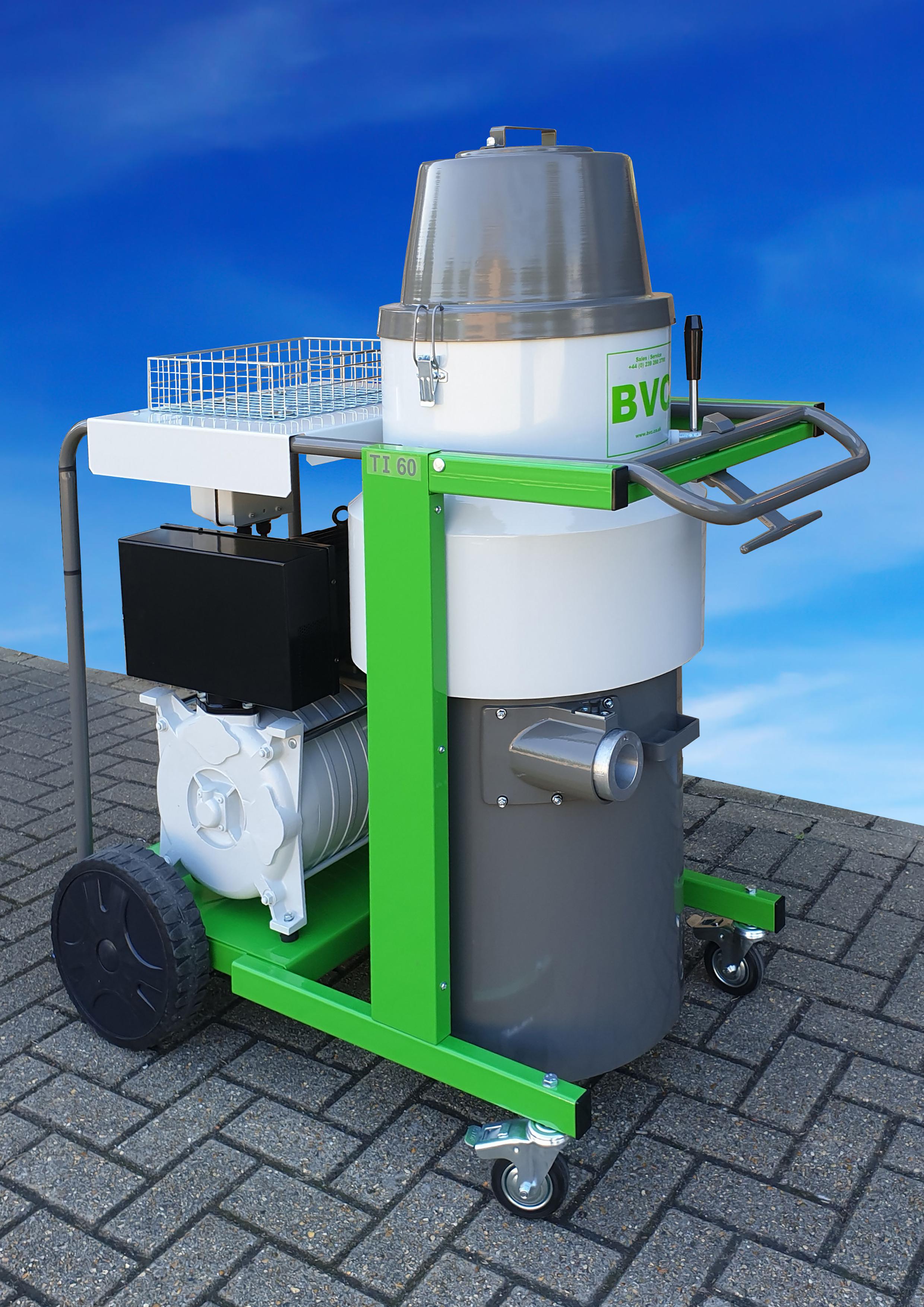
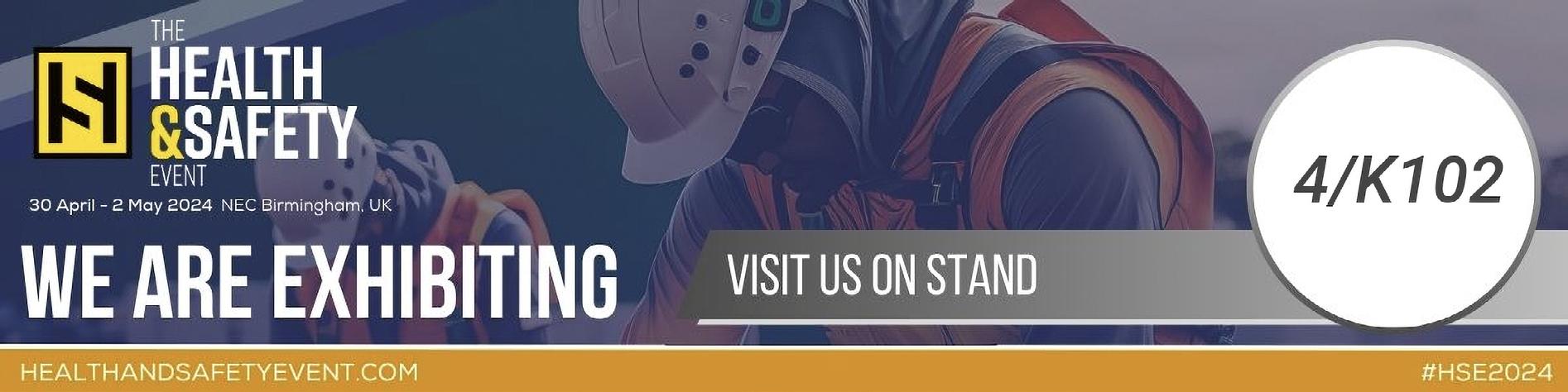
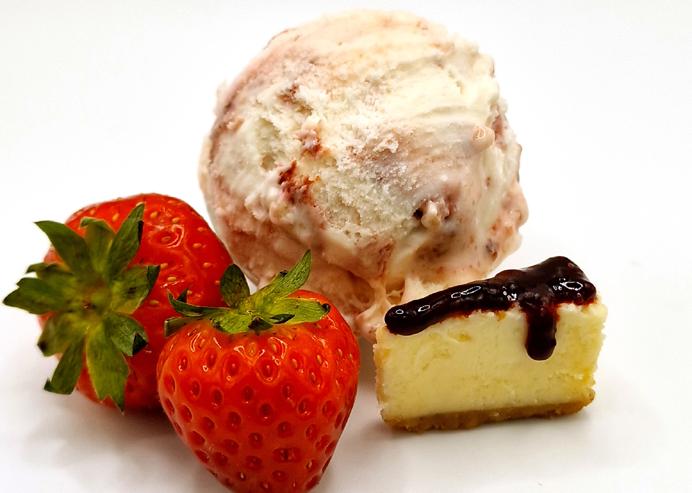

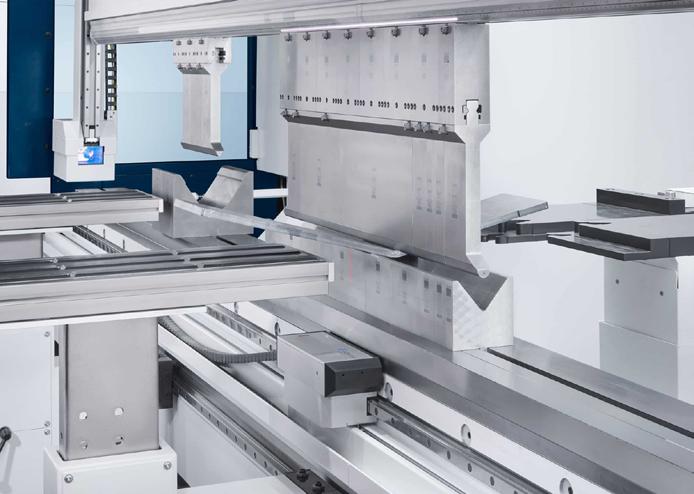

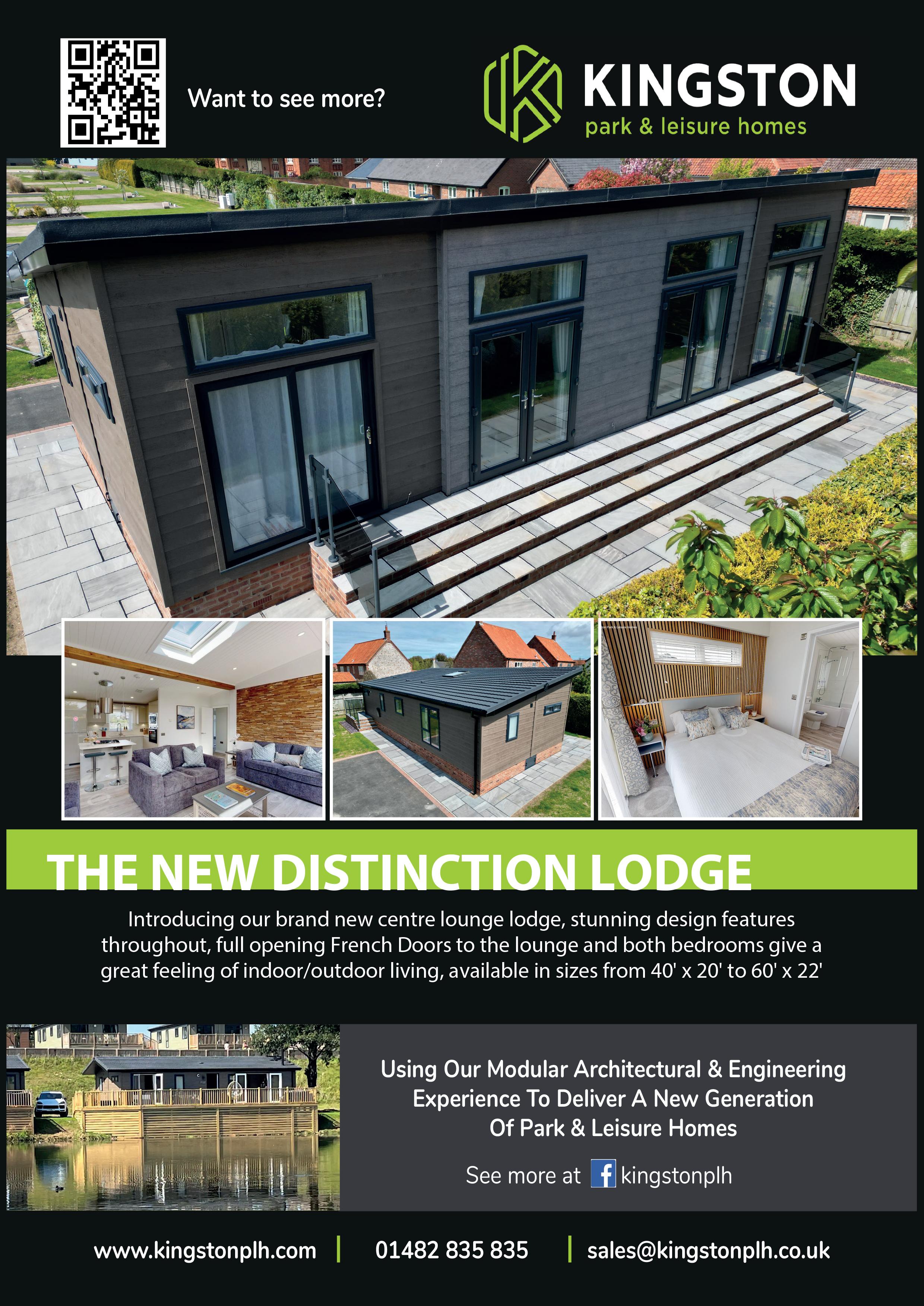
This month we continue to delve into the ever-evolving landscape of business and industry.
From gourmet delicacies to trending food and beverage concepts, we review The Leisure Food & Beverage Expo that was held at Birmingham’s NEC from the 6-7 of November 2023 alongside the Family Attraction Expo that showcased the latest innovations and trends in family entertainment.
Food enthusiasts and industry professionals marvelled at the number of diverse cuisines, artisanal food products and innovative beverages the show had to offer. Attendees were treated to a sensory journey being able to taste, sample, and discover an abundance of new flavours and gastronomic experiences.
Some of our best exhibitors from last year’s Leisure Food & Beverage Expo and Family Attraction Expo events include: Ariela’s
Gelato, Complete Weed Control, ICE Trikes, Ribble Valley Crafted & Sandpit Creations.
We also feature a great article that dives into the latest policies that cover driving safely for work. On pages 12-13, Driving for Better Business has provided some brilliant insight and information around its Driving for Work Policy Builder and access to a Driving for Work Policy Template that ensures you meet the required legal and compliance standards.
Other topics covered in this issue: Health & Safety, Warehouse & Logistics, Innovation & Business, Print & Packaging, Cleaning & Hygiene, Industrial & Machining.
Don’t forget to send us your latest Business, Industry and Sustainable news and updates and email us at: info@businessandindustrytoday.co.uk
Business Innovation 4-5
The Farm Business Innovation Show in November 2023 was a whirlwind of fresh ideas and inspiring conversations!
Ariela’s Gelato is committed to wholesale and supplying the hospitality industry with the best Gelato available on the market.
Fleetmaxx Solutions, a leading fuel and fleet cost reduction specialist, is thrilled to announce its strategic partnership with Artura Consultancy and Agile Developments.
Soyang Hardware displays leading print solutions at newly upgraded Cambridgeshire showroom.
10
12-13
Have you got a policy that covers driving safely for work? And if you do, are you confident that it’s good enough – that it meets legal requirements? And that it’s up to date?
Charles Day Steels increases sheet metal bending capacity with new machine investment.
BAIT Sales Manager, Harriet Parfitt – 0121 550 7510 harrietparfitt@businessandindustrytoday.co.uk
Editorial, Gina Burton – 07483 931474 – gina@businessandindustrytoday.co.uk
Production Manager, Robert Sharp – production@businessandindustrytoday.co.uk Accounts Department, Paul Whitaker – 0121 824 4742 accounts@businessandindustrytoday.co.uk
For more information or format requirements, see our Media Pack
The entire content of this publication is advertorial based. To place an advertorial or an advert, please call 0121 550 7510.
Farm Business Innovation 2023, held at Birmingham’s NEC from 6-7 November, brought visitors an incredible two days full of unmissable insights into the latest revolutionary products transforming the industry.
Farm Business Innovation is Europe’s largest event for farmers, country house estates, and landowners who are forward-thinking and looking to diversify into the leisure, hospitality and tourism industries. Co-located with 3 other shows, especially Holiday Park & Resort Innovation, which is also covered in this review.
