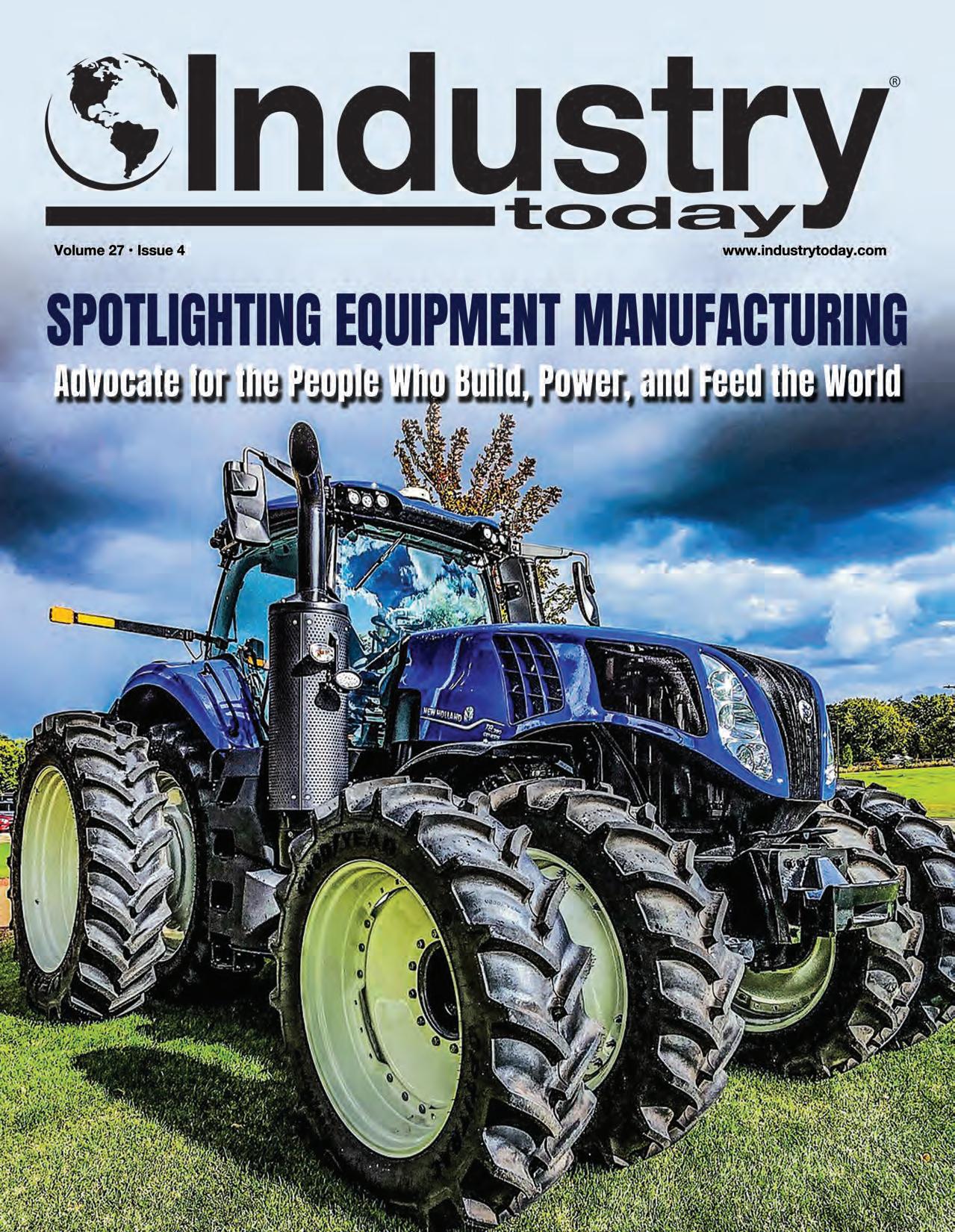

WALL-MOUNTED BOXES
JUNCTION BOXES
This is typically the time of year when people are making resolutions, and sometimes even keeping them. We at Industry Today remain resolute in bringing you pertinent news and information from key decision makers and influencers about manufacturing and industry. It’s a resolution we keep year after year.
We share the commitment to spreading the word about developments in our industry in our lead story, AEM Manufacturing Express: Celebrating the Backbone of America. Get on the bus with the Association of Equipment Manufacturers (AEM) and its AEM Manufacturing Express, a nationwide tour designed to promote the U.S. equipment manufacturing industry and its 2.3 million workers. Over the course of 18 weeks, the Express crisscrossed 13,500 miles, stopping at over 80 manufacturing facilities across 20 states and connecting with nearly 100 elected officials and engaging over 9,000 employees.
In other feature news, we take a look at how most auto manufacturers lack talent with nextgen skills to successfully transition to electric vehicles (EVs) and zero-emission transportation. Stella Ioannidou, industry analyst and Senior Research Director at human capital advisory firm The Josh Bersin Company, writes in How to Get to Cruising Speed in the Race to the EV Future, “The research shows that automotive manufacturers need to urgently invest in building a workforce equipped not only for traditional ‘metal-bashing’ production lines but also for emerging business models such as automated manufacturing, innovative product development, and directto-consumer sales...These new roles increasingly require IT and software expertise, skills that are also highly sought after in other tech-driven industries.”
Tech is also driving innovations in warehousing operations. Senior Editor David Soyka profiles America in Motion, which designs and builds all-in-one materials handling solutions deploying custom-built Automated Guided Vehicles (AVGs). These mobile robots can carry payloads ranging from several pounds to several tons and navigate independently within a facility. Read more about it in Mobile Automation is the Future.
In Together at Last: IT and OT, Matt Wyatt, VP of Professional Services at TeamViewer, points out that “A recent survey found that 90% of businesses report their IT and OT teams are isolated. Bridging this gap is more than improving efficiency, cost savings and quality – it’s about empowering frontline workers.” Learn how connecting IT and OT teams has the potential to create immense value.
BioMADE recently announced a $26.9 million investment in 17 projects to advance the domestic production of sustainable materials for consumer products and defense applications, while also building the manufacturing workforce of the future. The details are covered in Supporting U.S. Bioindustrial Manufacturing Innovation and Workforce Development.
Oklahoma is home to over 4,200 manufacturing businesses and nearly 130,000 workers. Read how the state powers this thriving industry in The Success and Resilience of Oklahoma Manufacturing.
What’s the secret to how Buffalo, New York created a pro-business environment to attract Canadian business expansion? Thomas A. Kucharski, President and CEO of Invest Buffalo Niagara, explains in Increasing Flow of Canadian Investment Into Buffalo Niagara. Also in this issue, we profile leading companies CIC Construction Group, Oldcastle APG, and Norfolk Naval Shipyard.
This digital edition is just one part of our comprehensive media platform. You can always find timely reporting on a weekly basis at industrytoday.com.
Thanks for reading this digital issue of Industry Today.
www.industrytoday.com spoeton@industrytoday.com
Publisher: Susan G. Poeton
Marketing Director: Alice Anne Coakley
Senior Executive Sales Manager: Jonathan Listig
Project Director: Brian McMillan
Production: Melissa S. Burge
Art Director: Seema Mazhar
Contributing Designers: Jorge Leandro Rodrigues
Profile Editor: David Soyka
472
This unique initiative brought an interactive experience, elected officials and industry leaders directly to local communities.
This summer, the Association of Equipment Manufacturers (AEM) embarked on a monumental journey with the launch of the **AEM Manufacturing Express**, a nationwide tour designed to shine a spotlight on the U.S. equipment manufac-
turing industry and the 2.3 million workers who drive it. Over the course of 18 weeks, the Express crisscrossed 13,500 miles, stopping at over 80 manufacturing facilities across 20 states. The tour concluded in October with a celebratory finale at AEM’s headquarters in
Milwaukee, Wisconsin.
The initiative, the largest in AEM’s 100-year history, celebrated the industry’s crucial role in building modern infrastructure, fueling the economy, and putting food on the table.
“Behind every piece of equipment is a story,”
said AEM President Megan Tanel. “We’re thrilled to tell the stories of grit, determination, and ingenuity that define the men and women of our industry.”
Each stop featured the “Manufacturing Challenge” game, an interactive experience
showcasing cutting-edge technologies that power the industry. Events also included food, entertainment, and thought leadership to connect communities with the innovations shaping America’s future.
