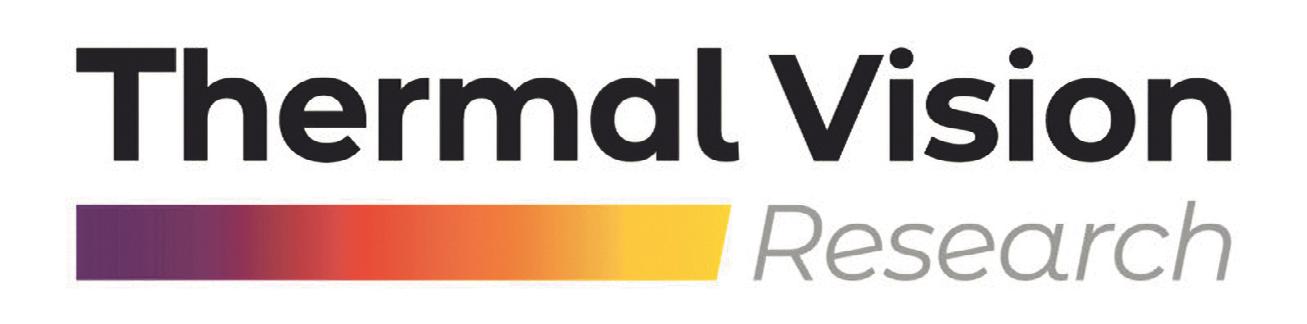
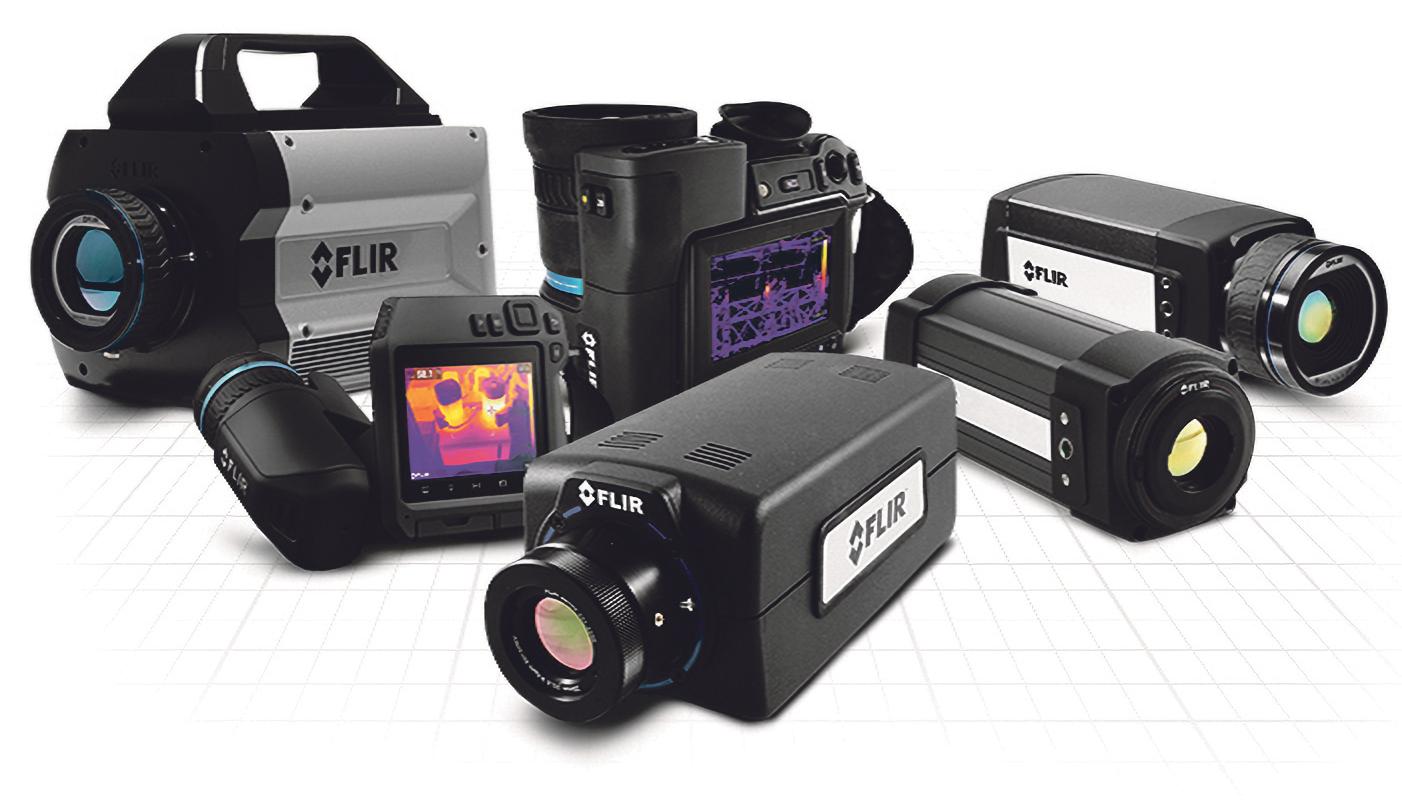
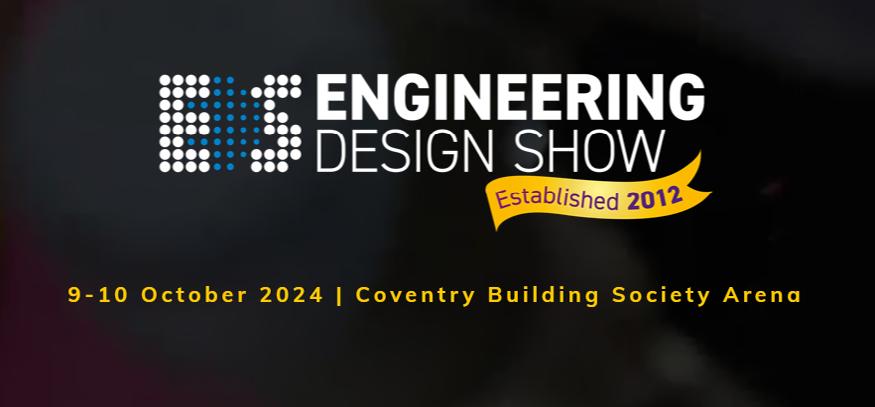
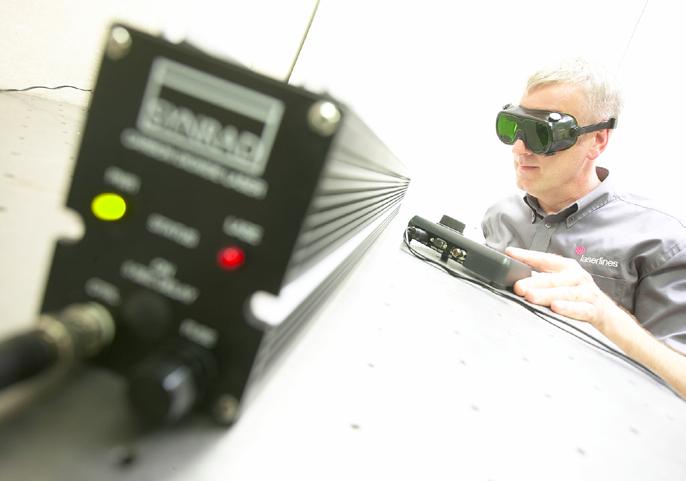
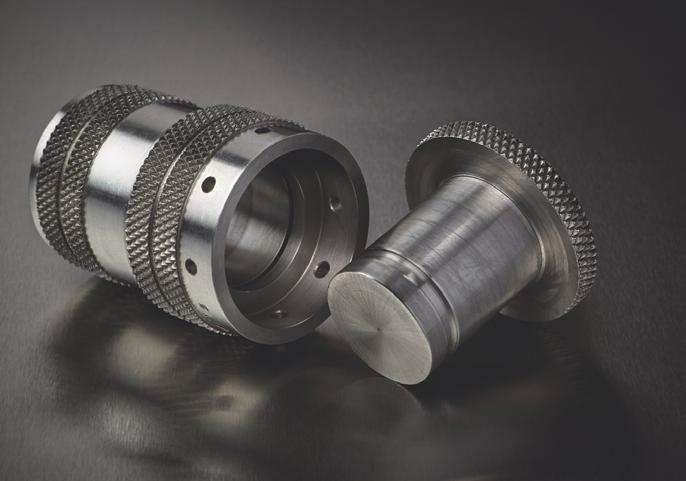
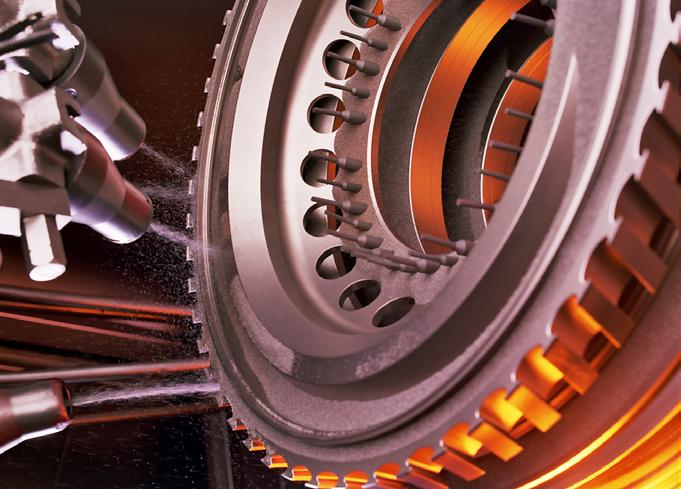
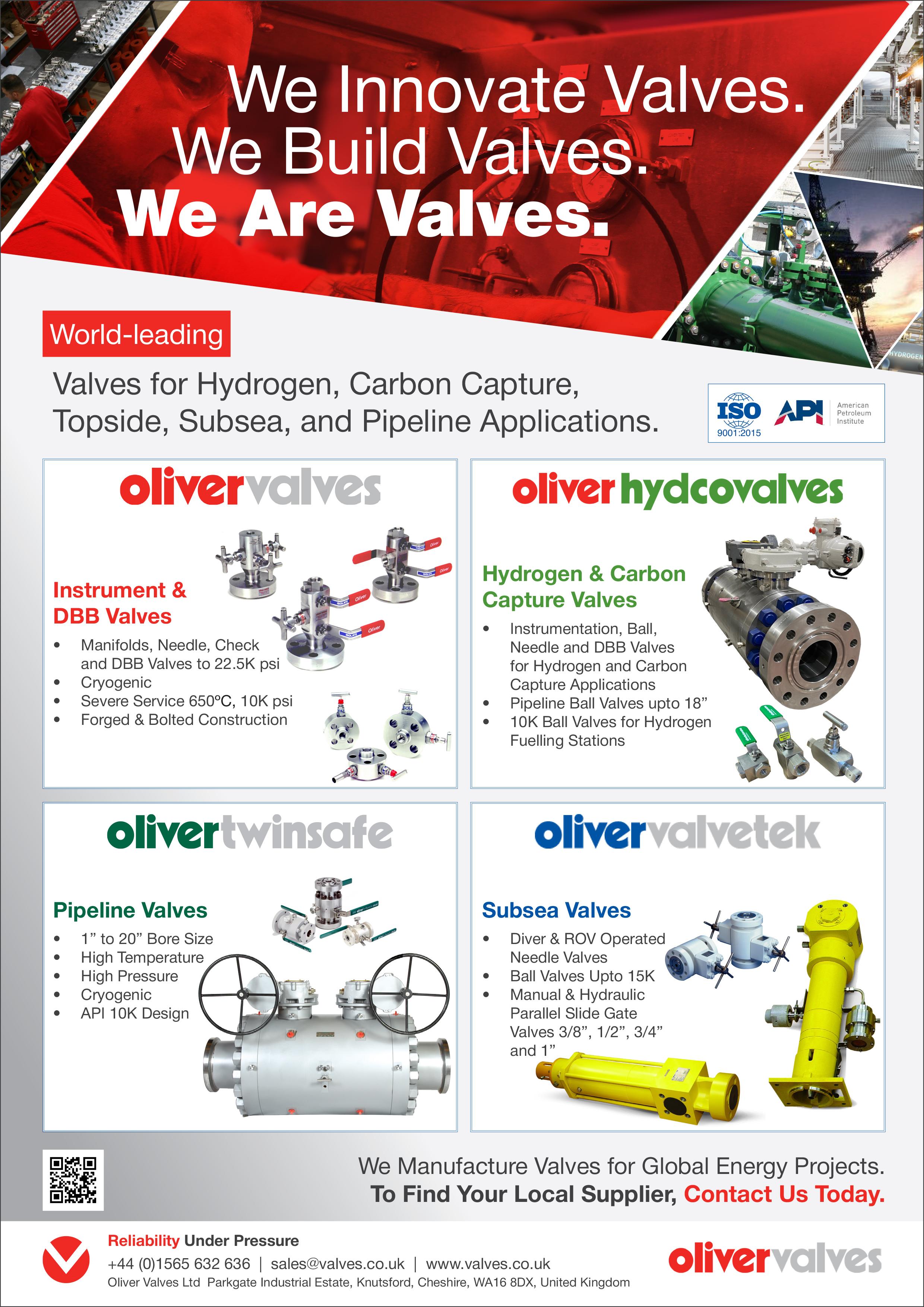
Welcome to the latest issue of Industrial Process News. This issue delves into the latest innovations, trends, and best practices shaping the industry, offering valuable insights for professionals navigating this complex landscape.
