Includes: Automechanika Birmingham review, Autotech supplement, TechFest report, Clutches, Steering & Suspension, Batteries, & much more!
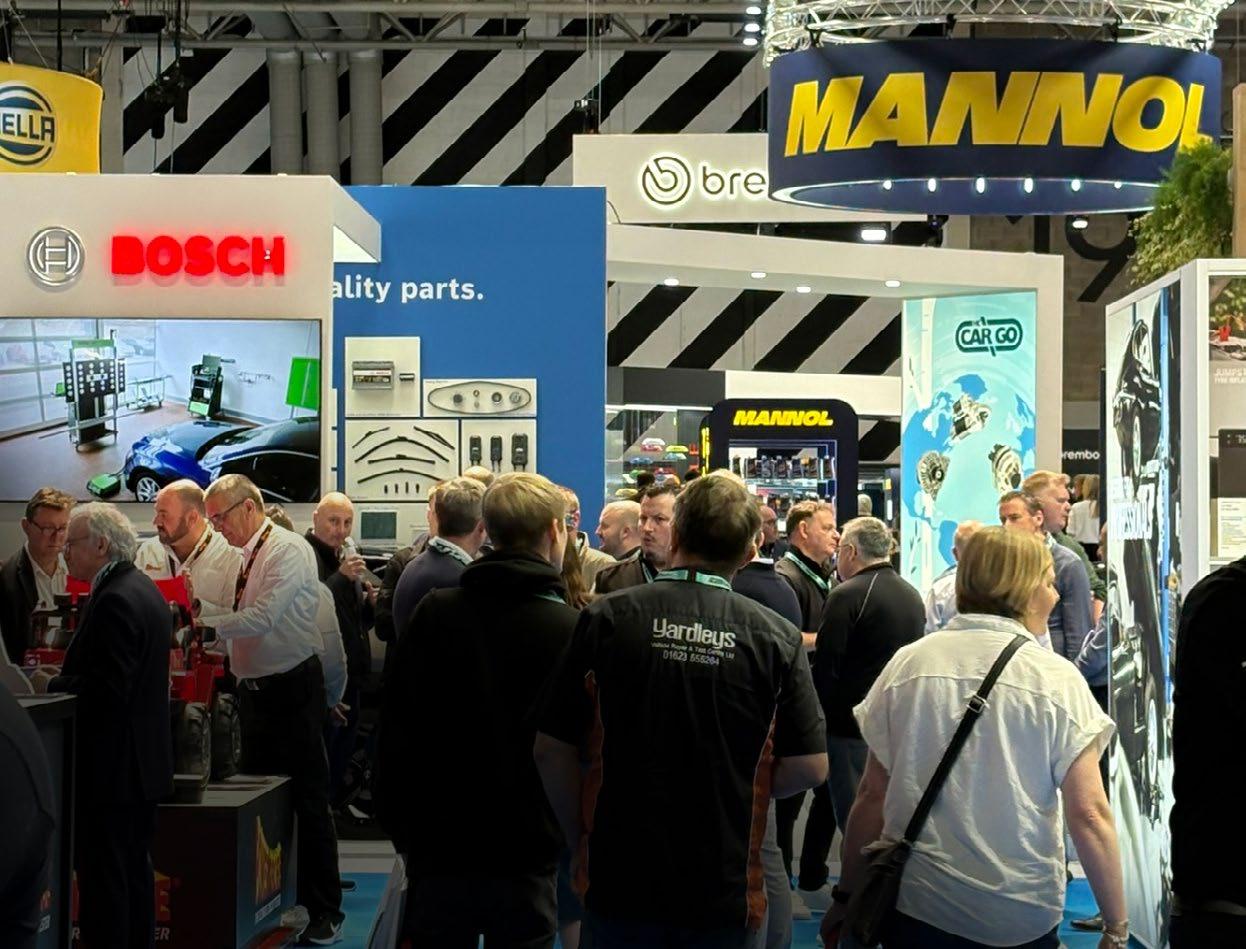
Includes: Automechanika Birmingham review, Autotech supplement, TechFest report, Clutches, Steering & Suspension, Batteries, & much more!
RECENT TRADE EVENTS HIGHLIGHT GROWTH OF PEER-TO-PEER SUPPORT AND A THIRST FOR KNOWLEDGE AND FUN!
The driveshaft assembly plays a vital role in transferring the driven force of the transmission to the wheels. At the same time, it has to flex and turn with the independent suspension system, enabling low rotational resistance and transferring axial and radial forces to the driven and steered wheels.
All febi driveshafts are developed to match OE performance and design specifications to ensure proper fit and function.
We supply over 340 Drive Shafts for popular vehicles like the BMW i3, VW e-Golf and Ford Transit. We also supply a huge range of peripheral parts like Drive Shaft Bearings, Joint Kits and CV Boot Kits.
Your No.1 for Driveshafts
Being a successful technician and/or workshop owner today is the result of an extensive amount of knowledge, experience and continuous learning to keep up with technology and trends. In addition to skills, modern repair demands access to reliable data, the right tools and the right attitude.
Trade shows provide a vital platform to discover the latest industry innovations and networking opens doors to new partnerships and valuable knowledge sharing. Continuous training and upskilling are essential to keep skills sharp and businesses competitive. Equally important is accessing support—not just for technical and business challenges, but for mental health too –ensuring resilience and well-being. These elements form the foundation for success, innovation, and sustainable growth and were the focus of exhibitors at Automechanika and also GSF TechFest Midlands. A full review of Automechanika begins on p48 and a report on the latter from p8.
We have two case studies in this issue and an additional video fault to fix from new contributor Ben Johnson –which can be found in our Autotech special feature from p20 – which highlights the technical and business support available from this year’s sponsors and inperson at our Workshop Live event in September – we hope to see you there!
Nicola St Clair Editor
Nicola@autotechnician.co.uk
P8 Report from GSF TechFest Midlands P10 Understanding Average Invoice Value
P14 Keeping Your Ramps Rolling: The Case for Contractors
P16 Case study: AdBlue investigation
P20 Autotech feature: Exclusive video case study, practical advice & support from sponsors & BM7 series fault-to-fix
P34 Clutch aftersales support
P38 Steering & Suspension: Beyond Parts
P44 The business of battery replacement
P48 Automechanika Birmingham Show Review
P59 Parts, Tools & Tips
* View and download previous digital issues at: www.autotechnician.co.uk instagram.com/autotechnician_magazine youtube.com/@AutotechnicianMagazine facebook.com/Autotechmagazine bsky.app/profile/autotechnician.bsky.social
Two Herefordshire garages have received prestigious national honours at the 2025 Automechanika Birmingham Garage Awards.
Oldfields Garage, based in Leominster, was crowned Garage of the Year, while Markhams Garage in Kingsland took home the award for Best Single Site Garage at a ceremony held at the NEC on Wednesday, June 4, in front of a packed audience of industry professionals, suppliers, and garage owners, and were held in partnership with the Independent Automotive Aftermarket Federation (IAAF).
Tim Benson, Managing Director at Oldfields Garage, accepted the top award alongside MOT tester Steve Neill. “We’re incredibly proud to have won this award, especially
with so many fantastic garages in the running,” said Benson. “Picking up seven awards in the last 18 months is just amazing, and it really shows the hard work and professionalism of our whole team.”
Benson also praised fellow Herefordshire winners Markhams Garage, highlighting the county’s high standards. “It’s great to see another Herefordshire garage getting national recognition,” he added.
Simon Powney, Director at Markhams Garage, expressed his excitement at winning Best Single Site Garage. “To have been named Best Single Site Garage is absolutely amazing,” he said. “We’ve worked so hard to get noticed in the industry and to give our customers the very best service.”
The Institute of the Motor Industry (IMI) has expressed disappointment over the government’s new ‘Invest 2035: The UK’s modern industrial strategy’, which offers little recognition of the automotive sector despite its vital role in the UK economy.
The strategy outlines a £1.2 billion investment in training for growth sectors such as defence, engineering, digital, and construction. However, the IMI noted a glaring omission of support for the automotive industry — particularly outside the manufacturing sphere — despite pre-election pledges by the Labour Party to implement a dedicated Automotive Strategy.
Sarah Sillars, Interim CEO of the IMI, welcomed the overall focus on skills but questioned the lack of targeted support for the automotive workforce. “It is encouraging to see investment in skills, but it appears the promise of a dedicated Automotive Strategy has been kicked into the weeds,” she said. “This is despite the sector providing 866,000 jobs and contributing £37 billion in GVA as of 2023.”
Sillars highlighted the sector’s crucial role in advancing electric vehicle (EV) adoption — key to the government’s net-zero targets — and warned that workers supporting these technologies are being overlooked in policymaking. She pointed to the underrepresentation of the aftermarket and technician workforce in recent government documents, including the Skills England Report.
The IMI reports over 16,000 current vacancies in automotive and estimates a need to replace 144,000 workers by 2032 due to retirement. The organisation warns that without urgent action, the sector may struggle to keep up with technological change and the ongoing transition to low-emission vehicles.
To address these concerns, the IMI’s manifesto, Driving the Future of Automotive Professionals, lays out practical steps to attract and train talent, including apprenticeships, upskilling programmes, and defined career pathways.
Despite the lack of focus in the new strategy, the IMI pledged to continue working with employers, educators, and government bodies to ensure the sector is equipped for the challenges ahead.
The Motor Ombudsman has unveiled its updated Motor Industry Codes of Practice, which play a central role in the self-regulation of motor industry businesses who have voluntarily committed to delivering high standards of work and service to consumers. The Codes of Practice have evolved in line with that of legislation , technologies and shift in customer buying trends.
More than 7,500 independent garages and franchise dealers, as well as 46 vehicle manufacturers and 21 extended vehicle warranty providers, abide by these Codes, which now reflect new technologies within vehicles, and the growing prominence of alternative fuelled vehicles (AFVs), such as electric cars (EVs).
www.TheMotorOmbudsman.org/consumers/our-codes-of-practice
The Independent Garage Association (IGA) has announced the finalists of its British Independent Garage (BIG) Awards 2025 – who are being recognised for going the extra mile and raising standards for the entire industry.
Stuart James, CEO of the IGA, commented: “We’re incredibly proud to reveal this year’s BIG Awards finalists. An outstanding line-up of individuals and businesses who are driving real progress across our industry. Their passion and determination are raising the bar and redefining what success looks like in the independent garage sector.”
Congratulations to all the finalists, who can be found at: https://independentgarageassociation.co.uk/meetthe-2025-big-awards-finalists/.
Winners will be announced at the BIG Awards ceremony on 12th September 2025 held at Hilton Birmingham Metropole. Tickets are available on the website.
For peace of mind always use a Garage Equipment Association member. GEA accredited engineers work to an industry code of conduct. Your assurance their skills and knowledge have been independently assessed.
GSF Car Parts has strengthened its network with the opening of a new branch in Chesterfield, Derbyshire, on 23rd June 2025. The new location, based at Broom Business Park, marks GSF’s fifth branch opening this year, with seven more planned before the end of 2025.
Regional Manager Rob Lambert said the new Chesterfield branch fills a strategic gap in GSF’s network, easing pressure on nearby locations in Mansfield and Sheffield and boosting local coverage.
Ivor Searle launches online vehicle look-up for international customers
Cambridgeshire-based engine and gearbox remanufacturer Ivor Searle has unveiled an online E-catalogue (E-CAT) system, believing it to be the first company globally to offer vehicle registration look-up across multiple countries. The innovation allows international customers—particularly in France, Italy, and Spain—to enter a vehicle’s registration details and instantly access the correct product codes and stock availability via its website.
The E-CAT system integrates with the global TecDoc aftermarket database and supports the company’s expanding European distribution of remanufactured petrol and diesel engines—currently averaging 600 units per month.
Commercial Director David Eszenyi highlighted the growing demand for remanufactured engines as consumers extend vehicle life cycles amid rising ownership costs and delayed electric vehicle transitions. Exports now represent nearly 20% of Ivor Searle’s annual turnover.
Aircon expansion in Europe
Kent-based aircon and leak control specialist Primalec has announced the establishment of Primalec srl in Turin, Italy. As well as the new commercial office, there will also be warehousing and production facilities, enabling the brands developed over the past 45 years to better serve the needs of customers and supplier partners in the region.
The Driver and Vehicle Standards Agency (DVSA) has completed a successful trial aimed at tackling ‘ghost’ MOTs – fraudulent tests where vehicles receive certificates without being physically inspected. As part of the sixweek initiative, 172 testers from 62 garages took photos of vehicles at the start of MOT tests, uploading over 13,000 images to the MOT Testing Service (MTS). This creates a verifiable digital record proving vehicle presence during the test.
The trial spanned a broad spectrum of testing stations, including independents, dealer chains, and local councilrun facilities, and covered all vehicle classes. Despite the added photo requirement, testing times remained unaffected, with the standard 40-minute duration maintained and retest times increasing only marginally –from 7 to 9 minutes. Garages responded positively, with
many describing the process as simple and stress-free. Chris Price, DVSA Head of MOT Policy, stated that although only a minority of testers engage in issuing ghost MOTs, the practice compromises road safety and undermines testing integrity. He emphasised the DVSA’s commitment to ensuring high standards and a level playing field for all operators.
The DVSA plans to initiate a second, larger-scale trial to further test the software’s effectiveness and usability across more garages.
The initiative forms part of DVSA’s broader efforts to enhance testing reliability and public trust in the MOT system, reinforcing the agency’s mission to keep UK roads safe and free from unsafe, uninspected vehicles.
ACTRONICS is
TechFest’s purpose is to build relationships between technicians and suppliers, while making learning both fun and personable. GSF Car Parts' desire to promote its speed of delivery was not subtle...
While there are plenty of trade events from which to choose, GSF Car Parts reckons its TechFest is different to a typical trade show; Rob Marshall finds that it is not wrong
It cannot be denied that GSF Car Parts is undergoing a revolution. Under fresh ownership and management, the turnaround has seen the firm grow by 20% every year for the last three. A new National Distribution Centre, increased product ranges, improved and increased nationwide branches, faster delivery times and more accurate product ID are proof that the extensive investment programme is bearing fruit, all funded through cash flow and not venture capitalists.
Doers rather than sayers
Interestingly, both the new CEO, Steve Horne, and Chairman, Sukhpal Ahluwalia, hail from competing suppliers, giving credence that not just that they are 'car people' but they also understand our industry. While they emphasise the importance of reaching out to the independent garage trade, GSF has put its money where its mouth is with TechFest, an automotive technology celebration, at which both men were not just present but also chatted freely with visitors.
What is TechFest?
Following the rousing successes of the inaugural 2024 event, which saw 2,000 visitors flock to Wembley Stadium, the event
headed to Manchester on the 21st of May. The following month, TechFest Midlands landed in Coventry, offering delegates opportunities to network, discover innovations, understand new tech, witness fresh repair techniques and experience the latest training schemes. Yet, GSF Car Parts has sprinkled a liberal dose of fun into proceedings, by blending a trade event with a car show, an evening out, chances to network and socialise, plus complimentary food and drink. Even access and parking were free.
GSF Car Parts' CEO, Steve Horne, explained that many technicians think that trade shows are not worth their time to attend, which explains why GSF has made considerable efforts to change perceptions. As engaging as they were, the tech talks were all optional and care was taken to ensure they did not become full-blown lectures, because each of which was restricted to between 15 and 30 minutes.
TechFest's casual but professional nature fostered opportunities for technicians to meet well-known brands personally, which supported the event with tools, demonstrations, training and competitions. GSF finds this particularly valuable for vehicle repairers, especially as CEO Horne has discovered from his visits to independent garages that customers are approaching technicians directly, with questions about which parts are being fitted to their cars. On the day, special deals included Delphi’s DS150 diagnostic VCI being reduced from £1,845 to £750, Bosch’s range of
reduced-price DAS3000 ADAS calibration bundles ranging between £9,650 and £10,400 and Ring offering a free head torch, when buying its flexible under bonnet lamp for the TechFest price of £25.95. As if this were not enough, every business attending received a £50 voucher to spend at the event.
