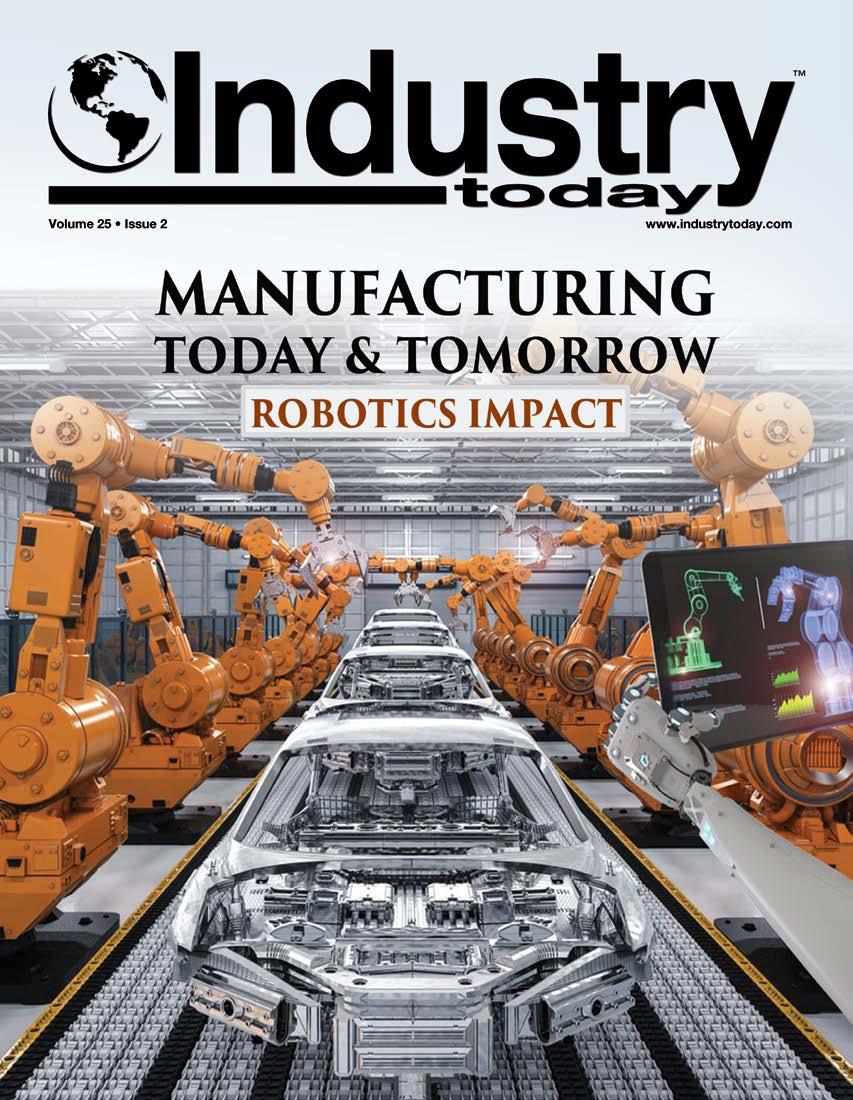
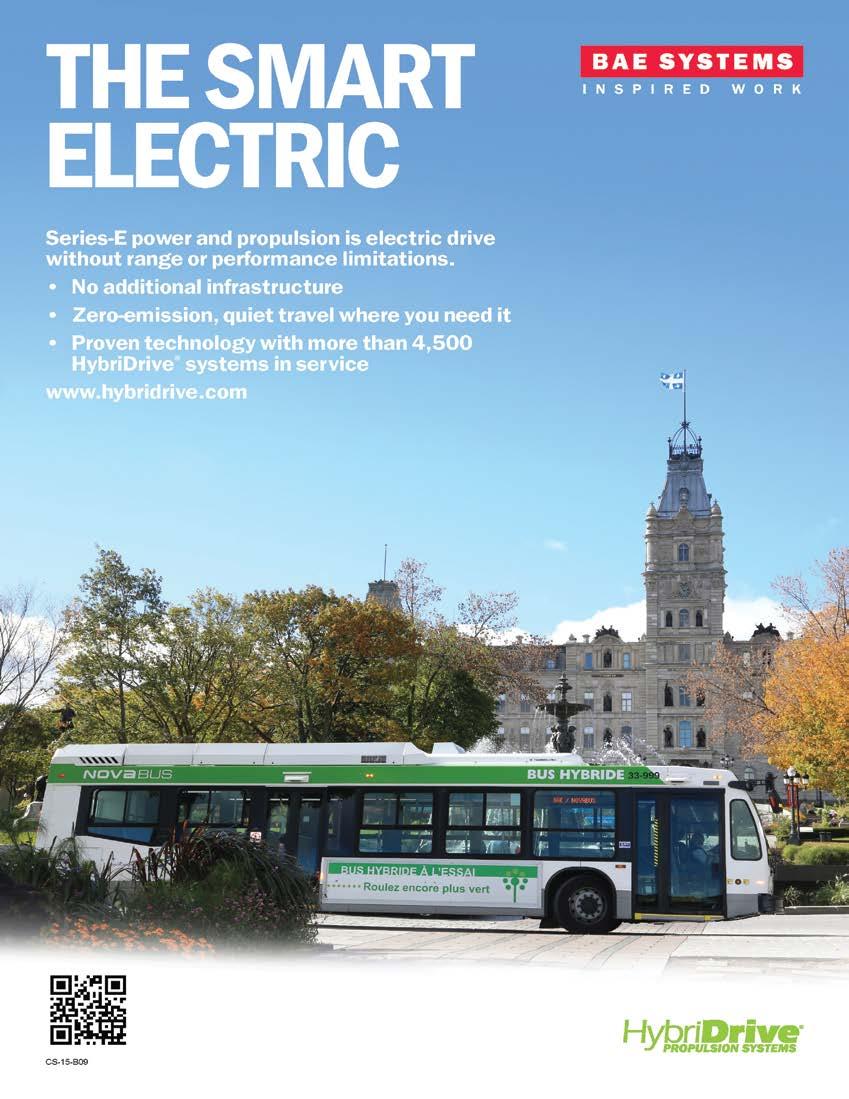
The U.S. currently ranks second only to China in terms of manufacturing productivity worldwide. Even so, improving operational efficiency is paramount if U.S. manufacturing is to adequately address a skills gap anticipated to result in some 2.1 million jobs unfulfilled by 2030, costing the economy as much as $1 trillion. How to close the gap?
For all we’ve heard over the years about robots replacing people, the answer actually depends on a combination of both robots and people.
Let’s start with the robots. The use of robots in manufacturing is nothing new. In fact, assembly line robots have been around for decades, though during most of that time affordable only by companies with deep pockets. New and developing robotic technology is now not only more affordable, but easier to integrate into just about any manufacturing process.
