
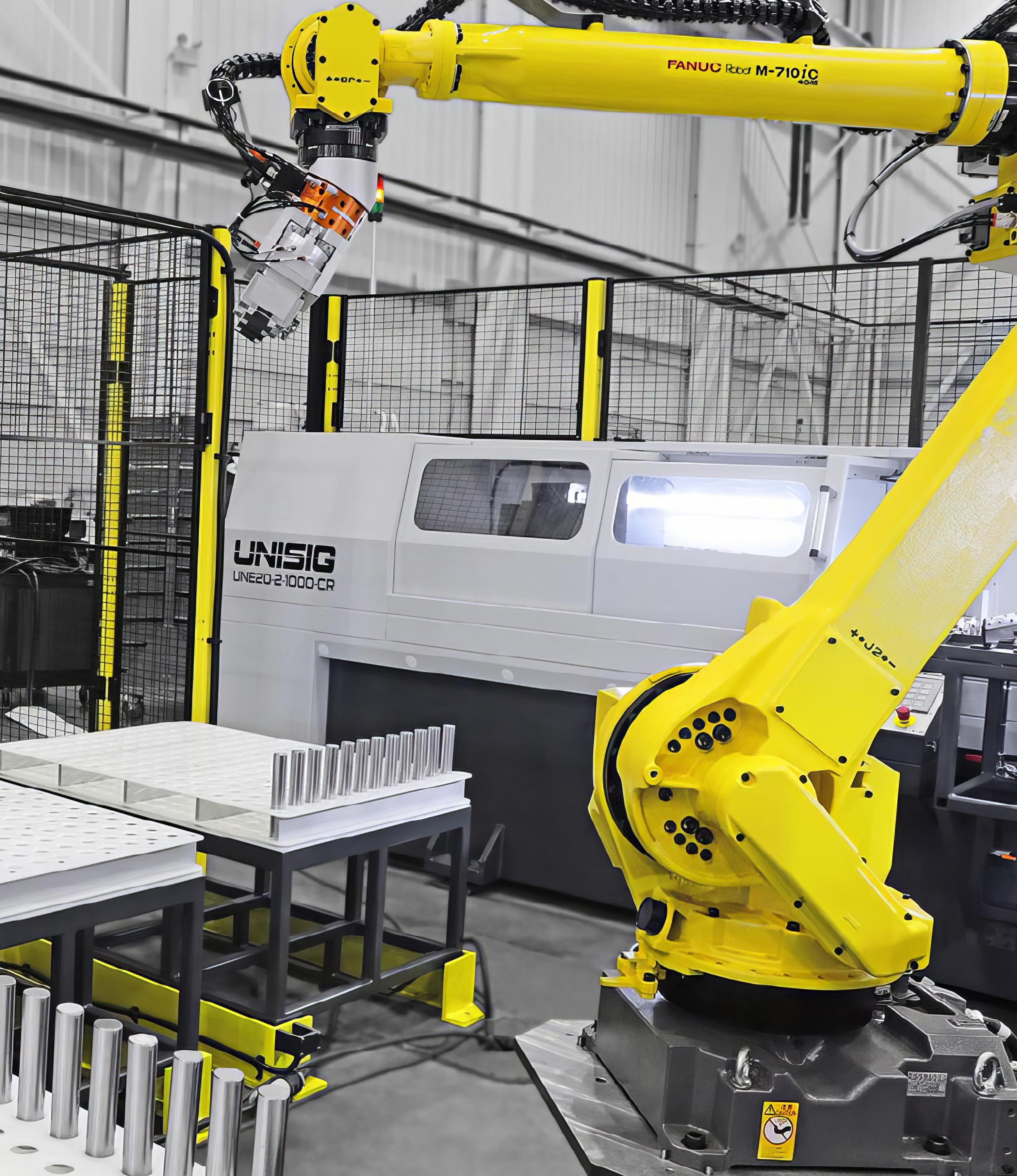
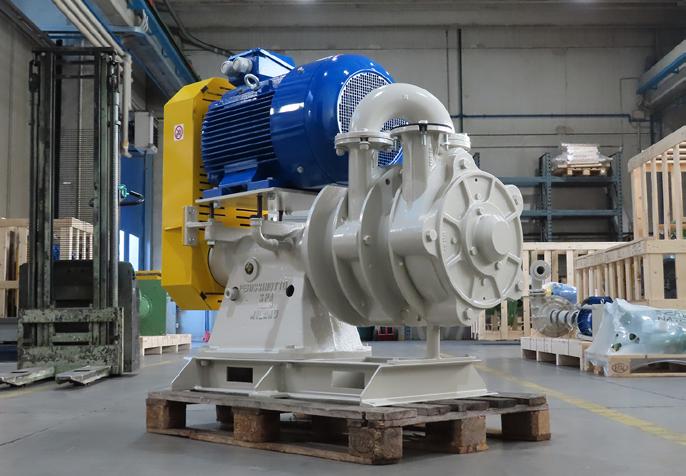
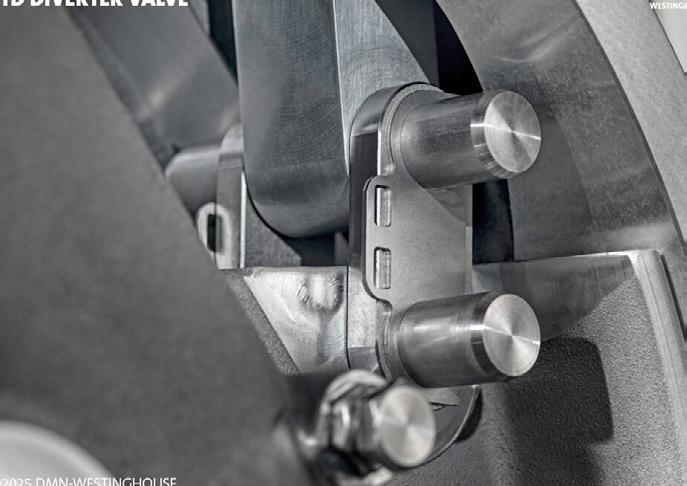
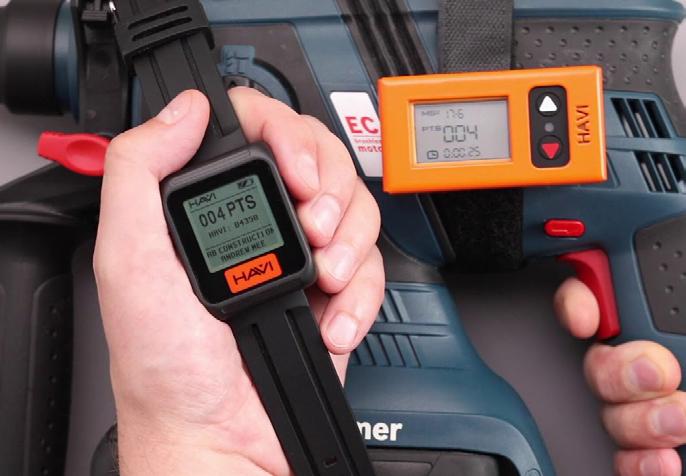
Written By LS Wastewater & Process Consulting Ltd for Leachate Solutions
PFAS, short for per – and polyfluoroalkyl substances, have become a major concern for regulators and the water industry, which means it will now impact on your business. Known as ‘forever chemicals’ due to their persistence in the environment, PFAS pose complex challenges for manufacturers, water authorities, and industrial dischargers alike.
Through our associate consulting company, LS Waste Water & Process Ltd, – Leachate Solutions Ltd works closely with clients across various industries to identify, assess, and manage PFAS risks in wastewater and process systems. Whether you’re in manufacturing, food processing, metal finishing, or chemical production, PFAS may be silently accumulating and contaminating your effluent streams, and regulators are paying attention.
What’s the problem for industry?
In the UK and across Europe, regulatory pressure is mounting. The Environment Agency has increased monitoring of industrial discharges for PFAS compounds, and tighter discharge limits are anticipated under evolving UK REACH, water and environmental legislation. Water companies are now seriously reviewing discharge consents and analysing effluent streams for PFAS contamination.
Industry are increasingly being held accountable not only for their direct discharges but also for contamination passed along through supply chains. This means all industrial processes could be liable for current and past PFAS discharges found in their process wastewater. Ignoring the issue is no longer an option!
At Leachate Solutions Ltd we offer a structured PFAS Assessment Pathway:
1) Site review: We look at your processes, raw materials, supply chain, and historical waste profiles to assess PFAS risk.
2) Targeted sampling & analysis: Using accredited laboratories, we conduct wastewater sampling focused on key PFAS compounds.
3) Gap analysis: We compare your current wastewater treatment against potential PFAS removal needs.
4) Strategic roadmap: A tailored action plan outlining mitigation options, timelines, and cost-benefit scenarios.
5) Regulators: We can help work with your regulator or Water Company to ensure agreement between all parties.
This approach helps our clients stay ahead of regulation and implement solutions that are pragmatic, scalable, and cost-effective, without affecting your day-to-day operations.
What is PFAS and why should you care?
PFAS are a group of thousands of synthetic chemicals used for their heat resistance, water repellency, and non-stick properties. They are found in everyday products, including cleaning products, water-resistant fabrics (umbrellas, raincoats), grease-resistant paper, nonstick cookware, personal care products, (shampoo, dental floss, nail polish, eye makeup), stain-resistant coatings (carpets, upholstery, fabrics) and electronics.
While PFAS make products more durable, they also resist natural breakdown. Once discharged to trade effluent, sewer or foul drains and subsequently released into the environment, often through wastewater discharge they can easily contaminate groundwater, surface water, and soil.
More importantly, due to the bioaccumulation effect, PFAS exposure has been linked to serious health concerns, including developmental issues, immune system disruption, and certain cancers.
For industrial operators, this presents issues with regulatory compliance.
What’s being done to sort this problem?
Managing PFAS is challenging because traditional wastewater treatment technologies, like activated sludge or standard filtration are not effective in removing them.
