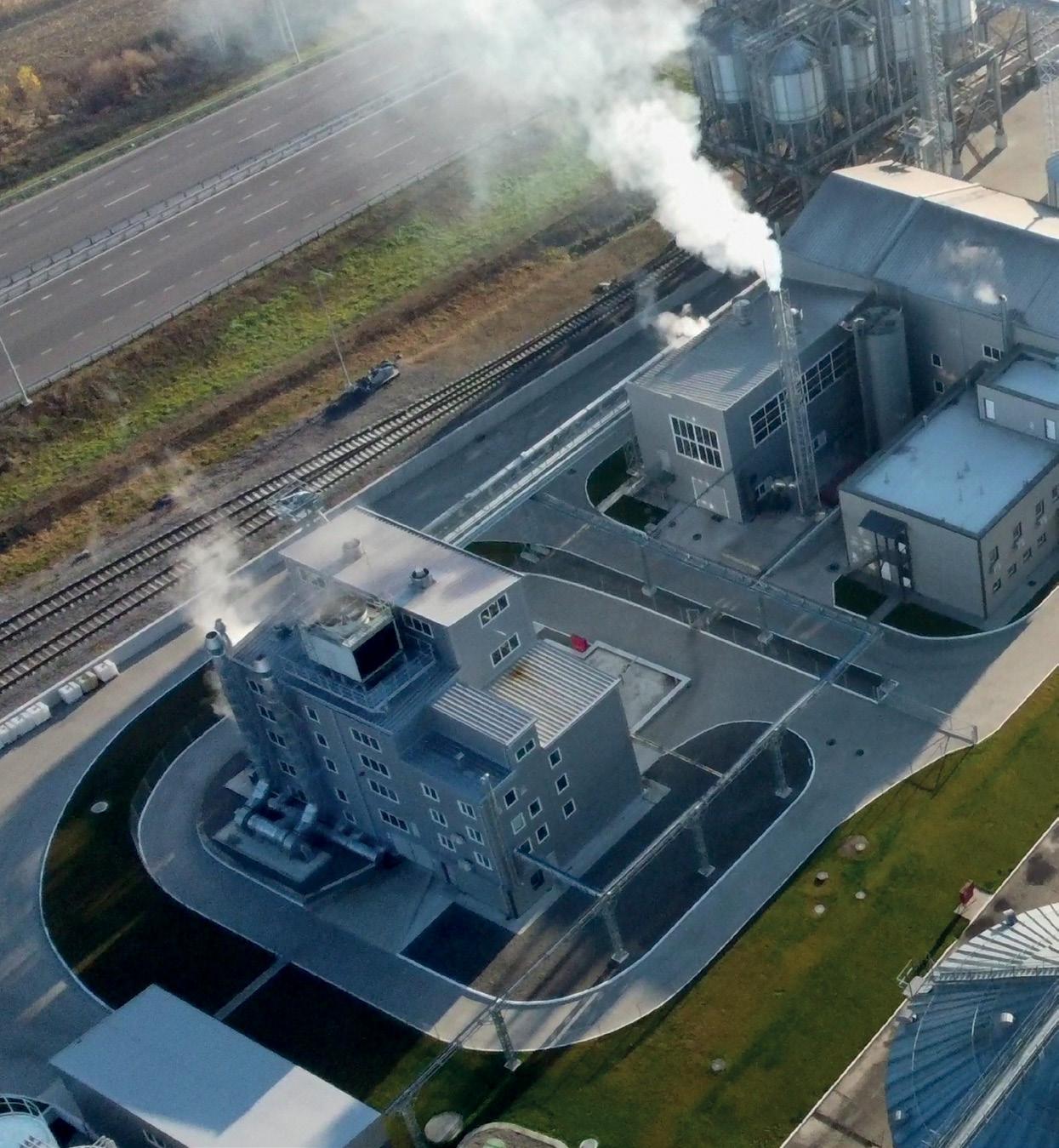
10 minute read
Molini, efficientare per risparmiare Mills-improve efficiency to save
Theenergy efficiency of Italian mills is a highly topical issue. In order to save up to 20 per cent on energy bills, it would be enough to reduce waste by introducing, for instance, state-of-the-art engines or optimising processes. Investments range from 150 to 300 million euros, but not all companies can afford them. New infrastructural models for the sector are under consideration, with plants built horizontally and no longer vertically.