66% of all farm businesses in England also run other enterprises – such as farm shops, wedding venues and B&Bs – generating an income of £680 million in 2017-18, to the UK economy. The event was specifically designed to
enable visitors to meet the faces of the industry, with 1,000 leading exhibitors ensuring visitors were able to try, touch and test all of the latest products, solutions, and systems from across the globe that are driving innovation.
Plus an incredible line-up of speakers allowed visitors to choose from over 500 seminars, where key individuals and experts in their field shared their insights and expertise, & divulged their own secrets to success, enabling visitors to return to their own business armed with ambition & brimming with ideas and inspiration.
In an exciting development that mirrors the ever-evolving landscape of the industries, the organisers are thrilled to announce the rebranding of these premier events – Farm Business Innovation, Holiday Park and Resort Innovation, Family Attraction Expo and Leisure Food and Beverage Expo – as the Land, Leisure and Tourism Show (LLTS).
The organisers want to assure exhibitors, attendees and partners that this exciting rebranding journey does not signal the end of Farm Business Innovation, Holiday Park and Resort Innovation, Family Attraction Expo, or Leisure Food and Beverage Expo. Instead, they’re embracing a new and dynamic way of bringing these
Established in 1903, Walter Geering stands as the UK’s leading manufacturer of luxury eco-friendly toiletries and welcome packs for the hospitality industry. At the forefront of innovation, Walter Geering unveiled ground-breaking, industry-altering, products at the 2023 Holiday Park Show, revolutionising the industry with 100% plastic-free welcome packs tailored for holiday park operators and accommodation providers.
Committed to empowering partners to establish new standards in guest satisfaction and environmental stewardship, Walter Geering offers exclusive access to a range of cutting-edge products.
These innovations not only elevate the overall guest experience but also cater to the surging demand for sustainable solutions within the hospitality sector.
With a legacy spanning over a century, Walter Geering epitomises excellence in crafting ecoconscious amenities that align with modern consumer values. By prioritising sustainability without compromising quality, Walter Geering remains steadfast in its dedication to driving positive change within the hospitality landscape.
From luxurious toiletries to meticulously curated welcome packs, each product reflects Walter Geering’s unwavering commitment to both guest satisfaction and environmental responsibility. As industry pioneers, Walter Geering continues to inspire and lead the way towards a more sustainable future for hospitality providers worldwide.
T 01233 658085
sales@waltergeering.co.uk www.waltergeering.co.uk
cherished events together under the Land, Leisure, and Tourism Show.
The commitment to these existing zones remains unwavering. They will continue to thrive and evolve within LLTS, offering dedicated spaces for farmers & landowners, holiday park owners, family attraction creators and culinary enthusiasts. This consolidation ensures that each sector retains its unique identity & focuses on the specialised knowledge and networking opportunities visitors have come to expect.
The newly rebranded Land, Leisure and Tourism show returns to Birmingham’s NEC from 6-7 November 2024. This is our pick of the best exhibitors from last year’s events, listed here in alphabetical order: Natural Habitat Bank & Walter Geering. Further details can be found on this page and the next.
www.lltshow.com
The Farm Business Innovation Show in November 2023 was a whirlwind of fresh ideas and inspiring conversations! At Natural Habitat Bank, we were thrilled to connect with so many passionate farmers and landowners eager to explore new ways to manage their land for both environmental benefit and financial gain.
For us, the highlight was the opportunity to discuss Biodiversity Net Gain (BNG) with a receptive audience. We met numerous landowners interested in allocating portions of their land for habitat creation, not only contributing to crucial biodiversity gains but also unlocking new income streams through participation in BNG projects. Our team enjoyed sharing their expertise on how Natural Habitat Bank can be the one-stop shop for landowners interested in BNG. We offer comprehensive support, from initial feasibility studies and habitat design to ongoing management and monitoring, ensuring successful BNG projects that benefit nature and the landowner's bottom line.
Beyond our specific focus, the entire Farm Business Innovation Show buzzed with
excitement. The energy from the diverse range of exhibitors showcasing innovative solutions was truly inspiring. From sustainable farming technologies to cutting-edge machinery, it was clear that the future of agriculture is bright and brimming with possibilities. We were proud to be part of such a forward-thinking event, where the focus lies on building a more sustainable and prosperous future for the farming industry.
Since the show, things haven’t slowed down one bit! We've been busy bootson-the-ground, creating diverse habitats across the country. We’re also actively engaging with local councils and developers, showcasing the value proposition of BNG units. The response has been incredibly positive, and we’re thrilled to be contributing to a nationwide shift towards a more biodiverse landscape.
Natural Habitat Bank stands at the intersection of environmental responsibility and economic opportunity for landowners. We look forward to fostering even more connections and collaborations as we continue to work towards a healthier planet – one thriving habitat at a time.
If you’re a landowner interested in exploring BNG opportunities, or simply want to learn more about how Natural Habitat Bank can help you create a positive environmental impact, get in touch today at: kate@naturalhabitatbank.co.uk
The Leisure Food & Beverage Expo, held at Birmingham’s NEC from 6-7 November 2023 alongside other co-related events, delivered a tantalising array of culinary delights. Visitors could explore diverse cuisines, artisanal food products, and innovative beverages, making it a haven for food enthusiasts and industry professionals alike. From gourmet delicacies to trending food and beverage concepts, this Expo offered a sensory journey for attendees to taste, sample, and discover new flavours and gastronomic experiences.
The Family Attraction Expo offered a comprehensive display of the latest innovations and trends in family entertainment. From thrilling rides to immersive experiences, attendees had the opportunity to explore a diverse range of attractions that are sure to captivate visitors of all ages. Whether you’re seeking adrenaline-pumping
adventures or interactive exhibits, this zone was a hub of creativity and excitement, providing valuable insights into the future of family attractions and entertainment.
The Expos served as a networking hub for industry professionals, providing a platform to connect with key players in the food & beverage and family entertainment sectors. From amusement park operators to suppliers of cutting-edge beverages, attendees could engage in meaningful conversations, exchange ideas, and forge valuable partnerships.
Show
The organisers want to assure exhibitors, attendees and partners that this exciting rebranding journey does not signal the end of Farm Business Innovation, Holiday Park and Resort Innovation, Family Attraction Expo, or Leisure Food and Beverage Expo. Instead, they’re embracing a new and dynamic way of bringing these cherished events together under the Land, Leisure, and Tourism Show.
In an exciting development that mirrors the ever-evolving landscape of the industries, the organisers are thrilled to announce the rebranding of these premier events – Farm Business Innovation, Holiday Park and Resort Innovation, Family Attraction Expo and Leisure Food and Beverage Expo – as the Land, Leisure and Tourism
The commitment to these existing zones remains unwavering. They will continue to thrive and evolve within LLTS, offering dedicated spaces for farmers and landowners, holiday park owners, family attraction creators and culinary enthusiasts. This consolidation ensures that each sector retains its unique identity and focuses on the specialised knowledge and networking opportunities visitors have come to expect.
The newly rebranded Land, Leisure and Tourism show returns to Birmingham’s NEC from 6-7 November 2024. This is our pick of the best exhibitors from last year’s Leisure Food & Beverage Expo and Family Attraction Expo events, listed here in alphabetical order: Ariela’s Gelato, Complete Weed Control, ICE Trikes, Ribble Valley Crafted & Sandpit Creations. Further details can be found on this page and the next.
www.lltshow.com
Ribble Valley Crafted (RVC) is located in the heart of Ribble Valley. We specialise in handcrafting durable and stylish seating solutions for a variety of commercial settings, from pubs and bars to restaurants, holiday parks, leisure venues, and commercial building projects.
Our journey of excellence took a significant stride when we showcased our craftsmanship at the 2023 NEC Autumn Fair. Since then, we’ve embarked on many diverse projects, from outfitting local pubs with our standard benches to our latest endeavour: a unique challenge faced by a pub landlord in Barrowford, Lancashire (see pictures). Troubled by the inadequacy of his current benches, which often caused customers’ drinks to slide and fall due to the uneven terrain, the landlord sought a solution that would enhance both safety and comfort for his patrons.
listed building set on a slope with traditional English cobblestones, we rose to the occasion. Head Engineer, Mark Robinson, personally surveyed the site and recognised the need for a bench solution that not only provided stability on uneven terrain but also enhanced the outdoor dining experience.
Challenged by the unique architecture of a Grade 2
Through meticulous measurements and inventive engineering, we crafted a multi-level sloping bench that challenged traditional design norms. Our powdercoated steel frames, boasting a 180-micron thick layer, promise durability surpassing industry benchmarks. By sourcing materials locally and adhering to BS EN 581-1:2017 certification, we surpass health and safety standards, ensuring an environmentally responsible product of superior quality. Moreover, our steel frames are engineered to endure up to 40 years, supported by a 5 year guarantee and come accompanied by touchup kits for hassle-free maintenance.
The meticulous craftsmanship is evident in every detail of our benches, with the wood expertly coated three times in premium wood stain to repel rainwater effortlessly. These benches are meticulously designed
to endure the elements, demanding minimal upkeep while guaranteeing longevity, even in the most unforgiving weather conditions.
The outcome? An exquisite bench that effortlessly harmonises with its historic environment, blending functionality with aesthetic charm. It’s more than just a piece of furniture; it’s a testament to our steadfast dedication to excellence, innovation, and customer delight.
At Ribble Valley Crafted, we don’t just create furniture; we craft experiences. Join us in redefining commercial seating solutions, one bench at a time.
T 01282 792674
M 07731 379661
www.ribblevalleycrafted.co.uk
www.facebook.com/ribblevalleycrafted www.instagram.com/ribblevalleycrafted
Sandpit Creations is an award-nominated creative workshop based in London, with a mission to create innovative sets, props, and experiences that both engage audiences and are built to withstand interaction.
Sandpit Creations works with a small but widely skilled group of individuals, bringing together carpenters, creative and concept designers, scenic artists, textiles specialists, creative technologists, prop makers, sculptors, and metalworkers as well as writers, directors and performers. Bringing these skills together under one roof ensures seamless communication and collaboration between each element of a project.
They have experience in a range of modern and traditional fabrication techniques including joinery, fibreglassing, textural effects, microelectronics, and robotics. They are also passionate about the latest developments in technology to deliver cutting edge special effects and interactive experiences.
Sandpit Creations launched in January 2023, and are proud to have worked with end clients including Samsung, Doc Martens, Aardman, Cupra, Kew Gardens and Wakehurst. They have ongoing projects with some of the UK’s foremost museums and attractions. They also work with many theatre and immersive companies to develop and build sets, props, costume pieces and even full show concepts.
Contact M 07547 352391 info@sandpitcreations.com www.sandpitcreations.com
Ariela’s Gelato is committed to wholesale and supplying the hospitality industry with the best Gelato available on the market.
From classic flavours to exotic creations bursting with fresh fruits and artisanal ingredients, Ariela’s Gelato promises a flavour adventure like no other.
Exploring the weird and wonderful, Ariela’s Gelato pushes the boundaries of ‘normal’ to the extreme. Think Black Forest Gateaux, Peanutella, Dulche de Leche (Argentinian Toffee), Cherry Bakewell, Avocado Sorbet, Eton Mess and Apple Crumble to name a few!
The company is also expanding its vegan friendly range to include a brand-new series of oat drinkbased Gelatos – guaranteed to be truly unique with no compromise on flavour.
Its artisan Gelato, Sorbet and Vegan Alternatives have been on the receiving end of numerous ‘Great Taste’ awards and are stocked by hundreds of stores across the UK.
Here to support you, Ariela’s Gelato also supply an extensive range of the highest quality waffle cones, cups, spoons, disposables and POS material to allow its customers to sell the best Gelato in the best way possible, ensuring you make the best margins. And, if that isn’t enough, they also provide ongoing support from the start, helping with layout decisions, finding the best equipment to suit your individual needs, menu design, and most importantly in-depth training on all things concerning the sale of Gelato.
If you’re interested in joining their list of stockists, see below.
T 020 8803 5344
info@arielasgelato.com https://arielasgelato.com/
First trading in 1972, Complete Weed Control is the longest established amenity weed control company in the UK and Ireland. We provide specialist services to a diverse range of clients and deliver to the highest standards through our local teams, utilising the most up-to-date equipment and technology.
Our services:
● Weed control
● Invasive plants
● Moss and algae
● Pests and diseases
● Aquatic weeds
● Grounds maintenance
● Baseguard urban tree protection
● Tree surgery
● Fine turf
● Winter maintenance
ICE Trikes are one of the most comfortable ways to cycle. They’re fun, stable and perfect for accessible cycling. Enjoy a relaxed countryside ride or the thrill of a sporty cycle through forest trails. ICE Trikes have accessible seating positions, easy to use controls, great looks with rugged ride capabilities. Cruise the open road and discover hidden trails. Trikes are super easy to ride with the rider needing no cycling experience.
From its headquarters in Falmouth, ICE makes 6 different models. The ICE VTX is one of the fastest trikes in the world, ridden by performance cyclists it even holds World Records. The Sprint X is a sports tourer that folds for easy transporting. The Sprint X Tour is built for comfortable touring
● Site cleaning
● Landscaping
Advanced technology, meeting the demands of today’s environmental targets.
Complete Weed Control has established WEEDit as the most advanced application equipment currently available for weed control on pavements and hard surfaces.
As used in the Cardiff Weed Trials, WEEDit is the most environmentally efficient method of weed control, with a typical herbicide reduction up to 80%.
T 0800 954 9679
info@completeweedcontrol.com www.completeweedcontrol.com
and is available with electric motors and fully automatic gearing. The Adventure range is ideal for accessible cycling with a more upright seating position. The ICE Full Fat is the off-road trike originally built to cycle to the South Pole.
Trikes are ideal for people with balance issues, disabilities, rehabilitation, mental health, fitness or simply cycling with friends and family.
ICE Trikes is an official partner to the British Cycling Limitless Cycling Programme. ICE has a network of UK dealers where you can try and buy. Visit: www.icetrikes.co for more details.
Fleetmaxx Solutions, a leading fuel and fleet cost reduction specialist, is thrilled to announce its strategic partnership with Artura Consultancy and Agile Developments. This collaboration aims to revolutionise fleet insurance claims processing with the introduction of the Fleetmaxx Vehicle Insurance Claims App.
The Fleetmaxx Vehicle Insurance Claims App, developed by Agile Developments Group in partnership with Artura Consultancy and Fleetmaxx Solutions, is set to transform the way fleets manage accident claims. This innovative app streamlines the claims process, offering step-by-step guidance to fleet managers and drivers, ensuring accurate and efficient reporting of accidents or incidents. By facilitating
swift capture of relevant claims data and vehicle damage assessment, the app expedites the claims process, reducing repair duration and claims settlement time.