However, several treatment and mitigation strategies are emerging, including:
t Granular Activated Carbon (GAC)
t Ion Exchange Resins
t Advanced Oxidation Processes (AOPs) t Membrane Filtration
The key is understanding whether you have a problem or not and choosing the right solution for your site’s specific PFAS profile, and that starts with a proper assessment.
How to start assessing if you have a PFAS issue Many companies don’t realise they are discharging PFAS until it’s too late, either due to regulatory enforcement or reputational damage. The first step is awareness, and the second is data.
What needs to be done now? If your business discharges process water or trade effluent, even indirectly, PFAS needs to be on your radar. Proactive steps and understanding now can prevent expensive process changes or remediation later. You’ll also demonstrate your proactive response to regulators, clients, and the public, something increasingly valuable in today’s Environmental, Social, and Governance (ESG) driven economy.
Leachate Solutions Ltd have the technical expertise, sector insight, and hands-on experience to help you navigate PFAS risks confidently. Whether you’re looking to assess a single site or standardise a PFAS strategy across multiple locations, we’re here to help.
Don’t wait for your water company to ask the question or for regulators to knock. Start your PFAS understanding today, contact Leachate Solutions Ltd for a confidential consultation.
T 01772 816593 enquiries@leachatesolutions.com www.leachatesolutions.com
PEMO is proud to announce its participation in the European Sanitation Summit (ESS) 2025, a pivotal event that brings together industry leaders, innovators, and policymakers to shape the future of sustainable sanitation. As a company committed to excellence in wastewater management and advanced pumping solutions, PEMO sees ESS 2025 as a strategic opportunity to contribute to global discussions and showcase its cutting-edge technologies.
Founded over 70 years ago, PEMO has built a strong international reputation for designing and manufacturing highly reliable, tailor-made pumps that serve a variety of demanding sectors - including mining, chemical processing, and, most notably, wastewater treatment. At ESS 2025, PEMO will highlight its latest innovations designed to meet the evolving needs of modern sanitation systems, such as high-efficiency slurry pumps, corrosion-resistant materials, and energysaving configurations.
Why ESS 2025?
PEMO’s decision to participate in ESS 2025 is driven by several key motivations:
1) Promoting Sustainable Solutions: Environmental sustainability is at the heart of PEMO’s mission. The company aims to share its latest advancements in energy-efficient pump technology, which help reduce carbon footprints and optimise water reuse in treatment facilities.
2) Connecting with Industry Stakeholders: ESS 2025 provides a unique platform for collaboration. PEMO looks forward to engaging with engineers, utility managers, public institutions, and NGOs to exchange
ideas and co-develop solutions tailored to the sanitation challenges of today and tomorrow.
3) Showcasing Innovation: PEMO will present a selection of its most advanced systems, including vertical and horizontal pump configurations designed for handling abrasive and aggressive liquids. Visitors will also get insights into PEMO’s customised approach, which ensures optimal performance and longevity in every application.
4) Supporting EU Green Goals: By participating in ESS 2025, PEMO reinforces its alignment with the European Union’s Green Deal and Circular Economy Action Plan, demonstrating how industrial innovation can actively support environmental and public health goals.
Through its presence at ESS 2025, PEMO aims not only to promote its technological expertise but also to affirm its commitment to building a cleaner, more efficient future for sanitation infrastructure across Europe and beyond.
We invite you to visit our Stand EN-E104, meet our experts, and discover how PEMO is redefining the standards of performance, sustainability, and reliability in the world of pumps.
Contact T +39 02 250731 peris@pemo.com www.pemopumps.com/en
In this issue of Industry Update, we are pleased to feature Adnet Precision Engineering as our HighPrecision Manufacturing Company of the Month
Founded in 1990 by Adrian Day, Adnet Precision Engineering is based in Gloucester and specialises in the manufacture of high-precision components with exceptional surface finishes.
Operating from a modern 4,200 sq. ft. facility in the UK, Adnet Precision Engineering combines robust quality management systems with advanced machining technologies and expert finishing processes.
“Adnet prides itself on our unmatched quality and customer satisfaction,” said Caroline Day, Managing Director. “We pride ourselves on our combination of technical expertise and commitment to quality. With over three decades of experience, we offer a highly personalised service, consistently delivering reliable, precision-engineered components. Our engineers are extremely hardworking, experienced and can tackle the most complex of projects with ease. Our attention to detail and transparent communication set us apart from larger, less agile competitors.”
As a key player in the precision engineering and advanced manufacturing sector, Adnet specialises in subcontract CNC machining and component manufacturing.
To further enhance this offering, the company is actively investing in new machinery and cutting-edge technologies, expanding both capacity and capabilities to
better serve its clients. The workshop houses eight CNC machine tools, all working together to produce precisionengineered components to the highest standards.
“Our recent installation of our Aberlink Axiom Too CNC CMM is ensuring quality with every micron; however, our most recent development is the arrival of our brand-new Hanwha XD 26II Sliding Head CNC Lathe, a cutting-edge addition to our space. Known for its exceptional speed, accuracy, and repeatability, the Hanwha enables us to take on even more complex components, reduce lead times, and increase production capacity,” stated Caroline. Plus, a brand-new Nakamura-Tome on the way is an exciting addition that will maximise efficiency in the new workspace.
Adnet works with key organisations that require toptier precision engineered components; this is across multiple industries including aerospace and defence, metrology, oil and gas, medical and pharmaceutical, and semiconductor sectors. In addition, the company contributes to specialised fields such as Formula 1 and rheology, machining precision components for these high-performance applications.
Some exciting news from Adnet is that over recent months, it has been undergoing a workspace transformation. Caroline explained more, “Our expanded workspace allows us to enhance our operations,
increase our capabilities and continue providing highquality solutions to our valued clients.”
“As part of our expansion, we have acquired an additional unit just across the road from our original site. This new facility is incredibly spacious, offering endless possibilities for the future of our company. The additional space will allow us to increase efficiency and ultimately take on more complex projects with ease. With this expansion, we are laying the foundation for long-term success, ensuring that Adnet remains at the forefront of precision engineering.”
“Renovations have been in full swing, helping shape the space to truly become our own. With improved layout and functionality, the vast space allows for a smoother, more efficient workflow for our team. Also, some new additions to our team include Ricardo, David and Martyn, who have already made a strong impact on our production line.”
“With a new workshop, new machinery, new team members, new clients and new relationships; we are blessed that 2025 is continuing to be Adnet's biggest year yet.”
For more information, please see below: https://adnetprecision.co.uk
Clearway Group today announces a leadership transition. Phil Doyle, the Group’s new CEO, assumes responsibility for the day-to-day management of the business, succeeding Peter Eglinton, Group Executive Chairman, who has successfully led the organisation through a significant period of growth and transformation over the past two years.
Phil joins Clearway with more than 20 years of senior leadership experience in the security and safety industry. His previous roles include Vice President at Bosch Security Systems, Regional Director at AXIS Communications, and most recently, Chief Business Officer at BauWatch. Phil’s deep industry expertise and commercial acumen will play a crucial role in driving the Group’s continued growth across its core markets.
Clearway has had an exciting two years, marked by acquisitions, entry into new markets and strategic customer success. This has included further development in the UK and France plus expansion into Germany and Austria, extending
its customer base to include national and international clients, accessing new sectors and realising a significant expansion of its security solution offerings throughout Europe.
This change marks a significant milestone in Clearway’s evolution, as it continues to deliver best in class security solutions across the UK and Europe. Under Phil’s leadership, the Group will embark on the next phase of its exciting strategic growth.
To find out more, please visit: www.clearway.co.uk
OHEAP Fire and Security have been awarded a place on the Building Safety and Fire Compliance Framework Agreement by NHS Shared Business Services (NHS SBS) to provide any NHS or Public Sector organisation fire or building compliance services and products.
As a response to The Building Safety Act (BSA), which overhauls the building safety system by focussing on building structural safety and fire safety throughout the lifecycle of a building, the NHS has awarded a select number of trusted, and approved companies to provide these critical services and products.
and regulated services for building safety and fire compliance for both planned and reactive works, removing the stress and risk from this process.
OHEAP Fire and Security
The framework agreement provides a PCR15 compliant route to market for any NHS or public sector organisation seeking fire or building safety work or products. The Building Safety and Fire Compliance Framework Agreement offers the flexibility to directly award to a single supplier or run a further competition saving valuable time and resources.
The framework agreement provides NHS or Public Sector organisations with compliant
As a fire safety and security company for more than 60 years, OHEAP offer passive and active fire safety including, fire risk assessments, fire alarm servicing, evacuation services, fire safety training and consultancy. This makes them the ideal company to support the NHS and wider public sector on their journey to safety excellence.
T 0330 999 8786 enquiries@oheap.co.uk www.oheap.co.uk
When it comes to maintaining interiors, prevention is always better – and more cost-effective – than cure. Yeoman Shield has been leading the way in wall and door protection for decades, delivering robust solutions that stand up to everyday wear and tear across all sectors.
Whether you manage a healthcare facility, school, commercial office, hotel or residential building, our protection systems help you safeguard interiors against costly damage. From impactresistant wall panels and corner protectors to full door protection and handrails, our products preserve surfaces, reduce maintenance budgets and extend refurbishment cycles.
One area where damage can be particularly costly – and even hazardous – is your fire doors. That’s why Yeoman Shield offers a comprehensive Fire Door Services package, including inspections, repairs and certified door protection products designed to maintain fire integrity while reducing scuffs, scrapes and impact damage. Fire doors are an essential safety feature and our solutions ensure they remain compliant and operational for the long term.
Our in-house Installation Team ensures every project is completed to the highest standard,
giving you complete confidence that your protection measures will perform as intended. From site surveys and measuring to installation and aftercare, Yeoman Shield is with you at every stage. We’ve made our products easy to install for those who prefer a self-installation option.
With a wide variety of products, colours and finishes, our solutions are fully customisable to suit any environment. All products all designed to be easy to clean, hygienic and visually appealing.
Investing in Yeoman Shield wall and door protection means you are choosing durability, compliance and peace of mind. Our products
have been proven to reduce reactive maintenance costs significantly, supporting your long-term building management strategy while enhancing the appearance of your premises.