On page 4, we feature a full review of Subcon 2024 as well as a list of our Top Exhibitors from the show. As the UK’s largest manufacturing supply chain event, the show drew over 4,000 manufacturing and engineering professionals, with 81% holding purchasing power or influence. The free conference explored many pertinent pain points such as escalating costs, supply chain shortages, recruitment, and sustainability.
Gina Burton Editor gina@industrialprocessnews.co.uk
EEMUA clinches the Industrial Training Company of the Year 2024 for its innovating safety and performance for the third time. EEMUA has continued to impress with its training innovations that support its role as industry’s not-for-profit association that helps safety, environmental and operating performance of businesses’ industrial facilities. On page 6, we delve into the company’s newly developed training courses: EEMUA 159 tankbasics, EEMUA 231 Mechanical Integrity Basics, and EEMUA 194 Subsea Engineering Basics.
We’re also pleased to spotlight Laser Lines Ltd as our Industrial and Scientific Laser Technologies Supplier Company of the Month. On page 5, we take a closer look into the role of lasers in manufacturing and speak to David Earl, Business Manager about how the company adapts its products to the ever-changing trends within industries. He also talks about their latest partnership with LC Lasers, a Barcelona based company that specialises in handheld laser welding systems and cleaning systems.
Other show reviews include: Smart Factory Expo 2024.
Other topics covered: Cleaning & Hygiene, Handling, Storage & Logistics, Print & Packaging, Electrical & Electronics, Health & Safety, Control, Drives & Automation, Green, Industrial Process Technologies, Chemicals, Training & Development.
Don’t forget to send us your latest Industrial news and updates and email us at: info@industrialprocessnews.co.uk
Thermal Vision Research have over 10 years’ experience in the thermal imaging market. Founded by Matthew Clavey, we supply FLIR’s range of specialist IR thermography cameras for the research and development (R&D) sector
Publication Management
Fallon Waldron, Publication Manager T 0121 550 2086
fallonwaldron@industrialprocessnews.co.uk
Production
Robert Sharp, Production Manager production@businessandindustrytoday.co.uk
Accounts
Paul Whitaker, Accounts Manager T 0121 824 4742 accounts@businessandindustrytoday.co.uk
Editorial Gina Burton, Editor gina@industrialprocessnews.co.uk
Industrial Process News is a multi-media digital magazine which circulates directly to 25,000 targeted businesses per issue, and is downloadable from multiple digital news stands and via social media.
Please contact 0121 550 2086 Email info@industrialprocessnews.co.uk www.industrialprocessnews.co.uk For more information on print or format requirements, please see our Media Pack
@ipn_uk The entire content of this publication is advertorial based. To place an advertorial or an advert, please call 0121 550 2086.
Subcon 2024 is a wrap and it was a blast! It’s the UK’s biggest manufacturing supply chain show and this year attracted over 4,000 manufacturing and engineering professionals, 81% who had purchasing power or influence. This year’s event was held from the 5th-6th June at the NEC Birmingham and united senior manufacturing buyers with potential new suppliers, all under one roof. With hundreds of UK and global suppliers, with many new innovations on show, visitors came from a variety of backgrounds including aerospace, automotive, defence and security, medical, energy, rail, and oil and gas.
The free conference explored many pertinent pain points such as escalating costs, supply chain shortages, recruitment, and sustainability.
The two-day event was the perfect opportunity for exhibitors involved in subcontract manufacturing and engineering to network with peers, increase brand awareness, showcase new innovations and services, meet buyers, procurement managers specifiers and key decision makers and on many occasions, start talking business.
Here at Industrial Process News, we were blown away by the following Three Top Exhibitors:
■ Aktis Engineering Solutions pvt. Ltd: This Surrey-based company has its headquarters in Bangalore and offices throughout the USA. This end-to-end solutions provider has wide-ranging capabilities in automation, heavy engineering, consume products, medical devices and irrigation sectors right across the product innovation cycle from concept design to series production. Aktis has always been the partner of choice for OEMs, Tier I and II companies around the world, with manufacturing capability in everything from injection moulded plastic parts and assemblies, precision machined components, forgings, sheet metal stampings to sheet metal fabrications and much more.
■ Grenville Engineering: Based in Stoke-on-Trent, this company specialises in precision engineering and manufacturing solutions, particularly in CNC machining and fabrication services: laser cutting, welding, bending and machining. Grenville works with a diverse range of applications and can provide sheet metal work, roll-forming, plastic injection moulding, presswork and more.
■ Santander Global Metal (SGM): This Spanish company offers an extensive range of services from engineering, material supply, casting and valves, precision machining, mechanical engineering, welding processes, industrial assembly, mechanised boilermaking, electroplating and recovery of parts, assembly and manufacturing of piping, process automation and more.
■ Tewkesbury (Diamond Chrome) Plating Co Ltd: This aerospace AS9100 and NADCAP accredited metal surface treatments and finishing company has an expertise spanning over 45 years and
This year marks a significant milestone for Grenville Engineering, which proudly celebrates its 40th anniversary. Over the past four decades, Grenville Engineering has grown into a trusted name in subcontract manufacturing, known for its unwavering commitment to quality, innovation, and customer satisfaction. Based in the Midlands, the company offers a comprehensive range of services, including laser cutting, punching, metal forming, welding, assembly, machining, and finishing. Their expertise in these areas has established them as a leader in the fabrication sector.
Grenville Engineering demonstrated its industry-leading capabilities again during its eighth consecutive appearance at Subcon. Their stand at the event consistently attracted significant attention, serving as a hub for industry professionals seeking diverse fabrication solutions, from simple laser-cutting tasks to full-scale bespoke projects. This year, they showcased their latest investments, totalling £280,000 in cutting-edge technology, including their first CNC milling machine, a second robotic welder, and a soon-to-bedelivered fifth flatbed laser.
Stuart Rawlinson, Sales Director, reflected on the company’s journey, stating, “From starting as an apprentice on the shop floor in January 1995 to witnessing the introduction of this cutting-edge machinery, I am immensely proud to have been a part of Grenville Engineering’s history. Our investment in technology goes beyond staying ahead; it’s about preserving the standards that have defined us for 40 years.”
As Grenville Engineering continues to innovate and expand, its dedication to delivering high-quality engineering solutions remains steadfast. This ensures that it meets the evolving needs of its valued partners and customers.
www.grenville-engineering.co.uk
is based in Gloucestershire. The company has worked in the surface finishing industry with leading aerospace and defence manufacturers, with the benefits of an on-site machine shop providing precision honing, cylindrical and centreless grinding.
This is our pick of the best exhibitors from this year’s event, listed here in alphabetical order: Grenville Engineering. Further details can be found below.
Save the date:
Subcon 2025 4th-5th June
NEC Birmingham
https://www.subconshow.co.uk
In this issue of Industrial Process News, we are pleased to features Laser Lines Ltd as our Industrial and Scientific Laser Technologies Supplier Company of the Month.
Founded in 1975, Laser Lines Ltd has grown into a leading UK supplier in the laser and additive manufacturing sectors. The company now represents over 20 suppliers and offers a full suite of services, including end-to-end solutions, training, installation, maintenance, and repair. They also provide subcontract 3D printing and additive manufacturing services.
Laser Lines Ltd is committed to delivering tailored solutions for diverse sectors such as university research, automotive production, tooling, and product design with a focus on enhancing efficiency with cutting-edge technology and innovation.
In recent decades, the role of lasers in manufacturing has evolved significantly. Laser markers now eliminate the need for labels by marking directly onto products, and lasers are increasingly replacing inkjet systems, reducing the reliance on messy consumables and revolutionising manufacturing processes.
Moreover, conventional welding systems like MIG and TIG, which were once manual tasks, have evolved with the advent of robotic automation. Today, lasers can be employed both manually and robotically, offering a superior alternative to these older technologies. By adopting laser processes, manufacturers benefit from significantly lower heat input during welding, allowing for precise control and minimal deformation when working with materials of varying thicknesses. This results in a more controlled, repeatable, and efficient welding process.
David Earl, Business Manager at Laser Lines stated, “Laser Technology represents the cornerstone of our business. We offer an extensive array of laser solutions, including laser markers, welders, turnkey systems, standalone lasers, accessories, and components. Our portfolio features esteemed brands such as Sisma, the Italian manufacturer of marking and welding laser systems; LC Lasers, the Spanish producer of handheld laser welders and cleaners; Novanta, the American specialist in CO2 lasers and galvo scanners for cutting and converting; and Laserline, the German innovator in high-power diode
lasers designed for integration into welding, brazing, cladding, and hardening production cells. Additionally, we provide industrial-grade nanosecond, picosecond, and femtosecond laser sources from Fluence Technology and Photonics Industries, along with laser power measurement accessories from Gentec-EO.”