Notably, the tour was also an advocacy platform. AEM leveraged its fiercely bipartisan approach to highlight the industry’s policy priorities during this critical election year. “The Express gave us a chance to engage workers in the political process, connect with elected officials, and advance policies that will strength-
en our economy,” said Kip Eideberg, AEM’s Senior Vice President of Government and Industry Relations.
The tour kicked off its historic bus tour with a stop at Weiler in Knoxville, Iowa on July 1. On a hot summer day, the might of American manufacturing was on full display, the facility courtyard, complete with skydivers, big iron, and a Weiler community nearly a thousand strong. Weiler employees wait for their turn to play
the Manufacturing Challenge.
The opening ceremony was held out in the open, and for good reason: out in the open is how Weiler does things. Pat Weiler, founder and CEO at the company that bears his name, feels strongly about hard, honest work.
“There’s a misconception people have,” he said. “Manufacturing isn’t dark, dirty, or dingy; it’s well-lit, safe, and fair to people.”
It’s true—equipment manufacturing has been good to the people of Knoxville. Founded less than 25 years ago, here at Weiler, prosperity
has sprung up where factory floors have been laid. Weiler has since grown to one of the most iconic equipment manufacturers in Iowa. But Pat Weiler isn’t one to self-congratulate, and neither are the workers alongside him. Addressing the crowd, Pat summed up what it means to work at Weiler: “We don’t wait for a pat on the back; we roll up our sleeves and work hard—it’s who we are.”
The tour continued its journey through Iowa and up into Minnesota, before stopping in communities in South Dakota, Nebraska,
Kansas and Missouri. In early August, the bus stopped at six different locations in Oklahoma, including McElroy Manufacturing.
Ask the folks at McElroy Manufacturing about what it takes to build a global leader in fintube manufacturing and pipe fusion machinery, and they’ll tell you two words: Hard Work. Ask them to explain further, and they’ll tell you that their belief is a simple one: only through the
hard work and the focused energy of their people can McElroy continue to build and maintain its reputation for decades to come. As the AEM Manufacturing Express visited McElroy’s Tulsa headquarters Thursday afternoon, generations of hard work were on display in the form of equipment—equipment handcrafted by men and women of this Tulsa manufacturing community.
The story of McElroy begins in 1954, when Arthur McElroy and his beloved wife, Panny, started up their family business in a tiny Tulsa garage. In the ‘60s, the company became a pioneer in the fintube machinery market, innovating state-of-the-art heat transfer technology that allowed for cheaper and easier refrigeration, among other applications.
Seventy years since its founding in that Tulsa
garage, McElroy has grown into a manufacturing powerhouse with hundreds of employees and offices across six continents. Even still, McElroy remains a family-owned and operated business, managed by President & CEO Chip McElroy and his siblings. But this new generation of McElroys isn’t content to simply tread water; Chip remains dedicated to taking McElroy Manufacturing to new heights.
In June, McElroy launched their brand-new facility in Broken Arrow, representing an investment in excess of $25 million in the northeast Oklahoma manufacturing community.
When the Manufacturing Express came to McElroy, we were greeted like family. Family is the focus at McElroy—and here, family means much more than the name on the door. As Chip McElroy tells, these 455 men and women don’t just work for the company; they are the company, and they’re part of the McElroy family. They’re proud of it, too: this community has given much to McElroy, and through decades of high-volume production and global distribution, McElroy’s worldwide presence is evidence of the power of Tulsa, Oklahoma manufacturing. “We’re showing what USA-based manufacturing means to us, and to the world,” Chip McElroy said. That’s the ethos present in every piece of kelly green equipment.
You don’t get to be an industry leader overnight; at McElroy, success is measured in years, not days, and that’s how McElroy has reached
seventy years of success. Here in Tulsa, there’s a feeling that the next seventy years begin today. Each morning, the men and women of McElroy show up to manufacture something that they can be proud of. To Chip McElroy, the philosophy is simple: “Underground, in the building, and around the world, we’re making the world a better place with better infrastructure—one project at a time.”
The final stretch of the tour was dedicated to Wisconsin, a state with a rich manufacturing legacy. Highlights included:
• CNH Industrial (Racine): Employees and community members celebrated 180 years of innovation at the Case IH Agriculture Racine Experience Center.
• Wacker Neuson (Menomonee Falls): A fall barbecue and remarks by AEM President Megan Tanel and Wisconsin Lieutenant Governor Sara Rodriguez highlighted the
PRESIDENT,
Association of Equipment Manufacturers (AEM) President Megan Tanel joined AEM in 1995, becoming Senior Vice President of Exhibitions and Events in 2016, Senior Vice President of Construction Equipment and Utility Sector in 2020, and her current role in 2022.
In her Exhibitions and Events Role, Tanel helped launch World of Asphalt in 2001, served as Show Director for The Utility Expo (formerly ICUEE), and served as Show Director of North America’s largest trade show, CONEXPOCON/AGG, growing overall trade show revenue by 80% over 12 years.
As President of AEM, Tanel sets the strategic direction and operation of all AEM programs, focusing on core service areas of market information, public policy advocacy, and exhibitions.
Tanel is a member of the select Ag CEO Council. She served as a member of the Milwaukee Women’s Leadership Group, previously served as Chair, and Education Committee Chair, of the International Association of Exhibitions and Events (IAEE), and served on customer advisory boards for the cities of Las Vegas, Louisville, Ky., and Orlando, Fla.
The IAEE recognized Tanel with both their Woman of Achievement Awards and Distinguished Service Award in 2017.
Tanel holds a bachelor’s degree in mass communications, PR, speech, and German from the University of Wisconsin-La Crosse, and a Certificate in Exhibition Management from IAEE.
company’s community impact.
• Super Products (Mukwonago): A local food pantry fundraiser brought together over 100 employees, showcasing the company’s charitable spirit.
• Husco (Waukesha): CEO Austin Ramirez announced plans to hire 250 employees, underscoring the exciting future of automation, robotics, and AI in manufacturing.
The final celebration at AEM’s Milwaukee headquarters was a fitting tribute, featuring a taco truck, raffles, and heartfelt reflections on the Express’s success.
The AEM Manufacturing Express achieved more than just miles on the road. It connected nearly 100 elected officials with the manufacturing sector, engaged over 9,000 employees, and amplified the voices of industry leaders. From
small towns to big cities, the tour celebrated the backbone of America’s economy: its equipment manufacturers.
While the bus has parked for now, the mission continues. AEM and its members remain steadfast in their efforts to advocate for the industry and support the hardworking people who build, power, and feed the world. For more about the Manufacturing Express and its journey, visit [www.manufacturingexpress.org](http://www. manufacturingexpress.org).
America in Motion designs and builds all-in-one materials handling solutions deploying custom-built Automated Guided Vehicles (AGVs).
By David Soyka, Senior Editor, Industry
Today.
he notion of automated artificial servants actually date back to antiquity, with the first primitive industrial robots appearing in the 1930s. While he might joke otherwise, Tommy Hessler, CEO of America in Motion, hasn’t
been involved with robotics quite that long, but his history as an innovator in mobile automation does date back to the 1980s.
“Back then it was more of a marketing tool,” Hessler says. “It was a novelty for companies that wanted to show off how modern they were
at red carpet presentations on how robots might work, but there were actually few real business cases. They might have had a few machines on the floor, though, and eventually discovered they actually could do something.”
Not only could they do something, they had a significant bottom line impact. “Back in
1990s, before the Internet, newspaper printers had these huge paper rolls that weighed 1500 pounds. Four to five hundred of these paper rolls were moved on forklifts at a total handling cost of about $1,000 per roll,” Hessler says.
“We put together an automated system to move those rolls and reduced material handling costs
by as much as 10 percent. Even if you only lowered costs by 3%, that’s still roughly a $35,000 savings.”
Of course, an automated forklift back then was primitive by today’s standards; since then, robotic technology has evolved from science fictional speculation to everyday reality.
Following his work in several previous automation and robotics companies, Hessler founded America in Motion in 2007, the same year as the introduction of the iPhone. And, like the iPhone, the technology has undergone exponential advancements.
“The first early mobile robots followed a wire track on the warehouse floor,” Hessler explains, “This was a limited, cumbersome application that required cutting up the floor to lay the wire. So you couldn’t change anything once the wire was in.”
The next development was a free ranging robot that was not physically bound to the floor. Instead, the robot used a laser scan to locate reflective targets to travel to, a much more flexible approach. Today, we have eleven different ways for a mobile vehicle to navigate through a set of programmable coordinates.”
