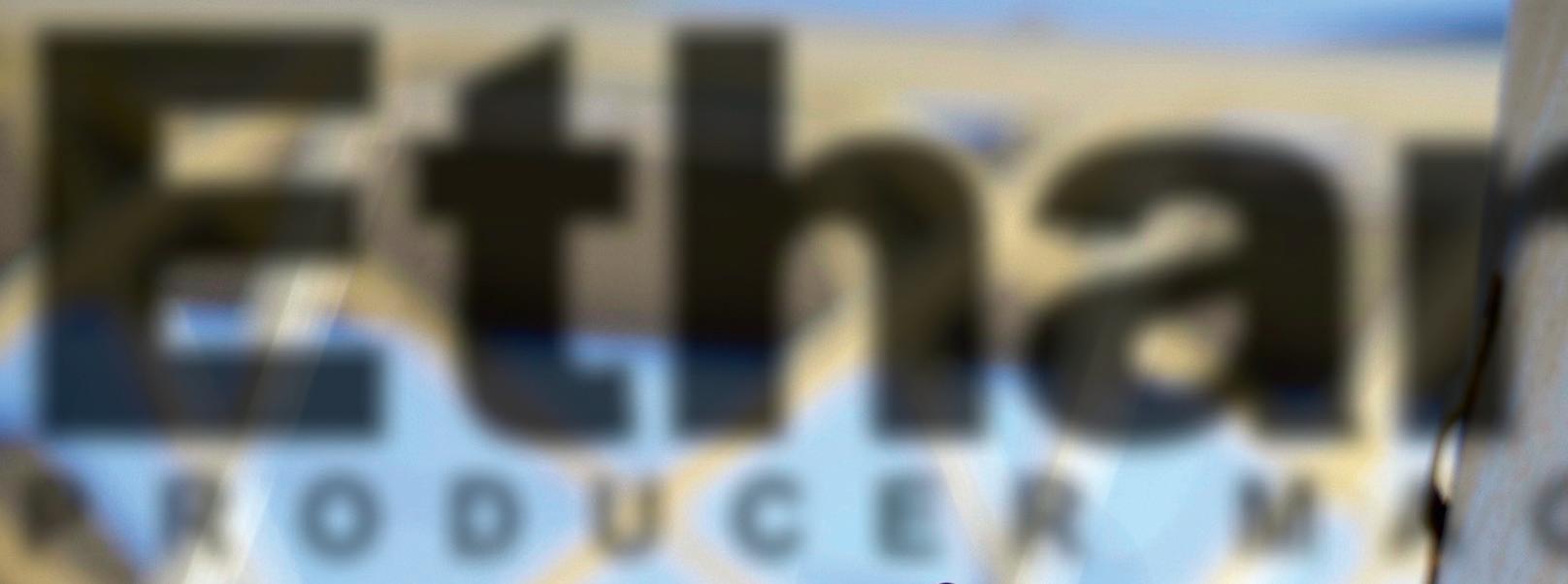
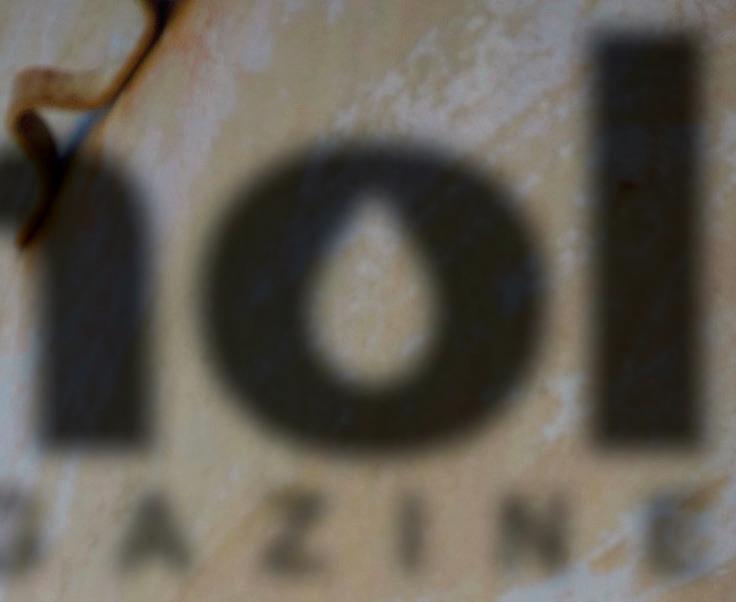
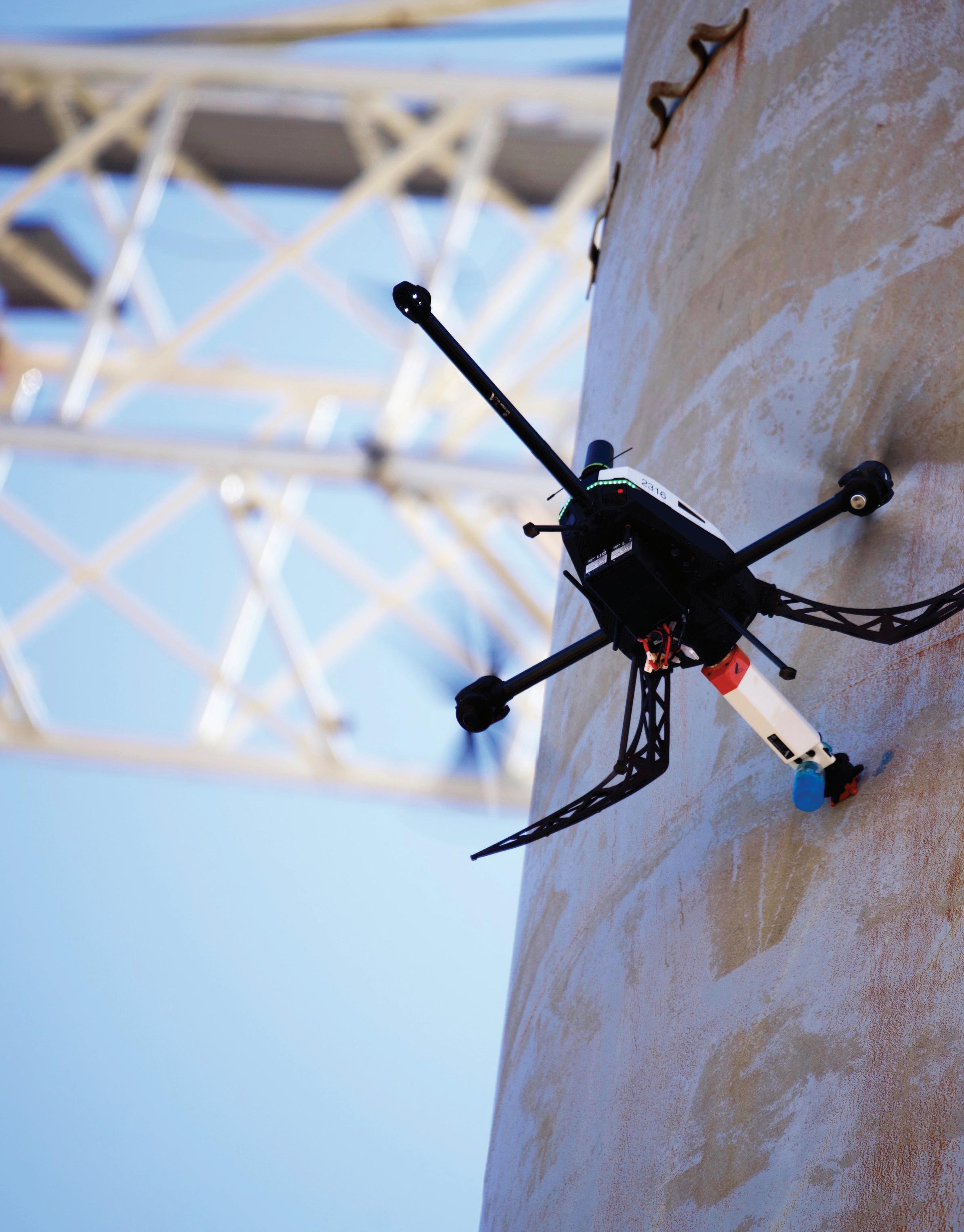
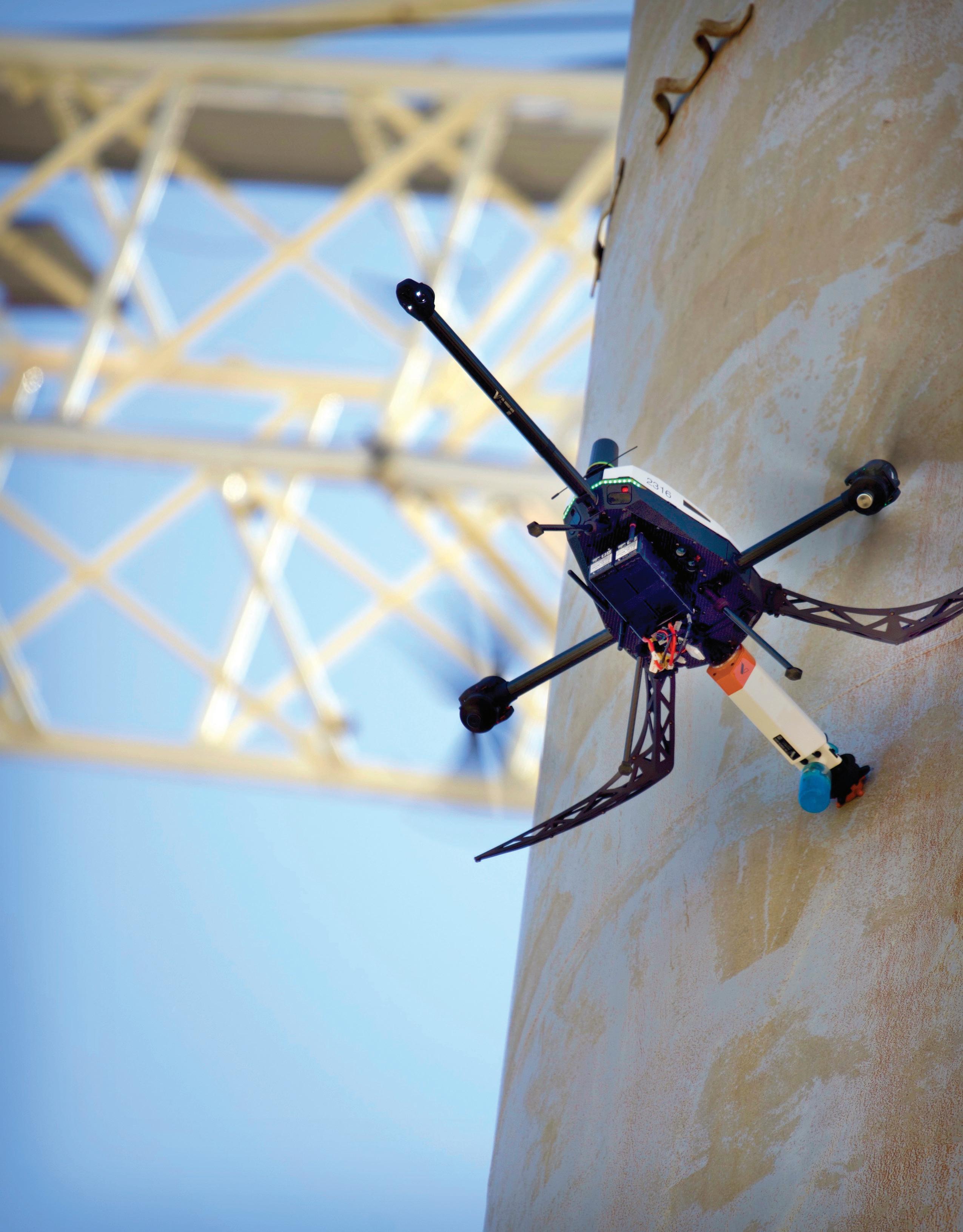
Non-Destructive Testing
Capabilities Evolve
Veto Keeps Iowa's CCS Projects Alive
Drones, AI and Robots
Data drives innovation. Th rough CTE InSight , advanced statistical analysis identifies opportunities for improvement and predicts the most impactful change for plant performance. Better data clarity enables optimization. Turn InSight into action.