In addition to simplifying claims processing, Fleetmaxx Solutions is delighted to offer an exclusive incentive to its customers. Fleetmaxx customers utilising the Claims App will receive £100 toward their insurance excess when making a claim through the app, further enhancing the value proposition for fleet operators.
Furthermore, Fleetmaxx Solutions extends special deals on fuel cards, AdBlue, and vehicle tracking to Artura Group (Braintree Motor Works, Braintree Insurance Services and Evolution Repair Group customers), enabling them to control and cut their vehicle running costs and enhance operational efficiency.
Businesses can download and register for the app here: www. fleetmaxxsolutions.co.uk/services/ vehicle-claims-app/ or by visiting the Fleetmaxx Vehicle Insurance App web page.
At Volkmann, ideas are born that find a home with customers all over the world. These ideas can benefit an individual customer application or can improve the general process solutions we offer.
Volkmann, engineers and manufactures high-quality, highperformance pneumatic conveying systems including pneumatic vacuum conveyors, additive manufacturing material handling systems, bulk bag unloaders, rip and tip stations, hoists, delumpers, dust collection systems, and weighing and dosing systems to offer a complete, fully contained powder handling system for the safe material transfer of fine chemicals, granules, pellets, tablets and small components. Volkmann systems are particularly well-suited to dust-tight, segregation-free and damage-free powder handling under vacuum. With features such as ‘No-Tools’ disassembly and easy cleaning, as well as designs conforming to cGMP standards, air-driven Multijector® vacuum generation and ATEX certification for explosionproof applications – it’s no wonder Volkmann is leading the industry with powder and granule pneumatic
conveying solutions.
The developments of our team are versatile and ingenious. As a partner in the process, we take on responsibility for the success, the safety, and the reliability of the final solution. Volkmann supports customers in solving their conveying tasks, from the idea right up to the finished plant. This is our strength.
T 01494 512228
https://uk.volkmann.info
Gransden UK, formally known as Lock N Pop UK Ltd, is the sole UK and Ireland distributor of the Lock N Pop pallet stabilisation systems, primarily known for reducing plastic pallet wrap and enhancing pallet stabilisation. The UK based company has been supplying the Lock N Pop solution to customers across the industrial and food and beverage applications for over 25 years.
Director, Duncan Potter, said, “We specialise in the Lock N Pop technology which is a water-based cohesive used for pallet stabilisation, applied on the production line prior to goods palletisation. We provide everything: machines, cohesive and fullservice support, with service engineers stationed around the country.”
“We are always interested in talking to customers using robotic or automatic layer palletisation at the end of production processes. Our solution works well with boxes, shrink wrap packs or sacks. We specialise in all products but have seen a real
increase in the last 18 months from customers palletising bagged products, often animal feed, chemical or industrial products such as cement bags.”
With the UK Government’s 2050 net-zero targets and a greater push towards the circular economy, all eyes are on sustainable best practices.
With this in mind, Lock N Pop is seen as the sustainable solution of choice across the industry for the following reasons:
● Lock N Pop reduces the need for plastic pallet wrap
● Cost-effective under the new UK Plastic Tax (Plastic Packaging Tax PPT): introduced in April 2022
● The definitive environmentally-friendly solution: cold, water-based and plastic-free
● Contains no hazardous, heated components or plastic consumables.
The Lock N Pop pallet stabilisation solution simply saves money by removing the costs associated with
palletised goods moving or collapsing in transit to endcustomers. The primary focus on streamlined production process efficiency and the end transit journey to high street shelf, distribution centre or even across international waters or airspace has been paramount and has afforded Lock N Pop gold-standard industry recognition.
Lock N Pop pallet stabilisation uses a cold, water based cohesive, that is carefully applied inline to the cases, bags, shrink-wrap trays etc. immediately before palletisation. The cohesive has high shear strength characteristics which binds the products together, resulting in a stable pallet. However, the additional bonus is that the cohesive combines this high shear strength with a low tensile strength, meaning that the items can easily be separated.
For more information, contact Gransden UK Ltd: T 01728 726621 M 07516 683314
locknpop@gransden.org www.locknpop.co.uk
Open now, the facility is based at the former Josero site in Swavesey, just 20 minutes from central Cambridge.
The showroom allows visitors to view live demonstrations of some of the market-leading hardware solutions available from Soyang.
Soyang Hardware, a leading supplier of wide- and superwide-format print production hardware solutions from many of the industry’s biggest and best-known printer brands, is delighted to announce the opening of its refurbished showroom in Cambridgeshire.
Open now, the facility is based at the former Josero site in Swavesey, just 20 minutes from central Cambridge. The showroom allows visitors to view live demonstrations of some of the marketleading hardware solutions available from Soyang.
Stand-out attractions at the revitalised and upgraded showroom include the Fujifilm Acuity Prime Hybrid LED UV machine that is capable of both rigid and roll-to-roll printing. Offering a top speed of 141m2/hr in roll-to-roll mode, the printer can handle media up to 51mm thick and offers printing across seven channels – CMYK+W+CI – plus primer.
Also being showcased at the Cambridge showroom is the Ricoh Pro Latex L5160e, offering a top printing speed of 46.7m2/hr. Featuring three staggered Ricoh print heads, it has an auto cleaning function to enable maximum uptime.
Additionally, visitors can view live demonstrations of several Mimaki wide format printers. A global brand widely renowned for its cutting-edge technology and high-quality products, Mimaki manufactures innovative, reliable and versatile print solutions which consistently produce excellent quality output.
The KeenCut Steeltrak is also on show, allowing visitors to see it up close and find out more about how it can support them with a range of applications.
In addition to live machinery demonstrations, visitors can speak with knowledgeable experts from the Soyang team about how the technology on display and other solutions from the expert supplier can help their businesses grow.
“We’re delighted to be opening another specialist showroom, allowing visitors from the south of the UK and further afield to find out more about our leading range of hardware solutions and how they can support their businesses moving forward,”
Sarah Fenna, Sales Director (Hardware Division) at Soyang said.
“While we are always happy to speak with visitors over the phone about our portfolio of machines, nothing quite beats seeing the technology in action. The upgraded showroom allows new and existing customers to get up close with some of our most popular solutions.”
The Cambridgeshire facility is in addition to Soyang’s existing showroom in Accrington which was opened in March 2023. Based at Soyang Europe’s headquarters, the Lancashire site houses a range of printing equipment, sewing machinery, flatbed printers, reel-fed printers, routers and cutters, all of which are available for live demonstrations.
Soyang runs its wide range of specialist materials on all the printers in-house, allowing visitors to see for themselves the quality of these solutions and how they perform in a print house environment.
To book an appointment at either of Soyang’s showrooms, please click here & select the ‘Book a Demo’ tab, or email: hardware@soyang.co.uk
Sustainability Today is always looking to champion the intersection of business and sustainability.
2024 will inevitably see a continued rise in the need for EV charger systems as there is now a real impetus for drivers to switch to cleaner vehicles, with the impending 2035 ban on the sale of new petrol or diesel cars. There has been steady growth, with an estimated 1.02 million zero-emission electric vehicles (cars) on UK’s roads today, alongside 615,000 plug-in hybrids.
On page 9, we feature Charles Endirect as our EV Charger Systems Supplier Company of the Month. In this article, we shine a spotlight on the company and the powerful role it has working within the EV power distribution sector.
On page 8, we feature an article on Kadaant PAAL Ltd that unveils its latest and exclusive Dicom Connect client platform that is now available to
customers new and old. Dicom Connect is the client platform where operators can navigate a dashboard to use key features to produce operational information for management and operational performance within their facility. Features such as live performance status, multiple device type access, managing user groups and notification subjects are just a few examples of how Dicom Connect will be an asset to your operation.
We also feature a preview of Hillhead 2024 on pages 12-16.
Other topics covered in this issue: Recycling & Waste Management, Greenbuild, Quality Air Monitoring, Water Management, Sustainable Farming & Agriculture, Heating, Ventilation & Air Conditioning.
Don’t forget to send us your latest Business, Industry and Sustainable news and updates and email us at: info@sustainabilitytoday.co.uk
SUS Sales Manager, Jess Machin – 0121 550 7510 jessmachin@sustainabilitytoday.co.uk
Editorial, Gina Burton – 07483 931474 – gina@businessandindustrytoday.co.uk
Production Manager, Robert Sharp – production@businessandindustrytoday.co.uk Accounts Department, Paul Whitaker – 0121 824 4742 accounts@businessandindustrytoday.co.uk
For more information or format requirements, see our Media Pack
The entire content of this publication is advertorial based. To place an advertorial or an advert, please call 0121 550 7510.
The presence of mercury in flat panel displays (FPDs), such as laptop monitors and LCD TVs, has brought into focus prospective health and safety issues.
Correctly designed and manufactured electrical distribution cabinets are an integral aspect of the EV charging infrastructure,
So why is addressing water heating in commercial buildings so significant? And how can it serve as a springboard for launching a sustainable strategy to more broadly support commercial organisations?
The next edition of the iconic quarrying, construction and recycling exhibition will take place from 25-27 June 2024 at Hillhead Quarry, Buxton.
Bluewater calls for global action on PFAS contamination on World Water Day 2024,
says manufacturers should assume full responsibility and halt production.
Agricarbon is a marketleading provider of soil carbon measurement at scale, serving all soil types across the UK and across Europe for farmers, landowners and businesses.
Sustainability Today is sponsored by Apex Pumps – see them on page V
The majority of Smart heating systems now turn ‘on or off’ but imagine if you could heat just one room or specific zones remotely using smart devices? This would allow business establishments or educational facilities to save 20-50% on energy bills and reduce carbon footprint. It’s a win-win situation.
EcoSync is a pioneer in heating management for commercial buildings and multi-occupancy residences, thanks to its innovative Smart Thermostatic Radiator Valves (TRVs). With a growing portfolio to date, of over 42 customers and more than 140 buildings across the UK, EcoSync has been instrumental in saving more than 1.565 MWH of energy and slashing carbon emissions by over 285 tonnes.
These next-generational TRVs, free from the constraints of batteries and maintenance, offer seamless installation and operation, making them an ideal heating solution for commercial buildings looking to optimise energy use and reduce waste. EcoSync's technology directly addresses the significant issue of heating energy wastage in unoccupied rooms, which can account for up to 40% of energy consumption in such spaces. By enabling precise heating control on a roomby-room basis, EcoSync's TRVs ensure energy savings of 25-50% for clients, showcasing their effectiveness as a heating solution.
EcoSync caters to the specific needs of Facilities and Utilities Managers, Energy Managers, Public Sector organisations, and Senior Buyers in the commercial sector who are focused on achieving low carbon, Net Zero, and energy efficiency goals. The addition of an AI-powered dashboard, in-room QR codes, a carbon meter, and room booking system integration enriches EcoSync's offering, making it a comprehensive energy management and heating solution for commercial and multioccupancy buildings.
The benefits of adopting EcoSync's TRVs as a heating solution over traditional, batterydependent systems are clear. Conventional systems require ongoing maintenance and regular battery replacements, which can be particularly burdensome in large commercial or multi-occupancy buildings. EcoSync’s TRVs eliminate these challenges, boasting an installation time of under a minute and zero maintenance requirements.
EcoSync provides high-quality data for ESG reporting, analysing buildings and identifying areas with higher-than-average heat loss.
EcoSync provides a multi-award-winning Smart Temperature Control System from the great minds at Oxford University. Established in 2018 by two entrepreneurial academics: Dr Zsuzsa Mayer and Yoav Gross, EcoSync is an active member of UKGBC and the Energy Managers Association. For two consecutive years: 2022 and 2023, the team has won the prestigious Property Week Student Accommodation, as part of the Climate Crisis Initiative together with Corpus Christi College of Oxford.
Dr Zsuzsa has a Ph.D. in Renewable Fuels & Bioenergy from Aston University of Birmingham and Yoav has a Master’s in Environmental Change and Management from the University of Oxford. Using exceptional R&D, they have devised a system that can reduce heating-related carbon emissions and energy bills by up to 50%.
“The demand-side control doesn’t rely on sensors,
instead the patented technology inputs QR codes scanned by users when leaving a room empty. The controller is intrinsically part of an intelligent IoT device, negating the use of wires or batteries due to the built-in energy harvesting feature.
By using LoRaWAN: our commercial communication technology, the data is collected to create the digital twins of the buildings that can be used for metering (real-time consumption and savings) or running various models - how would the building and the individual rooms behave with a heat pump instead of a gas boiler etc.
Furthermore, our 2nd generation is a plug-andplay technology that can be retrofitted by the client with minimal training requirements. It costs a fraction of the traditional building management systems (BMS) plus it can adapt to the dynamically changing occupancy levels,” explained founder and now Chief Innovation Officer: Dr Zsuzsa Mayer.
EcoSync has gone further than other Smart Temperature Control Systems: on top of AIpowered optimisation and control, it can collect data to support other building retrofitting projects such as monitoring the payback of installed doubleglazing. With the onus on the UK Government's 2050 net-zero targets, many businesses are looking to strengthen their Environmental, Social and Governance (ESG) policies.
“Going forward, we would like to support our clients not only with the energy efficiency improvement of their buildings but also with their next big challenge: decarbonising the grid, which mainly means replacing gas boilers with heat pumps. We would like to design a service that can provide data both at the planning stage and later for optimising the performance of their heat pumps.” explained Dr Zsuzsa.
Heat pumps are hugely energy-efficient as they produce more heat than they consume (supplementary) electricity and are rapidly becoming the cheapest, lowest carbon form of heating available. The UK Government has pledged to install 600,000 heat pumps by 2028, as part of the Energy Security Bill.
The UK is still playing catch-up with the rest of the EU, notably Norway, Sweden, Finland and Estonia for heat pump adoption rates but with reduced North Sea gas production, the UK is now urgently committed to futureproofing its energy security through renewable energy. Between 2021-2022 alone, the sale of heat pumps increased by 40% and the facts speak for themselves: more than 80% of global space and water heating demand could be met by using heat pumps instead of gas boilers, with significantly reduced carbon emissions. Buildings alone contribute to more than 40% of energy used, which equates to over a third of global emissions and with the real threat of climate change, reducing energy use and emissions is now a global priority.
“We are committed to meeting the real needs of climate change and fully understand that our clients need high quality data for their ESG reporting purposes and we can provide that. Moreover, it works in those commercial buildings where there is no budget for a BMS but data is needed for investment purposes.
“The launch day marked not just a milestone but served as a clarion call for the Commercial Real Estate sector to accelerate its journey towards Net Zero. The UKGBC's dedication to transforming the built environment through practical strategies, including optimisation, CAPEX-light, and significant investments in retrofitting, is truly inspiring. It's evident that the path to net zero is paved with innovation, collaboration, and actionable insights.
