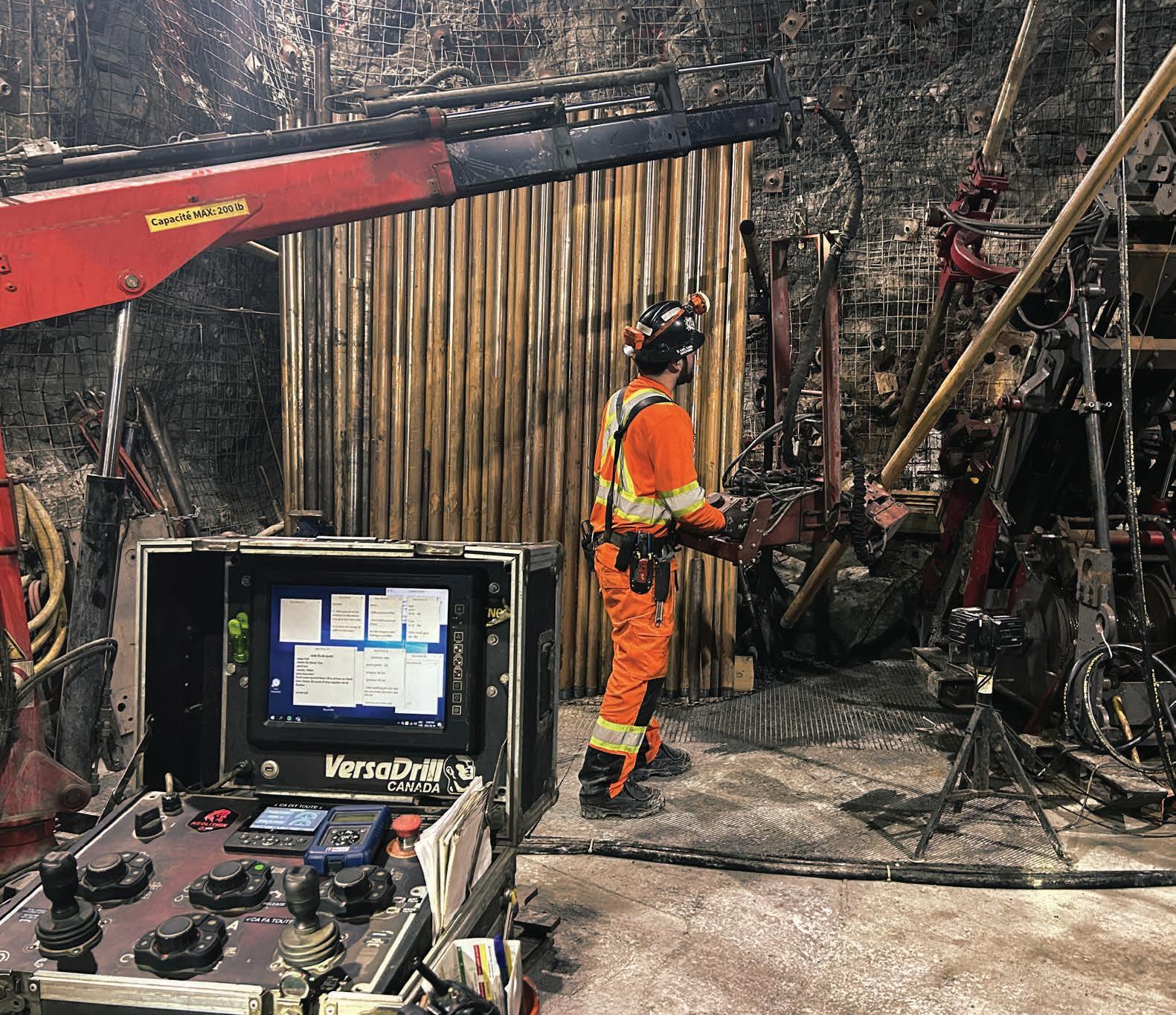
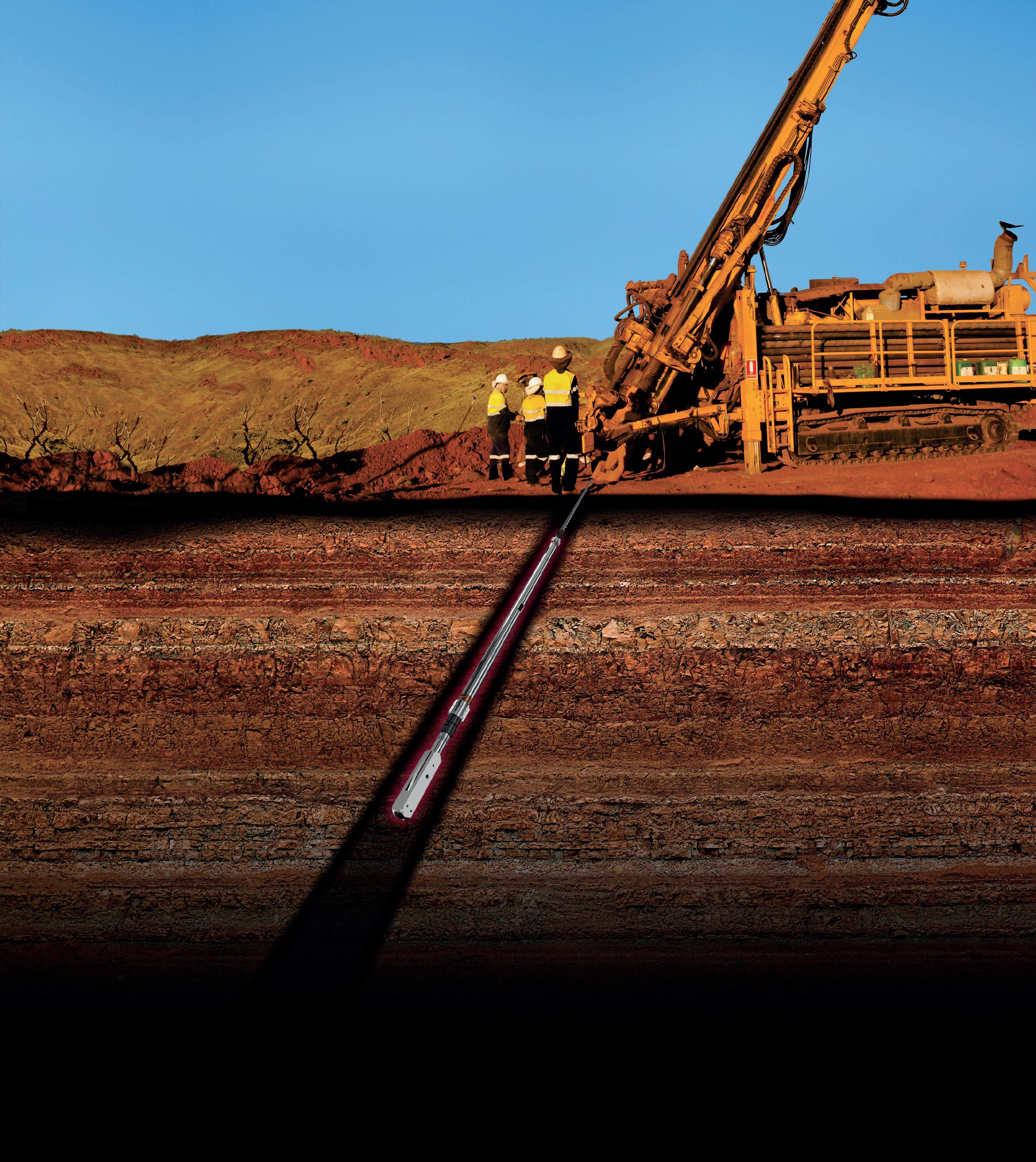
Team Drilling: 15 years of servicing the mining & exploration industry by Robert Fleming, President and CEO at Team Drilling
MBI Global unveils autonomous drill rig and a partnership with ASDR Canada by MBI Global
Ranger Exploration Drilling develops an automated RC drill rig by Stuart Baird, General Manager at Ranger Exploration Drilling Pty Ltd
28 Barge Drilling: Forage Fusion Drilling and Warkentin Fabricating battle the Canadian wilderness by Michael MacTavish, Owner at Forage Fusion Drilling and Jordy Warkentin, Owner at Warkentin Fabricating
32 40 years of Alton Drilling: Setting records while adhering to strict environmental regulations by Cory Ibbotson, Director at Alton Drilling /TECHNICAL ARTICLE
36 The importance of instrument calibration: Part I by Dag Billger, Owner & Business Manager and Duncan McLeod, Owner & Product Manager at Inertial Sensing One AB /EXPLORATION & MINING GEOLOGY
41 Q&A from the experts In conversation with David Rhys, Consulting Geologist at Panterra Geoservices
46 Power of the microscope: Petrographic analysis and mineralogy in the exploration and mining industry by Paul Ashley, Principal at Paul Ashley Petrographic and Geological Services
50 The call of the wild by Hugo Serra, Project Geologist
54 The traps and pitfalls to be aware of when releasing exploration results by Ivy Chen, Director & Principal at GeoReg Mining & Compliance
56 Drilling under the northern lights by Ashleigh Ball
Drilling services
Drilling equipment & accessories
Survey equipment
Miscellaneous
Ignus Storm COO at Hall Core Drilling
Cory Ibbotson Director at Alton Drilling
Paul Ashley Principal at Paul Ashley Petrographic and Geological Services
Robert Fleming President and CEO at Team Drilling
Dag Billger, Owner & Business Manager
Duncan McLeod, Owner & Product Manager at Inertial Sensing One AB
Hugo Serra Project Geologist
Stuart Baird General Manager at Ranger Exploration Drilling Pty Ltd
David Rhys Consulting Geologist at Panterra Geoservices
Ivy Chen Director & Principal at GeoReg Mining & Compliance
Ashleigh Ball
CORING MAGAZINE
May 2023
Cover photo
MBI Global
Issue 23
ISSN 2367-847X
Not for resale. Subscribe: coringmagazine.com/subscribe
Contact Us
Coring Media Ltd.
119B D. Petkov Str., Sofia 1309, Bulgaria
Phone +359 87 811 5710
Email editorial@coringmagazine.com Website coringmagazine.com
Publisher Coring Media
Editor in Chief Grigor Topev
Executive Officer & Editor Martina Samarova
Editor
Maksim M. Mayer
Section Editor – Exploration & Mining Geology Dr Brett Davis
Digital Marketing Manager Elena Dorfman
Graphic Design Cog Graphics
Coring Magazine is an international quarterly title covering the exploration core drilling industry. Published in print and digital formats, Coring has a rapidly growing readership that includes diamond drilling contractors, drilling manufacturers and suppliers, service companies, mineral exploration companies and departments, geologists, and many others involved in exploration core drilling.
Launched in late 2015, Coring aims to provide a fresh perspective on the sector by sourcing authentic, informed and quality commentary direct from those working in the field. With regular interviews, insightful company profiles, detailed product reviews, field-practice tips and illustrated case studies of the world’s most unique diamond drilling and mineral exploration projects, Coring provides a platform for learning about the industry’s exciting developments.
Open the box and GO. The GoGyro is fully integrated and designed specifically for simple, easy everyday use.
Configure your GoGyro as you need it for your surveys without unnecessary extra running gear. Simply add the needed fitting to run as:
• Core retriever
• Wireline
• Centralizers
Minimize downtime & Maximize efficiency. Simply GO Survey!
Fully integrated with SurveySafe for fast, convenient and secure online survey data management.
Chief Operating Officer at Hall Core Drilling
Ignus Storm dreamt of studying medicine, yet circumstances led him into the world of geology.
Ignus holds a Bachelor’s degree in Geology, followed by a Honors degree in Soil Chemistry & Mining Rehabilitation both from the University of Pretoria. After finishing his Honors degree in 2014, he started working at RHC Mining. He was a part of the first teams to successfully employ drones for commercial surveying.
Afterward, Ignus began working for Basil Read Mining and their client Anglo American, developing his managerial skills further. During the same time, he also completed a Master’s degree in Engineering from the University of Witwatersrand.
In 2018, he joined Hall Core Drilling (Hall Core) and quickly ascended through the ranks. First, he was a Head of Production, then a General Manager and Operating Manager. As such, he helped turn the company into one of the biggest contractors in Africa.
In March 2023, Ignus became the COO of Hall Core Drilling and, in his words, aims to bridge the gap between the technical and commercial sectors of mining operations through the development of systems for analysis.
Grigor Topev: Hi Ignus, thanks for taking the time to do this interview. Let’s start at the beginning: why did you choose Geology for your university degree?
Ignus Storm: Despite my lifelong dream of studying medicine, circumstances led me down a different path, and I ended up studying Geology instead. However, my passion for physical science never wavered, and I found myself intrigued by the subject matter from the very beginning.
Interestingly, my father’s hobby of collecting rocks also played a role in fueling my fascination with geology. As I delved deeper into the subject, I found myself drawn to the practical applications of geology in the field of mining engineering. The operations aspect of mining in particular captivated me, and I ultimately decided to pursue a Master’s degree in mining engineering to further explore this interest. Although my career path ended up being quite different from what I initially envisioned, my love of science and the natural world remains at the core of everything I do.
GT: How did you start working at Hall Core Drilling?
IS: I joined Hall Core Drilling after being recruited from Basil Read Mining, where I served as a Technical Manager. Hall Core was searching for someone with experience in mining operations, specifically drilling, and they needed a candidate who could better understand and manage their drilling activities. They were looking for someone with experience working at a larger mining company and with a strong technical background.
My skills and experience matched their requirements, and I was offered the role. Since starting at Hall Core Drilling, I have been able to apply my technical knowledge and experience to oversee drilling
operations and ensure we execute the highest quality of work. My time at Basil Read Mining prepared me well for this role, and I have been able to use my expertise to make valuable contributions to the Hall Core team.
GT: What’s the Hall Core’s story? When was it founded? How has it developed over the years? What were the biggest projects ever completed?
