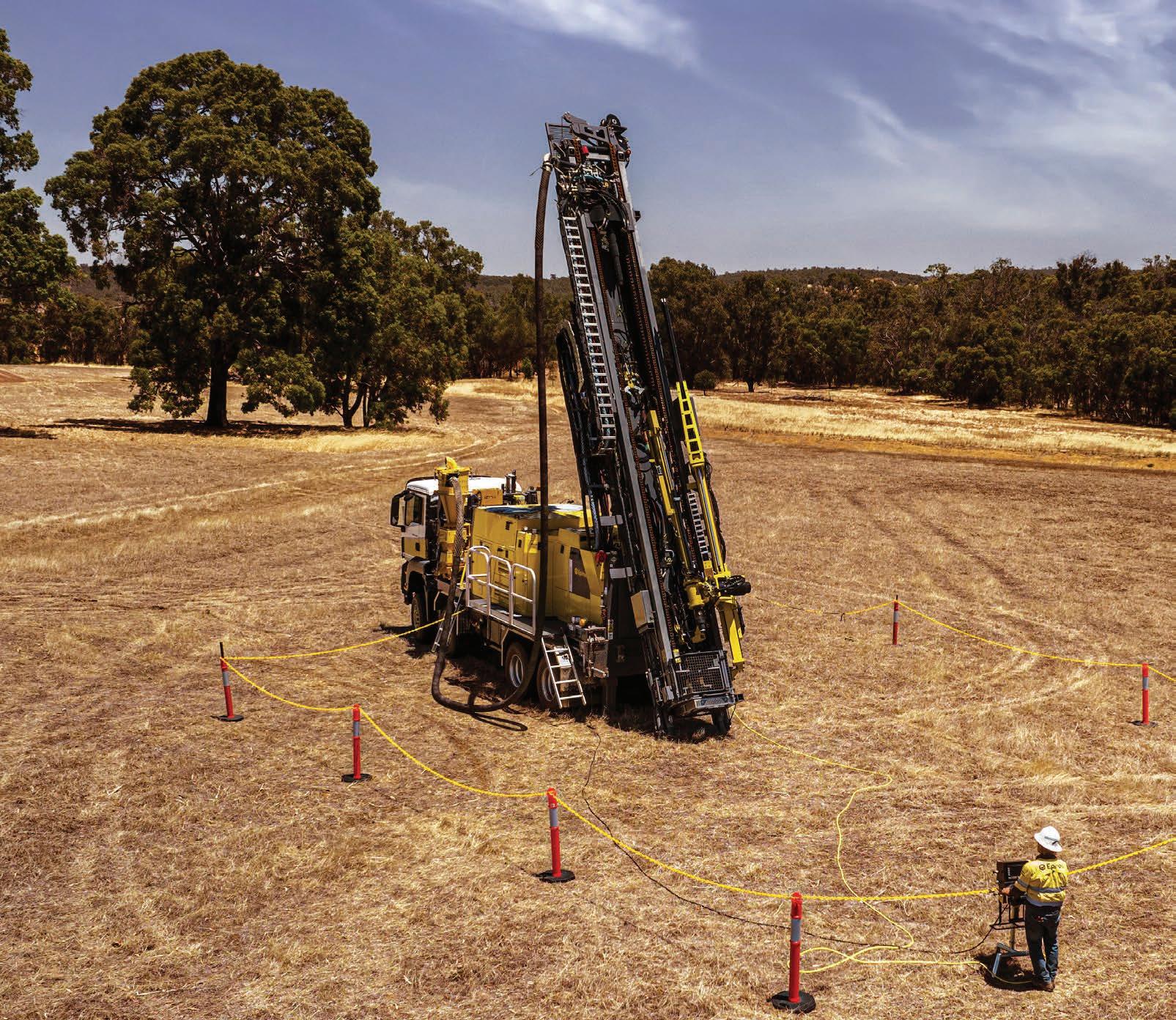
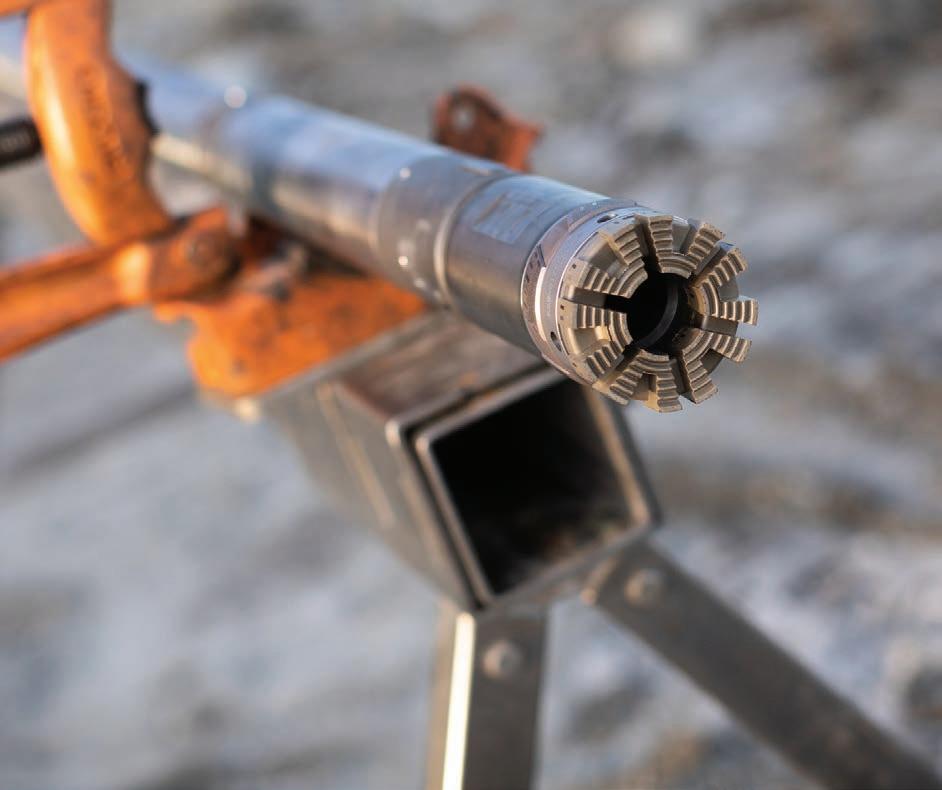
Ahead of
curve.
• Directional Core Drilling (DCD) • Rotary Steerable System (RSS)
Both coring (DCD) and non-coring (RSS) DeviDrill systems fit directly to a standard drill string and are fully compatible with N-size wireline systems. With integrated survey instruments and no need for additional water pumps or drill strings, DeviDrill is the ultimate choice for saving time, meters and money, whilst reducing environmental impact, on your next drilling project. With or without core. www.imdexlimited.com
Drilling: More than 100 years of experience combined by David Bradley, Co-Owner at RJLL Drilling
20 Top mineral exploration drilling contractors for 2022: Statistics of diamond drilling meters by Coring Magazine’s team
24 Epiroc’s Explorac RC30 Smart A meeting of minds between Australia and Sweden
28 Marcotte’s commitment to reliability, innovation and automation by Mathieu Audet, Mechanical Engineer at Marcotte
32 Directional core drilling: San Miguel Infill Program: A uniquely challenging gold exploration project by Nils Ivar Iversen, Chief Executive Officer and Daniel Popescu, Office Manager at Aziwell, and David DuCote, Operations Manager at IDS de Mexico /EXPLORATION & MINING GEOLOGY
39 Q&A from the experts: In conversation with Nick Tate Specialist Consultant Mapper of Geology, Alteration and Mineralization Systems
46 The airborne geophysics power for mineral exploration: An Amazonian Craton case study by Bruna de Freitas, Independent Exploration Expert Geologist and MSc in Mineral Resources
50 Hydrothermal system models: A great tool for understanding challenging geology by Mark Lindsay, Former Chief Geologist at GBM Resources
54 A short explanation why optical petrography knowledge is the key to preliminary identify hydrothermal magmatic processes by Paula Montoya-Lopera, Postdoctoral Research Fellow in Economic Geology at CODES, University of Tasmania
Drilling services
Drilling equipment & accessories
equipment
Colin Rice Owner of Colin Rice Exploration Drilling Advisory
,
and Daniel Popescu, Office Manager at Aziwell and David DuCote, Operations Manager at IDS de Mexico
Bradley Co-Owner at RJLL Drilling
Mathieu Audet Mechanical Engineer at Marcotte
CORING MAGAZINE
November 2023
Cover photo Epiroc Issue 25
ISSN 2367-847X
Not for resale. Subscribe: coringmagazine.com/subscribe
Nick Tate Specialist Consultant Mapper of Geology, Alteration and Mineralization Systems
Bruna de Freitas Independent Exploration Expert Geologist and MSc in Mineral Resources
Contact Us
Coring Media Ltd.
119B D. Petkov Str., Sofia 1309, Bulgaria
Phone +359 87 811 5710
Email editorial@coringmagazine.com Website coringmagazine.com
Mark Lindsay Former Chief Geologist at GBM Resources
Paula Montoya-Lopera Postdoctoral Research Fellow in Economic Geology at CODES, University of Tasmania
Publisher Coring Media
Founder Grigor Topev
Executive Officer & Editor in Chief Martina Samarova
Editor Maksim M. Mayer
Section Editor – Exploration & Mining Geology Dr Brett Davis
Digital Marketing Manager Elena Dorfman
Graphic Design Cog Graphics
Coring Magazine is an international quarterly title covering the exploration core drilling industry. Published in print and digital formats, Coring has a rapidly growing readership that includes diamond drilling contractors, drilling manufacturers and suppliers, service companies, mineral exploration companies and departments, geologists, and many others involved in exploration core drilling.
Launched in late 2015, Coring aims to provide a fresh perspective on the sector by sourcing authentic, informed and quality commentary direct from those working in the field.
With regular interviews, insightful company profiles, detailed product reviews, field-practice tips and illustrated case studies of the world’s most unique diamond drilling and mineral exploration projects, Coring provides a platform for learning about the industry’s exciting developments.
Open the box and GO. The GoGyro is fully integrated and designed specifically for simple, easy everyday use.
Configure your GoGyro as you need it for your surveys without unnecessary extra running gear. Simply add the needed fitting to run as:
• Core retriever
• Wireline
• Centralizers
Minimize downtime & Maximize efficiency. Simply GO Survey!
Fully integrated with SurveySafe for fast, convenient and secure online survey data management.
Owner, Colin Rice
Exploration Drilling Advisory
Colin Rice is the Owner of Colin Rice
Exploration Drilling Advisory, a company that provides consulting and training services to the exploration drilling sector.
In the early years, Colin was one of the founding partners of SAMCHEM (Pty) Ltd; Professional Diamond Drilling Equipment (Pty) Ltd; and Borehole Survey (Pty) Ltd, which was the first company in sub-Saharan Africa to utilize advanced electronic survey tools successfully.
Grigor Topev: Colin, thank you for agreeing to this interview. Let’s start at the beginning. How did you decide to replace a career in teaching mathematics with drilling? Which aspects of the drilling industry did you get involved in?
He played a key role in establishing the National Diploma in Drilling Practice at Technikon SA and has been teaching drilling and exploration-related courses at various institutions and in several Southern African countries for the past three decades.
Colin launched the Drilling Industry Certification Authority of South Africa (DICASA) and is a past President of the Borehole Water Association of Southern Africa. Furthermore, Colin has been recognized as an Honorary Fellow of the Geological Society of South Africa. Recently, he contributed to the development of the newly registered QCTO Driller qualifications as a member of the working group.
In 2013, Colin launched DrillSafe as a mechanism to share safety information and to improve the ability of the industry to manage safety on drill sites.
Colin Rice: When I went to university, I went for the sole purpose of becoming a Mathematics teacher and so I majored in Mathematics and Chemistry. After I finished university, I taught senior school mathematics in Zimbabwe for eight years.
In 1984, my wife and I decided to emigrate to South Africa. We left Zimbabwe with our little daughter, who was two at the time. I didn’t want to go back into teaching, so I looked for a job elsewhere. The mid-1980s was an incredibly difficult time in South Africa, and finding a job was not easy. Eventually, I was offered a job as a development chemist for a company that manufactured drilling fluids. I knew nothing about drilling, I didn’t know what drilling mud was, but I was desperate for a job, and I grabbed the opportunity with both hands. So, I didn’t make a conscious decision to move into the drilling industry – it just happened.
As I look back over the past 35 years, I consider myself to be extremely lucky because the lessons that I learned in those early days have been foundational for my career going forward.
GT: What was drilling like in the 1980s and 1990s?
CR: South Africa hosts the deepest gold mines in the world and so, many boreholes were drilled to depths of up to 4000 m (13 123 ft).
Back in those days, the South African gold mining industry was dominated by four major gold mining companies and each of those companies had its own ‘in-house’ drilling company that did the bulk of its drilling. The in-house contractors got work whether they were good or bad, it didn’t really matter because they were part of the family.
In addition, each of the major mining companies also owned their own equipment manufacturing company and it was very difficult for independent contractors or suppliers to get work from the four dominant drilling companies.
I am sure that many people would disagree with me, but I believe that the development of the industry was inhibited because of the structure of the industry.
Once the downturn hit in the late 1980s, deep gold exploration work dried up and the big in-house companies had to bid for shallower work in other sectors of the industry. They simply could not compete with the smaller, more agile independents and they all eventually closed.
GT: You mentioned that South Africa hosts some extremely deep holes. Please elaborate on that and share some stories from the 80s and 90s. What is the deepest hole you know of in the region?
CR: One of the first deep holes I worked on as a young mud technician, was a 3800 m (12 467 ft) gold exploration borehole. The contractor was having a problem with an over-pressured shale band, and I was asked to help stop the caving. I decided that a small increase in mud density would solve the problem and so I set about mixing up the mud system.
In those days, B-size wireline drill rods couldn’t reach deeper than 1400 m (4593 ft), so the borehole was drilled conventionally with a 3 m (9.84 ft) single-tube core barrel. Typically, it would take 45 minutes to fill the barrel, then 13 hours to pull and another 12 hours to lower the drill string! I had to be on site when the bit was on bottom, so I drove to site, watched them drill for about an hour and then I drove back to my office for a day’s work while they pulled and lowered. These deep and ultra-deep boreholes were very costly to drill and always involved a great number of deflections. All deflections
were done using steel wedges and so many boreholes took several years to drill.