To find out how Yeoman Shield can help protect your building, please visit: www.yeomanshield.com, call us on: 0113 279 5854, or email: info@yeomanshield.com. Our friendly team will be delighted to discuss your requirements, arrange a free survey or provide samples.
Yeoman Shield-protecting walls, doors, and budgets across every sector.
In this issue of Industry Update, we are
Hyde Park Environmental are specialists in Spill Control and Containment. Based in Antrim, Northern Ireland, their dedicated sales team covers the entire UK and Ireland, delivering top-quality solutions that help your business protect the environment, stay compliant, and confidently manage risks.
Hyde Park Environmental is a family-run business that truly puts its customers first. Founded in 2011 by Keith McMullan, the company lives by three simple but powerful values: We Listen, We Care, We Deliver. They take customer feedback seriously, often developing new products based directly on what their clients need. Every day, Hyde Park Environmental goes the extra mile to create and provide solutions that not only meet but exceed expectations – with great products, expert advice, and friendly, reliable service.
“Our huge range of cutting edge and innovative products –ranging from absorbent materials to advanced containment systems – are engineered to swiftly and efficiently manage
spills of all sizes, ensuring peace of mind and operational continuity,” stated Laura Mckay, Business Support Manager.
“Whether it is oil, chemicals or hazardous substances, we offer leading solutions that not only reduce risks but also minimise downtime, allowing your business to operate seamlessly. Trust us as your partner in spill prevention and containment, committed to safeguarding both your operations and the environment.”
Trusted by industry leaders such as BMW, Bentley, Caterpillar, JCM, JLR, Pfizer, and many more, Hyde Park Environmental enjoys a strong reputation across a diverse range of sectors. The recent move to their brand-new premises at Kilbegs Business Park, Antrim, marks an exciting milestone in the company’s growth and will further enhance the solutions they offer to customers.
What’s more, Hyde Park Environmental is set to launch specialised Spill Control solutions tailored for the Pharmaceutical, Aerospace, Engineering, and F&B industries –with the official announcement coming at the end of June 2025.
Committed to building a brighter future through environmental safety, Hyde Park Environmental understands just how important compliance is – especially when it comes to safety and spill control. To complement its services, the company has created a straightforward, practical compliance guide. This resource covers the essentials of environmental regulations, effective spill control solutions, and helpful tips to keep your workplace safe and responsible. Free to download here: https://hydepark-environmental. com/media/wysiwyg/Compliance_Document_-_ HPEnvironmental.pdf
Looking ahead, Hyde Park Environmental is entering an exciting new chapter in its journey. With a clear vision to protect companies, people, and the environment everywhere, the company is gearing up for significant growth. Here at
For more information, please see below: T 028 9446 7469 enquiries@hydepark-group.com https://hydepark-environmental.com
The Fire Safety Event 2025 was held at the NEC in Birmingham on the 8th-10th April 2025.
Showcasing the very latest in fire safety products, technologies, and solutions, the 2025 event welcomed an impressive 12,507 visitors and 264 exhibitors to its expansive 5,000+ sq. m event space.
As the UK’s leading fire safety exhibition, the event featured over 10,000 cutting-edge products and life-saving innovations from some of the industry’s most forward-thinking companies. Attendees were treated to hands-on experiences through Live Immersive Demonstrations and product launches, while also taking advantage of valuable networking opportunities with more than 12,000 fellow fire safety professionals.
The free-to-attend event drew a packed audience of industry professionals and fire safety experts, all eager to discover the latest innovations in the field. A standout feature of the three-day event was the series of engaging, CPD-accredited seminars, thoughtfully curated to enhance fire safety management. With the 2025 event welcoming even more comprehensive seminars, workshops, and keynote sessions than before, the curated agenda involving in-depth sessions delivered expert-led insights on critical aspects of fire safety, offering attendees valuable updates on current regulations, emerging trends, and influential case studies – ensuring they left better informed and better equipped to meet today’s fire safety challenges.
High-level fire safety professionals from all industries were on hand to network and share their passion for elevating fire safety standards at the Networking Café as well as at the end of the day complimentary Networking Drinks, which was accompanied with live music, curating the ideal space for new collaborations.
The Fire Safety Event welcomed exhibitors from all areas of fire safety who showcased their latest innovations and services in Emergency Lighting, Extinguishers, Alarm Receiving Centres, Fire Detection, Fire Prevention, Integrated Security & Fire, Passive Fire Protection, Sprinkler Systems, and Suppression Systems.
The Event was also designed to empower women within the sector, showing a commitment to, and celebrating women in fire safety management. Women Talking Fire had a stand where people could visit and network, as well as enjoy a thoughtprovoking panel discussion led by Andrea White.
The 2025 event also partnered with Worldskills UK to bring a fully immersive and interactive zone dedicated to the security engineers of tomorrow. Hosting the National Qualifiers on-site, this helped raise the standard for apprentices to excel in their careers, and took place at The Security Event which was co-located with The Fire Safety Event in hall 5.
The next Fire Safety Event will take place on the 28th-30th April 2026. To plan your visit to the 2026 show, please see below: https://www.firesafetyevent.com
Firerite’s debut at the Fire Safety Event (8th-10th April 2025, NEC) was a resounding success! As a new exhibitor, we were thrilled to showcase our extensive range of fire safety solutions, and the response was overwhelming. The event provided a fantastic platform to engage with industry professionals, including facilities managers, fire safety officers, and contractors, all keen to learn more about how we can help them navigate the complexities of fire safety.
The success of our first outing at the event highlights our commitment to raising fire safety standards and delivering solutions that not only meet but exceed industry expectations. It reaffirmed our dedication to safeguarding lives, protecting assets, and ensuring compliance in an ever-evolving regulatory landscape.
At Firerite, we recognise that every building has unique fire safety needs. Our fire risk assessments and fire strategy reports are comprehensive, indepth, and tailored to your property, ensuring that the risk isn’t just a tick-box exercise. We assess potential hazards, evaluate the current fire safety measures in place, and recommend solutions to reduce risks and enhance safety. Each report and assessment is designed to provide practical, actionable information that not only ensures compliance but creates a safer environment for everyone.
Our fire safety consultancy services are there to guide you through every stage of a project. From
initial planning to ongoing maintenance, we provide expert advice on fire strategy, fire alarm systems, fire doors, emergency lighting, and evacuation procedures. We help you navigate the complexities of fire safety regulations, ensuring that your building is designed and maintained with safety at the forefront, so you can be confident that you’re meeting both regulatory and practical requirements.
Maintaining a fully functional fire alarm system is crucial to ensuring the safety of your property. That’s why Firerite offers comprehensive fire alarm maintenance services. Regular checks and servicing are essential to ensure your alarms are fully operational in an emergency in line with BS5839 part 1. Our engineers are trained to a minimum level 3 and conduct thorough inspections, repairs, and upgrades to ensure that your fire alarm system
comply with current regulations and are ready for action when you need them most.
With over 30 years of experience in fire safety, Firerite is a trusted partner for your fire protection needs. We are accredited to BAFE SP101, SP203, SP205, NSI Gold, and SSI Acclaim standards, ensuring that you receive the highest levels of expertise, reliability, and professionalism. Whether you need a fire risk assessment, consultancy, or fire alarm maintenance, Firerite has the solutions to keep your building and its occupants safe.
Contact Firerite today to learn more about how we can assist with your fire safety requirements: T 02920 867222 sales@firerite.co.uk www.firerite.co.uk
For more than 35 years, the annual PPMA Total Show® has been a key event on the processing and packaging industry calendar. Taking place from 23rd–25th September at the NEC in Birmingham, the show is celebrated for drawing thousands of visitors and exhibitors from across the FMCG sector. Hall 5 is once again expected to be buzzing with energy and anticipation, offering an ideal platform for networking with leading exhibitors and exploring the latest cuttingedge technologies and innovative solutions.
Showcasing the latest in processing and packaging machinery, including robotics and industrial vision, this is going to be an unmissable three-day exhibition experience, so expect live demonstrations of exciting innovations, face-to-face contact with industry experts, and much more! The show is renowned for bringing together the very best suppliers of processing and packaging machinery, robotics and industrial vision systems
with the capability to deliver significant benefits to a wide range of businesses. These include cost reductions, increased efficiency, quality improvements, and reduced downtime and turnaround, all of which can deliver a healthy return on the investment in these technologies.
Visitors will be able to see the latest innovations from an impressive line-up of over 350 exhibitors, comprising over 1,500 brands. These exhibiting companies will be showcasing their latest cutting-edge solutions for the full spectrum of the manufacturing industry, including pharmaceuticals, food and beverages, building materials and suppliers, pet care, and microbrewers and distillers.
Supported by an insightful seminar programme featuring keynote speakers from leading brands, everyone can gain actionable insights from industry leaders on topics like sustainability, smart manufacturing, and operational efficiency.
There will also be a Live Demonstration Theatre, where you can see brand-new product launches brought to life through a highly interactive panel discussion. With morning and afternoon sessions on each of the three days, PPMA Total Show TV will also be recording live as experts from each exhibitor operate working machinery on their stands.
Each day you will have the chance to take part in one of the Daily Innovation Tours, designed to introduce you to the latest technological solutions and to expand your understanding of various machinery and their suitability
for your business needs. This is a great way to discover the latest breakthroughs in processing and packaging technology, with visits to selected exhibitors launching new technologies in the Demonstration Theatre.
Available in one handy app, make the most of your experience and get The PPMA Total Show® App on your mobile before you visit. One click is all it takes to open the app in your browser – no download is needed, which is why you won’t find it in the app store. Bookmark seminar sessions, browse event content, and even use SmartScan and ContentCapture within the app.
Find out more below: https://www.ppmashow.co.uk
In increasingly automated production and packaging environments, safeguarding people remains a critical concern. At Boplan, we offer high-performance polymer safety solutions that help protect workers, infrastructure and equipment in dynamic industrial settings.
