FEATURE
What’s new in maize and fodder beet equipment
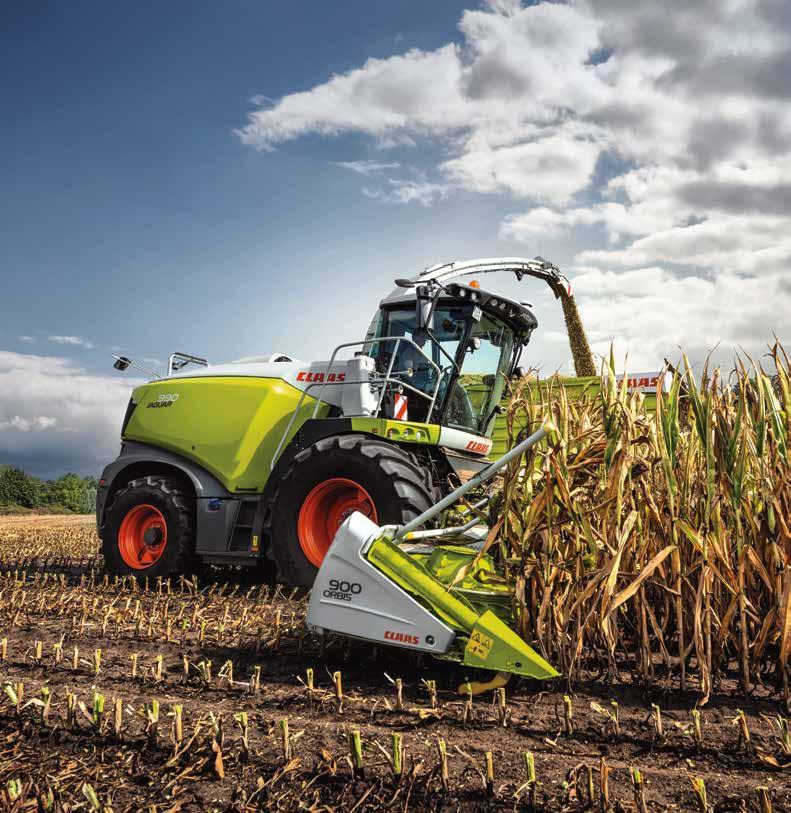
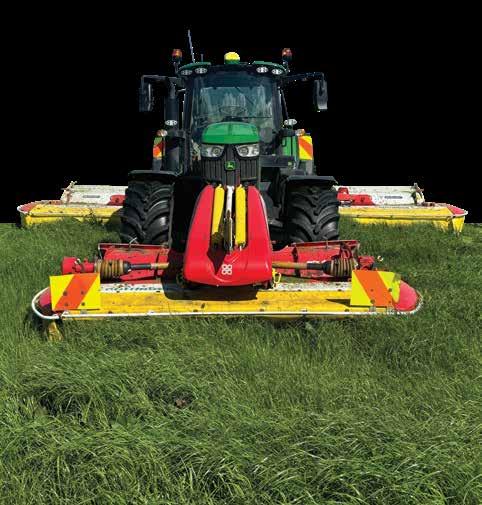
EQUIPMENT
Pöttinger gear at the forefront as contractor expands
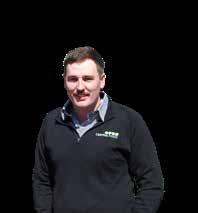
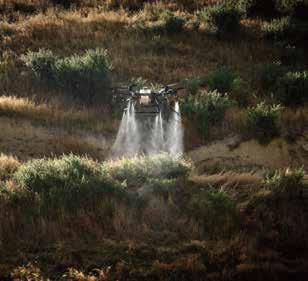
PROFILE
Lawns to high country stations Queenstown spray contractor covers the range
What’s new in maize and fodder beet equipment
Pöttinger gear at the forefront as contractor expands
Lawns to high country stations Queenstown spray contractor covers the range
Proceed can place the smallest of seed at the exact depth with millimetre precision. The even seed placement results in crops that mature uniformly and are more likely to reach their full yield potential. Proceed achieves this while drastically lowering the seed rate.
Available to order now.
04 FROM THE EDITOR: One last spin
INDUSTRY NEWS
03 Keith Andrews now sells Daimler Trucks in the Mainland
04 Testing and education antidote to drugs in rural businesses
06 Claas lifts its game with new telehandlers and loaders
09 Are healthy, happy animals more productive?
11 Rural contracting advocate wants your views and opinions
12 Video campaign spotlights dangers of fatigue
13 With 4R framework Hyslop Groundspread nails sustainable spreading
14 Tweak combines to get max grain yield
16 Don’t be afraid to ask about suicide
19 Maize silage made easy
19 Trelleborg has harvest covered with tyres for implements and tractors
20 Options available to farm with a lighter touch
21 Puma leaps on the hard jobs at Sallies’ training farm
22 Du-Wett super spreader boosts insecticide performance
TECHNOLOGY
24 Kiwi app for painless job management and invoicing
25 Novachem database can add power to digital tools
26 Latest row-hoes are mechanical weeding Swiss army knives
27 Robotics Plus takes autonomous sprayer on the road
28 After cyclones young contractor adaptswith hard work, new technology
34 Lawns to high country stations Queenstown spray contractor covers the range
38 Contracting supplements family’s deep roots in farming
42 Across the Ditch: Dion LeBrun and the art of reinvention
FEATURES
46 What’s new in precision agriculture
56 What’s new in maize and fodder beet equipment
EQUIPMENT
70 Pottinger gear at the forefront as contractor expands
72 Always a job for a Merlo telehandler
75 Wattie’s Elios trailed sprayer more of the same but better
76 Latest Deere 6M range offers more power, more smarts
78 Valtra’s sweet features impress sugarcane grower
80 Big NovaCat ideal for grass seed and silage
82 Agri-Spread AS65 makes life easier, more profitable
84 Precision mowing made easy with ISOBUS
PAUL TITUS, EDITOR
KIA ORA. IT IS TIME TO PARK THE TRACTOR IN THE SHED AND HAND THE KEYS OFF TO ANOTHER DRIVER. THIS IS MY FINAL ISSUE AS EDITOR OF NZ RURAL CONTRACTOR AND LARGE SCALE FARMER.
I jumped into the driver’s seat of this magazine back in 2001, and it has been a great ride.
While it might sound somewhat trite, it has indeed been a privilege to share the stories of the people in the engine room of New Zealand agriculture – Kiwi farmers, contractors, technicians and sales people.
Most townies like me who go to the supermarket and fill their trollies take for granted the men and women who work like crazy to produce what we eat.
It is the same with the machines they use to do that work. One of the perks I enjoyed as editor was the chance to visit several of the factories that produce the tractors and implements that farmers and contractors use to make the magic happen. Each of those factories is an impressive technological and logistical exercise that most of us are completely oblivious to.
For nearly 25 years I have had a bird’s eye view as agricultural machinery has become bigger and more sophisticated. The rise of GPS-based technology would be the most significant trend I have witnessed. It still amazes me that it works at all, much less repeatedly and at centimetre level accuracy.
No job is simply the work of one person. I want to thank the publisher, Agrimedia, for giving me a free hand to pursue the stories I wanted, freelance writers Joanna Ibell and David Hill, who have taken on all manner of assignments,
graphic designer Hannah Kincaid, who makes us all look good, and our proof reader, Jill McCracken, who tidies up our mistakes.
But, as we all know, life goes on. Angus (Gus) Kebbell is the new editor of NZ RCLSF. Gus has been working behind the scenes on the last two issues of the magazine. He takes over as editor for the first issue of 2025.
Gus is a Cantabrian. He grew up on a farm in North Canterbury and has spent his career in media with gigs at Stuff, Country-Wide and Dairy Exporter. He also produces the Factum-Agri podcast and radio show.
I will be in the background helping out on the first couple of issues of the New Year, so don’t hesitate to contact me if you have any questions or comments. One thing you will probably not miss is the Dad (or bad) jokes I inflict on you in these introductions. Well, here is my last effort to make you giggle or groan: Today my doctor told me I am colour blind. That really came out of the purple.
***
Want to know the last thing my grandfather said before he kicked the bucket?
“Watch how far I can kick this bucket.”
***
My friend was showing me his tool shed and he pointed to a ladder.
“That's my stepladder,” he said. "I never knew my real ladder.”
***
My hotel tried to charge me $10 extra for air conditioning. That wasn’t cool.
PO Box 36753
Merivale, Christchurch 8146 ph 03 329 6555 www.agrimedia.co.nz
Publishers of Rural Contractor & Large Scale Farmer, AgriBusiness, AgriVet, NZ Cropping, Australian AG Contractor & Large Scale Farmer, NZ Novachem Agrichemical Manual.
© RURAL CONTRACTOR AND LARGE SCALE FARMER - No part of this publication may be reproduced in any form without the prior written permission of the publisher. Opinions expressed in this publication are not necessarily that of the publisher and suggest independent advice be sought before acting on information or suggestions contained herein.
CONTRIBUTIONS - Editorial and photographic contributions are welcomed and should be sent directly to AgriMedia Ltd. Editing of submissions is at the sole discretion of the editor and will accept no responsibility for unsolicited material.
EDITOR
Paul Titus
87 Stanbury Avenue, Christchurch mob 021 655 092
email titus@agrimedia.co.nz
ADVERTISING MANAGER
Michael Lightbourne mob 021 403 853
email michael@agrimedia.co.nz
CIRCULATION
email admin@agrimedia.co.nz
PRODUCTION, LAYOUT & DESIGN
Hannah Kincaid email art@agrimedia.co.nz
CONTRIBUTORS
Joanna Ibell, David Hill, Angus Kebbell, Heather Chalmers, Brendon Burns, Charles Merfield, Dan Smith.
Printed by Blueprint Ltd
THE LARGE TRUCK AND OTHER COMMERCIAL VEHICLE DISTRIBUTOR KEITH ANDREWS HOLDINGS HAS OPENED NEW DEALERSHIPS IN CHRISTCHURCH, TIMARU AND DUNEDIN. WITH THIS STEP IT HAS BECOME THE NEW ZEALAND-WIDE SALES DEALER FOR DAIMLER TRUCK’S THREE BRANDS – MERCEDES-BENZ, FREIGHTLINER AND FUSO.
Prior to 12 September, Keith Andrews represented the three prominent truck brands in the North Island and CablePrice represented the brands in the South Island.
To deliver all NZ customers the full benefit of the general distributor appointment, Keith Andrews Holdings and CablePrice have now reached agreement on the sale and acquisition of selected South Island Daimler Truck dealerships.
Keith Andrews will begin trading at CablePrice’s trucks deal-
ership at 29 Waterloo Road in Christchurch together with sites in Timaru and Dunedin. CablePrice’s dealerships in Nelson, Greymouth and Invercargill will maintain their Daimler Truck service and parts status.
A Keith Andrews truck sales team will be located across the South Island, making Keith Andrews the New Zealand-wide sales dealer for Daimler Truck’s Mercedes-Benz, Freightliner and FUSO commercial vehicle brands.
An established South Island
FREIGHTLINER, FUSO AND MERCEDES BENZ TRUCKS ARE NOW AVAILABLE THROUGH NEW KEITH ANDREWS DEALERSHIPS IN CHRISTCHURCH, TIMARU AND DUNEDIN.
sales team has joined Keith Andrews. They include Andrew Buschl based in Nelson; Wayne Byrnes and Theo Ferreira in Christchurch; Hamish Stonehouse in Timaru; and Tristan Duffell in Dunedin and Invercargill.
Keith Andrews Holdings executive director Kurtis Andrews says that there is tremendous respect for the achievements in the South Island.
CablePrice NZ managing director Aidan Mahony says he is extremely proud of what the company’s team has achieved since becoming the South Island
dealer for Daimler Truck’s brands.
“I believe all customers will now benefit from having a New Zealand-based and focused general distributor,” he says.
Kurtis and Aidan say they share the goal of keeping their valued teams and customers updated as the transition progresses, and they are committed to keeping Daimler Truck customers moving.
“Keith Andrews Holdings and CablePrice aim to maintain all existing operations and personnel to ensure a smooth transition and a high level of customer support,” they say.
DRUGS AND ALCOHOL IN THE WORKPLACE IS NOT ONLY AN URBAN PROBLEM. THE SAME SPECTRUM OF DRUGS AVAILABLE IN CITIES IS PRESENT IN RURAL AREAS, WHERE THEY CAN BE A SERIOUS THREAT BECAUSE OF THE DANGER OF AGRICULTURAL WORK.
This is why farmers and contracting businesses need to stay up-to-date with drug trends, educate their employees, and conduct drug and alcohol testing to promote a safe working environment.
Glenn Dobson is CEO of The Drug Detection Agency (TDDA), which provides mobile drug testing and educational workshops throughout New Zealand and Australia.
Glenn says despite the economic downturn, testing shows a steady year-on-year increase in the presence of drugs and alcohol in workplaces.
“Drug and alcohol sales are inflation resistant. In the current economic climate, I anticipate more detections,” Glenn says.
“We are seeing more types of drugs in rural areas, including cocaine. We know from our contacts in law enforcement overseas that large international drug networks, like the Mexican cartels, are targeting New Zealand.
“I recommend that rural businesses review their substance policies, implement testing programmes, and engage professional educators for drug and alcohol awareness training.”
Glenn says this is particularly important for farms and contracting businesses.
“Farming businesses have a lot of moving parts and their employees often work in isolation with heavy machinery. Managers need to be aware of the risks that drugs can pose for them and their employees and then manage that risk as a fair and reasonable employer.
“Having an up-to-date and robust drug policy in place demonstrates that a company is serious about the wellbeing of its employees. Do not take shortcuts when people’s lives and livelihoods as well as your company’s reputation are on the line.”
A company that does not have policies to ensure their workforce is drug and alcohol-free as part of their health and safety programme (or who try to cut costs by using DIY kits or unaccredited testing providers) can be liable if there is an accident or injury.
TDDA is independent and accredited. It can carry out a variety of tests on-site and it has developed an electronic platform, Imperans, which can make drug testing and reporting much easier and efficient.
With Imperans there is no need to fill out paper forms in triplicate, which then end up in a desk drawer never to be seen again. It provides a secure digital dashboard where test results can be entered or called up instantly for review or reporting.
Although its headquarters are in Auckland, TDDA has 27 branches across Aotearoa NZ
WITH 27 BRANCHES ACROSS NZ AND 100 MOBILE TESTING VANS, TDDA CAN CARRY OUT TESTING AT WORKPLACES ANYWHERE IN THE COUNTRY.
TDDA CAN CARRY OUT ON-SITE TESTS OF URINE, ORAL FLUID, HAIR AND BREATH TO DETECT THE PRESENCE OF DRUGS AND ALCOHOL.
and 100 vans, which are essentially mobile labs that carry out testing anywhere in the country, no matter how remote.
Glenn says the three main times testing should be done are as a pre-employment check, random checks to act as a deterrent, and if there is a workplace incident or accident. If an accident happens, TDDA can be on-site straight away.
“We can do a range of tests, including urine, oral fluid, hair and breath. We tailor testing to what is best for each company and situation. The majority of the tests we do are urine and oral fluids,” Glenn says.
“We do a preliminary screen of the samples on-site. For example, we test urine samples for the major substances – meth, cannabis, cocaine, opiates, benzedrine and amphetamines – then and there.
“If drugs may be present, the sample is sent to a lab to determine exactly how much of the substance is present. We do the testing ourselves because our testing kits are controlled and verified. You have to know what you are doing with them and we do it on a daily basis.”
TDDA can also help companies set up a legally robust and up-to-date drug management policy and hold educational workshops for employers and employees on drug awareness and how to identify substances.
Glenn says his team can tailor to suit the needs of individual businesses. For example, one company might take a zero alcohol approach, while another might tolerate a low amount of alcohol if after work social drinks are part of their culture.
RANGE
PNEUMATIC PRECISION DRILLS
• 3-9 metre frame
• 6-16 row configuration
• High speed vacuum and pressure planter
• Granular and micro-granular fertiliser options
• Mounted and trailed options
LANDPOWER AND THE CLAAS HARVEST CENTRE NETWORK
ARE GIVING KIWI SILAGE CONTRACTORS AND FARMERS SOME POWERFUL NEW OPTIONS BY INTRODUCING CLAAS SCORPION
TELEHANDLERS AND TORION
AGRICULTURAL WHEELED LOADERS TO AOTEAROA.
Claas has been manufacturing agricultural wheeled loaders and telehandlers with German materials handling specialist Liebherr since 2018. Now three Claas Torion wheeled loaders are available here along with six Scorpion telehandler models.
rials handling and Claas’s expertise in powertrain management in agricultural environments.
Landpower chief executive Richard Wilson says the company is pleased to be building on its 40-year relationship with Claas by adding the two new product ranges.
“We are excited to be bringing these machines to extend our Claas range and offer further choice to our customers. We know that we are bringing in equipment that is right for our farming conditions because we have been selling both products in Australia for some time,” Richard says.
Claas Harvest Centre materials handling product manager Shane Barratt says Torion wheeled loaders combine Liebherr’s experience in construction and mate-
“The result is high-performance machines that can efficiently, effortlessly and safely move materials across a range of distances and heights, often in constrained spaces,” Shane says.
Three models from the Claas Torion range of agricultural wheeled loaders are available in New Zealand and Australia – the 1913, 1611 and 1611 P.
“The 1913 has the extra power and lift capacity required for grain handling or filling large loader wagons, while the 1611 and 1611 P models are medium-sized machines suitable for silage stacks.”
The Claas Torion 1913 has a four-cylinder, 7-litre Liebherr engine that delivers a maximum output of 222 hp.
“With the Claas low-speed,
high torque powertrain concept, maximum torque is produced at just 1100 rpm and maximum power at 1150 rpm,” Shane says.
“Dynamic powertrain management automatically adjusts the engine output to operating conditions, and an ‘on demand’ engine cooling system reduces fuel consumption.
“This is linked to a split-power Cmatic continuously variable transmission for smooth acceleration without losing traction or the need to shift gears.”
Torion 1913 has a maximum tipping load of 12.5 tonnes when fully articulated and a maximum tipping height of 4.2m. Hydraulic output of 234 litres/min enables faster load cycles of just over five seconds, while a long wheelbase and operating weight of 18.5 tonnes give balance and stability.
The 188-hp Torion 1611 and 252-hp 1611 P are both powered
AFTER SELLING CLAAS SCORPION TELEHANDLERS AND TORION WHEELED LOADERS IN AUSTRALIA FOR MANY YEARS, LANDPOWER IS NOW INTRODUCING THEM TO THE NZ MARKET.
by a six-cylinder, 6.8-litre DPS engine. They have maximum tipping loads of 9.4 tonnes and 10.25 tonnes respectively when fully articulated, and a maximum tipping height of 4m.
Shane says both the 1611 and 1611 P have longer lifting arms, larger hydraulic rams and more powerful hydraulic pumps that significantly improve their lifting and holding power. This means they can handle larger shovel volumes and heavier bale grabs.
All three models have Liebherr’s Z-kinematic system, which packages the lifting arms, hydraulic rams, and pumps into a single operating system.
“The working hydraulics allow the mast to be controlled safely with great precision. Automated lifting height, bucket return, lowering depth and tipping and shaking functions ensure quick, easy loading,” he says.
“All models can be equipped
CLAAS TORION WHEELED LOADERS ARE IDEAL FOR BUILDING SILAGE STACKS AND THEY CAN ALSO TAKE ON A RANGE OF OTHER MATERIALS HANDLING JOBS.
+8% ENLARGED CAB +18% FOOTPRINT
with a weighing device with additional memory and back-weighing function. They also have spacious cabs with 360-degree visibility and plenty of smart functions to reduce fatigue on long working days.”
Scorpion telehandlers are designed to meet requirements for agricultural work – shifting bales, loading and unloading or distributing forage. The range offers maximum lift heights up
to 9.75m (depending on the model) and max lift weights of 3-6 tonnes.
All Scorpions have a four-cylinder, high-performance Deutz engine with four-valve technology and turbocharger. They also have strong telescopic arms and powerful hydraulics.
Shane says Scorpion telehandlers achieve top performance thanks to their hightorque engines and efficient cooling system.
Dynamic Power automatically
adapts the engine speed to the demand of the job. With intelligent engine and ground drive control, the engine always runs in the optimum speed and torque range, based on the engine load. Dynamic Cooling ensures that the engine is cooled as required.
Claas also offers Smart Loading, which is a unique assistance system that helps operators carry out routine daily operations. Adjustable steps optimise the entire loading cycle, which
With a disc diameter of 645 mm, the Rubin 10 works to depths of up to 14 cm. The Rubin 10 operates without blockages, even with very moist and sticky soils. Discover its many benefits for yourself:
o Symmetrical disc arrangement to eliminate side draft
o Soil cultivation over the full width from only 14 cm working depth
o Harrow for optimum mixing and levelling action
o Maximum clearance to prevent clogging
boosts productivity and makes the operator’s job easier.
Scorpion 960 and 756 models have the infinitely variable VariPower Plus hydrostatic transmission as standard. Along with a wide-angle hydrostat (45°), it has a second, swivelling variable displacement motor with a 32° pivot angle, which delivers significantly more power in all operating ranges.
Other models feature a VariPower or VariPower2 transmission. They keep fuel consumption down even when operating at high capacity. VariPower2 drive is available with a twin motor.
Cabs on Scorpion telehandlers have a new high-flow air conditioning system, adjustable steering column, and automatic steering mode switch.
“In addition to the usual front, all-wheel and crab-steering modes, all models can be equipped with the new manual crab-steering mode that allows the front axle to be controlled,” Shane says. “This offers distinct advantages for certain applications, such as compacting silage stacks, moving along the walls of buildings or cleaning out bunkers.”
AN AMBITIOUS LINCOLN UNIVERSITY RESEARCH PROJECT WANTS TO WORK WITH FARMERS, CONTRACTORS, BUSINESSES AND OTHERS WHO ARE KEEN TO DEVELOP HEALTHIER AND MORE ETHICAL PASTORAL FARMING PRACTICES.
The starting point for the Integral Health Dairy Farm (IHDF) is the well-being of the land, animals and people. The team behind the IHDF says throughout human history, our nutrition has relied on plants and the animals that graze them.
Therefore, when we nurture our landscapes, we nurture ourselves. As the project leader, Professor Pablo Gregorini says, “We are what we eat”.
Pablo is the head of Lincoln University’s Centre of Excellence for Designing Future Productive Landscapes. The IHDF is one of the Centre’s projects.
It brings together specialists in such fields as genetics, animal nutrition, grazing management, design, sociology, human nutrition and grassland ecology from Lincoln University and around the world.
For IHDF, these specialists are taking a systems approach to view pastoral agriculture not purely in terms of productivity, but as part of wider ecosystems and economies. They call these ‘foodscapes’ and ‘healthscapes’.
While livestock productivity is certainly a priority for the experimental dairy farm, the researchers want to achieve this while they improve animal welfare and biodiversity and reduce inputs of synthetic fertiliser and pesticides.
The IHDF is a 40-ha farm that supports 100 dairy cows. Pablo and his team are using the IHDF for research and to put into practice some of their previous findings on livestock well-being and how it relates to human health.
TWO OF THE ‘FUNCTIONAL SWARDS’ AT THE DAIRY FARM – CHICORY TO THE LEFT AND RYEGRASS TO THE RIGHT.
For example, the farm is divided into paddocks that consist of adjacent 'functional swards' of different pasture crops. This is an extension of Pablo’s research on functionally diverse pasture.
He says that today most livestock in New Zealand receive a monotonous diet of ryegrass or ryegrass and clover. Another approach, which some advocates of regenerative agriculture support, is diverse pasture made up of as many as 30 different species.
Pablo says presenting this salad of different plants can be equally frustrating to animals because they struggle to eat what they want.
“It is like being offered a mixed salad that you eat with a spoon instead of a fork. They have to consume the mix, not what they want to eat.”
His alternative is functionally diverse pasture, which consists of pure swards of some of the plants in a diverse pasture mix. When the different species are presented to the animals in this way, they can choose what they eat to meet their own preferences and dietary needs.
The first functional diversity experiments Pablo and his team ran were with sheep. They found that compared to animals fed straight ryegrass pasture or a diverse mix, sheep who
PROFESSOR PABLO GREGORINI (CENTRE) WITH TWO OF THE RESEARCHERS BEHIND THE INTEGRAL HEALTH DAIRY FARM, ANNE SULLIVAN (LEFT) AND ANITA FLEMING.
could choose their own diet in the functional diversity treatment had 48 percent increase in live weights gains.
“Imagine, we could finish those animals in about half the time with half the amount of nitrogen excreted onto pasture and methane emitted. We also found urinary nitrogen was 30 percent lower for the animals on functionally diverse grazing.
“They also felt better because they had an 8 percent increase in total antioxidant status. This means they had much less oxidative stress and physiological stress.
“Another indicator of their better health was an 80 percent reduction in non-esterified fatty acids in ewes at lambing. This indicates the ewes were less stressed when giving birth. There was also a 5 percent reduction in cortisol in the wool of the new-born lambs, so they were healthier from the get-go of life.”
A study of dairy cows shows that those given an option of functional diversity showed comparable results. They produced more
milksolids and were healthier, with lower somatic cell counts.
Milk from cows fed a functionally diverse diet contained much less urea. This correlates with lower nitrogen levels in urine, so their environmental impact was lower.
Similar results were found with deer. Hinds on functionally diverse diets had less stress and higher live weight gains.
Another dimension to these findings is the benefits to human health from the meat and milk of animals on functionally diverse diets. Their milk has higher levels of certain beneficial elements (e.g. Vitamin B) and lower levels of TNO, which causes inflammation and fatty liver disease.
Pablo says this is a win-win-win. It is a win for farmers because production is higher, it is a win for animals because they are happier and less stressed, and it is a win for consumers because the milk and meat is healthier. And you can add another win because functionally diverse pastures are better for the environment.
The Integral Health Dairy Farm is an effort to put radical experimental findings into practice on-farm. Each paddock on the farm is planted in strips of plantain, chicory, fescue and legumes. Particular strips can be isolated with electric fences if they are overgrazed.
