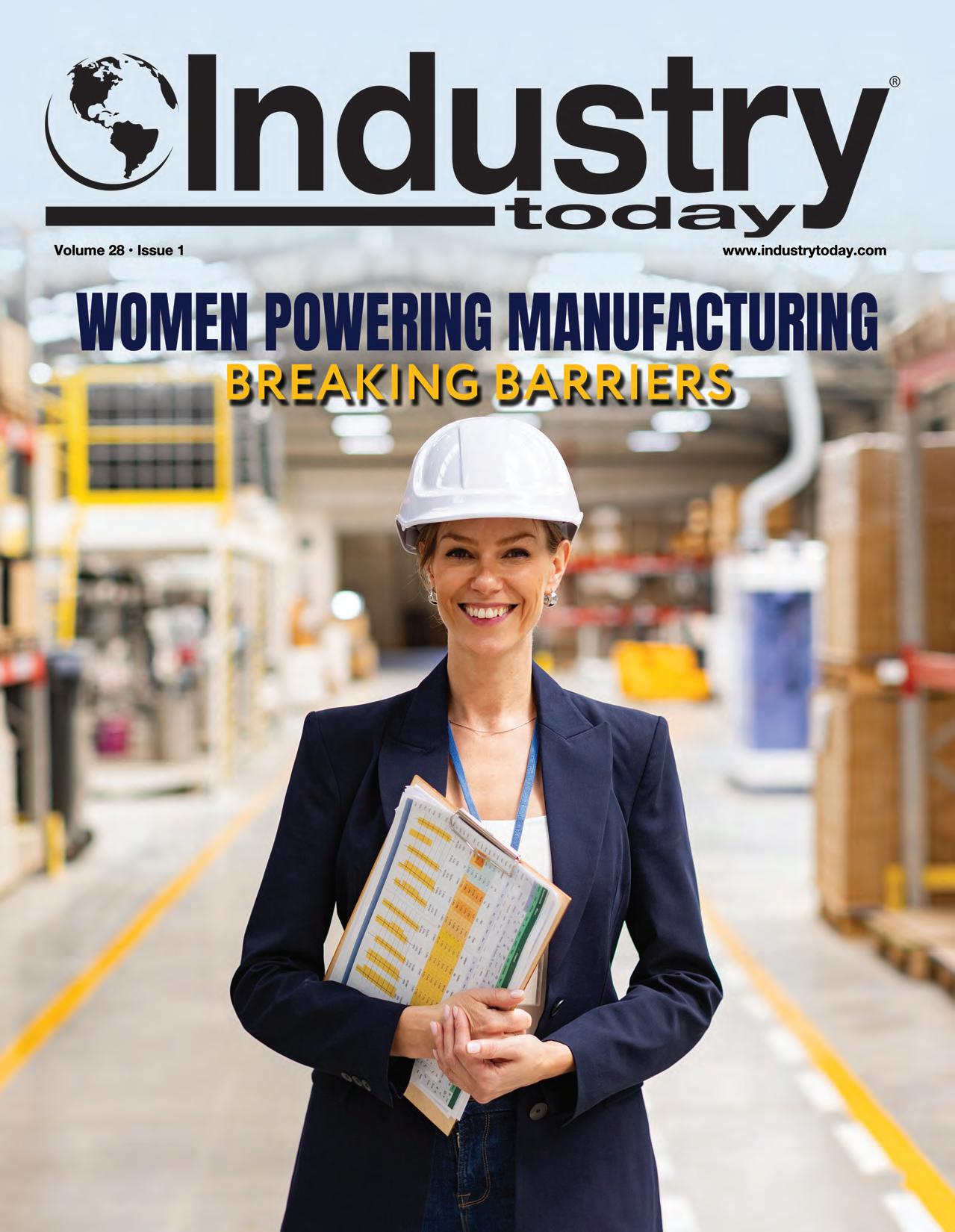
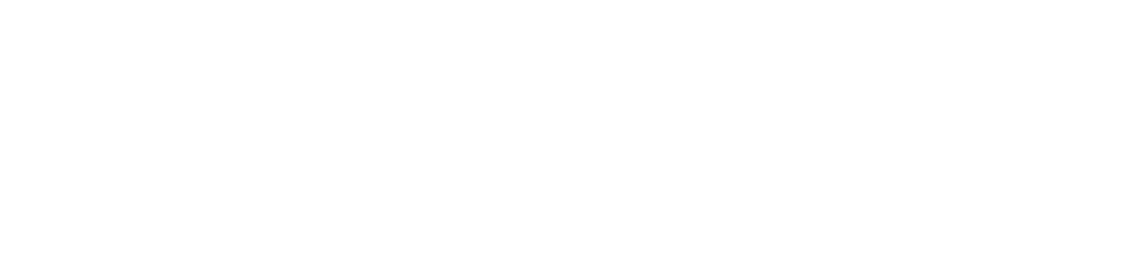
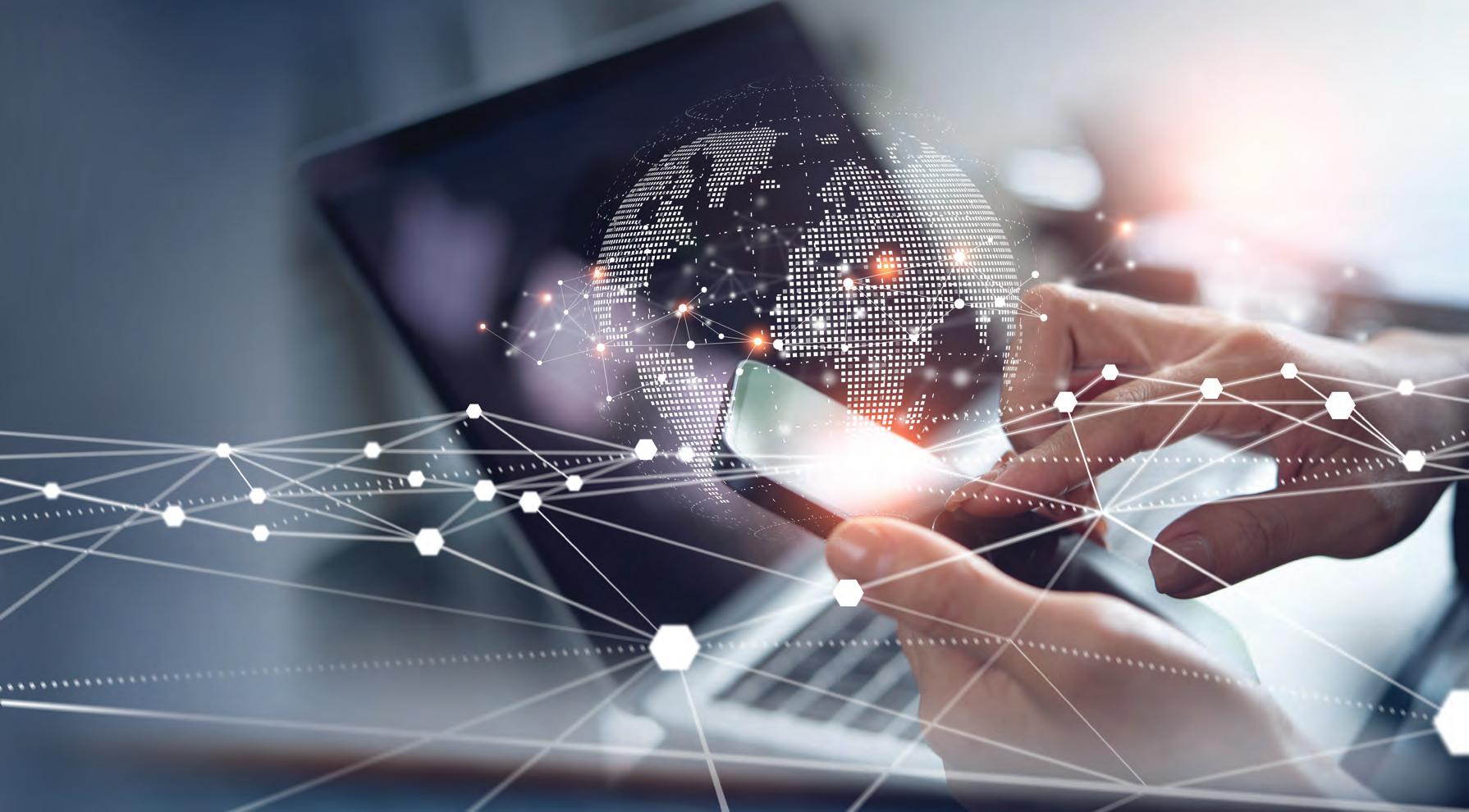
the digital media platform of choice for leaders and influencers in manufacturing and industry for nearly three decades. An approved Google news site and SEO compliant we offer bespoke media campaigns including
✓ Email and marketing automation
✓ Geo targeting based on behaviors and demographics
✓ Banners, customized e-blasts, sponsored newsletters, lead generation packages, sponsored articles and resources, webcast moderating, sponsored podcasts and videos
✓ Full pages and covers available in the digital magazine published quarterly and promoted to our opt-in subscriber base
Whatever your industry we have you covered with our team that boasts 30 years of editorial and promotional experience.
For further information contact: spoeton@industrytoday.com www.industrytoday.com
This issue of Industry Today focuses on women in manufacturing who are models for female achievement in STEM careers.
Helping U.S. Manufacturing Thrive in Manufacturing profiles two members of the ARM (Advanced Robotics for Manufacturing) Institute leadership team, which is 50% comprised of women, Suzy Teele, Chief Strategy Officer, and Lisa Masciantonio, Chief Workforce Officer. Helping women to thrive in manufacturing is important to Teele and Masciantonio, who have long been advocates for these roles, especially as advanced manufacturing technologies such as robotics and AI reduce the importance of physical strength in place of increased emphasis on problem solving, technical communication, and leadership skills.
In Raised by Women Redefining Normal, Olivia Morales, Senior Solutions Architect on the CESMII Smart Manufacturing Technology Team, writes about how women’s personal stories can inspire the next generation. Growing up, Morales says, “I feel lucky to have examples of strong women all around me, but no one was pointing them out to me as strong women. It was normal. It should be normal. It’s still not normal.”
Carolyn Lee, President and Executive director of the Manufacturing Institute (MI) describes how she has guided the organization’s growth and evolution, expanding its impact nationwide to strengthen the manufacturing workforce, change perceptions of manufacturing careers, and build a strong pipeline of skilled workers to close the industry talent gap.
Our regular industry coverage continues with an examination by Harry Moser, founder and president of the Reshoring Initiative®, in 2025 Reshoring Playbook: Turbulence, Tariffs, and Trump of how reshoring reduces import dependence, secures high-value supply chains vital to U.S. economic and national security, and mitigates risk.
Manufacturing continues to face a daunting labor shortage. Inspiring the Workforce of Tomorrow Through Education by Lauren Russell, Manager of Corporate Communications and Philanthropy at Nucor Corporation, discusses how manufacturers can build a reliable future workforce by connecting with K-12 students through various Discovery Education programs.
Speaking of the next generation of manufacturing, Lindsay Greene, President & CEO of the Brooklyn Navy Yard Development Corporation, writes about how the former naval shipyard now serves as an incubator for local new industries.
Last but not least are the company profiles: St. Mary’s Cement, Canadian manufacturer of high-quality cement products, woman-owned Rathburn Precision Machining, Midwest maker of machined metal components, and Eagle Picher’s Energetics business unit, a manufacturer of explosive and pyrotechnic devices.
In addition to the digital magazine, look for reporting on a weekly basis at industrytoday.com.