The main stages offered plenty of opportunities to update technical skills, from Schaeffler looking at common clutch installation issues to Brembo highlighting EV braking complications. You could also learn about the march of technology from Neil Pattemore (IAAF) to Matt Cleevely discussing the commercial decisions of embracing EVs. Garage owners could also discover more about recruitment, such as from Ambi Singh from easy2recruit, and how to bolster their digital marketing from Mat Watson at CarWow.
What to expect from GSF for the remainder of 2025 GSF’s expansion is not slowing, with existing sites being refurbished and 12 new branches being opened this year, including in Swindon, Bedford, Morpeth, Lee and Chesterfield. It is also expanding the range of parts in its Drivetec brand, such as radiators and air conditioning condensers. The firm also has bigger plans for 2026's TechFests. Before then, do not forget that it is not too late, because TechFest will return to Wembley on Thursday, 18th September, from 3pm to 10pm. More details can be found: https://gsftechfest.com/
By Tina Drayson, Head of the Garage Section, IAAF
In today’s competitive automotive industry, understanding your numbers isn’t just an advantage—it’s essential. I’m Tina Drayson, Operations Director of CCM and Head of the Garage Section with the IAAF, and I’m here to share valuable insights into the key data points that can drive real business improvement.
Average Invoice Value (AIV) is a term we hear frequently in the automotive aftermarket; it has become a bit of a buzzword. But what does it really tell us, and why should we pay attention? AIV refers to the average amount a customer pays per job. It is a key performance indicator that gives garage owners valuable insight into how much revenue is being generated per vehicle. It is also a useful metric for forecasting, helping us plan based on expected workload and business throughput.
There is often a perception that a higher AIV reflects a workshop firing on all cylinders, meaning that technicians are completing thorough vehicle health checks, identifying additional work, and service advisors are effectively communicating this to customers and securing authorisation. This not only drives revenue, but it also improves workshop efficiency, fewer cars through the door, less movement on and off ramps, and better use of technician time.
However, a higher AIV isn’t always straightforward. It can also indicate that your workshop is handling more complex jobs, such as diagnostics, engine work, or clutch and timing repairs. While this work brings in higher revenue per job, it also requires tighter management of time and parts and carries more risk if not carefully controlled as jobs can easily overrun. How often do you find yourself unable to charge the customer for all the time spent on these involved repairs?
On the other hand, a lower AIV typically reflects a high volume, quick turnaround environment. These are the MOTs, services, tyres, wiper blades and essential work, but often done on customer instruction only. It may suggest that your team are not consistently performing health checks, or that service advisors are hesitant to upsell additional work. This can be due to a lack of confidence, training, or the common misconception that “it’s too expensive for the customer” which we base on our own feelings about a value.
Low AIV means you will need more vehicles through the workshop each day to meet your revenue goals. That means more movement, which can cause reduced efficiency and more admin putting additional load on the service advisors.
While volume of jobs might make up for it on paper, lower margin jobs often leave little room for profit and missed opportunities to serve customers more thoroughly.
There is another important factor to consider when looking at AIV, the labour/parts split.
In a healthy garage, I would expect a split of at least 55% labour to 45% parts.
When AIV is low, especially in businesses that carry out high volumes of MOTs for retail and/or trade, we often see a split of 65% labour to 35% parts. That is because these jobs are labour only, without parts revenue.
Conversely, when AIV is higher, it's usually due to part heavy jobs (e.g. gearboxes, engine rebuilds, clutches), which can bring the split closer to 50/50 or even tip more towards parts. While that looks great for our average invoice value, we must remember that our core product as a garage is labour. That is where we make our real margin.
A balanced perspective
So yes, chasing a higher AIV can be beneficial, but it is not just about selling more. We have a duty of care to our customers, it is about doing a thorough job, identifying work customers need, and building trust through honest, informed communication.
It is just as important to focus on the right type of work, ensuring your labour sales remain strong and your team is confident in identifying and recommending necessary repairs.
And finally, don’t fall into the trap of comparing your AIV with other garages. Every business is different, your customer base, pricing model, and service offering will influence your numbers. A garage doing fast-fit work will have a very different AIV from one specialising in diagnostics or fleet maintenance. Instead, use AIV as an internal benchmark. Track it month to month, understand what is driving changes, and use it to shape your own improvement strategy. The goal is not to match someone else’s number; it is to optimise your own.
Food for thought, which would you prefer:
Total sales £95,689.00/jobs 226 = AIV £423.40 OR
Total sales £95,689.00/jobs 351 = AIV £272.62.
So many car enthusiasts are hungry for enhanced driving performance. Brembo’s Upgrade braking systems help them boost their potential.
Whether drivers want a sporty response on normal roads, own a supercar or spend their weekends competing on the circuit, there is endless demand for performance upgrades. Leading premium OE and Aftermarket braking specialist, Brembo, has designed a powerful parts programme expressly for drivers seeking that crucial edge. The company’s motorsports-inspired Upgrade series of brake calipers, pads, discs and accessories gives car lovers access to a world of unique details, superior quality, durability and exceptional vehicle performance. Brembo Upgrade simplify the replacement of OE braking systems with a custom set of more advanced, unmistakably sporty brakes, elevating cars to the next level of stopping performance. Every Upgrade part is built on Brembo’s 50-year motorsports experience, and manufactured in-house. Two, outstanding Upgrade families are available:
Is ‘the heart and soul of racing in a box’ and is the market’s most comprehensive offering of braking upgrades for high performance driving on the road or track.
Each kit includes a selection of distinctively painted, racing-style aluminium fixed calipers to suit every aspiration and aesthetic. Options include two-piece A calipers directly derived from Brembo’s most popular OE application; M monobloc designs for both road and racetrack; S calipers for club and weekend racers, and R calipers for the most challenging performance conditions.
For drivers who demand the very best for their car, Brembo’s BM calipers are made with ground-breaking 4D casting technology, allowing a level of design efficiency usually only feasible in racing billets or forged calipers. Each GT caliper is paired with slotted or cross-drilled discs, pads, brackets, hoses, hardware and brake fluid.
Options include
• BM8 WITH 8 PISTONS FOR HIGH END VEHICLES AND DISCS UP TO 420mm x 40mm
• BM6 WITH 6 PISTONS FOR SEDANS AND COUPES AND DISCS UP TO 410mm x 36mm
• SPORTY BM4 WITH 4 PISTONS FOR DISCS UP TO 380mm x 30mm
The Upgrade offering is completed by carbon ceramic (CCM) brake discs which are 50% lighter than cast iron, yet highly stable, corrosion-free and heat resistant when braking at speed, and dedicated CCM brake pads, providing a complete replacement solution for most performance cars.
Our biggest and best TechFest so far is coming soon.
Over 70 suppliers in our trade show zone
TechTalks and demonstrations
Supercars and collectors’ classics
Entertainment and main stage speakers
On-the-day only savings and giveaways
Award-winning food
Complimentary refreshments
Family-friendly - all welcome PRESENTED
Free parking, free entry, free food, free drinks Bring your team to Wembley
Please join us on Thurs 18th Sept from 3:30pm ‘til late.
Autotech Recruit explores how contractors are becoming an essential, flexible workforce solution, particularly for independent garages and fast-fit centres navigating ongoing technician shortages
The automotive industry is facing immense pressure. A persistent skills shortage combined with recruitment challenges has left many businesses scrambling to keep operations running smoothly. Whether it’s a nationwide fast-fit chain with a dedicated HR department or an independent garage juggling day-to-day operations and hiring responsibilities, one thing remains constant—unfilled roles create unacceptable risks for any business.
Putting it into context, an empty workshop ramp isn't just idle space; it’s an expensive problem. With the potential to cost up to £1,000 a day in lost revenue, prolonged vacancies can significantly affect a business’s bottom line. Hiring for permanent positions can take up to 44 days on average in the UK. For businesses in the automotive sector, where finding candidates with specialised skills can take even longer, these delays could be crippling.
While the ultimate goal for most businesses is to recruit and retain talented, permanent employees, relying solely on this approach during times of acute demand can be detrimental. This is where contractors become an essential part of the solution, filling critical gaps and providing the flexibility to maintain operations without long-term commitments.
Every single day that a workshop ramp remains empty directly affects revenue, productivity, and customer satisfaction. This is when temporary vehicle technicians and MOT testers can step in almost immediately to ensure business continuity. Their ability to hit the ground running offers a bridge solution, allowing businesses to keep operations steady while continuing the search for permanent staff.
Charlotte Hampson, Garages Agency Manager for Halfords, underscores this point by showcasing how contractors play a critical role in her company’s ability to maintain productivity. With over 560 garages across the UK in the Halfords network, including National Tyres and Autocentres, the pressure of consistent staffing is unrelenting. She explains, “With such a shortage of skills across the industry, highly skilled candidates are undoubtedly driven by salary and hours when seeking permanent employment. It’s a highly competitive pool which we are all fishing from, but it’s vital that, while we are sourcing
the right candidate, our ramps remain open. This is where contractors come in, it’s a resource we can turn on and off on demand.”
At Halfords, contractors play a key role not only in bridging resource gaps but also in ensuring seamless operations when permanent staff undergo training. This proactive approach allows Halfords to maintain exceptional customer service and steady revenue streams while investing in the continuous development of its team. It highlights the value of contractors as a strategic and flexible workforce solution that supports both business growth and employee advancement.
The hiring process is time-consuming and resourceintensive, a fact that automotive HR managers are all too familiar with. From advertising roles to shortlisting candidates and conducting interviews, the weeks quickly add up. For smaller garages where business owners or managers often handle recruitment themselves, this can place immense strain on already-stretched resources.
Contractors alleviate this challenge by offering immediate relief. Instead of leaving essential work undone or spreading current employees too thin, contractors step in to keep workflows uninterrupted. This is especially advantageous given the highly specialised skills required in the industry— skills that often make finding the right permanent candidate a lengthy and arduous process.
The automotive industry operates within a highly dynamic environment. Seasonal demand, fluctuations in customer needs, and new vehicle technology increasingly rolling onto forecourts requiring an updated skill, can all create workforce shortages. Contractors not only provide the support and skills necessary to weather these challenges but also offer unmatched flexibility.
Charlotte highlights how this flexibility gives Halfords a competitive edge: “We can typically secure cover within just a few days, ensuring our operations continue without disruption. And when demand shifts, we have the agility to adjust support as needed.' This adaptable approach to workforce planning
allows Halfords to stay responsive, efficient, and well-prepared for the evolving needs of the business and its customers."
Perhaps one of the biggest misconceptions about contractors is that they are inherently expensive. However, when you examine the full financial picture, the opposite often holds true. Consider that an empty ramp at £1,000 a day equates to a £30,000 loss in revenue over a month. Add to this the recruitment costs associated with advertising, interviewing, and onboarding, and the expenses of not hiring a contractor start to outweigh their fees.
Contractors not only minimise lost revenue associated with prolonged vacancies but also reduce strain on existing employees, ensuring that quality of service and employee satisfaction aren’t compromised. This, in turn, protects the business’s reputation in a competitive market where customer loyalty is paramount.
Temporary workers don’t just provide a stopgap solution— they offer businesses a chance to evaluate potential candidates for permanent positions. Trialling a contractor allows businesses to assess not just skills but also cultural fit, teamwork, and adaptability. When contractors prove they’re the right fit, transitioning them into permanent roles is seamless, turning what was initially a short-term necessity into a long-term asset.
This trial-before-commit process benefits both parties, creating opportunities for contractors to demonstrate their worth, while giving businesses confidence in their hiring decisions.
Relying solely on permanent recruitment strategies during times of staffing shortages can leave a business vulnerable. Whether it’s covering a temporary gap or addressing seasonal demand, contractors offer a practical and cost-effective alternative that ensure operations remain uninterrupted.
For businesses of all sizes, the choice isn’t always between permanent staff or no staff, it’s about integrating flexible solutions that support long-term goals. Contractors keep the ramps rolling, safeguard revenue, and provide the breathing room businesses need to find the right permanent team members.
As Charlotte Hampson aptly puts it: “Managed effectively, contractors quickly return our investment.” It’s a sentiment the entire automotive sector can adopt to overcome today’s challenges and build resilience for the future.
Navigating Staff Shortages is a new guide from Autotech
Recruit offering practical strategies to help independent workshops tackle today’s technician shortage. With insights from across the industry, it explores flexible staffing models, future-ready skills development, and smart use of technology. Download the guide now at: https:// autotechgroup.co.uk/navigating-talent-shortages/
Mercedez E220 Blue TEC 2.1 2014, Engine code: 651.924
Mileage: 80,670
Check engine light on fault codes: P229E13, P229F09, P13E400, P13F600, P13DF09
Customer complaint: AdBlue warning displayed on the instrument cluster, check engine light on and MOT fail
By Des Davies AAE MIMI, Top Gear Motor Services
A previous garage had cleared the codes and messages only for the codes, messages and the check engine light to display again after driving the vehicle a short distance. There is no point clearing codes and messages because they will reappear until you fix the problem. You can only clear the message with your fault code reader for approximately 1,000km, and then it will return and fail to start again.
I switched the ignition on and started the vehicle up to confirm the customer complaint that the check engine light was permanently lit and the AdBlue warning was displayed in the instrument cluster. I connected the scanner to the EOBD port to check for any codes displayed and to confirm the faults: P229E13, P229F09, P13E400, P13F600, P13DF09 were presented.
Understanding the P13F600 code
Definition – The engine cannot be started because the exhaust system aftertreatment has been tampered with or is malfunctioning, which is the Selective Catalytic Reduction (SCR) /AdBlue system.
Symptoms:
Engine will not start
Warning lights related to AdBlue system on the dashboard
Possible messages indicating a start prohibition or countdown to non-start
Common causes:
Faulty AdBlue components such as sensors, pumps or the injector
AdBlue fluid level issues or incorrect fluid
Order Now for immediate availability during the air conditioning season
Tested to Valeo O.E standards for optimal cooling efficiency and durability.
Ensure uninterrupted availability this season with Valeo
Access a free complete Technical support program
Wiring or connection problems within the AdBlue system
Software or programming issues in the control unit
Physical tampering with the AdBlue system components
NOx sensors
These were introduced to meet European Union environmental regulations, so that cars could have certifications for EURO 5 and EURO 6. Nitrogen and oxygen are present in the atmosphere so both diesel and gasoline engines are affected.
During combustion, these elements combine in an endothermic reaction to form nitrogen oxides or NOx. The amount of NOx formed varies with the peak combustion temperature – as that rises, so does the rate of NOx formation.
Diesel engines produce more oxides of nitrogen due to the engine operating on excess air; this is due to the absence of a conventional throttle valve. Oxygen and nitrogen react in the presence of high temperatures and combustion pressures to form NOx gases. The temperature in a diesel engine’s combustion chamber can reach as high as anywhere between 1,500°C and 1,800°C, which is optimal for the formation of NOx gases.
NOx gasses can be treated in two ways:
1. The formation of the chemical bond being disrupted during the combustion process (exhaust gas recirculation, internal and external)
2. The reduction of NOx gases using exhaust gas aftertreatment devices (catalytic reactions).
I checked the live readings to see if the data corresponded to the fault codes displayed on the scanner, looking at anything that stood out as incorrect data that could set the check engine light on. The NOx sensor codes needed to be addressed first to confirm that it was faulty and causing the check engine light to be permanently displayed on the instrument panel.
It was time to get my trusted PicoScope out to check and monitor the NOx sensor inputs and outputs for any anomalies.
NOx sensor wires from the sensor to its ECU module has 6 wires, 2 heater wires + and ground, 1st differential chamber, 2nd differential chamber, 02 concentration, and a ground wire. The module itself has four cable connections at its input coming to it from the harness end and these are the wires that I was interested in, checking these connections using the labscope. You can use a multimeter to test these wires, but I used the labscope because I needed to test the CanBus wires to confirm that they were connected to the ECM and to confirm good signal waveforms. I can check the voltages of the CanBus signals using a multimeter, but I cannot check the plausibility of the waveform to analyse the signals.
There is a 12V input to the module and we also need a good ground/earth. Use OBD2 (global) on the scanner to test.