As the name of the dairy farm suggests, one
of its main objectives is to create a healthier environment for the cows, in part because of the productivity benefits this creates.
This includes planting trees and shrubs that provide shelter and browsing options. The roots of the shrubbery also absorb nitrogen, which helps reduce leaching.
There is even some aromatherapy going on. Certain shrubs, herbs and flowers have been selected because their scent can improve the emotional state of the animals. Other shrubs are medicinal with anti-microbial, anti-inflammatory or even pain relieving properties.
“We are also using the latest technology,” Pablo says. “This includes green artificial intelligence which can be used to measure and report carbon and greenhouse gas emissions in real time.
“We will be using virtual fencing to control the movement of the cows, sensors to monitor soil moisture and satellite imaging to measure the health and density of our pastures.”
Initial results from the IHDF’s performance are promising. In its first milking season, milk production was higher than the rest of Lincoln University’s dairy farm, which is a kind of control since it matches the industry standard.
The IHDF achieved this even though its stocking rate had been cut from 3.4 to 2.8 animals/ha and the lactation period was 25 days less than standard.
Also, the IHDF unit achieved higher milk production while its fertiliser application
THE INTEGRAL HEALTH DAIRY FARM IS EXPLORING WHETHER DAIRY COWS WITH BETTER HEALTH PRODUCE MORE MILK AND MILK THAT IS BETTER FOR HUMAN HEALTH.
rates were cut from 190 kg N/ha to 83 kg N/ ha and its irrigated area was reduced by 20 percent.
Despite this nearly 50 percent reduction in N applied, pasture production only dropped by 15 percent. This means that the pasture’s N use efficiency was 46 percent higher. Animal health measures were up too, with better metabolic rates and calving performance.
Doing the nuts and bolts of better farming is only one aim of the IHDF. Another is to communicate what the farm is achieving.
Those behind it want to improve the public perception of dairy farming as they produce healthier products and reduce environmental impacts.
The ultimate goal is to promote a sense of belonging to the land and to transform the health of animals, people and the environment.
Pablo says the World Health Organisations' definition of health is a state of physical, mental and social well-being, not just the absence of disease.
“Society is increasingly aware of the connection between the health of the land, animals and humans. Aotearoa’s dairy farming systems must co-evolve with this thinking.
“The IHDF welcomes input from anyone who wants to get involved. We are a creative network that is building partnerships among researchers, industry, tech companies and farmers. We welcome new ideas, no matter how radical they may seem to be.”
For more information contact Pablo Gregorini on pablo.gregorini@lincoln.ac.nz or 021 851 250.
THE FARM HAS AREAS PLANTED IN TREES AND SHRUBS THAT WILL PROVIDE SHELTER AND BROWSING OPTIONS TO STOCK AND ALSO ABSORB NITROGEN TO REDUCE LEACHING.
LINCOLN UNIVERSITY
LECTURER DAN SMITH IS WRITING HIS PHD ON NEW ZEALAND’S RURAL CONTRACTING INDUSTRY, AND HE WANTS TO SURVEY AS MANY OWNERS OR MANAGERS OF AGRICULTURAL CONTRACTING BUSINESSES AS HE CAN.
Dan has published two articles on the earlier stages of research and he has reported on that work in this magazine. Last year he prepared a ‘warrant of fitness for rural contractors’ for our readers based on his findings.
The final push of his research is a nationwide survey of rural contractors. The survey gathers some basic information about the owner and their business and then asks rural contractors
to rank the importance of different aspects of their businesses and the different challenges they face.
It only takes 15 minutes or so to fill out the survey. Responses to the survey will help Dan refine the model he is developing on
what makes a successful rural contractor based on his earlier research.
“The findings of my research have already proved useful to a range of rural contractors and I will use my PhD to advocate for the industry,” he says.
Dan would love as many people as possible to fill out the survey. So scan the QR code or follow the link in the advertisement below and spend a small amount of time to share your views.
He understands that this is the busy season for most rural contractors, but he hopes as many as possible can fill out the survey while he spends his summer holidays working on a silage and fencing gxang.
This year Dan was named New Zealand’s Rural Professional of The Year, which is another plus for the rural contracting industry. The award from Far-
LINCOLN UNIVERSITY LECTURER (AND PART-TIME CONTRACTOR) DAN SMITH IS CONDUCTING A SURVEY TO LEARN ABOUT THE ISSUES CONTRACTORS FACE, AND HE WANTS YOUR INPUT.
max-FarmIQ and NZIPIM recognises industry professionals who have dedicated themselves to the agricultural industry and have contributed positively to farmers, clients, colleagues, and the rural field.
Dan was selected as the inaugural Rural Professional of The Year. The award recognises his efforts in teaching and mentoring Lincoln University students and for his work as a rural mental health ambassador through his relationship with Farmstrong and rural contractors.
SCAN HERE TO COMPLETE THE SURVEY
RURAL CONTRACTORS NZ IS FRONTING A CAMPAIGN THAT IS REMINDING PEOPLE ABOUT THE RISKS THAT FATIGUE CAN PLAY IN THEIR WORK.
CEO Andrew Olsen says because rural contractors work seasonally, drive big machines, and face time pressure due to weather and crop requirements, they need to manage fatigue.
“We are saying there are risks for everyone if you push yourself or others too hard,” he says.
Second-generation contractor and former RCNZ president Steve Murray, has fronted three short videos to get the message across. These include one video aimed at employers.
Ag machinery importer Power Farming has produced the videos and it is right behind the campaign.
“Rural contractors take their health and safety responsibilities
very seriously, but as the video says, they need to talk about the ‘F’ word – fatigue,” Andrew says.
“Our members are up against it with the weather, crop deadlines and client expectations so they can put themselves and their staff under too much pressure. They need to build in breaks and pace things so no one gets fatigued, which can cause stress and much worse.”
One of the videos is aimed at employees, who also have to do their bit to avoid fatigue. That includes not arriving at work really tired or stressed or hungover or unwell. If you are, or see others who are, you have got to sing out so people are not at risk.
The third video gives tips on
avoiding fatigue including eating good food, drinking lots of fluids and taking breaks. The videos are supported by more detailed material on the RCNZ website.
Andrew asks everyone involved in rural contracting to view and share the message, including with farmers and landowners.
“We all have a role to play. Rural contractors can sometimes be put under too much pressure to meet impossible deadlines, especially when the weather plays up and crops need harvesting.
“Big machines may be able to
CANTERBURY CONTRACTOR STEVE MURRAY STARS IN THE VIDEOS THAT REMIND CONTRACTORS, THEIR EMPLOYEES AND FARMERS ABOUT THE DANGER OF FATIGUE.
operate 24 hours a day but those behind the wheel need their sleep and breaks to be able to do the job safely.
“The last thing anyone wants is for a fatigued driver to do harm to themselves or someone else. We are saying let’s all work for a safe season by avoiding fatigue.”
BASED NEAR OAMARU IN THE WAITAKI DISTRICT, HYSLOP GROUNDSPREAD HAS A MISSION TO HELP FARMERS BE AS PRODUCTIVE AND ENVIRONMENTALLY RESPONSIBLE AS POSSIBLE WITH PRECISE NUTRIENT APPLICATION.
Nick Hyslop’s spreading business uses the 4Rs Nutrient Stewardship framework. It aims to apply the right product at the right rate and right time in the right place in every job.
The internationally-recognised 4Rs approach provides measurable benefits for farmers. A 4Rs framework gives guidelines that can optimise nutrient use.
By selecting the correct fertiliser, applying it at the ideal rate, timing applications strategically and ensuring accurate placement, farmers can boost productivity while reducing environmental risks.
It is an approach that can enhance crop growth and soil health, help farmers meet regulatory requirements and protect nearby ecosystems.
To uphold the 4Rs framework, Hyslop Groundspread is certified by Spreadmark, New Zealand's trusted quality assurance programme for fertiliser spreading.
Spreadmark-certified operators are trained to apply nutrients precisely. The programme ensures that all fertiliser applications meet high standards for
accuracy and environmental protection.
Spreadmark training covers:
• Skilled operators. Spreadmark training ensures operators are well-equipped to apply nutrients accurately, taking environmental factors like wind and terrain into account.
• Well-maintained equipment. Regular calibration and maintenance of equipment ensure even nutrient distribution.
• Independently audited. Audits give farmers and growers confidence that they can trust the Spreadmark tick.
By committing to Spreadmark standards, Hyslop Groundspread provides farmers with the assurance that nutrient applications are environmentally safe and comply with regulations. The Spreadmark process also reduces risks associated with misapplication.
Careful nutrient placement prevents over applications in sensitive zones and protects
HYSLOP GROUNDSPREAD IS SPREADMARK-CERTIFIED, WHICH MEANS THEIR SPREADERS ARE CALIBRATED AND WELL MAINTAINED AND THEIR OPERATORS ARE WELL-TRAINED.
local ecosystems.
Accurate application of fertilisers improves efficiency and reduces wastage, which in turn reduces costs to farmers.
For Hyslop Groundspread, adopting Spreadmark certification and the 4Rs framework is a commitment to lift industry standards, promote accountability, and foster a sustainable future.
By investing in the right technology, training and procedures, Spreadmark-certified operators like Nick provide farmers with effective, responsible nutrient application.
Head to the Groundspread NZ or FQC websites to learn more about becoming Spreadmark-certified.
Article supplied by the Fertiliser Quality Council.
A TEAM OF OVERSEAS COMBINE HARVESTER SPECIALISTS HAVE RETURNED FOR ANOTHER ROUND OF WORKSHOPS TO HELP KIWI FARMERS PUT MORE GRAIN AND SEED IN THE SILO.
Foundation for Arable Research (FAR) technology manager Chris Smith says the tips farmers learned at last season’s workshops led to instant harvesting gains and cost savings. Benefits were less crop losses, faster harvesting speeds, lower diesel consumption and better harvest samples.
“Getting the settings correct can make a dramatic increase in productivity and maintain harvest samples. One grower took 70 hours off his combining. Another cut fuel consumption by 30 percent and produced a clean sample.
“Some farms were already doing well and it was confirmation for them that they are running their combines efficiently.”
FAR’s combine harvester workshops provide practical and independent information so growers have the confidence to make changes on-farm, Chris says.
This season’s workshops will again be led by the same Australian team of experts as last year. Led by Peter Broley of Primary Sales Australia, the workshops examine combine harvesters of all colours from
the front to the back.
“They now have a season’s worth of experience working in New Zealand conditions and crops,” Chris says.
Each of the combine specialists concentrates on particular brands of combines. Kassie van der Westhuizen will advise on John Deere, Brett Asphar on Claas and Case IH, and Murray Skayman, who is from Canada, on New Holland and Case IH. All have 20-30 years of experience with the brands in dealerships and as independent consultants. Workshops cover all makes and ages of combines. The range includes rotary and straw walker machines and small and large tube rotors. While there are technicalities specific to each brand, all have some common features, Chris says.
Experts will focus on seed quality, how to achieve an optimum harvest sample, and how to minimise losses out the back. This can help address dressing losses in ryegrass and other small seed crops that seed cleaners have reported.
Eight key themes emerged from last season’s workshops:
1. Growers need to measure to know what they are losing in straw and over sieves.
2. Acceptable losses vary for different growers’ circumstances.
3. Make one change at a time.
4. Go extreme and work back to the sweet spot.
5. Don’t rely on your loss monitors if they have not been calibrated.
6. As part of your pre-harvest service, make sure the threshing system is square and aligned. Otherwise you can waste horsepower and compromise threshing, separation and sample quality.
7. Don’t be afraid to open the concave if you have rotor losses. You may need to let grain out of the straw
8. Different brands have unique settings and quirks. For
COMBINE SPECIALIST
KASSIE VAN DER WESTHUIZEN ADVISES ON HOW TO SET UP A MACHINE FOR OPTIMAL PERFORMANCE DURING HARVEST.
example, with an Axial Flow be aware of the step created by opening the concave over 32-45. And in New Holland combines, remove the hump pan.
Research in Australia supported by the Grains Research and Development Corporation (GRDC) shows that harvest losses due to incorrect combine harvester set-up are 2-5 percent in arable crops. When extrapolated to the total value of the Australian harvest, these losses can amount to more than Aus $320 million/year.
The FAR combine harvester set-up days were held in early December in Wairarapa, Waikato, Manawatu, South Canterbury, North Otago and Central Canterbury.
In February, during harvest, the team of advisers will return to gauge how well the adjustments made are performing in the field.
For more information and to register visit the FAR website: far.org.nz/events.
THE RIGHT COMBINE HARVESTER SETTINGS CAN PUT MORE GRAIN IN THE SILO AND CUT HARVESTING TIMES.
• 0.49% finance rate over 5 years*
• 20% deposit
• 6 year finance option available
• 3 year, 3,000 hour extended warranty^
• Offer valid to December 20, 2024
Now is the time to secure yourself the best deal on a Fendt with excellent finance rates, payment terms and an extended warranty.
Speak to your nearest Fendt dealer to find out more.
*Offer applicable on selected machines and ends December 20, 2024, while stocks last and applies to Fendt tractors only and excludes track tractor machines. Finance with an interest rate of 0.49% p.a. available over a 60 month term with monthly payments in arrears or a finance rate of 1.49% over a 72-month term with monthly payments in arrears. Both finance options available on a Hire Purchase agreement based on a minimum 20% cash deposit and the GST component repaid in the fourth month. Fees and lending conditions apply to approved ABN number holders who use the equipment for business purposes. Finance is approved by AGCO Finance Limited, NZBN: 9429035304203, Company No: 1530800, GST No: 88-831-861. ^3 year, 3,000 hour extended warranty consists of standard 2 year, 2,000 hour warranty plus additional 1 year, 1,000 hour extended warranty. Contact your local Fendt dealer for full terms and conditions.
WE ARE A SOCIAL SPECIES, SO IF WE BECOME ISOLATED AND THEN FACE A BUNCH OF OTHER STRESSORS, THE PRESSURE CAN BE HARMFUL OR EVEN FATAL.
When the busy spring season was kicking off in October, a number of Canterbury agricultural businesses sponsored a breakfast and workshop for contractors in Mid and South Canterbury to address the issue of mental health.
The Proag PreStart Check Breakfast in Ashburton was the initiative of Jayden Warner, operations manager at Central Feeds Ltd, a contracting business based in Temuka.
Jayden says he had the idea for the event after he lost a friend in the industry to suicide earlier in the year.
“I wanted to understand and learn more, and I figured it might be good to do something as a wider group, for our big contracting family.”
Jayden got together sponsors (including the naming sponsor, Proag) and set up a breakfast.
“I thought getting everyone in one room for a big tool box meeting was a fantastic way to get people opening up and talking,” he says.
“We aimed to inform business owners and staff about how to talk about mental health and suicide prevention. It is also about how our seasonal staff can build support networks while in NZ and who we can contact to help.”
Speakers included Dr Annette Beautrais with Health New Zealand, psychiatric nurse Greg
Dobson, Francis Beston and Jilly Haywood from the Rural Support Trust, and Paul (Pup) Chamberlain from Safer Mid-Canterbury.
An important point raised in the presentations is that the owners and managers of contracting businesses play an important role in their employees’ mental health.
Annette says the biggest group that is vulnerable to suicide is men of working age and especially those in the 20 to 49 age group. This means the workplace is an important site to promote well-being and prevent suicide.
Fatigue is a major issue for contracting businesses. Also many employees are from overseas and therefore cut off from their usual social and support networks should any problems arise.
Annette says suicidal thinking is not attention seeking. She compares it with heart attack. Both are life-threatening. Most people with chest pain will not die of a heart attack, but of those who do, most have chest pain.
Same with suicide – most people who think about it will not make an attempt, but of those who do die, they have thought about it.
“Replace attention-seeking with attention-needing. They are talking about suicide to communicate their distress.”
CONTRACTOR JAYDEN WARNER ORGANISED THE PRESTART CHECK BREAKFAST AFTER LOSING A FRIEND TO SUICIDE.
Risk factors for suicide include depression, substance abuse, and stressful life events (such as relationship break ups, child cus tody disputes, or grief).
Other risks are trouble with the law, bullying, or environmental factors (namely a readily availa ble method of suicide). Farmers have easy access to firearms giv ing them a lethal pathway.
“If anyone is having a tough time, get guns off the property,” Annette says.
ognised their distress and are not afraid to discuss the issue.”
Men and women tend to express depression different ly. Women typically display emotional responses - such as sadness and worthlessness. Men typically respond physical ly – they are tired, lose interest in things, are more irritable and angry or throw themselves into work. Men may try to mask the issues with drugs and alcohol.
If they do go to a GP they are more likely to say they are having difficulty sleeping rather than talk about depression or suicidal thoughts.
Annette says if you think some one is suicidal, ask them. “In my experience most people are incredibly grateful you have rec
Each one is a tragedy, but the
THROUGHOUT MID AND CENTRAL CANTERBURY TOOK PART IN A BREAKFAST AND ‘TOOL BOX MEETING’ TO HEAR PRESENTATIONS ON MENTAL HEALTH AND SUICIDE PREVENTION.
snap model –how to ask about sucide
• Summarise. Provide reasons for your concerns. ‘I am worried because I know things are tough at home at the moment.’ Or ‘I know your kid is ill…’
• Normalise. Suggest people facing similar stresses would be upset. ‘Anyone going through what you are going through would be upset. Some people might be so upset that they might even think about suicide'.
• Ask directly. ‘Are you thinking about suicide? Are you thinking about killing yourself? '
Do not say ‘commit’ suicide, because it sounds judgemental. Do not use a negative, such as ‘You are not thinking about suicide are you?'
If they say ‘not really’ ask follow up questions. ‘Can you tell me more?' Or ‘Do you know how to do that?'
• Plan – what support do they need? Pup says if in doubt, call for help.
Ask mates to stay with them until help arrives. Take them to their GP. If someone is suicidal and taking drugs, call 111 every time.
an uncommon event, and when things go wrong – get help,” Annette says.
Greg Dobson’s talk was titled: Suicidal thinking – a silent call for help.
Greg has been working in this area for 40 years. His work began in Central Otago when his community had suicides, one after another. This led Greg to ask What is the ‘why’ behind suicide?
“It became apparent to me that there is a cognitive pathway that people go on to get to that suicide,” he says.
The pathway is: 1) A catalyst. 2) Suicide thought. 3) Suicide intent. 4) Suicide plan. 5) Suicide activity. 6) Fixed focus.
The catalyst can be many things but is often the breakdown of a key relationship. It is always an overload of emotions.
“We get an emotional response
to stress – despair, jealousy, fear, hurt, embarrassment, guilt, sadness, or feeling threatened or trapped. Too many feelings at once. We can’t process so many emotions and suicide thought becomes a silent call for help,” Greg says.
Greg says the suicide thought often surprises people. He proposes it is a natural thought when resilience has waned with prolonged pressure and that pressure can no longer be borne. He says suicidal thinking is not a choice and not selfish – it is overload.
The first two stages are where the community can come in by listening, connecting and offering help. Further up the scale is the role of mental health workers. In that stage the role of community is to stay with them and connect them with that support.
Greg says that people can be stopped at every stage. “One
FORMER POLICEMAN PUP CHAMBERLAIN SAYS YOU CANNOT MAKE SOMEONE DIE BY ASKING THEM ABOUT SUICIDE. HE SUGGESTS USING THE SNAP MODEL TO ADDRESS THE ISSUE WITH SOMEONE YOU ARE CONCERNED ABOUT.
person was driving to the river bed to put in action their plan. He stopped at a store and met one person he knew, who asked him if he was okay and that was enough to stop him.”
Pup Chamberlain’s talk was titled: How to have a conversation about mental health.
When he was a police officer he had to deal with suicide and he continued in that area when he left policing. He spends much of his time talking to people at risk of suicide.
“If someone rocks up to work with an arm in plaster you ask about it. You don’t hesitate. But when it is mental health there is the fear that you are not trained and don’t know what to say. I have no mental health qualifications, but I have the ability to care and to learn.”
Pup emphasised that you cannot make someone die by asking
• Recognise that the workplace is often people’s sole place of support.
• Normalise asking about mental health and mental health support. “It’s because we care.”
• When taking on new staff, link them to new groups (such as rugby, tramping, fishing, or something arty) or perhaps someone who speaks their native language.
• Accommodation and transport – help them find decent, close accommodation and a way to get around on their time off.
• Help them have healthy habits:
1. Exercise – we are not designed to sit all day.
2. Sleep – it is not a luxury, it is vital for good health.
3. Nourish and hydrate. Power drinks and
pies are not real food.
4. Nature. Get out in the bush, rivers, or the ocean.
5. Connect – talk and listen, be there. Social connection can have a huge protective effect.
6. Focus on what you can control
• Fatigue management. Know when your crew is fatigued. Schedule lighter tasks or breaks.
• Alcohol. As well as health impacts, alcohol can result in worse sleep and aggressive behaviour. It can affect reaction times and decision-making.
(Every year a quarter of those who die by suicide do so with excess blood alcohol levels. Alcohol has a disinhibiting effect which can increase the risk of suicide.)
SUICIDE PREVENTION EXPERT ANNETTE BEAUTRAIS SAYS SUICIDAL THINKING IS NOT ATTENTION-SEEKING BEHAVIOUR. IT IS ATTENTIONNEEDING BEHAVIOUR.
them about suicide. He suggests using the SNAP model to guide how you ask people about suicide. (See sidebar.)
The workshop provided information on those who can help when pressure reaches a breaking point. They include the Rural Support Trust, which is run by rural people, helping other rural people in challenging situations. It is a free and confidential service.
Rural Support Trust says to think of mental health as a well-being bank account. Keep the account topped up when you can and then you can draw on it when times are tough.
Ways to keep topped up are to keep connected with other people, stay physically active, take notice and appreciate what you and others have done, give to others and keep learning.
Jayden and the speakers are delighted with the number of people who attended the breakfast, and by the number of people who reached out for help in the weeks after the event.
Annette says they have been connected to help
“This event and others like it can be very constructive. They provide practical ways getting information out about ways to help work colleagues, family members and yourself.”
Other groups who can provide support are Mental Health Helpline free text or phone 1737, Tautoko Suicide Crisis Hotline (0508 828 865), Youthline, GPs, counsellors, GoodYarn, Farmstrong, Lifeline and Healthline.
BIOSTART AND ASCOT PUMPS HAVE DEVELOPED AN APPLICATOR THAT MAKES IT EASY TO MONITOR VOLUMES AND CONTROL MAIZEKING APPLICATIONS FROM THE FORAGE HARVESTER’S CAB.
FARMERS AND CONTRACTORS WHO WANT TO PRODUCE TOP-QUALITY MAIZE WITH NO FUSS CAN LOOK TO MAIZEKING SILAGE PRESERVATIVE MADE BY NEW ZEALAND COMPANY BIOSTART.
MaizeKing can be applied direct from the drum without dilution and is stable at room temperature. It can be transported easily and, once the drum has been opened, it can be used over multiple days without any wastage.
Now BioStart has developed an applicator in collaboration with Ascot Pumps, which gives operators the ability to monitor volumes and easily control MaizeKing applications from the cab.
BioStart CEO Jerome Demmer says ease of use minimises workload, but it does not come at the expense of reliability.
“We have developed MaizeKing and tested it extensively to ensure it makes high-quality maize silage that stores well,” Jerome says.
MaizeKing is a mixture of fermentation extracts, nutrients and microbial stimulants. It
works in two ways.
Firstly, it stimulates the ensiling bacteria that naturally live on the maize forage in the paddock and, secondly, it supresses the spoilage microbes that can otherwise ruin the silage.
This dual action benefits the
maize feed quality by:
• Activating and increasing the number of beneficial ensiling bacteria that naturally occur on forage to produce more of the lactic and acetic acids required to properly ensile maize.
• Inhibiting the growth of the yeasts and fungi that use up feed energy, heat bales and produce mycotoxins that affect animal health.
“It is vital to always follow good silage-making practices. They include harvesting at the optimum moisture level, using the appropriate chop length and excluding as much oxygen as possible in the stack with tight compaction and sealing properly,” Jerome says.
For more information contact BioStart on 0800 274 524.
NEW ZEALAND’S
AGRICULTURAL SECTOR IS MADE UP OF DIFFERENT FARMING SYSTEMS, SO TRS TYRE AND WHEEL OFFERS A WIDE RANGE OF PREMIUM TRELLEBORG TYRES AND WHEEL SYSTEMS.
TRS national sales manager
Ivan Burrows says his company can show farmers and contractors how Trelleborg tyres can improve traction and maximise the efficiency of their machinery.
“Naturally, this means increased crop yields with greater sustainability. We are ready to show farmers how they can work more efficiently starting from the ground up.”
The range of Trelleborg tyres includes:
• The multi-award winning TM1000 ProgressiveTraction tyre. The TM1000 is made for the most advanced machinery. It delivers unbeatable traction with its extra-wide footprint and less soil stress thanks to its superior floatation.
Both in the field and on the road, this tyre can reduce fuel consumption and emissions and it offers premium handling and comfort, high load capacity and self-cleaning along with long-lasting tyre life.
• The Trelleborg TM3000 is
TRELLEBORG’S AWARDWINNING TM1000 TYRES DELIVER UNBEATABLE TRACTION AND LESS SOIL COMPACTION THANKS TO THEIR EXTRA-WIDE FOOTPRINT.
designed for combine harvesters, which are becoming bigger and are working in more critical environments due to extreme weather conditions. Its tread pattern and advanced carcass design maximise the tyre's load capacity at low inflation pressure. This preserves the soil and
its organic components while limiting mechanical damage from compaction.
• The Twin Radial is the first Trelleborg radial implement tyre. It can handle all working conditions and any type of soil. Its wide footprint and rounded shoulder profile ensure excel-
ALTERNATIVE TOOLS ARE NOW AVAILABLE FOR GROWERS LOOKING TO REDUCE THEIR RELIANCE ON AGRICHEMICALS IN RESPONSE TO MARKET AND RESISTANCE CHALLENGES, SAYS FOUNDATION FOR ARABLE RESEARCH CHIEF EXECUTIVE ALISON STEWART.
