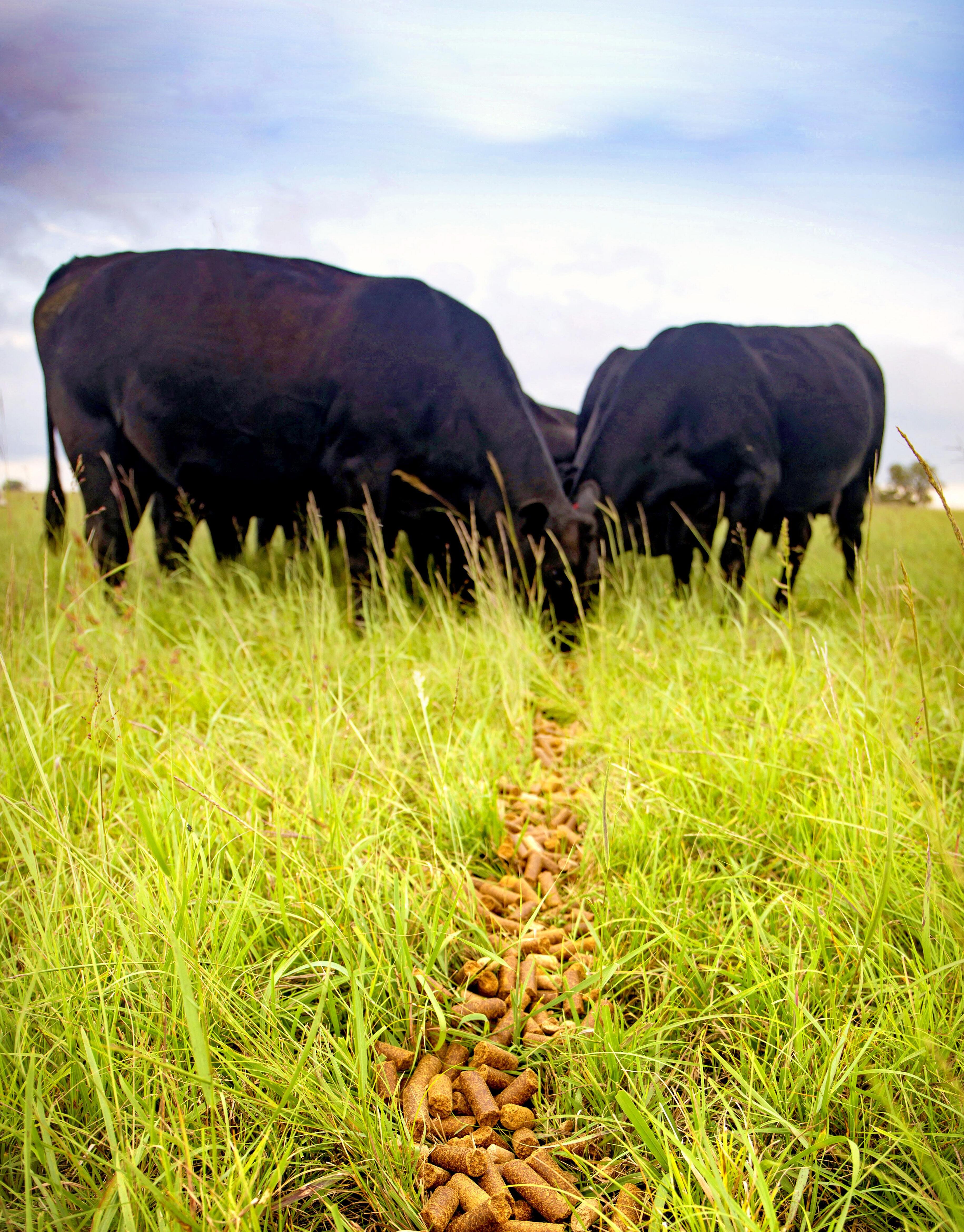


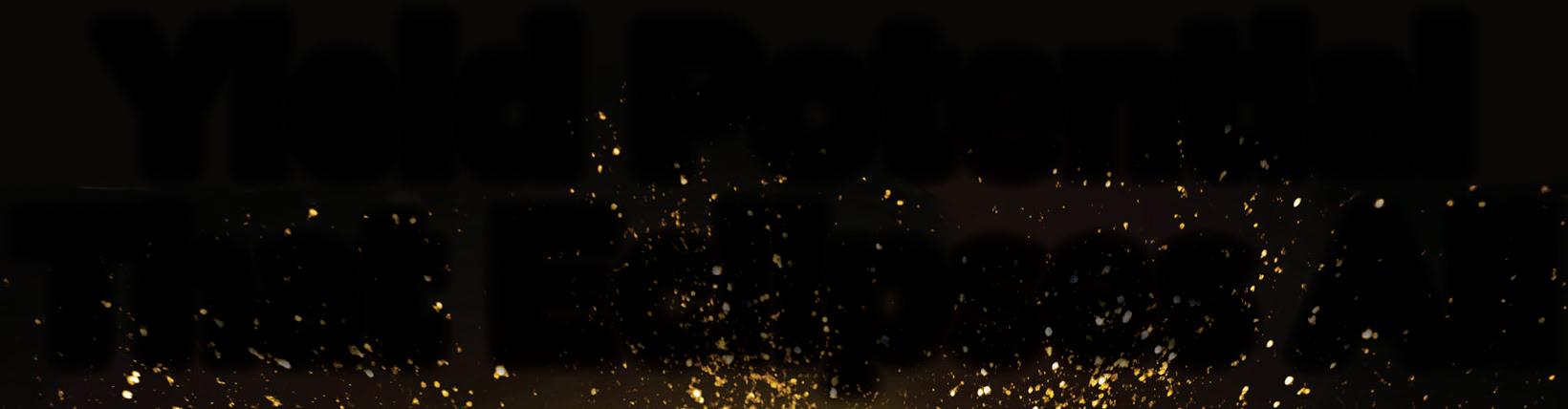
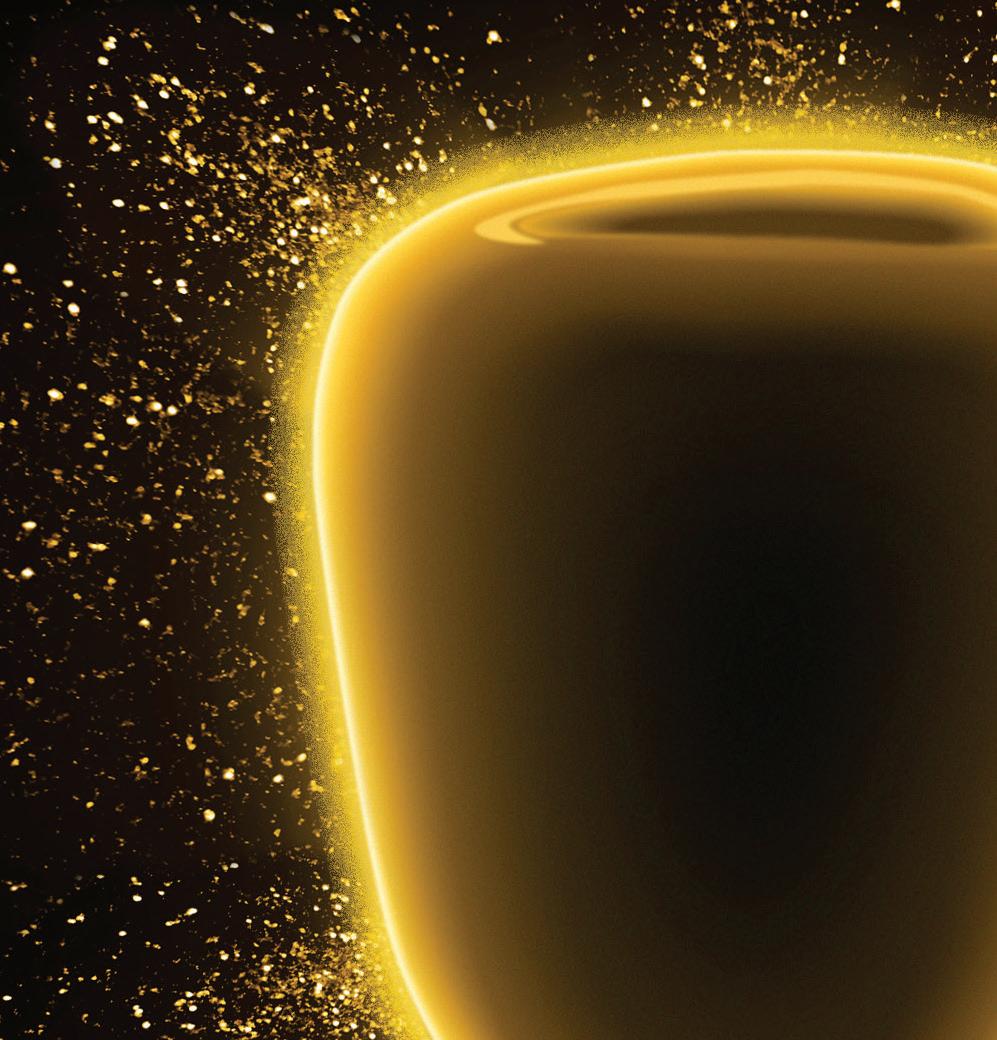
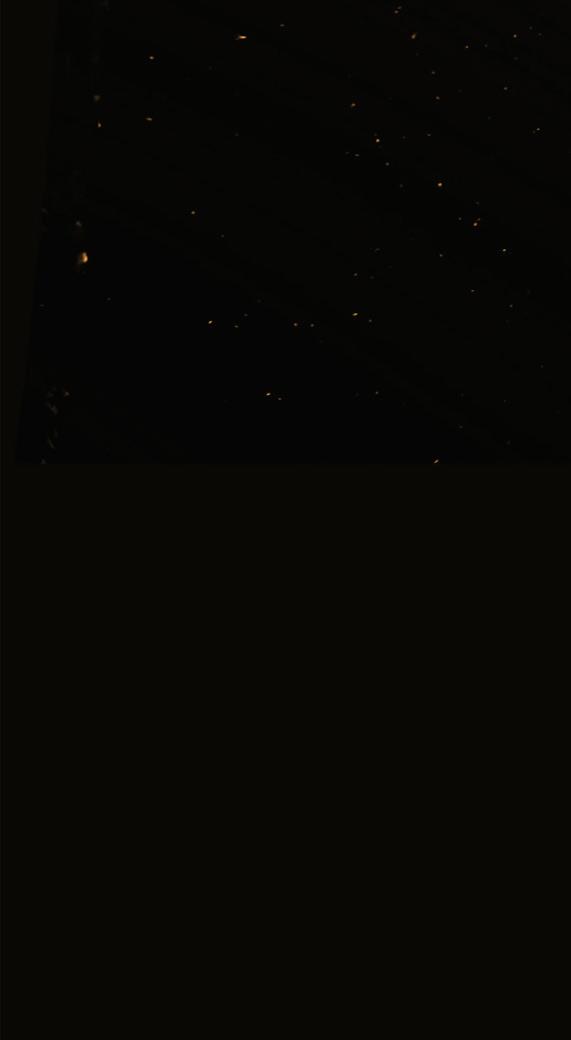
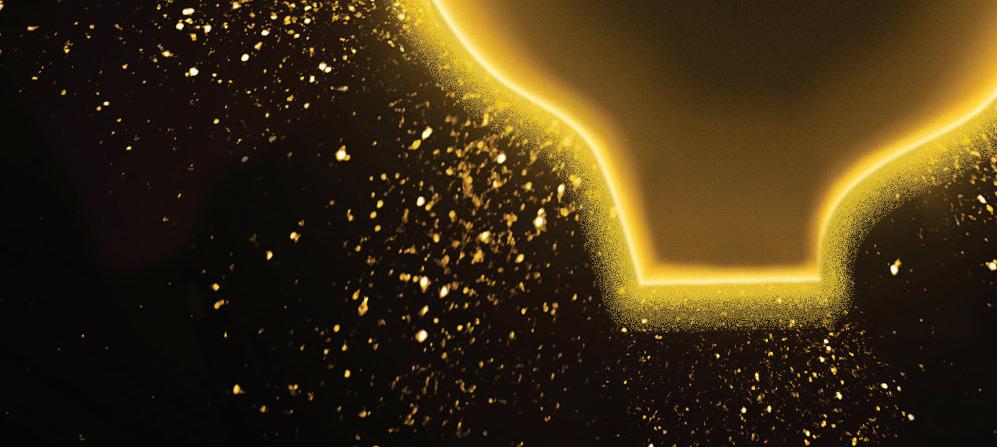
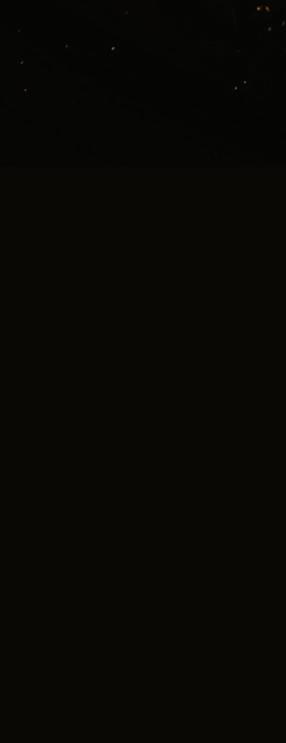

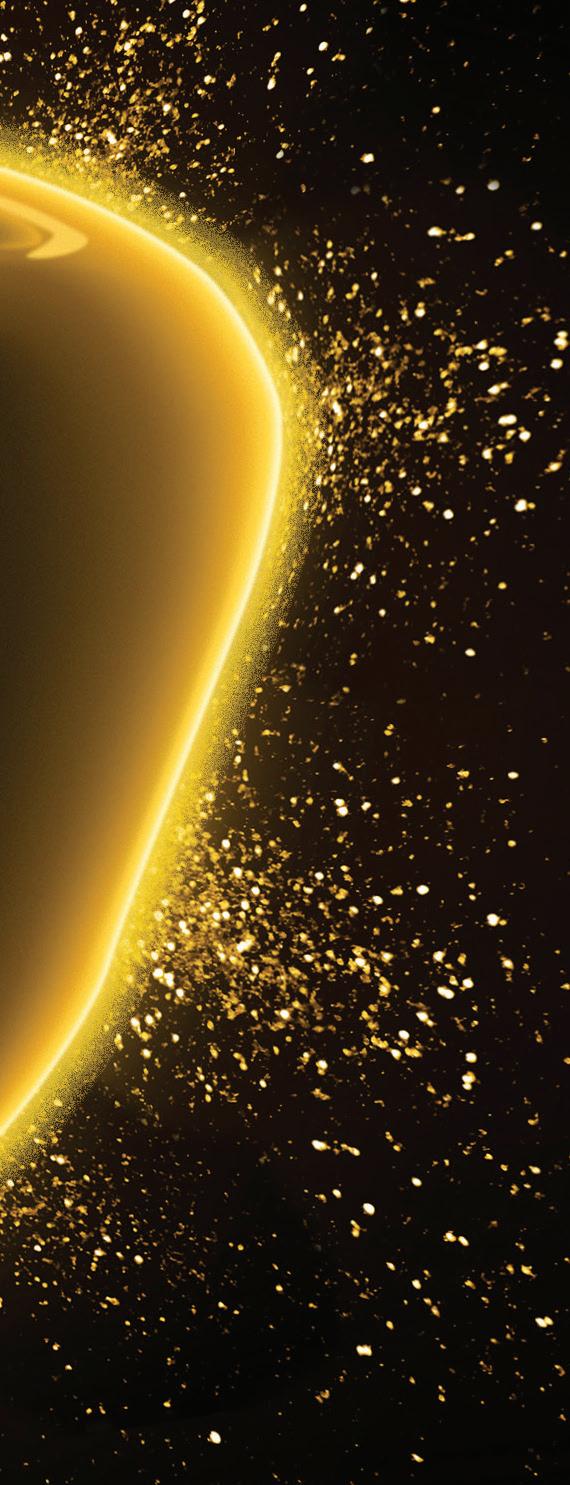
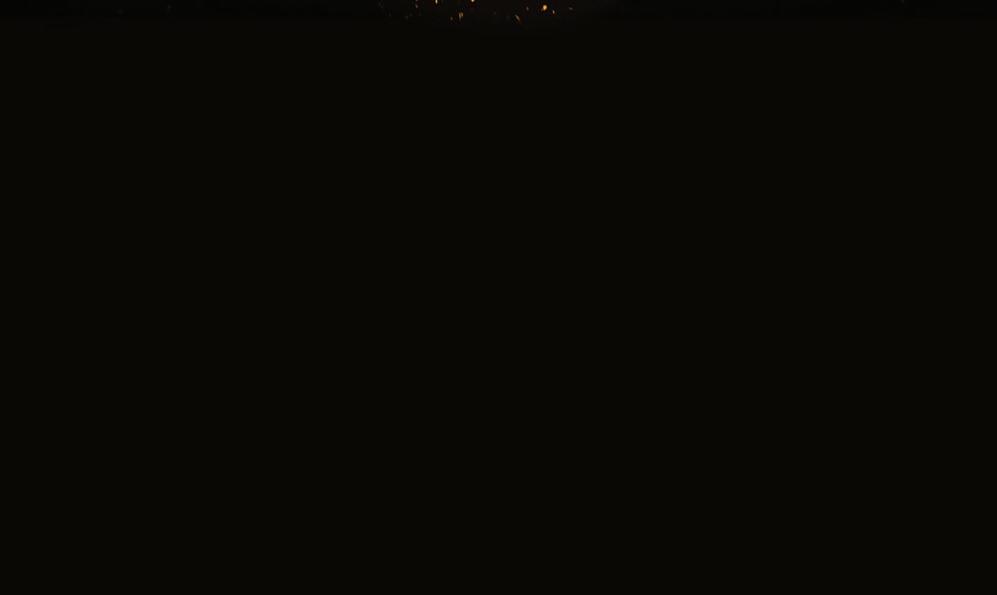
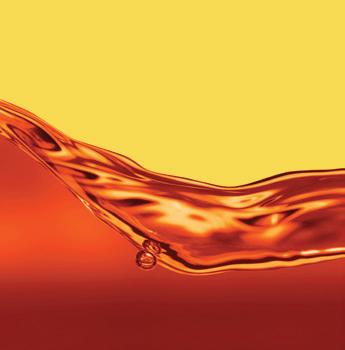
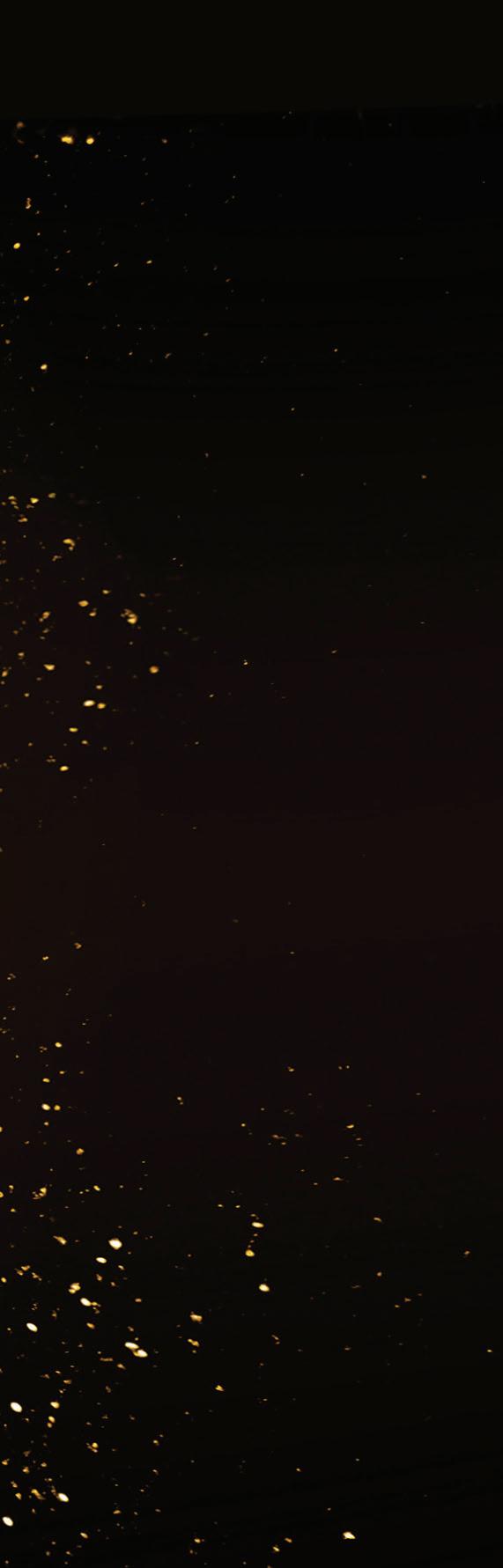

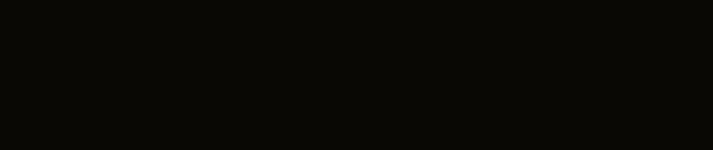

Why risk contamination? Or unnecessary downtime?
Get your tanks cleaner in less time! Even if you’re challenged by sticky, flammable or toxic residue or obstructions like paddles and agitators - we can work with you to remedy your operations.
With more than 100 sales o ces and 12 manufacturing locations worldwide, we are equipped to assist. From choosing the best nozzle, tank cleaner or tank cleaning machine, our field engineers are your partners to ensure we to meet your specific needs. We’ve helped others reduce cleaning time by as much as 90%. Let us do the same for you. Request a free evaluation of your cleaning operations from your local Spraying Systems Co. expert.
For unmatched service and support, visit spray.com/ethanol or call 1.800.95.SPRAY
5
6
By Tom Bryan8
9
MasterHand
14 INNOVATION
Revolutionizing the Range
MasterHand Milling's densified DDGS products find their place
By Luke Geiver
22 COPRODUCT
Thick with Nutrients
Mixed with DDGS or not, CDS is a valuable ingredient
By Katie Schroeder
28 PROCESS
Getting the Drop On DCO Yield Fluid Quip rolls out practical heat-and-hold system
By Katie Schroeder
34 PROFILE
Paired for Productivity
Reeve Agri Energy's storied colocation with cattle
By Luke Geiver
40
Improving
By
41
By
EDITORIAL
President & Editor
Tom Bryan tbryan@bbiinternational.com
Online News Editor
Erin Voegele evoegele@bbiinternational.com
Associate Editor
Katie Schroeder katie.schroeder@bbiinternational.com
Vice President of Production & Design
Jaci Satterlund jsatterlund@bbiinternational.com
Graphic Designer
Raquel Boushee rboushee@bbiinternational.com
CEO
Joe Bryan jbryan@bbiinternational.com
Vice President of Operations/Marketing & Sales
John Nelson jnelson@bbiinternational.com
Senior Account Manager/Bioenergy Team Leader
Chip Shereck cshereck@bbiinternational.com
Account Manager
Bob Brown bbrown@bbiinternational.com
Circulation Manager
Jessica Tiller jtiller@bbiinternational.com
Marketing & Advertising Manager
