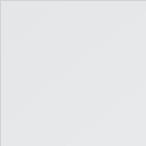



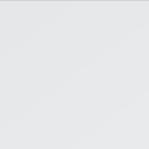

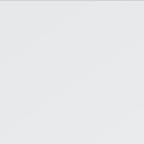

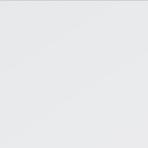

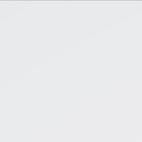

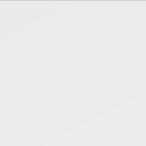


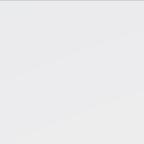



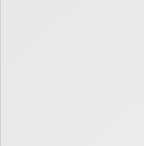
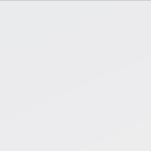
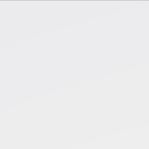

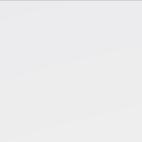

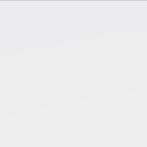



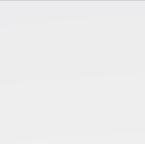


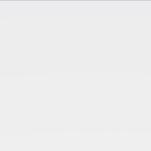
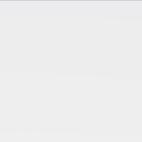

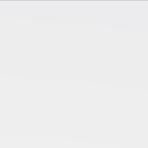













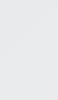

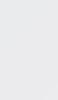


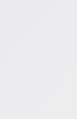
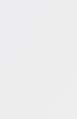
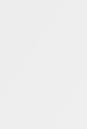
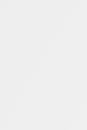
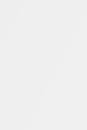
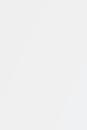
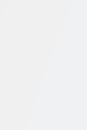
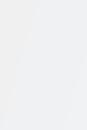

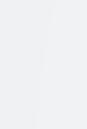
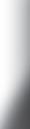


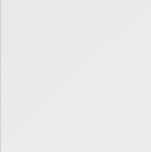







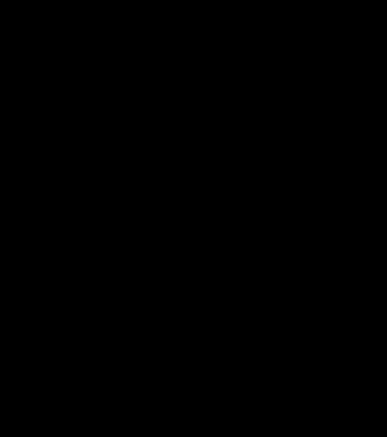


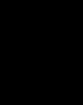
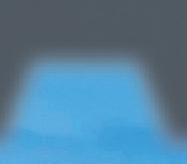
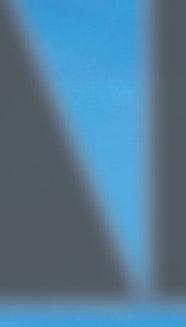


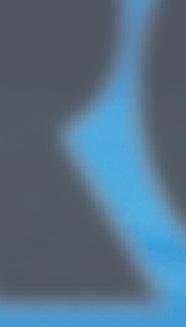
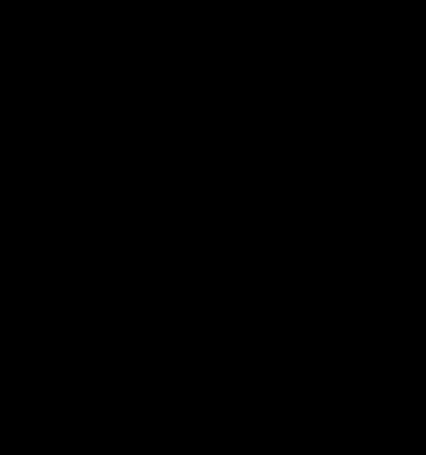
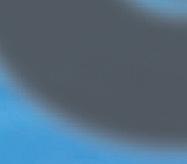
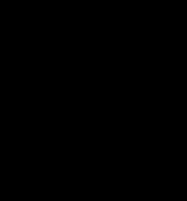
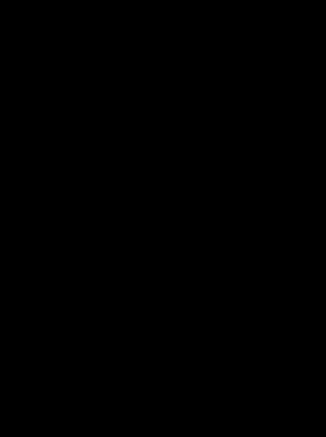
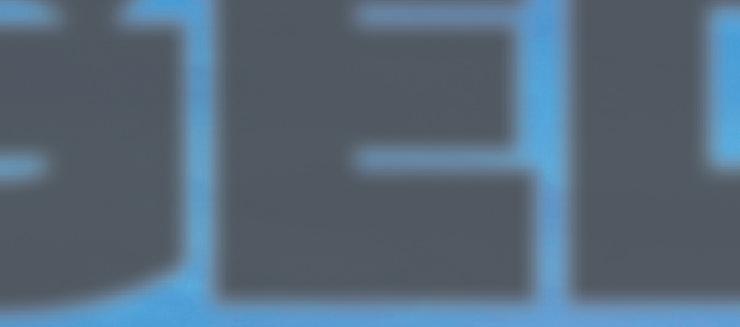










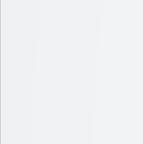
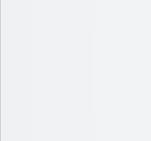
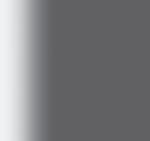
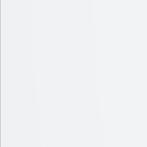



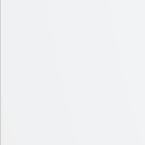
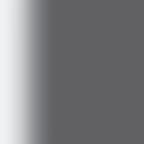

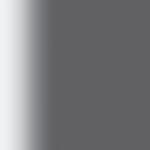
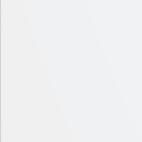
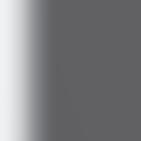
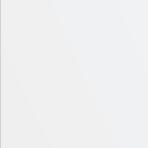

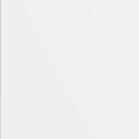
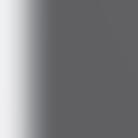
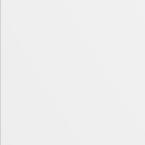
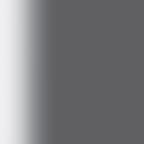

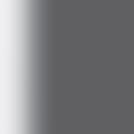

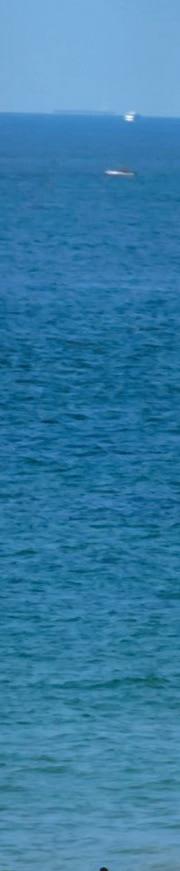
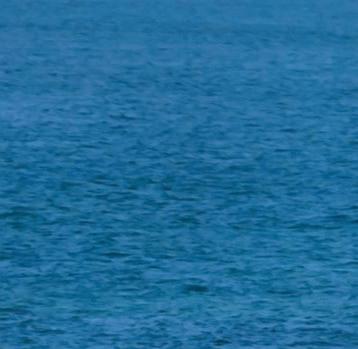
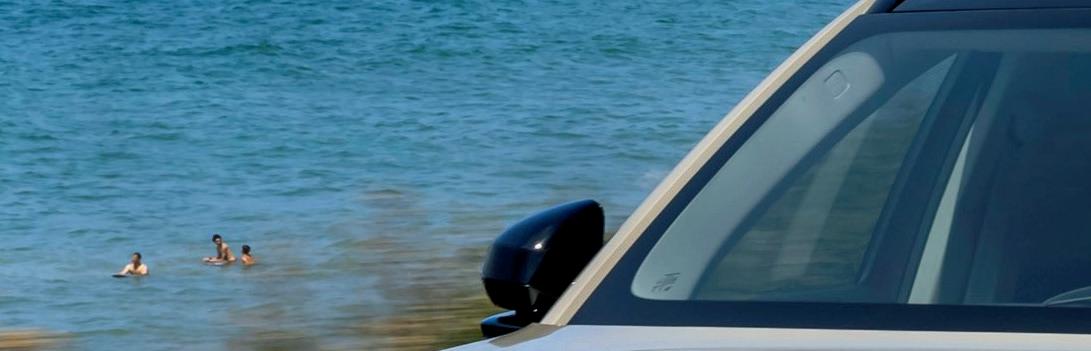
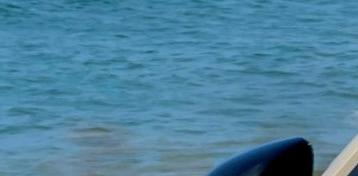
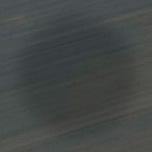
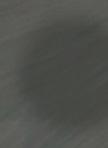

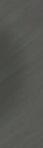
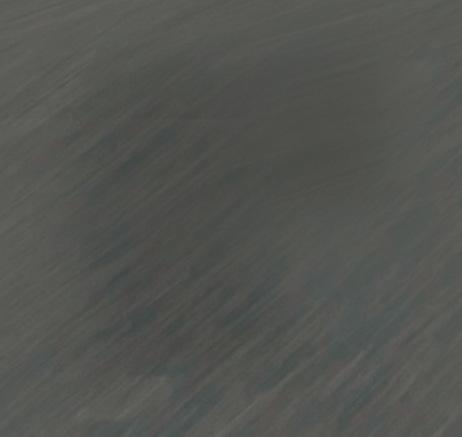
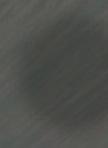

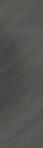
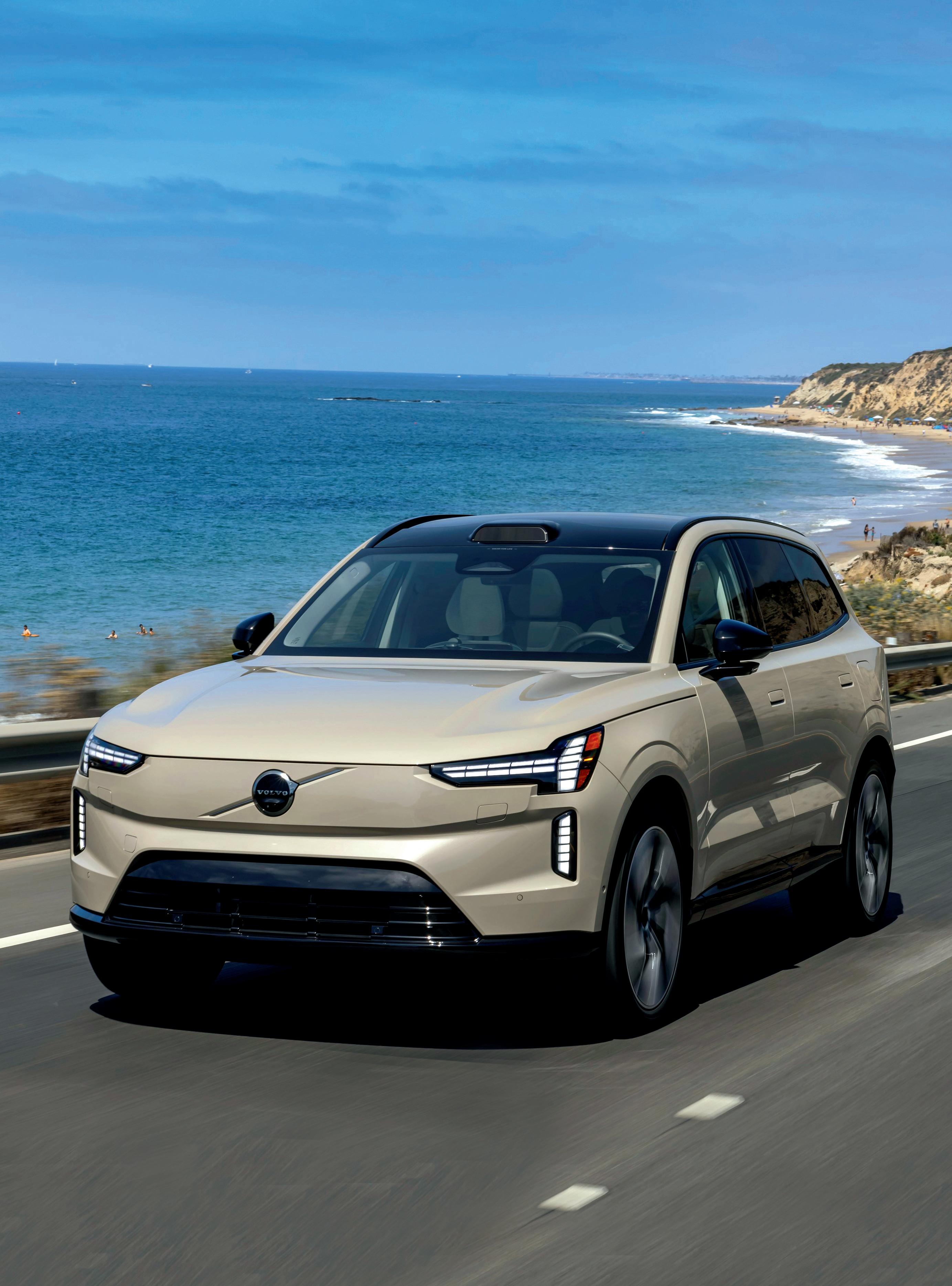
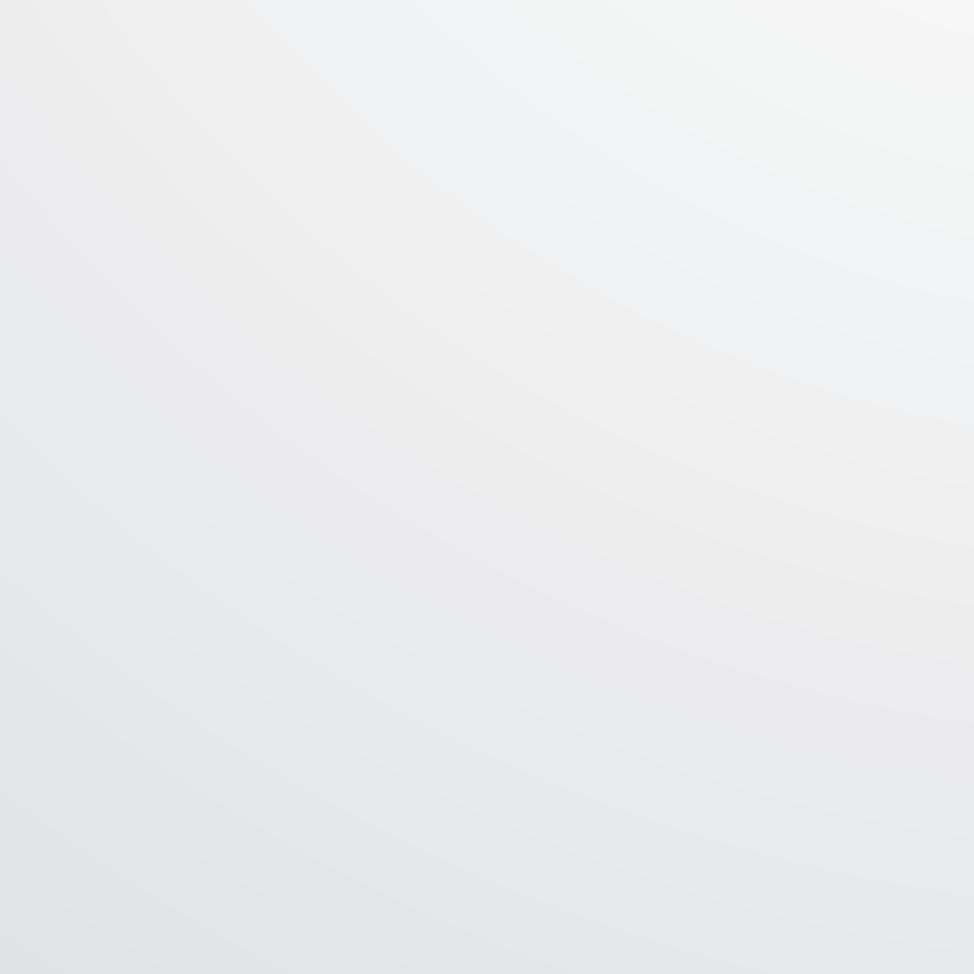

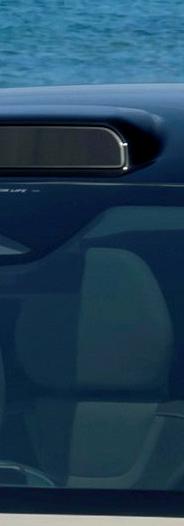
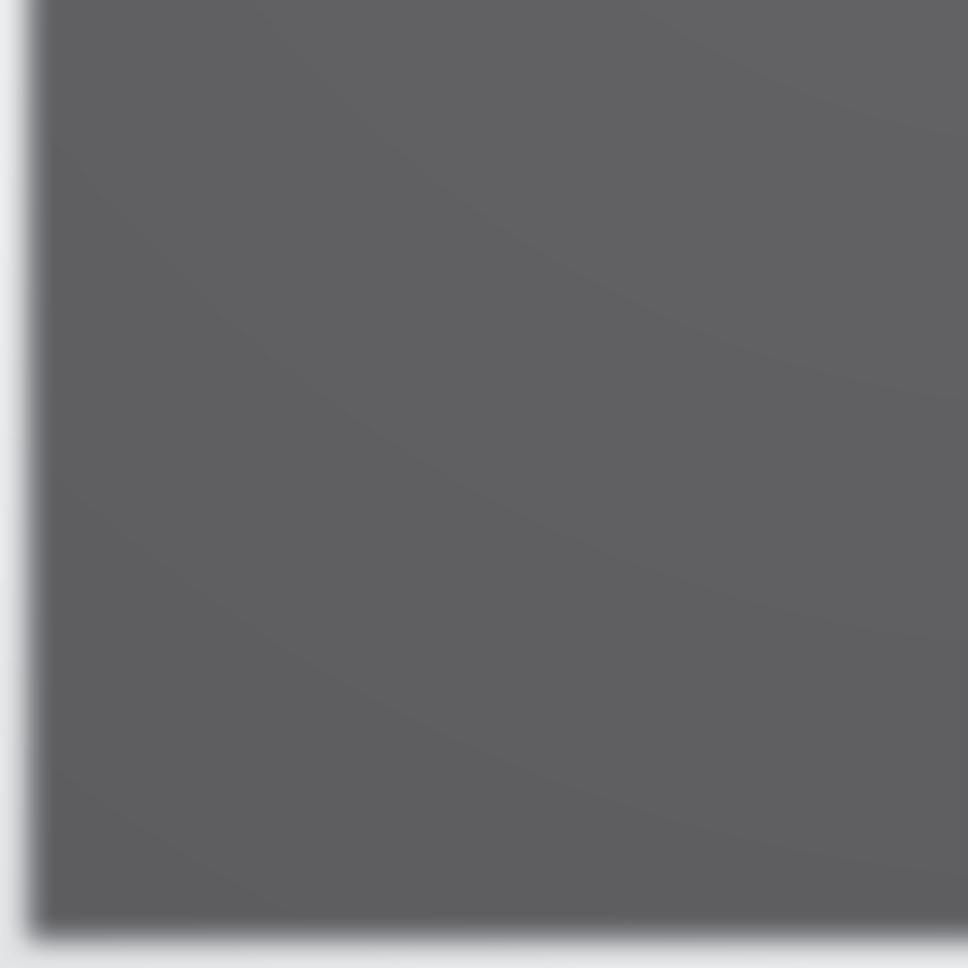

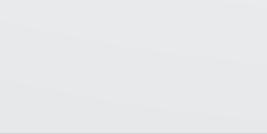
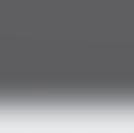
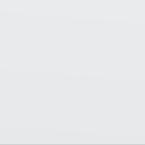
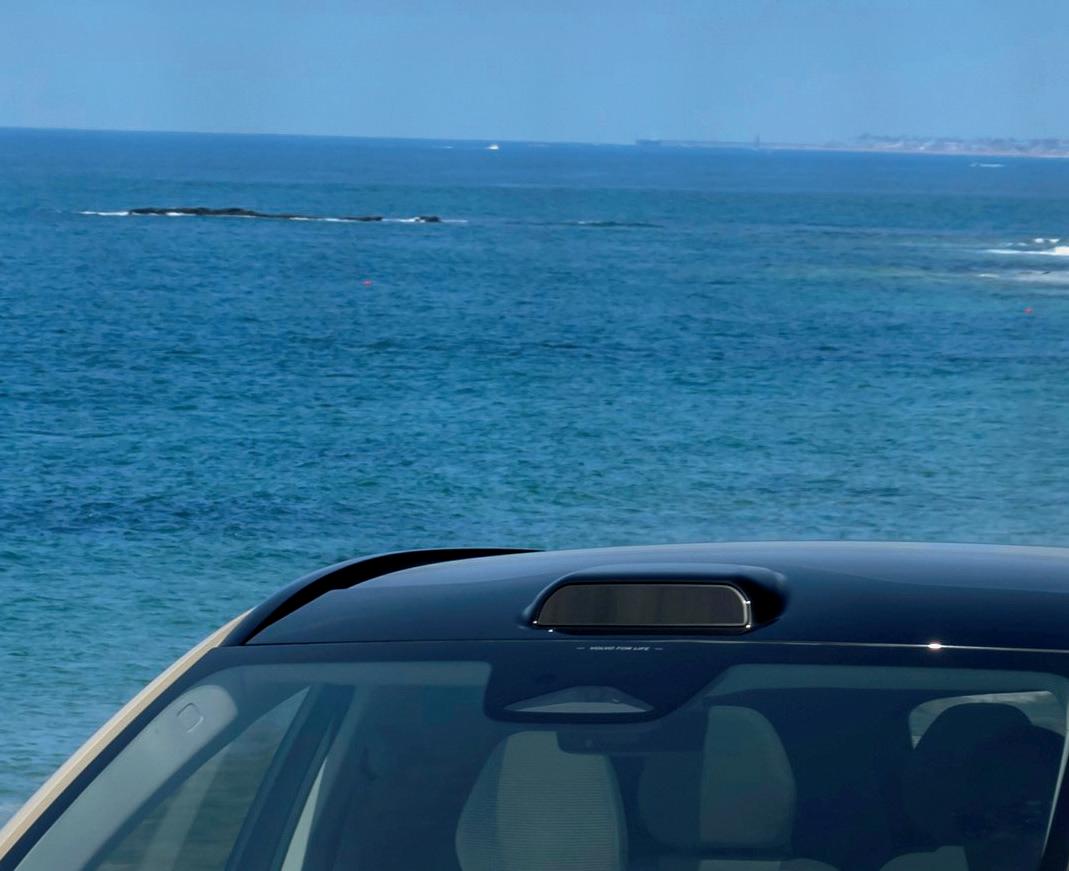
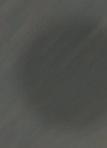
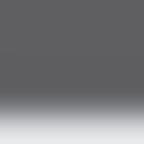
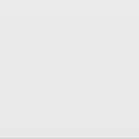

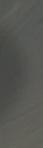
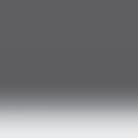