Unlike most of its competition, America in Motion is more than just a hardware provider of automated forklifts. Rather, the company is a provider of custom but open-source guided vehicle solutions comprised of:
• Automated Guided Vehicles (AGVs): mobile robots that transport materials within a facility following magnetic strips, lasers, or
Pictured previous spread: America in Motion designs and manufactures a variety of custom mobile robot vehicle types; above: Custom-designed AGV mobile robot.
cameras along predefined paths. Types of AGVs include fork, clamp, unit load, lift table, tugger or towing, turret truck, specialty, and eBot, a new vehicle type comprised of three mix and match components. Unlike traditional manual forklifts powered by gas or propane, AGVs run with either lithium or lead acid AGM batteries, which is more energy efficient and generates less noise pollution. Typically, AGVs can carry payloads ranging from a few hundred pounds
to several tons. All AGVs feature safety sensors and emergency stop functions to detect obstacles and prevent accidents.
• System Manager: The central control unit that “runs” the AGV operations. Similar to how Uber or other kinds of fleet manager software works to route vehicles to passengers or shipments and desired destinations, the system manager assigns AGVs to needed tasks and continually optimizes routes and processes to
obtain maximum efficiencies.
• Roadway Network: Defines the routes for the AGVs to navigate within a facility. These roadways can be changed within the system manager at any time to accommodate growing operations and physical changes in the plant.
Applications include high-volume material handling, repetitive transport tasks, hazardous and other high-risk transport, limited labor availability, and accident reduction. In addi-
tion, an AGV solution can be integrated with other existing automation, such as conveyer systems and robotic arms. “Unlike some of our competitors, we don’t believe in proprietary systems,” Hessler emphasizes. “Some companies like to keep you in their own ecosystem because that benefits them. We’re looking to benefit the customer.”
Pictured: Timeline showing the history of AGVs and America in Motion.
Pictured:Very high throughput is best handled with conveyors – and – low throughput is best handled with manual forklifts – but between the two, mobile robotics is the best solution;
right: A web-based drag-and-drop inventory management system recently used for a customer. The system provides real-time visibility of inventory, allowing the customer to track materials and products with precision.
In 2007, Tommy Hessler was appointed President and CEO of America in Motion. With extensive experience in the industry, he recognized a critical need for customizable AGV mobile robotics solutions. Tommy envisioned a customized mobile automation approach that meets the unique needs of each customer rather than the traditional cookie-cutter approach.
Originally from Sweden, Tommy has dedicated his entire career to the mobile robotics and AGV sectors. He spent several years at NDC Technology in Australia before taking ownership, further solidifying his expertise and commitment to innovation in this field.
www.weareAIM.com
The many benefits of AGV solutions are compelling:
• Increased efficiency. AGVs can operate 24/7 with faster material handling and reduced transit times.
• Lower costs. As much as a 70% reduction in labor costs. AGVs also minimize costly errors and damages that often occurs in manual handling of materials.
• Address Labor Gap. Automated solutions address labor shortages and high employee turnover that is a significant challenge in almost every industry.
• Reduce Physical Labor Strain. AGVs perform physically challenging tasks that strain and fatigue human workers, who can then be reallocated to other tasks, increasing employee satisfaction and retention.
• Enhanced safety. AGV safety features better
protect people and materials.
• Scalability and Reusability. AGVs are easily scaled as operational needs changes, and can be resold or repurposed rather than scrapped as waste.
• Data Analytics. AGVs can collect valuable data used to identify trends, optimize workflows, and make informed decisions on operational improvements.
While some customers do just order the AGVs, Hessler emphasizes that more benefits are realized employing a more holistic systems solution.
“For a lot of customers, the mindset is still like buying a microwave, they think of it as just another piece of hardware. You get it, you
plug it in, and it does a specific job,” he says. “The analogy I make is that what you are really buying is a kind of fighter jet that has a lot of sophisticated interlocking parts and requires specialized skills to operate. And there’s a lot more you can do with fighter jet kind of product than a microwave.”
Many of those benefits are quickly illustrated with a virtual session. “This is where customers try out various layouts and solutions and really see the value they can attain,” Hessler says.
“We don’t believe in a cookie cutter approach,” he adds. “We work with customers to learn about their workflows, develop several iterations of functional specs to ensure we’ve got everything right, then build the system at our 20,000 square foot facility in Charlotte, North Carolina, and finally install it and train the customer in its operation. Ideally, we continue the relationship to collect data to further refine and optimize the system.”
America in Motion has only 25 employees, though it partners with other companies preferably local to the customer whenever possible.
Automated Guided Vehicles (AGVs) are helping manufacturers cut costs by automating material handling tasks. By automating repetitive tasks like transporting goods, AGVs free up labor to focus on more value-added activities, such as process improvement or quality control. AGV mobile robots also reduce the need for forklifts, lower labor costs, and eliminate costly workplace accidents. Operating around the clock, they optimize routes, improve throughput, and reduce waste. Their ability to minimize damage leads to substantial savings and improved long-term profitability.
The typical lead time from consultation to installation typically takes about six months. True it its name, customers are primarily in the U.S., Canada, and Mexico, though it does have international customers as well.
Hessler originally came up with the America in Motion name to symbolize how AGVs can revitalize manufacturing while at the same time facilitating employee job security and satisfaction. “I saw automation as a way for American manufacturers to improve efficiencies and become more competitive with offshore low-cost labor,” Hessler says. “And the intent of auotmtion is not to replace employees,
but to relieve them of repetitive and sometimes dangerous tasks and retrain them for more rewarding careers. You need people to program the robots, manage them and maintain them. That’s why while Japan has the highest level of automation, it also has the highest levels of job retention.”
This integration of people and robots extends to the point where workers like to name AGVs. “We found that people interact better with a robot they give a name.” Hessler says. “By personifying the robot as ‘Bob’ as opposed to just ‘the robot’, people feel more comfortable working with it.”
Pictured left: Laser navigation is commonly used in AGV guidance. A laser beam is reflected by strategically placed reflectors allowing the mobile robot to navigate its surroundings; above: Example of a mobile robot fully customized to our customer’s needs.
Artificial intelligence is the next breakthrough in AGVs. “With AI capabilities, not only can the robots learn and adapt to new situations, they can also move in unfamiliar spaces,” Hessler says. “Right now, an AGV can’t go into a truck to unload materials, because its reference points are solely within the facility.
With AI, the AGV can recognize that it is a new environment, orient itself, and then perform its task.”
America in Motion experienced a boost in
sales during the pandemic, not surprisingly given concerns about hygiene and safer working conditions. However, Hessler says that this peak demand reflected short-term thinking.
“It goes back to are you buying a microwave or a fighter jet. What’s the point of buying a jet if you’re only using it to make popcorn,” he says. “Too often companies are focused on what’s going to happen five years from now, or even sooner, compared to companies in Japan that are focused on the next fifty years. Our AGV solutions are future-proof. Typically, you see an ROI in two years. But that’s just the start. You can continually build on an AGV solution to gain more efficiencies and free-up more time for important high value activities, further grow your business, stay competitive, and all the while engage your people in safer, more rewarding tasks.”
He adds, “AGVs aren’t just a trend, they are a core strategy for a more efficient, safer, and cost-effective workplace. We’ve been building AGVs for 17 years, and the future has never looked more promising to integrate AGV solutions to optimize workflows and improve working conditions. An investment in an AGV solutions isn’t just as investment in some hardware and software, it is an investment in a company’s future.”
Pictured: eBOT by AIM line of modular robotics. Each component can be mixed and matched to meet customer’s requirements.
The Norfolk Naval Shipyard (NNSY) is the oldest and largest industrial facility of the U.S. Navy.
The Norfolk Naval Shipyard (NNSY), located in Portsmouth Va. (despite its name, it is not located in Norfolk), is one of the largest, most comprehensive, and most significant shipyards in the United States. Originally established as the Gosport Shipyard in colonial America, destroyed and rebuilt twice in two wars, it became operational
under its current name in 1866.
During World War II, NNYS was a major shipbuilding hub, producing numerous naval warships, including aircraft carriers, battleships, and destroyers. Today, under the command since 2023 of Navy Captain Jip Mosman, the shipyard is a key component of the U.S. Navy’s fleet support infrastructure, specializing in
shipbuilding, repair and modernization, as well as support for decommissioning and dismantling older vessels. The shipyard is integral to the Navy’s lifecycle management of ships and submarines, providing critical support to ensure these vessels are mission-ready.