IS: Hall Core was started by Kobus Halliday with a single drill rig in the early 2000s in the small South African town Brits. The current owners bought the business from Kobus in 2007 and set out to build a sustainable exploration business by establishing a solid track record and offering unique value-added services to their clients. The business has evolved over the years and today Hall Core makes use of some of the most advanced technology in our industry to enable the team to supply safe and relevant information to our clients in their drive to deliver services that reach ‘Beyond the Core’.
GT: One of the highlights of your time as Head of Production is a program for increasing drill bit life. Many have tried achieving an improvement, though few have succeded. Tell us more about the program. Was it related to R&D or to the selection of the most efficient drill bit (price to performance)? Also, could you give some tips and tricks to our readers?
IS: We improved the average bit life by about 20% from 2019. This was achieved purely by selecting the correct bits, which we accomplished through infield testing and desktop studies. Our research has led to understanding of the geology and most importantly drilling muds management. It is incredibly important that the correct chemicals are used, and drill cuttings need to be separated from drilling fluids before being pumped back down the hole. A large portion of the success in increasing bit life was incentivizing exceptional operational performance. We further embarked on a campaign to teach operators and drill crews about the benefit of increased bit life and increasing time on the face; drilling. We have also implemented spot incentives for drill crews that get exceptional life out of drill bits.
GT: You worked closely on a project with Anglo American in 2019. Please tell us more about their operations at that time.
IS: In 2019, this project was started with only 14 drill rigs at a platinum mine in Limpopo,
South Africa. This project is now by far the biggest Hall Core has been involved in. We currently operate 35 core drilling drill rigs with a team of about 250 people. Since the start of the project, four years ago, we have drilled more than 300 000 m (984 250 ft), of which 150 000 m (492 126 ft) were drilled in 2022 alone.
GT: I absolutely must ask: did you try to do some drilling while in the field?
challenges and negative aspects are you facing?
IS: Yes, we are incredibly excited about this innovation, a first in our industry. We are busy replacing the mechanical over hydraulic valves of the controls on our machines in the fleet with electric over hydraulic solenoid valves. The machine is then operated from a distance via a wireless remote. We have completely removed the operator from the line of fire. We initially converted one machine as a trial and after a year of testing, we have now started to convert the rest of our fleet. One machine a month at the premises of our development partners, who are experts in the field.
‘We improved the average bit life by about 20% from 2019. This was achieved purely by selecting the correct bits, which we accomplished through infield testing and desktop studies. Our research has led to understanding of the geology and most importantly drilling muds management. It is incredibly important that the correct chemicals are used, and drill cuttings need to be separated from drilling fluids before being pumped back down the hole.’
IS: Unfortunately, I did not. The mine operations have very strict rules regarding the operation of machinery if you are not qualified and permitted. I have operated machines outside these operations but limited to the most basic of functions.
GT: Another thing I noted is that you are currently implementing remote-controlled drilling operations. How’s that going, what rigs are you using, and what
GT: Please share with our readers more about the drilling industry/market in South Africa and Hall Core’s place in it.
IS: The current position of the mining industry in South Africa is heavily influenced by commodity price volatility due to a weak currency, which has a major impact on the funds available to the sub-industry. The industry’s instability is further exacerbated by social and community-related obligations. Increasing work stoppages, corruption, policy and regulatory uncertainty and the lack of investment incentives are further eroding the potential profitability of mining operations, which further influences exploration expenditure and new project development. With the substantial mineral endowment of South Africa, it is concerning that exploration expenditure is at the lowest levels observed in decades.
Hall Core Drilling finds itself in a very privileged position to be involved in projects on the scale at which we are currently operating.
GT: What are the most common challenges that drillers face when drilling in South Africa? What solutions does your crew come up with?
IS: I believe that drilling crews find it difficult to adapt to new technologies. Most of the drilling crews, and especially operators, are old guard and rather set in their ways. Introducing new technologies and ensuring that they are utilized correctly has been one of our biggest challenges. The first step is to get the buy-in from the direct supervisors and production managers and then rely on them to teach the crews on not only the use, but the inherent benefits these technologies could have for both the crew and their output. The on-boarding process takes time and patience, but if you persevere it can be done.
GT: Whenever we can, we ask about the record-breaking deep holes over 3500 m (11 483 ft) deep in Africa. Since you are from the younger generation, have you heard any stories about them? What is their role nowadays… are they part of the mostly forgotten industry lore, or do they serve as examples/teachings for the drillers?
IS: The deepest we have drilled since I have been involved was just over 1400 m (4593 ft). Not a lot of stories are shared, and I am not aware of any other contractors drilling that deep currently. Our biggest achievement thus far has been the drilling of over 150 km (93.2 mi) in just 12 months on our current project.
GT: Which are the leading core drilling companies in South Africa?
IS: I would say that Hall Core is currently the leading core drilling company in South Africa.
GT: What are the hot spots for drilling in South Africa?
IS: I would say that there is currently a lot of drilling taking place in the following areas:
• Limpopo on the Bushveld Complex primarily for PGMs;
• Northern Cape for Iron ore. There are talks of drilling for gas in the Northern Cape, as well as offshore, but to my knowledge, this is not so far advanced yet.
Other than the big projects in these two provinces, other projects would likely be very small in scale and scattered across South Africa.
GT: Which directional drilling methods are being employed in South Africa? What is your opinion of this drilling technique? What makes it practical?
IS: Hall Core currently only uses directional wedges. We have not really used downhole steering motors for our current projects.
GT: What is your definition of a good driller?
IS: A driller that consistently drills the scheduled meters. Consistency, day after day after day. One that shows no massive spikes in production days and then very poor days thereafter. They take care of the bits, manage their drilling fluids, maintain good housekeeping, and have their paperwork in order. Most importantly, a crew that makes safety
their priority almost always proves that the production output naturally follows.
GT: How do you approach training Hall Core’s staff? What problems have you identified and resolved during staff training?
IS: There is a lot of cross-pollination between employees, and we tend to train each other internally. Where OEM training or legal training is required, we utilize accredited training providers and our employees are trained and certified by them. We then have internal assessments to verify knowledge. Furthermore, the mine assesses the employees, too. There are quite a lot of checks before employees are certified to grab the controls of machinery.
GT: In the process of doing this interview, you became the COO of Hall Core. Congratulations! What is your vision for the company? What are your first tasks?
IS: As the newly appointed COO, my vision for Hall Core Drilling is to continue to build on our success and steer the company towards becoming the preferred diamond drilling contractor on the African continent, if not the world. Our aim is to grow in stature and
Trusted, proven, and precise. For generations, Boart Longyear has designed and manufactured some of the most advanced exploration products in the industry
Longyear diamond bits represent a long tradition of innovation and dedication to the drillers and geologists who rely on us every day. Find your local sales team online.
change people’s lives for the better wherever we work.
To achieve this vision, we will maintain the utmost regard for safety as a top priority, and we will continue to prioritize innovation at our core. Our goal is for Hall Core Drilling to be recognized as the most innovative, productive, and safe drilling contractor in the industry.
We will work tirelessly to stay at the forefront of the industry by embracing emerging technologies and techniques that can enhance our capabilities and allow us to provide better solutions for our clients. We will also invest in our people and provide them with the tools, training, and resources they need to excel in their roles and deliver exceptional results.
In short, my vision for Hall Core Drilling is to build on our strengths, prioritize safety and innovation, and become the contractor of choice for diamond drilling projects around the world.
GT: Now being COO, how does your dayto-day work change? Are there things that you need to learn/skills to develop?
IS: As the COO, my day-to-day work will largely remain focused on ensuring that our day-to-day operations are managed safely and efficiently. I will be responsible for overseeing various aspects of our business, including production, logistics, and quality control, among others. I will also work closely with other senior leaders within the company to develop and implement strategies that will help us achieve our goals and grow our business.
While I have extensive experience in the industry, there will undoubtedly be things that I need to learn and skills I need to develop in order to excel in this new role. However, I am excited about the new opportunities that this role presents, and I am eager to learn and grow in my new position.
One of the biggest challenges that I anticipate will be learning to delegate effectively. As the COO, I will need to rely on my team to help me manage various aspects of our business. This will require me to trust in their
abilities and provide them with the support and resources they need to succeed. I am confident that with time and practice, I will develop the skills I need to delegate effectively and lead our team to success.
GT: I noted on LinkedIn that you’ve stated that you aim to bridge the gap between the technical and commercial sectors of mining operations through the development of systems for analysis. What does this mean and how can companies turn this into reality?
IS: Bridging the gap between the technical and commercial sectors of mining operations means creating a more cohesive and integrated approach to mining. Often, the technical and commercial sectors of a mining operation work in silos, which can lead to inefficiencies, communication breakdowns, and missed opportunities. By developing systems for analysis, companies can bring these two sectors together and create a more holistic approach to mining operations. These systems for analysis could include tools and techniques for data collection, analysis, and reporting that allow technical and commercial teams to work together more effectively. For example, companies could develop software platforms that integrate data from various sources, such as geological models, production data, and financial data. This could allow technical and commercial teams to analyze this data together and make more informed decisions about mining operations.
To turn this vision into reality, companies will need to invest in technology, talent, and training. They will need to develop or acquire software platforms and data analysis tools that can integrate data from various sources. They will also need to hire or train personnel with the skills to work with these tools and analyze the data effectively. Additionally, companies will need to foster a culture of collaboration and communication between technical and commercial teams, encouraging them to work together and share information.
GT: Is there anything you’d like to see changed in the relationship between a drilling company and the Client?
IS: A few years ago, my first answer would have been more transparent communication and an increasing sense of collaboration. In recent years, there has been a significant drive from our clients to promote a collaborative and partnership-based relationship, which has changed the way we communicate. This has had considerable net positive impacts on our operations.
GT: What would you like to see improved or fixed, within the drilling industry in South Africa and the world in the next ten years?
IS: I believe the exploration sub-industry outside South Africa is quite healthy and an increase in expenditure can be observed over the past few years. The South African focus remains on social and economic development, but a clear method to achieve this is often not discussed. Globally, the relationships between tax incentives, economic development, capital, policy, and regulation are prominent. Research suggests that those countries realizing significant growth in the sub-industry understand what mechanisms are required to ensure the sustainability of the sub-industry. A clearly defined program to stimulate growth needs to be formulated. The government needs to work closely with the private sector to determine if the current proposed mechanisms will be sufficient to ensure the growth of the industry. Reform cannot be formulated in isolation from the government. Without the support of the private sector, the programs will not be successful. The exploration sub-industry is vital in ensuring the sustainability of the mining industry. South Africa should look to the countries where exploration is healthy and thriving to determine which mechanisms these countries rely on and then develop and focus on similar programs in South Africa. The development of policies and regulations that encourage investment must be ensured and implemented. C For more information Get in touch with Ignus on LinkedIn
The Christensen CT20 is ready to take on core-drilling jobs in the toughest conditions. This safe, ergonomic, and versatile rig is available truck- or crawler mounted. The Christensen CT20 has all the power and capacity needed to ensure you get more core in the box. Find out more at epiroc.com United. Inspired.
by Robert
Before we joined forces to create Team Drilling in June 2008, Al Lamy, George Presseault, Sylvain Brisson and Robert Fleming each had over 20 years of direct experience of working for major companies in the diamond drilling industry. Each of us had a vision to lead our own venture.
We were able to turn our vision into reality thanks to a strategic partnership with Athabasca Basin Development. Athabasca Basin Development is an indigenous-owned investment company committed to building and investing in successful businesses.
We based our headquarters in Saskatoon, Saskatchewan, Canada. Originally, one of the main goals was to provide an industry-leading underground and surface drilling service to the mining and exploration industry. We wanted to consistently exceed our clients’ expectations by building a strong team-based relationship, providing a safe and empowering workplace for our employees, adhering to the
Team Drilling’s management from left to right: Robert Fleming, Al Lamy, Glen Sigstad, George Presseault
‘We wanted to consistently exceed our clients’ expectations by building a strong team-based relationship, providing a safe and empowering workplace for our employees, adhering to the highest standards, continuously striving for excellence, and developing innovative solutions to deliver optimal performance.’
highest standards, continuously striving for excellence, and developing innovative solutions to deliver optimal performance.
In 2008, we were fortunate enough to be awarded with our first drilling contract shortly after our start-up. The company that gave us that opportunity was Hathor Exploration and the project called for one fly drill on their Northern Saskatchewan property.
The program proved to be successful, and we were requested to provide additional drills the following year. Team Drilling was off and running!
Within our first two years of operating, we had grown from that one drill to 14, including two underground rigs because in the spring of 2009, we were awarded our first underground project at Rio Tinto’s Diavik Diamond Mine. We are very proud to say that we are still providing our drilling services at the mine site 14 years later.
As Team Drilling continued to grow, Sylvain Brisson moved on to other endeavors. At that time, we made our first acquisition, purchasing the assets of Elite Drilling, based in Saskatchewan and owned by Glen Sigstad. Glen was brought in as a shareholder of Team Drilling and his extensive surface and underground drilling experience from various domestic and international projects is a valuable asset.
For Team Drilling, finding and implementing creative solutions forms part of our everyday operations. We are always challenging ourselves to improve on every aspect of our business. Whether it’s providing a better service, improving safety, or reducing our footprint on the environment, we are constantly questioning things. We listen to the ideas of our employees and when we do find a new solution, we put our successes behind us quickly to meet the next challenge. Equipment innovations and customizations have led to some big improvements in service.
Thus, Team Drilling continued to grow organically, increasing our drill count to 30. In 2021, we made another acquisition, that of Aggressive Drilling. This purchase increased our drill fleet to 40 drills.
In 2023, Team Drilling is celebrating its 15th anniversary of servicing the mining and exploration industry. We have provided our drilling services to clients in locations across Canada. Throughout the years, we have been recognized by many organizations, such as the Saskatchewan Chamber of Commerce with the ABEX Award for Best New Venture, and Team Drilling was listed as one of Saskatchewan’s Top 100 companies. We are also a proud member of the Canadian Diamond Drilling Association (CDDA).
