

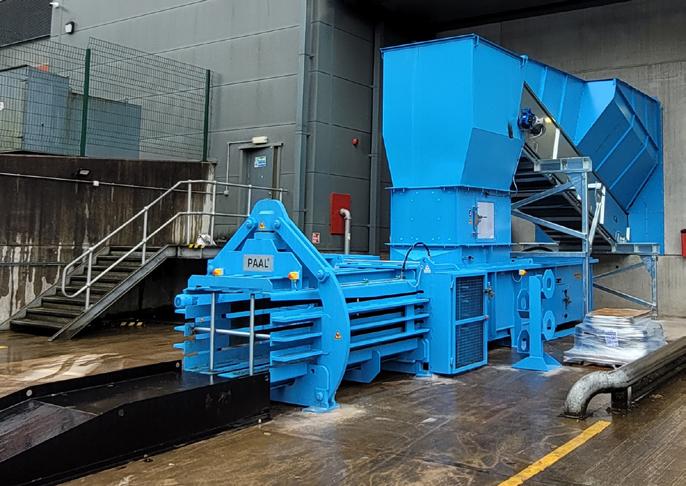
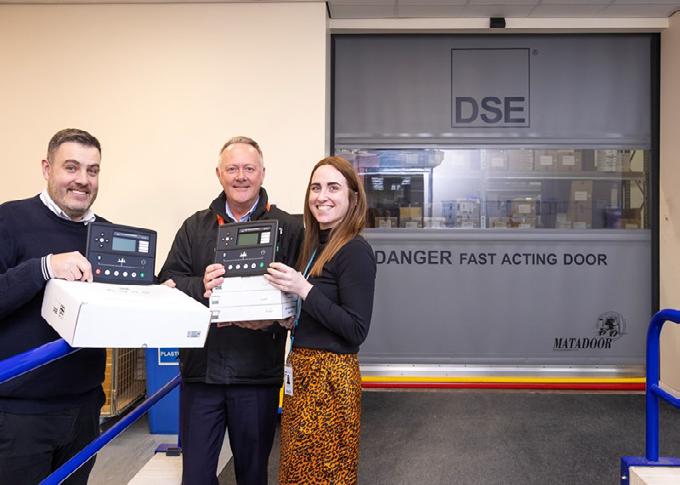
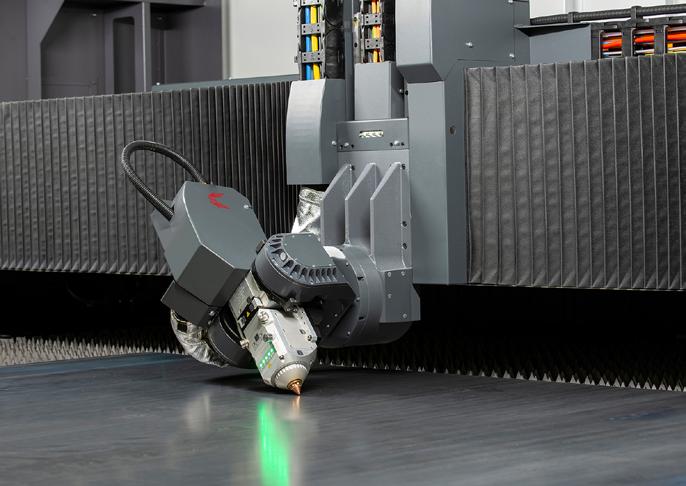
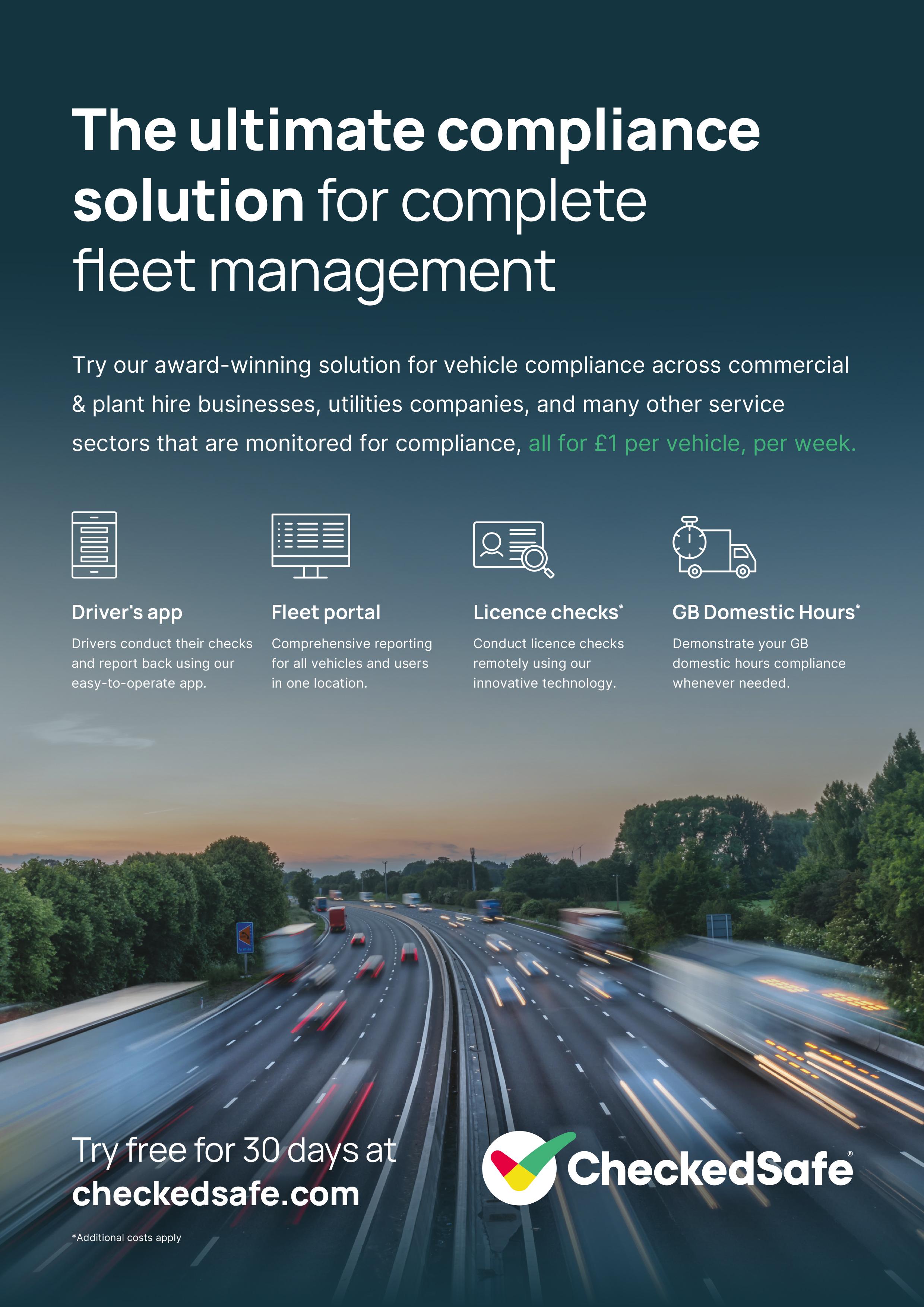

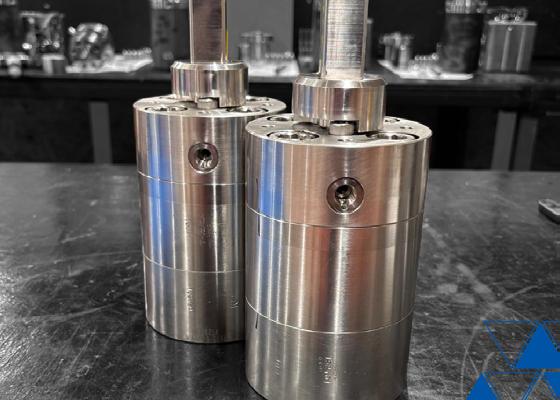


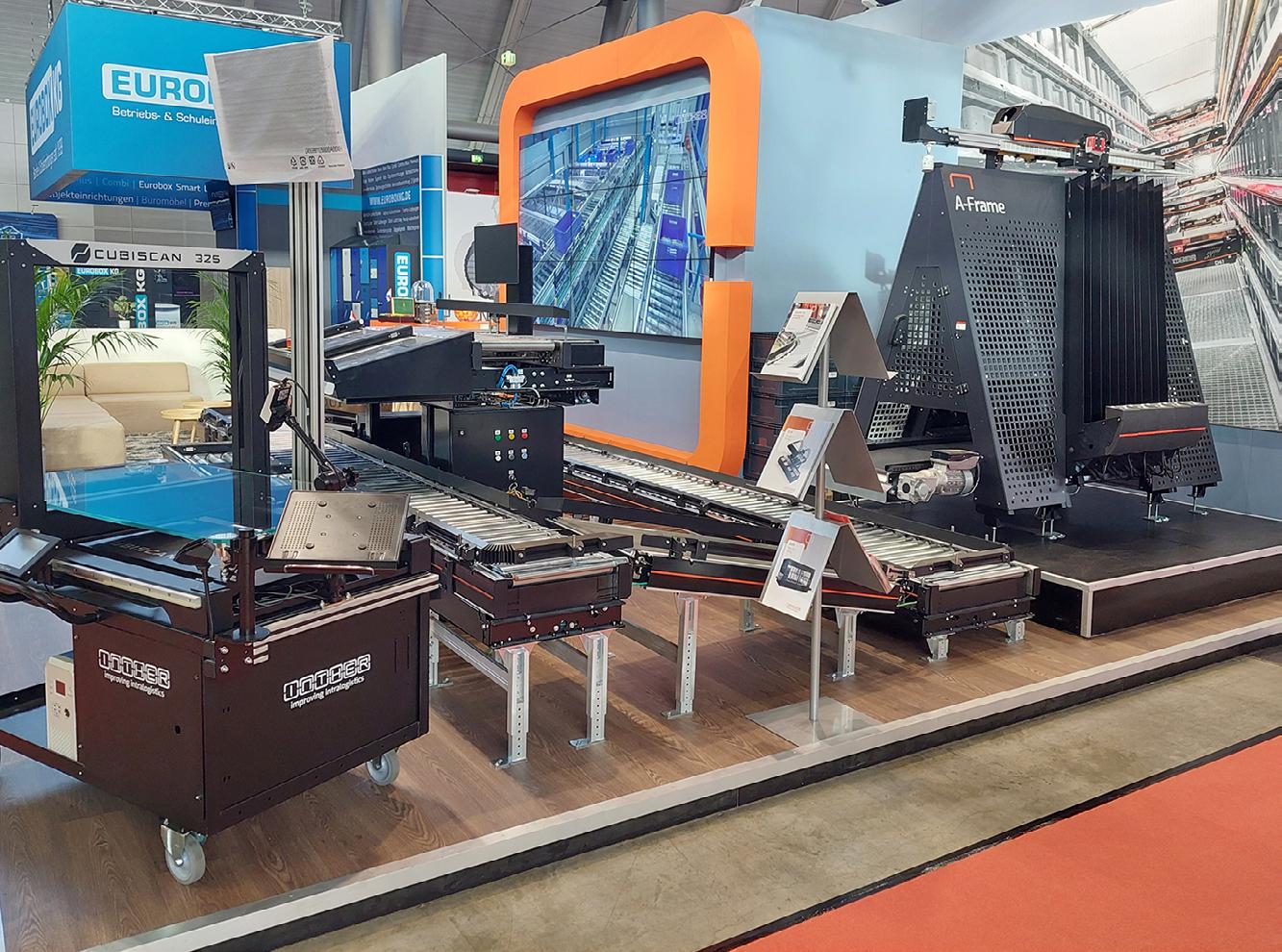

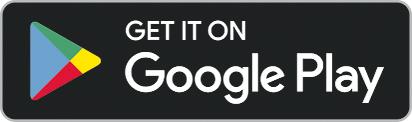
Metsä Group’s tissue paper business, Metsä Tissue, in partnership with the Cleaning & Services Support Association, is pleased to announce the shortlist for its 2025 Sustainability Awards.
The deadline for submitting entries for the 2025 Sustainability Awards passed on 30 September 2024, with an exceptional 91 entries received from 46 companies.
Nominations were submitted across all five categories and all were automatically entered into the Judges’ Choice.
After months of careful deliberation by the judges panel, the shortlist for the three best entries in each specific award category, in alphabetical order, are as follows:
Positive Climate Impact Award:
t Altum Technologies Ltd
t Landmarc Support Services Ltd
t Mindful Chef Ltd/Naked Sprout Ltd
Social Value Impact Award:
t Egal
t No Going Back Cleaning and Support Services
t The Hillingdon Hospitals NHS Foundation Trust and NWL Procurement Services
Best Sustainable Marketing Campaign Award:
t Bunzl Cleaning & Hygiene Supplies Ltd
t Mitie Ltd
t The Hillingdon Hospitals NHS Foundation Trust
Sustainable Collaboration Award:
t Birkin Group Ltd/Lime Supply Ltd
t Chamberlaine Cleaning Services Ltd
t Landmarc Support Services Ltd
New Sustainable Innovation Award:
t Altum Technologies Ltd
t BioVate Hygienics Ltd
t Shaanxi ORCA Electronic Technology Co Ltd (ORCAUBOAT®)
All entries will also be considered for the Judges’ Choice Awards, which will recognise the best achievements at both national and regional levels.
The winners of all awards, including the Judges’ Choice Awards, will be announced at the 2025 Sustainability Awards ceremony, which is being held on 19 March 2025 at The Pelligon in Canary Wharf, London.
About the 2025 Sustainability Awards
The Sustainability Awards were founded in partnership with the Cleaning & Services Support Association (CSSA) in 2023 with the aim of shining a spotlight on sustainability across the cleaning and hygiene industry.
The 2025 Sustainability Awards ceremony will be held at the Pelligon in Canary Wharf in London, on 19 March 2025. Tickets are now available to purchase from the website: https://2025sustainabilityawards.com/ request-tickets
Metsä’s 2025 Sustainability Awards nominated
charity is The Hygiene Bank: https://thehygienebank.com
