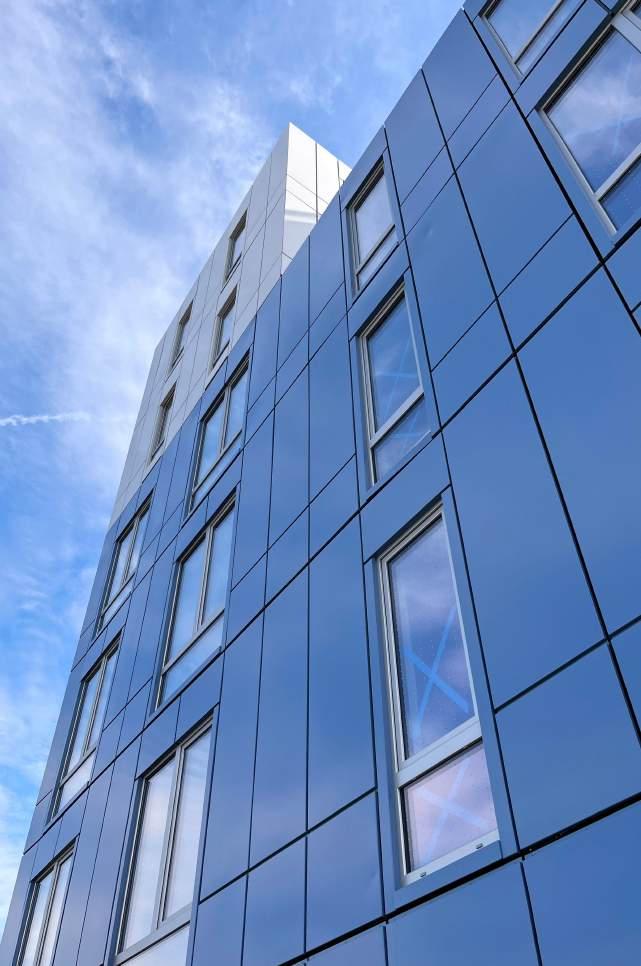
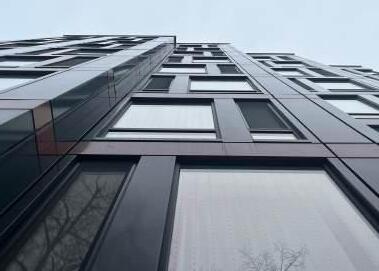
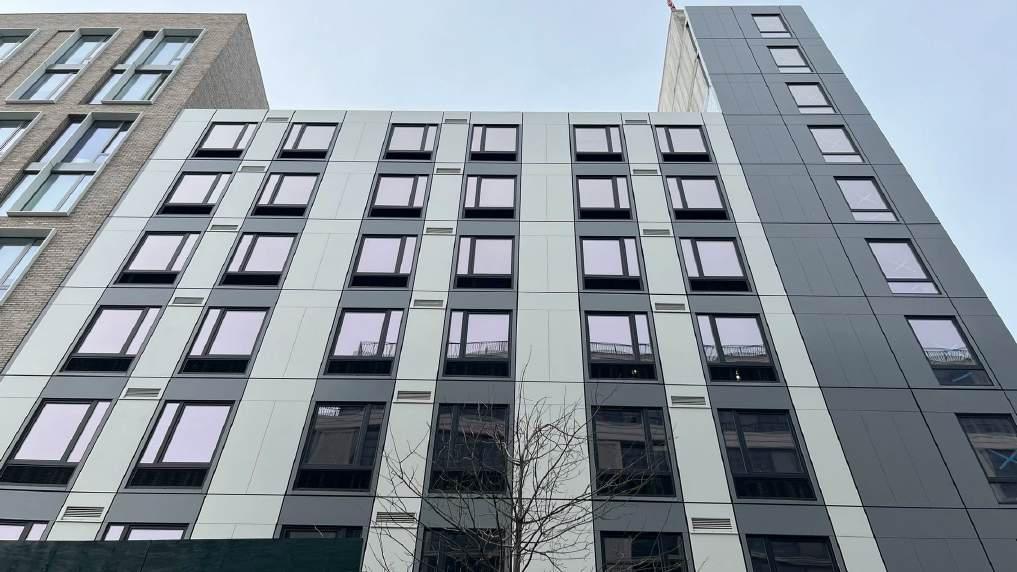
116th Street Project: A in Kew Gardens, Queens, NY. 9-story, 55-unit apartment building
Size: featuring Dextall’s pioneering 12,656 square feet, DWall 2000 system.