Earlier this year, Laser Lines Ltd established a partnership with LC Lasers, based in Barcelona. LC Lasers specialises in handheld laser welding systems with outputs up to 1.5kW, capable of welding stainless steel up to 6mm thick with minimal heat input. They also produce handheld laser cleaning systems with up to 500W power, designed for surface cleaning of both organic and inorganic materials.
Laser Lines Ltd has invested in both types of systems and now offers in-house demonstrations. Customers are invited to bring their own materials to experience welding or cleaning firsthand.
In a different arena, Fluence Technology, another partner of Laser Lines Ltd that specialises in femtosecond lasers, has showcased how their Jasper laser’s exceptionally short 250fs pulses enhance the ablation efficiency of metals such as stainless steel and titanium. These ultrashort pulses enable precise cutting and drilling without causing melting or thermal effects.
We asked David what trends the company is observing within the industries that use its products, “We serve a diverse customer base, from small subcontractors to large multinational companies across various industries, including Aerospace and Agriculture. While there is always a need for cost-effective small systems, recent trends show a growing demand for advanced solutions. These include laser marking systems with coaxial vision and pattern matching to eliminate fixturing and human error, as well as laser welding systems that use galvo scanners to track and weld complex paths. Additionally,
many customers are seeking high-quality improvements through shorter pulse lasers for precise applications.”
We then asked how they face common customer challenges, “We listen to our customers’ requirements and make it our priority to provide the best available solutions. By partnering with leading suppliers from around the world and always looking out for innovative manufacturers that we can add to our portfolio, we ensure that we can deliver cutting-edge products that meet the evolving needs of our customers.
For example, when a prospective customer approaches with a need for laser marking or welding, we first assess their requirements and conduct application trials to identify the best solution based on speed and budget. After selecting the ideal system, we ensure prompt delivery and arrange for a trained laser engineer to install and train them. If any issues arise, our engineers provide phone support and promptly address problems on-site. Our strong customer retention and repeat business reflect our commitment to exceptional support throughout the sales and after-sales process.”
Laser Lines also offers Additive Manufacturing Solutions. They have been partnered with Stratasys, a global leader in 3D printing technology for 30 years, and they offer a comprehensive range of their technologies, including FDM, PolyJet, SAF, DLP, and SLA. Our offerings also include cost-effective metal 3D printers from Xact Metal, FDM printers from UltiMaker, and advanced postprocessing systems from DyeMansion.
For more information, please see below: 01295 672500 info@laserlines.co.uk https://www.laserlines.co.uk
For a third time, Industrial Process News is proud to name the Engineering Equipment and Materials Users Association (EEMUA) as our Industrial Training Company of the Year 2024.
EEMUA has continued to press ahead with training innovations that support its role as industry’s notfor-profit association that helps safety, environmental and operating performance of businesses’ industrial facilities. We are continually impressed by EEMUA’s ability to keep driving relevant training content and deliver it through flexible methods that match the engineering community’s ability to learn within their busy work schedules.
best use them. These fit alongside live online lessons and 1-1s with seasoned, subject expert Tutors, and support from Mentors throughout – for direct interactivity that ensures correct understanding. The quality of training is complemented by certification valid for up to five years (through an endof-course assessment) to satisfy industries’ demands for people with proven skills.
EEMUA’s e-learning has reached new heights of usage, with companies customarily onboarding new staff by taking individual specialist modules or the whole range – to help joiners appreciate the practicalities of fitting different team members’ skills together in real-world engineering. Another fastgrowing audience has been company leaders who have been taking the Process Safety Management e-learning course. E-learning modules cover a dozen different areas, from cyber security to mechanical integrity, alarm systems to storage tanks, and pressure systems to subsea materials.
As a corporate membership organisation, EEMUA has a membership covering industries globally, and all its resources for engineers, courses included, are developed and verified by industry, for industry – a peer review process that produces practical ‘how to’ content for engineers, and keeps it up-to-date with technology, regulations, techniques, materials and good practice.
Building on the success of its earlier blended learning course the Mechanical Integrity Practitioner Certificate (MIPC®) course, EEMUA has developed ‘EEMUA 159 TankBasics,’ ‘EEMUA 231 Mechanical Integrity Basics,’ and ‘EEMUA 194 Subsea Engineering Basics,’ with more courses imminent – so watch out for announcements in Industrial Process News. The MIPC course runs twice a year, with learning starting on the next course in October 2024. It spans multiple months for the depth required by industry for practitioner-level engineers; with course work divided into weekly learning of around 4 hours per week, to fit around busy schedules of valuable personnel on-site, on-call or wherever suits them best.
Key attributes of EEMUA’s blended learning courses are: coursework adapted to the engineering needs of each Learner, their site/s and company (via a short induction ahead of learning) so that Learners immediately start to build a workbook tailored to fit factors on the ground directly relevant to them. All course resources are available online so that each Learner can access them when they can
EEMUA’s broad range of training options mean that individuals and their companies can select the type of training that most suits them at the time they can best use it. Options include: e-learning, classroom, blended, live online, in-house, in English, French, German, or Dutch languages. Courses in varied time zones to match work patterns in the UK, Europe, Americas, Middle East, and beyond. These training selections enable companies and individuals to compose entire careers of professional development, covering ‘Awareness,’ ‘Basic application’ and ‘Practitioner’ levels using the ‘how to’ of engineering good practice employed every day by the industry worldwide.
Having invested in an enterprise grade-learning platform, EEMUA is certainly making the most of it by extending the content and usage simultaneously. You can see how the experience and expertise that EEMUA shares with Members continues to give users an advantage. As EEMUA’s Operations Director John Lilley puts it, “We make the connection between courses and the market. Free from shareholders and owners, EEMUA invests all its revenue into sharing practical guidance resources, events, training, and more – founded in our guidance publications and accepted worldwide by both operators and regulators and all developed ‘for industry, by industry.’ It’s an honour to be recognised for this work as Industrial Process News’ Training Company of the Year.”
For more information, please see below: 020 7488 0801 ask@eemua.org www.eemua.org
Advanced Rework Technology Ltd (A.R.T.), the leading independent provider of IPC-certified and bespoke training services for the electronics assembly industry, is providing constantly updated courses that help prevent component damage during electronic assembly.
Comments A.R.T.’s Managing Director and Master IPC trainer Debbie Wade, “Modern electronics assembly is a complicated and intricate process that uses many different materials, machines, and techniques. Component damage is a challenge for any electronics assembler, but adhering to best practices as a matter of principle will help to avoid potential health and safety violations, financial costs and further electronic damage or failure, and will increase product performance and assembly efficiency.”
Electronic components and products risk many types of damage whilst on the assembly line, including:
■ Electronic Discharge Damage: This can result in immediate damage to sensitive components or it can lead to component failure further down the line.
■ Mechanical stress: Bending, dropping, and cracking are some of the ways that components can become damaged during assembly.
■ Thermal damage: Overheating during soldering can lead to the alteration of fundamental electronic properties.
■ Moisture, corrosion, and rust: Water can corrode certain metals, cause short circuits, and rust over time.
■ Overcurrent and overvoltage: Components that are subject to currents or voltages beyond their maximum ratings can degrade over time or destroy immediately.
■ Reverse polarity: Connecting components in reverse can cause instant damage, especially in diodes, capacitors, and ICs.
■ Chemical damage: Improper cleaning agents or exposure to harmful chemicals can corrode contacts, leads, and solder joints.
Contact Debbie Wade, Managing Director, Advanced Rework Technology Ltd, info@rework.co.uk https://rework.co.uk
Cool Energy, an international market leader specialising in complete temperature control solutions for manufacturing process and facilities applications, announced opening of a new training suite at its facility in Totton. The custom-made lab is designed to facilitate training and development of technicians in an environment tailored to their needs. It offers hands-on simulations and a classroom setup featuring all equipment that ICS Cool Energy sells hires and services including chillers, free coolers, temperature control units (TCU), heat exchangers, controls and more.
With the new training suite, ICS Cool Energy aims to equip technicians and sales engineers with enhanced skills and practical expertise to excel in the field. The facility, also featuring a water treatment fluid laboratory, allows for
hands-on, functional training that simulates real-life scenarios of how temperature control systems operate, ensuring optimal understanding and application of the equipment. This new training suite will also serve as an opportunity for customers, enabling them to learn and better understand the equipment they install and utilise in their facilities.
As new products and solutions are introduced to ICS Cool Energy offering, they will be incorporated into the training suite, making it future-proof and expansive.
For more information on ICS Cool Energy and its complete range of process temperature control solutions, please visit: www.icscoolenergy.com
Awaste management specialist has introduced a new ground-breaking service to identify unlabelled chemicals, allowing for safe disposal.
CSG has become the first waste management company in the UK to invest in a handheld Raman spectrometer, helping businesses and organisations, which produce chemical wastes to operate safely and meet their legal obligations.
Previously the only way to identify the contents of an unlabelled chemical container was to open it for sampling and analysis. CSG has invested in a Raman spectrometer, which enables accurate, through-barrier identification of hazardous chemicals at customers’ sites, without the need for containers to be opened
CSG or one of its trusted partners can then arrange to dispose of the chemicals compliantly and safely.
The Raman spectrometer can provide rapid results on liquids or solids through sealed, clear and coloured glass and plastic opaque containers, or by analysing the chemical directly in an open container, identifying the chemical from an inbuilt database.
The device works by scattering light from a high-intensity laser light source, producing different wavelengths or colours to determine the chemical.
Raman spectroscopy has been successfully utilised in hazmat response, law enforcement and parcel screening at border control and can be used to identify very hazardous materials, such as explosives and narcotics.
The only limitations on the Raman spectrometer are chemicals, which are in sealed containers through which the laser beam cannot penetrate, such as metal tins.
Visit: https://www.csg.co.uk/ hazardous-waste-quote for a quote, or call 0800 011 6600.
DOMO Chemicals, a global leader in engineered materials and sustainable solutions, proudly announces significant sustainability achievements in 2023, as detailed in its latest Sustainability Report published today.
In a year marked by substantial progress and innovative partnerships, the company obtained the International Sustainability and Carbon Certification PLUS (ISCC+) label for three production sites and over 300 PA6 and engineered materials products. This certification enhances DOMO’s ability to offer customers a wider range of circular and bio-based solutions, reinforcing its commitment to customer-centric innovation.
Further solidifying DOMO’s dedication to sustainability, DOMO Chemicals has been awarded the prestigious EcoVadis Gold Medal, improving
BASA has been representing the adhesives and sealants sector since 1983, and a new initiative open to all BASA member companies will recognise excellence and achievement within the adhesives and sealants industry.
“Sustainability and Innovation is really important to BASA and formally recognising our member companies’ achievements and excellence in these and a number of other areas is an exciting development,” says Lorna Williams, BASA CEO. “We are looking forward to maximum engagement and we are delighted by the responses from members who have entered for an award. We are looking forward to seeing everybody in November!”