I was also lucky enough to have worked on some small oil rigs that were brought into South Africa to drill some ultra-deep boreholes. The boreholes had to be drilled very quickly and so they were piloted using tricones to approx. 3000 m (9843 ft) and then cored 4.8 in (12.19 cm) to the target depth.
As with any new technology, the first few months were not terribly productive.
‘I consider myself to be the luckiest guy in the drilling industry because I have had exposure to a number of aspects of our industry and that has pretty much shaped how my career has developed.’
Open-holing the top sections through extremely hard rocks was difficult and slow and once the rigs got to coring, bit life was a huge problem. Eventually, they got things right and they did some amazing work.
I remember setting up the mud system on one of the last boreholes that the rigs drilled on the day they spudded. I was again on the rig 84 days later when the borehole was at 4048 m (13 280.84 ft)! 4048 m in 12 weeks –that has to be some sort of record.
GT: You managed a company called Professional Diamond Drilling Equipment (Pty). What products did you manufacture?
CR: After I left the mud business, I met up with an old friend, Graham Martin. We were both looking for something to do and we decided to purchase a company called Professional Diamond Drilling Equipment (Pty) Ltd (PDDE). PDDE was the Southern African agent for JKS Boyles, a very famous Canadian drilling equipment manufacturer. The products that JKS Boyles manufactured were a perfect fit for the Southern African exploration industry at that time and so the business grew very quickly. Graham was the most incredible business partner; we were business partners for 31 fantastic years.
In 2000, we saw an opportunity to purchase a diamond bit manufacturing company and that decision was probably one of the most significant decisions that we ever made. As a major manufacturer, we became a significant player in the Southern African industry, so much so that our company was acquired in 2003 by the Craelius Division of Atlas Copco.
GT: What are the main aspects of your current business - Colin Rice Exploration and Training?
RC: I consider myself to be the luckiest guy in the drilling industry because I have had exposure to a number of aspects of our industry and that has pretty much shaped how my career has developed. I guess my current business involves three main areas of activity:
• Consultancy: I do consulting work for a number of mining companies around drilling issues; I do a lot of development of tender specifications and evaluation of tender submissions. I have done a number of reviews of exploration projects, and I have developed a lot of cost models for a number of mining companies.
• Safety: I am involved in safety auditing for many different companies in several different countries.
• Training: The third aspect of my business probably developed because of my teaching background. Back in 1987, I started presenting training programs for geologists aimed at improving their understanding of basic drilling principles.
Over time the demand for courses on safety and drill site supervision increased and so I have developed and presented a fairly wide
range of training programs, for many mining companies, for industry organizations, for universities, and even for contractors.
As I have aged, my appetite for travel has diminished and so about six years ago, I migrated all of the programs onto an online platform. We now have people from all over the world involved in our programs.
Training is one of the most satisfying parts of my work – there is nothing more satisfying than seeing people being able to apply a skill or a piece of knowledge that you have taught them. I really love the training part of my business.
GT: Please share with our readers about DrillSafe Southern Africa. How did you start the initiative and what has been its impact? What’s its ultimate goal?
CR: DrillSafe was originally launched in 2013 as an attempt to improve safety performance in the industry. I have always believed that there is nothing proprietary about safety – if I know something that can save an arm or a life, it is my obligation to share that information.
Initially, we published technical articles with a safety focus, and we published safety information – incident and accident reports. Through a number of sources, I was given
incident and accident reports from many different places in the world. I would then ‘sterilize’ the report by removing all references to a person, a product, or a place. All I wanted were the learnings from the incident so that we could share the information on the website and hopefully prevent a repeat.
The website took off very quickly, but after a couple of years, some mining companies decided to no longer share incident and accident information across the industry and the initiative lost momentum.
By October 2017, I had been involved in a great number of safety audits and investigations and I became increasingly frustrated at seeing the same safety issues time and again at every project I visited. Large and small contractors alike had the same fundamental lack of understanding of basic safety principles and thus I decided to refocus and relaunch DrillSafe.
I believe that one of the biggest problems our industry currently faces is a lack of skills and contractors have people working on drill sites who have no, or very little experience or training. All training given to new entrants is focused on getting them onto site - little is focused on technical or safety issues. Every driller is expected to complete a pre-start check of his rig, but often the driller does not really know how to identify a defect. In many cases the driller has not been trained to identify defects in equipment or processes, and critical safety issues are not identified.
To help with this, I decided to create a series of ‘Drillers Resources’. These are a series of A3 posters that deal with specific safety aspects, such as how to inspect a flexible hose, how to inspect a steel wire rope, the risks associated with pressure relief valves and so on. These resources are available for free on DrillSafe.
Our overarching objective of the initiative is to encourage the sharing of knowledge and experiences, and we are fortunate to have the support of remarkable companies like Anglo American and Major Drilling who believe in the initiative. I am very proud of DrillSafe and I hope that more people in the industry use the resources on the website.
GT: How do you manage to adequately identify drill site hazards and associated risks when so many diamond drilling contractors refuse to reveal incidents, occurring at their drill sites?
CR: Despite what I said earlier, over the past few years there has been a dramatic shift in attitude among a number of mining companies and they now very openly share
information. I am part of a couple of ‘safety groups’ made up of safety leaders from all the major mining companies, Anglo American, Rio Tinto, Newcrest, First Quantum, Newmont to mention only a few. We meet on a monthly basis and have amazing discussions on safety issues, equipment and trends, and experiences and learnings are openly shared.
GT: What are the most common drill site injuries and how to avoid them?
CR: Instead of talking about common injuries, I would rather use this opportunity to talk about the significant risks on drill sites! I believe that drill site safety revolves around four key elements:
1. the equipment that is used, the drill rig, compressors, boosters, rod loaders, etc;
2. the people who interact with the equipment on a day-to-day basis;
3. the activities or procedures that take place on a routine and non-routine basis and,
4. the local environment that may alter the way that certain procedures are conducted.
All these elements are interrelated, and all affect one another, but very frequently mining companies and contractors focus only on equipment safety.
We must never forget that equipment doesn’t kill people, processes kill people. Very seldom do we hear of a catastrophic equipment failure in the industry, we only hear about failures in procedure that have caused an accident or a fatality. We have to rely on people, drillers and offsiders to conduct the procedures and everyone in the industry is acutely aware of the shortage of skills and experience in the industry.
Our greatest risk, I believe, is not the equipment that we use, it is the people that use and maintain it.
GT: Considering your extensive knowledge and experience, can you think of a drilling development that at one time was hailed as revolutionary, but turned out to be a fad lost to time?
CR: This is a difficult one, I don’t think I can identify one particular development that failed. Many lessons learned from an apparent failure have helped develop a new product or technique.
I have always tried to approach drilling issues from a technical perspective. Everything that happens on a drill site can be explained in terms of physical principles and
so, I am in full support of companies that innovate and try new processes or techniques. Unfortunately, many people often put more energy into explaining why something won’t work than they do trying to make it work - I find this attitude incredibly frustrating.
Back in the 1980s many of the old ‘conventional’ drillers said that wireline would never work – well it did!
GT: What is your experience with directional drilling?
CR: I got involved in directional drilling, not as a driller but as a supplier of technology to drilling contractors. Back in the early 1990s, all directional surveying was done with filmtype magnetic survey tools. There was only one major manufacturer and in South Africa, the sole distributor was very expensive, so we were asked by some of our customers if we could source the same equipment. It didn’t take much effort to source the same equipment at very much reduced costs and that was our entry into the surveying business. Eventually, we started a contract survey company, Borehole Survey, that used to survey very deep gold and platinum exploration boreholes using film-type multi-shot tools.
Surveying a 3500 m (11 483 ft) deep borehole using a film-type multi-shot tool was fraught with difficulty and in 1995, we decided to purchase two electronic multi-shot tools from Reflex, the Swedish manufacturer. These were the first electronic survey tools in sub-Saharan Africa and they totally revolutionized the deep hole surveying in Southern Africa.
satisfying projects that I have ever been involved in. This was a pivotal moment as directional drilling became a significant part of our business.
At that time, one of the large gold mining companies was drilling some very deep gold exploration boreholes in South Africa. On two of these holes, very long deflections were required to reach some hard to get to targets, so we got involved in running small diameter, 23/8-in, downhole motors at depths of 3000 m (9842 ft). Again, this was brand-new technology applied in very difficult conditions.
One of the boreholes was a remarkable success and the other was not so successful! In the second one, we got a bit ambitious with the build rate and we created a dogleg at very great depth that eventually caused the borehole to be abandoned.
Today, there are numerous successful directional drilling techniques that are widely applied in deep exploration boreholes. I think that the industry has developed a good understanding of what is and isn’t possible and I believe that directional drilling has a massive role to play in the exploration industry.
GT: What is the state of the drilling market in South Africa nowadays? Which are the main players, what are the biggest projects?
We became the local agent for Reflex and at one point our little business was responsible for selling 25% of Reflex’s production of electronic survey tools. This was how I started understanding the survey business.
One of our major customers was a large coal mining company that was attempting to develop a technique for drilling surface-to-inseam boreholes for dolerite detection. I believed that the steering technology that they were using was inefficient and I convinced them to change to a mud pulse telemetry system. This technology was well-established in the oil and gas industry but had never been used in a mining application before.
Eventually, they decided to switch to the new technology and the project really took off. The value of the information that the boreholes provided to the mining company was immense and I consider that particular project to be one of the most successful and
CR: South Africa is not enjoying its finest times in terms of exploration and mining, policy uncertainty and many other structural problems make investment in long-term projects unattractive. Most major mining companies have left the country and there is not as much greenfield exploration taking place as in other African countries. By far, the bulk of exploration work is ‘on mine’, essentially for ore body extension.
Drilling rates are extremely low compared to other countries and local contractors have had to become incredibly efficient to survive and make money. Companies like Rosond Exploration, Zaaiman Exploration, Hall Core Drilling and Master Drilling are among the largest local contractors.
GT: Building from the previous question, is there anything that the global industry can learn from the South African market?
CR: Wow, this is potentially a very dangerous question. From a technology point of view, the South African industry just does not have the critical mass that other countries have and so investment in technology has been far short of other countries. Having
Major Drilling is one of the world’s largest drilling services companies primarily serving the mining industry. We maintain field operations and offices in Canada, the United States, Mexico, South America, Asia, Africa and Australia.
said that, one South African contractor, Rosond, has undoubtedly led the way in terms of true, hands-free drilling technology. The company currently runs a massive fleet of state-of-the-art drill rigs involved in diamond core drilling, grade control and rotary percussion applications. To my knowledge, Rosond’s fleet is by far the largest of its kind in the world and that is something that they can be very proud of.
I would also add that in many respects standards of safety on some South African exploration projects are as good if not better than in many other countries. I think it is fair to say that South African contractors have embraced safety initiatives, therefore contractors are no longer part of the problem –they have become a part of the solution to improving safety standards.
GT: Various companies in our industry are releasing autonomous drill rigs and rod handlers. Please share your opinion on these developments… Do you think they can make the work of drillers truly safer?
CR: Mining companies and many manufacturers perceive drill string handling to be the most significant risk in an exploration drilling
operation, so ‘hands-free’ rod handling became the target. Unfortunately, mining companies did not define what hands-free means to them and many systems were released that were not at all hands-free. A great deal of time and money were expended for very little reduction in risk. In fact, many systems increased risk.
Designing a mechanical rod handling system for rotary percussion and RC drill pipe is relatively easy and many rod handlers have been developed that significantly reduce risk and make drilling safer. Mechanically handling wireline drill rods, however, presents several additional challenges – the requirement for accurate thread alignment, the requirement to clean and lubricate threads, and for correct compensation when making or breaking a connection are critical and unless these requirements are addressed, the consequential damage could easily outweigh any benefit. Some manufacturers have successfully managed these challenges and they will undoubtedly make the work of drillers safer.
I do not believe that drill string handling does in fact present the greatest risk in a wireline drilling operation. I think that wireline retrieval represents the greatest risk but
very little work has been done on mechanical inner-tube handlers. I have recently seen a couple of add-ons to existing drill rigs that assist in inner-tube handling, though I do not believe that they are the complete answer. The industry must be encouraged to look at solutions. I am absolutely convinced that some workable systems will begin to be introduced in the short term.
We must not forget that every piece of technology that we add to drill rigs brings with it its own set of risks and it is essential that these risks are fully assessed and mitigated. If we don’t, we will continue to hurt people in our industry.
GT: Teaching the new generation of drillers and mentorship are the cornerstones of our industry. How should companies approach teaching the ropes to newcomers? What can young drillers do to develop their skills and knowledge?
CR: I think that this question hits the nail on the head. Without a doubt, people represent the greatest risk in any drilling operation. While ‘human-free’ drills are the objective, we will still need human beings to interact with drilling equipment for the foreseeable future and the only way that we can manage
the associated risk is to ensure that people are correctly trained.
Based on many interactions with large and smaller contractors, training is focused on two objectives: getting the person approved to get onto site and teaching the person enough that they can produce meters. We need to do more than just this, we need to deepen drill crews’ understanding of basic drilling principles, the equipment, surface and downhole, that they use and how all systems in a drilling operation affect one another.
GT: What are the latest developments in drilling fluids and additives? Is there anything different today compared to when you first entered the industry?
CR: Bearing in mind that drillers used water instead of drilling fluids back when I started, I would say that there have been some significant changes in the drilling industry over the years.
One major shift is the increased emphasis on environmental considerations. Nowadays, drilling operations are much more environmentally conscious than in the past. In the old days, we didn’t pay as much attention to environmental impacts, but today, there’s a greater awareness of the need for responsible practices.
Another development is the improved understanding of fluid technologies. Drilling companies now grasp the benefits of using additives, both in terms of managing geological risks and enhancing drilling efficiency. This understanding has grown significantly since my early days in the industry.
While I don’t closely monitor the mud industry anymore, it appears that the industry has become quite competitive in recent times with some new companies making significant inroads, challenging the established players.
GT: What is the most important lesson that you have learned for yourself during your career?
CR: I guess there are three lessons that I would pass on to any young person entering the industry:
1. All business is based on relationships. relationships take many years to develop but they can be destroyed
in seconds. Build relationships and value them, don’t destroy them.