A testament to prefabricated construction's potential, offering enhanced efficiency and sustainability.
In collaboration with JLS Group Construction LLC and architect-of-record Chris Hwa Tan, of Tan Architects, PC , the project is noteworthy for its utilization of Dextall’s DWall 2000 product, marking a leap forward for both Dextall and the field of prefabrication at large.
Steven Li of JLS Group Construction LLC, the project developer, emphasized the importance of innovation in meeting project goals:
“Before we select anything, we’re looking at costs and time, and any kind of innovation that can bring those numbers down.
Li’s partnership with Dextall was driven by the potential to significantly impact the construction process’s efficiency and environmental footprint. The design, facilitated by Tan Architects,PC, was aimed at creating a building that seamlessly fits into the historical context of its neighborhood while embodying modern sustainability and efficiency standards.
001
Ensuring the new development was in harmony with the neighborhood's historic fabric, using alternating swatches of aluminum cladding to complement the area’s aesthetic.
004
002
Significantly reducing the construction timeline and labor resources compared to traditional methods, thereby accelerating occupancy and reducing carrying costs.
003
005 Integration with the Historic Streetscape Cost Reduction Environmental Responsibility Efficiency in Construction Innovation in Design and Fabrication
Slashing exterior construction costs by more than half, demonstrating substantial savings for the developer.
Showcasing Dextall’s DWall 2000 panels' versatility and efficiency from design through assembly, proving the system’s value in urban settings.
Minimizing material waste and carbon consumption through prefabricated panels, aiming for a zero-waste construction site.
These goals highlight the project’s broader ambitions: to illustrate the practical and environmental advantages of prefabricated construction in urban environments while maintaining aesthetic integrity and financial viability.
A building that fits the historic context and sets new sustainability standards.
A challenge was the sites unique wedge shape and ensuring that the panels met at the perfect angles. Dextall incorporated a lot of poured-in-place balcony slabs, which interrupts the unitized wall panel façade. Dextall provided lightweight panels which were hand installed between slabs, instead of being hoisted via crane. Loose windows were then installed into the panels on site. To achieve the tricky transitions at the balconies, 3D details and instructions were provided to the installers.
Aurimas Sabulis, Dextall's founder, highlighted the system’s all-in-one solution:
"Our panels arrive on site ready to install, which drastically cuts down on waste and inefficiency."
The choice of aluminum cladding not only aligned with the aesthetic goals but also contributed to the building's durability and maintenance savings.
The fabrication process, characterized by close to zero material waste and a focus on sustainability, underscores Dextall’s commitment to reducing the environmental impact of construction.
001
002
Efficiency Achieved Timeline and Labor Reduction
This efficiency allowed for the apartments to be ready for occupancy three months ahead of schedule, resulting in considerable savings on carrying costs for the developer. The utilization of Dextall’s system reduced the jobsite labor from the 47 workers typically required for a conventionally built exterior to just six, effectively minimizing the project's carbon footprint and eliminating traditional construction waste.
001
Enhanced Building
002
003
Façade Embodied Carbon Footprint Material Waste
DWall 2000 panels ensure optimal insulation and lower energy consumption. Reduced by 47% compared to traditional methods.
001
Optimal
The Dextall system’s impact extends beyond construction, promising longterm benefits for residents in terms of energy savings and maintenance costs. The durable, high-performance exterior contributes to optimal insulation, leading to lower energy consumption and enhanced tenant comfort. This translates to enhanced comfort levels, reduced energy bills, and a lower environmental impact over the building's lifespan.
JLS Group Construction LLC, Tan Architects, Dextall.