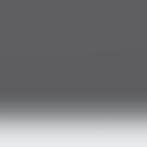
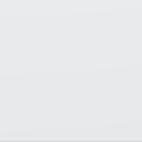
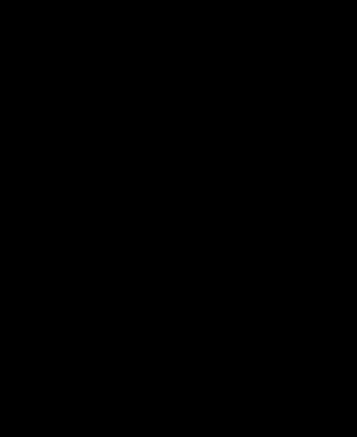


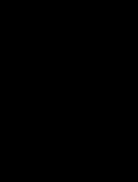
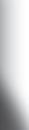
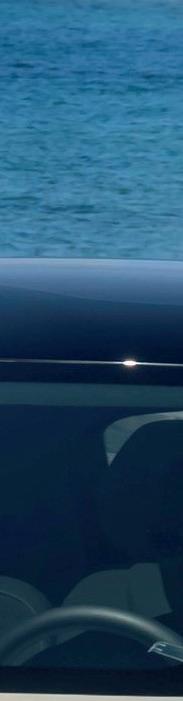




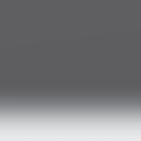
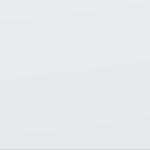




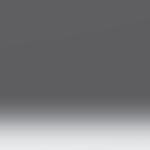
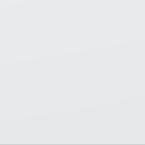
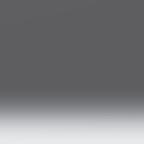







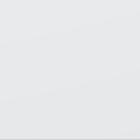
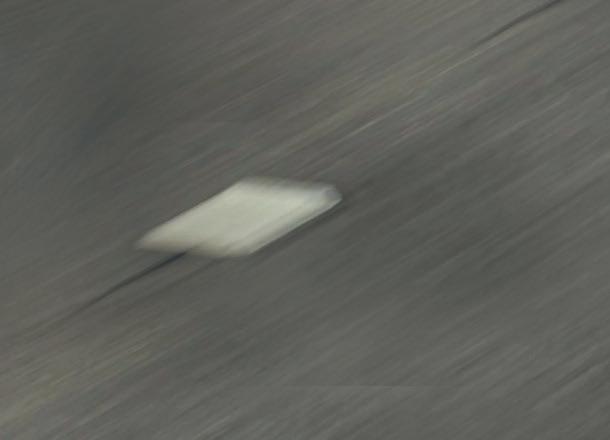
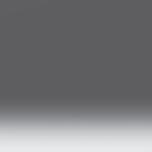
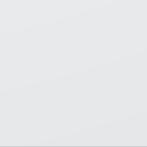
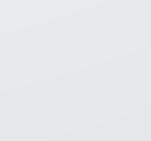
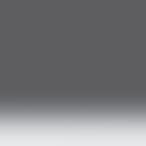
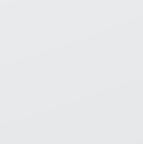





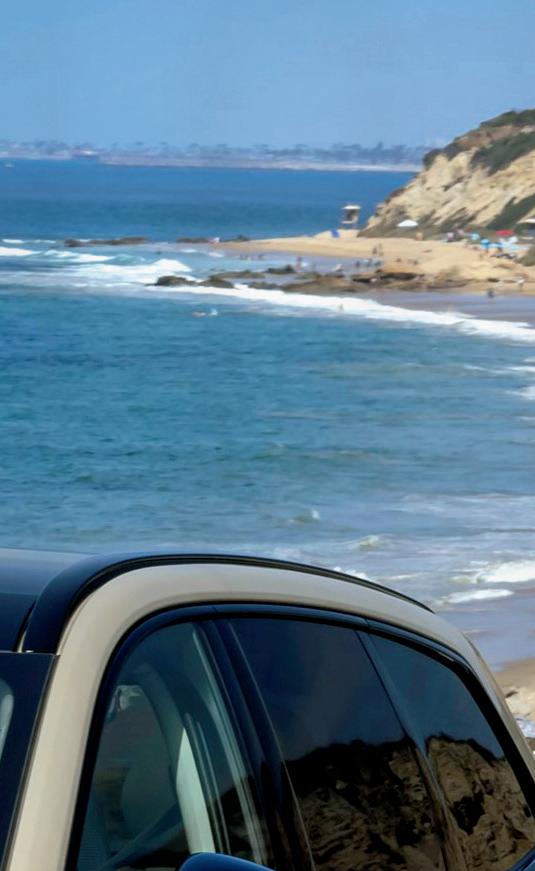

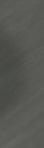


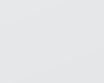

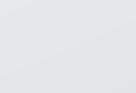

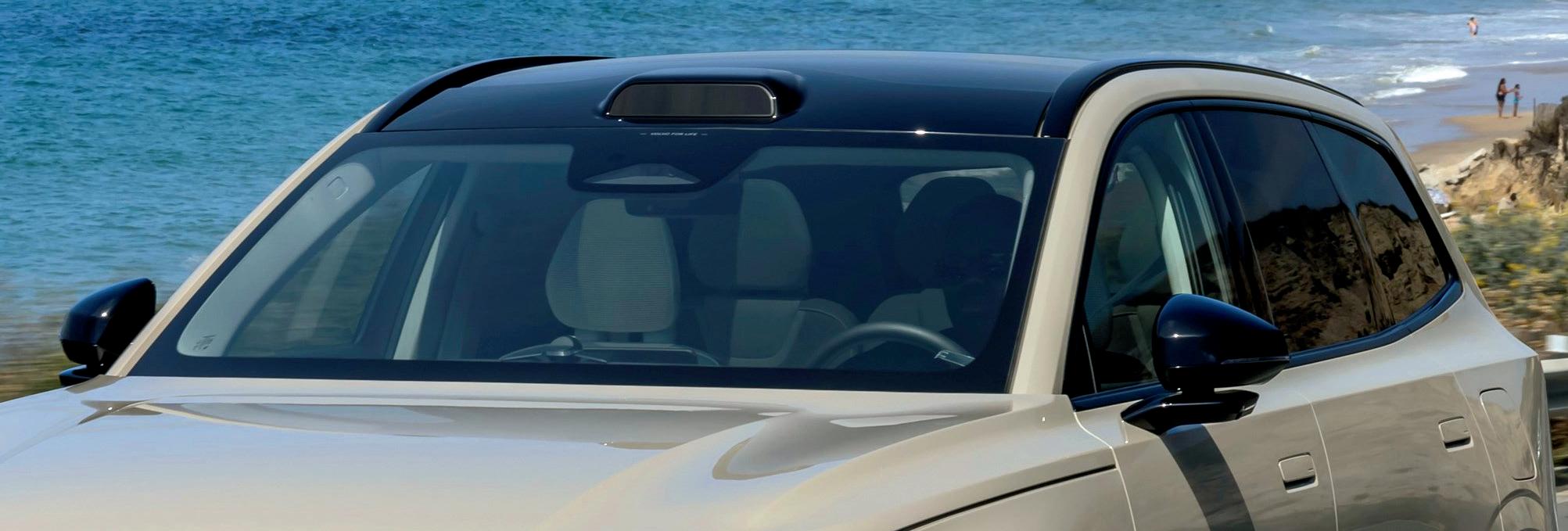


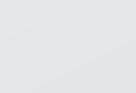

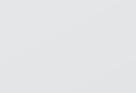



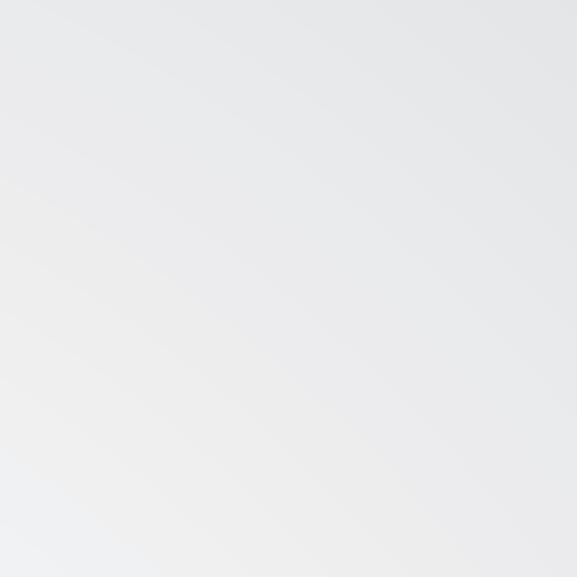
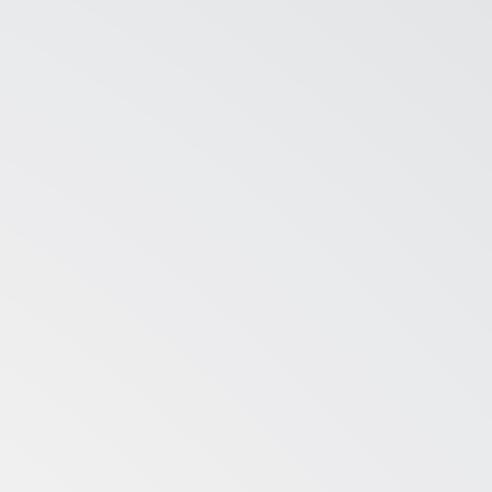
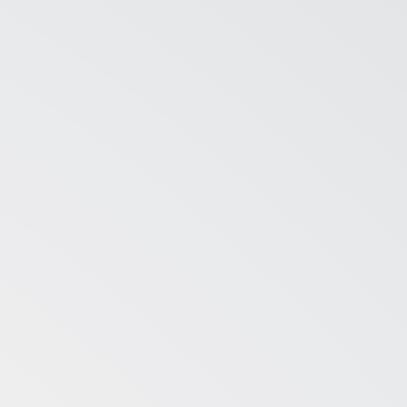
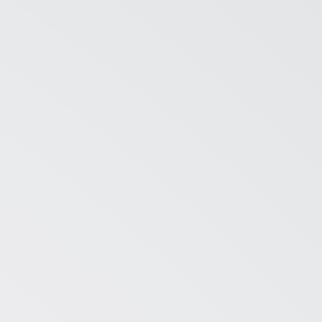
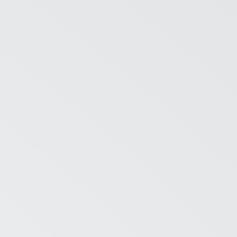
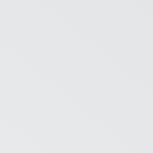
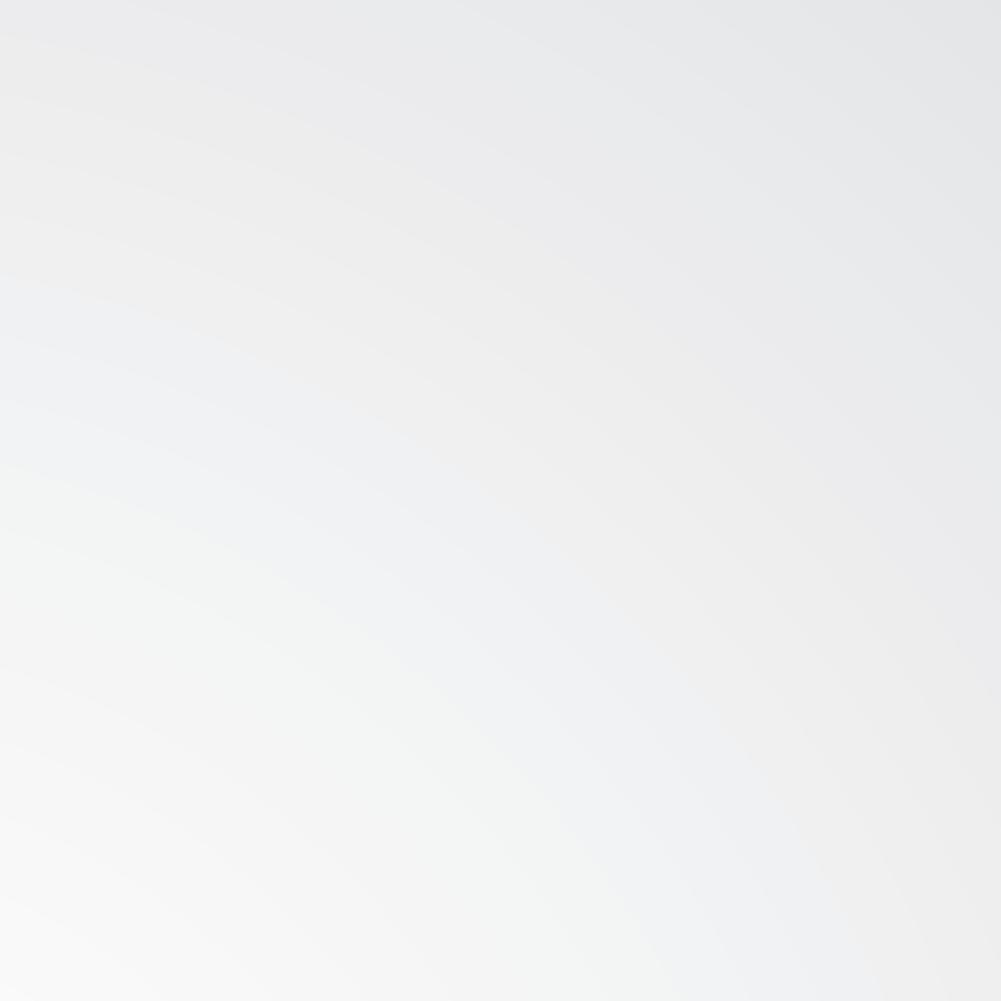
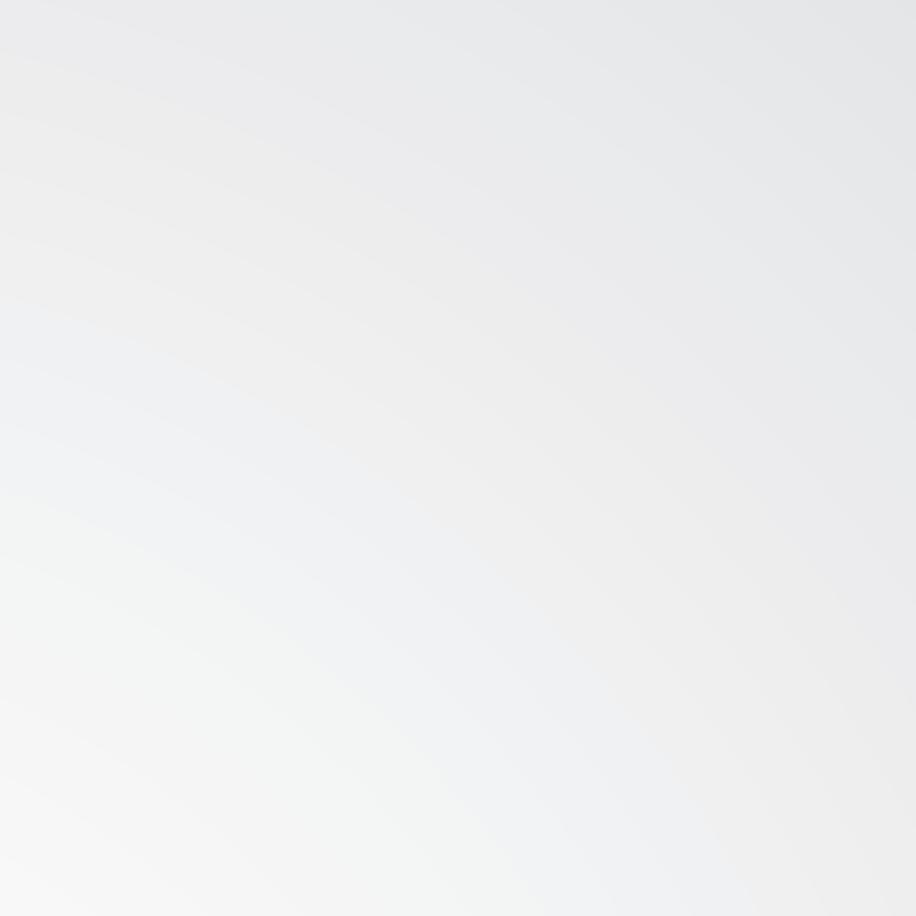
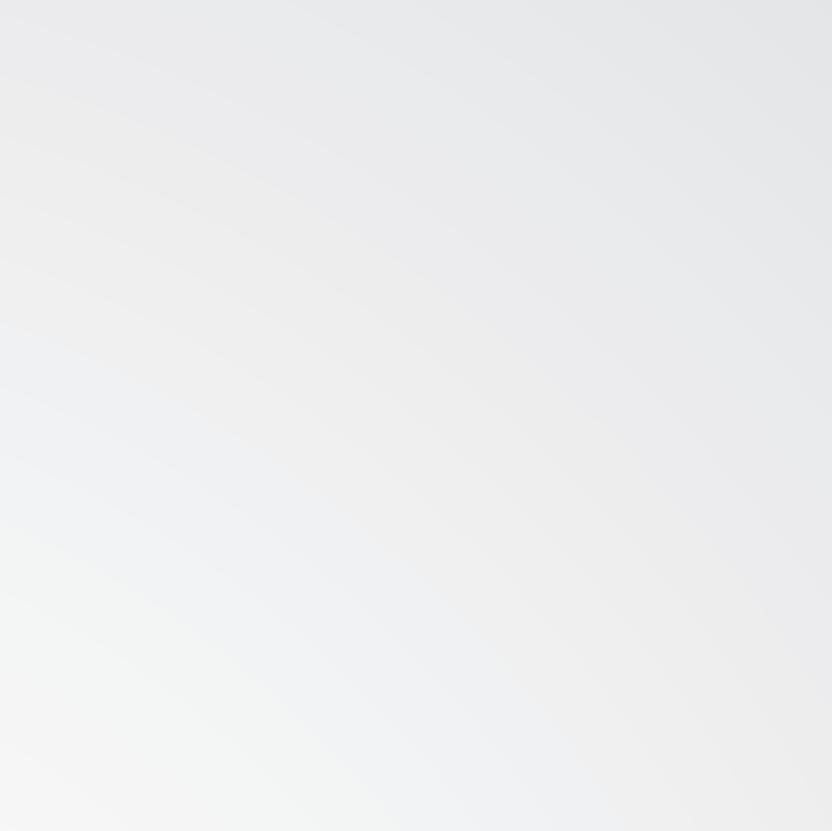
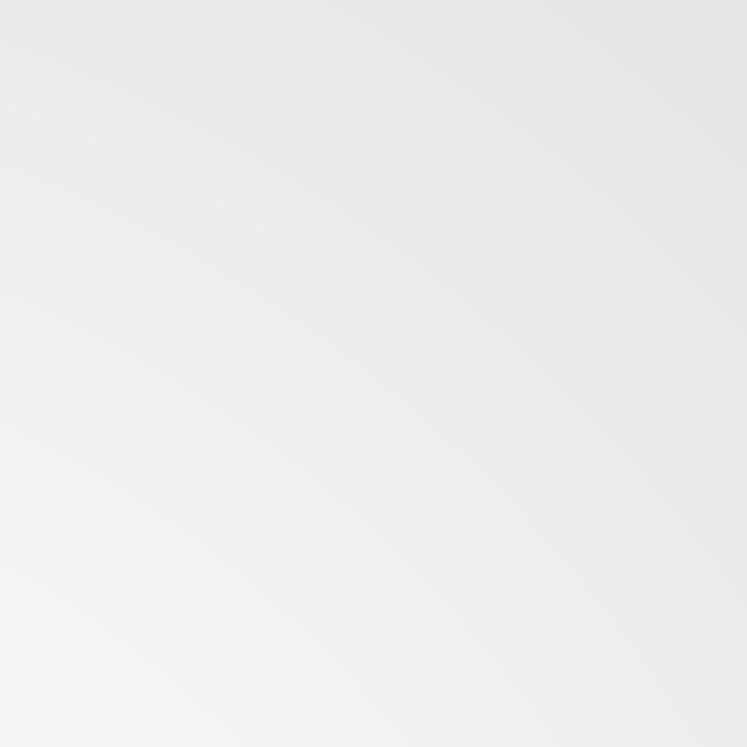
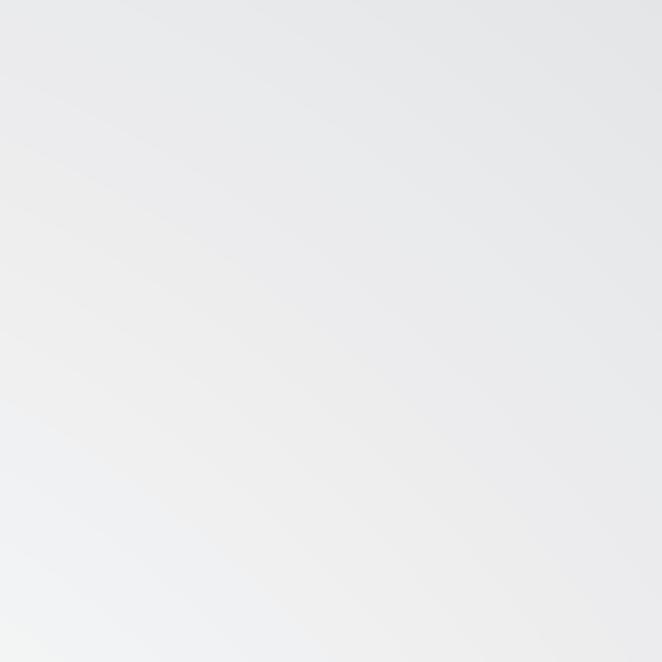
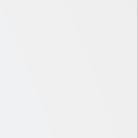







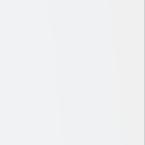

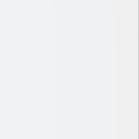

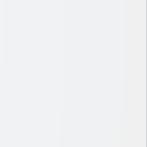

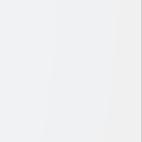

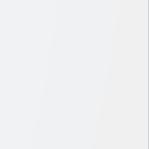

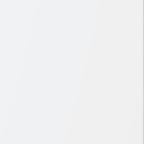

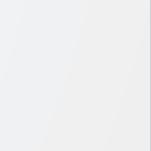



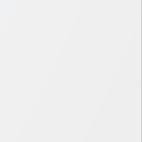

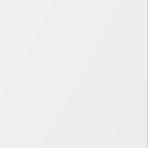

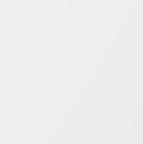

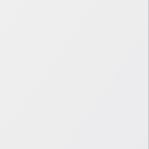

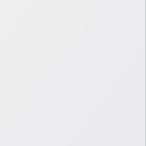

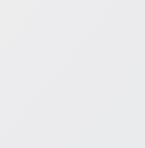

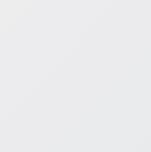
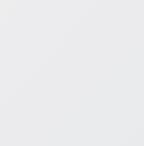


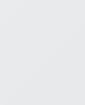

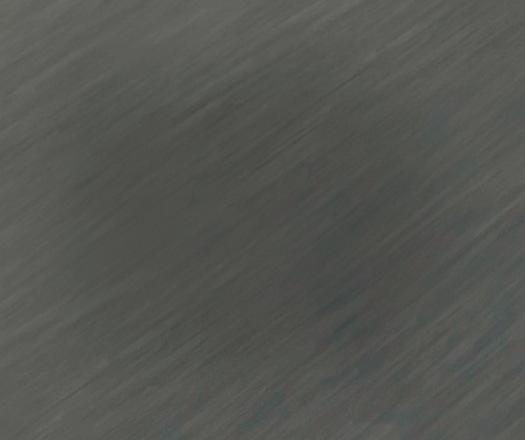


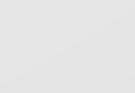
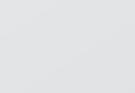





