
7 minute read
Fish protein concentrate can partly replace water as plasticizer in the fish feed extrusion process
Tor Andreas Samuelsen, Nofima
Consistent and high physical quality of feeds to aquatic species are crucial for efficient feed transportation, feeding logistics and reduced feed loss to the aqueous environment. Extrusion processing is a technology that enables the manufacturing of such quality and is the dominating technology used in commercial production. The extrusion process involves several processing steps to transform the dry recipe powder feed mix into expanded extrudates that can be dried to durable pellets and added oil in a vacuum coating operation. To obtain high physical pellet quality, the feed mix is moistened and heated by water and steam addition in the preconditioner and further heated by the use of mechanical mixing and viscous heat dissipation in the extruder barrel. During this processing, the powder is transformed into a plasticized and flowable material that can be shaped through the extruder dies. Normally a plasticizer in the form of water is added to reduce the temperature needed for this transformation and improve cooking efficiency in the extruder barrel. A plasticizer is a small molecule that penetrates the dry powdery feed mixture and weakens the intermolecular binding forces in the particles. The particle polymer chains then unfold and slide past each other creating a plasticized melt.
The use of fishmeal in salmon feed formulations has been reduced from 65% to 15% in the last two decades and has partly been replaced by alternative plant-based ingredients, with soy protein concentrate (SPC) and vital wheat gluten as the dominating protein sources. Plant proteins, especially SPC, demand high water level and temperature in the extrusion process to obtain satisfactory plasticization and durable pellets. This gives the feed manufacturing industry challenges related to pellet quality and drying costs. The use of alternative plasticizers to partly replace water can reduce extrudate moisture content and energy requirements in the dryer and improve physical feed quality. Our earlier studies have documented that the water-soluble peptides and amino acids in fishmeal have plasticizer effects comparable to water and improve physical pellet quality. We have also studied the plasticizing effect of the amino acid proline on SPC, and a near equal plasticizing effect for proline compared to water was found. This demonstrates that free amino acids and low molecular weight water-soluble peptides can be used as plasticizers and partly replace water in the extrusion process.
Figure 1. Capillary rheometer with pre-shearing capabilities. By setting the piston speed (shear rate) and measuring the pressure drop across the capillary die, melt viscosity can be calculated.
Fish protein concentrate
Fish protein concentrate (FPC) is a hydrolysate produced by acid conservation and autolysis of
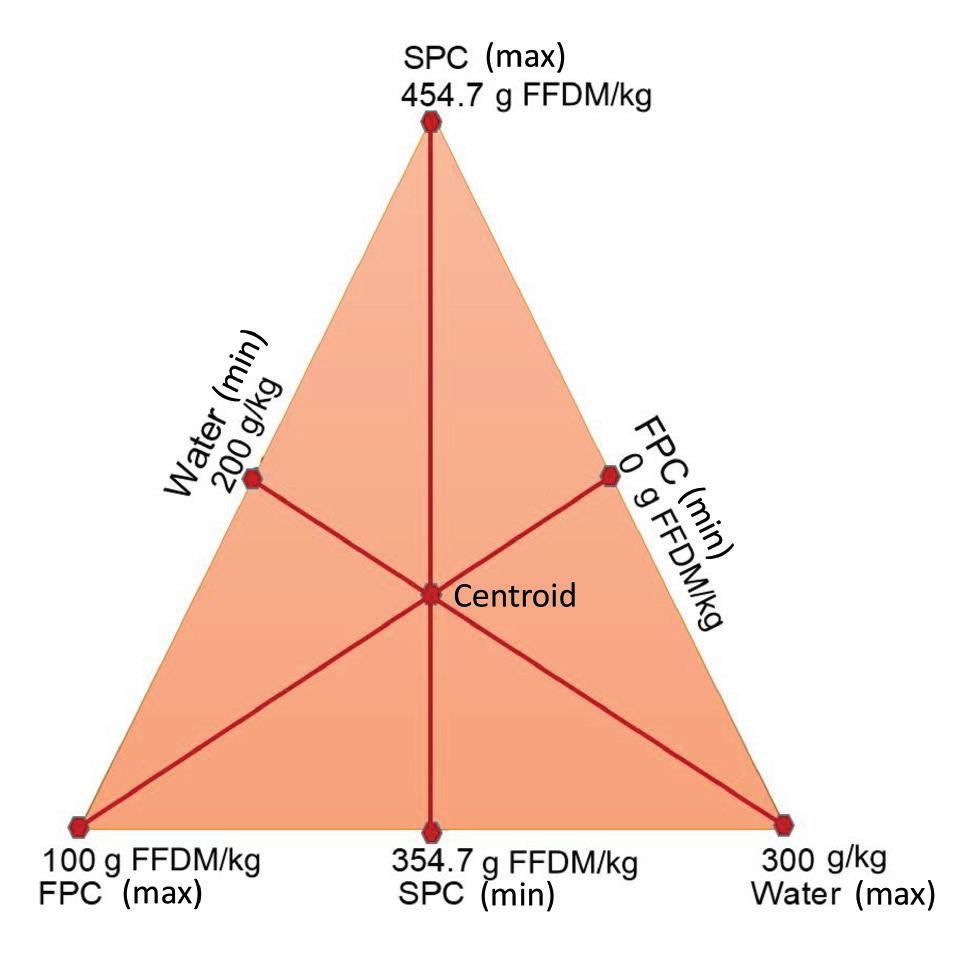
Figure 2. Levels of FPC, water and SPC in the design.
