
13 minute read
Sustainable manufacturing of shrimp feed with twin screw extrusion
Hadrien Delemazure, Clextral
In the global movement towards sustainable food sources, shrimp farming presents an important opportunity for aquaculture producers. Although the COVID-19 pandemic limited farming and temporarily reduced demand, worldwide consumption of shrimp is projected to reach $7.65 billion by 2023 (Global Shrimp Market 2019-2023). Consumers have come to value this small crustacean’s high nutritional impact and health benefits and are adding it regularly to their diet. Shrimp is a known source of the trace element selenium with antioxidant attributes that have been linked to increased immunity. Yet, with this market opportunity comes challenges: • How to produce high-quality feed that supports sustainable shrimp health and growth. • How to optimize Feed Conversion Ratios (FCRs) and minimize waste that negatively impacts the environment. • As the industry faces scrutiny about traditional feed ingredients (fishmeal and fish oil), combined
with periodic scarcity and resulting high ingredient cost, how to incorporate alternative and plantbased ingredients. • How to manufacture sustainably using fewer natural resources (energy, water, etc.). In this article, we will discuss these challenges and how shrimp feed processing with twin screw extrusion offers benefits both as a sustainable manufacturing method and also by producing shrimp feed that contributes to sustainable growth and environment conservation.

Processing for maximum nutrition and growth
Feed quality directly impacts the size and quality of harvested shrimp, however, shrimp feeding practices vary widely depending on the species and resources of the grower. For healthy growth to optimal size, shrimp require a nutritionally balanced diet, rich in protein and fats. For best absorption, feed ingredients must be properly managed, mixed and processed to fully combine the proteins and fats and integrate the carbohydrate components (starches) while protecting delicate enzymes and nutrients (vitamins and minerals). This is where the twin screw extruder excels. As ingredients are transported by the continuous, co-rotating screw action through the extruder barrel, the pressure, temperature and moisture can be precisely and independently controlled in every section. This complete control of production parameters ensures optimized starch gelatinization and complete protein cooking for best absorption. The intermeshing screw configuration of the extruder is key to positive transfer and uniform mixing when processing feeds with high-fat content.
Typically ingredients are processed in a preconditioner before extrusion, as this pre-processing step ensures homogenous distribution of the ingredients and initial starch gelatinization and denaturing of the proteins. The result of these combined processes, preconditioning and extrusion, is high-quality feed with excellent digestibility and textural qualities. Multiple studies by industry experts have shown that feeding high-quality feed to young shrimp significantly benefits their health and growth.
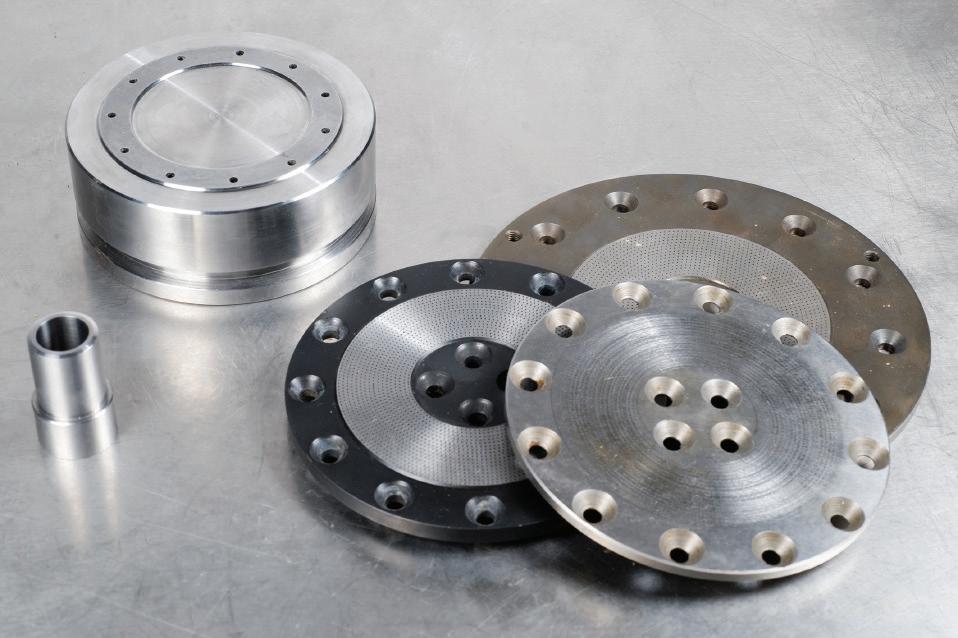
Processing for optimized Feed Conversion Ratio (FCR) with minimum waste
Whether shrimp are farmed in ponds or open nets,
virtually all are fed with commercial feed. Research has shown that feeds designed for the specific nutritional requirements for the species ensure optimal FCR, reduce waste and minimize farmers’ costs. The twin screw extruder has the flexibility to process a variety of feed types on the same machine by simply modifying the ingredients, production parameters and die configuration. Recipes and profiles are typically preset for access at the operator control station for the quick changeover on the production line.