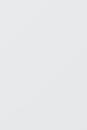
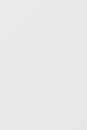
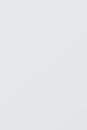

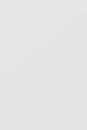
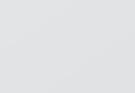
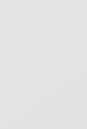
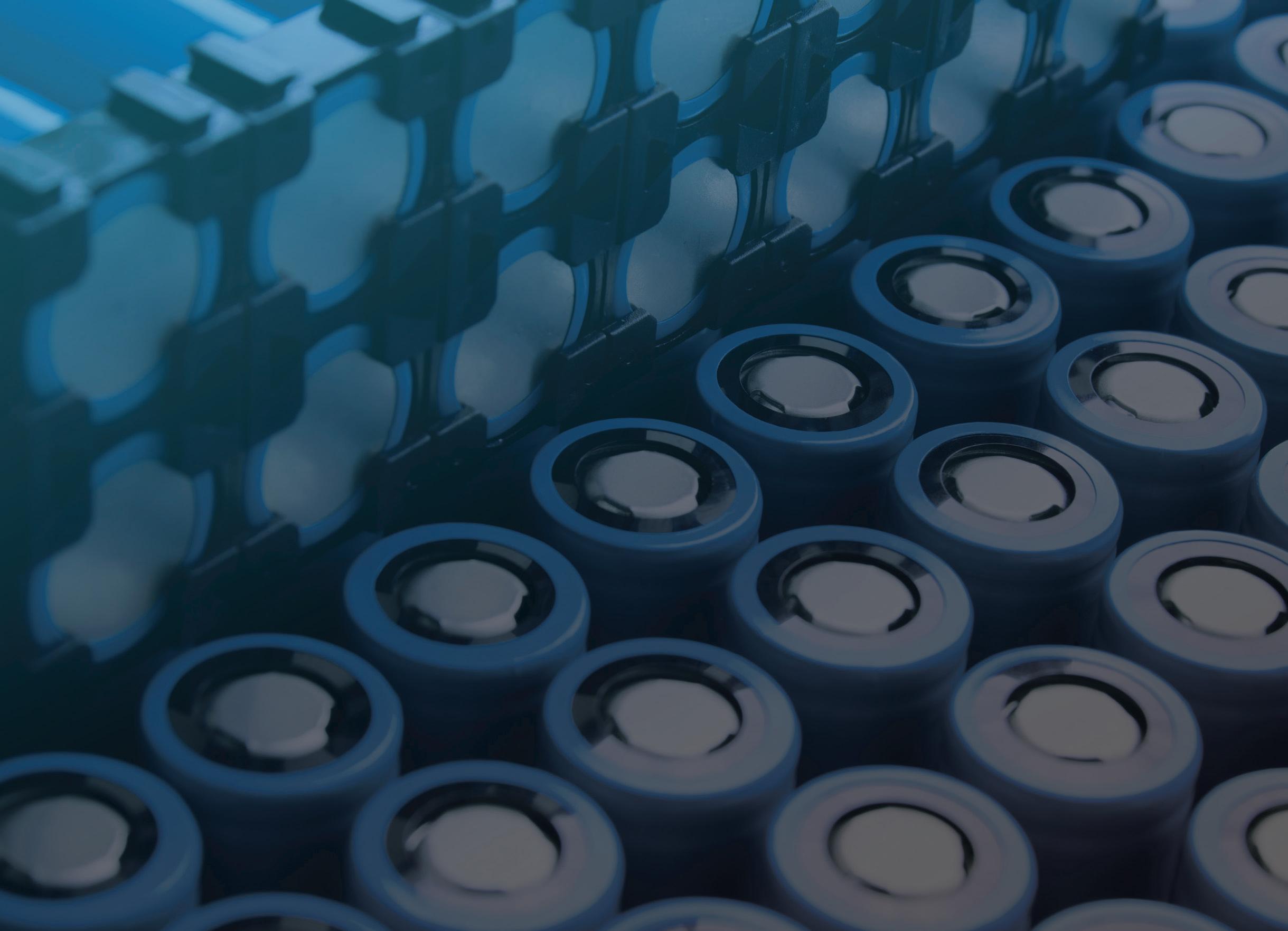