NNSY also serves as the U.S. Navy’s Naval Sea Systems (NAVSEA) Command’s chief East Coast repair, overhaul, and modernization facility, one of the largest such shipyards in the world as well as one of four public shipyards dedicated to maintaining the strength and preparedness of
America’s fleet. It is the sole builder of U.S. Navy aircraft carriers and one of two nuclear submarine builders. and has pioneered techniques in ship repair and modernization that have been adopted across all other Navy shipyards.
Located along the Hampton Roads harbor,
NNSY is strategically positioned for access to both Atlantic shipping routes and U.S. military operations. The proximity to Norfolk, a major naval hub, further enhances its logistical and operational importance. It is situated near other key naval assets such as Naval Station Norfolk, the largest naval base in the world.
The largest industrial employer in Virginia, NNSY employs some 6,000 military personnel 11,000 military civilian workers, and between 1,500 and 3,000 contractors, comprising a range of engineers, skilled tradespeople, and administrative staffs.
To recruit and retain the civilian talent
We specialize in marine decking and coating services, responding quickly to the needs of STC’s customers not only in facility areas but also throughout the country.
essential to carrying out its mission, NNSY offers a four-year apprenticeship program combining academics and trade theory with on-the-job training to quickly qualify journeymen tradespeople. Apprentices receive pay and academic tuition and book expense reimbursement as long as they remain in good academic standing. They get paid when working and are eligible to receive promotion upon successful completion of all program requirements. It held its most recent graduating class this November.
The shipyard encompasses several non-contiguous areas comprising 1,275 acres in total, with annexes along the Elizabeth River in Portsmouth and Chesapeake. The main 465acre main site, the Industrial Area Precinct, provides ship berthing, fabrication, maintenance and repair facilities, along with five operable dry docks and four major piers.
Home to the largest dry dock and crane in the Western Hemisphere, NNSY can dry-dock, overhaul and repair any ship in the U.S. fleet, as well as perform most any naval technical, fabrication, manufacturing and engineering work. Planners and shops are linked by stateof-the-art computer systems for computer-aided design (CAD) work and automated information systems that provide quality services on time and within budget.
The shipyard’s Rapid Prototype Center and Technology and Innovation Laboratory utilizes and impressive array of advanced capabilities, including additive manufacturing, a tie
bolt anti-rotation tool, a molded case breaker assembly test stand, a cable winch guide, and an ergonomic sanitary clamp wrench. All of these innovations aim to improve efficiencies and competencies, while also making work tasks
easier and safer. As the Navy’s fleet modernizes with new, more sophisticated ships, NNSY is adapting by investing in advanced technologies, improving its infrastructure, and modernizing its workforce training to handle the complex systems of new vessels.
With a legacy that spans over 250 years,
NNSY remains at the heart of U.S. naval power, providing world-class maintenance, repair, and modernization services for some of the most advanced warships in the world. Recognized as a world class organization in executing its
mission, developing its people, and aggressively improving performance at a state-of-theart facility, NNSY is continuously striving to achieve excellence and deliver service to the nation’s fleet safely with the right quality on schedule and within budget.
The Navy’s emphasis on readiness, coupled
with the increasing need to extend the service lives of older ships and submarines, is going to keep NNYS at the forefront of naval maintenance and modernization for some time to come. Its continued evolution is vital to ensure that the Navy remains ready to meet the demands of modern naval warfare and global security.
Most automotive manufacturers are lacking the critical skills needed to successfully transition to electric vehicles.
Despite its significance to the global economy, the automotive industry faces mounting pressure to transition toward greener alternatives, particularly electric vehicles (EVs). Governments worldwide are implementing stringent regulations to reduce carbon emissions, with a growing focus on zero-emission transportation. In the United States, for example, the Federal Government has set ambitious targets, mandating that at least 50% of all new American vehicles sold by 2030 be zero-emission.
The shift to EVs and other innovations, such as autonomous driving solutions, demands new
technologies and approaches, but also a new operating model where cars reach consumers directly rather than through dealerships. However, as our latest research has uncovered, a critical challenge remains: most automotive manufacturers lack the specialized talent they need to quickly adapt to these changes.
Our recent study of the automotive manufacturing industry’s current state, researched in collaboration with Eightfold, reveals a pressing issue: most manufacturers are grappling with a significant talent gap. The skills required for this transformation—ranging from electric
drivetrain engineering to advanced machine learning—are in short supply. As a result, many players in the industry are struggling to cross the finish line in their race toward EV innovation.
Automotive manufacturers must recognize that relying solely on new STEM apprentices or experienced automative workers isn’t enough to navigate the mandates of the EV transition. To truly succeed, they must shift toward delivering not just high-quality EVs but also digitally enhanced driving experiences—essentially “computers on wheels.” This demands advanced capabilities in areas like software engineering, AI, and data science, which are essential for integrating advanced digital fea-
tures and autonomous driving.
The research shows that automotive manufacturers need to urgently invest in building a workforce equipped not only for traditional “metal-bashing” production lines but also for emerging business models such as automated manufacturing, innovative product development, and direct-to-consumer sales. Companies that previously focused on conventional components like motors, interiors, drivetrains, and exhaust systems are now finding themselves ill-prepared to staff for radically different roles. These new roles increasingly require IT and software expertise, skills that are also highly sought after in other tech-driven industries.
Still, the analysis of the skills landscape in automotive manufacturing reveals a critical shortfall in next-generation expertise. While the sector is well-stocked with talent proficient in declining technology skills such as Java and SQL, there is a glaring deficit in the skills that will drive the future of the industry—machine learning, robotics, and data science. These are the capabilities needed to deliver the high-end driving experiences and on-demand, digitally enhanced vehicle-buying options that consumers of the late 2020s will increasingly expect.
This skills gap significantly hinders the sector’s ability to innovate and limits key players’ ability to remain competitive in the years ahead. Without the necessary expertise in areas
like machine learning, robotics, and data science, the industry will struggle to deliver the advanced, digitally-driven experiences that the future of transportation demands.
To overcome this barrier and ensure they are equipped with the right talent to meet future challenges, automotive manufacturers must invest in what we term “systemic HR”: thinking of the entire array of HR approaches rather than trying to “hire their way out of this challenge.” We have identified the following strategies:
Automotive manufacturers lag behind other
industries in HR maturity, with significant opportunities for improvement in understanding and applying the latest thinking and strategies around skills-based recruiting, retaining key talent, reskilling for the skills of the future, and redesigning work to automate and simplify the production line as much as possible.
Leading automotive manufacturers excel by strategically prioritizing roles that drive technology, transformation, and operational excellence. For instance, they have 23.2 times more quality experts and 4.9 times more software engineers than the industry average. By increasing roles like product specialists and technical project managers, companies can better manage complex projects and support the continuous improvement needed for the transition to electric vehicles (EV).
Pacesetter automotive companies employ three times more people with emerging technology skills compared to the industry as a whole. Key skills include .NET, Angular, AI, and robotics, essential for advancing vehicle tech and automation. Notably, pacesetters also have 3.1 times more employees with EV-specific expertise, such as electrical troubleshooting, safety man-
agement systems, and rapid prototyping. To achieve this, focus on creating future-oriented roles and building a talent mix with these critical skills.
In 2022, 1,022 U.S. schools produced graduates with degrees relevant to automotive
engineering, with the majority from mechanical engineering programs. Leading institutions like Purdue, Georgia Tech, and Texas A&M are key sources of this talent. EV-focused companies can enhance recruitment by partnering with top universities, particularly those with strong master’s and doctoral programs for advanced STEM talent. This approach to university partnerships, which prioritizes upskilling potential
over immediate readiness, broadens the candidate pool and attracts top talent aligned with the industry’s evolving goals.
By leveraging what we call “adjacent skills,” automotive manufacturers can create more efficient and targeted recruitment and talent development plans. For example, employees
with Jenkins, DevOps, or data science expertise can more easily acquire skills in Docker, machine learning, and AI, because they are highly relevant and therefore upskilling will be faster compared to other skilling plans. Identifying these skill relationships allows manufacturers to promote from within and develop robust L&D programs, helping employees transition from declining skills to those in demand. AI-powered talent intelligence platforms can further optimize this by analyzing workforce data at scale and recommending personalized upskilling paths.