Clextral extruders offer a density control system (DCS) that controls the thermal energy to be added or removed to adjust the feed pellet density, a benefit for shrimp feed production. This fully automatic tool increases the melt densities up to 750 g/L to achieve feed with high water stability and fast sinking properties. Water stability of more than 24 hours is key for optimizing feed consumption, as shrimp feeding activity is highest at night, while feed distribution is normally done during daylight hours. The ability to match feed characteristics with the shrimp’s habits is key to eliminating food waste and maintaining a healthy aquatic environment.
The feed size must also match the species’ mouth capacity. Clextral’s production dies for shrimp feed start at 0.5 mm. In order to form this small feed size, 100% of the mix granulometry must be less than one-third of the die holes, so in this case, 165 µm. This is achieved with a specialized grinding and pulverizing process. With die changes, the same extruder can process feed with perfectly calibrated dimensions from 0.5 to 3.0 mm and Clextral offers a range of die designs and cutters for this purpose. This flexibility enables specific matching for shrimp feeding patterns to ensure optimal feed consumption at every stage of growth.
Feed storage can also be a factor, especially for smaller farmers. Shrimp feed pellets produced by twin screw extrusion have proven to offer high shelf stability with minimum degradation due to their superior density and compact behavior.
Processing with plant-based ingredients
It has long been believed that shrimp feed must contain both fishmeal and fish oil for proper nutrition. However, with the increase in world aquaculture, these ingredients are often in short supply, resulting in higher costs. This has led researchers to explore new ingredients to obtain optimal nutrition. A recent study at Georgia State University demonstrated that shrimp feed based on soybean meal with added artificial chemostimulants was consumed as well as formulas that included krill, a known attractor.
Digestibility and palatability are top concerns when developing new shrimp feed formulations.
Clextral, as a major player in extruder technology for feed manufacture, has developed innovative techniques and technology for processing original recipes with raw materials that include pulses, proteins, insects, as well as processed animal proteins and seaweeds.
Sustainable manufacturing
Much has been discussed about sustainable manufacturing, in fact, the US Environmental Protection Agency (EPA) defined it as “the creation of manufactured products through economically-sound processes that minimize negative environmental impacts while conserving energy and natural resources.” If we look at twin screw extrusion processing, it is evident that this technology is well-aligned with this definition of a sustainable manufacturing operation. Let’s take a closer look. The twin screw extruder enables optimized processing with less waste. As a closed and continuous reactor, the extruder enables precise control and regulation of all parameters. Clextral preconditioners’ patented Advanced Filling Control (AFC) system is designed to control the filling ratio and residence time inside the preconditioner unit. The high output design of the Evolum+ extruder produces up to 40% greater volume than other systems, to generate more product at a reduced capital expenditure. The DCS system recycles fines and condensates from the extruder back into the preconditioner, forming a perfect closed loop system with no waste.
Efficient use of water in extrusion results in lower requirements and less effluent produced. In both the preconditioner and extruder, adjustable steam injection points are located for maximized absorption during processing.
Energy requirements are also lower due to several key features. In the preconditioner, steam injection can efficiently generate product temperatures of over 96˚C while limiting energy loss. At the extruder, a high torque gearbox generates maximum screw speed and
mechanical energy. Independent barrel modules are precisely heated or cooled by Clextral’s proprietary Advanced Thermal Control (ATC) system, a self-learning device that continuously monitors and adjusts to change in production parameters to achieve total process and product consistency. ATC has proven to reduce energy consumption by up to 20% with a 70% increase in stability.
