
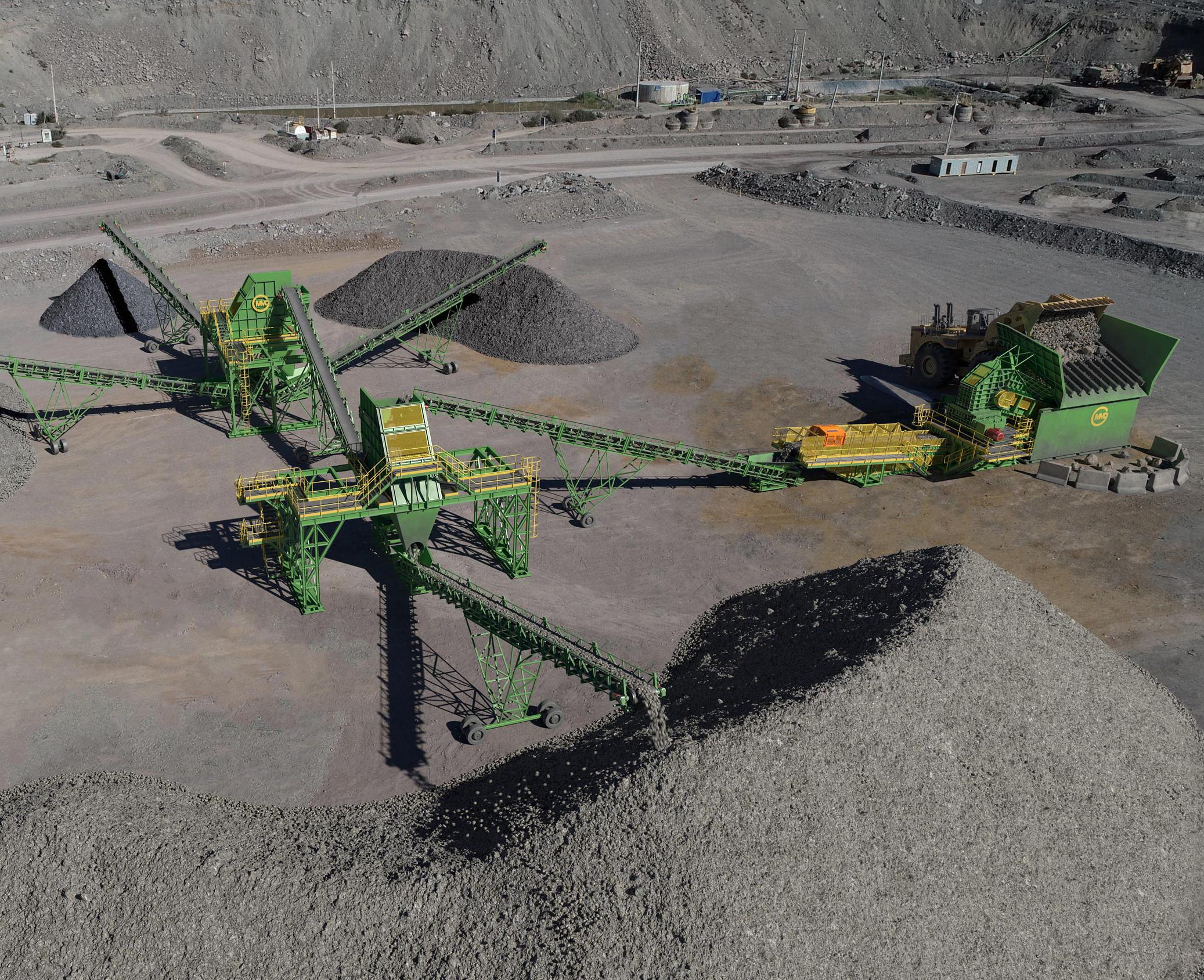


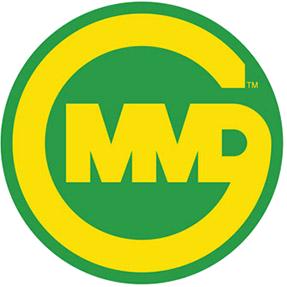
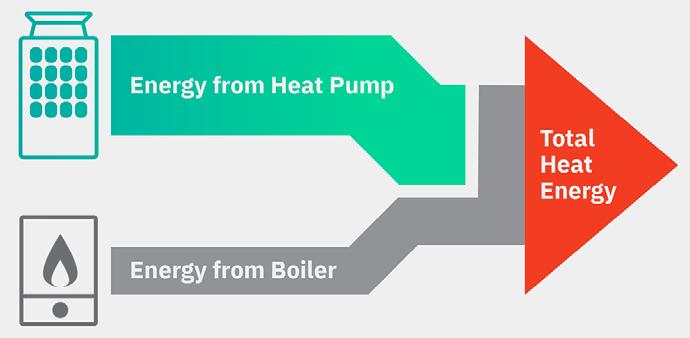

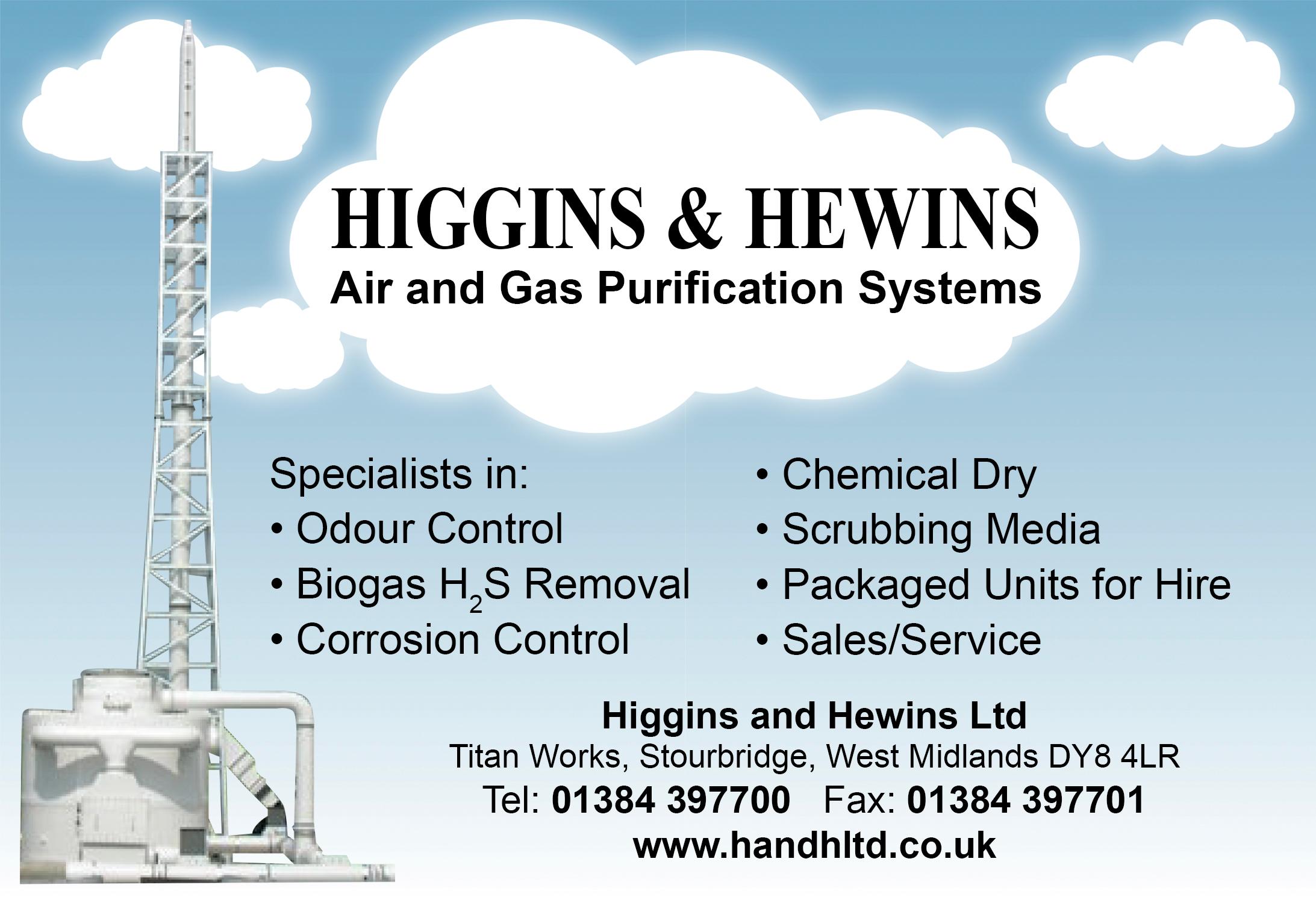
Sustainability Today is always looking to champion the intersection of business and sustainability.
