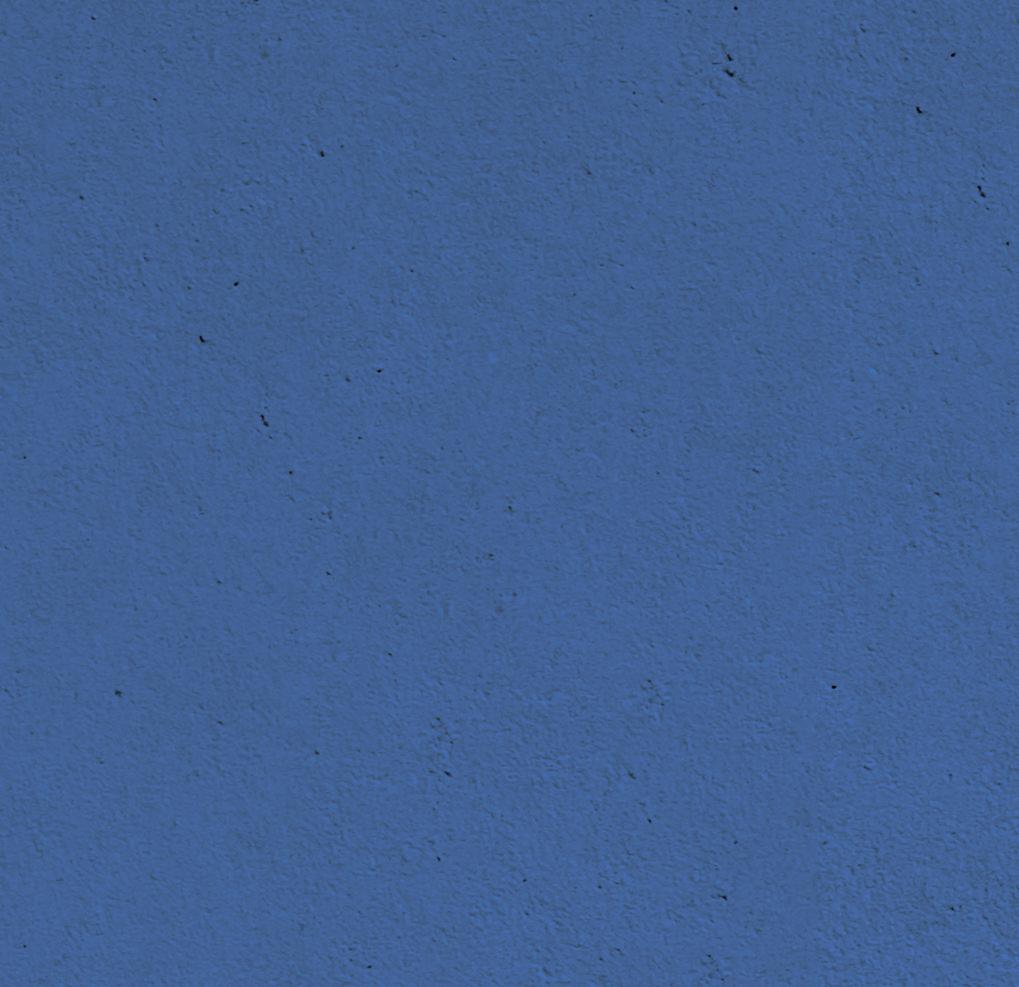
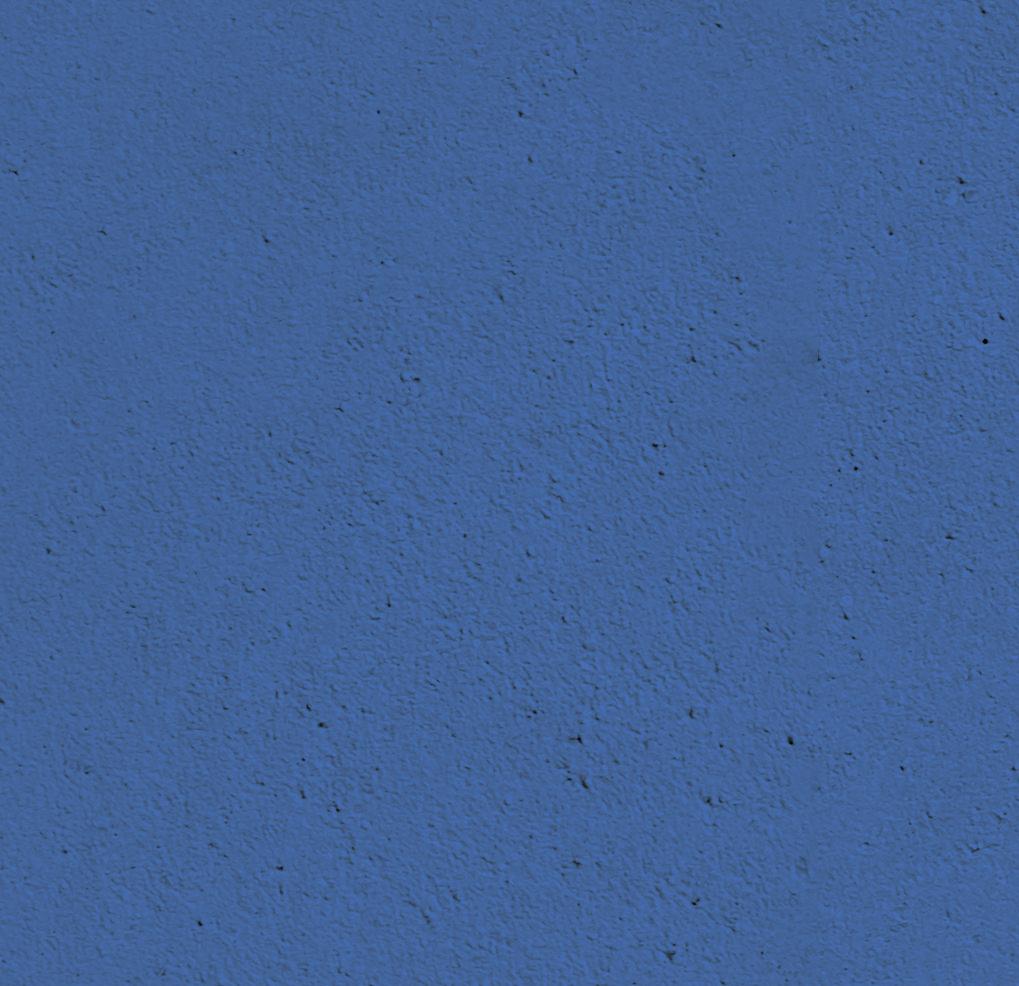
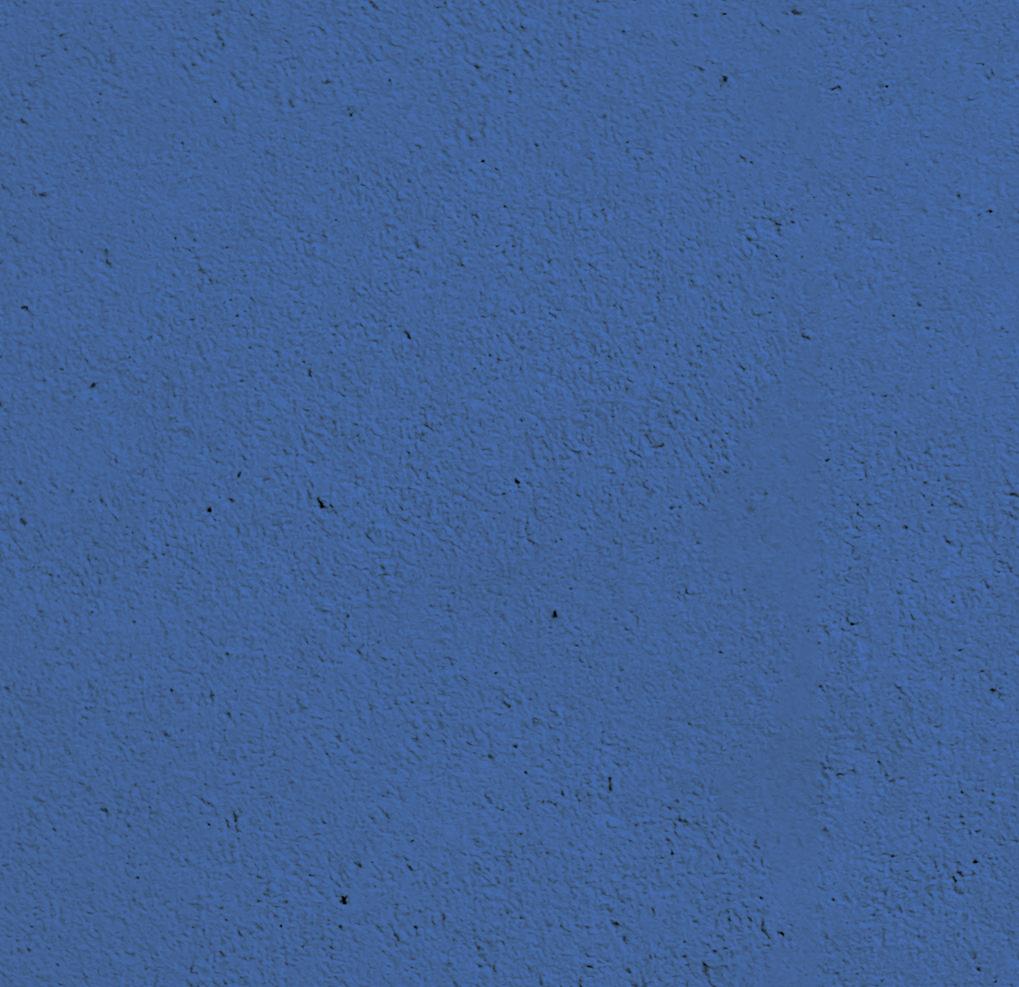
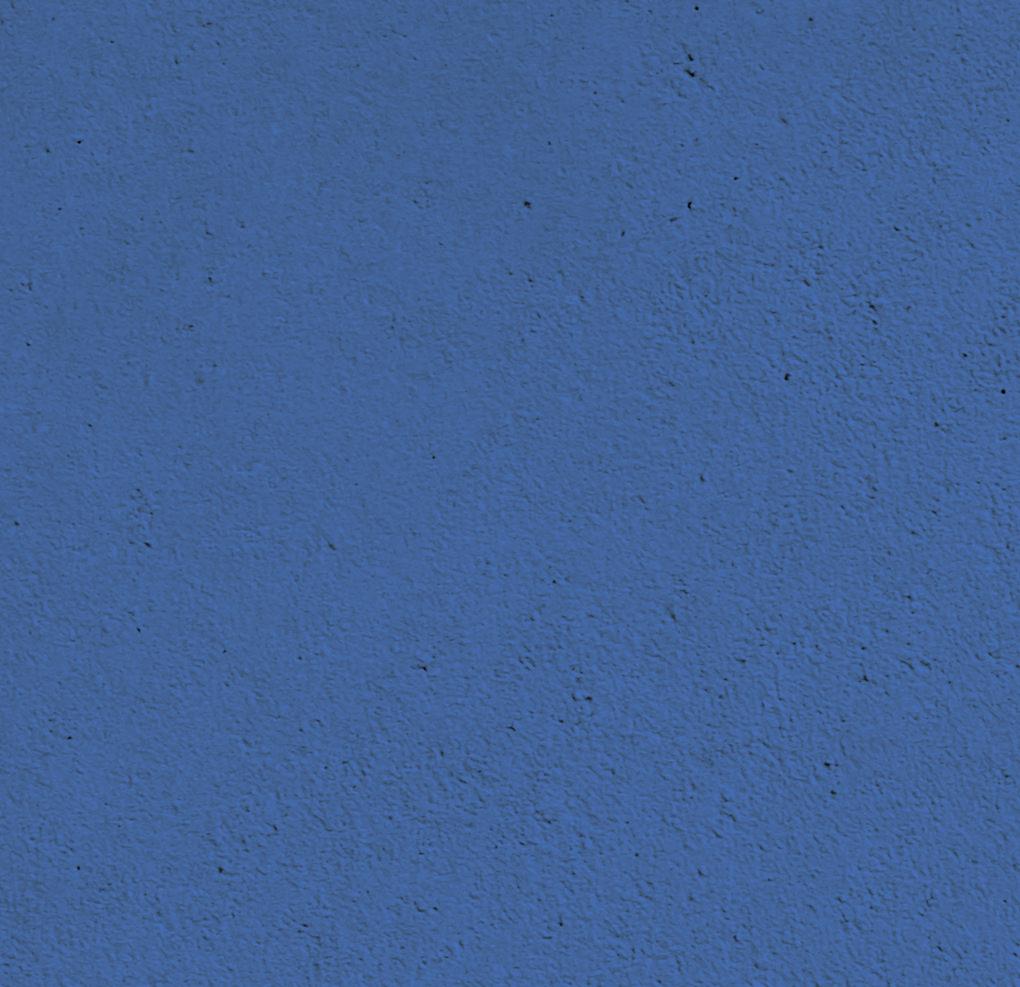
AWARD WINNING QUALITY SUPPLIERS TO THE WORLD
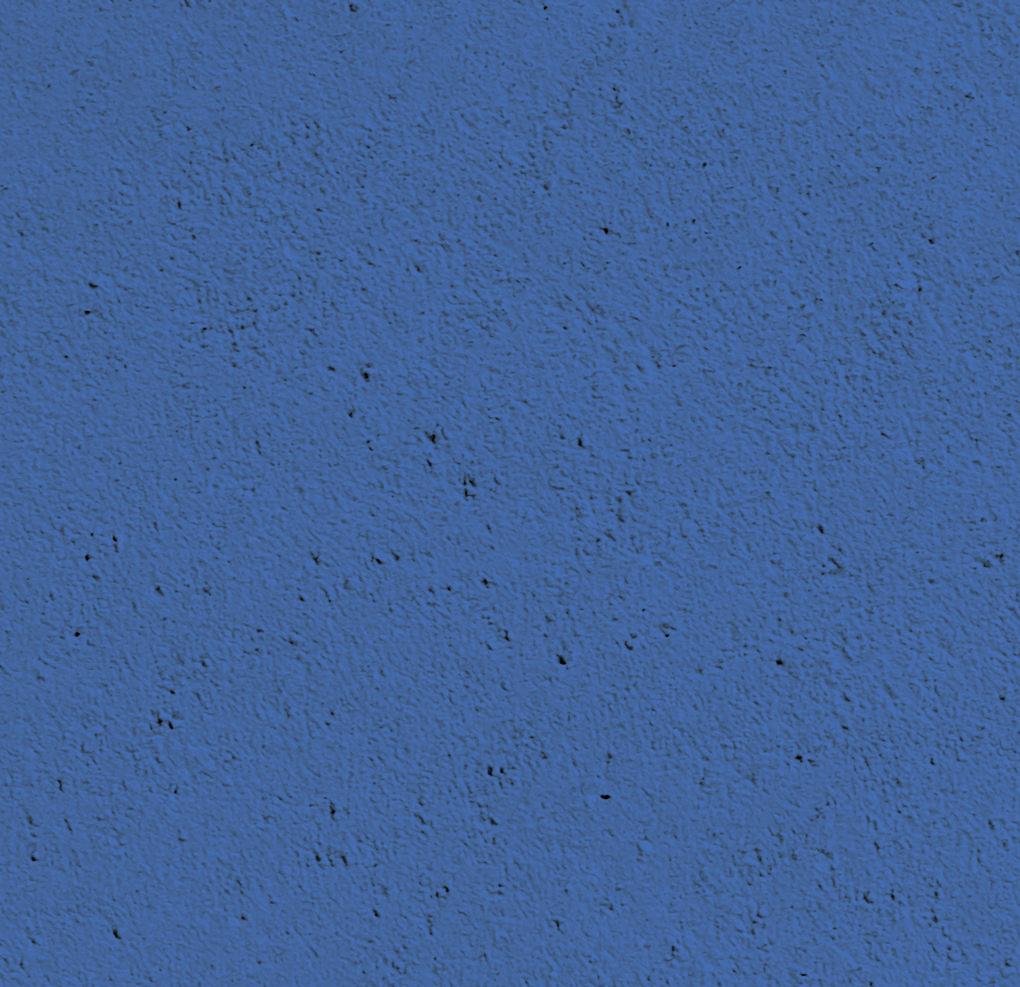
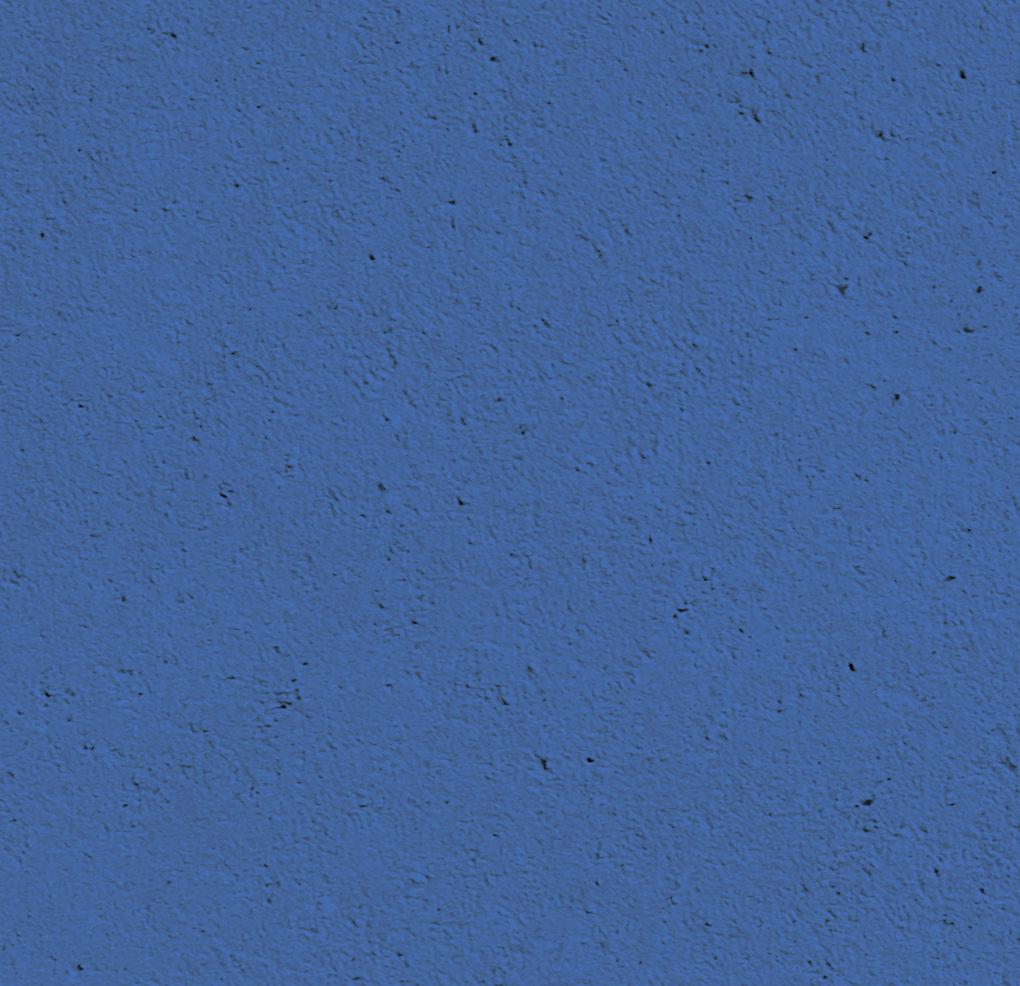
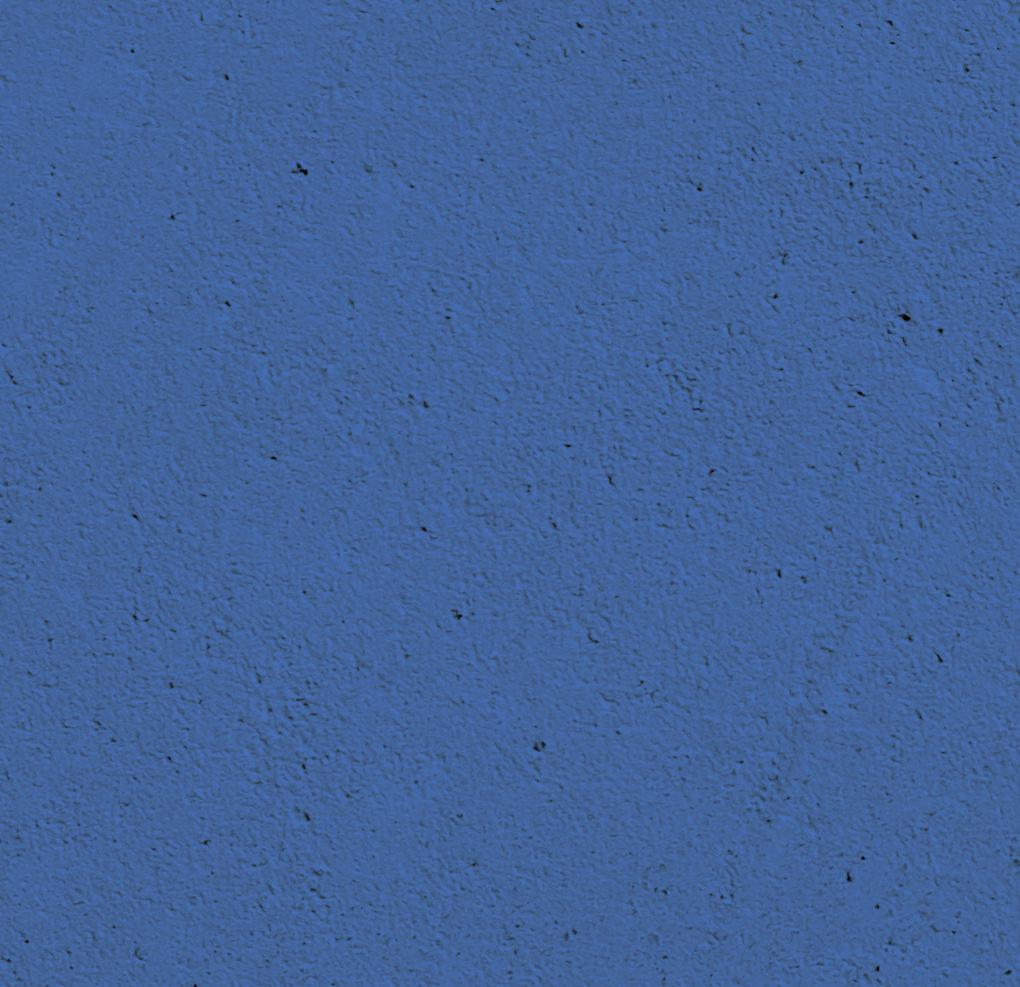

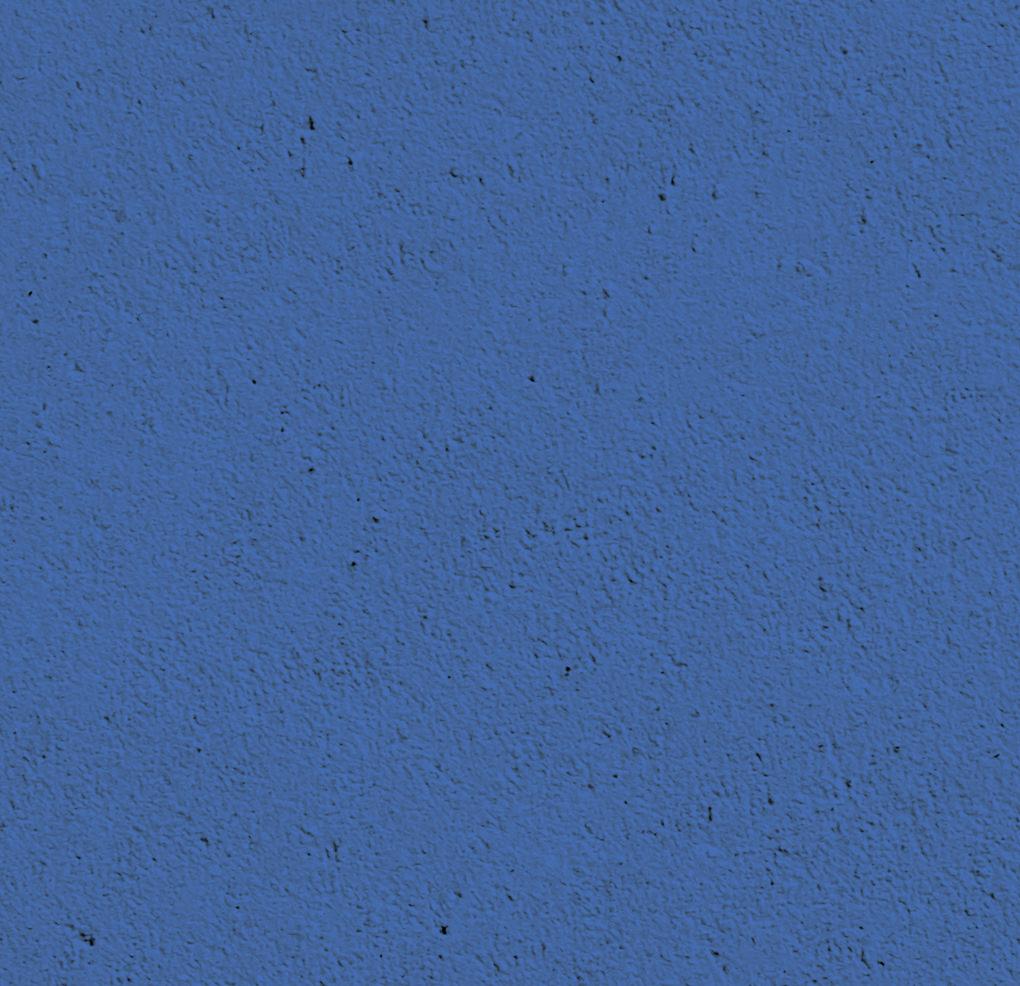