In this issue’s feature article, Robotics’ Impact on US Manufacturing Today and Tomorrow, we note how recent innovations have added to the type and measure of tasks robots can now perform. For example, many of today’s robots contain Light Detection and Ranging (Li-DAR) sensors that enable them to judge distances using laser reflections. This is just one example of how evolving robotic technology stands to improve the efficiency of machine operation, assembly line, packing and shipping. Indeed, robotic automation can yield up to 20 to 50 percent reduction in operational cost.
But while robots are replacing human workers in some areas, particularly the repetitive and in some cases dangerous jobs that historically characterized manufacturing, a skilled workforce is more important than ever. Robots don’t run themselves. How do manufacturers attract a new generation of workers that might not perceive manufacturing as the high-tech industry it is today?
Leo Goncalves, VP of the Workforce Group for the University of Phoenix, writes that apprenticeships are one way. “Apprenticeship programs today can be smart, cost-saving 21st century solutions to help you grow the skills you need in the employees you want,” he writes in the appropriately titled How to Fill Jobs and Save Money with Apprenticeships.
The U.S. Department of Labor estimates there were 26,000 apprenticeship programs nationwide as of 2020, a 73 percent jump in just over a decade. Among the many advantages to apprenticeship programs Goncalves cites is that you train apprentices for the specific needs and culture of your workplace—you don’t have to undo bad habits developed with a previous employer or try to close gaps on the fly. Many apprenticeship programs qualify for federal aid. And unlike internships where students are assigned to a variety of projects, an apprentice works full-time on a specific project at a discounted wage of a regular employee.
While apprenticeships aren’t a silver bullet that can solve all recruitment and retention problems, they are potentially a valuable component.
We hope you enjoy this issue of Industry Today and that it supplies you with some ideas to think about it in your own retention plans and productivity goals. Keep in mind you don’t have to wait for the next digital magazine issue; you can always find timely daily and weekly coverage at industrytoday.com about robots, recruitment and just about anything concerning manufacturing and industry.
www.industrytoday.com
Publisher: Susan G. Poeton
Project Director: Brian McMillan
Project Managers: Jonathan Listig
Production: Melissa S. Burge
Art Director: Seema Mazhar
Contributing Designers: Jorge Leandro Rodrigues
Profile Editor: David Soyka
164 Market Street, Suite 176, Charleston, SC 29401
973.218.0310
Industry Today is published by Industry Today LLC, 164 Market Street, Suite 176, Charleston, SC 29401.
Copyright © Industry Today 2022. All rights reserved.
part of this publication may be reproduced in any form or for any purpose without prior written consent from the publisher and payment of the agreed fee.
# 1521-8058
S manufacturers comprise an esti mated 11.5% of the country’s over-all output and employ about 10% of the workforce, according to the National Association of Manufacturers (NAM). And while the US cur rently ranks second in manufacturing productiv ity worldwide – surpassed only by China – there is need for improvement if we are to remain competitive with overseas sources. A key driver to up grading our standing now and in the future lies in the use of sophisticated or “smart automation” enabled by robotics.
The use of robotics in manufacturing is not brand new – in fact, large corporations includ ing GM, Ford, and Boeing have benefitted from this technology for several decades. Today, however, robotic technologies are available to less “deep pockets” companies, making it a game changer for basic manufacturing in this country.
Consider, as example, how hard tool manufac turers are working to lower costs; the use of robotics is both an affordable and practical solution to many more shops. With costs dropping and systemic integration getting easier, robotic automation will be a win-win for basic manu facturers and their customers, introducing ‘next level’ efficiencies in production, quality and cost.
Pictured above: Machine automation capable: Including automated doors, high intensity lighting, probing and communication; right: Automated tool and parts probe. Wireless intuitive probing allows for un attended tool setting, tool wear and parts QA probing. During automated production, its essential to assure good parts are made along with assessing tool wear in real time.
Since numbers often speak louder than words, consider this – robotic automation can yield upwards to a 20% - 50% reduction in cost. This savings is driven by greater production per labor hour, less rework and lights out manufacturing. Efficient, flexible, highly productive, accurate, and risk-controlled are just a few of the benefits of “smart automation” enabled by robotics. Ro bots can perform repetitive tasks, thereby stream lining assembly-based workflow. They can also take on jobs that may be dangerous to humans. That said; robots are able to collaborate with humans. These so-called “cobots” work along side humans with the end result being a more expedient and efficient workflow system.
Other ways in which robotics are currently active
in the manufacturing industry include “lights-out manufacturing.” This is more common at factories with few human workers; when integrated, machines handle production from start to finish and as such manufacturers can reap rewards in both productivity and labor costs.
While increased integration of robots in manufacturing remains ongoing, their use in other sectors, such as retail, e-tail (think Amazon) cus tomer service, and agriculture can provide “les sons learned” and hold some insight for the manufacturing industry.
Recent innovations have added to robot’s facili ties, enhancing the type and measure of tasks they are now able to perform. Robots used in basic manufacturing can identify and select materials based on size, shape or location. Moreover, some robots contain Light Detection and Ranging (Li
DAR) sensors, enabling them to judge distances through use of laser reflections. Using integrated inspection systems assures robot production can assure quality parts made throughout the night.
While the advantages of manufacturing robots are many, the “human factor” must be taken into consideration. Some question “at what cost” does increased implementation of automation have on workers whose jobs have been or will be taken over by technology, despite the ubiquitous “we’re hiring” signs seen on the lawns of manufacturing
facilities across the nation. It’s true that machine operation, assembly line, packing and shipping are the manufacturing related jobs most impacted by the evolving technology of robotics.
That said, having automation systems in place during the pandemic when stringent in-person restrictions were common turned out to be a financial savior for many manufacturers now chal lenged with finding people to refill assembly and factory posts. Couple this with an aging and retiring skilled labor workforce and therein lies the perfect equation for change, for with advanced technologies comes the need for skilled employ ees who are willing to learn and perform these processes. New types of jobs are being and will continue to be created by the widespread adop tion of automation, including the programming and operations along with the mechanical and software maintenance of robots.
Emerging technologies such as robotics are attracting a younger manufacturing workforce, some times referred to as “new collar.” Generally speak ing, new collar jobs are defined as skilled positions that don’t necessitate a Bachelor’s degree but do require some degree of technological acumen. In deed, the skills needed to manage, program, and operate automated technologies are advanced and require updated training, therefore jobs in these new technologies are attractive to both the vocationally trained and college educated.
Pictured: Ron Gerace is CEO of Precision Design Engineering in Wareham, MA. www.precisiondesignengineering.com; left: Robotics used for Part Loading.
This necessary shift in skill set resonates with younger workers who, growing up in the digital age, are naturally adept at working with automa tion. The need is evident for a new breed of work force, trained and educated to work alongside robots – a marriage of man and machine.