Thanks for reading Industry Today.
www.industrytoday.com spoeton@industrytoday.com
Publisher: Susan G. Poeton
Marketing Director: Alice Anne Coakley
Senior Executive Sales Manager: Jonathan Listig
Project Director: Brian McMillan
Production: Melissa S. Burge
Art Director: Seema Mazhar
Contributing Designers: Jorge Leandro Rodrigues
Profile Editor: David Soyka
472 Meeting Street, Ste C-156, Charleston, SC 29403, USA Ph. 973.218.0310
Industry Today is published by Industry Today LLC, 472 Meeting Street, Ste C-156, Charleston, SC 29403. Copyright © Industry Today 2025. All rights reserved. No part of this publication may be reproduced in any form or for any purpose without prior written consent from the publisher and payment of the agreed fee. ISSN # 1521-8058
WOMEN IN MANUFACTURING INTERNATIONAL WOMEN’S DAY
THE MANUFACTURING INSTITUTE
CAROLYN LEE
From family legacy to industry leadership
CESMII
OLIVIA MORALES
A manufacturing landscape that is future proof
THE ARM INSTITUTE (ADVANCED ROBOTICS FOR MANUFACTURING)
SUZY TEELE & LISA MASCIANTONIO
FEATURE ARTICLES
04 20 12 26 56 36
Leading the way to a future where people and robots work together
2025 RESHORING PLAYBOOK: HARRY MOSER RESHORING INITIATIVE®
TURBULENCE, TARIFFS AND TRUMP
How reshoring reduces import dependence and mitigates risk
ECONOMIC DEVELOPMENT
BROOKLYN NAVY YARD
A cornerstone of urban advanced manufacturing
EDUCATION IN THE WORKFORCE
DISCOVERY EDUCATION CAREER
CONNECT & NUCOR
Connecting with K-12 students
FEATURE ARTICLES
ENERGY
68
HYDROGEN AT THE TACTICAL EDGE
NovaSparks’ hydrogen technology enables cleaner, portable and resilient energy solutions
SAFETY SERVICES & PERSONAL PROTECTIVE EQUIPMENT (PPE)
SENTRY INSURANCE SAFETY SERVICES
Proper PPE, combined with training is essential for safety in manufacturing
COMPANY FEATURES
EAGLE PICHER TECHNOLOGIES ENERGETIC WORK
A manufacturer of a wide variety of explosive and pyrotechnic devices
RATHBURN PRECISION MACHINING MIDWEST CHARACTER INSPIRES HIGH-TECH SOLUTIONS
Customer solutions that meet demanding accuracy and quality goals for metal parts
ST. MARYS CEMENT SOLID FOOTINGS
Provider of high-quality cement products used in infrastructure, resident and commercial building construction
Carolyn Lee’s path to becoming the Executive Director and President of the Manufacturing Institute (MI), the 501c(3) workforce development and education affiliate of the National Association of Manufacturers, was shaped by a deep-rooted
family connection to manufacturing, a career in public service, and a commitment to building teams and empowering others. Her story is one of legacy, leadership, and a dedication to strengthen the workforce that drives American industry forward.
Manufacturing is more than a career for Carolyn, it’s part of her DNA. Her grandfather, a machinist, worked in manufacturing during the pre-World War II era and her
grandparents met at a global watch manufacturer’s factory outside New York City. This family heritage instilled in Carolyn a profound respect for manufacturing, its vital role in society and helped shape her view of service. Her father also carried on the family’s
legacy. He owned a screw machine business when Carolyn was young. The business provided for their family and gave Carolyn a firsthand view of the challenges and rewards of running a small manufacturing operation. She joined her father in the shop doing small jobs,
gaining early, hands-on experience with the precision and dedication the industry demands. Watching him manage the business and navigate the industry gave her a deep appreciation for the entrepreneurial spirit and the critical role that small manufacturers play in the
broader industrial ecosystem.
Early in her career, Carolyn worked on Capitol Hill, working first in the U.S. House of Representatives and then in the U.S. Senate.
During that time she saw firsthand how legislative policy shapes workforce development, and families. Serving as staff for former U.S. Representative Sue Kelly (NY), who was the Republican chair of the Congressional Women’s Caucus, reinforced the importance of building networks, coalitions and community.
While in the office of U.S. Senator Olympia Snowe (ME), one of her most memorable and formative experiences was working on the partially funded child tax credit, which was part of the 2001 tax law. It was the first piece of legislation she worked on that was enacted and
it would go on to provide thousands of families with additional support.
Her experience in Congress also gave her insight into the unique challenges women face in entering industries that are mostly male dominated, where the lack of role models can become a barrier. She recalls Rep. Kelly often
sharing how she was encouraged by others to run for office—a push that was and is often necessary for women seeking leadership roles. That lesson of needing allies and sponsors resonated deeply with Carolyn and became a guiding principle in her work at the MI, where she champions initiatives to support women in manufacturing and to reduce barriers to opportunities for all.
When the Executive Director position opened at the Manufacturing Institute, Carolyn initially hadn’t considered herself for the role. It took a suggestion from Jay Timmons, President and CEO of the National Association of
Manufacturers, and chair of the MI Board of Directors, for her to consider the opportunity to make an impact via programs instead of policy. His encouragement pushed her to step into a position where she could make a transformative impact on the industry.
When she first stepped into the role, the MI was a small organization of just eight people, working on several projects but without a clear strategic plan or vision. Under her leadership, the MI has grown dramatically in scale and reach. Today, the MI has become a trusted advisor for manufacturing employers – powering solutions to build and strengthen the
workforce needs of today and prepare the talent needed for the future. The organization is doing this by creating initiatives that empower individuals, strengthen communities, and address industry-wide challenges.
The MI’s success, however, is not Carolyn’s alone. Through her leadership she has empowered the dedicated teams working alongside her to think big and deliver impact. Together, they have transformed the MI into a national leader in workforce development, driving solutions that strengthen individuals, businesses and communities.
The MI’s flagship initiatives, including FAME
(Federation for Advanced Manufacturing Education), Heroes MAKE America, Women MAKE America, and its Student Engagement efforts, are expanding access to manufacturing careers and fostering a skilled talent pipeline. The MI also works with regions and communities to build new workforce development pipelines and develop new solutions.
During her tenure, the MI took over management of FAME. Originally founded by Toyota but then entrusted to the MI in 2019, FAME trains individuals for advanced manufacturing careers through a combination of paid, handson work experience and classroom instruction. The program is widely regarded for producing highly skilled graduates who are ready to meet the demands of modern manufacturing. FAME has scaled nationally, offering a proven model
Carolyn Lee is the president and executive director of the Manufacturing Institute, the 501(c)(3) nonprofit workforce development and education affiliate of the National Association of Manufacturers. Since 2017, she has guided the MI’s growth and evolution, expanding its impact nationwide to strengthen the manufacturing workforce.
A champion for the industry’s future, Lee is passionate about the MI’s work to tap into new talent pools and change perceptions of manufacturing careers so that every potential worker sees the opportunity for a family-supporting, rewarding career.
Parts of the MI portfolio include the Women MAKE America initiative, which empowers and elevates women in manufacturing to create role models and opportunities for the next generation, and the Heroes MAKE America initiative, which builds military-to-manufacturing pathways for veterans and transitioning service members. She is also committed to engaging students and fostering excitement for manufacturing careers. Through these and other initiatives, including apprenticeships, she works to close the industry’s talent gap and build a strong pipeline of skilled workers.
for building a skilled talent pipeline.
Recognizing the untapped potential of transitioning service members, in 2018, the MI launched Heroes MAKE America, a training and certification program that helps veterans and active-duty personnel transition into manufacturing careers. The program offers industry-specific training, career coaching, and connections to manufacturing employers.
Carolyn has been a champion for increasing female representation in manufacturing. Women MAKE America is elevating role models while creating mentorship networks and career development opportunities. The initiative aims to inspire more women to pursue and thrive in manufacturing careers by highlighting role models and fostering a community so that the next generation of women can see themselves in modern manufacturing. And in doing so, we can close the skills gap hindering manufacturing’s continued growth.
To address the need for a future-ready workforce, the MI has strengthened its student engagement tools, promoting manufacturing careers to young people through hands-on experiences, industry tours, and classroom resources. By sparking interest in manufacturing careers early, the MI is helping to cultivate the next generation of manufacturing talent.
At the heart of Carolyn’s MI leadership is the
belief that manufacturing is about people— strengthening individuals and, by extension, their families and communities. She recognizes that workforce development isn’t just about filling jobs, it’s about creating opportunities for growth and stability.
As she continues to lead the MI, Carolyn remains driven by the same values that brought her into public service: making a tangible impact through thoughtful leadership and a commitment to building a stronger, more dynamic manufacturing workforce. Her story is a reminder that meaningful change comes from persistence, adaptability, and a willingness to take on challenges, even the unexpected ones.
Women at the ARM Institute are leading the way to a future where people and robots work together creating the world’s most desired products.
When Suzy Teele (Chief Strategy Officer) and Lisa Masciantonio (Chief Workforce Officer)
joined the ARM (Advanced Robotics for Manufacturing) Institute, a fledgling Manufacturing USA Institute, in early 2017 as the 2nd and 3rd employees, respectively, it was because they believed in the mission – to secure U.S. global leadership in advanced manufacturing by connecting people, ideas, and technology. And 8 years later, they remain even more passionate about this goal.
The ARM Institute is a public-private partnership focused on advancing the use of robotics and Artificial Intelligence (AI) in manufacturing to strengthen U.S. industrial competitiveness. Established in 2017 through the Manufacturing USA network and supported by the Department of Defense (DoD), the ARM Institute brings together industry leaders, robotics and AI providers, academic institutions, Workforce Investment Boards (WIBs), Manufacturing Extension Partnerships (MEPs), manufacturing trade associations, and government agencies to drive innovation in
robotics and workforce development. Based in Pittsburgh, Pennsylvania, the ARM Institute collaborates with this comprehensive ecosystem to bridge the gap between research and real-world industrial applications, ensuring that robotics technology is accessible and beneficial across the sector. Its key goals include:
• accelerating the adoption of robotics and automation in manufacturing
• developing education and training programs to upskill the workforce for advanced manufacturing jobs
• enhancing U.S. manufacturing competitiveness by improving productivity and efficiency.
Pictured: Suzy Teele and her outreach team work tirelessly to coordinate ARM’s participation at nearly 100 conferences, tradeshows, workshops, and events every year; right: Lisa Masciantonio is presenting updates on the great work of the ARM Education and Workforce Development team at the ARM Institute’s annual Member Meeting.
International Women’s Day is a historic celebration of resilience, progress, and strives for equality. It’s a special day to honor the contributions and achievements of women around the country. It is also a time to envision a strong future for the great women in all industries. For Suzy and Lisa, this day is about amplifying these women’s voices, breaking down barriers, and ensuring a future where every woman has an opportunity to thrive.
Helping women to thrive in manufacturing is important to Suzy and Lisa, who have long been advocates for these roles, especially as advanced manufacturing technologies like robotics and
AI reduce the importance of physical strength with increased emphasis on problem solving, technical, communication and leadership skills. Manufacturing, robotics and AI are not traditional roles for women, but there is no reason why they can’t become traditional roles and rewarding careers, as robotics and AI reduce or eliminate dull, dirty and dangerous jobs of the past. Manufacturing is evolving with automation, robotics, and advanced technologies, creating exciting opportunities for women in STEM-related fields. Women in manufacturing gain technical skills and problem-solving abilities that are valuable across industries. An
Suzy Teele is the Chief Strategy Officer for the ARM Institute, the nation’s leading manufacturing innovation institute for robotics and artificial intelligence. In this role, Suzy drives the ARM Institute’s overall strategy related to new programs, outreach efforts, stakeholder strategy, and partnership activities.
Suzy Teele helped launch the ARM Institute and has been instrumental in growing its consortium of over 400 organizations committed to strengthening U.S. manufacturing through innovations in advanced manufacturing technology, particularly robotics and artificial intelligence (AI), and preparing the workforce to operate these technologies. Working across industry, government, and academia, the ARM Institute fosters collaboration between those who can create & maintain robotics with those who can leverage it for maximum economic impact.
Suzy has over thirty years of experience in technology-based business strategy, product commercialization, customer acquisition and retention, marketing, sales, and business development. Suzy was an executive at several international software companies, driving strategic revenue growth in roles that included General Manager, COO and CMO. Prior to joining the ARM Institute, she was an executive consultant and advisor to venture-backed, early-stage technology companies. She has mentored hundreds of technology companies on profitable growth strategies and product commercialization.
A graduate of Indiana University of PA (IUP), Suzy has been recognized as a Distinguished Alumni and has been inducted into the IUP Business Hall of Fame. She is also a board member of the IUP Research Institute. Other accolades include a Greater Pittsburgh Athena Award finalist and Businesswomen First Award. Suzy helped to start the Pittsburgh Chapter of WELD (Women for Economic and Leadership Development) and has coached many women-owned businesses. https://www.linkedin.com/in/suzyteele/ www.arminstitute.org
Industry Today article from July 30, 2024 “The Future of Manufacturing Depends on Women” shows key elements to how women are key to revitalizing manufacturing.
The U.S. is investing significantly to reshore manufacturing and is incentivizing leaders to
build manufacturing facilities in the U.S. This is leading to tremendous economic opportunities and career growth for the workforce. These exciting jobs often provide competitive wages and benefits, making them a solid career choice. Many roles do not require a four-year
degree, allowing for quicker entry into a stable career. And there are numerous opportunities for advancement, from entry-level roles to leadership positions.