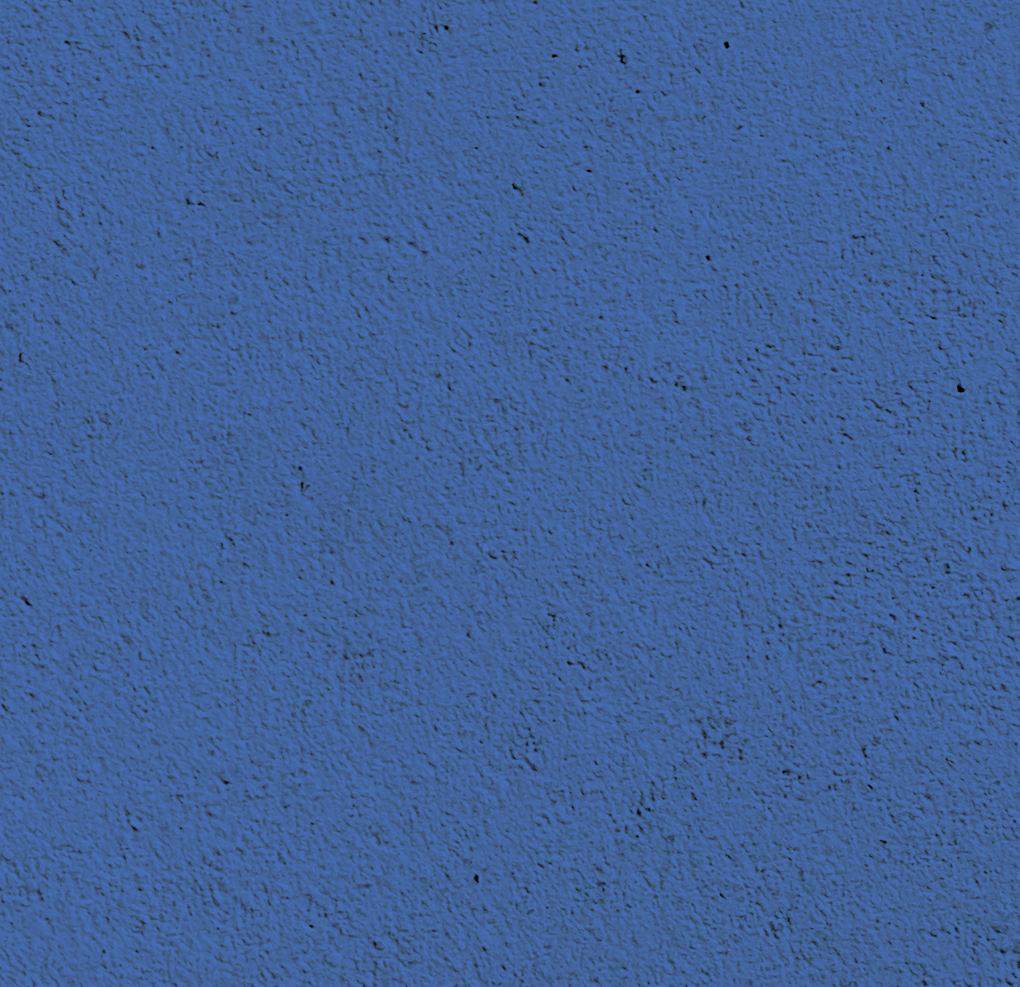
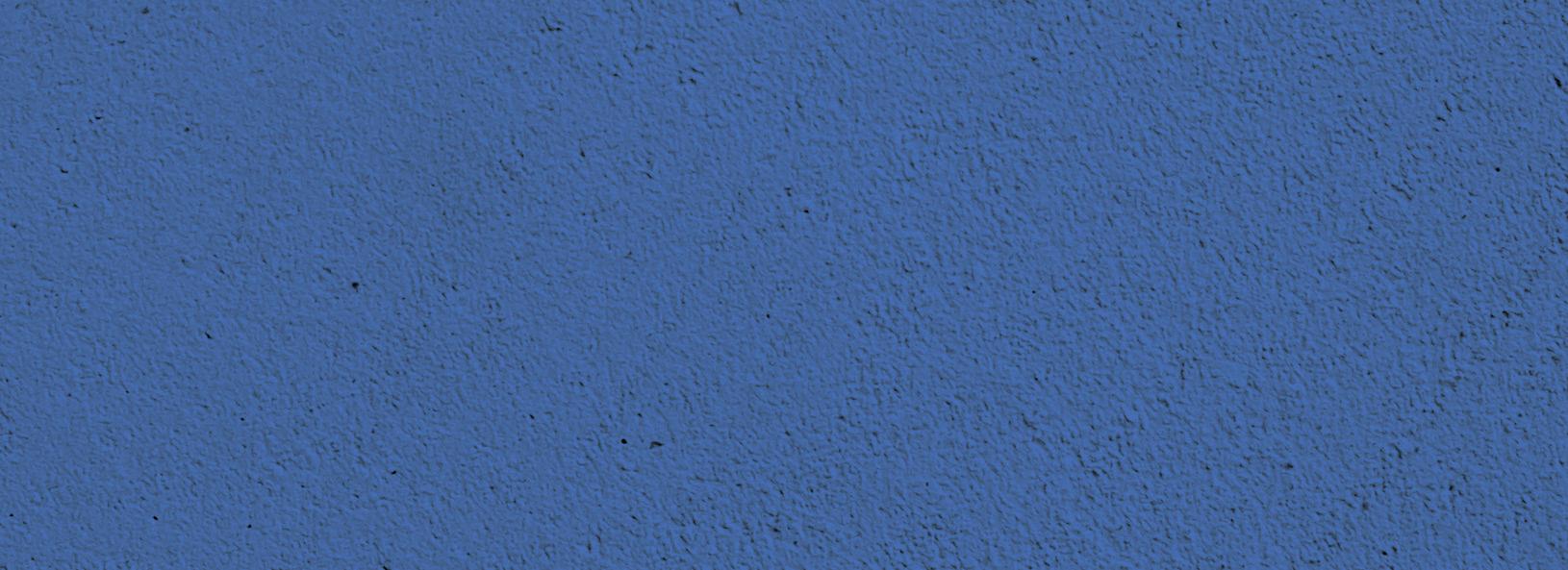
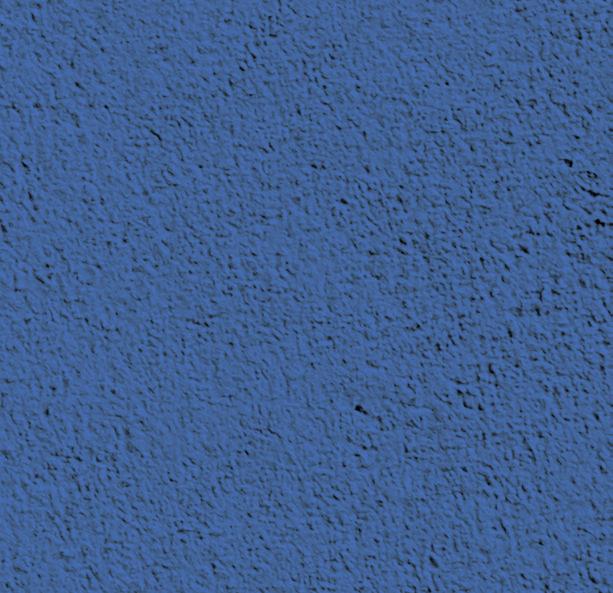


AWARD WINNING QUALITY SUPPLIERS TO THE WORLD
For 50 years Ronacrete has been at the leading edge of product development and performance. Innovation and brand leadership are enhanced by technical support which is considered the best in the industry.