This is not to say that the present and future of automation in manufacturing rests solely on a young workforce. The ability and desire to learn does not have a cutoff date! Workers of all ages can build new skills by embracing advancing technologies. Being able to adapt – companies and employees alike – is critical to being and re maining relevant in work and life, in general.
It is more than likely that the future of manufacturing in this country will feature both au tomated and human labor – sometimes working apart, more often working together – but both essential to creating a cost parity for the United States while maintaining our quality advantage.
Water, water everywhere and not a drop to drink. When poet Samuel Taylor Coleridge wrote that in 1798 he wasn’t making an analogy about data in a smart factory. But he could have been. That saying is used today when despite being surrounded by something, you cannot benefit from it. And that is overwhelmingly true today about data in many manufacturing operations.
Factories full of smart devices, automation systems, and software applications are awash in oceans of data. Intuitively, organizations know that there is value in that data. That they should be able to leverage that data to overcome challenges like supply chain disruptions, labor shortages, and skyrocketing energy prices. By harness ing the data, companies believe they can achieve
Connected enterprises with a cohesive data, analytics and visibility strategy can realize competitive advantage to deliver customer value.
competitive advantage and continue to deliver value to customers, despite adverse conditions.
But how?
Let’s start with what doesn’t work. Some com panies have tried an approach that can best be summarized as capture everything, dump it all in a data lake, and point some artificial intelligence (AI) and machine learning (ML) algorithms at it to look for insights that no one could have
predicted. While appealing in its simplicity it is often just magical thinking that results in enor mous costs and little value. Continuing the water analogy, this approach is like panning for gold in a rushing river. While there was occasionally a story of a miner getting lucky, it was Levi Strauss who got rich by selling tools to all of those who tried.
Instead, manufacturers today need a data
strategy that thoughtfully and clearly lays out the answers to some key questions.
First the strategy defines the sources of data. For most companies today there is no shortage of data sources. But more is not always better. Data storage is not free when considering the scale of data generation in a smart factory. And in some cases, the real data point of interest cannot be directly measured but instead must be derived from
simulation models and digital twins. Consider the temperature at the center of an oven. That might be impractical to measure directly, but, with a physics-based digital twin you can use easily and directly measured values as boundary conditions in a simulation model to accurately predict the temperature at the center of the oven.
When considering sources of data there is real benefit in providing many different types of data that, together, provide a more complete picture of the production system for the connected enterprise. Most manufacturers think first of OT (op erational technology) data. This is the data from sensors, devices, and control systems close to the production processes. Typically, these data points are captured at high frequencies that are matched to the speed of the production processes. This core data can be augmented with secondary data or sensors such as environmental data, power and utility data, video, point cloud data, and more.
There is a lot of value to be gained by augmenting this real-time data with operations management and manufacturing execution data such as sup plier and material tracking, involved workers and their qualifications, and quality system data such as non-conformances or approved deviations. Manufacturers are also tracking and managing the configuration of their production systems –the complete set of information that defines the machines, production software, and setting con figurations in place at every moment in time
Beyond data sources, the strategy further defines the data model that makes sense for their specific production system. The model provides
a structure for adding context and meaning to the raw data. Without this context, data is essentially useless. If I tell you the water temperature is 72 degrees but don’t tell you the units, the time, the location, the rate of change, the desired temperature, and much more, then the 72-degree data is useless.
The manufacturing data strategy must include planned uses. There are many ways that companies can create value from trusted data. Some companies want to use the data to help their front-line manufacturing workers make better decisions and be more productive and safe. This might take the form of operator
interfaces on machines, workflows or augmented reality experiences on mobile devices, or centralized dashboards that provide a shared source of visible truth of real-time manufacturing activity. Other companies want to make the data avail able and accessible to enterprise systems while abstracting out all of the complexity and domain expertise normally required to effectively use manufacturing data across the enterprise. Lowcode or no-code application development environments promise the rapid creation of special purpose software programs that are unique to a specific company, plant, or even manufacturing cell without requiring the skills of scarce and ex pensive professional software developers. Many
companies are also looking to take advantage of advanced data analytics and machine learning algorithms. The insights provided by such tools can be truly remarkable when the underlying data is contextualized and trustworthy. All of these uses of the production system data are new and substantial value creation opportunities.
Further, the strategy contemplates the optimum locations for the data between the edge and the cloud considering costs, performance, scalability, and accessibility. The organization must decide how they will govern and manage that data to ensure its fidelity and security. Afterall data that can’t be trusted is worse than no data at all.
Overall, the strategy puts data at the center of
their production system and creates a power ful reservoir that can be tapped for many new sources of value. By holistically harnessing the combined power of data, advanced technologies such as AI and ML, and expertise, manufacturers can optimize their entire operations. This powers tangible benefits and business outcomes for the organization, with actionable insights, across the manufacturing lifecycle - from the design of new
production system elements to shipping the fin ished product.
Beyond a data strategy, many companies are looking for additional ways to drive more value from manufacturing. Increasingly, that means implementing and using a set of operations man agement applications such as a manufacturing
execution system (MES), quality management system (QMS), supply chain management system (SCM), and asset performance management system (APM). These applications provide a plan ning and execution environment that coordinates activities, creates manufacturing records, and pro vides high levels of visibility across the spectrum of manufacturing activities.
Historically, those applications have been heavy-
weight on-premise software deployments requir ing the provisioning of on-site server-class IT infrastructures, long deployment programs, high levels of customization, and dedicated IT professionals to manage and maintain the installation. Those barriers to entry prevented many compa nies from fully embracing the value provided by these applications.
But of course, in manufacturing like in every other organization across the enterprise, the cloud changes everything. Using native-cloud, multitenant, highly available and secure SaaS offerings for operations management, more and more companies can quickly implement and get value from these applications. Even companies that have de ployed MES and related applications to some of their top-tier plants can now scale out those benefits across the rest of the manufacturing fleet.
Pictured: Brian Shepherd, senior vice president of software and control, Rockwell Automation.our business has a skills gap to close. You have positions to fill. You have a turnover problem.
You also have a potential solution: An appren ticeship program.
No longer the 19th Century system for training blacksmiths, apprenticeship programs today can be smart, cost-saving 21st century solutions to help you grow the skills you need in the em ployees you want.
Just ask the leaders – and successful apprentic es – at Microsoft, CVS Pharmacy or Lockheed Martin, and the nearly two million apprentices who’ve gained skills in a federal program since 2011. The U.S. Department of Labor estimates there were 26,000 apprenticeship programs na tionwide as of 2020, a 73 percent jump in just over a decade.
There are plenty of reasons employees and com panies are jumping on the apprenticeship bandwagon. Here are four:
1. Serious savings. You may be paying for
on-the-job training, but if you work within De partment of Labor guidelines, you’re paying a significantly lower wage than for a traditional employee. There also are significant efficiencies: An apprentice being trained by your business for your job doesn’t have to undo bad habits picked up from prior employers. Training can be tailored to fit your company’s skill gap.