For further information on the 2025 Sustainability Awards, please visit the website: www.2025sustainabilityawards.com –or contact Denise Nee by telephone on 0845 601 8266 or by email at: denise.nee@metsagroup.com
The CSSA is run by the Cleaning Industry for the Cleaning Industry. It exists to help businesses Grow, Comply, Change and Innovate. They do this through their accreditations, recognising greatness, key events, online and offline business advice, and having government representation.
Metsä Group: www.metsagroup.com/metsatissue
Metsä Group’s Tissue and Greaseproof Papers business, or Metsä Tissue, produces hygiene products for households and professionals, and greaseproof papers for food preparation and packaging. Our high-quality locally produced brands – Lambi, Serla, Mola, Tento, Katrin and SAGA – make daily life cleaner.
We promote a diverse, equal, and inclusive culture. Our 2023 sales were EUR 1.3 billion, and we have approximately 2,500 employees. Metsä Group’s parent company Metsäliitto Cooperative is owned by around 90,000 Finnish forest owners.
Kadant PAAL designs and manufactures efficient solutions for volume reduction to optimise transportation of recyclable materials, helping to reduce environmental impact and transportation costs.
We are recognised as Europe’s premier manufacturer of baling presses including Channel, Twin Ram, Closed End and Metal Balers. Kadant PAAL work globally within the recycling industry whether it is with national waste carriers, independent waste companies, local authority, or FM distribution centres.
The Kadant PAAL Group is a result of the merger of four European Companies, PAAL, COMDEC, FAES and DICOM, with the recent addition of BALEMASTER USA.
The experience within the group ensures that Kadant PAAL are best placed as a provider of proven, tried, and tested baling solutions.
Kadant PAAL UK manufactures its own DICOM Product range of popular vertical balers and waste compactors, distributing and installing the PAAL range of fully automatic horizontal balers and conveyors manufactured in Germany. With their own Technical and Design Team they can provide bespoke solutions with fabrication work manufactured at the factory based in Alfreton to suit all requirements. Our mobile engineers are strategically placed across the country in the event of any mechanical difficulties providing a rapid response call out. Furthermore, the Remote Service Support (RSS) system remotely connects technical experts to the machine in question, with the ability to quickly diagnose the cause of faults, alarms or any performance related issues to avoid unnecessary downtime.