2. Trust is everything. If your customers trust you, your chances of getting work from them are very good. Always act with integrity, always under-promise and over-deliver.
3. Never stop learning. Use every experience, whether it is a good or a bad experience, as a way of deepening your understanding. Ask questions and then ask more and more, but do not believe everything that you hear on a drill site!
GT: You claim that in order to be good in the drilling business you have to know the process from the beginning until the end. What are the main things in your view?
CR: As I mentioned earlier, an exploration drilling operation is made up of a great number of systems that affect one another and the better our understanding of these systems and their relationships, the more effectively we can manage an exploration drilling project.
None of these systems are terribly complex, but often, I see cases where a driller does not understand the most fundamental aspect of the work.
I recently completed a review of a very large number of drill rigs and not one of the drillers could tell me what their pump output was – not one!
Consequently, none of them knew what their annular velocity was, and none had any real idea of what flow rates should be.
These are very simple concepts and so to answer your question, the main things that we need to understand are basic drilling principles.
GT: You’ve had several truly successful businesses in your career. What do you think is the most important personal quality to run a successful business in the industry?
CR: I am very flattered that you believe that I have run successful businesses. I am not sure how one measures success in business, but if I have been successful then I guess my appetite for work has been a major contributor.
I truly love what I do, and I have absolutely no problems getting up in the morning to face the day.
I must also add that no one runs a business or develops a career in isolation, many people have been pivotal in my career: my wife held my family together all the times that I was away on business; Andre Ferreira gave me my first job, the late Mario Paro gave me my first order for drilling fluids in 1985; Stu MacGregor asked me to audit an exploration project that he was managing and that opened up the world of safety auditing for me; Graham Martin has been my business partner for over 30 years, and my daughter Erin played a huge role in developing the training part of my business. Without these people, I would not be where I am now, and I am forever grateful for their influence and help.
GT: Where are you currently located?
CR: My wife and I moved to Melbourne in April because all my children and grandchildren have been here for eight years now. We have a very close family, and it is fantastic to be able to spend a great deal of time with them. We have a beautiful home here and over the next couple of years, I would like to wind down so I can spend even more time with my children and grandchildren.
GT: How is a normal working day for you nowadays?
CR: I am still working on several projects in South Africa and other African countries, so my day usually starts at about 3 p.m. and runs through until about 10 p.m.! The time difference between Melbourne and South African time takes some getting used to! I am not sure that I have adapted fully yet, but I am grateful that I have so much work.
GT: What are your interests outside of the drilling industry?
CR: My wife would tell you that I have no interests outside of the drilling industry! I am extremely lucky that I am kept very busy on projects for the wonderful companies that have supported me over the years and I learn something new from every project I do. I guess, maybe my wife is correct – the industry is my hobby! C
AVAILABLE NOW. WORK SMARTER NOT HARDER.
The updated Quick Descent™ Head retains roller latching for reliability and adds automatic latch retraction and improved valving for maximum speeds. Combined with easier maintenance, it is a step ahead of the industry standard Link Latch™.
• Sealed bearings and simplified maintenance
• System descends 32% faster than our previous head design
• Threaded connections and no assembly pins
More than 100 years of experience combined
by David Bradley, Co-Owner at RJLL Drilling
RJLL Drilling (RJLL) was founded in 2014 by Réal Lemoine and Jérôme Lefebvre. They both started working for Bradley Brothers at the age of 16, climbing the ladder from helpers to drill rig operators to supervisors. In the last years of Bradley Brothers, Réal was the Canadian Operations Manager and Jérôme was the Arctic Superintendent. They worked for Bradley Brothers for 36 years up until Major Drilling bought the company in 2011.
Both Réal and Jérôme worked for Major Drilling for a few years, but the different culture between a private and public company was too difficult for them to bear, so they decided to start RJLL Drilling in 2014.
Réal and Jérôme’s objective at the time was to have a small but efficient drilling company that would surpass the industry standards. Since their sons were also drillers, they too saw the opportunity to build something with them and eventually pass the company down for generations.
In 2019, Réal and Jérôme asked David Bradley if he would like to join them on the adventure. Having worked together in Bradley Brothers for over 20 years, it was an easy decision for David to make. So, in January 2020, David officially joined as a shareholder. At the time RJLL had three surface drills in operation, one in Finland and two in Canada.
David had worked for his family business - Bradley Brothers for 23 years. He started working on drills as a summer job at the age of 13, then after college, he worked for six years as a helper and then as a drill rig operator.
At the age of 26, David started in the office as an assistant contract manager. A couple of years later, he became an operations manager for the Canadian operation and at the age of 30, David became VP of Operations and a co-owner of Bradley Brothers. When the family business was sold in 2011, David spent the next nine years as a co-owner of a management consulting firm until he joined RJLL.
In the fall of 2020, Marc-André Larouche joined the company as Financial Director and became a shareholder of RJLL in July 2021.
Powered by the Bradley Brothers culture, RJLL is committed to providing high-quality service and exceeding the expectations of our customers.
As of today, we cover mainly the provinces of Quebec and Ontario, the Canadian Arctic, and Finland. The main office is based in Rouyn-Noranda and we have a branch office in Timmins, Ontario. We do helicopter-supported drill jobs, shallow holes and deep hole drilling. We specialize in wedges, directional drilling, and complicated projects.
RJLL also has two important Joint Ventures. The first is RJLL/Nuvumiut with the Qaqqalik Land Holding Corporation out of Salluit, which covers the Québec Arctic. Another JV is with the Anishnabe Community of Lac Simon, which covers their territory in the Abitibi region.
We believe that our strength is our employees. RJLL has 145 employees as of today. We have great people in our administration and in the shop. Our in-field team is wonderful. Most of them have worked with Bradley Brothers and have many years of experience, and specialize in heli-portable work, deep hole, and directional drilling.
Everyone in the company is committed towards excellence. When a situation arises from a project, our approach is not to hide anything from our customers. We prefer to be honest and share with the client the information we gathered and then find and propose a solution that will make sense to all parties involved. We believe that the way management and employees react when facing an issue makes a big difference in customer satisfaction.
RJLL has 20 surface drills in operation. Our equipment consists mainly of drills made by Usinage Marcotte (learn more on p. 28), which are based in Val d’Or. We have 14 HTM 2500 rigs that can drill down to 2500 m (8202 ft) in N-size. We also have six Mancore 900H or equivalent that can do heli-portable and mobile drilling work with a depth capability of up to 900 m (2953 ft). All our drills come with the proper equipment that can move them to different hole locations. Our equipment of choice for such tasks are the Caterpillar D6-T tractors. Additionally, RJLL supplies the proper equipment to carry the crews to the drilling location. Our fleet consists of several Polaris 6x6 and Argo ATVs, and Prinoths and other snow machines in the winter. It is very important for us to have good and well-maintained equipment for the safety of our crews, particularly when working in the Arctic wilderness.
We believe that all drilling projects are important, yet we are extremely proud of the following:
We are presently working on a heli-supported job where we will have five drills. Considering that in the winter, we only have about eight hours of daylight to do drill moves with a helicopter, we are building tracked platforms, which will be able to carry the drills to new sites around the clock and maximize productivity. What makes this project special is that we have to be able to dismantle the platform into parts of no more than 2000 lb (907 kg), so we can sling them to the project site with the helicopter. Once there, our team will reassemble the platform and install the drill on top. The platform will be powered by the drill engine. This for us is adapting to our customer’s needs!
Going back in time over our many successful projects, the first one that stands out, in particular, is the Wasamac project with Yamana Gold in Rouyn-Noranda. We are truly proud that we solved the challenges we had on this specific project. All the drilling was being done in a residential area where houses were very close. One of the main challenges for this job was to work with Yamana in finding a way to minimize the sound of the drill to a point that had never been achieved before. Basically, the challenge was that the residents wouldn’t hear the drill at all!
When we started thinking of a solution to this challenge, there were two considerations: the first one was to eliminate the old-fashioned sound mitigation walls that were very heavy, therefore not safe to
manipulate, and build an effective sound mitigation system that was extremely efficient. We worked with a great supplier that had the sound mitigation expertise we needed. They helped us find the right solution for this specific project, while Yamana did all that could be done with the community; and they are having great success with project acceptability.
After a few months of planning and another month of testing, we surpassed our objectives. The system we developed was great because it was installed directly on the drill so there was no need for manipulation from the crews once set up, but if manipulation was needed, this system was extremely light. And the efficiency was excellent! At 10 m (32.8 ft) away from the drill, the noise was less than 60 decibels (for reference: roughly the level of a normal conversation). At 60 m (197 ft), you could barely hear the drill.
Another project we are very proud of is the O3 mining project in the Val d’Or area. When we began work on this project, we had to drill 2500 m (8202 ft) holes in soap stone. We were the first contractor to be able to get to the targeted depth.
To be able to go through this rock formation, our supervisors worked in close collaboration with mud suppliers to be able to find the right mixture that would allow to drill at depth without having the rock formation squeeze and stick our rods in the hole.
At the early stage of RJLL, we did a program for BHP Mining. Just qualifying to work for BHP made us proud because it meant that our organizational structure in safety and environment was excellent. To us this meant we could work for both major and junior mining companies.
Our next development phase is underground drilling. The objective is to have a total of 10 underground rigs in the Canadian market. Once we achieve this goal, we will be at our sweet size we had aimed for in January 2020 with 20 surface and 10 underground drills. In parallel, we are looking to develop in Scandinavia and other parts of the world. Outside of that, our main goals are to continue growing a great business with great values and to continue building good relationships with our Joint Ventures, customers, suppliers, and employees. This way we can become one of the leaders in the industry. We are not aiming to become the biggest drilling company, but we are aiming to provide exceptional quality!
Our dream would be to surround the next generation with great people and be able to pass it along! C
For more information
Visit: rjll.ca
Introducing CoreMatrix™, the new redesigned bit line-up from Di-Corp Drillers Edge.
The new CoreMatrix™ bits from Di-Corp are re-engineered for enhanced bit life and faster penetration rates across every ground condition.
With 21 matrices and a comprehensive matrix selection chart to guide you, it’s easier that ever to find the perfect CoreMatrix™ bit for your drilling conditions. Available with three waterway configurations and several specialty options for Abrasive conditions, Extended life, and Free-cutting matrices.
Drilling is tough. Get rugged to the core with new CoreMatrix™ bits by Di-Corp Drillers Edge.
by Coring Magazine’s team
Disclaimer
Coring Magazine is proud to present the new statistics of ‘Top mineral exploration drilling contractors for 2022’. Companies are classified by the number of meters achieved only through diamond drilling. These results were provided and confirmed by the companies themselves and have been rounded to whole numbers. The statistics present results for 2022, as at the time of publication (November 2023), complete data for 2023 was not available.
Other companies qualify but are not listed here for reasons beyond our control. We did our best to contact and include as many diamond drilling contractors as possible. However, many did not respond to our invitations; others were omitted per their request. Everyone is invited to get in touch and submit their numbers as long as their results equal or exceed 50 000 diamond drilling meters per annum.
Coring Magazine cannot be held liable for any errors or inconsistencies presented in this report.
In 2022, a wave of inflation washed across the world. The costs of labor, materials and fuel skyrocketed. Nonetheless, the interest in drilling services remained high.
2022 brought a slight contraction of over 5% in the meterage achieved by diamond drilling contractors in these statistics. We should stress that this contraction does not reflect an industry issue rather it may be a sign of increased drilling efficiency. This theory is supported by S&P Global data, as the approximate number of completed drillholes jumped to 70 008 in 2022 vs 69 000 drillholes in 2021. The number of drill projects globally climbed to 1751.
The economic conditions of 2022 have also reflected in the revenue reported. There is an increase in the range of 15-20% compared to 2021, possibly fueled by the increase of the cost per meter drilled globally. Reported profits, however, paint a complicated picture. Certainly, there are many companies with double-digit and even record-breaking increases, while others reported tame gains.
The number of drill rigs owned by the contractors in this list remains close to 2000, mostly unchanged from 2021. Most of the participating companies have augmented their fleets with new drill rigs, however. Rig utilization for the several companies that have reported it remained well over 75%.
Many companies also increased their staff in 2022, though some challenges to recruitment remain. Training and safety continue to be a focus for contractors, alongside ESG. Injuries remain low, and companies (including some that have chosen not to provide data) continued the zero-LTI streaks set in 2021.
Boart Longyear takes the first spot with reported 2 516 765 m (8 257 103 ft) achieved through diamond drilling, a less than 0.1% increase from the results of 2021. According to the annual report, the drilling services division of Boart Longyear remains the bigger portion of the company’s business and achieved nearly 20% growth in revenue and over 25% in EBITDA for FY22 (ended in Feb. 2023).
Major Drilling achieved 2 381 663 m (7 813 855 ft) through diamond drilling in calendar 2022. This result represents an increase of ≈40 000 m (131 234 ft) from 2021. Drilled meters for RC in 2022 were 1 193 372 m (3 915 262 ft). The company has 600 drill rigs (450 diamond), almost unchanged from 2021. Revenue and profits for FY22 (ended in April 2022) have increased by over 50%, while both revenue and profit for FY23 have increased by over 10% from 2022.
DDH1 Limited has skyrocketed to the third spot, partly due to the completion of the industry-changing merger with Swick Mining Services. The new entity, also consisting of DDH1 Drilling, Strike Drilling and Ranger Drilling, has achieved 2 123 267 m (6 966 099 ft) in diamond drilling and 1 283 156 m (4 209 829 ft) through RC for 2022. The group has a total of 183 drill rigs (149 diamond). DDH1’s earnings for FY22 increased by 14%, while EBITDA gained 10% over FY21. In late 2023, DDH1 Limited announced that it will reshape the industry again by merging with Perenti.
Orbit Garant Drilling has operations in North and South America and Africa. In FY22, the company achieved 1 356 033 m (4 448 927 ft) from diamond drilling and another 457 970 m (1 502 526 ft) through RC. These results mark an increase of ≈10% from 2021. Orbit Garant Drilling’s fleet was 217 rigs with 199 dedicated to diamond drilling and 18 to RC. These numbers were smaller than in 2021, because of a fleet upgrade, where six older rigs were retired from the fleet, and three new ones were purchased. Revenue for FY22 (ended on June 30 2022) was a record CAD 195.5 million, signifying a 19.7% increase from FY21.