2024 will inevitably see a continued rise in the need for EV charger systems as there is now a real impetus for drivers to switch to cleaner vehicles, with the impending 2035 ban on the sale of new petrol or diesel cars. There has been steady growth, with an estimated 1.02 million zero-emission electric vehicles (cars) on UK’s roads today, alongside 615,000 plug-in hybrids.
On page 9, we feature Charles Endirect as our EV Charger Systems Supplier Company of the Month. In this article, we shine a spotlight on the company and the powerful role it has working within the EV power distribution sector.
On page 8, we feature an article on Kadaant PAAL Ltd that unveils its latest and exclusive Dicom Connect client platform that is now available to
customers new and old. Dicom Connect is the client platform where operators can navigate a dashboard to use key features to produce operational information for management and operational performance within their facility. Features such as live performance status, multiple device type access, managing user groups and notification subjects are just a few examples of how Dicom Connect will be an asset to your operation.
We also feature a preview of Hillhead 2024 on pages 12-16.
Other topics covered in this issue: Recycling & Waste Management, Greenbuild, Quality Air Monitoring, Water Management, Sustainable Farming & Agriculture, Heating, Ventilation & Air Conditioning.
Don’t forget to send us your latest Business, Industry and Sustainable news and updates and email us at: info@sustainabilitytoday.co.uk
SUS Sales Manager, Jess Machin – 0121 550 7510 jessmachin@sustainabilitytoday.co.uk
Editorial, Gina Burton – 07483 931474 – gina@businessandindustrytoday.co.uk
Production Manager, Robert Sharp – production@businessandindustrytoday.co.uk Accounts Department, Paul Whitaker – 0121 824 4742 accounts@businessandindustrytoday.co.uk
For more information or format requirements, see our Media Pack
The entire content of this publication is advertorial based. To place an advertorial or an advert, please call 0121 550 7510.
The presence of mercury in flat panel displays (FPDs), such as laptop monitors and LCD TVs, has brought into focus prospective health and safety issues.
Correctly designed and manufactured electrical distribution cabinets are an integral aspect of the EV charging infrastructure,
So why is addressing water heating in commercial buildings so significant? And how can it serve as a springboard for launching a sustainable strategy to more broadly support commercial organisations?
The next edition of the iconic quarrying, construction and recycling exhibition will take place from 25-27 June 2024 at Hillhead Quarry, Buxton.
Bluewater calls for global action on PFAS contamination on World Water Day 2024,
says manufacturers should assume full responsibility and halt production.
Agricarbon is a marketleading provider of soil carbon measurement at scale, serving all soil types across the UK and across Europe for farmers, landowners and businesses.
Sustainability Today is sponsored by Apex Pumps – see them on page V
The majority of Smart heating systems now turn ‘on or off’ but imagine if you could heat just one room or specific zones remotely using smart devices? This would allow business establishments or educational facilities to save 20-50% on energy bills and reduce carbon footprint. It’s a win-win situation.
EcoSync is a pioneer in heating management for commercial buildings and multi-occupancy residences, thanks to its innovative Smart Thermostatic Radiator Valves (TRVs). With a growing portfolio to date, of over 42 customers and more than 140 buildings across the UK, EcoSync has been instrumental in saving more than 1.565 MWH of energy and slashing carbon emissions by over 285 tonnes.
These next-generational TRVs, free from the constraints of batteries and maintenance, offer seamless installation and operation, making them an ideal heating solution for commercial buildings looking to optimise energy use and reduce waste. EcoSync's technology directly addresses the significant issue of heating energy wastage in unoccupied rooms, which can account for up to 40% of energy consumption in such spaces. By enabling precise heating control on a roomby-room basis, EcoSync's TRVs ensure energy savings of 25-50% for clients, showcasing their effectiveness as a heating solution.
EcoSync caters to the specific needs of Facilities and Utilities Managers, Energy Managers, Public Sector organisations, and Senior Buyers in the commercial sector who are focused on achieving low carbon, Net Zero, and energy efficiency goals. The addition of an AI-powered dashboard, in-room QR codes, a carbon meter, and room booking system integration enriches EcoSync's offering, making it a comprehensive energy management and heating solution for commercial and multioccupancy buildings.
The benefits of adopting EcoSync's TRVs as a heating solution over traditional, batterydependent systems are clear. Conventional systems require ongoing maintenance and regular battery replacements, which can be particularly burdensome in large commercial or multi-occupancy buildings. EcoSync’s TRVs eliminate these challenges, boasting an installation time of under a minute and zero maintenance requirements.
EcoSync provides high-quality data for ESG reporting, analysing buildings and identifying areas with higher-than-average heat loss.
EcoSync provides a multi-award-winning Smart Temperature Control System from the great minds at Oxford University. Established in 2018 by two entrepreneurial academics: Dr Zsuzsa Mayer and Yoav Gross, EcoSync is an active member of UKGBC and the Energy Managers Association. For two consecutive years: 2022 and 2023, the team has won the prestigious Property Week Student Accommodation, as part of the Climate Crisis Initiative together with Corpus Christi College of Oxford.
Dr Zsuzsa has a Ph.D. in Renewable Fuels & Bioenergy from Aston University of Birmingham and Yoav has a Master’s in Environmental Change and Management from the University of Oxford. Using exceptional R&D, they have devised a system that can reduce heating-related carbon emissions and energy bills by up to 50%.
“The demand-side control doesn’t rely on sensors,
instead the patented technology inputs QR codes scanned by users when leaving a room empty. The controller is intrinsically part of an intelligent IoT device, negating the use of wires or batteries due to the built-in energy harvesting feature.
By using LoRaWAN: our commercial communication technology, the data is collected to create the digital twins of the buildings that can be used for metering (real-time consumption and savings) or running various models - how would the building and the individual rooms behave with a heat pump instead of a gas boiler etc.
Furthermore, our 2nd generation is a plug-andplay technology that can be retrofitted by the client with minimal training requirements. It costs a fraction of the traditional building management systems (BMS) plus it can adapt to the dynamically changing occupancy levels,” explained founder and now Chief Innovation Officer: Dr Zsuzsa Mayer.
EcoSync has gone further than other Smart Temperature Control Systems: on top of AIpowered optimisation and control, it can collect data to support other building retrofitting projects such as monitoring the payback of installed doubleglazing. With the onus on the UK Government's 2050 net-zero targets, many businesses are looking to strengthen their Environmental, Social and Governance (ESG) policies.