2. Tangible benefits. This year the U.S. De partment of Labor, hoping to broaden appren ticeship opportunities, gave $121 million to bol ster “earn-and-learn” partnerships nationwide. So, depending on the program you participate in, and where you’re located, linking up with the De partment of Labor may qualify you for significant grant dollars. Those dollars might cover 75 percent of an apprentice’s pay for up to six months, or they may reimburse you for 75 percent of your
In addition to federal help, many states also of fer tax credits for apprenticeship programs. More information on state programs is here.
While many apprenticeship programs are de signed to fill entry-level positions, there literally are hundreds of professions that qualify for fed eral contributions, from nannies and nurse practitioners to air conditioner installers and software developers. Right now the Labor Department is boosting a Cybersecurity Apprenticeship Sprint, with extra aid for employers seeking help in the IT Department, but different jobs are promoted with different programs as need arises.
3. Everyone wins. Unlike internships, where a student is assigned for a few months to a variety of projects, an apprentice works full time on a specific job – albeit performing at a lower level,
at least in the beginning – in exchange for a dis counted wage. When the six-, 12- or 18-month apprenticeship period ends, you get a grateful employee trained in the exact skills you need. That employee gets a paid position and may also receive a certificate or degree.
4. Intangible benefits. Most federally sanctioned programs connect an apprenticeship with a pathway to a degree or certificate. So, not only do you get more money in your pocket, you also get a windfall of employee loyalty that helps reduce turnover. Apprenticeship programs build bonds and relationships between longtime and incoming employees.
There are strings attached, of course. With the grant money comes reporting requirements and oversight. There are upsides, however. Govern ment programs often connect an apprenticeship program with a degree completion pathway,
which can be a real loyalty-builder. And, the over sight comes with a roadmap for how to run an effective apprenticeship program.
For an apprenticeship program to produce the results you want takes planning. Following are some dos and don’ts that can hold the keys to
Do be clear on which roles will best fit an apprenticeship program. Usually that means entry level positions and skill-based roles.
Don’t go it alone. Partner with a company that specializes in establishing apprenticeships and knows how to navigate government regulations, including mandated pay scales. That can greatly reduce your company’s administrative burden. It’s an upfront expense. But it’s one that can save you time and money in the long run.
Leo Goncalves is Vice President, Workforce Solutions Group, for University of Phoenix, leading development and value delivery of the university’s B2B relationships. He has significant experience developing growth strategies, turning around business performance, and shaping initiatives to enhance customer satisfaction in education and other private and public sectors. Prior to joining the University of Phoenix, Leo served as Chief of Staff at Kaplan Higher Education Group. Leo has a Master of Business Administration and a Master of Arts in International Studies from the University of Pennsylvania, and a Bachelor of Science in Computer Science from the Universidade Federal De Minas Gerais in Brazil.
Do utilize the expertise of companies that can tap into networks and their own experience to help you recruit and select the right candidates for your program. Hiring an apprentice isn’t like hiring other employees; you can’t rely on acquired skills and experience. It’s important to identify apprenticeship candidates with the attitude and am bition to fit into your company’s unique culture.
Don’t limit your program to the traditional model that ends with training. Instead, connect your program with continued skills development, or with a degree completion component. These drive retention, boost loyalty, and maximize re turn on your investment.
Do take the long view. Training an apprentice takes time. But ultimately, the benefits are
compounded and you’ve earned loyalty. And that spreads to other roles within the organization. That’s when you start unlocking value from that initial investment. Over time the trainee can progress and become the trainer – that’s when an apprenticeship program really can pay off.
The Labor Department says 93 percent of ap prentices retain employment after completion of apprenticeship programs.
The bottom line: apprenticeships aren’t a silver bullet that will solve all your recruitment and retention problems. But they can be a valu able component in your workforce development strategy.
Leo Goncalves is vice president, Workforce Solutions Group, University of Phoenix.
Two of my personal core values are lifelong learning and giving back to our industry, and I am motivated to fulfill both simultaneously when a cause allows. This is why I joined the Associated General Contractors of America (AGC) Middle Tennessee board four years ago and stepped into the role of president in 2021.
The AGC has played a vital role in my personal development and the growth of our company Hardaway Construction, a leading commercial general contractor building for almost 100 years in Nashville, Tenn. We have seen firsthand the AGC’s impact on the industry for over a century. As president, I can share an inside look into how we lead the organization today and why construc tion companies will see numerous advantages to investing in the AGC.
The AGC is the leading association for the
construction industry and represents more than 27,000 firms. We represent general contractors, joint ventures, specialty contractors, emerging contractors and associate firms. Compromised of qualified construction contractors and industry-related companies dedicated to skill, integrity, and responsibility, the organization has 89 local chapters, fulfilling the specific needs of their communities.
As president of the AGC of Middle Tennessee, I work with our executive director, who oversees many day-to-day activities of the organization. With the board, I lead monthly meetings where we discuss any local policies that may need to be addressed to meet the needs of our members. I also lead the review of our finances and monitor the management of dues.
This leadership opportunity has given me insight into the inner workings of building and
new business in Nashville, which is flourishing with growth. About 200,000 new residents are expected to move to the area over the next five years, with an estimated 109 people moving here daily. This consistent stream of new residents has spurred a major construction boom throughout my hometown of Nashville. Through the AGC, I have been able to keep a pulse on the status of the industry and how others are handling this influx, particularly amid supply chain issues. This insight comes from the networking and profes sional development opportunities the AGC provides its members.
Hardaway Construction’s team members have
taken advantage of many of these opportunities, especially the Construction Leadership Program for young professionals. This program educates young leaders on all facets of how to run a business and help shape a company’s future. We have sent ten of our employees through this program in the past four years, and I would highly recom mend that others do as well.
The AGC is a powerful voice of the construction industry because it improves the quality of construction, protects the public interest and shapes future industry leaders by providing excel lent training programs and dynamic networking opportunities. These member perks help retain
employees, positively impact members’ bottom lines and give members influence over the future of the industry.
Most importantly, the AGC offers its members protection in the legal and lawmaking processes. In Middle Tennessee, we work through our staff lobbyist to support legislation in the best interests of the construction industry and consumers alike. Members benefit from active participation in the legislative process at the local, state and federal levels affecting economic and infrastructure de velopment. A specific example is our yearly Day
on the Hill, where AGC members in Tennessee are encouraged to meet at the state capital building to speak with decision-makers in the state legislature.
The AGC also advocates for its members by reviewing proposed legislation and agency regulations, coordinating members’ responses to proposed rules and developing proactive policy state ments on major industry issues. For example, if we need to work through something with metro codes, we can call the AGC directly, and its legal team will work with the city to determine a solu tion that benefits both sides.