Details of the remaining sponsorship opportunities and how to book tickets to attend the event are available on the dedicated BASA Awards Night website
If you are interested in sponsoring the event, please contact us.
The event, to be held at East Midlands Conference Centre, Nottingham on 22nd November, will be hosted by comedian Jimmy McGhie and will include dinner and entertainment. Tickets are now available for purchase online.
Contact Lorna Williams, Chief Executive Officer, British Adhesives & Sealants Association, +44 (0)330 223 3290 lorna@basa.uk.com www.basa.uk.com
from a Silver Medal in 2022 with an impressive 13-point score increase. This recognition from the world's largest provider of corporate sustainability ratings underscores the company’s commitment to sustainable practices and continuous improvement. It also provides a clear benchmark for DOMO’s customers to evaluate the company's sustainability performance.
For more information about DOMO’s sustainability journey and to view the full 2023 sustainability report, titled ‘Caring for a Better Tomorrow,’ please visit: report2023. domochemicals.com.
www.domochemicals.com
Thermal Vision Research (TVR) is the UK premier distributor for Teledyne FLIR’s IR thermography camera range, designed for specialist R&D applications. Established in 2017 by Director Matthew Clavey, TVR is based at Aztec West Business Park near Bristol, in South Gloucestershire.
At last year’s Engineering Design Show (EDS): Held at the Coventry Building Society Arena from 12th-13th October, TVR featured at the show with Teledyne FLIR Business Development Managers.
The team showcased a state-of-the-art thermal lab, with a wide range of products including:
■ The RS Platform: Capable of seeing images in kilometres – perfect for military and defence operations
■ Microscope cameras: With images of two microns per pixel.
■ Premiere Uncooled A700 camera: 640x480 (60 Hertz) – with research studio – great sensitivity and perfect for university research and entry-level industrial applications.
■ The ‘King of Cameras’: The cooled HD 1280x1024 sensor, able to run at 180 Hertz, to 3kHz. Produces fine detail, down to 0.02 degrees.
The EDS show was a resounding hit, with stand fever pitch around the thermal selfies! Visitors were astounded by the high resolution and magnification capabilities of the Teledyne FLIR camera range.
We caught up with Matthew post-EDS show to find out how things have progressed, “We are excited to be showcasing the all-new FLIR’s 80-degree wide angled lens. It has full compatibility with A400/500/700 science range and is available now from our website.”
“That’s not all! We ran our first FLIR RS6780 advanced sensor showing during November. The RS6780 has a three-position motorised filter wheel, with premium quality thermal images across long-range and tracking. It is optimally-designed for researchers as a radiometric camera system, due to the calibration for temperature and radiance measurements. Our demonstration showed the optional extender lens up to 750mm, allowing tracking up to 30km away in the distance: perfect for defence operations, wind turbine monitoring, rocket launch monitoring through to wildlife research around the world!”
The R&D capabilities of FLIR thermal cameras are limitless, offering razor-sharp images and measurements, perfect for many applications from defence, military, renewable energy monitoring, battery testing, research, through to cutting-edge wildlife conservation monitoring.
Thermal Vision Research is well known for its outstanding research collaboration with The Aircraft Research Association (ARA): a dedicated UK aerodynamic research institute. This specific mission was to test the hybrid laminar flow control hypothesis. TVR loaned its Teledyne FLIR T1K to locate accurate temperature changes in the high-speed transonic wind tunnel, with speeds up to Mach 1.4 (1,000mph.) As a result of the air turbulence generated from the high speeds, the precise point of transition for airflow changes by less than 1.
The Teledyne FLIR T1K provides an accurate visualisation of the airflow in-situ, without adversely affecting the aerodynamic variable. These meticulous point of transition results allowed the Aircraft Research
Association (ARA) to prove the hybrid laminar flow control hypothesis, within controlled test conditions.
The ARA are now at the incredible, early stages of marketing the pioneering FLIR T1K wind tunnel concept design to engineering companies, as a blueprint towards long-haul sustainable flights.
A second collaboration involved working with Northern Rail, through the ingenious trialling of an ‘intelligence train,’ installed with a FLIR A6750sc cooled thermal camera. The camera works with acoustic monitors, G-shock Bogie, AI camera, radar dome, LIDAR horizonscanning cameras and precision-driven 180° thermal imaging software, providing precision-driven accuracy on railway track infrastructure problems. The camera captures clear, sharp images in transit, even at highspeeds: the pixels generated in sub-one milliseconds of track sections and full-frames of 125Hz. The cooled camera tracks up to 100 metres ahead on the tracks and automatically uploads detailed track date to a SMARTcloud platform, which can then be accessed by Northern Rail remotely.
Matthew explained the advantages of using the FLIR A6750sc in this manner, “It allows the train company to keep the track open for regular train services, saving costly downtime and thermal imagining target precise areas for track maintenance, earmarking for strategic future engineering maintenance.”
With the recent surge towards battery-electric cars across the UK, especially with the planned 2035 petrol and diesel ban, many businesses and households are considering the shift towards electric vehicles. One ongoing concern though is the safety around EV Batteries, with some high-profile media attention on cargo ship fires recently.
The Teledyne FLIR high-speed thermal camera offers accurate EV test safety reassurance, with more accurate high-speed imaging results than previous thermocouples and general IR devices, pinpointing the exact location of short-circuits and heat spreading.
The high-speed camera gives slow, thermal imaging captures at high temperatures of over 3,000°C and provide details of the thermal management system, during the EV battery testing period.
TVR are happy to visit businesses on-site to demonstrate camera range capabilities and offer camera hiring, lease and purchasing options.
TVR are set to repeat last year’s successful show for this year’s event. On the 9th-10th October 2024, TVR will be attending the Engineering Design Show at Coventry Building Society Arena. They will be located at Stand: G74.
For more information on TVR, please see the website below: 0333 200 4667 info@thermalvisionresearch.co.uk www.thermalvisionresearch.co.uk https://www.linkedin.com/in/ matthew-clavey-b8ab082a
ABLE are the official authorised UK representative for ARMADEX Ex-M OZC-3 Explosion Proof Digital Camera, available online with 128GB SD card included. This ‘point and shoot’ camera is certified for use in ATEX Zone 2 (Gas) hazardous areas and is a modified version of the TG-7 from OM System. Weighing in at only 249 grams (including the battery), the ARMADEX Ex-M OZC-3 ATEX camera has a compact yet rugged body meaning it is easy for engineers to carry either in a pocket, or with the included dropped safety strap. Furthermore, the camera’s hardware is perfectly suited for taking sharp pictures underwater even under low light conditions. The ATEX camera is also shockproof against drops up to 2.1m, freezeproof up to – 10 degrees Celsius and also dustproof.
With 4x optical zoom, the ARMADEX Ex-M OZC-3 has a ‘best-in-class’ 12.0 megapixel camera with Ultra 4K video recording capabilities. 4K Recording
is provided at 15fps, delivering the highest image quality. Furthermore, the ARMADEX 3rd Edition now comes with microscope mode, enabling you to capture extreme detailing.
Full list of package contents
■ ARMADEX Ex-M OZC-3 Explosion Proof Digital Camera
■ 128GB SD card
■ Pelicase
■ LI-92B Lithium-ion battery
■ USB cable (Type A to C)
■ Hand strap
■ User Manual
■ 1 year warranty
Key features:
■ Certified for use in ATEX Zone 2 (Gas) hazardous areas
■ Now comes with LED flash
■ IP68
■ Digital Microscope Mode
Have a particular application in mind? We’d welcome a call on: +44 (0)1189 169420.
For your info, ABLE are the exclusive UK distributor and stockist for ARMADEX Ex-M OZC-3 and can assist you and your customers in the following areas:
■ Handle future pre-arranged ‘call off’ quantities for expedient delivery
■ Offer after sales support utilising our in-house expertise
■ SanDisk SDXC Extreme Pro 128GB 200mb/s included
■ 3.0-inch, approx. 1,037k-dot monitor
■ Ultra 4K video recording capability
■ 12.0MP camera
■ Replaceable long life battery
■ Offer training into how the ARMADEX Ex-M OZC-3 can be used via a zoom call in our state-of the art training rig
Further to the above, ABLE can offer custom solutions based on your individual requirements. Email us now at: info@247able.com.
Vision Engineering, UK designer, manufacturer and exporter of ergonomic microscopes and measuring systems, today announces a new sub £1k entry point for its patented optical stereo microscope technology with the global launch of OPTA.
Available for only £900, with a choice of three stands and two lenses, OPTA redefines the entry point for users to benefit from Vision Engineering’s exceptional image quality, ergonomic design and ease of use.
Additionally, Vision engineering announces exciting advancements across its popular EVO Cam, Lynx EVO, and Swift PRO product lines. These enhancements broaden the appeal and applications of these powerful tools, making them more accessible to a wider range of industries and users.
EVO Cam ICON: Simply better for Quality Inspection The EVO Cam series now boasts a wider range of
configurations, offering even greater flexibility for digital inspection tasks. With the launch of a new, simplified ICON model, users can now choose from multiple software configurations and ergonomic stands to perfectly tailor their EVO Cam system, enabling effortless image comparison, capture, measurement, and reporting.
Award-winning Lynx EVO range extended for Superior 3D Viewing
Building upon its reputation for unparalleled ergonomic design and stunning 3D stereo imaging, the Lynx EVO series has been extended to include a simpler, non-zoom variant to appeal to a more price conscious market. This makes the benefits of Lynx EVO accessible to a much wider audience who have applications demanding exceptional image quality and clarity, useable working distance, and exceptional user comfort.
Swift PRO: Precision Measurement with a new EDGE Vision Engineering has enhanced the Swift PRO metrology line, its flagship range of bench-top optical
measuring systems, with the release of the new Swift PRO EDGE. Featuring a 6.5x zoom, the EDGE enables quick, precise measurements of a wide range of part sizes and features without time-consuming lens changes for different measurement tasks. Using our industry standard, user-friendly Metlogix software, operators of all skill levels will operate the EDGE more efficiently and more productively.
Commenting on the upcoming product launches, Paul Newbatt, Group Sales and Marketing Director at Vision Engineering says, “These products are the combined result of listening to our customers and continuously developing our innovative products. By bringing OPTA to market now, and enhancing the value propositions of our EVO Cam, Lynx EVO and Swift PRO ranges, we are confident that these new solutions will significantly broaden the appeal of our Inspection and Metrology portfolio. This enables a much wider range of customers in existing and new markets to better achieve their inspection and measurement objectives with Vision Engineering solutions.”
For more information, please visit: https://www.visioneng.com
Thermal Vision Research have over 10 years’ experience in the thermal imaging market. Founded by Matthew Clavey, we supply FLIR’s range of specialist IR thermography cameras for the research and development (R&D) sector.
Essentra PLC, the global manufacturer of essential industrial components, has become one of the first companies of its kind in the FTSE250 to publish a Climate Transition Plan since new rules were published on how listed companies had to report in accordance with the Transition Plan Taskforce.
The plan sets outs Essentra’s net-zero emissions reduction targets, and its approach to reducing Greenhouse Gas (GHG) emissions from its operations and value chain. The plan contains the actions, owners, timelines and anticipated costs to make the transition to net-zero.