Traditional cleaning methods expose your team to serious risks like injuries and heatstroke in hot, confined spaces. Automated tube cleaning keeps operators safe, using dual-direction high-pressure cleaning for better performance and heat transfer. Operators can remotely control the cleaning speed, ensuring consistent, thorough results. Protect your team and improve e ciency—contact NLB today to transform your operations!
Remove the operator from the blast zone. Increase tube heat transfer.
Enhanced operator control produces better results.
President & Editor
Tom Bryan tbryan@bbiinternational.com
Online News Editor Erin Voegele evoegele@bbiinternational.com
Contributions Editor Katie Schroeder katie.schroeder@bbiinternational.com
Features Editor
Lisa Gibson lisa.gibson@sageandstonestrategies.com
Vice President of Production & Design Jaci Satterlund jsatterlund@bbiinternational.com
Graphic Designer Raquel Boushee rboushee@bbiinternational.com
CEO Joe Bryan jbryan@bbiinternational.com
Chief Operating Officer John Nelson jnelson@bbiinternational.com
Director of Sales Chip Shereck cshereck@bbiinternational.com
Account Manager Bob Brown bbrown@bbiinternational.com
Senior Marketing & Advertising Manager Marla DeFoe mdefoe@bbiinternational.com
Ringneck Energy Walter Wendland
Commonwealth Agri-Energy Mick Henderson Western Plains Energy Derek Peine Front Range Energy Dan Sanders Jr.
September
Minneapolis, MN (866) 746-8385 | www.safconference.com
Serving the Global Sustainable Aviation Fuel Industry Taking place in September, the North American SAF Conference & Expo, produced by SAF Magazine, in collaboration with the Commercial Aviation Alternative Fuels Initiative (CAAFI) will showcase the latest strategies for aviation fuel decarbonization, solutions for key industry challenges, and highlight the current opportunities for airlines, corporations and fuel producers.
St. Louis, MO (866) 746-8385 | www.fuelethanolworkshop.com
Now in its 42nd year, the FEW provides the ethanol industry with cutting-edge content and unparalleled networking opportunities in a dynamic business-to-business environment. As the largest, longest running ethanol conference in the world, the FEW is renowned for its superb programming—powered by Ethanol Producer Magazine —that maintains a strong focus on commercialscale ethanol production, new technology, and near-term research and development. The event draws more than 2,300 people from over 31 countries and from nearly every ethanol plant in the United States and Canada.
St. Louis, MO (866) 746-8385 | www.sustainablefuelssummit.com
Please recycle this magazine and remove inserts or samples before recycling
Customer Service Please call 1-866-746-8385 or email us at service@bbiinternational.com. Subscriptions Subscriptions to Ethanol Producer Magazine are free of charge to everyone with the exception of a shipping and handling charge for anyone outside the United States. To subscribe, visit www.EthanolProducer.com or you can send your mailing address and payment (checks made out to BBI International) to: Ethanol Producer Magazine Subscriptions, 308 Second Ave. N., Suite 304, Grand Forks, ND 58203. Back Issues, Reprints and Permissions Select back issues are available for $3.95 each, plus shipping. Article reprints are also available for a fee. For more information, contact us at 866-7468385 or service@bbiinternational.com. Advertising Ethanol Producer Magazine provides a specific topic delivered to a highly targeted audience. We are committed to editorial excellence and high-quality print production. To find out more about Ethanol Producer Magazine advertising opportunities, please contact us at 866-746-8385 or service@bbiinternational.com. Letters to the Editor We welcome letters to the editor. Send to Ethanol Producer Magazine Letters to the Editor, 308 2nd Ave. N., Suite 304, Grand Forks, ND 58203 or email to editor@bbiinternational.com. Please include your name, address and phone number. Letters may be edited for clarity and/or space. TM
The Sustainable Fuels Summit: SAF, Renewable Diesel, and Biodiesel is a premier forum designed for producers of biodiesel, renewable diesel, and sustainable aviation fuel (SAF) to learn about cutting-edge process technologies, innovative techniques, and equipment to optimize existing production. Attendees will discover efficiencies that save money while increasing throughput and fuel quality. Produced by Biodiesel Magazine and SAF Magazine, this world-class event features premium content from technology providers, equipment vendors, consultants, engineers, and producers to advance discussions and foster an environment of collaboration and networking. Through engaging presentations, fruitful discussions, and compelling exhibitions, the summit aims to push the biomass-based diesel sector beyond its current limitations. Co-located with the International Fuel Ethanol Workshop & Expo, the Sustainable Fuels Summit conveniently harnesses the full potential of the integrated biofuels industries while providing a laser-like focus on processing methods that deliver tangible advantages to producers. Registration is free of charge for all employees of current biodiesel, renewable diesel, and SAF production facilities, from operators and maintenance personnel to board members and executives.
COPYRIGHT © 2025 by BBI International
This issue of Ethanol Producer Magazine is focused on maintenance, specifically high-tech applications—some powered by artificial intelligence (AI) that prescribes schedules based on predicted outcomes and probable risk. We also have fun covering some cool hardware—robotic vehicles and their payloads—being deployed to help maintenance personnel assess the health and structural integrity of their plants. From wall-crawling machines that collect ultrasonic data to high-flying drones that create geospatial records of whole biorefineries, we’ve got it all.
We begin with “Testing to Protect,” on page 17, which focuses a branch of maintenance called non-destructive testing (NDT), which is done by deploying myriad tools and technologies on industrial infrastructure to test for things like compromised structural integrity, leaks, wall loss, cracked welds and more. The data captured from these high-tech methods helps maintenance managers make informed, risk-based decisions based on the likelihood and consequences of equipment failure.
We trek even further into maintenance-related technology and gadgets in “Deploying Drones, Robots and AI,” on page 26. As the story’s author points out, there is a sort of inverse relationship between the age of our biorefineries and the novelty of the technologies being used to assess them. With many U.S. ethanol plants at or near two decades of operation, the tech needed to keep an eye on them is smarter and more sophisticated than ever: ultrasonic sensors, LiDAR and high-resolution georeferenced aerial imagery, to name a few. And with unmanned, AI-supported robotics in action, the work is done with almost zero risk.
Sandwiched between maintenance stories is a timely story about state policy—and a decision that may have saved carbon capture pipeline projects from outright cancellation in Iowa. In early June, Iowa Gov. Kim Reynolds vetoed a bill, HF 639, that many believe would have prevented most CCS projects from ever happening in the state. We explain what happened, and why, in a “A Path to Prevail,” on page 34. As most of our readers know, CCS is key to producing the ultra-low-carbon ethanol needed for sustainable aviation fuel—a market that is projected to create new demand for as much as 6.5 billion bushels of corn. That fact that was certainly not lost on Gov. Reynolds.
Finally, we reconnect with maintenance in “Ascending to Prescriptive Maintenance,” on page 42, a look at how Tranter is leveraging AI to monitor ethanol plant heat exchangers—which has broader implications than one might assume. While preventative and predictive maintenance continue to have their place in ethanol production, prescriptive platforms use AI to support scenario-based decision making that anticipates the need for maintenance through “digital twin” modeling, allowing producers to peek into the future and stave off problems before they occur.
Enjoy the read!
2.25 MILLION BUSHELS
BINS BETTER BUIL T
I wrote a column for Ethanol Producer Magazine a while back, featuring a version of one of my favorite Norm Macdonald bits—the “moth joke.” You kids can look it up on your internet machines. Some of the olds will know it. Here’s the Cliffs Notes/Sparks Notes/TLDR, or whatever you call it now, version.
A moth goes into a podiatrist’s office. The podiatrist greets him and asks how he can help, and the moth gives a long, painful explanation of how his life is falling apart all around him. After several attempts to redirect the conversation, the podiatrist finally interrupts forcefully and tells the moth, “You’re clearly troubled, but you need to talk to a psychiatrist, I’m a podiatrist.”
The moth apologizes, grumbles about proving again he can’t get anything right, and turns to leave. “Wait!” the podiatrist says, “While you’re here, can I ask you how you found us? Was it our TV ads? Radio? Our monster truck sponsorship—‘Big Foot’—clever, right? Or was it Twitter? Facebook? Instagram? What was it that brought you in here?”
“Dude. I’m a moth,” he answered. “Your light was on.”
At the time, and still today, the joke illustrates the fact that despite one’s best efforts to educate, inform, promote, or incentivize people to use your service or buy your product, sometimes they just do it anyway. Ethanol provides all kinds of different benefits, appealing to completely different types of consumers. To ethanol zealots like us, it’s the “something for everyone” fuel. We want drivers to be drawn to ethanol because it’s clean, or high-octane, or renewable, or American-made, or another of many benefits—and some are.
Over the years, millions have been spent telling consumers what’s great about ethanol. Some beautiful, creative, funny, clever ad campaigns have been launched to educate consumers, and while I feel good and proud when I see those ads, I’m not sure they register with Joe six-pack (or Joseph four-pack, if he’s a craft beer guy), because most ad campaigns have promoted what’s important about ethanol—to us—not the Joes. I’ve been critical of some ethanol advertising efforts—and most ethanol advertising expenditures, often pointing out that our competitor/partners in the oil industry hardly advertise at all while racking up half a TRILLION in annual sales. ExxonMobil is always in the top 10 in terms of revenue in the U.S. but never a top 100 advertiser. Last year they weren’t in the top 200—and they always spend extra in election years. And when oil companies do spend money on advertising, it’s usually by providing co-op ad dollars to their branded marketers who advertise their fuel for them. Those co-op funds come from a tiny portion of the increased cost retailers pay at the rack when they buy and market branded fuels—so it doesn’t cost anything.
