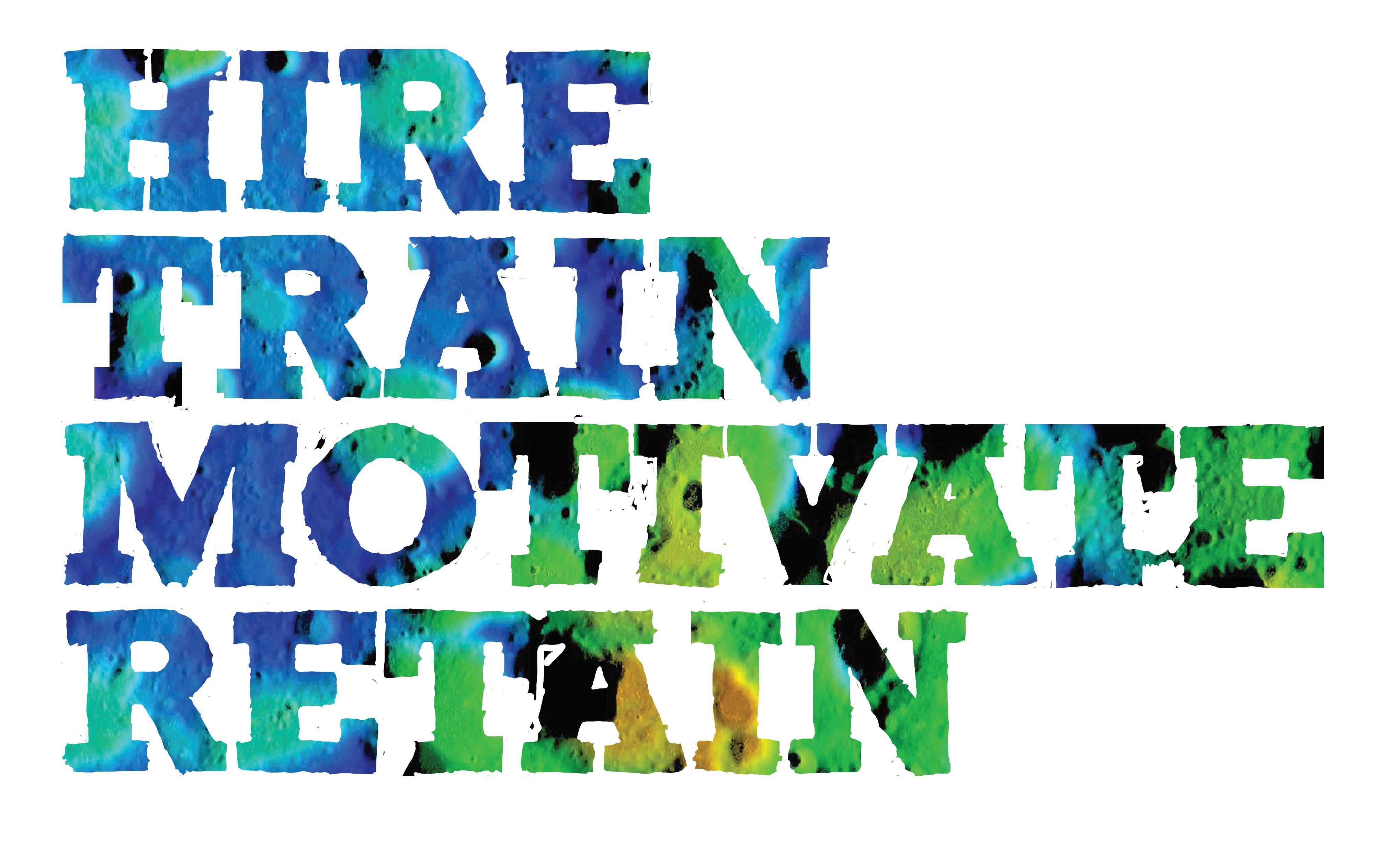
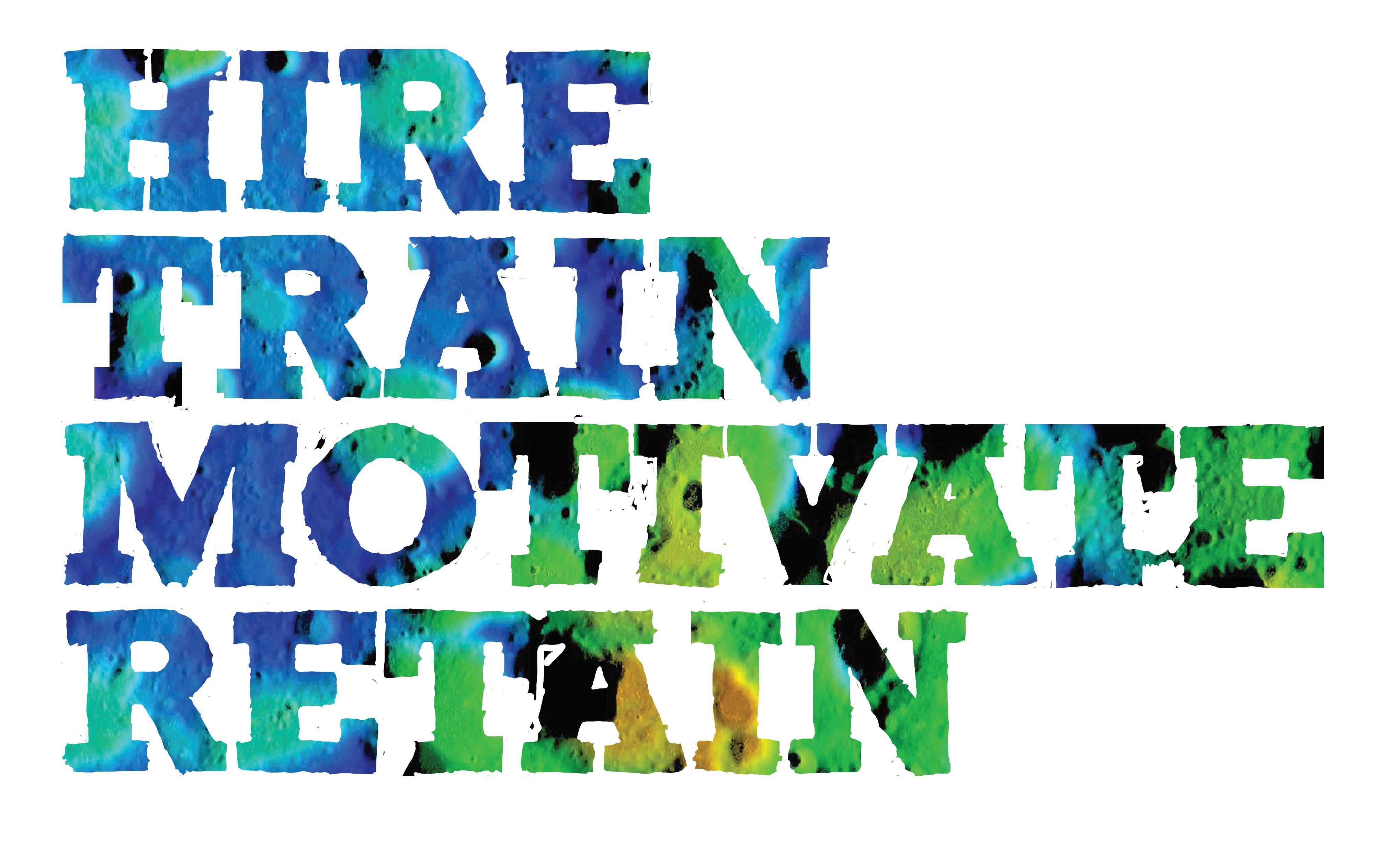
ready
Renewable energy solutions, like Entergy Mississippi’s 100-megawatt Sunflower Solar Station in the heart of the Delta, are becoming increasingly available across the state so industries can work smarter to achieve their goals while reducing greenhouse gas emissions. Maximize your savings with the power of renewable energy in Mississippi – where we are proud to be a leader in working toward clean and efficient energy usage.
SEE WHERE MIGHTY MISSISSIPPI CAN TAKE YOU. Visit MISSISSIPPI.ORG/energy to learn more.
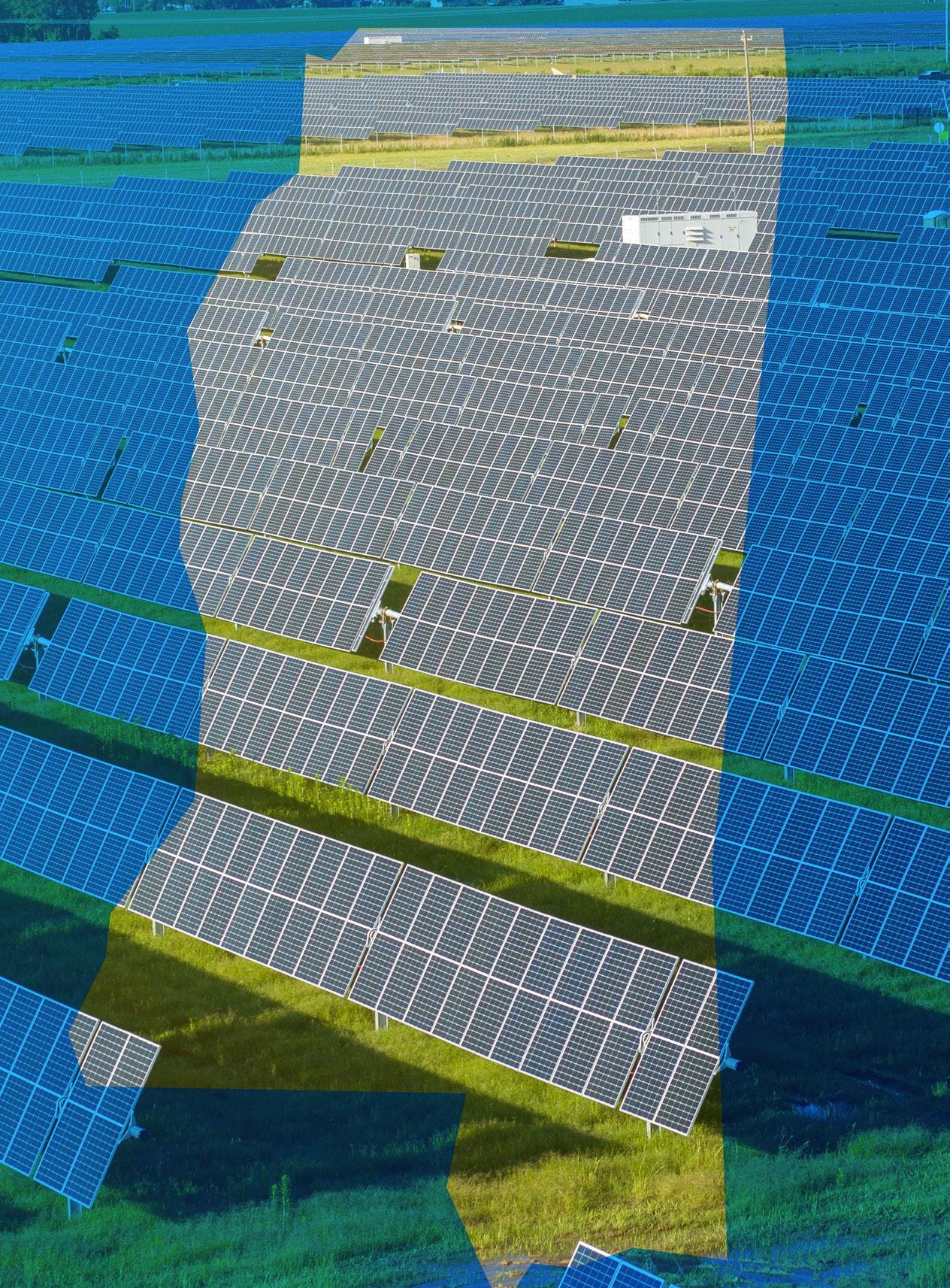
Top Talent. Top Companies. Arizona tops the list.

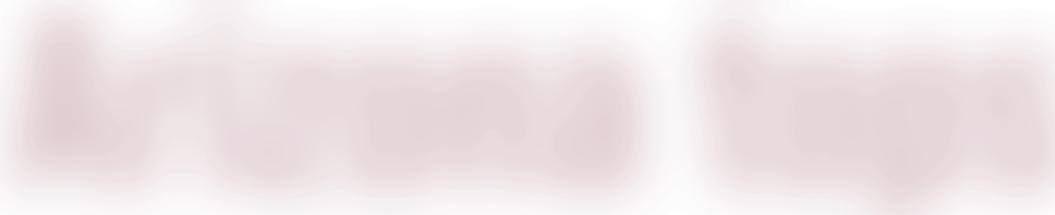

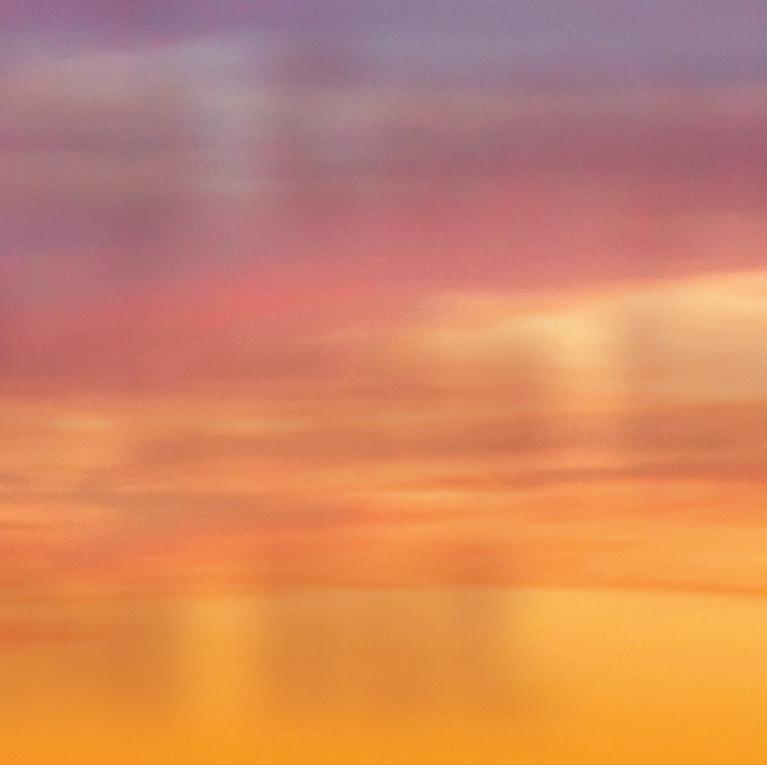
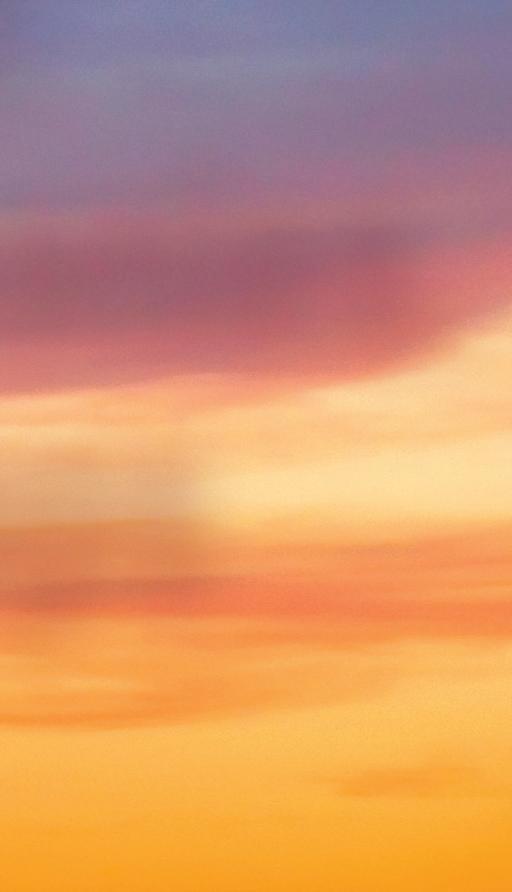



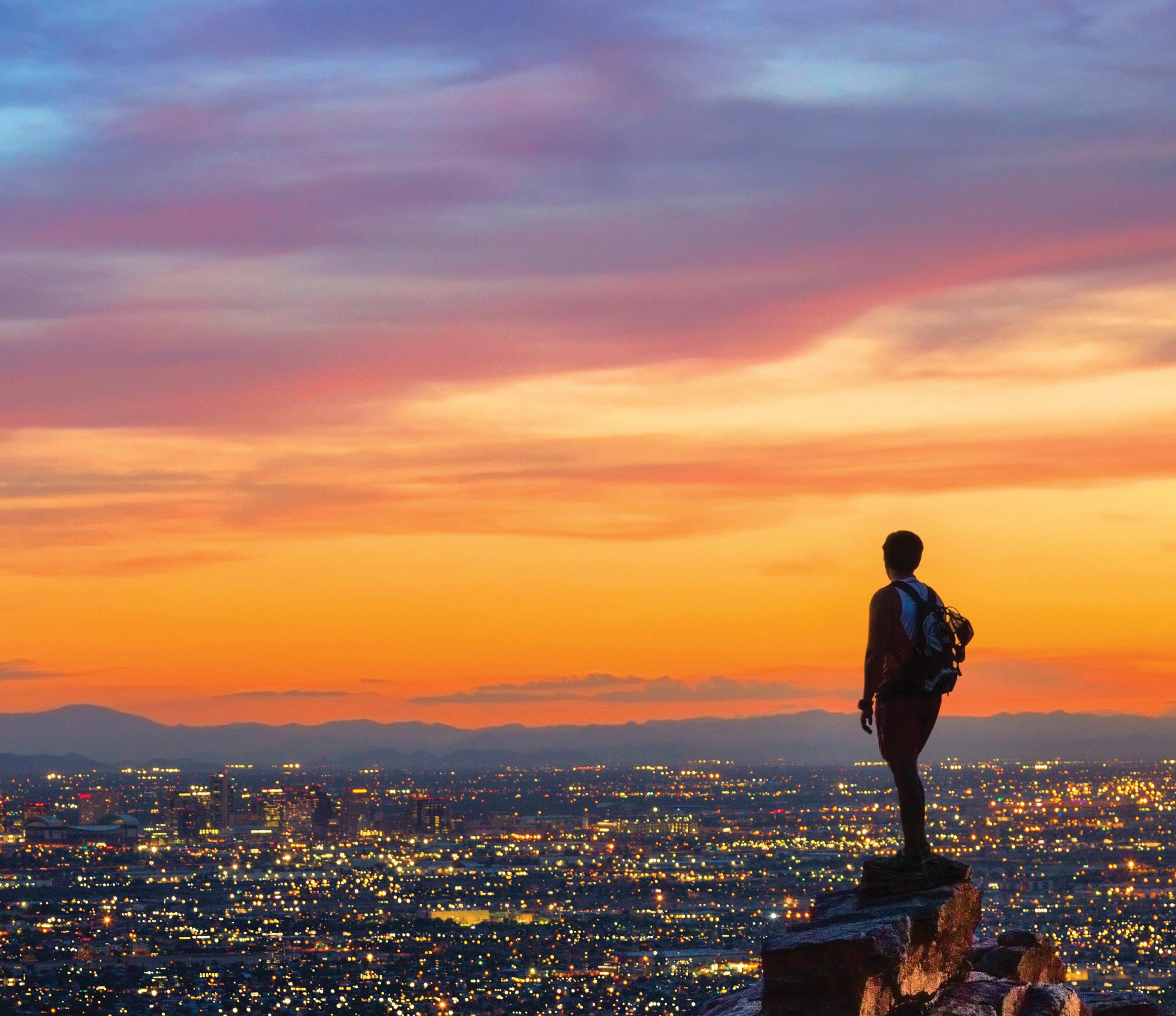
In Arizona, you’ll find the perfect balance of business opportunity and high-quality lifestyle that makes it a top state to live and work. Businesses benefit from pro-innovation policies and business stability. Residents enjoy a reasonable cost of living and beautiful scenery, all while taxes remain low for everyone. With a highly skilled talent pool and a commitment to future-forward industries like semiconductors, electric and automated vehicles and battery manufacturing, we’re maximizing our potential for generations to come.
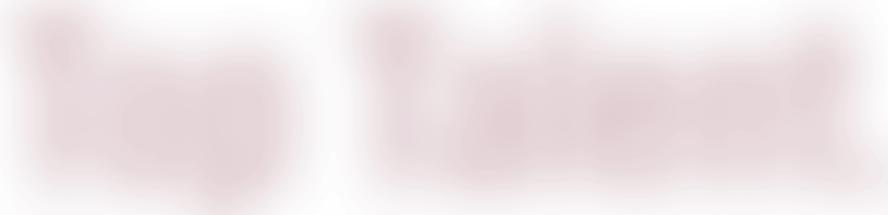
•
•
•
•
features

16 Inflation Reduction Act Promotes the Nation’s “Energy Security”

The clock is ticking for manufacturers to get maximum tax benefits on new projects under the Inflation Reduction Act.
20 ESG: The New Metrics in Construction and Real Estate
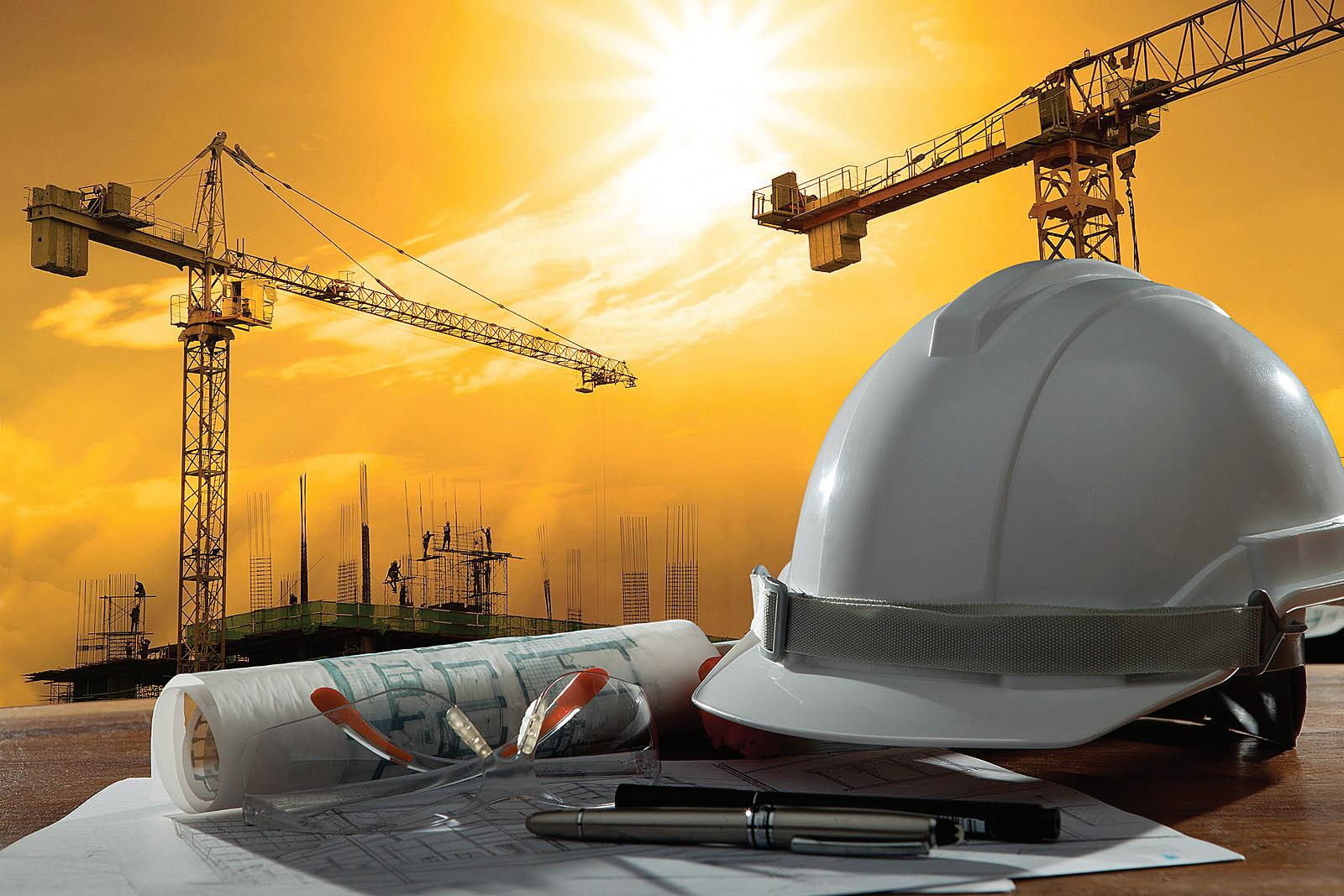
Key environmental, social, and governance (ESG) considerations include protecting the environment/ reducing energy use, making positive contributions to the community, adopting inclusive workplace policies, and maintaining high standards of governance.
23 Fixing the Supply Chain with AI and Robotics
Automation, industrial robots, and other technology solutions have allowed manufacturers to shorten their supply chains, while also making them more efficient and reducing labor costs.

26 To Cluster or Not to Cluster…That Is the Question!
Although clusters are here to stay in some sectors — think life sciences — other industries — among them EVs and semiconductors — are geographically branching out.
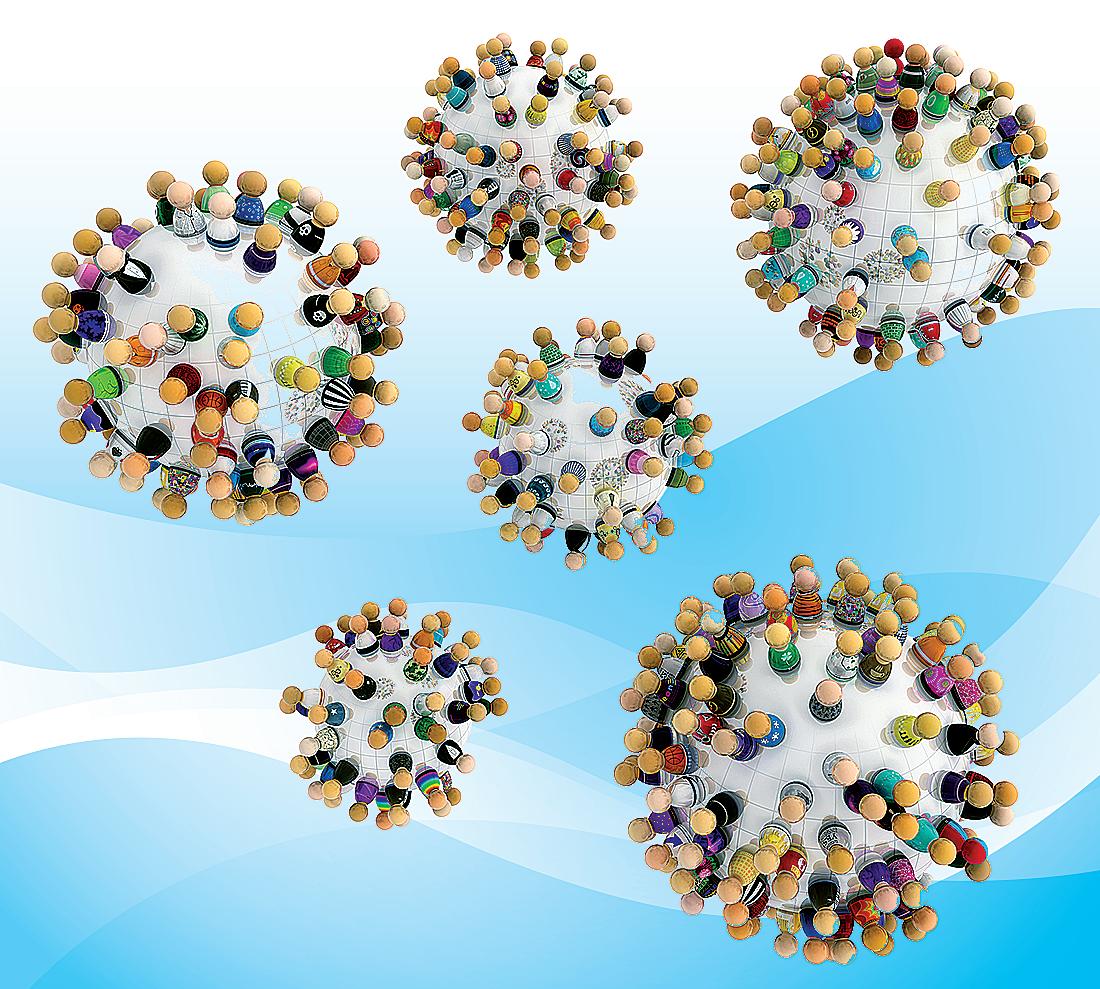
FOOD PROCESSING
66 Three Big Challenges Facing the Food & Beverage Industry
While every industry — and everyone — has faced disruptions over the last couple of years, the food and beverage industry has been disrupted on an almost unimaginable scale.
69 Food Processors’ Optimal Location Decision
Whether evaluating existing buildings or finding a location for a new facility, food processors must make sure all the variables involved align to support the final decision.
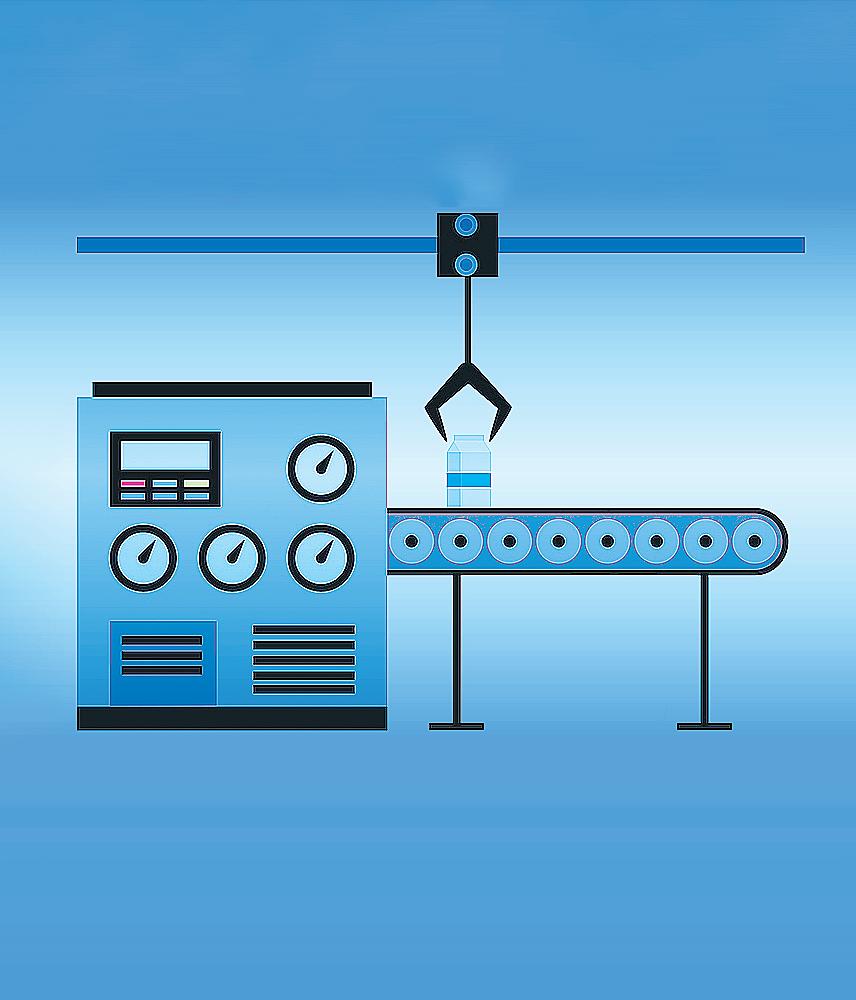
lOve we
what’s next-ers momentum builders game changers companies with vision world-first innovation industry revolutionizers competitive edge seekers
Wisconsin loves to help all sorts of companies find their version of success. That includes yours. From site selection through construction, opening and expansion, we provide support to ensure your vision becomes reality. After all, your success may inspire other companies to relocate or expand here, too. That’s how we look forward.
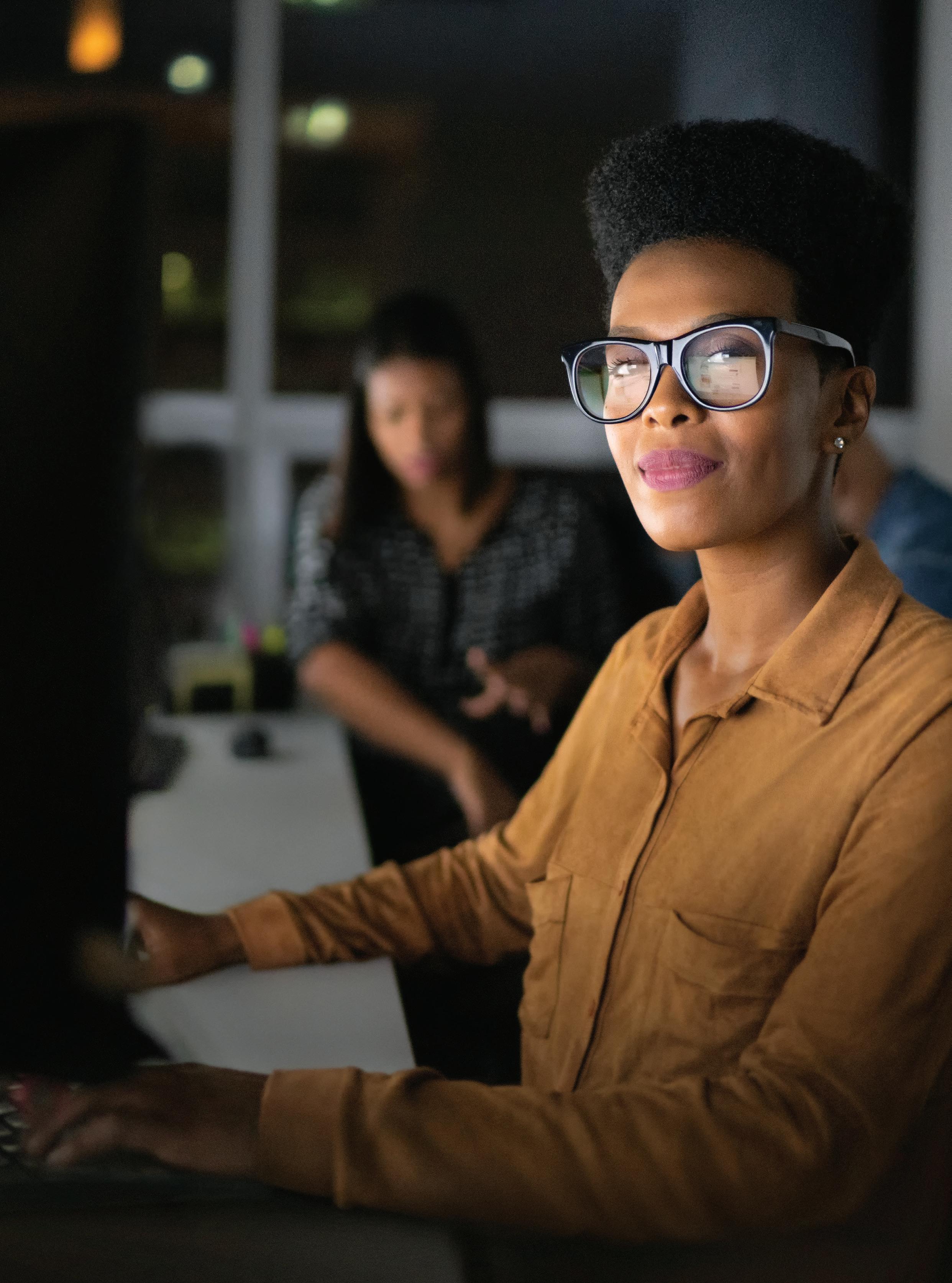
73 Bright
Spots of the Office Sector
The post-pandemic remote working trend has resulted in “emerging” or “other” metros performing better than the more established tech markets.
76 Factoring Mexico Into a Solution to the Global Supply Chain Crisis
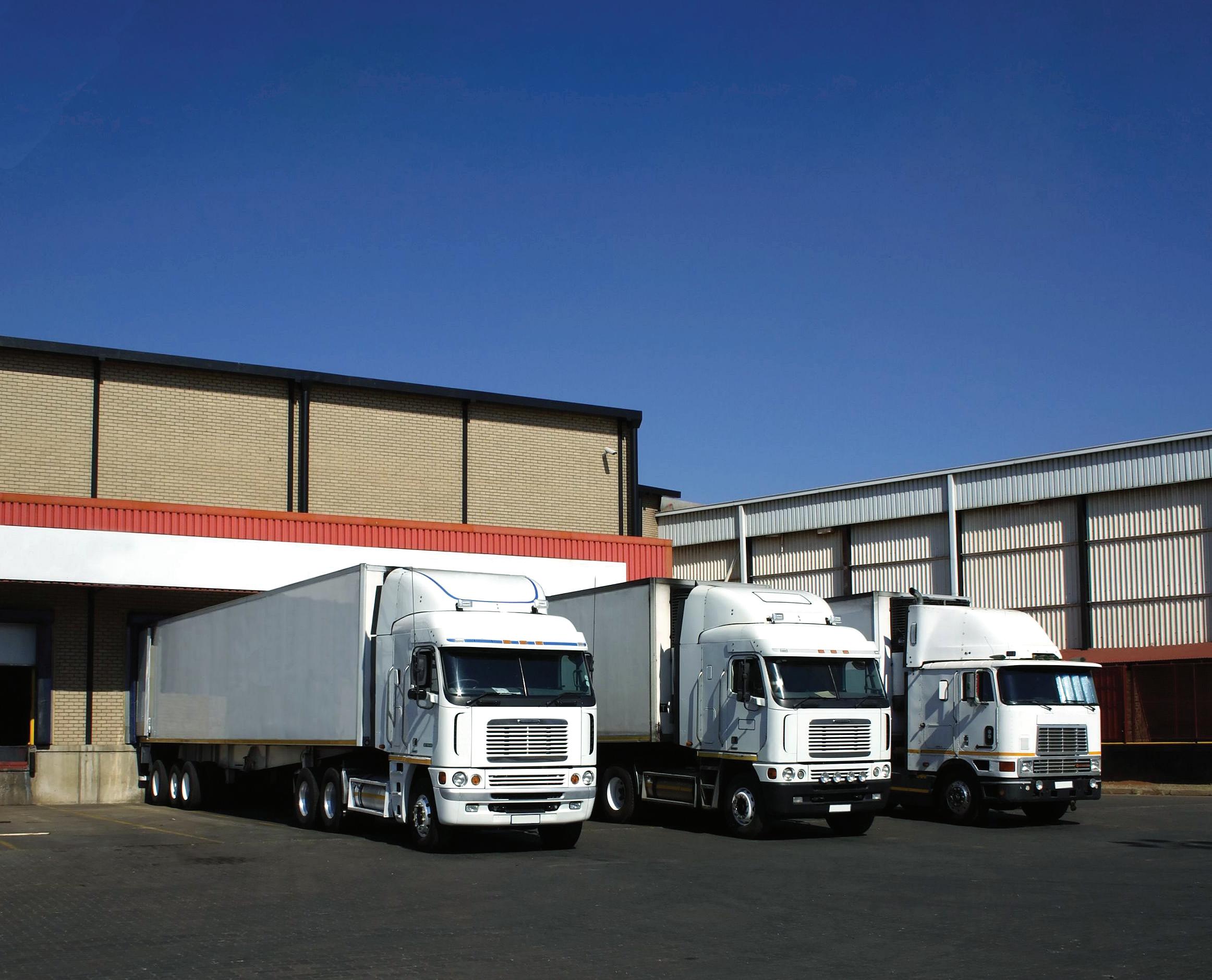
While its proximity to the U.S. and lower labor costs make Mexico a good location for a manufacturing operation, other costs may be higher, and its supplier base still lacks maturity.
INNOVATION CORRIDORS
From robotics to EVs, from semiconductors
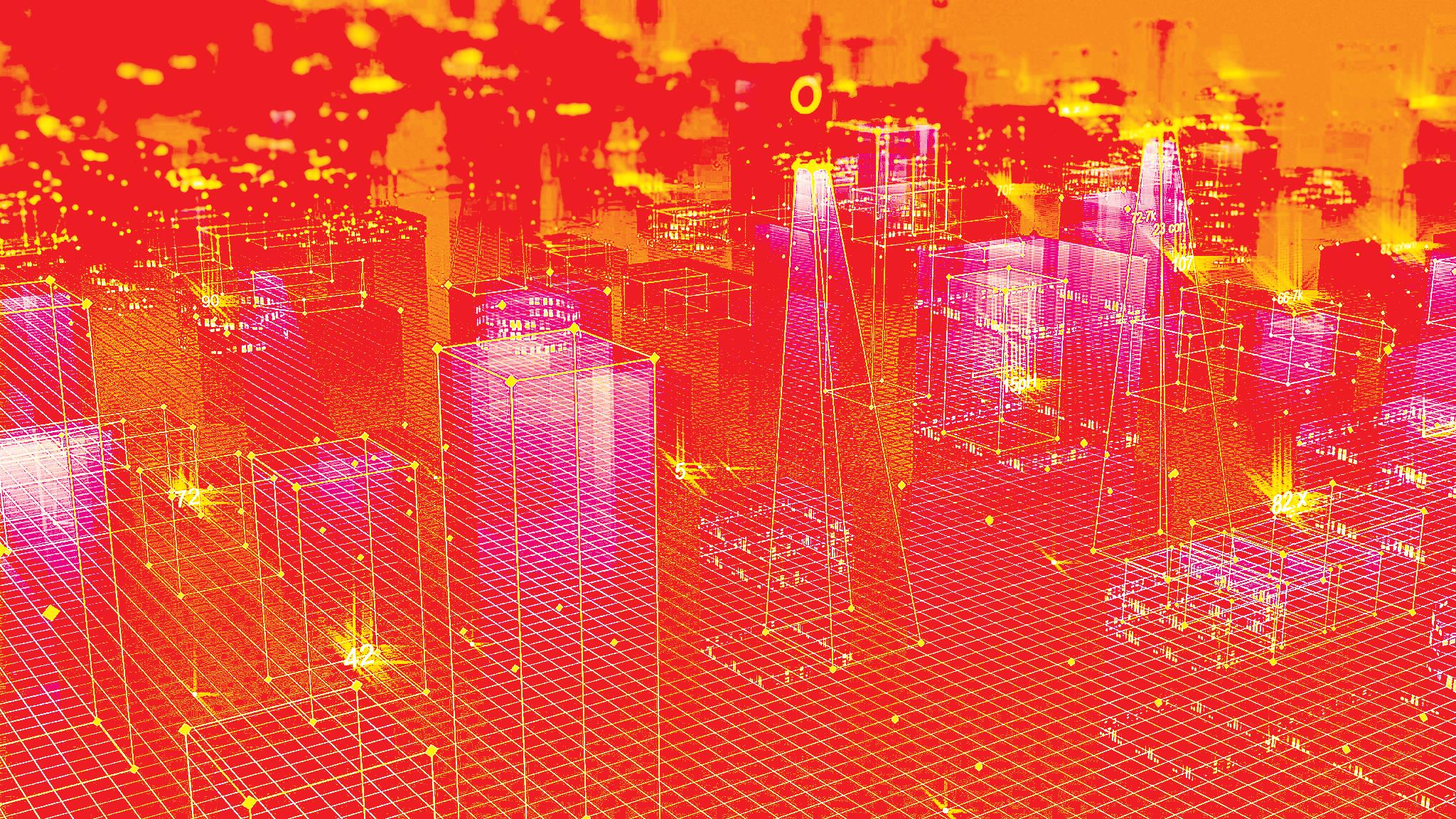
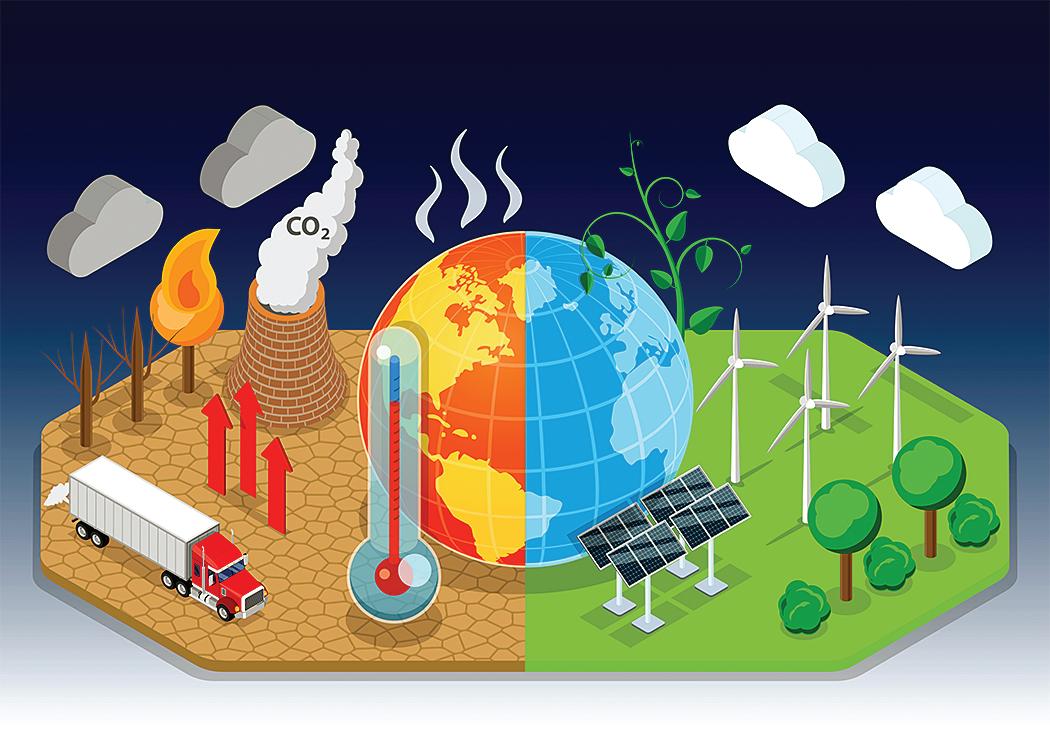
hubs of innovation are advancing economic development across the nation.
• Front Line: Taking a Deep Dive into Suppliers’ Labor Force
• Economic Impact and Importance of Social and Policy Issues
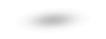
• Amid Rebound, U.S. Regains Position as World Leader in FDI
• Decision-Making Dynamics in an Uncertain World
• Only the Best Is Good Enough: The LEGO Group Chooses Virginia for U.S. Manufacturing Facility
• New Report Shows NYC Economy Going Strong
• Eight Public Private Partnerships Strengthening Michigan’s Talent Pool
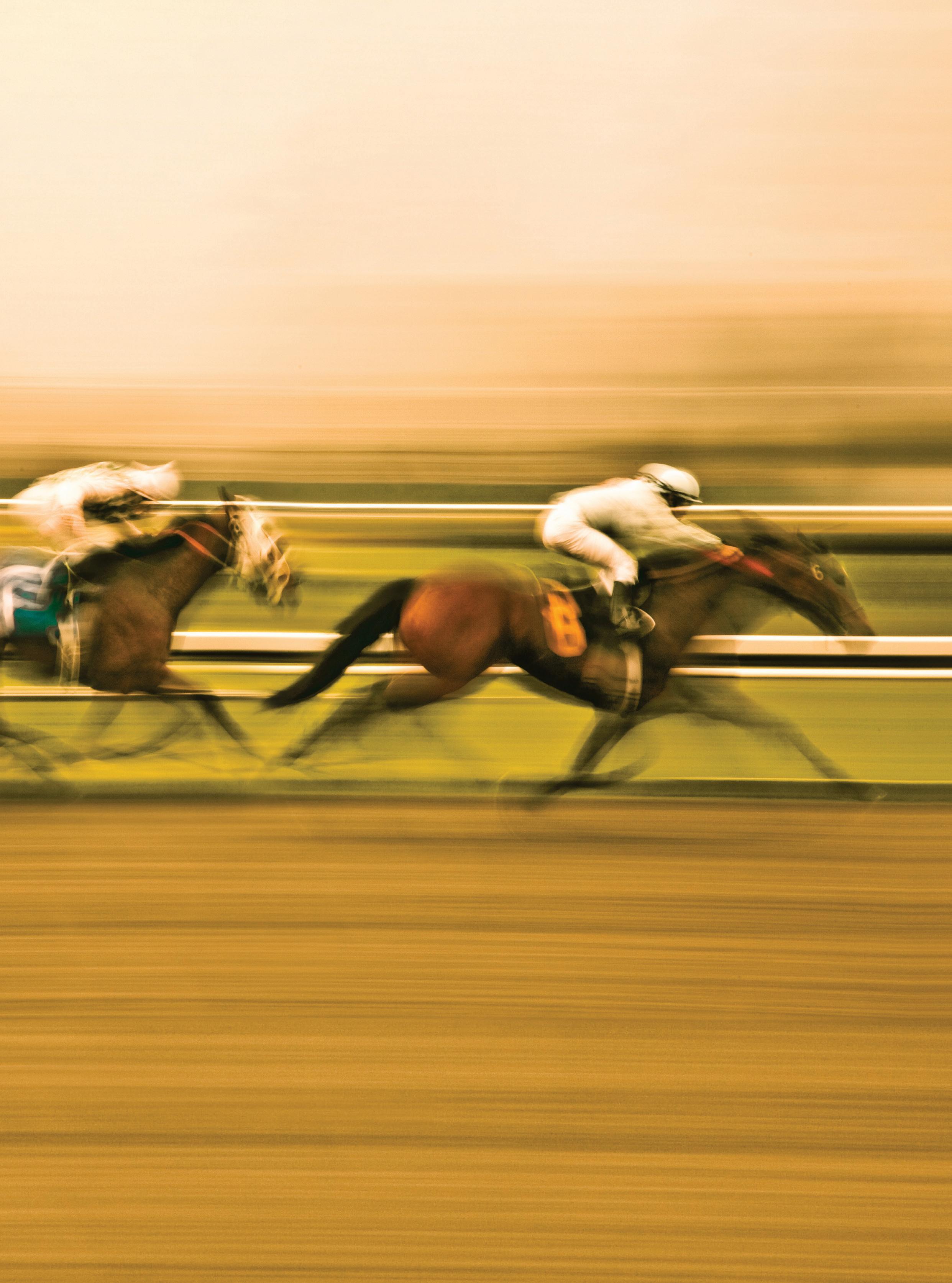
No Signs of the War for Talent Cooling Off
Much has been written about the Great Resignation that occurred in 2021 as a result of the COVID-19 pandemic as U.S. workers looked for a better work/life balance, increased compensation, safer working conditions, or a company culture more aligned with their values. Now, nearly three years after the global pandemic began, the number of people who are either working or looking for work has not fully recovered to pre-pandemic levels, let alone grown as it should have over the course of that time.
In the Workforce supplement to this issue (beginning on page 29), several consultants, who help companies satisfy their workforce needs when choosing a location, address the challenges businesses are facing and how they are navigating the post-2020 talent landscape.
The search can begin with an analysis of a location’s workforce data, i.e., demographics, wages, unemployment rates, etc. But qualitative information — such as information about competitors and community dynamics — also comes into play. In light of this, businesses are now looking at smaller less established markets to satisfy their labor force requirements. These markets often have lower living costs, thereby exerting less pressure on wages, and less competition for the available talent.
Companies need to have a better understanding of the reasons why individuals migrated to certain areas of the country during the pandemic in order to attract workers who are open to changing locations. They must also reprioritize their diversity, equity, and inclusion (DEI) efforts to acquire and retain the best talent. Increased diversity and inclusion in the workforce will enhance employee performance and increase company innovation.
The workforce trends highlighted above are also reflected in many of the articles comprising the rest of this year-end issue. For example, Moody’s data reveals that remote working trends have resulted in “emerging” or “other” metros performing better than more established tech markets. Graycor explains how a company’s adherence to ESG principals — which includes how the company treats its employees — is vital to the construction industry and its subcontractors. And food processors and makers of food processing equipment are among the manufacturers dealing with acute labor shortages.
It’s projected that the war for talent will continue in 2023 with many companies increasing their use of AI and automation to fill the gap and reduce labor costs. Savvy companies will also invest in upskilling current employees. Those that do will be one step ahead.
www.areadevelopment.com
2022 Editorial Advisory Board
Josh Bays, Principal site selection group
Marc Beauchamp President & CEO cai global group
H. Robert Boehringer III, Managing Director Global Location and Expansion Services kpmg
Brian Corde Managing Partner atlas insight
Kate Crowley Principal baker tilly capital
Dennis Cuneo Owner dc strategic advisors
Courtney Dunbar Site Selection & Economic Development Leader burns & mcdonnell
Amy Gerber Executive Managing Director Business Incentives Practice cushman & wakefield
Stephen Gray CEO gray
David Hickey Managing Director hickey & associates
Anthony Johnson President Industrial Business Unit clayco
Scott Kupperman Founder kupperman location solutions
Bradley Migdal Executive Managing Director Business Incentives Practice cushman & wakefield
Daniel Oney Managing Director newmark
Matthew R. Powers Managing Director Industrial Real Estate & EVP Retail/E-Commerce jll
Carolyn Salzer Director Americas Head of Logistics & Industrial Research cushman & wakefield