Many of these, including biologicals and digital decision support tools, were outlined at a FAR-organised series of events called ‘A Lighter Touch – A New Approach to Crop Protection’.
The $27 million, seven-year A Lighter Touch (ALT) programme was launched in 2020 to develop and promote arable and horticultural pest management options that reduce reliance on synthetic chemistry. It is jointly funded by government and industry.
Alison Stewart says FAR has had a crop protection research programme centred around agrichemicals since its inception almost 30 years ago but we will not necessarily have that luxury into the future.
“The challenge is how do we take our intensive arable agrichemical system and transition that to something that has a lighter touch.”
While agrichemicals are critical to management of pests and diseases in arable systems, their use and availability is being challenged by consumer pressure, growing resistance to existing agrichemicals and a reduction in new chemistry.
ALT industry advisory group chairman Dr Stuart Davis says that an impetus for the programme is the rapidly growing availability of biological products that can help growers tran-
lent ground care and provide exceptional traction. The central block structure and lug shape give efficient self-cleaning, even during high-stress transitions
sition into softer chemistry.
While new synthetic chemistry can cost $US300 million and 11 years to develop before commercial use, biologicals can be available in less than five years at a development cost of around $US5m.
“In the United States, it is predicted that the biologicals market could be as big as agrichemicals in 20 years at current annual growth rates,” Stuart says.
Already in the US, about 70 per cent of biologicals are sold to conventional farmers. In New Zealand, delays in getting approval for new products is causing frustration and the regulatory process is currently being reviewed by government.
“Biologicals need to be assessed and approved faster than they are now,” Stuart says.
FAR senior cereals researcher Jo Drummond says that while attracting premiums for using less and softer chemistry may be easier in sectors like horticulture or wine, for arable it may be more about market access.
She says other alternative crop protection tactics include plant breeding and resistant cultivars,
from field to road. This ensures safety and compliance with road regulations.
TRS Tyre & Wheel is owned by the Yokohama Rubber Co. It sup-
mechanical weed control, precision agriculture and digital support and monitoring.
“We still need agrichemicals. Ultimately our goal is to maintain the effective life of these products,” Jo says. “There is no option now but to layer up these strategies to help growers reduce their input costs and maintain or potentially increase profitability and yield.”
As a first step, growers need to pick a resistant cultivar. They also need to consider, understand and prioritise agrichemical application timings to reduce costs and protect existing chemistry.
“Do your homework on biopesticides and biological products and be realistic. You can’t just switch one product for another,” Jo says.
Decision support tools such as FAR’s online Aphid Chat are also available to assist with treatment timings.
Visiting UK plant pathologist Dr Aoife O’Driscoll says increasing fungicide resistance and rapidly rising fungicide costs is driving UK cereal growers to change their crop management and grow
plies a wide range of Trelleborg and Mitas tyres throughout New Zealand.
With more than 40 years’ experience in wheel manufacturing,
ABOVE LEFT: FAR RESEARCHER JO DRUMMOND SAYS FARMERS SHOULD SUPPLEMENT AGRICHEMICALS WITH OTHER PEST CONTROL STRATEGIES INCLUDING BIOLOGICALS, RESISTANT CULTIVARS, MECHANICAL WEED CONTROL AND PRECISION AGRICULTURE.
ABOVE: PLANT PATHOLOGIST AOIFE O'DRISCOLL SAYS AS FUNGICIDE RESISTANCE IN THE UK INCREASES, CEREAL BREEDING IS MORE FOCUSED ON DISEASE RESISTANCE.
more resistant cultivars.
“In the last four years, things have changed dramatically. The days are gone of growing susceptible varieties and then relying on a fungicide programme to obtain good yields,” Aoife says.
Cereal breeding programmes are now more focused on disease resistance and growing of wheat cultivar mixes is becoming common in the UK as growers respond to resistance issues and market signals.
TRS can meet the needs of any agricultural customer. TRS can be contacted via their website (trstyreandwheel.co.nz) or on 0800 336 334.
A SOUTHLAND FARM IS MAKING A BIG DIFFERENCE IN THE LIVES OF YOUNG PEOPLE WHO HAVE A PASSION FOR AGRICULTURE BUT LACK THE RESOURCES TO GET THE TRAINING NEEDED TO GET STARTED IN THE INDUSTRY.
Jeff Farm is a 2430-ha property near Gore. The Salvation Army has owned and operated it since the early 1950s after farmer Edmund Jeff bequeathed it with the stipulation it be used to train young people in farming who would not otherwise have that option.
Jeff Farm general manager Michael Benton has been with the farm for nearly three years, and says he has seen the difference the opportunities it provides have made in the lives of the young trainees.
There are five trainees at Jeff Farm at any one time. They do a two year cadetship and live on
the farm during their training.
They learn a raft of farming skills – from operating motorbikes, chainsaws and tractors, to fencing, stock care and training working dogs.
“We teach them the skills needed to make them attractive employees in the agriculture industry once they leave here,” Michael says.
The farm runs about 30,000 stock units – cattle, sheep and deer – and grows swedes, kale and fodder beet to support them during winter. They have a fleet of four tractors to prepare the ground for the crops and make balage.
OF THE
FARM
THEIR
Recently the Jeff Farm trainees welcomed a new tractor, a Case IH Puma 220. It is the first Case IH tractor Jeff Farm has run and it is now the biggest in their fleet.
“It’s our heavy lifter. It will do all the heavy ground work and discing, and the mowing for silage, with a double mower. Our other tractors are general tractors for feeding out and tasks like that. The new Puma is doing all the hard yards,” Michael says.
He says the team at the local Case IH dealership, Agricentre South, was keen to become involved in the farm.
“They wanted to know the story behind it, which was important to us. The service they have provided has been great. The new Puma has everything we need, and the trainees are certainly enjoying the additional horsepower and all the technology it offers,” Michael says.
While Jeff Farm does its bit to bolster the future of New Zealand agriculture, it also benefits the Salvation Army’s community outreach. It funds programmes such as drug rehabilitation and university scholarships. Michael says his role can be
IT IS ONE THING TO USE A PROVEN HIGH-QUALITY, EFFECTIVE INSECTICIDE. THAT’S BASICALLY A GIVEN. BUT GETTING THE SPRAY TO EVERY NOOK AND CRANNY IN A DENSE FORAGE BRASSICA CROP OR GETTING IT TO STAY, COVER AND SPREAD ON WAXY FOLIAGE IS A WHOLE DIFFERENT CHALLENGE.
As the climate is predicted to get warmer, insect damage to crops could have an impact on yields and profits. Farmers, agronomists, and field reps are focused on how to limit the harm.
UPL NZ adjuvant product manager David Lingan says white butterfly, diamondback moths, aphids, and fall armyworm, in particular, are real threats.
To maximise the results from insecticide applications, David recommends using the super spreader Du-Wett to deliver better crop coverage.
“That way you can save yourself a lot of time, reduce waste and, most importantly get a better outcome. Insects, by their nature, are all over the place, so effective control relies very heavily on actual contact or ingestion.
“The active in the spray needs to be present on the plant surface to get to the insects effectively. Du-Wett maximises spread and coverage giving you the results that everyone wants.”
David says farmers can be a hard sell at the best of times and this is especially true when everyone is cost conscious. Du-Wett will easily pay for itself, however.
“You get the most out of every drop of the spray. Contractors say they can see the difference.”
Particularly with helicopter application and other low-volume application technologies,
Du-Wett can reduce water use and provide significant reductions in time and fuel.
“Du-Wett allows you to cover a greater area faster, with a much-reduced water volume and still get better protection for the crop. Until relatively recently, the volume of water in spray programmes hasn’t been that big a concern.
“With rising fuel, labour and spray costs and with low water volume applications, attitudes toward the use of water itself is changing. People are having to get on-board with that.”
David says contrary to popular belief, more water does not deliver better spray coverage. Water’s high surface tension doesn’t give the spread or coverage insecticides need for optimal performance.
“Du-Wett reduces the surface tension of spray droplets. One spray droplet containing Du-Wett can provide up to 20 times the spread of active compared to an insecticide applied without an adjuvant and at least 6-8
UPL’S DU-WETT ADJUVANT CAN GIVE BETTER INSECTICIDE COVERAGE IN DENSE FORAGE BRASSICA CROPS.
times compared to a conventional, non-ionic adjuvant.”
Du-Wett is compatible with major insecticides including Sparta, Exirel and Aphidex.'
It is recommended that Du-Wett be used at 200 ml/ha for most insecticides. Exceptions are Attack (use at 300 ml/ha) and chlorpyrifos (use at 250 ml/ha).
Water volumes are 50-250 litres/ha for ground applications and 50-100 litres/ha for aerial applications. Optimum spreading and wetting from Du-Wett will occur between pH 5 and pH 9.
For more information on getting the most out of insecticides with Du-Wett talk to your local technical advisor or contact UPL NZ adjuvant product manager David Lingan on 021 804 450.
demanding, but he gets lots of satisfaction from it.
“It’s amazing to watch these young people grow and change. Trainees who started at the beginning of this year have come such a long way already. They arrive here as teens and they leave with much more maturity and confidence.
“Even the difference in the way they hold themselves and present themselves is huge,” he says.
For more information on the Case IH range of machinery, contact your local Case IH dealer.
THE PUMA 220 PREPARING WINTER FORAGE CROP GROUND AT JEFF FARM.
KAITAIA Kaitaia Tractors 09 408 0670
WHANGAREI Piako Tractors Northland 09 438 1319
SILVERDALE Brandt NZ 09 427 9137
PUKEKOHE Brandt NZ 09 237 0043
MORRINSVILLE Piako Tractors 07 889 7055
MATAMATA Matamata Tractors & Machinery 07 888 6292
HAMILTON Brandt NZ 07 847 0425
CAMBRIDGE Brandt NZ 07 827 5184
ROTORUA Piako Tractors Ltd 07 345 8560
TAUPO Taupo Tractors & Machinery 07 378 4533
STRATFORD FeildTorque Taranaki 06 765 8643
HASTINGS Stevenson and Taylor 0800 4273 2273
WAIPUKURAU Stevenson and Taylor 06 858 6041
DANNEVIRKE Lancaster Tractor Services 2022 Ltd 06 374 7731
FEILDING TRC Tractors 06 323 0309
MASTERTON Brandt NZ 06 377 3009
NELSON Drummond & Etheridge 03 543 8041
BLENHEIM Drummond & Etheridge 03 579 1111
KAIKOURA Drummond & Etheridge 03 319 7119
GREYMOUTH Drummond & Etheridge 03 768 5116
CHRISTCHURCH Drummond & Etheridge 03 349 4883
ASHBURTON Drummond & Etheridge 03 307 9911
TIMARU Drummond & Etheridge 03 687 4005
OAMARU Drummond & Etheridge 03 437 1111
MOSGIEL JJ Limited 03 489 8199
GORE
IT IS SAFE TO SAY THAT CONTRACTORS AND THEIR EMPLOYEES ARE CRAZY ABOUT FARMING AND OPERATING MACHINERY, AND THEY ARE NOT SO PASSIONATE ABOUT PAPERWORK.
This can make life difficult for the person in the office who does the invoicing and payroll, especially when they have to wade through paper dockets to get the information they need to bill clients for completed work.
Southlander Bevan Caldwell knows this from experience. His family runs a large contracting business, and when he went looking for a digital system to manage staff and do invoicing, he could not find one that suited their business.
You can guess what comes next. Bevan thought there must be a better way, so he
set out to create it.
The result is Task Pilot, a mobile phonebased app that gives contractors the ability to assign tasks to their operators, record details about completed jobs, and use that information to do paperless invoicing and employee time keeping.
“We designed Task Pilot for agricultural contractors, but it will also work for contractors in other sectors like construction. It is a flexible system. It is cloud-based and can be used with a web browser or phone, so you can schedule work from the office or any-
SOUTHLAND CONTRACTOR BEVAN CALDWELL COULD NOT FIND A DIGITAL WAY TO MANAGE HIS STAFF AND DO INVOICING SO HE DEVELOPED HIS OWN – TASK PILOT – WHICH IS NOW AVAILABLE TO BUY.
where else,” Bevan says.
“You can tailor Task Pilot to your operation. For example, when you send a job to an operator’s phone, you can include a prestart safety check for the specific machine that will be used on that job.
“You can also include a map when you make the assignment. This is a point of difference with some other job management systems.”
Bevan says Task Pilot is built with family businesses in mind and is ideal for contractors who do their own invoicing.
It can keep track of multiple machines and drivers and tally how much time they spend
TASK PILOT IS A MOBILE PHONE APP THAT GIVES CONTRACTORS THE ABILITY TO ASSIGN TASKS, RECORD DETAILS ABOUT JOBS, AND USE THAT DATA TO DO INVOICING AND PAYROLL.
Rising costs, unpredictable weather, meet your new secret weapon.
We're not just selling precision; we're future-proofing farms. Your challenges are our challenges. Together, let's steer toward a future that's sustainable, profitable, and resilient.
THE PUBLISHERS OF THE NOVACHEM AGRICHEMICAL MANUAL SAY THEIR DETAILED DATABASE OF ALL CROP PROTECTION PRODUCTS USED IN NEW ZEALAND HAS THE POTENTIAL TO ADD A HUGE AMOUNT OF INFORMATION TO DIGITAL JOB ALLOCATION, PROOF OF PLACEMENT AND PRODUCT ORDERING TOOLS.
Existing precision farming companies are expanding their offerings to rural contractors and at the same time start-ups now offer new apps and services.
As this technology evolves there is greater ability for them to link to one another and to rural retailers. This makes it easy for farmers and contractors to share information or place orders with their suppliers.
Novachem publisher Michael Lightborne says it really is the definitive source of information on all things agrichemical. Available online or in book form, it provides a comprehensive alphabetical listing of products, active ingredients, crop and weed tables, and weed and pest identification.
The online version is updated daily and it has links to suppliers’ documentation. This
includes the label, safety data sheet and Haznote for each product. The safety documentation has become increasingly important for anyone who stores, uses or transports agrichemicals.
The latest edition has new hazard codes and safety precautions, as the local industry transitions from New Zealand’s own HSNO classifications and wording to internationally standardised language.
“Information from Novachem can be made available to the new apps and Web-based services that farmers and contractors now use to keep track of their work and provide proof of placement,” Michael says.
“A job allocation app could, for example, provide a sprayer operator the relevant safety data sheet to them in the cab as they head out for a job. They could use it to keep a digital spray diary, and contractors and farmers could use it to record the chemicals in their shed with all necessary information about them.”
Novachem’s digital database has already been integrated into all the main rural retailers’ systems and a number of rural software development companies have approached the publisher to provide essential agrichemical information.
“Novachem is up-to-date, accurate and comprehensive, so there is no need for
agrichemical suppliers or software developers to reinvent the wheel in order to add this information to their digital services,” Michael says.
on different jobs. All this data can be stored, tallied and used to produce invoices.
It can also be used to keep track of machine hours as well as employees’ work hours. This can provide an insight into costs versus income, and it can help you schedule maintenance.
Task Pilot links directly to Xero. Once the manager has approved the numbers for the job, they can send it straight to the accounting system, which produces and sends the invoice.
When an operator gets an assignment, they also get the farmer’s contact details. The farmer can send them a map or a photo that shows the paddocks where they will be working or you can send a map from the office.
Only employees who have administrator status in Task Pilot can see sensitive information, such as charge-out rates and client invoice details. All sensitive data is encrypted to ensure your information remains secure. Other staff can do the standard operations such as select customers, assign tasks and equipment or add machine hours.
“We worked with Auckland based software developers to build Task Pilot, and we are
Task Planning. The contracting season can be hectic when multiple drivers and machines have to be coordinated to get work done in a hurry. With Task Pilot it is simple to send an employee a precise assignment, whether they are in the yard or already on the road.
Timesheets. Task Pilot makes it easy to keep track of paid hours for individuals or teams of drivers. The system keeps track of both work hours and machine hours, so it can be used to compare paid time and on-task time.
Invoicing. Once a job is complete, it just takes a few clicks to generate an invoice and deliver it to the client’s inbox.
Health and Safety. Task Pilot can be tailored to provide set-up instructions and safety checks for different machines. It can also provide a procedure to check for hazards at the work site and it can send prompts to the members of a crew to make sure they are taking breaks to manage fatigue.
Machinery Management. Because Task Pilot can record machine hours, it can be used to schedule maintenance, report repairs or keep track of machines.
Client Details. The team sent to carry out a job can be sent the client’s contact details so there is no need to make calls to track down phone numbers or people.
continuing to add new features to it. We have trialled the app for the past two years with four different contractors. Over the last couple of months several more contractors have come on board,” Bevan says.
“It is easy to sign up for a trial or a demon-
stration on our website. The website also has a cost calculator so you can see how much you can save when you use the app.”
For more information or to sign up for the Task Pilot app visit the website www.taskpilot.app.
A REVOLUTION IS HAPPENING IN WEED MANAGEMENT. MECHANICAL WEEDING IS MAKING A COMEBACK IN THE FORM OF INTER-ROW HOES DUE TO THE EVER INCREASING PROBLEMS OF HERBICIDES OF RESISTANCE AND THE WITHDRAWAL OF ACTIVE INGREDIENTS.
Such is the size of this resurgence, that some of the biggest names in ag machinery – Lemken, Kverneland, Väderstad – have bought mechanical weeding companies and rebranded them.
John Deere never got out of mechanical weeding, even if they did not shout about it. Along with their subsidiary Monosem, they also offer a range of mechanical weeders.
In Europe, squeezed by herbicide resistance, legislative withdrawal, and a low rate of new chemistry, farmers are returning to mechanical weeding. But these are not the weeders of our grandparents’ generation, they are something else.
Over the last 50 years mechanical weeders have been evolving. There is something of an arms race among manufacturers as they try different approaches and to achieve ever better weeding.
The main winners of this race are what are now called ‘row-hoes’, because unlike their predecessors, inter-row hoes, these machines weed both the inter-row (between the crop row) and the intra-row (among the plants in the crop row). This means that they can control all weeds in the paddock.
Such are the technological advances that these modern machines are like a self driving electric vehicle compared to their predecessors’ horse and cart.
Row-hoe design has also consolidated around a modular parallelogram based ‘weeding unit’. These weeding units are now a technology platform onto which a range of inter-row and intra-row weeding tools can be
This means any crop – from delicate direct sown vegetables such as carrots and onions through to cereals like wheat and barley, and even wide row crops such as maize – can be weeded by the same machine. With modularisation, the size of the row-hoe can be easily varied, with working widths now reaching 30m.
The two key breakthroughs that have revolutionised row-hoes are computer guidance systems and intra-row weeding tools.
Before computer guidance, row-hoeing was a task that required specialist tool carrier tractors, extra staff to steer, or front mounting, as well as highly skilled drivers. Now it can be done on an ordinary rear three point linkage and any driver can do it.
There are two main approaches to accurate guidance – either RTK GPS autosteer or computer vision systems. The simplest approach is to use standard RTK tractor autosteer to steer the tractor and the row-hoe on the three point linkage.
There are a number of issues with this approach. Some of them are addressed with implement steering (also known as ‘double steer’) where both the tractor and imple-
VISION GUIDANCE USING CAMERAS GIVES MECHANICAL WEEDERS THE ABILITY TO FOLLOW CROP ROWS, EVEN WHEN THEY WERE PLANTED USING MANUAL STEERING.
ment have an RTK antenna and their own, but linked, steering systems.
Despite this, after nearly three decades of development, vision guidance systems are now the clear winner for weeders. They use a camera to identify the crop rows, and they are accurate enough that even crops that were hand steered at drilling can be followed and weeded. Combining tractor autosteer with a vision system for the hoe is the ultimate dream team.
The second breakthrough is intra-row weeding tools that weed the crop row. The Achilles heal of inter-row hoes was that they only weeded the inter-row, which left the weeds in the crop row because the weeds within the row are the ones that will be the most competitive with the crop.
A whole bunch of new intra-row weeders that use finger weeders, mini-ridgers, torsion weeders and vertical wire weeders. They can work in a wide range of arable and vegetable crops and can achieve high levels of in-row weed control.
They are also complementary. They can be ‘stacked’ and used at the same time or in sequence over multiple weedings to further increase the weed kill.
Such are the advances in row-hoes that they are split into first and second generation machines. The first generation are entirely
THE LATEST MECHANICAL ‘ROW HOES’ CAN WEED BETWEEN CROP ROWS AND BETWEEN THE PLANTS IN A CROP ROW.
INTEREST IS GROWING OVERSEAS IN PROSPR, THE MULTI-USE AUTONOMOUS AGRICULTURAL VEHICLE DEVELOPED BY KIWI AGRITECH COMPANY ROBOTICS.
Launched last year, Prospr is already transforming orchard and vineyard operations in the US, Australia and New Zealand. In September Robotics Plus exhibited the robotic sprayer at the FIRA USA, a major agricultural robotics show in California.
Robotics Plus CEO Steve Saunders says growers around the world face the challenge of producing more food while reducing their environmental impact.
“That is why we developed Prospr. It is a robust autonomous vehicle with unique modular architecture that can run all day. Prospr’s design centres on flexibility. It can adapt different tools for different crops, growing heights and applications, which maximises return on investment,” Steve says.
“Prospr’s capabilities include automated intelligent spraying. With its hybrid diesel-electric system, it can cut fuel consumption by 70 percent. This improves environmental sustainability and reduces cost. It also solves the problem of hard-to-find machine operators.”
Robotics Plus chief engineering officer Dr Alistair Scarfe says he is excited to demonstrate Prospr’s capabilities.
“It has advanced artificial intelligence capabilities and a user-friendly interface. We have designed Prospr to alleviate labour challenges and to drive efficiency, safety and precision for vineyards and orchards.”
At the core of Prospr’s innovation is its advanced artificial intelligence (AI) system. It combines intelligent features to maximise efficiency, safety and uptime.
mechanical. Adjusting them requires getting off the tractor and taking out the socket and spanners.
Second generation row-hoes have a range of automatic systems, such as downpressure, ISOBUS section control, and crop gap width adjustment.
Row-hoes can therefore achieve exceptional whole-of-paddock weed control. These machines have wide widths and can operate at speeds above 20 kph. They can approach the effectiveness of herbicides to achieve clean fields and high work rates.
They are not getting the recognition they deserve, however, and often it is the robotic weeders using high tech tools, such as lasers, that take the limelight. Robotic solutions are
Among the notable features Prospr has is a state-of-the-art collision avoidance system that integrates laser-based Light Detection and Ranging (LiDAR) technology, sensors and cameras to detect and identify obstacles. This ensures safe navigation in complex environments.
This system enables Prospr to autonomously adjust its speed, avoid obstacles, and stop when necessary, so that it can maintain high working speeds while ensuring safety.
LiDAR uses laser pulses to create detailed 3D maps of the surroundings and distinguish between critical obstacles and harmless elements, like plants and foliage.
Prospr uses this technology to work while autonomously navigating row crops. It only slows or stops for major obstacles. When it sees other obstacles, it slows to a safe speed and relies on triggering the front bumper to bring it to a stop if necessary.
Growers can use a range of Prospr spray-
ers. These include tower sprayers for grapes, apples, or tree crops.
Spray rates and air speed are controlled in zones or by individual fans to maximise spray efficacy and produce more targeted applications than traditional sprayers. The fine mist and turbulent air produced by the sprayers put spray on the backs of leaves.
Prospr’s highly intuitive user interface empowers operators to manage and monitor tasks remotely and efficiently. This interface simplifies complex operations, making it easy for operators to harness the full potential of autonomous technology.
For example, operators can organise the day's jobs for multiple machines from a single location. They can remotely track job status in real-time and maintain a detailed record of work in progress and completed jobs.
Operators can set parameters to ensure safe operations that protect people, crops and the environment.
often vastly more expensive to buy, however, and, even with far lower work rates, a good row-hoe with computer guidance will beat robotic weeders any day.
So for farmers who want to get into mechanical weeding, the options are now as complex and confusing as herbicides.
What guidance system to choose? What are the best inter-row and intra-row weeding tools for my crops? What are the traps for new players?
To fill this need, the BHU Future Farming Centre (FFC) has released a report entitled ‘Understanding (Inter) Row-Hoes and Guidance Systems — A Comprehensive Guide'. This can be downloaded for free from the bhu. org.nz website.*
The author of the report is Dr Charles ‘Merf’ Merfield, head of the FFC. Merf is a world leading physical weeding expert with more than 30 years’ experience, including practical on-farm management, machinery design, and research.
His guide answers questions you did not even know to ask. So, as herbicide resistance continues to increase, fewer new herbicides come to market and consumers ask more questions about herbicides, mechanical weeding is going to be an increasingly positive part of arable and vegetable weed management.
Download the full report for free from https://bit.ly/4hgqbOF or email ffc@bhu.org. nz.
LIVING IN THE WAKE OF CYCLONE GABRIELLE AND MULTIPLE WEATHER EVENTS SINCE HAS BEEN A CHALLENGE BUT TOBY PARKER IS DETERMINED TO KEEP GOING.
Toby runs Broadlands Contracting Ltd from his parents’ farm in Tolaga Bay, north of Gisborne. He does drainage, levels paddocks, plants and harvests maize for himself and other farmers, and does long-haul trucking to deliver feed wherever it is needed.
“The last two seasons have been extremely challenging which has taken a real toll on all of us. We pretty much had a rain event every month leading up to Cyclones Hale and Gabrielle and afterwards, it still didn’t stop.”
Everything was covered in silt and slash, fences were gone, and heavy rain left paddocks flooded, and unable to drain. The Parker family farm was particularly hard hit.
“Imagine waking up to every single inch of the property covered in silt. Every house, every
AFTER CYCLONE GABRIELLE, TOBY PARKER BEEFED UP HIS FLEET OF EARTHMOVERS WITH A 13-TONNE DIGGER, A 21-TONNE DIGGER AND A KOMATSU BULLDOZER.
shed, yard and gate buried, with no idea where to start.
“Almost two years on, we are still very much in recovery mode. Only now are we at a stage where we can start putting fences back up.”