SERVIREBBERO DAI 150 MILIONI
Advertisement
AI 300 MILIONI DI EURO PER AVVIARE UN PROCESSO DI EFFICIENTAMENTO ENERGETICO DEI MOLINI ITALIANI
150 TO 300 MILLION EUROS WOULD BE NEEDED TO START A PROCESS OF ENERGY EFFICIENCY IN ITALIAN MILLS di Mariangela Latella Giornalista professionista esperta del settore agroalimentare
Molti grandi impianti molitori hanno già introdotto interventi per ottimizzare il consumo di energia. Nonostante tutto, oggi, secondo le stime degli esperti, l’industria molitoria italiana, energivora per definizione, consuma 3 miliardi di kWh l’anno, circa un quinto del consumo energetico di tutto il settore produttivo agroalimentare italiano. Potrebbero bastare poche opere (a partire da investimenti nell’ordine di 50mila euro), tutte ammortizzabili - dicono gli esperti - nel breve e brevissimo periodo (massimo tre anni), perché la bolletta dei mugnai italiani possa ridursi fino al 20%. La variabilità non è data solo dal tipo di interventi ma anche dal tipo di molino su cui si effettuano gli interventi.
Ridisegnare il modello architettonico del sistema molitorio italiano
Per alcuni esperti, la riduzione dei costi energetici potrebbe essere ancora maggiore se si ridisegnasse ex-novo il modello architettonico del sistema molitorio nazionale. Il fatto che gli impianti siano strutturati in verticale comporta un risparmio di elettricità legato all’attività di movimentazione verso il basso dei semilavorati della macinazione che passano da una fase all’altra del processo molitorio sfruttando la gravità terrestre. Ridurre l’altezza degli edifici che ospitano impianti molitori, potrebbe comportare un risparmio di energia legato al trasporto dei prodotti verso l’alto. Secondo una stima prudenziale, il consumo attuale dei molini italiani corrisponde a circa 65-75 kWh per tonnella- ta macinata. Questo dato conduce a una bolletta complessiva di tutti i mugnai italiani di quasi un miliardo di euro l’anno, calcolata su un costo dell’energia, peraltro attualmente piuttosto volatile, attestato sui 25 centesimi di euro per kWh. Gli interventi di ammodernamento degli impianti che potrebbero portare a risultati immediati vanno, ad esempio, dalla semplice taratura del motore in base al reale fabbisogno energetico di macinazione per la capacità del mulino (eliminare la cosiddetta sovrastima del motore), all’introduzione