So, I’m happy to see some very positive changes to ethanol advertising and promotion happening over the past several years. The South Dakota Corn Utilization Council’s latest efforts are a great example. Their new “It’s OK to Go Low” campaign focuses squarely on what matters to consumers: Price. More impressive is the fact some of their ads don’t even mention ethanol. That takes both humility and confidence—being OK knowing the word “ethanol” carries unearned negative juju, while being confident ethanol will be in the lowest priced fuel. SD Corn is also doing a cooperative ad campaign and E15 promotions with Kwik Trip/ Kwik Star. The ads are a little corn-y to me, but drivers trust retailers’ endorsements of fuel quality more than ours.
Whether drivers like ethanol or not, they buy it, and that’s the goal. Current campaigns recognize people are begrudgingly drawn to the nearest gas station and the lowest priced fuel—containing ethanol—because a light is on—the blinking “low fuel” light on their dashboard. Like moths to a podiatrist.
• Delivers up to 15% increased corn oil recovery
• Enables pathway to produce low-CI cellulosic gallons
• Dewaters corn kernel fiber for reduced natural gas consumption
• Maximizes plant operability
To learn more, contact your account manager.
As the U.S. Grains Council celebrates its 65th Anniversary this year and hosts its flagship biannual Global Ethanol Summit (GES) in October; it is an opportunity to reaffirm the Council’s steadfast commitment to developing export markets for agricultural products, including increasing visibility around the benefits of ethanol as a fundamental tool to reduce global carbon emissions.
Marketing year 2023/2024 saw a record-setting level of export volumes of U.S. ethanol to the world, reaching 1.746 billion gallons (6.609 billion liters), for a total value of $4.1 billion. This figure does not include exports to Japan. Current ethanol exports are on track for a similar performance this year.
While Canada, the United Kingdom, India and the European Union figure among U.S. top export destination markets, rapid expansion and uptake is also occurring in other less mature global markets. For example, several countries throughout Central America (Costa Rica, Guatemala and Panama) are moving forward with commitments to implement an E10 blending mandate, while Colombia and Peru are exploring ways of increasing current blending rates to higher levels. Similarly, Japan recently announced its intention to transition to E10 by 2023 and E20 by 2040, and the Philippines continues to blend at E10 but allows E20 on a voluntary basis.
Several drivers fuel this demand for U.S. ethanol, including economic, environmental and public health considerations. Concerns about air quality have led many foreign governments to consider ethanol as a readily available resource that provides immediate reductions in outdoor air pollution. Another aspect of USGC’s engagement involves ethanol educational programming, specifically to help raise awareness about the benefits of ethanol and its ability to help countries meet their climate goals.
Beyond ethanol’s role in on-road applications, there is tremendous potential for its use in sustainable aviation fuel (SAF), particularly via the alcohol-to-jet (AtJ) pathway. There are also growing opportunities for its use as a sustainable marine fuel (SMF), in the chemical space, household energy and other emerging sectors. Council staff recently travelled to the Philippines, China, South Korea, Taiwan and Japan to showcase how ethanol can play a role in SAF and SMF development, while supporting new research initiatives and engaging with stakeholders.
U.S. ethanol is poised to play a critical role in the energy transition. In response to global demand, U.S. ethanol is consistently improving its carbon intensity score. To be effective as a decarbonization tool, policy frameworks must allow for the use of ethanol in all forms. Policies that constrict ethanol use in the form of feedstock restrictions and/or quantitative limits in favor of other technologies or fuels render the path to carbon neutrality more costly, placing a premium on clean energy and increasing the cost of decarbonization for consumers.
Ethanol production benefits American growers and represents a source of homegrown energy that stimulates rural communities and dynamizes their economies. U.S. ethanol is a readily available and affordable resource supported by existing supply infrastructure with a demonstrated record of effectiveness, and USGC will continue its efforts to assist countries around the world as they integrate this plentiful high-octane oxygenate into their energy matrix.
Experience the Alcohol School like never before. With revamped sessions, fresh topics and more opportunities to connect, this year’s event blends cutting-edge innovation with expert-led education.
Se ptember 7-12, 2025 | Montreal, Quebec, Canada REGISTER TO DAY
El evate your exper tise.
cal, or converted into isooctane and jet fuel.
A.E., an agriculture-oriented buyer group based in Minnesota, will acquire the ethanol plant and a portion of the land with the intent to restart ethanol production, which has been idled since 2022.
Gevo announced that it has entered into a definitive agreement to sell AgriEnergy LLC, a wholly owned subsidiary of Gevo, to A.E. Innovation for $7 million. The transaction includes Agri’s 18 MMgy ethanol production facility located in Luverne, Minnesota. Gevo will retain ownership of certain isobutanolproduction-related assets and a portion of the vacant land at the site for future use. With these retained assets, Gevo could potentially produce up to 1 million gallons per year of isobutanol, which can be sold as a specialty chemi-
A.E. intends to operate the plant as an innovation facility providing companies with the opportunity to certify that new technologies can transition from laboratory or bench-top status to full production-level performance.
boosts the amount of distillers corn oil available for recovery, ensuring oil remains accessible throughout the process rather than being lost in the wet cake.
ICM has signed a new agreement with Little Sioux Corn Processors to install ICM’s proprietary FOT Oil Recovery system at the company’s 170 MMgy ethanol plant in Marcus, Iowa. The project includes engineering, equipment procurement and construction, with completion targeted for the first quarter of 2026.
FOT Oil Recovery is ICM’s proprietary two-step separation technology that improves solids-liquid separation after distillation. It includes a dedicated solids-washing step that significantly
The system has now been successfully deployed at several ethanol facilities across the U.S., and ICM has reported reliable, high-impact results and positive customer feedback.
Conestoga Energy announced the successful completion of drilling operations for its first Class VI well designed for carbon capture, utilization and sequestration (CCUS). The well, located near the company’s Bonanza BioEnergy ethanol plant in Garden City, Kansas, will serve as the cornerstone of Conestoga’s initiative to permanently store carbon dioxide emissions generated during the ethanol production process.
Conestoga intends to submit its full Class VI permit application to the U.S. EPA this summer, marking the next critical step in the company’s fully integrat-
ed CCUS/ethanol production strategy that will significantly reduce the carbon intensity score and increase margins of its bioethanol.
The project will enable Conestoga to capture and store 100% of the CO2 emissions generated from its bioethanol production process. Once operational, the facility will sequester over 150,000 metric tons of CO2 annually. Additionally, the project presents opportunities to store CO2 from third-party sources, allowing Conestoga to earn additional carbon credits.
Whitefox Technologies has announced the successful installation of the Whitefox ICE membrane dehydration system at ALCO Energy Canada (formally IGPC Ethanol ) in Aylmer, Ontario.
This project increases ALCO’s ethanol production capacity by just over 50 million liters (13.5 MMgy) per year, an increase of 15%, while also making the plant operate more efficiently throughout distillation and dehydration.
Representing Whitefox’s 18th installation and first project in Canada, it marks a significant step in the company’s North
American growth strategy and commitment to improving the overall efficiency of the ethanol industry with cutting-edge membrane technology.
Whitefox Technologies has had a strong presence in Canada for over 20 years, with an Engineering, Research and Development center in Calgary, Alberta. The project with ALCO Energy Canada underscores the company’s dedication to delivering innovative, sustainable solutions tailored to the evolving needs of the Canadian ethanol industry.
Our team of experts have over 20 years of ethanol plant maintenance expertise. We o er full service and parts for all Fluid Quip equipment to ensure peak performance.
• OEM Parts Warehouse
•$2 million+ inventory on-hand
Novonesis, formerly Novozymes, announced the launch of its most advanced yeast technology yet. Engineered to deliver exceptional substrate to ethanol conversion while withstanding fermentation rigors, Innova Eclipse-L, an advanced yeast, plus Innova Total A6, its companion enzyme, ensures the most effective operational performance and flexibility for ethanol plants operating with long fermentation times. Together with Innova Eclipse launched in September 2024, the Eclipse biosolution offers unmatched performance for the industry helping our customers push what’s possible with their plants.
Built on the industry’s most robust yeast platform, Innova Eclipse-L and Innova Total A6 are designed for plants operating with greater than 55-hour fermentations—breaking bottlenecks that prevent them from reaching their full potential. The result is maximum starch conversion and carbon utilization: +12% more ethanol yield, up to 40% less glycerol, consistently higher ethanol titers >16%, up to 100% reduction in costly urea and yeast nutrition supplements, and exceptional stress tolerance.
•Factory Trained & Certified Techs
•MZSA™ Screens
•Paddle Screens
•Grind Mills
•Centrifuges
•Gap Adjusters
Pittsburgh International Airport and Avina Synthetic Aviation Fuel are partnering to develop the first on-airport sustainable aviation fuel (SAF) production facility utilizing one of the very first alcohol-to-jet pathways in the U.S.
Avina will build a state-of-the-art facility to provide ASTM certified fuel on airport property just south of PIT’s terminal by deploying KBR’s innovative PureSAF alcohol-to-jet technology, developed and owned by Swedish Biofuels AB and exclusively licensed globally by KBR.
The facility, through multiple phases of development, is expected to produce over 100 million gallons of SAF annually, to meet local and regional commercial and cargo needs at PIT and beyond. When constructed, Avina’s SAF facility will provide the opportunity for hundreds of fulltime jobs. The plant will have a carbon intensity that is at least 65% lower than that of conventional jet fuel.
The U.S. Grains Council signed a renewed memorandum of understanding (MOU) with Vietnam’s Ministry of Agriculture and Environment to strengthen bilateral trade of animal feed and biofuels and expand technical support to the Vietnamese agricultural industry.
USGC Chairwoman Verity Ulibarri signed the MOU on behalf of the council with USGC President and CEO Ryan LeGrand observing. The signing took place during a USGC board of directors’ meeting at its Washington, D.C. headquarters,
allowing council leaders to greet the Vietnamese delegation and discuss further U.S. agricultural exports to Vietnam.
As part of the agreement, the USGC will work with MAE and other related agencies to organize workshops, publish educational information and engage in relevant regional and international conferences. It also includes a focus on additional activities in both countries including trade teams, technical missions and industry networking events.
Iowa Secretary of Agriculture Mike Naig announced that the Iowa Renewable Fuels Infrastructure Program Board recently approved an additional 90 applications from Iowa fuel retailers to support new and expanded ethanol infrastructure projects. These investments help drivers save money by providing expanded access to lower cost and cleaner burning homegrown biofuels like E15 (Unleaded 88).
The cost-share grants were awarded by the
RFIP Board during its quarterly meeting on June 4.
The approved project sites are in 48 different counties and total $1.23 million in state cost-share.
