
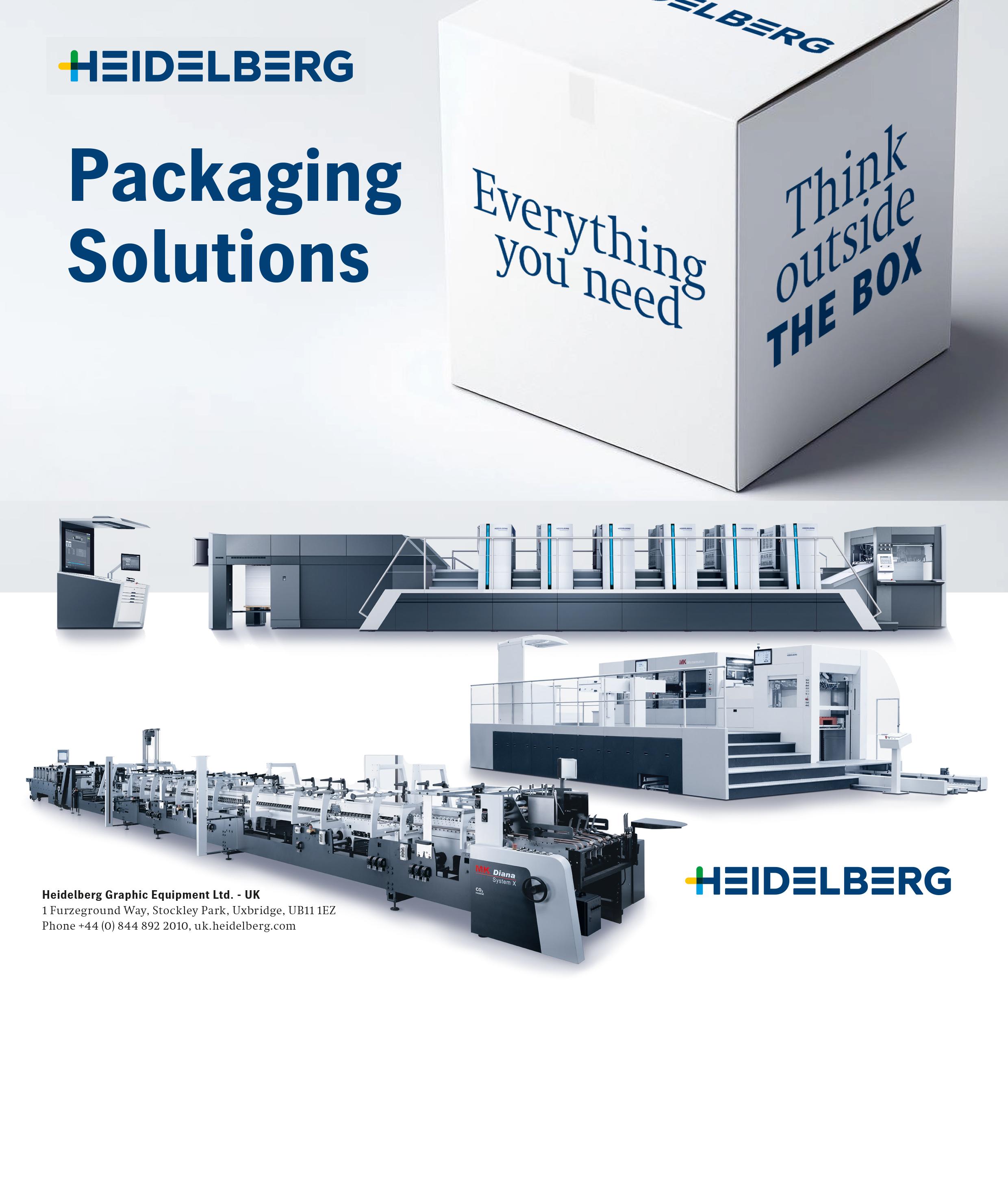
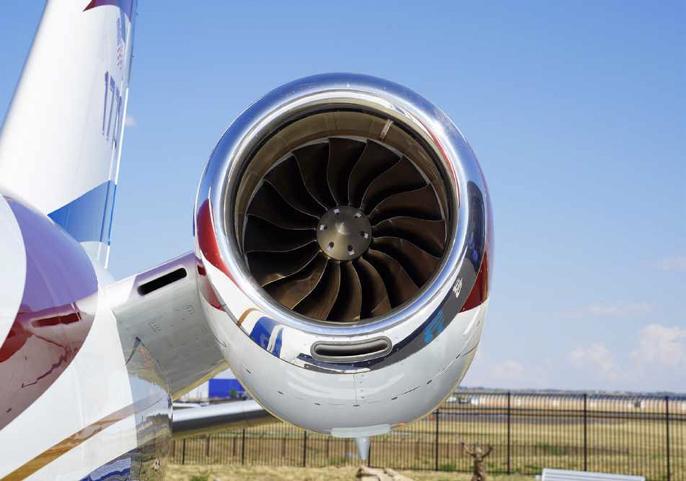
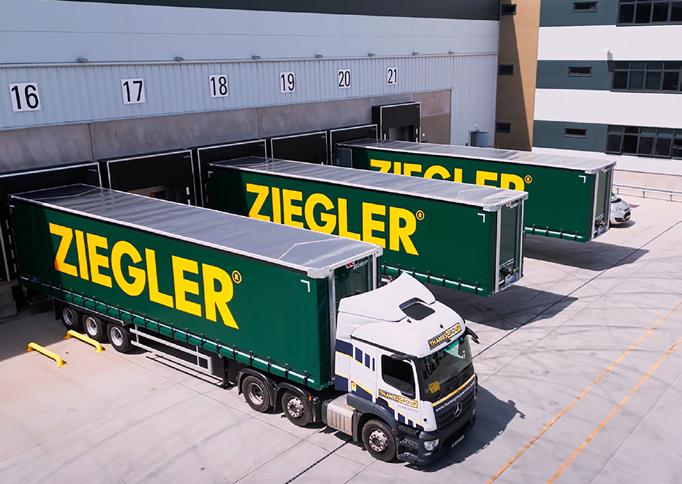
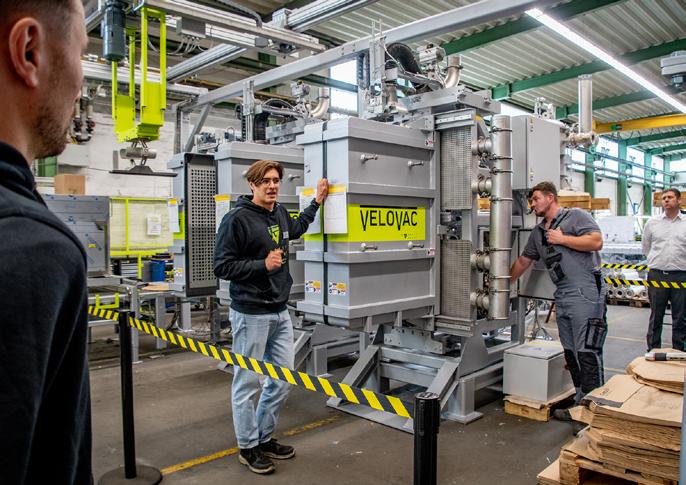
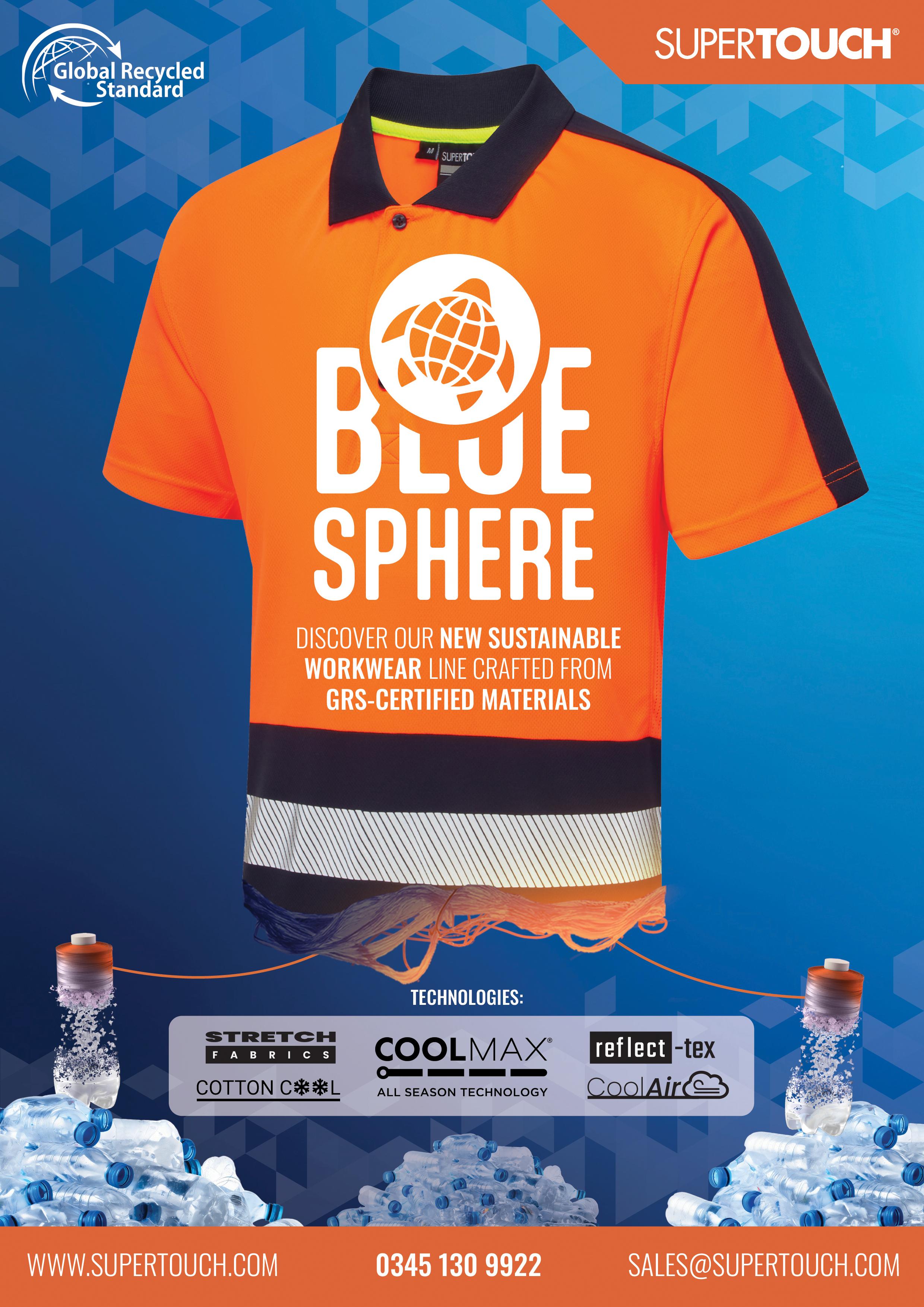

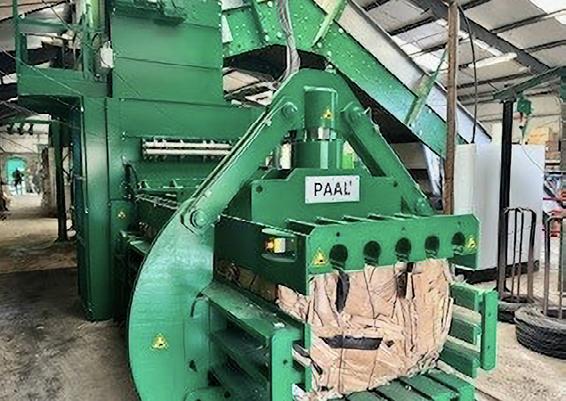
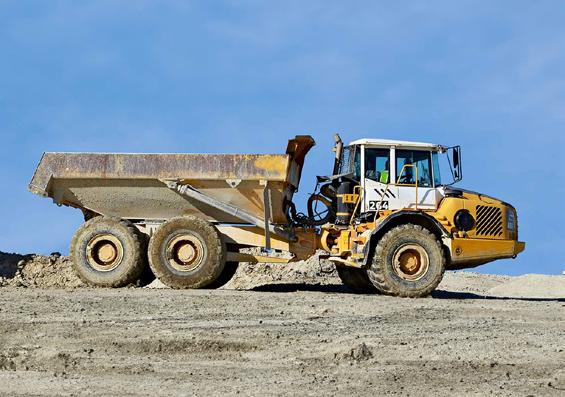

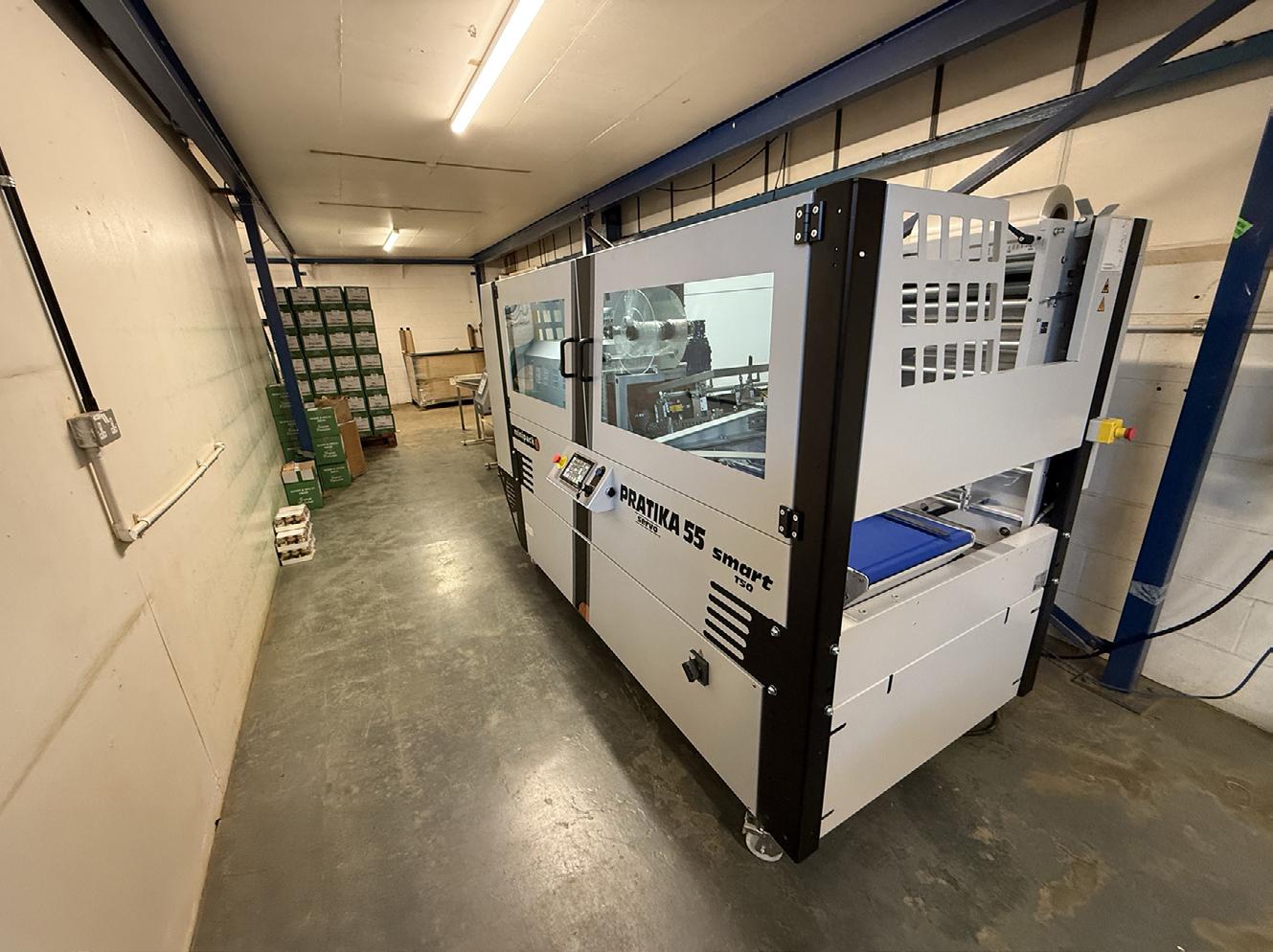
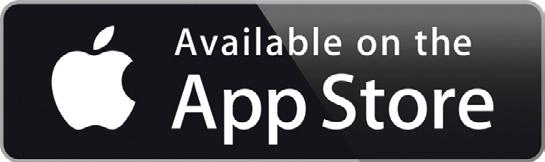
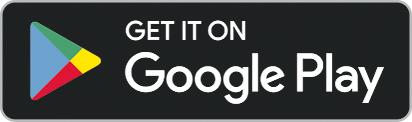
Founded in 1948, E-T-A pioneered the development of precision performance circuit breakers which provide overload and short circuit protection for equipment and assets. Today, we now offer the most comprehensive product portfolio of devices, whether mechanical or electronic solutions, single components or complete systems, standardised or for customer-specific applications. All our products are designed and manufactured to exacting performance and quality standards; produced in our own production facilities and supplied by our world-wide network of E-T-A subsidiaries and channels.
Our intelligent power distribution systems capabilities for server and network cabinets include flexible power distribution units as standard products and customised solutions. From purely electronic overcurrent protection to a fully integrated complete system with remote access - thanks to its flexibility, the system covers all needs and guarantees maximum system availability. Using our unique circuit breaker technology ensures precise overcurrent protection and also enables remote control, monitoring and analysis. Many customers from the telecommunications, data center, industrial, energy and railroad infrastructure sectors place their trust in us. Please do not hesitate to get in touch.
T +44 (0)1296 420336 info@e-t-a.co.uk www.e-t-a.co.uk
Elektromotoren designed a compressor motor for modular installation, observing the maximum crane capacity of 16 tons at this UK installation site. An industrial gasses producer ordered the motor to replace a 1957 built existing gas compressor motor.
Since structural changes and any roof removal in the plant were unwanted, Menzel replicated the mechanical interfaces of the existing motor. The motor’s outstanding feature is its massive base at 3 tons. Base, motor (14.7 tons) and cooler (2 tons) were installed in three lifts one after the other.
Menzel won the contract due to its ability and willingness to respond to such special requests. The family firm built the three-phase squirrel cage motor based on its MEBKSW series, which is characterised by high power density and offers flexible equipment
options such as various cooling types.
The motor, with its specific base plate, features a total shaft height of 1,120mm, 6MW nominal power, 11kV nominal voltage, 57,995 nominal torque and 988rpm nominal speed. It has an IP54 protection rating with air-to-water heat exchanger (cooling type IC 86W). Like all Menzel machines, the compressor motor underwent comprehensive inspections in the manufacturer's load test field before shipping. The customer traveled to Berlin to witness testing.
More about customised motors: www. menzel-motors.com/modification
In this issue of Industry Update, we are pleased to feature Ionic Systems as our Window Cleaning Equipment
Since launching the revolutionary Reach and Wash© System in 1997, Ionic has led the way in ground-based, ladder-free window cleaning. Applying the same safety-first innovation across its product range, the company has transformed professional cleaning worldwide.