Ronacrete provides a specialist range of products for installation by expert contractors. Technical advice is freely available (call 01279 638700 or email technical@ronacrete.co.uk) to ensure the most appropriate product is selected. Products are widely specified and it is not uncommon for the Ronacrete team to be called in to provide the solution to a problem others cannot overcome.
The product range is specialised and deliberately limited. Consequently this allows for full and meaningful support for each material. Ronacrete is a member of several trade bodies, including the Concrete Repair Association, The Concrete Society, FeRFA and BALI. As a result, we are able to discuss the market requirements
with the contractors in the industry. To ensure that all our customers get the best possible service and highest quality product all of our materials are manufactured to a Quality Management System and are certificated to BS EN ISO 9001:2008. We also work to a strict Environmental Management System and Health and Safety Management System. Furthermore, we have also been certified to BS EN ISO 14001:2004 and OHSAS 18001:2007. NQA (UKAS accredited body) regularly audit our Quality Management System, Environmental Management System and Health and Safety Management Systems. In addition to this the company was proud to receive the Queen’s Award for Export Achievement.
The Ronacrete philosophy is to constantly strive to be the best in all activities. We are one of the few, successful, family run independent British companies in the building materials industry. This therefore allows us to have a flexible attitude and genuine commitment to customer service.
Ronacrete offers a number of RIBA approved CPD seminars as part of its commitment to training. CPD seminars are held at your office at a time to suit you. Our seminars discuss the importance of specifying the most appropriate material for the application and installation techniques and procedures required for successful realisation of design. Our RIBA approved CPD seminars are also available to view online through the Ronacrete CPD Academy which can be found on our website. importance of specifying the most appropriate material for the application and installation techniques and procedures required for successful realisation of design. Our RIBA approved CPD seminars are also available to view online through the Ronacrete CPD Academy which can be found.
“Ronacrete works closely with trade associations to promote high standards at all levels of the legislative and regulatory process. We aim to work towards the improvement of training and education, promotion of high standards and quality of service”
Ronacrete was founded by Fran and Maurice Osen on 1st April 1969. The first office was in the corner of their bedroom with a hand made desk and a second hand typewriter. They saw a gap in the market for alternatives to epoxy and polyester mortars, which were extensively used for concrete repair and screeding. They came up with the idea of offering Ronafix, which is an SBR polymer admixture designed to be mixed with cement and sand to form a strong and durable mortar.
1971
We start distributing internationally and our pre-packed rapid setting mortars were used extensively in the Middle East for the bedding of movement joints in road construction.
1978
Ronafix was awarded its first BBA certificate. 3 more certificates were to follow.
Following the success of a large project at the new HSBC HQ in Hong Kong and high demand for our products, Ronacrete (Far East) Limited was founded.
1974
Large quantities of Ronafix were supplied to the Barbican Centre in London for bedding brick slips, laying thin screeds, repairing fire damaged concrete and bedding of block paviours.
Ronacrete was founded by Fran and Maurice Osen in 1969. Still agile at 50, Ronacrete remains a family owned company and was recognised by Her Majesty the Queen when awarded The Queen’s Award for Export Achievement. Below is a brief timeline of events, taken from an idea to the Ronacrete you know today.
Over 300,000 litres of Ronafix were supplied to the new headquarters of HSBC in Hong Kong. A special formulation was required to create a spray applied polymer/ cement coating to protect the steel.
Ronacrete were awarded the Queen’s Award for Export Achievement and were invited to attend one of the famous Royal Garden Parties at Buckingham Palace.
We celebrated 30 years. The RonaDeck hard landscaping range was introduced to the industry.
Awarded BS EN ISO 9001. Later awarded BS EN ISO 14001 and OHSAS 18001.
Large volumes of RonaScreed 8 Day Overlay were supplied for the screeds at Heathrow Airport Terminal 2.
Ronafix Pre-packed Screed 6-50 was specified and used for the screeds at the Shangri-La Hotel at the top of The Shard
RonaDeck Resin Bound Surfacing was introduced to the market. We supplied materials for nearly 4,000m2 of paving for Newmarket Racecourse
Move to our new state of the art production and laboratory facilities in Harlow, Essex.
Following successful works in the early 80’s, Ronacrete was contacted again to supply materials for extensive refurbishment works to podiums at the Barbican Centre. Success at the Barbican was followed by a similar project at the Brunswick Centre. The futures bright...
The RonaBond Concrete Repair and Coatings range offers all the products required to carry out a detailed concrete repair and provide long term protection to the concrete and reinforcement.
The RonaDeck Resin Bound and Bonded Surfacing range delivers high quality resin based materials for hard landscaping. Whether for your home or a large commercial project we will have the product for you.
The RonaFloor Flooring and Bedding range includes a wide range of resin based coating and screed products for commercial and industrial use as well as specialist polymer modified bedding mortars.
The RonaScreed Specialist Screeds range provides a comprehensive range of site batched and prepacked screeds for domestic, commercial and industrial use ranging from fast drying to moisture tolerant flowable screeds.
The RonaStop Waterproofing and Tanking range comprises of materials designed to protect your property from water ingress. Our damp proof membranes and polymer modified renders ensure your property is protected in the harshest of environments.
TECHNICAL INFORMATION
A series of articles written by Ronacrete’s expert technical department. Subjects include drying of screeds, carbonation of concrete and polymer modification of mortars. Further articles can be found on the Ronacrete website.
The RonaBond Concrete Repair and Coatings range encompasses all the components required for a full repair system in line with BS EN 1504, whether repairs are structural, protective or cosmetic. Polymer modified cementitious primers provide protection to reinforcement and ensure a durable bond between the substrate and the repair mortar. A number of polymer modified repair mortars are available, ranging from high strength mortars to lightweight mortars for overhead repairs and fast setting mortar for cold weather work. Levelling coats are available to provide a fair faced finish and a brush applied polymer cement coating is available to improve equivalent concrete cover where low cover threatens durability. The system is completed with a pure acrylic anti-carbonation coating or waterproof, crack-bridging acryl-siloxane anti-carbonation coating systems, to cover dynamic cracks from fine hairline to 2mm and resist ingress of CO2 and chlorides.
▶ Ronafix for Concrete Repair
▶ RonaBond Concrete Repair Mortar
▶ RonaBond HB40
▶ RonaBond HB40 Ultra Rapid
▶ RonaBond HB25
▶ RonaBond Flowable Micro Concrete
▶ RonaBond Concrete Cover Elastic
▶ RonaBond EasySkim FC
▶ RonaBond FC for Prison Cells
▶ RonaBond Re-profiling Mortar
▶ RonaBond Slurry Coat
▶ RonaBond Crack Bridging Anti-Carbonation Coating WB
▶ RonaBond Anti-Carbonation Coating WB
▶ RonaBond MCI
A repair incorporating the product will have at least the life of the surrounding concrete
Polymer modified concrete repair mortar
▶ Size: 25kg
▶ Conforms to BS EN 1504-3
▶ Excellent long term durability
▶ Pre-packed for ease of use
▶ Provides protection to steel reinforcement
▶ High strength
▶ Waterproof and frostproof
RONAFIX FOR CONCRETE REPAIR
Polymer admixture for use with concrete repair mortars
▶ Sizes: 5L, 25L, 210L, 1000L
▶ 50 year track record
▶ Application from 6mm
▶ High compressive strength
▶ High flexural strength
▶ High tensile strength
▶ Protect steel reinforcement
RONABOND
HB40 ULTRA RAPID
High build concrete repair mortar
▶ Size: 18kg
▶ Conforms to BS EN 1504-3
▶ Apply multiple layers in one day
▶ Repairs from 6mm - 75mm
▶ Just add water
▶ 40N/mm2 compressive strength
▶ Allows for a smooth surface finish
HB40
High build concrete repair mortar
▶ Size: 18kg
▶ Conforms to BS EN 1504-3
▶ Repairs from 6mm - 75mm
▶ Just add water
▶ 40N/mm2 compressive strength
▶ Allows for a smooth surface finish
HB25
High build concrete repair mortar
▶ Size: 18kg
▶ Conforms to BS EN 1504-3
▶ Repairs from 6mm - 75mm
▶ Just add water
▶ 25N/mm2 compressive strength
▶ Allows for a smooth surface finish
FLOWABLE MICRO CONCRETE
Pre-packed flowable repair concrete
▶ Size: 25kg
▶ Conforms to BS EN 1504-3
▶ High strength
▶ Flows freely in to shuttering and through reinforcement arrays
▶ Shrinkage compensated
▶ Protects steel reinforcement
RONABOND EASYSKIM FC
Pre-packed fairing coat mortar
▶ Size: 25kg
▶ Conforms to BE EN 1504-2
▶ Skim coat prior to surface coatings
▶ Level concrete surfaces
▶ 1-3mm application
▶ Covers minor blemishes
▶ Easy to apply
Coating to increase equivalent concrete cover by 150mm
▶ Size: 19kg
▶ Protective coating for concrete
▶ Elastic - covers fine cracks
▶ Only requires 2mm application
▶ Waterproof
▶ Easy to apply
FC FOR PRISON CELLS
Hard wearing fairing coat
▶ Size: 25kg
▶ Conforms to BS EN 1504-2
▶ Provides a ‘harder than plaster’ finish
▶ Set time of less than one hour
▶ 1-3mm application
▶ Covers minor blemishes
COATING WB
Elastomeric, waterproof and carbonation resistant coating
▶ Size: 16L
▶ Excellent CO2 resistance
▶ Self cleaning properties
▶ Superior workability
▶ Dynamic crack accommodation up to 2mm
▶ Permanent elasticity
▶ Water based
▶ Large colour range
Pre-packed mortar for facade levelling
▶ Size: 25kg
▶ Forms textured substrate prior to application of surface coating
▶ Apply 1-3mm thickness
▶ Pre-packed for ease of use
▶ Waterproof and frostproof
▶ Apply by brush, roller or trowel
Mortar for reprofiling vertical and overhead surfaces
▶ Size: 25kg
▶ Conforms to BS EN 1504-3
▶ Can be applied from 3mm
▶ Excellent resistance to shrinkage
▶ Excellent substrate adhesion
▶ Pre-packed for ease of use and consistent performance
COATING WB
Water based anti-carbonation coating
▶ Size: 16L
▶ Excellent CO2 resistance
▶ High resistance to UV degradation
▶ Excellent vapour permeability
▶ Suitable for facades and soffits
▶ Smooth finish - low dirt retention
▶ Large colour range
Surface applied migratory corrosion inhibitor
▶ Size: 208L
▶ Migrates through normal and dense concrete structures
▶ Protects steel reinforcement
▶ Does not require removal of sound concrete
▶ Enhances durability of reinforced concrete
▶ Traffic can resume minutes after application
▶ Organic, safe and environmentally friendly
For over 20 years, Sussex Heights has been protected against driving rain and airborne salts by RonaBond Crack Bridging Anti-Carbonation Coating WB. Situated close to the West Pier, immediately behind the Brighton Hilton Metropole Hotel, Sussex Heights is a 24 storey landmark block of luxury apartments.