Working in Nashville, the AGC has helped
develop impactful solutions for builders that also consider the best interests of city residents.
The AGC is a premier educational resource for the construction industry, providing a wealth of educational opportunities and discounted Safety Services from one of the AGC’s full-time safe ty directors. The AGC helps reduce injuries and illnesses, reduce industrial-insurance premiums, create a safe working environment, promote job site safety within the industry and the public, prevent regulatory violations and represent in dustry viewpoints to safety regulators.
The organization offers in-person and virtual safety training and certifications, which most
of Hardaway’s employees have completed. They offer classes in CPR/First Aid/AED, excavation training, rigging, signaling for cranes and more. They also provide job site safety inspections, which Hardaway has utilized on many of our sites to ensure the team’s welfare and the building’s integrity.
The AGC offers two training programs, the Supervisory Training Program and the Construc tion Leadership Program, which I recommend for any leaders in the industry. The programs have proven to be highly beneficial to our employees because the knowledge and experience gained make them better managers and leaders,
David Frazier is the CEO and owner of Hardaway Construction.
In 2018, Frazier bought Hardaway Construction after serving as president and operations manager in 2017. David is committed to preserving the company’s legacy and forging the future with a motivated leadership team, a straightfor ward yet flexible approach and a genuine, company-wide commitment to collaboration and transparency in client rela tionships. Frazier graduated from Vanderbilt University with a master’s in construction/engineering management in 2009. He also served in the U.S. Navy as a pilot for seven years and graduated from the United States Naval Academy in 1996 with his bachelor’s degree in mechanical engineering.
which trickles down to the rest of the team.
The Supervisory Training Program is a sixcourse comprehensive training that focuses on the knowledge and skills that every supervisor must have to manage people, time, equipment
and materials effectively. The Construction Leadership Program educates young leaders on the inner workings of a business and how they can shape the future of their companies. It also provides leadership training and networking
opportunities broken out into 13 classes with focuses ranging from Conflict Management to Bonding and Construction Law.
Arguably the most significant impact that the AGC has had on construction companies hap pened during the early months of COVID-19. The industry did not have experience with a crisis of that magnitude, and it was impossible to predict what would happen over the next two years. The industry needed a place to come together and determine the best way to move forward with a unified effort. In response, the AGC released a set of standardized guidelines and procedures that contractors could follow to best protect their businesses during the pandemic. Many companies shut down during this time, but knowing the necessity of continued build ing, the AGC’s advocacy allowed construction to proceed safely.
My experience leading the AGC of Middle Tennessee on the board and as president has sig nificantly impacted our team at Hardaway Con struction. Through our membership, our company has grown professionally, networked with other businesses and utilized the safest building practices. This experience ensures that we can provide excellent, transparent and collaborative service to our customers. We also have peace of mind knowing that we have an advocate protect ing and uplifting our company and the construc tion industry as we move forward into the next 100 years.
Accelerated vaccine development in response to COVID-19 demonstrated the resourcefulness of science. That resourcefulness depended upon the concerted efforts of a number of collaborators, including ThermoFisher Scientific, which produced well known items such as testing kits, PPE (Personal
Protective Equipment), ventilator components and even hand sanitizer, as well as also com plex laboratory equipment such as ultra-low temperature refrigeration to store perishable vaccines.
“The urgency of the pandemic required us to figure out new ways to develop and deliver
highly efficient
separators have been important components in Thermo Scientific’s Ultra Low Temperature Freezers for over 35 years. Temprite oil separators provide
vital high oil separation efficiency needed to enable Thermo Scientific’s
achieve
ultra-low temperatures required to safely store Covid
If the freezer does not reach the required low temperature, vaccine doses may be at risk of spoilage.
Temprite specializes in energy-efficient coalescent and conventional oil separators, oil reservoirs, drier housings, liquid receivers, suction accumulators and more.
Thermo Fisher Scientific Inc. (NYSE: TMO) is the world leader in serving science, with annual revenues of approximately $40 billion, delivering innovative technologies through industry-leading brands, includ ing Thermo Scientific, Applied Biosystems, Invitrogen, Fisher Scientific, Unity Lab Services, Patheon and PPD.
products,” says Michael Meguiar, VP of Global Operations for the Laboratory Equipment Division. “ThermoFisher Scientific brands help our customers push science and technology a step beyond.”
One example is the Thermo Scientific™ TSX Series Ultra-Low Temperature Freezers which
replaces ozone depleting refrigerants with more environmentally friendly hydrocarbon refriger ant and utilizes technology that adapts to usage patterns, such as door openings, substantially reducing energy costs without compromising performance. Even the manufacturing site is focused on science and technology as a zerowaste facility, using water-blown foam insula tion, compliant with the U.S. EPA’s Significant New Alternatives Policy (SNAP), the European Union’s F-Gas compliance and other sustainability standards.
Pictured: Fisher Scientific empowers innovation with world-class products and services.
Another science enhancing product is the GP Pro centrifuge. Centrifuges are a workhorse of the science world, used for separating the con stituents of liquids and chemicals by spinning them extremely rapidly in a safe, controlled manner. This technologically advanced centri fuge can run various speed and ramp profiles automatically. The advanced rotor management system (the part of a centrifuge which holds the test material as it spins) automatically maximizes acceleration, braking a residual load imbalance for each rotor and bucket option to optimize safety and improve separation, while also reducing energy consumption by 40 per cent.
These products are among the many which actualize the ThermoFisher Scientific corporate mission statement “to enable our customers to make the world healthier, cleaner and safer. We do this by helping our customers accelerate life sciences research, solve complex analytical
Pictured: Quiet operation, easy to read controls and other thoughtful design features make Thermo Scientific ULT freezers the right choice for the laboratory.
challenges, improve patient diagnostics, deliver medicines to market and increase laboratory productivity.”
That mission, Meguiar notes, is the guiding principle for product development throughout the company, from conception to execution. “We look to develop solutions that are highly customizable and scalable that we deliver in partnership with our customers.”
Meguiar’s specific responsibility is ThermoFisher Scientific’s Laboratory
Pictured: Freezers are energy efficient and offer reliable sample storage in a variety of formats.
Peerless of America, LLC was founded in 1912 as a manufacturer of extruded aluminum shapes for heat transfer. Peerless is a manufacturer all aluminum and aluminum/copper heat transfer coils and pioneered the use of our aluminum tubing in refrigeration equipment.
In the early 1930’s we introduced the first all aluminum fin coils for commercial refrigeration. By 1960, Peerless introduced all aluminum fin coils for frost -free household refrigerators. Our aluminum coils can be provided with copper tips joined with Peerless ’ patented “eutectic” joint or flux less solder joint.