Over the past 8 years, Suzy and Lisa have seen the number of women working in manufacturing increase, although the total percentage is still smaller than the number of women in the U.S. workforce overall, at around 30% in comparison to 47% overall, according to the U.S. Census Bureau. Much growth has come in both operational roles as well as technology roles, as more women consider STEM careers.
Pictured: The ARM Institute is headquartered at Mill 19 in Pittsburgh. Mill 19 is the catalytic redevelopment of the former Pittsburgh Jones & Laughlin Steel Company mill.
At the ARM Institute, over 50% of the staff are women and they fill roles in all areas of the organization – from technical, to workforce development, marketing and finance. The leadership team – of which Suzy and Lisa are part of – is 50% women.
They regularly encourage women to consider manufacturing careers as they travel the country presenting at conference and through audio and video podcasts. A great resource for women looking to enter or grow in the manufacturing industry—especially in robotics and automation—is RoboticsCareer.org. This national resource, started as an industry-informed vision developed by Lisa and Suzy several years ago at the ARM Institute, helps individuals:
• find the right training programs to build
Lisa Masciantonio is the Chief Workforce Officer for the Advanced Robotics for Manufacturing (ARM) Institute. She joined the ARM Institute in May 2017 as the Director of Membership and Outreach. She moved to the position of Chief Workforce Officer in 2019 and she is responsible for driving the Education & Workforce Development vision for ARM in conjunction with the ARM membership, the federal and state government partners, and other expert stakeholders.
Lisa brings with her over 25 years of experience as a performance-driven leader with notable success in cultivating and executing business strategies and formulating long-term strategic client relationships. She has proven success in developing business solutions, commercialization of products, technology transfer, and technological initiatives that have supported organizational growth, improved staff productivity, and increased value to many communities of practice. Critical to her success is the ability to increase awareness and drive thought leadership position by designing and executing innovative programs as well as developing and launching new, value-add offerings for ongoing competitiveness. Lisa received a Bachelor’s degree from the Pennsylvania State University and 2 Master’s degrees from Carnegie Mellon University.
In 2021, Lisa was recognized as one of 20 world-wide Exceptional Women in Robotics and Automation by SME. In 2022, she was recognized by the Pittsburgh Business Times as a Women of Influence and was also part of the inaugural Technical.ly Pittsburgh RealLIST Connectors list, which recognizes the top 100 influential leaders in Pittsburgh tech.
https://www.linkedin.com/in/lisa-masciantonio-88ab246/
skills and knowledge in robotics and advanced manufacturing
• explore job opportunities that align with career goals and interests
• create a user profile to showcase skills and experience, making it easier for employers to find and connect with interested candidates. By leveraging RoboticsCareer.org, women can understand the key competencies needed for robotics in manufacturing, access person-
alized career pathways, training resources, and networking opportunities, helping to break barriers and advance in the industry. Over 16,000 training programs – from micro-credentials to Ph.D. degrees - are listed on the site that can be searched in a variety of ways. Some of these programs have passed an ARM-led audit and are officially “Endorsed” as offering best practice training solutions. This resource also provides a unique SkillsMatch™ capability that
matches job seekers with employers based upon the skills in a user’s profile.
Looking back, Suzy and Lisa realize that they have come full circle, in a way, in their careers. They both grew up in Pittsburgh when manufacturing was a critical industry during their childhood but then lived through its devastating reduction in the 1980s, when factory unemployment hovered around 25 percent. Now the Pittsburgh region is committed to advanced manufacturing and robotics and AI are a major growth industry because of the influence of regional resources like the ARM Institute, Carnegie Mellon University, the Pittsburgh Robotics Network, the Robotics Factory, and over 100 robotics and AI companies. By witnessing firsthand how manufacturing lifts communities and commerce, they are playing a critical role to ensure that it continues to do so, not only in Pittsburgh, but throughout the United States.
Pictured: Lisa Masciantonio and Suzy Teele are part of the close-knit ARM Institute team – here they are enjoying time at the ARM Institute summer social.
Their advice to women looking to enter the manufacturing sector is that it can be both rewarding and transformative. Women can break barriers so advocate for yourself and explore the many opportunities throughout the manufacturing industry, where over 800,000 manufacturing jobs are open in the U.S. today. They encourage women to be courageous and confident that they can gain the skills to preserver and succeed in these exciting careers.
As we celebrate International Women’s Day, there has never been a better time to consider a career in the exciting and ever-growing manufacturing sector.
Personal connection and women’s stories impact our paths more than any other type of outreach
International Women’s Day is, in many ways, just another day. It’s not a big holiday that garners a lot of attention, and is likely overlooked. If you’d asked me a month ago what its date was, I wouldn’t have been able to tell you. But I’m a woman! Shouldn’t I be aware of a day that honors me and my rights? Maybe that’s a symptom of why such a day must exist – to force us to look a little more closely at this half of the population. When I think about International Women’s Day, I think about all the incredible women in my life. This year, I think about my grandmother. Little Jean was born in a small town during a time when women had fewer choices and less independence than today. They did not get to grow up thinking they could be just anything. She wanted to go to university; she did not. I think she had professional ambitions, but pursued them only after fulfilling the requirements of the time: to raise her family, two girls and two boys. Perhaps I have unintentionally reduced her to this story. I wish I could ask her. I have always wondered what life she wanted, and how it compared to the life she had. What
did little Jean want to be when she grew up? Did she do it? What got in her way? Here’s what I do know: she lived a big life. At age 50 she became the Executive Director of her city’s Habitat for Humanity Chapter. She was one of the few founding members tasked with developing a local branch of the organization, eventually leading Habitat until she retired. She traveled the world – she had deep relationships – she was an incredible mother, grandmother, friend, leader.
But what did little Jean want? She lived through significant social movements; she performed what many may call the most quintessential roles of the time: homemaker, party hostess, community volunteer. Women are complex. Our desires are often bound by our circumstances. Where is the balance? Our paths are set not by explicit rules, but by expectations and examples - both of the era, and for
Pictured: Blowing out candles (1998).
the individual. I am no exception.
This is an industrial publication, and I would be remiss to stay silent on the topic of being a woman in manufacturing, or being a woman in a male-dominated field. There are certainly interesting things to say on these topics, but what matters more to me is acknowledging the incredible women in my life. The ones I look to for advice and who helped me become the woman I am today.
My work life is in stark contrast to the environment in which I was raised. I grew up in a female-dominated family, then landed in a male-dominated field. The concept of “girl power” was not explicitly emphasized in my home, but it was modeled daily in the ways that my grandmother and mother lived their lives and raised me. My mom made sure I took time to analyze my passions, cultivate my skills, and
get out of my comfort zone. She insisted I could be whatever I wanted. I feel lucky to have had examples of strong women all around me, but no one was pointing them out to me as strong women. It was normal. It should be normal. It’s still not normal.
It should be unremarkable to see women leading and succeeding in all the same ways as men.
But to get there, we first need to see those examples. Young girls and boys need to see them early. Humans are wired to model themselves after examples they see. Those examples do not need to be trend-setting, social disruptors. Most people are not that. The examples simply need to feel achievable and encourage a practice of challenging perspectives and expectations. Urging young women to consider a career in manufacturing is even more challenging. Manufacturing careers are less visible and accessible compared to others. Few young people actually know about them, let alone know that they can offer opportunities for women. When was the last time you saw a TV show about manufacturing? There are dozens about
Pictured: Little Jean pictured growing up.
Olivia Morales is a Senior Solutions Architect on the CESMII Smart Manufacturing Technology Team. She works with manufacturers and technology providers on the Smart Manufacturing Innovation Platform by advising on architecture, development and implementation, and by expanding resources for developers. Olivia has focused her career on Software Development for Manufacturing Systems and her knowledge of technology and manufacturing provide the foundation necessary to lead CESMII and its members towards a manufacturing landscape that is future proof, collaborative and rooted in standards. She leads and participates in industry joint working groups with a shared mission to create reusable interoperable manufacturing technology. Previously, Olivia was with Rockwell Automation where she received a patent for her work on an innovative product that delivered an industrial hardened AI directly to the automation control platform.
https://www.cesmii.org/
doctors, lawyers, and teachers. Storytelling of any kind goes a long way in its ability to influence what we define as normal, or possible. Those stories can have an impact regardless of whether they are personal ones, ones in the media, or even fictional ones.
International Women’s Day celebrates the women’s rights movement, but the day is increasingly commercialized and leveraged by corporations. Movements form at a personal level – sustained by individual connections, stories, and a little serendipity. I owe my ability to embrace the opportunities in front of me to the women who raised me, like my grandma.
My grandma wanted to be an actress. She was smart, creative, klutzy, strong-willed. She went from being a horrible cook to a great one. She never stopped trying new things. She was adventurous. She created community. She was always reading a new book.
Women are complex and deserve a world where they can choose from a vast set of potential paths, or forge their own. Little Jean may have begun her life as a product of her circumstances, but she built a life that was so much more.
Because of everything she was, I am everything I am. I am honored to tell part of her story.
The U.S. has shifted from producing the lion’s share of the world’s goods to now relying heavily on imports. In the mid to late 1940s America produced half of the world’s manufacturing output, much higher than the 28% that China produces today.
Offshoring: how the U.S. lost its edge
Offshoring became prevalent in the late 1970’s when large U.S. corporations began moving manufacturing to low-cost countries. Not only did OEMs offshore much of their own manufacturing but suppliers were also encouraged to migrate offshore. This “asset-light” business model minimized physical assets like manufacturing facilities, relying instead on outsourced offshoring and focusing on R&D, marketing, and finance.
Assets were reduced and margins increased, driving ROA. Offshoring grew to a value proposition that could sidestep strict U.S. workplace and environmental regulations while taking advantage of low offshore wages and foreign government subsidies.
The bottom fell out in 2001 when China joined the World Trade Organization (WTO), removing barriers to its exports globally. A surge of inexpensive Chinese goods flooded the U.S., transforming manufacturing towns and the U.S. economy itself. The U.S. lost millions of manufacturing jobs, a phenomenon economists call “China Shock”.
America’s competitive edge dulled as institutional knowledge, intellectual property, technology, mission critical components and process engineering were transferred to foreign competitors. U.S. manufacturing communities experienced higher unemployment, lower wages, higher disability payments, higher rates of child poverty, and elevated mortality. The ramifications were reduced competitiveness, more
Pictured: Currently, at least half of what we consume is imported, with major supply chain gaps such as personal protective equipment (PPE), semiconductors, and rare earth minerals: the key ingredients for glass, lights, magnets, batteries, electronic components, and used in everything from cell phones to cars; right: Figure 1: Primarily as a result of the increasing trade deficit, US manufacturing employment as a percent of total U.S. employment declined dramatically from about 26% in 1970 to about 9% today.
vulnerability to geopolitical risk and a depleted U.S. workforce.
Growing trade deficits from globalization eliminated six million U.S. manufacturing jobs over 6 decades and approximately 70,000 factories.
Our large trade deficit, a measure of offshoring or lack of self-sufficiency, is primarily due to the U.S. not being price competitive on a broad range of products. The strong correlation between the trade deficit and declining manufacturing employment is clear in Figure 1.
For the US to recover millions of lost jobs, China’s growth has to slow. China’s economy enjoyed an average annual growth of 9.5% from 1978 until 2019 and then began to feel the effects of a structural slowdown. China’s economic growth rate slumped to a three decade low in 2023 (5.2%) as a result of the 4D’s: demographics, debt, drought and decoupling. Birthrates in China are falling, and its population is aging. Risky investment activity has led to inflated real estate, land bubbles and unsustainable debt. China’s unequal water distribu-
tion is contributing to a water shortage crisis. In 2024, China’s net Foreign Direct Investment (FDI) inflows turned negative to -4.6B as foreign firms repatriated earnings back home instead of adding new China investments.
The US has to reshore to avoid further hollowing out of manufacturing before China peaks.
To facilitate an economic rebound from the 4D’s, Beijing doubled-down on investments in industrial overcapacity, flooding global markets with low-priced hi-tech exports, exacerbating global trade tensions. China’s excessive investments are a $450 billion tsunami that threatens the market over the next three years.
This overcapacity push is ushering in a sequel
to the first “China shock.” The export surge will depress global prices and, if left undeterred, will inhibit development of U.S. hi-tech industries, enabling China to capture important sectors. To thwart China’s overcapacity and its impact on trade, section 301 tariffs have been extended, increased and broadened on a range of hi-tech Chinese goods.
Since the beginning of the trade war, China has targeted U.S. companies with legislation like the “unreliable entry list” and the “anti-foreign sanctions law.” Penalties imposed on companies or individuals include restriction of trade, investment and visas, and even sweeping powers to seize assets and block business transactions of actors that China perceives as harming
its interests.