We provide comprehensive baling solutions. Over the last 150 years we have learnt that each application is unique, each operation having its own particular requirements and needs, processing varied materials.
We understand each project is unique, therefore we have a wide range of options that have been developed to ensure once the customers’ needs have been assessed and identified, we can offer an option that will fulfil the baling requirements, supplying a well-designed, robust and reliable solution. It is inconceivable to produce an individual bespoke baler for each application in the same way that one size does not fit all. With our extensive range of waste management options which are used in applications from MRFs to retail stores, we are also able to offer bespoke adaptations to provide solutions for your environment.
dicom.sales@kadant.com
www.kadantpaal.com www.dicompaal.co.uk
TEC Transnational, the only specialist provider of end-to-end aerospace and defence training solutions in quality, has recently announced its e-learning had increased by over one third this year, which has contributed to 19% growth in overall sales.
The company first dipped its toes in e-learning before the pandemic and this capability has grown significantly and now accounts for more than a fifth of the whole business. It has more than doubled its turnover since 2021, largely due to e-learning.
This exceptional growth not only reflects TEC’s resilience but also its role as a trusted partner in driving success for businesses navigating the rapidly changing standards and regulatory world. The
HPC KAESER’s efficient compressed air technologies enables customers to significantly reduce their energy requirements more than most.
How? Our compressors are designed to ensure they have the best ‘Specific Power’: the ratio of total energy used by the compressor and its compressed air output (at a stated pressure).
The lower the Specific Power of your compressor, the greater the efficiency, and the greater the savings.
Equivalent non-HPC compressors are typically less energy efficient with a higher Specific Power. So, investing with HPC saves you costs in the long-term.
In fact, we save our customers up to £25k a year – and in some cases, much more than that.
Our compressed air systems are not only designed to be exceptionally energy efficient, but energy consumption is also minimised as much as possible during their production.
So, not only are your energy costs reduced, but natural resources are increasingly protected, too.
And, until March 31st, we are offering Sustainability Discounts across our range of energy efficient belt-driven rotary screw compressors.
So, for the duration of this campaign, you can save TWICE with us. Save on energy costs – and save with discounts, too.
To find out more, visit: www.hpcplc.co.uk/sustainability or contact us via: offers@hpcplc.co.uk
increase came about as businesses sought innovative solutions to adapt and thrive in a ‘new reality’.
TEC Transnational, established in 1977, delivers expert training, coaching, and support tailored to the Aerospace and Defence industries. ISO 9001-certified, plus other international approvals/certifications, the company ensures clients meet and maintain top industry standards.
The company has leveraged a significant shift in demand as aerospace and defence companies seek alternative methods to improve the skills and attitudes of its workforce, which has traditionally been carried out face-to-face.
Responding to this industry shift, TEC has expanded
its e-learning offerings substantially, enhancing its core training and support services to ensure an efficient mix of in-person and online, so that both arms work in synergy. All courses are available in English, German, French, Arabic and several other languages.
www.tectransnational.com
RPI, the world’s largest manufacturer of high precision rotary measurement and angular positioning devices, recently announced that it had increased its turnover by 55% last year and the installation of its 3,000th device.
Most of the growth came from the USA, which now accounts for half the business, and is where the 3,000th device was installed. Large OEMS manufacturing turbines for energy production have placed orders to the value of over $2m for the company’s iMAPs since May.
The company is reaping the benefits from a strategic investment in the US, after listening carefully to its customers. It set up a sales and technical support service for repair and calibration which has reduced turnaround times from four months to two weeks. The first major repair started last month.
30 years of innovation, engineering and precision in measurements – all “made in Dresden, Germany”. This is what we wanted to celebrate in 2024. To mark the occasion, we put up invited people to an international roadshow that took us to numerous cities around the world. We wanted to showcase our latest developments and technologies in metrology, as well as explore synergies and present research topics in expert talks.
Last year was a significant milestone for the company as it secured its start-of-the-art premises for another 10 years. Its location within the engineering hotspot of Bristol & Bath and its excellent transport links makes it an attractive employer, with four engineers joining the team to meet this growth and plans for another three this year.
RPI has more than 3,000 devices operating within the industry worldwide. It has been manufacturing since the 1940s and is planning for a high-growth future by investing 12% of its turnover in R&D. It will also integrate a new large volume, dual axis, precision rotary grinder into its operations.
So, our thanks go from our supporters from the very beginning to our valued suppliers and loyal customers, our 100 employees in Dresden, our sales team at APS Dynamics in the USA and our entire partner network in 39 countries worldwide.
At the 2 anniversary festivities in September, we celebrated those without whom this milestone would not have been possible. On the one hand, our customers, suppliers and partners, and on the other, our own colleagues who, with a heart for engineering and precision, research, develop, design & improve every day in the service of our customers.
Contact: Audrey Stein, Business Development/Head of Marketing T +49 (0) 351 400 240 marketing@spektra-dresden.de
Union Industries, the UK’s leading manufacturer of bespoke industrial doors, has assisted Deep Sea Electronics with improving access and traffic flow through the installation of its high-speed Matadoor.
The robust high-speed door has been installed in-between the company’s warehouse and production area in Hunmanby, North Yorkshire, and completes a significant on-site investment programme. The Matadoor replaces an existing sectional door, which slowed access between the warehouse & production areas due to the amount of time it took to open and close. Additionally, the Union Industries Matadoor helps to complete the smart new finish of the warehouse refurbishment.
Deep Sea Electronics is one of the world’s leading manufacturers of generator controllers, auto transfer switch controllers, battery chargers and vehicle and off-highway controllers. It employs more than 150 people across four continents and sells products to 150 countries, direct from its UK head office and through its comprehensive distributor network.
The Matadoor, which can be used via remote control or swipe-card, joins two Bulldoors already installed by
Union Industries almost eight years ago.
It is engineered from heavy duty materials and components, hence why it is generally used for high use internal doorways, and where extreme reliability is required.
Matadoor, introduced to the UK by Union Industries in 1992, was the first ever high-speed door on the market with a ‘Crash-Out & Auto-Reset’ feature, which not only allows the bottom beam to swing out of the way if hit by a speeding forklift truck, but automatically resets itself back into the side guides so the door can continue to operate even if damaged.
Adam Sheader, Industrial Engineer at Deep Sea Electronics, said, “We approached Union Industries having experienced the reliability and robustness of its two high-speed Bulldoors in 2016, which are supported by excellent customer service.
“We were seeking a solution to operational challenges of an older, sectional door which was left over following a refurbishment and was proving problematic due to the length of time it took to operate.
“We are not only pleased to have found a solution in
Union Industries’ Matadoor, but also thrilled to support British manufacturing.”
Steve Moultrie, Technical Sales Engineer at Union Industries, said, “Once again, Union Industries is the go-to for reliable and efficient high-speed doors, which are known for their longevity.
“Deep Sea Electronics recognised that they needed a much faster solution and came back to us having experienced the quality and robustness of our doors.
“We were also able to link into the customer’s existing fob access system to maintain controlled access for this opening, which meant minimal disruption during installation.”
Contact T 0113 244 8393 enquiries@unionindustries.co.uk www.unionindustries.co.uk
Union Industries, the UK’s leading manufacturer of bespoke industrial doors, has assisted Crown Lift Trucks in addressing multiple operational challenges with the installation of its cutting-edge high-speed Ramdoor.
Crown Lift Trucks, based in Warrington, faced several issues at its facility, including the need to segregate two adjoining units with different temperature requirements while allowing the movement of high-mast forklift trucks through a large opening.
To tackle these challenges, Union Industries produced a bespoke solution to accommodate the building configuration, ensuring the required opening height could be achieved without compromising functionality. Additionally, the limited space at high-level, between structural steel frames, posed a significant obstacle.
Since launching their UK operations in 1960, Crown Lift Trucks have become one of the world's leading manufacturers of forklift and material handling equipment. Designing and manufacturing up to 85% of its forklift components, Crown provide their wide customer base with forklift rentals, servicing and maintenance, used equipment and a variety of support services.