Equipment Division, which employs about 5,000 people throughout the world. The Divisions Operation Leadership is based in Asheville, North Carolina with additional manufacturing operations in Ohio, California, Puerto Rico, Massachusetts, and global locations in China and Germany. “Our customers are worldwide, so we have facilities to be close to our custom ers,” Meguiar notes. “At the same time, many of our locations are their own centers of excellence that develop products, solutions and practices to share throughout our operations and with our customers worldwide.”
Like every manufacturer since the onset of the pandemic, ThermoFisher Scientific faces supply chain disruptions. Meguiar says the company
works closely with valued suppliers, such as Temprite, which supplies refrigerant management products, to identify issues and allocate resources to meet demand and minimize issues created by raw material shortages, price increas es, and shipping bottlenecks.
To address these challenges, the compa ny recently implemented a supply chain risk management program to map, monitor, and lower supply chain risk based on supplier performance, geographic exposure, and environ mental practices. In addition, the company employs the globally recognized EcoVadis plat form to assess and help drive improvements in supplier health and safety, labor, and
Pictured: Employees at various locations through out the facility in Asheville, N. Carolina.
Temprite specializes in energy-efficient coalescent and conventional oil separators, oil reservoirs, drier housings, liquid receivers, suction accumulators, and other refrigerant and oil management products for all refrigerants, including traditional and natural refrigerants: ammonia (NH3), carbon dioxide (CO2), and hydrocarbons (HCs).
Temprite’s highly efficient oil separators have been important components in Thermo Scientific’s Ultra Low Temperature Freezers for over 35 years. Temprite’s oil separators provide the vital high efficiency oil separation needed to enable Thermo Scientific’s freezers to achieve the ultra-low temperatures required to effectively store Covid vaccines. If the freezer does not reach the required low temperature, the vaccine doses in the freezer may be at risk of spoilage. With Temprite products, your system will:
• Perform at maximum refrigeration capacity
• Consume minimal energy
• Emit less carbon
• Have clean oil and clean refrigerant Refrigeration systems work most efficiently when they are properly designed, properly constructed, and clean. Temprite’s oil separators remove more dirt out of the oil and refrigerant than other separation technologies, saving money on electric bills and reducing the freezer’s carbon footprint.
Temprite’s coalescent oil separators, compliant with several regulatory standards from around the world are manufactured to stringent quality standards.
We use customers’ input to continually develop products that meet the changing needs of a dynamic market. Temprite’s products meet the standards for manmade and natural refrigerants, (including CO2, ammonia, and hydrocarbons). An experienced, dedicated, and conscientious work force, along with a talented engineering team ensures you have products that enable your refrigeration system to perform at its optimal level.
sustainability performance. The platform also helps ThermoFisher Scientific monitor com pliance with its Supplier Code of Conduct and adherence to its four core values of integrity, intensity, innovation, and involvement.
ThermoFisher Scientific sells both directly and
Pictured: For more than 70 years, Thermo Scientific Ultra-Low Temperature Freezers have been protecting and preserving some of the world’s most valuable biological samples.
through third-party channels. Meguiar stresses that end-users can rely on one-stop life sci ences shopping. “What makes ThermoFisher Scientific stand out worldwide is our longstanding customer and channel partner relation ships,” he says. “Price is always a consideration, but our ability to consistently develop and deliv er world-class products is why so many in the life sciences community rely on us.”
Beyond the Laboratory Equipment Division, ThermoFisher Scientific also leads the way in the quest to support science. Most recently, ThermoFisher Scientific developed a test to detect monkeypox, which was just declared a public health emergency. There are currently fewer than 100 laboratories across the country capable of handling monkeypox specimens, and this capability will expand testing. ThermoFisher Scientific also recently announced a $105 mil lion manufacturing site in greater Nashville to meet growing demand for bioprocessing materials required to produce vaccines as well as breakthrough therapies for other diseases. The facility manufactures customizable, single-use BioProcess Containers and fluid transfer assembly systems in high demand by biopharma companies.
Meguiar attributes the ability to continue to deliver world-class products on “our extremely committed team and the value of our human capital. The true purpose of every associate is to our customers, and making the world healthier, cleaner and safer.”
John F. Kennedy once said, “The time to repair the roof is when the sun is shin ing.” CMR Construction & Roofing first opened its doors 20 years ago to help families and businesses repair their roofs and recover when the sun wasn’t shining during catastrophic storm damage.
Since then, CMR has expanded to over 30 states, employing more than 500 and expanding its services beyond storm-related roof repairs and replacements. Today, CMR installs roofs for residential, specialty, commercial, and historical restoration projects. It also has major motorsports sponsorships in alignment with its
company motto, When Speed Matters.
“CMR has been ranked among the top-100 roofing companies in America every year since 2007,” CEO Steven Soule points out. “We con tinue to excel year after year and attained the tenth leading position last year.”
He adds, “We have invested a great deal into
our culture, training and employee experiences, which helps us attract top-quality talent. We sponsor a range of events that are unique in our industry to provide fun opportunities for our team and their families to participate. People are looking to work for a company that gets them excited, and that’s the energy we try to
maintain here. We focus on building our team with people who are passionate about what they do and are experts at it so we can deliver supe rior products, services and experiences for our customers.”
CMR also partners as needed to perform work and meet customer expectations. “We leverage all our assets, including trusted partners and subcontractors, to provide fast, expert, high quality and reliable services to our customers. We’ve built our nationwide network to ensure we can deliver on that promise.”
Pictured: Previous spread: Forbush Performance’s Toyota-Gazoo Racing Supra in the GT4 Michelin Challenge; left: NASCAR Xfinity Series #39 Ryan Sieg; above: Ludowici Elite Crown Roofer Certification class; P1 Offshore Powerboat Race - Cocoa Beach, FL; Shaun Torrente P1 Offshore.
Working in national markets serving vari ous customers helps assure CMR’s continued growth. “There has been a healthy demand for residential and commercial jobs across the nation,” Soule says, adding, “Of course, the storm markets are active for most roofing companies. We’ve been very busy in south ern Louisiana since Hurricane Ida and across Florida and parts of Texas. But CMR’s strategy is different from traditional storm chasers or roofers focused on a few local markets. We have built the resources, processes, and reputation we need to ensure we can serve our custom ers where and when they need us—no matter
where they are located.”
Some examples include repair work in Louisiana’s Terrebonne Parish school district, while another CMR team installed a custom copper roof on the Governor’s mansion in Utah. “CMR has dedicated account managers, crews, and resources available in each area so we can continue servicing and maintaining properties long after the projects are complete,” Soule says.
One particularly challenging project illustrates CMR’s ability to respond to unique customer needs with creative solutions that exemplify its motto of When Speed Matters. “One of our commercial projects came to us after anoth er contractor could not complete the job and was months behind the original schedule. The Pictured left: Ludowici Roof in Florida; above: Utah Governor’s Mansion.
more homeowner confidence
America’s #1 selling shingle just got better again. In 2020, GAF introduced Timberline HDZ® Shingles with Layerlock™ technology and the StrikeZone™ Nailing Area.