Testing with ignition on, there are 4 wires to the sensor module:
Pin 1 Can high
Pin 2 Can low
Pin 3 Ground
Pin 4 Live wire
If we have a problem with the live wire, we can then check the fuse and relay. Can wires should be 60Ω using the ohmmeter and Can signals Can high and Can low should mirror each other.
Can voltages Can high and ground around 2.5V higher voltage than Can low
Can voltages Can low and ground around 2.5V lower voltage than Can high
Both Can wires should then add up to 5V, this is the correct voltages for the circuit.
Testing the 4 wires to the NOx sensor module
The ECU/ Module supply wire and earth/ground wire were tested under load using my test light between the live supply
and earth/ground wires. First, we test the ground wire, see Figure 4. Next, probing the supply and ground wire with the ignition on pin 3 and pin4. To test the circuit, we now connect a test light to the power and ground wires to put the circuit under load to check for any voltage drop, see Figure 6. Now we check both the Can high and Can low signals to confirm the integrity of the circuit signals.
Both these signals were good therefore we now need to remove the NOx sensor 2 and replace it with a new sensor (easier said than done!)
The old NOx sensor was seized solid. I had to apply gas to the sensor and cut off the old sensor to attach a socket to the sensor as the old sensor started to round with my NOx sensor spanner. As the sensor was removed it damaged the threads in the exhaust pipe, I then had to cut and rechase the old thread in order to fit the new sensor back to the exhaust system.
I fitted a new genuine NOx sensor to the exhaust system. These Mercedez vehicles must be fitted with new genuine parts from the dealer; I have come across a few of these NOx sensor problems being fitted with non-genuine parts that do not operate correctly.
My next step was to address the AdBlue fault codes stored in the ECM. First, I tested the AdBlue fluid with my hydrometer to confirm that the fluid was good and then topped up the tank with AdBlue to the correct fill level, if two discs are floating, the DEF has the correct concentration of urea and water, see Figure 11
I decided next to remove the DEF injector and clean the nozzle and the orifice for the injector with fluid, a pick and spray to clear any blockages. After refitting and checking the
DEF injector, I reconnected my scanner to the EOBD port to recheck the AdBlue system and that it was now operating correctly, see Figure 13
I now had to reset the new module after fitting for the ECU to Relearn the correct adaption's for this system, the AdBlue and the new NOx sensor. I cleared all the codes, test drove the vehicle and all messages and fault codes cleared.
AdBlue faults can be difficult and complicated to understand and rectify, but they are possible to fix if you have the correct equipment and knowledge of the systems involved. Clearing fault codes and conducting forced regens on these vehicles does not work, as after driving the vehicle for a short distance, the fault codes reappear as you have not fixed the underlying faults on the vehicle.
Training and system knowledge is important if we are to comprehend and diagnose faults correctly.
This vehicle is now fixed with one happy customer!
Imagine having a secret weapon in your toolkit, an ever-growing library of expert-led assessments, training material, and exclusive live events – all designed to turn you into a Top Tech. That’s exactly what Autotech offers!
Created to fuel your passion and sharpen your skills, Autotech is your go-to online platform for free, confidential assessments crafted by top independent automotive trainers. Whether you're looking to test your knowledge or learn something new, it’s all just a click away. Simply head over to https://autotechnician.co.uk/registration, pop in a few details, and watch your skills soar! Once you get the email, just click the link, and you’re in.
Here’s the best part... these assessments are completely confidential, so you can challenge yourself without any pressure. You’ll get instant scores, correct answers, and detailed explanations to boost your understanding. Ready to level up? Dive into as many assessments as you like, absolutely FREE!
Can you crack this adaptive headlamp mystery?
Here’s a real-world challenge to test your diagnostic skills: A customer rolls in with his 2006 BMW E61, insisting on a new Xenon bulb for the right headlamp. He claims it
suddenly stopped working after a heavy downpour. You step outside to check it out.
What you find is intriguing: the left headlamp works perfectly. On the right side, the side marker, angel eyes, and high beam are all shining bright. But the low beam? Completely dead.
Based on your experience, you quickly realize that swapping out the Xenon bulb probably won’t fix this issue. Instead, you suggest a thorough diagnosis – just an hour of your time – to uncover the real problem.
Using the detailed circuit schematic provided, you methodically troubleshoot the fault, guided step-by-step. No guesswork, no unnecessary part replacements; just, confident diagnosis.
Are you ready to become the technician everyone trusts?
Log in or register now at https://autotechnician.co.uk/ registration and unlock the full library of confidential assessments. Elevate your skills, solve complex problems, and stand out as a true Top Tech!
Our Autotech sponsors provide revenue opportunities, best practice guides and more in the following pages and don’t miss our new contributor Ben Johnson who details the fallout from bad design on a BMW 7 Series…
Ready to elevate your skills and stand out as a top technician? The Autotechnician Workshop Takeover is your ticket to mastering the latest automotive innovations. Whether you’re looking to refine your diagnostic skills or learn new repair techniques, this event is designed to empower you.
Autotechnician’s team of trainers and top-notch technicians will get together at the impressive Cleevely Motors in Cheltenham on Saturday 6th September and we invite you to join us for this year’s Workshop Takeover and tackle live faults together. Guests can expect various vehicles, including ICE and EVs, and receive ‘just-in-time’ learning to get to the root of the problem with minimum fuss, alongside workshop owners and industry experts such as Matt Cleevely, Gareth Davies and Alistair Finch and event sponsors ACtronics, ALLDATA, JLM Lubricants and NAPA.
Why should you join us?
Exclusive Access: Get behind-the-scenes insights from expert trainers who live and breathe automotive repair.
Practical Skills: Dive into real-world diagnostics, repairs, and troubleshooting that you can apply immediately in your workshop.
Interactive Learning: Ask questions, participate in demonstrations, and learn by doing—no passive watching here!
Stay Ahead of the Curve: Keep up with the latest vehicle technologies & repair techniques.
Numbers are kept to a minimum to ensure delegates receive an immersive experience and the chance to draw valuable insights and practical tips to take back to the workshop.
Both experienced diagnosticians, as well as those with less years of experience under their belt, will gain valuable takeaways on how to find faults more effectively on both combustion and electrified vehicles. Guests also have the opportunity to enjoy dinner and drinks with the team the night before and are welcome to bring along partners to this.
Don’t miss out—visit https://autotechnician.co.uk/ training/ to secure your spot. Gear up for an unforgettable learning experience that will leave you inspired, confident, and ready to tackle any challenge on the workshop floor!
Saturday day ticket plus Friday dinner with the team: £152.00 + VAT (£182.40)
Saturday day ticket only £122.00 + VAT (£146.40)
Ben Johnson, fault finder, writer and YouTube creator with 30 years’ experience fixing many brands, specialising in BMW, has joined the autotechnician team. He has created the latest autotech online assessment and provides a 39-minute video case study just for us on a BMW X3 repair. Over to Ben: “This involves a common fault I wished I’d known about – it is the worst job I’ve ever done! I have chosen this topic because it exposes how systems work and how they can create false fault codes. It also highlights problems with the way the hardware is made and implemented and how bad grounding can confuse almost everything.”
Watch the video at: https://youtu.be/oGC4A89ZpQM or scan the QR code.
"Gather evidence, work through it methodically and cleanly"
In association with:
To view the video roundup on YouTube, click here or scan the QR code
From ABS and ECU testing to instrument cluster repair, our team are experts in remanufacturing electronic car parts, ensuring they will perform as new.
With 20 years of experience under our belts, we’re proud to be one of Europe’s market leaders in automotive remanufacturing, providing a quick, effective, and affordable remanufacturing solution.
Why repair when you can remanufacture?
Whilst repairing a malfunctioning car part can provide a quick fix, there is a better, longer-lasting alternative that will ensure your electronic unit performs to the highest standard. A repair will only fix the defective parts, but a remanufacture identifies and addresses all these malfunctions as well as the weak points commonly found in that unit.
As statistics show that automotive electronics will account for up to 50% of the total cost of a new car by 2030, it’s clear that short-term repairs can quickly become expensive. But with remanufacturing, you are guaranteed a higher-quality result that also promotes more sustainable practices and feeds into a circular economy.
Here, we detail two new products to overcome common faults.
AdBlue Tank Assembly Repair – Peugeot Partner / Citroën Berlingo (2008–2018)
AdBlue was introduced along with Euro 6 emission standards as an aid for reducing the harmful nitrogen oxide (NOx) emissions that diesel engine vehicles produce.
A common symptom of failure is an “Emission Control Fault” message appearing on the dashboard, often accompanied by the engine warning light. If not addressed in time, the vehicle may even enter limp mode or display a countdown indicating that it will not restart after a certain number of miles.
One of the most common issues involves defects in the integrated AdBlue control unit (mounted within the tank). These may include: Internal corrosion or water ingress; short circuits or internal electrical faults; crystallisation of AdBlue fluid around the injector or level sensors; faulty temperature, level, or quality sensors within the tank.
These faults may also cause communication issues with the engine ECU or other systems within the vehicle. Often, the complete AdBlue tank assembly must be replaced; however, a remanufacture is often a far more cost-effective and sustainable solution.
Technicians may notice during diagnosis that the system is no longer heating the AdBlue fluid, even when required (e.g. in colder temperatures). A short circuit in the control unit may also prevent diagnostics communication, or a fault may be stored with a permanent status that cannot be cleared.
In some cases, crystallisation caused by AdBlue residue may
block the injector or damage internal wiring and sensors, contributing to system errors and inaccurate readings.
Fiat group: Blue & Me Repair – Body Control Units
ACTRONICS offers a high-quality remanufacturing solution for the common problems with the Blue&Me Module, an infotainment system used in various Fiat Chrysler Automobiles (FCA) vehicles between 2006 and 2017. This module is known for enabling hands-free calling, music control, and voice control functions, but can develop malfunctions over time that affect the use of the car.
We are aware of several problems that can be caused by a malfunction in the Blue&Me: Flashing odometer reading; no communication; no Bluetooth connection; an unstable Bluetooth connection; USB port not working; steering wheel controls not working; battery draining; media player not working; error codes ‘Blue and Me’.
U1733 and P0022 error codes are common with the FCA Blue & Me module. If one of these error codes occurs during vehicle diagnosis, an overhaul of the Blue&Me control unit is necessary.
The Blue&Me module is usually located under the passenger seat. By sliding the seat forward and removing a black cover, the module becomes visible. In some models, such as the Fiat 500, the module is located at the rear of the vehicle, near the speaker on the passenger side. In the Fiat Punto, the module is located in the glove compartment. This can therefore vary per model, so consult the manual of the specific vehicle for the exact installation location.
Models in which the Blue&Me Module is used:
Abarth 500/595/695 (from 2008)
Abarth Grande Punto (2008 - 2014)
Alfa Romeo Giulietta (2010 - 2020)
Alfa Romeo Mito (2008 - 2018)
Fiat 500 (from 2007)
Fiat Bravo (2006 - 2014)
Fiat Doblo (2009 - 2022)
Fiat Fiorino (from 2007)
Fiat Grande Punto (2005 - 2011)
Fiat Panda (from 2012)
Fiat Punto (1999 - 2012)
Fiat Punto (2012 - 2018)
Fiat Punto Evo (2009 - 2012)
Ford Ka (2008 - 2016)
Lancia Delta (2008 - 2014)
Opel Combo D (2012 - 2018)
ACTRONICS repairs, overhauls and restores the Blue&Me module and many other electronic car components. A good diagnosis of the defect is essential for a successful overhaul. ACTRONICS has a specific test setup for each BCM, so that we can make the correct diagnosis, check all functions and perform a final test. In this way, the success rate is extremely high.
ACTRONICS offers specialised repair services for Blue&Me BCMs that restore the original functionality of the system while saving up to 80% of the costs compared to a new part.
You get the Plug & Play part back. We revise the original part, so that it is immediately ready for use to be reinstalled. No reprogramming is required.
We always offer a 2-year warranty on the revision of your Blue&Me Module, so that you are assured of a sustainable and high-quality solution. And speaking of sustainable, because we know how to reuse many of the components, having the Blue&Me Module repaired is also better for the environment!
Have your Blue&Me Module repaired by ACTRONICS
If you have a car in your workshop with a defective Blue&Me Module, simply follow the process below to submit your revision request:
Submit revision order: Start the revision order at the top of this page, fill in your details and follow the steps indicated, after which you can send the part to us, or have the part collected from your workshop.
Diagnosis and Revision: Our technicians carry out a comprehensive diagnosis and revise the module according to the highest standards.
Return and Installation: You will often receive the module back within a few days, ready for immediate installation. That's it!
The experts in remanufacturing car electronics
Our range is continually expanding – in 2024, we remanufactured more than 15,000 parts. If you have an electronic control unit, we can help! Our range covers over 1,200 different components from over 60 brands.
Over the past decade, the number of Battery Electric Vehicles on UK roads has increased tenfold. At ACTRONICS, we have followed this trend closely to ensure we can support these developing vehicles. We’re continually working to expand our range of onboard chargers and are now able to offer remanufacturing solutions for chargers from 15 different OEMs.
At this year’s Automechanika Birmingham, ALLDATA Europe took to the Workshop Hub stage – organised by Autotechnician – to host a panel discussion focused on the importance of having the right people, tools, and data in today’s increasingly complex automotive landscape
Addressing the 60-strong audience were James Dillon, the founder of Technical Topics and diagnostics expert; Tim Benson, owner of Oldfields Garage; and Steve Derham, a technical support specialist at ALLDATA. All three possess different skillsets, but all are united in their desire to illustrate how these attributes marry up to ensure independent workshop owners and technicians can thrive in the face of rising vehicle complexity.
Professionals with decades of experience will recall when vehicles were simpler – fewer or no ECUs, easy access, diagnosis based on intuition and experience, minimal tools required, and repairs could often be completed in under a day – but those days are firmly in the rearview mirror.
Modern vehicles are vastly more complex. The diagnostic process now demands a structured, well-informed approach long before a technician physically interacts with the vehicle. Even basic components – like pressure sensors or airflow meters – require background research. That means knowing what systems the vehicle has, understanding how they’re supposed to operate and using that knowledge to plan the diagnostic path.
With the rise of electronics, ECUs and software, gut instinct and practice won’t cut it. ALLDATA believes that access to original, accurate, brand-specific data is essential to enabling professionals to service and repair vehicles efficiently,
returning them to customers with the issues resolved and in roadworthy conditions – first time.
Modern vehicles can contain between 70 and 100 ECUs, controlling everything from brakes and power steering to infotainment and heated seats. Technologies, like ADAS, EV platforms and OTA (over-the-air) updates, are not fringe developments; they are now part of everyday work for technicians. Add to that the increasing importance of vehicle-to-cloud communication and diagnostics that involve software bugs or CAN communication faults, and it’s clear that technicians need both deeper insight and better resources.
Ultimately, ALLDATA believes that the more complex the system, the more precise the diagnostic process must be –and the greater the risk of error unless original, accurate data is available from the outset.
Process before wrench
What does the panel think of that assessment? Tim was asked by Matthew Wright, director of information and OEM relations at ALLDATA, how he and his team prepare to meet the demands of modern repairs while keeping customer satisfaction high. He replied: “It’s all about following a process. Vehicles today are not simple machines and technicians need to have a good solid process to follow to ensure we are working in the right direction. Having the right data is a key part of this process. Understanding how the system works is critical, so we know what tasks need to be done.
“Once we accept a job, we need to understand what’s involved, the steps, the tools and the data needed. Then we can deliver properly. It’s about assessing things before we even touch the vehicle!”
Tim also emphasised that data is central: “If we can show the customer that we understand their vehicle and can fix it –
A potentially tricky job emphasised the value of repair instructions direct from the VM – with safety and accuracy the priorities
Replacing a broken window on a 2001 BMW 3
Series E46 requires careful preparation and a solid understanding of the vehicle’s specifications. Frameless windows, in particular, can be challenging; without accurate data and step-by-step instructions, the process can be time-consuming and error prone. Having the correct procedure, therefore, is essential for a safe, efficient and precise repair.