U.S. manufacturers should consider reshoring to mitigate the risks of retaliation. Localizing production and sourcing will not only reduce geopolitical risk but also make supply chains more resilient and sustainable, encourage investment in infrastructure and workforce development, strengthen the U.S. economy and generate well-paying jobs in manufacturing and other industries through the multiplier effect.
Reshoring hi-tech manufacturing ecosystems reduces offshore dependence and secures high-value supply chains that are vital to U.S. economic and national security. Studies show that geopolitical turbulence and the need for resilient/sustainable supply chains, is disrupting
offshoring.
Localization plans jumped to 81% (2024) from 63% (2022) with 64% reporting ongoing investment and execution in reshoring and nearshoring. Companies shifting operations out of China rose to 69% (2024) from 55% (2022).
Today, reshoring and foreign direct investment (FDI) trends are demonstrating strength and longevity, driven by risks associated with global politics, and climate change, and by supportive U.S. industrial policies. Investment in U.S.
Pictured: China’s structural slowdown is caused by the 4D’s: demographics, debt, drought and decoupling; above: China’s new overcapacity surge will depress global prices and, if left undeterred, will inhibit development of U.S. hi-tech industries, enabling China to capture important sectors.
manufacturing has been rising with a key focus on shortening supply chains. The cumulative number of jobs announced coming back since the manufacturing low in 2010 is now approximately two million.
U.S. policy has created favorable conditions
for reshoring and FDI via the Infrastructure Investment and Jobs Act (IIJA), Inflation Reduction Act (IRA), and CHIPS and Science Act. U.S. reshoring is driving a manufacturing construction boom with investment in manufacturing facilities reaching a new record of
US$238 billion in 2024, contributing the most to real year-over-year GDP growth since 1958. But as government subsidies run out, new reshoring and FDI announcements are slowing. Future progress will depend on new policies that make U.S. manufacturing broadly cost competitive, rather than subsidizing specific industries.
Acceleration of the trend depends on the government leveling the playing field. We should quantify the competitiveness gap with a unified, quantified, broadly supported proposal for the nation. The Reshoring Initiative’s Competitiveness Toolkit is a good start on
Pictured: Geopolitical risk is a top driving force in the reshoring and FDI trends.
Founder/President, Reshoring Initiative®
Harry founded the Reshoring Initiative® to bring five million manufacturing jobs back to the U.S. after serving as president for high end machine tool supplier GF AgieCharmilles. Harry was inducted into the Industry Week and Association for Manufacturing Excellence’s (AME) Halls of Fame and was named FAB Shop Magazine’s Manufacturing Person of the year. Harry participated actively in President Obama’s 1/11/12 Insourcing Forum at the White House and won The Economist debate on outsourcing and offshoring. He was recognized by Sue Helper, then Commerce Department Chief Economist, as the driving force in founding the reshoring trend and named to the Commerce Department Investment Advisory Council in August 2019. Harry testified at the June 9, 2022 Senate commission Hearing on U.S. supply chains and China.
Harry is regularly quoted in the national business media and seen on national TV programs. He received a BS in Mechanical Engineering and an MS in Engineering at MIT in 1967 and an MBA from U. of Chicago in 1981.
the reshoring and job impact of most of these actions.
Continuation of the trend depends on companies reevaluating their offshoring. Companies can use the Reshoring Initiative’s free online TCO Estimator and our new Geopolitical Risk measure to compare alternative sources.
Workforce development is a top priority. It is essential that the United States have a sufficient
number of workers with the skill-level necessary to use the most modern equipment and technologies to achieve the required cost competitiveness and quality. This factor is the sine qua non of reshoring and rebuilding.
Automation is essential to bridging the cost gap. Reshoring and increased domestic demand are critical to enabling automation. When factories are busy and profitable, they can justify
the investment.
President Trump has promised more tariffs and lower taxes. Companies are closely monitoring the situation. But the unpredictability and “tariff whiplash” are creating uncertainty for U.S,
Pictured:Reshoring packs a punch. Localization plans jumped 81% in 2024.
manufacturers’ supply chains and investment plans.
The potential tariff threats do however seem to be moving the needle on reshoring and FDI consideration. To mitigate potential tariffs, some U.S. companies like 3M and Polaris are already considering reshoring and foreign companies like Samsung, LG, Hyundai Steel, Volkswagen Group’s premium brands Audi and Porsche, and South Korean biopharma contract manufacturer Celltrion are considering FDI.
If we are going to use tariffs, I believe that they should apply to all products from all countries forever. The best way to do a tariff is through a value-added tax (VAT) because, unlike a direct tariff, it would not lead to retaliation since US peers all already have a VAT so they have no grounds to retaliate. And yet it would tax, say, 15% of everything coming in, and then subsidize our exports at the same percentage.
Our main mission is to get companies to do the math correctly using our free online Total Cost of Ownership Estimator® (TCO). By using TCO, companies can better evaluate sourcing, identify alternatives and even make a case when selling against offshore competitors. For help, contact me at 847-867-1144 or email me at harry.moser@reshorenow.org.
Have you reshored a metal component or product? Apply for the National Metalworking Reshoring Award.
Manufacturing companies can build a reliable workforce by connecting with K-12 students today. Nucor shares examples of how to do so.
Today’s manufacturers play a vital role in our modern economy. The sector contributes more than $2.3 trillion to the total U.S. GDP and employs 15-16 million workers, which is approximately 10% of the entire U.S. workforce. As critical as manufacturing is to our success as a nation, manufacturing industries face a stark challenge in the notso-distant future. Research reveals that there are projected to be over 2.1 million unfilled jobs by 2030 due to a lack of skilled workers.
According to a National Association of Manufacturers Outlook Survey, “attracting and retaining a quality workforce” is one of the industry’s biggest concerns in the coming years. And in an aging sector like manufacturing, where the median age of workers is over 44 years old, this challenge is compounded by the
difficulty of recruiting younger workers to fill the growing gap. As a result, it is critical that manufacturing companies strategically focus on engaging and inspiring tomorrow’s workforce today. Achieving future success requires companies to take proactive steps to connect with the next generation of workers and address skills gaps.
As a large industrial manufacturer and the largest steel company in America, Nucor is taking a forward-looking approach to connecting with today’s youth early through targeted employee volunteerism.
At Nucor, we believe that connecting our teammates in technical and professional roles with students is an impactful way to positively influence their aspirations, and by modeling passion for their work, our Nucor teammates are showing students that today’s modern manufacturers offer a diverse range of incredibly exciting and rewarding career opportunities.
Nucor teams in Nebraska are fostering student interest in STEM careers through FIRST® (For Inspiration and Recognition of Science and Technology), a global nonprofit that offers STEM programs to K-12 students. Nucor established its Nucor Robotics Team in 2023 with five children of Nucor team members. Within one year, the team grew to over 30 student participants under the guidance of Nucor volunteer mentors. In 2024, students on the Nucor
Robotics team worked an average of four hours each week with their coaches and mentors in order to prepare for their “first” FIRST Robotics competition. Their hard work paid off when the Nucor Robotics Team walked away with second place in Innovation, an extraordinary feat for a first-time participant.
While we realize the importance of providing exposure and igniting an early interest in
STEM careers for middle and high school students, it’s equally imperative that we connect with older students who are continuing their education and seeking a rewarding future.
With that in mind, Nucor’s three industrial operations in rural Norfolk, Nebraska, invested $250,000 in the Northeast Community College (Neb.) iHub. The Nucor donation will fund the Nucor Robotics Lab, a space aimed at developing youth robotics programs. When complete, the iHub will provide essential resources for robotics teams, such as practice space, coaching support and access to technology, and will ensure that students in their rural area have the
same opportunities as their urban ‘competition’.
In addition, the iHub will house woods, metals and prototype labs for community use, as well as electromechanical and industrial automation spaces to support workforce development. The $8.5 million facility is expected to be completed by Spring 2026, and is funded by both governmental support and private donations – a great example of the public-private partnerships supporting our education system.
While our Nebraska team serves as a wonderful example of Nucor’s commitment to fostering STEM education among young learners, there are many similar examples throughout our company. At Michigan Technological
University in Houghton, Michigan, Nucor proudly sponsors summer youth programs, where high school students have an opportunity to explore various STEM-related careers through hands-on learning. Nucor teammates who are Michigan Tech alumni actively participate in these summer programs, working with students and sharing their career experiences to inspire the next generation of American steel manufacturers. “Early exposure to STEM-
Pictured: Nucor Steel Memphis partnered with the Greater Memphis Chamber and local colleges and universities to create a well-rounded and engaging experience for local high school students on MFG Day. [https://mfgday.com/]
related careers can make a huge difference in a student’s decision to pursue them,” said Tessa Kriz, Michigan Tech alum and Process Development Analyst at Nucor. “The opportunity to give students a glimpse into what their futures could be is invaluable.”
By investing in these students, Nucor is not only supporting their individual growth, but also contributing to the broader goal of developing top engineering talent for the future.
Students cannot aspire to careers they do not know exist. That is why participating in partnerships and programs that introduce realworld examples of what it looks like to work in a STEM field opens the doors to many possible future careers, especially in communities where access to mentors and role models is
limited. This helps students better understand the demands of the job market and improves broader career readiness.
Our Nucor Steel Memphis team has taken a vested interest in its local community, because not only do they share in our belief that the earlier students can see themselves in STEM fields, the better, but they also know that Memphis is often seen as one such area where access to mentors and role models can be hard to find. As a result, our Nucor Steel Memphis Engineered Bar division participates in the annual Manufacturing (MFG) Day, an initiative affiliated with the National Association of Manufacturers. Each year on MFG Day, local manufacturers open their doors to students, community partners, and educators to inspire future generations to pursue careers in the industry. In 2024, our Nucor Memphis team
Manager of Corporate Communications and Philanthropy at Nucor Corporation
Lauren is focused on aligning community relations and philanthropic efforts with Nucor’s strategic initiatives and values. Lauren is experienced in both internal and external communications and handles corporate projects, public affairs, and company-wide communications.
With a background in non-profit work and a master’s in industrial and organizational psychology, Lauren is a true believer that doing good for your community and for your team is good for business. Lauren joined the Nucor team in 2013.
Nucor is the largest steel and steel products producer in North America.
hosted more than 20 students from Power Center Academy High School, which included a tour of our steelmaking facility and an onsite college fair with local colleges and universities. Students asked insightful questions about working at Nucor Steel Memphis, and gained valuable insights into the educational pathways that will enable them to pursue a career in manufacturing.
“Our partnerships with local schools and interacting with students where our teammates live and work are a huge part of igniting curiosity in a Nucor career,” said Aubrey Houston, Human Resources Recruiter from Nucor Steel Memphis. “Building a presence in our local
schools and communities is key to helping young people understand the opportunities in their own backyards.”
By partnering with global education technology leader Discovery Education, Nucor is expanding its footprint beyond the communities where Nucor has operations to inspire students using Career Connect. This digital network provides employee volunteers with opportunities to meet virtually with classrooms around the country,
Pictured: High school students on the Nucor Green Team won 2nd place Alliance at the State competition held at Metro Community College in Omaha.
share their industry expertise and experiences, and introduce students to potential career paths. These direct-to-classroom connections help fill a critical gap for students, as research shows that 67% of students think that school is not evolving to meet workplace needs.
Another way to support students is to ensure that they have access today to the STEM resources they need to build the skills that they will need tomorrow. To further these efforts, Nucor is a proud partner of the STEM Careers Coalition, an alliance of industries and non-profit organizations that has provided more than 11 million students with access to
free standards-aligned STEM resources and career planning tools since 2019.
“Helping educators equitably incorporate STEM into everyday learning is exactly why we are excited to work with Discovery Education on programs like Career Connect and the STEM Careers Coalition,” said Kristin Perkins, Talent Manager at Nucor. “By combining our teams’ expertise with their curriculum specialists, we can create authentic learning materials that benefit everyone. Teachers need engaging tools, and through these corporate partnerships, we can provide free, inspiring resources anyone can access.”
STEM education focuses on teaching problem-solving skills, with many of the most innovative thinkers being individuals who have overcome early challenges or lacked confidence in math and science.
The steel industry, in particular, still faces outdated misconceptions about modernization, its environmental impact and the general experience of working in industrial manufacturing. An added bonus of interacting with younger students is the opportunity to head off any negative or outdated opinions before they are formed. This includes ensuring students understand that there are many diverse career paths for all types of skills and interests.
Within the steel industry alone, there exist over 140,000 jobs that are directly created from today’s modern steel production process, ranging from manufacturing and engineering careers and roles in project management, to sales, accounting, logistics and construction positions. The possibilities are endless!