A key element of the plan is the transition to the use of 100% renewable energy across all of its sites, worldwide by the end of 2030, and a target that 50% of the polymers used in the manufacture of new products will be sustainable by 2030, rising to 100% for its general protection and security seals ranges.
This will be helped by the continued investment into its Centre of Excellence at its UK site, which is enabling the trial of innovative materials with lower emissions and improved environmental impacts. It has a longer-term ambition to publish the precise carbon impact of every component within its product range – data it can currently calculate in response to a direct customer request.
Such has been the dramatic rise in requests for this data (from six in 2023 to 80 already this year), the business
is now looking at how the relevant carbon data can be published on its website for all 45,000 of its products.
The publication of the Climate Transition Plan coincides with the launch of Essentra’s 2023 Annual Report that shows that the business has reduced its scope one and scope two emissions by an impressive 38% since 2019. It also reveals that 94% of all solid waste was diverted from landfill across all operations – an 18% improvement on its performance in 2022. Almost 8,000 (7,981) products across its entire range now have sustainability attributes, of which 750 have been launched within the last 12 months.
Jennifer Spence, ESG Director at Essentra PLC, says that 2023 has been a year of significant progress for the business across all areas of environment, social and governance (ESG): “In our first year as a pure-play components business, we have been able to sharpen our focus on the ESG topics that will drive us towards our goal of building a sustainable future,” she says.
“Our purpose is to help customers build a sustainable future. With our unique business model combining manufacturing and distribution, we are ideally placed to provide a low-carbon service to our customers from design to delivery, and support them through a lowcarbon transition.”
Contact www.essentracomponents.com www.essentraplc.com
Essentra PLC, a leading provider of essential components and solutions, has released details of the ‘future products and innovations’ promised in Q2 and following its recent acquisition of BMP TAPPI, having completed trials of more sustainable alternatives to single use plastics.
In terms of product, new releases include an extension to its highly successful ILU range of polyethylene ribbed pipe-end plugs, used to protect pipes during transit against the ingress of dust, water and other contaminants, as well as during sandblasting, painting, and other surface treatments.
The company, which already manufactures in excess of 1,500 individual product lines, has also extended its range of tube inserts to
accommodate square, round or rectangular openings to give a more aesthetic finish to metal fabricated tubes.
Among the more important innovations is the successful trial of a sustainable post-consumer recycled (PCR) plastics material that will reduce the company’s reliance on single use plastics and will result in the launch of a new range of plastic components later in the year.
The company has also further expanded production capacity in expectation of new lines, with further moulding machines on order.
Nicolas Karoui, Integration Director at Essentra, says the firm is realising the benefit of being part of a larger global operation, “We continue to work closely with our colleagues at the Essentra Centre of Excellence in Kidlington, UK, to see how PCR content and biodegradable bioplastics can help make future manufacturing more sustainable, and meet the future demands of our customers in Italy and Southern Europe.”
Based in Milan, BMP TAPPI has more than 60 years of history serving thousands of customers predominantly across Europe, in multiple end-markets, including industrial equipment, automotive and metal fabrication sectors.
www.essentracomponents.com www.essentraplc.com
What do we do?
Electric Materials, a premier copper mill headquartered in Pennsylvania, USA, has been a global leader since 1915, specialising in the extrusion, casting, and forging of high-quality copper electrical components and commutators.
Commutators:
We are internationally recognised for its expertise in commutator manufacturing including V-ring, Glass band and shrink ring commutators. Our comprehensive capabilities encompass start-to-finish commutator production accompanied by compression seasoning, spin seasoning and profiling.
Busbars:
Our busbars are not simply ‘off the shelf’ stock that may (or may not) fit the job, but if needed can be custom designed
and built to your exact specifications in any shape and configuration needed.
What does One-stop shop means?
All our high-quality extruded shapes, rods, rings and bars are produced from billets we cast in-house. The necessary materials are carefully combined in our two large induction furnaces, and before pouring each heat, the chemical composition is evaluated in our laboratory.
Do we work globally?
Certainly! With a century-long legacy of excellence, Electric Materials ships its highquality electrical components globally. Just get in touch with us for your inquiries.
Contact Selim Yetkin, +44 (0)7387 140988 syetkin@elecmat.com www.elecmat.com
GCE®, a global market leader for gas control equipment, has introduced its SmartControl line of cylinder pressure regulators to expand its industry provenportfolio of reliable and robust gas control products.
This straightforward, compact and lightweight designed regulator provides a steady gas supply and accurate pressure settings, as well as the safety and heavy-duty performance worthy of the GCE brand yet is priced competitively. SmartControl regulators are available for common cutting and welding industrial gases: oxygen, acetylene, propane, and argon/CO2 mixes.
“The SmartControl provides efficiency through flow stability to deliver consistent welding or cutting results,” says Tommy Jönsson, Business Development Manager, GCE. “As with all our regulators, the new SmartControl
meets ISO 2503 certification. Prioritising safety, GCE is one of very few companies that offers the Oxygen Shock Test to meet the highest safety standard of welding and cutting processes and inlet pressures of up to 300 bar.”
Applications
■ The SmartControl for Oxygen applications provide accuracy of the pressure setting, which is an important factor for quality especially in combination with the high flow needed for cutting and strong preheating operations typical for Oxygen-only applications like oxyfuel cutting, oxyfuel welding and brazing.
■ For Acetylene and propane applications traditionally used for oxyfuel cutting, welding, brazing, and heating, GCE’s SmartControl provides the safety features necessary for this powerful gas.
■ Argon/CO2 shielding gas are the most common applications for GMAW welding. SmartControl provides the precision and accuracy of the shielding gas flow to create high quality welds.
Contact Shaun Heys, +41 41 560 07 00 +44 (0)7935 711355 shaun.heys@gcegroup.com www.gcegroup.com
Expromet Technologies Group is opening a new base in the Philippines to offer customers extended sourcing solutions, inventory management, faster delivery times and local precision CNC machining capability.
De-risking the manufacturing supply chain
Expromet Group companies provide UK-manufactured precision casting and machining solutions alongside extensive supply chain partnerships with global manufacturers. Global economic, political and social considerations now make it more important than ever to offer an increasingly wide range of sourcing options.
Expromet Asia Inc will initially provide a new logistics and inventory call-off facility. CEO Robert Guest confirms this is part of the group’s drive to optimise Expromet’s end-to-end supply chain from trusted manufacturers, “Expromet’s increased presence in Southeast Asia will enable us to reinforce existing supply routes and establish direct links with a more extensive manufacturing base. Local warehousing and call-off will further de-risk the supply chain for our customers.”
Worldwide customers will benefit from:
■ Increased security of supply, minimising risk in the supply chain
■ Reduced lead times through warehousing and inventory management
■ Cost efficiencies and enhanced operational reliability.
On-site CNC machining
Expromet is further investing in state-of-the-art CNC machining technology with the aim of offering CNC
machining on-site in the Philippines. This will deliver expertise directly where it is needed; helping to optimise the speed and efficiency of Expromet’s worldwide manufacturing supply chain. It will also provide opportunities to eliminate tariffs and benefit from significantly lower taxes, giving customers a competitive edge.
Turnkey supply chain solutions from Expromet
Expromet Asia will ultimately provide an umbrella service that encompasses product development, sourcing and inventory management. The Philippines facility will provide local technical and engineering expertise to accelerate product development, alongside advice on manufacturing methods to optimise cost and lead times without impacting on quality. With supplier-managed inventory and flexible scheduling, Expromet Asia will provide a turnkey solution that adds significant value to customers’ supply chain management.
Enhanced relationships with a range of sectors
responsible for building and developing Expromet’s presence in Southeast Asia.
Expromet group companies supply precision-engineered solutions for performance-critical applications to a wide range of industry sectors, including Aerospace, Automotive and Electronics.
“Expromet’s base in the Philippines will improve supply options and reduce lead times, providing a fantastic opportunity for customers across demanding sectors to benefit further from strategic sourcing,” says Jason Tyas,
“Building a strong presence in Asia means that Expromet can meet local customers and manufacturers face to face, ensuring that we develop robust relationships and meet customer expectations. It enhances Expromet’s ability to provide turnkey solutions sourced from international supply chain partners, building on Expromet’s reputation as a fully integrated, leading-edge supplier of engineered solutions.”
To find out more about overseas sourcing through Expromet Technologies Group, please call: +44 (0)1271 866200 or email: enquiry@expromet.com.
Operators in manufacturing facilities have long depended on Human Machine Interfaces (HMI) to offer a visual summary of process systems that simplifies the monitoring of crucial status and control data. A well-crafted graphical user interface enhances situational awareness, decreases workload, and empowers operators to oversee the entire process – facilitating their focus to quickly address any abnormal scenarios.
Most of this HMI/SCADA software runs on a dedicated computer system. “Today, sophisticated web server technology facilitates access to HMI screens and the viewing of SCADA systems. Newer PLCs and RTUs frequently incorporate web servers that allow diagnostics and monitoring via browsers as well,” says Paul Shu
of ARISTA Corporation, a leading provider of computing platforms and visualisation display products for manufacturing environments across all industrial sectors.
Facilitating Implementation of WebBased HMIs
Historically, HMI/SCADA client software has run on a dedicated computer with a compatible Operating System installed that exhibited slow loading times during startup and restart procedures. This reduced productivity on a routine basis, cutting into valuable production time. Updating and maintaining software on individual PCs resulted in higher cost of ownership and even more downtime.
For more information, contact ARISTA Corporation at (510) 226-1800 or email: sales@goARISTA.com.
On the 5th-6th June, the NEC in Birmingham hosted Smart Manufacturing Week 2024. For two whole days, visitors and exhibitors were able to network, build a community and have fun whilst discovering new manufacturing & engineering technologies and solutions.
Smart Manufacturing Week is the largest UK festival of advanced manufacturing & engineering of the year, and featured a series of digital and live events that showcased end-to-end manufacturing & engineering solutions whilst encouraging conversation, business knowledge sharing and actionable steps.
Each year, every aspect of Smart Manufacturing Week celebrates manufacturing & engineering excellence hosting expert speakers, industry-shaping influencers, visitors from the best manufacturers & engineering businesses around the world and the brightest emerging talent.
Smart Manufacturing Week hosts six co-located events: Smart Factory Expo, Maintec, Design Engineering Expo, Fluid Power & Systems, Air-Tech and Drives & Controls –accessible with one FREE pass!
Welcoming over 12,500 attendees, 450+ exhibitors and 200+ speakers, this year’s show had an abundance of live events including the Industrial Data & AI Summit, the Manufacturing Automation & Robotics Summit, the Manufacturing Digitalisation Summit, and The Manufacturer Directors Forum.
Now in its ninth year, Smart Factory Expo is firmly established as the go-to manufacturing technology event curated by the leading and trusted industry brand, The Manufacturer. Designed to allow manufacturers to be the most efficient, the most sustainable, and the most profitable in the world, Smart Factory Expo is where change-makers can find the insights, the solutions, and the connections for their digital transformation projects.