While risk assessments, training, and signage play a key role, physical protection is essential to prevent accidents. Boplan safety systems are engineered for integration into fast-moving, high-traffic zones – whether near conveyors, robot cells, or loading docks.
Tailored safety for production and packaging lines
Automated production lines, high-speed conveyors, robotic arms and AGVs bring efficiency – but also increase the potential for accidents. Boplan offers modular safety systems that seamlessly integrate into dynamic industrial environments, helping you meet your safety targets without compromising on workflow or space.
t Safety gates: Our self-closing gates and sliding or swing gates provide controlled access to hazardous areas such as pedestrian areas, machine zones, or maintenance corridors. They are ideal for guarding operator access points on filling lines, wrapping stations, or palletisers.
t Safety barriers with handrails: Designed to absorb the impact of forklift or pallet truck collisions, these barriers also guide foot traffic along designated walkways. This dual functionality enhances spatial organisation and reduces the risk of pedestrian-vehicle incidents.
t Handrails: Installed alongside internal transport routes, production lines or mezzanines, handrails
clearly separate pedestrians from moving machinery and automated guided vehicles (AGVs), contributing to a safer working environment without interrupting operations.
t Kick rails with handrails: Combining ground-level impact protection with visible pedestrian guidance, these systems are often used near case packers, depalletisers and warehouse transfer points – where low-level impacts are common but often overlooked.
Whether you’re designing a new packaging line or upgrading safety in an existing facility, Boplan solutions adapt to your layout and operational flow. Our safety systems are made from advanced polymers that outperform steel in terms of durability, corrosion resistance, and maintenance – ideal for food-grade, chemical or cleanroom environments.
The DG250R AE: setting the standard for dock safety
Unveiled at PPMA 2025, the DG250R AE Dock Gate is a motorised safety gate with double bars that acts as fall protection at loading docks or as an impact-resistant barrier arm to close off access to a specific area. It provides robust impact protection of up to 10.2kJ. The design is very compact, so no precious space is lost.
About Boplan
Boplan® develops and produces high-quality polymer safety solutions for industrial environments. Our innovative and durable fall and impact protection is the reference in impact absorption and protects people, vehicles, buildings and infrastructure worldwide in warehouses, production sites, logistics centres, cold storage facilities, (petro-) chemical sites, car parks and airports.
With over 25 years of experience, our comprehensive range of products is designed to withstand extreme conditions and meet the strictest safety standards.
Visit Boplan at PPMA Total Show 2025
From 23rd–25th September 2025, join us at Stand E96, Hall 5 at the NEC Birmingham to explore our full portfolio of safety solutions. Our team will be on hand to demonstrate how Boplan products integrate into modern processing and packaging environments.
Contact T +44 (0)1902 824280 info@boplan.co.uk www.boplan.com
For the global label printing industry, the increasing focus of consumers and governments on sustainability is a call to action. With every aspect of the printing supply chain now under scrutiny, from the biodegradability of substrates to the VOC content of inks and the energy efficiency of printing presses, an up-to-date sustainability strategy is an essential part of future proofing your business. In this article, we’ll look at how sustainability can be achieved effectively in the print sector without compromising quality, cost control, or efficiency.
Why sustainability is essential for print businesses
Consumer brands and printing businesses are often in the spotlight for their environmental impact. This stems from the high energy costs associated with many production processes, as well as prevalent wasteful practices in packaging disposal, and the carbon footprint of producing traditional printing materials. Achieving greater sustainability is, therefore, a multipronged approach for most label supply chains. Some of the main strategies include:
t Designing for recyclability: Many labels now feature an ‘eco-conscious’ design that makes it easier for consumers to separate labels from products to aid recycling, and avoid multi-material labels that could make substrates non-recyclable.
t Investing in energy efficient printing presses: Reducing the energy consumption of your printing assets
makes sound financial sense as well as benefitting the environment. Upgrading to more energy-efficient machinery could deliver a good ROI in energy savings without impacting your production line throughput. For example, when considering a new Pressor upgrading older UV equipment, why not look at the latest LED drying option? Not only reducing VOC emissions, but also reducing running costs with a less energy hungry press.
t Minimising substrate waste: There are various areas in which waste can be reduced or eliminated in the label printing process, and many of these have been addressed by recent technology innovations. Basically, only produce what you need, avoid overruns and holding large stock quantities for call off. Digital and hybrid printing technologies, for instance, avoid the need for over production, try to separate plate making and elaborate setups, which reduces the time and energy associated with print management. At the same time, lean inventory management processes mean that businesses only order the substrates, inks, and consumables that are required for each print run, avoiding the costs associated with overstocking. Precision Servo machinery, advance software, and recalibration tools all contribute to less energy and fewer resources being wasted during production.
How our label printing technology supports greater sustainability
There are several ways that our modern digital label printing machinery can support your sustainability initiatives, including:
1) Planned production: Advance planning to ensure ALL orders can be produced on the specified time & day. There is nothing more wasteful than a press ready to go only to find an element of production is missing, be that Inks, Plates or even substrates.
2) Multi-substrate compatibility: Our presses work with a variety of eco-friendly materials, including FSC-certified paper and biodegradable film, are recycled substrates a possible option to win business?
3) Automation: The goal of automated print technology is to reduce setup time and material waste. From precise ink delivery mechanisms to automated alignment systems, our Flexo & digital label presses help you conserve resources and make each run more sustainable and cost-effective.
4) Personalised sustainability support: We can help you rethink your production strategy, providing tailored insights on how you can integrate eco-friendly technologies into your business model and production goals.
5) Hybrid printing solutions: Our digital label presses combine the best features of flexographic and digital printing, helping control energy and carbon emissions on both large-scale and small batch print runs, plus Variable data and Personalisation.
Find out more
To find out more about sustainability and how it could impact your print operation this year, please contact the experts at Focus Label today by clicking here, by calling: 01949 836223 or get a quote
Please visit: www.focuslabel.com
For more than five decades, health and safety practitioners have turned to noise monitoring equipment such as handheld sound level meters and personal noise dosimeters to assess noise levels in the workplace. However, with more and more businesses choosing to operate from multiple sites as opposed to across one site, it’s possible that these more traditional methods of noise measurement and monitoring may no longer be the most efficient.
Quantum; the future of noise measurement
Quantum Indoor from Cirrus Research is a powerful noise monitoring solution with built-in cloud connectivity, perfect for continuous occupational noise monitoring, identifying the source and type of noise that is occurring, and highlighting where noise control measures are required.
With this instrument, it has never been easier to measure and monitor workplace noise continuously and remotely across one or multiple sites.
The cloud technology that is built into the Quantum instruments allows health and safety practitioners to connect multiple noise monitors on one account, allowing for data from each noise monitor to be viewed and assessed on one platform. This creates a network of interconnected instruments, whose data can be viewed and analysed side-by-side, removing the need to download information from separate handheld instruments one-by-one.
Additionally, Quantum indoor provides a constant ear to the ground, offering live and historical data round-the-clock that practitioners can access from anywhere, at any time and on any device. Whether users are on the other side of the planet to where the instrument is installed, or they’re stood in the next room, the data is always accessible on demand via the online Quantum portal, powered by MyCirrus.
With a network of cloud-connected noise monitors, the need for users to be physically on-site to measure noise levels is vastly reduced. Cloud-connected monitors, such as Quantum Indoor, can be installed and left to do their jobs completely unattended. They can then be configured remotely to send users real-time alerts when noise events occur, which provides greater control to health and safety practitioners in the workplace.
With Quantum Indoor, you can:
t Link multiple units to form a cloud-connected network of noise monitors to make viewing the full picture of your workplace noise impacts easier.
t View your live and historical data in the Quantum portal anytime, anywhere around the world on any device.
There is a common misconception that all breather valves are rigorously tested to a certain standard before they are sold, but unfortunately, this is definitely not the case. Many breather valves on the market are not subject to stringent testing protocols, leading to significant safety and operational risks. When these untested and, more importantly, unsafe breather valves are procured, the end user unknowingly takes on many risks.
It is crucial to know the facts by conducting thorough due diligence from the initial purchase and throughout the entire lifecycle of the unit. First, ask yourself: Are your breather valves set correctly?
t Create numerous audio triggers and notifications based on your personal set of conditions for acceptable noise emissions, and receive these notifications via email, SMS or push notification.
t Use the frequency analysis screen on the Quantum portal to further view and analyse your noise data and better understand the exact nature of the noise.
t Create detailed reports directly though the Quantum portal based on direct data captured by your Quantum Indoor units.
The Quantum Portal; powered by MyCirrus
With the Quantum Portal there are no fixed fees or set up charges. With Cirrus Research, users are offered subscription packages that are flexible to fit in with your noise monitoring programme and your preferred level of usage. These flexible plans means that you have the ability to change your subscription up or down on a monthly basis.
Powered by MyCirrus, this portal is suitable for all Quantum noise monitoring devices, and can also be used with other instruments such as the Cirrus Research Environmental Noise Measurement Kits.
Contact
T +44 (0)1723 891655 sales@cirrusresearch.com www.cirrusresearch.com
Incorrect settings can lead to valve malfunction, causing potential overpressure or vacuum conditions that could compromise tank integrity. Are your breather valves performing safely? Regular testing ensures they function within safety parameters, preventing hazardous situations.
Do you know your breather valve leak rates, and is your media hazardous, flammable, costly or toxic? Understanding leak rates is vital for environmental, occupational health and safety compliance. Do they function as per intended design and specification, and do they meet the set point? This ensures that valves operate as required under specific conditions.
Has your breather valve been tested in accordance with API2000 Section 5.4? Compliance with this standard guarantees that valves meet industry requirements. Do you monitor your breather valves as part of your aging plant management plan? Regular monitoring can identify wear and tear before it leads to failures. Lastly, are you confident that all your breather valves maintain optimum efficiency and performance? Ensuring this can prevent costly downtime and environmental hazards.