The installation of the Ramdoor not only addressed the temperature control and safety concerns but also enhanced operational efficiency. Union Industries designed the door to accommodate Crown Lift Trucks’ requirements while incorporating a pedestrian access door to segregate
traffic flow, ensuring a safer working environment.
The Ramdoor features a dual height opening facility, allowing for optimal heat retention while accommodating different forklift sizes. Furthermore, the engineered seals and infills achieve a seamless finish, enhancing both functionality and aesthetics.
It has also been designed to achieve a Class 5 wind resistance rating, making it able to withstand strong winds and to remain operational even during severe weather conditions.
Achieving this rating is supported by a number of the Ramdoor’s features, including its thick Ramhide door curtain material, which is high frequency welded to give the strongest fabric joins available.
In addition, it features heavy-duty wind-brace and wind-bar systems for added strength, plus extra-deep side-guides, which all contribute to the Ramdoor’s ability to cope with high wind loads and pressures. Like other doors in the Union range, it also benefits from a ‘Crash Out’ facility, in case of vehicle or personnel impact to the bottom beam, thus ensuring minimal downtime and repair costs.
Alan Hirst, Sales Director at Union Industries, said, “We are delighted to have assisted Crown Lift Trucks in overcoming their operational challenges with our high-speed Ramdoor. This project highlights our ability to provide innovative solutions tailored to our customers’ specific needs.”
Mark Eccleston, Branch Manager, at Crown Lift Trucks, said, “Union Industries’ Ramdoor has revolutionised our operational efficiency and safety standards. Their dedication to understanding our unique requirements and delivering a bespoke solution underscores their commitment to customer satisfaction. The Ramdoor not only enhances temperature control and traffic segregation but also contributes to our sustainability goals. We are grateful for their expertise and partnership in achieving our objectives.”
T 0113 244 8393 enquiries@unionindustries.co.uk www.unionindustries.co.uk
Let’s face it – how confident are you that your commercial drivers are truly prioritising safety on the roads? Can you be certain that daily walk-around checks are performed accurately? How do you know your drivers are actually getting out of their cabs to inspect their windscreens and tyres before ticking every box and going on their way? For many commercial fleets, the truth is that you don’t.
It is well-documented that driving for work is one of the most dangerous things you can ask your employees to do. A staggering 33% of road deaths and 20% of serious injuries involve someone driving for work. So what are you doing about it?
The reality of road safety in commercial fleets Managing a fleet of commercial vehicles is no easy task. The logistical challenges are immense, and ensuring the safety of each driver is paramount. However, safety protocols can often become mere checkboxes in a long list of daily duties. When the pressure is on to meet delivery schedules and performance targets, it’s easy for thorough inspections to fall by the wayside.
But this isn’t just about meeting regulatory requirements or avoiding fines. The human cost is significant. When a driver skips a safety check, it could lead to severe consequences – an accident that could have been prevented, injuries, or even fatalities. These incidents not only affect the driver and their family but can also have a profound impact on your business, from increased insurance premiums to the potential loss of contracts.
The importance of thorough walk-around checks
Daily walk-around checks are a crucial part of ensuring vehicle safety. These inspections are designed to catch potential issues before they become serious problems. A cracked windscreen might seem like a minor issue, but it can obstruct the driver’s view and become a major hazard. Worn tyres can lead to blowouts, especially at high speeds, putting the driver and others on the road at risk.
accurately and efficiently. With our system, you can digitise your inspection processes, making it easier for drivers to complete checks and for you to monitor compliance.
Ensuring that these checks are carried out properly is vital. This means making sure that your drivers are not just ticking boxes but are actually getting out of their cabs and performing the inspections thoroughly. However, manual checks can be inconsistent. Fatigue, complacency, or simple oversight can lead to missed steps, and without a robust system in place, these errors can go unnoticed until it’s too late.
Choosing CheckedSafe for safer roads
This is where CheckedSafe comes in. CheckedSafe is a comprehensive SaaS solution designed to ensure that your fleet’s safety checks are carried out
We provide a userfriendly app that guides drivers through each step of the inspection process, making sure that no item is overlooked. We do this by dating, timestamping and geolocating every time they press a button, so you can see if they have raced through the checks in two minutes or carried it out properly. The software also uses an accelerometer to make sure they’re walking around the vehicle to do the checks, not just sitting in their cab.
Meanwhile, from your offices, you’ll be able to monitor user activity, view comprehensive maintenance reports in real-time, identify outstanding tasks and vehicle defects, and schedule services with our intuitive system. We also offer secure data storage and a clear end-to-end audit trail, so that you can protect your business in the event of investigations.
Don’t just tick boxes, commit to comprehensive safety
Don’t wait for a serious incident to highlight the gaps in your safety protocols. Act proactively to mitigate risks and ensure that every journey your drivers make is a safe one. With CheckedSafe, you gain peace of mind knowing that your fleet is compliant, your drivers are protected, and your business is safeguarded against avoidable accidents and their associated costs. Prioritise safety, protect your drivers, and ensure the longevity of your business with CheckedSafe.
Take the first step towards a safer fleet today by visiting our website at: www.checkedsafe.com or ring us on: 01282 908429.
One of the technical highlights at ACHEMA 2024 was KSB Group’s new 3D-printed containment shroud for mag-drive pumps of the Magnochem type series. Named MagnoProtect, the component offers the same safety as a doublewalled containment shroud – without the latter’s disadvantages of heating up strongly and having high eddy current losses.
AtWhile providing comparable safety, the overall efficiencies of the new mag-drive designs clearly exceed those of canned motor pumps. Designed with a structure of channels, the new containment shroud offers a second, redundant, static safety barrier preventing leakage of the fluid handled.
A pressure transmitter monitors the vacuum generated, which is present during normal operation in the channels of the containment shroud. If the monitored pressure rises to atmospheric pressure, the outer containment shell is leaking. If the pressure rises above the ambient pressure, the
inner containment shell is damaged. The containment shroud design is characterised by high mechanical strength and good wear properties. It has been optimised to minimise heat losses and eddy currents.
Converting a standardised chemical pump with mechanical seal to a magnetic drive is easier and more cost-efficient than retrofitting it with a canned motor. The geometry and dimensions of the new containment shroud are integrated in the modular system of Magnochem, allowing metallic or ceramic containment shrouds to be replaced easily. This enables operators to upgrade older pump sets that are still in service without difficulty.
www.ksb.com/en-gb
Oliver Valvetek, innovation drives our commitment to advancing critical technologies. Over the past few years, we’ve increasingly focused our research and development efforts on creating solutions for Carbon Capture, Utilisation, and Storage (CCUS), a key component in the global drive toward reducing carbon emissions.
We are excited to share that we have developed two 3/8” subsea rotary gate valves, part of a group of prototypes heading to a customer for a pioneering carbon sequestration project in a subsea environment. This milestone showcases our dedication to pushing the boundaries of valve technology through advanced R&D.
Our subsea rotary gate valve is
specifically engineered for the demanding conditions of carbon sequestration projects. Its compact size ensures easy placement in constrained spaces, while its costeffectiveness makes it ideal for scalable solutions in large-scale CCUS applications. Additionally, it features the same proven metal-on-metal seal technology as our standard gate valves, delivering top performance even in the harshest subsea environments.
This advancement reflects Oliver Valvetek’s ongoing commitment to developing cutting-edge solutions that contribute to a more sustainable future.
For more information on Subsea valves, contact Oliver Valvetek on: +44 (0)1565 632636, email: sales@ valves.co.uk or visit: www.valves.co.uk
The safe laser scanner UAM-05LP offers maximum vewrsatility for safe area monitoring
The Schmersal Group continues to expand its range of products for safe area monitoring: the company is now selling the UAM-05LP safety laser scanner from Japanese manufacturer Hokuyo in Europe, beginning with markets in Germany, France, Austria and Switzerland. The safety scanner is characterised by its extremely compact design and low weight, as well as its flexible integration options and high safety standards. This helps it to ensure maximum personal protection in logistics, manufacturing & the process industry.
