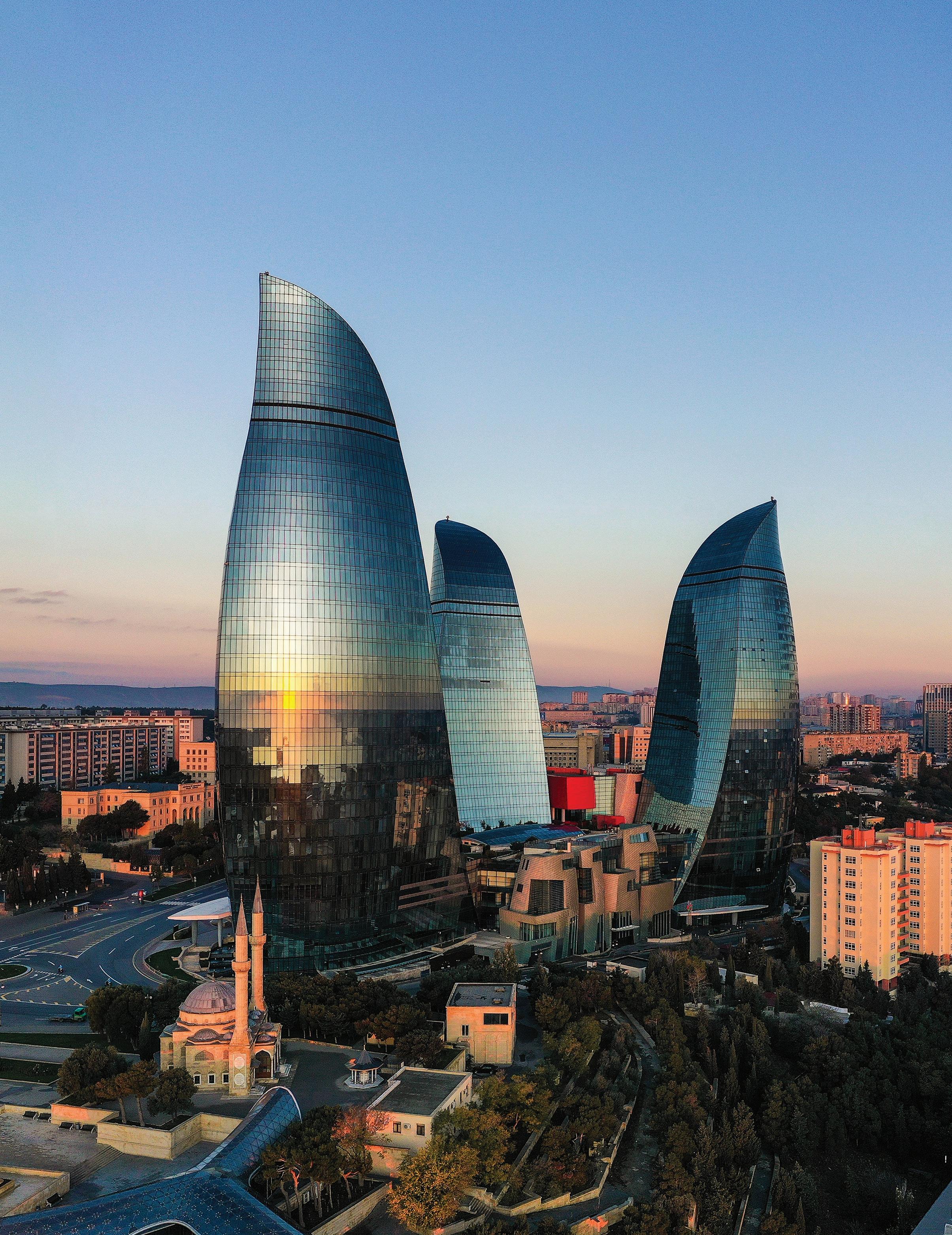
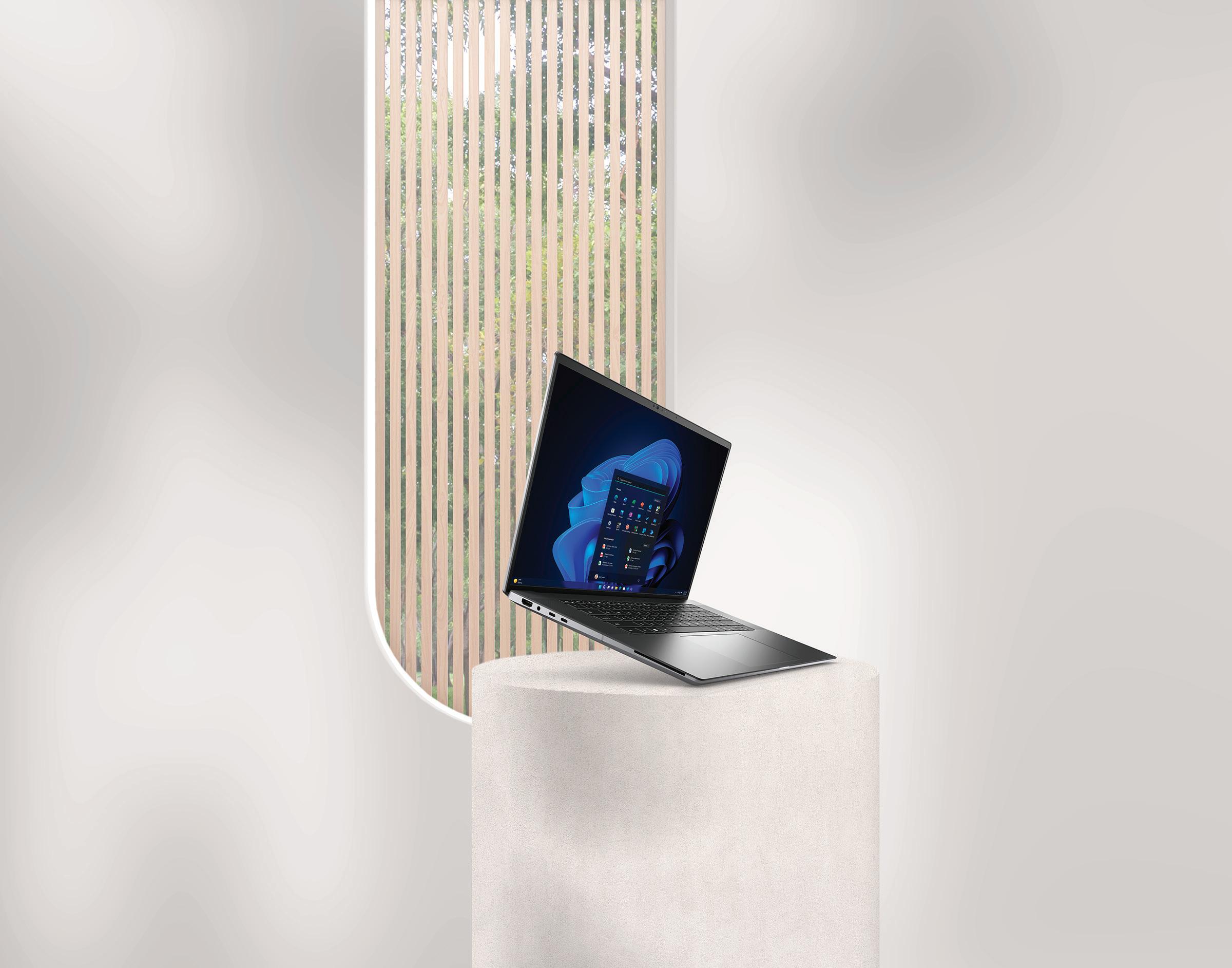
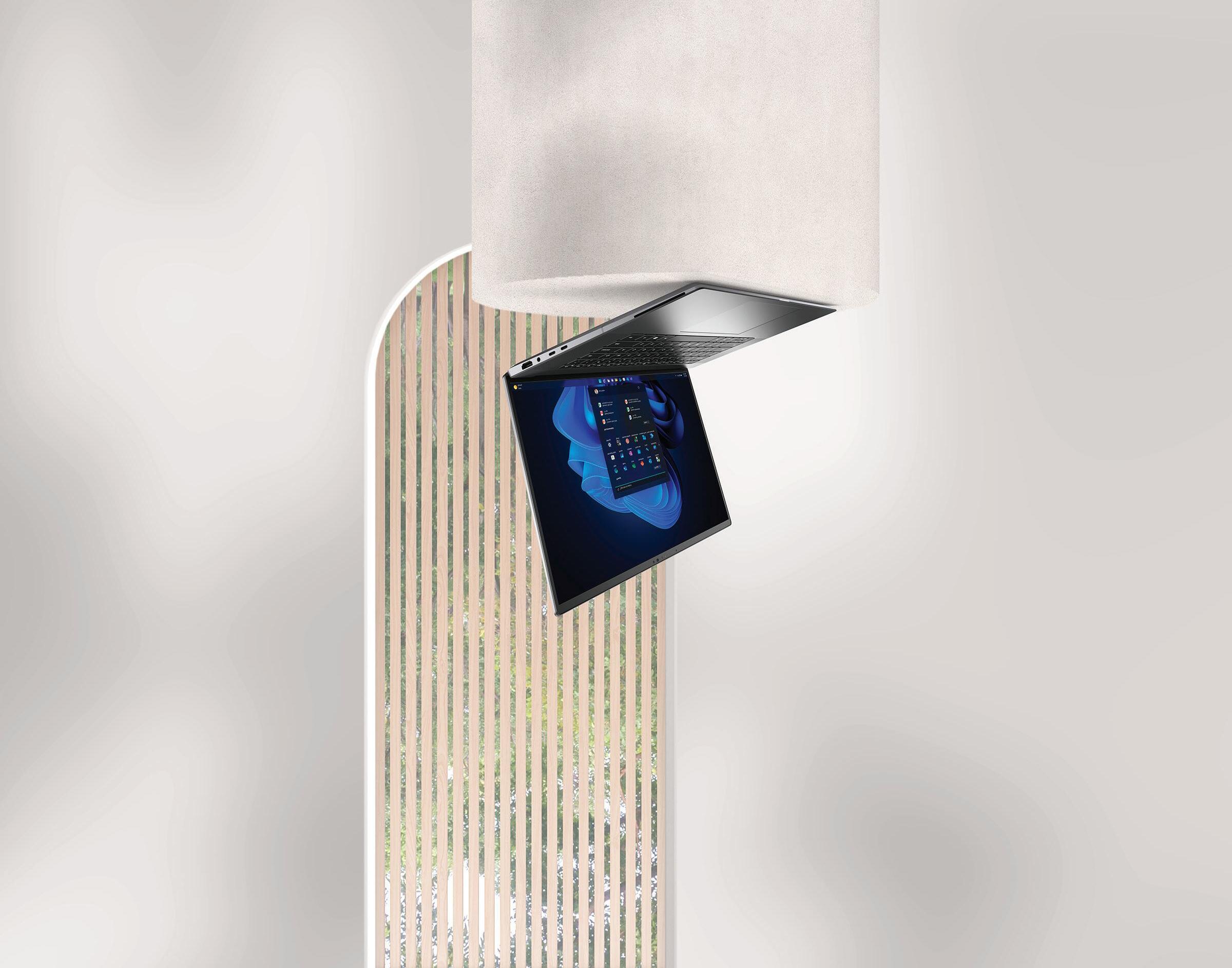
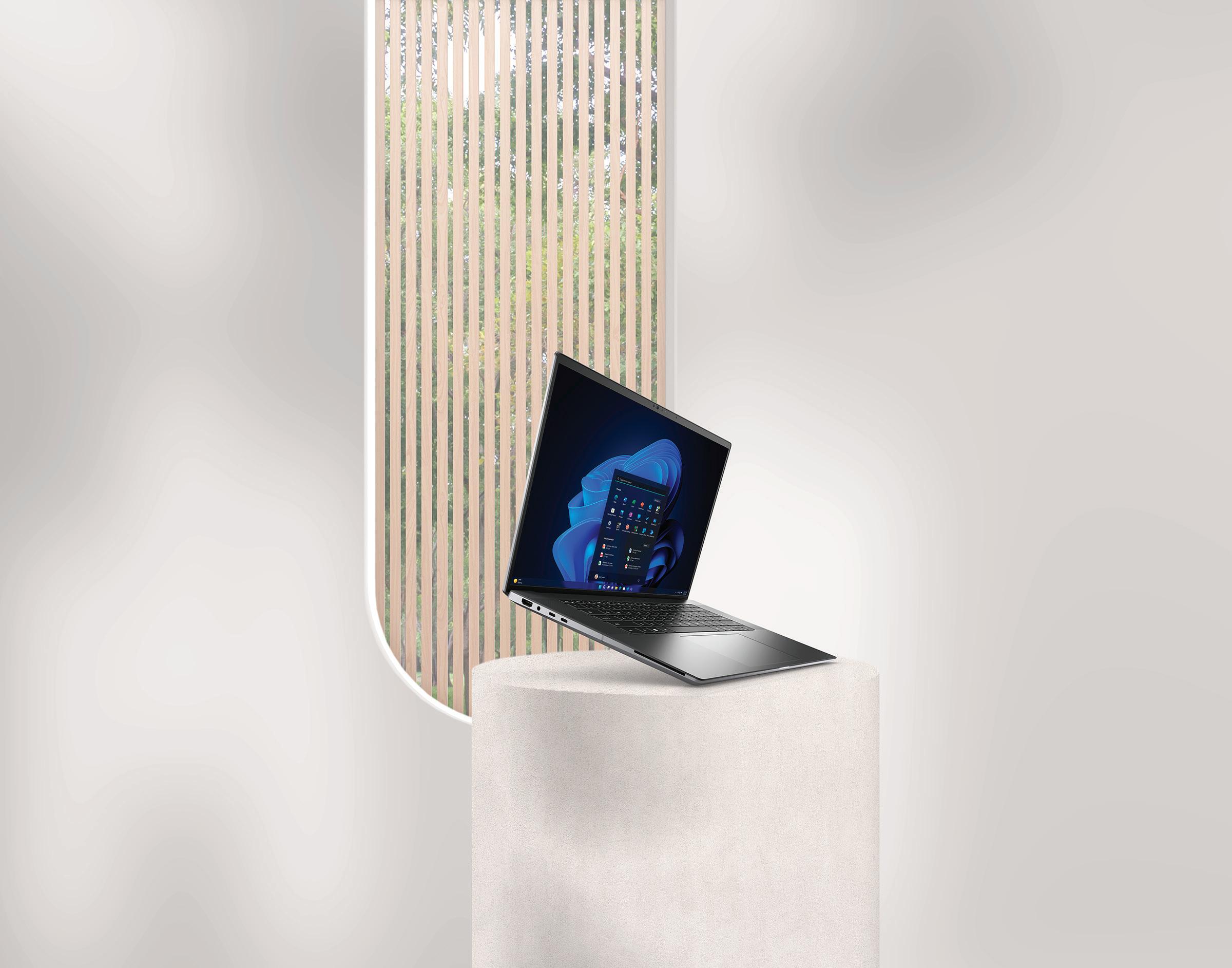
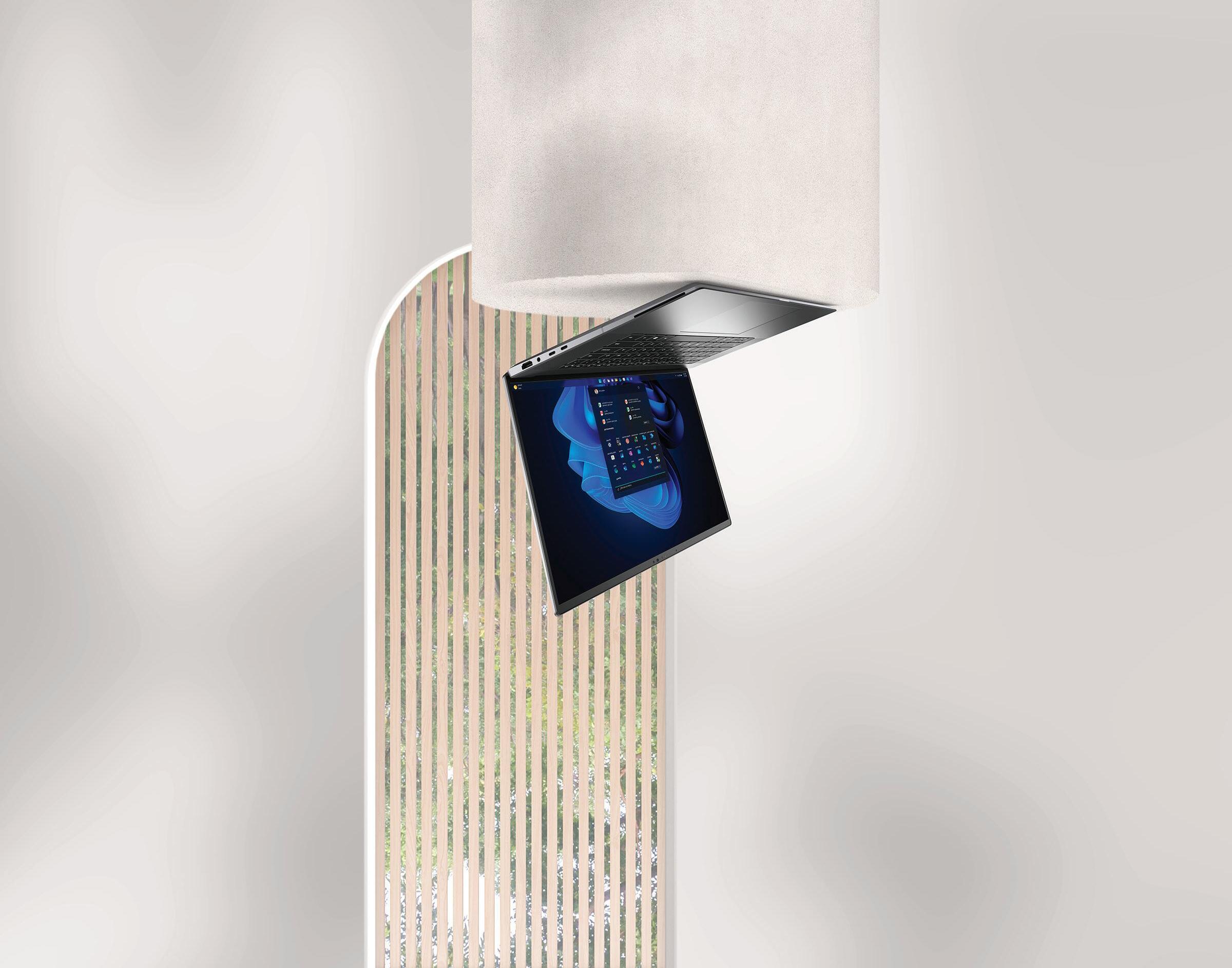
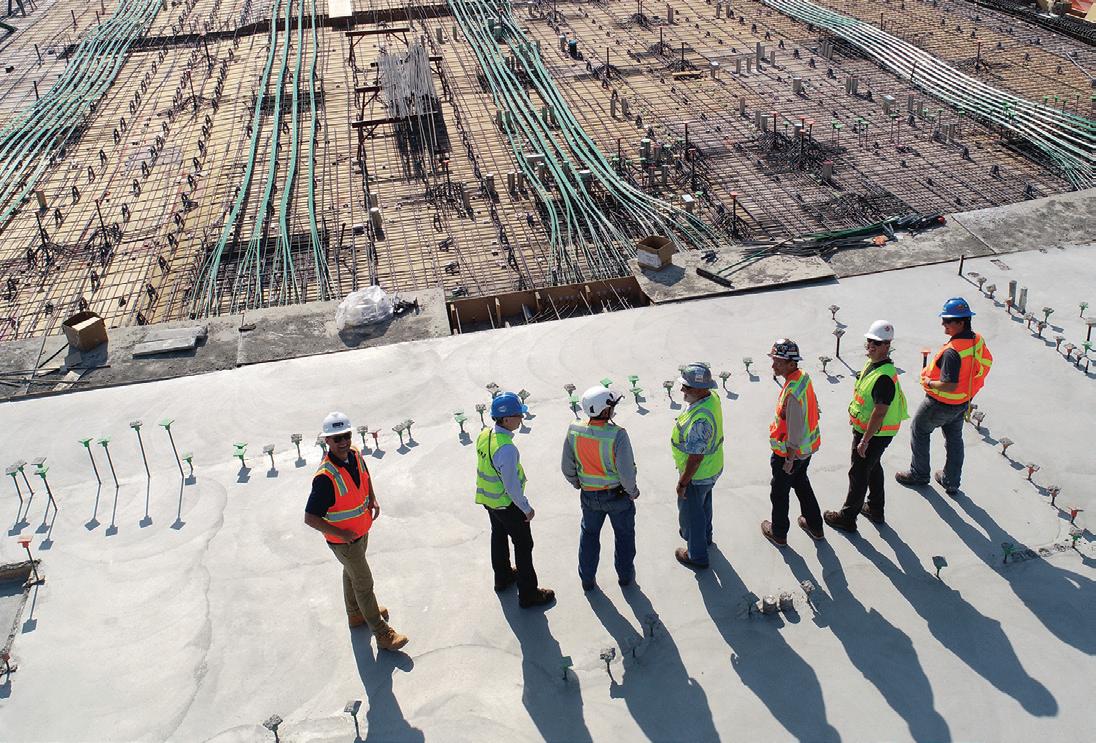

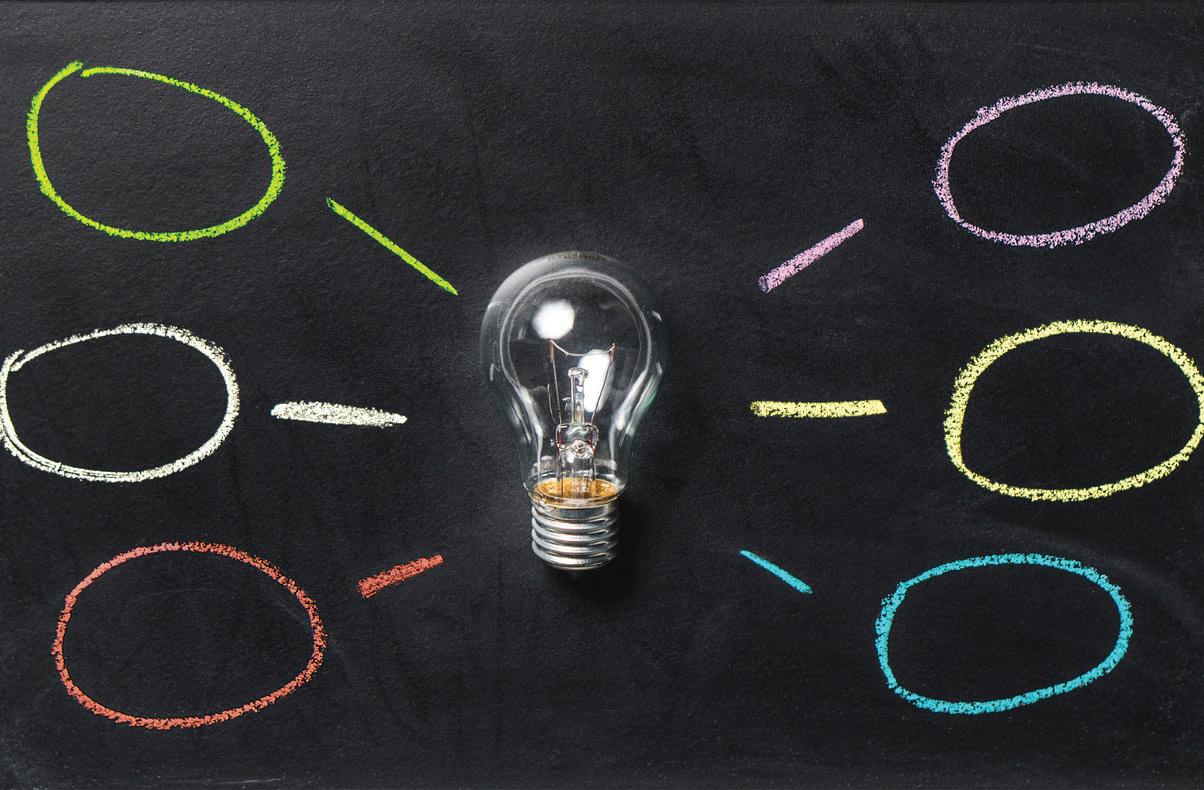
This month’s focus is implementation. Just in time for us here at Walter P Moore to roll out the 2024 versions. We only roll out every other year. I determined that the even years seem to work better than the odd years. I guess I learned this from the R13 version of AutoCAD, which was a complete disaster. They definitely stepped their game up for R14, which in my opinion, was the best release ever.