First, the groundwork needs to be done in accordance with the OE standard: remove and replace the windowpane. This is done by removing the sound insulation of the front door, which provides access to the relevant components.
Next, for vehicles with side airbags, it is essential to adhere to the safety precautions to protect the system. Furthermore, particular care must be taken when removing the window glass; a left-handed screw must be loosened clockwise – the opposite way to a standard thread. Additionally, when removing the glass, be wary of damaging the rubber ring. For convertible models, the window glass may have an Aquapel coating, which is indicated by a white dot on the glass. This coating needs to be protected during installation.
This is a detailed and patient process, one that should only be carried out cautiously and with original data and instructions by the technician’s side.
ALLDATA Repair a workshop’s companion
Without these particular instructions, it would be virtually impossible for technicians to understand the exact requirements and safety precautions. This example is a powerful reminder that – irrespective of knowledge – precise, manufacturer-specific data is an invaluable addition to any workshop and job.
ALLDATA Repair provides instant access to instructions from 42 VMs, comprising of more than 90 million articles, over eight-and-a-half million technical drawings and wiring diagrams with electrical connector views. That is procedures for more than 153,000 year, make, model and powertrain combinations – or, simply, 97% of vehicles on the road today.
For more information about ALLDATA Repair or sign-up to a trial, visit www.alldata.com/eu/en/ repair-europe
because we’ve got the tools, the skills and the data – then we gain their trust. It’s about being prepared and professional.”
From the front line
That’s one view from an independent workshop owner –but what about the technical support side? ALLDATA’s Info Centre Service provides subscribers with on-demand access to OEM repair data and expert technical support for complex or unpublished vehicle issues. One of its specialists, Steve, drawing on 30 years of experience in diagnostics, manufacturer systems and customer support, explained how the needs of technicians have evolved.
He said: “Ten years ago, most of the questions we handled were about core systems, like ABS, airbags, engine ECUs. Today, we’re being asked about ADAS, EV safety, vehicle architecture and shutdown procedures. It’s not just about where the fault is either; it’s why the system failed and how it behaves under certain conditions. Technicians want to understand the design, not just diagnose the outcome.”
He added that with EVs in particular, safety comes first – he told the audience: “You can’t even start the job until you’ve properly shut the vehicle down. That requires accurate, manufacturer-approved procedures – you can't guess. And customers expect you to know this; safety isn't optional.”
This emphasis on understanding before action became a defining theme of the session. Technicians are increasingly shifting from reactive to proactive approaches – researching, planning and preparing before opening the bonnet.
The panel was clear that even the best data and equipment are only part of the solution: trained technicians, confident front-of-house staff and clear internal processes are as important as the repair job itself. Everyone must be in sync; everyone must know and understand what they're doing — diagnostics, customer communication or complex repairs –which makes training absolutely essential.
“Confidence grows when staff know they’re using accurate, reliable information,” added Tim, “which, in turn, converts into greater trust, improved fix-first-time rates and, ultimately, customer satisfaction.”
For independent workshops, getting the job done right the first time is no longer a differentiator – it’s an expectation. A comment from the audience drove this point home: “The customer doesn’t care if the job takes 10 minutes or three hours – they care if it’s done right. Data gives us the confidence to charge for our expertise, get the job done correctly first time and deliver on that promise.”
ALLDATA’s message is clear: workshops already have the passion and expertise. When that’s complemented by the right tools, data and people, there is a clear pathway to improved diagnostics, greater workshop efficiency, stronger communication and better value for the customer.
In an increasingly complex, fast-paced industry, that might just be the simplest formula for success.
For more information about ALLDATA Europe or request a free trial, visit www.alldata.com/eu/en
A 2024 eBay survey found that to save money, 35% of car owners were willing to repair their own vehicles, instead of taking it to a professional. 34% were also delaying their car’s MOT. Worryingly, the Driver Vehicle Standards Agency stated that “a large proportion of MOT failures are likely down to poor maintenance and if vehicles are maintained well, there is a good chance that the MOT pass rate will be higher.”
What can workshops do to buck this trend?
“Although most of our work is with professional motor factors, we talk regularly to technicians from all over the UK,” says Mike Schlup, MD of JLM Lubricants UK, sponsors of Autotech.
“They tell us they’re resisting the urge to lower prices. It’s neither fair nor feasible. Workshops are now having to absorb some of the increased costs of materials, energy and labour.
To then reduce their prices to appeal to ‘lowest- priceplease’ customers, should be avoided.”
“The name of the game is adding value,” continues Mike. “Trade trusted additives can boost a workshop’s profits and kerb appeal. JLM Lubricants is a global brand with a reputation for supplying top tier additives with the highest concentration of active ingredients, to thousands of
“The feedback was incredible to the point that customers, mainly garages, started to order these products in multiples because they deliver on their promises. I can also add that the service and technical help and guidance that my customers receive, is second to none.”
Matthew Perring, Manager, CR Marks Banbury
technicians worldwide. In the UK, JLM Lubricants is trusted by award winning technicians such as AJ Fleetcare. A technician can trust a product with JLM on the label to deliver every time. And if a trusted additive can take the place of a repair or a part reducing workshop bills, everyone’s a winner.”
The top selling JLM Lubricants products include:
For engine oil and filter change – JLM Oil Flush and JLM Bortec
For fuel filter change – JLM Rapid Fuel System Clean
“Over the last 6 years we’ve used JLM Lubricants’ additives on a range of vehicles in our workshop. JLM is like a partner in our business, offering exceptional quality products that deliver every time.”
AJ Fleetcare, award-winning family garage
For sparkplug change – JLM Injector and Sparkplug Loosener
For petrol GDI service – JLM Direct Valve Cleaner, JLM Direct Injector Cleaner
For MOT testing – JLM Emission Reduction Treatment (petrol or diesel)
For turbo change – JLM Turbo pre lube, JLM Oil Flush, JLM Extreme Clean
“We had a 2017 Skoda Octavia, with massive running issues – suffering from under boosting, rapidly blocking up the DPF system. The intercooler which is part of the inlet manifoldcharge air cooler, to be technical, was blocked, restricting air flow, throwing everything out. We could see with a borescope how blocked it was. Before deciding to remove the manifold, I thought we could try a can of JLM EGR and Air Intake Cleaner with nothing to lose. I had been impressed with other JLM products including the Diesel DPF Spray. The difference between before and after was massive. Air flow issues restored and visually cleaner, re-checked with a borescope. It saved the customer a fair bit of money which is always nice, especially in today’s economic climate! I wouldn’t hesitate to use anything else with the JLM name on it. From previous experience with their products, it’s good stuff!
Ryan Lee, RSL Autos
For DPF clean (spray or two-step) – JLM Diesel DPF Spray, JLM DPF Cleaner, JLM Diesel DPF Cleaning Toolkit with the DPF Cleaning Fluid and DPF Flush Fluid Pack.
For air intake cleaning – JLM Air Intake Cleaner and JLM Intake Extreme Clean.
Unrelenting focus on quality
“Diesel is still big business for garages,” says Mike. “And this is where JLM Lubricants DPF products are leading the market for quality and performance. What do these products contain that others don’t? The JLM DPF Cleaner contains a high concentration of Cerium and Platinum. This allows regeneration to take place at a much lower temperature and in a much shorter time, making it effective in city vehicles, without the risk of damaging the DPF at an excessively high temperature. Platinum coats cylinders, promotes soot reduction, extends the life of the DPF and promotes DPF regeneration. Plus, Cerium reduces ash which helps to extend the life of the DPF. Other products tend to have a much higher ferrous metal content, which burns at a very high temperature and produces more ash in the long term.”
fellow mechanics. Oli will be spending a week with AJ Fleetcare, working with the team, and seeing the JLM products in action. After this, he’s on the road, visiting our technician customers. If you’d like him to call on you, with goody bags and limited-edition mugs, email info@kalimex. co.uk
Order your JLM Lubricants’ bestseller starter pack! Contact us to discuss a starter pack of JLM bestsellers, fine-tuned to your workshop.
For more information visit www.jlmlubricants.co.uk, email info@kalimex.co.uk or call on 01273 891162.
Oli’s on the road – can he visit you?
Oli Schlup is a trained motor sport mechanic and a UK Legends car racing driver. When he’s not racing, he loves nothing more than getting under the hood and meeting
Corrosion is the natural process of metal deteriorating after a reaction with the environment. The most common example of this is rust, which forms on the surface of metals when they’ve been exposed to oxygen and moisture.
This is a dangerous and costly problem when it affects the braking system.
Several braking components are manufactured from cast iron, most notably brake discs. With high distortion resistance, excellent durability when subjected to different types of forces, and the production of great friction coefficients, the high iron content is essential for safe and efficient braking. However, cast iron is highly corrosive.
When corrosion is present on the brake disc surface, NVH (noise, vibration, and harshness) will increase, and braking
efficiency will worsen. In extreme cases, corrosion adhesion between the disc and pad can occur, leading to severe damage.
Some corrosion build-up on the surface of a brake disc is cleared naturally when the brakes are applied while driving — but NAPA goes a step further to prevent corrosion from occurring in the first place.
NAPA Brake Discs are expertly manufactured to match the OE design. The disc edges and hub are coated with a premium Onyx Guard anti-rust coasting, providing effective protection and a long-lasting smart aesthetic. There’s no coating on the friction surface to ensure the brake pads aren’t contaminated.
Brake Pads
Brake pads also suffer from corrosion, particularly on the backing plates. Corroded backing plates can cause delamination of the friction material. This can lead to an
increase in NVH, the complete detachment of the friction material from the plate, and the loss of braking efficiency and stability.
To prevent this, NAPA coats the backing plate of its brake pads with an anti-corrosion layer.
Components surrounding the discs and pads are also prone to corrosion, and this process can be accelerated by certain cleaning methods and materials.
For example, pressure washing can introduce moisture and acidic detergents to tight crevices between the disc and hub. This can cause corrosion build-up and other issues like disc misalignment or detachment of the caliper slider boots.
At the point of installation, cleaning the hub surface and protecting it with a suitable lubricant, alongside lubricating all susceptible contact points, will help to prevent corrosion build-up. It’s also vital that the caliper slider boots are removed, inspected, cleaned or replaced, and then lubricated with a hydrophobic lubricant that is compatible with the rubber boots.
Do not use copper grease to lubricate the braking system. The metal within the grease will cause galvanic corrosion, accelerating the corrosion process, restricting movement, and increasing NVH.
NAPA Brake and Clutch Cleaner is a tailor-made, solventbased blend of hydrocarbon and alcohol, ensuring that even the most stubborn contaminants aren’t immune to its fastcleaning action.
Likewise, NAPA Brake Grease and NAPA Caliper Grease are copper-free, anti-rust lubricants designed to restore and maintain peak braking performance. NAPA Brake Grease is also suitable for use in ABS brakes, and NAPA Caliper Grease is reinforced with a high film strength to avoid the deterioration of rubber parts.
How can NAPA support you?
At NAPA, Know How is everything, and that’s why NAPA is backed by expert support and guidance to give technicians the confidence to fit and forget. NAPA Braking offers consistent OE-quality performance and a 3-year/36,000-mile warranty guarantee.
Technical bulletins are available to address frequently asked questions. Meanwhile, the in-house technical team is on hand to provide support and guidance on the full NAPA range, including installation best practice, troubleshooting, and more.
If you’re in need of in-person support, NAPA is partnered with TechMate, the direct technical support specialists with coverage of the entire United Kingdom. All TechMate specialists have an expert understanding of the NAPA product catalogue and the finer points of aftermarket installations. They offer NAPA customers a variety of services including garage workouts, classroom visits, installation demonstrations, and more.
Quality may begin with the product, but there is never an end to our Know How.
NAPA Racing UK drivers Dan Rowbottom and Cam Richardson visited our NAPA Brake Pad production facility in Spain last summer, accompanied by our technical partner, TechMate.
Join them to learn more about the production process, R&D, quality control, and more in the NAPA Brake Pad Factory Tour video, live on YouTube @NAPAUKI.
The BMW 7 Series: Over £100k as new! Note the extreme rideheight – a sporty look, although highly impractical.
By Ben Johnson
It’s always the posh ones, isn’t it? The flagship models, the rolling showcase of automotive engineering, packed with every conceivable convenience and cutting-edge tech — except, apparently, a basic understanding of puddles.
This story begins, as so many do, with a phone call from a flustered customer, followed shortly afterwards by the sorry sight of a BMW (G11) 7 Series sat outside like a wounded cruise ship. Not sagging slightly. Not “a bit low on one corner.”
I’m talking full front-end collapse, nose dragging along the tarmac, rear end reluctantly following suit. It had the visual appeal of a collapsed camping chair and the dignity of a tired old Labrador trying to stand on an ice rink.
Once the check control messages were done with, I managed to enjoy a Nat Geo documentary whilst loading the trouble codes on the scan tool – it’s not every day one is offered this level of luxury during a workday! As if the job wasn’t already frustrating enough, this particular G11 came fitted with one of
those Dräger alcohol interlock systems. You know the type — breathalyser wired into the ignition, designed to stop a driver from starting the engine if they’ve been on the sauce. Clearly, the customer had been caught indulging in a bit too much Merlot behind the wheel, and this was part of the court-mandated slap on the wrist. But of course, he hadn’t left a spare mouthpiece, just one well-used, manky plastic nozzle rattling around in the centre console like a biohazard. So, before I could do anything, I had to disinfect the thing thoroughly — not exactly the start to the day I had in mind.
The system gives you about five minutes after shutting off the engine before it starts shrieking at you to blow — or worse, do a kind of simultaneous
Not very Practical when trying to find a fault. Stay off the pop folks!
blow-and-suck manoeuvre that feels like you’re playing a very undignified brass instrument. And while you’re fault- finding or sitting with the ignition on, it’s constantly bleeping away in the background like R2-D2 having a panic attack. Not helpful. Not pleasant and certainly not conducive to calm diagnostic thinking. Woe betide you fail the test more than a few times, too. Then the system really throws a wobbly — starts warning that test conditions have been violated, the screen flashing as though you’re about to be electronically handcuffed for breathing wrong. I do hope it’s not wired into any kind of remote monitoring system. Otherwise, our poor sauceswigging customer might find himself bundled into a van and carted off to some open-air rehabilitation centre, all because the fault-finder couldn’t master the dark art of sample submission under pressure.
Honestly, you couldn’t make it up.
Naturally, the dash was lit up like a Christmas tree, ‘Suspension Failure. Chassis Function Restricted. You may continue driving’, it helpfully offered, as though that was a realistic option when the front bumper was threatening to catch a speed bump and rip clean off. The button in the centre console to raise or lower the ride height? Completely nonresponsive. It might as well have been a volume knob for all the good it did.
What made it worse — and more suspicious — was the fact that the compressor had already been changed six months earlier. Genuine part. Professionally installed. Worked perfectly, until it didn’t. Now it was back, and looking very much like it had given up on life.
Initial checks were all as expected. System pressure was low. Compressor was attempting to run. Relay was clicking, fuse was intact, but every time it tried to lift, you’d hear the compressor kick in, then wind down shortly after, as if the car had changed its mind mid-way through standing up.
"Nowt wrong wi that!" My old mentor would have said and he would have been correct. Great delivery pressure yet the other half of the compressor was goosed. Pressure can build but no use if it bleeds off at the same time.
No leaks from the airbags. No burst lines. No hissing from the usual suspects. So off came the compressor for a proper bench inspection — and that’s when things got a bit more… aquatic. Before pulling the whole system apart, I did what any good tech should do — I started with some simple, old-school
"Nowt
tests. First, I removed the rear-left air bellow feed line. Then, with the compressor commanded on, I slipped a rubber glove over the pipe and watched it inflate instantly like I was prepping for surgery. No hesitation, no limp half-hearted puff — just a crisp, confident swell of pressure. That told me the compressor was pushing air. Properly.
To be thorough, I rigged up a pressure gauge directly onto the compressor’s feed into the valve block. The result? Huge output. This compressor wasn’t just functioning — it was delivering serious pressure. You could run a small sandblaster off it. So now we had a mystery – strong compressor, but the car was still sagging like a forgotten soufflé.