Specialising in pure water window cleaning equipment, Ionic are the creators of the modern waterfed pole window cleaning system, Reach & Wash©, and new innovations such as the Foamion and Roof Wand.
Based in the UK with in-house manufacturing, R&D, and distribution, Ionic also supports a global customer base through a strong international distributor network.
“Our core products include vehiclemounted pure water window cleaning systems, static and portable filtration units, waterfed poles from 9ft to 80ft, and specialised tools for roof cleaning, gutter vacuuming, and softwashing – all designed for safe, ground-based operation using the Reach and Wash method.
“We focus on engineering complete, integrated systems that tackle real-world challenges. While others prioritise upfront cost, Ionic Systems delivers lasting value through durability, performance, and efficiency – reducing manual labour and meeting the demands of daily professional use,” said Reuben Reynolds, Managing Director.
All Ionic’s components are purposebuilt to work harmoniously together. One of its latest products is the new
Dual Protector Pole Handles which provide electrical safety protection up to 50,000 volts. Ionic Systems go to extraordinary lengths to make sure that your safety isn’t compromised, and remains the ONLY supplier of water-fed pole equipment to be awarded the FMVSS-208 certification.
“This comes in light of the tragic electrocution of Jason Knight, and we've been working closely with others in the industry to help raise awareness of electrical safety for window cleaners,” added Reuben.
Two other notable products include the Roof Wand and Foamion soft wash system.
Roof Wand
Constructed from High-Modulus carbon fibre, the wand pole offers superior strength and rigidity, while also ensuring lightweight handling. Providing a seamless cleaning experience regardless of the height of the surface being cleaned, the wand consists of 10 poles – 2 adjustable telescopic Glass Fibre poles, with protective non-conducting insulation. 8 quick release Carbon Fibre pole sections (2m each), with a total possible length of 20m.
Foamion soft wash system
It is cost-effective, helps reduce chemicals, and works in conjunction with the existing Reach & Wash© System, allowing operators to provide
additional softwashing services as part of their regular round. It is mainly used to treat algae on hard exterior surfaces and moss on roof tiles, using a contactless and gentler approach than pressure washing.
that's simple for their teams to use, even across large sites.
“We already provide solutions for window cleaning, softwashing and roof cleaning, which all fit our core values of working safely from the ground and efficiency of cleaning to an unrivalled quality. We plan to expand our reach into other markets where the equipment can be used, ie. Aviation Cleaning and Solar.
Looking ahead, Ionic is focused on addressing two of the most important areas in its industry: electrical safety and safe working at height. While expanding its range, Ionic continues to find ways for facilities managers to access durable, reliable equipment
“We have experienced good growth in all areas of the business in the UK and Export, and with rolling out our online training school we are seeing further demand for our products,” stated Reuben.
