A dverti $ er Component manufaCturing
Serving the Structural Building componentS induStry
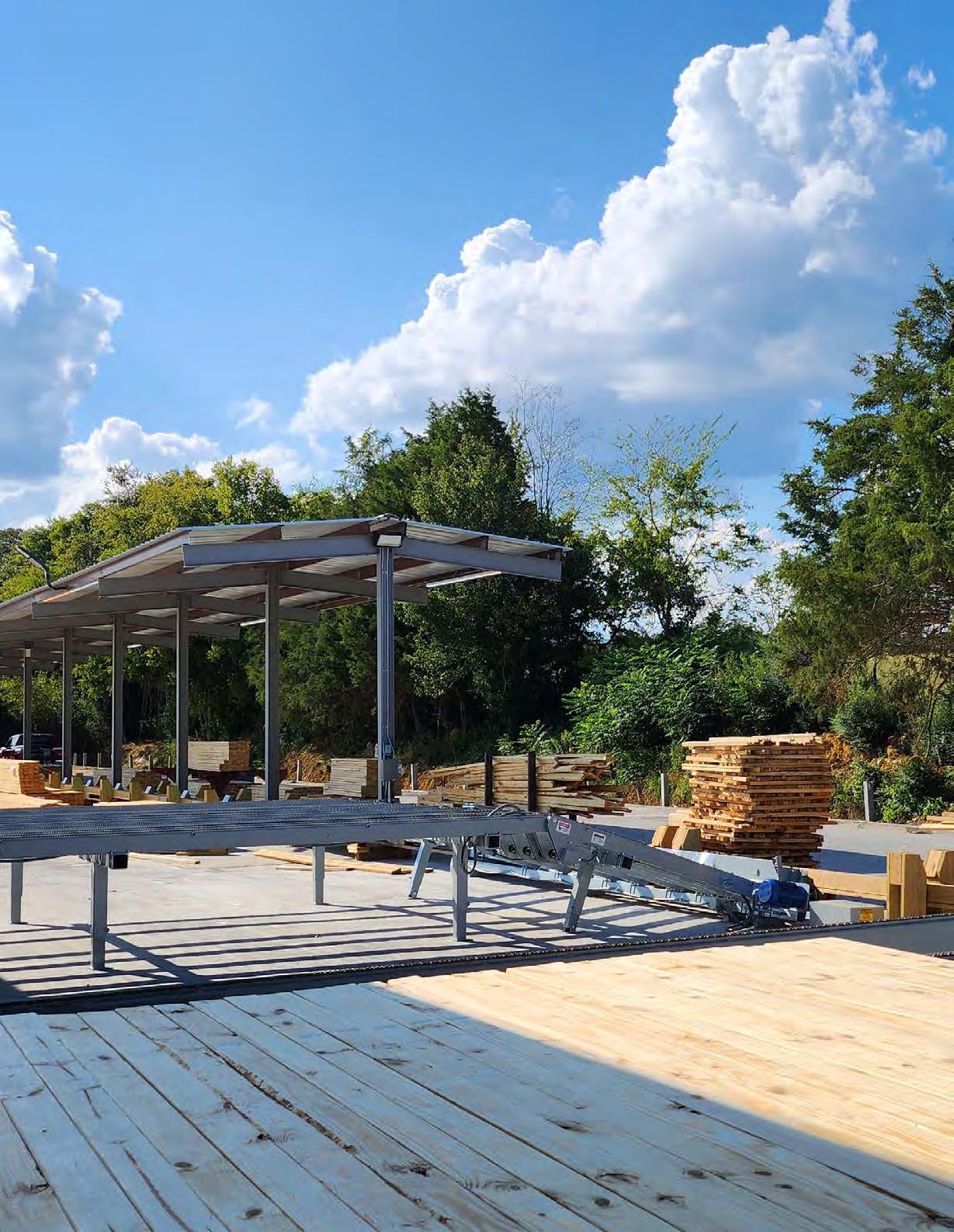
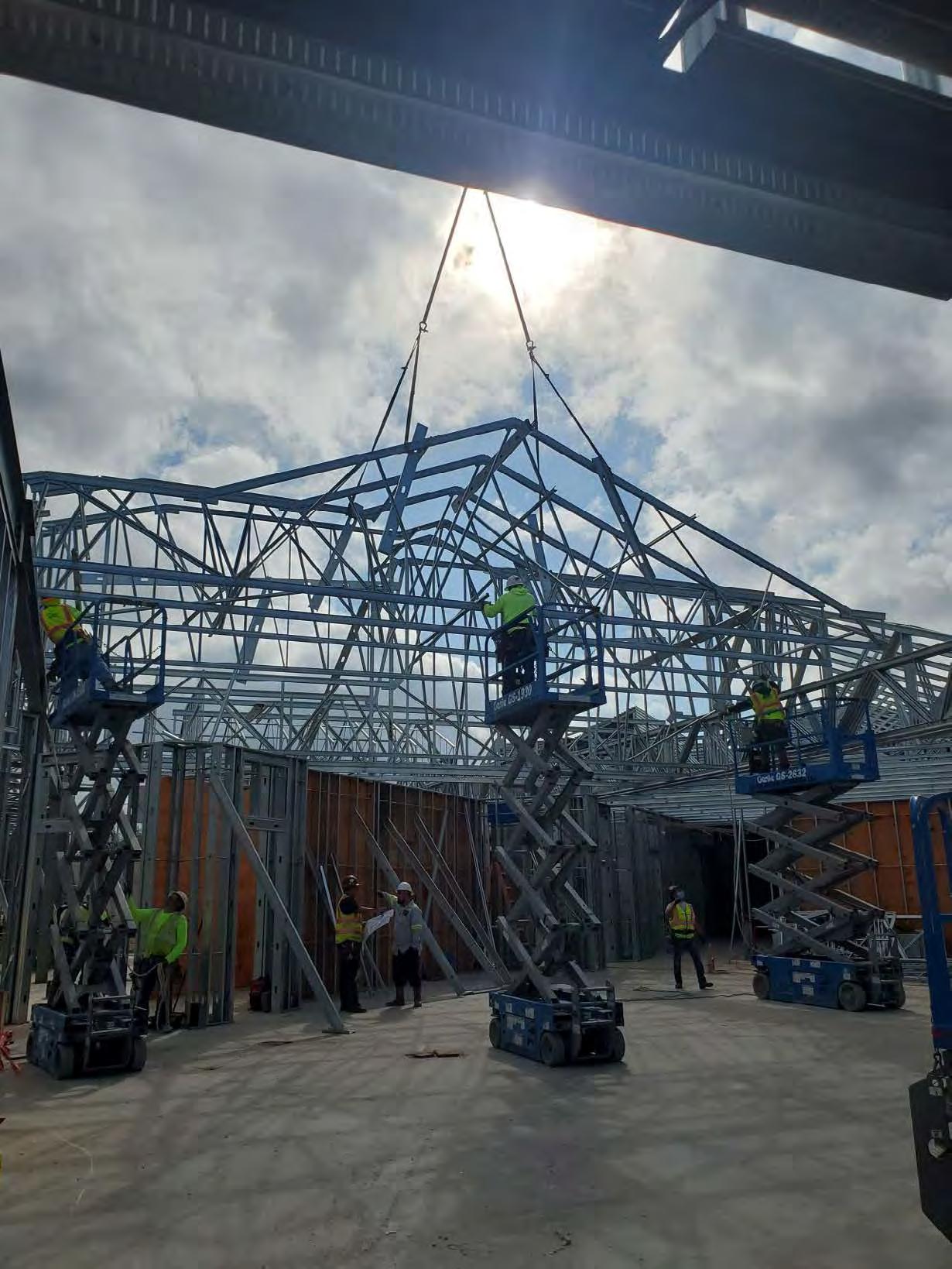

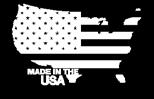
INCREASE PRODUCTION. MAINTAIN A SMALL FOOTPRINT. EXPANDABLE.
FRAMING STATION
SQUARING STATION
SHEATHING STATION
The Panels Plus 3-Table Router Line is similar to the 3-Table line and includes a Squaring & Routing Station in place of a Squaring Station. This station incorporates a manual X-Y router bridge for routing out rough openings. This production line consists of a Framing Station, Squaring and Routing Station, Sheathing Station, Subcomponent Tables and Roller Conveyors.
Anna Stamm – Advertiser Forum: Problem Solving 101—A Refresher
Joe Kannapell: Home Building Technology, Part IV: The $6,000 Question
Wendy Boyd – Spida Machinery: Importance of Factory Layouts and Investing in the Right Machinery!
Todd Drummond Consulting, LLC: Proper Time Management is Essential for Proactive Management Best Practices
Glenn Traylor: Do You Use Sub-Components to Aid in the Assembly of Components?
Ed Lim – LimTek Solutions: Giant Kanban!
Ed Serrano – Vekta: A Fork in the Road
Steve Shrader – Hundegger: Labor Tweaks Won’t Save Manufacturing—Automation Will
Marco Gagnon – Element Equipment: Custom Equipment for Any Project
Jesse Southard – Stiles Machinery: Constructing a Safer Tomorrow: The Safety Advantages of Off-Site Framing
Carl Villella – Acceptance Leasing: Tariff Pressures Squeeze Wood Building Component Manufacturers, Financial Solutions Sought
Kathryn Pedde –JAX, The Wood Retriever: Hardware + Software Integration with JAX, The Wood Retriever
Valerie Hansen – BuyMetrics: Component Industry’s Latest Nightmare: Tariffs
Steph Karlstad – LFT Strategies: Built Over Time, Not Overnight: Why Truss Plant Owners Must Lead Through the Next Season
Thomas McAnally – TheJobLine: Standards of Performance for Manufacturing and Their Role in Annual Reviews
Geordie Secord – Design Connections: Fewer Inspections = Better Quality?
Yoonhwak Kim, P.E. – Alpine: Hand Calculations for Maximum Gravity Reaction on Truss Design Drawings
MiTek Staff: The Evolution of Product Testing in Engineering and Manufacturing
Simpson Strong-Tie Staff: Using Truss Self-Weight
Joe Kannapell – The Last Word: Material Handling, Saw to Table
Serving the Structural Building componentS induStry
New & Used Equipment
Saws
Truss Equipment
Panel Equipment
Trucks & Trailers
Misc. Equipment
Door | Stair | Window Equipment
Safety First
Calendar of Events
TheJobLine - Jobs & Candidates
Industry News
Directory
Hiring Zone
4Ward Solutions Group
Acceptance Leasing & Financing
Acer, Inc
Advanced Component Solutions
All Points Technical
Alpine
BuyMetrics
Clark Industries, Inc.
Eagle Metal Products
Eide Machinery Sales, Inc.
Element Equipment
Fitzgerald Group
HOLTEC USA
Hundegger USA
JAX, The Wood Retriever
LFT Strategies
LimTek Solutions
MiTek
Panels Plus
Paragon
Precision Equipment
ROGworx Automation
Simpson Strong-Tie
Spida USA
Stiles Machinery
The Hain Company
TheJobLine
Timber Products Inspection
Todd Drummond Consulting, LLC
Triad
Merrick Machine
Truss Builder Parts
Vekta Automation
Wasserman & Associates
West Fraser
Wolf X Machina
Wood Tech Systems
Publisher Thomas McAnally twm@componentadvertiser.org
Editor Anna L. Stamm 800-289-5627 x 3 anna@componentadvertiser.org
Distributed FREE Via e-mail subscription Download PDF or Read on line at www.componentadvertiser.com
News of Interest and Advertising inquiries can be submitted to: anna@componentadvertiser.org An Open Forum for many sources.
Deadline 20th of each month. Articles, Trade Names, and Logos are the property of their respective owner or creator unless otherwise noted
Disclaimer: We reserve the right to refuse any advertisement or material that we deem not in the interest of the industry or the Advertiser. Permission to use content is the responsibility of the contributor including permissions to use any likeness of persons.
The Advertiser is provided “As Is” including typographical errors, omissions, and mistakes both intentional and unintentional.
Believe it at your own risk! Copyright 2008-2025
Component Manufacturing Advertiser
The Advertiser 7586 Becks Grove Road Freetown, Indiana 47235 no reproduction in whole or in part without permission from the component manufacturing advertiser
Archive Copies Available On Line www.componentadvertiser.com
Anna L. Stamm Director of Communications and Marketing Component Manufacturing Advertiser.
Large and small, we’re confronted with problems on a daily basis. Often, they’re something routine and simple, so we don’t even think of it as problem solving. But other times, they hit us like a roadblock, at which point it helps to have a strategy so we can move forward.
Understanding exactly what a problem is will go a long way toward solving it. Most importantly, you have to be honest. It’s not about assigning or avoiding blame – it’s about identifying why something is not working as it should. You need to be objective and logical, so you don’t waste time on distractions or incidentals.
After you have a clear picture of the problem, then you can devise your plan to address it. These strategies may help you navigate your path.
1. Ask for Opinions: If the problem is affecting other people too, then be sure to listen to their input when diagnosing it and taking action. Even if the solution is your responsibility, you would do well to include others when assessing a situation.
2. Do Your Research: Let’s face it – the internet is a vast resource that we can use. Of course, not everything you read is true, but now more than ever you can find enormous amounts of information online. Importantly, do not simply do one search and call it done. Dig deeper, vet your answers, and keep researching until you have a complete picture.
3. Plan Ahead for Next Time: Especially if you have, or think you will have, a recurring problem, take that into consideration when you’re trying to resolve it. Is there more you can do now so that your fix lasts longer? A few extra steps or extra cost now may help you avert your next roadblock, or at least extend the time before you’re stopped again.
Sometimes, it’s tempting to ignore a problem, even though we all know that won’t make it go away. Large or small, the problem will still be waiting for us – and the sooner we accept that, the sooner we can (try to) fix it.
Monet DeSauw FWA 500 Floor Web Cutter
• Push Button Powered Blade Angulations
• Single Push Button Setting for 2 Blades per Side
• Electronic Digital Readouts
• Backup Mechanical Indicators
• Cuts 4 Angle Webs, Cantilever Webs (2 piece webs) & Square Blocks
• Magazine Lumber Feed for 3x2, 4x2 and 6x2 Lumber 12 1/2” to 48 1/2” Length Capacity (7” Minimum on Square Blocks)
• 60 Pieces per Minute
• (4) Internal 16” Blades & (1) External 16” Cut-Off Blade
• Pneumatic Blade Brake on External Blade
• Dust Hoods
• Belt Waste Conveyor (under saw)
• Add $4,300 for 12’ Incline Waste Conveyor (adjacent to saw)
• Add $2,100 for Extra Set of Blades
• 480 Volt / 3 Phase FOBMO Call For Pricing
• Automated (Truss Design Software Download) or SemiAutomated (Touch Screen Entry) Operation
• All Movements are Computer & PLC Controlled
• Comprehensive Setup Screens Display Each Piece with Setup Data
• 22” x 40 Tooth Blade on PAE Cut 1 or 2 Boards up to 20’ (2 Second Plunge Cut)
• Cut Chords, Webs, Rafters, Wedges & Stair Stringers
• Cut Long Scarfs by MultiPlunging
• Servo Positioning on Infeed, Angle & Outfeed Pusher
• Over Travel Protection
• Ink Jet Printer
• Lumber Optimization Program
• Belt Waste Conveyor
• 480 Volt / 3 Phase / 60 Amp
• Includes 5 Day Onsite Installation & Training
• Optional Monet DeSauw Live Deck, Bunk Feeder & Incline Belt Waste Conveyor FOB MO Call For Pricing
• Touch Screen User Interface with Backup Mechanical Controls
• 3 Operating Modes: Auto, SemiAuto & Manual
• All 20 Axes of Movements are Computer & PLC Controlled
• Comprehensive Setup Screens Display Each Piece with Setup Data
• Anti-Collision & Optimizing Programming
• Auto Calibration Productivity & Time Tracking
• Maintenance Diagnostics
• Variable Speed Conveyor (0-50 Flights per Minute)with Powered Hold Downs
• (1) 30” x 80 Tooth Blade (27 3/4” Scarf on PAE)
• (4) 16” x 40 Tooth Blades (13 1/2” Scarf on Centerline)
• Pneumatic Blade Brakes on all 5 Blades
• 16 1/2” to 20’ Length Capacity (11” Minimum on Square End Blocks)
• Vibrating Waste Conveyor Under Saw
• 480 Volt / 3 Phase
• Includes 4 Day Onsite Installation & Training
• Add $2,900 for Extra Set of Blades
• Optional Live Deck, Label Printer, Ink Jet Printer, Catcher Display & Incline Belt Waste Conveyor.
Automatic Truss Jigging System to drastically reduce setup times. Allows for 100% embedment on the table, with top & bottom chord pucks in the same slot. TopSider or standard configurations available for conventional kick-leg, walk-thru, or our new trackless 8' and 10' continuous table systems. Systems for other roller & hydraulic gantries are coming soon. Available in new machine installations or for retro-fitting your existing table. The TopSider is exclusively applicable for “kick or flip leg” style truss presses such as the Tri-Axis & Lumbermater®
• Capable of 100% On-Table Nail Plate Embedment
• Two Pucks Per Slot
• 24", 26", and/or 30" Spacing
• Compatible with all current major design software
• Multiple Simultaneous Layouts
That'sallthetimeittakes todrillstudsforrunningRomexorotherelectricalwireinthewallpanels
Motor: HeavyDuty5HP-3phase-220vor440v(Pleasespecifywhenordering)
MotorcarriagebearingandspindleassemblymountedonBlanchardgroundsteelplate LinealmotionishardenedandgroundVbearingsandrails
BlockSizes: 2x4through2x12infiniteheightsettingtocenter
AirSupply: 100psi10CFM
Drills: 2wing3/4'”CarbideTippedcanaccommodatesmallerorlarger
Spindles: AlloySteelpolishedandgroundprecisionshafting
Frame: 2"SteelWithPowderCoatFinish
Covers: 10Gauge(1/8"Thick)Aluminumremovable
Dimensions: Height-60inches,Width-33inches,Depth-33inches
Shippingweight: 750lbs.-(Includingcrate)
MADEINAMERICABYAMERICANS
By Joe Kannapell
Unions opposed it, builders dismissed it, but the American homebuyer would embrace prefabricated housing as soon as they could afford it. Despite fierce opposition, the government made it a reality by allowing FHA financing on prefabricated homes with loans of $6,000 or less. In announcing this expansion, FHA’s administrator proclaimed, “What America needs is a good $6,000 house!” And, with that, American entrepreneurship kicked into high gear in 1948.
Jim and George Price responded immediately, building a model home that incorporated their decade-long experience prefabbing nearly 14,000 homes in their Lafayette, Indiana factory. When they listed this two-bedroom model for $5,750 with a lot included, they drew a crowd of 3,000 people on the first day they showed it, booking 300 orders. Afterward, inquiries came from other builders, many of whom were from out-of-state, lending credence to the Price’s ambitions of taking their company, National Homes, into the national market.
Meanwhile, traditional builders like William Levitt of Levittown acclaim went back to stick framing after the war. Others tried building components on site, but few could realize enough savings to get under the $6,000 threshold.
But an increasing number of builders realized that they could not build components efficiently in the field, so they began ordering packages from prefabbers. By 1951, over 3,000 builder-dealers had allied themselves with one of 60 prefabricators. This impromptu arrangement produced a torrent of desperately needed affordable houses, delivering the American Dream to millions of World War II veterans and average middle-class Americans.
The lasting legacy of the prefabbers is that they embedded the use of trusses into residential framing practices. Because the prefabbers installed windows and doors in wall panels, once the trusses were installed
and sheathed, the entire structure was closed in and finish work could begin. There were a few large multi-plant firms, including National Homes and Scholz Homes, that framed rafters and ceiling joists 4’ on center, and dropped in premade 2x4 ladder-framed roof and ceiling panels between them. However, these holdouts would soon convert to trusses to recover space on their delivery loads, since trusses would consume only one-tenth the volume as roof and ceiling panels.
In the summer of 1950, National Homes purchased a 175,000 sq. ft. former army depot in upstate New York to build homes for their eastern dealers, producing 10,000 homes that year. By then, they were the dominant producer in the country, building approximately onethird of all prefabbed units. Gradually their practices were being accepted by the building community, leading to their appearance at the NAHB Exposition in 1952. Co-owner and VP George Price attributed their success to volume buying, affordable pricing, and shipping the whole house on a single truck.
The turn of the half century brought amazing tracts of entry-level housing and uplifted millions of families across America. The majority of these homes have weathered well, as shown in these present-day pictures of two 75-year-old beauties.
Also in 1950, The University of Illinois set up its Small Homes Council to determine the best ways to design and build the most affordable homes, those typically 24’ x 36’ in size. They began by studying the most efficient interior wall layouts, and in the early 1950s erected houses to determine the optimal construction techniques, paving the way for wider acceptance of panelization and truss use. Also, at this time, a young engineer named Cal Jureit was testing the best way to connect trusses in a small lab in south Florida, and his work would soon blossom with the invention of the modern truss plate.
Next Month: The Earliest Housing Innovator
Get the industry-leading software and automation technology you need to scale your business. Overcome market challenges, boost productivity, and confidently meet demand when you choose MiTek as your solution partner.
Are you ready to scale your success?
Elevate Your Wall Panel, Floor Truss or Roof Truss
Manufacturing with 4Ward Design Solutions’
Precision Component Design Services!
When you work with us, you get: and
Speed and Scalability
Adjustable Hours
No Need for Training
Reduced Regulatory Burdens
Reliable Timelines
Extend your existing capabilities with 4Ward's design expertise. Without the hassle and expense of training your own designers, partnering with us guarantees that each wall panel, floor truss or roof truss will be designed for structural integrity and production and field efficiency.
Achieve cost efficiency without compromising on excellence. Our costsensitive approach ensures maximum value for your investment.
Leverage our expertise, ensuring every component is attentively designed for optimal performance and durability.
We understand that every component project is unique. At 4Ward, we create custom designs, tailored to your exact specifications. Contact us today for a complimentary consultation.
Enhance your expertise with wall panel design services from Simpson Strong-Tie. Whether you’re a framer, component manufacturer or LBM, our regional project managers and designers know the standards and practices in your area. Based on your plans, we use leading software with automated saw systems, such as EasyFrame™, to customize wall panels for efficient assembly, stacking and jobsite delivery. You also get IFC and 3D model files for seamless integration and review by local trades. Along with innovative hardware and cutting equipment, our wall panel design services can add value to your customer relationships and the structures they build. Learn more at go.strongtie.com/cs or contact your sales representative.
We’ve expanded our global manufacturing capabilities with a new facility in Jacksonville, Florida. Our customers in America and Canada now benefit from even greater, local responsive service and support.
Wendy Boyd Chief Customer Officer Machinery Group Spida Machinery
Factory layouts are important in any industry, and none more so than in the structural building components industry. Not only do factory layouts allow you to simplify and streamline workflow processes, but they can also assist you in maximizing your productivity and improving overall efficiency
So, what is needed to ensure an effective and optimal layout? How can you choose the right machinery that supports the effectiveness of your factory layout and also supports increased market share? Consider these critical points.
Never underestimate the importance of a factory layout. There are a number of key elements you need to consider when creating a factory layout to ensure you get the best outcome. When you partner with us, we’ll work alongside you and discuss each of these key areas in relation to your manufacturing goals.
Space utilization takes into account how much space you have available and the best way to utilize this space for optimal results. Taking time to do space planning will ensure your workflow processes flow within your manufacturing factory and are safe and efficient. When looking at the space available, consider other elements such as material handling, easy access and movement of staff, clear pathways within and between areas, tasks to be performed inside and outside of areas, and of course equipment placement to maximize floor space.
Ultimately you want to have equipment, workstations, and storage areas placed in the optimal position for workers and material handling.
When it comes to your workflow, a factory layout is critical and if you get this right, you have much greater control over quality and efficiency. The goal here is to position machinery and work areas to achieve an uninterrupted flow, where the manufacturing process logically and safely moves from one stage to the next. Effective factory layouts with workflow optimization in mind allow you to implement a layout that minimizes material handling, transit times, and potential bottlenecks.
•
They say time is money, right?! A smart factory layout considers material handling and considers the most efficient way to move materials throughout the manufacturing process. To streamline your production flow, you want to consider how you can logically and safely move and store material in a way that requires the least distance to travel and the least amount of manual handling. Clear pathways and purpose-designed trolleys and equipment can help, with automation increasingly being used with great advantages.
•
Of course, you need a factory layout that is efficient and increases productivity, but worker safety is also a top priority. Your layout will not be optimal unless it takes safety considerations into account. The positioning of equipment and workstations should be done in a way to achieve easy access for workers, limit the amount of heavy lifting required and physical strain, reduce worker fatigue, and minimize the chance of an injury or damage.
•
When you’re in business, you naturally think ahead and plan for the future to ensure ongoing success of your manufacturing operations. This ‘future’ view is a key consideration when designing a factory layout, so it’s a good idea to think of scalable layouts that will meet your manufacturing needs now and in the years ahead. If you’re wanting to end up with a full wall panel line but are starting off with just a few machines, plan for this at the start so it’s an easy addition in the future with less disruptions and costs.
When you partner with Spida Machinery, we work alongside you on your factory layout. Our collaborative approach means we learn what your manufacturing goals and requirements are, go through the key considerations with you, discuss some options, and then recommend a solution that’s best for you. Each of our layouts is unique to the customer given everyone’s factories and workflow processes are different – it’s not one size fits all when it comes to layout.
We’ve been in the structural building components industry for well over 40 years, and collectively we have decades more experience with factories and machinery, so we have extensive insight that we utilize for layout design and installation.
As explained by Cullen Ellis, Spida Machinery Product Specialist, “[At the layout stage], we take pride in taking the time to understand our customers – what their pain points and challenges are, where they have bottlenecks, what they are wanting to achieve with machinery now and in the future. This requirement-gathering stage is a fundamental part of our customer journey and input into our factory layout, allowing us to deliver a tailormade, fit-for-purpose solution.” We take the time to understand your needs so we can make the best recommendations for your business.
In addition to an effective layout, it is critical to select the right machinery to maximize efficiency and productivity, quality and consistency, cost reduction and profitability as well as increasing safety. Most importantly, we realize you are not starting from scratch but have existing machinery too! That’s why we begin with a CAD drawing of your factory that we can populate. Your current machinery is put in place and then we add our new ideas. This gives us a shared diagram that we can discuss, adjust, and refine as we go.
Whatever your manufacturing goals are – streamlining processes, increasing output, growing capabilities, reducing downtime, alleviating bottlenecks, reducing manual labor or minimizing heavy lifting – selecting the right machinery can assist with the realization of these goals.
The end outcome of investing in the right machinery and installing it as per a well-planned factory layout is the opportunity to increase your market share.
Investing in the right machinery, that’s designed for the environment it’s intended, allows you to increase production while lowering your manufacturing costs.
Also, choosing machinery that provides versatility and flexibility means you’re maximizing the footprint in your factory while best utilizing the operator and the outputs of the machine. For example, the Spida Raked Wall Extruder is designed to assemble and simplify the process of making raking wall frames as well as common wall frames, from the same machine! No need for two separate lines with multiple machines.
Finally, when investing in the right machinery, consider the advances in technology and how this can support your goals. The increasing use of automation (which we specialize in) is a game changer!
At Spida Machinery, our customer journey begins with you. We listen to what your manufacturing goals are and what you’d like to achieve for your factory. We then recommend the best Spida machinery and equipment to meet your needs now and in the future. We design a factory layout alongside you, taking into consideration your space available, your workflow processes, moving of material around the factory, safety, and your future plans. We know that when you make the decision to invest in machinery, you want it to reap optimal benefits. Talk to us today about how we can help you achieve such benefits in your factory!
A starting point for exploration. If you’re new to Paragon, our free plan provides:
1 User
Paragon Truss Link with TDDs
Live and Dead Loading Analysis
View-Only Layouts
Basic Support
5 Prototype Trusses without Plates
Perfect for individual modeling and estimation professionals who need tools for layout, pricing, and preliminary truss designs without plates.
1 User
250 Prototype Trusses/mo
Paragon Truss Link with TDDs 3D Layout Tools
Truss-to-truss Connections
Truss Lumber Analysis without Plates
Modify All Load Settings
Lumber and Connector Lists
Access RESTful API
Estimation Downloads
Access Engineering Network
Perfect for individual component manufacturer designers needing production-ready truss designs and manufacturing features.
1 User
250 Manufacturer Trusses/mo
Paragon Truss Link with TDDs
3D Layout Tools
Truss-to-truss Connections
Full Truss Analysis with Plates
Modify All Load Settings
Lumber and Connector Lists
Access RESTful API
Premium Downloads
Access Engineering Network
Precise cutting up to 4-boards high! The ProCut™ UC Linear Saw Series is configurable to any assembly line; providing a safe, accurate way to cut your lumber, while keeping your materials moving on your line. The ProCut™ UC Linear Saw Series offers many variations to suit your plant & assembly line.