That’s when I knew the issue wasn’t at the source. It was after the compressor — somewhere in the valve block or downstream. And from there, the investigation got a lot wetter. And the height sensors? All displaying perfect plausible values.
Like an object from RMS Titanic not a compressor frame from a premium 2018 built luxury BMW. Note, the wholly inadequate exhaust outlet hose in the lower right part of the image.
When I cracked open the compressor and drier unit, I found exactly what I was expecting — which is to say, everything I wasn’t hoping to see. The brass scrubber was oxidised.
The desiccant chamber was full of saturated silica beads, clumped together and stained the colour of old engine coolant. It looked less like a high-end air-drying system and more like something you’d dredge out of the bottom of a dishwasher.
The drier is designed to prevent moisture from contaminating components such as this solenoid valve. Clearly, in this case, it had failed.
But what really nailed the diagnosis was the condition of the inner chamber where the fill/drain solenoid bolts to. If this was corroded then odds were high that the inner valve block was too. This thing uses a pair of one-way valves — essential components that keep air flowing in the right direction when the compressor is working.
The very wet and mouldy removed dessicant
Except one of them, I suspect, had seized open, meaning the compressor was doing something truly daft; pumping and venting at the same time. It was trying to inflate the system while bleeding off pressure just as quickly, like trying to fill a paddling pool with the drain still open.
And here’s where it gets even more maddening: the cause of all this? Water. Plain, old-fashioned road water. Not from a flood, not from driving through a lake. Just an everyday puddle. So how does water get into a sealed compressor system with a desiccant dryer? Simple. Bad design.
Let me walk you through the setup. The G11’s air suspension compressor is clever, in theory. It has a sealed drier unit filled with silica beads to absorb moisture from the air it compresses. These beads even regenerate themselves during rest cycles by drawing air through a vent — a neat trick that makes use of a reversible flow through the internal valve system. A small brass scrubber sits at the end of the line, acting as a filter. Behind that, a rubber hose routes the vent to the outside world.
And where does that vent exit? You guessed it — horizontally, level with the bottom edge of the rear bumper right in line for anything wet.
Perfect.
Six port distribution valve block controls each of the four air suspension bellows. The other two provide air to the two pressure accumulators
That means everytime the car reverses through standing water, or splashes into a kerbside puddle, or gets blasted by an overzealous pressure wash, there’s a chance that water will sit in the exhaust hose.
And when the pipe is submerged completely? It’ll happily draw that water backwards — through the scrubber, into the drier, past the valve block — until you’re left with a corroded, waterlogged paperweight that was once a precision air system.
This isn’t speculation. The compressor was only six months old, and the internal corrosion was exactly what you’d expect from repeated water exposure. The customer even remembered driving through a deep puddle a week before the symptoms started.
You’d think someone in Munich might have seen this coming. So, what’s the fix? Simple. First, I replaced the compressor with a valve block, external 6 port distribution block and drier unit. No point trying to save components that had turned into a
rust sculpture. Then, during refitting, I addressed the actual cause of the problem.
I removed the factory rubber hose, added a 90-degree elbow, and routed it upwards, lifting the exhaust vent six inches higher than its original location. It now sits neatly tucked into the top corner of the compressor frame, safely out of the splash zone. It looks OEM, works better than OEM, and, most importantly, it won’t be sucking up half the A406 next time it rains.
It’s not rocket science. It’s common sense. But apparently, common sense is in short supply in the design department these days.
Note the newly routed, dare I say it, vastly improved exhaust venting design compared to the best that BMW factory engineers could come up with
This wasn’t a software problem. No coding. No flashing modules. No wild goose chases with fibre optics or FlexRay. It was mechanical. Simple. Brutally obvious once the compressor was open.
And yet, it was entirely avoidable.
It’s a frustrating reminder of the gap between engineering theory and real-world experience. On paper, the venting system is neat and tidy. Efficient. Compact. But in the real world — you know, the one with weather — it becomes a liability. Because when you put a breathing hose for a precision air system right where every splash and puddle can find it, you’re asking for trouble.
They went to great lengths to route the compressor’s intake high up, complete with a 180-degree bend to fend off water ingress — a thoughtful bit of engineering, clearly aimed at keeping the system dry. And yet, they overlooked a fundamental truth of human behaviour: people don’t always make wise decisions. Sometimes, they’ll plough through standing water that’s halfway up the door, because it’s quicker than taking the long way round — or just because they’re curious to see if they’ll make it. In other words, even clever design can be undone by the unpredictable genius of the average driver.
A sealed air system shouldn’t be ingesting water. That’s basic. But here we are, six months into the life of a new compressor, binning it because someone routed a hose 30cm too low.
Back on the road, and riding high
Once everything was reassembled, the G11 lifted immediately. No faults. No warning lights. No sulking. Ride height adjustment returned. Suspension functions fully restored. And thanks to that subtle routing change, the compressor will now live a longer, drier life — as it should’ve done in the first place.
I explained the modification to the customer, and he nodded politely, the way most people do when they realise their car was taken down by a bit of wet air and just plain bad luck. But he’s happy. The car’s happy. And I’m happy, because I got to fix something properly — not just replace parts and clear codes, but solve the problem at its source.
This job sums up what being a good technician is really about. It’s not just about plugging in a scan tool and reading faults. It’s about thinking. Looking. Using the experience gained from years of seeing what actually happens to cars in the real world — not in perfect test conditions or engineering diagrams.
Because when you lift a car and see a vent hose sticking out like a snorkel made by someone who’s never heard of rain, you realise it’s not about how clever a system is. It’s about whether it actually works where it lives.
And sometimes, the smartest fix is just raising a pipe six inches.
Ben Johnson, fault finder, writer and YouTube creator with 30 years’ experience fixing many brands, specialising in BMW, has joined the autotechnician team. He has created the latest autotech online assessment and provides a 39-minute video case study just for us on a BMW X3 repair. Over to Ben: “This involves a common fault I wished I’d know about – it is the worst job I’ve ever done! I have chosen this topic because it exposes how systems work and how they can create false fault codes. It also highlights problems with the way the hardware is made and implemented and how bad grounding can confuse almost everything.”
Watch the video at: https://youtu.be/oGC4A89ZpQM or scan the QR code.
"Gather evidence, work through it methodically and cleanly"
While most garages realise the importance of offering parts that meet OE quality, Rob Marshall looks at aftersales support and why you might need it
They say that a good teacher is hard to forget. A good friend lives her life from her physics teacher, whose mantra was, "If something is worth doing, it is worth doing badly... first." The idea is to encourage learning from mistakes. This may be good advice in a GCSE laboratory experiment but it is far from ideal, when fitting a clutch. After all, an error tends to be realised after the car is reassembled and the clutch does not function correctly. The resolution is likely to involve having to tear down the car again, destroying both your morale and profitability in one fell swoop. It is unsurprising, therefore, that the real philosophy should be to do the job well from the outset.
As the bilstein group (home of the febi brand) acknowledges, as vehicle technology has evolved, removing the transmission to replace the clutch has become more time-consuming, due to the number of components that require removal. Yet, technicians need to be aware of common mistakes. Even if you are making no fundamental errors, it is worth becoming better, by enhancing your technique and brushing up on ever-evolving best practice tips.
ZF Aftermarket (maker of Sachs clutches) highlights four main errors that it sees technicians making. It highlights improper
spline greasing, due to its warranty department seeing a large number of clutches returned with a slipping complaint, but close inspection reveals friction material lubricant contamination. The main cause is excessive grease being thrown outwards from the splines and onto the driven plate as engine speeds increase. ZF Aftermarket warns that undergreasing, or applying copper slip to the splines, can cause the driven plate to drag on the spline, causing the clutch not to release properly. To help, Sachs clutch kits come with a packet of the correct spline lubricant.
ZF Aftermarket admits to receiving many returned clutches with distorted covers/pressure plates, bearing excessive scoring around the fixing points. The problem is incorrect fitting. The clutch cover should be torqued down following a cross, or star, pattern sequence. Working your way around a clutch cover, tightening the bolts sequentially, risks causing distortion. The result of this is an inconsistent clamping force, causing slip and judder.
A further problem is poor alignment. Again, this issue can be caused by not centring the driven plate correctly and the resultant forces will wear the driven plate's splines. Misalignment can occur also during the physicallydemanding task of lifting the gearbox back into the engine bay and manipulating the input shaft splines into those of the driven plate. The warning is never to allow the transmission's
Comprehensive Range Coverage – With over 1,250 Clutch Kits for Asian and European vehicles, our ‘Fast to Market’ approach ensures workshops stay ahead with options for the latest makes and models.
SMARTFIT - Blue Print’s professional, cost-effective and SMART repair solution! Our Conversion Kits are the premium, reliable and easy-to-install Aftermarket alternative for lasting performance.
Unmatched Quality - All clutches meet OE standards, offering a seamless premium replacement experience.
Installation Made Easy - Helpful instructions ensure effortless understanding and implementation, even for complex repairs.
Proven Precision - Every clutch passes rigorous testing at the bilstein group’s Clutch Competence Centre, ensuring it fits Right First Time®
weight to hang on the input shaft. Rather than bending the shaft, the driven plate becomes the sacrificial part and can become damaged. Ensure that the transmission's weight is supported by the dowels between the engine and bellhousing. ZF Aftermarket warns that not aligning these components correctly will lead to the driven plate hub splines wearing very quickly and, in extreme cases, this will cause the input shaft to mill the splines from the hub. It can also distort the driven plate, a situation that results in excessive runout and clutch clearance issues.
Yet, the biggest technician mistake that ZF Aftermarket finds is not using a self-adjusting clutch mounting tool for the assembly of its Sachs Xtend clutches to the flywheel. This can lead to the adjusting mechanism releasing as the cover is tightened down, causing clearance issues and cover distortion. Schaeffler (LuK clutches) agrees that this is a very common issue, revealing that a worrying proportion of technicians are installing its self-adjusting clutches without the appropriate tools.
It can be easy to forget that the clutch replacement procedure extends beyond the three-piece unit. First Line (makers of the Borg & Beck brand of clutches) recommends that technicians must consider the consideration of any input shaft seals (especially if it is leaking), plus clutch forks, pivot balls, release bearing guide tubes and, of course, the Dual Mass Flywheel.
Schaeffler says that best practice recommends that you replace the DMF at the same time as a new clutch. This is because DMFs have a service life that is shortened by driving style and conditions. Understandably, it is very difficult (if not impossible) for a second, or third owner to assess how the DMF has been treated. Febi agrees, especially if the clutch has lasted over 80,000 miles. Yet, should the customer have concerns, you can measure DMF wear status with a DMF
Many quality brands supply significant online and digital support but many of them report that technicians are putting themselves at a disadvantage, by not using the support available at their fingertips.
Whether you wish to improve on your technique, or tackle twin-clutch automated manuals, support includes practical technical training.
Testing Tool and compare your readings against the tolerance data, which can be found on Schaeffler's Repxert app. Borg & Beck agrees, stating that you will need to measure both rotational free play and rock angles. Should the DMF be out of spec, it can cause premature wear to the new clutch.
ZF elaborates that DMF free play is a popular technical question. Many garages reject a sound flywheel, because they view movement as excessive. ZF Aftermarket reports that, like LuK, its DMFs require special tools to test them and the application of a specified torque. DMFs have differing levels of movement and some of them can be as many as 75 degrees of rotation before the internal springs are compressed. Therefore, consider that there is no universal value and you should consult your data source.
The first route to a successful clutch change is being supplied with the correct item and it arriving safely. Borg & Beck highlights its WebCat, with its vehicle-specific parts lookup function and the ability to cross-reference OE numbers and competitor parts. It also emphasises its fast and real-time stock availability through its regional distributor network and dedicated technical support to assist with part identification and ordering.
Information on Schaeffler's WebCat and Repxpert is updated daily and includes a free VRN lookup facility. Furthermore, Schaeffler trains its distributors on how to use its cataloguing systems, to improve the service that independent garage customers receive.
Sachs reports that customers can contact its UK customer services by e-mail or phone, to help identify the clutch kit they need. Its online catalogue is also available for everyone to use on the ZF Aftermarket website.
However, it is no good getting the right part, if it arrives damaged. Alliance Automotive, Borg & Beck, Schaeffler and ZF told us that they pay special attention to developing robust packaging but they all warn garages that they cannot guarantee fully against damage, especially if the box has been dropped in transit. They all recommend strongly that technicians inspect components carefully as they are unboxed and reject anything that appears damaged.
Clutch manufacturers do their best to ensure the correct clutch is supplied quickly and the protective packaging does its job. Even so, check every part for damage, as it is removed from the box, especially if there is any damage to the packaging.
Schaeffler is pushing its Repxpert portal hard and with good reason. The company has spent considerable efforts to put all specifications, fitting instructions and technical bulletins in one place. LuK clutch boxes have a OneCode printed upon them; all technicians have to do is scan the box with their mobile telephones and the relevant information is displayed. Should you get stuck, Schaeffler emphasises the team of experienced technicians at your disposal, including former VM master mechanics, on the Repxpert hotline.
Borg & Beck and febi-branded clutches have comprehensive fitting instructions included within clutch kit boxes, in addition to online training modules, videos, and downloadable guides. All of these firms offer a real-time technical helpline, although ZF Aftermarket has introduced a video call facility, so its technical help team can see the problem with you, increasing the chance of a swift resolution.
Some clutch suppliers support workshops with special tools. Without them, you are increasing your chances of making an error.
Whether you are looking to improve your techniques of fitting clutches to conventional manual transmissions, or to upskill on tackling the latest dual-clutch automated manuals, training is a worthwhile time and money investment.
Schaeffler's two-day IMI-certified dual-clutch training course is offered mainly through its distribution partner programs. It covers the most common wet and dry double-clutch systems that are manufactured by Schaeffler for the OEMs, including Volkswagen Group's DSG. ZF Aftermarket offers a dual-clutch training course, too, catering for a wide range of cars from the German DSG through to Hyundai/Kia applications. Alliance Automotive highlights not just the technical specialist support and knowledge through its TechMate partnership but also IMI Certified clutch training.
So, there you are. Selecting your clutch is more than just buying the part. You must consider the support that is offered – unless, of course, you wish to follow the advice of my friend's physics teacher...
“Whether you are looking to improve your techniques of fitting clutches to conventional manual transmissions, or to upskill on tackling the latest dual-clutch automated manuals, training is a worthwhile time and money investment."
Some clutch kits supply extra common wear components. However, before ordering, check for any technical advice and technical bulletins that your preferred brand supplies and enquire which extra parts are included.
Choosing parts is more than just cost. Consider the extra support offered, such as availability, speed of delivery, whether (or not) ancillary parts are supplied, kits are offered, plus any UK-based rapid back-up if you get stuck.
Do you even need support for bread-and-butter steering and suspension repairs? It turns out that there are plenty of resources available to technicians and Rob Marshall finds that all you have to do is reach out and use them.
While it cannot be denied that modern motor cars are becoming increasingly digitally tech-heavy, it is a stretch too far to say that all future car repairs will require an AI-driven laptop. As fascinating as digital technology might be, Artificial Intelligence cannot change a worn tyre, Swarm Intelligence cannot replace a knocking inner steering joint and you can do as much ADAS calibration as you want but it cannot resolve a leaking damper. Considering that almost 25% of all MOT Test failures last year were caused by faults in either the steering, or suspension systems, the majority of these mechanical defects required a capable human touch to resolve.
Not helped by increasing vehicle weights and neglected potholes growing sufficiently large to swallow small children, even EVs are not immune to chassis-related repairs and maintenance. Therefore, with suspension and steering repairs forming a significant chunk of many all-makes independent garages' bread-and-butter current (and future) work, it is not a bad idea to be aware of the support offered by suppliers, or brands, with whom you work.
Diagnosis is not always easy, especially when noises occur intermittently and are not easy to replicate. Meyle acknowledges this ongoing challenge and highlights its joint play tester as especially valuable, when dealing with more complex systems, including multi-link axles. The firm concludes that such repairs, generally, might not be rocket science but this does not mean that training and awareness are irrelevant.