The definition of implementation, taken from Wiktionary.com, states, “The process of moving an idea from concept to reality. In business, engineering, and other fields, implementation refers to the building process rather than the design process.”
Templates, deployments, standards, and more, are all forms of implementation. It’s important to note that creating an implementation plan prior to implementing will save you hours of rework and/or fixing what was pushed out if you had not manufactured a plan and put it in place.
I hope you enjoy this issue, as there are some great authors that have taken the time to implement their articles for this June issue. Also, don’t forget to check out our AUGIWORLD Podcast, hosted on several platforms, for your listening pleasure.
Editor-in-Chief
www.augi.com
Editors
Editor-in-Chief
Todd Rogers - todd.rogers@augi.com
Copy Editor
Isabella Andresen - isabella.andresen@augi.com
Layout Editor
Tim Varnau - tim.varnau@augi.com
Content Managers
3ds Max - Brian Chapman
AutoCAD - Mathew Marrero
AutoCAD Civil 3D - Shawn Herring
Bentley
BIM/CIM - Stephen Walz
BricsCAD - Craig Swearingen
Dassault Systèmes - Rafael Testai
Electrical - Mark Behrens
Manufacturing - Kristina Youngblut
Tech Manager - Mark Kiker
Inside Track - Shaun Bryant
Advertising / Reprint Sales
Kevin Merritt - salesmanager@augi.com
AUGI Executive Team
President
KaDe King
Vice-President
Frank Mayfield
Treasurer
Todd Rogers
AUGI Board of Directors
Eric DeLeon
KaDe King
Chris Lindner
Frank Mayfield
Todd Rogers
Scott Wilcox
Publication Information
AUGIWORLD magazine is a benefit of specific AUGI membership plans. Direct magazine subscriptions are not available. Please visit www.augi.com/account/register to join or upgrade your membership to receive AUGIWORLD magazine in print. To manage your AUGI membership and address, please visit www.augi. com/account. For all other magazine inquires please contact augiworld@augi.com
Published by:
AUGIWORLD is published by AUGI, Inc. AUGI makes no warranty for the use of its products and assumes no responsibility for any errors which may appear in this publication nor does it make a commitment to update the information contained herein.
AUGIWORLD is Copyright ©2023 AUGI. No information in this magazine may be reproduced without expressed written permission from AUGI.
All registered trademarks and trademarks included in this magazine are held by their respective companies. Every attempt was made to include all trademarks and registered trademarks where indicated by their companies.
AUGIWORLD (San Francisco, Calif.)
ISSN 2163-7547
As part of the Global Implementation Team here at Bricsys BricsCAD®, we have met a variety of companies spanning dozens industries all with various local and network setups, a plethora of customizations, whether those are third-party applications or inhouse API development, LISP functionality, and much more. While we could compose an entire article on each migration aspect, we want to touch on a few of those and supply an overview of what our team has learned from our experiences. That way, when you make the transition to BricsCAD, it is a migration made simple.
Before we go any further, we would like to clarify and define “Migration” as the term can be perceived differently depending on the person. Migration, in a general sense, could be moving from one program to another. Migration could also be understanding the similarities between the programs. In this case, we are discussing the migration of custom tools and customizations. This includes but is not limited to plot styles (.ctb/.stb) CUI’s, tool palettes (.xtp), fonts (.shx), .LSP, plotter configuration files (.pc3), command alias (.pgp) hatch patterns (.pat), and more. See Figure 1.
Now that you have decided to download and install BricsCAD®, let’s discuss where to start. Our
Implementation Team best practice suggests forethought and investigation before expecting BricsCAD to replicate your current UI and overall environment. Grant Dott, BricsCAD® Global Implementation Consultant based in the United Kingdom asks, “How do you expect to be successful migrating CAD programs if the proper tools aren’t in place?” Excellent point Grant! I’m glad he spoke up.
The most effective way to adapt to BricsCAD is to make BricsCAD look and feel exactly like you want it. The appearance of the BricsCAD application window varies slightly depending on which profile you selected. The main user interface elements, however, apply across profiles even if the tools differ. Those elements can be controlled through the settings, CUI, and profile manager. Workspaces also can control what tools are available.
Before diving deep into design and exploring all of the timesaving, machine-learning features in BricsCAD, we need to locate all of the needed resources and their specific locations. This might be something you conduct on your own or you establish a team within your organization to investigate. Considerations also include multiple offices, departments, and even regional languages. Any files or folders contained in the current software folders would need to be copied to the BricsCAD support folder. The same would apply to any local folders on individual machines. At some point, your current CAD program will be deactivated and uninstalled, therefore you will need to ensure nothing erroneously disappears. That investigative team should also be the team that creates a test project and uses BricsCAD just like they would in the other software.
This is also a terrific time to investigate company standards. As your investigation grows, so will your perspective on your company standards. Your files and tools might be specific to a location, a department, or even individuals. Be diligent in discovering as much as you can before you start. As we discussed regarding standards in the February 2023 edition of AUGIWORLD, this might be the time to hop on the company intercom and call a “Clean-Up in Aisle 5” and now would also be the time to reorganize locations for blocks, templates, or custom tools. The resources needing to be migrated would include but are not limited to .ARX, LISP routines, custom hatch patterns, toolbar customizations, tool palettes, and fonts. This a reminder that there may need to be a recompilation of LISP/ARX/VB and .NET or custom code that may require more resources.
While many of the mentioned items above can be used with little to zero modifications, one item of interest that cannot be migrated is the user profile. While there are many similarities in the user profile between BricsCAD and other CAD solutions, the file structure and pathing are
completely different. So our first order of business is modifying the settings in BricsCAD to duplicate your existing CAD environment. Pathing and file folder structure will vary but we need to do a healthy comparison between the two, as you will need to open your current Cad software and compare folder paths for templates, sheet sets, tool palettes, etc. The BricsCAD settings dialog box can be accessed with two different commands. The BricsCAD development team knows the users so well that both “Settings” and “Options” will open the BricsCAD settings dialog box. How about that! See Figure 2.
And while the crosshairs and picking options are important, the most important aspect of the profile is the file pathing. This is where things can get wonky if not applied correctly. As well, pay special attention to the file locations as your folders may be in a network location and not locally. Lastly, not everyone should be doing this. This should be completed by your assembled team and, as a team, compile one profile to be distributed throughout the company. Of course, if there are other server locations involved in housing templates and other items, then a subsequent profile should be created.
Before I go any further, I would like to address the elephant in the room. That elephant is the perception that everything will be correct and function exactly 100% after the first attempt.
Whether that is the profile, CUI, or the settings, file/folder locations, it will take more than one attempt to get it perfect. Continue to test and make adjustments. Grant wants to remind us that, “Before modifying the settings, best practice recommends exporting or creating a copy of the default profile in case there is a need to revert.” Excellent point Grant! See Figure 3.
Notice that the BricsCAD CUI contains tabs for the Menus, Toolbars, Ribbons, Workspace, etc. Adjustments to these features are completed within the CUI. Add toolbars or create your own.
Now that we’ve completed our comparison and transferred the appropriate file pathing to BricsCAD, let’s move over our custom CUI’s. While we cannot migrate proprietary tools from other software, we can easily migrate your custom, inhouse tools. As long as those tools are contained within their own CUI, it is simple to migrate them. Access the Customize Dialog Box with the “CUI” command.
Right-Click on the BricsCAD file menu header to “Load a Partial CUI”. Assuming you have already exported your CUI’s from your current software, locate/select that CUI to import. See Figure 4.
BricsCAD commands and functions are very familiar, so familiar that your current muscle memory should kick in just a few minutes. However, if you are accustomed to your current command alias’ and keyboard settings, you can make those modifications with the Command Alias tab in the BricsCAD CUI in the Default.pgp file. Allowing users to get immediately familiar with how they have been working for decades. Grant suggests, “Just make sure not to overwrite the entire .pgp file, and only take the custom alias’ you created.” Absolutely Grant. Keep in mind, some commands in BricsCAD may be slightly different than what you’ve been used to. For example, “Attach” is a common command. The BricsCAD equivalent is “XAttach.” While that may not seem like much, it stops any LISP routine, command alias’, or macro.
Tool Palettes
Tool Palettes are also an essential part of any CAD user’s workflow. Before we wade into migrating tool palettes, Grant is waving his hand to let us know that tool palette pathing is also stored as a part of the settings. Within the settings, the tool palette pathing should be set to the out-of-the-box location. If your desire as a company is to have no user customization allowed with the tool palettes, then a read-only network location is where these should be stored, and that location can be added to the palette pathing.
The transferable tool palette file we want to import is the .xtp file. This is the file to be exported out of your current software and the file we will import into BricsCAD. Once again, only in-house blocks and customizations are allowed to be migrated. If you are
familiar with importing palettes, creating groups, and modifying individual palette properties, you will feel right at home. (See Fig.5)
“Hey Craig,” Grant exclaimed. “Before we go, let me show you how the best way to navigate the settings dialog box. Hear me out, chaps. Often we think of search bars as a bit of a pain, but not this one. Especially if you are new to BricsCAD settings, the settings search bar is a thing of beauty. Located at the top of the setting box, and using the arrows, it toggles you right to the search term, eliminating monotonous searching.”
Awesome Grant, and thank you for the pro tip. He’s right, chaps. The settings search bar greatly assists with locating the correct settings, system variable, or related search term in milliseconds. Speaking of milliseconds, that’s about all of the time we have left for today.
“Wait Craig,” Grant uttered. “We have a lot more to discuss regarding migration and implementation, and what about sheet sets, templates, blocks, and drawings?
The short answer is, as long as those blocks, sheet sets, templates/drawings are not in a specific CAD software folder, then they can remain in the same location. The long answer goes back to the point I made earlier about gathering information, and how vital it is to the success of migration. Thankfully, anyone can check out the free Bricsys Lessons and visit the BricsCAD Migration Page which contains blog posts and a Migration Guide that provides additional information and migration assistance.
Explore all the BricsCAD® editions and features by downloading the free, 30-day trial of BricsCAD® Ultimate. The latest BricsCAD® V23 improves the tools and features users love, as well as new functionality and UI that supercharge productivity.
Mr. Craig Swearingen is a Global Implementation Specialist and Consultant at Bricsys. Currently, Craig provides migration and implementation guidance, management strategies, and technical assistance. Craig spent 19 years in the civil engineering world as a technician, Civil 3D & CAD power user, becoming a support-intensive CAD/ IT manager in high-volume production environments. Craig is a longtime AUGI member (2009), a Certified Autodesk® AutoCAD® Professional, and he enjoys networking with other CAD users on social media.
Mr. Grant Dott is a Global Implementation Specialist and Consultant at Bricsys. He is a part of the EMEA Brisys team based out the the UK. Grant has a strong client-facing background with the ability to adapt and focus across many disciplines and environments. Grant has a demonstrated history of working in the computer software industry, skilled in BricsCAD, AutoCAD, Production Management, Construction-based cloud technologies, and Software Development. Grant can be found on YouTube, promoting BricsCAD and demanding that you let him show you how.
Implementing a true BIM | CIM design and project, especially your first one, is not accomplished easily. There will most definitely be some hiccups and some growing pains experienced along the way. You may even find yourself reaching a breaking point of frustration where you think that the only viable option is to go into survival mode and let old habits kick in, essentially abandoning the model completely and reverting to throwing some additional 2D components on the plans to make sure the printouts and the final deliverable(s) look good.
If you or your company has any intention of handing off design models electronically to a client or contractor, or if there is an expectation for you to produce an as built model after construction, this finishing touch workflow of adding 2D components will not put you in an ideal situation, as it will be much more difficult to update your model dynamically later on through the remaining phases of the project.