The only irrefutable test method is using the Vent-Less test bench. This groundbreaking technology is revolutionising testing, ensuring that breather valves are tested prior to installation and during
the life term of the unit. The award-winning Vent-Less test bench aligns with the API2000 Section 5.4 test protocol, and the instantly generated certification stands up to regulatory scrutiny. The documented leak rate is also invaluable for LDAR, IED, and Regulation 61 reporting. These questions are critical for assessing your vulnerabilities and ensuring the safety and efficiency of your operations. Don’t leave it to chance – make sure your breather valves are thoroughly tested and maintained using the Vent-Less test bench.
Contact T +44 (0)1726 844707
info@assentech.co.uk www.assentech.co.uk
What if speed isn’t just an advantage but the new standard in servicing? Every second counts – and downtime counts tenfold.
As an established supplier of rotary and diverter valves for a large range of dry bulk solids processing industries, DMN-WESTINGHOUSE is committed to providing future-proof value. This is why we launched the improved PTD plug diverter valve.
The PTD plug diverter valve at a glance
The PTD is designed to route powders and pellets in pneumatic conveying systems with minimum degradation. This diverter valve minimises service time, ensuring more uptime and lower costs. This isn’t just servicing – this is efficiency. Every single time.
t Aluminium housing & end covers, dual-pipe plug
t Stainless steel product contact surfaces
t No outside moving parts, no atmospheric leakage
t Suitable for systems with positive pressures 3-6 barg, pressure shock resistant up to 10 barg*
t Static belly seals with solenoid valve & inductive position sensors; optional: terminal box
t Inflatable belly seals with electropneumatic control system (Inc. solenoids, terminal box, inductive position sensors)
t Standard version suitable for product temperatures -25-80°C (ambient temperatures -10-40°C); versions for higher temperatures available
t Versions with electrical drive and/or wear-resistant pipes available
t EC 1935/2004 compliant; ATEX 2014/34/EU certification available
*Size 200 excluded
The PTD plug diverter valve is suitable for a range of dry bulk solids processing industries:
t Aquaculture
t Animal feed
t (EV) Batteries
t Biomass
t (Petro) Chemicals
t Cosmetics
t Dairy
t Food
t Infant formula
t Minerals
t Paint
t Pet food
t Pharmaceuticals
t Plastics
t Recycling
t Rubber
Benefits of the PTD plug diverter valve
These features help your operators work smoother and faster, leading to minimal downtime:
t Easy, two-sided access – service from the most convenient side
t Adhesive-free belly seals
t Quick-connection position sensors
t Easy-release actuator linkage
t Reinforced jacking points
t Minimal service required
Your benefits? The PTD sets a new standard in servicing efficiency, ensuring more uptime and reduced costs.
The PTD plug diverter valve exemplifies DMN-WESTINGHOUSE’s commitment to providing dry bulk processing industries with future-proof value. It slashes servicing time and offers unparalleled ease of use. The PTD provides the fastest way to efficiency.
T +44 (0)1249 818400 dmn.uk@dmnwestinghouse.com www.dmnwestinghouse.com
Award-winning British valve manufacturer strengthens its presence in the Kingdom through new strategic partnership.
Oliver Valves and Oliver Twinsafe Limited are proud to announce the signing of an exclusive agency agreement with Abdul Rahman Ali Al Turki Company (ATCO), further cementing our presence and commitment to the Kingdom of Saudi Arabia.
The agreement was formalised during an official signing ceremony held at ATCO’s headquarters in Dammam. The event was attended by senior representatives from both organisations, marking the beginning of a strengthened and strategic collaboration.
From ATCO, the signing was witnessed by Chairman Ziad Abdulrahman Ali Al Turki, alongside Director Adnan M. Iqbal. Representing the Oliver Valves Group were Trevor Spencer, Managing Director, and Anurag Srivastava, General Manager Middle East, joined by Mohammed Aleemullah, Business Development Manager.
The agreement follows Oliver Valves’ recent recognition with the King’s Award for Enterprise in International Trade, one of the highest honours for UK businesses. The partnership with ATCO reflects the company’s continued commitment to bringing British engineering excellence to key global markets.
Trevor Spencer commented, “Saudi Arabia remains one of the most vital markets in our global strategy. This exclusive agreement with ATCO represents a major step forward in how we support our customers and projects across the
Kingdom. Partnering with a company of ATCO’s calibre enables us to deliver even greater value, responsiveness, and local alignment.”
This partnership reflects Oliver Valves’ long-term vision to deliver British-engineered excellence to the region, backed by local expertise and trusted partnerships.
Contact T +44 (0)1565 632636 sales@valves.co.uk www.valves.co.uk
Wieland Electric presents the latest generation of highly efficient safety light grids and safety light curtains.
The importance of occupational safety grows in modern industrial and logistical environments as machines and systems become more complicated. Against this backdrop, Wieland Electric introduces its next generation of safety light curtains and safety light grids, which complement the existing array of optoelectronic protection devices and are distinguished by a high level of safety, flexibility, and use.
The new SLG4 series safety light grids were designed for applications requiring dependable access protection over wide areas on machines or in production sites. While withstanding temperatures as high as 70°C, the light grids may be put into action swiftly thanks to their simple software configuration and plug-and-play installation. Clearly visible LEDs also enable immediate on-site diagnostics, reducing downtimes.
Furthermore, the durable aluminium housing and protection rating IP65/67 in accordance with EN 60529 ensure that the optoelectronic protective devices perform reliably even in adverse environmental situations.
The SLC4 series safety light curtains are perfect for protecting fingers and hands in the machine's danger zone. When the machine is used frequently, they cut access times compared to physical guards, increasing production. Advanced functionalities like muting ensure safe material flow and contribute to cost-effective material supply and removal.
Cascading two devices enables vertical access and horizontal presence monitoring in a single system.
The SLC4 safety light curtains, like the SLG4 safety light grids, have a simple software-free configuration and the ability to do quick on-site diagnostics. This improves productivity and safety in industrial applications.
www.wieland.co.uk
The oxygen sensor MFOxy-Comp has been specially developed for use in composting plants. The materials used meet the high requirements of this field of application. The measurement method is based on a dynamic process at two zirconium dioxide slices, which form a hermetically sealed chamber. The entire measuring range is linear.
During operation the sensor system monitors its own function and reports in case of hardware and sensor malfunction.
The calibration is done without reference gas in atmospheric air. The output of the measurement values takes place via an analog (420mA) and a digital channel, the latter transmits the error messages.
The oxygen sensor MF-OxyComp is designed for the measuring range 0.1 to 25 vol% oxygen and equipped with an analog interface with 4-20mA and has a digital output as well.
sales@logidatatech.com www.logidatatech.com
Showing the world what production technology is capable of is the promise of EMO Hannover 2025 that will take place on the 22nd26th September 2025 in Hannover Fairgrounds.
EMO Hannover is the world’s leading trade fair for production technology – the industry’s highlight of the year under the banner Innovate Manufacturing! The 2025 edition promises to surpass the 2023 event, which drew over 92,000 visitors from 140 countries and featured around 1,850 exhibitors.
Since 1975, EMO has stood for innovation, international reach, inspiration and the future of global metalworking. Held every two years in Hannover and Milan – celebrating its 50th anniversary this year – EMO offers an unmatched platform to forge international connections, unlock new business opportunities and gain a comprehensive view of the industry’s global landscape.
EMO (Exposition Mondiale de la Machine Outil) 2025 will showcase a vast range of metalworking products including cutting and forming machine tools, manufacturing systems, precision tools, automated material flow, computer technology, industrial electronics and accessories.
Organised by the VDW (German Machine Tool Builders’ Association), Frankfurt am Main, Germany, no other trade fair presents the full breadth and depth of international manufacturing technology like EMO. It is the place for exhibitors and visitors with a high level of expertise to discuss the biggest trends in manufacturing, exchange ideas with representatives of international production research and develop solutions for existing challenges.
EMO creates a platform where tomorrow’s trends are conceived and discussed and transformed into solutions and business models.
EMO Hannover 2025 will focus on three main topics: Automation, AI & Digitisation, and Sustainability.
Automation takes centre stage, with 1,400 global exhibitors set to showcase innovations driving efficiency, precision and flexibility. Discover how robotics, intelligent controls and fully automated production lines are transforming manufacturing and securing competitive advantages.
Exhibitors will also showcase how digital technologies and AI are transforming production and advancing Industry
4.0. Showing how connected machines, IoT, intelligent data analysis and cloud computing can boost efficiency, optimise processes and create new opportunities. Explore the innovations shaping the market – and the challenges still ahead.
Sustainability is a key theme. Exhibitors will present innovations in environmental protection, resource conservation and energy efficiency. From green technologies and circular economy solutions to energyefficient production – discover how sustainability is shaping industry’s future and boosting competitiveness. There is still time to get your tickets, don’t miss out! https://emo-hannover.com
Representing a leap forward in programming, UNISIG’s next-generation operating system further improves the human-robot interface and slashes programming times.
The new operating system, featured on UNISIG’s UNE6-2i-750-CR small-diameter gundrilling machine, streamlines the setup of dozens of different part handling combinations to reduce new part setup times by 80% or more. The system significantly improves the communication between the machine’s human machine interface (HMI) and the robotic controller. This enables centralized data storage or a single source of truth – the coding and data for the gundrilling operation and the program for the part handling are stored together for ease of recall.
Because it works within a parametric programming environment, the new operating system automatically adjusts its parameters to any dimensional part changes, without the need to manually calculate and enter in new parameters. Such intelligence eliminates the need to start over and create entirely new and independent programs, while greatly simplifying and shortening programming times for part families.
The UNE6-2i-750-CR gundrilling machine with integrated robot ships with a handheld programming console/teach pendant connected to the machine. Prior to the use of parametric programming, all part handling operations were pre-programmed using the pendant. Users can now enter & store all machine & robotic parameters in the machine HMI. This allows for
a more centralized user experience and greatly reduces the depth of robotic experience required.
The machine HMI has built-in parametric selection guides, allowing users to toggle between data entry and the programming guides. Each data value, and its function, are graphically displayed in the on-screen programming guide. This prevents the guide from being misplaced and makes it available at all times, which is especially advantageous when periodically adding new parts involving large time gaps between them.