T 01793 871386
info@ionicsystems.com www.ionicsystems.com
With global trade tensions and shifting tariffs reshaping supply chains and market dynamics, there’s never been a more crucial time for professionals to come together. It’s a vital opportunity to explore adaptive strategies, connect with peers facing similar challenges, and gain insights from the industry’s most knowledgeable voices.
Packed with expert-led content, hands-on networking opportunities, and the latest advancements in hardware, software, and industrial solutions, it remains the UK’s premier festival of advanced manufacturing and engineering. Addressing today’s most pressing industry challenges, the event showcases nextgeneration technologies that are shaping the future. Stay ahead of the curve and cut through the complexity of this fast-evolving sector.
In partnership with Forest Nation, we’ve once again
measured the emissions generated by our live shows and have now planted a total to 40,634 trees!
With 13,500+ manufacturing & engineering business professionals in attendance, it’s THE place to engage with like-minded people across the full spectrum of industry from design, engineering, manufacturing and maintenance.
Returning for 2025, to help visitors navigate the presentations and exhibitors most relevant to them, we’re bringing back ‘Visitor Trails’ based on specific topics to help you make the most out of your visit at the show. Visitors will be able to discover the enabling capabilities of our exhibitors and sponsors a lot easier than reading through all the listings in the event app!
Explore 450+ companies showcasing software, hardware and services from established brands and emerging start ups that truly support the manufacturing
A&S International is excited to be exhibiting at MAINTEC for a third year in a row after the success of our previous events. We are pleased to once again showcase a range of our innovative maintenance solutions to the UK market – all of which are proven to help to improve the sustainability as well as the reliability of our clients' businesses by reducing energy, fuel & lubricant consumption and cleaning of hydrocarbon contamination:
t Fluitec – B Corp Certified Fill4Life solutions – identifying & treating varnish contamination – including MPC & RULER ASTM tests and SOLVANCER products such as DECON, DECON AO & DECON AW.
t HOSEPATCH – emergency, temporary, reusable hydraulic hose repair kits
t MAK CHEM International – range of maintenance chemicals including biodegradable MAK FOX Degreaser & MAK WELDING Anti-Spatter Liquid.
t MAK LUBES International – range of industrial lubricants including biodegradable ML253 Ecology EAL Wire Rope Grease, EP greases & gear oils.
t Sulnox Eco Fuel Conditioner – proven cost-effective decarbonisation product with 5-8% fuel savings & significant GHG emission reductions
t SYLMASTA – cost-effective pipe repair solutions for a wide range of industries
t Viper WRL – efficient cleaning & lubrication of wire ropes ranging from 6mm to 165mm in diameter at speeds of up to 2,00m per hour.
Come see us on Stand 5/K12.
T 0118 930 4321
hello@aands-international.com
and engineering sector. Discover all the latest technologies, products and solutions for your current and future design, engineering, manufacturing or maintenance projects.
Located at the very heart of Smart Factory Expo, Innovation Alley is the UK’s leading showcase of all the new and developing technologies that will change the landscape of manufacturing over the next 5-10 years.
Visit our Best of British Showcase in a celebration of domestic manufacturing, featuring world-beating new designs, innovative modes of manufacture, products that redefine categories, and export successes that plant the flag in overseas markets.
This year, we’ve levelled up our Solution Theatres with seven fully curated spaces, each laser-focused on a core industry theme. What’s new? Tighter programming, zero content overlap, and sessions designed to go deeper –so you get actionable insights, not just inspiration.
www.smartmanufacturingweek.com
We pride ourselves on providing innovative and highly customised force measurement solutions for various industries. One recent project highlights our customisation expertise in aerospace, where we developed specialised custom load pins to measure forces on components within a jet engine nacelle. This case study delves into the unique challenges, the tailored solutions we provided, and an overview of our broader customisation services.
Client challenge: Measuring forces on a jet engine nacelle
An aerospace client required precise measurements of forces acting on about 20 different bolts and mountings within a jet engine nacelle. The testing environment and stringent requirements of aerospace engineering made this an intricate project, with the following challenges:
t Multiple Component Sizes – The load pins needed to replace bolts and mounting pins of varying sizes.
t Threading and Locking Mechanisms – Several pins required threads or locking nuts to ensure secure installation.
t Preload Sensitivity – Over-tightening risked preloading the pins, potentially skewing measurements.
t Orientation – Correct orientation of load pins was essential for accurate force measurement.
t Varied Capacities – The pins needed to handle loads ranging from 2kN to 33kN.
t Multi-Axis Measurement – Some components required force measurement in two axes.
t High-Temperature Tolerance – Components had to be temperature-compensated up to 300˚C.
t High Accuracy – Measurement accuracy needed to be within 1% or better.
Our solution: Customised load pins for precise force measurement
Addressing these challenges required a close collaboration between our design team and the client, involving detailed discussions, customised
engineering, and iterative approval processes. The resulting solution included:
t Custom-Designed Load Pins – Each load pin was engineered to replicate the client’s existing components, such as bolts or mounting pins, with required modifications for accuracy and fit.
t Enhanced Durability and Safety Features –To ensure measurement reliability, we added features like specific threading, precise orientation markers, and high-temperature compensation.
t Rigorous Testing and Backup Plan – To guarantee accuracy & reliability, we manufactured spare units, which were essential to avoid delays due to unforeseen issues during testing.
Despite the challenges posed by the COVID-19 pandemic, our team delivered these customdesigned devices on time and within budget. The client’s testing was successful, and they praised the reliability and performance of our load pins.
Customisation services and broader applications Beyond aerospace, our customisation service addresses force measurement needs in various sectors where standard devices may not suffice.
Common applications for our load pins include:
t Luggage Carousels – Wireless load pins for predictive maintenance, monitoring load and identifying potential issues.
t Stage Lifting Equipment – Load pins replace pully pins to monitor safe weight limits.
t Wind Turbines – Load monitoring on blades, gearboxes, and towers to enhance operational safety and efficiency.
t Winch and Tow Systems – Real-time tension measurement to prevent overloading.
t Structural Monitoring – Force measurement in buildings, bridges, and other structures for structural health assessment.
Conclusion
Our customisation service provides tailored solutions that are precise, reliable, and engineered to meet the most demanding requirements. Whether in aerospace, energy, transportation, or construction, our commitment to understanding unique needs and delivering quality products ensures that we are a trusted partner in force measurement solutions.
Come see us on Stand 5/C110.
T +44 (0)1344 776666 info@interface.uk.com https://interfaceforce.co.uk
Vision Engineering, a UK based manufacturer of ergonomic microscopy and digital 3D visualisation technology unveils the EVO Cam HALO, a new 4K digital microscope that redefines the standard for clarity, precision and consistency in inspection and measurement tasks.
Suitable for a wide range of inspection applications, EVO Cam HALO combines stunning 4K image quality with advanced, adaptive illumination, and new intelligent software, empowering users to capture the most challenging details with unparalleled accuracy.
HALO’s key features include 4K resolution which reveals previously obscured details with remarkable clarity, ensuring nothing escapes the user’s view. A Super-Wide Dynamic Range ensures the user captures images with exceptional brightness and contrast, even in challenging lighting conditions. Additionally available with HALO comes a new enhanced Illumination package, including a quadrant light, panel light, and white/UV light, to optimise illumination for a variety of inspection needs.
New Intelligent Hardware and Software automatically detects lenses and adjusts magnification settings, ensuring seamless workflow and accurate results. Real-time insights are available providing intuitive image capture, measurement, and analysis tools, enabling faster and more informed decision-making. Vision Engineering’s popular 360 Direct/Oblique Viewer also works with HALO, enabling users to inspect details from different angles, revealing hidden features that would otherwise be inaccessible.
HALO is suitable for a wide range of applications, including Medical Devices Manufacture and testing especially in the practices of inspecting translucent tubes, electro-polished devices, and other medical components with enhanced clarity and accuracy.
It is also effective at capturing fine details on small,
reflective metal parts for precise inspection and quality control – perfect for Micro Mechanics. In the laboratory HALO cam improve the examination of Petri dishes with translucent samples, enhancing contrast and clarity for detailed analysis, and in Industrial Manufacturing, intricate assemblies, solder joints, and other components are inspected with much improved precision and efficiency.
Pricing and availability: EVO Cam HALO is available for purchase now, with
configurations starting at 6,500GBP.
Commenting on the launch, Paul Newbatt, Group Sales and Marketing Director at Vision Engineering, says, “We are delighted to bring EVO Cam HALO to market, confirming our reputation for innovation, while improving the inspection performance available within digital microscopy. 4K image quality plus fully controllable lighting and flexible software available in multiple configurations means that our customers in a wide range of sectors can easily choose the most accurate and consistent digital system for their inspection requirements.”
For more information, please visit: www.visioneng. com/products/digital-microscopes/evo-cam-halo
Representing a leap forward in programming, UNISIG’s next-generation operating system further improves the human-robot interface and slashes programming times.
The new operating system, featured on UNISIG’s UNE6-2i-750-CR small-diameter gundrilling machine, streamlines the setup of dozens of different part handling combinations to reduce new part setup times by 80% or more. The system significantly improves the communication between the machine’s human machine interface (HMI) and the robotic controller. This enables centralized data storage or a single source of truth – the coding and data for the gundrilling operation and the program for the part handling are stored together for ease of recall.
Because it works within a parametric programming environment, the new operating system automatically adjusts its parameters to any dimensional part changes, without the need to manually calculate and enter in new parameters.
Such intelligence eliminates the need to start over and create entirely new and independent programs, while greatly simplifying and shortening programming times for part families.
The UNE6-2i-750-CR gundrilling machine with integrated robot ships with a handheld programming console/teach pendant connected to the machine. Prior to the use of parametric programming, all part handling operations were pre-programmed using the pendant. Users can now enter & store all machine & robotic parameters in the machine HMI. This allows for a more centralized user experience and greatly reduces the depth of robotic experience required.
The machine HMI has built-in parametric selection guides, allowing users to toggle between data entry and the programming guides. Each data value, and its function, are graphically displayed in the on-screen programming guide. This prevents the guide from being misplaced and makes it available at all times, which is especially advantageous when periodically adding new parts involving large time gaps between them.
The UNE6-2i-750-CR with integrated robotic automation also features interchangeable part trays. The robot services both the machine’s spindles and accommodates drilling of different diameters from each end.
The optional lantern chuck system on this machine model allows workpiece loading into the rear of an automatic collet chuck to ensure accurate workholding, especially for uniquely shaped workpieces.
UNISIG’s UNE6 Series of precision gundrilling machines generate holes from 0.8mm to 6.0mm (0.03” to 0.24”) in even the most challenging of materials. Such capability makes the machines well suited for a wide range of applications, including medical part manufacturing.
Further information on all machines and the complete UNISIG machine program is available at: www.unisig.com or follow the company on LinkedIn and Twitter (@UNISIG). You will also meet us at the EMO 2025 show in Hannover, Germany, from 22-26 September.
The 18th annual Multimodal exhibition at Birmingham's NEC from 17-19 June 2025 is poised to deliver unparalleled insights for logistics professionals with its most comprehensive speaker programme to date.
