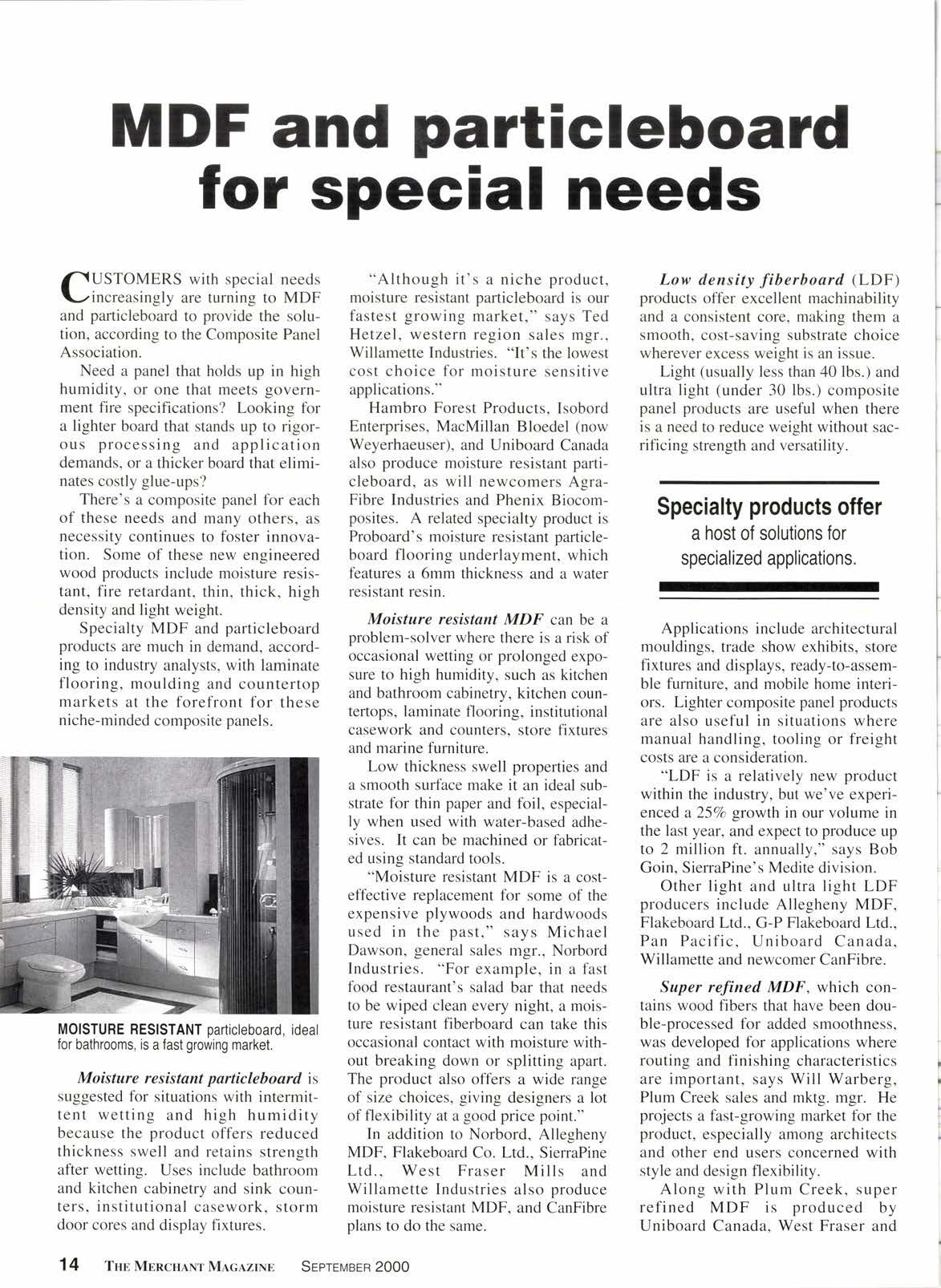
5 minute read
MDF and particleboard for special needs
f\USTOMERS with special needs
\-rincreasingly are turning to MDF and particleboard to provide the solution, according to the Composite Panel Association.