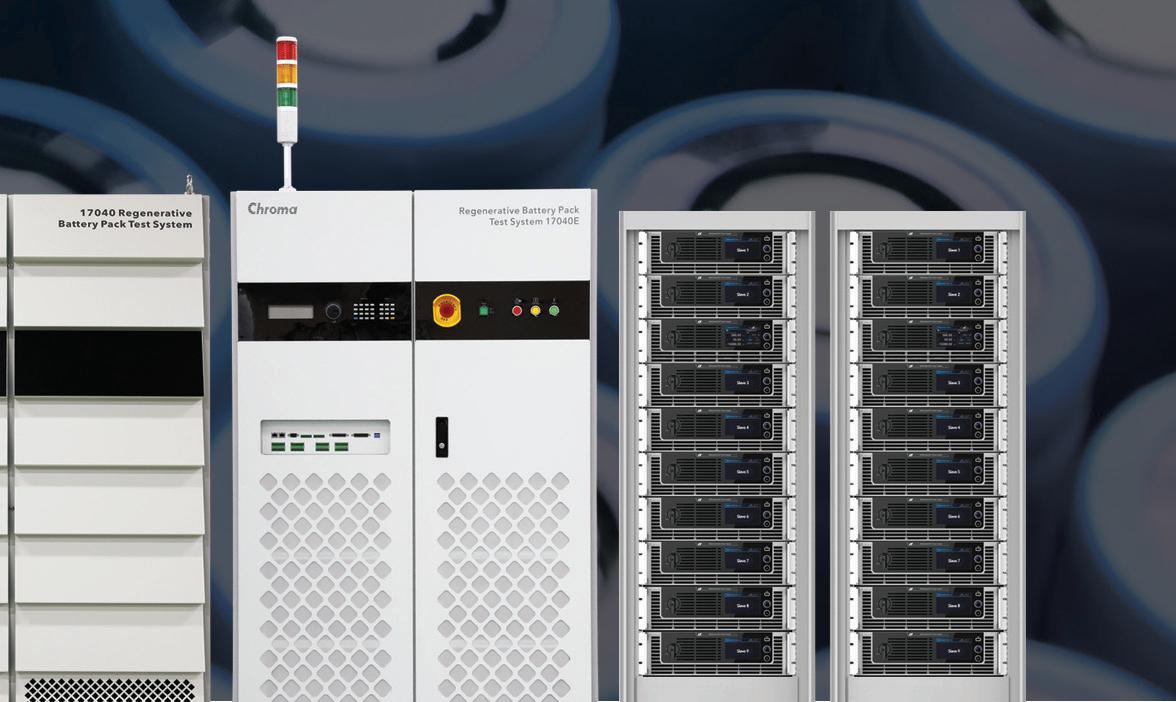
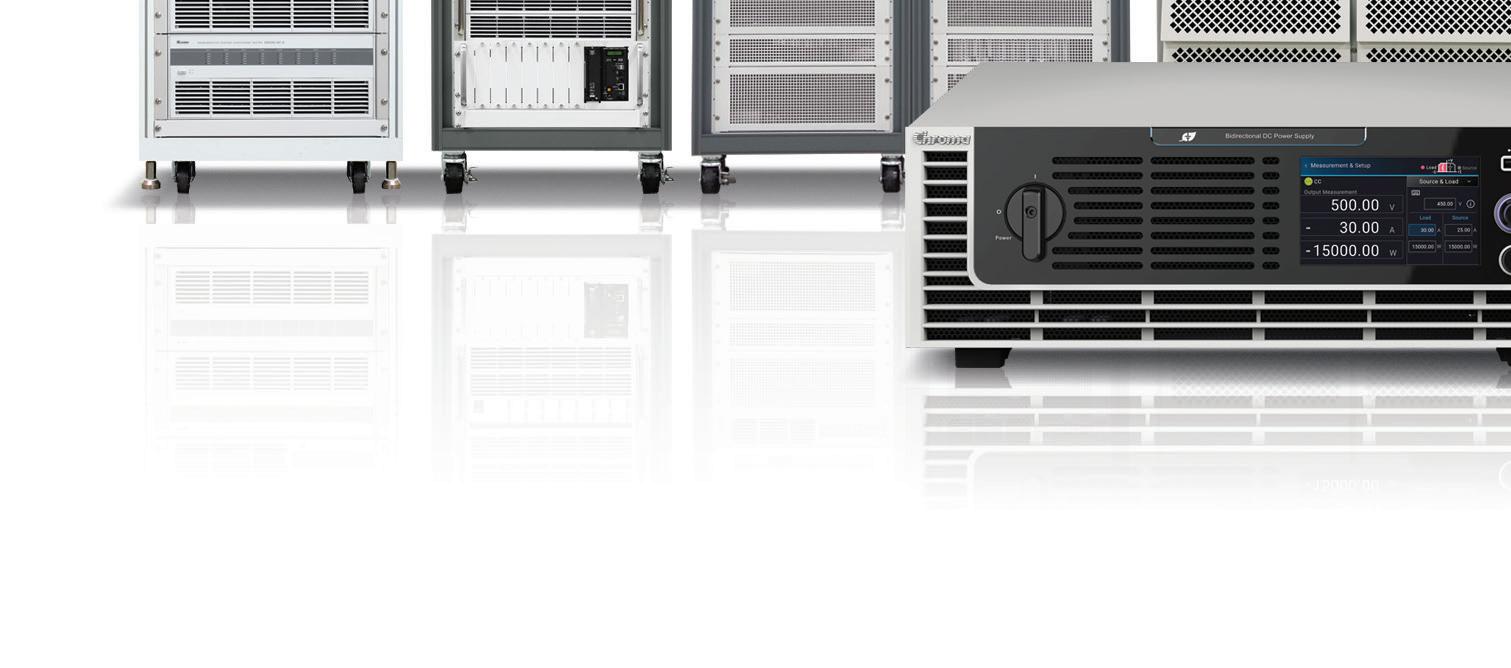
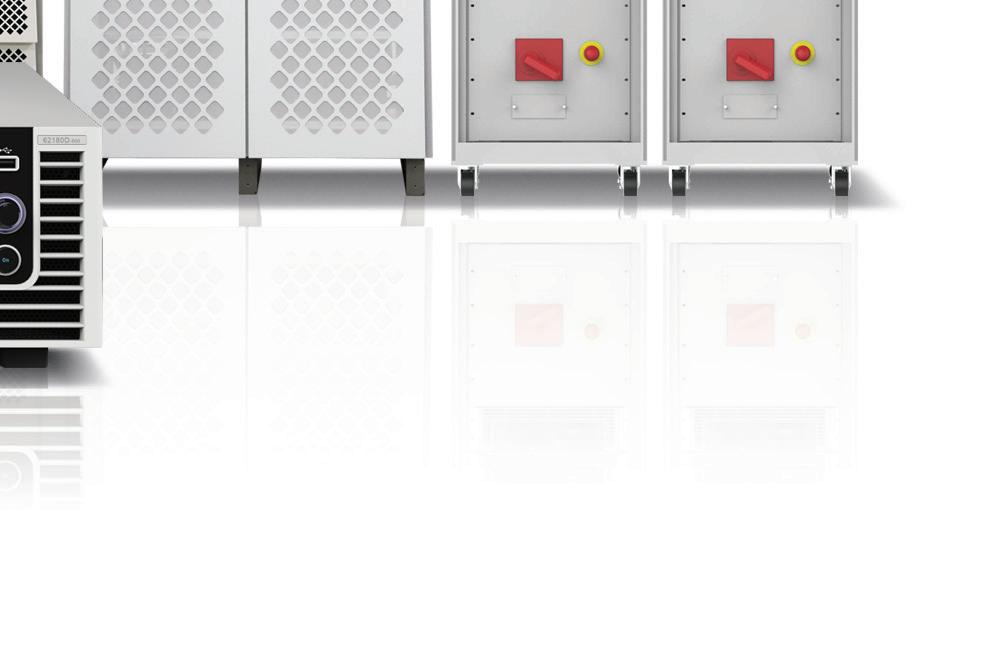
GM and LG partner on prismatic cell development
Stellantis and Zeta Energy to develop lithium-sulfur EV batteries
Elaphe’s new Sonic.1 front in-wheel motor delivers up to 347 peak hp
Danfoss launches 690-volt motor for off-highway applications
American Battery Factory partners with KAN Battery ahead of US launch
ZF to supply OEM with brake-by-wire technology for 5 million vehicles
Honeywell releases a new generation of battery safety sensors
German testing agency finds EV batteries last longer than expected
CATL’s new Bedrock Chassis for EVs can withstand high impacts
Wevo-Chemie unveils silicone filler for power electronics and batteries
Ascend Elements to increase US lithium carbonate production
Power Integrations’ wide-creepage IC switcher targets 800 V applications
Yamaichi upgrades connector system for EV battery applications
Novonix receives $755-million conditional DOE loan for US graphite plant
Study finds recycling battery metals could supply a quarter of Europe’s EVs
Stellantis and CATL to invest up to €4.1 billion in Spanish LFP battery plant
Toshiba releases automotive photorelay for 400 V battery control systems
MP Materials establishes rare earth magnet production in the US
Mining firm Fortescue orders $400 million worth of electric mining equipment
ICF’s PowerGuide helps utilities identify the best fleets for electrification
Isuzu begins customer deliveries of its NRR-EV Class 5 electric truck
Thomas Built Buses unveils second-generation Jouley electric school bus
Rio Tinto and SPIC partner to test electric mining trucks with battery swapping
Other automakers “knocking on the door” to access EV tech from Rivian/VW
SkyDrive and SAI Flight to develop electric air taxi routes in South Carolina
Stockholm construction site uses 50% electric construction equipment
Daimler Truck begins series production of Mercedes-Benz eActros 600 truck
Bollinger Motors delivers first Class 4 B4 electric trucks to West Coast
Polestar starts US production of single-motor variant
Scout Motors is confident it will win the right to sell EVs directly to customers
Lake Tahoe to link 14 ski resorts with Candela P-12 electric hydrofoil ferry
Lyteflo closes $3-million seed round to help dealers sell EVs
ABB and Black Box partner on management system to avoid panel upgrades
Smiths Interconnect’s new socket boasts more efficient energy transfer
GM and Reliant offer free nighttime charging to Chevrolet EV owners in Texas
Multi-story garage with charging spots for 2,000 EVs opens in Canada
Lectron producing up to 12,000 NACS-to-CCS charging adapters per week
EVgo to install up to 480 fast charging stalls at Meijer grocery stores
XCharge and Grensol to improve recycling for EVSE supply chain waste
PHYTEC and PIONIX release EVCS-Cube development kit
California revises LCFS regulations to favor EV charging over biofuels
Charging software provider AMPECO raises $26 million in funding
GM and EVgo surpass 2,000 co-branded public fast charging stalls in the US
Tritium to start “a new chapter” under CEO Arcady Sosinov
UK’s Project EV introduces MCS charger with vehicle-to-grid features
and Treehouse collaborate on home
charging management
Publisher Senior Editor
Technology
Editor
Business Development
Graphic Designers
Christian Ruoff
Charles Morris
Jeffrey Jenkins
Joel Franke
Mark Rogers
Greg Schulz
Tomislav Vrdoljak
Jeffrey Jenkins
Charles Morris
Christian Ruoff
Jonathan Spira
John Voelcker
Volvo Car Corporation
Kelly Ruoff
Sebastien Bourgeois
For Letters to the Editor, Article Submissions, & Advertising Inquiries Contact: Info@ChargedEVs.com
1. PUBLICATION TITLE: CHARGED ELECTRIC VEHICLES MAGAZINE. 2. PUBLICATION NUMBER: 18170. 3. FILING DATE: SEPTEMBER 29, 2024. 4. ISSUE FREQUENCY: QUARTERLY.
5. NUMBER OF ISSUES PUBLISHED ANNUALLY: 4. 6. ANNUAL SUBSCRIPTION PRICE (IF ANY). 7. COMPLETE MAILING ADDRESS OF KNOWN OFFICE OF PUBLICATION: CHARGED ELECTRIC VEHICLES MAGAZINE, 136 4TH STREET NORTH, STE 201, SAINT PETERSBURG, FL 33701. CONTACT PERSON: CHRISTIAN RUOFF. TELEPHONE: (727) 522-0039. 8. COMPLETE MAILING ADDRESS OF HEADQUARTERS OR GENERAL BUSINESS OFFICE OF PUBLISHER: CHARGED ELECTRIC VEHICLES MAGAZINE, 136 4TH STREET NORTH, STE 201, SAINT PETERSBURG, FL 33701. 9. FULL NAMES AND COMPLETE MAILING ADDRESSES OF PUBLISHER, EDITOR, AND MANAGING EDITOR: PUBLISHER, EDITOR, AND MANAGING EDITOR: CHRISTIAN RUOFF, 136 4TH STREET NORTH, STE 201, SAINT PETERSBURG, FL 33701.10. OWNER. FULL NAME: CHRISTIAN RUOFF. COMPLETE MAILING ADDRESS: 136 4TH STREET NORTH, STE 201, SAINT PETERSBURG, FL 33701. 11. KNOWN BONDHOLDERS, MORTGAGEES, AND OTHER SECURITY HOLDERS OWNING OR HOLDING 1 PERCENT OR MORE OF TOTAL AMOUNT OF BONDS, MORTGAGES, OR OTHER SECURITIES: NONE. 13. PUBLICATION TITLE: CHARGED ELECTRIC VEHICLES MAGAZINE.14. ISSUE DATE FOR CIRCULATION DATA BELOW: #69, JULY-SEPTEMBER 2024. 15. EXTENT AND NATURE OF CIRCULATION. A. TOTAL NUMBER OF COPIES (NET PRESS RUN). AVERAGE NO. COPIES EACH ISSUE DURING PRECEDING 12 MONTHS: 12250; NO. COPIES OF SINGLE ISSUE PUBLISHED NEAREST TO FILING DATE: 12500. B. LEGITIMATE PAID AND/OR REQUESTED DISTRIBUTION (BY MAIL AND OUTSIDE THE MAIL): (1) OUTSIDE COUNTY PAID/REQUESTED MAIL SUBSCRIPTIONS STATED ON PS FORM 3541: 9685; 9675. (2) IN-COUNTY PAID/REQUESTED MAIL SUBSCRIPTIONS STATED ON PS FORM 3541: 0; 0. (3) SALES THROUGH DEALERS AND CARRIERS, STREET VENDORS, COUNTER SALES, AND OTHER PAID OR REQUESTED DISTRIBUTION OUTSIDE USPS: 0; 0. (4) REQUESTED COPIES DISTRIBUTED BY OTHER MAIL CLASSES THROUGH THE USPS: 0; 0. C. TOTAL PAID AND/OR REQUESTED CIRCULATION (SUM OF 15B (1), (2), (3), AND (4)): 9685; 9675. D. NON-REQUESTED DISTRIBUTION (BY MAIL AND OUTSIDE THE MAIL): (1) OUTSIDE COUNTY NONREQUESTED COPIES STATED ON PS FORM 3541: 0; 0. (2) IN-COUNTY NONREQUESTED COPIES STATED ON PS FORM 3541: 0; 0. (3) NONREQUESTED COPIES DISTRIBUTED THROUGH THE USPS BY OTHER CLASSES OF MAIL: 72; 32. (4) NONREQUESTED COPIES DISTRIBUTED OUTSIDE THE MAIL: 973; 855. E. TOTAL NONREQUESTED DISTRIBUTION [SUM OF 15D (1), (2), (3) AND (4)]: 1045; 887. F. TOTAL DISTRIBUTION (SUM OF 15C AND E): 10730; 10562. G. COPIES NOT DISTRIBUTED: 1520; 1938. H. TOTAL (SUM OF 15F AND G): 12250; 12500. I. PERCENT PAID AND/OR REQUESTED CIRCULATION (15C DIVIDED BY 15F TIMES 100): .9026; .9160. I CERTIFY THAT 50% OF ALL MY DISTRIBUTED COPIES (ELECTRONIC AND PRINT) ARE LEGITIMATE REQUESTS OR PAID COPIES. 17. PUBLICATION OF STATEMENT OF OWNERSHIP FOR A REQUESTER PUBLICATION IS REQUIRED AND WILL BE PRINTED IN THE ISSUE OF THIS PUBLICATION: ISSUE 70, OCTOBER-DECEMBER 2024. 18. I CERTIFY THAT ALL INFORMATION FURNISHED ON THIS FORM IS TRUE AND COMPLETE. CHRISTIAN RUOFF, PUBLISHER, SEPTEMBER 29, 2024.
With the rise of hybrid and electric vehicles, the automotive industry is undergoing an unprecedented shift marked by significant engineering and design changes.
At Shell, we are supporting this transformation by working in close technical partnership with equipment manufacturers to develop a range of fluids specifically for high-tech hybrid and EV powertrains.
Much has changed in the US federal government, and I’ve read many di ering takes about what it will mean for our EV industry. One thing is certain: it’s tough to discern between political theater and concrete policies that will have a tangible impact on the auto industry. However, there is a long list of trends that are not likely to change.
Technological genies don’t go back into their bottles, ever. An astonishing amount of engineering resources have been poured into EV tech in the past decade, and, as a result, the nal products have gotten much better and simultaneously much cheaper. When you consider that Wall Street continues to reward EV leaders while punishing the laggards, it’s hard to imagine that any global automaker will stop investing heavily in the EV race.
ese engineering achievements helped to make 2024 a record year for EV sales, and trends point to faster growth. Entry-level EVs that are much better products and cost less than comparable legacy ICE cars are appearing worldwide (and not all of them are Chinese-made). At the same time, the uncertainties surrounding various charging challenges that have plagued EVs for years are being solved one a er another. e charging industry is coalescing around common standards and protocols that will make the EV owner’s experience much more consumer-friendly. Innovations in areas like better corridor fast charging and curbside chargers for urban drivers are popping up everywhere.
Obviously, there are areas in which anti-EV politicians could impact the market, although I think any e ects would be short-lived. e example of Germany shows how important purchase incentives are for new consumer EV adoption. While it seems very possible the federal tax incentive for EV buyers could go away, in other areas, I’m not that pessimistic.
ere are still funds from the National Electric Vehicle Infrastructure program, established under the Bipartisan Infrastructure Law, that could be clawed back, delayed or diverted away from EV charging. However, billions have already been sent to states to deploy, and shovels are in the ground. ere are also plenty of important projects in the works that will proceed without government funding. en there is the In ation Reduction Act of 2022, which has signi cantly incentivized battery and automotive manufacturing in the US through a series of strategies to promote domestic production. e early results are in: it’s working. If these incentives are not reversed, which would require passing new legislation, I think history will view the IRA as one of the biggest boons to US manufacturing ever. And, as it turns out, a massive amount of the new EV/battery supply chains and factories are now being built in states and districts represented by politicians who originally opposed the bills that made it happen.
Will there now be enough political will (and attention span) to pass a new law to kill all these projects and jobs, including those designed to keep at-risk auto factories open? When e Verge recently asked former Transportation Secretary Buttigieg, he said, “For every conservative legislator publicly threatening to reverse our work, there’s two or three who look like they’re trying to take credit for it.” For the good of the US auto industry, we hope this is what happens. A er all, it’s much easier—and more common—for politicians to try to take credit for popular projects they initially opposed than it is to repeal and replace them.
One thing that de nitely will not change is our mission at Charged—to keep you informed of the latest developments in the global EV industry. We’re more excited than ever about the progress we’re seeing worldwide and we have some awesome new projects rolling out this year to help you keep up with it all.
Christian
Ruoff | Publisher EVs are here. Try to keep up.
CNC BENDING TECHNOLOGY FOR BUSBARS
Busbar Bending Machine for large wire dimensions
Unstripping of the insulation coating by laser or milling process
Device for Twisting the Busbar
Transfer of actual geometries and correction values
Real-time simulation for calculating cycle times and for collision monitoring
US automaker GM is extending its 14-year collaboration with South Korean battery maker LG Energy Solution to develop prismatic cell technology.
GM expects the cells that the companies develop to power its future EV models, as part of its strategy to diversify its supply chain, using multiple chemistries and form factors. GM will continue to use the pouch battery cells produced at the companies’ Ultium Cells joint venture plants in Warren, Ohio and Spring Hill, Tennessee.
Prismatic cells are at and rectangular in shape and have a rigid enclosure, which saves space within battery modules and packs. is can reduce EV weight and cost, while simplifying manufacturing by reducing the number of modules and mechanical components. LG Energy Solution has experience with prismatic cell production and an extensive patent portfolio on battery design and manufacturing technologies, including packaging.
“Together with LG Energy Solution, we’ve built Ultium Cells into one of the largest battery cell manufacturers in North America, powering our diverse EV portfolio,” said Kurt Kelty, GM VP of Batteries. “We’re focused on optimizing our battery technology by developing the right battery chemistries and form factors to improve EV performance, enhance safety and reduce costs.”
Netherlands-headquartered automaker Stellantis and US battery technology rm Zeta Energy have signed a joint development agreement to develop lithium-sulfur EV batteries that have energy density comparable to that of lithium-ion technology.
e collaboration includes pre-production development and planning for future production. Stellantis aims to use the batteries in its vehicles by 2030.
Lithium-sulfur battery technology has the potential to create a lighter battery pack with the same usable energy as lithium-ion batteries, enabling greater driving range, improved handling and enhanced performance. e technology can potentially improve fast charging speeds by up to 50%. Sulfur, being widely available and cost-effective, reduces production expenses and supply-chain risk. Lithium-sulfur batteries are expected to cost less than half the price per kWh of current lithium-ion batteries.
Zeta’s lithium-sulfur battery design uses waste materials, methane and unre ned sulfur, a byproduct from various industries, and does not require cobalt, graphite, manganese or nickel. e technology is intended to be manufacturable within existing gigafactories and would leverage a short, entirely domestic supply chain in Europe or North America.
“ e combination of Zeta Energy’s lithium-sulfur battery technology with Stellantis’s expertise in innovation, global manufacturing and distribution can improve the performance and cost pro le of electric vehicles while increasing the supply chain resiliency for batteries and EVs,” said Tom Pilette, CEO of Zeta Energy.
The Supply Chain Expo & Technical Programme for the Global Magnetics Industry
The Pasadena Convention Center, California May 14 – 15 2025
Elaphe, a Slovenia-based developer of in-wheel motor technology, has introduced a new front-wheel in-wheel motor for electric and hybrid vehicles.
e motor integrates a large 400 mm brake disc in a 21-inch rim, making it well-suited to high-performance vehicles in which space and weight are key considerations. e motor delivers continuous power output of 272 horsepower per wheel, and can reach up to 347 peak hp.
e scalable design o ers potential axle peak power of up to 1 MW in rear-wheel-drive con gurations and 8 kW/kg of continuous speci c power.
Traction control and torque vectoring improve vehicle handling, acceleration and braking, o ering faster wheel response compared to conventional wheel and suspension setups, according to the company.
e Sonic.1 is designed to be easily integrated into existing and new supercar models, and to enable vehicle designers to improve aerodynamics as well as component placement and styling.
Danfoss Power Solutions has announced the launch of the Editron EM-PMI375 690 Volt electric motor. Based on synchronous reluctance-assisted permanent magnet technology, the EM-PMI375 functions as both a motor and a generator. It is designed to work with the Editron EC-C1700B inverter, o ering a system solution for 690 V AC and 1,050 V DC applications such as winches, cranes, marine vessels, and mining and material handling machinery.
e motor o ers up to 96% e ciency throughout its operating range, and Danfoss says it’s smaller and lighter than competing products. Developed especially for demanding applications, the motor features a compact and robust aluminum frame structure with an IP67 ingress protection rating.
“Our new EM-PMI375 690 Volt motor and ECC1700B inverter are the rst two pieces of our 690-volt ecosystem, with more to come,” said Chao Wang, Head of Portfolio Management for the company’s Editron division. “ ere are few, if any, options out there for true 690-volt mobile-grade inverters and motors. Most are based on industrial solutions, and thus o er much lower vibration and shock tolerance.”
e EM-PMI375 electric motor is available in four sizes to suit a range of torque and power needs. Models o er continuous torque ratings of 200 Nm to 1,100 Nm and power range from 63 kW to 296 kW.
All models feature a speed range of up to 4,000 rpm. e motors are liquid-cooled and have low coolant ow requirements.
Lithium iron phosphate (LFP) battery cell manufacturer American Battery Factory (ABF) has formed a partnership with Chinese manufacturer KAN Battery to develop a pilot line of battery cells at its facility and accelerate its US production launch.
As part of the collaboration, ABF will secure training in the latest analytics and machining for its workforce, re ne battery cell production and launch its subsidiary ABF China.
At the facility in China, ABF will work alongside KAN Battery to run an initial 1 GWh factory line to produce high-capacity prismatic cells o ering 105 to 300 Ah outputs. e 750,000-square-foot line will enable the company to immediately start production at scale. ABF will supply select battery cells produced at the factory to o -takers such as Lion Energy ahead of its full US cell production.
By re ning the production process while it prepares for the construction of its rst gigafactory in Tucson, Arizona, ABF will bring together its experience in machining, battery chemistry and business analytics at launch. e company expects to complete the rst phase of the Tuscon plant in the second half of 2026. e site will include the company’s headquarters, an R&D innovation center and the initial 2 x 2 GWh factory module. ABF’s battery cells are designed to last up to 10,000 life cycles or an average of 20-30 years.
“ e United States is 10 years behind the leaders of battery cell production. To develop a domestic supply chain, we must work together with the best in the world,” said John Kem, President of American Battery Factory.
German automotive parts supplier ZF has signed a deal with a global manufacturer that includes planned volume production of brake-by-wire technology to equip nearly 5 million vehicles with electro-mechanical braking (EMB) over the length of the contract.
Featuring electro-mechanical brake and by-wire technology on the rear brakes, the project will also include ZF’s integrated brake control (IBC) and traditional front calipers, creating a hybrid braking system of by-wire and hydraulics that o ers the manufacturer increased exibility.
e agreement will also provide steering technology with ZF’s Electric Recirculating Ball Steering Gear (RBSG). EMB, as a key component of the brake-by-wire technology, lays the foundation for the so ware-de ned vehicle that will lead to new functions and features, such as autonomous braking and steering in a crash, according to the company.
ZF’s EMB is at the center of its “dry brake” system, which does not require brake uid. Brake pressure is not generated by the pressure of uids in the hydraulic system, but by electric motors. Braking signals from the pedal to the electric motor are also transmitted electronically.
e EMB works with the IBC, a non-vacuum, fully integrated electro-hydraulic system providing high brake performance for automatic emergency braking, full energy recuperation and redundant fallback options up to full automated driving for passenger car and light truck segments.
e hybrid system is created by an electric system on the rear axle and hydraulics at the front, featuring ZF’s Colette-type caliper, which is available for passenger car and light commercial vehicles in single and twin piston designs.
e RBSG is a 48 V electrically powered gear designed to replace current hydraulic applications as an integrated unit that reduces vehicle assembly costs. It allows for ADAS features up to Level 2 as well as improved steering and performance.
Honeywell has released a new generation of battery safety sensors. e Battery Safety Electrolyte Sensor (BES) series is designed speci cally for enhanced safety in lithium-ion battery onroad applications, and exceeds industry standards for performance and reliability, according to the company.
e new BES uses Honeywell’s proprietary Li-ion Tamer [clever!] electrolyte gas detection technology to identify “ rst vent” events. ese events serve as early warning signs of potential battery malfunctions, enabling the system to issue alerts 5 to 20 minutes prior to a risk of re.
e sensors can detect multiple gases released during thermal runaway, which minimizes the risk of false negatives. e integration process is facilitated by a rate of change algorithm, which eliminates the need for target gas threshold testing. is feature is designed to reduce integration costs and shorten project timelines.
e sensors incorporate the CAN communication protocol, and feature two operating modes, which can be selected via CAN commands. In Normal mode, the sensor operates at full functionality with active CAN communication. In Eco mode, CAN communication is disabled, which reduces power consumption by 60%—however, the sensor automatically reverts to Normal mode to send alarm signals to the Battery Management System (BMS) in the event of an alarm condition.
German testing organization DEKRA has developed a standardized test that measures the health of an individual EV’s battery, and has now completed more than 25,000 state-of-health tests using its patented procedure. DEKRA reports that “the batteries of electric cars are more durable than consumers sometimes fear.”
DEKRA’s rapid battery test, which was introduced in 2022, is currently available for around 130 di erent vehicle models and is o ered in several European countries. e procedure takes 15 minutes, and includes a static test and a short acceleration drive of around 50 to 100 meters.
e real-world results of an individual test are compared to the “parameterization” of the individual vehicle models, which includes data gathered from complex test drives under a wide variety of conditions. “ is creates a kind of coordinate structure that our system uses to analyze and evaluate the actual measured values during the test,” explains Christoph Nolte, Executive Vice President of DEKRA. “ e bottom line is a statement on the battery condition that no other method on the market can o er as quickly and at the same time as precisely.”
e growing data pool enables the DEKRA experts to make more general statements about battery aging, and they say that “even with higher mileages, the vast majority of traction batteries are still in good condition.”
As one example, DEKRA cites a eet of Jaguar I-Pace electric taxis that went into service in Munich in 2018. DEKRA tested six of the vehicles in 2024, and found that, with mileages between 180,000 and 260,000 kilometers, the state of health of the traction batteries was between 95 and 97 percent.
“On average, we charged the vehicles about one and a half times a day, and not particularly gently, but always fully charged to give the drivers the appropriate level of safety in terms of range,” said Gregor Beiner, Managing Director of the Munich Taxi Centre (MTZ). “ e batteries are very, very durable and, especially with the safety bu ers that the manufacturers install, they retain their capacity for a very long time.”
Chinese battery manufacturer CATL has launched the CATL Bedrock Chassis, a skateboard chassis that can withstand 120 km/h frontal impacts without catching re or exploding.
e battery-centered design uses cell-to-chassis integration technology, which directly integrates the battery cells into the chassis and allows for a shared structural design. Based on the decoupling of the chassis from the upper body, the Bedrock Chassis can absorb 85% of the vehicle’s collision energy, compared to around 60% absorbed by traditional chassis, according to the company.
e speed for frontal impact safety tests in the commonly used China New Car Assessment Program (C-NCAP) is 56 km/h, which, when experiencing a frontal impact at this speed, generates collision energy equivalent to falling from a 12-meter-high building. In comparison, a frontal impact at 120 km/h generates a collision energy 4.6 times that of collision at 56 km/h.
e Bedrock Chassis incorporates three core characteristics: internal integration; decoupling of the chassis from the upper body; and external openness.
e CATL Bedrock Chassis introduces a three-dimensional biomimetic tortoise-shell structure—the body and energy unit framework are integrated to protect the energy unit. Its aircra carrier-grade arresting structure disperses impact forces across multiple pathways during a crash, gradually decelerating the vehicle and signi cantly reducing the depth and speed at which obstacles intrude into the cabin. e utilization of submarine-grade hot-formed steel with a strength of 2,000 MPa, aerospace-grade aluminum alloy with a strength of 600 MPa and multiple barrier structures further enhance the rigidity of the chassis.
e chassis instantly disconnects its high-voltage circuit within 0.01 seconds of impact and completes the discharge of residual high-voltage energy in the vehicle within 0.2 seconds. e battery cells have undergone tests including high-speed sled impact tests at 60 km/h, 90-degree bending tests and sawing tests.
German adhesives and sealants producer Wevo-Chemie is expanding its portfolio of thermal interface materials with an optimized silicone gap ller.
WEVOSIL 26040 FL features high thermal conductivity of 4 W/m*K for e cient heat dissipation for large surfaces. e material has been formulated to be resistant to sedimentation, allowing it to be stored, used and transported over long distances for at least three months without having to be rehomogenized.
e material’s specially developed ller combination and the resulting low bond line thickness of <70 µm bridge small gaps. Material properties such as reactivity can be customized to individual needs, according to the company.
e optimized dosing properties permit simple and e cient handling, high dispensing speeds and ne dosing patterns. is ensures greater precision and exibility in production compared to thermally conductive pads, particularly when manufacturing large unit volumes.
e ller provides high temperature resistance of up to 200° C, ame-retardant properties in accordance with UL 94 V-0 (at a thickness of just 2 mm) and mechanical properties including elongation at break of more than 30%.
When cured, WEVOSIL 26040 FL meets the requirements of the PV 3040 test speci cation for low-volatile emissions in the automotive industry.
“Whether it’s high dosage volumes, reliable heat dissipation for large surfaces or mechanically demanding thermal joints that are needed, the new silicone gap ller from Wevo is a solution for numerous requirements in contemporary electronics and electrical engineering,” the company said.
US battery materials manufacturer Ascend Elements will commission a new lithium carbonate recovery line at its battery recycling facility in Covington, Georgia in 2025 to start producing 99% pure lithium carbonate (Li2CO3) recovered from used lithium-ion batteries.
e company plans to produce up to 3,000 metric tons of lithium carbonate annually. Its Hydro-to-Cathode direct precursor synthesis technology produces new cathode material from spent lithium-ion cells more e ciently than traditional methods, according to the company, resulting in lower costs and carbon emissions.
Ascend’s Covington facility has been operational since August 2022. It has the capacity to recycle up to 30,000 metric tons of lithium-ion battery materials—the equivalent of approximately 70,000 EV battery packs—annually.
“ is new domestic supply of a critical battery material will help US industries meet growing demand while avoiding the possibility of tari s on imported materials,” said Eric Gratz, co-founder and CTO of Ascend Elements.
US-based Power Integrations, which produces high-voltage integrated circuits for energy-e cient power conversion, has introduced a wide-creepage package option for its InnoSwitch3-AQ yback switcher IC for automotive applications.
A wide drain-to-source-pin creepage distance of 5.1 mm eliminates the need for conformal coating, making the IC compliant with the IEC60664-1 standard in 800 V vehicles while simplifying manufacturing and increasing system reliability.
e 1,700 volt-rated CV/CC InnoSwitch3-AQ switching power supply ICs incorporate a silicon carbide (SiC) primary switch capable of delivering up to 80 watts of output power. e highly integrated ICs reduce the number of components required to implement a power supply by as much as 50%, saving space, enhancing system reliability and mitigating component sourcing challenges, according to the company. An increased drain-pin width assists in withstanding high levels of shock and vibration, especially in eAxle automotive applications.
Target automotive applications include battery management systems, DC-DC converters, control circuits and emergency power supplies in the main traction inverter.
e new ICs in the range start up with as little as 30 V on the drain without external circuitry—which is critical for functional safety. Additional protection features include input under-voltage, output overvoltage and overcurrent limiting.
Yamaichi Electronics, a manufacturer of test and burn-in sockets, connectors and test contacts, has released the newest version of its Y-Lock Pullforce connector system to meet the requirements of battery applications.
e exible at cable (FFC) or the exible printed circuit board (FPC) is inserted into the connector using the pre-assembled sti ener. e Y-Lock V4 series has a double locking function, via two lateral locking hooks and a central locking mechanism on the long side of the insulator.
e two-part sti ener design ensures that the FFC or FPC are protected against contact, so that the cable can be handled safely during servicing. is feature also ensures that the plug cannot be inserted at an angle or upside-down, preventing short circuits. e sti ener can be permanently locked to the connector by an additional plastic part.
e Y-Lock V4 series is available with gold or tin plating. It is currently available in a 90° version, and its 4.5 mm height is well suited to the tight installation spaces in battery applications.
e connector system is available with di erent contact spacings: 1.0 mm, 1.2 mm, 1.8 mm and 2 mm, for various clearance and creepage distances.
Novonix, a battery materials and technology company, has received a conditional commitment from the US Department of Energy for a direct loan of up to $754.8 million for a proposed graphite facility in Tennessee.
If nalized, the nancing from the DOE’s Loan Programs O ce would be applied towards partially nancing the construction of the new facility to manufacture synthetic graphite, primarily for use in EV batteries.
e new facility is expected to produce approximately 31,500 tonnes of synthetic graphite annually, supporting the production of lithium-ion batteries for approximately 325,000 EVs each year. e plant is expected to reach full production capacity by the end of 2028.
Novonix has previously discussed plans to build a new facility in the southeastern US that could expand to 75,000 tonnes of annual production capacity.
e proposed loan is being o ered under the LPO’s Advanced Technology Vehicles Manufacturing (ATVM) Loan Program. It would be structured in two tranches based on a phased completion of infrastructure and production lines from a total eligible investment of $943.6 million. e rst tranche would support the site and infrastructure for the new facility and 21,000 tonnes per year of production capacity, while the second tranche would support an additional 10,500 tonnes.