“Going forward, we would like to support our clients not only with the energy efficiency improvement of their buildings but also with their next big challenge: decarbonising the grid, which mainly means replacing gas boilers with heat pumps. We would like to design a service that can provide data both at the planning stage and later for optimising the performance of their heat pumps.” explained Dr Zsuzsa.
Heat pumps are hugely energy-efficient as they produce more heat than they consume (supplementary) electricity and are rapidly becoming the cheapest, lowest carbon form of heating available. The UK Government has pledged to install 600,000 heat pumps by 2028, as part of the Energy Security Bill.
The UK is still playing catch-up with the rest of the EU, notably Norway, Sweden, Finland and Estonia for heat pump adoption rates but with reduced North Sea gas production, the UK is now urgently committed to futureproofing its energy security through renewable energy. Between 2021-2022 alone, the sale of heat pumps increased by 40% and the facts speak for themselves: more than 80% of global space and water heating demand could be met by using heat pumps instead of gas boilers, with significantly reduced carbon emissions. Buildings alone contribute to more than 40% of energy used, which equates to over a third of global emissions and with the real threat of climate change, reducing energy use and emissions is now a global priority.
“We are committed to meeting the real needs of climate change and fully understand that our clients need high quality data for their ESG reporting purposes and we can provide that. Moreover, it works in those commercial buildings where there is no budget for a BMS but data is needed for investment purposes.
“The launch day marked not just a milestone but served as a clarion call for the Commercial Real Estate sector to accelerate its journey towards Net Zero. The UKGBC's dedication to transforming the built environment through practical strategies, including optimisation, CAPEX-light, and significant investments in retrofitting, is truly inspiring. It's evident that the path to net zero is paved with innovation, collaboration, and actionable insights.
We are currently working extensively with boarding schools, higher education and PBSAs (purposebuilt student accommodation) providers, to provide our Smart Temperature Control System. This not only reduces energy bills in a cost-of-living crisis but wholeheartedly commits to ESOS compliance and substantially less carbon emissions, allowing companies to exercise sustainability best practices.” added Dr Zsuzsa.
EcoSync is helping businesses join the green agenda and was recently delighted to attend the Advancing Net Zero hosted by the UK Green Building Council (UKGBC) in March this year.
By focusing on low-cost, high-impact adaptive and intelligent retrofit solutions, we help buildings not just meet, but exceed their sustainability targets.” outlined Simon Brown, Partnership Director.
EcoSync is much more than a provider of smart heating solutions; it is a key stalwart in the path to a sustainable future for commercial buildings and multi-occupancy residences.
For more information about how EcoSync can transform your energy management and heating practices, contact them at: contact@ecosync.energy www.ecosync.energy
The presence of mercury in flat panel displays (FPDs), such as laptop monitors and LCD TVs, has brought into focus prospective health and safety issues when considering the WRAP (The Waste Resources Action Programme) commissioned study into the technical and commercial potential for recycling the items.
The research, which was carried out by environmental consultancy Axion Consulting, aims to help WRAP identify viable recycling outlets. However, due to an increased uptake in items, WRAP anticipates that the number of FPDs in the WEEE waste stream will rise ‘dramatically’ (It is considered that there will over 145,000 tonnes of flat panel displays in the waste stream by 2018) in the next few years bringing pressure to automate suitable commercial recycling processes in the UK and Europe.
In particular the study looked at the presence of mercury in the cold compact fluorescent light in the ‘backlighting’ system for LCD TVs, laptop computers and desktop monitors. The existence of this mercury means that end-of-life FPDs are classed as hazardous waste.
protective equipment and local extract ventilation.
Mercury is extremely toxic, with inhalation of the vapour producing harmful effects on the brain, nervous, digestive and immune systems, lungs and kidneys. Mercury poisoning can result in several diseases,
and duration of exposure.
Humans are mainly exposed by inhaling vapours. These are absorbed into the body via the lungs and move easily from the bloodstream into the brain. However, when elemental mercury is ingested, little is absorbed into the body.
The conclusion of the WRAP study highlighted that employees at an FPD recycling facility would be subjected to levels of mercury ‘higher than is acceptable’. However, it suggested that this could be reduced with personal
Hunter-
Russell syndrome, and Minamata disease. Symptoms typically include sensory impairment (vision, hearing, and speech), disturbed sensation and a lack of coordination. The type and degree of symptoms exhibited depend upon the individual toxin, the dose, and the method
ABLE’s Jerome J405 gold film Mercury vapour analyser delivers highly accurate, repeatable and specific measurements, g/m3 Hg. Jerome series analysers are used extensively throughout the electrical waste recycling industry as well as by government agencies and regulatory bodies such as the EA, Natural Resources Wales, SEPA and the HSE.
The Jerome J405 can be utilised for mobile monitoring work and also for fixed-point analysis in key locations. Users typically monitor in key processing areas with personnel access and within extraction systems, to verify filter efficiency. On-board alarms can be configured to Public Health England’s guidelines for air quality, which recommend exposure limits of 1µg/m3.
The Jerome J405 combines the industry proven performance of its predecessor (the Jerome™ 431), with several new features. These include USB connectivity, onboard data logging, extended battery life, a lower detection limit and improved resolution. Its intuitive display and menu system aid operation by personnel with only very minimal training.
Results can be output live to a plant control system and the analyser’s 20,000 data-point storage capacity also provides excellent traceability on results, with time and date stamping.
T 0118 931 1188 info@able.co.uk www.able.co.uk www.247able.com
Impact Air Systems, the world’s leading air-based technology provider for the environmental, waste, recycling, and resource management industry, announces they are to exhibit their innovations at three major tradeshows to cover the USA and Europe – WasteExpo, Las Vegas, May 6-9, IFAT in Munich, May 13-17 and RWM in Birmingham 11-12 September 2024.
“We are excited to formerly announce our latest innovations at these key industry events. Impact strives to be at the cutting edge of technology to offer solutions built for the industry. The promotion of resource recovery and the circular economy is a common theme across all our innovations this year with our Airlift and Zigzag Air Classifier (ZAC) solutions at the forefront, which enables waste operators to effectively recover materials such as flexible plastic packaging, glass, and aggregates, with a remarkably high success rate.” – Nick Ball, Impact’s Managing Director.
Impact Air Systems pride themselves on their British engineering roots along with innovative air system design applied to solutions to separate materials, which catapulted
them into the recycling equipment market back in the early 1990s. Many years of working with industry professionals and listening to their issues with regards to separating waste to recover valuable materials, has resulted in Impact’s catalogue of impressive solutions which add value while easing the pressure to produce quality material streams.
After conquering the UK market, Impact’s solutions were noticed, and are now in high demand, by US waste operators for their distinctive ability to separate material effectively and efficiently, while being engineered to an exceptionally high standard, providing minimal maintenance and downtime.
Find out more at: www. impactairsystems.com or contact the team on (619) 642-8649 or email: sales@impactairsystems.com
We are now ready, after comprehensive in place testing, to unveil and launch our exclusive Dicom Connect client platform to all our customers new and old (if their existing Dicom equipment is fitted with RMS and they would like to upgrade the equipment as an optional extra). This system links to our already proven Remote Monitoring System (RMS). It is crucial that you can make quicker and more informed costeffective decisions regarding your business operation and make the most of your investment in equipment.
Here at Kadant PAAL we understand this and can make the changes you need to operate your compaction and baling equipment effectively. One of the many benefits of having the Dicom Connect on compaction equipment at source is that it will communicate directly with the client’s waste management services. This becomes efficient and effective practice on both sides in terms of transport only being despatched for full load collections and less charges being made to the source for part loads being collected, Sustainability being increased, and environmental impact being reduced.