Marla DeFoe mdefoe@bbiinternational.com
Minneapolis Convention Center | Minneapolis, MN (866) 746-8385 | www.fuelethanolworkshop.com
Celebrating its 40th year, the FEW provides the ethanol industry with cutting-edge content and unparalleled networking opportunities in a dynamic business-to-business environment. As the largest, longest running ethanol conference in the world, the FEW is renowned for its superb programming—powered by Ethanol Producer Magazine—that maintains a strong focus on commercialscale ethanol production, new technology, and near-term research and development. The event draws more than 2,000 people from over 31 countries and from nearly every ethanol plant in the United States and Canada.
Minneapolis Convention Center | Minneapolis, MN (866) 746-8385 | www.fuelethanolworkshop.com
Capturing and storing carbon dioxide in underground wells has the potential to become the most consequential technological deployment in the history of the broader biofuels industry. Deploying effective carbon capture and storage at biofuels plants will cement ethanol and biodiesel as the lowest carbon liquid fuels commercially available in the marketplace. The Carbon Capture & Storage Summit will offer attendees a comprehensive look at the economics of carbon capture and storage, the infrastructure required to make it possible and the financial and marketplace impacts to participating producers.
Saint Paul RiverCentre | Saint Paul, MN (866) 746-8385 | www.safconference.com
The North American SAF Conference & Expo, produced by SAF Magazine, in collaboration with the Commercial Aviation Alternative Fuels Initiative (CAAFI) will showcase the latest strategies for aviation fuel decarbonization, solutions for key industry challenges, and highlight the current opportunities for airlines, corporations and fuel producers. The North American SAF Conference & Expo is designed to promote the development and adoption of practical solutions to produce SAF and decarbonize the aviation sector.
Saint Paul RiverCentre | Saint Paul, MN (866) 746-8385 | www.nationalcarboncaptureconference.com
The National Carbon Capture Conference & Expo is a two-day event designed specifically for companies and organizations advancing technologies and policy that support the removal of carbon dioxide (CO2) from all sources, including fossil fuel-based power plants, ethanol production plants and industrial processes, as well as directly from the atmosphere. The program will focus on research, data, trends and information on all aspects of CCUS with the goal to help companies build knowledge, connect with others, and better understand the market and carbon utilization.