The UNE6-2i-750-CR with integrated robotic automation also features interchangeable part trays. The robot services both the machine’s spindles and accommodates drilling of different diameters from each end.
The optional lantern chuck system on this machine model allows workpiece loading into the rear of an automatic collet chuck to ensure accurate workholding, especially for uniquely shaped workpieces.
UNISIG’s UNE6 Series of precision gundrilling machines generate holes from 0.8mm to 6.0mm (0.03” to 0.24”) in even the most challenging of materials. Such capability makes the machines well suited for a wide range of applications, including medical part manufacturing.
Further information on all machines and the complete UNISIG machine program is available at: www.unisig.com or follow the company on LinkedIn and Twitter (@UNISIG). You will also meet us at the EMO 2025 show in Hannover, Germany, from 22nd26th September.
Held at the NEC in May this year, The UK’s largest chemical B2B trade show saw a 12% increase in visitors from last year, hosting 550 exhibitors and over 5,000 visitors.
Launched in 2019, CHEMUK is renowned for its diverse range of exhibitors from across the chemical industry, as well as its varied and impactful speaker line up, growing year on year to become a must attend event for the industry.
CHEMUK showcased its specialist exhibitors and expert speakers across five show zones in 2025. Here’s what visitors experienced over the two-day, free event:
Chemicals Supply Show Zone
Here visitors met manufacturers and distributors of chemicals, raw materials and ingredients. Giving attending R&D, product development and supply chain teams a unique opportunity to meet chemical distributors and manufacturers supplying industries like; chemical manufacturing, food ingredients, lubricants, metalworking, homecare, industrial cleaning, water treatment, pharmaceuticals, agriculture, coatings, adhesives, sealants, elastomers, beauty and many others.
The Chemical Supply zone also hosted a series of sustainability sessions at Stage 2. Composed of industry keynotes speakers and expert panel sessions discussing the very latest intelligence, strategy and progress updates towards a sustainable future.
Chemicals Management Show Zone
In this show zone attendees had the chance to meet specialist suppliers dedicated to the handling, storage, transportation, regulation and disposal of chemicals. The Chemicals Management Show Zone also hosted the CHEMUK Regulatory Affairs Programme. This mini
conference provided a two-day programme bringing together cross-industry groups to discuss the biggest issues in areas such as UK Reach, EU Reach, Chemicals Regulatory Compliance, Safety Data Sheets, GHS/CLP and more.
Furthermore, the UK & Ireland Spill Association Helpdesk was on hand to run a chemical spill prevention and immediate response drop-in clinic; where attendees were able to meet with a number of specialist regulatory groups that partnered and exhibited at the show. These included the Chemical Hazards Communication Society (CHCS), BADGP, and Chemical Regulations Self Help Group.
Process and Chemical Engineering Show Zone
At the Process and Chemical Engineering Show Zone hundreds of process engineering suppliers were exhibiting under one roof. Showcasing the latest technology and specialist services to attending process, plant, and control engineering and safety professionals across the chemical, food and beverage, pharma, oil and gas, water, waste and energy sectors.
CHEMUK was also proud to welcome IChemE and IMechE as headline partners of the Process and Chemical Engineering Show Zone. Visitors had the opportunity to engage with representatives from both organisations, who also delivered expert panel discussions and keynote sessions throughout the event.
Chemical Laboratory Show Zone
Here laboratory equipment suppliers, supporting analytical and process chemistry, showcased specialist laboratory chemicals and equipment for research and development, analysis, process design and development, scale-up and quality testing professionals.
The Chemical Laboratory Show Zone also hosted the Innovation to Industry poster zone. Here startups, university spinouts and research groups from across the chemical,
bio-chemical and process industries networked with specialist industry groups to support their development journey towards full-scale implementation and commercialisation.
The Henry Royce Institute, the UK’s national institute for advanced materials research and innovation, was also based in the Chemical Laboratory Show Zone. Visitors to CHEMUK were able to meet with the HRI team to discuss how Royce could assist in supporting their projects to reach the next phase of their innovation journey towards full-scale commercialisation.
Formulated Product Manufacturer Show Zone
New for 2025 was the Formulated Product Manufacturer Show Zone, connecting formulated product brand owners and retailers with specialist ingredient, contract manufacturing, logistics, packing, and fulfilment partners.
The BCMPA was also housed in this zone. As a headline partner to this new show, the BCMPA exhibited alongside several of their members, including Briar Chemicals, Cod Beck Blenders, Rutpen, Safapac and Libra Speciality Chemicals.
CHEMUK’S 2025 speaker program also impressed this year. The two-day programme hosted some 150 expert speakers discussing the big challenges and opportunities affecting the UK’s chemical and chemical product industries.
The UK Government was one of this year’s standout speakers with a special Regulatory Briefing containing updates from Defra, DESNZ, DBT & HSE on topics related to chemicals regulation in Great Britain. Panel members discussed the latest developments and took questions from the audience, providing an in-depth look at the UK’s current chemical policy and trade plans.
The Royal Society of Chemistry was also at CHEMUK this year. The new RSC President, Dr Annette Doherty gave a stellar keynote presentation where she laid out her goals for the organisation. As well as this the RSC ran a mini conference recognising excellence in science and sustainability.
CHEMUK 2026 will take place at the NEC, Birmingham on May 20th and 21st.
For more information on CHEM UK and to register for next year’s show, please see below: https://www.chemicalukexpo.com
With over a century of logistics expertise, RJJ Freight is an independent UK freight forwarding company specialising in compliant, efficient transport solutions for the chemical industry. Since our founding in 1918, we’ve built a reputation for reliability, precision, and customer first service, offering global shipping via land, sea, and air.
We understand the complex regulatory landscape chemical industry face, especially in a post-Brexit world. Our dedicated team offers tailored support, Dangerous Goods handling, and seamless customs clearance. As specialists in UK import and export processes, we ensure full adherence to safety, documentation, and environmental controls.
Our AEO (Authorised Economic Operator) status underlines our commitment to security, transparency, and operational excellence. Whether managing sensitive cargo or co-
ordinating multimodal cross-border shipments, we deliver responsive, costeffective logistics to meet demanding industry standards.
As a family-run business, our customerfirst ethos is woven into everything we do. From navigating new border regulations to streamlining timesensitive shipments, RJJ Freight delivers with professionalism, transparency, and care. From multinational manufacturers to niche chemical suppliers, we’re here to move your business reliably, efficiently, and across borders.
Contact T 01394 673466
sales@rjjfreight.co.uk www.rjjfreight.co.uk
KSB made a confident return to CHEMUK, drawing strong interest with a well-rounded display of advanced pump and valve technologies. The stand featured the Magnochem pump with MagnoProtect, the MegaCPK process pump, and a versatile range of valves including the SISTO-20 with PTFE lining and the KE Plastomer.
Each product demonstrated KSB’s commitment to innovation, reliability, and performance across chemical processing applications. Visitors were particularly engaged by the detailed cutaway models, which offered a rare, in-depth look at the inner workings of KSB’s pumps and valves – highlighting the engineering precision behind each solution.
The event proved to be a valuable platform for reconnecting with long-
standing customers and welcoming new prospects. With a high volume of quality leads now in active discussion and follow-up meetings already underway, KSB’s presence at CHEMUK has reaffirmed its role as a trusted partner in the industry.
KSB looks forward to building on this momentum and continuing to deliver tailored solutions that meet the evolving needs of the chemical sector.
For more information, contact KSB at: +44 (0)1509 231872 or email: sales@ksb.com.
Worcester-based toxicology consultancy Toxiqua made a striking impression at CHEMUK 2025, the UK’s largest chemical supply chain Expo, held on 21st-22nd May 2025 at the NEC Birmingham. As a first-time exhibitor, the company brought a fresh energy and scientific clarity to the event.
Founded in 2024 by experienced toxicologist Jason Manton, Toxiqua has already become a trusted partner for clients across the chemical, agrochemical, pharmaceutical, and biocide sectors. The consultancy supports organisations navigating complex regulatory landscapes with services grounded in many decades of hands-on toxicological expertise.
From its position on Stand C124 near the regulatory stage, Toxiqua offered visitors tailored insights on Developmental and Reproductive Toxicology, GLP study oversight, and strategic technical opportunities. The team, including experts in reproductive and developmental toxicology, fielded high levels of interest from manufacturers, consultants, CROs, and regulatory professionals.
Key service areas such as developmental and reproductive toxicology, developmental immunotoxicity, endocrine disruption, and developmental neurotoxicity drew particular attention. Toxiqua also demonstrated its capability in delivering scientifically robust alternatives to traditional animal testing, using read-across, QSAR, and other New Approach Methodologies (NAMs) to help clients achieve both compliance and efficiency.
“CHEMUK gave us a great opportunity to showcase how our deeply specialised expertise can simplify what are often overwhelming regulatory challenges,” said Managing Director Jason Manton. “We’re proud to have sparked so many productive conversations and look forward to building lasting client relations and partnerships.”
Visitors praised Toxiqua’s hands-on approach, scientific integrity, and responsiveness, a reflection of the company’s founding values: toxicology with precision, quality, and purpose.
About Toxiqua
Toxiqua is a specialist consultancy focused on developmental and reproductive toxicology, offering a rare depth of expertise in one of the most complex and highly scrutinised areas of chemical safety. The company supports clients through every stage of DART-related programme design and execution, whether it’s testing strategy, study monitoring, regulatory interpretation, or dossier submission.
Led by Managing Director Jason Manton, and supported by experienced toxicologists, the team is particularly experienced in foetal pathology, reproductive hazard assessment, and addressing regulatory concerns under REACH, PPP, and BPR. Toxiqua is grounded in scientific rigour and tailored to meet evolving regulatory expectations in human health protection.
For more information, please visit: www.toxiqua.com Contact Charlotte Holland, T +44 (0)7944 934079 info@toxiqua.com
At Recontainers Ltd, we’re proud to be one of the UK’s leading specialists in the reconditioning, supply, and purchasing of Intermediate Bulk Containers (IBCs) and plastic drums. Based in Lancashire and family-run since 1991, we combine over three decades of industry expertise with a strong commitment to quality, safety, and sustainability.