Inspired by ten years of intensive field experience and the ample and detailed feedback of numerous customers, we’re pleased to introduce the most advanced, most enhanced and high-performance Terminailer yet-Terminailer V.8. Drawing on invaluable time in the trenches closely evaluating Terminailer’s performance under varying conditions, our engineers have incorporated critical learning and insight to enhance simplicity, performance and operator control. Just part of what V.8 offers includes:
•Vastly enhanced operator control for even greater productivity
•A redesigned nail-feed supplying EverWin PN90-PAL industrial nail guns
•Simplified pneumatics featuring direct air-supply to all six nail guns
•Even more sub-component profiles for wall design flexibility
•Rugged durability with pharmaceutical grade assembly
Developed by people who know well the mechanics, safety considerations and business aspects of wall-panel production, Terminailer V.8 combines more enhancements & operator-friendly features than ever to take your productivity to the next level and beyond. Contact us to learn even more and to put the V.8 performance in motion at your facility.
When it comes to the daily tasks of any executive, there doesn’t seem to be enough time in the day to implement everything that needs to be done. From sales to troubleshooting, there are constant interruptions in your day that keep you from accomplishing those goals you tell yourself need to happen. However, as an executive, your primary duties should be improving the processes and not performing the daily tasks others should accomplish without your input.
Proper time management is essential, and smart executives need to find ways to prioritize their most important responsibilities. An example may be that you have decided to implement a tool to vastly improve the pricing, scheduling, and shop efficiency benchmarks of your wood truss manufacturing. How are you going to undertake this and make it happen?
Let’s revisit the time management strategy by Stephen Covey’s 7 Habits of Highly Effective People. The displayed matrix shows two columns of “Urgent” and “NonUrgent” and then two rows of “Not Important” and “Important.”
Why the repeating pattern of insufficient time? — Suppose you are an executive or department manager and don’t seem to have enough time to implement better processes. If that is the case, you are too tied up in quadrant #1 of necessity, which is urgent and important. Your time is consumed with crises, pressing problems, firefighting, and answering repeated questions only you can answer. To resolve this repeating pattern of not having enough time because of reactive management, you need to be proactive and spend more and more time in quadrant #2, which is quality and improvement, which is not urgent but is important.
Quadrant #2 of quality and improvement — Preparation, prevention, education and training, professional development, relationship building, recognizing new opportunities, and planning are all very good things you need to spend time doing every day. Once this is accomplished, your time-consuming activities of reactive management practices will fade away the more time you spend implementing better processes. So, how are you going to find the time to do this? Did you overlook where it clearly states education, training, and professional development? I know this may shock some, but investing in someone coming to your location is wise to help you and your group implement better solutions. You can spend an entire year trying to accomplish an important task that could be performed in a few weeks spread over a few months with assistance from someone who has achieved that very task many times before.
Implementing a tool to improve pricing, scheduling, and shop efficiency — I have written many times about the importance of time standards; please refer to Truss Manufacturing Time Standards (Man-Minutes) Time and time again, too many component manufacturers think they can simply develop time standards (man-minutes, work minutes, R.E., or S.U.) by tracking their work orders in the shop. To everyone without professional industrial engineering training, you will inevitably incorrectly sort and categorize which labor to track, group processes that should not be grouped, and try to develop time standards for labor that should not be developed. Let me save your team a lot of trouble and state that it is a complete waste of time when you do this, which 90% of component manufacturers do with no formal industrial engineering training.
“Depending on the department and task, most case studies state an average gain of 5% to 25% in productivity directly related to training programs.”
Our solution — TDC has repeatedly accomplished this task and refined the best practices of implementing proper time standards many times. Why reinvent something that someone else has done many times before? We’re here to help you succeed.
“But the Helper, the Holy Spirit, whom the Father will send in My name, He will teach you all things, and bring to your remembrance all things that I said to you.” — John 14:26
There is no better value than TDC for getting the best ROI for professional consulting services. TDC is your best source for learning about proven and practical lean manufacturing best practices combined with industrial engineering principles to keep your company at the leading edge of competitiveness. Cost savings and net profit gains that usually take months or years can be accomplished in weeks or months with TDC. No one is better at providing your team with proven results for good employee practices, pricing, truss labor estimation, and so many other best-in-class practices. All areas are addressed, not just manufacturing. Please do not take my word about TDC’s services, though. Read the public testimonials many current and past clients with decades of expertise and experience have been willing to give.
Website: www.todd-drummond.com • Phone (USA): 603-748-1051
E-mail: todd@todd-drummond.com • Copyrights © 2025
The industry’s most powerful integrated component design, engineering, and management software for steel and wood-framed structures.
iCommand
Manage projects, customers, materials, pricing & inventory
iModel
Design truss layout & profiles
iDesign
Optimize material usage & engineer trusses
iPanel
Design wall layouts, panelize, bundle, break & stack
eShop
Maximize crew productivity & improve manufacturing efficiency
The IntelliVIEW Suite is a fully integrated software solution for the layout and design of a building’s rough framing elements—including roof and floor trusses, wall panels, solid sawn, EWP, sheathing and various ancillaries.
The IntelliVIEW Suite provides the industry’s most complete analysis of the design, cost information and bill of materials—promoting increased profits by reducing plate and lumber use.
Ask those who know. They’ll tell you about the people at Alpine who make a difference.
Upgrade your truss-building workflow with our precision engineered jigging tables – the industry standard for quality and efficiency. Built to accommodate all truss jig parts and accessories, our tables ensure a flawless fit, every time.
We combine unmatched craftsmanship with competitive prices to deliver the best value for your business. Choose us – trusted by truss builders nationwide!
We offer Machinery Services Before
Recondition | Rebuilds Replace Components
Framework | Fabricate Guards Repaint Equipment Etc.
Precision. Efficiency. Affordability..
After Restoration
info@trussbuilderparts.com 2810 Parkway St. Unit 4 | Lakeland, FL 33811 863 602 2019 www.trussbuilderparts.com
T+/- .010 Inches
Stop Rail: 2 x 4 x 1/4 Aluminum Extrusion
he Hain Systems Framer (HSF) will help you build square and accurate wall panels for residential or commercial construction applications. It will help you cut building costs by saving time and improving your quality. It’s a reliable, efficient and proven system that features a ruggedly simple design. The HSF is based on a proven design with over 20 years of actual production use and maintenance experience. It comes fully assembled and is designed for portable job site framing or in-plant permanent installation. The table has many optional attachments and will support Mylar Tape wall layout or any other type of layout. The optional gun rails can also be retro-fit to any table.
Stops: Jig Bored Steel
Stop Blocks: Machine Billet Aluminum
Details:
Internal Components: Hardened, Ground and Polished Steel and Billet Aluminum
Table Construction: Thick-wall Structural Steel Tubing, Jig Welded for Accuracy
Dimensions: Length: 5 feet (60”) to 60 feet (720”)
Height: 12 inches
Air Supply: 90 psi (10 CFM Air Flow Recommended)
Depth: 12 inches
Electrical Supply: 120 VAC
Powder Coat: Industrial Gray
Dimensions: Height: 43”
Length: 16’ or 20’
Width: Adjustable 8’ to 10’ or 8’ to 12’
Shipping Weight: 3000 lbs
If you are looking for the fastest, most consistent way to measure and cut your product, then the Hain Measuring System (MEA) is your answer. The MEA changes from one length t any length instantly, up to 60’, without changing the operator’s position on the line. It is also highly accurate (+/- .010) and quickly moves from one length to the next in seconds. The MEA is designed for quick and easy setup and is simple to use. Even a first time user will be productive with little or no training required. It can adapt to any saw and can be mounted to any surface so that you can integrate the MEA with your existing setup. The MEA is versatile allowing “left” or “right” handed operation and measurement in “feet and inches” or “inches” depending on your preference. The MEA is also available in a “Skid Mounted” version.
Off-site construction solutions built around your business.
Build higher-quality components and modules more efficiently.
Stiles has been a trusted name in the U.S. woodworking industry for over six decades. Today, we continue to lead the way with a consultative approach to off-site construction, partnering with you to increase speed, precision, and productivity, while providing ongoing parts and service support when you need it.
Invest in equipment built to perform—and last.
Stiles is the exclusive North American provider of WEINMANN, the world’s leading machinery and equipment manufacturer for off-site construction. Whether it’s an individual machine or fully automated system, Germanengineered WEINMANN machines provide innovative solutions that revolutionize your production.
Make your good decisions work even better. Learn More
lnnovationen fur den Holzbau
HUNDEGGER
Hundegger leads the way in automation innovation for the truss component industry. Our advanced CAMBIUM software offers cutting-edge automation and digitalization solutions, revolutionizing operations, boosting productivity, and driving sustainable growth for manufacturers like you.
We go beyond standard mechanization; we champion true Automation. The Hundegger TD-II isn't just a saw-it's a transformative, comprehensive solution designed to streamline your production process. From retrieving lumber to optimizing, nesting, stacking, destacking, sorting, buffering, and precise delivery, our system ensures peak efficiency and productivity, tailored specifically to truss component manufacturing.
Harness the power of data with Hundegger's advanced CAMBIUM TACTICAL software. It meticulously tracks and optimizes your production, ensuring more automated operations and significant productivity gains.
We provide state-of-the-art automation and control solutions that set the industry standard. Our focus on industrial automation and robotics positions Hundegger as the leader in enhancing performance and efficiency in truss component manufacturing and beyond.
Hundegger products are essential for future-proofing your business. Elevate your productivity and secure your competitive edge with our advanced technologies and automation solutions, meticulously designed to meet the unique demands of component manufacturers today and tomorrow.
Don't get left behind. Invest in the future with true automation from Hundegger and see your business thrive.
2004 MiTek Cyber A/T Component Saw – Frame #398, Fully automated five-blade component saw, cutting performed by 2-16″ x 7 HP, 2-20″ x 7 HP, 1-32″ x 13 HP. Touch screen monitor w/Remote PC in enclosure. Belt scrap conveyor and gravity outfeed conveyor included. 240v, 3ph power / 90psi air required.
• T1 Axis Rod and Pillow Bearings replaced in 2023
• 7.5 HP Motor (230 Volt/3 Phase) with 20" Blade
• Touch Screen Computer
• Ink Jet Printer
• Powered Infeed Roller Tables & Outfeed Queue System
• (2) Manual Bunk Feeders (saw can be used with or without bunk feeders)
• Waste Conveyor (includes new belt which needs to be installed)
• 240 Volt / 3 Phase
• Motion Control Upgrade in 2018
• New Computer with Touch Screen in 2019
• (4) T1 Linear Bearings replaced in 2023
• (4) Z1 Linear Bearing replaced in 2023
• (8) Be lt Drive Linear Bearings replaced in 2023
• Several Belt Drive Wheels replaced in 2023
• New Z1 Actuator in 2023
• Spare Parts: 2 White Drive Belts, Spare Power Cable, Rebuilt Z1 Actuator
• Video available upon request
Cuts wall and truss parts from lumber depths 2×4 through 2×12, 60”+ scarf cuts, internally optimizes material (up to 11 7/8″ x 1.5″ EWP) Includes 20 foot OEM auto-infeed conveyor and 15 foot OEM outfeed conveyor, and under-saw scrap conveyor with belt-type incline. All servo controlled functions, Microsoft Windows XP OS, 7.5 hp motor with 20” carbide tipped blade. Includes spare infeed/outfeed belt and any available spare parts. No printer is included. The door latch needs to be repaired. 220v / 3 ph power, 125 PSI air required.
2003 Alpine AutoMill RS Component Saw, Model 344
Computer controlled saw sets up in 2 to 19 seconds and downloads from a network or by using a touch screen for ease of operation. Five-head automated component saw works in both automated (downloading files) and semi-automated control via touchscreen input. It has [23] axes of automated movement, enhanced diagnostics, auto management reporting. The RS cuts from 13″ to 20′ long material in size ranging from 2×3″ through 2×12″, includes [3] 18″, [1] 22″ and [1] 32″ blades with air brakes, shaker pan waste conveyor to incline scrap conveyor, one set of spare blades and any available spare parts. (Infeed conveyor needs electrical service). 480v/60Hz/3Ph power.
$17,997 NOW $12,497 FOB AZ
Wood Tech Systems
765-751-9990
www.woodtechsystems.com
Striebig Optisaw, model
Optisaw Automatic (Type # 5164) vertical panel saw station, with angled frame supporting material being cut: Max. cutting height (vertical) 5′-4″, max. cutting length (horizontal) 15′-1″, max. cutting thickness 2.36″. Both vertical and horizontal analog measuring scales on frame. Cutting head manually rotates from ve rtically t o horizontally for rip vs. cross-cutting, adjustable spacers for repetitive cuts, 5.25 HP saw motor, 9.84″ diameter blade, guide bearings for travel , push button controls, e-stop button and dust extraction hose (no vacuum included). Overall footprint of station 19′-1″ wide x 4′7″ deep x 7′-10″ height. Sold for $36,000 new. 208 volt, 3 phase electrical required.
$14,490 FOB AZ
Wood Tech Systems
765-751-9990
www.woodtechsystems.com
2000 Alpine AutoMill Component Saw
2000 Alpine AutoMill model 343H, (5) blade component saw, cuts lumber from 2×3 through 2×12, from 18″ to 20′, 4-angle floor webs from 18″. Includes powered length and angulation, digital readouts, (1) 32″, (3) 18″ & (1) 20″ blade, shaker under-saw scrap conveyor, incline, PC with Windows 98 o/s, and outfeed conveyor. Decommissioned in 2018. Stored indoors. 480 volt ,3 phase electrical required.
$10,497 FOB ON Wood Tech Systems
765-751-9990
www.woodtechsystems.com
Idaco Webmatic Saw
• Roof & Floor Web Saw
• Four 5 HP Saw Motors
• Cuts 2x4, 4x2 and 2x6 up to 16'
• Manual Angulation
• Waste Conveyor (under saw)
• Incline Waste Conveyor (adjacent to saw)
$8,500 FOB CO
Wasserman & Associates
800-382-0329
www.wasserman-associates.com
Hain 210' Powered Measuring System Adapts to Any Saw. Left or Right Hand Operation. Feet & Inches System (Stops at 12” Centers) or Inches System (Stops at 10” Centers). Motor: 1/4 HP Linear Actuator (110 Volt). Stop Rail: 2 x 4 x 1/4” Aluminum Extrusion. Stops: Jig Bored Steel. Stop Blocks: Machine Billet Aluminum. Optional Lengths from 5’ to 60’. Optional Gang Stop. Add $890 per 10’ Section of Heavy Duty Roller Conveyor with Stands
$8,990
Wasserman & Associates
800-382-0329
www.wasserman-associates.com
The truss industry relies on 3rd party quality assurance services to provide random visits to review the plants Quality Assurance program along with their operations. If your plant needs to comply with the IRC, IBC and to those who depend on solid, experienced QA expertise, we ask you to consider selecting Timber Products Inspection, Inc. (TP) as your choice for 3rd party inspections.
Proudly serving the forest products industry for over 50 years, TP brings the expertise you need to ensure your business is successful. As a responsible partner, TP delivers to clients, employees, and the industries we serve the confidence to drive value through the effective use of our diverse professional team.
TP would like to welcome the following authorized agents to our inspection team, each of whom have many years of experience in the truss industry! • Al Coffman
Jean Hart
Curt Holler
Chuck Ray
Glenn Traylor
Elliot Wilson
If you have questions about how you can make this selection, please contact your authorized agent above or Glenn Traylor at 919-280-5905 or trusguy@gmail.com. https://www.tpinspection.com/ https://www.tpinspection.com/auditing-services/truss
By Glenn Traylor
Managing a truss with multiple pieces can affect productivity. For example, maintaining compliance with ANSI/TPI 1 Chapter 3 requirements for nearly thirty pieces can be challenging. To improve cycle time while preserving quality, using sub-components may be a practical solution.
Most likely, some truss builders have objected to separating projects into sub-components. They may argue that it increases labor (and therefore cost), but does it? When you have a complicated build, it may be more efficient to break it down into smaller steps that can be more clear and more easily managed. The quality of the end result will likely be improved too.
As a real-world example, let’s consider the following attic truss. Taking a closer look at the design, it can be argued that panel points 14 to 25 should be constructed on a separate assembly table that is concentrating on just the floor section of the attic area. Doing this will make it a little easier to keep gaps out of the assembly, thereby producing a higher-quality end result.
Here is another great example. It’s difficult to even read and interpret the drawing, so a subassembly that is adjustable by slight trimming might be a better solution.
Without the availability of a separate press, the assembly shown is laid out on the regular assembly table. Note that most joints are stapled to hold joints together. The component manufacturer is also pre-back-plating joint 26, which is a critical joint to aid in accuracy.
Then, the sub-assembly is easily inserted into the larger assembly.
Complex components can be simplified by breaking them into smaller pieces, which can enhance quality and improve productivity. This approach also prevents un-plated connections. Additionally, controlling pushing and slipping when the finish roller moves the design left and right during gantry cycling is another advantage that is gained when using sub-components.
Rather than seeing sub-components as extra work and extra cost, they can be easier for truss builders to manage and execute properly. If you’re not already, you too should consider using subcomponents in your assembly process.
An ANSI/TPI 1 3rd Party Quality Assurance Authorized Agent covering the Southeastern United States, Glenn Traylor is an independent consultant with almost four decades of experience in the structural building components industry. Glenn serves as a trainer-evaluator-auditor covering sales, design, PM, QA, customer service, and production elements of the truss industry. He also provides project management specifically pertaining to structural building components, including on-site inspections and ANSI/TPI 1 compliance assessments. Glenn provides new plant and retrofit designs, equipment evaluations, ROI, capacity analysis, and CPM analysis.
Glenn Traylor Structural Building Components Industry Consultant
http://www.linkedin.com/in/glenntraylor
This is a ground-up opportunity to bring your skills as a top Truss Design Manager to an exciting new venture. Can you combine individual strengths into one unified team effort? The company has invested in state-of-the-art manufacturing equipment from Alpine and needs a dynamic leader to take existing personnel and build a strong, efficient, and motivated team to support this location. As with any startup, the ideal candidate must be willing to wear many hats within the design department. Responsibilities include:
• Hiring, motivating, and developing team members
• Assessing, training, and managing design staff
• Implementing and optimizing processes to align with production needs
• Driving success and innovation in truss design
• Touch Screen Computer
• Automated Infeed Deck
• Infeed/Outfeed Roller Table
• Ink Jet Printer (does not work)
• 230 Volt / 3 Phase
• Excludes: Outfeed Queue Rollers & Waste Conveyor
Year Warranty and are custom built. We use blast prep for our powder coat
and paint
air-ride suspension and we now offer Galvanized Rollers as
We build
and 53’-80’ Extendable Truss Trailers, 26’, 32’ and 36’ Gooseneck Truss Trailers (Split Truss Available as well on Goosenecks) and 40’, 48’, and 53’ Standard Truss Trailers.
Quality components and meticulous assembly minimize downtime.
After comprehensive testing, each Ranger is carefully packed for shipping.
Trolley assembly process— the heart of the Ranger. Run
Infeed deck assembly—versions available for 5 saw brands.
Rangers can be installed in one day. Modular construction and thorough labeling of cables and components make the job easy.
2006 Alpine AutoMill SC Automated Component Saw
• Model 348B
• Automated Setup via Download or Semi-Automated Setup via Touch Screen Input
• 23 Axes of Automation
• Sets up in 2 to 15 Seconds
• Five Blades cut 2x3 thru 2x12 up to 20'
• Waste Conveyor (under saw)
• Excludes Incline Waste Conveyor (adjacent to saw) and Live Deck (in fronnt of saw)
• 480 Volt / 3 Phase
• Video available upon request
$38,900 NOW $10,000 FOB TX Wasserman & Associates 800-382-0329 www.wasserman-associates.com
Safety Speed Manufacturing Model 7400 XL Panel Saw
Safety Speed Manufacturing, model 7400 XL*, vertical panel saw, 3 HP induction motor, 64 inch crosscut, 2 1/8" maximum thickness, accuracy within 0.005 inches, 13 foot long welded steel frame with integrated stand and linear V-guides, enclosed counterweight system, adjustable vertical and horizontal rules. Quick changes from vertical to horizontal cutting. Includes machined aluminum material rollers, hold down bar, wheels, quick stop gauges and material hold downs. Dust collection ready. Options available include digital readouts for vertical cuts, automated length measuring, laser guide, stop bar, vacuum and midway fence. 208-230/460 volt, 3 phase electrical (208-230 single phase, 2 HP power optional +$100.00).
$14,499 Base, FOB MN. Wood Tech Systems 765-751-9990 www.woodtechsystems.com
Safety Speed Manufacturing model 7000, vertical panel saw, 3 HP induction motor, 64 inch crosscut, 2 inch maximum thickness, accuracy within 1/64th of an inch, 10 foot welded steel frame with integrated stand and linear V-guides, enclosed counterweight system, adjustable vertical and horizontal rules. Quick changes from vertical to horizontal cutting. Includes machined aluminum material rollers, hold down bar, wheels, quick stop gauges and material hold downs. Dust collection ready. Options available include lower frame extensions, digital readouts, laser guide, stop bar, vacuum and midway fence. 208-230/460 volt, 3 phase electrical (208-230 single phase, 2 HP power optional +$100.00). $10,199 Base, FOB MN.
Edmond Lim, P.Eng. LimTek Solutions Inc.
anban systems are designed for “just in time” workflow to optimize production efficiency and inventory levels. The Enventek Lumber PickLine is essentially a “Giant Kanban System” designed to improve lumber handing and to efficiently cull lumber away from the saws. Did you know that the main design criteria of the PickLine was to improve truss build production by having the lumber picker follow the tablet picking software to facilitate the organization of cut lumber in front of the truss build tables? With Enventek’s invention of the auto-feeding RetroC and auto-catching SpeedCatch carts, the system was too efficient for ordinary arrangements to keep up, and “one could not feed the beast even with multiple forklifts running around all day fetching lumber.” Hence, Larry Dalson invented the Enventek Lumber PickLine.
In the first picture, one can see how a forklift followed this path to get lumber to the saw — now that’s been replaced with a “passive lean” PickLine and SmartConveyor. No Kanban card system required (Giant Kanban!). Everyone can easily see what lumber needs to be refilled and what lumber is getting depleted. Please note the lumber storage shed and the dense storage lumber in the background. Daily picking lumber is not lumber storage. Lumber PickLines can feed any automated saw with the same benefits of more productive cutting/batching schemes and of increased sawing production by eliminating saw idle time.
There’s always room for an Enventek Lumber PickLine by strategically placing the lumber chain trough on an existing forklift path. This saves on operating costs by significantly reducing forklift travel and by replacing a dedicated forklift operator with a dedicated lumber picker. The important process of culling lumber at the PickLine away from the saw will improve sawing throughput with better quality lumber — for another example, see my article, “To Cull or Not to Cull (at the Saw).”
Space limitations in front of truss build tables require hand-stacked lumber to be organized for “left, right, and middle” of truss to speed up truss building as shown in the next photo. Without a Lumber PickLine, these truss building cutting schemes would be difficult to “pick” and would require a lot of communication between the sawyer, forklift picker, and lumber stackers. Having the software determine the lumber picking based on the detailed stacking sequence of lumber standardizes the material handling workflow and streamlines teamwork.
There are many tips and guidelines on how to envision and layout a lumber PickLine in my article, “The Art of a Lumber PickLine.” The only space limitation is how close the lumber trough can be placed alongside your existing building/driveway! The general rule is 35 ft from the building to the centerline of the lumber trough, if there is limited or no overhead door access along the side of the building. This is so forklifts can easily replenish lumber along the building side. To get more building clearance access, increase the length of the Smart Conveyors up to 80 ft long, which gives plenty of building access. In the next picture, because this plant has a Side-Loading Forklift and they wanted to keep the existing driveway as open as possible, they put the centerline of the lumber trough to the building at only 16 ft.
Even with a “Single-Sided Lumber Trough,” this customer is boasting a 30% sawing increase compared to their previous forklift lumber picking following the same path with significant operating cost savings. As shown here, the lumber is two bunks wide (different grades/sizes) and the picker manages the picking lumber accordingly.
Most importantly, the Lumber PickLine never cares what type of saw you have! Of course, I can personally recommend the RetroC, but you can read about other options too in my article, “Feed Any Component Saw with a Lumber PickLine.”
When you’re ready to Feed Your Beast and see these efficient and effective systems for yourself, let us know! Inside and out, LimTek Process Organization Technology will help you squeeze out more truss production and deliver quality trusses with shorter lead times to better service your customers by organizing your truss fabrication processes to maximize your investment in automation.
https://limteksolutions.com/#solutions
To see meaningful labor savings, quality improvement and production gains, SL Lasers with their easyto-see green light are nothing short of illuminating. They enhance worker accuracy and productivity, regardless of experience or primary language. They can reduce tedious setup time by up to 70%. No complex training or costly service agreements are required. And SL Lasers integrate seamlessly with any component design software and are quickly installed over existing equipment. We’ve been trailblazers in wood component laser projection since its very beginning, and we’re still delivering more rapid ROI for roof truss, wall and floor panel producers every day. Contact our enlightening team at Wood Tech Systems to see how SL Laser can deliver for you.
2021 Powermatic Model 511 Panel Saw 2021 Powermatic model 511 panel saw. Vertical panel saw features a powerful 3HP worm-drive motor which rotates in the carriage, adding the versatility to perform rip cuts. The solid aluminum rollers assure smooth feeding of stock and perfect 90° cuts every time. This saw will handle panels up to 5-ft tall in unlimited length. Includes horizontal and vertical scales and casters for mobility, the counterweight system keeps the saw carriage in the desired position when loading or unloading panels. Features dual 4″ dust collection ports with nylon brush surrounding the blade for superior dust collection from the front and the rear side of the panel. 115v, 1-phase electrical required.
$6,799 NOW $1,999 FOB AZ
Wood Tech Systems
765-751-9990
www.woodtechsystems.com
2023 Northfield Model 410 Upcut Saw NEW 2023 Northfield model 410 upcut saw available for immediate shipment. 90/90 degree cuts to 4″ x 10″ capacity (fence forward position) to 2″ x 14″ (fence rearward position). Saw is configured for material from left to right, with 3″ x 6″ air operated cylinder, filter, regulator, lubricator, 10 HP motor, enclosed steel base with cast iron table, magnetic starter and adjustable operating speed from 20 to 60 CPM. Includes optional two-palm controls, additional 4″ dust outlet, NEMA 12 electrics with fused disconnect and two 18″ diameter 60 tooth blades with 1″ diameter bore. 460 volt, 3 phase electrical required.
$18,630 FOB MN
Wood Tech Systems 765-751-9990
www.woodtechsystems.com
Model 1000 Cut-Off Saw
• 5 HP Motor with 14" Blade
• 2 3/16" x 8 1/4" Capacity
• Pneumatic Blade Guard/Lumber Clamp
• Foot Pedal Control
• Dust Collection Outlet
• 460 Volt / 3 Phase
• 1 Left Hand & 1 Right Hand Model
Available
$3,500 NOW $2,800 Each FOB NC Wasserman & Associates 800-382-0329
www.wasserman-associates.com
1982 SpeedCut MetraCut
Centerline Saw
26’, 32’ & 36’ sizes available, Split Rollers available too! 2 YEAR WARRANTY
ALL TRAILERS NOW AVAILABLE WITH OPTIONAL GALVANIZED ROLLERS
Scan the QR Code to take you directly to our website. For more information or to request a quote Call or Email: 1-800-237-5161 sales@precisionequipmfg.com
1982 Speed Cut Metra Cut, model SSA-11, centerline saw, 16″ blade, maximum cutting depth of 6″, maximum cut length of 31″, 164 deg. cutting range and 5 HP motor. Includes push-button on/off controls and analog angle measure on turntable with air stop, 20′ long infeed conveyor with OEM SpeedMeasure, 20′ long outfeed conveyor and one (1) spare blade. 208 volt, 3 phase electrical required (can be converted to 240v/440v).
$6,990 FOB WY Wood Tech Systems 765-751-9990
www.woodtechsystems.com
New Monet DeRobo Linear Saw
New, DeRobo linear saw by Monet organizes "fill" boards to increase optimization of each board, can produce unlimited scarf cuts, cuts 1 or 2 boards at a time and cuts webs, chords, wedges, rafters and open-stair stringers. Works with all major connector plate manufacturer's software. Features include 22 inch blade, left-to-right feed direction standard, lumber push and pull grippers for more accuracy, ink marking on the 1 1/2" face of the incoming boards and small piece capture and delivery to the front of the saw for easy access. Infeed deck and bunk feed are shown as options only. 480 volt, 3phase.