Let’s be honest. When most of us stand around a highboy cocktail table at a conference talking coproducts—if the conversation even goes there—we maybe hit on exports, high-protein, corn oil and CO2. It’s coproducts casual. Feedlots, rumen health and growth rates are out of our wheelhouse. And that’s okay. We’re not ranchers or animal nutritionists. That said, it’s critical to not lose sight of how important standard, domestic coproduct use is to our industry—and we haven’t.
This issue starts with stories about conventional coproduct use: the colocation of distillers grains and beef cattle production, and the still-important role of condensed distillers solubles (CDS). We wrap up with more progressive ideas about coproduct yield optimization and post-production coproduct enhancement.
Our page-14 cover story, “Revolutionizing the Range,” shares the story of Dusty Turner and MasterHand Milling. The Nebraska company has, for a decade, been transforming DDGS into pellets and cubes for both feedyard and grazing operations. Like other trailblazers in this business, Turner is an entrepreneur and a risk taker. He’s experienced the ups and downs of the ethanol and cattle businesses—many have—but he’s still passionate about where the two industries intersect. It’s been a long journey, but MHM now has a network of about 60 dealers across nine states. Its future looks solid.
If rumen health isn’t the subject of cocktail gatherings, neither is CDS, which may be the least celebrated coproduct of ethanol production. CDS is, however, an important feed ingredient, both as a component of DDGS and apart from it. As we report in “Thick with Nutrients,” on page 22, despite the fact that CDS has been in continuous production for decades, it has a low profile because it typically doesn’t reach the market as a stand-alone coproduct, but mixed in with distillers grains. However, a select number of U.S. plants do sell CDS straight up. Our story revisits SweetPro, longtime maker of CDS-laden lick tubs. SweetPro has been using CDS for years, and experts say the use of liquid supplements is now growing because they are more widely available, affordable to transport, and easy to mix.