Chris Schwinden Senior Vice President site selection group
Eric Stavriotis Senior Vice President Advisory & Transaction Services cbre
Steven Tozier US-East Region Credit & Incentives Leader ey
AREA DEVELOPMENT
Publisher Dennis J. Shea dshea@areadevelopment.com
Sydney Russell, Publisher 1965-1986
Business/Finance Assistant Barbara Olsen (ext. 225) olsen@areadevelopment.com finance@areadevelopment.com
Advertising/National Accounts advertising@areadevelopment.com
Art
Circulation/Subscriptions circ@areadevelopment.com
Production Manager Jessica Whitebook jessica@areadevelopment.com
Business Development Manager Matthew Shea (ext. 231) mshea@areadevelopment.com
Digital Media Manager Justin Shea (ext. 220) jshea@areadevelopment.com
Web Designer Carmela Emerson
Halcyon Business Publications, Inc. President Dennis J. Shea
Correspondence to: Area Development Magazine 30 Jericho Executive Plaza Suite 400 W Jericho, NY 11753
Phone: 516.338.0900 Toll Free: 800.735.2732 Fax: 516.338.0100
Chris Volney Senior Director Americas Consulting/Labor Analytics cbre
Dan White Director Government Consulting & Fiscal Policy Research moody’s analytics
Joshua Wright Vice President Economic & Workforce Development emsi
Scott J. Ziance Partner vorys
‘Tis the Season for
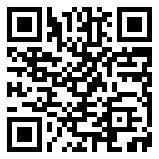
Even Saint Nick knows Kentucky is the best location to ship products anywhere in the world in a single night

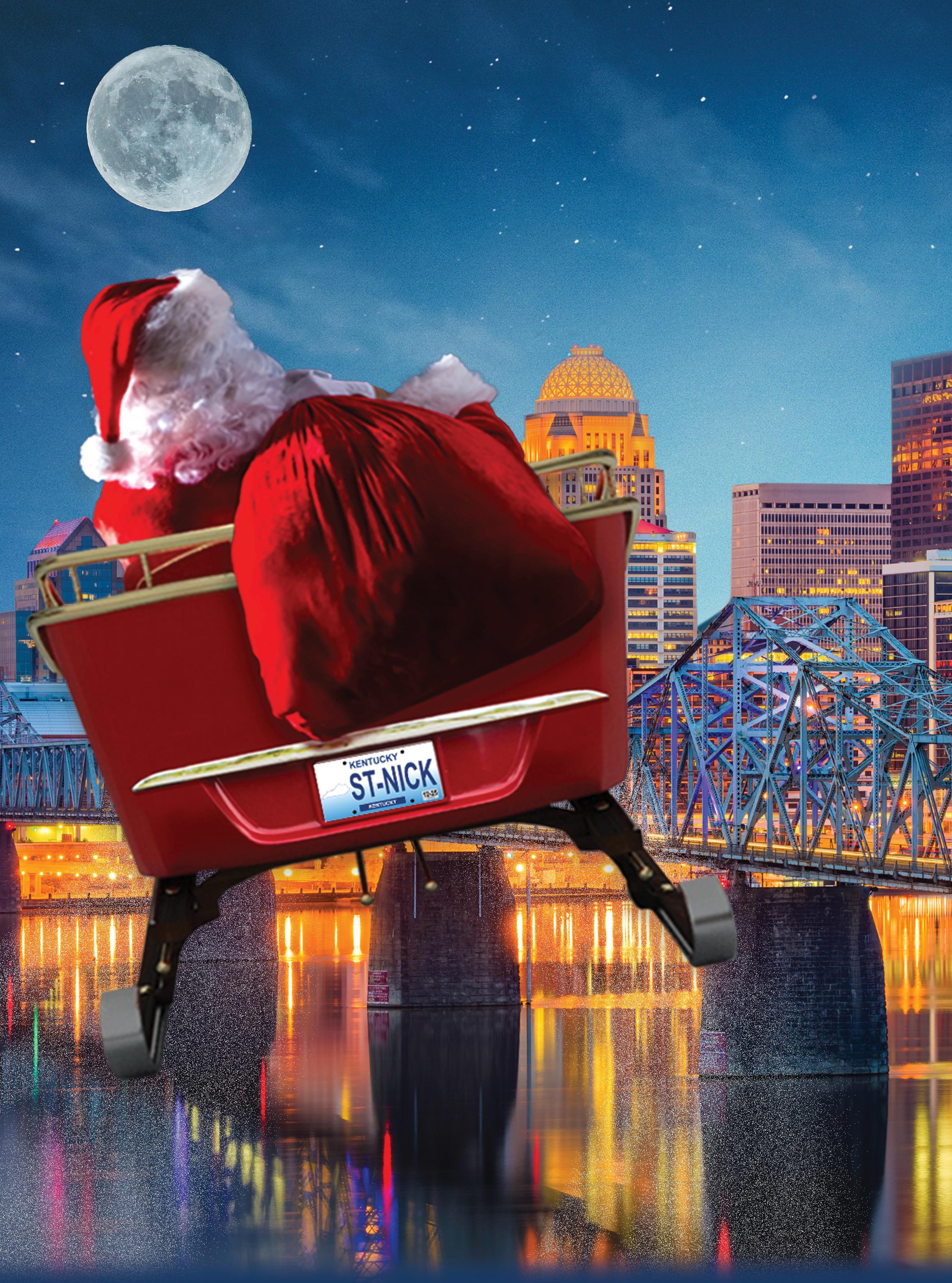
The CHIPS Act: A Historic Investment in Our Future
By helping to provide a critical domestic supply chain, the CHIPS Act represents a new era of American industrial competitiveness.
BY QUENTIN L. MESSER JR., CEO, MICHIGAN ECONOMIC DEVELOPMENT CORP.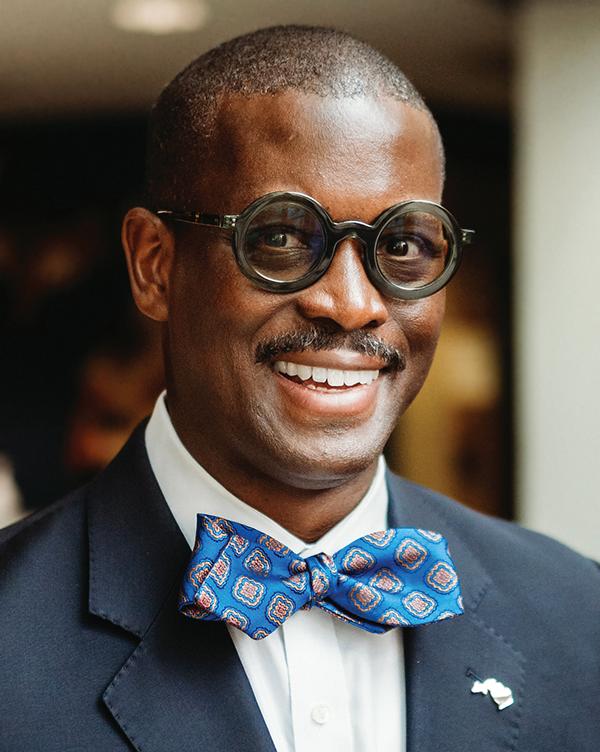
Since this summer’s passage of federal legislation aimed at boosting domestic semiconductor manufacturing, several chipmakers have announced plans to build new fabrication facilities in the United States. Fortunately for the country, the CHIPS and Science Act won’t just be a gamechanger for the semiconductor industry.
Encouraging the manufacturing of microchips at home means providing critical domestic supply chain support for businesses dependent on these critical electronic compo-
conductor chip availability. Chips are a key component of emerging technologies, including 5G wireless devices, artificial intelligence software, electric and autonomous vehicles, and cryptocurrencies — in short reaching every single business sector.
The global chip shortage has hurt the production of cars and other essential American products. Increasing the access and availability of semiconductors is crucial for our national and economic security
American semiconductor industry will also foster a vibrant innovation ecosystem that creates new opportunities. It’s easy to forget that Americans invented the transistor, a tiny semiconductor device that allowed for the precise control of the amount and flow of current through circuit boards. The birth of the semiconductor industry was the force behind the computer revolution. The next great digital invention is being built in an American garage as we speak. In Michigan, we celebrate the CHIPS Act! Michigan helped lead the bipartisan charge for the bill’s passage because we know the stable supply of chips is vital to building a championship economy in our state and nationwide. The average passenger vehicle may have 1,200
CREATING A MORE ROBUST AMERICAN SEMICONDUCTOR INDUSTRY WILL ALSO FOSTER A VIBRANT INNOVATION ECOSYSTEM.
as we compete for technological leadership on a global playing field, ensuring that Michigan-based companies like Whirlpool, GM, and Ford are able to
different chips that serve as the brains of a variety of automotive systems, from cruise control and entertainment to lane-departure warnings and other modern safety features. The transition to EVs and other propulsion systems will only increase the demand for chips, thus underscoring the necessity of a domestic chip supply chain.
Federal economic policies like the CHIPS Act validate all the work we’re doing in Michigan to support industrial sectors critical to our economic growth and future.
Michigan is home to several companies driving
a growing semiconductor supply chain ecosystem domestically and advanced research in semiconductor device and circuit fabrication at the University of Michigan among other Michigan universities. In 2018, KLA, a high-tech, Fortune 500 company specializing in systems and software integral to chip and electronics manufacturing, chose Michigan for the location of second headquarters facility, creating 600 jobs in Ann Arbor.
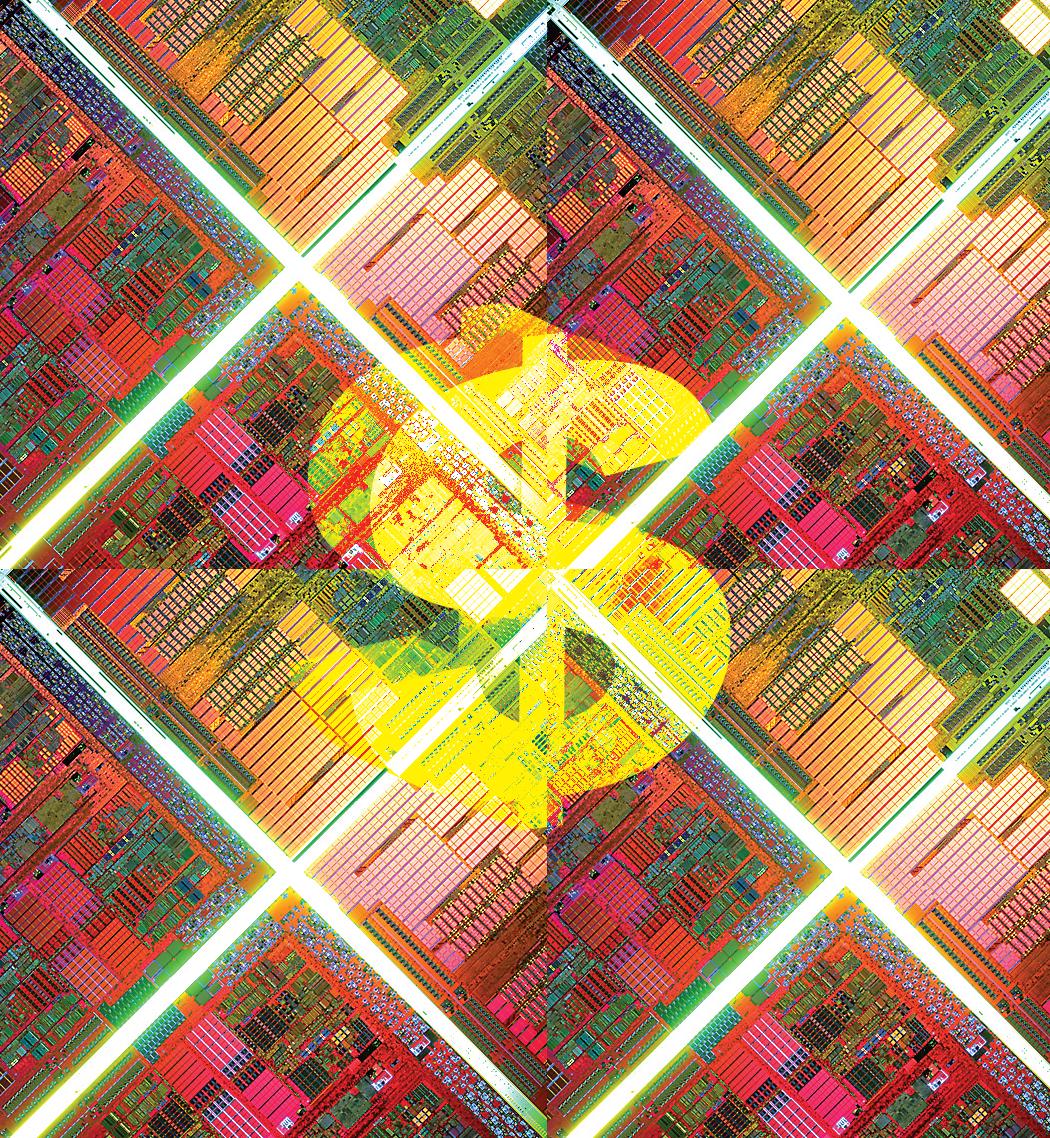
SK Siltron CSS has invested $300 million in a new semiconductor wafer manufacturing and R&D facility near Bay City. SK Siltron CSS will expand the production of much-needed silicon carbide wafers, considered the future of the industry because of their ability to efficiently transfer energy. Hemlock Semiconductor Operations, the largest producer of polysilicon in the United States, recently announced plans to invest $375 million to modernize and expand operations in the state. And in the Upper Peninsula, Calumet Electronics on Michigan’s scenic Keweenaw Peninsula is positioned to be one of the few domestic IC (integrated circuit) substrate suppliers in the U.S.
The CHIPS Act represents a new era of American industrial competitiveness. Building upon Michigan’s innovative tradition and unsurpassed advanced manufacturing heritage and cognizant of the hard work ahead, we are moving with confidence to create a better future to ensure we take full advantage of economic opportunity afforded by the CHIPS Act.
for free site information, visit us online at www.areadevelopment.com
“ IN MICHIGAN, WE DREAM BIGGER.”
Dreaming. Innovating. Growing. It's how Michigan talent is making an impact on the world in key industries. From tech to mobility to advanced manufacturing, there's a different kind of hustle here. Expand your business in Michigan and get access to support, camaraderie and new opportunities.
Make the move at michiganbusiness.org/pure-opportunity
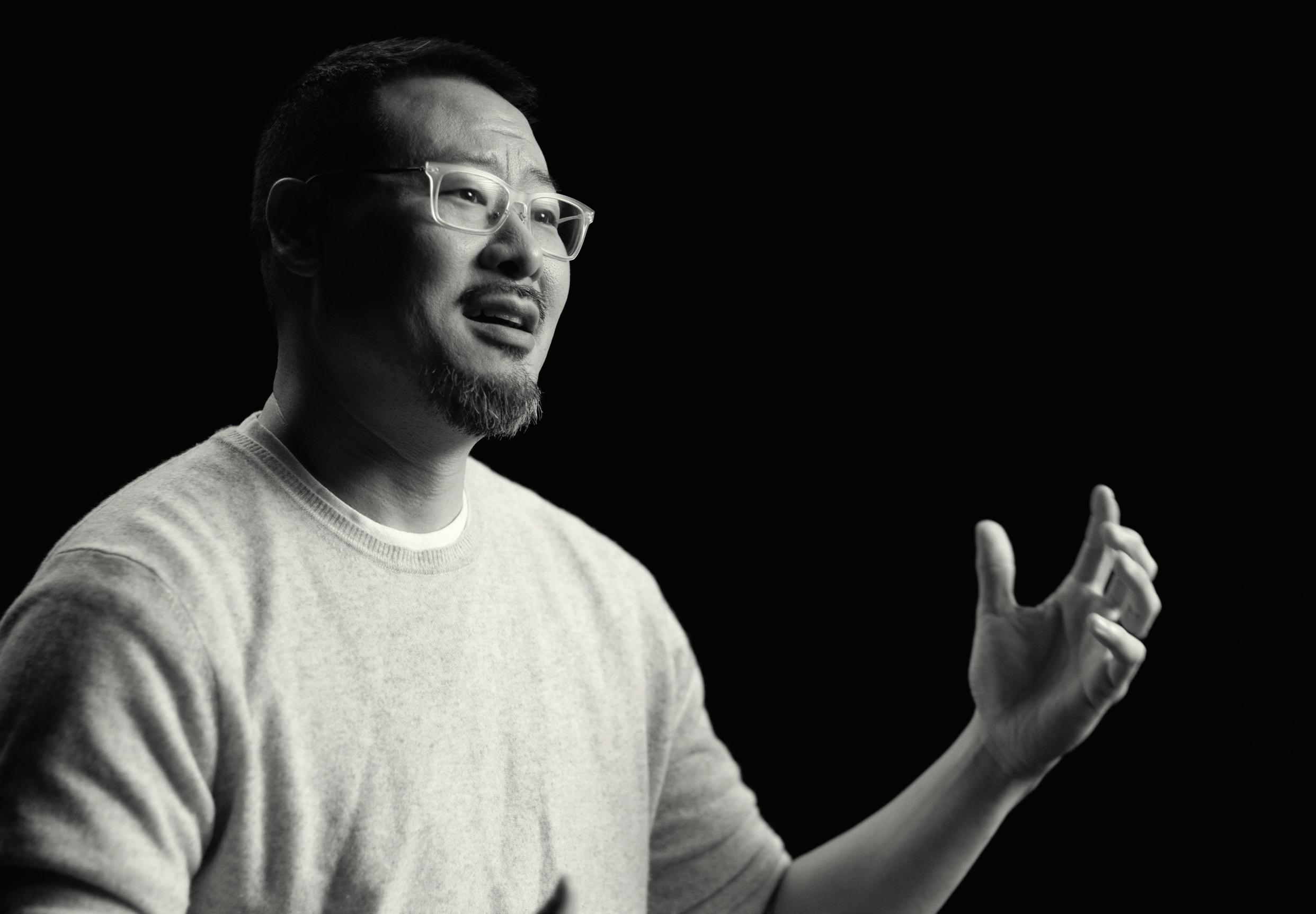
Taking an Expanded View of Climate Change
Climate change, corporate sustainability/ESG ratings, and the use of renewables are becoming increasingly important to companies as the planet heats up.
These concerns have begun to affect facility design, according to Wassmansdorf. He has worked with a client who wants to have a manufacturing facility using “new to the world” renewable power. Also, in the event of power loss from the grid, how can solar or a company’s own resources combined with batteries or backup generators provide better continuity?
BY DAN EMERSONSummer 2022 — a season marked by historic heat waves, widespread drought, and torrential rains — ranks among the hottest on record, according to data from NASA and the National Oceanic and Atmospheric Administration (NOAA).1
During a triple-digit wave in California, Governor Gavin Newsom issued a state of emergency, ordering some manufacturers to cease operations, encouraging electric vehicle drivers to charge at night, and allowing ships in harbor to keep their engines on instead of using shore power from the grid.
With climate data showing that summer 2022 was part of a long-term trend, and not a fluke occurrence, it’s no wonder that climate change has become a more urgent factor for companies in many industries, particularly manufacturing. In fact, the Urban
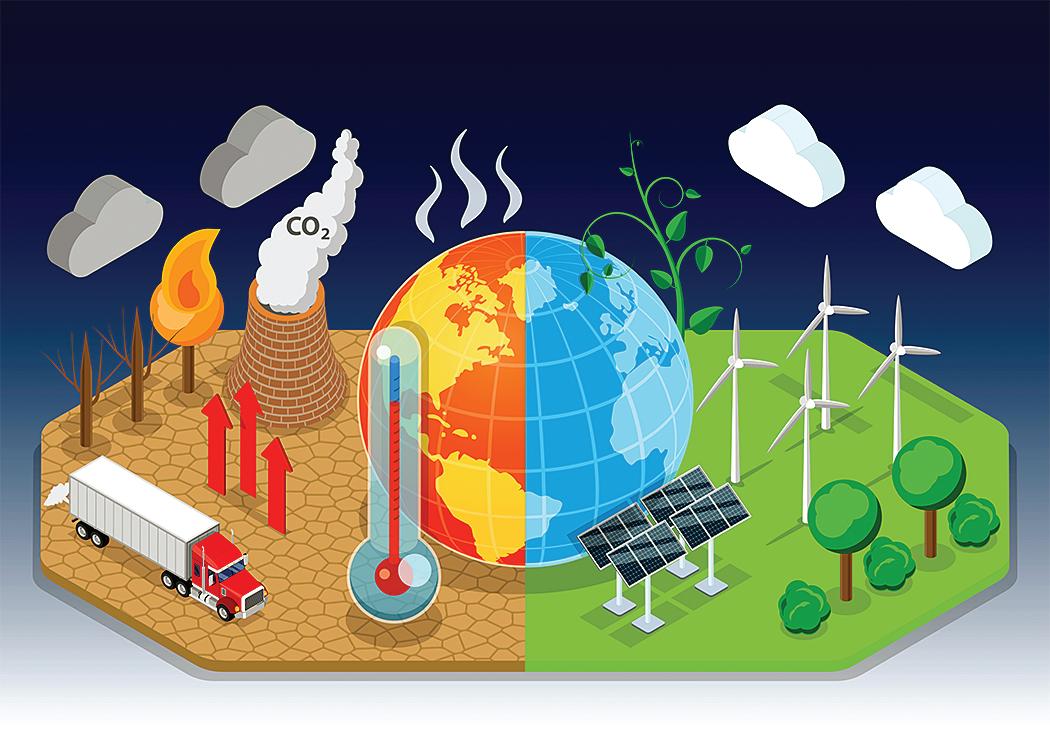
Land Institute and LaSalle Investment Management recently released a new report on how climate risk assessment can help protect people and property.2
Part of the Site Selection Equation
The risk of natural hazards has always been part of the site selection equation, says Gregg Wassmansdorf, senior managing director of Global Consulting for New-
Will climate concerns cause manufacturing companies to start favoring locations in more northern latitude locations, or farther inland? It’s too soon to say, Wassmansdorf says, “but I think that will be a natural outcome and a specific function of what a specific business needs for that operation.” For example, “if your process relies heavily on water for cooling or being consumed in process, as in food and beverage manufacturing, the likelihood you would go to drought-prone locations is going to be reduced.”
Reliability of the Electric Grid
One of Wendt’s manufacturing clients doesn’t want to source energy from coal, so it factored in the percentage of renewable kilowatts a local utility could deliver. Doing so would reduce its environmental impact and also lower the carbon intensity score, which is part of the company’s ESG (environmental, social, and governance) rating, he says. The client company hopes to take advantage of wind production offsets offered by a particular locale.
ESG is a proposed corporate sustainability disclosure by the U.S. Securities and Exchange Commission, which other non-SEC companies are adopting as a common standard to benchmark how their corporate commitments, performance, and business model compare with their peers.
THE RISK OF NATURAL HAZARDS HAS ALWAYS BEEN PART OF THE SITE SELECTION EQUATION.
mark. Risks like hurricanes, earthquakes, and floods have always been assessed either as a “fatal flaw” to eliminate a particular location, or as part of the short list considerations to pick one location over another, he says. But in recent years, “more and more climate change-related factors are expanding the field of view around natural hazard risk,” Wassmansdorf says.
Cory Wendt, a principal with Baker Tilly who focuses on manufacturing and distribution advisory, says the reliability of the local electrical grid has grown in importance as a site selection concern. One example: for manufacturers whose processes discharge a large amount of water, a municipality’s capacity to handle high-strength wastewater — or its ability to expand its capacity — might be major factors in choosing a locale.
Companies are also re-evaluating their supply chains with the goal of reducing “upstream” shipping-related impact on the environment, Wendt says. He notes that the 2022 Inflation Reduction Act includes multiple incentives for manufacturers to invest in infrastructure that helps reduce their energy footprint — changes that can also help make many otherwise non-economical sites now possible.
One incentive example is investing in a digester that can be used to turn high-strength wastewater into energy. Doing so can earn an Investment Tax Credit to cover 30 to 50 percent of capital costs, Wendt explains.
1 https://www.noaa.gov/news/us-sweltered-through-third-hottest-summer-onrecord
2 https://www.lasalle.com/company/ news/uli-lasalle-provide-framework-forreal-estateindustry-to-assess-climate-risk
for free site information, visit us online at www.areadevelopment.com
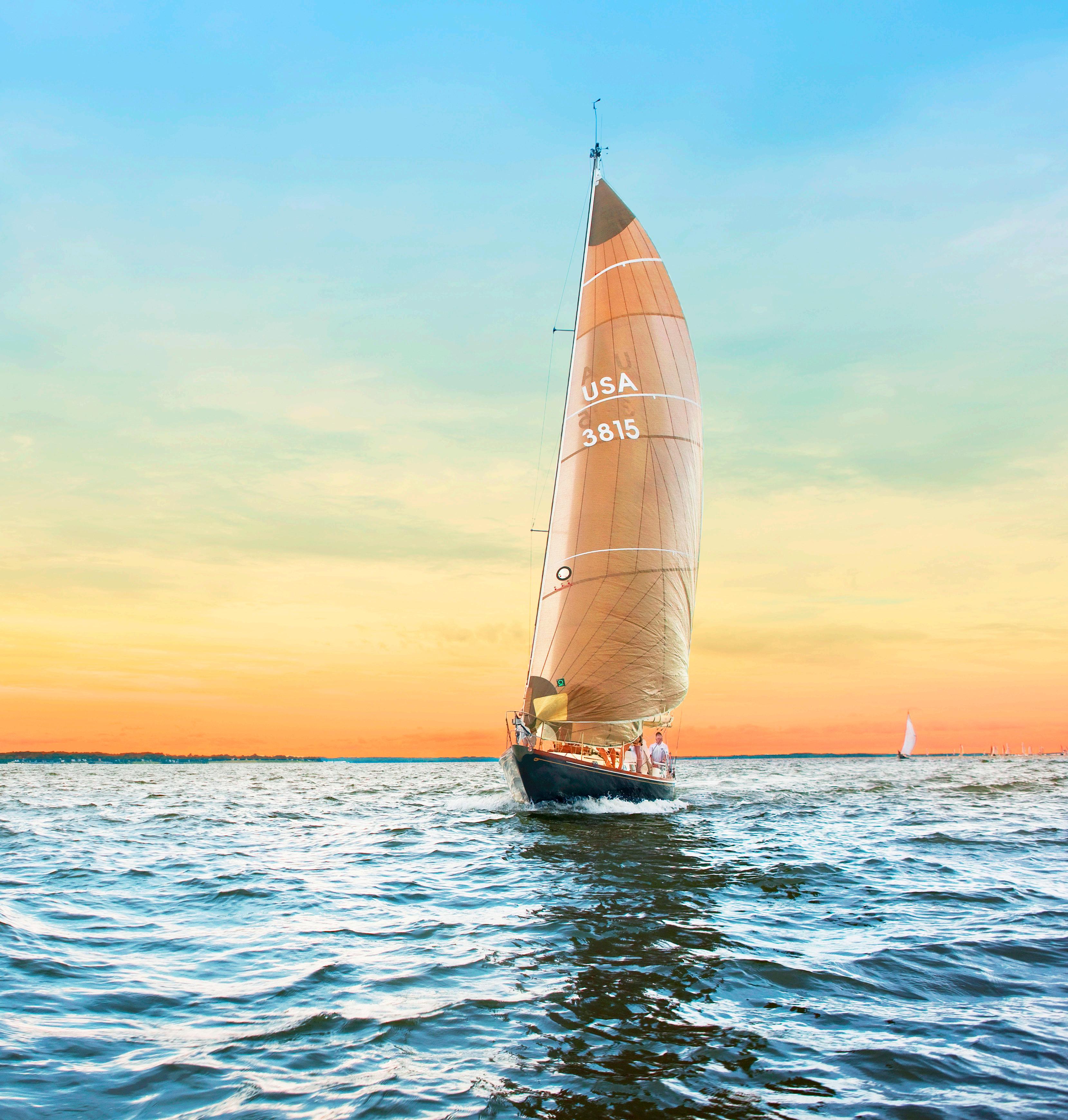
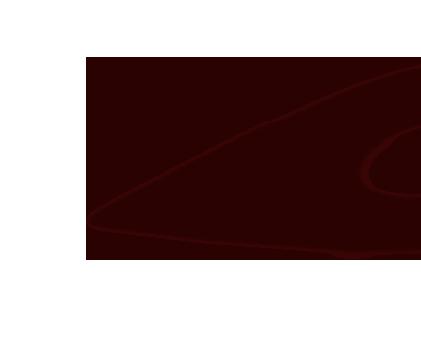

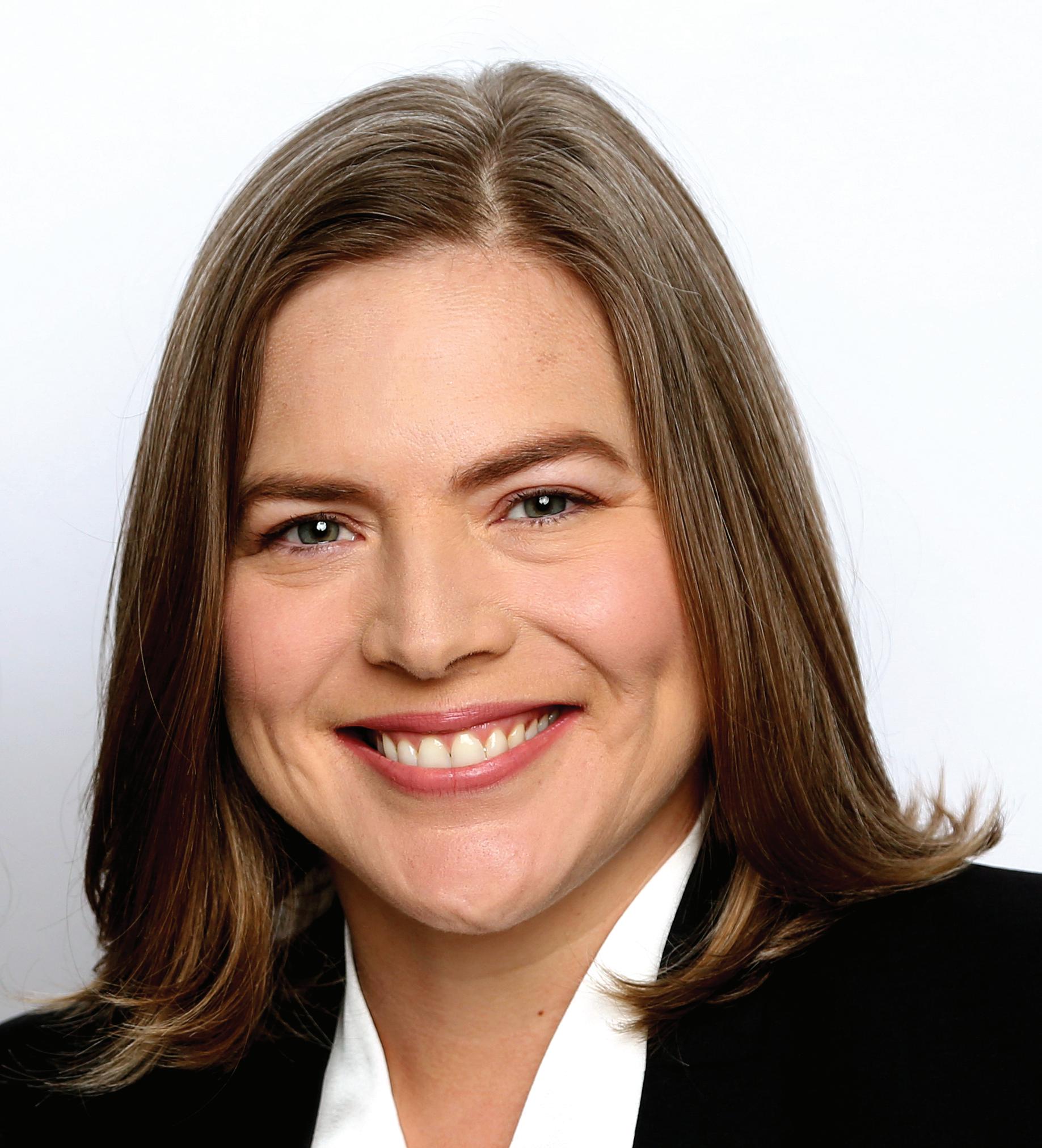
What were your company’s major challenges caused directly by the pandemic, and how did you handle them?
Norheim: Our major challenges matched those of many other companies, including supply chain hurdles, remote workforce management, and obstacles caused by operating during the pandemic since we were classified as an essential business. But our workforce rallied. We persevered and overcame many obstacles in our path, even though it was difficult.
Do these problems continue to be “pain points” for American Crane and other manufacturers as well? Will the industry get back to “normal”?
Norheim: The pandemic was a painful experience to endure, but it also presented us an opportunity to grow and innovate our skills to meet the challenges before us. For example, we implemented digital transformations that were at least three times faster when compared to what we would normally accomplish in a year, giving us more tools to better meet our customers’ needs.
Leveraging several technology partners as well as internal innovation teams has helped us remain
focused on the future, while appreciating the “now.” That, coupled with our amazing people and culture, remains integral to our success. I want to build upon what we have learned and the advancements we have made. Our growth as a company has prepared us to not just survive the future but also to thrive among whatever challenges come our way.
What problem has been most difficult for manufacturers to overcome in a timely manner due to the pandemic, and why?
Norheim: As businesses and individuals, we are collectively brought out of our comfort zone, but to remain at the top of our game, we must expand our comfort zone. This leads to an incredible speed of innovation and creation of organizational and digital transformation.
A new business landscape was unfolding before COVID-19, with a 10X speed increase on digital advancements affecting industry. We’re in a period of time where you either disrupt or you get disrupted. This, coupled with workforce issues, means companies need to double down on developing culture and planning their digital transformation road map. Our company’s culture — our secret weapon — gave us the strength to endure, adapt, manage, and leverage disruptive change.
What is the most surprising lesson you’ve learned as the leader of a U.S. manufacturing company to help your company stay competitive?
Norheim: The most surprising lesson I learned is that many of us do not have a good worklife balance — or, as I like to say, a work-life integration. The pandemic shined a light on this and provided an opportunity for us to become more aware of needing self-care and boundaries, myself included.
You’re no good to your people or your company if you’re burnt out. We must encourage our people to take care of themselves and practice disconnecting. That means taking time away from work and devices to recharge, refresh, refocus, and rejuvenate. This often provides new perspectives, cre-
ative boosts, and enhanced clarity that improves productivity and other key measurable results.
The future of manufacturing includes AI and other new and evolving technologies. What tech innovations are you most excited about and why?
Norheim: As manufacturing companies, our need for embracing and leveraging technology is evident. I think the very best companies, the ones most successful at implementing and leveraging technologies of the future, will do so because they value technology and humanity. It’s not “either/or” but the merging of the two that will grant us a prosperous future.
I’m most excited about how we’re embracing technology versus which one we’re focused on. At American Crane we created an Innovation Lab in 2019 to give us the framework to stay on top of not just the emerging technologies of today, but also those of tomorrow. I believe it’s very important to experiment with new technologies, remain ahead of the curve, and allow space for your team to learn and find ROI.
Fewer than one in three manufacturing professionals today are women, despite representing nearly half of the overall U.S. workforce. Why is that, and what can be done to get more women professionals into the industry?
Norheim: Our biggest hurdle is that many women are just not aware of the opportunities available in manufacturing. There is significant overlap between what women want in careers and the attributes of careers in manufacturing. That’s why we need to educate others about the opportunities and benefits of a manufacturing career.
That’s why I invite women already in manufacturing to be role models to inspire the next generation of women (and men) to enter our industry. I encourage them to promote their pride and passion for manufacturing by sharing why they love their jobs, their companies, and this industry.
In what ways can women proactively help solve critical problems that could negatively
impact the future of U.S. manufacturing?
Norheim: Creating an inclusive and diverse workforce brings different perspectives together. This builds an environment fostering the appreciation of all members’ creative diversity through trust, respect, and openness.
Leveraging our company’s creative diversity also can be a competitive advantage by its ability to improve management, communication, and teamwork throughout our organization and to increase our company’s efficiency. All of these things help create cognitive diversity to solve problems more effectively. The greater perspective gained on an issue, the better the solutions will be. In the end, employees will be more engaged and eager to come to work as a result of the welcoming environment, and productivity and overall profitability will go up.
How can American Crane and other manufacturing companies best prepare for the next national or global crisis?
Norheim: In the recent sea of chaos, we all have been touched by tsunami-like waves in our personal and professional lives. And while often overwhelming, among the waves of change we find our direction. We cannot direct the wind, but we can raise our sails and adjust as needed.
It has never been more important to communicate with your people in order to adjust your [operational strategies] and keep your team engaged and productive. Leveraging the growth and skills you have obtained from this crisis helps maintain agility and responsiveness to manage the coming crests and troughs. Rough seas make stronger sailors. Tough times build greater people. And storms don’t last forever.
THE ASSIGNMENT
Area Development’s staff editor, Lisa Bastian, recently posed some question to American Crane’s CEO & President, Karen Norheim, about how overcoming pandemic challenges has strengthened the company for what lies ahead, as well as opportunities for women in manufacturing.
New Report Shows NYC ECONOMY GOING STRONG
A new report on New York City’s economy shows that the city still lives up to its long-standing reputation as the global business capital.
The New York City Economic Snapshot, a report released for the first time in October by New York City Economic Development Corporation (NYCEDC), aggregates and highlights data to measure the strength of the city’s economy.
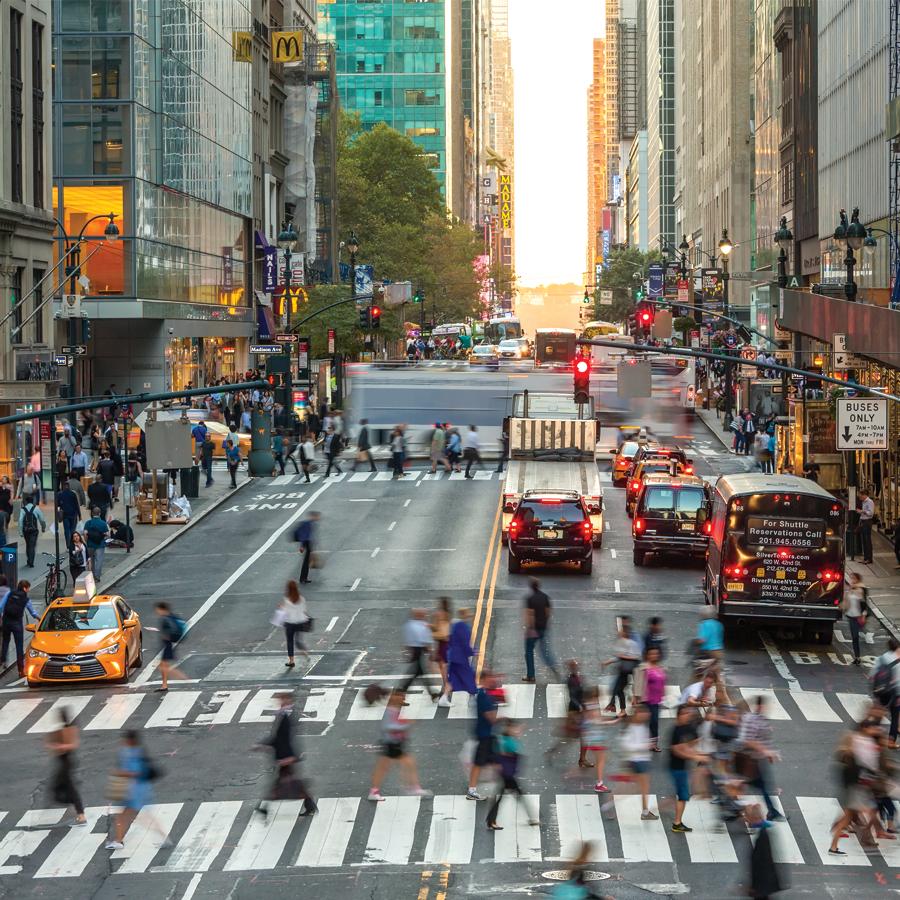
NYC is the largest city in the country, and with a gross metropolitan product (GMP) of $1.66 trillion, it produces more value than the entire state of Texas. The city ranks as the #1 U.S. destination for foreign direct investment (FDI) and #4 globally for total FDI inflows since 2014. It’s also the #2 global startup ecosystem, now valued at $371 billion. And, with the nation’s biggest consumer base at over 20 million, companies in NYC can test their ideas and products at scale — with a diverse audience that represents the world.
At 20M+, the NYC consumer base represents the world.
“The Snapshot helps inform NYCEDC’s work not just in leading the city’s recovery from COVID, but in building a more vibrant and inclusive economy for the future,” said Andrew Kimball, NYCEDC President & CEO, in a note introducing the October report.
According to the report, one in 10 businesses in the city have opened in the last year alone, with the NYC metro area adding 450,000 jobs in that time — almost 200,000 more than runners-up Los Angeles and Dallas.
The report goes on to present metrics for tourism, transit, office and retail occupancy, and more — all data points that businesses can use to get a clear picture of the city’s economy.
REAFFIRMING A GLOBAL BUSINESS CAPITAL
While the Snapshot gives a monthly picture of recent trends, these trends only reaffirm New York City’s long-standing status as a premier business destination.
Visit edc.nyc/Business to contact the team at NYCEDC and get started today.
To read, and subscribe to, the NYC Economic Snapshot, Visit edc.nyc/Insights
When it comes to talent, the city has the nation’s largest and most skilled labor force at over four million, with 2.3 million holding a bachelor’s degree or above — more than Los Angeles; San Francisco; Washington, D.C.; Philadelphia; and Boston combined.
Companies are already taking notice. In 2022, Suntory, a global beverage industry leader, celebrated the opening of its New York City office, while monday.com, a work-operating system, opened its new North American headquarters in the city — with Mayor Eric Adams cutting the ribbon. Funders are seizing the opportunity too — within the past year, leading international tech VCs including Index Ventures, Sequoia Capital, and Andreessen Horowitz have all opened offices in NYC.
A ONE-STOP SHOP FOR BUSINESSES
T he Business Development team at NYCEDC has the connections and experience to help companies succeed in the diverse NYC business ecosystem.
The team can guide companies through every step of the expansion or relocation process, offering solutions and guidance on site selection support, access to talent and workforce development programs, financial incentives analysis, city and state agency navigation, connections to industry associations and local chambers of commerce, and more.
The center of industry. The center of everything. NYC: A global innovation hub

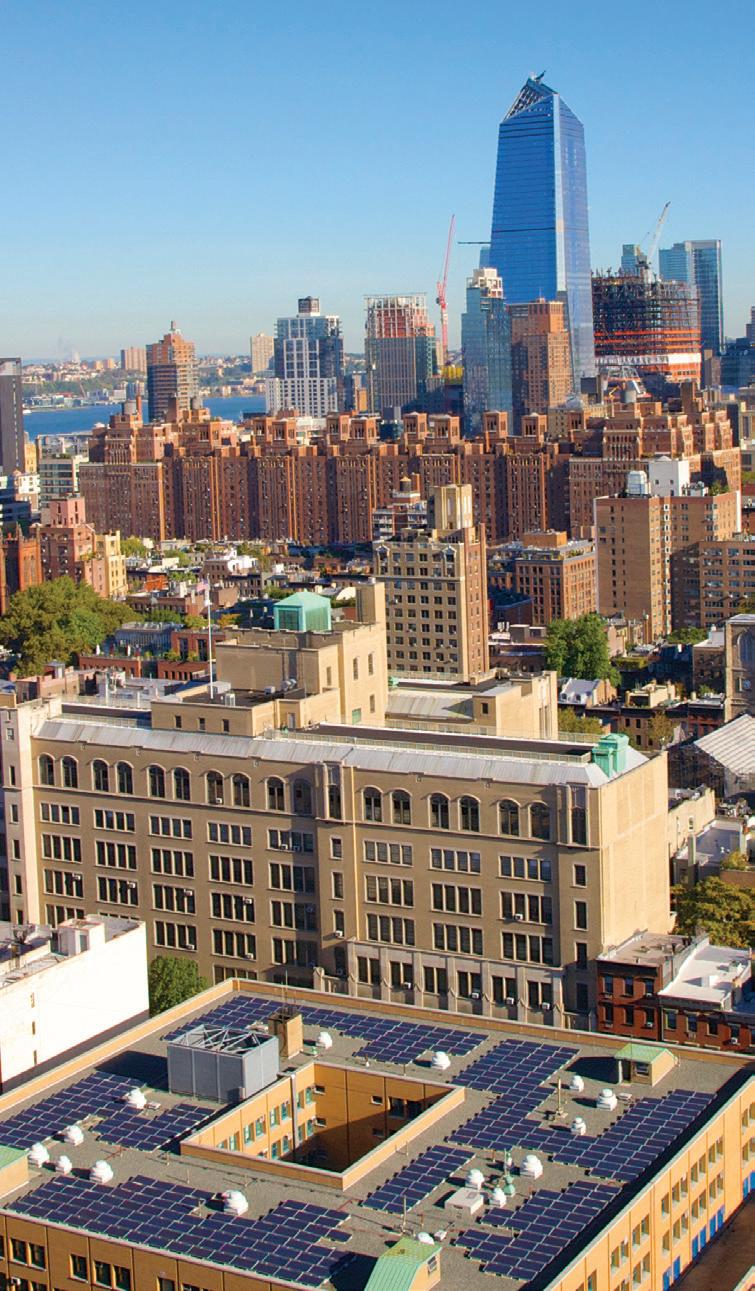
With unmatched talent, diverse funding sources, and a robust workforce and opportunity pipeline, NYC is a thriving business ecosystem and a powerhouse of equitable innovation—in industries from offshore wind to tech to life sciences and beyond.

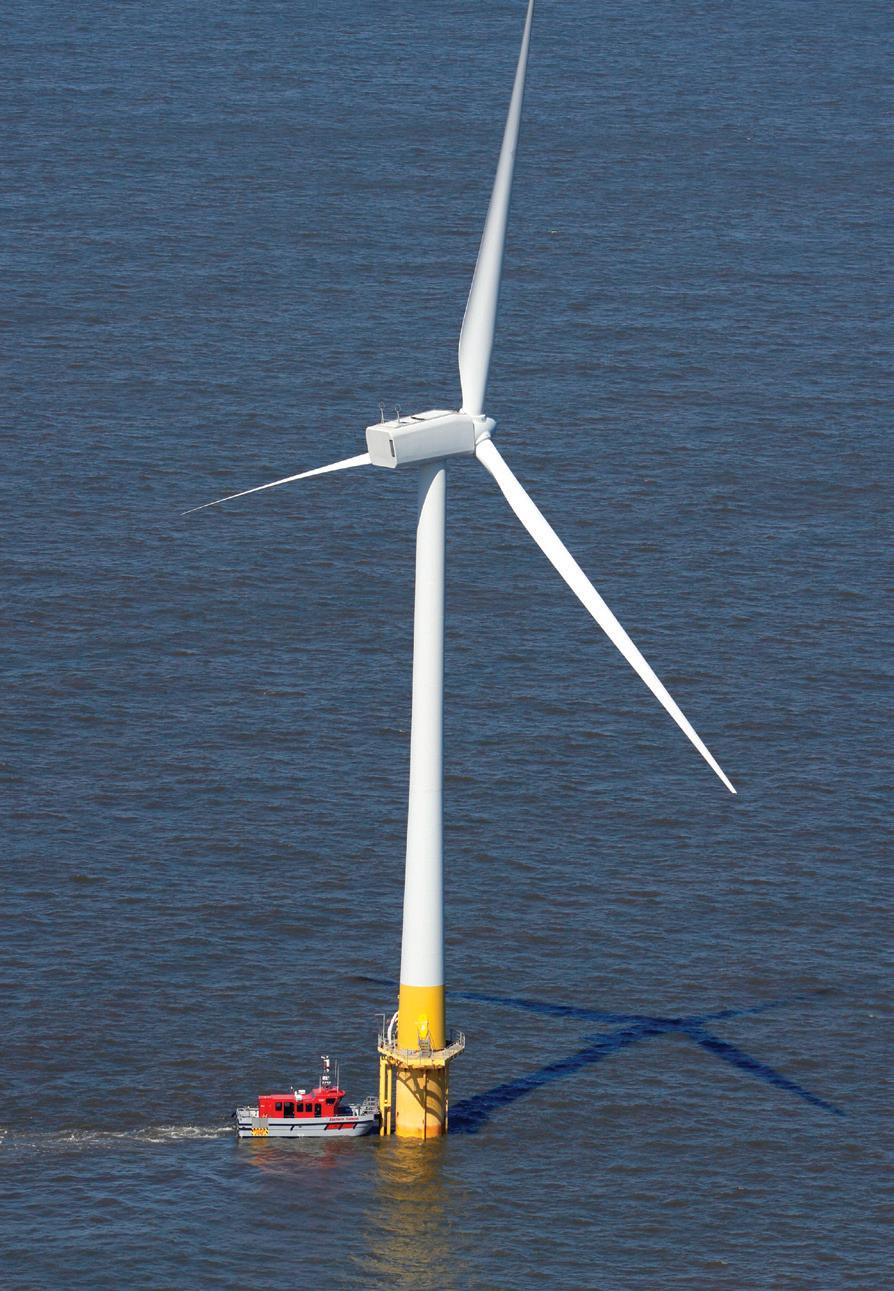
Bring your business to NYC, with NYCEDC by your side—helping you make connections, forge strategic partnerships, and hit the ground running.
Visit edc.nyc/business.
Inflation Reduction Act Promotes the Nation’s “Energy Security”
The clock is ticking for manufacturers to get maximum tax benefits on new projects under the Inflation Reduction Act.
By Cory Wendt, Principal, Baker TillyThe Inflation Reduction Act of 2022 (IRA) includes the largest legislative energy incentive in U.S. history, promoting the transition to efficient use of renewable energy. It includes over 70 separate investment, production, or excise tax credits, most of which are effective through 2032. However, manufacturers and other entities that are eligible for the tax incentives can preserve maximum benefits now if they can begin construction on qualified projects leading up to the end of 2022.