Extruders by design are sustainable machines with continuous processing and closely controlled parameters that enable extended operational lifetime. Screw and barrel wear are factors in feed production and most manufacturers offer premium metallurgy to extend time between replacements. Pretreating the ingredients in a preconditioner also greatly reduces screw and barrel wear. In addition, extruders allow complete production versatility. One system can easily make multiple products interchangeably and can be repurposed for different production lines when required.
Helping shrimp feed manufacturers reach sustainability goals
As consumers search for sustainable food sources and nations seek to feed growing populations, farmed shrimp will likely face the same scrutiny as other farmed fish. By implementing sustainable practices, feed manufacturers can help shrimp farmers around the world to meet sustainability goals and produce highquality shrimp thus enabling all players to prosper from this growing market.
More information: Hadrien Delemazure
Process Engineer and Feed Expert Clextral, France E: hdelemazure@clextral.com
LACTIC ACID BACTERIA FOR AQUACULTURE Believe in what you see

We can see it inside, you will see it from the outside! BACTOCELL activates and associates with the gut mucosa, which is the key to a true probiotic effect. If you need to see more, years of research and field applications have provided compiling evidence of BACTOCELL’s modes of action and benefits at cellular, animal and farm level. Discover the world of BACTOCELL, the pioneering probiotic in aquaculture.
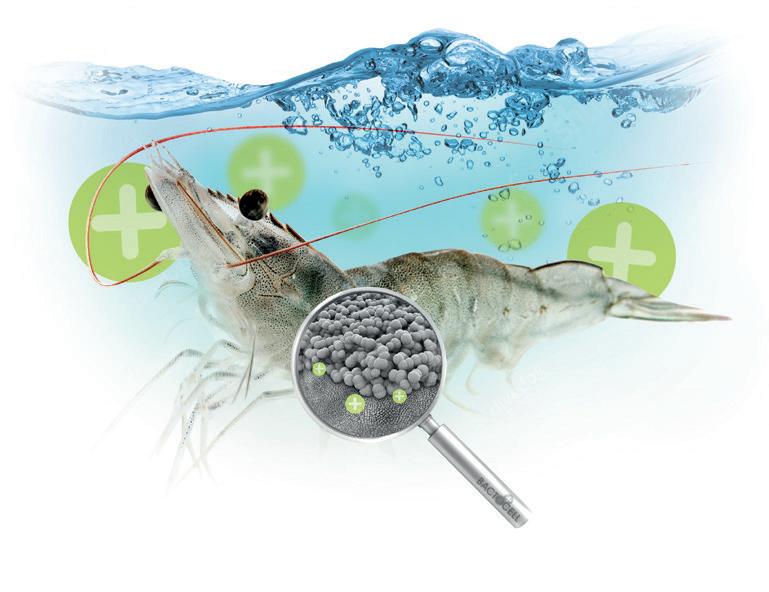
Not all products are available in all markets nor all claims allowed in all regions.
LALLEMAND ANIMAL NUTRITION SPECIFIC FOR YOUR SUCCESS
www.lallemandanimalnutrition.com
High moisture extrusion: A promising new method for making aquafeed with unique properties
Keshun Liu, USDA
Over the past several decades, extrusion processing has become the primary technique for making fish feed (Welker et al., 2019; Tacon, 2020). The method involves compressing a mixture of raw materials (a mash) through the barrel of a single or twin-screw extruder, applying heat to the mash as it passes through the barrel by rotating screw(s) and forcing the cooked mash through the small aperture of a die attached to the end of the extruder’s barrel. The whole process occurs at a high-temperature condition with a moisture content of the inner mash in the range of 15-45%. Upon exiting the die, the extrudate undergoes a sudden drop in pressure, causing rapid moisture loss and volume expansion. It is then cut into pellets and dried. The fish feed produced has a porous texture and acceptable durability. Starch (as in a grain flour) and/or other binder is often added to the raw mash at 5-20% to facilitate feed expansion and improve durability. However, the increased carbohydrate content is generally undesirable for carnivorous fish (Hemre et al., 2002). Compared with the prior technologies, such as expansion processing and steam pelleting, the high temperature and lowmoisture extrusion cooking has significantly improved both the physical and nutritional quality of feed (Welker et al., 2019). This popular method for making fish feed is commonly known as thermoplastic extrusion.