In “Getting the Drop on DCO Yield,” on page 28, we look at how Fluid Quip Technologies is giving ethanol producers another practical way to maximize DCO output with thermal pretreatment. Overdrive, FQT’s latest DCO optimization platform, is designed to boost DCO yield with a “heat-and-hold” system that treats syrup before it enters the centrifuge for oil extraction. They say it’s a “bulletproof” setup that can increase yield by 10-20%.
Finally, we come full circle to beef cattle in our closing feature, “Paired for Production,” on page 34. We share the story of the historic colocation of Reeve Agri Energy and Reeve Cattle Co. in southwest Kansas. The Reeve family has owned the land where the biorefinery and feedlot sit for more than a century, and the ethanol plant is one of the oldest operating facilities of its kind in the nation. The story is a shining example of a business that has leveraged the efficiency of onsite distillers grains consumption for more than four decades, and counting.
Enjoy the read.
The U.S. Department of Agriculture recently made a $25 million investment in a Regional Conservation Partnership Program being led by the American Coalition for Ethanol. The RCPP is designed to unlock corn ethanol access to clean fuel markets and new tax incentives, such as the 45Z clean fuel production credit, based on the adoption of climate-smart agricultural practices that reduce greenhouse gas (GHG) emissions.
We are immensely grateful for the USDA’s vote of confidence in the work ACE is doing to ensure corn ethanol has a strong future as a meaningful part of the climate solution.
The USDA’s investment builds on ACE’s successful South Dakota-based RCPP, which has already enrolled more than 15,000 acres in climate-smart practices across seven counties around Dakota Ethanol LLC, a corn ethanol plant in the eastern part of the state.
The new RCPP funding will help farmers adopt reduced tillage, nutrient management, and cover crops on nearly 100,000 acres across 167 counties surrounding 13 ethanol facilities partnering with ACE to implement the project in the 10-state region of Illinois, Indiana, Iowa, Kansas, Minnesota, Missouri, Nebraska, Ohio, South Dakota, and Wisconsin. The sites were strategically chosen to provide our project’s scientific team with statistically significant data regarding the GHG effect of conservation practices in different soil types and climates.
ACE and our partners will accomplish three important objectives through this RCPP project. First, we will incentivize farmers in 10 states to adopt conservation practices, with three-fourths of the funding going toward that goal. Second, our team of soil scientists and agronomists will monitor, measure, and verify how the conservation practices adopted by participating farmers reduce GHG emissions from corn production. The data they collect will be shared with the U.S. Department of Energy, which will use it to pressure test existing models, such as GREET, to address real and perceived “information gaps” that currently prevent farmers and ethanol producers from adequately monetizing climate-smart ag practices. Third, our ultimate objective is to empower ethanol producers and farmers with modeling and calculator tools to earn higher tax credits and premium prices in clean or low-carbon fuel markets based on climate-smart ag practices. We want to establish an alternative to burdensome and costly quantification and verification protocols that would discourage farmers and ethanol producers from reaping maximum benefits from these practices in the future.
We have been working with the 13 ethanol plants, along with a team of technical experts, and we are all eager to get started. Our near-term goal is to work with farmers in the 167 eligible counties to adopt conservation practices after the 2024 harvest. Given the progress we have already made on our existing South Dakota RCPP project, with more than 15,000 acres under contract for climate-smart ag practices, we are in a good place to hit the ground running.
The economic potential of capitalizing on climate-smart farming practices to produce corn ethanol for clean fuel markets or new tax incentives is significant. Through the 13 partnering ethanol facilities, there’s the potential to remove over 2,679,843 metric tons of CO2 per year, equivalent to taking 596,346 cars off the road annually. Across the 10-state project area, this could amount to over $500 million per year in estimated maximum value from clean fuel markets—a $266 per acre benefit for farmers based on the three-year average carbon price in the California Low Carbon Fuel Standard. This potential economic value is similar to what the carbon benefits could be worth under a properly implemented 45Z tax credit.
Visit ethanol.org/usda-rcpp to learn more about this project.
The EU’s ambitions to be a world leader in the fight against climate change are admirable but daunting—which makes it all the more vital for policymakers to take a pragmatic approach that uses every available sustainable emissions reduction technology.
This is especially clear in the latest EU figures on renewable energy compiled by Eurostat, which show that the bloc is still heavily dependent on fossil fuel in transport once the influence of artificial multipliers is removed—more than 92% in 2022, compared to just 7% renewables. It’s clear that more needs to be done to promote real renewables in transport.
Unfortunately, in some cases the EU has chosen a more dogmatic approach that excludes practical solutions. This is especially true when it comes to biofuels. That’s why the European renewable ethanol industry has chosen to challenge two of the flagship policies of the EU’s Green Deal for failing to recognize the proven benefits of crop-based biofuels.
In December, European ethanol producers launched a legal challenge to the EU’s FuelEU Maritime Regulation, which aims to decarbonize the shipping industry; in January, the industry filed a similar case against the ReFuelEU Aviation Regulation, which seeks to decarbonize air transport.
Those two regulations, as devised by then-Commission Executive Vice President Frans Timmermans and inherited by his successor as the Commission’s Green Deal chief, Maroš Šefčovič, marginalize or prohibit the use of crop-based biofuels to reduce emissions—even those such as renewable ethanol that meet the strict sustainability criteria enshrined in EU law.
In the maritime case, companies representing nearly all of the EU’s production of renewable ethanol seek to annul a section of the legislation that considers crop-based biofuels to have the same emission factors as the least favorable fossil fuel pathway. In the aviation case, these companies seek to annul specific sections of the RefuelEU Aviation Regulation that exclude crop-based biofuels from the definition of sustainable aviation fuel.
The legal actions are based on several arguments. In the maritime case, the suit argues that the European Parliament and Council committed a manifest assessment error by failing to rely on scientific and technical data in preparing their policy on the environment; violated the principle of proportionality by considering that crop-based biofuels that are compliant with the Renewable Energy Directive (RED) have the same emission factors as the least favorable fossil fuel in maritime transport; and violated the principle of equal treatment because the methodology used to calculate the GHG intensity of the energy used to power ships is not consistent with how RED calculates biofuel GHG emissions.
In the aviation case, the industry argues that the European Parliament and Council once again contradicted available scientific and technical data in preparing their policies; and that they violated the principle of proportionality by effectively enacting bans on the use of RED-compliant crop-based biofuels.
This patchwork approach to crop-based renewable ethanol—confirming its sustainability and importance within RED but sidelining it in FuelEU Maritime and RefuelEU Aviation—is more than just discriminatory. It also jeopardizes the EU’s ability to meet ambitious decarbonization targets. Given the importance of achieving Europe’s goals for climate change mitigation, energy independence, food security, and strategic autonomy, the EU should make better use of proven domestic solutions such as renewable ethanol.
Carbon America has submitted a Class VI CO2 injection well permit application to the U.S. Environmental Protection Agency’s Region 8 office to permanently store carbon dioxide produced by two ethanol plants in Colorado. The application was submitted in late 2023, determined to be
complete by the EPA in early January, and is now in the technical review phase.
“We are thrilled to take this significant step toward advancing our mission to quickly and safely capture and store as much carbon dioxide as possible,” said Brent Lewis, CEO of Carbon America.
Raízen, Brazil’s largest ethanol producer, and Wärtsilä, a global leader in power system technologies for marine and energy markets, have partnered to help decarbonize the marine sector through ethanol use. By studying the effects of applying ethanol as a marine fuel, the initiative aims to reduce greenhouse gas emissions, pro-
vide novel options to customers seeking sustainable fuel alternatives, and substantively contribute to an energy transition in marine shipping.
“Ethanol is a promising marine fuel that is readily available now,” said Paulo Neves, vice president of trading at Raízen. In addition to testing ethanol as a primary
Cardinal Colwich LLC, a wholly owned subsidiary of Cardinal Ethanol LLC, has completed the acquisition of Element LLC, a 70 MMgy corn ethanol plant located in Colwich, Kansas, that was previously owned by a joint venture between ICM Inc. and The Andersons Inc.
The facility, capable of producing ethanol, corn oil, and high-protein feed, origi-
nally began operations in 2019. Last April, The Andersons and ICM announced that market-based disruptions had adversely affected the facility’s profitability and that the plant had been placed in receivership.
According to U.S. Securities and Exchange Commission filings, Cardinal Colwich LLC entered into an asset purchase agreement to acquire the former Element
If approved, the injection well will permanently store up to 350,000 metric tons per year of CO2 produced annually by Colorado Agri Products’ Yuma and Sterling ethanol plants in northeastern Colorado.
marine fuel, the companies are engaging in discussions with ship designers and shipowners, and also examining regulatory and compliance issues related to the use of ethanol as a marine fuel. Ultimately, using cellulosic ethanol in marine applications is their goal.
plant in October. The acquisition was completed on January 31. The plant is now listed as Cardinal Colwich LLC on Ethanol Producer Magazine’s plant list.
Enerkem, a Canada-based advanced biofuels production company, is retiring its Enerkem Alberta Biofuels plant in Edmonton. According to the company, the EAB facility achieved its main objective of completing the commercial scale-up of Enerkem’s process technology.
With more than 15,000 hours of operation producing ethanol and methanol, the plant validated Enerkem’s waste-tobiofuels platform. It also allowed Enerkem to attract global partners and investors while developing a world-class team with expertise in the design and deployment
of advanced gasification technology. With those objectives achieved, Enerkem made the decision to retire the EAB plant. The company said it will continue to focus on the global deployment and commercialization of its technology.