Background
The IRA’s “energy security” subtitle includes provisions providing tax credits for the production and/or consumption of clean energy, carbon emissions reduction, and electric vehicle purchases as part of the effort to promote domestic energy security and manufacturing. Manufacturers could get the tax benefit related to an in-progress or planned project at an existing facility or if they produce renewable energy equipment compo
nents. Almost any entity with environmental, social, and governance (ESG) initiatives will likely benefit from use of IRA tax incentives.
The IRA provides for a direct offset to federal tax liability in the form of a tax credit. Eligible entities (including manufacturers) can use the tax credit against their own tax liability. If a company doesn’t have tax liability or taxable income, they can transfer/sell the credit to another taxpayer. Tax–exempt entities (like state and local governments, the Tennessee Valley Authority, tribal governments, and colleges and universities) can receive a direct payment from the IRS. This credit will be tied to costs related to eligible projects placed into service after December 31, 2022.
Types of Tax Credits
There are three types of tax credits that will help manufacturers and other entities decrease their capital cost for projects that promote energy conservation, whether that relates to storage of energy, a reduction of net new energy/emissions, or the creation of renewable energy at their facility:
• • The investment tax credit (ITC) is a percentage of eligible energy capital cost for new construction related to new property that captures or generates different types of renewable energy. The credit will vary in amount based on energy property type, project location, and American content. It likely will be the most accessed credit, as the credit is earned when the project is placed in service.
• • The production tax credit (PTC), which can be for a variety of alternative fuels (solar, wind, biomass, geothermal, hydropower, to name some), is paid based on unit production over 10 years.
• • The excise tax credit (ETC) offers benefit per gal-
GREATER PHOENIX
A game changer for business growth and development
Companies that relocate here are scoring big wins with reliable power, diverse water resources and a robust dark fiber network. Add SRP to your lineup and reap the rewards of a true team player.
Learn more at PowerToGrowPhx.com
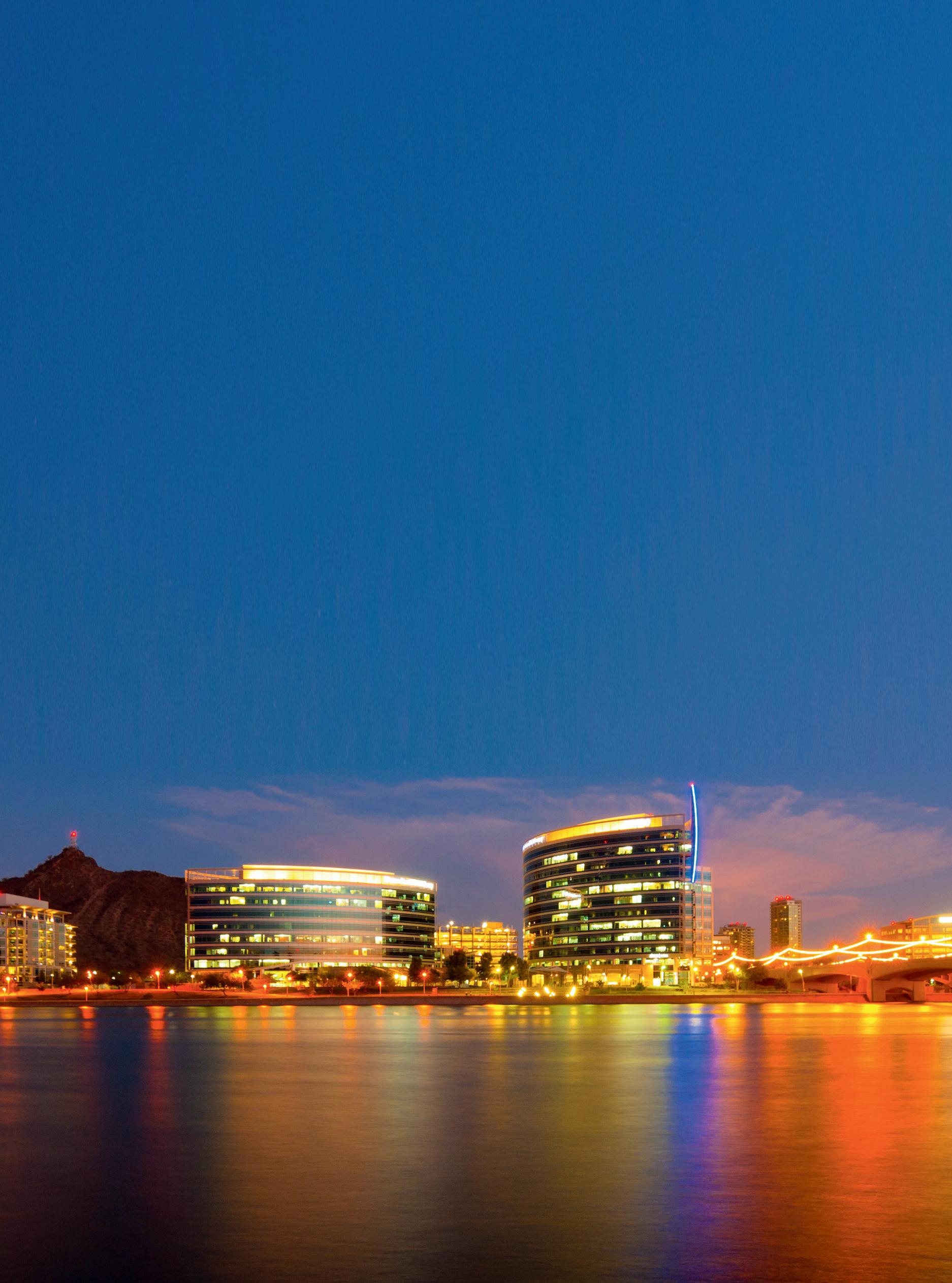
lon for any biodiesel mixture, alternative fuel, alternative fuel mixture, sustainable aviation fuel sold or used by a company.
Both the ITC and PTC have a base credit and a 5X bonus criteria value for projects meeting prevailing wage and apprenticeship criteria. The IRA will give additional bonus credits to those who can produce or use domestic content in the energy projects.
Additional bonus credits will be given to projects locating in a named “Energy Community.” These Energy Communities are specific census tracts that are defined and targeted areas where prior economies were tied to coal, oil, and/or natural gas heavy industry sites. These targeted areas are meant to drive investment in new energy production infrastructure.
For certain wind and solar projects, an additional credit yet is additive to above credits for projects located in Environmental Justice areas.
The significance of the legislation has been slow to resonate among the primary beneficiaries of the law, perhaps because the energy credits are a new entitlement buried as a subtitle in a much larger law. A manufacturer may be surprised to hear that a 30 percent — even now up to 50 percent — benefit of a $20 million project may be eligible for an ITC.
In addition to tax credits for energy projects, there are also more than 20 ITC and PTC tax credit types for manufacturers who invest in their U.S. facility production lines to make energy equipment (or will make certain components going into that energy equipment) that will go into energy projects.
The spirit of the IRA tax incentives is to help American companies maximize existing energy resources using a range of new, advanced, efficient technologies. The incentives encourage companies undertaking a major building project to ask, “Will it really cost any more to build a property that will be more efficient in the long-term?”
Wastewater Projects
If a company is attempting to use less energy or reduce its carbon footprint, an IRA tax credit can help. A company may not even have “renewable energy projects” as a priority, but if they need to install a wastewater treatment plant, that could qualify for the credit.
The food and beverage industry, for example, may not use a lot of energy compared to others in the manufacturing sector. But food and beverage companies do create a byproduct water that needs to be treated. Because that wastewater is rich in nutrients, it can also generate energy.
That wastewater is often the biggest point of interaction with the municipality because it’s discharging to the municipality. Companies are always considering whether they pretreat wastewater or whether they discharge and let the municipality treat it. Municipalities generally charge a rate per gallon per unit of strength that is applied to that discharge. If they needed to expand their wastewater treatment facility, the cost of that expansion
would generally be passed on to industry in the form of higher rates.
Because of the IRA, municipalities now have a tax incentive to expand their wastewater treatment facilities without increasing their wastewater treatment rates as much. They can use this expansion as an incentive to retain an expanding local company or to draw new industries to the area.
The IRA tax credits also may influence the site selection of non-American companies looking to relocate to expand their market share.
The Clock Is Ticking
The most important thing for manufacturers, and other qualified entities, is taking action soon to preserve the tax credit.
In order to preserve the tax credit, without needing to meet any prevailing wage and apprenticeship requirements (and as a result securing the 5X bonus criteria), a project must begin construction before 60 days after the IRS issues guidance on those requirements. That guidance has not been issued but is likely to be issued soon.
Prior IRS guidance has established two ways to meet “begin construction” — physical work of a significant nature or meeting the 5 percent safe harbor provision. Either test can allow you flexibility if you are not yet permitted to get dirt moving on your site.
How Do I Take Advantage of the IRA’s New or Expanded Credits?
• Are you considering a plant expansion where you are changing the use, consumption, or storage of energy at your facility?
• Do you manufacture components qualifying as renewable or which have high domestic content?
• Does your company have an ESG strategy driving future capital investments?
• Are you planning or currently executing a project to enhance heat or carbon capture, utilize wind, solar or hydropower, or harness biogas to make heat, electricity, or a transportation fuel?
If you can answer “yes” to any of the above, here is what your business needs to know now:
• Approximately 70 different energy property types are eligible for their own federal tax credit.
• The federal tax credits can be used by an owner of the project or be sold to another taxpayer.
• To preserve and maximize the tax credit value percentage, you can take early steps to meet safe harbor.
• Most credits are good through 2032 — the longest ever U.S. “energy policy” timeframe.
• Significant enhancements have been made to the USDA and DOE loan programs (some for direct, low-interest loan funding).
• If structured optimally and timed correctly, a credit could be worth 50+ percent of total qualifying costs. n
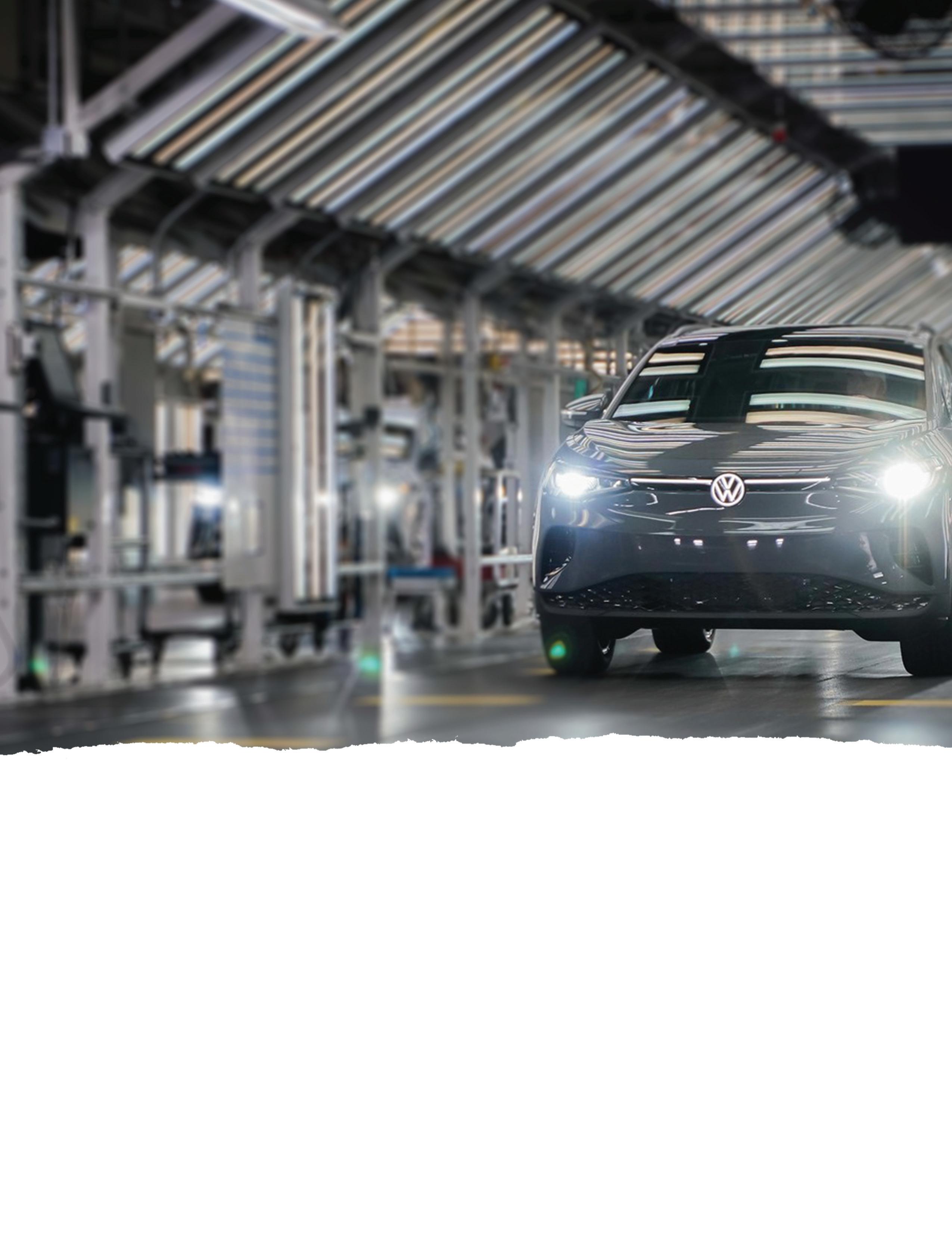
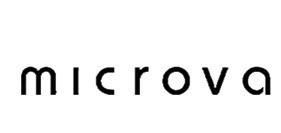

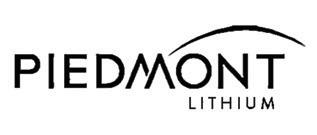

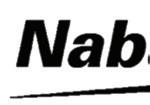
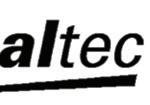

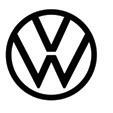
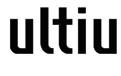

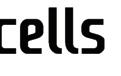
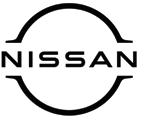
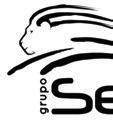
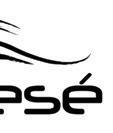
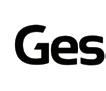

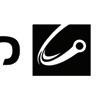
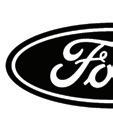
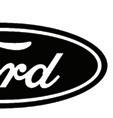
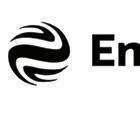
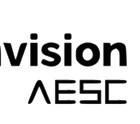

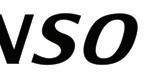
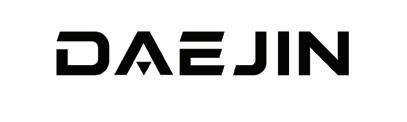

ESG: The New Metrics in Construction and Real Estate
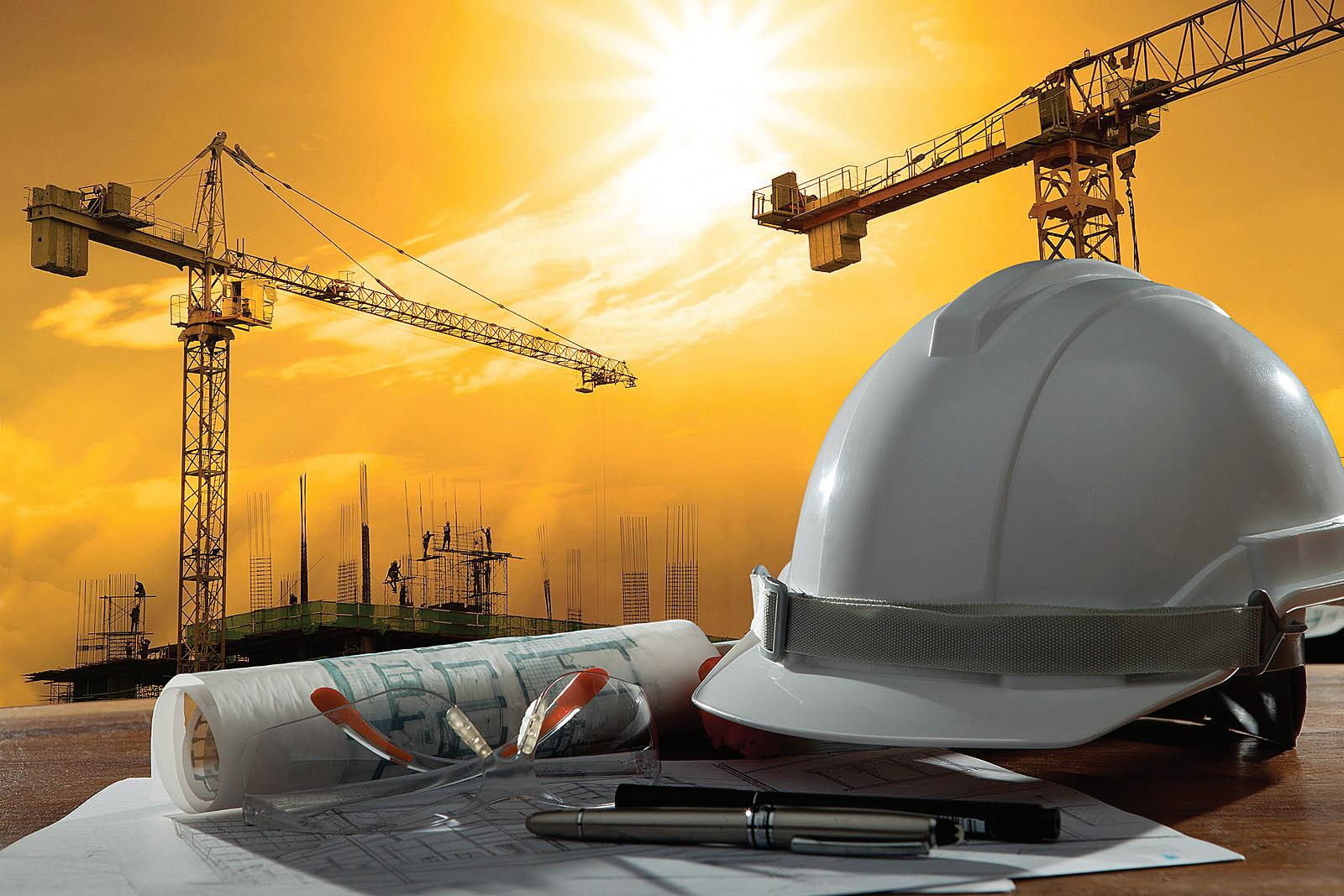
Key environmental, social, and governance (ESG) considerations include protecting the environment/reducing energy use, making positive contributions to the community, adopting inclusive workplace policies, and maintaining high standards of governance.
By Michelle Palys, Vice President of Performance Excellence and ESG; and Brian Gallagher, Vice President Corporate Development; GraycorWith engineering and construction making up more than 11 percent of global domestic product, there is a growing focus on how the building industry conducts business. What started as a movement among institutional investors and their financial partners has expanded across almost all sectors, and environmental, social, and governance (ESG) considerations now impact many real estate decisions and capital project planning. Consumer behavior is partly responsible for the change. So is the fact that investors and lenders increasingly view a company’s ESG policies as indicative of how that company is positioning itself for success in the marketplace.
Regulatory decisions further heighten the importance of ESG. A change that will soon make itself felt is the Securities and Exchange Commission (SEC) release of ESG disclosure rules for Scope 3 emissions. (The Environmental Protection Agency defines Scope 3 emissions1 as “the result of activities from assets not owned or controlled by the reporting organization, but that the organization indirectly impacts in its value chain.”) Combined, these factors mean one thing for developers and corporations undertaking capital
Governance
Social
projects: not only will they have to institute, track, and report their own ESG efforts, but they will have to include those of their contractors and other project partners.
What are the New Metrics?
Requiring all business partners to demonstrate responsible practices for environmental, social, and governance concerns is a broad request. To achieve success, the entire project team will have to break their processes down into
manageable pieces, identifying metrics and outlining specific rules for meeting, measuring, and reporting those metrics. Fortunately, some contractors and other stakeholders are poised to meet them more than halfway.
• • Environmental/Sustainability — Sustainable building has been an important topic in the construction industry for years. Great strides have been made in identifying life-
for free site information, visit us online at
cycle costs/benefits and balancing competing considerations across the lifetime of a structure. Many contractors are now well-versed in the kind of early planning that makes these assessments and decisions possible. Thorough pre-construction planning and sourcing phases are the key, and these phases should prioritize:
• Sustainable site planning
• Safeguarding water and water efficiency
• Energy efficiency and renewable energy, with a focus on:
• Conducting a comprehensive energy analysis
• Enhancing a building’s environmental management system (EMS)
• Installing sensor systems to monitor and adjust environmental conditions
• Installing demand-based fresh air distribution
• Installing ventilation heat recovery systems
• Retrofitting indoor and outdoor lighting systems using LED or other technology
• Implementing solar solutions
• Pursuing LEED certification
• Conservation of materials and resources
• Indoor environmental quality
contractors who have funding programs), supporting charitable 501(c)(3) nonprofit organizations that align with the team’s values. Often this means providing basic needs to area residents, such as food, shelter, education, and healthcare, as well as civic, environmental, and cultural programs. Along with financial assistance, volunteer involvement on the part of project stakeholders is also desirable.
Diversity, equity, and inclusion (DEI) is another pillar of social responsibility. Advancing DEI should begin with team culture and employee development, then extend to trade partners and communities. Because there are many factors for achieving success with DEI efforts, contractors and other partners should demonstrate that they have set up a company-wide council, with council members from across different departments. The goal should be to not only increase the participation of women and minorities, but also to make changes in operations and communications to sustain diversity. This means identifying and removing biases in recruiting, hiring, and promotion as well as educating people already within the organization to make them inclusive leaders and individual contributors.
Supplier diversity is another aspect of strengthening the social fabric. Working with and supporting minorityowned, women-owned, and small businesses contributes to the economic growth and expansion of communities. It is a good idea for owners and contractors to have established supplier diversity programs in place to support this goal.
•
• Social — Responsible social behavior begins with how a company, organization, or team treats its own employees. For the construction industry, safety and health are fundamental considerations. In addition to workplace safety programs, the individual as well as collective health and safety of employees should be an area of focus. Wellness programs that incentivize physical activity with reduction in insurance premiums should be instituted to proactively support employees’ health.
Promotion of healthful foods at events and provision for standing desks and ergonomic furniture in offices are other options. Benefit packages should include healthcare and retirement plans, family and medical leave, and a budget for training and education. The good news, when it comes to starting or maintaining such programs, is that they enable better productivity, ensure quality, and control insurance costs, improving employee retention and advancing employers’ competitive position within the industry.
To comply with the principles of ESG, teams are also expected to enhance the quality of life of the people in surrounding communities. A direct way to accomplish this is to establish a funding program (or partner with
The International Living Future Institute (ILFI), through their Just Program, encourages organizations to disclose employee-related indicators to measure social performance. The good news is that most organizations have progress on one or more of the institute’s indicators. Disclosing program results can demonstrate a firm’s formal commitment to social well-being.
Indicators include:
Employee benefits
Healthcare
Retirement provision
Family/medical leave
Training and education
Stewardship
Local communities
Charitable giving
Diversity, equity, and inclusion
Gender/ethnic diversity
Engagement
for Successful Site Selection, set
Sights on Georgia Ports
• Full-time employment • Pay-scale equity
• Purchasing and supply chain • Equitable purchasing
• • Governance — With societal and environmental concerns making daily headlines, the “governance” aspect of ESG can get overshadowed. However, to understand why the “G” in “ESG” is given equal weight, one has only to think of headlines that have been generated as a result of poor governance — i.e., rules, procedures, and decisionmaking hierarchies that have allowed company representatives to make missteps that ended up reflecting poorly on their organizations. It becomes apparent that the governing bodies of all companies involved in a given project should meet benchmarks for good governance, demonstrate strong management capabilities, and effectively manage risk.
Furthermore, all business development strategies and business practices should support the team’s core values, which, in turn, should emphasize honesty and integrity, commitment and follow-through, and full transparency (a “nosurprises” management style). Team interactions should be based on a thorough understanding of customer and project needs and on long-term continuity in client and subcontractor relationships. A commitment to innovation and investment in new technology, along with a system of subcontractor prequalification, further contributes to solid project outcomes.
If you want to position your business in the most desirable area of the country right now, the Savannah corridor, take the easy route: use the Georgia Ports’ Site Selection Tool. This robust online resource allows you to easily compare land and building availability, work force readiness, plus, important utility and transportation options.
Real-time data. Really fast.
Go to GAPorts.com/SiteSelection and set your sights on success.
To assure that all participants in a construction project are meeting the demands of ESG, the team should pursue mastery of logistics and coordination. Implementing ESG should involve inventorying current efforts, performing a GAP analysis, developing a system of metrics and tracking, and informing and educating internal stakeholders.
Taking all of its components together, ESG’s requirements for owners and their partners to not only protect the environment and reduce energy use, but make positive contributions to their communities, adopt inclusive policies, and maintain high standards of governance require a new level of planning from the top down. Once plans are in place, tracking and reporting — underpinned by transparent and comprehensive team-wide communications — is the recipe for success. n 1 https://www.epa.gov/climateleadership/scope-3-inventory-guidance
Fixing the Supply Chain with AI and Robotics
Automation, industrial robots, and other technology solutions have allowed manufacturers to shorten their supply chains, while also making them more efficient and reducing labor costs.

One of the many lessons learned from the COVID-19 pandemic was just how fragile the global supply chain is. For decades, much energy has been spent streamlining the supply chain, building efficiencies, and finding low-cost options — but the result has been an increased vulnerability to shutdowns, labor shortages, and other disruptions tied not just to the pandemic but also to the global economy and the war in Ukraine.
“With COVID, the level of volatility in supply chains rose to a level that was unprecedented and caught a lot of people by surprise — and not in a very good position,” says Claudio Knizek, global leader of Advanced Manufacturing and Mobility at EY-Parthenon. “There’s always been interest and appetite to understand and predict the supply chain, but now more than ever many companies are looking for technologies and software to predict supply chain issues before they happen.”
Technology solutions range from an ever-increasing use of industrial robots to tapping into more powerful uses of data, artificial intelligence, and machine learning to gain effective insights. Organizations are looking for new ways to run their manufacturing and distribution operations with fewer people, while making more prescient decisions that can help avert shortages.
Adding Automation to the Supply Chain
The digital technology conglomerate ABB surveyed hundreds of American
and European business executives on topics including supply chain plans. Just under half said they plan to use robotics and automation to build supply chain resiliency.1
A key aim, of course, is increased efficiency, and one result of relying a bit less on human efforts is added flexibility when making location decisions. A big factor in the recent supply chain turmoil has been the increasingly global reach of operations. If finding cheaper labor was a big driver behind overseas operations, automation can make it more feasible to locate operations closer to home.
Indeed, the ABB survey found that more than a third of executives were making plans to bring production back to the U.S., and a third said they’d look at nearshore loca-
tions for new operations. In all, the survey found that 70 percent of companies are considering reshoring or nearshoring projects.
“There is an increased appetite to bring manufacturing and supply chains closer to end markets, closer to the U.S.,” Knizek says. “There are benefits to having sourcing closer to the U.S., Mexico, or South America.”
To be sure, costs remain lower in China and Southeast Asia, he says, and China has noteworthy supplier infrastructure advantages. “But increasingly, firms are looking to find ways to move production back to U.S. but need to lower costs and make the return on investment work.”
“Around 2015 to 2016, technology kind of finally caught up to a certain extent with promises it was making,” says Jason Bergstrom, Deloitte’s Smart Factory GoTo-Market leader and a partner in the firm’s manufacturing practice. Manufacturing, he says, has really started to shift from a human-centered operation to a process that’s increasingly automated. “We’ve seen technology really catch up and advance at an exponential rate and have made that shift to what we now think of as a hybrid — humans and machines operating together.”
The Future of Automation
Automation is getting better and cheaper all the time, on the production line and in the warehouse, according to Bergstrom. “The level of the bar between what should be done by a human and what can be done by a machine continues to fall on a cost basis and rise on a capability basis,” he says. “What made sense to automate in 2015 looks very different today because of the continually falling costs to automate combined with the fact that you can now do so much more as you transition from weak automation to strong automation.”
Less than a decade ago, he says, “you’d see just the automating of transactional, discrete tasks that required really no logic,” he explains. “A series of steps…a human used to do them, now a machine does them — easy to codify, with almost no logic.”
To use an automotive manufacturing example, imagine having a piece of plastic move into a fender press, and rather than have a human run that press, a machine conveys the plastic through and sends a fender out the other side. That was typical automation circa 2015, he says.
“Fast forward to today for that same operation,” Bergstrom continues. “It’s still automated, but with more advanced learning capabilities and vision capabilities. You take that same piece of plastic, use vision systems to do quality scans in an automated way, and kick out components and raw materials that don’t meet specs to eliminate quality issues downstream.”
Plainsight Corp., based in San Francisco, is one of many companies offering this kind of AI-powered computer vision capabilities in manufacturing. It promises such benefits as process automation and risk reduction, safety and productivity monitoring, precision counting along the assembly line, automated product and packaging inspections, quality monitoring, and defect detection.
“Currently, clever machines are used to improve and automate production processes, influencing quicker decision-making, better safety precautions, and highquality improvements,” according to a white paper produced by Heriot-Watt University in Scotland.2 “With every manufacturer’s goal being to reduce risks and improve production efficiency, the role of artificial intelligence in this sector will continue to intensify.”
It’s no longer simple automation with robots assembling widgets, Knizek says. “You have intelligent robots, ‘cobots’ (collaborative robots) able to work side-by-side more effectively. You’re improving processes through more use of Big Data, predictive maintenance to reduce downtimes, or finding ways to anticipate process disruptions,” he says. “Firms able to leverage all of these technologies concurrently will be best positioned.”
“In the supply chain, AI can be used as a virtual assistant for robotic process automation and predictive analytics,” according to Ryan Prindiville, partner at the technology and consulting firm Armanino. “In today’s digitally connected world, AI is not just a nice-to-have; it’s an imperative to stay competitive. According to Gartner, supply chain organizations expect the level of machine automation in their supply chain processes to double in the next five years.”3
Better Insights into the Supply Chain
Aside from employing more physical automation on the factory floor and at distribution centers, technology can enable a healthier supply chain by providing more visibility into operations and potential problems. A couple of key concepts, says Knizek, are supply chain control tower and digital twin solutions.
“Essentially you are trying to monitor the full end-toend supply chain in an integrated and holistic manner, and trying to anticipate shortages before they occur,” he says. “This field has advanced significantly. You have firms that are still susceptible to issues in transportation and shortages of labor, but they are better able to get a handle on it.”
A supply chain control tower is essentially a dashboard of data and metrics. But to really provide the kind of visibility and insights that organizations need, it can’t just be a display of numbers. It must tap into advanced technologies such as AI with machine learning.
Extending control tower functionality with AI and machine learning can cut down on manual processes and offer the most actionable information. “Companies further along in this journey really use these tools on a dayto-day basis, and can anticipate problems weeks before they happen,” Knizek says.
Similarly, a supply chain digital twin is basically a simulation model of the actual supply chain. It brings in real-time data to help predict how the supply chain will behave and what unusual situations lie around the corner. It’s good for spotting bottlenecks before they become a problem, optimizing inventory, planning transportation, and testing any changes that might be
planned for the supply chain.
The Impact on Location
The supply chain challenges of recent years have put the spotlight on the downsides of sourcing goods and materials from all over the planet. Onshoring and nearshoring are great remedies to some of those problems, but then you’re faced with costlier labor and the worker shortages happening closer to home. Automation can come to the rescue, Knizek says.
“It’s very hard for U.S. firms that have production overseas to bring production to the U.S. without putting in any kind of automation technology or artificial intelligence and machine learning that improves your efficiency,” he says. “There are still significant labor costs, and with inflation the way it is in the U.S., labor rates will go up. People will pay attention to tools they can use to lower the costs, to make them more in line with costs overseas.”
That doesn’t mean you have to match costs exactly when moving back closer to home, he adds. “The U.S. will never be able to compare with places like Vietnam and Indonesia,” he says. But if through automation you can get the total costs close enough, some of the benefits of producing goods closer to home start to win the day.
Beyond mitigating potential supply chain disruptions, those benefits include the elimination of international shipping costs, according to Saman Farid, CEO of Formic Technologies, speaking on a Thomas Industry Podcast.4 “We think that we can match, if not exceed, the kind of productivity of a Chinese factory here in the U.S. through technological innovation, and that innovation is in the form of drastically better automation, used at a much greater scale.”
Increasing automation may mean fewer humans, but it doesn’t mean no humans, Bergstrom points out. Deloitte has clients visit its “Smart Factory” in Wichita, Kansas, which is a showcase of production capabilities maximizing such technologies as AI, machine learning,
Big Data, robotics, and vision solutions. “We intentionally talk to them about the machine-human interface that will never go away. The lion’s share of everything manufactured will always have a human component.”
That said, it requires a different labor mix to run such facilities. “Instead of a low-cost hourly person, you now have a different mix of people — developer, coder, maintenance. Although you are replacing an operation with an automation step, you have support roles that come into play,” he says.
“Right now, there’s a real need to hire people with more advanced skills such as mechatronics — you can’t hire enough of these folks,” Knizek says. “There’s a tremendous need for data scientists, and those are even harder to come by. There’s a real challenge right now in the manufacturing space to really get enough people with these skills.”
Bergstrom notes that in the past, manufacturing that wasn’t offshored was often set up in rural parts of North America, to achieve lower operating costs. That isn’t as easy to do with a more automated facility. “You’re actually seeing manufacturers get closer to urban centers than in the past, for that very reason,” he says. “Through automation and what we’re doing, it requires capabilities you’re not going to find in rural environments.”
“That drives all kinds of second-order questions,” Knizek says. “Where do you recruit? Do you set up your own training program? Do you need to raise wages to attract these people?”
Workforce development is always a vital topic in location decisions, but this reality is adding new twists, he says. “Any government looking to really position itself as a manufacturing hub with advanced manufacturing needs to be investing in all these topics.” n
1 https://www.globenewswire.com/en/news-release/2022/06/28/2470499/0/en/ABB-surveyfinds-70-of-US-businesses-looking-to-bring-production-closer-to-home-robotic-automationand-workforce-upskilling-essential-to-return-of-operations.html
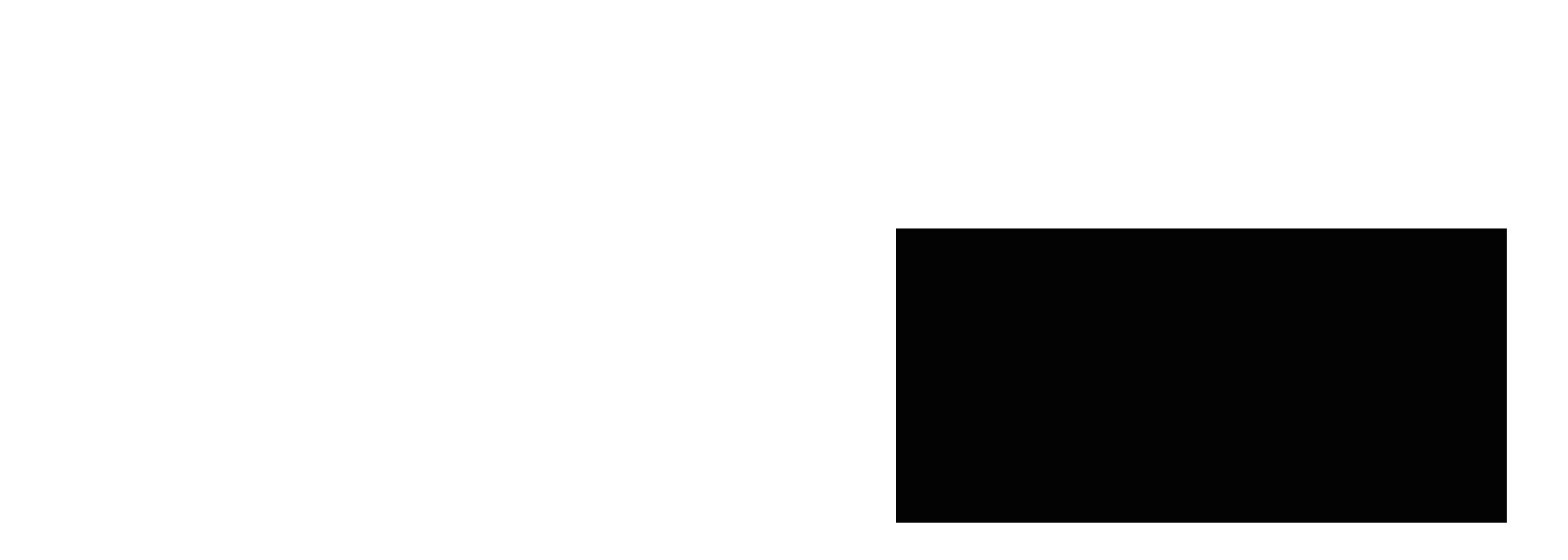
2 hhttps://www.hw.ac.uk/uk/study/undergraduate/subject/computer-science.htm 3 https://www.gartner.com/smarterwithgartner/gartner-predicts-the-future-of-supplychain-technology
4 https://www.thomasnet.com/insights/how-automation-can-propel-manufacturinginnovation-in-the-u-s
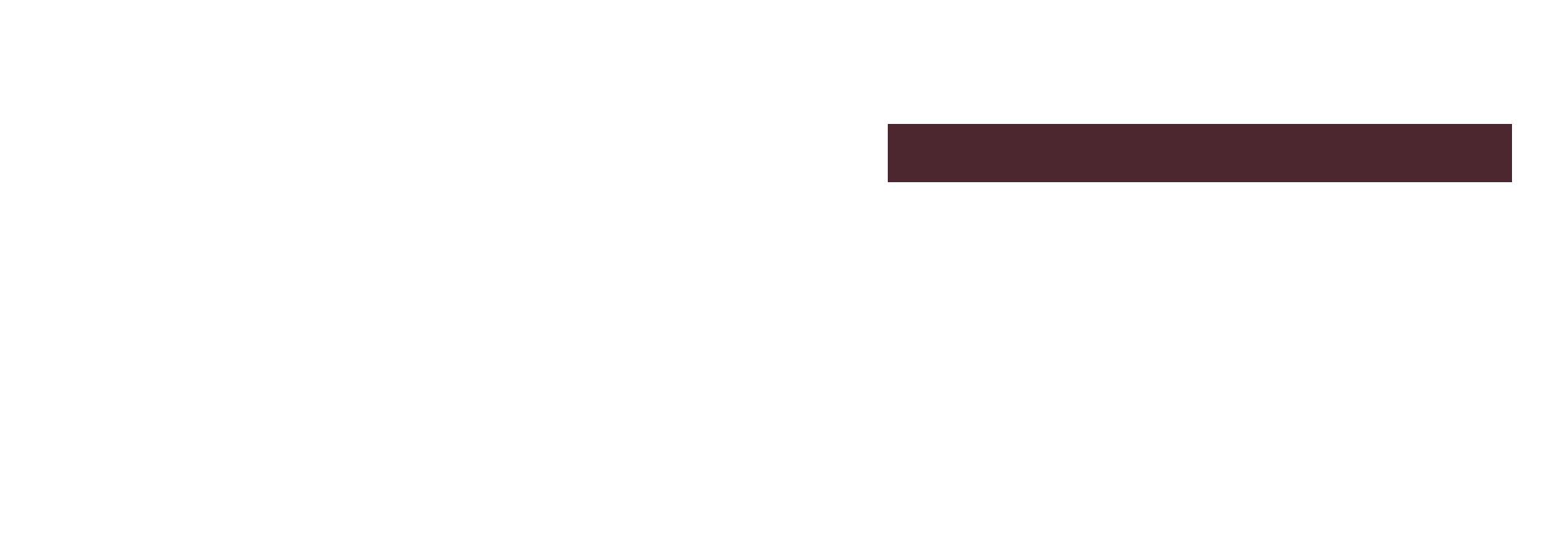
To Cluster or Not to Cluster… That Is the Question!
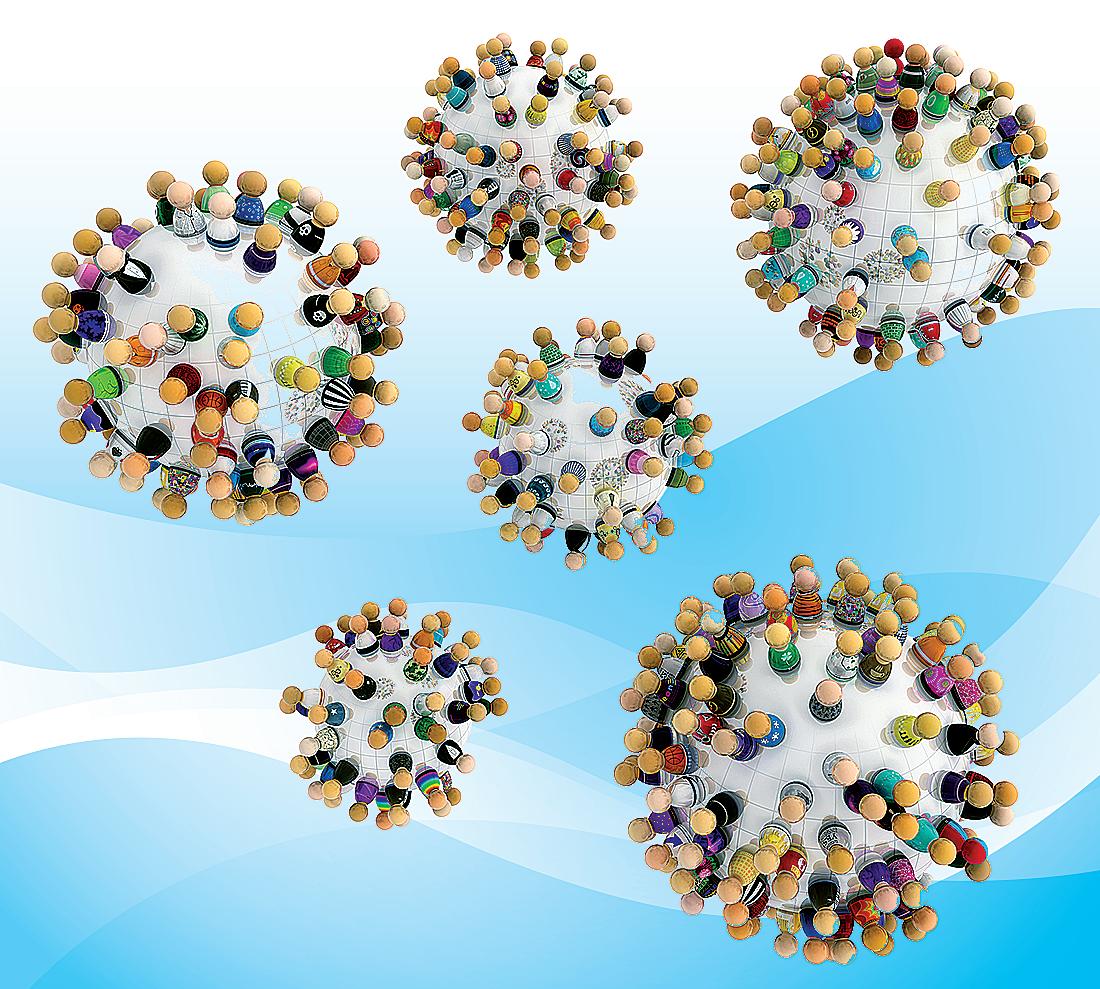
Although clusters are here to stay in some sectors — think life sciences — other industries — among them EVs and semiconductors — are geographically branching out.
By Rich Thompson, International Director, Supply Chain & Logistics Solutions, JLLOne of the unanticipated outcomes of the COVID-19 pandemic is the reconfiguration of global manufacturing and supply chains. While you might expect manufacturers to be attracted to traditional “industry clusters” where talent and suppliers will come together in a certain market or geography — think of the close ties between automakers and Detroit — that isn’t necessarily the case today. In some sectors, traditional industry or logistics clusters are less important than they have been at any point in the past.
Disruption has created opportunity for U.S. manufacturing. Following various supply chain disruptions and lengthy logistics logjams beginning in 2020, many manufacturers have been near-shoring or on-shoring their manufacturing operations and reconfiguring their supply chain networks.
Shifting Manufacturing and Supply Chain Footprints
No wonder JLL Research finds that demand for U.S. manufacturing-related facilities soared 93 percent year-
over-year from the first quarter of 2021 to the first quarter of 2022.1 More than 1,800 companies reshored manufacturing in 2021, and reshoring is expected to create 350,000 new U.S. jobs by the end of 2022, up from 260,000 in 2021, according to The Reshoring Initiative®’s IH 2022 Data Report.2
To be clear, the shifts are not limited to the United States. Manufacturers with customers around the world are looking to keep operations close to customers to reduce the risk of future supply chain delays and facilitate product delivery. Moving manufacturing closer to consumers — whether in the Americas, APAC, or EMEA — also helps mitigate risk and the impact of high shipping costs.
Many companies also have diversified their supplier networks to avoid over-dependence on any single company or country. The life sciences, pharmaceuticals, heavy equipment, electronics, and semiconductor industries, in particular, suffered serious impacts when supplies became unavailable as the pandemic disrupted manufacturing and business activity in APAC.
Meanwhile, the conflict between Russia and Ukraine has disrupted global energy markets and added pressure to skyrocketing energy costs, with particular impact on chemicals, resins, plastics, fertilizers, paper, and pulps industries reliant upon natural gas. The United States and Canada have emerged as countries of choice and highly attractive locations for high energy, gas-reliant manufacturers.
Within the United States, however, the industries most affected by current trends are not necessarily locating in or near industry clusters. Multiple factors are pushing manufacturers beyond the traditional cluster markets. The tight market for labor — in particular for skilled manufacturing jobs — has made access to labor more of a challenge than in that past, driving manufacturers to areas with available labor pools. Tax incentives are always a factor, as is access to rail, highways, and other shipping infrastructure. Large developable land sites are also harder to come by, as manufacturers are
Bahama Buck's® is the Greatest Sno on Earth®
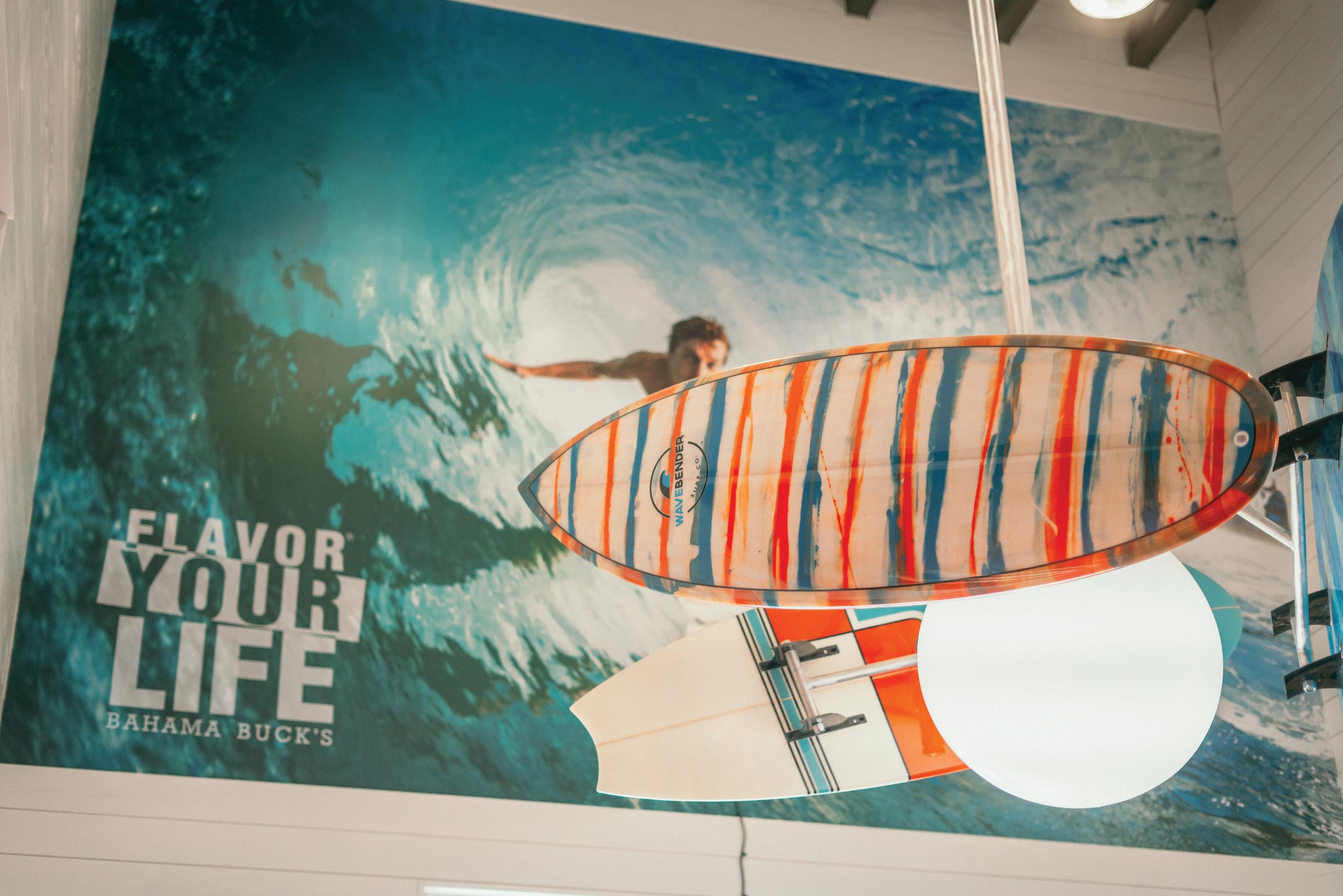
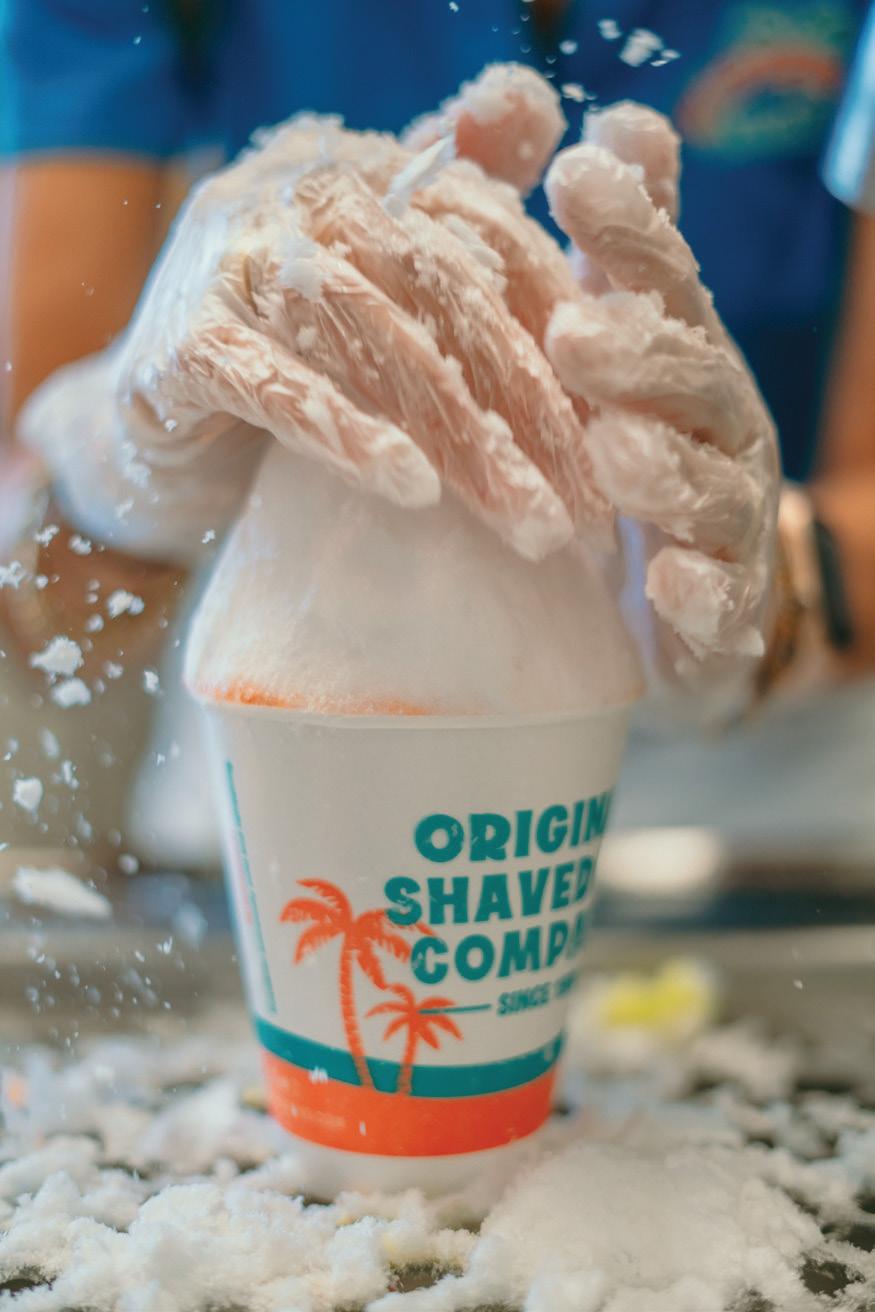
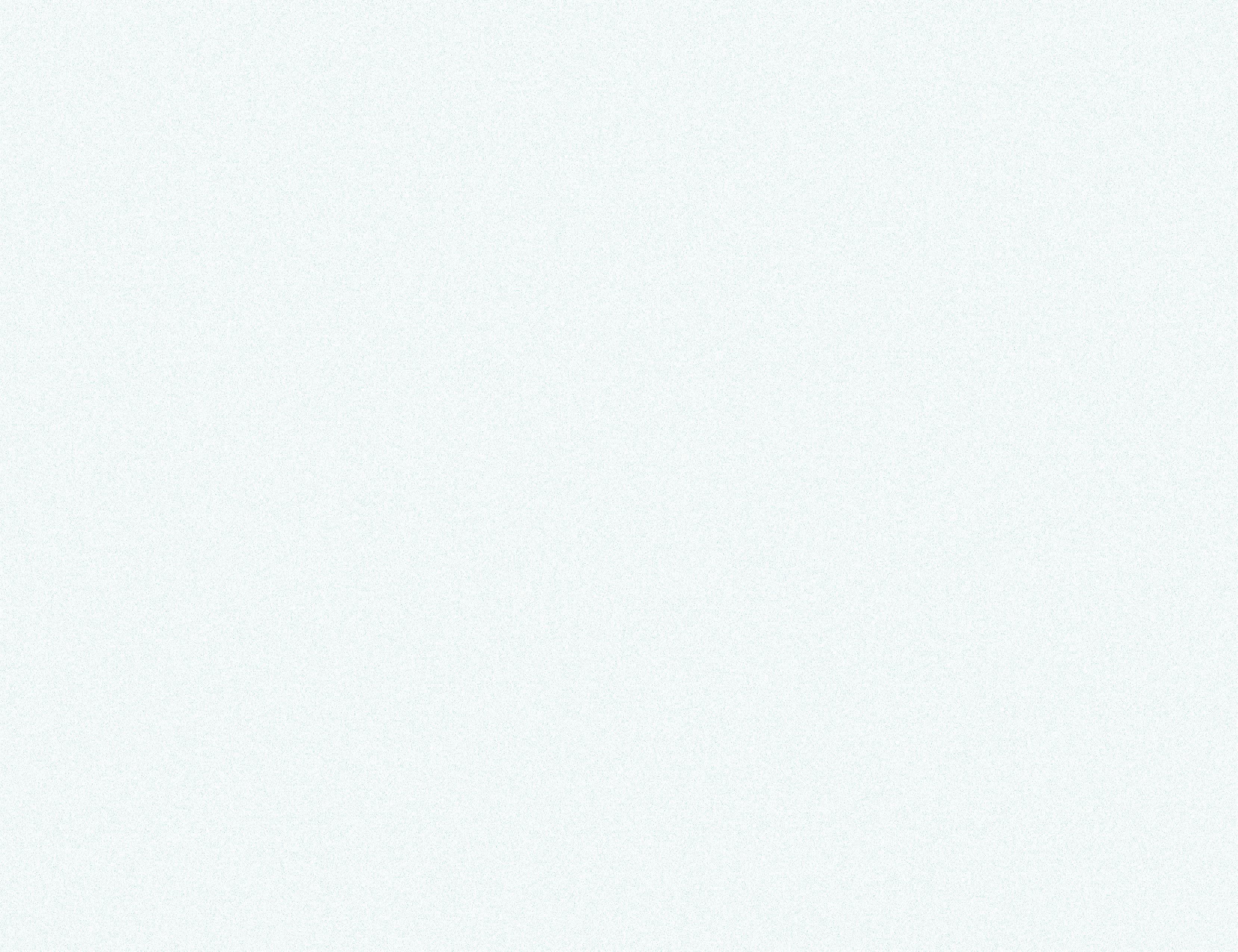
In 1990, Blake and Kippi Buchanan started a snow cone shack in the heart of Lubbock, Texas with a passion for people and tasty treats. Today, this international brand services 107 stores throughout the U.S. and Puerto Rico.