di motori altamente efficienti, come gli IE3 e gli IE4. Questi due interventi, effettuati congiuntamente, permetterebbero di ridurre i costi energetici con tempi di ammortamento brevissimi, 36 mesi, ai quali poi seguirebbero guadagni di lungo periodo. Tra questi, un minor costo dovuto anche al risparmio energetico oltre che la maggiore capacità molitoria ottenuta con l’ottimizzazione delle linee di processo. In realtà, poiché alcuni tra i molini più grandi e strutturati hanno già realizzato investimenti di miglioramento energetico, la maggior parte dell’inefficienza energetica che incide sulla bolletta complessiva dell’industria molitoria nazionale, riguarda per lo più, gli oltre 200 piccoli molini, più dei due terzi del totale, che sono stati costruiti senza piani industria-
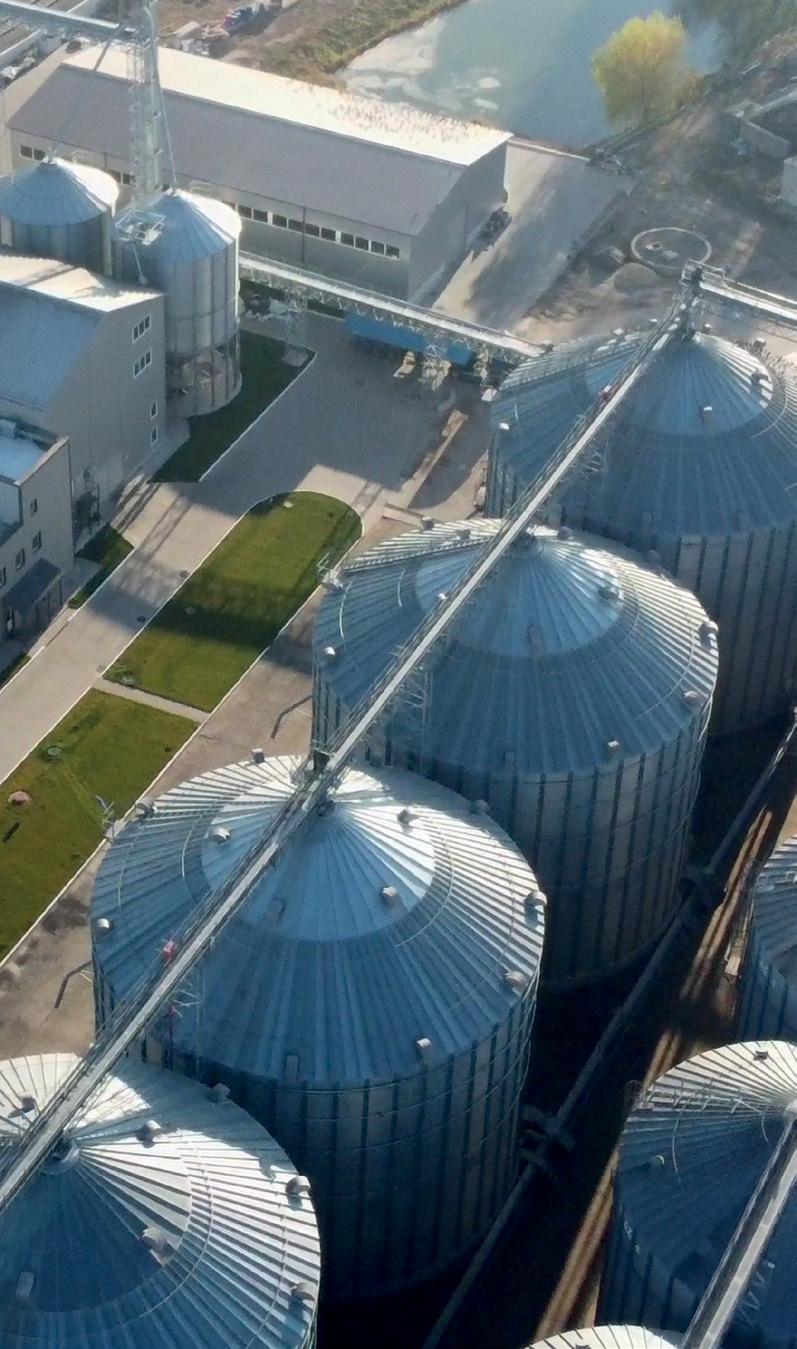
Intervenire Su Motori E Inverter Potrebbe
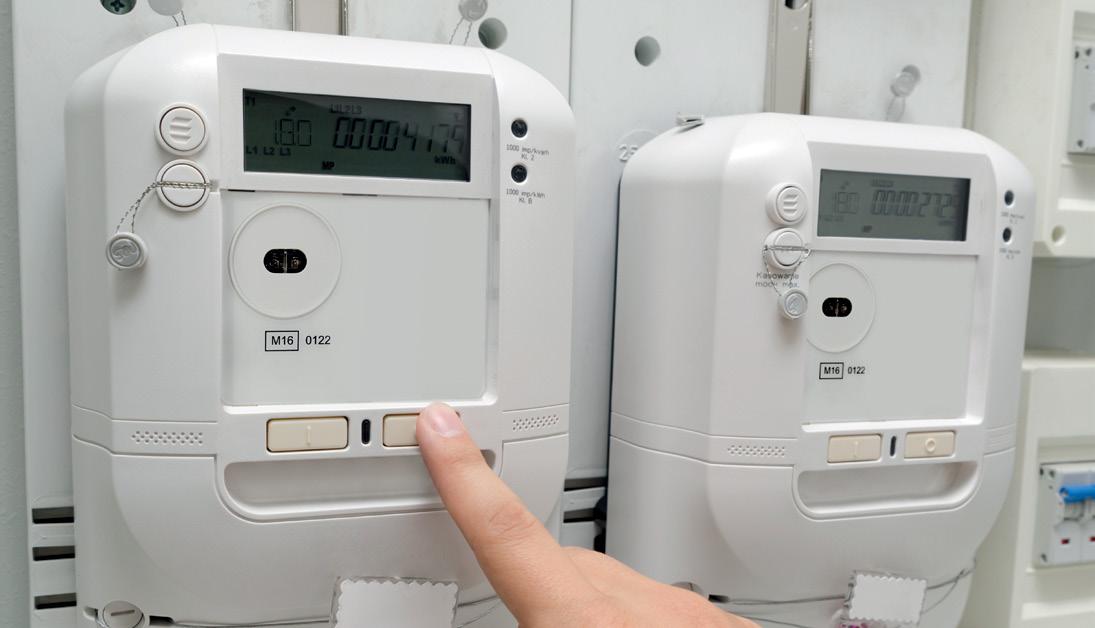
Portare A Netti Risparmi
li a monte tarati ad hoc. In pratica, senza una precisa stima del fabbisogno energetico degli impianti in base alla loro capacità di macinazione e senza un adeguato dimensionamento della taglia delle macchine e scelta dei motori.
Si tratta di riflessioni che assumono un certo rilievo alla luce del processo di transizione ecologica in atto nell’Unione europea che si è posta l’obiettivo della “carbon neutrality” al 2050. Riflessioni che non possono non toccare il tema del crescente deficit energetico dell’Italia sempre più dipendente dall’estero per il suo fabbisogno.
Il problema “energia”
“La coniugazione dei temi di transizione energetica, industria molitoria e produzione della pasta di cui l’Italia è leader mondiale - spiega a “Molini d’Italia” Davide
Tabarelli, presidente di Nomisma Energia - e gli obiettivi di efficienza energetica e di sovranità alimentare richiedono una risposta molto complessa. Anche perché l’obiettivo della neutralità per le emissioni di carbonio che l’Unione europea si è prefissata di raggiungere entro il 2050, è molto ambizioso. Per seguire la road map ufficiale, in Italia bisognerebbe riuscire ad arrivare, a quella data, al 70% di energia da fonti rinnovabili e continuare a importare la restante parte del fabbisogno fino al raggiungimento, certamente non vicino, della tecnica della fusione nucleare e realizzare i relativi impianti per soddisfare la restante