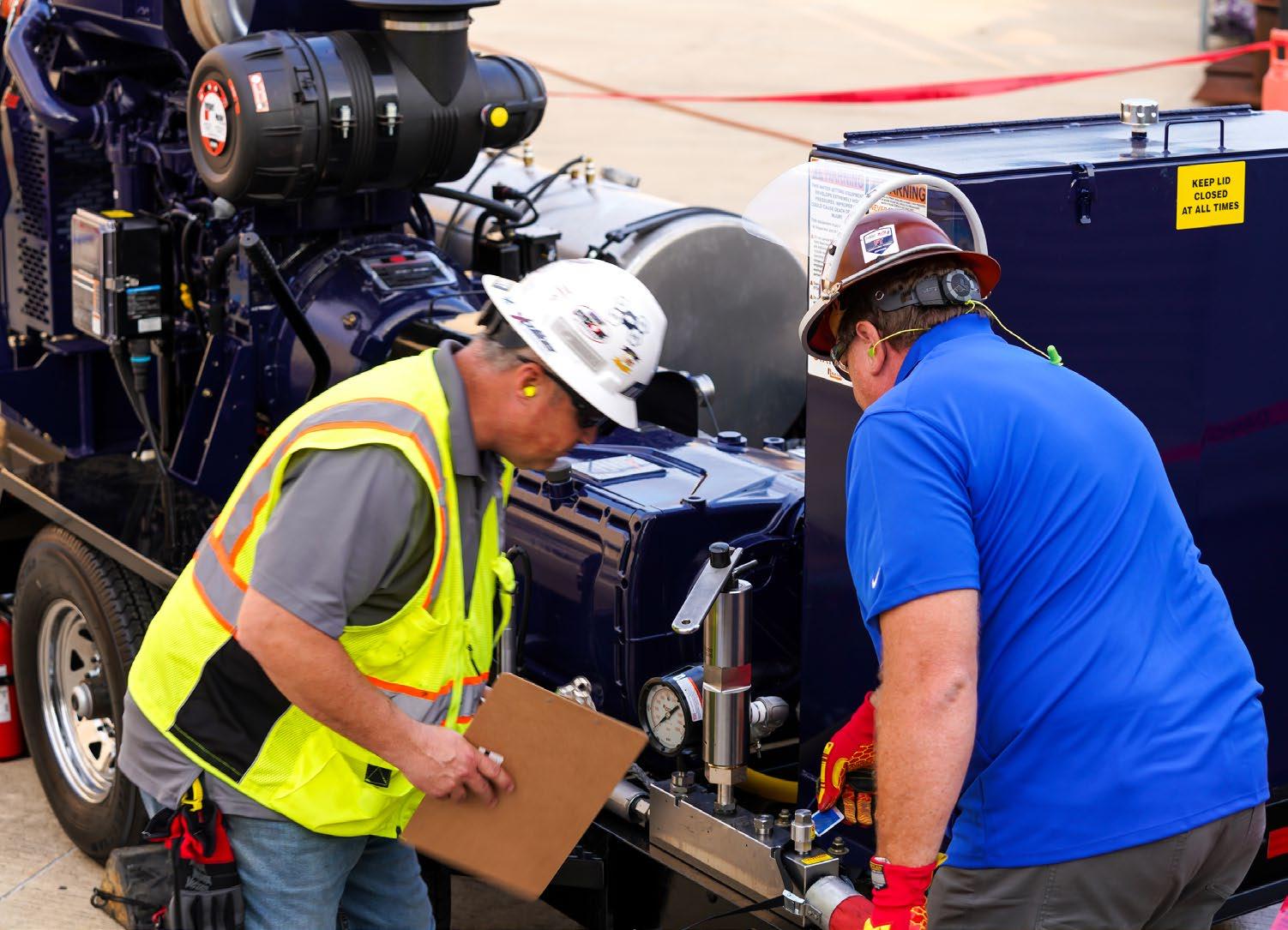

By Jimmy Peck, WJTA President/MPW GM of Industrial Services
Investigator Jim Ashmead is the WJTA Board Secretary and an asset owner with a unique and fascinating point of view on the WJTA’s role in the industrial services industry.
With more than 36 years of experience at DuPont, Jim has developed expertise in various fields, including machine design, robotic automation, micro-fluidics, hygienic design and industrial cleaning. Jim is actively involved in updating DuPont’s safety standards for industrial hydroblasting and leading the company’s industrial cleaning and hydroblasting team.
I’m pleased and honored that Jim agreed to sit down to a question-and-answer session to reflect upon the WJTA and the waterjetting industry’s relationship with its asset owners.
Q. What is your vision for the WJTA and its future? Is there anything you want the association to focus on in particular as an asset owner?
A. My vision for the WJTA foremost is safety. I believe this is the foundation of the WJTA. The WJTA needs to be the leading voice for safety in hydroblasting and industrial services. When I first got involved with the WJTA, the Orange Book was considered the minimum standard for hydroblasting.
I believe the WJTA can develop and deliver the gold standard in hydroblasting safety. This will include basic and thorough advanced training and certification. With the Blue Book and its expansion into vacuum truck safety, the WJTA is well on its way to develop and deliver safety standards and training for industrial services.
The world of hydroblasting is evolving rapidly. With the development of hands-free and automated equipment, we no longer have an operator handling a shotgun for 8 to 12 hours a day. The WJTA does a good job of attracting technology developments to the WJTA trade show, where suppliers and asset owners can be educated.
continued on page 4
With advances in automated technology, new or different safety concerns can be created. The operator is no longer controlling a simple tool, but in some cases a sophisticated piece of equipment. Educating the operator on these new safety concerns is critical for safe operation. I see the WJTA as the key leader in identifying and addressing all of the safety concerns.
Q. You represent an asset owner who has high standards when it comes to waterjetting. Please tell us a bit about what’s going on at DuPont in regard to industrial cleaning.
A. Like every asset owner, we are always striving to achieve safe and cost-effective methods to clean our plants. One of the elements we are pushing is hands-free and automated technology. This technology starts to remove the operator from the highly pressurized components and allows for a safer cleaning operation. I have always believed that hands-free technology is the gateway to automation.
As technology advances, we now can capture, almost free of charge, critical data from each job. Let’s take heat exchangers for example. With automated cleaning systems, we can start to collect data that we can use to drive continuous improvement in cleaning. Data such as the traverse speed of the tool, the number of passes to clean a tube, pressure and flows used for the job, what tool was used, orifice size, what tubes were plugged and so on.
foulant to be removed to be slightly different. Capturing this data for future cleaning is priceless for driving cost effective cleaning outcomes. It’s not always the cleaning vendor’s fault that the job was unsuccessful. Accurate and plentiful data will be one of the tools used to develop safe, repeatable and cost-effective cleaning outcomes in the future.
Q. How important is it to you and DuPont that all the sites have WJTA trained people and that you have the same people working at the sites day after day?
A. If I were to compare industrial cleaning to the electrical trade levels, being WJTA trained and certified carries the same weight. If you have a journeyman or master electrician come through the gate to work on your site, you know they have received the education and training to perform the work safely and according to standard. No additional training is required, other than site specific.
This data can show us where the deficiencies are and how to improve them. Or, if this cleaning worked exceptionally well, here are the conditions that we can use to have another successful, safe and cost-effective cleaning. Time and again we have had cleaning jobs fail. And then, when we ask ourselves what was different, how was it cleaned last time and what pressure and flows were used this time, we struggle to find answers.