“Not helped by increasing vehicle weights and neglected potholes growing sufficiently large to swallow small children, even EVs are not immune to chassis-related repairs and maintenance"
PART IS A PART OF US
Our founder Wulf Gaertner was a passionate car enthusiast. As a racing driver in the 50s, he needed spare parts he could count on, which is why he set up his own company. His tireless pioneering spirit paved the way for our company. The aspiration: Do the IAM better. With every part. With every solution. With every movement of the hand. Or screwdriver.
Dayco advises that most vehicle manufacturers recommend inspecting steering and suspension components every 36,000 miles or 36 months. Yet, it is wise to check them more often, such as during brake servicing or whenever tyres are changed, in addition to the MOT inspections.
While wear can be narrowed to a single component, it tends to be more cost-effective for the customer if any other associated parts that may not be as worn, but are in a borderline state, are replaced at the same time. It also avoids potential confrontation, when the associated part causes an issue soon after and the customer blames the technician for not performing an effective repair. This is a time, when quality suppliers can help, because they will know from their sales experience which parts fail close together. Some of these firms group these components under one part number. Take the bilstein group (febi) as an example. In its ProKit anti-roll bar range, not only is the bar supplied but so are the bushes and stabiliser/drop links.
Febi acknowledges that all vehicles suffer from corroded nuts and bolts in their suspension system as they age. Therefore, these fixings are included within a ProKit, thus saving time and money. Motaquip (a Comline brand) highlights the same issue, using the rear lower suspension arms, fitted to certain Volkswagen Group models, as examples. On these arms (part numbers LVSA1764 and CCA3037), the fixings cannot be reused and so it includes all of these fitting accessories with the replacement part. Motaquip also encourages feedback from technicians about real-world problems that they encounter. Some of these seeds germinate into fruit, an example of which is a lower arm fitting kit, which Motaquip offers for the Land Rover Discovery III, IV, V and the Range Rover Sport. As you may need to remove the arm, not necessarily to replace it, but to change the bushes (for instance), the securing bolts tend to be destroyed. Part number LVSK3001SK contains new fixings that you need to refit the arm, once it is repaired.
A common problem that the spring and damper specialist, KYB, experiences is technicians believing, quite reasonably, that they have been supplied with incorrect dampers, because the new items appear to be shorter than those that have been removed. KYB explains that many OE struts feature a rebound spring but, later in the production run, some car
After suspension or axle repairs, do not forget the importance of wheel alignment and ADAS calibration.
manufacturers remove it to reduce costs. Therefore, should you compare an OE part with a KYB replacement, it can be normal for the dimensions to differ. KYB explains that this does not mean that the part is incorrect. Instead, this intentional design feature protects the piston rod from damage and adds stability when extended fully. Yet, it is positive that technicians are noticing a difference and are querying it. For more details on this situation, plus more technical bulletins, KYB highlights its resource on https://kyb-europe.com/technicalbulletins/
Naturally, downtime is costly, especially when worn suspension tends to be spotted at MOT Test time, and the customer is placing you under pressure to conduct repairs and the retest as quickly as possible. KYB explains that it has invested hard in making replacement part identification quick and accurate. The Japanese firm explains that it has a dedicated European team working around the clock, ensuring utmost accuracy in its online catalogue. Its efforts have been rewarded with KYB being awarded TecDoc Premier Data Supplier status for several years. It advises technicians can search by VIN, or registration number, and many of the parts include 360° images. This function allows the technician to zoom and rotate the image, making it easier to match the part, reducing further delays and the inconvenience of resending parts and awaiting replacements.
Consider that, even if you are not replacing a component, you may not be able to re-use the fixings and so check if new nuts/bolts/washers might be required.
Support is available with air suspension repairs, from febi's technical support document supplied in the box to Arnott's installation www.arnottmanuals.com. Both firms have YouTube installation videos on www.youtube.com/@ArnottAir/ and www.youtube.com/watch?v=hVcNjQdq1pg
Naturally, parts availability for newer models, especially, is a major challenge. With Chinese BEVs from unknown and unproven brands flooding the UK market, their longerterm success, or failure, rests on aftersales. It is interesting, therefore, that Alliance Automotive has announced a series of quality steering and suspension parts for the BYD Atto 3. We suspect this is only the beginning and shows that the aftermarket has an opportunity to make parts available for brands that might struggle to support the cars they sell with spare parts.
Febi, incidentally, reminds us that its parts range includes components that tend to be available only via main dealers. These include power steering fluid reservoirs, ignition lock housings and even air suspension compressors and solenoid valves.
Meyle agrees that availability is a vital means of reducing workshop downtime. It highlights digital tools, including its relaunched website, as a major part of its strategy to ensure that the correct parts are supplied, first time. Additionally, its refreshed online catalogue is integrated with independent software ordering solution providers, including MAM Autopart, TecDoc and national distributors for optimum accuracy. Coupled to this is the focus that the German firm has on maintaining high UK stock levels within its dedicated UK warehouse, in which distributors can view real-time stock levels via TecCom.
Meyle also has invested heavily in technical communication, too. These include installation guides and QR codes printed on parts packaging that link directly to technical sheets and tutorials. Additionally, the firm offers live training events/ webinars with its distributors and has a dedicated travelling technical team that supports independent workshops with visits. It is also worth keeping abreast of the regular Technical
It might cost more initially but fitting a kit of parts is likely to offer longer-term savings.
Service Bulletins that Meyle publishes in its newsletter: www. meyle.com/en/newsletter
While febi offers fitting instructions on its partsfinder site, too, (https://partsfinder.bilsteingroup.com/), its YouTube videos are a resource that is worth visiting, especially because of the greater detail that they include. You can access a vast library of technical information about springs and dampers on KYB's website, including installation videos (https:// kyb-europe.com/fitting-videos). Yet, KYB is keen to avoid information overload. Therefore, where a particular part number is known to be difficult to fit, it provides a QR code next to a spanner symbol on the parts packaging, which takes the technician straight to dedicated fitting instructions.
KYB says that, as an OE manufacturer, it has a deep engineering knowledge of the parts it offers to the aftermarket, because they are the same. Where it can, it also shares the OE information. This relationship allows KYB to provide part-specific information, including accurate installation guides. Should you get stuck, you can get quick and direct access KYB’s UK Technical Team.
Febi underscores the advantage of choosing a firm that insists on OE quality, especially when it looks upon OE support as a springboard, not a target. Febi's three-year warranty is a clear example of this. Aside from its standard OE-quality range, Meyle is promoting its HD parts range hard. Part of the support is where the OE part has been reengineered to either enhance durability, or installation ease. Where relevant, some 'MEYLE HD' parts are preassembled to make the task quicker for the technician and they include all the necessary accessories, such as fixings. In addition, Meyle supports workshops with marketing support to help upsell its HD parts. These include point-of-sale materials, such as flyers, posters and comparison tools, plus social media content, national campaigns and even training through online videos and at events. Added to this is the four-year warranty support for
“It might cost more initially but fitting a kit of parts is likely to offer longer-term savings"
these upgraded components, which Meyle reasons helps technicians build trust with customers.
While it is true that vehicles have become more dependent on electronics and many technicians are upskilling accordingly, do not forget that support is available to help you maintain and repair the analogue side of the motorcar, which is worth using to your advantage.
While most steering and suspension repairs are analogue, we admit that some repairs dictate understanding the network system. BMW's Vehicle Dynamics Control, for instance, is networked linked through the ultra-fast flex-ray protocol with other ECUs, including via the X-drive (where fitted) system.
Air suspension systems offer superior comfort and handling, but proper maintenance and repair are essential to ensure they function optimally. Arnott Suspension Products provides you here with six essential tips for maintaining, diagnosing, and repairing your vehicle's air suspension system.
1. Prioritize
Air suspension systems can operate at high pressures, so ensure the system is depressurized and power is disconnected. Prevent contamination by keeping grease and dirt away. Always wear proper protective gear and securely lift the vehicle. Safety measures protect both the technician and the system.
2. Depressurize
Controlled depressurization prevents damage. Never remove fittings abruptly - some vehicles require diagnostic tools to open solenoids to release air. If available, activate “jack mode” to stop the system from adjusting when the vehicle is lifted.
3.
Improper handling can lead to system failure. Always support the vehicle when the system is depressurized and never pressurize air springs during installation, as both can cause improper unfolding and crimp ring damage. Lowering a vehicle without pressurization can overwork and overheat the compressor and possibly damage the compressor relay.
Follow torque specifications - especially with VOSS connectors. These typically require no tightening, and overtightening can cause leaks or thread damage. Arnott recommends using a torque wrench when needed.
4.
Catching failing parts early saves time and money. Signs of a failing compressor include melted lines, discoloration, or a burnt smell - often due to leaks causing overuse. A drop in
ride height overnight suggests a leak; use soapy water to find it. Uneven height may point to a faulty valve block as well.
Inspect struts for oil leaks. Oil can degrade air sleeves and reduce lifespan, while internal damper leaks hinder performance, overburdening the air spring.
Replacing a failed part without resolving the underlying issue may lead to repeat failures. For instance, a leaking shock might damage an air spring, which in turn stresses the compressor. Always replace relays with compressors to prevent premature failure due to constant running. Once repairs are complete, perform a comprehensive system check.
After service, proper calibration is essential to ensure everything works as intended.
Recalibrate ride height sensors with a diagnostic scan tool to verify and adjust ride height settings to avoid faults and ensure correct function. After test driving the vehicle, confirm that no diagnostic fault codes have reappeared in the system.
info@arnotteurope.com | www.arnotteurope.com
Battery testing and replacement might seem elementary work, but support will help you. Can you identify what this is, for instance?
Many technicians are aware of the need for battery support but what support is offered for you? Rob Marshall consults with the experts to find out.
Considering the colossal developments in automotive electrics, it is amazing that lead-acid chemistry remains dominant. While batteries have changed considerably, especially since the introduction of AGM, even these topspec batteries rely on good old lead-acid interaction.
At least modern batteries are easier to look after. No longer do they need frequent inspection and distilled water replenishments but this does not mean that they should be ignored. This is not helped by some manufacturers using the term "Maintenance Free" to give them a marketing advantage, when the intent behind the message is to indicate that the battery does not require periodic top-ups. Therefore, viewing any 12-volt lead-acid car battery as a fit-and-forget item could not only be a mistake in terms of lost revenue but you could also put your customer at risk of an engine non-start. Do not forget that a dying low-voltage battery will prevent Battery Electric Vehicles from entering Ready mode – so even EVs are not exempt.
Many suppliers recommend that you check batteries not just at service but every time a car enters your workshop. Some of these checks remain as they have been for years: is the battery secure and at no risk of moving in its tray? Are the terminals tight and uncorroded? Is the casing showing any
sign of damage, or warning signs, such as a bulging, or split, plastic casing? These visual checks remain just as pertinent today as they ever were.
Yet, your diagnosis does not stop there. You will also need to assess the battery's state of charge (measured in volts) and its capacity, known otherwise as state of health (assessed in amps). These might be separate measurements but they are interconnected. A battery with a charge level that drops below 12.5 volts will see a gradual reduction in its CCA – i.e. its capacity/state of health. The rate at which this deterioration occurs depends on how far below the 12.5-volt threshold the charge level has fallen and for how long.
The enemy is sulphation – a chemical process, where sulphate atoms remain attached to the plates, preventing the acid from contacting the lead, thus reducing the battery's capacity. Acid stratification causes a further complication for flooded batteries – excluding AGM. Due to the acid being heavier than water, the concentration level can become higher at the battery base than at the top.
There is some hope, however. Should you discover a low state of charge, a successful recharge should restore the voltage levels. Preferably, your charger should possess an anti-stratification mode to encourage the acid to mix, thus ensuring even acid strength throughout the battery.
While a recharge might restore voltage, there may not be sufficient capacity remaining within the battery to crank a cold engine. This might be because of inadequate acid/lead interaction. The cause might be sulphation, where the battery has been discharged deeply for so long that the sulphates cannot be shifted from the plates. A possible solution is highvoltage pulse-charging. This is how the desulphation mode on some smart chargers works, which may help to prolong a dying battery's life.
Yet, it might not. As the acid is corroding the plates' lead content continually, the paste will, eventually, fall from the plates and collect in the battery base. This also results in a capacity drop, indicating that the battery has reached the end of its life. The only consolation is that lead-acid batteries possess a decent scrap value, due to being over 95% recyclable.
While some supposed technically(ish)-minded customers might insist that Grandad's voltmeter is all that is needed to assess batteries properly, you must be supported by more sophisticated equipment.
Ring Automotive's battery analyser (RBAG950) provides a complete 12v and 24v battery health check, by assessing not just volts but also amps, thus indicating battery capacity, not just state of charge. It also checks for future starting problems, by measuring battery voltage drop during engine
Recognising that battery-related issues remain a leading cause of breakdowns, Ecobat Battery promotes a "test every battery" approach to help workshops boost customer service and profits. Silver Street Motors in Tiverton trialled this method using the Ecobat EBT780 battery tester and branded materials. Over three months, every vehicle entering the workshop had its battery tested, regardless of the service booked. Owner Steve Webber, initially sceptical, saw both customer engagement and battery sales improve.
cranking. Additionally, the RBAG950 can detect that the earth connections between the battery, engine and chassis are in good order.
Banner GB's HD1+ is designed for 6v and 12v batteries. It also assesses the state of charge and state of health and, like the Ring, possesses an integral printer, allowing for the findings to be taken away as 'evidence' by the customer. An over-extended cable is particularly useful for batteries in inaccessible locations, along with the option of eight different languages. As with the RBAG950, the HD1 can be used to assess EFB, AGM and GEL battery technologies.
which technicians can choose, dependent on their needs. The Accucharger, with its 15, or 25A, maximum outputs, was introduced last year and possesses seven charging modes, including those that address sulphation and acid stratification. Accuchargers possess a supply mode as well, to prevent vehicle data from being lost during charging.
Aside from its retail range, Ring's Professional smart charger range includes the RSCP5024, which the firm states is a complete battery support unit. A nine-stage charging algorithm is provided for lead-acid batteries and, like Banner's Accucharger, the RSCP5024 can charge other battery types, such as Lithium. Yet, Ring's RSCP5024 cannot only be left connected to batteries permanently but it also can maintain a constant battery voltage level for both 12V and 24V systems, when either programming or vehicle diagnostic equipment is in use for long periods.
battery replacement right, first time
Modern cars are increasingly fussy about many replacement parts; batteries are no exception. Banner Batteries reports that the most significant challenge facing suppliers is fitting the wrong technology type, especially with start-stop technologies.
The firm highlights that most cars in the UK are on their third battery and Banner Batteries have found it not uncommon for them to have an incorrect one installed. To help technicians, Banner has its www.bannerbatteryfinder.co.uk online portal to help you confirm the correct one. All technicians need to do is input the registration number.
Banner Batteries highlights that its portal contains extensive technical support information, such as the battery’s dimensions, layout, engine compartment location and an estimated fitting time. Should technicians need fitting support, this information is available after you have logged in.
As battery life is linked directly with usage patterns, you may deduce that a customer might benefit from an upgraded battery. This might comprise one that possesses a higher capacity (CCA), or more sophisticated technology.
Banner GB highlights its UK Technical Hotline, open Monday to Friday from 9.00 am to 5.00 pm. The number is 01889 571100. Alternatively, non-urgent enquiries can be directed to: office.bgb@bannerbatteries.com
Varta's Partner Portal is also a free-to-access online platform that supports technicians with the correct battery recommendation, once a registration number is inputted. Varta highlights that its system provides the correct replacement battery part number, as well as an upgrade option, should one be available.