These investments are helping more Iowa fuel stations come into compliance with the E15 Access Standard. Iowa is the first state to enact an E15 Access Standard, which requires most fuel retailers to offer E15 by January.
With the E15 waiver in place, consumers can unlock billions in fuel savings this summer. Lower cost. Higher octane. Made in America.
From new technology to upgraded approaches, non-destructive testing methods are expanding into and across the ethanol sector.
By Luke Geiver
With many U.S. ethanol plants at or near two decades of operation, the toolbox of available non-destructive testing (NDT) tools and methods has evolved to meet their needs. Age-related issues are being examined with more sophisticated tech. New strategies and data-capture methods are helping plant managers understand the needs and challenges of their physical infrastructure. Data from the findings is helping maintenance teams make better decisions based on risk.
The number of companies equipped to service the biofuels sector is growing as well. NDT providers from the wind or oil and gas sectors are bringing their technologies, experience and capabilities into the biorefinery sector. And some NDT teams that started in biofuels are branching into other industries. Today, NDT is not just relevant to ethanol plant maintenance, but integral to it.
Several NDT methods have been used across the ethanol sector for years, including: dye penetrant, leak testing, magnetic particle testing, ultrasonic and visual testing. Most conventional NDT methods are non-invasive, cost-effective, reliable and provide real-time assessments on active equipment.
Dye penetrant testing relies on a liquid dye applied to the surface of a structure. After the dye dries, the surface is cleaned and any cracks will be exposed. The tried-and-true method is good for checking welds, pressure vessels and piping.
Magnetic particle testing utilizes magnetics to reveal issues on ferrous materials, welds in particular, and to ensure material integrity. The surface in question is magnetized and a fine material is applied. Any issues, such as cracks,
are revealed through disruption of the fine particles on the magnetic surface.
Radiography uses an X-ray to reveal an internal image of a vessel or tank, much like a human bone.
Ultrasonic testing has become a widely used approach for testing pressure vessels, heat exchangers and pipelines. The process relies on reading wavelengths as they pass through various materials, both solid and liquid.
Visual testing methods are also commonly used to simply inspect tanks, piping, vessels, coatings and other equipment. The use of remote-control robots that can crawl in all directions without falling off a vessel are now common, too, according to PROtect LLC, an NDT service provider.
PROtect offers all of the standard NDT methods, and more than a dozen advanced options. The company started in the ethanol space in 2006 and has since diversified into other industries.
Nathan VanderGriend, CEO of PROtect, says NDT methods have gotten more sophisticated, incorporating many new technologies over the past five years. The tools used today help collect more and better data, he says. All forms of radiography are growing, he adds, as the industry better understands construction standards. Infrared has also dramatically improved as a screening tool with new applications to help producers with everything from energy efficiency to integrity issues.
The team has seen a big difference between old ethanol plants and new. VanderGriend uses an analogy of the human body. “The older it gets, the more inspection it needs,” he says. “As your body ages, those that take really good care of it and have kept it up will age better. If you do it right, you can know a lot about your plant and actually make your inspection program a competitive advantage.”
Although the list of common NDT methods is already long, it continues to grow.
Through automated ultrasonic, NDT providers like ScanTech are using high-precision remote-control scanners to analyze tough-to-reach and tight areas. Some of the scanners can crawl, while others, such as those used by Voliro, can fly. Voliro has custom built a multi-rotor drone with swappable sensor units that can allow a user to quickly change between high-temp ultrasonic testing to electromagnetic testing in the time it takes to insert a different sensor package into the drone.
Computational radiography (CR) can take a traditional X-ray image and provide a digital read via an imaging plate, instead of requiring physical films to read on an Xray light. The digital format allows for faster read times, better shareability and contrast adjustability for better viewing.
Eddy current or IRIS (internal rotary
inspection systems) testing is a newer approach to testing pits, corrosion, cracking and other issues in tubes, most commonly present at an ethanol plant in the heat exchangers. IRIS testing relies on a probe and a couplant—sometimes simply water—to read ultrasonic waves.
Eddyfi Technologies uses pulsed eddy current to detect wall loss on ferromagnetic structures such as carbon steel. According to Eddyfi, the advanced NDT method “provides a relative volumetric measurement converted into an averaged thickness measurement based on the calibration data.”
For hard-to-reach piping, guided wave testing (GWT) is now used to transmit volumetric ultrasound waves into structures from a distance.
Infrared thermography inspections, while not new, are a more advanced NDT testing technique used by PROtect and others to show thermal heat signatures of equipment and systems such as storage tanks, electrical systems and heat exchangers.
PROtect has also had success at ethanol plants using magnetic flux leakage (MFL) testing. The systems use magnetics and sensors to detect leakage within a magnetic field.
The technique proved reliable on an 8.5-year-old denatured ethanol storage tank, finding areas of the floor showing discontinuity of 90% to 100%. A second company found no issues using more conventional testing methods (basic ultrasonic testing).
PROtect advised facility management to cut up a section of floor to get a visual on the most significant areas of discontinuity. Indeed, pinhole leaks were found, along with denatured ethanol that had pooled under the tank.
Eddyfi Technologies also uses MFL regularly and has provided the service for a few big-name clients including SpaceX and Chevron.
Mistras Group uses phased array ultrasonics to test for corrosion and other issues. Unlike conventional ultrasonic testing, this
approach relies on an array of transducers working in unison to create a beam that can be pulsed and applied to very specific areas like welds or rivets.
Remote field testing, another magneticsbased approach, is used for tubing inspections. A magnetic field is created by transmitter coils and placed along the piping to be tested. A transmitter reads the magnetic field and tests for abnormalities within it.
Intertek Group uses an advanced NDT method for weld inspections called time of flight diffraction. The ultrasonic testing method has many benefits, according to Intertek. The process can take place during production—with no shutdown required, no radiation produced—and production data can be stored digitally. Inspection results are available immediately and accommodate sensitivity to all weld types, Intertek explains.
To perform the test, a pair of ultrasonic probes are placed on either side of a weld or item to be tested. One of the probes acts as a transmitter and the other a receiver. An un-
• API 510 - Pressure Vessel Inspector
• API 570 - Piping Inspector
• API 581 - Risk Based Inspection
• API 653 - Above Ground StorageTank Inspector
• API QUPA, EPRI Certified
• ASNT-TC-1A Level II UT, MT, PT
• Automated Ultrasonic Testing (AUT)
• AWS Certified Welding Inspector
• Certified Welding Inspector (CWI)
• Computed Radiography (RT)
• Eddy Current Testing (ET) /IRIS
• Electromagnetic Acoustic Transducer (EMAT)
• Guided Wave (GWT)
• Infrared (IR)
• Light Detection and Ranging (LiDAR)
• Magnetic Flux Leakage Testing (MFL)
• Magnetic Particle Testing (MT)
• Penetrant Testing (PT)
• Phased Array Ultrasonic Testing (PAUT)
• Pulsed Eddy Current (PEC)
• Radiographic Testing (RT)
• Remote Field Testing (RFT)
• STI-SPO01 - Above Ground Storage Tank Inspector
• Time Of Flight Diffraction (TOFD)
• Touch Point Corrosion
• Ultrasonic Testing (UT)
• Ultrasonic Thickness Testing (UTT)
• Visual Testing (VT)
LONG LIST OF NDT TOOLS: The types of services performed by leading non-destructive testing firms like PROtect LLC for ethanol clients has become extensive.
SOURCE: PROTECT LLC PHOTO: STOCK
There’s no one -size - ts-all solution when it comes to fall prevention equipment. To ensure a safer work environment it’s critical to work with a trusted vendor like Carbis who can design and manufacture a solution to t your speci c needs.
damaged weld shows normal wave pattern from the transmitter and receiver. A damaged weld creates an ultrasound pulse from the tip of the crack. By measuring the time of flight of the pulse, Intertek can determine the depth of the crack.
The number of companies providing NDT methods (both conventional and advanced) is increasing. In 2024, Mistras Group joined the Renewable Fuels Association. The global company provides asset protection solutions for several major industries.
Gennaro D’Alterio, executive vice president and chief commercial officer for Mistras, said in a statement that his team understands the unique challenges faced by biorefineries.
“Joining the RFA allows us to bring our advanced NDT and data analytical solutions to the forefront, helping members improve their biofuel processing capabilities and bioproduct output,” he said.
Mistras says its proprietary technologies will enable advanced NDT inspection services and inline inspections that will ultimately help producers make better decisions, enhance safety, meet regulatory and insurance compliance, and achieve better operational performance.
Senseven is another tech developer trying to help ethanol producers perform NDT without calling in a service provider. In 2023, the company released a sensor that attaches to a common smartphone. Using the phone, plant staff can perform acoustic emissions testing and valve leak detections.
In 2024, Senseven was named startup of the year in the Deep Tech category by Ernst & Young.
Investors are taking notice of NDT providers, too. Last year, Sterling Investment Partners acquired a controlling equity interest in PROtect. The partners at Sterling
said PROtect has impressive growth potential in biofuels and other industries.
Part of the potential for both PROtect and Mistras appears to be their ability to provide more than just NDT solutions. NDT companies handle a great deal of data and some are building special software packages or services to help clients properly utilize their findings.
Mistras offers what it calls plant condition management software. The features include asset management on piping, pressure vessels, tanks and more; activity tracking; corrosion management; risk-based inspections; maintenance management leak tracking; software interfaces for data transfer, drawing links and valves; and reporting tools. Through its risk-based inspection offering, Mistras is able to help teams prioritize inspections and maintenance based on the likelihood and consequences of equipment failure.
PROtect has helped ethanol plants with data, as well as with carbon and sustainability monitoring, reducing carbon
scores through proper data analysis.
The team has also developed a proprietary inspection data management system called Shield. VanderGriend says the system helps manage all inspection intervals based on regulatory requirements as well as asset wear and tear. The system has a risk-based feature that helps producers create inspection intervals based on the calculated risks of failure and consequence of the asset.
Young plants today have the opportunity to learn more lessons—or run more risk—by tapping into industry networks, VanderGriend says. Older plants that have retained institutional knowledge have seen more and know more, though their assets are aged and pose a different risk.
But no matter the age of the plant, VanderGriend says there’s a way to protect it.
Author: Luke Geiver writer@bbiinternational.com
How Premium Plant Services is transforming industrial cleaning through automation.
Premium Plant Services is setting a new standard in industrial cleaning—boosting safety, consistency and performance through cutting-edge automation. Dan Rice, vice president of operations, says the company’s automated lancing and bin whipping technologies help keep employees out of hazardous situations.
Premium Plant Services targets 100% automation application on the job. This commitment stems from a desire to keep technicians out of “the line of fire,” explains Rice. Without the use of automation, employees must clean vessels—such as evaporators or condensers—manually, using a hydroblasting lance. Rice adds that manual cleaning comes
with the possibility of injury for the operator if the lance or tooling were to rupture. Technicians operate the automated lancing system from outside of the confined area, pressure washing the vessels with an air motor driven unit. The automated lancing system moves on an XY axis, cleaning each tube thoroughly. One to three lances may be deployed depending on the amount of space available within the vessel.