We also need to collect data on the process side of things. I have run into scenarios where vendors were not successful in cleaning. They did it the same way they always did, and we do not understand what was different. I always ask, was there any type of excursion to the process, any change in feed stock, etc.?
Usually, this type of questioning uncovers some difference in the process that could have caused the
Internal to Dupont, we have developed our own standard for hydroblasting. One of the requirements is that vendor personnel must have worked on a Dupont site for a prescribed number of hours. This translated into us paying someone to observe, but not work, on our site until they have achieved that number.
The reasoning behind this was to ensure the personnel were exposed to the Dupont Safety Culture and understand that safety is Job One. The collective of people who develop the standards and training certification for the WJTA are leaders in the industry.
This produces, what I believe, are the highest quality of training and certification standards. As the WJTA training and certification become the standard for all the industry, the asset owners will no longer have to develop their own internal standards and training requirements and rely solely on the WJTA. This will drive safety, performance and costeffective industrial services.
Q. What are some of the toughest challenges you’ve seen in the industrial cleaning world and how were they addressed, assuming that they have been?
A. I believe the toughest challenges are still ahead of us. As the world strives to protect our natural resources, we are
continued on page 6
starting to see pushback with using water as a cleaning agent. Disposing of contaminated water in some areas is very prohibitive; alternative methods of cleaning will need to be developed to minimize the environmental impact.
I am not sure what the future will look like, but I believe there needs to be a collaboration between asset owners, industrial cleaning suppliers and contractors to develop the future of cleaning, and the WJTA is poised to lead and drive this collaboration.
Q. One of the roles you’ve inherited is that your voice represents an entire industry of asset owners (customers). We’d appreciate hearing the final word from you regarding how the following three aspects of industrial cleaning can improve their impact on the industry:
• What would you say to industrial cleaning suppliers?
○ Innovate, look to the future and evolve with the times.
○ Work to expand your offerings.
Chairman of the Board
Kerry Siggins
Email: kerry.siggins @stoneagetools.com
Phone: (970) 259-2869
President
Jimmy Peck
Email: jpeck
@mpwservices.com
Mobile: (740) 808-0460
Office: (740) 927-8790
Vice President
David Beckum
Email: d.beckum
@augustaindustrial.com
Phone: (706) 798-8437
• What would you say to contractors?
○ Embrace and drive change. Reputation is everything.
○ Listen to the voice of the customer.
○ Stand your ground. Cutting corners with safety is hazardous to everyone.
• And finally, what would you say to other asset owners?
○ How clean is clean? This needs to be defined for every job. How do you validate?
○ What can we do to make our assets easier to clean? Clean in place.
○ Collaboration is the key to safe, cost-effective desirable outcomes.
Special thanks to Jim for participating. We look forward to future Q&A sessions with other board members, and we look forward to seeing all of you at the October 28 WJTA Texas golf tournament event! If you haven’t signed up yet, please do so as soon as possible because it’s almost time! We’re seeing a lot of
Treasurer
Drew Waltenbaugh
Email: drew.waltenbaugh @nlbusa.com
Phone: (248) 624-5555 Ext. 10167
Secretary
James W. Ashmead
Email: james.w.ashmead @usa.dupont.com Phone: (302) 695-1173
Association Managers
Mark S. Birenbaum, Ph.D.
LeAnn Hampton
Peter Wright
from page 4
interest from sponsors and the event is nearing capacity.
Also, the 2025 Conference & Expo is finalized for November 5-7 in New Orleans. The 2025 event will be outstanding! New Orleans has been a great location for us; however, we’re expecting to move to another venue in 2027. Moving the show should help us expand its audience.
Sincerely,
Jimmy Peck, President Office: (740)927-8790, Mobile: (740)808-0460
MPW Industrial Services, Hebron, Ohio
For more information: Peter Wright, WJTA Association Manager Office: (314)241-1445
Email: WrightP@wjta.org ■
Richard Bass
Email: richard.bass @kuraray.com Phone: (281) 221-4668
Hans Borgt
Email: hgborgt @dow.com Phone: [31](61)4772124
Jerry Carter
Email: jerryc@spirstar.com Phone: (281) 664-7800
Bradley Coble
Email: bradley.coble @covestro.com
Phone: (281) 383-5971
Dee Green
Email: dgreen @usadebusk.com Phone: (832) 205-1622
Bill Krupowicz
Email: bkrupowicz @waterblast.com
Phone: (832) 590-1347
Bill Shaw
Email: bill.shaw@enais.com Phone: (281) 478-5800
Ext. 211
JTA has introduced a new annual eLearning refresher for certified hydroblasting Verified Trainers. The brief, computer-based course is accessed through the safety council network or remotely through the Health and Safety Council (HASC)’s Live Online Proctoring system (course code 19HBVT).
The annual refresher for WJTA-certified trainers is an opportunity to communicate updates in WJTA Training and Certification Program policies and curriculum; the
Share Your News!
Do you have a new product? A project that you’re excited about? Staff promotion? New employees? Tell us about your news!
• Case studies
• White papers
• Innovations
• New product releases
• Personnel changes, including promotions and new hires
Sharing corporate member news in Jet News is a service to our members and to Jet News readers.
Questions? Email HamptonL@wjta.org or call (314)241-1445, attention: LeAnn. ■
association’s best practices; and tips for delivering WJTA Field Verification.
For current Verified Trainers, the eLearning refresher will be required effective for the year 2025.
For more information on the new refresher module or how to become involved in WJTA’s training and certification program, contact Peter Wright at wrightp@wjta.org or 314241-1445. ■
An extremley compact, lightweight, simple, ecomomic 140kW (190hp) pumpset
USA Distribution
APEX Waterjetting Global LLC
Phone: +1 866 273 9109
Email: dave@apexwaterjetting. com
Perkins 4 cylinder, Tier 4/5 engine
67lpm at 1000bar (18gpm at 14,500psi)
51lpm at 1400bar (14gpm at 20,300psi)
44lpm at 1800bar (11.6gpm at 26,100psi)
30lpm at 2800bar (7.9gpm at 40,600psi)
Web: www.hughes-pumps.co.uk
We welcome international enquiries from potential distributors and resellers
Arecent WJTA Hydroblaster
Train-the-Trainer course was held August 6-8 at NLB Corporation in Wixom, Michigan. Seven new Verified Trainers were approved to deliver WJTA Field Verification training. The train-the-trainer course, delivered by WJTA Master Trainers, includes the Field Verification curriculum, WJTA program policies and procedures, and assessment of each candidate’s command of the curriculum.
Another train-the-trainer course is scheduled for Houston in November. Anyone interested in participating can reach out to Peter Wright at wrightp@ wjta.org or 314-241-1445. The trainthe-trainer courses have limited capacity and are expected to fill up.
WJTA’s waterjet and vacuum medical alert cards have been translated from English into Portuguese. Additionally, the WJTA vacuum medical alert card has been translated into Spanish for the first time. The cards are currently available free of charge to WJTA members as soft copy PDF documents. Members can arrange for printing locally or use the translated documents as a reference.
Uma lesão causada por jatos de água de alta pressão pode ser grave. Em caso de qualquer lesão por jato de água:
It is recommended that cards such as these be carried by all waterjet and/or vacuum operators to provide information on the possible nature of the injury and treatment considerations in the event of a fluid injection incident.