For 2022, Foraco International reported 1 017 485 m (3 3382 05 ft) achieved through diamond drilling and 393 348 m (1 290 512 ft) for RC. The result for diamond drilling represents ≈5% increase from 2021. The company fleet consists of 302 drill rigs. For FY22 (ended Dec. 31), Foraco reported a 23% increase in revenue and significantly higher profitability compared to FY21. The company’s operations have grown the most in South America, as demand for drilling services has increased tremendously in the region.
Explomin Perforaciones is among the largest companies in Latin America. In 2022, they achieved 604 194 m (1 982 264 ft) through diamond drilling. This result represents a decrease of less than 4% from 2021. The company’s fleet, however, has increased to 107 rigs (101 diamond). Explomin has reported working on 26 diamond and four RC drilling projects in 2022.
Hy-Tech Drilling achieved 594 422 m (1 950 203 ft) through diamond drilling in 2022; a decrease of less than 2% from the previous year. The company’s fleet has grown significantly to 69 diamond drill rigs from 46 in 2021. Furthermore, Hy-Tech Drilling’s number of projects has more than doubled to 35. Hy-Tech Drilling also reported excellent revenue of CAD 124.7 million for 2022.
For 2022, Canadian contractor Forages Rouillier Drilling reported a decrease in meters achieved through diamond drilling to 582 769 m (1 911 972 ft). While this is a double-digit decrease compared to the results from 2021, the company has increased the number of diamond drill rigs to 60 (50 in operation; 10 on standby).
Geodrill and their subsidiary in South America Recon Drilling reported 407 103 m (1 335 640 ft) achieved through diamond drilling in 2022. The results for RC drilling are 942 410 m (3 091 896 ft). Although the meterage for both diamond and RC is lower compared to 2021, Geodrill has a larger fleet – 76 drills (70 diamond/multipurpose and six RC), drastically more projects (48 vs 25), and has reported back-toback record fiscal years.
Capital Drilling achieved 368 958 m (1 210 492 ft) through diamond drilling in 2022. Of these, 190 591 m (625 299 ft) were through underground diamond drilling. The results represent a significant increase from 2021 driven by major contract renewals. Capital had 15 projects and 57 rigs. For FY2022 (ended March 2023), the drilling division contributed USD 209 million in revenue; a 21% growth from FY21.
This year, Team Drilling is celebrating its 15th anniversary and over 2960 days without a loss time injury. These achievements come on the back of a strong 2022 with 210 000 m (688 976 ft) achieved through diamond drilling, a fleet of over 40 rigs (24 diamond), and 13 diamond drilling projects across Canada.
One of the biggest Turkish contractors, Ortadoğu Drilling, reported 193 249.7 m (634 021 ft) achieved through diamond drilling for 2022. The company services the Eurasian region with its in-house-manufactured 35 drill rigs (29 diamond), and it is one of the few contractors that can produce everything required for a drilling operation. Ortadoğu Drilling had 23 diamond drilling projects last year.
Hall Core Drilling is the only contractor in this list with one project – the platinum mine in Limpopo, South Africa. In 2022, the company achieved 161 331.51 m (529 302 ft) through diamond drilling; a tremendous increase of nearly 60% from 2021, fueled by the expansion of drilling operations in Limpopo. As a result, Hall Core’s fleet more than doubled to 35 diamond drill rigs.
Brazilian contractor DrillGeo has achieved 124 629.25 m (408 889 ft) through diamond drilling and 9325.12 m (30 594 ft) by RC in 2022. The company is a new entry into Coring’s statistics, boasts a fleet of 36 rigs (34 for diamond drilling) and had 14 diamond drilling and one RC project. C
Helicopter Portable Diamond Drill
1400 Meter NWL Depth Capacity
Cummins Power Unit 160 or 260 HP
‘P’ Size Rotation Unit & Clamp
Safety Package: Full Guarding, Multiple E-Stops, Interlock Rod Guard & Power Lock-Out
Available in Heli-Portable, Skid Shack Mounted and Track Carrier
A meeting of minds between Australia and Sweden
The story of Explorac RC30 Smart began in 2018 when contractor Ausdrill was faced with a strong demand from the exploration industry for automated drill rigs. They decided to partner with Swedish Epiroc, as they had worked closely in the past on the development of other rigs. The goals were lofty from the start: keep operators away from the danger zones, develop advanced interlocks and monitoring for both processes and safety, while still providing improvements to reliability and maintenance. All of this had to be done fast.
About five years later, Epiroc introduced to the world the Explorac RC30 Smart surface drill rig for Reverse Circulation. It promises to be a robust and reliable solution with highly automated functions, better capabilities both in terms of safety and productivity, and advanced rod handling functionality. All of this comes without any compromises to performance, as Explorac RC30 Smart provides 30 tonnes (67 442 lb) of pullback delivering sufficient capacity to take on deep work while not being excessive for shallower projects. It is available on a robust truck carrier which offers great mobility and gets you right where you need to be with the minimum of fuss.
Perhaps the first and most important innovation for Ausdrill could be summarized with the motto ‘Hands off steel’ or removing manual work from rod handling. For deep holes, rod handling is a complicated, dangerous, and tiresome process often requiring two people. There is the added challenge that automated rod running needs to be faster than manual work, otherwise drillers would continue doing it by hand to save time. The engineers at Epiroc obliged.
The Explorac RC30 Smart’s automated rod handling seamlessly combines automated sequences and embedded interlocks to execute the repetitive task of rod feeding. Not only does the automated rod handler improve safety but it also reduces fatigue and crews are freed up to perform other tasks. Wear and tear on consumables is also reduced, as the automated rod handler executes the task in exactly the same way every time, so uptime is increased and predictive maintenance is easier.
All of this happens with the push of a button on the Explorac RC30 Smart controls.
To remove drillers from dangerous situations also means smarter controls. Explorac RC30 Smart builds on the RCS platform, which has been tried and tested across the industry, by including radio remote control with multiple interlocks, a software-based safety system, and an emergency stop button, which protects both the rig and the operator during autonomous operation. Having the controls away from danger adds the benefit of reduced noise and vibrations, improving the work of drill crews.
Explorac RC30 Smart comes with a litany of other smart features, such as mast centralizers with variable grip force and an advanced breakout system with automatic application of thread grease. All of these help to optimize the life of drilling consumables and the need to go into the hazardous area is reduced.
Of course, it is sometimes necessary to approach the drill rig. Explorac RC30 Smart features high-visibility LED safety lights that indicate rig-status and whether it’s safe to be near the machine.
With the rapid development of new drilling technologies, scalability is an important part of Explorac RC30 Smart. The rig was designed to be scalable, meaning it can be expanded or upgraded with new automation features and functionalities over time. Epiroc’s excellent global after-sale support with both genuine parts and services safeguards the productivity of the rig. This ensures that contractors, such as Ausdrill, can easily support and upgrade their Explorac RC30 Smart rigs and get the highest possible returns on their investment.
Improvements to safety, smart and autonomous features and technological breakthroughs make a real change only when the rig has the performance to match and exceed the vast demands of exploration companies. With the 30 tonnes (67 442 lb) of pullback force, Explorac RC30 Smart offers the largest pullback capacity on any Epiroc exploration rig to date. This rig makes it possible to quickly and safely collect core samples down to a depth of 600 m (1968 ft).
The mast is 11.55 m (37.89 ft) long (including the jib) and can be angled between 45° and 90°. There is also a unique angle package with internal locking cylinder, meaning that setup can be performed quickly and safely from a distance.
‘We
have listened to the market and pushed to reach the high level of automation that drilling companies require. Drilling contracts today are more demanding than ever, both big and small contractors must meet a high safety level while maximizing the return on capital employed - automation simply makes sense. It removes personnel from dangerous environments, at the same time changing the game when it comes to operational efficiency and planning’, explained David Benton, Epiroc’s Global Product Manager for Exploration.’
Explorac RC30 Smart comes with a standard on-board 35-bar Atlas Copco two-stage compressor and cone splitter. The truck-mounted pipe rack for the automated rod handler can hold up to 15 pipes of 6 m (20 ft) in length (OD 4.5 in or 11.43 cm). The maximum rod holder clamping diameter is 124 mm (4.88 in). The power unit is a diesel CAT C18 Tier III ACERT ATAAC with a maximum torque of 2769 Nm at 1800 rpm (2042 lb) with an output of 522 kW (700 hp) at 18002100 rpm.
In total, Explorac RC30 Smart weighs 30 000 kg (66 139 lb) including a full rod rack, so it can be fitted on a variety of truck models.
Developing the breakthrough Explorac RC30 Smart required a great deal of effort from both Ausdrill and Epiroc, recounted Eric Gobbert, Senior Manager Business Development and Improvement of Ausdrill. He shares that in the first years of the collaboration, there were problems with parts wearing more quickly and the rig not staying in auto-drilling mode.
Finding solutions required open communication, innovative thinking, and a great deal of understanding of the specific requirements that make a great drill rig, especially with COVID-19 causing delays and wreaking havoc across the world. Despite all the challenges, the prototype Explorac RC30 Smart has now been delivered to Ausdrill. Early results show great promise but require some adaptation from drillers and technicians. One thing is clear, Explorac RC30 is merely the beginning, a strong foundation, for innovations towards the complete automation of the drilling process from start to finish. C
For more information Visit: epiroc.com
The Christensen CT20 is ready to take on core-drilling jobs in the toughest conditions. This safe, ergonomic, and versatile rig is available truck- or crawler mounted. The Christensen CT20 has all the power and capacity needed to ensure you get more core in the box. Find out more at epiroc.com United. Inspired.
by
Marcotte has been manufacturing drill components since 1992. Starting from a simple parts manufacturer, it reached the status of a complete drill manufacturer within a decade. From the notorious HTM-2500 to the versatile Mancore 900, Marcotte has since then developed a full array of robust and innovative drill rigs to answer the needs of its ever-growing customer base.
Be it for surface exploration, remote operations, underground operations and all the accessories that go with it, Marcotte has been committed from day one to ensure that its customers get the reliability of Canadian-built machinery every time they acquire equipment with its name on it.
temperatures while having everything it takes to deal with the harsh conditions known to Central and South America.
The STM-1500 was the first underground model designed by Marcotte and it allowed its users to drill deep holes thanks to its robust construction. The STM-1500 has made its place in the world of underground exploration as a reliable deep hole machine and is now one of Marcotte’s flagship products that benefit from a wide array of options. Its heavy construction gives this model the capacity to withstand a beating from high-hp power units in the hardest conditions an underground hole can get you. The STM-1500 can be found around the world in various configurations and equipped with power units ranging from 125 hp to 300 hp.
From this model were derived the STM-600 and STM-300, which were developed to work in much more limited space. These models benefit from many field-tested parts of its predecessor which make them a reliable and versatile choice for specific operations where high depths are not the main factor.
The HTM-2500 was the first popular model built for North American surface drilling. It is an unstoppable workhorse that will get the core samples out no matter the depth. With its 275 hp diesel prime mover, the base model can reach a pull capacity of over 66 000 lb (29 937 kg). Evolution has led it to incorporate many different key options. Its reputation opened the door for the arrival of the HTM-2500TA, which is a completely different model of very capable surface drill but built on top of a set of heavy-duty tracks. The TA was designed for drilling projects that require highly mobile equipment in milder
The Mancore 600 has been developed for remote projects that could only be accessed by foot or helicopter. Like most of the products in that category, it has a light modular design and Marcotte made sure that its configuration would allow intuitive assembling and dismantling while enabling its users to choose amongst multiple power unit options. Mostly found in southern parts of the world, this model has made its place with its simplicity and its robust mechanics.
The Mancore 600 paved the way for the development of its big brother the Mancore 900. However, this model has the capacity to access remote locations in northern parts of the world thanks to its modular configuration compatible with various shack options. The Mancore 900 also benefits from a single more powerful engine (instead of two or three separate ones) which enables it to reach higher depths. It possesses an impressive list of standard options:
heli-portable platform, skids, steel shack, composite shack, heavy-duty tarpaulin, rod handler, and a lot more which makes it the machine of choice when the job requires extra mobility all year long in challenging conditions.
Another sequel to the Mancore 600’s success is the Mancore 600TA. This model, running on a single diesel engine uses all the main components of the Mancore 600 to transform it into a heli-portable unit mounted on tracks and remotely controlled for the moves. Despite its modules being heavier, the heaviest one being the track frame weighing 1600 lb (726 kg), it allows faster moves between multiple distanced holes at remote locations while leaving the smallest possible footprint.
While continuously improving its most popular existing products with the help of its wide customer base, Marcotte also strives to supply the drilling market with new ideas. Improving mobility, reducing setup times, enhancing safety, achieving higher reliability, and incorporating automation are only a few of the many ways Marcotte sets new standards for the development and manufacture of its existing products and innovative projects.
The STM-600ME, a statement to Marcotte’s commitment to improving the core drilling industry in the underground world, is a unit that’s been developed for a very specific task in a very dynamic environment. The 600ME is a carrier-mounted, self-contained drill rig that allows super-fast mobilization and demobilization while providing a complete working platform (Canadian patent #2880877) to quickly
drill a hole and be ready to move to the next one within a single shift. This model carries all the equipment, tools, and consumables required for underground core drilling so it can move by itself from one drill site to the next without any need for extra machinery to get the work started. The carrier to which it is attached has two seats so that the helper can be with the driller when the machine arrives on site.
The latest innovation developed by Marcotte is the automated rod handler for surface drilling (Canadian patent #3021385). This unique accessory has been developed as an add-on to the HTM-2500TA model but has the still-untapped potential to be implemented on any other brand or model of surface drill. Achieving an impressive loading and unloading cycle below 1 minute per string of rods and having the capacity to manipulate strings of up to 9 m (29.5 ft), the current version of this equipment eliminates the need for human intervention when the time has come to change the bit. The Cyborg Rod Handler not only allows the workers to limit their exposure to repetitive heavy lifting but also helps management to forecast how much time it will take to proceed to a complete removal and re-insertion of a drill string in the ground.
Marcotte is committed to giving the best after-sales support in the industry to all its customers so that no drill stays out of service when it should not be. Backed by a professional and readily available team of technicians, Marcotte will answer every service call within an unmatched timeframe. Marcotte understands the value of an equipment that keeps on producing 24/7. So does its field support team. C
MARCOTTE is your key partner in mining exploration! Our passion for innovation is reflected in all our products, pushing back the boundaries to meet your exacting requirements.