The Manufacturer Top 100 Awards Ceremony and Enginuity Skills Awards delivered a real festival vibe whilst publicly recognising the heroes of UK manufacturing. The Closed Door Summits were a real highlight that spanned across eight Solution Theatres: Digital Transformation, IIoT & Connectivity, Industrial Data & AI, Innovation, Maintenance, Drives & Technology, Air-Tech Solutions, and Fluid Power & Systems.
Showcasing the latest technology offerings, products and services from start-ups, as well as established brands and companies that truly support and advance the manufacturing sector, the Smart Factory Expo acted as a carefully-curated shop window for manufacturers
Since 2016, Factbird has been empowering UK manufacturers with real-time production data and analysis. Factbird’s plug-and-play tools make it easy for manufacturers to boost productivity and reduce waste, offering a fast time-to-value solution.
For many manufacturers, gaining real-time visibility on the shop floor has seemed too challenging due to long setup times, extended training demands for overly complex software, and high installation costs. This often forces companies to rely on experience, hunches, and manually collected data to guide improvement efforts.
Chris Hutton, former Engineering Manager at Star Brands, said, “The installation was quick and straightforward. It was impressive that we could get the live data immediately.”
Jonathan Bell, Operations Director at Broxburn Bottlers, added, “It helped our understanding of each line and each machine’s downtime and the key areas that we needed to focus our resources on for improvement.”
Whether you’re starting your automated production monitoring journey or enhancing your existing processes with advanced capabilities like condition monitoring and video analysis, Factbird can help. Visit us at the PPMA Show in Birmingham at Stand F50 for a no-obligation demo and discover how Factbird can transform your operations.
Contact Tais Roden, +44 (0)770 015 8561 www.factbird.com
at all stages of their digital journey featuring practical workshops, keynotes and live demonstrations to enhance the visitor experience.
Don’t miss out on next year’s event. Smart Manufacturing Week 2025 takes place on the 4th-5th June at the NEC in Birmingham.
This is our pick of the best exhibitors from this year’s event, listed here in alphabetical order: Bex Design & Print, Chronos Technology & Factbird APS. Further details can be found on this page and the next.
Register your interest now: https://www.smartmanufacturingweek.com/ register-interest-2025
Digital transformation of your processes and policies, and the way you measure and manage them, using Industrial Internet of Things/ Industry 4.0 technologies, can support your aims to reduce your impact, waste, and costs, and increase efficiency and productivity.
Carbon Footprint and Sustainability Chronos can help you meet and exceed your short and long-term goals for Carbon Footprint, Sustainability and Environmental Social & Governance (ESG) by take data from a variety of sources (including Building Maintenance Systems and Heating, Ventilation and Air Conditioning systems and Building Access Controls) and providing you with a single ‘Dashboard of Dashboards’ to measure, monitor and manage to successful outcomes.
We present this data in dashboards and reports in whatever ways suit your departments or projects best.
Typically, we will first identify the data you currently
have available that can help in meeting your goals, including data siloed or indeed not even collected. We enhance this data by using a range of sensors, such as temperature and humidity, granular power usage, water and waste usage, and occupancy and people movement.
From there we can help you develop a baseline picture of your business, giving insights into the activities required to meet your goals – including identifying any ‘low hanging fruit’ to kickstart the process.
As your policies, and indeed your facilities, evolve then so can we. New data sources can easily be integrated into UCentric Dashboard and as the project proceeds, we will develop your in-house knowledge and skills to create views and reports in UCentric as your requirements change.
Asset Tracking and Real Time Location Services
We have been involved in GPS and other GNSS
signals for both timing and position for many years, but these signals do not really penetrate indoors. A range of wireless technologies are now available that allow asset tracking and RTLS – Real Time Location Services – both inside and outside your facility.
For manufacturing and industrial sites, this could be to track WIP and finished goods, raw materials, high value jigs and tools, and plant and machinery both indoors and out.
As a Master Systems Integrator with over 35 years of experience, Chronos has a range of technologies and the capability to supply, install, commission and integrate hardware and software platforms to deliver the right solution for your asset tracking and RTLS needs.
Contact our team to discuss how we can help: 01594 862200 www.chronos.uk
In 2023, Ahlsell continued to develop its sustainability work in line with the company’s long-term strategy and vision of contributing to a more sustainable society. Ahlsell has joined the Science Based Target Initiative (SBTi), made the carbon footprint of its own brand products visible, expanded its sustainable offering and taken more steps towards circular initiatives to accelerate the green development of society.
The new and ambitious climate goals, which have now been submitted for validation to SBTi, clarify Ahlsell’s goal of being a leader in the climate transition. Approval of the targets is expected in spring 2024, but work has already begun to realise them.
“Over 90% of our emissions come from purchased products and services. Working towards scientifically validated climate targets is vital to make a difference. We look forward to contributing to strengthening our customers’ competitiveness with the help of sustainable products and services, which also reduce their climate emissions,” says Christina Lindbäck, CSO Ahlsell Group (pictured).
Further initiatives for a greener transition include investments in tools that publish third-party approved environmental
product declarations and provide customers with facts about Ahlsell’s own brand products’ carbon footprint.
For Ahlsell, the work is now continuing to build a forward-looking company with a dedicated organisation with the right expertise that together develops the sustainable offering.
For more information: Ahlsell Sustainability report 2023: https://www.ahlsell.com/ sustainability/sustainability-report
Contact Christina Lindbäck, CSO, Ahlsell AB: +46 8 685 70 00 christina.lindback@ahlsell.se www.ahlsell.com
Carbon usage extends to so much more than petrol mileage and paper, and that’s what Ed Crowther, founder of My Square Metre is trying to help people to understand.
A passionate entrepreneur who’s love for biodiversity has turned into a planetsaving business – My Square Metre uses a carbon calculator and wildflower planting to help individuals and businesses offset carbon usage.
ecological strategy to improve the performance of its wildflower planting.
Using simple and flexible carbon calculation tools, so far 715kg of CO2 has been offset by 239 square metres of meadowland containing 179k of wildflowers.
With interest climbing, these numbers are only expected to flourish and working alongside experts at the University of Lincoln, My Square Metre has developed an environmental and
If you’d like to talk about the power of wildflowers and Ed’s to vision inspire others to start their wildflower-fuelled carbon-free journey, please come back to me.
For further information, take a look at Ed’s recent TED talk on a microoffset mindset – https://youtu.be/ f5NQM52J2jM?si=gTsOkxR7U kLFcM9G
www.mysquaremetre.co.uk
Metsä Group’s tissue paper business, Metsä Tissue, is pleased to announce that The Hygiene Bank has been chosen as the nominated charity for the 2025 Sustainability Awards.
As part of its 2025 Sustainability Awards event, to be held on 19th March 2025, Metsä Tissue has chosen to support The Hygiene Bank, a UK-registered charity dedicated to ensuring that everyone living in the UK has access to essential hygiene products.
The Hygiene Bank is a grassroots charity and social movement dedicated to providing hygiene essentials to those in need across the United Kingdom. Founded on the belief that everyone deserves access to basic hygiene products, The Hygiene Bank works tirelessly to address hygiene poverty and advocate for systemic change. Its network of local projects is powered by volunteers, who collect donated hygiene products and distribute them to people in need via local community partners such as food banks, schools and shelters.
The Hygiene Bank believes that everyone deserves to feel clean. They challenge the injustice of hygiene poverty and advocate for a future where everyone has access to the basics they need.
“Metsä Tissue has chosen The Hygiene Bank as our preferred charity for the event because we know
that access to good hygiene can promote health for everyone. The Hygiene Bank aims to ensure that everyone across the UK has access to everyday hygiene products, protecting their mental and physical health, and their social wellbeing. Its network of local community partners and its help for those in poverty, in particular women and children, is aligned with Metsä Tissue’s strategic goals of locality and social value, where children’s charities are a priority,” says Mika Paljakka, SVP for UK & Ireland, Metsä Tissue.
“We are thrilled to have been chosen by Metsä Tissue to support The Hygiene Bank during the Sustainability Awards 2025. This partnership not only helps us provide the basic hygiene essentials to people pulled into hygiene poverty across
the UK, but also highlights the power of unity in making a difference. Together, we can end hygiene poverty, once and for all,” says Ruth Brock, CEO of The Hygiene Bank.
In addition to the funds raised at the 2025 Sustainability Awards ceremony, Metsä Tissue will be supporting The Hygiene Bank between now and 19th March 2025, and encouraging its customers and partners to do the same.
For more information about the important work of The Hygiene Bank, including the locations of its local projects and donation drop off points, please visit: www.thehygienebank.com
https://www.metsagroup.com/metsatissue
The Royal Society for the Prevention of Accidents (RoSPA) has crowned the winner of its Fall Prevention Trophy following a virtual event this week that saw three shortlisted companies go head-to-head for the industry accolade.
L’Oréal Pune, based in India, were awarded the top trophy following a vote by event attendees, comprised of award winners from the RoSPA 2024 awards scheme. The other two shortlisted companies were support services company Compass Group Healthcare sector, and engineering firm Jacobs Field Services – who were both commended.
RoSPA’s Fall Prevention Trophy seeks to draw on best practice and showcase innovation around fall prevention, both by selecting a high-performer as the overall trophy winner, and also sharing advice and learning on the subject with the wider awards community as part of the selection process.
L'Oréal Pune’s three-step initiative saw a communication campaign that saw all its workforce take RoSPA’s Fall Fighter course, the formation of an exemplary risk assessment strategy and the successful implementation of L’Oréal’s Safe@Work-
Safe@Home programme. The programme, which seeks to take the lessons learned from occupational health and safety into homes and communities, was rolled out to over 2,500 people on the Pune area, including orphanages and assisted living centres.
L’oreal Pune’s main objectives included site surveys of old age homes and identification of STF improvement opportunities, inspections by in-house tech experts and a steady commitment to the Fall Fighters programme.
This holistic approach was especially for combatting the high rate of slips, trips and falls (STP) within the over 65-age bracket, whereby Pune factory workers pledged themselves ‘Fall Fighters’ (a RoSPA-developed slips, trips and fallsprevention course).
https://www.rospa.com
Hydro Aluminium UK Ltd, a subsidiary of the global aluminium and renewable energy company Norsk Hydro, has demonstrated its commitment to elevating health and safety standards by entering the UK’s leading health and safety awards scheme and scooping two accolades from The Royal Society for the Prevention of Accidents (RoSPA).
Hydro Aluminium UK Ltd was awarded both a Gold Achievement Award and a Best New Entry Award (UK) at this year’s RoSPA Awards for its strong commitment to health and safety. It was awarded the accolade after it took a thorough approach to clearly explaining and demonstrating its health and safety management system in action during the past year.
Erika Curnow, an apprentice interim manager at Hydro Aluminium UK Ltd, was also announced as the winner of RoSPA’s Inspiring Women in Safety Award, for her own personal
inspirational impact within health and safety at the organisation.
Sponsored by EcoOnline, a leading provider of EHSQ software solutions, RoSPA’s Best New Entry Award recognises outstanding submissions made by organisations entering the RoSPA Awards for the very first time.