The association’s hydroblasting and vacuum training courses continue to gain momentum, with both the Vacuum Operator Foundational Training and Hydroblaster Foundational Training already surpassing 2023’s year-end total. ■
by the WJTA. The vacuum medical alert card was introduced in 2021 to address considerations for a vacuum suction injury.
– Procure atendimento médico imediatamente. Não demore!
– Informe ao médico a causa da lesão.
– Mostre ao médico este cartão.
The waterjet medical alert card is currently available in English- and Spanish-language as both digital and print copies. Print copies of the vacuum medical alert card are currently only available in English.
– Informe ao médico o tipo de projeto que estava sendo realizado com jato de água no momento do acidente e a fonte da água.
Since the introduction of the waterjet medical alert card in 2000, over 250,000 physical cards have been distributed
To access the new digital files, visit the “Members-only Resources” page on the WJTA website. To inquire about a print run of the translated cards or for more information, contact Peter Wright at 314241-1445 or wrightp@ wjta.org. ■
Email addresses and other member contact information published in the WJTA Corporate Member Directory are meant to encourage helpful, informative communication between members. The information is not provided to circulate spam or junk mail.
LEIA ESTE CARTÃO DE PLÁSTICO E MANTENHAO EM SUA CARTEIRA. EM CASO DE LESÃO POR JATO DE ÁGUA, MOSTRE O CARTÃO AO SEU MÉDICO.
Distributed by: WaterJet Technology Assn. 906 Olive Street, Suite 1200 St. Louis, MO 63101-1448
Phone: (314)241-1445, Fax: (314)241-1449 Email: wjta@wjta.org Website: www.wjta.org
The WJTA leadership requests that members respect the contact information of fellow members and not use that information for the dissemination of spam or junk email. Membership information is not meant to be circulated beyond the WJTA membership.
NLB’s new HydraFlex™ drive gives our latest pumps more water jet control than ever before, plus dry shut-off that practically eliminates wasted water. This groundbreaking hydrostatic drive makes the pump speed independent of the engine, letting you right-size speed, flow and horsepower to each job.
Replacing the usual PTO with a HydraFlex drive reduces emissions, noise, and maintenance, and even the unit footprint. And these pumps feature NLB’s wireless Esync™ technology for remote operator control and enhanced safety.
With the HydraFlex drive, NLB delivers truly customized performance from a standard water jet pump. Call today for a demo.
A61-year-old man was operating a vacuum truck to remove debris from a hole dug for a powerline pole when a boom arm on the vacuum truck was extended and made contact with power lines. The electrocution sparked a fire that quickly engulfed the vacuum truck. The man did not survive.
We can’t stress enough the importance of always being vigilante, aware of your surroundings, and observing all safety practices when operating industrial vacuum equipment.
For your information and practice, following is an excerpt from the WJTA’s Recommended Practices for the Use of Industrial Vacuum Equipment, Fourth Edition, Section 6.1 Variable Hazards.
A potential electrical shock hazard exists with the operation of mobile equipment near high voltage power lines. All OSHA and site rules and regulations must be followed.
High reaching equipment includes radio antennas, crane booms and masts. NEVER dump under power lines. Contact the local electrical utilities for identification of the power rating and proper procedures for working near the lines.
Exceptions are permitted for travel under or work near a power line only when both of these conditions exist:
• The electrical department is notified for a qualified electrical person to de-energize the power line and the Tag-Lock-Try procedures are followed.
• A trained person properly grounds the mobile equipment.
In most cases trailing cables run along service roads. If a trailing cable blocks your desired route do not drive over continued on page 14
Parflex PFX waterblast hoses feature working pressures up to 55ksi and low volumetric expansion. The compact design promotes easy handling and reduced operator fatigue. Prevent failures and unexpected downtime by incorporating a Colorgard™ sheath under the jacket to give operators easy visualization to core tube erosion.
PFX38-05 8mm 55ksi
PFX38-05TJ 8mm 55ksi
PFX30-05 8mm 43ksi
PFX30-05TJ 8mm 43ksi
PFX25-05-TJ 8mm 36ksi Learn more at parker.com/waterblast
it, go back to the main road and find another route to your destination.
To prevent contamination and injury wear chemical resistant gloves, chemical resistant suit, long sleeves, trousers, and dust-proof or splashproof goggles as appropriate. Face shields may be required as well. Seek immediate medical attention if exposure or contamination is suspected.
Unless otherwise specified, never make adjustments or repairs while the machine is moving, the blower is engaged, or the engine is running.
Equipment, components, and attachments should be properly supported when working beneath them. Any attachment can fall if a control is moved, or if a hydraulic line fails.
Everyone should be clear of the unit before any engine is started. Stay clear of all rotating and moving parts.
Be aware of pinch points. Where there are attachment linkages or articulating equipment, the clearance in the linkage area will increase or decrease with movement of the attachment or articulation. Never be on the rear door platform while the rear door is being operated.
Liquid material being loaded should not exceed 120°F. If material is over 120°F, the operator shall wear a full slicker suit (material capable with liquids up to 180°F), steel toed rubber boots, rubber/PVC gloves and face shield.
All gaskets, seals, valves, gauges shall be compatible with the temperature of the liquid being loaded.
Engine coolant is hot and under pressure at operating temperature. The radiator and all lines to heaters or the engine contain hot water or steam, and any contact could cause severe burns.
Allow cooling system components to cool before draining. Do not allow hot oil or components to contact skin as they can cause personal injury.
At operating temperature the oil in the hydraulic tank is hot and can be under pressure. Remove the filler cap only after the engine has been stopped and the filler cap is cool enough to remove with your bare hand. Remove slowly to relieve pressure.
Relieve all pressure in air, oil, fuel, or cooling systems before any lines, fittings, or related items are disconnected or removed.
All fuels, most lubricants and some coolant mixtures are flammable. Smoking in fueling and lubricating areas is prohibited. Also, no smoking is allowed where batteries are charged or where other flammable materials are stored.
Clean and tighten all electrical connections. Check for frayed or loose electrical wires daily and have them repaired or tightened if needed.
Keep all fuels and lubricants stored in properly marked containers and away from unauthorized personnel. Always store oily rags and other flammable material in protective containers. Ether is flammable; do not smoke when using ether and use only in well ventilated areas.
An appropriate, currently inspected, working fire extinguisher shall be with the unit at all times.
Refer to Section 5.5 Grounding and Bonding for more information on vacuuming flammables and combustibles.
Open manholes and other access openings create risks of trips and falls. Be aware of such locations and do not step in or over them. Ensure that manhole cover and other covers are in place when job is completed. Failing to follow these precautions may cause serious injury or death.
Be aware of traffic and pedestrians on the job site. Use extreme caution while moving around the vehicle to avoid contact with moving vehicles. When moving the boom or vehicle make sure pedestrians are clear of the area. Use orange safety cones to mark the work area.
For complete details, refer to the WJTA’s Vacuum Equipment Recommended Practices. The manual also includes a section covering hydroexcavation, updates to the prejob inspection checklist, and additional recommendations and updated information regarding flammables and combustibles and grounding and bonding. Other topics: injury potential, seeking medical attention, damage, explosion, types of trucks, getting started, pre-job preparations, working safely, job completion, loading/offloading, equipment maintenance, and regulations and certifications.
Copies of the manual are available for purchase through the WJTA online store at www.wjta.org or by calling (314)241-1445. ■
Arecent alert shared by AUSJET* details an August 2024 incident involving an operator and a vacuum combination unit. A summary of the incident and some of the preventative actions and learnings as reported by AUSJET appear below.
