
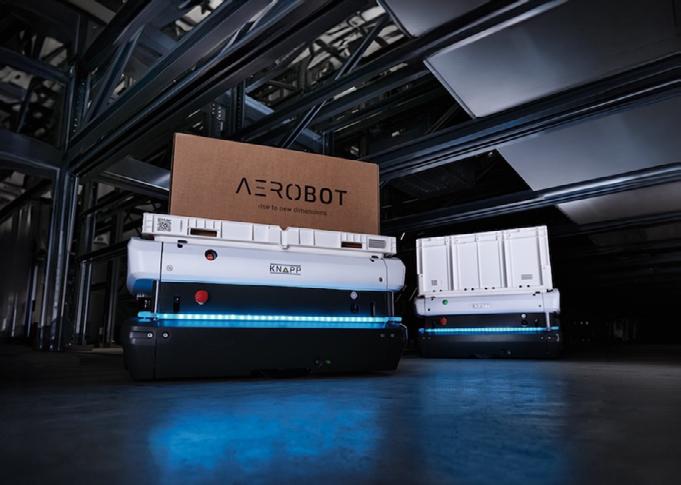
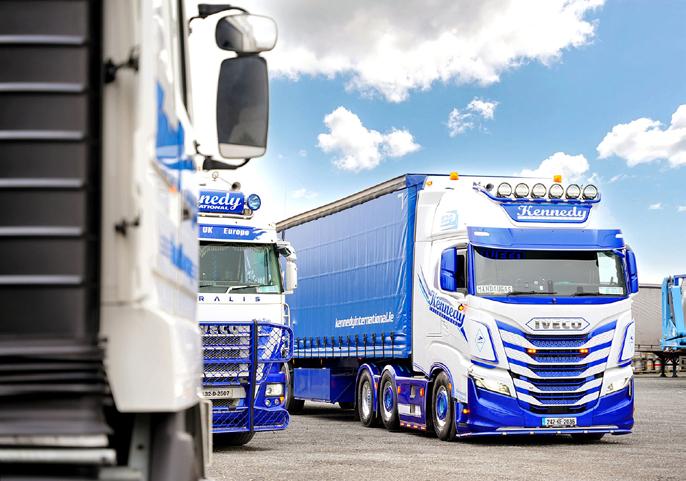
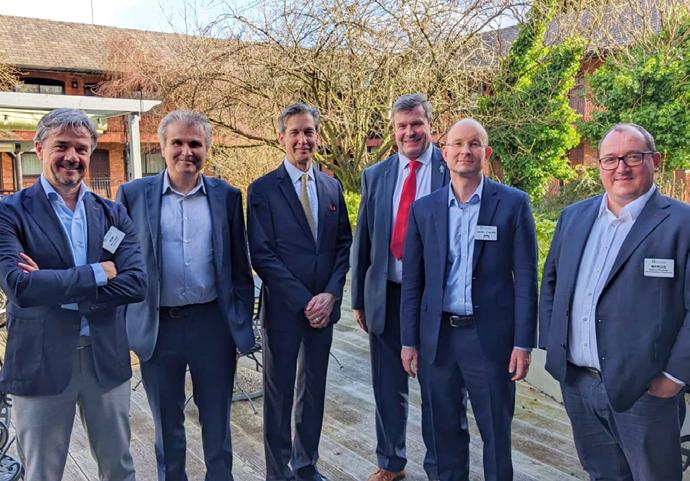
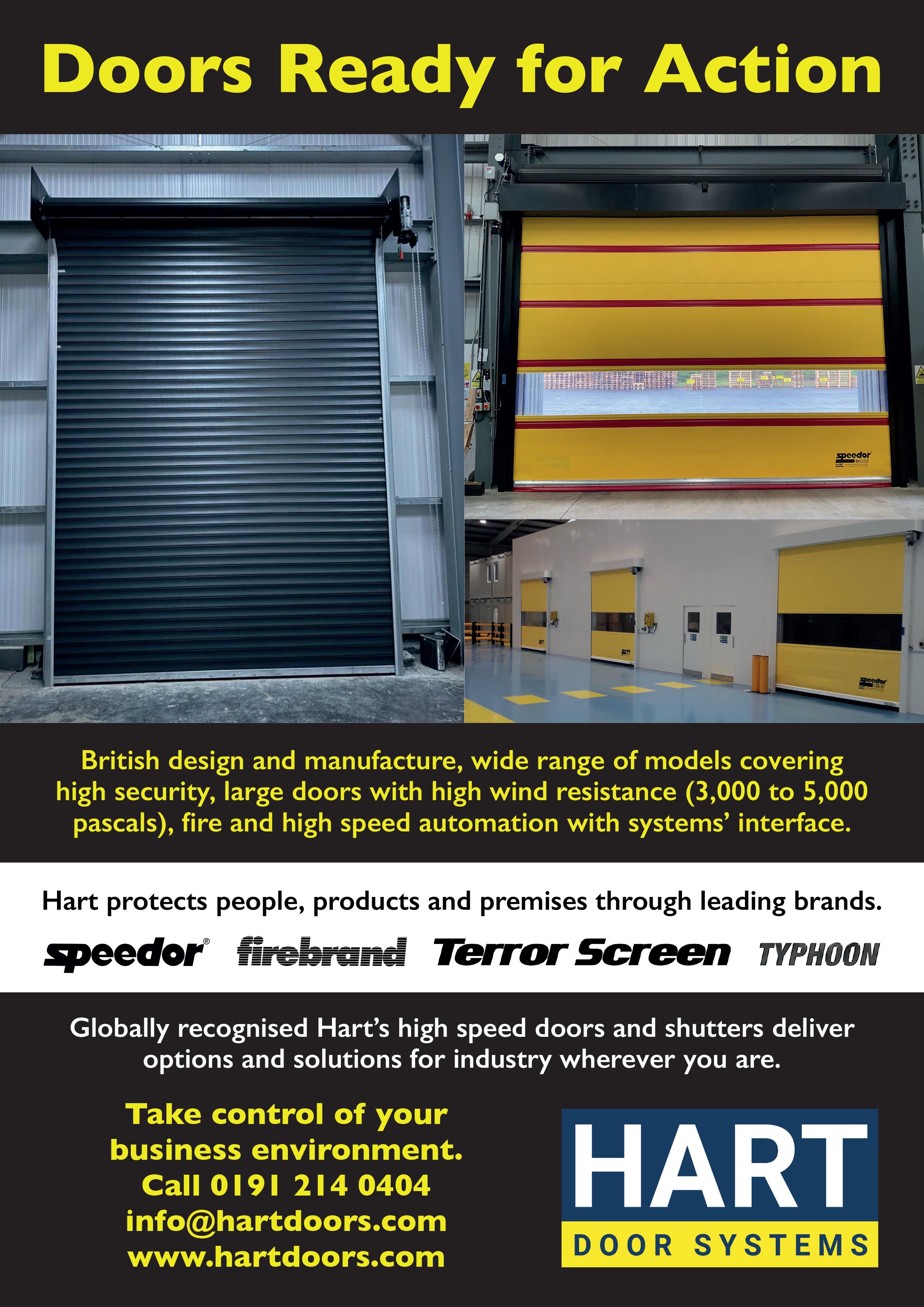
Our commitment is to be the first choice partner to the print media industry by providing the best products, best networking and unparalleled service and support to customers of all sizes and in all market segments in the UK and Republic of Ireland.
Welcome to our June/July edition of Packaging Warehouse & Automation! In this issue, we showcase a curated selection of features on innovative companies across diverse industries, exploring the technologies and solutions shaping the future of packaging, logistics, and automated systems.
Gina Burton Editor
gina@industrialprocessnews.co.uk
IntraLogisteX is the UK’s largest intralogistics event, bringing together the entire industry. On page 4, we have a full review of the 2025 event, including the co-located events Robotics and Automation and the Sustainable Supply Chain Exhibition.
The King’s Awards for Enterprise stand as the highest official UK accolade for business excellence, celebrating outstanding achievements across four vital categories: Innovation, International Trade, Sustainable Development, and Promoting Opportunity through social mobility. On page 9, we have a brilliant feature that delves into the credibility these awards bring to businesses, as well as a full break down of the entry criteria by category for all future applicants.