We have been operating our RMS since Q1 2016 which has been very popular with our clients. For those not already aware the RMS allows Kadant PAAL to dial into our client’s machinery for diagnostics and managing factory settings to suit individual operational needs. This gives our clients a huge advantage of being able to diagnose and solve any issues by communicating directly with the machine user. Benefits being lower service call out costs and also massively reducing downtime by identifying parts required and enabling our Field Service Engineer to attend site fully equipped if required.
Dicom Connect is the client platform where operators can navigate a dashboard to use key features to produce operational information for management and operational performance within their facility.
This system is available for our range of Dicom Static Compactors, Dicom Portable Compactors and Dicom Vertical Balers allowing high level data to be produced and used within the organisation for optimal performance. Data collection will allow you to follow your waste management performance, enabling you to compare historical with live performance and have a location and status overview. All these factors ensuring you create an efficient, cost-effective facility.
Features such as live performance status, multiple device type access, managing user groups and notification subjects are a few examples of how Dicom Connect will be an asset to your operation. By choosing our product you will be able to access valuable data to maximise your waste management operation.
PH Hull & Sons Recycling Services have played an integral part in the initial testing of the Dicom Connect product. Initially with stringent and comprehensive testing of three Dicom Connect systems supplied for different compaction equipment, PH Hull & Sons put the system through its paces. Proof of the pudding is that now to date
they have 12 installed Dicom Connect systems on compaction equipment that processes different materials such as food waste, ie. vegetable, bread, Category 3 waste and general waste. They regularly share performance read outs from the equipment enabling them to show the high performance they can achieve with this monitoring, reaping benefits for the client and the recycling services alike.
This is what J Brown, Financial Director at PH Hull & Sons Recycling Services, had to say, “Dicom’s telemetry and vast servicing network have allowed our business to become market leading nationally, for Total Waste management services within the food production industry.”
www.dicompaal.com
There is now real impetus for drivers to switch to cleaner vehicles, with the impending 2035 ban on the sale of new petrol or diesel car. There has been steady growth, with an estimated 1.02 million zero-emission electric vehicles (cars) on UK roads today, alongside 615,000 plug-in hybrids.
The number of public charging stations are growing too across workplaces, council-owned car parks, hotels and numerous other places, to keep up with demand.
One of the biggest questions remains though: How do you maintain reliable and ever-increasing charging speeds while keeping the users and installers safe, through adherence to BS7671:2018 amendment 2:2022?
The role of electrical distribution cabinets for EV chargers
Correctly designed and manufactured electrical distribution cabinets are an integral aspect of the EV charging infrastructure, providing optimised safety and reliable electrical connections for EV charging equipment. They are typically configured to provide automatic disconnection of the supply for a given fault condition such as a short circuit, overcurrent, earth fault, and open neutral conductor (O-PEN fault on the incoming supply side cable where PME is used).
Who is a trusted manufacturer/supplier of electrical distribution cabinets to power EV Chargers?
Charles Endirect is a family-based company with an expert history celebrating forty years in the design and manufacture of metal fabrication and electric equipment originally for the street lighting market. Working with the EV power distribution sector is a natural progression for the Company. Founded by
engineer Eric Charles in 1984, the company has built up its strong industry reputation through the recruitment and retention of talented mechanical and electrical engineers.
Eric designed the Central Earth Terminal for use on the construction of the M1 motorway and with an eye on exceeding industry benchmarks, the company has undertaken innovative R&D over the decades.
Eric’s son, Nic Charles, took over the running of the company and after outgrowing its Sherborne premises, the company relocated to Wincanton, Somerset. With fabrication factory and sales and delivery offices all on-site, Charles Endirect prides itself on working with Local Authorities, National Highways and numerous other public and private bodies across the UK and further afield.
Charles Endirect is a founding member of the Highway Electrical Manufacturers & Suppliers Association (HEMSA), prominent existing member of the Highways Electrical Association (HEA.) and are long-standing members of the Institution of Lighting Professionals (ILP).
We spoke to Andrew Jackson, Sales & Marketing Director, for more information, “Our company holds ISO 9001:2015, ISO 14001:2015 and ISO 45001:2018 accreditation and we pride ourselves on delivering products that are market-leading.
“Our pre-wired distribution cabinets for example are designed using cutting-edge OEM equipment, parametric 3D modelling and AutoCAD software. A full range of distribution boards are available in polycarbonate IP65, steel and 304 grade stainless steel.
Over the last five years, the company has seen a surge in demand for EV charging stations and with its reputation for quality products and service in the design and manufacture of metal fabrication and electrical equipment, provides pre-LV Distribution Cabinet solutions to meet that demand.
Expert guidance and distribution for EV charging
The Somerset-based company provides a wide range of EV charging solutions, from the slow (nonrapid) 3kW to the Ultra-rapid DC 350kW chargers.
The range of feeder pillars and distribution cabinets include the slimline and compact Mini pillar range, Mega pillars, with customised metalwork and build service available beyond standardised models. The cabinets are designed and pre-wired to requested customer specifications and are robustly tested to an internationally recognised standard before dispatching.
Charles Endirect offers a full in-house solutions service from design, manufacture, testing, certification and delivery to customer expectations.
“The MEGA electrical cabinet range, originally launched in 2021 has been purposefully designed for the larger, feeder pillars in the EV supply industry. Cabinets are usually pre-wired providing a ‘fit and forget’ solution for the installer.
“We also offer a range of concealed in-ground pillars, which reduce street clutter and the risk of vandalism. This is perfect for heritage sites such as Piece Hall in Halifax and has also been used in contemporary settings such as the new Tottenham Hotspur football stadium.
“The key components of isolation and earthing remain essential, and so we can share our forty years of expertise in training sessions and presentations to consultants and industry stakeholders on large TEAMS meetings and in faceto-face meetings.”
Charles Endirect will be at: t Passive Safety Conference & Workshop: National Conference Centre, Birmingham. 9th May 2024 t and NRSC2024: Hilton Birmingham Metropole Hotel: 6th-7th November 2024.
For more information, contact the sales teams below: T +44 (0)1963 828400 info@charlesendirect.com www.charlesendirect.com
The importance of launching a sustainable strategy for commercial buildings has never been more important. According to recent data from the EU’s climate service global warming has, for the first time, exceeded 1.5ºC across an entire year. This temperature limit, promised by world leaders in 2015, has been seen as crucial to help avoid the most damaging impacts of global warming. A 2018 UN report said that the risks from climate change – such as intense heatwaves, rising sea levels and loss of wildlife – were much higher at 2ºC of warming than at 1.5ºC.
Limiting long-term warming to 1.5ºC above pre-industrial levels has been a key symbol of international efforts to tackle climate change, and whilst the report notes that this first yearlong breach doesn’t break that landmark Paris Agreement, it does bring the world closer to doing so in the long-term.
All the major datasets agree on the recent warming trajectory and that the world is in by far its warmest period since modern records began –and likely for much longer. Berkeley Earth reported that the calendar year 2023 was more than 1.5ºC above pre-industrial levels. Other science bodies, such as NASA, put the past 12 months slightly below 1.5ºC of warming. Fluctuations in reporting are expected, but at the current rate of emissions, the Paris goal of limiting warming to 1.5ºC as a long-term average – rather than a single year –could be crossed within the next decade.
This new data sends out yet another clarion call to the commercial sector, where sustainability has
become a defining theme for modern businesses increasingly seeking ways to reduce their environmental impact. While numerous avenues exist, prioritising water heating in a commercial sustainability strategy offers unique advantages, making it the optimal starting point for many organisations.
So why is addressing water heating in commercial buildings so significant? And how can it serve as a springboard for launching a sustainable strategy to more broadly support commercial organisations?