As most of you know, traditionally, design costs and efforts typically take the biggest hits during the intermediate and final design phases of a project.
With a fully implemented BIM | CIM project design, costs will be more front loaded and taper off as the project design development progresses. Your company and clients will need to understand this significant change, as it will affect where dollars and hours need to be allocated throughout the design development process.
Additionally, working in a 3D model-based environment drives an individual to really think about what they’re designing and how it impacts the rest of the project. More time is spent upfront detailing a 3D model dynamically and intelligently in preparation of drawing generation and detailed analysis. As a result, any changes or revisions you encounter during the latter phases of the project design will take significantly less time to update and adjust. It’s at this point that you will begin to realize the major benefits behind generating a BIM | CIM design.
During project initiation or startup, all project stakeholders should be sitting down and looking at the overall picture of the project, documenting what they want the final constructed product to represent, and collectively best determine how to get there. 3D models have the potential to contain much more rich data and valuable information
than your typical 2D designs, making content more useful to us during the design process and for downstream uses, but can also leave us very exposed to unforeseen errors and omissions. Model Managers and Project Managers must work closely together to manage risk here.
BIM | CIM Execution Plans, or Digital Delivery Execution Plans, are becoming more commonplace, where design teams collaborate early on to put together a document outlining all of the BIM | CIM Workflows and Uses to be applied throughout the project lifecycle that will be most beneficial to reach that final constructed product. This phase is probably the most critical as the flow of the remainder of the project will be determined here.
Although there are way too many BIM | CIM Uses to list here, we must recognize that each Use has its own purpose/function within a project’s lifecycle and can be used in either one phase of the project or multiple phases (Planning, Design, Construction, Operations). Each project comes with its own unique set of requirements and design intricacies, so we certainly don’t want to go overboard with defining all of the Uses that can be applied if there is no real value added to the outcome. That said, we really want to stick to the BIM | CIM uses that are required to achieve the expected final delivered product.
It’s quite often said that there are four common BIM | CIM uses that definitely should be applied to all projects regardless of which market you may be developing a design for. These four fundamental BIM | CIM Uses are: Design Authoring, Drawing Generation, 3D Coordination, and Design Reviews.
Design Authoring is the process in which software is used to develop a 3D+ model based on information required for accurate translation of the design. With Quality Control (QC) having a place in every phase of design and every BIM | CIM use, we should note that the QC process related to design authoring typically focuses on the accuracy and completeness of BIM | CIM elements at a granular level during interdisciplinary design, while the 3D Coordination and Design Review BIM | CIM Uses provide a broader look at interdisciplinary design and focus more specifically on errors and completeness. In
practice, these lines are not distinct, and quality plays a pervasive role like it does in all aspects of the project lifecycle.
The most important factor to consider when modeling Existing Conditions is determining the Level of Detail (LOD) needed in the model. This is typically addressed while developing scope and fee and should be discussed between the project manager and a lead modeler. We should note that designing with an imprecise Existing Conditions model will create constructability issues and will create a risk to your company. On the flip side excessive detail increases survey costs and processing time, so there needs to be a level of balance here to identify LOD and boundary to limit overruns.
Next, we have drawing generation which essentially means the process of taking our BIM | CIM components and creating drawing sets (i.e., Issued for Bid, Construction, etc.). The broader objective here is to define model elements once and use that information with no loss of accuracy or integrity to generate your drawings. This improves the overall quality of the drawings and reduces effort and errors in the design process.
For most projects, plans are the primary deliverables so drawing generation really isn’t a new concept. The difference between drawing generation before and after a BIM | CIM implementation is that designers can now show information in any 2D Plan View rapidly with little to no loss of precision or accuracy. Plans, profiles, sections, and detail sheets can all be generated from your model.
Next, we have 3D Coordination, which is more often referred to as Class Detection. 3D Coordination is the process in which 3D design software is used to identify spatial interferences of modeled objects such as structural elements, utility pipes, pilings, etc. in one or more 3D models. The goal of 3D Coordination is to eliminate major system conflicts prior to construction. 3D Coordination is a continual cycle throughout the design process and should begin prior to the first project milestone as defined in our BIM | CIM execution plan.
On the flip side, the time to start 3D Coordination and frequency can have budgetary implications. 3D Coordination on conceptual drawings can
potentially produce false positives. Because elements have approximate dimensions and solutions to design challenges and constrained areas have not been investigated. Furthermore, excessive 3D Coordination can waste time and project budget.
We should also recognize that we should not rely solely on 3D Coordination software to verify that there are no conflicts with your project. Yes, clash tools are helpful in identifying physical conflicts, but everything has to be set up perfectly for 3D Coordination to work as a sole basis for verifying your design. Ultimately, the responsibility of avoiding conflict falls on the design team, and a no conflict report from a program is not a basis to defend a problem within the design.
Lastly, we have Design Review, and by that we mean nothing more than taking our 3D design models and/or drawings and sharing the content with other project stakeholders. Design Review isn’t typically formalized, but it does typically take on two primary purposes.
The first is to verify quality with a focus on problems that are otherwise difficult to identify. The second is to communicate design information to other designers or outside audiences as quickly and accurately as possible.
Projects require us to deliver services that meet a high standard of care, necessitating plans free from errors and omissions. Compared to omissions, errors are relatively easier to detect since they are visible on our drawings or in our models. Omissions are challenging to identify as they do not appear on plans or in our models. BIM | CIM can assist in identifying omissions by providing a comprehensive view of the project, which also helps identify constructability concerns.
Another aspect of Design Review requires communication of design intent, which can also have a couple challenges. First, audiences may lack the technical skills and software required to navigate 3D files, making it an accessibility issue that design review meetings can overcome through in-person discussions, teleconferencing, and media sharing. Secondly, different groups of designers or stakeholders have varying interests in design, presenting a content challenge. That said, we’ll need to have a good idea of the anticipated
audience and what design information is necessary to include that is most relevant.
As I’m sure you’ve realized already, there’s quite a bit of information, planning and collaboration that goes into properly executed a full BIM | CIM design project, with many considerations and decisions to be made along the way. If you’re just getting started on implementing BIM | CIM at your workplace, I hope I’ve been able to shed some light into the overall process. Whether you’re just starting out or are seasoned vet and well into implementing BIM | CIM at your workplace, please reach out and connect! Would love to have your experiences and stories shared through AUGIWORLD Magazine for all our readers to learn from!
Stephen Walz is, not only the BIM | CIM Content Manager for AUGIWORLD Magazine, but also the Digital Design Lead within HDR’s Applied Technology Office, a global leader in Engineering, Architecture, Environmental and Construction services. Stephen has been in the AEC Industry since 2003, and with HDR since 2004 supporting multiple offices and regions and now support all Business Groups and Market Sectors across HDR at a corporate level. In Stephen’s current role, his primary focus is to work with HDR’s Business, Technical and IT Leadership, as well as our technology vendors, to identify, evaluate and implement new platforms/tools/technologies supporting BIM | CIM processes and workflows, drive consistency with how HDR is leveraging various tools and platforms, and identifying ways to build skillsets and overall awareness across HDR to better serve their clients. Stephen can be reached for comments or questions at Stephen.Walz@hdrinc.com or subscribe to his YouTube Channel for BIM | CIM, Data Integration, and Visualization workflow video demonstrations.
Civil 3D is a powerful and complex software, and we’ve all had our ups and downs with figuring out the best way to implement the software, especially across a large firm. It can streamline the design and documentation of civil engineering projects, from roads and highways to land development and water resources. However, implementing Civil 3D can also be a challenging task, especially for those who are new to the
software or have limited experience with it. In this article, we will discuss some best practices for Civil 3D implementation, based on industry expertise and real-world experience.
Before beginning a Civil 3D implementation, it is essential to define the objectives and
goals of the project. This can help ensure that the implementation meets the needs of the organization and its stakeholders. Some common objectives may include improving design efficiency, reducing errors and rework, efficient change management or increasing collaboration between team members.
Civil 3D implementation is a team effort, and it is essential to establish a project team to lead the effort. The team should include individuals with a range of expertise, including civil engineers, surveyors, CAD specialists, and project managers. It is also important to involve stakeholders from across the organization to ensure that the implementation meets the needs of all parties.
3. Develop a Project Plan
A detailed project plan is essential for a successful
Civil 3D implementation. The plan should outline the scope of the project, including timelines, milestones, and deliverables. It should also identify key stakeholders, roles and responsibilities, and resources needed for the project.
Developing standards and templates can help ensure consistency and efficiency in Civil 3D design. Standards should define how objects are named, labeled, and organized within the software.
Templates can include pre-defined styles for objects such as surfaces, alignments, and profiles, as well as pre-configured settings for drawing sheets and scales.
Civil 3D is a complex software tool, and training and support are essential for successful implementation. This can include formal training sessions, online resources, and on-the-job coaching. It is also important to provide ongoing support to users, including troubleshooting assistance and guidance on best practices. My suggestion is to put together a company “starter pack” of freely available videos, or some fundamental level online courses that are inexpensive. Allow your new users to finish those prior to having them jump right into a live session or any advanced sessions.
CIVIL 3D IS A COMPLEX SOFTWARE TOOL, AND TRAINING AND SUPPORT ARE ESSENTIAL FOR SUCCESSFUL IMPLEMENTATION.Figure 1
Before implementing Civil 3D across the organization, it can be beneficial to conduct pilot projects to test the software and identify any issues or challenges. Pilot projects can also provide an opportunity to refine standards and templates and train users on the software in a controlled environment. I’ve seen companies use previously finished projects, but my personal recommendation is to choose an upcoming project and just jump on in!
7.
Defining workflows and processes can help ensure that Civil 3D is used efficiently and effectively. Workflows should outline how different team members will use the software to complete different tasks, while processes should define how data is exchanged and shared between team members. Documentation is key!! In many of my implementations, we documented with videos AND written documentation of standards and workflows. To me, if it’s not documented, it’s not standard!
Civil 3D can be integrated with other software tools, such as GIS software, project management software, and BIM platforms. Integration can help streamline workflows and improve collaboration between team members. However, it is important to ensure that the software is properly configured and tested before integration.
Effective data management is critical for successful Civil 3D implementation. This can include creating a central data repository, establishing data backup and recovery procedures, and defining data access and security protocols. It is also important to establish data standards and protocols to ensure consistency and accuracy in data exchange.
Monitoring and evaluating the success of the Civil 3D implementation is essential to identify areas for improvement and ensure that the software is meeting the needs of the organization. Regular evaluation can include collecting feedback from users, reviewing project performance metrics, and identifying opportunities for further training and support.
So that’s just a few of the things to think about prior to launching an implementation, but let’s now explore some of the common implementation failures that can occur when using Civil 3D.
1.
One of the most common implementation failures is the lack of planning and training. It is essential to have a clear understanding of the project requirements, and how Civil 3D can help to achieve those requirements. This involves identifying
the software’s strengths and limitations, setting up project standards, and developing training programs for the users. Failing to do so can result in mistakes and inconsistencies in the final designs, as well as user frustration. Knowing the limitations of any software is just as important understanding the highlights of the software.
Civil 3D is a powerful software package that requires a high-performance computer system to operate correctly. Failing to provide the required hardware and infrastructure can result in slow performance and even system crashes. It is essential to ensure that the computer system meets the software’s minimum requirements and has sufficient storage and memory to handle large data sets. I recently did an implementation of Civil 3D 2023 with the company coming from LandDesktop 2004, and Windows XP systems!! Needless to say, Civil 3D was the least of their worries.
Data management is an essential aspect of Civil 3D implementation. The software requires a significant amount of data to operate, including topography, geospatial data, and project standards. Failing to manage this data effectively can result in lost or corrupted files, incorrect data, and inconsistencies in the final designs. With Civil 3D, understanding and managing your data shortcuts, sheet sets, templates, etc., is essential to establish clear data management protocols and ensure that all users follow them.
Civil 3D implementation requires consistent project standards to ensure that all designs meet the same quality and accuracy standards. Failure to establish these standards can result in designs that are inaccurate, inconsistent, and difficult to manage. It is essential to define project standards and ensure that all users follow them. Many times I come in after a firm has attempted to do their own implementation, and many times they have failed and/or switched platforms because it was too tough to create the initial set of standards, and too time consuming to maintain/manage.