Sussex Heights was built in 1965 and was originally clad in mosaic tiles, but by 1990 it was clear that the tiles were no longer protecting the structure against water ingress from rain, driven by the prevailing South Westerly winds. To restore the building to its former glory and to prevent further damage, the tiles were removed, repair works were carried out and the entire building was coated with RonaBond Crack Bridging AntiCarbonation Coating WB.
RonaBond Crack Bridging AntiCarbonation Coating WB is a waterproof, elastomeric anti-carbonation coating, chosen to provide a rainproof envelope to the structure and protect the reinforced concrete against attack by airborne
salts and acidic CO2 gases. Key to the specification was a 10-year insurancebacked guarantee, underwriting the performance of the product and the application. The guarantee was the first to be underwritten on such a contract in the U.K.
By 2001 the coating was reaching the end of its 10-year warranty period and the client’s building consultant, Lambor Associates Surveyors, approached Ronacrete Ltd to prepare recommendations to re-coat Sussex Heights, to enable continual cover and a 10-year extension. Inspection of the existing coating showed that it was in good condition, free from defects and well bonded to the substrate, a testimony to the performance and longevity of the product in a very aggressive environment.
RonaBond Crack Bridging Fabric, a glass fibre reinforced coating product, was specified for the second contract, to provide extra durability and resistance to structural movement and substrate cracking, with a top layer of RonaBond Crack Bridging Anti-Carbonation Coating
WB to provide rain resistance and prevent dirt retention. A further 10 year guarantee was issued on successful completion of the works.
Concrete Repairs Limited, a contractor with specialist knowledge of concrete protection was awarded the contract to re-coat the building in two phases. The phases were carefully planned to be carried out over a two year period around the migration habits of the Peregrine Falcons that nest on the roof of Sussex Heights. The existing coating was cleaned and refurbished to a very high standard under difficult access conditions, requiring extensive use of cradles to provide a cost effective and timely solution to the client.
Daren King, Senior Contracts Manager for the project, said: “The difference between the completed phase and original condition highlights the benefits that the application of RonaBond Crack Bridging Anti-Carbonation Coating WB has made to the appearance of the block. The success of this project can be gauged by the fact that both the residents and client are extremely happy.”
In 1993 it was billed as Europe’s Largest Concrete Repair Project. It was Loughborough Estate in Lambeth, South London. The Client was London Borough of Lambeth. The engineer was Ove Arup. It was home to 239 families.
As with concrete repair and protection projects before and after this one, the contractor was allowed to select and price one of two approved repair specifications provided by Arup; one was for a Ronacrete system, the other from another manufacturer used a combination of more materials, resulting in higher contract cost, neither did it offer the assurance and comfort of a 10 year Insurance Backed Guarantee, something many local authorities came to rely upon after suffering early failures of products from other manufacturers.
Three nine storey blocks of flats were refurbished; works included not only concrete repair but also roofing and window replacement. The concrete repair works required the removal of
existing coatings to the concrete using low pressure water and grit blasting – low pressure to reduce the noise nuisance to residents and to minimise the amount of concrete removed in the process. RonaBond Fungicidal Treatment was then applied to kill off mould, fungal growth and algae.
The damaged concrete was identified by the surveyors and cut out to expose sound concrete and clean steel. Rust was removed from exposed steel by wire brushing – no need to grit blast to bright steel when using Ronacrete materials which saves further time and money – and then primed with two coats of Ronafix and cement. The Ronafix mix design D repair mortar of cement, sand, Ronafix and water was mixed and applied to replace the removed concrete.
When repairs were complete a roller applied textured slurry was applied to the walls and soffits to mask the repairs and provide a regular surface to receive the RonaBond Crack Bridging Anti-
Carbonation Coating WB. The coating system used was a solvent primer (water based primers were not yet available), followed by an intermediate coat of RonaBond Crack Bridging Anti-Carbonation Coating WB and a top coat of RonaBond Crack Bridging Anti-Carbonation Primer WB was used to achieve surface texture and appearance. RonaBond Anti-Carbonation Coating WB was applied to soffits and at dpc level to allow water to pass through as required.
To indicate the size of the project, 14,000 litres of Ronafix, 31,000 litres of RonaBond Crack Bridging AntiCarbonation Coating WB and RonaBond Anti-Carbonation Coating WB were used, 20,000m2 of vertical surfaces and 10,000m2 of soffits were treated.
Installation was supervised by Arup engineers, and by Bureau Veritas who ensured materials were applied in accordance with the specification and the requirements of the 10 year Insurance Backed Guarantee scheme.
Any nurse knows that you can’t just stick a plaster on a serious wound and expect all to be well; some cleaning up and repair work may be required! The situation is similar with buildings; in this case, a concrete repair treatment is necessary. You cannot restore a building structure simply by giving it a new coat of paint! Careful examination, diagnosis and finally treatment are required to ensure recovery back to full health.
The nurses’ accommodation at Grantchester House, is a high rise block of flats situated at Addenbrooke’s Hospital, Cambridge. The windows needed replacing, and the facades required restoration. First of all RonaBond HB40 concrete repair mortar was used for the concrete repair. Finally, the ‘operation’ – the finished facades were coated with RonaBond Anti-Carbonation Coating WB.
RonaBond HB40 – Concrete Repair
A pre-packed high build, medium strength repair mortar for repairing concrete and protecting reinforcing steel. It is used to repair
concrete facades and is suited for overhead applications. Its combination of ease of use and strength makes it an ideal product. It can be applied in thick-section layers up to 75mm on walls and soffits. As a result, it provides good cover to steel reinforcement.
RonaBond Anti-Carbonation Coating WB – Protection
A smooth, coloured, water-borne acrylic anti-carbonation coating for use on vertical surfaces, soffits and at DPC level. It allows the passage of moisture vapour so it is particularly suited for application to substrates which may contain entrapped moisture. The coating can be applied to external walls and facades and protects against water, frost, and weathering. In addition, it is also an effective barrier against the damaging effects of carbon dioxide gas.
Notably, RonaBond Anti-Carbonation
Coating WB is available in a standard range of more than 300 colours. BS or RAL colours can be produced, and the life expectancy of the system is more than ten years.
In Hong Kong more than 300,000 litres of a specially modified form of Ronafix was chosen for corrosion protection to the steel structure of the headquarters building of the Hong Kong and Shanghai Banking Corporation designed by Sir Norman Foster.
The Ronafix modified mortar was chosen for protection of the steelwork, after permeability and adhesion testing proved it to be the right weight and performance for the crucial task of protecting the structure from corrosion in the humid marine environment. Without the protection of the two layers of Ronafix modified mortar, exposure to water, airborne salt and CO2 gas would have shortened the life of the building. The design life of the protective Ronafix layer was calculated as being at least 60 years.
The bulk of the concrete protection was applied off-site by sub-contractor ContechWhitmor JV, to ensure that the shot blasting of the steel and spray application of the two layers of Ronafix mortar was achieved under the strictest quality controlled conditions. This meant that the mortar needed to be not only impermeable but also resistant to the impact and abrasion of being loaded onto junks, transported to site, unloaded and erected. After erection, joints and other sections that had to be left untreated were spray applied on site.
The total contract value for the construction of this world renowned building which has 44 storeys, covers 99,000m2and graces the famous Hong Kong skyline was over $650 million.
The RonaDeck Resin Bound and Resin Bonded Surfacing provide highly decorative and functional systems for exterior pavement surfacing. RonaDeck Resin Bound Surfacing, RonaDeck EcoPath UV and RonaDeck Eco Tree Pit consist of UV stable resin and natural aggregates (RonaDeck EcoPath UV also incorporates recycled rubber granules) producing highly permeable and slip resistant surfacing systems. The UV stable resins used in RonaDeck products are unaffected by the discolouration, embrittlement and degradation which is characteristic of resin products which are not UV stable. RonaDeck Resin Bonded Surfacing is typically self-priming and provides excellent slip resistance for pedestrians and high friction surfacing for vehicles. RonaDeck products are tested for slip resistance in accordance with BS 8204-6:2008+A1:2010 Appendix B. RonaDeck UV Wet Pour Rubber Granule Surfacing, RonaDeck Soft Feel Pool Surround and RonaDeck Rubber Granule Tree Pit consist of coloured EPDM rubber granules and UV stable resin, producing surfaces which are soft and safe underfoot; they provide noise absorbency and they are sufficiently resilient to absorb the impact of falls. UV stable resins ensures that surfacing systems are unaffected by discolouration, embrittlement and degradation caused by UV light.
▶ RonaDeck Resin Bound Surfacing
▶ RonaDeck Stone Carpet
▶ RonaDeck EcoPath UV
▶ RonaDeck Drive Base
▶ RonaDeck Thixotropic Surface Sealer
▶ RonaDeck Eco Tree Pit
▶ RonaDeck EcoAgg
▶ RonaDeck UV Wet Pour Rubber Granule Surfacing
▶ RonaDeck Soft Feel Pool Surround
▶ RonaDeck UV Rubber Granule Tree Pit
▶ RonaDeck Resin Bonded Surfacing
▶ RonaDeck Resin Bonded Scratch Coat
▶ RonaDeck Resin Bonded Pore Filler
▶ RonaDeck Resin Bonded Seal Coat UV
RonaDeck Resin Bound Surfacing is a SuDS compliant, UV stable, slip resistant resin bound aggregate surface for pedestrian and vehicular traffic. RonaDeck Resin Bound surfaces are highly decorative and functional, seamless and slightly flexible. The open matrix allows water to drain through to the base, eliminating water ponding and allowing water to drain to planted areas or land drains. The surfacing may be applied to SuDS compliant bases and sub-bases, reducing the impact of urban development on flood risk and allowing water to flow into water courses. Edgings created from brick, stone, timber or steel should be installed to retain and protect the resin bound surfacing.
SuDS compliant, permeable paving system
▶ Sizes: Resin only 7.5kg, full batch 113.75kg
▶ UV stable
▶ Highly permeable surfacing
▶ Slip resistant
▶ Application from 15mm
▶ Low maintenance
▶ Wide range of colours
Images used are for illustrative purposes only.
Sustainable drainage systems (SuDS) are a natural approach to managing drainage in and around properties and other developments. Sustainable drainage systems work by slowing water run off from a site, allowing natural processes to break down pollutants. Water draining through SuDS compliant paving may be allowed to flow naturally to groundwater or diverted to a soakaway when natural drainage is poor, as in heavy clay soils, or diverted to a rainwater harvesting storage tank and used for irrigation, car washing etc. Permeable paving reduces surface water run-off and the risk of flooding, reduces the risk of sewer flooding during heavy rain and recharges groundwater to help prevent drought, all important elements of SuDS. RonaDeck Resin Bound Surfacing and RonaDeck EcoPath UV are paving products suitable for use where a fully permeable construction is required; the polyurethane resin used to bind the aggregate in both products is UV stable, ensuring that the resin will not yellow or darken. RonaDeck Resin Bound Surfacing is applied to a solid base and may be used for car parks, driveways, footpaths, terraces, patios, swimming pool surrounds and other light vehicle traffic or pedestrian traffic areas. RonaDeck EcoPath UV is suitable for pedestrian traffic and may be applied directly to a Type 3 aggregate base. The depth of construction required for permeable pavement will vary according to predicted traffic conditions, the type of base to be laid and how well the subsoil drains. Heavy clay soils may require laying
RONADECK RESIN SURFACE COURSE
Hand applied & troweled to a smooth finish by a trained installer
SUB-BASE
Laid by trained installer
Or Geotextile Layer
Geotextile layer to prevent upward migration of soil
Capping Layer
If required, depending on sub-grade condition
WELL COMPACTED MOT TYPE 3
of pipes to divert water draining through the construction to existing the drainage, a soakaway or a rainwater harvesting system. The use of a waterproof membrane is typical in such cases, applied before laying of pipes and Type 3 aggregate sub-base. It may be necessary for a capping layer to be applied to the sub-grade if the soil is too soft. Information about minimum depths and the constituents of permeable pavement construction for car parks, driveways and footpaths can be found in the RonaDeck Resin Bound Surfacing technical data sheet, the following is a typical build-up.
RonaDeck Resin Bound Surfacing
Base Course: AC14 open graded asphalt concrete maximum 100/150 pen binder to BS EN 13108-1
Or No-fines concrete
Granular Sub-base
Well compacted Type 3 granular sub-base or similar approved
Optional Impermeable Membrane
Impermeable membrane for use when a storage system is to be installed
RonaDeck Resin Bound Surfacing is a highly porous surfacing which, when applied to porous base and sub-base materials, forms a hard wearing, slightly flexible and decorative topping to permeable pavement constructions.
RonaDeck Resin Bound Surfacing is available in a wide range of natural aggregates chosen for their appearance and performance. All standard aggregate blends have been tested to determine their slip resistance in wet and dry conditions in accordance with BS 82046:2008+A1:2010 Appendix B, and all exceeded the minimum Pendulum Test Value required for low slip potential, test results for slip resistance are available on request. All Ronacrete products are developed, manufactured and supplied in accordance with BS EN ISO 9001, the standard for Quality Management Systems. Ronacrete’s Environmental Management System has been assessed and registered in accordance with BS EN 14001 and Ronacrete’s Health and Safety Management System has been assessed and registered in accordance with BS OHAS 18001.
Resin bound surfacing incorporating recycled rubber
▶ Size: 102kg
▶ UV stable
▶ Install directly on to MOT type 3
▶ Environmentally friendly
▶ Incorporates recycled rubber granules
▶ Slip resistant
▶ Flexible
A resin bound aggregate surface for pedestrian traffic. RonaDeck EcoPath UV surfaces are decorative and functional, seamless and slightly flexible. The open matrix allows water to drain through to the base, eliminating water ponding and allowing water to drain to planted areas or land drains. The system is designed to be SuDS compliant reducing the impact of development on flood risk and allowing water to flow into water courses.
Resin and aggregate base for resin bound surfacing
▶ Size: 6kg (to be mixed with 100kg washed aggregate)
▶ Epoxy formulation
▶ Alternative base to tarmac and concrete
▶ Highly permeable
▶ Install resin bound after 24 hours
▶ Use with wet aggregates
▶ Quick and easy to install
Resin bound system for pedestrian traffic
▶ Size: 113.25kg
▶ Install directly on to MOT type 3
▶ UV stable ▶ SuDS compliant
▶ Slip resistant ▶ Low maintenance
Sealer to minimise entry of water into resin bound systems
▶ Size: 10kg
▶ Polymeric water based gel
▶ Squeegee applied
▶ Reduces the porosity of surfacings
▶ Typical 3 layer application
▶ Single component product
▶ Easy to use
UV stable aggregate and recycled rubber resin bound surfacing system
RonaDeck Stone Carpet is a resin bound aggregate surface for pedestrians and for occasional use by light vehicles. It is used to create decorative and durable surfaces which are seamless and slightly flexible. The surfacing will withstand heavy footfall, light traffic from trolleys and even occasional powered vehicles. Noise from foot traffic is lower than for other hard floorings with noise being absorbed and baffled by the voids. Warm air in the voids makes the surfacing warmer than solid hard flooring and the slight “give” in the system provides a more comfortable experience for pedestrians. RonaDeck Stone Carpet must be laid onto a sound, stable and solid base such as concrete.