Supply chain and logistics professionals attending Multimodal 2025 are set to gain invaluable knowledge from a record-breaking line-up of industry experts. The event will feature over 100 speakers across 71 conference sessions, alongside 275 exhibitors, making it the most comprehensive event in its 18-year history.
Each day of the three day event will offer attendees the opportunity to engage with thought leaders from across the logistics sector, with keynote sessions addressing the most pressing challenges and opportunities facing the industry today.
Leading the impressive roster of speakers is Gary Jeffreys, Managing Director of Maersk, who will headline a panel discussion on ‘Unlocking UK Connectivity Puzzle’. The session will explore how crossmodal connectivity between roads, railways, ports and warehousing clusters can drive productivity improvements whilst supporting decarbonisation objectives.
Alex Salden, Managing Director of The Sofa Delivery Company/DFS, will share his journey in ‘Transforming Fulfilment from Couch to Car’, offering insights into the unexpected benefits realised through supply chain modernisation.
In a particularly timely session, Andrea Pearson OBE, Deputy Director of International Rail and Rail Freight at the Department for Transport, will join an expert panel exploring ‘International Rail Freight - Time for a New Opportunity’, examining the potential for expanded rail freight solutions.
Cameron Bowie, Managing Director - UK & Ireland at Hapag-Lloyd (UK) Ltd, will deliver a crucial analysis of how new US industrial and trade policies are set to impact global shipping. His session will delve into the implications of recent geopolitical shifts, including tariffs, near-shoring, trade-wars, freight rates, and domestic trucking operations.
Sustainability and geopolitical insights at the forefront
Sustainability remains a key focus, with Kate Broome, Sustainability and Social Impact Director at Kuehne+Nagel UK, leading a panel that will showcase existing case studies on decarbonisation within multimodal logistics. Attendees will benefit from real-world examples of eHGV implementation, charging networks, and the decarbonisation of rail and water freight.
David Wells OBE, Chief Executive of Logistics UK, will launch groundbreaking research examining the impact of ongoing geo-political instability on the UK's trading relationships and the resulting implications for the logistics industry.
The comprehensive speaker programme also includes representatives from leading organisations across the supply chain spectrum, including Malcolm Logistics, DP World, Maritime, MSC, Peel Ports, CMA CGM, Freightliner, Kuehne + Nagel, Hapag-Lloyd, ASM, Ocean Network Express, DHL, and CEVA.
Conference places are offered on a first-come, first-served basis and are free when visitors register to attend. Registration for Multimodal 2025 is now open and visitors can secure their place via: https://forms.reg.buzz/multimodal-2025
We possess the experience, people, and resources necessary to identify the optimal transport solutions for your export and import needs. Our highly skilled staff are available to provide you with exceptional service, whether you require transportation for Foodstuffs, Excise Goods, Agricultural Products, Furniture, Machinery, Equipment, or any other commodity via Road, Sea, or Air. We are here to assist you!
Our small-business approach to relationship building, combined with our extensive resources, ensures that you will receive all the advantages of working with a larger organisation while also enjoying the personalised customer care typically associated with smaller operations. Consider us an extension of your organisation. Our knowledgeable staff can guide you through every step of your shipment and provide advice on the best course of action and requirements to ensure your goods reach their destination.
ACP Freight Services Limited will be
exhibiting at Multimodal at the NEC Birmingham UK, from 17-19 June 2025, for the second consecutive year. Come by and to discuss how we can assist you in achieving your goals for 2025 and beyond.
Originating from Belgium and with a 117-year history, Ziegler is a 4th generation, family-owned logistics powerhouse that has learned to evolve with the ever-changing landscape of freight transportation. In a market where many larger providers stick to rigid service offerings, Ziegler’s mantra is simple: make it happen, no matter how complex the requirement.
Ziegler’s bespoke approach to logistics ensures that clients receive customised solutions that meet their unique challenges. Whether it’s out-of-gauge ‘ugly freight,’ complex customs requirements, or the handling of hazardous materials, Ziegler excels at finding solutions where others might see
obstacles. Their ability to think creatively and adapt to specific needs sets them apart in an industry that often relies on one-size-fits-all offerings.
This outside-the-box thinking is backed by a solid foundation of cutting-edge technology, sustainability practices, and a highly skilled workforce. Ziegler invests continuously in both innovation and their people, ensuring that their team can handle even the most demanding logistical challenges.
Ziegler’s comprehensive supply chain services, which include multimodal distribution, warehouse storage, customs clearance and other valueadded services are designed to provide flexibility and efficiency, giving their clients the peace of mind that their logistics needs will always be met.
For the 4th consecutive year, Ziegler will be showcasing their solutions at Multimodal 2025 at the NEC in Birmingham. Visit them on Stand 4030 to explore how their creative approach can help solve your most complex logistics needs.
sales.enquiries@zieglergroup.com www.zieglergroup.com/uk
We are now KLN Freight. Kerry Logistics Network has recently announced a rebranding initiative to change our name to KLN Logistics Group Limited. This strategic move aims to establish a more unified corporate identity and strengthen our company's brand positioning in the global logistics market.
This rebranding initiative reinforces our dedication to delivering high-quality, reliable logistics services that empower our customers to excel in their respective fields. It highlights our role as a trusted partner and opens doors to new opportunities.
At Samskip Multimodal, we redefine efficiency across Europe’s logistics landscape. As a leading provider of sustainable, door-to-door transport solutions, we specialise in combining rail, road, sea, and inland waterways into a seamless, cost-effective network. Our extensive multimodal services connect major European hubs, offering unmatched reliability and reduced carbon emissions – keeping your cargo moving and your footprint light.
From containerised cargo and refrigerated transport to bulk and hazardous goods, Samskip ensures flexible, customised solutions tailored to your supply chain. Our innovative use of digital platforms provides milestone tracking, smart booking tools, and data-driven optimisation to enhance transparency and control at every stage of the journey.
In addition, Samskip Logistics offers comprehensive forwarding global logistics services, including sea, air, and road freight, customs clearance, and supply chain solutions designed
for smooth international transport. With a strong presence in over 39 countries and decades of expertise, Samskip operates more than 22 vessels, 20,000 containers, and an extensive rail and trucking fleet. Our strategic terminals and green logistics focus make us a trusted partner for businesses looking to simplify operations and achieve their sustainability goals.
Choose Samskip Multimodal for your European logistics – where performance meets responsibility. Efficient. Reliable. Sustainable.
Come see us on Stand 4026. T +31 88 400 1000 rotterdam@samskip.com www.samskip.com
logistics service provider and underscores our commitment to helping customer achieve excellence in their operations through top-tier logistics solutions.
Offering a diverse range of services, including sea, air, rail, and road transport, tailored to meet your specific needs, our flexible approach ensures that, regardless of market conditions, we can provide the most costeffective and efficient logistics solutions.
Come and speak to a member of our team at Multimodal. You will find us on Stand B6 on the BIFA Pavillion.
Our transition to KLN represents more than just a name change. It symbolises our evolution as an independent, forward-thinking
Contact T 0161 873 8777
UK.CustomerService@kln.com www.kln.com
The Inside Warehouse Logistics Expo (IWLEX) is the UK’s only dedicated event focused on warehouse operations and internal logistics, with exhibitors such as warehousing providers, system suppliers and the industry’s best packaging and equipment companies.
This year’s event takes place at NAEC Stoneleigh, Kenilworth, Warwickshire from 3-4 June 2025 and welcomes attendees to meet with a diverse range of suppliers from aerospace, automotive, manufacturing, food and drink, solar energy, to warehousing and 3PLs and much more.
Running alongside the exhibition is an expert-led series of two conference streams, including presentations on hot topics such as: automation, safety and compliance, the role of women in logistics, and sustainability.
IWLEX 2025 mirrors how
the sector is shaped by the industry for the industry and runs with two parallel purposes: supporting the professionals within and encouraging business across the sector.
IWLEX is thrilled to provide a FREE World Class conference for attendees of the show. If your organisation runs a warehouse and you want to understand how you can improve that operation, this conference is for you. Equally, we will explore external challenges that impact warehouse operations and share examples of how we can overcome them.
information you need to know about the warehousing and logistics sector. This really is a conference not to be missed.
The result is a jam-packed conference stream full of unmissable content delivered by leaders from in and around the Warehouse Sector. Shaped by the industry, for the industry, our conference is set to be curated by our advisory board to provide the
Last year, visitors praised the organisers at IWLEX 2024 for a fantastic, well-organised show, with opportunities to meet with the right decision-makers to discuss ‘real-world problems’ with the potential for long-term relationships, “We thoroughly enjoyed our time at IWLEX. It is a valuable exhibition for companies looking for the highest quality visitors. Visitor numbers may be lower than at other exhibitions, simply because the organisers have done a fantastic job in screening out time-wasters! Everyone who came onto our stand was a motivated buyer and we have had several high-quality leads since the exhibition. We recommend IWLEX to anyone looking for relevant leads within the world of warehousing and logistics,” commented NLT Mechanical.
Working with and supported by many of the UK’s trade associations and key sector media, IWLEX will provide a fresh and modern marketplace for a broader range of visitors and exhibitors to meet and do business. A free conference program will provide industry-driven content which empowers visitors to generate and implement new actionable ideas.
www.iwlex.co.uk
Ibstock Brick is the UK’s leading manufacturer of clay products and employs nearly 1,400 people in the UK spread over 19 sites.
The sites are located throughout the UK and most have associated quarrying operations at or near to them. In order to meet the increasing demand for the supply of bricks, Ibstock Brick has extended its manufacturing capability at the new Ibstock site in Coalville, Leicestershire.
The new factory can produce 100 million bricks per annum, coupled with the existing manufacturing on site; it will mean 190 million bricks per annum total output from the Ibstock site, or an amount equivalent to around 28,000 new homes per year.
The challenge
Silica is a natural substance found in materials common on construction sites, like concrete, rocks and sand. The dust created by cutting, grinding or drilling concrete products can contain respirable crystalline silica. Over time, exposure to these silica particles causes scarring in the lungs.
Silica dust poses health and safety and compliance challenges in many work environments. Controlling the extremely fine dust is a complex task requiring both proper engineering controls and effective housekeeping practices.
The control of airborne silica dust is a constant challenge for industries that create the dust. The key to preventing silica exposure is to keep silica dust out of the air. That’s a tall order for giant manufacturing sites like Ibstock Brick. Former methods like broom sweeping are neither efficient nor
effective, which is why Ibstock Brick contacted Tennant to help find a solution.
Industrial cleaning machines from Tennant can play an important role in helping teams on site manage the silica dust challenge, and can support silica exposure control plans that help create safe, healthy, productive work environments, and work toward OSHA compliance.
The solution Tennant offers three types of dust control methods that can be used to support silica control housekeeping requirements. As Tennant developed its offering, they worked closely with Ibstock Brick to test their HEPA enabled S20 sweeper.
The Tennant S20 is a versatile and durable midsized industrial sweeper with a three-stage primary filter system, plus the option was made available for a 4th stage HEPA dust filter.
The S20 picks up everything from dust to broken glass in shopping centres, warehouses and industrial facilities, has a compact size that manoeuvres easily, and features innovative Tennant technologies that reduce costs by extending run times, improving operator safety and simplifying maintenance.
moisture and dirt in the hopper removing 90% of particulates from the air stream.