An operator was shutting down a vacuum combination unit when he heard a hissing noise. He investigated the source of the noise, going to the debris tank rear and, standing directly behind the dewatering end cap, released the end cap camlock. Once released, stored air pressure in the debris tank escaped, throwing the operator backwards off his feet and he struck the ground.
The operator was unaware the debris tank was pressurized when he attempted the removal of a pressurized camlock fitting.
The injured operator received immediate medical attention. An investigation and notification of the regulator followed.
Preventative actions include ensuring the pressure gauge is incremented to show low pressure readings inside the vessel (the pressure gauge that was fitted didn’t have a noticeable scale for low pressure reading) and installation of a visual alert system.
Operators should be educated on potential “line of fire hazards.” Training should include checking pressure readings inside the debris tank before attempting to open any ports.
What Immediate Action
• When using air pressure systems, ensure the tank is open (i.e., dewatering valve or debris door open) and that all pressuring systems (i.e., cyclone cleaners, dewatering) are off before the door or valve is closed.
• Always check the pressure gauge for pressure; any positive pressure can be a hazard.
• If the tank is pressurized, follow the manufacturer’s procedure to release the pressure under control. Any positive pressure can be hazardous; ensure it is at zero.
• If you are unsure of the process, stop operations, call your supervisor, and do not proceed any further until the hazard is rectified.
• Line of Fire – Never stand in the path of something that can hurt you. Stay out of the line of fire.
Corrective Action
Medical attention for the injured operator. Investigation commenced Notification to the Regulator
Any pressurized tank creates a significant risk of forceful release from the tank. Most vacuum interceptors are not able to be pressurized. Due to the new design of internal cleaning systems, the possibility of pressurizing the interceptor has increased on these newly designed units.
Preventative Action
Thanks to AUSJET for sharing this incident alert, which serves to remind us how important it is to follow safety practices.
See the WJTA’s safety manuals, Industry Best Practices for the Use of High Pressure Waterjetting Equipment and Recommended Practices for the Use of Industrial Vacuum Equipment, for detailed safety recommendations. For more information, call (314)2411445, email wjta@wjta.org, or visit www.wjta.org and follow the ONLINE STORE link.
*AUSJET is the Australasian High Pressure Water Jetting Association (AUSJET), incorporating the Australasian Drain Cleaning and Vacuum Association (ADCVA). For more information, visit www.ausjetinc.com.au. ■
or barriers
The text below is excerpted from the WJTA’s Industry Best Practices for the Use of High Pressure Waterjetting Equipment, Second Edition, Section 7.0 – PreOperating Procedures. Refer to the Industry Best Practices for complete details.
7.1 Planning – Each job shall be planned prior to work beginning. Personnel familiar with the equipment, structure, area/items to be waterjetted, material to be cut and the work environment shall meet with the personnel who will be doing the work and shall outline potential hazards of the work area, environmental problems, safety standards, and emergency procedures. Hazards shall be mitigated or removed in the planning phase.
7.2 Operating Pressure and Flow – The contractor shall inform the owner of the anticipated pressures, flow rates, and hazards associated with the work to be carried out.
7.3 Checklist – A checklist shall be used to verify proper procedures and equipment selections. (See Appendix C on page 20 of this issue of Jet News.)
See the complete section in the Industry Best Practices for the Use of High Pressure Waterjetting Equipment
The Industry Best Practices includes information about responsibility, accidents, pre-service and operational checklists and procedures, PPE, training requirements, waterjet team responsibilities, care and maintenance of equipment, automated equipment, permanent cleaning areas, design criteria, and a glossary of definitions and guidelines.
Copies of the manual are available for purchase through the WJTA online store at www.wjta.org or by calling (314)241-1445. ■
• Kevlar inner layers with Hydropel outer layer.
• Available in Standard and Full Coverage
• Complete Suits or apparel sold
• Available with your company’s color and logo.
from page 18
Unit Number/Division:
Mileage/Hours Front:
Date Inspected: Mileage/Hours Rear: PASS FAIL
REMARKS
Condition of Trailer: Stands/Wheels/Lights
Waterblaster Grouding System/Condition
Engine: Fluids/Electrical/Gauges
Clutch: Grease Points Greased
Waterblaster Items PTO Grease Points Greased/Oil Level
Power End Oil Condition/Level Belt Condition & Tension
Filters Checked/Replaced if Required
Supply Piping Routed Correctly/Condition
Pressure Gauge Condition/Last Certification
Pressure Relief Valve Condition/Rating
Rupture Disk(s) Condition/Rating Bypass Valve Cartridge/Diffuser Condition
Safety Warning Decals Present/Condition
Supply Lines Flushed
Lubrication Lines Flowing Coffee Cup Filter Test Hoses Inspected/Condition
Couplings Inspected/Condition
Whip Checks Inspected/Condition
Gun Stock/Trigger/Trigger Lock Inspected Gun Barrel 4' Minimum/66" Overall Length
Shotgun Cartridge/Cap Inspected/Condition
Safety Shroud/Whip Hose Inspect/Condition
Foot Pedal Cartridge/Inspected/Condition
Lances Inspected/Condition Fittings Inspected/Condition
Field Items
All Employees have Waterblast Safety Card Delivery Lines Flushed
Tip Condition/Proper Size
Anti-Withdrawal Inspected/Installed
Anti-Reversal Inspected/Installed
Barricades & Barriers Installed/Inspected
Area Clean/Good Footing
PPE Proper/Inspected Leak Check Performed (1,000 psi)
Line of Sight Established
Operator at Pump Area Cleaned Upon Completion Hoses Drained and Re-coupled Pump Antifreezed (if required)
Inspectors Name/Signature
Managers Name/Signature
By Jonathan Frye, Transportation and Safety Supervisor, MPW Industrial Services
When it comes to ensuring the safety and efficiency of commercial motor vehicles, adhering to Department of Transportation (DOT) best practices for vehicle maintenance is of utmost importance. DOT regulations are in place to ensure that commercial vehicles are properly maintained, reducing the risk of accidents and promoting overall road safety.
One of the key aspects of DOT best practices for commercial motor vehicle maintenance is conducting regular and thorough inspections.
This includes checking essential components such as brakes, tires, lights and fluid levels to ensure that they are in optimal working condition. Additionally, adhering to a strict schedule of routine maintenance, including oil changes, filter replacements and thorough inspections of critical systems is crucial for the safe operation of commercial vehicles.
Accurate record-keeping of all maintenance and repairs is another fundamental aspect of DOT best practices. Keeping
detailed and up-to-date records not only ensures that all maintenance tasks are performed on time but also provides valuable documentation in the event of inspections or audits.
Adhering to DOT best practices for commercial motor vehicle maintenance is not only a regulatory requirement but also a commitment to the safety of drivers, passengers and other road users. By following these guidelines, commercial vehicle operators can help prevent accidents, reduce the risk of breakdowns and maintain a high standard of safety and reliability on the road.
Following DOT best practices for commercial motor vehicle maintenance is essential for ensuring the safety and efficiency of these vehicles. By prioritizing regular inspections, maintenance and record-keeping, commercial vehicle operators can contribute to safer roads and a more reliable transportation system. ■
By Luis Garcia, President, Gulf Coast Region, Würth Industry
Ahealthy safety culture is a major element of a successful organization. This kind of environment promotes employee health and protection, but also enhances productivity, boosts morale, and reduces turnover.