Quality is at the heart of our approach. Robust and reliable, our products are specially designed to meet the challenges of mining exploration. For ultra-portable solutions, underground or surface work, join the professionals around the world who trust MARCOTTE and experience innovation, reliability and customer satisfaction at every stage of your project.
by
About 260 km (162 mi) southwest of Mexico City, on the southern bank of the Balsas River in Guerrero state, Torex Gold planned an intense infill drilling program at its Media Luna project.
Due to the site’s topography, environmental regulations, lack of hydrological resources, and highly variable geologic conditions, a conventional drilling program would have been almost impossible to execute with the desired accuracy and within budget.
Phase I of the program began in October 2018 and consisted of 117 targets divided into 16 blocks, reached from only nine drilling sites. Each collar comprised of one block with nine targets, designed on a 30- by 30-meter (98.4 x 98.4 ft) grid spacing, to upgrade the deposit to ‘measured’ status.
The authors would like to acknowledge and give a special thanks to Nicolas Landon, Exploration Manager at Torex Gold.
Media Luna is a skarn deposit located in the Morelos district, itself a part of the Guerrero Gold Belt. Its geological setting is dominated by limestone, siltstone, and other sedimentary formations cut by several intrusive bodies. The resulting contact metamorphism led to the formation of skarns, rich in gold, copper and silver.
The varying, thick sedimentary layers and the variety of intrusions create a unique set of circumstances that come with their own unique set of challenges for anyone attempting to drill through them.
One of the main issues encountered was the lack of hydrological resources. Considering drilling is dependent on having a reliable water supply, any planned program had to contend with the limitations of having to bring water to the project by tanker trucks.
Throughout its geological setup and structural deformation, the limestone in the area has been heavily affected by karst processes.
That presented another problem for the drilling program, where the underground caverns created could lead to a total loss of water in a drilling well, further exacerbating the previously mentioned issue.
Extreme magnetic anomalies were also present due to the iron-rich exoskarn. This prevented the reliable use of magnetic measurement instruments.
To save costs and reduce water consumption, the total number of meters drilled to intercept each target had to be cut drastically.
The only way to reduce meters while still reaching the same number of targets is to use directional drilling. In the simplest terms, it consists of producing an intentional and controlled deviation of a borehole to pre-determined target coordinates (Northing/Easting/Elevation). And of course, multiple deviations can be made from a single pilot hole.
The way to reduce water consumption is to use a directional core drilling tool. Directional drilling itself can be done with ‘full-face’ tools, or with ‘DCBs’ (Directional Core Barrels).
An advantage of the DCB is that it uses far less water compared to a full-face tool, such as a mud-motor, since it has no turbine that requires a higher flow volume. Furthermore, its ability to extract core increases the production rate compared to the alternative. As such, the AZIDRILL® NB DCB was chosen for the task. The AZIDRILL® cuts an N-sized hole and collects a B-sized core sample. In addition, the DLS (Dogleg Severity – a measure of the drill hole curvature), tool face (orientation), and borehole trajectory can be continuously monitored to make timely adjustments and maintain the planned course of the curve. In particular, DLS needs to be kept within ‘safe’ parameters, so as to not create an unacceptable amount of torque in the drill string which can then lead to a host of additional problems.
In every case, the mother hole was aligned to the center target and drilled to total depth before planning the daughter holes. This allowed the exploration team to select KOPs (Kick-off Points) in favorable zones, and eliminate the risk of setting wedges or beginning directional operations in unfavorable ground conditions. Each mother hole became the origin of eight additional daughter holes.
Due to the relatively shallow depth of the deposit of approximately 450-600 m (14761968 ft), every directional curve was designed to be completed with a length of about 40 m (131.2 ft) (on average). Although the AZIDRILL® collects a core sample during operation, extracting full-sized N core samples from the deposit was imperative, so the AZIDRILL® would have to be switched for the conventional core barrel after the curve was completed.
Mother holes began with collar alignment set to the central target based on the known natural deviation from the area. This was the only hole in the block where drill rig alignment was required. In all cases, holes were started with P-sized diameter for the collar and were advanced up to a depth of approximately 170-210 m (558–689 ft), where lithological and structural conditions demanded a reduction to H-size. The holes in which directional steering control was used were further reduced from H-size to N-size using conventional core barrels and casing wedges.
Upon the completion of the directional curve, the AZIDRILL® was pulled out of the
borehole and conventional drilling continued until the target was drilled and the borehole surpassed the limit of the skarn deposit.
In addition to drilling the curved sections, AZIDRILL® was also utilized to control conventional sections, such as mother hole corrections, where ground formations caused substantial natural deviation.
↑ Aziwell and Layne crew at the drill rig preparing directional drilling operations
After analyzing the core samples of each Mother hole, lithological and deviation information was considered to confirm the KOP, or if necessary, to propose an alternative KOP depth with better borehole conditions. Afterwards, anchors were installed as the base for the wedges.
For this project, two types of wedges were used: permanent bypass and P/H-size Casing, the latter of which is recoverable and reusable. Once on the hole bottom, the wedge was oriented with a tool face directed at the target. Subsequently, the wedge ramp was drilled off using a bull nose bitball bit, reducing the diameter from H to N-size. This methodology yielded three daughter holes per KOP (approximately 120° of separation between each tool face orientation).
In general, it is not necessary to extract the casing wedge upon completion of a daughter hole. Simply lift the drill string, rotate to the desired orientation, and set it down upon the
anchor again. This is a very effective method for eliminating the amount of time involved in setting permanent wedges.
To monitor the trajectory of each borehole and create an accurate model of the deposit, it is necessary to collect frequent deviation measurements as the drilling advances. Due to substantial magnetic interference in the area, all deviation surveys were collected via a North-seeking gyroscope. These instruments are unaffected by magnetism. Additionally, these gyroscopes were utilized to validate the survey data collected by the AZIDRILL® during the curves.
Due to the success of Phase I, the infill program grew subsequently throughout Phase II and III. At its peak of operation, eight di-
amond core rigs (CT14 /CS1500/CS4000), two AZIDRILL® systems, and two gyroscope survey crews operated around the clock.
With this methodology, the accuracy of target interception was significantly improved while dramatically decreasing the need for additional drilling. As a result, not only were funds and water saved by drilling less, but much fewer rig moves were required, leading also to less need for further pad creation and environmental permitting.
To date, there have been more than 1000 targets hit and 30 000 m (98 425 ft) of directional drilling. The joint venture efforts between AZIWELL, International Directional Services de Mexico, and Layne de Mexico have saved the projects millions of dollars and years of drilling while putting more than 4 Moz of gold equivalent in the ‘proven’ category.
The team is unaware of any other infill programs globally that have reached the same number of targets in such a short amount of time! C
In this Issue:
Q&A from the experts
In conversation with Nick Tate Specialist Consultant Mapper of Geology, Alteration and Mineralization Systems
The airborne geophysics power for mineral exploration: An Amazonian Craton case study by Bruna de Freitas, Independent Exploration Expert Geologist and MSc in Mineral Resources
Hydrothermal system models: A great tool for understanding challenging geology by Mark Lindsay, Former Chief Geologist at GBM Resources
A short explanation why optical petrography knowledge is the key to preliminary identify hydrothermal magmatic processes by Paula Montoya-Lopera, Postdoctoral Research Fellow in Economic Geology at CODES, University of Tasmania
Nick
Tate Specialist Consultant Mapper of Geology, Alteration and Mineralization Systems
Brett Davis: Firstly, thanks for giving Coring the opportunity to interview you, Nick. Very few people have a geological profile as well-respected, or as well-known, as you. So, it’s a real pleasure to sit down and chat with you. Can we start off by telling us what interested you in a career in geology?
Nick Tate: My father was an organic chemist at the Waite Institute (now part of the University of Adelaide) for most of his career. We went to a barbeque with one of his students at the house of her boyfriend, who was a paleontologist. I was about 5 years old at the time. The story goes that I spent the entire evening looking at shelves full of fossils that he had collected. Apparently, I was determined to be a paleontologist when I grew up until I was informed that there was no money in that career, but there was money in geology! Shortly after that, someone taught me how to pan gold and I would regularly borrow Mum’s cooking utensils to prospect for gold in the backyard.
Mum loved being outdoors. She designed and built her own sailing boat and rode dirt bikes so that fostered my love of being outside. Dad was only interested in the out-
Nick Tate graduated with a BSc in Geology from James Cook University. In the 40 years since, he has worked on dozens of contracts worldwide, becoming a specialist consultant mapper of geology, alteration, and mineralization systems.
His expertise has led to multiple notable discoveries in Laos, Mongolia, and Argentina, as well as an excellent reputation in the industry.
Nowadays, Nick runs his successful YouTube channel GeologyUpSkill and a series of courses providing young geologists with the necessary skills for fieldwork.
doors if it involved fishing. He used to say that it was the only time that he didn’t think about chemistry, but I think he was lying. It was really the time when his mind was undisturbed by the clutter of the chemistry lab, and he would sometimes scribble furiously some new formula that had come to mind when we got home. I find I do the same thing now on long traverses between outcrops. Mum also loved photography and she taught me how to shoot film, process it and make prints in a home darkroom. That skill set would have a fundamental influence on my career many decades later.
At high school, I had a friend who lived on a farm next door to an old alluvial goldfield, so we used to go there on weekends to dig dirt out of the shafts and pan real gold. I still have that gold! From then on, there was no question about my future career.
I remember being quite shocked when I arrived at university and most of my compatriots were still trying to decide what career they would like!
I was a serial underperformer at primary school because I was hopeless at rote learning and numbers didn’t excite me. I went to an ‘alternative’ school for grades 4 and 5 where I had lots of fun digging in the gar-
den and making model airplanes, but I didn’t learn much of the 3Rs. Grades 6 and 7 back at ‘normal’ school were a real struggle to catch up, but thanks to my parents and two very helpful teachers, I recovered lost ground. I found high school much easier, but I couldn’t study geology even though it was an available subject because it conflicted with the prerequisite science and mathematics subjects required for university entry.
I was kind of a nerd at high school, and I was too short to play any of the team sports with kids the same age so, along with a couple of similar friends, we set up a darkroom and made an unofficial photography club. I entered a print of my girlfriend at the time in a competition run by the local paper. It won first prize and that created a problem for us because the prize involved a camera for the winner and some equipment for the club, so we had to hastily make the club ‘official’ to accept the prize. That camera became a fundamental tool for my future geology work because I understood that a picture was worth a thousand words, and I hated writing! When I went to Flinders University in South Australia, I found studying easy because I could learn the underlying theory for a process and apply it to whatever problem was
posed. That just suited the way I learn, and I also had a few geology subjects in first year that made learning fun for me.
During my undergraduate studies, I took a few short holiday jobs to get some experience. All of those jobs involved some geological mapping, and I just loved it. There is something addictive about the instant gratification that comes when you add a little more to the picture each day. It’s like working on a difficult jigsaw puzzle with lots of pieces missing, so when you find a piece that fits, it is very satisfying. On top of that, there is always the carrot of potential discovery dangling in front of you if you are in the mineral exploration business. Because I loved what I was doing, I never had a problem going the extra mile to collect more data and make it into maps. I also had a bit of a talent for drawing, so I enjoyed the artistic side of making the data into maps. I didn’t realize it at the time, but the connections I made during those jobs sowed the seeds for almost all of my future jobs.
Then I went to James Cook University to study for an Honors degree with Prof. Roger Taylor because he had a project mapping a tin system in the jungle south of Cooktown in North Queensland. His enthusiasm for geology and irreverent way of deconstructing complex topics into the simple stuff that matters was a perfect fit for my way of doing things. He also had a lot of industry contacts and was very good at getting them involved in student projects which laid even more seeds for my future clients.
My honors year was extremely hard work, but I loved every minute of it because I am a learning junkie, and I was in my element. My problem was that I couldn’t stop collecting data and sit down to write the thesis. All that came in the last two weeks before the deadline and my hours of sleep shrank to zero as the ‘D’ day approached. Part of the problem was that I had shot hundreds of photographs to illustrate my work and I had to print and put together four copies of the thesis which ran to two volumes because of all the pictures. It was quite a change from the usual
dry black and white diagrams in theses, but it must have made an impression because after some harrowing defense, I was awarded First class Honors.
After I graduated, those connections I had made on holiday jobs started calling me up and offering me short mapping contracts and I just kept accepting them because I loved the work and I got to look at new things every few weeks. It just snowballed from there as I developed a reputation as a ‘professional mapper’. As a result, I’ve never actually had a real ‘job’ and my CV looks like a log sheet from a drill hole to the MOHO.
Being ‘respected and well-known’ is really a very recent thing for me. I have only ever published a couple of descriptive papers, so I have no academic profile. I very rarely attend conferences or present in person so very few people outside my client network even knew what I looked like. I had a LinkedIn profile for about 10 years, but I never used it. All that changed when I started making videos and sharing them on YouTube.
I think YouTube and other online platforms have had a great democratizing effect. The scientific journals and major media houses had evolved into very narrow channels that were the only path to mass audiences. Any system with that kind of concentrated control makes it extremely difficult for new or unorthodox talent to get recognized. It also inevitably leads to abuse of the power generated by the narrow funnels of information. The digital platforms have disrupted all of that. Now, you don’t have to publish in Nature to become a famous scientist. Anyone who does good work and knows how to present it can reach a global audience. Of course, the unfiltered access to publishing for everyone has resulted in a kind of anarchy where it is difficult to rise above the sea of chaos, but it can be done. The platforms are still evolving rapidly, and monopolistic power is concentrating in different ways with platform owners, algorithms and AI police influencing what gets viewed, so the future may be not quite so democratic. Right now however, we are in a golden age where you can blow your own trumpet and if it’s good, people will listen.
BD: Coring is a drilling magazine, and we like to keep to our roots. So, I’ll ask you a drilling-related question. I know you are predominantly a field geologist, but do you do much work with diamond core? Do you have any drilling horror stories?
NT: Even though I’m a mapping geologist, I often look at available core on a project early in the job if possible. It gives me a great introduction to the rock types and alteration facies in their pristine state. That makes it much easier to unravel outcrops that are masked by the ravages of oxidation and other weathering processes. Critical relationships between rock types and mineralization paragenetic sequences are also much easier to sort out in clean cut core than broken oxidized
rock which helps enormously when you are trying to understand what you are seeing on surface.