Typical Applications include showrooms, shops and supermarkets, nightclubs, leisure centres, offices, public buildings, schools and colleges, hotels and private homes.
STONE CARPET
Internal resin bound surfacing system
▶ Size: 108kg (primer required)
▶ Highly decorative flooring system
▶ Alternative to common floorings
▶ Warmer and quieter than other flooring
▶ Easily cleaned
▶ Very durable
▶ Wide range of colours
ECO
Permeable paving for tree surrounds
▶ Sizes: Resin only 1.5kg and 6kg and full batch 113kg
▶ UV stable
▶ Alternative to tree grilles
▶ Design accommodates tree growth
▶ Application from 40mm
▶ Low maintenance
▶ Wide range of colours
RonaDeck Eco Tree Pit is a resin bound natural aggregate finish surround for planted trees in public and private areas. Surrounding the tree in a solid, semi-flexible construction ensures that litter can be easily removed and hazardous items such as syringes and needles cannot be hidden or become lodged under grilles. RonaDeck Eco Tree Pit is a two component polyurethane resin and a range of selected rounded attractive aggregates, The system is highly porous and able to receive light foot traffic. Its porosity allows a rate of flow >850 litres/ m2/minute through 6/10mm aggregate.
Resin bound rubber surfacing system for tree pit surrounds
▶ Size: 60kg
▶ UV stable
▶ Highly permeable surfacing
▶ Soft and safe underfoot
▶ Suitable for pool surrounds and other leisure facilities
▶ Wide range of colours
Resin bound rubber surfacing system for play areas
▶ Size: 60kg
▶ UV stable
▶ Highly permeable surfacing
▶ Soft and safe underfoot
▶ Suitable for play areas and other leisure facilities
▶ Absorbs noise and impact
▶ Wide range of colours
Resin bound rubber surfacing system for tree pit surrounds
▶ Size: 60kg
▶ UV stable
▶ Highly permeable surfacing
▶ Soft and safe underfoot
▶ Alternative to tree grilles
▶ Design can accommodate tree growth
▶ Wide range of colours
RESIN BONDED SURFACING
High friction surfacing system
▶ Size: 7.5kg (aggregates available in 25kg bags)
▶ High slip resistance
▶ Rapid cure resin
▶ DDA compliant
▶ Self priming on to concrete and asphalt
▶ Suitable for pedestrian and vehicular traffic
▶ Wide range of colours
RESIN
Polyurethane scratch coat
▶ Size: 20kg
▶ Fills defects in concrete and tarmac
▶ Use prior to RonaDeck Resin Bonded Surfacing
▶ Reduces amount of resin required on porous surfaces
▶ Quick curing
▶ Overlay after 1-2 hours
RONADECK
RESIN BONDED PORE FILLER
Fast cure cementitious pore filler
▶ Size: 25kg
▶ Scrape on scrape off pore filler
▶ Use prior to RonaDeck Resin
Bonded Surfacing
▶ Reduces amount of resin required on porous surfaces
▶ Quick curing
▶ Overlay after 1-2 hours
RESIN BONDED
SEAL COAT UV
Polyurethane sealer for resin bonded surfacing
▶ Clear polyurethane coating
▶ UV stable
▶ 1 or 2 coat application
▶ Increase abrasion and frost resistance
▶ Improved chemical resistance
▶ Supplied ready to use
WET POUR RUBBER GRANULE SURFACING RESIN BOUND SOFT FEEL SURFACING AND SHOCKPAD FOR PEDESTRIAN TRAFFIC
RonaDeck UV Wet Pour Rubber Granule Surfacing is a UV stable resin bound rubber granule surfacing for pedestrian traffic. It is used to create flexible seamless safety surfaces which absorb sound and impact. A solid edging should be installed as necessary to protect edges. RonaDeck UV Wet Pour Rubber Granule Shockpad is a base layer for absorbing impact below and around play equipment. The system must be laid onto a sound stable and solid base; concrete is the preferred substrate, the system may be applied to asphalt concrete but there is a risk of migratory staining from the bitumen binder. The system may be applied directly on to MOT Type 3 aggregate when the minimum thickness exceeds 40mm. It is suitable for applications in areas such as play areas, swimming pool surrounds and other leisure environments.
Samples available on request
In brief Over 300m2 of RonaDeck Resin Bound Surfacing with Quartz Parallel aggregate was laid at Conisbrough Castle, Doncaster.
The project Conisbrough Castle is a 12th century Grade I listed castle, one of the country’s best examples of medieval architecture, featuring a rare Norman hexagonal keep. The castle was closed for six months for major redevelopment work amounting to £1.1m. The project was funded by the Heritage Lottery Fund, English Heritage and Doncaster Metropolitan Borough Council and included a new visitor centre, larger education and exhibition rooms, interactive displays, improved access, signage and parking.
The new visitor centre was built onto an existing Victorian lodge and the surrounding park was landscaped.
The car park and the area in front of the centre and its surrounding path were surfaced with RonaDeck Resin Bound Surfacing by Ronacrete Approved Contractor Route One Highways.
Product and application The RonaDeck Resin Bound Surfacing System was supplied as a two-component UV stable polyurethane resin and a blend of kiln-dried aggregates; the two resin components were mixed by Route One with a slow speed drill and paddle before being added to a forced action mixer containing the Quartz Parallel aggregate blend. The RonaDeck Resin Bound Surfacing was spread to level and the surface was smoothed with a steel float. RonaDeck Resin Bound Surfacing was applied at a thickness of 15mm on the path and 18mm in the car park.
RonaDeck Resin Bound Surfacing
satisfies SuDS requirements, allowing rainwater to quickly and easily drain through the porous surface. The surfacing is tested to BS 8204-6 and this test shows the risk of slip to be low, an important factor to consider at a busy tourist attraction. RonaDeck Resin Bound Surfacing is also suitable for wheelchair ‘traffic’ as wheels will not sink and get caught as they do in loose gravel paths. The resistance of the resin to ultra-violet light ensures that the resin will not yellow or darken and will remain elastic, lengthening the service life of the system.
Conclusion By improving the access and parking facilities at Conisbrough Castle, RonaDeck Resin Bound Surfacing has played a role in a major redevelopment project that will bring history alive to thousands.
The Queen’s Silver Jubilee was marked with the creation of the Jubilee Walkway, an integral part of which was the introduction of pedestrian access along the south bank of the Thames, known as Queen’s Walk.
As part of preparations for the Diamond Jubilee thirty five years later Lambeth Council made the decision to have the area ‘smartened up’. Part of this operation was to replace the worn resin bound surfacing on the Queen’s Walk between Waterloo and Blackfriars bridges. The surfacing needed to be laid in time for the Jubilee celebrations which would attract many tourists, particularly for the Jubilee Pageant when crowds would line the banks of the Thames watching over 1,000 vessels participate in a flotilla from Battersea to Tower Bridge.
FM Conway were contracted to lay new resin bound surfacing to 2700 square metres of the 5 metre wide pathway and Sesame Gold aggregate was selected to brighten up the route.
The RonaDeck Resin Bound Surfacing System was supplied as a two-component UV stable polyurethane resin, the two components were mixed with a slow speed drill and paddle before being added to a large forced action mixer containing the Sesame Gold aggregate blend. FM Conway spread the RonaDeck Resin Bound Surfacing to level and smoothed the surface with a steel float. The finished surface was ready for foot traffic within four hours.
Ronadeck Resin Bound Surfacing satisfies SuDS requirements, allowing rainwater to quickly and easily drain
through the porous surface, avoiding puddling. Slip testing shows risk of slip to be generally low, an important consideration for a busy walkway.
The resin bound surfacing was completed in time for the crowds to watch the Jubilee Pageant. Now the ‘golden path’ provides a route which takes tourists and commuters past many well known buildings and locations in the capital city. Starting at Waterloo Bridge it runs past the National Film Theatre and the National Theatre through Gabriel’s Wharf, past the IBM building and London Television Centre alongside Bernie Spain Gardens and through Oxo Tower Wharf passing the art-deco Oxo Tower and Sea Containers House, finishing at Blackfriars Bridge close to the Tate Modern.
Newmarket is the historic home of horseracing, offering a treasure trove of sights and sounds for the racing enthusiast. Crowds flock to the racecourses on race days as well as to the concerts and festivals held in the grounds, putting considerable wear and tear on paving around the courses.
Two of Ronacrete’s hard landscaping systems were successfully applied by alGEK Flooring to a concourse, roads and steps at Newmarket’s July Course. More than 800m2 of RonaDeck Resin Bound Surfacing and almost 3,000m2 of RonaDeck Resin Bonded Surfacing were laid.
The products were chosen for both appearance and safety, with care being taken to ensure that the surfaces did not create any additional risk of slip in the wet or dry. Slip testing shows RonaDeck Resin Bonded Surfacing with bauxite aggregate to have an extremely low risk of slip in wet and dry condition and stopping distances for vehicles are reduced. The potential for slip of RonaDeck Resin Bound Surfacing is generally low in wet and dry conditions and slip resistance can be improved by casting RonaDeck Resin Bound Surfacing Fine Aggregate into the freshly laid material.
Wembley Stadium, home to the England football team and venue for the football finals of the 2012 Olympics, can house 90,000 seated fans and a further 15,000 standing. At the Take That concert in the summer of 2011, 623,737 people attended the eight shows at the stadium.
These enormous crowds of sport and music fans enter the stadium via a series of ramps which lead into the stadium at five levels.
RonaDeck Resin Bonded Surfacing was chosen to provide a hard wearing and slip resistant surfacing to the tarmac ramps, ensuring that crowds can gain access to the Stadium in safety in even the wettest of weather conditions.
Specialist contractor Entech Services Ltd was employed to apply RonaDeck Resin Bonded Surfacing with Medium Grade Guyanan Bauxite slip resistant aggregate to macadam on 4,500 square metres of ramp.
The surface of the macadam was mostly tightly closed – ideal for this highly specialised
surfacing system. Open textured areas were closed using RonaDeck Resin Bonded Scratch Coat to prevent the resin draining through and to ensure an adequate thickness of resin to secure and bond the aggregate to the surface.
RonaDeck Resin Bonded Scratch Coat was mixed with a slow speed drill and paddle and scraped across the surface of the macadam, filling the voids in the surface. After just one hour the surface was ready to be receive the RonaDeck Resin Bonded Surfacing.
The resin components were mixed with a slow speed drill and paddle before application by squeegee and roller to the surface at the specified thickness. The Guyanan Bauxite aggregate was immediately scattered into the wet resin and left to cure for four hours.
Excess aggregate was then vacuumed away and RonaDeck Resin Bonded Surfacing Seal Coat UV roller applied to bind and protect the surface for ease of cleaning, leaving the ramps ready for foot and service vehicle traffic.
The RonaFloor range includes epoxy resin screeds, coatings, sealers and liquid DPM, polyurethane stone carpet and polyurethane and acryl/ polyurethane floor/ wall sealers. Fast setting and drying floor repair mortars complete the range. The epoxy flooring range comprises type 1 water based sealer, types 2 & 3 solvent free coatings, types 5 & 7 self-smoothing screed and types 6 & 8 industrial screed, “type” refers to FeRFA resin flooring classifications. RonaFloor Stone Carpet consist of UV stable resin and natural aggregates producing highly permeable, slip resistant surfacing systems which are unaffected by discolouration and degradation caused by UV light, aggregates are either self-finished or coloured with UV stable coatings. RonaFloor PU Coating & RonaFloor PU
Acryl Coating WB are clear UV stable, single component floor and wall sealers, RonaFloor PU Coating may be supplied pigmented if required. RonaFloor 1 Hour Repair products are polymer modified fast setting patch repair materials, which are sufficiently dry after 24 hours for application of resin flooring, resilient flooring, tile and stone flooring.
▶ Ronafix for Bedding Mortars
▶ RonaBond Bedding Mortar
▶ RonaFloor HB100
▶ RonaFloor HB200
▶ RonaFloor EWB
▶ RonaFloor Epoxy Floor Mortar
▶ RonaFloor Matt Floor and Wall Sealer WB
▶ RonaFloor PU Coating
▶ RonaFloor SL
▶ RonaFloor Epoxy DPM
▶ RonaFloor Concrete Dustproofer
▶ RonaFloor Repair 1 Hour 25mm+
▶ RonaFloor Repair 1 Hour 6-50mm
Produces durable adhesion to concrete and masonry elements for the design life of a building
Pre-packed bedding mortar
▶ Size: 25kg
▶ Polymer modified
▶ Apply from 6mm
▶ Ideal for bedding brick slips and paving
▶ Enhanced physical properties
▶ Monolithic adhesion
▶ Pre-packed for ease of use
Solvent free epoxy coating
▶ Size: 5kg
▶ Excellent wear resistance
▶ Chemical resistant
▶ Hygienic surface
▶ Slip resistant
▶ 100 microns per coat
▶ Range of colours
HB200
Solvent free epoxy coating
▶ Size: 5kg
▶ Excellent wear resistance
▶ Chemical resistant
▶ Hygienic surface
▶ Slip resistant
▶ 200 microns per coat
▶ Range of colours
RONAFLOOR
EWB
Water based epoxy coating
▶ Size: 5kg
▶ Good abrasion resistance
▶ Chemical resistant
▶ Rapid drying and chemical curing
▶ Slip resistant
▶ 50 microns per coat
▶ Range of colours
Polymer modified bedding mortar
▶ Sizes: 5L, 25L, 210L, 1000L
▶ 50 year track record
▶ Apply from 6mm
▶ Ideal for bedding brick slips and paving
▶ Enhanced physical properties
▶ Site batched mortar
RONAFLOOR EPOXY FLOOR MORTAR
High performance epoxy resin mortar
▶ Sizes: 5kg and 25kg
▶ Epoxy screed and repair mortar
▶ Extremely hard wearing
▶ Resistant to mechanical and chemical attack
▶ Installed from 5mm
▶ Good surface finish
▶ Available in rapid grade
RONAFLOOR MATT FLOOR AND WALL SEALER WB
Clear silicate based floor and wall sealer
▶ Sizes: 5L and 25L
▶ Single component surface sealer
▶ Water repellent
▶ Matt finish
▶ Eliminates dusting
▶ Superior abrasion resistance
▶ Solvent free and non flammable
Self smoothing epoxy screed
▶ Sizes: 20.5kg
▶ Seamless screed
▶ High strength
▶ Good chemical resistance
▶ Applied from 2mm
▶ Easy to clean
▶ Range of colours
RONAFLOOR
EPOXY DPM
Solvent free damp proof membrane
▶ Size: 4.8kg
▶ Epoxy resin formulation
RONAFLOOR
CONCRETE
DUSTPROOFER
Surface dustproofer and hardener
▶ Size: 16.5L and 205L
▶ Binds surface to reduce or eliminate dust formation
▶ Easy to apply
▶ Durable
▶ Economical
RONAFLOOR PU COATING
Single component polyurethane floor and wall sealer
▶ Sizes: 5L and 25L
▶ Single component surface sealer
▶ Increased abrasion resistance
▶ Eliminates dusting
▶ Chemical resistant
▶ Very durable
▶ Simple to use
RONAFLOOR
REPAIR 1 HOUR
25MM+
Ultra rapid floor repair
▶ Can be applied on to surfaces with 97% RH
▶ Use before screeds and epoxy coatings
Images used are for illustrative purposes only.
