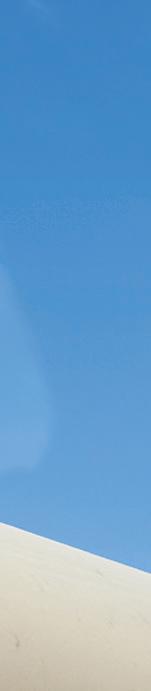
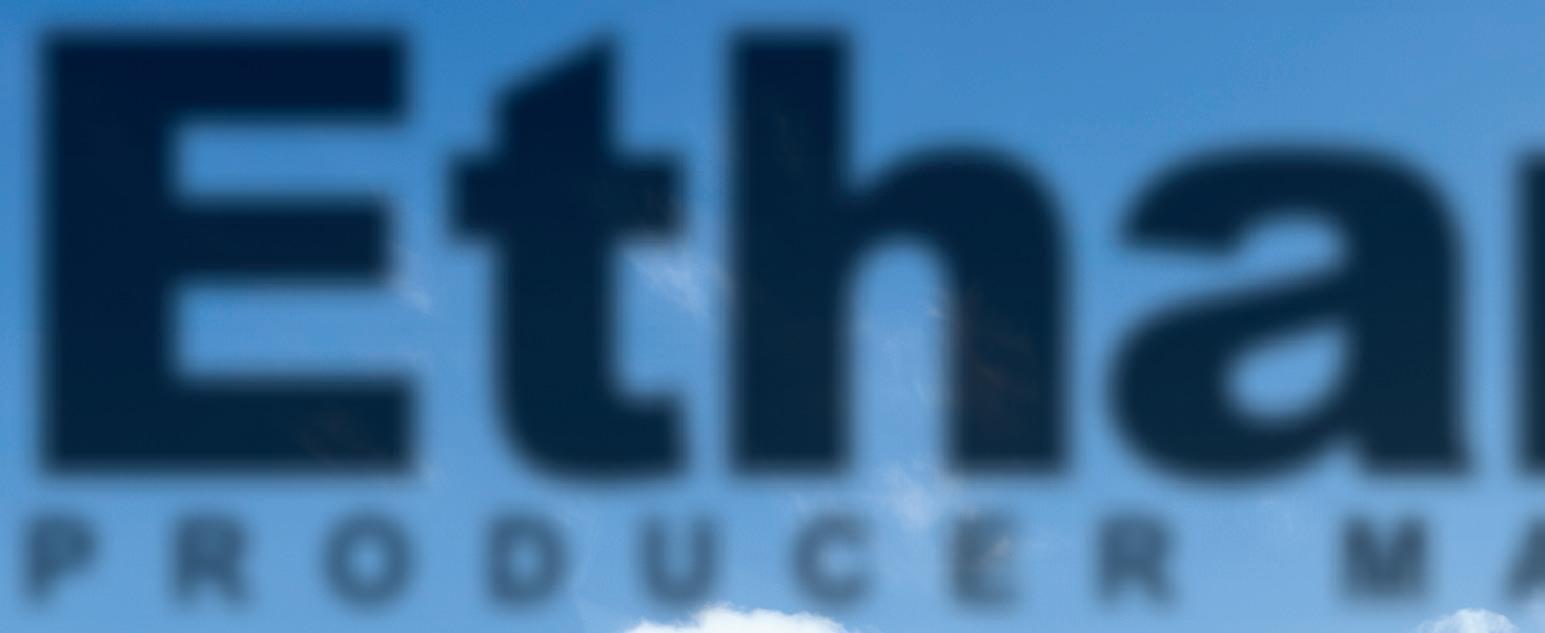
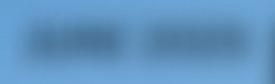

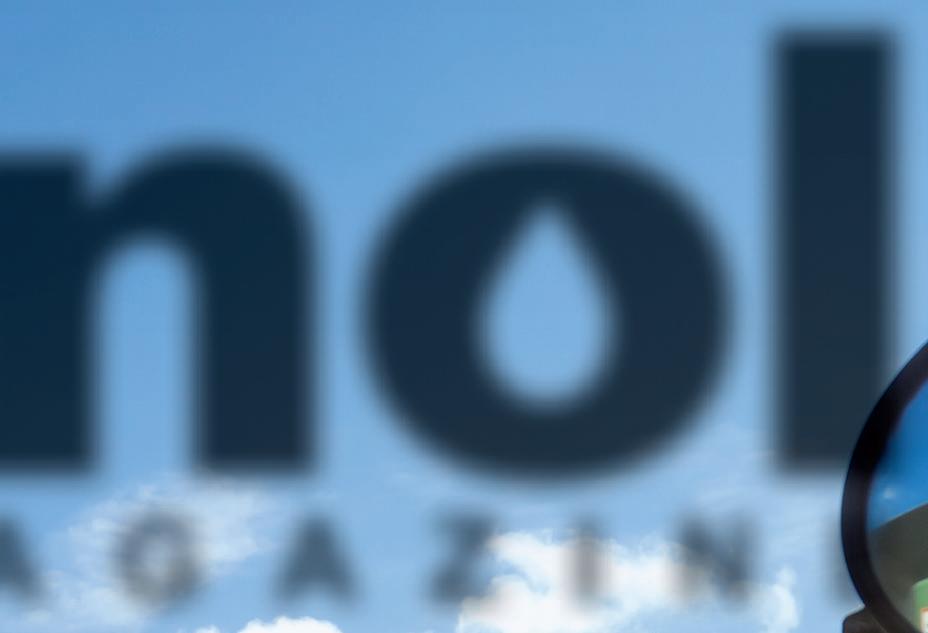
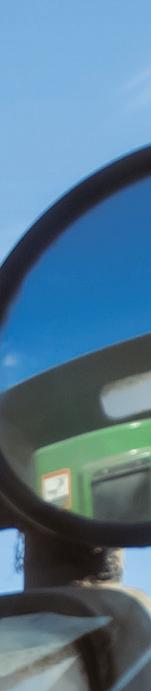
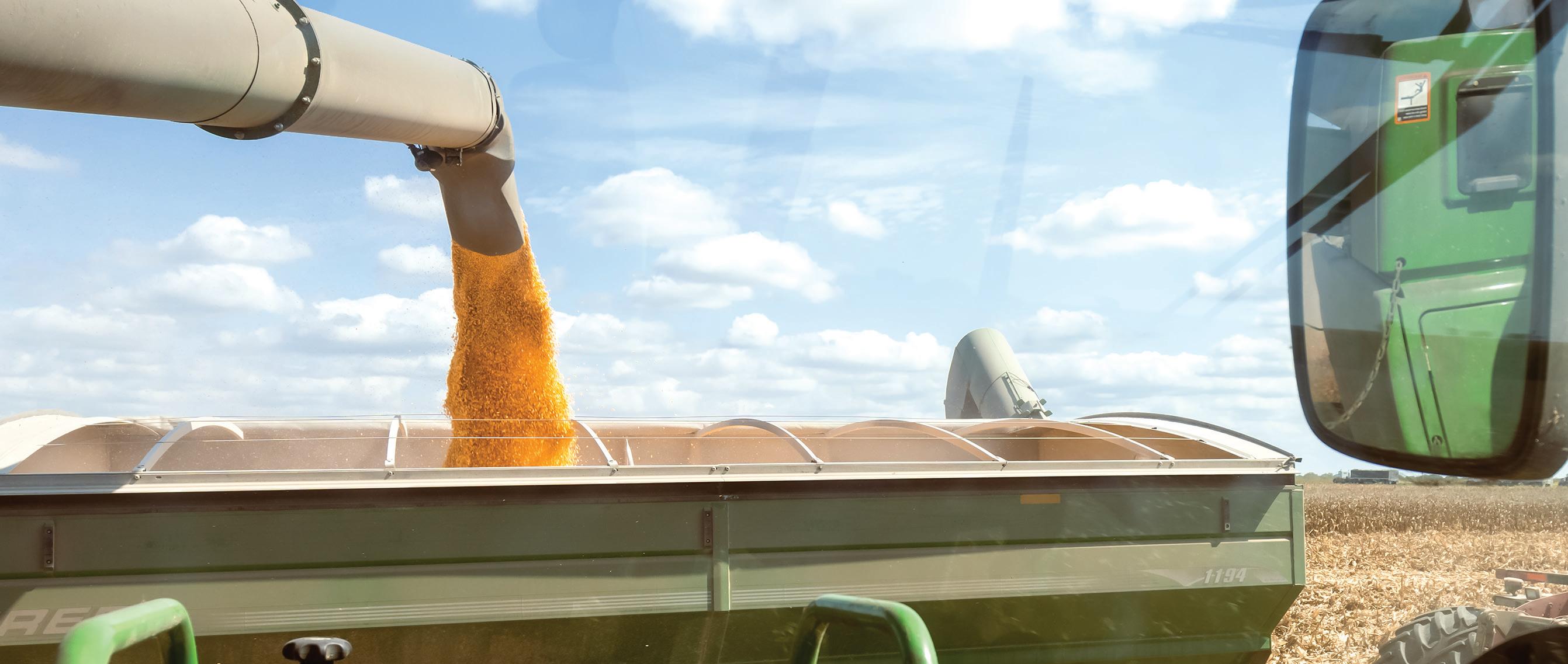
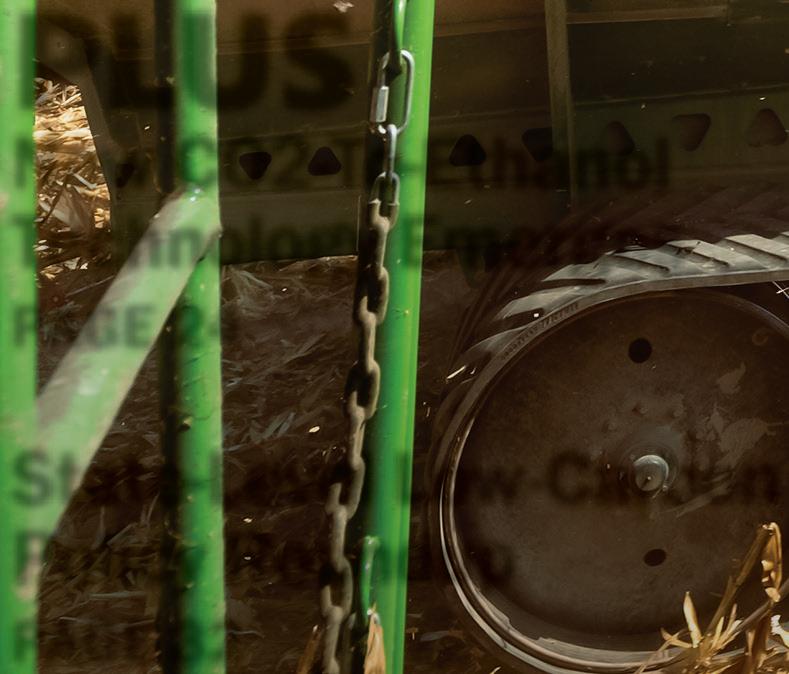


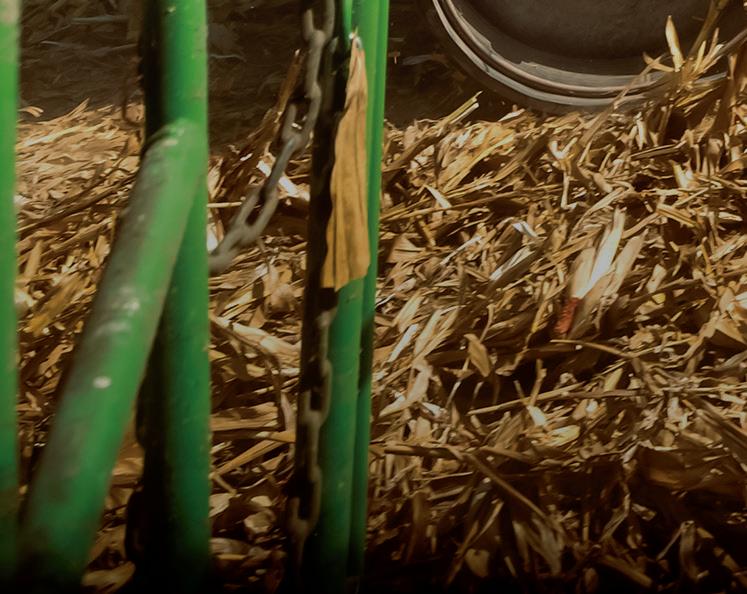
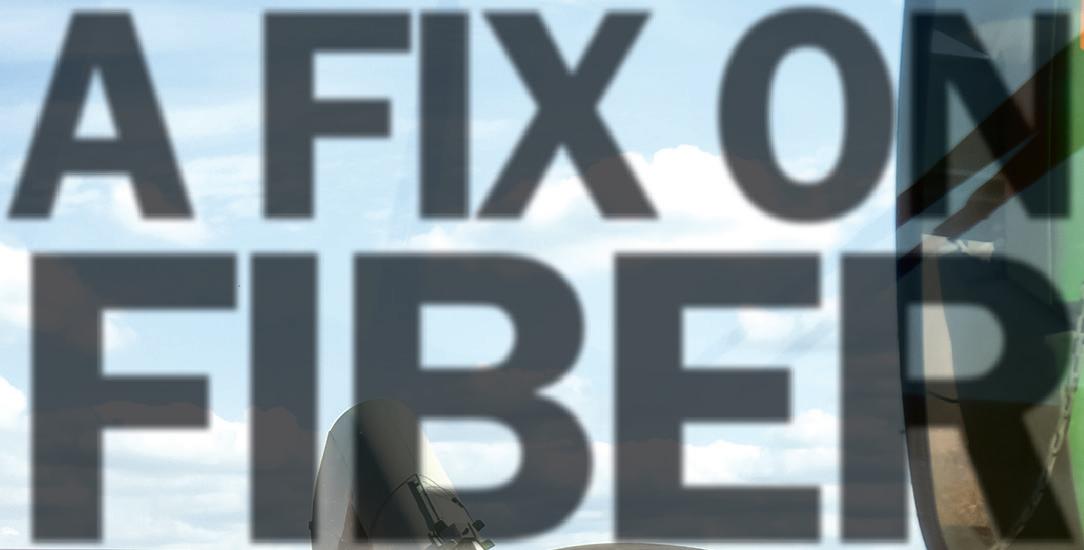

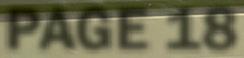
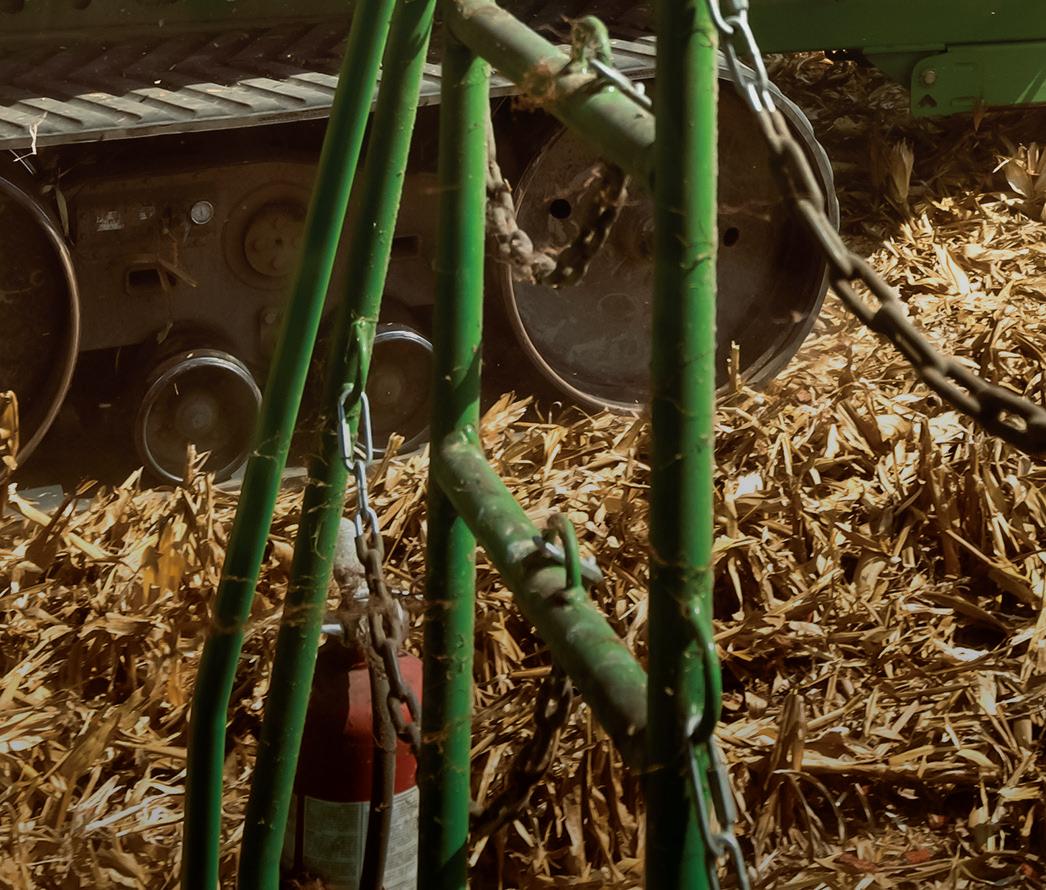

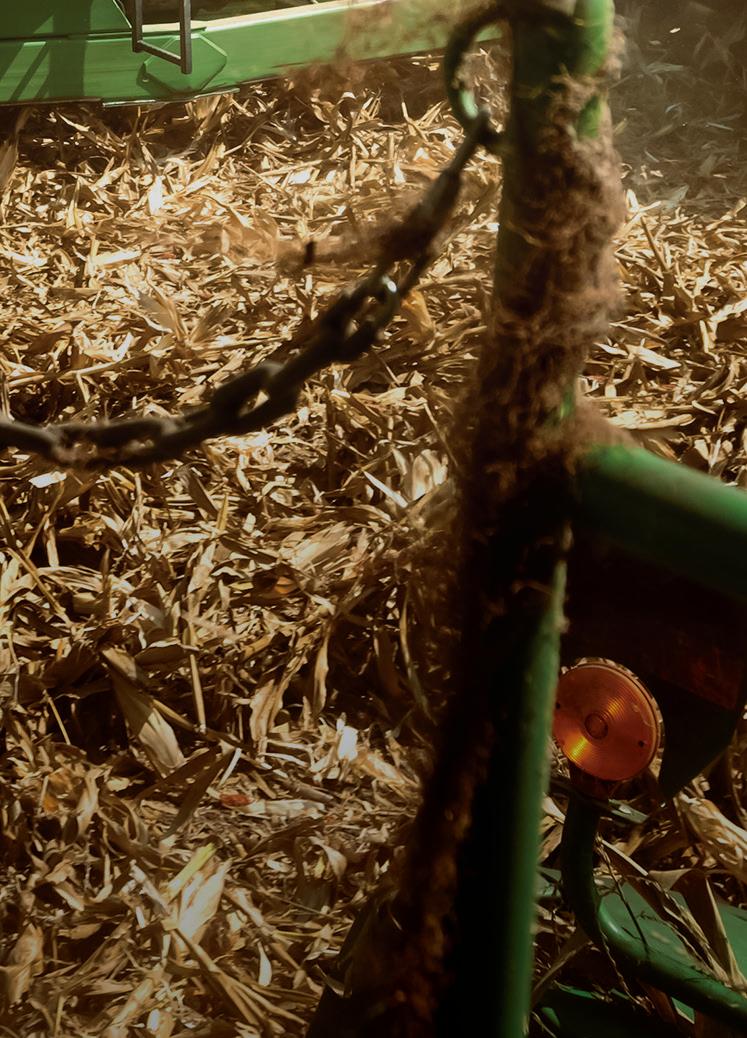
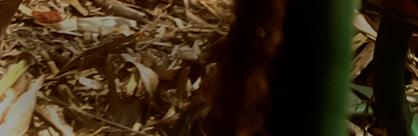
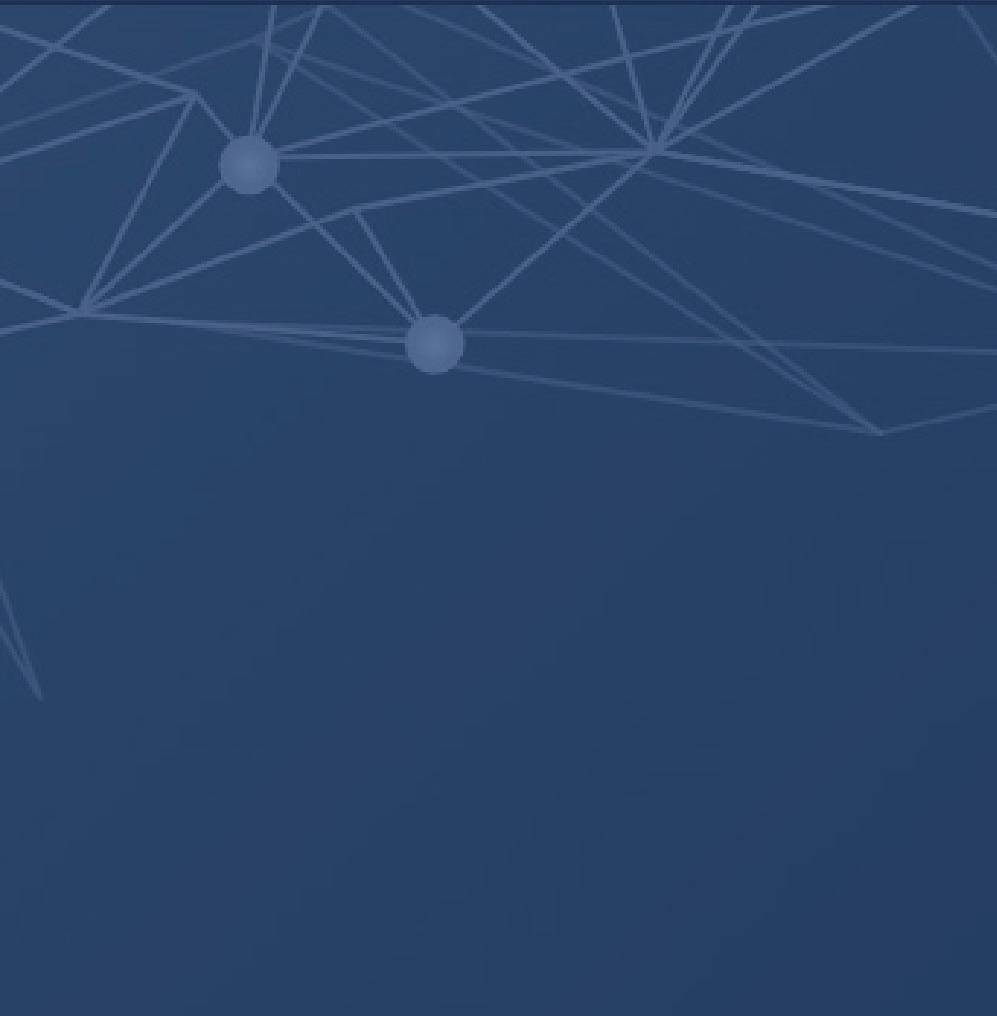