Scan the QR code below to learn why the Buchanans find there is no better place to inspire a people-first culture than in the "Hub City."
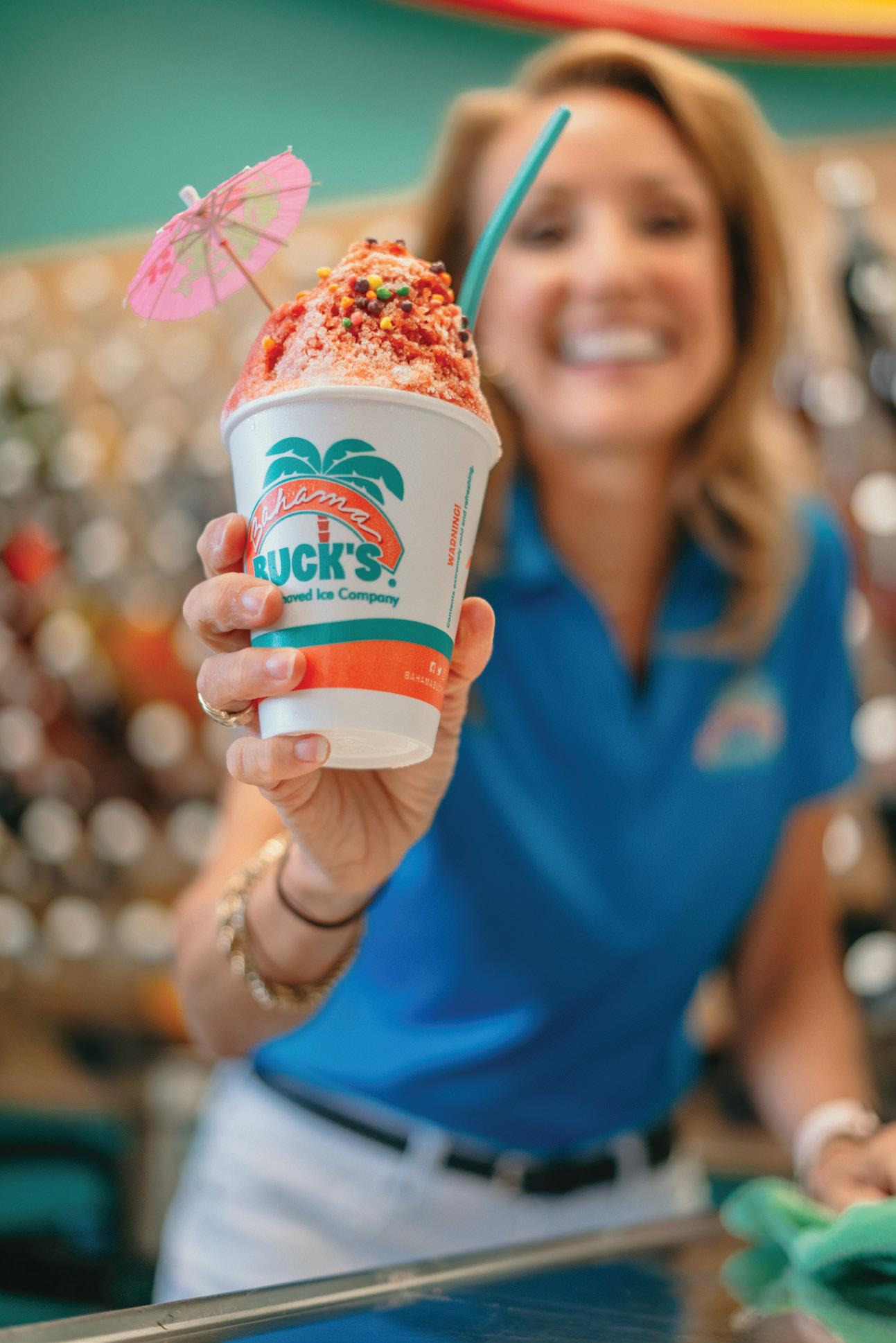
often competing with logistics companies for major parcels.
The
Dispersed
Footprint of EV Manufacturing
EV manufacturing, in particular, is not developing around the historic automotive centers of Detroit. While some EV manufacturing has settled in Michigan, the largest U.S. manufacturing developments are under way in 17 different states, including Arizona, Texas, Georgia, Ohio, Tennessee, and Indiana.
The United States is becoming a location of choice for companies producing electric vehicles (EV) and EV batteries as major domestic automakers shift production to EVs in response to soaring global demand. Recent federal legislation — including the 2021 Infrastructure Investment and Jobs Act (IIJA) and the 2022 Inflation Reduction Act (IRA) — has provided funding and expanded tax credits to accelerate the transition to clean energy infrastructure and EV vehicles for public transit and the commercial and consumer markets.
AS SOME INDUSTRIES DEVELOP IN DIVERSE LOCATIONS, OTHERS [E.G., LIFE SCIENCES] CONTINUE TO BENEFIT FROM LOGISTICS CLUSTERS.
Instruments began construction on a new facility in May 2022. GlobalFoundries also is expanding its U.S. manufacturing, investing in additional capacity at its Malta, New York, headquarters.
Most recently, Idaho-based Micron announced that it will invest up to $100 billion to build semiconductors in New York State — reportedly the largest semiconductor fabrication facility in the history of the United States and possibly the largest in the world. The state is providing $5.5 billion in state tax incentives for the project, which is also likely to tap CHIP tax credits.
Clusters Here to Stay in Some Industries
It is hard to “cluster” big manufacturing operations, such as EV and EVrelated manufacturing, when each plant requires large ready-to-develop land sites, supply chain infrastructure, access to labor, as well as tax and economic incentives. EV manufacturers also are attracted to areas with comparatively low energy costs to reduce production costs.
Semiconductors Nationwide
With factories coast-to-coast in 18 states, the U.S. semiconductor industry is another that is not clustered around a particular location, according to the Semiconductor Association’s 2021 State of the U.S. Semiconductor Industry report.3 Semiconductor manufacturing is resurging in the United States, with new manufacturing facilities planned in locations far beyond the industry’s roots in Texas and Silicon Valley. Intel, for example, is expanding its U.S. footprint by investing billions of dollars into two chip production plants in Arizona and two in Ohio, and an advanced packaging facility in New Mexico.
In 2020, TSMC also announced plans to build a factory near Phoenix, Arizona, to be near the talent and suppliers already supporting Intel. Meanwhile, Samsung Foundry announced in late 2021 that it is building a plant near Taylor, Texas. Near Sherman, Texas, Texas
As some industries develop in diverse locations, others continue to benefit from logistics clusters. Life sciences organizations, for example, continue to cluster in such markets as the San Francisco Bay area, New Jersey, San Diego, Boston, and Raleigh-Durham. Manufacturers of petrochemical products, resins, and plastics tend to cluster around ports to streamline exports.
One reason is that clustering reduces the cost and time of delivering product to end-users. With proximity to multiple downstream manufacturers, suppliers can exploit economies of scale while offering customers faster, lower-cost deliveries. Clustering also can produce a labor pool with specialized industry knowledge — which is a major reason why life sciences companies tend to cluster around major life sciences research organizations. In addition, geographic proximity can spur innovation as small entrepreneurs and established manufacturers come together in economic activity as well as research and development.
Whatever the industry, a myriad of factors enter into site selection decisions for manufacturing operations. With access to strong labor pools, logistics infrastructure, energy, and large shovel-ready sites among the primary concerns, companies are willing to look outside traditional industry clusters with regard to their strategic U.S. manufacturing location decisions. n
1 https://www.us.jll.com/en/views/resurgence-for-made-in-america 2 https://reshorenow.org/content/pdf/2022_1H_data_report-final5.5.pdf 3 https://www.semiconductors.org/state-of-the-u-s-semiconductor-industry/
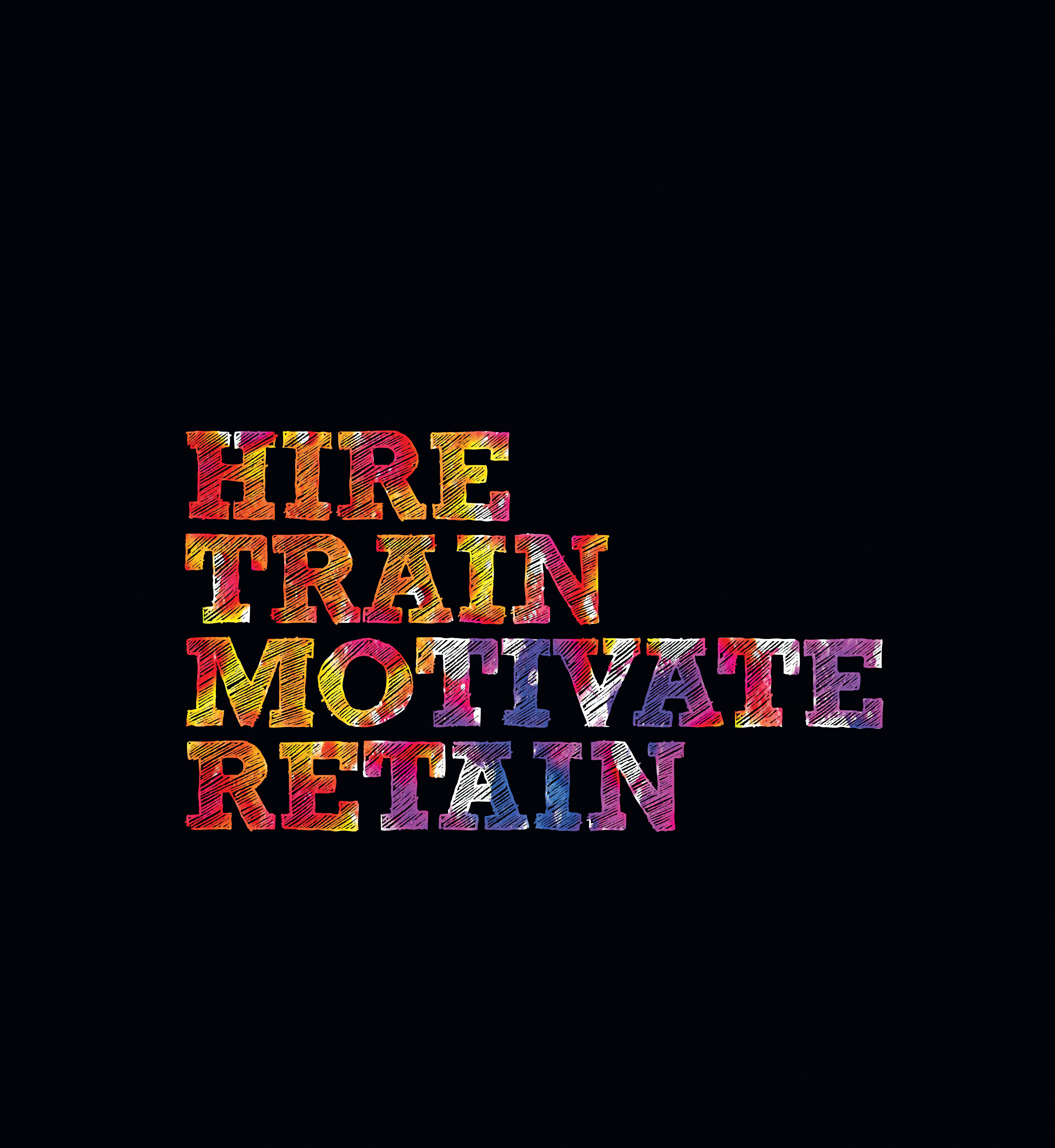
The great thing about Virginia is the prevalence of technical talent that we have here. That’s due to many other technical companies being located here as well as the excellent graduates that we get from all of our state universities.

See the advantages Virginia can offer your business at vedp.org


THE GREAT MIGRATION OF WORKERS
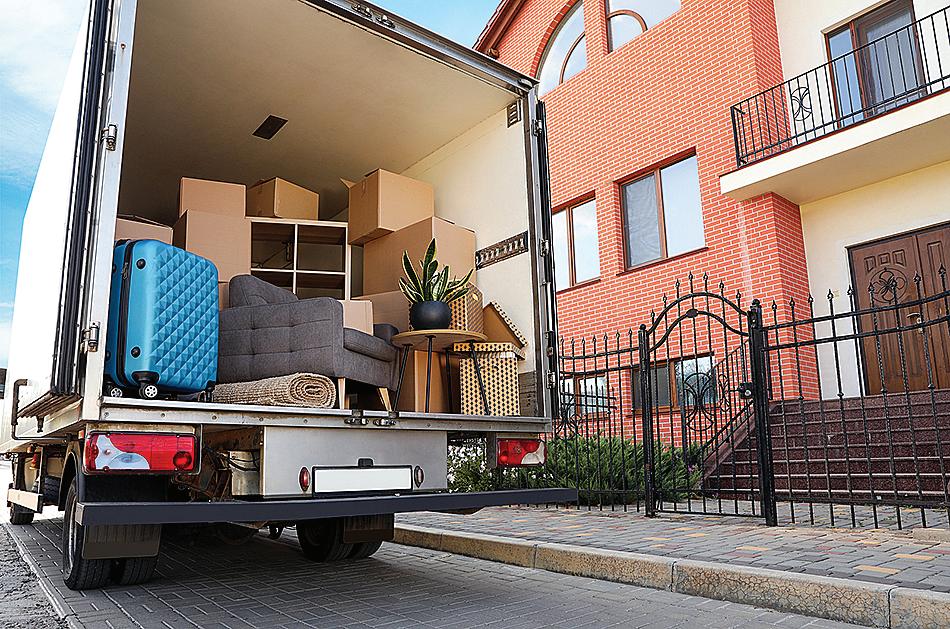
“Now Hiring” — the sign that we see across the country, from main street to downtown to the county road. This sign now seems to be a permanent fixture in windows of small and large businesses alike. Competing billboards along the highway shout to us from the roadside why you should consider working for “company A” as we read the same reasons that the last three billboards gave for their respective companies. Online advertisements and virtual recruiters constantly let us know of the opportunities just on the other side of the cyber fence. The workforce issue has always been around; however, the pandemic and further economic impacts since
then have accelerated this shift in the last few years. What can we discern in the now years since the pandemic? Prior to 2020, wages were in a price war to try to keep employees from moving from one location to another down the street. In 2022, employers continue to struggle with keeping employees interested in coming to work, especially in the office. What are the drivers for migrating away from a current employer? Where are people going? What are prospective employees seeking? Let’s dive into the various forces that are influencing the workforce today and subsequently the employers and communities so desperate to find (and retain) them.
Movement
Despite the disruptions of the pandemic, 2020 was a pivotal year — knowing it was also a census year. As a result, we can dig into data provided on a decade basis as a starting point for further analysis. In March of 2022, the U.S. Census bureau1 produced a report noting the migration patterns of people within the United States. This data is produced at the county level, so you see a significant amount of “hot spot” data for inference purposes.
When comparing the data migration patterns from 2019–2020 and 2020–2021, there are several notable differences. The 2019–2020 migration data (i.e., preand early pandemic months) indicates movements from “rural” areas to more suburban areas. Metro areas noted the largest increases in population, though not all these increases occurred in a “downtown
ByCompanies must understand how a shift in workforce development and remote work will impact their location decisions.
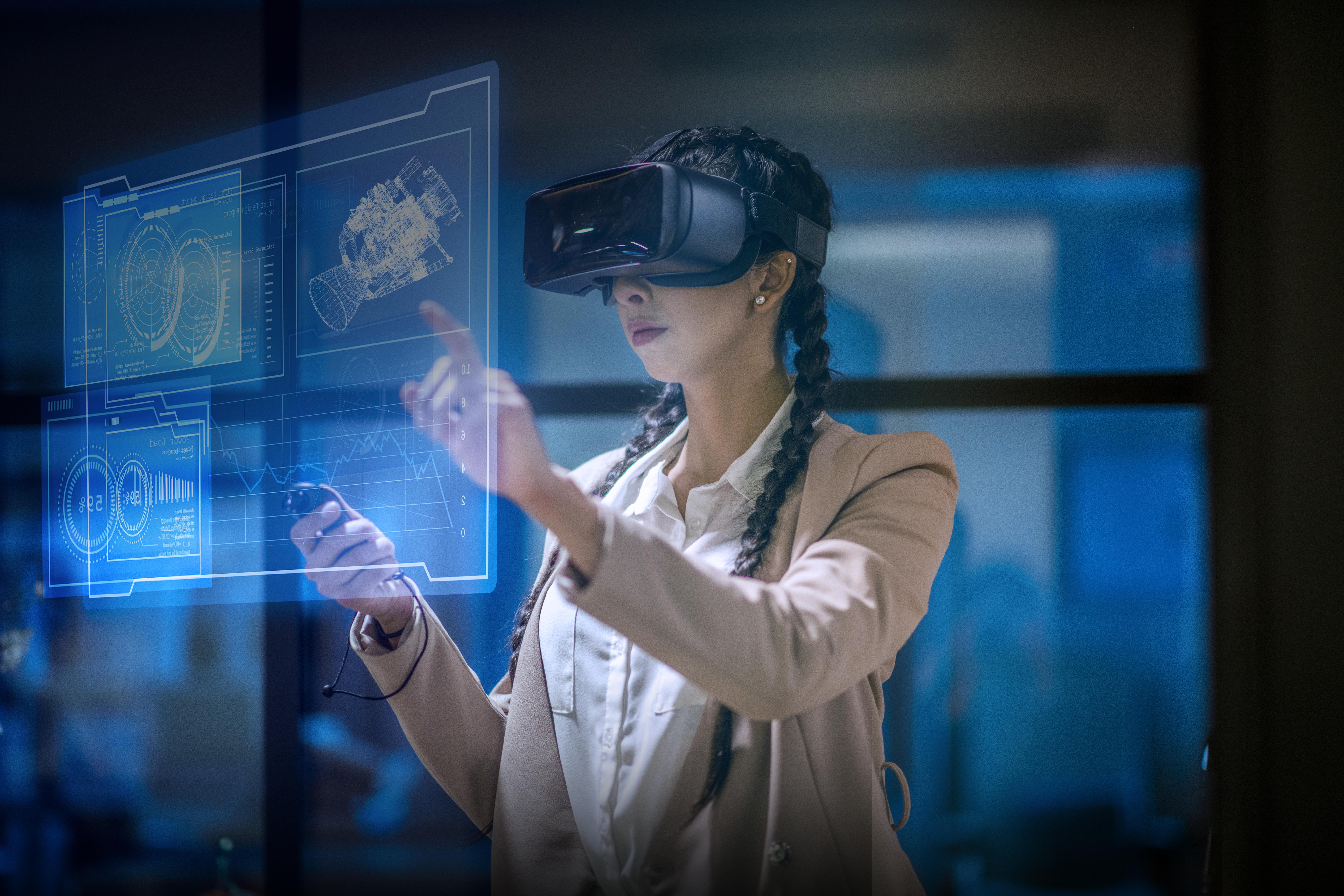
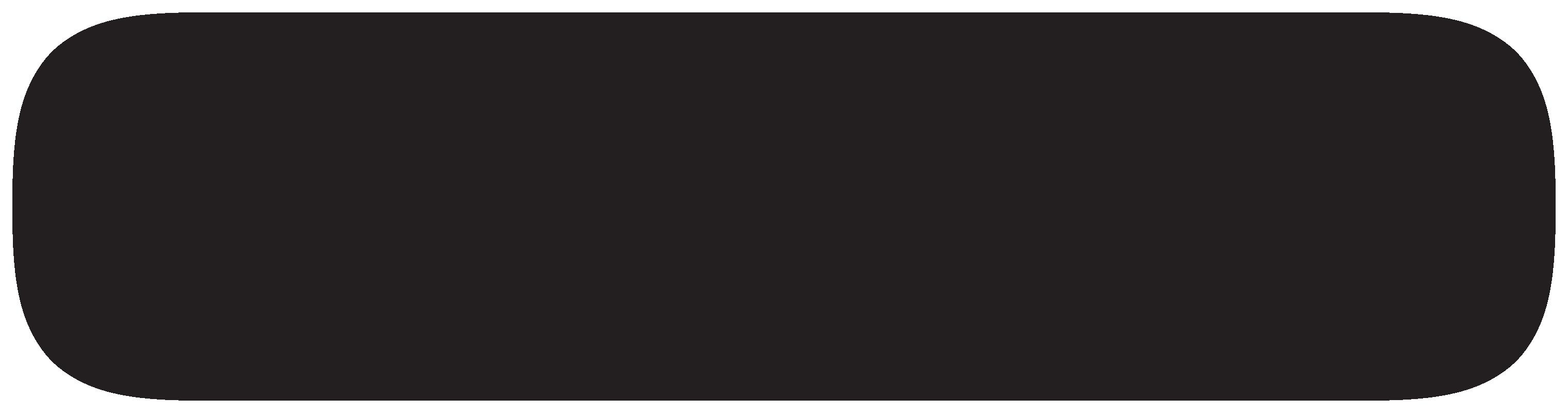


core” (centralized, urban county). Surrounding urban areas appealed to many people due to amenities, job opportunities, and available supply of housing options. This data appears to indicate a move toward places that offered more due to the convenience and proximity of the urban core, though life in the urban core was not as sought after.
The data changes substantially in 2020–2021 (midpandemic to waning pandemic months). Core urban areas, especially in the North and East/West coasts, and in the Midwest and South, saw some of the largest decreases due to net migration patterns. The largest increases in net migration patterns appeared to be the suburban areas around urban “cores,” and these increases were weighted toward areas in the South and Midwest. According to the data, the state of Florida saw some of the highest increases in net migration, taking four spots out of the top 10 largest migration net increases. The largest decrease areas were New York-Newark, San Francisco-Oakland, Los Angeles, Seattle, and Washington, D.C.-Baltimore.
However, this data does not tell us “who” was making these transitions. Further analysis needs to be done to sort out the timing of this information too: were these migration patterns unique to this time? For example, does the data reflect retirees seeking to capitalize on the white-hot housing market, trying to get the best bang-for-their-buck and move to their retirement home? Or were these patterns indicative of the closures of higher education institutes and travel opportunities and the movement of young people back “home”?
For further insights into the “who” we can look at other data produced by a unique source: moving and storage companies. Extra Storage Space2 notes that
all age demographics participated in the movements during and after the pandemic, from young professionals to retirees. A Pew Research study3 noted that nearly one in four people in 2020 moved or knew someone who moved due to the pandemic environment. However, of that population, over a third of the moves were made by young people aged 18–29. While the pandemic possibly had a stronger migration influence on young people, the data still notes participation from all age levels. Therefore, with the population shifting during this time, what were the main drivers for these decisions to move?
Forces
Several studies of this time note the prevailing factor for moving was the cost of living. Communities and campuses that closed due to the pandemic could not provide the long-term financial security that people rely on. As the economy struggled through the mid- and late-pandemic months, many people could not afford to stay in the places they were, so they started to look for areas where their dollar would go farther.
This was especially impactful on young families due to the costs of childcare or the absence of options for childcare and the requirement for a caregiver to stay home. Move.org notes the average cost of childcare for a household in America is $175/week for a four-year-old or 13.9 percent of the median household income (across the United States). Some states have much higher costs associated with childcare and a greater impact on a family’s budget.4 With increases in costs like this for the working-class family and an uncertain future, many families looked to move “home” to be nearer other family members

THE LARGEST INCREASES IN NET MIGRATION patterns appeared to be the suburban areas around urban “cores.”
To learn more about how inspiring businesses are leading the way to a strong economy, visit ArkansasEDC.com/ whyarkansas
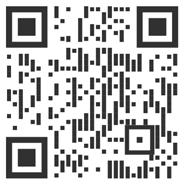
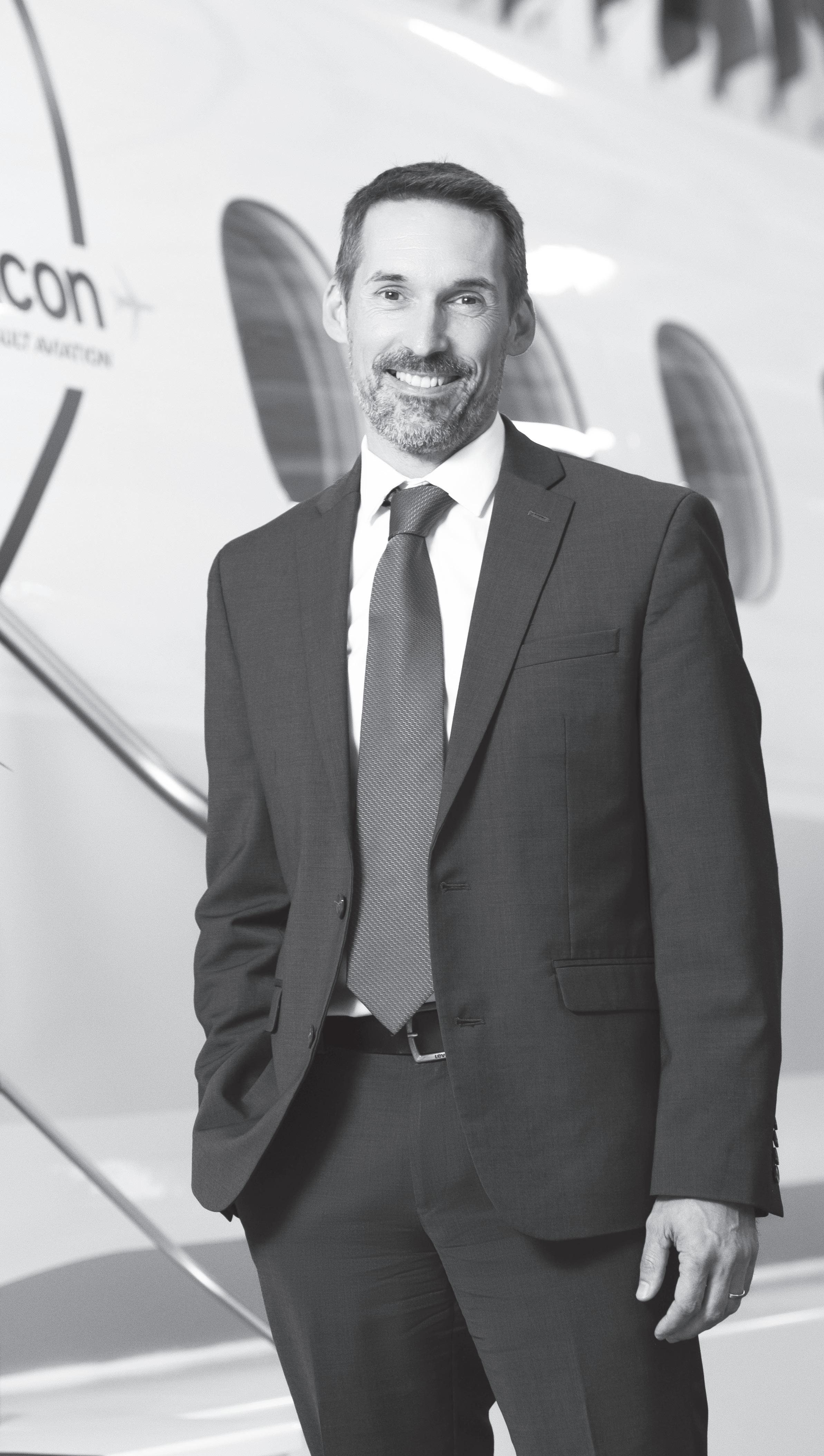
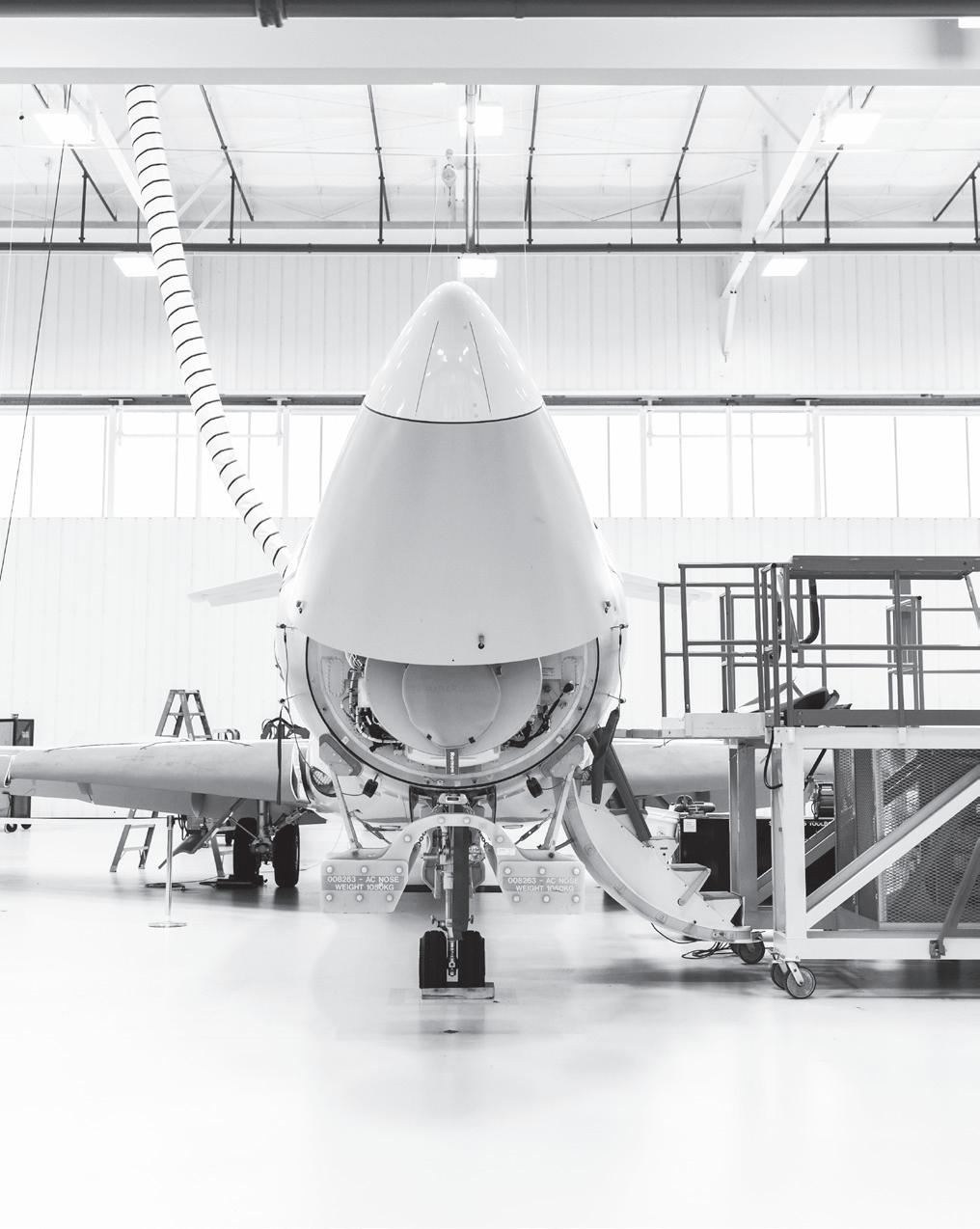
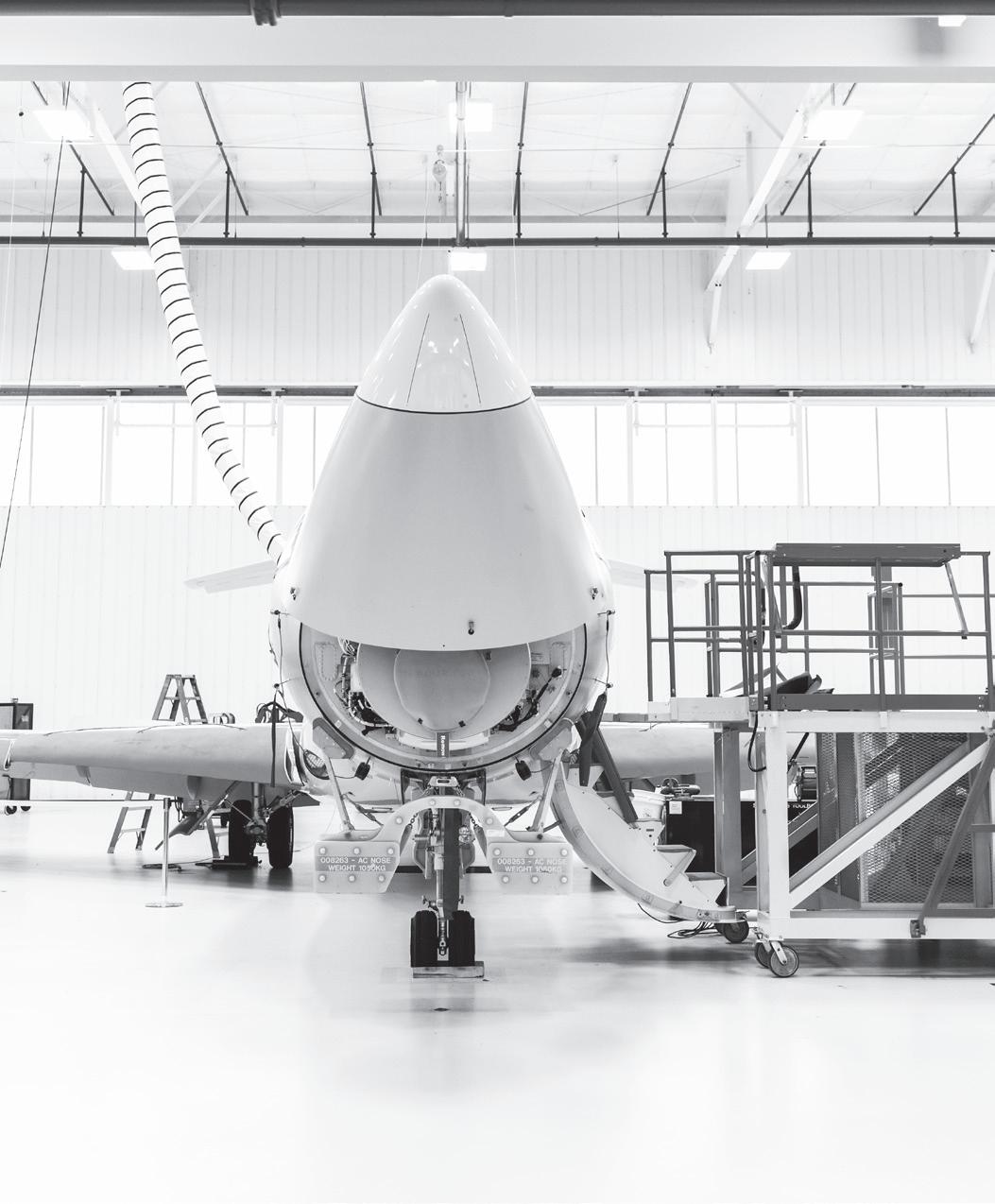
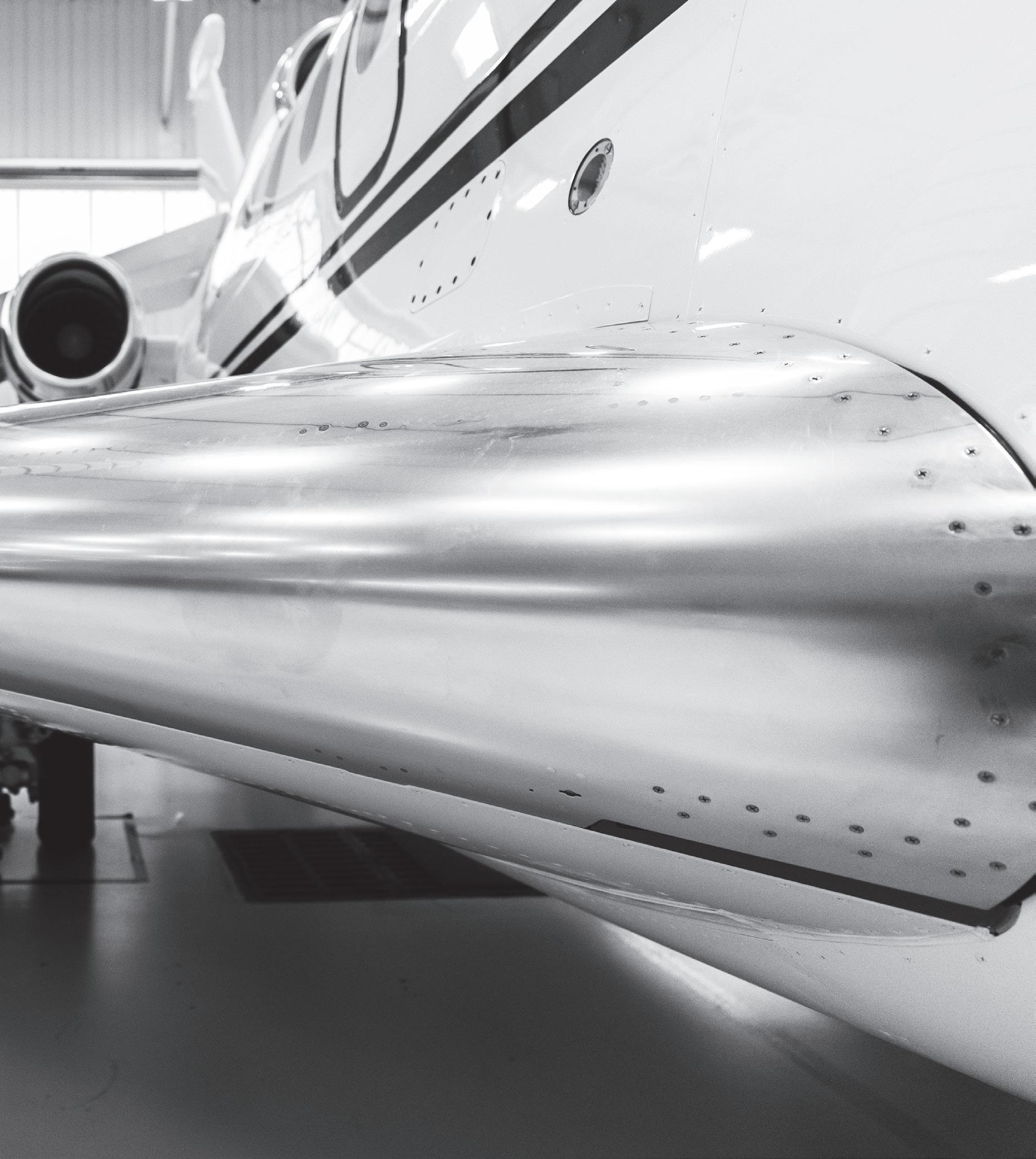
“
Arkansas is the perfect fit for Dassault Falcon Jet environment that encourages business and attracts the best people. And the people are the key to our success.”Sebastien Deltheil - General Manager, Dassault Falcon Jet, Little Rock
who could support them.
Simultaneously, the great migration saw a necessary and, in many cases, mandated requirement for remote work. Many businesses had to quickly adapt working models to accommodate this new factor. As the pandemic began to subside, many workplaces maintained the remote policies created in one fashion or another. However, with the rise of remote work options, working professionals could also benefit from flexibility in location. If employees can work from anywhere, why not be in a place that benefits your wallet the most!
Not all moves were just for families — many areas that saw migration growth were outside of historically large urban areas to smaller suburban communities, even rural areas. Individuals and families, according to real estate, finance, and moving companies like Zillow, 5 BankRate,6 and Neighbor.com,7 were looking for more space and the ability to stretch their dollar.
Communities that saw the largest net migrations bring some common amenities and features. Outdoor activities were on the rise during and following the pandemic as indoor spaces were shut down or severely restricted in capacity. Areas for year-round outdoor activities naturally occur more in the Sunbelt states. Other states that saw increases include Tennessee, the Carolinas, Utah, Idaho, Montana, and Arizona — all states known for adventurous recreation and support of the scenic outdoors. Areas that provided options and a better cost of living saw the benefits of an increase in population.8
Another force that drove the migration from larger urban areas included crime. Urban areas will inherently see a larger percentage of crime due to population densities. Statistics highlight the increases in crime across the country, especially in urban areas over the last two to three years.9 Families and individuals want to feel safe within their community, and if the community cannot offer that, they will find a better opportunity.
Assessments
With a better understanding of the forces that migrated people to different areas during and postpandemic, what can be done by employers and communities to attract the attention of workers who are
open to the idea of changing location?
Employers have felt and will continue to feel the incredible balancing act of offering flexibility while still maintaining a strong workplace culture. How do you bridge the two? For some employers, a flexible “in-office” schedule or an entirely remote option is advisable. As long as the work is getting done and productivity is maintained, many employers have embraced a lighter in-person workplace. This is beneficial for workers within professional or service industries.
Employers in areas that have seen a decrease in employees may have to look for workers who are not within traditional “reach.” Employers will need to assess whether they can accommodate a worker in another area of the state or even the country to fill talent shortages. While technology can expand the reach of some tasks to remote settings, many still seek to be a part of their workplace culture and community. Employers must be willing to offer flexibility (to the degree they can) and at the same time offer a workplace that people want to be a part of. Otherwise, employers will struggle to fill roles and retain top talent.
Alternatively, many businesses, such as manufacturers and retail operations, will always need in person operations due to fixed location tasks, such as running equipment or serving a customer. Hospital workers need to be at the hospital to perform surgeries and deliver direct medical care. Employers in these settings continue to struggle with maintaining optimal workforces at optimal levels. When employees are not available or present, there are significant pushes toward automation or reductions in services. For these employers, company benefits continue to be flexed to maintain workforce buy-in. However, as these expenses continue to increase, the costs will be pushed to the consumer, which, in turn, dictates what they are ultimately willing to pay for and at what time.
Similarly, employers may need to consider alternative workforce pools, such as retirees, employees with little to no experience, and the disabled community. Flexibility will be even more important in these employment pools as retirees will likely not want full-time working hours. Young employees may not be able to bring the experience needed to do more
READY TO EXPAND OR RELOCATE YOUR BUSINESS?
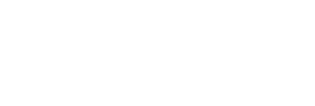
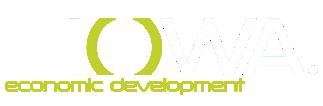
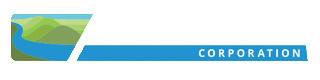
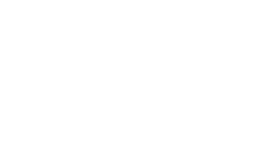
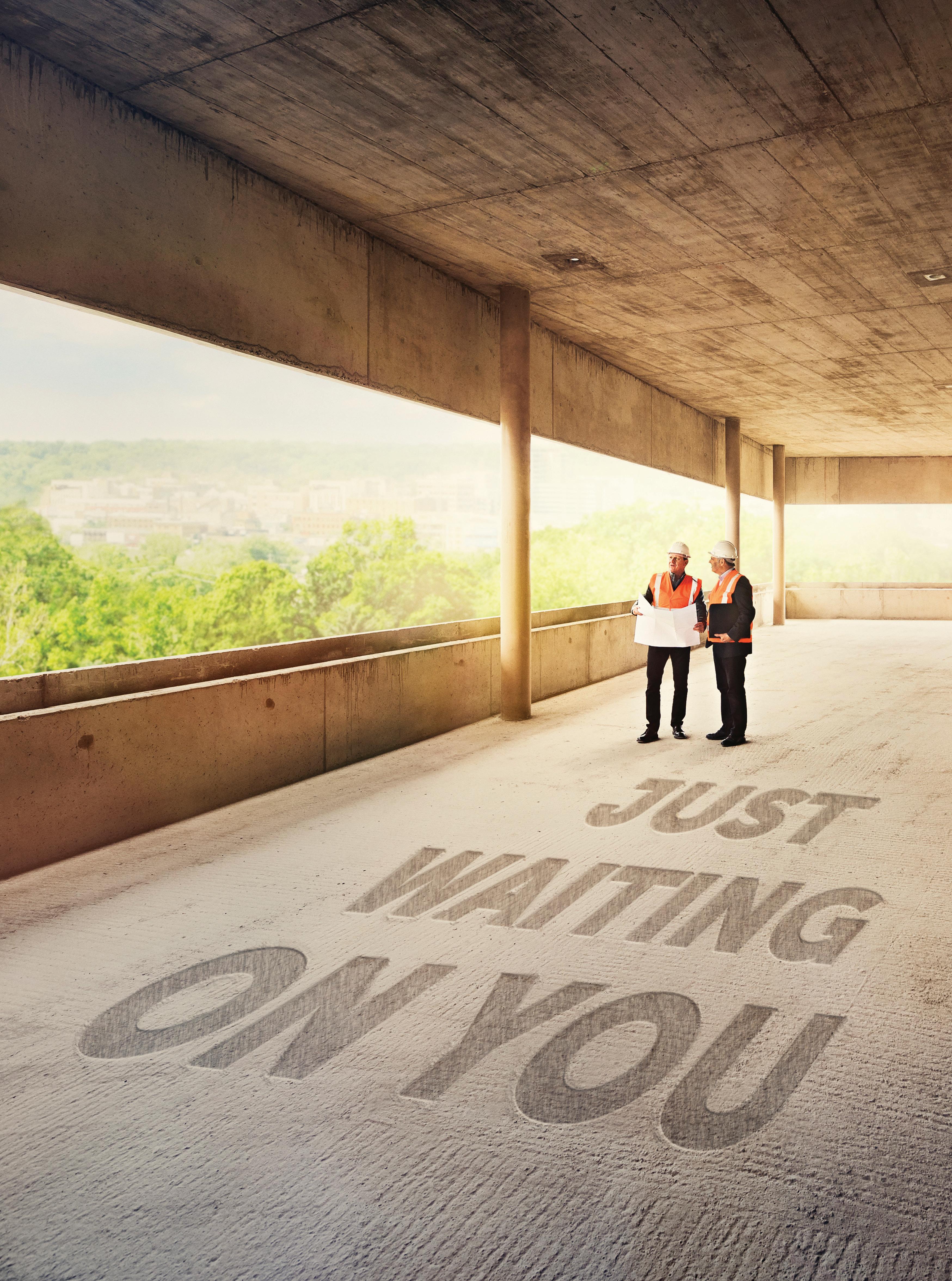
What makes Iowa a best-in-class option for business? If our pro-business environment, low operating costs or the state’s move toward one of the most competitive tax structures in the nation came to mind, you’re correct. But our skilled workforce really sets us apart. The evidence is all across the state, including the Iowa South region, which is experiencing a renaissance thanks to a world class workforce with the skills today’s employers need. Head west to Council Bluffs , where local schools and colleges work with area businesses on workforce development initiatives to ensure a robust talent pipeline. And just a few hours up the road in the Iowa Lakes Corridor region, businesses provide customized, on-site training at local universities and community colleges.
These are just a few of the many forward-thinking communities across Iowa making major moves thanks to our unwavering commitment to fielding a workforce ready to meet your needs.