Lallemand Biofuels & Distilled Spirits, a fermentation ingredients supplier to alcohol producers, has formed a partnership with Braskem, a prominent polyolefins producer and market leader in the biopolymers space, to jointly develop renewable chemicals.
The partnership between LBDS and Braskem provides a joint technological
and commercial framework for the research, development, and commercialization of next-generation biobased alternatives to fossil fuel-based chemicals. Using LBDS’s biotechnology as a basis for their platform, the two companies will collaborate to develop biobased chemicals for Braskem’s technological and commercial partners, first exploring products for the
The Denmark-based biotechnology and biosciences companies Novozymes and Chr. Hansen have officially merged to create Novonesis.
“We have successfully combined Novozymes and Chr. Hansen, and today we come together as one leading global bio-
solvents segment. Their goal is to produce 100% renewable, drop-in chemicals derived from “bio-origin” feedstocks like ethanol.
“This new technology will bring higher value coproducts to the fuel ethanol industry,” said Angus Ballard, president of LBDS.
solutions partner,” said Ester Baiget, president and CEO of Novonesis. “Novonesis combines our joint strengths and the wonders of biology.”
Cees de Jong, chairman of Novonesis, added, “I am pleased to witness the realization of the Novozymes and Chr.
Hansen combination. We will continue to create powerful biosolutions for our customers and partners based on our more than 100 years of innovation and application expertise.”
Dusty Turner helped develop and lead Conestoga's ethanol plants in Kansas before setting out on his own to produce coproduct cubes and pellets that have gained broader acceptance over the past decade.
By Luke GeiverLike the early renegades and risk-takers of ethanol production, Dusty Turner has always been a progressive cattleman willing to explore unconventional ways of getting things done. And it was through ethanol that Turner found a way to bring an innovative feed product to ranches and feedyards from Texas to South Dakota—what is ultimately a 900-mile swath of American cattle country. About 10 years ago, he left a successful career in ethanol production after serving as the chief operating officer of a multi-plant operation he helped start. Along with a small group of fellow co-founders, Turner is largely credited with the idea of building a pair of biorefineries that became the foundation for a diverse, multi-plant operation known today as Conestoga.
In 2006, Turner helped spearhead the development of the company's first two ethanol plants, both in Kansas. The now 62 MMgy plant in Garden City came first, followed by the now 115 MMgy facility in Liberal. In 2012, Conestoga acquired Diamond Ethanol in Levelland, Texas (the former Levelland Hockley Ethanol plant). The origin of the company’s Kansas facilities, like
a lot of things in the southwest part of the state, is tied to cattle. The founders wanted to build the plants to bring cattle feed— specifically, distillers grains—closer to their feedyard. In fact, much of Turner’s life and career has been about cattle. Before Conestoga became a reality, he was running a 75,000-head feedlot. Getting ethanol plants built represented a steady supply of highprotein energy for the cows without the need for trucks hauling it in from 150-plus miles away. So they built the plants and got their distillers grains. Turner was an integral part of the company’s original management team, serving as COO, but he never stopped being a cattleman. His legacy, however, may ultimately be tied to both industries—a cattle guy known for producing densified feed products from grain ethanol’s principal coproduct.
“I’ve always been the guy who has looked at issues and found the fixes for them,” Turner says. “I did that with Conestoga to bring cattle feed closer, and now I’m trying to do that with MasterHand Milling.”
Turner has always been an entrepreneur across the cattle and ethanol indus-
tries. While he was still with Conestoga— and also running a trucking company and a feed business—he hired a team to help stand up MasterHand Milling, or MHM, which makes a variety of densified cattle feed products from DDGS.
“I’ve learned that pain is the path,” he quips. “If you truly believe in something, it’s not so much about if it’s right or wrong; it’s just about not giving up.”
After several years in the ethanol industry and running various other endeavors on the side, Turner decided to make an all-in commitment to MHM. “I chose to basically go out on my own and really put all of my effort into it,” he says.
During his time at Conestoga, he held a few different roles. He frequently worked with ICM Inc., the prodigious U.S. ethanol process technology firm, to improve the company’s plants. And prior to his role as COO, he was in charge of marketing Conestoga’s 150-plus loads of wet distillers grains per day coming out of the company’s plants, so he was familiar with the process and benefits of the product. In many cases, the plants had more demand than supply for the distillers grains they were able to produce.
“I was on the other side of the table from my peers in cattle. We were talking dis-
tillers instead [of cattle operations],” he says. “I think my relationship with some of those customers gave them confidence that our wet distillers grains products produced via ethanol were dependable and could benefit their entire system.”
Turner was successful in growing the distillers grains market for the ethanol plants. But at a certain point, he was ready for a pivot back toward his true cattle passion. So,
PHOTO: MHMhe combined his firsthand knowledge of the ethanol and distillers grains production process with an idea sparked from a visit to the International Fuel Ethanol Workshop & Expo, where he and a colleague saw a pelletized DDGS product. Using those experiences, Turner laid the foundation for MHM, a company that uses unique milling technology to transform loose DDGS into consistent, high-protein, high-energy
range pellets and cubes. Picture a rancher in a flatbed truck bouncing along a grass field during a summer day in Kansas. Thanks to MHM, that rancher can now spread pelletized or cubed feed for the animals.
It should be noted that Conestoga produced DDGS pellets and cubes at its Texas ethanol plant, starting about nine years ago, but halted operations of the pellet mill last September due to production economics,
Turner learned early on that the traditional rancher wasn’t as progressive in adding or changing feedstuffs as the cattle feeder. He needed to be more patient with the ranchers running cattle on grass. He needed to take on less debt. He also needed to provide more performance data on his
product. Working with Oklahoma State, MHM ran trials on the product, collecting data that verified the feed’s effectiveness and value.
Turner and his team of cattlemen had never had an issue explaining or showing the benefits of the cubes used in a feedyard, but grass operations were a whole different story. As it turned out, the Oklahoma State
data helped them work with grass ranchers, too. They found out that cattle grown on grass and supplemented with the distillers grains cubes throughout the grazing period were heavier going into the feedyard and more efficient with processing feed, as seen through rumen health. Carcass characteristics also showed a higher red meat yield in animals feeding on the cubes.
The data also helped prove that the pellets and cubes could do everything on the ranch from summer through winter. The product could feed mama cows, weaning calves, help grow stockers, and even be used in the diet of finishing cattle. Sometimes animals have difficulties transitioning from one food source to another, but according to Turner, animals tend to take to the pellets and cubes quickly. The cubes offer a unique combination of concentrated energy that is roughly 95% digestible protein and low residual starch that accelerates growth, reduces digestive issues, improves forage utilization and boosts reproductive performance in lactating cows, weaning calves, yearling calves on winter grass, and yearling calves on summer grass, among others.
The ingredients used in the cubes and the smaller pellets are one of two things: corn distillers grains with solu-
bles or grain sorghum distillers grains with solubles.
The return on investment from using the cubes is 100%, Turner says, which is fortunate for MHM because the products are more expensive than a traditional feed counterpart—sometimes up to $100 per ton more. The price often requires justification, and Turner consistently emphasizes the same point: Once ranchers and cattle operations understand that the gains from using the product are going to be greater in the end than the price difference they incur at the beginning, using the cubes becomes a “no brainer.”
The Oklahoma State data helped to show another piece to the MHM cube story that also seems like a nobrainer. In the winter, feedlots and ranchers rely on some form of wet distillers grains or a dried version for their feed rations. But in the summer, the demand for distillers grains prod-
ucts decreases. The pellets and cubes, however, have been shown to make a major difference in cattle performance and carcass characteristics when provided to cattle grazing on summer grass. (Remember Turner’s statement about his product revolutionizing the range?). The cube is now being viewed as a risk management tool. In the ranching world, rainfall amounts are always a constant worry and major determining factor of herd health. Too much, too little, not at the right time. All of it matters to the grass quality and availability for the cows out on pasture. As several
real-life videos on the MHM website show, ranchers can sprinkle, dump, or leave out the cubed products on the range in the summer to supplement or improve the rations of the herd.
“If a ranch really wants to make its operation sustainable year over year and take the variability out and put certainty in, they are choosing our product,” Turner says.
As passionate as Turner is about his products and the cattle business in general, he’s still fond of and excited to talk about the ethanol sector. He hopes the ethanol industry will continue developing its understanding of DDGS and how valuable the coproduct truly is as a reliable option for the cattle industry.
In his next phase of work at MHM, Turner hopes to continue the evolution of the milling process and the distribution network he’s established. For the ethanol sector in general, he wants to
build bigger buzz and demand nationwide for distillers grains in a way that will inspire increased investment in new products that can continue to add value to ethanol production while, of course, benefitting American cattle producers.
Author: Luke Geiver Contact: writer@bbiinternational.comIt may be the least heralded coproduct of corn ethanol production, but condensed distillers solubles—CDS—has an important role in the animal feed market, both as a component of DDGS and apart from it.By Katie Schroeder
When it comes to ethanol production coproducts, you simply don’t hear about condensed distillers solubles (CDS) very often. Despite being in continuous production for decades, CDS has a relatively niche marketplace presence and low profile compared to higher-volume, higher-margin dry mill coproducts like distillers corn oil (DCO). That’s because CDS typically doesn’t reach the market as a standalone coproduct, but as a component of DDGS (giving the dried distillers grains acronym its S). However, a select number of U.S. plants do sell CDS straight up—by choice or necessity—and the product has a real place in the animal feed industry.