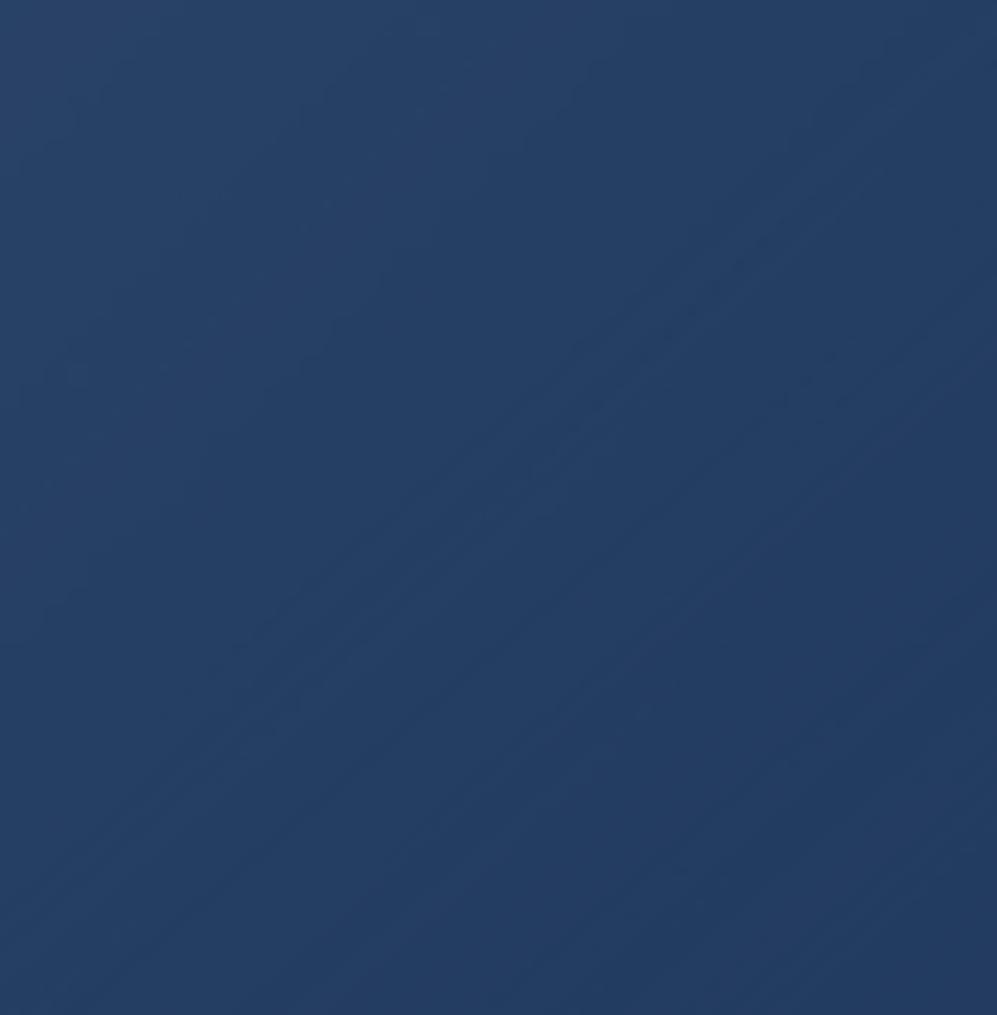
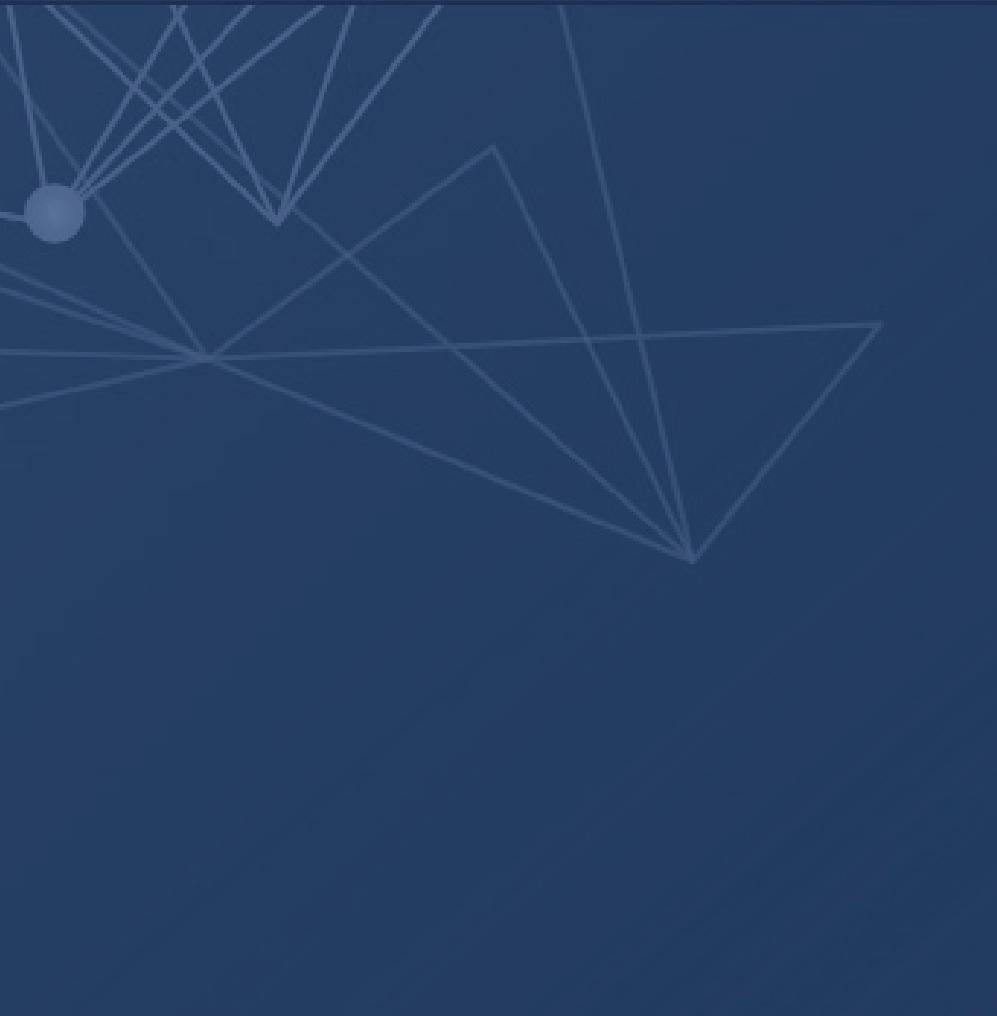
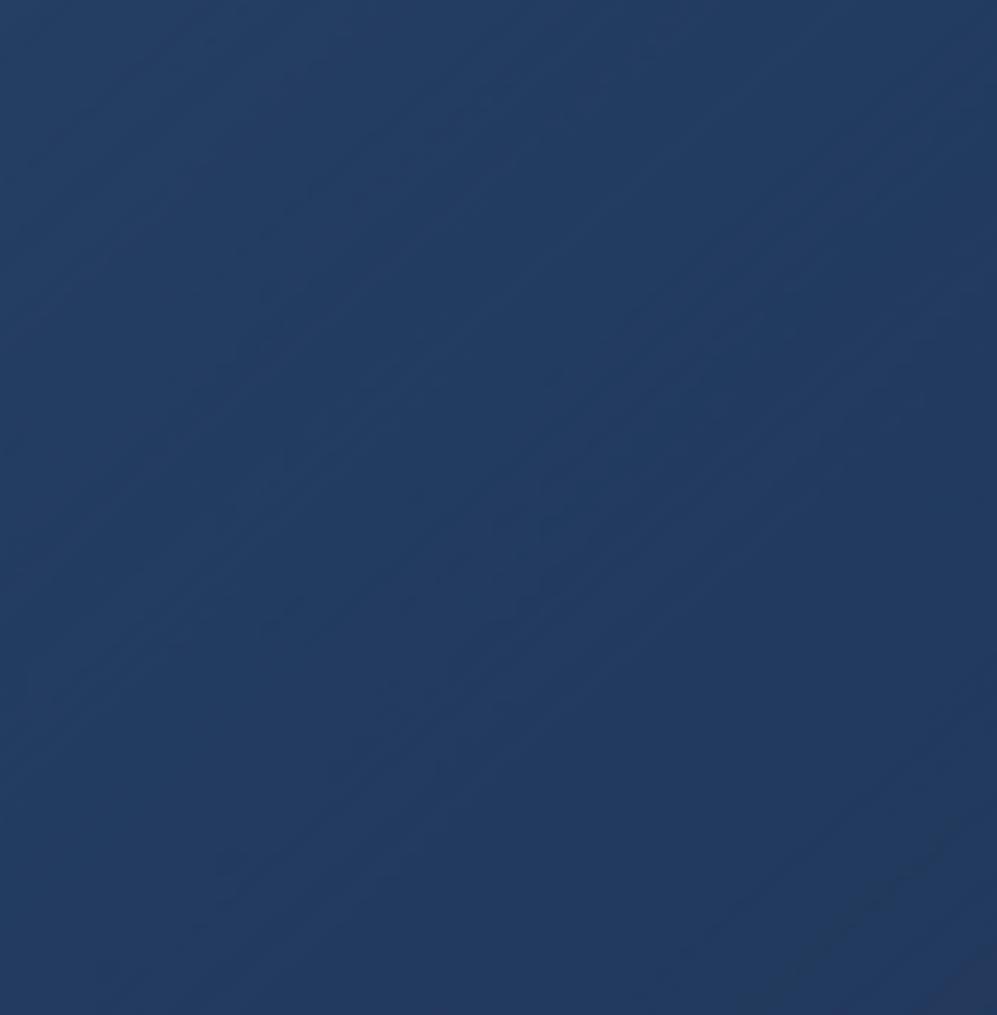

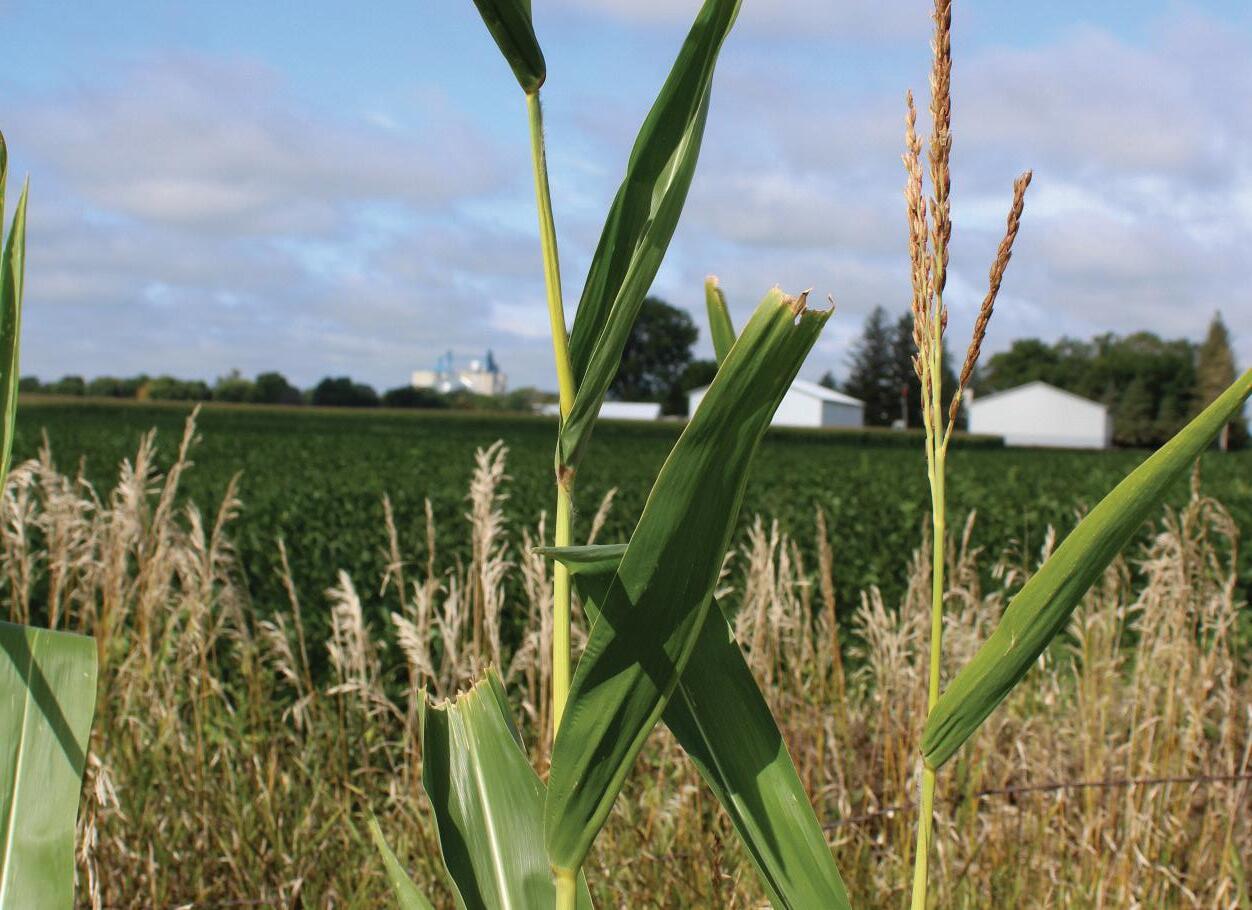

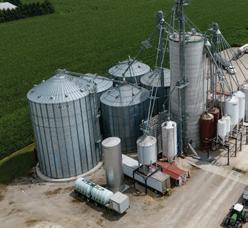
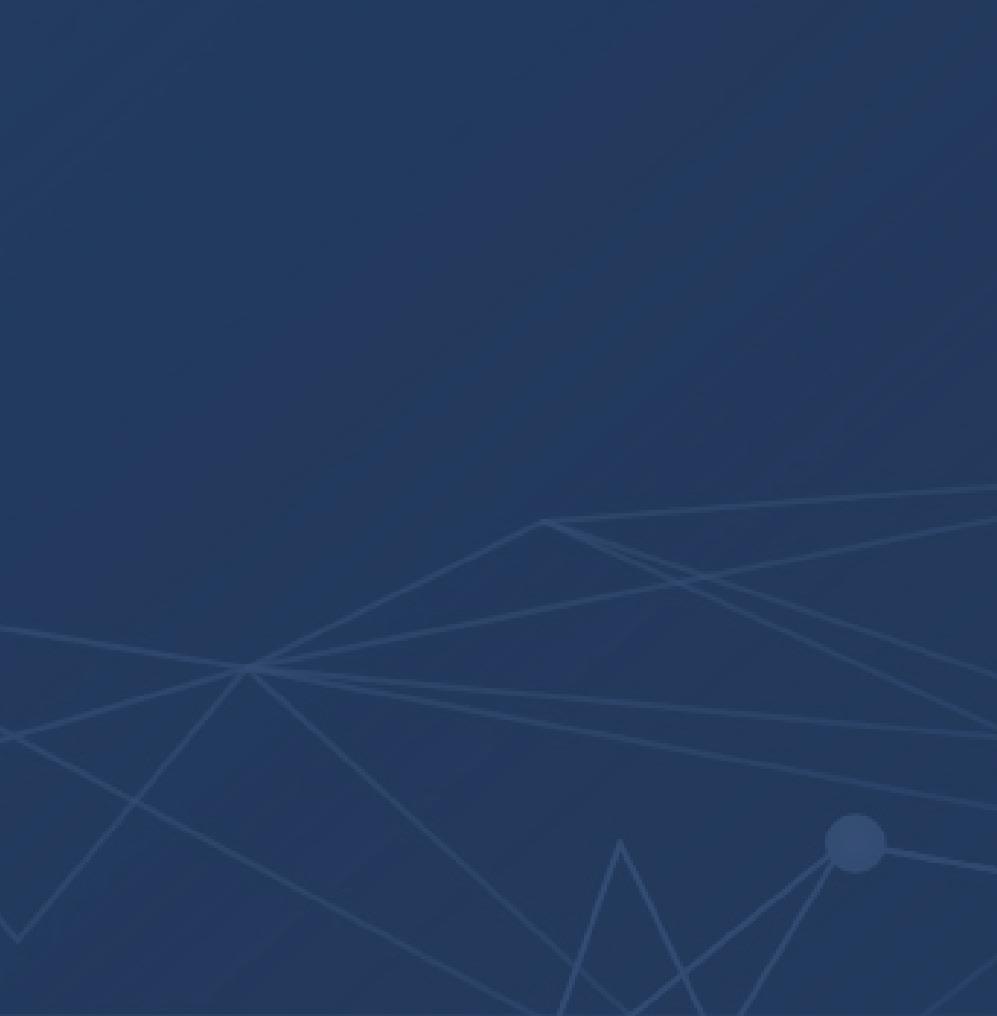
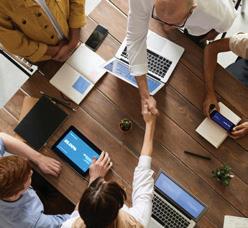
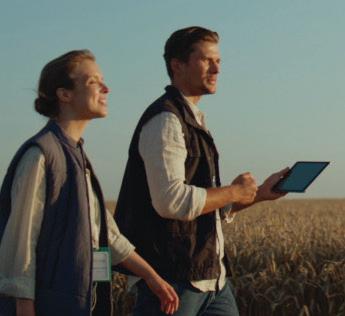

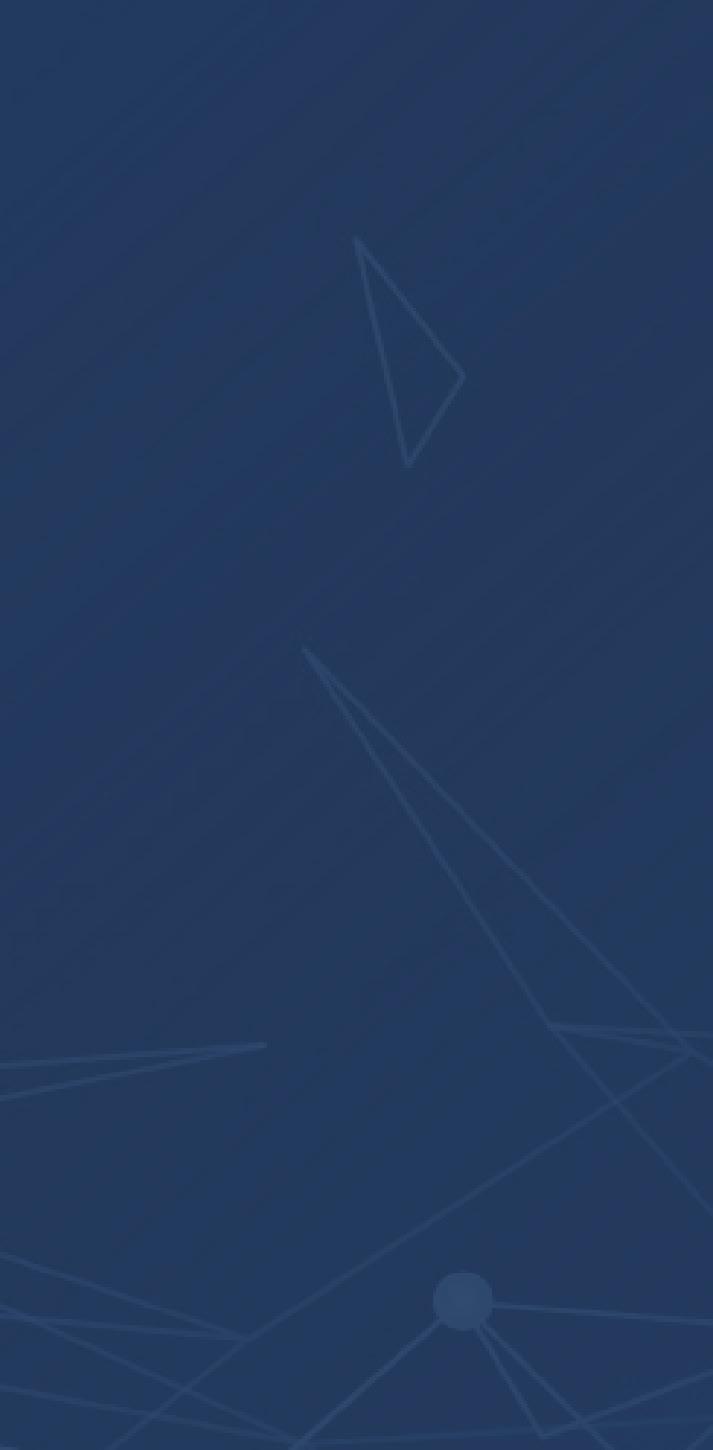
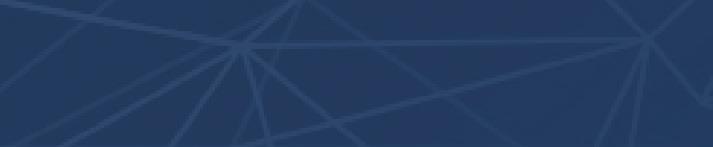
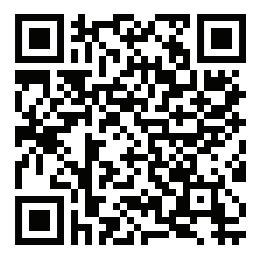
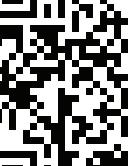
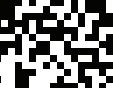



OK, so our IRmadillo™ may have a long nose and a funny look.