We buy, sell, and clean IBCs and drums – making us a one-stop solution for businesses looking to manage their industrial packaging needs responsibly and costeffectively. We offer fast turnaround, competitive pricing, and reliable UK-wide delivery.
Our reconditioned IBCs go through a rigorous cleaning and inspection process – including full electronic pressure testing – to ensure they meet the highest standards for reuse.
We also stock a full range of IBC parts and accessories, from replacement lids to IBC heaters. All products are available via our easy-to-use online store.
Looking to clear empty containers? We offer a professional, nationwide IBC and drum collection service
If your business has 10 or more clean, empty containers, we can assess, collect, and (potentially) pay for them –helping you reclaim space and generate revenue while contributing to a circular economy.
We’re trusted by customers across the UK’s chemical, food production, and manufacturing sectors who value our consistency, flexibility, and customer-first approach. Our
At Recontainers Direct, we go beyond containers to bring your business everything it needs – all in one place.
Whether you’re storing, transporting, cleaning, or safely managing hazardous goods, we offer an extensive range of industrial packaging and workplace products to keep your operations running smoothly and compliantly.
Launched as an expansion of our long-established sister company, Recontainers Ltd, Recontainers Direct was created to serve as a comprehensive, online hub for commercial and industrial supplies. From IBC containers and plastic drums to spill control kits, bunded storage, ladders, racking, traffic management, and cleaning equipment, we’ve curated a
product range designed to meet the real-world needs of UK businesses.
We supply:
t New & reconditioned IBCs and drums
t IBC parts and accessories: Taps, valves, caps & more
t Spill containment: Pallets, bunds, trays, and emergency kits
t Workplace essentials: Safety signage, PPE, absorbents, tools
t Warehousing essentials: Racking, shelving, picking crates, ladders
mission is to make bulk packaging safer, cleaner, and more sustainable – helping businesses reduce waste and save money without compromising on quality.
With fast delivery, expert support, and a huge inventory of reconditioned and new containers, Recontainers Ltd is the smart choice for any company using IBCs and drums.
Contact T 01706 211112 https://recontainers.co.uk
Whether you operate in manufacturing, agriculture, automotive, chemical handling, logistics, or waste management, Recontainers Direct provides high-quality, compliant products at competitive prices – with UK-wide delivery and bulk-buy discounts available.
Our platform is designed for ease. With secure online checkout, transparent pricing, and helpful customer support, sourcing what your business needs has never been simpler. We serve everyone from small independent traders to national corporations, offering the same level of care and professionalism that has made Recontainers Ltd a trusted name for over 30 years.
Looking to streamline your procurement process? Recontainers Direct is your supply partner, giving you access to both everyday consumables and specialised equipment – all from one reliable source. With more products being added monthly, we can help you source the right tools at the right price.
T 01706 482060
info@recontainersdirect.co.uk
https://recontainersdirect.co.uk
Camida is a customer service-driven supplier of specialised raw materials to the Life Sciences, Ingredients and Industrial sectors worldwide. Founded in Ireland in 1988, Camida has built a reputation for reliability, technical expertise and strong partnerships with both suppliers and customers.
We’re your sourcing team – performance partners in procurement. One touch sourcing and supply. To simplify your working life. Camida shape a team around your specific needs, comprising of experts in sourcing, quality, and logistics. Our clients come to think of us not simply as suppliers, but partners, people they can trust to address every challenge
with fresh thinking and new ideas.
Our commitment to quality, safety and sustainability is central to our operations and we have achieved a Silver EcoVadis rating, reflecting our dedication to continuous improvement in environmental, social and governance practices.
At M Seals, our global network of 12 CNC machines allows us to offer fast turnaround times and responsive service to our customers. Our in-house manufacturing capabilities enable us to meet both standard and bespoke requirements with precision and efficiency.
At our Engineered Seals Division in Sheffield, we can produce parts up to 850mm in diameter using our largest CNC machine. Equipped with live tooling for milling and drilling, this machine ensures high-quality production with unmatched versatility and ensures that every part we manufacture meets the high standards our customers have come to expect. We also excel at producing seals just a few millimetres in size – demonstrating our capabilities across the full range of seal sizes.
rotary, rod, piston, and spring-energised seals and more, we support many markets with certified, industry-standard solutions.
Contact Ireland Head Office +353 526125455 Manchester Office +44 (0)161 2662226 info@camida.com https://camida.com
Additives & Chemicals UK Ltd is a fast-growing distributor specialising in petrochemicals such as Lubricant Additives, Base Oils GRP I-IV as well as other semispeciality products. It is a dynamic force in the global petrochemical industry. As a leading supplier of industrial and specialty chemicals, Solvocoat’s reach spans the Middle East, the Asian Subcontinent, Europe, and North America.
Our in-house design and manufacturing processes often provide faster, more costeffective solutions, improving both time efficiency and operational performance. From PTFE and high-pressure seals to
We believe that ‘small things make GREAT things possible.’ Getting the small details right – like seals – can prevent breakdowns and ensure lasting performance. At M Seals, our products are engineered for excellence, reliability, and durability.
T +44 (0)114 243 2777 sales.esd@m-seals.co.uk www.m-seals.com
Solvocoat solutions are used worldwide to compliment in the manufacturing process of a wide range of intermediate and finished products. By combining scientific expertise with a practical, human approach, Solvocoat is able to tackle virtually any challenge related to solvents and semi-specialty products. In today’s fast-evolving market, the company remains committed to delivering consistent quality and stability across its product range.
As a global leader in petrochemicals supply, Solvocoat delivers reliable and effective solutions through a diverse product portfolio, backed by exceptional customer service, efficient operations, and deep technical expertise.
With industry leading technical expertise and reputable supply chains, Solvocoat sources only the highest quality products from some of the world’s most renowned and trusted manufacturers. Whether you need paints raw materials, adhesives, sealants, additives, modifiers, surfactants, solvents, or other specialty chemicals – for applications in floor coatings, hygiene, personal care and cosmetics, metalworking, or beyond – Solvocoat has the solutions you’re looking for.
For more information, please see below: T 07762 855193 danial@solvocoat.co.uk https://solvocoat.co.uk
As it celebrates 90 years in business, the Darcy Group has announced its transition to an Employee Ownership Trust (EOT), making the company 100% employeeowned. This milestone secures long-term independence and reflects the Group’s continued commitment to environmental protection and innovation.
Founded in 1935, Darcy provides essential pollution control solutions for chemical and industrial businesses; helping prevent, contain and clean up spills while ensuring environmental compliance through spill care consumables, liquid containment, drain closure and liquid monitoring.
The team was proud to exhibit at CHEMUK 2025. It was fantastic to meet so many new faces on the stand.
Thank you to all the delegates who stopped by – your interest and conversations made the event.
As part of its programme of continuous product development, Aquasentry (a division of the Darcy Group) has recently introduced refinements to its separator alarm range, offering enhanced flexibility within site monitoring systems. The Group also continues to deliver its Chemical Hazard Awareness Training; a one-day, Royal Society of Chemistry-approved course designed to help employers educate staff about the risks associated with chemical hazards in the workplace.
To find out more, please visit: www.darcy.co.uk, telephone: 0800 0370 899/+44 (0)1732 762338 or email: sales@darcy.co.uk.
In this issue, we are pleased to feature HAVi as Vibration Management Company of
Recognising the need for better worker protection, Mike Swan founded HAVi Technologies in 2008. Motivated by the limited solutions available at the time, he developed a product that not only met legislative requirements but also prioritised the improvement of hand health outcomes for workers.
17 years later, HAVi remains steadfast in its mission: to enhance hand health outcomes for workers exposed to vibration and to ensure organisational compliance with health and safety regulations, offering a range of innovative solutions designed to monitor and manage vibration exposure effectively.
Leading the health & safety sector, HAVi is the only provider of a holistic solution to the management of HAVs. We spoke to Kate Louise Cole, Managing Director, who explained the benefits to working with HAVi, “We assure compliance by starting with an audit of the current processes. We then measure tool vibration magnitude in compliance with BS EN ISO 5349-2 and BS EN 8041 to create an asset database of tools and use unique sampling methodology of vibration exposure to produce a suitable and sufficient risk assessment for our clients.”
“Furthermore, our trademarked HAVi ActivIQ and HAVsRiskIndex make it easy for our clients to take action on exposure data by providing bespoke insights.
Underpinning all of this, is our bespoke training and engagement activity to ensure that the clients project succeeds, maximises ROI and most importantly, the workers remain protected.”
HAVi ACTIVIQ is an exciting new solution from HAVi Technologies. The contents of which comes from over 16 years of working with companies to help them comply with the Control of Vibration at Work Regulations Act 2005. Featuring the unique HAVSRiskIndex™, a groundbreaking innovation that not only visualises your HAV data outcomes at a glance, but also drives your ‘ALARP’ policy to managing HAV for your business, HAVi ACTIVIQ will help you to make better decisions, faster, enabling you to quickly demonstrate that you are lowering your exposures in line with the HSE’s guidelines.
Offering a simple solution that quickly identifies the level of HAVs Risk in your organisation, the new HAVi ACTIVIQ breaks information down to the exact tool, task, team, division, or site that is at the greatest risk, and provides a foundation for a ‘continual improvement’ culture for your whole business. Including bespoke smart recommendations to help you focus on the areas that matter most, HAVi ACTIVIQ also keeps you competitive in the market, enabling you to compare your risk with others in your industry.
An estimated 5 million people in the UK are exposed to vibration-related risks in the workplace. HAVi offers a scalable, proven solution that effectively serves organisations of all sizes – from SMEs to multinational blue-chip companies – across industries such as Construction, Manufacturing, Landscaping, Facilities Management, Automotive, Rail, and Oil & Gas.
Looking ahead, HAVi remains committed to advancing innovative technologies that support the management of HAVS in the workplace, pledging to always listen to its
customers, ensuring that every solution developed is driven by their needs and focused on delivering measurable, positive outcomes.