At the heart of this culture lies effective employee training, but not the one-and-done kind. Ongoing training, whether in toolbox talks or more formal settings, improves safety culture and reduces costly, painful on-the-job accidents.
The Innumerable, Diverse Benefits of Ongoing Training
• Regular training ensures employees are equipped with the latest safety knowledge and skills like understanding workplace hazards (machinery, chemicals, etc.), emergency procedures (evacuation, medical, etc.), and the use of safety equipment (eye wash, fire extinguishers, etc.).
Regularly assess the training needs of your workforce to identify knowledge gaps, skill deficiencies, and emerging hazards. Develop your training programs specific to the tasks and risks associated with each job’s role and working environment and instruct workers what to do in an emergency. Implement a schedule and recordkeeping.
Remember, people learn in different ways. Employ a mix of training methods, including classroom instruction, hands-on demonstrations, simulations, and online courses to keep people engaged. Tailor training to the cultural backgrounds and needs of your workforce. Ensure training materials and methods are accessible to employees with disabilities. Reinforce safety concepts and address changes in regulations or procedures during refresher sessions. Don’t forget to gather feedback from employees and managers regarding the effectiveness of training programs and make necessary adjustments to improve future installments.
• Ongoing training helps organizations stay compliant with industry regulations and standards. This is crucial for avoiding legal issues and maintaining both a positive reputation and affordable insurance rates.
• Well-trained teams are more likely to recognize potential hazards in their work environment. They can then take proactive steps to mitigate risks and prevent accidents.
• Training empowers employees to take ownership of their safety. It cultivates a sense of responsibility and encourages them to report unsafe conditions or practices.
• A safe work environment fosters higher employee morale and reduced absenteeism. When workers feel valued and protected, they are more likely to be engaged and productive.
• Time Constraints: While training may seem timeconsuming, it’s a long-term investment in safety that’s worth the effort, so try to keep on schedule.
• Resistance to Change: Some employees may resist training. Don’t assume this is just workplace grumbling. Chat with them and emphasize the benefits of continuous learning.
• Cost: While there may be initial costs associated with training, the lasting benefits, such as reduced accidents and improved productivity, often outweigh the expenses.
There are some elements to a training program that help ensure its success. By showing commitment and attending sessions, safety managers and executives display support that creates a positive culture. The training initiatives
continued on page 28
“If you are serious about acquiring the top management talent in our industry, BIC Recruiting must be considered. You won’t be disappointed”
Aaron Shermer, President, Bayou City Industrial Contractors
“BIC Recruiting provided qualified candidates quickly. The recruiter maintained great communication and was very hands-on from start to finish. The time saved by having BIC’s recruiter handle the candidate search as well as coordinating all the interviews was a tremendous help to us. They allowed us to find the right fit in half the time.”
Dan Braud, Head of Turnaround Services Americas, Sulzer Chemtech Ltd.
“I was very pleased with the level of talent BIC Recruiting brought to the table. It is obvious BIC Recruiting’s Thomas Brinsko and the entire team know the industry well.”
Josh Causey, President, Repcon Inc.
The U.S. Department of Labor’s Occupational Safety and Health Administration (OSHA) has unveiled an online tool giving users the ability to search its severe injury report database and view trends related to workplace injuries occurring in states covered by federal OSHA.
The Severe Injury Report dashboard allows users to search and download data by year, industry, state, establishment name, and Occupational Injury and Illness Classification System codes. The dashboard includes information on all severe injuries reported by employers covered under federal OSHA since 2015.
industries and use the agency’s available resources to help prevent workplace injuries. Visit OSHA’s Severe Injury Reports page at https://www.osha.gov/severeinjury to access the Severe Injury Dashboard and an instructional video, which demonstrates how to use the dashboard.
Federal law requires employers to notify OSHA of a work-related in-patient hospitalization, amputation or loss of an eye within 24 hours of the incident. The agency’s compliance assistance specialists and on-site consultations are available across the country and in U.S. territories to help employers. For more information, visit www.osha.gov. ■
OSHA encourages workers and employers to use the dashboard to learn how severe injuries happen in their
The U.S. Department of Labor has announced the opening of the public comment period for its proposed rule, Heat Injury and Illness Prevention in Outdoor and Indoor Work Settings. The standard would apply to all employers conducting outdoor and indoor work in all general industry, construction, maritime, and agriculture sectors where OSHA has jurisdiction, with some exceptions.
It would be a programmatic standard that would require employers to create
a plan to evaluate and control heat hazards in their workplace. It would also more clearly set forth employer obligations and measures necessary to effectively protect employees from hazardous heat.
The rule – if finalized – would help protect approximately 36 million workers in indoor and outdoor work settings and substantially reduce workplace heat injuries, illnesses and fatalities.
should be aligned with other safety events, such as hazard assessments, incident investigations, and emergency response planning.
Finally, implement metrics to track the impact of training on safety performance. This data can be used to refine training programs and demonstrate their value.
OSHA encourages public participation in the rulemaking process to help the agency develop a final rule that adequately protects workers, is feasible for employers and is based on the best available evidence. Directions on how to submit comments are included in the Federal Register notice. For more information, visit https://www.osha.gov/heat-exposure/ rulemaking. ■
from page 24
Ongoing employee training is not merely a compliance requirement; it is a strategic investment in the health and well-being of your workforce. By prioritizing safety training, you can create a culture of prevention, reduce accidents, and foster a more productive and positive work environment. If you have any questions on improving your safety training, call the technical support reps at Würth Industry: (800)922-8553. ■
By Kerry Siggins, CEO, StoneAge Tools, and Chairman of the WJTA Board
As business leaders, we’ve all been there: an employee doesn’t respond to an email, and suddenly we are spinning stories about disengagement or lack of respect. A colleague misses a deadline, and assumptions about their dedication begin to form. These narratives feel real, but more often than not, they’re inaccurate and can significantly impact team dynamics, trust, and communication.
Our brains are wired to make assumptions, and it’s a natural part of how we navigate uncertainty. However, when it comes to the workplace, these assumptions can do more harm than good. As leaders, understanding the science behind these mental shortcuts and learning to reframe our thinking can transform how we interact with our teams.
Human beings are wired to seek coherence. When information is incomplete or ambiguous, our brains fill in the gaps with stories to make sense of what we see. While this can be helpful in some situations, it often leads to misunderstandings in complex environments like the workplace.
Cognitive biases are at the core of this process—mental shortcuts that help us make quick decisions but can also distort our perceptions. Three common biases that influence workplace storytelling are confirmation bias, fundamental attribution error, and negative bias:
• Confirmation bias: We tend to interpret information in ways that confirm our pre-existing beliefs. If you believe a team member is disengaged, you’re more likely to notice signs that reinforce that story and ignore evidence that contradicts it.
• Fundamental attribution error: We often attribute others’ actions to their personality or character rather than considering external factors. For example, if someone misses a deadline, we might assume they’re lazy or unorganized rather than thinking about their potential challenges.
• Negative bias: The human brain focuses on and remembers negative experiences or information. In the workplace, this means we’re more prone to noticing problems or conflicts, and we may overlook positive actions or intentions. For example, you might focus on one piece of critical feedback in an otherwise positive review, amplifying a negative story in your mind.
These mental shortcuts served us well in our evolutionary past but can create toxic workplace dynamics today. As leaders, we are responsible for recognizing when we’re falling into these patterns and actively seeking to challenge them.