$245,000 FOB MO.
We provide high quality precision machinery suitable for cutting and assembly of walls, roof trusses and floor trusses. All your needs are covered.
$349,000 Location: MO
New, Monet DeSawyer 2000, computerized, five-bladed component saw, sets up in 15 to 17 seconds, can run in manual mode, downloads projects from a network or manually using display screen controls. Features all powered movements, cuts from 15" 90/90 cuts to 20 foot length, 2 x 3" to 2 x 12" lumber depths and internal brakes are standard. Options include enhanced servo controls featuring autocalibration, catcher's display and either shaker or belt scrap conveyor and incline. 440 volt, 3 phase electrical.
By Ed Serrano Managing Director VektaUSA
“My
only regret is that I didn’t do it sooner.”
(— You, probably)
t’s a common refrain from recent automation adopters, and you might just find yourself saying it one day. So, what makes that initial step feel like such a big leap and not just another step in your journey?
The price can sometimes be intimidating, bringing to mind all the possible financial implications and concerns. We often worry about the cost of change, but what about the cost of not evolving? Often, standing pat is the riskier choice.
When you embrace automation, you’re not alone. You gain the support of a dedicated team of people on your side, working with you to make sure your new solution serves your needs. You’ll see labor savings, safety improvements, training reduction, and of course, increased production and efficiency.
Any supplier can tell you the cost of their machines, but the number transcends a simple number on a page. In 30 minutes, Vekta could sit down with you and tell you your throughput improvements, return on investment, leasing or buying terms, and the number on the page would still feel like a big step — because it’s more about changing the status quo.
Okay, let’s talk straight. If you’re running a prefabricated frame and truss plant, you’ve probably thought about automation. Maybe you’ve even checked out the price tags.
Automation isn’t just about cost, it’s about what that investment unlocks: efficiency, scalability, and resilience in an ever-changing industry. To truly grasp it, you need to envision a future where your business thrives, unburdened by the limitations of manual processes. Investing in modular systems you can upgrade later isn’t just a short-term gain; it’s about making sure your plant is ready for the future and offsetting costs in the long run. It’s about looking beyond
the day-to-day and thinking about the big picture for your business and where it is headed in the years to come.
You’ve built your plant to where it is today through dedication and hard work. Automation is not about replacing that foundation but about empowering it for continued success. It is also about ensuring you have the right support system in place. Consider the stability and affordability of the support offered by your automation partner. Choosing a dependable provider means investing in a partnership that will stand by you as you grow.
But what about the consequences of doing nothing? In today’s fast-moving industry, standing still might be the biggest cost of all.
The best time to think about automation was yesterday, but thankfully, you’ve picked the secondbest time to think about automation.
In a continually evolving and competitive industry, plants at all levels are actively adopting innovative technologies to gain a leg up on the competition. The “cost” of maintaining the status quo is not merely about forgoing opportunities for increased profit and efficiency, it encompasses the significant risk of falling behind, finding difficulties in attracting and keeping talent, and losing your established niche in the market.
Let’s think about the cost of just sticking with what you’re doing – that feeling of safety from the familiar. You might be thinking, “We have operated successfully this way for years, why change now?” The answer is straightforward: the world around you is evolving. Your workforce evolves; individuals retire, seek new opportunities, or move on. Relying heavily on individual employees with years of accumulated wisdom and skill presents a considerable risk. What happens when those key individuals need to be replaced?
Construction is already seeing a trend towards deskilling in certain manual roles, highlighting the increasing value of the consistent, high-quality prefabrication that automation delivers. The demand for prefabricated frames and trusses, driven by efficiency and cost considerations, is only set to increase.
Consider this: would a carpenter who has experienced the precision and speed of a modern power saw willingly revert to using only hand tools? Similarly, would someone who has experienced the efficiency of automated frame and truss manufacturing willingly return to relying on multiple pull saws with multiple operators? The answer, in most cases, would be a resounding “no.”
Don’t let the cost of complacency hold your business back. Vekta is ready to help you take the step into automation and unlock a future of greater efficiency, productivity, and success. Let’s talk about how Vekta can future proof your frame and truss plant. Contact us today to explore automation solutions tailored to your business.
It takes all the right players to build a winning team. That’s why Simpson Strong-Tie provides truss and component manufacturers with a broad selection of versatile hardware products. Choose our code-listed truss connector plates, framing angles and straps, heavy-duty girder hangers and holdowns for strength and durability. Secure them with speed and ease using Strong-Drive ® structural fasteners, along with our Titen HD ® heavy-duty screw anchor and other mechanical anchors. Along with software, cutting equipment and professional design services, our hardware is widely available and backed by expert support. Learn more at go.strongtie.com/cs or contact your sales representative.
•
•
•
•
Saw Safety Speed Manufacturing, model 7400 XL*, vertical panel saw, 3 HP induction motor, 64 inch crosscut, 2 1/8" maximum thickness, accuracy within 0.005 inches, 13 foot long welded steel frame with integrated stand and linear V-guides, enclosed counterweight system, adjustable vertical and horizontal rules. Quick changes from vertical to horizontal cutting. Includes machined aluminum material rollers, hold down bar, wheels, quick stop gauges and material hold downs. Dust collection ready. Options available include digital readouts for vertical cuts, automated length measuring, laser guide, stop bar, vacuum and midway fence. 208-230/460 volt, 3 phase electrical (208-230 single phase, 2 HP power optional +$100.00).
Price: $237,900
FOB: ND
The Terminailer all but shatters the stereotypical myth that sub-component equipment is essentially peripheral – unimportant. And it does so by quickly and accurately driving far more framing nails in your wall panel jobs than ever before. Whether in your shop or in the field, one operator sets the pace for production and quality, which reduces labor costs and other aspects of overhead.
The new Terminailer V.8 improves on the previous generation Terminailer in several key ways:
All new HMI/Software
• Siemens Pivoting HMI Touchscreen display to operate from either side
• On-screen tutorial for all menu items
• Operator now controls functions such as process speed, nail spacing, nail patterns, etc.
• Simplified input commands
Nail Feed Complete Redesign
• All new frame to allow for redesigned nail coil placement with direct feed path
• EverWin PN90-PAL industrial tools now standard equipment
• New nail guides with spring-loaded tensioners
• Nail coils move with vertical travel of the nail guns
Reengineered air system
• SMC “Soft–Start” Pneumatics
• Simplified air for control to all components: lift–cylinders, triggers, stop–gate, etc.
• Direct air supply to each nail gun for improved nailing performance
• All pneumatic elements are clearly labeled for EZ service and adjustment
Overall Features
• Pharmaceutical grade assembly, industrial grade durability
• “Block–wheel” redesign for 3X increased applied force
• Approximately 1,200# of applied clamping force resulting in straighter finished
• Subcomponents from even the poorest lumber
• Larger doors for easier access to interior elements including coil–nail spools
Terminailer is an event-driven, sub-component assembler that will quickly and accurately drive 30% to 70% of the framing nails in any wall panel job. In your shop or in the field, one operator sets the pace for production and quality. The Terminailer functions independent of design software, requires zero set-up time when switching between any configuration, and requires no special operator training.
The Terminailer is easy to move around the shop so its location can evolve as your shop evolves. With all of the nailing occurring in the closed main chamber, nail injuries and nail location misfires are eliminated, making your plant that much safer.
With nearly ten years of development from people that know machinery, it is assembled to exacting standards, well supported, and it is easily maintained with shelf-item parts. Terminailer: vetted, tested, and ready to drive maximum productivity for you. Be sure to check out our videos below for a quick review of this revolutionary machine!
240 volt, 1-phase, 30 (full load) Amps, 60 Hz electrical required. 50 SCFM @ 120 PSI air required. Net weight 7,000 lbs.
2006 Alpine Speed Rafter Cutter
• Simplified compound cutting for hip, valley and jack rafters (double & single compound cuts)
• Two Worm-Drive Circular Saws (110 Volt / 30 Amps)
• Saw Turntable (for angle cutting)
• Saw Carriage (for up to 45 degree bevel cutting)
• Infeed & Outfeed Roller Conveyor with Stands
$4,900 NOW $4,250 FOB CA Wasserman & Associates 800-382-0329 www.wasserman-associates.com
Used - Metra Cut Radial Arm Saw (2x) Parts Machine
$500 – Make Offer
Eide Machinery Sales, Inc. 612-521-9193 www.eidemachinery.com
Used - 2005 Model 305 Infeed Conveyor Designed for use with all component saws. To include: Soft Start ~ Soft Stop Inverter System. Programmable load sensing; Overload / Jamb sensing shut down feature. Gear motor providing conveyor speed of 36' per minute. Forward and reversing controls for location at both ends of conveyor unit. Material capacity range - 4' through 24' lumber. Chain deck pedestals 20' long with cross bracing. Staging area at the saw independent of the live deck system. 30,000lb. Deck capacity. Call for pricing
Eide Machinery Sales, Inc. 612-521-9193
www.eidemachinery.com
New Monet FWA 500 Floor Web Saw
New, Monet five-head, floor truss web saw, cuts 4-angle, 4×2 floor truss webs from 13 inches and 90-90 blocks from 7 inches, to 4 foot long maximum length. Features 10-board magazine feed, powered, fixed-quadrant angulation, manual carriage standard, scrap conveyor and cut-off blade. Options available for longer carriage length, incline scrap conveyor, and choice of shaker or belt scrap conveyor. 440 volt, 3 phase, 60 Amp electrical. 50 PSI air at 5 CFM required.
$75,000 FOB MO Wood Tech Systems 765-751-9990 www.woodtechsystems.com
1995 SpeedCut Timbermill 620 Component Saw
1995 SpeedCut Timbermill component saw, model MH6G-20, six blades cut lumber from 2″ x 4″ through 2″ x 10″, 4″ x 2″ lengths from 5 feet to 20 feet, including four-angle floor webs from 5-feet. All powered movements. Saw includes (2) 30″, (2) 22″ and (3) 14″ blades, analog scales, chain-drag scrap conveyor with matching OEM long scrap incline. Scrap conveyor drive, brakes and wiring harness need replacement. 220 volt, 3 phase electrical required.
$7,993 FOB IN Wood Tech Systems 765-751-9990 www.woodtechsystems.com
New SpeedWorx Automated Sheathing Station by Safety Speed Manufacturing- Reduce labor and operator fatigue by taking advantage of the SpeedWorx automated vertical panel saw. This one-person station cuts wood sheathing sheets up to 50-inches x 10-feet, and up to 2-inch thickness, using a fast 1-button cutting setup with CNC accuracy to 1/32 of an inch (0.03125″). The photos of raw materials illustrate the drastic reduction of scrap material thanks to implementing the Rogworx saw station.
Visual user interface makes choosing the job and sheet cutting order easy to determine. Files are downloadable allowing for minimum waste. Saw station reads WBX file format (Alpine) or EHX file format (MiTek) or CSV files with manipulation.
Automated sequencing of sheets provides optimum usage of each sheet. The cutting chamber changes from ri to cross-cutting automatically. All this in a very small machine footprint, so it can fit easily into your existing building.
Visual user interface with standard ‘Auto Fill’ feature makes choosing the job and sheet cutting order easy to determine. System offers full optimization and sequence panel parts looking ahead through the job based on your specification. The cutting chamber changes from rip to cross-cutting automatically. All this in a 100 square foot footprint, approximately 25′ long x 4′ deep, so it can fit within existing facilities.
Includes advanced dust collection. Integrated Printing for labeling parts is available as an option. 208-230V volts, 3-Phase, 25 Amp electrical required, 5 CFM at 100 PSI air required.
“Alpine’s
industry-leading engineering, software, and production equipment allow us to remain competitive in today’s market. Alpine’s commitment to the industry is second to none!”
— Bill Weber Cascade Mfg. Co.
Alpine has it all—the right equipment, user-friendly software and dependable hardware to improve your teams efficiency. Alpine delivers the complete package for success—including comprehensive support and service that sets us apart within our industry.
Ask those who know. They’ll tell you about the people at Alpine who make a difference.
Used Hain Quick Rafter Cutter
• Reconditioned in December 2020
• Board Sizes: 2x4 and 2x6
• Motors: Two 1 HP / 220 Volt or 440 Volt / 3 Phase
• Saw Blades: 7 1/4" Carbide Tipped (set at 45 degrees)
• Angle Adjustment: Manual Rotation with Air Brake
• Air Supply: 90 PSI
• Carriage: Steel Rails with Steel Dual V Rollers
• Pedestal: 3/16" Formed Steel
• Saw Housing: 1/2" Billet Aluminum
• Covers: 10 Gauge (1/8" thick) Steel
• Fully Enclosed for Safety
$12,500 NOW $9,900 FOB AZ Wasserman & Associates 800-382-0329 www.wasserman-associates.com
Clary 329-2 4-Blade Component Saw
Clary Web Saw, model 329-2, cuts from minimum 18-inch long to 11-ft long, fourangle floor webs, and minimum 11-inch blocks at 90/90. Manually adjusted length and angles. Includes (4) 14″ diameter blades, incline, manual, any available spare blades, and chain-driven under-saw scrap conveyor. 230 volt, 3 phase electrical required.
$7,995 FOB AR Wood Tech Systems 765-751-9990 www.woodtechsystems.com
In answer to the demands of high-volume customers comes the Monet DeSauw FWA 500 CA (Automated Controls) floor web saw. The 500 CA is perfect for component manufacturers who routinely run floor trusses in high volumes with variable web geometry. Another primary feature is enhanced safety through automation which eliminates the need to open the saw motor cabinets other than for periodic service. The 500 CA includes automation for all blades, including the fixed cut-off blade for minimal waste. Lumber infeed speed is variable up to sixty (60) boards per minute, while the powered carriage utilizes rack and pinion drive with airlock for set accuracy throughout the production run. Your operator will easily download batches to the 500 CA saw from your design software via an ethernet connection to a MS Windows 10 industrial PC with a 17″ monitor housed in a stand-alone console. If you frequently batch floor web cutting, and if enhanced safety with increased productivity are a concern, then an automated Monet FWA 500 CA may be the right selection for you. More information Here
Price based on configuration.
That'sallthetimeittakes todrillstudsforrunningRomexorotherelectricalwireinthewallpanels
Motor: HeavyDuty5HP-3phase-220vor440v(Pleasespecifywhenordering)
MotorcarriagebearingandspindleassemblymountedonBlanchardgroundsteelplate
LinealmotionishardenedandgroundVbearingsandrails
BlockSizes: 2x4through2x12infiniteheightsettingtocenter
AirSupply: 100psi10CFM
Drills: 2wing3/4'”CarbideTippedcanaccommodatesmallerorlarger
Spindles: AlloySteelpolishedandgroundprecisionshafting
Frame: 2"SteelWithPowderCoatFinish
Covers: 10Gauge(1/8"Thick)Aluminumremovable
Dimensions: Height-60inches,Width-33inches,Depth-33inches
Shippingweight: 750lbs.-(Includingcrate)
MADEINAMERICABYAMERICANS
By Steve Shrader, Business Development / Operations Hundegger USA
Manufacturing, in truss production, means transforming lumber and plates into engineered components through machinery, labor, and precise processes. In 2025, it’s more than labor—it’s automation. Some cling to the old beat, stacking bodies and tuning schedules as if headcounts alone can hammer out profits. Others see the shift: machines that slice and stack, software that optimizes, processes that pull work through with lean crews. In an era of vanishing workers and rising costs, betting on labor tweaks isn’t just narrow—it’s a relic. Manufacturing in 2025 demands systems that scale, and automation delivers.
Certain voices in the component manufacturing (CM) world swear by a labor-heavy rhythm: pack the shop floor with more workers, bump their pay, and tune every task to a fine edge. They argue “you cannot” trim headcounts with automation without cratering profits, brushing off robotic systems as overhyped flops. Picture the pitch—a plant drowning in chaos, bleeding cash, turns it around fast by hiring extra hands and sweetening the deal to keep them. Machines? They’ve seen them sputter, unable to cut labor while pumping out trusses, so they stick to manpower. Their secret sauce? Ditch “useless” board footage metrics for time standards carved from years of tinkering— man-minutes, realistic expectations, whatever keeps the crew humming.
It’s a gritty tune—until 2025’s reality cuts in. They nod to a shrinking workforce—400,000 fewer entering yearly than exiting, ballooning to 900,000 by 2030—blaming obesity and a glut of desk-bound grads. Fair play: BLS (2024) pins participation at 62.7%, and the CDC clocks 42% of adults too heavy for trades. But their fix leans on rounding up skilled folks happy to pound nails all day on a slab. With construction wages climbing 5.2% yearly (BLS) and turnover scraping 30% (industry avg.), that’s a fading echo. Manufacturing in 2025 is more than labor—it’s automation, and extra hands don’t materialize from thin air.
There are those who chant an old refrain—120+ factors, motion studies, daily production reviews— promising 10% labor savings. It’s pitched as lean, wringing efficiency from every hammer swing. But it demands a steady crew you can mold and measure. Today, new hires ghost before mastering a jig, let alone hitting “realistic expectations.” The hand-eye coordination they call undervalued? It’s scarce—42% obesity isn’t just data; it’s a wall for trades. And the college grad overhang—6 million non-degree jobs vs. 3.4 million takers (NCES, 2021)—leaves a workforce that’s not just thin, but checked out.
Their staffing math frays fast. Two assemblers hit $6–7k/shift; three climb to $9–10k, with $100+/hour margins lost if you skimp. Sure—if labor’s plentiful. But “wasting hundreds daily per vacancy” stings worse when slots stay empty. And their equipment gripes—never feed more than two stations into one finish roller, or crews stall—miss the mark: manufacturing in 2025 is automation, sidestepping manual choke points with tech that flows.
Some brush off automation, claiming it can’t trim headcounts without gutting output. They’re staring at relics. Manufacturing in 2025 is more than labor—it’s automation, with CNC systems like the ACER WoodRanger or Hundegger’s TURBO-Drive selecting lumber on demand, stacking and cutting 3 to 4 high, nesting and optimizing multiple trusses at once, then sorting, destacking, and buffering parts to the right station, right on time. Slicing lumber from 2” x 4” to 6” x 18” in one pass, they don’t tweak—they transform.
Take Hundegger’s TACTical system: one operator cuts and delivers 9 parts per minute, each averaging 5.5 board feet. That’s 2,970 board feet per hour (9 parts × 5.5 BdFt × 60 minutes), and over an 8-hour shift, 23,760 board feet—one person overseeing all picking, cutting, sorting, and delivery. Compare that to 50 laborers scrambling to keep up: no turnover, no wage fights, no idle hands at a clogged roller. Manufacturing is automation—a live, data-driven pull-through that decides faster and smarter than a crew ever could. Software tracks, optimizes, and adjusts on the fly,
slashing waste and human error. Less handling, fewer bodies—yield soars.
Can small firms foot the bill? CNCs pay back in 18–24 months (Woodworking Network, 2024), driven by labor savings and throughput leaps. McKinsey (2023) pegs automation’s margin boost at 15%–25%, dwarfing the 3%–6% from staffing tweaks. With 60% of timber firms running CNCs (Woodworking Network, 2024), it’s not a gamble—it’s the pulse of 2025. Those finish roller jams? Smart buffering and sequencing keep output humming, no extra hands required.
The labor-first camp isn’t wrong— skilled hands shape quality. But their answer—more assemblers, bigger checks, endless fine-tuning—fit a bygone beat, not 2025’s. Some call it a “light switch”—instant gains from staffing up. Maybe once. Now, the bulb’s dim—labor’s too sparse, too pricey, too fleeting. Manufacturing in 2025 is more than labor—it’s automation and innovation, rewriting the game. It’s not about ditching every worker; it’s about arming them with tools to program, oversee, or refine— where humans outshine machines.
The numbers don’t bend: betting on headcounts in a shrinking market is a broken record. Manufacturing is automation—machines that don’t flake, don’t strike, and don’t need 120 factors to schedule a shift. Some might hum the old tune. The rest of us? We’re building 2025’s rhythm—one precise cut at a time.
To see meaningful labor savings, quality improvement and production gains, SL Lasers with their easyto-see green light are nothing short of illuminating. They enhance worker accuracy and productivity, regardless of experience or primary language. They can reduce tedious setup time by up to 70%. No complex training or costly service agreements are required. And SL Lasers integrate seamlessly with any component design software and are quickly installed over existing equipment. We’ve been trailblazers in wood component laser projection since its very beginning, and we’re still delivering more rapid ROI for roof truss, wall and floor panel producers every day. Contact our enlightening team at Wood Tech Systems to see how SL Laser can deliver for you.
lnnovationen fur den Holzbau
HUNDEGGER
Hundegger leads the way in automation innovation for the truss component industry. Our advanced CAMBIUM software offers cutting-edge automation and digitalization solutions, revolutionizing operations, boosting productivity, and driving sustainable growth for manufacturers like you.
We go beyond standard mechanization; we champion true Automation. The Hundegger TD-II isn't just a saw-it's a transformative, comprehensive solution designed to streamline your production process. From retrieving lumber to optimizing, nesting, stacking, destacking, sorting, buffering, and precise delivery, our system ensures peak efficiency and productivity, tailored specifically to truss component manufacturing.
Harness the power of data with Hundegger's advanced CAMBIUM TACTICAL software. It meticulously tracks and optimizes your production, ensuring more automated operations and significant productivity gains.
We provide state-of-the-art automation and control solutions that set the industry standard. Our focus on industrial automation and robotics positions Hundegger as the leader in enhancing performance and efficiency in truss component manufacturing and beyond.
Hundegger products are essential for future-proofing your business. Elevate your productivity and secure your competitive edge with our advanced technologies and automation solutions, meticulously designed to meet the unique demands of component manufacturers today and tomorrow.
Don't get left behind. Invest in the future with true automation from Hundegger and see your business thrive.
Monet DeSauw model Desawyer ESC enhanced servo-controlled ( ESC) component saw with touch screen user interface with backup mechanical controls. Includes three operating modes: Auto (download setups from LAN or USB), Semi-auto (touch screen setup entry), and Manual (backup push-button switches for powering all movements). Includes over-travel protection, comprehensive setup screens, auto sequencing, auto-calibration and pneumatic brakes on all five () blades. One (1) 30” blade and four (4) 16” blades. Manual cut limits are 18” min., 11” min. square edge blocks, 20’ max cut. Belt under-saw waste conveyor. Voltage: 480 volt/3 phase/60 Amp. Air: 50 PSI at 5 CFM. One-year warranty included. Can be paired with a model PD-6 lumber feed system at an additional cost. Heavy duty 80 RIV chain feed system. 16’ wide x 20’ long x 36” deck height. Transfers 3’ to 20’ lumber. Includes auto-feed control, foot pedal override, forward & reverse, variable speed control with HD double-bearing construction. Other additional-cost options include, inkjet marking, label printing, backside screen display, spare blades and incline scrap conveyor.
$369,900 FOB MO
A complete wood processing system proven to profitably feed cut lumber to truss plants of all sizes.
Easy to use, simple robust automation that is scalable with less labor. A RetroC holds calibration.
Auto-Feeding, no upper hold-downs (just 15 automation axes) with electronic braking. Efficient material handling that will significantly increase cut piece production with reduced operating costs and improve truss build times with consistently accurate cut pieces.
Catching labor is eliminated with our optional SpeedCatch cart system. Sophisticated SpeedCatch software enhances the efficiency of truss production by effectively collating and organizing the lumber at the truss tables. SpeedCatch upgrades the RetroC to a comprehensive one-person (sawyer) wood processing system.
Alpine AutoMill HP, model 349C component saw. Servo controlled computerized saw sets up in 2 to 19 seconds and downloads from a network, or by using a touch screen for ease of operation. Five-head automated component saw works in both automated (downloading files), semi-automated control (via touch-screen input) or manual mode. It has (23) axes of automated movement, enhanced diagnostics, and auto management reporting.
The HP cuts from 2′-6″ to 20′-0″ long material in size range from 2×3″ through 2×12″, and 4-angle floor webs from 2′-0″. Includes [3] 18″, [1] 20″ and [1] 30″ blades with air brakes, Windows 7 o/s and under-saw scrap conveyor. The Windows 7 o/s can be upgraded to a version of Windows 10 that will be supported until 2032, at an additional expense.
Also includes over $8,000 in spare parts. 480 volt, 3 phase, 100 Amp electrical required. 90 PSI @ 69 SCFM air required.
$129,997 - FOB OR
By Marco Gagnon
At Element Equipment, we pride ourselves in our custom machinery solutions. Since entering the market in 2021, we’ve made it our mission to look for additions to our equipment offerings that will add more automation to ease the pain of assembling building components. We are committed to innovation, and our drive to consistently add equipment sets us apart from our competitors.
Our drive to design and build the best equipment for any project, however, has also led us to successful collaborations for other industries and organizations too! We have over 40 years of company experience in designing and building equipment for various industries including agriculture, sawmill, and pulp and paper, and over 25 years in the building components industry.
Recently, we were approached by the University of New Brunswick’s Wood Science and Technology Centre (UNB-WSTC) when they asked our strong team of engineers and technologists to tackle the complex job of building a wood press for their testing program. This one-of-a-kind press was needed to enable UNB-WSTC to assist Canada’s wood industry in developing cross-laminated timber that has been deemed as next-generation green building materials.
We actually got to know the Wood Science Center when we ran a truss plant, doing various research and development projects with them on building components and in factory wall building. They knew our strong equipment fabrication capabilities, so when they started looking for a manufacturer that could bring their project to life, they contacted us. Basically, we took their idea from concept drawing to execution. They supplied us with general machine capacity that they were looking for and we went from there.
Beyond building the press they needed, we also helped them with the automation and programming, making this a great example of how much we can offer customers in terms of support. We did everything from the design to the installation.
With all of our projects, we focus on automation and keeping things simple for the worker. When we design new equipment or look at improving existing processes, we always ask: does it make sense, are we adding value to the design, and what else can be done to simplify life for the user.
In fact, our team members love the challenge presented with creating new machines and then going on to manufacture products that we sell and service. Seeing opportunities for improvement while running our own truss plant and today by visiting existing plants and talking with assemblers provides inspiration for new process and improvements. Working in various industries also allows us to garner additional knowledge, so that we can repurpose processes and equipment into the building components industry. Enhanced automation, while keeping a close eye on monetary constraints, will provide both a return on investment and an increase in productivity.
We’re not novices when it comes to designing and building our own equipment, and we’re pleased we have the opportunity to apply that knowledge and skill to the truss industry. In an everchanging business landscape, adaptability is key. Our custom machinery solutions are designed with flexibility and scalability in mind. As your business evolves and your needs change, our machinery can be easily modified, expanded, or upgraded, providing you with a future-ready solution that grows alongside your success. We will continue to grow our company, and we invite you to grow with us.
• 3 3/8" Maximum Thickness
• 13 1/2" Maximum Distance from Rip Fence to Outer Saw
• 100 HP Arbor Motor
• 2 HP Feed Motor
• 7 1/2 HP Dust Collector
• 480 Volt / 3 Phase
• Waste Conveyor with Short Incline
$35,000 NOW $21,900 FOB MN Wasserman & Associates 800-382-0329
www.wasserman-associates.com
STRAIGHT LINE RIP SAW
• 10 HP Arbor Motor
• 3 HP Variable Speed Feed
$10,500 FOB MI Wasserman & Associates 800-382-0329 www.wasserman-associates.com DANCO GANG-RIP SAW
• 4" Maximum Thickness (when using 18" Blade)
• 48" Throat
• Adjustable Rip Fence
• Overhead Holddown
• Automatic Chain Oiler
• Dust Outlets
Baumeister Lumber Splicer
• Vertical Hydraulic Press with 3"x 12" Platen Size
• 2x3 and 2x4 Lumber Material (3" x 10" maximum plate size)
• Magnetic Platens to hold plates in the correct position
• Working Pressure: 1600 PSI
• Dual press cycle activation for safety
• 208, 240 or 480 Volt / 3 Phase (10 HP)
• Video available upon request
• Excludes: Infeed/Outfeed Roller Conveyor
• Optional 2x6 Capacity (up to 16" long plate) Splicer is available
$29,500 FOB PA Wasserman & Associates 800-382-0329
www.wasserman-associates.com
40′ Tee-Lok Floor Truss Gantry (Video available here.)
40′ Tee-Lok floor truss gantry features gantry head with new 18″ diameter rollers with 3/4″ wall with removable shaft. Gantry head has a 7.5 HP motor with VFD. Table features fire hose clamping and pin ejectors (never used by seller). Build floor trusses from 12″ to 32″ deep. Includes all available spare parts. 230/460v, 3 phase power.