On page 16, we have a full preview of UKPackaging Expo 2025, due to take place on the 3rd-4th September at Manchester Central. This year promises to be the event’s most dynamic yet. Hosting retail, e-commerce, food & beverage, beauty, and pharmaceutical industries all under one roof, the event will offer tailored insights, state-of-the art technologies, and key industry connections.
Other topics include: Warehouse Automation, Storage & Racking, Transport & Haulage, Print, Packaging & Labelling, Customs & Logistics, Food & Drink & Health & Safety.
Got news to share? Email: gina@industrialprocessnews.co.uk
Publication Management
Fallon Waldron, Publication Manager T 0121 550 2086 fallonwaldron@industrialprocessnews.co.uk
Production
Robert Sharp, Production Manager production@businessandindustrytoday.co.uk
Accounts
Paul Whitaker, Accounts Manager T 0121 824 4742 accounts@businessandindustrytoday.co.uk
Editorial Gina Burton, Editor gina@industrialprocessnews.co.uk
The entire content of this publication is advertorial based. To place an advertorial or an advert, please call 0121 550 2086.
Packaging, Warehouse & Automation is a multi-media digital magazine which circulates directly to 25,000 targeted businesses per issue, and is downloadable from multiple digital news stands and via social media.
Please contact 0121 550 2086
Email info@industrialprocessnews.co.uk www.industrialprocessnews.co.uk
For more information on print or format requirements, please see our Media Pack
Find us on LinkedIn and follow us on Twitter @ipn_uk
IntraLogisteX is the UK’s largest intralogistics event, bringing together the entire industry – from warehouse automation, robotics, and materials handling to packaging, labelling, software, transport management, and more. Held this year from 25th–26th March at the NEC Birmingham, the event welcomed thousands of visitors.
Co-located with Robotics and Automation and the Sustainable Supply Chain Exhibition, IntraLogisteX offered the UK’s most comprehensive showcase of robotics, automation, and sustainable supply chain solutions – providing attendees with access to innovations spanning the entire warehouse, supply chain, and manufacturing process, all under one roof.
Now in its 10th year, IntraLogisteX offered exhibitors a chance to connect with thousands of high-level decision makers actively looking for the latest solutions. The event supplied exhibitors with an audience of unrivalled quality, and visitors had an average of £2.3 million to spend with 80% of them having buying influence.
The event was a great place to meet industry leading exhibitors and discover how the latest technology could be applied to your operations to provide massive improvements in productivity and accuracy.
One of the standout features was the completely free comprehensive Conference Theatre. This learning opportunity gave visitors the chance to hear directly from the minds behind the latest technology, whilst listening to industry leaders as they shared their insights and gave real world examples of how they have automated their own, and their customers, operations.
The Theatre featured standout talks from expert speakers such as Adam Coventry – Former Director of Warehousing, Boots UK Ltd; Alistair Barnes – Senior Programme Manager, Land & Maritime Transport, Innovate UK; Anna Krajinska – UK Director, Transport & Environment; Phil Taylor – Key Account Manager, BS Handling Systems Ltd; Reuben Henry-Fellows – Deputy Editor, CiTTi Magazine; Sarah Hyde –UK&I Sales Director: Manufacturing, Transport and Logistics, Zebra Technologies; and many more.
A wealth of world-leading companies attended, bringing the industry’s key connections together
under one roof. The floor was bustling with potential suppliers, exhibitors, and industry influencers, all engaging in business and benefiting from the unique value of face-to-face interactions.
Companies like Allpack, AmbaFlex, Assa Abloy (Traka), Aurora Insights, Makestation Projects, Lucas Systems, Modula Storage Solutions, Netstock, Palband, and many more were in attendance, showcasing their latest innovations and putting on live demonstrations of their latest solutions.
Robotics and Automation offered the unique opportunity to gain an insight into the latest innovations and technology available to improve efficiency, reduce errors, drive down costs and gain a competitive advantage.
Companies specialising in robots and robotic systems that exhibited at the event included Fives Group, Deli, Crescent Industrial, Karcher, JBT, KNAPP UK Ltd, LAC Conveyor Systems Ltd, and many others. They showcased a wide range of products and services, including intelligent warehousing logistics systems, equipment integration, safety solutions, consultancy, performance-driven automation, and more.
The 2025 exhibition excelled in providing dynamic spaces for visitors to connect with industry-leading exhibitors – including robot manufacturers, system integrators, and automation and machine vision experts – and explore how the latest technologies can drive significant gains in productivity and accuracy across their operations.
The Robotics & Automation Theatre featured casestudy presentations from exhibitors highlighting the benefits of their products, alongside seminars by industry thought leaders and experts on the latest trends and developments in robotics and automation. Each session concluded with an open forum, allowing visitors to ask questions and explore how cuttingedge technology could be applied to their businesses.
In addition, the IntraLogisteX Theatre and the Sustainable Supply Chain Exhibition Theatre hosted industry experts and exhibitors sharing insights into operational success within their fields. A single visitor
pass granted access to all three shows, enabling attendees to move freely between them under one roof.
The feedback from exhibitors this year was overwhelmingly positive, with many openly expressing their enthusiasm for the show, praising the number of sales leads generated, and highlighting the consistently high-quality footfall.
Comments included:
“It’s so great to hear what our customers and potential customers think about our SAP solutions and services, in person.”
“Unbelievable couple of days at IntraLogisteX Exhibition at the NEC. Non-stop conversations regarding mobile working, asset tracking, and locating with the use of technology.”
And, “Lots of great discussions with many connections, old and new.”
Showcasing the smartest innovations in warehousing and logistics, IntraLogisteX 2026 will take place on 18th–19th March 2026 at the NEC Birmingham, in Halls 6 and 7. The event will once again be co-located with Robotics and Automation, as well as the Sustainable Supply Chain Exhibition.
This is our pick of the best exhibitors from last year’s show, listed here in alphabetical order: Ambaflex, Interoll & Troax. Further details can be found on the next page.
https://www.intralogistex.co.uk
Stationed at Stand 622, Troax made the most of the 2025 IntraLogisteX Exhibition. The team forged new relationships, strengthened existing ones, and captivated a keen audience showcasing how Troax safety systems protect people, property and processes.
Troax has been at the forefront of safety innovation since 1955, developing advanced solutions for warehouse safety, machine guarding, secure storage, and commercial partitioning. With over 70 years of expertise, they have become the global leader in secure partitioning and are trusted by industries worldwide. Their durable, adaptable, and high-performance systems are used across warehousing, automation, logistics, and manufacturing, helping businesses operate with confidence and peace of mind.
Over the years, Troax has earned a strong reputation for creating safer environments across global industries – particularly within the fast-growing automated warehouse sector. Specialising in warehouse and industrial wall solutions, Troax offers a versatile range of products including machine guarding, partitioning systems, cages and mesh shelving.These
solutions serve a dynamic customer base, from pallet stacker manufacturers and system integrators to major players in e-commerce, pharmaceuticals, and logistics.
With a presence in over 40 countries, Troax combines global expertise with local insight to deliver high-quality, industry-critical solutions. Troax is deeply committed to both sustainability and quality, forging strong, long-term partnerships with customers while promoting environmental responsibility. This dual focus ensures that safety and sustainability go hand in handsupporting smarter, greener operations across industries.
For more information, please see below: T 01793 542000 info.uk@troax.com https://www.troax.com/uk
In the dynamic world of the bakery industry, accumulation plays a crucial role in optimising production processes and increasing efficiency. AmbaFlex, as a global leader in spiral conveying and accumulation solutions, offers innovative solutions specifically designed to address the challenges in the bakery market.
Improved efficiency and continuity Accumulation in bakery production lines, such as for cookies in flowpacks, is a proven method to eliminate micro stops in crucial processes, such as the tray-loader (cookies in tray. The AccuVeyor type AVh from AmbaFlex provides a unique way to enhance efficiency in packaging lines for flexible and sensitive packs which are most common in bakery. Thanks to the fully contactless and pressure-free operating principle of the AccuVeyor, producers can finally achieve accumulation in their lines, resulting in a significant boost in the efficiency and Overall Equipment Effectiveness (OEE) of the packaging line.
Sustainability and waste reduction In addition to improving efficiency, accumulation also contributes to
optimising sustainability. Unnecessary stops are significantly reduced, leading to less lost product and packaging material. This is especially in the bakery industry, where the shelf life and quality of products are of great importance.
Practical applications
Multinational producers of bakery products, such as cookies in flowpacks, pastries in stand-up bags/ pouches have experienced that the AccuVeyor type AVh offers significant improvements in their production processes. Due to the contactless and pressure-free operation, these products can be accumulated without damage, resulting in higher output and improved packaging processes.