▶ Size: 25kg
▶ Can accept foot traffic after 1 hour
▶ Application from 25mm
▶ Suitable for very heavy traffic
▶ Low temperature use - down to -10°C
▶ Can also be used as a bedding mortar
RONAFLOOR
REPAIR 1 HOUR
6-50MM
Ultra rapid floor repair
▶ Size: 25kg
▶ Can accept foot traffic after 1 hour
▶ Application from 6mm
▶ Suitable for very heavy traffic
▶ Low temperature use - down to -10°C
▶ Can also be used as a bedding mortar
An ambulance is dispatched to the scene. The patient is too ill to move by road, and road isn’t fast enough anyway. London’s Air Ambulance takes on the responsibility of airlifting the patient to The Royal London Hospital in Whitechapel, East London.
The helicopter lands on the roof of the building, a steel structure designed to accommodate the helicopter, its support and safety equipment, and of course the medical staff whose primary concern is the wellbeing of the patient. As they run across the steel deck, often wet from rain and sometimes snow, it is essential they don’t slip. The metal deck is therefore coated with an anti-slip coating with different colours used to mark safe and hazardous areas.
RonaFloor HB100 Rapid was recently applied to the deck to refurbish and replace the existing coating which had become worn. The use of the unique 4 hour cure formulation provided a coating which was quick to apply and fast curing but without the use of harmful, dangerous or flammable solvents. After cleaning down the existing surface and removing any loose, flaking or peeling paint, two coats of RonaFloor HB100 Rapid were applied by roller, which has an intercoat and foot traffic waiting time of only 4 hours, ensuring the landing pad was only out of service for minimal time.
As part of a refurbishment of its Studio complex, Pinewood Studios in Iver, Buckinghamshire asked specialist industrial flooring contractor Aedean Limited, to lay almost 1,000 m2 of Ronacrete’s RonaFloor SL self-smoothing epoxy resin screed in both Studio J and Studio K. The studios were being converted from film to television usage.
It is important for TV cameras to be able to move around the Studio smoothly without the slightest jolt, unlike film cameras which usually run on tracks, so RonaFloor SL was specified as it provides easy to clean finish that allows troublefree removal of studio floor paints.
Studios J and K previously had filmstyle timber flooring covering a concrete floor laid in sections. This timber floor
was removed, the concrete mechanically prepared after priming a thin layer of RonaFloor SL self smoothing epoxy screed was placed on top.
Depending on the programme being produced, each new set in the Studio may require the floor to be repainted with water-soluble peelable paint, and it is therefore necessary that the floor screed is able to withstand the constant application and removal of these paints. RonaFloor SL also provides good wear resistance with high chemical resistance, making it the perfect application in this situation. RonaFloor SL is available in seven standard colours, although special colours may be specified, the specification from Pinewood Studios was for a pale grey colour.
The Edinburgh-Glasgow Improvement Programme (EGIP) is an improvement programme focusing on the Edinburgh to Glasgow rail corridor. Its aim is to make Edinburgh airport and nearby business developments more accessible by public transport by improving the train services and integrating them with the Edinburgh tram system. Part of the programme included the construction of a new tram depot at Gogar.
The depot building includes a two storey accommodation block incorporating staff offices and associated staff facilities plus the tramway system control room. The depot also houses main workshop areas, an internal tram wash area, maintenance pits for tram maintenance as well as stabling areas where the trams are due to be located overnight.
The client’s design brief called for a robust anti-slip coating for the floor, it needed to be: hard wearing, slip resistant, easily cleaned and resistant to chemicals. After consultation with Ronacrete’s technical department, Parsons
Brinckerhoff specified RonaFloor HB100, a solvent free epoxy resin coating with additional anti-slip aggregate.
RonaFloor HB100 is suitable for use on concrete, screeded and granolithic floors. Its resistance to abrasion by constant traffic, its tolerance of train wash chemicals and oil spills made it particularly suitable for the tram depot. It is available in a variety of colours to clearly define hazardous areas.
The main contractor, Barr Construction appointed Industrial Floor Treatments Ltd to carry out the coating works. After approval of a trial, Industrial Floor Treatments laid approximately 5000m2 of RonaFloor HB100 in the specified colours. The concrete substrate was prepared by captive shotblasting before the first coat of RonaFloor HB100 was applied by roller. Kiln dried aggregate was scattered into the fresh resin to provide slip resistance and a second coat was applied to encapsulate the aggregate and produce a hygienic and wear resistant surface.
The Barbican Centre was constructed between 1969 and 1980 restoring a bomb damaged part of the City. Architects Chamberlin Powell & Bon planned a network of pedestrian precincts above and separated from traffic. This enclave contains the renowned Barbican Arts Centre, residential towers and blocks, a school, college, commercial premises, gardens and lakes.
The Centre took over a decade to build and was opened by The Queen in 1982, who declared it ‘one of the modern wonders of the world’ with the building seen as a landmark in terms of its scale, cohesion and ambition. Its stunning spaces and unique location at the heart of the Barbican Estate have made it an internationally recognised venue, acknowledged as one of the most significant architectural achievements of the 20th century.
Ronacrete was involved with construction at the Barbican. During construction, Ronafix was used at the Arts Centre by John Laing Construction and by other contractors working on various other parts of the scheme. Ronafix was used for bonding of tiles, for bedding of paving, for bonding large areas of render in the concert hall, for screeding and for repairing firedamaged concrete. A Grade II listed building; the Barbican is Europe’s largest multi-arts and conference venue and one of London’s best
examples of Brutalist architecture.
Maintaining the quality of the surroundings requires a continuous programme of maintenance and replacement. By late 2011 the City of London concluded that a comprehensive replacement of the paving was required to address recurring problems with waterproofing of the pedestrian decks, raised over commercial premises.
Bickerdike Allen Partners, a practice with a strong background in providing remedial solutions to building defects, was appointed to prepare a scheme to address water ingress through the podium, which was affecting commercial premises below. Following extensive discussion with Ronacrete between November 2011 and September 2012, Bickerdike Allen Partners specified Ronafix Mix Design A1 high strength polymer modified mortar for screeds to be laid to falls, Ronafix Mix A1 was chosen for its ability to be laid over insulation boards at a minimum thickness of 35mm, maximizing achievable falls and for its low permeability. Ronafix Mix Design C waterproof high strength polymer modified mortar was specified for bedding of tiles, chosen for its thin bed depth, high adhesion strength and waterproof properties. Ronafix used in a mortar mix enhances long term flexural and
tensile strengths of a mortar, ensuring that materials remain durable for decades longer than unmodified materials. When moisture sensitive materials are to be applied, the shorter drying time of Ronafix mix designs reduces waiting time from months to days or weeks..
VolkerLaser was appointed as the principal contractor; the main elements of the project were re-waterproofing, upgrading of insulation, hard landscaping and the installation of new structural movement joints. Liquid resin waterproofing was applied to the existing asphalt membrane of a large podium, located within the centre of a residential area and insulation was upgraded. The hard landscaping included the removal of existing tiles, adhesive beds and screeds. Ronafix screeds were laid to falls and Ronafix thin bed waterproof mortars for bedding of tiles.
Tiles were bedded on a nominal 15mm thickness of Ronafix Mix C waterproof bedding mortar by A.T. Knott & Sons Ltd; selected for their extensive knowledge of the site, gained by their involvement in the original project.
VolkerLaser laid 10,000m2 of Ronafix Mix
A1 to adjust falls on the deck, thus improving water shedding from the paving to the drains.
The RonaScreed range of products comprises polymer modified screeds, fast drying screeds, fast setting screeds and self-smoothing screeds. Most are available as either factory batched screed products requiring no addition of materials on site or as additives for site batching of screeds. Ronafix polymer modified screeds are suitable for thin bonded wearing toppings, levelling of irregular bases, thin floating and heated floating screed applications and unbonded screed applications. All polymer modified screeds are suitable for interior and exterior use. Fast drying screeds are available for drying times from 1 day to 15 days at 75mm thickness in good drying conditions. RonaScreed Concrete is ready for pedestrians after 6 hours and vehicle traffic after 12 hours; it is dry after 3 days in good conditions. The range of self-smoothing screeds comprises an exterior screed, an industrial topping, a base screed and a floating screed; all are fast setting and fast drying. RonaScreed DPM is a polymer cement surface damp proof membrane to separate screeds from drying concrete or to facilitate early application of resin flooring, resilient flooring, tile and stone flooring.
▶ Ronafix for Screeds
▶ Ronafix Pre-packed Screed 6-50mm
▶ Ronafix Pre-packed Screed 25mm+
▶ Ronafix Pre-packed Wearing Screed 15mm+
▶ Ronafix Pre-packed Floating Screed 35mm+
▶ Ronafix Pre-packed Fine Concrete 25mm+
▶ Ronafix Underfloor Heating Screed Admixture
▶ Ronafix Pre-packed Underfloor Heating Screed 40mm
▶ RonaScreed Fast Drying Underfloor Heating Screed Additive
▶ RonaScreed 8 Day Overlay Fast Drying Screed
▶ RonaScreed 1 Day Overlay Rapid Drying Screed
▶ RonaScreed 4 Day Overlay Quick Drying Screed
▶ RonaScreed Concrete
▶ RonaScreed Mortar
▶ RonaScreed DPM
▶ RonaScreed Self Smoothing Exterior Screed
▶ RonaScreed Self Smoothing Levelling Base
▶ RonaScreed Self Smoothing Levelling Topping
Polymer modified screed
▶ Size: 25kg
▶ Thin section screed from 6mm
▶ Enhanced physical properties
▶ Foot traffic after 24 hours
▶ Excellent wear resistance
▶ Excellent resistance to passage of water and water vapour
▶ Pre-packed for ease of use
Polymer admixture for thin section and high strength screeds
▶ Sizes: 5L, 25L, 210L, 1000L
▶ 50 year track record
▶ Admixture for site batched screeds
▶ Application from 6mm
▶ Enhanced physical properties
▶ Waterproof
▶ Fast drying
Rapid strength gain floor screed
▶ Size: 25kg
▶ Ready for light vehicle traffic after only 6 hours
▶ Ready for heavy vehicle traffic after only 24 hours
▶ Apply from 25mm
▶ Excellent wear resistance
▶ Enhanced physical properties
▶ Pre-packed for ease of use
Polymer modified screed
▶ Size: 25kg
▶ Thin section screed from 25mm
▶ Enhanced physical properties
▶ Foot traffic after 24 hours
▶ Excellent resistance to passage of water and water vapour
▶ Pre-packed for ease of use
Polymer modified wearing screed
▶ Size: 25kg
▶ Thin section wearing screed from 15mm
▶ Excellent wear resistance to very heavy traffic
▶ Enhanced physical properties
▶ Foot traffic after 24 hours
▶ Excellent resistance to passage of water and water vapour
▶ Pre-packed for ease of use
RONASCREED
FAST DRYING UNDERFLOOR HEATING SCREED ADDITIVE
Fast drying screed additive
▶ Sizes: 20L, 210L and 1000L
▶ Promotes rapid drying of floor screeds
▶ Can receive floor coverings after 8 days at 50mm thick
▶ Can receive floor coverings after 15 days at 75mm thick
▶ Commissioning of underfloor heating can begin after 10-14 days
▶ Minimises site delays and access times
▶ Simple and cost effective
RONASCREED
4 DAY OVERLAY QUICK DRYING SCREED
Powder additive for quick drying screeds
▶ Size: 18kg
▶ Can receive moisture sensitive floor coverings after 3 days
▶ Light foot traffic after only 24 hours
▶ Application from 35mm
FAST DRYING SCREED
Fast drying screed additive
▶ Sizes: 20L, 210L and 1000L
▶ Promotes rapid drying of floor screeds
▶ Can receive floor coverings after 8 days at 50mm thick
▶ Can receive floor coverings after 15 days at 75mm thick
▶ Can be installed by non licensed contractors
▶ Minimises site delays and access times
▶ Simple and cost effective
▶ Can be installed by non licensed contractors
▶ Minimises site delays and access times
▶ Compatible with underfloor heating systems
RONASCREED
1 DAY OVERLAY RAPID
DRYING SCREED
Cement replacement for rapid drying screeds
▶ Size: 20kg
▶ Can receive moisture sensitive floor coverings after 24 hours
▶ Light foot traffic after only 6 hours
▶ Application from 6mm
▶ Can be installed by non licensed contractors
▶ Minimises site delays and access times
▶ Compatible with underfloor heating systems
Polymer modified fine concrete screed
▶ Size: 25kg
▶ Thin section concrete screed from 25mm
▶ Foot traffic after 24 hours
▶ Enhanced physical properties
▶ Excellent wear resistance to very heavy traffic
▶ Pre-packed for ease of use
RONAFIX UNDERFLOOR HEATING SCREED ADMIXTURE
Polymer admixture for screeds incorporating underfloor heating
▶ Sizes: 5L, 25L, 210L, 1000L
▶ Fast drying allows earlier commissioning of underfloor heating
▶ Application from 40mm (only 20mm cover over pipes)
▶ Can receive floor coverings after 10 days at 50mm thick
▶ Enhanced physical properties
▶ Site batched mortar
▶ Excellent resistance to passage of water and water vapour
RONAFIX PRE-PACKED FLOATING SCREED 35MM+
Polymer modified floating screed
▶ Size: 25kg
▶ Thin section floating screed from 35mm
▶ Fast drying - allows earlier commissioning of underfloor heating
▶ Can receive floor coverings after 10 days at 50mm thick
▶ Foot traffic after 24 hours
▶ Enhanced physical properties
▶ Pre-packed for ease of use
PRE-PACKED UNDERFLOOR HEATING SCREED 40MM
Polymer admixture for screeds incorporating underfloor heating
▶ Size: 25kg
▶ Commissioning of underfloor heating can begin after 10-14 days
▶ Application from 40mm (only 20mm cover over pipes)
▶ Can receive floor coverings after 10 days at 50mm thick
▶ Enhanced physical properties
▶ Pre-packed for ease of use
▶ Excellent resistance to passage of water and water vapour
Rapid strength gain floor screed
▶ Size: 25kg
▶ Ready for foot traffic after only 12 hours
▶ Ready for heavy vehicle traffic after only 24 hours
▶ Apply from 6mm
▶ Excellent wear resistance
▶ Enhanced physical properties
▶ Pre-packed for ease of use
Surface damp proof membrane
▶ Size: 10kg
▶ Water based membrane system
▶ Reduces water and water vapour permeability
▶ Designed to accept thin bonded screeds
▶ Quick drying two or three coat application
▶ Non-hazardous, solvent free
▶ Compatible with most Ronacrete screeds and toppings
Water tolerant flowable screed
▶ Size: 22kg
▶ Does not require trowelling
▶ Suitable for internal and external use
▶ Foot traffic after only 4 hours
▶ Application from 5mm
▶ Excellent wear resistance
▶ Very fast application reduces disruption and down time
Self smoothing underlayment screed
▶ Size: 22kg
▶ Does not require trowelling
▶ Up to 1500m¬≤ installed in a day
▶ Suitable for wet areas and external use
▶ Application from 10mm
▶ Base layer for floorings such vinyl and tiles
▶ Very fast application reduces disruption and down time
Water tolerant flowable screed
▶ Size: 22kg
▶ Does not require trowelling
▶ Suitable for internal and external use
▶ Foot traffic after only 4 hours
▶ Application from 5mm
▶ Excellent wear resistance
▶ Very fast application reduces disruption and down time
The skyline of London has changed a lot over the last few decades; starting in 1991 with the appearance of One Canada Square and its neighbouring Canary Wharf tower blocks.