$49,890 FOB SC Wood Tech Systems
765-751-9990 www.woodtechsystems.com
New Monet 5-head, floor truss web saw, cuts 4-angle, 4×2 floor truss webs from 13 inches and 90-90 blocks from 7 inches, to 4 foot long maximum length. Features 10-board magazine feed, powered, fixedquadrant angulation, manual carriage standard, scrap conveyor and cut-off blade. Options available for longer carriage length, incline scrap conveyor, and choice of shaker or belt scrap conveyor. 440 volt, 3 phase, 60 Amp electrical. 50 PSI air at 5 CFM required.
765-751-9990
$79,000 FOB MO
www.woodtechsystems.com
• 10 Each - Standard 20 Ton Track Mounted Heads with 10" x 10" Platens (refurbished in 2011)
• 6 Each - 2011 Double 40 Ton Track Mounted Heads with 10" x 15" Platens
• 2 Each - 2021 Double 40 Ton Track Mounted Heads with 10" x 15" Platens
• 2 Each - 10 HP Two Stage Hydraulic Systems with Controls (230 Volt / 3 Phase)
• Track System for 55' Scissor & Flat Bottom Trusses
• 1 Each - Peak Head Track (perpendicular to base line)
• 2 Each - Movable Bottom Chord Tracks (to adjust for pitch)
• 8 Each - Floating Tracks for Top Chord Head
• Clamping Package: Peak, End Stop, Camber Stops & Air Clamps
• Air & Hydraulic Manifolds with Quick Connectors for Heads
• Pn eumatic Pop-Up Skatewheel Ejectors (for truss removal)
• 56' Powered Transfer Roller with Stands
• 26 Each - 14' Powered & Idle Exiting Rollers with Stands
$89,900 NOW $85,900 FOB AR
Boost production output by up to 30% with the SAWTEQ sheathing saw by HOMAG. This horizontal panel saw preps sheathing material utilizing optimized cutting plans for peak efficiency.
• Requires only one operator
• Maximizes yield through software optimization
• Provides just-in-time delivery with various destacking options for your panel line
Build on better with Stiles Machinery.
Stiles has been a trusted name in US manufacturing for over 60 years and is a proud member of the HOMAG Group, a global leader in industrial manufacturing machinery.
Contact us today to discover automated solutions that take your business to the next level.
$229,300 FOB NY
End-eject (EE), raised–recessed–rail roof gantry table with finish press, 14’ x 70′ working length with 18″ aisles. System includes a RT gantry head with 24″ dia. roller, and elevated riding platform. Production area features (14) HD slotted-steel tables with (7) EE roller ejectors, feeding to an inclined park station for single-pass truss ejection to a matching Pacific Automation Auto-Roll 14′ final roller press. Tables feature (28) Gen 1 Wizard PDS automated set-up rails. Table includes approx. 140 lf of rail′ (70′ per side) with base plates, all available hardware, and OEM system manuals. No conveyor included. 208V 3Ph/44 Amp. power required.
Field Service Installation
Our team ensures your retrofit is perfectly installed to work with your equipment.
Retrofit your tables for Jack and small truss production, a growing percentage of what you do! The New ‘Double Jack Retrofit’ allows you to double your production by operating on both sides of the table, allowing assemblers to quickly build four or more trusses in half the space. Unlike conventional setups that demand longer lines, this retrofit optimizes floor space by consolidating jack production on a shorter, standalone workstation or retrofit the end of your existing line.
Your table, automated.
We bring the best together!
Two C-Clamp Presses with Unistrut Jig Table
• Hydro-Air Mark-8 Mono Press (C-Clamp, Hydraulic Power Unit, Boom Assembly & Trolley)
• Panel Clip TK C-Clamp Press (C-Clamp, Hydraulic Power Unit, Boom Assembly & Trolley)
• Unistrut Jig Table/Stands (up to 80' long trusses)
• Electric Feed Rail
• Overhead Steel Beam
• Price is in US Dollars
$20,900 NOW $18,500 FOB MB Wasserman & Associates 800-382-0329 www.wasserman-associates.com
2021 CMF Floor Truss FRP with Conveyors
2021 CMF floor finish roller press for 3×2 and 4×2 floor trusses. Features 7-ft wide throat, with dual-sized rollers one half larger diameter rolls to press 3×2 material, the other half presses 4×2 material. Press includes 4″ diameter guide rollers, Dual (2) 5 HP drive motors, (2) safety bars, push button controls and e-stop button. Included are (19) 4″ diameter x 6-ft long, stand alone idler conveyors and (6) 6-ft long manual floor-truss stacking racks. 240 / 480 volt, 3 phase electrical required. $29,997 FOB ON Wood Tech Systems 765-751-9990 www.woodtechsystems.com
2007 Clark Industries
Horizontal Truss Stacker
Model HVS, Two Unit, 2-Zone, 14’ Horzontal Stacking System. Two lifting units (one master and one slave) with integral electrics. A truss sensing system consisting of adjustable laser sensors mounted on slide rails. One indoor electric control enclosure & panel w/PLC and manual controls. A stacker-conveyor interface package comprised of (1) mounted 3-push button enclosure and (1) remotely mounted 2-push button enclosure (pause/ emergncy stop). Hand-held Wampfler Remote Control System. 8 stacking rails and 4 stripping posts. Stack 1 5/8” thick x 14’ tall trusses up to 30 high. Stack a truss in approximately 40 seconds (cycle time). Stack up to 55’ or longer trusses on each side of the conveyor with minor assistance for truss sag, shorter lengths can be stacked unassisted. Excludes 77’ Walk Through Conveyor System. Two systems available at $25,000 NOW $19,900 Each. FOB NE. Wasserman & Associates 800-382-0329
www.wasserman-associates.com
The
EMSI Field Repair Press
EMSI 10 Ton Field Repair Truss Press System. Complete with: 1/2 HP, 115 Volt, 50/60 Cycle Universal Motor – Operates at voltage as low as 60 volts. 10,000 PSI Portable Power Pack with Two Speed Operation – 200 cu in/min @ 0–200 psi, 20 cu in/min @ 200–10,000 psi and Externally Adjustable Relief Valve (unit weight 55 lbs.). C-Clamp Assembly with 8" Maximum Reach, 4" x 5" Pressing Platen (optional platen available for 4” x 2”). Independent 10 Ton Hydraulic Cylinder. 10’ Hydraulic Hose Assembly with Quick Disconnect Coupling. Handle with 24 Volt Remote Electrical Pendant. Call for Price Eide Machinery Sales, Inc. 612-521-9193 www.eidemachinery.com
By Jesse Southard Off-Site Construction Regional Manager
In the construction industry, safety is a paramount concern no matter what task is being completed. For years, traditional on-site framing and assembly have exposed workers to significant risks, including falls, heavy lifting injuries, and adverse weather conditions. As construction elements shift to being produced in a controlled factory environment, there is significant improvement in safety of the workforce. Plus, framing off site also improves efficiency and overall quality of the construction elements being produced.
One of the most significant safety benefits of off-site framing is the controlled environment of the factory. Unlike traditional construction, where workers are exposed to unpredictable weather, uneven terrain, and high elevations, factory-based framing takes place on level ground with proper ventilation, lighting, and ergonomic workstations. A proper and well-thought-out factory footprint reduces the likelihood of common jobsite injuries and allows for a safer, more comfortable working environment. At Stiles, we aim to provide solutions that help automate these processes (especially the more hazardous ones) to help create the safest possible workspace for employees.
Falls from heights remain one of the leading causes of construction-related fatalities, as reported by the Occupational Safety and Health Administration (OSHA). In traditional framing, workers often operate at high elevations, relying on scaffolding or ladders. Off-site framing eliminates much of this risk by allowing most of the work to be completed at ground level in a controlled environment. Workers can assemble walls, floors, and roof components safely before shipping them to the jobsite for final installation.
Additionally, heavy lifting and repetitive motion injuries are common in traditional framing. In a factory setting, automated equipment, such as WEINMANN’s WALLTEQ M-500 bridges, significantly reduce manual material handling. These machines efficiently cut, process, and assemble components with precision, minimizing the strain on workers and decreasing injury rates.
Traditional jobsites expose workers to dust, chemical fumes, and noise pollution, all of which can contribute to long-term health issues and make each day a challenge. Factories equipped with advanced dust extraction and ventilation systems create a healthier working environment. For instance, WEINMANN’s automated cutting and milling systems are designed to minimize airborne particles, ensuring better air quality for workers. Furthermore, noise-reducing technologies in factory settings help lower hearingrelated risks compared to loud construction sites where high-decibel hammering and sawing are constant.
Factory-based framing also enables companies to enforce consistent safety protocols and training. While jobsites try to be consistent with training protocols, the variety of site conditions and different subcontractors on a jobsite can lead to inconsistent safety practices and differing definitions of safety standards by all team members involved. Workers in a factory environment receive specialized training to operate machinery and follow standardized safety procedures in a more predictable and consistent environment, making it easier to comply with safety standards.
Off-site framing in a factory setting offers a safer alternative to traditional field construction by reducing fall risks, minimizing material handling injuries, improving air quality, and ensuring consistent safety protocols. With the integration of advanced equipment like WEINMANN’s automated framing systems, the construction industry can continue to prioritize worker safety while enhancing efficiency and quality. Companies can create safer workplaces and contribute to the overall well-being of their workforce all while increasing quality and volume of the elements that are being produced.
If you are considering switching to off-site framing and construction, contact Stiles Machinery at (616) 698-7500 or visit StilesMachinery.com/OSC to learn more. We welcome the opportunity to talk with you and build a custom solution that meets your needs and helps make your production safer and more efficient.
From essential components to custom solutions, we’ve got everything you need to build trusses with precision and confidence. Our inventory includes parts for all leading truss jigging tables, OEM replacements, and custom components tailored to your needs. Choose from high-quality materials in custom lengths and widths, including durable plastic, unistrut, and steel.
We work with a nationwide vendor network, ensuring fast delivery. Don’t waste time searching – call us first to keep your projects on track.
Dave Walstad - Panama City Beach, FL
Dave.AllPoints@gmail.com
$217,997 FOB AR
2005 Alpine RAM Easy-Rider roof gantry model 756A, side-eject, 14′ x 70′ working length table, slotted steel building surface with (9) ejectors, (1) 6-ft long parking station, electrical supply cord runs in trough, and all available jigging hardware. Gantry head with 24″ diameter gantry roller, 7.5 HP drive motor with gearbox, operator riding platform with joy-stick control, and (2) safety bars. (8) stand-alone receivers included. No finish-roller or exit conveyor included. 230/460v, 3 phase, electrical required.
Carl Villella, CLFP President, Acceptance Leasing & Financing Service
ood building component manufacturers are facing increasing financial pressures as tariffs and supply chain disruptions drive up the cost of essential materials and equipment. Industry insiders report rising concerns over the impact on production costs and project timelines.
The effects of increased import taxes on steel, machinery, and technology are rippling through the manufacturing sector, with wood building component producers feeling the strain. Key challenges include:
• Escalating Material Costs: Tariffs are directly contributing to higher prices for essential manufacturing equipment, impacting overall production expenditures with higher lumber and plate costs.
• Supply Chain Volatility: Uncertainty surrounding trade policies is causing disruptions in supply chains, leading to potential delays and shortages of vital components.
• Cash Flow Constraints: To mitigate future price hikes, many manufacturers are resorting to stockpiling inventory, which ties up significant capital and creates cash flow challenges.
These challenges are affecting everyone in the industry with varying intensity. For example, one truss manufacturer in Colorado has said, “We’re seeing a dramatic increase in lumber prices already.” Furthermore, he went on to say, “The increased cost of equipment is forcing us to explore financing options to maintain our production capacity without straining cash flow.”
In response to these challenges, many manufacturers are seeking flexible financing solutions to:
o Acquire necessary equipment without depleting working capital.
o Secure equipment purchases before further price increases take effect.
o Obtain quick (usually the same day) credit decisions for equipment purchases.
o Maintain operational efficiency amidst supply chain disruptions.
Financial experts suggest that brokers specializing in equipment financing can play a crucial role in helping manufacturers navigate these turbulent times.
The current economic climate presents a significant opportunity for Acceptance Leasing and Financing Service, Inc. to provide valuable support to wood building component manufacturers. By offering tailored financing solutions, we can help your business overcome cash flow challenges and ensure continued growth, because we know the industry and the equipment.
The industry is closely monitoring ongoing developments in trade policies, with many manufacturers taking proactive steps to mitigate potential risks. As the situation evolves, the ability to adapt and secure flexible financing will be critical for the long-term success of wood building component manufacturers.
We are Acceptance Leasing and Financing Service, Inc. We were established in 1992, which puts us in our 33rd year of business. We pride ourselves on our Certified Leasing and Financing Professional designation. We are a member of SBCA and a frequent attendee of the BCMC tradeshows. We can provide financing for any new and, regardless of age, used equipment. We invite you to contact us at 412 262-3225 to discuss your particular situation.
"We have seen positive results using the Squote and Squofe quoting system. Bids that would take hours for a designer to complete are now being accurately priced within minutes. We are excited to continue working with Dan and his process to better serve our customers"
Chad Witkowski - GM Truss Design Franklin Building Supply
Boise, ID.
Request a demonstration today advancedcomponentsolutions@outlook.com www.advancedcomponentsolutions.net
$389,795 FOB PA
(Video available here.)
2021 MiTek 40′ Auto-10 with Wizard PDS® automated pin system (commissioned Jan. 2022). The Auto-10 features a fully integrated 50 Ton hydraulic press with a 10’x24″ pressing platten (overall Gantry width 14’10”). Gantry features 4-Wheel Drive, and an operator platform with joystick control that travels up to 4.5′ per second. The Auto-10 press is capable of handling 2”x4”-12″, 4”x2”, and it is further optioned for 6″x2″ material with no adjustment. No finish press required, this system features a HDPE plastic/steel T-slot tabletop and includes a substantial quantity of auxiliary T-Slot jigging hardware. This state-of-the-art production system features (18) Wizard PDS® @ 16″ O.C. spacing with 36 jiggingpins covering 24′ of automated setup. Set up capabilities are further enhanced by manual T-Slot positions on either side of the Wizardsetup area , System is complete with (5) electrical control boxes, all cabling and gearbox drive components, main control box, computer kiosk, and system computer. System sold for $442, 300 new.
Buyer must provide appropriate voltage/amperage: Auto-10 – 230v, 3Ph , Wizard – 208v, 3Ph, 40A (3-phase transformer included), 120v AC clean power supply to control computer. Professional installation by OEM representatives required.
$202,000 FOB MB
2008 Alpine C4 roof gantry line, model 757A, solid-top, trackless, side-eject, 14′ x 63′ working length table, slotted steel building surface includes (9) tables, (8) ejectors, (2) 6-ft long parking station, electrical supply cord running in trough, (6) powered roller conveyors, (6) idler roller conveyors, (20) exterior idler conveyors, and all available jigging hardware. Includes one gantry head with 24″ diameter gantry roller, 7.5 HP drive motor with gearbox, operator riding platform with joy-stick controls. No finish-roller included. 240 volt, 3 phase, 20 Amp electrical service required.
The TruStance Pedestal Jig System was developed to solve the problems associated with pedestal jig systems, while retaining and enhancing all the advantages. The system features track mounted pedestals with a track and lockdown design, movable pedestals, and a roller lift assembly. The pedestal tops are 30″ above the floor, creating a comfortable working height. The ability to configure the system in a very small footprint makes it ideal for any size truss plant. It is designed to use with a ‘C-clamp’ type press.
With the ability to install the interchangeable crossmembers and angle iron stops on both track mounted and movable pedestals, the system can be configured to meet the needs of even the most complicated truss designs.
Movable pedestals can be moved and locked down efficiently; the 4″ thick steel base provides the weight needed to keep them in position.
Bottom chord pedestals are installed on the steel track mounted to the floor. Pedestals are easy to move and rigidly lock into place with threaded rod locks.
The optional air activated roller lift assembly raises the truss above the jig to be easily ejected. Its versatile design allows it to be configured for any set-up.
TruStance recommends a (16) pedestal system for roof trusses to 60-ft in span. 120 volt, 1 phase, 20 Amp electrical required. 50 PSI air required.
By Kathryn Pedde
When we started down the path of creating the JAX automated retrieval system, it had to work with our existing saws from three different suppliers. So, one of our first tasks was to bring their disparate cutting files into a common format to feed JAX. We also had to bring the sequence of jobs from our supplier’s management system, and our inventory levels and costing from Quick Books. Our goal was to enable JAX to function with any vendor’s software and any manufacturer’s hardware. After two years, and with the assistance of Q4US, we developed browser-based software that compiled data from multiple sources and displayed it in a universal format. We call this the JAX Universal Compiler, or JAX-UC for short.
Building browser-based software was incredibly appealing to us, because we could display live views of our JAX processes anywhere in our plant, or even at a remote location. Then, these views could be updated and enhanced as we connected JAX-UC to our accounting software, and eventually to the PLC driving the JAX hardware, as will be illustrated here.
We condensed much of the data we gathered and displayed it beneath the bunk location number, conforming to the arrangement of bunks within JAX. Onto this display, called the Production Manager, we’ve overlayed a red dash so that we can tell at a quick glance when any bunk needs to be replenished. In this example, the red dash appears in the top half of both SKUs, and indeed, they are 60% and 90% full, respectively. Likewise, we created a Sawyer Report so that each sawyer can see which jobs are next on the conveyor coming to their saw. These have formed the beginning of a stream of useful reports that we’ve created to manage our shop, each of which is easily accessed by clicking on a link.
Each sawyer receives a report summarizing what is coming to him on the conveyor from JAX, and if any substitutions occurred. In fact, JAX is able to select a higher grade or a longer length if material is out of stock. In this example, 52 pieces of #3 lumber were substituted with #1 grade, so this report alerts the sawyer that these are web members and signals to him that more bow and crook is permissible than if they were chords.
One of the most powerful features of the JAX-UC software is its ability to communicate with JAX hardware through its onboard computer, the Programmable Logic Controller (PLC). This interaction enables everyone on the network to view the operational status of JAX and the safety light curtains surrounding it. Since we have divided JAX’s working area into two light curtained zones, in one of the zones the light curtain can be broken and lumber carts replenished, while JAX continues to retrieve lumber in the other zone, which remains protected.
On the large monitors in our shop, we now display JAX’s status. In this example, the display is covered with red cross-hatching, indicating that the gantry head is locked in place after being stopped by an operator over bunk 27. Prior to this stoppage, it had picked lumber from bunk 20 and delivered it to the Blade Saw.
With these reports, everyone in our shop is able to have all the information that they need to keep material flowing from JAX to the saws. But, we haven’t stopped there. From this foundation, we’ve continued to add more features, which we’ll talk about next month. In the meantime, if you have questions, please reach out to me or Richard at 980-404-0209 to learn more about JAX, The Wood Retriever.
• 9 Each - 6'-0" x 13'-11" Steel Slotted Top Tables with Ejectors
• 7 1/2 HP Motor (460 Volt / 3 Phase)
• E xcludes: Inside Powered Exit Conveyor, Finish Roller and Outside Conveyor
$61,900 FOB HI Wasserman & Associates 800-382-0329 www.wasserman-associates.com
Virtek LPS-6R Laser Projection Heads
• 8 Each - Virtek LPS-6R Laser Projection Heads
• Excludes: Computer, Virtek Software License & Service Agreement
$2,000 Each or $15,000 for all 8 Heads Price in US Dollars
Wasserman & Associates 800-382-0329
www.wasserman-associates.com
• 14' Long x 4" or 5" (Inside Diameter) Schedule 40 Pipe
• Tube Steel Stands (7" Height Adjustment - Height to be Specified)
• 4 Bolt Flange Bearings
• Idle and Motorized Rollers
• 1/4 HP Motors (240/480 Volt-3 Phase) with Controls
• 1" and 1 1/4" Cold Rolled 24" Shafts Baffled
• 6 to 8 Week Delivery
New Wescana floor truss machine, available in side-eject or end-eject models. Builds floor truss depths from 12 inches to 26 inches, to 40-ft long. Features under-table cylinders powering the clamping system, built-in camber, truss flip arms, truss pop-ups, control valves for clamps, flip arms and pop-ups, with parking stations at each end of the table, and emergency shut-off bars on each side of the press head.
A starting point for exploration. If you’re new to Paragon, our free plan provides:
1 User
Paragon Truss Link with TDDs
Live and Dead Loading Analysis
View-Only Layouts
Basic Support
5 Prototype Trusses without Plates
Perfect for individual modeling and estimation professionals who need tools for layout, pricing, and preliminary truss designs without plates.
1 User
250 Prototype Trusses/mo
Paragon Truss Link with TDDs 3D Layout Tools
Truss-to-truss Connections
Truss Lumber Analysis without Plates
Modify All Load Settings
Lumber and Connector Lists
Access RESTful API
Estimation Downloads
Access Engineering Network
Perfect for individual component manufacturer designers needing production-ready truss designs and manufacturing features.
1 User
250 Manufacturer Trusses/mo
Paragon Truss Link with TDDs
3D Layout Tools
Truss-to-truss Connections
Full Truss Analysis with Plates
Modify All Load Settings
Lumber and Connector Lists
Access RESTful API
Premium Downloads
Access Engineering Network
Featuring precision Gen. 2 controls, this system squares and sheathes wall panels ranging up to 16′ in length and up to 12′ -3″ wall height with dimensional material from 2×4 through 2×10. This late-model system includes a servodriven bridge with joy-stick controlled motion on the operator’s riding platform. The single, large-coil capacity tool carriage travels across the wall frame inserting sheathing fasteners at the spacing set by the operator. The stitchers will automatically insert fasteners through the sheathing into the top and bottom plates at your chosen spacing during the auto-return process. The bridge has 9 programmable presets for fastener spacing. Other features include: Single Beam Bridge, top and bottom plate stitchers, Operator Platform with Windows industrial touchscreen, and joystick control. Squaring table features a squaring edge, footswitch & push-button controls for telescoping side and horizontal outfeed rollers. 120 PSI at 60 CFM air.120 volt AC electrical required. Utilizes large-coil 15º wire-collated nails. (No nail tools included).
2022 Panels Plus Floor Cassette Station
• Assemble Dimensional Lumber, I-Joists & Open Web Floor Truss Panels from 12' Wide up to 45' Long
• Po wered (120 Volt/1 Phase) Telescoping with Foot Pedal Control
• Color Coded Joist Locators
• Pop-Up Skatewheel Conveyors
• Squaring Stops
• Price is in US Dollars
$55,000 FOB Ontario Wasserman & Associates 800-382-0329 www.wasserman-associates.com
2023 2-Head 30 mW LAP
www.woodtechsystems.com
• Automated Component & Linear Saws (2010 & Newer)
• Monet DeSauw or TimberMill Manual Component Saws
• Floor Web Saws
• Spida (Apollo) Saws with Truss Automation
• Bunk Cutters
Truss Equipment
• Roller Gantry & Hydraulic Press Systems
• Finish Rollers
• Truss Stackers
• Floor Truss Machines
• Lumber Splicers
• Jack Tables
• C-Clamp Presses
Equipment
• Pacific Automation or MiTek Mobile Home Press
&
By Valerie Hansen Founder and Chairman, BuyMetrics Inc.
Today, 93% of America’s new homes are built of wood-frame construction. If fully enacted, the implemented and pending tariffs will reduce lumber supply and trigger an increase in lumber price, resulting in a one–two punch for the wood-frame construction industry.
As we once again brace for a volatile cycle, we can look back at other significant lumber cycles of the 21st century and see what we might be able to learn from them: the 2006 boom cycle, the 2009 bust cycle (Great Recession), and 2021 Covid-driven cycle.
Observation #1: The 2021 cycle (Covid) was supply driven, while the 2006 boom and 2009 bust cycles were demand driven. Commodity traders across markets/exchanges know it is changes in supply, not demand, that dictate most price movements. Even a small imbalance in supply produces outsized movement in price.
Observation #2: When markets ‘go postal’, extending vendor reach improves outcomes. Volatile markets reward quick and accurate price discovery. During Covid, it paid to shop.
Periodically, BuyMetrics measures the effect shopping via our service has on the Cost-of-Goods (CoG lumber) of large clients using our technology. The full report is available on BuyMetrics’ website at https://www.buymetrics.com/papers/CaseStudy.OutsizedCoGSavings2021.pdf and the following are some highlights.
Price Spread: During the 2006 boom and 2009 bust cycles, the average spread between an awarded purchase order (lumber PO) and next-best vendor offer was 1.9%–2.2%. During Covid, the gap between the best offer and next-best offer doubled to 4.06%.
Reach: During the 2009 bust cycle, lumber buyers shopped on average 7.5 vendors per PO awarded. During 2021 Covid, lumber buyers (using BuyMetrics) shopped on average 20.6 vendors per awarded PO, tripling (3X) their vendor contact as they reached to cover urgent need for wood. Expanding reach, particularly in volatile markets, improves the odds of: (1) successfully sourcing supply-constrained material, and (2) purchasing from the vendor with lowest cost/best value.
Low Win/Low Share Suppliers: In all three cycles, the percent of purchase orders (POs) awarded to low win/low share suppliers remained relatively constant at about one-third of client purchases (29%–36%). In fast-moving, volatile markets, deals need to get done before they vanish. When markets run, reach is too often sacrificed for speed. CMs (shopping via traditional methods) missed the value secondary suppliers contribute to the mix.
Lost Opportunity Cost: During Covid, consistently shopping more primary and secondary vendors produced twice (2X) the overall CoG lumber savings achieved during the demand-driven cycles, 4.06% vs 1.9%–2.2%. In 2021, secondary suppliers added $390,000 in lumber savings to the bottom line for every $10 million in lumber purchased.
If implemented, tariffs will trigger a supply-driven cycle. Buckle up.
Valerie Hansen is the Founder and Chairman of BuyMetrics Inc. She is a 47-year industry veteran and the former owner/CEO of Custom Components Company, Racine, WI (sold 2008). From 2000–2019, she earned 21 U.S. patents for inventions in the technical areas of finance and data management. Privately serving industry-leading CMs since 2000, the BuyMetrics® commodity procurement platform automates and informs the purchase of lumber and other volatile commodities.
This is the first, self-contained, truly portable FRP unit used to press metal truss plates into dimensional lumber at virtually any location. Wood component (roof and floor truss) manufacturers, as well as builders, frequently require a tool to repair metal plate connected, wood truss components. The complete unit is mounted to a wagon built from square tubular steel. Extremely compact at only 28” wide and about 32” long the wagon features four wheels on soft-rubber solid tires, and a steering axle on the front with a handle that makes the unit easily maneuverable. The wagon contains the hydraulic power unit and an area for a portable gas generator. A rack in the back securely stores the C clamp, a standard 25′ hydraulic hose, and an electric power-supply cable. The clamp is manufactured from T1 steel, cut into a C-shape with a steel tube welded to the front that securely holds the hydraulic cylinder. Pressing is easily performed with a 4×4 magnetized steel platen that holds and presses the truss connecter plates. The C-clamp that weighs less than 30 pounds, features a throat that opens to 4-1/2” inches to accept either 4 x 2 or 2 x 4 lumber. It has a push on and release off switch to cycle the unit. A 10,000-psi electric-over-hydraulic power unit pumps hydraulic fluid through a 10,000-psi hose to activate a 10-ton hydraulic cylinder with a 3.9 inch stroke. The unit can be powered by 120v electric power or an optional 120v, 2200-amp, gasoline powered generator, which can also act as a portable power supply out in the field for other single-phase equipment.
• Pressing Capability: 4.5” throat opening presses 2×4 through 4×2, includes a standard 25-foot, HD 10,000 PSI hose, with a 10 TON, 4”x4” magnetized pressing plates
• Electric/Hydraulic: SPX Hydraulic Technologies – Rockford, IL USA 10,000 PSI / 700 BAR. 10 ton pressing capability
• Power Source: 110V Dual Power via outlet plug in and/or optional gas-powered inverter generator at an additional price. Optional generator is a Honda EB 2200i Industrial, inverter motor, manual start, GFCI Protected,120 VAC at an additional cost of $1,450.00.
• Warranty: One year from date of purchase on manufactured unit, OEM warranties on hydraulic and gas motor. $9,779 FOB
New Wescana roof finish roller presses, available in either a 14-ft or 16-ft throat models. Travel speed of 2-ft per second. Both models feature 24″ diameter steel rolls with 3 1/2″ diameter shafts with baffles, (2) 5-horsepower drive gear motors with controlled motor drive systems for starting and stopping, along with taper-lock sprockets, sealed flange roller bearings and reversing magnetic starters.. Includes safety shutoff bars, electric eyes, amber running light, red reversing light with buzzer, and e-stop module. 240 / 480 /575 volt, 3 phase electrical required.
