Achieving 23% Cost Savings, 33% Less Film Usage, and 30% Increase in Load Containment
A major medical supplies distribution player faced product damage during transit. They also had inconsistent stretch wrap practices. Operating an extensive warehouse seven days a week, we recognized the need to optimize their end-of-line packaging process. Since they were very price-conscious and focused solely on the price per roll, we needed to demonstrate the difference between the cost per roll and the cost in use. Our goals were clear – to show them improved product protection, enhanced efficiency, and, therefore, significant cost reduction.
Challenge
• Incidents of product damage during transit.
• Lack of standardized and optimized stretch wrap practices.
• Using lower-performance-level stretch film.
Solution
• Initial testing of Crawford’s stretch film produced twice the load containment compared to their current stretch film.
• The maximum skid weight was 1500 lbs; the containment level with Crawford’s stretch film, using unchanged stretch wrapper settings, was sufficient to wrap a 3000 lbs skid.
• Crawford’s Packaging Specialists scaled back the containment, removed the top and bottom wrap, and increased the carriage speed to reduce overlap and shorten the cycle times.
Impact
• Significant cost savings: 23% reduction in stretch film costs.
• Reduced film usage by 33%, contributing to sustainability efforts.
• Improved load containment (force-to-load) by 30%.
• Reduced the roll changeovers by 50%, reducing the chance of roll edge damage during changeover.
• Achieved a significantly higher number of pallets wrapped per roll.
• Enhanced efficiency and performance of end-of-line packaging process.
23% reduction in stretch film costs
33% reduction in film usage
30% improved load containment
50% reduction in roll changeovers
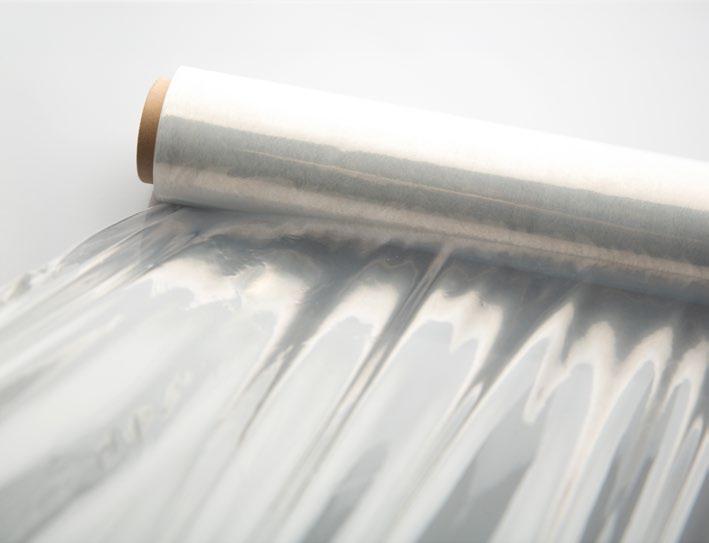