But that nose can sni out exactly what’s going on inside every one of your processes. Every single second of the day.
And if you know the precise chemical composition inside all your lines and tanks, there’s virtually nothing you can’t improve
Filled with ground-breaking new technology, IRmadillo™ helps keep yeast happy, eliminates failed batches, reduces enzyme use, and much, much more.
So while you’re sitting around waiting for your next set of HPLC results, why not visit our website, and read up on the whole amazing IRmadillo™ story?
States
Engineering
Exploring KATZEN's legacy of integrity and design prowess
Peace of Mind for Ethanol Corrosion Control
ENGINES INC.
Model E: Empowering Laboratories and Terminals By
Rethinking Energy Efficiency By ICM
Membrane Technology Is Ushering In a New Era In Ethanol Distillation, Dehydration and Evaporation
Closing the Gap In DCO Separation: Four Proven Best Practices By Chris Clausen
Claiming the 45Z
Kari Buttenhoff
Advances In CIP and Foulant Prevention Technologies By Steve Rust
Railroad 101: How the Pros Do It By Jordan Davis
President & Editor Tom Bryan tbryan@bbiinternational.com
Online News Editor Erin Voegele evoegele@bbiinternational.com
Contributions Editor Katie Schroeder katie.schroeder@bbiinternational.com
Features Editor Lisa Gibson lisa.gibson@sageandstonestrategies.com
Vice President of Production & Design Jaci Satterlund jsatterlund@bbiinternational.com
Graphic Designer Raquel Boushee rboushee@bbiinternational.com
CEO Joe Bryan jbryan@bbiinternational.com
Chief Operating Officer John Nelson jnelson@bbiinternational.com
Director of Sales Chip Shereck cshereck@bbiinternational.com
Account Manager Bob Brown bbrown@bbiinternational.com
Circulation Manager Jessica Tiller jtiller@bbiinternational.com
Senior Marketing & Advertising Manager Marla DeFoe mdefoe@bbiinternational.com
Customer Service Please call 1-866-746-8385 or email us at service@bbiinternational.com. Subscriptions Subscriptions to Ethanol Producer Magazine are free of charge to everyone with the exception of a shipping and handling charge for anyone outside the United States. To subscribe, visit www.EthanolProducer.com or you can send your mailing address and payment (checks made out to BBI International) to: Ethanol Producer Magazine Subscriptions, 308 Second Ave. N., Suite 304, Grand Forks, ND 58203. Back Issues, Reprints and Permissions Select back issues are available for $3.95 each, plus shipping. Article reprints are also available for a fee. For more information, contact us at 866-746-8385 or service@bbiinternational. com. Advertising Ethanol Producer Magazine provides a specific topic delivered to a highly targeted audience. We are committed to editorial excellence and high-quality print production. To find out more about Ethanol Producer Magazine advertis
ing opportunities, please contact us at 866-746-8385 or service@bbiinternational.com. Letters to the
letters to the editor. Send to Ethanol Producer Magazine Letters to the Editor, 308
58203 or email to editor@bbiinternational.com. Please include your
edited for clarity and/or space.
June 9-11,
Omaha, NE (866) 746-8385 | www.fuelethanolworkshop.com
Now in its 41st year, the FEW provides the ethanol industry with cutting-edge content and unparalleled networking opportunities in a dynamic business-to-business environment. As the largest, longest running ethanol conference in the world, the FEW is renowned for its superb programming—powered by Ethanol Producer Magazine —that maintains a strong focus on commercialscale ethanol production, new technology, and near-term research and development. The event draws more than 2,300 people from over 31 countries and from nearly every ethanol plant in the United States and Canada.
June
Omaha, NE (866) 746-8385 | www.sustainablefuelssummit.com
The Sustainable Fuels Summit: SAF, Renewable Diesel, and Biodiesel is a premier forum designed for producers of biodiesel, renewable diesel, and sustainable aviation fuel (SAF) to learn about cutting-edge process technologies, innovative techniques, and equipment to optimize existing production. Attendees will discover efficiencies that save money while increasing throughput and fuel quality. Produced by Biodiesel Magazine and SAF Magazine, this world-class event features premium content from technology providers, equipment vendors, consultants, engineers, and producers to advance discussions and foster an environment of collaboration and networking. Through engaging presentations, fruitful discussions, and compelling exhibitions, the summit aims to push the biomass-based diesel sector beyond its current limitations. Co-located with the International Fuel Ethanol Workshop & Expo, the Sustainable Fuels Summit conveniently harnesses the full potential of the integrated biofuels industries while providing a laser-like focus on processing methods that deliver tangible advantages to producers. Registration is free of charge for all employees of current biodiesel, renewable diesel, and SAF production facilities, from operators and maintenance personnel to board members and executives.
Ringneck Energy Walter Wendland Commonwealth Agri-Energy Mick Henderson Western Plains Energy Derek Peine Front Range Energy Dan Sanders Jr. COPYRIGHT © 2025 by BBI International
Minneapolis, MN (866) 746-8385 | www.safconference.com
Serving the Global Sustainable Aviation Fuel Industry Taking place in September, the North American SAF Conference & Expo, produced by SAF Magazine, in collaboration with the Commercial Aviation Alternative Fuels Initiative (CAAFI) will showcase the latest strategies for aviation fuel decarbonization, solutions for key industry challenges, and highlight the current opportunities for airlines, corporations and fuel producers.
June is always our largest issue of the year, and this 88-page installment of Ethanol Producer Magazine is no different with six spotlights, four contributions and half a dozen features. I typically preview the big stories in every issue, but this month, let me tell you about the folks who wrote them.
I’m privileged to work with some of the most qualified journalists in the biofuels business, writers and editors who have covered production, policy, energy and technology for decades. They’ve written books, worked for major producers, launched magazines, covered the industry under three U.S. presidents—even met one or two—and traversed the country chasing stories, touring plants, covering speeches and, not infrequently, making them.
Lisa Gibson, our adept features editor, is a former communications manager for one of the largest ethanol producers in North America and the past editor of this publication. After spending her early career in newspapers, Lisa worked here at BBI International for years. Today, she runs Sage & Stone Strategies out of Omaha, Nebraska, helping clients form smart, structured communication to optimize their messaging and enhance their reach. She reconnected with us last year, and we’re thrilled to be working with her again. This month, Lisa delivers our cover story, “Every Molecule Matters,” a piece about corn fiber ethanol on page 18.
Luke Geiver, who writes more features for EPM than anyone on the planet, is a South Dakota-based freelancer who, like Lisa, is a former BBI staffer. Luke has done it all in energy, tech and business writing, covering ethanol, biomass, biodiesel, SAF, oil and gas, unmanned aerial systems and more over the past 20 years. A self-taught magazine and event planning guru, Luke helped BBI launch numerous media products during his tenure with us. These days, we’re fortunate to have him supplying us with features written in his patented style of storytelling. Luke’s bylines show up atop three stories this month, including “A New Twist on Existing Tech,” a piece about CO2-to-ethanol on page 24, “Fermentation Forward,” an exclusive on IFF on page 40, and “Operating On the Edge,” an update on Aemetis on page 62.
The author of our page-32 report, “States Support Low-Carbon Futures,” is also a veteran industry journalist and part of the BBI family. Sue Retka Schill, who lives in North Dakota, is well known in our industry for being a fabulous writer, a past editor of this magazine, and a perennial speaker and host at the FEW’s annual Ethanol 101 seminar. Recently, after working on a book about the history of U.S. ethanol production, Sue offered to graciously host the Homegrown Fuels Podcast featuring conversations with industry pioneers through our online platform.
I would be remiss to not mention Katie Schroeder, our indispensable contributions editor and the author of “Engineering Excellence,” a profile on Katzen Engineering on page 52. Katie juggles several responsibilities here at Ethanol Producer Magazine, procuring columns and contributions, producing Spotlights, hosting podcasts and so much more.
Last but not least, our talented graphic designer, Raquel Boushee, is the artist who makes this magazine excel visually, applying her design magic and gracefully turning our editorial chaos into sophisticated, beautiful content each month.
Appreciated, all.
Overdrive™ Technology
• Boost oil yield with your existing system by creating optimal syrup conditions for oil recovery
• 5% or more increase in oil yield
DCO Technology™
• Wash more oil to thin stillage and remove fine solids from evaporators to increase oil yields and reduce energy consumption
• 15-20% increase in oil yield
Selective Grind Technology™
• Secondary milling to release more oil from germ particles and increase ethanol yields
• 10-20+% increase in oil yield
Optimization Solutions
• FQT conducts oil optimization studies to optimize operating conditions and help you evaluate the best options for improvements
CEO of Growth Energy
Earlier this spring, the Trump administration formally announced a summer waiver allowing uninterrupted sales of lower-cost E15. Action on the waiver fulfills a key element of President Trump’s executive order directing the U.S. Environmental Protection Agency to leverage E15 “to meet any projected temporary shortfalls in the supply of gasoline across the Nation.”
The decision takes the guesswork out of summer fueling options, giving our retail partners the regulatory certainty they need to manage inventory and protect a critical market for U.S. farmers. It could not come at a better time.
E15 demand is growing at a record pace. American families have been hit hard by inflation, and more and more consumers are seeking out lower-cost options at the pump. In April, both Minnesota and Iowa (the only states that specifically report E15 sales) announced record breaking sales in 2024, with sales in Iowa surging by an impressive 45%.
Other states aren’t far behind. Just weeks ago, Growth Energy’s Technical Director for Market Development Reid Wagner was one of the first customers to take advantage of Costco’s new Unleaded 88 (or E15) fuel offering. Located at the Costco in La Vista, Nebraska, it is the first Costco location in the country to offer the higher blended fuel. And thanks to Nebraska’s E15 Access Standard, Nebraskans will soon have access to low-cost Unleaded 88 at even more locations.
Of course, retailers and motorists aren’t the only winners. E15 can also help deliver on the President’s trade agenda, which includes securing domestic markets for domestic goods, so U.S. producers are less vulnerable to foreign trade barriers. It provides American farmers with more certain and reliable markets for their corn.
The bottom line is that E15 presents a huge opportunity to boost the rural economy and lower prices at the pump. And with a temporary waiver in place, our champions in Congress and the White House can focus on passing legislation restoring permanent, unrestricted access to E15 for all months, all states, all stations and all fuel dispensers.
That is Growth Energy’s goal, and we urge readers to help us keep up the momentum by visiting GrowthEnergy.com/E15Now, where biofuel supporters can quickly connect with their members of Congress. We have a coalition that is bigger and broader than it’s ever been, and with a permanent E15 fix in place in advance of the 2026 summer driving season, the need for temporary EPA waivers will be a thing of the past.
Past-President and Board Director
This column is being written immediately after Canada’s federal election. The Liberals have secured a historic fourth term while Conservatives reached their highest vote count in 40 years. Yet, amid this, one of the most striking features of Canada’s 2025 election is how dramatically the narrative shifted: in particular, on climate.
The passionate climate debates that dominated 2019 gave way to kitchen-table economics and trade concerns. Yet here’s the key insight: even as climate concerns fade from campaign speeches, Canada’s need for smart, growth-oriented clean fuel policies has never been more apparent. For the new Prime Minister, incoming lawmakers, investors and skeptics alike, ethanol presents a rare opportunity: rural economic growth that also offers environmental protection. The proof transcends politics.
A major change leading up to the election was the repeal of Canada’s national consumer carbon tax—a signature policy of Justin Trudeau—dismantled by his successor, Prime Minister Mark Carney. The former central banker, known for his climate finance leadership, argued that while carbon pricing had served its purpose, the time had come for a more practical approach. Few solutions have proven more practical than ethanol for both emissions reduction and economic growth. Case in point: the Clean Fuel Regulations (CFR) which ensures fuel producers lower their carbon intensity over time but allows flexibility in how to achieve it. Thanks to the ease and affordability of higher ethanol blending in the CFR, Canada’s ethanol blending has increased by 25%, and in 2024 it removed nine million tonnes of CO2 which is equivalent to taking two million cars off the road.
Crucially, ethanol’s environmental gains don’t come at the expense of consumers and affordability. Ethanol-blended fuel is often cheaper than straight gasoline, thanks to ethanol’s lower per-gallon price. Take Minnesota, where drivers saved $24 million USD in 2024 by filling up with E15 (15% ethanol), about 17 cents per
gallon cheaper than regular unleaded. Canadian drivers enjoy similar savings with E10 at the pump.
Ethanol also directly strengthens the rural economy. The newly formed Farms and Fuels Alliance (FFA)—which unites Canada’s dedicated ethanol producers and grain farmers—demonstrates how the domestic ethanol industry fuels strong rural growth. It creates jobs in small towns, generates tax revenue and produces co-products like high-protein animal feed that strengthen other agricultural sectors.
For those worried that Canada’s climate progress might stall without a carbon tax, look no further than other jurisdictions that cut transport emissions through strong ethanol mandates. The United States has achieved sizable reductions through its Renewable Fuel Standard, requiring biofuel blending in gasoline. Every gallon sold in America contains 10% ethanol (E10), cutting emissions while saving consumers money— all without a federal carbon tax. Brazil offers another compelling example. Their mandatory 27% ethanol blend and widespread use of flex-fuel vehicles cut 71 million tonnes of CO2 in 2022 alone. Like the U.S., Brazil achieved this through smart mandates rather than fuel taxes. Canada is now following a similar path.
With Canada moving away from a consumer carbon tax, the focus must shift to smart, investmentdriven measures like the CFR and other pro-ethanol investment tools. This new direction allows Canada to move past tax-based politics, reinforce its performancebased approach, and maintain ethanol’s role as a cornerstone of rural prosperity and economic growth in Canada, just as it is in the U.S. and elsewhere.
Political priorities may shift, but the fundamental value of ethanol does not. Ultimately, what voters most want from any government is competence, making ethanol a blueprint of how practical, homegrown solutions can work across party lines and well beyond the ballot box.
The American Coalition for Ethanol hosted a fly-in to Washington D.C. during which participants visited members of the legislature to advocate for year-round E15 and unleashing new market opportunities at home and abroad. According to Brian Jennings, CEO of ACE, the fly-in started over ten years ago when the Renewable Fuel Standard was implemented by the Environmental Protection Agency.
“It’s really important, especially with a new Congress, that we get as many people from as many walks of life out to Washington to talk to members of Congress about our priorities,” Jennings said.
Fifty people attended the fly-in, including members of ethanol plant leadership, farmers, ethanol plant board members and investors, corn growers, fuel retailers and industry advocates. Many came from the
LRQA, a global assurance partner backed by Goldman Sachs Alternatives, has acquired EcoEngineers, a U.S.-based consulting, auditing and advisory firm with an exclusive focus on the energy transition. This marks LRQA’s fifth acquisition in five months, reinforcing its commitment to accelerating growth and expanding its support
for global corporate clients navigating the energy transition.
EcoEngineers was recently recognized as one of the Top 10 Sustainable Consulting Firms in the world by Sustainability Magazine and offers deep technical expertise in lowcarbon fuel production, climate regulations, carbon markets and innovative technolo-
gies—areas in high demand amid growing regulatory complexity and uncertainty. Against this backdrop, businesses still have to respond to pressures from investors, consumers and stakeholders to uphold transparency and integrity in their climate commitments, particularly in the agriculture and energy sectors.
