Circular
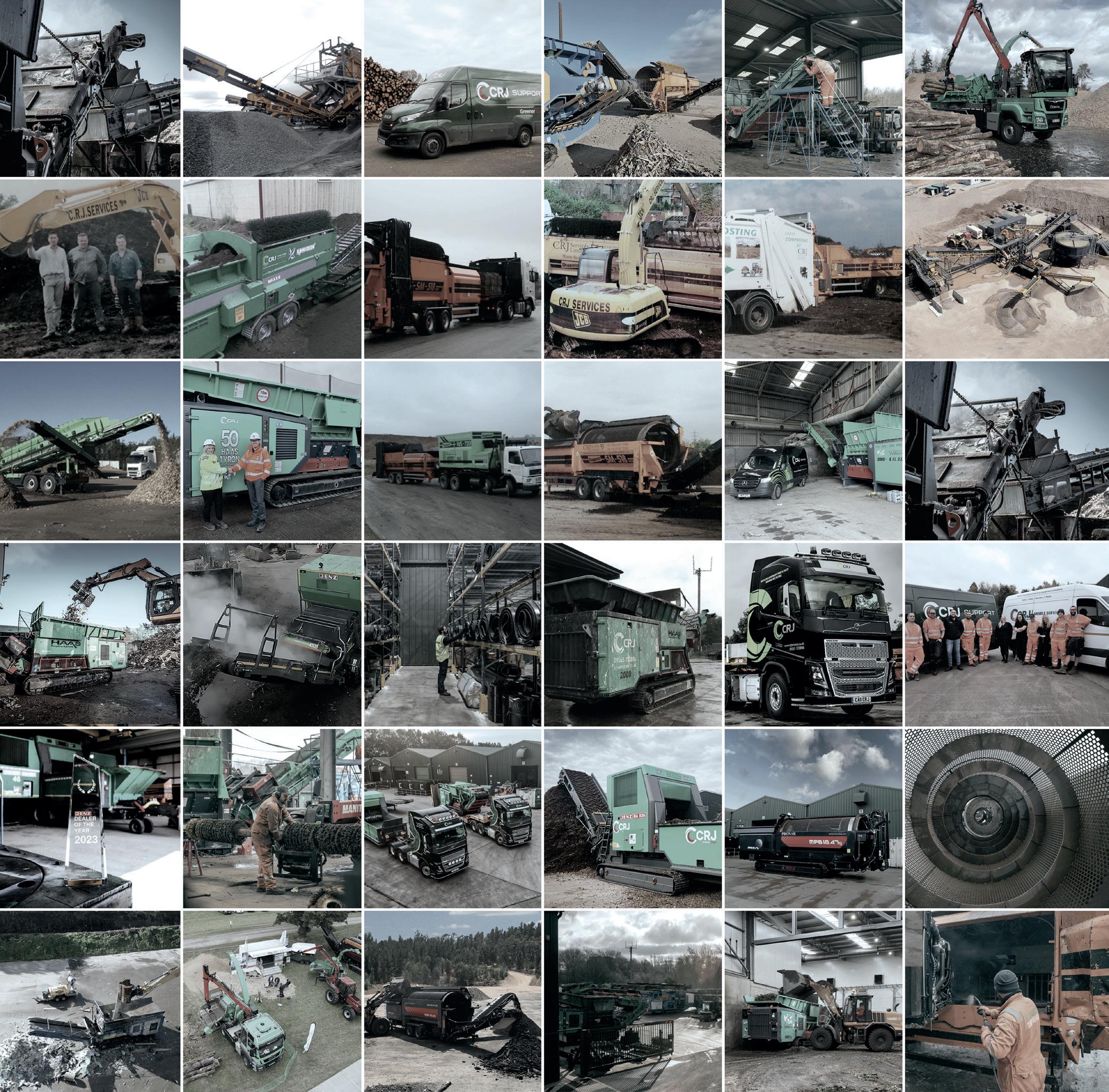
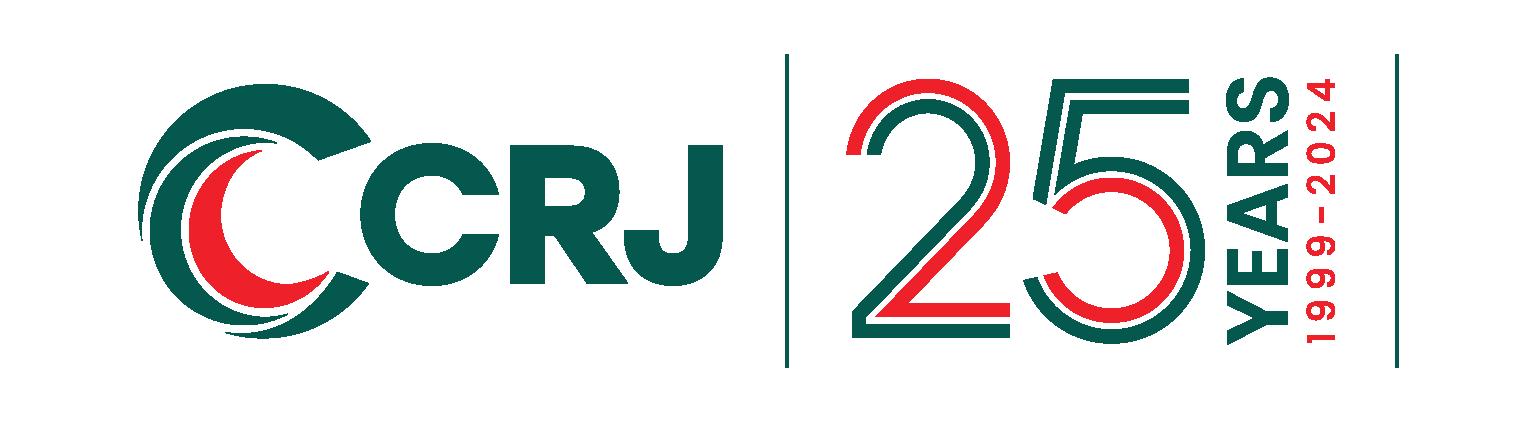
As we mark 25 years of CRJ Services, we find ourselves reflecting on an incredible journey that began with a simple vision: to revolutionise the recycling industry and contribute to a more sustainable future. That vision has not only endured but has grown stronger with each passing year, thanks to the extraordinary people who have been part of our story.
Each milestone in our journey, from our first machine hire to our position today as one of the industry’s most respected recycling specialists, showcases why CRJ Services is trusted as a leading authority in waste processing solutions. Our advanced recycling technologies and deep technical expertise have established us as the go-to specialists for businesses seeking optimal material recovery. These achievements represent not just our success, but validate the trust our clients have placed in CRJ’s proven track record of innovation and excellence.
To our loyal customers, your trust in our full service offering has enabled us to push boundaries and continuously improve. Your feedback and partnerships have been instrumental in shaping our journey and helping us better serve the recycling industry’s evolving needs.
To our trusted suppliers, your reliability, innovation, and support have been crucial in maintaining our high standards and enabling us to deliver exceptional value to our customers. Together, we’ve built a supply chain that not only meets today’s demands but is prepared for tomorrow’s challenges.
To our dedicated employees, your passion and commitment have been the driving force behind our success. Whether you’ve been with us for decades or have joined us more recently, each of you plays a vital role in delivering the excellence that CRJ Services is known for.
As we look to the future, we’re more excited than ever about the opportunities ahead. The recycling industry continues to play an increasingly critical role in building a sustainable UK, and CRJ Services remains committed to leading the way with innovative technology, exceptional service, and environmental stewardship.
This 25 year milestone is not just about looking back, it’s about looking forward to the next chapter of our story. With strong foundations, a clear vision, and the continued support of our exceptional customers, suppliers, and team, we’re confident that the best is yet to come. Thank you for being a part of our journey. Here’s to the next 25 years of growth, innovation, and shared success.