According to the U.S. Bureau of Labor Statistics, the number of workers in STEM fields is projected to increase by almost 11% by 2031, over two times faster than the total for all other occupations combined, while also offering salaries that are over twice as high. This makes careers in STEM-related fields both highly competitive and desirable.
However, a report from Gallup and Walton
Family Foundation found that while 75% of Gen Z are interested in STEM fields, “only 29% list a STEM role as their first-choice career.” This data highlights a significant lack of exposure to STEM careers, including those in manufacturing. And this is far from an isolated issue — only 33% of 2023 graduates felt
their schools regularly exposed them to diverse career options.
As society and industries face increasingly complex issues, providing students with opportunities to practice these skills and engage with STEM professionals will help create a more talented future workforce. By being proactive
in their local communities, manufacturers have an incredible opportunity to not only provide students with valuable real-world insights, but companies can also enhance their future workforce pipeline by sparking early interest in their industries and establishing meaningful connections with the next generation of professionals.
The Energetic Strategic Business Unit of EaglePicher Technologies, manufactures a wide variety of explosive and pyrotechnic devices.
nergetics are explosive or pyrotechnic devices that take a small input of mechanical or electrical energy and through a precisely controlled reaction make it, basically, more explosive. The amount of released energy and how that energy is used depends on the design of the device and its application. The inherent advantages of these devices include high power-to-weight ratio, compact size, low input energy requirements, and, as you might expect from something involving an explosion, extreme reliability.
The Energetics Strategic Business Unit is an outgrowth of EaglePicher Technlogies long-
standing specialty battery business in support of major defense, space, aviation, and commercial programs. Eagle Picher qualifies as a certified small business that is the leading U.S. maker of thermal batteries. Founded as a mining and lead business in 1843, the company started making batteries in 1922. With manufacturing operations and research and development sites based in the Midwest and Northeast, EaglePicher Technologies supplies over 90 percent of the U.S. military’s munitions and mission critical systems.
“The Energetics unit supplies explosive and
pyrotechnics devices to prime contractors, such as Lockheed Martin or Rockwell,” explains Jantzen Westfall, Director of Operations. “Although we do some commercial work, we primarily support defense programs.”
Explosive devices are used in artillery, mortar, cannon and bomb fuzing, and warhead detonation. Pyrotechnic devices are primarily used to initiate motion, ignite materials, pressurize a container, close or open a circuit, and generate gas, among other applications.
Typically, the prime contractor supplies the build specifications. “We’re essentially a kind of job shop,” Westfall says. “We primarily build to order though we can sometimes modify existing designs to meet customer requirements. The
MAPP Technologies is a high-performance Aerospace & Defense OEM manufacturing and aftermarket repair organization. For over 70 years, we have proudly served the Maritime, Aerospace, and PowerGen industries.
We value our partnership as a trusted supplier to EAGLEPICHER, supporting their commitment to excellence.
We deliver to our clients, precision-engineered solutions that drive mission-critical success through a variety of highly technical internal special processes. Going above and beyond for our OEM clients, we offer: Engineering & Product Development | Machine & Fabrication | Repair & Overhaul | Quality & Nadcap Accreditation
Energetics unit of EaglePicher provides defense customers with a single source of high quality, high volume devices custom built under quick lead times.”
Stefan Holt Marketing Director at MSIViking, notes, “Our Hexagon Coordinate Measuring Machines (CMMs) delivers leading metrology solutions to EaglePicher Energetics as well as its many other business units that ensure the highest accuracy, reliability, and effi ciency. These solutions encompass multi-sensor systems and high-speed scanning to provide unparalleled data quality and inspection issues. Working with Hexagon CMM, EaglePicher attains the highest level of quality control to achieve consistent results with minimal downtime.”
in researching pyrotechnic devices in 1984, eventually going into production of an igniter in 1995. By 2003, demand necessitated cre ation of a separate Energetic Business Unit to engage in numerous contracted ventures rang ing from explosive leads, detonators, bellows,
Hexagon Manufacturing Intelligence. Hexagon’s Manufacturing Intelligence division is at the forefront of innovation, providing cutting-edge solutions that empower manufacturers to enhance productivity and quality. www.msi-viking.com
igniters, and burst assemblies to fully assembled lanyard start assemblies and bottle cutters. In June 1995, EaglePicher acquired a licensing agreement and exclusive production rights to a line of specialized explosive devices developed
As part of one of the two largest domestic battery suppliers, the Energetics unit is in a particularly good place to win competitive contractor bids. In addition to longstanding relationships with the major defense contractor customers, Westfall points out that EaglePicher providing additional advantages qualifying for
Also, there the many synergies with other business units within EaglePicher that create
For over 60 years, Networks Electronic Company (NEco) has provided innovative, miniature pyrotechnic and ordnance solutions to the aerospace and defense markets. Our diverse product family includes igniters, initiators, cord and cable cutters, pressure cartridges, gas generators, piston and retracting actuators, thermal relays and squib switches. NEco’s commitment to customer responsiveness, design excellence, manufacturing flexibility, and product reliability is the foundation for our strong industry partnerships. ptitechnologies.com
Joplin, Missouri based MAPP Technologies L.L.C. is a privately-held Aerospace & Defense manufacturing and aftermarket services company delivering critical components to OEM print specifications using specialized process capabilities; from raw material through complex machining, welding, coating, assembly, and final inspection – providing best-in-class value, quality, and just-in-time delivery to our global customers throughout the maritime, aerospace, and power generation industries. We contribute to a world in which people reliably feel protected, safe, and secure.
At MAPP, we optimize supply chain operations to maximize customer value and create a sustaining competitive edge. Our expertise in highly technical internal special processes enables us to deliver innovative, high-quality solutions tailored to our clients’ needs. With Nadcap accreditations, we uphold the highest industry standards, demonstrating our unwavering commitment to precision, reliability, and excellence. We specialize in managing supply chain activities to maximize customer value and achieve a sustainable competitive advantage. Our Nadcap accreditation demonstrates our organization’s ongoing commitment to quality and we excel in a variety of internal technical process that provide our clients with one-stop-shop solutions.
Contact us for further information. Sales & Service: sales@mapptechnologies.com | mapp-technologies.com
new business opportunities. “All the divisions are involved in working with one another to develop and supply product,” Westfall says.
Westfall notes that the Energetics unit expects business growth of 30 to 50 percent over the next three to four years. Which is why construction of a new 55,000 square foot facility is underway, representing a $30 million investment in that expected growth. The new manufacturing facility features state-of-the-art advancements in manufacturing technology with semi-automatic capabilities, as well as advanced software for data retrieval and tracking.
Thanks to the Missouri Works program, the company is eligible for certain capital withholdings or tax credits for job creation and may also receive assistance from Missouri One Start, a division of the Department of Economic Development, for assistance with its recruitment and training needs.
“We are currently based in Seneca, Missouri,” Westfall notes, “on the border of Oklahoma. The new facility is co-located with four other EaglePicher manufacturing and research and development sites in Joplin, about 20 minutes away. Joplin, Missouri has been the heart of EaglePicher since the company was founded. So, in addition to a new facility, we’ll be located in a bigger city that should help us draw more interest in getting people to fill new jobs.”
Energetics currently employs about 100, but
expects that number to double in the next three to four years. “EaglePicher is a great employer,” Westfall says, “offering competitive pay, generous medical benefits, paid holidays and vacation, performance-sharing and tuition reimbursement. Plus, we’re working in a brand new climate-controlled environment that is a lot different from the perception of manufacturing as a hot, dirty workplace.”
He adds that, “An additional advantage with our move to Joplin is we can work with surrounding colleges to develop programs and
recruit students interested in manufacturing careers. It’s going to help us develop a better prospect pool. We’re basically looking for people with a manufacturing background who we can train and who fit in with our culture. Our needs range from assembly workers to material scientists to robot programmers.”
As an American manufacturer, the Energetics unit emphasizes a local supply. “Of course, we’re always looking to diversify and expand
our supply chain to ensure we can get what we need, when we need it, at the highest quality we require,” Westfall says. “To maintain products that meet the high quality we demand, any supplier providing parts, materials or services must maintain a quality system certified to ISO 9001.”
He adds that, “Our goal is to provide customers with the highest quality energetics solution from concept through final production for their applications. We are committed to continuous improvement, with the rigorous application of
Jantzen Westfall Director of Operations – Energetics
Six Sigma methodologies, as well as our ISO 9001:2009 and AS9100C certifications.”
The explosive organic growth of EaglePicher’s Energetics unit is fueled by brand name reputation, history of quality products and innovation. “We’re always looking to develop new opportunities that make sense for us, and make sense for our customers,” Westfall says. “We’re always striving to make a better cutting-edge product.”
Brooklyn Navy Yard once symbolized industrial might by launching warships. Now, it’s proving industry can flourish in the heart of a city.
For nearly two centuries, the Brooklyn Navy Yard was a bastion of American industry, churning out vessels that powered our nation’s military and maritime endeavors. Today, it stands as a cornerstone of urban advanced manufacturing, hosting over 550 businesses at various scales that generate more than $2.5 billion annually for New York
City’s economy and employ over 13,000 people. While the Yard is no longer fitting out and launching warships, our mission to innovate, produce and employ New Yorkers remains.
Modern manufacturing, often called advanced manufacturing, looks and feels nothing like the traditional images we see in everyday culture.
We might still picture the old photographs from the Yard’s archives, showing men— and occasionally women—laboring in difficult, hazardous tasks, but those scenes no longer reflect the reality of today’s high-tech, safety-focused manufacturing environments. The reality of today’s factories and R&D centers differ
Pictured: The Brooklyn Navy Yard (the Yard) is a mission-driven industrial park that is a nationally acclaimed model of the viability and positive impact of modern, urban industrial development. The Yard is home to 450+ businesses employing more than 11,000 people and generating over $2.5 billion per year in economic impact for the city. Building on the Yard’s history as the economic heart of Brooklyn, the 300-acre waterfront asset offers a critical pathway to the middle class for many New Yorkers; right: The CNC Operator Training Program at the Brooklyn Navy Yard focuses on preparing Brooklyn communities for in-demand careers in advanced manufacturing. Led by the Workforce Development Department’s Employment Center and through partnerships with BNYDC employers, this program provides industry-driven training that directly meets workforce needs and offers job placement support for free.
Photo credit: Brooklyn Navy Yard Development Corporation.
dramatically from the pasts but bridging that gap has required – and still requires – intentional planning, strategic investment and a hefty bit of aspiration and persistence. Our story at the Brooklyn Navy Yard is a model for cities worldwide for how to reinvent underutilized or historical industrial spaces and transform them into ecosystems of equitable economic growth and community development in the 21st century.
Truly incubating and growing industries locally is not merely about siting physical production
plants, but also creating ecosystems where shared resources, ideas and opportunities converge and where businesses grow through stages of their life cycle in one place. By rehabilitating and repurposing the Yard’s historic buildings, we’ve created spaces that reflect our rich history while flexibly accommodating the infrastructure needs of today and tomorrow’s advanced manufacturing companies.
The message is clear: history can serve as inspiration rather than an obstacle. Many of our tenants, and even the investors who visit them, point to the Yard’s history as a reason why they are here and what makes the Yard special.
Instead of constructing nondescript facilities
on the city’s outskirts, rooting a manufacturing business ecosystem within a vibrant urban setting enables immediate access to a diverse talent pool, accessible transportation, educational institutions and business connections. Furthermore, a campus setting allows multiple companies to converge in the same place and add value to each other. It creates enough scale where beneficial services – such as talent sourcing and placement, worker training and original research facilities – can be localized very close to business operations. Companies choose the Yard for several reasons that are “bigger” than the spaces they are leasing – they want
Pictured: The Market @ 77 is a vibrant food hall located on the ground floor of Building 77 in the Brooklyn Navy Yard. This culinary destination offers a diverse array of beloved food vendors – some of whom manufacture their wholesale products on-site – offering Market visitors everything from freshly baked bagels with lox to piping hot pizza and delicious tacos;
right: BNYDC’s mission is to fuel New York City’s economic vitality by creating and preserving quality jobs, growing the City’s modern industrial sector and its businesses, and connecting the local community with the economic opportunity and resources of the Yard.
Photo credit: Brooklyn Navy Yard Development Corporation.
to be in New York with its array of talent and general urban vibrancy, and they want an ecosystem of like-minded entrepreneurs. The synergy between place and purpose fosters a collaborative ecosystem, ensuring big ideas have a place to be tested and advanced with ample though partnership.