parte di domanda interna. Da un punto di vista storico, bisogna precisare che per noi italiani è sempre stata un’abitudine dovere fare economia sull’energia, perché abbiamo i prezzi più alti del mondo. Pensiamo al costo della pasta francese che è inferiore anche perché i cugini d’Oltralpe pagano meno l’energia elettrica che ottengono dagli impianti nazionali di produzione di energia nucleare. Lo stesso dicasi per i paesi dell’est Europa e per la Turchia, altri produttori e trasformatori di derrate agricole primarie, i quali ricevono l’energia dalla produzione nucleare e dal carbone che pagano a prezzo molto inferiore rispetto a quello pagato dall’Italia che si affida molto al gas, fon- te tradizionalmente più cara ma che poi ha subito la crisi del 2002. La situazione oggi si è appesantita, inoltre perché stiamo assistendo a una crescita del deficit energetico a causa dell’embargo russo. È vero che abbiamo diversificato le fonti di approvvigionamento, per ridurre il rischio di riduzione delle forniture, ma in passato lo abbiamo fatto meno di altri Paesi”. In Italia, l’energia elettrica deriva per il 50% da gas che è quasi tutto importato. Mosca nel 2021 è stato di gran lunga il primo fornitore di gas, per il 40% delle importazioni. Dopo le sanzioni commerciali internazionali, le importazioni dalla Russia si sono dimezzate passando al 20% e sono state compensate da un aumento delle importazioni dai gasdotti del Mari del Nord; dall’Azerbaijan; dall’Algeria e, via nave, dal Qatar da dove arriva in forma liquida. Tuttavia, gli aumenti delle importazioni da questi paesi non sono riusciti a compensare del tutto le forniture dalla Russia sicché, si registra comunque una riduzione dei flussi di gas in arrivo. Guardando alla produzione interna di energia elettrica, oggi il 30% deriva da fonti rinnovabili: il principale è l’idroelettrico che è in calo a causa della siccità; il fotovoltaico; l’eolico; le biomasse, i bioliquidi e la geotermia. Sono tutti impianti progettati per soddisfare, per lo più, il fabbisogno dei territori in cui sono situati. “A tal proposito, la geotermia si rivela un settore strategico - specifica Tabarelli -. Se per l’uso abitativo stiamo parlando di un tema del tutto nuovo, per quello industriale elettrico, essa appartiene a una tradizione ormai secolare. Si pensi, ad esempio, ai soffioni boraciferi