The market landscape is so dynamic that relying on gut feeling decisions around talent is risky. Understanding the capability landscape both within and outside of the organization and leveraging AI to map skills (what we call “talent intelligence”) can help manufacturers go beyond the narrow focus of job roles, making it easier to map potential career transitions across the organization. For example, the shift
The author is an industry analyst and Senior Research Director at human capital advisory firm The Josh Bersin Company that provides insights on work, talent, learning, leadership, and HR technology. You can read the full report, Automotive Manufacturing: Navigating the EV Metamorphosis, here.
to direct-to-consumer sales in the automotive industry is rendering traditional, in-person sales models obsolete. Instead of relying on showroom interactions, sales associates can be transitioned into marketing specialists or inside sales advisors, based on skill adjacencies.
The message is clear: there’s work ahead, but if you start now, you can truly reach a more sus-
tainable skill-enabled transport future—keeping your brand attractive and relevant. And it’s not just car makers who should be concerned about this. Valued at an estimated $3 trillion, the global automotive industry stands as one of the most economic drivers of the global economy. Securing a good future for this sector helps us all.
The secret behind how Buffalo, NY has created a pro-business environment to attract Canadian business expansion.
With two of the planet’s ten largest economies sharing the longest international land border, it only makes sense Canada and the United States are close
trading partners. Both are resource rich and have held a peaceful relationship for centuries, making it natural that they’ve worked closely for each other’s benefits. Buffalo Niagara, in Western New York, has taken advantage of their position on the map to become a powerhouse in attracting foreign direct investment, especially from Canadian organizations looking to grow.
The city is a gateway for over $90 billion in trade annually, approximately 15 percent of all trade between the two economic powerhouses. In fact, more trade flows each year between Buffalo Niagara and Canada alone than the entirety of the United States and other leading economic juggernauts, such as France, Brazil and Australia. Building this sort of reputation didn’t happen overnight. Instead, the city has tediously built itself up as the ideal candidate for businesses to expand and grow over the past few decades through its unique geographical position and instituting business-friendly policies.
When the Erie Canal first opened in 1825, it was Buffalo that was the critical gateway to accessing the newly established trade route from the Atlantic Ocean. Today, Buffalo Niagara has evolved into the region now being the first major U.S. port of call when entering the Great Lakes, which are responsible for an additional $278 billion in bilateral trade between the United States and Canada.
But the evolution hasn’t stopped with progression on the Buffalo Niagara region’s waterways; investment has continued because of Buffalo’s unique position as an unlikely global logistics hub. For starters, Toronto’s massive $265 billion economy is only a 90 minute drive away.
New York City and its more than $2 trillion economy isn’t much further, just being a six hour drive away. In fact, despite being in the Northeast corner of the United States, Buffalo Niagara has positioned itself as a central hub, with over 40 percent of the combined United States and Canadian population being located within only a day’s travel of the city.
Sucro Sourcing is a prime example of a company that has benefitted from the Buffalo and Canadian cross-border exchange. The sugar refinery has two locations: one in Lackawanna, New York, and another in Hamilton, Ontario. Raw sugarcane arrives by cargo ships from
Pictured: Hundreds of millions are being invested in the development of Buffalo’s downtown.
South and Central America and is processed into sugar and molasses at both sites. Molasses from the Hamilton refinery is then shipped to Lackawanna for further sugar extraction to make more products. At just 68 miles apart, this proximity has led Sucro to expand operations in both locations.
Accessibility to other markets, coupled with the region’s seven international ports of entry via auto, rail and water, and two of the largest Foreign Trade Zones in North America, makes it an incredibly effective springboard from which to launch, build and expand businesses.
It’s not hard to find a community that calls itself
“business friendly”, but it is rare to find one that has relentlessly worked to create such a smooth runway for businesses to grow as Buffalo has. Invest Buffalo Niagara – the region’s nonprofit economic development organization – has made it especially easy for Canadian companies, as well as those from other regions, to
expand into the Western New York market. This includes free project management services, incentive coordination, site coordination, as well as expert connections to help companies navigate any thorny regulatory requirements as they grow into a new territory that may have different restrictions than their own.
But once those businesses are established in their new communities, Buffalo Niagara
provides other incentives to keep growth sustainable. The city doesn’t impose any sales tax on production or research and development equipment and it has no inventory/real personal property tax. We offer dozens of programs focused on investing in workforce training, energy efficiency, providing grants and loans, and much more to help businesses plant their roots, and ensure they grow deep. The wide base of experienced workers, as well as up and coming graduates from dozens of higher-education institutions like Niagara University and the University at Buffalo, provides our businesses with a robust talent pipeline.
Thomas A. Kucharski has served as President and CEO of Invest Buffalo Niagara since 2000. Under his leadership, Invest Buffalo Niagara has grown from a start-up initiative to an innovative regional economic development organization that has secured more than 400 successful project wins representing $6 billion in investment in the region and over 65,000 jobs created and/or retained. From the onset, Tom helped Invest Buffalo Niagara form strong, enduring partnerships with business, development and academic leaders throughout the Buffalo Niagara region. Learn more at Invest Buffalo Niagara.
As a result of these factors mixing together, we’ve seen an incredible amount of Canadian direct investment, especially from companies looking to gain a foothold in the American market for the first time. The region is already home to hundreds of Canadian companies that have opened new operations or invested in job creation.
Earlier in 2024, Ontario’s Lifco Hydraulics invested over $2 million into the region, creating over 40 new jobs. Another Ontario-based company, Norgen Biotek, made a similar move this year, investing $5 million for a new 2,800 square foot manufacturing facility in Niagara Falls, as well as a research and development lab at the Buffalo Niagara Medical Campus.
This growth is only expected to continue, especially in manufacturing. With a zero percent state corporate income tax for manufacturing companies and a deep talent pool of nearly 70,000 advanced manufacturing workers, Buffalo Niagara is a prime location. Canadian manufacturers launching in the U.S. are already leveraging these benefits and we expect this to develop into a larger trend.
For instance, we have seen increased interest and traction in green energy projects. Both Electrovaya and Worksport – Canadian manufacturers in battery storage – underwent significant expansions into Buffalo Niagara over the last few years, creating over 400 new jobs.
This growth is spreading into the life sciences, food and beverage processing, and advanced business services, all industries that can benefit from the unique proposition Buffalo Niagara offers.
For Canadian companies looking to expand their scope into the United States, or even just expand their international business operations, Buffalo Niagara has proven to be a great springboard, across a number of different industries. It’s never been more important to build out a globalized company, taking advantage of all potential markets, and taking advantage of business-friendly environments in Buffalo Niagara is one of the best ways to get started.
Pictured: Buffalo’s Canalside is seeing an increase in tourism and business activity.
CIC Construction Group builds long-term client relationships by delivering exceptional quality, safety, and value.
CIC Construction Group is a leading provider of integrated construction and project management services, specializing in large-scale commercial, residential, and industrial projects. With a reputation for delivering high-quality, cost-effective solutions, CIC’s commitment to safety, sustainability, and innovation has built a diverse portfolio of successful projects across various public and
private sectors, including energy, healthcare, life sciences, office buildings, education, housing, infrastructure, warehouse and distribution, and hospitality, among others.
CIC services encompass:
• General Contracting: Offering end-to-end construction services, including field engineering, site preparation and management, schedule development, subcontractor management, construction, and project closeout. CIC manages all aspects of the project to ensure timely and efficient delivery.
• Project Management: Providing expert project management services, from initial concept through to completion, ensuring that all aspects of the project are coordinated and delivered on
time and within budget.
• Design-Build: Integrating architecture and construction into one cohesive service, CIC ensures streamlined communication, faster timelines, and reduced risk for clients.
• Construction Consulting: Offering strategic advice on cost estimation, scheduling, risk management, and procurement strategies to help clients optimize their projects.
• Renovation and Retrofitting: Specializing in modernizing and upgrading existing structures to meet new standards, codes, and client needs, from office buildings to historical landmarks.
• Sustainability and Green Construction: CIC is committed to environmental sustainability, delivering energy-efficient buildings, LEED-
certified projects, and green building techniques.
• Self-Performed Trade Work. Wherever possible, CIC uses their own equipment and skilled tradespeople to deliver the best quality standards and efficiencies. This includes concrete work, demolition, metal framing, dry-
wall, flooring installation, painting, and the manufacturing and installation of structural steel. In addition, CIC maintains a fully-managed fleet of over 450 vehicles and machines; modern. This ability to manage significant portions of their construction projects internally not only enhances quality control but also leads to greater cost efficiency for clients.