Figure 3. CT-scan of extrudate samples for maximum concentrations of SPC, FPC and water and equal mixture of the three (centroid). Black is air, grey is the pellet structure, and white is bone fragments from fishmeal.
fish offcuts and residues from filleting, gutting and other fish processing operations (silage process). It is a sustainable alternative protein ingredient. The raw material is minced and added formic acid to reduce the pH ≤ 4. This gives optimal conditions for protein hydrolysis by the fish digestive enzymes and a microbiological stable product. The hydrolyzed crude fish silage is heated and processed over a 3-phase decanter centrifuge to remove oil and particles before concentrated to FPC with a dry matter (DM) of 40-50%. A typical FPC can have a water-soluble protein content >90 g/kg DM where >60% is free amino acids (<200 Dalton) and >80% with molecular weight less than 500 Dalton, components with potential plasticizing effect. In industrial manufacturing practice, FPC may thereby represent a cost-effective and sustainable plasticizer solution.
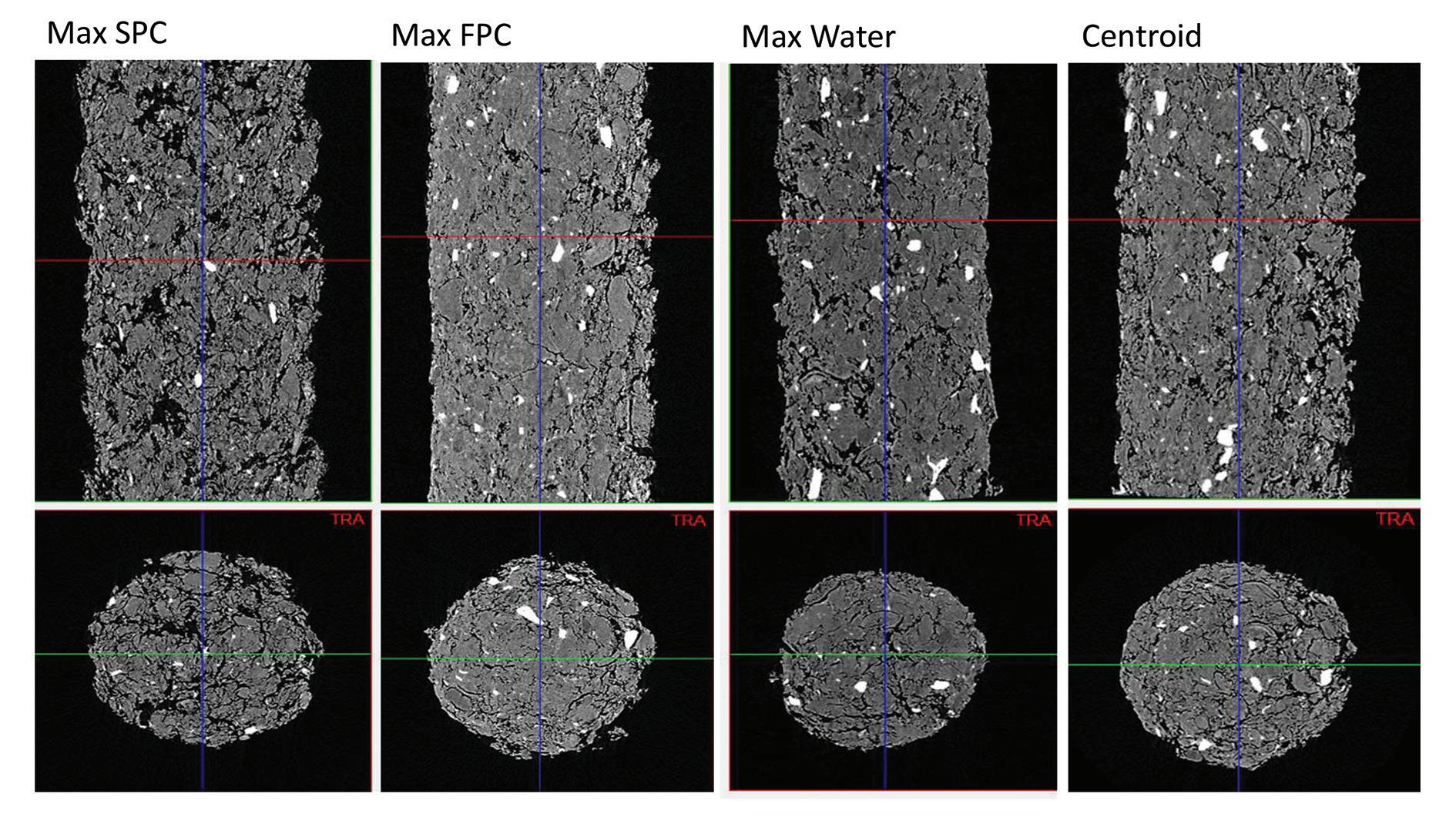
Plasticizing effect of fish protein concentrate
To document a possible plasticization effect of FPC, we performed a technical trial by using a capillary rheometer with pre-shearing capabilities (Fig. 1). This rheometer has been reported to give results comparable to the extrusion process and enabled us to produce a plasticized/melted feed mass in a conical shear cell prior to viscosity measurements through a capillary die and evaluation of dried extrudate physical properties. In the trial, we chose to vary the three ingredients, FPC, SPC and water in feed mixes. This was performed by use of a mixture design where the three ingredients always sum up to 100 g in a triangle (Fig. 2). The SPC and FPC have different fat and water content and we, therefore, varied the amount of SPC and FPC based on fat-free dry matter (FFDM). We held the rest of the feed mix constant (900 g) with a fixed composition consisting of fishmeal (100 g FFDM/kg), vital wheat gluten (100 g FFDM/kg), whole wheat flour (100 g FFDM/kg), SPC (354.7 g FFDM/kg), water (200 g/ kg; sum of moisture content in the ingredients + added water) and