is year, Novonix signed binding o ake agreements to supply synthetic graphite to Panasonic Energy, Stellantis and Volkswagen’s PowerCo. e company’s Riverside facility, located in Chattanooga, is scheduled to start commercial production in 2025, with plans to increase output to 20,000 tonnes annually to meet current customer commitments. Expansion of the new plant would depend on customer demand and access to additional nancing.
Novonix has been awarded a $100-million grant and $103-million investment tax credit by the DOE’s O ce of Manufacturing and Energy Supply Chains (MESC) towards the funding of the Riverside facility.
Materials recovered from end-of-life batteries and gigafactory scrap have the potential to supply up to 2.4 million EVs in Europe by the end of the decade, cutting the continent’s reliance on mineral imports, according to research by non-governmental sustainability group Transport & Environment (T&E).
Recycling spent battery cells and production scrap could provide 14% of the lithium, 16% of the nickel, 17% of the manganese, and 25% of the cobalt that Europe will need for electric cars in 2030, the study found. e region has the potential to be almost self-su cient in supplying cobalt for EVs in 2040.
Recycling could replace the need for primary ores, avoiding the need to build twelve new mines globally by 2040: four lithium, three nickel, four cobalt and one manganese. is would also reduce the potential negative environmental e ects on water, soil and biodiversity from those mines. However, to reap the economic and sustainability bene ts, Europe needs to scale up its recycling industry. e EU and the UK will not be able to harness this potential unless they secure recycling projects that are at risk of being canceled, T&E said. Almost half of the recycling capacity that has been announced for the region is on hold or uncertain whether it will go ahead.
T&E called on the EU and the UK to urgently prioritize support for recycling across their policies and funding programs.
“If Europe delivers on its recycling plans, it can slash its reliance on imported critical metals. e expected volumes of locally recovered materials can enable Europe to build millions of clean electric vehicles locally,” said Julia Poliscanova, Senior Director at T&E. “Neither the EU nor the UK are ready to capture the recycling opportunity. Almost half of the planned recycling capacity is at risk due to high energy costs, a shortage of technical expertise or a lack of nancial support. It’s time to start treating battery recycling like another clean tech and prioritize it in our policy and grant making.”
Netherlands-headquartered automaker Stellantis and Chinese battery manufacturer CATL have agreed to invest up to €4.1 billion to form a 50/50 joint venture that will build a large-scale lithium iron phosphate (LFP) battery plant in Zaragoza, Spain.
e battery plant is targeted to start production by the end of 2026 at Stellantis’s Zaragoza site. It will be implemented in several phases, and could reach up to 50 GWh of annual capacity. is will depend on the evolution of the EV market in Europe and continued support from authorities in Spain and the European Union, the companies said.
e agreement follows a non-binding memorandum of understanding (MOU) the companies signed in November 2023 for the local supply of LFP battery cells and modules and a long-term collaboration on two strategic fronts—creating a technology roadmap to support Stellantis’s EVs and identifying opportunities to further strengthen the battery value chain.
CATL operates battery manufacturing plants in Germany and Hungary. e Spanish facility will enhance its capabilities to supply European automakers as well as the global market.
Stellantis is employing a dual-chemistry approach— using lithium-ion nickel manganese cobalt (NMC) and lithium iron phosphate (LFP) batteries. e JV will enable the automaker to o er more electric passenger cars, crossovers and SUVs in the B and C segments with intermediate ranges in Europe.
Toshiba Electronics Europe has introduced a high-voltage transistor output photorelay for 400 V automotive battery-related control systems.
e automotive-compliant TLX9150M is housed in a compact SO12L-T package. Its space-saving form factor of 7.76 mm × 10 mm × 2.45 mm is 25% smaller than Toshiba’s existing package SO16L-T. is helps to miniaturize the battery unit and reduce costs.
e photorelay delivers a minimum breakdown voltage (VOFF) of 900 V with a maximum reaction (TON/ TOFF) time of 1 ms. is is important for control-sensitive applications such as battery and fuel cell control and battery management systems (BMS) for monitoring voltages, as well as detecting mechanical relay sticking and ground faults.
e TLX9150M consists of an infrared (IR) emitting diode optically coupled to a photo-MOSFET, providing electrical isolation between the primary (control) side and the secondary (switch) side, enabling safe switch control across varying ground potentials.
e trigger current (IFT) is more than 3 mA, minimizing system energy consumption. e device’s o -state current (IOFF) is 100 nA maximum at ambient temperature, drawing minimal power while inactive. e IR LED has a forward current (IF) rating of 30 mA, while its photodetection element has an on-state current (ION) rating of 50 mA at ambient temperatures.
MP Materials produces specialty materials that are vital inputs for the EV and renewable energy industries. e company is expanding its manufacturing operations downstream to provide a full supply chain solution from raw materials to magnetic products.
Now MP Materials says its agship Independence facility in Fort Worth, Texas has begun commercial production of neodymium-praseodymium (NdPr) metal and trial production of automotive-grade, sintered neodymium-iron-boron (NdFeB) magnets.
NdFeB magnets are essential components in vehicles, drones, robotics, electronics, and aerospace and defense systems. For decades, the US has relied almost entirely on foreign sources for these critical materials.
e Independence facility is poised to produce approximately 1,000 metric tons of nished NdFeB magnets per year, and production will ramp up beginning in late 2025. e facility will supply magnets to GM and other manufacturers, sourcing its raw materials from Mountain Pass, MP Materials’ mine and processing facility in California.
In 2024, the Mountain Pass mine delivered more than 45,000 metric tons of rare earth oxides (REO) contained in concentrate, as well as approximately 1,300 metric tons of NdPr oxide, in addition to cerium, lanthanum, and other separated and re ned products.
“ is milestone marks a major step forward in restoring a fully integrated rare earth magnet supply chain in the United States,” said James Litinsky, founder, Chairman and CEO of MP Materials.
Figure 1: The differences in the voltage waveforms produced by the conventional 2-level inverter vs. 3-level and 5-level MLIs.
5-Level
By Je rey Jenkins
The vast majority of EV traction motors must be supplied with sinusoidal 3-phase alternating current with the frequency proportional to RPM, and the overwhelmingly favorite way to do this is with a triple half-bridge voltage source inverter, or VSI.
In this topology, each bridge switch can connect its output terminal (i.e. motor phase winding) either to the positive or the negative rail of a voltage source (i.e. the battery in an EV, herea er referred to as +Vbatt and -Vbatt), ignoring the useless choice of both switches being o , and the destructive choice of both being on, hence this type of inverter is further described as “2-level.”
e output waveform of a 2-level inverter operating at the fundamental frequency is a square wave, and while it is possible to drive AC motors with square waves, they don’t much like it because of the high harmonic content, which produces excessive heating, a reduction in maximum achievable torque at any RPM, and more vibration. e traditional approach to reducing the harmonic content is by chopping each output pulse up into many slices and modulating their on times, or duty cycles, sinusoidally. e inductance of the motor windings then integrates this pulsating voltage waveform into a sinusoidal current, with a consequent improvement in torque, vibration and losses. e higher the PWM frequency—i.e. the more slices for each output pulse— the lower the total harmonic distortion, or THD, in the current waveform, which can only be a good thing...up until it isn’t, anyway.
e rst major obstacle to increasing the PWM frequency without end is that the percentage of time spent in the switching transitions (i.e. o to on and on to o ) increases unless the switches are also proportionally faster. As the switch e ectively acts like a resistor during the transitions, these so-called switching losses increase with PWM frequency, all else being equal. However, employing faster switches—such as the latest technology SiC MOSFETs and GaN HEMTs (High Electron Mobility Transistors)—leads to its own set of headaches, as just because you can switch 400 to 800 V in 10-30 ns with these technologies doesn’t mean you should; the extremely high dV / dt of such rapid switching produces prodigious amounts of RF noise, and also causes winding insulation and sha bearing-destroying common-mode currents to ow. In fact, a rule of thumb says that the effective RF bandwidth, in MHz, of a switching transition, in ns, is 350 / dV / dt; e.g. a 10 ns switching time will generate signi cant RF energy out to 35 MHz.
One solution to so en the switching transitions without slowing down the switches is to add an LC low-pass lter directly a er each inverter output (especially if the motor is more than a few meters away, as the intercon-
nect cables make embarrassingly good radio antennas). Setting the lter’s cuto frequency to 1/10th the e ective bandwidth frequency as calculated above (e.g. 3.5 MHz for the previous example) will su ce for so ening the transitions, which will drastically reduce o ending RF noise emissions while not introducing enough phase shi to cause problems with vector motor control schemes. ese so-called dV / dt lters won’t help much with reducing the common-mode currents, though, as the motor voltage waveform will still very much consist of pulses that span the full battery voltage.
To e ectively integrate the chopped voltage waveform into a nice sine wave (i.e. same as the current waveform) would require the LC lter cuto frequency be no higher than 1/10th the actual PWM frequency, and that would take up a lot more volume (and cost more) while almost certainly introducing enough phase shi to interfere with vector control schemes if not addressed in hardware and/or so ware.
Another way to lower the THD and reduce the magnitude of common-mode currents is to add more steps to the voltage waveform generated by the inverter—a multilevel inverter, or MLI, in other words. Figure 1 illustrates the di erences in the voltage waveforms produced by the conventional 2-level inverter vs 3-level and 5-level MLIs. It’s di cult to see how the 2-level inverter even produces a
Multilevel inverters obviously need access to separate voltage sources for each output voltage level, or else must create the voltage levels indirectly.
sinusoidal current, whereas it’s much more obvious in the 3-level and 5-level MLIs. Note also that each PWM pulse in the 2-level inverter swings the full battery voltage, but only half Vbatt for the 3-level MLI, and a quarter of Vbatt for the 5-level MLI, etc. e price you pay for lower THD and common mode currents at a given PWM frequency with all multilevel inverter topologies is that they are much more complicated than their 2-level progenitor (ridiculously so, in some cases), and might very well not be worth paying for when compared to the more band-aid-type solutions of additional LC ltering, hardening of the motor against common-mode currents, etc.
Multilevel inverters obviously need access to separate voltage sources for each output voltage level (and each motor phase, for some MLI topologies), or else must create the voltage levels indirectly (typically with capacitive voltage dividers). An example of the former type of MLI is the
Cascaded H-Bridge, which has found some use in industrial applications because the separate DC voltages can be supplied by a mains transformer with multiple secondaries, but won’t be considered further here because it would require a Rube Goldberg-like arrangement of isolated battery packs and chargers in an EV.
A far simpler way to generate the di erent voltage levels is the capacitive voltage divider (examples of such for 3- and 5-level MLIs shown in Figure 2), which acts just like a resistive voltage divider, though only for alternating currents. Wiring two equal-value capacitors in series will divide the bus voltage in half, and the midpoint will become a new 0 V reference for the MLI (i.e. the power stage of a 3-level MLI generates pulses with amplitudes of +Vbatt / 2, 0 V, or -Vbatt / 2, with respect to the midpoint).
e divider function can be extended by adding more pairs of capacitors, in which case the midpoint of each junction becomes a new voltage level (so the 4-capacitor divider string for a 5-level MLI creates voltage levels of +Vbatt / 2, +Vbatt / 4, 0 V, -Vbatt / 4 and -Vbatt / 2, once again assuming all capacitor values are equal).
As advantageous as reducing the voltage swing of the pulses might be, the law of diminishing returns will kick in at some point, as the sheer volume of the capacitors required—and the complexity of the rest of the MLI—scales directly with the number of voltage levels. It is also important to note that the capacitors in the voltage dividers have to carry considerable ripple current, both at the fundamental (motor) frequency and the PWM frequency, meaning that they will likely need to have relatively large capacitance values (to minimize ripple voltage from the low-frequency currents) and a lm dielectric (to minimize losses from the high-frequency currents), which is not terribly cost- or volume-e ective.
Two of the original multilevel inverter topologies that could be used in EVs are the Neutral Point Clamped (NPC) and Flying Capacitor (FC) types, shown in Figures 3 and 4, respectively, which use the same basic power stage structure but di erent methods of generating the 0 V
Capacitor types of multilevel inverter topologies use the same basic power stage structure but different methods of generating the 0 V output level.
output level. In each of these 3-level MLIs, a phase winding is connected to +Vbatt when the upper two switches are on, or -Vbatt when the lower two switches are on, but the 0 V output level is generated directly in the NPC type by turning on the inner two switches, while in the FC type it is generated indirectly by turning on the upper and lower-inner switches at the same time to charge the ying capacitor, followed by the upper-inner and lower switches to discharge it. Neither of these methods allow for actively balancing charge on the divider capacitors, so there tends
to be more voltage ripple across them, and as mentioned above, the more ripple on the divider capacitors, the higher the THD. e NPC type is easier to control (far easier, in fact), while the FC type has higher fault tolerance (a capacitor is in series with the motor windings during the 0 V state) and can achieve a lower ultimate THD, but it is endishly di cult to control and introduces the thorny problem of how to pre-charge its ying capacitors during startup.
Two MLI topologies that use active switches to better maintain charge balance on their divider capacitors while preserving the ability to handle loads with a wide power factor range (read: induction motors) are the Active Neutral Point Clamped (ANPC) and the T-type, shown in Figures 5 and 6, respectively.
e ANPC MLI replaces the clamping diodes in the NPC with switches that are turned on in conjunction with their respective middle bridge switch to clamp that winding to a capacitor midpoint. e key di erence in operation compared to the passive clamping with diodes is that the on time of the clamping switches can be varied to better control the charge balance on the divider capacitors.
e T-type MLI operates in a similar fashion but saves two switches by replacing the clamping and inner bridge switches with a single bidirectional switch (composed of two conventional unidirectionally-blocking switches wired back-to-back) that directly connects a phase winding to a divider midpoint while allowing for bidirectional current ow when on, and bidirectional blocking when o . e main advantage of the T-type inverter is that it uses a standard triple half-bridge for driving the motor, but that also means the bridge switches must be rated to comfortably withstand the full battery voltage, whereas all of the other MLI topologies considered here stack two switches in series at the outer (highest
voltage) bridge positions (the inner switches only see a fraction of Vbatt), so all of the switches can theoretically be rated for half the blocking voltage (in a 3-level MLI). at’s particularly helpful for current-technology GaN HEMTs as they most commonly top out at a 650 VDC rating, but not so relevant with SiC MOSFETs (or older-technology Si IGBTs) as they are widely available in the 1.2 kV and 1.7 kV ratings that would be appropriate for battery voltages in the 600-800 VDC range. ere are numerous other MLI topologies that are even more complex, but they won’t be considered here—the considerable increase in component count going from a 2-level VSI to any of the 3-level (much less 5-level!) MLI topologies is enough of an obstacle to their adoption as it is. Another obstacle is that all of the MLI topologies require changes to the power stage switch control schemes, which means their development will be far more costly (and take more time than anticipated—but isn’t that always the case?). When one also considers that just the AC voltage divider capacitors required by most MLI topologies will likely take up as much volume all by themselves as a complete 2-level VSI (to say nothing of the ying capacitors also required in the FC MLI), and that a substantial reduction in RF noise emissions—and even common-mode noise currents— can be achieved in the 2-level VSI simply by adding LC lters to each phase output, the argument for MLIs in EVs is a tough one to sell.
Multiphysics simulation software feeds the innovation of electric components, batteries, sound systems, and other automotive parts. By building models that accurately represent the real world, engineers are able to develop, test, and verify their designs faster.
» comsol.com/feature/automotive-innovation
$400 million worth of electric mining equipment from
Australian mining company Fortescue has placed a $400-million order with Chinese heavy equipment maker XCMG (Xuzhou Construction Machinery Group). e sale, which includes over 100 pieces of electric equipment, is the largest single export deal in XCMG’s history. e massive contract includes a wide range of battery-electric heavy equipment, including electric wheel loaders, dozers, semi-trucks and graders, which will be delivered to Fortescue’s mining operations in Pilbara, Australia, in stages between 2025 and 2030.
Fortescue says the use of this equipment will displace millions of gallons of diesel fuel at the company’s iron ore operations over the life of the assets.
“We’re moving rapidly to decarbonize our Pilbara iron ore operations and eliminate our Scope 1 and 2 terrestrial emissions by 2030,” said Fortescue Metals CEO Dino Otranto. “To achieve this target, we will need to swap out hundreds of pieces of diesel mining equipment at the end of their life with zero-emissions alternatives.”
XCMG is embracing electri cation across its product lines. “XCMG is dedicated to long-term sustainable development, o ering high-end, intelligent and green product+scenario full-life-cycle solutions to global customers,” said XCMG Chairman Yang Dongsheng. “ e company has achieved electri cation across its entire product range, and new energy products account for 18 percent of revenue.”
ICF’s new PowerGuide helps utilities identify likely candidates for fleet electrification
ICF provides energy e ciency, electri cation and demand management programs to over 60 utilities across North America, including Duke Energy, Con Edison and National Grid.
Now the company has launched PowerGuide, a cloudbased customer engagement, education and analytics platform designed to provide utilities and their customers real-time insights on the costs and bene ts of eet electri cation.
Drawing from a data collection of over 200 eets across 16 US states and a database of over 600 EV models, PowerGuide o ers utility customers market awareness, education and modeling to help make the transition to electri ed eets easier. e platform is designed to support informed decision-making on vehicle costs, maintenance schedules, grid impacts and community bene ts.
e platform also helps utilities to identify prospective customers for eet electri cation, including businesses and communities that could generate high environmental bene ts.
“PowerGuide gives us the ability to coordinate with customers who will bene t the most from eet electrication, allowing us to make real and lasting impacts on emissions,” said Ryan Hawthorne, VP of Electric Engineering and Operations at Central Hudson, a New York utility that is an early adopter of the platform.
“Utility customers are trying to navigate a complex landscape to make decisions about their eet electrication programs,” said ICF Executive VP Anne Choate. “Our new platform, supported by our industry-leading energy experts, will help utilities successfully guide their customers through their electri cation journey, provide tailored resources, eet insights and ultimately a ordable choices.”
Red Bull North America has become the rst customer for Isuzu’s new NRR-EV Class 5 electric box truck. e medium-duty trucks are now delivering cans of the neon-red sugar-and-ca eine concoction in Southern California. (We haven’t been able to learn how many units Red Bull bought, but a photo provided by the company shows six of the trucks.)
e NRR-EV is available with several battery con gurations, ranging from three to nine 20 kWh battery packs (60 kWh to 180 kWh total). e nine-pack version boasts up to 235 miles of range with a 19,500-pound GVWR. A 150 kW (200 hp) electric motor delivers 380 lb- of torque.
Red Bull’s Isuzu trucks ship with a “big enough” battery capacity of 100 kWh, are tted with a lightweight aluminum 6-bay beverage body, and have a 9,000 lb payload.
Isuzu began assembling NRR-EV trucks at its Charlotte, Michigan assembly plant in August 2024, and plans to expand customer deliveries nationally in Q1 of 2025.
“Watching the NRR-EV evolve from a concept to a viable operating product is a big deal,” said Shaun Skinner, President of Isuzu Commercial Truck of America. “Our teams and our clients have put so much time and e ort into making this happen, and it speaks to our teamwork and dedication to more sustainable transportation solutions.”
omas Built Buses, a subsidiary of Daimler Truck, has announced the launch of the second-generation Saf-T-Liner C2 Jouley battery-electric school bus.
At the core of the second-generation Jouley is the 14Xe eAxle from Accelera by Cummins, an all-in-one unit that integrates the motor, two-speed transmission, disc brakes and rear-drive gear set into one package mounted on the rear axle. is eliminates the need for a traditional drivesha , which omas explains makes the drivetrain lighter, more e cient and less complex. e streamlined design of the eAxle simpli es maintenance by reducing the number of moving parts. e eAxle, coupled with Accelera’s ELFA inverter, delivers power directly to the wheels, enhancing acceleration and torque for a smoother ride.
Accelera’s eAxle enables shorter wheelbase architectures. e second-generation Jouley o ers a new 219inch wheelbase, which improves the overall maneuverability of the vehicle.
“ e 14Xe eAxle elevates expectations for performance, e ciency and serviceability, setting a new standard for the industry. School buses are an ideal application for electri cation,” said Brian Wilson, General Manager of eMobility for Accelera.
e second-gen Jouley is equipped with an 800-volt Proterra battery system. “ e higher voltage along with the eAxle makes it ideal for diverse terrains, including hills and mountains,” omas explains. “ is upgrade also supports the integration of additional components like air conditioning, heaters and other essential features without compromising performance.”
“With features that enhance e ciency, performance and serviceability, the new Jouley delivers unmatched value for both current electric bus operators and new adopters who are ready to embrace cleaner, smarter solutions,” said T.J. Reed, President and CEO of omas Built Buses.
Mining giant Rio Tinto will partner with China’s State Power Investment Corporation (SPIC) to demonstrate battery-swap-capable electric haul trucks at the Oyu Tolgoi copper mine in Mongolia.
e technology is already in use on haul trucks in mining operations in China, and this collaboration will enable Rio Tinto to demonstrate a complete battery-electric truck and charging ecosystem.
e two-year project will demonstrate 8 mining haul trucks (91-tonne payload), 13 batteries (800 kWh), and a robotic battery swap and charging station. Technical experts from Rio Tinto and Oyu Tolgoi have worked closely with SPIC and truck manufacturer Tonly to align the equipment design with Rio Tinto’s requirements. e trucks will perform non-production activities in the aboveground operations—speci cally, tailings dam rehabilitation work and topsoil movement.
Rio Tinto operates about 700 haul trucks across its global operations, of which 100 are classi ed as small or medium class (100-200-tonne payload).
Each battery charge is expected to last up to 8 hours, depending on the work performed, and the battery swap process takes around 7 minutes.
e rst truck is scheduled to arrive at Oyu Tolgoi this year, and the remaining 7 trucks, along with the battery swap and charging infrastructure, will be in operation by mid-2025.
e joint venture between Rivian and Volkswagen could someday supply EV tech to other automakers.
Developing the so ware that is a critical component of modern autos has proven to be a struggle for legacy automakers, including VW, but comes more naturally to an internet-era startup such as Rivian. Volkswagen plans to invest $5.8 billion in the joint venture, which was ocially launched last November. e JV will focus on the development of electrical architecture and so ware for a new line of so ware-de ned EVs, which are expected to start appearing in 2027.
It’s a win/win deal: higher production volume should allow Rivian to negotiate better supplier deals and reduce costs, and VW’s investment shores up the company’s capital position. Meanwhile, Volkswagen will get access to the so ware mojo it lacks. Now Rivian says other legacy automakers want a piece of the action.
“I’d say that many other OEMs are knocking on our door,” Rivian Chief So ware O cer Was-sym Bensaid said (as reported by Reuters). “Any other OEM who wants to make a leap from a technology standpoint, the joint venture today becomes one of the key partners with whom they can make that collaboration.”
Bensaid didn’t name any of the interested automakers, or discuss what stage the talks were at.
Rivian’s next-generation architecture requires fewer electronic control units and signi cantly less wiring than its rst generation (which was already ahead of the legacy brands’ tech), reducing vehicle weight and simplifying manufacturing.
Volkswagen CEO Oliver Blume recently told Der Spiegel that VW might expand the partnership with Rivian: “We are thinking about sharing modules and bundling purchasing volumes.”
Japan-headquartered eVTOL aircra manufacturer SkyDrive, South Carolina-based private jet charter company SAI Flight and Greenville Downtown Airport have signed an agreement to jointly develop air cargo, air taxi and emergency service opportunities using SkyDrive’s aircra .
e three organizations are collaborating with local and state governments and local businesses to design practical routes originating from Greenville Downtown Airport to such destinations as the city center and Greenville-Spartanburg International Airport.
SAI Flight has placed a pre-order for 10 SkyDrive aircra , and its SAI Flight Services division will oversee operations and maintenance from its base at Greenville Downtown Airport.
“ is partnership marks a milestone in our e orts to drive business growth in South Carolina,” said SkyDrive CEO Tomohiro Fukuzawa. “We will continue to deepen our cooperation with local partners, while making strategic preparations to fully realize our innovative business model.”
Construction vehicles and equipment are rapidly going electric, and Volvo Construction Equipment is a major purveyor of electric equipment—so it’s not surprising to nd that a construction site in Stockholm is a testing ground for sustainable construction technologies.
A construction site in Slakthusområdet, a former meat-packing district in central Stockholm that has been rejuvenated as a trendy nightlife destination, has reached a milestone: 50% of its operations are now performed by electric equipment.
Volvo CE electric machines in use on the project include two EC230 Electric crawler excavators and an L120H Electric Conversion wheel loader. ese are supported by two Volvo electric trailer trucks.
“ e rst phase [of the project] showed the e ectiveness of electric machines in performing tasks while signi cantly reducing CO2 emissions,” said Fredrik Tjernström, Head of Electromobility Solutions Sales at Volvo CE. In the next phase, which is scheduled for completion in 2025, Volvo aims to reduce emissions even further, reaching target of 3.5 tonnes of CO2 per SEK 1 million in turnover. “ is is a dramatic decrease on the 11 to 29 tons typically emitted in similar projects.”
e city of Stockholm has set a goal of becoming climate-positive by 2030.
“ is proactive approach creates a ripple e ect throughout the entire value chain, pushing all stakeholders to explore new possibilities and expand the boundaries of what can be achieved in sustainable construction,” said Anna Göransdotter, Project Manager at construction company Skanska.
Daimler Truck has begun series production of the Mercedes-Benz eActros 600 at its plant in Wörth am Rhein, Germany.
Mercedes-Benz’s third electric truck model a er the eActros 300/400 and the eEconic, the eActros 600 is designed for long-haul applications. It boasts up to 500 km of range, depending on the speci c application and ambient conditions. Its three battery packs, each with 207 kWh, provide a total installed capacity of 621 kWh.
e eActros 600 is manufactured on the existing assembly line of the Wörth A-series production alongside diesel-drive trucks. It is the rst electric truck from Wörth to be assembled in one production hall. Its battery-electric drive components, including electric axles, transmission components and front boxes, are supplied by company plants in Mannheim, Gaggenau and Kassel.
e truck will contribute to the complete electri cation of delivery tra c into the Wörth plant by the end of 2026, according to the company.
“Our eActros 600 is addressing the long-haul segment in Europe which is responsible for two thirds of CO2 emissions from heavy road freight,” said Daimler Truck CEO Karin Rådström.
Michigan-based electric truck maker Bollinger Motors, a majority-owned company of California-headquartered Mullen Automotive, has delivered three 2025 Bollinger B4 Chassis Cabs to TEC Equipment dealerships on the West Coast.