● Stage 2 – SweepMax® Plus Cyclonics Longer filter life with exclusive cyclonics dust control that removes an additional 90% of dust particles from the air stream before reaching the filter.
● Stage 3 – Canister Nanofibre Filter MERV 15rated, flame retardant Donaldson Ultra-Web® filter loads and shakes-back 70% more effectively, and provides cleaner air from filtering sub-micron dust particulates down to .5 microns at 99% efficiency.
● Stage 4 – HEPA Dust Filter Dry system providing a filtration efficiency of 99.97% to .3 microns.
Ibstock Brick’s new Eclipse site was awarded the Industry Pledge Award for measures to control dust within a factory.
"A HEPA filter has a special filter media that can clean to a very high standard by removing microscopic particulate from the air,” said Jamie Harris, Head of Industrial for Tennant Company in the UK.
Based on Ibstock Bricks testing, the HEPA filter should last at least six months, possibly up to a year depending on the customer’s application. Proper usage and maintenance practices will help increase the effectiveness of the machine’s filtration stages and the life of the HEPA filter.
Filtration stages
● Stage 1 – PermaFilter™ Tennant engineered design helps keep bulky debris,
"Without the Tennant Machines we would not be able to keep the site clean and safe, the S20 and T20 in particular helps us maintain a clean site and are easy to use and do a great job helping us keep the dust levels low on site and help us keep the floors clean and safe." – Ibstock Brick Hygiene and Cleaning Supervisor for Ibstock Eclipse.
"Tennant have provide us support and helped us identify machines that have helped us in keeping the new factory clean. The Tennant equipment helped us gain the Industry Pledge Award for measures to control dust within a factory in December 2018 which is something that we are very proud of and would have not achieved this without the Tennant machines that we have on site." – Senior Production Manager for Ibstock Eclipse.
Arrange a free on-site machine demonstration at your facility – contact your Tennant account manager or Danny Cross on 0161 728 8306 or email: danny.cross@tennantco.com, and view the full range online at: www.tennantco.com or come see us on Stand B20 at IWLEX 25.
Packing speed and quality have been significantly improved for one food production company, regardless of the limited space in their production facility. A compact automatic l-sealer was supplied by Yorkshire Packaging Systems (YPS) to achieve their goals.
Green Cuisine are specialist producers of herbs, spices and seasonings. Established in 1990, they supply several million packs per year to the UK and Europe. Their range of over 150 different products are supplied in jars, tins and boxes, plus specially shaped gift packaging.
Green Cuisine previously operated a semi-automatic packaging line. However, this line was becoming increasingly unreliable with poor quality seals and had always been time-consuming to operate. They discussed their requirements for a faster and higher quality alternative with a number of packaging equipment suppliers, before opting for YPS’ proposal.
“YPS really listened to our specific needs and offered us equipment
that was a little different to the norm, so that it perfectly suited all our requirements,” commented Jules Pike, Director at Green Cuisine.
YPS supplied a Pratika Smart 55 compact l-sealer. “This machine offers the benefits of an automatic l-sealer, such as speed, precise sealing and fast changeovers, all with a much smaller footprint, ideal for the limited space available at Green Cuisine,” explained YPS Sales Manager, Jacques-Pierre Macchi.
The Pratika Smart 55 combines sealer and tunnel in one machine, resulting in a total line length that is at least 1.5 metres shorter than one made up of a sealer and separate tunnel.
The intuitive HMI provides complete control of the sealer, shrink tunnel and conveyors to achieve an optimal finish to the seal. Additionally, over 250 separate ‘recipe’ combinations can be saved, to significantly
speed up changeovers between different products or collations and minimise downtime.
“As well as YPS’ fresh approach to supplying the equipment, their back up and support convinced us that they were the right partner to work with. We’ve been very happy with the installation, commissioning and continued running of our new compact l-sealer,” concluded Jules.
T 01484 715111 info@yps.co.uk www.yps.co.uk
Rotech is excited to announce a new partnership with LEIBINGER, a globally recognised manufacturer of advanced industrial coding systems. This collaboration marks a significant leap forward in Rotech’s commitment to delivering the best coding and marking solutions for every application, ensuring customers have access to the best technology for their needs.
“Our mission has always been to provide reliable, easyto-use systems that meet our customers’ needs and solve their challenges,” said Richard Pether, General Manager at Rotech. “Over the years, we've offered various technologies, from hot foil to thermal transfer and thermal inkjet, each with unique features and benefits. The LEIBINGER range of continuous inkjet printers is a welcome addition to our range and has been well received by our customers, across many applications.
“We are very excited about our collaboration. I’d say this is a perfect match! Rotech and LEIBINGER share the same commitment: Innovative technology that delivers real value to customers, empowering them to achieve their goals - maximum productivity and efficiency. For over 75 years, this has been the foundation of LEIBINGER, ensuring smooth production and packaging processes,” adds Tim Richards, International Area Sales Manager at LEIBINGER.
Unlocking new possibilities with CIJ technology While Rotech’s range of Thermal Inkjet (TIJ) printers
remains a trusted solution for many applications, the technology isn’t without its limitations – particularly on high-speed production lines or in harsh or changing environments. Continuous inkjet (CIJ) systems excel in these conditions, offering the perfect complement to Rotech’s portfolio and enabling a more versatile offering that meets every customer requirement.
LEIBINGER printers stand out for their innovation and meticulous craftsmanship. With 85% of manufacturing carried out in-house, LEIBINGER guarantees exceptional quality, making them a sound investment for businesses seeking long-term performance and reliability.
“To succeed in a mature market, a new product must offer clear advantages,” added Richard. “LEIBINGER printers do just that, takings convenience, cleanliness, and cost-effectiveness to new levels. Having witnessed the birth of the CIJ printer back in the 1980s, it has been fascinating to see how the technology has evolved. This perspective has allowed us to fully appreciate how much of a step forward the LEIBINGER range of printers are.”
Introducing the IQJET: A new standard in CIJ Printing As part of the Rotech-LEIBINGER partnership, Rotech proudly introduces the IQJET, a revolutionary printer that redefines CIJ performance. Winner of the German Innovation Award 2024, the IQJET is the world’s first intelligent coding system, offering up to five years of service-free operation.
The IQJET boasts an impressive five years of service-free operation, driven by its unique design and fully automatic nozzle seal technology - a signature feature of all LEIBINGER printers. No printhead cleaning, no routine maintenance, just reliable high-quality coding, day in and day out. With Plug & Print functionality, integration is effortless, enabling instant setup with no delays.
The SMART.EFFICIENCY system is another key feature that sets the IQJET ahead of the competition. By automatically adjusting parameters in real time, it optimises ink consumption, reduces waste, and enhances operational efficiency. This leads to cost reductions of up to 50% compared to traditional continuous inkjet (CIJ) systems. The system intelligently manages ink flow, ensuring that every drop is used effectively, while the IQJET’s ultra-low ink consumption and XXL cartridges, designed to empty completely, eliminate the need for separate disposal, making it a cost-efficient solution.
T 01707 393700
sales@rotechmachines.com www.rotechmachines.com
From scale manufacturer to global market leader
Packaging machinery
manufacturer Greif-Velox is celebrating 80 years of company history at its Lübeck location in Germany and invites guests to the in-house trade show Greif-Velox Connect on May 13, 2025. Reflecting on a rich tradition while keeping a firm eye on future innovations, the company underscores its role as a technology leader in the packaging industry.
From the ‘Greifenmühle’ to high-tech manufacturing
The roots of Greif-Velox trace back to the year 1100, with the founding of the Greifenmühle (‘Griffin Mill’) by monks in Pomerania, in what is now Poland. A key turning point came in 1936 when Ernst Mahlkuch founded the Greif-Werke in Klützow, Pomerania, after inventing and patenting the automatic bagging scale ‘Velox’. Following the company’s relocation from Pomerania, a new chapter began in Lübeck in 1945. “The past eight decades have been shaped by challenges – but above all, by the development of outstanding innovations for the industry,” says Sebastian Pohl, Managing Director of Greif-Velox.
Milestones of industrial progress
From manufacturing certified Velox scales to developing fully automated packaging systems, Greif-Velox has continuously advanced filling technology over the past decades. Key technological milestones include the introduction of valve bag filling machines in 1957, sealing machines in 1966, and the establishment of a strong
research partnership with the Lübeck University of Applied Sciences beginning in the 1980s. One major leap was the development of the VeloVac vacuum technology, which enabled dust-free packaging of ultra-light powders such as carbon black and silica— securing the company’s position as a global market leader in this segment.
Structural change and strategic turning points
Following the insolvency of Greif-Werke in 1997, a new beginning was marked by the founding of Greif-Velox Maschinenfabrik GmbH. The acquisition of filling and dosing specialist LogDos in 1999 significantly expanded the company’s portfolio, including the addition of automated liquid filling systems. In the years that followed, GreifVelox continued to drive its internationalisation. With the founding of Greif-Velox America in 2020 – now based in Houston, Texas – the company currently operates in more than 90 countries worldwide.
Lübeck remains a strategic hub
By extending the lease for its premises for another ten years, the company has once again reaffirmed its commitment to the city of Lübeck as a strategic location. “The combination of innovation, entrepreneurial
vision, and a strong connection to the Lübeck site will continue to drive our success in the future,” says Managing Director, Sebastian Pohl.
Greif-Velox Connect: Where innovation meets networking
As part of its anniversary celebrations, Greif-Velox will host Greif-Velox Connect at its Lübeck headquarters on May 13, 2025. Under the motto ‘Explore. Innovate. Network.’ the event will feature expert talks, live machinery demonstrations, discussions with industry specialists, and exclusive insights into the company’s in-house InnovationHub. “Greif-Velox Connect is a key meeting point for our partners, customers, and employees,” says Managing Director, Thorsten Köll. “Our aim is not only to reflect on the past but to actively engage in conversations about the future of packaging technology and to spark new ideas together.”
www.greif-velox.com
In September last year Scotland’s recycling infrastructure got a massive boost when Wyllie Recycling purchased and installed their second Cross-Tie baler from PAAL, a Konti J 275 X XL.
With contracts for 7 Councils, representing over 1 million people, their Perth Site is the only recycling facility in Scotland with 2 x PAAL Cross-Tie balers.
Business investment decisions are not to be made lightly, they have to be based on performance, reliability and trust, therefore as part of a £3M capex investment, the PAAL Konti Cross-Tie was chosen for these reasons as it uniquely stops the expansion of baled plastics and avoids bale bursts so ensuring maximum payloads of HDPE Nat & Jazz, PET Nat & Jazz and PP.
Wyllie Recycling relies on their balers to consistently perform to the highest standards and their initial Cross-Tie baler, purchased in March 2020, has already made 87,604 bales without any breakdowns.
Their Perth Facility has grown into a thriving 5-acre site using Optical Sorting equipment with 1 x PAAL
baler dedicated to plastics e.g. 5 tonnes per hour of empty plastic milk bottles and 1 x PAAL baler exclusively for cardboard, paper and aluminium UBC cans.