di Larderello, nella valle del diavolo in Toscana, che sono veri e propri geyser del cui potenziale energetico si registra un grande sfruttamento storico. La produzione italiana di questa forma di energia è facilitata dal fatto che la nostra Penisola ha una grande complessità geologica e un’attività sismica costante. Soprattutto su tutta la fascia tirrenica, dalla Toscana fino all’arcipelago siciliano delle isole Eolie. Quest’areale è pieno di vulcani la cui potenzialità energetica che deriva dal profondo della terra, potrebbe ben essere sfruttata. Da più parti si discute per arrivare al 70% di produzione di energia rinnovabile di modo da soddisfare in maniera green il fabbisogno interno. A me sembrerebbe un po’ un azzardo perché, allo stato dell’arte, non siamo arrivati a un livello di efficienza delle tecnologie su cui si basano questi sistemi e soprattutto di garanzia di continuità delle forniture. In secondo luogo si registrano una serie di impianti di produzione di energia rinnovabile dispersi sul territorio italiano, per lo più orientati al fabbisogno di chi li realizza. In terza battuta, non si può ignorare che l’industria in generale e, in particolare, quella molitoria, ha bisogno di forniture energetiche di grande intensità e soprattutto programmabili. Questi ultimi sono due punti fondamentali che, con le energie verdi, non si riuscirebbe, almeno per il momento, a raggiungere facilmente. Persino con l’energia idroelettrica ci sono problemi: è la principale fonte di energia verde, ma sta subendo le conseguenze della lunga fase siccitosa in cui versa il Mediterraneo e in particolare l’Italia, dove gli invasi e i bacini sui quali insistono questi impianti energetici, sono molto al di sotto della loro capacità ordinaria”.

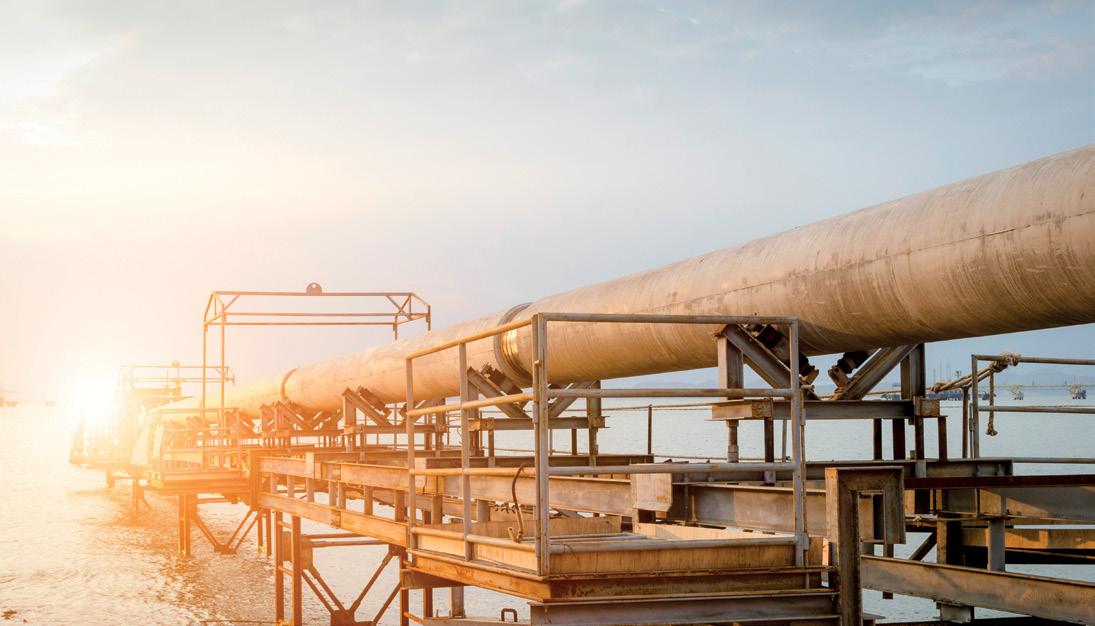
Efficientamento energetico dei molini: la situazione
Il risparmio energetico di un’industria molitoria è il risultato di un lavoro di efficientamento sulle diverse fasi che compongono il processo produttivo e non possono riassumersi in un unico intervento. In alcuni casi, queste operazioni posso richiedere impegni finanziari importanti da un punto di vista economico, in realtà, secondo quanto riferito da alcuni esperti dell’industria molitoria, si tratta di investimenti che possono essere ammortizzati nel giro di un triennio per poi