The RoSPA Health and Safety Awards is one of the largest occupational health and safety awards programme in the world. Now in its 68th year, the Awards have almost 2,000 entries annually, covering nearly 60 countries and reaching millions of employees. The programme recognises an organisation’s commitment to continuous improvement in the prevention of accidents and ill health at work by looking at entrants’ overarching health and safety management systems, including practices such as leadership and workforce involvement.
https://www.rospa.com
7in 10
organisations operating in some of the UK’s biggest industries admit that they are unlikely to comply with on-the-spot
Health & Safety Executive (HSE) inspection due to a lack of data proving that their fixed and moveable assets are managed and maintained to the required regulatory standards.
Nearly one-fifth (17%) have received enforcement action in the past due to assets not meeting HSE compliance standards, with over 10% receiving an HSE fine.
The new research on 2,000 UK businesses, commissioned by enterprise asset management (EAM) solutions specialist, BPD Zenith surveyed organisations operating in the utility and renewable industries, including telecoms and broadband, as well as the defence, transport, pharmaceutical, and healthcare sectors.
The findings revealed that nearly 50% of these organisations’ moveable or fixed asset data isn’t detailed,
nor updated or recorded accurately enough to comply with the Health and Safety at Work Act 1974 or other HSE regulations that apply to their sectors.
Latest HSE figures for 2022/2023 show that there were 60,645 employee nonfatal injuries reported by employers during this period and 135 deaths as a result of work-related accidents. The Health and Safety at Work Act 1974 legally and duty bounds companies to ensure the safe working environment for employees and third-parties, including the general public, who may be affected by an organisation's activities. The HSE compliance standards work alongside the Health and Safety Act, designed to protect people and the environment. Penalties for failure to comply can include fines, orders for operations to cease, and imprisonment if the misconduct is found to be serious enough.
https://www.bpdzenith.com
Menzel
Elektromotoren has celebrated the opening of its new headquarters near Berlin with a grand inauguration party. In honor of company founder Kurt Menzel, the date was set for his 120th birthday on 14th May 2024. With increasing numbers year on year, the German manufacturer successfully markets its industrial motors and tailor-made drive systems worldwide. This continued success, now required more space with modern production facilities designed for efficient processes, and larger, heavier machines. In addition to state-ofthe-art machinery, efficient paint shops and test fields that can accommodate even the largest motor configurations; the new plant is prepared for further growth. In coming years, the workforce at this site can be expanded from around 100 to 150, allowing the manufacturer to meet all customer requests.
Menzel manufactures its own motor series and also specializes in custom models and exact replicas of existing machines. Menzel builds new motors with outputs up to and beyond 25MW from scratch, stocks a large range of motor variants up to 15MW and adapts
Menzel Elektromotoren has found a suitable location for a new factory building with state-of-the-art equipment in Hennigsdorf, just outside Berlin
them at short notice for various drive tasks. The company also offers testing of motors, generators and rotary converter sets. Since the official factory commissioning on 2nd January 2024, the quality management system has already been certified according to DIN EN ISO 9001:2015.
More information: https://www.menzel-motors.com/ article/moving-to-new-motor-plant
+49 30 349 922-0 info@menzel-motors.com www.menzel-motors.com
In stock at Powell Electronics, the supplier of connectors and more for high-rel applications including defence, aerospace and industrial, are Series 806 Mil-Aero connectors from Glenair. The products offer significant size and weight savings while meeting key performance benchmarks for a broad range of applications such as commercial and military aerospace, industrial robotics, transportation systems and more.
Designed for use in harsh vibration, shock and environmental settings – as well as high-altitude, unpressurized aircraft zones with aggressive voltage ratings and altitude immersion standards, Series 806 connectors feature numerous mechanical design innovations including durable mechanical insert retention, radial seals and triple-ripple grommet seals. The reduced thread pitch and reengineered ratchet prevents decoupling problems which solves one of the major problems of shell size 9 and 11 MIL-DTL38999 Series III connectors.
Glenair Series 806 Mil-Aero connectors feature size 22HD and 20HD contacts as well as size 8 power and high speed El Ochito®, quadrax, and fiber optic
Apex Dynamics has launched its new high-performance MG/MGK and MGH/MGHK series planetary gearboxes.
Both ranges have been specifically designed for enhanced axial and radial loads, with easy installation and adjustment for rack and pinion applications.
The new gearboxes are ideally suited to CNC machine tools, robotics and heavy-duty automation applications, and have been optimised for rack and pinion applications. Both the high efficiency MG and MGH ranges come with optimised moment of inertia, long service life, best backlash of ≤ 3 arc per min and long-term persistence of low backlash, while the hypoid right-angle K-series offers identical input-output rotating direction.
Potential applications for the new MG and MGH series include: industrial and mobile robots for tasks like assembly, welding and material handling, reliable movement and positioning of heavy loads; and in-flight simulators, aircraft control surfaces and weapon systems for precise movement and positioning.
The high precision MG and MGK gearboxes come with a ratio of 4 ~ 10,000, high torque and high torsional rigidity and are suitable for high-end applications, as are the MGH/MGHK and MGHC/ MGHCK gearboxes. The latter series has extra high torque (typically 25% more than the MG/MGK range), a ratio of 4 ~ 5,500, and is available in Standard Flange or patented Curvic Output.
With these new ranges, Apex Dynamics once again demonstrates its impressive ability to introduce drop-in replacements for leading competitors’ products, which combined with its market-leading delivery times and guarantees, ensures customers find it simple to transition to high performance precision solutions.
www.apexdynauk.com
options. The devices offer up to twice the number of contacts with no reduction in performance. Independent laboratory testing has demonstrated that the connectors meet, and in many cases even exceed, the requirements of the MIL-DTL38999 specification. A ‘top hat’ insulator with raised bosses ensures foolproof alignment of insulator cavities. An O-ring radial interface sealing design instead of a flat gasket allows for easier metal-tometal coupling, improved sealing, and better EMI performance.
For further information, please visit: https://shop.powell.com
For further information about Powell, please visit: www.powell.com For project design or procurement support, please contact: europe@powell.com.
Industrialtechnology and thermal systems provider, Watlow, has announced the launch of its new Prime Distributor Programme across Europe. The Prime Distributor Programme will be offered through a network of well-qualified distributors that have both strong local presence and a history of supplying Watlow products. The programme will provide customers with improved support and easier access to the full line of Watlow products and solutions.
responsibility for managing its own business as well as an extended network of Endorsed Distributors within their respective markets. Endorsed Distributors will assist Primes with other localised and unique needs as they arise.
To qualify as a Watlow Prime Distributor, each business is required to demonstrate the ability to continually invest in and scale their organisation and adhere to Watlow’s requirements for service and support. This applies to both Watlow and Eurotherm product lines — an industrial technology company that Watlow acquired in 2022. These key partners will bear a certified ‘Prime Distributor’ logo to demonstrate their affiliation with the company.
Watlow will have one Prime Distributor in the UK, Germany, France, Spain and Italy. Each distributor will have primary
The first market in which the Prime programme will be introduced is the UK, with Watlow selecting Electroserv as the Prime Distributor for this key market. Throughout 2024, the company will be transferring a significant number of UK based customers and distributors to Electroserv and will be working with relevant groups within Watlow to ensure a smooth transition for all parties. The company’s website, which currently offers Eurotherm’s product line, is currently under development to also provide access to Watlow offerings.
To discover more about Watlow’s thermal solutions, please visit: www.watlow.com
We are a leading provider of pumps, power equipment, and fluid handling solutions to a wide range of industries throughout the UK and export markets. Our expertise extends to manufacturing and selling pressure washers, pumping systems, and component assemblies. With a deep understanding of our products and a network of industry experts, we can cater to the specific needs of our customers.
We are recognised as offering exceptional service, characterised by speed, accuracy, & flexibility. Our customers can count on us for support & assistance, allowing them to focus on serving their clients.
We value open communication and respect in all our interactions and strive to be helpful, personable, and friendly. We take responsibility for our actions and always follow through on our commitments.
With over 48 years in the industry, a dedicated team, and our own warehouse, production, and testing facilities, we are wellequipped to meet the demands of our partners and stock a wide range of quality products.
Located in Melton Mowbray, Leicestershire, in the heart of the East Midlands, we have good transport links and offer nextday delivery to most of the UK. Good access to East Midlands, Birmingham, and London Stansted international airports enables easy travelling for overseas visitors.
We pride ourselves on longlasting relationships with our customers and suppliers built on trust and excellent service
■ Customer Care & Sales team are ready to take your orders and help with enquiries.
■ Technical experts to offer advice.
■ Dedicated export sales advisor for European and international export matters.
■ Dual Pumps has a proud tradition of longserving staff.
■ 99% of customers surveyed, rated our service as good or excellent.
■ In a typical month, 99% of more than 2,400 calls are answered within a minute.
■ More than 96% orders fill on active products over a typical monthly period.
Our experienced distribution team ensures you and your customer’s consignments are despatched securely and on time
Unrivalled stocks are ready for your choice of delivery. Optional plain cover delivery direct to your customer.
Our purchasing team liaises with suppliers daily, placing orders and negotiating the best possible prices
The warehouse team receives daily deliveries from suppliers and replenishment of stock is constant.
+44 (0)1664 567226 info@dualpumps.co.uk www.dualpumps.co.uk
Leading food and beverage manufacturers are facing increasing pressure to eliminate the risks of product contamination.
With stricter hygienic controls required, the key to success is the rigorous and effective cleaning of the process line itself. Clean-In-Place (CIP) systems are universally recognised as the most effective solution for maintaining dependable, consistently repeatable results.
Responding to demand for a more versatile approach, Axium Process have launched an adaptive Mobile CIP System for all industry sectors, offering a costeffective and compact plug-and-play solution in place of traditional fixed-inplace methods.
The new CIP package is a highly versatile and easy-to-maintain clean-in-place solution, designed with mobility and hygiene at the forefront of its design. Fully customisable with options ranging from manual to automatic, the system can be adapted to include an integrated control unit via a panel-mounted touchscreen HMI and PLC. With remote
monitoring and ongoing technical support available if required, the system can be programmed to record historic data, accessible on site by an operator, or remotely by one of Axium’s own engineers.
Developed with decades of hands-on experience across multiple process applications, Axium’s new Mobile CIP System offers an advanced alternative for sanitary maintenance.
For further information, please contact: 01792 883882 jamie.george@axiumprocess.com www.axiumprocess.com
We are a membership organisation that strives to bring recognition of the vital role cleaning operatives play in everyone’s day-to-day life. Whether you’re shopping, travelling, working, holidaying, or recuperating, every one of these scenarios has cleaning staff striving to ensure that the environment is not only clean but also safe. Founded over 60 years ago, BICSc key objective is to promote the value and professionalism of the cleaning industry, providing training in the key skills required to enhance a cleaning operative’s core role whilst keeping them safe and encouraging them to work in a more effective and
efficient manner. With a range of both practical and theoretical qualifications available, BICSc has something to help further the career of every cleaning professional – from entry level, through to supervisor level, and up to an employer with your own business tendering for cleaning contracts. Check out our website www.bics.org.uk for our full range of courses – many of which can now be taken online via the virtual training suite to fit in with your lifestyle – some of them are free for anybody.