From humble beginnings to becoming a leading provider of waste, recycling, and forestry equipment with a full-spectrum of services, we’ve dedicated ourselves to driving the UK and Ireland towards a greener future.
When our founders Lee Carter, Kevin Jones, and Andrew Reed incorporated CRJ in 1999, we started with a simple mission: processing green waste. Today, we’ve grown into something much bigger, offering comprehensive services including equipment hire, sales, aftermarket parts, and service expertise across waste, recycling, and forestry sectors.
We’ve always focused on becoming the best provider in the industry, and we’re proud to have achieved significant milestones along the way. We’ve become the exclusive dealer for JENZ GmbH, HAAS Recycling Systems, and Pronar Trommel Screeners in the UK and Ireland. With our expanding hire fleet of over 110 machines, we’re better equipped than ever to deliver top-tier solutions to our customers. Our success has been built on our unwavering commitment to helping the UK recycle, a dedication that has been recognised through nominations and awards from various renowned industry bodies.
Everything we do at CRJ is guided by our core values:
These aren’t just words on a wall, they are the principles that unite our entire CRJ family. We take pride in our work and we’re committed to providing exceptional service. Whether we’re tackling a challenging project or handling day-to-day operations, our team goes the extra mile to exceed our customers’ expectations.
CRJ thrives under a leadership team that blends deep industry experience with proven innovation.
Andrew Clarkson, Finance Director, architects our financial strategy with nearly three decades of business transformation experience. Since joining in 2022, he’s streamlined our operations and strengthened our investment in sustainable growth.
Ben McQuaid transformed CRJ’s market presence when he joined as Sales Director through the 2016 Matpro merger. Under his guidance, we’ve evolved from equipment supplier to industry leading solutions provider, expanding our reach across the recycling sector.
As Compliance Director and founding member, Lee Carter champions our environmental mission. His vision has established CRJ as a pioneer in sustainable practices, setting new benchmarks for environmental responsibility in the waste management industry.
Rob Symons embodies CRJ’s commitment to excellence. Rising from driver/operator in 2004 to Operations Director, his hands-on experience and customer-first approach have become legendary in the industry.
In preparation for the next 25+ years, we’re focused on expanding our brand across the UK and Ireland, establishing ourselves as industry experts ready to share our knowledge and experience with corporate and government leaders. With a strong leadership team, a dedicated workforce, and a commitment to sustainable practices, we’re excited to continue our growth, helping advance the UK and Ireland toward a greener, more sustainable future.
1st Hire to Manchester Waste (high-speed shredder) from CRJ Services, and secured waste processing contract from Macclesfield council
We welcomed Rob Symons to CRJ.
We partner with Matpro Machinery, officially welcoming Ben McQuaid to the CRJ team, inevitably gaining exclusive dealership rights for HAAS Recycling Systems
CRJ is founded on Brookhouse Farm, Cheshire, and awarded a green waste processing contract from Cheshire County Council and Congleton council
Secured waste processing contracts from Nantwich and Crewe Councils
We began servicing large accounts incl.
CRJ Services and Steelweld collaborate to design a tracked Eddy Current Separator.
We were appointed as a dealer for Bruce Engineering and achieved a hire fleet of 100 active machines.
We became the exclusive dealer for Pronar Trommel Screeners in the UK & Ireland.
CRJ celebrated 20 years and installed our first HAAS static wood recycling plant. Welcomed Andrew Clarkson as contractual Finance Director (changing to full time in 2022)
We secured exclusive dealership rights for JENZ GmbH, while expanding our stores with £2,000 000 worth of aftermarket parts.
We’ve turned 25! CRJ grows to over 70 employees across the UK, with 110 active machines within our hire fleet, and received 4 industry awards.
Celebrating 25 years at CRJ Services is not just a milestone, but a testament to the dedication and hard work of our entire team. From our early days with just a handful of machines to becoming a leading provider in the industry, our journey has been driven by a commitment to excellence and a shared vision of a greener future. We are proud of what we’ve accomplished and excited for what lies ahead as we continue to innovate and grow.