Civil 3D implementation requires collaboration between engineers, architects, and other stakeholders involved in the project. Failing to establish effective collaboration processes can result in misunderstandings, mistakes, and delays. It is essential to develop effective communication and collaboration processes and ensure that all stakeholders are involved in the design process. In conclusion, implementing Civil 3D requires careful planning, training, and collaboration to ensure that the software is used effectively. Failure to address these issues can result in design inconsistencies, inaccurate data, and user frustration. By addressing these implementation failures, you can ensure that your projects are designed accurately and efficiently, resulting in better outcomes for all those involved.
Shawn Herring has been a part of the design engineering community for roughly 15 years in all aspects of design, construction and software implementations. He has implemented and trained companies across the Country on Civil 3D and other infrastructure tools and their best practice workflows. Shawn can be reached for comments or questions at sherring@ prosoftnet.com.
CIVIL
TO ENSURE THAT ALL DESIGNS MEET THE SAME QUALITY AND ACCURACY STANDARDS.
Please understand that I am not implying that any individual would be better suited to develop a standard than another at any time in this article.
Your business, large or small, must be built around solid decisions. The choices made when establishing a company will have long-term effects in many areas. The repercussions of poor initial choices will affect all levels of an organization.
Depending on the organization’s size, these effects will go unrecognized for quite a while. When a
business grows, a parallel increase in activity is required to maintain forward momentum.
A company that fails to review its corporate culture regularly as part of its overall development will become a stressful, tension-filled workplace. This will lead to employee burnout and fatigue. Ultimately, your best, however, now overworked and stressed out, employees will leave, putting management in a potential bind.
As each business has its ecosystem, the foundation they started with will be unique to them. If good planning and due diligence were done initially, there is a good chance of success and sustained growth.
Failure will eventually result if the initial setup is not well thought through.
In this article, I will discuss the critical areas that regularly need to be reviewed and considered to create a healthy and productive business. Identification of areas that are failing is crucial to moving forward.
I will focus on best reviewing a business’s existing corporate culture. This is a core value in developing an effective business plan with farreaching implications.
After learning to identify areas of weakness, positive goals and a plan to develop and implement them must be established. This plan must include all levels of an organization, or the resulting culture will suffer.
Every business, large or small, is a living organization. If they want to remain competitive and move forward, its activity and plans must target constant improvement and future growth. This detail is easily overlooked when daily activity ramps up and today’s economy takes over the corporate world’s responsibilities.
The business that relies on the established routine, since it, “Just works, no need to change it,” will find themselves watching other organizations moving forward as they stagnate.
Reviewing corporate environmental and organizational standards must be done in an organized and well-planned manner. Identifying and examining areas of required organizational change must start at the root level.
This often brings up unpopular issues that many people will not like discussing. The best effort will be wasted if the corporate mindset mutes these potentially divisive concerns.
Developing any “standard” that will include multiple people will create friction among those people at some point with someone involved. This is guaranteed to happen.
Employees are the very lifeblood of an organization. Their value must be recognized and must be included when considering policies impacting dayto-day activity.
Basic parameters and ground rules must be established before any discussion of standards is considered. Without this, everyone will be an expert on the topic, and they will defend their opinions fiercely.
This will generally create a situation in which many people will either shut down, not including valuable input, or the loudest voice will be the one to take over. Both of these situations will be failures.
To include as many employees as is practical, an organization will often employ the “committee” approach as their first plan of attack, which is typically flawed. Let me explain where I am coming from.
A committee established to handle the standards task must represent all involved parties. Including
all departments affected by any policy, while required, can become the committee’s most challenging hurdle to overcome.
The typical mindset when organizing this group is to include as many individuals as is deemed necessary to represent all areas of the business, possibly impacted by the standards development process.
The issue will require efficiency when selecting potential personnel with similar responsibilities. Having the critical personnel represented is necessary for success. However, it must be carefully managed.
When organizing a committee, one must remember that the higher the number of individuals included, the better the chance of disagreement between those individuals.
This disagreement can be productive in many ways, as multiple inputs will ensure that critical issues are brought to the table.
However, as I have seen firsthand, even though all are working towards a common goal, the selected
personnel will infuse a discussion with some personal bias.
When a previous employer first established CAD standards, they set up a committee for the task. The team included individuals representing all appropriate groups. However, while it would have been functional with six people, the committee was set up with more than a dozen individuals.
The outcome was different from what management hoped for. Due to a lack of focus by the personnel involved, plodding progress was caused by too many opinions and ideas being thrown into the mix.
The issues that a standards committee decides on must encompass everything that will be impacted the process, down to the individual CAD operator’s daily activity. Yet including all personnel down to this level is not a practical approach.
One or two individuals per invested group who take the said group’s concerns into a committee will be much more efficient. A clear direction and forwardlooking plan can then be achieved.
The return on investment (ROI) of this effort will suffer if this occurs, turning the people crucial to a business’s success against its future progress possibilities.
Management, from their perspective, is interested in having a stable and smooth running operation. The key to this being successful is to have people who are respected and valued in an organization.
Typically standards and their development are considered overhead expenses. This issue is on management’s mind, I guarantee it. The hourly value of several employees, now sitting and discussing non-revenue-producing matters, does not go unnoticed.
The personnel involved in this process are also active in many other activities necessary to facilitate day-to-day activity.
Even though standards are a basic tenet of every viable business, their development cannot impede daily business activity.
The bottom line for a business is to be profitable. A company lacking a solid foundation, including an efficient set of standards, will constantly react to daily fires.
This preoccupation with today’s issues will preclude any thoughts of improving the working environment. If this situation exists for an extended period, the business will suffer.
Mark Behrens' current employer designs Automated Guided Vehicles (AGVs) and test machines. He has worked with AutoCAD software for forty years, starting on version 1.4. Having been with his current employer for almost sixteen years and CAD manager by the necessity for at least ten, he has seen their culture change many times in attempts to improve processes and become more efficient. CAD standards have become a high-profile topic recently. Mark is excited to share his process of implementing a user-friendly system of CAD standards with others.
THIS ARTICLE IS BEST READ AND VIEWED IN THE ELECRONIC VERSION OF AUGIWORLD
https://youtu.be/-wzyDWdOzco
Ever wondered what it would be like to be mentored one-on-one by a senior engineer that’s using SOLIDWORKS to successfully deliver solutions to industry clients? My name is Rafael Testai, and in this video series “Mechanisms & Mentorship,” we’ll take a look behind the scenes to see how a hand-picked engineer has designed one of their mechanisms in granular detail. We’ll “open the hood” to analyze their CAD design and thought process behind the solution. I’ll ask them questions about the project, roadblocks, challenges, specific insights they learned, and how they’re using SOLIDWORKS to solve real world problems.
You’ll learn a mixture of soft skills and hard skills. This series is perfect for viewers who are already proficient in SOLIDWORKS (CSWA, CSWP, CSWE) and want to take the next step in their careers.
In this episode of Mechanisms & Mentorship, I’ll interview Mechanical Engineer & Owner of TeamPipeline.us, Aaron Moncur. We’ll focus on his journey from getting laid off, to successfully starting his own mechanical engineering and product development firm that’s going on 13 years strong.
What’s the Story of Your Company, TeamPipeline. us? (Min 0:29)
Aaron leads the interview with honesty, one of his core values. He explains how the story of Pipeline, the company he owns, begins with failure, and how he was fired from his previous position. He accredits his former employer as being absolutely correct for firing him. Listen to the segment to gain an understanding of how Aaron turned a negative into a positive.
More about Pipeline: Pipeline partners with medical & other device engineering teams who need turnkey equipment such as cycle test machines, custom test fixtures, automation equipment, assembly jigs, inspection stations and more. You can find more here: www. teampipeline.us
Why is the Company Called “Pipeline” if you Don’t do Pipelines? (Min 4:45)
Aaron grew up surfing in Hawaii. “Pipeline” happens to be the name of the beach in Hawaii that had the best waves and where all the top surfers would go.
The company was named Pipeline because it’s ideal for the best projects, engineers, and work.
The company doubled down on its niche of custom equipment and automation. The timing was impeccable, because while the pandemic was forcing workers from other industries to work from home, the manufacturing industry couldn’t be done remotely. Hence, there were a lot of companies looking to automate manufacturing. Preparation met opportunity, and Pipeline scaled.
Aaron launched the “Pipeline Academy,” a faster, less expensive, and more effective process to train mechanical design engineers than the traditional college route. You can watch the video playlists below for free:
• Top used hardware by mechanical design engineers
• MFG Processes
• Instrumentation
• Mechanics
Rafael Testai also helped him create the content. The initiative was discontinued due to lack of funds, but the videos remain on YouTube. The idea behind monetizing the academy was to sell the packaged training to mechanical engineering firms so they could train their staff quicker. If you’re interested in contributing and/or helping finance this mechanical design engineering academy, please reach out to Aaron Moncure here and tell him you read this blog. The world needs this academy!
To learn more about Aaron Moncur, visit his LinkedIn.
If you read until the very end, I greatly appreciate it. I would encourage you to follow me on Linkedin so that we can stay in touch, and you can be notified when more articles like this one get published. I lead with value and my writing style is direct and to the point. https://www.linkedin.com/in/testai/
Any recommendations on who you think I should interview next? Feel free to reach out to me on Linkedin or Instagram. I read all correspondence. Linkedin: https://www.linkedin.com/in/testai/ Instagram: https://www.instagram.com/rafael_ testai/
A quote that inspired Moncur was when his business coach shared with him that a company in the 2008-09 recessions stated: “We refuse to participate in the economic downturn.” Aaron mentions how he borrowed that metaility and applied it during COVID.
What
(Min 9:55) Aaron explains his strengths, and his philosophy that technical skill can only take you so far.
Rafael Testi is a SolidWorks Influencer. Follow to watch exclusive videos he creates that quickly teach you the inner working mechanism of interesting products l Mechanical Product Designer LinkedIn/Instagram/TikTok/ Podcast/ More articles: https://linktr.ee/testai
We have tried to add a few apps that assist with the implementing BIM, projects, and standards and just making things a bit easier!
The Autodesk App Store is full of useful apps for all Autodesk applications, so make sure you search the store, as I’m sure you will find many apps that will help you work smarter, not harder.
So, on that note, here are this month’s opportunities to advance your skills, processes, and workflows with the most current industry-related software and hardware updates available.
https://apps.autodesk.com/ADSTPR/en/Detail/ Index?id=2670972604380037744&appLang=e n&os=Win32_64
Autodesk AutoCAD
Version: 2024, 2023, 2022, 2021, 2020, 2019
Autodesk AutoCAD Electrical
Version: 2024, 2023, 2022, 2021, 2020, 2019
Autodesk Advance Steel
Version: 2023, 2022, 2021, 2020, 2019
Autodesk AutoCAD Mechanical
Version: 2024, 2023, 2022, 2021, 2020, 2019
Autodesk AutoCAD Architecture
Version: 2024, 2023, 2022, 2021, 2020, 2019
Autodesk AutoCAD MEP
Version: 2024, 2023, 2022, 2021, 2020, 2019
Autodesk® Civil 3D®
Version: 2024, 2023, 2022, 2021, 2020, 2019
Autodesk AutoCAD Map 3D
Version: 2024, 2023, 2022, 2021, 2020, 2019
Autodesk AutoCAD Plant 3D
Version: 2024, 2023, 2022, 2021, 2020, 2019
Every time you want to open a drawing, attach external references, insert a drawing as a block or want to create a block, you will have a Current Folder item on the left of your file selection dialog box (in the custom places’ area). This app will bring your active drawings’ path, which is often some clicks afar, to just one click away at your fingertip.
A simple but great app with many drawing/project implementation uses!
GEMINIBIM TOOLS
https://apps.autodesk.com/RVT/en/Detail/Index ?id=7553979608040885624&appLang=en&os= Win64
Autodesk Revit
Version: 2023, 2022, 2021, 2020
Add Filters+
This add-in alleviates the difficulty of manually adding or modifying view filters assigned to multiple view templates by providing a robust user interface that allows various methods to add or modify filters. You can manually add and configure filters and assign them to multiple view templates or automate the process by copying view filters from an existing Revit template and assigning them to other templates, copying all aspects of visibility control and the graphical setting assigned to the view filter.