We are currently working extensively with boarding schools, higher education and PBSAs (purposebuilt student accommodation) providers, to provide our Smart Temperature Control System. This not only reduces energy bills in a cost-of-living crisis but wholeheartedly commits to ESOS compliance and substantially less carbon emissions, allowing companies to exercise sustainability best practices.” added Dr Zsuzsa.
EcoSync is helping businesses join the green agenda and was recently delighted to attend the Advancing Net Zero hosted by the UK Green Building Council (UKGBC) in March this year.
By focusing on low-cost, high-impact adaptive and intelligent retrofit solutions, we help buildings not just meet, but exceed their sustainability targets.” outlined Simon Brown, Partnership Director.
EcoSync is much more than a provider of smart heating solutions; it is a key stalwart in the path to a sustainable future for commercial buildings and multi-occupancy residences.
For more information about how EcoSync can transform your energy management and heating practices, contact them at: contact@ecosync.energy www.ecosync.energy
The presence of mercury in flat panel displays (FPDs), such as laptop monitors and LCD TVs, has brought into focus prospective health and safety issues when considering the WRAP (The Waste Resources Action Programme) commissioned study into the technical and commercial potential for recycling the items.
The research, which was carried out by environmental consultancy Axion Consulting, aims to help WRAP identify viable recycling outlets. However, due to an increased uptake in items, WRAP anticipates that the number of FPDs in the WEEE waste stream will rise ‘dramatically’ (It is considered that there will over 145,000 tonnes of flat panel displays in the waste stream by 2018) in the next few years bringing pressure to automate suitable commercial recycling processes in the UK and Europe.
In particular the study looked at the presence of mercury in the cold compact fluorescent light in the ‘backlighting’ system for LCD TVs, laptop computers and desktop monitors. The existence of this mercury means that end-of-life FPDs are classed as hazardous waste.
protective equipment and local extract ventilation.
Mercury is extremely toxic, with inhalation of the vapour producing harmful effects on the brain, nervous, digestive and immune systems, lungs and kidneys. Mercury poisoning can result in several diseases,
and duration of exposure.
Humans are mainly exposed by inhaling vapours. These are absorbed into the body via the lungs and move easily from the bloodstream into the brain. However, when elemental mercury is ingested, little is absorbed into the body.
The conclusion of the WRAP study highlighted that employees at an FPD recycling facility would be subjected to levels of mercury ‘higher than is acceptable’. However, it suggested that this could be reduced with personal
Hunter-
Russell syndrome, and Minamata disease. Symptoms typically include sensory impairment (vision, hearing, and speech), disturbed sensation and a lack of coordination. The type and degree of symptoms exhibited depend upon the individual toxin, the dose, and the method
ABLE’s Jerome J405 gold film Mercury vapour analyser delivers highly accurate, repeatable and specific measurements, g/m3 Hg. Jerome series analysers are used extensively throughout the electrical waste recycling industry as well as by government agencies and regulatory bodies such as the EA, Natural Resources Wales, SEPA and the HSE.
The Jerome J405 can be utilised for mobile monitoring work and also for fixed-point analysis in key locations. Users typically monitor in key processing areas with personnel access and within extraction systems, to verify filter efficiency. On-board alarms can be configured to Public Health England’s guidelines for air quality, which recommend exposure limits of 1µg/m3.
The Jerome J405 combines the industry proven performance of its predecessor (the Jerome™ 431), with several new features. These include USB connectivity, onboard data logging, extended battery life, a lower detection limit and improved resolution. Its intuitive display and menu system aid operation by personnel with only very minimal training.
Results can be output live to a plant control system and the analyser’s 20,000 data-point storage capacity also provides excellent traceability on results, with time and date stamping.
T 0118 931 1188 info@able.co.uk www.able.co.uk www.247able.com
Impact Air Systems, the world’s leading air-based technology provider for the environmental, waste, recycling, and resource management industry, announces they are to exhibit their innovations at three major tradeshows to cover the USA and Europe – WasteExpo, Las Vegas, May 6-9, IFAT in Munich, May 13-17 and RWM in Birmingham 11-12 September 2024.
“We are excited to formerly announce our latest innovations at these key industry events. Impact strives to be at the cutting edge of technology to offer solutions built for the industry. The promotion of resource recovery and the circular economy is a common theme across all our innovations this year with our Airlift and Zigzag Air Classifier (ZAC) solutions at the forefront, which enables waste operators to effectively recover materials such as flexible plastic packaging, glass, and aggregates, with a remarkably high success rate.” – Nick Ball, Impact’s Managing Director.
Impact Air Systems pride themselves on their British engineering roots along with innovative air system design applied to solutions to separate materials, which catapulted
them into the recycling equipment market back in the early 1990s. Many years of working with industry professionals and listening to their issues with regards to separating waste to recover valuable materials, has resulted in Impact’s catalogue of impressive solutions which add value while easing the pressure to produce quality material streams.
After conquering the UK market, Impact’s solutions were noticed, and are now in high demand, by US waste operators for their distinctive ability to separate material effectively and efficiently, while being engineered to an exceptionally high standard, providing minimal maintenance and downtime.
Find out more at: www. impactairsystems.com or contact the team on (619) 642-8649 or email: sales@impactairsystems.com
We are now ready, after comprehensive in place testing, to unveil and launch our exclusive Dicom Connect client platform to all our customers new and old (if their existing Dicom equipment is fitted with RMS and they would like to upgrade the equipment as an optional extra). This system links to our already proven Remote Monitoring System (RMS). It is crucial that you can make quicker and more informed costeffective decisions regarding your business operation and make the most of your investment in equipment.
Here at Kadant PAAL we understand this and can make the changes you need to operate your compaction and baling equipment effectively. One of the many benefits of having the Dicom Connect on compaction equipment at source is that it will communicate directly with the client’s waste management services. This becomes efficient and effective practice on both sides in terms of transport only being despatched for full load collections and less charges being made to the source for part loads being collected, Sustainability being increased, and environmental impact being reduced.
We have been operating our RMS since Q1 2016 which has been very popular with our clients. For those not already aware the RMS allows Kadant PAAL to dial into our client’s machinery for diagnostics and managing factory settings to suit individual operational needs. This gives our clients a huge advantage of being able to diagnose and solve any issues by communicating directly with the machine user. Benefits being lower service call out costs and also massively reducing downtime by identifying parts required and enabling our Field Service Engineer to attend site fully equipped if required.
Dicom Connect is the client platform where operators can navigate a dashboard to use key features to produce operational information for management and operational performance within their facility.
This system is available for our range of Dicom Static Compactors, Dicom Portable Compactors and Dicom Vertical Balers allowing high level data to be produced and used within the organisation for optimal performance. Data collection will allow you to follow your waste management performance, enabling you to compare historical with live performance and have a location and status overview. All these factors ensuring you create an efficient, cost-effective facility.
Features such as live performance status, multiple device type access, managing user groups and notification subjects are a few examples of how Dicom Connect will be an asset to your operation. By choosing our product you will be able to access valuable data to maximise your waste management operation.
PH Hull & Sons Recycling Services have played an integral part in the initial testing of the Dicom Connect product. Initially with stringent and comprehensive testing of three Dicom Connect systems supplied for different compaction equipment, PH Hull & Sons put the system through its paces. Proof of the pudding is that now to date
they have 12 installed Dicom Connect systems on compaction equipment that processes different materials such as food waste, ie. vegetable, bread, Category 3 waste and general waste. They regularly share performance read outs from the equipment enabling them to show the high performance they can achieve with this monitoring, reaping benefits for the client and the recycling services alike.
This is what J Brown, Financial Director at PH Hull & Sons Recycling Services, had to say, “Dicom’s telemetry and vast servicing network have allowed our business to become market leading nationally, for Total Waste management services within the food production industry.”
www.dicompaal.com
There is now real impetus for drivers to switch to cleaner vehicles, with the impending 2035 ban on the sale of new petrol or diesel car. There has been steady growth, with an estimated 1.02 million zero-emission electric vehicles (cars) on UK roads today, alongside 615,000 plug-in hybrids.
The number of public charging stations are growing too across workplaces, council-owned car parks, hotels and numerous other places, to keep up with demand.
One of the biggest questions remains though: How do you maintain reliable and ever-increasing charging speeds while keeping the users and installers safe, through adherence to BS7671:2018 amendment 2:2022?
The role of electrical distribution cabinets for EV chargers
Correctly designed and manufactured electrical distribution cabinets are an integral aspect of the EV charging infrastructure, providing optimised safety and reliable electrical connections for EV charging equipment. They are typically configured to provide automatic disconnection of the supply for a given fault condition such as a short circuit, overcurrent, earth fault, and open neutral conductor (O-PEN fault on the incoming supply side cable where PME is used).
Who is a trusted manufacturer/supplier of electrical distribution cabinets to power EV Chargers?
Charles Endirect is a family-based company with an expert history celebrating forty years in the design and manufacture of metal fabrication and electric equipment originally for the street lighting market. Working with the EV power distribution sector is a natural progression for the Company. Founded by
engineer Eric Charles in 1984, the company has built up its strong industry reputation through the recruitment and retention of talented mechanical and electrical engineers.
Eric designed the Central Earth Terminal for use on the construction of the M1 motorway and with an eye on exceeding industry benchmarks, the company has undertaken innovative R&D over the decades.
Eric’s son, Nic Charles, took over the running of the company and after outgrowing its Sherborne premises, the company relocated to Wincanton, Somerset. With fabrication factory and sales and delivery offices all on-site, Charles Endirect prides itself on working with Local Authorities, National Highways and numerous other public and private bodies across the UK and further afield.
Charles Endirect is a founding member of the Highway Electrical Manufacturers & Suppliers Association (HEMSA), prominent existing member of the Highways Electrical Association (HEA.) and are long-standing members of the Institution of Lighting Professionals (ILP).
We spoke to Andrew Jackson, Sales & Marketing Director, for more information, “Our company holds ISO 9001:2015, ISO 14001:2015 and ISO 45001:2018 accreditation and we pride ourselves on delivering products that are market-leading.
“Our pre-wired distribution cabinets for example are designed using cutting-edge OEM equipment, parametric 3D modelling and AutoCAD software. A full range of distribution boards are available in polycarbonate IP65, steel and 304 grade stainless steel.
Over the last five years, the company has seen a surge in demand for EV charging stations and with its reputation for quality products and service in the design and manufacture of metal fabrication and electrical equipment, provides pre-LV Distribution Cabinet solutions to meet that demand.
Expert guidance and distribution for EV charging
The Somerset-based company provides a wide range of EV charging solutions, from the slow (nonrapid) 3kW to the Ultra-rapid DC 350kW chargers.
The range of feeder pillars and distribution cabinets include the slimline and compact Mini pillar range, Mega pillars, with customised metalwork and build service available beyond standardised models. The cabinets are designed and pre-wired to requested customer specifications and are robustly tested to an internationally recognised standard before dispatching.
Charles Endirect offers a full in-house solutions service from design, manufacture, testing, certification and delivery to customer expectations.
“The MEGA electrical cabinet range, originally launched in 2021 has been purposefully designed for the larger, feeder pillars in the EV supply industry. Cabinets are usually pre-wired providing a ‘fit and forget’ solution for the installer.
“We also offer a range of concealed in-ground pillars, which reduce street clutter and the risk of vandalism. This is perfect for heritage sites such as Piece Hall in Halifax and has also been used in contemporary settings such as the new Tottenham Hotspur football stadium.
“The key components of isolation and earthing remain essential, and so we can share our forty years of expertise in training sessions and presentations to consultants and industry stakeholders on large TEAMS meetings and in faceto-face meetings.”
Charles Endirect will be at: t Passive Safety Conference & Workshop: National Conference Centre, Birmingham. 9th May 2024 t and NRSC2024: Hilton Birmingham Metropole Hotel: 6th-7th November 2024.
For more information, contact the sales teams below: T +44 (0)1963 828400 info@charlesendirect.com www.charlesendirect.com
The importance of launching a sustainable strategy for commercial buildings has never been more important. According to recent data from the EU’s climate service global warming has, for the first time, exceeded 1.5ºC across an entire year. This temperature limit, promised by world leaders in 2015, has been seen as crucial to help avoid the most damaging impacts of global warming. A 2018 UN report said that the risks from climate change – such as intense heatwaves, rising sea levels and loss of wildlife – were much higher at 2ºC of warming than at 1.5ºC.
Limiting long-term warming to 1.5ºC above pre-industrial levels has been a key symbol of international efforts to tackle climate change, and whilst the report notes that this first yearlong breach doesn’t break that landmark Paris Agreement, it does bring the world closer to doing so in the long-term.
All the major datasets agree on the recent warming trajectory and that the world is in by far its warmest period since modern records began –and likely for much longer. Berkeley Earth reported that the calendar year 2023 was more than 1.5ºC above pre-industrial levels. Other science bodies, such as NASA, put the past 12 months slightly below 1.5ºC of warming. Fluctuations in reporting are expected, but at the current rate of emissions, the Paris goal of limiting warming to 1.5ºC as a long-term average – rather than a single year –could be crossed within the next decade.
This new data sends out yet another clarion call to the commercial sector, where sustainability has
become a defining theme for modern businesses increasingly seeking ways to reduce their environmental impact. While numerous avenues exist, prioritising water heating in a commercial sustainability strategy offers unique advantages, making it the optimal starting point for many organisations.
So why is addressing water heating in commercial buildings so significant? And how can it serve as a springboard for launching a sustainable strategy to more broadly support commercial organisations?
Water heating often accounts for a significant portion of a building’s energy consumption, ranging from 15-40% depending on the industry and usage patterns. This makes hot water both familiar and more often than not business critical, so reducing hot water demand and implementing efficient heating methods translates to substantial energy savings and emission reductions that have recognisable advantages to its users across the built estate.
energy demands means initial investment is often quickly recovered. This economic attractiveness makes it a compelling entry point for sustainability efforts.
Addressing water heating can also have wider positive impacts on a business. One area which has seen far greater focus since the COVID-19 outbreak has been improved Indoor Air Quality (IAQ). Renewable water heating solutions such as air source heat pumps and solar thermal as well as electric boilers eliminate the need for combustion processes, reducing harmful emissions and potentially improving air quality for occupants.