Rob Symons Operational Director CRJ
Services “
Scan the code to watch the machine feature video.
Long-term JENZ operator R J & C Chancellor partnered with CRJ Services to upgrade his green waste and biomass processing machinery with t he latest JENZ BA916D high-speed shredder , significantly enhancing his operational capabilities across multiple sites.
R J & C Chancellor’s green waste and biomass processing operation required a specialised shredding solution that could deliver consistent performance across multiple daily sites. His business needed equipment that could maintain high throughput for both composting and biomass production while minimising setup time and maintenance delays. The challenge lay in balancing mobility with processing power, the equipment needed to be robust enough for continuous operation yet agile enough for quick relocation.
Site transitions had to be streamlined, as every minute spent on setup directly impacted daily productivity targets. The ideal solution had to combine rapid deployment with reliable processing capacity, transforming downtime into productive hours while maintaining consistent output quality regardless of location. These operational demands meant traditional static processing equipment wouldn’t suffice; instead, Rob needed a solution that could adapt to varying site conditions and material types while maintaining efficiency throughout multiple daily moves.
Based on Rob’s extensive 20-year history with JENZ equipment, CRJ Services recommended the JENZ BA916D high-speed shredder. The machine’s 32-hammer system doubles processing capacity, while its advanced control interface and remote functionality offer enhanced operational control. Key features include a covered rear conveyor and quick fold/unfold capabilities, optimising mobile operations. The BA916D’s specifications aligned perfectly with Rob’s requirements, enabling a smooth transition and immediate gains in processing efficiency and mobility.
In my experience, the Jenz shredder consistently outperforms all competitors in green waste processing. The upgrade from 16 to 32 hammers delivers a finer shred size and increased throughput, eliminating the need for smaller screens.
Though this setup requires more blades, their longer lifespan keeps costs similar.
“
Rob Chancellor Owner R J & C Chancellor
As soon as the JENZ BA916D was delivered, CRJ provided comprehensive support to ensure a seamless transition. The implementation began with in-depth operator training that covered the shredder’s sophisticated control systems and remote operation features. Working side-by-side with Rob, CRJ’s technical specialists fine-tuned the hammer configurations to achieve optimal performance across different materials, maximising efficiency for both composting and biomass production. This systematic approach helped maintain productivity as the team mastered the BA916D’s advanced capabilities, ultimately streamlining operations across multiple sites.
Since implementing the JENZ BA916D, Rob has experienced significant performance improvements across his operations. The upgraded 32-hammer system has delivered superior shred quality while increasing overall throughput, eliminating the need for smaller screens. Despite the higher number of hammers, the system has demonstrated extended blade life, effectively maintaining operational costs. The machine’s enhanced cleaning and maintenance efficiency has substantially reduced downtime between sites.
The operational impact has been equally impressive, with the BA916D’s quick fold and unfold capability streamlining site transitions. The covered rear conveyor design has minimised cleaning requirements between jobs, while the new control interface and remote functionality have given Rob greater control over the shredding process.
The JENZ BA916D installation at Rob’s site went smoothly with support from our sales and technical teams. When initial challenges arose, we worked quickly to resolve them and keep operations on track. Our aim is to provide reliable equipment backed by consistent support to help our customers succeed.
The JENZ BA916D is a diesel driven, high-speed shredder, ideal for organic waste, biomass, wood, and tree roots.
Key Features:
• Free swinging or fixed hammers.
• Rotor speed control for optimum shredding.
• The outfeed belt can be swivelled to one side to allow easy access to the shredding chamber.
• Simple replacement of the 2-piece screening basket.
• An extremely aggressive feed with a height-adjustable top roller.
• Innovative ‘Easy2’ control system with remote control.
• IPS impact protection system, with foreign object detection.