produrre, però, risparmi (in termini di minor consumo energetico) e guadagni di lungo periodo. Gli interventi di efficientamento cambiano in relazione a tanti fattori: dalla struttura del mulino, per fare qualche esempio, alla sua capacità di macinazione, alla sua dimensione. “Con un investimento di circa 1,5 milioni di euro ammortizzati in tre anni, inserito nel piano industriale di un importante molino, abbiamo ottenuto un abbattimento del consumo energetico da 72 kWh per ogni tonnellata macinata a 58 kWh, realizzando un risparmio di 14 kWh per tonnellata macinata”. A parlare è Francesco Nuzzi, uno dei più importanti esperti italiani di tecnica molitoria, titolare della società di consulenza NMT Srl di Bologna che ha costituito dopo avere maturato una solida carriera in Barilla dove ha svolto la funzione di gestione della parte tecnica su tutti gli impianti della multinazionale italiana sparsi nel mondo. “Se guardiamo alla sola filiera del grano duro e quindi al settore pasta - spiega Nuzzi - l’industria molitoria italiana ha un consumo medio per
Il Maggior Spreco Del Comparto Si Registra Nei Piccoli Impianti
tonnellata macinata che oscilla tra i 65 e i 75 kWh. Questa misura si riferisce al consumo complessivo che è la risultanza di tutti i processi dell’attività di un molino: dalla ricezione della merce alla sua uscita dall’impianto. Il progetto che ho curato è partito da un’analisi energetica dell’impianto e ha portato, dopo una serie di interventi tarati su misura, alla riduzione di consumo di 14 kWh per tonnellata. Tra questi, quelli relativi, ad esempio, alla sostituzione delle lampade tradizionali con quelle a led o agli investimenti, economicamente più importanti, legati all’attività di macinazione vera e propria che poi rappresenta l’attività più energivora di tutto il processo molitorio. In questo caso, abbiamo introdotto motori ad alta efficienza energetica, cosiddetti IE3 e IE4. Abbiamo ridotto il consumo energetico di quasi il 20% con un investimento che oscilla tra il milione e il milione e mezzo di euro e un piano di ammortamento triennale. Oltre alla riduzione del consumo energetico della struttura, siamo riusciti a ottenere, per l’efficientamento energetico e meccanico, anche un aumento della capacità produttiva giornaliera da 350 a 500 tonnellate, semplicemente modificando il diagramma di macinazione”.