Probably my worst drilling story would be a run of 0.8 m (2.6 ft) to demolish a new diamond bit after drilling a long interval of alunite alteration in a high sulphidation system at Frieda River (Papua New Guinea) and then encountering a zone with corundum as the main alteration mineral.
BD: You’ve worked in a lot of countries and on a lot of continents. Are there any skills or mindsets that have helped you in your roles in these places?
NT: Working overseas is invaluable experience. There are so many boundaries to the way you think, and you don’t even know that they exist until you see people from other cultures do things differently because the tools are different, the risk tolerance is different, the laws are different, and the culture is different, but the needs are the same. You also learn what it’s like to be a minority group with different colored skin who struggles with the local language. That gives you a real appreciation for the challenges faced by others at home. Perhaps most importantly, you will learn that the outlook you had on the rest of the world was extremely narrow before you left!
BD: One topic we commonly talk about but rarely put into print is the health hazards of working in different countries and environments. Has your health ever been particularly challenged and, if so, what happened?
NT: I have been extremely lucky, despite working in some pretty hazardous places. By far, the biggest risk in most countries is vehicle accidents. I had an extremely narrow escape riding a scooter in Laos.
While waiting at an intersection, a drunk guy on another scooter with two children on board ran into the back of my scooter at high speed. There are a few seconds of missing time from my life on that day during which my scooter was catapulted from under me, and the other scooter miraculously went over or around me. The next thing I knew was that I was standing in the middle of the intersection minus a scooter, but with only a small bruise on my right leg. The other rider, the children and the scooters were in a pile 20 m (65.6 ft) down the road. Fortunately, none of them had serious injuries, but it was a stark reminder that getting to and from the office is the riskiest part of the job. The worst disease that I acquired was Dengue fever (also in Laos). It has similar symptoms to a bout of Malaria, but it lasts for up
to six weeks and there are no preventatives or curative drugs. Definitely not a recommended experience!
BD: Would you believe that one of the earliest pieces of geological literature that I read and can remember was your Honours thesis, which had a focus on tourmaline? Has there been any formative piece of geological work from a colleague that influenced you, and who have been some of the positive influences in your career?
NT: I always recommend the book ‘The Tin Scratchers’ by Ion Idriess. It is part-adventure story and part-instruction manual for prospectors. It inspired me to follow in the footsteps of those people with dreams and determination to make discoveries.
BD: Given the high profile of energy metal companies, are you doing a lot of work outside of the commodities and deposit styles you have traditionally worked on?
NT: Generally, no. I am still getting more work than I can handle in the systems that I know best (gold and copper). It would be interesting to try mapping some of the lithium and rare earth systems. The process is basically the same. Understand what controls ore and figure out what parts of those controls can be mapped in a sensible way. There is a little bit of crossover for me in tin, since that’s what I studied for my honors project and it's now becoming a critical metal.
BD: As a widely traveled geologist, what part of the world do you think is highly
prospective for finding new world-class orebodies?
NT: You just can’t escape the Ring of Fire (from the southern tip of South America, up along the coast of North America, across the Bering Strait, down through Japan, and into New Zealand) and the other fossil subduction zones, but I have learned the hard way that above ground risk is more important than geological risk. That puts places with stable jurisdictions up near the front of the pack. I include Australia in that pack, even though it has been intensively explored: Rule #20!
BD: Is there a particular mineralization style or deposit type that interests you, and why?
NT: I just love porphyry systems (and related IRG systems) because they have huge zoned alteration systems that can be mapped. The alteration is commonly unrecognized or unmapped, so my work can make a big contribution in those systems.
BD: Leading on from the previous question, everyone has a handful of deposits that have left a mark on them, be it because of the amazing geology, the hideous conditions, the people they worked with, etc. Which deposits do you hold dear, and which ones really were difficult to work on?
NT: Both of those categories are filled by the Frieda River system in Papua New Guinea. It has a cluster of giant porphyry Cu-Au systems and the classic high-sulphidation Nena Cu Au deposit all in mountainous, jungle covered terrain where it pelts down rain every afternoon. Amazing geology and some of the best local people I have ever worked with.
BD: You wrote a fantastic article on Artificial Intelligence (AI) for a previous issue of Coring. So, where do you see the most exciting technological developments being made in mineral exploration going forward?
NT: I think there must be great potential in applying the kind of computer tomography that is used in medical imaging to geophysics, particularly seismic data. It’s a challenge because it’s hard to get sensors all around the target, but in mature projects where there are deep drill holes or extensive mine workings, I think there is great potential to define brownfields targets.
BD: Do you think that there are any mineral exploration strategies or technologies that are under-employed, but could make a big difference to an exploration campaign if people used them more?
NT: Ha-ha! Mapping of course! It seems to be a dying art, but it is even more valuable as a tool today because we have such amazing remote data sets that can speed up the process and put boots on the ground where they make a difference.
BD: We hear all about the advances and benefits of technologies, such as 3D modelling, geochemical analysis, and utilization of drones. Have you noted any negative impacts to effective exploration and mining as a result of these, e.g. less people out kicking rocks?
NT: None of those technologies are a problem in themselves. As per my answer to the previous question, they can all make exploration fieldwork faster and more effective. The problem comes when they are viewed as a replacement for fieldwork. The most valuable skill for people in the future will be critical thinking. As AI generates models for almost every aspect of our lives, the ability to assess what is real and what is just an attractive model will separate the explorers from the discoverers.
BD: There would be very few geologists who have not watched your Fieldcraft videos. This is an amazing resource, with content varying from academic to truly quirky, but always overwhelmingly pragmatic. With this in mind, what is your opinion of the geological skillsets, experience, and knowledge of geologists today, especially those who are newly graduated?
NT: I started out making the videos to share the knowledge that I had accumulated in the field, so I wasn’t thinking about the basic technical stuff that students learn at university. From the responses to my videos and working with young geologists, I can see that the quality of university geology courses is falling seriously and the number of students is following a similar curve. That is an absolute tragedy for Australia because we spent 200 years building that pool of people with the best exploration and mining skills in the world and we will lose it in a generation if we don’t get serious about rebuilding the geological education system.
BD: What are your software programs of choice? And what are your opinions on pricing and their usefulness?
NT: I am still using Mapinfo 2012 on a Windows 7 laptop with Discover Mobile running on Windows Mobile 6 because they were the last versions that you could buy outright. The current trend to move everything to annual subscriptions is part of the process of ‘enshittification’ that afflicts almost all tech companies these days. Look up that term on YouTube for a detailed definition, but it’s basically the process of squeezing financial returns out of software or platforms that have become popular because they were useful to users. The results are inevitably increased cost and reduced usefulness for end users. It usually leads to a demise when a new startup comes in to fill the usefulness gap, but when users pile in because the startup gives better service, it has to expand rapidly, and
they usually do that with venture capital. Sooner or later, the venture capitalists want their pound of flesh and the process of enshittification starts again. QGIS is the new guy on the block now and that will probably be my next package when my old laptop finally dies, but you just have to get used to moving on when the rot sets in.
BD: Has there been any single satisfying geology-oriented moment in your career that rates above all the others?
NT: The discovery of the copper orebody at Phu Kham in Laos has to rate highly there. The previous explorers had drilled over 100 holes and still missed the orebody. We (Pan Australian Resources) found it after I re-logged all the old holes and redrew the sections (by hand). The system sits above a thrust fault and there was just one drill hole that went below where the thrust should be, but was still in ore. The only way I could make that work was to put in a vertical fault that cut the thrust between previous holes (which were mostly vertical). We tested the idea with a big-angled hole and discovered a large down-thrown block of ore that was twice the grade of the previous resource because it also contained lots of skarn. That made the mine and the company.
BD: I’ll ask a question on the flipside to the previous one. Many of us have interfaced with less than savory individuals or experienced toxic workplaces. Has there been any incident or incidents that really disappointed you?
NT: My virgin discovery story of a huge platinum system in Laos led to a JV with Australian Dominion Mining. They were great people to deal with and we spent a lot of time drafting a watertight agreement that would materialize the JV if Dominion managed to get an exploration license granted. Unfortunately, during the application process,
Dominion was taken over by Kingsgate Consolidated (an Australian listed company that owned the Chatree Mine in Thailand). When the license was granted, they simply refused to honor the agreement to sign the JV, knowing full well that they could out-spend me in a court battle. In the end, I waited them out, but the experience was a hard lesson about dealing with valuable discoveries.
BD: You are one of the rare breeds of geologists who work in the industry but manage to maintain a high professional profile. I’d hate to think about the amount of time you have devoted to your videos. Monetary gain aside, what inspires you to keep producing them and how do you overcome the challenges, such as finding the time?
NT: ‘High professional profile’ might be a bit of an overstatement. I don’t belong to any professional organizations anymore and I don’t write papers for journals or make presentations at conferences. I’m really just a field geologist who learned to make videos. I have streamlined that process quite a lot now, although the longer videos take a bit more time on research and editing. The direct monetary side is still far behind the effort employed. YouTube earns me about a coffee a day. The paid course versions have now paid for the camera gear and computers for editing and for that I am eternally grateful to all of my paid subscribers. Each one of them has contributed to making the videos to help educate future generations of geologists. That alone is motivation to continue, but shooting and editing the videos is also a creative outlet for those camera skills acquired from my mother half a century ago. If people enjoy them and learn something, I am happy. The real financial return comes from the increase in people who know what I do and the work that flows from that. Those jobs take me to new and places with differ-
ent geology, so I have a constant supply of new subjects for videos and the bills get paid.
BD: What does Nick Tate do in his downtime (assuming he takes some)?
NT: What is this ‘downtime’ you speak of?! I used to have downtime, but now I have a son instead. We do the same stuff I used to do but now I’m teaching it all over again!
BD: What have you learned from field practice and your job experience that is not taught at university?
NT: See my YouTube channel! I have learned that geology is fractal. The closer you look, the more detail you see, ad infinitum! The most valuable skill is to be able to step back and answer the question: ‘What really matters here?’. When you can answer that, you will know what data to collect and how to assess the prospects you are looking at.
BD: If you had abundant financial funding, is there a fundamentally annoying geology question you’d like to solve or a topic you’d like to work on?
NT: ‘Where is the next Mt Isa Copper orebody?’. I think the works of Bill Perkins and more recently Dr Richard Lilly and students at the University of Adelaide have shown that there are probably lots more of them out there and the zinc deposits are the key to finding them. With an unlimited drilling budget, I would like to find one!
BD: Finally, any concluding comments or words of wisdom from an industry veteran?
NT: I leaned to ride a unicycle because it seemed impossible, so I knew that if I mastered it, the sense of achievement would be amazing. Challenging yourself occasionally to do something difficult, but not impossible, keeps your spirit alive. C
For more information
Subscribe to Nick Tate’s YouTube channel: GeologyUpSkill
by Bruna de Freitas, Independent Exploration Expert Geologist and MSc in Mineral Resources
The fast improvement of geophysical tools in recent decades has transformed mineral research at the same rate, allowing prospective ore deposits to be identified without the lengthy and expensive on-site exploration procedure. Many geophysical methods are available for surveys and quick estimating of large areas during prospecting and mineral exploration work.
Advancements in geophysical data processing, depth inversion, and estimation techniques can determine the lateral extension and depth of anomalies with good assertiveness. These advancements have avoided high and unnecessary costs, which often face the impossibility of implementing an undertaking that will not guarantee a return. Therefore, the methods must be applied appropriately and have their surveys planned correctly and consistently with the local geology.
Geophysics and its artifices have increased assertiveness in rock drilling programs, reducing costs, and simplifying the characterization of mineralized bodies and structures. When a commodity concentration shows a potential economic value and sufficient volume to pay for the entire extraction, the geophysics practices have become increasingly valuable and competent, allowing inefficient methods to be abandoned in favor of more efficient ways.
Geophysics has enabled correct planning of positive and negative holes during resource estimates, which is critical during mining ex-
ploration. In the implementation phase of a mine and during its operation, geophysical profiling methods have brought significant advantages, such as the precise determination of contact depths and geological structures, given the inefficiency of total rock recovery during drilling. Accurate knowledge of contact depths and geological structures has relevant implications for determining mineralized zones and surveying geomechanical parameters.
Analogous to the prospecting in mineral research, geophysics has been a great resource in defining areas for dams and tailings piles, and during the observation of the behavior of these earthworks, which suffer due to the seasonal climatic variations, still, geophysics has greatly supported environmental monitoring in the stages that follow a mining life cycle.
Airborne geophysics is one of several aspects of geophysics methods applied to mineral exploration. It uses data collected from aircraft to characterize large areas with mineral potential, both at the preliminary recognition level, aiming at the subsequent
application of classic geophysical methods in selected regions, and the level of detail, aiming to improve the information available in previously studied areas.
Geophysics can be used to interpret surface and depth geological features. Studies can be developed to define contacts, tectonic structures, lithology, and mineralizations by analyzing geological and geophysical data.
The most used geophysical methods in airborne geophysics are magnetometry and gamma-spectrometry; when performed by airplanes, these fly over the region of interest at altitudes that generally vary between 150 and 300 m (492 and 984 ft) above the ground. Detecting minerals with several physical and/or chemical properties, such as density, electrical conductivity, magnetic susceptibility, and radioactivity, can indicate mineralized zones through airborne geophysical methods.
Mineral occurrences and deposits of gold, copper, chromium, molybdenum, tin, nickel, platinum, tungsten, and iron are associated with specific lithologies and hydrothermal alteration systems that can be identified by airborne geophysics, whether by magnetism, gamma-spectrometry, or gravimetry.
Furthermore, many deposits have extensive hydrothermal alteration zones that airborne geophysical methods can detect. The potassic, sericitic, propylitic, argillic alterations, and silicification zones can present different behaviors in response to airborne geophysical data, mainly due to the aid of the gamma spectrometric signatures of the minerals in the alteration halos.
The effectiveness of geophysics methods for application in the mineral exploration sector is associated with the recognition of anomalies and mineralized zones, which can be very efficient if there are occurrences of magnetometric structures and good gamma spectrometric responses.
When we compare its costs versus benefits and the importance of the results for the mining company to better understand where to extract the ore, geophysics becomes a cheaper tool to better understand the subsoil with the need to drill a smaller number of holes, immensely more expensive, or drilling holes that are more accurate for mineralization. Furthermore, without geophysics, these drilling holes would be based only on the outcropping rocks in that region and not
on the chemical and physical parameters of the rocks in the subsurface, which could significantly increase the cost of drilling, as this would be more imprecise.