Building a business to become a significant player in the Scottish Recycling Market is no mean feat, but this is exactly what the family-owned Wyllie Recycling has achieved.
To enable this growth Wyllie Recycling has been progressive, innovative and invested in the latest recycling technologies to ensure they maintained and grew their reputation and excellent services to the UK market.
Kadant PAAL have had the pleasure of being involved in Wyllie Recycling’s growth through our Scotland Agent, Davy Knowles, Clydesdale Technical Services. He started the PAAL baler relationship in 2006 when Jim Wyllie MD was running a recycling site for a multi-national company in Glasgow.
Becoming friends, over that business bonding ritual ground of the golf course, and “from that day to this we have purchased exclusively PAAL equipment and been provided with great service back up by Davy and his team,” said Jim.
Jim Wyllie says, “We find the PAAL range offers us
the best possible package of reliability of output with parts and service when needed. Kadant PAAL have also been chosen when providing our customers with vertical mill-size balers or static compactor units.”
In this difficult business climate from all angles this is a testament to all the people involved in this journey; proving friendships, teamwork and a passion for growth are all key to our growing recycling infrastructure.
www.kadantpaal.com www.wyllierecycling.co.uk
CECO Environmental (EIS) provides market-leading solutions such as VOC abatement, odour control and acid gas removal for industrial applications requiring air pollution control. Offering turnkey solutions, EIS offers comprehensive, compliant solutions across the global industrial sector. With all eyes on air quality, EIS is dedicated to safer, cleaner solutions to protect people, the planet and industrial equipment. The sales and design offices are based in Bromsgrove, Worcestershire, with equipment manufactured globally. EIS was formed in 2005 by four experienced colleagues who had worked together within the abatement industry for many years.
Favourable acquisition
In 2020, EIS was acquired by CECO Environmental: A global player serving industrial air, industrial water and energy transitions markets through engineered systems and industrial process solutions headquartered in Dallas, USA. CECO Environmental has industrial expertise dating back over 150 years and now across more than 40 countries. In January this year, CECO Environmental was ranked 20 on the prestigious Forbes 2024 list of America’s Most Successful Small-Cap Companies. CECO Environmental works actively to optimise air quality and the energy value chain through bespoke solutions for petrochemical processing, power generation, refining, midstream oil & gas, EV production, general industrial, poly silicon fabrication, battery recycling, water/ wastewater treatment and much more.
This acquisition has further leveraged CECO’s North American supply chain for EIS and given CECO access to the European production partners through EIS. This consolidates EIS as a UK hub for CECO’s industrial solutions, allowing for a greater push across European industrial markets.
Spotlight on EIS
EIS operates as a worldwide solutions provider in air pollution control, specialising in turnkey VOC abatement, odour control and air pollution control systems. The best solutions are selected for air pollution control applications from our range of technologies available.
These include:
t Regenerative Oxidisers, (RTO)
t Recuperative Oxidisers
t Direct Fired Thermal Oxidisers (DFTO)
t Catalytic Oxidisers
t Zeolite Concentrators
t Carbon Adsorption Systems
t Dust Extraction & Air Filtration Systems
t Heat Recovery Systems
t Ductwork Systems.
“EIS operate in a variety of industries which are not exclusive of automotive and automotive parts, chemical and process industries, can manufacturing, waste and water industry, printing and flexible packaging, pharmaceutical, oil and gas, electric vehicles and EV battery plants and many more.”
“With various technologies and solutions available to us, EIS have a reputation as experts in the field with strong project management capabilities. EIS are known for robust and reliable designs while providing energy efficient solutions.” explains Peter Hill, Sales Manager, Environmental Integrated Solutions Ltd: CECO Environmental.
Case study: Supporting EV manufacturers
EIS are currently working on a large project for an electric car manufacturer with air to water heat recovery. The heat exchanger recovers up to 3,000kW of heat per hour. The hot air from the RTO pre-heats boiler water. This is
then pumped back to the central heating hub.
Looking to 2025: Future developments
“During 2024, EIS exhibited at CHEMUK24 for the first time: It’s the UK’s largest annual event dedicated to the development, manufacture and management of chemicals and formulated products. We were fortunate that this year’s event had a record attendance and we’re now looking for new opportunities to showcase our solutions.
“
This year, we also joined forces with NEPIC- who mainly operate in the North East as we felt that this cluster of businesses offered an idea opportunity to work alongside other process providers, manufacturers and professional partners engaged in the usage of our technologies.”
“Looking to 2025, there are impending legislative changes in emission regulations in the water industry, particularly regarding methane and nitrous oxide. EIS is actively working with partners to provide solutions with abatement systems for the water industry sector on their journey to Net Zero.”
For more information on how EIS can support your industry, please see the details below:
T +44 (0)121 550 7079 phill@OneCeco.com www.eisuk.co.uk
For over 25 years Walker Plant Services Ltd has provided essential services to the construction industry with a primary focus on Volvo Construction Equipment for both maintenance purposes and spare parts.
Based in Nottingham, Walker Plant is a privately owned company with a highly skilled and experienced team committed to delivering a firstclass service. Equipped with fully fitted workshop facilities, the team is capable of handling a wide range of services, including routine refurbishments of engines, transmissions, drop boxes, and more –specifically for all Volvo ADT models. This allows Walker Plant to offer major components on a service exchange basis, helping customers save both time
and money compared to traditional ad hoc repairs.
Whether you’re working in mining, construction, or quarrying, Volvo Articulated Haulers are built to conquer whatever comes your way. Offering maximum safety, uptime and efficiency across the toughest terrains, these machines ensure that you can move more material for less money.
As a specialist in the sale of used Volvo Articulated Haulers & Dump Trucks/ parts, Walker Plant has established itself as the largest stockist in the UK with a comprehensive range of parts to including Engine Overhaul Kits, Transmission and Suspension parts, Loader Frame Pins, Bushes, Seals, Bearings and Cylinder Kits. Walker Plant’s
capabilities also include the remanufacture of all Volvo transmissions, and offers a ‘NO QUIBBLE’ 6 months/750 hrs warranty, or a repair only service to suit your budget.
Following their appointment as a factory-approved SLP stockist, Walker Plant is now your trusted source for high-quality off-road Volvo dump truck and loading shovel parts, backed by renowned Swedish engineering. When you choose genuine SLP parts or services from Walker Plant, you can count on OEM specifications – without the OEM price tag – offering you exceptional value and total peace of mind.
T 01777 709533
sales@walker-plant.co.uk www.walkerplant.com
There is a common misconception that all breather valves are rigorously tested to a certain standard before they are sold, but unfortunately, this is definitely not the case. Many breather valves on the market are not subject to stringent testing protocols, leading to significant safety and operational risks. When these untested and, more importantly, unsafe breather valves are procured, the end user unknowingly takes on many risks.
It is crucial to know the facts by conducting thorough due diligence from the initial purchase and throughout the entire lifecycle of the unit. First, ask yourself: Are your breather valves set correctly?
Incorrect settings can lead to valve malfunction, causing potential overpressure or vacuum conditions that could compromise tank integrity. Are your breather valves performing safely? Regular testing ensures they function within safety parameters, preventing hazardous situations.
Do you know your breather valve leak rates, and is your media hazardous, flammable, costly or toxic? Understanding leak rates is vital for environmental, occupational health and safety compliance. Do they function as per intended design and specification, and do they meet the set point? This ensures that valves operate as required under specific conditions.
Has your breather valve been tested in accordance with API2000 Section 5.4? Compliance with this standard guarantees that valves meet industry requirements. Do you monitor your breather valves as part of your aging plant management plan? Regular monitoring can identify wear and tear before it leads to failures. Lastly, are you confident that all your breather valves maintain optimum efficiency and performance? Ensuring this can prevent costly downtime and environmental hazards.
The only irrefutable test method is using the Vent-Less test bench. This groundbreaking technology is revolutionising testing, ensuring that breather valves are tested prior to installation and during
Maintec is the longest standing exhibition for the predictive maintenance, reliability and asset management industry, and Chris Hansford, Managing Director of Hansford Sensors Ltd, has been attending the show for almost 40 years.
As a globally recognised leader in industrial vibration monitoring, Hansford Sensors designs & manufactures a broad range of high-performance equipment. Its offerings include accelerometers, vibration sensors, 4-20mA transmitters, cable assemblies, and industrial enclosures. At Maintec 2024, Hansford Sensors highlighted key products like its Accelerometer Power Supply Modules and Vibration Sensors, showcasing its commitment to delivering reliable solutions for industrial applications.
Vibration monitoring products are crucial in industry because they help detect early signs of machinery malfunction, such as misalignment, imbalance, or bearing failures. Hansford Sensors systems are ideal to support various outputs like AC acceleration and velocity, ensuring versatility in usage. Its products are designed for robustness with IP ratings suitable for harsh environments, making them ideal for industries such as manufacturing, power, and mining.
As well as Vibration Systems and Switches, Hansford Sensors also offer a range of accessories for vibration monitoring that include DIN rail mounted monitoring and protection modules, vibration switches and charge amplifiers.
What’s more, Hansford Sensors also provide an online calculator designed to simplify your vibration analysis. From an input of acceleration, velocity or displacement the Vibration Calculator converts the amplitude and frequency into a range of engineering units to optimise analytical performance.
For more information on all products, or to use the calculator, please see below: T 0845 680 1957 sales@hansfordsensors.com https://hansfordsensors.com
the life term of the unit. The award-winning Vent-Less test bench aligns with the API2000 Section 5.4 test protocol, and the instantly generated certification stands up to regulatory scrutiny. The documented leak rate is also invaluable for LDAR, IED, and Regulation 61 reporting. These questions are critical for assessing your vulnerabilities and ensuring the safety and efficiency of your operations. Don’t leave it to chance – make sure your breather valves are thoroughly tested and maintained using the Vent-Less test bench.
Contact T +44 (0)1726 844707
info@assentech.co.uk www.assentech.co.uk
Hansford Sensors is a leading global manufacturer of industrial vibration monitoring equipment. We design, develop and manufacture a range of high-performance industrial accelerometers, vibration sensors, 4-20mA transmitters, cable assemblies, industrial enclosures and ancillary equipment. These products can be used in a wide range of industries including petrochemical, metal, paper & recycling.
Visit hansfordsensors.com, contact 0845 680 1957 or email sales@hansfordsensors.com
One of the technical highlights at ACHEMA 2024 was KSB Group’s new 3D-printed containment shroud for mag-drive pumps of the Magnochem type series. Named MagnoProtect, the component offers the same safety as a doublewalled containment shroud – without the latter’s disadvantages of heating up strongly and having high eddy current losses.
AtWhile providing comparable safety, the overall efficiencies of the new mag-drive designs clearly exceed those of canned motor pumps. Designed with a structure of channels, the new containment shroud offers a second, redundant, static safety barrier preventing leakage of the fluid handled.
A pressure transmitter monitors the vacuum generated, which is present during normal operation in the channels of the containment shroud. If the monitored pressure rises to atmospheric pressure, the outer containment shell is leaking. If the pressure rises above the ambient pressure, the
inner containment shell is damaged. The containment shroud design is characterised by high mechanical strength and good wear properties. It has been optimised to minimise heat losses and eddy currents.