Template Transfer
the Template Transfer utility that provides an intuitive and efficient method to apply changes across a single view template or multiple templates in a Revit project by specifying a source view template and settings to transfer from and target view templates to modify.
Workset Prompt
A simple and effective plug-and-play type solution to help with this problem that many BIM Managers encounter while at the same time instilling good modelling habits for users by making them always verify the active starting workset.
Good BIM tools provide a good BIM implementation! This app provides some GREAT BIM tools!
https://apps.autodesk.com/ACD/en/Detail/Inde x?id=4397898311965520050&appLang=en&os= Win32_64
Autodesk AutoCAD
Version: 2020, 2019, 2018, 2017
Autodesk® Civil 3D®
Version: 2020, 2019, 2018, 2017, 2016
Layout Creation Assistant has several tools for automatizing the hard work of creating drawing sheets. With this Application, you will be able to:
• Create hundreds of layouts with your custom paper format and plot settings.
• Store your company’s paper format and plot settings.
• Rename all your layouts.
• Apply and edit plot settings. Create a viewport with its view projected to the Modelspace as a dynamically linked polyline.
• Add dynamic grids to your viewports. Fill title block attributes using a spreadsheet.
Standardizing drawing sheets during project implementation can be challenging. This app is a great help!
https://apps.autodesk.com/RVT/en/Detail/Inde x?id=1208465312471232826&appLang=en&os= Win64
Autodesk Revit
Version: 2023, 2022, 2021, 2020, 2019, 2018
Digitteck® NameConvention™– Whether working on small or large-scale projects, naming convention will always be an important component of your work. Naming conventions and standards are required whether you implement BIM or not. Variability and inconsistencies often lead to confusion, error, and loss of time.
With this app, you can easily apply naming conventions to your elements. You get a great overview of the names currently used in your project and ensure they are properly set. The features “find and replace” and “wrap” allow group changes for a selection or all elements in a table.
With the key features “export to Excel” and “export Lexicon to Excel” you can make changes in Excel or even define a set of possible values for an element (one example is to create data for multiple languages). You can easily save your changes into the Autodesk® Revit® model by clicking the Sync button.
Name conventions can be a real chore during a BIM implementation. This app provides that help you need!
The Engineering Industry has helped humanity usher in the modern world like no other time in humanities revolution and history. If one were to try and define the industry with a single word, Implementation comes to mind, as this is at the core of what the industry does on a daily basis. All those meetings, all the mass data, physics, and math, etc., are fundamentally being applied to help implement some final goal to create something, be it a road, building, car, or any other ‘Built Concept’; the list goes on and on; it is endless. Without Engineering, we would all live in a world of chaos.
Good Engineering is all about good control, yes? So, it could be safe to say, ultimate control is the best form of Engineering. Yet with my 43+ years in the industry here in Australia and now, with my recent venture into the online world of all things CAD-related and listening to all the CAD Managers on Eric Deleon’s CAD Manager Confessions it would appear this is a global problem. I have not worked in a CAD office that was not embroiled to some degree in a state of chaos on a daily basis. I cannot help feeling that the industry thinks this is normal, it is just the process and there is nothing that can be done about it. Any attempts to get the full CAD process under control over the past 40 years has yielded only great expense, failure, and disappointment. And here we are in 2023 still asking the question, “Why can we not get it under control and work in a less stressful and more unified, efficient and consistent environment?” Is this not the whole point of the technology’s creation/purpose?
Back in the early 1990’s I became rather burnt out by all this chaos and constant problems within the industry, it was never-ending and relentless. So much so that I left it for a year and started my own business in the fitness world. But the recession of
that era put a quick end to that plan, and I was faced with contemplating the idea of having to go back to Drafting. I managed to find a new fire in my belly to return with the realization I was not actually a ‘Draftsman’; I was a ‘Problem Solver’ and drafting was just my tool to convey my Engineering comrades and my ideas, insights and solutions with accurate documentation to support the next stage of the process; the construction and/or manufacture of the clients project with a clear vision of what is required.
Big global Engineering companies with 10’s of thousands of employees spend millions of dollars on software every year. One of the biggest expenses is their CAD systems software and hardware. Despite it being the ‘Engineering Industry’, the CAD department is the engine room of the industry. Engineering is a goods and services type industry and the Drawings produced within the CAD department are one of the products they sell to their clients. Yet so few assign the correct proportional percentage of this budget to the CAD systems development, configuration, and most importantly, implementation in the hope to gain greater Drawing quality, produced more efficiently, on time, and on budget. What would even a meager 10% improvement be worth to their bottom-line profit margins? It would be significant for sure.
The fact that this is not happening to the degree required does not make sense, one can only assume. Therefore, my own personal assumptions, beliefs, and observations are the Engineering industry is over (tired) of all the past broken promises and disappointments made by wellintended CAD Managers suffering, innocently from what is known as the Danning-Kruger Effect (please research this for full clarity). Hence, they have given up; believing it is just not possible.
Back in 2003, I worked as an employee for what was one of the most chaotic (out-of-control) Engineering companies of my 43+ year career. Ironically, they should have been one of the most controlled, because it was at this very company I witnessed and used my first version of a fully customized AutoCAD, (AutoCAD R14 still but that is another story).
In the typical fashion that fits my super-curious nature, I was excited, fascinated and as the
months passed, I naturally delved into the customization to attain a full understanding of why, who, when, where etc. to fully understand AutoCAD customizing features and power that I was witnessing, saving all those thousands of daily mouse and keyboard movements, and standardizing the finished drawing product quality in a unified, efficient and consistent manner. This was the first Implemented system I had ever seen and used and one of a few I have ever seen since.
20 years later and approximately 20,000 hours of Research and Development, I believe I have found all the answers for implementing the perfect CAD system and office. What was once complex even to me seems rather simple now. There are certain systems, staff and strategies that need to be in place for it to work properly but these are all achievable with a clear vision, effort, and implementation. And no, I do not believe that I am suffering from the Danning-Kruger Effect anymore that I also once was that night I sat-down and started developing the AutoMENU CAD system in 2003. We can obtain those ‘Prefect Set of Plans’ as Eric Deleon talks about in his ‘CAD Manager Confessions’ podcasts.
Anyone with the funds can purchase the CAD technology (hardware and software), anyone can hire CAD staff and then try and manage it all (The Trilogy). But if you feel you are ‘Flying Blind’ into something you do not understand, with constant, on-going, common CAD issues; then may I suggest you STOP, re-group and re-think your strategies. Are you just purchasing and installing software or does your company have an implementation strategy to develop the technology to try and standout of the crowd. Without it, your company cannot legitimately claim to be better than any other, because you are all on a level playing field.
Adam Black is a CAD solutions and technologies professional with over 43 years of experience within the Engineering and Construction community. His main focus i s on providing innovative AutoCAD based solutions for the Engineering Infrastructure and Resources sectors. He is also the creator of the AutoMENU CAD System.
This issue is concentrated on implementation, so I wanted to focus on how implementing new tech impacts your standards. I suggest expanding or updating your standards from time to time. It might be a total revision, an update or expansion. But how often should that be? Your standards need to be stable, so folks know what is expected. They need to be flexible, so folks know they are not locked in processes from years ago that do not serve the current tech needs. They need to be up to date and changed to keep up with tools and talent. But what drives the changes and how often should you change them? Implementations impact standards, so I provide some guidelines for when these standards updates and expansions should be done and talk a little about why.
Bottom line on when, is generally this… I like to update my standard whenever there is a totally new tool introduced, or when a new feature of an existing tool is making an impact. I also update when the standard has not been changed or updated for an extended period. That period is defined by your company. Some are excited to bring in new tools and
methods and others are resistant. You could make it a time frame, like every two years. Or you could tie it to the version upgrades you do with the tools. Either way, going longer than three years tends to have people settle into a rut and change is very hard. You probably have a cycle already. If you do not, you want to create one. If the cycle is not working, you need to break it and redefine it. Too short? Too long? Or just right? You decide.
Make documentation updates and expansions coincide with software rollout. Provide training as needed. Get the documents in the hands of the users and monitor the embrace of new tools or methods. Introduce changes at the proper time, like when a new project starts or when a new office is opened. Lingering old-fashioned ways of doing things can come back to bite you. If it is not a major change, you could issue amendments or addendum to your existing standard. Or just replace a few pages.
Why do you need to update or expand your standard? Some of the answers are embedded in the ‘When’ part of this article, but there are others.
You need to update your standard to keep up with new tools and new features of existing tools. When your standard gets so outdated that it no longer serves the design team because it no longer covers what is needed, you need to update. When new features are added to existing tools, you need to expand your standard to address them.
When something new comes along, you need to get out in front of it. It could be a totally new tool, or a major upgrade to an existing tool. I suggest that you let the design team wander around for a while. They need to try things out, see what works, what improves your output and what is not worth the trouble.
When implementing a totally new tool, hopefully you have investigated its use and proven that there is value in the new offering. Then you can bring others in. It might be a free version, trial version or a low seat count purchase so that you are not overextended if it does not pan out. You can escort them through the process or research by giving them specific things to try out, or you can just let them play around with it. There is value in both methods, and you can mix them up as needed. If one feature rises to the top and becomes the focus, encourage people to try that specific feature. If some have been playing, ask them for input on what stood out then encourage them to focus. If others have been focused, suggest that they play around a little. Usually, most folks will do both on their own.
Ready to lock down a method of use? If it is a totally new tool, I suggest a separate standard just for that tool. You end up with a focused standard that allows new tools to not be jammed into old habits and methods. You want to keep the general approaches in tack, but not handcuff a new tool with outdated guidelines.
If it is a new feature in an existing tool, then update your existing standard to reflect the new features use. If you have old workarounds that the new feature addresses, through out the workaround and adopt the new feature. Don’t let people hang on to outdated methods.
Sometimes software developers retire features or do not continue support or development of those features. What do you do then. You document what NOT to use. You may need to add items to your standard that are not used any longer. You can continue to use them until projects that have used them are completed, but you need to move along. Write it down. Document it in new project kickoff meetings. Outline what is not to be used any longer.
Developers may stop updating, selling, and supporting tools that your team may use. It may be something that you heavily relied on but is no longer versioning up. It is just totally gone. But wait – the version I have still works… When that happens, have a wake and call it a day. Get rid of the tool gradually, but totally. Uninstall it. Do not keep old copies alive that might still work. Migrate all data out of any repository dependent upon the tool. It is gone and you need to move on. Provide a departure schedule and remind people that the old tool is being retired. Then stick to the timeline.
Standards are meant to improve processes and production. If they are old, limited or outdated, they may hinder productivity. Take a fresh look at your standard and see if it is current and covers the needed processes that drive improved design. Finding a better way to be productive and drive it into your standards and staff.
Mark Kiker has more than 30 years of hands-on experience with technology. He is fully versed in every area of management from deployment planning, installation, and configuration to training and strategic planning. As an internationally known speaker and writer, he is a returning speaker at Autodesk University since 1996. Mark is currently serving as Chief Technology Officer for SIATech, a non-profit public charter high school focused on dropout recovery. He maintains two web sites, www. caddmanager.com and www. bimmanager.com. He can be reached at mark.kiker@augi. com and would love to hear your questions, comments and perspectives.
The world is leading toward a society more integrated with AR/VR with the continued advancements exhibited throughout media and our professional worlds. Delivering content to attract an audience and meet the demand of this era is challenging. This article isn’t for the weak at heart, the unmotivated, or the lazy. It is for the serious professional who wants to meet that demand head-on. With planning, preparation, and implementation of modern tools and modular procedures, we can add scalability and efficiency to ensure maximum return on investment.
Let’s start with the bad news. Eliminate baking and texture customization. High-res to low-res baking allows for adding details to elements such as weathering, cracks, and realism. However, it’s one of the most time-consuming and least controllable processes in a production and modeling pipeline. That leaves us relying on various tools, UV tricks, modeling, and shaders to push as far as possible without it. With these, we can create virtual content that is scalable, efficient, and fit for a powerful pipeline.