Price based on configuration
ton
gantry with 15 HP motor, and two stage pump. Drives on four 8″ dia. steel wheels with two individual hydraulic motors on two drive wheels running on 60# crane rail. Gantry speed up to 300 fpm. (2) 7″ x 5″ hydraulic cylinders. Pressing platten 24″ x 14″, 2″ thick steel. Includes (10) 14′ x 3′ 5″ tables with 1/2″ thick drilled and tapped steel tops. 5 ejectors included. 240v, 3 phase, 100 amp power.
$87,990 NOW $44,990 FOB MN Wood Tech Systems 765-751-9990 www.woodtechsystems.com
Klaisler 40′ Floor Truss System
Model G2640 kick-leg, gantry head with 18″ dia. roller and push button controls and dual safety bars. System builds trusses from 12″ to 24″ depth and up to 40′ in length with built-in camber, side-eject, with air clamping, dual park areas. Twin 5 h.p. drive systems, 85lb.crane rail, includes festooned cable/power supply line with single support mast. 230/460v, 3 phase, 90lb+ PSI air required.
$29,920 FOB KY Wood Tech Systems 765-751-9990 www.woodtechsystems.com
• Klaisler Model GR1424 Gantry Roller
• Re cessed Floor Mounted Rail
• (5) 6' x 14' WEG-IT Tables with Ejectors
• 460 Volt / 3 Phase
• Excludes: Inside Exiting Conveyor, Finish Roller & Outside Conveyor
• Price in US Dollars
By Steph Karlstad
ou don’t wake up one day and decide to start a truss plant. This kind of business isn’t a side hustle. It’s not something you launch from a playbook. A successful truss plant is built slowly—through long hours, tight margins, and a steady stream of challenges most people will never understand. It’s earned.
Those who have endured know this well. You’ve faced supply chain disruptions, labor shortages, design backlogs, and unpredictable swings in material pricing. And through it all, you kept moving—because that’s what truss plant owners do. But even the most seasoned owners are asking the same question right now: “What happened in 2024?”
After the boom from 2020 through 2023, the sudden slowdown has left a lot of owners scratching their heads. Margins have thinned. Sales cycles have shifted. And that sense of momentum many felt just a year or two ago? It’s fading.
Look back at your last five years: 2019 to 2024. Forget revenue for a moment. Forget even net profit. Instead, ask:
• How many trusses and/or board feet was produced each year?
• What was the output compared to the labor?
• Did efficiency improve—or decline—year over year?
Achieve Excellence with LFT Strategies
This is the data that tells your real story. In the growth years, higher sales volume masks inefficiencies. Labor costs were absorbed by sheer demand. But when volume tightened and prices leveled, any production misalignment was exposed.
At LFT Strategies, we empower truss plant owners to elevate their business by delivering customized solutions and unmatched expertise.
Truss plants that adjusted early are still stable. But the ones that didn’t—those still operating on bloated labor-tooutput models—are feeling it now. It’s not that your business failed. It’s that the margin for error got smaller—and many plants were never structured to operate lean when demand cooled.
Streamlined Operations: Cut costs, eliminate inefficiencies, and boost productivity.
Enhanced Design Accuracy: Achieve precision and maintain exceptional quality in every project.
Innovative Strategies: Stay ahead with forward-thinking solutions tailored to industry trends.
Alongside those pressures is another challenge: the leadership gap. The deeper issue isn’t just cost. It’s stability. Many truss plants were built by people who could walk the plant and know, on instinct, what was off. But that knowledge isn’t always being passed down. The next generation may know software, but not system flow. They may know numbers but not distinction.
We’re more than consultants—we’re your trusted partner in driving sustainable growth, fostering strong relationships, and positioning your business to thrive in an ever-changing industry.
What’s at stake isn’t just efficiency, it’s legacy. And if the systems aren’t built to outlast the owner, the business won’t either.
Like farming, truss plants follow seasons: Plan in winter. Plant in spring. Push hard through summer. Reap in fall. If you don’t know what season you’re in—growth, reinvestment, stabilization, or transition—you’re probably operating in reaction mode. And that’s where chaos and burnout thrive.
The strongest plants aren’t just well-built. They’re well-led. And that starts with stepping back and asking the hard questions:
• Have I clearly defined the future of this business?
• Is my team aligned around that vision—or am I carrying it alone?
• Am I still doing everything myself, or building a team that can grow with me?
There’s plenty of talk about automation—and yes, that has a place. But automation won’t fix broken fundamentals. And it won’t clarify your vision. Before you grow, go back. Back to what worked in 2017–2019. Back to knowing your local market, your true production flow, and your labor benchmarks.
Back to asking the right questions:
• What is a truss, and how do we build it better?
• What movements on the floor are costing us time?
• What metrics matter—really?
Most importantly, ask: Am I still pulling the plow, or am I preparing the field for the next generation? The most successful people in any business had a mentor. They learned from someone that taught them and helped them avoid the struggles they went through. Who is your mentor? Who is your coach? Remember success leaves clues. The question is, are you looking for them?
Whether you’re running a truss plant, scaling a business, or leading a team through uncertainty, the answers are usually already out there, hidden in past performance, in mentors’ stories, in decades of experience, pointing to what works. The best owners don’t guess. They listen. They observe. And they act on the clue’s success has already been left behind. Because this isn’t just about what happened in 2024. It’s about building a business that’s ready for 2026, 2030, and beyond.
You only get one full season—if you’re lucky. Make it count.
Pointer
Auto Return -Bridge Tilt at Sheathing Seams -Programmable Fastener Patterns -Pop-Up Skatewheel Conveyors
to 12’-5” Wall Heights
Squaring Stops
Floor Rails
• Wall Lengths to 20' / 6' to 12' Wall Heights
• Length Stops Position the Top & Bottom Plates for Nailing (as directed by Wall Panel Design Software output)
• Touch Screen Computer/Enclosure
• 4 Everwin PN80PAL Coil Feed Nail Guns
• Transfers Wall Panels from the Wall Extruder to the Squaring Table STUD EXTRUDER
• Nail C, L, U Sub-Assemblies and Double/Triple Studs
• Touch Screen Computer/Enclosure
• 2 Everwin PN80PAL Coil Feed Nail Guns
• Transfer Sub-Assemblies & Studs to the Wall Extruder Operator
• Squaring the Wall Panel before attaching Sheathing Excludes: Installation/Training and Annual Technical Support Fee EQUIPMENT FINANCING available from Fidelity Leasing $249,000 NOW $239,000 FOB AZ
INCREASE PRODUCTION. MAINTAIN A SMALL FOOTPRINT. EXPANDABLE.
FRAMING STATION
SQUARING STATION
SHEATHING STATION
The Panels Plus 3-Table Router Line is similar to the 3-Table line and includes a Squaring & Routing Station in place of a Squaring Station. This station incorporates a manual X-Y router bridge for routing out rough openings. This production line consists of a Framing Station, Squaring and Routing Station, Sheathing Station, Subcomponent Tables and Roller Conveyors.
2007 VIKING 16' X 12' SQUARING TABLE WITH SHEATHING BRIDGE
• 16' x 12' Squaring Table with Powered Width Adjustment & Powered Chain Conveyor
• Wall Panel Lengths up to 16', Wall Panel Heights from 4'-0" to 12'-2"
• Swing Gates at Both Ends of Squaring Table
• Automated Field & Edge Nailing Driving by Panel Pro Event Software & Your Programmed Nailing Patterns
• Simple Touchscreen Controls
• 2 Tool Carriages for Sheathing Nailing with Tilt Function for Seams
• 2 Paslode Nail Guns with High Load Coil Tray
• Auto Sheathing Bridge Return
• Includes 4 Pallets of Magnum Coil Nails (2 3/8 x .113)
• 480 Volt / 3 Phase
$29,900 FOB KS.
Wasserman & Associates 800-382-0329
www.wasserman-associates.com
Used Panels Plus Wall Panel Lift
• Two available at $1,175 Each Wasserman & Associates 800-382-0329
www.wasserman-associates.com
IBS Exterior Wall Panel Line
• 16' x 12' Framing Table with Tool Dollies
• 16' x 12' Squaring Table
• Router/Plate Stitcher Bridge
• 16' x 12' Sheathing Table
• Double Tool Bar Panel Bridge
• 230/460 Volt - 3 Phase
• Excludes: Nail/Staple Guns and Router Motor
$28,500 FOB IL
Wasserman & Associates
800-382-0329
www.wasserman-associates.com
IBS Tilt Table
• 16' Length Capacity
• 7' to 12' Wall Heights
• Hydraulically Powered (3 Phase)
• Video available upon request $22,500 NOW $13,900 FOB WI Wasserman & Associates 800-382-0329
www.wasserman-associates.com
2022 Prairie Mechatronics 12' Portable Sheathing Bridge
• Programmable Fastener Spacing with PLC Touch Pad Entry
• One Touch Selection for Field or Seam Pattern
• Gun Tilt at Sheathing Seams
• Laser Pointer for Stud Location
• Sensors to Detect Sheathing
• Nail/Staple 8' Wall in 6 to 8 Seconds
• Quick Tool Changeout
• Weight: 150 Lbs
• Extra Gun Mounts & Spare Parts
• Excludes Nail or Staple Guns
• 120 Volt / 1 Phase
• Includes Custom Pneumatic Supports (adjustable from 35" to 47" above floor)
• 2 Available at $18,500 NOW $14,500 Each Wasserman & Associates 800-382-0329
www.wasserman-associates.com
• 2022 Triad Mobile Diamond Quad Framing Table (never used)
• Wall Lengths up to 16', Wall Heights from 6'-9" to 10'-3"
• 2 Tool Dollies with Senco FP752XP Nail Guns
• Stud Locators at 16" and 24" Centers
• Pop-Up Skatewheel Conveyors
• Squaring Stops
• Telescoping Hitch System (pivots out of the way when framing)
• 4 Down Riggers
• Not DOT certified (to be shipped to the jobsite and moved around)
• Video available upon request
$79,500 NOW $72,500 FOB HI
IBS FRAMING TABLE
• Wall Panel Lengths to 16'
• Powered Height Adjustment (3-11' to 12'-3" wall heights)
• Pop-up Skatewheel Conveyor
• Pop-Up Center Support (for transfer of window/door assemblies from the side)
• NO Tool Dollies, NO Stud Locators
20' ROLLER CONVEYOR WITH STANDS
• One section is on casters to accommodate variable wall heights
IBS SQUARING TABLE WITH PANEL/ROUTER BRIDGE
• Wall Panel Lengths to 16'
• Powered Height Adjustment (3'-11" to 12'-3 wall heights)
• Multi-Tool Panel Bridge with Laser Pointer & Bridge Tilt
• Palode F350S Nail Guns (guns mounted on 6" centers with 3" shift)
• Industrial Router Motor
Reconditioned by Doug Dodd in 2020
$47,500 FOB PA
In 2025, SBCA is Offering Quality Bootcamps to All Component Manufacturers (CMs)
These two-day live events are being held in all six regions of the country, giving CMs the opportunity to learn from SBCA instructors on how to maximize the benefits of SBCA’s Digital QC software, enhance your quality management program, and better understand how to get the most value out of Third-Party Quality Assurance (QA) audits. Level up your Quality Management program, register today!
To learn more about when a Quality Bootcamp will be held near you, check out: sbcacomponents.com/quality-bootcamps
• Wall Lengths to 12'
• Wall Heights to 40'
• Powered Height Adjustment
• Manually Adjustable Rake Side (0 to 12/12 pitch)
Not producing the results you need or want – getting conflicting info about what to do and the equipment and the systems you may need?
If you want an Independent Guide that has your bottom-line results as the #1 priority, Call Me. If the salesman will do - we'll talk later...
Also, don't let Financing Deals influence your best solution. FitzGroup can arrange – Zero down & No payments for 90 Days!
• Stud Locators at 16" and 24" Centers
• Center Support Bar with Stud Locators
• Excludes Tool Doilies
• Adjustable Squaring Stop • Pop-Up Skatewheel Conveyors
• Price is in US
The Panels Plus Subcomponent Tables are designed for building rough opening sections. They feature pop-up rollers, a squaring edge, and a manual telescoping side to easily adjust and set the wall height. The pop-up rollers make it easy to move product down the production line.
Please be assured that your investment with any of our selected partners will not cost one penny more with the Fitzgerald Group as your purchasing contact. In addition, you will receive the full advantage of our Partner Relationships and Services NOT offered elsewhere.
Subcomponent Tables can be adjusted to match the height of your station or system, making it easy to transition subcomponents from the Component Tables to your desired location.
By Thomas McAnally TheJobLine.com
Manufacturing operations rely on efficiency and accuracy. But is that limited to the literal manufacturing process only, or can companies take the same logical approach to evaluating all aspects of employee performance?
A well-defined set of Standards of Performance ensures employees understand their roles, management expectations, and key metrics that define success. The Standards of Performance serve as a structured framework for both employees and supervisors, fostering a culture of accountability, continuous improvement, and fair assessment. Likewise, annual reviews provide a structured opportunity to evaluate an employee’s contributions over the past year, reinforcing the importance of Standards of Performance in manufacturing environments.
Standards of Performance provide a clear benchmark for employees, ensuring they understand what is required to fulfill their roles effectively. Unlike arbitrary or subjective evaluations, Standards of Performance are based on measurable, achievable goals that reflect the level of performance required—not an expectation to exceed or be exceptional but to consistently meet the standards of the position. Benefits of well-defined Standards of Performance in manufacturing include:
1. Clarifies Job Expectations – Employees understand the minimum performance level required to fulfill their responsibilities successfully.
2. Ensures Consistency – Establishing clear Standards of Performance eliminates favoritism or subjective assessments, ensuring fair evaluations across all employees.
3. Enhances Accountability – Employees take ownership of their work, and supervisors have a clear framework for assessment.
4. Supports Continuous Improvement – Standards of Performance identify areas where employees may need additional training or support to perform at the required level.
Annual reviews are a critical component of performance management but are only effective when aligned with Standards of Performance. Manufacturing roles depend on measurable, objective criteria to determine success. Without clear Standards of Performance, annual reviews can become arbitrary and ineffective. To ensure these evaluations are meaningful, organizations should:
• Align Standards of Performance with Business Goals – Employees should see a direct connection between their performance expectations and the company’s overall objectives.
• Use Measurable Criteria – Standards of Performance should incorporate key performance indicators (KPIs) such as safety objectives, production efficiency, budget adherence, and schedule accuracy.
• Provide Constructive Feedback – Reviews should focus on ensuring employees understand their strengths and areas for improvement.
• Be Adjusted Annually – Supervisors should review Standards of Performance with each employee, discussing any challenges or advantages experienced over the past year and setting the framework for the next year.
• Incorporate Areas for Improvement – Any deficiencies identified during the annual review should be included in the next year’s Standards of Performance, with clear expectations and an allowable time frame for correction.
• Imply a Formal Agreement – Both the supervisor and the employee should sign the Standards of Performance, signifying mutual understanding and agreement to the expectations set forth.
Annual reviews should not be the only time employees receive performance feedback. Manufacturing success depends on continuous improvement, and Standards of Performance should be reviewed regularly to ensure employees remain on track. Supervisors must engage with employees throughout the year to provide coaching, identify roadblocks, and adjust as necessary.
Furthermore, the key benefits of year-round performance measurement include:
1. Prevents Surprises in Annual Reviews – Employees should always be aware of where they stand in relation to Standards of Performance.
2. Encourages Incremental Improvements – Regular feedback allows employees to adjust performance in real time, rather than attempting to correct issues at year-end.
3. Boosts Engagement and Accountability – Employees who understand how they are measured feel more empowered and invested in their performance.
4. Eliminates Focus on Only Recent Events – Evaluations should reflect the full year’s performance, not just the last few months.
In manufacturing, performance is often tied to financial incentives. Annual bonuses can hinge on an employee’s ability to meet or exceed Standards of Performance. This means that Standards of Performance are not just a management tool but a direct factor in an employee’s financial rewards.
• Bonuses Based on Performance – Employees who meet their Standards of Performance may qualify for performance-based bonuses. Exceeding these standards may result in higher incentives, while failing to meet them may impact compensation.
• Transparency in Compensation – When bonuses are linked to Standards of Performance, employees understand exactly what is required to earn additional financial rewards.
• Motivation for Continuous Improvement – Employees have a clear incentive to maintain or improve their performance year over year.
Just as manufacturing relies on precise, quantifiable performance measures, Standards of Performance should reflect realistic expectations, not unattainable goals. These benchmarks define when the job is being performed at the level management expects. Some key Standards of Performance metrics in manufacturing include:
• Adhering to Safety Protocols – Clear standards can ensure that safety protocols and training are followed without exception (e.g., no lost-time injuries during the year).
• Meeting Annual Budgets – Employees and teams should keep budget variances within an acceptable range (e.g., no more than X% variance).
• Adhering to Production Schedules – Performance should be measured by the ability to keep schedules within a specific deviation range (e.g., no more than X days or hours of variance per week/month).
• Managing Worker-Hour Budgets – Employee and team performance can be evaluated based on whether they meet the expected labor hours per project or schedule window.
Many organizations still rely on discretionary reviews, which can be highly subjective and inconsistent. In contrast, Standards of Performance provides a structured, fair, and transparent method of evaluating employees. Key benefits of using Standards of Performance over discretionary reviews include:
1. Objectivity and Fairness – Standards of Performance eliminate bias by using clear, predefined benchmarks.
2. Employee Trust in the Process – Employees are more likely to accept reviews when they are based on measurable performance data which they have agreed to in advance.
3. Accountability for Employees and Supervisors – Employees are responsible for meeting expectations, while supervisors must set reasonable and achievable Standards of Performance.
4. Data-Driven Decision-Making – Standards of Performance allow companies to make fair, consistent decisions about promotions, raises, and job placements.
5. Clear Definition of Success – Employees know exactly what is expected, reducing uncertainty and improving job satisfaction.
For Standards of Performance to be effective, organizations must establish a structured and transparent process that integrates standard setting, performance tracking, and regular feedback. Key implementation steps include:
• Annual Standards of Performance Review with Employees – Each year, supervisors should sit down with employees individually to review the current Standards of Performance and set expectations for the next year. Employee input should be encouraged.
• Employee Feedback on Performance Barriers – Supervisors should discuss any issues that have helped or hindered performance, ensuring Standards of Performance remain reasonable and achievable.
• Utilizing Performance Management Tools – Software can track employee progress, document feedback, and provide analytics to improve Standards of Performance adherence.
• Training Supervisors on Standards of Performance Implementation – Supervisors must be trained to create fair and attainable Standards of Performance and to evaluate employees consistently.
• Encouraging Employee Self-Assessment – Employees should reflect on their performance to identify areas of improvement proactively.
• Involving Human Resources and Legal Counsel – Your organization should also include your human resources department and/or legal counsel in this process, so that all Standards of Performance comply with employment laws and avoid potential discrimination risks.
In manufacturing, Standards of Performance are essential for ensuring employees meet performance expectations without ambiguity. Annual reviews must be rooted in Standards of Performance, with supervisors regularly engaging employees to review and refine them. By linking Standards of Performance to compensation and maintaining clear, measurable metrics, organizations create an environment of accountability and continuous improvement. When Standards of Performance are structured, fair, and transparent, both employees and management benefit— resulting in improved efficiency, better decision-making, and long-term success.
Stacking wall panels at the end of your production line can be a real labor-intensive and safety-challenging task. But it doesn’t have to be now, thanks to ProStack . This innovative wall panel stacker literally stacks from the bottom up, reducing awkward overhead lifting & placement, and the risk of head injury. Plus, ProStack frees up at least one worker to return more productively to your core task—building wall panels. Enhanced worker safety and productivity is what ProStack is all about.
By: DAK Automation
Setup and installation is easy too, without the need for complex training or disruption to workflow. So, free up your team to do what they do best, and you need to do most, and let ProStack stack your wall panels instead. Contact us to learn more today. For a ProStack demonstration video, scan the QR code below.
• Model SRDE6.5 Stock Reel
• Model RS35-4-12" Roller Straightener
• Model FR5-12 Feed Roll
• Hydraulic Press System with Three Feature Dies (36" Feeds)
• 22' Powered Entry Conveyor
• M odel 420 STR Rollformer (10 Forming Stations)
• Roll Tooling
• Beck Automation Controller
• Citronix CIJ Ink Jet Printer
• 3 5/8" and 6" R-Stud
• Coil Inventory
• Refer ence Uploaded PDF for Additonal Details & Layout
Reliable automated machinery, built to last for generations!
“The equipment is extremely durable to stand up to the beating it takes in a truss plant”.
Wall Panel Lift
* 8’- 12’ Wall Height
* 1,000 LB Capacity
* Easy Adjustment
* Hoist and Crane Sold Separate
Handle Bar Router
* 8’ - 12’ Wall Height
* 2 Person Operation
* 3 ¼ hp Production Router
* 120 Volt /1 Phase/15 Amp
Lay-Up Tables
* 10’ x 10’ Working Area
* Lift & Extend Rollers
* Squaring Lip
* Nail Tray
Skate Rollers
* 15’ Standard Length
* Adjustable Height
* Sturdy Stands
* Custom Lengths Available
$13,900.00
$3,500.00 $3,000.00 $1,950.00
New Component Table with Skatewheel Conveyors
Lift & Extend Skatewheel Conveyors. 10' x 10' Work Area with Squaring Lip. Gun Holster & Nail Tray.
$13,900 FOB NE
Wasserman & Associates
800-382-0329
www.wasserman-associates.com
• 8' to 12' Wall Heights
• 1,000 Lb Capacity
• Weight: 120 Lbs
• Excludes: Electric Hoist & Freestanding Bridge Crane
$1,950 FOB NE
Wasserman & Associates
800-382-0329
www.wasserman-associates.com
Consider Panels Plus wall panel assembly equipment for manufacturers of wood or steel wall panels, floor-panels, and related framing components. Panels Plus is an employee owned, ISO certified, manufacturing company that builds state-of-the-art equipment featuring durable construction, with fit and finish second to none in the structural building component industry. The referenced base framing table allows you to assemble from 7-12 foot wall heights, at industry standard 16 foot lengths, at a working height of 29 to 32 inches. This framer design includes controls at each end of table, squaring stops and pneumatic clamping for consistent wall panel quality. Frames 2x4 or 2 x 6 walls, with color-coded, steel stud locators at 16 and 24 inches O.C. spacing. Includes pop-up skate wheels for easy transfer of completed wall frame. Framing table can be configured to receive wall framing light bars, other options include custom buildable wall heights, lengths and auto-indexing of optional 2 or 3 tool carriages.
Additionally from Panels Plus are sheathing tables with features that include foot pedal control at squaring end of table, with squaring stops, roller conveyors at both sides, single pendant controls for bridge, tool spacing at 6 inch centers with 3 inch bridge shift for offset nailing. Tool bridges can accommodate from 2 x 4 to 2 x 8 walls, with seam tilt being standard equipment Panels Plus Tool Bridges are available with single beam or dual beam design for two different tool mounts on one bridge. Squaring stations, sub-component tables, conveyors and panel lifts are also available to complete the configuration of the wall panel assembly line. Price includes factory installation and training. 50 CFM at 120 psi air. 120 or 230 volt, 1 phase electrical.
765-751-9990
Solving the problem of missed fasteners on exterior sheathing remains one of the primary reasons for call back charges and exceptions noted during jobsite building inspections. Clearly finding and resolving missed fasteners or “shiners” becomes mission critical before a sheathed wall panel leaves the production line. Our shop-proven, tilting conveyor makes the process safe, fast, and labor efficient. The ProStack tilt in-feed safely lifts wall segments to 45º in 5 seconds for inspection and on to 75º for easy to reach repairs. This tilt system is also excellent for installing blocking , windows, and other details in your wall panel segments. More information click here. 72,657 FOB ND
$37,525 FOB ND
ProStack powered in-feed conveyor was engineered to deliver wall panel segments at a matched speed and height into the ProStack automated wall panel stacker. Built for smooth operation and assembled with laser cut, powder-coated finish steel. Base model conveys wall panel segments up to 12’ in height and up to 16’ in length for wall segments up to 1,600 lbs. Extended length systems come in standard 20′ and 24’ length capacity. All models come with adjustable working heights and variable conveyor speeds.
Powered in-feed conveyor section, synchronized chain drive under top and bottom plate for open access, 5-HP, 208v, 3Ph power. Adjustable working height from 28” to 34”. 16′ length capacity.
“What do you mean you are stopping the QC inspections?” I could not believe what the operations manager was telling me when it was decided that we would no longer have each truss inspected at completion.
Our truss company had always prided itself on delivering the highest quality trusses in our market. We used top-notch materials, were renowned for tackling the most complex roof designs (even before 3D truss layout software became commonplace), and rarely encountered quality issues on job sites.
Before QC programs became mandatory in Canada and the U.S., we’d experienced a few near-misses in production. In response, the owner implemented a rigorous inspection process: every single truss run had to be fully inspected before the first truss of the run was pressed. For our medium-sized plant, this meant a full-time QC inspector on each shift, with production managers often jumping in to keep things moving. The rule was crystal clear – no truss left without a complete inspection.
Initially, this approach significantly improved our site-ready quality. But over time, an unexpected problem emerged. Our builders were growing complacent. Why worry about plate placement or lumber grade when an inspector would catch any issues? What was once a quality boost had morphed into a productivity killer and, ironically, was breeding a culture of carelessness.
The operations manager’s solution was bold. He eliminated full-time inspectors and instead placed the responsibility squarely on the build crews. They would be accountable for their own quality control. Random spot checks – at least two per setup per shift – would keep everyone alert. The message was unambiguous: take pride in your work and maintain high standards.
The results were remarkable. The build crews responded with renewed enthusiasm, reclaiming their commitment to craftsmanship. (This approach aligns closely with current QC inspection guidelines from TPI/SBCA and TPIC/CWTA.)
The design department faced similar challenges. Every job’s design book underwent exhaustive review, checking for geometric and engineering accuracy. But this came at a cost. Senior designers spent more time checking others’ work than completing their own designs. Morale plummeted, and careless errors became frustratingly common – wrong pitches, incorrect overhangs, you name it.
We implemented a parallel approach in the design department. Each designer became fully accountable for their work’s accuracy. If production or site problems arose from poor workmanship, it would reflect directly on them. We encouraged collaboration – designers were encouraged to seek help from peers or management. New team members had their work regularly checked until they proved their independence.
The outcome? Design throughput jumped. Mistake rates didn’t increase, and – most importantly – the design team’s job satisfaction improved dramatically.
My key takeaway? Sometimes solving a problem isn’t about adding more layers of complexity. It’s about stepping back, understanding the root cause, and setting clear expectations. We need to provide support, offer training, and hold people accountable. When team members feel trusted and empowered, they rise to the challenge.
I am genuinely curious – how does your organization handle quality control? Drop me a line and share your experiences.
If you want help finding that next perfect component designer or design job in Canada, please contact me. If your work is in the mass timber world anywhere in North America, I’d love to talk to you about connecting you to that next great job or candidate. You can reach me at secord@thejobline.com, or 800-289-5627 ext. 2. I’m also happy to engage at: LinkedIn.com/in/geordiesecord www.thejobline.com
The MSR Lumber Producers Council (MSRLPC) represents the interests of machine stress rated lumber producers in the manufacturing, marketing, promotion, utilization, and technical aspects of MSR and MEL lumber. Suppliers, customers, and professionals may join as Associate members to enjoy:
• Online Marketing
• Networking Opportunities
• Reliable Market Data
• Education
“There is no question that the MSR Lumber Producers Council meetings are worth your time to attend. The information you will receive from the guest speakers and members of the Council is unparalleled!”
—Sean Kelly,
Automated Products Inc.
2021 Panels Plus light gauge steel (LGS) framing station, builds steel stud wall panels from 6′-9″ to 16′-0″ heights, from 1′-0″ to 20′-0″ long. Includes four (4) Graber SuperDrive tools with mounts, two tools per dolly, adjustable top and bottom plate stops, squaring stops and pop up conveyors. 110 volt, 1 phase, 30 Amp electrical required. 80 PSI at 10 CFM air required. $71,993 NOW $59,000 FOB PA
• Pop-up Skatewheel Conveyor
• Powered Height Adjustment (6'-11" to 12'-5" wall heights)
• Fixed Squaring Stops
• Excludes Tool Dollies
• 110 Volt / 20 Amps
• Add $6,000 for Stud Locators at 16" & 24" O.C.