In the wake of the disaster, Toby had more work to do than hours in the day. That included piling up slash and moving mountains of silt.
Today, he is future proofing paddocks by levelling them with
TOLAGA BAY CONTRACTOR TOBY PARKER FOCUSES ON DRAINAGE, EARTHMOVING AND MAIZE PLANTING AND HARVESTING.
new technology, so water can run off as quickly as possible.
Having 50 ha of maize on his lease land completely wiped out by Cyclone Gabrielle and unable to be harvested, was a huge hit financially.
“It was soul destroying to watch entire paddocks of maize fall over, and not be able to do a thing about it. Maize and drainage is my passion, but it’s been a real struggle to keep our heads above water. Now, with the sun shining and our 2024 crops in the ground early things are finally starting to look up.”
Last year he planted 630 ha of crops on his parents’ farm, leased properties and neighbouring farms. Most of that was maize and some sweet corn, but he also sowed grass and chicory.
“Pretty much 90 percent of the farms we work with are local. I have enough area around me to keep me busy, so I don’t have to go far. It is all about keeping a
good relationship with farmers close by.”
Toby wasn’t always dead set on being an agricultural contractor. He spent his school years following in his fathers’ footsteps as a boarder at King’s College in Auckland. After that he took a year off to work as a teacher’s aid in England and travel around Europe.
Upon returning home, Toby found a passion for engineering, took a course at the Eastern Institute of Technology and worked for Gisborne Engineering where he learned the trade. He then headed out on his own to set up Parker Engineering.
“I loved the challenge. My business was running for about five years, but I worked too hard and just got burned out. A lot of what we did was heavy duty welding for forestry companies. There were plenty of nights staying late on site to get the job done.”
He realised those hours weren’t sustainable in the longterm, and it was difficult finding staff willing to travel.
When his parents decided to grow organic kiwifruit for Zespri, Toby took the opportunity to join them on the farm.
“I moved back to Tolaga and we got to work researching and building the kiwifruit orchard. Having no previous experience constructing something like this,
ALTHOUGH IT IS PRIMARILY DESIGNED TO LAY DRAINAGE TILES, TOBY PARKER ALSO USES HIS SOILMAX GOLD DIGGER (RIGHT) TO MIX SILT FROM THE CYCLONES INTO THE TOPSOIL.
it was a great learning curve.”
After about a year, the project finished and Toby was ready for a new challenge. With house prices skyrocketing he sold his renovated property in Gisborne, and bought some machinery off his parents.
As work began to pick up, more clients came on board, so starting Broadlands Contracting Ltd
The ELHO TR 300 tedder can be used to turn, spread and move swaths. The ELHO TR features a large diameter rotor and double tines that are secured with lock plates. They are the highest capacity machine of their type on the market. Able to handle the largest swaths with a removable kick panel at the front of the machine.
The ELHO V-Twin 600 front-mounted swather enables you to reduce passes in a field by allowing one pass raking and baling. The V-Twin 600 swather is designed to swath all types of forage cleanly, gently and efficiently. Able to mount to a loader, front linkage, or with a drawbar attachment to be pulled from the rear.
TOBY
seemed like the natural next step.
“It’s been a hell of a journey –a lot of highs, some real testing lows, but we are pushing through and making good progress. Everything we do is to get a step ahead of the game and grow the
best crops we possibly can.
“It is one thing to deliver in the good times, but as we have learned the past couple of years, we need to be prepared for the bad.”
Having owned the agricultural contracting business for about four years now, he has expanded to take on several staff, all with a different set of skills.
“They are all pretty flexible, some of them like having a break in the winter, but I try to keep work going with the digger and some engineering. There is always plenty to do, year-round,
so it is important to have the right people for the job.”
Putting his engineering background to good use, Toby maintains and services his machinery. He also makes hoses and fixes gear for others.
The Parker family has eight John Deere tractors in all, including Toby’s 370-hp 8RX 370 on tracks. All up the fleet also includes three big tractors in the 300-hp range and two smaller 125-hp tractors, which are perfect for planting and spraying.
There’s an ‘old classic’ John Deere 4450, which is 160hp and dates from the 1980s and two 85-hp orchard tractors.
“The 8RX arrived just as Gabrielle hit, so it is not even twoyears-old, but it has been an incredible investment already. There is just no way we could have even attempted planting some of our paddocks without it.
“It’s basically my home now, it has a massager, heated seat and a fridge, so it keeps your back warm and beers cold,” Toby jokes.
“Having a quad track tractor means there is not much we can’t do, the problem is there is only one of them. In areas where a wheeled tractor would get stuck the 8RX makes it look easy. It has changed the game for us because we are able to push through even in some really tough conditions.”
Toby admits John Deere machinery is expensive, but it is all about parts and support. Brandt Gisborne is the John Deere dealer in town and offers a wide variety of machinery with a big presence and “there is not really anyone else who comes close”.
Single/tandem axle spreaders & muck spreaders
Renowned high quality, durable design and easy operation Advanced precision tech
TOBY PARKER SAYS THE 9770 STS IS THE BEST COMBINE JOHN DEERE HAS EVER MADE AND WITH TRACKS IT CAN HARVEST IN PRETTY MUCH ANY CONDITIONS.
Brandt has a number of mechanics on deck, meaning someone is able to get out in the field to offer support at short notice.
The Parkers brought an eightrow planter and John Deere 6125R tractor brand new in 2015. Back then they were top of the line, but in recent years Toby has upgraded with Precision Planting technology.
“It allows me to see soil temperature and how clean and uniform the soil is. It helps to get the best planting conditions possible and in turn, increases yields. The planter keeps track, so I can vary planting depths based on optimal conditions for growth.
“Maize isn’t the highest value crop out there, but if you can produce a high yield it’s rewarding. That is why I am so passionate about levelling and drainage, because every hollow is costing money in a dry or a wet year. Having an even paddock gives you the best chance to be as productive as possible.”
He has made a significant investment to his planter in the last three years, adding speed tubes, which means he can now plant twice as fast.
Toby has a Freightliner truck
BROADLANDS
CONTRACTING’S
FREIGHTLINER TRUCK HAS A 38.5 TONNE PAYLOAD AND IS USED TO BRING IN FERTILISER AND TAKE AWAY GRAIN.
Looking ahead, Toby says he would like to buy his own land and to build a house. He would also like to get married.
“I made a vision board in 2017 and I have just about ticked it all off. My goal for 10 years was to get a grain dryer in place, an 8RX John Deere tractor and a combine harvester on tracks, and I have managed to do that.”
For now his focus is on getting the family farm back looking like it did before Cyclone Gabrielle and level every contour and drain in Tolaga Bay.
There are always new dreams, big plans, and Toby has no intention of slowing down any time soon.
“For now it is about looking to the future. It finally feels like there’s light at the end of the tunnel, and as always I have plenty more projects on the horizon.”
and trailer unit, and he runs a couple of diggers, a bulldozer and a John Deere 9770 combine harvester on tracks.
“It’s the best combine John Deere has ever made. She’s a bit of a beast. It goes over the ground without too much compaction and you can pretty much harvest in any conditions. The tracks have been worth their weight in gold.”
The truck is his newest addition. He uses it to cart maize from sources to suppliers. It can carry a 38.5-tonne payload and gives him the ability to bring fertiliser in and take grain away.
After Cyclone Gabrielle, he bought his 13-tonne digger to help remove slash and silt from paddocks. He also added a 30-tonne dump trailer on Stryder tracks, which has been invaluable for clean-up work and har-
vesting in wet conditions. This year he added a 21-tonne digger and a Komatsu bulldozer.
The Parkers built a grain drying complex in April, which has proven to be a good move already, Toby says. It means maize can come off the paddock and into a silo, without having to wait for trucks or drier space.
“Living in a relatively remote location, logistics can be a nightmare, especially with road closures and delays. Having these systems in place takes the pressure off and gives us a lot more control.
“I love having a great team of staff around, living in Tolaga. We are always on the lookout for people with varied skills so we can tackle most jobs in house.
“We are about to start building a large storage dam to store water, so we can protect our-
selves and the wider community in case of a drought.”
As technology evolves, Toby’ can use data to make small adjustments that have a big impact over time.
Levelling paddocks using Trimble GPS and OptiSurface prevents water from pooling in low lying areas, meaning less re-planting and higher yields. Trimble GPS knows where all the highs and hollows are, which has allowed him to level 180 ha on his parents’ farm to increase efficiencies.
AFTER THEIR MAIZE PADDOCKS ARE HARVESTED, THE PARKER FAMILY OVERSOWS ANNUAL RYEGRASS, WHICH THEY GRAZE SHEEP ON OR CUT FOR SILAGE.
LEVELLING AND DRAINING PADDOCKS REMOVES WET, BOGGY AREAS THAT REDUCE MAIZE YIELDS AND MAKE HARVESTING DIFFICULT.
“It’s eliminated wet areas making the paddocks far easier to work. After the Cyclone we had a lot of very wet, boggy spots that were putting pressure on our machinery. We were getting stuck multiple times a day just trying to get the crops harvested before they fell over.”
A Polaris buggy makes it simple for Toby to take data off
paddocks and send it to OptiSurface in Australia, who map out the area and help get the best results for his clients.
“They basically design each paddock from across the Ditch. A couple of phone calls later we hop in the tractor and go round and round to get it looking like Eden Park. You don’t see any puddles on Eden Park.
“There are massive areas in many paddocks which aren’t performing. It is my passion to help people sort that out, so they can start making money off their land. They need to, because costs only keep rising.
Once it is level, you see instant benefits so you don’t have to worry.
“Whether it is lush green grass or lush green maize crops, as far as I’m concerned if you are not producing more off the same land, you are going backwards. As soon as a crop turns yellow, you are losing money – it is as simple as that.”
The Parker family has been farming in Tolaga Bay since 1956, when Toby’s grandfather first moved into the area.
His parents, Mike and Bridget
TO IMPROVE MAIZE YIELDS, TOBY PARKER LEVELS PADDOCKS USING TRIMBLE GPS AND OPTISURFACE EARTHWORKS DESIGN SOFTWARE.
THE PARKER FAMILY RECENTLY INSTALLED THEIR OWN GRAIN DRYING COMPLEX, SO THEY CAN DRY MAIZE IMMEDIATELY AND GET IT INTO A SILO WITHOUT TRUCKING IT TO A DIRER.
Parker, have around 250 ha, while sisters Penny and Clare and their husband’s Matt and Ben have 40 ha. Toby leases an additional 100 ha of land.
Having sold his house in Gisborne two-years-ago, Toby is now living on the family farm with his partner Amy and his three-year-old step-daughter Freya.
With his parents looking to retire, he is gradually taking over the farming operation alongside Clare and Ben. The farm is a mix of horticulture and agriculture, with the kiwifruit orchard taking up 7.3 ha.
“It is really starting to come on now. We should get a big harvest in March, which will all be destined for export.”
They grow maize over the spring and summer period on 80-100 ha. Once they have harvested it, they oversow a crop such as grass. They can either harvest it or put sheep on it, depending on the season and the price.
“The biggest challenges are the rising cost of inputs, including diesel, parts and freight. Farming right now is the toughest it has been for quite a while.”
A 30-TONNE DUMP TRAILER ON AUSTRALIANMADE STRYDER TRACKS HAS BEEN INVALUABLE FOR CLEAN-UP WORK AND HARVESTING MAIZE IN WET CONDITIONS.
You deserve technology that’s both compatible with your existing fleet and easy to use. That’s why PTx Trimble leads the way in engineering solutions – including displays, steering systems and guidance control – that allow you to connect your farm, your way for seamless work all season long.
This farmer uses: GFX-1060™ display with Precision-IQ™, Autopilot ® steering system, NAV-900 guidance controller, and Trimble ® CenterPoint ® RTX correction service. Scan to learn more and contact a local dealer.
WHEN IAN HUTTON RETIRED FROM CONTRACTING IN THE WAKATIPU BASIN IN 2015, ONE OF HIS SONS, JARED, TOOK OVER THE BALAGE AND HAY WORK AND THE OTHER, HAMISH, WENT SPRAY CONTRACTING.
Hamish had been working for Ian since 2002. They had been doing their own spraying and Hamish could see there was a need for a local spraying contractor.
“There was a gap and no one really servicing the area. I asked around clients and said I was spraying, and most put their hands up. I went into spraying 100 percent.”
The new business is Oregon Agriculture Ltd. ‘Oregon’ came from the tree species Hamish worked with in his previous career. He studied forestry at Lincoln University and worked around the North Island for three years before coming back to help out Ian.
Hamish met his wife Alyson at Lincoln University. She is from Opotiki and was studying Resource Studies. Alyson is now town planning manager at the Queenstown Lakes District Coun-
cil, but she also does the bookwork for Oregon Ag.
“I used to drive, and helped out Ian back in the day. I drove the hay rake and trucks around farmland. I enjoyed it, but haven’t done it for a while, since having children and working full time,” Alyson says. (Their kids are now 14 and 11 years.)
She says because Hamish specialises in spraying, he is quite particular that it is done right.
“Spraying is such an important part of the farming year in terms of getting ready for crops.”
HAMISH AND ALYSON HUTTON WITH THEIR CHILDREN LUKE AND JESSICA.
They are based in Dalefield, between Arrowtown and Queenstown, and their business has grown through word of mouth. Most clients run extensive high-country properties. These include in Glenorchy, and across Lake Wakitipu on Cecil Peak and Halfway Bay Stations, where they travel courtesy of the clients’ barges.
THE MAIN SPRAY TRUCK FOR AGRICULTURAL JOBS IS A LANDCRUISER WITH A 12M HARDI BOOM, A 190 LITRES/ MIN COMET PUMP AND ARAG SPRAY CONTROL GEAR.
Hamish says most farmers used to do their own spraying because they had to. Now, however, his clients don’t want to deal with the chemicals, which means keeping up with the rules regarding storage, keeping records and being certified.
“It is a lot easier and safer to call in the experts. For most of our clients I supply and apply all chemicals they need. I store it and supply it.”
Hamish works north as far as Makarora, occasionally east as far as Alexandra, and south to Kingston.
If you think getting staff is hard in other parts of rural New Zealand, it is a nightmare around Queenstown. He says the cost of living in Queenstown is “mental”.
Up until the last few years Hamish employed a full-timer, but very few people can afford to live there long term if they have to pay market rent, and training up someone who may only be there a year on a working holiday is not economical.
“You need them to stay two to three years, otherwise it’s a waste of time.”
Instead he works with other contractors if necessary.
Weather willing, spraying happens most of the year. Over win-
FROM THEIR BASE AT DALEFIELD, OREGON AGRICULTURE SPRAYS CROPS FOR FARMERS AND LIFESTYLERS IN THE WAKATIPU DISTRICT, INCLUDING SOME PROMINENT HIGH COUNTRY STATIONS.
ter, lucerne is sprayed whilst it is dormant. Then during spring most of the work is spraying out to get paddocks ready for winter crops. Over autumn, Hamish sprays pre-emergents for winter wheat.
He says work has become more varied over the years.
“When I started, most work was spraying glyphosates for winter
speciality crops.”
Apart from eye-catching sun-
”For more than 20 years we’ve been steering NZ tractors down exactly the same lines using my local land-based RTK correction stations.”
We achieve superior accuracy and repeatability because our local land-based RTK stations are not affected by the modeling errors found in large wide-area networks, and they are less susceptible to coordinate drift that occurs due to NZ’s unstable earthquake-prone landscape. Call me for friendly advice and expert knowledge.
John Ahearn GPS CONTROL SYSTEMS LTD
021 2234 911
usual brassicas, fodder beet and turnips.
But most of the farming is extensive, with the most intensive being winter crops.
Most clients are in the High Country, while the rest are on lifestyle blocks. Being Queenstown, some land use seems a tad odd to farmers, but four-hectares of lawn helps keep Hamish employed.
“They may want the clover sprayed out, or want 20-acres of grass mulched a couple of times a year.”
He keeps a side-by-side ATV set up with a 3m spray unit for these smaller jobs.
“The total hectares I spray is a drop in the bucket compared with Canterbury contractors, so I do all these other things to fill in the gaps.”
Not all lifestyle blocks are lost to farming. Hamish ends up managing blocks and then the neighbours ask him to look after their land.
“There is more farming on them than you think. We have had so much subdivision of
OVERVIEW’S DJI T40 DRONE HAS A 9M WIDTH AND A 40-LITRE TANK, AND HAMISH HUTTON SAYS IT IS SURPRISINGLY QUICK.
PHOTO COURTESY OF BEN RUFFELL, OVERVIEW.NZ.
OVERVIEW HAS USES A CUSTOM-MADE TRAILER TO MIX CHEMICALS AND FILL THEIR DRONES.
land, but people still like seeing farming. It’s not just a couple of sheep, it could be 200 cattle and a new crop going in.”
He and Alyson lease 100 ha of land. Sometimes they winter-graze dairy cows and sometimes they buy in calves for fattening.
Hamish is interested in regenerative ag. A friend was using products from Invercargill company, Bioactive Soils. It is a solid fertiliser based on seaweed, fish waste and oyster shells, with RPR and trace elements added.
“The client had good results and now a few others are trying it. I think a solid mix hangs in the soil longer. We have such a short growing season here, so we feed the soil and the plants take it when they need it.
“I am also trialling liquid alternatives. I have the gear and want to service my own farm. I have done a lot of liquid fertilisers, using the same gear.”
One Oregon Agriculture client is Royalburn Station on the Crown Range, farmed by Nadia Lim and Carlos Bagrie from the TV programme ‘Nadia’s Farm’. They are high on the list of people embracing regenerative ag and trying new things and speciality crops.
“They are trying to go down the regen path. They are not organic and not trying to break records. They are trying to be sustainable and give the land a bit of love and some balance.”
Part of the regenerative vision is planting mixed pastures.
“There are lots of regenerative mixes for soil aeration, to stop compaction and crank along the soil biology. There could be 20 different seeds in a mix which
HAMISH HUTTON HAS WORKED WITH SPRAY CONTRACTOR OVERVIEW TO SPRAY ON BROOM AND GORSE STEEP SLOPES WHERE A HELICOPTER COULD NOT GET TO.
PHOTO COURTESY OF BEN RUFFELL, OVERVIEW.NZ.
can be a pain to drill because they range in size from beans to little, tiny lucerne seeds.”
Many of the mixes come from Wholesale Seeds.
Another new thing Hamish is experimenting with is spraying by drone. For four years he has been returning to a Wanaka property to spray weeds. He has done most of it with a ute and hand gun, but now they are down to just a few steep faces.
“It’s not big enough for a chopper job, and anyway there would be too much by-kill. We are trying to leave the matagouri.”
This time he worked with another contractor, Joshua Dunn. Joshua and Ben Ruffell formed the drone company Overview in 2015 for the film industry. They now also work in the ag sector mapping, seeding and spraying.
“It worked really well. You are not taxing yourself, and it is better for health and safety because you are not out on steep slopes, and it is low noise and low impact. Josh could target the broom and gorse, where the chopper couldn’t get it or it would damage other things.”
The Agras T40 drone from DJI can spray a 9m swath.
“I never thought it could complete the job because it only carries 40-litres, but it is actually bloody quick.”
Joshua has a trailer set up with a 300-litre mixer tank and fills the drone with a hand gun. He uses a generator to recharge batteries, so it is not free of fossil-fuels, but is a lot less than a helicopter.
Hamish is going to investigate using Overview for broadacre applications.
“Maybe if you have a fodder beet crop or brassicas up to your knees and you don’t want a truck to crush them, then you could use a drone.”
The drone is likely to become another tool. He says on the big jobs it wouldn’t be as effective as a helicopter, but there is definitely a place for it.
Mulching is a job that Hamish keeps for days when the weather does not cooperate for spraying.
He has a 2.5m Seppi M mulcher which goes on the three-point linkage. It is designed for stubble,
and he does use it on that, but has found it is also good on green spaces.
The main tractor is a Kubota M135GX. It provides the muscle for cultivation and planting on Hamish and Alyson’s lease land, and for a few clients, but that is not a part of business they push.
For primary cultivation they use a 4Ag disc cultivator. Hamish likes that the angle of front and back gangs of discs are controlled with one adjustment.
“They are never fighting each other. We also use if for finishing work sometimes. If you play around with the angle you can use it like a speed disc.”
After the discs they use a 6m Flexi-Coil Cambridge roller drill with levelling paddles on the front. It has an Einbock seeder for small seeds like lucerne and pasture mixes.
He also uses a Hubbard folding
good relationships make wheels go round
Hamish Hutton has happy relationships with lots of people in the industry.
He uses EziCover adjuvant oil from Pure Oil based in Rolleston. Its core ingredient is rapeseed oil.
“It is a really good wetting agent and competitively priced. We get good support from Pure Oil.”
He also values his Farmlands reps, people from Wholesale Seeds, and Gerard McCarthy from PGG Wrightson. “He’s near retiring now and has been a mentor and bloody helpful to me.”
cultivator and an Amazon power harrow.
The main spraying workhorse is a Landcruiser spray unit. Hamish bought the truck, deck frame and tank and built it up.
It has a 12m Hardi boom, a 190 litres/min Comet pump and ARAG spray control gear. He has tried different nozzles and prefers Hardi mini-drift.
“Hardi are really good. They are nice and compact. I still use flat fan nozzles.
“Around here I spray whole pasture, mainly fine-leaf grasses like browntop, so you have to get the droplet size down to penetrate through.”
A key part of the set-up is the Tracmap guidance with differential GPS. That coupled with the
air-induction nozzles ensures the spray goes where it is meant to, which is both more efficient and saves annoying the neighbours.
“From my personal experience, I have had hardly any bother from the wider public voicing concerns over what I'm doing, but there are so many lifestyle blocks and grapes that I'm always very careful about where we spray.”
THE PULL OF THE FAMILY FARM CAN BE STRONG, ESPECIALLY IF IT HAS BEEN IN THE FAMILY FOR FIVE GENERATIONS.
The Armstrong family has owned their farm near Becks, Central Otago since the late 1880s. Over the past 15 years brothers Chris and Nathan Armstrong have joined their parents James and Linda to run the family’s 370 ha sheep and cattle farm and contracting business.
“Nathan is my older brother. He drove tractors for contractors around here and in North America before he came back to help manage the farm. Nathan and my father set up the contracting business,” Chris says.
“I came back to the farm about 10 years ago. At first I looked after the farm, helped manage another farm and filled in for the contracting business as a go-fer
or driving a baler, rake or wrapper.
“Then, about three years ago, Nathan left to work for Norwood. He still lives on the farm but he works out of Norwood’s branch in Mosgiel. He is their Kuhn specialist for the South Island.”
The Armstrong family farm supports 2000 breeding ewes and finished about 150 calves each year. They establish their own pasture, whole crop silage and winter crops – swedes, rape and kale – and they bring in a contractor to establish about 15 ha fodder beet each season. Thanks to local dams some of their paddocks are irrigated.
“We have one centre pivot that covers 70 ha. We converted an
CENTRAL OTAGO’S ARMSTRONG CONTRACTING WRAPS MOST OF THE BALAGE IT PRODUCES WITH THEIR TWO WEBBLINE TUBE WRAPPERS.
old flood irrigation system into the centre pivot in 2014. We also have some old soft hose guns that were put in during the 1980s. Each one covers about 4 ha per day.”
Balage is the mainstay of the contracting business. They also have a cultivation side of the business, which prepares former pasture and winter cropping ground for new crops or grass. They concentrate on the ag work
in August, September and October, before the balage season kicks off in a big way.
Chris also built up experience working elsewhere before returning to the farm. Most that time he had either a handpiece or a big tractor’s steering wheel in his hands. After he finished high school, he spent six years as a shearer. Then he did a two-year stint in Canada driving trucks and tractors for a large hay contractor.
“I was with a contractor in Lethbridge in southern Alberta. We did thousands of big square bales of alfalfa for farmers and thousands more on land that the contractor leased. A lot of it was for export to the US. We drove trucks full down to the States, mostly to Idaho and Washington. It was great fun.”
He then did a season operating a big air drill for a big grain grower in northern New South Wales sowing barley.
“It was fun driving the really big gear. In Australia I drove a fourwheel drive John Deere. In Canada I ran Fendt and John Deere tractors and JCB and John Deere telehandlers.”
tralia, he worked on an irrigated beef and dairy support farm at Tarras (near Wanaka). When he returned to work with the family, he focused on the home farm and also helped manage a dairy support and deer breeding farm that ran about 1000 red breeding hinds.
It is perhaps no surprise that Nathan decided to work for Norwood given the Armstrong family’s history of running brands of equipment Norwood has supported. This includes a lot of New Holland equipment.
Their primary baler is a NH RollBelt 180. They also have an old
er NH baler that is usually used as back up but has done a lot of work this season. It generally joins the fray to meet demand during the busy hay baling season.
Tractors are a NH T6050 and a NH T7185. Over the past several seasons they have also leased a NH T7225s. As the names suggest, the T7185 boosts to 185 hp while the T7225s boost to 225 hp.
“We leased the 200-hp tractor to run the baler. Last year, when Norwood and New Holland separated, we bought the T7225 that we had been leasing.”
While the bigger tractors are used to do ag work, run the baler or work the double mower, the T6050 is the loader tractor. “It is a nice little nimble loader tractor,”
Chris says.
The brothers have also held on to an older Case IH Puma 140, which generally sits on a four-rotor rake.
“We only mow for about 50 percent of our clients. A lot of farmers like to do their own mowing. We don’t mind because rocks are everywhere in Central Otago and they can be hard on gear. Most people are pretty good though. They roll their paddocks, so rocks
BALAGE IS THE MAINSTAY OF ARMSTRONG CONTRACTING AND THEY MAKE UP TO 7000 BALES IN A TYPICAL YEAR.
During the winter Chris gets to spend more time with his wife Jess and their two-year-old son, Gus. He also gets to play a bit of golf.
Jess is the South Island assets manager of Heritage NZ-Pouhere Taonga with responsibility to look after the historical properties that the government agency owns.
Those properties include Totara Estate near Oamaru and Hayes Engineering in nearby Oturehua, where the Hayes family produced wire strainers, rabbit bait cutters, wind turbines and other agricultural tools in the 19th century.