Converting a standardised chemical pump with mechanical seal to a magnetic drive is easier and more cost-efficient than retrofitting it with a canned motor. The geometry and dimensions of the new containment shroud are integrated in the modular system of Magnochem, allowing metallic or ceramic containment shrouds to be replaced easily. This enables operators to upgrade older pump sets that are still in service without difficulty.
www.ksb.com/en-gb
Oliver Valvetek, innovation drives our commitment to advancing critical technologies. Over the past few years, we’ve increasingly focused our research and development efforts on creating solutions for Carbon Capture, Utilisation, and Storage (CCUS), a key component in the global drive toward reducing carbon emissions.
We are excited to share that we have developed two 3/8” subsea rotary gate valves, part of a group of prototypes heading to a customer for a pioneering carbon sequestration project in a subsea environment. This milestone showcases our dedication to pushing the boundaries of valve technology through advanced R&D.
Our subsea rotary gate valve is
specifically engineered for the demanding conditions of carbon sequestration projects. Its compact size ensures easy placement in constrained spaces, while its costeffectiveness makes it ideal for scalable solutions in large-scale CCUS applications. Additionally, it features the same proven metal-on-metal seal technology as our standard gate valves, delivering top performance even in the harshest subsea environments.
This advancement reflects Oliver Valvetek’s ongoing commitment to developing cutting-edge solutions that contribute to a more sustainable future.
For more information on Subsea valves, contact Oliver Valvetek on: +44 (0)1565 632636, email: sales@ valves.co.uk or visit: www.valves.co.uk
The Cleaning Show 2025 at London’s ExCeL (18-20 March) solidified its position as the UK’s premier cleaning and hygiene event, attracting over 8,000 visitors and fostering invaluable industry connections.
The largest Cleaning Show to date, this premier event solidified its reputation as the go-to destination for cleaning professionals.
It showcased cutting-edge technologies, products, and trends while bringing together industry leaders, innovators, and thousands of eager participants looking to learn, network, and discover transformative solutions, highlighting the latest innovations in cleaning, sustainability practices, and
emerging technologies.
The event highlighted the sector’s growth and collaboration, with over 150 exhibitors showcasing the latest advancements. A key focus was sustainability and workforce development, underscored by the British Cleaning Council’s (BCC) launch of its annual report, revealing the industry’s £66 billion economic contribution in 2022. The BCC also unveiled a new "Career Development Zone" to attract younger talent, addressing the sector’s ageing workforce challenges.
Discussions at the conference emphasised the importance of technology, sustainability, and training. Panels explored regulatory compliance, AI integration, and the need for accurate environmental claims. The event also featured the return of the Window Cleaning World Cup, with France’s Frank
PEVA UK, a trusted name in skin protection for over 55 years in Germany, is bringing its expertise to British industries with an innovative range of professional-grade skincare solutions.
Specialising in products that protect, heal, and enhance skin health, PEVA UK stands out for its quality and commitment to environmental responsibility. Unlike competitors who use plastic particles, PEVA UK products contain natural abrasives by utilising exfoliants like walnut shell and corn cob meal.
The company’s comprehensive range includes protective barrier creams for harsh environments, cleansing products, and restorative skincare solutions. All products are manufactured under strict GMP guidelines at their Velbert facility in Germany, backed by independent dermatological testing.
Darren Isherwood, national sales manager at PEVA UK, said, “We were excited to attend The Cleaning Show, where we were on Stand J6 This was an excellent opportunity to meet industry professionals and potential distributors, as well as showcase our high-quality, affordable skin protection solutions to the UK market.
“Our skin protection products offer individual and combination solutions for skin protection, cleansing, and care, catering to various applications in the industry and handicraft sectors.
“We look forward to demonstrating how our decades of expertise can benefit British businesses and consumers.”
T 03330 919996
sales@pevauk.co.uk https://pevauk.co.uk
Burrows, Guinness World Record holder for the fastest window cleaning on the planet.
Paul Sweeney, Event Director, said, “The energy and innovation at this year’s record-breaking show demonstrate the industry’s dynamic future. The connections made here will drive progress for years to come.”
The Cleaning Show 2027 returns in two years’ time to London’s ExCeL from 16-18 March. Before then, The Cleaning Show 2026 is held at Manchester Central from 18-19 February. This is our pick of the best exhibitors from this year’s London show, listed here in alphabetical order: BISCc & PEVA UK. Further details can be found on this page and the next.
https://cleaningshow.co.uk/london https://cleaningshow.co.uk/manchester
BICSc is launching a brand-new event to inspire young people to explore careers in the professional cleaning and facilities management industries. The first-ever BICSc Youth Event will take place on 9th July 2025 at IET Birmingham: Austin Court, during Youth Employment Week 7th11th July.
This one-day event will spotlight the wide range of career opportunities available in the cleaning and FM sectors. Neil Spencer-Cook, Group MD, said, “This event is designed to give young people a comprehensive understanding of the diverse job roles available after leaving school, college, or university. Those attending will leave with a clearer picture of the multiple career paths that await them, and the skills needed to succeed.”
In collaboration with Youth Employment UK, BICSc aims to create an engaging, youth-focused experience that highlights the importance and potential of the industry. The event reflects BICSc ongoing commitment to supporting young talent and being a positive force in the local community. Don’t miss this opportunity to learn more about the future of cleaning and facilities management – and how you could be part of it. Discover the possibilities and take the first step towards an exciting and rewarding career.
Contact www.bics.org.uk/bicsc-youth-event
Since its inception in 2000, it has evolved into the largest and most influential gathering of commercial vehicle manufacturers, dealers, distributors, and suppliers. This event, held at Birmingham’s NEC from 29 April to 1 May 2025, is where the industry’s leaders – senior decisionmakers, directors, managers, and engineers – come to see the latest innovations in vehicles, trailers, equipment, and cutting-edge technology.
For those who keep the wheels of industry turning, this is the unmissable event of the year. It's where you gain essential insights, uncover next-level practices, and stay ahead of the toughest challenges and emerging trends. This is your chance to connect with peers, drive your business forward, and solidify your position in the industry.
Attending The Commercial Vehicle Show is crucial
for anyone serious about the future of road freight, transport, distribution, and logistics. This is your chance to connect with industry leaders, explore the latest innovations, and stay at the forefront of key trends and challenges. Don’t miss the chance to experience the groundbreaking technology that will keep you ahead of the competition.
Visiting the Commercial Vehicle Show offers a unique chance to explore the latest innovations in road freight transport, distribution, and logistics – all in one place.
Whether you're interested in cutting-edge vehicles, equipment, and technology, or seeking insights into industry trends and challenges, this event is a mustattend. It’s the ideal platform for networking with key decision-makers, connecting with suppliers, and staying ahead of the competition.
Exhibiting at The Commercial Vehicle Show provides unmatched access to the key decisionmakers driving the road freight, transport, distribution, and logistics sectors. It’s the ultimate platform to showcase your products, elevate your brand, and connect
with potential customers and industry leaders.
This year, over 15,000 road freight, distribution, and logistics professionals will take over the NEC for the Commercial Vehicle Show – the ultimate event for the UK and Ireland’s road transport sector. This is where the serious players connect.
The Commercial Vehicle Show is the only event in the UK where fleet operators can meet industry leaders, discover game-changing products, and find solutions to streamline operations and reduce costs. This is where the best in the business come to drive the industry forward and set new standards.
This year, the Commercial Vehicle Show is focused on maximising your ROI. With a revamped floorplan, new features, new content, and a range of new initiatives throughout the year, you’re guaranteed a marketing campaign and exhibiting experience finely tuned to your customers. Our team is here to act as an extension of your own, ensuring you build important relationships and kick-start your sales pipeline.
www.cvshow.com
Bradshaw Electric Vehicles, one of the UK’s leading manufacturers and suppliers of electric vehicles and waste management solutions, has launched a new range of Refuse Collection Vehicles which are specifically engineered to tackle the challenges of urban waste collection.
The Refuse Collection Vehicle range, which includes the Goupil G4, the longwheelbase G4L and Bradshaw’s pedestrian PFB1500, are each expertly designed to improve how local authorities and waste management companies operate in confined urban areas.
All three models have been made available in 3 body configurations; hopper only, hopper and bin lift as well as hopper, bin lift and compaction arm.
Both the Goupil’s and Bradshaw’s RCVs are compact, agile, highly manoeuvrable and ideally suited to towns, high streets and pedestrianised areas. Their compact dimensions enable access through street barriers and around street furniture, while electric powertrains ensure a silent and pollution-free operation, making them an efficient alternative to traditional refuse collection methods.
The road-legal Goupil G4 is available with two lithium battery options, offering either a 62-mile or 101-mile range
on a single charge. The standard G4-RCV has a 2.0m3 hopper and a payload of up to 740kg and works with 120, 240, and 360-litre bins. The G4L Long-Wheelbase adds 500mm to its chassis, increases the volume to 3.5m3 and works with larger 660-litre bins.
Based on the popular PFB1500, which is available with a number of body options, including cage body, Bradshaw’s pedestrian-controlled walk-along RCV is designed to tackle the challenges of urban waste collection in areas with high pedestrian footfall and limited vehicle access.
The pedestriancontrolled RCV handles 120, 240 and 360-litre bins and features a corrosionresistant aluminium hopper. The ergonomic tiller head provides a comfortable and precise operation and can be driven easily with either hand. With five braking systems, automatic hill hold, and advanced safety
features, it ensures safe operation on slopes.
All three RCVs feature corrosion-resistant aluminium bodies with a 90° tipping angle for easy waste disposal into larger containers or larger RCVs for satellite operations, streamlining waste collection rounds and reducing overall time on the streets.
The vehicles are set to be showcased for the very first time at the Commercial Vehicle Show at Birmingham’s NEC later this month on the Bradshaw EV Stand 5A60
With increasing pressure on local authorities to reduce emissions and improve air quality, traditional dieselpowered waste vehicles are no longer viable. Bradshaw’s latest offering addresses these concerns by providing a zero-emission, cost-effective solution tailored for urban environments.
The Goupil G4 RCV in particular arrives at a crucial time for waste management operations following the introduction new recycling regulations coming into effect on 31st March 2025, requiring businesses across England that produce more than 5 kg of food waste per week being legally required to segregate food waste from general waste.
T 01780 782621 enquiries@bradshawev.com www.bradshawev.com
The event returns from 3-5 June 2025 to the NEC, and is an automotive trade show like no other in the UK. In 2025 it will bring together 550+ leading brands from 25+ countries and 15,000 senior UK based visitors from across the automotive industry, for three days of networking, learning and invaluable face-to-face time to do serious business.
Network and connect with quality buyers and top customers from the UK aftermarket in one place. Educate and influence forward thinking business owners from the garage, bodyshop and detailing sectors. Network with engineering and procurement professionals from the supply chain across 3 days.
Visitors can expect to get their hands on new products, fully test tools and technology in our 13 interactive features areas. There will also be a 3 day Innovation4Mobility conference where leaders can come together to debate and tackle the big industry challenges head on.