Iowa is the perfect place.
EMPLOYERS WILL NEED to assess whether they can accommodate a worker in another area of the state or even the country to fill talent shortages.
complex tasks; therefore, employers will be required to consider tasks that can be done and shift roles and responsibilities appropriately. The disabled community can also bring a tremendous amount of opportunity to employers who can accommodate needs, be they mobility or other support services. In all cases, employers placing expectations from just a few years ago on this new workforce will likely continue to struggle finding and maintaining employees. Flexibility on both employers and prospective and current employees will be critical to meeting the challenges presented in the modern workforce environment.
Communities’ Role
Communities and their economic development partners will play a pivotal role in attracting and maintaining workers who are open to moving. As described before, workers today are allowed more flexibility from an employment location standpoint, so they are actively choosing where to live based on what the area offers, and not just from an occupational standpoint. Family-friendly options and amenities are key drivers for many moves. Communities need to ask themselves:
• What are we doing to invest in infrastructure to support this shift?
• Are we taking active steps to upgrade communication and fiber infrastructure to support remote work?
• Are we investing or supporting downtown areas or unique districts that give community flavor?
• How are we working with first responders and non-governmental agencies to address crime and problem areas?
• Are we reviewing zoning and master plan documents (from 15 years ago) to anticipate future
growth needs in housing, business, and industrial areas?
• How are we making it easier to do business within our community by streamlining processes and cutting red tape?
• What creative incentive options could we explore to attract new businesses and workers to our community?
• Do we have a regular business retention and expansion program and are we executing on it?
There are many factors communities and businesses do not have direct control over: the economy, inflation, criminal activities, just to name a few. However, there are opportunities that can be explored and enacted in the short term to impact longer-term outcomes. Communities and businesses must come together to work through these complex problems and the first step is openly reviewing the issues at hand. By collaborating on problem areas, people — community leaders, business owners, and the employees and families who live there — can share ideas and invest wisely in new initiatives that position themselves for the best opportunities. This workforce migration issue and opportunity will not disappear overnight, but with solid planning and collaboration, communities can begin to make an impact and move in the right direction. ~
1 https://www.census.gov/library/stories/2022/03/net-domestic-migration-increasedin-united-states-counties-2021.html
2 https://www.extraspace.com/blog/moving/where-are-people-moving/ 3 https://www.pewresearch.org/fact-tank/2020/07/06/about-a-fifth-of-u-s-adultsmoved-due-to-covid-19-or-know-someone-who-did/
4 https://www.move.org/child-care-cost/
5 https://zillow.mediaroom.com/2021-04-06-Zillows-2021-Mover-Report-The-OpportunityEmotion-and-Trends-Behind-the-Great-Reshuffling 6 https://www.bankrate.com/mortgages/housing-heat-index/ 7 https://www.neighbor.com/storage-blog/more-americans-plan-to-move-in2021/#small
8 https://sparkrental.com/hottest-real-estate-markets/ 9 https://www.safehome.org/resources/crime-statistics-by-state

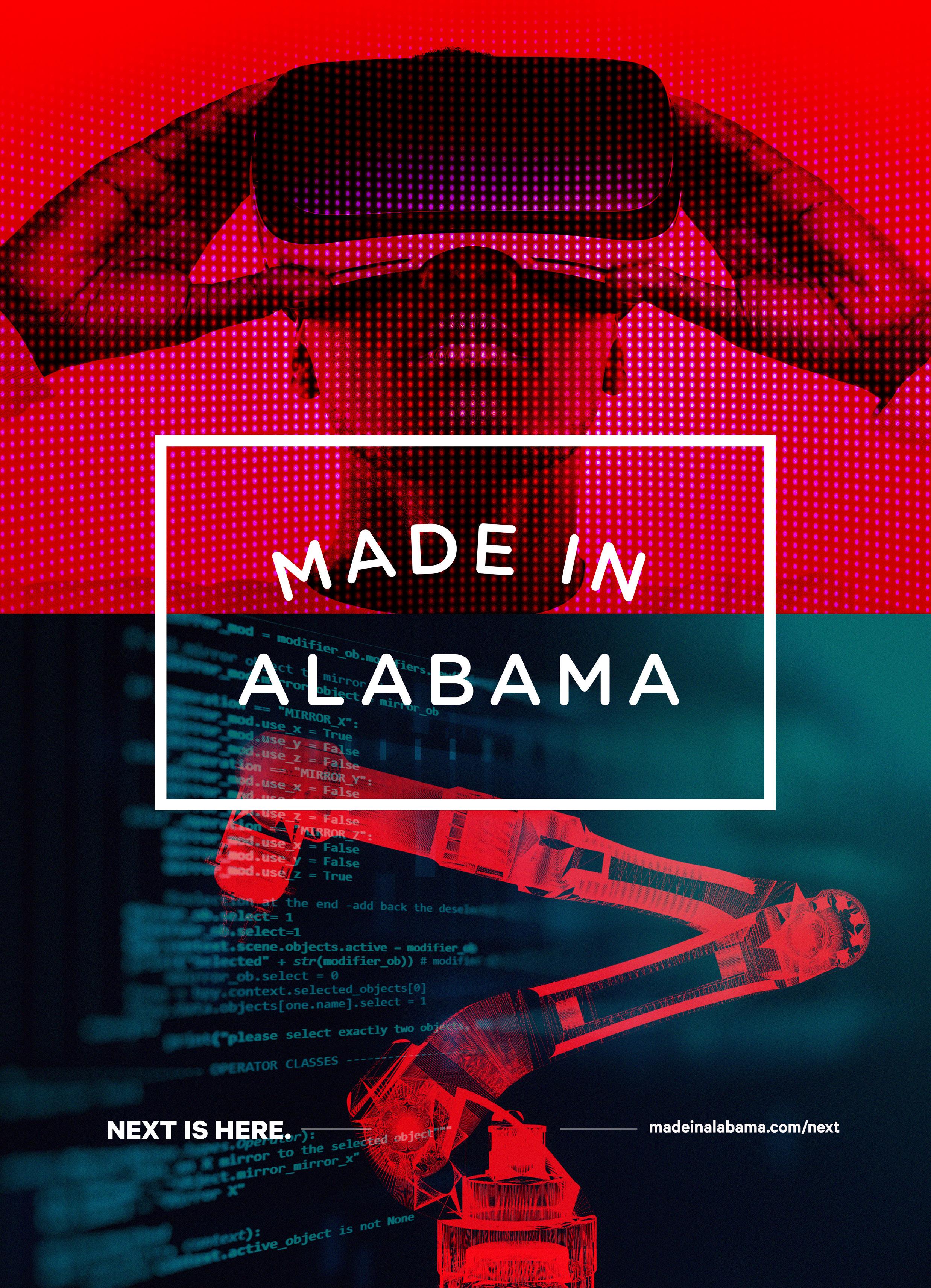
The ability to attract and retain quality talent is typically the key determinant behind a company’s current and future success. While the COVID-19 pandemic hasn’t changed this, it has shifted the overall talent landscape, forcing employers to evaluate new talent geographies in different ways. This piece explores the various talent-related factors employers are using to determine where to hire and how their prioritization of these factors continues to change.
New hiring locations are typically assessed based on three broad categories: talent supply (including quality), talent cost, and talent demand. These factors still drive most talent-based location selections, but the priority placed on each has changed as a result of the constricted talent environment, accelerated by the pandemic, that has employees decidedly in the driver’s seat across most occupations and industry sectors.
Pre- and Post-Pandemic
Prior
WE LIKE TO SEE BUSINESSES GROW. NOT TAXES.
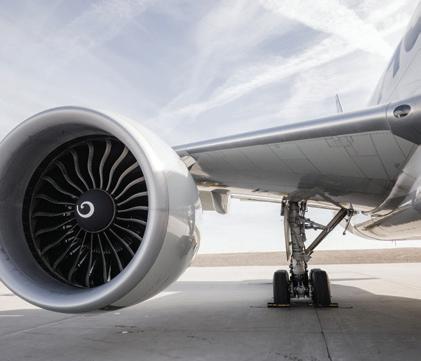

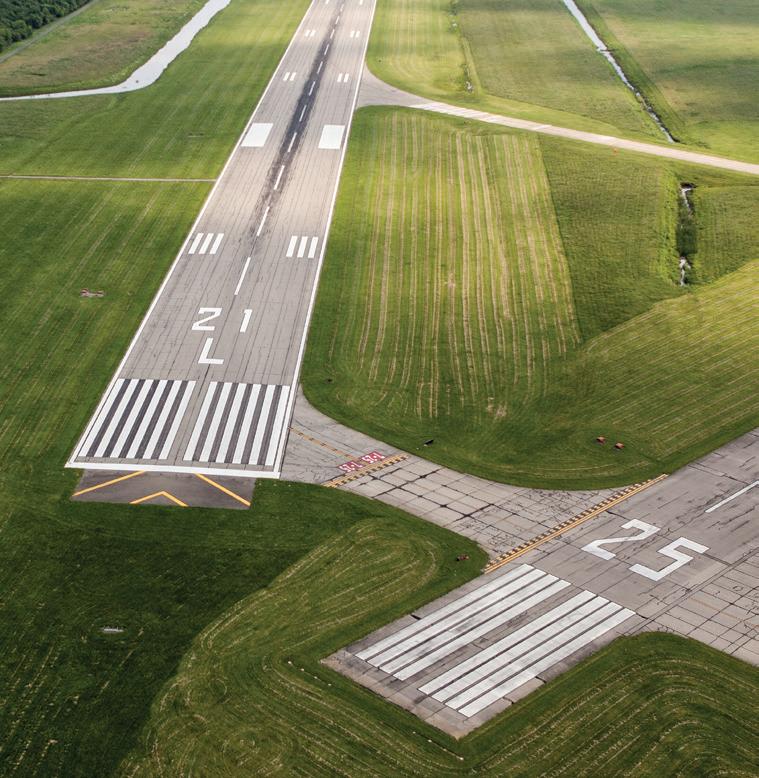
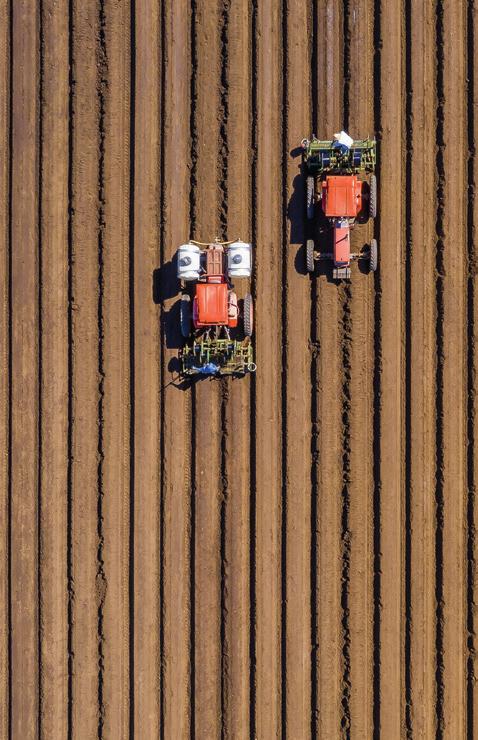
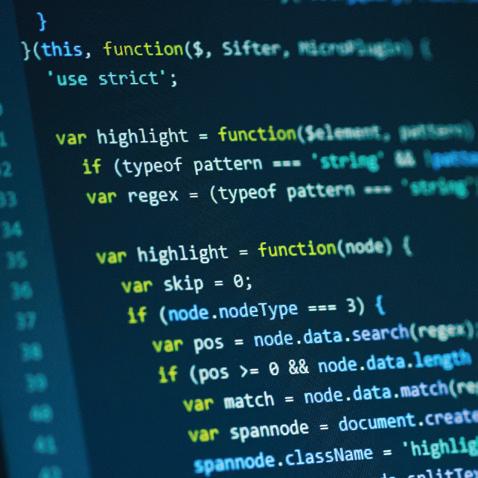
At just 2.5% and dropping, North Carolina is home to the lowest corporate tax rate in the United States. Picture what that can mean to your business. See why North Carolina was named “America’s Top State for Business 2022” by CNBC at ALLinNC.com.
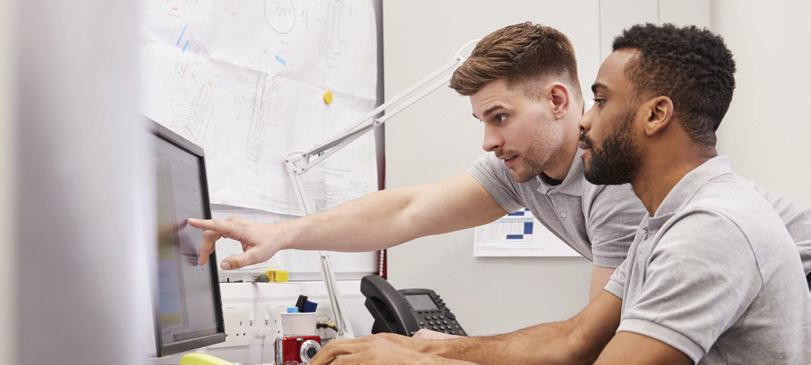
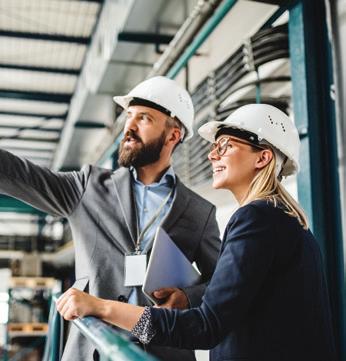
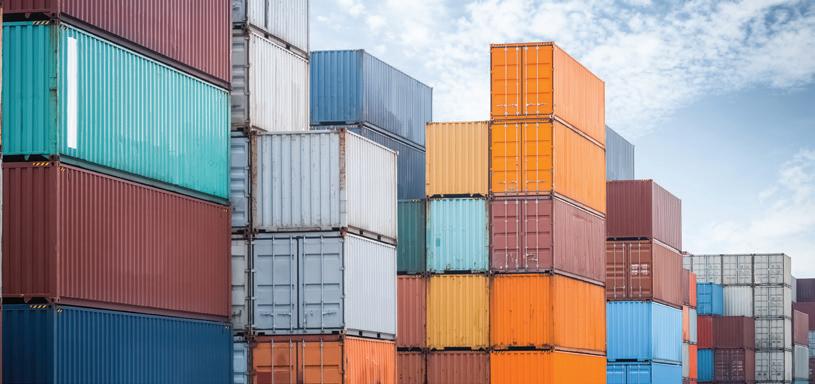
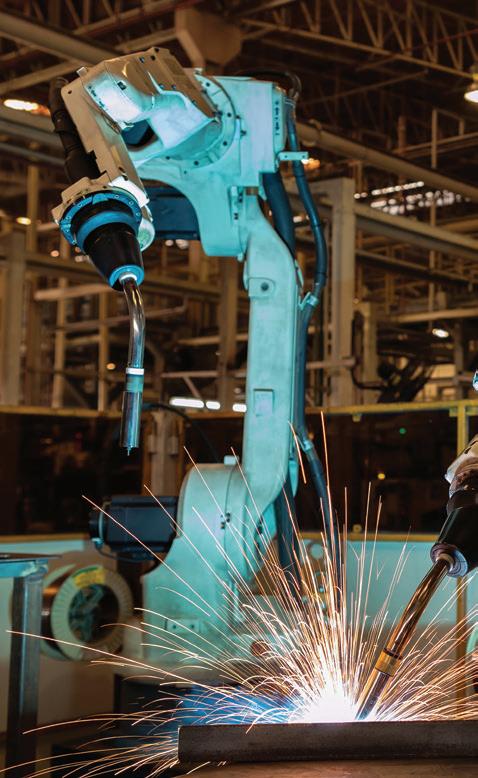
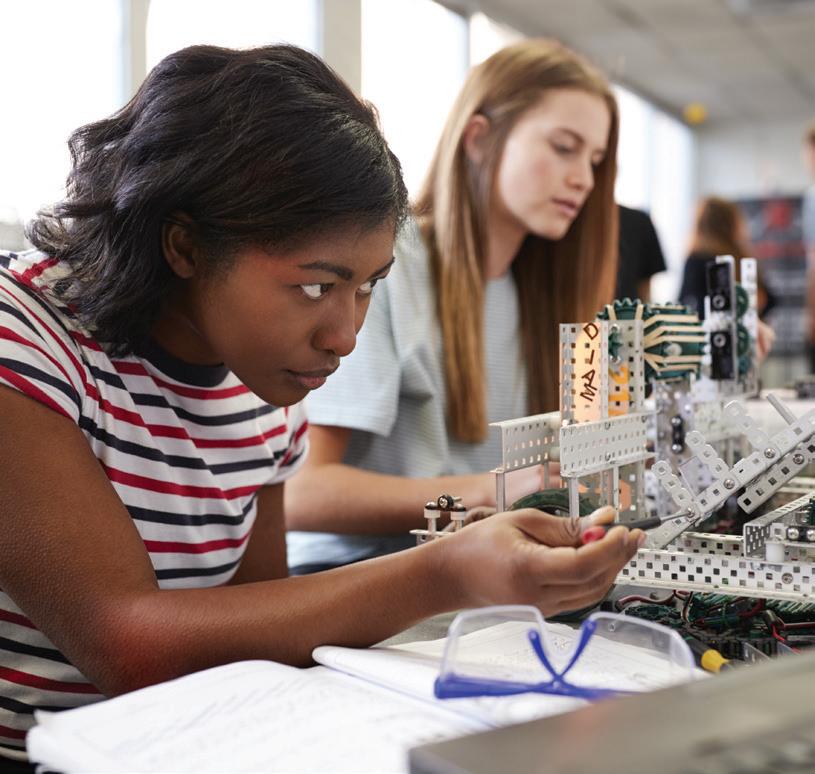
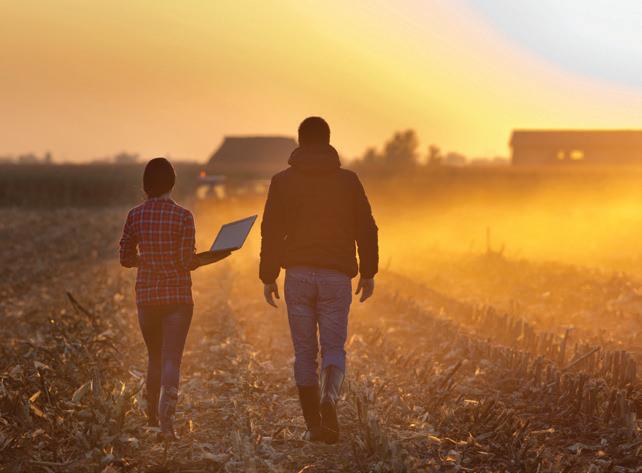

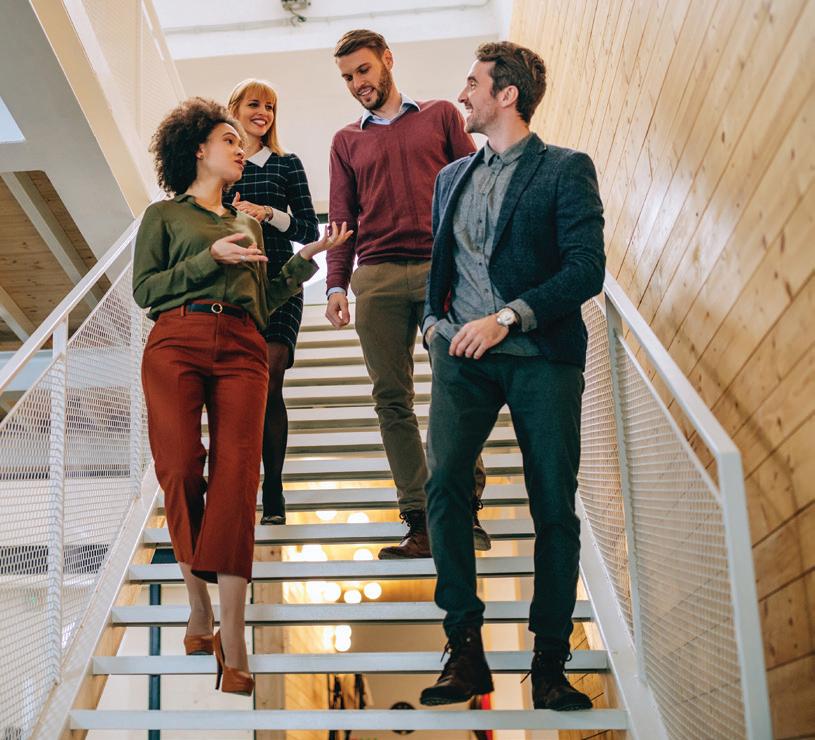

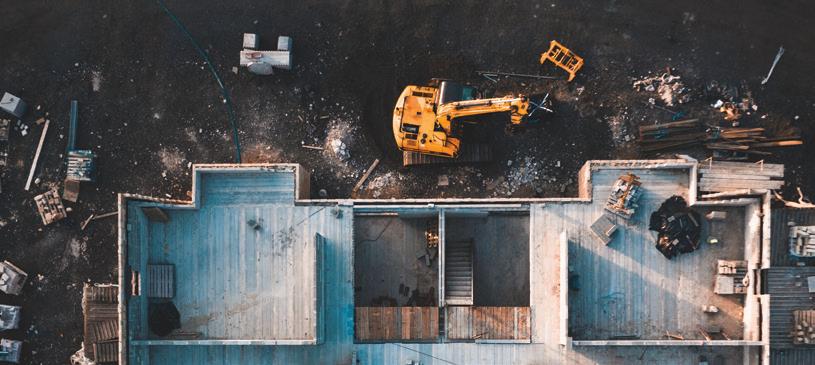
ALL IN NORTH CAROLINA
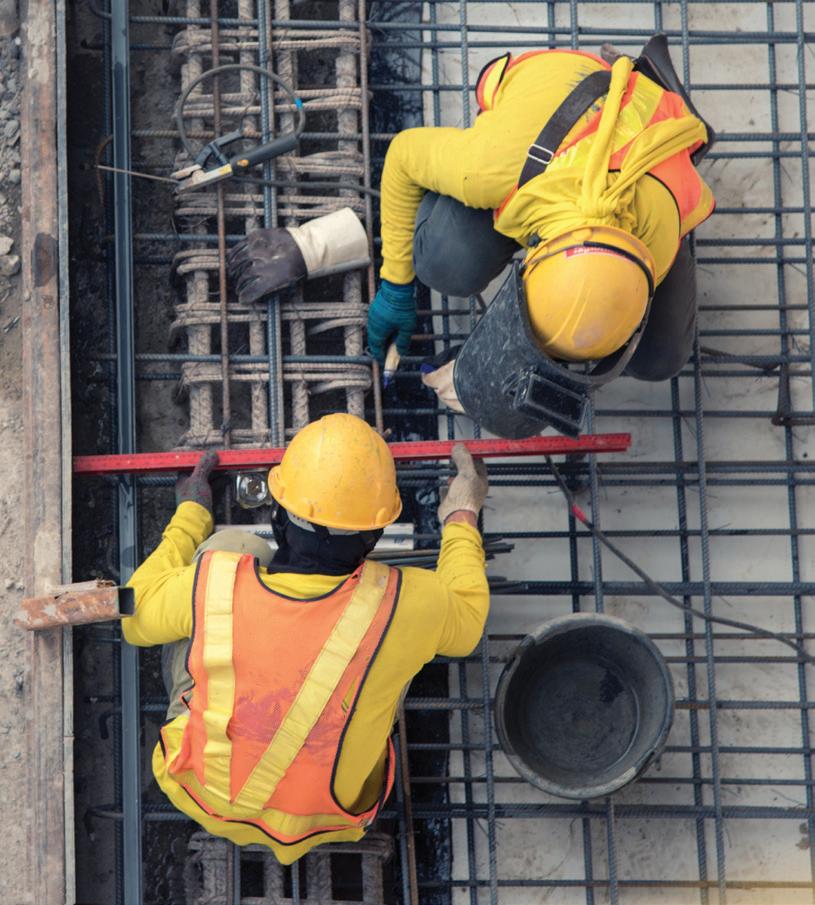
the current hiring environment, which is characterized by slower supply growth in the face of a rapid escalation in demand. Identifying locations with deep pools of cost-effective talent is no longer enough to guarantee a company can enter a new market as a preferred employer with a strong potential to attract and retain top talent over the longer term.
Ignoring a candidate market’s demand environment will significantly increase an employer’s near- and long-term risk. The COVID-19 pandemic accelerated the geographic distribution of hiring de -
mand across the United States. Demand share decreased in larger, more established costal markets and shifted to a wider variety of locations dispersed throughout the country.
For example, many high growth “Tier 2” talent markets offering sizable pools of quality talent at a significant cost discount to more established costal markets have seen dramatic spikes in the demand for their talent. In most cases, this demand growth has significantly outpaced the supply growth occurring through in-migration and new talent creation

within the local university pipeline. Because of this imbalance, many talent markets in metros like Nashville, Austin, Denver, Raleigh/Durham, and Atlanta are seeing higher rates of turnover and wage inflation than more traditionally competitive markets such as DC, Boston, Los Angeles, Seattle, and the San Francisco Bay area. This represents a major change in U.S. talent market fundamentals.
As employers encounter recruiting challenges, they’re increasingly incorporating the demand environment into their location selection process to avoid competitively saturated locations where it will be difficult to scale and retain headcount. The new goal is to identify markets with growing pools of specialized talent that have fewer competitive pressures and a more stable and predictable cost environment. This is leading many companies to break away from the herd by exploring smaller and previously off-the-radar talent markets with strong fundamentals and future growth potential.
Even within the three evaluation categories of supply, cost, and demand, companies are realigning on what individual decision drivers are important to them in each of these buckets. The following section explores each category in more detail to explain the most common metrics evaluated and how their importance may have changed since 2020.
Evaluation Categories
Talent supply generally includes any indicators related to the size and specialization of a local area’s workforce. It also includes measures related to the quality of the workforce such as educational pipeline, language skills, and diversity.
The most common evaluation metrics within this category include:
• Existing talent count (by job title and/or skill set)
• Existing talent density per 10,000 workforce (indicating a market’s specialization)
• Talent pool and population growth rates
• Recruiting radii *
• Unionization rates
• Net migration by skill set and age *
• Educational attainment levels
• Size of annual graduate pipeline by degree program*
• Size and breadth of the local university system
• Size and breadth of local workforce training programs
• Workforce diversity (racial/ethnic, gender and age/professional experience) *
* Factors with increased importance since the onset of the COVID-19 pandemic
Several of these supply-related factors are seeing an increased focus since the pandemic began in March 2020. Specifically, diversity, equity, and inclusion (DE&I); net talent migration; university pipeline size; and the likely target recruiting radii are all receiving increased scrutiny as companies evaluate new locations for hiring. Net migration and university pipeline are being used to assess the growth capacity of the local market and its ability to attract (or create) new qualified talent. Recruiting radii for talent has changed, particularly for industrial occupiers, and many companies are realizing that they are not able to draw candidates from as wide of a radius for lower-paying jobs that require full-time attendance.
DE&I is being actively considered by companies across industry sectors. This was accelerated in 2020 as a result of nationwide protests associated with racial inequality. Diversity is being measured in multiple ways including racial/ethnic identity, gender, and age. In some cases, companies are interested not only in the total diversity across a local population but are also keen to understand the “representation gap” between the overall local population compared to representation in the workforce for a particular industry sector or occupation group. For example, tech sector diversity in a given market may lag behind the local population overall. Some companies are seeking to take proactive roles in closing this gap by “fostering” greater diversity within their given industry by hiring a more diverse workforce more closely resembling the composition of the overall local population.
Talent cost covers factors related not just to the cost an employer pays in salaries/wages but also a market’s macro cost environment, which impacts an employee’s quality of life. For example, cost of living and housing is an increasingly important consideration in hiring strategies, especially as it relates to overall affordability compared to average local market wages. Markets with greater housing
EIGHT PUBLIC PRIVATE PARTNERSHIPS
Strengthening Michigan’s Talent Pool
Michigan’s No. 1 asset is its people — a workforce defined by integrity, grit, and a culture of innovation — who not only see what’s possible but rise to the challenge of making what may seem impossible a reality. To address today’s tight labor market, meet eight public private partnerships in Michigan producing everything from hands-on industry experience to semiconductor apprenticeships.
FORD AND THE UNIVERSITY OF MICHIGAN ADVANCE TALENT INNOVATION
Developed in cooperation with Ford Motor Company and the Michigan Economic Development Corporation, the University of Michigan (U-M) Battery Lab, a full-service, 9,000-squarefoot battery cell fabrication and testing facility, is helping to advance the battery and robotics fields.
Ford further partnered with U-M on the Ford Robotics Building. The 134,000-square-foot complex allows students to collaborate with industry in state-of-the-art autonomous aerial vehicle fly zones, walking robot obstacle courses, an imitation of Mars’ surface, and more.
PREPARING THE SEMICONDUCTOR AND TECH TALENT PIPELINES
Michigan has positioned itself as a leader in advocating for and supporting the semiconductor industry, from urging the passage of the CHIPS Act to developing workforce initiatives.
In May 2022, Michigan announced the $1.5 million Semiconductor Career and Apprenticeship Network (SCAN) Program grant. The SCAN Program will engage key microelectronics employers, end-users in automotive and manufacturing industries, and workforce development and education partners to build a more robust and knowledgeable talent pipeline for the industry.
Michigan’s collaborative approach to workforce preparedness is well underway in IT and computer science. Grand Valley State University’s Applied Computing Institute is connecting students with industry collaborators to solve computing problems, gaining the attention of Fortune 500 companies like Michiganbased Whirlpool. In Michigan’s Upper Peninsula,
Michigan Technological University and nearby printed circuit boardsmaker Calumet Electronics are partnering to bring hands-on manufacturing experience to engineering students.
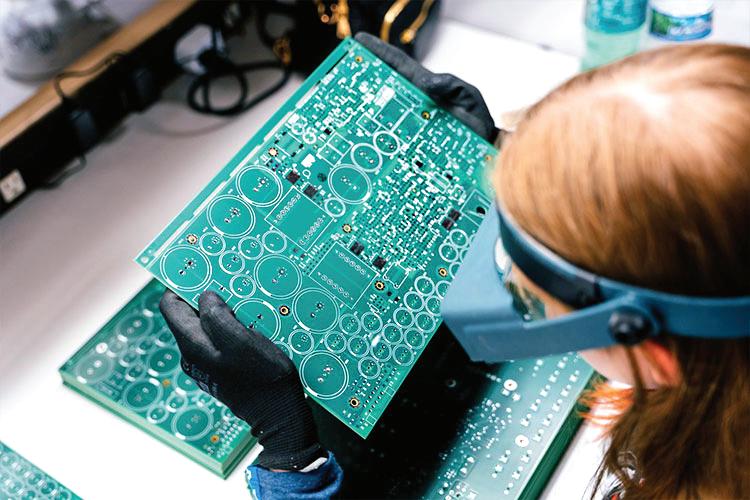
BUILDING AN EQUITABLE TALENT PIPELINE
Communities and institutions across the state are making sure Michiganders have access to quality K-12 education and beyond, readying them to jump into the workforce as skilled talent in their chosen professions and fill in-demand occupations.
The Detroit Regional Chamber’s Detroit Drives Degree is collaboratively working to increase the region’s post-secondary attainment rate from 43% to 60% and cut the racial equity gap in half. Meanwhile, the Urban Alliance in Kalamazoo partners with Kalamazoo Valley Community College and the Northside Association of Community Development to provide technical
training for unemployed and underemployed individuals.
At the state level, the Sixty by 30 Alliance, comprised of economic development organizations, colleges and universities, workforce development initiatives, and professional associations, is working toward 60% of working-age Michiganders to hold a certificate or college degree by 2030. Its programs include last-dollar scholarship program Michigan Reconnect and essential workers scholarship program Future for Frontliners, which have received over 170,000 applicants and counting.
Michigan is proactive and intentional in its workforce development as it prepares talent across the state for in-demand occupations that will innovate the future. Learn more about public private partnerships, tools and programs to support your corporate growth at MichiganBusiness.org
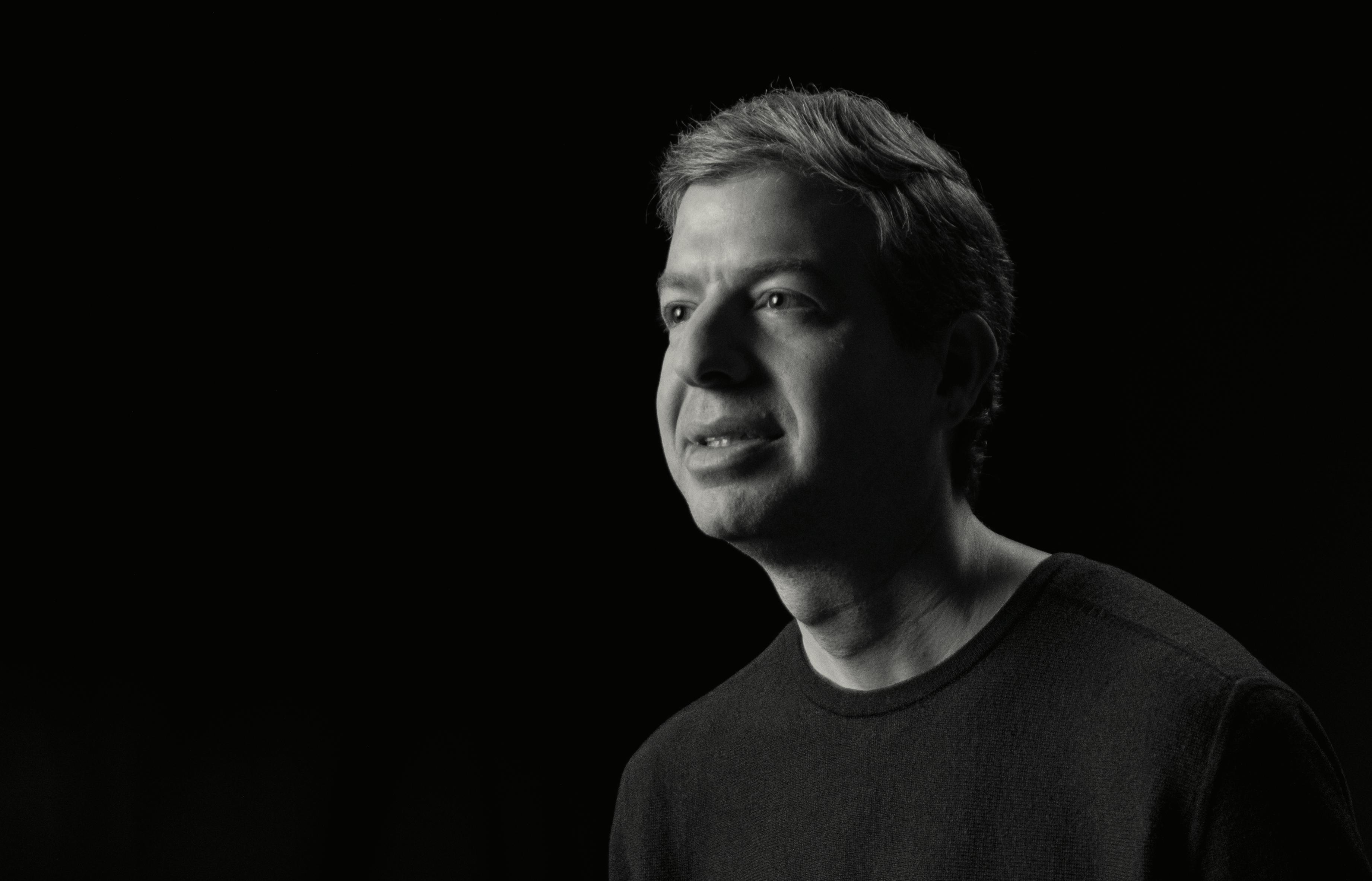
“
THE GRIT AND DETERMINATION WE HAVE IN MICHIGAN IS PREVALENT.”
Dreaming. Innovating. Growing. It's how Michigan talent is making an impact on the world in key industries. From tech to mobility to advanced manufacturing, there's a different kind of hustle here. Expand your business in Michigan and get access to support, camaraderie and new opportunities.
Make the move at michiganbusiness.org/pure-opportunity
THE CURRENT HIRING ENVIRONMENT is characterized by slower supply growth in the face of a rapid escalation in demand.
How Companies Are Navigating – Continued from page 43
affordability and a generally lower cost of living, and especially those with slower rates of growth in these categories, are viewed favorably in that employees will have more purchasing power in these locations and there will likely be less upward wage pressure and lower turnover risk.
The most common evaluation metrics within the talent cost category include:
• Current market wage/salary
• Local/state minimum wage policies (current and proposed)
• State/city taxes and fees (to be paid by employer)
• Wage inflation (1-, 3-, 5-year growth rates)*
• Housing cost as percent of average annual income*
• Cost of living*
• Change in cost of housing/living*
*Factors with increased importance since the onset of the COVID-19 pandemic
While talent cost remains a critical input in any talent strategy, the way cost is being evaluated has shifted. Companies are interested not just in the current talent cost today but also in the recent historical trajectory or rate of wage inflation. Markets with relatively lower talent costs that have recently experienced rapid year-over-year increases are avoided in favor of other lower-cost markets with less of an inflationary risk. Wage growth is seen as a major risk factor that can erode future cost savings potential and is typically indicative of an overheated talent market that will be more challenging for most employers.
Talent demand is the third primary evaluation category. As previously mentioned, this is a critical evalu-
ation category in today’s very tight talent environment, which gives candidates the upper-hand over employers. While talent supply addresses the total amount of talent, talent demand measures the volume of competition chasing that same talent pool as measured through unique active job postings. The comparison of supply versus demand helps determine a market’s likely saturation and thus the ability for a company to compete for talent in a given market.
The most common evaluation metrics within the talent demand category include:

• Total competitive job postings *
• Competitive job posting growth *
• Job postings vs. supply (hiring risk ratio) *
• Turnover rate *
• Wage inflation (cost and demand) *
• Company tenure *
• Time to fill job posts *
* Factors with increased importance since the onset of the COVID-19 pandemic
All of these factors are being featured more prominently in talent-based location strategies as employers struggle to attract and retain the volume of talent they need to support their business operations. Markets with a tighter ratio between talent supply and demand often exhibit higher rates of turnover, rapid wage inflation, and a demonstrated disadvantage in terms of the time to fill open job requirements.
In Sum
The COVID-19 pandemic accelerated the trend of geographically dispersed hiring particularly for
Top Talent. Top Companies. Arizona tops the list.

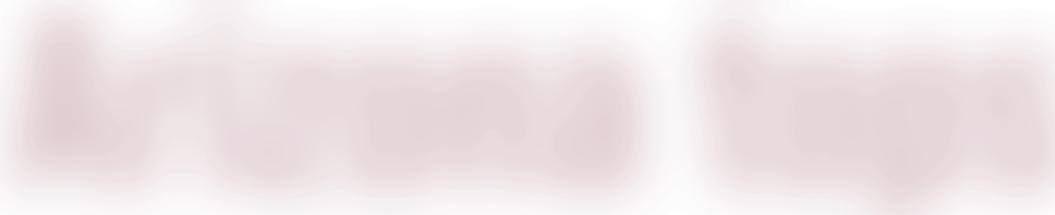

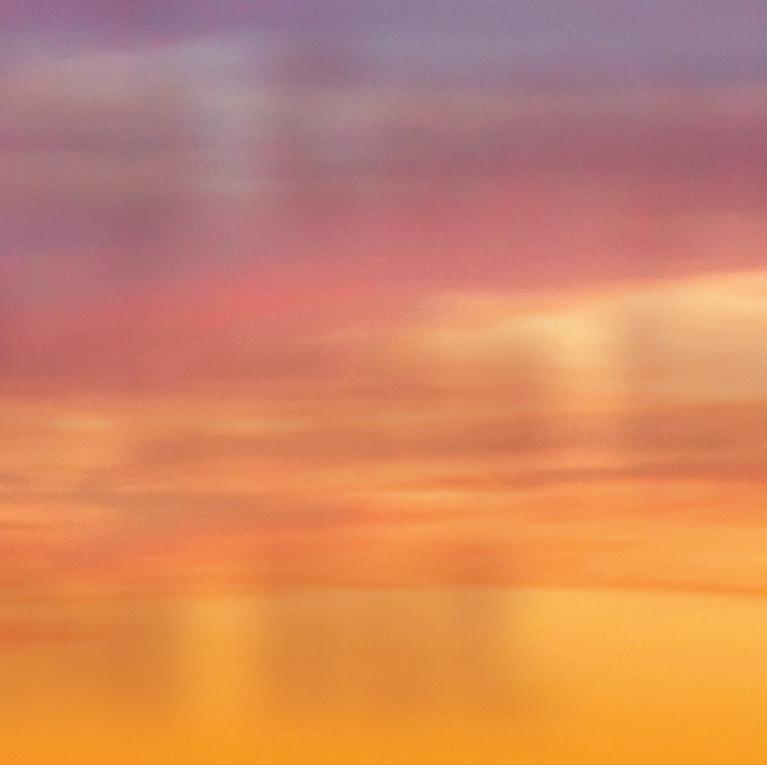
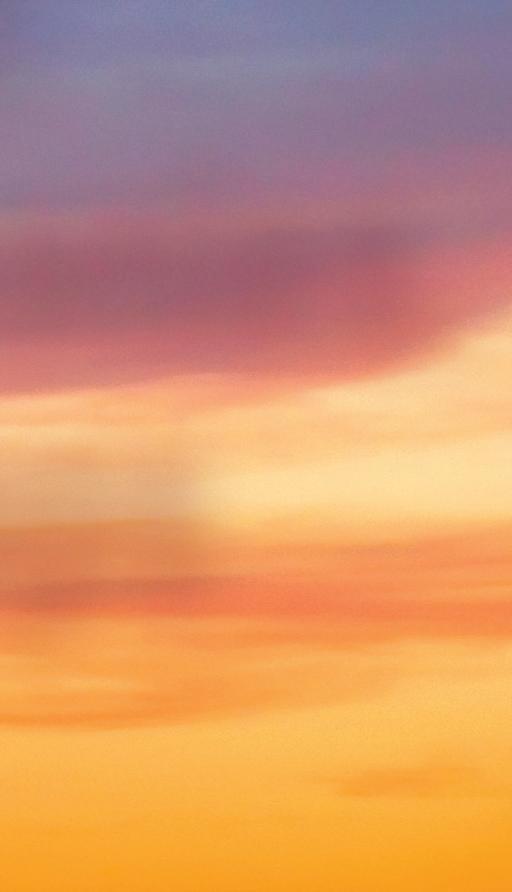



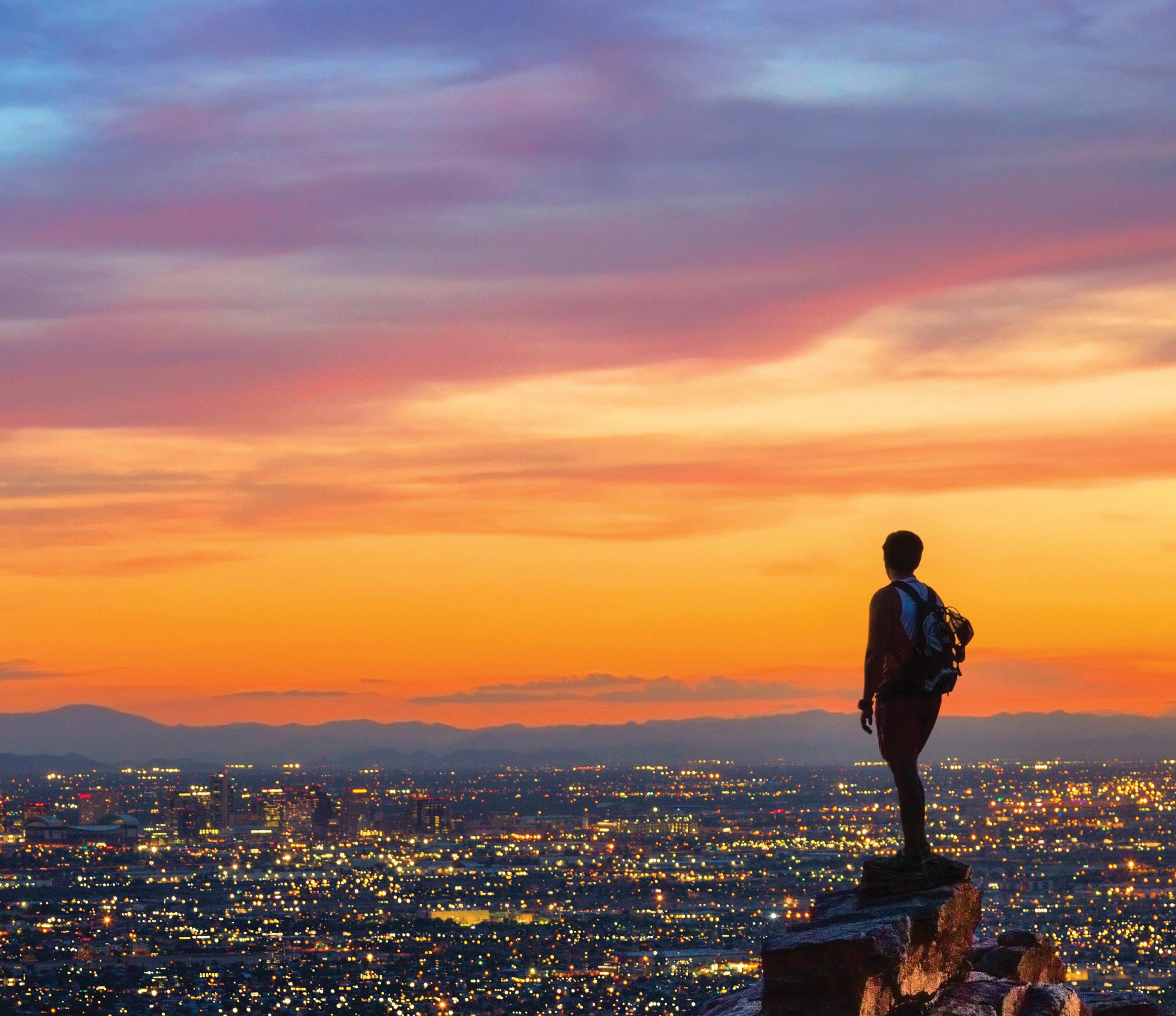
In Arizona, you’ll find the perfect balance of business opportunity and high-quality lifestyle that makes it a top state to live and work. Businesses benefit from pro-innovation policies and business stability. Residents enjoy a reasonable cost of living and beautiful scenery, all while taxes remain low for everyone. With a highly skilled talent pool and a commitment to future-forward industries like semiconductors, electric and automated vehicles and battery manufacturing, we’re maximizing our potential for generations to come.
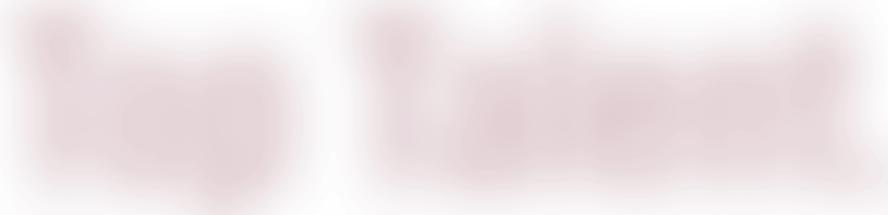
higher-skilled roles, such as tech and life sciences, that were historically highly clustered in a small number of mostly costal, gateway markets. This accelerated demand shift to a wider number of smaller markets has quickly changed the hiring landscape in these less established talent markets.