Only biofuels can unlock the investments & jobs needed to revitalize the rural economy.
Verity Holdings announced a partnership with Minnesota Soybean Processors (MnSP) to implement Verity’s proprietary track and trace software. This collaboration aims to unlock additional value for MnSP through export premiums while streamlining compliance reporting and auditability.
solutions, MnSP can document key attributes with confidence, ensuring that sustainably grown soybeans translate into real value for farmers, processors and international buyers alike.”
“This partnership with MnSP is a great example of how Verity’s technology empowers producers to capture and communicate the value of sustainable agriculture,” said Kimberly Bowron, president of Verity. “By leveraging our advanced data verification and supply chain transparency
The partnership reinforces Verity and MnSP’s commitment to expanding opportunities in international markets for sustainably certified products, such as those derived from regeneratively grown soybeans.
Verity, a wholly-owned subsidiary of Gevo Inc., is also actively engaged with multiple U.S. ethanol producers.
Growth Energy recently announced four new additions to its staff.
Emily Marthaler joins as director of global policy, bringing her experience as senior trade advisor with USDA’s Foreign Agricultural Service to support Growth Energy’s engagement with the current administration on foreign trade issues.
Reid Wagner joins as technical director of market development, leveraging his background as executive director of the Nebraska Ethanol Board to lead Growth Energy’s efforts to clear technical hurdles that hinder the wider adoption of higher ethanol blends.
Michael Lozier joins as director of membership and stakeholder engagement, where he will work with Growth Energy members and biofuel producers and industry supporters, having previously served as U.S. portfolio marketing leader at Corteva Agriscience.
Ciara Markoski joins as PAC manager for the Government Affairs team. Prior to this, Markoski worked as a PAC assistant at Delta Air Lines.
California motorists in 2024 nearly set another record for E85 use, based on data from the California Air Resources Board. Last year’s total of 114.7 million E85 gallons trails only the 118.5 million gallons fueled up in 2023. E85 is a renewable, biomass-based fuel for use in flex fuel vehicles (FFVs).
Pearson Fuels, the state’s largest E85 distributor, expected cheaper gasoline in 2024 would weigh on E85 sales numbers. Average gasoline prices last year were 24 cents per gallon below the previous year’s average and 76 cents per gallon lower than in 2022.
Sustained low gas prices are unlikely for 2025. California’s Division of Petro-
Green Plains announced it is continuing the refreshment of its board of directors through appointments of three highly qualified and independent individuals: Steven Furcich, Carl Grassi and Patrick Sweeney. The three appointees collectively possess additive experience in key areas such as the agriculture and commodities sector, capital allocation, finance, long-term planning, and
strategic reviews and transactions. From the time of appointment until the company’s 2025 Annual Meeting of Shareholders, the appointments will result in an expansion of the board to at least 10 members. The company expects the board to shrink thereafter due to two tenured directors not standing for re-election at this year’s Annual Meeting.
leum Market Oversight noted a $0.42 per gallon price surge earlier this year after a refinery fire in Northern California. Pearson Fuels distributes E85 to more than 430 retail stations throughout California. E85 in the Pearson Fuels station network is typically $1.50-$2.00 per gallon cheaper than unleaded gasoline.
Green Plains also announced that its board has formed a new Strategic Planning Committee to provide analysis and recommendations pertaining to value-creation initiatives.
• Delivers up to 15% increased corn oil recovery
• Enables pathway to produce low-CI cellulosic gallons
• Dewaters corn kernel fiber for reduced natural gas consumption
• Maximizes plant operability
To learn more, contact your account manager.
A surge in corn kernel fiber as a feedstock is sweeping the industry, driven by incentives for low carbon intensities and EPA-approved testing methods for D3 RIN qualification.
By Lisa Gibson
The steps are simple, with low capital and strong ROI: Engage with the appropriate analytics labs to help calculate in-situ cellulosic ethanol production from corn kernel fiber; register those gallons with the appropriate markets; and enjoy the new competitive advantage. McCord Pankonen, ethanol and biodiesel service director with EcoEngineers, says in-situ CKF ethanol is seeing a surge as a result of its accessibility and its advantages over firstgeneration ethanol in programs such as the
Renewable Fuel Standard and California’s Low Carbon Fuel Standard.
In January and February of 2025 (the most recent data available at press time), 13.6 million D3 RINs were generated for cellulosic/CKF ethanol. For the same months in 2024, approximately 374,000 were generated.
“What’s neat about the opportunity is ethanol producers really don’t have to do a ton of altering of their plants,” Pankonen says. “It increases revenue for the same kernel that’s going through the process, so really the lift is to get it registered and then engage markets.”
Pankonen also strongly recommends ethanol producers looking into CKF ethanol (also called generation 1.5) partner with the right enzyme provider to maximize value in fiber-degrading packages and strengthen cellulosic production. EcoEngineers, for its part, helps consult, advise, audit programs and train plant staff across a wide area of opportunities, including adherence to cellulosic compliance standards in the RFS and LCFS.
Certainly, the process to register and continue compliance is complicated, but producers can see significant benefits through the work, he says.
“When we’re in a market calculating carbon intensity, every molecule matters.”
“One of the first decisions an ethanol producer needs to make is whether they want to maximize the value of their corn kernel fiber or just enter the cellulosic ethanol market,” says Laura Bostic, global marketing manager with Novonesis.
Novonesis’ trademarked Fiberex portfolio has multiple solutions designed to meet a customer’s specific needs in CKF conversion. “We know ethanol producers’
priorities are diverse and finding the right combination of products to maximize a plant’s value and meet those needs is crucial,” Bostic says.
“Is the focus generating D3 RINs, participating in state markets like CARB (California Air Resources Board), increasing ethanol and oil yield, or a combination of other drivers? Essentially, what is the customer hoping to achieve?” she adds. “Novonesis’ fiber-degrading enzymes can help a plant achieve their goals and maximize the value from their corn kernel fiber across all of these areas.”
Fiberex products contain powerful cellulases to generate cellulosic ethanol for D3 RINs or state low-carbon markets, Bostic says. “Hemicellulases work to further break down and hydrolyze the fiber matrix, releasing trapped cellulose, starch and oil. Meaning, in addition to cellulosic ethanol, more glucose is released, giving a bump to starch ethanol, plus a significant increase in extractable oil potential.”
Fiber-degrading enzymes have more complex work to do than a traditional firstgeneration starch enzyme. Traditional firstgeneration glucoamylases and proteases do not degrade cellulose or hemicellulose—the
main components of corn kernel fiber, Bostic explains. So when a cellulase or hemicellulase is used to break those down, they’re also hydrolyzing the fiber into fermentable sugars the yeast can convert into ethanol.
“The fiber matrix is a very tightly bound structure, and as the cellulases and hemicellulases are working on that fiber, it loosens it up, which then enables components trapped in that very tight structure to be released,” Bostic says, adding that without cellulase and hemicellulase, that valuable fiber goes out with the wet cake as a waste product.
IFF Staff Scientist Brad Kelemen emphasizes fiber’s complexity as well. “Cellulose is really tough. It’s a recalcitrant substrate so it’s highly insoluble. It’s problematic and requires chemical pretreatment or other treatment to get access to cellulose.” It’s much tougher, he says, than the starch part of the process in terms of the speed of the reaction and the challenges working with it. “The hemicellulose—
the fiber—is difficult in that it’s complex. There’s a lot of variety in it and there’s a lot of branching, a lot of cross linking, a lot of different bonds to work on.”
Because of the complexity, a fiberdegrading enzyme package can be more complicated to produce, Kelemen says. “We have a world-class R&D group that understands the application of our enzymes very well in these processes. So I’m very excited about the things to come. But they’re complex, so it takes some time to develop them.”
IFF also focuses on downstream processes with its fiber-degrading enzymes— Optimash F200, Optimash AX and Optimash Cellulase. “The biggest concern is that these enzymes can have some impact on downstream parts of the process. It’s a concern when working on them to look for suspended solids development because they can start producing greater suspended solids and those will increase the viscosity in the syrup or start fouling the evaporators.
So it’s important to develop things that act on the fiber but don’t necessarily exaggerate any downstream effects that might come.”
IFF focuses on dual purposes for its enzyme packages, seeking to maximize the value of other CKF coproducts such as corn oil and other benefits such as cellulosic RINs and LCFS qualification, Kelemen says. “It’s by design that these things are beneficial in multiple places.”
Neogen has captured interest in the ethanol industry for its work on the in-situ cellulosic ethanol testing and quantifying method that was approved by the EPA in March 2024. Neogen started with a method developed by Justin Sluiter with the National Renewable Energy Laboratory, using it as a “backbone” for its method, according to Matthew Nichols, director of biofuels strategic market for Neogen.
“Previously, Justin had come up with a method for detecting corn kernel fiber, but
a number of challenges remained,” Nichols says. “When you would test a sample pre- and postfermentation, the post-fermentation would commonly have more fiber than pre-fermentation.
“That doesn’t really make a lot of sense, so we realized that what was happening was the fiber from yeast was being counted as part of the process,” he adds. “We came up with a yeast-degrading cocktail and modified the method on a number of steps, and we were able to eliminate that fiber from the yeast.”
The ASTM approval process, required for EPA approval, is robust, Nichols says. It requires full publishing of the method and unanimous approval by voting members. After several iterations with the ASTM process, the testing method was approved by the EPA and prompted an influx of EPA Efficient Producer Pathway approvals. As of April 2024, a total of 14 ethanol-related operations had approved D3 RIN pathways, according to the EPA. As of April 2025, that number had increased to 117. Not all of these approved D3 RIN pathways, of course, are for CKF.
Nichols points out that the accomplishment was the result of industry-wide collaboration, with input from producers as well as top CKF analytics labs. “The industry came together and worked through some scientific inquiry; we did meet the requirements and we got the method across the finish line, so it has met the EPA specifications and we’re just really happy about everyone working together.”
The National Corn-to-Ethanol Research Center of Southern Illinois University Edwardsville also has created an in-situ CKF ethanol testing method, though it is not approved for RFS pathways or for California’s LCFS. Yanhong Zhang, interim executive director of NCERC, says it is a VCSB method, but the lab has not sought EPA approval.
“In my opinion, the reason NCERC’s method was not popular among the industry ... was because our method only delivers results to support about 1% ethanol increase for 1.5-generation processing versus some other popular methods will deliver results to support over 3% ethanol increase (for the same fermentation batch),” Zhang says.
Different analytical methods report varying ethanol yield lifts, Pankonen explains. “There are calculations out there on the content of cellulosic. It’s important to make sure folks are engaging with analytical labs accordingly.”
According to Zhang, NCERC’s method first optimized the total starch testing method by improving the conversion of starch in the corn matrix to glucose. Next, Zhang’s team developed a total cellulosic method based on the NREL cellulose in biomass method, using acid hydrolysis to convert starch, cellulose and yeast cell wall to glucose, then subtracting the glucose from starch to estimate the cellulose level in the sample.
Producers using an approved pathway can generate D3 RINs through the EPA’s Efficient Producer Pathway program. D3
RINs have a value of $2 to $3 more than D6 RINs at any given time, depending on market fluctuations. “When we talk about why ethanol producers really want to look at the benefits for registering for D3 RINs or kernel fiber ethanol, it really boils down to the higher RIN value,” Pankonen says. “It’s worth the opportunity for ethanol producers to register their facilities for D3 RINs. The impact can be pretty significant.”
LCFS, in contrast, is based solely on carbon reduction. CKF ethanol, through the program, has a score 30 points lower than that of first-generation starch ethanol, Pankonen explains. “So, literally, the more carbon reduction you have at your facility, the higher price per metric ton of CO2 produced you would receive,” he says, adding that potential revenue per gallon can range from $1.50 to $3. Assuming a 1% yield lift, a 100 MMgy plant can qualify for a 30-point reduction on 1 million gallons.
For both RFS and LCFS, producers need to submit a third party-validated pathway and, following approval, conduct quarterly and annual compliance reporting.
“You have to have a carbon-reduction strategy, and this is something that pays itself back pretty well in terms of return on investment within a year,” Pankonen says.
The Clean Fuel Production tax credit in 45Z is another area where producers can potentially cash in on their carbon-reduction strategies. “45Z is really about making sure you understand what your carbon intensity is first and foremost,” Pankonen says. “I wish that more cellulosic ethanol could qualify that’s inside a kernel of corn, but there’s only so much you can get.” Guidance and supporting frameworks were released in early 2025, but the timeline for implementation of 45Z remains unclear.
The qualifying threshold, as proposed, for 45Z is 47.4 grams of CO2 equivalent per megajoule. “If you’re at 48 points and cellulosic ethanol can bring your overall volume down, maybe that pushes you into that tier where you can take advantage of 45Z,” he says.
It’s clear that valuable opportunities are accessible for CKF ethanol, whether through direct monetary benefits or in market access via low carbon-intensity gallons. “It really allows ethanol producers to be more competitive on the gallons they’re processing through the ethanol plant,” Pankonen says.
Author: Lisa Gibson lisa.gibson@sageandstonestrategies.com
We stand for quality, integrity, and defensibility in lab analysis and data all the while bringing innovation and the best value in the industr y.
We employ all available analytical methods for corn kernel fiber conversion pathways.
NREL approved by EPA for RFS D3 RINs
ASTM approved by EPA for RFS D3 RINs
Our Proprietar y Analytical Methods have been approved by CARB for LCFS and provide an unrivaled level of accuracy and precision.
We are an ISO 17025 Accredited Laborator y and a member of ASTM International.
LET’S TALK.
By Luke Geiver
Nataqua is a startup company that aims to help ethanol producers profit from carbon dioxide emissions by producing more ethanol on site. Last year, the small company joined the Renewable Fuels Association as an associate member in a move it says shows its commitment to the ethanol industry specifically.
The company isn’t yet ready to offer its unique carbon dioxideto-ethanol reactor to producers, but Alex Motey, co-founder and CEO, says Nataqua’s approach to commercialization is on the right track. Randall Doyal, past chairman of the RFA and former CEO of Al-Corn Clean Fuel, agrees and serves as an advisor to the company. Chris Barile, a professor at the University of Nevada, Reno, is the electrochemist helping lead the technical efforts of the startup.
Motey admits that Nataqua is not the first entity with the idea to develop a commercially viable technology to convert CO2 to ethanol. He does say, however, that his team is one of only a handful that is focused on serving the ethanol industry first and foremost. Since researchers came across a unique catalyst capable of making electrolysis for CO2-to-ethanol feasible back in 2016, several firms have attempted the task. Some, like LanzaTech, have been successful.
Alex Motey Co-Founder and CEO, Nataqua
More than 65 groups have demonstrated that the process is feasible, Motey estimates. Cert Systems in Canada is developing an electrochemical process that could be similar to Nataqua’s. Adkins Energy and CapCO2 are already building out a facility that can turn CO2 into green methanol. Twelve, a company that has collaborated with LanzaTech, is developing a plant to produce what it calls E-Jet SAF in a process that converts CO2 into a renewable fuel. Avfuel Corp. is developing a CO2-to-SAF process using electrochemistry and special catalysts. And AirCo is focused on serving the SAF industry with its trademarked Airmade tech after rebranding and refocusing this year toward fuels and away from alcohols and fragrances.
According to Motey, most groups developing CO2 conversion technologies eventually choose one of three options: making syngas from carbon dioxide and water, directly converting CO2 into ethylene or transforming it into jet fuel. These pathways remain popular
because of prevailing beliefs about chemical conversion efficiencies and projected hydrogen feedstock costs, he says.
Should Nataqua’s unique approach prove out at scale, Motey believes it can offer solutions for several challenges facing the ethanol industry.
Motey and Barile’s team has developed an electrolyzer reactor that requires three simple ingredients to function—CO2, water and electricity. The system splits water into hydrogen and oxygen internally. The hydrogen created in the system immediately reacts with CO2 to form ethanol and water, producing a mixture that integrates seamlessly into an ethanol plant’s existing pre-distillation process. The current iteration of their process uses an inexpensive catalyst to convert the CO2 into ethanol at room temperature and is protected by multiple pending patents. To date, the system has proven to be highly faradaic, meaning capable and efficient at transferring an electrical charge through a system to get the desired result.
In 2016, Ethanol Producer Magazine first wrote about a new catalyst made of carbon, nitrogen and copper that was capable of converting CO2 into ethanol. At the time, the researchers from Oak Ridge Nation-
al Laboratory who discovered the catalyst said several parties were interested in helping commercialize the product. Since then, several other catalyst breakthroughs have been announced on the CO2-toethanol front. In 2020, a team of researchers from Argonne National Laboratory, the University of Chicago’s Pritzker School of Molecular Engineering and Northern Illinois University discovered an electrocatalyst capable of converting CO2 into ethanol. Their version, also copper-based, proved to be more efficient than other versions and was viable at low voltage.
In 2021, an international team of researchers under the U.S. Department of Energy’s Brookhaven Lab made the cover of the Journal of the American Chemical Society for their work developing a catalyst and process for turning CO2 into ethanol.
Last year, scientists at Stanford released insight on work to make a different catalyst capable of producing ethanol from CO2, but the process and catalyst needed further study due to the costs associated.
Motey and Barile have focused on developing specialized electrochemical catalysts to go with an electrolysis system. Electrolysis systems typically involve the introduction of current in a vessel containing an electrolyte solution. An internal electrode fires and creates a charge in the solution. The electricity creates a non-spontaneous reaction and splits water into hydrogen and oxygen.
Nataqua is working to create a practical and smooth integration option that will work with existing ethanol plants. Essentially, the process would convert CO2 exhaust streams directly into ethanol prior to entrance into the pre-distillation mix.
“Historically, many groups have struggled to scale because they optimized one attribute at a time, such as maximizing ethanol production volume without addressing overall system economics from the outset,” Motey says.
Barile is focused on minimizing the cost per gallon for CO2-toethanol conversion rather than prematurely perfecting upfront capital costs. After scaling the prototype electrolyzer, Nataqua intends to collaborate with ethanol plant partners.
“Our CO2-to-ethanol technology addresses common objections to CO2 storage, eliminating the need for complicated new supply chains or distribution networks,” Motey says.
In addition to diminishing the need for some plants to connect to a CO2 pipeline or invest in carbon capture and sequestration networks, technologies like Nataqua’s could help plants transition from traditional feedstocks to alternative options like switchgrass or miscanthus, Motey says.
When switching feedstocks from corn to miscanthus or switchgrass, ethanol concentrations from fermentations would drop significantly from the 12% to 16% seen in corn, to only 4% to 10%.
Such decreases would dramatically increase distillation costs, Motey says, and decrease total yield.
“Our technology can resolve this challenge by converting fermentation-produced CO2 directly into additional ethanol on site,” he says.
The process restores pre-distillation ethanol concentrations seen with corn to economically viable levels using switchgrass or other alternative feedstocks.
Motey, an inventor and financial analyst prior to founding Nataqua, has always believed in the importance of pairing long-term thinking with an understanding of people’s beliefs and actions. Combining those perspectives, he says, can yield impactful results.
“When the world paused during the pandemic, I found myself diving into materials science and engineering, craving to develop a product,” he says. “I spent countless hours reaching out to experts, researchers and entrepreneurs, and that’s how I connected with Dr. Barile. Our relationship, driven by a shared excitement and curiosity, eventually led us to work on what became Nataqua.”
When Motey initially reached out to Barile and talked about working together, the pair clicked from the start. Motey even used his personal savings to sponsor a project in Barile’s lab at UNR that involved using a hydrothermal reactor to synthesize CO2capturing sponges for vehicle tailpipe filters. The concept was based on the idea that drivers could remove the filters after use, convert the captured CO2 into ethanol, and produce ethanol-based household items like cleaning solutions or disinfectants.
BCI equipment is built to last, one piece at a time, by a team that still believes quality matters.
From custom design, to fabrication, to service & support...