Clients include Amgen, Bristol-Meyers, Squibb, Walmart, Nordstrom, Pfizer, Boston Scientific, and Merck, among others. CIC’s vast construction experience enables it to cater to the unique demands of a wide variety of clientele, ensuring that projects are delivered on
time and within budget, while adhering to the highest quality standards.
Founded in 1983, CIC’s leadership team brings decades of experience in construction, with deep knowledge of both local and national markets, ensuring that each project is managed with expertise and efficiency. CIC has offices in Puerto Rico, North Carolina, and Florida. It also engages in projects in the Caribbean region.
One of CIC’s latest construction projects is an eight-story multi-family senior living building in Guaynabo, Puerto Rico., developed by Égida 837, LLC Senior and designed by Young & De
la Sota Architects, PS. The $53 million project features 192 one-bedroom residential units, as well as a gym, laundry facilities, a community lounge with a kitchen, a reading room, and a public community courtyard.
For Aerostat, CIC reconfigured Terminal D at Luis Muñoz Marín International Airport CIC’s Aerostar client to improve Custom Border Patrol (CBP) operations and make international travel smoother with easier access to baggage
claim. The project involved constructing new offices, training areas, storage rooms, workstations, restrooms, as well as streamlining inspections facilities and other corresponding facilities, including holding rooms, triage, and
enforcement offices.
Other recent projects include a new manufacturing facility for Terumo Scientific in Caguas, Puerto Rico. Spanning 34,044 square feet, this facility is designed to host manufacturing zones, offices, a warehouse, a central utility building, and multiple support areas.
CIC was the general contractor for all civil, structural, and architectural work for Bard’s medical device manufacturing facility. The $48 million project comprised construction of a 223,500 square foot building and support facilities, including a clean room, on an 18.4 acre lot.
In Durham, North Carolina, CIC executed site preparation for an $8.6 million project, Activities included demolition, tree lodging, clearing and grubbing, building pad, new access entrances, construction laydown areas, and temporary construction parking.
Every construction project involves sometimes potentially hazardous challenges that poses risks to both people and project timelines. At CIC, safety is an integral part of its corporate culture.
Which is why CIC recently received two prestigious awards from the Puerto Rico Manufacturers Association. The Distinguished Safety Performance Award recognized CIC’s recordable injury and illness frequency rate that significantly outperformed the national averages. The Excellence in Safety Award is the highest level of recognition for safety excellence,
granted exclusively to companies that consistently earned the aforementioned Distinguished Safety Performance Award for five consecutive years. This achievement underscores CIC’s unwavering commitment to the well-being of its team members and the communities it serves.
Green building practices to reduce environmental impact to reduce waste, improve energy efficiency and sustainability are increasingly the norm for any construction project. CIC is dedicated to staying at the forefront of this trend by offering innovative solutions that meet the unique sustainability needs of its clients.
These solutions incorporate wherever possible the integration of IoT and automated systems to enhance building efficiency and reduce energy use. Modular and prefabricated construction accelerates project timelines and reduces waste through off-site assembly.
Equally important is the deployment of solar panels. CIC believes solar is no longer just an option, but a strategic necessity as a cost-effective, eco-friendly way to power lighting, heating, air conditioning, and water heating. The price of solar panels has dropped significantly in recent years as technology and production processes have dramatically improved efficiencies and economies of scale.
The construction industry shares the growing
problem of most industries, that of attracting and retaining a skilled workforce. A number of factors contribute to this labor shortage, including an aging workforce, a decline in vocational training programs, and a general misconception about construction jobs and careers.
CIC aims to recruit the workers it needs
through a positive company culture where workers feel valued and motivated. It also offers opportunities for professional growth and development, and partners with vocational and trade programs to develop the next generation of skilled workers.
All CIC projects are delivered by experienced teams working closely with its clients to deliver exceptional quality, project management and value. CIC has only one standard of service and that is to deliver Excellence Beyond Expectations.
Oklahoma is home to over 4,200 manufacturing businesses and nearly 130,000 workers. Here’s how the state powers this thriving industry.
The manufacturing sector in Oklahoma has always been a crucial part of the state’s economic fabric, shaping the lives and livelihoods of Oklahomans while contributing significantly to
the nation’s industrial output. In recent years, Oklahoma’s manufacturing industry has not only survived global challenges but has thrived by leveraging innovation, skilled labor, and a strong network of local support.
Oklahoma’s manufacturing sector covers a wide array of industries from aerospace and defense to food processing, energy, transportation, and more. With over 4,200 manufacturing businesses and approximately 130,000 workers, the state has long been a hub for industrial success. This growth is driven in large part by Oklahoma’s central location, multi-modal transportation system, affordable cost of living, business-friendly policies, and a commitment
to developing a highly skilled workforce. Manufacturing accounts for 11% of Oklahoma’s GDP—an output of $18.6 billion—and 12% of the nation’s GDP. This figure is especially impressive when considering the challenging economic landscape many manufacturers face, from inconsistent supply chains to workforce shortages. Nevertheless, Oklahoma’s manufacturing sector continues to expand. 2023 was a particularly strong year with at least 71 projects from new and expanding companies statewide.
Pictured: Access Optics – based in Broken Arrow, Oklahoma – is a medical manufacturer, specializing in micro optics, optical assemblies, glass-to-metal seals and advanced coating; right: Production at Advantage Controls in Muskogee, Oklahoma, which manufactures water control technology for industrial use.
(Photo credit: Oklahoma Manufacturing Alliance)
Recent project wins in the manufacturing sector include:
• Pratt & Whitney recently opened its new 845,000-square-foot military engines manufacturing facility in Oklahoma City, representing an investment of $255 million and creating 100 jobs.
• Solar energy company NorSun selected Tulsa for its first U.S.-based factory, a $620 million investment that created 320 new jobs.
• Stardust Power Inc., a manufacturer of battery-grade lithium products, selected the state for its domestic supply chain facility, representing a $1 billion investment.
The U.S. manufacturing industry will require some 3.8 million jobs to be filled in the next decade, while 65% of manufacturers say attracting and retaining talent is their primary business challenge. With initiatives aimed technical skills development, Oklahoma is ensuring a steady pipeline of talent to fill high-demand manufacturing roles.
Oklahoma has 28 colleges and universities offering manufacturing technician-related programs, and the CareerTech system projects 10,000 completions of these programs over the
next five years.
The Oklahoma Manufacturing Alliance (OMA) works closely with local manufacturers to optimize operations, improve efficiency and implement new technologies. OMA provides technical expertise, training, and business consulting services through programs that focus on lean manufacturing, energy management, and workforce development.
Here are some examples:
• Developed by OMA in partnership with the
Oklahoma Department of Commerce (ODOC), Connex Oklahoma is a powerful supply chain database tool for the manufacturing industry to help Oklahoma companies better connect with each other, increase business opportunities and be more easily discovered as suppliers.
• OMA’s “Supply Chain Academy” is a comprehensive program designed to assist business owners and managers dive into the world of supply chain management.
• Registered apprenticeship programs devel-
Rowland is president
CEO of the Oklahoma Manufacturing Alliance, which is a statewide organization with experts working to help companies grow, become more efficient, and integrate technology. OMA is part of the national Manufacturing Extension Partnership with centers in every state and Puerto Rico.
oped in collaboration with OMA are targeted specifically toward manufacturing skills.
• OMA recently opened an Advanced Manufacturing Center. The 1,375-squarefoot lab is designed to showcase cutting-edge technologies and process improvements while helping manufacturers engage a more capable workforce. Demonstrations center around applications involving collaborative robots, welding and industrial robots, 3D printing, dimensional
measurement, and other automated systems.
Companies looking to relocate or expand their production also enjoy low-cost, clean energy in Oklahoma. The state is one of the top U.S. producers of renewable energy derived from solar and wind, with nearly 40% of its total electricity coming from renewable sources and producing 68% more energy than it consumes.
In terms of accessibility, an international airport in Tulsa, along with 135 public-use
Pictured left: Claremore, Oklahoma-based, United Axle developed the first threaded axle tube allowing spindles to be easily installed and removed; below: Production at Advantage Controls in Muskogee, Oklahoma, which manufactures water control technology for industrial use. (Photo credit: Oklahoma Manufacturing Alliance)
airports across the state, offers access to domestic and international destinations. Major highways connect Oklahoma within a day’s drive to all U.S. markets. The state is home to four inland ports and 20 rail operators, providing Class I and II service throughout the state.