Premium Plant Services also implements bin whipping technology within its bin cleaning service. The whip technology loosens built up material within the bin, while keeping the technician out of an environment where rescue would be challenging in an emergency situation.
Bringing innovation and automat ion to industrial cleaning - protecting people, improving consistenc y, and delivering exceptional performance. Premium Plant Ser vices o ers a wide range of solutions tailored to your unique needs, maximizing e ciency and safety.
• Abrasive Blasting
• Automate d Lancing
• Bin Whipping
• Dr y Ice Blasting
• Hydroblasting
• Industrial Vacuuming
• Robotic Ser vices
• Surface Chemical Cleaning
Automation provides more consistent results compared to manual labor. “The technician performing the work is going to get tired,” says Rice. “They’re going to wear down, work at different speeds, or make inconsistent judgments. Automation eliminates that subjectivity and ensures consistent performance.” Operator fatigue also impacts cleaning consistency—especially in vertical vessels.
Premium Plant Services’ pursuit of excellence drives its application of automation. “We’re making sure that we provide a safe working environment, reducing onsite hazards that we don’t want to be associated with,” Rice says. “In addition to that, the consistency and performance of the cleaning will be improved, which will help the customer’s processes down the line.”
Book Your Ad AD SPOTS LIMITED
Winter 2026 Map
Ad Deadline: August 20, 2025 Mailed with the January 2026 Issue of EPM
All major Ethanol related events
- Growth Energy Executive Leadership Conference
- Iowa Renewable Fuels Summit
- National Ethanol Conference
- Plant Manager Meeting
- International Biomass Conference & Expo
Receive 6 Months FREE Online Advertising! Advertise now on Ethanol Producer Magazine’s U.S. & Canada Ethanol Plant Map. It is the easiest and most cost-effective way to get your name, product and/or service in front of ethanol producers and ethanol industry professionals for 6 months at a time.
Need more info on advertising opportunities? service@bbiinternational.com - 866-746-8385 - EthanolProducer.com
Scoular helps ethanol producers keep operations running smoothly with consistent grain supply and reliable offtake services tailored to operational needs.
Ethanol producers know their success depends on a guaranteed supply of grain from a broad footprint.
Scoular delivers both. The company, an independent leader in grain since 1892, trades more than 1 billion bushels annually. Scoular’s Grain Division leverages strong relationships with its producer network as well as large suppliers to meet the changing needs of ethanol facilities.
The company also provides consistent offtake services and marketing to help ethanol producers reach new markets with their co-products.
Supported by Scoular’s experts from logistics to trade across its Grain and Feed Ingredients Divisions, ethanol facilities gain the confidence to focus more on building for their future while Scoular handles procurement and offtake.
Melissa Norem, general manager in Scoular’s Grain Division, says: “In addition to ensuring a consistent supply of corn, Scoular provides market insight, logistics expertise and thought partnership on evolving trends and opportunities in the ethanol industry.”
Merchandising partners like Scoular play a critical role in helping ethanol producers consistently move distillers grains and corn oil efficiently and profitably.
Joel Mueller, product group manager within Scoular’s Feed Ingredients Division, leads a team that specializes in connecting ethanol coproducts to diversified end markets, leveraging deep logistics capabilities, transparent reporting and longstanding industry relationships.
“In today’s volatile markets, producers need more than just a buyer—they need a strategic partner who understands the entire value chain. At Scoular, we don’t just market
your feed coproducts, we help maximize their value through logistics expertise and demand creation. If you’re looking to unlock new revenue streams and simplify execution, we’re ready to help.”
Scoular is a reliable partner for customized solutions in grain supply and offtake agreements that meet the unique schedule, volume, and financial requirements of domestic ethanol producers. Headquartered in Omaha, Nebraska, Scoular is an employeeowned company leading the way since 1892. For more information, email info@scoular. com.
Grain procurement exper tise with co- product o take and marketing tailored to your operational needs . Keep operations running wit h reliable supply & o take
Technology—activated in, on and above plant infrastructure— is taking maintenance to new heights.
By Holly Jessen
It’s no secret that aging infrastructure is a big issue across many industries, including ethanol. In their quest for optimal reliability— and to stay in compliance—maintenance workers have traditionally had to physically examine assets like tanks, pipes, boilers and more. That can mean donning protective equipment, climbing inside enclosed spaces or using scaffolding or ropes to access hard-to-reach places.
“Historically, when these plants are trying to do these types of inspections, it’s slow, it’s expensive and it can be dangerous,” says Ben Lawrence, director for industrial artificial intelligence (AI) and robotics for Gecko Robotics.
Now, growing numbers of ethanol producers are turning to technologies that offer newer, better tools to assess the health of their facilities. Gecko Robotics,
for example, deploys wall-climbing robots, robot dogs and drones when working with its ethanol clients. Sky Ladder Drones and Pinnacle Engineering Inc. also provide services in the ethanol industry.
“Drone-based inspections are a leap forward, offering smarter, data-driven maintenance strategies,” says Frank Segarra, chief revenue officer for Sky Ladder Drones. “With each inspection, you’re building a digital record of asset health, which can be integrated with asset management systems or digital twin platforms. It’s a modern solution for a highly competitive and regulation-sensitive industry.”
There are plenty of reasons to deploy drones, particularly keeping employees out of danger, says Mike Braulick, senior engineer for Pinnacle Engineering. “The safety thing is always at the top of everybody’s mind,” he says.
Lawrence agrees. “The No. 1 driver for a lot of customers is the safety aspect. We don’t have to put humans in harm’s way anymore—just send a robot. I would say that’s value category No. 1.”
Segarra points to the time element. Doing a full-plant assessment with boots on the ground could take months. With drone power, it can be done in mere days. “The dirty jobs, the difficult jobs, the hard-to-enter jobs and the risky jobs, that’s where we see drones being mostly adopted,” he says. Regardless of what type of equipment is used, and by what company, it’s all about
gathering a lot of data in a very precise and detailed way. While the three companies have some differences in how they do business, one thing they all have in common is that they send trained employees to operate the equipment. “There is a big difference between being insured and a commercial pilot, and just doing it recreationally,” Braulick says.
Sky Ladder Drones has been working in the unmanned aerial systems space for about five years. Segarra says a drone can
be used to inspect ethanol plant infrastructure in a variety of ways. Some sensors deployed on drones harness light detection and ranging, known as LiDAR, by using lasers to capture precise information to generate a 3D point cloud map. Cameras capture videos for visual data while ultrasonic testing inspection measures the thickness of the materials, which helps identify areas of corrosion or degradation. The company can also send drones into confined spaces where it isn’t safe to send a human, often to obtain video or scans, but also to detect the presence of gases and other hazards.
“We’re collecting that information so fast and so accurately, we’re actually creating a geospatial archive of all of the locations inside, we’ll say, an ethanol tank that might be degrading,” Segarra says, adding that once the data is collected it can be passed on to an engineering company to make maintenance plan recommendations.
Braulick says Pinnacle Engineering utilizes drones equipped with cameras and LiDAR, as well as the ability to generate orthomosaic maps—high-resolution georeferenced aerial images. The company has done some work with drones inside con-
fined spaces, he says, but it isn’t one of their specialties.
What Pinnacle Engineering does have is a more than 30-year history as an environmental engineering firm, which provides services such as environmental
compliance, safety, emergency response and more. In 2016, drones were added to its list of services, right after the Federal Aviation Administration first finalized rules for commercial use of drones. “We’ve kind of ingrained our drones in
DETAILED MAPPING: Drones
help assess tank containment using LiDAR—light detection and ranging.
almost all the aspects of our company,” Braulick says.
The company is well-positioned to go beyond data acquisition. Pinnacle’s team of engineers can analyze drone-collected data to identify maintenance and safety
risks and provide recommendations to their customers on next steps, he says.
Gecko Robotics utilizes robotics equipped with cameras and ultrasonic sen-
sors, Lawrence says. The robots travel across the plant infrastructure horizontally and vertically, gathering data on things such as potential failure points and weld quality.
“These robots have, I’d say in simple terms, the equivalent of superman vision,” Lawrence says. “These robots, they walk, they crawl, they fly. They are able to take literally millions of these health readings, [where], previously, the plant was only able to take 100 readings.”
The old way of gathering this type of information can be compared to listening to a heartbeat with a stethoscope, Lawrence says. “Think of a little stethoscope that they can put onto a piece of piping or onto a boiler tube or the side of a tank and they can try to take a small reading to understand the health of the asset,” he explains.
With Gecko’s robots, the stethoscope is tossed aside in favor of a full-body scan. “Instead of a handheld stethoscope that might take one reading every 10 feet, these robots are taking thousands of readings every 10 feet,” he says. “So, you end up with a three-dimensional digital twin of the asset that tells you on an inch-by-inch, and sometimes a millimeter-by-millimeter, basis what the health of that asset is.”
Gecko Robotics got its start about 13 years ago, with the company’s founder building data-collecting robots out of his college dorm room. In 2019, the company made massive investments in AI software, putting it on a path to being a frontrunner in the AI space. Lawrence says the company’s clients are telling them: “We don’t need more data, we need to know what to do with the data.”
Today, Lawrence calls the company’s AI-powered software, trademarked Canti-
lever, the “secret sauce” used to help clients prioritize maintenance plans. It can analyze large data sets in ways that are beyond human capability.
“The AI, within minutes, literally, will build out precision repair plans on exactly where the plant needs to send its skilled tradespeople,” he says. “So that every time they cut into one of these assets or do a repair, it’s exactly where it needs to be, and the AI is telling them exactly what kind of repair to do.”
Pinnacle Engineering regularly sees the presence of deferred safety upgrades and facility infrastructure improvements related to buildings, pipes, foundations, tanks and more, Braulick says. Stormwater issues are also common, often cropping up as a result of changes in discharge limits, he adds.
“A lot of ethanol plants are reaching the 20- to 30-year mark and starting to show wear,” he says.
Lawrence doesn’t mince words. “In almost every case, the infrastructure of these plants is in rough shape,” he says. “It’s old. Nobody is entirely certain of the health of that infrastructure. And almost all the maintenance and investment that goes into trying to maintain that, in fact, is rough guesswork.”
He points to several factors complicating efforts to stay on top of maintaining plant infrastructure. First, there’s the “Silver Tsunami,” a term used to describe an ag-
ing population. The current average age of a maintenance technician is 57. “They are old,” he says, adding with a laugh, “I am in my 50s, I can say that.”
These older maintenance workers have years of experience and understand the equipment in ways no one else does. When they retire, they take with them a vacuum of knowledge and skill with few workers available to take their place.
The next factor is that a lot of plants are focused on fixing problems as they come
up. “That’s reactive maintenance,” Lawrence says. “That’s very dangerous and very expensive.”