T +31 229 285130 inquiry@ambaflex.com https://www.ambaflex.com/en
Kardex are well known for the manufacturing, implementation and ongoing support of the Vertical Lift, Vertical Carousel, Horizontal Carousel, and Vertical Buffer Modules. Specifically designed for Automated Storage and Retrieval Systems (ASRS), Order Fulfilment, Buffering and Sequencing and much more!
As a global AutoStore partner, together we offer a high-performance and space-saving storage and retrieval solution to rapidly process small parts orders with autonomous robots. All of which can also be combined with integrated material handling systems and high-bay warehouses if needed from Karex Mlog.
The Kardex portfolio also includes clean room and temperature-controlled storage environments to fit various needs of hospitals, pharmaceutical companies, electronics manufacturers or food & beverage producers. By combining technology
with an aim to improve efficiency, Kardex offers standardised, stand-alone subsystems that are both modular and scalable. With over 140,000 installations, Kardex has a broad existing customer base that counts on first-class after-sales services.
Why is it important to transform warehouse operations with automation?
By automating repetitive and labour-intensive tasks, businesses can significantly enhance operational efficiency, reduce errors, and minimise dependency on manual labour. Automation has transitioned from a luxury to an essential progression, especially in sectors where speed, accuracy, and cost-efficiency are paramount to success.
With labour shortages becoming more frequent, businesses increasingly use automation to overcome workforce challenges and unlock new levels of efficiency and scalability. Automation is not intended to replace workers but to enhance their capabilities, fill gaps, and make labour-intensive roles more accessible and attractive.
In today’s dynamic business environment, companies constantly face the hurdles of managing limited warehouse space, navigating complex inventory systems, and striving for increased performance. At Kardex, we recognise these challenges and present solutions that address them and set you on a path of growth and efficiency. Our commitment is to walk with you through your entire journey, offering scalable, flexible solutions that evolve with your business. With Kardex solutions you can recover up to 80% of floor space and improve accuracy in picking and inventory levels up to 99%.
Kardex Systems UK Ltd, T +44 (0)800 9390800 info.remstar.uk@kardex.com www.kardex.com
As a critical part of its overall strategy to optimise and modernise a large portion of its B2B and B2C storage and distribution operations, Eram Group’s Fashion division has selected Dematic to automate the company’s new distribution centre in Chemillé-enAnjou in the department of Main-et-Loire.
The family-owned company, based in France and operating internationally, wants to consolidate the flows of its footwear activities for its various brands, including Gémo, Eram, Bocage and Mellow Yellow in its new facility covering more than 40,000 square metres in the Loire Valley region.
The Dematic solution features several advanced
technologies with a compact and scalable design. The automation covers both picking and palletising processes and includes a large AutoStore system to enhance Eram’s Group order processing. The system contains 80,000 bins, 84 robots and 16 workstations for order processing. Additionally, a receiving conveyor with two unloaders will unload trucks or containers and a conveyor will sort packages for palletising.
A robot will open cartons while another robot loads totes into the system. For the order picking process, a packing station with a conveyor forwards orders to the dispatch area.
The project is now underway and scheduled to be
Order picking is complex and costintensive, whether in e-commerce or at OEMs. Traditional automation technology reaches its limits here. The Stuttgart-based company Sereact solves this challenge with a complete solution consisting of AI software and robotics: robots understand their environment situationally, develop solution strategies for an efficient pick and place process and implement these autonomously.
Sereact Pick and Place identifies products in real time based on their appearance and selects the
appropriate picking method, taking into account object characteristics such as shape, color or texture –even for complex products such as food, textiles or fragile objects. It then automatically switches between different gripper types such as suction cup or two-finger grippers. One of Sereact‘s own new developments is a patented gripper consisting of three individually functioning vacuum grippers with which the robots can pick up a wide range of products of different dimensions.
Even in complex environments, the software detects the scope and context of tasks. If objects are on top of each other or too close to the edge of the container, the robot moves them into a position where it can grip them ideally.
T +49 711 90777712 contact@sereact.ai https://sereact.ai
Warehouse automation and software specialist Dematic has recently signed a contract with Globalpesca – a leading Italian provider of frozen foods and food services to the hotel, restaurant, and catering industries – to ensure operational efficiencies at a new lowtemperature warehouse for frozen goods.
Headquartered northwest of Milan in Gravellona Toce, Italy’s Piedmont region, Globalpesca S.p.A. is a familyowned business whose roots date back nearly 125 years.
Due to rapid growth in the hospitality and catering industry in Italy, food service companies must be able to manage higher order volumes and be prepared to continuously improve service levels. Globalpesca recognised that automation would support its operations by bringing improvements in two key areas: better planning and managing of its inbound product
process and better handling in storage and restocking of its picking areas.
The Dematic solution is going to be installed in a new warehouse facility adjacent to Globalpesca’s distribution centre in Gravellona Toce. The solution calls for a self-supporting structure designed to meet the load and temperature requirements of the warehouse, the second temperaturecontrolled warehouse adjacent to the distribution centre.
For more information on Dematic, please visit: dematic.com and follow us on LinkedIn and Facebook.
At LogiMAT, held from March 11th-13th, in Stuttgart, Germany, Dematic wanted visitors to come away with a clear sense of the crucial role its software plays when combined with partnerships to design customised solutions for them providing facility agility.
At its Hall 1/H61 stand, the leading provider of intelligent automation technology has showcases that take visitors on a warehouse journey filled with live technology demonstrations, customer service training demonstrations, discussions on where the industry is heading as well as opportunities to meet with some technology partners, that when combined, help customers meet their supply chain ambitions.
Whether its learning how Dematic comes together with fellow KION Group brands, strong partnerships with companies such as AutoStore™, or the recently announced KION collaboration with NVIDIA, visitors can experience first-hand the benefits they reap from a seamless combination of automation, software, industrial trucks and other advanced technologies in an integrated solution developed by Dematic. On display will be an innovative, autonomous shuttle for high-density pallet storage solutions involving the Dematic partnership with EuroFork.
For more information about Dematic, please visit: dematic.com
Rack-clad warehouses where the rack installation columns also act as a supporting structure for the roof and sidewalls are an attractive option for companies that quickly need weather-protected storage capacities. They offer a significant cost advantage over standard buildings with separate rack systems. OHRA also enables its customers to reduce costs further by performing work themselves. Hungarian companies Farkas-Fa, a woodworking business, and timber dealer Sarok-Fa made and mounted the roof constructions for their OHRA rack-clad warehouses with their own wood.
New storage capacities in no time Both companies quickly needed new capacities for storing planks, beams and other wood protected from the weather. Farkas-Fa and Sarok-Fa opted for rack-clad warehouses based on cantilever racks. Warehouse construction and rack assembly are done at the same time and not separately, enabling significantly faster construction times.
Custom solutions
At Farkas-Fa, two cantilever racks each measuring 12.4 metres in length form the walls. As the columns of the OHRA racks are made of hot-rolled
steel profiles, offering high load bearing capacities, they enable large spans for the roof construction: At Farkas-Fa, the distance between the two rows of racks measures 15 metres.
Roof construction
Both companies had the workforce and expertise to build the roof construction themselves. OHRA simply tailored the supports at the racking columns to the respective roof construction in consultation with the two companies.
A new video shows the construction and use of the two rack-clad warehouses: https://youtu.be/ dC8gAB4K5gU
T + 49 2237/64 0 info@ohra.co.uk https://www.ohra.co.uk
Alwayse Engineering Ltd has entered a strategic partnership with Rapid Racking Ltd, the UK’s leading specialist in shelving and racking solutions, to integrate its precision range of ball transfer units into custom tables for roll-on/roll-off capability.
This collaboration between the two UK businesses aims to reduce the risk of physical strain and fatigue for warehousing and logistics workers when loading and unloading shelves, particularly when handling heavy items.
The integration of Birminghambased Alwayse Engineering’s 3016 series ball transfer units into Rapid Racking’s tables also offers enhanced customisation and flexibility for warehousing operators. They can be introduced during the design stage for new storage systems, as well as to improve the efficiency of existing installations.
The ball tables will be available across Rapid Racking’s Rapid 1 workbench range and are available in 1,830x760mm and 1,830x915mm tables.