We’ll start by reviewing modular construction, an incredibly efficient method of production that adds value to every industry. Whether it’s in the production of crops or the design of office buildings, consistency, and repetition lead to costeffective results. That is especially true in the construction industry, where using standardized modules can improve the skills of construction crews, resulting in greater efficiency and innovation as experience is gained. Any deviation from this consistency can lead to increased costs and unpredictable results. In short, modularity is the most efficient path forward for any industry, including construction. The same is valid for technology, especially 3D and virtualization. Adhering to it will produce substantial long-term benefits. We ignore this simple principle to our demise.
Modeling is the most essential aspect of a modular workflow. Without baking, high-fidelity visualization can be more challenging. To address that, we can take
advantage of 3ds Max’s tools. Almost a near singular purpose for baking is to produce the edge quality needed for engines to render content with some realism. We control normal conditions and edge quality through that procedure. These normals help reflect light and render edge conditions more realistically. After all, every edge on the planet has some flatness that impacts light reflection (even blades at a near-microscopic level). We use some powerful tools in the 3ds Max arsenal to represent this properly. Take a look at Figure 2.
This figure starts with a simple spline. Then apply the extrude modifier to add thickness. The Turn to Poly modifier is added to convert that object into a triangulated form (eliminating the ngons). The chamfer modifier is applied to provide the edge details we lose from eliminating the timeconsuming baking procedure. Finally, we add the weighted normal modifier to eliminate the faceted appearance providing a clean, smooth object with edge details that are great for rendering engines and lighting. While this adds some triangulation, triangulation has become far less of an issue than complex texture maps for today’s software and hardware. The time-saving component of this procedure is impossible to ignore. Take a look at Figure 3. This example shows a similar process can be utilized for more complex architectural
elements. The only difference is that the spline isn’t closed, so a shell modifier needs to be used to give it thickness after the extrude is applied to the spline. Tip: This is also one of the most common methods for creating curtains.
That addresses the primary visual component. Now let’s move on to more profound aspects of modular construction. The idea is to apply code to generate the content randomly. If you review Figure 4, you’ll notice the sections on top are uniform in length and height. That is significant for many factors. Some render engines operate more cleanly this way. Primarily, for a modular workflow, this allows us to streamline their connections, similar to Lego blocks. By maintaining this relationship, we apply conditions through coding that prioritize the pieces. So, if the piece is on the ground floor or meant for the corner of a building, we can code it accordingly. The consistent length and height make coding simpler. As 3D modelers, we apply nodes to each modular piece that our code can use to connect them. In the case of these architectural elements, the nodes are placed on all sides of the walls. As you can imagine, this becomes a coding exercise to connect the pieces based on priority. As long as the dimensions are maintained, we don’t have to get too complicated about what pieces go where. In a similar fashion, we can push it further by utilizing a
single UV trim sheet template for every piece. That’s a more advanced workflow that must be discussed at another time.
The final step is to add details, such as columns, signs, etc. This is as easily accoemplished by having the 3D artist place additional nodes for those details in positions they should apply. Then, as coders, we apply a random selection, say for signs, to attach to that location.
That concludes the overview of a modular, bakeless procedure. If you’re interested more in all these processes, a similar example was shared by Cryptic Studios in their youtube video “Trim My Starship: Building Flexible, Modular Hero Assets in 3ds Max”
for the Star Trek Multiple Player Online Roleplaying games here: https://youtu.be/Be4m9EGOv2U
Brian Chapman is a 2D/3D design professional located in Las Vegas creating content for the AEC industry, games, film, entertainment, and software development. Brian can be reached at pictelforge@gmail. com
We live in a society of fast innovations and expanding technologies. In the world of manufacturing, companies are always searching for new and cost-effective ways to stay ahead of their competition and keep up with the demands of a constantly evolving industry. Visualizing and implementing new products takes time, understanding, and consideration prior to when the actual manufacturing process can begin.
Success relies on many conditions and factors, which sometimes can be hard to control and foresee. One way to reduce some of the unknowns and a crucial step in seeking success is setting clear and specific goals related to implementation. By defining and establishing a clear direction and focus for the implementation process, we can ensure all parties involved are working towards a common objective.
This article will help you get into the right mindset as we explore the importance of setting clear goals in the manufacturing sector. The importance of communication and collaboration from initial
conception to manufacturing. How to identify your must-haves and MVP in the early stages of design. Thinking about your future by identifying phases and iterations.
Work towards your success and take a strategic approach to implementation and become a fierce competition within your specific design industry.
Hear me out. This might sound backward, but
where do you start? At the end. Without knowing what you want and where you want to go, will you know what it will take to get there. Take this opportunity, grab a pen and paper, write ‘What do I want’ and write whatever comes to mind. You don’t need me or this article to get the creative juices flowing. If you are reading this, you already have an idea and are looking for ways to get started.
A simple design sketch, a mind map, an outline, or keywords will allow you to put your thoughts down and solidify them as real ideas. Something you can hold in your hand and share with others to begin the journey.
Once you have the initial idea, you will then need to assemble individuals who will be part of this idea. You must identify project or product goals, features, expectations, and potential roadblocks related to the end result. In a collaborative environment, multiple individuals may have different ideas or goals. These should all be written down, like User stories. No information is bad information when you are looking to start. You can sort it out later.
There are predefined strategies for setting clear goals when implementing any product or solution. Such as identifying the specific outcomes you want to achieve, breaking down goals into smaller, achievable tasks, and involving all stakeholders in the goal-setting process. Take time to discuss this. It cannot be solved in one conversation. People need time to decompress, absorb, and reflect after these types of conversations. Be prepared to meet again. Be open to ideas and listen.
In the manufacturing sector, implementation of any new idea or changes requires the involvement of multiple stakeholders, ranging from investors to customers. Effective communication and collaboration between these stakeholders is crucial for the success of any implementation, as it ensures that everyone is working towards the same objective. A well-informed and cohesive team can better understand the goals and objectives of the implementation, leading to a more efficient and productive process.
To ensure effective communication and collaboration, various strategies can be implemented. One strategy is the establishment of clear lines of communication among stakeholders, ensuring that everyone can easily reach out to one another, discuss issues, and share ideas. Regular meetings and updates can also be scheduled to keep everyone informed and engaged in the implementation process.
In addition to these strategies, involving all stakeholders in decision-making discussions and processes can also be beneficial. This not only ensures that everyone is working towards
Setting clear and specific goals is essential to successfully implementing products or services within the manufacturing sector. You need to be open and properly communicate goals to all involved. If one group is unaware or unsure of the goals related to the final product, the potential for issues and roadblocks that you will not be able to foresee increases significantly. All projects have unexpected situations that arise regardless of how much we plan. Defining clear goals helps recover from those surprises, as all involved parties understand what the objectives are.
a common goal but also creates a sense of investment and ownership among stakeholders, leading to greater motivation and commitment to the implementation.
By prioritizing clear communication and collaboration among stakeholders, the manufacturing sector can implement changes smoothly and efficiently, ultimately leading to greater success and growth.
Implementing new processes or products can be complex and challenging. It’s important to anticipate potential roadblocks and challenges that could arise during the implementation process, and to have strategies in place to overcome them. Some things to consider include:
• Investment
Will you have enough funding to cover the costs, including any necessary equipment or personnel?
• Timelines
How will the implementation process be managed across multiple stakeholders, and what is the expected timeline for completion?
• Logistics
Are there any logistical challenges that could arise, such as transportation or supply chain issues?
• Regulations
Are there any regulatory requirements that need to be met, such as safety or environmental regulations?
• Production Quality
How will you ensure that the product or process is of high quality and meets customer expectations?
Is there a market for the product or process, and what is the competition like?
• End User
How will the product or process be received by end users, and what are their needs and preferences?
It is important to consider these factors and developing strategies to address potential roadblocks can help ensure a smoother and more successful implementation process.
Determining the Minimum Viable Product (MVP) is a critical step in the product development process. It ensures that you are building a product that addresses the core needs of your target customer while also being cost-effective and efficient. Prioritizing the core needs of the target customer, you may need to conduct market research, analyze customer feedback, and study the competition. This information can help you identify what features are essential for your MVP and what can be developed later.
Once you have a clear understanding of the core needs of your target customer, it’s important to compare this to the goals you set out for your product and assess any potential roadblocks that may hinder your success. This comparison can help you determine what features are essential for your MVP and what can be developed later. It’s important to consider what is both important and feasible for your MVP in order to get the best product to market in a timely and costeffective manner.
Once the MVP is established and launched, it’s important to keep in mind that the product is not set in stone. Customer needs and market trends are constantly changing, and it’s important to be prepared to adapt and iterate the product accordingly. This involves planning for future iterations of development and identifying additional features and functionalities that can be added to the product to meet the evolving needs of the target customer.
This planning for future iterations is not a trivial task and requires a lot of thought and consideration.
The work done in identifying the core needs of the target customer during the MVP stage can be leveraged to identify potential future phases of development. Were there any features, functionalities, or potential customers that were not identified during the MVP stage? These can be considered in future phases of development to help evolve the product or solution and provide investors with a clear business scope for the future.
By taking a thoughtful approach to planning for future iterations of development, companies can stay ahead of the curve and continue to meet the needs of their target customers. This can help to establish a competitive advantage and drive continued success in the market.
new technology or processes, it’s important to keep in mind that the success of your implementation ultimately depends on the people involved. By fostering a culture of collaboration, communication, and shared ownership, you can ensure that your implementation is not only successful but also sustainable in the long run.
Remember that you’re not alone on this journey, and don’t hesitate to reach out to others for support and guidance. With the right mindset and approach, you can achieve great things and make a positive impact in your organization and beyond. Best of luck on your journey!
The world of manufacturing is continuously evolving, and success in this industry requires a strategic approach to implementation. Setting clear and specific goals related to the final product, promoting effective communication and collaboration among all stakeholders, and identifying potential roadblocks and challenges are essential steps in the implementation process. By doing so, companies can reduce uncertainty and ensure that all parties involved are working towards a common objective.
In addition, identifying the must-haves and MVP of the product or solution is a critical step in the product development process. It ensures that the product addresses the core needs of the target customer while also being cost-effective and efficient. Prioritizing the core needs of the target customer positions you and your product in a more competitive position. Limiting the bells and whistles that will absorb time and money which can be used elsewhere.
Regardless of the industry or application for your implementation, the starting point is the same for all of us. At the end. Whether you’re implementing
Kristina Youngblut is an accomplished expert in the field of CAD solutions and technologies, with over 20 years of experience in the Architecture, Engineering, and Construction (AEC) industry. Her extensive knowledge and expertise are focused on providing innovative solutions and technologies to professionals in the manufactured products sector, helping to optimize workflows and improve collaboration within teams.As an Autodesk Expert Elite member, Kristina is recognized for her exceptional skills and contributions to the Autodesk community. She is also an AUGIWORLD author, a BIM Coordinators Summit Ambassador to Canada, and a dedicated community member. Kristina has a passion for empowering her clients to achieve their goals through the utilization of advanced technology and tailored solutions.Throughout her career, Kristina has worked on various projects, from initial conception to completion. She has been instrumental in creating standards and formats that unify content and maintain file and data integrity. Her expertise has been recognized in various web series, podcasts, and articles, where she has shared her insights and knowledge with industry greats.
On second thought, I better not go there since I don’t want to offend any Auto “CAT” lovers. But seriously, the Auto “CAD” program from the beginning has always offered more than one way of doing the same thing. For example, with the latest AutoCAD version, command entries can be entered ranging from typing it in on the Command Line to selecting it from icons on Toolbars, Palettes or the Ribbon. Likewise, AutoCAD comes loaded with built-in commands that may generate similarly looking objects like LINE versus POLYLINE or TEXT versus MTEXT. Relative to the aforementioned examples though the reasons to choose one command versus another may be fairly simple. But when it comes down to choosing the command to INSERT versus XREF a Block, this warrants a deeper discussion.
To kick off this discussion since AutoCAD categorizes both an Insert and Xref as a BLOCK, it’s important to go over what makes up a Block in AutoCAD. The following is the definition from the AutoCAD help screen:
“A block is one or more objects combined to create a single object.”