Geophysics makes it possible to investigate the subsurface, that is, to make measurements carried out using modern equipment on or close to the surface. These surveys are often carried out using small aircraft coupled to specific geophysical sensors. Currently, technologies are being developed for the use of drones in their execution, reducing costs and improving the resolution of this type of image.
Before the process, the flight lines are planned in the area to be executed. Different products can be generated from these data depending on the processing and filtering. Each map can be used for prospecting many
ores, and its resolution depends on the spacing of the executed flight lines.
These images are being used increasingly, as they greatly facilitate geological mapping, helping to delimit targets to be investigated in the field and thus providing greater assertiveness to find certain differentiated features on the ground that may indicate some ore or rock that may contain ore.
The main advantage is that the processing will present a targeted result for the ore that intends to prospect in the region. This
way, the resulting map will indicate relevant points on the terrain that the geologist must visit to verify its characteristics. This will make the geologist more assertive during geological mapping, reducing costs and increasing efficiency.
The larger the survey area, the more indicated this type of procedure is performed, as in an extensive area, mapping can be time-consuming and inaccurate if the ore is concentrated only in a specific location on the ground.
The region of São Félix do Xingu (SFX) is located in the Amazon Craton, State of Pará –Brazil. Geologically, the area is located in the eastern part of the Central Amazon province, close to the western limit of the Carajás Archean Mineral Province and is considered a promising area for the mineralization of epithermal gold and porphyry and base metals. The SFX region is composed mainly of andesites to rhyolites (ca. 2.0–1.88 Ga), generally undeformed and affected only by very
low-grade metamorphism. These units are considered part of the significant Uatumã Magmatic Event, consisting of several intermediate to felsic magmatism events generated in continental magmatic arcs, with a final orogenic event (ca. 1.87 Ga), including intrusive volcanic, volcaniclastic, plutonic rocks, and sedimentary sequences. Several Au-Ag mineralizations of high, intermediate, and low sulfidation and Au-Cu-(Mo) porphyry were recognized in these units over 400 km (249 mi) from the Tapajós Province to the SFX region, encouraging research in this critical area.
However, due to its high prospective potential, the region lacks more geological details and a limited database. Using airborne geophysical techniques for difficult access areas, emphasizing mineral prospecting was
essential for characterizing new domains and creating target areas in the region of interest. Through predictive techniques, using gamma-spectrometric and magnetometric data, it was possible to develop favorability maps for exploratory targets. With geophysical and magnetometric data integration, regions of high favorability were highlighted by applying relationships between channels and structural complexity analysis techniques of the area.
The result, published in the shape of a master’s degree thesis by the author at the University of São Paulo, demonstrates that both methodologies effectively identified promising regions for mineral prospecting. There was a total of six areas highlighted as favorable, two classified as ‘High priority’, two as ‘Moderate priority’, and two as ‘Low
priority’. Areas with potential mainly for Au, Cu, Fe, Pt, Ni and Sn were defined based on the correlation between the magnetic data, where zones of significant geological discontinuities can host mineralization, and between the gamma spectrometric data, characterizing regions of interest based on geostatistics and the study from areas with anomalous concentrations of potassium, uranium, and thorium.
In short, geophysics has become a mandatory tool in mineral research work and mining. Geophysics will bring a great return to the mining enterprise if used consciously and coherently. For this, an interpretation consistent with geology and understanding its limitations is fundamental. C
For more information
Get in touch with Bruna de Freitas on LinkedIn
IT HAS NEVER BEEN EASIER TO CONTROL A LARGE NUMBER OF BOREHOLES
Are you looking for a fast, economical and reliable solution, also to advance your digitalisation process?
LiPAD®-100 is the answer.
The LiPAD®-100 has proven to be the fastest and easiest to-use-tool during hole surveys.
Rickard Lindström CEO at Xploration Products AB
Book your live demo now!
by Mark Lindsay, Former Chief Geologist at GBM Resources
GBM Resources Limited recently acquired the Twin Hills project that comprises the 309 and Lone Sister ore deposits and in 12 months grew the resources by 58% from 633 000 oz Au to around 1 Moz Au (see GBM ASX Release: 05/12/2022, Twin Hills Gold Project Upgrades to ~1 Moz Mineral Resource).
Though the geology of Lone Sister was well documented by previous workers, the geology and controls on mineralization at 309 were poorly understood. Constructing an observation-driven hydrothermal system model by systematically recording the key features of the deposit facilitated a new understanding of the 309 Deposit geology and importantly, provided a significant increase in resource confidence. Here’s how we did it.
The best way to undertake this process is to have time to concentrate on the geology for long periods every day. You’ll need time to think about the rocks, the relationships you’re seeing, and how they might fit together.
The key challenge for GBM was to resolve the geology and controls on the distribution of mineralization at the 309 Deposit in order to develop a new resource estimation model. Previous workers variably interpreted the host rocks as a prograding alluvial fan, diatreme/maar complex, and phreatic/phreatomagmatic breccia in a graben, with mineralization described as fault-controlled, breccia-controlled, epithermal, and components of mesothermal. The historic logging was inconsistent within programs and between companies and several logging codes combined lithology with mineralization and brecciation. Initial attempts to use historic logging as the basis for interpretations quickly indicated a relog with revised codes was required.
Geologists generally record most features of ore deposits in substantial detail, particularly if diamond core is being logged. The abundance of data is then viewed on screen and detailed models of various aspects of deposits are created, often in isolation from other deposit features. A Hydrothermal System Model as discussed here aims to show the broad patterns of the key aspects of a hydrothermal system in a single simplified model. The overall geometries and patterns are used to resolve the geological setting and broad controls on the distribution of mineralization.
Selecting the features to log is a significant step, but the process of building the model will help to define which features are important. The features that are logged will likely change as the work proceeds so don’t feel that you must get it right immediately.
Start by laying out the core from a selection of drill holes that pass from the least to most altered/mineralized parts of the system and encompass the main features of the deposit. Look through each drill hole and note the main features you see; this will form the basis for logging. The key features of the hydrothermal system will vary between systems but usually include various types of Lithology, Structure, Brecciation, Alteration, Mineralization, and the nature of Contacts between the logged features. Alteration was not logged for the 309 Deposit model as the entire system is overprinted by strong to intense silicification with little evidence of other alteration styles in the hand specimen. Mineralization was simplified into four main types of veins and breccia fills. More than 20 lithologies were initially recorded
↑ A - THRCD814 72 m, 1 m @ 449.0 g/t Au and 997.0 g/t Ag from 72 m (236 ft). Ginguro banding with visible gold in breccia pipe.
B - 3209DD22002 139.7 m, 79 m @ 1.09 g/t Au from 131 m (430 ft). Coarse bladed fluorite.
C - 309DD22003 128.5 m, 15 m @ 3.96 g/t Au from 118 m (387 ft). Quartz-chalcedony-pyrite replacing bladed fluorite.
D - 309DD22005 327 m, 1 m @ 129.4 g/t Au and 55.4 g/t Ag from 327 m (1073 ft). Abundant visible gold as electrum. Mineralization is hosted by chalcedony veins that cut earlier-formed breccia.
E - 309 deposit 3D view
(looking NNW)
F - 309 deposit schematic model
↑ Figure 1 - 309 Deposit Hydrothermal system model. 1A–D show variation in mineralization styles across the deposit with sample locations shown on 1E. Abundant bladed fluorite and fluorite replaced by silica forms in a distinct zone that we interpret to result from boiling. The fluorite-rich boiling zone marks an inflection point in deposit geometry above which mineralization forms two pipe-like bodies along ax NNE trend (1E and F). Note that elevated gold grades form in layers sub-parallel to the inflection horizon/boiling zone. 1F schematic model displays the spatial relationships of key mineralization features at 309.
to reflect the complexity of host rocks evident in the drill core. These were simplified into eight types after the sedimentary and volcanic facies relationships were resolved during logging. The nature and orientation of contacts between logged features can be very important and resolve the genesis of specific lithologies (e.g., breccia pipe vs. mass flow) or controls on the distribution of mineralization (e.g., fault vs. lithological).
Basic observations and interpretations of relationships between key features of the system and how those features change across the deposit are fundamental to building a great model. If there is a heavily altered rock type that you don’t understand, then can you find a less altered rock with the same textures elsewhere in the deposit? Is there a recognizable unit that you’ve seen in a few holes that could be used as a marker bed? Logging core is not just about recording various geological features, there are plenty of automatic core logging machines that can do that, it’s about recognizing patterns and making interpretations.
If time permits, several sections through the deposit should be relogged and preferably with at least one section that is perpendicular to the other sections. Ensure that the sections selected are representative of the deposit geology including the unaltered/unmineralized parts and where possible select sections from across the length of the deposit. In most instances, initial logging will need to be on the drill core. Once you can easily recognize the key features of the system, then logging can proceed using core photographs. Logged units should be recorded at a scale that can be easily displayed on a section with recorded intervals preferably > several meters thick. The aim is to illustrate the overall geometry of system components, not the detail. Exceptions to this may include planar features such as contacts, faults, dykes, lodes, and marker beds.
To aid interpretation, it is useful to compile a reference library of photos with notes (I use PowerPoint for this as it’s easy to annotate and sort the photos) showing key relationships, logged lithologies, alteration, mineralization, and any other significant features or interpretations. There were plenty of rocks that we did not understand when we started relogging the 309 Deposit core. By compiling a reference photo library, we were able to identify gradational variation from sedimentary to volcanic facies. Combined with structural and geometrical data, we could interpret the environment of formation.
The hydrothermal system model is developed by combining observations and interpretations of the relationships between various features of the system made whilst logging in conjunction with other drill hole information, such as geochemistry and mapped surface geology. As is often the case, the key to unraveling the 309 Deposit wasn’t the focus of previous explorers and the real answer lay in compiling lithology, veining, and gold distribution data.
Mapping out lithology showed that the 309 Deposit is hosted by a simple sequence of calcareous and variably carbonaceous well-bedded siltstones with abundant sedimentary structures that are progressively interlayered upwards with ash, crystal, and crystal lithic tuff that starts as occasional beds 1–5 cm (0.39–1.97 in) thick and increases to tuff layers that are several meters thick. A marker bed was
also identified within the interbedded siltstones and tuffs and helped correlation across the deposit. The siltstones and tuffs are cross-cut and overlain by a thick unit of breccia. Historically described as ‘milled matrix breccia’, this breccia is typically matrix-supported and comprises a rock flour matrix with angular to sub-rounded clasts of the underlying siltstones and tuffs. The basal contact of the milled matrix breccia is broadly parallel to bedding and we interpret this unit to represent a mass flow. Thus, we have the first part of our model, the host stratigraphy.
Plotting 309 Deposit mineralization styles in 3D showed that sinter crops out along an arcuate trend that rings near surface gold mineralization. Bonanza grade ginguro style colloform banded chalcedony veins are present at the top of the system (Figure 1A). Spectacular bladed fluorite-chalcedony-quartz ± adularia-pyrite-gold veins (Figure 1B) and breccia fill form throughout the deposit but are most common in the middle and upper parts of the deposit. The fluorite-bearing veins are progressively replaced by later stages of silicification (Figure 1C) and corresponding higher gold grades. Quartz-chalcedony-pyrite veins with visible gold as electrum and bonanza grades > 100 g/t Au (Figure 1D) appear to post-date most other mineralization and were observed in the deeper parts of the deposit. Thus, we have the second part of our model, mineralization styles suggesting a vertically zoned epithermal system.
Gold, or whichever commodity you are working on, is arguably the most important part of the hydrothermal system. The overall distribution of high grades often outlines the fluid conduits and likely reflects key controls on the system. A plot of gold grades >0.4 ppm Au at the 309 Deposit displays a complex shape. At depth, gold mineralization is predominantly focused along WNW and, to a lesser extent, NNE structural zones as stockwork veins and breccia fill. The best grades form in two 50–70 m (164–230 ft) high layers broadly sub-parallel to bedding and presumably the palaeo surface (Figure 1 E). Comparison with logged mineralization styles shows that the uppermost of the two zones contain abundant bladed fluorite-chalcedony-quartz veins and breccia fill. The bladed fluorite suggests this zone may represent a boiling and/or fluid mixing zone with associated abundant silicification potentially having formed a cap that allowed later gold-rich fluids to be concentrated.
The fluorite-rich zone also marks an inflection point in deposit geometry above which near-surface gold mineralization forms in two pipe-like bodies along an NNE trend (Figures 1E and F). A hydrothermal breccia with rounded pebble-sized clasts has formed at the intersection of the WNW and NNE structural zones and marks the center of the southern pipe (Figure 1F). The northern pipe is elongated parallel to the NNE structural zone. This pipe comprises shatter breccia and stockwork veins, but a clearly defined breccia conduit was not seen. Thus, we have the third part of our model, structural and hydrothermal controls on the distribution of mineralization.
Figure 1 shows the final hydrothermal system model of a structurally controlled hot spring epithermal system with a boiling zone marked by abundant bladed fluorite and pervasive silicification. Two breccia pipes propagate from close to the boiling zone and vent to the surface to produce an arcuate ring of sinter. The distribution of gold mineralization is controlled by structures at depth and boiling and brecciation near the surface. C
gbmr.com.au
by Paula Montoya-Lopera, Postdoctoral Research Fellow in Economic Geology at CODES, University of Tasmania
Ore deposits are developed on specific magmato-tectonic environments, on this subject exploration geologists should identify features that help to elucidate those specific zones. This short article describes the importance of understanding textural and mineralogical associations as a key exploration tool.
Most of the hydrothermal processes start in magmatic chambers at different depths, so ‘How could we identify those processes by field or optical petrography inspection?’. Well, to answer this question let’s start with the ‘beginning’, when mafic magmas cool down slowly, crystallizing and solidifying anhydrous crystals such as calcic plagioclases, pyroxenes or olivines (Bowen 1956) (Fig. 1A, B, C). Consequently, as crystallization progresses, high-temperature magmas dehydrate the host rock through metamorphic processes, liberating volatiles such as water which is increasingly concentrated in the residual melt. Then, when crystallization progresses to some point, the residual melt is saturated with water, silica, cations and anions changing the magma initial chemistry (Fig. 1D to J). The supersaturated magma by further crystallization results in vesiculation, bubble formation and magma fractionation (Toramaru 2022). Such vesiculation triggered by the cooling crystallization of melt is known as secondary boiling (Melnik and Sparks 1999; Toramaru 2022). At this point, supersaturated magmas are developing (Fig. 1D to I).