Since 2018, the Department of Commerce has seen a 90% rise in economic development projects in the pipeline—a number it anticipates will keep climbing due to Oklahoma’s pro-business environment, which offers some of the nation’s most competitive tax rates and incentives.
To support this growth, the state launched proactive initiatives like the Oklahoma SITES Program, which focuses on strengthening site infrastructure. This program is designed to meet the needs of both established and new businesses seeking to expand or relocate to Oklahoma. Currently, there are 27 certified,
site-ready locations and 4,500 industrial sites available, with active efforts underway to further expand these resources.
With continued support, strategic planning, and a commitment to excellence, the manufacturing industry in Oklahoma is poised for a future as bright as its storied past.
BioMADE recently announced a $26.9 million investment in the U.S. bioeconomy. These 17 projects will advance the domestic production of sustainable materials for consumer products and defense applications, while also building the manufacturing workforce of the future.
The next five to ten years will determine a leader in the global bioeconomy. While the U.S. is uniquely positioned to seize this opportunity, strategic funding is needed to develop bioindustrial manufacturing infrastructure and prepare an American workforce to fill this demand for technical jobs.
In late October, BioMADE announced $26.9 million of funding for 17 innovative new projects that will drive the scale-up and commercialization of American biomanufactured products. BioMADE is a Department of Defensesponsored public-private partnership created to develop domestic bioindustrial manufacturing capabilities, or the use of biological systems to produce materials incorporated into products
we use every day, like bio-based cement, plantbased nylon, paints and adhesives, and more.
These projects highlight the breadth and depth of the rapidly growing U.S. bioeconomy, providing funding to 30 organizations that represent the private and nonprofit sectors,
Pictured: previous spread: Community college educators at a bioindustrial manufacturing training session led by BioMADE;
right: Researchers in the lab at Invizyne; right: Squitex materials made by Tandem Repeat.
academic research institutions, and community colleges across 18 states. Projects will look into producing biodegradable plastics, upcycling waste to create new products, developing cellfree systems for commodity chemicals, and launching certification programs to prepare the manufacturing workforce of tomorrow.
This work will continue to revitalize American manufacturing by advancing and commercializing the bioindustrial production of components incorporated into everyday items. The 17 projects will also help to reshore manufacturing
jobs and bolster a domestic supply chain of commodity and platform chemicals, translating the rich history of biotechnology innovation in the U.S. into manufacturing leadership on the global stage.
The US’s leadership in research must be paired with equally strong leadership in process development and scale-up capabilities to
transform our visionary developments into tangible outcomes. By engineering living cells to sustainably produce chemicals, materials, and structures, we have the potential to revolutionize industries and drive sustainable innovation. These bioindustrial manufacturing processes are powered by feedstocks from the U.S., such as corn, woody biomass, waste gases, and
Douglas Friedman is CEO of BioMADE. In founding BioMADE, Doug seeks to secure the growth of the U.S. industrial biomanufacturing ecosystem and advance the non-health bioeconomy. He also serves as consultant (special government employee) at the White House Office of Science & Technology Policy focused on a broad range of policy matters in non-health biotechnology and biomanufacturing as drivers for economic growth and opportunities in national security. Prior to BioMADE, Doug was the founding Executive Director and President of Engineering Biology Research Consortium (EBRC). He earned a Ph.D. in Chemistry from Northwestern University and a B.S. in Chemical Biology from the University of California, Berkeley.
agricultural waste. As a result, the impact of investment in bioindustrial manufacturing is felt across sectors of the U.S. economy, creating new markets for farmers, spurring rural job growth nationwide, ending U.S. reliance on foreign materials imports, and manufacturing sustainable products on American soil.
The $26.9 million investment includes $13.9 million of federal funds from the U.S. Department of Defense and $13 million through non-federal cost sharing. The U.S.
has all the foundational pieces to overcome the challenges of commercialization and build a flourishing bioeconomy. These projects will help to bridge the gap between bioindustrial manufacturing and U.S. consumers, stocking store shelves with more sustainable products
and giving ‘Made in America’ a renewed meaning. With continued cross-disciplinary collaboration and funding in bioindustrial manufacturing, the U.S. can lead the world into the bioeconomy of the late-21st century and beyond.
Integrating IT and OT teams is key to industrial efficiency, reducing costs, and driving innovation for a more competitive edge in industrial manufacturing.
Imagine a high-precision manufacturing plant where machines must operate with exact calibration. To do so, its IT systems monitor equipment vibration and calibration data closely to detect when a machine drifts out of tolerance. However, when they
find issues, they are not communicated to the technicians in front of the actual machines. The technicians therefore remain unaware of these issues and are unable to solve them, leading to flawed products and costly rework. By the time they discover the problem, it’s too late.
This is the reality for many factories with disconnected IT and OT teams. IT holds the data to predict issues, while OT manages operations. Without bridging these worlds, on-site technicians are unable to take action.
A recent survey found that 90% of business-
es report their IT and OT teams are isolated. Bridging this gap is more than improving efficiency, cost savings and quality – it’s about empowering frontline workers. When IT and OT work in sync, technicians receive real-time alerts, allowing them to adjust calibration before
problems escalate. This integration increases employee engagement, prevents downtime and reduces waste.
Integrating IT and OT ensures that machines, data and personnel work together seamlessly, driving efficiency and giving businesses a competitive edge.
A recent study highlighted that a lack of connection between IT and OT leaves behind an immense amount of potential, such as failure to train teams together, integrate data or align their strategies. That’s because too many orga-
nizations keep these departments siloed. Nearly half (47%) of the leaders surveyed say their IT and OT teams aren’t even on the same page when it comes to cybersecurity – a necessity for keeping businesses safe and secure.
Syncing IT/OT offers companies predictive maintenance, faster reaction times to market
changes, and even reduced energy use, with fewer breakdowns, more streamlined operations, and a happier workforce.
With that comes reduced costs, increased revenue, improved operational performance, greater agility and so much more.
It seems like an obvious decision to connect IT and OT, but the barriers are both technical and cultural. On the technical side, many OT systems don’t play well with existing IT infrastructure. For example, OT devices and sensors might not be compatible with existing IT networks, which leads to fragmented data and inconsistent workflows. In fact, 71% of industrial manufacturing professionals say this lack of comprehensive overview of IT and OT assets and data impedes the effective management of
their technology infrastructure.
Culturally, the two teams often have different priorities, budgets, and they even speak slightly different languages. IT tends to be all about cybersecurity and data integration, while OT is laser-focused on operational efficiencies.
In an industrial setting, IT managers are often
at the forefront of data and analytics – they are well-versed in new technologies and how to leverage integrations to identify inefficiencies –whereas plant managers may downplay IT as device administrators or even blockers of innovation due to their strict cybersecurity policies.
For example, IT might insist on a rigorous
security patch for network-connected equipment to prevent cyber threats. The OT team, however, might resist because applying the patch requires downtime, and their priority is minimizing any disruption to production. These differing priorities can lead to tension, with IT seen as overcautious and OT resistant to change.
It’s all about communicating these benefits to both teams. And without strong leadership, that makes both sides feel seen and heard, these departments may stay stuck in their own silos.
Closing this gap between IT and OT will require
As the Vice President of Professional Services at TeamViewer, Matthew oversees Technical Project Management, Software Development for Projects, and Client Operations. His role focuses on delivering exceptional results and ensuring TeamViewer’s clients achieve an expeditious return on investment and long-term success. Before stepping into his current position, Matthew served as the Director of Solution Delivery for TeamViewer Americas, where he led a team of specialists dedicated to delivering world-class Operational Technology experiences. Prior to TeamViewer, Matthew was responsible for delivering global IoT asset tracking and monitoring solutions to Fortune 500 clients in the manufacturing and logistics industries. His career began as an aerospace manufacturing engineer and later as a systems and field engineer in both the onshore and offshore Oil and Gas industries.
Contact Info: https://www.teamviewer.com/en-us/
simultaneous actions on numerous fronts.
First, leadership needs to step in and create a clear, unified vision to ensure both IT and OT operate off the same page – essentially, a common purpose.
Once the human dynamics are sorted, the focus can shift to the technology that brings the two together: technical compatibility between IT and OT is essential to the success of these initiatives.