Now we’re making our most popular shingle even better - with the addition of WindProven™ - the wind warranty with no maximum speed limitation1.
Contact CMR for more information or find out more at gaf.com/windproven.
protect what mat
building still didn’t have a roof, and the grand opening was just two weeks away,” Soule says. To make matters worse, Soule points out, “The roof, wall panels and MEP (mechanical, electri cal, plumbing) were all unfinished. And moving the grand opening wasn’t an option.”
A further problem, according to Soule, was that “The project schedule we inherited was out of sequence and overlapped with the work of other companies. Six hundred members of various crews had to share the same space over 14 days with access to only four service eleva
Pictured above: Ludowici Roof on a Louisiana home; below: Old Red Courthouse in Dallas.
tors. While our team worked 24-hour shifts to complete the project on time, we had to adjust to provide other companies with access to the roof throughout the installation.”
The solution was to move materials at night, install them during the day, and continuously lay protection down on the new roof to shield it from damage while the other crews worked. In addition, CMR constructed scaffolding with aerial platforms that enabled the other teams to work simultaneously in the surrounding areas and avoid project delays.
“Two weeks from the initial call to action, our crew successfully completed the multi-level roofing project, including a new gutter sys tem that ran adjacent to the building’s laser
When you buy materials from ABC Supply, you’re not just getting the latest products from the industry’s top brands. You’re also receiving world-class customer service. Call or stop by your nearest location to learn how we make it easy to order products, get your deliveries and more.
For two decades, CMR’s team of award-winning experts and artisans have been dedicated to protecting and preserving American communities - one roof at a time.
equipment. The collaborating teams were also able to complete their jobs, and the building opened as scheduled and on budget,” Soule says.
He adds, “This project demonstrated how important it is to have the decades of expe rience CMR offers. We’ve overcome similar challenges on previous projects—from mimicking centuries-old roofing practices for historical buildings to collaborating with complex teams on one-of-a-kind roofs.”
Up on the Roof Roofing materials and construction play an important role in achieving energy efficiency and sustainability goals. Soule notes, “Trends toward sustainability and energy efficiency have been steadily rising for a while now. CMR has always paid attention to both trends in the mar ket and government incentives or restrictions
to determine the best course of action for us to follow. One piece of legislation can quickly take down a portion of your growth strategy in this industry. That said, solar seems to be on the rise again, so we are excited about providing that offering to our customers.”
These days, almost every company is dealing with supply issues. CMR is no exception. “Supply chain challenges are difficult indus try-wide,” Soule says. “CMR is lucky to be in a position where we have the cash flow and stor age capacity to keep certain supplies and roofing materials on hand, enabling us to ride out shortages for a reasonable amount of time. We also maintain excellent relationships with our suppliers, which provides many benefits, including cost efficiencies and priority treatment.”
Still, prolongated supply chain issues require
Pictured: Seminole Hard Rock Hotel & Casino.
Congratulations to CMR for 20 years of Elite Roofing!
For over 130 years architects, homeowners, universities, commercial, and government clients have turned to Ludowici for uniquely beautiful architectural terra cotta clay tile products that stand the test of time. Crafted in Ohio, our clay tile products are infinitely customizable and carry a 75-year warranty.
ROOFING
more creative thinking. “Since many of our customers are in areas that suffer from frequent and severe storms, we needed to find options that would help them resolve their immediate problems, such as leaks,” Soule says. “We came up with some innovative product options that
Pictured: Part of the CMR team celebrates the company’s 20th anniversary at the Win The Storm event.
enable us to seal the roofs and protect them from leaks while they wait for their preferred permanent roofing materials to arrive.”
CMR’s motto aligns perfectly with its racing team sponsorships. “We succeed at roofing the same way they succeed at motorsports...speed combined with performance,” Soule notes. “To
drive faster and outperform the competition, you need a talented driver, crew expertise, teamwork, top-quality materials and workman ship, as well as an optimal design. Fractional changes and measurements—inches, seconds, degrees—make all the difference. The very same is true in roofing.”
CMR sponsorships include #39 Ryan
Sieg Racing for NASCAR Xfinity, Kalitta Motorsports for NHRA, the Forbush
Performance team for IMSA, ThorSport
Racing for NASCAR Camping World Truck Series, and Shaun Torrente for Powerboat P1.
In addition, CMR sponsorships extend to a slower-paced sport, but one with equal empha sis on performance and accuracy. “We are also participating in PGA Golf with our new brand ambassador, Chad Pfeifer,” Soule says. “It’s a great honor to sponsor Chad, who fought bravely for our country and is dedicated to leveraging his success to champion various organizations that support wounded veterans and their families. CMR has always prioritized bettering our community and supporting veter ans, which makes Chad and his passion projects the perfect fit for CMR.”
Soule emphasizes that CMR is unique with its combination of 20 years of roofing experi ence and reputation for speed, performance and excellence serving residential, commercial, and historical renovation customers across the nation. “CMR blends traditional craftsman ship with advanced technology and strategies to install the most innovative roofing systems, respond immediately to customers and com plete projects on tight deadlines without sacri ficing quality. We can deliver on this promise because of the top-quality people, partnerships, processes and expertise we’ve built over two decades in business.”
CMR Construction & Roofing is America’s 10th-largest roofing company.
f you are going to name a company “Innovative,” it had better be, well, innovative. Over the near 30 years since its founding, Innovative Refrigeration Systems has repeatedly lived up to its name in providing engineering, manufacturing and constructing, as well as aftermarket service, for refrigeration projects used in logistics/distribu-
tion, food and beverage, industrial and process sectors.
The company’s latest innovation: prefabricat ed mechanical enclosures literally delivered to a customer’s doorstep and even rooftops.
“These are skid-mounted, fully-lit and fully insulated enclosures with removable walls and roof,” explains John Stoklosa, VP of
Innovative Refrigeration Systems provides single-source design, fabrication, and installation of customized turnkey industrial refrigeration systems.
Engineering. “It contains the ‘brains’ of an industrial refrigeration system—all the operat ing components including the full set of con trols. Our standard package can interface with separate evaporators. The Master Series offers more flexibility with customization to house evaporators and compressors in one package.”
Under normal circumstances, and depending on customer requirements, pre-fabricated units can be built and delivered in about 12 weeks. Completely outfitted enclosures are truck delivered, sometimes in sections. “A 30-foot wide enclosure, for example, isn’t going to fit on a truck, so it is designed in two to three parts
that we connect on site,” Stoklosa says. ”The prefab enclosure length, however, is always built to fit on a truck bed.”