As a reaction to this, companies have become especially focused on the competitive environment
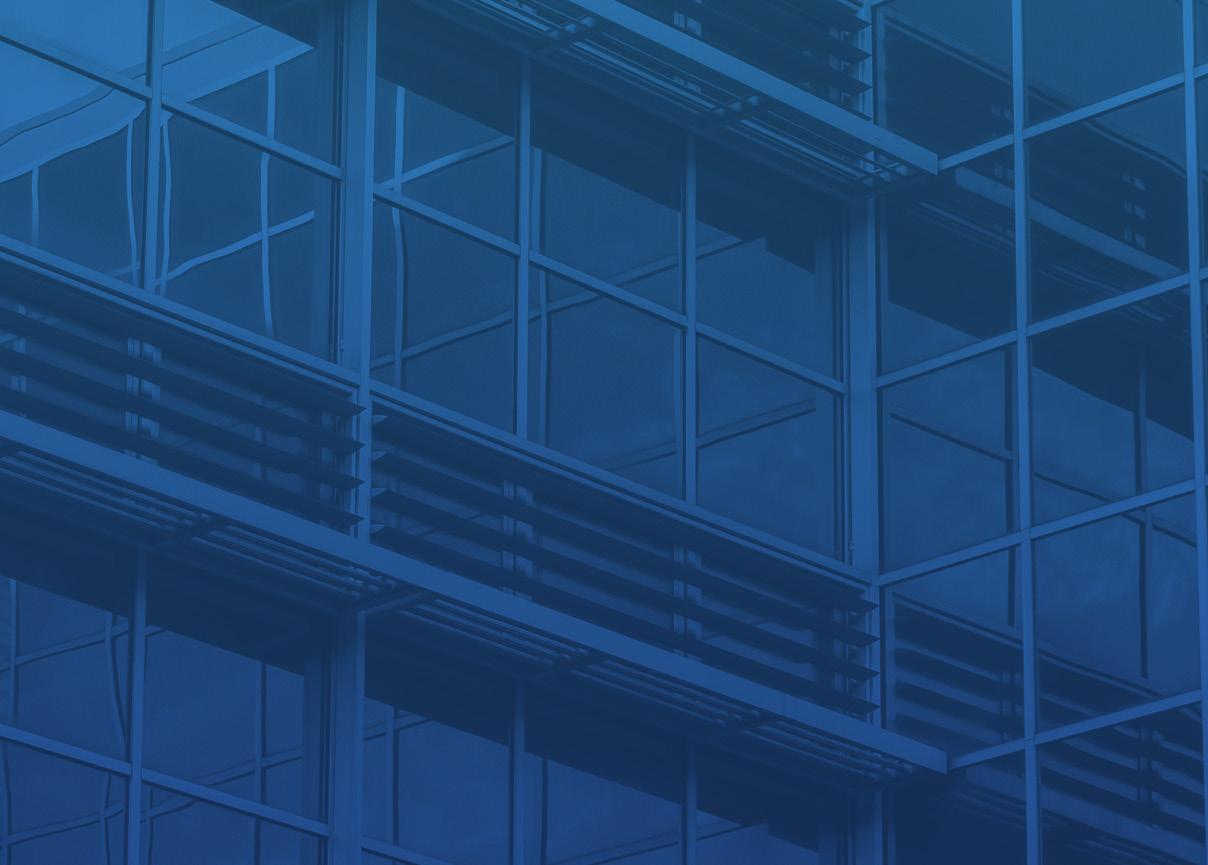
for talent as they’re considering new locations. Luckily, there remains a wide variety of markets in the United States offering specialized talent pools that are both cost-effective and have relatively lower levels of competition that can help employers achieve the coveted “employer of choice” status that positions them to attract and retain the top talent in the market over the long term. ~

TALENT SUPPLY generally includes any indicators related to the size and specialization of a local area’s workforce.
UNLOCKING LABOR ANALYTICS
While assessing a prospective location’s workforce may begin with a review of the data, a qualitative evaluation can provide new information not easily apparent from any desktop research.
There are few subjects about which more ink has been spilled in the last three years than the state of the U.S. workforce. From the impact of business shutdowns and enhanced unemployment benefits on labor participation, to pent-up challenges bringing critical supply chain workers to the verge of major strikes, and the more recent “quiet quitting” trend impacting even the most progressive office environments — HR and executive teams tasked with selecting new company locations are faced with more complexity than ever before. Even in the face of such fast-changing dynamics, growing companies must still
plan for a stable workforce, separating the short-term impacts from the long-term realities, and compare potential communities accordingly.
While none of us has a crystal ball, there are proven methods to evaluate and measure a community’s workforce “fit” for a specific project. In this evaluation, it is important to look not only at the data, but also at the qualitative factors that are specific to each market to ensure you can recruit competitively and retain the workforce needed to be successful.
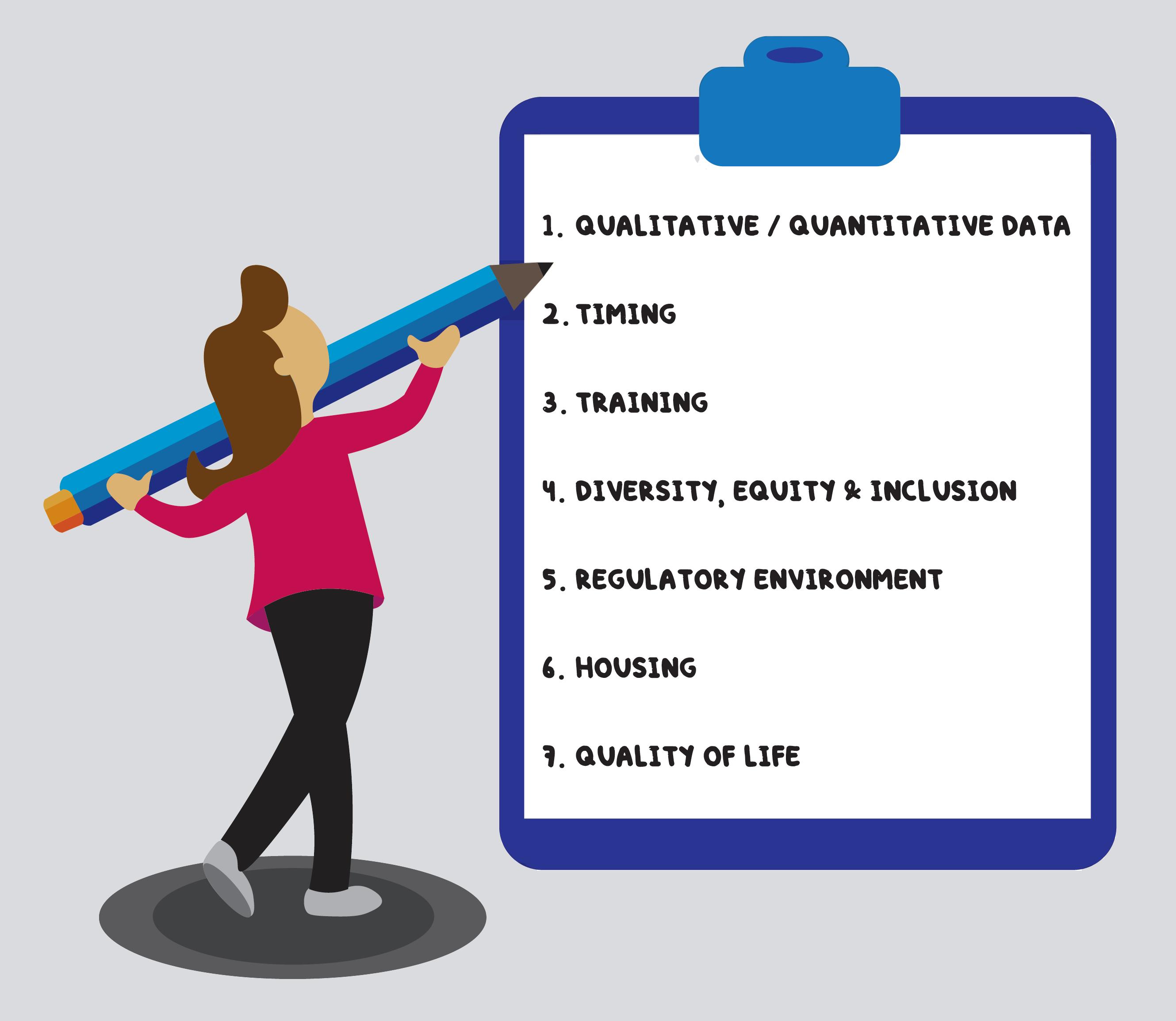
My team and I are spending more time evaluating labor than ever before, and it continues to be a major concern for our clients in making a final location decision. Our reports are comprised of both robust data analytics and thorough contextual examination of our client’s potential locations.
Quantitative
Our labor evaluations begin with a detailed look at a community’s workforce data: population size, population growth, average age, wages, labor participation, unemployment rates, etc. In addition to the community’s overall workforce, we use standard occupation classification (SOC) codes to analyze particular segments of the labor pool relevant to our client’s employment profile.
An important consideration when performing such an analysis is how to set the geographic region to evaluate. Employment data, especially for key metrics like wages, can be highly localized. Unfortunately, too
By Lauren Berry, Manager, Location Analysis and Incentives, Maxis Advisorsoften the data is reported at levels — such as by MSA or county — that skews its usefulness for evaluating a particular site or building. Some economic development organizations (EDOs) and research platforms report population and labor data using a mileage radius, which — particularly in any large metro — may vastly overstate the actual commutable area. Our team uses granular zip-code-level data based on driving distances to ensure accuracy in our methodology and reporting.
We also pay close attention to data trends. While not perfect (and COVID certainly added an interesting wrinkle to most data sets!), past performance is still the best predictor of future outcomes. Our team examines growth rates in population, industry metrics, wages, and other customized topics to understand a community’s dynamics and how our client’s needs fit into the long-term outlook.
Qualitative

In addition to the data review, as part of our labor analytics for site selection projects, we conduct dozens of interviews each year with existing employers across the U.S. to help our clients understand what’s working — and what isn’t — in local labor markets. This information can not only illuminate and contextualize the data trends but can also provide new information that won’t be easily apparent from any desktop research. Information about major competitors, shift schedules, wage pressures, community dynamics, and other variables are factors all decision-makers should be investigating as they select a new location for any type of operation.
Key Issues
• Time — COVID left us with many lessons, but for the U.S. workforce, the most significant realization may be that life is short and precious — leading many employees to reassess their work-life balance. Understanding how your competitors are approaching this issue in your finalist locations can ensure you can meet prospective employee expectations and be competitive in hiring.
In some communities, this trend has impacted how employers are scheduling shifts. In particular, workers are pushing back against mandatory overtime or shift schedules extending five, six, or seven days. Many manufacturers and distributors who can shift to a schedule of four 10-hour shifts with a three-day weekend, or even three 12-hour shifts, and still meet production requirements, are doing so. It is important to understand how your preferred shift schedule fits with what’s offered in your target community (or provides an alternative not currently in the market).
In communities that have seen a slower rebound to pre-COVID labor participation rates, this is sometimes due to factors such as childcare availability or schooling impacting working parents. To account for this, some companies are supplementing with part-time opportunities to replace full-time roles or backfill absent employees where needed. I’ve heard from companies hosting job fairs for part-time-only roles for which they’ve received hundreds of applicants — among them, parents needing a second income, college students, or even baby-boomers who have retired but may want to reenter the workforce
WHILE NONE OF US HAS A CRYSTAL BALL, there are proven methods to evaluate and measure a community’s workforce “fit” for a specific project.
less than full-time. This move to include part-time roles can take some time to accomplish but can help companies tap into an additional pool of candidates not currently participating in the workforce or underemployed in part-time service roles.
• Training — Just as every community is “a great place to do business,” you’d be hard pressed to find a community without an extensive workforce development ecosystem. Nearly every city and county has resources in place — regionally, if not locally — to support workforce development for groups ranging from K–12, technical, and community college students to exiting service members and formerly incarcerated persons. Without clear quality indicators to provide benchmarks, it can be confusing and difficult to assess a community’s workforce resources and their ability to provide customized training and qualified candidates for your project.
A great place to start is identifying existing programming for alignment with your skill and credential needs. Visit the training centers to view equipment and speak to instructors about coursework. Request the school’s data on enrollments, graduations and credentials earned, and placement. Ask about partnerships serving middle- and high-school students. Are the existing industries engaged and providing hands-on opportunities to explore students’ career pathways?
If your company’s needed training isn’t available, or existing programming needs to be tailored to meet your needs, ask for case studies based on similar efforts for other projects. Get feedback from the HR teams of existing companies using the training to understand its ease of use, flexibility, and ability to meet relevant industry standards.
Finally, don’t discount the importance of training and leadership development for non-production roles. Turnover data reveals what most of us already know anecdotally: workers don’t leave bad companies; they leave bad bosses. Due in part to the wave of early retirements — which is still ongoing — there is a tremendous gap in leadership development for the first-time managers who fill many supervisor positions. It is important for decision-makers to understand what a community’s resources are for training not only technical skills but interpersonal, communication, and management skills for these roles as part of their training plans, as well as supporting existing
internal company training programs.
• Diversity, Equity, and Inclusion — As the national conversation about company stewardship in environmental, social, and governance (ESG) areas has progressed, it is important to consider how your company’s priorities for diversity, equity, and inclusion (DEI) can be met in the community you select. This begins with learning about the diverse populations and their history in each community you are evaluating, as well as how an equity and inclusion framework is part of the existing workforce and education programs. The history, population composition, and culture of your final location can support (or hinder) your company’s ability to successfully build an equitable and inclusive team, so it should not be ignored in the evaluation process.
• Regulatory Environment — Another factor employers want to evaluate in their location decision is the region’s legalization of marijuana for medical or recreational purposes. In states that have any form of legalized use, as well as states with stricter controls, employers and staffing agencies are seeing higher incidences of THC on pre-employment drug-testing panels. Many manufacturers and transportation industry employers maintain a zerotolerance policy for safety and insurance reasons, but many others have chosen to relax their standards. If your company is considering a new location in a state that’s legalized cannabis for any purpose, it is important to evaluate how that will impact your potential labor pool based on your company’s policies and insurance requirements.
• Housing — Another factor often missed or neglected in a location decision is the community’s available housing at all price points. We’ve seen many communities interested in recruiting manufacturing and distribution operations that aren’t willing to support multifamily housing or affordable single-family developments. Evaluate a community’s number of new units built and pipeline of new developments to ensure that your workforce can sustainably commute a reasonable distance to the facility and that the community’s housing can support a growing workforce.
• Quality of Life — Quality of life is one factor that is hard to pin down but remains as important as
ever for every type of workforce. The important thing to remember when comparing multiple locations is that quality of life often means different things to different types of workers and different generations. Quality of life for recent graduates often means walkable urban communities, outdoor recreation assets, and entertainment amenities, while quality of life for mid-career professionals may place more emphasis on excellent schools, lower commuting times, and familyoriented amenities. If you can’t have all of these in one place (which is often the case), understand the workforce you’re targeting (or relocating) and how to choose a location that can meet those needs.



In Sum
The question of how long this new normal dynamic will last is an open one. As the economy moves into a potential recession, employees may lose some of the leverage they’ve been accustomed to through the pandemic. As labor costs continue to increase, our clients are also investing heavily in automation to reduce their labor profile. While this is nothing new, it indicates that more changes are in store for the talent market of tomorrow. This is why it is essential to conduct a multifaceted evaluation of your potential locations to ensure long-term success in your location of choice, as well as periodic evaluations of your market once you are operational to ensure you are adapting to stay competitive as an employer of choice in your new home. ~


WHAT OPPORTUNITY LOOKS LIKE.
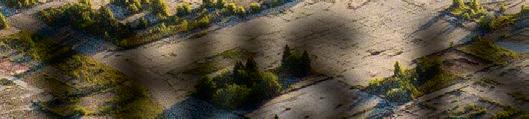
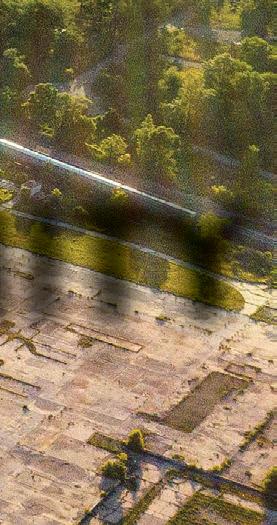
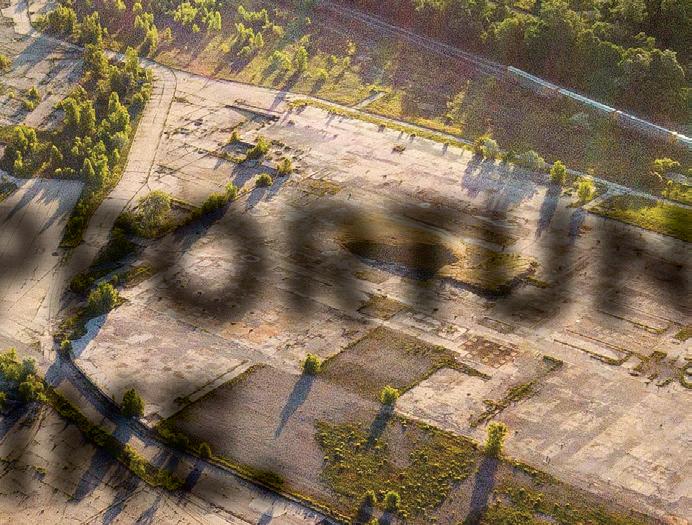
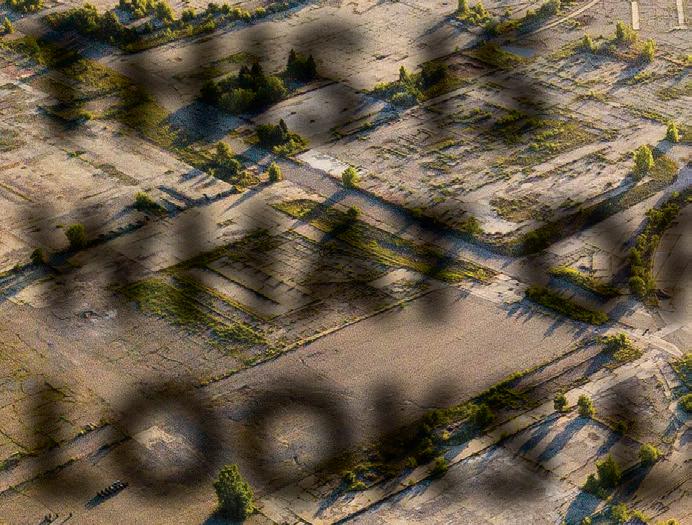
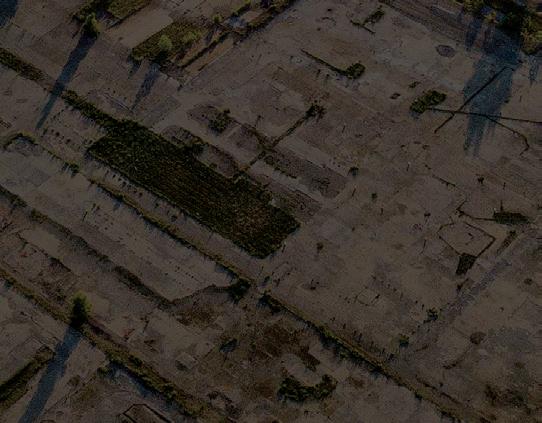
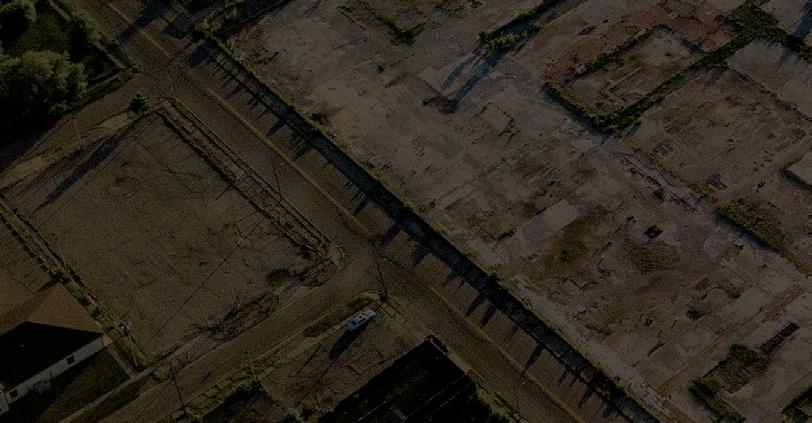
REPRIORITIZE DIVERSITY, EQUITY & INCLUSION INITIATIVES
Manufacturers must reprioritize their DEI efforts in order to acquire and retain the best talent, which will lead to enhanced employee performance and increased innovation.
Amid increasing recession concerns and mounting pressure from key stakeholders to mitigate supply chain disruption risks, industrial products (IP) sector leaders continue to grapple with workforce issues, leaving social commitments like DEI initiatives to fall to the back burner. These initiatives involve strategies to attract and retain a diverse workforce, implementing programs
to increase inclusion, and supporting community values, all while measuring company progress for accountability along the way. With so many investors increasingly advocating for improved DEI efforts, it is no longer a nice to have, but a must. If manufacturers continue to let DEI fall to the wayside, they risk losing potential candidates who can bring creative innovation,
Survey Reflects Need to Reprioritize DEI
77 percent of industrial products (IP) sector leaders agree that problems surrounding talent acquisition and retention pose risks to their business.
69 percent describe their businesses as “very or moderately” agile in responding to the shifts in the workforce and in attracting talent.
64 percent of IP executives are already embracing flexibility, expanding permanent remote work options in roles that allow for it.
By Terri McClements, DEI Consulting Leader, PwC Workforce Transformation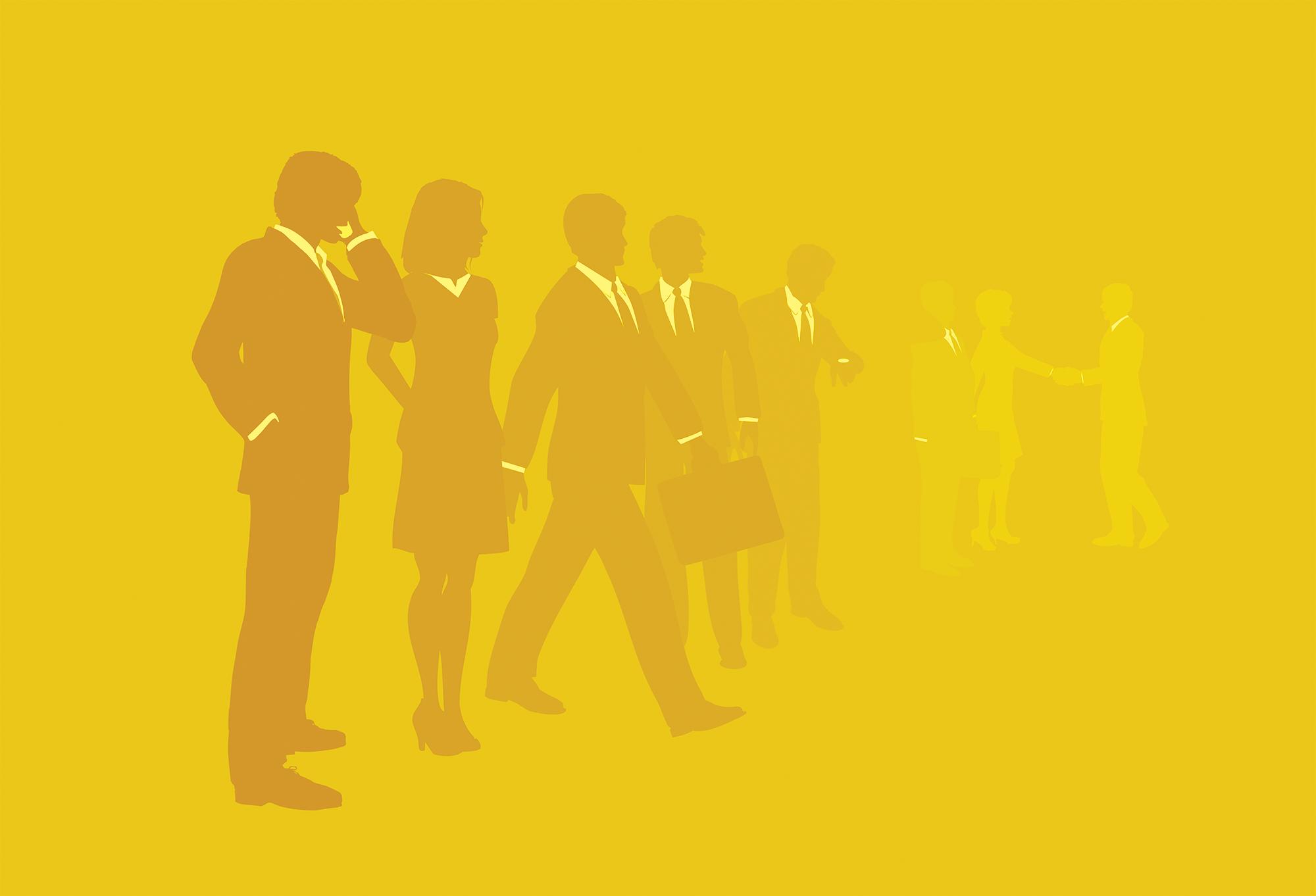
drive equitable outcomes. With all the challenges that manufacturers are currently facing, managing and improving DEI initiatives to elevate talent acquisition and retention is not something on which to lose focus.

PwC’s Managing Business Risks Pulse Survey 1 recently found 77 percent of IP sector leaders agree that problems surrounding talent acquisition and retention pose risks to their business, and 71 percent say that supply chain woes pose either a moderate or serious risk. Despite the challenging workforce environment, most IP leaders (69 percent) describe their businesses as “very or moderately” agile in responding to the shifts in the workforce and in attracting talent. PwC’s survey found that 64 percent of IP executives are already embracing flexibility, expanding permanent remote work options for roles that allow for it in an effort to attract a more diverse talent pool. As manufacturers look to manage shifts in talent among existing supply chain woes, it is important that they reprioritize DEI efforts into their retention strategies as well, to deliver on DEI promises in ways that will build trust with their workforce and improve the employee experience.
With manufacturers taking on more ambitious business and societal goals, leaders must remember that employees can be a force multiplier or a detractor, as talent management directly impacts overall growth. Understanding workplace power in all its aspects can help leaders energize their workforce, tap into the power of their people, and accomplish bolder goals. This starts with understanding your employees’ needs and values and creating an inclusive environment for your workforce to thrive.
DEI Talent Management
When it comes to DEI in the workplace and retaining employees, compensation is a top factor, especially given the historic increases in inflation in recent months, which are projected by many economists to continue in the year ahead. We recently found that men were more likely than women to say they’re fairly rewarded financially and were 9 percent more likely than women to say they planned to ask for a raise. 2 Both of these findings appear to reflect longstanding problems in wealth inequity, and they highlight the need to advance not only the gender-equity agenda — in relation to pay transparency and higher female participation in the labor force — but also the need to advance DEI efforts as a whole in the industry.
Historical data shows that the manufacturing industry is a white and male-dominated field, which makes it even more difficult in trying to change its perception and attract a wider representation of diverse, female cohorts. As of 2021, the manufacturing industry still consisted of roughly 80 percent white workers and only 30 percent women in total. 3 For manufacturers, expanding DEI initiatives will continue to become more important, as the industry continues to struggle with drawing new, diverse talent into its ranks.
IP organizations are making strides in helping to translate DEI strategy into action, though there is still work to do in the industry. As employees, customers, and investors increasingly demand that the organizations they do business with model values of equity and inclusion, organizations have invested
WITH SO MANY INVESTORS increasingly advocating for improved DEI efforts, it is no longer a nice to have, but a must.
at unprecedented rates in DEI programs, with 75 percent of IP organizations now saying it is a value or priority, according to our latest Diversity & Inclusion Survey. 4 Despite this heightened commitment, organizations still have progress to make in designing and executing DEI programs that meet these objectives, with about a third of industrial products respondents indicating that they still view diversity as a barrier to employee progression. Similarly, nearly half of IP organizations surveyed (44 percent) view their DEI program primarily as a way to attract and retain talent, but far fewer are connecting DEI directly to responding to customer expectations or enhancing the external reputation. So, what’s causing this disconnect?
One reason to account for this dissonance between what organizations are doing versus employee perception is that organizations are failing to empower their leaders on topics of DEI. Against our DEI maturity model, 80 percent of leadership engagement on DEI remains at the basic or emerging levels, and only 6 percent of surveyed IP organizations’ DEI programs reach the highest level of maturity when assessed against the four dimensions of PwC’s DEI maturity model. A lack of knowledge on social issues that are valuable to your workforce and key stakeholders will only hinder the innovation and enhanced performance that could be achieved with increased diversity and inclusion in the workplace.
DEI Measurement
Driving sustainable change requires effective monitoring efforts. Most organizations track employee demographics, but significantly fewer measure discrepancies in compensation, performance, or promotions based on these attributes.
Success cannot be measured without a clear picture of where you are now — and where you want to go. The journey begins by capturing the status of DEI programs and policies via metrics on DEI-related employee recruitment, hiring, retention, and promotions, as well as employee exits. It continues by responding coherently to the outcomes of the various programs and policies. Measuring diversity is nothing new to most organizations; however, measuring inclusion (the degree to which an employee feels valued, respected, welcome, and understood) can be a challenge.
As the conversation around measuring inclusion continues to grow in value, IP leaders need to take
time to align and map out strategies for how they want to measure progress on DEI initiatives and meet employee needs around transparency. Considering employee perspective in creating benchmarks for inclusion and determining what it is that makes them feel most valued when it comes to DEI and related social issues will be key in developing strong measuring standards for accountability.
By holistically measuring employee demographics in addition to tracking progress on supplemental DEI goals, industrial products leaders have an opportunity to grow engagement with key stakeholders through transparency and to lower the disconnect in employee perception. Transparency is the foundation of building trust, and measuring your DEI goals, especially in an industry that historically lacks diversity in the workplace, will show your employees that you’re serious about change and following up on your commitments. With 71 percent of employees saying they’re likely to leave a company if they lose trust in their employer,5 it is imperative that manufacturers leverage DEI reporting tools to build trust with their employees through transparency and accountability.
Consistency Is Key
In addition to prioritizing DEI programs and measuring and tracking progress, consistency is also key. In order to maintain structure, leaders have to stay consistent with building trust. DEI success hinges on executive leadership, and IP leaders can’t afford to stand on the sidelines for these issues. By following through on DEI promises and continuing to look for new ways to improve, the industry can seek to change issues of inclusion in the workplace and attract more candidates in the future who align with company values.
It is important that IP leaders realize that their people are the most important asset that their organization has. With all of the challenges the manufacturing industry is facing, DEI is not something that can be put on hold. If IP leaders hope to remain agile in today’s shifting workforce environment, they must reprioritize and re-strategize to put employee needs first, and that starts with delivering on DEI. ~
1 https://www.pwc.com/us/en/library/pulse-survey/managing-business-risks. html#sectors
2 https://www.pwc.com/gx/en/issues/workforce/hopes-and-fears-2022.html#retentionstrategies
3 https://www.bls.gov/cps/cpsaat18.htm
4 https://www.pwc.com/gx/en/services/people-organisation/global-diversity-andinclusion-survey.html
5 https://www.pwc.com/us/en/services/consulting/library/consumer-intelligence-series/ trust-new-business-currency.html
SPONSORS
ALABAMA
Alabama Department of Commerce
The Alabama Department of Commerce is the state’s lead economic development agency. In addition to business development activities, Commerce promotes exporting and international opportunities for Alabama companies, assists small businesses, and positions the state for film productions. Commerce is home to the state’s primary workforce development program, AIDT.
Greg Canfield, Secretary
Alabama Department of Commerce 401 Adams Ave., P.O. Box 304106 Montgomery, AL 36130-4106 800-248-0033
contact@madeinalabama.com madeinalabama.com
ARIZONA
Arizona Commerce Authority
The Arizona Commerce Authority (ACA) is the state’s leading economic development organization with a streamlined mission to grow and strengthen Arizona’s economy. The ACA uses a three-pronged approach to advance the overall economy: attract, expand, create — attract outof-state companies to establish operations in Arizona; work with existing companies to expand their business in Arizona and beyond; and help entrepreneurs create new Arizona businesses in targeted industries.
Sandra Watson, President & CEO
Arizona Commerce Authority (ACA) 100 N. 7th Ave., Suite 400 Phoenix, AZ 85007 602-845-1200 AZcommerce.com
ARKANSAS Arkansas Economic Development Commission
The Arkansas EDC creates economic opportunity by attracting higher-paying jobs, diversifying local economies, increasing investment, and generating growth throughout Arkansas. Arkansas is a pro-business environment operating leaner, faster, and more focused through a streamlined state government that acts on corporate interests quickly and decisively.
Clark Cogbill, Director of Marketing
Arkansas EDC
1 Commerce Way, Ste. 601 Little Rock, AR 72202 501-682-5996
ccogbill@arkansasedc.com arkansasedc.com
IOWA
Iowa Economic Development Authority
Explore Iowa, U.S. News & World Report’s #1 state for opportunity. Iowa’s thriving economy is fueled by a pro-business environment, low operating costs, and a skilled workforce. The state is also moving toward having one of the most competitive corporate tax structures in
the nation. Learn more about available sites and Iowa’s Certified Sites program at IowaEDA.com/locations.
Iowa Economic Development Authority 1963 Bell Ave., Suite 200 Des Moines, IA 50315 515-348-6200 www.iowaeda.com/locations/
MICHIGAN
Flint & Genesee Economic Alliance
The Flint & Genesee Economic Alliance, located in Genesee County, Michigan, is invested in your success — ready to connect you to the resources, partnerships, and incentives your business needs to thrive. Our dedicated team will work with you every step of the way toward reaching your goals.
Tyler Rossmaessler, Executive Director
Flint & Genesee Economic Alliance
519 S. Saginaw St., Suite 200 Flint, MI 48502 810-600-1404 info@flintandgenesee.org developflintandgenesee.org
Michigan Economic Development Corporation
The MEDC markets Michigan as the place to do business, assists businesses in their growth strategies, and fosters the growth of communities across the state. The mission of the MEDC is to achieve economic prosperity for Michiganders by investing in communities, enabling the job growth, and promoting Michigan’s image worldwide.
Susan Proctor, Director, Strategic Initiatives, Growth and Development Michigan Economic Development Corp. 300 N. Washington Sq. Lansing, MI 48913 517-719-0393/888-522-0103 proctors1@michigan.org Michiganbusiness.org
MISSOURI
Missouri One Start
Missouri One Start provides a tailored workforce strategy to address your unique business needs. At no cost to eligible businesses, the team at Missouri One Start will customize services ranging from pre-employment screening and recruitment to designing jobspecific training both during and after the onboarding process.
Kristie Davis, Director
Missouri One Start P.O. Box 478, 301 W. High St. Jefferson City, MO 65102 573-526-9239 MissouriOneStart.com
NORTH CAROLINA
Economic Partnership of North Carolina North. South. East. West. No matter where you look, North Carolina is the
home of endless opportunity. From the mountains to the coast, everything that makes life fulfilling can be found right here, right now. Named America’s Top State for Business 2022 by CNBC. Economic Partnership of North Carolina Wells Fargo Capitol Center 150 Fayetteville St. #1200 Raleigh, NC 27601 919-447-7777 https://edpnc.com/
OHIO
JobsOhio
JobsOhio is Ohio’s private economic development corporation that highlights Ohio’s unique competitive advantage. JobsOhio works outside, but alongside, state government to support the creation of jobs and act as a catalyst for highgrowth business investments to propel the state’s talent, innovation, and economic diversification and prosperity forward.
Nick O’Bruba, Marketing Director JobsOhio 41 S High St. #1500 Columbus, OH 43215 330-207-9034 JobsOhio.com
PENNSYLVANIA
Lehigh Valley Economic Development Corporation Lehigh Valley, Pennsylvania, is a short trip from both New York City and Philadelphia. We’re home to 15,000 businesses and have the fastest-growing population in the key 18–34 age group in Pennsylvania.
LVEDC markets the Lehigh Valley’s economic assets, creating partnerships that attract employers, help businesses grow, and address talent supply needs.
Don Cunningham, President and CEO Lehigh Valley EDC 520 N. New St. Bethlehem, PA 18018 610-266-6775 www.lehighvalley.org
VIRGINIA
Virginia Economic Development Partnership
Virginia continues to raise the bar when it comes to talent development. Programs such as the Virginia Talent Accelerator Program and the Tech Talent Investment Program make sure Virginians are prepared for the jobs of today and the future.
Jason El Koubi, President and CEO
Virginia Economic Development Partnership
901 East Cary Street Richmond, VA 23219 804-545-5600 info@vedp.org www.vedp.org
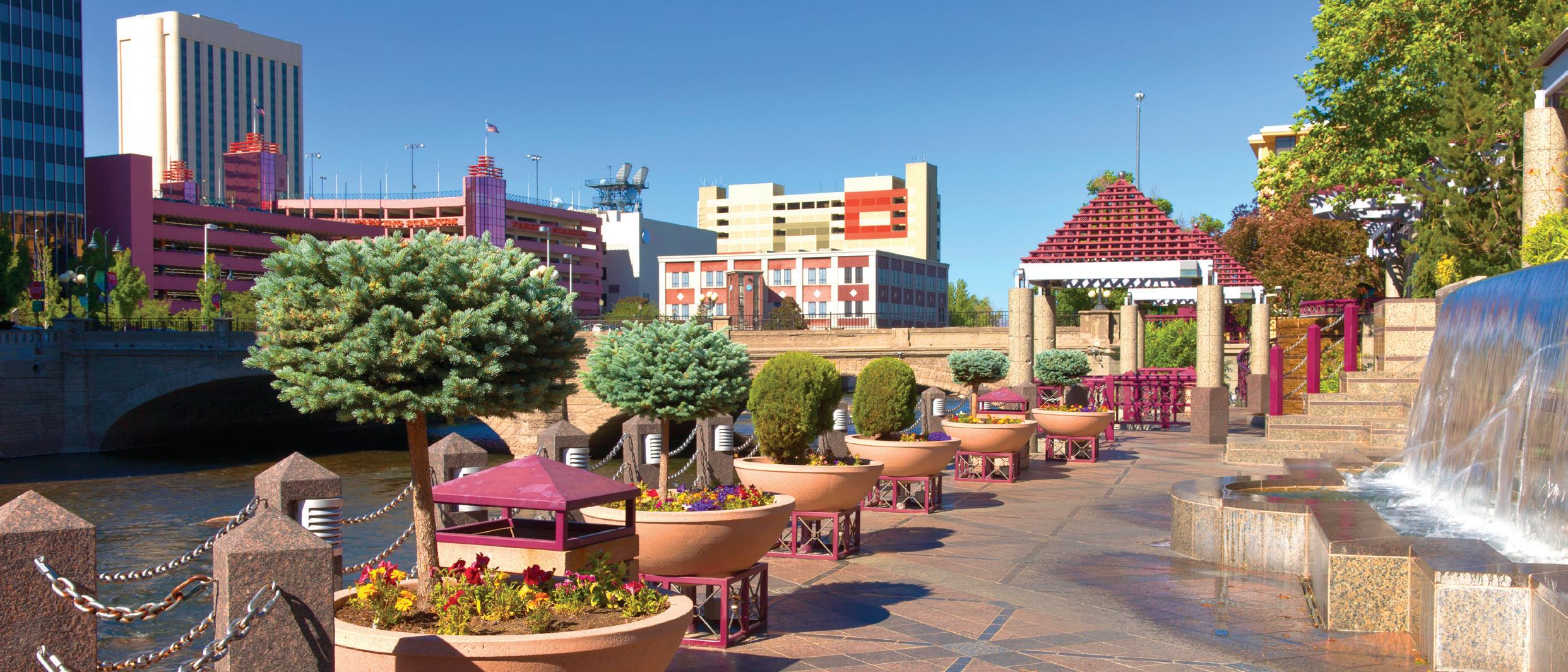
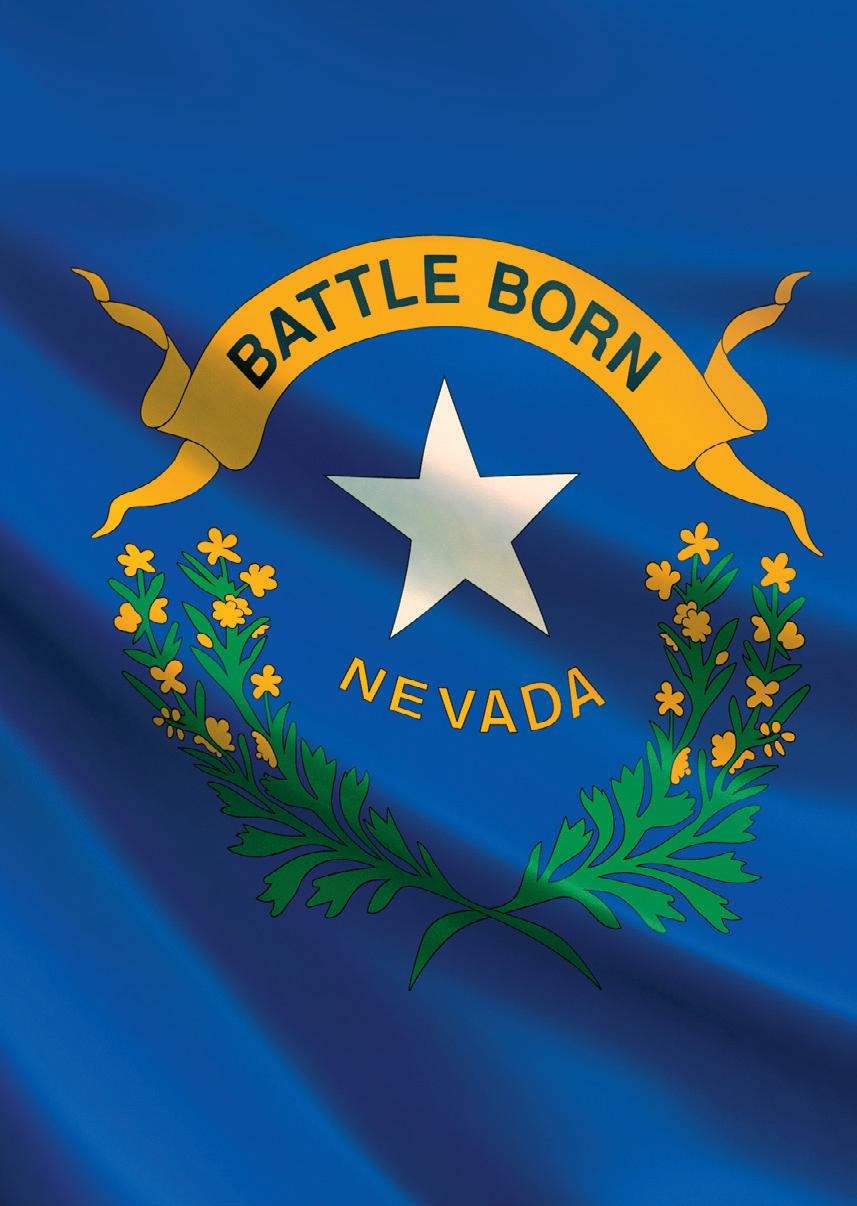
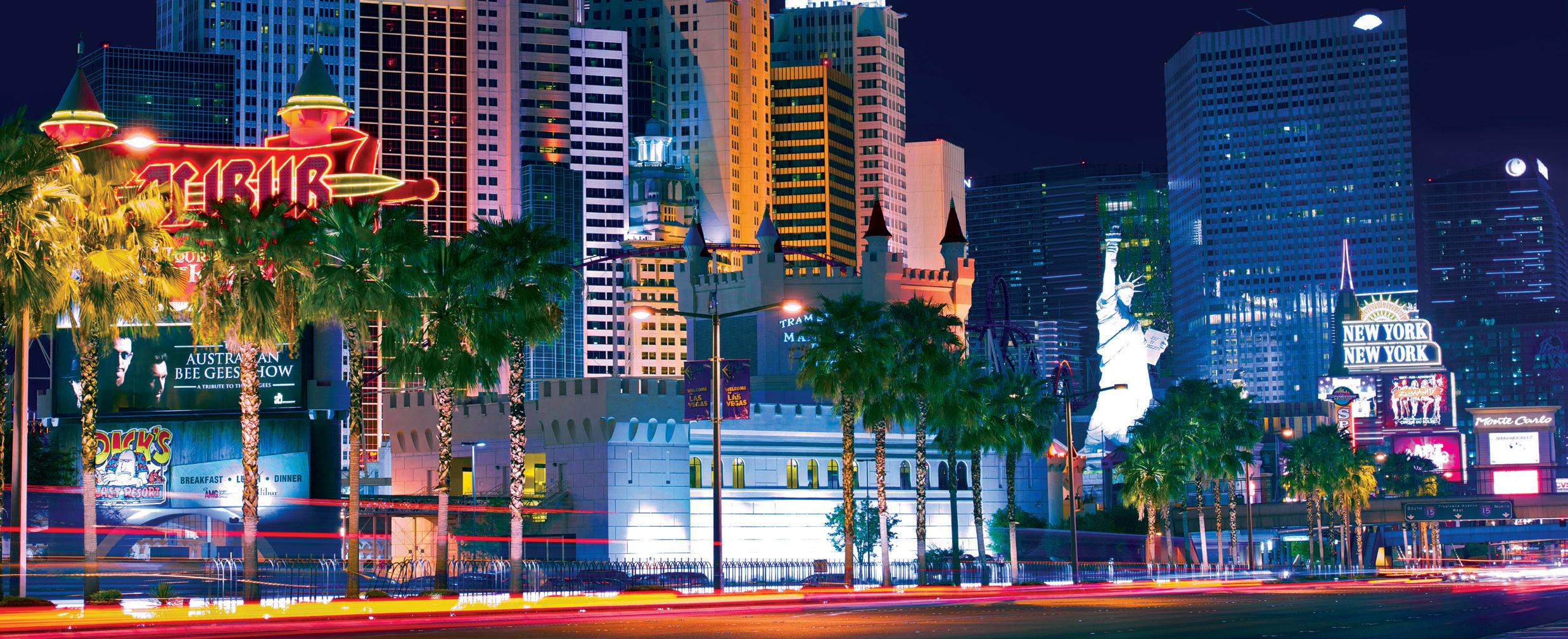
Products coming out of U.S. centers of innovation are ramping up the economies of cities/regions across the country, shortening critical supply lines, and, in the case of some newly announced projects, helping ensure national security. Some of the breakthroughs will eventually find their way into space missions.
These hubs of innovation stretch from coast to coast. Following is a look at what a selection of these centers are doing to push their respective technological envelopes.
INNOVATION CORRIDORS
From robotics to EVs, from semiconductors to the life sciences, metro and regional hubs of innovation are advancing economic development across the nation.
BY JOHN MCCURRYA Robotics Hub
Pittsburgh has long been a nexus of robotics research. The Wall Street Journal nicknamed the city “Roboburgh” more than 20 years ago. In the ensuing years, robotics has continued to help the city emerge from its Rust Belt reputation of the last century. Robotics R&D has accelerated over the past decade, and the city is now one of the leading U.S. centers of robotics development. From autonomous vehicles to aerospace to warehousing and logistics, estab -
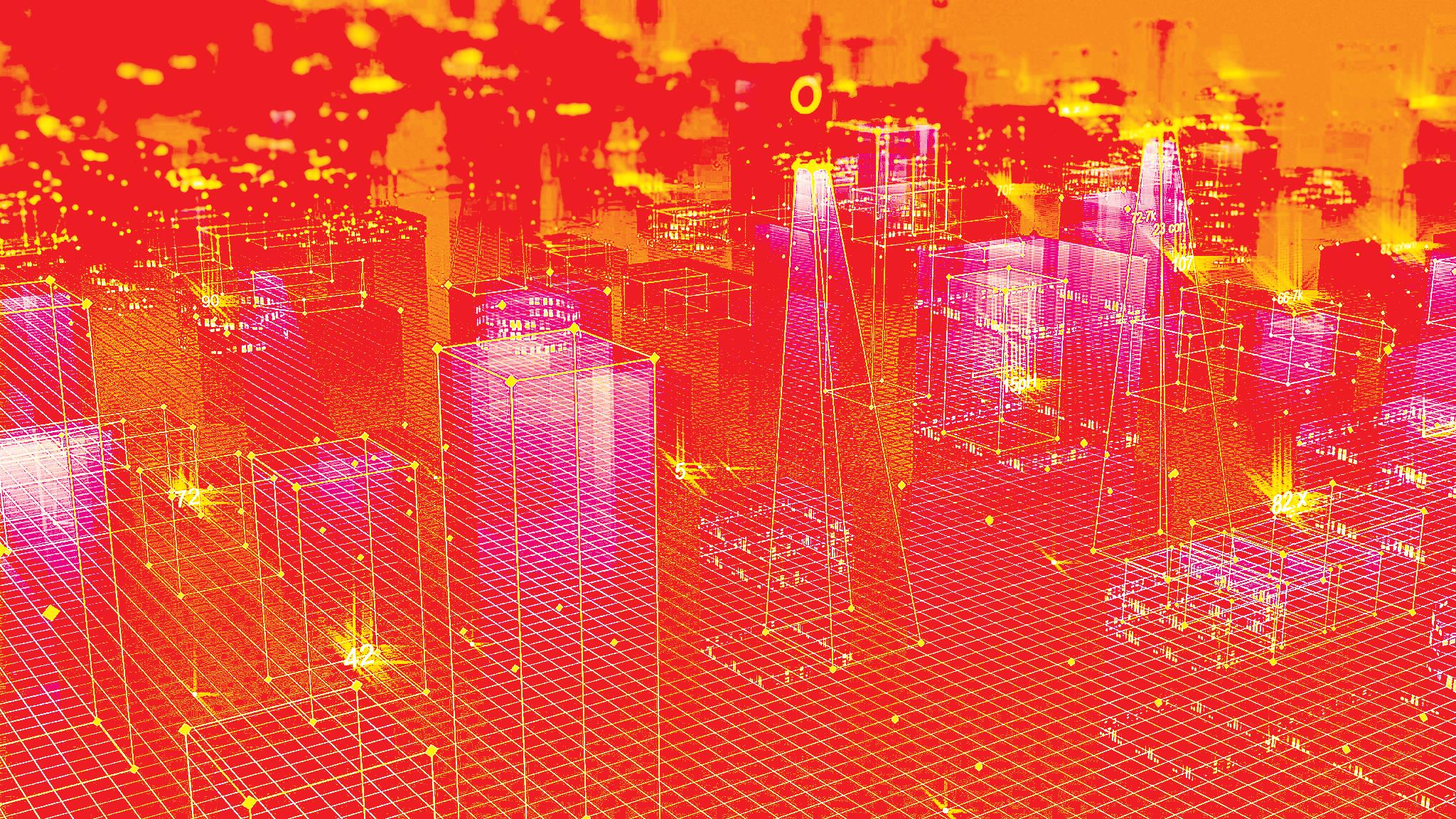
lished firms and startups are exploring new frontiers in robotics.
The city’s Carnegie Mellon University has a long history as a center of developmental research related to robotics. A report released by the university in late 2021 credits the university’s National Robotics Engineering Center (NREC), founded 26 years ago, as being the catalyst for a “dramatic transformation of the Pittsburgh economy, the region, and the robotics industry.” The NREC has been a driving force in development of the city’s “Robotics Row,” an area now home to more than 80 of the region’s robotics and artificial intelligence companies.
During the past decade, Pittsburgh’s robotics cluster has evolved from one centered on academic research to become more focused on commercialization, according to Joel Reed, executive director of the Pittsburgh Robotics Network, an organization formed in 2018 to promote the fast-growing sector. The Pittsburgh area now has a critical mass of commercialized robotics companies numbering more than 100. “During the last 10 years, we have really seen the commercial aspects explode in numbers, and with success,” Reed says.
Up until about five years ago, much of the area’s robotics development occurred organically, driven by Carnegie Mellon, as well as the University of Pittsburgh, according to Reed. More recently, there has been an influx of companies drawn to Pittsburgh to be a part of the region’s burgeoning ecosystem, to have access to talent and to share in the overall understanding of the intellectual property surrounding the industry.
The Pittsburgh Robotics Network estimates 7,000
people work directly in Pittsburgh’s robotics industry and more than 45,000 technology workers at large.1 In the five years prior to 2022, the region saw $4.3 billion in corporate and venture capital investment in Pittsburgh companies, Reed says.
Jared Glover, CEO and co-founder of CapSen Robotics, a developer of software that guides robotics used in warehousing, is a product of Carnegie Mellon. He founded CapSen after finishing his Ph.D. at MIT.
“The draw of Pittsburgh was strong enough to bring me back here to start the company,” he recalls. “It took a couple of years to figure out what industry we were going to go into, and to raise some money. We started building our team in 2016, and we are just about to make a large expansion push.”
CapSen creates software that gives robots more spatial intelligence with 3D cameras so that they can understand what they are looking at, in places like inside a cluttered bin, or on shelves inside factories and warehouses. The company also produces motion planning software to be able to perform complicated packaging and assembly tasks.
As CapSen grows, it will draw from what Glover terms a “fantastic talent pool” in Pittsburgh: “There is a never-ending supply of top-trained talent from the local universities,” he says. “Also, with so many robotics companies here, it’s easy for us to retain people, because there are so many options.”
Astrobotic Technology touts its 47,000-squarefoot facility in Pittsburgh as the “largest private facility dedicated to lunar logistics.” The expanding company has emerged as a significant participant in space-related robotics.
“The power, or the gears working behind the growth of robotics in Pittsburgh, is the university system,” says John Thornton, Astrobotic’s CEO. “That creates the economic engine and the talent engine that has created new businesses and new opportunities, particularly in robotics, but also a lot of different technological engineering fields. That is the engine that is making Pittsburgh work as a region.”
INNOVATION CORRIDORS
The company’s growth has been rapid. Employment has risen from 19 people in early 2019 to about 200 currently. Thornton says Astrobotic continually sees opportunities to expand its business in the space industry.