Knowledge, experience, and achievements aren’t everything. We know that we are the strongest when we work as a team. That’s why we focus on building strong relationships with our clients based on honesty, integrity, respect, and open communication. We welcome feedback from our clients and employees, and we continually evolve and adapt to satisfy changing industry standards. A strong partnership is the key to not only meeting and exceeding expectations but delivering the best possible service.
The end result? A history of providing long-term safe and productive drilling services.
Our drills are customized to deliver the industry’s best surface, underground and specialty drilling, and our team gets the job done with
them in even the most challenging conditions. Lightweight and pow erful, our drills are modified to accommodate different sizes, depths, tracked-mounted, skid-mounted, flyable to drilling on a barge or fro zen bodies of water, and any other requirements for our client’s proj ects to deliver a safe and optimal performance. In all, the fleet con sists of the following rigs and equipment:
• 14 TD-1500 surface drills capable of depths to 1500 m (4921 ft) N-size;
• 10 A5 Zinex drills;
• 10 TD-2500 surface drills capable of depths of up to 2500 m (8202 ft) N-size;
• 5 TD-1500 underground drills;
• 1 HC 2000 Hydracore drill;
• 80 pieces of mobile equipment consisting of skidders, dozers, loaders, and snowcats to facilitate drill moves and trail access.
Since 2008, Team Drilling has provided industry-leading drilling ser vices to some of the best companies in the mining and exploration industries. Each team brings over 100 years of drilling experience to every project. Each one of us is focused on providing a safe and em powering workplace for our employees, continually striving for excel lence, and developing innovative practices and solutions that adapt to the industry’s changing demands. Because of these unceasing efforts, Team Drilling has the reputation for drilling excellence and consistent results that exceed our clients’ expectations.
Team Drilling has successfully undertaken many diverse and special ized drilling projects:
• Underground specialized core drilling techniques to overcome high water pressure;
• Core drilling from B- to P-size core and depths to 2200 m (7218 ft);
• Directional drilling utilizing wedging, mud motor, Devico and Aziwell directional core barrels;
• Drilling off barges and frozen bodies of water;
• Small reverse drilling sampling.
↑ A happy drill assistant working in a heated core/rod sloop in Northern Saskatchewan
Additionally, as a result of our success, Team Drilling has been awarded other freeze-hole drilling projects for other clients.
Team Drilling has undertaken many interesting projects over the 15 years of our operations. Most notable would be Cameco’s Cigar Lake Freeze Hole project.
Team Drilling was awarded this project in 2011. At the peak of the drilling, our team had five drills operating. We continue working on this project (our second longest-running project) having completed over 1200 freeze-holes.
The challenges our team faced on this project were various. Probably the biggest was that the team had to maintain a hole target of 2 m (6.56 ft) from vertical P-sized holes to a depth of 461 m (1512 ft).
To keep the drill holes on target, we utilized directional drilling techniques with a 4.75 ft (1.45 m) mud motor and in-hole retrievable wedges. Overall, the project was a huge success and continues to be.
Another challenging project wasn’t so much related to the drilling, but the mobilization, support, and demobilization of the job. The challenge was to access the project area, which was 180 km (112 mi) away in the wilderness. Trails and ice roads needed to be made and maintained to support the drilling campaign.
Winter was the only time that the area could be reached since numerous lakes had to have ice roads made safely in order to mobilize all the drilling and support equipment for the client. Needless to say, lake ice had to have sufficient thickness to safely move the equipment. This meant constant GPR (ground penetration radar) readings, ice building, and plowing 180 km (112 mi) of snow. A one-way trip with a skidder and load of equipment would take upwards of 22 hours. Bunkhouses were placed along the trail, enabling the crews to have a place to eat and sleep.
The underground projects we tackle are challenging as well. Our current projects require ‘hole security’, meaning we are drilling into high water pressurized zones. The drills are outfitted with hole collar security, which includes Blowout preventers, HD gate valves and Rot-packs. We use a quad latch coring system for core retrieval in high-pressure zones and utilizing a Kelly valve system to safely retrieve the core.
As a result of our success on these jobs, we have been awarded additional long-term projects.
Our Number One priority is making sure all members of our team go home safely to their families! We have a responsibility to every team member - our employees, contractors, clients and shareholders - to proactively work on strengthening safety.
We believe safety starts with the people who make up our team. Fostering and encouraging a culture, where safety is a part of every process, is paramount to achieving a zero-incidence record. We also believe that investing in training for our employees keeps everyone safe. A single investment per team member isn’t enough, though. To keep everyone sharp, we provide annual safety refresher course updates for our supervisors and field crews.
Recognizing the need for a standardized safety and management program, Team Drilling is D.E.C (Driller Excellence Certification) certified. We worked closely with MiHR providing input into their development of the National Occupational Standards. Additionally, Team Drilling was the first diamond drilling company in Saskatchewan to have signed with the Saskatchewan Health and Safety Leadership Charter and pledged to accept and encourage Mission: ZERO - a pledge to support the principle that nothing is more important than the health, safety and well-being of employees, contractors, clients, visitors, and whenever possible the surrounding community. On top of that, we have received numerous safety awards from AMEBC, CDDA and our clients for outstanding safety records.
Our company strives to ensure our drilling and ancillary equipment is state of the art. We are committed to outfitting our drills with rod handlers, ergonomic work areas, such as enclosed road sloops with core tables and vices, to assist the helpers in performing their duties without excessive bending, and complete guarding of all rotating parts and interlock systems on the guards.
As proof of this philosophy, Team Drilling is proud to say that we have worked 2960 days without a Lost Time Injury.
In addition to the yearly safety refresher courses, Team Drilling actively provides training for northern residents. The goal of the course is to prepare participants for potential upcoming jobs in the drilling industry. Each year, Team Drilling conducts two to four training courses, with up to five people per course.
We organize these courses because Team Drilling recognizes that most of the work that we are involved in is located on indigenous traditional lands, therefore the focus on recruitment is from these communities. We have had great success with these courses.
Team Drilling recognizes the importance of working closely with Indigenous communities that are impacted by the work that we do. We have formed numerous partnerships and joint ventures within indigenous regions. Most recently, we have signed a partnership with Clearwater River Dene Nation providing many opportunities for local employment and giving back to the communities.
Being that Athabasca Basin Development is a shareholder and represents seven communities in Northern Saskatchewan, we are proud that our efforts are invested back into these communities.
Team Drilling has provided drilling services to major and junior mining companies. No job is too big or small for us. We have drilled every ground condition and formation out there and we have successfully completed projects for:
• Hathor Resources’ Roughrider project (uranium);
• Shore Gold (diamonds);
• DeBeers (diamonds);
• Rio Tinto Exploration (diamonds and uranium);
• Diavik Diamond Mines;
• Ekati Diamond Mines;
• IOC / Rio Tinto (iron Ore);
• Forum Energy (base metals);
• Alamos Gold;
• Argonaut Gold;
• Fortune Bay Resources (gold/ uranium);
• Evolution Mining (gold);
• SSR Mining (gold);
• Teck Resources (coal and copper);
• Cameco (uranium);
• Orano (uranium);
• NexGen Energy (uranium);
• Denison Mines (uranium);
• Nutrien (Potash).
With an emphasis on reducing our carbon footprint, we see a bright future for the diamond drilling industry. The need to explore and find new mineral resources will continue to be ongoing. Exploring for minerals that provide a ‘greener’ impact on our daily lives will continue to be strong.
Team Drilling has aligned itself on a number of long-term contracts with our clients that our actively exploring for those alternative resources both from the surface and underground. C
One tiny gyro. Many great solutions.
Whether it’s diamond or RC drilling, mining or civil, the DeviGyro has a setup to suit your requirements.
Available in a range of ultra robust, purpose-built running gear configurations, the miniature rate gyro helps you to maximise accuracy and productivity no matter the application.
Now with a step-by-step guided app-flow, surveying with the DeviGyro has never been easier.
by MBI Global
MBI Global unveiled its VersaDrill autonomous drill rig to the world during PDAC 2023. The KmN autonomous drill is the product of years of research and development, testing, and perfecting.
The mining industry is beset by challenges. Labor shortages, skyrocketing operating and material costs, and safety requirements demand constant innovation. Automation is the key.
This is why MBI Global’s exploration drilling segment, opted to increasingly turn towards automation technologies to tackle the challenges of today and tomorrow.
The KmN rig comes with a set of distinct advantages and offers surprising results in terms of performance, safety, and time and money saved.
The autonomous KmN rigs come packed with many game-changing features improving driller safety and protecting the operators, such as:
• an optical guard;
• an inner tube puller;
• pressure and safety control;
• a direct communication tool that allows the underground driller to communicate with the surface team if the mining operation has LTE communication capacities.
Other autonomous features, which drastically improve safety, are:
• the automated thread breaking/making;
• the opportunity for the rig to operate while using rod handlers with an optical safety device;
• automated wireline ascend and descend functions.
Thanks to these functions, the autonomous KmN rig only requires one operator. During shift changes, the drill can automatically complete a 3 m (9.84 ft) run without any supervision. This enables complete 24/7 non-stop operation, saving time, money and improving productivity.
Each drill has a fully electronic interface with a 10-inch, touchscreen color display. Alongside the controls, it can be placed away from the ‘line of fire’, while still providing complete, clear, and easy-to-understand information. Even at a glance. Additionally, thanks to the drill’s connectivity, all data can be shared and monitored remotely, allow-
ing for adjustments to be made during operation and reducing costly equipment changes.
The many features and improvements of the automated KmN drill rig do not sacrifice performance. KmN rigs are available in three configurations.
The standard KmN 1.4UA configuration has a 125 hp, 1750 RPM engine. It is equipped with a 26 000 lb (116 kN) pull mast with 66 in (1.68 m) feed stroke. KmN 1.4UA is capable of drilling up to:
• 6391 ft (1948 m) B-size;
• 5014 ft (1528 m) N-size;
• 3372 ft (1028 m) H-size;
• 2228 ft (679 m) P-size.
The KmN 2.0UA configuration comes with a feed cylinder increase to 37 000 lb (165 kN) of pullback force. This in turn results in capabilities of up to:
• 9095 ft (2772 m) B-size;
• 7135 ft (2175 m) N-size;
• 4798 ft (1462 m) H-size;
• 3171 ft (967 m) P-size.
The third configuration, KmN 2.5UA, comes with higher main feed frame and feed cylinder increase. The pullback force jumps to 45 000 lb (200 kN) and 4500 psi working pressure (both KmN 1.4UA and 2.0UA come with 4100 psi). Consequently, KmN 2.5UA has a higher depth capacity over the other two configurations:
• 8678 ft (2645 m) N-size;
• 5835 ft (1779 m) H-size;
• 3857 ft (1176 m) P-size.
‘By distributing ASDR’s technology, MBI Global is positioning itself as a pioneer in sustainable applications for mining exploration with solutions that easily integrate with drilling equipment and meet the strictest of environmental standards,’ stated Daniel Misiano, President of MBI Global.
All three configurations have additional customization options to fit and exceed the requirements of drillers. The KmN rig is now a part of MBI Global’s strong product line and is available to everyone, everywhere.
Days before PDAC 2023, MBI Global announced its partnership with ASDR Canada Inc., a company specializing in water treatment for the mining industry.
The partnership allows MBI Global to distribute ASDR’s ECOMUD technology, further expanding its vast product range. ECOMUD is synonymous with the efficient management of mud and water, including effective water recirculation and sludge dewatering, which increases the efficiency of operations while reducing their carbon footprint.
With 50 years of combined experience in the mining industry, the two companies are leveraging their strengths to offer even more innovative solutions for the current environmental concerns and the need for sustainable development.
‘By distributing ASDR’s technology, MBI Global is positioning itself as a pioneer in sustainable applications for mining exploration with solutions that easily integrate with drilling equipment and meet the strictest of environmental standards,’ stated Daniel Misiano, President of MBI Global.
MBI Global provides quality products and services for the drilling and mining industry. With offices in Rouyn-Noranda, Val-d’Or, Saskatoon, Lima (Peru) and Santiago (Chile), as well as an international network of distributors, MBI Global serves over 30 countries. The company relies on a solid partnership with manufacturers and distributors working together for the strongest products and services. C
For more information Visit: www.mbiglobal.ca www.asdr.ca
OOur company, Ranger Exploration Drilling (Ranger), partnered with two Western Australian businesses to innovate on drill rig design and manufacture through the inclusion of technologies being applied across the mining industry.
by Stuart Baird, General Manager at Ranger Exploration Drilling Pty Ltd
ur company holds progressive attitudes and values to improvement on work practices, and equipment as on all our key values. Seeing the development of equipment, particularly automation in mining as well as general equipment, increased our curiosity in this area.
A reverse circulation drill was the target, with a reduction of human input into the operation of the machine. Our partners in the project, Western Drill Maintenance and Compliance (WDM) and Cortex Intelligence Systems (Cortex) have built significant expertise in this area through previous experience and projects. So, as expected, they stepped up to the plate and took on the challenge.
WDM took on the mechanical engineering and build of the machine, with Cortex developing the control systems. We had previously developed, in partnership with Cortex, MDP system that is fitted onto our rigs. The MDP is made up of Monitor While Drilling (MWD) equipment, as well as systems that provide remote monitoring of equipment on a live basis. We run dashboards in our head office where we can see the status of all rigs, production statistics, hole depths and activities (amongst other things). From this system, the development of automation onto the drill became a natural progression.
Thus, the design brief was to utilize automated control, where possible, to improve the operating reliability, consistency and reduce the need for human input into repetitive operating tasks.
The result is an RC drill rig with the ability to set itself up on angle, handle single and multiple rod handling cycles, with additional functionality available to fully automate as the programming maturity develops – including RC bit changes, sampling and eventually auto drilling.
Whilst automation has been incorporated into exploration machines by other businesses, WDM and Cortex are among the first (that we are aware of) to commercialize an exploration machine of this nature.
The base design was approached to enable the retro fitment of the automated components to a range of currently available RC machines.
The rigs are capable of remote monitoring, including cameras for eyes on the task. The Cortex MDP systems are fitted to capture the operating parameters of the machine including, but not limited to:
• head position;
• feed rate;
• time drilling;
• time rod handling;
• hole depth, rod count;
• daily meter production;
• rotation speed and torque;
• holdback/pulldown pressure.