BCI is Elevating Conveying Standards
• Chain Conveyors
• Bucket Elevators
• Parts & Accessories for all makes/models of conveying equipment
Over 200 Years of Combined Experience. Made in the USA.
It was Barile’s deep expertise as an electrochemist that helped the team decide that although the filters would have been feasible and economical, they could think bigger. After joining the RFA in 2024, the company went so far as to say that its technology produced in Barile’s lab held the potential to revolutionize ethanol production.
Barile has an extensive background and list of accomplishments in his field. He has earned multiple awards from the National Science Foundation. At the University of Nevada Reno, he operates the Barile Laboratory to study electrochemistry, inorganic chemistry and materials used to solve energy conversion, storage and efficiency.
In 2021, prior to the formation of Nataqua, Barile’s lab was working to create catalysts suitable for CO2-to-ethanol conversions along with the creation of an electrolyzer prototype. Much of that work has been translated to Nataqua.
The lab created a vessel to push unfavorable reactions to completion. Through customization, the team added a gas chromatograph to the unit to identify and measure the products (gases like methylene or ethanol) generated during the process. Using polymer modified metal electrodes, the vessel and catalysts from the lab, they were able to make ethanol from CO2.
By designing catalysts with different structures, the lab team learned they could control how reactions happened and what fuel
could be made. Coating the catalyst with a fluoropolymer was the key. To go fully commercial, the lab team believed they needed a CO2 capture unit to concentrate the gas directly from the air. The electrodes in the vessel also needed to be more robust to handle large quantities of gas.
Motey believes that Barile’s expertise combined with his own background will help the company make it from startup to commercial success. Through his finance and innovation background, Motey is focused on setting realistic milestones and identifying clear next steps. “Too often, startups chase grand visions without practical roadmaps or real market understandings,” he says. “Such an approach can distort reality, allowing impractical ideas to gain undue popularity while more practical, efficient solutions are overlooked.”
The Nataqua team has already learned a great deal from the ethanol industry. Producers are practical, economically minded and savvy, Motey says. “Ethanol operations aren’t theoretical—every change, every new technology must clearly simplify operations or directly boost profitability.”
Plus, Nataqua knows producers deal daily with tight margins, volatile commodity markets, regulatory complexities and community expectations. No technology, Motey explains, gains traction unless it clearly cuts costs, enhances efficiency or increases profit-
ability in a straightforward way. “When initially pitching Nataqua to investors outside the Midwest, it quickly became clear they didn’t fully grasp the intricacies of the ethanol industry or appreciate the potential of biobased chemical innovations,” Motey says.
When Nataqua joined RFA, President Geoff Cooper called the company’s technology “exciting,” adding that it holds great promise for reducing carbon intensity and enhancing operational efficiency.
Motey says the ethanol industry has been welcoming. In the future, he hopes to work with producers or industry partners to run tests and pilot its electrolysis reactor and catalyst technology. Anything from practical feedback to letters of interest to simple expressions of support would help the team on its path to commercialization, he says.
“Converting CO2 into ethanol on-site offers a tangible path toward genuine carbon negativity, energy independence and economic growth,” Motey says. “We strongly believe this is an innovation everyone can proudly support.”
Author: Luke Geiver writer@bbiinternational.com
The industry’s maintenance managers will come together later this summer to learn, network and troubleshoot shared challenges at the annual Team M3 Meeting.
A staple conference of the ethanol industry, the team M3 Meeting offers ethanol plant maintenance managers an opportunity to maintain connections, solve problems and explore innovations. Slated for August 5-6, 2025, the meeting offers maintenance managers from across the U.S. ethanol industry an opportunity to discuss their profession and explore new technologies. Jon Osland, event organizer and retired maintenance manager, explains that the event will include breakfast and lunch sessions followed by roundtable discussions amongst maintenance personnel to talk about solutions to shared challenges they encounter on the job.
This year’s meeting will be held, once again, at the Marriott Riverfront in South Sioux City, Nebraska, according to Osland. “We’ve done two there … and then last year they were remodeling [so we went] across the river to Sioux City,” he says. “This year, we’re going back [to the Marriott’s] newly remodeled facility. They’ve got a nice place there, lots of room, so the vendors aren’t packed in. So, if you want to sit and talk with the vendor about something, you [have] plenty of room.”
Osland anticipates that nearly 150 vendors will come to the 2025 meeting to inform ethanol plant staff about technological innovations. Attending the meeting for the last 10 to 12 years, Andy Daly is one of those vendors. Daly works as an outside field engineer with The Heat Exchanger Group. He explains that the meeting gives him a chance to share solutions and educate maintenance managers, however the meeting’s relaxed environment gives him a chance to talk about recent hunting trips and simply build solid relationships with clients.
“We try to help educate the maintenance guys and the operators on what a plate and frame heat exchanger is, how they’re designed, how to look for things that could point to problems and help you identify those,” Daly says. “A lot of times these guys are expanding their production capabilities, and we talk [through] the importance of knowing data points so that we can help them do that properly.”
The number of plant staff attending is likely to reach around 150 with around 80 ethanol plants represented, according to Osland. Aaron Godell, maintenance manager at Corn LP, an 87 MMgy ethanol plant in
Goldfield, Iowa, shares that the meeting has a “huge” value in his eyes. Giving maintenance managers an opportunity to compare notes and talk about problems they are facing within their facilities provides them an opportunity to figure out solutions. The expertise of participating vendors lends more opportunities for learning and resolving issues. “And it’s seeing and [networking] with all those people and giving us the advantage of just coming to that meeting and learning from all that knowledge … over the couple days that we’re there,” he continues.
During his 20-year career, Godell believes the collaboration fueled by the team M3 Meeting makes an impact in the industry. “I think there have been a lot of improvements in the industry that have, [in part], come about through this meeting,” he says.
For more information, contact Osland at (507) 829-7660 or teamm3jlo@outlook. com. More information about the event can be found at team3managers.com.
Leveraging a combined 200 years of experience, RCM - Thermal Kinetics’ engineers empower ethanol producers to improve energy efficiency.
By Katie Schroeder
Thermal Kinetics, a division of RCM Corporation, specializes in advanced process design for distillation, evaporation, and dehydration unit operations. When founder Chris Brown established Thermal Kinetics, ethanol was just one of the many chemical and energy industries the company served. Over time, however, ethanol became a key focus, now accounting for 80% of the company’s business.
According to Brown, the patented distillation, evaporation and dehydration (DDE) process developed by Thermal Kinetics reduces energy consumption by 20% compared to competing systems, driving greater profitability for ethanol producers. “There’s a strong push towards net zero and reducing
a major role in that,” Brown explains. Lowering carbon scores starts with minimizing CO2 generation at the source, rather than just capturing it. Thermal Kinetics is dedicated to enhancing energy efficiency for every client, utilizing technologies like mechanical vapor recompression (MVR) systems and advanced systems integration.
One of the company’s breakthrough innovations, its New Ethanol Expansion Technology (NEXT), enables ethanol producers to increase yields and efficiency without significant capital investment. Roy Viteri, Chemical Engineer at RCM Thermal Kinetics and the developer of the NEXT program, draws on techniques he honed from the refining industry. He describes the hands-on approach:
RCM Thermal Kinetics delivers high efficiency process solutions for ethanol plants. From Distillation, Evaporation and Dehydration technologies, we help plants reduce energy use and optimize performance.
the DD&E unit equipped with pressure and temperature gauges, tool bags and pipe fittings gathering data to establish a baseline of the unit at its current capacity. Since we understand equipment performance and the fundamentals of equipment design, including distillation column internals, heat exchangers, pumps, controls and hydraulic circuits, this allows us to effectively identify problem areas and confidently develop cost-effective solutions to overcome each of them, requiring careful consideration of the entire unit impact based on individual modifications.”
Thermal Kinetics empowers ethanol producers to reduce carbon scores, boost yields and unlock additional capacity—driving long-term success and sustainability.
Now, with NEXT—New Ethanol eXpansion Technology, boost production, integrate patented RCM Thermal Kinetics energy integration designs and increase profitability without compromising reliability and uptime.
Terry Wanzek sells corn to Dakota Spirit AgEnergy down the road from his farm near Jamestown in eastern North Dakota. And, since his farm is located near Interstate 94, his corn often heads to one of the western North Dakota ethanol producers, serving as a backhaul for truckers hauling sunflowers or beans to eastern buyers.
Wanzek also serves in the state legislature. So, when approached by the state’s ethanol association to sponsor legislation, he needed little convincing. “We grow a lot of corn and you can draw lines from our
corn to the ethanol to the market that all comes back to us who raised the corn,” he says.
He was in the state senate over two decades ago when the state redirected its 1980s-era fuel tax credit that incentivized blending into a counter-cyclical program to aid the state’s producers during challenging market conditions with payments based on market costs of corn versus market value of ethanol.
“Back then, it did a couple things,” says Jeff Zueger, CEO of Harvestone Low Carbon Partners, owners of Dakota Spirit AgEnergy and Blue Flint Ethanol in western North Dakota. “It incentivized plants
to get built in North Dakota, and made sure that, should you build a plant, there was a support mechanism around the commodity components.”
Though much smaller when compared to neighboring South Dakota and Iowa, North Dakota’s 550 million-gallon annual production still lands it in the top 10 ethanol producing states. Zueger points out that the North Dakota ethanol industry contributes nearly $1.7 billion annually to the state’s economy. While two of the original ethanol plants built in the 1980s closed (one in Grafton and one in Walhalla), six plants opened between 2007 and 2020. Five of them are operating today, and each has maxed out the
North Dakota takes unique approach as other states target sustainable aviation fuel tax incentives.
By Susanne Retka Schill
counter-cyclical program’s caps of 10 years or $10 million per facility.
The North Dakota legislature is poised to redirect the continuing appropriation passed in 2003 to another program unique to North Dakota. “It’s about meeting the next phase for our industry,” Zueger says. “Commodity prices are relevant to our business, but sustainability relies on differentiating yourself and lowering the carbon intensity and energy inputs into your process so you can offer the product the market is asking for. The markets are asking for lower-carbon feedstock for SAF and lower-carbon products for the transportation industry.”
The legislation redirects the continuing appropriation consisting of 40% of the sums collected from farm vehicle registrations to a new low-carbon fuels fund. Eligible capital projects would include carbon capture and sequestration, energy efficiency upgrades and ethanol yield improvements. The low-carbon fuel incentives would be limited to 50% of the cost of a single project, with no more than $3 million per facility every biennium, capped at $10 million and 10 years for any one facility.
“This provides an additional support mechanism to cover some of the uncertainty in making these investments,” Zueger says. “Rulemaking in the regulatory front
presents risk and the low-carbon fuel markets move around as well, so we’re making investments on two fronts with associated risks.”
The legislation has passed the state Senate and House, but was not yet signed by the governor at press time. Support was primarily positive, though Wanzek says some legislators want to get into discussions around climate change or the legitimacy of green initiatives. “I’m looking at it totally differently, from the business perspective. If there’s an opportunity to meet our customers’ needs, it could open up a whole lot more markets for ethanol and ultimately for corn farmers. We’re trying to assist the eth-
anol industry in North Dakota to address those market forces and help them position themselves to apply for those markets.”
North Dakota’s approach to positioning its ethanol production for future markets is unique in that it is directed at helping its producers bring lower carbon intensity (CI) products to emerging markets. Most states are adapting the 1980s-era tax credit approach aimed at lowering the cost of using the new, higher-priced sustainable aviation fuel (SAF) to support in-state production and infrastructure.
Illinois’ SAF incentive was first implemented in 2023. Washington State, Minnesota and Nebraska have also implemented SAF programs. New York and Michigan are currently considering measures. Chris Bliley, vice president of regulatory affairs for Growth Energy, also lists Arkansas, Hawaii and Alaska among states considering leg-
islation. He expects other states with large aviation sectors, or those that have been on the cutting edge of carbon programs, to join the movement.
States vary in how they structure the incentive and their approaches to feedstocks.
Illinois’ $1.50-per-gallon tax credit started July 1, 2023, and covers SAF sold or used by an airline carrier in the state. To be eligible, SAF must achieve a 50% CI reduction when compared to petroleum-based jet fuel. Credits are not applicable to SAF from palm oil or soy-based SAF once air carriers have collectively purchased SAF made from 10 MMgy soybean oil feedstock. The credit can be claimed for fuel derived from biomass resources, waste streams, renewable energy sources or gaseous carbon oxides. Beginning June 1, 2028, feedstocks must be domestic biomass only.
Nebraska has a 75-cent-per-gallon income tax credit for SAF sold and used in the state, beginning Jan. 1, 2027. The credit
applies to SAF reducing CI by at least 50%, with a supplementary credit of 1 cent for each percentage point better than 50%, capped at 50 cents. It excludes SAF derived from coprocessing and palm derivatives. This year, the legislature is considering removing a $500,000 annual limit.
Beginning July 1, 2024, Minnesota began offering a $1.50 tax credit for each gallon of SAF meeting a 50% CI reduction threshold, produced or blended in Minnesota, and used in aircraft departing from a Minnesota airport. The legislation excludes palm fatty acid distillates. Minnesota also offers a tax exemption for materials and supplies used in the construction or retrofitting of facilities located in the state to produce or blend SAF between June 2027 and July 2034.
The 2025 Minnesota legislature is considering increasing the incentive by 2 cents per gallon for each 1% CI reduction beyond 50%, capped at 50 cents per gallon (a max
of $2). The credit would also be expanded to include liquid fuel derived from gaseous carbon oxides, increase the credit limits and allow unused credits to remain available for allocation through 2035.
Washington’s $1-per-gallon tax credit on SAF goes into effect once one or more facilities are operating with a production capacity of at least 20 MMgy, and expires nine years later. The credit applies to SAF achieving a 50% CI reduction compared to conventional jet, and increases by 2 cents for each additional 1% CI reduction, to a maximum of $2 per gallon. The credit applies to SAF produced or blended within the state of Washington for flights departing the state. Washington accepts SAF that has been coprocessed.
New York is considering one proposal for a $1.25-per-gallon producer tax credit that would increase to $1.50 per gallon for SAF made with domestically produced corn or soybeans. A second proposal under con-
sideration by the legislature would peg the incentive at $1 per gallon, increasing by 2 cents for every 1% reduction below the 50% threshold, not to exceed $2 per gallon.
Michigan also has legislation to offer a $1-per-gallon tax credit for SAF that reduces life cycle emissions by at least 50% and is purchased in the state for departing flights. An additional 2-cent credit would be granted for each percent reduction greater than 50%, not to exceed $2.
Hawaii’s 2025 legislative session has two bills before it. One would mandate at least 10% SAF in intrastate airline flights by any commercial airline beginning in 2030 and increasing each year to 100% SAF in 2045. The bill calls for the state department of transportation to collaborate with other agencies and stakeholders to support the development of in-state SAF production, develop compliance procedures and incentives to promote SAF fuels, with an annual appropriation of $5 million. A second bill
in Hawaii would establish a SAF credit on income taxes amounting to $1 per gallon sold for distribution in the state that meets a 50% reduction threshold in greenhouse gas emissions compared to fossil fuel.
Arkansas legislators are considering an end user income tax credit equal to $1.09 per gallon of 100,000 gallons of SAF purchased, limited to 50% of the taxpayer’s income tax liability. For SAF producers, the bill offers an income tax credit equal to 30% of the cost of SAF production equipment up to $10 million for an investment over $2 billion and creating at least 75 new fulltime permanent jobs. The bill also provides a sales-and-use tax exemption on utilities used in SAF production. The bill defines SAF as jet fuel derived from wood biomass.
In early April, Wisconsin lawmakers announced they were seeking co-sponsors for proposed legislation that would create a $1.50-per-gallon production tax credit for sustainable aviation fuel. To qualify for the
credit, the SAF would need to be produced in Wisconsin and meet certain other conditions. This includes a requirement that at least 90% of the fuel be derived from synthetic, renewable and nonpetroleum sources, such as energy crops. In addition, the legislation requires eligible SAF feedstock to be produced in the U.S. If signed into law, the credit would take effect in 2028.
The Biden administration’s SAF goals and the passage of SAF credits in the 2021 Inflation Reduction Act precipitated the state-level incentives, which mirror the 50% CI reduction threshold set in the IRA. Those incentives add to the SAF pathways already approved to generate renewable identification number (RIN) credits under the Renewable Fuel Standard.
“Because SAF is so new, it’s going to take a great deal of policy support,” Bliley
says. “It’s important how all of these federal and state incentives stack up to help get a new fuel off the ground.” Asked whether the change in administrations will diminish SAF interest, Bliley responds: “These are important conversations happening not only here in the U.S., but there’s growing international appetite for SAF in places like Europe and Japan and other places. I think this continues. And I know a number of airlines continue to be heavily engaged, especially with the implementation of [the tax credits in the IRA under] 45Z.”
Details of the 45Z regulations and, indeed, the fate of the entire program itself, are in the hands of the Trump administration. The name itself is in flux, with the administration declaring the term “sustainable” will be replaced with the word “synthetic,” even though the fuels industry historically used the term for fuels made from coal or natural gas rather than petroleum.
“We don’t see a real change,” Bliley says. “It doesn’t change the way we view the market or the potential for ethanol for our producers.”
The potential for ethanol to contribute to carbon reduction is significant, Bliley says, citing the study, “A Strategic Roadmap for Decarbonizing the U.S. Ethanol Industry.” Released in September, the study was conducted by the Energy Futures Initiative Foundation, led by former DOE Secretary Ernest Moniz, lending credibility to the findings, Bliley says. “It emphasizes what we know already—ethanol’s ability to decarbonize. Just yield improvement can decarbonize ethanol by 6%, but we have the ability to drop carbon intensity by as much as 160%.”
Author: Susanne Retka Schill writer@bbiinternational.com
A new day is dawning for ethanol production. Our industr y-leading lineup of yeasts and yeast nutrition, plus our newly added Spar tec® enz ymes, are pushing the limits of fermentation and reaching levels of performance never achieved before. Paired with our renowned educational programs and expert ser vices, we’re setting a course for even greater yields and performance.
With LBDS, THE FUTURE OF FERMENTATION IS BRIGHT AND THE POSSIBILITIES ARE ENDLESS.
Veolia’s novel corrosion inhibitor makes it easy on ethanol producers by ensuring simple and reliable testing, and performance that significantly cuts traditional dosage rates.
By Katie Schroeder
Utilizing Veolia’s decades of expertise in petroleum fuel additives development, the company launched the Spec-AidTM BIO family of products; proprietary corrosion inhibitors specifically for the ethanol space.
Brad Thompson, subject matter expert – biofuels with Veolia, explains that corrosion inhibitors for ethanol are important to mitigate adverse effects on downstream assets such as tanks and pipelines. Because many inhibitors use brightly colored fluorescent tracers to measure concentration in the fuel, they can deteriorate, impacting testing accuracy. Thompson adds that those tracers’ strong
less at any dosage. Veolia’s tracer is also stable, so its fluorescence does not deteriorate while in storage. Thomspon explains that with other inhibitors, producers must conduct frequent standardization procedures to take into account tracer deterioration. The fluorescent tracer in Spec-Aid remains stable for many months; a quality that makes it easier for producers to run tests, ensure they do not overuse or underuse the treatment, and obtain optimal protection at minimum cost.
Veolia’s labs have the capability to test the corrosion protection performance of the inhibitor on producers’ systems, something they
“We provide maximum corrosion protection without them having to go to extraordinary lengths to re-standardize, to continually have to retest to ensure accuracy,” he says.
The Spec-Aid BIO’s impressive corrosion protection results mean it can halve the treatment dosage when compared to other corrosion inhibitors, explains Corwin. In addition, the product has pHe adjustment properties, helping raise ethanol’s pH within the required range without the need for supplemental additives. Spec-Aid’s stability, high performance and complete all-in-one formulation provides a unique solution for ethanol producers that seek simple, cost-effective and worry-free operation around their corrosion inhibitor pro-
Model E delivers dependable performance wherever ethanol analysis is needed.