• Add $2,750 for 1 Pair of 15' Skatewheel Conveyor with Stands
• Add $11,900 for Sub-Component Layup Tables with Pop-up Skatewheel Conveyors
• EQUIPMENT FINANCING available from SLS Financial Services $38,750 FOB NE
2021 Panels Plus light gauge steel (LGS) framing station, builds steel stud wall panels from 6′-9″ to 12′-3″ heights, from 1′-0″ to 20′0″ long. includes four (4) Graber SuperDrive tools with mounts, two tools per dolly, adjustable top and bottom plate stops, squaring stops and pop up conveyors. 110 volt, 1 phase, 30 Amp electrical required. 80 PSI at 10 CFM air required.
$71,993 NOW $59,000
Reduced labor, increased safety, the benefits just keep stacking up. Stacking wall panels at the end of your production line can be a real labor-intensive and safety-challenging task. But it doesn’t have to be now, thanks to ProStack. This innovative wall panel stacker literally stacks from the bottom up, reducing awkward overhead lifting & placement, and the risk of head injury. Plus, ProStack frees up at least one worker to return more productively to your core task—building wall panels. Enhanced worker safety and productivity is what ProStack is all about.
Developed for commercial wall panel production facilities this is the remarkable ProStack, fully automated wall panel stacker. The ProStackrelieves your build team from creating a stack of wall panels and keeps them building walls instead. Stacks 2×4 through 2×8 walls up to 20′ in length and up to 12′ in height (taller by special order). The ProStack will automatically center or left or right justify each layer including multiple wall segments on the same layer. For ease of loading in your yard or on the build site, fork pockets are created in two ways: The operator can attach blocking up to 5″ tall to the last wall of the stack prior to entering the stacker, or two shorter walls can be spread apart prior to the second to last row of the stacker. Designed without any overhead frame or apparatus, so no crane inspections are required. The ProStack is “event driven”, so there is no need to read a file. Setup and installation is easy too, without the need for complex training or disruption to workflow. So free up your team to do what they do best, and you need to do most, and let ProStack stack your wall panels instead. ProStack can even operate with your existing powered conveyors or select our optional matching conveyors (see the video shown below). 208 volt, 3 phase, 43 Amp base model electrical required. No air required. Footprint is 26′-5″L x 19′-3″W.
• Sources for MSR Lumber
Filter by species, grade and dimension to locate products from MSRLPC members.
• Educational Resources
Find helpful information for current and potential MSR lumber users.
• NEW! Design Values
Comparison Tool
Compare MSR lumber reference design values with visually graded dimensional lumber by species. The MSRLPC website is a
to make informed purchasing decisions as well as those exploring design optimization with MSR Lumber. Check it out!
By Yoonhwak Kim, P.E., Senior Alpine Engineer
Building engineers rely on maximum gravity reactions (R+) from Truss Design Drawings (TDD) to design structural components. These maximum reactions are calculated based on load combinations specified by building codes, representing the highest downward forces which allow engineers to determine the stability requirements for the structure. The R+ values are essential in determining the size and capacity of columns, lintels, dowels, foundations, as well as other structural elements.
The standard loading of a 32-foot roof truss, as illustrated in Figure 1, is 20-7-0-10 with 24” spacing (see the Loading Criteria section). The IntelliVIEW® Software calculates and displays the maximum reactions of each bearing as 1,183 pounds (lbs) with a total of 2,366 lbs.
This result can be manually verified using the following formula:
Reactions = (TCLL + TCDL + BCLL + BCDL) × truss span × truss spacing
Equation with values: (20 + 7 + 0 + 10) psf × 32 ft × 2 ft = 2,368 lbs
This result is within 1% of the value displayed on the TDD, demonstrating consistency between hand calculations and the software results.
Unlike standard trusses, a girder truss supports concentrated loads from other trusses or structural framing, making it an essential element in a building’s design. These require stronger structural components to meet the higher load-carrying demands.
The hand calculation for a girder truss follows the same basic formula as standard trusses but includes concentrated loads. For instance, in Figure 2, the girder truss carries fourteen 200 lbs point loads at the bottom chord. The reaction can be calculated as follows:
(20 + 7) psf × 32 ft × 2 ft + (0 + 10) psf × 32 ft × 1 ft +14 × 200 lbs = 4,848 lbs
The blue font is the top chord calculation, while the green font is the bottom chord calculation. The result is close to the TDD value of 4,866 lbs confirming the accuracy of the calculations.
Figure 2. TDD of Girder Truss with Point Loads on One Face.
Figure 3 examines a situation where point loads are applied to both faces of a truss. Specifically, three 50 lbs point loads are placed on one face, while fourteen 200 lbs point loads are attached to the other face. The reaction is calculated as:
(20 + 7) psf × 32 ft × 2 ft + 14 × 200 lbs + 3 × 50 lbs +10 psf × (32 – 6) ft ×1 ft = 4,938 lbs
While the top chord loading (blue) remains unchanged, the bottom chord loading (green) must account for the distribution on both faces. For the face with fourteen 200 lbs point loads, the calculation remains as before. For the opposite face with three 50 lbs point loads, the remaining tributary area is calculated as: 10 psf × (32 – 6) ft × 1 ft.
Figure 3. TDD of Girder Truss with Point Loads on Both Faces.
Here, the 32 ft is the total truss span, while the unoccupied area accounts for the spacing of the point loads: 32 ft – (3 trusses × 2 ft). The calculated result of 4,938 lbs closely aligns with the TDD reaction value as well.
Typically, the maximum reactions shown on the TDD surpass the hand calculated values because IntelliVIEW Software considers all loading cases per code, displaying the highest reactions. If the TDD maximum reactions are lower than the hand calculations by more than 15 percent, truss designers should review the loadings on the truss. This discrepancy is often due to missing or underestimated loads on the girder truss. By understanding and verifying maximum gravity reactions (R+), engineers can help ensure accurate, safe, and efficient structural components.
For additional information or questions, please contact your local Alpine Sales Representative or the Structural Engineering Team (info@alpineitw.com).
References:
1. Important check points for a truss design drawing. Good Connections, Yoonhwak Kim, P.E., Winter 2021.
2. ASCE 7-22 Minimum Design Loads and Associated Criteria for Buildings and Other Structures.
3. IntelliVIEW Suite: The software solution for Component Manufacturers (alpineitw.com).
2022 Peterbilt 579 S/A Day Cab Truck #1
Paccar MX-13 / 12.9L / 405 HP Engine
249,300 Miles / 5,566 Engine Hours
Auto Transmission Engine Brake
12,000 Lb Front Axle / 22,700 Lb Rear Axle / 34,700 Lb GVWR
Air Trac Air Ride Suspension
148 Inch Wheelbase
Dual Fuel Tanks Tires are Very Good
$35,000 FOB PA
Wasserman & Associates
800-382-0329
www.wasserman-associates.com
Reconditioned Lakeside 36'-51' Stretch Roll-Off Trailer
• Self-Contained Hydraulic Front End
• Sliding Tandems
• Roller Locks
• Headache Rack
• New Axles (Undercarriage)
• New Wheels, Tires & Brakes
• New Hydraulic System
• New Wiring & Light Sockets
• Sandblasted & Epoxy Painted
• DOT is Current $40,000 NOW $29,900 FOB ME
Wasserman & Associates 800-382-0329
www.wasserman-associates.com
features hydraulic lift, locking rollers, sliding tandem, ABS brakes, and a fifth wheel neck. Six tires have 75% tread remaining and two tires have 50%. 68,000 GVWR. Iowa DOT inspection valid until October 2025.
$26,997 FOB IA Wood Tech Systems 765-751-9990 www.woodtechsystems.com
2021 Big John Extendable Pole Truss Trailer
Extendable pole trailer
Used for 60' span roof trusses, peak down
Retracted length - 35'. O.A.
Extended length - 45' O.A.
Adjustable 2' Increments
Outer tube frame - 8" square tube
Inner tube frame - 6" square tube
Axles - (2) 25,000 LB Capacity Each
Axle width -102"
Anti-lock brake system
Parking brakes on both axles
Wheels - 10 stud outboard drums
Tires - 11 R 22.5 radials
Rims - 22.5 steel unimount (8) alum wheels
Suspension - Watson air ride with dump valve
Landing gear - 2 speed
Bumper - standard
Lights - DOT Specs, LED Package (2) truss stands (4) winches with straps
$29,900 NOW $23,900 FOB SC
Wasserman & Associates
800-382-0329
www.wasserman-associates.com
1995 Pines 45' Chip Trailer
• Modified by LMI TENN
• 8" Floor Cross Members
• Reinforced Roof
• 22.5 Tubeless Tires
• Sl iding Tandem Axle (for weight distribution) (FOB PA) $9,900
Wasserman & Associates
800-382-0329
www.wasserman-associates.com
1997 Lakeside JDH Trussmaster
36-51 ft Stretch Trailer (OR-1)
1997 Lakeside JDH Trussmaster 36′51′ – Lakeside trailer features 5th-wheel connection, sliding tandem axle, locking rollers and hydraulic lift neck. Current DOT inspection September 2023. 50% brakes and 50% tire tread remains. 26,000 GVWR $28,997 NOW $21,997 FOB MO Wood Tech Systems 765-751-9990
www.woodtechsystems.com
Features sliding tandem axle, fifth wheel connection, locking rollers, ABS brakes, and hydraulic lift neck. This trailer does have a current DOT inspection. Estimated 50% tire tread remaining.
$28,990 FOB WI Wood Tech Systems 765-751-9990
www.woodtechsystems.com
Due to manufacturing efficiency upgrades we have increased production and have various trailers with various options on our lot READY TO GO! * Large Toolbox and/or Headache Rack can be added as Options # Does NOT INCLUDE FET or Freight ## DOES NOT include Freight EXTENDABLE TRUSS TRAILERS
38’-53’ (T-1267) - No Options*- $65,670#
38’-53’ (T-1375) - No Options*- $65.670#
38’-53’ (T-1418) - No Options*- $65,670#
42’-60’ (T-1413) - Front Lift Axle*- $71,857#
42’-60’ (T-1392) - Headache Rack, Large Toolbox - $71,239#
42’-60’ (T-1393) - Sliding Winch* - $71,754#
42’-60’ (T-1414) - No Options* - $68,970#
42’-60’ (T-1416) - No Options* - $68,970#
42’-60’ (T-1415) - No Options* - $68,970# 42’-60’ (T-1417) - No Options* - $68,970#
42’-60’ (T-1298) - No Options* - $68,970#
50’-70’ (T-1277) - Headache Rack, Large Toolbox, Sliding Winches - $81,959#
50’-70’ (T-1346) - Headache Rack, Large Toolbox, Lift Axle - $76,700#
50’-70’ (T-1421) - No Options* - $76,700# 50’-70’ (T-1347) - No
- $76,700# 50’-70’ (T-1422) - No Options* - $76,700#
50’-70’ (T-1186) - Headache Rack, Large Toolbox - $78,369# 50’-70’ (T-1377) - Headache Rack, Large Toolbox - $78,369# 53’-80’ (T-1419) - Sliding Winches, Large Toolbox, Headache Rack - $83,919# 53’-80’ (T-1420) - Lift Axle, Large Toolbox, Headache Rack - $83,610# 53’-80’ SHOW TRUSS TRAILER (T-1274)
32’ Gooseneck (T-1381) - Front Roller - $50,825##
32’ Gooseneck (T-1382) - No Options - $48,485##
36’ Gooseneck (T-1291) - No Options - $50,515##
36’ Gooseneck (T-1385) No Options - $50,515##
36’ Gooseneck (T-1384) 12K Axles, Front Roller-$53,163##
36’ Gooseneck (T-1383) 12K Axles, Front Roller-$53,163##
All of our Trailers come with a 2 Year Warranty and are custom built. We use blast prep for our powder coat prime and paint system, air-ride suspension and we now offer Galvanized Rollers as an option. We build 38’-53’, 42’-60’, 50’-70’ and 53’-80’ Extendable Truss Trailers, 26’, 32’ and 36’ Gooseneck Truss Trailers (Split Truss Available as well on Goosenecks) and 40’, 48’, and 53’ Standard Truss Trailers.
You Can Truss our Truss Trailers! Call Bryan Shinn today to purchase one of the trailers listed above or to get a Quote and have us build a NEW Truss Trailer for you call or emailBryan Shinn - Sales Manager 701-941-2017 or 1-800-237-5161 bryan.shinn@precisionequipmfg.com
Precision 50-70′
Roll Off Trailer (R158) 2015 Precision 50-70′ stretch roll off trailer features sliding tandem axle, fifth wheel connection, locking rollers, ABS brakes, and hydraulic lift neck. This trailer does have a current DOT inspection. Estimated 50% tire tread remaining.
$27,990 FOB WI
Wood Tech Systems 765-751-9990 www.woodtechsystems.com
2014 Precision 48′ Roll Off Trailer (R156)
2014 Precision 48′ roll off trailer features tandem axle, fifth wheel connection, locking rollers, ABS brakes, and hydraulic lift neck. Estimated 50% tire tread remaining.
$17,990 FOB WI Wood Tech Systems 765-751-9990 www.woodtechsystems.com
2014 Precision 48′ Roll Off Trailer (R157)
2014 Precision 48′ roll off trailer features tandem axle, fifth wheel connection, locking rollers, ABS brakes, and hydraulic lift neck. Estimated 50% tire tread remaining.
$17,990 FOB WI
Wood Tech Systems 765-751-9990
www.woodtechsystems.com
2022 Stoll 36-ft TrussTran Roll-off Gooseneck Truss Trailer (Black) 2022 Stoll 36′ TrussTran roll-off truss trailer (Black) STOT-2022, features remote pendant-control operation for hydraulic lift/tilt function, GVWR 10,896, integrated load straps, Locking, split rollers for delivering roof truss up to 50′, floor trusses, and material packages. Has current DOT inspection in January, 2025.
$41,997 FOB IN Wood Tech Systems 765-751-9990 www.woodtechsystems.com
2021 Big John Extendable Truss Pole Trailer
2021 Big John peak down extendable pole trailer. Transports up to 60′ peak down trusses with a retracted length of 35 ft. O.A., and an extended length of 45 ft. O.A. Adjustable in up to 2 ft. increments. Outer tube frame is 8″ sq. tub and inner frame is 6″ sq. tub. Features 2 axles with anti-lock brake system and parking brakes on both axles. Trailer features air ride suspension with dump valve and 2 speed landing gear.
$23,890 FOB NC
Wood Tech Systems 765-751-9990
www.woodtechsystems.com
Used - 2014, R157 48” Roll -Off
Precision Trailer
Tandem Axles | Air Ride Suspension : Air Operated Load Control, Air Operated Pin
Locks | Mesh Between Rollers | Beaver Tail | Strap Locks and Winches | LED Lighting | 11.4 Ton Self Contained Power | (1) Heachache Rack
$17,500 NOW $12,500 Eide Machinery Sales, Inc. 612-521-9193
www.eidemachinery.com/equipment/ trailers
Used - 2014, R156 48” Roll -Off Precision Trailer
Tandem Axles | Air Ride Suspension : Air Operated Load Control, Air Operated Pin
Locks | Mesh Between Rollers | Beaver Tail | Strap Locks and Winches | LED Lighting | 11.4 Ton Self Contained Power | (1) Heachache Rack
$17,500 NOW $12,500 Eide Machinery Sales, Inc. 612-521-9193
www.eidemachinery.com/equipment/ trailers
2015 JLG G10-55A Telehandler Lift
• 10,000 LB Capacity
• 55' Lift Height
•
•
•
•
•
•
2004 and 2005 Pratt 53' Roll-Off Trailers
Hydraulic Front End
Sliding Tandems
Roller Locks
Winches and Straps
Headache Rack
Tool Box
Several cross member have rust holes and need to be replaced
$12,500 Each or $24,000 for Both Trailers
Wasserman & Associates 800-382-0329
www.wasserman-associates.com
2022 Stoll 36-ft TrussTran Gooseneck Truss Trailer (Red)
2022 Stoll 36′ TrussTran roll-off truss trailer, model STOT-2022, features remote control operation for hydraulic lift/tilt function, GVWR 10,896, integrated load straps, locking, split rollers for delivering roof truss up to 50′, floor trusses, and material packages. Has current DOT inspection in January ’25.
$41,997 FOB IN Wood Tech Systems 765-751-9990 www.woodtechsystems.com
1993 JDH Trussmaster 48'-70' Stretch Roll-Off Trailer
• Fixed Tandem
• Spring Suspension
• Roller Locks
• Winches & Straps
• Headache Rack
• Tires are Good (less than 5,000 miles on tires)
• DOT is Current
• Video available upon request
$19,900 NOW $13,900 FOB IN Wasserman & Associates 800-382-0329
www.wasserman-associates.com
1995 ASI 48'-70' Stretch Roll-Off Trailer
• Slanted Profile
• No Hydraulic Lift (has been removed)
• Fixed Tandems
• Spring Suspension
• New Landing Gear and New Springs/ Shackles on the rear axles within the last year
• Tires are Good (4 new tires in Summer of 2024)
• Roller Locks
• Headache Rack DOT is current (February 2025)
$12,800 NOW $9,980 FOB WI Wasserman & Associates 800-382-0329
www.wasserman-associates.com
2003 JDH TRUSSMASTER SIDEOFFLOADING TRUSS TRAILER
10,000 Lb Tandem Axles (Dual Wheels). 26,000 GVWR. Deliver Trusses Vertically. Stretch from 18' to 38'. Raise Loads Hydraulically. Air Brakes. $6,900 FOB CA Wasserman & Associates 800-382-0329 www.wasserman-associates.com
2000 Haulin 36' Truss/Panel Roll-Off Trailer
• Bed Length: 36'
• GVWR: 26,000 Lbs
• Battery Operated Hydraulic Tilt
• Electric Brakes
• Locking Rollers
• Trailer Inspection is current
• One location needs steel plate/weld repair (reference photo)
$19,900 NOW $10,900 FOB PA Wasserman & Associates 800-382-0329 www.wasserman-associates.com
Used Precision 50’-70’ Stretch Trailer Tandem Axles | Air Ride Suspension, Air Operated Load Control, Air Operated Pin Locks | Mesh Between Rollers | Beaver Tail | Strap Locks and Winches | LED Lighting | 11.4 Ton Self Contained Power Unit | (1) Heachache Rack
$27,500 Eide Machinery Sales, Inc. 612-521-9193
www.eidemachinery.com/equipment/ trailers
2012 Precision Equipment 36' Gooseneck Roll-Off Trailer
• 10,000 Lb Tandem Axles with Dual Wheels
• Self Contained Hydraulic Lift
• Roller Locks
• Extra Roller on Gooseneck
• Electric Brakes
• Price in US Dollars
$29,900 NOW $28,500 FOB Ontario Wasserman & Associates 800-382-0329
www.wasserman-associates.com
Electrical Supply: 110 VAC
Motor: 1/4 HP, 110 VAC, Linear Actuator
Highly Accurate: +/- .010 Inches
Stop Rail: 2 x 4 x 1/4 Aluminum Extrusion
Stops: Jig Bored Steel
Stop Blocks: Machine Billet Aluminum
Internal Components: Hardened, Ground and Polished Steel and Billet Aluminum
Dimensions:
Length: 5 feet (60”) to 60 feet (720”)
Height: 12 inches
Depth: 12 inches
If you are looking for the fastest, most consistent way to measure and cut your product, then the Hain Measuring System (MEA) is your answer. The MEA changes from one length t any length instantly, up to 60’, without changing the operator’s position on the line. It is also highly accurate (+/- .010) and quickly moves from one length to the next in seconds. The MEA is designed for quick and easy setup and is simple to use. Even a first time user will be productive with little or no training required. It can adapt to any saw and can be mounted to any surface so that you can integrate the MEA with your existing setup. The MEA is versatile allowing “left” or “right” handed operation and measurement in “feet and inches” or “inches” depending on your preference. The MEA is also available in a “Skid Mounted” version.
Alpine Lumber Carousel
• 7 Bunk Capacity (up to 12' Lumber)
• Pushbutton Control Station
• 10 HP / 3 Phase Motor
• In working condition when removed in August 2023
$11,900 FOB Manitoba
Wasserman & Associates 800-382-0329
www.wasserman-associates.com
2002 Atlas Copco Rotary Screw Air Compressor
• Model GX11FF
• 15 HP Rotary Screw Air Compressor (230/460 Volt - 3 Phase)
• 13,443 Hours
• 51.7 CFM at 128 PSI
• 80 Gallon Tank
• Built-in Air Dryer does not work
• Includes separate 2012 Pneumatech AD-50 Air Dryer (1 Phase)
$4,250 FOB TX
Wasserman & Associates
800-382-0329
www.wasserman-associates.com
SL-Laser Model ProDirector 7 Projection System
Improved model ProDirector 7, green-color laser projection system from SL-Laser. Projects roof truss, floor truss and wall panel design images accurately onto building surface for faster setup and fabrication times. New employees are productive more quickly, with less training required. Each laser head provides 21′ projection length (at 15-foot ceiling heights). New model PD7 projector heads are smaller in size than previous models, have diodes that are easier than ever to swap out and maintain, and project an even clearer line onto the building surface.
System includes projector heads, cables, mounting hardware for attachment to customer’s structure, factory installation, training, and options for computer controls. Works with each connector plate manufacturer’s design software. Modular nature of the laser heads allows for easy future expansion of system length. 120 volt, 1 phase.
FOB NC Wood Tech Systems 765-751-9990 www.woodtechsystems.com
New Monet Power Deck Infeed Decks Heavy-duty, 5-chain feed system to bring material to the infeed of the component saw. 16′ wide x 20′ long x 36″ high. Transfers 6′ to 20′ lumber lengths. Option for 6-arm Power Deck available at an additional cost. Features auto-feed advance, foot pedal override forward and reverse, variable speed control, double bearing construction, softstart and soft-stop and e-stop cable. Base price shown. 480 volt, 3 phase, 15 Amp electrical required. (Prices start at $31,000.)
Wood Tech Systems 765-751-9990
www.woodtechsystems.com
Champion Valve Plus Compressor
2023 Atlas Copco Compressor in Container Housing
2023 Atlas Copco type G7FF rotary screw compressor with internal dryer and external tank. Compressor capacity is 145 PSI, has a 10 HP motor, external air tank includes bleed valve and manual output valve. System comes contained in a custom shipping container with locking entry door, thermostat controlled electric fans, throughwall induction vent grills, interior lighting, electrical panel and utilities for a second compressor. Container size is 8′ width x 10′-6″ long x 8′-8″ height. Hours as of 19 September ’24 were 986. 480 volt, 3 phase / 120VAC electrical required.
$34,490 FOB AZ Wood Tech Systems 765-751-9990 www.woodtechsystems.com
Champion Valve Plus – Reciprocating twostage compressor, model 7.5–V80E, with Eaton controls, 7.5 HP motor, 80 gal vertical tank, rated for 22 cfm @ 175 PSI. 208/230/ 460 volt, 3 phase electrical required.
$2,495 FOB AZ Wood Tech Systems
765-751-9990
www.woodtechsystems.com
2023 Triad Flow Through Component Nailer
• Assembles Trimmers, Partition Leads, Corners, Headers, Ells, Jack Studs
• Length Capacity: 10'-2"
• Clamp Opening: 3" x 3" to 12" x 12"
• Vertical & Horizontal Clamping Pressure: 300 Lbs at 100 PSI
• Foot Pedal Control
• On/Off Switches for Each Nail Gun
• Pop-Up Stop
• Nail Trays
• 10' Infeed & 10' Outfeed Roller Conveyor with Stands
• Excludes Nail Guns
$19,900 FOB ON Wasserman & Associates 800-382-0329
www.wasserman-associates.com
• 2 Each - 35' Span Gantry Bridges with 1 Ton Harrington Electric Hoists
• 20' Height
• Internal Electric Bus Bar (eliminates festoon system) $45,000 NOW $33,900 FOB AZ
By MiTek Staff
roduct testing is the backbone of quality control in engineering and manufacturing, ensuring products are reliable, durable, and safe before reaching the market. Over the years, the testing processes have evolved dramatically, transitioning from manual inspections to highly sophisticated automated systems. This article will explore how product testing has advanced, focusing on the evolution of testing machines, the role of data analytics (like MS Excel), and how modern standards such as ASTM and ICC-ES Acceptance Criteria influence today’s rigorous testing environments.
Organizations like ASTM International, ICC-ES, and ISO have been pivotal in developing testing standards and criteria. ASTM develops and publishes technical standards for a wide range of materials and products, setting the baseline for how tests should be conducted. These standards ensure consistency across the industry, allowing manufacturers to meet internationally recognized benchmarks for product quality.
The ICC-ES Acceptance Criteria is another set of guidelines that provide a basis for testing innovative products that may not yet have established testing protocols. These criteria allow for flexibility while ensuring that new products still meet rigorous safety and performance standards.
In the early 20th century, product testing was predominantly manual and labor-intensive. Engineers relied on visual inspections and rudimentary mechanical tests using basic machines like tension testers and compression testing rigs. These machines were relatively simple—often hand-cranked—and measured basic properties like tensile strength, compression, and load-bearing capacity.
One example of early testing machines was The Little Giant by Tinius Olsen, which could test materials under tension, compression, and bending. These machines laid the foundation for more complex testing techniques and standards such as ASTM E8, which is the oldest standard for metal testing that is still in use today.
As manufacturing scaled up in the mid-20th century, so did the need for more precise testing. Mechanical testing machines became motorized, allowing for more consistent force application. Over time, electronic controls were introduced, improving accuracy and repeatability. Early machines operated using simple load gauges, but the development of strain gauge-based testing systems in the 1950s allowed for more accurate measurements of material deformation and stress.
The introduction of digital control systems in the 1970s revolutionized product testing. Machines could now be programmed to perform complex tests automatically, allowing for precise control over testing conditions like cyclic loading and displacement control. Cyclic loading, for example, simulates repeated stresses on materials to evaluate fatigue life—a crucial test for products exposed to constant forces, like bridges or aircraft wings. This advancement led to new testing standards for cyclic loading such as ASTM E2126. Displacement control testing, on the other hand, maintains a constant deformation rate, measuring how a material reacts over time under a controlled strain, which is essential for materials like steel and concrete. This allowed standards such as ASTM D7147 to include cross head rates for testing.
In parallel with mechanical testing, the industry developed durability tests to ensure products could withstand environmental conditions. Corrosion testing, for instance, became essential for materials exposed to the elements. Salt spray chambers simulate corrosive environments to measure how materials like steel and aluminum degrade over time which led to the creation of ASTM B117 to standardize salt spray testing.
The introduction of computers to testing labs in the 1980s dramatically improved the ability to analyze test data. Programs like MS Excel became vital tools for engineers. Data from mechanical and environmental tests could now be recorded, processed, and analyzed efficiently. Engineers could use Excel to create detailed reports, graph trends, and identify patterns in test results, vastly improving the decision-making process.
In particular, pivot tables and macros allowed for more advanced analysis, reducing human error and enabling the processing of larger datasets. As a result, Excel enabled engineers to correlate test results with product failures, leading to improvements in design and manufacturing processes.
As computers became more powerful, simulation software started to replace some physical tests. Programs like ANSYS, SOLIDWORKS Simulation, and Autodesk allowed engineers to model products digitally and simulate how they would perform under various conditions, including mechanical stress, heat, and pressure. These simulations are typically based on real-world test data, enabling the software to replicate physical phenomena with increasing accuracy.
SOLIDWORKS Simulation. (Retrieved from https://www.solidworks.com/ product/solidworks-simulation.)
While simulation testing has reduced the need for extensive physical prototypes, it is typically used in conjunction with real-world testing to validate the models. Physical tests remain essential for verifying the assumptions and inputs used in simulations, ensuring that the digital models reflect real-world behavior.
As product testing has evolved, so too has the understanding of scaling effects—how a product’s behavior under stress or load changes with its size. In structural testing, the impact of scaling is critical, especially when testing components that will be scaled up or down from the prototype stage. Engineers have found that certain materials or configurations behave differently when tested in small samples versus full-scale implementations, affecting measurements like tensile strength, compression resistance, and fatigue life. The advent of advanced simulation software has aided in addressing these scaling effects, enabling engineers to predict performance changes based on size adjustments.
Today, calibration of testing machines is a critical aspect of ensuring accurate results. Equipment must be regularly calibrated against known standards to guarantee precision. For example, load cells in modern testing machines are calibrated to ensure that force measurements are accurate to within specific tolerances, often governed by standards like those from ASTM E74.
Product testing has come a long way from manual inspections and simple mechanical tests. Today, testing is a complex process involving cutting-edge machines, data analytics, simulation software, and rigorous standards. As industries continue to evolve, so will the methods of testing—driven by the need for ever-greater precision and reliability in the products we use every day.
For additional information, or if you have questions, please contact the MiTek Research and Development or the MiTek Engineering department.