Chris says the 2024-2025 season is looking good for Central Otago. By mid-November Armstrong Contracting had done 1500 bales and they had another 1000 bales to wrap. They have had regular rain and he is hoping it will continue.
are not too much of a problem.”
The Roll-Belt 180 baler is a variable chamber round baler that produces bales from 90 to 180 cm in diameter. It is a straight baler and to make silage they wrap the bales with either a tube wrapper or individual wrapper.
“We run two Tubeline tube wrappers from Webbline. Our main one is a Super Wrap XL model and it is a nimble little thing. The other one is a ‘Contractor’ model. It can wrap square bales as well as round bales. We use a Scania truck to cart the bales to the wrapper,” Chris says.
“We also have a Goweil individual bale wrapper, but we do not have a lot of demand for individual silage bales. We did around 200 bales with it last year.”
The rake is a four rotor Fella,
which has a few years under its belt, and the mower is a front-rear Fella double mower.
Chris says in a typical year Armstrong Contracting does 60007000 silage bales. In Central Otago farmers can generally get two cuts off their pasture paddocks. Often the first cut goes to pit silage and the additional cuts in summer go into balage.
Armstrong Contracting mainly does its cultivation work in spring – helping farmers get ready to sow winter forage crops. Many farmers in the area are also on irrigation schemes. Water availability tends to drop off early in the new year so they often devote their water quotas to winter crops rather than balage.
Tillage tools in the family’s arsenal include a James aerator,
MANY FARMERS PREFER TO MOW THEIR OWN SILAGE, BUT ARMSTRONG CONTRACTING CAN USE ITS TWO FELLA MOWERS TO DO THE JOB IF REQUIRED.
a seven furrow Kverneland conventional plough, Proforge speed discs, and a Rata Maxi-Till tine cultivator with leveller.
“Around here compaction is a big issue, so the aerator is the first tool we use on most of the winter cropping ground that we do. Its legs penetrate to 500 mm, and it can rip down and break up a pan.
“After that we go in with the discs. Depending on what the farmer wants we can then do another pass with the discs or a pass with the Maxi-Till and leveller. We use the plough to turn over pasture that is going into crops or back into grass.”
The amount of hectares the plough does depends on the season and where farmers are at in their renovation schedules. Last year Armstrong did 30 ha with the plough for one farmer, but this year he only wants 15 ha done. Another farmer has asked Chris to plough another 20 ha, however.
“We do not do any drilling for farmers because it is better for us to have our tractors out doing balage,” Chris says.
The family does have a 3m Taege 3000 direct drill to establish winter crops in their own paddocks, however. The Taege is a tine drill that can direct drill or work in cultivated ground.
“We do a lot of drilling where we just spray out pasture and direct drill kale or swedes. It is a very quick way to establish a crop. Even though we do not get really high yields, if you consider the cost versus the output and the speed it is a cost effective way to go.”
Armstrong Contracting’s clients are mostly within a 30 km radius of Omakau and Becks. Some are in the Ida Valley-Poolburn area on the other side of the hills and a few are as far south as Alexandra.
THE CULTIVATION SIDE OF THE BUSINESS FOCUSES ON GETTING FORMER PASTURE AND WINTER CROPPING GROUND READY FOR NEW CROPS OR GRASS IN SPRING.
They are mainly sheep and beef farmers and they do include a few dairy farmers. Chris says he is on call for the dairy farmers because they can decide quickly when they want to shut up a paddock and take bales off it. Usually that means baling up 100 to 200 bales, which does not take long.
During the busy part of the year, the contracting business has two or three drivers. They include Chris’s Dad, James, who comes on board as needed, and two seasonal workers.
For the past four years local driver Julie Beale has worked for them and for the past three years Samuel Reed from the north of England has joined the team.
“Julie is a jack-of-all-trades. She is our main rake driver but you can put her on anything and she will figure it out. She doesn’t break as much gear as Dad, Samuel and I, which is good. After she works for us, she rolls maize silage stacks for another contractor. Then in winter she works on a big Dairy Holdings farm feeding out,” Chris says.
“Samuel can also operate anything. He runs our baler, rake and wrappers until early March, when he has to return home for lambing on his own farm.
“We can all operate most of the equipment so we can switch around when we need to. During winter things get quiet. We feed balage and winter crops to cattle and ewes and we do maintenance on the equipment to get ready for the next season. I used to do some shearing but not anymore.”
A place to socialise, stock up on groceries and stock feed, and agricultural equipment. But the fortunes of rural service towns are closely tied to the highs and lows of the local agricultural economy.
An effort to lessen the impacts of these financial fluctuations, and improve the economic outcomes for businesses in his own town of Tumby Bay, has surprisingly led cropping farmer Dion LeBrun into the global art world.
backbone of that area.
The painted silo is one of around 18 in South Australia, and one of 53 on the Australian Silo Art Trail.
But how did Dion’s likeness, when he is not a local of Wirrabara, nor a forester, end up on a silo four hour’s drive away from his farm?
on the close-knit forestry town’s silo.
across
And, while he may be heading into his retirement years, Dion has found unexpected fame in one small corner of South Australia.
Off the beaten track at the timber town of Wirrabara, Dion’s rugged face looks out from a 28m high grain silo. With a wellworn hat shading his face and an axe swung over his shoulder he looks the picture of the old-time timber workers that were the
When the town folk at Wirrabara were looking to become part of an early wave of silo art springing up across rural Australia six years ago, the image of an outsider would eliminate any friction over who should be painted
“The community there decided they didn’t want a local person portrayed on the silo as it could cause problems. Why wasn’t this person picked or that person, or why was this person picked because they’re a bloody idiot –that sort of thing,” says Dion.
THE PAINTED SILO AT TUMBY BAY WAS THE START OF TOURISM BECOMING AN IMPORTANT NEW REVENUE STREAM FOR THE
Though not a forestry worker Dion’s face fitted the bill.
“I’ve got a farmer’s face. I’ve spent too much time out in the sun - weather beaten and busted up,” he reckons.
But Dion’s towering art story begins earlier than this and closer to home.
Although Dion reckons his own skills see even stick figure drawing as a challenge, he became involved in the art world after a move to improve the economy in his own small coastal home town of Tumby Bay, 380 km down the coast from Wirrabara, on the Eyre Peninsula, and 600km west of Adelaide.
At a business breakfast put on by a local bank seven years ago, a speaker from a similar small rural town had given the local Tumby Bay commercial group some insights into how they had grown the economy of their area by looking beyond the local agricultural community. Based around the natural attractions of their area, tourism had become their new economic driver.
As president of the Tumby Bay Progress Association, Dion, along with other local business owners, began brainstorming on how to bring tourism into the Tumby Bay area.
Silo art was just getting off the ground then, and painting a local grain silo was a popular suggestion. Design company Juddy Roller, who developed the concept of silo murals, were contracted for the project. Along with managing the projects, they also locate the artists.
Choosing a local theme to make their mural stand out from the crowd was recommended.
Leading Argentinian street artist Martin Ron was brought in and saw him painting a mural based on an image of a couple of local boys jumping off the Tumby Bay jetty.
The painted silos became the catalyst for a major change for the town.
While the mural would get people to pull off the highway, the challenge became how to draw them down the side road to Tumby Bay township, a couple of
kilometres away.
With Dion at the helm, a street art festival was decided on. This saw around 30 murals painted on walls in the town by some world class artists.
“We’ve gone for quality,” says Dion. “People will drive a long way for quality but they won’t cross the road for average.”
Turning the town into what is basically an art installation has been a big success.
The influx of visitors has benefitted the entire community, and has meant that, for a small town, they actually have a decent café culture, with tourists also underpinning other local business, he says. The bakery and supermarket are as well stocked as a major centre because of the tourist dollars that come through.
Dion’s wife Maria, who has been administrator on the farm since they married, has now become a barista in the bakery.
While she doesn’t drink coffee herself, Maria enjoys making it. The added income goes toward their increasing semi-retirement travels.
One of the artists who worked on the town street murals and goes by the name of Smug - aka Sam Bates - is something of a ‘rock star’ in the art world. Originally from Melbourne, he now lives in Glasgow.
Along with the Tumby Bay street art, Smug was also commissioned to paint the silos at Wirrabara.
Now in need of a timber worker model, and having gotten to know Dion, Smug suggested his
rugged outdoor looks would be a good fit for the silo. This saw Smug spending nearly three weeks in a boom lift bringing the design, which included Dion’s likeness to life.
The LeBrun family have farmed on the Eyre Peninsula since the early 1900s with Dion the sixth-generation on the land.
The original coastal farm has been added to over the years until they now have six parcels of
land scattered over an area within 60km of Tumby Bay.
The sandy loam of the coastal farm also harbours shallow limestone rock caps. Breaking this rock down has been a work in progress over the years with a contractor brought in periodically, operating a Reefinator. This equipment rips the soil, bringing the rock to the surface where a heavy, water-filled roller following behind crushes it.
Cropping is the biggest and most profitable part of the business, with around 3500 hectares in a three crop, three-year rotation.
grown although 90 per cent is wheat, the rest mostly barley. Nitrogen-fixing legumes follow – mostly lentils, and depending on the soil type and rainfall environment, a small area has fava beans. Oil seed like canola follows on behind.
Depending on how the season or markets are going, another
crop instead of oil seed.
Variable rainfall across the farms from 320mm to 400mm annually sees maximizing rainfall an important issue, with measures in place to conserve moisture in the ground and subsoils.
This sees no-till cultivation and preparation for next year’s
‘beer can’ height cut close to the ground.
To reduce weeds, which suck up moisture they need for the crop, the headers have Seed Terminator seed destructors on them. These help to overcome chemical spray resistance in weeds, by collecting all the weed seed that comes off the header/harvester sieves, and putting them through big cage mills which pulverize the seed.
When summer rain falls and weeds start to grow, they spray to keep the soil bare. Over a period of time, destroying the seed using the Seed Terminator runs down the seed bank, so they don’t have to be as reliant on chemical control, Dion says.
Some of the land is granite-based and too steep and rugged for cropping. Here Dion runs around 1200 self-replacing Merino ewes and a couple of hundred hoggets. Meat is the money spinner here with wool a sideline.
Always mindful of the local economy Dion prefers to buy farm equipment at the local dealers. He knows he’s going to get good after-sales service there, but also feels it’s important to support the business so it stays
This sees him with a mix of mostly Case and New Holland tractors and machinery used across the various properties. The big articulated 500 tractor is a New Holland while the utility tractor which tows the spreader and the chaser at harvest is a Case. There’s also a Case self-propelled sprayer, and a couple of New Holland harvesters.
While farming has become traditional for the LeBrun family on Eyre Peninsula, it is a far cry from their pre-settler European traditions. And their beginnings in Australia in the 1850s certainly don’t follow the usual settler storyline.
From a traditional French military family, with his father aidede-camp to Napoleon Bonaparte and his grandfather having been Governor of Genoa, young Barron Frederick Le Brun, in his early 20s, had caused a family scandal by rebelling against a future in the French cavalry in the late 1840s, and absconding from service. He was sent back to France in disgrace by his uncle in the United States after heading there in search of a new life, Frederick then sailed to Australia. Here he joined the gold rush at Ballarat before heading to Port Lincoln in 1853 after the French military came looking for him. There he ‘went bush’ until they gave up the search and left, with Frederick later marrying, raising a family and spending the
rest of his days in the area.
And life on the peninsula has had much to offer the LeBrun family over the years. Dion has enjoyed an upbringing that included plenty of surfing, fishing, and diving. His four sons are all surfing mad, he reckons.
Having never been fishing before, when artist Martin Ron stayed at their farm - while painting the local silo, he proved to be an enthusiastic fisher when Dion took him out in the boat.
In stark contrast to the family expectations the rebellious Frederick had rejected, Dion and Maria have always said their four sons needed to get some life experience before they made any decision about their future.
Lenny, Isaac, Jordan and Harry have all been encouraged to get a trade or try another line of work first, and to travel as much as they can before deciding whether to work the farm.
“You need to be passionate about farming as it’s not an easy job at times,” Dion comments.
Isaac and Jordan, both in their 30s, have tried farming, but decided it isn’t for them and have gone on to other things. At just 17, Harry is still figuring out what he wants, while 40-yearold Lenny has largely taken over the running of the farm from Dion.
Pleased with how he is running the place, Dion says he has been happy to relinquish the reins to Lenny and his Scottish wife Debs, who he met while travelling. Their two young sons are now the eighth generation on the farm.
For his part, farming was always likely for Dion who had spent the last two years of schooling at an agricultural college before going home to the farm.
But he had also experienced working life outside the farm gate.
At times when the farms finances were down, Dion and his brother Steven would work off-farm. Dion went shearing,
and then both of them became involved with the tuna fishing industry.
The farming operation was small enough their father could largely manage it himself with Steven coming home for busy harvest times, while Dion would come home for crop planting. After Steven tragically died young from melanoma, Dion came home full-time.
His father was happy to relinquish control early to him and Dion has continued this with Lenny.
“Families working together can be a balancing act,” Dion says. “But you’ve got to respect the generation coming after you. They’ll have different ideas, but they’re the future, and will reap the consequences of whatever their decisions.”
Dion is taking more of a back seat these days and is semi-retired. Unless it’s a particularly busy time like seeding or harvesting, he doesn’t have to go to work, although he can’t imagine ever giving up farming entirely.
Meanwhile the coastal town of Tumby Bay is busier with a more diverse business mix and is less impacted by agricultural cycles.
“While people move to the regions for the quiet and tranquility, we all need the businesses in our towns. If they’re going to survive, they need more than just the local residents. And it creates jobs, so kids don’t have to leave town. They can get jobs in town in hospitality and things like that,” says Dion.
“Rural towns need to evolve or they will stagnate or die.”
More information on Australian Silo Arts Trail https://www. australiansiloarttrail.com.
GPS TECHNOLOGY PROVIDES THE MEANS TO ACHIEVE HIGHER YIELDS WITH FEWER INPUTS WHILE PROTECTING THE ENVIRONMENT. IT CAN ALSO HELP CONTRACTORS MANAGE LARGE FLEETS OF MACHINERY. IN THIS FEATURE THE INDUSTRY’S LEADING MANUFACTURERS AND DISTRIBUTORS OF PRECISION FARMING PRODUCTS DETAIL THEIR GUIDANCE SYSTEMS, SECTION CONTROL, MAPPING, TELEMATICS, DATA MANAGEMENT, AND OTHER PRECISION FARMING PRODUCTS.
In October, Ag Leader released the next generation of its InCommand displays. The InCommand Go 16 and InCommand Go 10 will allow farmers to see more information and enhance the user experience in the cab, while making it simpler to stay connected to every activity on the farm.
InCommand Go displays offer a high-resolution touchscreen with an intuitive interface. They give the operator easy access to real-time information without compromising mapping visibility and are ideal for farmers or contractors with a mixed fleet, regardless of the size of their operation.
With faster processing times and more visibility, InCommand Go displays make it easier for farmers to manage complex operations in the field and improve decision making on the go through a single display.
Ag Leader product specialist Luke Bunkers says with today’s advanced equipment, farmers
need access to a significant amount of information to ensure accuracy and operational efficiency.
“This means the farmer is interacting with the display more frequently, which often requires more button pushes or monitoring multiple displays to get to the information they need in the cab,” Luke says.
“This can be cumbersome and takes the operator’s attention away from where it needs to be. We think we can offer a better user experience, and that is where we started as we began
thinking about what the next generation of the InCommand display should look like.”
InCommand Go includes several user enhancements that improve visibility. Operators can, for example, view machine diagnostics and multiple layers at one time, so there is no need to navigate different screens for different operations.
The InCommand Go 16 boasts a 16-inch widescreen that gives farmers and contractors easy access to all the information they need while never losing sight of the map. The dashboard
Considering the environmental, economic and climatic challenges that New Zealand agriculture is faced with, farmers are looking closely for proven returns on investment (ROI) for any investment they make in technology.
Kyle Baxter is the Asia-Pacific-Africa (APA) marketing manager for PTx Trimble (formerly Trimble Agriculture) and has been involved in New Zealand agriculture for the past 20 years.
He says the industry here is well versed in the adoption of precision farming technology. It provides farmers an edge in maximising accuracy, efficiency, and productivity.
Kyle says no matter where you are in adopting technology to manage your farming or contracting operations, it is important to stay focused on the future.
“When deciding which technologies offer the greatest benefit to your operation, ask: Will it expand existing capabilities or help accomplish more than you are able to do today?
“Does it deliver a measurable return, by way of added cost savings (such as lessening chemical usage, or freeing up time and labour)? Can it guarantee higher yields?”
With those questions in mind, Kyle identifies a few trends he recommends farmers and contractors explore.
Retrofitting technology can add capabilities to existing equipment. For example, adding a PTx Trimble GFX connected display to a machine gives the ability to seamlessly transfer data to and
from the farm office.
This approach provides the latest technology without the need to spend capital on buying new equipment.
PTx Trimble’s earthworks and water management tools can help improve the use of water across the entire farm. WM-FieldForm provides a wide range of options for controlling the movement of water onto, off of, and within fields using uniform surfaces.
Landforming options extend from simple topsoil levelling to complex multiplane grading, levelling, and terracing. This system helps farmers efficiently use water and improve crop yields by mitigating the variations experienced through irregular rainfall and irrigation.
Kyle says we will continue to see more intelligent machines and implements. Look particularly for advances in smart spraying technology.
Green-on-brown and Greenon-green spot spray systems, like PTx Trimble’s retrofit WeedSeeker 2 and the Bilberry system, deliver herbicide only where it is needed. This improves yields and lowers costs substantially.
Smart sprayers also help optimise field practices. PTx Trimble’s Field-IQ ISOBUS Advanced Sprayer system allows operators to customise features so they can have added control over the rate, section and boom. Prescription and coverage maps can be easily managed through any PTx Trimble GFX display.
Kyle says ‘autonomy’ is an
industry buzzword that farmers in New Zealand should keep their attention on. It is one of the most promising ways that capabilities of machinery will advance and it can help better use labour.
Whilst full autonomy and driverless machines may be seen as the pinnacle, many technologies available today can immensely improve machine and operator efficiency when retrofitted on existing machines.
“When you implement new technology, it is valuable to involve trusted advisers who can help you adapt your practices,
especially around input usage, to get the most out of your investment,” Kyle says.
“This can translate into even higher returns on your technology investment and builds confidence in the level of risk you assume.
“Farmers and contractors who leverage the expertise of their dealer when it comes to implementation and field practices will have the best available information. This means they can position themselves as leaders in the next chapter of agricultural evolution in New Zealand.”
provides flexibility, by showing real-time data through dynamic tiles and a mapping viewpoint that adjusts as more details are displayed.
“Because farmers and contractors are performing and managing several functions at once, they need to be able to see all that information at the same time. The larger viewing area on the InCommand Go 16 lets you see more without the hassle of pressing buttons to switch between screens or compromising the visibility of the
map,” Luke says.
“The ability to view and map real-time data and layer historical reference maps allows you to make better decisions while operating.”
The 10-inch display is a cost-effective option that serves as a great standalone display or companion to the InCommand Go 16.
It is loaded with features like advanced seed monitoring and variety tracking. This means the InCommand Go 10 can also
provide additional flexibility for operators who want to maximise their potential.
An entry-level guidance package is also available for farmers just stepping into steering who may want additional display functionality in the future.
Vice president of finance and engineering at Ag Leader, Mike Myers, says the company has set a standard with the InCommand display, and farmers and contractors have come to rely on its usability and functionality.
“We know they expect their
display to do more in the cab including giving them access to more data. It’s crucial our display continues to evolve with our customers’ needs, while maintaining the familiarity of the features they’ve grown to love,”
Mike says.
“With the new InCommand Go displays, Ag Leader can greatly enhance the user experience while maintaining the core things that make InCommand the best display on the market.”
For more information, visit agleader.com.
Precision agriculture technology and digitised workflows are becoming essential tools in the tool kit for rural contractors.
As economic, environmental and regulatory landscapes shift for farmers, it is crucial that their contractors keep pace and offer variable-rate spraying and spreading services as well as manage their operation digitally.
Farmers need to lower input costs, boost yields and meet compliance requirements, so they are adopting self-spreading and precision ag technology in record numbers. Those who rely on groundspreaders or rural contractors expect the same high-tech capabilities from their partners.
Increasingly, farmers are connecting technology across their farms to assign jobs, automate reporting, and manage workflows seamlessly. For contractors, connecting to this ecosys-
tem isn’t just an advantage, it is essential to stay competitive and deliver more value and return on investment for their farmer clients.
Managing these changes may seem daunting, as contractors are juggling multiple clients, products, and jobs. Solutions are available to streamline this connectivity, however.
There are options that allow contractors to connect with multiple farmers on different farms, simplifying job management through tablets and smartphones. They are both easy to use and cost-effective.
Once connected, the benefits expand. Contractors can integrate with systems like MyBallance or Hawkeye to receive job assignments, use digital farm maps to improve accuracy, minimise wastage, and automatically send proof of application back to the farmer's fertiliser supplier.
The true potential, however, emerges with variable rate spreading (or spraying). Here, application jobs from the farmer feed directly into the contractor’s guidance and VRT systems to maximise precision and efficiency for both stakeholders. From simple job management to deeper data analysis, the technology can provide signifi-
cant upside to both farmers and their contractors.
This is the direction of future farming. To stay ahead, the rural services ecosystem must be as connected as the farmers they support. Contractors who invest time and resources in adapting to this evolving environment will be well-positioned to lead in 2025 and beyond.
Topcon Agriculture has announced the release of its new Value Line Steering system, which is designed for farmers using mid-range tractors on small to medium-sized farms.
Autosteering is typically used on larger machinery, and Value Line is a significant step in mak-
ing the technology accessible to a broader range of farmers.
Topcon Agriculture executive vice president and general manager Antonio Marzia says Topcon is committed to the democratization of technology and putting precision agriculture technology in the hands of more farmers
throughout the world.
“With the Value Line, we are opening up opportunities for farmers who have older or smaller machinery and smaller specialty farmers to boost the value of their machinery with autosteering technology that is based on our proven premium steering technology used for decades on larger machines,” Antonio says.
“It is an integrated system designed to seamlessly work with a variety of tractors. It is compliant with ISOBUS-UT functionality to offer universal compatibility and ease of use.
“Our goal is to provide high-quality, reliable, affordable, value-added technology that works across a wide range of applications, machinery and brands. This is in keeping with our philosophy of being a partner to farmers and supporting their independent brand choices.”
Value Line steering is a comprehensive package that includes a Global Navigation Satellite System (GNSS) receiver, electric steering wheel controller, touchscreen console, and Horizon Lite software. It is compatible with front-wheel-steer tractors.
Farmers have the option to add local, satellite or RTK correction services such as Topcon’s Topnet Live for greater precision.
Autosteering gives more efficient use of resources – seed, fertiliser and fuel – which reduces input costs. This improves the farm’s bottom line and contributes to more sustainable
Making irrigation decisions can be stressful and costly, but it doesn’t have to be.
Potential costs in time, money, and yield losses from overwatering and underwatering can be tough to manage. That said, tools are now available that vastly increase farmers’ knowledge of what is actually happening at the soil and plant level, so they can make well-informed agronomic decisions.
CropX is one of these tools. It offers its users data-driven insights to make irrigation decisions with confidence. Users of the CropX system can reduce irrigation water by up to 50 percent while still protecting and even improving the productivity of their fields.
CropX’s agronomic farm management system links sensors in fields and satellite data with Cloud-based advanced agronomic analytics. The system delivers field, weather, and crop
data and recommendations via mobile or desktop app.
The data that CropX soil sensors collect is transformed into helpful visualizations and insights that farmers can use to guide the timing and amount of irrigation, crop protection, and planting and harvest dates. It also acts as a recording repository for on-farm management activities.
In New Zealand, the Dairy Holdings dairy collective covers more than 20,000 hectares. It has used CropX to reduce irrigation use by 30 percent while improving the quality and quantity of their yield.
While the soil sensor is the gold standard for tracking soil moisture in a field, CropX has introduced a first-of-its-kind above-canopy sensor that takes measurements of field-based evapotranspiration (ET) to offer an unprecedented view of crop water usage.
This new ET sensor can be used alongside a soil moisture sensor to gain a complete picture of water use in a field. It can also be an alternative to a soil moisture sensor when rocky soils make an in-ground option challenging. Regional evapotranspiration values have been used by farmers for years to estimate how much and when to irrigate, but the CropX option offers the first measurement that covers a specific field on a daily basis. Specificity like this can reveal microclimate differences and crop stage water uptake differences. It can also provide an early detection method for crop stress.
CropX acquired its evapotranspiration technology when it acquired Tule Technologies, a California-based agricultural technology company that developed and patented the technology. CropX has further refined the technology and developed a version that can be mounted on
a center pivot.
CropX Australasia managing director Eitan Dan says it is exciting to bring evapotranspiration sensing to New Zealand and Australia. “It expands the universe of tools we offer for effectively managing water, the most valuable natural resource we have.”
Additional benefits of the evapotranspiration sensor include the reduction on the reliance on weather stations for ET and field-scale insights that offer a clearer view of field water-use dynamics.
Seasonal ET data can provide insights into how factors like temperature swings and droughts impact water use that can help inform irrigation planning and water budgeting for future seasons.
In New Zealand, CropX is sold through local dealers. To find a local dealer or to become one, contact us at info.nz@cropx. com.
farming practices. The increased accuracy in field operations can also lead to improved crop yields, further enhancing profitability.
Farmers from various agricultural sectors, including commodity crops, specialty crops, and mixed farming systems, can expect significant benefits in their operations when they
adopt autosteering.
“There is tremendous potential for growth in the agriculture industry. Value Line is another step for Topcon in being a preferred partner in this evolving landscape by fostering adoption and effective collaboration both with original equipment manufacturers and the farmer,” Antonio says.
“We are a global company with decades of precision technology experience with engineering, R&D, and manufacturing operations on multiple continents along with a global network of dealers for sales and support.
“Designed with quality in mind, Topcon facilities across the world, such as Germany, Italy, and the United States, are
providing the display consoles, steering wheels, and receivers.”