Once the first drill design and manufacture were completed, we hit a quarry near Perth, Australia, for field testing. The testing program went well, there were issues, but mainly with some programming and communication dropouts. These were quickly identified and rectified. The rig structure and functions performed well, with no major rework required. The machine spent around three weeks in the quarry before mobilization to a contract and an operating site.
On-site work presented a few more development challenges. We were fortunate to locate the rig at a site where mobile network communications (3G/4G) were available, making it easier for the tech team to remote into the control systems for monitoring and to update things as required. The learning curve for our drillers was the most interesting. They picked up the operating system of the machine very well – certainly, there were some challenges, frustrations and long phone calls, but to their credit, they hung in there and spent time understanding stuff they haven’t dealt with before.
Automation is a funny thing. From my perspective, it all depends on what I call ‘knowing’. If an autonomous device knows where it is, it knows where everything else is. Therefore, it knows where it needs
to go... makes sense? A couple of early learning frustrations for the drillers related to things shifting slightly out of adjustment or home position, meant the machine wouldn’t move, as it couldn’t confirm the location of something. The drillers adapted well once they understood some of the basic principles and were able to assist the technicians, who were remoting into the drill.
Aside from highlighting the efforts of our drillers, the client was a great support. Any innovation comes with risk – safety, production and so on. Without clients like ours, these projects would never get off the ground. Our client was willing to support through input, assistance and bear the costs for low production and testing during the early times. I suppose ultimately, they see the long-term benefits and will reap those rewards as they manifest.
The automated functions have seen improvements in the following tasks/areas:
• manning on the machine has been reduced as rod handling now only requires the driller;
• sampling duties have become more fluent, as no rod handling operations are carried out by the offsiders;
• the consistency and fluency of the rod handling equipment reduces wear of components – the machine is a smoother operator than a person;
• damage through poor operating practices has been reduced.
Prior to field testing, Ranger reached out to some of our key drillers – people we knew had the motivation to challenge themselves and have a go with this type of equipment. It is funny, at first, they were all a bit stand offish. Roll forward a bit of time and they have adjusted well and enjoy operating a little further away from the machine. Some of them bring their ‘tunes’ to work now and place their personal speakers on the control module for entertainment.
The improvements listed above are the obvious ones. We are seeing other benefits to our staff – no more standing next to the drill hole
area with its dust, noise and potential for projectiles. The vibration emanating from the drill stands is gone – people are more alert and less fatigued
We have two of these machines operating in the field, with a third under build. For those who would question reliability and productivity, the following metrics have been taken year-to-date (YTD) against rigs operating under the same contracts, same geology and region: Not a lot of difference, and in some cases an improvement.
Model WDMES270
Rig Type Exploration – RC
Control System
Ranger Exploration Drilling is one of the operating brands of DDH1 Limited. The business specializes in the Pilbara region of Western Australia, with iron ore as our favorite geology. The business currently has 22 operating rigs, with 17 RC drills and five diamond drills. We currently employ in the vicinity of 190 people and have been operating for 17 years. C
Visit: www.rangerdrilling.com.au www.wdmdrillmaintenance.com www.cortexintelligence.com.au
Forage Fusion Drilling and Warkentin Fabricating
battle the Canadian wilderness
by Michael MacTavish, Owner at Forage Fusion Drilling and Jordy Warkentin, Owner at Warkentin Fabricating
Our company Forage Fusion Drilling was first invited to bid in the fall of 2020 for a 1000 m (3281 ft) N-size lithium drill program for Patriot Battery Metals in their Corvette Property in James Bay, Québec, Canada. Lithium really seems to be the go-to commodity in the world right now.
In the years since winning the contract, our work has grown tremendously. Currently, we have 55 active employees on-site, and come summer, we should be ramping up and expect to have around 70 people with an increased number of active drills. The team comes from all over Canada – east to west, and it is tackling several different tasks to meet and exceed the requirements of our clients.
We have faced several challenges on this project. One of the most significant was the 27 km (16.78 mi) winter road access in 2023, we had to do bridge installations, and we had to do heli-portable barge work in 2022, while drilling on very shallow lake/river systems doing 45°-angled holes. None of these challenges were too big for our team, as the crew is well-experienced, and the guys are always looking for a new challenge. So far, everything they have been asked to do, they have accomplished. As a company, we wouldn’t be where we are today without them. We must take our hats off to the guys on the ground.
We have a fleet of MPP Discovery drills from British Columbia, Canada, and along with Odyssey Fluid Power of North Bay, Ontario, we were able to modify them to our specifications. Our Discovery drills can reach a depth of 800 m (2625 ft) N-size, which is far more power than the project requires. They remain as light as possible, which is particularly important while drilling in 2-3 ft (0.6–0.91 m)
of water, and helicopter hole-to-hole moves are required.
The Discovery drills really shined.
Our barge was designed by one of our operation managers, who had come up with the idea after drilling a winter program. He knew that the client needed to get the information from what was lying under the lake. A road at the time wasn’t worth it because the site was still in the early exploration stage. That’s why he came up with the idea and proposed it to the client.
At first, it seemed a bit crazy, but after putting the numbers and doing some calculations on paper, it made sense. And since the client really wanted them holes drilled, we drew up the plan.
That’s when we contacted Warkentin Fabricating in Harrow in South-Western Ontario and we sat down with Jordy Warkentin, the owner, and his team and came up with a course of action. They were going to manufacture a 35-section barge, made out of Canadian-sourced steel, with each section weighing less than 2000 lb (907 kg). Each of these sections would be able to be flown in by a helicopter, and together, they would be stable enough to support the drilling team. Then, Warkentin’s team got to work.
After Jordy and his team were done, we hauled the equipment to James Bay, where we assembled the barge a few times, while making minor adjustments to ensure that the team on the ground didn’t have too much trouble putting this all together, which was going to be a difficult task either way.
Once satisfied, we flew the barge to the site via an Airbus Astar B2 helicopter. It took over a week to reach
↑ Inside frame work for 35 sections, each to not exceed 2000 lb (907 kg) when complete
the drill site, because of the weather. The assembly was much faster, thanks to our preparation. It took two men in wetsuits and a 12-hour workday, as the 35 squares didn’t really float too well. In the end, the men got it done and by the next day, we were welding spud pockets and slinging the drill into position.
There was a big risk involved in this approach, as drilling in very shallow lakes/rivers can be very challenging - boulders and current can be your worst enemy while trying to line up a rig on a 45°-angle. However, this barge approach worked out and we were able to drill off several holes to an average depth of 400 m (1312 ft).
Forage Fusion Drilling is a company owned and operated by Michael MacTavish. We specialize in heli-portable/skid/limited access drilling. We strive for challenges and as in this project, we achieve them with safety being one of our top priorities. For all inquiries, please call 613-632-0120 or email mike@foragefusiondrilling.com
Warkentin Fabricating commenced as marine contractors and organically started building barges that were needed for the company’s own projects. This turned into an entirely new business plan and department of building barges for projects across the world. The company is quickly becoming a household name in the barge industry and intends to continue its aggressive plan for growth in the coming years. The company offers barges of all sizes, with many customizable options and prides itself on building the barge that has best suited Forage Fusion’s needs, which is demonstrated in the 35-piece project with them.
For barge pricing and inquiries: call 519-992-0639 or email warfabsales@gmail.com. C ↑ Final material drop for on-water assembly
↑ The successful collaboration of the Forage Fusion and Warkentin Fabricating teams hard work is shown in action, drilling to a depth of 400m (1312.34 ft)
Helicopter Portable Diamond Drill
1400 Meter NWL Depth Capacity
Cummins Power Unit 160 or 260 HP
‘P’ Size Rotation Unit & Clamp
Safety Package: Full Guarding, Multiple E-Stops, Interlock Rod Guard & Power Lock-Out
Available in Heli-Portable, Skid Shack Mounted and Track Carrier
Setting records while adhering to strict environmental regulations
by Cory Ibbotson, Director at Alton Drilling
Alton Drilling (Alton) is a New Zealand-based drilling company, and we are making a name for ourselves by embracing innovation and versatility in our approach to drilling and rig manufacturing. We are committed to delivering customized solutions for clients with complex drilling needs, including heli-portable rigs for remote and hard-to-reach locations, as well as drilling in sensitive environments.
Our partnership with OceanaGold started when we were tasked to supply drilling services and expertise to the Wharekirauponga (WKP) project. This got some serious legs in 2015, and our work continues to this day. Primarily the project is based on a two-week on, one-week off roster with our exploration team accommodated in our Alton Drilling-built and serviced heli-camp and facilities with all day-to-day supplies and consumables flown in when weather permits. We are excited to be a part of the underground target and the challenges it brings.
The WKP project is situated within the Coromandel region on the northeast coast of the North Island. The project has varied terrain and environment, characterized by rugged mountains, steep valleys, and dense native forests and is beneath a forest park administered by New Zealand’s Department of Conservation. The prospect hosts a high-grade epithermal gold/silver deposit. It is planned to access the deposit by tunneling in from OceanaGold-owned land, therefore minimizing any impact on flora and fauna.
The operational areas must be no larger than 150 m2 (492 ft2) - sites are only granted in areas after extensive site ecological surveys to mitigate impacts to a range of flora and fauna and particularly to locate and avoid any native frogs. Thus, all drilling and other equipment is installed by a helicopter onto large, raised platforms built above ground usually from 8 x 8 in- and 6 x 2 in-timber. This allows us to work with the undulating ground and gives the luxury to recycle; that together limits our impact.
Many of our clients now have a no-dig policy due to environmental regulations, meaning that sumps are no longer an option for water retention and reticulation. To assist with keeping our drilling footprint as minimal as possible, we are developing new systems with our Solid Recovery Units (SRUs) and running multiple-stage pump systems for remote high-altitude sites.
Another recent challenge was to extract water samples at depth. There was nothing on the world market, so our team set to and designed and manufactured an overshot water sampler tool for both H-size and N-size. This tool runs on conventional wireline drilling equipment and provides uncontaminated water samples to be extracted at specified depths for geochemical analysis. We have settled on the modified heli-portable SC11 drill rigs for their small footprint. We opted for these rigs because they have the ability to drill up to P-size, can drill at low angle mast setups to -20° off horizontal and have rod handling capability.
Our hole depths are achieved through careful planning and mitigation of the day-to-day challenges. P-size is used to case off the top several hundred meters, while target depths are then achieved with H-size. This is due to the unexpected nature and ground conditions in New Zealand. It is not uncommon to run PWT casing down to depths of 60–100 m (197–328 ft). All drilling is orientated triple tube drilling. With this in mind, a recent company milestone was achieved when Rig 82 SC11 completed a heli-supported exploration hole, drilling over 1308 m (4291 ft) at -20° angle from a timber platform, utilizing pumpup equipment and a heli-portable SRU for solids recovery.
Another success on the WKP project was the completion of a sizeable heli-supported geotech program where one of the holes was drilled to 458 m (1503 ft) at -25 degrees and five vibrating wire piezometers were installed then fully stage grouted to the surface.
Established in 1983, Alton Drilling is a proudly Kiwi-owned and operated company. We provide quality, professional service with a friendly business approach. Continual research and using and developing the latest drilling equipment and technology, combined with a wide range of experience, Alton Drilling is at the forefront both in New Zealand and globally.
Alton Drilling’s rig manufacturing business is built with the same values. The company’s rigs are designed to be modular and portable,
with minimal electronics, highly interchangeable parts, and the ability to be broken down into components weighing no more than 500 kg (1102 lb). This allows exploration in previously unreachable zones.
Alton Drilling’s commitment to innovation and versatility is reflected in the success of the company’s operations. The company’s rigs have been sold globally, and they continue to build on their turn-key packages including new rigs, downhole consumables, muds, supply pumps, rig spare parts, hyd motors, concept to design and more. With their ongoing investment in people, infrastructure, and stock levels, Alton Drilling is well-positioned to meet the increasing demand for exploration and geotechnical drilling both surface and underground. C
For more information
Visit: www.altondrilling.co.nz or call: +64 508 425 866
↓ Drilling on a heli-portable supported site from a wooden platform setup on a -20 degree angle has its own challeneges. Our Waihi surface crew also were faced with testing ground conditions. A great team effort for successfully reaching a depth of 1308 m (4291 ft) exceeding expectations.
↑ Rig 82 setup on a low angle and positioned on the 12 x 12m-timber platform keeping everything contained within the operational parameters. The site is careful selected to minimize any tree disturbance, native trees and step terrain surround the site.
Drillers Edge drill rods by Di-Corp are earning a global reputation for reliable, long-lasting performance under some of the most challenging conditions.
What makes Drillers Edge drill rods different? Our choice of premium quality steel. Our approach to stress relieving heat treatments, precision machining, intense quality controls, and the unique, specialty finishing process we use to harden our R™ Thread for unmatched pull-back strength.
All these differences help Drillers Edge to produce premium coring rods that deliver:
• More even pin and box wear.
• Better deviated drilling performance.
• Superior drill string life.
1.800.661.2792 info@di-corp.com
by Dag Billger, Owner & Business Manager and Duncan McLeod, Owner & Product Manager at Inertial Sensing One AB
Downhole survey instruments rely on a range of sensors to produce data that gives position information about a borehole. One class of sensors that has undergone rapid change over recent years are MEMS gyros and inclinometers. In the last decade, these have gone from single- and dual-axis systems on a large chip to very small multi-axis, multi-sensor components. These components often include a basic calibration and a basic ‘navigation engine’ that can directly output the heading angles of the system. The natural temptation is to exploit this technology to create a survey gyro. In fact, several such tools have appeared on the market in recent years, but things are not as simple as they seem. These micro IMUs have an ‘off-the-shelf’ navigation performance adequate for simple consumer-grade applications but fall short of the requirements for precision borehole navigation over any significant distance.