Diverse solutions, from upgrading equipment, especially gas-fired to more efficient gas or gridelectric, and utilising renewables such as solar thermal and air source heat pumps can be tailored to various building sizes, budgets, and hot water demands. This scalability makes hot water systems a readily addressable target for sustainability initiatives, with easily quantifiable impact that can be demonstrated to stakeholders. Critically, many water heating efficiency measures offer attractive payback periods, this is especially true of solar thermal where up to 30% offsetting of annual
By demonstrating commitment to sustainability through water heating upgrades, companies not only meet regulatory compliance helping to avoid potential fines or penalties, but can demonstrate active corporate social responsibility which resonates positively with customers, employees, and investors, boosting brand image and reputation. This function of a business is increasingly being recognised, with notable examples of organisations across the leisure and catering markets in particular, embracing a sustainable approach to enhance engagement with customers and define services from competitors. This also resonates with employees, meaning that an initial focus on water heating,
which is both familiar and often business critical can be a starting point for engaging employees in broader sustainability initiatives, fostering a culture of environmental awareness and responsibility.
So where do you begin? The most valuable, yet possibly single lowest cost, activity you can start with is to conduct an energy audit to assess your buildings’ hot water consumption patterns and identify key areas for improvement. Adveco provides a comprehensive service that incorporates live metering of your system and creates an accurate, cost-effective system design that can deliver carbon reductions and meet all your business hot water demands. This provides the data you need to evaluate any upgrade and a benchmark against which to explore various alternatives all available from Adveco, whether high-efficiency gas or electric boilers, heat pumps, and solar thermal systems, which can be deployed in isolation, although most renewables still work best when deployed to supply system preheat as part of a hybrid system. It also enables consideration of other factors like budget, space constraints, and fuel availability, which all factor into launching a sustainable strategy for a building. Working with Adveco at this early stage gives you access to expert guidance from qualified professionals who can provide necessary consultation to determine the most suitable approach for your building’s specific needs and provide a working design that can help secure funding from within the organisation, or externally via government grants, financial incentives, or green loans to offset the initial investment costs of your chosen system design.
The most consistent issue we see in commercial hot water systems is oversizing, whether through a lack of understanding of application design or
concerns over providing suitable backup to ensure system continuity. The result of oversizing is however always the same, unnecessary capital costs for system supply, installation and ongoing excess operational costs associated with higher energy demands and therefore greater carbon emissions.
Correct sizing with metered data can reduce the costs of purchasing and installing new hardware, potentially saving tens of thousands of pounds depending on the scale and complexity of the DHW application. Recognising a need for lower-cost electric systems, Adveco has developed the awardwinning FUSION range, combining an electric boiler, a specially designed cylinder and pipework that is fast to install and resilient to operate. Iterations with a monobloc air source heat pump deliver a reduction of up to 56% in carbon emissions over equivalent gas-fired systems. Integration of solar thermal to deliver mid-system heating reduces demands for water heating by as much as 30% for further carbon cutting and reduced operating costs. Because the systems are now more accurately sized, even the additional upfront capital investment associated with a more complex hybrid system can be offset for a more rapid return on investment.
With a live metered dataset, you gain insight into those prospective carbon reductions and operational costs of the new system. These can be tracked and monitored against, to demonstrate real-world savings in energy consumption and emission reductions, which can be applied toward regulatory compliance as well as used to celebrate achievements by sharing sustainability efforts with stakeholders through transparent communication.
Whichever route is decided upon, organisations should choose environmentally responsible suppliers and prioritise products with low environmental footprints as part of the procurement process. Increasingly building consultants will factor this into a project design, calculating the embodied carbon of any new system, whether water heating, space heating, ventilation and so forth. It’s an important consideration when launching a sustainable strategy, ensuring that a project meets, or preferably exceeds current building regulations ensures projects are not held up or shelved, which will be costly to both the business and the environment.
While water heating serves as a powerful launchpad, achieving true sustainability requires a holistic approach. Once successful water heating initiatives are implemented, businesses can leverage this momentum to expand their sustainability efforts by investing in wider energy efficiency across other building systems such as lighting, ventilation and especially space heating, all of which can require greater levels of physical alteration, operational disruption and accompanying costs. Also, greater attention should be given to further integration of renewable energy, exploring options for onsite renewable energy generation such as installing solar PV panels alongside the higher-efficiency solar thermal collectors used in water heating. PV enables the generation of electricity that can be deployed to a range of building systems. Since PV requires greater roof space than solar thermal, clear decision-making is required when available space for solar collection is limited, with solar thermal recommended to be prioritised as the more effective means of delivering water heating for a smaller physical footprint.
Focusing on water heating presents a strategic and impactful starting point for commercial buildings embarking on their sustainability journey. By addressing this often-overlooked area, businesses can achieve significant energy savings, emission reductions, and tangible business benefits. Furthermore, this initial success creates a springboard for wider sustainability initiatives, ultimately contributing to a more responsible and environmentally conscious future. Remember, sustainability is a continuous journey, and by starting with water heating, businesses can unlock a pathway towards a greener and more sustainable future.
Contact www.adveco.co
The next edition of the iconic quarrying, construction and recycling exhibition will take place from 25-27 June 2024 at Hillhead Quarry, Buxton.
Hillhead returned with a bang in 2022 as The QMJ Group celebrated the show’s 40th anniversary over three gloriously sunny days in June. Exhibitors and visitors took the opportunity to reconnect with their industry peers, marvel at the plethora of live machinery action taking place, discover the latest product launches, and explore the latest technology and innovations driving digitalisation and decarbonisation across the sector.
With 18,500 unique visitors in attendance and more than 600 of the world’s leading equipment manufacturers, suppliers and service providers taking part, 2022’s Hillhead exhibition was a record breaker, cementing its status as the world’s biggest working quarry event for the mineral products, construction, and recycling sectors.
The organisers will be extending the numbers of
toilets for the next event with additional plumbed units being installed at the top of the showground adjacent to the Registration Demo area. To reduce queues at peak times, there will also be a higher provision of urinals throughout the Showground.
More seating and communal areas will be introduced at various locations around the showground, allowing visitors to take a break and enjoy their picnics and other refreshments.
Two new hydration stations will be located on the showground where visitors and exhibitors can top up their water bottles with fresh, cold, filtered water free-of-charge.
The renamed Showground Pavilion (previously the Main Pavilion) is being extended by around 1,300m3. As well as generating more indoor stand space, this will also house a newly designed Hillhead Café offering a wider range of hot and cold food and drink, as well as an outdoor terraced seating area. There will also be a meeting lounge equipped with free Wi-Fi & charging points where visitors can grab a coffee & catch up on emails.
Additional catering areas are being organised across the site (including within the Registration Pavilion). These new outlets will deliver more choice and meet a wider range of dietary requirements. They will also help to reduce queuing times during busy periods.
1,000 additional car parking spaces have been added together with a new dedicated helicopter landing area. This will help to maximise entry to the parking areas from multiple access points and reduce queuing times to a minimum throughout the busy morning rush.
Brand new for 2024, exhibitors will now have their own dedicated entrance taking them directly into the showground as part of a reconfigured Registration Pavilion. This will ensure fast track access at the beginning and end of the day for exhibitors.
Contact www.hillhead.com
MMD have been a global leader for over 45 years in the design and manufacture of innovative material processing equipment. Our core products, the Mineral Sizer™ and Apron Plate Feeder, feature in groundbreaking in-pit solutions that enhance productivity, profitability, safety, and promote sustainability in the mining industry.
MMD’s revolutionary Bulk Ore Sorting System combines the benefits of In-Pit Sizing and Conveying with pioneering ore analyser technology. The ore analyser distinguishes between grades of material, enabling the separation of ore from waste at the mine face. By allowing this to happen earlier in the process, trucks need only to haul ore, not waste, to the processing plant. The
results are up to 10% less energy usage and a lower cost per tonne. Efficiency advantages are passed on to the downstream processes too, with less water consumption, ore grade uplift, and SAG mill benefits. These MMD systems are currently operating in South Africa, Chile and Brazil, processing copper, platinum and nickel ore.
We invest heavily in developing new technology that maximises efficiency. We are committed to helping our customers achieve their sustainability targets and lead the way towards a greener future for the industry.
Come see us on Stand W15. T +44 (0)1773 835533 info@mmdsizers.com www.mmdsizers.com
With hundreds of these systems installed globally, DESMI in the UK supply a fully compliant, UK manufactured, pump package for additive dosing. Our package has been continuously developed in partnership with Evotherm and, collectively, we can provide chemical and dosing advice along with specific on-site support for the full dosing system to ensure the right chemical composition and pump system is selected for your specific plant.
Our Bitumen Additive Systems are supplied with a heavy-duty ROTAN pump, control panel, pulse-output flow meter, pre-wired, pre-piped, and packaged in a rugged container. DESMI UK further provides contractor co-ordination to aid ease of
installation. Options include batch and continuous plants (with variable frequency controller and force ventilated motors) and low dosing rates for smaller systems. DESMI’s ROTAN internal gear pumps are also widely acknowledged as one of the leading pumps for bitumen and are used in asphalt plants for bitumen off-load and for duty and/ or blending. We can provide on-site advice to replace existing bitumen pumps to ensure the correct size of pump is selected. We also offer a service exchange programme to minimise downtime.
Contact Ray Jeffries on 07854 007593 or 01782 566900 or email: rayj@desmi.com to arrange a site visit or for further information. Come see us at Hillhead on Stand C6.
Celebrating its 50th anniversary, MIT is thrilled to announce its return to Hillhead for an impressive third exhibition. This milestone reflects MIT's enduring commitment to the heavy-duty machinery industry, providing life-extending aftermarket services and showcasing innovative solutions.
MIT has been a beacon of sustainability, supporting machinery longevity with expert parts supply, repair, overhaul, and service capabilities. Their aftermarket expertise ensures equipment performs, beyond typical warranty periods.
At Hillhead, MIT will exhibit driveline systems design and supply, highlighting the role of these components in constructing sustainable, reliable, and durable OEM machinery. Additionally, MIT's future propulsion technology for heavy industry will be a cornerstone of the display, signalling the company’s forward-thinking ethos.
With enduring partnerships with industry titans like Twin Disc, Transfluid, Reich, and ZF, MIT delivers OEMapproved servicing for a variety of driveline components. This golden jubilee is more than an anniversary; it's a testament to MIT's dedication to innovation, customer service, and eco-friendly practices that will propel the industry towards a more sustainable future.
Visit MIT at Hillhead on Stand M14 to explore the future of heavy-duty machinery.
T +44 (0)330 383 0333 info@mitgroup.co.uk www.mitgroup.co.uk
Discover FRUTIGER and the brand MobyDick, the hallmark of excellence in wheel washing, dust control, and demucking systems for over 30 years.
Trusted by 6,000 sites in 72 countries, the FRUTIGER solutions are renowned for reliability.
Serving a diverse clientele of 2,500 international partners, including industry leaders like Vinci and Rio Tinto, FRUTIGER caters to various sectors, from SMEs to military organisations and NATO.
With 35 years of experience, a global network of independent companies and sales offices, and ISO-certified production facilities in Switzerland, the Czech Republic, China, and the USA, FRUTIGER guarantees consistent quality and performance, delivering unparalleled solutions worldwide.
Visit us at Main Pavilion, Stand PB3 and see for yourself why FRUTIGER is the trusted choice in the industry. We look forward to meeting
you. We would be pleased to visit your site and discuss your requirements and arrange a visit to a reference site so you can see our systems in action and discuss with the site manager directly.
Contact: Tony Morgan M 07534 225087 a.morgan@frutiger.ch www.mobydick.com
Flender, the leading manufacturer of drivetrain solutions, is pleased to be exhibiting again at Hillhead in 2024.
This year we will be featuring the new revolution in gearbox design: The Flender One, and the award-winning AIQ products including the AIQ Core – a new standard in gearbox condition monitoring, and AIQ Detect – a world’s first in elastomeric coupling condition monitoring. Alongside these we will also present our couplings range, the best fit for the aggregate, recycling, and construction industries, and our marketleading service portfolio that includes on-site inspections, retrofits, and upgrades including 3rd party products
and many other solutions.
With 125 years of experience in the mining and process industries, Flender is wellplaced to support your business in maintaining high plant availability and reducing unplanned downtime.
Come visit us at Stand PD26 in the Showground Pavilion to see our live demos and presentations, free brochures and light refreshments whilst discussing your drivetrain requirements.
Email us at: flenderuk.gb@ flender.com to book your free live demo in advance. Get to know more about our products and services by visiting: www.flender.com
Heavy equipment plays a vital role in shaping the future. Timken designs engineered bearings and industrial motion products (chain, couplings, lubrication systems) to support machine builders in manufacturing hard-working aggregate equipment.
At its core, a bearing is an inherently efficient product. Its function is to transfer motion in a way that reduces friction. But Timken engineers work constantly to optimise bearings against power
loss and deliver solutions that exceed industry standards and customer expectations.
We design with sustainable in mind. Our objective is to develop light, powerdense solutions that minimise power loss and are manufactured in a manner that reduces energy inputs, processing steps, and waste while achieving operational excellence.
With more than a century of innovation, we also help operators to maximise uptime, reduce maintenance costs and improve productivity.
We know that product sustainability is also about making installation and maintenance easier, reducing steps and requirements, and extending service life through predictive modelling.
Finally, bearings are made of steel. Most of the steel we purchase is recycled, and most bearings are 100% recyclable.
Timken posted $4.8 billion in sales in 2023 and employs more than 19,000 people globally, operating from 45 countries.
Come see us on Stand Q12. T +44 (0)1977 665010 www.timken.com
Discover VEGA's comprehensive solutions for bitumen systems at Hillhead 2024
As bitumen system regulations evolve under HSE and DSEAR, ensuring compliance is paramount. Explore VEGA’s comprehensive range of ATEX/ UKEX approved sensors and panels, tailored to meet the newest explosion protection standards.
Witness firsthand how our instrumentation, including the remote inventory system (VIS), revolutionises aggregate handling procedures, enhances security and efficiency in quarries at Hillhead on Stand PD19.
We will have on display live working demonstrations of our
next generation non-contact level radar sensor - THE 6X®, abrasion-proof ceramic pressure sensors, point level switches and our remote inventory system (VIS), conveyor mass flow measurement solutions and noncontact blockage and object detection.
Our dedicated team is ready to showcase our comprehensive solutions for all budgets and requirements. Backed by excellent on-the-ground service, our knowledgeable team is available to address your queries and provide expert guidance. Experience the ease of instrumentation setup and operation, designed to streamline processes for quarry operations.
T +44 (0)1444 870055 info.uk@vega.com www.vega.com/uk
Bein with a chance to win a £100 gift voucher by helping leading Aggregates and Asphalt supplier and manufacturer, FM Conway, name its new asphalt granulator. Supplied by CAMS Srl, the new hybrid powered machine will be making its debut at Hillhead 2024.
Featuring a combination screen and oversize recirculation conveyor, the granulator will begin its life at FM Conway’s Heathrow asphalt plant and recycling centre after the show. Here it will be put to work producing reclaimed asphalt pavement (RAP) for use across FM Conway’s asphalt plants across London and the South East.