Saws
• Automated Component & Linear Saws (2010 & Newer)
• Monet DeSauw or TimberMill Manual Component Saws
• Floor Web Saws
• Spida (Apollo) Saws with Truss Automation
• Bunk Cutters
Truss Equipment
• Roller Gantry & Hydraulic Press Systems
• Finish Rollers
• Truss Stackers
• Floor Truss Machines
• Lumber Splicers
• Jack Tables
• C-Clamp Presses
& Trailers
• Stretch Roll-Off Trailers
• Go oseneck Roll-Off Trailers
• Pacific Automation or MiTek Mobile Home Press Contact Wasserman & Associates for a Fair Market
Value Assessment of your Used Equipment
Operational, Needs Work, and Parts Only equipment will be considered!
• Automated Wall Panel Parts Cutting & Marking as directed by Wall Panel Design Software Output
• 20' Roller Conveyor with Servo Motor Controlled Length Stop/Plate Pusher
• 10' Infeed Roller Conveyor
• 24" Lenovo Touch Screen Computer (Windows 11 Pro OS)
• ASI Bas ic L Plate Cutting/Marking Operating Software
• 4 Head Ink Jet Plate Marker (marks 2 plates on edge)
• 110 Volt / 1 Phase
• Includes Onsite Installation & Training
• Excludes Saw & Dust Collector
• Approximately $50,000 USD with DeWalt Sliding Miter Saw including Freight, Customs Brokerage Fees & Installation
• Other Saw Options Include: Existing Saws, ASI Radial Arm Saw, Lauderdale Hamilton Up Cut Saw & Vista Angle Boss Saws
• Video available upon request
EMSI Teeter Cart
Width – 46” / Length – 73” / Load Capacity
– 2850 pounds / Pneumatic tires – 14.5 inch / Maximum utility in truss plants, panel plants, and lumber yards / Quick Assembly by bolting parts together / All hardware is supplied / Upright 2 x 4’s not supplied / Medium duty tires rated at 1500 lbs each are included.
Call for Price
Eide Machinery Sales, Inc.
612-521-9193
www.eidemachinery.com
Used - Quincy 25 Horsepower Screw Compressors (2x) Taken from service | Optional: Refrigerated Air Dryer - $500 $3500 each
Eide Machinery Sales, Inc. 612-521-9193 www.eidemachinery.com
NEW GALVANIZED STEEL STRAPPING
1 1/4" wide x .035 thick. $95 per coil. $1,900 per skid (21 coils). FOB PA. Wasserman & Associates 800-382-0329 www.wasserman-associates.com
AMI Industrial Floor Carts
AMI's industrial floor trucks (material carts) are designed of hardwood construction, fitted with space-age phenolic, roller-bearing wheels, and ball bearing swivel casters for strength and durability. AMI's phenolic wheels resist shock without chipping. They are non-sparking, non-marking, and can be operated continuously between -50℉ and 260℉. They are unaffected by grease, oil or debris on your shop floor.
Series "B" AMI Industrial Floor Truck
Our swivel casters are precision built with perfectly aligned raceways. All cold-form parts are made to exacting tolerances from heavy-gauge steel, and are hardened for severe service and long wear. Series B-4 carts include four casters, one at each corner, to prevent "tri-cycling" of long lumber loads.
Standard Models Available Max Load Weight (lbs.)
2748 27" x 48" Series "B" & "C" 2500
3248 32" x 48" Series "B" & "C" 2500
3260 32" x 60" Series "B" & "C" 2800
3660 36" x 60" Series "B" & "C" 2800
3672 36" x 72" Series "B" 4000
4072 40" x 72" Series "B" 4000
3696 36" x 96" Series "B" 4000
4896 48" x 96" Series "B" 4000
*Other models and sizes are available on request. FOB NC. Wood Tech Systems 765-751-9990 www.woodtechsystems.com
2005 Koorsen Connector Detector (For Repair or Parts)
6 detection zones to locate missing plates. Horn & zone lights indicate missing plates. 12" to 60" adjustable height from floor. 110 Volt / 1 Phase. New control panel switches & lights in 2014. Needs circuit board repair or replacement and new tower light. Includes 4 extra detection zone boxes.
$2,500 NOW $1,500 FOB NE Wasserman & Associates 800-382-0329
www.wasserman-associates.com
Fully Automatic Laser Guided
Builders Automation Machinery (BAM) model 2220, stair wedge saw station automatically produces wood wedges used to lock stair treads and risers into slots cut into the stair stringers…
Price based on configuration FOB FL
765-751-9990
www.woodtechsystems.com
BAM Pre-Hung
Door Machine
Titan Series
Builders Automation
Machinery (BAM) Titan series pre-hung door machine. Designed to produce between 150 and 250 doors per day. Multi-function door machine capable of doors 1′-6″ to 4′-0″ in width, and both 6′-8″ or 8′-0″ door heights. Processes both 1 3/8″ and 1 3/4″ thick door slabs. Machines the door, hinge jamb and strike jamb all at the same time. Capable hinge sizes include 3 1/2″ x 3 1/2″, 4″ x 4″, 4 1/2″ x 4 1/2″ with 5/8″ radius. Cycle time with flush hinge routing is 45 seconds. 10′ long x 7′-6″ wide footprint. Shipping weight 4,000 lbs.
More information Click Here
Price based on configuration
765-751-9990 www.woodtechsystems.com
BAM Staircase
Assembly Clamp
Builders Automation
Machinery (BAM) staircase assembly clamp, model 2210, accommodates up to 20 foot long stringers with a maximum width of 54″…
Price based on configuration FOB FL
BAM “Ovation”
Door Machining Center (DMC)
New Builders Automation Machinery
“Ovation” series, door machining center (DMC). Fully programmable, two-stage door machine featuring (27) axes of operation. Can be specified with either two or four front machining heads. Machine is side-eject, direct-drive with helical gear racks and gear protection from dust. The door loader is driven by an absolute encoder; no stepping motors, belts or exposed ball screws are used.
More information Click Here
Price based on configuration Wood Tech Systems
765-751-9990 www.woodtechsystems.com
$4,900 NOW $3,600 FOB GA
Wasserman & Associates 800-382-0329 www.wasserman-associates.com
Since 2006, we've been helping businesses of all kinds build their online presence. We make websites and software for the construction industry to empower companies to reach a wider customer base and engage their audiences. Companies all around the world work with us to make websites and apps that people actually want to use. Reach out to Wolf X Machina if you're a business and you want a website that actually drives results.
Builders Automation
Machinery (BAM) door loader, model 2001. Allows you to stack door slabs horizontally and feeds them into a horizontal door machine like the BAM model 996E-TS. Mechanically adjusts door stack height vertically as slabs are fed into machine. Clamp automatically adjusts to type and size of door slab: steel, solid-core or hollow-
manages the
By Simpson Strong-Tie Staff
Abenefit of using Simpson Strong-Tie’s CS Truss Studio™ is managing the relationship between the truss self-weight and the dead load. Truss self-weight is checked against all applied dead loads to verify that there is enough assumed “extra” dead load to account for the dead load of the truss itself.
Steps for managing the truss self-weight and the dead load:
1. Open a truss and analyze.
If the dead load for the truss is not adequate, a message displays. The message is either an error message or a warning message. In the example shown below, the following error message displays:
• Dead Load does not include enough to cover self-weight of truss! Dead Load = ####, Weight = ####, Deficit = #### (##%)
• #### indicates the actual values used
The error message indicates that the total dead load on the truss is 672 lbs. Because of the heavier lumber used and the gable truss design, the weight of the truss itself is almost 650 pounds. This leaves approximately 22 pounds of dead load to carry anything above the truss weight, which is not adequate.
2. To resolve the error, you must calculate what is required for the truss dead load and how much is extra and can be used to counteract the self-weight of the truss.
In the following example, the applied dead load is 672, as indicated.
3. When designing trusses for Wind Loads, you must run a factored dead load case (typically 60% of the dead loads used in combination with wind loads); this ensures that the weight of materials is not overstated to reduce uplifts.
• In the example below, the factored dead load (402#) is subtracted from the dead load (672) = 270. This amount represents the “extra” amount, above the truss weight. Subtract the extra amount from the weight of the truss (650#). The result is the deficit indicated in the error message. In the example below, the deficit for this truss is 380#.
• You can adjust the deficit threshold in Env Data > Analysis > Overall Controls > Report Self-Weight deficit larger than % as Error. This value can be set from 0% to 50% (default is 10%). This could be expressed as a decimal instead of a percent, with values Min = 0.00, Max = 0.50, Default = 0.10. If the deficit divided by the weight (times 100, if using %) is more than this setting allows, the truss fails and an error displays. Adjusting this setting may result in a warning as opposed to an error that prevents the truss from passing analysis.
• Adjust standard loads on the truss. Go to Load Template Manager > Standard Load and adjust dead loads for the truss.
• If you know the actual weight of the materials, you can override the dead loads. Go to Load Template Manager > Wind Loads and enter the actual material weights. Be aware that if you enter amounts that total more than 60% of the dead load, you will actually be reducing the amount of available dead load for the weight of the truss.
• Add additional load to the truss. Remember that when you add load, Truss Studio uses only 40% of that load as part of the truss self-weight. Go to Component > Component Loading > Distributed Load and adjust the Dead Load values. Adding a Description of Self Weight may be helpful to anyone reviewing the truss design.
If this added weight is the only additional load on a single-ply or two-ply truss, check the User Load is applied over 3 or more trusses checkbox to maintain repetitive lumber values. If there are other loads that disqualify the use of repetitive lumber values, do not check this box.
Note: Verify that the repetitive member factor is used properly. See Repetitive Members.
Note: If a warning displays regarding the truss self-weight, this is informational only. You can decide whether it is necessary to adjust the dead load for the truss.
Additional benefits of truss self-weight include:
• Verify the truss can support itself, in addition to all other material weights
• Warnings or errors are presented to the user when the truss self-weight exceeds the design dead loads
Simpson Strong-Tie’s Component Solutions® CS Truss Studio™ software has the ability to use truss self-weight. Contact your Simpson Strong-Tie Representative or email CSHelp@strongtie.com for more information.
Copyright © 2025 Simpson Strong-Tie Company Inc. All Rights Reserved
Inspired by ten years of intensive field experience and the ample and detailed feedback of numerous customers, we’re pleased to introduce the most advanced, most enhanced and high-performance Terminailer yet-Terminailer V.8. Drawing on invaluable time in the trenches closely evaluating Terminailer’s performance under varying conditions, our engineers have incorporated critical learning and insight to enhance simplicity, performance and operator control. Just part of what V.8 offers includes:
•Vastly enhanced operator control for even greater productivity
•A redesigned nail-feed supplying EverWin PN90-PAL industrial nail guns
•Simplified pneumatics featuring direct air-supply to all six nail guns
•Even more sub-component profiles for wall design flexibility
•Rugged durability with pharmaceutical grade assembly
Developed by people who know well the mechanics, safety considerations and business aspects of wall-panel production, Terminailer V.8 combines more enhancements & operator-friendly features than ever to take your productivity to the next level and beyond. Contact us to learn even more and to put the V.8 performance in motion at your facility.
Drug use and alcohol consumption are normally considered personal issues. They only become an employers concern when they affect safety and worker performance. Drug and alcohol abuse cost employers through high absenteeism and sick pay. Abusers hurt themselves and their families if they lose their job as a result of their actions. If they are fired or cannot function on the job, the company loses the services of an experienced worker. Those under the influence of drugs or alcohol cause friction in the work group, lower morale and work efficiency, use poor judgment that results in bad decisions, and give the company a poor public image.
Certain times of the year individuals should be especially aware of their alcohol and drug consumption. In the winter months when the days are dark and dreary, some people experience a sense of depression or seasonal affected disorder (SAD). They may turn to drugs or alcohol in the mistaken belief it will relieve the symptoms of the disorder.
El uso de drogas y el consumo de alcohol se consideran generalmente asuntos de índole personal. Éstos solamente incumben al empleador cuando afectan la seguridad y el desempeño del trabajador. La drogadicción y el alcoholismo tienen un costo elevado para los empleadores por ser causas del ausentismo laboral elevado y de las ausencias por enfermedad con goce de salario. Los drogadictos y los alcohólicos se lastiman a sí mismos y a sus familias si pierden sus trabajos como resultado de sus acciones. Si se les despide o si no pueden desarrollar las funciones del trabajo, la empresa pierde los servicios de un trabajador con experiencia. Aquéllos que se conducen bajo la influencia del alcohol o las drogas causan fricción en el grupo de trabajo, bajan la moral y la eficiencia en el trabajo, utilizan el mal juicio que resulta en malas decisiones, y dan una mala imagen pública a la empresa.
The holiday season, with increased social gatherings or added financial stress, leads some people to misuse drugs or alcohol, especially during this year of millennium celebration. Those who over-consumed alcohol or drugs yesterday and are hung over today may feel out of sorts, still trying to recover, and may not give all their attention to the safety aspects of their job. Their judgment and safety performance becomes impaired and the likelihood of an accident or injury to themselves or coworkers increases.
Sometimes a personal or health problem persists. In most cases, the problem gets resolved. But if it is not resolved some people turn to alcohol or drugs. Even some prescription drugs can interfere with job performance. The individual cannot think clearly or becomes distracted. This can lead to accidents. Irresponsible consumption of drugs or alcohol not only jeopardizes the safety and health of the worker and coworkers but it can impact the employers business and affect the future of all families involved.
Durante algunas épocas del año, las personas deben estar especialmente conscientes de su consumo alcohólico y de drogas. Durante los meses de invierno, cuando los días son opacos y lúgubres, algunas personas padecen de algún tipo de depresión o de síndromes estacionales (SAD, por sus siglas en inglés). Ellos pueden optar por consumir drogas o alcohol con la falsa esperanza de que eso les aliviará los síntomas del trastorno.
La época de las fiestas de fin de año, con un mayor número de reuniones sociales o de mayor tensión nerviosa por problemas económicos, conduce a muchas personas a excederse en el uso de drogas o en el consumo de alcohol, especialmente este año de celebración del nuevo milenio. Todos aquellos que consumieron alcohol o drogas en exceso ayer, y tienen resaca hoy, pueden sentirse faltos de coordinación, aún tratando de recuperarse y quizá no le presten completa atención a los aspectos de seguridad que su trabajo requiere. Su juicio y desempeño seguro se verán seriamente disminuidos y aumentará la posibilidad de que ellos o sus compañeros de trabajo sufran accidentes o lesiones.
Algunas veces los problemas personales o de salud persisten. En la mayorìa de los casos, el problema se resuelve. Pero si no se resuelve, algunas personas recurren al alcohol o a las drogas. Incluso algunos medicamentos recetados pueden interferir en el desempeño del trabajo. La persona no puede pensar claramente o se distrae. Esto puede llevar a accidentes. El consumo irresponsable de las drogas o del alcohol no solamente pone en peligro la seguridad y la salud del trabajador y sus compañeros, sino además, puede repercutir en las actividades empresariales del empleador y afectar el futuro de todas las familias involucradas.
The above evaluations and/or recommendations are for general guidance only and should not
They are based solely on the information provided to us and relate only to those conditions
or implied, that your workplace is safe or healthful or that it complies with all laws,
April 2–4
April 2–4
April 7–8
April 7–10
April 8–10
April 9–11
April 10–13
April 13–15
April 16–17
April 27–30
April 27–May 2
May 5–7
May 5–8
May 6–7
May 19–21
May 19–21
May 26–30
NASCC: The Steel Conference Louisville, KY
Natl Frame Bldg Assoc (NFBA) Annual Conference & Expo Knoxville, TN
American Bldg Materials Alliance (ABMA) Advocacy Day Washington, D.C.
Modular Bldg Institute (MBI) World of Modular Conference & Tradeshow Las Vegas, NV
AGC—The Construction Assoc. Annual Convention Columbus, OH
Structural Engineering Institute (SEI) Structures Congress Phoenix, AZ
Assoc Bldg Mat Distrib of America (ABMDA) Convention Ponte Vedra, FL
Western Wood Products Assoc (WWPA) Annual Meeting Vancouver, WA
Virginia Tech Short Course: Structural Design of Wood Structures Blacksburg, VA
LBM Advantage NextGen Leadership Conference 2025 Grapevine, TX
North American Wholesale Lumber Assoc. (NAWLA) Executive Management Institute (EMI) Evanston, IL
Builder 100 Leadership Summit Dana Point, CA
Lumber Quality Institute (LQI) Lumber Quality Workshop Atlanta, GA
Engineering News-Record (ENR) FutureTech 2025 San Francisco, CA
Building Innovation Conference 2025 McLean, VA
Cold-Formed Steel Engineers Institute (CFSEI) Expo Raleigh, NC
LIGNA 25 Hannover, Germany
May 27–30 University of Texas Building Professional Institute (BPI) Irving, TX
June 4–5
June 4–6
June 4–7
June 8–10
June 10–13
June 10–13
June 13
Global Softwood Log & Lumber Conference Vancouver, BC, Canada
Structural Building Components Assoc. (SBCA) & National Framers Council (NFC) Open Quarterly Meeting (OQM) Washington, D.C.
American Institute of Architects (AIA) Conference 2025 Boston, MA
Groundbreaking Women in Construction (GBWIC) Conference San Diego, CA
National Assoc. of Home Builders (NAHB) Spring Leadership Meeting & Legislative Conference Washington, D.C.
Pacific Coast Builders Conference (PCBC) Anaheim, CA
Offsite Construction Summit Berkeley, CA
June 22–26 World Conference on Timber Engineering (WCTE) Brisbane, Australia
JULY 2025
July 16–18 Frame & Truss Mfrs Assoc (FTMA) of New Zealand Conference Rotorua, NZ
July 23 Mountain States Lbr & Bldg Mat Dealers (MSLBMDA) Golf Golden, CO
July 24–27 Bldg Mat Suppliers Assoc (BMSA) Summer Conference Virginia Beach, VA
July 31–Aug 4 Am Institute of Bldg Design (AIBD) Design & Build Conference Asheville, NC
2025
August 6–8 So Forest Prod Assoc (SFPA) Forest Prod Machinery Equip EXPO Nashville, TN
August 12–14 Ace Hardware Fall Convention Chicago, IL
August 14 Mountain States Lbr & Bldg Mat Dealers (MSLBMDA) Clay ShootBrighton, CO
August 19 Offsite Construction Summit Atlanta, GA
2025
September 22 Woodrise 2025 Vancouver, BC, Canada
Sept 29–Oct 3 Bldg Component Mfrs Conference & Framers Summit (BCMC | FS)Omaha, NE
Don’t see your event? Increase attendance and participation by listing your industry focused events here! E-mail details and event web-link to Anna@componentadvertiser.org. We can’t guarantee space for all events, but all industry related events will be added on a space available and interest to our reader priority.
The truss industry relies on 3rd party quality assurance services to provide random visits to review the plants Quality Assurance program along with their operations. If your plant needs to comply with the IRC, IBC and to those who depend on solid, experienced QA expertise, we ask you to consider selecting Timber Products Inspection, Inc. (TP) as your choice for 3rd party inspections.
Proudly serving the forest products industry for over 50 years, TP brings the expertise you need to ensure your business is successful. As a responsible partner, TP delivers to clients, employees, and the industries we serve the confidence to drive value through the effective use of our diverse professional team.
TP would like to welcome the following authorized agents to our inspection team, each of whom have many years of experience in the truss industry!
• Al Coffman
• Jean Hart • Curt Holler • Chuck Ray
Glenn Traylor • Elliot Wilson
If you have questions about how you can make this selection, please contact your authorized agent above or Glenn Traylor at 919-280-5905 or trusguy@gmail.com. https://www.tpinspection.com/ https://www.tpinspection.com/auditing-services/truss
4x10
Are you a skilled Truss Designer or Wall Panel designer seeking a better work-life balance? Look no further! Our client is offering a unique opportunity for talented designers like you to thrive in an environment that respects your personal and professional needs.
In this position, you'll have the flexibility to choose from various working arrangements to accommodate your lifestyle. Some of our employers offer a 32-hour workweek with full benefits, allowing you to strike a perfect balance between your career and personal life. You can work in the office, remotely, or in a hybrid setup, depending on your location and skill level.
More Details Here
Measures 9 areas of Skills and Experience Compairs Results to National Averages Identify Strengths and Areas For Improvement
$145 per Exam (Volume Discounts Available)
Test your design team to have a better understanding of individual strengths and areas for improvement.
Use your team's results to measure potential new hires!
Truss Design Manager - Apline J15366 Texas
Remote Truss Designer - MiTek J15361 Mid Atlantic
Truss Designer-J15349 Western Canada
Truss Designer - Multifamily/MiTek J15362 TN
Truss Designer - Multifamily/MiTek J15363 TX
Remote Multifamily Truss Designer J15356 Texas
Technical Outside Sales Truss & Wall Panel J15358 Colorado Front Range
Truss Designer J15357 East Texas
Implementation and Support Specialist J15306 100% RemoteNortheast
Sales Representative - J15355 Central Ontario
Truss & Wall Panel Designer J15226 Northeast
Remote Truss Designer J15307 Full Time Remote
Truss Production Manager-J15354 Greater Toronto Area
Truss Designer - MiTek - Remote or OS J15312 Florida, AL, or GA for Remote
Remote Truss Designer - Alpine J15246 Midwest Candidate preferred
Senior Truss & Wall Panel DesignerMiTek J15352 Midwest
CFS Truss Designer | Wall Panel Designer J5323 Midwest
Outside Sales - Truss/Lumber J15345 Southeast
Truss Designer - On-site - MiTek J15346 Florida
Truss Designer J15348 South
Senior Truss Designer - J15342 Mountains
Remote Truss Designer J15313 New England
Truss Designer J15339
New England
Project Coordinator J15272 TN
Remote Truss Designer - MiTek J15228 Florida
Truss Designer J14165 Carolinas
Mass Timber Sales/Business Development-J15338
Central Ontario
Mass Timber Engineer-J15337
Central Ontario
Truss Designer-J15334
Southern Alberta
WE WORK WITH OVER 100 LOCATIONS IN THE UNITED STATES AND CANADA SOME ARE HIRING NOW AND SOME ASK US TO CALL WHEN QUALIFIED CANDIDTES ARE AVAILABLE
WE RESEARCH OPPORTUNITIES
ID: C18426
Remote Truss Designer
Relocation: Colorado, Illinois, Indiana, North Carolina, South Carolina, Texas, Utah, Maryland, Florida, Georgia, Nebraska, REMOTE, Costa Rica, Pennsylvania, Tennessee, Virginia, Wisconsin, Wyoming, Washington DC, Rhode Island, Saskatchewan, Oregon, Ontario, North Dakota, New York, New Mexico, New Jersey, New Hampshire, Nevada, Montana, Mississippi, Minnesota, Massachusetts, Kentucky, Delaware, Conneticut, California, Arizona, Alaska
Offshore Truss Designer with MiTek experience. The candidate is a civil engineer with 6 years' truss design experience for companies in Texas and Florida. Prior work for BFS and smaller manufacturers. Bilingual Spanish/English with a company set up to make paying easy. Scored 89 on our truss design skills evaluation, which is near the senior designer level. He is also SBCA I & II certified. He is willing to go to work immediately.
Compensation: $65-75k as a subcontractor, no benefits or taxes.
We haven't represented offshore candidates in the past but feel this candidate is worth a shot. Please contact Thom for additional details.
ID: C18549
Remote Wall Panel Designer
Relocation: USA - ALL States Wall panel designer with 10 years' experience including production builders, single family custom and small to MegaMultifamily projects. MiTek Sapphire software experience.
ID: C18836
Truss Designer / Wall Panel Designer / Design Manager
Relocation: USA - ALL States Intermediate level designer with wall and roof truss design skills using MiTek software. Candidate has both MiTek Sapphire Structure and Management, plus AutoCAD experience. Products include wall panels, roof and floor trusses for single family custom, tract, and small commercial/ multifamily projects. Estimating roof and floor trusses, with my speed I could keep about 7-9 new projects a week
ID: C10122
Designer/Design Manager - Truss Relocation: Iowa
Senior Designer. - Advanced. Candidate has 24 years Truss Ddesigner experience and 5 years Truss Design Manager experience. Products include floor trusses, roof trusses, I-Joists, and hardware. Markets include single family, custom, high end, multi-family, light commercial, and agriculture. Primary duties include design, layout, optimization, cutting/production documents, and takeoff.
Secondary duties include checking others work, repairs, customer service, inside sales, software maintenance, training, and filling in for the Design Manager as needed. Software experience includes MiTek and Keymark. Training received includes WTCA Level 2. Education: High School Graduate and Batchelors degree.
Motivating factors: advancement, compensation, benefits, work location, job security, and relocation.
ID: C18604
Truss Designer - Remote (MiTek) Relocation: Alberta
I currently design & layout roof trusses, floor trusses, I-Joists and EWP from PDF plans and specifications for pricing. Also does engineering using MiTek, then uploads to Management or MBA in the past. Once sold, and field measurements are provided, I update the project and clean up the layouts, trusses and release them to the shop. I also answer questions from sales and the shop as needed as well as training newer designers. Most of my projects are single family, but I have also done several apartments, hotels, assisted living centers, and other commercial projects. I want to grow, learn, and become a better designer to be a valued team member.
ID: C10968
Senior Wood Truss Designer - Part Time Relocation: Florida, Alabama, Georgia, REMOTE
Candidate desires to use his career long industry experience to be the best Part Time Remote Designer you have. Prior truss plant owner for 10 years, strong production and operations management background, and JobLine Senior Designer rating in truss design using MiTek software. Also has FASTBeam experience. Products: floor & roof trusses. Markets: Single family custom, multi family, tract and light commercial. Was successful in creating strong teams in production, design and customer service, but the local economy and overwhelming competition was more than he could overcome from a small plant perspective. Degree: BSEE
Compensation: Based on employee or 1099 status.
Thom's Notes: I have worked with this candidate as an employer for years. Very detail oriented. Fair, honest, and customer service oriented. Very design/liability conscious. Scored 98
ID: C10853
Remote Design Manager | Remote Offshore Design Project Manager Relocation: Texas, Georgia, USA - South
Top level Engineering/Design Management candidate, 14+- years experience Truss, 4+- Panel experience. Has experience
building and integrating offshore design resources with internal design departments and training design managers to better utilize offshore capabilities. Large volume manufacturer experience. MiTek Sapphire design/layout proficient. Too confidential to go into more detail.
Compensation: $120k+
ID: C11370
General | Plant Manager/Operations - Truss/ Panel/Framing Package Relocation: Texas, Arizona
20 years' experience. Started in production, advanced to Saw Supervisor, Production Manager, Plant Manager, now General Manager. As General Manager operated a $125M truss plant. Tripled output and reduced errors and labor cost. Developed and implemented standards and procedures to manage quality and costs. As Plant Manager (4 years), manage all the operation of the manufacturing plant, such as Productivity, logistics, efficiencies, costs. As Production Manager (12 years), manage all the areas of the manufacturing across the plant. Safety, quality control, efficiencies, HR, etc... Software: MiTek, Word, Excel, OptiFrame. Products: R & F Truss, Panel, Framing package. Markets: Single Family, Multifamily, Custom Homes. Bilingual English/Spanish spoken and written. Degree in Industrial Engineering.
Compensation: $90's+ bonus ($100k min)
ID: C10897
Design Manager/Senior Designer/PE/ Optimizer - Truss/Panel/EWP Relocation: REMOTE
30 year industry veteran, started as a Truss Designer, earned his way to Design Manager over 20+ designers. MiTek - Advanced, AutoCAD proficient. BSCE - PE.
Compensation: Open??
Thom's Notes: PE with Mid Atlantic seals
ID: C18565
Designer: Truss/Panel, Wood/Steel, BIM Relocation: North Carolina Material take-offs, proposals, job-site meetings, Submittal Tracking, Excellent Problem-solving Skills, Material Ordering, Field Measuring, 3-D Modeling Program (3-D and 4-D BIM in-house), Generated material take-offs from the BIM model, Coordinated RFI's thru the BIM model, Clash detection between wood trusses, structural steel and LVL's. 3-D Scan's of job-sites. Scheduled / Distributed work to 6 designers Cross-trained all designers in roof floor and wall panels for whole-house design.
ID: C18370
Plant | Location | General Manager - Truss/ Panel
Relocation: California, Nevada
Highly experienced (20+ years) roof and floor truss, and wall panel manufacturing manager. Started in the plant as builder, then sawyer, supervisor, truck driver, maintenance manager, designer, outside sales, plant manager, operations manager, and general manager. OSHA trained, developed and implemented safety programs. Successful turn around experience, hands on ability to work with departments to combine individual strengths into one team effort, lower costs, and meet quality and volume expectations. Past experience negotiating better vendor programs to lower costs and improve inventory turns.