The customer pours a concrete slab. Once it has sufficiently hardened, the mechanical enclosure is delivered, connected and start ed-up. “Customers are still amazed that in one day they are looking at an empty space, and the
Pictured: Interior view of completed prefabricated mechanical enclosure ships with piping, wiring, electrical, life safety, painting and labeling; below: Exterior view of insulated metal panel walls with fully attached membrane roof walls with an access ladder, safety railing, ventilation system and suspension tank.
next day there is a fully assembled refrigeration system in place,” Stoklosa says.
In addition, there are roof-mounted mini-pent house air handling units which are pre-built to standardized or customized specifications for various cooling applications. Mini-penthouses typically contain access doors, interior grat ing, partitions, ammonia detectors, temperature probes, lighting, stainless steel piping, galva nized steel drain lines, insulation, among other features, and can even be seismic or hurricane rated.
“There are a lot of advantages to prefab construction,” notes company president Mike
left: Only hours before this would have been a bare concrete slab. A few well-coordinated deliveries, a dedicated crew and a crane and this pre-fabricated mechanical enclosure, condenser steel platform and cooperative condensers are only a few weeks away from refrigerating another facility; above: Pre-fabricated mechanical enclosure being prepared to be lifted from the truck deck to its new home.
McGinnis. “It’s built faster, for one thing. You don’t have to dispatch crews to a construction site that gets disrupted by weather, you don’t have to deal with contractors not showing up when they are supposed to or system parts not arriving at time. There is better quality control and system reliability because everything is con structed under one roof by a dedicated team in a climate-controlled environment. All of which contributes to significant costs savings of prefab compared to on-site construction.”
He adds, “A factory-built prefab structure also offers a greater safety factor. “An exam ple is how mini-penthouses are built so that everything is accessible by means of a four-foot ladder. “It reduces the possibility of falls from taller heights as well as the danger of trying to reach for something that isn’t quite within grasp.”
Innovative Refrigeration Systems has a long-established history as a one-stop-shop, single-source for customized and turn-key
Pictured: Pre-fabricated mini-penthouse air unit loading onto flatbed truck with combi-lift straddle carrier at our manufacturing facility. Next stop is the customer’s facility ready for final connection and operation; below: All piping systems are 3-D modelled, drafted and fabricated in our facility ready to be field erected at the customer’s facility.
industrial refrigeration, coupled with a reputa tion for mastering and implementing modern technology to improve customer interactions, conserve energy and improve refrigeration efficiency. All of which makes it uniquely equipped to successfully provide prefabricated industrial refrigeration systems and solutions.
One example is a project for a major distributor of natural and organic foods that needed to upgrade from a Freon-based refriger ation system to a more environmentally-friendly system. Innovative Refrigeration Systems designed a new ammonia/CO₂ cascade system that included 11 mini-penthouses, four screw compressors, and three reciprocating
at Innovative Refrigeration’s Virginia-based manufacturing facility and shipped cross-coun try and installed by Innovative Refrigeration construction teams which replaced their old equipment and integrated everything into one new system. This brought the total footprint of the facility to 800,000 ft. Most significantly, the upgrade/expansion took only 16 weeks, from mobilization to commissioning.
Another is the recent installation of nine pent houses on the top of an automated storage and retrieval facility. The challenge confronting Innovation Refrigeration Systems was that the facility is 100 feet higher than a typical facility. This required building stands and installing duct
Thank you Innovative Refrigeration for being a great FRICK factor and partner, and for trusting us to provide the best equipment for your projects.
All of our solutions are designed with you in mind and aim to give you the high performance, ultra-reliability and robust efficiency you need, whatever the project.
But why stop at equipment? We’ve taken the same revolutionary approach you see in our products and applied it to our training offerings too. All of our trainings are engaging and easy to follow, providing you with everything you need to operate our products, all in one convenient place.
For all of your training needs, simply visit www.fricktraining.com today.
www.johnsoncontrols.com/FRICK to learn more.
the penthouse units up to the top. The project also included installing a full ammonia refriger ation system with two low-stage compressors, six hanging evaporators, and an evaporative condenser, as well as redundant evaporators for a new 45-foot tall freezer room.
“When we first started out, pre-fab made up about five percent of our business,” McGinnis says. “Now it’s about 65 to 70 percent. There are just so many advantages to it that, in most cases and depending on specific customer situations, prefab is more economical and more efficient.” The popularity among customers led to the company’s recent shop expansion that adds some 40,000 square feet to its existing
182,951 square feet of office and shop space, in part to expanded mini-penthouse manufac turing. To increase the safety and productivity of min-penthouse manufacturing, the company also acquired a remote-controlled straddle carrier Combilift system, capable of lifting 95,000 pounds over 16 feet high. The new facility also added 35 manufacturing workers and six
Miller Transport specializes in moving heavy-haul loads and high-end specialized freight. We pride ourselves in moving loads that other companies deem “impossible” and we set ourselves high expectations to ensure we haul freight in a time-sensitive, cost-efficient but most importantly safe manner. With a team of mostly owner operators we are a verified federal contractor as well as HAZMAT certified. Based in Christiansburg, VA with offices in Logan, UT and Hampstead, NC our dedicated staff, both on the road and in our logistics division, will work with you to haul overweight or oversized loads and all types of equipment.
Innovative Refrigeration Systems, located in Lyndhurst, Virginia, is a leader in the design, fabrication and installation of customized turn-key industrial refrigeration systems, as well as industry-leading refrigeration-re lated wen-based software programs. A sister company, Industrial Refrigeration Technical College, offers hands-on training at their state-of-the-art, 4000 square foot facility for ammonia and CO2 operators.
engineers, helping to eliminate weekend and overtime work for full-time employees. McGinnis points out that while imitation is the best form of flattery, almost no other vendor offers the same range of capabilities as Innovative Refrigeration Systems. “There are a few companies that are starting to offer
prefabricated industrial refrigeration units, but they typically rely on other entities to fulfill the project. They don’t have the capabilities to provide complete end-to-end service.”
A key selling point for Innovative Refrigeration Systems, in contrast, is that it is the single-source for prefabricated construction. McGinnis notes
new standard for satisfying your
USA’s
that, “We’ve been offering full-service, in-house design and engineering, manufacturing, con struction, project management and aftermarket support performed by experiencing professionals since our inception. As design-build con tractors, we’re fully competent in every step of the process. Which makes it easy for us to apply these same disciplines to build our prefabricated units.”
Which is why Innovative Refrigeration prefabricated enclosures are so cool.
Pictured: Pre-fabricated mini-penthouse air units being manufactured in our factory. Once fully assembled, Quality Control steps in to do a full inspection before rolling out the door to a customer’s facility.
And we all like a comfortable climate. The right temperature is just what you expect on board a New Flyer bus. MCC provides the ultimate cooling and heating solutions for New Flyer electric, hybrid and diesel buses. The rear mounted ECO RM35 and the new roof mounted ECO Xcel from MCC are designed for performance, efficiency, flexibility, connectivity and care for the environment.
MCC – for a better climate.