All of that leads to unplanned downtime. “The unplanned downtime villain ruins your day,” he says. “It puts lives at risk.”
Making the shift from the old way of doing things to embracing new methods and technologies, like drones and robots, can have big payoffs. “Most, if not all the plants that we work with find that their maintenance costs drop dramatically,” he says. “[They see reductions of] at least 30%, just by eliminating reactive maintenance and replacing it with proactive maintenance.”
Then there’s the cost of capital expenditures such as replacing tanks or major repairs on a boiler. Lawrence says companies are making the wrong decisions on where to allocate money much of the time because they lack the data new technologies can provide. “They are replacing something that if they had the data, could easily be repaired for pennies on the dollar and get them the same amount of useful life as brand new,” he says.
Segarra says a Sky Ladder drone inspection once revealed internal beam corrosion inside a tank. The issue, which had gone unnoticed for years, had the potential to cause an emergency shutdown that would have resulted in $250,000 or more in production losses. Identifying it through drone inspection allowed the company to schedule the repair during a planned outage.
At another plant, a drone inspection detected thermal anomalies in a tank bottom. In that case, trapped moisture was causing corrosion under the insulation layer. “Addressing this early prevented a potential leak that could’ve triggered environmental compliance violations and fines,” he says.
All in all, traditional maintenance inspections can cost significantly more than drone inspections, once the cost of downtime, confined space entry permits, insurance liability and scaffolding are factored in. “The cost benefits are huge,” Segarra says. “Typically, we see ROIs of 90% or better.”
Author: Holly Jessen writer@bbiinternational.com
We’r e making it ea sy to ma ximize pr oduc ti vity and pr ofi tability.
Simply adding the Phiber Flex™ pr ogram to your oper ation can have major impacts down the line. By combining the power of XylaPlus® and CelluMax™ enzymes, PhiberFlex can:
Impr ove cellulosic ethanol conver sion —quali fy ing for D3 RINs
Impr ove corn oil pr oduc tion
Incr ease ethanol y ields
Lower residual star ch
A sk your Phibro repr esentative about tr ialin g the Phiber Flex pro gram.
While far from certain, Iowa once again appears open to CO2 pipelines following its governor’s landmark veto of a bill designed to impede them.
By Luke Geiver
Iowa corn growers and ethanol producers now have a fighting chance to capture future market share thanks to the veto power of Gov. Kim Reynolds. In early June, Reynolds chose to veto HF 639, a bill that many believed would have prevented carbon capture and sequestration (CCS) projects from happening in Iowa.
Several prominent voices affiliated with Iowa’s farming economy spoke out in favor of Reynolds’ decision. That support was accompanied by a respectful acknowledgement of the complexity of CCS projects, specifically pipelines, and their impact on property rights and eminent domain.
While South Dakota’s openness to carbon pipeline projects remains in flux, Iowa now joins Nebraska, Minnesota, Illinois and North Dakota as states with a foundation in place for the operation of current or future carbon pipeline routes. On December 12, the Minnesota Public Utilities Commission approved the state’s first carbon pipeline route. On the same day, North Dakota’s Public Utilities Commission took essentially the same action. Nebraska has approved multiple pipeline routes to move CO2, as has Illinois.
Although there was no specific language in HF 639 that outright banned CCS projects in Iowa, provisions in the bill would have prevented such activity through the use of new restrictions on eminent domain for CO2 projects and new restrictions on permitting.
Reynolds provided a lengthy explanation regarding her decision to veto: “Reasonable
A BETTER VIEW: With some farmers struggling this year due to high input costs and low commodity prices, the promise of increased corn demand for SAF production is a bright spot.
people can—and do—disagree about when the government, or a private company acting with government approval, should be allowed to take private land,” she wrote. “That debate is as old as the Republic. At its core, it asks how we protect individual property rights while still building the infrastructure—roads, utilities, pipelines—that modern life depends on.
“I respect both sides of that debate. I’ve consistently said that if eminent domain is used, it must be rare, fair, and a last resort. But HF 639 isn’t just about eminent domain,” she continued. “It goes much further—and in doing so, sets a troubling precedent that threatens Iowa’s energy reliability, economy and reputation as a place where businesses can invest with confidence.”
The day after Reynolds’ veto, Iowa House Speaker Pat Grassley called for a special session to consider overriding her decision; the idea received support from over two-thirds of the House. Senate leaders, however, said a special session—also needing sign-off from two-thirds of the lawmakers in that chamber—was unlikely. At press time in late June, a special session did not appear to have momentum.
Ryan Sauer Vice President of Market Development, Iowa Corn Growers Association
Speaking to Ethanol Producer Magazine after the veto in early June, Ryan Sauer, vice president of market development for the Iowa Corn Growers Association, said, “In the end, property rights are important, but so is finding new demand outlets as farmers continue to produce more corn.”
Sauer says ICGA’s members are seeing significant challenges in the farm economy right now, specifically farm profitability due to high input costs and low commodity prices. The ability of Iowa farmers to grow corn for lower-carbon ethanol production over the next decade will, in part, be made possible through CCS. It’s key to the industry’s future.
“This will help unlock low-carbon fuel markets around the world such as sustainable aviation fuel,” he says, explaining that the global jet fuel market is projected to grow to about 120 billion gallons over the next decade. If just 10% of that market could be made into SAF from corn ethanol, that would generate an additional 6.5 billion bushels of new corn demand.
Crop projections from the USDA highlight the significance of Sauer’s point. As of early June, the USDA had projected that 1.8 billion bushels of corn will have unmet demand from the 2025
planted crop. That unmet demand could grow as high as 2.5 billion bushels over the next several years.
“These new markets are key to ensuring farmers have new demand for their corn as yields continue to increase and countries like South America continue to grow more corn,” he says.
Reynolds included a specific example of a CO2 pipeline in the works (by Southwest Iowa Renewable Energy) as a reason why the bill needed to be blocked. Reynolds said the bill’s call for new insurance mandates and an arbitrary 25-year limit on CO2 pipelines would have killed projects like the one SIRE is developing.
Emily Skor, CEO of Growth Energy, said Reynolds’ decision will allow farmers and producers alike to accelerate investment in U.S. energy innovation. Skor also said her team looked forward to working with elected officials to find a balanced policy solution.
For Iowa Renewable Fuels Association Executive Director Monte Shaw, part of the issue with the legislation was its inaccuracies. “Any thoughtful review of this bill would determine that it would lead to higher energy prices for Iowans, hamper future
economic development, hold back job creation and stifle new markets,” he said. Shaw believes that Reynolds studied and deliberated over the legislation, ultimately looking beyond anti-pipeline rhetoric that was “as inaccurate as it was loud.”
The bill’s impact would not have been limited to CO2 pipeline projects. Some of its provisions applied to all hazardous liquid pipelines. Those provisions would change permitting rules across the board and inject uncertainty into critical energy projects, including those focused on oil, gas and fertilizer, Reynolds wrote.
The premise that safety concerns provided justification for stopping CO2 pipelines in Iowa was also dismissed by Reynolds in her decision rationale. She cited robust regulations already in place by the U.S. Department of Transportation’s Pipeline and Hazardous Materials Safety Administration (PHMSA).
Pending updates to CO2 pipeline safety requirements under review by PHMSA could also enhance protocols currently in place. Since December 2023, PHSMA has seen a 10-fold increase in CCS projects under development nationwide. A report provided
to PHMSA by the Congressional Budget Office estimates that, by 2050, the mileage of CO2 pipelines in the U.S. could expand by as much as 10 times the current number of more than 5,000 miles in operation. This projected growth, in part, is prompting PHMSA to consider enhanced federal pipeline safety requirements.
In addition to addressing safety concerns, Reynolds also spoke to the economic reality of CO2 pipelines in relation to other states. She pointed out that other states have already created a framework that will enable such development and Iowa will not be left out.
“Iowa leads the nation in biofuels,” she said in her decision. “We are at the forefront of turning corn into low-carbon energy— a leadership position we risk losing if we block the infrastructure that makes it possible. Other Midwestern states, like Nebraska, Illinois and North Dakota are already moving forward with carbon capture projects that would put Iowa at a competitive disadvantage if this bill became law.”
Sauer echoed Reynolds’ rationale related to the economic possibilities for Iowa. The decision to block the bill, “will ensure ethanol plants remain here in Iowa, and that Iowa remains the most competitively advantaged to produce ethanol,” Sauer says. “This will set Iowa ethanol plants up for potential expansions.”
Every state understands the repercussions of stalling CO2 pipeline development, including Sauer and his team at ICGA. Keeping the door open for CCS to happen in Iowa will ensure it doesn’t become disadvantaged to places like Nebraska that have already begun pursuing a carbon pipeline as the markets build out for low-carbon fuels.
POET, the world’s largest producer of biofuels, commended Reynolds’ veto. “At a time when commodity prices are low, these CO2 investments will expand market access for Iowa corn, biofuels and bioproducts across the globe, increasing the value of every bushel of corn and every acre of Iowa cropland,” said Jeff Broin, POET founder and CEO. “This decision will bring benefits to Iowa farmers for generations to come.”
POET has already started working to develop a CO2 capture plan with Tallgrass, an infrastructure company with pipeline operations in multiple states for several products including oil, natural gas and CO2. POET’s Fairmont bioprocessing facility in southern Nebraska will capture CO2 and transport it via the Tallgrass Trailblazer line to a permanent underground sequestration site in Wyoming. Tallgrass is converting an existing natural gas pipeline that has operated for more than a decade.
Under the Trailblazer Community Benefits Agreement, POET’s commitment will also support additional direct funding to the landowners who have agreed to site the pipeline on their property and the communities that are hosting the infrastructure.
Although Iowa’s current stance on CCS infrastructure and CO2 pipeline development is (post veto) ostensibly affirmative, the full realization of a project like Summit Carbon Solutions may not be quite as clear as some may have hoped.
Minnesota’s PUC has said that before any work begins on the portion of the pipeline that runs through the state, work must have already started in neighboring North Dakota, the storage destination for the CO2 that would be moved by Summit. North Dakota has had its share of regulatory wrinkles with CO2, but like Nebraska and Illinois, it does now appear primed for pipeline work to begin.
And then there is South Dakota. Like Reynolds, South Dakota Gov. Larry Rhoden also made a momentous decision on CO2 pipeline development. Rhoden’s determination, however, was nearly the opposite of Reynolds’. “I am no stranger to discussions
'The ethanol industry will remain a crucial part of our state’s economy'
- Larry Rhoden, South Dakota Governor
about eminent domain and property rights,” Rhoden wrote, explaining his long history fighting for private property rights as a legislator and landowner.
Rhoden signed HB 1052, a bill that bans eminent domain for carbon pipelines. Although the decision may be viewed as a setback to those in favor of using the tool to help develop the South Dakota portion of Summit’s multi-state project, Rhoden offered another perspective.