ID: C10507
Senior Management - Truss/Panel/Lumber/ Installed Services
Relocation: USA - Western
I am a Diverse driven individual seeking a position in the fast paced construction component industry where my professionalism in sales, business and leadership skills along with a strong proven background in, General Management, Operations, Sales Management, strategic alliances, business development, team building, P&L experience and Customer Satisfaction will play an integral part in growing new business, nurturing existing business or developing company operations to meet the highest level of efficiencies, standards and safety while having fun doing it!
March 19, 2025— Simpson Strong-Tie, the leader in engineered structural connectors and building solutions, celebrated the grand opening of its newest distribution center, located on Buffalo Drive in Las Vegas, on March 18, 2025. The 59,436-square-foot facility now serves as the primary distribution center for the company’s products throughout the Las Vegas region, allowing for faster and more convenient service to contractor and lumber and building material (LBM) supplier customers.
The facility also houses offices and a spacious training center for company, customer and industry partner meetings, professional development and collaboration. This versatile 4,470-square-foot space has capacity for 297 guests and features a state-of-the-art audio/visual system. It also includes a demonstration room to facilitate hands-on training with Simpson Strong-Tie products.
“The Las Vegas area is not only one of the largest territories in our Southwest region, it is a growing market for us, offering abundant opportunities to serve our customers and industry partners,” said Zack Harrison, senior vice president for Simpson Strong-Tie’s Southwest Region. “This new facility will help us to expedite products to customers in the area within 24 hours and enable same-day will-call, providing customers with improved access to a wide variety of inventory as well as our in-house support and field staff expertise.”
As of the grand opening, the facility housed 872 separate SKUs across product lines that are most popular in the Las Vegas territory. These include connectors for wood and steel construction, screws and nails, anchoring systems, shearwalls and outdoor decorative hardware. At full capacity, the distribution center can hold more than 1,000,000 pounds of products.
To learn more, visit www.strongtie.com or call 800-999-5099.
March 18, 2025 — Stanwood, WA — 4Ward Design & Labor, LLC is excited to announce the acquisition of All-IN Design, LLC, a respected leader in component design founded and led by Allen Washburn. This strategic move further reinforces 4Ward’s commitment to delivering industry-leading design solutions and expanding its innovative offerings.
As part of the acquisition, Allen Washburn joins the 4Ward team as the new Director of Component Design for 4Ward Design Solutions. Allen brings with him years of experience, deep industry knowledge, and a passion for excellence, making him an invaluable addition to the organization.
“I’m incredibly excited to join the 4Ward team,” said Allen Washburn. “This opportunity allows us to combine the strengths of All-IN Design with the forward-thinking approach of 4Ward Design Solutions. Together, we’re positioned to deliver even greater value to our clients while continuing to innovate and elevate component design across the industry.”
In addition to Allen’s new role, 4Ward is proud to announce the promotion of Roger Wagner, who previously served as Design Manager, to the position of Director of Design Training and Development. Roger will spearhead the growth and mentorship of 4Ward’s design team, ensuring the highest level of training, innovation, and consistency across all projects.
“These moves reflect 4Ward’s unwavering dedication to investing in both people and process,” said Ben Hershey, CEO at 4Ward Design & Labor. “We’re thrilled to bring Allen’s leadership and expertise into the fold, and to elevate Roger to a role where he can help shape the next generation of top-tier designers. Together, they will play a critical role in advancing our mission to provide comprehensive, forward- thinking design solutions to our clients.”
The integration of All-IN Design’s operations and leadership is effective immediately.
Posted March 19, 2025 on NAHB Now | The News Blog of the National Association of Home Builders
Reprinted with permission.
The 2025 International Builders’ Show (IBS) boasted its largest attendance in 17 years with more than 81,000 builders, remodelers, developers and other home building professionals filling the halls of the Las Vegas Convention Center (LVCC).
While hundreds of students participated in the industryleading education and networking opportunities offered at the show, their attention was on the prestigious NAHB Student Competition they’d been working toward for months.
Over the span of two days, the aspiring project managers, land developers and designers from NAHB Student Chapters across the country presented intricate building proposals to an audience of construction company executives.
“I think this is the realest experience you can get while in college,” said Sean Ross, a student at California Polytechnic State University. “You’re able to tackle actual development. You can take your plans and build it. There’s nothing like it.”
“You can have a residential class, and that sets you up well,” said California Polytechnic State University student Emily Edmondson. “But to dive into the level of detail needed for a project like this, it’s a whole other educational experience that you don’t get from class.”
Seventy-six teams participated in the competitions, up from 63 a year ago. The winners were announced in front of a packed crowd during NAHB’s Student Chapters Awards Ceremony at the LVCC on Feb. 28.
“We worked hard,” said Gage Redman, a student at the University of Oklahoma. “We had weekly meetings and collaborated whenever we had a chance outside of classes at school. But my favorite part was getting to Las Vegas, flying with the team, checking into the hotels with everyone’s been a lot of fun.”
Registration for the 2026 Student Competition will open Aug. 22, 2025. Looking to start a new student chapter to compete in the 2026 Student Competitions? NAHB’s New Student Chapter Toolkit is the premier guide to getting started.
Posted March 17, 2025 on NAHB Now | The News Blog of the National Association of Home Builders
Reprinted with permission.
Economic uncertainty, the threat of tariffs and elevated construction costs pushed builder sentiment down in March even as builders express hope that a better regulatory environment will lead to an improving business climate.
Builder confidence in the market for newly built single-family homes was 39 in March, down three points from February and the lowest level in seven months, according to the National Association of Home Builders (NAHB)/Wells Fargo Housing Market Index (HMI) released today.
“Builders continue to face elevated building material costs that are exacerbated by tariff issues, as well as other supplyside challenges that include labor and lot shortages,” said NAHB Chairman Buddy Hughes, a home builder and developer from Lexington, N.C. “At the same time, builders are starting to see relief on the regulatory front to bend the rising cost curve, as demonstrated by the Trump administration’s pause of the 2021 IECC building code requirement and move to implement the regulatory definition of ‘waters of the United States’ under the Clean Water Act consistent with the U.S. Supreme Court’s Sackett decision.”
“Construction firms are facing added cost pressures from tariffs,” said NAHB Chief Economist Robert Dietz. “Data from the HMI March survey reveals that builders estimate a typical cost effect from recent tariff actions at $9,200 per home. Uncertainty on policy is also having a negative impact on home buyers and development decisions.”
The latest HMI survey also revealed that 29% of builders cut home prices in March, up from 26% in February. Meanwhile, the average price reduction was 5% in March, the same rate as the previous month. The use of sales incentives was 59% in March, unchanged from February.
Derived from a monthly survey that NAHB has been conducting for more than 35 years, the NAHB/Wells Fargo HMI gauges builder perceptions of current single-family home sales and sales expectations for the next six months as “good,” “fair” or “poor.” The survey also asks builders to rate traffic of prospective buyers as “high to very high,” “average” or “low to very low.” Scores for each component are then used to calculate a seasonally adjusted index where any number over 50 indicates that more builders view conditions as good than poor.
The HMI index gauging current sales conditions fell three points to 43 in March, its lowest point since December 2023. The gauge charting traffic of prospective buyers dropped five points to 24 while the component measuring sales expectations in the next six months held steady at 47.
Looking at the three-month moving averages for regional HMI scores, the Northeast fell three points in March to 54, the Midwest moved three points lower to 42, the South dropped four points to 42 and the West posted a two-point decline to 37.
HMI tables can be found at nahb.org/hmi. More information on housing statistics is also available at Housing Economics PLUS
Posted March 25, 2025 on NAHB Now | The News Blog of the National Association of Home Builders Reprinted with permission.
A slight decline in mortgage rates and limited existing inventory helped new home sales to edge higher in February even as housing affordability challenges continue to act as a strong headwind on the market.
Sales of newly built, single-family homes in February increased 1.8% to a 676,000 seasonally adjusted annual rate from a revised January number, according to newly released data from the U.S. Department of Housing and Urban Development and the U.S. Census Bureau. The pace of new home sales in February was up 5.1% compared to a year earlier.
“New home sales have been roughly flat thus far in 2025, as ongoing limited inventory of existing homes in many markets continues to support the need for new homes,” said Buddy Hughes, chairman of the National Association of Home Builders (NAHB) and a home builder and developer from Lexington, N.C. “Although policy uncertainty may be holding back some home buyer and business decisions, builders have hope that regulatory reform and tax policy extension will act as tailwinds later this year.”
“Lower mortgage rates helped to lift demand in February, despite other near-term risks such as tariff issues and affordability concerns,” said NAHB Chief Economist Robert Dietz. “While new home inventory is at an otherwise elevated 8.9 months’ supply, total home supply—new and existing—is a relatively lean 4.2 months’ supply for February.”
A new home sale occurs when a sales contract is signed, or a deposit is accepted. The home can be in any stage of construction: not yet started, under construction or completed. In addition to adjusting for seasonal effects, the February reading of 676,000 units is the number of homes that would sell if this pace continued for the next 12 months.
New single-family home inventory in February continued to rise to a level of 500,000, up 7.5% compared to a year earlier. This represents an 8.9 months’ supply at the current building pace. The count of completed, readyto-occupy homes available for sale increased again, rising to 119,000, up 35% from a year ago and marking the highest count since mid-2009.
The median new home sale price in February was $414,500, down 1.5% from a year ago. The count of sales was supported by a gain of transactions priced between $300,000 and $400,000 in February.
Regionally, on a year-to-date basis, new home sales are up 12.4% in the South but are down 6.7% in the West, 13.5% in the Midwest and 50.8% in the Northeast.
Posted March 18, 2025 on NAHB Now | The News Blog of the National Association of Home Builders Reprinted with permission.
Limited existing inventory helped single-family starts to post a solid gain in February, but builders are still grappling with elevated construction costs stemming from tariff issues and persistent shortages related to buildable lots and labor.
Overall housing starts increased 11.2% in February to a seasonally adjusted annual rate of 1.50 million units, according to a report from the U.S. Department of Housing and Urban Development and the U.S. Census Bureau.
The February reading of 1.50 million starts is the number of housing units builders would begin if development kept this pace for the next 12 months. Within this overall number, single-family starts increased 11.4% to a 1.11 million seasonally adjusted annual rate, the highest pace since February 2024. The multifamily sector, which includes apartment buildings and condos, increased 10.7% to an annualized 393,000 pace.
“While solid demand and a lack of existing inventory provided a boost to single-family production in February, our latest builder survey shows that builders remain concerned about challenging housing affordability conditions, most notably elevated financing and construction costs as well as tariffs on key building materials,” said Buddy Hughes, chairman of the National Association of Home Builders (NAHB) and a home builder and developer from Lexington, N.C.
“Despite elevated interest rates and policy uncertainty, ongoing lean levels of single-family existing home inventory helped to boost single-family production in February,” said Jing Fu, NAHB senior director, forecasting and analysis. “NAHB forecasts that single-family starts will remain effectively flat in 2025 as prospects of a better regulatory business climate are offset by uncertainty on the tariff front. Meanwhile, multifamily construction is expected to remain soft in early 2025 due to challenging financing conditions, before stabilizing in the second half of the year.”
On a regional and year-to-date basis, combined single-family and multifamily starts were 4.7% lower in the Northeast, 21.5% lower in the Midwest, 8.3% lower in the South and 20.2% higher in the West.
Overall permits decreased 1.2% to a 1.46-million-unit annualized rate in February and were down 6.8% compared to February 2024. Single-family permits decreased 0.2% to a 992,000-unit rate and were down 3.4% compared to the previous year. Multifamily permits decreased 3.1% to a 464,000 pace. Looking at regional permit data on a year-to-date basis, permits were 30.1% lower in the Northeast, 2.3% higher in the Midwest, 2.1% lower in the South and 12.5% lower in the West.
The number of single-family homes under construction in February was down 6.7% from a year ago, at 640,000 homes. In February, the count of apartments under construction increased 0.3% to an annualized 772,000 pace. It marks the first gain after 18 months of consecutive declines. But it was down 20% from a year ago.
March 17, 2025—Overall, investment in building construction rose 1.8% (+$393.7 million) to $22.1 billion in January. The residential sector increased 2.3% to $15.4 billion, while the non-residential sector was up 0.8% to $6.7 billion. Year over year, investment in building construction grew 5.7% in January.
On a constant dollar basis (2017=100), investment in building construction increased 1.5% from the previous month to $13.2 billion in January and was up 2.5% year over year.
Ontario’s multi-unit component leads increase in residential sector
Investment in residential building construction increased $342.0 million to $15.4 billion in January. Gains were seen in four provinces and two territories, driven by Ontario (+$354.8 million; +6.3%), while Manitoba (-$61.6 million; -12.3%) led the decline.
Investment in multi-unit construction was up $497.5 million to $8.2 billion in January. Gains were led by Ontario (+$421.0 million).
Single-family home investment declined $155.5 million to $7.2 billion in January, with declines being recorded in eight provinces and one territory.
Non-residential investment continues to reach record highs
Investment in non-residential construction increased $51.7 million to $6.7 billion in January. This marked the sixth consecutive monthly increase. Much of the recent growth stemmed from the institutional and industrial components, which both reached a record high in January.
The institutional component rose $38.8 million to $2.0 billion in January. Gains were recorded in six provinces and three territories, led by Ontario (+$18.3 million) and British Columbia (+$11.5 million). Quebec (-$6.1 million) partially offset these gains, as it recorded its 10th consecutive monthly decrease.
Investment in the industrial component increased $22.5 million to $1.5 billion in January, driven by Ontario (+$15.2 million) and Alberta (+$5.1 million).
Meanwhile, the commercial component decreased $9.5 million to $3.3 billion in January following five consecutive monthly increases. Declines in six provinces and two territories were tempered by growth in Ontario (+$16.3 million).
For more information on construction, please visit the Construction statistics portal. For more information on housing, please visit the Housing statistics portal.
March 3, 2025—Wilson Lumber Company has reached an agreement to acquire Nashville Lumber, a wellestablished supplier of lumber and building materials located near Nashville, Tennessee. The acquisition expands Wilson Lumber Company’s ability to serve builders, contractors, and construction professionals in this region while maintaining the exceptional service and quality products that both companies are known for.
Wilson Lumber Company, a family-owned company for three generations, has been a trusted partner in the building industry since 1949. With this acquisition, Wilson Lumber Company will expand its market footprint to better serve customers in Tennessee.
“For 75 years, Wilson Lumber Company has been committed to providing on-time, in-full deliveries and superior customer service,” said Josh Hendrickson, President of Wilson Lumber Company. “Nashville Lumber has built a strong reputation in the industry, and we look forward to combining our expertise to continue meeting the needs of our customers.”
With the acquisition, Nashville Lumber’s customers will have access to Wilson Lumber Company’s expanded services and manufacturing capabilities, including:
• Lumber & Building Materials – High-quality materials for residential and commercial construction.
• Truss Manufacturing – Precision-engineered components to improve construction efficiency.
• Windows Manufacturing – Window solutions designed for durability and performance.
• Millwork & Doors – Interior and exterior doors, trim, and custom millwork.
• Reliable Delivery & Logistics – Ensuring materials arrive on time and in full to keep projects on schedule.
The acquisition is now finalized and Wilson Lumber Company will begin to operate at Nashville Lumber’s location under the Wilson Lumber Company name.
Wilson Lumber Company, located in the metropolitan Huntsville area (population 502,000) has been family-owned and operated for three generations. Since 1949, Wilson Lumber has been the supplier of choice for homebuilders and building materials consumers in the region. Today, the thriving building materials supplier, with over 300 employees, is led by the third generation of founder Clyde J. Wilson.
EIGHTY FOUR, Pa. (March 26, 2025) – 84 Lumber, the nation’s largest privately held supplier of building materials, has been named to Newsweek’s list of Most Trustworthy Companies in America 2025 for the second consecutive year. This recognition underscores the company’s enduring commitment to excellence and the trust it has earned from both its associates and customers
“We are truly honored to receive this recognition, which is my favorite ranking that 84 Lumber earns each year,” said 84 Lumber’s owner and CEO Maggie Hardy. “At 84 Lumber, trust is more than just a core value—it’s the cornerstone of our success. It forms the foundation of the lasting relationships we have built with our associates and customers. Being recognized by Newsweek is a testament to the unwavering dedication of our entire team.”
Ranked No. 4 in its category of Materials & Chemicals, 84 Lumber was among the 700 companies recognized. The rankings were determined through a comprehensive evaluation of trust, focusing on pillars such as customer and employee trust. The complete list of companies that made the list can be found here.
The Most Trustworthy Companies were identified through a three-step process. First, public and private companies with revenues exceeding $500 million were selected. Next, a score was calculated for each company based on a significant number of evaluations. Finally, an extensive survey of 25,000 U.S. residents was conducted, focusing on three key factors: trust, recognition, and the assessment of a company’s reputation across various online media platforms. This process resulted in the creation of a list of the Most Trustworthy Companies, organized by industry.
84 Lumber is the leading supplier of building materials, manufactured components, and industry-leading services for single and multifamily residences and commercial buildings.
Founded in 1956 and headquartered in Eighty Four, Pennsylvania, 84 Lumber Co. is the nation’s largest privately held supplier of building materials, manufactured components, and industry-leading services for single and multifamily residences and commercial buildings. The company operates 320 facilities which include stores, component manufacturing plants, custom door shops, and engineered wood product centers in 34 states. 84 Lumber also offers turnkey installation services for a variety of products, including framing, insulation, siding, windows, roofing, decking, and drywall. 84 Lumber, a certified women’s business enterprise owned by Maggie Hardy, has earned widespread recognition for its industry leadership and commitment to excellence. Named one of Newsweek’s Most Trustworthy Companies in America for both 2024 and 2025, 84 Lumber was also honored as one of USA Today’s Top Retailers in 2024. For three consecutive years, 84 Lumber has been honored as one of America’s Best Large and Mid-Size Employers by Forbes and has also earned a spot on the list of America’s Top Private Companies from 2019 to 2024. In 2023, the company was also honored with a spot on the Inc. 5000 list of America’s Fastest-Growing Companies. For more information, visit 84lumber.com or join us on Facebook, Instagram or LinkedIn.
March 13, 2025—Nation’s Best Holdings, LLC hosted their Third Annual Golf Tournament on Monday, March 3rd in support of Nation’s Best Cares, the charitable arm of Nation’s Best Holdings. In addition to the tournament, Nation’s Best hosted a vendor market providing store managers with the opportunity to connect with more than 75 vendors and make on-site promotional purchases.
Thanks to the event’s overwhelming success, Nation’s Best Cares donated $250,000 to the Arrivederci ALD foundation to support research for Adrenoleukodystrophy (ALD), a rare genetic condition that can cause severe disability and life-threatening complications. The foundation is dedicated to finding a cure for ALD through raising funds to support research by Harvard and Stanford physicians focused on advancing treatments and finding a cure. Nation’s Best began its partnership with Arrivederci ALD in 2021 by allowing customers to “round up” their purchase to the nearest whole dollar.
Additionally, Nation’s Best Cares donated $65,000 to the NB Cares Scholarship Program, which awards scholarships in the local communities of its stores. The NB Cares Scholarship program was created to cultivate a skilled workforce, fostering growth, innovation, and community strength through investments in education and support for careers in the trade and construction industries, ensuring individuals have opportunities to thrive in fulfilling professions.
The Third Annual Golf Tournament was held at the Gleneagles Golf Course in Plano, Texas. The day began with the vendor market, showcasing over 75 vendor partner booths. The vendor market delivered significant value to our stores, featuring 147 exclusive deals and category offers, representing a portfolio of over 10,000 unique items. Following the vendor market, over 180 golfers, a mix of vendor partners, customers, and employees, teed off in the tournament. The day concluded with an awards dinner, where Nations Best Cares presented donations to Arrivederci ALD and the NB Cares Scholarship Fund, honoring the shared commitment to giving back.
“Once again, the support our vendor community continues to show simply warms my heart. Our event this year was the biggest yet, and I couldn’t be more proud of our team for putting together such a detailed day. Giving back to our communities is at the core of our culture, not only at the national level but at each individual market we serve.” Chris Miller, President and CEO of Nation’s Best Holdings, LLC., said. “We look forward to the future of NB Cares and the causes we give to, and I want to thank everyone who was involved that made it such a memorable annual event.”
Nation’s Best would like to thank the growing list of participating vendor sponsors of this year’s event. We would like to extend special recognition to this year’s title sponsors, DW Distribution, YellaWood, Milwaukee, Azek-Timber Tech, Blue Linx, PrimeSource, and Pennsylvania Lumbermens Mutual Insurance Company.
Nation’s Best Holdings, LLC was founded in 2019 and currently owns and operates a growing number of locations across the United States. Nation’s Best is committed to identifying and acquiring best-in-class independent home improvement stores to ensure their continued relevance as vibrant community resources. To learn more, visit nationsbest.net
March 27, 2025 – The SLB’s work to aggressively grow market share in nonresidential and multifamily construction has generated more than 15 BBF of incremental lumber demand since 2012.
This collaborative work has put the industry in a stronger position than ever before, but more can be done to accelerate the rate of market share capture. Here’s a look at how the SLB has found and converted opportunities for market growth—and where we see room for new gains in the years to come.
One of the opportunities the SLB has spotted is to expand wood’s role in steel and mass timber hybrid construction systems. Alongside organizations such as the World Steel Association, the SLB is promoting hybrid wood construction, encouraging builders to leverage the benefits of both materials to build efficient, cost-effective, lower-carbon buildings.
The SLB’s success in spurring new demand has been driven by trailblazers: early adopters of mass timber and taller multistory light-frame construction. Growing wood’s market share means appealing to design professionals and developers who value confidence: the reassurance of precedent and complete solutions over sustainability attributes and innovation. The industry must make mass timber and taller light-frame construction predictable: the easy, obvious, and most profitable solution.
Multifamily projects, affordable housing, education, and offices present the greatest opportunity to reach an incremental annual volume growth of 4.9 BBF—versus 1.6 BBF in 2024. The share of apartment buildings with 20 to 49 units has grown over five years from 26% to 34%, according to the U.S. Census Bureau. Today, light-frame construction represents 77% of the market share in the 1- to 4-story segment and 48% of the 5- to 8-story segment, offering significant incremental growth opportunities for lumber.
Education is another market with significant volume, as pent-up demand from postponed projects boosts activity and demographic trends lead the under-25 population to increase by nearly 2 million by 2030. With less than 5% of market share over the past six years and 1.7 BBF of annual potential, there is a significant margin for the taking, specifically in the K-12 segment. Offices and banks represent an additional 1.2 BBF of potential as developers look to differentiate their buildings with beautiful and biophilic wood-based construction systems that enhance the tenant experience.
With every accomplishment, we clarify a vision for what more we can do. It’s important for lumber producers of all sizes to align on a plan to accelerate demand for lumber, granting a new mandate for the SLB to forge a consensus path toward diversification and market expansion for our products. Read our full article on softwoodlumberboard.org to learn more about our vision for reaching lumber’s market share potential.
707-333-4507
Truss Designer 25-0227-1
Posted on Thursday, February 27, 2025
Employer: Company: Villa Truss
Wooden Roof and Floor truss designer. Should be versed in the Mitek Software. Experience preferred.
Remote Multifamily Truss Designer J15356
Posted on Thursday, January 30, 2025
Employer: Client Confidential
We have a client in Texas who needs Remote Multifamily Truss Designer(s) familiar with the Houston, San Antonio, Austin, and DFW areas. In addition to Texas, they sell to multiple other states. They have multiple plants and are bringing on another plant this year. If you inquire about this job, know that we will represent you to the best of our ability. With over 30 years of experience, The JobLine is your source for career moves that offer advancement and better-than-average compensation.
Truss & Wall Panel Designer 20-1130-1
Posted on Friday, April 12, 2024
Employer: Woodhaven Lumber
Located in central coastal NJ is a growing truss and wall panel manufacturer looking for an experienced truss & wall panel designer. The ideal candidate would be local to our central NJ market, but remote design is also a possibility. Previous experience with the Mitek suite of software is a plus.
We offer a competitive salary, paid holidays, paid time off, medical/ dental/life/disability insurance, 401k and profit sharing.
Truss Designer J15339
Posted on Thursday, August 01, 2024
Employer: Client Confidential
We seek Truss Designers to join our client's team and support their New England office. In this role, you will design various truss products, focusing on floor and roof trusses for single-family custom projects. Experience with MiTek software is highly desirable, and panel experience, while not required, is a valuable asset.
Truss Designer J15307
Posted on Wednesday, January 08, 2025
Employer: Client Confidential
Truss Designer - Single Family, Custom, and Multifamily. Experience required: 5 years industry experience, 3 years experience in this position, and will consider a move up if qualified. Primary duties include design, layout, optimization, cutting/ production documents, and takeoff. Work Schedule: Monday/Friday, limited Saturdays, average 40-45 hours a week, and work from home - full time if qualified. Your hours can be semi-flixible. Components include: floor trusses and roof trusses. Markets include Single Family, Custom, and Multifamily. Educational requirements: GED and High School graduate. Compensation Relocation is acceptable with limited assistance and open to negotiation. Remote if you are qualified.
Truss Designer J15312
Nestled in the serene landscapes of Central Florida, away from the hustle and bustle of the city, their location offers a picturesque setting with abundant lakes, perfect for boating, fishing, and outdoor enthusiasts. (Iused to live there and know it is truer) If you
For Additional Information twm@componentadvertiser.org or Call: 800-289-5627 x1
Visit our website: www.componentadvertiser.com/Hiring-Zone
appreciate the balance between work and the great outdoors, you've found the right place.
Our client, located in Florida, is seeking two Truss Designers. Remote is acceptable if you live in Florida, Alabama, or Georgia as they are able to offer benefits if you live in one of these three states.
Get the industry-leading software and automation technology you need to scale your business. Overcome market challenges, boost productivity, and confidently meet demand when you choose MiTek as your solution partner.
Are you ready to scale your success?
Joe Kannapell, P.E.
What’s inside your home today, and what will be on top of your house in the future, was or will have been handled by Automated Guided Vehicles (AGVs). These are the small under-riding robots that carry all sorts of items from point A to B in plants or warehouses, eliminating manual handling. Amazon, Kroger, and Porsche have scores of these work-savers in use today, transporting everything from books to bacon to bumpers. Kroger, for example, initiated use of AGVs in 2019 in their huge new customer fulfillment centers (CFCs) near Cleveland and Orlando, and have at least 18 more CFCs in process. So, if Kroger can afford to use AGVs to handle groceries, which is one of the least profitable products, why shouldn’t a component plant be able to use them to deliver truss parts, a much more profitable product? Fortunately, there is at least one proven company implementing their use.
AGVs work well because they are always on the move and don’t otherwise take up space. They can deliver a cart with the next group of cut parts as soon as the preceding cart has been emptied. When they disengage from the newly delivered cart, they can engage the empty one and return it to receive another group of truss parts. AGVs can save 20% of the assembly floor space, enabling the truss lines that formerly required a 250’ wide building to fit into a 200’ wide building (see The Last Word: The Rise, Fall, and Rise of Big Truss Plants.)
The utility of AGVs is that they can be used in any existing component plant with little change in infrastructure, as long as floors are smooth and level. AGVs are designed to complement workers, and they avoid collisions by employing one of several available navigation guidance systems, which would have to be adapted to account for the cantilevering of lumber beyond the frame of the AGV. Carts would have to be designed to receive the AGV underneath their frame, to ensure that sticks of lumber don’t protrude beyond the sides of the cart. Carts with a cradle and/or sufficient uprights to contain cut parts and those that are elevated to near-table height are preferable.
The mechanical drive system of AGVs is technically advanced, as is the software that guides them. Integrating AGVs into a running plant would be a significant challenge, but, fortunately, Hundegger has already developed their TRUSSLinc® System around AGVs. They have employed technology similar to that used in the largest Mercedes plant in the world (which has 600 AGVs servicing its production line).
TRUSSLinc®’s operation is well described in this video filmed at Hundegger’s Demonstration Center on their large headquarters campus. Like Hundegger’s conveyor-based system, it is specifically designed to handle truss-by-truss fabrication (see The Last Word: Material Handling Bunkto-Table). Key features are its ingeniously designed carts with a cradle built of flexible, fabric-like material that holds cut parts in a neat bundle.
Also a key feature of TRUSSLinc® is the sorting device that enables parts to be cut in the most lumber-saving sequence, and then separated and deposited into bins, truss by truss. When a given bin contains all necessary parts, the AGV drives beneath it, rises up, and carries it to the truss line.
Clearly, we are witnessing the most flexible, space-saving, material handling equipment on the market. Expect to see it soon in a plant near you.