With lower energy consumption and improved outputs compared to conventional asphalt recycling equipment, this is just one example of how FM Conway is committed to a net carbon future.
As a leading asphalt manufacturer
in the UK, FM Conway’s products offer sustainable options and a broad range of high-performance pavement solutions. Meet the team at Hillhead to learn more about their asphalt materials, including their SurePol range of polymer engineered bitumen solutions and their technology centre which provides testing & design services.
To take part in the naming contest, visit FM Conway at Stand PC49 in the Showground Pavilion.
T 0800 276 1122 aandaorders@fmconway.co.uk www.fmconway.co.uk
Come see us on Stand PD2. T 01332 227500 info@davisderby.com www.davisderby.com Come see us on Stand D4
Afrequent exhibitor at Hillhead is Davis Derby, a world leading conveyor protection and forklift fleet management system manufacturer. This leading Derby-based company supplies to quarries, mines and warehouses around the world and loves to demonstrate its StedFAST and TruckLOG products during the exhibition.
The StedFAST conveyor range protects workers in hazardous working conditions such as quarries, mines, tunnels, processing plants and railway depots. With a built-in speed monitor, emergency stop pull system key and digital sequencing through a WiPAN enabled and wireless management system, this is a world-leading conveyor protection system.
Health and Safety reports estimate that 30% of all fatalities are caused by fork lift truck vehicles. The TruckLOG TK5 system offers driver access control, pre-op checks, shock alerts and utilisation reporting through Cloud-based software. With the Trucklog zoning systems, forklift
speeds can be controlled to reduce the risk of vehicle to pedestrian collisions. The TK5 TruckLOG is the UK’s leading independent MHE fleet management system and with its advanced features, warehouse companies are assured of ultimate driver safety. All Davis Derby systems are fitted by electrical engineers to new or retrofit systems and a fully tailor-made conveyor control system can be designed for any company.
Founded in 1947, Perissinotto SpA manufactures a wide range of heavy-duty slurry pumps for tough abrasive and corrosive applications.
Hard metal, Special Alloys, and rubber lined pumps with customised design for single-stage, multistage, submersible, and vertical configurations.
Some of the most appreciated features are: t Longer life, thanks to ABRASION RESISTANT PEMO design and materials.
t CORROSION RESISTANT, using the most suitable alloys for aggressive fluids.
t NON-CLOGGING, thanks to the special design of casings and impellers.
t SINGLE, DOUBLE or CARTRIDGE MECHANICAL SEALS to prevent leakages and contaminations.
t Flowrate up to 2,000m3/h.
t TDH up to 160mcl.
PEMO Pumps are commonly used in Mining, Aggregate Washing, Quarry and Mineral Extraction Process.
PEMO PUMPS are designed and manufactured to resist and operate with the heaviest abrasive slurry and are commonly used to feed the classifier, to deliver the slurry to the flotation system, tailing thickener, and finally to the filtration/dewatering system.
Mining and aggregate excavation
Pemo Slurry Pumps are used extensively in these markets due to the wide variety of Models and Configurations. Pumps available for this application include Horizontal, Vertical & Submersible Designs.
Pemo Slurry Mining Pumps used for this application are designed specifically for abrasive and or acid/ corrosive fluid applications and are available in a number of materials including Rubber Lined, Hardalloy PEMO (750-800 HB), Stainless Steel and Hastelloy.
Some Models can operate to a maximum pressure of 20 bar (290 psi).
Some of the applications for PEMO pumps include, slurry transfer in ponds, hydrocylone feed and yellowcake slurry transfer.
Come see us at Hillhead from 25-27 June 2024 on Stand PC20.
Contact today our consultants to learn more about the complete range of Pemo Pumps: www.pemopumps.com/en/contact-us/
After recently celebrating its 30th anniversary in 2023, the United Kingdom Society of Trenchless Technology (UKSTT) remains at the forefront of environmental preservation with its trenchless methods that harness innovation.
Going into its fourth decade, UKSTT has achieved many milestones across its history, and today its mission still remains the same: To advance the science of practice of trenchless technology for the public benefit and to promote education, training, study and research in the practice and to publish the results.
focus is to continue supporting and engaging its membership within the utility sector.
UKSTT’s range of trenchless solutions offer key advantages across inspection & detection, cleaning methods, renovation, new installations, and keyhole & other techniques.
Addressing the urgency of climate change is a priority for UKSTT moving forward and by putting itself in the centre of the action enables the company to remain focused on promoting its technology for the benefit of the environment and everyone involved.
Through sustainable impact, effective collaboration, lasting partnerships and knowledge transference, UKSTT’s main
UKSTT is excited to announce its first masterclass of 2024 that will take place on the 20th March at Woodland Grange, Leamington Spa. CIPP for Pressure Pipes Masterclass is a one-day masterclass that comprehensively covers CIPP for pressure pipes and much more. Including presentations from speakers from Wessex Water, Thames Water, IKT –Institute for Underground Infrastructure, WRc Group, Picote Solutions, Applied Felts and RPS, reserve your place today!
M 07745 781500 www.ukstt.org.uk www.ukstt.org.uk/calendar/cipp-forpressure-pipes-masterclass
Bluewater calls for global action on PFAS contamination on World Water Day 2024, says manufacturers should assume full responsibility and halt production.
In response to recent findings exposing the presence of harmful PFAS contaminants in the tap water of 70 million Americans, Bluewater, a pioneering brand delivering water purification solutions and beverages, is urging for increased public vigilance and intervention from national health and water authorities this World Water Day 2024. Bluewater is spotlighting the intensifying global crisis of water contamination by PFAS persistent chemicals, now widely detected in tap water worldwide and posing a threat to human health.
“Our mission at Bluewater is to protect people by preventing hazardous chemicals such as PFAS from getting into their bodies. PFAS isn’t a localised issue. It’s a global health crisis spiralling out of control,” says Bengt Rittri, a leading Swedish environmental entrepreneur who founded & leads Bluewater as CEO.
In recent investigations to raise
public awareness of the problem in London and Stockholm, Bluewater found evidence in both cities of worrying levels of the most hazardous PFAS chemicals, PFOA and PFOS.
“As we commemorate World Water Day 2024, Bluewater encourages everyone to consider tap water quality and to take action towards better health and a sustainable planet. We also urge the manufacturers of PFAS chemicals to take responsibility for the pollution they are causing and — preferably — stop their production of such chemicals entirely,” said Bengt Rittri.
M 07785 302694
david.noble@bluewatergroup.com www.mynewsdesk.com/bluewater
The highly anticipated Groundswell Event in Hertfordshire on 28th and 29th June did not disappoint, with farmers, researchers and experts in the agricultural industry coming together from across the world to learn and share knowledge on sustainable food production through regenerative farming practices.
Interagro (UK) Ltd, leading adjuvant and biostimulant experts, were among the growing number of exhibitors in attendance offering practical solutions to help farmers achieve more sustainable and profitable food production through superior plant health.
offers a more natural and eco-friendly approach to crop establishment, by boosting seeds rather than treating plants.
Growing in popularity year-on-year the ‘Glastonbury-for-farmers’ style event was full of buzz, learning and positive attitudes, with Interagro part of the Knowledge Trail showcasing how its plant-based seed treatment Newton,
Newton is increasingly being adopted by farmers due to the recognition of its proven abilities to enhance plant growth, productivity, and resilience. Newton’s potential to improve crop establishment, work in harmony with soil biology, and put plants in the best possible position to acquire moisture and nutrients throughout its lifetime – so they are less reliant on synthetic inputs – has contributed to its increasing use.
To find out more about Newton and Interagro’s adjuvant and biostimulant range visit: www.interagro.co.uk
Get in touch on: 01279 714970 or email: info@interagro.co.uk
Follow on Twitter: @InteragroUK
Agricarbon is a market-leading provider of soil carbon measurement at scale, serving all soil types across the UK and across Europe. For farmers, landowners, and businesses looking to assess their soil carbon stocks, Agricarbon offers scientifically driven, evidence-based sampling and analysis at its on-site processing facility.
The company is at this year’s Groundswell Agricultural Festival from 26-27 June 2024, the leading, annual regenerative agricultural event, to showcase its leading soil testing technology.
Agricarbon is committed to expanding its unparalleled soil carbon technology across European countries and further afield in North America.
It is well known that increasing soil carbon has a twofold impact: improved soil health and higher yields for crops.
Supporting natural soil microbes such as fungi, archaea and protozoa is great for worm populations and enhanced eco-biodiversity.
The data speaks for itself – Agricarbon has sampled over 32,000 hectares and quantified an astonishing 2 million
tonnes of carbon, which amounts quite possibly to the biggest database on soil carbon in the world.
The talented leadership team include world renowned soil scientist: Dr Helaina Black and her team of soil science experts, helping facilitate how soil can work as a carbon sink, while simultaneously supporting food production and natural biodiversity.
T +44 (0)1382 413 270 info@agricarbon.co.uk https://agricarbon.co.uk
Following on from the successful launch into the UK and Irish market at this year’s Groundswell Festival, Gaiago is encouraged by the interest and commitment to its sustainable products.
there is a need to embrace and engage with a new way of thinking around soils. Soils should be treated as one of the biggest assets we have to avoid the continuing loss of fertility and current negative impacts on nature.
Gaiago’s portfolio harnesses the very latest innovation for revitalising soils, any farmer, grower, horticulturist or land manager’s biggest asset. The solutions consist of unique formulations of natural elements, protecting yields and empowering growers to evolve their practices to a more regenerative farming. Products registered as biostimulants are now available in the UK.
The current portfolio is supported by a strong R&D pipeline developed both internally and externally, notably through a scientific joint-venture with a renowned Agricultural University, UniLaSalle.
Soils – understanding the problem As a global issue, it is clear that
Gaiago is making the change within soils and their whole team is committed to educating and offering solutions to growers for the production of healthy, fertile, and sustainable products. “Mankind thrives when soils thrive” is Gaiago’s mantra
Innovative solutions on the ground Alongside Gaiago’s leading soil probiotics FreeN100 & FreePK, its prebiotic biostimulant Nutrigeo® offers improved soil structure in less than 6 months, enhances fertility and growth, and accelerates the humification process – the source of carbon storage in soils.
Find out more at: www.gaiago.eu
When it comes to decarbonising buildings it’s crucial to balance effective heating with low upfront investment and low running costs – Chris Newman, Zero carbon design team manager at Mitsubishi Electric, explains
We all know that decarbonising the UK’s building stock is vital for hitting the country’s net-zero targets. At the same time, this can pose challenges for building developers, energy managers, installers and even tenants. One area of complexity is how buildings are heated, because heating has traditionally contributed significantly to overall building emissions, and changing how we heat spaces is high on the net-zero agenda.
But while effective in helping to reduce carbon emissions, changing how we heat spaces isn’t always simple. For example, traditional gas-fired heating systems operate with relatively high water flow temperatures of 70-80ºC (in comparison to today’s typical designs of ≤55ºC). Swapping to an electrically driven alternative to match those temperatures can be straightforward – but it can also have a big impact on the operating cost of equipment.
This is made particularly apparent by the current disproportionate cost per kWh of gas compared to electricity, and the capital cost of technologies such as heat pumps compared to fossil fuel alternatives. This is where a bivalent approach can help to balance the ability to decarbonise a space with lower overall costs.
Focusing on utilising heat pumps as part of a bivalent solution, we can consider two broad types of configuration (see Figure 1).
It is typical in the UK for peak space heating capacity (ie. 100% load) to only be required for a small number of hours in the year and therefore this makes up a relatively small amount of the total kWh of heat energy delivered. This then opens the possibility of deliberately undersizing your heat pump in comparison to peak load and only operating it for certain parts of the year, allowing the gas boiler to provide the extra peak capacity or peak flow temperatures when needed – this approach can help to reduce up-front costs and plant space requirements.
We know that operating a heat pump at the lowest possible flow temperature and the warmest source temperature will usually deliver the highest efficiency and lowest operating cost, but we must also consider how any heat generated is emitted into the building
– this is where the infrastructure of the existing system begins to influence the design approach.
The existing heat emitters (fan coils, AHU coils, radiators, etc) must be assessed to understand their deliverable output capacity at different mean temperatures – this will demonstrate what mean temperature is needed at certain ambient conditions to deliver the required capacity. This is a key piece of information needed to model bivalent parallel and bivalent changeover configurations.
Boiler topping up
A bivalent approach can involve a heat pump being the lead heating source, with a boiler topping up when needed. Alternatively, a heat pump can work in isolation, and swap over entirely to a boiler when it can no longer meet requirements.
In a bivalent changeover arrangement, the heat pump is deliberately designed not to deliver the peak flow temperature or capacity of the heating system.
This means that it will only operate up to a specific temperature and capacity chosen, and then it will reach a changeover point.
The heat pump will operate in isolation to the boiler, and provide heat until its maximum flow temperature and capacity is reached. At this point, the heat pump will turn off and the boiler will take over delivering the higher temperature water and increased capacity required to meet the increasing building load.
This arrangement will deliver a lower proportion of annual space heating kWh from the heat pump compared to a bivalent parallel solution, but as the heat pump will not operate at peak design conditions and will not be asked to deliver high flow temperatures, it will benefit from increased efficiency, resulting in a lower operating costs.
A bivalent parallel approach, on the other hand, requires the heat pump to be capable of delivering the peak flow temperature of the system, so it can work alongside a boiler at any time of year. This allows the heat pump to be sized at any capacity and either deliver heat energy on its own when it has the capacity available, or in conjunction with the boiler when the load is greater than the heat pump capacity.
Flow temperature can be either fixed or weather compensated, but the key design principle is that the heat pump is able to deliver the required flow temperature to meet peak heating demands.
This arrangement will deliver a large proportion of heating from the heat pump and will most likely result in the lowest overall carbon emissions. However, operating the heat pump at potentially high flow temperatures and low ambient conditions will reduce its efficiency, meaning that this configuration could result in an increased operational cost compared to the gas boiler only system.
Special consideration must also be given to the selection of heat pump to ensure it can deliver the necessary flow temperature and capacity at all operational conditions.
Opting for a bivalent solution – whether parallel or changeover – can be the most effective way to balance effective heating with low upfront investment and low running costs.
Contact https://les.mitsubishielectric.co.uk
Imagine Arriving At Work To Find A Door That Wasn’t There Yesterday, And When You Open The Door You Discover...
A well-dressed lady who, upon seeing you, rises from behind her desk and, with a big smile, hands you a sheet of paper.
“Good morning,” she says, “here are the details of a company who want to see you to discuss how you can help them. I’ve told them all about Business And Industry Today Limited,” she continues, “and they’re very eager to meet with you. You’re scheduled in with the MD for 10am next Wednesday.” The company she has made the appointment with has been on your ‘most wanted’ list for a while.