By April Zamora
The Model E Ethanol Analyzer from WI Instruments, a CFR Engines Inc. brand, is revolutionizing ethanol analysis by delivering accuracy speed, and simplicity in one compact system. Designed for both ethanol and fuel laboratories, as well as the dynamic demands of terminals and pipelines, Model E brings advanced performance and compliance into every environment where ethanol quality matters.
While traditional gas chromatography is still a common choice, it has drawbacks, including extended analysis times, consumable use, and complex calibration routines. Model E replaces these hurdles with streamlined mid-infrared (mid-IR) spectroscopy, offering rapid, accurate readings and minimal maintenance. It eliminates the need for extensive cleanings and intensive sample prep, mak-
ing it easier for labs to improve throughput, reduce costs and maintain regulatory confidence.
Model E measures ethanol and methanol concentrations in conformance with ASTM D5845 and supports up to 100% ethanol and methanol purity, correlated with ASTM D5501. It features multi-analyte functionality, allowing one instrument to perform the work of many, enhancing lab and field efficiency.
Out in the field, Model E continues to perform. It provides on-the-go analysis of ethanol and denaturant concentrations for blending accuracy at terminals and pipelines, with an integrated density measurement compliant with ASTM D7777. Whether installed permanently or used as a portable device, it offers the flexibility operators need.
It also supports ASTM D7923, D6839, D6730 and D4815 for correlated contaminant detection, enabling consistent blend quality and actionable insights. Operators can quickly make informed adjustments and reduce variability between batches.
With a user-friendly interface and rugged design, Model E bridges the gap between lab-grade accuracy and field-ready practicality. Whether increasing speed in the lab or improving compliance in the field, Model E empowers teams to achieve more without sacrificing accuracy.
From precise lab work to fast-paced terminal operations, Model E delivers dependable performance wherever ethanol analysis is needed. It’s a comprehensive solution for professionals who demand accuracy, reliability and efficiency every step of the way.
Behind the scenes with IFF’s biofuel team and its work to bring new yeasts, yeast blends, AI and next-gen research to the ethanol industry.
By Luke Geiver
To bring any new commercial yeast, enzyme or additive product to the ethanol industry, IFF completes years of research across its global network of R&D facilities through a team of experienced scientists equipped with the newest tools modern technology has to offer, including selective breeding programs, genetic improvement capabilities, artificial intelligence and sometimes even robots.
The size of the actual yeast strains used in any given plant may be micrometers small, but the amount of time and resources that go into proving out and producing strains capable of helping ethanol producers operating in fluctuating market conditions is huge. In most cases, IFF’s line of yeasts can increase ethanol yields by up to 3%.
Beyond the extensive and expensive work performed behind the scenes, IFF’s biofuel team spends a significant amount of time with plant managers or lab personnel inside customers’ ethanol plants. Developing cutting-edge fermentation products that provide yield, speed, robustness or all three is an intense job that requires year-round attention, says Caroline Peres, principal scientist for IFF.
Peres has visited multiple ethanol plants in her 20-year career at IFF, sometimes for more than a month at a time. When on site, IFF scientists ensure all lab data matches real-world plant conditions. They track the viability of their yeast cells over time, comparing parameters in a plant’s lab and their own. “You get the whole package when you work with us,” Peres says. “It is amazing what we can do with ethanol.”
Peres leads the Fermentation Bioactives team at IFF and was crucial to the commercial success of IFF’s current trade-
marked synerxia Gemstone Collection of yeasts and yeast blends. The product line offers producers the option to use individual yeast strains or to combine different products in the same batch. According to Peres, her team was one of the first in the industry to embrace the idea of combining yeast strains instead of relying on a single option.
“It is nice to have a collection of yeast,” Peres says. “You always have the right yeast at the right time.” If corn is expensive, for example, a producer can swap out yeasts for a more favorable option that matches operational changes made because of market conditions.
When the team first brought the idea of yeast groupings, or collections, to the market, IFF had already conducted feasibility testing. “We had the small-scale data to show the results of individual yeasts versus yeast blends,” Peres says.
The customized approach to yeast blends has worked because it is hard to achieve desired numbers for rate, titer and
PRINCIPAL VIEW: Caroline Peres, principal scientist for IFF’s fermentation team, has helped usher in the company’s new strains and yeast combination options. PHOTO: IFF
robustness in a single batch. A single yeast can struggle to achieve all three, she says, because the conditions in modern fermentation can include high temperatures, stress from organic acids, the presence of dry solids and high ethanol titers.
Yeasts perform better together than apart, Peres says. A yeast combination can get a batch through a lot of scenarios. “We know the fast yeasts are going to go early and then the robust yeasts are going to produce more at the end,” she says. Because the IFF products are selected for robustness, the blends can endure and perform as they should despite the harsh operating conditions of fermentation.
Ethanol plants are diversifying in different ways to make different products, a factor the research team always has to consider. Even regional corn differences can change
the effectiveness of a yeast product, which is another reason Peres believes in the collection approach to yeast offerings. Plants today run their operations at different rates for different reasons. Some choose high yields over efficiency, while others need the right balance to maintain the kind of bottom line a board, investor group or leadership team requires, Peres says.
An advanced yeast breeding program helps the IFF research team find results or the “diamond in the rough,” says Larry Anthony, R&D technical manager for Grain Processing at IFF.
The yeast strain used by ethanol plants across the world is well-known, well-studied and has more than 6,000 genes, Anthony says.
“It’s very hard to tell looking at the genome which modifications are going to have an impact on the strain performance,” he says.
Strain performance testing, breeding and selection protocols help the team match customers’ needs with the abilities of each strain. Anthony believes there is still a long way to go in improving yeast strains for ethanol producers.
Most producers utilizing the synerxia Gemstone Collection now prefer to run a combination of products that allow them to “start fast and finish high.”
For many years, producers have been using IFF’s synerxia multi-generational yeasts alone or in combination. synerxiaJade is the fastest and suitable for maximum plant throughput, in part, for its ability to tolerate ethanol titer during fermentation. synerxia sapphire is IFF’s most robust yeast and like all IFF strains, provides glucoamylase expression. It is known for its ability to tolerate high heat and infection. For the highest yield yeast, synerxia ruby is robust and offers minimal byproducts. IFF
now provides its synerxia products to the U.S. and Brazil, as well as Argentina’s 185 MMgy ethanol industry.
Minimizing certain byproducts during fermentation is an important part of ethanol yield maximization. Peres is currently pushing her team to look at options that further reduce the production of glycerol or CO2, or that can better tolerate the presence of high glucose.
To optimize current yeast offerings or develop the next version, Peres and her team utilize advanced resources in labs across the world, insight from artificial intelligence, and yes, even robots.
Peres performs her research out of Palo Alto, California. Other team members work in Wilmington, Delaware. In the Midwest, a lab in Cedar Rapids, Iowa, helps clients directly in the heart of North
American ethanol production. The lab in the Netherlands is equipped with robotics.
To help clarify how modern technology helps leading-edge researchers, Peres says to think of a normal lab first. Within a normal lab setting, a single human researcher can only prepare one test plate containing only a handful of yeast colonies for review and testing. Using the robotic setup in the Netherlands, IFF’s team can easily screen 50 plates at once (each plate with roughly 96 yeast colonies). The system allows IFF to screen millions of colonies to find the best options for further research and development.
In addition to the mechanical technology, the team utilizes an array of screening conditions and growing techniques to bring new yeasts to market.
Bringing a new yeast product to market takes at least a year of research in the lab, Peres says. She is trying to bring different
projects throughout the greater IFF biofuels team together while also working with different scientists that may have new ideas about how to maximize the possibilities of greater yield potential and yeast robustness.
Peres knows she has her work cut out for her, given the breadth and type of solutions her team has already delivered to the industry. In addition to yeast products, IFF’s biofuels team provides innovative options for liquefaction, saccharification and fermentation and accessories. Optimash F200 and Optimash AX enzymatic solution for liquefaction helps to optimize corn-oil production while reducing the amount of oil lost to wet cake.
In its group of products for saccharification and fermentation solutions, IFF provides several options that increase yields
or speed up fermentation times. The trademarked distillase shortens fermentation times and increases yields through a precision blend of concentrated enzymes that produce glucose from liquefied starch. The trademarked Fermgen product also helps to deliver faster fermentation times by hydrolyzing proteins under low pH conditions. With its trademarked FermaSure, IFF can provide producers with a non-antibiotic option to attack and decrease harmful bacteria that occurs during fermentation.
Part of IFF’s success, in terms of both research and the commercial application of its products, stems from AI. Using its trademarked xCelis AI system, researchers can predict certain outcomes before they hap-
START WITH SACCHAROMYCES: The saccharomyces cerevisiae strain is typically used for fermentation in ethanol.
and her team hope to find new strains in the coming years.
pen. IFF calls it the “crystal ball,” helping producers make future decisions. Peres’ team uses the system as a complement to check on testing parameters and results.
At the plant level, IFF customers can use the system to ask questions. Given the right question, the AI platform will predict changes in operational performance, fermentation and more based on preestablished baselines. If a producer wants to know how changing a yeast or enzyme combination might impact fermentation results, the AI system—built on custom IFF software—can provide insight.
In one case study (unrelated to yeast deployment), xCelis AI was used to analyze the energy and economic differences of running front-end processes at two different temps, 185 degrees or 195 degrees Fahrenheit.
The AI analysis examined overall steam use, dryer natural gas use, mash cooler duty, liquefaction dry solids and economics. The analysis found that a higher temperature would result in increased beer feed temperatures. In conclusion, the AI answered, hotter liquefaction would ultimately draw more natural gas and mash cooler duty, thus reducing overall economics.
According to the IFF team, the xCelis AI digital platform used today was being developed or used well before the AI-race began.
IFF is currently working on its next line of yeasts using AI in combination with all of its other labs, technologies, robotics and most importantly, Peres says, its years of direct-from-the-plant know-how and insight. Although current yeast strains are very good, much of the focus will be on reducing side products, diversifying strains
and increasing rate. IFF has evolved xCelis AI to better understand the carbon intensity (CI) of its products and the impact on the ethanol plant to help customers meet their CI goals. The team’s work with natural and GMO options will only expand.
Inside IFF, the R&D trials are complex and include several stakeholders. The team hosts weekly review meetings of its work and findings to share ideas or note traits that could lead the researchers in the right direction.
As Peres says, bringing the next-best yeast lineup to the ethanol market won’t happen by a single effort. It will require a collection of tools, resources and researchers.
Author: Luke Geiver writer@bbiinternational.com
ICM discusses the importance of evaporators in plant efficiency and outlines strategies for success.
By ICM
The ethanol industry continues to evolve, with rapid advancements in energy optimization and oil recovery. Emerging opportunities such as carbon sequestration, methanol production and sustainable aviation fuel (SAF) are reshaping the market. Capitalizing on innovation grants ethanol producers a way to future proof their facilities, strengthen operations and maintain a competitive edge.
Energy efficiency and oil recovery are two of the biggest drivers of ethanol plant profitability, yet many facilities may be missing opportunities. This raises a critical question: Are current operational choices maximizing performance, or are hidden inefficiencies quietly eroding margins?
One often underestimated factor in plant efficiency is water balance. Many ethanol plants that struggled financially did so not because of fluctuating corn prices or regulatory changes, but due to poor water management. When excess water cannot be efficiently removed, plants face increased costs in transportation, drying and overall energy consumption, directly impacting their bottom line.
Water management is directly linked to energy efficiency, and evaporator performance plays a central role in making ethanol production more efficient. Every stage of the process, from fermentation to distillation, depends on effective evaporation to separate water from valuable co-products. If evaporators are not optimized, plants experience increased energy consumption and higher operating costs.
When evaporation is inefficient, more water continues downstream either to dryers or into syrup production. While dryers serve
an important role in ethanol plants, particularly when production exceeds wet cake market capacity, they typically require more energy to operate.
To reduce energy waste, plants can implement different strategies such as improving heat transfer efficiency, enhancing recirculation rates and maintaining proper viscosity control. Poor heat transfer and scaling within evaporators create inefficiencies that force the system to work harder, consuming more energy than necessary. By addressing these inefficiencies early, ethanol producers can reduce the burden on post-evaporation processes, limit low-value syrup sales and support more stable, energy-efficient operations.
A combination of strategies significantly improve evaporation performance. Multieffect evaporators enhance heat transfer efficiency by using energy from one evaporator stage to drive the next, significantly reducing energy consumption.
Viscosity management is equally critical, as higher viscosity reduces heat transfer efficiency and disrupts recirculation rates. Removing suspended solids from thin stillage before evaporation plays an important role in controlling viscosity. Reducing viscosity improves circulation and decreases energy demand, allowing more centrate to reach boiling temperature and facilitating greater water removal.
Effective recirculation management further enhances system performance by preventing scaling. Reduction of scaling minimizes unplanned downtime, maintains evaporator efficiency and ensures continuous operation.
Oil recovery is another critical factor directly tied to evaporator performance. When evaporators operate efficiently and with suffi-
cient capacity, plants can send more decanter centrate to the evaporators, rather than relying solely on backset recycling. This helps maintain oil availability throughout the process and improves the likelihood of getting more oil to the recovery system, rather than losing it in the wet cake.
Beyond evaporator optimization, ethanol plants can further improve oil recovery by implementing the right separation strategies. These include increasing decanter efficiency and using multi-pass oil recovery methods to minimize losses, enhance oil separation efficiency and maximize overall yield.
The next phase of ethanol plant optimization revolves around reducing energy consumption and improving oil recovery, both of which are closely tied to evaporation performance. The cost of inefficiencies is too high to ignore and plants that invest in proven technologies will gain a competitive edge.
ICM offers a range of proprietary and patented solutions designed to help ethanol producers maximize efficiency. Multi-effect evaporators enhance heat transfer and reduce energy costs, while Selective Milling Technology™ optimizes particle size for improved downstream separation. The Thin Stillage Solids Separation System™ boosts evaporator performance, viscosity control and recirculation by removing suspended solids before evaporation. FOT Oil Recovery™ improves yield through a multi-step separation process that minimizes oil loss in the decanter cake and increases the amount available for recovery.
The ethanol industry is advancing, and those who invest in strategic improvements will position themselves for long-term success. As market demands evolve, continuous innovation will be essential for enhancing operational performance and profitability.
Seventy years after its founding by Raphael Katzen, the company that bears his name remains committed to his core tenets: integrity, objectivity and excellence.
Robert Eickelberger, Katzen’s vice president business development, explains that the company’s founder was a pioneer in the ethanol space.
A chemical process design, engineering and consulting firm, most of the company’s work over the last 35 years has been ethanolrelated. “We have vast experience in many biochemicals and some of this [experience] helped us become who we are now,” Eickelberger says.
David Lococo, president and CEO of Katzen, has been with the company for over 30 years. He aims to build on the foundation of customized process design, close client partnerships and industry collaboration. “Dr. Katzen created a remarkably resilient business model, and my goal is to preserve that foundation while expanding our capabilities so that we can deliver to the
industry more effectively into the future,” he says. “We have a strong vision of biotechnology being a key driver for the sustainability of our planet.”
Katzen began his career developing processes for paper pulp production and acid hydrolysis processes to convert biomass into useful products like plastics and biochemicals. During World War II, he led the team that designed and started the United States’ first commercial-scale cellulosic ethanol plant that converted wood waste into ethanol.
In 1954, Katzen expanded the sole proprietorship he founded the year before, bringing on additional consultants to meet grow-
Katzen’s long legacy of process design prowess and innovation informs its present as the company moves forward, continuously improving ethanol plants worldwide.
By Katie Schroeder
ing demand. The business was incorporated the following year as Raphael Katzen Associates International Inc. (RKAII)—later shortened to Katzen. The company developed and introduced a myriad of technologies still used in the ethanol industry today. In the 1980s, RKAII designed the first simultaneous saccharification fermentation (SSF) system, which later became the industry
standard for batch fermentation. The company also brought high-temperature jet cooking to commercial ethanol production and implemented the first commercial molecular sieve dehydration technology, just to name a few.
The SSF process was first implemented at South Point Ethanol in South Point, Ohio, in 1980. Eickelberger explains that, at the time, the 60 MMgy South Point plant was the world’s largest known motor fuel-grade ethanol facility.
High-temperature cooking was a breakthrough for ethanol producers’ yields, explains Ethan Campbell, lead process engineer with Katzen. The process allowed more starch conversion by keeping the temperature high enough that bacteria, which would consume
the sugars instead of the yeast, were unable to survive.
Vice President Business Development Katzen
The design recovers some of the energy used to achieve those high temps by flash cooling the slurry. According to Campbell, killing the bacteria without antibiotics was vital for Katzen’s European market, where the use of antibiotics in ethanol production is strictly regulated.
As biotechnology has progressed, yeast and enzymes are able to achieve even higher levels of conversion efficiency. In response, Katzen engineers adapted their process designs to capitalize on these enhanced biological capabilities. “We had to make substantial adjustments,” Campbell explains. “The available steam pressure was significantly lower than we typically design for, which ruled out high-temperature cooking as an option. This challenge drove a complete rethinking of our
plant-wide energy integration strategy and led us to develop an entirely new low-temperature cooking process.”
The company takes a vendor agnostic approach, working with whichever enzyme supplier the client prefers. With the help of enzyme providers, Katzen engineers tailor a unique enzyme and yeast combination system optimized to fit the producer’s specific feedstock. Campbell explains that this collaboration “gives our clients the best opportunity for
• Conf ined space rescue
• Dr y ice blasting
• Hydroblasting
• Hydro reclamation
• Indus trial vacuuming
• Restoration
• Sandblas ting
• Slurr y blasting
• Spongeblasting
• Surface chemical cleaning
Tube bundle and heat exchan ger cleaning
commercial success.” Katzen’s design precisely controls cook temperatures to provide an optimal environment for enzymes to do their work.
On-site logistics and customer input differentiate Katzen’s plant designs from other engineering firms, explains Campbell. The company takes a custom approach, working closely with the plant owners on decisionmaking to determine process specifications and select vendors. “We have a good understanding from beginning to end what the customer sensitivities are, site logistics that guide the way that we layout our equipment—it guides the way that we design our control schemes,” Campbell says. “Some things that we add into our designs on paper, the mass and energy balance is completely unaffected. But we know that having this extra line here or having these valves arranged in a different way makes it way easier to start up [or shut down].”
Katzen’s engineers take an inquisitive approach when starting a project, seeking to understand their customers’ goals. “We’re always asking questions about … their project drivers and how we can customize a design to their specific location, their specific needs and to give them a competitive advantage,” he says.
Seeking to give their clients a bespoke ethanol facility makes each Katzen designed facility unique in its own way. “It’s never a cookie cutter design,” Campbell says. “Our designs are continually adapted to accommodate different feedstocks, climates, plant logistics and utilities constraints around the world. Because the same people doing the design work in Cincinnati often travel to the plant site overseeing construction and startup, we are able to see operator pain points first-hand and implement those insights in future projects.”
Campbell emphasizes Katzen’s commitment to honest and fair estimates of process yields. Ethanol plants will not produce their highest volume with new operators, he explains. Because of this, the company gives
customers a modest estimate for the plant’s production capability, ensuring that the number given can be achieved on day one. As the operators become more experienced, Campbell expects the facility’s yield could increase by 15% and energy usage reduce by around 10% to 15%. “We don’t want to over promise and under deliver; we would rather somebody go in eyes wide open,” he says.
The company’s Lean team enables a close relationship with customers throughout the design process. “We are a group of lifelong learners and teachers—that’s how we view ourselves,” Eickelberger says. “We learn through research and industry relationships, literature and our empirical experience.” Often the same people who meet with a client for sales discussions and initial introductions will also be there sharing champagne to celebrate the plant’s completion. Katzen’s staff makeup demonstrates its dedication to process engineering—about 60% are engineers, 25% handle business operations and the remaining 15% provide technical support. Lococo plans to add staff to the team to maximize the company’s ability to simultaneously handle more projects, while preserving the work-life balance of its engineers.
Katzen uses innovation to help producers access new markets, empowering them to maximize their competitive edge. The company’s Very High Quality (VHQ) distillation system enables ethanol producers to diversify by producing an ultra-pure true neutral spirit.