Indeed, it is the miniaturization of these components that led to the launch of Inertial Sensing’s 21.6 mm (0.85 in) diameter SlimGyro in January 2015. During the course of the SlimGyro development, it was quickly discovered that the built-in calibration and navigation algorithms could not satisfy the demands of borehole surveying. In parallel with the growing convenience of the miniaturized components, it was necessary to continuously develop and refine the calibration and navigation theory and algorithms. It is clear that a precision survey instrument must be founded on a triad of (1) detailed knowledge of the sensors down to the raw signal behavior, (2) navigation algorithms founded in mathematics and physics, and (3) precision calibration and alignment.
This article outlines the impact on survey results in the absence of proper precision
calibration. The aim is to illustrate that, despite the proliferation of easy-to-use miniature components, rigorous individual component calibration is still paramount for obtaining reliable and accurate results.
All sensors tend to have a change of output as the tool temperature changes, for the same input. For instance, a gyro may measure 10.0ᵒ/s at 20ᵒC, but 10.1ᵒ/s at 25ᵒC for the same turn rate. These small variations have a major impact on the survey results. A calibration of each individual sensor’s response to temperature is required, for both gyros and inclinometers, if precise and repeatable results are to be obtained in the
field. This requires sophisticated calibration equipment to rotate and orient the sensors while also setting and maintaining numerous constant temperatures over a required temperature operating range. Multiple temperature test cycles are needed to validate the statistical confidence necessary to qualify or discard a sensor component from use in a system to be delivered.
A compact MEMS sensor component is typically comprised of three gyro axes and three inclinometer axes. These are manufactured ‘on the chip’ to be perpendicular to each other, but in practice, there is a wide variation from chip to chip. The variations are between the three gyro axes as a group and the three inclinometer axes as a group, but also as a
variation between the triads formed by the gyros and by the inclinometers. Computing and compensating for these small misalignments is a critical stage of calibration to avoid skewed results.
What happens if a proper calibration of the IMU component is not performed, or is done inadequately? This is the same as relying on the default ‘factory’ calibrations from the manufacturer. These are usually linear temperature models that are approximately good for an entire class of mass-produced sensor components. Since they are produced in the tens of millions, there is no way that the manufacturer can conduct individual and exact calibration of every individual axis in an IMU. The system alignment is also approximate and assumes that the manufacturing process produces sensor axes that are sufficiently perpendicular. The typical variations are usually noted in the data sheets, with wording like ‘variation of scale factor over temperature’ of 3%, or a ‘cross-axis sensitivity’ of 2%.
A basic improvement to the factory temperature calibration would be to measure the gyro and inclinometer response at room temperature and obtain a gross correction. This shows better performance when the survey tool is tested near room temperature, but quickly degrades as the tool is warmed or cooled in a borehole.
A simple correction to the alignment is to roll the survey tool about its long axis to get a better fix on where the sensors are pointing. But this is insufficient to properly align all the axes and to align the gyros with the inclinometers. Such a gross correction may help in standard situations where the tool is in an inclined borehole and not subject to rotation. But with typical in-hole rotations and/or coming near a vertical section, errors quickly blow up to unacceptable levels.
All of the above can be rigorously proven mathematically but is far beyond the scope of this article. By using a real survey that exemplifies these effects it can be shown just how bad the problems can be. All of Inertial Sensing’s gyro systems maintain a record of raw sensor data. This means complete access to the unadulterated sensor signals at very high data rates for every survey. It is there-
fore possible to take surveyed data from any of Inertial Sensing’s gyros and reprocess this under the conditions of interest here.
The surveyed hole used as an example is nearly 1900 m (6234 ft) in depth, begins at a near-vertical inclination of -89.5ᵒ, builds about 2ᵒ of inclination at 700 m (2297 ft), and then rapidly built to -78ᵒ inclination over approximately 100 m (328 ft). The azimuth holds at about 240ᵒ in the vertical section and is steered to about 340ᵒ in the inclined section. The surveying was done in late-2022 using a GoGyro in fast continuous surveying mode, with data output processed using 3 m (9.84 ft) station intervals.
The initial data is processed with the normal high-precision calibration that is standard in all Inertial Sensing gyro models, using full temperature calibration and alignment. The resulting azimuths and inclinations are shown in green in Figures 1 and 2 respectively.
By disabling the full alignment calibration for the GoGyro and relying on the manufacturer’s tolerances the results shown in orange are obtained. This reveals the tell-tale of a
poor alignment: strong ‘oscillations’ in the angles due to the coning of the sensing axes around the instrument’s physical axis as the tool rolls going down the hole. Each oscillation corresponds to one roll of the tool. In this case, the error caused by the oscillation is about 1ᵒ in the inclination and 5ᵒ in the azimuth! The nature of inertial navigation means that an alignment error of a fraction of a degree can blow up to several degrees in the results. A naive approach would be to try to improve these results by smoothing these oscillations, but this also seriously degrades the results, grossly blunting any true turning and biasing the survey angles. On top of this, the fractional misalignment error means that a very significant error of 12ᵒ is picked up in the azimuth as it passes near or through vertical. This is mathematically unavoidable. In inclined or horizontal holes, the effect becomes a decreased sensitivity to turns, leading to unusually ‘flattened’ borehole profiles.
Next, the precise temperature calibration is removed, entirely falling back on the manufacturer’s bulk calibration. The effects are shown in Figures 1 and 2 in blue. This adds an additional 9ᵒ of error in the azimuth and
1ᵒ to 2ᵒ in the inclination. Detailed analysis shows that there is also a drift of the results as the temperature changes. Another naive mitigation strategy is to enforce roll on the tool as it traverses the hole to spread the angle error around an ‘average’ value. However, this will in general still be biased and worse, feeds straight back into the misalignment oscillations.
The effect on the final position of the hole is dramatic. Figure 3 shows the coordinates of the borehole reconstructed with standard minimum curvature calculations. The misalignment effect causes an error in the final hole position of ~50 m – or ~164 ft - (2.6% of depth) while the poor temperature calibration adds another ~40 m (~131 ft) for a total of 90 m (295 ft) in error (4.7% of depth).
In recent years, the proliferation of compact inertial measurement units comprising triads of gyro and inclinometer sensors has led to the possibility of making survey instruments without the apparent need for high-precision calibrations. However, by doing so the results from borehole surveys are seriously degraded. Unavoidable problems with uncontrolled oscillations, drift and biases due to inadequate temperature calibration and alignment are introduced.
Attempts to mitigate these problems by using ad-hoc filters on already processed survey angles destroy the detailed profile of the borehole or give unexplainable variations. These attempts smooth and flatten the borehole profile, making it appear more acceptable and severely reducing the dogleg severity. False confidence in the results is created. The final error profile can be grossly affected, being as much as several percent of hole depth.
While each new generation of miniaturized sensor packages brings advantages in instrument design, a proper high-precision calibration in temperature and alignment for each individual tool is absolutely required for precise and reliable survey results.
This is part 1 of a 2-part series. In the next article, we discuss more specific calibration effects. C
Safety is the challenge, CX Line is the answer. Compact design, hands-free rod handling system for fully automated and remote controlled operations: the future of exploration drilling is already here. Are you ready to join in?
In this Issue:
Q&A from the experts In conversation with David Rhys Consulting Geologist at Panterra Geoservices
Power of the Microscope by Paul Ashley, Principal at Paul Ashley Petrographic and Geological Services
The call of the wild by Hugo Serra, Project Geologist
The traps and pitfalls to be aware of when releasing exploration results by Ivy Chen, Director and Principal at GeoReg Mining & Compliance
Drilling under the northern lights by Ashleigh Ball
David Rhys Consulting Geologist at Panterra Geoservices
David Rhys is a Consulting Geologist based in Vancouver, Canada, who applies geological studies with a structural focus to exploration, development and mining. Dave has extensive experience in many deposit types, and especially gold deposits, having worked globally for a variety of clients including both major and junior companies. His focus is on advanced projects and active mining operations, aiding in the interpretation of mine site ore controls and applications of mine geology to local and district scale exploration activities, and training of geological teams. He is an advisor to several companies.
Brett Davis: Firstly, thanks for giving Coring the opportunity to interview you, Dave. Very few people have a career like yours, where you’ve worked across the spheres of academia, mining, and exploration, plus gained enormous respect in the geological community while you’ve been doing it. Can you tell us what interested you in a career in geology?
David Rhys: Thanks for having me, Brett, it’s an honor to be invited to contribute to this column. I grew up in Vancouver, Canada, where the wilderness and mountains begin at the city’s edge. That’s how I was able to see first-hand the effects of geological processes during outdoor trips from a young age. Geology became a career I worked towards early on, especially with the influence of the government geological surveys and the mining industry based in Vancouver at the time.
BD: Coring started as a drilling magazine, and we like to keep to our roots. So, I’ll ask you a drilling-related question. Do you do much work with oriented core? Do you have any horror stories with regard to core orientation?
DR: I frequently contribute to the set-up of data collection protocols and the review of data obtained through oriented core. In disasters, I’ve seen years of client data rendered useless even with good orientation marks from the drillers, due to poorly traced reference lines and inconsistent protocols. The latter principally occurs in inconsistencies in beta orientation collection due to the use of different tools, software, or poor training.
Another ongoing issue I see is that even where the core is well-oriented, there is often insufficient or inconsistent subdivision of
structural features, and often collection of irrelevant or biased data. These issues obscure principal structural features. In general, these issues can be aided by training on both outcrops and/or core, and by the use and plotting of the data by the same people who gather the data, which allow geologists to recognize and focus on the most useful and representative features.
Geologists are also sometimes restricted to data collection with only a small number of fixed generic structure codes within the software provided to the site. This limits the effectiveness of the utility of the database. Given the associated costs and efforts of core drilling, orientation efforts and geologists’ time, this is counterproductive and based more on the ease of imposed database design and maintenance than on the reality of finding and interpreting ore deposits. The most effective databases are generally customized to the conditions and geology of the project.
Televiewer technology can work well as an alternative to oriented core under appropriate conditions. However, where imagery is obtainable and of sufficient resolution, it is most effective when the geologist logging the core correlates and tags features in the imagery for measurement, so that relevant data is obtained and not lost in a sea of uncoded data points.
BD: You’ve worked in a lot of countries and on a lot of continents. Are there any skills or mindsets that have helped you in your roles in these places?
DR: Respect and interest in the people one works with, of course, are some of the principal approaches, which bridge cultural, technical and individual divides, and bring people out of their shells to provide them with the confidence to interact, learn, and convey their ideas
and observations. Respect breeds respect and enjoyment of the task and downtime with the people one works with are also generally contagious and motivating.
BD: One topic we commonly talk about but rarely put into print is of the health hazards of working in different countries and environments. Has your health ever been particularly challenged and, if so, what happened?
DR: I’ve been fortunate to avoid any dangerous health or major personal safety issues. Usually, if the water supply in an area is good, food safety is generally higher with the regular cautions. In parts of Africa and South America, I’ve found it’s often the cities after the fieldwork where one can pick up ailments more readily, since in the countryside food is generally cooked more thoroughly and water is always bottled. Never underestimate the risk of malaria or dengue fever in the tropics because while there are often few mosquitos, a high proportion of them can carry it. Taking or carrying antimalarials and basic exposure prevention is important, even when passing through airports in highrisk areas where watered plants can provide a breeding site for mosquitos. But the greatest health risk is often the drive to the field or the hotel in countries where road safety is an afterthought.
BD: Who have been some of the positive influences in your career?
DR: Just after graduating from undergraduate studies, I traveled through Australia and ultimately ran out of money in Darwin. In those days, there was no internet or email, so I took a stack of coins to a phone booth and called local mining companies, ending up with two offers in the Pine Creek area. Both offers led to the first major mentors in my career, including Greg Partington and Michelle Stokes, who gave me the opportunity to run the exploration of a property package there.
In the early 1990s, the merging of plate tectonics and metallogeny was well underway with and geochronology was providing better constraints on geological cycles and the positions of different styles of deposits within them. After returning to Canada from Australia, I was fortunate to be involved for my MSc in the first MDRU project in the Iskut area of BC. There, James MacDonald, Colin Godwin, John Thompson and Peter Lewis together helped shape my geological approach and understanding, which continues through my colleagues and co-collaborators. Despite being an independent consultant, it is important for me to often work in a team with other professionals who provide ongoing interaction and differing perspectives that continue to positively influence my professional work.
BD: Given the current multi-commodity mineral boom, are you doing a lot of work outside of the commodities and deposit styles you have traditionally worked on?
DR: No major changes yet, although I’ve done work in the past on deposits with metals which are now part of the increasing critical metals focus. As the range of deposits in this broad boom becomes better understood, I’m sure there will be practical structural aspects to define in some of these for both exploration and internal grade understanding even in deposits that don’t have obvious external structural controls.
BD: Is there a particular mineralization style or deposit type that interests you, and why?
DR: In part because of their high degrees of structural control and also with seeing a large number of them, which allows comparisons between the deposits and districts of different ages and regions, gold deposits of different types are my general focus and area of principal interest. Epithermal deposits, which are not significantly eroded, often have synvolcanic histories that may allow evaluation of the whole
system scale, including the paleosurface and lithological architecture. This in turn can also influence the position and nature of the deposits. These more than other deposit styles can therefore provide a mineral systems view allowing applications to district exploration, and the opportunity to assess relationships of other associated arc-related deposit types.
BD: Leading on from the previous question - everyone has a handful of deposits that have left a mark on them, be it because of the amazing geology, the hideous conditions, the people they worked with, etc. Which deposits do you hold dear and which ones really were difficult to work on?
DR: The deposit, which was the subject of my MSc thesis, the Snip Mine, encapsulated a wide range of aspects that made for a perfect research topic, including its association with a CuAu porphyry system and skarns. This is an unusual occurrence in a ductile shear zone in the thermal aureole of the porphyry which formed at a critical time during the development of the Jurassic arc in BC, and consequently for a very holistic study. It was also a good place to be at the time, on a beautiful camp with great people in a spectacular setting.
In the Abitibi, I was involved during the early development of the Hoyle Pond Mine, and have been regularly going back since the mid-1990s. Following the orebody downward and seeing it evolve as mining continues to nearly 2 km (1.24 mi) depth has been particularly informative.