Collaboration for success between and Steven Li’s decision to adopt Dextall’s prefabricated system was driven by the desire to innovate in terms of cost, time, and performance. Steven Li notes the significance of this partnership: "We’re already looking at several more projects together on the horizon," indicating a strong endorsement of Dextall’s technology and its potential for future developments. This partnership has set the stage for future projects, with plans already underway to incorporate Dextall’s panels in additional developments in Queens.
The completion of the 116th Street project has set new benchmarks for the construction industry, achieving:
Construction Timeline reduced by 15%
90% reduction in waste
Labor ExteriorEfficiency: assembly labor reduced from 47 to 6 workers
Cost Savings: 52% reduction in exterior construction costs, saving nearly $1 million
47% reduction in carbon footprint
The 116th Street project has not only achieved its goals of reducing construction timelines and costs but has also provided a model for prefabricatedintegratingtechnology into urban environments. This success has solidified the client's decision to continue partnering with Dextall for future projects, indicating a shift towards more sustainable, efficient construction practices in the industry.
Reduced from an average of 30% to close to zero.
The completion of the 116th Street project marks , offering a glimpse into the future of sustainable urban development. Dextall’s innovative approach to design, fabrication, and installation has proven that it is
As Dextall continues to collaborate on new projects in Queens and beyond, the 116th Street building will remain a landmark achievement, a significant achievement in the field of prefabricated construction possible to deliver highquality, energy-efficient housing at a reduced cost and with a lower environmental impact.
demonstrating the tangible benefits of prefabrication technology in transforming the built environment.
Completed in 2023
1
A New Construction in Queens, New York, featuring 8-story mixed-use marvel38 residences, community spaces, and retail.
3 2
Dextall’s DWall 1750
Area: of groundbreaking design using system. 14,211 square feet
4
Location: 132-77 Metropolitan Avenue, Jamaica, Queens, NY.
A model for future urban development, blending affordable housing with sustainability
This project is not just a construction endeavor but a model for future developments seeking to integrate mixed-use spaces in urban settings.
43% reduction in embodied carbon with Dextall’s prefab walls.
80% faster installation, optimizing construction schedules and costs.
Technological advancements in construction for improved safety and labor efficiency.
The Metropolitan project was conceived with ambitious objectives that align closely with Dextall’s commitment to transforming the construction industry through sustainability, efficiency, and innovation.
The project's life cycle assessment underscores this, revealing a The choice of materials, such as aluminum, further supports the sustainability objective by combining durability with environmental responsibility. 43% reduction in embodied carbon compared to conventional construction methods.
43% reduction in emboided carbon
80% faster installation time compared to traditional on-site construction processes
The project sought to redefine efficiency in construction through the use of Dextall’s digital system and prefabricated unitized exterior walls. These innovations allowed for an , significantly improving construction schedules. The streamlined design and construction process facilitated by Dextall's technology also offered end-to-end project cost analysis from the earliest design stages, optimizing both time and financial resources.
80% faster installation time compared to traditional on-site construction processes
These goals highlight the project’s broader ambitions: to illustrate the practical and environmental advantages of prefabricated construction in urban environments while maintaining aesthetic integrity and financial viability.
At the heart of the Metropolitan project is a drive for innovation, reflected in the integration of Dextall’s precision-manufactured structural wall panels that require no wet-sealing and eliminate the need for scaffolding. This not only accelerates the construction process but also enhances safety and reduces labor needs. The project stands as a testament to how technological advancements can overcome skilled labor shortages by lowering barriers to entry and raising the capability level of the construction workforce.
Aligned with Dextall’s vision, the Metropolitan project serves as a pioneering example of how to decarbonize the construction sector while addressing the urgent need for mixed-use developments that are both affordable and sustainable. It demonstrates a holistic approach to building that considers environmental impact, operational efficiency, and the wellbeing of residents and the community, setting a new benchmark for future projects in the industry.
001
Architectural vision for sustainability and efficiency, supported by Dextall Studio
002
Facade design to meet energy codes and integration of mechanical systems.
003
Collaboration with Angelo Ng & Anthony ArchitectsNgStudio, P.C.
Dextall worked closely with architects: Angelo Ng & Anthony Ng Architects Studio, P.C. from the early stages to ensure that the building's design incorporated sustainable practices and efficient use of materials. This partnership enabled the integration of high R-value prefabricated walls, high-performance triple pane windows, and other energy-efficient features right from the design phase.