Contactless protective devices, such as laser scanners, offer many benefits in the implementation of safety requirements. In contrast to guard fences and guard doors, there is no manual opening and closing requirement, and they do not impede materials transport. In addition, they also enable a clearer view of machinery and processes.
infrared beams to scan the environment and detect the entry of people and objects into the safety zone. This also allows the Hokuyo UAM to achieve a wide range: with a detection range of up to 270°, a safety clearance of up to
The UAM safety laser scanner handles presence control on stationary machinery and robot systems, with the UAM’s sensor utilising
5m and a warning detection area of 20m, the laser scanner can be used in various machinery safety applications.
The laser scanner can be easily configured for
a wide range of uses and also has the ability to monitor two hazardous areas at the same time, eg. two adjacent robots. Each of the two safety zones switches its own OSSD output.
Furthermore, the safety laser scanner is also able to undertake access control as well as arm and hand protection for safety-critical areas in work zones, eg. as part of insertion and assembly workflows.
Another advantage of the Hokuyo laser scanner is its encoder input: with the help of encoders, the speed and direction of travel of automated guided vehicles (AGVs) are transferred to the laser scanner, so that the safety zones can be dynamically adjusted to stop the AGV in case of danger.
The Hokuyo UAM-05LP is suitable for use in machinery safety applications up to PL d, Cat. 3 in accordance with EN ISO 13849 and SIL 2 in accordance with IEC 61508.
Contact: Steve Watkins, Marketing Manager T 01684 571987 swatkins@schmersal.com www.schmersal.co.uk
With colder weather in our midst, it is essential to keep roads safe by having the storage facility for salt or grit in an easy-access container ready to use in the event of ice or snow.
To help weather-proof your streets, Grit Bins of either 200 or 400 litre capacities are included in Leafield Environmental’s range of street furniture. They are ideal for grit, salt or general storage and are made with an extremely hard-wearing premium plastic material.
As standard, the Grit Bin’s extra strong lid has double wall edges, a moulded-in
‘GRIT SALT’ sign, and a fork-lift space for easy manoeuvrability. Custom signage, labels, or crests are available as an optional extra.
Find out more: https://leafieldrecycle. com/product/grit-bin/
Leafield Environmental is an awardwinning UK manufacturer of premium litter and recycling bins, and street furniture. For more information about Leafield’s products, visit: www.leafieldrecycle.com or call 01225 816500 or email: recycle@leafieldenv.com
Apioneer in metal profiling, Charles Day Steels, proudly announces the launch of their progressive 50degree Laser Bevel Cutting machine.
This innovative addition to their extensive suite of laser cutting and profiling services promises to redefine efficiency and precision in metal fabrication.
One of the stand-out features of the new laser is its unparalleled versatility, enabling cuts
at any angle up to 50 degrees from a 12kw laser power source. Set to revolutionise the industry with its ability to eliminate the need for manual grinding and weld preparation, this investment serves as a powerful complement to their existing Waterjet Bevel capabilities.
The new machine boasts a large 6,510mm x 2,600mm bed, allowing for the rapid processing of substantial bevel parts up to 40mm thick. This advancement ensures a seamless transition from cutting to assembly, offering drastically reduced post-processing time and labour costs.
The ability to laser bevel cut offers two key benefits. First, it significantly cuts costs for downstream fabrication by providing parts that are already prepped for fabrication with weld preps. This eliminates the need for additional preparation, saving both time and money. Second, it efficiently handles parts that would otherwise require bevelling or countersinking through traditional machining methods, which are both expensive and time-consuming. By incorporating laser bevel cutting, the process becomes more streamlined and cost-effective. This is particularly effective when dealing with harder material such as wear and amour plate which carry with them the challenges of machining harder materials.
Charlie Day, grandson of the Founder and Sales and Business Development Director at Charles Days, spoke about their latest investment, “With the launch of our new Laser Bevel Cutting technology, we are taking a significant step forward in our service capabilities by providing fabrication-ready parts in a single process. This addition means we can offer clients the very best value not just in our cutting service, but also through reduction downstream fabrication costs.”
Established in Sheffield, the city of steel, Charles Day continues to lead the way in profile-cutting innovation, leveraging over four decades of expertise and cutting-edge technology to serve their customers across various sectors, including construction, automotive, and aerospace, all with industry leading capacity and reliability.
For more information regarding Laser Bevel Cutting and Charles Day’s services, or to request your free bevel sample, please get in touch with their team today.
T 0114 244 5544
Apioneer in metal profiling, Charles Day Steels, proudly announces the launch of its progressive 50degree Laser Bevel Cutting machine.
This innovative addition to their extensive suite of laser cutting and profiling services promises to redefine efficiency and precision in metal fabrication.
One of the stand-out features of the new laser is its unparalleled versatility, enabling cuts at any angle up to 50 degrees from a 12kW laser power source. Set to revolutionise the industry with its ability to eliminate the need for manual grinding and weld preparation, this investment serves as a powerful complement to their existing Waterjet Bevel capabilities.
The new machine boasts a large 6,510mm x 2,600mm bed, allowing for the rapid processing of substantial
bevel parts up to 40mm thick. This advancement ensures a seamless transition from cutting to assembly, offering drastically reduced post-processing time and labour costs.
The ability to laser bevel cut offers two key benefits. First, it significantly cuts costs for downstream fabrication by providing parts that are already prepped for fabrication with weld preps. This eliminates the need for additional preparation, saving both time and money. Second, it efficiently handles parts that would otherwise require bevelling or countersinking through traditional machining methods, which are both expensive and time-consuming. By incorporating laser bevel cutting, the process becomes more streamlined and cost-effective. This is particularly effective when dealing with harder material such as wear and amour plate which carry with them the challenges of machining harder materials.
providing fabrication-ready parts in a single process. This addition means we can offer clients the very best value not just in our cutting service, but also through reduction downstream fabrication costs.”
Established in Sheffield, the city of steel, Charles Day continues to lead the way in profile-cutting innovation, leveraging over four decades of expertise and cutting-edge technology to serve their customers across various sectors, including construction, automotive, and aerospace, all with industry leading capacity and reliability.
www.daysteel.co.uk
For more information regarding Laser Bevel Cutting and Charles Day’s services, or to request free bevel sample, please with their team today.
Charlie Day, grandson of the Founder and Sales and Business Development Director at Charles Days, spoke about their latest investment, “With the launch of our new Laser Bevel Cutting technology, we are taking a significant step forward in our service capabilities by
Representing a leap forward in programming, UNISIG’s nextgeneration operating system further improves the human-robot interface and slashes programming times.
The new operating system, featured on UNISIG’s UNE6-2i-750-CR small-diameter gundrilling machine, streamlines the setup of dozens of different part handling combinations to reduce new part setup times by 80% or more. The system significantly improves the communication between the machine’s human machine interface (HMI) and the robotic controller. This enables centralised data storage or a single source of truth – the coding and data for the gundrilling operation and the program for the part handling are stored together for ease of recall.
Because it works within a parametric programming environment, the new operating system automatically adjusts its parameters to any dimensional part changes, without the need to manually calculate and enter in new parameters. Such intelligence eliminates the need to start over and create entirely new and independent programs, while greatly simplifying and shortening programming times for part families.
The UNE6-2i-750-CR gundrilling machine with integrated robot ships with a handheld programming console/teach pendant connected to the machine. Prior to the use of parametric programming, all part handling operations were pre-programmed using the pendant. Users can now enter and store all machine and robotic parameters in the machine HMI. This allows for a more centralised user experience and greatly reduces the depth of robotic experience required.
The machine HMI has built-in parametric selection
Producing a customised explosionproof high-voltage motor within just 12 calendar days, Menzel Elektromotoren saved an oil refinery a considerable amount of money. The failure of the previously installed compressor motor was causing enormous financial damage.
The team of the German family business Menzel worked on this project with considerable commitment, including weekend shifts, and thus completed all necessary works in record time.
An in-stock MEBKSW-type threephase squirrel-cage induction motor
in size 710 was enabled for ignition protection type Ex ec, increased safety, with purging.
Menzel’s certified explosion protection experts gave it the ATEX marking II 3G Ex ec IIA T3 Gc and prepared the extensive documentation required by the customer within the tight time frame. The motor generates an output of 10MW and 64,132Nm rated torque at 6,600V rated voltage. It features IP55 protection and IC 81W cooling (air-to-water heat exchanger) and is suitable for outdoor installation and the increased ambient temperature range of -20°C-48°C.