Technical Specifications:
Power: 530 HP / 390 kW
In-feed: 1500mm x 900mm
Loading length: 4400mm
Hopper volume: 7.5m3
Discharge height: 4,400mm
Weight: 19,000kg
For information about our JENZ product range and services, contact Mike and the sales team.
015657 23886 / 07808 282750
JENZ HEM 700
PTO Chipper (YOM 2017)
Price: £200,000.00 (excl VAT)
Bruce BWB 120
Wash Bath (YOM 2020)
Price: £58,000.00 (Excl VAT)
Arjes VZ750
Slow-Speed Shredder (YOM 2019)
Price: £165,000.00 (Excl VAT)
JENZ HEM 582
Wood Chipper (YOM 2010)
Price: £115,000.00 (excl VAT)
HAAS Tyron 2000 XL 2.0
Slow-Speed Shredder (YOM 2021)
Price: £195,000.00 (Excl VAT)
Each used machine has been quality checked by our expert heavy plant mechanics to ensure they are in good working condition.
Scan to view full range of used machines, ready to purchase or email enquiries@crjservices.co.uk.
When Wastewise’s HAAS Tyron shredder needed a major overhaul, our comprehensive refurbishment service, combined with temporary relief equipment, helped keep their business running smoothly throughout the process.
Wastewise, a prominent player in the waste management industry, encountered a significant challenge with their HAAS Tyron 2000 XL 2.0 slow-speed shredder. To ensure the machine’s optimal performance and extend its operational life, a comprehensive overhaul was necessary.
Wastewise entrusted CRJ Services with this critical task, confident in our expertise and reputation for delivering high-quality service. This case study outlines the challenges faced, the solutions provided, the implementation process, and the successful results achieved.
The complexity and scale of the HAAS Tyron 2000 XL 2.0 refurbishment required specialised attention and resources. It was determined that the work would be best performed at CRJ Services’ facility rather than on-site. This decision was made to ensure a faster turnaround and higher quality of service. The challenge also included managing the logistics of transporting the machine to and from the site efficiently, minimising downtime for Wastewise.
All components for the overhaul were hand-picked from our extensive parts store unit, ensuring the machine would return to service operating at peak efficiency. Additionally, CRJ supplied and delivered a relief shredder to Wastewise to maintain their operations during the refurbishment period. CRJ also arranged the transport for both the relief shredder and the one needing repairs, showcasing their commitment to comprehensive service and support.
The HAAS Tyron 2000 XL 2.0 machine was transported to CRJ workshop in Cheshire, where the team conducted the refurbishment. This approach allowed for better control over the quality and speed of the repairs. The CRJ mechanics meticulously disassembled, inspected, and replaced the necessary parts of the machine.
Throughout the process, communication with Wastewise remained fluid, ensuring all repairs were completed on time. This transparent communication helped build trust and ensured that Wastewise was always aware of the project’s status. The refurbishment process involved several key steps:
1. Initial Assessment: A thorough inspection of the HAAS Tyron 2000 XL 2.0 machine to identify all necessary repairs and parts replacements.
2. Disassembly: Careful disassembling of the machine to access and replace worn-out components.
3. Parts Replacement: Sourcing and installing high-quality replacement parts to ensure the machine’s optimal performance.
4. Reassembly and Testing: Reassembling the machine and conducting rigorous testing to verify that all repairs were successful and the machine was operating at peak efficiency.
The refurbished HAAS Tyron 2000 XL 2.0 shredder was returned to Wastewise and immediately put back into service. The machine is now performing well, meeting all operational expectations.
As one of the first large-scale third-party engagements, it was important for us to demonstrate our team’s ability to commit to high standards in both service quality and client collaboration.
CRJ Services did an outstanding job refurbishing our HAAS Tyron 2000 XL 2.0 machine. We were kept informed throughout the entire process, and all repairs were completed on time. The machine is now back in service and performing exceptionally well. Excellent communication and service from start to finish.