Banner GB has introduced a dedicated mobile technical training and support vehicle, equipped with the latest battery testing and charging equipment. The firm offers technical training free of charge to garages and motor factors, which is offered on a one-to-one, or group, basis. Should you wish to upgrade your knowledge not just with charging but also in replacement battery programming, contact Banner on 01889 571100, or office.bgb@bannerbatteries.com
Varta, too, is dedicated to enhancing your knowledge about batteries. Its Partner Portal contains free E-learning modules with unlimited access that are designed not just to help technicians but also front-of-house staff. Yet, this is not the only place that Varta provides support. Varta Automotive's 'Knowledge' section should not be overlooked either, because it contains useful information, including how technicians code a new battery, how 12-volt batteries are charged correctly and how to support the electrical system, while replacing a battery
Heavy discharges shorten lead-acid battery life considerably. This is one reason why AGMs last longer than their flooded battery cousins, because they can tolerate a deeper discharge, down to 50%, without damage.
As lead-acid batteries prefer to be recharged slowly, it might be worth you offering an overnight recharge service to customers who cover short journeys frequently, to maximise battery life.
It is vital not to get your lead-acid technology types wrong. To help, Varta updated its battery labels to make it easier for technicians to identify which technology lies within the battery. ‘AGM’ Absorbent Glass Mat has a gold label. ‘EFB’ Enhanced Flooded Batteries have silver and ‘SLI’ Starter Lights Ignition (traditional flooded batteries) possess a blue marker.
As a dedicated mechanic, staying ahead of the latest industry developments, technological innovations, and market trends is essential to maintaining a competitive edge. Automechanika Birmingham is a must-attend for anyone serious about their craft and the future of automotive repair.
Automechanika Birmingham 2025 roared into the NEC with record-breaking momentum – for the first time, over 15,000 visitors walked through its doors—an achievement that underlines the industry’s resilience, innovation, and hunger for connection.
Across three exhilarating days, garages, bodyshops, detailers, suppliers, and technicians came together for a packed agenda of learning, networking, and hands-on discovery. With 550+ exhibitors from over 35 countries, the show floor buzzed with new products, live demos, and face-to-face energy like never before.
The launch of Motorvate brought a fresh edge to the event, engaging students, apprentices, and early-career professionals through competitions, interactive talks, and immersive experiences. It wasn’t just a feature—it was a vision for the future of automotive talent.
Returning crowd favourites — Workshop Hub (in partnership with autotechnician) Aftermarket Hub, Modern Garage, Paint & Spray Live — offered more than 150 hours of free training on everything from EV servicing and ADAS calibration to business strategy. Innovation4Mobility added a futurefocused edge, spotlighting emerging tech and sustainability in a dedicated theatre.
Among the highlights was the debut of the Thirty Under 30 Awards, honouring rising stars in the sector with a packed audience at the Motorvate Ignite Arena. The Garage Awards, hosted by the IAAF and supported by LKQ Euro Car Parts, celebrated excellence across the aftermarket.
Exhibitors showcased cutting-edge products, real-time support solutions, and game-changing innovations, reinforcing the show’s role as a business-critical event and demonstrating the appetite for in-person connection and progress is stronger than ever.
Joanne Knowles, Event Director at Messe Frankfurt, summed it up: “This year’s Automechanika Birmingham has been our strongest yet—not just in numbers, but in energy, ambition and impact. The industry has chosen Automechanika as the place to unite, tackle challenges, and shape a stronger future.”
Next up? The UK Garage and Bodyshop Event 2026— returning in June with even more tools, tech, and training tailored to workshops and repair professionals.
LKQ Urges aftermarket to build on collaborative momentum post-automechanika
Following a standout showing at Automechanika Birmingham 2025, LKQ Euro Car Parts is calling on the UK automotive aftermarket to harness the collaborative energy displayed at the event and channel it into long-term, industry-wide progress.
Matt Robinson, B2B Trading Director at LKQ Euro Car Parts, praised the unity on display at the show and highlighted the growing importance of partnerships in addressing key sector
challenges – from closing the skills gap to navigating the EV transition.
“There’s an incredible sense of connection in the aftermarket, which was on full display at Automechanika,” Robinson said. “It’s clear the industry is ready to work together, but we need even more of it to overcome the biggest hurdles and secure the future of the sector. No one business can do this alone.”
At the show, LKQ supported the newly launched Motorvate feature, a dedicated space designed to inspire and inform the next generation of automotive professionals. There, education providers and students engaged with industry leaders— including Bosch and Toyota GB—about the vast career opportunities available across the sector.
LKQ partnered with show organisers Messe Frankfurt to deliver the Modern Garage stand—offering hands-on insight into how workshops can evolve their technical capabilities and customer service to stay ahead of shifting trends.
Robinson pointed to LKQ’s broader commitment to industry progress, referencing recent advocacy efforts at both UK and European levels. In the EU, LKQ played a key role in shaping feedback for the Motor Vehicle Block Exemption Review, uncovering 16 examples of anti-competitive practices. In the UK, the company co-signed a letter to the Transport Secretary outlining key policy recommendations to protect the independent aftermarket.
“Collaboration isn’t just something we do at trade shows—it’s part of our everyday approach,” Robinson added. “By working together, we stand the best chance of delivering the skills, revenue streams, and technological innovation that will define the future of the aftermarket.”
As the dust settles on a record-breaking Automechanika Birmingham, LKQ’s message is clear: Industry unity is not just a moment—it’s a movement.
Trade trusted worldwide A complete range of professional additives and tools from JLM for reducing emissions and improving performace in diesel, petrol and hybrid engines.
“This year’s Automechanika Birmingham has been our strongest yet—not just in numbers, but in energy, ambition and impact. The industry has chosen Automechanika as the place to unite, tackle challenges, and shape a stronger future.”
Joanne Knowles, Event Director
At Automechanika Birmingham 2025, ALLDATA Europe announced the addition of Mitsubishi Motors as its 42nd OEM partner on the first day of the show. Since 2023, the company has expanded to cover 97% of Europe’s car parc with original mechanical and collision repair data. Key platform enhancements include smarter EV taxonomy, license plate-based vehicle identification (VRM), and improved search functions. Light commercial vehicle support has also been bolstered.
On day two, it launched its fully integrated API for all authorised partners, enabling real-time access to OEMcertified repair data directly within workshop systems. This breakthrough enhances workshop connectivity, offering verified procedures, diagrams, and diagnostics for over 42 brands. First adopted by TOPMOTIVE, the API supports scalable, flexible integration for garages of all sizes.
On day three, ALLDATA highlighted its commitment to the next generation of automotive professionals. Through its growing education initiative, ALLDATA is providing colleges across Europe with access to the same OEM repair data used by professional workshops. In the UK, 14 colleges now use the package, giving students hands-on experience with diagnostics, mechanical, and collision repair across 42 vehicle brands. This practical exposure boosts confidence, employability, and readiness for real-world workshops. With tailored packages for vocational programs, ALLDATA is bridging the gap between education and the evolving demands of the automotive industry.
Bosch demonstrated ADAS calibrations, diagnostics using its Secure Diagnostics Access, EV services with its next-generation Battery Tool and Tesla Diagnostics with Bosch ESI[tronic].
NAPA celebrated its centenary year and discussed its catalogue with stand visitors, which spans more than 40 product categories. It also presented NAPA 360, the digital platform for easy access to parts and tools & visitors had the chance to win NAPA Racing merchandise and other prizes.
Comma celebrated its 60th anniversary at Automechanika Birmingham 2025, presenting its latest products and showcasing myComma, a new loyalty programme offering rewards for workshop owners, plus tools and training to help mechanics grow their knowledge.
The IAAF hosted the Automechanika Birmingham Garage Awards at the Show, celebrating the best of the garage industry – acknowledging the commitment and dedication of independent garages and technicians.
The IGA team provided insights and discussed the most pressing issues and opportunities facing independent garages. Visitors learnt about SERMI and how the IGA is working to support businesses in staying competitive in a continually evolving industry.
Snap-on had several show deals on offer, giving visitors thousands of pounds off its alignment and diagnostic equipment.
Maverick Diagnostics hosted the Ultimate OE Diagnostic Challenge – competitors won up to £1,000 towards OE equipment, with second and third prizes including vouchers and a training course.
Arnott displayed its aftermarket suspension products including remanufactured OE air struts, Arnottdesigned new air struts, magnetic shocks, innovative air springs, OES air suspension compressors, coil spring conversion kits, valve blocks and ride height sensors.
TOPDON UK welcomed Danny Versluis (Diagnose Dan) onto its stand demonstrating the DDTSB system and explaining its benefits to workshops. A FREE 6-month subscription is included with most of the Phoenix range of diagnostic tools.
BM Catalysts’ stand attracted visitors with its interactive Spin the Wheel game and exclusive prize draws. Alongside the fun, the company showcased its Garage Pro and Rewards Pro platforms, designed to boost workshop efficiency and reward customer loyalty. BM Catalysts also offered insights into its latest technologies and commitment to a greener future. Attendees explored new products using QR code systems, streamlined access to information, and support.
Brembo showcased its full fftermarket range, organised into five product families tailored to diverse vehicle and customer needs. Brembo Essential offers an accessible entry point with brake drums and remanufactured calipers. Brembo Prime,
the premium line, delivers OE-quality brake discs, pads, and accessories for cars, trucks, and motorbikes. Brembo Beyond focuses on sustainability and new mobility, with its Greenance Kit cutting PM emissions by 80%, and an EV Kit offering corrosion-free performance up to 100,000 km. Brembo Xtra caters to performance enthusiasts with stylish, highperformance products like drilled discs and coloured calipers. Brembo Upgrade brings track-level innovation to everyday driving with its Gran Turismo and Pista Kits, along with Carbon Ceramic Material (CCM) discs now available for aftermarket supercar applications.
Duckhams, the original British motor oil brand since 1899, marked its 125th anniversary at the event. Founded by Alexander Duckham, the brand has pioneered numerous innovations, including Europe’s first multigrade and synchromesh gear oils.
Duckhams announced a new direct-to-market strategy for the UK and Ireland, supported by new distributor partnerships for workshops and retailers. CEO Mike Bewsey and the team showcased the brand’s full product range, from QXR oils for modern cars to the Classic range. Visitors enjoyed interactive competitions and the chance to win merchandise. Racing driver Max Coates and his Duckhams-liveried Porsche Carrera Cup car attracted strong attention. Bewsey said, “It’s an exciting time for us at Duckhams as we build on the brand’s unique heritage and scale our business both in the UK and globally.”
Autotechnician speaks with Duckhams Chief Executive Officer Mike Bewsey about the brand's 125 year anniversary, its discussions with workshops at Automechanika Birmingham 2025, and the Duckham's ducks! https://youtu. be/b0tFngc9EQU
ELTA Automotive announced a three-year extension to its supply contract with Halfords, continuing to provide over five million automotive bulbs annually across the UK and Ireland. As the official licensee of the Lucas brand, ELTA supplies both Lucas and Halfords’ own branded bulbs, with the Lucas range proving popular for its trusted quality. The extension coincides with Lucas’ 150th anniversary and reflects strong confidence in ELTA’s product quality, reliability, and sustainability—highlighted by a shift to 100% plastic-free packaging, eliminating 28 tonnes of plastic from the supply chain each year.
The Elta stand highlighted its range of exhaust sensors, engine management programme, ignition coils, wipers and fans.
Autotech Training showcased its advanced online Learning Management System, Autolearn, designed to transform technician training and support Continued Professional Development (CPD) in line with IMI TechSafe standards.
As the industry continues its shift toward electric vehicles (EVs) and ADAS technologies, Autolearn offers technicians a flexible, modular e-learning experience—allowing them to upskill anytime, anywhere. With EV-certified technicians required to complete 18 hours of CPD over three years, and ADAS-certified professionals needing 10 hours, Autolearn delivers bite-sized content that covers both technical topics and essential soft skills. It enabled users to stay compliant, efficient, and future-ready.
The platform is also customisable, allowing businesses to white label the system and create tailored training journeys aligned with their development goals, supported by Autotech Training’s industry expertise.
Also featured on the stand was Autotech Connect, which unveiled the latest developments in its Assisted Reality headsets. These wearable devices provide hands-free, real-time expert guidance—helping to boost skills and productivity.
Among the new features launched were AI-driven tools designed to support neurodiverse users and simplify administrative tasks, fostering more inclusive and efficient work environments. Additionally, a thermal imaging camera was introduced, allowing technicians to instantly identify live electrical components—speeding up diagnostics and reducing errors.
Visitors to the Kalimex stand at this year’s show were greeted with a warm welcome, free goodies, and the chance to win tickets to the European Rally Championship in either Rome or Wales. There was also an exciting competition to win the JLM Lubricants DPF Toolkit with the Clean and Flush Fluid Pack— worth over £250.
This professional-grade kit enables mechanics to clean severely blocked DPFs without removing them from the vehicle. Trusted and used by thousands of technicians worldwide—including DPF specialists across Europe, Australia, and the UK—it proved to be a popular attraction. Attendees also had the opportunity to learn more about JLM’s top five technician-trusted products: the DPF Refill Fluid, a universal alternative regeneration fluid offering excellent value; the JLM DPF Cleaner, a best-selling cerium and platinum-based formula; the JLM Petrol GDI Cleaner, independently tested and proven to outperform all competitors; Diesel Extreme Clean; and the JLM GPF
Staff shortages, pre-planned holiday & sickness cover
Skilled & experienced techs and MOT testers
Contracts from one day to six months
450+ vetted contractors across the UK
Weekday & weekend cover available
Cleaner, an emerging favourite for cleaning petrol particulate filters.
Also highlighted were two more standout Kalimex products: K-Seal Permanent Coolant Leak Repair, a global bestseller with over 13 million units sold across the UK and USA, and Quiksteel, widely recognised as the world’s strongest epoxy putty.
Auto3iii showcased its AI-powered electronic vehicle health check (eVHC) platform designed to turn ‘workshop potential into profit’. The platform’s predictive maintenance tools, digital reporting, and gamified user experience – trained on over 250 million part images – is designed to boost productivity and customer loyalty.
HELLA made a strong return to thermal management at Automechanika Birmingham, unveiling an initial range of 1,200 air conditioning and engine cooling parts, set to expand to 6,000 by 2027. The lineup includes compressors, radiators, and intercoolers, with plans to introduce advanced EV components like coolant control hubs and electronic valve actuators. HELLA aims to integrate thermal management with its electronics range, supported by Gutmann diagnostics, software, and training via HELLA Tech World, ensuring
workshops access quality parts and expert resources.
Hella Gutmann’s mega macs S 20 diagnostic tool is designed to tackle challenges posed by manufacturer security gateways and speed up fault-finding. It supports advanced protocols like Diagnostics over Internet Protocol (DoIP) and CAN-FD, with built-in access to over 20 OEM security gateways. Julian Goulding, Head of Garage Equipment, highlighted its ability to reduce downtime and boost productivity affordably. The tool features Cyber Security Management for one-time authentication across OEM platforms, enabling comprehensive diagnostics on securityprotected vehicles. It includes a rugged Android tablet and connects via Bluetooth or USB-C for easy use. Priced at £2,150+ VAT, it comes with two years of software updates, with optional HGS Data for detailed technical info, helping workshops deliver fast, accurate repairs on complex vehicles.
MEYLE showcased its latest innovations, including the rear axle control arm for Volkswagen Group’s MQB platform, a Volvo driveshaft, and a high-precision PDC sensor—all reflecting MEYLE’s commitment to OE-comparable, repairfriendly solutions. Visitors explored a broad portfolio covering steering, suspension, brakes, engine, and electronics.
The Motor Ombudsman announced its expanded Codes of Practice and also partnered with automotive charity Ben to launch Steer, a free printed and downloadable guide aimed at helping automotive businesses identify and support workers facing mental health and wellbeing challenges. This initiative responds to a survey revealing that nearly half of vehicle repairers are concerned about the rising mental and physical health pressures caused by increasing living costs. Ben’s recent Health and Wellbeing survey of over 1,000 UK automotive workers highlighted stress (57%), poor sleep (52%), and anxiety (44%) as top issues, with figures rising
above the national average amid financial strains.