One of the more challenging projects I’ve recently worked on is the Yanacocha mine in Peru since - in addition to logistical challenges of the work - with more than eight million years of overprinting, telescoped alteration-mineralization events, late faults, and deep supergene alteration in an intense lithocap, the important ore controls are largely obscured.
BD: Do you think that there are any mineral exploration strategies or technologies that are under-employed, but could make a big difference to an exploration campaign if people used them more?
DR: Human brains to help guide, constrain and filter these technologies!
BD: We hear all about the advances and benefits of technologies, such as 3D modelling, geochemical analysis, and utilization of drones. Have you noted any negative impacts to effective exploration and mining as a result of these e.g. less people out kicking rocks?
DR: This is particularly notable in the reduction of surface and open pit geological mapping, and therefore lack of good outcrop maps and interpretations that can form a foundation for exploration and mine ore controls. There is often an incorrect perception that geophysical interpretations and drilling models can replace good maps where outcrop exposure is available, and there is a diminishing number of geologists with mapping experience through retirement attrition and fewer university training programs. As the industry relies on more data, the importance of a good base map that incorporates such field interpretation only increases and forms an essential source for modeling and targeting in many projects. Those who become proficient at geological mapping tend to be some of the best and most observant geologists: good mappers will always be in demand.
BD: Has there been any single satisfying moment in your career that rates above all the others?
DR: In the early 2000s, when conducting ongoing consulting for Placer Dome in Timmins, Greg Hall visited in his capacity as Chief Geologist. Greg involved me in both expanded regional camp scale modeling there and an exchange with the talented Kalgoorlie-based team, as well as technical sessions and mine visits. These highly productive exchanges provided the impetus for further exploration and understanding of ore controls through comparative work between the regions, and lead to many associations with colleagues that I continue to have today.
BD: I’ll ask a question on the flipside to the previous one. Many of us have interfaced with less-than-savory individuals or experienced toxic workplaces. Has there been any incident or incidents that really disappointed you?
DR: Early in my career especially, during work for a minority of junior clients, I’ve been exposed to some questionable promotional tactics, and in one case suspicious activity, which ultimately proved to be fraudulent. In the latter case, the lack of correlation between assays, assay intervals and geology in one project I worked on was sufficiently concerning to seek legal advice, although there was no clear proof of fraud at that stage.
↑ David Rhys in the field
After a couple of consultants subsequently provided reports on the project which appeared to validate the company data, my concerns diminished. However, a third group later determined that assays had been indeed manipulated and the single perpetrator in the company was ultimately found guilty. My initial report, which documented the inconsistencies I observed, was used in the legal proceedings.
In retrospect, I’m sure that my requested presence at the site was to provide credibility and cover without anticipating that I’d complete as much review as I could. I’d hope that under the current regulatory regime and higher expectations for QA/QC that this may not have occurred or could have been detected earlier.
BD: You are one of the rare breeds of geologists who work in the industry but manage to maintain a publishing career. What inspires you to publish and how do you overcome the challenges, such as finding the time?
DR: While it’s a bit of an arduous task at times, especially during the writing and editing process, publishing is ultimately quite satisfying. It takes the consulting work to a higher technical standard that involves further research and learning, and allows the dissemination of otherwise invisible internal work to the broader geoscience community. As many of my projects are long term and advanced, there is the opportunity to develop concepts and make for substantive contributions. I’ll often set aside a month or two a year for this process, which benefits from already having a base for the papers from what has been written and illustrated in my consulting reports. Ultimately, the papers, as well as short courses I’ve given that benefit from reference to the
published material, make up for the voluntary time and elevate my profile, leading to more new work opportunities and added value and demand from my long-term clients.
BD: Are you undertaking any active research now?
DR: I’m fairly steady on that front working towards a series of papers as time and field projects continue. While also doing work for clients in areas of research interest, I’ll often set aside some personal time to conduct traverses and visit adjacent mines to place the deposits or districts into a better context. As my wife does petrographic work, we can also address the paragenetic, textural and microstructural aspects on most of our projects. She has connections with the local university for more rigorous analytical and geochronological work, together contributing to the research aspects.
With these approaches, I’m currently continuing work on the understanding of the structural controls and setting of the Carlin gold deposits in Nevada, USA, and finishing up a major multidisciplinary review of the Fosterville deposit with the mine team that will lead to a paper addressing its deposit structure and vein evolutionary history. I am also working on papers based on my many years of ongoing work in the Timmins area and other deposits in the Abitibi Belt. I have planned a collaboration to provide review papers on the structure of orogenic gold deposits with Stephen Cox, and orogenic gold diversity with Rich Goldfarb. We will continue to flesh out both papers during an upcoming SEG short course in London. While these projects may seem quite ambitious, I treat them as multi-year objectives which I work toward as time permits.
BD: Do you think that geological societies, such as the Society of Economic Geology (SEG), have adapted to the times in terms of being useful entities for their members? Or are there basic things that such societies should be providing and/ or promoting?
DR: The SEG and other societies are doing their best to adapt to changing commodity demands, technologies, demographics and social concerns, as it is illustrated by many of the themes in the upcoming conference in London. But while there is a paid staff at the larger societies that run the business and administration and oversee the editorial aspects of their publications, the technical and educational offerings are determined and provided by volunteers and the financial support of the fees and company contributions. These societies are therefore dependent on the time we in the industry, who have technical, educational and/or management skills, are willing to provide to make them successful and relevant. So, as a community, I’d encourage your readers with the time and skills to offer to give back to these societies. This could be through volunteering, presentation of courses, by publishing scientific contributions, or by participation in community outreach.
Participation could also be by simply attending conferences and courses provided by the societies, to be part of the overall communi-
ty and exchange of ideas, as well as through the fees generated from these events and membership which provide funds for the societies to function. As we are facing a diminishing pool of young geologists, and a need to train international geologists within their home countries, educational outreach is also becoming increasingly important to support the industry. Education can only be provided by those of us who volunteer our time or participate.
BD: Finally, any concluding comments or words of wisdom from an industry veteran?
DR: For early career geoscientists, I’d encourage obtaining as much field experience as possible, even if it means some sacrificed time away from family and friends. Regardless of the ultimate path you may follow in the industry, this initial base can give you the diverse experience and context to draw from in the future, as well as the immersion in the culture and camaraderie of a worksite or project. Try to practice and encourage critical thinking, observation and good evidence-based interpretation in your work, especially with the introduction of so many new technologies. You were trained to be a geologist, not a technician. This is often one of the more satisfying parts of the job. C
For more information
Get in touch with David Rhys on LinkedIn
by Paul Ashley, Principal at Paul Ashley Petrographic and Geological Services
Most minerals industry geologists, after their initial university training, leave behind skills that they learned about the use of the petrographic microscope, much of which at university is aligned towards academic pursuits and not necessarily economic geology. In part, this situation arises due to the multiplicity of other industry work avenues that geologists must pursue, and due to the fact that most companies do not possess a suitable microscope. Consequently, the potential knowledge and deductions that can be obtained from petrographic examination of the wide range of geologic materials may be foregone. As an alternative, some companies use the services of consultant petrologists/mineralogists. B A C D E
↑ Figure 1 - Typical materials used for petrographic and mineralogical examination: A) drill core, B) mine samples, C) regolith (gossan), D) RC drill chips, E) mineral concentrate.
Petrographic examination generally follows careful examination of sample material with a hand lens, and ideally uses both transmitted and reflected light optics on petrographic sections that can include standard thin sections, polished thin sections and polished blocks, prepared from the complete range of geological sample media. The latter can encompass outcrop samples, drill core and chips, mine samples, quarry products, regolithic materials, sand and heavy mineral concentrates, and processed material such as mill products and tailings (Fig. 1). Interpretations from petrographic observations can commonly be enhanced if there is access to accompanying geological and geochemical data. The information acquired can be the springboard for more detailed material investigations where necessary. Some examples may be using techniques that include electron microprobe analysis, hyperspectral scanning, X-ray diffraction, QEMSCAN and fluid inclusion thermometric and compositional determinations.
In comparison to macroscopic and hand lens observations, e.g. during drill core or drill chip logging, petrographic examination can provide significant benefit in being able to give insights through the plethora of imposed processes that have commonly been imposed on rocks that are associated with mineral systems, e.g. one or more of hydrothermal alteration, metamorphism, deformation and supergene alteration.
Petrographic examination has the ability to deliver major benefits, including the following:
A C
• Assisting the development of geological models in greenfields exploration by being able to quickly verify rock types, alteration and mineralization potential.
• Determination of primary rock types: relevant in exploration and assessment of ore systems such as porphyry Cu-Au (Fig. 2), layered intrusion and ultramafic-hosted Ni-Cu-PGE, granite-related Sn-W-Mo, carbonatite-related critical metals, etc.
• Be able to ‘look through’ imposed processes to recognize features, such as relict textures and minerals, or assess metamorphic or hydrothermal mineral assemblages to assist the determination of primary rock type (Fig. 2).
• Determine hydrothermal alteration mineral assemblages and use these as vectors towards mineralized systems, e.g. porphyry Cu-Au, volcanic-associated massive sulphides, orogenic Au, with related benefits of confirming hyperspectral results (Fig. 2).
• Use the observed mineralogy to explain geochemical data: e.g. occurrence of particulate gold in gold-anomalous samples, occurrence of enargite or tennantite to explain high As in a porphyry Cu system, presence of relict chromite in an altered rock to confidently state that the protolith was of ultramafic type (Fig. 2), presence of rutile in a high-Ti-altered rock to indicate that the protolith was of basalt type.
• Use of observed mineralogy to explain geophysical data: e.g. graphite and Fe-sulphides in electrical conductivity anomalies, magnetite (and/or pyrrhotite) in magnetic anomalies,
B
↑ Figure 2 - A) Typical texture in a porphyry Cu-related intrusive and with propylitic alteration characteristic of a peripheral position in a mineralized system. B) Relict phenocrystal quartz grain in an intensely phyllic altered felsic volcanic rock associated with a massive sulphide system. C) Relict chromite grains (grey), enclosed by magnetite (pale brown-grey) and hosted in bornite-chalcocite-hematite rock, proving that the high-grade Cu mineralization replaced an ultramafic composition protolith.
and K-feldspar and U- and Th-bearing minerals in radiometric anomalies.
• Interpretation of vein and breccia textures, including timing relationships, formation processes and infill mineralogy.
Examples of mineralogical and textural characteristics that are directly relevant to the minerals industry include the following:
• In sulphide ores, e.g. from porphyry Cu-Au-Mo, volcanic-associated and sediment-hosted massive sulphides, Ni-Cu-PGE deposits, and some epithermal precious metal, orogenic gold and skarn systems, the following aspects can be determined: ore mineralogy, mineralogical location of minor (including deleterious elements, e.g. As), metal deportment and textural relationships relevant to ore processing (e.g. particle size and intergrowths relevant to liberation characteristics) (Fig. 3).
• In gold ores (e.g. epithermal systems, orogenic gold, intrusion-related, IOCG/ISCG and alluvial deposits), determination of gold mineralogy, location, and particle size relevant to processing recoveries, refractory (invisible gold) issues, gold fineness and the mineralogical presence of associated beneficial or deleterious elements, e.g. Cu, As, Sb, Te, Hg (Fig. 3).
• In metal sulphide and gold ores, determination of the mineralogy in variably oxidized (supergene-affected) systems to enhance metal recoveries, e.g. liberated (particulate) versus sulphide-hosted gold, knowledge of oxidized/sulphide mineralogy
A B
C
‘Industries can add an additional layer of knowledge to standard techniques, particularly those involving geological observation and geochemistry. They can also provide augmentation to more detailed analytical methods, such as hyperspectral logging, and rapidly acquired field data from portable XRF and XRD analyzers.’
↑ Figure 3 - A) Where’s the deportment of high-grade Ag in the massive sulphides? In this case, it’s in tetrahedrite (pale olive-grey). B) Easy-to-liberate cassiterite grains (brown) in a quartz-tourmaline greisen. C) Different size gold particles in complex sulphide ore (sphalerite-galena-pyrrhotite-chalcopyrite) dictates optimal grind size.
in copper heap leach operations, and whether cyanide leaching is an optimal route in certain gold ores.
• Critical metal deposits: mineralogy and metal deportment in deposits associated with pegmatites, carbonatites, fractionated granitic rocks and mafic-ultramafic igneous rocks, e.g. commodities such as Li, REE, Ta, W, Sn, Mo, V, Cr, Ni, Co and PGE (Fig. 2). Prediction of liberation characteristics of minerals during ore processing (Fig. 3). Mineralogical siting of trace critical metals such as Co, In, Ga, Ge.
• Mine-focused environmental issues: due diligence before mining to determine potential problems and solutions with rock types and minerals, e.g. acid production and neutralization, and toxic element (base metals, As, Sb, Cd, Hg, U) release. Characterization of waste rock and mill tailings. Assessment of mineralogical issues with rocks that could produce hazardous dusts, e.g. fibrous and acicular minerals.
• Engineering (including ground stability) issues at metalliferous and coal mines, and characterization of rock behavior in crushing and milling. Nature of quarry products such as the characterization of problematic rock types (e.g. sheared, layer-silicate dominated rocks, altered igneous dykes), assessment of suitability of quarry products for engineering and construction
purposes (e.g. presence of swelling clays, other layer silicates, zeolites, sulphides, fractures/veins).
In conclusion, petrographic and mineralogical investigations on materials typically encountered in the minerals exploration and mining industries can add an additional layer of knowledge to standard techniques, particularly those involving geological observation and geochemistry. They can also provide augmentation to more detailed analytical methods, such as hyperspectral logging, and rapidly acquired field data from portable XRF and XRD analyzers. In mine development, mining (or former mining) and processing operations, this easily acquired information can assist in developing mineral processing routes without making ‘mineralogical mistakes’, prediction of waste rock and tailings behavior and their environmental consequences, and rock quality issues from an engineering perspective during mining, and in quarry products.