The first full VHQ system was installed at Golden Triangle Energy in Craig, Missouri, in 2007. Since then, it has been installed in 11 facilities worldwide. VHQ produces a true neutral spirit with less than one part per million of impurities and no detectable organoleptic properties. Because the alcohol produced has no smell or flavor, it has buyers from a variety of industries, including food and beverage, pharmaceuticals, personal care, cosmetics and more. One use for VHQ’s alcohol is as an additive for wine companies that need to increase their beverages’ alcohol content.
The system can also be dialed in for production of pharmaceutical-grade alcohol, which can be sold as an ingredient in cosmetics, solvents, printing inks and more.
Campbell explains that VHQ distillation can be implemented as either a bolt-on addition or integrated system, enabling the production of super high-quality alcohol alongside fuel-grade alcohol. The feed is an intermediate stream from the fuel ethanol process, and the congener draws are recycled into the fuel-
grade product. The system can also be tuned to produce various specifications of potable and industrial alcohols.
Lococo says Katzen did not participate much in the U.S. ethanol boom in the 2000s. “The U.S. market at the time prioritized speed, uniformity and zero perceived risk,” he says. “Producers wanted the plants built fast, identical to one another, and with minimal custom-
ization. That copy-and-paste model was just not our forte.”
Europe’s ethanol boom was happening at a similar time, and Katzen’s customized approach fit that market’s needs well. According to Lococo, the company provided the process technology for around half the plants that make up Europe’s ethanol industry. Designing facilities in Europe gave the company experience adapting to new and different challenges
around the world, such as different code requirements, feedstocks and grades of alcohol.
Experience and knowledge gained in the European market furthered Katzen’s worldwide exposure and evolved into designing projects in over 40 countries around the world, including Australia, Vietnam, China, Brazil, Canada and more. The company’s engineers are always looking for ways to continuously improve, explains Eickelberger, adding Katzen has enhanced plants with its own designs, as well as those designed by other process engineering firms. One such expansion during 2024 at an Inpasa Agroindustrial facility located in Sinop, Mato Grosso, Brazil, resulted in the creation of the world’s largest grain-based dry mill ethanol plant with a yield of 550 MMgy.
Lococo and his team continue pursuing new ways to help the ethanol industry move forward. Technologies such as chemical up-
grading, which Campbell and Lococo call “ethanol-to-x,” could turn fuel-grade ethanol into sustainable aviation fuel or even convert CO2 into methanol. Lococo is enthusiastic about these new innovations and revenue streams, but explains that Katzen wants to assess the commercial viability of these technologies before committing to implementation.
“We will continue to develop those technologies as they come along, but we’re not in the business of promoting a non-commercially viable technology,” he says. “We’re happy to work with partners who want to explore or do independent testing. But we’re also truth tellers in the industry. We don’t want to see failures. It’s not good for the industry as a whole. It’s not good for our clients and it’s not good for Katzen to have a technological failure.” Instead, the company wants to partner with innovators that possess pathways with a high likelihood for financial success, helping them move toward commercial viability, Lococo explains.
This tenet of careful development comes from Katzen himself, according to Lococo. While the company is not afraid to engage with and advance new technologies, doing it responsibly is paramount. “We’ve always operated under the premise that proven technology should be the foundation for advancing new ideas. We never take a risk without making sure our clients fully understand the challenges associated with … some aspect of the project,” he says. “And generally, we work closely with them to mitigate those risks— whether through lab testing, pilot trials or other validation processes.”
Another encouraging trend that Lococo recognizes is the shift toward more sustainable processes and advanced biotechnology. Katzen sees greater interest in driving energy usage down and increasing efficiency. Lococo points out that energy usage in the U.S. ethanol industry back in the 1980s was double the energy per gallon used at European ethanol plants in the 2000s, and that figure has halved
again over the last 20 years. “It’s amazing,” he continues. “I mean, it’s really quite an advancement.”
Keeping pace with the industry’s advancement demands a workforce capable of engaging with a growing number of producers. For Lococo, investing in the ethanol industry’s future means investing in the next generation. “We are excited for the future,” he says. “We’re excited about the technology, focused on growth, and we’re investing heavily in our people to make our business model sustainable. We think we have a really good approach to technology development and engineering that’s delivered results around the world. And I want that legacy to continue.”
Author: Katie Schroeder katie.schroeder@bbiinternational.com
• 165’ Diameter Bins (up to 2.25 Mil. Bu.)
• Up to 21’ Peak Decks & 150K lbs. Rating
• Patented Double-End Stud Bol ts
• Patented Laminated Splice Plates
• Tower Dryers (up to 12K BPH)
• QuadraTouch Pro TM Controls
• Remote Web Access
• Balanced Moisture Content
• Paddle Sweeps
• Capacities up to 12K BPH
• Patented Pivot Point
• Industrial Grade Pushers
SCAN HERE TO FIND YOUR LOCAL SUKUP DEALER
Whitefox Technologies is advancing ethanol distillation, dehydration and evaporation (DD&E) by replacing molecular sieves with membrane technology, achieving up to 50% reductions in both energy and water consumption in the most energy-intensive plant operation.
As ethanol producers seek new efficiencies and lower carbon intensity scores, operational strategies are evolving. Beyond incremental process optimizations, plants are investing in infrastructure capable of supporting long-term decarbonization and readiness to navigate regulatory change. Western Plains Energy identified Whitefox ICE® XL as a key asset in its Net Zero strategy. Commissioned in October 2024, this system delivers substantial operational efficiencies and resource savings.
“This project is probably the largest step change you can make in energy, period,” said Western Plains CEO Derek Peine. “We set the goal to become a Net Zero carbon intensity fuel supplier. We’re on the path and this project is helping us get there.”
The ICE XL system introduces two core improvements:
• Membrane-based dehydration, replacing molecular sieves for immediate efficiency gains
• Reengineered DD&E energy management, leveraging proprietary heat integration to further reduce energy demand
Whitefox’s initial product for the U.S. ethanol market, the Whitefox ICE system, integrates a membrane unit alongside existing molecular sieves as a bolt-on debottlenecking solution. The system processes regen streams without pressure fluctuations or reflux loops, improving process stability and uptime. Its broad operating range accommodates streams with up to 50% moisture, while proprietary heat recovery reintegrates latent energy from the ICE system, reducing thermal loads and cutting natural gas consumption by 10–15%.
The Whitefox ICE XL removes molecular sieves entirely, enabling a new energy optimization model for ethanol downstream processing.
“The way that the traditional DD&E system was designed was the best way to go about it with the molecular sieve incorporated,” said Jeff Scharping, Commercial Director at Whitefox. “However, once you swap in the membrane, it changes the variables you use to design the system, changing the energy equation, and allowing it to use the energy more times throughout, ultimately delivering a 50% reduction in natural gas consumption.”
By starting with energy optimization that doesn’t increase electrical load, it allows producers to broaden their strategies to include additional technologies, such as Mechanical Vapor Recompression (MVR), as they continue on the path towards Net Zero. In addition, the Whitefox ICE XL reduces cooling water demand by 50%, addressing limitations in water-scarce regions and facilities constrained by cooling tower capacity.
“This project helped us not only have a sustainable future for the bottom line, but also be able to use fewer natural resources,” said Rick Holaday, Western Plains Plant Manager.
As ethanol producers pursue carbon reduction strategies and operational resilience, early adopters like Western Plains demonstrate how infrastructure investments can deliver immediate resource savings while positioning plants for long-term regulatory and market shifts.
“At Whitefox, we appreciate the challenge that ethanol producers take on as they look towards the next 25 years,” said Whitefox CEO Gillian Harrison. “We are doing the same as we celebrate our 25th anniversary in 2025. Regardless of market in-
fluences, one thing we can bet safely on is the value in reducing operating costs and scaling back reliance on natural resources. Helping industry to do that, plant by plant, is how we achieve our mission to produce more with less.”
By the end of 2025, membranes will be operational in 16 North American plants, with several sites demonstrating membrane lifespans exceeding four years under continuous operation. For technical specifications and project inquiries, visit Whitefox.com or email solutions@whitefox.com.
Despite its geographical location and forward-thinking approach toward trying new tech, Aemetis Inc. believes its story can be central to the future of biofuels.
By Luke Geiver
Aemetis Inc. has always known how to operate on the edge. From its Keyes ethanol plant in California’s Central Valley well outside traditional U.S. ethanol country, to its non-stop efforts to install, upgrade or test cutting-edge technologies across its renewable energy portfolio, Aemetis has proven how comfortable it is with navigating unique challenges. For the company’s leadership team, that also includes figuring out how to capitalize on or keep up with California’s one-of-one policy and regulatory framework designed to prioritize low-carbon energy through the state’s Low Carbon Fuel Standard (LCFS). In February this year, the company announced it had surpassed $2 billion in revenue from the Keyes plant, operating since 2011. In a state with hot and dry weather conditions most of the year, along with a regulatory system that ties the value of every ounce or watt of energy produced and consumed to an intricate carbon calculation scheme, Eric McAfee, Aemetis CEO, believes he knows why his team has thrived on the edge from day one.
“I think that the core of our success is in our understanding of the regulatory environment here, and knowing that we always have opportunities to keep innovating to improve production and economics across our business.”
Andy Foster, president of Aemetis North Americas, is always busy with new innovations, he says, because the company is focused on thinking ahead. Foster has led the tech upgrades and expansion work for Aemetis at the plant, the company’s growth into dairy renewable natural gas production, working to create a carbon capture and sequestration system through injection wells, and also the recent permitting of a SAF and renewable diesel facility.
CORE OF SUCCESS: Aemetis Inc. stays on the cusp of innovation through constant improvement projects and its skill in navigating policies, such as California's LCFS.
PHOTO: AEMETIS
The 65 million-gallon-per-year corn ethanol plant delivers wet distillers grains to more than 80 California dairy operations. Corn oil is made for animal feed or as feedstock for renewable fuels. Through his work with Aemetis RNG, Foster has established a dairy and biogas capture network that could soon make Aemetis one of the largest producers of dairy RNG.
Even when he laughs about being busy, he doesn’t laugh for long. In the past few years, the Aemetis team has performed several efficiency upgrades in Keyes. In 2023, the team shut down the plant to perform the most extensive upgrades since purchasing the facility in 2011. Upgrades have included everything from converting to electric ethanol dehydration to adding more than 1,100 sensors.
Working with PG&E through a special program designed to incorporate modern, energy-efficient tech, the plant has been analyzed inch by inch, Foster says. The team has added variable speed drives, energy-efficient pumps, and electrified anything possible, all the way down to changing out light bulbs. Foster says the plant’s financial operations depend on a constant push to be more efficient and to work within the framework of the state. In 2023, the plant added high-effi-
ciency heat exchangers and, in 2024, a solar microgrid with battery storage.
“On average, we pay about 50 % more in natural gas costs than most of our Midwest peers,” Foster says. “We just pay a lot higher utility rates in California.”
To combat the high costs incurred through the plant’s cooling towers running during high external temp conditions, Aemetis installed a solar microgrid system. The main purpose of the system is to capture energy and store it for later use. According to Foster, temps in the Central Valley can regularly reach and stay at 110 degrees Fahrenheit. During the peak hours of the day when pulling power off the grid is most expensive, the plant uses roughly 2 MW of solar-generated power stored in on-site batteries. The stored power helps to run the fans on the cooling towers when the plant is load shedding, which helps the plant avoid peak power rates during high-usage times.
Solar panels situated above large storm water storage ponds and parking areas provide low-carbon electricity that is integrated with a distributed control system equipped with artificial intelligence. Through a grant from the California Energy Commission, Aemetis was able to install an entirely new Allen-Bradley distributed control system sys-
tem that can switch the power sources for the plant back and forth throughout the day.
The next big project at Aemetis will involve mechanical vapor recompression (MVR), a process that replaces steam boilers with electrical compressors that can reuse vapors generated during evaporation. MVR systems are starting to appear across the ethanol industry, and Foster and his team are excited to add the energy efficiency and carbon reduction system to its operation.
Foster plans to link AI with the MVR once the unit is up and running next year. “We’ll go from big natural gas boilers to using efficient electric turbo fans,” he says. “The design will give us an opportunity to preprogram a lot of the parameters of how the plant operates.”
Praj Industries is designing the MVR and fabricating a good portion of the build. Piller, a commercial fan and compressor provider from Germany, will supply the fans.
Outside the confines of the plant, Foster is also overseeing the construction of a carbon capture well that, once complete, could store 1.4 million tons of CO2 7,000 feet below ground in a saline formation. A characterization well is already under construction and will form the basis for the Class VI well permit required by the EPA. Aemetis is cur-
rently working to line up additional CO2 customers as the CO2 volumes from the plant and the RNG production sites that will be connected to the well won’t fully use its annual capacity. Foster is always busy.
Baker Hughes, an oil and gas drilling company, is leading the underground engineering and drilling work, including consultation and project design. ATSI, an EPC and project management firm, is helping on the project as well.
McAfee and team are also continuing work on the renewable diesel and sustainable aviation fuel project they began circa 2021 by buying a former 125-acre Army ammunition plant. To date, the company has completed an Environmental Impact Report, obtained California Environmental Quality Act permits and received the Authority To Construct air permit. The design plan for the future plant is to utilize nonedible oils as feedstock, ranging from distillers corn oil to used cooking oil. At the plant, Foster says the design produces renewable SAF, propane, naphtha, and hydrogen.
At the Keyes plant, the team has also explored alternative feedstock options. Because the plant is surrounded by orchards, the team is continually looking at utilizing orchard debris or almond-based biomass as a feedstock, explains Foster.
“If there is a way to take orchard wood and turn it into ethanol, you better believe we are going to do it.”
Our team of experts have over 20 years of ethanol plant maintenance expertise. We o er full service and parts for all Fluid Quip equipment to ensure peak performance.
• OEM Parts Warehouse
•$2 million+ inventory on-hand
•Factory Trained & Certified Techs
•MZSA™ Screens
•Paddle Screens
•Grind Mills
•Centrifuges
•Gap Adjusters
Foster believes that Aemetis’ willingness to evaluate, assess and regularly adopt cutting-edge tech or new operational processes is, in part, linked to the physical location of the plant. “We’ve lived near Silicon Valley for a long time and the culture here encourages that innovation,” he says
The state’s unique LCFS and other regulatory frameworks also mean the team has to monetize anything and everything it can. Sometimes that includes adding more projects or products, or running existing operations more smoothly.
“We are ever vigilant in lowering the CI score,” he says.
As the chief visionary behind Aemetis’ evolution, McAfee never shies away from learning about new tech. According to Foster, he’s been in thousands of meetings over the years with McAfee and tech providers pitching or educating their team about the newest offerings.
Aemetis runs several pilot programs and tests at the Keyes facility. When a company approached Aemetis about testing out radio-frequency identification (RFID) sensors to detect vibrations on pumps and other equipment throughout the plant, Foster agreed. Today, the Keyes plant still uses the technology to help with preventative maintenance. A different company trying to develop a new coating for the inside of tanks has also worked with Aemetis. Many of the tests don’t pan out, but that doesn’t stop the team from keeping an open mind.
“We really try to be early adopters,” Foster says.
Both Foster and McAfee can talk at length on biofuel technology. And the same can be said of biofuel policy and regulatory issues at both state and federal levels. Through March of this year, McAfee had already traveled to D.C. multiple times. And Foster and McAfee are both active in the state’s policies on biofuels, carbon and most recently, E15. California is the only state left that hasn’t allowed the adoption of E15.
“If we adopt E15 in California, it’s major news for the entire ethanol industry,” McAfee says.
The 600 million-gallon increase in the size of the ethanol market by adopting E15 in California is significantly larger than the annual production at Keyes, he adds.
The Aemetis team dedicates significant time speaking with members of the state legislature, in part because of term limits. There are always new people to educate. McAfee focuses on informing state agencies such as CARB about the impact of their policies, as well as meeting with Gov. Gavin Newsom.
“Our job is to bring them the message of how these policies work in the real world,” McAfee says.
The Aemetis CEO believes the current administration has a significant opportunity to put America in a leading place for energy generation, biofuels and more, starting by administering the 45Z tax credit. Aemetis’ MVR project shows the impact of such policy on biofuel producers working to expand domestic energy production and reduce their CI score. The MVR would reduce the CI score at Keyes by roughly 15 points and improve the plant’s cash flow by an estimated $0.50 per gallon, the company projects, or roughly $32 million per year.
LCFS credits are expected to increase over time, the company believes. The MVR, through the generation of LCFS credits, could increase revenues at the plant by another 10 cents per gallon. Changes to the LCFS program, which were approved last November, should be adopted in 2025, which will help as the program requires more carbon-intensity reductions for producers that participate and supply energy into the program. Such a change could reduce the supply of LCFS credits on the market and reward those that invest heavily in CI-reduction tech. Should LCFS credits reach $150 per metric ton, Aemetis estimates it could generate another $12 million per year from the addition of its MVR system.
Installing or continuing on with E15 mandates, LCFS revisions, the 45Z (incen-
tivizes new fuel with low CI) or 45Q (incentivizes carbon capture and sequestration) tax credits isn’t just about revenue generation— it’s also about access to markets.
Through a greater opportunity to access more markets or maybe just more of the markets it already serves, the ethanol industry can help the country unleash its energy dominance, McAfee states.
Investments should come to the renewable energy sector, including ethanol production, Foster adds.
“Now is the time to be aggressive. This is an American-made industry,” Foster says. “Of any industry that you can point to that has grown from the ground up, this industry really touches all parts of the economy.”
Both Foster and McAfee agree with the idea that their work at Aemetis is often on the edge—in location, through new strategies, and as reflected in their willingness to adopt or try new technologies. They may not always have a blueprint to follow in their new ventures, but they can talk with the
greater biofuels industry to share ideas or go over options. In today’s industry, everyone talks and shares insights. They believe that right now the Aemetis story isn’t just about them and their unique and ever-expanding operations in California’s Central Valley. The ethanol industry can be a continued success story if the policies are kept or put in place to help it grow—no matter where the biofuel is produced in the U.S. The real takeaway from what they are doing, from what the entire ethanol and renewables industry is or can do in the future, they agree, is actually central to unleashing American energy dominance.
Author: Luke Geiver writer@bbiinternational.com
Trucent provides practical strategies for optimizing corn oil recovery and quality.
By Chris Clausen
Distillers corn oil (DCO) is a valuable coproduct and strategic revenue stream for ethanol producers. Because it is often the highest value product per pound, optimizing oil yield is essential to profitability. Recovery rates vary from plant to plant, even when operating similar equipment. The difference often lies—not in a single fix—but in the many best practices that affect the whole DCO separation process.
Drawing on over 17 years of fieldwork with ethanol producers, the technical team at Trucent has identified four best practices that result in higher yields, better oil quality and more consistent DCO recovery.
The single best practice that a plant can implement is comprehensive testing, trending and analysis of trends. Having a broader picture of the oil content and concentration beyond just inlet and outlet streams empowers operations with valuable knowledge. Oil levels can be mapped from raw corn intake through to the back end of the plant. Tracking establishes a baseline oil expectation at various points in the process. Operators can then check against baseline when a new batch of corn enters the plant, new enzymes are trialed, different chemical
additions are used, de-emulsifier dosages are changed, or during any process upset. Routine mapping of the oil can show operators where little adjustments can make meaningful improvements to yield and quality.
The best practice is for producers to routinely sample, test, trend and analyze the results of oil content in raw corn, whole stillage and thin stillage. Plants should also perform routine mapping along with daily testing, trends, and analysis of oil concentration, solids by volume, emulsion and free oil concentration, and moisture of the centrifuge feed. This should be done before, during and after any pre-treatment and chemical additions, heavy phase, light phase and finished oil.