“We are thrilled to partner with Rapid Racking and begin integrating our ball transfer units into their custom tables,” said James Turner, Head of UK and Ireland Sales at Alwayse Engineering. “Poor manual handling is one of the biggest causes of workplace injury, so finding a safe, efficient and repeatable way to improve processes was a key driver behind the partnership.”
For more information, please visit: www.alwayse.co.uk and www.rapidracking.com/en
AeroBot, the brand-new storage technology from KNAPP, features intelligent storage bots that move in three dimensions: lengthwise and crosswise on the floor and vertically by climbing the racks.
Launched earlier this year at the LogiMAT exhibition – where it won the coveted Best Product award – the AeroBot system is ideal as a combined storage and picking solution for e-commerce, micro fulfilment or omnichannel fulfilment in various sectors, as well as being suitable for applications in manufacturing and industry.
The AeroBots at the heart of the solution use intelligent lidar technology to navigate through the entire system, without having to rely on lines for their routes. Powered by their innovative friction drive technology, the AeroBots move in every dimension: along the floor – also running below the rack system to find the most efficient route – and vertically along the racks.
Maximum storage density
Handling containers weighing up to 35kg in racks up to 12m high, the AeroBots store goods four deep to maximise storage density. “The system can work around beams, slanted walls and sloping ceilings,” explains Ben Carroll, KNAPP’s IT Business Development Manager, “Allowing you to make the most of your existing space, even when integrating
the AeroBot system into an existing building. Controlled by our own KiSoft software,” continues Ben Carroll, “The AeroBots can access any area of the system and work independently of one another, resulting in high availability and reliable operation.”
The AeroBot system was created with simplicity in mind, from startup to maintenance. Its intelligent design means that the solution is easy to implement and goes live quickly. In addition, standardised components simplify maintenance and reduce servicing costs.
The AeroBot system can grow as required. “You can add more storage locations if you need more space,” says Ben Carroll, “or add AeroBots to the system to boost your
throughput. Both factors can be changed independently of each other, allowing you to scale the solution to the precise needs of your business.”
The AeroBot system can also be combined with other technologies in KNAPP’s portfolio including goods-to-person workstations, picking robots, pocket sorter systems, other automated mobile robots (AMRs) or conveyors.
Renowned for its customer service, KNAPP has successful long-term partnerships with clients including Alliance Healthcare, Boots, Clarks, John Lewis, Marks & Spencer, Matalan, Next, The Very Group and Wincanton.
T 01865 965000
sales.uk@knapp.com www.knapp.com
The King’s Awards for Enterprise stand as the highest official UK accolade for business excellence, celebrating outstanding achievements across four vital categories: Innovation, International Trade, Sustainable Development, and Promoting Opportunity through social mobility. These prestigious awards honour organisations that are driving progress, breaking boundaries, and creating lasting impact both within the UK and internationally.
Winning a King’s Award boosts credibility, reputation, and visibility – nationally and globally. It signals excellence to customers, partners, and investors, opening doors to new opportunities.
Winners can use the official King’s Awards emblem for five years, building brand trust and authority. Externally, for companies targeting international growth, the award supports increased exports, partnerships, and investment. Internally, it lifts employee morale, attracts talent, and reinforces a culture of excellence and innovation.
One of the standout moments for winners is the invitation to a Royal reception, followed by a formal presentation of the award by one of the King’s representatives, a Lord-Lieutenant. This not only generates positive media attention but also offers valuable networking opportunities with fellow winners, government officials, and key industry stakeholders.
Far more than just a badge of honour, the King’s Award is a strategic asset – one that can accelerate growth, enhance visibility, and inspire future success.
The King’s Awards are open to UK-based organisations of any size or sector – including businesses, non-profits, and public bodies.
Applicants must:
ä Be based in the UK (including Channel Islands and Isle of Man)
ä Employ at least two full-time staff
ä Be a self-contained enterprise with its own management and accounts
ä Have a strong HMRC compliance record
ä Demonstrate solid environmental, social, and governance (ESG) practices
Entry criteria by category
International trade:
Minimum £100,000 in overseas sales in year one, with strong year-on-year growth over 3 or 6 years (no dips), relative to size and sector.
Innovation:
Must have introduced a new innovation available for at least 2 years, with proven commercial success. Eligible areas: goods, services, marketing, distribution, or after-sales. Innovation must have recovered its costs or be on track to do so.
Sustainable development:
At least 2 years of embedded sustainability efforts with clear, measurable environmental, social, or economic impact.
Promoting opportunity (social mobility):
At least 2 years of support for individuals from disadvantaged backgrounds – e.g., through mentoring, training, or work experience – with clear benefits to participants and the wider community.
The King’s Awards for Enterprise are free to enter, and organisations can apply for as many categories as they wish.
To register, you’ll need to submit your application by 1pm on 9th September 2025.
https://www.gov.uk/ kings-awards-for-enterprise
Global Graphics Software, a developer of core digital printing technologies, received the King’s Award for Enterprise in Innovation for its ground-breaking SmartDFE™ – intelligent digital front end components that drive high-speed, single-pass industrial inkjet presses.
The company developed SmartDFE in response to their customers, who increasingly needed to build inkjet presses that could handle extremely large files while printing at high speed.
Part of the proud team at Global Graphics Software, who have been honoured with a King’s Award for Enterprise for Innovation 2025 for their intelligent SmartDFE™ printing software. From the left: Eric Worrall, VP of Products & Services, Peter Goodwin, Group Finance Director, Justin Bailey, Managing Director, and Ben Gilbert, Engineering Manager
Global Graphics leveraged artificial intelligence to develop software that can process these files in real time as the press operates, enabling faster, more flexible production, reducing delays and minimising waste. A key innovation was embedding print expertise directly into the software, reducing reliance on skilled
operators who are increasingly scarce in the industry.
Managing Director Justin Bailey says, “We are proud to be honoured with this most prestigious award. Developing SmartDFE has been a journey that has seen us transition from supplying software development kits to a complete platform that our customers can develop into their own digital front ends to be sold with their digital inkjet printers.”
SmartDFE has the potential to transform digital printing: with its built-in intelligence, SmartDFE empowers press manufacturers to consistently deliver first-class products without the need for specialised knowledge, and makes adding a print subsystem to a smart factory as straightforward as adding any other industrial component.
T +44 (0)1954 283100 https://www.globalgraphics.com
Kennedy International will be exhibiting at Multimodal 2025 at the NEC in Birmingham on the 17th-19th June at Stand: 1052.
Kennedy International has been revolutionising the transportation industry with its innovative approach to international haulage transport and logistics for over 40 years. As a family run transport company, based in the heart of County Kildare, Ireland, it is ideally located just 30 minutes from Dublin Port to offer a complete haulage service, acting as a one stop shop for all logistical requirements. Kennedy International, also have depots in Newry, Northern Ireland and Liverpool.
Kennedy International brings decades of experience and industry expertise, proudly holding one of the longest-standing histories among Irish haulage companies.
Operating one of the biggest and most modern fleets of vehicles in Ireland, Kennedy International is committed to offering a flexible and comprehensive service at an affordable price.
Their comprehensive range of transport services handle everything from small packages and single pallets to multiple pallets and full loads. Additional offerings include break bulk handling, pick and pack, palletisation, and complete logistics management, overseeing customer goods from their arrival in the country through to final delivery to the end consumer.
For warehousing and distribution, Kennedy offers both indoor and outdoor storage solutions. With adaptable racking and multiple capacities of forklift trucks, they can offer keen rates on both storage and distribution of many packaging types in all types of delivering trailers. They also offer yard space for storage of machines and vehicles, as well as 40ft and 20ft static, onsite containers which can be rented for short or long term, and personal or business use.
All transport services are delivered using the company’s own substantial fleet of over 75 vehicles and over 150 trailers. Each truck is fitted with mobile phones and satellite tracking systems so that they can offer all customers quick response in understanding collection times, delivery times and any other queries.
Three rising stars at Guyhirn-based Bretts Transport are set to embark upon a degree course as part of an ongoing investment programme to futureproof the business.
Wayne Minney, Transport General Manager, Kim Wyatt, Customer Service and Logistics Manager and James Norris, Warehouse Manager will complete the four-year BSc (Hons) Supply Chain Management degree course run by Peterborough-based Anglia Ruskin University.
The course will cover every aspect of supply chain management, with modules including Operational Design and Management, Inventory and Warehouse Management, Finance and Procurement Management, International Supply Chain Management, Forecasting and Decision Making and Contemporary Issues.