To better integrate knowledge gained from drill core/chip logging, geochemical and geophysical results, with petrographic and mineralogical information, some companies might be encouraged to utilize (or invest in) their own petrographic microscopes, and their geologists who still retain the observational and interpretive skills.
I thank Luke Milan and Damien Wilkinson for their exploration view
● Near in-situ continuous core samples.
● Highly accurate mineral resource value determination.
● Geotechnical and environmental program drilling.
● Install straight pre-collars through difficult overburden for diamond coring.
● Can easily be converted to drill diamond coring tails on short holes.
by Hugo Serra, Project Geologist
↑ Pick-up time at the end of a great trekking day
The Grenville Province characterizes the youngest geological entity accreted to the Canadian shield (Laurentia) around a billion years ago. The province represents a significant area of the North American continent, it is structured in a northeast/southwest orientation from Newfoundland to Mexico. Today, the region expresses the remains of a gigantic mountain range that was equivalent to the current Himalayas at the end of the Mesoproterozoic period, and it is now sufficiently eroded to allow the structures of the Precambrian middle crust to outcrop at the surface. The formation of the belt takes place in the Precambrian context of North America in which the continent-continent collision between the Archean/Paleoproterozoic cratons Laurentia and Amazonia (the South American shield) have formed the supercontinent Rodinia, between 1.26 and 0.90 billion years ago. The construction of the mountain range was structured by a succession of metamorphic thrust belts formed in medium to high-pressure regimes during the Grenvillian orogen. The region consists of pre-Grenvillian volcano-sedimentary rocks intruded by plutonic sequences metamorphosed from the amphibolite facies to the granulite facies then intruded by gabbroic and syenitic intrusions dated from the Grenvillian orogen until the post-Grenvillian period (1.09 to 0.99 billion years ago), eventually the whole sequence has been injected by pegmatitic dykes cross-cutting the older formations. During the team meeting before dinner of the previous day, my project geologist Abdelali defined for myself and my field assistant Max
In order to keep improving the geoscientific knowledge of Quebec, the Ministry of Energy and Natural Resources (MERN) of Canada deploys mapping teams throughout the territory during the summer period, since the weather and temperatures permit it from early-June. The acquisition of this field data is primarily aimed at improving and updating the overall knowledge of the targeted area and secondly, at enhancing its mining potential (mines, quarries). Following a geological survey carried out during the summer of 2017, a new geological map of the Borgia Lake region (western zone of the Grenville Province) has been produced at the scale of 1:50 000, the mapping of the area was based on a systematic outcrop survey in a kilometer-spaced grid. The zone where the study has been conducted is situated 300 km (186.4 mi) North-West of Quebec City, in a controlled ecological zone made up of dense forest on hilly terrain dotted by numerous forest tracks, few main roads, rivers and lakes, and an active wildlife during summer (moose, black bears, wolves, foxes, beavers, and a lot of various flying insects willing to drink your blood).
an approximatively 10 km (6.2 mi) long route oriented north/south in the middle of the forest where geological data was missing. Due to predominant vegetation in the region, the bedrock exposure rate is less than 10%. Using a topographic map, I prepared the traverse by defining the best path along our transect in order to intersect the relief, increasing our chances of finding outcrops as much as possible. As the area mapped had no access road, we had to be dropped and picked up by helicopter, thus I had to find landing spots using a satellite map. I selected two swamps for the starting point, and I decided to extend
↑ Outcrop sampling along an old lumberjack track before lunch
our traverse by roughly 2 km (1.2 mi) north as a large river with meanders was cutting through the impenetrable forest, and the sand benches on the edges of rivers are a good landing zone while swamps can be trickier. After writing down the geographic coordinates of these three spots on Johann’s notebook (the pilot), it was time to have a good rest to make the best out of the next day.
I woke up early the next morning, as I was overexcited to spend a day of work in the world’s best office: the wilderness. After having a champion’s breakfast, I double-checked my backpack making sure I had all the geological equipment: Android tablet, GPS, geological compass, hammer, and chisel; and safety gear: ‘SPOT’ GPS tracker, walkie-talkie to help the helicopter pilot to find us during the pick-up, foldable hand saw, first aid kit, 5 L (1.3 gal) of water, bear spray and bear banger, plus some extra survival equipment in case we must sleep on the field, and last but not least, lunch. All this equipment represented three quarters of the volume available in my backpack (roughly 10 kg or 22 lb), knowing that we had to sample every lithologies of each outcrop (with 10 outcrops on average per day), thus it was necessary to have a good swing with the hammer to fit everything inside while making sure the sample size was decent enough to allow all the potential analyses. Ready for the day, we sat in the helicopter, while Johann was typing the GPS coordinates of the arrival spot I wrote the night before and we took off. Why heading to the arrival point first would you say? It allows the pilot to check and confirm that the landing zone is safe.
If it isn’t, he just had to seek a better landing spot in the vicinity, and I would just have to change the GPS coordinates of the pick-up and voilà! After this step, we headed towards the starting point by overflying of the zone to be mapped, which is useful for geologists as it allows them to adjust the traverse after seeing the terrain for the first time. We landed on the grassy swamp that looked the safest for the helicopter and started the walk north.
The geological surveys carried out by the MERN involve the systematic filling of a ‘geofile’ for each outcrop, where the outcrop is identified (petrological and structural analyses), geolocated, photographed and sampled. The data entry, the photos, and the geolocation of the outcrop are done by using an Android tablet, and associated GPS data via Bluetooth. Publicly broadcasted via the Geomining Information System (SIGEOM website in Quebec), the content of each outcrop can thus be directly downloaded and compiled in the different geographic information systems (GIS). Before reaching the edge of the forest, we encountered a several meter-wide stream blocking our progress, it was too deep to be crossed on foot, so we improvised a bridge of small trees we cut with the hand saw. We managed to cross the stream without falling and kept going. Several hundred meters further we found the first outcrop of the day, a beautiful 10 m (33 ft) high face of moss hiding a mangerite formation behind the vegetation. After cutting some squares of moss with my bowie knife, I started the geological analysis, as Max was sampling the outcrop.
After several hours of work, our bags started to get heavier while the forest was getting denser, slowing our progress. Luckily, we found an old track just before lunch and we followed it for a kilometer to catch up. We discovered another outcrop on the side of the track, we analyzed it, then we enjoyed a little rest and had lunch. During this break, I sent a message with the ‘SPOT’ GPS tracker to the project manager detailing our good progress.
Heading back into the pristine forest, we left the track behind for a steeper terrain heading north. The area was particularly complicated as tens of dead trees were lying on the abrupt slope, we probably spent half an hour to get through this 200 m (656 ft) wide obstacle due to the really slippery conditions of decaying trees, the weight of the backpacks, and the steep topography. After this little challenge, we found our eighth outcrop at the top of the mount and then progressed downhill until we reached the valley. After crosscutting some water bodies thanks to beaver dams, we found and analyzed our last
two outcrops before going to the pick-up spot. Two chairs probably left by hunters were waiting for us on the sand bench allowing us to relax a bit after this hectic journey in the heart of the forest. I turned on the walkie-talkie and a short time after, heard the voice of Johann, I confirmed to him we were waiting for the pick-up while starting to hear the noise of the helicopter. With the strong wind created by the blades smashing sand into our faces, we took the equipment that we put in the side rack and flew towards the camp. Johann dropped us on the pad at the camp and kept going on his pick-up mission with the other pairs of geologists/field assistants still in the field. We emptied our heavy load and I took some time to double-check every geofile before transferring the data collected during the field day into the computer system. After a good shower and some time to unwind, we joined the team meeting for the next day, ready for another adventure, deep in the forest a call was sounding. C For more information
by Ivy Chen, Director and Principal at GeoReg Mining & Compliance
A company has spent thousands of dollars on mapping, sampling, and drilling and now has some exciting results it would like to share. How might the company go about achieving this, maintaining the momentum and excitement of the discovery, without falling foul of the regulators?
It is a bit of a minefield (pardon the pun). In most jurisdictions, the first consideration would be the legal framework of corporate law, and the requirement for public statements to have reasonable grounds. The basis for reasonable grounds, is then generally established by industry specific guidance. It seems simple, but as with any area of specialized knowledge, such as the minerals sector, the detail is important.
The main mining jurisdictions all apply a principles-based approach to public disclosure, the CRIRSCO template. This template derives from Australia’s JORC Code, which was the first to have been drafted, following the Poseidon Nickel Scandal in Australia in 1969. And from the CRIRSCO website:
‘CRIRSCO, which was formed in 1994 under the auspices of the Council of Mining and Metallurgical Institutes (CMMI), is a grouping of representatives of organizations that are responsible for developing mineral reporting codes and guidelines in Australasia (JORC), Brazil (CBRR), Canada (CIM), Chile (National Committee), Colombia (CCRR), Europe (PERC), India (NACRI), Indonesia (KOMBERS - KCMI), Kazakhstan (KAZRC), Mongolia (MPIGM), Russia (NAEN), South Africa (SAMREC), Turkey (UMREK) and the US (SME). The combined value of mining companies listed on the stock exchanges of
these countries accounts for more than 80% of the listed capital of the mining industry.’
Table 1 of CRIRSCO (and JORC) summarizes the principles of public disclosure in the minerals space. Read the relevant Code applicable to the reporting jurisdiction and check the guidance. For ease of discussion, the remainder of this article will use the Australian context.
Firstly, what are reasonable grounds? Unfortunately, there is no single definitive answer; and ‘it depends’ is not what someone desperately trying to write a market announcement and head off a market suspension wants to hear. Reasonable grounds in our sector, generally start with reporting in accordance with the JORC1 and VALMIN Codes. Clauses 18 and 19 of the JORC Code outline disclosure of Exploration Results. ‘Exploration Results include data and information generated by mineral exploration program that might be of use to investors but which do not form part of a declaration of Mineral Resources or Ore Reserves.’ And ‘Public Reports of Exploration Results must contain sufficient information to allow a considered and balanced judgement of their significance… Public Reports of Exploration Results must not be presented so as to unreasonably imply that potentially economic mineralization has been discovered’.2
1 The JORC Code is currently under revision and an update is imminent.
Context is critical here. The disclosure needs to inform, but not mislead. And it is important to remember here that the intended audience is the investor. The JORC and VALMIN Codes are disclosure frameworks for discussing our discoveries, aimed at the people we hope will invest in our projects. We need to present the information clearly with a focus on what is material – what makes this particular result significant: and why it matters to a potential investor. Importantly, in language that does not require a geology degree to understand. We are not communicating with fellow geoscientists, we are telling investors (and possibly their expert advisers) about the merits of our projects and describing the risks and potential upside in a balanced way to allow them to make an informed investment decision. When disclosing drilling results, provide enough context:3
• how the samples were collected, and how they were analyzed;
• what the typical background assay results might be;
• how many assays were collected that were nondescript, compared to the assays that are worth getting excited about.
Remember the investors: there is more than just the reporting Codes. This is where we the technical people must extend ourselves outside our comfort zones and consider that we are informing non-technical people. We are also interacting with the market, usually as part of a company that is listed on a stock exchange governed by listing rules and regulated by legislation. For this article, assume that it is the Australian Stock Exchange (ASX) listing rules; and the Australian Corporations Act, regulated by ASIC (the Australian Securities and Investments Commission) which regulates compa-
2 Note the use of bold in this article is purely for emphasis and does not reflect the same usage as applied in the JORC Code.
3 JORC Clause 18: ‘… Reports must include relevant information such as exploration context, type and method of sampling, relevant sample intervals and locations, distribution, dimensions and relative location of all relevant assay data, methods of analysis, data aggregation methods, land tenure status plus information on any of the other criteria listed in Table 1 that are material to an assessment’.
ny and financial services and enforces laws to protect Australian consumers, investors, and creditors.
Exploration Targets are covered in the JORC Code (JORC Clause 17). Context is critical again here. The Exploration Target must (not should!) be expressed as a range of tonnes and a range of grades, and the basis or derivation of the target must be provided. And importantly, cautionary language must be included ‘… within the same paragraph as the first reference of the Exploration Target in the Public Report, stating that the potential quantity and grade is conceptual in nature, that there has been insufficient exploration to estimate a Mineral Resource and that it is uncertain if further exploration will result in the estimation of a Mineral Resource.’
The amount of work that has been done, and remains to be done, should be described. But ultimately, do not rely wholly on this article, please read JORC Clause 17, and then read it again. Always refer back to the JORC Code every time a public report is being prepared.
The ASX Listing Rules that are most pertinent to our sector when it comes to releasing Exploration Results are in Chapter 5 (ASX Ch 5 LR 5.7). These relate to material mining projects for the company, and when the company is an exploration junior almost every project will be a material mining project. Make sure that the five bullet points in ASX Ch. 5 LR 5.7.2 are addressed and included in the announcement, either as a table or in narrative form. Avoid Exploration Targets as headline statements. To remove any doubt, ASX Mining FAQ 20 clarifies that ASX interprets ‘headline statements’ broadly. It includes not just the title or heading to the report, but also any highlights, dot points or summary statements at the beginning of the report.
This rigor around the release of Exploration Results and Exploration Targets can sometimes seem over the top to us in the industry. After all, everyone knows how uncertain exploration is – we all know that it is a high-risk industry. But this is the perspective of highly-trained and experienced geoscientists, not that of the investor. We all agree to use these Codes and reporting frameworks so that we can retain the trust of our investors, to help the investors compare different projects, and select the ones that fit their
risk profiles. Make sure that the appropriate jurisdictional guidance is used, and always keep in mind that while industry codes are helpful guidance, the law of that jurisdiction always takes precedence. A list of useful (but not definitive) documents for the main mining jurisdictions is below.