The production of CDS actually jumped from 102,605 tons in October 2022 to 114,333 tons in October 2023, according to the USDA’s Grain Crushings and Coproducts Production report for De-
cember 2023. Chuck Gallop, director of innovation at ICM, and Ryan Mass, ICM’s director of animal nutrition and a self-identified “voice for the animals,” outline the unique role and benefits of CDS as a feed ingredient and explain why producers typically don’t prioritize it as much as other coproducts. “Whoever is buying condensed distillers solubles, or this syrup, is doing it because it’s on the market,” Gallop says. “It’s not the primary pathway with which [producers] want to market that material because it’s normally sold at a much lower value than if it was dried and sold [within DDGS]. It’s better mixed together.”
CDS is a blend of the fine suspended solids, yeast, fine fiber and protein found in the thin stillage stream condensed five to ten times in the evaporators. “From an animal feed perspective, it makes a great feed. It’s concentrated in the things the animals need; it can also be concentrated in things that the animals really don’t need like salts,
sulfur, sodium, and impurities that come in with the corn,” Gallop says. “We try to mitigate those things by how we operate the process.”
Another component found in CDS that benefits animals is glycerin, explains Mass. Glycerin is a high-energy compound that does not impact the glycemic index and insulin response of the animal. Solubles provide an easy-to-transport solution for cattle farmers that are looking for ways to deliver these nutrients in a palatable way. “Anything we make in an ethanol plant is highly palatable: animals love the taste, smell, aroma, flavor—all of those [characteristics],” Mass says. “So, another way to think of it is, not every animal producer has across-the-road access to different kinds of feeds. They might not have an ethanol plant nearby, but [if they are trying to incorporate] a flavor component to [their operation], solubles is a great way to do that.”
FEED THAT FLOWS: Condensed distillers solubles, or CDS, is a blend of the fine suspended solids, yeast, fine fiber, and protein found in the thin stillage stream condensed five to ten times in the evaporators. While it is usually mixed back into DDGS, it is sometimes sold to customers straight up, in its viscous, yellow form.
PHOTO: ICM INC.
Cattle and swine need a variety of nutrients that both CDS and DDGS provide. However, the logistics of acquiring a feed ingredient is an important factor in its usability. Mass explains that every ingredient must be purchased, transported, mixed, and delivered to the animals. “The key driver is the cost of the nutrient delivered to the bunk,” he says. Liquid supplements require far less infrastructure to make and are easy to mix, and cattle producers are taking advantage of that. Additionally, Mass explains, many feed lots are showing interest in using CDS because the availability and understanding of liquid supplements, in general, has increased.
Cattle need several elements to be healthy. The first and most important need is water, Mass explains, the cheapest source of which is a nearby stream or water tank. Secondly, cattle need energy—some type of carbon-based compound—including glycerin and any excess protein. Amino acids and phosphorous are key as well.
Since ethanol producers started making DCO out of the fats found in the syrup stream, the fat content of the CDS and DDGS has dropped. Because DCO extraction has resulted in drier DDGS, swine farmers have started adding other humectants to moisten the feed and keep it from blowing around, explains Mass. Some farmers use molasses, but it lacks significant nutritional benefits other than some phosphorous. CDS is a more nutritional option, due to the higher amount of digestible phosphorous in it, among other nutritional benefits. Corn has a lot of natural phosphorous in its raw state, but pigs are not able to digest it properly. However, after corn goes through the ethanol process, enzymes have broken down the phosphorous into a “very, very digestible” state, making it an appealing ingredient for swine farmers.
The palatability of CDS is a key rea-
son it is in demand as an ingredient, explains Gallop. “Syrup used to be referred to as cow Kool-Aid,” he says. “And the reason why is you could add it to just about anything, and if whatever it was added to was previously unpalatable, like Canadian thistle, if you mixed the syrup with it, cattle would eat it.”
Bob Thornberg, CEO and founder of SweetPro, used his experience in the ethanol industry and knowledge of CDS to create higher-value feed supplements. “Solubles had limitations in the early days, so [knowing] how to deal with them is what prompted our use in feeds,” Thornberg says. SweetPro’s primary product is 50- to 250-pound lick tubs for cattle, horses, goats, and sheep. The company also makes bagged products. The tubs use a combination of CDS and DDGS, but the bagged product does not include syrup. “We’re looking for [our bagged products] to be more free flowing—[as the] tackiness [of CDS] is a benefit in the tubs but a detriment in loose meal products—so we only use solubles in our tubs,” he says.
CDS is challenging to use as an ingredient because its characteristics are not con-
sistent, Thornberg explains. Ethanol plant processes vary, causing the CDS to have different dryness or viscosity. When ethanol producers started extracting DCO from the CDS it lowered the fat content of the ingredient significantly. Thornberg and his team adapted by adding canola oil or flax oil to compensate for the lower oil content and increase the feed’s Omega 3 content. “Now, [with] some of the fat being stripped out of solubles, it changes their characteristics, and so it kind of limited our use and created a variable for us from a feed industry standpoint,” Thornberg says. “We’ve put oil back into our feed product [to compensate for the fact that we’re not] getting [a conventional] CDS.”
Today, a dry mill ethanol plant may produce around 15 to 16 pounds per bushel of DDGS, and roughly a third of that weight is CDS, Thornberg explains. SweetPro uses both DDGS and CDS to make its signature lick tubs by recombining the two ingredients, packing them, and adding a mineral to make the tubs harden. DDGS brings a different type of protein than CDS, along
with more soluble fiber than DDGS. These components have helped SweetPro’s brand of lick tubs stand out in the industry. Thornberg explains that the lack of starch and sugars, replaced with a high amount of
fiber, gives his company better options for nutrition.
“Condensed solubles, I’ve always thought, are just a spectacular feed ingredient,” he says. “And if you can use it appropriately, the nice fiber content, the nice protein content, the nice everything about it is good. But it does have its limitations— trying to deal with it from each plant, [with each product stream] being a little different.” SweetPro’s two manufacturing plants source ingredients from ethanol producers in North Dakota, Nebraska, Kansas, and Missouri, with most of the CDS used in its products coming from the latter two states. Thornberg says a working partnership between an ethanol producer and feed maker can be tricky to create, but a good partnership matches the feed company’s needs with the ethanol producer’s operating conditions.
These partnerships are challenging, in part because an ethanol producer’s goal is usually to reduce the production of syrup, Gallop explains. Producers achieve this by
Our team of experts have over 20 years of ethanol plant maintenance expertise. We o er full service and parts for all Fluid Quip equipment to ensure peak performance.
• OEM Parts Warehouse
•$2 million+ inventory on-hand
•Factory Trained & Certified Techs
•MZSA™ Screens
•Paddle Screens
•Grind Mills
•Centrifuges
•Gap Adjusters
mitigating the amount of glycerol made in fermentation, pulling out suspended solids, and managing the amount of enzymes used. Glycerol is a humectant that keeps CDS in a liquid state. Making a lot of glycerol is a problem for ethanol producers because it makes distillers grains with solubles harder to dry. Higher glycerol can be a good quality for making some types of feed, but a problem for ethanol producers trying to keep their natural gas costs low.
Producing more stand-alone CDS does have the potential to help lower carbon intensity (CI) scores since drying DDGS with higher solubles content uses more natural gas. However, this strategy may not end up drastically reducing CI because transporting the syrup tends to offset any carbon reduction. When operating above nameplate capacity, ethanol producers often make more CDS because their evaporators can’t handle the extra volume of liquid. When that happens, they will end up with a lot of water left in their thin stillage, and since the dryers cannot handle the extra moisture, producers may choose to sell the CDS as a liquid rather than combine all of it with their DDGS.
Ethanol producers are able to customize their product streams—including feed
products such as DDGS and CDS—to fit the feed market in their area. Gallop points to a couple of ICM’s products that help producers customize and improve their coproducts. TS4, the company’s thin stillage solids separation system, has the potential to help producers concentrate the CDS to maximize its feed value and minimize the volume of syrup produced, explains Gallop. This technology uses highspeed decanters to remove fine suspended solids to concentrate the syrup. Another approach is to send the thin stillage stream through third- or fourth-effect evaporation. A higher concentration reduces the water load in the solubles, a key part of increasing the nutrient value of the syrup.
ICM’s other technology that assists producers in concentrating the CDS is its FOT for Oil Recovery. Gallop explains that this two-part technology dewaters the whole stillage cake and washes out any residual starches and sugars, along with DCO and minerals. These components end up in the centrate stream, which is concentrated into the syrup. “By performing this washing step of the cake, we can force the migration of all of these solubles, salts, and sugars and fat into one product stream where it can be concentrated,” Gal-
lop says. “We can use it for liquid feeds, or it can actually be fractionated out even farther at that point. We can move the glycerol into one bucket, try to move the yeast and other things into another bucket, and get the salts
and acids into another bucket, so each one of those fractionated streams bring a higher value at the end.”