In all there are 11 modules to be completed over the four years, each with their own assessments. They will be completed over a series of fortnightly webinars, each three hours long, along with one week of training on campus every trimester.
Over the four years the three will work towards the End Point Assessment which is made up of a 9,000-word report, a 20-minute presentation followed by a 10-minute question and answer session, and a 40-minute viva examination.
As part of the course Bretts Transport has also committed to supporting the three by allocating time in work to study towards the degree, providing a number of work-based opportunities and experience to help them build a portfolio of evidence required by the assessment plan, liaising with the university on the candidates’ progress, and providing a mentor throughout the four-year course.
Please visit: www.brettstransport.co.uk
Kennedy International is fully equipped to meet all your temperature-controlled transport needs with a fleet of over 20 refrigerated units – including straight boxes, meat railers, twin evaporators, double-deck trailers, tail lifts, and undermount gensets. Maintaining precise temperatures from -25°C to +25°C.
Since its founding in 1996, Kennedy International has built a strong reputation as a leader in transhipping. The company offers a full suite of services including container loading and unloading, cross-docking, palletising, and secure storage solutions.
What’s more, Kennedy International and its subsidiary TankTrans Ltd. have vast experience in the carriage of both hazardous and non-hazardous liquids and powders. Tanktrans also hold waste collection permits for all of Ireland, Northern Ireland and the UK. This combined haulage on ro/ro and lo/lo basis amounts to 60 years and is expedited by a large fleet of vehicles and drivers.
For more information, please see below: T +353 1 836 5277 info@kennedyinternational.ie https://kennedyinternational.ie
Aegis Energy, the company building the UK’s first network of clean, multi-energy refuelling hubs for commercial vehicles, today launched the Aegis Trailblazers – a new initiative to recognise and support the fleets leading the transition to clean transport.
The Aegis Trailblazers offers a range of perks for forwardthinking fleet operators who are committing early to clean refuelling. This includes discounted electric charging rates that can be competitive with depot infrastructure, networking opportunities, and the chance to help shape Aegis Energy’s infrastructure plans, from fuel options to driver welfare facilities.
has been a significant barrier to fleet decarbonisation. Aegis Energy is addressing this challenge with its plans to open five public-access multienergy hubs by the end of 2027 and 30 by the end of the decade.
Members will join a growing community of businesses that are responding to increasing consumer and regulatory demand for decarbonisation, getting a head start on the transition and their competitors, whilst helping set the pace for the rest of the industry.
Commercial vehicles contribute 10% of the UK’s total emissions, but a lack of tailored clean refuelling infrastructure
Through its Trailblazers initiative, Aegis will provide early adopters with tailored support, including decarbonisation advice, financial incentives and a voice in where and how its infrastructure is developed. This aims to make the transition more accessible for all operators – from small local van fleets to large mixed-fleet businesses.
Please visit: http://www.aegisenergy.uk
Delegates from the wooden pallet and packaging industry heard how new regulations will soon impact on their businesses at a general meeting of the Timber Packaging & Pallet Confederation (TIMCON).
Held in Manchester at the end of February, the event featured presentations on the development and implementation timelines of new UK and EU packaging rules. In an update on the Packaging & Packaging Waste Regulation (PPWR), Marcus Kirschner of German association HPE said European recycling targets are set to increase to 25% this year and 30% by 2030.
As the EU continues to develop the new rules, Kirschner said the packaging industry was seeking greater clarity on PPWR definitions – and acknowledged the role of continued industry lobbying by organisations such as HPE, FEFPEB, and TIMCON in securing key exceptions and special considerations for wood pallets and packaging.
Meanwhile, David Daw of environmental compliance specialist Valpak outlined the expected impact of Extended Produce Responsibility (EPR) regulations on the UK
industry, adding that finalising complex details could lead to a delay in the implementation of the new regime.
The meeting also featured updates on the wooden pallet and packaging sector from Heikki Vidgren of AFRY – which produces TIMCON’s monthly market index – and the worldwide timber market by Rob Driessen of pallet and packaging wood purchasing specialist Connec3.
Jeff May, Deputy Chief Executive of the Construction Products Association (CPA),
gave an overview of the construction industry’s priorities including its sustainability goals of decarbonising industry and ensuring compliance with government expectations.
TIMCON President, John Dye, said, “TIMCON meetings always aim to provide key updates for our membership, and our speakers this time gave essential insights into the changes in packaging rules that will affect their businesses in the months ahead. This meeting also showed how important our engagement in the lobbying process is to achieving positive results for our business – and the fantastic turn out shows how much our members value the opportunity to hear first-hand and discuss updates on regulations and other aspects of the business.”
“Working closer with pallet and packaging using industries, our forest-based sector counterparts, and our international colleagues makes all our businesses stronger and in today’s increasingly complex global market, is more important than ever.”
For more information or images, please contact TIMCON: T +44 (0)116 274 7357 info@timcon.org
In late summer 2025, Faller Packaging will start producing folding cartons at its new site in Horsens, Denmark. The company is thus implementing a project that was already announced in April 2023: the establishment of an additional production facility for the Nordics. The aim is to reliably meet the growing demand.
The new plant will complement Faller Packaging’s existing facility in Hvidovre, Denmark, and is a targeted response to the growing demand for pharmaceutical packaging. The plan is to increase total capacity in Denmark to around 900 million units per year. In Horsens alone, the packaging manufacturer plans to produce up to 600 million folding cartons per year.
The decision to open a second production site is part of the growth strategy for the folding carton division of the Faller Packaging Group. The packaging specialist had already taken over a 5,700 square metre building complex in Horsens in 2023 and modernised it extensively. The production facility will now go into
operation in stages – the future employees will first undergo extensive training in Hvidovre.
More capacity, more customer proximity
“The new factory is lean and combines efficiency and quality. This not only allows us to significantly increase capacity, but also strengthens our customer service on site,” explains Managing Director Christian Holmskov. A major advantage of the new plant is that the modern full-format printing presses enable a much higher output per sheet than the half-format technology previously used.
T +49 7681 405 0 info@faller-packaging.com www.faller-packaging.com
Packaging manufacturers are under pressure to meet increasingly complex brandowner demands with impeccable accuracy while maximising productivity, quality and sustainability. Flexible Packaging Europe (FPE)’s European FlexPack Summit, took place February 24th to 26th in Barcelona, Spain, addressing these challenges head-on. BW Converting demonstrated how the latest innovations under its Paper Converting Machine Company (PCMC), Hudson-Sharp and Baldwin Technology brands have set new standards to propel the industry forward.
The event, which took place at the five-star Torre Melina Gran Meliáh hotel, was the first FlexPack Summit where suppliers joined converters for three days of presentations from industry and regulatory experts who covered a range of topics relating to global market developments, trends, sustainability issues and current European legislation.
Among the dozen inaugural exhibitors, BW Converting showcased its PCMC ION digital hybrid press, Hudson-Sharp Ares stand-up pouch line and Baldwin Defender® 100% inspection system.
BW Converting’s PCMC ION hybrid printing platform provides the ability to produce larger digital runs costcompetitively, meeting market needs for wider, faster printing with highest quality. It is designed to handle up to 127 metres per minute with web widths of 914, 1,066 and 1,320 millimetres for paper, film and board applications. ION is a fully modular system with digital CMYK and flexo print stations that can be custom configured to meet a variety of customer challenges.
Click here to book a slot with McGill and visit: https://www.bwconverting.com for more information.
ThePackHub was excited to announce the finalists for the 2025 Packaging Startup Awards, which celebrated the cutting-edge innovations from startups that are transforming the future of packaging. Sponsored by Ocado Retail, the prestigious competition culminated in a highly anticipated awards ceremony at Packaging Innovations & Empack 2025, held at the Birmingham NEC on February 13th, 2025. These awards spotlight the most impactful packaging solutions from around the world, with finalists spanning five categories: Alternative Materials, Connected Packaging, Refill & Reuse, Waste Reduction, and Online.
This year’s competition has seen an impressive increase in submissions, showcasing the entrepreneurial spirit reshaping the packaging landscape. A distinguished panel of 20 experts from leading global brands has selected the finalists,
whose forward-thinking solutions are set to reshape packaging and drive sustainability. Notable finalists include Blue Ocean Closures, which is set to transform packaging with its fully recyclable cellulose fibre closures, and Kelpi, creating biodegradable seaweed-based alternatives to plastic. PulpaTronics is pushing the boundaries of smart packaging with interactive features, while ecoSPIRITS is reinventing the spirits industry with a closed-loop distribution system.