Inaccurate stories lead to misunderstandings, mistrust, and disengagement within teams. The stories we tell ourselves—whether it’s about an employee’s performance or a peer’s behavior—often result in decisions that are out of alignment with reality. This disconnect can cause tension, erode relationships, and foster a culture of negativity.
For example, imagine a manager who assumes an employee is disinterested because they didn’t participate in a meeting. Without seeking to understand why the employee was quiet (perhaps they were feeling overwhelmed or dealing with a personal issue), the manager might distance themselves from the employee or exclude them from future decisions—creating a cycle of disengagement that stems from a false assumption.
To break free from inaccurate stories, leaders should pause and reflect before reacting. Start by practicing mindfulness to become aware of the assumptions you’re making. Challenge these assumptions by asking, “What evidence do I have?” and “What else could be true?” Finally, try to see the situation from the other person’s perspective, considering their challenges and pressures. Reframing allows you to approach situations with clarity and empathy, leading to better communication and more constructive outcomes.
As leaders, it’s crucial to seek understanding before jumping to conclusions. Instead of making assumptions, cultivate curiosity by asking open-ended questions like,
continued on page 30
“Can you help me understand what happened?” and actively listening with the intent to understand, not just to respond. Doing so creates space for genuine dialogue and empathy, fostering a culture of trust and reducing misunderstandings. Remember, when in doubt, assume good intentions—this simple shift can transform team dynamics and create a more positive work environment.
Reframing assumptions and seeking understanding is a key component of leadership. Reducing inaccurate stories and creating space for curiosity and empathy fosters a workplace where people feel valued and understood. As a leader, committing to the following can have a significant impact on your team’s success:
• Pause, Reflect, Reframe: Notice when you’re making assumptions and practice challenging your initial thoughts.
• Embrace Curiosity: Ask questions and seek to understand before forming conclusions.
• Assume Good Intentions: Approach every interaction with the belief that others mean well, creating a culture of trust and openness.
By embracing these practices, you’ll not only improve your own leadership capabilities but also create a more positive, collaborative, and high-performing workplace for your team.
Kerry Siggins is the CEO of StoneAge, Inc., a leading manufacturer of high pressure waterblasting and sewer cleaning tools and equipment based in Durango, CO. She has been key in building StoneAge’s strategic vision,
worldwide sales, and employee ownership culture. Her passion lies in organizational and leadership development, and she enjoys helping StoneAge employees and those in our industry to grow both personally and professionally. She is also the chairman of the WJTA board. For more information, contact Kerry Siggins at kerry.siggins@stoneagetools.com. To read her blog, visit kerrysiggins.com/blog. ■
By Rich Gomes, Director of Sales, Jetstream of Houston, LLP
Extreme weather conditions, especially freezing temperatures, require special care for waterblasting equipment. Routine maintenance is always important, but requirements ramp up when temperatures drop below freezing. Winterization is critical to keep the equipment in good working condition and maintain operator safety. For example, a unit damaged by freezing water has an increased risk of having hoses burst or fittings fly away from the unit. Knowing the condition of the machine and the weather conditions of the worksite help determine what precautions to take.
Review these tips on when and how to winterize a waterblasting unit.
Does a waterblasting unit need to be winterized if it’s in use?
Waterblasting units can be used in cold weather — even in freezing temperatures. When in use, the unit creates enough heat to avoid freezing. However, it does need to be run continuously when in freezing temperatures. If the unit will sit idle, operators can either winterize it or place it in heated storage. Some contractors use storage units or insulated shipping containers to protect their waterblasting unit when it sits idle in the winter. Other contractors who choose to leave the unit outdoors for extended periods winterize instead.
If the waterblasting unit is used periodically throughout the season, winterization can be
Winterization is critical to keep waterblasting equipment in good working condition and maintain operator safety. Water should be completely drained from the waterblasting tank and system when the unit will be sitting idle in cold weather.
If a waterblasting unit is used periodically throughout the season, winterization can be completed multiple times as needed. Make sure to drain the water before any idle time to keep the equipment in top condition — even when traveling between jobsites.
completed multiple times as needed. Make sure to drain the water before any idle time to keep the equipment in top condition — even when traveling between jobsites.
Some contractors travel long distances with their equipment. Take caution from one contractor, who transported their waterblasting trailer through a mountain pass where they reached a high elevation, and the temperatures dipped below freezing. When they reached the jobsite, they found that the waterblasting unit sustained damage because they didn’t drain the water from the system. Knowing the weather and temperature in locations where the unit will travel can help protect it against inclement weather, including conditions caused by high altitudes.
Water should be completely drained from the waterblasting tank and system when the unit will be sitting idle in cold weather. First, disconnect the water lines and allow water to drain fully. Then, add a glycol-based antifreeze into the waterblasting system. The amount required will vary depending on the system. Run the antifreeze through the system by turning on the engine and letting it idle. Apply light pressure to the clutch handle to gently “feather” the engine. Let the plungers move back and forth slowly until the antifreeze discharges from the system. Once this happens,
continued on page 32
Waterblasting in a Winter Wonderland from page 31
disengage the clutch and shut off the engine. Drain the lines fully of antifreeze and completely clean off the unit to ensure the water piping system is protected.
While most waterblasting units follow these general guidelines, be sure to read the owner’s manual and follow the specific procedure for each unit to ensure proper winterization. Make sure to complete all winterization requirements to manufacturer specifications to keep the waterblasting unit safe throughout the winter months.
Weather directly impacts the safety of a waterblasting unit. Make sure to keep an eye on the forecast when working and traveling to ensure the unit doesn’t require winterization before, during or after. When in doubt, the best option is still to winterize the machine to protect against damages. ■
Kidextractor has announced the availability of 100T Rollers, heavy duty rollers that easily rotate tube bundles for cleaning. The rollers have oversized capacity to hold a heavy load.
During the cleaning process of a heat exchanger, whatever type of robot you are using, external or internal, the
rollers allow the tube bundle to rotate for thorough, uniform cleaning.
The rollers are driven by a hydraulic motor and operated by the simple movement of a lever.
Learn more about this easy way to rotate tube bundles during cleaning. Contact Kidextractor: info@ kidextractor.com. ■
Vac2Go, a provider of industrial vacuum truck rentals, is taking swift action to support communities impacted by the recent hurricanes by providing specialized equipment to aid in recovery efforts.
“We understand the devastating effects that hurricanes can have on families, businesses, and infrastructure,” said Kevin Podmore, vice president of operational excellence at Vac2Go. “Our team is committed to helping during this critical time by supplying essential equipment to support cleanup efforts, debris removal, and recovery services in the hardest-hit areas.”
Vac2Go is prepared to send its full range of equipment, including combination units and liquid vacuum trucks, which are particularly suited for hurricane recovery efforts. These units are crucial for debris removal, cleanup, and other vital recovery tasks, ensuring that local
municipalities, contractors, and disaster response teams have the support they need. Vac2Go is prioritizing areas in urgent need and ensuring rapid response times.
As part of Vac2Go’s ongoing commitment to delivering the highest quality customer experience in the industry, the leadership team is dedicated to making Vac2Go’s resources available where they are needed most.
“Our goal is to support recovery efforts by providing essential equipment that can help restore impacted communities as quickly as possible,” added Dustin Culverhouse, vice president of sales.