Need a panel that holds up in high humidity, or one that meets government fire specifications? Looking for a lighter board that stands up to rigorous processing and application demands, or a thicker board that eliminates costly glue-ups?
There's a composite panel for each of these needs and many others, as necessity continues to foster innovation. Some of these new engineered wood products include moisture resistant, fire retardant, thin, thick, high density and light weight.
Specialty MDF and particleboard products are much in demand, according to industry analysts, with laminate flooring, moulding and countertop markets at the forefront for these niche-minded composite panels.
"Although it's a niche product, moisture resistant particleboard is our fastest growing market," says Ted Hetzel, western region sales mgr., Willamette Industries. "It's the lowest cost choice for moisture sensitive applications."
Hambro Forest Products. Isobord Enterprises, MacMillan Bloedel (now Weyerhaeuser), and Uniboard Canada also produce moisture resistant particleboard, as will newcomers AgraFibre Industries and Phenix Biocomposites. A related specialty product is Proboard's moisture resistant particleboard flooring underlayment, which features a 6mm thickness and a water resistant resin.
Moisture resistant MDF can be a problem-solver where there is a risk of occasional wetting or prolonged exposure to high humidity, such as kitchen and bathroom cabinetry, kitchen countertops, laminate flooring, institutional casework and counters, store fixtures and marine furniture.
Low thickness swell properties and a smooth surface make it an ideal substrate for thin paper and foil, especially when used with water-based adhesives. It can be machined or fabricated using standard tools.
Low density fiberboard (LDF) products offer excellent machinability and a consistent core, making them a smooth, cost-saving substrate choice wherever excess weight is an issue. Light (usually less than 40 lbs.) and ultra light (under 30 lbs.) composite panel products are useful when there is a need to reduce weight without sacrificing strength and versatility.
Specialty products offer
a host of solutions for special ized applications,
Applications include architectural mouldings, trade show exhibits, store fixtures and displays, ready-to-assemble furniture, and mobile home interiors. Lighter composite panel products are also useful in situations where manual handling, tooling or freight costs are a consideration.
"LDF is a relatively new product within the industry, but we've experienced a 257o growth in our volume in the last year, and expect to produce up to 2 million ft. annually," says Bob Goin, SierraPine's Medite division.
MOISTUBE BESISTANT particleboard, ideal for bathrooms, is a fast growing market.
Moisture resistant particleboard is suggested for situations with intermittent wetting and high humidity because the product offers reduced thickness swell and retains strength after wetting. Uses include bathroom and kitchen cabinetry and sink counters, institutional casework, storm door cores and display fixtures.
"Moisture resistant MDF is a costeffective replacement for some of the expensive plywoods and hardwoods used in the past," says Michael Dawson, general sales mgr., Norbord Industries. "For example, in a fast food restaurant's salad bar that needs to be wiped clean every night, a moisture resistant fiberboard can take this occasional contact with moisture without breaking down or splitting apart. The product also offers a wide range of size choices, giving designers a lot of flexibility at a good price point."
In addition to Norbord, Allegheny MDF, Flakeboard Co. Ltd., SierraPine Ltd., West Fraser Mills and Willamette Industries also produce moisture resistant MDF. and CanFibre plans to do the same.
Other light and ultra light LDF producers include Allegheny MDF, Flakeboard Ltd., G-P Flakeboard Ltd., Pan Pacific, Uniboard Canada, Willamette and newcomer CanFibre.
Super refined MDF, which contains wood fibers that have been double-processed for added smoothness, was developed for applications where routing and finishing characteristics are important, says Will Warberg, Plum Creek sales and mktg. mgr. He projects a fast-growing market for the product, especially among architects and other end users concerned with style and design flexibility.
Along with Plum Creek, super refined MDF is produced by Uniboard Canada, West Fraser and including fire retardancy in their requirements, continued growth is projected. It is produced by CanFibre, Medite and Willamette. foil doors, according to Flakeboard Co.'s Shotbolt.
Willamette Industries.