In 1999 the London Eye appeared on the horizon at the South Bank; then in a project lasting from 2009 to 2012 the Shard rose above them all, creating another vantage point from which to view the capital.
The Shard is a magnificent feat of architecture and engineering and is the tallest building in the European Union. It is 306 metres high and has 87 floors; it incorporates state of the art offices, apartments, a hotel, restaurants, retail outlets and of course a viewing gallery.
A thin screed was needed for several
floors in the Shard’s upper levels and Ronafix Pre-packed Screed 6-50mm was specified because of its durability and it’s high compressive, flexural and tensile strengths. As a pre-packed system it provided the specifier with assurance of consistent high quality.
Ronafix Pre-packed Screed 6-50mm is supplied as a two component product comprising powder and polymer gauging liquid; used with Ronacrete Standard Primer it bonds to suitably prepared surfaces and is water resistant. It can be used as thinly as 6mm for bonded screeds or 35mm for unbonded or floating screeds. Used as a floating screed it is compatible with under floor heating systems.
The Café Royal in central London dates back to the 1860s and was a popular place to eat and drink for many well known literary and theatrical figures over the years. It was refurbished in the 1950s but closed for business in 2008.
The Café Royal was reopened as a luxury hotel during the summer of 2012. The opening followed a major interior refurbishment which retained the original detailing, combining it with contemporary décor.
The hotel’s newly marble-fitted bathrooms required a thin, water resistant floating screed to be applied to the insulation boards
providing a base for the marble flooring. The screed needed to withstand the weight of the marble baths and other fixtures. Specialist building and construction distributor Resapol, after consultation with Ronacrete’s technical team recommended Ronafix Pre-packed Floating Screed 35mm+ as a suitable screed to be laid above the underfloor heating system in the 159 Café Royal bathrooms. Ronafix Pre-packed Floating Screed 35mm+ is a thin section, high strength, waterproof screed particularly suitable for the project requirements.
Terminal 2 at London Heathrow Airport was replaced as part of a £4.8bn development programme at the airport. The Terminal 2 project which is estimated to have cost around £2.5bn included the main building, a 522-metre satellite pier, a 1,340 capacity car park, an energy centre, cooling station, and road refurbishment.
The project was completed in 2014 and is home to STAR Alliance, Aer Lingus, and Virgin Atlantic’s domestic routes.
The lead architect for the new terminal was Luis Vidal Architects collaborating with Foster and Partners and Pascall and Watson. To replace the original old and outdated building which opened in 1955 they designed a bright and modern space, with Impressive runway views from the departure lounge, making use of the natural light that pours in through the ten metre high windows and north facing skylights. The terminal is also designed to give priority to environmental issues and energy-efficiency.
The complete terminal covers a floor
space of 185,000m2, extending into the existing Terminal 1 site. The floor takes heavy traffic from the 20,000,000 passengers plus associated trolleys and airport vehicles who are estimated to cross it annually.
Vetter UK, the specialist contracting arm of Laing O’Rourke needed to specify a fast drying 135mm deep screed so that the project could continue with minimum disruption, saving time and costs. RonaScreed 8 Day Overlay Fast Drying Screed was specified for its fast drying properties and the fact that it could be mixed at ground level and then pumped up the three storeys to the point of application, saving on time and cost.
RonaScreed 8 Day Overlay Fast Drying Screed is a screed additive which when added to a screed enables earlier access by following trades and reduces drying time. Screeds can be laid later in the construction program, reducing likely damage by following trades and saving unexpected bills for surface DPMs.
South Court is a Grade II Listed Building owned by Sidney Sussex College, part of the University of Cambridge. Building Surveyors and Architects Pleasance Hookham and Nix Limited were commissioned to refurbish the property and part of the work required re-waterproofing of the first floor terrace. The terrace provides access to student accommodation and waterproofing to the rear of the shop units below.
Pleasance Hookham and Nix Limited specified Ronafix Pre-packed Screed 6-50mm to be laid to falls to provide drainage to the new terrace construction, which was to be waterproofed with mastic asphalt and finished with a tiled surface, providing protection to the existing structure below. Ronafix Pre-packed Screed 6-50mm is designed to be laid as a thin bonded screed
and has very low permeability, high strength and negligible shrinkage. All components of Ronafix Pre-packed Screed 6-50mm are pre-measured in Ronacrete’s factory, giving assurance to the specifier that the screed will perform as expected.
Pleasance Hookham and Nix Limited appointed Cocksedge Building Contractors Limited to carry out the works. The concrete deck was prepared in accordance with Ronacrete’s recommendations and primed with Ronacrete Standard Primer before Ronafix Pre-packed Screed 6-50mm was laid to falls on the freshly applied primer. Early application of the asphalt waterproofing was possible because Ronafix Pre-packed Screed 6-50mm dries faster than traditional sand and cement screeds, reducing the delay between application of the screed and waterproofing.
RonaStop is a range of waterproofing products including Ronafix pre-packed renders, a surface DPM, an elastic waterproof membrane and a fast setting water plug. Ronacrete AR Glass Fibre Mesh may be used to reinforce renders and waterproof coatings. Ronafix Pre-packed Tanking Render is a polymer rich mortar which withstands 30m head of negative and positive water pressure and is therefore suitable for basement and swimming pool waterproofing. Ronafix Pre-packed Render/ Screed is a polymer modified weatherproof render which prevents ingress of water through porous masonry and improves equivalent concrete cover where low reinforcement cover threatens durability. Monoprufe DPM is a polymer cement surface damp proof membrane to separate screeds from drying concrete or to facilitate early application of resin flooring, resilient flooring, tile and stone flooring. Monoprufe WP Elastic is a crack bridging, elastic polymer cement waterproof membrane.
▶ Ronafix for Waterproofing
▶ Ronafix Pre-packed Render / Screed
▶ Ronafix Pre-packed Tanking Render
▶ Monoprufe WP Elastic
▶ Monoprufe DPM
▶ RonaStop Water Plug
Prevents transmission of liquid water when bonded to concrete and masonry elements for the design life of a building
Polymer admixture for use with waterproof and tanking renders
▶ Sizes: 5L, 25L, 210L, 1000L
▶ 50 year track record
▶ Admixture for site batched renders
▶ Excellent resistance to passage of water and water vapour
▶ Application from 6mm
▶ Will withstand water penetration by a 30m head of water
▶ Enhanced physical properties
Pre-packed mortar for weatherproof renders and screeds
▶ Size: 25kg
▶ Weatherproof
▶ Application from 6mm
▶ Pre-packed for ease of use
▶ Improved physical performance
▶ Traffic after 24 hours
Pre-packed mortar for tanking
▶ Size: 25kg
▶ Waterproof
▶ Application from 6mm
▶ Pre-packed for ease of use
▶ Suitable for swimming pools, lift pits, vaults and more
▶ Improved physical performance
▶ Traffic after 24 hours
MONOPRUFE
WP ELASTIC
Elastomeric damp proof membrane
▶ Size: 11.25kg
▶ Suitable for above and below ground use
▶ Adheres to concrete, mortars, brick and block
▶ Highly elastic
▶ Water based
▶ Excellent adhesion
RONASTOP WATER PLUG
▶ Size: 5kg and 25kg
▶ Rapid setting water plugging system
▶ Rapid-set water stop
▶ Mix with water and apply
▶ Non-toxic
▶ Easy to use
▶ Can be quickly rendered or painted
Liquid applied surface damp proof membrane
▶ Size: 10kg
▶ Conforms to BS EN 1504-2
▶ Water based membrane system
▶ Reduces water and water vapour permeability
▶ Designed to accept thin bonded screeds
▶ Quick drying
▶ Non hazardous
London’s Trafalgar Square is one of the capital’s most popular tourist attractions, playing host to millions of people every year. From his vantage point hundreds of feet in the air Admiral Nelson observes the tourists, the cars, the taxis and the buses every hour of every day.
Water work trouble
More recently however he has seen a new kind of activity which may well cause him to raise a pigeon stained eyebrow in wonder. For his normally full water fountains have been emptied, administered to by men in overalls and hard hats, and then filled up again with clean water.
To the untrained observer such activity would seem strange but to Tarmac Construction and the PSA it is all part of a carefully devised scheme to overcome operational difficulties with the water and drainage systems and a general improvement of the Square which was constructed in the 1840s.
No problem for New Year
This £2.3 million scheme was completed in 1989
although special contingency plans were made to allow the Christmas and New Year celebrations to proceed unhindered. Work to the fountains includes re-rendering the underside of the concrete copings to align it with the circular underhang. A Ronafix modified render was specified to be placed over the brickwork lining of the tanks to level and seal the surface prior to a waterproofing lining being placed.
After emptying the tanks the brickwork was inspected. This showed it to be in poor condition and unable to support the Ronafix render in its present state. The specification was consequently changed and a stainless steel mesh was shot fired into the brickwork and the render applied through it. This ensured that the render would remain in position even if the surface of the brick was not sufficiently stable to bear its weight.
Ronafix was used as a priming coat brushed on to the brickwork to secure the render to the main structure and also in the render mortar to provide waterproofing, strength, resistance to change in water temperature and the ability to be applied in thin section.
In brief
A basement in North London which had not been used for some time needed to be waterproofed as part of a conversion project.
project
The basement of Fairfax Mansions on the Finchley Road in North London had not been used for some time although it had previously housed a café. The building was being converted into a branch of the coffee house chain Caffè Nero and the basement needed to be waterproofed as part of the overall conversion. Harrison Waterproofing was contracted to carry out the waterproofing work.
After discussion with the Ronacrete technical team, Harrison Waterproofing recommended that Ronafix Mix E should be used to provide a durable high strength waterproof render to the basement walls. Harrison Waterproofing
prepared the surface by scabbling with a bush hammer to provide a mechanical key for effective bonding of the render; glass fibre mesh was used locally over brickwork of uncertain quality. Ronafix admixture and Portland cement were mixed to produce a slurry to prime the brickwork and the first layer of render. Ronafix was used as the gauging liquid to produce Ronafix Mix Design E, a blend of Portland cement, sharp sand and Ronafix admixture. The render was trowel applied in two layers; day joints in the render were positioned so that joints in the second layer did not coincide with joints in the first layer, to ensure there was no direct path for water ingress through joints.
Conclusion
The basement was given a new surface finish using Ronacrete Ronafix Mix E polymer modified render, providing a securely bonded durable waterproof render, ready for interior decoration.
Drying of standard sand/ cement screeds. BS 8204-1 “Concrete bases and cementitious levelling screeds to receive floorings — Code of practice” section 6.11.1 suggests the following calculation for drying of screeds with no fast drying additive“with levelling screeds, one day should be allowed for each millimetre of thickness for the first 50 mm, followed by an increasing time for each millimetre above this thickness. It is therefore reasonable to expect a levelling screed 50 mm thick, drying under good conditions, to be sufficiently dry in about 2 months.” It is generally accepted that between 50mm thickness and 75mm thickness, 2 days should be allowed for drying of each millimetre of thickness and a 75mm thick screed with no additive might be expected to take 100 days to dry to 75% humidity in good drying conditions. In poor drying conditions when humidity.
Wood flooring – different dryness requirements
Please note that BS 8201:2011 Code of practice for installation of flooring of wood and woodbased panels refers to 75% screed humidity as being acceptable for installation of wood flooring, this is disputed by many wood flooring suppliers who say that this figure applied to floating wood flooring only, some of these suppliers recommend a variety of lower screed surface humidity figures or
Drying of standard sand/ cement screeds
BS 8204-1 “Concrete bases and cementitious levelling screeds to receive floorings.
screed moisture contents (some very low) as the maximum acceptable. Ronacrete products are not tested to determine the time taken for screed surface humidity to fall below 75% and we are unaware of any data which may be available. Some competitor products are sold as being suitable for early application of wood flooring but no claims are made for screed dryness at the stage when they claim wood flooring may be applied, such claims should be viewed with scepticism and evidence should be sought.
When comparing specific drying claims made by other producers, it is advisable to look at the drying conditions under which samples were tested. Ronacrete products are tested after drying at a room temperature of 20°C temperature and 60-65% air humidity. Tests carried out on samples cured at higher temperature and lower air humidity will produce apparently better drying data, the specifier or contractor should consider how close the curing conditions are to the reality of site conditions.
Ronacrete produces a number of screed products, both pre-packed screeds, additives and a cement replacement, all of which produce faster drying screeds: Ronafix polymer modified screed mix designs, site batched with Ronafix admixture, Ronafix Pre-packed Screeds, a range of two component factory produced polymer modified screed products, composed of a blend of CEM I RHPC and graded kiln-dried silica sand and a bottle of gauging liquid containing Ronafix admixture
RonaScreed 1 Day Overlay Pre-packed Rapid Drying Screed, single component factory produced polymer modified screed product RonaScreed 1 Day Overlay Rapid Drying Screed, single component factory produced
polymer modified cement replacement product, for batching on site with sand and water in accordance with the mix design
RonaScreed 4 Day Overlay
Quick Drying Screed
Powder additive for batching on site with sand, cement and water in accordance with the mix design
RonaScreed 8 Day Overlay
Fast Drying Screed
Liquid additive for batching on site with sand, cement and water in accordance with the mix design
Limiting factors
There are a number of key factors involved in how quickly flooring may be applied to a screed:
1. Temperature in the room – lower temperature will increase drying time
2. Humidity in the room – higher air humidity will increase drying time
3. The mix design of the screed, for example
RonaScreed 8 Day Overlay Standard Mix
Design is 3 parts sand: 1 part Portland cement by weight and will reach 75% RH after 8 days @ 50mm thickness and after 15 days @ 75mm thickness – increasing the sand content will increase drying time, a 4:1 (by weight) screed laid at 75mm thickness typically produces to following results:
Time to reach 80% RH 14 days
Time to reach 75% RH 21 days
4. Mixing equipment, the mixer must be a forced action mixer; free fall mixers are not acceptable.
5. The use of retarders – retarders added to the screed at a batching plant or in volumetric mixers will severely affect drying of the screed.