e trucks, equipped with 158 kWh battery packs, were delivered to Lacey, Washington; Fontana, California; and Oakland, California.
TEC is headquartered in Portland, Oregon, and has more than 30 locations across eight states.
Swedish EV manufacturer Polestar has started US production of the long-range single-motor variant of its Polestar 3 SUV at the plant near Charleston, South Carolina, that it shares with Volvo.
e model has a certi ed WLTP range of up to 438 miles and a certi ed EPA range of up to 350 miles. It uses the same 111 kWh battery pack as the dual-motor version and has the same 250 kW peak charging capability.
e motor produces 220 kW and 490 Nm of torque and can accelerate from 0 to 100 km/h in 7.8 seconds. e long-range single-motor variant uses the same Brembo braking system as the rest of the Polestar 3 range. It comes with a new entry price in Germany of €79,890.
“ is new entry point for our full-sized agship electric SUV means Polestar 3 is now accessible to even more consumers than before,” said Polestar CEO Michael Lohscheller.
Scout Motors, a brand of the Volkswagen Group that builds rugged, o -road-capable electried vehicles, has announced plans to sell its electric trucks directly to consumers when they launch in 2027, with transparent pricing, online orders and company-owned stores. Dealer groups are already organizing legal challenges.
InsideEVs’ Mack Hogan writes that Volkswagen dealers are “furious” that Scout plans to cut them out of the picture. “To just show these new vehicles that would have t very nicely into VW’s portfolio, it’s like rubbing salt in the wound here,” National Auto Dealers Association CEO Mike Stanton told Automotive News.
California dealers are planning to sue, arguing that Scout is competing with VW’s own dealers. Scout contends that it’s a di erent company than VW.
Scout execs believe they’ll be able to stave o the legal challenges. “We’re highly con dent we’re going to prevail,” Cody acker, Scout Motors’ VP of Growth, told InsideEVs. “We think we have the right position here, and it’s never a bad spot to be advocating for consumer choice and consumer freedom in car buying.”
e car dealer groups’ claims are “what you would expect from a lobbying entity,” acker added. “It’s what you would expect from a trade association. We don’t believe that there’s any validity to the claims.”
“To me there is no doubt that if we can o er a buying process that is transparent, that is seamless, that is fast and that is truly enjoyable, that’s what we’re doing,” Scout CEO Scott Keogh told InsideEVs. “I think these things should be decided by the American consumer and businesses should innovate and compete.”
e legal battles will probably be fought ought state by state over the course of years (as is the case with Tesla’s ongoing saga), and Mr. Hogan notes that Scout does not need to win in every state. Rivian and Tesla get around local prohibitions by simply doing the paperwork for a sale in one state, and delivering the vehicle in another.
Lake Tahoe, the largest Alpine lake in North America, became a transportation hub a er the 1848 California Gold Rush. Mail delivery then took place via a sailboat that visited each community, and steamboats began plying the river in 1863. e advent of automobiles in the 20th century diminished the steamers’ popularity, but the pendulum might swing back to greenwater transit a er FlyTahoe launches its rst Candela P-12 electric hydrofoil boat.
FlyTahoe plans to link the 14 ski resorts that encircle the lake by electric ferry. At 30 minutes, the travel time from the northern to the southern part of the lake via the FlyTahoe ferry service will compare favorably with driving around the lake, which can take up to two hours in the winter.
Because Lake Tahoe does not freeze, the delays and disruptions caused by road closures due to heavy snow will be greatly reduced.
e P-12, thanks to its hydrofoil design, o ers passengers a much smoother ride than traditional ferries and o ers operators improved e ciency.
e P-12 seats up to 30 passengers, with plenty of room to stow skis and bikes. It is 39 feet in length, has a 14-foot beam, and displaces 11.02 tons. e rst P-12 ferry went into service in Sweden at the start of November and o ers green travel among Stockholm’s 14 islands.
e ferry’s manufacturer, Candela recently raised an additional $14 million in its Series C round, putting the company’s total secured funding in 2024 at over $40 million. e investment will help Candela meet the increased demand for its vessels and allow it to ramp up production.
“ is is the dawn of a zero-emission revival in waterborne transportation,” said Gustav Hasselskog, Candela’s founder and CEO.
Lyte o, a new EV merchandising company, has received $3 million in seed funding.
Lyte o’s platform integrates into auto dealership web sites to help them move their EV inventory faster and appraise EV batteries with precision. It provides data-backed sales tools to answer customers’ most prominent questions.
Lyte o’s EV Revenue Platform provides a suite of tools that communicate VIN-speci c EV savings including fuel and maintenance savings, state, federal and local tax incentives, a charger and trip planner, personalized ownership reports and EV data enrichment, adding EV-speci c information to a dealership vehicle’s detail pages.
Dealerships are embedding Lyte o into their web sites to increase EV lead conversion and ultimately sell EVs faster. e company is working on integrating additional tools into the platform, including EV battery testing and health reports.
Lyte o also recently announced a partnership with DealerOn, connecting the company with 7,000 dealers around the US.
By John Voelcker
Kia kicked it off last year with the EV9, but the latest EV three-row utilities—the Volvo EX90 and Hyundai Ioniq 9—are far from the last.
It all started, of course, with the Tesla Model X. Only the second vehicle built and sold in volume by the Silicon Valley EV startup, it was instantly recognizable—for its whalelike shape, its lack of any pretense at a front grille, and most of all the Falcon Wing doors that elevated vertically from the spine down the roof and hinged in the middle as they rose.
Seven years would pass before another maker launched a three-row electric SUV. at was the Rivian R1S, including a seven-seat option, from a di erent EV startup—one that had already launched an EV pickup truck. First deliveries of the R1S took place during 2022; it’s built in Illinois.
at meant the 2024 Kia EV9, on sale for much of 2024 and now built in the US to boot, was a revelation: the rst three-row EV utility from an established carmaker. Its striking looks, capacious third row and 800-volt battery charging positioned it as a mass-market successor to the Model X—which by this point had become a low-volume, high-performance ancillary model to Tesla’s high-volume Model Y, which only o ered ve seats.
Now the 2025 Volvo EX90 has gone into production in the US as well; it can be found at Volvo dealers throughout North America. (See separate feature story on page 42.) It’s the high end of Volvo’s EV range, and is likely to be joined in due course by a midsize EX60, along with the subcompact EX30 now starting deliveries in small volumes.
At November’s Los Angeles auto show, the 2025 Hyundai Ioniq 9 broke cover as well. While it uses many of the same underpinnings as its Kia counterpart, the design and interior ttings di er signi cantly. It too will be US-built—and Hyundai promises 300 miles of EPArated range from every version.
After the launch of Tesla’s Model X in late 2015, seven years would pass before another maker launched a three-row electric SUV, Rivian's R1S.
Hyundai Ioniq 9
And that’s hardly the end of it. e 2025 Cadillac Vistiq will go on sale during 2025 as well, the last of four Cadillac EVs that started with the midsize Lyriq. e full range of four EVs will shortly add the compact Optiq, and top out with the seven-row Vistiq and its even larger sibling, the truck-based Escalade IQ (which will also have seven seats).
While the US EV market as a whole promises to be turbulent over the next few years, it’s clear that the most American of all vehicle types—the seven-seat “family SUV”—is sticking around, whether powered by gasoline or electricity. We wouldn’t bet on the EV models we’ve named here being the full list, either. So far, Chevrolet, Ford and Dodge have no o erings in the segment. Nor do Toyota, Honda, Nissan or Volkswagen. Ditto the German luxury brands. We expect that to change over the next ve years. Meanwhile, US EV shoppers have plenty to choose from—and there’s more on the way.
While the US EV market as a whole promises to be turbulent over the next few years, it’s clear that the most American of all vehicle types—the seven-seat “family SUV”—is sticking around.
Volvo’s flagship all-electric SUV is quiet, competent and safe, but it has its quirks.
By John Voelcker
The 2025 Volvo EX90 three-row electric SUV has been a long time coming. First unveiled in Sweden back in November 2022, its production at a new plant in Charleston, South Carolina, was delayed for many months to resolve so ware issues. e EX90 entered production there in June 2024 for North American and European markets. ( e same plant also builds the sleeker Polestar 3 SUV, with which the EX90 shares underpinnings—that model went into production a couple of months later.)
Now on sale at Volvo dealers, the EX90 is Volvo’s batteryelectric agship, at the high end of the range that’s anchored at its low end by the EX30 subcompact crossover. at EV too has been delayed in its launch, though Volvo has imported a small number of the cars from China to satisfy its earliest reservation holders before production for North American markets starts in Belgium in mid-2025.
We drove a very early production EX90 for most of a day in late summer in and around Newport Coast, California. e temperate weather and an a uent suburb in the most EV-friendly state in the US o ered the perfect backdrop for Volvo’s new agship.
You’re unlikely to see the EX90 and identify it as anything other than a Volvo. e big electric SUV updates the classic shape and proportions of the gasoline XC90, while appearing cleaner and more modern both inside and
The big electric SUV updates the classic shape and proportions of the gasoline XC90, but appearing cleaner and more modern both inside and out.
out. Its wheelbase is identical, at 117.5 inches, but it’s 3.3 inches longer and 1.6 inches taller. e biggest giveaway is the blanking plate between the headlights, where you’d expect a grille. Only tech geeks will be likely to notice a small bulge in the roo ine, just above the windshield, that houses a Lidar sensor for partial self-driving functions to come in the future.
Riding on 22-inch summer tires, our test car was painted in a light beige shade called Sand Dune, which one reporter accurately pegged as “vintage Band-Aid color.”
Inside, the interior was light and airy, helped by the massive glass roof—though the lack of a sunshade made the inside of the roof hot to the touch. (An a ermarket sunshade is o ered in some markets as a dealer accessory.) Interior materials use Volvo’s customary quiet palette, in this case a bio-based leather-free upholstery called Dawn Quilted Nordico o set by a light ash trim that’s lit from the back at night—a startling but memorable touch.
A massive 111-kilowatt-hour nickel-manganese-cobalt battery pack, of which 107 kWh is usable, powers the EX90 Twin Motor.
For the moment, the EX90 comes only as a three-row vehicle, with seven seats provided by the rear bench, or six if you opt for the $500 second-row captain’s chair option.
Behind the steering wheel, the design language could be called the evolved, digital version of Volvo, but it di ers considerably from that of the XC90. A short, wide 9-inch digital display sits behind the steering wheel, similar to that of the Ford Mustang Mach-E (it also adjusts with the wheel), to give running information to the driver. A head-up display also projects speed, navigation directions, and other vital information onto the windshield. A vertical 14-inch touchscreen sits proud of the dash as well; it has permanent icons at the bottom for home, climate control and hazard ashers. Audio, phone and other infotainment functions are activated via widgets.
Volvo and its sister brand Polestar are migrating all their vehicles to use Android operating so ware. at company’s voice recognition is head and shoulders above any other maker’s, though it wasn’t clear how o en the Google Maps navigation system for EVs updated its list of public charging locations. To reassure anxious shoppers who’ve seen GM’s latest EV o erings, the EX90 still o ers cellphone mirroring via both Android Auto and Apple CarPlay.
A massive 111-kilowatt-hour nickel-manganese-cobalt battery pack, of which 107 kWh is usable, powers the EX90 Twin Motor. Both versions are EPA-rated at 300 or more miles combined. e standard powertrain is rated at 296 kilowatts (402 horsepower) and 568 lb- of torque, while the Performance model boosts that to 380 kW (510 hp) and 671 lb- , courtesy of its more powerful rear motor. In both versions, the vehicle moves away from a stop using both motors, but then defaults to cruising on
It’s the car’s overall hush inside that left the biggest impression. This thing is genuinely tomblike.
only the front motor as soon as conditions permit. At roughly 3 tons, the EX90 is faster than you might expect, with quiet, no-nonsense acceleration. But it’s the car’s overall hush inside that le the biggest impression. is thing is genuinely tomblike, which means the optional 25-speaker Bowers & Wilkins stereo can show o its Dolby Atmos sound in utter silence. e dual-chamber air springs and adaptive dampers together isolate occupants from all but the worst road-surface irregularities. Overall, this is one very re ned big luxury SUV.
Within the Driving Dynamics menu, the Performance AWD icon boosts accelerator response and tightens the steering—a er the user executes ve separate actions on the center screen to get there. Drivers can also separately tune the steering feel and the air suspension to So or Firm, although even on the Firm setting, the big Volvo is hardly a sports car.
Regenerative braking is good, as in other electric Volvos, and one-pedal driving can be turned on, o , or set to Auto, which lets the car glide in certain circumstances to use minimal energy and works with the adaptive cruise control to recapture energy while slowing.
Unless they also own a Tesla, XC90 owners looking to make the transition to an all-electric version of the big Volvo SUV will have some adapting to do. A common query among reporters testing the car was whether the company has gone too digital in putting vehicle control functions into soware, versus physical knobs and buttons.
A few examples: Volvo expects EX90 owners to unlock and activate the car using the digital-key function on their Android or Apple phones, though it provides an NFC card as a backup. A fob? Oh, yes, you will get one of those too—though Volvo seems not to think many owners will want one, mentioning only the digital key and NFC solutions at the press launch.
Need something from the glove box? You’ll need to learn where the touchscreen icon to open it sits. All climate control is done via the center screen, though at least occupants can aim the vents by hand. Adjusting the steering wheel and door mirrors is done by tapping on Driver Adjustments in the Quick Controls menu, a er you’ve tapped the car icon on the screen, then using buttons on the steering-wheel center to move them around. e driver’s armrest has only two electric-window switches. Just as in the Volkswagen ID.4, you have to toggle a Front/Rear switch to operate the rear windows from the front. It’s just as irritating in the Volvo as it is in the VW; asked why they’d done this, the team said the plastic saved by eliminating a fourth widow switch contributes to the car’s sustainability pro le. In a luxury SUV of 5,500 to 6,000 pounds, that seems...a stretch.
While one of the media test cars (not ours) locked up solid due to a so ware glitch, Volvo stressed in late summer that it was still re ning the so ware before it released any cars to buyers. So we’ll wait until we get an EX90 for a longer test before weighing in on the solidity and usability of its production so ware. e old advice may hold, though: “You should never buy a product for the promise of what it will one day be.” Owners’ forums and word of mouth should offer at least some guidance as to whether Volvo has squashed the so ware bugs that are all too common in new vehicles, on new platforms, built in new factories.
Sooner or later, Volvo will have any remaining so ware problems licked. at will give the brand a quiet, luxuri-
Need something from the glove box? You’ll need to learn where the touchscreen icon to open it sits. All climate control is done via the center screen.
ous, long-range electric SUV to top its range and serve as a halo vehicle for its EV aspirations. e high-end EX90s now at Volvo dealers start around $90,000, but there will be less pricey models coming in due course as well.
Volvo provided airfare, lodging, and meals to enable Charged to bring you this rst-person drive report.
REE Automotive’s modular REEcorners enable an unprecedented amount of fl exibility in vehicle design.
By Charles Morris
o a large extent, vehicles are designed around their propulsion systems. e rst generation of modern EVs shoehorned an electric motor and a battery into a vehicle that was designed around an engine, a transmission and a gas tank. It soon became apparent to vehicle designers that designing an EV from the ground up would deliver many advantages, including better handling and more space for passengers and cargo. When a certain American startup designed its second-generation vehicle, it put the battery pack on the bottom, in a at platform. is arrangement, which
has since come to be called a skateboard, is the basis of most modern EVs.
An Israel-based startup called REE Automotive has taken the skateboard concept a step further: since there’s no need for a longitudinal drivesha or transmission, why not make the wheel assembly a modular component separate from the skateboard platform, so it can be placed wherever it’s convenient for the design of a particular vehicle? is allows almost unlimited exibility in vehicle design—a huge advantage in the commercial vehicle market, where one size de nitely cannot t all.
e REEcorner integrates the motor, steering, suspension, braking and control into a single compact module. Each REEcorner is completely independent, and is controlled by its own electronic control unit (ECU). e REEcorners are attached to what REE calls a platform (and others might call a skateboard chassis), which contains the battery packs and other vehicle systems. REE’s x-by-wire system (drive-by-wire, steer-by-wire, brake-bywire), which earned FMVSS and EPA certi cation earlier this year, controls all vehicle functions electronically. is eliminates drivesha s, control cables and other hardware vestiges of the ICE era, and allows performance parameters to be adjusted in so ware.
REE is setting its sights on the North American commercial vehicle market—the company currently has 78 sales and service locations in the US, and approximately $60 million worth of orders in its order book at last count. e company has begun customer deliveries of its P7-C electric demo trucks, and eet heavyweights including Penske and U-Haul are evaluating its vehicles.
Charged spoke with Dr. Peter Dow, REE Automotive’s VP of Engineering.
Q Charged: What are some of the advantages of your modular design concept?
A Peter Dow: Our corner can be used on each of the four corners of a truck, so there’s no le - or right-handedness, there’s no front or rear, and that gives you all the exibility that is so important in the commercial vehicle market. We can change wheelbases reasonably quickly and easily for di erent applications, which means that customers haven’t got a massive investment in a platform. ey can take the corners and position them in the optimum setup for their applications.
Q Charged: You’ve got basically two products—the corner and the skateboard chassis, which you call the platform. Does each of these come in just one variety, or are there di erent options?
A Peter Dow: e corner comes in one variety, so it has one part number. We manufacture that as a unit that will t a range of applications. We’ll do a Class 3, Class 4 or Class 5 truck with the one corner—the systems have been sized to apply to all of those di erent trucks. e platform is also a modular design, but it can be sized to
We can change wheelbases for different applications, which means that customers haven’t got a massive investment in a platform. They can position the corners in the optimum setup for their applications.
meet di erent applications. So, we could position three of our battery packs in a truck to give you one wheelbase and a certain range, or we could make the wheelbase longer and put four battery packs in.
e corners are very much the building blocks. e rest of the components—the mechanical chassis, the batteries, the cooling systems—are designed to be exible, to expand or contract to meet what customers need.
Q Charged: Each corner includes a motor, but this is not an in-wheel motor.
A Peter Dow: No. e corner has an inside and an outside component, and the inside component has all of the drive mechanisms. We have a three-in-one electric drive unit (EDU) that contains the motor, the gearbox and the inverter, and there’s one of those in every corner.
We have a steering actuator, which operates on a 48-volt system, which controls the steering, so you get steering on all four corners, both front and rear, which is another bene t. We also have a brake actuator that controls your brake pressure. We have a hydraulic brake system—fairly conventional—but the electrical actuator that controls it sits within the corner. All that—drive, braking and steering—is controlled through the electronic control unit (ECU) that sits in the corner.
If you need to replace a corner, it’s a very simple operation of a few bolts to replace it with a new unit and have the truck operational again. We’ve shown examples of replacing that whole corner within an hour.
Q Charged: You have an electric truck for sale now, but you can also work with customers to custom-design vehicles for their speci c applications.
A Peter Dow: Yeah. We’ve got a network of dealerships in all the key states that we want to be operating in within the US. ey’ll be o ering a standard product—our P7-C, a Class 4 chassis cab—as a starting point. It has a single wheelbase as an application to show the di erent kind of boxes, platforms, etc, that can be up tted to that. We’re also working with other customers on di erent ideas—maybe a longer-wheelbase version, maybe a kind of walk-in van.
For the customers, we’re looking at what they need in terms of volume, weight capacity and maybe EV range. For some, range is a critical part, so we can look at optimizing the battery packs for them. For some, the weight capacity is critical, and we can optimize the vehicle for that. We have an ability to listen to our customers, understand what they want, and then easily modify the end product.
Q Charged: e platform can be up tted to create just about any kind of vocational truck, right?
A Peter Dow: Correct. We’ve been working closely with a number of up tting partners and trying to make it so that you can put di erent applications onto our truck. One of the bene ts of the REE system is that we’ve got a very low platform, but we also have the ability to build what we call a high- oor application, so you can go to the conventional dock heights that you normally get with a box truck. Within the chassis design, we’ve put in connection points for both the electrical and mechanical up tters, so it is very much an easy application for them to use. e up tters have given us some really positive feedback that it’s been an easy truck to work with.
Q Charged: Do you have some prototypes out there of di erent types of trucks?
A Peter Dow: Yes, we have a number of trucks in the US within our dealer network that have di erent con gurations on them. What we want to do is to get people driving our trucks, and one of the messages we want to get across is that our by-wire system is designed to give a lot of bene ts in terms of the drivability of the trucks. We’ve had a lot of feedback from people that have driven our trucks. At ACT in Las Vegas, we had numerous people driving the truck on the ride-and-drive event, and the feedback was that it’s more like driving an SUV, not like driving a Class 4 truck. You
The upfitters have given us some really positive feedback that it’s been an easy truck to work with.
can actually control the feeling of the steering wheel, the feedback you get. We’ve got four-wheel steer, so the maneuverability at low speeds is really high.
Q Charged: So, the drive-by-wire system allows you to customize the driving feel of the truck?
A Peter Dow: Absolutely. Conventionally, in a lot of trucks you look at maybe putting some customization into the throttle, you could maybe change the acceleration pro le, but we can look at the amount of steering feedback and the amount of rear steer that we’re bringing in. At the moment, at low speeds we bring in the rear, so it gives you a lot more maneuverability. At higher speeds we take the rear steer out. We can tune that to what customers want. We can also do things like change the amount of regeneration we have from the electrical motors. It’s very easy for us to change things because it’s a so ware change, not a hardware change.
Q Charged: So maybe one customer likes a Ferrari feel and another customer prefers BMW-like handling.
A Peter Dow: Exactly. For example, if we had one customer that was a bakery, maybe he wouldn’t want the Ferrari because he doesn’t want to squash his cakes. Somebody might want to have a very gentle acceleration pro le because he’s got goods in the back that he wants to protect.
Q Charged: And somebody else might want plenty of acceleration because they want to get to the next job fast.
A Peter Dow: Absolutely. at’s the ethos of understanding what the customer wants, and within reason, we can provide whatever they need.
Q Charged: How many of the components do you manufacture in house? I know you work with a lot of Tier 1 suppliers.
A Peter Dow: Yes, we do. We own all the design. We tend to use our supply chain to do the main manufacturing activities, and we do an assembly process. We assemble the corners here in the UK. We have what we call our Integration Center, which is our robotic assembly line for the corner. And that takes some systems and some pre-assembled manufactured parts, and assembles that into the full corner. en we use contract manufacturers to assemble the rest of the truck in terms of putting the components together. We’ve designed everything, and have actually gone through a number of iterations of design. For example, the corner design itself, we started three years ago and since then, we are probably on the fourth iteration in terms of optimization. We’ve just nished a long-term durability test on the corner, where we’ve actually simulated a 20-year usage. So we know that we’ve got the durability that is going to be needed out there.
We’ve designed the system so that we can have different battery packs installed into our chassis.
Q Charged: What can you tell us about your suppliers? Who’s making the motors and the battery packs?
A Peter Dow: We have a number of options. At the moment, we have two di erent motor suppliers, and the same for our steering system and our braking system. We won’t go into details of who they are, but we don’t want to be constrained to one supplier because there’s always a risk associated with using one supplier. Same with our high-voltage battery—we’ve designed the system so that we can have di erent battery packs installed into our chassis, so we are not constrained to one supplier. We want to be agnostic so that we can go with di erent suppliers. Some customers say, “We want to use certain battery packs,” or “We’ve got an association with a certain supplier we want to use.” We’ve got our supply chain in place, but we want to have that exibility as well.
Q Charged: Tell me more about your modular battery pack. e customer can select di erent sizes. Can they also select di erent chemistries or di erent formats?
A Peter Dow: Again, we’re pretty agnostic to the chemistry and the battery pack itself. At the moment
we have a modular system based on essentially NMC Li-ion 42.8 kWh battery packs. In our P7-C application, we have three packs, which gives us 128 kWh total capacity for the truck. But we can look at replacing that with di erent options. We can also look at other power sources if need be, because all we worry about is making sure we have 400 volts going to our corner system. We’ve always had a design philosophy of being power source-agnostic. We can look at di erent battery cells, or even a range extender.
Q Charged: So you could add a gas or diesel engine if a customer wanted that.
A Peter Dow: Yes, if the customer decides.
Q Charged: Tell me more about the charging.
A Peter Dow: e platform is broken down into what we call ve zones. Zone one at the front has all of the cooling system: pumps, radiators, compressors, etc. Zones two and four actually house the corners. And then zone three in the middle has the batteries, the DC-DC converters for the 12-volt system on the truck, the 48-volt system for our control system. It also has the onboard charger, which can support both AC and DC charging. At the moment, we support 22 kW AC charging and up to 140 kW DC charging.
We can also look at other power sources if need be, because all we worry about is making sure we have 400 volts going to our corner system.
Q Charged: We’ve written about di erent kinds of motors, and we’ve had experts describe the pros and cons of di erent kinds. What kind of motors do you like? Do you see using di erent ones for di erent applications?
A Peter Dow: Our initial application is a high-speed induction motor. We’ve got about a 22-to-1 ratio on the gearbox. We’ve got a lot of innovation in the rest of the truck, but we wanted to keep the motor technology kind of as established as possible. We don’t need to do anything special with our motors for the application we’re looking at, as long as we’ve got decent e ciency. We also have an application with a permanent magnet motor. e ability to be able to ex between di erent motor types in the future is something we believe would be helpful.
Q Charged: Give me a brief history of the company and your background.
A Peter Dow: I’ve been working in automotive new product development for 30 years. I’ve worked across a number of global automotive consultancies, technology startups and Tier 1 suppliers, including Lotus Cars,
Geely Auto, Ricardo Technical Consultancy, Getrag Transmissions and Tata Group.
I joined REE 3 years ago. REE has been active for about 10 years in di erent forms, and came out of stealth mode about 4 years ago. I came in to help build the engineering activity.
We’ve got a team of about 150 people here in the UK working on mechanical engineering, vehicle engineering, and some so ware engineering. We do all our vehicle tests and development work here, but we also work very closely with the team in Israel that are doing a lot of the electrical system development, the so ware development. We’ve also got a team in the US that are looking at a er-sales and sales support.
We’re selling just in the US at the moment. We’ve got our development here in Europe, and we are looking at other markets, but we’re very much focused on the US at the moment.