It’s crucial to invest in integrated platforms and technologies that are helping to bridge the gap between IT and OT systems, such as
solutions that support data exchange, interoperability and seamless integration between IT applications. For example, data analytics platforms and OT systems such as sensor networks. Data compatibility should be a particular area of focus, as IT and OT teams must understand each other’s data needs.
Digitally advanced businesses realize that connecting their IT and OT assets can create immense value, but for many organizations
these functions still remain too far apart.
Combining the two is all about creating harmony between teams that were never meant to be separated in the first place. It causes inefficiencies and frustrations for all parties involved. But when businesses do manage to bridge that gap, they’ll not only drive efficiency and revenue but also be better positioned to tackle unpredictable challenges.
Together, systems will run more smoothly and both teams can focus on what really matters, instead of being at odds.
Oldcastle APG is part of one of the largest global networks of architectural product manufacturers specializing in exterior environments.
Oldcastle APG (Architectural Products Group) is a leading manufacturer of building materials, specializing in products used in the construction, landscaping, and infrastructure sectors. As a global maker of concrete building and hardscape products, Oldcastle
APG covers a wide spectrum of applications— from the structural masonry used in erecting cityscapes and urban centers to the finishing touches of a homeowner’s backyard oasis. The company’s family of brands have set the standard for design, technical acumen and thought leadership in their related categories,
helping homeowners as well as design and landscape professionals craft their vision from concept to installation.
With a comprehensive range of offerings ranging from stadiums to outdoor kitchens, Oldcastle APG is recognized for high-quality, innovative, and sustainable products designed to enhance both residential and commercial construction projects.
Oldcastle APG offers the most complete collection of outdoor brands in the industry, backed by expert design support. Its exterior products
work together to create the inviting outdoor spaces people need to connect, reflect, and recharge.
As the North American leader in outdoor building materials, Oldcastle APG offers a wide array of products under a family of brands that come together to create a complete exterior environment across multiple building categories:
• Outdoor Flooring: Pavers, composite decking, porcelain.
» Brands: Belgard, Moisture Shield®, EP Henry
• Shade, Security, and Privacy. Railing, pergolas, fencing and gates, screens.
» Brands: Barrette Outdoor Living®, rdi® Railing, ActiveYards®
• Landscaping: Stones, gravel, mulch, edging, potting soil, lime, steps and coping.
» Brands: Belgard, Soil Doctor, Jolly Gardener, Timberline
• Backyard Features: Fire pits, outdoor kitchens, grills and accessories, pool and water features.
» Brands: Belgard, Pebble Technology®,
Elements Outdoor Essentials
• Wall Surfaces: Brick, block, and veneer, composite cladding, wall systems, pool finishes and surrounds.
» Brands: Echelon® Masonry, Pebble Technology®, Moisture Shield®, Permacon, Anchor Diamond™
• Set, Seal, and Repair. Concrete, sealants, sands, mortars, grout.
» Brands: Amerimix®, Sakrete, Techniseal® Working together with builders, developers, and contractors, the Oldcastle APG family of brands help create complete exterior environments. No one delivers end-to-end solutions— from site planning to installation to maintenance—quite like Oldcastle APG to ensure every project fulfills goals for both aesthetics and durability. And thanks to its streamlined
supply chain, ordering, logistics and invoicing is greatly simplified.
The team of experts at Oldcastle APG works closely with its customers to meet their design goals to create a site plan design that is both practical and aesthetically pleasing, using the
highest quality, highest performing materials.
Headquartered in Atlanta, Ga., but with operations across North America, Oldcastle APG has over 8500 family members throughout its
more than 200 North American locations and manufacturing facilities supported by some 1,000 sales professionals, the company blends big reach with local service attention. All of its products are manufactured regionally under the most rigorous quality control standards.
Parent company CRH plc, a global leader in building materials, was founded in Ireland in 1970, with operations in the Americas beginning in 1978. CRH’s commitment to safety, innovation, and sustainability further strengthens Oldcastle APG’s capabilities in delivering high-performance products for a wide range of outdoor construction needs. As part of the CRH family of companies, Oldcastle APG has access to expertise in raw materials, infrastructure, stormwater structures, and construction accessories to develop a truly holistic outdoor building solution for residential and commercial customers.
In addition, Oldcastle APG continually seeks to strengthen its product accessibility and capabilities. A recent example is to integrate its signature products in partnership with the custom design platform of Yardzen, the leading technology-enabled landscape design and build platform. Along the same lines, the company’s most recent acquisition, the assets of Certain Teed, expanded its operational capabilities, including two facilities in Buffalo, N.Y., and Orem, Utah.
Oldcastle APG places a strong emphasis on sustainability and innovation. The company actively pursues environmentally responsible manufacturing processes that focus on reducing energy use, minimizing waste, and using recycled materials whenever possible. Many of their
products are designed to be environmentally friendly, ensuring that both the materials and production methods support green building initiatives and a smaller carbon footprint.
The company’s commitment to climate positive innovation means customers can enjoy a one-of-a-kind yardscape while also knowing they are treading lightly on the planet. As a company statement puts it, “Our materials, products, and services define how our world is built. That’s why every time we make something, we work to make it better. We rethink, reimagine, and reinvent solutions for the build environment, making homes, buildings and infrastructure that stand the test of time.”
Oldcastle APG is committed to making a positive impact on the communities it serves. The company is involved in a variety of corporate social responsibility initiatives, including charitable donations, employee volunteerism, and sustainability projects aimed at reducing its environmental footprint. Oldcastle APG strives to shape the next generation of sustainable building materials and solutions.
Another example of Oldcastle APG’s social responsibility is its continual promotion of safe construction practices, supporting industry best practices and enhancing employee well-being. According to a company statement, “Over the years, our growth has been fueled by an entrepreneurial spirit and a family mindset. We
believe in doing business the right way, which means that safety is a top priority and when we give our word, we keep it.”
As the company promotes itself, “As a CRH company, Oldcastle APG is part of one of the largest global networks of manufacturers in the architectural products industry. We create. We build. We innovate. Most importantly, we
care for our people and our planet. Across the globe, we stand together to reinvent the way our world is built.”
“Living your best life begins with enjoying more time outside,” is an Oldcastle APG motto it lives up to with the most complete collection
of outdoor brands in the industry, backed by the expert design support to make the perfect outdoor oasis a reality.
Its exterior products work together to create the inviting outdoor spaces people need to connect, reflect, and recharge.
Oldcastle APG, has everything its customers need to “Live Well Outside.”
spoeton@industrytoday.com
www.industrytoday.com
Tel: 973.218.0310
Our state-of-the-art, multi-channel digital media platform allows you to define your target audience when and how you want to, whether by industry, title or geography. This is why, when companies have a story to tell, time and time again they choose Industry Today to tell it.
For over two decades Industry Today has developed comprehensive editorial coverage on leading companies. Our stories cover the challenges, the victories and the many innovations at work as companies reinvent their operations to compete in this fast-growing global environment.
Our articles are published on our media platform www.industrytoday.com, permanently archived and posted on all social media.
Established in 1998 as a print magazine, Industry Today evolved into a digital magazine and comprehensive digital media platform. We promote the news of the day combined with thoughts about what that news means to businesses and the people who lead them.
Google News and SEO Compliant, Industry Today creates bespoke media campaigns that target key decision makers and buyers to achieve your marketing and promotional goals. We offer a variety of channels to reach the right audience for our partners.
Whatever your industry we have you covered. Led by a seasoned and knowledgeable team of top industry experts, writers, graphic designers and influencers we offer nearly 30 years of editorial and promotional experience.
For further information contact: spoeton@industrytoday.com www.industrytoday.com • Tel: 973.218.0310
Producing high quality components for the rail, defense, mining and recycling industries.
Short lead times are just a part of our everyday business:
• Managing your order from PO to delivery
• Delivering your quality parts and assemblies on time and on budget
• Boosting production with robotic welding
• Full complement of CNC fabrication technology
• Wide range of machining and welding equipment
• Metal finishing and assembly services
• Quality engineering for customer specific and conceptual design
Accumetal Manufacturing is a registered ISO 9001-2015 Company
300 Wright Blvd, Stratford, ON N4Z 1H3 (519) 271-6710
info@accumetal.com
1039 Ridgeway Road Woodstock Ontario Canada N4V 1E2 (519) 537-6284 info@bfteck.com