01604 678710
info@bics.org.uk www.bics.org.uk
Companies are investing in AI and automation to drive warehousing efficiency, but the results are being hampered by a lack of investment in suitable storage solutions. Tim Steer, Commercial Director at Twinplast, explains how a joined-up approach is the only way to maintain maximum reliability.
AI and automation are revolutionising warehouse operations. Companies are investing in AI-powered robots with the ability to identify, pick and sort items, and transport them for despatch. AI algorithms are used to manage the storage and retrieval of goods with enhanced precision, reducing the time required to complete these tasks.
AI and automation are not new technologies, but their development and uptake have accelerated in recent years, and other aspects of warehousing are not in step with the speed and nature of change. Issues are starting to emerge with growing evidence of a malfunctioning relationship between robotics and traditional storage solutions.
For all the advances that automated technology has made in navigating the complex warehouse environment, it is not foolproof. While investment in technology is higher than ever, budgets for warehouse storage containers are largely still driven by cost savings. Standard mass-produced storage might provide economy of scale, but it is not designed and manufactured to keep in sync with the cameras and sensors that interpret visual information.
Folds, overhangs and stacking create blind spots preventing the detection of stock labelling. Cheaper materials such as cardboard are prone to tear or sag,
obscuring key signifiers. Mould, water damage, dust and discolouration can make printed information illegible. As a result, robotics are failing to identify stock and creating fault lines in their automated inventory management.
These vulnerabilities are not immediately obvious and usually take time to become apparent to warehouse operators. By the time they are finally identified as a drag on efficiency, numerous items have been left unpicked for months and profits have been severely dented.
In recent years, we have encountered a wide range of organisations that have fallen foul of these underlying problems. We have worked with them to develop bespoke replacements for their established storage systems. Each container should be custom-designed for maximum compatibility with robotics operating in the specific physical environment of the warehouse. That objective often benefits from site visits along with the development and testing of prototypes driven by consultation and collaboration between the warehouse operator and the manufacturer. It may seem like a fairly time-consuming process, but it’s nothing compared to countless hours lost through inventory and subsequent diagnostics.
Strength and durability are essential characteristics for containers serving automated systems. Solutions must be designed and manufactured to resist damage caused by moisture/water, extreme temperature fluctuations, static, and industrial environments. Polypropylene has the inherent properties to serve this purpose. It has high tensile strength and impact resistance, excellent electrical insulation, exceptional water repellence and strong resistance to chemicals, solvents and corrosion. This combination of attributes ensures that
polypropylene solutions retain their shape and surface appearance, ensuring that robotics record every item with reliable accuracy.
Treatments can be applied to enhance resistance to degradation. Anti-microbial additives prevent the growth of a multitude of bacteria and fungal growths by up to 99.99%. Anti-static or conductive additives prevent fibre and dust build up.
Developing warehouse storage solutions that will remain fit for purpose in the automated age requires an initial investment in design and material quality, but the benefits are compelling: if AI and robotics are all about maximising efficiency, that goal cannot be achieved without complete harmony between the digital and the physical world.
https://twinplast.co.uk
Union Industries, the UK’s leading manufacturer of bespoke industrial doors, has helped food importer and distributer, Taj Foods, improve efficiency through the installation of high-speed freezer doors – the Eiger Door.
Taj Foods, specialists in frozen exotic food and prepared meals, was established in 1980 and recently expanded its cold storage at its Sheffield warehouse to meet growing demand. The project undertaken by EJM refrigeration, involved improving its energy efficiency and carbon footprint with the installation of a new CO2 refrigeration system.
The two Eiger Doors will enhance operational efficiency in the high-demand environment and will maintain consistent freezer temperatures, while ensuring unimpeded access to cold stores.
Since its launch in 2002, the Eiger Door has been installed as a fast-access traffic door at major food retailers, 3PL cold storage and distribution, and frozen food manufacturers across the UK.
The Eiger Door ensures that consistent temperatures can be maintained and features an innovative dehumidification system, which prevents snow and ice build-up on the door blade and frame. This feature tackles a consistent issue plaguing other door types, as the freezer encounters humid ambient air entering the cold store.
Minimising downtime is also supported by the Eiger Door’s robust construction and its tried and tested crash-out and reset system. Due to the modest difference in size between Forklift Trucks and the door opening, as well as the busy nature of this freezer, this is of particular benefit at this depot when considering the long-term reliability of the Eiger Door.
Rob Howe, Union Industries’ Technical Sales Engineer, said, “The installation of the Eiger Doors at Taj Foods showcases our commitment to providing cutting-edge solutions that prioritise efficiency and reliability.
“Over the past 20 years, the Eiger Door has consistently proven to be a superior and effective innovation for cold storage access, overcoming challenges such as ice build-
up and excessive energy use to maintain consistent temperatures.
“We are confident that the Eiger Door will significantly contribute to Taj Foods’ operational success.”
Anil Solanki, managing director at Taj Foods, said, “We were looking for a reliable door solution to fit in with the redevelopment of our Sheffield warehouse, and after reading about the success of the Eiger Door we approached Union Industries to assist us to improve operational efficiency as we doubled our capacity.
“We believe that the advanced features of the Eiger Door will not only enhance the efficiency of our cold storage but also contribute to long-term reliability, minimising disruptions in our day-to-day operations.”
Contact +44 (0)113 244 8393 enquiries@unionindustries.co.uk www.unionindustries.co.uk
■ Plant in Tibi is second production site of the Food&Beverage division in Spain operating under CCL Label Spain
■ Goal is to support Spanish and multinational brands to achieve their recycling targets and to comply with upcoming European legislation (PPWR)
■ Premium sleeve labels are a growing segment in product decoration
CCL Label, a world leader in labels and packaging, announces the inauguration of a brand-new production facility for shrink sleeve labels in Tibi, Spain near Alicante.
“We are very excited to offer shrink sleeves produced in Spain for local brands and multinational brands operating in Spain. Investing into local production follows CCL’s strategy to stay close to the production sites and filling lines of major food and beverage as well as home and personal care brands and service them locally and efficiently,” explains Lukas Nachbaur, Commercial and Technical Director at the new facility.
“Our first brand customers have placed and received orders and were happy with the quality and service.”
Modern printing technology for premium shrink sleeves
“The investment in this greenfield facility is a commitment to the growing Spanish consumer products market. There are many great brands that call Spain their home and the country has a proud tradition to produce outstanding highquality food and drinks including beer, wine and spirits,” Reinhard Streit, VP and Managing Director Food&Beverage at CCL Label points out. “We installed state-of-the-art assets to service these premium brands in the best way possible – we see that we can offer our customers very special printing technology that is unique in Spain.”
The installed assets offer customers premium-printing technology. The combination of offset and gravure printing offers customers the greatest flexibility when it comes to changing designs frequently.
Award-Winning floatable EcoFloat sleeve technology a focus
Although all shrink sleeve materials will be available, there will be a focus on the award-winning EcoFloat shrink sleeves made from polyolefin that are approved for PET, HDPE and PP bottles and containers and have been embraced by renowned brands.
Shrink sleeves are applied by heat and conform to a variety of container shapes, acting like a second skin. They are made from floatable low-density polyolefin
The EU Green Deal is a hot topic, and rightly so. With 94% of consumers saying it’s a brand’s responsibility to create products that are not harmful to the earth (Deloitte), it was only a matter of time before ecofriendly efforts were put into legislation.
Set out by the European Union, the EU Green Deal was approved in 2020 and aims to make Europe the first ‘climate neutral’ continent by 2050. The deal encompasses a range of strategies, including a target to reduce emissions by 55% by 2030, with an additional goal of a 90% reduction by 2040.
a sustainable and green future for the EU.
In this blog, we will be focusing on the second pillar, circular economy as this lies at the heart of everything we do at Smurfit Westrock. We’ll be looking at waste, recycling, sustainable production, and the efficient use of resources.
This deal is centred around five pillars that collectively drive the Green Agenda. These are climate action, circular economy, biodiversity, fighting pollution, and sustainable food systems and rural areas. Each of these five pillars represents a key aspect of the Green Agenda, which works together to create
If your packaging needs to change to meet the new legislation, we’re here to help. At Smurfit Westrock, we have tools that can assess your packaging and even one that can instantly verify its compliance with PPWR. We stay at the forefront of evolving packaging legislation and regulations to help our customers reap the rewards of EU Green Deal-compliant packaging. Give consumers what they want through packaging that drives profit and purpose.
Get in touch to find out more: www.smurfitwestrock.com
material, which is at the forefront of sustainable shrink sleeve technology. The design of the sleeves allows for easy separation from the primary container during the recycling process, thus supporting material separation and enhancing recycling efficiency.
“Just as other European countries, Spain will have to deliver on the ambitious new packaging and packaging waste (PPWR) regulation. The regulation also includes mandatory Design for Recycling and our low density, floatable EcoFloat polyolefin sleeves have been endorsed by several recycling associations like RecyClass and the European PET Bottle Platform (EPBP),” says Marika Knorr, Head of Sustainability and Communication at CCL Label. “PET bottles that are combined with an EcoFloat sleeve are fully recyclable and this helps increase the yield of food-grade PET resins that then can be fed back into new bottles – closing the loop. Mandatory recycled content targets are also an integral part of PPWR legislation.”
Sustainability a priority at production site
The sleeve production will be ultimately be co-located with the In-Mould Label production site (formerly Creaprint) that was acquired about a year ago. The IML Business is expected to move to the new site in Tibi in 2026.
“IML is a rapidly growing decoration technology. The label becomes an integral part of injection or blow moulded plastic containers without the need for adhesives, typically using the same resin material as the container for easy recycling,” comments José Vincente Guillem, general manager of the CCL Spain IML plant. https://ccllabel.com
Loctite 55 has been awarded the German Packaging Award 2024. Henkel received this prestigious award for the packaging of the 160m pack of its leading thread sealant cord in the ‘Functionality and Convenience’ category. The jury particularly pointed out the optimisation of the conventional combination of dispenser can with separate lid by adding an attached closure, “This guarantees that the conventional separate lid can no longer be lost during use and extends the shelf life of the pipe sealing cord it contains,” according to the official statement.
Loctite 55 is used by numerous professional fitters and plumbers to seal pipe threads and fittings made of metal and plastic. Since this year, the product has been available in a new sustainable packaging, which Henkel has further developed and improved on the basis of an extensive customer survey. This makes applying the thread sealant even easier and more convenient for users.
An ideal choice for sealing metal and plastic threaded joints, Loctite 55
replaces hemp and PTFE tapes and proves to be an essential item for any toolbox. The product requires no curing time and results in an immediate, full pressure seal. Simply wind it onto the thread with tension and then cut the thread sealant with the integrated cutter.
The official award ceremony for the German Packaging Award will take place on September 24th at FACHPACK in Nuremberg. Loctite 55 160m has been available from specialist retailers in its new packaging since June. More information at: LOCTITE 55 – Thread Sealing Cord – Henkel Adhesives (henkel-adhesives.com)
Contact www.henkel.com