fat (45.3 g/kg; sum of fat content in the ingredients + added sunflower oil). Fat is a lubricator, and it was therefore set equal in all samples to prevent fat from affecting the results. We aimed to simulate the conditions at a preconditioner outlet for a “normal” salmon diet with a moisture content ranging from 20-30%, prior to simulating the extrusion process in the capillary rheometer.
Results
We operated the capillary rheometer at 110°C and a wall shear rate of 300 1/s, and
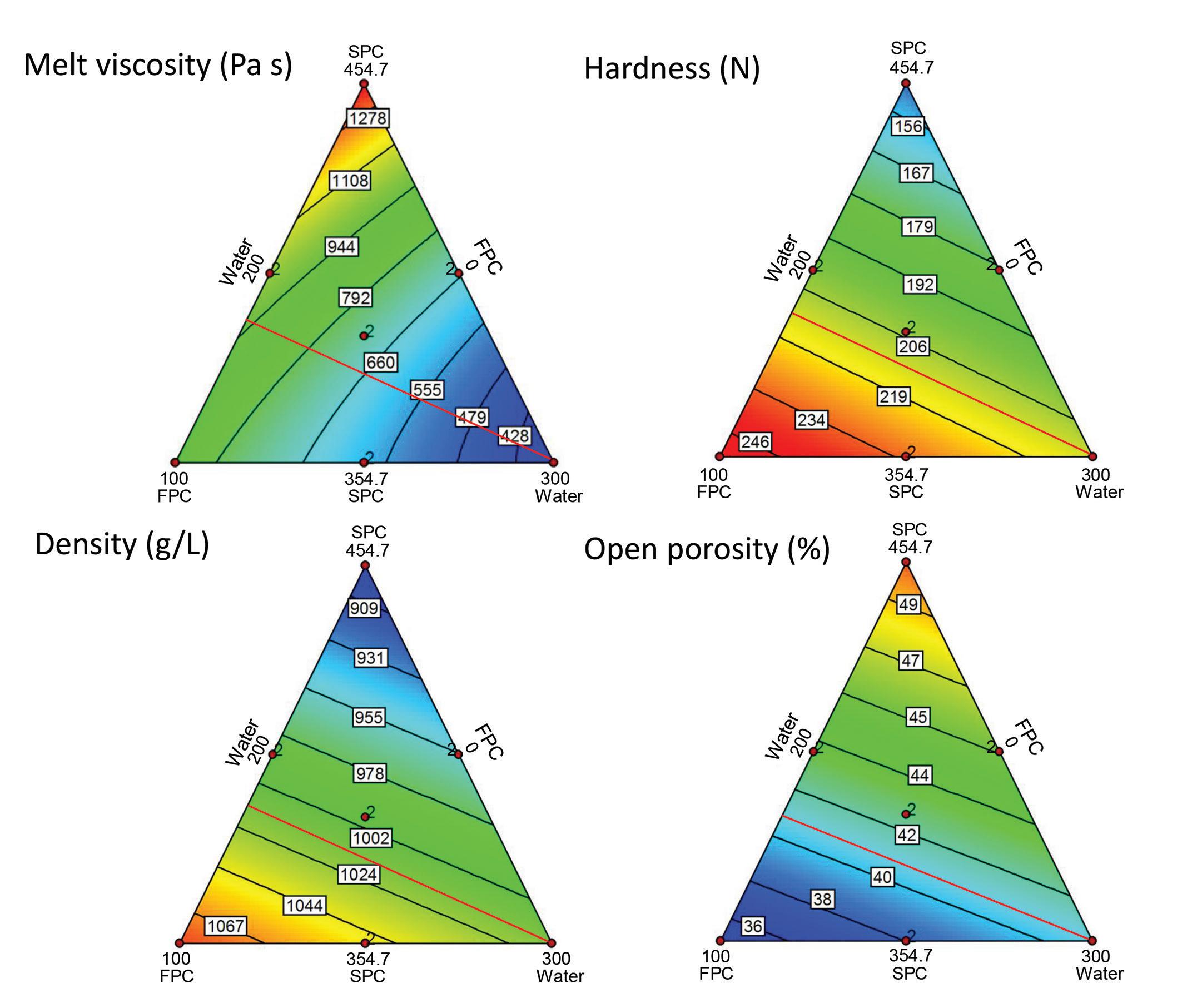
Figure 4. Results for melt viscosity (Pa s), extrudate hardness (N) and density (g/L), and the extrudate microstructure parameter, open porosity (% of total porosity). The contours are flagged with the actual units. The red line represents feed mixes with similar values for hardness, density, and open porosity.
freeze-dried the extrudates into durable pellets. We thereafter measured pellet hardness by use of a texture analyzer, density, and microstructure by use of X-ray microtomography (CT-scan). The measured parameters showed high variation (Fig. 3 and 4) and with the physical pellet parameters hardness and density negatively correlated to the microstructure parameter, open porosity (i.e., % of total pore volume connected to the pellet surface).
Effect on melt viscosity
We observed a decrease in melt viscosity when SPC was replaced with FPC and/or water but with a sharper decrease by using water (Fig. 4). This may be a result of the much lower viscosity of water compared to FPC and differences in how they interact with the other ingredients in the feed mix. We chose to hold the temperature, shear rate, and die diameter constant and the observed reduction in viscosity with increased concentration of FPC and/or water reflects a higher effect of temperature on viscosity reduction in the feed melt phase. This confirms a plasticizing effect of the two ingredients.
Effect on hardness, density and open porosity