“I also want to ensure that we keep South Dakota ‘Open for Opportunity,’” he wrote. “HB 1052 does not kill the proposed project. Rather than viewing this legislation as an obstacle, I encourage Summit and others to view it as an opportunity for a needed reset. Voluntary easements for this proposed project will still be able to move forward and are not impacted by HB 1052.
“The ethanol industry will remain a crucial part of our state’s economy,” Rhoden said. As South Dakota’s place in any in-state or multi-state CO2 project continues to play out, Sauer and his team believe the stakes and situation are clear in Iowa.
“We are working hard on E15 expansion, but we need more,” Sauer says. The ability for CCS projects to happen in Iowa “will ultimately position corn farmers to take advantage of any low-carbon fuel market and ensure future generations of farmers can enjoy the same success and prosperity we have seen for the past two decades.”
Author: Luke Geiver writer@bbiinternational.com
Think of IRmadillo™ as your early warning system. Always monitoring what’s going on inside your fermentation tanks. Instantly alerting you to anything out of the ordinary IRmadillo gives you lab-grade accuracy in real time, continuously measuring the concentrations of lactic acid, ethanol and more. All from a device that’s been called “the most robust instrument we’ve seen.”*
So while other plants wait 8 hours for the HPLC to inform them of a disaster that’s already started, get ahead of the lactic acid curve while you can still do something about it.
Buy an IRmadillo
*Julian Parra, Engineering Manager, Pannonia
Bio
Leveraging artificial intelligence to monitor heat exchangers, Tranter is providing optimized maintenance regimens that help producers strategize their operations for the best economic outcome.
By Katie Schroeder
Always necessary but rarely convenient, maintenance is vital to avoiding expensive and unexpected downtime. Fortunately, ethanol producers have access to technologies and tools that can minimize and expedite shutdowns.
With decades of expertise in a key component of the ethanol process—the heat exchanger—Tranter has unveiled such a technology. As artificial intelligence (AI) makes its way into nearly all industries, Tranter’s Fullserv Digital AI system takes advantage of new software to prescribe maintenance solutions and help customers on their digitalization journey. Iuri Bazalia, business development manager for the Americas, outlines how the system helps ethanol producers identify issues with their heat exchangers—and connected processes—while revealing the financial impact of deferring maintenance and finding solutions.
David Lusignolo, director of aftermarket sales for North America with Tranter, explains that the new system creates a digital twin of an ethanol plant, allowing its
technicians to prescribe necessary maintenance and offer ethanol producers an opportunity to simulate different outcomes based on their operational decisions. The system can be set up to track certain plant priorities, such as CO2 emissions.
Tranter provides heat exchangers for multiple industries, including ethanol, petrochemical and HVAC. Heat exchangers play a key role in the ethanol system, with over 20 integrated throughout a typical plant for heating and cooling mash, distillation and more.
Although Tranter has been making heat transfer-related products since 1932, the company started making gasketedplate heat exchangers in the mid-1970s. Tranter now makes several types of heat exchangers, including welded bloc, welded shell and plate, and gasketed, which are widely used in the ethanol industry.
With over 15 years of experience in the business, Lusignolo is a leading expert on servicing heat exchangers, having done so across the U.S. and Canada. He explains that Tranter’s service division became
prevalent in the 1990s as an early wave of ethanol plant construction began; the company’s heat exchangers were installed in ICMdesigned ethanol plants. “Before that, thirdparty companies were doing aftermarket, just local providers who would come and open heat exchangers, buy plates from us when they needed to, but then in the mid-90s, our aftermarket presence started to grow,” Lusignolo says.
Tranter built its first service shop in Farmersville, Illinois, right in the heart of ethanol country, then went on to build more shops in Virginia, California, Texas and Alberta, Canada.
Russell Kee, ethanol sales manager for North America, says Tranter’s plate refurbishment service starts when a plant’s maintenance team swaps out dirty plates for a new set of plates and sends the old plates to the Tranter service shop. Tranter’s team examines the plates first, looking for any visible damage. Then, the plates are cleaned using a pressure washer and a chemical solution,
which helps remove the glue that connected the gasket to the plate. Next, Tranter sprays a dye check chemical on the plates, looking for any pin holes. After the plates are cleared, the company re-gaskets them, assembles the packs and sends the refurbished plates back to the plant.
The company’s long history with heat exchangers grants its team an intimate understanding of the maintenance needed to keep them running.
Kee has been with Tranter for nearly 30 years and started servicing the ethanol industry in 2002 as a field technician. With a comprehensive understanding of maintenance and the role heat transfer equipment plays in an ethanol facility, Kee is able to offer insight into the variables that cause certain heat exchangers in the ethanol process to deteriorate more quickly than others. For example, he says, the heat exchangers used for beer mash
and mash coolers should be swapped out every two to three years, but those serving yeast props may go a decade without refurbishment.
Kee explains that the regen condenser used to distill the alcohol from a vapor to a liquid causes the most significant disruption if it goes down. Because the exchanger pulls a vacuum to get the alcohol vapor into the unit, when it loses that vacuum, the plant must either shut down or significantly decrease production.
Heat exchangers that contain abrasive chemical compounds at high temperatures will also need rebuilding more often because the rubber gaskets are not made to withstand those chemicals and will break down from consistent exposure. “If you run a compound or a fluid through there that is not compatible with the gasket material and the plate material, you can run into issues pretty quick,” Kee says.
The heat exchangers used in fermentation also often run into issues due to the ve-
locity of the fluid running through them, causing erosion in the plates over time.
When Kee started working in the ethanol space, ethanol plants needed to shut down in order to work on heat exchangers. Now, most plants carry spare parts, streamlining maintenance. Some heat exchangers can be replaced without shutting down the plant, but not all.
Because heat exchangers are so ubiquitous throughout the process, Lusignolo explains that maintaining them helps avoid downtime. “When it comes down to the maintenance of the heat exchangers, it’s all based around the ideology of that plant and that facility and what they want to do and how they want to maintain it,” Lusignolo says. The four primary maintenance ideologies producers employ include reactive, preventative, predictive and prescriptive. Tranter seeks to meet producers’ needs in whichever approach they pursue.
A reactive maintenance strategy addresses maintenance needs as problems arise. “Some plants will run almost until there's an issue, and
then they’ll go in and change things out,” Kee says.
The preventative approach dominates the ethanol industry, Lusignolo explains. Producers will put their heat exchangers on a schedule and choose to replace gaskets or clean the exchanger at regular intervals, regardless of its condition. “Tranter tries to meet that approach through service contracts,” he says. “We’ll take a list of all the heat exchangers a customer has in their plant, help them build a schedule and put that on a contract.”
The third approach, predictive maintenance, executes maintenance when certain key performance indicators (KPIs) are demonstrated. “For example, pressure drop through the heat exchanger rises too high or heat transfer performance degrades to a certain point,” Lusignolo says. “Boom, I’m predicting that any further degradation would be too costly, so it’s predictive.”
A fourth maintenance strategy—prescriptive maintenance—has arrived with Tranter’s Fullserv Digital AI solution. “This prescriptive approach ... recognizes that the heat exchangers are components of a system—a revenue-producing, cost-creating system,” Lusignolo says. “An ethanol plant is a system that produces revenue that in-
cludes heat exchangers, but it includes pumps and chillers and cooling towers. It includes costs like electricity ... to energy [for running] pumps and CO2 emissions that influence a plant’s CI score. So, in order to make a maintenance decision that includes all of those factors, you need an advanced approach.”
The Fullserv Digital AI system helps producers “foresee” which heat exchangers will need maintenance next and determine
if a heat exchanger on the schedule to be maintained needs that maintenance immediately, explains Kee. Plugging the plant’s parameters into Tranter’s system helps the plant run more efficiently and minimizes rebuilding exchangers. “If you get it in early enough, you can head off a problem, and it doesn’t cost you as much money being down where you can kind of plan it versus ... all of a sudden you have an issue, and you’ve got to scramble to get things done right,” Kee says. Bazalia explains that in order to set up
EXPERIENCED INNOVATION: Although Tranter has been in business making heat transfer-related products since 1932, the company started making gasketed-plate heat exchangers in the mid-1970s.
the solution, Tranter needs to get operational data like pressure, temperature and flow. Once the information is entered into the AI solution, Tranter’s team creates optimization models that meet the plant’s needs. “This digital twin is built by heat transfer PhDs, and it is undergirded with all of the thermohydraulic calculations and AI that is necessary to purify the data to an acceptable level of confidence, analyze that data and make conclusions about what’s happening in the system,” Lusignolo says.
Fullserv can detect when fouling or plugging occurs, which degrade heat exchanger performance, he explains. Beyond identifying and recommending a heat exchanger to clean, the system also suggests what response would work best, such as running clean in place or postponing cleaning certain heat exchangers
until the next shutdown. Lusignolo adds that the system can also show the financial benefit or detriment incurred from delayed maintenance. “For example, they can see how much money they are spending on the production side, on the energy side and on the CO2 emission,” he says. “So, they can have all this information to take an action.”
The solution also allows ethanol producers to compare different scenarios and predict the impacts of their decisions to act or defer maintenance. Fullserv offers a scheduling tool to bring in maintenance teams from Tranter to swap out the plates, rebuild or clean exchangers.
After creating the models, the digital twin solution runs online and customers will have access through a web portal.
“These plants have to be running, and they have to keep making money,” Kee says.
“And when you have an issue with a heat exchanger, then it can cost [you] downtime. And when ... you’re not running, you’re not making money. ... [L]ooking at it from the heat exchanger side, being more proactive versus reactive can really make a big difference in your facility.”
Ethanol producers are accustomed to operating on tight margins, which makes determining financial decisions complex. With the Fullserv Digital AI solution, ethanol producers can weigh their options, peek into possible futures and examine whether putting off maintenance could save them money or cost them in the long run. Looking at the ethanol plant as a full system allows Tranter to show ethanol producers the big picture.
Author: Katie Schroeder katie.schroeder@bbiinternational.com
Exploring how Preventive Maintenance Optimization helps ethanol producers cut costs and reduce risk.
By Natae Shreeves
Reliability strategies are gaining momentum in the ethanol industry, and Novaspect and Laurentide Controls are helping manufacturers move beyond OEM guidelines with smarter, data-driven strategies. Ethanol plants rely on a wide range of equipment—from fermenters and distillation columns to boilers and dust collectors. Keeping these assets running safely and consistently is critical to ensuring steady throughput and revenue.
Emergency repairs can be expensive, often requiring overtime labor, expedited parts and unplanned downtime. Producers have been modernizing their reliability strategies by implementing predictive (PdM) and preventive (PM) maintenance programs that identify issues early and allow for planned interventions which are far less costly.
A Midwest-based company, Novaspect, along with Laurentide Controls, the creator of the Asset Performance Management (APM) software trademarked Spartakus, have been guiding customers in their move from a reactive, fragmented maintenance program to a proactive, data-driven strategy that supports long-term reliability.