How we at the Brooklyn Navy Yard create that ecosystem is based on our foundational relationships with anchor partners who share our
vision for creating a modern manufacturing and innovation hub. To state the obvious, incubating industries requires actual incubators and organizations that support businesses in their infancy. At the Yard, we have two such institutions: Newlab and The Research Yard.
Almost a decade ago, we partnered with Newlab, a multi-faceted business that helps startups grow and achieve impact by leveraging a unique space built with shared fabrication and product development labs. These labs are surrounded by flexible office spaces and shared amenities like a self-serve food & beverage area,
conference rooms and an event space for conferences and product showcases. The concept of Newlab was created through the same public-private collaborations that allow the broader Yard to flourish – a mix of real estate, property
management and program expertise working together to support job and company creation and growth. Newlab played a huge role in seeding the idea that modern manufacturing can thrive in an urban setting. Today, over a dozen
companies have evolved from their infancy at Newlab and are part of a growing group of maturing startups with their own dedicated spaces at the Yard, such as Amogy and 10xBETA. Dozens of new entrepreneurs have taken up residence in the spaces left at Newlab, creating a virtuous cycle of new economic activity.
Similarly, in the last two years, we worked with Pratt Institute to create a multi-institution academic research facility focused on “producing” activities. Faculty and students from the university come to the Yard to work on projects they hope to turn into business endeavors, ranging from robotics to sustainable materials like AquaSteady.
These partnerships exemplify our ability to support a business from research to early stage through growth and commercial operations. Having this variety is only possible through partnerships with other institutions who share our goals.
Successful business growth campuses and communities don’t just host startups; they help fuel growing industries and prepare the future workforce. This is truer in the rapidly evolving
Pictured: The Yard was once the nation’s most storied naval shipbuilding facility, which for over 150 years built and launched America’s most famous fighting ships, including the USS Maine, USS Arizona, and USS Missouri. The Yard also served as an important point of the passage, home, and workplace for countless veterans as they served our country. Through its public programming, the Yard continues to honor and preserve this rich history.
Photo credit: Brooklyn Navy Yard Development Corporation.
manufacturing sector. One of the Yard’s unique flagship initiatives is our CNC Operator Training Program. Participants gain skills, industry certifications, and most importantly, an upskilled pathway to employment in advanced manufacturing. Once complete, our employ-
ment center connects them with job opportunities at the Yard and beyond – ensuring a steady pipeline of skilled workers to support the very businesses we host. This also grows the talent pool required to fill in-demand jobs. Crucially this program does not require prior technical
Pictured: By delivering NIMS certifications in core CNC skills, the CNC Training program helps individuals gain entry into high-demand fields, creating pathways to economic advancement while strengthening NYC’s manufacturing workforce and meeting industry demand.
Photo credit: Brooklyn Navy Yard Development Corporation.
experience or degrees, simply familiarity with a production environment and general technology comfort.
This program, along with our on-site employment center, is centered on the Yard’s commitment to diversity, equity and inclusion, actively recruiting women, people of color and economically disadvantaged individuals who have historically faced barriers to entry in the manufacturing industry. By breaking down hurdles, we pave the way for participants to achieve economic mobility and attain higher-paying leadership roles. In many cases, newly certified workers are also armed to pursue their own entrepreneurial pathways—launching micro-enterprises or applying their expertise to product development—ultimately fueling a virtuous cycle that transforms job seekers into job creators and energizing the entire urban industrial ecosystem.
Additionally, we incubated and are an anchor partner to the Brooklyn STEAM Center, an on-site “next generation” technical high school that trains students in six pathways. The pathways are rooted in growing industries in our local economy and supported by industry-based faculty who work alongside traditional teachers with curriculum, internships and work-based learning experiences, often developed and hosted by the modern manufacturing businesses at the Yard. STEAM scholars not only graduate with advanced high school diplomas, but also with professional credentials
and college credits.
Integrating workforce development throughout stages of growth has proven to be an investment among tenants, trainees and established companies. Startups gain access to a local labor pool that is well-trained and diverse and aspiring professionals find a clear route to growth in interesting, tactile industries.
When incubators actively cultivate these connections, they become the nucleus of a healthy, thriving economic ecosystem.
To achieve real success, economic development projects cannot exist in a silo or isolate themselves from surrounding neighborhoods. We’ve learned the power of this principle through our public facing amenities—like the Market @77 food hall and intentionally curated public programming that supports small businesses while bridging the gap between community and industry.
Inviting the public to experience the fruits of manufacturing innovation—whether it’s accessing quality jobs or attending an open house or middle school tour—breeds awareness and plants seeds of opportunity. In turn, this fosters a culture where local communities champion the success of projects and see themselves as part of the project, rather than viewing them as gentrifying forces or unapproachable sites.
Lindsay Greene is the President & CEO of the Brooklyn Navy Yard Development Corporation, which includes managing and operating six million square feet of industrial real estate across 300-acres in the heart of New York City. Greene is charged with deepening and expanding the Yard’s mission, investing in future career pathways, and creating pipelines for underserved communities to fill these jobs. She previously served as Chief Strategy Officer of the New York City Economic Development Corporation, where she oversaw economic analysis, business development, inclusive job growth, and innovation strategies. school group.
Urban manufacturing centers must help solve the challenges of our time—one prime example being the sustainable use of energy and resource scarcity. Through adaptive reuse of our historic buildings, investments in renewable energy and educational events, we’ve shown that sustainability can coexist (and thrive) in an industrial manufacturing setting.
Tenants at the Yard span cutting-edge fields like clean energy, sustainable transportation and building decarbonization, all benefiting from an environment that encourages responsible, forward-thinking production practices. This focus on sustainability is a global imperative and
drives markets forward.
More recently, the innovation ecosystem at the Yard has seen the growth of med-tech and medical device businesses working to solve healthcare challenges for people with disabilities or rural preventive care access. Many of these companies are collaborating with each other and with other producers at the Yard, reinforcing that disparate industries can be value-add neighbors.
Finally, for manufacturing ecosystems to succeed, they must be more than just a collection of startups sharing buildings or production space. They need to offer structured avenues for collaboration, supply chain connectivity and
scalability, and a network of service partners to support the evolution of small businesses (i.e. capital providers, experts in operational systems and advisors in marketing and legal issues). Furthermore, these business advancement resources must also be well-crafted to support entrepreneurs from various backgrounds across industries. At the Brooklyn Navy Yard, we’ve built relationships with local universities, government agencies and industry partners all under the mission to connect businesses and entrepreneurs with resources to grow beyond the prototype stage. From city procurement opportunities to research and development collaborations, our network helps innovators expand within the supportive ecosystem that nurtured them.
Cultivating modern manufacturing communities in the U.S. where “factories” have an outdated and relatively one-dimensional identity and the idea of working in manufacturing no longer carries the same level of dignity and pride that it once did, requires consistent commitment to a vision. The road will be tough. All manner of stakeholders will doubt why you are doing what you are doing. The national dialogue around industrial policy and how the U.S. has or has not succeeded with its policies exemplifies this tension. Some of the new companies that seem promising in their early days will not survive and some established companies will struggle to
evolve. Do not let these examples and the skepticism they create be a deterrent. Entrepreneurs must think bigger than they can immediately see or realize. Charting a new path for economic development that supports entrepreneurs and builds real and accessible middle-class careers and economic opportunities for all requires that same mindset.
Manufacturing and innovation ecosystems do more than just propel fledgling companies — they catalyze entire industries, invest in neighborhoods and make cities stronger. In an era where manufacturing is taking center-stage in the national economic conversation, the Brooklyn Navy Yard can serve as a model for business incubation centers in industries where rapid advancement and strategic investment is most critical. If we want economic development projects that sustainably deliver on the promise of industry growth, they must be thoughtfully integrated into the communities where they are located, provide robust workforce development opportunities, cultivate a diverse group of entrepreneurs and support the formation of an ecosystem that supports strong partnerships and helps emerging companies scale.
We have seen firsthand the revitalizing impact a well-rounded manufacturing incubator model can have on businesses and communities, growing meaningful job opportunities in urban environments.
How NovaSpark’s hydrogen technology enables cleaner, portable, and resilient energy solutions for mission-critical military operations.
Modern militaries depend heavily on fossil fuels
to power vehicles, aircraft, bases, and critical systems. This dependency creates significant logistical, economic, and strategic challenges. Transporting fuel to remote or contested areas is both costly and hazardous, as supply lines are prime targets in conflict zones. Furthermore, fluctuating global oil markets can destabilize budgets and operational planning, leaving forces vulnerable to resource shortages at critical moments.
This reliance also poses strategic vulnerabilities. Disruption of energy supply chains can undermine mission success, as demonstrated by the ripple effects of a single attack on a fuel convoy, which can compromise mobility, communications, and overall combat effectiveness. Additionally, the environmental impact of fossil fuels can strain relationships with host nations and detract from sustainability goals.
To address these challenges, there is an urgent need for energy systems that are secure, sustainable, and adaptable to remote or austere environments. Renewable technologies such as hydrogen and solar provide a path to reduce reliance on fossil fuels while enhancing energy resilience. These solutions also align with emerging military priorities, including improving energy efficiency, reducing carbon emissions, and extending mission endurance.
Portable energy systems are particularly valuable for forward-deployed units and remote installations, where resupply missions are costly and high-risk. Innovations in on-site energy generation and scalable storage are critical to ensuring operational success in increasingly complex and unpredictable environments.
NovaSpark is leading this energy revolution with advanced hydrogen-powered solutions
designed to meet the demands of modern militaries. Our mobile hydrogen generators extract moisture from the air and convert it into clean hydrogen fuel. This eliminates the need for fuel convoys, reduces logistical risks, and provides a portable, self-sustaining energy source that operates in resource-scarce environments.
With hydrogen’s high energy density and
Pictured: Training on the NovaSpark Atmospheric Hydrogen Generation Technology; right: NovaSpark Fueling Training for Drones and Ultralight Vehicles.
NovaSpark’s modular system design, our solutions power a wide range of applications, from forward operating bases (FOBs) to advanced drones and autonomous systems. This capability enhances operational flexibility, reduces carbon footprints, and increases energy independence, directly addressing the vulnerabilities inherent in fossil fuel dependency.
NovaSpark’s patented atmospheric hydrogen generation technology uses moisture in the air to produce pure hydrogen on-demand. This breakthrough eliminates reliance on tra-
ditional water sources or complex infrastructure, enabling sustainable energy generation in remote or contested environments.
By producing hydrogen on-site, NovaSpark eliminates the logistical challenges and costs associated with transporting fuels. This innovation is ideal for military operations in resource-limited areas, ensuring energy availability in even the most challenging conditions.
NovaSpark’s hydrogen systems offer unparalleled versatility and reliability for both stationary and mobile applications. Integrated with hydrogen fuel cells, these systems provide
Pictured: Mobile Power and Fueling Unit on JLTV (Joint Light Tactical Vehicle) Trailer; right: NovaSpark Rendering of Solar Panels Deployed.
efficient, zero-emission energy for various military operations:
• Mobile Power: Portable hydrogen generators and fuel cells provide energy for vehicles, command centers, and mobile medical units, ensuring consistent power on the move.
• Fixed Operations: For bases and infrastructure, NovaSpark offers scalable systems that power communications, radar, and critical life-support systems, enabling uninterrupted operations in harsh environments.
NovaSpark’s hydrogen technology addresses a range of operational needs with innovative solutions:
• Drone Fueling: Hydrogen-powered drones offer extended flight durations and payload capacities compared to battery alternatives.
NovaSpark enables on-site hydrogen genera-
Rick Harlow, Co-Founder of NovaSpark Energy, has been instrumental in driving the company’s rapid growth in the hydrogen energy sector. His leadership has secured capital, forged strategic partnerships, enhanced manufacturing operations, and integrated Industrial IoT to elevate NovaSpark’s technological edge. Under Rick’s vision, NovaSpark is transforming energy and job creation in manufacturing that help accelerate economic development in the United States.
tion for drone refueling, reducing logistical burdens and improving mission readiness.
• High-Altitude Reconnaissance Balloons: These platforms rely on hydrogen to remain operational for long periods. NovaSpark’s solutions provide the necessary fuel for sustained surveillance and communication without frequent resupply.
• Fuel Cells for Vehicles and Equipment: Hydrogen fuel cells deliver a quiet, efficient, and emission-free energy source for tactical vehicles and equipment, enhancing stealth and mobility while reducing reliance on supply lines.
• Forward Operating Bases (FOBs): NovaSpark’s systems ensure energy self-suffi-
ciency by generating hydrogen on-site, reducing the dependency on vulnerable fuel convoys and supporting critical operations such as surveillance, communications, and life support.