"Super refined MDF's uniform results make it a viable, less costly substitute for solid wood, especially with painted finishes," Warberg says. Uses include raised panel doors, interior mouldings and other architectural millwork and store fixtures.
"Superior raw materials are essential to what we do," says Kevin Leuning, general mgr., American Millwork Inc., a manufacturer of primed and prefinished mouldings and millwork for residential homes and luxury hotels. "This MDF substrate is consistent all the way through, with no pits or holes, allowing us to achieve the smoothness our customers exDect."
Thick MDF, usually more than 1-112", is used for residential and commercial furniture, architectural mouldings and millwork, door stiles and rails, and picture frames. Pan Pacific, for example, makes three densities of fiberboard in thicknesses up to 3".
"Thick MDF has solved some major issues in a variety of situations," says Bob Metzger, sales mgr., Creative Products, Inc., a custom profile wrapper. "For example, it saves labor and time to use a single thicker panel without having to glue parts. Of equal importance, a single piece is more dimensionally stable than two glued-up pieces, avoiding problems of bow and warp for designs like large sleigh bed rails or crown moulding. And thick MDF offers excellent machinability."
THICK MDF helos create dramatic veneerwrapped architectural and industrial mouldings.
FIRE RETARDANT particleboard provides the perfect wall substrate for public spaces where lire retardancy is a concern.
Fire retardant particlebourd from Willamette Industries was developed 25 years ago in response to stricter building code requirements. The smooth, grain-free Class 1 rated substrate is used in malls, offices, hospitals, hotels, restaurants, elevator cabs, jet ways and other locations where fire retardancy is a concern.
"Our fire retardant particleboard is used primarily for wall panels since it's an excellent substrate for both wood and laminate veneers," Hetzel explains. "And it can be routed, drilled, bullnosed, beveled and precision-machined."
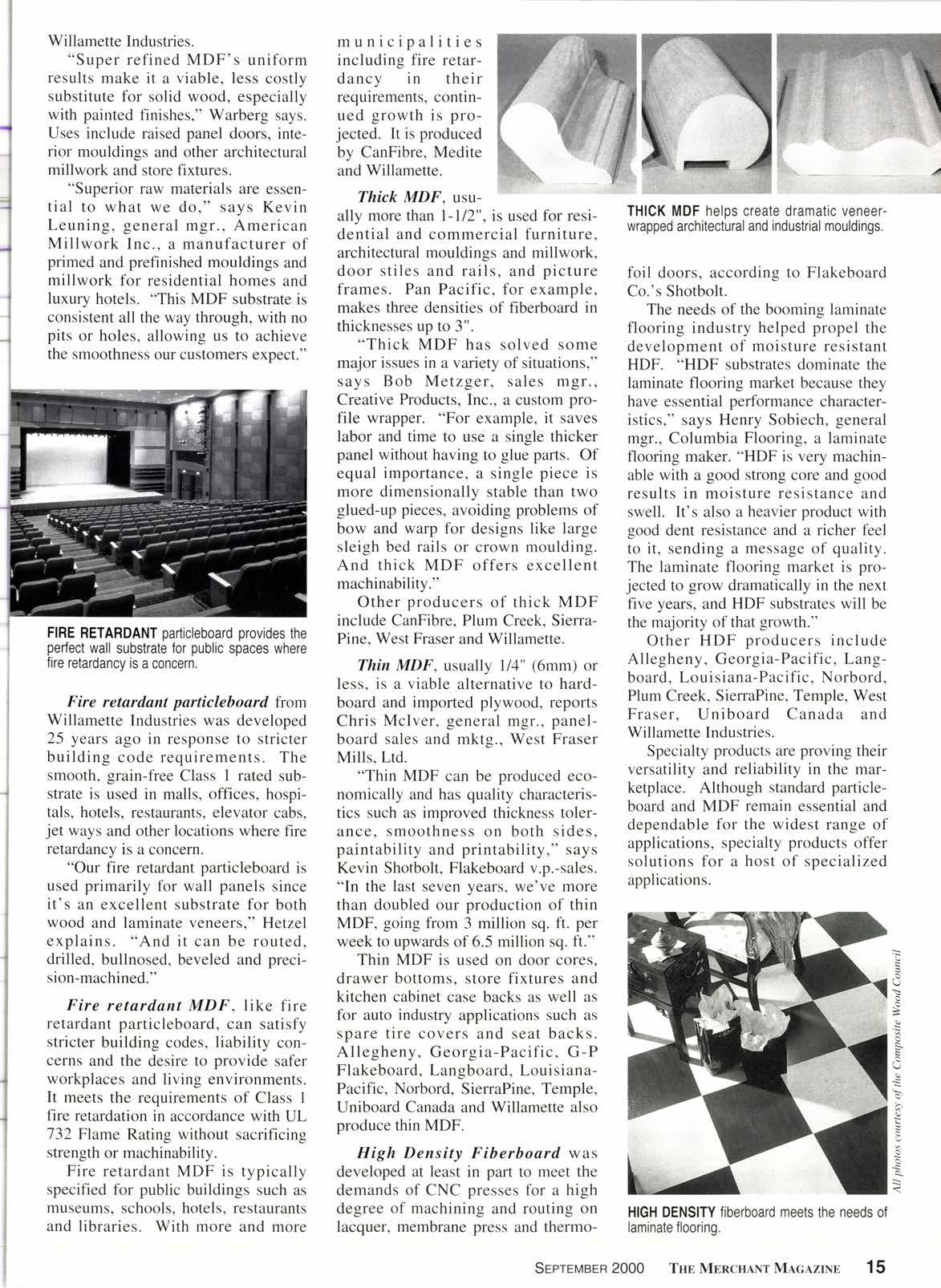
Fire retardant MDF. like fire retardant particleboard, can satisfy stricter building codes, liability concerns and the desire to provide safer workplaces and living environments. It meets the requirements of Class 1 fire retardation in accordance with UL '732 Flame Rating without sacrificing strength or machinability.