In the above example for magmas located in the deep crust, the temperature inevitably decreases due to e.g., host rock interaction, and water gets gradually concentrated in the melt because of crystallization. But ‘What would have happened if the magma started ascending?’. So, continuing with the latter magma example, which is
phasing secondary boiling, bubbles were formed somewhere in the magma chamber, because bubble formation causes volume expansion; the magma chamber is about to expand and exerts a force on the surrounding (Melnik and Sparks 1999; Toramaru 2022). However, the magma chamber cannot easily expand because it is surrounded by rock. Both cooling and crystallization unavoidably progress and magma vesiculation and bubble formation inevitably proceed. In this manner, the pressure of the magma chamber is highly increased, and at a point (the critical state; Wilson et al. 1980; Toramaru 2022) where the surrounding rock cannot withstand the pressure with all its strength, the surrounding rock cracks, and the magma flows out through the crack (Toramaru 2022). The magma that allows to somewhat increase its volume is decompressed (i.e., Solubility decreases and a degree of supersaturation increases; Fig. 1J to P) and increasingly vesiculates, leading to the increase in the fractionation of a gas phase (Melnik and Sparks 1999; Toramaru 2022). The fractionated and vesiculated magma decreases its density, expands the crack, and ascends towards the surface by buoyancy at an accelerated pace (Fig. 2A to D). In this way, second boiling can be considered as an overpressure that not only explains the dyke formation (Melnik and Sparks 1999; Toramaru 2022) but also triggers eruptions (Bowen 1956).
So, let’s complicate the processes a little bit more. As it is known, most of the ore deposits are associated with continental subduction zones; in that area magma chambers can recharge it by crust assimilation (e.g., thin or thick crust), multiples magmatic chambers, asthenosphere, upper mantle, oceanic slab dehydration or even from continental sediments as a part of accretion wedge (Fig. 3), and other. If the magmatic chamber is recharged by hotter magma (e.g., evidenced by mafic xenoliths; Fig. 2G to P), and supersaturated with water, silica (e.g., assimilation of asthenosphere, slab dehydration, continental sediments; Fig. 1D to U, Fig. 2F), it would reach the second boiling phase faster (no matter the depth of the chamber, commonly at shallow depths, Fig. 1Q to U). In addition, if the chamber goes through faster devolatilization processes releasing the volatiles richer in water, silica, Mg, Fe, Ca, cations and anions (e.g. hotter hydrothermal fluids, Fig. 1D to I), the dehydrated magma will be represented by porphyritic felsic hypabyssal dykes with euhedral pyroxenes overimposed to the general texture (Fig. 2D; Montoya-Lopera et al. 2019, 2020), even hydrothermal veins will be formed following the same dyke structural controls (Montoya-Lopera et al. 2020).
→ Figure 1
A Ophitic texture
B, C Subophitic textures
D Myrmekite texture
E, F Graphic texture
G, H Hypogene chlorite in matrix in andesitic porphyry
I Crowded sphene in andesitic porphyry
J, K Sieve textures in micas
L Sieve textures in feldspar
M–P Reabsorption texture in quartz
O, P Silica recrystallization around broken reabsorbed quartz
Q–U Porphyritic intrusive textures
Q–R Anhedral quartz
T Glomerophyric texture in plagioclases
U Broken quartz in phaneritic textures in plutonic rock
The development of each texture is based on the thermodynamic and chemical conditions of the magma, e.g. subophitic textures indicate high temperaturepressure and Ca excess, meanwhile ophitic is contrary to the latter; myrmekite and graphic texture are associated to silica saturation in the system, same as crowded or higher amounts of sphene or zircons; sieve, reabsorb and broken crystals textures imply chamber decompression, however those textures should be analyzed in detail with other microtextures in the same sample to obtain an accurate description, as those also could be interpreted as magma mixing; hypogene, basic hydrous aluminum-silicate minerals in matrix indicate hotter magma saturation. Photo A and B source: www.alexstrekeisen.it; C to U: by the author at Sinaloa and Durango State, Sierra Madre Occidental, Mexico). Microphotographs are in Cross Polarized Light (XPL).
A Panoramic basalt dykes hosted in granodiorite
B Basalt dykes hosted in granodiorite
C Basalt dykes hosted in lava sequence
On the other hand, if the saturated magma preserves the volatiles (e.g., water, silica, Mg, Fe, Ca, cations and anions) and crystallizes faster in structural traps, a most common product will be made, e.g., porphyry type deposits.
So, ‘Is there evidence that supersaturated fluids, secondary boiling occurred in a magma chamber, remain in crystalized rock or even eruptive materials?’. Well, the answer is yes, the most common evidence of those processes is rock, mineral texture, microtextures and mineral assemblage. As was cited through the above paragraphs, there are some key textures that help us to identify evidence of specific elementary processes that a geologist may take into account in order to create their own hypothesis, which should be supported later with more advanced experimental laboratory tests. It is highly important to observe those textures by thinking that something happened there when a magma chamber crystallized. C
References
• Bowen, N.L. (1956). The evolution of the igneous rocks. Dover
Publications
• Frisch, W., Meschede, M., Blakey, R. (2022). Plate tectonic, continental drift and mountain building. Springer. DOI 10.1007/978-3-54076504-2
D Dacite porphyry with crowded and anhedral pyroxenes overimposed
E Diorite xenoliths in granite
F Classic sinuous quartz veinlets in andesitic porphyry rock
• Melnik, O., and Sparks, R.S.J. (1999). Nonlinear dynamics of lava dome extrusion. Nature. V 402 : 37-41
• Montoya-Lopera, P., Ferrari, L., Levresse, G., Abdullin, F., Mata, L. (2019). New insights into the geology and tectonics of the San Dimas mining district, Sierra Madre Occidental, Mexico. Ore Geology Reviews. https://doi.org/10.1016/j.oregeorev.2018.12.020
• Montoya-Lopera, P., Levresse, G., Ferrari, L., Hernández, G., Orozco, T., Abdullin, F., Mata, L. (2020). New geological, geochronological and geochemical characterization of the San Dimas mineral system: Evidence for a telescoped Eocene-Oligocene Ag/Au deposit in the Sierra Madre Occidental, Mexico. Ore Geology Reviews. https://doi. org/10.1016/j.oregeorev.2019.103195
• Neukirchen, F. (2022). The formation of mountains. Springer. https:// doi.org/10.1007/978-3-031-11385-7
• Toramaru, A. (2022). Vesiculation and crystallization pf magma, Fundamentals of the volcanic eruption process. Springer. https://doi. org/10.1007/978-981-16-4209-8
• Wilson, L., Sparks, R.S.J., Walter, G.P.L. (1980). Explosive volcanic eruptions – IV. The control of magma properties and conduit geometry on eruption column behavior. Geophys. J. R. astr. Soc. V63: 117-148
For more information Contact Paula at: paula.montoyalopera@utas.edu.au
Drilling Contractors (A-Z): Diamond Drilling, Reverse Circulation, AirCore
BRYSON DRILLING
Phone 306-323-2202
Fax 306-323-2203
info@brysondrilling.ca www.brysondrilling.ca Canada
CAPITAL DRILLING
Phone +230 464 3250
info@capdrill.com www.capdrill.com East, North and West Africa
DDH1 DRILLING
Phone +61 08 9435 1700 admin@ddh1.com.au www.ddh1.com.au Australia
DIAFOR Phone (819) 860-3957
info@diafor.ca www.diafor.ca Canada
KATI OY Phone 0207430660 info@oykatiab.com www.oykatiab.com Finland
MITCHELL SERVICES
Phone +61 7 3722 7222 Fax +61 7 3722 7256 info@mitchellservices.com.au www.mitchellservices.com.au Australia
ATELIER VAL-D’OR
Phone (819) 824-3676
Fax (819) 824-2891
info@avddrills.com www.avddrills.com
BARKOM
Phone 90-312 385 60 50
Fax 90-312 385 35 75 info@barkomas.com www.barkomas.com
DISCOVERY DRILL MANUFACTURER
Phone 1-506-542-9708
Fax 1-506-542-9709 info@discoverydrills.com www.discoverydrills.com
www.terrasonicinternational.com
sales@terrasonicinternational.com
+1 740.374.6608
+1 740.374.3618
WE ARE YOUR SONIC DRILLING PARTNER
Terra Sonic International knows what it takes for you to succeed. We are committed to making the world’s most productive and reliable SONIC Drill Rigs and SONIC Tooling while providing the best service and support in the industry. Experience the Terra Sonic Difference today.
Swick Engineering has been building quality mobile rigs for over 18 years.
Available now, the Swick Gen II Mobile Drill Rig delivers intense power with a small footprint. Perfect for underground grade control, reverse definition, and exploration.
Key Features:
• Drilling automation
• HMI (Human Machine Interface) screen provides real-time updates
• 112kW drilling power
Spare parts
Training
Global Footprint
Aftermarket support
• 95% mechanical availability in field
• 360° versatility
• Small footprint, compact design
FIND OUT HOW SWICK’S GEN II CAN HELP YOU PERFORM ON ALL LEVELS
PROLENC
Phone (250) 563-8899
Fax (250) 563-6704 khodgins@prolenc.com www.prolenc.com
BOART LONGYEAR
Phone 1-801-972-6430
Fax 1-801-977-3374 www.boartlongyear.com
FORDIA POWERED BY EPIROC Phone 514-336-9211 Fax 514-745-4125 info@fordia.com www.fordia.com
NORTH BAY MACHINING CENTRE
Phone (705) 472-9416 Fax (705) 472-2927 luc@nbmc.ca www.nbmc.ca
PROLENC Phone (250) 563-8899 Fax (250) 563-6704 khodgins@prolenc.com www.prolenc.com
Diamond Products (A-Z)
www.boartlongyear.com marketing@boartlongyear.com
www.diatoolglobal.com anthonygraham6@gmail.com
DIATOOL is a young and dynamic company, founded in 2010. The company manufactures impregnated and set core bits, casing shoes, reaming shells, and geotechnical drilling bits. DIATOOL products are sold in North and South America, Australia, Asia, Africa, and Europe. DIATOOL Diamond Products are manufactured in a modern well-equipped plant, using the latest manufacturing technology.
DIAMANTINA CHRISTENSEN
Phone +562 2620 7808 christensen@christensen.cl diamantinachristensen.com
DIASET
Phone 1-800-663-5004 bits@diaset.com www.diaset.com
BOART LONGYEAR
Phone 1-801-972-6430
Fax 1-801-977-3374 www.boartlongyear.com
HOLE PRODUCTS
Phone 909-939-2581
Fax 909-891-0434 www.holeproducts.com
Drill Rods & Casings (A-Z)
BARKOM
Phone 90-312 385 60 50 Fax 90-312 385 35 75 info@barkomas.com www.barkomas.com
CORE TECH
Phone +51 983 856 666 info@coretech.com.pe www.coretech.com.pe
SINOCOREDRILL
Phone 86-510-82723272 Fax 86-510-82752846 sales@sinocoredrill.com www.sinocoredrill.com
FORDIA POWERED BY EPIROC
Phone 514-336-9211 Fax 514-745-4125 info@fordia.com www.fordia.com
Terra Sonic International knows what it takes for you to succeed. We are committed to making the world’s most productive and reliable SONIC Drill Rigs and SONIC Tooling while providing the best service and support in the industry. Experience the Terra Sonic Difference today. www.terrasonicinternational.com sales@terrasonicinternational.com
+1 740.374.6608
+1 740.374.3618
FORDIA POWERED BY EPIROC
Phone 514-336-9211
Fax 514-745-4125 info@fordia.com www.fordia.com
REFLEX
Phone 1-705-235-2169 Fax 1-705-235-2165 reflex@imdexlimited.com www.reflexnow.com
SONDA PARTS
Phone 55 – (31) 3391 3810 Fax 55 – (31) 3391 3810 comercial@sondaparts.com.br www.sondaparts.com.br/
Drilling Fluids (A-Z)
AMC
Phone 1-705-235-2169 www.amcmud.com
DI-CORP
Phone +1 (705) 472-7700 info@di-corp.com www.di-corp.com
Mudex
Phone +61 (8) 9390 4620 info@mudex.com.au www.mudex.com.au
Surveying & Geophysics (A-Z)
CORE TECH
Phone +51 983 856 666 info@coretech.com.pe www.coretech.com.pe Peru
DIGITAL SURVEYING
Phone +27 18 788 6349 sales@digitalsurveying.co.za www.digitalsurveying. com.za Africa
TRUST SOLUÇÕES
GEOLÓGICAS
Phone +55 62 992720023 contato@trustsg.com.br Brazil
CORE TECH
Phone +51 983 856 666 info@coretech.com.pe www.coretech.com.pe
DYNAMICS G-EX
Phone +61 7 54826649 sales@dynamicsgex. com.au www.dynamicsgex.com.au
PROSPECTORS
Phone +61 (02) 9839
3500
Fax +61 (02) 8824 5250 sales@prospectors.com.au
COREFINDER
Phone +55 62 992720023 contato@corefinder.com.br www.corefinder.com.br
DEVICO AS Phone +47 72870101 devico@devico.com www.devico.com
Basic listing
110 USD per issue
330 USD per four issues
A text-only listing including your company name and contact details (phone, fax, email and website).
Featured listing
275 USD per issue 830 USD per four issues
A business card-sized listing featuring your choice of image as a background, your logo and strapline, 240 character spaces and your company contact details.
Combined listing
1250 USD per year (four issues)
A featured listing published both in our print and web catalog. For more info, get in touch at: editorial@coringmagazine.com
• Enhances both bit-life and penetration rates during drilling operations.
• Extremely effective for lubricating down hole motors and eliminating magnetization of drill rods.
• Protects drill rod wear when using wedges in diamond drilling.
• Increases tool joint life by reducing torque in the hole.
• Inhibits swelling of clay-like materials such as saprolites, talcs and kimberlites.
• Enhances the effectiveness of powdered mud systems.
• Non-sheening when accidentally introduced into a water course.