Steer raises awareness of mental health’s impact on workforce morale and performance and offers practical strategies, communication tips, case studies, and signposts to Ben’s free, confidential support services. Bill Fennell, Chief Ombudsman, emphasised the importance of open dialogue and support for staff wellbeing, while Ben CEO Rachel Clift highlighted the guide’s role in reducing stigma and encouraging vulnerability. The guide promotes a positive mental health culture within automotive workplaces and can be accessed at www.TheMotorOmbudsman.org/Steer
Autotechnician spoke with Rachel Clift, CEO, Ben automotive charity at Automechanika Birmingham 2025 about its partnership with The Motor Ombudsman and the comprehensive support available to technicians and the wider automotive community https://youtu.be/ XMyQ5xdhfR8
OSRAM launched its new LEDinspect® torch range, with six models split into two categories: the ESSENTIAL (batteryoperated) and PRO (USB-C rechargeable) series. The ESSENTIAL line includes the TORCH 250, 350, and 450 (£7.99–£14.99), offering brightness from 250 to 450 lumens, twist focus from flood to spotlight, multiple light settings, and robust aluminium casings. The PRO series—TORCH 500, 800, and 1200 (£19.99–£32.99)—boasts higher lumen output, longer runtimes (up to 48 hours), five light modes including Eco and flash, and beam distances reaching 680 metres.
OSRAM’s new LEDinspect® 3-in-1 inspection light kit (LEDIL417) offers versatile lighting for workshops. Housed in a compact case, the kit includes three interchangeable attachments: a standard torch, a slim inspection lamp with dual hinges (180° and 230° rotation), and a flexible gooseneck light ideal for illuminating hard-to-reach areas. Each attachment connects to a single handle base, featuring four lighting modes—high, medium, low, and flash. The base and gooseneck tip are both magnetic, enabling hands-free operation and aiding in the retrieval of small metal parts.
The THINKTOOL Euro 399 is a brand new 14-inch AI diagnostic device developed by THINKCAR in 2024. The unique design features an optimised Ul interface and powerful THINKCAR operating system (TCOS). The 399 supports dual vehicle diagnostics with additional VCI, and also has a split-screen function to show data and modules etc. Coverage includes passenger cars, LCV, EVs, and commercial vehicles, making the 399 the ideal choice for the advanced workshop.
• OE-Level diagnostics, including full system diagnostics, special function, actuation test, bi-directional control, advanced coding etc.
• Newly released AI diagnostics with optimised user experience, the device can quickly and easily follow instructions.
• Advanced TCOS system with brand new UI interface for optimised user experience.
• Includes enhanced EV coverage as well as HGV as standard.
• Online reprogramming for 19 brands, plus remote diagnostics.
• Supports additional VCI for dual-car diagnosis.
• Equipped with a fast charging stand, the tablet can be fully charged in 2 hours.
• Supports video remote diagnostics.
• 14-inch HD IPS touch screen, 256G ROM, 8G RAM, 20MP Rear Camera, 8MP Front camera.
• Brand-new industrial design, the body is constructed using 8.15mm titanium alloy, providing light-weight and exceptional druability, easily passing a 1.2M drop test.
• VCI data can be synchronised to the tablet in real time with split screen. 2-Years free updates for passenger cars.
• Integrated 41 maintenance resets.
• Optional: Thinkeasy Bluetooth, Video Scope, Scope Box, THINKCAR TPMS Tool, PROG, TKey 101, Printer.
• Supports ADAS calibration services.
Meanwhile, the Ring Automotive brand has expanded its popular Xenon range with the launch of Xenon220, its best-performing halogen bulbs yet. Designed as a direct replacement for standard H4, H7, and H11 bulbs, Xenon220 offers up to 220% more light on the road and 20% whiter light than the legal minimum. The enhanced brightness and clarity improve visibility, helping drivers respond faster to road conditions for safer driving.
Supertracker launched its next-gen CCD wheel alignment systems, the STR130 TC and STR420 TC. The compact systems feature 6 or 8 sensor technology and are controlled via a robust WindowsTab with magnetic mounting. Key benefits include a cabinet-free design, improved mobility, and compatibility with rims up to 27”.
The Verification of Lubricant Specifications (VLS) marked a successful three days, engaging with workshops to raise awareness about the complexities of modern lubricants and risks of non-compliance. As vehicles age and OEM specifications proliferate, workshops face mounting challenges in selecting the correct oil. VLS, backed by Trading Standards, plays a critical role in investigating lubricant complaints and verifying product claims to ensure consumer and vehicle protection.
Chairman Harald Oosting highlighted concerns over economic pressures driving workshops to reduce lubricant ranges and opt for cheaper oils. However, using low-quality or incorrect oils can lead to severe consequences—damaging emission control systems, increasing wear, and even causing engine failure. He emphasised that modern engines require highly sophisticated lubricants, and even small formulation changes can have a significant impact on performance and engine longevity.
The shift toward smaller, high-efficiency engines has increased the demand for synthetic and semi-synthetic oils,
creating further complexity. Additionally, the assumption of backward compatibility with new oils is becoming less reliable due to evolving OEM specifications and performance requirements.
VLS expressed concern over the integrity of products from new entrants in the additives market, which may use untested ingredients that fail to meet industry standards. At the show, VLS launched a new white paper reviewing 123 product investigations and released findings from its UK Workshops Attitudes to Engine Oil Survey, which revealed confusion around oil specifications and a troubling emphasis on price over quality.
VLS continues to push for better industry understanding and compliance, protecting workshops and end users alike.
Autotechnician spoke with Alan Outhwaite, Head of the Technical Review Panel & VLS Company Secretary David Wright about oil quality, stock control and compliance... https://youtu.be/Kib8rIri7lQ
“It’s clear the industry is ready to work together, but we need even more of it to overcome the biggest hurdles and secure the future of the sector. No one business can do this alone.”
Matt Robinson, B2B Trading Director at LKQ Euro Car Parts
Castrol, in partnership with UK distributor The Race Group (part of Certas Energy), showcased its full product portfolio across three stands. Together, they highlighted Castrol’s current and heritage products, alongside its Castrol Service offering.
Visitors to stand S70 discovered Castrol’s digital solutions for workshops and collected a £50 voucher towards a 200-litre order. Rally driver Meirion Evans appeared on 3 June to meet fans and answer questions. A token slot machine gave guests the chance to win Castrol-branded mechanics gloves and Castronomy merchandise. Visitors who signed up to Castrol Service or registered for a partner product were entered into a prize draw to win a limited-edition MEM Rally Team Castrol barrel table and chairs—an attendee favourite in previous years.
On stand C88, the Castrol Technical team stressed the importance of using the correct oil, offering the chance to win an ATF Transmission Flush Machine worth £3,500. Guests explored Castrol’s 126-year product legacy, including the Castrol ON range, designed for electric vehicles to go further, charge faster, and last longer. Also featured was Castrol’s new Car Care Range, a six-product line designed to simplify and enhance workshop maintenance.
SMP Europe launched its new Ride Height Level Sensors range, designed to address a common MOT failure caused by faulty sensors affecting headlight alignment. The sensors are crucial for vehicles with adjustable suspension and their malfunction can lead to MOT test failures. Alongside the new range, SMP showcased its full product portfolio, including Intermotor AdBlue Injectors, air mass meters, EGR valves, ignition coils, and more.
Thinkcar UK launched an exclusive promotion offering workshops a free HaynesPro Electric Pack (worth £350 + VAT) with purchases of its THINKTOOL Euromax or THINKTOOL Euro 399 diagnostic tools. Managing Director Alex Gillbanks explained the deal aimed to help technicians work more efficiently by combining powerful diagnostics with quick access to essential wiring diagrams and technical data. The Euro 399 features split-screen functionality, enabling users to view diagnostics and wiring diagrams side by side. It also provides EV system integration. The THINKTOOL Euromax, its flagship tool, deliveres OE-level diagnostics for over 300 manufacturers, online programming, ADAS support, a fourchannel oscilloscope, and Topology Mapping for system visualisation. It supports the latest protocols and compatible with both passenger and heavy-duty vehicles.
NGK celebrated its 50th anniversary, joined by motorsport brand ambassadors Charlene Martin and Max Coates. The centerpiece of the stand was the iconic John Player Special Lotus F1 car – a symbol of Niterra’s long-standing ties with motorsport excellence.
Autotechnician magazine ran three days of training seminars and panel debates at the Workshop Hub, which incorporated a live fault finding area, hosted by Matt Cleevely of Cleevely EV and trainers from Delphi
Matt delivered two impactful sessions encouraging independent garages to embrace electric vehicle (EV) work. Speaking at the Workshop Hub, he shared his journey from running a family garage to establishing a nationally recognised EV service centre, highlighting the importance of building capability ahead of demand.
Matt emphasised that transitioning to EV servicing doesn't require a massive financial investment — just safety training, essential tools, and a willingness to learn. His key message: mindset and confidence are the most important assets for success in the growing EV sector.
Now operating an 8,000 sq ft workshop, a 4,000 sq ft EV showroom, and a mobile network with 12 EV technicians, Cleevely Group demonstrates the potential for independents to thrive in EV servicing. Matt also discussed practical topics like high-voltage insulation testing, tyre replacements, and ongoing EV maintenance, supported by live demos using a Nissan Leaf.
With EV adoption accelerating, Matt urged garages to act now or risk falling behind.
New products, fitting tips & technical advice to ease fault-finding and installation
Castrol offer for Stellantis servicing Castrol is offering free Magnatec lubricant to workshops that service Stellantis-group vehicles when they make a bulk purchase in July.
Castrol MAGNATEC can be used to service a large proportion of vehicles on UK roads, and is suitable for many cars from brands within the Stellantis group, including Alfa Romeo, Citroën, DS, Fiat, Jeep, Peugeot, and Vauxhall.
The range has been developed to meet the demands of modern driving – a significant 75% of engine wear happens at the start of a journey and continues when cars accelerate, slow down and idle in city driving. Castrol MAGNATEC is designed to cling like a magnet to critical engine parts and locks in place to deliver 50% better engine wear protection; safeguarding vital components, including the valvetrain, timing chain, pistons and bearings from damage and wear.
Contact your local distributor for details.
Step-by-step tutorial: Peugeot Boxer 2023 transponder clone
In a new series of step-by-step guides, Autowave is supporting workshops and locksmiths with clear, detailed instructions on how to get the most from their replacement key and programming equipment.
The series covers individual vehicle transponder cloning to advanced diagnostics, key coding and remote programming, and will help technicians save time, reduce errors and tackle specific vehicles with confidence.
To start the series, Autowave’s Ravi Kotecha explains how to clone a transponder on a Peugeot Boxer 2023. A video tutorial can be found at https://youtu.be/WMRzfef3Tdc or snap the QR code.
Cooper Barnes Automotive created a dedicated 5,000sqft calibration and repair workshop to sit alongside its bodyshop at its Cambridge site following a sharp increase in the demand for ADAS calibration.
“Every other car we see now needs some form of calibration. That simply wasn’t the case 12 months ago,” said managing director Matt Cooper. “We’ve been in this industry for 40 years. While we’ve always known autonomy was coming, the speed at which it’s landed has been staggering.”
Until this expansion, all calibration and coding work was undertaken on-site by mobile technicians from A1 ADAS. Matt could not fault their work but said: “We’re seeing so many ADAS-equipped vehicles that it reached a point where I was seeing more of A1’s team than my own. That’s when we knew it was time to bring it in-house”.
Matt chose A1 to specify, supply, and support the full setup. Working closely with A1’s Iain Molloy and Matt Hume, the business invested in the Autel IA900WA system, which combines ADAS calibration with fourwheel alignment functionality and also upgraded its existing diagnostic tablet to the MS909 and purchased all the necessary targets, boards, and mats to cover a wide range of vehicle makes. https://a1adassolutions.co.uk/services/
Attain OE-level coding & programming
Workshops can access OE-level coding and programming at a reduced cost by taking advantage of Thinkcar Uks new promotional price on its Euro Master diagnostic tool. This normally retails for £1,695+VAT but is now available for £1,195+VAT through its national dealer network.
Developed to bring OE-level diagnostics to independent workshops, the Euro Master combines full-system fault finding with the ability to perform online programming and coding on vehicles including BMW, Mercedes, Volkswagen Group, Land Rover, Nissan, and more. Secure gateway access for FCA vehicles is also supported.
The Euro Master is also modular, allowing garages to add capabilities over time, such as ADAS calibration and oscilloscope modules.
Schaeffler introduces NOx sensors Vitesco was integrated into the Schaeffler family some months ago and the first joint product launch has been announced Nox sensors, and are available to order from the Hereford distribution centre.
The replacement part supports exhaust after-treatment, helping to ensure compliance with strict emissions standards.
Schaeffler Sales & Marketing Director, Matt Selby, said: “The range covers all vehicle sectors, from passenger cars and LCVs to trucks and tractors, for both 12V and 24V systems. Vitesco have manufactured over 140 million NOx sensors since 2002, with more than 50% of that total coming in the last 7 years, so we know there is enormous potential in the independent aftermarket for this product, which delivers a significant contribution to clean mobility.”
Information on products, including fitting instructions, can be found on the REPXPERT app, or at: www.repxpert.co.uk
NAPA has launched six new high-quality steering and suspension components for the BYD ATTO 3, the first BYD model available in the UK and Ireland. This includes two stabilisers, two tie rod ends, an inner tie rod, and a ball joint, all manufactured to OE standards. These parts are part of NAPA’s 3,800+ SKU range and feature cataphoresis plating for 10-year anti-corrosion protection, tested with 900 hours of salt spray and come with a 3-year/36,000-mile warranty.
Following the introduction of water pumps to the DriveTec cooling range earlier this year, radiators and condensers are also now available through GSF Car Parts, providing 120 radiator SKUs for more than 78% of the market and condensers covering 70% of both cars and LCVs.N
Both products are OE-matching design, treated to protect from corrosion and backed by a three-year/36,000-mile warranty.
TPS has expanded its range of products available through its 83 UK centres, adding six leading brands Bosch, ZF, Mahle, SKF, Hella and Valeo.
This will offer around 2,000 third-party parts at launch, with plans to increase this to over 10,000 as the range develops and new brands are added.
TPS is a supplier of Volkswagen Group approved genuine parts and these new brands will offer a greater choice of parts to fit Audi, Seat, Cupra and VW cars and CV models. Catherine Baker, Head of TPS, said: “We are proud to launch ‘Brands at TPS’ and in doing so boost our parts offering to our customers… We remain dedicated to Genuine as our primary offer, but we can now offer a one-stop-shop for our mechanical customers’ needs, including a wide-ranging selection of third-party branded parts.”
The Air Mass Flow Meter (MAF sensor) plays a pivotal role in ensuring the correct air-fuel mixture in ICE vehicles. Valeo explains that a faulty MAF sensor can cause poor acceleration, rough idling, and increased fuel consumption. Diagnosis involves:
Checking signal voltage with a multimeter
Using live data from a scan tool
Inspecting for dirt or oil contamination
Examining wiring and connectors for faults.
Contamination: Dirt buildup affects readings, causing rough performance. Cleaning with MAF sensor cleaner restores accuracy. Electrical Faults: Wiring damage leads to erratic signals and check engine lights. Inspect and repair connections. Sensor Degradation: Over time, hot wires or films lose precision, requiring sensor replacement.
Valeo Service has a comprehensive range of MAF sensors, recently adding 150, bringing its offering to a total of 240. New releases include applications for hybrid vehicles such as the Volvo XC60 II T8 Plug-In Hybrid 2022 and the Peugeot 408 II Hybrid 225 2022
Comma’s Bag-in-Box range of oils provides a more sustainable alternative to traditional 20-litre pails and the new programme introduces nine of its most in-demand engine oil grades. They use 75% less plastic, feature a stackable design and an integrated tap makes dispensing cleaner.
Schaeffler’s range of Vitesco NOx Sensors is the ideal addition to its constantly evolving Vehicle Lifetime Solutions portfolio. Thanks to their proven original equipment (OE) quality, these sensors set the highest standards in accurate nitrogen oxide measurement, supporting efficient exhaust after-treatment and helping to ensure compliance with strict global environmental standards. By choosing to install genuine Schaeffler Vitesco NOx Sensors, you are trusting in our market-leading OE quality – which delivers precise emission control, reliable operation and a long service life. www.repxpert.co.uk