“Thank you very much,” you reply, a little bewildered, “I’ll put it in my diary.”
so you understand why the appointment was made.
“Sorry,” you say, “but who are you and where’ve you come from?”
“Ah, you didn’t get the memo; I’m here to help you win new clients,” she explains. “I’ve researched your markets and am now making direct contact with all the companies identified as needing your
You feel yourself getting mildly excited at the prospect of winning a steady stream of business from this work and start thinking about the difference it’s going to make to the company's performance.
As you step back out into the corridor the fire alarm goes off, which, after a couple of seconds, turns into your alarm clock. You sit upright in bed, gathering your thoughts. “Aahhh, a dream,” you sigh to yourself as you start to come to, “just a dream.”
services. If you give me enough time I will provide your company with quality appointments that will lead to £1,000s worth of appointments and often £Ms worth of pipeline. Call back at lunchtime,” she continues, “as I’ve a conference call at 11am with another company who are keen to meet with you.”
“No need,” she says with a wave of her hand and another smile. Already done, along with directions, a link to their website, a resume of their core activities and the recordings of the calls with them
“Oh, ok,” you say, “I will,” adding, “this is great, thanks very much.” You’re not sure how she’s doing it but feel very grateful that she is!
As you flop back down onto your pillow to allow yourself an extra five minutes you begin wondering ‘what if?’ What if there was such a person, capable of making such good quality appointments; someone as competent, as professional and as effective as her, even if only for just one or two days per week? If she did exist, you conclude, you would definitely like to meet her.
For advice on all services provided by Newton Fox, please contact Chris Newton on 07760 161677 or email: chris@newtonfoxbd.com for immediate attention.
Most organisations have many policies, whether that is for safe working practices when using dangerous equipment, to prove that certain regulatory standards are being met, or to satisfy client requirements regarding quality and management systems.
But, have you got a policy that covers driving safely for work? And if you do, are you confident that it’s good enough – that it meets legal requirements? And that it’s up to date? Driving for work is, after all, probably the most high-risk activity most employees ever undertake.
What do you think the odds are that someone who works for you, and drives as part of their job, will be involved in a crash that injures either themselves or, worse, another road user? The vast majority of those casualties are other vulnerable road users such as cyclists or pedestrians.
Would it surprise you learn that the odds are just one in 500? Yet, we think it will never happen us.
Compare that to the odds of winning the National Lottery jackpot.
Their website says the odds of winning the jackpot are a staggering 1 in 45 million and yet still we think we have a chance. We really don’t.
Why is there such a disconnect between these massively different odds and our perception of the risk they represent?
How did I arrive at odds of 1 in 500? According to government figures, every year, almost 40,000 people are injured on Britain’s roads each year in crashes that involve someone who was driving for work.
There are approximately 20 million vehicles used for some form of work journey across the UK which is about half of all registered vehicles. That includes company cars, company managed commercial vehicles, such as vans and trucks, grey fleet – which is where employees use their own personal car for a work journey – and mopeds or motorcycles.
If you take those 20 million vehicles and divide by the 40,000 injury collisions above, you’ll see that the odds are just 1 in 500. That means if you have a 500 vehicle fleet, you’re statistically likely to deal with an injury collision every year, if you manage 100 vehicles, then once every 5 years.
Of course, if you don’t manage your drivers and vehicles well, then the odds could get a lot worse.
If you want to ensure your employees are not part of the problem, it’s vital to set out the importance of driver safety – and the standards you expect of any staff who drive for work.
Your organisation needs to do this for three reasons:
1. It’s the right thing to do. We have a moral responsibility to ensure all our staff and other road users to get home to their families safe and well at the end of each day.
2. It makes good business sense. Poor driving, collisions and injuries cost money so good management of drivers means significant business benefits in the form of greater cost control and improved sustainability, as well as a reduction in reputational risk.
3. But if you’re not going to do it for either of those reasons, you need to understand that it is a legal requirement –the law says all companies must have policies and procedures to minimise risk – and that includes the recognised risks around driving. In the event of a serious incident, you could be asked to prove what you do to promote driver safety.
To communicate your
commitment, and the required standards to drivers, you need a driving for work policy.
What should be included in a driving for work policy?
Here’s a summary of what needs to be included.
A Policy Statement which explains to drivers why the policy exists and why it is important they follow it at all times. This should also a statement from senior leadership that sets out the importance of driver safety to the organisation.
This statement is from Paul Edgar, Head of Workspace and Safety at Heineken UK – winners of the inaugural Safety & Health Excellence Award for Best Driver Risk Management Performance in 2023. The award is sponsored by National Highways and Driving for Better Business and was presented by TV’s Tess Daly.
“At Heineken UK, safety is our number one priority; we want to ensure that our people go home safely every day. For field-based colleagues driving millions of miles annually, driving presents our highest risk. Managing driver risk is a huge priority for us, so we always look to improve through updating policy, technology and awareness programmes to positively reinforce good behaviours. We can repair or replace bent metal, but that isn’t always the case for the lives of colleagues and their families involved in serious road traffic collisions.”
That’s a strong statement and clearly sets the tone for the standards expected of both drivers and their managers.
A Driver Management section covering licence checks, medical conditions, driver competence and fitness to drive including impairment, fatigue and wellbeing.
A Vehicle Management section including vehicle roadworthiness, safe loading, vehicle security, private use of vehicles and towing, if applicable.
A Journey Management section including driving standards, use of mobile phones, dealing with fines and penalties, and what to do in the event of a collision or breakdown.
A Grey Fleet Drivers section – for those employees who use their own car for business journeys. It’s an area often missed but every time an employee uses their own vehicle for any work purpose, you have the same legal responsibilities for managing safety.
What happens if it all goes wrong?
In the event of a serious incident, questions about whether you had a policy, how good it was and whether it was followed would form a core part of any investigation and prosecution. This year’s Health and Safety Event at the NEC (30th April to 2nd May) sees the return of the Driving
for Better Business Driver Safety Theatre with three days of content dedicated purely to driver risk managers. After the success of last year’s mock trial, we are going to be running it on all three days but with a different follow-on session on each day. Tuesday’s trial will be followed by a detailed driving for work policy session, Wednesday will be legal Q&A with our trial prosecutor and Thursday will focus on good practice for internal incident investigation.
The incident in the trial covers a whole range of driver and management failures that were either not adequately covered by the firm’s driving for work policy, or else corners were routinely cut that rendered the policy ineffective. Some of the myriad issues we looked at included vehicle roadworthiness, driver impairment, work schedules, fatigue, mobile phones, overloading and, of course, corporate risk management systems.
The team at Driving for Better Business has just created a brand-new resource to help you with your policy. Our new Driving for Work Policy Builder is a free online tool:
● It allows you to access a driving for work policy
template and checklist to make sure you’ve got everything covered,
● Using these templates, you’ll be able to create a policy document that meets legal and compliance standards;
● You’ll get email alerts when there are any changes in guidance or legislation that could affect your policy;
● And you’ll receive an annual reminder to review your policy, along with any changes that may be required since the last review;
The Driving for Better Business Policy Builder gives you access to a Driving for Work Policy Template that ensures you meet the required legal and compliance standards. You can use these templates to create a brand new policy or check your current policy.
Signing up to the driving for work policy builder means we can also keep you informed when there are any important changes to legislation, official guidance or the Highway Code, that may need to be reflected in your policy.
We’ll also send you an annual reminder to review your policy. This will include any changes or updates that have occurred since you last reviewed it, so that you remain legally compliant.
Find out more at: www.drivingforbetterbusiness.com or scan the QR code.
Click on a photo or headline below to learn more about a given new product
Industrial software developer, COPA-DATA has launched a Module Type Package (MTP) suite as part of its zenon software platform. The technology has been developed for the pharmaceutical, chemical, energy, food and beverage and marine sectors and is designed to enable plug-and-produce
manufacturing. MTP is the cross-industry and cross-manufacturer standardisation of the interfaces of different pieces of machinery which form a module. In a manufacturing facility, this functionality is achieved through the integration of MTP on the Process Orchestration Layer (POL).
Softing Industrial is expanding the smartLink product family with two new members: smartLink HW-PN and smartLink SW-PN enable access to PROFINET networks. The hardware gateway smartLink HW-PN and the Docker container software
Molex recently introduced a Brad® IP67 solution portfolio based on IO-Link and PROFINET technologies. Brad IO-Link solutions include IP67 PROFINET IO-Link master modules in 60mm format and IP67 IO-Link digital hubs. The PROFINET master
smartLink SW-PN enable controllerindependent access to PROFINET field devices. The application areas of smartLinks PN range from parameterisation and asset management to the monitoring of PROFINET and PROFIBUS devices.
module features eight M12 ports with each port an IO-Link master channel and a configurable digital I/O channel. The digital hubs are available in 16 Inputs or 12 Inputs + 4 Outputs versions.
Phoenix Contact has a new PROFIsafe safety controller that operates as an expansion module for its AXC F 2152 or AXC F 3152 PLCnext controllers. The AXC F XT SPLC 3000 controller adds a safety PLC for PROFINET networks to PLCnext. It can be used in applications up to SIL3 or PLe. When operating as an F-host, the SPLC
3000 can communicate with up to 300 F-devices and operate simultaneously as an F-device. Combining with the PROFIsafe I/O extensions of the Axiobus that can be added to the right-hand-side of a PLCnext controller, offers a high degree of modularity.
SEW-Eurodrive says it is redefining what ‘standard’ means with a compact frequency inverter that can be used for applications from open-loop speed control and encoderfree torque control, to dynamic positioning. Its new Movitrac Advanced inverter offers a high degree of standardisation and is suitable for use in more than 50
countries. The inverter – part of SEW’s Movi C modular automation system – can control asynchronous and synchronous AC motors, with or without encoders. The drive can connect with control systems via PROFINET, and safe communications can be implemented via PROFIsafe. https://profinews.com/
AdCo UK is one of the largest manufactures of shaped hotmelt adhesives and water-based adhesives for use in packaging and product assembly markets for over 21 years, from its Head Office and manufacturing facility in Liphook Hampshire with additional distribution facilities based in Leeds UK and a network of approved distributors based throughout the UK.
As well as supplying adhesives for all requirements, AdCo supplies a wide range of specialist applicators – from ProFlex industrial, heavy duty and professional glue guns to total melt, cartridge and bulk systems, we also manufacture and supply UF resins, PVA Adhesives, PU Adhesives, Tapes and much more
As part of our commitment to
offer our customers the correct solution for their needs AdCo are continually investing in research and development along with new state of the art manufacturing equipment to ensure we continue to meet the ever changing needs of all types of industry.
Thanks to our unrivalled knowledge of adhesives and application techniques, our highly skilled technicians can offer a ‘find and supply’ service to all our customers.
With a combined industry experience of over 120 years, our technicians can ensure that any bonding problem can be solved quickly and efficiently.
T 01428 751755 enquiries@adco.co.uk www.adco.co.uk
With a variable transformer design, there is usually a significant difference between the kWs needed to melt glass and the kilo volt amperes (kVA) rating of the transformer. This means that this type of system must be oversized, typically by up to 50%, which increases cost.
For example, for a two MW at 200V system with three single boosting zones, the system would typically be designed at three mega-volt amperes (MVA).
For only 2,000kW power needed to melt the glass, the system needs to be designed at typically a minimum of 3,000kVA, with three 5,000A at 200V busbar systems to the electrodes.
With Eurotherm’s power box solution, an alternative design using a much more standard medium voltage transformer with a secondary voltage between 400 and 480V is possible. Power skids can be placed as close as possible to the electrodes to control and step down the voltage to the desired operating range.
The high amperage is only after the power skids and therefore on much shorter cable distances to the electrodes. The power skids include power controllers operating in automatic load tap changer mode, which provides control of power on the full operating voltage range at very high-power factor and without the traditional mechanical wear.
To learn more about Eurotherm and its solutions for glass manufacturing, visit: www. eurotherm.com – to learn more about Watlow’s thermal solutions, head to: www.watlow.com
Quirepace manufacture the BVC range of Industrial Vacuum Cleaners. BVC is the original ‘British Vacuum Cleaners’ and the core range is still manufactured here in the UK in Quirepace’s Fareham factory.
The largest range of BVC machines is the Ti series consisting of the Ti60 and Ti80. These are available with several choices and variations of motor size, capacity, filtration and hoses/ tools. The range spans from 4kW up to 15kW. All electric units require a 3-phase supply, although petrol and diesel variations can also be supplied.
The power of BVC Ti series Industrial Vacuum Cleaners is required primarily when heavy aggregates and materials have to been cleaned and recovered. Typical customers come from manufacturing, heavy engineering, and construction.
Ti60 and Ti80 have 60 litre and 80 litre collection tanks respectively, but for heavier materials it is often appropriate to use an intermediate interceptor skip which can be both manoeuvred on its own wheels or picked up and carried by FLT. Similarly, the Ti80 is equipped with fork lugs.
Using a separate skip interceptor provides several advantages; a single vacuum unit can be shared between several interceptors, for emptying the vacuum unit does not have to be detached from the power supply, and having the vacuum plant separate from the collector reduces the weight to be carried from the work place to the disposal point.
The motive power for BVC Ti series Industrial Vacuum Cleaners is a combination unit consisting of a continuously rated 3 phase electric motor of a size suitable for the application combined with a BVC multistage vacuum pump designed for heavy duty use. The BVC multistage design is much more forgiving in an industrial application than typical side channel exhausters and vacuum pumps found on competitor machines. Side channel units are
efficient at handling air, but the tight internal tolerances are rapidly destroyed should anything else find its way into the unit. BVC multistage vacuum pumps operate with much wider tolerances between Impellers and casings and in many cases are not affected by accidental ingress of some material or liquid, giving the units a very high durability in the toughest environments.
As in all Industrial Vacuum Cleaners, filtration is as important as the machine power in determining the overall efficiency of the unit. Filters must not blind easily, or performance quickly degrades, and must also be robust enough to handle continual operation with aggressive materials. All BVC Ti series vacuum cleaners may be specified with either standard bag filters or, for finer materials, the unique BVC Clearflow filter which naturally agitates continually in use helping to prevent filter blinding. All standard filters may be combined with HEPA secondary filters for enhanced filtration where required.
BVC Ti series machines are available with 38mm, 51mm, 76mm
and 102mm hoses and various combinations and lengths of hose may be used depending on the application. Additionally, the larger machines are capable of operating multiple users simultaneously through either Y pieces or fixed pipework systems.
Similarly, heavy-duty tools are available in several different designs depending on the application. For some materials special aerating tools are necessary to mix the material with air to enable it to flow easily.