For more information, please see below: T 0115 932 7002 info@thehavi.com https://www.thehavi.com
Rotork has supplied over 200 actuators to ONE-Dyas for the N05-A upstream gas processing platform, located in the Dutch North Sea.
The Skilmatic SI intelligent self-contained electrohydraulic actuators, IQT3 Pro intelligent part-turn electric actuators and CVA continuous unrestricted modulating actuators will support the electrification and automation of the platform.
HSM Offshore was contracted to build N05-A – which will turn upstream wet natural gas into dry natural gas for pipeline export – by Dutch exploration and production company ONE-Dyas.
The next generation platform, scheduled for production in the winter of 2024/2025, is expected to reach ‘near zero’ operational emissions (Scope 1 and 2) and will be the North Sea’s first fully electrified gas production platform. Electrification is central to ONE-Dyas’ nearzero strategy, with power primarily supplied by a nearby German offshore wind farm, Riffgat.
Reduced maintenance visits and limited unplanned helicopter flights also form part of the near-zero initiative. The platform will be fully automated
High-pressure upstream gas pipelines
and normally unmanned, with all plant equipment controlled autonomously. Reliability is also key to reducing unplanned visits to the platform, and digital solutions further supports reliability and availability of assets.
The energy efficiency of Rotork’s actuators will further support the near-zero emissions target. Electric actuators only consume power when in operation, unlike pneumatic actuators and controls, which need
a constant supply of either gas or locally produced compressed air.
Rotork performed a factory fit of the Skilmatic SIs with free issued valves for the N05-A project, which were fitted and calibrated at Rotork’s Rotterdam Service Centre then shipped to the HSM Offshore yard.
Please visit: https://www.rotork.com/en
SPE Offshore Europe (OE) 2025 will take place from 2nd–5th September at P&J Live in Aberdeen – the heart of the UK’s oil and gas industry. As Europe’s leading energy event, OE 2025 is set to welcome over 30,000 energy professionals and more than 500 exhibitors, offering a dynamic platform to explore key themes including energy security, decarbonisation, and emerging low-carbon technologies.
As the premier biennial event driving the offshore energy sector’s transition to a sustainable future, OE 2025 brings together industry expertise, cutting-edge knowledge, and innovative technology to accelerate progress across the entire value chain.
Renowned for fostering a strong sense of community within the offshore energy industry, OE continues to evolve, with the 2025 edition set to introduce even more forward-thinking initiatives to advance the upstream sector.
The exhibition floor will host a broad range of exhibitors, each showcasing the latest solutions and technologies –creating a dynamic, engaging environment for all those active in the UK’s domestic offshore energy market.
OE is widely recognised as a world-class event, celebrated for its high-quality presentations, impressive exhibitor stands, and unparalleled networking opportunities. With many attendees praising the 2024 edition as the best they’ve ever experienced, expectations are high – and OE 2025 is set to rise to the occasion.
OE 2025 will showcase a diverse array of exhibitors driving sustainability across the offshore energy sector. With a strong focus on innovation in Oil & Gas, Offshore
Wind, Carbon Capture, Utilisation and Storage (CCUS), Decommissioning, and Digitalisation, attracting a wide range of professionals – from industry leaders and decisionmakers to engineers, technical experts, project managers, procurement specialists, and business development professionals.
Attendees will have the opportunity to explore cutting-edge solutions throughout the exhibition, as well as through in-depth technical sessions, thought-provoking panel discussions, and valuable networking opportunities. These elements reinforce OE 2025’s role as a vital platform for knowledge exchange and collaboration within the Offshore Energy Industry.
In the Offshore Oil & Gas sector, OE continues to focus on upstream energy production and supply chain activities. For 2025, the event will expand its scope to encompass key aspects of the energy transition and the evolving commercial landscape – spotlighting new opportunities across the region and throughout the wider energy mix.
At the event, you can expect a diverse showcase of products and services across key sectors such as facilities & construction, digital technologies, drilling & completions, health, safety & environment, management & information, people & skills development, and reservoir description & dynamics. Attendees will include representatives from leading companies like Baker Hughes, Oceaneering, Petrogas, Shell, SLB, Subsea 7, Dana Petroleum, and many others.
With the UK leading the way in Offshore Wind Technology through major advancements and strong commitments, OE 2025 will feature a wide range of cutting-edge products and services. These include Installation vessels and equipment, cables and electrical infrastructure, operations and maintenance services, environmental and geotechnical services, project management and consultancy, logistics and transportation, grid connection and integration, as well as monitoring and control systems. If you’re seeking solutions in offshore wind, OE 2025 offers the ideal platform to connect with key industry players such as SSE, RWE, ScottishPower Renewables, Equinor, Ocean Winds, Orsted, Bilfinger, TotalEnergies, and many more.
With over 30% of past OE attendees directly involved in energy transition operations, OE 2025 will continue to reflect the evolving landscape of the Offshore Energy Sector. The conference will feature dedicated Net Zero content, highlighting the industry’s pivotal role in achieving a low-carbon future.
The Energy Transition Zone is set to expand, occupying approximately 50% of Hall 2, and will spotlight innovative technologies and solutions driving the transition. Meanwhile, the Energy Transition Theatre in Hall 3 will serve as a key platform for thought leadership – enabling the industry to explore both the opportunities and challenges in delivering a sustainable energy future and achieving a net-zero economy.
Some of the products and services in demand for this sector include automation, carbon capture, utilisation & storage, decarbonisation solutions, electrification, energy efficiency, floating offshore wind, geothermal, as well as hydrogen, offshore wind – fixed & floating, on-site power generation, operations & maintenance, ports redevelopment, smart technologies, and other marine renewables.
The Decommissioning sector will be prominently featured at OE 2025 through a comprehensive showcase of products and services across the exhibition floor, dedicated content in the Future Opportunities Theatre (Hall 1), and focused sessions within the Technical Conference. As the decommissioning of North Sea oil and gas infrastructure becomes an increasingly vital component of the UK’s sustainable energy transition, this sector presents significant opportunities for innovation, collaboration, and growth within a rapidly evolving landscape.
Other sectors will also include key talks and seminars on applications such as bio energy ccs (beccs), development of transport infrastructure, onshore & offshore pipelines – repurpose & construction, satellite communications, wearable technology, production - gasification & electrolysis, storage, blue/green hydrogen, and much more.
This jam-packed exhibition should NOT be missed! https://www.offshore-europe.co.uk
ProTech Global is a UK-based manufacturing company that creates innovative solutions for the Industrial, Marine, Building Services, and Chemical Markets. With our Insulating Cladding Solutions, Vapour Barriers, and Sealing Systems, we are addressing industry challenges from the outside in. Our portfolio of products showcases a systems approach, providing our clients with long-lasting solutions.
Margel (A ProTech Global Brand) has been developed to deliver alternative solutions to corrosion-related challenges across various markets, from CUI (Corrosion Under Insulation) to CUF (Corrosion Under Fire Protection). Margel can be formulated to provide mid to long-term protection for both new and pre-existing assets.
Margel offers comprehensive protection for all metal surfaces; its vapours saturate the air within the vapoursealed systems on pipes and vessels, penetrating microscopic crevices and other inaccessible areas of the metal surface. The vapour chemically adsorbs to the metallic substrate, creating a robust coating and forming a barrier that prevents oxygen and moisture from attacking the metal substrate. This formula can work alongside existing
coatings that have deteriorated due to mechanical damage or serve as a preventative solution for new applications.
Margel corrosion solutions have been utilised within the UK and internationally, providing protection for oil lines, marine vessels, and large structural assets. The formulation can be adapted to meet a variety of corrosion challenges.
In conjunction with Margel, Proclad Plus 350 has served as the external weatherproofing solution, offering external protection to any insulated system. Come and visit our stand to find out more information.
See them at Stand Number: 2C84
Contact T +44 (0)1934 318468
sales@protechglobal.co.uk www.protechglobal.co.uk
GISMA Steckverbinder GmbH designs and produces high performance underwater connectors that are deployed deep-sea down to 10.000m. The actual production line comprises more than 15.500 different electrical, coaxial, fibre-optical, hybrid connectors and penetrators for Offshore, R&D, Renewables and Defence applications. Connectors are available with up to 265 contacts, suiting to a maximum current rating of 1.000 amps and 10.000V working voltage.
As an independent, medium-sized company with >100 highly qualified employees, we attach particular importance to customer satisfaction, quality, delivery reliability and a partnership-based cooperation. In order to achieve these goals, we consistently
rely on our high proportion of in-house production.
Our core competencies are found in underwater connectors that are specially designed for wet underwater mating, large water depths and demanding environmental and operating conditions. Additionally, we constantly offer new, innovative connectors and complete cable system solutions from one source.
Our motivated team consisting of technical sales, project management, design and development is dedicated to customer requests with efficient processes to quickly achieve the optimal solution. With passion, we support in complex projects: from the selection matrix and the design sketch, project sketches, 3-D models and rapid prototyping to the end product and it’s testing or qualification.
Our stand number is 1N31.
T +49 4321 9835 30 info@gisma-connectors.de https://www.gisma-connectors.de
Come and visit ABLE Instruments, the Process Control Experts, on Stand 1X31.
ABLE’s stand will be focused on two of our major strength: flow and level. On the flow side, this will include the latest ATEX
non-invasive technology, precise Coriolis mass flow & the V-Cone DP Meter with its space saving, integrated flow conditioning capability. For level, we will be displaying Ametek Magnetrol’s ‘best in class’ guided wave radar and the ground-breaking Genesis Multiphase Detector for interface level detection.
ABLE’s own FlareMaster FT flare gas flow meter and flare metering enhancement system will also feature, as will our comprehensive range of field communications/asset management devices.
ABLE are suppliers of a wide diversity of both cutting edge & traditional instrumentation to the process and research industries. As an EOT and in our 40th year of operation, we continue to remain
the world of process control and analytical measurement and developed our own solutions to some of the more difficult measurements across the oil & gas, petrochemical, chemical, utilities, food and pharmaceutical sectors.
T +44 (0)118 9311188
info@able.co.uk www.able.co.uk