“
Michael Wheatley Operations Director Wastewise
By representing world renowned brands such as HAAS, PRONAR, JENZ, and more, we offer a diverse selection of OEM parts and high quality aftermarket parts for waste
management, recycling and forestry machinery, ensuring delivery within 24 hours.
For more information, contact Alan and his team.
parts@crjservices.co.uk 015657 23886 (4)
CRJ Services is driving operational transformation through the implementation of Kaizen methodology across its machine hire department and engineering operations.
Understanding Kaizen at CRJ Services
Kaizen, meaning “change for better” in Japanese, represents our dedication to continuous, incremental improvements across all aspects of our operations. The initiative began with an intensive week-long training program led by Kaizen experts, laying the foundation for a company-wide transformation in how we approach our daily operations.
One notable improvement already in action is the introduction of standardised digital job cards, which have reduced equipment handover times by eliminating paper-based processes and ensuring consistent documentation across all service points. This strategic integration of the renowned Japanese continuous improvement philosophy marks a significant milestone in our commitment to operational excellence and service delivery.
The implementation of Kaizen principles is projected to deliver significant improvements:
• 20-30% reduction in machine maintenance turnaround time.
• Enhanced workplace organisation through 5S methodology (Sort, Set in order, Shine, Standardise, Sustain).
• Improved team communication and problem-solving capabilities.
• Reduced operational costs through elimination of waste.
• Increased customer satisfaction through consistent service quality.
Our workshop engineering team is enhancing efficiency through Kaizen-driven improvements, including streamlined troubleshooting procedures and optimised workspace layouts. The implementation of visual management systems and refined inventory control has significantly reduced diagnostic times and parts wastage, while strengthened quality control checkpoints ensure consistent repair excellence throughout our operations. This commitment to continuous improvement ensures we maintain our competitive edge while delivering superior value to our customers.
As one of the UK's premier events for forestry, woodland, and arboriculture professionals, APF provided an excellent platform to demonstrate our latest equipment offerings in the heart of the forestry sector.
Our stand was bustling with activity, as we showcased a selection of machines designed to meet the rigorous demands of the forestry industry. Among the equipment on demo were our popular Jenz HEM 583 R-Truck wood chipper and the Jenz BA 926 high speed shredder, both known for their efficiency, power, and user-friendly design. These machines drew a crowd, sparking great discussions with industry pros on how our lineup can help them meet their operational needs while supporting sustainable practices. In addition to the live demonstrations of our Jenz chipper and shredder, we showcased a Jenz HEM 542z Wood Chipper pulled by a vintage Tractor - Case 1455, and a Pronar MPB 20.55 Trommel Screener.
Adding to the experience, attendees enjoyed a barista-made coffee from our on-stand coffee bar—a perfect way to start a conversation about forestry and recycling. Our team appreciated this relaxed setting to catch up with familiar faces and connect with new ones, strengthening our industry network.
We were also joined by Michael Hourtz, Export Manager at Jenz GmbH, who provided insights into the innovative technologies behind Jenz machines. Michael’s presence was invaluable, as he shared firsthand knowledge and connected with customers to discuss the latest advancements from Jenz, as well as their practical applications for UK forestry.
We’d like to extend our heartfelt thanks to Martin Robinson at Robinson & Son Timber and Louis Saer from Chalford Timber for their invaluable help and support at the APF show.
Thank you to everyone who visited us at APF 2024! If you couldn’t meet us at the show, scan the code to watch the highlights:
When Enva faced the complex challenge of processing end-of-life wind turbine blades, one of the most demanding materials in renewable energy waste, they turned to CRJ Services for an innovative solution.
With the growing wind energy sector, Enva faced the complex challenge of processing end-of-life wind turbine blades - one of the most challenging materials in the renewable energy waste stream. Wind turbine blades, primarily composed of durable composite materials like fiberglass and carbon fiber, pose significant recycling challenges due to their resistance to breakdown. Their enormous size, often up to 95 meters, complicates transportation to recycling facilities, making the process logistically challenging and expensive. Current recycling technologies, including mechanical processes, pyrolysis, and solvolysis, are limited and not yet cost-effective or widely adopted. Environmental concerns arise from disposing of blades in landfills or through incineration, which can generate microplastics and release pollutants, harming ecosystems and air quality. Additionally, the high cost of recycling and the lack of economic incentives deter investment in recycling technologies. While efforts are ongoing to develop more sustainable methods, such as repurposing materials for cement production or new composite products, these solutions are still in early implementation stages.