If materials to be cleaned are organic such as wood or plastic products and where fine material dusts may create an explosive atmosphere, it is necessary to use ATEX rated vacuum cleaners. Both Ti60 and Ti80 are available in ATEX rated versions with similarly rated hoses and tools.
Whilst the BVC range of Industrial Vacuum Cleaners manufactured by Quirepace is available in a wide range of standard configurations, it is also possible to manufacture special units for particular applications. For example, it is possible to equip machines with PLC interfaces so that the equipment starts and stops automatically determined by external signals and processes. This is particularly of interest where the Industrial Vacuum is integrated in to the production line.
All BVC Industrial Vacuum Cleaners are manufactured for durability in the most aggressive environments, and have stood the test of time in many diverse industries. Machines used in the UK are provided with a 5 year parts warranty against manufacturing defect, and spare parts are available for all units from a comprehensive warehouse in Fareham.
BVC from Quirepace – Tough Machines for Tough Jobs.
T 023 9260 3700
bvcsales@quirepace.co.uk www.quirepace.co.uk
Boasting over four decades of experience and rooted in Sheffield’s rich steel heritage, Charles Day Steels is thrilled to introduce their latest cuttingedge machinery acquisition – a new sheet metal bender. This state-of-the-art machine is engineered to cater to a wide spectrum of bending requirements with unparalleled efficiency and quality; emphasising Charles Day Steels’ ongoing investment strategy and commitment to advancing their bending and sheet metal pressing services.
Building on a foundation of excellence and innovation, Charles Day Steels’ latest in a long line of machine investments underscores their commitment to providing customers with cutting-edge solutions. This strategic move not only improves their in-house capabilities but also broadens the range of services available to their clientele. Boasting a tonnage of 320 tons and a bending length capacity of 4,100mm, this newest investment marks a significant upgrade over previous capabilities; allowing them to accommodate larger and thicker materials, and expand their service offerings to include more complex and demanding projects. With this investment, Charles Day Steels reinforces its position as a leader in the metal processing
Renowned for its unparalleled precision and flexibility, this machine investment is a gamechanger in the industry, equipped with dynamic crowning and Pressure-Reference technology to ensure the highest repetition accuracy and consistent quality across all projects. Its modular machine concept, coupled with a broad power spectrum, allows for the optimal configuration for specific sheet metal work, significantly enhancing production efficiency and flexibility.
Charlie Day, grandson of the founder and Sales and Business Development Director at Charles Days, had this to say about their latest investment, “With our larger cutting beds and higher power lasers, the demand from customers for larger, thicker, and more complex parts is growing, so naturally we invest to satisfy that demand.”
This new addition seamlessly integrates with Charles Day Steels’ existing array of services, including laser cutting, waterjet cutting, bevel cutting, and etching, to offer a comprehensive one-stop shop for metal processing solutions; effectively downstreaming production and enhancing customer experience. The higher tonnage and extended part length capabilities of the new machine allow for the bending of thicker materials across larger dimensions than ever before. Supported by a robust tooling library, Charles Day Steels is well-equipped to handle the most complex part requirements, further establishing their commitment to providing versatile and highquality solutions to their clients.
T 0114 244 5544 sales@daysteel.co.uk www.daysteel.co.uk
Transforming precision engineering and productivity, The Laser Cutting Co is proud to unveil its latest addition of the Trumpf TruBend Series 5000, a state-of-the-art bending machine, to its series of cutting-edge metal profiling machinery. This investment not only elevates the Sheffield-based company’s capabilities in metal bending and profiling, but also aligns with its Smart Design Production services; reinforcing its commitment to excellence in laser cutting, metal fabrication, and now, with an increased focus, on advanced metal bending techniques.
For over four decades, The Laser Cutting Co has led the way in the metalworking industry, adapting and evolving to exceed the various demands of its clients. The integration of this newest investment is a testament to the company’s commitment to innovation, quality, and the holistic approach of Smart Design Production.
This service optimises parts for efficient downstream processes and assembly, significantly reducing component volume, material waste, and overall complexity for customer projects.
With an ethos of continuous re-investment, this latest addition introduces unparalleled flexibility, speed, and efficiency to The Laser Cutting Co’s operations. Featuring an energy-efficient On-Demand Servo Drive and a 6-axis back gauge, the machine enhances the company's bending capabilities, allowing for the processing of thicker materials over larger part lengths, up to 4,250mm. The innovative automatic tool changer, ToolMaster, also enhances the company’s ability to produce complex parts with ease and precision, significantly improving its bending capabilities.
Regarding their latest investment, James Day, The Laser Cutting Co’s Operations Director, had this to say, “Pressing is a rapid growth area for the business so investment into larger and more capable machinery fits comfortably within our approach to ensuring a happy customer base.”
This latest investment is a clear indication of The Laser Cutting Co’s commitment to enhancing its service offerings and meeting the evolving needs of its customers; underscoring not only The Laser Cutting Co’s dedication to enhancing its service offerings, but also complementing its existing range of services, including laser cutting, sheet metal bending, laser engraving and etching, and much more.
By integrating this machinery with its Smart Design Production services, the company is poised to deliver even more optimised, efficient, and high-quality fabrication solutions, further cementing its position as a leader in the metalworking industry.
T 0114 242 0101
sales@lasercutting.co.uk
www.lasercutting.co.uk
In BASA’s 41st year of operation, we are still excelling in our mission to remain the umbrella organisation for UK adhesives and sealants manufacturers. Focusing on technical and legislative aspects and on promoting awareness of the industry and technology by providing guidance on technical and compliance issues, we create a variety of networking opportunities for members and provide a huge library of documents on the website. Our SME members are our lifeblood.
BASA is the voice of the adhesives and sealants industry and an information source for manufacturers and suppliers. We lobby on behalf of members and liaise with Government on
legislation, keeping Members well informed of UK, EU and International proposals and initiatives.
With the growing concerns around the environment and using sustainable products and raw materials, BASA is dedicated to helping its members minimise harmful chemical usage and educate the public on the industry’s drive for safer products. BASA members work hard to formulate innovative products that positively contribute to the sustainability agenda whilst maintaining performance and durability.
BASA hopes to continue to reach more potential members, looking at ways to support its manufacturers post Brexit and help them to navigate potential new legislation and trade rules.
Come and see us at CHEM UK on Stand Q90.
Contact: Lorna Williams T +44 (0)330 22 33 290 secretary@basa.uk.com www.basa.uk.com @BASA_updates
Vision Engineering Ltd, a multinational designer and manufacturer of innovative, patented ergonomic stereo optical and digital instruments has relocated its anodising arm, Milturn Finishing, to a brand new facility in Measham, Leicestershire following its acquisition in 2022. The Leicestershire location is beneficial as the Midlands serves as a major hub for UK manufacturing, innovation, and skilled workforce.
The new ISO9001 certified site delivers modern new facilities which include large 3m x 1.5m anodising tanks, which accommodate larger work pieces, enabling efficient processing of entire components without needing to break them down. This reduces processing time and cost. Larger tanks enable deeper immersion for uniform anodising. The increased depth allows for complete submersion of parts, ensuring consistent coating thickness and quality across the entire surface and reduced handling needs for smaller parts, meaning that batch processing of smaller parts
Suurmond have, for many years, held distribution agreements with the very best gear-pump manufacturers. Maag Pump Systems (now incorporating Witte Pumps), Gather Industrie GmbH, HNPM and additionally Suurmond UK Ltd hold the distribution agreement with Dynisco, a world leading manufacturer of melt sensors and instrumentation.
In 2024, Suurmond group celebrate 50 years in business and Suurmond UK celebrate 20 years. At the end of 2023, Suurmond UK moved into new premisses which will allow us to further improve our
becomes more efficient, minimising handling time and potential damage.
Milturn Finishing’s high load crane delivers safe and efficient handling of heavy work pieces, improved productivity and throughput including faster handling of parts, and handling multiple parts at once, boosting productivity.
Services include accurate masking and demasking of complex parts pre and post anodising which delivers high accuracy selective anodising, maintaining dimensional integrity, improving process efficiency, and ultimately contributing to consistently high-quality results.
Extensive experience and professional advice in anodising and finishing plus competitive pricing, fast track service, free delivery & collection, together with free quotation and sampling services complete the picture for the new Milturn Finishing offer. www.milturnfinishing.co.uk
service to customers in the UK. We now have a workshop that allows us to service and repair gearpumps of any size. We have a larger stocks of emergency spares for Maag Pumps. We also have a lab facility to run melt flow tests using our Dynisco LMI5500 melt flow analyser.
As we move through 2024 and into the future, Suurmond UK plan to further expand to support the future of fluid processing in the fine chemical, pharmaceutical, polymer and extrusion industries. As these industries recover from the impact of Brexit and COVID, we see great opportunities to work with manufacturing plants in the UK & Ireland to develop better, more efficient processes. #letstalk
T 01386 423756 info.uk@suurmond.com www.suurmond.com
The machinery health industry is at the heart of many applications today, down to the monitoring of each bearing and pump rotation. From shipping containers, cruise liners, to manufacturing and the automotive sectors, the smooth running of machinery is the chief concern of engineers. The annual scheduling of manual maintenance checks has been the modus operandi for decades but is no longer seen as the most efficient system.
What happens during the rest of the year between inspections, if the filters get blocked and cause pump cavitation? An untimely pump overhaul is expensive, costing thousands, especially when it was only the filters that needed changing in the first place.
CMServices Global is a leading consultancy, offering AI condition monitoring to diverse sectors from marine and offshore, automotive, manufacturing, food and beverage, postal sorting through to chemical, oil and gas.
Condition monitoring involves the real-time tracking of machine functionality but with the added bonus of predictive maintenance and remote diagnostics across a whole system. AI brings automated processing to the table and with that, a superior result-driven accuracy. Predictive maintenance analyses senor data previously installed on equipment to determine when maintenance is needed. AI can analyse huge chunks of data in real-time and identify patterns proactively, before a problem arises, such as pump cavitation. This allows on-site engineers to schedule checks and repairs before a more costly machine failure or malfunction occurs, later down the line.
We spoke to Director, Simon Edmondson, for more insight, “Our software has been precision-designed to ascertain faults, using strategic comparison to known fault signatures. The cause of the problem can be quickly sourced, saving unnecessary downtime and costly repairs. Through continuous AI monitoring, anomalies can be spotted before further catastrophe strikes, through the smart analysis of sensor data
and the comparison to standard historical data.”
“Traditionally, service engineers respond to faults manually but our computer-generated system spots the fault before it materialises at the early stage. This early detection system can essentially save companies thousands in downtime and repairs.”
“For some companies, asset optimisation allows them to really hone in on energy usage or machine productivity.”
“We are confident in the accuracy of our Maintenance in Balance (MiB) software service. Just in the marine industry alone, the annual lifecycle costs of operating one ship amounts to £60M and a third of the annual budget is spent on repair and maintenance, to keep ships buoyant and operational. Yet studies show that a staggering 60% of all maintenance is actually unnecessary and can in fact cause more issues going forward. As a total 80% of unplanned maintenance is not age-related and circumvents inspects and service, there has been growing demand for an AI-driven, continuous, accurate and automated condition monitoring and maintenance platform to be designed and implemented.”
“MiB creates a bespoke integrated software platform for prescriptive maintenance monitoring on machinery and all systems, which results in a real-time ‘helicopter view’ of the set-up, from each vessel.”
Maintenance in Balance (MiB) ingeniously combines Machine Learning and Artificial Intelligence (AI) to supply diagnostic support for assets, through condition monitoring techniques that identify anomalies and provide further diagnostic guidance. The MiB asset condition assessment software provides a cutting-edge, integrated platform for foresighted ship machinery maintenance.
MiB drastically reduces inspection and maintenance costs, up to £500 thousand per ship across the year, with predictive fault monitoring and can decrease ship downtime from 7 to 1.5 days. What’s more, MiB helps shipping vessels meet compliant seaworthy regulations, giving quality assurance.
MiB has the added benefits of supplying an extra level of real-time prescriptive maintenance outputs, based on accurate condition and systems performance data and provides next-level operational performance across safety, regulatory, environmental and business areas.
CMServices Global is the brainchild of Simon, who after a career in the Royal Navy and subsequent petroleum industry saw first-hand the importance of accurate, efficient marine maintenance. The company was established in 2016, when CMServices was asked to consult and then join a government-funded grant programme in 2019, highlighting the importance of AI in the shipping business. Simon quickly realised that the same type of programme could be replicated across many different industries, offering an ingenious way to offer condition monitoring.
“We work on a global scale, across Europe, USA, Asia and Australia, supporting many on and offshore companies.”
“CMServices Engineers are maritime professionals, with expertise in vibration/IR technology but we are looking to extend our services further to the other sectors like manufacturing and the renewable energy sector, namely wind turbines.”
“It is impossible to analyse wind-turbines in real-time, due to the fluctuating nature of gearboxes, generators, bearings, through to the speed of the rotating blades. Our state-of-the-art AI-system will demonstrate condition monitoring and predictive maintenance, allowing wind farms across the UK to save money and time on repairs,” concluded Simon.
For more information on MiB and other services, please see the website below: https://cmservicesglobal.com
With enhanced customer service in mind, UNISIG, a global manufacturer of deep hole drilling machines, has commissioned two new SSI Schafer LOGIMAT® vertical lift modules (VLM) into its parts warehouse. Integrated with UNISIG’s enterprise resource planning (ERP) system, the 20 foot tall, high-density storage units keep parts organised and optimise inventory tracking.
Touchscreen interfaces at the VLM modules allow personnel to add or remove inventory pieces, while the purchasing team can access real-time data and reports from their desktops. The module’s trays tilt toward the operator for improved ergonomics when reaching into bins located toward the back of the tray, and a laser highlights the correct bin or location of the part requested.
With 28 tons of inventory capacity in their tray systems, the VLMs exponentially increase UNISIG’s inventory storage capability. This, in turn, allows the company to provide the spare parts customers need as quickly as possible.
“We continue to seek out & identify areas in which we can improve efficiency as well as operational excellence at UNISIG, and this inventory system is a result of that,” said UNISIG CEO, Anthony Fettig. “It also complements our commitment to having the inventory we need to serve our customers.”
The installation of the inventory warehouse VLMs is the most recent of several significant investments
designed to add value to UNISIG’s customer offerings. Earlier this year the company unveiled its newly constructed 5,000 square foot fabrication department.
Equipped with $1.5 million in state-of-the-art technology, the expansion supports the company’s strategy to develop in-house, design-to-finish
production of high-quality sheet metal components used in UNISIG’s product line. By producing many of its parts in-house, the company will preserve and maintain component quality and quantity while optimising the mix of parts that are made internally versus those that are outsourced for production.
www.unisig.com