The event promises to be an exciting and insightful experience, bringing together the brightest minds in packaging innovation. For more information on the Packaging Startup Awards 2025 or to attend the awards ceremony at Packaging Innovations & Empack 2025, register as a visitor today
Please visit: https://thepackhub.com
Gerhard Schubert GmbH and the Berlin-based Berndt+Partner Group packaging consultancy are combining their expertise with the Packaging Competence Centre (PCC). The new organisation brings together experts in regulation, packaging design, materials and automation technology. The aim of the PCC is to advise manufacturers on the development of sustainable packaging and to find viable solutions for implementation. The focus is on meeting the challenges of PPWR as well as other sustainability issues.
sustainable and to reduce the negative environmental impact of packaging waste. However, it presents manufacturers with major challenges due to extremely tight deadlines, different implementation timelines and the current lack of detailed regulations. Companies need to evaluate as quickly as possible how they will respond to the often complex requirements. This can have far-reaching consequences for their packaging and production processes – and requires efficient, compliant implementation, for which PCC provides a wide range of support.
The EU Packaging and Packaging Waste Regulation (PPWR) aims to make the packaging industry more
Please visit: www.schubert.group
In its latest phase of growth plans, familyowned plastic packaging manufacturer Measom Freer has relaunched its company website to showcase its range of sustainable packaging solutions to a wider audience.
The new website promotes the company’s products and services, sharing their commitment to sustainability and extensive knowledge of the plastic packaging sector.
Established in 1937, Measom Freer is a fourthgeneration family run business specialising in the design, manufacture and supply of injection and blow moulded plastic packaging.
Producing more than 20 million plastic bottles, scoops, closures and containers each year from its state-of-the-art facility on Chartwell Drive in Leicester, the company prides itself on delivering
The website features professional videos and images illustrating the products and services available to customers, improved navigation
and search functions together with an upgraded resource centre providing visitors guidance on current plastic legislation and useful information.
Measom Freer production manager Ben Freer commented, “As a UK packaging manufacturer that prides itself on delivering an excellent customer experience, we needed a new website that could showcase our exceptional service and manufacturing capabilities to our existing and future customers.”
“We have ambitious plans to grow the business over the next 12 months. With the recruitment of an experienced business development manager and investment in a new blow moulding machine the new website will support our strategy.”
To visit the new website go to: www.measomfreer.co.uk
XPO, a leading provider of innovative and sustainable end-to-end logistics solutions across Europe, held its fifth annual UK Female Driver Forum this week. The forum provided a safe space for female drivers to bring matters of concern to the attention of XPO’s senior management and to network.
Workplace, which is at the heart of XPO’s workplace equality and diversity values. It also hosted an interactive session for female drivers to provide operational feedback to help the company best support them.
As in previous years, all XPO Logistics female drivers were invited to attend the forum, which took place at the company’s national distribution centre in Crick, Northamptonshire. This is the second UK Female Driver Forum, which took place in 2024. Since the first one, held in April, XPO Logistics has increased its number of female drivers by 20 in the UK and Ireland and hopes to boost this number even further this year.
The forum covered several topics, including Neurodiversity in the
XPO Logistics is a leading innovative supply chain company in Europe, offering end-to-end logistics solutions that combine fulltruckload, less-than-truckload, pallet distribution, last-mile delivery, global freight forwarding, and warehousing services. The company tailors its solutions to the specific needs of its customers in a wide range of industrial and consumer sectors.
For more information, visit: xpo.com and europe.xpo.com.
From airside to landside, DIMOS pallet movers ensure safe and efficient handling of ULDs throughout the entire airport terminal. While retaining the standard model, the system service provider has developed two new versions with scales and lift tables. Carrying out typical stationary processes with a flexible vehicle saves users space, time and, most importantly, money.
Handling unit load devices (ULD) at airports requires high levels of flexibility and efficiency, as large quantities of baggage and freight must be loaded as quickly and safely as possible in a confined space. Pallet movers are commonly used for transporting ULDs in the terminal. However, Petersbergbased machine manufacturer
DIMOS has modernised its standard model to create two new variants and now offers a product range that can also be used landside. The standard version with crosswise seat cabin and 360° steering remains unchanged but also formed a solid basis for development. With a load capacity of up to 7t, the entry-level model lifts the ULDs to 508mm so that they can be seamlessly transported to the dollies. The truck’s three characteristic forks have been replaced in the new variants in order to expand into further areas of application.
For further information on DIMOS’ air cargo solutions, please visit: https://www. dimos-maschinenbau.de/ de-de/luftfrachtlogistik
UKPackaging Expo is poised to become the UK’s leading event for the packaging industry. Strategically located in Manchester – the ideal location for an event focused on innovation, collaboration, and business growth.
Manchester is known as the beating heart of the UK’s manufacturing and industrial sectors, as well as the birthplace of the industrial revolution, boasting innovation and progress. By hosting the event in this dynamic city, UKPackaging Expo can better serve the packaging needs of businesses across the UK, particularly in the North, where much of the country’s manufacturing and industrial activity takes place.
What’s more, with its rich legacy of industrial innovation and vibrant, forward-thinking economy, Manchester offers a unique environment for collaboration and discovery, boasting a diverse and growing economy that is ideal for an event focused on shaping the future of packaging.
Known as Europe’s leading event dedicated to platforming sustainable packaging solutions, UKPackaging Expo 2025 will take place on September 3rd and 4th 2025 at Manchester Central, Hall 1, for two days of innovation, sustainability, and business growth – bringing together the North’s industry leaders and future trends.
This year promises to be the event’s most dynamic yet. Hosting retail, e-commerce, food & beverage, beauty, and pharmaceutical industries all under one roof, the event will offer tailored insights, state-of-theart technologies, and key industry connections to help you stay ahead in an ever-evolving market.
The event is dedicated to connecting businesses with cutting-edge technologies, offering access to eco-friendly materials, smart automation, and costeffective solutions that improve efficiency and drive profitability. So, whether you’re looking for insights into sustainable packaging trends, innovative design concepts, or supply chain optimisation, UKPackaging Expo 2025 is the place where forward-thinking businesses come together to inspire and lead the industry forward.
Offering unparalleled opportunities for brands and manufacturers to connect, innovate, and grow, the event brings together leading minds, cutting-edge technologies, and vital business networks.
UKPackaging Expo 2025 will feature: 100+ Innovative Exhibitors and 2,500+ attendees: The event will feature a wide range of exhibitors at the forefront of the packaging industry ready to showcase their latest solutions to a highly engaged audience. From launching a ground-breaking product, to unveiling sustainable packaging solutions, or demonstrating state-of-the-art technologies, UKPackaging Expo 2025 will provide the ideal platform to drive brand awareness, forge valuable partnerships, and gain a competitive edge in the evolving packaging landscape. The event will be a great place for brands to extend their reach across many industries, generate high-quality leads, and take advantage of the opportunity to place their business at the centre of industry transformation.
There will be suppliers, manufacturers and service providers at the event, exhibiting from a number of key sectors including Packaging Materials, Packaging Machinery & Equipment, Printing & Labelling, Supply Chain & Logistics, Sustainability & Recycling, Design & Innovation, Food & Beverage Packaging, Pharmaceutical & Healthcare Packaging, and Retail & E-Commerce Packaging.
20+ Inspiring Speakers & Thought-Provoking Panel Debates: Don’t forget to visit the highly anticipated Future Packaging Conference. It will be the ideal place where attendees can gain insights and inspiration from the brightest minds in the industry.
One session not to miss taking place on the 4th September is ‘What do EPR, RAM, and disposal fees really mean for your packaging strategy moving forward?’ taken by Michael Jennings, Policy & Affairs Advisor at Beyondly. The session will explore the challenges, opportunities, and the long-term translation of EPR legislation and what it means for brands, suppliers, and the broader packaging ecosystem.
Networking Opportunities: The event will offer attendees the opportunity to network with procurement managers, packaging engineers, and C-suite executives from major brands. With over 70% of attendees having direct purchasing power, valuable conversations and sales opportunities are guaranteed! This is also a great opportunity for brands to showcase themselves to a highly targeted audience of professionals actively looking for solutions.