For more information on Vac2Go’s recovery efforts or to inquire about services, please visit www.vac2go.com or call (855) 822-7246 ext. 111. ■
When working with high water pressures most operators know they need to wear protection to be safe if an accident were to happen. However, being properly protected on a worksite filled with potential hazards often is easier said than done. Operators can slip and couplings can break unexpectedly. So, how does one make sure everyone is properly protected and prepared for the unexpected?
The first thing a waterjet operator and/or supervisor needs to do before starting any job is to conduct a risk assessment together with the client. Together they assess what hazard the job itself entails as well as where it is taking place and the challenges with that environment. For example, if multiple operators are working in the same area there’s always a risk of hurting each other and if the operator is working in a public area other people’s safety, like passersby, might need to be considered.
One important thing to remember when making a risk assessment is that even the most experienced operator can slip, trip, or accidentally hit something that makes them lose control of the waterjet gun. Equipment may malfunction, pinhole leaks may occur, and couplings may break. All waterjetting jobs require protective clothing, even those that might only take five minutes as one never knows when an accident might happen. Consider the water pressure and flow used as well as nozzle type, then choose protective clothing accordingly. When in doubt, opt for higher protection to ensure the operator is equipped for today’s task and whatever comes their way tomorrow.
To ensure complete protection, it’s important to both wear protective clothing and use protective gear, such as the pictured hose protection and whip stop.
TST Sweden, a front-runner in the industry, offers protective clothing for waterjetting up to 3,000 bar / 43,500 psi and a variety of options depending on what job is being performed.
There are many factors to consider when choosing PPE. Besides the obvious parameters like pressure, flow, and nozzle type being used, it is important to look at what type of job the operator is performing. Do they need to move around and climb or crawl, or do they mostly do stationary work? And if they’re working in a warm environment ventilated PPE is a good choice, says Peder Lindström, market and sales director at TST Sweden.
Waterjetting is both a tough and sweaty job and it’s important that the operator feels well and stays alert to reduce the risk of accidents. Therefore, when working in a warm environment, ventilated clothing can be a great option, as well as taking frequent breaks. TST Sweden offers a ventilation solution in both their trousers and overalls, allowing compressed air to flow through the clothing. Shortly, they will also launch a ventilation vest that can be worn under any jacket. The compressed air keeps the operator cool during the work shift, lowering the risk of heat stress and increasing the operator’s comfort and endurance.
The parts of the body that most often sustain waterjet injuries are the hands, underarms, feet, and legs. The hands, in particular, are difficult to protect as operators require full movement of their fingers and adequate grip to perform
continued on page 34
their work safely. Therefore, gloves with good grip and high protection that does not compromise too much with flexibility are a good option. TST Sweden offers waterproof gloves with protection up to 500 bar, which combined with their hand protections, gives good protection without hindering the operator.
An area on the body many often forget to protect is the neck, a sensitive area where injuries quickly could become lethal. If the operator puts the hose over their shoulder and a pinhole leak occurs, it can—and has—led to fatal injuries.
A waterjet operator protected from head to toe in TST Sweden’s EliteOperator® range for waterjetting up to 3,000 bar / 43,500 psi.
For protecting the neck, TST Sweden offers two different options. Either the operator wears neck protection that is fastened on the helmet and protects the sensitive area between the helmet and the collar of the upper body protective clothing. Or they can go directly to the source of the hazard, the hose. Using hose protection will protect the operator from possible pinhole leaks in the hose close to their neck, arm pit, and side of their body, areas often difficult to protect with protective clothing, says Peder Lindström.
In addition to protective clothing TST Sweden offers something they call WSS, Workplace Safety Solutions:
products developed for when you need to protect people, sensitive equipment, or machinery, from water, waterjetting, gravel spray, and ricochets.
Apart from protecting the operator, it is extremely important to consider the safety of the worksite, especially around the hose and pump. Safety curtains can be used to protect people passing by and nearby equipment.
A scuff guard reduces wear on your hoses and thereby the risk of accidents with leaks and tears. Whip stops are important to secure hose ends and prevent broken hoses from whipping. The safety funnel and safety pipe cap make cleaning out heat exchangers and pipes both safer and smoother by preventing flying objects and water from hitting and injuring people and damaging equipment. There are many safety measures that one could—and definitely should— take, concludes Peder Lindström.
Ensuring operator safety involves many considerations, but creating a routine for conducting a risk assessment before every job will guide you in the right direction. By then taking appropriate action, the job can be done safely, with operators protected throughout their workday, from head to toe. ■
October 7, 2024
NOCO LLC, a full-service energy company and provider of environmental services, announced the acquisition of assets of Global Environmental Industrial (GEI), a Dunkirk, New York-based industrial and environmental cleaning company.
September 16, 2024
Painters USA, a commercial and industrial painting, cleaning, and flooring contractor, acquired Lakeside Painting, a Wisconsin-based painting contractor.
September 12, 2024
GenNx360 Capital Partners, a private equity firm investing in middle market business-to-business industrial and business services companies, announced an investment in Shenandoah Industrial Solutions, LLC, a Florida-based provider of underground infrastructure services.
September 12, 2024
Coalesce Capital, a private equity firm focused on investing in business services companies, announced that it has entered into a definitive agreement to acquire Miller Environmental Group, a provider of waste, industrial, and environmental services, from GenNx360 Capital Partners
September 6, 2024
Team Group, provider of total facility management, paint shop cleaning solutions, and industrial services, has acquired S.&T. Group, a Sault Ste. Marie multi-trade company based in the Algoma District.
mvt AG has introduced its expanded nozzle series, specifically designed for the demanding ultra high pressure (UHP) market in the Americas and beyond. These nozzles, equipped with American NPT (National Pipe Thread) threads, seamlessly integrate with a wide range of high-pressure water tools, offering a perfect solution for professionals in the UHP industry.
The mvt nozzle series also features Unified National Fine (UNF) threads, commonly used in imperial measurement systems, including popular sizes like 3/8 inch-24, 7/16 inch-20, and 1/4 inch-28. These threads provide better sealing and stronger connections in even the most challenging environments, making them ideal for highpressure applications that require maximum durability and precision.
Features include:
• American NPT Threads: Optimized for the UHP market, ensuring seamless compatibility with tools designed for imperial threading standards in the U.S.
• Durable and Reliable: Built to withstand extreme pressure, mvt nozzles offer long-lasting performance in demanding environments.
• Comprehensive Product Range: With the addition of Type 977, mvt’s portfolio now includes Types 972, 971, and 976, covering a wide array of high-pressure tool requirements.
• Ceramic Option Available: The popular Type 972 nozzle is also available in a ceramic version for enhanced durability and extended lifespan.
Whether working with UHP tools or systems that rely on imperial thread standards, mvt nozzles provide reliable performance. From manufacturers specializing in highpressure equipment to professionals operating in tough industrial environments, mvt’s products help ensure exceptional results.
Learn more about how mvt AG’s high-performance nozzles can optimize your tools and applications. Visit www.mvt.ch. ■
J
etstream of Houston, LLP, has announced the rebranding of its rental division, FS Solutions, to Jetstream Rentals. The rebrand aligns with Jetstream’s commitment to providing a unified brand experience and further strengthens its position as a premier provider of waterblasting solutions across the U.S.
The transition to Jetstream Rentals reflects the company’s dedication to consistency and excellence in serving its customers. By integrating the rental division under the Jetstream name, customers benefit from a more streamlined and cohesive experience with access to the company’s complete range of high-quality waterblasting equipment, tools and services.