Q Charged: We’ve seen a lot of commercial EV companies come and go. Is there anybody out there that’s o ering the kind of thing that you are?
A Peter Dow: In some ways, we feel we’re a bit of a last man standing, and we are quite proud of that because we’ve been really clear on what we want to deliver. Because we’ve got our by-wire and our corner technology, we are very di erent. When we go to the trade shows, we never really look around because we don’t think we’ve got any direct competition. It’s not something that distracts us. We just carry on and stay focused on getting our rst product out there, the P7-C.
ABB Electri cation Canada has announced a licensing agreement with Canadian electrical equipment supplier Black Box Innovations to manufacture EV energy management systems. e systems will use Black Box’s patented technology that supports the installation of EV chargers on an existing electrical panel.
e range of energy management systems will be available through ABB’s distribution partners across Canada in 2025. ABB’s team will also collaborate on the design and manufacture of new models, components and parts licensed under the ABB Electri cation brand.
Black Box Innovations’ technology enables EVs (or other devices) to be charged when there is su cient electrical capacity available and to automatically stop, or reduce usage, when capacity is limited. e technology is compatible with existing residential or commercial electrical services from 60 A to 200 A, and is designed to eliminate the need for electrical service or panel upgrades.
“Our collaboration with Black Box Innovations will help address our customers’ current challenges,” said Mike Shenouda, Canada Region Leader and General Manager, ABB Installation Products. “Together we will streamline the installation process and provide reliable and accessible EV energy management that meets their evolving needs.”
Smiths Interconnect’s new socket boasts more efficient energy transfer, uses no lead or beryllium
Smiths Interconnect touts several advantages of its new Hypertac Green Connect socket for CCS chargers. Designed to IEC 62196 and SAE J1772 standards, Hypertac Green Connect o ers “unprecedented energy transfer, durability and long-term performance.”
Smiths explains that Joule heating (aka resistive heating) within CCS sockets causes power loss, leading to increased charging time.
e Hypertac Green Connect contact o ers “unmatched low contact resistance and temperature rise even a er 10,000 insertion and withdrawal cycles.” e hyperboloid contact reduces heat buildup, and the improved crimp design of the socket o ers increased contact area between the contact body and the multi-stranded cable. e sockets are built to endure up to 60,000 mating cycles.
e connector is designed to minimize insertion and extraction force, making the ergonomics of the plug more user-friendly while reducing wear and tear on the connector.
Hypertac Green Connect technology is lead-free and beryllium-free, and the connectors are fully compliant with RoHS and REACH regulations, which restrict the use of hazardous substances in products. Eliminating beryllium and lead signi cantly reduces the burden of compliance documentation, according to the company, and eliminates the future costs associated with environmentally safe disposal of these materials.
Reliant and GM Energy are rolling out a new program that will o er free nighttime charging for Chevrolet EV drivers. Some 150 Chevy dealerships in Texas can now o er the plan upon vehicle purchase.
e Reliant Free Charge Nights plan, available to Reliant electricity customers, provides a monthly bill credit that o sets the energy charges incurred from charging a qualifying EV between 11 pm and 6 am. Customers must designate one EV to receive the charging credit in their GM Energy Smart Charging Portal.
Reliant Energy, a subsidiary of NRG Energy, provides electricity to over 1.5 million Texans.
“As we continue to shape the future of EV charging and energy management for our customers, our work alongside Reliant in Texas is a sign of our commitment to working with industry leaders to facilitate more solutions that make EV adoption an easy decision,” said Aseem Kapur, Chief Revenue O cer, GM Energy. “ e Reliant Free Charge Nights plan is a great example of how an automaker and an energy company can work together to build the ecosystem to support the all-electric future.”
“With a reputation for bringing innovative new plans and products to market, Reliant continues to make power personal for Texans. We’re excited to help Chevrolet EV drivers o set the cost of charging their vehicle all while having access to a renewable electricity plan,” said Rasesh Patel, President, NRG Consumer.
Concord Paci c Development has unveiled what it calls the world’s largest EV charging parkade in Burnaby, British Columbia, which provides capacity to charge nearly 2,000 vehicles simultaneously.
“Parkade” is a Canadianism for a multi-story parking garage. e Burnaby parkade o ers 1,974 underground parking spaces, which have 24/7 access to EV charging. e developers contend that the electrical infrastructure at the facility is robust enough to supply power to all access points at the same time.
e parking spaces are distributed in two separate zones, each with two entrance and exit points for ecient vehicle access and egress to and from the parkade. Each plug-in is individually monitored and each residence is only billed for the charging power it consumes.
“ is milestone is in keeping with our longstanding commitment to sustainable future communities,” Hui said. “We have a portfolio of wind, solar and hydro projects that has grown signi cantly over the past 15 years and has now expanded to ve Canadian provinces. Creating infrastructure like this helps close the loop on sustainable transportation options.”
“Achieving carbon neutrality is a community-wide e ort that includes residents and businesses in Burnaby, and it’s great to see Concord moving forward with this development,” said Burnaby Mayor Mike Hurley. “Making it easier for folks to drive electric vehicles, ride their bike or take transit will help us cut down on carbon emissions and achieve our climate goals faster.”
Since Tesla opened up its Supercharger network, demand from drivers of other brands of EVs has been massive. So massive that Lectron, a provider of portable chargers, adapters and charging stations for all charging standards, has ramped up production of its NACS-to-CCS adapter to as many as 12,000 units per week.
“Our expanded production guarantees that every EV driver with a compatible vehicle can access the largest fast charging network in the US,” said Lectron CEO Christopher Maiwald.
Lectron’s Vortex Plug is an adapter that enables non-Tesla EVs equipped with CCS1 charging ports to charge at Tesla Superchargers. It’s rated for 1,000 volts and 500 amps.
Ford, GM, Rivian, Polestar and Volvo gained access to Tesla Superchargers in 2024, and other automakers are in the pipeline, so the demand for Tesla adapters is expected to grow. Lectron is strategically strengthening its relationships with automakers, retailers and dealerships.
“ e NACS-to-CCS adapter serves as an essential component for automakers transitioning to the NACS standard, enabling them to o er their customers seamless access to Tesla’s Supercharger network,” says Lectron.
EVgo to install up to 480 new fast EV charging stalls at Meijer grocery stores in the Midwest
EV charging network EVgo is expanding its longstanding partnership with Meijer, a Midwest grocery retailer, to bring more public EV charging infrastructure to Meijer store locations throughout its six-state footprint. EVgo plans to deploy up to 480 new DC fast charging stalls at Meijer properties across Michigan, Illinois, Wisconsin, Indiana, Ohio and Kentucky.
Meijer currently o ers EV charging options at more than 35% of its store locations. To date, EVgo has opened 24 public fast charging stalls at six Meijer stores in Michigan and Ohio. As part of the expanded partnership, the company expects to open up to 30 new stations at Meijer stores by the end of 2026, and 30 more by the end of 2027.
“Fast charging should be an e ortless part of drivers’ daily routines, and nothing is more routine than a trip to the grocery store,” said EVgo President Dennis Kish. “EV adoption is growing in the Midwest, and adding hundreds of new fast charging stalls with the region’s leading supercenter shows our companies’ shared commitment to delivering an elevated charging experience for EV drivers.”
“Access to EV charging is an essential pillar of our broader sustainability goals, and we’re proud to partner with EVgo as part of our ongoing environmental stewardship e orts,” said Erik Petrovskis, Director of Environmental Compliance and Sustainability at Meijer.
XCharge North America, a provider of DC fast charging solutions, is working with Swiss startup the Grensol Group to address the challenge of reducing the endof-life waste associated with EVSE—speci cally EV charging cables and modules.
E ective immediately, XCharge NA will provide broken or worn-down EVSE materials to Grensol and its research partner Worcester Polytechnic Institute (WPI), for the development of an industrial recycling solution for such equipment. Grensol will use its metals recovery and photolysis technologies, among others, to process the waste and produce useful raw materials, including critical metals for new charging stations.
“EVSEs have a particularly short useful life due to constant wear and tear, so the need for a recyclable material solution is the driving force behind this partnership,” said Rajiv Singhal of Grensol. “Partnering with XCharge NA will provide us and WPI with more materials and information for our development of breakthrough lowcost circular materials solutions for the future that keep resources onshore and materials in use for longer, while avoiding carbon emissions.”
“ is recycling-focused partnership will allow us to achieve an improved product lifecycle by promoting sustainable solutions,” said Aatish Patel, co-founder and President of XCharge North America, “We’ll work with Grensol to determine the best mechanical, chemical and thermal recycling methods to create a continuous lifecycle for our charging materials and reduce our carbon footprint.”
Germany-based PHYTEC, which produces embedded components for industrial electronics, has partnered with EV so ware charging rm PIONIX introduce the EVCSCube, a development kit for EV charging systems.
EVCS-Cube combines PHYTEC’s phyVERSO-EVCS charger controller and PIONIX’s BaseCamp operating system, which is based on the open-source rmware stack EVerest. e ready-to-use development kit is designed for EV charging station developers and manufacturers to use in order to start testing and developing their products quickly.
ere are two versions of the kit. EVCS-Cube Basic includes all components such as power meters, contactors, residual current detection, charging indicators and a stop button. e EVCS-Cube PoC enables DC charging, and includes additional components such as DC power supply unit, insulation monitoring and power meter. Both versions can be optionally expanded with WiFi, LTE, display, NFC, fan, temperature sensor and other modules.
e Basic version is available as an AC test kit. e PoC version will follow during the rst quarter of this year.
“ e package of tried-and-tested charging electronics and future-oriented operating system supports common industry standards (IEC61851, ISO 15118-2 (AC+DC), DIN SPEC 70121 (DC) for CCS and TYPE 2 charging solutions, OCPP 1.6 and OCPP 2.0.1), application scenarios such as Plug & Charge, and the communication protocols relevant for communication with the infrastructure, vehicle and payment system,” the companies said.
e California Air Resources Board has approved an update to the state’s Low Carbon Fuel Standard (LCFS) that will make it more di cult for biofuel producers to generate regulatory credits, and seems likely to result in the largest share of credits going to support electricity for EV charging.
e program, which is funded by fossil fuel suppliers whose product emissions exceed legislators’ emissions targets, delivered $2.8 billion to suppliers of biofuels and electricity for EVs last year.
BloombergNEF estimates that the program will provide something between $500 million and $1.4 billion to the charging sector per year, based on today’s credit prices. Recipients will include EV charging infrastructure providers, grid operators and automakers. Biofuels producers such as Phillips 66 and Marathon Petroleum will see their funding reduced.
Bloomberg predicts that other states and countries around the world will be taking note of the updates, as many have similar programs or are planning to introduce them. Like California, some have found that an oversupply of credits has caused prices to fall.
LCFS credit prices fell from $187 in 2021 to $66 recently. Credits in Germany’s program, the GHG quota, have been trading for less than $100 from previous highs of more than $400.
BNEF expects California’s new rules to reduce the supply of credits and stabilize credit prices. Under the new rules, transport fuel emissions must be at least 30% below 2010 levels by 2030, and 90% below by 2045. e previous target was a 20% reduction by 2030.
BNEF expects EV sales to reach 65% of California’s passenger vehicle sales by 2030, making electricity generation the largest producer of credits in 2030. BNEF predicts that biofuels’ share of the credits will fall from 74% in 2023 to 45% in 2030.
AMPECO o ers a white-label, hardware-agnostic EV charging management platform that covers public, private and home charging and currently serves over 160 clients across 60 markets and powers some 120,000 charging stations on all 6 continents. e customer list includes (in Europe) E.ON Drive Infrastructure, ChargeGuru, INDIGO Group, Wattif and Elaway; as well as (in the US) Free2Move. (Read our Q&A with AMPECO CEO Orlin Radev at www.chargedevs.com.)
Now AMPECO has raised $26 million in a Series B funding round led by Revaia, with support from existing investors Cavalry Ventures, BMW i Ventures and LAUNCHub Ventures, bringing total funding to $42 million since the company’s founding in 2019.
e new funding “will fuel AMPECO’s growth plans while accelerating product enhancements and expanding into key markets like Western Europe, the Nordics, the UK, North America and Southeast Asia.” e company aims to double the size of its team over the next two years.
“With this funding, we’re poised to further drive innovation in EV charging management so ware, helping our clients build and scale robust charging networks,” said Orlin Radev. “ e positive market feedback has reinforced our vision for 2025 as we prepare to launch new platform capabilities focused on operational excellence and network scalability.”
GM and EVgo surpass 2,000 co-branded public fast EV charging stalls in the US
US automaker GM and EV charging provider EVgo have surpassed 2,000 co-branded public fast charging stalls. e partners’ 2,000th stall is part of a new charging station in Murrieta, California, which o ers ve 350 kW fast chargers capable of serving up to ten EVs simultaneously.
EVgo and GM have collaborated to build fast charging stalls at more than 390 locations in 45 metropolitan markets across 32 states. e collaboration focuses on grocery stores, retail complexes and city centers, and also aims to serve customers who are unable to charge at home, including renters and those living in multifamily dwellings.
e companies opened their 1,000th public fast charging stall in August 2023. ey plan to complete a total of 2,850 DC fast charging stalls nationwide, including 400 public fast charging stalls across major metropolitan markets in Arizona, California, Florida, Georgia, Michigan, New York and Texas.
“EVgo’s longstanding collaboration with GM has helped us bring public charging to communities in more than 30 states across the US,” said EVgo President Dennis Kish. “As we work to deploy our rst agship destinations next year, we are thrilled to celebrate today’s milestone of reaching 2,000 fast charging stalls built through this program.”
When EV charger manufacturer Tritium fell from its perch in April, it caused tremors in the EV charging industry, as the company has sold 13,000 chargers in 47 countries, and claimed some 30 percent of the US market share for DC fast chargers in 2023.
In August, India-based Exicomm agreed to take over the company, promising to keep Tritium’s factory in Lebanon, Tennessee open. As far as we know, the company has continued to operate with minimal disruption— good news for its customers, which include some of the biggest names among US charging providers.
Now Tritium has appointed Arcady Sosinov, a seasoned leader in the EV charging industry, as its new CEO.
“With a proven track record in driving innovation, Arcady brings with him a deep understanding of the industry and the expertise needed to deliver transformative products to market,” says Tritium. “As the founder and former CEO of FreeWire Technologies, Arcady demonstrated exceptional vision in pioneering clean energy solutions.
“With the unwavering backing of Exicom, Tritium now has the nancial and operational stability and security to accelerate the development and delivery of next-generation products that rede ne the future of EV charging.”
Commercial EV charging providers are gradually rolling out chargers compliant with the new Megawatt Charging System (MCS). Now UK charge point supplier Project EV has presented a charger that supports vehicle-to-grid (V2G) technology, which could provide an additional source of income for electri ed commercial eets.
As Electrive reports, Project EV’s new charger was “designed for high-demand charging environments such as commercial locations, large eet operations and highway rest stops.” e power cabinet can support up to ten outlets, and is compatible with liquid-cooled and aircooled systems. Few other technical details are available at the moment.
e new charger was developed in collaboration with the UK’s Department for Energy Security & Net Zero and Innovate UK. It is part of the Electric Heavy Goods Vehicles— rst roll-out and demonstration of V2X and grid decarbonisation project, which aims to demonstrate the “V2G services potential of electric HGVs (eHGVs)— load-balancing, frequency stabilization and resilience.”
e project is headed by Kaasai Services and received 1.4 million pounds in funding from the UK government.
“Over the past year, our team has worked tirelessly to design and deliver the cutting-edge hardware for this trial,” said Richard Pink, Chief Technology O cer at Project EV. “We are immensely proud of the innovative charging solution we’ve developed, featuring exceptional versatility with multiple charging guns tailored to meet diverse customer requirements.”
Multinational power management company Eaton and San Francisco-based home EV charging provider Treehouse have partnered to accelerate the adoption of EV charging and electri cation in US homes.
Under the agreement, Eaton will be the preferred supplier of technology, including its AbleEdge home energy management ecosystem and Green Motion EV chargers, for Treehouse residential installations that are designed to facilitate EV charging, energy storage, heat pumps and more, and powered by Eaton home energy management systems. e collaboration will enable installation programs at scale for automotive OEMs, utilities and hardware manufacturers.
Eaton and Treehouse will provide consumers with pricing and access to licensed electricians for installations. Treehouse will apply Eaton’s hardware options to speci c installations and scope projects to ensure that the most e cient systems are deployed at scale. e Eaton Certi ed Contractor Network will have access to Treehouse’s end-to-end installation platform that supports scoping, design, permitting and installation for both retro t and new projects.
“We’re con dent this collaboration will streamline and expedite US electri cation projects, driving consistency, reliability and sustainability—while saving time and money,” said Paul Ryan, General Manager of Connected Solutions and EV Charging at Eaton.
Pando’s minimalist solution allows more EVs to charge in less space at less cost, with fewer reliability issues.
By Charles Morris
During times of rapid technological development, many companies address the new technology by adapting the trappings of the old (Remember internet portals and online malls?). However, those who think “outside the box” (Remember that tired old phrase? It’s back!) are sometimes able to unlock major savings by jettisoning vestiges of the old way of doing things.
Back in the previous century, we had to stop at gas stations to fuel our cars. Now we need to replace those with EV charging stations, right? Well, maybe not. Pando Electric’s solution for multifamily properties provides simple, compact boxes equipped with standard NEMA 240-volt receptacles, and requires drivers to use the portable charging cables
that come with their cars. is means a property can install more charging ports in less space, for much less cost—while eliminating interoperability issues and vandalism risk as a side bene t. But it doesn’t mean sacri cing must-have features such as load management and revenue metering.
Pando founder Aaron Li explained to Charged why he thinks his company’s solution is the best one to address today’s biggest impediment to EV adoption.
Q Charged: ere are many avors of EV charging, and each has its own technical requirements and its own business opportunities. You’re targeting just one segment—the multifamily EV charging market.
We’re laser-focused on the multifamily housing market, because we think this is the biggest pain point for EV adoption in our country.
A Aaron Li: We’re laser-focused on the multifamily market, because we think this is the biggest pain point for EV adoption in our country. e biggest hurdle for EV adoption is charging, and 80% of charging happens at home. e issue of single-family home charging has been solved, but multifamily home charging, we see that as a big disaster. at is why Pando is focusing on that market. We do two things—EV charging and energy management—and we do them really well.
Q Charged: Your system doesn’t use a charger with the typical 1772 plug. As I understand it, you simply provide a 240-volt outlet, and the driver uses their own portable charger. Is that pretty much the way it works?
A Aaron Li: Yes and no. Yes, if you look at the form factor, it is an outlet, so it has all the advantages over an EV charger, such as small size, low cost and zero maintenance. Also, it ts into the tightest parking spaces. But no, it is not as simple as it looks. We beefed it up with a lot of core technologies. Some safety features are baked into the outlet. We also o er revenue metering, so it can be used to report exactly how many kilowatt-hours are used for billing purposes, and features such as tap-and-charge.
If you look at the form factor, it is an outlet, but it is not as simple as it looks. We beefed it up with a lot of core technologies.
Users can activate the charging outlet without the need to connect to a server, and the adaptive load management functions through the local system. We have to connect all the charging outlets, so that they do not blow up the panel, and individually each can support as high as 10 kilowatts—this is like 50% higher than the average Level 2 EV charger. So putting all that together, yes, it is much simpler than a regular EV charger, but it supports all those technologies, making it the most powerful and the smartest charging outlet.
Q Charged: So pretty much any portable charger will work with your system, as long as it has the right AC connector?
A Aaron Li: Yes. We see a big problem with the EV charging industry—a lot that’s happening is about the connectivity. at means not only connecting to the cloud, but also the charger and the car need to talk to each other. ere’s a lot of issues there. ere’s also a debate between the J1772 connector and the NACS, which is de ned by Tesla. ere is going to be tons of confusion down the road between those two standards, and all those interoperability issues, but we believe we’ve found the shortcut. With the NEMA 14-50 outlet we are o ering, all that is gone. It supports all di erent OEMs, without adapters.
Q Charged: Did you develop your own proprietary so ware?
A Aaron Li: Yes, and our system relies on two things: number one, we have an open system for the application; number two, we have vertical integration between the hardware and so ware.
Regarding the open system, Pando is part of OCA, the Open Charging Alliance. We believe OCPP should be the
standard, so if some tragedy happens to a company like Juicebox [which recently went out of business], other companies can take over their networks. at’s the disengagement between a so ware application and the hardware. And to be an advocate for that, we are the rst EV charging outlet company that has its so ware backed by OCPP.
We have done a lot of things that are rsts. We are the rst high-power charging outlet. We are the rst charging outlet that has a GFCI baked in. We are the rst one to have revenue grid metering. Our API is also open, so that means the Pando charging outlet can work seamlessly with other property technology so ware, such as smart parking and more—a lot of services can be integrated.
We believe not only that an open platform is important, but also that so ware-hardware integration is critical. To give an example, we see tons of companies that only make so ware. ey white-label the hardware from Taiwan, from China, from Vietnam. It does not work. It makes the system very fragile when it comes to the rmware and the hardware.
With Pando, we do not see that issue. We design our own hardware. at is why we can de ne all the features
so beautifully to t the needs of our customers. We have temperature, voltage and current protection because we designed it that way to be safe. We have tap-and-charge through near- eld communication [NFC] so that users can activate the charger through their mobile phones. And we have adaptive load management through the ConnectUS application, which means all the chargers are connected to each other to support the best possible load management. All of that is impossible if you build an EV charging company by only making so ware.
Q Charged: I believe a big part of the reliability problem is that there are so many di erent companies involved: hardware, so ware, installation. Are you providing a turnkey service?
A Aaron Li: Yes. We believe that the EV charging industry has a big challenge: people think when you sell the hardware the problem is solved. It’s not the case. We see many charge points that are well-engineered pieces of hardware, but they are dead, not working at all—because the companies fail to think of the lifetime value. Pando does it di erently. Number one, we o er a turnkey solution. at means besides hardware, we also think about the installation, the commissioning and even the local incentives and rebates.
Number two is that we care about value for the EV driver. at means we push the uptime to the limit. at means if some hardware is broken, we do not repair, we replace. We want to ensure high uptime because we do not want the customer to be disappointed. at is not only about operations and maintenance—it is baked into the design of our hardware from the beginning.
Q Charged: We did an article about a condominium complex in Palo Alto that’s a customer of yours. Are there any other customers you can talk about?
A Aaron Li: We have many customers. e range is nationwide, from a big apartment company such as Great Star to condo buildings in Manhattan. One exciting project I can bring up is in New York. ey had all ChargePoint EV chargers. ey weren’t happy with them. ey break all the time, and it limits them from upgrading the system. When they have more EVs, people have no chargers to use. ey got us, they decided immediate-
Most EVs come with an OEM-provided cable, and the value of that is often underestimated.
ly, within 48 hours, they wanted to upgrade. ey upgraded from 10 ChargePoint chargers to 30 Pando charging outlets. Not only does this serve more EVs in a much more tightly packed parking space, but they also leverage the existing capacity of their panel because of our schedule-based load management so ware. ere are tons of buildings out there waiting to be retro tted for the EV charging solution that the residents deserve. e best solution is to scale up the EV charging infrastructure without upgrading the panel or the utility connection. Coming back to the project in East Palo Alto, this has been a perfect example not only for the city, but for the whole state, and we want to spread it nationwide. If you want to provide scalable and equitable EV charging to people living in multi-family dwellings, this is the right solution. It is so e cient in terms of spending and in terms of operation and maintenance, that we believe this is not one of the solutions—this will be the solution.
Q Charged: So, the customer brings their own portable EV charger. If they don’t have one, can they buy one from you?
A Aaron Li: Yes. Most EVs come with an OEM-provided cable. e value of that is o en underestimated. at cable comes with the warranty from the car, so if something happens, the OEM is on the hook. And that mobile cable is the best solution for that car, because it’s provided by the OEM. It is tested all the way to t that vehicle. But if I l buy a used car, or if I lost the cable, what do I do? You can purchase such a cable online for about $200. [Editor’s note: Make sure you’re buying a cable that’s safety-tested and certi ed.]
Whenever you move out of the apartment, that investment will continue working for you because when you’re moving into a single-family house, very likely behind your dryer, you’ll see a similar NEMA 14-50 outlet. We believe this is a really good idea. On one hand we think
it is superior compared to a regular EV charger. On the other hand, if we consider the cordless EV chargers used in Europe, we see that our system is the best. A lot of other startups are doing that, but you can only buy that particular cable from that startup. If the company dies or if you move out of the multi-family, that cable will be wasted. But Pando’s cable, the NEMA 14-50, this is the standard for the whole of North America, has been for over a hundred years. [Editor’s note: itselectric, for one, uses a J3068 detachable cable, which it says is the same standard cable used in the EU and the UK.]
Q Charged: Are there any interoperability issues at all? Have you ever had a problem with a charger that won’t work with your plug?
A Aaron Li: Simple answer is no. We did intensive tests. We’re humble enough to say that there may be some corner cases, but so far we have seen no interoperability issues with any EVs using our solution.
Q Charged: Once the system is set up, your customers pay you a monthly fee for maintenance and so ware support?
A Aaron Li: Yes. It’s like 20 bucks per month, or $200 per year. at fee powers the maintenance, the operation, the customer service, the app, the in-app billing with credit cards, the ongoing so ware support and the warranty, everything. We keep the price very low for two reasons. Number one, we’re con dent in our hardware. It’s very unlikely to fail. Number two, we believe this will lower the barriers for the public to adopt EVs.
ere’s also a business model where they don’t have to pay that fee. We just mark up the per-kWh rate so that we are still recouping that cost. ey pay us and then we reimburse the property. We are working on a system in which we’re able to provide sub-metering—that’s part of PG&E’s new initiative, but that’s not going to be rolled out for a while.