• Disaster Response and Humanitarian Missions: NovaSpark’s portable systems provide clean energy for disaster-stricken areas, accelerating response efforts and supporting essential infrastructure like water purification and medical equipment.
NovaSpark is redefining energy strategies for militaries in the 21st century. Our hydrogen solutions provide reliable, sustainable, and
portable energy, empowering military forces to operate more effectively in unpredictable and contested environments. From powering UAVs to fueling FOBs, NovaSpark delivers the tools needed to enhance resilience, reduce environmental impact, and maintain a strategic edge.
NovaSpark has successfully partnered with
the U.S. Marines, U.S. Army, and Defense Innovation Unit (DIU) to deploy hydrogen-powered technologies tailored for mission-critical applications:
• Drone Fueling Systems: NovaSpark collaborated with the Army and DIU to develop hydrogen fueling systems for UAVs (unmanned aerial vehicles). By enabling on-demand hydrogen generation at the tactical edge, NovaSpark extended drone flight ranges and operational
endurance, improving situational awareness and reducing resupply requirements.
• Mobile Hydrogen Generators for Remote Bases: In remote or austere locations, NovaSpark’s systems enabled energy self-sufficiency, reducing reliance on traditional fuel supply chains and ensuring operational sustainability.
• Hybrid Backup Solutions: NovaSpark’s hydrogen systems provided reliable backup power for critical infrastructure such as command centers and communication hubs, ensuring operational continuity in all scenarios.
• Operational Resilience: Hydrogen reduces dependence on fossil fuel supply chains, providing a secure and consistent energy source even in contested areas.
• Enhanced Agility: Portable hydrogen sys-
tems allow military units to operate effectively in remote locations without relying on extensive logistical support.
• Reduced Environmental Impact: Zeroemission hydrogen technology aligns with global sustainability goals and military decarbonization efforts.
• Cost-Effectiveness: On-site hydrogen production minimizes transportation costs and risks, delivering long-term financial and operational benefits.
• Technological Superiority: Adopting cutting-edge hydrogen systems positions militaries as leaders in innovation, ensuring a strategic advantage in future operations.
NovaSpark’s hydrogen technology aligns with broader sustainability initiatives by reducing
Pictured: Training on Electrolysis and Power Management of NovaSpark System.
NovaSpark is revolutionizing energy with patented atmospheric hydrogen generation technology. From powering military logistics, drones, and aerospace to supporting civilian transportation and infrastructure, our solutions provide clean, on-demand energy while reducing emissions and enhancing resilience. By integrating hydrogen across sectors, we are addressing global energy challenges with scalable, sustainable innovations. NovaSpark invites collaboration with partners to accelerate hydrogen adoption and build a cleaner, more secure energy future.
emissions and promoting renewable energy adoption. By integrating hydrogen into their energy strategies, militaries can contribute to international environmental agreements while maintaining mission readiness.
Adopting hydrogen technologies also strengthens partnerships with allies and host nations, demonstrating a commitment to shared sustainability goals and energy resilience.
NovaSpark envisions hydrogen as a cornerstone of energy solutions for both defense and civilian sectors. From military applications like autonomous vehicles and mobile bases to civilian uses such as disaster response and off-grid energy systems, hydrogen offers unmatched versatility and sustainability.
We invite partners to collaborate with NovaSpark to accelerate the adoption of on-site, on-demand hydrogen technologies, driving innovation for a cleaner, more resilient future.
NovaSpark’s hydrogen-powered solutions deliver reduced logistical challenges, lower emissions, and enhanced energy independence, enabling militaries, the Federal Government, State Governments and commercial companies
to operate more effectively in the most demanding environments. By addressing critical energy vulnerabilities, NovaSpark paves the way for more efficient and sustainable operations, setting a new standard for energy in modern battlefields
In addition to transforming military energy strategies, NovaSpark is driving economic growth and creating new job opportunities in advanced manufacturing. By investing in state-of-the-art production facilities and innovative technologies, NovaSpark is contributing to the revitalization of American manufacturing industries. These efforts not only generate high-quality jobs but also enhance workforce development in areas such as engineering, technology and of course energy.
NovaSpark’s commitment to bolstering the U.S. economy extends beyond domestic operations. By collaborating with foreign partners to bring manufacturing jobs back to America, NovaSpark is strengthening domestic supply chains and reducing reliance on overseas production. These partnerships support economic resilience while positioning the United States as a global leader in hydrogen energy innovation.
Through its dedication to sustainable energy, economic revitalization, and global collaboration, NovaSpark is advancing a vision of reliable energy solutions that empower militaries, create jobs, and drive growth in the U.S. economy, all while fostering strong international partnerships.
Rathburn Precision Machining is an agile partner for customer solutions that meet demanding accuracy and quality goals for metal parts.
When Vietnam war veteran Jerry Rathburn started his company in 1983, he focused on quality parts made by good people who cared about the work they did.
Today, Rathburn Precision Machining is led by one of Jerry’s daughters, Angie Holt, and is a certified woman-owned company. Though the
leadership has changed, the company’s focus on quality people and parts has not. In 2024, Rathburn changed their name from “Tool & Manufacturing” to “Rathburn Precision Machining”.
According to company President Angie Holt, the change was a reflection of the brand’s growth. “We have evolved considerably from a
job shop to a full-service company offering high precision quality production parts. Our name needed to reflect both the evolution and help people clearly understand what we do.”
Based in Auburn, Indiana at a 40,000 squarefoot facility, Rathburn is strategically situated to serve customers in the Midwest and beyond that need quality, American-made metal components. Rathburn specializes in precision-machined metal components (aluminum, cast iron, steel, brass, stainless steel and superalloys) in a turning envelope of 38mm diameter for Swiss, 8” diameter for gantry-fed lathes, 10” diameter for chucker work, and a 20” cube for milling. The company can produce quantities between 100 to 200,000 or more per year, depending on complexity, with an ideal part weight of less than 30 pounds.
“For the first 30+ years of our history our customer base was focused on the heavy trucking industry,” Holt explains, “While we still work with customers in that space, we have expanded to other sectors and connect well with customers looking for automotive-level quality from a company that is more than just a supplier. We work best with people who want and need an agile partner who is working side-by-side with them to find great solutions to their challenges. Our engineers meet with customers to fully understand their needs, tolerances, volume,
Pictured: Rathburn is committed to having the latest equipment to enable its skilled employees to craft the highest quality parts.
Plex, by Rockwell Automation, is a leader in cloud-delivered smart manufacturing solutions, empowering the world’s manufacturers to make awesome products. Our platform gives manufacturers the ability to connect, automate, track, and analyze every aspect of their business to drive transformation. The Plex Smart Manufacturing Platform™ includes solutions for manufacturing execution (MES), ERP, quality, supply chain planning and management, asset performance management, production monitoring, process automation and analytics to connect people, systems, machines and supply chains, enabling them to lead with precision, efficiency and agility. To learn more, visit http://www.plex.com.
materials, and other requirements, and then create a plan to meet those needs.”
Holt says the typical solution is built to customer-provided prints, but Rathburn is also asked at times to develop prototypes or alternative solutions in partnership with customers. “We proactively help address customer issues.”
In one example, a manufacturer was facing increased demand at a time when their supplier was failing to meet their quality and delivery needs. Rathburn was able to ramp up quickly to address their machining needs, improve quality and delivery, and enable more scalability as the market flexed.
Rathburn’s engineering team met with the customer’s Engineer and Quality Manager to review prints, understand critical features, and hear frustrations. Doing this before starting manufacturing enabled the team to proactively solve challenges and ensure the customer got the quality parts they needed from the start.
For instance, during the review, the Rathburn team discovered that the finish expectations weren’t detailed on the prints. By identifying the issue before manufacturing, the first samples delivered exceeded expectations and resulted in the customer placing regular monthly orders.
Holt identifies several critical components that uniquely enable Rathburn to meet customer needs—quality standards, technology, people, and small-town values.
“We meet or exceed the quality expectations of our customers,” Holt says. “Rathburn has a Quality Management System compliant with ISO 9001, IATF 16949, and AS9100 standards. Our dedicated team of experienced professionals achieve the highest quality by following established processes and adhering to customer specifications.”
She adds, “Many of our customers rely on Rathburn to provide parts as needed and scale up or down according to market demand, with the same level of quality and speed of delivery. That could be in the next quarter, the next year, or even once every ten years.”
Repeatability and high quality are achievable with Rathburn’s advanced automation and robot technologies. Equipment includes the latest CNC (Computerized Numerical Control) mills and lathes outfitted with bar feeders, parts catchers, robotics, and live tooling. Latest investments include a twin spindle gantry lathe, a pair of automated saws, wire EDM and collaborative robots that improve precision and greatly reduce the potential for human error.
Rathburn also maintains a climate-controlled Quality Lab that utilizes three Coordinate Measurement Machines (CMM), an Optical Comparator, a Surface Roughness Tester, and other metrology equipment that ensure consistent and precise gauging and measurement inspections. These quality tools and processes enable Rathburn to manage a significant volume of parts with <1% internal scrap rate.
“In late 2024, we transitioned to the Plex Smart Manufacturing Platform by Rockwell Automation as our Enterprise Resource Planning (ERP) / Material Resource Planning (MRP) system.” Holt notes. “It is helping us
Pictured: Rathburn leverages the latest in CNC, Wire EDM, and Quality Lab equipment to deliver precision solutions.
to access real-time data, monitor efficiencies, manage our inventory, and streamline production, among other capabilities. We are also using it to transition to a fully digital shop floor, which will include digital work instructions and inspections.”
She adds, “This software system combines the functionality of our previous programs to allow for one true source of data, from customer-specific requirements to causes of internal scrap to employee training progress. It allows our employees to have more time to better utilize their talents and reach their full potential.”
A commitment to technology does not interfere with the company’s commitment to its people. Which is why Rathburn was recently named one of the Best Places to Work in Indiana. “We have 30 employees, many of whom have been with the company for five years or more,” Holt explains “Many of them started as temps who we eventually hired permanently. It’s easier for us to train people who have the right attitude, are willing to learn, and are a good fit with our culture.”
She adds, “Rathburn is a family business and we treat our employees like family. We offer good wages with benefits including healthcare, matching 401K plans, and wellness programs. We also invite employee suggestions about how to make their jobs more efficient and achieve continuous improvement. If something makes sense, we’ll try it. If it doesn’t work out, we’re open to try the next idea.”
Last but not least is what Rathburn touts as “small town values.” According to Holt, “Our company character is represented every day in how we operate, how we work together, and how we commit to working hard to make a difference every day with deliverable, manufacturable solutions. Our aim is to make working with Rathburn as easy and enjoyable as it is effective. When done well, our values will show in the people who work here and the quality of work we produce every day.
Ontario’s St Marys Cement manufactures high-quality cement products used in infrastructure, resident and commercial building construction.
As a major North American producer of cementitious materials, with a commitment to innovation and sustainability as well as community involvement, St Marys Cement is a construction cornerstone trusted by building contractors for well over a hundred years. Founded in 1912, St Marys Cement is a subsidiary of Votorantim Cimentos North America (VCNA). Votorantim Cimentos is a global company focused on building materials, mining, agricultural lime, co-processing, and waste management.
The St Marys Cement legacy includes such landmark projects as CN Tower, Roy Thompson Hall, Maple Leaf Gardens and the Darlington Nuclear Station, as well other
Blast furnace slag granulation is the greenest product available to the cement industry. With one new system recently commissioned, and two under construction, SMS group is leading the industry in this technology.
Technological leadership, improving sustainability & decarbonization
The Paul Wurth INBA® slag granulation system is an advanced technology designed to transform slag into a valuable product for the cement industry. This process involves granulating the slag using water, followed by dewatering with the dynamic INBA® dewatering drum. The system is highly flexible and compact, allowing it to be integrated seamlessly into various plant configurations.
Key Benefits:
• Efficient slag processing
• Produce high-quality granulated blast furnace slag
• Green direct replacement for Portland Cement
• Reduced emissions
renowned engineering, civic and residential projects that have contributed to the growth and prosperity of the region. Company operations are based in St Marys, Ontario, Canada with a head office in Toronto and various strategically located production and distribution facilities in New Brunswick, Nova Scotia, Quebec, and the Great Lakes region of the U.S.
Product lines include:
• Portland Cement. This finely ground powder is mixed with sand, stone, and water to produce concrete.
• Blended Cement. This produced provides enhanced performance and durability with reduced environmental impact by reducing the energy required to produce concrete. Consequently, “green” blended cement can help achieve LEED points.
• Slag Cement. Produced by finely grinding granulated blast furnace slag, a glassy by-product of iron production, blended with Portland cement. This long-lasting product is also a “green” cement.