Stokes’ Law, which governs centrifugal separation, highlights two key variables: oil droplet size and viscosity. Increasing droplet size significantly speeds up separation. De-emulsifier chemicals are used to enlarge droplets and perform best under specific temperature and time conditions. Adding a hold tank after dosing allows control over the chemical reaction time. To determine the necessary retention time, dose several feed samples with the same de-emulsifier and concentration. Spin one sample im-
mediately in the lab centrifuge and keep the rest in a water bath at process temperature. Spin additional samples at 15, 30 and 45-minute intervals, comparing the oil layer volume. Regularly performing these tests with different de-emulsifiers and dosages optimizes results.
The best practice is to dose the deemulsifier to the centrifuge feed at a point allowing maximum retention time. If possible, install a hold tank for additional retention. Perform benchtop tests with various de-emulsifiers, dosages and hold times to find the best combination. Repeat these tests each season and when new corn crops are processed. If DCO yield drops, check the hold tank for an oil layer and keep it gently mixed. A “smart” dosing system that adjusts dosage rates to match process flow can maintain efficiency and reduce chemical usage.
Whether horizontal or vertical, a clean centrifuge is more efficient. As a centrifuge becomes dirty, the fluid dynamics in the bowl or scroll are disrupted. This not only decreases separation efficiency but can lead to unplanned and costly downtime, due to high vibration, damage and quicker bowl/ scroll erosion. Whether it’s a dip in yield or
CONTRIBUTION: The claims and statements made in this article belong exclusively to the author(s) and do not necessarily reflect the views of Ethanol Producer Magazine or its advertisers. All questions pertaining to this article should be directed to the author(s).
efficiency, or a sound that just isn’t normal, running a process condensate or caustic clean-in-place (CIP) cycle is often the best first step when an operator notices something out of the ordinary. Make a habit of listening to the centrifuge (including vertical centrifuge discharges). Establishing a baseline of how the centrifuge system normally sounds allows operators to quickly understand when something sounds off. Ensure CIP effectiveness by checking the light phase (DCO) flow rate after cleaning. Increased flow indicates better separation. If flow meters are unavailable, use a bucket test, though it’s less accurate. During planned maintenance, inspect for solid material, erosion or discoloration. In horizontal centrifuges, check for solids buildup in the feed area and scroll. In vertical centrifuges, inspect the underside and edges of discs for buildup and cracking. Ineffective CIP is often due to inadequate rinsing or dirty, cold or weak caustic solutions.
In this scenario, the best practice is to follow recommended CIP schedules but also listen to the centrifuge and run a CIP cycle if there is an abnormal sound or efficiency drop. Ensure CIP cycles are effective by monitoring performance before and after CIP and inspecting during planned maintenance. Dirty caustic can lower cleaning effectiveness and cause damage. Caustic cleanup systems, like Trucent’s TruCIP, help maintain clean and consistent caustic solutions.
It is crucial to focus on the ultimate goal: capturing all the free oil. If the oil isn't on spec, there are options to address it. However, if the oil is missed; it's gone for good. It is better to take a dirty cut at the centrifuge than to send oil to the dryers. If the raw oil is high in solids or moisture, a decant system like the Trucent Oil Concentration System (TOCS) can be used to precisely dial the oil properties to the
specification. If oil is sold for renewable fuels, other specifications may need to be considered, and further refinement may be needed. To detect oil loss, test heavy phase and de-oiled syrup samples, microscopically. If oil is present in the heavy phase, adjust the centrifuge. If oil is in the de-oiled syrup but not the heavy phase, troubleshoot for bypassed flow or oil in the solids phase. Check for leaking or improper valve positions and review centrifuge pre-treatment, feed rate, discharge times and volume, or scroll torque and differential speed.
Best practice is to remember that separating dirty raw oil is better than losing free oil. Regular heavy phase and de-oiled syrup samples should be inspected for oil. Dirty raw DCO can be brought into specification with some additional equipment and steps.
Author: Christopher Clausen Director of Technology, Trucent cclausen@trucent.com
Here is what you need to know about third-party verification.
By Danielle Anderson & Kari Buttenhoff
The 45Z Clean Fuel Production Tax Credit presents renewable fuel producers with a valuable opportunity to capitalize on their low-carbon fuel production while incentivizing further reductions in carbon intensity (CI).
Recent guidance issued in January 2025 by the Internal Revenue Service and the United States Department of Agriculture outlines the compliance requirements for
claiming and maximizing the credit, highlighting the critical role of third-party verification to ensure accuracy and traceability. Additionally, the guidance provides pathways for producers to increase their credit value through further reductions in carbon intensity.
This article unpacks the verification requirements based on the IRS guidance for transportation fuel and the USDA’s Climate-Smart Agriculture (CSA) program as they relate to the 45Z tax credit.
For transportation fuels other than sustainable aviation fuel (SAF), third-party verification is not required to claim the 45Z tax credit. However, voluntary market demands—such as buyers requiring assurance under transferability provisions—may lead producers to seek verification.
For non-SAF fuels utilizing the 45ZCFGREET model, a Safe Harbor provision is
CONTRIBUTION: The claims and statements made in this article belong exclusively to the author(s) and do not necessarily reflect the views of Ethanol Producer Magazine or its advertisers. All questions pertaining to this article should be directed to the author(s).
available for those claimants who choose to substantiate their emissions rates. To qualify for this provision, taxpayers must provide the certifier with all inputs into the 45ZCFGREET model, along with the specific fuel type and category from the applicable emissions rate table and supporting data consistent with SAF certification requirements.
For SAF claimants, third-party certification is mandatory. The IRS requires certification from an independent, qualified certifier to ensure compliance, traceability and accurate lifecycle greenhouse gas (GHG) emissions assessments. The SAF certification process includes:
Production and Sales Statements:
• A statement confirming the accuracy of the SAF production process and inputs used to determine lifecycle GHG emissions.
• Verification of the number of SAF gallons sold in a qualifying sale.
Conflict of Interest Declarations:
• The certifier must confirm they have no financial interest in the value of the 45Z credit, no involvement in SAF transactions and no familial or employment ties to the taxpayer.
Qualified Certifier Statement:
• This includes the certifier’s name, contact information, qualifications and a description of their accreditation. If the certifier acts as part of an organization, additional organizational details are required.
Facility Information:
• Information about the qualified facility, including data on metering devices and confirmation of their calibration and accuracy.
• Emissions rate accuracy must be within ±5% or 2 grams of CO2e per mmBTU, whichever is higher.
Supporting Documentation:
• Any additional documentation required by the certifier’s accrediting body and circumstances of the facility.
While certification is mandatory for SAF producers utilizing the 45ZCFGREET model to determine their emissions rate, non-SAF producers who opt for certification must also use entities accredit-
ed by the American National Standards Institute National Accreditation Board or the California Air Resources Board Low Carbon Fuel Standard (CARB LCFS) program. Alternatively, SAF producers using the CORSIA or CORSIA Actual model to determine their emissions rate must engage a certifier accredited by International Sustainability and Carbon Certification (ISCC), The Roundtable on Sustainable Biomaterials (RSB), or other International Civil Aviation Organization (ICAO)-approved sustainability schemes.
The USDA’s interim rule provides guidelines for quantifying, reporting and verifying GHG reduction benefits from CSA practices. By integrating third-party verification into the biofuel feedstock supply chain, renewable fuel producers can unlock new opportunities to reduce the fuel’s overall carbon CI, resulting in greater value from the 45Z tax credit.
Verification standards for CSA practices ensure the authenticity of net GHG emissions reductions, bolstering credibility and trust, expanding market opportunities for U.S. farmers cultivating biofuel feedstocks.
The USDA’s CSA guidelines aim to establish a transparent and accountable system that rewards sustainable practices, further driving the adoption of climate-smart agricultural methods in biofuel production.
Under these guidelines, third-party verification is required at every stage of the supply chain once feedstock leaves the farm. The responsibility for initiating the audit process falls on the first point of aggregation—the first location where the crop is collected after leaving the farm. This could be a storage facility, a processing facility (such as a soybean crushing plant) or a biofuel refinery. From that point onward, audits are mandated at every subsequent transfer of ownership.
Annual Audits:
• All first points of aggregation, intermediary entities and biofuel refiners must undergo annual audits by accredited thirdparty verifiers.
Farm Audits:
• Farms supplying reduced-CI crops may be selected for audits by the first point of aggregation’s verifier. Selection criteria includes geographic location, crop type, quantity supplied and associated CI values.
Mass Balance and Traceability:
• The CSA process follows ISCC prin-
ciples, incorporating mass balance, traceability, chain of custody and verification protocols.
• Each entity in the supply chain relies on sustainability declarations and audits of mass balance data and forward-looking certificates.
First Point of Aggregation Responsibilities:
• These entities must provide detailed farm producer information to third-party verifiers, enabling sample selection and verification. Information includes the number of farms supplying feedstock, geographic location, crop types, amounts and CI data.
USDA guidance specifies that certification bodies conducting CSA audits must be accredited to ISO 14065, a globally recognized standard for validating and verifying environmental information. While few verification bodies currently meet this rigorous standard, ISO 14065-certified verifiers can operate throughout the supply chain, serving as the auditor for storage facilities, processing facilities and biofuel refiners.
For farms selected for audit, thirdparty verifiers ensure CSA practices, recordkeeping and farm-level crop-specific CI calculations comply with the rule. Farms audited under these standards may be exempt from additional audits if they provide prior audit results to the verifier at the first point of aggregation, which determines the need for further review. Farms
can also proactively hire ISO 14065-accredited verifiers to coordinate audits with their schedules.
Intermediary entities must have thirdparty verification for their mass balance systems and recordkeeping of reduced-CI crops or products.
Biofuel refiners must verify CI tracking systems and adhere to additional audit standards if acting as first points of aggregation. Facilities processing reduced-CI feedstock must ensure accurate calculations of reduced-CI product quantities and maintain records supporting mass balance compliance.
The 45Z Clean Fuel Production Tax Credit offers biofuel producers a compelling opportunity to enhance revenue and market positioning. However, success depends on navigating stringent third-party verification requirements, particularly for SAF and CSA practices. Beyond regulatory compliance, these verifications enhance transparency, build stakeholder trust and open doors to voluntary markets.
By proactively embracing these requirements, biofuel producers can optimize their 45Z credit eligibility and demonstrate their commitment to sustainability and innovation in renewable fuels.
Authors: Danielle Anderson, Senior Government Policy and Advocacy Manager Christianson PLLP
Buttenhoff, Partner Christianson PLLP
Improving plant efficiency and performance through innovative solutions.
By Phibro Ethanol Staff
As fuel ethanol plants continue to face challenging market conditions, they are focused on reducing operating costs while improving production efficiencies. As part of this trend, many have turned to advanced CIP and foulant prevention technologies to optimize plant performance and reduce operating costs.
Phibro TCP (Total Cleaning Program) provides ethanol plants with an effective foulant reduction and CIP program designed to
optimize plant operational efficiency while reducing CIP frequency and costs.
Phibro TCP is fully customized to meet unique plant operational demands. The system uses deposit-prevention technologies that reduce how fast and how much foulant forms, thereby keeping plants running more efficiently between cleaning events. It then applies advanced detergent rinse aids and CIP formulations that effectively and efficiently remove deposits that negatively influence plant performance.
An automated central PLC system integrated into the plant’s distributed control system (DCS), controls all product dosing using state of the art dosing skids, which provide accurate and consistent
CONTRIBUTION: The claims and statements made in this article belong exclusively to the author(s) and do not necessarily reflect the views of Ethanol Producer Magazine or its advertisers. All questions pertaining to this article should be directed to the author(s).
dosing. The control system also provides plant management with product tracking tools to confirm dosing levels and monitor product usage and cost.
An integral part of Phibro TCP is OptEvap, which addresses the unique foulant prevention and CIP challenges presented by evaporator and corn oil systems. Specifically, OptEvap adapts the TCP technology platform by incorporating customized equipment and dosing strategies. In particular, OptEvap applies Phibro DC and Phibro SI deposit-prevention technologies using Phibro’s multivalve patented pulse dosing system. This system provides flexibility to customize and adjust dosing levels and dosing frequency to each individual evaporator and the corn oil system. This allows plants to optimize their dosing strategies to address the specific and unique foulant prevention challenges of each unit.
Jim Ekenstedt, Phibro TCP Area Manager, comments, “Ethanol plants have long recognized that each evaporator has its own unique fouling challenges that can vary widely, even within the same system. OptEvap’s ability to deliver a unique foulant prevention dosing strategy to each evaporator and the corn oil system allows plants to customize their foulant prevention program to optimize system performance. Our patented dosing system also allows plants to easily modify dosing levels and frequencies to focus foulant prevention dosing where it is most needed and to easily implement modifications in dosing strategy as changes in plant operating conditions dictate.”
The table above (Figure 2) demonstrates the effectiveness of OptEvap fou-
lant prevention strategies. Using the OptEvap program, a 50-million-gallon ICM plant reduced the number of CIP’s from 57 per year to 7 per year and eliminated all first effect CIP’s, which would have required the plant to slow down, and eliminated its bi-annual hydroblasting. Controlling foulant formation also reduced the rate of pressure buildup in the evaporator system, improving evaporator efficiency and performance (Figure 3).
While OptEvap’s foulant prevention formulations significantly reduce CIP frequency, the program also includes advanced CIP technology for when CIP is needed. These technologies include PhibroClean detergent for the rinse cycle and the CIP formulation, and Phibro AC to optimize CIP effectiveness.
Adding PhibroClean to the rinse cycle, effectively removes more material in less time than water alone, reducing the length and number of flush cycles needed to remove material prior to CIP. Applying Phibro AC as the CIP has significantly reduced CIP cycle times compared with other CIP programs. Improved CIP performance combined with a significant reduction in CIP frequency provides significant cost savings, with less down time and more efficient water usage.
OptEvap provides an avenue to improve evaporator and corn oil system performance, delivering operational improvements that include:
• Improved energy efficiency
• Increased corn oil production
• Improved efficiency at higher production rates
• Reduced CIP frequency
• More operating time and less down time
• Improved evaporator and corn oil performance under upset conditions
Mohammed Mousa, Process and Innovation Specialist at Greenfield Global’s Chatham facility, summed up the advantages and benefits his plant has achieved as a direct result of OptEvap performance.
“We reduced steam to evaps by 75% since starting our OptEvap program at the plant, now relying primarily on heat from distillation for evaporation, which cuts energy usage significantly. This has improved our CI score, matching the value of energy savings.” Mousa also noted savings from decreased high-pressure wash (HPW) time and frequency: “We cut HPW from 120 to 8 hours during our biannual maintenance shutdown and eliminated our regular 3-month boil out CIP, saving on operations, third party contractor, and chemical costs.”
Regarding the OptEvap dosing system and the value it brings to his operation, Mohammed stated, “Phibro’s equipment and engineering are exceptional. The precise dosing system, efficient pump and automatic valve setup, accurate installation and thorough product usage monitoring via the PLC system make it highly user-
friendly and effective in managing the program. Among all the vendors we collaborate with, Phibro’s system is unmatched.”
Dave Fowlie, Phibro Process Aids Product Manager, describes how Phibro is partnering with OptEvap customers. “It has been rewarding working with our customers to address their specific plant challenges and deliver value for each operation based on their plant design and individual goals and priorities,” Fowlie says. “We are truly working and learning together with our customers how our technology can best improve operational performance given the diversity of potential improvements our technology can provide.”
Phibro Ethanol is a division of Phibro Animal Health Corporation. Phibro supplies the fuel ethanol industry with a range of antimicrobials, cleaning solutions, enzymes and yeast, all backed by comprehensive technical support programs that help our customers run their plants more efficiently.
For optimal ethanol size reduction, CSE Bliss has the system to meet your needs. From single units to complete turnkey systems, our custom configured hammer mills provide precision, efficiency and a superior finished product. Contact us today to find out how we can help you improve your process!
www csebliss.com (580)749-4895 | sales@csebliss.com
Ensuring employee safety on and around the railroad plays a vital role when working with an ethanol producer’s key transport access.
By Jordan Davis
In today’s hybrid workforce, many employees manage multiple tasks daily, enhancing operations through increased versatility, productivity and reduced downtime. While multitasking boosts overall output, it is crucial to remember that each task carries inherent risks, and less familiarity with a task heightens the danger. While some administrative tasks can be mastered through trial and error, others are far less forgiving.
Rail transport remains the most efficient method for shipping and receiving goods nationwide, especially in bulk. Many ethanol and other hazardous material facilities have rail spurs, track systems or loadout tracks used daily by employees. Some even possess equipment to move railcars, com-
plete with train horns for safety. Rail has been integral to the United States’ development, though it has evolved significantly since the days of folk tunes celebrating the railroad.
Major railroads train their crew members rigorously, with training periods ranging from three months to over a year per craft. This training includes qualifications for operating various equipment and understanding different track layouts and characteristics. Crew members undergo extensive classroom and direct training to develop safe practices and adhere to governing rules. These rules exist because someone has been injured or worse.
Introducing railroad cars and equipment into industrial operations does not reduce the associated risks; it may even increase them. Employees tasked with work-
ing on or around rails deserve thorough training. At RailPros, we have received numerous inquiries following incidents, highlighting the importance of proactive safety measures. Most incidents are preventable, and an initiative-taking approach is essential when dealing with rail equipment and other high-risk tasks.
Training is often sidelined in favor of productivity, but even a single training event can significantly boost an employee’s confidence. This leads to happier, more productive employees alongside greater accountability. Employees gain confidence in performing tasks correctly, rather than just getting the job done.
The benefits found when moving forward with a training initiative for employees on and around the rail include significant risk reductions and cost savings. Risk reduc-
CONTRIBUTION: The claims and statements made in this article belong exclusively to the author(s) and do not necessarily reflect the views of Ethanol Producer Magazine or its advertisers. All questions pertaining to this article should be directed to the author(s).
tion comes in the form of better equipped staff, component and equipment familiarity, and infrastructure protection. Cost savings are found in reduction or complete elimination in downtime on rail operations, efficient loading/unloading techniques resulting in higher volume, and shipment fines from regulatory agencies and service partners can be avoided via simple inspections performed by knowledgeable, well-trained staff.
What does this training look like in an industrial environment? After all, we already covered the multiple tasks plants must manage daily. We cannot realistically mimic the robust rail training we see utilized by railroads. So, where does that leave us? In need of assessment.
In the fuel and ethanol industry there are no two plants that move or utilize rail
in the exact same way. Step one to an effective rail training initiative is to take a look at what currently exists to determine what is operating and effective versus where there are clear areas of improvement in the operations safety and efficiency. There is no need to reinvent the wheel in most operations. Take the good and supplement with in-depth training designed to pinpoint the areas of improvement. A couple of things to look for in this assessment: Are rail cars being inspected prior to use and do we know how to inspect? Look at crew communication. Is everything being done well communicated, leaving no areas for misunderstanding? What is the track condition? If crews do everything in their power to
Their valuable contents are at risk. But if your site planning included J.C. Ramsdell secondary containment systems, you’re protected from the unthinkable. Your contents are safe— the environment is safe. Ramsdell has been protecting them both since 1988.
move safely, can the infrastructure support the operation’s needs? And the all-important track rule—can we see the leading end of each piece of equipment when moving, and verify that no hazards exist throughout that move?
These are just a few things commonly examined in a facility assessment that then allows for the implementation of new or supplementing procedures introduced via plant specific training programs. There is no one-size-fits-all program, but industry best practices have been improved for the past 200 years of railroad history. Those that fit your operation could save in more ways than one!
Safety should always be the top priority, regardless of industry, occupation or organization. Embrace a proactive approach and use training to enhance workforce knowledge and confidence. Whether it is rail work or other job hazards, prepare your employees to prevent minor issues from becoming major concerns.
Author: Jordan Davis, Director - Training Sales and Delivery, RailPros
SAF Magazine, in collaboration with the Commercial Aviation Alternative Fuels Initiative (CAAFI) will showcase the latest strategies for aviation fuel decarbonization, solutions for key industry challenges, and highlight the current opportunities for airlines, corporations and fuel producers.
The North American SAF Conference & Expo is designed to promote the development and adoption of practical solutions to produce SAF and decarbonize the aviation sector. Exhibitors will connect with attendees and showcase the latest technologies and services currently offered within the industry.