To ensure a smooth installation in the existing plant environment, Menzel made various mechanical adaptations such as machining the motor shaft, manufacturing a new base frame and providing flanges for the purging system.
More about electric motors with ignition protection type Ex ec, increased safety: www.menzel-motors.com/ex-na
guides, allowing users to toggle between data entry and the programming guides. Each data value, and its function, are graphically displayed in the on-screen programming guide. This prevents the guide from being misplaced and makes it available at all times, which is especially advantageous when periodically adding new parts involving large time gaps between them.
The UNE6-2i-750-CR with integrated robotic automation also features interchangeable part trays. The robot services both the machine’s spindles and accommodates drilling of different diameters from each end. The optional lantern chuck system on this machine model allows workpiece loading into the rear of an automatic collet chuck to ensure accurate workholding, especially for uniquely shaped workpieces.
UNISIG’s UNE6 Series of precision gundrilling machines generate holes from 0.8mm to 6.0mm (0.03” to 0.24”) in even the most challenging of materials. Such capability makes the machines well suited for a wide range of applications, including medical part manufacturing.
www.unisig.com
IntraLogisteX, to be held at Birmingham’s NEC from 25-26 March 2025, is for logistics professionals who are looking for solutions to their current and future challenges, from the latest materials handling technologies to full-scale warehouse automation options. This event is designed for end-user practitioner logistics professionals such as warehouse managers, heads of distribution, IT directors and lead project managers.
Now in its 10th year, IntraLogisteX offers exhibitors a chance to connect with thousands of high-level decision makers actively looking for the latest solutions.
We supply exhibitors with an audience of unrivalled quality. Our visitors have an average of £2.3 million to spend and 80% of them have buying influence.
Meet industry leading exhibitors and discover how the latest technology can be applied to your operations to provide massive improvements in productivity and accuracy.
There will be a completely free comprehensive Conference theatre. This free learning opportunity means you can hear directly from the minds behind the latest technology. Listen to industry leaders as they share their insights and give real world examples of how they have automated their own, and their customers, operations.
Condense weeks of online research into just a few hours – all the companies you need to talk to are gathered together in one venue. There’s no way better way of doing business than meeting face-toface so get more value from your interactions with potential suppliers and ensure they really understand your organisation’s complex needs.
Watch Live demonstrations of the latest solutions
Celebrate 30 years of innovation with Carlton at IntraLogisteX 2025, Stand 410. We’re showcasing cutting-edge solutions designed to optimise your packaging operations for efficiency, cost-effectiveness and sustainability.
Experience the wrapX pallet wrapping system, revolutionising warehouse operations worldwide. Achieve faster, safer and more efficient wrapping while reducing material usage by up to 65% and improving load stability. Its lightweight, carbon fibre dispenser and wrapX Elite film ensure ergonomic, consistent wrapping, with magnetic mounts for seamless storage and accessibility.
evident seal for cartons, reinforcing our commitment to eco-friendly packaging. See how the Xtaper simplifies carton sealing with a professional finish.
Our expert team will be on hand to discuss your specific packaging challenges and demonstrate how Carlton’s comprehensive range of solutions can optimise your entire process. Explore live demonstrations of wrapX, the Xtaper, and other innovative products designed to address global packaging needs.
Don’t miss exclusive giveaways and the chance to explore the future of fulfilment packaging. Visit Carlton on Stand 410 at IntraLogisteX and join us in building a smarter, more sustainable future.
taking place throughout the exhibition so you can get first hand insight into how they work in practice. Be one of the first to see the latest innovations perform right before your eyes.
Join your industry – network and share ideas with others who do the same job as you. Make brand new contacts through the plentiful networking opportunities available at the exhibition.
The event will also host a Robotics & Automation Theatre and a Sustainable Supply Chain Exhibition Theatre will also host industry experts and exhibitors who will share the secrets to their operational success in their respective fields. The Sustainable Supply Chain Exhibition and Robotics & Automation Exhibition are co-located with the IntraLogisteX Exhibition and your visitor pass will allow you to move freely between the three shows.
www.intralogistex.co.uk
AtPPS Group, we specialise in providing innovative Returnable Transit Packaging solutions and services, tailored to meet the needs of diverse industries. Our offerings include rental, pooling, management, washing, and repairs. These services are delivered not only through PPS Ltd but also via our trusted sister companies, Alison Handling and GW Containers.
with a strong focus on industries such as meat, poultry, and food production. By collaborating closely with these sectors, we ensure our solutions are efficient, cost-effective, and perfectly aligned with the demands of supply chain operations.
Sustainability is at the very heart of PPS Group. We are passionate about supporting a greener, more
Alongside wrapX, discover the Xtaper handheld water-activated paper tape machine. This sustainable alternative to plastic tape offers a secure, tamper-
T +44 (0)1908 277181 info@carltonpackaging.com www.carltonpackaging.com
PPS expanded its portfolio by acquiring Alison Handling and GW Containers. This strategic acquisition has significantly enhanced our capabilities, allowing us to offer an even broader range of returnable transit packaging products and services. Alison Handling and GW Containers are leaders in the sales of high-quality, and products, enabling us to provide an unmatched selection to meet varying customer needs.
Our expertise spans multiple sectors,
environmentally responsible future. By promoting reusable and returnable packaging, we help businesses reduce waste, minimise their environmental impact, and adopt sustainable practices.
Comes see us on Stand 1230. T 01283 821502 rebecca.elston@ppsequipment.co.uk
Loading docks are high-traffic areas that require appropriate safety measures to ensure the well-being of employees and pedestrians. Workers often use the dock to load and unload goods, while forklift trucks move in and out of the area. Unfortunately, accidents can happen, and workers can fall into the void of the dock or lose their balance and fall in.
To prevent such accidents, a reliable fall protection system is essential, and a Boplan Dock Gate offers the perfect solution. This safety gate provides optimum fall protection and ensures a safe working environment for employees and pedestrians in loading areas. With this Dock Gate, employees can work with confidence, knowing that their safety is guaranteed.
The Boplan Dock Gate: Unmatched strength and versatility
The new and improved Dock Gate sets a new standard in fall protection and impact resistance for loading areas. Designed with a tube-in-tube structure and robust base plates, it offers unparalleled protection against impacts up to 16kJ, both to the posts and the rails.
The safety gate, made of high-performance
polymer, features ergonomic handles and an assist mechanism for effortless manual operation. For even greater convenience, a motorised version is now available, making it easier than ever to secure loading docks or restricted areas. Compact, efficient, and easy to install, this dock gate is the world’s strongest polymer safety gate.
About Boplan
Boplan® develops and produces high-quality polymer safety solutions for industrial environments and sporting events. Our innovative and durable fall and impact protection is the reference in impact absorption and protects people, vehicles, buildings
With over fifty years of industry experience, Metreel specialises in advanced mechanical handling and powerfeed solutions. During the trade show, the company will showcase its unmatched solutions alongside business partner Akapp-Stemmann, known for their high-performance conductor bar systems designed for warehouse automation.
At the forefront is the Pro-Ductor conductor bar series, which offers an ideal balance of quality and costeffectiveness. This system features a long operational life, requires minimal maintenance, and provides exceptional reliability for crucial operations.
Introducing the new 2-pole Pro-Ductor conductor bar system. The system is compact and powerful, delivering high performance while optimising space. Alongside the Pro-Ductor series is the PowerPOZ conductor rail, which seamlessly integrates power transmission with precise positioning for cranes and machinery.
Visitors will also find the ergonomic Met-Track® workstation bridge crane in action. Designed for effortless movement and precise load positioning, it helps reduce operator fatigue and eliminates the need for manual handling, streamlining workflows.
Located at Stand 560, join Metreel and Akapp-Stemmann at Intralogistex 2025 and discover the impact of overhead cranes, renowned cable reeling drums and conductor systems for an elevated future of automation.
Contact T 0115 647 0422 sales@metreel.co.uk www.metreel.co.uk
and infrastructure worldwide in warehouses, production sites, logistics centres, cold storage facilities, (petro-) chemical sites, car parks and airports.
With over 25 years of experience, our comprehensive range of products includes safety barriers, handrails, bollards and column protectors. All solutions are designed to withstand extreme conditions and meet the strictest safety standards.