Water heating often accounts for a significant portion of a building’s energy consumption, ranging from 15-40% depending on the industry and usage patterns. This makes hot water both familiar and more often than not business critical, so reducing hot water demand and implementing efficient heating methods translates to substantial energy savings and emission reductions that have recognisable advantages to its users across the built estate.
energy demands means initial investment is often quickly recovered. This economic attractiveness makes it a compelling entry point for sustainability efforts.
Addressing water heating can also have wider positive impacts on a business. One area which has seen far greater focus since the COVID-19 outbreak has been improved Indoor Air Quality (IAQ). Renewable water heating solutions such as air source heat pumps and solar thermal as well as electric boilers eliminate the need for combustion processes, reducing harmful emissions and potentially improving air quality for occupants.
Diverse solutions, from upgrading equipment, especially gas-fired to more efficient gas or gridelectric, and utilising renewables such as solar thermal and air source heat pumps can be tailored to various building sizes, budgets, and hot water demands. This scalability makes hot water systems a readily addressable target for sustainability initiatives, with easily quantifiable impact that can be demonstrated to stakeholders. Critically, many water heating efficiency measures offer attractive payback periods, this is especially true of solar thermal where up to 30% offsetting of annual
By demonstrating commitment to sustainability through water heating upgrades, companies not only meet regulatory compliance helping to avoid potential fines or penalties, but can demonstrate active corporate social responsibility which resonates positively with customers, employees, and investors, boosting brand image and reputation. This function of a business is increasingly being recognised, with notable examples of organisations across the leisure and catering markets in particular, embracing a sustainable approach to enhance engagement with customers and define services from competitors. This also resonates with employees, meaning that an initial focus on water heating,
which is both familiar and often business critical can be a starting point for engaging employees in broader sustainability initiatives, fostering a culture of environmental awareness and responsibility.
So where do you begin? The most valuable, yet possibly single lowest cost, activity you can start with is to conduct an energy audit to assess your buildings’ hot water consumption patterns and identify key areas for improvement. Adveco provides a comprehensive service that incorporates live metering of your system and creates an accurate, cost-effective system design that can deliver carbon reductions and meet all your business hot water demands. This provides the data you need to evaluate any upgrade and a benchmark against which to explore various alternatives all available from Adveco, whether high-efficiency gas or electric boilers, heat pumps, and solar thermal systems, which can be deployed in isolation, although most renewables still work best when deployed to supply system preheat as part of a hybrid system. It also enables consideration of other factors like budget, space constraints, and fuel availability, which all factor into launching a sustainable strategy for a building. Working with Adveco at this early stage gives you access to expert guidance from qualified professionals who can provide necessary consultation to determine the most suitable approach for your building’s specific needs and provide a working design that can help secure funding from within the organisation, or externally via government grants, financial incentives, or green loans to offset the initial investment costs of your chosen system design.
The most consistent issue we see in commercial hot water systems is oversizing, whether through a lack of understanding of application design or
concerns over providing suitable backup to ensure system continuity. The result of oversizing is however always the same, unnecessary capital costs for system supply, installation and ongoing excess operational costs associated with higher energy demands and therefore greater carbon emissions.
Correct sizing with metered data can reduce the costs of purchasing and installing new hardware, potentially saving tens of thousands of pounds depending on the scale and complexity of the DHW application. Recognising a need for lower-cost electric systems, Adveco has developed the awardwinning FUSION range, combining an electric boiler, a specially designed cylinder and pipework that is fast to install and resilient to operate. Iterations with a monobloc air source heat pump deliver a reduction of up to 56% in carbon emissions over equivalent gas-fired systems. Integration of solar thermal to deliver mid-system heating reduces demands for water heating by as much as 30% for further carbon cutting and reduced operating costs. Because the systems are now more accurately sized, even the additional upfront capital investment associated with a more complex hybrid system can be offset for a more rapid return on investment.
With a live metered dataset, you gain insight into those prospective carbon reductions and operational costs of the new system. These can be tracked and monitored against, to demonstrate real-world savings in energy consumption and emission reductions, which can be applied toward regulatory compliance as well as used to celebrate achievements by sharing sustainability efforts with stakeholders through transparent communication.
Whichever route is decided upon, organisations should choose environmentally responsible suppliers and prioritise products with low environmental footprints as part of the procurement process. Increasingly building consultants will factor this into a project design, calculating the embodied carbon of any new system, whether water heating, space heating, ventilation and so forth. It’s an important consideration when launching a sustainable strategy, ensuring that a project meets, or preferably exceeds current building regulations ensures projects are not held up or shelved, which will be costly to both the business and the environment.
While water heating serves as a powerful launchpad, achieving true sustainability requires a holistic approach. Once successful water heating initiatives are implemented, businesses can leverage this momentum to expand their sustainability efforts by investing in wider energy efficiency across other building systems such as lighting, ventilation and especially space heating, all of which can require greater levels of physical alteration, operational disruption and accompanying costs. Also, greater attention should be given to further integration of renewable energy, exploring options for onsite renewable energy generation such as installing solar PV panels alongside the higher-efficiency solar thermal collectors used in water heating. PV enables the generation of electricity that can be deployed to a range of building systems. Since PV requires greater roof space than solar thermal, clear decision-making is required when available space for solar collection is limited, with solar thermal recommended to be prioritised as the more effective means of delivering water heating for a smaller physical footprint.
Focusing on water heating presents a strategic and impactful starting point for commercial buildings embarking on their sustainability journey. By addressing this often-overlooked area, businesses can achieve significant energy savings, emission reductions, and tangible business benefits. Furthermore, this initial success creates a springboard for wider sustainability initiatives, ultimately contributing to a more responsible and environmentally conscious future. Remember, sustainability is a continuous journey, and by starting with water heating, businesses can unlock a pathway towards a greener and more sustainable future.
Contact www.adveco.co
The next edition of the iconic quarrying, construction and recycling exhibition will take place from 25-27 June 2024 at Hillhead Quarry, Buxton.
Hillhead returned with a bang in 2022 as The QMJ Group celebrated the show’s 40th anniversary over three gloriously sunny days in June. Exhibitors and visitors took the opportunity to reconnect with their industry peers, marvel at the plethora of live machinery action taking place, discover the latest product launches, and explore the latest technology and innovations driving digitalisation and decarbonisation across the sector.
With 18,500 unique visitors in attendance and more than 600 of the world’s leading equipment manufacturers, suppliers and service providers taking part, 2022’s Hillhead exhibition was a record breaker, cementing its status as the world’s biggest working quarry event for the mineral products, construction, and recycling sectors.
The organisers will be extending the numbers of
toilets for the next event with additional plumbed units being installed at the top of the showground adjacent to the Registration Demo area. To reduce queues at peak times, there will also be a higher provision of urinals throughout the Showground.
More seating and communal areas will be introduced at various locations around the showground, allowing visitors to take a break and enjoy their picnics and other refreshments.
Two new hydration stations will be located on the showground where visitors and exhibitors can top up their water bottles with fresh, cold, filtered water free-of-charge.
The renamed Showground Pavilion (previously the Main Pavilion) is being extended by around 1,300m3. As well as generating more indoor stand space, this will also house a newly designed Hillhead Café offering a wider range of hot and cold food and drink, as well as an outdoor terraced seating area. There will also be a meeting lounge equipped with free Wi-Fi & charging points where visitors can grab a coffee & catch up on emails.
Additional catering areas are being organised across the site (including within the Registration Pavilion). These new outlets will deliver more choice and meet a wider range of dietary requirements. They will also help to reduce queuing times during busy periods.