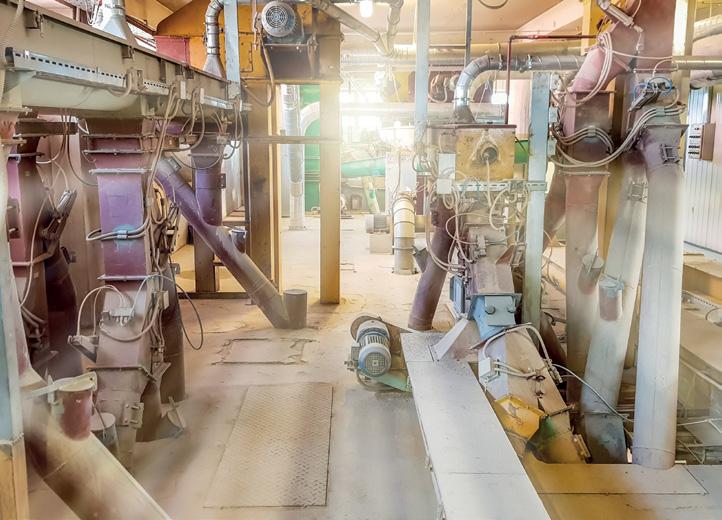
Conti alla mano, si tratta, in sostanza, di un risparmio energetico di oltre 500mila euro l’anno che, una volta superati i tre anni di ammortamento per rientrare delle risorse investite, hanno iniziato a generare un guadagno netto di pari misura per l’in- dustria che va ad aggiungersi all’aumento della capacità molitoria di 150 tonnellate al giorno in più a parità di costi fissi. Il problema principale è che i piccoli molini, che rappresentano la maggior parte del tessuto industriale del settore molitorio, non sono in grado di affrontare investimenti di questa portata. Una cosa non da poco perché sono proprio i piccoli molini che rappresentano il perno del dispendio energetico. In parte per una mancanza di economie di scala che regolano il modello economico dell’attività: più è piccola, in sostanza, più è costosa da un punto di vista energetico, sopperendo a questi costi con turni di lavoro importanti. D’altro canto, il consumo di elettricità non è direttamente proporzionale alla quantità di grano macinato anche a causa dei progetti realizzati a monte della costruzione dei molini.
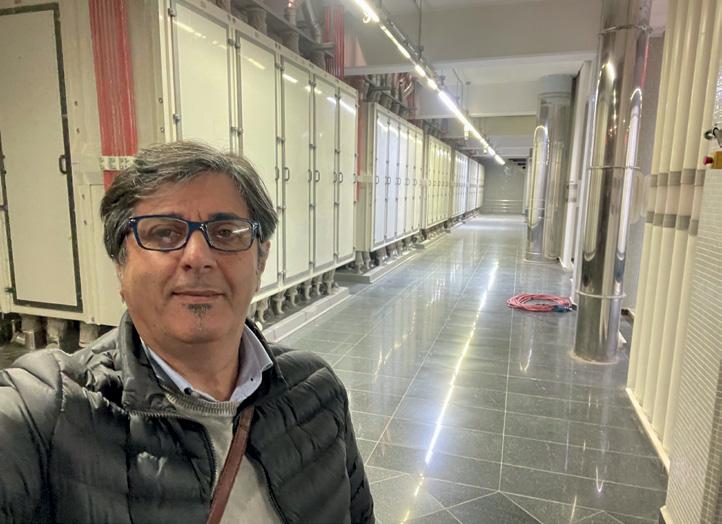
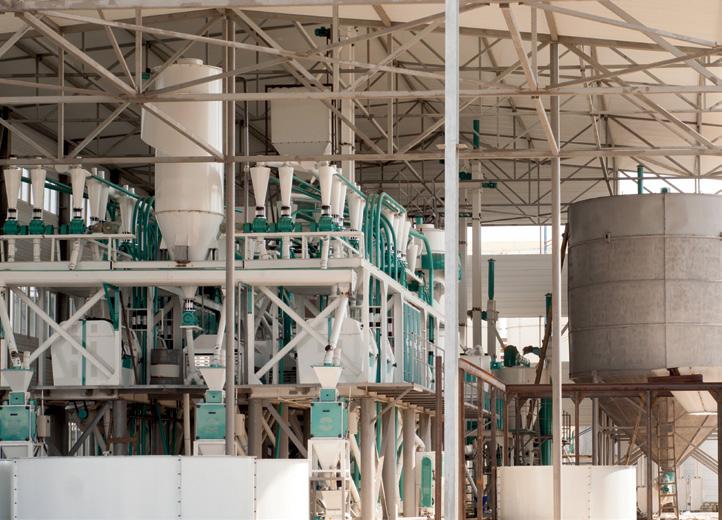
“La stragrande maggioranza degli impianti italiani sono piccoli e vengono gestiti da storiche famiglie di mugnai, attive nel settore, in molti casi, da generazioni - spiega Riccardo Scarcelli, titolare di RAM elettronica ed esperto di automazione molitoria -. In quasi tutti questi molini, si è proceduto all’installazione, all’avvio dell’attività, di motori molto spesso sovrastimati, ossia che consumano più di quanto sia necessario in relazione alla reale esigenza per cui quell’utenza è installata nel processo molitorio. Questa discrasia deriva soprattutto dalla mentalità del mugnaio che per tanti anni ha considerato come costi fondamentali non tanto quelli energetici, quanto quelli della manodopera. Sicché, installando motori potenti, sovrastimati, pensava di potere incidere sulla riduzione del costo della manodopera. Il risultato è che oggi abbiamo molti molini con motori importanti che non sempre vengono impiegati correttamento, per i quali basterebbe semplicemente ritararli in base alle effettive necessità dell’impianto per ottenere già un risparmio significativo. Emerge che il costo della manodopera è accessorio e che la riduzione della bolletta energetica contemporaneamente all’aumento dei costi energetici si ottiene ottimizzando tutti i processi produttivi, nel loro insieme. Per avere efficienza energetica bisogna lavorare sull’80-85% dell’efficienza del motore”.