Although CDS production is not a priority for most ethanol producers, those that
MAXIMIZING VALUE: ICM Inc. has multiple technologies that help producers customize and improve their coproducts. TS4, seen here, the company’s thin stillage solids separation system, has the potential to help producers concentrate their CDS to maximize its feed value and minimize the volume of syrup produced.
have a local market for it are contributing to the quality of life and production efficiency for animals in the Midwest, and giving farmers an option for a liquid feed ingredient rich in protein, glycerin, and fiber. “All in all, the thing that we’d like the most to capitalize on is the fact that it has sticky, gooey, molasses-like characteristics without sugar or starch,” Thornberg says. “We feel like that gives us the better nutritional option.”
Author: Katie Schroeder Contact: katie.schroeder@bbiinternational.comDistillers corn oil prices have come down from a 70-cents-perpound peak in recent years but still remain between 45 and 50 cents, yielding strong production margins for the high-demand coproduct. The interest in maximizing DCO production has not abated, and producers are still looking for ways to improve yields. Overdrive, Fluid Quip Technologies’ new DCO optimization technology, is a robust and straightforward solution capable of increasing oil yields by up to 20%. Michael Franko, vice president of FQT, shares the development process behind the technology as well as its operational impact, production potential, and process integration.
At its core, Overdrive is a “heat-andhold” system for treating the syrup before it enters the centrifuge for oil extraction, Franko explains. It is common knowledge among ethanol producers that heating the syrup before running it through oil extraction helps release more oil from the emulsion, increasing DCO yields. He explains that FQT, through experimentation and fabrication, has built a “bulletproof” skid-mounted system that has the potential to provide a return on investment in one year or less. Franko explains that process syrup is piped into the skid and essentially held in a heated tank to create “optimum con-
ditions for the oil centrifuge to recover those yields day in and day out,” he says.
FQT is deliberate about making sure its technologies are additive, or complementary to one another, rather than redundant. For example, the company’s DCO Technology uses a different approach, washing the stillage thoroughly to maximize oil production—a more involved technology than Overdrive. Although oil yields would benefit from using DCO Technology and Overdrive together, most of the producers that have installed Overdrive thus far are running it as a standalone technology. “We look at it like Lego blocks. We have different pieces that we can plug and play throughout the plant,” Franko says. “But it’s not, ‘Oh, you installed that, so now this one doesn’t help you.’ We have our preferred technology for each step in the process, and you kind of gain exponentially as you’re putting those together.”
Franko explains that the high profit from DCO has driven up prices for chemicals in the past, but a one-time technology purchase is a simpler solution. “I’m not going to tell a client to stop using any chemistry, because it’s probably worth it for the additional oil you get, but this is an opportunity where you can make that capex investment,” Franko says. “It just sits and runs, and you’re not spending money over and over again on more and more chemicals.”
Process
ILLUSTRATION:
The design and development of Overdrive involved a lot of experimentation to determine what temperature range is optimal for oil recovery. “There was an understanding from the start that [many producers were] not feeding these centrifuges optimum conditions for oil recovery,” Franko says. “You look at what’s in the syrup and [if] you still have oil in your syrup, fat in your syrup, that tells us right there, there’s more to get out.”
Overdrive is based on the well-known fact that warming the syrup helps with oil extraction—it’s not “magic nuclear fusion,” Franko says. He explains that this phenomenon is well established and easy to recreate in a lab. In fact, some producers have attempted to implement a version of this technology on their own. In development, FQT’s team of engineers optimized the company’s technology for the precise temperature range that benefits yields, while figuring out a realistic amount of time to heat and hold the liquid in the context of limited tank space. After this information was gathered, FQT began the process of designing a robust technology with the specs needed to meet those requirements.
PHOTO: FQTOne of the challenges that FQT faced in development was handling the heated syrup. Heating the syrup is messy and can cause fouling in machinery over time. Knowing this would be an issue, the company designed the technology with a built-in solution. “We use a proprietary plate set in the exchangers and figured out the right flow rates to get the best and ... most energy-efficient temperature transfer, [while also limiting] fouling to reduce [clean-in-place, or CIP] and optimize uptime and performance,” Franko says. “We have a single-exchanger design and also a dualexchanger option with full automation for zero CIP downtime,” he adds.
Through R&D trials, FQT worked out how to balance the need for efficient energy use with minimal fouling, while optimizing the technology by working with producers on site. “We’ll do all of our R&D lab work, [and] all of our study work [independently], but
BENCH TO BIOREFINERY: In development, FQT’s team of engineers had to figure out optimal heat-and-hold parameters in the context of limited tank space at the actual plants. So while the work started in the lab, it needed to translate to large-scale production and realistic plant setups.
PHOTO: FQTwe’re working with our partner plants in the field, we’re looking at what we’ve got—how those temperatures affect things—[and] trying to make adjustments with them, within reason, to do [commercial-level] development,” Franko says. “We like to do only what’s necessary in the lab. We want to show proof of concept and then find a partner—so we are in the real world operating these things and not in a vacuum—because we all know there’s a lot more variability out there; we want to see that robustness.”
Overdrive is able to increase producers’ oil yields by over 10% on average, though this yield boost will vary based on the efficiency of each plant’s existing process, which involves myriad factors. A corn oil study can be a great tool for helping producers accurately evaluate how much DCO they can gain by adding a certain technology, explains Franko. During a DCO study, FQT applies its understanding of chemical engineering to examine a plant’s operating parameters—everything from milling to fermentation—to give the ethanol producer better information on how to optimize its
current operation, and how a new technology will impact its process.
The placement of oil extraction is one factor FQT evaluates in a corn oil study, according to Franko. The process of DCO production starts when the stillage left over after distillation is separated into a fiber stream, which goes to the dryers, and a thin stillage stream, which goes to evaporation. At the evaporation stage, the oil, fine fibers, proteins, and other components are concentrated into a syrup known as corn condensed distillers solubles, or CDS. Extraction of DCO happens during or after evaporation, depending on the individual producer.
Franko explains that integrating Overdrive into an ethanol plant’s process is straightforward. The technology is brought in on a skid and set on the ground; then FQT works with the plant to connect the syrup stream, heating source, and CIP solution. A holding tank is necessary to ensure the syrup has time to reach the correct temperature. Franko explains that if a plant doesn’t already have a tank with ample capacity—most plants have one installed in front of the centrifuge as a buffer—FQT will supply a small tank, in-
stalling it alongside the pretreatment system. Larger holding tank capacity may be necessary to ensure that the syrup maintains the desired temperature for the right amount of time.
“If somebody doesn’t have that tank, or it’s very small and they’re basically slamming everything through [an undersized] machine, then we would say, ‘Hold on, we’re going to put a little wide section in the pipe here to give it time to sit before it goes forward,’” Franko says. With the installation of a new tank, a new pump between the tank and centrifuge is also necessary, he explains. If the producer already has a right-sized holding tank set up, only existing pumps are needed for installation. Once the technology is integrated, it functions as a larger section of the pipe and has a minimal impact on production time.
Along with improved yields and noninvasive installation, Franko emphasizes the low maintenance, “set it and forget it” nature of the technology. Thanks to the built-in CIP solution, downtime for cleaning is minimal. Franko explains that a standard pressure washing during shutdowns probably wouldn’t hurt, but overall, the technology is low maintenance. “With our two-exchanger set up, it’s just back and forth, it’s totally automated,” he says. “Set it, plug it—[producers have] bigger things to worry about—and just let it run.” The lower-cost version of Overdrive uses a single exchanger and is bypassed for a few hours every eight to 10 days for CIP.
As DCO prices remain strong—around 48 cents per pound in January—Overdrive gives producers a simple and easily integrated solution to optimize production. Franko emphasizes the importance of it being an investment that keeps on giving, rather than an approach that requires repeated investment, and continuous inputs. “It’s a really good ROI [on DCO yield optimization] that’s not related to buying more chemicals,” Franko says. “And it helps produce more of a product that we’re already working hard to make.”
Author: Katie Schroeder Contact: katie.schroeder@bbiinternational.comReeve Cattle Co. has a storied history in ethanol and beef cattle production in southwest Kansas, and an even longer family legacy there. For the past 40plus years, the company’s footprint has included a 17 MMgy ethanol plant—Reeve Agri Energy—which is a sister company to RCC. The ethanol plant and connected 50,000-head feedlot are co-located outside the town of Garden City, the county seat of Finney County. The small corn biorefinery was brought online in 1982 for the express purpose of supplying the feedlot with distillers grains. Both operations sit on land that’s been operated by the Reeve family for over a century. Brothers Chet and Oliver Reeve originally homesteaded the land. Chet’s son, M.P. “Jack” Reeve, took over the operation in the 1950s. And today, M.P.’s son, Lee, oversees both RCC and Reeve Agri Energy.
Along with the ethanol plant and feedyard, RCC runs a center-pivot irrigation operation on several thousand acres. Catching Lee Reeve in between his duties with the feedlot and the ethanol plant can sometimes be a challenge, but Ethanol Producer Magazine caught up with him in mid-February. Even after all these years of operation, Reeve says, ethanol production, and the constant supply of on-site feed it provides, remains integral to the business.
Reeve is well known in Kansas for his role in developing and championing ethanol production. Since first convincing his family and team at RCC to pursue building the ethanol plant in the early ’80s, he has been heavily involved in the ethanol space. Ag outlets, universities, and TV stations in Kansas have all highlighted Reeve and his Garden City-based businesses. It’s hard not to discuss the past when talking to Reeve, whether he’s reflecting on the history of his family’s 5,000-acre ranch, changes in the cattle business, or the evolution of ethanol production since the early ’80s. He’s seen it all.