1,000 additional car parking spaces have been added together with a new dedicated helicopter landing area. This will help to maximise entry to the parking areas from multiple access points and reduce queuing times to a minimum throughout the busy morning rush.
Brand new for 2024, exhibitors will now have their own dedicated entrance taking them directly into the showground as part of a reconfigured Registration Pavilion. This will ensure fast track access at the beginning and end of the day for exhibitors.
Contact www.hillhead.com
MMD have been a global leader for over 45 years in the design and manufacture of innovative material processing equipment. Our core products, the Mineral Sizer™ and Apron Plate Feeder, feature in groundbreaking in-pit solutions that enhance productivity, profitability, safety, and promote sustainability in the mining industry.
MMD’s revolutionary Bulk Ore Sorting System combines the benefits of In-Pit Sizing and Conveying with pioneering ore analyser technology. The ore analyser distinguishes between grades of material, enabling the separation of ore from waste at the mine face. By allowing this to happen earlier in the process, trucks need only to haul ore, not waste, to the processing plant. The
results are up to 10% less energy usage and a lower cost per tonne. Efficiency advantages are passed on to the downstream processes too, with less water consumption, ore grade uplift, and SAG mill benefits. These MMD systems are currently operating in South Africa, Chile and Brazil, processing copper, platinum and nickel ore.
We invest heavily in developing new technology that maximises efficiency. We are committed to helping our customers achieve their sustainability targets and lead the way towards a greener future for the industry.
Come see us on Stand W15. T +44 (0)1773 835533 info@mmdsizers.com www.mmdsizers.com
With hundreds of these systems installed globally, DESMI in the UK supply a fully compliant, UK manufactured, pump package for additive dosing. Our package has been continuously developed in partnership with Evotherm and, collectively, we can provide chemical and dosing advice along with specific on-site support for the full dosing system to ensure the right chemical composition and pump system is selected for your specific plant.
Our Bitumen Additive Systems are supplied with a heavy-duty ROTAN pump, control panel, pulse-output flow meter, pre-wired, pre-piped, and packaged in a rugged container. DESMI UK further provides contractor co-ordination to aid ease of
installation. Options include batch and continuous plants (with variable frequency controller and force ventilated motors) and low dosing rates for smaller systems. DESMI’s ROTAN internal gear pumps are also widely acknowledged as one of the leading pumps for bitumen and are used in asphalt plants for bitumen off-load and for duty and/ or blending. We can provide on-site advice to replace existing bitumen pumps to ensure the correct size of pump is selected. We also offer a service exchange programme to minimise downtime.
Contact Ray Jeffries on 07854 007593 or 01782 566900 or email: rayj@desmi.com to arrange a site visit or for further information. Come see us at Hillhead on Stand C6.
Celebrating its 50th anniversary, MIT is thrilled to announce its return to Hillhead for an impressive third exhibition. This milestone reflects MIT's enduring commitment to the heavy-duty machinery industry, providing life-extending aftermarket services and showcasing innovative solutions.
MIT has been a beacon of sustainability, supporting machinery longevity with expert parts supply, repair, overhaul, and service capabilities. Their aftermarket expertise ensures equipment performs, beyond typical warranty periods.
At Hillhead, MIT will exhibit driveline systems design and supply, highlighting the role of these components in constructing sustainable, reliable, and durable OEM machinery. Additionally, MIT's future propulsion technology for heavy industry will be a cornerstone of the display, signalling the company’s forward-thinking ethos.
With enduring partnerships with industry titans like Twin Disc, Transfluid, Reich, and ZF, MIT delivers OEMapproved servicing for a variety of driveline components. This golden jubilee is more than an anniversary; it's a testament to MIT's dedication to innovation, customer service, and eco-friendly practices that will propel the industry towards a more sustainable future.
Visit MIT at Hillhead on Stand M14 to explore the future of heavy-duty machinery.
T +44 (0)330 383 0333 info@mitgroup.co.uk www.mitgroup.co.uk
Discover FRUTIGER and the brand MobyDick, the hallmark of excellence in wheel washing, dust control, and demucking systems for over 30 years.
Trusted by 6,000 sites in 72 countries, the FRUTIGER solutions are renowned for reliability.
Serving a diverse clientele of 2,500 international partners, including industry leaders like Vinci and Rio Tinto, FRUTIGER caters to various sectors, from SMEs to military organisations and NATO.
With 35 years of experience, a global network of independent companies and sales offices, and ISO-certified production facilities in Switzerland, the Czech Republic, China, and the USA, FRUTIGER guarantees consistent quality and performance, delivering unparalleled solutions worldwide.
Visit us at Main Pavilion, Stand PB3 and see for yourself why FRUTIGER is the trusted choice in the industry. We look forward to meeting
you. We would be pleased to visit your site and discuss your requirements and arrange a visit to a reference site so you can see our systems in action and discuss with the site manager directly.
Contact: Tony Morgan M 07534 225087 a.morgan@frutiger.ch www.mobydick.com
Flender, the leading manufacturer of drivetrain solutions, is pleased to be exhibiting again at Hillhead in 2024.
This year we will be featuring the new revolution in gearbox design: The Flender One, and the award-winning AIQ products including the AIQ Core – a new standard in gearbox condition monitoring, and AIQ Detect – a world’s first in elastomeric coupling condition monitoring. Alongside these we will also present our couplings range, the best fit for the aggregate, recycling, and construction industries, and our marketleading service portfolio that includes on-site inspections, retrofits, and upgrades including 3rd party products
and many other solutions.
With 125 years of experience in the mining and process industries, Flender is wellplaced to support your business in maintaining high plant availability and reducing unplanned downtime.
Come visit us at Stand PD26 in the Showground Pavilion to see our live demos and presentations, free brochures and light refreshments whilst discussing your drivetrain requirements.
Email us at: flenderuk.gb@ flender.com to book your free live demo in advance. Get to know more about our products and services by visiting: www.flender.com
Heavy equipment plays a vital role in shaping the future. Timken designs engineered bearings and industrial motion products (chain, couplings, lubrication systems) to support machine builders in manufacturing hard-working aggregate equipment.
At its core, a bearing is an inherently efficient product. Its function is to transfer motion in a way that reduces friction. But Timken engineers work constantly to optimise bearings against power
loss and deliver solutions that exceed industry standards and customer expectations.
We design with sustainable in mind. Our objective is to develop light, powerdense solutions that minimise power loss and are manufactured in a manner that reduces energy inputs, processing steps, and waste while achieving operational excellence.
With more than a century of innovation, we also help operators to maximise uptime, reduce maintenance costs and improve productivity.
We know that product sustainability is also about making installation and maintenance easier, reducing steps and requirements, and extending service life through predictive modelling.
Finally, bearings are made of steel. Most of the steel we purchase is recycled, and most bearings are 100% recyclable.
Timken posted $4.8 billion in sales in 2023 and employs more than 19,000 people globally, operating from 45 countries.
Come see us on Stand Q12. T +44 (0)1977 665010 www.timken.com
Discover VEGA's comprehensive solutions for bitumen systems at Hillhead 2024
As bitumen system regulations evolve under HSE and DSEAR, ensuring compliance is paramount. Explore VEGA’s comprehensive range of ATEX/ UKEX approved sensors and panels, tailored to meet the newest explosion protection standards.
Witness firsthand how our instrumentation, including the remote inventory system (VIS), revolutionises aggregate handling procedures, enhances security and efficiency in quarries at Hillhead on Stand PD19.
We will have on display live working demonstrations of our
next generation non-contact level radar sensor - THE 6X®, abrasion-proof ceramic pressure sensors, point level switches and our remote inventory system (VIS), conveyor mass flow measurement solutions and noncontact blockage and object detection.