After consulting with CRJ Services’ hires team, Enva opted to hire the HAAS Tyron 2000XL 7/7-4, specifically configured for processing composite materials. Using a large slow-speed shredder, offers efficient size reduction, as the shredder can handle the tough composite materials of the blades, breaking them down into smaller, more manageable pieces. It also reduces the need for extensive blade preparation, streamlining the recycling process. Operating at lower speeds, the shredder minimises dust generation, maintaining a safer and cleaner working environment. The versatility of the shredded material allows it to be repurposed for various applications, such as in cement manufacturing or as composite materials for industrial use. While this method shows great potential, it is part of a broader strategy to improve the sustainability of wind turbine blade disposal. Continuous advancements in recycling technologies and methods are essential to address the growing volume of decommissioned blades.
This robust slow-speed shredder was recommended by our hires team for its exceptional processing capabilities. The HAAS Tyron 2000XL 2.0 features a robust dual-shaft shredding system and independent shaft speed control. Its enhanced cutting system with a 7/7-4 tooth configuration, combined with heavy-duty construction, makes it uniquely capable of handling tough composite materials while consistently producing uniform output sizes. The machine’s advanced hydraulic drive system ensures optimal torque delivery, allowing for efficient processing even under heavy loads. Furthermore, its reinforced chassis design provides excellent stability during operation, even when processing challenging materials.
Following a thorough quality check at CRJ, the HAAS Tyron 2000XL 2.0 was deployed to Enva’s processing facility with a specialised setup designed to optimise performance. The installation included custom-configured cutting tools specifically designed for composite materials, carefully adjusted shaft speeds to handle the fibrous nature of turbine blades, and implementation of specific loading procedures to maximise throughput. A comprehensive maintenance schedule was also established to ensure optimal performance throughout the operation.
Since handover, the HAAS Tyron shredder has shown impressive results in processing wind turbine blade sections. Key performance metrics include consistent reduction of blade sections to manageable output sizes, sustained reliability under challenging conditions, and adherence to environmental compliance standards. The shredder’s efficiency in processing complex composite materials has reduced manual handling and maintained consistent output sizes suited for further processing, with minimal operational downtime. CRJ Services has supported this hire with comprehensive operator training, continuous technical support, regular maintenance checks, and remote troubleshooting.
The successful implementation of this solution has positioned Enva to handle increased volumes of wind turbine blade waste as the renewable energy sector continues to grow. The hire arrangement provides flexibility to scale operations based on demand while maintaining access to CRJ’s technical expertise and support.
For more information about our hire solutions for specialised waste processing applications, contact Becky and her team.
hire@crjservices.co.uk 015657 23886 (2)
The mobile Haas Tyron shredder is the most powerful, twin-shaft, slow speed shredder in the industry. It can shred a wide range of materials and waste.
Key Features:
• Twin shredding shafts enable greater control and consistency of shred size.
• Can be used in any location (comfortable transport measurements)
• Easy and quick positioning thanks to crawler tracks and radio remote control
• Shreds different materials with just one tool configuration
• Resistant against foreign objects
• No wrapping of long fibrous material (self-cleaning system)
• Low wear costs and a long lifetime
• Quiet main drive
• Service and Maintenance friendly.
Technical Specifications:
Power: 400 HP / 294 kW
Shredding Chamber: 700mm x 2000mm
The CRJ Service team delivers comprehensive maintenance and breakdown services through our service desk and network of OEM-trained engineers strategically positioned throughout the UK and Ireland .