6. Dryness requirements of the flooring – most flooring products require a screed surface relative humidity of 75% for application. Bonded wood floorings generally require a considerably lower moisture content and RonaScreed 8 Day Overlay Mix
Design 1 is not tested for the requirements of wood floorings.
7. Dryness testing – the following is the only equipment recognised by Ronacrete for accurate testing of screed surface relative humidity:
Drying of Ronacrete products cured at 20°C and approximately 60-65% relative air humidity
When tested in the laboratory at ≥ 50mm thickness, RonaScreed 1 Day Overlay screed will typically achieve 75% relative humidity in approximately 24 hours, when cured at 20°C and approximately 60-65% relative humidity, thinner screeds may take 36 hours. 75% relative humidity at the surface indicates that the screed is sufficiently dry for application of resilient floorings, carpet, quarry tiles, ceramic tiles and stone tiles. Lower temperature and higher humidity may extend the drying period.
Protimeter Hygromaster fitted to Protimeter Humidity Box BLD4711
Rapid Drying Screed ≥ 50mm thickness will typically achieve 75% relative humidity in approximately 24 hours, when cured at 20°C and approximately 60-65% relative humidity; thinner screeds may take 36 hours. 75% relative humidity at the surface indicates that the screed is sufficiently dry for application of resilient floorings, carpet, quarry tiles, ceramic tiles and stone tiles. Lower temperature and higher humidity may extend the drying period.
Will dry after 4 days of air curing at a thickness of 50mm, a temperature of 20°C and air humidity of 60-65% and 75mm –100mm thickness of screed will dry to a screed humidity of ≤ 75% after 3 days of air curing. 75% screed humidity is the maximum acceptable level for application of vinyl flooring, carpet, tiles and stone flooring. Lower temperature and higher humidity may extend the drying period; changing the mix design to increase the sand content will increase drying time.
Design 1 (3:1 by weight) has been tested at 50mm and 75mm thickness. At 50mm thickness, 20°C temperature and 60-65% air humidity, RonaScreed 8 Day Overlay Mix Design 1 dries to 75% RH after 8 days of air curing and at 75mm thickness, 20°C temperature and 60-65% air humidity, RonaScreed 8 Day Overlay Mix Design 1 dries to 75% RH after 15 days of air curing. 75% relative humidity at the surface indicates that the screed is sufficiently dry for application of resilient floorings, carpet, quarry tiles, ceramic tiles and stone tiles. Ronacrete Laboratory tests and independent tests by Vinci Technology confirm the predictability of results shown in the technical data. Drying time on site will vary according to site conditions. Increased screed thickness, lower temperature and higher humidity will lengthen the drying period; increasing the aggregate/ cement ratio will also increase drying time.
When tested in the laboratory at 50mm thickness, Ronafix polymer modified screeds achieve 75% relative humidity at the screed surface after approximately 10 days of air curing at 20°C and approximately 60-65% relative humidity; 15mm thickness of Ronafix polymer modified screed will typically dry in 3 days. 75% relative humidity at the surface indicates that the screed is sufficiently dry for application of resin floorings and waterproof membranes, resilient floorings, carpet, quarry tiles, ceramic tiles and stone tiles. Increased screed thickness, lower temperature and higher humidity will lengthen the drying period; increasing the aggregate/ cement ratio will also increase drying time.
Screeds should be sufficiently dry and strong before forced drying commences, at a temperature of 20°C and air humidity of 60-65%, RonaScreed 8 Day Overlay Mix Design 1 dries to 80% RH after approximately 10 days of air curing at a thickness of 75mm and will gain a high proportion of its ultimate strength after the same period of curing. At this stage, forced drying may commence. Forced drying should be delayed at lower temperature and when air humidity is high or when RonaScreed 8 Day Overlay has been added to a weaker mix design.
Screeds should be sufficiently dry and strong before commissioning of underfloor heating commences, at a temperature of 20°C and air humidity of 60-65%, RonaScreed 8 Day Overlay Mix Design 1 dries to 80% RH after approximately 10 days of air curing at a thickness of 75mm and will gain a high proportion of its ultimate strength after the same period of curing. At this stage, underfloor heating may be turned on and the temperature may be gradually increased in accordance with the instructions of the heating manufacturer. Commissioning should be delayed at lower temperature and when air humidity is high or when RonaScreed 8 Day Overlay has been added to a weaker mix design, but it should still be possible to use the heating system to reduce drying time at lower temperature, which may be important in thicker sections of screed.
Carbonation is the single most common cause of reinforcement corrosion in above ground structures and although many construction professionals and contractors are familiar with the progression of carbonation through concrete and the consequential effects on reinforcement, some may not be familiar with research carried out in recent years. This research suggests that loss of reinforcement passivity, as the carbonation front progresses, occurs at a higher ph than previously thought.
The ph of new concrete is typically 12-13, which surrounds embedded reinforcement with a passivating layer of highly alkaline cement, protecting reinforcement against corrosion. The rate of carbonation in new concrete will be affected by the water/ cement ratio and the cement content; the
connectivity of the capillary pore structure and size of the pores in concrete with a W/C ratio ≤ 0.4 and a cement content ≥ 400kg/ m3 will be reduced when compared to concrete with a W/C ratio > 0.4 and a cement content ≤ 400kg/m3, making progress of the carbonation front slower in cement rich concrete with low W/C ratio.
The Chemical Process of Carbonation – accepted wisdom
Atmospheric carbon dioxide reacts with calcium hydroxide (Ca(OH)2 + CO2 =CaCO3 + H2O), a cement hydration product in the cement paste. The reaction produces calcium carbonate. This reduces the alkalinity of the concrete to a level where the cement paste no longer provides a passive environment for embedded steel, this is said to occur when the ph of concrete falls to approximately 8.6. Steel reinforcement is then though to be susceptible to corrosion. The reaction of
carbon dioxide and calcium hydroxide only occurs in solution and so in very dry concrete carbonation will be slow. In saturated concrete the moisture presents a barrier to the penetration of carbon dioxide and again carbonation will be slow. The most favourable condition for the carbonation reaction is when there is sufficient moisture for the reaction but not enough to act as a barrier.
See also the later paragraph by the Concrete Society headed Loss of Passivity (Concrete Society – Carbonation of concrete)
The presence of oxygen initiates surface corrosion of the reinforcing steel through oxidation, where iron oxides form on the steel’s surface. These oxides, although porous and flaky, have a larger volume than the original steel—up to six times greater depending on the composition of the corrosion products, Broomfield notes. The iron oxides expand against the concrete, and the resulting stress causes the concrete cover to crack and eventually spall. He comments that a steel loss of only 0.05 to 0.10 mm (0.002 to 0.004 in) will cause concrete to spall. (Broomfield)
Some doubt has been cast on the assumption that a ph of ≤ 9 is required before CO2 induced corrosion is initiated and some believe that a phenolphthalein
Reinforcement Rust
Uncarbonated depth
Carbonation depth
Cover depth
test, which provides evidence of carbonation of concrete at a ph of ≤ 9, may be only a guide to corrosion risk. It is now thought that corrosion is initiated some 5-10mm ahead of the carbonation front as indicated by phenolphthalein testing (or 20mm in concrete containing chlorides), where the ph of the concrete may be up to 11 or higher. Investigations suggest that reinforced concrete structures are not at risk of carbonation induced corrosion if the un-carbonated depth, as revealed by a phenolphthalein test, is further than 5–10 mm from the reinforcement. Thermogravimetric analysis (TGA) of drillings at 5mm depth intervals and phenolphthalein tested samples were taken from the inside and outside of a 36 year old in-situ concrete framed building. The phenolphthalein results and the TGA data for complete carbonation indicated that outdoor exposure was more severe but TGA data for the deepest penetration of carbon dioxide suggested that the thickness of concrete with a reduced ph (9-11) was greater inside, suggesting that sufficient CO2 may be
present in concrete to initiate corrosion at a higher ph threshold than may be detected by a phenolphthalein test. (L.J.Parrott, D.C.Killoh)
Loss of passivity occurs at about pH 11. Carbonation of the concrete, caused by carbon dioxide in the atmosphere, has the effect of reducing the pH. Hence there may be corrosion in the zone ahead of the front defined by the phenolphthalein indicator. In general the change in pH occurs in this zone, which is only a few millimetres ahead and the phenolphthalein method provides a good indication of the location of the de-passivation front. (Concrete Society –Carbonation depth)
In concrete with a ph of 12-13, about 7,000 to 8,000 ppm of chlorides are required to start corrosion of embedded steel. This threshold is reduced is to below 100ppm in concrete
with a ph of 10-11. Conversely the progress of carbonation was significantly slowed down due to the existence of chlorides in concrete samples; the depth of carbonation boundary was decreased and the profile of consumed OH- became modest.
Results of studies suggesting CO2 induced corrosion may occur 5-10mm ahead of the carbonation front as indicated by the phenolphthalein test are clearly a cause for concern, especially with rising global CO2 concentrations being likely to increase the threat of corrosion in reinforced concrete and construction professionals should consider the results of such studies and the implications for acceptable reinforcement cover. It may be that an increased depth of reinforcement cover will be required (if previously specified cover was based on research where the phenolphthalein test has been used to determine behaviour) if the desired service life of a structure is to be achieved.
Compressive strength of unmodified concrete and mortars can continue to increase slowly after the initial curing period. However, other physical properties are reduced as the concrete or mortar ages. Published independent data relating to the effect of ageing on cementitious mortars is scarce. But testing of compressive strength, tensile strength and elastic modulus has been conducted on samples taken from 23-30 year old concrete. The results indicated that capacity to withstand loads degraded with age. Testing of samples showed that ductility was reduced, with elastic modulus increased by approximately 30%. Embrittlement of the concrete meant that its resistance to tensile stress was reduced by up to 50% compared to new concrete. The expectation of the researchers was that this degradation would continue to worsen over decades; reducing the capacity of the concrete to withstand tensile and shear loads.
Polymer modification of cementitious mortars is an accepted method for improving the physical properties of mortars. Screeds, renders, concrete repair, bedding and other applications requiring durable high strength mortars. Polymer modification may improve compressive strength to some extent because of the reduced water demand. However compressive strength should be adequate in most cases without polymer modification. The compressive strength of mortar with a polymer cement ratio of approximately 1:7 will be lower than the compressive strength of mortar with a polymer cement ratio of approximately 1:10.
The reduction comes with considerable gains in flexural and tensile strength. Compressive modulus is also reduced in mortars with high polymer contents, reducing stress on the bond between mortar and weaker substrates. The greatest strength gains in polymer modified mortars are in tensile and flexural strength. This allows thinner screeds to be laid. This reduces the risk of cracking caused by tensile and flexural stress in screeds, concrete repairs and renders. Wear resistance, which is generally poor in traditional screeds, is also improved by polymer modification.
The capillary pores in cementitious mortars produced in accordance with Ronafix mix designs, particularly those with a Ronafix content of ≥ 9 litres per 50kg Portland cement are narrower and have fewer connections to other pores than in unmodified mortars with the same proportions of sand and cement and the same water: cement ratio. This considerably reduces the permeability of Ronafix modified mortars to liquid water, moisture vapour and acidic gases. Permeability is low or extremely low, depending on the mix design. This makes Ronafix mix designs waterproof or weatherproof, resistant to carbonation and very resistant to damage by freeze thaw cycling. Typical shrinkage of Ronafix modified mortars with a Ronafix content of ≥ 9 litres per 50kg Portland cement is 0.01%. This is similar to that of epoxy resins. The image shows a microscopic view of a polymer modified mortar with many of the voids filled in.
The addition of Ronafix admixture to sand/ cement mortars improves physical properties during the curing period and in the longer term. Flexural and tensile strengths are considerably increased and the reduced water cement ratios of Ronafix modified mortars will in many cases improve compressive strength. The rate of increase in physical properties of
polymer modified samples tested beyond the initial 28 day curing period is greater than increases in unmodified samples.
Heat ageing testing indicates that after simulated life of 20 years, tensile strength of Ronafix modified samples was similar to unaged samples and after 40 years of simulated ageing, tensile strength was reduced by 14%. At the same age, tensile strengths of unmodified control samples were unmeasurably low. After 260 years simulated ageing, tensile strength of Ronafix modified samples was 34% lower than unaged samples but similar to tensile strength of samples tested after 80 years ageing, indicating that reduction in tensile strength had stopped.
Heat aged samples subjected to flexural strength testing showed that after 40 years accelerated ageing, flexural strength of Ronafix modified samples had increased by nearly 50% while unmodified samples had lost approximately 30% and were 68% lower than the flexural strength of Ronafix modified samples. After 260 years simulated ageing, flexural strength of Ronafix modified samples was 9% lower than the 40 year aged samples. It was also considerably higher than samples tested after 20 years simulated ageing.
Ronafix mix designs dry faster than unmodified mortars, when tested in the laboratory at 50mm thickness. Ronafix polymer modified screed mix designs achieve 75% relative humidity at the screed surface after approximately 10 days of air curing when cured at 200C and approximately 60-65% relative humidity. In general 75% relative humidity at the surface indicates that the screed is sufficiently dry for application of resilient floorings; carpet, quarry tiles, ceramic tiles and stone tiles. The typical drying time of unmodified mortars in the same drying conditions is 50 days.
RonaScreed
RonaScreed Self Smoothing Exterior Screed
RonaScreed
RonaScreed
We understand that it can be a difficult decision when it comes to choosing the colour of your finished surface. It can be even more difficult when you can only choose from pictures. For that reason we are able to send out a selection of cured samples so that you can have a closer look at the colours and finishes available. We are able to provide samples for a number of products. Please select the product from the samples shown on the relevant pages.
You can contact the Ronacrete office directly on 01279 638700
Open from 08:00 til 17:00 Monday to Friday.
Alternatively, you can email us using the email addresses.
CPD Seminars cpd@ronacrete.co.uk Sales sales@ronacrete.co.uk
Technical technical@ronacrete.co.uk
Office/ warehouse Ronac House, Flex Meadow, Harlow, Essex CM19 5TD
Our warehouse is open for collections between 07:30 and 16:00
Ronac House, Flex Meadow, Harlow, Essex, CM19 5TD t +44 (0)1279 638700 e technical@ronacrete.co.uk w ronacrete.co.uk