CRIRSCO Template (International):
• International Reporting Template for the Public Reporting of Exploration Targets, Exploration Results, Mineral Resources and Mineral Reserves, November 2019
• JORC Code 2012 (especially Clauses 17-19, Figure 1, Table 1 Sections 1 and 2)
• VALMIN Code 2015 (Section 5 Public Reports and Section 7 Technical Assessment)
• ASX Listing Rules Chapter 5, LR 5.7
• ASX Mining FAQ 15-21
• ASIC Information Sheet 214
• National Instrument 43-101, the national instrument for the Standards of Disclosure for Mineral Projects
• CIM Definition Standards for Mineral Resources & Mineral Reserves
• CIMVAL Code for the Valuation of Mineral Properties
• Overview: Toronto Stock Exchange and TSX Venture Exchange Technical Guide to Listing (see Appendix A: Listing Requirements For Mining Companies)
• The South African Code for The Reporting of Exploration Results, Mineral Resources and Mineral Reserves (SAMREC Code)
• The South African Code for the Reporting of Mineral Asset Valuation (SAMVAL Code)
• JSE Limited Listings Requirements Europe/UK
• PERC Standard for Reporting of Exploration Results, Mineral Resources and Mineral Reserves
• AIM Note for Mining and Oil & Gas Companies. C
Designers and manufacturers of inflatable packers and
by Ashleigh Ball
Exploration in Alaska is a remote, challenging and often an expensive endeavor. In a place where untested veins still outcrop at surface and huge swathes of underexplored to completely unexplored ground still exists the rewards can be high.
In 2020, I was given the opportunity to swap exploration in Western Australia’s Goldfields for exploration in interior Alaska. I encountered immediate differences. The obvious ones were a mountainous landscape, the need for helicopters, hazardous wildlife and extreme weather. But there were also the less obvious ones that took time to understand such as subtle differences in culture, recruitment challenges and collecting and working with data in mountainous terrain.
I had visions of summer field campaigns involving hiking from ridge to ridge under the midnight sun, measuring quartz veins with towering mountains in the background. While some of this turned out to be true, many of my preconceived ideas also turned out to be completely wrong. I quickly realized that exploration in interior Alaska could be very challenging, both physically and technically, and that exploring in the outback was like a walk in the park compared to this. The following are some of the biggest myths that were busted during my time in Alaska: The first myth: there are mountains, therefore there will be good outcrop.
Compared to outback Australia where there is commonly less than 2% outcrop to none at all, I was under the illusion that the mountainous Alaskan terrain would mean excellent outcrop. I had romantic visions of hiking from outcrop to outcrop with my compass at hand and map book outstretched.
The reality is that outcrop in interior Alaska can actually be quite poor. Due to the yearly freeze-thaw cycle, outcrop is often slumped and ‘creeps’ downhill. This means that despite a lot of rocky exposure outcrop often cannot be relied on for measuring structural features such as foliation, folding or vein orientation. This resulted in a lot more float mapping than I had anticipated. Thick vegetation away from ridgetops meant that outcrop and float were also often obscured, leaving huge
parts of the map devoid of information. I quickly realized that in some places outcrop was as sparse as it was in the outback.
A new set of skills were also required to understand geochemical signatures and dispersion patterns. This was not only due to the effects of topography and mountainous terrain but also because of unusual weather phenomena, such as solifluction formed by the freeze-thaw of permafrost. This made the interpretation of geochemical data an entirely new challenge.
The second myth: helicopter-assisted drilling means that you have more options on where you can drill.
Due to the remoteness and a lack of roads, most exploration drilling in Alaska is only possible with the assistance of a helicopter. Unlike Western Australia where the terrain is flat and you can generally drill out a target as desired, the terrain in interior Alaska is reasonably mountainous which limits the number of suitable drill site locations and therefore narrows your drilling options.
I learned very quickly that siting helicopter drill sites can be difficult. What looks like a small hill in 3D software can actually turn out to be a monstrously steep formation when you stand on top of it. Steeper terrain means a taller pad with more timbers, and while it was incredible to see what drill crews can build, larger and more expensive pads could be difficult to justify on greenfield targets.
The ideal drill design and what could actually be achieved were often two vastly different things. It was not always possible to move the rig along strike or down dip to follow up an intercept and you often had to get creative. Key lessons I took away were to always site pads in the field with the pad building crew and that good planning was more necessary than ever.
The third myth: the animals in Alaska couldn’t be any worse than the cohort of venomous creepy-crawlies and snakes in Australia.
When Americans claim that Australia is full of dangerous animals, it’s good to remind them that at least there are no large four-legged predators there that may want to eat you up.
Bears are a serious concern when working in Alaska and precautions must always be taken. Both black and grizzly bears inhabit the interior and it wasn’t uncommon to see them around camp or from the helicopter. Although bears are generally afraid of humans and likely to run away at the sound or scent of us, strict bear safety protocols were always necessary when mapping in the field and running drill programs. My ears are still ringing with the shout, ‘hey bear!’.
Other four-legged creatures that required caution included the Alaskan moose, which although often docile-looking had to be provided with a wide berth due to its notorious unpredictability, as well as wolves and lynx that were occasionally spotted but are generally quite reclusive.
A particularly honorable mention should be also given to the mosquito, rightly nicknamed the Alaska state bird. These menacing pests would form a dense cloud around you in the field and could bite through even the thickest of pants and shirts unless those were smothered in the strongest of Deet. I’d never complain about outback flies again after having experienced Alaskan mosquitos.
The fourth myth: field work would involve hiking along alpine ridge tops and hammering rocks under the endless midnight sun. Whilst there certainly were days of hiking along beautiful ridge tops with incredible views of the Alaska Range, I wasn’t aware of how thick the bush could be until we were battling our way through it. Hiking involved everything, from pushing through dense alder that made for a whole new type of bushwhacking (and getting invariably soaked if it had been raining), to bouncing along on thick tundra that was not unlike walking on a trampoline; to also picking your way down rocky talus slopes covered in ‘banana lichen’ (appropriately named for if it rained, you would invariably end up on your backside). While the vegetation was luckily not viciously spikey like that in Australia it could still make for exerting days in the field.
The fifth myth: drilling can only occur during the summer months.
The summer drilling season in Alaska is typically very short, particularly when drilling at higher elevations. One must wait for the snow to thaw (around May), then for all of the ensuing mud to harden, allowing road access and pad construction (sometimes not until June), then hope you don’t get too fogged out when the rain starts and unable to operate helicopters (in August) and keep drilling until the snow comes again (around October but sometimes as early as late-September).
At the right elevation and terrain, however, I was surprised to learn that drilling can continue throughout the winter. In the right conditions, drillers were able to drill even in -40°F (-40°C), by erecting huts around the rig and keeping everything warm with space heaters thus making sure that the machinery, the drilling muds (and personnel) didn’t freeze. Decked out in Carharrt, racerbacks and heavily insulated boots, North American drillers are a tough breed! One perk of drilling through winter for them was that they had some of the best aurora photos I’d ever seen.
There were numerous other lessons learned, ranging from becoming aware that there wasn’t any running water in the core facility because pipes froze in winter, to not touching a metal doorhandle in -40°F (-40°C), to leaving frozen core in its box until it thawed, to not hiking through muskeg (ever) and also realizing that being exposed to the midnight sun meant chances of overheating and sunburn in the field were just as real in Alaska as they were in Australia.
Working in interior Alaska had some unique challenges but was an incredibly rewarding experience. It is a stunning part of the world, hugely endowed and with new discoveries waiting to be made. Stepping out of our comfort zones and into something new always entails a steep learning curve and opportunities to grow, both professionally and personally. As well as, of course, a few surprises along the way. C
BRYSON DRILLING
Phone 306-323-2202 Fax 306-323-2203 info@brysondrilling.ca www.brysondrilling.ca Canada
DDH1 DRILLING
Phone +61 08 9435 1700 admin@ddh1.com.au www.ddh1.com.au Australia
DIAFOR Phone (819) 860-3957 info@diafor.ca www.diafor.ca Canada
GÜNZEL DRILLING CC
Phone + 264 81 322 89 28 info@guenzeldrilling.com www.guenzeldrilling.com Namibia
KATI OY
Phone 0207430660 info@oykatiab.com www.oykatiab.com Finland
MITCHELL SERVICES
Phone +61 7 3722 7222 Fax +61 7 3722 7256 info@mitchellservices.com.au www.mitchellservices.com.au Australia
ATELIER VAL-D’OR
Phone (819) 824-3676
Fax (819) 824-2891
info@avddrills.com www.avddrills.com
BARKOM
Phone 90-312 385 60 50
Fax 90-312 385 35 75 info@barkomas.com www.barkomas.com
DISCOVERY DRILL
MANUFACTURER
Phone 1-506-542-9708
Fax 1-506-542-9709
info@discoverydrills.com www.discoverydrills.com
Drill Rigs & Accessories Cont. Drill Rigs & Accessories Cont.
WE ARE YOUR SONIC DRILLING PARTNER
Terra Sonic International knows what it takes for you to succeed. We are committed to making the world’s most productive and reliable SONIC Drill Rigs and SONIC Tooling while providing the best service and support in the industry. Experience the Terra Sonic Difference today. www.terrasonicinternational.com sales@terrasonicinternational.com
+1 740.374.6608
+1 740.374.3618
Drill Rig Parts (A-Z)
PROLENC
Phone (250) 563-8899 Fax (250) 563-6704 khodgins@prolenc.com www.prolenc.com
RC Equipment (A-Z)
BOART LONGYEAR
Phone 1-801-972-6430 Fax 1-801-977-3374 www.boartlongyear.com
FORDIA POWERED BY EPIROC
Phone 514-336-9211 Fax 514-745-4125 info@fordia.com www.fordia.com
Specialized Machine Works (A-Z)
NORTH BAY MACHINING CENTRE
Phone (705) 472-9416
Fax (705) 472-2927 luc@nbmc.ca www.nbmc.ca
PROLENC
Phone (250) 563-8899
Fax (250) 563-6704 khodgins@prolenc.com www.prolenc.com
Swick Engineering has been building quality mobile rigs for over 18 years.
Available now, the Swick Gen II Mobile Drill Rig delivers intense power with a small footprint. Perfect for underground grade control, reverse definition, and exploration.
Key Features:
• Drilling automation
• HMI (Human Machine Interface) screen provides real-time updates
• 112kW drilling power
Spare parts
Training
Global Footprint
Aftermarket support
• 95% mechanical availability in field
• 360° versatility
• Small footprint, compact design
FIND OUT HOW SWICK’S GEN II CAN HELP YOU PERFORM ON ALL LEVELS
www.boartlongyear.com marketing@boartlongyear.com
www.diatoolglobal.com anthonygraham6@gmail.com
QUALITY AND EXPERTISE
DIATOOL is a young and dynamic company, founded in 2010. The company manufactures impregnated and set core bits, casing shoes, reaming shells, and geotechnical drilling bits.
DIATOOL products are sold in North and South America, Australia, Asia, Africa, and Europe. DIATOOL Diamond Products are manufactured in a modern well-equipped plant, using the latest manufacturing technology.
DIAMANTINA CHRISTENSEN
Phone +562 2620 7808 christensen@christensen.cl diamantinachristensen.com
DIASET Phone 1-800-663-5004 bits@diaset.com www.diaset.com
WE ARE YOUR SONIC DRILLING PARTNER
Terra Sonic International knows what it takes for you to succeed. We are committed to making the world’s most productive and reliable SONIC Drill Rigs and SONIC Tooling while providing the best service and support in the industry. Experience the Terra Sonic Difference today. www.terrasonicinternational.com sales@terrasonicinternational.com
+1 740.374.6608 +1 740.374.3618
BARKOM Phone 90-312 385 60 50 Fax 90-312 385 35 75 info@barkomas.com www.barkomas.com
CORE TECH Phone +51 983 856 666 info@coretech.com.pe www.coretech.com.pe
FORDIA POWERED BY EPIROC Phone 514-336-9211 Fax 514-745-4125 info@fordia.com www.fordia.com
FORDIA POWERED BY EPIROC Phone 514-336-9211 Fax 514-745-4125 info@fordia.com www.fordia.com
REFLEX Phone 1-705-235-2169 Fax 1-705-235-2165 reflex@imdexlimited.com www.reflexnow.com
SONDA PARTS
Phone 55 – (31) 3391 3810 Fax 55 – (31) 3391 3810 comercial@sondaparts.com.br www.sondaparts.com.br/
COREFINDER
Phone +55 62 992720023 contato@corefinder.com.br www.corefinder.com.br
DEVICO AS Phone +47 72870101 devico@devico.com www.devico.com
REFLEX INSTRUMENTS
Phone 61 8 9445 4020 Fax 61 8 9445 4040 reflex@imdexlimited.com www.reflexnow.com
www.reflexnow.com reflex@imdexlimited.com 1-705-235-2169
REFLEX - A LEADING IMDEX BRAND REFLEX forms part of Imdex Limited, a leading Mining-Tech company. Our unique end-to-end solutions for the mining value chain integrate IMDEX’s leading AMC and REFLEX brands. Market leading REFLEX technologies enable drilling contractors and resource companies to drill faster and smarter, obtain accurate subsurface data and receive real-time information for critical decision making.
CORE TECH
Phone +51 983 856 666 info@coretech.com.pe www.coretech.com.pe
DYNAMICS G-EX
Phone +61 7 54826649 sales@dynamicsgex. com.au www.dynamicsgex.com.au
PROSPECTORS
Phone +61 (02) 9839
3500 Fax +61 (02) 8824 5250 sales@prospectors.com.au
AMC
Phone 1-705-235-2169 www.amcmud.com
DI-CORP
Phone +1 (705) 472-7700
info@di-corp.com www.di-corp.com
Mudex
Phone +61 (8) 9390 4620 info@mudex.com.au www.mudex.com.au
Surveying & Geophysics (A-Z)
CORE TECH
Phone +51 983 856 666 info@coretech.com.pe www.coretech.com.pe Peru
DIGITAL SURVEYING
Phone +27 18 788 6349 sales@digitalsurveying.co.za www.digitalsurveying. com.za Africa
TRUST SOLUÇÕES
GEOLÓGICAS
Phone +55 62 992720023 contato@trustsg.com.br Brazil
A business card-sized listing featuring your choice of image as a background, your logo and strapline, 240 character spaces and your company contact details. Combined listing
USD per year (four issues)
A featured listing published both in our print and web catalog.
For more info, get in touch at: editorial@coringmagazine.com