At CRJ, we believe our equipment support is second to none, delivering industry-leading equipment maintenance and breakdown support to both our hire and sales customers, across the whole of the UK and Ireland.
Our strategically positioned field engineers and headquarters-based workshop teams ensure swift response times, typically same-day or within 24 hours. Each engineer arrives in a fully equipped service vehicle, prepared to handle immediate repairs and maintenance needs.
• Strict adherence to OEM servicing standards.
• Extensive spare parts inventory.
• Remote diagnostic capabilities.
• Emergency replacement machinery when needed.
• Bespoke servicing agreements tailored to your operations immediate repairs and maintenance needs.
Flexible Service Solutions
• Regular maintenance scheduling.
For more information about our breakdown and maintenance services contact Darren and the service team.
service@crjservices.co.uk 015657 23886 (1).
• Rapid breakdown response.
• Remote diagnostics and troubleshooting.
• Custom service plans for all equipment types.
• Replacement machinery provision.
CRJ Services proudly acknowledges the dedicated employees who have been recognised for their long service to the company. Their unwavering commitment and hard work have been instrumental in driving the company's success and growth. Each of these individuals has played a vital role in shaping CRJ Services' journey, and the company is deeply grateful for their contributions. Congratulations to all the award recipients.
Ben McQuaid Sales Director
Brian Parker Purchasing Manager
Griffiths Mobile Heavy Plant Mechanic
Barton Driver
Stephen Robinson Project Accountant
Sid Smith, British GB4 Championship Driver and 2022 Fiesta Junior Champion, is making waves in the racing world! To support his journey, Operational Director Rob Symons proudly sponsored a set of tyres.
CRJ Services is proud to sponsor Craig Finnikin, a distinguished F1 stock car driver. Craig has made a name for himself in the racing world with numerous accolades, incl. becoming the F1 Stock Car European Champion in 2019 and the World Champion in 2014. Craig’s dedication and skill on the track make him a perfect ambassador for CRJ Services, and we are thrilled to support his continued success in the racing arena.
This Christmas, CRJ Services is proud to support The Trussell Trust and a network of local food banks in Cheshire East as our chosen charity, helping to combat homelessness and hunger. For every Christmas gift sent to a CRJ customer, we will donate one meal to someone in need in our community.
Four of our staff members (Deon Swanepoel, Stian Mostert, Ben McQuaid, and Gary Molloy) will spend the night on the streets of London to raise awareness and funds for the homeless community, who face another Christmas in harsh conditions. By spending one night on the streets, our team hopes to gain a small glimpse into the challenges faced by the homeless. They will join the RESTART LIVES community on 6th December, outside St Columba’s Church, London.
RESTART LIVES empowers homeless people to overcome the personal and systemic barriers they are facing and to reach their self-defined goals. From housing and employment, to mental and
Join us in making a meaningful impact by donating to our ‘JustGiving’ fund.
physical health, they offer wraparound casework and group programmes aimed at empowering each person to take any steps that are right for them. We believe everyone deserves a safe home.
CRJ Services is pleased to announce the appointment of Tony Jakub as our new Area Sales Manager for Scotland. Tony brings over a decade of expertise in the recycling, forestry, quarrying, and fabrication sectors. His technical background in Mechanical Engineering and comprehensive knowledge of OEM machinery positions him perfectly to support our Scottish customers.
If you are in the market for a new or used machine, contact Tony at tony.jakub@crjservices.co.uk or 07350 397120.
As we approach the festive season, we’d like to extend our heartfelt thanks to our valued customers, trusted suppliers, and dedicated team members for their continued support throughout 2024. Your partnership and commitment have been instrumental in our success this year.
Our offices will close for the holiday period from 1pm on December 24th, reopening at 8am on January 2nd.
For any urgent matters during this time, please contact our emergency line on +44 (0)1565 723 886.
From all of us at CRJ Services, we wish you a peaceful Christmas and a prosperous New Year. We look forward to working together in 2025.
+44 (0)1565 723 886 enquiries@crjservices.co.uk