• Masonry Cements. These products consist
of a balanced mixture of Portland cement, limestone, and proprietary additives to produce types N and S mortars in compliance with ASTM C-270 requirements for both proportion and property specifications to meet a range of challenging fabrication needs.
Hutton Transport Limited, a subsidiary of St Marys Cement, delivers bulk and bag cement products employing more than 90 tractors and 115 trailers to markets in southern Ontario, western New York and Michigan. Hutton also provides logistics services to a wide variety of other shippers of commodities such as silicates, fly ash, barite, slag, steel, lumber, concrete
beams and blocks, paving stone, and fabricated assemblies.
St Marys Cement’s focus on innovation puts them at the forefront of the industry, particularly in terms of eco-friendly products and technologies aimed at reducing the environmental impact of cement manufacturing. As a VCNA company, St Marys Cement is part of the global Cement Sustainability Initiative (CSI) developed in partnership with the World Business Council for Sustainable Development (WBCSD) to reduce CO2 emissions.
One example of the company’s environmental best practices is its work with Verdera, the
waste management business unit of St Marys Cement parent company, to employ waste materials as low-carbon fuels and resources in cement manufacturing. While cement manufacturing typically employs limestone, shale or clay, sand, and iron ore, St Marys Cement kilns also use other industry by-products that reduce carbon emissions and provide cleaner thermal energy.
St Marys Cement operates the first-of-its-kind algal biorefinery demonstration project that employs carbon dioxide waste as a fuel. The
$4 million, 1500 square-foot plant utilizes technologies developed by Pond Technologies, an algae production company based in Markham, Ontario, with additional support from Canada’s National Research Council (NRC) through its Algal Carbon Conversion Program. How it works is that untreated emissions from the kiln smokestack at the St Marys cement plant are channeled into a custom photobioreactor developed by the Pond team. Fast-growing algae inside the reactor consume the gases, creating tons of biomass in the process.
Currently, the biomass is used primarily for further NRC studies, but the long-term goal is
OPTIMIZE YOUR CEMENT PRODUCTION WITH GRANULATED BLAST FURNACE
The granulation process of Blast Furnace Slag, enhanced by INBA® dewatering technology, transforms it into a valuable additive for the cement industry. Granulation rapidly cools the molten slag, forming a glassy, granular material that is easy to store, transport, and integrate into cement production.
The INBA® dewatering system efficiently removes excess water, ensuring optimal moisture content and reducing energy consumption during processing. Additionally, the granulation process, combined with INBA® dewatering, reduces dust and environmental impact, promoting safer and cleaner handling compared to dry-pit activities.
By incorporating an INBA® system, you achieve a sustainable, cost-effective, and high-performance solution, meeting the demands of modern construction while supporting eco-friendly practices.
Scan the QR code to learn more:
for the use of the biomass to produce a range of other products such as bio-fuel, animal feeds, soil amendments, pharmaceuticals, and nutritional supplements. While the pilot project at St Marys, Ontario utilizes only about 1% of all CO2 produced on-site, plans are to scale the technology for fully commercial facility at the Bowmanville cement plant. Up to 40% of the project’s build-out may be covered as part of a $74-million clean tech innovation initiative sponsored by the Ontario Centres of Excellence (OCE).
A company spokesperson notes, “For our business, sustainability means serving customers and growing responsibly, while respecting the present and future needs of the environment, society, and the communities where we operate. We achieve this by researching, developing and using eco-efficient processes and advanced materials to provide world-class products and support for the North American construction industry.”
This commitment includes maintaining work environments that emphasize safety before productivity and profitability. In addition, St Marys Cement considers itself as a vital economic engine in the communities where it operates, supporting local causes and promoting active engagement that leads to more transparent and collaborative business relationships. The company regularly supports local charitable organizations, educational initiatives, and environmental conservation projects. It also main-
tains a close working relationship with local stakeholders to ensure that its operations align with community goals and values.
St Marys Cement stands as a leader in the Canadian cement industry, combining a century of experience with a commitment to innovation and sustainability. The company’s blend of high-quality products, responsible business practices, and community involvement cements its reputation as an essential part of Ontario’s construction sector.
Proper PPE, combined with training and a strong safety culture, is essential to preventing electrocution risks in manufacturing.
Electrocution risks in the workplace are a serious concern, particularly in the manufacturing sector, where workers are exposed to high-voltage equipment daily. While construction sites are often perceived as the most hazardous for electrical accidents due to their changing environments and temporary wiring, manufacturing facilities also present serious and unique risks to workers. Factory floors and production lines are controlled environments with established workflows, but this consistency can lead to complacency, making workers underestimate the potential electrical dangers.
The severity of this issue is clear. The manufacturing industry ranks among the top sectors with high fatalities, and 28% of electrical fatalities occur on industrial premises,
underscoring the vulnerability of workers in these environments. Other industries face risk as well. According to Occupational Safety and Health Administration (OSHA) and Bureau of Labor Statistics (BLS) data compiled by the Electrical Safety Foundation International, 74% of workplace electrical fatalities occur in non-electrical occupations, showing that even workers who don’t directly handle electrical
systems can be at risk.
Beyond the human toll, electrical incidents can have severe financial repercussions for businesses. According to the BLS, 2.6 million nonfatal workplace injuries and illnesses were reported in 2023, with over 900,000 cases involving days away from work. These incidents disrupt operations, reduce productivity, and lead to increased insurance premiums.
Randy Dombrowski is the Director of Safety Services for Sentry Insurance. Sentry provides insurance and risk management solutions to manufacturing businesses throughout the country, helping companies maintain safer workplaces and reduce liability risks.
Furthermore, non-compliance with OSHA and National Fire Protection Association (NFPA) 70E standards can result in substantial fines and legal liabilities.
However, electrocution risks are preventable with the right safety training, strict adherence to regulations, and proper use of personal protective equipment (PPE). PPE plays a critical role in mitigating electrical hazards and, when combined with a strong safety culture, can significantly reduce the likelihood of injuries or fatalities.
Manufacturing environments are filled with high-voltage machinery and electrical systems, which pose significant risks to workers, including arc flash injuries. Unlike construction sites, where hazards frequently change due to evolving job sites and temporary wiring, manufacturing facilities operate in a more stable and controlled setting via factory floors and production lines. However, this consistency can create a false sense of security, leading to lapses in safety
practices within established workflows.
Most electrical accidents and injuries happen abruptly or unexpectedly, especially when working with or around electrical live circuits or current. This is why it’s vital to assess each work task, identifying what electrical safety is required that might help lower the risk factors of an incident occurring with having the proper protective equipment.
One of the most common causes of electrical injuries in manufacturing is improper Lockout/ Tagout (LOTO) procedures. LOTO violations have led to severe and sometimes fatal incidents where machines were unexpectedly energized during maintenance. Even experienced workers may bypass safety protocols to speed up operations, increasing the risk of electrocution.
Additionally, equipment failures can expose workers to live electrical parts. If machinery malfunctions without warning, employees may inadvertently come into contact with hazardous voltages, leading to severe injuries or fatalities. These risks make it essential for manufacturers to enforce stringent electrical safety measures, including the use of appropriate PPE.
Preparation is the first step in prevention. The following best practices can help ensure safety when working with or around electricity.
1. Conduct a risk assessment
The first step in preventing electrocution
incidents is conducting a thorough risk assessment. This assessment identifies potential electrical hazards in the workplace, evaluates voltage levels, and determines the proximity of workers to live electrical parts. By understanding these risks, employers can implement appropriate safety measures and ensure that workers are equipped with the necessary PPE. A risk assessment should include:
• Evaluating the presence of live electrical circuits
• Identifying potential arc flash hazards
• Determining the likelihood of accidental contact with electrical components
• Assessing environmental factors, such as moisture or confined spaces, which can exacerbate electrical hazards.
By proactively identifying these risks, manu-
facturers can implement preventive measures that minimize the likelihood of accidents and ensure workers are adequately protected.
2. Select the right PPE for the job
Once risks are identified, selecting the appropriate PPE is essential to protect workers from contact with electrical hazards, including shock, arch flash, and fire protection. The type of PPE required depends on the specific risks present in
the workplace. Some key categories of PPE that can reduce electrocution risk include:
• Insulated gloves: Designed to prevent electric current from passing through the body, insulated gloves are essential when working with live electrical systems
• Voltage-rated tools: These tools provide an additional layer of protection, preventing accidental electrical contact
• Flame-resistant (FR) clothing: Arc-rated FR clothing helps protect workers from burns in the event of an arc flash
• Arc flash suits: These suits provide comprehensive protection against extreme heat and thermal hazards associated with arc flashes
• Closed-toe safety shoes with non-conductive soles: These shoes minimize the risk of electrical currents traveling through the worker’s body
• Insulating mats: Used in high-voltage areas, these mats provide an additional barrier against electrical grounding.
PPE must comply with OSHA and NFPA 70E standards to ensure maximum protection. Employers should regularly inspect PPE for wear and damage, replacing any equipment that no longer meets safety requirements.
3. Implement supporting safety practices
While PPE is essential, it should be part of a broader safety strategy that includes training, enforcement of safety protocols, and ongoing risk management. Key supporting practices include:
Comprehensive electrical and LOTO training
• Workers should receive regular training on recognizing electrical hazards, following safe work practices, and responding to emergencies.
• Employees must be trained in proper LOTO procedures to ensure machinery is fully de-energized before maintenance work begins.
Circuit protection measures
• Install circuit breakers and fuses to prevent overloads and short circuits that could cause fires or electrocution.
• Ensure all electrical systems are properly grounded to reduce shock hazards.
• Use Ground Fault Circuit Interrupters (GFCIs) in high-risk areas to cut off power in case of a fault.
Avoiding overloaded circuits
• Proper load management is essential to prevent overheating and electrical failures.
• Conduct routine inspections of electrical panels and wiring to identify wear, corrosion, or damage before issues arise.
• Reduce reliance on extension cords and instead install permanent wiring solutions where needed.
Using the right equipment
• Use explosion-proof electrical devices in environments with flammable substances.
• Ensure all electrical equipment meets OSHA and NFPA 70E safety standards.
Adopting safe work practices
• Never bypass safety mechanisms such as
interlocks or machine guards.
• Maintain clear access to electrical panels and emergency shutoff switches.
• Avoid handling electrical equipment with wet hands or working in damp conditions.
• Post warning signs near electrical hazards to reinforce safe work practices.
• Ensure that emergency response procedures for electrical incidents are well-documented and communicated to all employees.
By implementing these practices, manufacturers can build a culture of safety that prioritizes hazard awareness and proactive risk mitigation.
Electrocution risks in manufacturing are a serious concern, but they’re preventable with the right combination of safety protocols and personal protective equipment. A proactive approach that includes conducting risk assessments, selecting appropriate PPE, and implementing comprehensive safety programs can significantly reduce the likelihood of electrical injuries and fatalities. By fostering a strong safety culture, manufacturers can protect their workers, improve operational efficiency, and ensure compliance with regulatory standards.
The Paul Wurth INBA® slag granulation system is an advanced technology designed to transform slag into a valuable product for the cement industry. This process involves granulating the slag using water, followed by dewatering with the dynamic INBA® dewatering drum. The system is highly flexible and compact, allowing it to be integrated seamlessly into various plant configurations.
Key Benefits:
• Efficient slag processing
• Produce high-quality granulated blast furnace slag
• Green direct replacement for Portland Cement
• Reduced emissions
over two decades
and
| www.sms-group.us
spoeton@industrytoday.com
www.industrytoday.com
Tel: 973.218.0310
Our state-of-the-art, multi-channel digital media platform allows you to define your target audience when and how you want to, whether by industry, title or geography. This is why, when companies have a story to tell, time and time again they choose Industry Today to tell it. Our articles are published on our media platform www.industrytoday.com, permanently archived and posted on all social media.
Producing high quality components for the rail, defense, mining and recycling industries.
Short lead times are just a part of our everyday business:
• Managing your order from PO to delivery
• Delivering your quality parts and assemblies on time and on budget
• Boosting production with robotic welding
• Full complement of CNC fabrication technology
• Wide range of machining and welding equipment
• Metal finishing and assembly services
• Quality engineering for customer specific and conceptual design
Accumetal Manufacturing is a registered ISO 9001-2015 Company
300 Wright Blvd, Stratford, ON N4Z 1H3 (519) 271-6710
info@accumetal.com
1039 Ridgeway Road Woodstock Ontario Canada N4V 1E2 (519) 537-6284 info@bfteck.com
WALL-MOUNTED BOXES
JUNCTION BOXES