Visit us at IntraLogisteX in Birmingham – 25th & 26th March 2025
Discover the Dock Gate range and other innovative safety products at IntraLogisteX 2025, Stand 446 For more information on our solutions, feel free to contact us ahead of the event or visit our stand during the exhibition.
T +44 (0)1902 824280 info@boplan.co.uk www.boplan.com
We are a global, innovative system integrator with 250+ employees and offices in 6 countries, from the USA to China. Since 1998, we have been automating the storage, sorting, picking and packaging of goods in distribution centres. Our range of services extends from analysis, design, construction and delivery (software & hardware) to global 24/7 service and support.
We offer integrators a comprehensive and reliable hardware portfolio, including order picking systems like A-Frame and GRIPP, automated document handling machines, and an extensive range of plug-and-play conveyors. All our solutions are specifically designed to optimise intralogistics projects and are easy to install, configure, and
maintain. They have already proven their worth in numerous projects over all those years – renowned, satisfied customers such as BMW, Estée Lauder, Skechers, DHL, HEMA, Quickbox, Picnic, Zeeman, and CoolBlue have all benefited from our solutions already.
Let us realise your intralogistics ambitions and take your company to the next level: Visit Inther Group at the IntralogisteX on March 25th-26th at Stand 550 for a live demonstration of our A-Frame with its unique PUMA application!
Learn more at: www.inthergroup.com or contact your dedicated account manager, Maarten Peeters, at +31 614 912 582 or mpeeters@inthergroup.com
Bubble Duck Marketing, in collaboration with The Cleaning Show – the UK’s largest cleaning and hygiene event – announces a strategic partnership designed to elevate both exhibitor and attendee experiences at the upcoming Cleaning Show, set for 18-20 March 2025 at ExCeL London.
Anticipated to be the largest Cleaning Show to date, this premier event has solidified its reputation as the go-to destination for cleaning professionals. It will showcase cutting-edge technologies, products, and trends while bringing together industry leaders, innovators, and thousands of eager participants looking to learn, network, and discover transformative solutions.
This partnership merges Bubble Duck’s marketing expertise with The Cleaning Show’s extensive platform, providing exhibitors and participants with unmatched opportunities
As a rising name in the industrial cleaning space, the V-TUF team are poised to make waves at The Cleaning Show 2025, showing off the newest additions to their range of reliable cleaning equipment.
Positioned as a market-leader in the design and manufacture of powerful cleaning machines, V-TUF will showcase their impressive array of vacuums, pressure washers, and floor cleaners, engineered to tackle any challenge faced by the cleaning space.
Sustainability in action
Alongside the raw power and toughness that V-TUF products offer, sustainability underpins the full manufacturing process. From tanks made of recycled plastic, metal frames/ components sourced from scrap metal and cleaner, lower emission engines, V-TUF fully commit to the idea that power and sustainability aren’t mutually exclusive.
Why The Cleaning Show 2025?
As a premier event for UK industry professionals, the Cleaning Show gives V-TUF the perfect chance to engage with customers in person and showcase what their products are made of. The latest additions to their signature floorcare range highlight the ongoing focus on product longevity, efficiency, and user-friendly
to enhance their visibility and drive business growth.
Key benefits of the partnership:
t Tailored Marketing Support for Exhibitors – Bubble Duck will deliver customised marketing strategies that empower exhibitors to maximise their presence and extend their reach before, during, and after the event. From engaging social media campaigns to targeted advertising, this collaboration ensures that each exhibitor can effectively showcase their unique offerings.
t Dynamic Content Creation and Digital Strategy –Exhibitors will have access to Bubble Duck’s expertise in creating compelling content that resonates with The Cleaning Show’s audience. Expect a diverse range of engaging materials – from video interviews and product demos to blogs and case studies – that enhance attendee experience and boost brand awareness.
t Showcasing Innovation – The Cleaning Show will leverage Bubble Duck’s innovative marketing strategies to highlight the most exciting trends and breakthroughs in the industry. This partnership guarantees that pioneering products and services receive the spotlight they deserve, igniting discussions that could lead to significant advancements within the sector.
This collaboration reflects a progressive approach to the cleaning and hygiene industry, as both organisations are committed to fostering growth, development, and to ensure the event continues to appeal to a new generation of industry professionals.
“We are thrilled to partner with Bubble Duck to reach new audiences and provide innovative marketing solutions for our exhibitors,” said Paul Sweeney, Event Director of The
Show. “With
2025 event poised to be the largest yet, this collaboration will significantly enhance our offerings.”
“Teaming up with The Cleaning Show is an incredible opportunity for us,” said Merci Marosi, Director of Bubble Duck Marketing. “We are passionate about helping each exhibitor shine and truly connect with their audience.”
“By integrating our marketing expertise with The Cleaning Show’s robust platform, we aim to empower businesses of all sizes in this competitive landscape,” added Michelle Brightly, Director of Bubble Duck Marketing. “We’re excited to see the positive impact this partnership will have on exhibitors and the broader cleaning community.”
The Cleaning Show 2025 is expected to attract over 7,000 industry professionals, showcasing the latest innovations in cleaning, sustainability practices, and emerging technologies. With Bubble Duck Marketing driving engagement and visibility, this year’s event promises to be the most impactful yet.
https://cleaningshow.co.uk/london www.bubbleduck.co.uk/cleaning-show
design, ensuring there’s always something new to offer industrial cleaning.
Visit the V-TUF team at Stand H35. Visitors to Stand H35 will have the chance to chat with the friendly V-TUF team of experts face to face, and see firsthand what their
powerful industrial cleaning and floorcare products can do when unleashed.
Contact T 01522 787978 enquiries@v-tuf.com www.v-tuf.co.uk
Kornbusch & Starting GmbH & Co KG, a familyowned enterprise with a rich textile heritage spanning four generations, is set to showcase its latest innovations at the upcoming Cleaning Show in London this March. With headquarters in Borken, Germany, and production facilities in both Germany and the Czech Republic, the company has established itself as a leading manufacturer of high-quality cleaning cloths and sponges.
Specialising in the development of private label cloth, wipes and sponges for major international retail chains, Kornbusch & Starting supplies supermarkets, discounters, and drugstores across Europe, North Africa, and the USA. Their commitment to quality is underscored by a comprehensive quality management system that ensures products meet the highest standards.
At the London Cleaning Show, attendees can expect to experience Kornbusch & Starting’s dedication to innovation firsthand. The company prides itself on its ability to anticipate market trends and develop advanced solutions in collaboration with clients. A key focus of their innovation strategy is sustainability, with initiatives such as self-produced solar energy and plastic reduction
efforts highlighting their commitment to environmentally friendly practices.
Kornbusch & Starting’s participation in the Cleaning Show represents an opportunity for industry professionals to engage with a company that seamlessly blends tradition with modern manufacturing techniques. Their extensive experience and global presence make them a valuable partner for businesses seeking reliable and innovative cleaning solutions.
Visitors to the show are encouraged to connect with the Kornbusch & Starting team to explore potential collaborations and discover how their products can meet diverse cleaning needs. With a steadfast commitment to customer satisfaction, the company fosters close, cooperative relationships with clients, ensuring that their products not only meet but exceed expectations.
PEVA UK, a trusted name in skin protection for over 55 years in Germany, is bringing its expertise to British industries with an innovative range of professional-grade skincare solutions.
Specialising in products that protect, heal, and enhance skin health, PEVA UK stands out for its quality and commitment to environmental responsibility. Unlike competitors who use plastic particles, PEVA UK products contain natural abrasives by utilising exfoliants like walnut shell and corn cob meal.
The company’s comprehensive range includes protective barrier creams for harsh environments, cleansing products, and restorative skincare solutions. All products are manufactured under strict GMP guidelines at their Velbert facility in Germany, backed by independent dermatological testing.
Darren Isherwood, national sales manager at PEVA UK, said, “We are excited to attend The Cleaning Show, where you’ll find us at Stand J6. This is an excellent opportunity to meet industry professionals and potential distributors, as well as showcase our high-quality, affordable skin protection solutions to the UK market.
“Our skin protection products offer individual and combination solutions for skin protection, cleansing, and care, catering to various applications in the industry and handicraft sectors. We look forward to demonstrating how our decades of expertise can benefit British businesses and consumers.”