Value Line steering is now available through Topcon Agriculture’s global network of authorized dealers. For more information about it and Topcon Agriculture’s full range of precision farming technologies, visit the website topconpositioning. com/value-line.
Kuhn offers advanced equipment that prioritises precision, efficiency, and durability. From fertiliser spreaders to baler-wrappers, Kuhn’s innovative machinery meets the diverse needs of farmers and contractors working in demanding environments.
The Axis range of fertiliser spreaders delivers precise applications and capacities from 1000 to 4200 litres to suit different farm sizes and crop types.
Notable models include the Axis 50.2 H-EMC W with spreading widths up to 50m and a load capacity of 4200 kg, and the Axis 40.2 M, with spreading widths up to 42m and a 3200 kg capacity. Both are ISOBUS-capable machines.
Kuhn’s CDA distribution system ensures consistent application by adjusting fertiliser drop points on the fly, regardless of spreading width or product type. Metering outlets are positioned near the disc’s centre to maintain a steady flow and eliminate the 'dose effect,' which can disrupt spreading accuracy
during application rate changes. To protect granules and ensure smooth fertiliser flow, the agitator rotates at a slow 17 rpm, improving product quality.
All Axis models feature the Electronic Mass Control (EMC) system, which monitors and adjusts fertiliser flow independently for each disc every second using torque sensors. This ensures accuracy even on uneven terrain, with no need for manual calibration.
The integration of GPS main-
tains correct application rates across the field. It minimises overlaps and reduces fuel consumption by operating efficiently at lower engine speeds.
Kuhn’s Varispread system allows the spreading width to be adjusted directly from the tractor’s ISOBUS terminal.
With Varispread 8, the fertiliser rate can be progressively reduced across eight sections –four per side.
Varispread Pro uses two SpeedServo electric motors for
rapid, continuous adjustment. These motors enable highspeed adaptation of drop points and application rates in one-metre increments, perfectly tailoring coverage to plot shapes, even at high speeds.
The SpreadSet mobile app helps users identify the right settings for every fertiliser application by factoring in fertiliser type, working width, and speed. These settings can be transferred directly to the machine via WiFi, eliminating manual input
The all-new Continental Farm Tyre range has extra grip to help lower fuel costs and get the job done faster. Then there’s N-Flex resilience for extra damage resistance and a longer lasting, more comfortable ride. All backed by a 10-year manufacturer's warranty.
Technology that’s ahead of its field. So you can stay ahead in yours.
A recent independent trial undertaken by three respected European trade publications echoed what Valtra customers have been saying for years, says Valtra NZ product marketing manager Mark Hamilton-Manns.
“Valtra’s autoguidance capabilities and user interface were found to be the best of all systems tested,” Mark says.
The field study was undertaken in Denmark and evaluated different brands’ autoguidance and automatic headland turning capabilities.
“Seven tractors were assessed, including a Valtra Q285 and six competitors. The Valtra came out on top, scoring a total of 43.5 points compared to 40.1 for the next closest tractor and 33.6 points for the poorest result.”
The judges acknowledged that all brands tested offered good guidance features that make work easier, however, Valtra came out on top thanks to its ease of use and functionality. The judging panel concluded that: “Valtra is the best when it comes to the user interface in general.”
In terms of speed, its system also scored highly. The SmartTouch terminal took only 20 seconds to start up, compared to about 55 seconds for the slowest tractor tested. Simplicity is another area where the machine impressed.
The judges noted that the Valtra Go Mode made everything much simpler and they liked the fact
that the information icon (SmartTouch Help) remained in the top right corner of the display in most menus.
When it comes to headland management and automatic headland turns, the trial results again showed, Valtra offered the best performance because four or even more headlands modes can be individually adjusted.
“Complementing the simplicity of the Smart Touch terminal and guidance package is Valtra’s SmartFarming technology,” says Mark.
Operators benefit from completely automatic headland turns. Together with Auto U-Pilot headland automation and Valtra Guide automated steering, the SmartTurn feature completes field task automation by automatically turning the tractor on the headland.
The operator does not have to touch the steering wheel. This improves precision, saves time and fuel, prevents soil compaction and enables the driver to focus entirely on the job.
Working with SmartTurn begins by defining the field boundary and headland. The turning radius is calibrated according to implement type. The final step is to select between four turning options.
U-turn mode: The tractor turns automatically in the headland into the adjacent undriven wayline. The tractor makes a small U-shaped turn in the headland
according to the maximum turning radius. This requires a relatively large headland.
Part-field mode: The tractor turns automatically in the headland into the third, fourth or further wayline. This requires a smaller headland than U-turns.
K-turn mode: The tractor turns away from the worked area, reverse must be triggered manually. It then follows a straight reverse line and the operator must then trigger forward shuttling manually before the tractor turns toward new line.
Y-Turn mode: The tractor turns towards the worked area, reverse must be triggered manually, following a curved line, shuttling forward must be again triggered manually, and then the tractor turns toward new line.
U-turns and part-field mode are suitable for both mounted and trailed implements.
“Guidance and headland management are pivotal to precision agriculture and now Valtra customers can benefit from Section
and reducing errors. The app can also track the amount of fertiliser remaining in the hopper, ensuring precise loading and preventing waste.
An E-Click control box adds simplicity by removing the need for hydraulic valves. It has two
switches that open and close outlets via electric cylinders. It is available for MDS version C models, enhancing operator ease and precision.
Telimat is a border limiter with a double row of deflectors, preventing excess fertiliser appli-
cations along borders to comply with environmental directives. It is controlled via a double-acting cylinder and flap.
For specialised applications, a spreading control kit for seven rows is available, ideal for row crops like vegetables and straw-
Control 96 with Multiboom feature,” Mark says.
“Previously section control could divide the boom of an ISOBUS-compatible sprayer into 24 or 36 sections, for example. Valtra’s new Section Control 96, by comparison, can divide the boom into up to 96 different sections, while the Multiboom feature makes it possible to simultaneously control up to three different booms.
“On a seed drill, for example, fertiliser can be spread in the first feed system, seed in the next and starter fertiliser or small seed in the third. Depending on the implement, the seed and fertiliser hoppers are often divided between two or more sections.
“The new Section Control 96 with Multiboom can control each of these sections and feeders with centimetre accuracy,” says Mark.
Alternatively, one implement can be in front of the tractor and the other at the rear. As the width of implements grows year by year, ISOBUS management is increasingly required to control them precisely. The more irregular the fields, the greater the benefit.
“Valtra’s section control is very easy to operate from the touchscreen on the SmartTouch armrest. The tractor must have Valtra Guide auto guidance and ISOBUS implement control,” Mark adds.
berries, with adjustable spacing down to 90 cm.
By combining advanced technology with durable construction, Kuhn delivers equipment that helps farmers and contractors work efficiently and profitably.
Discover the KUHN mounted AXIS 50.2 H EMC fertiliser spreader with a capacity of up to 4200 kg.
KUHN offers unique solutions for absolute application accuracy: the EMC (“Electronic Mass Flow Control”) system regulates flow automatically and independently left and right during work.
CONTACT YOUR LOCAL KUHN DEALER TODAY
CNH Industrial has launched new precision farming technology for Case IH and New Holland that put the experience of farmers and contractors at the forefront.
They are also bringing down the cost of using digital farming technology by making data monitoring from CNH machines as well as from other farming operations free and easy to use.
The all-new FieldOps mobile and Internet application from CNH is now available for download from the App Store and GooglePlay.
FieldOps allows fleet owners and managers to monitor all their machine and agronomic data from anywhere they have a Wi-Fi connection.
CNH Australia-NZ head of precision technology Jeremy Duniam says FieldOps fulfills the three main needs farmers have with connectivity and precision tech –ease of use, data transfer and the ability to be used with different machines.
An important feature of FieldOps is the remote display view.
This allows mangers to see the cab’s entire monitor remotely. They can then guide operators to solve problems or operate at peak performance.
With FieldOps, a farmer can monitor crop health, growth stages and field conditions to make informed decisions. Contractors and farmers can track machinery usage, fuel consumption and machine performance.
FieldOps also allows fleet managers to customise their view based on what’s important to them. They can adjust notifica-
tions, alarms and the settings for each machine, and set up preferred settings for different functions.
It consolidates all CNH data and information into one consistent, user-friendly interface across mobile devices and web browsers. This means users can get easier access to their agronomic and operational data.
FieldOps also eliminates the hurdles that occur when navigating in different digital platforms and ultimately it boosts productivity.
CNH has also announced the Connectivity Included policy. This removes subscription fees from Case IH and New Holland technology for qualifying machines built after 1 October, 2024. With Connectivity Included, farmers and contractors can access all the benefits of connectivity without ongoing subscription costs.
This is a completely new approach to connectivity. It makes data accessible by simply making it part of the machine. As
a baseline feature on selected models, it can expand the reach and utility of connected features, and help farmers and contractors improve their productivity and their use of agronomic data.
Jeremy says some CNH customers can activate Connectivity Included for their existing machines by contacting their dealer. They must have compatible telematics modems and a FieldOps account and they will have to pay a one-time fee.
Case IH machine owners can convert to a FieldOps account from an AFS Connect account and New Holland owners can convert to FieldOps from MyPLM.
“By simplifying subscription management and providing continuous access to our technology, farmers and contractors can unlock the benefits of the technology now, and in the resale process.” Jeremy says.
For more information about Case IH precision technology, please visit caseih.com or talk to contact your local dealer.
Precision guidance systems offer the accuracy needed to cut input costs, boost yields, and improve sustainability. But if you are flat out with spreading, silage, balage, seeding and a whole bunch of other tasks, you have probably found that guidance alone doesn’t quite cover it.
The question is: Can this essential technology help you manage the ever-growing demands of day-to-day operations?
Tabula says their team has seen first-hand that managing large-scale farms or contracting businesses is no small feat. They have to juggle clients, coordinate mixed fleets, and manage multiple jobs across different locations.
On top of that, they have to ensure the safety of operators and equipment, which is becoming more challenging as equipment, vehicles and jobs become more complex.
The solution lies in going beyond guidance to think about tools for job management, fleet tracking, communication, and invoicing. All of these can work together to help you run safer, more efficient operations.
Imagine being able to create detailed job plans for your team, complete with guidance instructions, and send them directly to equipment in the field.
Weather playing havoc? No problem. Update those plans in real time, keeping everyone on the same page. Add fleet tracking into the mix, and you’ve got a clear view of where every piece of machinery is, helping you allocate resources effectively and reduce downtime.
Once the job is done, you can easily compile proof of application reports for clients and pass job details through for invoicing. By centralising these tasks, you can avoid burning the midnight
oil to finish job reports or manually create invoices. Automated admin processes mean fewer headaches, fewer errors, and more time to focus on growing your business.
With larger machinery and multiple worksites, safety has to come first. But traditional safety measures might not keep up with the fast pace of today’s operations. Integrated safety tools such as pre-start checks, job plans that highlight hazards and exclusion zones, and even automated on/ off switches for application work offer a better way.
If something goes wrong, operators have a way to signal for urgent support in seconds. Communication tools are just as essential for managing progress and ensuring operator safety.
With real-time updates, you can monitor each team member’s location and track their progress. This improves job efficiency and ensures you know where everyone is in case of an emergency.
Agricultural technology is evolving fast, and any system you invest in needs to grow with
your business. Scalable systems are designed to adapt, with components that can be updated as technology advances.
With improved connectivity like 4G and 5G reaching more rural areas, the potential for precision, tracking, and safety features will only grow.
For contractors, this isn’t just about solving today’s challenges. It’s about setting up for the future, staying ahead of the curve, and embracing tools that will make life easier for years to come.
As the demands on New Zealand’s rural contractors and farmers grow, the tools to manage operations efficiently are evolving to meet the challenge. Centralising key tasks – like job planning, fleet tracking, communication, reporting and invoicing – can help streamline day-to-day work while prioritising safety and flexibility. With technology continuing to advance, the future of farming looks set to combine tradition with innovation, helping operators navigate complexity with greater ease and confidence.
MAIZE AND FODDER BEET PLAY A UNIQUE ROLE IN NEW ZEALAND AGRICULTURE THANKS TO THEIR ABILITY TO PRODUCE HIGH VOLUMES OF DRY MATTER TO MEET FEED DEFICITS DURING WINTER. BOTH CROPS ARE BEST ESTABLISHED WITH PRECISION PLANTERS AND ARE HARVESTED WITH SPECIALIST MACHINES. IN THIS FEATURE WE CHECK OUT THE LATEST MAIZE AND BEET PLANTING AND HARVESTING TECHNOLOGY.
Since its launch 12 years ago, Vaderstad’s Tempo high-speed precision planter has gained a leading position in the planter market. In 2025, the Tempo row unit will be upgraded with Vaderstad's new WSX electronic system with brushless motors and better cabling performance.
Greg Moore is Norwood brands manager for equipment, and he says in addition to the new WSX system a number of other new features improve the accuracy of the Tempo.
Firstly, automatic seed singulation now ensures a precise seed singulation in the seed meter, without the need for manual setting. Each row unit has sensors that continuously monitor seed singulation and then automatically adjust the singulators for the optimum setting.
Farmers and contractors who regularly change crops will appreciate how much automatic singulation saves time and
increases productivity.
Secondly, active hydraulic row unit downforce now ensures precise planting depth, regardless of the soil condition. It adds or releases row unit ground pressure depending on the soil conditions.
On an area of a paddock with lighter soils, the pressure will decrease. Then, if you enter an area with harder soils, the pressure will increase.
Tempos can be equipped with active hydraulic downforce
with feedback and control for the full width of the machine, or with individual active hydraulic downforce for each row unit.
Individual row control can be used to improve tramlining and prepare un-planted tracks for the sprayer. With active hydraulic downforce for each row unit, the planter can relieve pressure and lift individual row units when making the tramlines.
To do this, the active hydraulic downforce works with the Tempo’s dynamic tramlining system. This means the tramlines will be clearly visible to the sprayer
operator before the crop has emerged.
The Tempo’s third new feature is curve compensation, which ensures consistent metering output over the planter’s full width when turning. During a turn, the inner row units temporarily decrease their metering rate, while the outer row units will increase their rate.
Greg says gyro sensors identify when the machine is turning and adjust the metering output of each row unit to always ensure a consistent rate over the full planter width.
Additional options available on Tempo for 2025 include pointed closing wheels, which are recommended when direct seeding or in heavy clay soils. Another option is the Pro-Drain closing wheel attachment, which is mounted outside the closing wheel and creates a weatherproof surface.
Vaderstad has also designed a liquid fertiliser system for its Tempo L planter. The liquid fertiliser system has a 2000-litre plastic tank. The liquid fert can be applied in the seed row via the row units or beside the seed row via fertiliser coulters.
“The system works with a wide
range of liquid fertiliser rates without changing nozzles. It can handle liquid fertiliser doses of 30-200 litres/ha without changing nozzles, at a row spacing of 750 mm and 15 kph driving speed,” Greg says.
Flow sensors constantly monitor the output rate of the liquid fertiliser. With this real-time feedback, the system automatically maintains the selected output rate.
The new Vaderstad Proceed is a single seeding machine that can increase the yield in a range of crops, including wheat, barley, oilseed rape, sugar beet, peas, maize, sunflower, and many more.
Proceed removes the distinction between grain seed drills and precision planters. By merging both technologies into one, it brings the precision of planters to grain crops, but maintains the ability to plant at wider row distances.
At the heart of Proceed is its high-precision row units. Individual ‘pre-consolidation’ wheels consolidate the field to ensure the same conditions for each
seed. The pre-consolidation wheels are individually mounted, using hydraulic downforce to ensure high performance.
The Proceed V 24 detects its angle in two directions and automatically adjusts to maintain precise operation. For lateral adjustment in hilly conditions, the machine monitors the position of the parallel linkages of the outer row units and adjusts downforce to ensure even results.
In the driving direction, it actively senses the angle between its two sets of row units. If there’s a deviation, it adjusts the downforce on the pre-consolidation wheels to keep all row units parallel to the ground.
Each row unit on Proceed is
electrically driven, which allows GPS-controlled individual row shut-off. By eliminating overlaps on headlands and irregular field areas, yield losses and input costs are reduced.
The most important factor for increasing yield is seed depth precision. In a field where tillage has produced uneven consolidation, excessive air may be present in parts of the soil profile.
After seeding, this air escapes, causing the soil to settle, so the actual seed depth may be shallower than intended. Row-by-row pre-consolidation wheels treat each row individually to ensure a well-consolidated profile above every seed, guaranteeing precise seed depth.
Kverneland’s Pudama spot fertiliser system for maize is available in New Zealand for the 2025 planting season. Instead of applying fertiliser in bands during planting, Pudama precisely places a targeted amount of starter fertiliser just beneath the maize seed.
This targeted fertiliser deposit ensures the maize seedling’s roots can better access essential nutrients as the plant grows. Because the fertiliser is not applied in a band, it lowers the amount of starter fertiliser needed, which reduces nitrate and phosphate leaching.
Typically, maize is sown with a fertiliser band around 15-20 mm below the seed depth. Because plants cannot fully absorb all the fertiliser in these bands, the surplus can impact the surrounding ecosystem.
Pudama uses up to 25 percent less starter fertiliser without compromising yield potential. The system works by loading fertiliser at the coulter and propelling it into the soil with an airstream.
A sensor linking the fertiliser coulter and seeding unit ensures the timing of seed and fertiliser placement is synchronised. The frequency with which the valve opens and closes to deliver fertiliser depends on the tractor's speed and the pre-set seed spacing within the furrow.
Pudama can operate at speeds up to 15 kph when paired with Kverneland’s pressurised Optima SX sowing unit.
Kverneland’s Optima F and TFprofi models can be equipped with high-speed, pressurised SX sowing units. SX units offer precise seed singulation and placement at working speeds up to 18 kph.
SX metering units use a pressurised airstream to push seeds into disc holes, rather than a vacuum system. When seeds reach the release point, the airstream propels them directly down the
seed tube into the trench. They land under a large rubber press wheel, which prevents bouncing and ensures great seed-to-soil contact.
Because the SX unit relies on an airstream instead of gravity, seed placement remains consistent, allowing for accurate sowing even at higher speeds.
Kverneland’s HD-II universal vacuum sowing units offer another option for the Optima F
Without predator control, these habitats and the native wildlife that depends on them will continue to decline — even with stock exclusion. Our toolbox will guide you through how to manage pests in these unique spaces.
Claas has once again set a new standard for forage harvesting with the introduction of the V-Flex chopping cylinder, now available as an option for the Jaguar 900 Series forage harvesters.
The V-Flex chopping cylinder advances harvesting productivity, flexibility, and efficiency. It builds on Claas’s expertise in forage harvesting that it has built up over 50 years to give farmers and contractors more precision and user-friendly operation.
Among the improvements Claas has made to its latest Jaguars are faster sharpening and shear bar adjustment. It now takes just one minute to carry out both tasks, which minimises downtime
Claas product business manager Luke Wheeler says reduced setup times, lower fuel consumption, increased throughput, and faster sharpening and shear bar settings prevent delays during harvesting.
The V-Flex chopping cylinder is an optional alternative to the V-Max for 2025 Jaguar 900 and Jaguar 900 Terra Trac models. The V-Flex cylinder supports multiple knife configurations, so operators can adjust chop lengths for different crops and conditions.
The knives are triple-bolted for stability and feature a durable 23 mm anti-wear coating and a 10-degree angle to the shear bar. Together, they provide longer operational intervals and reduced wear. This new design also delivers a quieter and smoother operation, especially at chop lengths over 12 mm.
Available in four configurations – with 20, 24, 28 and 36 knives –the V-Flex cylinder offers settings such as full-knife, half-knife, and one-third knife modes. This gives chop lengths from 3.5 mm up to 53 mm.
and TFprofi models. HD-II sowing units are ideal for planting crops such as fodder beet and other specialist crops.
Featuring open gauge wheels, they follow ground contours closely, and their heavy construction ensures precise depth control, even under challenging conditions. An additional 100 kg
The V-Flex 36 model is a new option. With 36 half-knives, it enables longer cuts to achieve optimal crop flow and chopping quality. It can be configured with 36 knives for full capacity, 18 knives in half mode, or with 12 knives.
These configurations support maize harvesting at lengths up to 30 mm when paired with Multi Crop Cracker (MCC) Classic, MCC Max, and MCC Shredlage. They can deliver smooth crop flow, precise cuts, and reduced processing costs.
The pick-up 300 for Jaguar 800, 900 and 900 Terra Trac models also sees advancements. With improved intake it gives less soil contamination and more consistent throughput.
The auger has been redesigned with four offset central feed paddles for a uniform crop flow, which boosts throughput. The intake now has an extended dust screen that covers the entire working width of the pickup.
This prevents material buildup on key components, such as the feeder housing, cutting cylinder, and front windscreen, and effectively reduces harvest losses.
The screen’s wide-mesh design enables a clear view of crop flow from the cab, and it can be easily swung open for maintenance, Luke says.
The MCC Classic and MCC Max corn crackers now operate with a speed difference of up to 40 percent. MCC Classic offers an optional fine sawtooth profile, ideal for small-seed crops such as sorghum.
MCC Classic, MCC Max and MCC Shredlage corn crackers give efficient processing of kernels, leaves and stalks across various cut lengths with a speed differential that has increased from 30 to 40 percent. A larger maintenance compartment makes it easier to install and remove the corn cracker when switching
between grass and maize.
Model year 2025 Jaguars also have the new Carraro rear axle, which supports a load capacity of 9 tonnes. This axle allows operators to engage four-wheel drive under load, with available wheel spacers of 460 mm for the standard axle and 620 mm for the Power Trac, providing greater track width flexibility. This innovation ensures excellent traction and stability in varying conditions.
Claas has manufactured more than 45,000 Jaguars over the past five decades, and it has established a reputation for productivity, efficiency and reliability. Its commitment to ongoing improvement ensures the Jaguar consistently delivers cost-effective, high-quality chopping.
of pressure per sowing unit can be applied via a spring-loaded system if required.
Kverneland precision planters can also be paired with the F-Drill front fertiliser hopper.
The F-Drill provides flexibility for farmers and contractors, as it is compatible with other Kverneland seed drills, strip tillers, and
even some other brands of drills and planters.
Besides fertiliser, the F-Drill can handle both fine and larger seeds, enabling farmers to seed and fertilise in one pass or to plant seeds alongside companion crops.
Pipes fitted along the side of the cab transport seed or fer-
tiliser to the coulters using an airstream. The compact F-Drill model has a 1600-litre capacity, while the larger version holds 2200 litres, and both can be equipped with the Eldos fully electric ISOBUS metering unit known from and found on both the Udrill and DG seed drills.
Rotary strip till and mechanical strip till offer two distinct approaches to strip-tillage, both of which can improve efficiency, soil health and crop yields.
While both systems minimise soil disruption and optimise field preparation, they are tailored to different farming needs and provide different options based on field conditions, crop types and farming priorities.
FarmChief’s Rotary Strip Till system integrates seamlessly with the front fertiliser tank and Xact Precision Planter. It enables farmers to cultivate, fertilise and plant in a single pass.
This saves time and preserves soil integrity by limiting the number of field passes, which reduces compaction and helps retain moisture. It conserves the soil conservation because only the areas intended for planting are tilled, which leaves the rest of the soil structure undisturbed and prevents erosion.
Its powered blades allow the Rotary Strip Till to handle heavy clay soils that can be difficult to work up or dairy pasture that has recently been sprayed off.
The rotary till applies fertiliser in the strips, directly in front of the tiller, incorporating it into the soil where it is needed most. This targeted fertilisation reduces costs.
With these advantages, Rotary Strip Till is attractive to contractors. They can work efficiently without worrying about previous
crop conditions or waiting for perfect weather.
The FarmChief Rotary Strip Till system is versatile thanks to adjustable subsoiling tines, highspeed tiller blades, and a hydraulic packer roller that can be modified on-the-go to suit changing field conditions. An oil-cooling system ensures consistent performance during extended operation.
When combined with the Xact Precision Planter, it ensures every seed is placed accurately. This promotes healthy crop emergence and high yields.
In contrast, FarmChief’s Mechanical Strip Till offers a simpler, faster approach that is well-suited for large-scale crops like maize. It prioritises speed and efficiency, and allows growers to cover larger areas quickly.
Mechanical Strip Till uses three cutting discs per row to slice through crop residue. Two additional residue management discs ensure an unobstructed seedbed.
Adjustable limitation discs allow operators to match various crop layouts, while multiple rear roller options provide a smooth finish to encourage even emergence.
One of the Mechanical Strip Till’s standout features is its ripper leg, which penetrates the soil down to 250 mm deep to improve aeration and water infiltration. With fertiliser applied in a band behind the ripper leg, root systems benefit from early access to nutrients, supporting vigorous growth.
This system suits growers who can control when, where and
what the implement is working into, and who can utilise strip spraying for better weed management. While it is less effective in recently sprayed grass or challenging conditions, it offers greater flexibility for those who prefer to wait for the best conditions.
Both excel in preparing paddocks for spring fodder beet or maize planting, two of the more commonly planted spring crops. They are reliable options for Kiwi farmers and contractors who want to reduce soil disturbance and maintain soil health during spring cultivation.
Because rotary strip tillage combines multiple steps into one pass, it is ideal for operations where precision and time-saving are crucial, especially with high-value crops that demand exact seed placement and fertilisation.
FarmChief’s Mechanical Strip Till is a more traditional, straightforward approach. It is less complex and has fewer moving parts, which reduces maintenance and improves durability.
It is ideal for operations that cover large areas at high speeds. Its transport-friendly width and relatively light weight add to its practicality, particularly for operations that require frequent relocation.
Farmers who manage different crops and require precise planting and fertilisation may favour the Rotary Strip Till because it carries out multiple tasks in one pass. Conversely, Mechanical Strip Till is ideal for larger-scale crops that require robust soil preparation at speed.
TITAN HERCULANO
HT 5000
To maximise the potential of today’s larger, more powerful forage harvesters, contractors need to have high-capacity silage wagons to work alongside them.