There will also be many live demonstrations and interactive experiences where the latest materials, technologies, and solutions will be showcased, highlighting the next-generation in packaging.
UKPackaging Expo is known as being more than just an event; it's seen by many as a hub for innovation, education, and collaboration. It’s not just another industry show, it is making noise, and for a good reason. The event is building something bold, focused, and designed around the industry, the brands, buyers, and packaging professionals who are shaping the future.
Mark your calendars for the 3rd-4th September at Manchester Central. From sustainability to shelf impact, from circular formats to connected packaging, this is where the UK’s packaging community comes together to see what’s new, what’s changing, and what’s actually working. Secure your FREE ticket today for the UKPackaging Expo 2025!
https://ukpackexpo.co.uk
Countrywide Freight Group is a market leader in GB-IrelandGB transport. With depots in Gateshead, Manchester, Melton Mowbray, London, Belfast and Dublin, we offer part load and full load services across Eire and Northern Ireland.
We are proud to count some of Europe’s biggest names in packaging amongst our customer base. Our packaging customers know that outsized freight and non-standard pallets don’t faze us. They rely on us to deliver on time to Ireland’s largest consumer goods manufacturers, knowing that we will take care of the booking in process from start to finish.
Our 50 years’ experience in the market means we take the hassle out of customs too, however complex the declaration.
Group Sales Director, Diane Carroll, says, “Our customers stay with us for our personal service, reliability and great value for money – all increasingly critical in the fast-paced world of FMCG packaging. We’re delighted to be exhibiting at UK Packaging Expo – our first dedicated packaging event and an opportunity to demonstrate our service excellence to the indirect goods market.”
Meet the team at Stand B28, or visit our website to chat to us sooner.
T +44 (0)330 383 0032 sales@countrywide-freight.co.uk www.countrywide-freight.co.uk
A new campaign promoting metal packaging recycling has been introduced by Leicestershire County Council. In a bid to improve recycling rates, households across the county are being encouraged to recycle their metal packaging including food and drink cans, aluminium wrapping foil and foil trays, as well as empty aerosols and metal screw tops.
Spearheaded by the Aluminium Packaging Recycling Organisation (Alupro), the ‘MetalMatters’ programme will use targeted social media and digital messaging to communicate the widespread benefits of recycling metal household packaging.
Starting in January, it is hoped that within the six-week long campaign, Leicestershire County Council can engage with the majority of the 316,000 households in Leicestershire. Since its launch in 2012, more than 128 local authorities have adopted MetalMatters, with recycling rates improving as a result.
GEN GRINDERS is a leading Turkish manufacturer specialising in high-tech plastic packaging for the global spice industry. We produce premium-quality, sustainability-focused grinders, PET jars, and closures designed to meet the highest industry standards.
As a BRC packaging-certified company, we proudly export to over 40 countries, supplying a wide range of clients including co-packers, major global spice brands, and packaging solution providers. Our strong focus on quality, innovation, and environmental responsibility makes GEN GRINDERS a trusted partner in the international packaging market.
Our headquarters and production facility are located in Izmir, Türkiye, supported by dedicated sales offices in Austria and the UK, ensuring close communication and efficient service for our European clients.
With in-house moulding and R&D capabilities, we offer custom solutions including tailor-made product development, rapid prototyping, and
short lead times-enabling our partners to bring their products to market faster. Whether you're looking for a standard packaging solution or a unique design that fits your brand, GEN GRINDERS delivers with quality, flexibility, and speed.
Choose GEN GRINDERS for packaging solutions that combine advanced manufacturing, sustainable practices, and global reach.
Contact mert.artun@gengrinders.com info@gengrinders.com https://gengrinders.com
Jim Farquhar, Sales Director at CSL, discusses the issue of excess packaging use, the reasons behind it and how this can be addressed using technology.
Funded by the metal packaging industry, MetalMatters aims to educate householders about the benefits of metal packaging and encourage them to recycle. Designed to support recycling schemes, MetalMatters can be run by any local authority, either region-wide, by collection round or even by demographic targeting.
For more information about MetalMatters, or to register interest, please visit: www.metalmatters.org.uk
For ecommerce businesses, 3PLs, warehouses, and fulfilment centres, lowering your carbon footprint is not just a goal but also a responsibility. Some positive progress has already been made with many major ecommerce businesses now avoiding plastic and using paperbased packaging instead. But there is still much room for improvement, particularly in terms of the amount of packaging used.
The scale of the problem
More often than not, consumers end up with boxes that are way oversized compared with the size of the product they’ve ordered. The more the ecommerce industry grows, the worse the problem is becoming. Paper packaging production has increased by 65% throughout the
past two decades,1 equating to billions more trees being cut down each year.
It’s great that the UK ecommerce industry is booming. But with this increase, it’s more important than ever to consider the environmental and financial impact of sending goods to the customer.
For more information, please visit: https://conveyorsystemsltd.co.uk
1 https://www.bbc.com/worklife/ article/20240415-why-your-small-goodscome-in-gigantic-boxes
Atlas Copco, a leading brand in the beer industry for compressors and N2 generator systems, recently introduced a new innovative solution for the beer bottling process – the Beer Foam Separator (BFS 900). Built to be used in combination with its industry 4.0 ready GHS VSD+ screw vacuum pump, the addition of the beer foam separator is primed to improve energy efficiency, reduce lifecycle costs and lower the rejection rate of over and underfilled bottles in the process.
Better protection, cleaner processes, higher savings The beer foam separator was designed and developed in partnership with leading brewery customers and in direct response to the excess foam production that hampered the beer filling process. The high amount of foam generated at the end of the filling process would enter the vacuum line and disrupt the process leading to poor quality, reduced output.
KM Packaging, a leader in innovative flexible packaging solutions, is celebrating 40 years of delivering reliable, cuttingedge packaging across many varied sectors, including fresh produce, ambient, chilled and frozen convenience foods, confectionery, and snacks.
This milestone highlights four decades of dedication, growth, and strong partnerships that have consolidated the company’s standing in the industry.
Since its inception in 1984, KM Packaging has established a reputation for close collaboration with customers, ensuring their products are wellprotected, presented, and preserved.
KM Packaging’s ability to adapt to the ever-changing market has fostered long-term loyalty, with key customers staying with the company from its inception. This enduring trust reflects KM’s commitment to providing highquality, tailored packaging solutions.
The company’s longevity and market leadership are also attributed to its
robust supply partnerships, which have been carefully nurtured over the years. This strategic approach allows KM Packaging to offer one of the most comprehensive ranges of lidding films around the world.
Looking ahead, KM Packaging is committed to sustainable growth, ensuring long-term business viability.
The company’s expansion into Australia and more recently North America highlights its commitment to growing its global presence while maintaining exceptional customer service.
For further details, please contact: T +44 (0)1832 274944 contact@kmpack.co.uk www.kmpackaging.com
Tough design meets smart functioning
The BFS 900 is fabricated from 304 stainless steel for high durability with an auto-draining tank and associated logic control system. When the excess foam enters the vacuum system, it is effectively collapsed in the foam separator by a calming section with a large diameter for foam settling. The rising liquid level is detected by appropriate sensors and an automatic separation process is initiated by an air lock consisting of electro-pneumatic actuators and a receiver tank to enable drain in continuous operation.
Please visit: www.atlascopco.com
The food and packaging market is facing major challenges: longer transport routes and growing demands on products today require better shelf life. In addition, there are increased demands in terms of environmental compatibility, legal requirements and consumer wishes. In order to fulfil these criteria, it is necessary to carry out leak tests on packaging during production to prevent leaks and damage. These tests ultimately serve to ensure product safety and consumer protection –such as in the case of vacuum-sealed coffee capsules and packaging. Here, manufacturers attach particular importance to brand-relevant quality features such as freshness, color, creaminess and aroma and flavour intensity.
Expertise in the food and packaging industry
Established suppliers of leak testing systems have proven to be reliable partners for coffee producers. With its extensive expertise in the food and packaging industry, INFICON, for example, has tried-and-tested products for this application in its portfolio. The easy-to-use systems are used where
quality requirements are particularly high: for coffee packaging. “This is not least due to the special properties of the popular hot beverage,” argues Arman Khazali, Operations Manager at Italian coffee manufacturer and INFICON customer Bialetti from Coccaglio, in the province of Brescia. According to Khazali, coffee is a luxury foodstuff that, like wine, is based on a raw material. Due to natural influences, such as the climate or soil conditions, the fruit is not identical for every harvest.