“Rebranding as Jetstream Rentals is a strategic move to enhance our brand identity and better serve our customers,” said Alberto Albuquerque, senior manager of rentals at Jetstream of Houston. “Our focus has always been on providing top-tier equipment and unparalleled service. This allows us to present a unified front, making it easier for customers to recognize and trust the Jetstream name.”
Jetstream Rentals will continue to offer an extensive selection of waterblasting units, pumps, fluid ends and automated equipment, with most rental units being less than three years old. The rebranded rental locations will provide the same expert service and training that customers have come to expect, with equipment that offers minimal downtime and optimal performance.
This rebranding follows the recent expansion of Jetstream’s rental network, with a new location that opened in Corpus Christi, Texas, in August and facilities in Aurora, Colorado, and Tampa, Florida, that opened earlier this year. With the addition of these facilities, Jetstream Rentals now operates 13 rental locations across the United States.
For more information on Jetstream Rentals locations, visit https://waterblast.com/rentals/ or call Jetstream at (832)590-1300. ■
Co-Chief Executive Officers
Michael Battles and Eric Gerstenberg have joined Clean Harbors’ Board of Directors.
“Eric and Mike are talented, proven executives with lengthy track records of valuable contributions to Clean Harbors,” said Alan S. McKim, the Company’s founder, executive chairman and chief technology officer. “The first year and a half under their leadership as co-CEOs has been an incredibly successful period for the Company, its employees and its shareholders as we execute our Vision 2027 growth strategy. Their collective insights in the areas of operations,
finance, sales and capital allocation further strengthens our Board.”
Gerstenberg, 56, joined Clean Harbors in 1989 and during the past thirty years he has held a variety of positions of increasing responsibility throughout the organization. Prior to being named co-chief executive officer, he was the Company’s chief operating officer – a position he has held since 2015 – where he had responsibility for the environmental sales and service organization, all its facilities including incinerators and re-refineries, and oversaw the majority of its workforce.
Battles, 56, joined Clean Harbors in 2013 as chief accounting officer after a long career in public accounting at Deloitte & Touche, and as a finance leader at PerkinElmer, Inc. He was elevated to chief financial officer in 2016 and became co-chief executive officer in 2023. During his tenure as the Company’s CFO he oversaw the entire finance organization, including multiple debt raises and refinancings, as well as taking on some strategic and operational oversight. ■
Vacuum Truck Rentals (VTR) has converted its entire fleet of vacuum and jetting rental units to Vacall brand AllJetVac, AllExcavate, AllJet and AllVac machines. Vacall machines are designed, manufactured, sold and supported by Gradall Industries Inc.
VTR has one of the largest fleets of specialty equipment in the U.S., including trailers, tankers, roll-offs, dump trucks, and jetters. A third of VTR’s rental machines are vacuum and jetting machines. In addition to full-service rentals and sales, VTR offers maintenance and repair for many types of equipment as well as parts sales.
VTR is a leading supplier for contractors serving municipalities and private industry. Founded in 2001, the company grew out of an environmental service contractor business – Vacuum Truck Services, which was founded in 1998. As the business continued to grow, a sister company, Vacuum Truck Sales & Services, was founded in 2006 and now sells new and used trucks and other machines in six states.
For more information about VTR and its 17 locations, visit www.vactruckrental.com. ■
Applications for WJTA’s Student Scholarship Program are being accepted through March 31, 2025. WJTA members and their spouses, dependents and grandchildren are encouraged to apply.
These scholarship awards are gifts to be applied toward the cost of tuition. They place no obligation on the recipients other than that they do the
best possible work as students. In the spirit of such gifts that recipients are not obligated to repay any money to WJTA, but it is hoped that they, too, will help others to obtain an education when they become successful in the field of their choice.
The program was launched in 2021 with the first awards presented in 2022. The impressive number and
quality of applicants led the WJTA leadership to increase the number of awards presented. Now in its third year, the program has awarded nearly $63,000 in scholarships to WJTA members and their dependents.
For more information or to apply, visit https://www.wjta.org/wjta/ Scholarships.asp. ■
Spectrum Cleaning Company W.L.L
Hisham Kooheji Building 22 Road 6003 Block 624 Al Akr Al Gharbi, Bahrain Phone: +973 77122441 Website: spectrum-cleaning.net
Guilherme Bacinello
Alfajet Servicos Especializados Ltda. Rua Geraldo Gregorio da Silva, 65 Nova Olimpia, Mato Grosso 78.370-000 Brazil Email: gzbacinello@hotmail.com
Mid South Septic
Michael Gurley 11284 Gulf Stream Rd Arlington, Tennessee 38002 Phone: (901)867-2085 Website: www.midsouthseptic.com
Benoit Beaudoin 12480 Rue April Suite 103
Montreal, Quebec H1B 5N5
Canada
Email: bbeaudoin @amnorindustries.com
ICC Commonwealth
Patrick Jenkins
Cody Costello 795 Wurlitzer Dr North Tonawanda, New York 14120 Phone: (412)396-9162 Website: www.icc-commonwealth.com
Rich Speidel Rain for Rent
221 McDonald Avenue Joliet, Illinois 60431
Email: rspeidel@rainforrent.com
Richard Walsh
Walsh Service Solutions
1087 W 6 Mile Road
Sault Ste. Marie, Michigan 49783 Email: rich@walsh-ss.com
Billing Address (if different from above): Address____________________________________________________________________________________________
Shipping and Handling Charges are calculated on a per pound basis that is based on shipping by FedEx Express Saver within the United States or FedEx International Economy/FedEx Ground for international destinations. When ordering online at www.wjta.org the shipping is calculated automatically. If ordering by fax, phone or mail, contact the WJTA office for a shipping and handling total.
Waterjet Equipment Industry Best Practices. English, Second Edition (2021) (formerly Recommended Practices for the Use of High Pressure Waterjetting Equipment) Published in a newly redesigned full-color format
11-99 copies ___ # of copies of Waterjet .............................................................................................................x
100 or more copies ___ # of copies of Waterjet .............................................................................................................x
Vacuum Equipment Recommended Practices. English, Third Edition (2018)
.............................................................................................................x
Pocket Handbook - Vacuum Operator Mini Blue Book. English, First Edition (2019) 1-10 copies ___ # of copies of Waterjet .............................................................................................................x
Pocket Handbook - Hydroblaster Mini Orange Book. English, Second Edition (2021) 1-49 copies ___/___ # of copies (Hydroblaster/Vacuum Operator)..................................................................x
50 or more copies ___/___ # of copies (Hydroblaster/Vacuum Operator)..................................................................x
Currently under revision, new editions available soon.
Waterjet Equipment Industry Best Practices Video on DVD (2018)
Vacuum Equipment Recommended Practices Video on DVD (2009)
Contact the WJTA office for shipping and handling charges before processing your payment.
WAYS TO ORDER
Online: Go to www.wjta.org and click on "Online Store." Phone: Call (314)241-1445 and have your credit card information ready. Fax: Fill out the order form with your credit card information and fax to our 24-hour fax number at: (314)241-1449. Mail: Fill out the order form and mail with applicable payment to: WJTA, 906
At SPIR STAR, we do things a little differently. We prioritize listening to and adapting our business practices to best serve our customers. We understand that product quality, on-time delivery, and exceptional customer service go hand in hand. It's what sets us apart from ....well, you know. With our specialization in high pressure, we maintain an extensive inventory, offer a wide selection, and boast some of the best technical expertise in the industry. Whether it's something custom or a stock item you need, we' ll get it right and get it to you on time.