Come see us on Stand J6. Contact T 03330 919996 sales@pevauk.co.uk https://pevauk.co.uk
For more information about Kornbusch & Starting and their participation in the London Cleaning Show, please visit the website at: www.kornbusch. com – here, you can learn more about their production capabilities, sustainability initiatives, and the dedicated team driving the company's success.
Do not miss the chance to engage with Kornbusch & Starting at the Cleaning Show in London this March on Stand H15, where tradition meets innovation in the world of cleaning solutions.
For over 25 years, Ionic Systems has been at the forefront of revolutionising the exterior cleaning industry through our unwavering commitment to British manufacturing excellence, innovation, and above all, safety. From our headquarters in the UK, we’ve consistently delivered solutions that not only enhance efficiency but fundamentally transform how cleaning professionals work.
Our journey began in 1997 when we introduced the groundbreaking Reach and Wash© system, eliminating the need for dangerous ladder work in window cleaning. We’ve since applied this same ground-based safety principle to roof cleaning with our innovative Roof Wand, allowing operators to effectively clean roofs while keeping their feet firmly on the ground. In 2017, we raised the bar
again with our ‘Protector™’ handle waterfed pole, manufactured to meet BS8020 standards for electrical safety – a feature that has since become the industry benchmark.
Today, we continue to lead the charge in addressing one of the industry's most critical challenges:
electrical safety. We invite you to see our innovations firsthand at the London Cleaning Show (18th20th March 2025) on Stand A1, where we’ll be showcasing our revolutionary Roof Wand© and the brand new anti-rotational Endura© waterfed pole.
www.ionicsystems.com
Jangro is a dynamic, forwardthinking company at the forefront of innovation in the cleaning and hygiene industry. As the largest network of independent janitorial distributors across the UK and Europe, Jangro delivers sustainable and high-quality solutions, all tailored to meet the diverse needs of facilities managers and cleaning professionals. Jangro’s extensive product portfolio – from catering to chemicals, paper to PPE – is designed to be practical, cost-effective, and easy to use, helping enhance hygiene and operational efficiency for businesses.
Built on long-term relationships with its distributors and customers, Jangro offers tailored solutions for a wide range of industries and sectors.
From retail and hospitality venues to education hubs, healthcare facilities, and transportation sectors, Jangro’s customer-centric approach ensures exceptional service and value for its clients. Its local network provides a comprehensive and personalised service, combining regional knowledge with a commitment to large-scale operational excellence and efficiency. Every product is supported by various resources, including training programmes, safety data, and online tools designed to empower cleaning professionals.
Jangro is a leader in sustainability, ensuring its products meet high environmental standards
without compromising performance, such as Planet Mark, ISO 14001 – Environmental Management System, and the EcoVadis Gold Medal, which puts Jangro in the top 5% of companies globally for sustainability excellence. Its NTRL range, for example, is a collection of eco-friendly cleaning solutions that are Vegan Society Accredited, free from harmful chemicals, biodegradable, and sustainably packaged. This range supports Jangro’s wider sustainability pledge, which incorporates responsible sourcing, reducing carbon emissions, and promoting a circular economy.
Kingdom Canvassing Ltd is the renowned trustworthy canvassing company dedicated to enhancing domestic customer growth through our proven direct canvassing strategy.
Our approach begins with a pre-consultation initiative prior to canvassing commencement. Preparation is part of our commitment to understanding your requirements, such as target areas, pricing, access points and housing types. We only utilise your branded material.
Our professional direct canvassers, represent your company throughout the canvassing process. Utilising our tailored customer forms, we gather essential information along with committal agreed on conditions. Comprehensive spreadsheets are provided which can be integrated into software systems like Cleaner
Planner and Squeegee.
Our meticulous processes will not only expand your customer base but will upscale your services leading to excellent profits. Our assurances and partnerships within the industry shows the credibility and capability that Kingdom hold.
t Our team covers the UK
t Our rates start from only x 3.3
t Our 3 clean guarantee promise
t Our 25% customer buffer
Kingdom’s sure footing is what’s needed to make your exterior cleaning business excel.
We’ve proved businesses grow from our direct marketing strategy but in addition your company will have increased word-of-mouth, exposure and referral opportunities all at no extra cost.
Come see us on Stand 18.
Contact: Luke Jenkins T 0207 117 6060
M 07985 582102
luke@kingdomcanvassing-ltd.uk www.kingdomcanvassing-ltd.uk
Jangro wants to drive even further change in the industry when it comes to sustainability, as the company recently created its own sustainability scoring system, with the aim of getting set standards agreed upon and implemented across the sector.
Innovation is at the heart of Jangro. By leveraging advanced technologies like AI and IoT, Jangro enhances the customer experience and drives efficiencies. Its AI tools, like Carpet Care, help to streamline product selection and offer tailored solutions to improve hygiene standards. This commitment to pioneering solutions ensures that Jangro remains a trusted leader in the cleaning sector.
With a strong focus on safety, sustainability, and innovation, Jangro continues to set the benchmark for excellence in the cleaning and hygiene industry. Whether it’s through its ecofriendly offerings, industry-first Keep it Clean podcast, advanced technologies, or unparalleled customer support, Jangro remains committed to helping businesses thrive in a cleaner, greener, and safer world.
Come see us on Stand E55 at The Cleaning Show 2025. T 01204 795955 enquiries@jangrohq.net www.jangro.net
Are you ready to transform your cleaning routine with innovative, ecoresponsible solutions? Visit SoluCLEAN at the London Cleaning Show on Stand G1 and discover how our cutting-edge cleaning products are making a real impact on sustainability.
t Dramatic Plastic Reduction –Say goodbye to bulky plastic bottles! Our pre-dosed soluble sachets eliminate the need for singleuse plastics, significantly cutting waste and reducing landfill impact.
sachet contains the perfect dose, preventing overuse and saving money without compromising performance.
t Sustainable Without Sacrifice – Proudly UK-manufactured, our products are Cruelty-Free International & Vegan Society approved, offering powerful cleaning with plant-derived ingredients.
t Lower CO2 Emissions – Traditional cleaning products are often 90% water, leading to unnecessary transport emissions. With SoluCLEAN’s lightweight sachets, we remove excess water, cutting transport-related CO2 emissions and reducing your carbon footprint.
t Cost-Effective & Easy-to-Use – Each
Come and see how SoluCLEAN can help your business save costs, reduce waste, and meet sustainability goals. Let’s clean smarter and greener—visit us at the London Cleaning Show!
Better for the planet. Better for business.
Find out more at: www.soluclean.co.uk
T 01924 565120
M 07423 714197
sales@solupak.com
marcus.mcdonald@solupak.com
Wieland Electric presents the latest generation of highly efficient safety light grids and safety light curtains.
The importance of occupational safety grows in modern industrial and logistical environments as machines and systems become more complicated. Against this backdrop, Wieland Electric introduces its next generation of safety light curtains and safety light grids, which complement the existing array of optoelectronic protection devices and are distinguished by a high level of safety, flexibility, and use.
The new SLG4 series safety light grids were designed for applications requiring dependable access protection over wide areas on machines or in production sites. While withstanding temperatures as high as 70°C, the light grids may be put into action swiftly thanks to their simple software configuration and plug-and-play installation. Clearly visible LEDs also enable immediate on-site diagnostics, reducing downtimes.
Furthermore, the durable aluminium housing and protection rating IP65/67 in accordance with EN 60529 ensure that the optoelectronic protective devices perform reliably even in adverse environmental situations.
The SLC4 series safety light curtains are perfect for protecting fingers and hands in the machine's danger zone. When the machine is used frequently, they cut access times compared to physical guards, increasing production. Advanced functionalities like muting ensure safe material flow and contribute to cost-effective material supply and removal.
Cascading two devices enables vertical access and horizontal presence monitoring in a single system.
The SLC4 safety light curtains, like the SLG4 safety light grids, have a simple software-free configuration and the ability to do quick on-site diagnostics. This improves productivity and safety in industrial applications.
www.wieland.co.uk
Working with light since 1931, CML is the market leader in the field of miniature lighting for signalisation. As one of the first companies to introduce LED lamps, nearly 30 years ago, CML is now the supplier with the broadest range of miniature lighting products in the world.