At one time, the area where the current feedlot and ethanol plant reside was a national park. Or at least it was supposed to be. According to Reeve, the government planted trees in western Kansas and planned to designate the area as a national park or
Lee Reeve,
a multi-generational Kansan who operates a feedlot colocated with a small ethanol plant, explains how producing fuel and feed has impacted his family business for over four decades.By Luke Geiver
preserve. But the plan didn’t stick. The area is low in moisture, especially during the winter. While not good for growing trees, the dry conditions make western Kansas a good place for feedlots. In fact, within 50 miles of RCC’s operation, there are several other high-volume feedlots. Reeve estimates that nearly 20,000 head of cattle are processed in the area every day. Behind only aircraft parts, Kansas generates its second highest amount of revenue from chilled beef cuts, followed by wheat, soybeans, and then frozen beef cuts.
The first time Reeve and his team ever heard about ethanol was from a Colorado School of Mines professor who was an advocate for blending ethanol into gasoline. That was in the 1970s. The professor’s research included insight on using ethanol’s principal coproduct, distillers grains, for cattle feed.
“In the ’70s, there was a big push to include ethanol blended fuels in clean air legislation,” Reeve says. “There was some research out there talking about how ethanol cleaned up fuel. It wasn’t just about how to get rid of corn.”
After talking with an engineering firm that built ethanol plants, RCC invested in and built a 1 MMgy corn ethanol plant.
“Most people were probably pretty skeptical, but we saw the numbers and it made sense,” he says.
The whole point of the ethanol plant was to provide consistent feed rations for the feedlot, according to Reeve. “The plant, [even] back then, produced some really good feed,” Reeve says. “We have the same feed today. Cattle are really good at cleaning all of this up and we knew that from day one.”
Over four decades, the plant has expanded from 1 MMgy to nearly 17 MMgy—an impressive legacy of expansion but still a small biorefinery by today’s standards. Milo is Reeve Agri Energy’s preferred feedstock, when available, but corn is typically easier to source. According to Reeve, milo, or grain sorghum, can often be difficult to obtain due to foreign buyers, China among them, procuring much of the available product in the region. Most of the ethanol produced at Reeve Agri Energy is sold into the Denver area or to nearby terminals. Some of the plant’s ethanol ends up in Oklahoma City, Amarillo, and other lower-
central U.S. markets. While many ethanol producers rail their ethanol to market, all of Reeve Agri Energy’s biofuel leaves the plant via truck. The employee headcount at the plant ranges from 12 to 15, about a third of the people employed at larger corn dry mills.
Although the plant may have started at very small scale, the team never considered it to be a pilot or demonstration facility. Katzen Engineering Inc. was instrumental in the creation of the original plant, providing the first process design package, detailed engineering, operator training and start-up service. Katzen continued working with Reeve to expand the plant over the years—a few million gallons at a time—from 1985 to the modern era, as the feedlot expanded almost ten-fold. In the early days, the ethanol plant’s waste heat was utilized for a colocated aquaculture operation. The main focus of each stage of growth was always creating synergy between the ethanol plant and the feedyard.
The centrifuges are in the feed mill. Instead of creating multiple byproducts out of the beer stripper, the plant’s design only produces a wet product and forgoes drying. The wet stillage is dropped out into the feedyard for cattle rations.
Several years ago, ICM Inc. did a renovation on some of the equipment that was 25 years old and needed to be replaced. The plant added an ICM frontend with a vacuum system that, Reeve says, is quite efficient. Although Reeve says the ethanol sector has always been a good business, he also says it hasn’t been easy.
“Even though we think there is good synergy in having the plant and feedlot together, through the years it has been rocky,” he says.
There has been opposition to aspects of the colocated operation dating back to ’82, and sometimes it has come from people and places that have surprised Reeve. Financial institutions were afraid of ethanol early on. The fight with oil has always been just that, a fight.
He specifically points to a rough period in the ’90s when the oil industry de-
veloped and promoted a product known as methyl tert-butyl ether (MTBE). A byproduct of the hydrocarbon refining process, MTBE became the darling of the oil industry for a time due to its ability to increase oxygen levels by adding octane to gasoline, Reeve recalls. Had MTBE continued without being regulated out of use due to safety and environmental issues, Reeve believes ethanol production and usage wouldn’t have taken off like it did.
Reeve and his team in Kansas have helped promote ethanol across the state and in Washington D.C. While the Kansas plant’s ethanol production capacity is limited by the size of the feedlot, he still wants to see the overall ethanol market expand. “We need a bigger market or more exports,” he says, pointing to developments in corn and cattle.
Genetics are improving in corn, leading to an increase in yield every year. The cattle industry, currently on a headcount decline across the entire sector, isn’t going
What can 5% more oil mean to your operation?
Contact us today to learn more about how Overdrive™ can help you turn oil production all the way up
to expand. However, the cattle produced at places like RCC are bigger and more efficient than ever with feed and nutrient consumption.
Although the Garden City plant doesn’t have a clear path to expansion, Reeve still follows the latest technology trends across the industry. One of those improvements is corn oil extraction. His plant doesn’t extract oil. They actually buy palm oil for the feedyard because they need more fat than they are currently getting out of the stillage ration.
Reeve is amazed at how far the industry has come since the early '80s, and how producers have persevered through rough periods. He says there were times when he and others thought the industry wasn’t going to make it. The Kansas State alumni is proud of everything he’s added to RCC’s legacy, especially the introduction of ethanol. Given the accomplishments of those before him, it should come as no surprise that he and his team have accomplished so much in Garden City.
In 2023, Jack Reeve, Lee’s father, was posthumously inducted into the Cattle Feeders Hall of Fame after a career that included a degree in veterinary medicine from Kansas State, time in the U.S. Army, starting the feedyard in 1962, and running it until Lee took over.
Today, there is a largely undefined nextstage for RCC and Reeve Agri Energy. But with how efficient their current operation is, Lee isn’t worried. “It has all evolved the way it needed to,” he says, “just as the ethanol industry has.”
He continues, “It has done what it set out to do from the time we got into it. Ethanol cleaned up a lot of gasoline. It provided a lot of rural jobs for rural areas. Now, it could play a big role with aviation fuel, and for us, it’s been a good business the whole time.”
Author: Luke Geiver Contact: writer@bbiinternational.comDisc stack centrifuges and tricanters are familiar and effective tools in distillers corn oil (DCO) extraction. However, challenges arise from upstream processes and over 50 unique plant variables, influencing optimal extraction. While upstream process variability is inherent, enhancing DCO yield involves focusing on modifiable variables to improve syrup feed conditions. Some of the feed stream variability, particularly viscosity, particle size, and oil droplet size, can be confined to more manageable conditions, directly impacting DCO separation efficiency and, consequently, the bottom line.
Optimal syrup conditioning hinges on the fundamental principles of Stokes' Law, where the manipulation of particle size, viscosity, and
fluid density directly influences oil droplet size, resulting in improved separation efficiency. Achieving this level of syrup conditioning is streamlined through TruShield-SC modular technology. This advanced syrup conditioning module is tailored to selectively eliminate large particles from syrup, effectively reducing viscosity and increasing oil droplet size for enhanced extraction efficiency.
Use of an advanced filtration technology, such as TruShield-SC, goes beyond enhancing syrup conditioning and boosting DCO yields. It serves as a robust safeguard for DCO extraction equipment, protecting against inevitable process upsets and consequently reducing maintenance requirements and un-
scheduled downtime. Unique in its modular design, TruShield-SC boasts easy installation with a plug-and-play process and connections for utilities and communication. Its compact footprint easily integrates into all plant designs and processes, providing a versatile and reliable solution.
TruShield-SC is a DCO efficiency enhancement manufactured exclusively by Trucent Separation Technologies LLC. Trucent’s process-oriented approach is experience-driven and backed by a diverse team of engineers, research scientists, and seasoned service technicians committed to innovation and service excellence.
Spraying Systems Co., a seasoned partner to the ethanol industry, has expanded its offering of fermentation tank cleaning technology.
By Katie SchroederSpraying Systems Co. offers custom solutions for sanitizing ethanol producers' fermentation tanks. Ethanol producers face various challenges in tank cleaning, from hard-to-reach areas to stubborn residues. In 2023, Spraying Systems Co. acquired Cloud Company, which gives ethanol producers quick access to technical support, with technicians able to reach the plant within two days or less.
Tank cleaning nozzles can last 10 to 20 years with regular maintenance. “Many of these machines have been out there for 40 years,” says Dominic DeMaria, tank cleaning business development leader with Spraying Systems Co. “And we want to make sure ethanol plants are maintaining them correctly, at the right time to achieve increased longevity,
better effectiveness in cleaning their tanks, and more efficient cleaning.”
Through ongoing collaboration with technical field engineers, systems are tailored to meet producers’ needs and ensure superior sanitation results. With nearly 90 years of experience in nozzle engineering, manufacturing, and developing spray technologies, Spraying Systems Co. collaborates closely with customers to develop customized strategies, optimizing cleaning effectiveness, machine maintenance, and equipment longevity.
For more information, visit www.spray.com