Visitors can expect to get their hands on new products, fully test tools and technology in our 13
interactive features areas from Innovation4Mobility, The Modern Garage, Workshop and Aftermarket Hubs, Paint & Spray Live, the Vehicle Detailing Hub, Body Repair Live where visitors can choose from 150+ hours of skills training for collision repair, digitalisation, EV & Hybrid, ADAS and more.
Experience the future of mobility at Innovation4Mobility – a dynamic hub where cutting-edge technology, electrification, autonomy, and sustainability converge. Connect with start ups, industry leaders, and visionaries driving innovation. Engage in thought-provoking discussions, hands-on demos, and immersive experiences.
In association with Autotechnician, a packed programme of technical seminars will be delivered by respected specialists, addressing the advancements and challenges facing the service, repair and maintenance sector. Covering a range of topics such as engine fault diagnostics, MOT, diesel, ADAS and more.
Presenting key industry trends and insights, designed to inform managers and business owners so they can optimise and futureproof the running
of their Aftermarket business in an environment of fast-paced change. Seminars will be presented by respected industry figureheads, giving access to free expert advice and insights covering a range of topics including UK & global trends, the MOT, EV, legislation, digitalisation in the aftermarket and more.
As the education partner and co-curator of the programme, The UK Detailing Academy invites the community to join them at this brand new feature for practical demos and to discuss the sector's challenges and opportunities.
https://automechanika-birmingham. uk.messefrankfurt.com/birmingham/en.html
The Turbo Guy Ltd will be exhibiting at Automechanika 2025 at Birmingham, NEC in Hall 20 Stand: G50.
Founded in 2010, The Turbo Guy Ltd was established to address a gap in Scotland’s turbo remanufacturing market. Today, it is recognised as one of the UK’s largest manufacturers, remanufacturing approximately 1,000 turbos each month. The company operates exclusively with trade customers, supplying turbos and DPFs to independent repairers, motor factors, and buying groups across the UK.
Aside from its team of expert engineers and broad product range, The Turbo Guy Ltd takes pride in stocking the latest turbos and DPFs to land on the market. Its extensive range includes turbochargers, diesel particulate filters, seals and gaskets,
particulate filters for gasoline engines and fitting kits.
As the UK's top 10 expert supplier for re-manufactured, OE genuine and new aftermarket turbochargers, and DPF supply and cleaning, The Turbo Guy Ltd has received BSI approved Quality Management System certification, ensuring customers receive the utmost precision and reliability.
Having already taken part in Automechanika Birmingham 2023 and visiting Automechanika Frankfurt in 2024, the team are yet again excited to meet potential suppliers and new customers while showcasing some exciting new products at the 2025 event coming soon in June.
Contact T 0141 649 9426 sales@theturboguy.com www.theturboguy.com
Kärcher, global leader in cleaning technology, is pleased to announce its presence at Automechanika Birmingham 2025 this June.
Located on Stand C84, Kärcher will be spotlighting its best-in-class pressure washers, which deliver unbeatable versatility. Whether using hot or cold professional pressure washers, Kärcher provides the solution to suit any automotive cleaning challenge.
Alongside its pressure washers, Kärcher will also be unveiling its new eco!Booster power nozzle. The eco!Booster is suitable for cold and hot water high-pressure cleaners, compatible with the EASY!Lock interface and has a nozzle size of 040. The increased jet width ensures reduced energy and water consumption and therefore better efficiency. This revolutionary nozzle concept directs the water stream with the help of air drawn into the system. This enables impressive cleaning results fast, which is particularly crucial to meet the demands of fleet cleaning in the automotive sector.
Alongside the new nozzle accessory,
Kärcher will be spotlighting their best-in-class pressure washers which deliver unbeatable versatility. Whether using hot or cold professional pressure washers, Kärcher provides the solution to suit whatever the cleaning challenge.
The Kärcher team is excited to provide attendees of Automechanika with an exclusive preview of the new eco!booster and will be available throughout the event to discuss how those in the automotive industry can enhance cleaning efficiency through adoption of the latest technologies.
For more information on how Kärcher can supercharge your cleaning operations, please visit: www.kaercher.com/uk
What if speed isn’t just an advantage but the new standard in servicing?
Every second counts – and downtime counts tenfold.
As an established supplier of rotary and diverter valves for a large range of dry bulk solids processing industries, DMN-WESTINGHOUSE is committed to providing future-proof value. This is why we launched the improved PTD plug diverter valve.
The PTD plug diverter valve at a glance
The PTD is designed to route powders and pellets in pneumatic conveying systems with minimum degradation. This diverter valve minimises service time, ensuring more uptime and lower costs. This isn’t just servicing – this is efficiency. Every single time.
t Aluminium housing & end covers, dual-pipe plug
t Stainless steel product contact surfaces
t No outside moving parts, no atmospheric leakage
t Suitable for systems with positive pressures 3-6 barg, pressure shock resistant up to 10 barg (Size 200 excluded)
t Static belly seals with solenoid valve & inductive
position sensors; optional: terminal box
t Inflatable belly seals with electro-pneumatic control system (inc. solenoids, terminal box, inductive position sensors)
t Standard version suitable for product temperatures -25-80°C (ambient temperatures -10-40°C); versions for higher temperatures available
t Versions with electrical drive and/or wearresistant pipes available
t EC 1935/2004 compliant; ATEX 2014/34/EU certification available
The PTD plug diverter valve is suitable for a range of dry bulk solids processing industries:
Aquaculture • Animal feed • (EV)
Batteries • Biomass
• (Petro) Chemicals
• Cosmetics • Dairy •
Food • Infant formula
• Minerals • Paint •
Pet food • Pharmaceuticals • Plastics • Recycling • Rubber.
Benefits of the PTD plug diverter valve
These features help your operators work smoother and faster, leading to minimal downtime:
t Easy, two-sided access – service from the most convenient side
t Adhesive-free belly seals
t Quick-connection position sensors
t Easy-release actuator linkage
t Reinforced jacking points
t Minimal service required
Your benefits? The PTD sets a new standard in servicing efficiency, ensuring more uptime and reduced costs.
Conclusion
The PTD plug diverter valve exemplifies DMNWESTINGHOUSE’s commitment to providing dry bulk processing industries with future-proof value. It slashes servicing time and offers unparallelled ease of use. The PTD provides the fastest way to efficiency.
www.dmnwestinghouse.com
The Royal Association of British Dairy Farmers, the organiser of the UK’s flagship dairy event, record this year’s event (Wednesday 7 February 2024) as the most successful since its launch in 2018.
With a plethora of dynamic speakers, a host of over 80 new products and the highest visitor number to date the event was a resounding success.
Tech-giant Google delivered this year’s keynote session discussing all things consumer focused.
The Dairy Hub also played host to several key industry names including Arla’s Paul Savage, Bali Nijjar from Freshways and Agriculture Counsellor Hillary Curnow from New Zealand High Commission.
The Innovation Hub showcased new
concepts throughout the day with talks on new technology, breeding innovation, grazing strategies and new diversification opportunities, concluding with a session focused on all things science and research.
The day saw the presentation of several prestigious industry awards, the pinnacle of which was the announcement of the NMR RABDF Gold Cup winner. Bisterne Farms were victorious, with Farm Manager George Brown graciously accepting the award from RABDF Chairman Robert Craig.
RABDF Managing Director, Matt Knight, said the show was without doubt the most successful yet.
“It’s amazing to see Dairy-Tech growing each year, the content across all aspects of the event this year were second to none, with top quality exhibitors, speakers and products.
“With uncertainty still ongoing within the sector it’s imperative we are able to provide a platform, through Dairy-Tech, to help equip farmers and businesses with as much insight and knowledge as possible to aid their success and profitability.”
Next year’s Dairy-Tech event will take place on Wednesday 5 February 2025. More information is available at: www.dairy-tech.uk
With over 30 years of experience in specialised calf rearing, Holm & Laue is THE expert in advanced calf feeding technology. Our innovative solutions are trusted in more than 56 countries worldwide. Our product development is driven by science, research and a focus on healthy calves.
At the heart of our technology is the CalfExpert, the market’s only fully individual calf feeder – a smart feeding system that precisely tailors nutrition to each calf’s needs. This not only ensures optimal growth, but also provides
MandA has been a trusted name in the mechanical feed industry since the 1980s. As a familyowned company, it brings decades of hands-on experience and in-depth knowledge of feeding machinery. This expertise has earned them a strong reputation— not only as a reliable supplier of new feeding equipment for baby animals and as a provider of machine servicing, but also as a dependable source of technical support with a commitment to helping its customers identify and implement the right solutions for their needs.
calves and come with numerous feeding stations depending on your requirements and specifications.
M and A also stocks spare parts and feeding machines from other major feeding machine manufacturers such as URBAN, VOLAC, BRITMIX an HIKO.
accurate, real-time data accessible from anywhere in the world.
We’re also celebrating our MilkTaxi’s 20th anniversary this year. Two decades of innovation have led to a lot of intelligent features – for example SmartMix that tells you exactly how much milk powder is needed for perfect mixing every time. Feeding curves can be defined individually and pasteurising whole milk helps to prevent disease transmission.
Our product range is completed by various housing systems for every need. Igloos for various group sizes, single and twin hutches – all combined with intelligent feed fences. Healthy outdoor housing for better growth.
Holm & Laue – Because healthy calves mean a productive future.
Visit us at: www.holm-laue.com
Based in Leicestershire, M and A are specialists in Forster Technik equipment including spare parts, second hand machines, repairs, as well as brand new equipment like the new ECO feeder and Vario Smart Feeder that are suitable for lambs or
From lamb teats and teat holders to calf teats, bucket feeders, Ewe2 feeders and parts, starter kits, feeder pipes, and a wide range of accessories, M and A offers a comprehensive, costeffective product portfolio coupled with a fast and reliable delivery service that ensures you get what you need, when you need it.
Contact T 01572 850021
M 07836 387632
macsorder@live.co.uk www.mandacalfsystems.co.uk
Since 1968, AgriKing has been at the forefront of innovation in livestock nutrition. As industry leaders in nutritional analysis and forage preservation technologies, AgriKing, we believe that capturing the nutritional value in feeds is the key to profit, animal health, and sustainability.
By researching and developing highquality, data-driven nutritional solutions, Agri-King empowers UK & Ireland farmers to optimise their operations by delivering reliable, science-backed solutions that promote animal health, sustainable practices, and economic success.
At Dairy Tech 2025, Agri-King proudly presented its industry-leading products and services to the dairy farming
community, equipping farmers with the tools and expertise needed to optimise feeding strategies, boost animal performance, and drive overall farm productivity.
One innovative product showcased was Ru-Max®, an enzyme-based rumen enhancer designed to improve digestion and feed efficiency while reducing mineral antagonism for cows. Ru-Max® as well as other products in their Dairy Programme range such as AKMC, Hoof King, Dry Cow MicroPak and VT-Max® are all formulated using the latest technology and research to treat forages and improve digestibility and nutrient availability in cattle/cows.
Contact www.agriking.co.uk