Challenges such as accommodating the mechanical system within the prefabricated panels were addressed through engineering solutions that allowed for thru-wall vents and exterior louvers, demonstrating the flexibility and adaptability of Dextall’s approach.
One significant challenge was designing a facade that could meet stringent energy codes while also fitting the aesthetic character of the neighborhood. Through Dextall Studio, the team was able to iterate designs quickly, selecting materials and systems that aligned with both performance goals and visual identity.
Another challenge involved optimizing the design for the limited access site. Dextall’s prefabricated systems were chosen for their ability to be installed from the interior, minimizing disruption in the high-traffic area.
This project has three elevations of unitized panels and one elevation of EIFS. Dextall was tasked to develop a detail that can easily transition from prefab panels to EIFS construction. To achieve this goal, Dextall incorporated their proprietary gasketed system onto the site-built EIFS wall which easily connected to the prefab panels, maintaining the air/ water line of the building’s façade.
With R-value of R 29.64, emphasizing aluminum’s durability and recyclability.
The benefits of these materials included not only superior insulation and energy efficiency but also minimal maintenance requirements and adaptability to various design aesthetics.
Precision manufacturing reduces waste to 3-5%, enhancing efficiency.
Dextall’s fabrication process emphasizes efficiency and waste reduction, with materials precision-manufactured in a controlled factory environment. The use of dry perimeter gaskets for the panels eliminates the need for wet- sealing on-site, further streamlining the installation process.
Dramatic reduction in on-site labor
With a six-member crew and approximately 4 days of panel installation per floor.
002
Completing exterior installation 80% faster
003
Innovative use of cranes
"Plug-and-play" panel installation eliminated the need for scaffolding- further reducing costs and improving safety on-site.
This reduction in labor not only but also resulted in
accelerated the timeline substantial cost savings in terms of labor and insurance premiums.
The project also showcased the effectiveness of Dextall’s industrialized design, engineering, fabrication, and installation process in improving the quality of the finished product, reducing embodied carbon impacts, and minimizing unused materials costs.
001
Prefabricated walls and highperformance windows
Leading to significant energy efficiency improvements.
002
Life cycle assessment shows a 43% reduction in embodied carbon
002
Sustainable material selection
Prioritizing responsibilityenvironmental and performance.
Sustainable Material Selection
The project prioritizes materials that offer durability and environmental benefits. Aluminum was chosen for their low maintenance requirements and longevity, in addition to their recyclability, supporting the circular economy.
Recycling-Ready at End of Life
At the conclusion of its lifecycle, the Metropolitan building's materials are designed to be easily recyclable, ensuring that the environmental impact is minimized even beyond its operational phase.
By incorporating Dextall’s innovative building solutions, the Metropolitan project not only complies with current energy codes but significantly exceeds them. The project’s design and materials selection are geared towards surpassing the standard requirements for energy efficiency, setting a new standard for the industry.
001
Superior insulationthermal and air quality advancedthroughventilation systems
002
Enhanced natural lighting contributes to a healthier, more comfortable living environment
The Metropolitan project places a strong emphasis on tenant comfort and building performance, integrating features that enhance the living environment while ensuring energy efficiency. Key aspects include:
Thermal Insulation
The use of Dextall's prefabricated exterior walls with high R-values significantly improves the building's thermal insulation. This not only reduces energy consumption but also ensures a stable indoor temperature, contributing to a more comfortable living environment year-round.
The design incorporates advanced ventilation systems that work in conjunction with the prefabricated walls to enhance indoor air quality. By ensuring proper ventilation and minimizing air infiltration, the building promotes a healthier indoor environment for its occupants.
High-performance windows and strategically placed balcony doors maximize the use of natural light, reducing the need for artificial lighting during the day and offering tenants a connection to the outdoor environment.
Feedback from occupants and post-occupancy data, while not explicitly provided, would likely reflect positively on these features, highlighting improvements in comfort levels, satisfaction with the indoor environment, and potentially lower energy costs for residents.