Actually, this description is not 100% accurate or perhaps not 100% complete. A Block actually can be created without a single object in it. For example, you may want to create a drawing with just Layer names assigned with Colors and Linetypes. Or perhaps you may want a drawing to contain just Text style names and or Dimension style settings. In either case there are no objects in this kind of drawing. But such a drawing can still be brought in as a Block and used as a Template to begin a project.
Now a Block at the minimum must contain the features shown in Figure 1.
1. At time of creation (Block Definition) and placement (Insert or Xref):
a. A Name – up to 255 characters in length with the following thirteen characters not supported: \ / : * ? ” < > | ; , = `
Note: The Microsoft Windows operating system does support the following four characters in a file name: ; , = ` So when a
file name contains any one of these four characters at time of Insert or Xref AutoCAD will request for a different name entry using only supported characters.
b. A Base or Insertion point – X, Y,Z coordinates which can be a different location from 0,0,0
2. At time of placement (Insert or Xref):
a. A Scale – uniform or unique for X, Y, Z
b. A Rotation angle – 0 to 359 degrees
Other possible features a Block may contain are:
1. Units – Option to define a unit setting using the Insunits system variable introduced in AutoCAD 2000
2. Explodability – Option to prevent the Block from being exploded introduced in AutoCAD 2006
3. Annotative – Option to set various scales for Texts and Dimensions to appear introduced in AutoCAD 2008
Next, let’s go over what is a Block Insert. Inserting Blocks into a drawing has been a built-in command since AutoCAD was first released back in 1982. The
source of Block Inserts can come from Blocks stored only internally in the current drawing database or drawings saved externally. After an external drawing (a.k.a. the source drawing) is inserted into another drawing (a.k.a. the target drawing), then the Block definition now resides inside the target drawing database. There’s no longer any connection to the original source drawing.
Now to share an internally stored Block Insert for use externally to other target drawings you’ll have to execute the WBlock command. On the Write Block window under Source select Block and then from the drop-down list click on the name of the Block to share externally. As long as the Destination File name matches the Block name then the Block is successfully written out as a source drawing for inserting into other target drawings (see Figure 2).
As a caveat, since the source drawing when used as a Block Insert can be made up of other Blocks (a.k.a. nested Blocks), if the target drawing already has any of the matching nested Block names stored internally, these will not change. Instead, the nested Blocks inside the target drawing will remain as they are different from those inside the source drawing. So, it may be a good idea for a Block to contain only basic elements without nested Blocks to avoid this problem.
Initially the process of inserting a Block into the current drawing can only be executed from the Command Line. By entering the “Insert” command you’ll have to respond sequentially to the remaining prompts to complete a Block Insert. Then in 1992 AutoCAD R12 came out accompanied with a lisp function called DDInsert.lsp. The DDInsert command implements a customized graphic user interface (GUI) option for Block insertion. Now all the required responses to inserting a Block can be seen and completed at once using the GUI shown in Figure 3.
This Insert command method continued to be the typical method to insert a Block until many more releases later when AutoCAD 2020 introduced the Blocks Palette. In addition to having the Palette stay floating on the screen, now a graphic thumbnail representation of all the Blocks in the current drawing can be seen. Also, the selected Block can be inserted by dragging & dropping it from the Blocks Palette onto the graphics drawing area (see Figure 5).
But it took a few more releases until AutoCAD 2000 came out before the Insert GUI became a built-in AutoCAD command. This new Insert command (a.k.a. ClassicInsert as of AutoCAD 2020) added the additional feature of seeing a preview of the Block prior to insertion (see Figure 4).
So, in summary, the Block Insert offers the following features:
1. Embedded – Block definition exists inside the target drawing database.
2. Attributes – editable and extractable text can be included introduced in AutoCAD 2.0 in 1984.
3. Dynamic – visibility control to display different graphic geometry introduced in AutoCAD 2006.
Now, let’s go over what is an Xref Block. Support for external reference files or Xrefs did not occur until AutoCAD R11 in 1990. The introduction of the much-needed Xref command eight years after the initial release of AutoCAD was long overdue. This made it possible for drawing files saved outside of the current drawing database to stay where they’re
located and at the same time be placed into the current drawing as a reference. Whenever that file (a.k.a. the source drawing) is changed every location where it’s referenced (a.k.a. the target drawing) would automatically reflect the latest and greatest updates.
Since an Xref Block remains located externally from the target drawing database, whenever target drawings are shared outside of your network environment all source drawings will need to be included. To accomplish this AutoCAD provided the ETransmit command. When executed from within the target drawing a list of all source Xref Blocks can be seen in the ETransmit command window. You can also click on the Transmittal Setups button to define the drawing format to use from current to all the previously supported versions. The end result is a compressed set containing both the target and all source Xref Blocks (see Figure 6).
view where Xrefs are listed in column format. List View offers the flexibility of sorting the list based on the column heading. The second viewing method is called Tree View (activated by pressing F4 on the keyboard). In this alternate view only a single Xref can be selected at a time to perform an operation. Tree View visually differentiates top level from nested level Xrefs (see Figure 8).
As for the method to execute the Xref command, like the Insert command, AutoCAD initially only offered a Command Line interface. So, when AutoCAD R12 came out with the DDInsert.lsp function but still provided no Xref GUI I decided to use DDInsert.lsp as a template to develop my own DDXref.lsp function. I also used this opportunity to add a Pick function to select an already placed Xref on the screen to perform various Xref Options (see Figure 7).
Then after five more years AutoCAD R14 in 1997 came out with a built-in Xref GUI called the Xref Manager (a.k.a. ClassicXref as of AutoCAD 2008). Though everything was still text based, the Xref Manager offered two ways of viewing all the Xrefs that are contained in the current drawing. The first viewing method is called List View (activated by pressing F3 on the keyboard). This is the default
Finally, after another decade, AutoCAD 2007 introduced the External References Palette. In addition to supporting all the functions Xref Manager offered the External References Palette can remain open and provides a graphics preview of the Xref as the cursor hovers over it (see figure 9).
As a side note, since there are some operations AutoCAD does not support with managing Xrefs, I recently developed an app to fulfill my wish list. I call this app Xref Object Manager or XOM as the shortcut command to launch the app in AutoCAD (see Figure 10).
So in summary, the Xref Block offers the following features:
1. Automatic Updates – changes in the source drawing are reflected in the target drawing
2. Separate Layers – comes with Layer names prefixed with the name of the Xref allowing the option to separately control Layer status
3. Bound – can be converted to an Insert Block using the Xref Bind or Insert option.
For convenience XOM does replicate a couple of operations that are already available on the External References Palette like Attach and Detach (Delete). But for the most part XOM includes a few additional operations that are not currently supported.
One of the added operations XOM offers to manage Xrefs is Copy. The Copy operation makes a duplicate instance of the source file giving the Xref another name. I typically use this operation so I can separately control the Layers prefixed with the Xref name grouping. For example, I can have Floor Plan
Xref Copy 1 and Reflected Ceiling Plan Xref Copy 2 both referencing the same source file: Floor Plan Sample.dwg. This way whenever Floor Plan Sample. dwg is updated both Xref Copy 1 & Xref Copy 2 updates as well. Also, with the separate Xref Layer name prefixed groupings, I can have certain Xref Copy 1 Layers Frozen and at the same time leave On and change all Xref Copy 2 Layers to a grey tone using Color 8 as shown in Figure 11.
A second XOM added operation is the ability to Rename any Xref. Since the External References Palette limits renames to top level Xrefs only, I would have to run a separate Rename command to change nested level Xrefs. Granted, renaming nested Xrefs is only temporary since the next time a Reload occurs the nested level Xref will return to the original name. But there are times I want to be
currently pathed to Design Scheme 1, this can be changed or repathed to Design Scheme 2. But when this operation occurs AutoCAD does not automatically rename Xref to match with the repathed drawing name. XOM’s RePath operation will do both a repath and a rename of the Xref. Likewise, EqPath will automatically rename any Xref to match with the corresponding pathed drawing name (see Figure 13).
The last XOM operation I added is Show. Though an Xref selected on the External References
Palette can show up highlighted in the current graphics area, it does not
able to use the same GUI to Rename Xrefs regardless of their level (see Figure 12).
A third and fourth XOM additions are RePath and EqPath operations which offer similar features. There are times when I want to preserve the Xref placements in the current drawing but change the source drawing (the path) to another. For example, in the current drawing where an Xref is
zoom up to the location where the Xref is located. This made me develop the Show operation so that it’ll both highlight and zoom full screen to the first Xref instance found. When the Show operation is completed the graphics screen view will return back to the original location (see Figure 14).
Now that everyone is thoroughly informed about Blocks, Block Inserts and Xref Blocks, it’s time to return to the original question as to when to use a Block Insert versus an Xref Block. Obviously, if you plan on using Attributes or Dynamic Blocks, then a Block Insert is the only option since an Xref Block does not support these features. Likewise, if a Block contains lots of complex objects, is frequently updated and shared to multiple drawings, then an Xref Block would be most appropriate to meet these objectives.
I remember at my previous office I had received a site plan drawing from a lighting consultant. All the lighting symbols placed in the drawing were Xref Blocks. This would work well if the lighting symbols changed frequently. Otherwise, I would have used Block Inserts instead.
Typically, a Block Insert is ideal for simple geometric symbols that are used repeatedly. Symbols like a company’s logo or a parking stripe arrow will most likely not change throughout the life of the project. On the other hand, a Block that’s made up of numerous objects on many Layers, like a set of structural columns and shear walls that need to be referenced on multiple floor plans would be best served as an Xref Block.
Here’s a more specific example of when to use a Block Insert: Typically, the title block may contain the same information throughout the life of a project. The project name, client name & address will most likely remain constant. This is the ideal situation to use the Insert command to place the title block into the entire drawing set. In addition, Attributes can be incorporated to this Block. These Attributes can include items that are unique to each drawing such as Sheet Title, Scale, Page number and etc.
Here’s a more specific example of when to use an Xref Block: You frequently receive updated drawings from team members outside of the
office for use as background coordination. In an Architectural office, drawings are typically received from other engineers and externally referenced instead of inserted. This way whenever the engineers reissue updated drawing sets all target locations where the source drawings are referenced are automatically updated without user input.
Since AutoCAD has a history of continued development on enhancing existing as well as adding new commands, who knows what changes will come with future releases. But one thing for certain, AutoCAD will always offer variety and flexibility giving users multiple options to reach the same goal. It is up to the end user to be fully informed of all that AutoCAD offers. Then better educated decisions can be made to help everyone successfully cross the finish line.
Mr. Paul Li graduated in 1988 from the University of Southern California with a Bachelor of Architecture degree. He worked in the Architectural field for small to midsize global firms for over 33 years. Throughout his tenure in Architecture he has mastered the use and customization of AutoCAD. Using AutoLISP/ Visual Lisp combined with Dialog Control Language (DCL) programming he has developed a number of Apps that enhance the effectiveness of AutoCAD in his profession. All the Apps actually came out of meeting challenging needs that occurred while he worked in the various offices. He has made all the Apps available for free and can be downloaded from the Autodesk App Store. Though he recently retired from the Architectural profession, Paul continues to write articles depicting his past work experience. Some of these articles can be found in AUGIWorld Magazine where he shares his knowledge learned. Paul can be reached for comments or questions at PaulLi_apa@hotmail.com.
Basic members have access to:
• Forums
• HotNews (last 12 months)
• AUGIWORLD (last 12 months)
DUES: Free
AUGI is introducing three new Membership levels that will bring you more benefits than ever before. Each level will bring you more content and expertise to share with fellow members, plus provide an expanded, more interactive website, publication access, and much more!
Student members have access to:
• Forums
• HotNews (last 24 months)
• AUGIWORLD (last 24 months)
• AUGI Educational Offerings
DUES: $2/month or $20/year
Professional members have access to:
• Forums
• HotNews (full access)
• AUGIWORLD (full access and in print)
• AUGI Library
• ADN Standard Membership Offer
DUES: $5/month or $50/year
Are you ready to upgrade yourself and your membership? Access additional benefits and upgrade at www.augi.com
AUGIWORLD brings you the latest tips & tricks, tutorials, and other technical information to keep you on the leading edge of a bright future.