“In general, Pittsburgh has a lot of real estate, but the challenge is finding the flex space that robotics typically requires, which are facilities with both office space and lab space, a place to actually build and produce something,” Thornton says. “We’ve bought our facility and renovated it, and that was a pretty significant investment for us. We wanted to remain in this region and continue to foster robotics talent, and to encourage more robotics companies to come to town.”
Thornton believes Pittsburgh’s robotics cluster will grow much larger over the next five to 10 years. “The opportunities continue to expand,” he says. “I think of it as being a bit like how the computer revolution occurred. There are aspects of the robotics field that could be applied to almost any industry. As more applications are discovered, you will see more businesses sprout up here.”
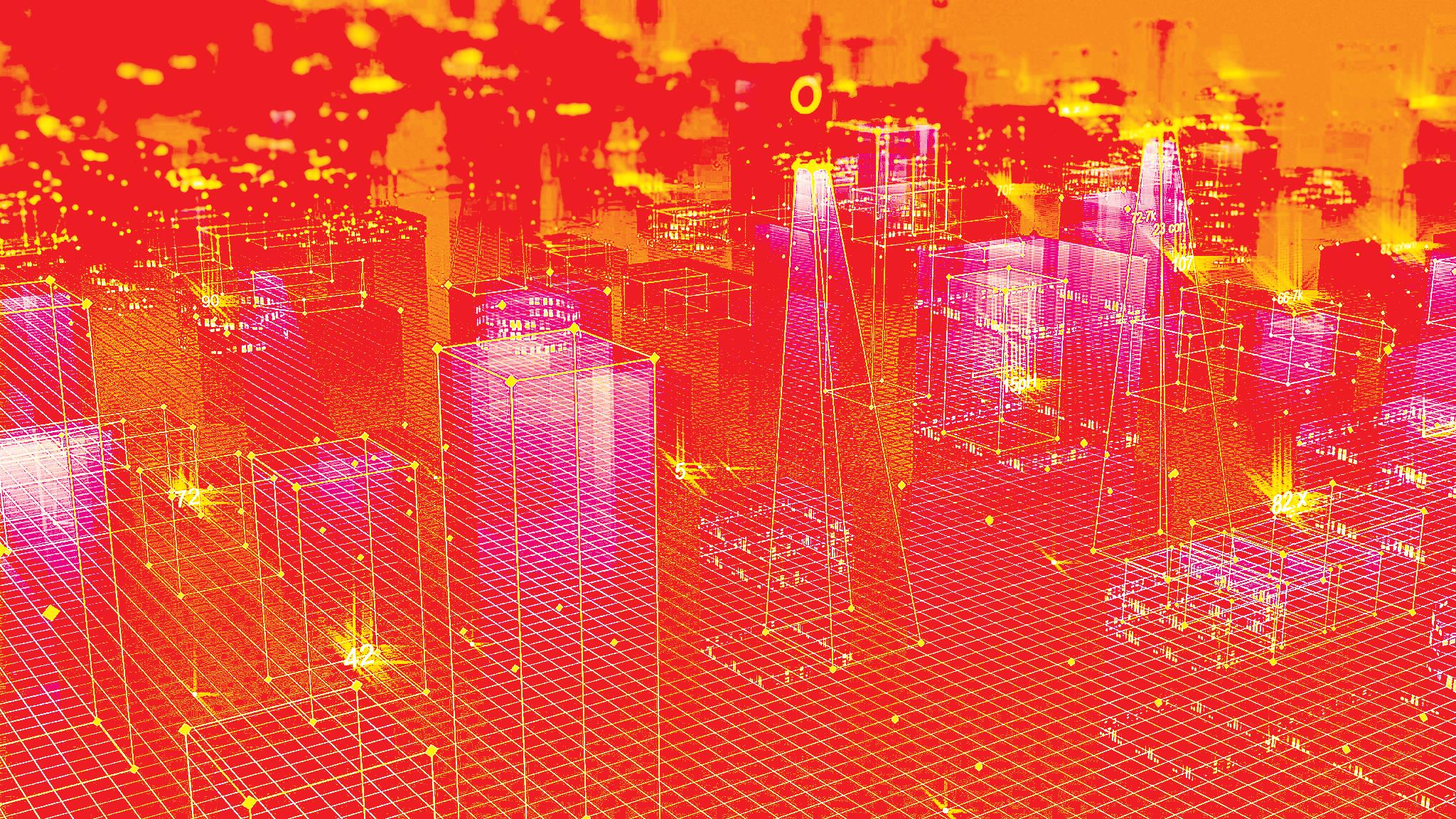
Electrifying Developments
Arizona boasts an eager market for electric vehicles, helping to boost progress of an EV manufacturing cluster. The state has the seventh highest number (40,740 as of June) of electric vehicle registrations in the U.S., according to the U.S. Department of Energy’s Alternative Fuels Data Center.2 That number is projected to increase in the coming years, as the state receives $76.5 million in federal funds through the National Electric Vehicle Infrastructure Formula Program to establish publicly accessible EV charging stations. That
project, set to begin in 2023, will initially target interstate highways.
“The future looks very good for Arizona and EVs, says Jim Stack, president of the Phoenix chapter of the Electric Automobile Association. “We have three EV makers in the state, a new battery recycling location, and a large battery-maker now. We will have more in the future.”
“Arizona has become a national hub for electric vehicle manufacturing,” says Sandra Watson, president and CEO of the Arizona Commerce Authority. About two dozen companies with ties to the EV or autonomous vehicle industry are in Arizona, including parts manufacturers, battery makers, and OEMS. These include Tesla, ElectraMeccanica, Lucid Motors, and Nikola. Two of the latest additions are battery-related companies.
Logistics considerations and proximity to customers helped lure KORE Power, a Coeur d’Alene, Idaho, developer of battery cell technology to Maricopa County. The company is building the first lithiumion battery manufacturing facility wholly owned
The California Option for solid state memory R&D
Greater Sacramento is home to: 5 of 6 of the world’s leading memory chip manufacturers 1/6 of California’s semiconductor jobs 718K 2- and 4-year students within 100 miles GreaterSacramento.com/semiconductors
INNOVATION CORRIDORS
by a U.S. company. Plans call for the plant to open during the second half of 2024. KORE’s twomillion-square-foot facility will produce 12 gigawatt hours of batteries per year, with half going into production in 2024 and the other half in 2025.
Lindsay Gorrill, KORE’s founder and CEO, says his company found the “total package” in Arizona. “We are close to the Long Beach port, and we ship to South America and Europe. We can get a shipping container to Long Beach and have it picked up in one day. Arizona has done a good job of luring our customers here, and more are on the way.”
The region’s strong workforce pipeline was also enticing. KORE has been working on cultivating that pipeline for more than 18 months, with Arizona State University and the Maricopa County Community College District. “We are working with them on new curriculum for what we need,” Gorrill says. “We have the education people behind us. That is part of the whole package of why it makes sense for us to be in Arizona.”
Li-Cycle, a recycler of lithium-ion batteries, describes its new location of Gilbert, Arizona, as sitting at the nexus of expected robust growth in the supply chain. “Li-Cycle’s patented technology is proven in the North American market as the leading way to recycle lithium-ion batteries, and we are building a network of spoke facilities, like the one in Arizona, around the world,” says Alan Ferguson, Li-Cycle’s commercial VP. “As the world continues to electrify and the demand for lithium-ion batteries accelerates, it is important for recycling capac-
ity to be established where there is expected to be a significant amount of both end-life batteries and battery manufacturing scrap.”
Ferguson says, “We believe that Arizona will continue to present a significant opportunity for lithium-ion battery recycling, due to its own emerging supply chain in addition to its proximity to other markets, such as California.”
Chris Camacho, president and CEO of the Greater Phoenix Economic Council, notes that “California and historically the Midwest’s Rust Belt have been the juggernaut of OEMs, but we are seeing the new age EV companies evaluate locations differently. We are able to compete in an entirely different way.”
A Nexus of Computers and Semiconductors
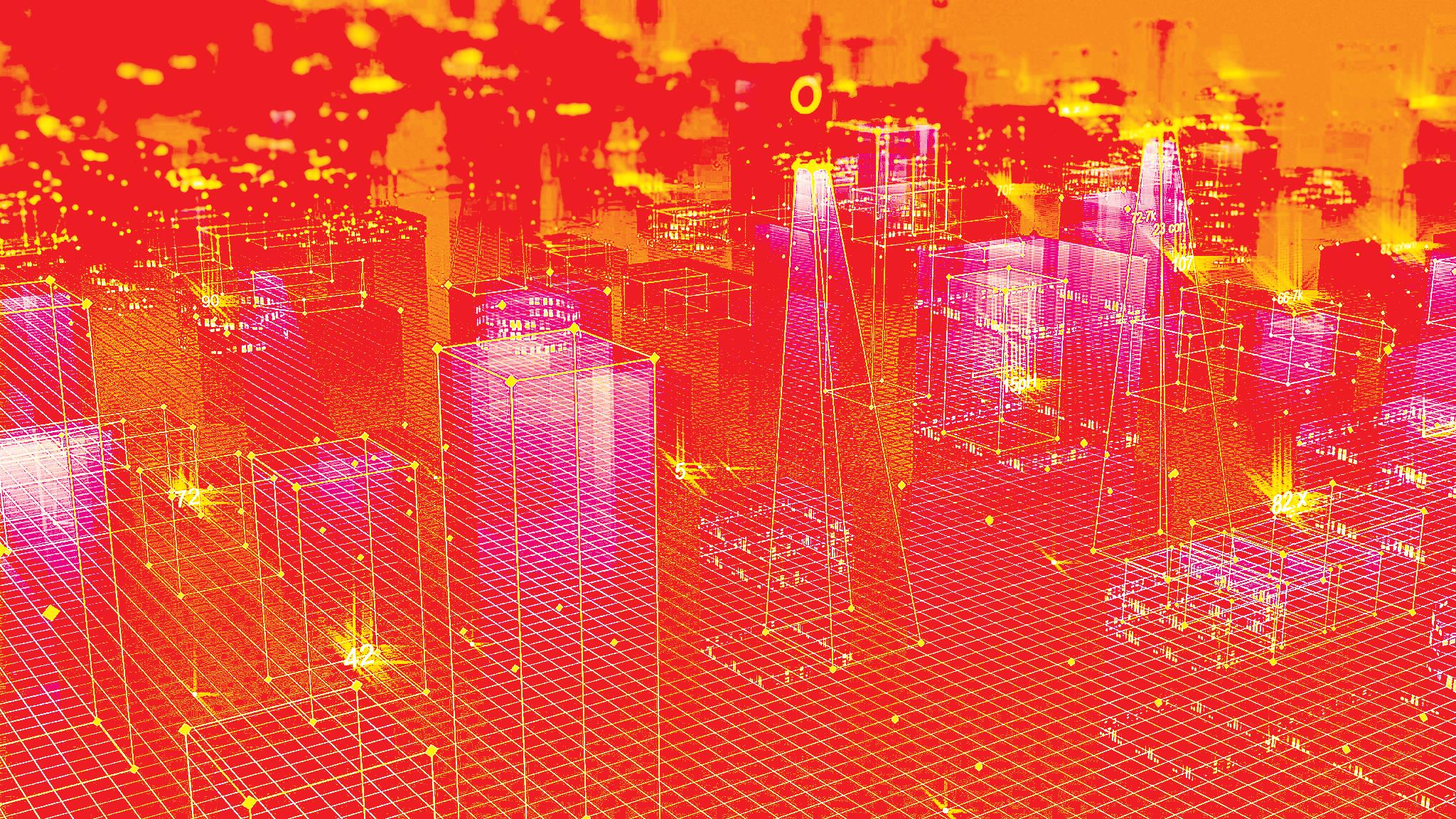
New York State scored two major computerrelated coups in October when Micron and IBM announced colossal projects in the Syracuse and Hudson Valley areas, respectively.
In October semiconductor heavyweight Micron Technology announced plans to build the largest semiconductor fabrication facility in the history of the U.S. The new mega fab will increase domestic
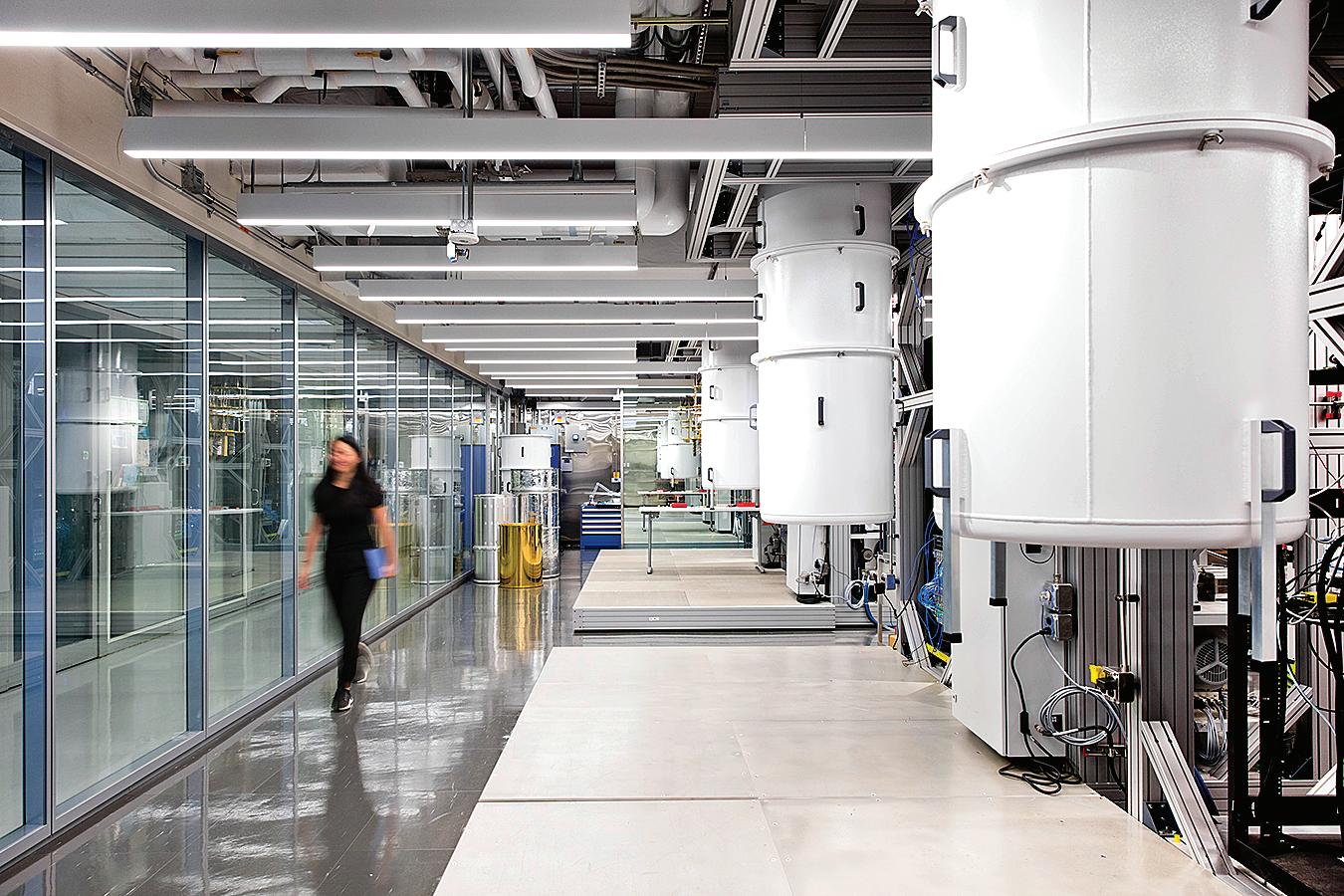
IBM builds mainframe computers in Poughkeepsie, N.Y., which is also home to its Quantum Computation Center.
for free site information, visit us online at
supply of leading-edge memory and create nearly 50,000 New York jobs, including approximately 9,000 highpaying Micron jobs.
Micron plans to invest up to $100 billion over the next 20-plus years to construct its new mega fab in Clay, N.Y., with the first phase investment of $20 billion planned by the end of this decade. This represents the largest private investment in New York State history. The site could eventually include four 600,000-square-foot cleanrooms.
IBM plans to invest $20 billion across the Hudson Valley region over the next 10 years. IBM’s goal is to “expand the vibrant technology ecosystem in New York to unlock new discoveries and opportunities in semiconductors, computers, hybrid cloud, artificial intelligence, and quantum computers.”3 IBM has long had a huge footprint in New York State and currently employs more than 7,500 in the Hudson Valley.
IBM builds mainframe computers in Poughkeepsie. The site also is home to IBM’s first Quantum Computation Center — where a large number of real quantum computers run in the cloud. IBM’s vision is for Poughkeepsie to become a global hub of the company’s quantum computing development, just as it is today for mainframes.
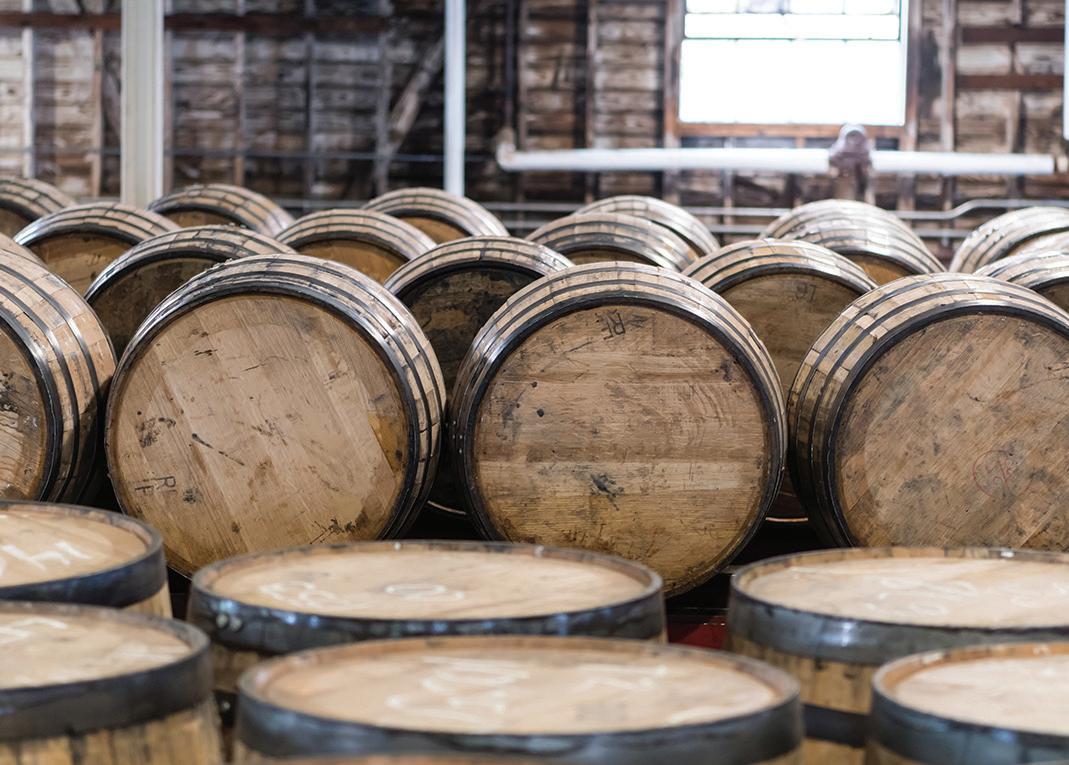
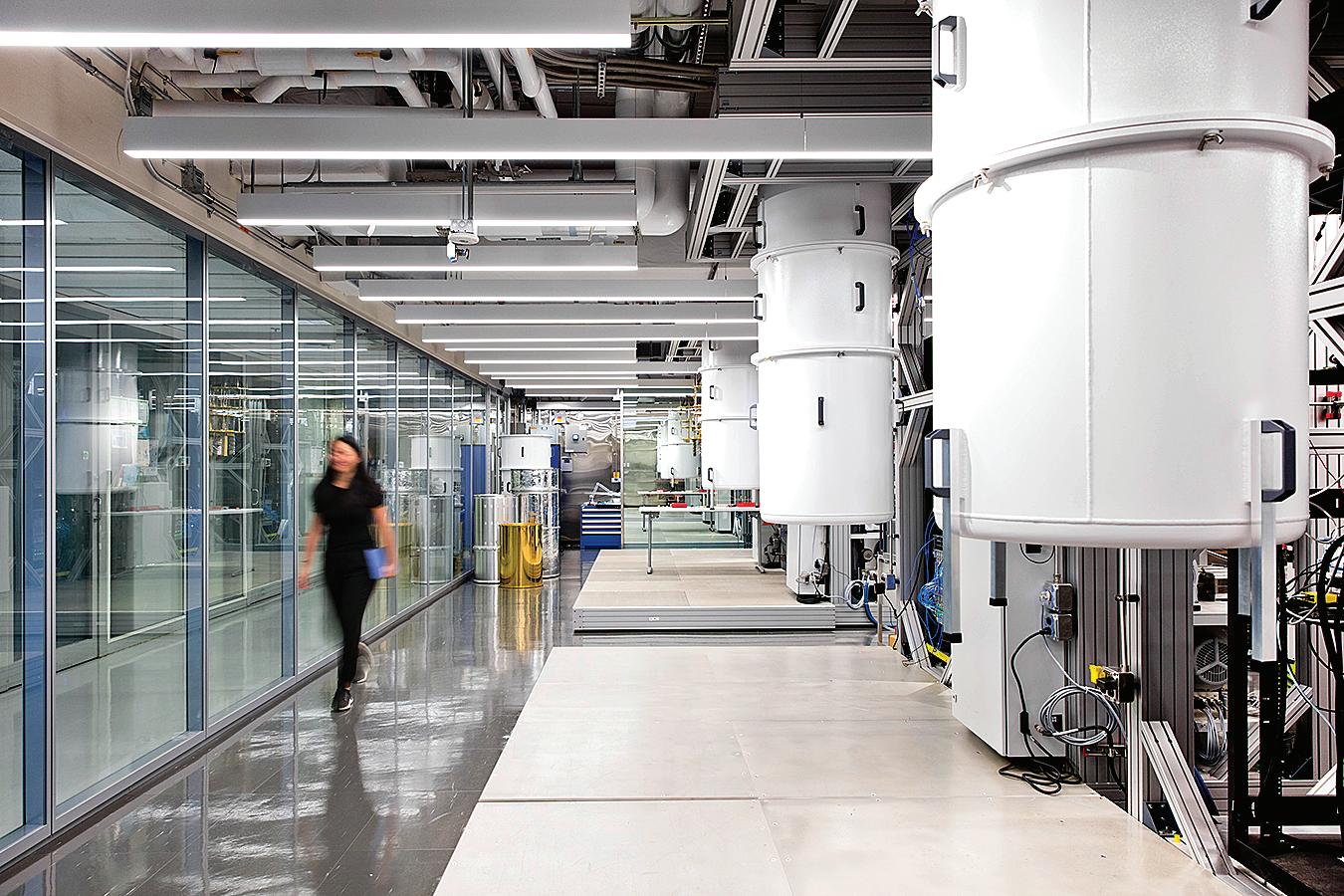
Ron Hicks, assistant county executive for Dutchess County, says President Biden’s visit in October for IBM’s announcement confirms that Poughkeepsie’s center of computer development is vital to the country’s national interests. He expects IBM’s announcement to attract further investment from startups and small businesses that support the quantum computing industry.
Chip R&D cluster
Further chip development is taking
INNOVATION CORRIDORS
place across the country in a cluster in California. The Sacramento area continues to grow its semiconductor R&D cluster. The latest company to choose the area is Solidigm, a U.S.-based subsidiary of SK hynix, which announced plans in September to invest more than $100 million to build its global R&D campus in Rancho Cordova. The company expects to create more than 1,900 high-paying jobs over the next five years. Area economic developers tout it as the largest such project the region has seen over the last decade.
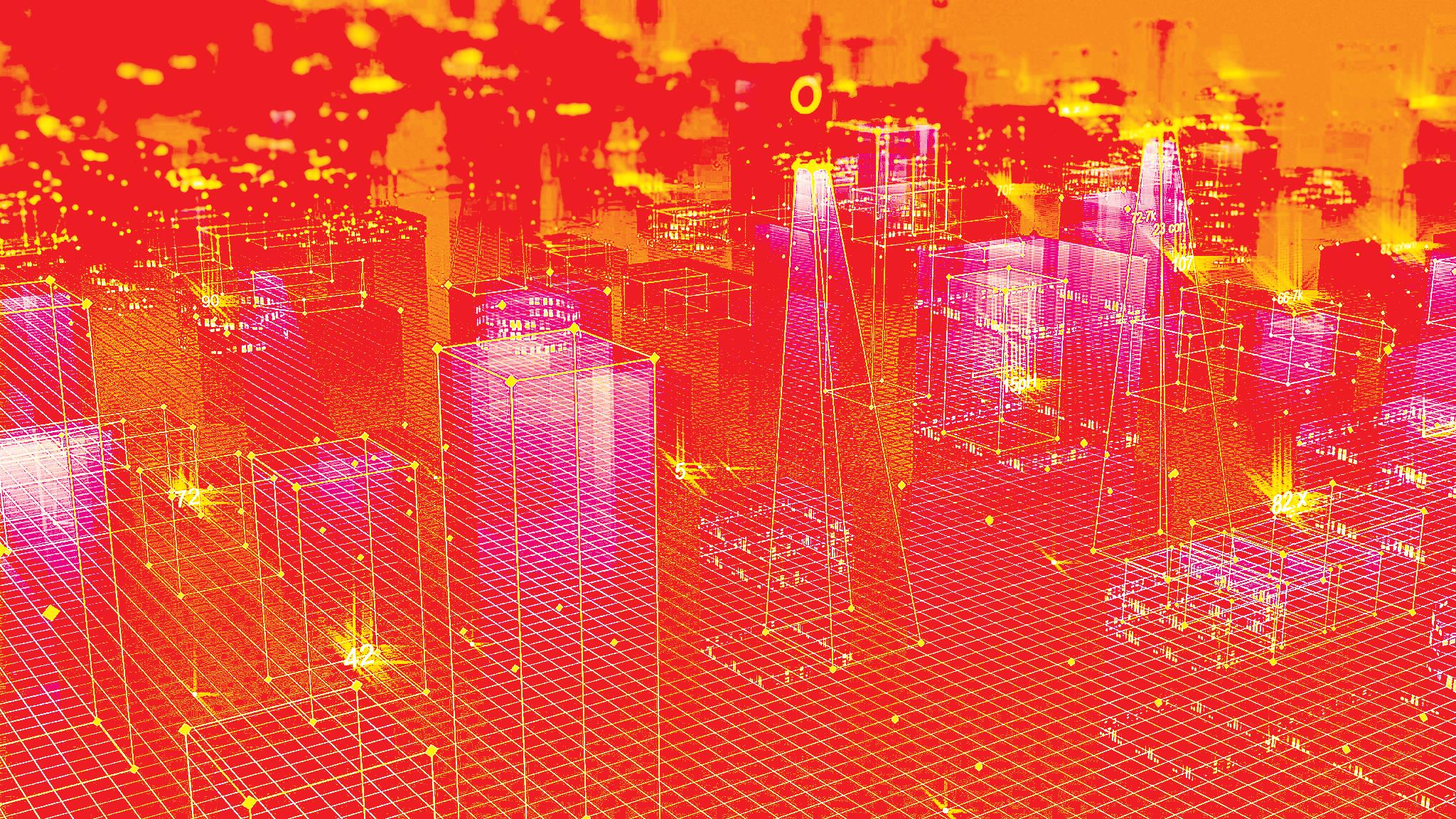
Solidigm, a developer of NAND flash memory products, is working on tenant improvements to the 230,000-square-foot R&D campus and is targeting a move-in date in the first quarter of 2023. The site was chosen for its ample office and lab space, proximity to where Solidigm’s workforce lives, availability of public transportation, nearby amenities, and the ability to expand to accommodate a growing workforce.
Much of the region’s R&D cluster is sprinkled along the Highway 50 corridor, a route running east to west and connecting Sacramento to the San Francisco Bay Area. Intel has a large campus in the area, which has grown to nearly 6,000 employees since the late 1980s.
“The region is home to global leaders conducting R&D in the memory space,” says Jasmine Ward with the Greater Sacramento Economic Council. “We are at a turning point, where we are starting to see an acceleration of interest in the area.”
Folsom, Calif., a town about 25 miles northeast of Sacramento, has been a primary location of Micron since it acquired Numonyx from Intel in 2010. The acquisition gave rise to what Micron now calls its Embedded Business Unit, which is essentially headquartered in Folsom, according to Chris Jacobs, vice president and general manager of embedded market segments in Micron’s Embedded Business Unit, “which is one of the fastest-growing units at Micron,” Jacobs says. “We focus on delivering innovative memory and storage semiconductor solutions in automotive, industrial, and certain consumer applications.”
Micron recently refurbished its Folsom facilities, which Jacobs says is a testament to the ongoing investment the company has in the area. “This is a great place to live and work,” he says. “It is a bit more affordable than other areas of California. The area is perfectly located, close to both urban centers and easy access to outdoor activities. We have had a great experience attracting talent, and currently have 350 employees, and growing. We have the space to support the growth that we see over the next few years.”
Tri-State Region Life Sciences Cluster
The tri-state region of Connecticut, New York, and New Jersey continues to attract investment from innovative life sciences firms.
Connecticut’s thriving life sciences cluster boasts more than 1,000 companies. One of the state’s fast-growing hubs in this sector is in New Haven, home of Yale University. An example of the city’s robust biotech growth is Arvinas, a company developing therapies for a variety of diseases. Arvinas is developing 160,000 square feet of lab and office space on three floors of a 10-story tower at 101 College St.
“New Haven has been an exciting place in the last few years,” says John Houston, Arvinas’ president and CEO. “Clearly, the number of companies that have been spun out of Yale, as well as those that have come to New Haven, has been quite significant. There are probably hundreds of small companies. The idea that there will be even more of a busy downtown cluster is very exciting.”
for free site information, visit us online at www.areadevelopment.com
Houston says when he moved to Connecticut 25 years ago, he didn’t see New Haven as being anything like a biotech cluster. That changed over the last 10 years.
“I think the growth of our company is acting as a catalyst to attract other companies here. It is already happening. Other companies are looking at New Haven, looking at the new buildings going up. One of the things that may have caused hesitation in the past about locating here was the available space for labs, and also the concern about having enough of a talent pool to recruit from. I think both of those questions have now been answered fairly strongly.”
In other tri-state developments, New York City is developing the Science Park and Research Campus Kips Bay, a job and education innovation hub that will be the first of
its kind in the state. Officials say the project will help New York City become a global leader in creating and attracting accessible jobs in life sciences, healthcare, and public health by creating a pipeline from local public schools.
And Rocket Pharmaceuticals, a clinical-stage company developing genetic therapies for rare childhood disorders, is developing an R&D, manufacturing, and headquarters facility in Cranbury, N.J.
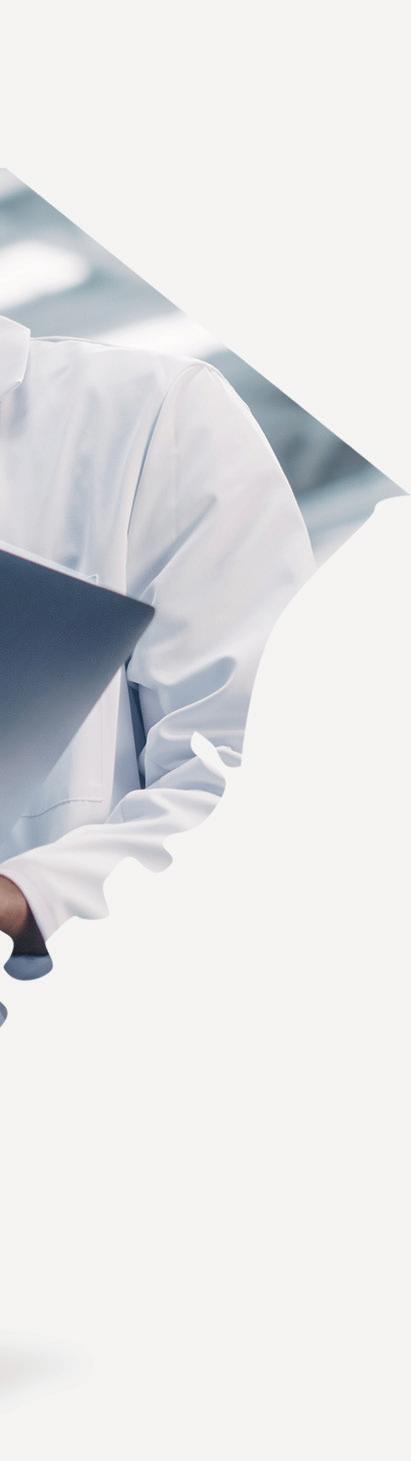
1 https://nextpittsburgh.com/city-design/how-pittsburgh-is-transforming-into-the-roboticscapital-of-the-world/
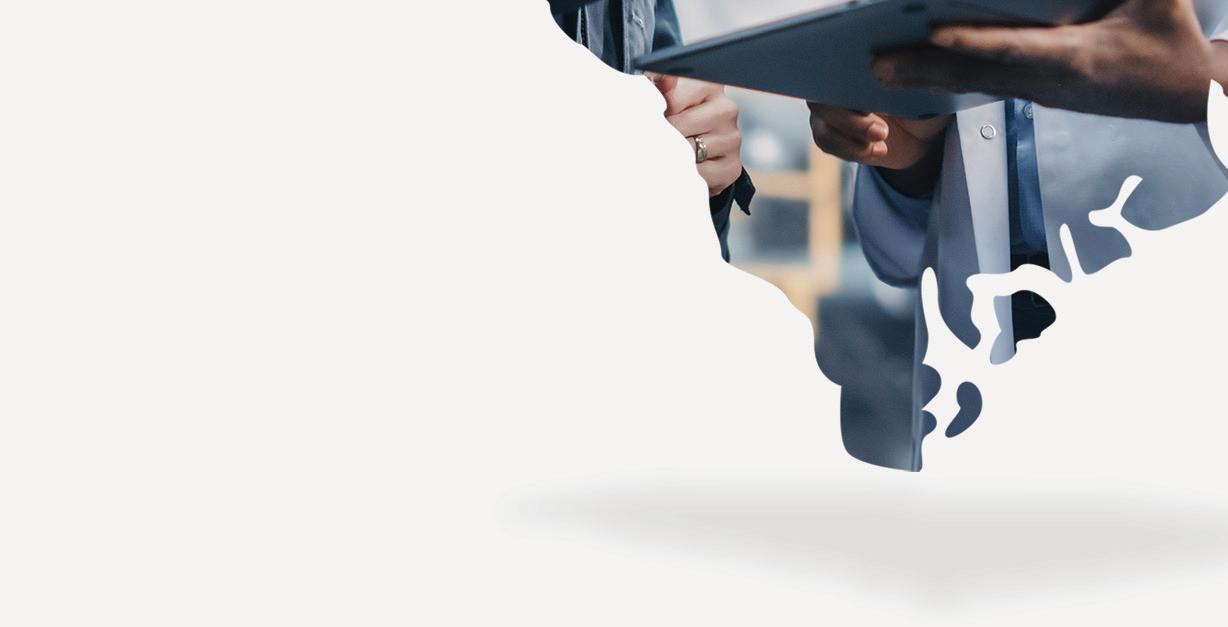
2 https://afdc.energy.gov/data/
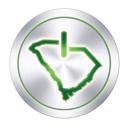
3 https://newsroom.ibm.com/2022-10-06-IBM-and-CEO-Arvind-Krishna-Welcome-President-Biden-to-Poughkeepsie-Site,-Company-Plans-to-Invest-20-billion-in-the-HudsonValley-Region-Over-10-Years
POWERING GROWTH
With resources like low-cost, reliable power, creative incentive packages and a wide-ranging property portfolio, Santee Cooper helps South Carolina shatter the standard for business growth.
In fact, since 1988, Santee Cooper has worked with the state’s electric cooperatives and other economic development entities to generate more than $17.2 billion in capital investment and helped bring more than 85,000 new jobs to our state. It’s how we’re driving Brighter Tomorrows, Today www. poweringSC .com
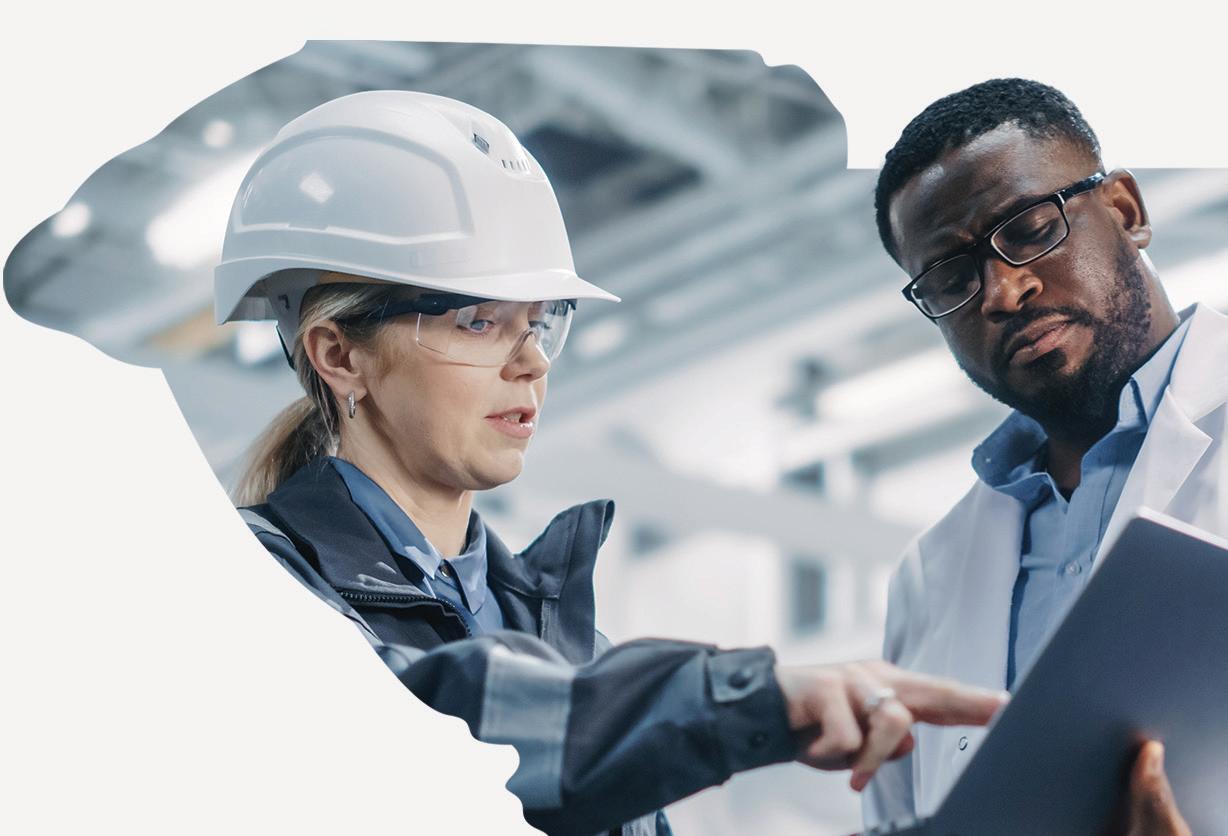
Three Big Challenges Facing the Food & Beverage Industry
While every industry — and everyone — has faced disruptions over the last couple of years, the food and beverage industry has been disrupted on an almost unimaginable scale.
By Stephen Gray, President & CEO, Gray, Inc.Huge spikes in demand for retail products, while food service demand virtually disappeared… supply chain disruptions1 that revealed previously unknown weaknesses in the flow of ingredients and materials…already existing labor shortages exacerbated by COVID outbreaks and shutdowns, as well as existing staff missing time due to illness, caring for family members, or juggling work in an essential industry with remote school and other logistical challenges — these are among the challenges food and beverage processors have faced. While these disruptions have stabilized as food and beverage processors have figured out how to adapt and improvise, they still exist. And they are existing throughout the entire process, even extending to how food and beverage plants are being built or remodeled.
Whether it’s building a food and beverage plant or operating one, three major disruptions persist: supply chain challenges, labor shortages, and e-commerce, which has seen explosive growth during the pandemic as consumers looked for new ways to shop. What they all have in common is they are forcing food and beverage processors to reimagine what their processes look like, how they will carry out those processes, and even the facilities they will use to make their products.
Supply Chain Challenges
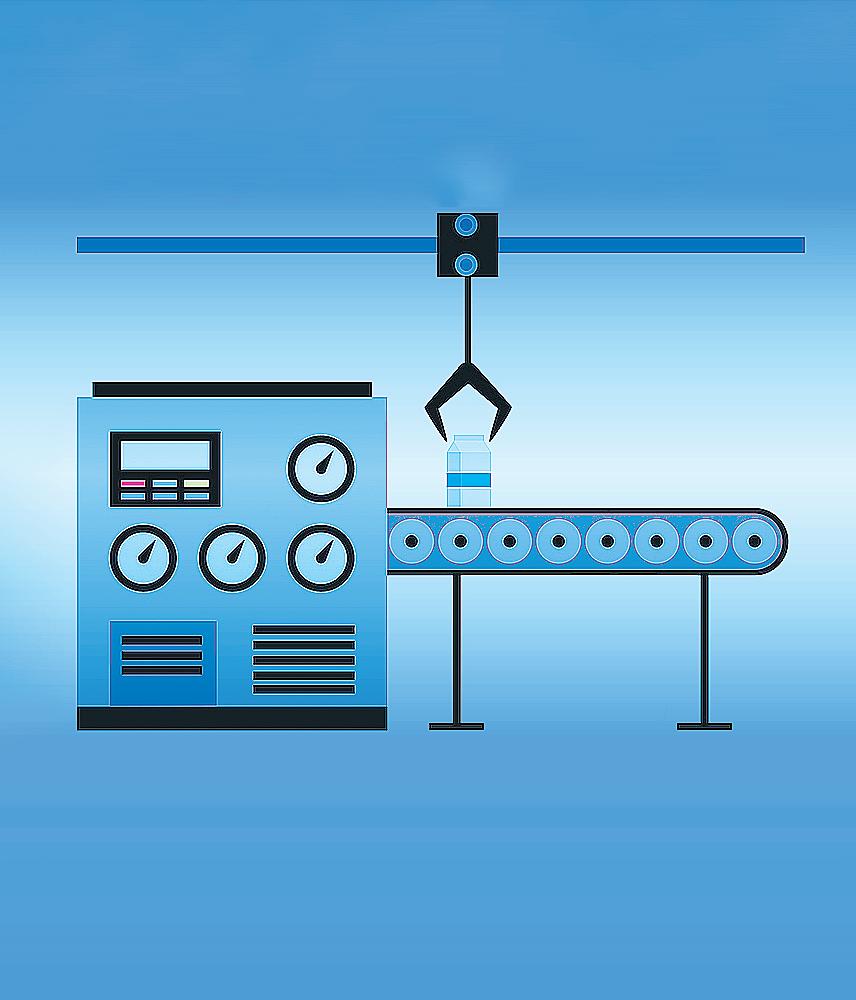
In many industries, the answer to supply chain challenges is a relatively simple one: Look to a new provider or stockpile the materials you need to guard against future shortages.
But it’s not that simple for food and beverage processors. Ingredients have a shelf life, so you can’t just stock up on extra perishable items because you expect them to be in short supply in the future. Producers of livestock and crops cannot ramp up production the way a supplier of cardboard boxes can. And many ingredients only come from one region, so disruptions in that region — whether COVID outbreaks, natural disasters, or any other disruption — can force processors to scramble to meet their needs. Many ingredients are shipped to arrive just in time for production, but disruptions to the supply chain have interfered with that timing, as well as making it harder to find new supplies on short notice.
“The expectation has changed. Our food and beverage customers continue to grow. In response, we continue to innovate with engineering, design, construction, automation and controls, and equipment manufacturing techniques that allow us to be more efficient,” says Tyler Cundiff, president, Food & Beverage Group, Gray, Inc. “This hasn’t happened just as a result of COVID, but it’s been happening for the past several years. We’ve been moving our subcontractors and our own construction professionals to work more closely with material suppliers and design technologies to have greater ability to pre-fabricate various builds for part of the facility, part of the equipment, or infrastructure for the equipment.”
Food and beverage processors face another supply chain challenge on the construction and renovation side. Delays and cost spikes in materials lead to longer lead times and more expensive building materials, replacement parts, and new machines. A project that may have

been measured in weeks before the pandemic can now take months, and larger projects face can face even longer delays.
Building a single piece of process equipment involves hundreds of steps, and many of them are in sequence. A delay at one point in the process doesn’t mean fabricators can just move on to a different part of the process and come back later. It stops the process entirely until the needed parts are in hand. The disruptions of the pandemic era have been felt throughout the manufacturing process, says Perry Henderson, vice president, Marketing and Business Development, Anderson Dahlen Inc., a Gray company.
“It was a disruption of manufacturing businesses, including material-producing businesses; with mining and processing of things you need to make components and electronics,” says Henderson. “Almost every piece of processing equipment was directly impacted by not being able to get certain electronics for the controls, and not being able to get certain components for pumps, valves, and other ancillary parts.”
Labor Shortages
Materials shortages have forced food and beverage processors and their suppliers to adapt. But even when they have materials in hand, they need people to operate production lines, build and maintain equipment, and undertake construction projects. Skilled labor was in short supply even before the pandemic hit, and it has only gotten worse since then.
Consider the process of building a new food plant. An engineering or design-build firm works with the customer to design and engineer the building, then hires contractors to build it. Those contractors often hire subcontractors for specializations such as plumbing, electrical, or HVAC. The firms have existing relationships with a number of high-quality contractors, who in turn have a stable of subcontractors they can rely on.
But if a subcontractor has three plumbers assigned to a project and they are all out of work for a couple weeks because of a COVID outbreak, it can slow down the entire building project. And it’s not as easy as simply hiring new plumbers, because subcontractors need to be vetted to ensure they are performing work that is up to the necessary standard.
There’s another issue as well. That plumbing subcontractor may already be committed to another project, because after an initial slowdown due to shutdowns or engineering firms and tradespeople working through how to safely do their jobs, construction has continued at a breakneck pace. Skilled tradespeople have no short-
age of work, so there’s no guarantee that a firm or a contractor will be able to get their usual subcontractors, which means new subcontractors have to be evaluated and hired to get the work done.
One other challenge: If everybody’s looking for employees, they might try to hire yours away.
“Your manufacturing infrastructure is one thing,” says Cundiff. “The labor and what everybody’s calling the Great Resignation — that’s impacted manufacturing jobs as well. So, maintaining a high level of retention, whether it’s with our engineering teams or manufacturing teams, is a constant challenge, and it just brings to light the focus on people and culture.”2
From the equipment side, finding enough people — and keeping them safe — forced manufacturers to rethink their entire process, says Henderson.
“Acute labor shortages popped up a lot because of people being out, or needing to be isolated, or having to change work patterns to not have people come into contact as much with each other,” says Henderson. “This affected all types of operations, but it affected equipment manufacturing as well. You had to rethink your workflows and how you manage your movement of materials back and forth within the building, or even receiving it into the building. And that’s everything from inspection, to parts movement, to handoff between departments, or project managers going to check on things in production.”
But the disruptions have also provided a learning opportunity for Anderson Dahlen, and one of the takeaways has been adapting to operate more like a food and beverage plant. Managing material and worker movement throughout a building has long been a staple of food and beverage due to allergen control3 and managing cross-contamination. What Henderson learned is that those trusted principles can also work in an equipment manufacturing environment.
The company realized its team members were spending a lot of time moving from one place to another within the building, and they didn’t necessarily need to be doing so. For example, if fabrication had a question for engineering, then a common solution was for someone to walk over to engineering, explain the issue at hand, then walk back to the piece of equipment in question with the engineer accompanying them. The company realized that by modifying the way people and materials moved both throughout the building and the fabrication process, it could eliminate much of the unnecessary movement throughout the building.
“We actually kept it that way because it gained efficiency in the end,” says Henderson.
Clemens Food Group selected Gray to design and build a smoked pork processing facility on a greenfield site in Hatfield, Pa., which was recently completed.