Q Charged: Tell me about your load management so ware. Does it allow the property owner to set di erent parameters?
A Aaron Li: Sure. e background for load management is that about 95% of apartment buildings are existing
Not only is the installation of those WiFi repeaters, those hotspot routers, expensive and diffi cult and labor-intensive, but those are also one of the major failure points.
ones, they’re not new buildings. And in California, above 92% of the existing buildings are having capacity issues to support so many EVs. e buildings were not designed that way, and when there’s a capacity issue, it’s super-expensive to make a call to the utility, to upgrade the transformer. It’ll take you years and millions of dollars. at’s why, if we want to support so many EVs in multi-family, we have to do load management. is is not something nice to have. is is a must-have.
I see a lot of companies that do xed load management. at is, if I have 20 kilowatts, I divide that into 10 pieces. Every car gets 2 kilowatts. at means if I only have one car, the other 18 kilowatts are wasted and it’ll take that driver over 30 hours to get a full battery, which makes zero sense. So, the number-one idea for Pando is to be able to adaptively increase the load.
Given this principle, our algorithm is a schedule-based load management. at means the charging speed is so fast that when every car nishes charging, it’ll only take you about 4 to 5 hours. For overnight parking in an apartment, you park the car about 12 to 15 hours, so it’s easy for you to get every car fully charged for 3 times the possible EV charging capacity for a regular EV charger.
We take that one step further. If some vehicle wants to jump the line—say they have to pick someone up at the airport at midnight—they can pay a premium to get charged rst. In that sense, we optimize the whole system. You have to do it this way, otherwise in multifamily, given the limited capacity, if you do not do holistic load management, it is physically impossible to charge every car at the same time.
e last piece I want to mention here is our hardware-so ware integration. Typically all the chargers
If the WiFi is down, if the cellular is off—for example if there is a big storm—the charger will still work.
WiFi is down, if the cellular is o —for example if there is a big storm—the charger will still work. And I want to take it one step further—down the road the whole system will communicate with other energy appliances in the building. We put that into our roadmap. We believe that load management is such a beautiful thing, it should not be limited to EV charging, it should include all the other appliances, say the water heater, the thermostat.
Q Charged: You said you are laser-focused on multiunit properties. But it seems to me this could be useful for other applications too, like city curbside charging. Do you have plans to target other markets in the future?
A Aaron Li: We de nitely have a lot of potential customers who are super-interested in our solutions, say for eets, student housing and even curbside charging. But as a company we need to see, given the limited bandwidth, how we want to spend our energy and time Our technology is applicable to many di erent scenarios, but we want to cut to the biggest pain point, which is multi-family charging.
Q Charged: So that’s a business decision, not a technical limitation.
right now on the market, they need every charger to be connected through WiFi or cellular to the cloud. But in Pando we see that as a big pain for two reasons. Not only is the installation of those WiFi repeaters, those hotspot routers, expensive and di cult and labor-intensive, but also those are one of the major failure points. ey fail all the time. So that’s why we designed our hardware-soware integration so it’s no WiFi, no cellular, no problem.
Q Charged: Where does the load management so ware run? Is there a computer at each installation?
A Aaron Li: Every outlet has a processor board inside it, running on Linux. It is very powerful—it recognizes others in the same network and they talk to each other. If the
A Aaron Li: You are absolutely right. And although our main business development is towards multi-family, the real estate industry, there are customers knocking on our door, and we are not rejecting them—we have one o ce building right now that is under the design phase. Pando is not just a company trying to sell our hardware. We are trying to build the standard to lead the industry. We want to make a robust, healthy, cordless EV charging concept, and make it nationwide, because we believe this is the best thing that can lead to a sustainable future. Not only are we actively participating in lobbying, we want to raise the awareness of the public that cordless EV charging is safe, it’s powerful and it’s very smart and cost-e ective. To make that happen, I’m happy to talk with anyone in the industry. I’m even talking to our competitors. I’m talking to the people who set the rules. I’m talking to the legislators and the utilities to promote the idea of cordless socket-based EV charging. And to that end, I’m happy if someone shares a similar vision, wants to reach out to us and build a coalition.
APRIL 02-03, 2025 IN AACHEN/GERMANY WWW.BATTERY-POWER.EU
The 17th International Advanced Battery Power Conference on 02-03 April 2025 will set new superlatives in terms of the number of participants, exhibitors, diverse lecture program and more than 350 poster authors! Over the course of two days, international scientists, developers, and users will provide in-depth insights into the latest developments and solution strategies in battery technology – from innovative materials and production techniques to energy density, lifetime, secondary use, and recycling.
At the parallel Vehicle-2-Grid Conference, you can discuss with experts from business, the public sector and science how this potential can be realized in your company or field of activity! The focus will be on current trends and implementation possibilities in the coming years.
Organised
by
By Charles Morris
t’s not news to Charged readers (or anyone who makes EV road trips) that public charging has a reliability problem. But whose problem is it? Many of the entities that installed public EV chargers over the last decade (businesses, municipalities, utilities) appear not to have realized that ongoing maintenance would be required, and when stations go down, it can be di cult to get any of the players involved (hardware manufacturers, so ware providers, network operators) to take responsibility.
IStartup ChargerHelp will take on that responsibility, and commit to keeping your EV chargers up and running—for a price. Under the company’s Reliability as a Service contract, customers pay a xed monthly fee for unlimited Operations & Maintenance (O&M) support and a guaranteed level of uptime.
ChargerHelp’s business model is a bit like that of an insurance company or an extended warranty provider, in that ChargerHelp takes on the risk that charging stations will malfunction. However, the company does much more—it proactively maintains the charging stations to try to prevent malfunctions.
As CEO Kameale Terry explained to Charged , the issues that cause chargers to go down tend to arise at the connection points between di erent so ware systems, and typically fall outside the scope of product warran-
ties. ChargerHelp addresses the gaps and smooths out connection points.
rough a large data set collected from eld service work orders, the company has identi ed patterns in how so ware failures occur, and it uses this data to detect failures and understand station behaviors that might otherwise go unnoticed. Furthermore, ChargerHelp continuously trains its model to improve its ability to provide support, whether on-site or over the air.
Q Charged: Public charging reliability is a scandal, so I imagine there’s plenty of business for a company like yours. Who are your customers?
A Kameale Terry: Most of our customers sit in three di erent verticals: utilities, eet operators and resellers. ey tend to be people that have multiple so ware providers, multiple hardware providers, and are coming out of warranty on the hardware.
Q Charged: Do you take over the reliability guarantees that they had from the hardware providers?
A Kameale Terry: Most of them don’t have reliability guarantees—actually, reliability guarantees don’t necessarily exist in the industry. at is what we are o ering.
Most folks who deploy infrastructure don’t believe that it’ll break, so a product like ours doesn’t necessarily make sense to them yet. They think, “The hardware warranty will cover the issues that I’m experiencing,” or, “The software provider will send someone out.”
They don’t understand that that’s not in their contract. Neither the software provider nor the hardware provider technically have to provide support, if they can’t confirm that it’s their problem. And most of the problems that we see sit in a gray space. Is this a communication issue? A firmware issue? An issue with the charge management system? Those are the problems that we see making up most reliability issues, and they don’t necessarily fit into anyone’s responsibility. That’s why I built the company.
I started out at EV Connect, where I was in charge of EV driver support. Often when drivers phoned in, they would describe behavior of a station that I couldn’t see in our log data. I led the deployment of EV charging infrastructure in the US, Canada and Australia, and I always saw instances of stations behaving in ways that weren’t coming through on Open Charge Point Protocol.
In 2020, I decided to leave EV Connect to help my mom with some health problems. Then I wrote a curriculum, because I had found that most of the electricians or technicians that were being sent out to repair charging stations didn’t know what OCPP was. They didn’t have an EV.
The LA Cleantech Incubator bought a license to that curriculum, started to train people, and I was trying to get folks placed. My contacts at EV Connect were like, “We don’t want to hire field service staff—we’re a soft-
ware company—but if you hire them, we will hire you.”
So my first contract was with EV Connect and Southern California Edison on the Parks and Schools program, and I started to deploy technicians there. But what I quickly found out was that simply having a body on site did not necessarily mean you would fix the station, because there was so much troubleshooting involved. Then I got interested in getting data from the field and figuring out how to find patterns. Eventually that moved into Reliability as a Service and developing this product that we felt confident enough to offer at a fixed price.
Q Charged: So, in four years, have you seen improvement? Can we say that reliability in general is better than it was then?
A Kameale Terry: I think so. When I first started this company, people would say, “Wait, stations break?” They didn’t realize it was a problem. Another issue was the lack of an agreed-upon calculation for uptime. People would claim, “I’m 99.9% up,” but everyone had their own way of calculating it. We worked with the California legislature to create a bill called the EV Charging Reliability Act, which passed last year. It established an agreed-upon formula and includes stipulations regarding down stations.
Q Charged: I’m amazed at how many charger deployments seem to have no provision for maintenance. When they start breaking, nobody knows who’s supposed to be responsible.
The reliability issues often have little to do with the physical components. It’s usually a software sensor communicating with the hardware that fails, or a handshake issue.
For the rest of the industry, the lack of vertical integration and limited emphasis on O&M means missing out on those learnings. When multiple companies are involved, everyone has di erent priorities. For example, if the rmware you just pushed isn’t working on my speci c hardware, will you prioritize a new rmware update if I represent only 1% of your deployed assets? Probably not.
While this fragmented system is a challenge, I believe it’s a solvable one. Look at computer systems, the internet, or telecom—those industries faced signi cant interoperability issues, yet they gured it out. Collaboration and information sharing are key.
A Kameale Terry: I’m less amazed, mainly because this is a new technology, and people were relying on hardware warranties. What many didn’t realize is that these devices are smart assets, and integrating so ware into the built environment requires a completely di erent approach to O&M [Operations & Maintenance].
All the stations come with parts warranties, but the reliability issues o en have little to do with the physical components. It’s usually a so ware sensor communicating with the hardware that fails, or a handshake issue. During the early deployment phase, I don’t think the industry could have predicted these challenges.
On top of that, the business models in this industry are problematic. In many cases, companies are losing money le and right. Was the business model robust enough to support a more comprehensive O&M package? I don’t think so. In the early days, I doubt customers would have been willing to pay for it.
Q Charged : A lot of people tell me that part of the problem is that so many deployments involve a dozen different companies—hardware, software, site owner, network operator, payment provider, maybe a utility or a municipality...
A Kameale Terry: I would agree, but I don’t think this has to remain the problem. Tesla has a vertically integrated system, and invested early in eld service operations. When labor is on-site, they gather unique data points to build a better system. O&M should be a part of the ywheel that improves reliability because you’re continuously learning from the eld.
Q Charged: at’s a good point, and maybe when people say, “It’s because there’s all these di erent companies involved,” that’s just a cop-out, because they’re not really identifying where the problem lies.
A Kameale Terry: Yeah, we have to collaborate. I’ve been advocating for a council of CEOs from network providers and hardware manufacturers to agree on a bare minimum implementation of OCPP. Right now, everyone implements it slightly di erently. ere are fundamental elements in the OCPP code that aren’t being implemented, and OCA [the Open Charge Alliance] doesn’t test for them today. We need to sit down and agree to share this data set and implement OCPP in a standardized manner.
e next question is: who regulates this? How do we ensure that implementations serve the best interests of the entire ecosystem? Other industries have tackled this by establishing baselines that everyone must follow for the good of the industry. Companies can still compete on other aspects, but reliability shouldn’t be something we compete on.
For example, we were part of the ChargeX Consortium, which created a standard set of error codes. OCPP includes about 30 suggested error codes, but only 10 are required. With every new rmware push, additional error codes emerge, but there’s no standardized understanding of what those error codes mean or, more importantly, what actions they require.
e Consortium wrote a white paper, but the critical question remains: who is committing to implementing these standards, and who will hold everyone accountable? Honestly, I’m young, and I don’t have all the answers. I look to history for guidance—how have industries in
competitive markets done this before? How do you take a white paper, get everyone to agree, and set a deadline for implementation?
Q Charged: An all-too-common story: thick reports get written, but no action gets taken. So, if I understand correctly, these common error codes have not yet been implemented.
A Kameale Terry: As far as I know, it’s only a white paper today. I am not aware of anyone making commitments to the implementation of those error codes.
Q Charged: Tell us about your EMPWR so ware package.
A Kameale Terry: Today, if something breaks, typically you have to pay an hourly rate. If it breaks again, you have to send someone out again. A lot of these issues are so ware-related, and not necessarily only for one device. Usually if I nd a so ware problem, I’m nding it across multiple devices. But what typically happens is that you send someone on site to cycle breakers, the site starts working a little bit, and then in three months, you have to go on site to cycle the breakers again. With the EMPWR platform, we touch stations every single day. We’ve touched over 30,000 charging stations in the last four and a half years, and we have over 19 million unique data points that we’ve gotten from the eld. We intercept charge management data, and we try to paint a better picture. Why is that station getting stuck? Where is the failure? Is it the hardware? e car? e so ware? Are there any patterns in rmware updates? If I’m seeing an
Companies can still compete on other aspects, but reliability shouldn’t be something we compete on.
issue in California, am I also seeing an issue in New York? All the data that we’re getting from the eld is going into a central mainframe. We’re also bringing in a lot of the OCPP data, and we’re looking for patterns. e last time I solved a problem, could I have detected that problem ahead of time? at’s what EMPWR does, but the product itself is called Reliability as a Service, and that’s a xed contract where we’re putting a bet on not having to roll a truck, and increasing uptime over the air.
Q Charged: In your Annual Reliability Report, you de ne categories for some common so ware issues that cause problems for drivers, including Ghost Stations (which appear online but are actually o ine) Zombie Stations (which appear o ine but are actually online) and Dead-End Stations (which fail to deliver a charge despite appearing operational). I encountered a Zombie Station the other day—PlugShare says it’s been down for months, but I went there and it was working. Would that be a communications problem?
A Kameale Terry: It could be comms or it could have been put in a free vend mode. A free vend mode is when the so ware on the station is turned o and the station is able to operate as a dumb station.
Q Charged: Well, you may not approve, but I love dumb stations. I plug in, they work, I charge. My favorite is at a grocery store near my house—it’s been there for 10 years. It’s not connected to anything—no network, no app. It’s retro and it’s rusty, but it always works.
A Kameale Terry: I think what you just said is the problem of the industry. It’s a fact that the so ware o en doesn’t work. People just want to charge. So no, what you’re saying is true. A lot of EV drivers believe that, and it puts the onus on the industry to gure it out.
Q Charged: I’d like to add one to your list, and I’ll propose a name for it: a Crap App station. It’s a station that requires some special app to use, and the app doesn’t work for some drivers. You download the app and set up your password, and then it just won’t work. And having to use all these di erent apps anyway— that’s too complicated.
A Kameale Terry: Yes, you’re totally right. I was chatting this morning with Hubject’s North American CEO Trishan Peruma. at’s what they’re working on—you just use one app for all the stations—but he said there still are certain network providers that want to own the EV driver and don’t want to do roaming, don’t want to sign on. at goes back to my previous point that we have to gure out where we’re going to compete and where we’re going to collaborate. Electric vehicles are new, they’re stylish, people like them. e car OEMs are doing their part, and we as an ecosystem have to make sure that we’re doing our part.
Q Charged: How far are we from that ideal ecosystem? Are we making progress?
A Kameale Terry: I think we have one year. ese things that we’re chatting about—roaming, Plug & Charge, more reliable infrastructure, I think we have until the end of 2025 to save consumer trust. ere’s a lot of consumers today that do not trust the infrastructure, so my goal for 2025 is to put together this coalition around error codes. My goal is to support organizations like Hubject and Chargeway, to highlight companies that are doing things to improve the driver experience and not to grab a quick dollar.
Q Charged: When you say we have a year, you mean that if we fail to x the reliability problems in a year, we’re facing disaster?
A Kameale Terry: I think so. I think a lot of people are looking at the administration change, and people are getting antsy about EV adoption. In 2024 we were faced with a lot of negative press around broken charging stations. If we have another year of people having poor experiences, you’ll see more charging companies go under, and it’ll be hard to see consumers, and folks who are doing eet electri cation, putting their dollar into EVs. But I
think if we continue to highlight the businesses that are doing well, if we double down on reliability, it will show that it wouldn’t matter what administration is in o ce.
Q Charged: Do you have any competitors that are doing something similar to what you’re doing?
A Kameale Terry: Not today. ere are people that do traditional O&M, like rolling a truck, and some that say they can use AI to solve things over the air. But solving how we are solving? No. Selling an unlimited truck-roll package? No. We will roll trucks forever for this xed cost. All my investors think I’m crazy. But we’ve been doing well so far because I think we’ve gured out how to solve this problem.
Q Charged: Do you get involved with commercial eet charging as well?
A Kameale Terry: Yeah, we do. We’re selling an insurance-like product, so we’re looking at the risk level
of covering the uptime of particular charging stations. So, we look at our data set to price it out, and if with some projects we have enough data to say, “Oh no, that station is probably going to be down 40%, 50% of the time,” or we know that a company does not prioritize reliability, I’m not going to cover that station.
We will work with eet operators, but there are some so ware and hardware makers that I can just look at and say “You’re always going to have a problem.” Because we’re like insurance, I have to be mindful of my risk, right? ere is a certain makeup of assets that I can cover, but we can’t just cover everybody.
Q Charged: I imagine you have to carefully analyze each potential customer and get a detailed picture of their system before you sign them up.
A Kameale Terry: Exactly. And we have a lot of procurement managers working with us, because we can give them a breakage rate. We worked with McKinsey with our data set, and for every hardware or so ware product, we can tell you what your breakage rate and your O&M costs will likely be.
Q Charged: So, companies that provide Charging as a Service should be natural partners for you, because you can advise them on what brands of hardware are the most reliable.
A Kameale Terry: Absolutely. We work with some turnkey providers. We call them our reseller partners— they will resell our insurance product as their O&M. ere are some hardware partners that we are working with as well—they add our Reliability as a Service as part of their hardware package.
What we o en see with people who end up hiring us, is that they have multiple so wares, multiple hardwares, and on top of that, they may have a load management system. And load management so ware doesn’t always play nice with OCPP in regards to the integrations and how it understands error codes, or even how it understands the other so ware.
We just put out a case study with one of our depots. ey have about 100 buses, and we were seeing core interoperability issues between the load management system and the multiple manufacturers. at’s hard for
Americans, we like to spend money on good products. If you can wow us, make our lives easier in an affordable way, we will give you a dollar.
depots, working with multiple platforms, so we tell a lot of eet operators, either work with a company like ours or go with one so ware, one hardware. Sometimes mixing multiple so ware and hardware products will open you up to more pain than anything else.
Q Charged: What do you see ahead with the new US regime? Are they going to sabotage the EV industry?
A Kameale Terry: We just had the LA Auto Show. Almost 80% of those vehicles were electric. At the Super Bowl last year, all of the car commercials were electric car commercials. And I don’t think that’s because of federal incentives. I think the OEMs have bought the idea of being able to create a better experience through an electric vehicle. Do they care about the environment? Maybe not, but you can put in more technology, you can drive e ciency, you can do a lot without having an ICE.
e other thing that I pay attention to is the competitiveness of the US. I was in Mexico City recently, and half of the EVs, if not all, were from BYD. e EV market outside of the US is booming, and if we’re going to be competitive in the global space, we have to gure something out. So that’s a big indicator to me that I don’t think is connected to the federal government.
I think now it’s in the hands of the consumer. Americans, we like to spend money on good products. If you can wow us, make our lives easier in an a ordable way, we will give you a dollar. So now it’s just like, “Let’s make good experiences.” I think that it’s all reliant on the EV charging experience at this point. And we need to make EVs more a ordable. ere’s a lot of things outside of government participation that the private sector needs to gure out for itself.
• EV, DC FAST CHARGING
• INFRASTRUCTURE
• WIRELESS CHARGING
• AUTONOMOUS VEHICLE
• DIGITAL SIGNAGE EV
• FLEX & HI POWER CHARGING
• E-MOBILITY, EVS & HEVS
• SITE DESIGN & MANUFACTURE
• CHARGER UPTIME
• MICRO & POWER GRID
• ZEV, AFV, BUS & TRUCKS
• ADVANCED BATTERY
• FUEL CELLS, LI-ION, H2
• EV EQUIPMENT SUPPLY
• BATTERY TESTING & CERT
• OEM PRODUCTS & COMPONENTS
• DIESEL TO EV & COMMERCIAL EV
• ENRGY DEMAND EV FLEETS
• EV, PHEV, HYBRID, FLEET CHARGEING
• TRANSPORTATION ELECTRIFICATION
By Charles Morris
n the early days of the internet, a million owers bloomed, and entrepreneurs all over the world came up with ideas—some good, some bad, some really weird. As I’ve o en noted (and as regular readers may be tired of hearing), today’s evolving EV ecosystem has much in common with the Wild West internet frontier era.
Back then—just as on today’s EV scene—companies came and went as their products went in and out of fashion. Concepts that were touted as essential for a few months or a few years are now forgotten. ese tend to fall into certain categories, which we see recapitulated in today’s EV universe.
New tech always has limitations, and companies invent workarounds. For the internet, the constraint was bandwidth. For EVs, it’s range and charging speed. Once these limitations ease, some transitional technologies become obsolete (RealAudio, ISDN). Others stick around (MP3s), because the limitations still exist to some extent, and/or because they’ve established themselves as trusted standards.
In the automotive world, the hybrid is the epitome of a transitional technology, but it’s likely to be with us for a while, not only because cars last a lot longer than internet so ware trends, but also because, while 250-300 miles of range is enough for the vast majority of drivers, there are some who simply need more.
Battery swapping is a transitional tech that we thought was history a er Tesla abandoned it and Better Place went under. However, NIO is making a go of it, as are a couple of e-truck startups. It seems handy for commercial e-bikes (delivery services), but we’ll see if it nds other applications.
Seeing the new tech through the lens of the old
People o en assume that structures that supported the old tech will simply be updated to accommodate the new. Others (thinking “outside the box”) realize that certain concepts are no longer relevant. Internet “shopping malls” were a thing in the very early days, before it sunk in that there’s no physical location in cyberspace. Web “portals” attracted much media coverage and investment until people grokked that browser bookmarks accomplish the same thing.
In the early EV era, many overestimated the demand for public charging infrastructure, imagining that gas pumps would need to be replaced by EV chargers. In fact, most charging happens at home (or for urban drivers, at a curbside near home), so the main function of public charging is to enable long road trips. (Prime locations are along highways and at destinations such as hotels.)
We’ve already seen one wave of ill-conceived charger rollouts crash and recede—lured by federal incentives, local
governments installed Level 2 chargers at city halls, colleges and other locations where installation would cost them nothing. No one had yet coined the term “site selection,” and in hindsight, we can see that there were never going to be customers at these locations.
We may be on the verge of another upheaval. Pando founder Aaron Li (see our feature story on page 66 of this ish) considered the challenges of providing EV charging for multi-family dwellings, and asked, “Who needs conventional charging stations?” Most EV drivers can get a portable Level 2 charger provided from their OEM—one that’s speci cally designed to work with their EVs. Instead of ripping up parking lots, waiting for utility upgrades and installing bulky stations, Pando simply runs some conduit and installs a little box with a standard 240-volt NEMA outlet (billing, load management and other necessary features are built in).
Could the very concept of vehicle ownership become a vestige of the ICE era? Vehicle autonomy is more of a quiet evolution than the revolution that some once envisioned, but it’s coming. at said, robotaxis aren’t going to replace private cars any time soon. Some of us need to own cars to get our work done and most of us simply want to own things.
For commercial eets however, choosing not to own trucks can be a fast track to electri cation, and the concept isn’t new. Companies have always leased trucks for nancial reasons. Given the advantages of vertical integration in the eet infrastructure eld, it’s no surprise that practically every charging provider is o ering Charging as a Service these days. Some companies (Zeem, Revolv, Zenobe) are going further and o ering Fleet as a Service—they own not only the infrastructure but the trucks too. If you could electrify your whole eet overnight by simply signing up for a monthly fee, why wouldn’t you?
In the converse of the previous category, people envision new structures for the new tech, failing to realize that the structures of the old are still t for purpose.
In our day, many have envisioned EV “charging hubs,” with well-lit canopies, rest rooms, and food and drink for sale. More recently, people are realizing that such handy facilities have been hiding in plain sight all along—they’re called “convenience stores” in the US (the term “gas station” was already dated), or “motorway services” in the UK. Truck stop chain Love’s has been getting rave reviews from EV drivers for its fast chargers, which have their own canopy (and even their own logo) right next to the gas pumps—where poor old ICE drivers can see how much fun the cooler kids are having.
n Charging the Future of Mobility: Markets, business models and trends
n Experience innovations: Smart charging systems, electric vehicles and mobility services
n Knowledge2Go: Conference, exhibition forum, test drive and much more
n Industry meeting point: 110,000+ energy & mobility experts and 3,000+ exhibitors at four parallel exhibitions