We also observed that increasing the level of both FPC and water in the feed mixes increased pellet hardness and density and reduced the open porosity (Fig. 4). This may be a result of increased plasticization (cooking efficiency) and reduced melt viscosity, contributing to the formation of denser and harder pellet with a smoother outer surface as shown in Figure 3. From Figure 4, it can be seen that adding FPC had a higher effect compared to water. In contrast to water, which needs to be removed from the dryer, FPC will be carried over to the dried pellets. This will change the viscoelastic properties of the pellets and also give less pore structure, denser pellet, and increased hardness. We performed all the measurements under equal conditions in the capillary rheometer and as can be seen
from Figure 4, SPC plasticized with FPC gave different extrudate properties compared to water plasticization. However, FPC added at a concentration of 65 to 70 g/kg FFDM at 20% moisture content gave values of hardness, density, and open porosity similar to SPC added 100 g/kg of water (30% moisture content; Fig. 4, red line). This documents that FPC can partly replace water as a plasticizer in the extrusion process, with a potential for a significant reduction of the energy consumption during drying of the wet extrudate.
Conclusion
The pre-shearing capillary rheometer enables plasticization of the sample material prior to rheological and physical measurements relevant to extrusion cooking. The ratio between the ingredients SPC, FPC and water gave different melt viscosity, extrudate hardness, density and microstructure. At equal levels, SPC plasticized by FPC gave different extrudate properties compared to water, but by knowledgebased use, FPC can be a sustainable plasticizer and nutrient in extruded fish feed and partly replace water in the extrusion process.
Acknowledgments
This article is based on Ahmad, R., Oterhals, Å., Xue, Y., Skodvin, T., Samuelsen, T.A. (2019) Impact of fish protein concentrate on apparent viscosity and physical properties of soy protein concentrate subjected to thermomechanical treatment. Journal of Food Engineering, 259, 34-43. Laboratory and pilot equipment for technical ingredient characterization, feed production and product evaluation are now available at the new Aquafeed Technology Center hosted by Nofima (https://aquafeed.science/).
References available on request.
More information: Tor Andreas Samuelsen
Senior Scientist Nofima E: tor.a.samuelsen@nofima.no