4Ag has the perfect option to meet this need, the Titan Herculano HT 5000, a Hardox tridem axle trailer with a removable silage bin with a capacity of 50m3 (or 38 tonnes).
4Ag product specialist Darren Raikes says the trend in the industry is for contractors to move toward fewer, bigger machines and more skilled operators who can move between them.
“Contractors need support equipment that will let them realise the capacity of their high value capital assets. With choppers, such as the latest Jaguar 960s and 980s, a 25m3 or 30m3 silage trailer is not going to cut it,” Darren says.
“A Herculano trailer HT 5000 on a decent tractor with a decent operator, is a much better option than a truck and trailer. Even though the truck and trailer might
be able to carry 80m3 , the driver needs a Claas 5 license and you have to remove the trailer to empty the truck, which adds time at the stack.
“While you wouldn’t want to put a 15-year-old on a big silage trailer like this, the operator does not need a special license, or COF or vehicle compliance.”
The Herculano HT 5000 has full air brakes and its tridem axle has a steering axle for better manoeuvrability. It also has an automatic greasing system. The operator activates the central-
ised greasing system at the push of a button in the cab.
Darren says another option with the Titan Herculano trailers is advanced weigh scales. They are installed in New Zealand and they are certified to allow contactors to use them to sell forage.
“If they are calibrated annually, you can sell maize or grass silage off them without the need to go over a weighbridge. And if your forage harvester has a certified John Deere or Claas NIR sensor, then you can use both to sell silage.
“This is a game-changer for contractors because they can just invoice off the printout from the scales.”
4Ag collaborates closely with its European manufacturing partners to deliver Kiwi contractors and farmers equipment that is suited to tough New Zealand conditions.
Herculano HT 5000 trailers have the specs needed to stand up to hard work. With its Hardox steel body, it will deliver a long working life and it can easily cart rock, sand, gypsum or oth-
» PTO powered strip tiller with ripping shank » 8-Row folding units operational in NZ! » Fertilizer tank packages available » Suit 200-350Hp
Lemken has announced the arrival of the first Equalizer planter – the Precision CII 8/762N – in New Zealand.
Equalizer is a South African company that produces precision planters, seeders and air carts. Lemken acquired the Equalizer company and has expanded sales of their equipment to Australia, Eastern Europe, North America and now New Zealand.
The innovative machinery that the company Equalizer builds is robust and accurate and it can help contactors and farmers boost crop yields.
It has earned Equalizer a reputation for innovative seeding equipment while Lemken has proven expertise in soil cultivation. Their collaboration promises to deliver world-class machinery that can meet the needs of today’s farmers.
The Equalizer Precision CII 8/762N planter has advanced features that ensure each seed is planted precisely. It has a highstrength steel frame that allows it to stand up to tough field conditions and its user-friendly design ensures easy maintenance.
Models in the Equalizer Precision CII range offer from eight to 24 row units. For precise seed placement, the CII 8/762N comes factory-fitted with Precision Planting’s vDrive metering system.
Even greater planting control can be achieved with the optional DeltaForce row pressure system, which adjusts pressure depending on field conditions. This level of precision can create consistent crop stands, which enables maize growers to achieve optimum yield potential.
A standout feature of the planter is its three-tank hopper system. Two of the tanks have a capacity of 1500 litres and the other carries 1650 litres. They provide flexible options for dry or liquid fertiliser, or even a combination of both.
With this design, contractors and farmers can fine tune their fertilisation strategies, to enhance plant growth from the outset. Each row unit also features a 75-litre seed hopper, ensuring efficient planting operations with minimal downtime for refilling. Pre-emergence spray nozzles can be positioned directly behind the row units.
Lemken Equalizer planters can be configured to plant crops ranging from maize and fodder beet to sunflowers and pumpkins, with adjustable row spacings as tight as 50 cm. This versatility makes it ideal for contractors or farmers who grow a range of different crops.
Transport width for Equalizers with row spacings of 50 and 76 cm is 3.5m. A telescopic axle prevents the planter’s wheels from running within the planted strip to reduce soil compaction.
To maintain planting accura-
er abrasive material as well as silage.
The rear of the trailer is 80 mm wider than the front, and this tapered design gives quick, easy emptying. The HT 5000 also has big 600/65R26.5 wheels, which give a wide footprint for stability and low rolling resistance, which
makes it easier to tow heavy loads or work in damp ground conditions.
The silage bin is held in place by 10 quick-release J hooks. It takes just 45 minutes to an hour to put the bin on or take it off using a telehandler or frontend loader.
Unlike other silage trailers that might have a 14- or 15-tonne ram to empty the bin, the Herculano has a 30-tonne ram. This means it has enough power to easily empty the bin, even if its full of dirt or metal.
There are three trailers in the Titan Herculano range. In addi-
cy in soft or uneven ground, the planter has adjustable trailing gauge wheels that improve flotation. To create an ideal seedbed, row cleaners ensure that debris is cleared ahead of planting.
For ease of maintenance, the frame lifts high enough to allow farmers to service the machine comfortably from a standing position.
Lemken has established a dealer network across New Zealand that can supply the Equalizer range. They plan to introduce additional planters and seed drills in the future.
Contractors and farmers in the Waikato region were the first to experience the Precision CII 8/762N. Demonstrations started there at the end of September, and the planter is now on tour in other maize-growing regions across the North Island.
Lemken says the demonstration campaign will highlight the unique advantages Equalizer planters offer. Interested contractors and farmers can contact Lemken’s area managers or their nearest Brandt dealer to learn more about demonstration opportunities.
tion to the HT 5000, there is the HT 3600 with a capacity of 36m3 and the HM 3100 with a capacity of 31m3 . All are Hardox trailers with removable silage bins.
For more information on 4Ag Herculano trailers, call 0800 424 100 or visit the website 4ag. co.nz.
Amazone is expanding its range of precision seeders with the new trailed Precea 6000TCC, 9000-TCC and 12000-TCC models, in working widths of 6m, 9m, and 12m respectively.
This new Preceas will suit contractors and large-scale farmers. They offer high-performance overpressure singling, large tank capacities, and the new Central Seed Supply seed delivery system. High-precision seed placement ensures optimum crop emergence, even at increased forward speeds of up to 15 kph.
Central Seed Supply carries the seed from the central hopper to the singling units via an air stream. The seed for each row is temporarily stored in a small reception unit.
When this reception unit is full, the air stream automatically cuts off, shutting off further seed supply. Once the fill level decreases, the air stream restarts, conveying seed from the main hopper to the individual rows.
With this intelligent air stream
system, each singling unit is independently supplied with seed, without the need for complex sensor systems or electronic controls.
Precea 9000 and 12000 models feature a central seed hopper that has a capacity of 2000 litres and can accommodate up to two big bags of seed. The Precea 6000-TCC model has an 850-litre central seed supply and 70-litre seed hoppers.
Amazone NZ product manager
Steve Gorman says the 6000TCC encompasses all of the features of the Precea in a more compact version.
For seed singling, Amazone employs its precision PreTeC singling units. They work on an overpressure principle, which means that air pressure presses the seed against the singling disc. The seal rotates along with the singling disc, which reduces power consumption of the electric drives across individual rows.
The SmartControl stripper fingers are remotely controlled automatically using optical sen-
sors. This eliminates misses and doubles.
At the same time, the electrically-driven singling discs adjust according to the forward speed and seeding rate to send the seed into the propulsion channel. When the contact pressure breaks, the seed is shot precisely into the seed furrow, where the catcher roller embeds it securely in the furrow bottom.
Furrow formers ensure precise seed placement, while two carrying rollers and hydraulically-ad-
justable coulter pressure ensure uniform depth control.
Amazone also offers SmartForce automatic coulter pressure regulation, which maintains a constant set contact force. This gives uniform seed placement even in variable soil conditions. With ElectricDrive electric metering, the operator can set the seed rate with the ISOBUS terminal. It can be used to set part-area rate control using GPS and field zone maps. Section control reduces overlaps in wedge-
The Kuhn Maxima 3 precision planters are built to deliver performance and flexibility to meet the diverse needs of contractors and farmers.
With the Maxima 3 system you can configure the planter to suit a variety of crops, soil types and field conditions. This modular approach paired with high-end technology ensures optimal seed placement and fertilisation and that means better crop establishment and efficient use of inputs.
The Maxima 3 system does not compromise on precision. Its seeding units weigh 120 kg and can apply up 180 kg of pressure. They are robust enough to handle challenging field conditions. Whether working on tilled, minimum-till or no-till soils, the Maxima 3 maintains a steady working speed between 5 and 10 kph.
Maxima planters can be specified with either mechanical or electric drive options. Electric drive offers row shut-off and seed population control via GPS, which reduces seed waste and ensures consistency.
The seed distribution system uses an ejector to guide individual seeds smoothly and precisely to their intended position. It has minimal risk of clogging or double-seed placement.
Fertilisation options with the Maxima 3 range can boost crop performance. A fluted metering system ensures fertiliser is distributed uniformly, with rates adjustable from 50 to 700 kg/ ha, depending on the forward speed and crop type.
Kuhn offers a number of different options for fertiliser hoppers
on its Maxima precision planters. The range extends from twin 190-litre hoppers to single 1350-litre units. Different fertiliser applicators are also available. They include a non-stop shoe or disc system.
Maxima planters are available with a single-bar, telescopic chassis or folding frames. Working widths extend up to 9m.
The telescopic chassis allows operators to quickly change row spacings from 45 cm to 80 cm, which makes it easy to switch between crops. You can change row configurations without tools in just 20 minutes.
Folding and telescopic chassis ensure that transport is safe and convenient. All models fold to comply with road regulations. Moving quickly between paddocks reduces downtime.
The trailed version, designed for maize planting, comes with a 1500-litre fertiliser hopper, providing high autonomy and compatibility with lower-powered tractors.
A Maxima 3 planter with electric drive system requires less frequent greasing and wear-related repairs over time. Each planting unit has its own alternator, which eliminates the need to draw electrical power from the tractor. This ensures smooth operation across different speeds, inclines and environmental conditions.
Kuhn offers a number of different rear roller options. V-HD rollers are standard across the Maxima 3 range. They are versatile and perform in a range of conditions.
For more intensive applications, the V-Max rollers offer higher ground pressure, which is ideal for heavy soils and highspeed sowing. Contractors and farmers working in lighter or sandy soils may benefit from Otiflex rollers, which minimise soil disturbance and help retain moisture around the seed.
ISOBUS connectivity is another benefit of Maxima 3 planters. CCI 800 and CCI 1200 ISOBUS
terminals provide intuitive control over all Kuhn machines. These terminals can display different types of information at the same time, during planting.
Operators can streamline work with applications such as PreciSeed, which can guide adjustments of planting density, depth, and fertilisation rates.
Kuhn’s CCI Connect packages allow contractors to monitor and manage operations remotely via a MyKuhn account. They can transfer data through Agrirouter and update software online without hassle. This digital integration ensures the Maxima 3 system remains future-proof, with software updates and remote support readily accessible.
Maxima 3 planters offer precision, adaptability and advanced technology. Whether planting different crops, adjusting row configurations or integrating fertilisation with sowing, the Maxima 3 gives contractors the ability to maximise yields and streamline their operations.
shaped fields and on headlands, and it can set the ideal conditions for mechanical weed control.
The electric metering drive in individual rows maintains evenly-spaced seed placement across the entire working width, even when navigating bends. A yaw sensor calculates the difference between forward speeds on the inside and outside of the bend, which allows CurveControl to
adjust each singling disc’s speed accordingly.
Uniform seed spacing around bends gives all adequate nutrients and promotes uniform crops and even ripening.
Precea-TCC 9000 and 12000 planters have a twin-chamber hopper, which gives a total volume of 6000 litres. Each chamber has its own electric metering unit connected to a distributor head,
enabling standard half-side shutoff.
One hopper can be used for fertiliser, which is placed by the FerTec twin fertiliser coulter. It sets the placement depth in relation to seed depth and automatically adjusts this if the sowing depth changes.
The Precea 9000 and 12000TCC models provide 12 or 16 rows with row widths of 70 cm, 75 cm
or 80 cm, while the Precea 6000TCC offers eight rows on the same spacings.
A telescopic axle on the running gear allows oversized tyres to be positioned between seed rows during field operation. This prevents compaction directly beneath the rows. With wheels fully retracted, the Precea-TCC can be transported on roads with an overall width of 3m.
Wairarapa company Scott’s Ag Contracting is betting that its financial and environmental benefits will give strip tillage a big role to play in New Zealand agriculture going forward.
For that reason it has just bought a second Kiwi-made Precision Cultivation strip tiller, which will be dedicated to fodder beet, other forage crops and close row maize.
Scott’s Ag already had an eight-row Precision Cultivation strip tiller on 750 mm spacings, which it used to prepare ground for maize. Now it has added a 12 row version on 500 mm spacings, which is ideal for fodder beet and swedes.
Jason Scott says Scott’s Ag Contracting provides crop establishment and harvesting services to arable, dairy, and sheep and beef farmers in Wairarapa and Hawke’s Bay. Most years they also grow 100 ha of maize silage on their own and leased land to sell.
Jason says the demand for fodder beet has dropped off after it came in with a hiss and a roar about 10 years ago. With strip tillage, he believes it can become a more popular option for winter feed, however.
“One of the big problems with fodder beet is the damage that the animals do to the winter grazing paddocks. Because you only till a fraction of the paddock with strip till, more of the ground stays firm under grazing,” he says.
“Strip tillage preserves soil structure and moisture retention. It also reduces carbon losses and it can reduce soil erosion. We have clients in Hawke’s Bay who are worried about losing their topsoil through wind erosion. We can now strip till fodder beet and maize for them.
“Some of our customers are sheep farmer who are interested in swedes as a winter crop because it eliminates some of the dietary problems that fodder beet can cause. We believe strip tillage will deliver good tonnages of swedes and protect their ground better.”
Precision Cultivation strip tillers are PTO driven. They use both ripping tines and PTO-powered rotary hoe units to prepare 20-cm wide cultivated bands into which a precision planter can place the seed.
Scott’s Ag runs two Vaderstad precision planters that match the spacings on their two Precision Cultivation strip tillers. The maize planter is on 750 mm spacing and the beet planter is on 500 mm spacing.
Jason says they do separate passes with the strip tiller and the planter.
“We have a front tank that we can run with the strip tiller to put fertiliser precisely in the row where the plants will use it. It means we can prepare a paddock in one pass before planting rather than three or four passes it would take to plough, disc, power harrow and then roll.
“Our aim is to drive efficiencies so that we can keep establishment costs low as we can so that cropping remains an affordable option for farmers.”
They use John Deere Green-
star Autopath GPS, which gives repeatable RTK level accuracy. It records where the strip tiller has gone, so that the planter can come in and line-up exactly with the tilled strips.
Despite its 12-row working width, Jason says the new Precision Cultivation strip tiller does not have a huge power demand. They operate it with a 345-hp John Deere 8R345. Jason says it runs the PTO-powered row units with ease.
“The only issue with the tractor is traction. We have to make sure the ground is dry enough before we use it.
“Some of our clients still like to do traditional cultivation with the plough and discs but as environmental issues come more into play, we think more and more of them will take a closer look at strip till,” Jason concludes.
The latest John Deere S Series combine harvesters have undergone a comprehensive redesign to optimise automation in order to achieve greater efficiency and productivity.
John Deere production systems manager Royce Bell says the significant updates can deliver productivity gains up to 20 percent and fuel reductions of around 10 percent compared to previous models.
The new engines enhance fuel efficiency, a redesigned grain loss sensing system provides more accurate measurements, and advanced automation boosts operator performance.
“S Series combines are proven workhorses and they have since they were introduced in 2012. Now it is even better, and we have updated the cab and exterior styling,” Royce says.
Productivity gains, based on tonnes of crop harvested per hour, can be achieved with anonymous Ops Center data, which compare models with and without Predictive Ground Speed Automation. (Results may vary depending on model, crop, field, and operating conditions.)
At the heart of the new S7 combine Harvesters is either a JD14 13.6-litre engine or the JD9 9-litre engine, which are designed to deliver higher power at lower rpm. Both engines deliver outstanding perfor-
mance in all conditions and have advanced diagnostic capabilities that keep the S7 running smoothly throughout the day.
Royce says that the new engines’ fuel savings will be a much-appreciated advantage for farming and contracting businesses.
The S7 combine introduces a high-efficiency residue management. It has straight knives, a mechanical tailboard drive and the Premium PowerCast tailboard option. This system consistently sizes and spreads fine or extra-fine residue up to 13.7m, but it requires the power used for residue management by up to 15 hp.
An adjustable unloading spout ensures precise grain flow into the bin, and the cross-auger shutoff feature completely empties the unloading system after each tank to reduce weight in the unloading auger and wear on its belts.
John Deere’s new grain loss-sensing system is up to three times more accurate at detecting grain compared to previous models. It shows the grain loss rate on the in-cab display so the operator can make adjustments in real time.
Base S7 models come equipped with advanced technology, including the G5Plus CommandCenter, the Integrated StarFire 7500 receiver, a JDLink modem, and a new corner post display. These additions pave the way for future automation features.
For operators who want to streamline their work, 2025 model S7 and X combines offer three technology packages –Select, Premium and Ultimate.
Options available in the Ultimate package include ground speed automation, which controls combine speed based on inputs such as grain loss, engine load and rotor pressure.
Another option is Harvest Settings Automation which manages rotor speed, fan speed and other clearances. This ensures a consistent, high-quality harvest regardless of operator skill level. Or there is the choice of Predictive Ground Speed Automation, which builds on Ground Speed Automation. It uses forward-looking cameras and satellite imagery to create a predictive field map. This enables the combine to proactively adjust ground speed to maximise throughput even in changing crop conditions.
“These automation packages can maintain peak performance all day long, regardless of variations in crop yield and down crops. Even less experienced operators can maximise productivity at harvest,” Royce says.
For a demonstration of the new S Series or the X Series combine harvester, contact your local John Deere dealer.
Precision and timing are key to successful planting, crop development, and ultimately, what matters most: yield. Horsch brings these principles to life with its Focus TD strip tillage tools and Maestro precision planters.
These machines have cutting-edge technology that can optimise planting efficiency while safeguarding soil health. Their features provides farmers and contractors versatile solutions tailored to modern agricultural demands.
The Horsch Focus TD combines two essential steps, soil loosening and fertiliser placement at depth. The addition of the Maestro planting system ensures precise seed sowing.
At the heart of the TD system is the Horsch TerraGrip tine. In conjunction with a disc coulter, it clears residues, loosens soil, and delivers nutrients. It can work \varying conditions and it gives different fertiliser placement options, including deep soil application or a 50:50 split between the surface and root zone.
This adaptability ensures plants have the nutrients they need to thrive, whether in challenging wet conditions or ideal growing environments. For crops such as maize or cereals, the Focus TD’s coulter system and packer technology deliver uniform seeding and optimal consolidation, which enhances roots’ access to moisture and their ability to develop.
Equipped with Low Draft (LD and LD Plus) points, the tines provide deep soil cultivation with minimal mixing, which is crucial for maintaining soil structure. The tines also minimise clods moving to the soil surface and they bring moisture and nutrients into the germination zone, which supports healthy crop emergence.
These features, combined with optional carbide coating (on the LD plus) for durability in wear-intensive soils, make the Focus TD a good choice for contractors.
Followed by a large-diameter tyre packer, the loosened soil is consolidated to ensure a level surface and even water distribution below the seed horizon. This precise soil preparation sets the
stage for optimal germination and strong root growth.
A rear linkage enables the Focus TD to be fitted with a Maestro precision planter or a TurboDisc double disc coulter toolbar to establish cereals at narrow row spacing.
TurboDiscs optimise crop emergence by maintaining consistent seed depth, even at high operational speeds. The result is a uniform and healthy crop stand, which is crucial for maximising yield.
The Maestro V series of planters is designed to fully take advantage of the narrow planting windows critical for spring crops. Their large bins have the capacity that enables farmers to cover larger areas in less time.
This is particularly valuable in variable field conditions, where the ability to plant at faster
speeds without sacrificing precision ensures crops are established quickly.
The Maestro V excels in precise seed placement. With its Auto Force system, it gives automatic downforce adjustment as soil density changes during planting.
With AutoForce, the Maestro SV adapts seamlessly to changing field conditions and maintains consistent, accurate seed placement. It eliminates shallow placement that risks moisture loss or deep placement that hinders emergence.
The robust row unit design incorporates a parallelogram mechanism to stabilise the double disc opener, maintaining perpendicular engagement for accurate seed furrow creation.
Another standout feature of Maestro V series planters is their innovative weight transfer system. . By evenly distributing the weight of the chassis across the
toolbar, it eliminates pinch rows that can compromise yields in compacted soils. This design supports uniform soil structure and reduces the machine’s overall footprint. It improves manoeuvrability in challenging conditions.
Large tyres create a lighter footprint, which minimises compaction and protects the soil’s structure and health.
The Maestro V series offers numerous models that have industry-leading seed and fertiliser capacities. They reduce downtime so operators can spend more time planting during critical windows.
The addition of features like electric drive meters and ISOBUS implement control enables variable rate planting, curve compensation, and precision farming.
Together, the Focus TD and Maestro SV 8800 redefine planting efficiency and precision.
The eight-row, PTO-powered Oekosem strip tiller is the perfect tool for contractors who want to take maize planting to the next level, says the New Zealand importer, 4AG.
4AG product specialist Darren Raikes says the eight-row Oekosem gives contractors the ability to establish maize (or fodder beet) crops faster, using less fuel while preserving farmers’ soil structure and reducing their environmental impact.
“Most contractors who plant maize also make silage. Because the two overlap, they really want to get through the planting as quickly as possible so they can get onto the grass. In mid-November we worked with a Hawke’s Bay contractor who strip tilled 100 ha of sprayed out annual ryegrass in a week,” Darren says.
“It was typical hot Hawke's Bay weather and the ground was hard but the sprayed out pasture retained good moisture. The contractor has a tank on the front of his strip till tractor so he could apply fert, and he had his planter on another tractor, so he can till the strips and plant on the same day.
“He has one man and one tractor on his strip tiller and another man and tractor on his planter. He can cultivate the ground and fertilise a paddock in one pass using 18-21 litres of diesel/ha. Compare that to the conventional way to prepare maize ground doing three or four passes with a ripper, multi discs and power har-
row burning 15-20 litres of fuel/ ha on each pass.”
Designed and built in Switzerland, Oekosem Power Strip strip tillers use a rotary tilling action to create thoroughly cultivated strips in a range of soils and conditions.
Each tillage unit has a subsoiler shank and multiple rotary hoe blades. They work together to create a deep strip into which maize, beet or other precision-sown crop can be planted.
4Ag imports the full Oekosem strip tiller range, which includes four-row, six-row and eight-row machines.
Darren says PTO-powered Oekosems are designed specifically to strip till in pasture. They are ideal machines for contractors because they can work in grass, no matter when it has been sprayed out.
“A farmer may be able to use a smaller, non-powered strip tiller because they can control all the conditions they work in. They can spray out well before they strip till, for example.
“Contractors need to be able to work in any conditions, often at short notice. The Oekosem can strip till in long or short grass, green or dead grass. It can also work quite well in stony soils.
“Lots of contractors now have eight-row precision planters, and the eight-row Oekosem is the perfect match for them. It is a folding machine and it contours well.
“It can work at 4-7 kph with a 290-350 hp tractor, and with a
fert tank on the front of the tractor, you can put down 300-350 kg/ha while you strip till.”
Oekosem Power Strip is available on 75-cm or 50-cm spacings. The rotary hoe units produce a 33-cm wide tunnel. This width gives plenty of space for soil and even rank, stalky annual grasses to flow through.
Multiple rotary hoe blades run on each side of the ripping shanks. The working depth of the ripping shanks can be adjusted, but they always sit below the depth of the hoe blades.
With this configuration, the shank creates an explosive lifting action that prevents the rotary hoes from creating a pan.
Darren says another important feature of Oekosem strip tiller is the 400 hp gearbox, which has split drives that take the torque to the outer tillage units. This is different to the more common set up where the power is taken out to a side drive gear case and
then distributed to all power units from there.
“The centre four tillage units on the Oekosem sit on a rigid frame and are powered by the central gearbox. Power for the outer units on each side, is split off via cross shafts. This evenly splits the load on the whole transmission and drivetrain, extending the life of all components.”
While it is possible to attach a precision planter to the rear of the Oekosem Power Strip, with a trailing kit for one pass tillage and planting, 4Ag says the best option is to do the two operations in separate passes.
Powered strip tillers work at slower forward speeds than today’s high speed precision planters. Keeping the two operations separate, means both implements are working in the most efficient way, due to the contrast in working speeds. Both operations also have different needs in terms of tractor size and horsepower.
The McHale V6750 variable chamber round baler has been designed with the demands of today’s farmer and contractor in mind.
• High-Intake 2.1m pick-up
• 15 knife heavy-duty chopper unit and feed rotor
• Double drive system with auto greasing
• Net and bale density can be adjusted from the cab through the console
The Fusion 4 Plus is a fully automatic integrated baler wrapper which can apply film or net wrap to the barrel of the bale, delivering optimum bale density.
• Maximum output whilst keeping the machine short and compact at 5.8 metres in length
• 25 knife-chopping unit
• Patented unique bale transfer technique
• ISOBUS ready
VARIO PLUS
The Fusion Vario Plus is a fully automatic integrated baler wrapper that applies film or net wrap to the barrel of the bale, delivering optimum bale density.
• Hay and straw bales from 0.6m to 1.68m
• Haylage or silage bales from 1m to 1.45m to allow for wrapping
Find your local dealer
AS HE HAS BUILT UP HIS BUSINESS OVER THE PAST DECADE, WEST COAST CONTRACTOR MATT KNIGHT HAS RELIED ON POTTINGER GRASS HARVESTING EQUIPMENT.
The Pottinger gear he currently runs includes a loader wagon, triple mower conditioners, rake and tedder.
MJ Knight Contracting is based at Ahaura in the Grey Valley, midway between Greymouth and Reefton. Matt and his team look after a wide variety of customers, including dairy, dry stock and lifestylers. The work is largely in the Grey Valley with the odd client further afield in Hokitika and Murchison.