The successful completion of the Metropolitan project was the result of collaborative efforts among key stakeholders:
43% reduction in embodied carbon
Enhanced environmentliving for tenants, setting a precedent for future developments
Streamlined construction process due prefabricatedto panels
001
The projectMetropolitanshowcases the potential transformativefor urban development
002 002
Sets a blueprint for future projects with a focus on sustainability, efficiency, and tenant comfort
Dextall’s innovations signal a shift towards more sustainable and efficient construction practices
Dextall’s innovations could significantly influence industry trends
Looking ahead, , driving the adoption of prefabricated building systems, digital design integration, and sustainability-focused construction practices. As the industry continues to grapple with challenges like labor shortages, environmental impact, and the need for affordable housing, the lessons learned from the Metropolitan project provide valuable insights and solutions.
The project's success underscores the potential for transformative change in the construction industry, paving the way for a future where sustainable, efficient, and comfortable urban living is the norm.
Completed in 2024
3
1
The 30th Street project is an 11-story residential building
Area: designed as a multifamily residential building 37,313 square feet
4
2
Location: 9 - 26 30th Street, Long Island City, NY
A testament to Dextall’s capabilities in buildings delivering cost-competitive, highperformance
OBJECTIVES: The primary objectives of the 30th Street project were to:
001
002
003 Efficiency Sustainability Innovation
Achieve high sustainability standards. Implement innovative building practices.
Enhance construction efficiency.
Collaboration between Dextall, architects, and the design team ensured that sustainable and efficient building practices were incorporated from the outset.
Prefabricated Products and Specifications. The project utilized Dextall’s 7-inch insulated panel system, featuring:
001 R-VALUE
Met and exceeded code requirements, ensuring superior thermal performance.
002 MATERIALS
003 SUSTAINABILITY ASPECTS
Powder-coated painted aluminum composite material.
Factory-installed cladding and windows, reducing on-site waste and improving energy efficiency.
Dextall’s fabrication process includes precision cutting using CNC and laser machines, optimizing material orders, and pre-assembling components. This approach minimizes waste and enhances efficiency. The materials were selected for their performance characteristics and sustainability, such as steel, aluminum, gaskets, sheathing boards, stone wool, tapes, fixing materials, and windows.
Air and Water Tightness: A significant advantage of Dextall's factoryassembled products is the rigorous quality control procedures that ensure the highest levels of air and water tightness. This controlled environment allows for meticulous inspection at every stage, reducing the likelihood of defects and ensuring that the panels perform exceptionally well once installed on-site. This level of precision is difficult to achieve in traditional onsite construction, further highlighting the benefits of prefabrication.
savings. The panels not only meet but exceed code requirements, providing superior thermal insulation compared to traditional construction methods. This leads to significant reductions in heating and cooling energy requirements, translating to lower utility bills for residents and a reduced carbon footprint.
techniques and sustainable building practices, were employed. These methods improved durability, reduced waste, and minimised the environmental impact.
001 Sustainability Features: The 30th Street project incorporated several sustainability features:
001 Energy Efficiency Measures
Superior thermal insulation provided by the 7-inch insulated panels.
Use of recycled and recyclable materials in the panel construction.
Reduced through efficient material use and waste management practices.
The building’s energy efficiency measures contribute to lower utility costs for residents. Specific calculations show that the enhanced R-value of Dextall panels leads to approximately reduction in energy consumption for heating 30-40%
The use of Dextall panels over traditional construction methods in the 30th Street project has led to a substantial decrease in CO2 emissions, underlining the environmental benefits of Dextall’s prefabricated solutions.
Dextall Panels: Globalpotentialwarming of
80.46 kg CO2 eq/m²
143.11 kg CO2 eq/m² warming potential of
Developer/General Contractor: JLS Group Construction (Flushing, NY)
tenant comfort. The integration of Dextall’s technologies and performance building delivered
impacted the local community by providing a modern, efficient residential building. It serves as a model for future sustainable in urban settings.
The 30th Street project exemplifies Dextall’s commitment to pioneering sustainable and efficient construction practices. As the industry evolves, the lessons learned and technologies developed through this project will play a crucial role in shaping the future of building construction.
The team's competence with