Our dedicated team is ready to showcase our comprehensive solutions for all budgets and requirements. Backed by excellent on-the-ground service, our knowledgeable team is available to address your queries and provide expert guidance. Experience the ease of instrumentation setup and operation, designed to streamline processes for quarry operations.
T +44 (0)1444 870055 info.uk@vega.com www.vega.com/uk
Bein with a chance to win a £100 gift voucher by helping leading Aggregates and Asphalt supplier and manufacturer, FM Conway, name its new asphalt granulator. Supplied by CAMS Srl, the new hybrid powered machine will be making its debut at Hillhead 2024.
Featuring a combination screen and oversize recirculation conveyor, the granulator will begin its life at FM Conway’s Heathrow asphalt plant and recycling centre after the show. Here it will be put to work producing reclaimed asphalt pavement (RAP) for use across FM Conway’s asphalt plants across London and the South East.
With lower energy consumption and improved outputs compared to conventional asphalt recycling equipment, this is just one example of how FM Conway is committed to a net carbon future.
As a leading asphalt manufacturer
in the UK, FM Conway’s products offer sustainable options and a broad range of high-performance pavement solutions. Meet the team at Hillhead to learn more about their asphalt materials, including their SurePol range of polymer engineered bitumen solutions and their technology centre which provides testing & design services.
To take part in the naming contest, visit FM Conway at Stand PC49 in the Showground Pavilion.
T 0800 276 1122 aandaorders@fmconway.co.uk www.fmconway.co.uk
Come see us on Stand PD2. T 01332 227500 info@davisderby.com www.davisderby.com Come see us on Stand D4
Afrequent exhibitor at Hillhead is Davis Derby, a world leading conveyor protection and forklift fleet management system manufacturer. This leading Derby-based company supplies to quarries, mines and warehouses around the world and loves to demonstrate its StedFAST and TruckLOG products during the exhibition.
The StedFAST conveyor range protects workers in hazardous working conditions such as quarries, mines, tunnels, processing plants and railway depots. With a built-in speed monitor, emergency stop pull system key and digital sequencing through a WiPAN enabled and wireless management system, this is a world-leading conveyor protection system.
Health and Safety reports estimate that 30% of all fatalities are caused by fork lift truck vehicles. The TruckLOG TK5 system offers driver access control, pre-op checks, shock alerts and utilisation reporting through Cloud-based software. With the Trucklog zoning systems, forklift
speeds can be controlled to reduce the risk of vehicle to pedestrian collisions. The TK5 TruckLOG is the UK’s leading independent MHE fleet management system and with its advanced features, warehouse companies are assured of ultimate driver safety. All Davis Derby systems are fitted by electrical engineers to new or retrofit systems and a fully tailor-made conveyor control system can be designed for any company.
Founded in 1947, Perissinotto SpA manufactures a wide range of heavy-duty slurry pumps for tough abrasive and corrosive applications.
Hard metal, Special Alloys, and rubber lined pumps with customised design for single-stage, multistage, submersible, and vertical configurations.
Some of the most appreciated features are: t Longer life, thanks to ABRASION RESISTANT PEMO design and materials.
t CORROSION RESISTANT, using the most suitable alloys for aggressive fluids.
t NON-CLOGGING, thanks to the special design of casings and impellers.
t SINGLE, DOUBLE or CARTRIDGE MECHANICAL SEALS to prevent leakages and contaminations.
t Flowrate up to 2,000m3/h.
t TDH up to 160mcl.
PEMO Pumps are commonly used in Mining, Aggregate Washing, Quarry and Mineral Extraction Process.
PEMO PUMPS are designed and manufactured to resist and operate with the heaviest abrasive slurry and are commonly used to feed the classifier, to deliver the slurry to the flotation system, tailing thickener, and finally to the filtration/dewatering system.
Mining and aggregate excavation
Pemo Slurry Pumps are used extensively in these markets due to the wide variety of Models and Configurations. Pumps available for this application include Horizontal, Vertical & Submersible Designs.
Pemo Slurry Mining Pumps used for this application are designed specifically for abrasive and or acid/ corrosive fluid applications and are available in a number of materials including Rubber Lined, Hardalloy PEMO (750-800 HB), Stainless Steel and Hastelloy.
Some Models can operate to a maximum pressure of 20 bar (290 psi).
Some of the applications for PEMO pumps include, slurry transfer in ponds, hydrocylone feed and yellowcake slurry transfer.
Come see us at Hillhead from 25-27 June 2024 on Stand PC20.
Contact today our consultants to learn more about the complete range of Pemo Pumps: www.pemopumps.com/en/contact-us/
After recently celebrating its 30th anniversary in 2023, the United Kingdom Society of Trenchless Technology (UKSTT) remains at the forefront of environmental preservation with its trenchless methods that harness innovation.
Going into its fourth decade, UKSTT has achieved many milestones across its history, and today its mission still remains the same: To advance the science of practice of trenchless technology for the public benefit and to promote education, training, study and research in the practice and to publish the results.
focus is to continue supporting and engaging its membership within the utility sector.
UKSTT’s range of trenchless solutions offer key advantages across inspection & detection, cleaning methods, renovation, new installations, and keyhole & other techniques.
Addressing the urgency of climate change is a priority for UKSTT moving forward and by putting itself in the centre of the action enables the company to remain focused on promoting its technology for the benefit of the environment and everyone involved.
Through sustainable impact, effective collaboration, lasting partnerships and knowledge transference, UKSTT’s main
UKSTT is excited to announce its first masterclass of 2024 that will take place on the 20th March at Woodland Grange, Leamington Spa. CIPP for Pressure Pipes Masterclass is a one-day masterclass that comprehensively covers CIPP for pressure pipes and much more. Including presentations from speakers from Wessex Water, Thames Water, IKT –Institute for Underground Infrastructure, WRc Group, Picote Solutions, Applied Felts and RPS, reserve your place today!
M 07745 781500 www.ukstt.org.uk www.ukstt.org.uk/calendar/cipp-forpressure-pipes-masterclass
Bluewater calls for global action on PFAS contamination on World Water Day 2024, says manufacturers should assume full responsibility and halt production.
In response to recent findings exposing the presence of harmful PFAS contaminants in the tap water of 70 million Americans, Bluewater, a pioneering brand delivering water purification solutions and beverages, is urging for increased public vigilance and intervention from national health and water authorities this World Water Day 2024. Bluewater is spotlighting the intensifying global crisis of water contamination by PFAS persistent chemicals, now widely detected in tap water worldwide and posing a threat to human health.
“Our mission at Bluewater is to protect people by preventing hazardous chemicals such as PFAS from getting into their bodies. PFAS isn’t a localised issue. It’s a global health crisis spiralling out of control,” says Bengt Rittri, a leading Swedish environmental entrepreneur who founded & leads Bluewater as CEO.
In recent investigations to raise
public awareness of the problem in London and Stockholm, Bluewater found evidence in both cities of worrying levels of the most hazardous PFAS chemicals, PFOA and PFOS.
“As we commemorate World Water Day 2024, Bluewater encourages everyone to consider tap water quality and to take action towards better health and a sustainable planet. We also urge the manufacturers of PFAS chemicals to take responsibility for the pollution they are causing and — preferably — stop their production of such chemicals entirely,” said Bengt Rittri.
M 07785 302694
david.noble@bluewatergroup.com www.mynewsdesk.com/bluewater
The highly anticipated Groundswell Event in Hertfordshire on 28th and 29th June did not disappoint, with farmers, researchers and experts in the agricultural industry coming together from across the world to learn and share knowledge on sustainable food production through regenerative farming practices.