Dennis Uhl, who leads development for Novaspect’s Reliability Solutions business unit, explains, “Many companies just take the manufacturer’s recommended PMs and run with them as-is. But those are often generic and not tailored to actual operating conditions. That’s where PMO comes in—we help them refine those tasks so they’re doing the right maintenance at the right time.”
PMO isn’t just about trimming down maintenance schedules— it’s about making them smarter. By analyzing data and understanding failure modes, teams can identify which tasks truly add value and which may be introducing unnecessary risk or cost. “Not all maintenance is good maintenance,” says Jean-Francois Murphy, a reliability specialist with Laurentide Controls. “You don’t want to spend time doing maintenance you don’t need to do. Eliminating redundant tasks directly lowers costs because less labor is needed, and fewer parts are being replaced.”
This approach also helps reduce the cognitive load on technicians, who are often juggling a multitude of tasks. “When you al-
CONTRIBUTION: The claims and statements made in this article belong exclusively to the author(s) and do not necessarily reflect the views of Ethanol Producer Magazine or its advertisers. All questions pertaining to this article should be directed to the author(s).
leviate their workload and give people clear, meaningful tasks, they’re more engaged and more effective,” Murphy says.
The partnership between Novaspect and Laurentide Controls blends deep industry knowledge with reliability expertise and advanced digital tools like Spartakus APM. Spartakus APM acts as a central hub for reliability data, allowing teams to visualize asset hierarchies, track failure modes, and embed detailed instructions and photos directly into PM tasks.
modes, embed photos and instructions directly into the PM program, and to track key performance indicators (KPIs) and measure the impact of the changes,” Murphy says.
The PMO workshop uncovered approximately 680 failure modes across more than 25 components (e.g., sprockets & chains, blowers, belts & sheaves, fan bearings, rotary arms, rotary valves, dampers) on the dust collectors. These included common issues like leaks, vibration, deformation, belt wear, cracks, overheating, misalignment, damaged filters, lack of grease, broken/loose bolts and seized bearings.
Uhl shared an example of how a major player in the Midwest biofuels sector recently put PMO into practice to cut costs, reduce risk, and gain a clear roadmap for future reliability.
Like many others in the industry, the plant had built its PM program over the years using a mix of OEM manual recommendations, technician experience and reactive adjustments. The result was a long list of PM tasks—some redundant, others undocumented and many with unclear value.
The plant’s maintenance team turned to Novaspect and Laurentide Controls to support their reliability initiatives, and together the companies planned to perform a PMO workshop at the customer’s site.
The purpose of a PMO Workshop is to review existing maintenance strategies to identify opportunities for improvement. The team evaluates current PM tasks and frequencies, failure modes and effects, and historical performance. The goal is to identify real failure risks, eliminate inefficiencies, and build a more effective, data-driven maintenance strategy.
“There are multiple ways to do PMO,” Murphy says. “We follow a standardized framework that combines the elements of Failure Modes and Effects Analysis (FMEA) and Reliability-Centered Maintenance (RCM). We focus on the component level to determine what can go wrong and to evaluate the risk associated with said failure based on its probability of occurring and the severity of its impact.”
Novaspect and Laurentide Controls began by working with members of the plant’s maintenance team to identify a pilot area that would deliver meaningful results quickly. They selected four Hammermill baghouse dust collectors—critical assets that are essential to both safety and production, with a high frequency of maintenance activities, making them ideal candidates for optimization.
From there, the PMO team gathered and examined the current PM tasks, tools and data available for the dust collectors. Then, the team broke each asset down to the component level, identified potential failure modes, and evaluated each based on risk, frequency and operational impact.
After that, they entered the data into Spartakus APM. “The team used it to visualize equipment hierarchies, document failure
Based on the findings, the team standardized and aligned PM tasks with each failure mode to improve reliability without overmaintaining.
The final step of the PMO workshop entailed sending the team a complete package of deliverables, which included: the new PM routes with updated tasks and frequencies, failure analysis based on historical data, equipment status requirements, and before-and-after KPIs, all packaged in a ZIP folder with documentation and visuals.
The results of the PMO workshop were measurable. “The facility achieved a 55% reduction in total risk across the four dust collectors,” says Murphy.
“When you compare the risk levels before and after the PMO workshop, the facility was able to quantify its progress and demonstrate the value of the initiative to leadership and stakeholders,” Uhl says.
The workshop provided a clear framework, and the team now has a repeatable process for expanding PMO to other asset classes across the plant, including fermenters, distillers and conveyors.
For ethanol producers facing similar challenges, this story offers a clear path forward for planning PMO initiatives.
Murphy explains: “Start with your most critical assets, use a structured methodology to identify failure risks, determine the right PdM/PM tasks and eliminate what doesn’t add value. You can probably do one or two pieces of equipment per day. It’s more manageable, and the impact is immediate. And most importantly, involve your team in the process.
“PMO isn’t just about fixing maintenance, it’s about building a culture of reliability. And with the right tools, structure and support, any plant can make that shift.”
Author: Natae Shreeves +1 224-483-4756 nshreeves@novaspect.com www.novaspect.com
DUSTY ENVIRONMENTS: DDG storage areas are one of the major areas where dust accumulates in ethanol facilities, constituting a potential fire hazard.
Why ethanol producers must shift from cleanup to prevention in 2025.
By Jordan Newton
If you’re running an ethanol plant, you’re not dealing with ordinary housekeeping issues. You’re managing a critical safety risk every day: combustible dust. It clings to your overhead pipes, settles in cable trays and drifts into overhead beams. You invest in dust collectors, ventilation and manual cleaning. But no matter how many systems you put in place, dust still finds a way to accumulate.
And that dust? It’s not just an inconvenience. It’s fuel waiting for you to be too busy to worry about it and an ignition source just waiting for a spark.
Dust buildup overhead is one of the most overlooked hazards in ethanol production. It’s easy to treat it like a basic cleaning task, but the reality is much more serious. Combustible dust can lead to devastating secondary explosions, which often cause the most damage. The Occupational Safety and Health Administration and the National Fire Prevention Association both identify this risk as a top safety concern. OSHA even started a National Emphasis Program, and for good reason: it only takes a thin layer of dust and
a single ignition to cause a chain reaction that can level a facility and claim lives in the process.
Even if you’re compliant today, dust can reaccumulate tomorrow. The risk is constant. That’s why prevention needs to be part of your everyday operation. You cannot afford to fall behind. Prevention is not a luxury; it is a necessity.
Your facility likely uses dust collectors to remove particulate from conveyors and transfer points. You’ve probably installed ventilation systems to help improve air movement and added manual cleaning into your shutdown routines. These are solid steps, and they help. But they have limits.
Here’s where traditional methods often fall short. First, dust collectors never catch everything. Fugitive dust always escapes at some point. Secondly, ventilation systems can’t reach every pocket of stagnant air. Also, manual cleaning is expensive, timeconsuming and reactive. Finally, explosion suppression systems only respond after danger has already escalated.
Each of these tools has a role in your overall safety strategy, but none of them
prevents dust from settling in the first place. That is the missing piece in most facilities.
What if you could keep dust from ever building up in overhead spaces? SonicAire’s BarrierAire technology does exactly that.
BarrierAire is the use of high-velocity airflow to create a continuous curtain of air. This curtain interrupts the natural thermal currents that pull airborne dust upward into beams, ducts and ledges. Instead, particles are agitated, clump together and stay low to the ground. Once on the ground, dust is much easier to remove safely.
This is not just moving air around. It is a targeted, engineered solution designed to prevent dust from becoming a hazard. BarrierAire works alongside your existing systems, making them more effective.
BarrierAire technology helps address these issues in four key ways.
When you keep overhead spaces dustfree, you remove a key part of the explosion pentagon. That means fewer conditions that can lead to devastating secondary explosions.
2. Fewer Shutdowns and Less Cleaning
CONTRIBUTION: The claims and statements made in this article belong exclusively to the author(s) and do not necessarily reflect the views of Ethanol Producer Magazine or its advertisers. All questions pertaining to this article should be directed to the author(s).
You can reduce or even eliminate cleaning shutdowns. Your team stays focused on production instead of dealing with lifts, vacuums and scaffolding.
3. Stronger Compliance Position
BarrierAire supports NFPA 660 and OSHA requirements for proactive housekeeping. It shows regulators and inspectors that your facility is taking real, proactive steps to maintain safety.
4. Cost Savings You Can Measure
Most facilities see a return on invest-
ment in one to five years. Savings come from reduced labor, fewer shutdowns, extended equipment life and even lower insurance premiums.
You do not need to replace what is already working. Instead, you need to build on it.
When you add engineered airflow to your current dust control setup, dust collectors capture more efficiently; ventilation
systems distribute air more evenly; manual cleaning becomes easier and less frequent; and the entire system operates with fewer gaps and greater impact.
This is what OSHA refers to as a layered defense. Prevent what you can. Control what you must. Be ready for what remains. When you approach dust control this way, you build resilience and readiness into your operations.
Facilities using SonicAire fans report cleaner overhead spaces and a sharp drop in the need for inspections and shutdowns. One plant completely eliminated monthly overhead cleanings. Another facility saw an immediate improvement in worker morale, thanks to reduced time spent in respirators and confined spaces.
In a controlled study, two similar facilities were compared: one with SonicAire fans and one without. In the facility with fans, particulate levels in the air averaged just 2 milligrams per cubic meter. In the non-fan facility, levels spiked over 40 milligrams per cubic meter during regular operations. That difference is not just measurable. It is transformational for safety, compliance and employee well-being.
No two ethanol plants are the same. That is why SonicAire creates a custom-engineered fan layout for every client. Whether your facility includes tall blending towers or long conveyor paths, SonicAire systems are optimized to match your dust types, airflow patterns and production processes.
Even hazardous environments can benefit. SonicAire now offers the first and only Class II Division 1 certified dust control fans. These models are specifically built for explosive dust zones and are fully UL certified.
SonicAire offers peace of mind with its Compliance Guarantee. If SonicAire fans are installed and maintained according to engineered recommendations and do not eliminate the need for overhead housekeeping, SonicAire will reimburse you for the cost of the fans or any fines, whichever is lower.
This guarantee shows SonicAire’s confidence in the technology and its results. It also provides reassurance that you are investing in a solution that works and that stands behind its promises.
You have already taken important steps.
But if dust keeps returning, then your current tools are not enough. It is time to stop reacting and start preventing.
SonicAire can help. We will review your facility layout, dust types and operational needs. Then we will design a preventionfirst solution that keeps your people safe and your plant compliant.
Your ethanol plant powers a cleaner energy future. Let’s make sure dust never interrupts that mission.
Dust is done. Guaranteed.
Author: Jordan Newton Chief Operating Officer, SonicAire moreinfo@sonicaire.com 336-712-2437
www csebliss.com (580)749-4895 | sales@csebliss.com For