High moisture extrusion
In parallel to the development of the low moisture extrusion technology for making aquafeed, over the past several decades, high temperature and high moisture extrusion with a twin-screw extruder and inner mash moisture above 45% has been developed to impart a fibrous, meat-like texture to proteins of various sources in the food science community (Noguchi, 1989; Liu & Hsieh, 2008; Pietsch et al., 2019). The textured protein products can be used as meat analogs or meat extenders in a wide variety of ready-to-eat products. Therefore, in the food industry, high moisture extrusion has become an emerging technology for transforming vegetable proteins into palatable and consumeracceptable products.
In contrast, in the aquafeed industry, there has been no single report on using high moisture extrusion to make aquafeed until recently when a pilot study was first published (Liu et al., 2021). According to the report, as part of a Trout-Grain Project, a prototype method

Figure 1. Schematic diagram of a specially designed cooling die for the new extrusion method. Source: adapted from Liu et al. (2021).
Figure 2. Front view of an extruder in making the new high moisture feed. Source: Keshun Liu.


Figure 3. Cross-section views of conventional (left) and new (right) fish feed. Source: Keshun Liu.
of high moisture extrusion was developed at the U.S. Department of Agriculture research facilities in Idaho and Montana to make fish feed. The developing team consisted of Rick Barrows, a well-known fish scientist and now retired, Keshun Liu, a research food chemist with the USDA, and Jason Frost, a former USDA technician. The new process requires a twin-screw extruder, a uniquely designed cooling die (Fig. 1), and careful controls of extrusion parameters.
During operation, a raw mash is mixed with water injected into the barrel, so that it has a moisture of 45-75%. The wet mash is then kneaded, heated and melted under high-moisture and high-temperature conditions, and then enters the specially designed die attached at the end of the extruder. Within the die, the extruded mash is channeled into multiple elongated tubes, which are spaced so that cooling water can be circulated around within the outer house through the inlet and outlet connected to a water-circulating system. With this unique process, the hot extrudate is cooled immediately upon exiting the extruder’s barrel, while the pressure drop is controlled and gradual so that expansion of the extrudate is minimized (Fig. 2). Rapid cooling and controlled expansion prevent moisture loss and the formation of large air pockets within the extrudate.
High moisture extruded feed properties
There are significant differences in physical properties between the high moisture extruded feed (HME feed) and a conventional feed made by the low moisture extrusion. The HME feed has a smaller diameter, denser structure and smoother surface (Fig. 3).
When freshly made, the HME feed has an elastic feel and soft texture, with a hardness value approximately the same as that of a fish fillet. Upon contact with water, conventional feed (fresh or dried) rapidly disintegrates, while dried HME feed slowly returns to