Interagro (UK) Ltd, leading adjuvant and biostimulant experts, were among the growing number of exhibitors in attendance offering practical solutions to help farmers achieve more sustainable and profitable food production through superior plant health.
offers a more natural and eco-friendly approach to crop establishment, by boosting seeds rather than treating plants.
Growing in popularity year-on-year the ‘Glastonbury-for-farmers’ style event was full of buzz, learning and positive attitudes, with Interagro part of the Knowledge Trail showcasing how its plant-based seed treatment Newton,
Newton is increasingly being adopted by farmers due to the recognition of its proven abilities to enhance plant growth, productivity, and resilience. Newton’s potential to improve crop establishment, work in harmony with soil biology, and put plants in the best possible position to acquire moisture and nutrients throughout its lifetime – so they are less reliant on synthetic inputs – has contributed to its increasing use.
To find out more about Newton and Interagro’s adjuvant and biostimulant range visit: www.interagro.co.uk
Get in touch on: 01279 714970 or email: info@interagro.co.uk
Follow on Twitter: @InteragroUK
Agricarbon is a market-leading provider of soil carbon measurement at scale, serving all soil types across the UK and across Europe. For farmers, landowners, and businesses looking to assess their soil carbon stocks, Agricarbon offers scientifically driven, evidence-based sampling and analysis at its on-site processing facility.
The company is at this year’s Groundswell Agricultural Festival from 26-27 June 2024, the leading, annual regenerative agricultural event, to showcase its leading soil testing technology.
Agricarbon is committed to expanding its unparalleled soil carbon technology across European countries and further afield in North America.
It is well known that increasing soil carbon has a twofold impact: improved soil health and higher yields for crops.
Supporting natural soil microbes such as fungi, archaea and protozoa is great for worm populations and enhanced eco-biodiversity.
The data speaks for itself – Agricarbon has sampled over 32,000 hectares and quantified an astonishing 2 million
tonnes of carbon, which amounts quite possibly to the biggest database on soil carbon in the world.
The talented leadership team include world renowned soil scientist: Dr Helaina Black and her team of soil science experts, helping facilitate how soil can work as a carbon sink, while simultaneously supporting food production and natural biodiversity.
T +44 (0)1382 413 270 info@agricarbon.co.uk https://agricarbon.co.uk
Following on from the successful launch into the UK and Irish market at this year’s Groundswell Festival, Gaiago is encouraged by the interest and commitment to its sustainable products.
there is a need to embrace and engage with a new way of thinking around soils. Soils should be treated as one of the biggest assets we have to avoid the continuing loss of fertility and current negative impacts on nature.
Gaiago’s portfolio harnesses the very latest innovation for revitalising soils, any farmer, grower, horticulturist or land manager’s biggest asset. The solutions consist of unique formulations of natural elements, protecting yields and empowering growers to evolve their practices to a more regenerative farming. Products registered as biostimulants are now available in the UK.
The current portfolio is supported by a strong R&D pipeline developed both internally and externally, notably through a scientific joint-venture with a renowned Agricultural University, UniLaSalle.
Soils – understanding the problem As a global issue, it is clear that
Gaiago is making the change within soils and their whole team is committed to educating and offering solutions to growers for the production of healthy, fertile, and sustainable products. “Mankind thrives when soils thrive” is Gaiago’s mantra
Innovative solutions on the ground Alongside Gaiago’s leading soil probiotics FreeN100 & FreePK, its prebiotic biostimulant Nutrigeo® offers improved soil structure in less than 6 months, enhances fertility and growth, and accelerates the humification process – the source of carbon storage in soils.
Find out more at: www.gaiago.eu
When it comes to decarbonising buildings it’s crucial to balance effective heating with low upfront investment and low running costs – Chris Newman, Zero carbon design team manager at Mitsubishi Electric, explains
We all know that decarbonising the UK’s building stock is vital for hitting the country’s net-zero targets. At the same time, this can pose challenges for building developers, energy managers, installers and even tenants. One area of complexity is how buildings are heated, because heating has traditionally contributed significantly to overall building emissions, and changing how we heat spaces is high on the net-zero agenda.
But while effective in helping to reduce carbon emissions, changing how we heat spaces isn’t always simple. For example, traditional gas-fired heating systems operate with relatively high water flow temperatures of 70-80ºC (in comparison to today’s typical designs of ≤55ºC). Swapping to an electrically driven alternative to match those temperatures can be straightforward – but it can also have a big impact on the operating cost of equipment.
This is made particularly apparent by the current disproportionate cost per kWh of gas compared to electricity, and the capital cost of technologies such as heat pumps compared to fossil fuel alternatives. This is where a bivalent approach can help to balance the ability to decarbonise a space with lower overall costs.
Focusing on utilising heat pumps as part of a bivalent solution, we can consider two broad types of configuration (see Figure 1).
It is typical in the UK for peak space heating capacity (ie. 100% load) to only be required for a small number of hours in the year and therefore this makes up a relatively small amount of the total kWh of heat energy delivered. This then opens the possibility of deliberately undersizing your heat pump in comparison to peak load and only operating it for certain parts of the year, allowing the gas boiler to provide the extra peak capacity or peak flow temperatures when needed – this approach can help to reduce up-front costs and plant space requirements.
We know that operating a heat pump at the lowest possible flow temperature and the warmest source temperature will usually deliver the highest efficiency and lowest operating cost, but we must also consider how any heat generated is emitted into the building
– this is where the infrastructure of the existing system begins to influence the design approach.
The existing heat emitters (fan coils, AHU coils, radiators, etc) must be assessed to understand their deliverable output capacity at different mean temperatures – this will demonstrate what mean temperature is needed at certain ambient conditions to deliver the required capacity. This is a key piece of information needed to model bivalent parallel and bivalent changeover configurations.
Boiler topping up
A bivalent approach can involve a heat pump being the lead heating source, with a boiler topping up when needed. Alternatively, a heat pump can work in isolation, and swap over entirely to a boiler when it can no longer meet requirements.
In a bivalent changeover arrangement, the heat pump is deliberately designed not to deliver the peak flow temperature or capacity of the heating system.
This means that it will only operate up to a specific temperature and capacity chosen, and then it will reach a changeover point.
The heat pump will operate in isolation to the boiler, and provide heat until its maximum flow temperature and capacity is reached. At this point, the heat pump will turn off and the boiler will take over delivering the higher temperature water and increased capacity required to meet the increasing building load.
This arrangement will deliver a lower proportion of annual space heating kWh from the heat pump compared to a bivalent parallel solution, but as the heat pump will not operate at peak design conditions and will not be asked to deliver high flow temperatures, it will benefit from increased efficiency, resulting in a lower operating costs.
A bivalent parallel approach, on the other hand, requires the heat pump to be capable of delivering the peak flow temperature of the system, so it can work alongside a boiler at any time of year. This allows the heat pump to be sized at any capacity and either deliver heat energy on its own when it has the capacity available, or in conjunction with the boiler when the load is greater than the heat pump capacity.
Flow temperature can be either fixed or weather compensated, but the key design principle is that the heat pump is able to deliver the required flow temperature to meet peak heating demands.
This arrangement will deliver a large proportion of heating from the heat pump and will most likely result in the lowest overall carbon emissions. However, operating the heat pump at potentially high flow temperatures and low ambient conditions will reduce its efficiency, meaning that this configuration could result in an increased operational cost compared to the gas boiler only system.
Special consideration must also be given to the selection of heat pump to ensure it can deliver the necessary flow temperature and capacity at all operational conditions.
Opting for a bivalent solution – whether parallel or changeover – can be the most effective way to balance effective heating with low upfront investment and low running costs.
Contact https://les.mitsubishielectric.co.uk