Fire retardant MDF is typically specified for public buildings such as museums, schools, hotels, restaurants and libraries. With more and more
Other producers of thick MDF include CanFibre, Plum Creek, SierraPine, West Fraser and Willamette.
Thin MDF, usually 1/4" (6mm) or less. is a viable alternative to hardboard and imported plywood, reports Chris Mclver, general mgr., panelboard sales and mktg., West Fraser Mills, Ltd.
"Thin MDF can be produced economically and has quality characteristics such as improved thickness tolerance, smoothness on both sides, paintability and printability," says Kevin Shotbolt, Flakeboard v.p.-sales. "In the last seven years, we've more than doubled our production of thin MDF, going from 3 million sq. ft. per week to upwards of 6.5 million sq. ft."
Thin MDF is used on door cores, drawer bottoms, store fixtures and kitchen cabinet case backs as well as for auto industry applications such as spare tire covers and seat backs. Allegheny, Georgia-Pacific, G-P Flakeboard, Langboard, LouisianaPacific, Norbord, SierraPine, Temple, Uniboard Canada and Willamette also produce thin MDF.
High Density Fiberboard was developed at least in part to meet the demands of CNC presses for a high degree of machining and routing on lacquer, membrane press and thermo-
The needs of the booming laminate flooring industry helped propel the development of moisture resistant HDF. "HDF substrates dominate the laminate flooring market because they have essential performance characteristics," says Henry Sobiech, general mgr., Columbia Flooring, a laminate flooring maker. "HDF is very machinable with a good strong core and good results in moisture resistance and swell. It's also a heavier product with good dent resistance and a richer feel to it, sending a message of quality. The laminate flooring market is projected to grow dramatically in the next five years, and HDF substrates will be the majority of that growth."
Other HDF producers include Allegheny, Georgia-Pacific, Langboard, Louisiana-Pacific, Norbord, Plum Creek, SierraPine, Temple, West Fraser, Uniboard Canada and Willamette Industries.
Specialty products are proving their versatility and reliability in the marketplace. Although standard particleboard and MDF remain essential and dependable for the widest range of applications, specialty products offer solutions for a host of specialized applications.