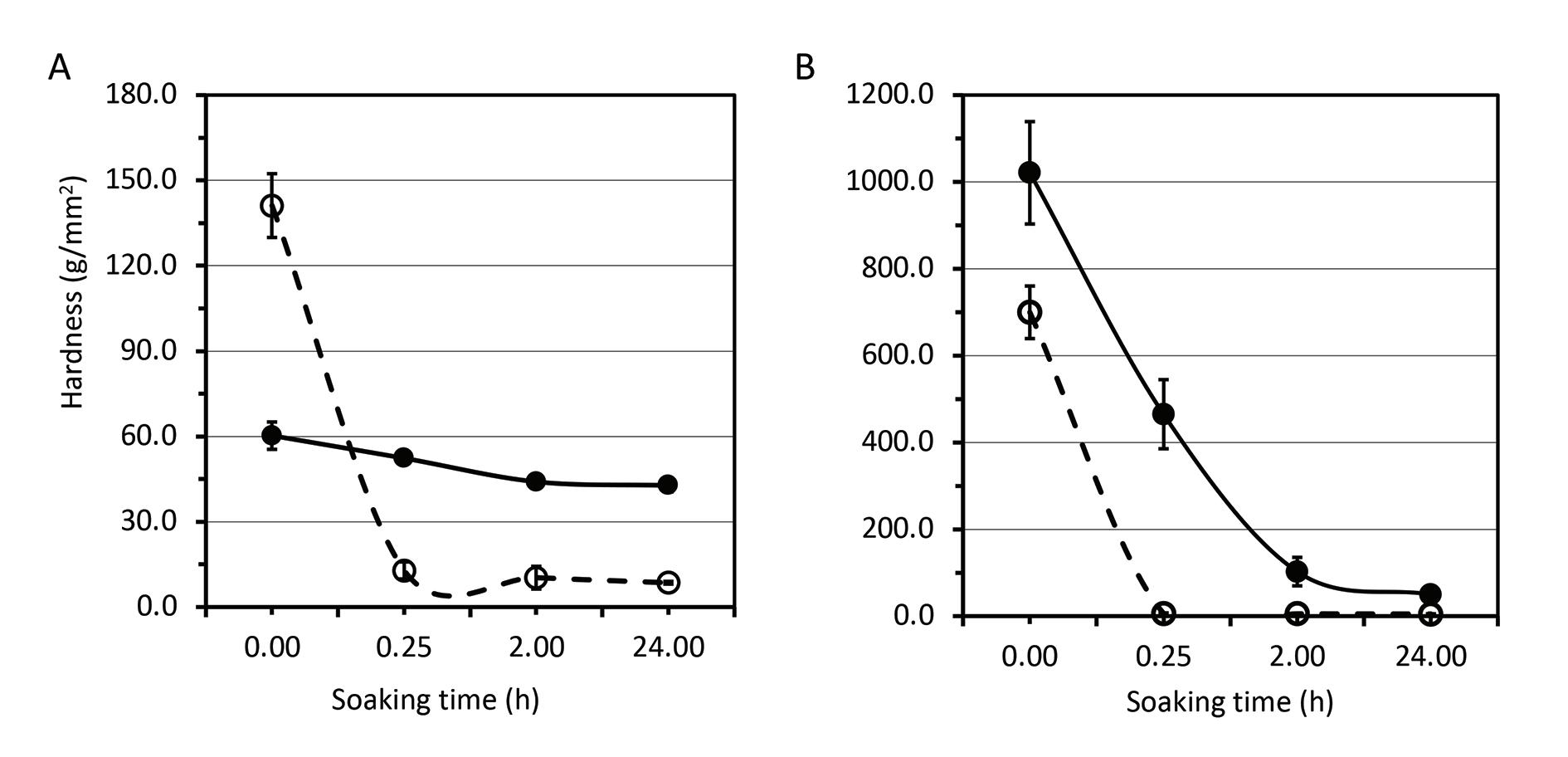
Figure 4. Changes in hardness of conventional and HME feeds with soaking time. (A) fresh feed. (B) dried feed. Solid circle: HME feed. Empty circle: conventional feed. Source: adapted from Liu et al. (2021).
the soft texture of its fresh stage, and both fresh and dried HME feed show resistance to breakage even after soaking in water for as long as 24 h (Fig. 4). Dry matter loss from the HME feed is significantly lower than the conventional feed after agitation in water for 6 h. Therefore, the HME feed has a softer texture, better pellet durability and significantly higher water stability than the conventional feed. Furthermore, the addition of a binding agent (such as wheat flour) becomes unnecessary when using the new method.
Yet, the HME feed has some undesirable features as well. First, because of its denser structure, the HME feed has about 85% oil absorption capacity of the conventional feed. This makes it more difficult to produce floating and/or high-energy feed with this new method. Second, although the HME feed can be dried for easy handling and storage, its drying cost can be significantly higher than drying the conventional feed, due to the much higher moisture content of the former.
In feeding aquatic animals such as fish, the interaction of feed with an aquatic environment poses problems not encountered in the feeding of terrestrial animals. This makes the physical properties of feed for aquatic animals more important than for terrestrial animals (Sorensen, 2012). Poor feed durability and water stability can negatively impact aquaculture profits and surrounding environments. In fact, the presence of lost nutrients and uneaten feed in fish farm effluent has been a major constraint for the expansion of commercial aquaculture (FAO, 2017). From this perspective, the desirable features of the HME feed, which include soft texture, high pellet durability, high water stability, plus no requirement for a binder, can compensate for the undesirable feature of high drying cost and dense structure. Therefore, the new method of high moisture extrusion developed by the USDA scientists to make fish feed represents an emerging technology for the aquafeed industry with exciting implications. For example, it can be a better way to produce soft pellets that more closely resemble natural feed and thus are more attractive for Atlantic salmon and other species. More importantly, the new process can potentially revolutionize how feed is made and serve as a promising strategy to mitigate water pollution issues associated with aquaculture. Further research is needed for optimizing the new method and exploring its possible applications in making various types of aquafeed.
References available on request.
More information: Keshun Liu, Ph.D.
Research Chemist National Small Grains and Potato Germplasm Research Unit USDA, Agricultural Research Service, USA E: Keshun.Liu@usda.gov