For more information about INFICON and its products, please visit: www.inficon.com
Macsa id UK highlighted a wide range of advanced coding and marking equipment at PPMA 2024 last year. Amongst the machines on show were the high speed SPA2 NANO UV laser system which offers high contrast, damage free operation, and clean and uniform marking making it ideal for a variety of delicate or difficult substrates including flexible packaging films. There was live demonstrations of a conveyor mounted Macsa low cost idTIJ thermal inkjet printer. With significant ease of use and low maintenance benefits, the idTIJ is aimed at fast, high resolution applications. Macsa’s affordable SPARK small character laser coder and Fiber laser coder for marking aluminum beverage cans were also highlighted.
Macsa’s versatile SPA2 NANO UV laser system is compact, lightweight and simple to install and delivers
a high quality beam that is used for precision marking of delicate or difficult substrates such as flexible packaging films or high strength, high heat resins. The machine’s digital galvos and drivers together with new dual processor facilitates easy integration in the most demanding production lines.
The NANO UV can mark multiple materials with similar parameters, reducing the need for operator intervention and increasing line up time and efficiency. It is capable of generating greater contrast for more appealing aesthetics and improved readability of 2D codes. Through suppressed heat effects, burns and yellow tinting are eliminated which allows for a virtually perfect finish.
Please visit: www.macsa.com
Brothers Lloyd and Jim Kershaw join family business
Macpac (www.macpac.co.uk)
– one of the UK’s largest family run thermoformed packaging manufacturers has welcomed Lloyd and Jim Kershaw to the business.
The sons of owner and Managing Director, Graham Kershaw, have joined Macpac as part of a longterm plan designed to drive the business to the next generation of sustainable packaging.
Founded by the Kershaw family in 1973, Macpac has been an independent and highly innovative thermoforming business for over 50 years.
The brothers bring nearly two decades combined experience in design, marketing, and engineering, specialising in sustainability from outside the industry.
The brothers certainly achieve this with Jim joining after spending nearly a decade working in the pharmaceutical marketing consultancy industry. His master’s degree in environmental
sciences and clean technology bring insights into the needs of clients and patients in the medical sector, whilst having a deep knowledge of modern manufacturing.
Jim is excited by the challenges of developing new production techniques to keep improving Macpac’s environmental strengths.
Graduating from Cambridge University with a master’s in general engineering, Lloyd spent nine years as a Chartered Structural Engineer and Associate to a prestigious London design studio.
For product enquiries please contact: Macpac, contact: 0161 4421642 or email: info@macpac.co.uk.
Narrow web printing ink specialist Pulse Roll Label Products (Pulse) has welcomed Przemysław Juszczyk to its team in Poland, strengthening the company’s position in the country and beyond.
Mr Juszczyk brings vast experience to the narrow web ink manufacturer’s operation in Poland – Pulse Polska. He has a strong background in print, having trained in printing, worked at a printing house, and most recently served as a sales manager at Reprograf Grafikus for almost 15 years.
In his new role, Mr Juszczyk will support Pulse’s customers in Eastern Poland and Slovakia. Colleague Artur Mansfeld, Pulse Polska Sales Manager, will focus on serving customers in Western Poland and Czech Republic.
Pulse Roll Label Products Managing Director Gary Seward said, “We are delighted to welcome Przemysław to the Pulse family. His experience and skills make him a highly valuable asset to the Pulse Polska team and our growth ambitions for the region.”
The Pulse Polska facility was formally
opened at the start of 2024, giving the narrow web ink specialist a direct presence in the country as well as growing its position in Central and Eastern Europe.
For information on Pulse Roll Label Products and Pulse Polska, please visit: pulserl.com
The Pulse Polska team can be contacted directly on: sales@pulsepolska.pl.
A Leicester based family-owned plastic packaging manufacturer has appointed a new Business Development Manager to support its strategy to diversify into new markets.
Measom Freer has appointed Craig Edwards to the role of Business Development Manager to help drive strategic growth and generate new business within the chemical market.
Craig brings a wealth of industry experience to the business having previously worked at plastic packaging manufacturer Faerch UK, and more recently, packaging distributor Pont Packaging.
As part of his role, Craig will be responsible for shaping strategy and product development to generate new business in the chemical market with a focus on sectors such as janitorial and car care.
Craig will also work closely with the production team to roll out a ‘On Time in Full’ inventory service to customers. The new offering will provide customers with ‘their allocated’ products as and when they are needed, with manufacturing to replace
stock as it’s taken, reducing order fulfilment times.
Established in 1937, Measom Freer is a fourth-generation family run business specialising in the design, manufacture and supply of injection and blow moulded plastic packaging.
Producing more than 20 million plastic bottles, scoops, closures and containers each year from its state-of-the-art facility on Chartwell Drive in Leicester, the company prides itself on delivering quality, sustainable packaging solutions.
For more information, please visit www.measomfreer.co.uk
KM Packaging, a global provider of flexible packaging and lidding films, is pleased to announce the appointment of Matt Gilks as Business Development Manager.
In his new role, Matt will serve as a key contact for clients seeking optimal packaging solutions within the UK and Ireland. Commenting on his appointment, Matt said, “Together with the team, I navigate the technical complexities, ensuring we meet all food-grade requirements and lead times while truly understanding the customers’ requirements to provide a positive packaging experience.”
staying ahead in a fast-paced industry will be key, but I’m confident in my ability and proactive approach.”
He added, “I have always been passionate about packaging, and joining KM Packaging has been a long-time aspiration. The company’s skills, knowledge, and the quality they deliver to customers set them apart in the industry.”
Looking forward, Matt stated, “Managing client expectations and
Outside of work, Matt enjoys an active lifestyle. He shared, “I love mountain biking - the bigger the hill, the better. I also enjoy playing and watching football and spending quality time with my wife and our three sons.”
For further details, please contact: T +44 (0)1832 274944 contact@kmpack.co.uk www.kmpackaging.com
A growing number of businesses are exploring automated projected safety signage as a more effective way to highlight hazards, reduce accidents and improve workplace safety.
That’s according to Projected Image, leading UK suppliers of LED gobo projectors and experts in providing projected safety signage for businesses in sectors ranging from warehousing and logistics to automotive and food and beverage.
The specialists say that by combining powerful LED gobo projectors with motion or light sensors, projected signage is proving extremely beneficial in improving safety for many workplaces.
“Traditional painted and printed safety signs can easily be ignored or missed, especially in busy environments where they become faded or viewed so often that workers become subconsciously ‘blind’ to them. However, by automating signage – and using projections which are bright, clear and difficult to ignore – workplaces are not only transforming their workplace safety, but making their facilities more efficient too.” says Ian Spoors, Managing Director of Projected Image.
According to Projected Image, projected signs are especially impactful in areas where traditional floor or wall signage is likely to become worn, obscured or ignored. Projected signage remains clear even in low light, on wet surfaces or where layouts frequently change.
In sectors like logistics, manufacturing, food production and cold storage – which typically
operate within busy warehouses or facilities – automated projected signage is more likely to be adhered to as it’s only visible when it’s needed most.
“Automated projected signage consists of a gobo projector shining a bright safety message only when triggered by a sensor, such as when an approaching forklift or pedestrian is detected. By only projecting safety messages when needed, automated projected signage systems improve sign visibility, reduce sign blindness and help teams respond to potential risks in real time, creating a safer workplace!” adds Ian.
Projected Image have implemented projected
signage for a wide range of businesses across the country, including leading names like Coca-Cola, Mercedes-Benz and Dunbia.
As projected signage becomes increasingly popular, more and more businesses are pairing it with automation too.
“We recently delivered an automated system for a leading manufacturer of renewable energy. The system warns pedestrians of forklifts when approaching roller doors, which has significantly improved their health and safety measures. Signs are brighter and clearer, less likely to be ignored and are helping to reduce the risk of accidents.” says Ian.
Projected Image are the only business in the UK who supply both powerful, IP-rated LED projectors and the bespoke gobos which go in them.
Their durable LED projectors offer up to 50,000 hours of lamp life, providing maintenance-free safety messaging.
“Automated projected signage isn’t just a visual upgrade for businesses – it’s a smarter, more responsive way to communicate safety messages. By combining bright, clear signs with automation, businesses can manage workplace risks in a way that traditional signage simply can’t.” concludes Ian.
More information about Projected Image can be found at: projectedimage.com