The Effect of E-Commerce
E-commerce places different demands on a food and beverage plant than retail and food service do, so flexibility is paramount. Whether it’s processing lines, packaging equipment, or shipping, processors who have seen significant growth in e-commerce business4 have had to adapt their operations to meet that demand. People may be returning to the grocery store, but that doesn’t mean they’ve stopped ordering certain things online.
E-commerce is also offering opportunities for startup companies that make products such as meal kits or other items sold directly to consumers. Not shipping to grocery stores or wholesalers creates a need for a different kind of food plant, as well as different demands for processing and packaging equipment.
But for processors who already have retail or food service customers in addition to e-commerce, it’s more about adapting current equipment and processes to meet the needs of each market. Equipment manufacturers are adapting to offer more flexibility in equipment, and engineering firms are rethinking the design of packaging lines and other aspects of the production process to ensure they are able to change over with minimal time lost.
And, of course, supply chain challenges and labor shortages play into the e-commerce side as well, because just like any other food product, materials and people are needed to produce the products.
All these challenges tie into each other, and they all create disruptions. As Cundiff says, there’s no set answer to solving any of them, but the industry is tackling them head-on and it is continuing to focus on future growth.
“In spite of all these challenges, we continue to see food and beverage companies wanting to heavily invest in larger, more modern processing facilities,” he says. “We’ve never seen the demand like it is now, and there’s no indication that it’s going to slow down.” n
1 https://www.foodengineeringmag.com/articles/99366-big-things-to-know-aboutsupply-chains

2 https://www.foodengineeringmag.com/articles/98748-training-plays-a-part-in-employeehappiness-and-retention
3 https://www.foodengineeringmag.com/articles/96778-successful-allergen-control-requiresclose-attention-to-detail
4 https://www.foodengineeringmag.com/articles/99058-pet-food-e-commerce-boomhas-major-influence-on-manufacturers-operations
The #1 site selection newsletter
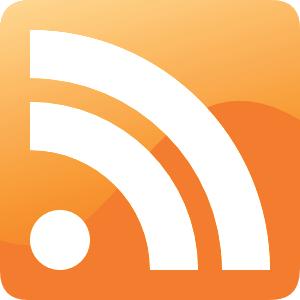
The #1 site selection website areadevelopment.com twitter.com/ areadevelopment
Join our growing list of followers
Stay in touch with the latest news, case studies, white papers and the industry’s most insightful site selection content and current contacts.
Food Processors’ Optimal Location Decision
Whether evaluating existing buildings or finding a location for a new facility, food processors must make sure all the variables involved align to support the final decision.
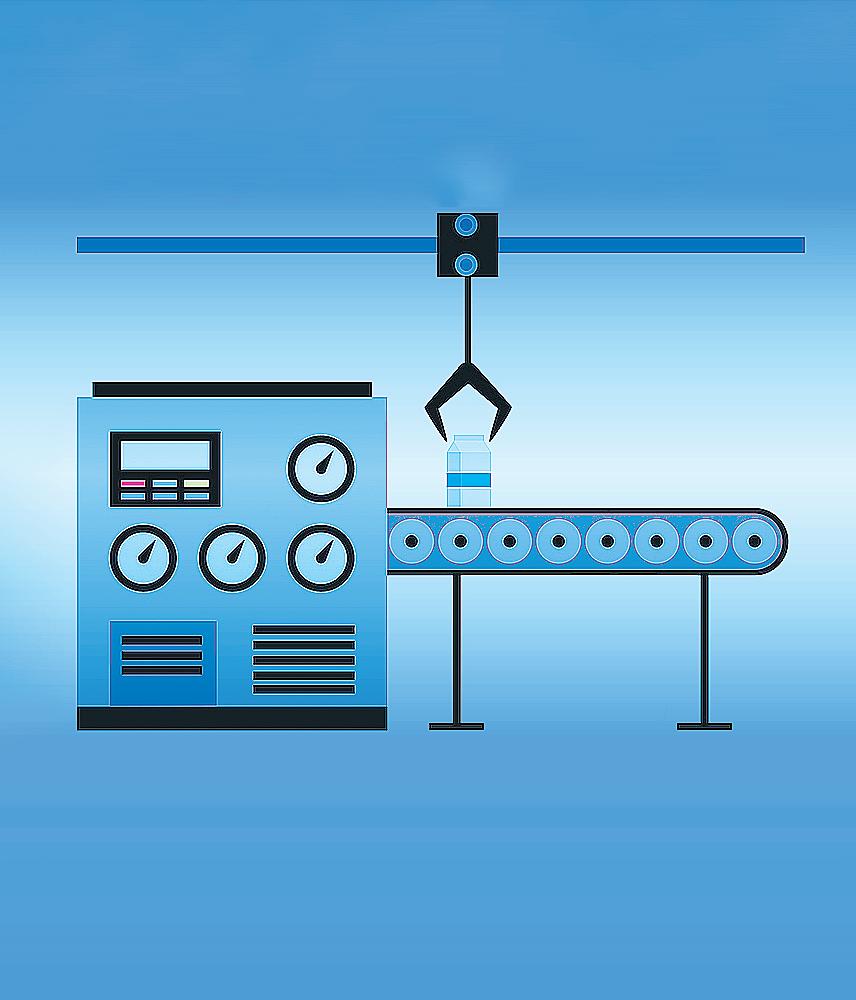
In today’s quick moving market, companies need to start running multiple lanes of site selection work when searching for their next production facility. Some of the most frequent reasons we see companies looking for new facilities involve the need to update older inefficient operations, achieve transportation savings, increase market share, address a lack of labor, and obtain business incentives.
Each one of these reasons creates a different problem and requires a creative solution.
ing or parcel of land that allows them to better fit their lines and flow.
The major question is, are available buildings located in the existing area that can deliver this opportunity? Locating in the same area, if possible, provides the ability to keep existing labor and save on downtime and cost of retaining employees. Although, there’s a national shortage of food processing and refrigerated distribution buildings.
Once a company determines it doesn’t have an exist-
Evaluating Many Variables, One Integrated Project
Existing Building Options Infrastructure Analysis Labor Analysis
Incentive Negotiations Real Estate: Lease or Build
DECISION SUPPORT
OPTIMAL LOCATION
Updating Inefficient Operations, Existing Buildings
Companies tend to operate in buildings for many years, adding on and demising buildings to fit new operations and put off major expansion plans in light of the cost and the time take-away from their daily grind of keeping up with their business. The only way to update these operations is to start fresh and find a build-
ing building in its own market, it’s time to start looking regionally and or nationally. Now is an ideal time to look for additional savings, evaluating factors such as labor, incentives, and new construction. To investigate the prospects in full, a company should run a full site selection process.
The best way to start this process is by determining what are the optimal locations for the business. The
for free site information, visit us online at www.areadevelopment.com
first step is performing a supply chain transportation study. This study will identify where the best location is for a new facility based on costs savings in the supply chain. This study can also determine the location best for a company to gain market share, either through shifting capacity or moving closer to target suppliers or customers. This is a simplified description of a complex modeling and business strategy project.
Addressing a Lack of Labor
Labor has become a key driver of site selection since the pandemic. Therefore, the next lane in the location process is performing a labor study, making sure there is an adequate supply of labor and that it matches the skill level of the jobs to be offered at the facility. Other questions include, is there a seasonal demand? How deep is the labor pool? And what is the drive-time for that labor pool? Also, are there state or local incentives and options to assist with recruiting and training? Will company executives be relocating? These are all factors that need to be accounted for. Labor can make or break an operation.
Satisfying Infrastructure Needs
The third lane to start running is infrastructure. Power and water are key, and both can be constrained so ensuring that there is adequate supply is essential.
The second part to the water question is discharge. How much will the facility discharge and what are the discharge options? Can it be treated and sent to a municipal system or is setting up a private system an option and does that require more land on or off site? Does the target area offer incentives or financing options for infrastructure? This is one of the most limiting factors when looking to locate a new food processing facility.
Obtaining Incentives
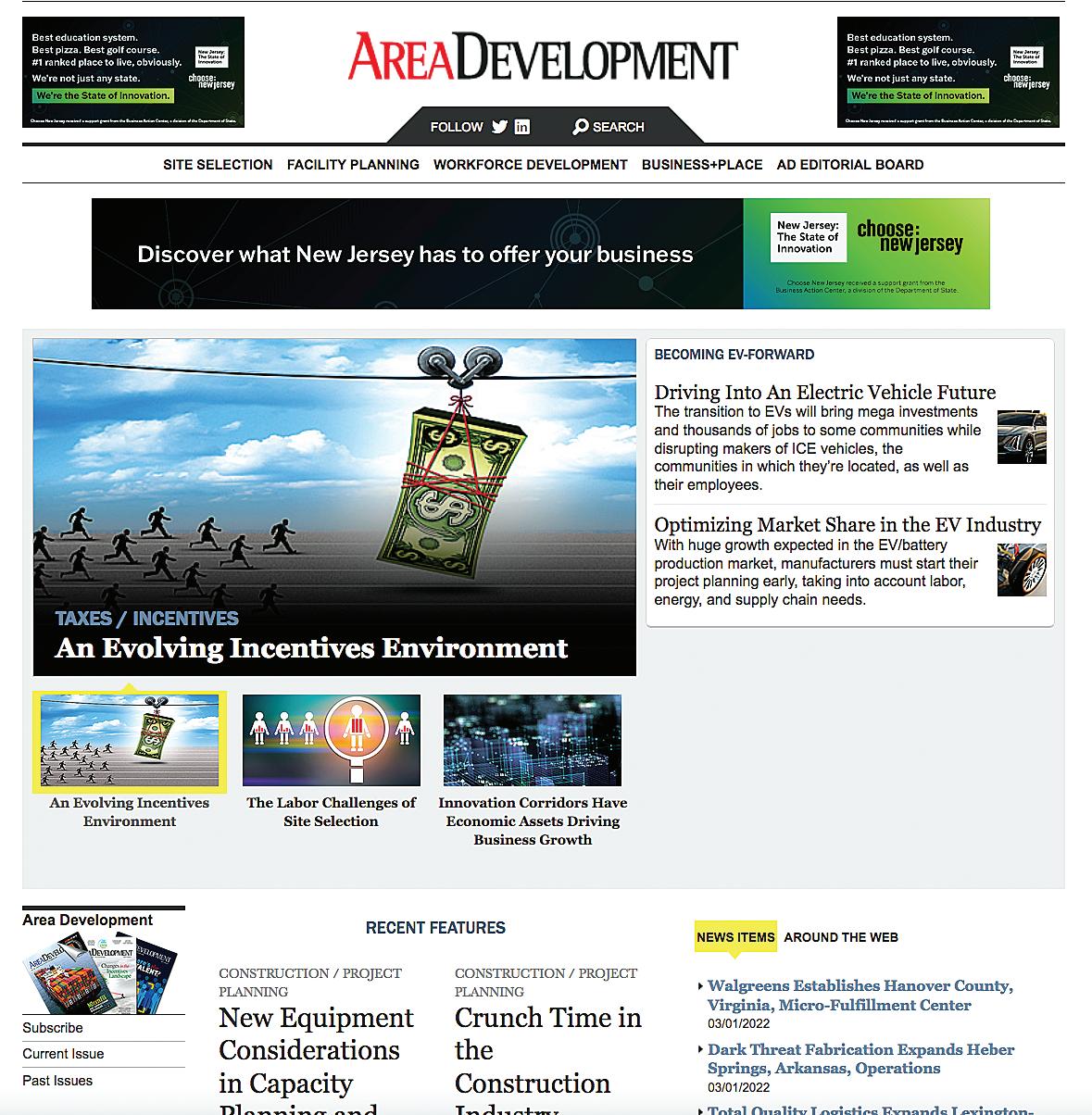

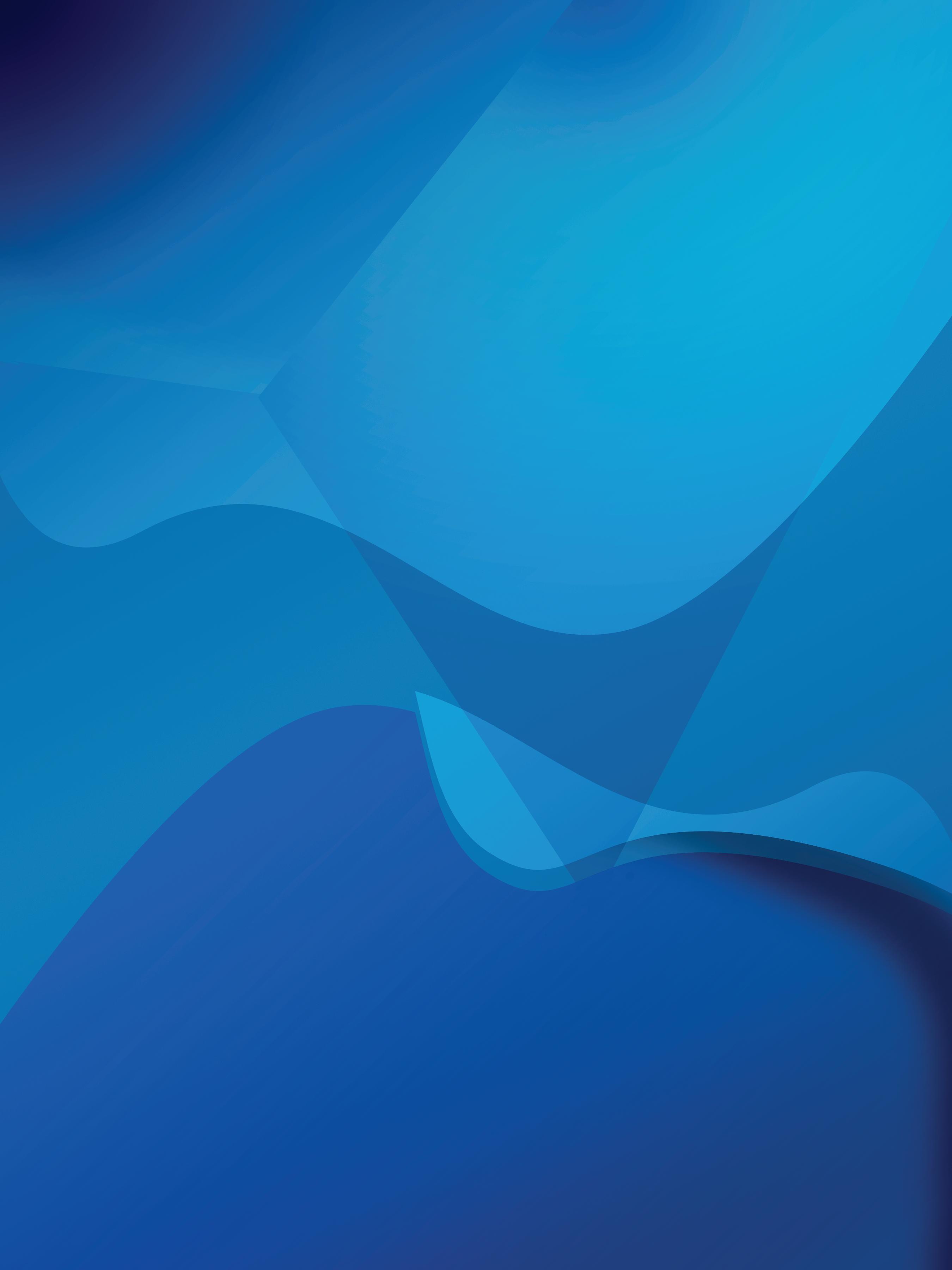
The fourth lane is local and state business incentives. These can be in the form of everything from free land and delivering utilities, to worker training and expedited permitting. Incentives are different in every community and state. It’s best to engage a professional business incentive consultant with national experience to manage the C-suite’s expectations of what is possible in a community. Once again, like infrastructure studies and labor analysis, correctly evaluating and obtaining incentives requires a certain professional training and experience.
Real Estate Search
The infrastructure study, labor analysis, and incentives will generate several locations, such as different municipalities in the same state or in several states. Real estate should be searched in each area as it is ap-
Higher Borrowing and Construction Costs Impacting Industrial Users
By David Welch, President and Robinson Weeks PartnersThe Federal Reserve’s rate hikes are prompting many industrial developers to be more mindful of the pace of their starts as higher borrowing costs run tandem with higher construction costs. Following two years of pandemic-fueled highs, developers are slowing down their construction pipelines and recalibrating their expansion strategies to get ahead of cost increases.
Although owners are erring on the side of caution, the industrial construction pipeline remains at record levels, reaching an all-time high of 716.9 million square feet, according to a recent report by Cushman & Wakefield.1 Despite this, current low vacancy rates (3 percent +/- in most markets) and limited space availability are compounding to make the leasing environment less than ideal for industrial tenants. While developers are right to be careful to avoid overextending their pipelines in an evolving environment, the wait-and-see approach could aggravate an already tight market for industrial users that are looking to expand their existing portfolio of space and locate in emerging industrial hubs.
Shifts in consumer demand have prompted many retailers and third-party logistics providers to improve supply chain processes by leasing additional warehouse facilities to store more goods and to develop more efficient operations. However, they’re finding higher rents and fewer space options that meet their specific needs are limiting their choices. It’s a challenging environment on both sides of the equation, with industrial developers ramping down on activity in the face of an expected recession and industrial users trying to navigate supply chain complications and consumer demand that may change
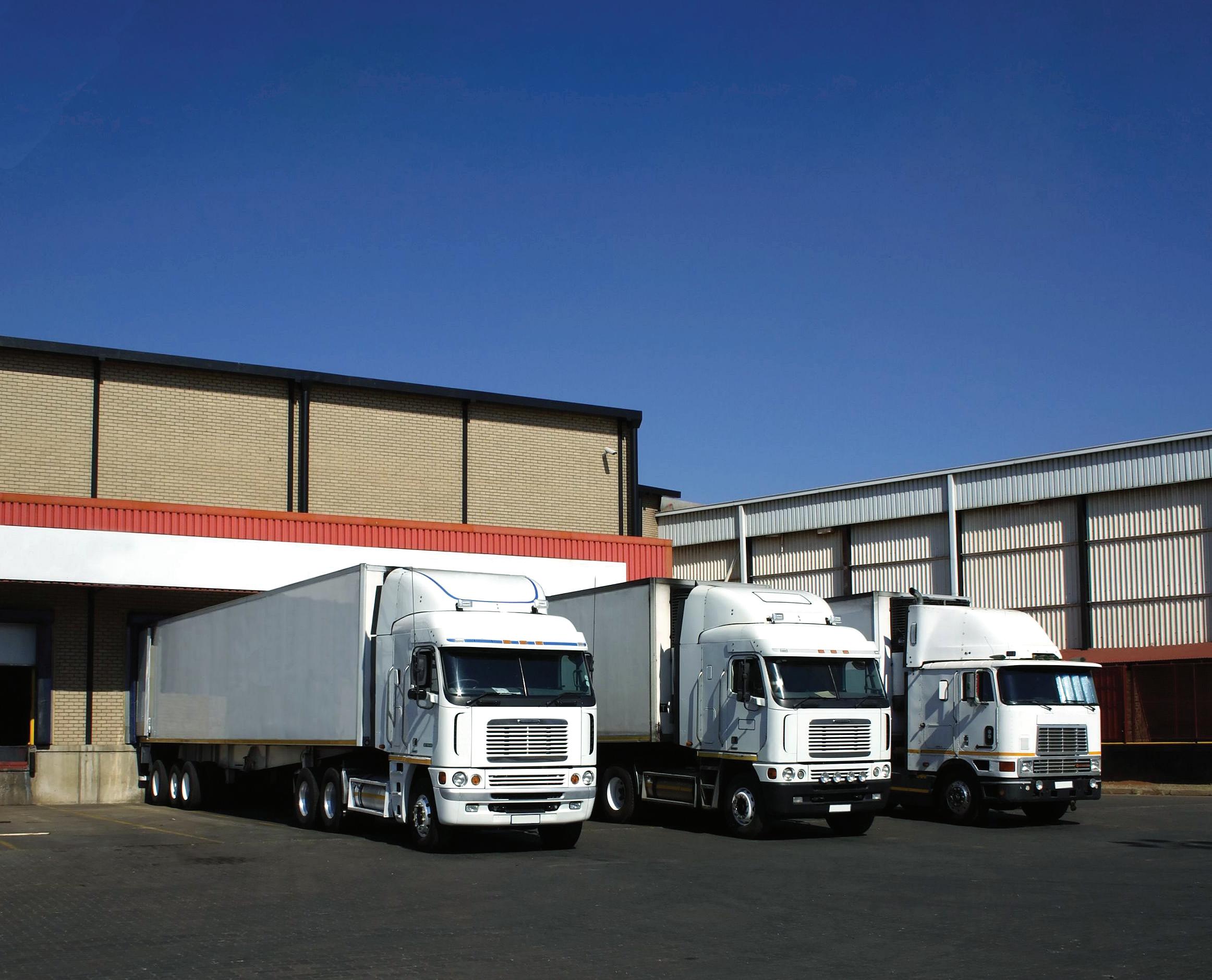
with a slowing economy.
Vacancy Rates Trigger Higher Rents
With vacancy rates remaining at historically low levels — which are holding steady at around 3 percent, substantially below the five-year historical average of 4.7 percent as reported by Cushman and Wakefield — rental rates will remain elevated as demand for space surges and supply remains tight.
In Atlanta, where growth is being fueled by strong market fundamentals including significant population jumps in the metro area and transportation accessibility along three interstates (I-75, I-85, and I-20), average rental rates are up 33 percent year-over-year, marking the first time in history asking rents have tallied above $6.2 Even so, leasing activity remains robust, with more than 70 percent of speculative facilities delivered in the first half of the year being claimed by an expanding mix of 3PL providers, manufacturers, and retailers.
As interest rates continue to climb and construction costs swell, rental rates will continue to make headlines, as developers try to stabilize their returns to make projects pencil. While most developers aren’t slamming on the brakes given the strong market fundamentals, the threat of fewer starts will also drive upward pressure on rents, at least in the short-term.
The Rise of the One-Million-Square-Foot Facility
The market continues to see strong demand for one-million-square-foot or larger facilities. To put this size footprint in perspective, 20 football fields (50 yards wide by 100 yards long) could fit inside one of these buildings. They are massive facilities. Much of this demand for large boxes is being powered by traditional retailers, e-commerce, and 3PL tenants, which are increasingly requiring more space to keep up with demand.
In Q1 2022, the market saw a record 37 warehouse transactions of one million square feet or more, up from 24 year-over-year, according to a CBRE report.3 While these large facilities will continue to be developed, there will also continue to be demand for all size increments, and industrial developers should focus on building-size
niches that aren’t being provided. Industrial users may find limited choices for smaller-size increments and should be mindful of this when planning their future space needs.
Build-to-Suits Are Challenging
Tenants looking for specialized industrial buildings (build-to-suits) that address their unique needs may be hard pressed in this environment to find a developer to accommodate their request. Build-to-suits, by their specialized nature, take longer to plan and execute. In a rising interest rate and construction cost environment, it is very difficult to lock in final pricing and deal terms that both developer and tenant can agree on. There is just too much economic risk to absorb for most build-to-suits to make sense. Further complicating the issue is the aging warehouse stock in the country, with the average age around 40 years old. Many users need more modern warehouse facilities with higher ceilings, larger truck courts, and added parking for vehicles and trailers. As a result, industrial developers are focusing on speculative facilities (buildings that do not have a signed tenant when construction begins) that can be brought to market more quickly. Cushman & Wakefield reports that speculative warehouses made up 70.3 percent of facilities that came to market as of Q3 2022. But with the market for build-to-suits so challenging, plans for these advanced facilities are hindered.
Although certain construction materials are beginning to stabilize, such as the price of steel and lumber, the rising interest rate environment and looming recession are causing more industrial developers to be less aggressive in this current climate. We can anticipate continued, yet fewer starts as development pipelines are recalibrated to address these cost challenges. While the full impact on tenants remains to be seen, rising interest rates and volatile construction costs will surely affect the pace, size, and supply of industrial facilities for the near term. n
1 https://www.cushmanwakefield.com/en/united-states/insights/us-marketbeats/us-industrialmarketbeat
2 https://www.cushmanwakefield.com/en/united-states/insights/us-articles/atlanta-industrialfast-facts
3 https://www.cbre.com/press-releases/bigger-and-bolder-large-warehouse-leases-fueledus-industrial-and-logistics-market-in-h1-2022
Rising INTEREST RATES and volatile construction costs will surely affect the pace, size, and supply of INDUSTRIAL FACILITIES for the near term.
Bright Spots of the Office Sector
The post-pandemic remote working trend has resulted in “emerging” or “other” metros performing better than the more established tech markets.
By Lu Chen, Senior Economist, Moody’s AnalyticsAfter more than two years since the beginning of the pandemic, over 50 percent of the office-using employees are still spending most, if not all, of their working days at home. The office, once an undisputed necessity, has become a pandemic luxury at least for some of the wellestablished tech markets located along the coast. As landlord and investors closely monitor and assess the future of office, Moody’s Analytics developed tools to rank each metro’s performance and future prospect using trend and forecast data. The results show many bright spots that are creating positive momentum and shining lights into the future of the office space.
Top Performers
The Performance Index is designed to measure a metro’s office sector performance (effective rent growth and vacancy changes) compared to its own performance history and cross-metro performances. As shown in Table 1, four Midwest metros — Wichita, Omaha, Dayton, and Indianapolis — secured top-10 spots in the third quarter of 2022. In general, firms in the Midwest are benefiting from lower salary levels and office rent as compared to other regions. Wichita ($12.15/sq. ft.) and Dayton ($11.95/sq. ft.) offer the
Table 1:
Top 10 Performers in Q3 2022
lowest office effective rent among our 82 primary metros, and all four are among the most affordable places for employees to live.
Two West metros — Tucson and San Bernardino/Riverside — made it to the top performer list. On the other end, well-known coastal markets including San Diego, Los Angeles, San Francisco, or San Jose all ranked in the bottom third. Tucson’s economic development was boosted by the boom of semiconductor manufacturing and high-tech/R&D/logistics support. San Bernardino/Riverside benefited from its emerging tech presence and still relatively affordable resi-
Table 2:
Top 10 Future Stars
Rank Metro Name Forecast Effective Forecast Effective Forecast Effective Revenue Growth Revenue Growth Revenue Growth (1 year) (3 year) (5 year)
1 Tucson 5.4% 7.0% 13.0% 2 Knoxville 5.3% 8.2% 15.0% 3 Westchester 2.6% 5.5% 9.0% 4 Ventura County 3.5% 7.4% 13.0% 5 Salt Lake City 3.8% 8.2% 15.0% 6 Birmingham 2.0% 5.2% 11.0% 7 Central 4.1% 6.5% 11.0% New Jersey 8 Omaha 4.7% 6.0% 10.0% 9 Dayton 3.5% 5.4% 11.0% 10 Greensboro/ 1.4% 5.0% 11.0% Winston-Salem
Table 3: Bright Spots of the Office Sector
Source: Moody’s Analytics CRE
dential market.
On the East Coast, Central New Jersey and New Haven, Conn., outperformed their peers surrounding the broader New York area, and their office sectors had significant improvement as compared to a year ago. Diversified industry played a key role in both metros’ success, and New Haven is especially bolstered by its tech and life sciences industries.
Oklahoma City and Palm Beach, Fla., shined in the South, along with three Tennessee metros close behind: Memphis (#11), Nashville (#12), and Knoxville (#13).
Population in-migration, skilled labor force, low cost of doing business, and diversified industries are some of the common advantages to consider for these five southern metros.
Will the Top Performers Sustain Their Growth?
One quarter of good performance doesn’t always guarantee longer-term prosperity. To account for future performance, we used a Prosperity Index, which compared a metro’s one-year (near-term), three-year (mid-term), and five-year (long-term) forecast with other
metros’ forecasts and against its own history.
The rankings of metros were shuffled, but all top-10 performers’ futures remain bright. As shown in Table 2, Tucson (#1), Central New Jersey (#7), Omaha (#8), and Dayton (#9) all secured their top-10 rankings in both performance and prosperity measures.
The Midwest and South Atlantic led the nation with above-average construction activities pre-pandemic, and cities in these regions have been gathering momentum in the post-pandemic period. Emerging semiconductor and tech industries are also fueling the growth for places such as Salt Lake City; Knoxville, Tenn.; and Ventura County, Calif., which were once down at the middle or even bottom third on the performance list during the same time last year.
What to Look for in the Future of Work
To account for every office market’s current state and future trajectory, we combined their Performance and Prosperity Indexes into a Total Index. Table 3 lists the top 10 office markets which performed well in the third quarter and will continue to deliver above average performance in the next five years.
Further, we classify all 82 primary office markets by their level of tech-related employment into “established,” “emerging,” or “other”1 markets. Unsurprisingly, 26 out of 28 metros in the top third of the Total Index ranking are “emerging” or “other” metros, while nearly half of the established tech markets ranked in the bottom third from both the current performance and future prospective.
The three Bay Area metros — San Francisco, San Jose, and Oakland-East Bay, which supported the rise of Silicon Valley — are now ranked at the bottom. Many local tech companies have moved their headquarters to states such as Texas, Tennessee, Arizona, or Nevada due to lower cost of doing business and living. For companies that are staying, many offer technology and continued flexibility for employees to work from anywhere without losing connection with the team.
3
As market participants continue to explore the opportunities and challenges created by the future of work, these are some of the important trends we need to watch for:
1. Metros with higher remoteworking percentages tend to experience higher office vacancy increases; and a higher share of technology employees can tilt vacancy up further.2
2. In the post-COVID era, office and apartment rent growth in a given metro may no longer be in lockstep. Workforce used to follow where the physical offices are, but the reverse is happening at many places.3
3. The decision of office lease renewals will not only depend on trajectory of future office use, but also its pivotal role in talent recruiting, retention, or even promotion.
4. Diversified industry, skilled workforce, and affordable housing options are important factors to hedge the market risk.
5. Offices loaded with amenities such as meeting spaces, food and beverage options, health and cleanliness processes, and technology capabilities such as virtual reality and larger screens for video conferencing stand a better chance to draw employees back.4 n
1 Established” — a metropolitan area as one if computer and math employment makes up 5% or more of total employment OR the metro has over 100,000 jobs in those occupations, including Seattle, Atlanta, San Francisco, San Jose, Raleigh, Dallas, Chicago, Los Angeles, New York, Baltimore, Austin, Colorado Springs, Boston, Denver and Washington, D.C. “Emerging” — a metropolitan area that has at least 10% more growth in employment for computer and math occupations than the national average since 2018 OR at least 4% more median annual wage growth for computer and math occupations since 2015 compared to nationally. The 12 qualifying metros were Ventura, Buffalo, Greensboro, Miami, Greenville, Knoxville, New Orleans, Norfolk, San Bernardino, Nashville, Lexington, and Wichita.
2 Where Office Vacancy Stands as Working from Home Becomes Mainstream: https://cre.moodysanalytics.com/insights/cre-trends/where-office-vacancy-stands/
The Great Divergence — Multifamily and Office Rent Growth Are No Longer in Lockstep: https://cre.moodysanalytics.com/insights/cre-trends/the-great-divergence-multifamilyand-office-rent-growth-are-no-longer-in-lockstep/
4 Are You Asking the Right Questions About Office? https://cre.moodysanalytics.com/insights/cre-trends/are-you-asking-the-right-questionsabout-office/
One quarter of good performance doesn’t always guarantee longer-term prosperity.
As manufacturers seek to bolster their global supply chain capabilities, we are seeing a significant uptick of interest in Mexico as a platform to serve the U.S. marketplace. While operating costs may be higher in Mexico versus many Asian locations, companies are opting to locate in Mexico in order to build resiliency into their global supply chain.
In a recent conversation with one of our clients who recently established their fourth production facility in Mexico, I was told that they are paying very high prices to express ship components from Asia by air to their production operations south of the border. They are doing this precisely because they have learned that it costs more to have a manufacturing line inoperable than to pay a higher price for components and materials. Clearly, this is not a sustainable strategy.
Mexico, the United States’ second-largest trading partner behind Canada, is an outstanding manufacturing location, but it’s not for every company. This article explores both the advantages and challenges of placing a production operation in Mexico.
An
Economy
Geared
Factoring Mexico Into a Solution to the Global Supply Chain Crisis
While its proximity to the U.S. and lower labor costs make Mexico a good location for a manufacturing operation, other costs may be higher, and its supplier base still lacks maturity.
By Bob Cook, Senior Vice President, Site Selection GroupFigure 1 WORKFORCE: Mexico Manufacturing Employment by Industry
Source: INEGI, Banco de Informacion Economico, October 2022
percent compared to the first eight months of last year, while those from Mexico have grown 21 percent over the same time period.
for
Export Mexico’s manufacturing economy is geared for export…primarily to the U.S.
Mexico has been gaining ground on China as a key link in the global supply chain for companies serving the U.S. marketplace. During the three-year period of 2018–2021, U.S. imports from Mexico have increased 11.9 percent to $384.6 billion, while those from China have actually decreased by 6.2 percent to $504 billion over the same time period. However, from January through August of this year, imports from China are rebounding — up 18.3
The manufacturing sector provides almost 4.5 million jobs in Mexico, almost two-thirds (65 percent) of which are provided by companies involved in the IMMEX (manufacturing for export) program. Also referred to as “maquiladoras,” these companies lost 123,000 IMMEX jobs during the first four months
of the pandemic in 2020. The jobs were fully recovered by Oct 2020, just 7 months into the pandemic. IMMEX manufacturers in Mexico have added more than 200,000 new production jobs since that time and in August 2022 reached their highest level in history at almost 4.458 million.
While two industry segments provide almost half (46.5 percent) of Mexico’s manufacturing employment — food and beverage (1.042 million jobs) and transportation equipment (1.034 million jobs), there is still solid diversity in the country’s manufacturing base. As seen in Figure 1, there are four additional manufacturing sectors that employ at least 250,000 people south of the border.
Our project activity with companies considering Mexico reflects this diversity. Over the past few years we have worked with producers of industrial equipment, furniture, automotive parts, medical devices, and others who are contemplating operations in Mexico. In fact, almost every one of our clients that is looking to reposition facilities or expand their current capacity requires us to analyze both Mexico and the U.S. for their projected operations.
What types of companies should consider Mexico as a production location? We believe Mexico is wide open for almost any type of manufacturer — especially if it is not hypersensitive to electric and logistics costs. (These two issues are discussed later in the article.) While there are no hard and fast rules about this, any company contemplating an operation with at least 200 production jobs — or at least 15 percent of their total product cost comprised of labor — could potentially benefit from a location in Mexico. Having said that, we have seen companies with smaller headcount and lower labor content also find success there.
From a supply chain perspective, the most important relationship between the U.S. and Mexico is found in the transportation equipment sector, primarily the automotive industry. Automotive OEMs in the United States depended upon Mexican suppliers to provide almost $53 billion in auto parts last year, 41 percent of the total value of all car parts imported into the U.S. Imports from Canada were a distant second with only $13.1 billion. Additionally, Mexico ranks #1 or #2 for imports into the U.S. for other industry segments such as medical devices ($8.5 billion in imports in 2021), consumer electronics ($71.0 billion), electrical equipment and appliances ($34.7 billion), food and beverage ($20.1 billion), and fabricated metal products ($11.3 billion). Clearly, Mexico has shown strength in a wide range of industry segments and is an integral part of the global supply chain equation.
Labor & Location — Mexico’s Traditional Supply Chain Advantages
Mexico offers two principal value propositions to a manufacturer — labor cost and proximity to the United States marketplace.
Labor costs in Mexico will be a fraction of those paid in the U.S. Figure 2 depicts average base wages for each country for certain production jobs; however, benefits in Mexico can add another 70 percent to 115 percent to the base wage versus 28 percent to 35 percent in the United States. Common benefits in Mexico include productivity bonuses, attendance bonuses, free transportation to/from work, partially subsidized meals (two per day), on-site doctor or nurse, and others. All of these, plus a whole host of benefits mandated in Mexican federal labor law (housing subsidy, healthcare subsidy, Christmas bonus, etc.) are calculated in the fully burdened wage. Even with the higher benefits load in Mexico, it is not uncommon to see fully burdened labor rates in Mexico that will be 15 percent to 25 percent of fully burdened labor rates in the U.S.
The second advantage to Mexico is its proximity to the United States. You can transport a finished product (component or sub-component) in Mexico from almost any location in the country, cross at one of many ports of entry along the U.S.-Mexico border, and have that product land in almost any community in the United States within a matter of days. Of course, it will take several weeks for that same product, component or sub-component to be shipped from Asia (20–22 days to Long Beach), and then the shipment will encounter additional berthing delays when the container arrives at port. Coupled with truck driver shortages and significant rail backlogs, transit times are often difficult to predict. A location in Mexico doesn’t completely solve this problem, but it does provide a much better solution than purely relying upon suppliers from Asia.
Close to one third (30.9 percent) of IMMEX companies, representing 34.4 percent of IMMEX employment in Mexico, are taking full advantage of logistics by locating in a Mexican city located immediately on the 2,000-mile border with the United States. For most products manufactured in one of these border cities, they are crossing in less than half a day and are on their way to the final destination in the United States.
An additional benefit of locating on the border is that your management team, engineers, and other professionals can live in a U.S. city and commute to the Mexican operation on a daily basis. Most of these managers will be enrolled in a trusted-traveler program like SENTRI that allows them to experience almost no wait
Figure 2 Base Wages for Selected Production Jobs (USD per Hour)
Job U.S. Average Mexico Average (USD)
Welder-Cutter
$23.84 $2.98
Assembler (Mfg.) $17.69 $3.03
QA Inspector $19.12 $3.35
Warehouse Laborer $19.18 $2.67
Machine Operator $20.28 $3.28
Tool & Die Maker $29.50 $5.08
Painter (Production) $18.48 $2.62
Source: ERI Global Salary Assessor, October 2022
at the border when they cross northbound at the end of the day. Additionally, the cost of living in these U.S. border cities tends to be well below U.S. averages.
Mexico’s Commitment to STEM Higher Education
Although labor cost and proximity to the U.S. are the principal drivers to a Mexican location, the nation has been positioning itself to attract higher value-added operations by investing in STEM education at its institutions of higher education. Today, Mexico is one of the top eight producers of engineering talent in the world, and this past school year (2021–2022), Mexico had over 847,000 students enrolled in engineering and related programs and conferred 135,765 engineering degrees. This was up from 129,600 graduates just three years ago. Higher education south of the border is also doing a good job of responding to the needs of industry by creating special programs related to aerospace, automotive, and biomedical industries to name a few.
A small handful of companies like Aptiv (formerly Delphi) are taking full advantage of this talent. Aptiv’s Mexico Tech Center in Cd. Juarez (on the border across from El Paso, TX) employs a large number of engineers (at one time more than 2,000) who have generated hundreds of pieces of intellectual property in new products, process improvements, and more.
Labor Laws Strongly Favor the Employee
When the USMCA (formerly NAFTA) was adopted during the Trump Administration, Mexican workers were given greater standing in collective bargaining agreements, and many states in Mexico now require companies to formally accept a labor union. A data point we closely monitor is labor disputes that are registered with the appropriate Mexican authorities in each of the cities across the country. We apply the number of annual disputes to a ratio such as “per 100,000 population,” and the higher ratios can be an early warning signal about
the potential “militancy” among unions in that area.
Perhaps the most significant HR issue to be aware of is unilateral termination of an employee. There is no “employment at will” in Mexico, like we see in the U.S., so terminations must be “for cause.” Employees that are laid off or otherwise terminated without cause are entitled to severance pay that starts with 12 days of wages for each year of employment. Severance pay may also include proportional amounts of various benefits like a Christmas bonus, vacation pay, and any agreed-to benefits that have not been paid as of the termination date.
On the plus side, federal labor law allows the worker to work eight hours per day and 48 hours per week before overtime is incurred. Overtime pay will be either two or three times the hourly pay rate depending upon the amount of overtime incurred on a daily or weekly basis.
Be aware that labor turnover in Mexico will likely be higher than at your operations in the U.S. Successful labor turnover rates (for your direct and some indirect personnel) will be less than 3 percent per month, a metric that would be deemed unacceptable in most of the U.S. Companies that successfully manage labor turnover will give great attention to three things in the following order of priority:
1. Enter Mexico with a strong understanding of the family-oriented culture, and make sure you establish policies and a plant culture that promote this.
2. Choose the right location within a given community. Locations that offer lower employee commute times will be more competitive.
3. Pay competitive wages and benefits. You do not have to be in the upper echelon of pay and benefits for a given community.
It should be noted as well that higher skilled operators and professionals like engineers tend to have labor turnover rates that will more closely mirror those in the United States.
Certain Operating Costs Will Be Higher in Mexico
Due to driver shortages that are even more acute than in the U.S., higher maintenance costs for fleets given lower quality of the infrastructure, and higher insurance costs, transportation lane rates will be higher in Mexico. We typically will budget 20 percent to 25 percent higher per mile costs in Mexico vs. the U.S. and
for free site information, visit us online at
will consider an additional half to one full day of transit time as trucks arrive for northbound clearance at the U.S.-Mexico border.
Electric rates are determined by size of load and time of day use. Rates will be lower in non-peak hours, and manufacturers that can balance their load over a 24hour period will be rewarded. Still, most electric rates you will incur can fluctuate between $0.10 and $0.20 per kwh, with the average typically around $0.13 per kwh.
Supplier Base Lacks Maturity
If your company depends on suppliers of raw materials or certain types of components, be aware that while the supply base is growing in Mexico, it still lacks maturity. An estimated 75 percent of the value of Mexico’s exports start as a component part or raw material from somewhere else, principally the U.S. or Asia (China). We suspect that this will begin to change somewhat as companies pay more attention to supply-chain resiliency than supply-chain cost by expanding their presence in Mexico.
Multiple Options to Commence Operations
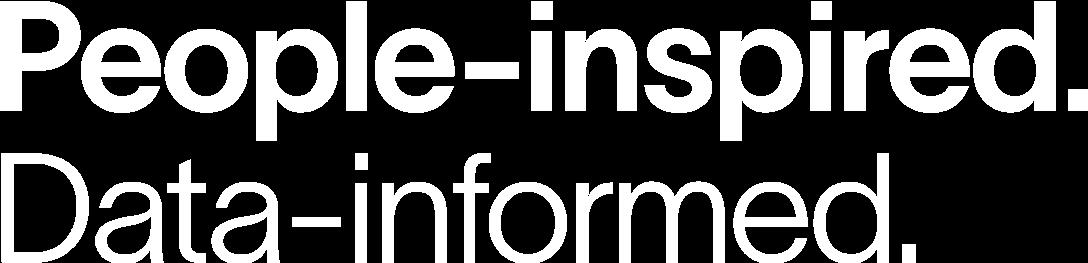
Since Mexico’s manufacturing for export program
(maquila) was created in the late 1960s, the country has liberalized its investment laws that allow companies to own 100 percent of the assets related to their production facilities, including land and building. Service providers across the nation have stepped up to offer various types of “soft landing” options to manufacturers seeking to establish a manufacturing presence in Mexico. Contract manufacturers have sprung up across the country (albeit not in large numbers) that can handle every aspect of manufacturing your products.

A more popular option for many companies entering Mexico for the first time is through a “shelter service” provider. These companies will provide a combination of services to include HR support, import/export assistance, environmental compliance, facilities management, transportation services, purchasing and more — and allow you to be operational in a matter of months under their corporate umbrella. Many companies will “graduate” from these programs after a few years, having learned how to successfully operate in Mexico through their shelter service provider.
Whether it is stand-alone, outsourcing to a contract manufacturer, or contracting with a shelter service provider, each option provides a unique blend of cost and risk that companies must assess. n
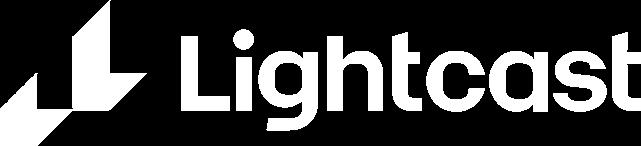
ALABAMA
Alabama Department of Commerce 39 contact@madeinalabama.com www.MadeInAlabama.com
ARIZONA
Arizona Commerce Authority 1, 47 www.AZCommerce.com
Salt River Project 17 www.PowertoGrowPHX.com
ARKANSAS
Arkansas Economic Development Commission 35 ccogbill@arkansasedc.com www.ArkansasEDC.com
CALIFORNIA
Greater Sacramento Economic Council 61 www.GreaterSacramento.com/ semiconductors
GEORGIA
Georgia Department of Economic Development 5 www.Georgia.org
Georgia Ports Authority 22 www.GAPorts.com/Site Selection
KENTUCKY
Commerce Lexington 63 www.LocateInLexington.com
Kentucky Cabinet for Economic Development 7 www.CED.KY.gov
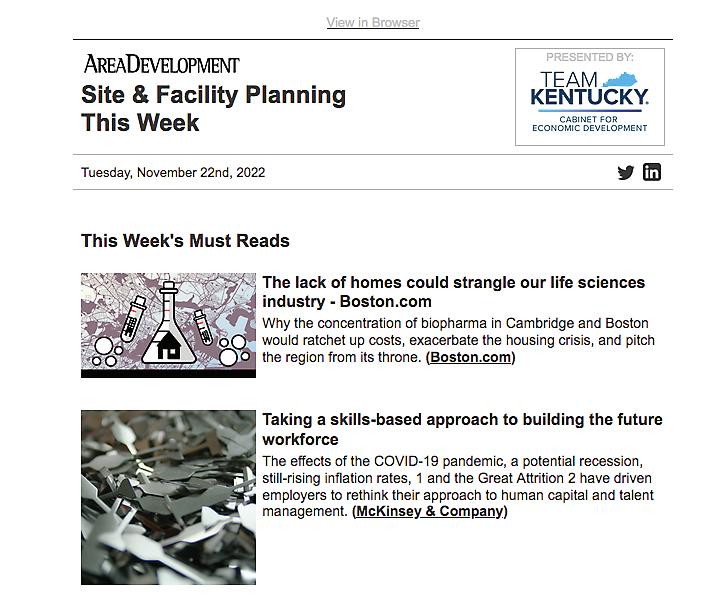
IDAHO
EMSI/Lightcast 79 Lightcast.io
IOWA
Iowa Economic Development Authority 37 www.IowaEDA.com/locations
MARYLAND
Maryland Department of Commerce 11 Open.maryland.gov/siteselection
MICHIGAN
Flint & Genesee Group 52 info@flintandgenesee.org www.DevelopFlintAndGenesee.com
Michigan Economic Development Corporation 9, 44–45 proctors1@michigan.org www.MichiganBusiness.org/ Pure-Opportunity
MISSISSIPPI
Golden Triangle Development Link 25 www.GTRLink.org www.DevelopNorthStar.org
Mississippi Development Authority C2 www.Mississippi.org
MISSOURI
Missouri One Start 33 www.MissouriOneStart.com
NEVADA NV Energy 57 www.NVenergy.com
NEW YORK
National Grid C3 www.ShovelReady.com
NORTH CAROLINA Economic Development Partnership of North Carolina 41 www.EDPNC.com
OHIO JobsOhio C4 www.JobsOhio.com
PENNSYLVANIA
Lehigh Valley Economic Development 48 www.LehighValley.org
SOUTH CAROLINA Santee Cooper 65 www.PoweringSC.com
TENNESSEE
Tennessee Department of Economic & Community Development 19 www.TNecd.com
TEXAS
Lubbock Economic Development Alliance 27 https://lubbockeda.org
VIRGINIA
Virginia Economic Development Partnership 30–31 info@vedp.org www.VEDP.org
WISCONSIN
Wisconsin Economic Development Corporation 3 www.WEDC.org
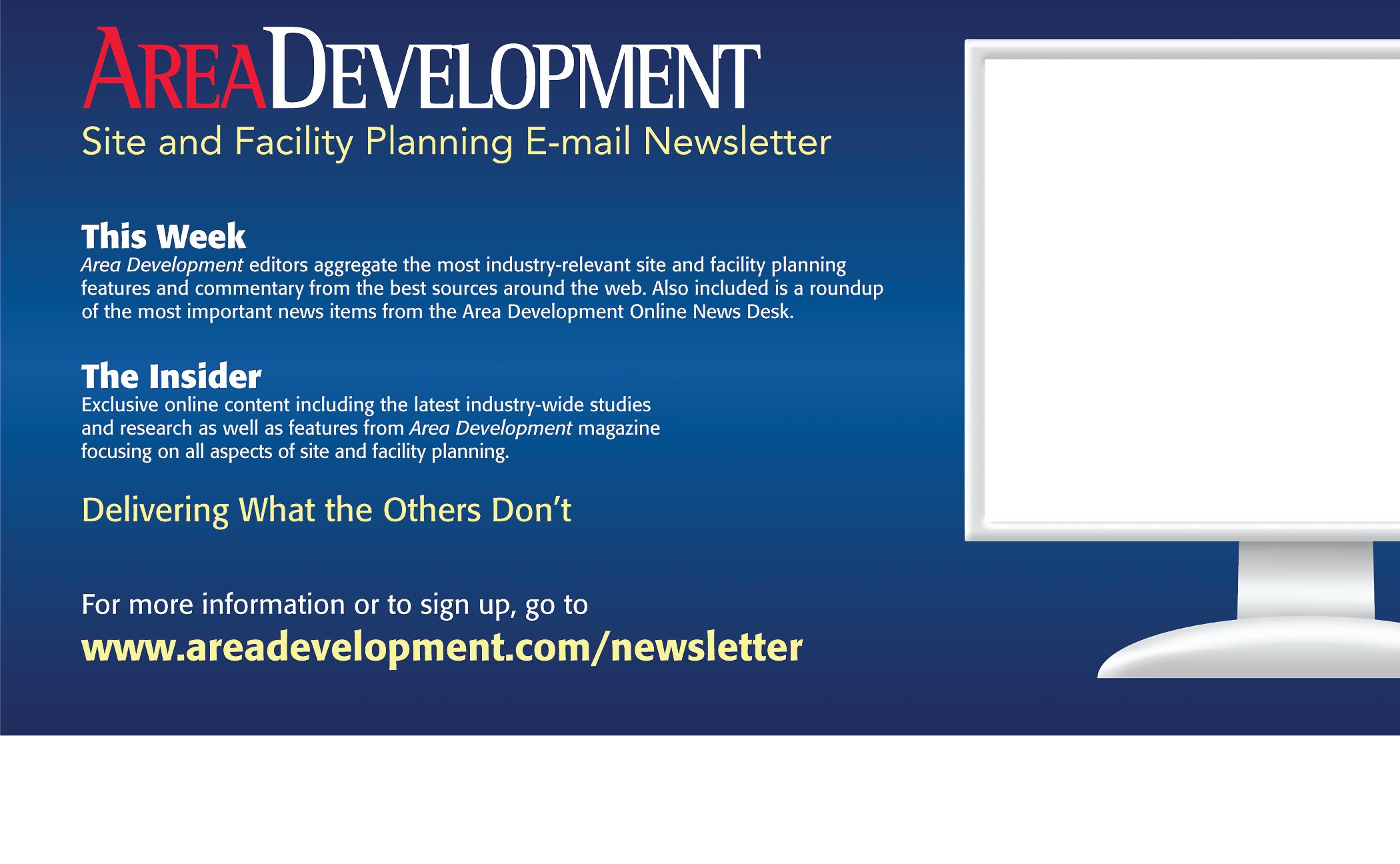
14–15 www.edc.nyc
NYCEDC
Our grant programs have provided over $100 million in assistance, helping to create or retain 50,000 jobs in New York communities.
Learn how our programs can benefit your business. Visit www.shovelready.com
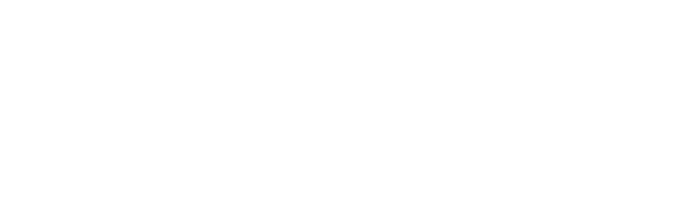
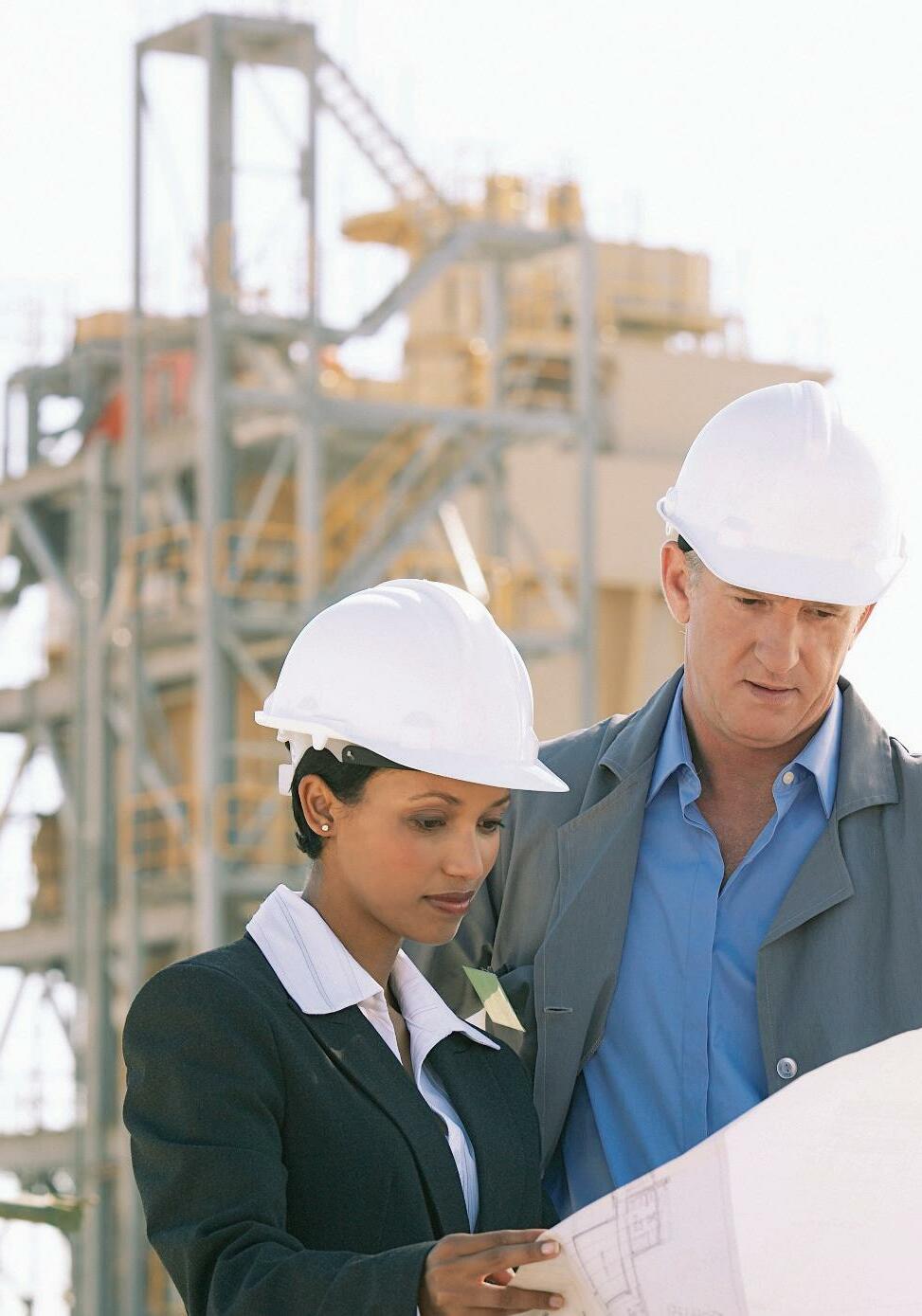
We’re committed to Economic Development and a clean energy future in New York State.
Ohio Moves Business Forward

With shovel-ready sites, low costs, skilled workforce, and 21st-century infrastructure, JobsOhio matches companies with the perfect location to meet their diverse needs. We embrace innovation and are committed to working with bold leaders who are ready to experience all Ohio has to offer.
Find Out Why Companies Are Moving to Ohio.