Secondo una stima prudenziale, circa il 30% dei molini italiani ha dei motori sovrastimati rispetto alla loro effettiva esigenza, determinando questa sola inefficienza di processo, un aumento del consumo energetico che oscilla tra il 7 e il 9%. “Si può arrivare a ottenere risparmi importanti anche con piccoli investimentiprecisa Scarcelli -. Ridurre il costo in bolletta dall’8 al 13% intervenendo nella sola fase di macinazione oppure ottenere abbattimenti dei consumi fino al 15% se sommiamo alle ottimizzazioni legate alla riduzione dell’eccessiva potenza del motore anche l’inserimento di macchine più efficienti energeticamente. Per intervenire in maniera incisiva sul risparmio in bol- letta dei molini, servirebbe una riprogettazione delle loro infrastrutture. Oggi sono strutturati su più piani, ad esempio, ma questo richiede un consumo di elettricità maggiore legato alla movimentazione verticale della materia prima, dall’alto verso il basso e viceversa”.
L’altezza del molino, quindi, ha un’incidenza sul consumo energetico. Un grande molino italiano che lavora su diversi livelli, per fare un esempio generico, spende non meno di 350mila euro solo per la verticalizzazione della sua attività. In questo senso, la fortuna dei piccoli molini e che non hanno l’altezza. “Mettendo da parte la questione infrastrutturale, che non è di poco rilievo - chiosa Scarcelli -, si può ottimizzare il consumo energetico con alcuni investimenti di base. Basterebbero, ad esempio, tra i 200mila e i 250mila euro per ridurre l’eccesso di potenza dei motori ed introdurre quelli di ultima generazione nella fase di macinatura. Se si introducessero degli inverter, laddove è necessario perché non si può ovviare, ad esempio, con l’inserimento di cinghie e pulegge che sono sempre preferite, basterebbe una spesa che oscilla tra i 100 e i 150mila euro. Gli interventi di domotica industriale costano circa 50mila euro e permettono di utilizzare l’energia solo quando essa è effettivamente richiesta dalle macchine. Tutte queste spese prevedono rientri brevi dell’investimento: circa tre anni. In compenso, porterebbero a risparmi minimi del 10% per tutta la vita del molino se si considera che i motori si cambiano ogni 15 anni, mentre gli inverter ogni cinque”.