“We began contracting in 2011. We mainly do fine chop silage and baling plus some cultivation and deep ripping in the spring. I gained my experience in my younger years doing grass work for my parents, who are dairy farmers in the area,” Matt says.
“About three-quarters of our harvesting work is pit silage and the other quarter is balage. During the peak of the season I have four local guys working for me.”
MATT KNIGHT’S POTTINGER 8400 ED TRIPLE MOWER CONDITIONER HAS A 9M CUT AND EXCELLENT SUSPENSION SO IT COVERS THE GROUND QUICKLY.
Along with their contracting business, Matt and his wife Anna also have a 250-ha dry stock farm that carries 600 bulls.
Pottinger harvesting equipment has been part of Matt and Anna’s contracting and farming story since the beginning. When Matt started out, he replaced the family’s old loader wagon with a 40m3 Pottinger Jumbo 6610.
He also had a Pottinger Novacat front-rear mower combination and a Pottinger rake, which have now been upgraded with larger Pottinger equipment, and a Pottinger tedder that is still doing the rounds.
THANKS TO THE TINE CONDITIONERS ON THE POTTINGER 8400 ED, MOWN GRASS WILTS QUICKLY, WHICH IS VITAL ON THE SOUTH ISLAND’S WEST COAST.
“Our business has slowly grown over the years and to keep up with demand we have upgraded with larger machinery. We bought a new Pottinger Top 842C twin-rotor rake in 2023, and this year we bought a new Pottinger 8400 ED triple mower conditioners. We also added a
second loader wagon in 2023.”
Matt says the performance of his first Pottinger mowers made it an easy decision to stick with the brand when he wanted to upgrade to a butterfly mower.
“Our first front mower was a Novacat Alpha Motion 301 and our rear mower was a trailing Novacat 307 with a grouper. Pottinger mowers cut clean, and the Alpha Motion suspension system is really good. With the suspension, they handle uneven ground and the conditioners improve our drying times, giving us the ability to get mowing done in short weather windows.
“I believe our new Pottinger 8400 triple mower is the first one sold in New Zealand. It is a mower conditioner with finger tine conditioners.
“These days, dairy farmers want to cut grass when it is shorter to get better quality. That means crops are lighter so we needed to increase the size of our rows. The 8400 has a 9m cut, which lets us cover the ground quickly and it still floats really well. The tine conditioners on the new mower wilt the grass fast.”
MJ Knight Contracting runs the triple mower with a John Deere 195M, which boosts to 220 hp or a John Deere 170R that boosts to 210 hp. They use John Deere autosteer to avoid misses and overlaps and to make the whole mowing job more efficient.
While the triple mower is new this season, the Pottinger 842C rake has one season under its belt and is performing extremely well. With its 8.4m working width, Matt can use the rake to pull three rows into one, whereas
THE POTTINGER JUMBO CAN CUT SILAGE DOWN TO LENGTHS OF 32 MM, WHICH IS WHAT WEST COAST DAIRY FARMERS WANT.
he could only pull two into one with his old rake.
Among the features of the rake that he likes are the MultiTast jockey wheels, which give good ground tracking.
“The 842 rake makes nice square rows that feed into our loader wagon and combi baler really well. It has really good ground following. It floats up hills and avoids hollows,” he says.
“It also has individual rotor lift. Separate hydraulics go to the left and right rotors, so you can lift only one rotor to avoid water troughs and other obstacles. You can work efficiently in triangular-shaped paddocks by lifting one rotor and then the next.
“It has a very strong main chassis and frame, so it is very sturdy and very well balanced. And with its big wheels on the back, it can work on soft ground.”
His Pottinger Jumbo loader wagon also gets the thumbs up from Matt. He likes the way that the knife bank swings out, which makes it easy to change or sharpen knives.
With a 40m3 capacity, it is a good-sized loader wagon. It has a twin axle with a steering axle, so despite its size, it is easy to manoeuvre and does not scuff pasture paddocks.
“We can vary the loader wagons chop length from no chopping down to 32 mm. A shorter chop length is better for filling up the wagon and milking cows, and for compacting the stack.”
Matt and his team mostly use
their 5.4m Pottinger Hit tedder during the shoulders of the season. During spring and autumn it can be necessary to turn grass over to get it dry if rain is coming or if unexpected rain falls on a mown crop.
“We use the tedder for early balage, and also in summer to speed up hay drying. We run both the rake and tedder on a John Deere 6330.”
The local dealer for Pottinger equipment is Drummond and Etheridge in Greymouth. Matt says he gets good support from them and from the importer, Origin Ag’s South Island sales man-
ager Darryl Chambers.
“Drummond and Etheridge sort out any mechanical issues that we have, and Darryl gives us really good technical support. When we got the new triple mower, he came out and helped us set it up on the tractor. He went through and made adjustments and showed us how to run it in different ways to get the most out of it.
“We definitely plan to stay with Pottinger. Right now I am sorted with our new mower and rake, but we will have to replace one of our loader wagons soon and I will be looking to them when we do,” Matt says.
TO MEET DEMAND AS HIS BUSINESS HAS EXPANDED, MATT KNIGHT HAS BOUGHT BIGGER POTTINGER HAY TOOLS, INCLUDING A TOP 842C TWIN-ROTOR RAKE AND A 8400 ED TRIPLE MOWER.
GREY VALLEY CONTRACTOR MATT KNIGHT SAYS HIS POTTINGER 842 RAKE FLOATS OVER UNEVEN GROUND, AND IT MAKES NICE SQUARE ROWS THAT FEED INTO HIS LOADER WAGON AND COMBI BALER REALLY WELL.
IT IS NOT UNCOMMON TO HEAR FARMERS OR CONTRACTORS SAY THAT BEFORE THEY GOT A TELEHANDLER, THEY COULD NOT IMAGINE WHAT THEY WOULD NEED ONE FOR AND AFTER THEY GOT ONE, THEY COULD NOT IMAGINE HOW THEY EVER GOT ALONG WITHOUT IT.
Two quite different Canterbury agricultural businesses illustrate the point that telehandlers are the true multi-tools of the farming world. Both bought Merlo telehandlers to serve a particular purpose but then went on to use them for so much more.
First we speak with Andrew Darling, who manages his family’s large arable farm south of Timaru. They have run a Merlo P34.7 Plus telehandler for the past 10 years.
Second we speak to Jason Brown, who, along with his brother Hamish, works in CWT, their family’s contracting business. Based in Rolleston, CWT began as a rural transport operation and that is still part of what they do. They have since branched out into an interesting arena – farm machinery assembly, storage and delivery.
In Andrew’s case the Darling
family bought the Merlo P34.7 telehandler primarily to shift grain into and out of bays in a large storage shed. The P34.7 has a max lifting capacity of 3.4 tonnes and a max vertical reach of 7m.
It has the capacity to work the big grain bucket Andrew uses to shift grain and rape seed but still small enough to manoeuvre around in the barn and storage bays.
“We store most of our grain in silos but we also put 2000 tonnes in our storage barn, which has five bays. Truck and trailers dump the grain on the ground and then we use the Merlo to push it up into the bays.
“Our grain bucket can hold two tonnes and the extendable boom makes the job easier. We used to do it with a tractor and front end loader but after we got the Merlo, we sold the loader because we never used it,” Andrew says.
But its main job is just the beginning because the telehandler is useful for so many other jobs around the yard, the farm, and the farm house and garden.
“We use it to clean traps and culverts, and we put a chain or strop on it to lift machinery for repairs or just to move it across the yard. With a man cage we use it to clean gutters and trim trees.
“We also have bale forks so we
CWT ORIGINALLY GOT ITS MERLO TELEHANDLER FOR ITS FEED CARTAGE OPERATION, AND, WHILE IT STILL DOES THAT, IT NOW TAKES ON ALL SORTS OF OTHER JOBS.
THE DARLING FAMILY ORIGINALLY GOT THEIR MERLO P34.7 PLUS TO SHIFT GRAIN IN THEIR STORAGE SHED, BUT NOW IT IS USED VIRTUALLY EVERY DAY TO CARRY OUT ONE TASK OR ANOTHER ON-FARM.
can use it shift straw bales. We mostly use a contractor to do that but it we have to do it ourselves, we can.”
It is also used to heft a halftonne of one-bags of seed or fertiliser to fill seed drills or spreaders. Thanks to its extendable arm they do not need to fold the seed drill up to get close enough to fill it.
Andrew says with its fourwheel steer the Merlo P34.7 is much more manoeuvrable than a tractor, and with crab steer it is easy to get it into the right position to do a job.
The Darlings’ Merlo has been really reliable. It has not had any major mechanical problems, and when it did have one little electrical issue, the local dealer, Power Farming Timaru, sorted it out very quickly.
“In the past 10 years we have used the Merlo nearly every day but it has only done about 2000 hours. It is the ideal machine for so many jobs. You know how handy it is because whenever you want to use it, it is somewhere else on the farm,” Andrew says.
Shane and Leanne Brown started their rural transport company Canterbury Westland Transport to cart stock and feed between Canterbury and the West Coast.
When their sons Jason and Hamish got involved in the business, they kept the part of business that focused on shifting bales but they dropped the stock transport in order to establish an inland transitional facility in Rolleston.
They receive containers of farm and forestry implements from all over the world on behalf of major Canterbury importers. They then assemble and deliver the equipment to customers around Canterbury, the South Island and even the North Island.
Jason says since they have taken on this work they have always had a Merlo telehandler on hand to load and unload bales on farms and do other jobs around their facility. They have had three over that time, replacing them when they reached 3000-5000 hours.
The latest is a new Merlo 50.8, which has a max lifting capacity of 5 tonnes and a max vertical reach of 8m.
“The 50.8 is bigger than the Merlos we had before because, along with the ag contracting work, we wanted a telehandler that we could use to move machinery around the yard when we are processing and assembling it. A lot of it is really heavy,”
Jason says.
Sometimes, CWT brings it to a site away from the yard to shift or assemble a piece of machinery. For example, they used it to relocate a firewood company’s processing equipment from one part of Christchurch to another.
During the busy harvest season a CWT crew is out with the Merlo
and a truck and trailer doing long days shifting bales of balage, hay and straw.
To add to its versatility, CWT ordered their new Merlo 50.8 with a number of additional features.
“We got it with cab tilt, which you can use to get the cab level when you are lifting heavy loads in uneven terrain. We also ordered an attachment for a blade so that we can take it hedge trimming.
“Rear hydraulic remotes are another extra we specified. We can use them to power some of
assembling machines, we can hook them up to the hydraulics to test them.
“We have weigh scales, which are quite handy when we are carting bales. With the scales, our operators have a rough idea of the number of bales they are carting and they can avoid overloading trucks and trailers.”
Jason says he has always received good support for his Merlos from his local dealer, Power Farming Canterbury. The service they provide has been good and whenever there has been a problem they have pounced on
Capacity, capacity, capacity and extreme endurance with the Condor range of sprayers from 5,000-8,000 litres. The most innovative sprayer in the world. Condor offers the most stable spraying with StabiloPlus, every drop hits the right spot and booms available up to 55 m. Full circulation and no rest liquid with GreenFlowPlus. Optimal control and intuitive operation with EcoTronicPlus.
(topographic, soil type or pest maps) combined with boom mounted cameras to reduce chemical usage.
WHEN THE MANAGER OF WATTIE’S CROPPING OPERATIONS IN HAWKE'S BAY DECIDED IT WAS TIME TO REPLACE THE TRAILED BARGAM ELIOS SPRAYER HE HAD BEEN USING FOR MORE THAN A DECADE, HE WAS SO IMPRESSED WITH HOW IT HAD PERFORMED THAT HE ORDERED THE LATEST VERSION OF THE SAME MACHINE.
Each year Wayne McDonald looks after 150200 ha of crops that Wattie’s produces on leased land in Hawke's Bay. He grows beet root, tomatoes and sweet corn in rotation for the process factory.
Wayne says tomatoes and beet root require a variety of herbicides, insecticides and fungicides – first to prepare the ground for planting and then to maintain the health of the crops.
“We spray out and do our own strip tilling and planting. Tomatoes require weekly sprays of fungicides and insecticides, whereas beet root requires more herbicides and fungicides,” he says.
“Our sprayer is a crucial tool for us. Spraying determines the health and productivity of our crops. We cannot leave it to a contractor because our plans can change on the fly depending on the wind and the weather.
“I do all of our spraying myself. When you spray, you get a close look at the crop. You can see any defects and whether the plants need irrigation. I was the only person who ever operated our old Elios, which we had for 13 years.”
The new Bargam Elios sprayer has a 3200-litre tank and 24m boom. It also has a raft of advanced features that were not available on the old sprayer, including section control, full airbag boom, wing lift and ISOBUS.
While the new Elios has variable width axles, Wayne keeps it set on 2m wheel centres. This suits the planting configuration of the tomatoes and beets, which are planted in beds on 500-mm centres.
“I like using a trailed sprayer versus a three-point linkage unit combined with a front tank because it gives us the volume but also makes it easier to switch the tractor to another machine.
THE NEW BARGAM ELIOS HAS AUTOMATIC SECTION CONTROL, SO SECTIONS OF THE BOOM AUTOMATICALLY SHUT OFF TO AVOID OVERLAPS ON HEADLANDS AND IN TAPERED ROWS.
“We opted for a two point hitch with the new Elios. It tows better and it is user-friendly when it comes to taking the sprayer on or off the tractor.
“The air bag on the boom came factory-fitted. It does a great job of opening up the canopy and drawing the chemical into the plants. It is all hydraulically driven and runs with digital controls.”
Wayne operates the big sprayer with a 155hp John Deere 6155R. Both the tractor and sprayer are on narrow tyres.
He says the 6155R has plenty of power to run the Elios, which it does quite efficiently at 1500-1600 rpm. The nozzles are TeeJet 11005s and the tractor can comfortably maintain three bars of pressure while working at 8 kph.
“We have pivot irrigators and the wheel ruts can get quite deep at the end of the season. That can be hard on gear, so we just take our time.”
Another feature on the Elios that Wayne likes is the fresh water flush out system. It runs fresh water through nozzles on the inside of the main tank and then through the boom to completely eliminate the old chemical from the system.
“Its agitation tank is also really good. It
JOHN DEERE’S LEGENDARY 6M HAS BEEN GIVEN A MAJOR UPDATE FOR MY2025 WITH MORE SPEED AND POWER, AND THE 13-MODEL RANGE, FOR THE FIRST TIME, NOW INCLUDES FOUR MODELS ABOVE 200 HP AND A 50 KPH TRANSMISSION.
John Deere production systems manager Stephanie Gersekowski says the update will give customers never-before-seen customisation to create the ideal mid-size utility tractor.
“The new 6M builds on its reputation as the ready-for-anything workhorse of the farm by adding more optionality, so our customers can build the tractor that perfectly matches the unique needs of their operation,” Stephanie says.
“We have taken some of the key features of our larger machines and introduced them to the mid-size tractor market. This answers the calls of those who want extra speed for transport with the new option of 50 kph transmissions.”
The new 6M will be available in five frame sizes with models ranging from 95 hp to 250 hp so they can tackle anything from mowing and baling to feeding livestock.
Intelligent Power Management comes standard in all machines, except for Tier 2 models (6M 140 and 6M 110). IPM gives a 20-hp boost for operations that use rear PTO in high-power applications or transport.
John Deere has taken on customer feedback and given the new 6Ms 50-kph capability with AutoQuad, CommandQuad and AutoPowr IVT transmissions. AutoPowr IVT allows operators to change seamlessly from low creeper speeds to as high as 50 kph during transport. It is now available on all 6M tractors, with the
pumps water around the inside of the tank during filling. It gives us 100 percent mixing of the chemical.
“With the Visio flow meter, we know exactly how much water goes into the tank and how much we have left when we are spraying. We can type in the amount of water we want to use if we are doing a partial tank and it beeps to let us know when it has reached that amount.”
To achieve the accuracy needed to grow beet root and other row crops, Wattie’s cropping operation uses Trimble guidance with an RTK base station to plant, spray and run other implements.
AB lines and other data can be transferred between tractors and implements using the
exception of the 6MH and the Tier 2 models.
The new models have updated styling with a sleek, modern look. The name and numbering conventions have also been aligned with the 6R, 7R, 8R and 9R tractors, which display the series separately from the rated engine horsepower.
Other features of the new 6M models include:
• Sloped hood design for excellent visibility and manoeuvrability.
• Single or dual rear wheels or larger tyres for better traction and power to the ground.
• Optional reversible fan technology quickly cleans radiator screens from the comfort of the cab.
• A corner post display features state-of-
Trimble system, so they all can operate along the same wheel tracks with the same information.
Its ISOBUS connection allows the Elios sprayer to connect with the Trimble system through the tractor.
“By linking with the guidance system, ISOBUS also gives us section control. The boom has nine sections that automatically shut off to avoid overlaps. It reduces our chemical use, saves us time and eliminates over spraying.
“At the headlands, the tapered rows automatically shut off, which reduces damage compared to when you have to guess when to shut each section down manually. It has been a real game changer.”
Wing lift also gives the Elios greater accu-
THE THREE TRANSMISSIONS AVAILABLE ON THE LATEST JOHN DEERE 6M TRACTORS ALL GIVE 50 KPH ROAD SPEEDS.
the-art instrumentation, connectivity, and precision technology.
“The redesigned 6M has everything you know and trust from this dependable all-rounder but with more power, more smarts and additional features to make it a go-to tractor for a diversity of farms including dairy and beef operations,” Stephanie says.
To learn more, talk to your local dealer or visit johndeere.com.au.
racy. When the operator sets the spraying height using the joystick in the tractor cab, it consistently maintains that height over all terrains.
Wayne says another major reason he opted to stick with the Bargam Elios is the support and knowledge he can tap into from the local Croplands dealer, Spray Shop.
“If I ring Greg Deck and his team at Spray Shop, they will answer any questions I have or come out to help me if necessary. There is never an issue getting parts and they have so much experience,” Wayne says.
“When the new Elios arrived, Croplands spent a lot of hours testing it with me, changing things and calibrating it until it was spot on.”
At Trelleborg, we start from the soil up. Our tyres are crafted to maintain the earth’s balance while boosting your productivity. This seamless fusion of performance and sustainability means you can maximise the results with minimal impact. Experience how our innovation transforms into tangible benefits, driving your success and enhancing your work every step of the way.
THE ONLY CRITICISM A QUEENSLAND SUGARCANE GROWER CAN MAKE ABOUT VALTRA IS THEY DO NOT PROMOTE THEMSELVES ENOUGH.
Anthony and Sonya Girgenti grow sugarcane on 340 ha in the Herbert River flood plain in Queensland, 230 km south of Cairns. The Herbert River region has 55,000 ha of sugarcane, which produce about half a million tonnes of raw sugar each year for export around the world.
In 2011 Anthony and Sonya started to purchase their farms from Anthony’s parents. They have since bought more land.
They plant cane between May and October, and a crop is then harvested for the next five years. After that, the paddock goes into grass or pulse crops for 6-12 months before re-planting the following year.
Anthony and Sonya bought their first Valtra tractor, a 320-hp S324 model, in June 2024. There is plenty of broadacre work for it in the sugarcane operation, including discing, ripping and hoeing.
They have 11 tractors now, including a 1964 International, and most of them are still used on a weekly basis. Previously the biggest tractor in the fleet was 230-hp and it is 32 years old.
Buying another tractor (and the first Valtra) was not a casual decision. Anthony did his research by riding with various neighbours in their tractors to see what they liked and what they did not.
A big question he asked was ‘Would you buy another?’ The only Valtra S324 in the area was some 60 km away, but it came out on top in his survey.
Now that he has the Valtra, Anthony cannot
believe they are not better known and promoted in the area.
“They don’t sell themselves enough. They should be pushing their product in Australia, like at major sporting events,” he reckons.
Anthony is a very happy customer because his Valtra ticks all the boxes on his wish list. They include:
Step-less transmission. “It is one of the best features. I can go at the speed I want for the implement to perform at its best, for example, discing at 8.3 kph,” he says.
Simple. It is Tier 2 compliant so he does not need AdBlue. He optioned his S324 without GPS so he can use his third-party Topcon unit. “It was easily connectable and I didn’t have to learn another unit.”
TWO GENERATIONS OF THE GIRGENTI FAMILY (FROM LEFT – FRANCES, SAM, ANTHONY AND SONYA) WITH THE VALTRA S324, WHICH HAS BOOSTED THE EFFICIENCY OF THEIR SUGARCANE FARM.
Front linkage and PTO. “I have a heavier block weight on the front of the Valtra to balance it. It is easy to remove when I don’t need it. With my other tractor I was doing a few front wheel stands with the hoe on.”
Anthony says the front linkage and PTO future-proof the tractor. “We may be able to put tanks on the front linkage for planting. It’s much easier than building a frame.”
The front PTO provides another benefit. The sugarcane industry is now shifting to mulching cane stalk residues. Currently most people have the mulcher on the rear, which means the tractor rides over the cane crop first, but this can damage the paintwork.
“If we put the mulcher on the front, it mulches down the cane stalks to a residue before driving over it and helps keep the cosmetic look of the tractor.”
Suspension. Anthony has a minor back injury and wears a lower back strap. He wanted a tractor with the smoothest ride possible. The Valtra has pneumatic cab suspension, front-axle suspension and Evolution seat suspension.
“The Evolution seat is fantastic. The sus-
SOME OF THE PEOPLE WHO MAKE THE GIRGENTI FAMILY’S SUGARCANE FARM TICK ARE (FROM LEFT) SAM GIRGENTI, ANTHONY GIRGENTI, TIM GIDDINS AND BRENDAN VELLA.
THE GIRGENTI FAMILY’S VALTRA
pension not only works vertically, but longitudinally in both directions. There is no jolting when I work rough ground.”
He says the pneumatic cab is adjustable through the SmartTouch display. “I have it as soft or hard as the job requires.”
Anthony has put in some long days preparing ground for planting. Stints in the cab can last up to 18 hours.
“Fatigue management was great. I wouldn’t have lasted as long without the suspension, the climate control air conditioning and the radio. It is better than I was expecting.”
For someone whose previous main tractor was 30-years-old, the SmartTouch display might have been overwhelming. But it wasn’t.
“It is very user-friendly. I did read the manual, but it wasn’t hard to learn.”
His local dealer, Russo and Vella Machinery, spent a lot of time giving him a full rundown of all controls when they delivered it.
“I don’t expect everything to go perfectly. No tractor is bullet-proof. But they were all over it. It was only a phone call to find out why it was doing this or that. If they couldn’t tell me over the phone, they were there within an hour.
“Russo and Vella played a major part in my decision to buy this tractor. They have three dealerships in the north and are very thorough with servicing. They are always calling to make sure everything is okay.”
Another of the features Anthony rates is the counters built into the SmartTouch display. He has set them up to show when individual implements are working.
“The rotary hoe has three gear boxes that use oil. I set the servicing based on the coun-
A hazard on Anthony and Sonya Girgenti’s farm are crocodiles that live in the surrounding creeks and rivers. They range in size from 1m to 4m.
Anthony is very relaxed about what seems alarming to non-locals. Apparently the tricks to avoid them are not to fish alone and do not get into a routine when approaching rivers.
“They love consistency. That’s how people lose dogs. They drink in the same place and crocs get to know that,” Anthony says.
ter. I have another counter for new blades. I know how many hectares and how many hours those blades have done and it helps me to forecast when to order spare parts.”
The layout of controls is also a plus, as is the ability to change them.
“I have six hydraulic remotes and can assign them to any switch on the arm controls. I have set up a profile for each implement on the screen and I set up all the switches to how I like to use them.”
Working at night is a reality for many farmers and contractors. Valtra’s LED package was extensive and adaptable.
“The lights are really good. We could angle them to suit our environment and our implements. It made it easy for us,” Anthony says.
QuickSteer is another handy feature. Anthony adjusts the steering sensitivity on a headland so at low speeds he can do a fast turn with 1.5 to 2 turns of the wheel, rather than the usual 3.5 to 4 turns.
The six-cylinder AGCO engine is 8.4-litres
Receive digital job requests & streamline job management
Automate proof of application returns
Accurate variable rate control
Connect to leading guidance systems with ease or utilise our cost-effective app
Automated reporting for self-spreading and self-spraying
Cost-effective upgrade options for 3G roll-over
Connected to MyBallance, Hawkeye www.precisionfarming.co.nz
and very fuel efficient. Anthony says some of that efficiency is thanks to the twin-turbo, which gives better torque at lower revs.
“The tractor is usually on auto at between 1270 and 1500 revs to pull non-PTO implements. There is plenty of power.”
When running the rotary hoe on loamy soils the Valtra S324 uses about 26 litres/hour and around 32 litres/ hour on heavy clays. This compares favourably with the previous tractor which used 40-litres/hour.
Anthony says his new Valtra also had to be affordable. It was priced reasonably well compared to other brands. Also it came with an extended warranty out to four years or 4000 hours, and finance at a low rate over five years.
He has taken lots of his neighbours for a ride in his new tractor and is doing his part to spread the love for Valtra.
“Around our district the best form of advertising is word of mouth. I am very happy with the purchase.”
Start for as little as $25/month
NZ Rural Contractor is available free of charge to readers who qualify under the publisher’s criteria and who supply proof of occupation (printed letterhead, business card, invoice etc) and to others via subscription and payment of the $68.00 inc GST annual NZ Subscription. Australian Subscription $130, Rest of World $270.
If you are not a registered reader, but would like to receive a regular bi-monthly copy, fill in the details of your contracting or farming business below.
Subscription criteria for owners/sharefarmers:
Dairy milk over 600 cows
Sheep & Beef 12,000+ stock units
Cropping over 250 ha in arable
Main contracting services offered:
Total farm Ha.: No. of sheep: No. of dairy cows: No. of beef cattle: Area in arable crop:
Equipment operated Make, Year, Model
To subscribe to NZ Rural Contractor & Large Scale farmer, please complete the credit card form below: $68.00 (NZ), $130 (Australia), $270 (Rest of World).
Name:
Company:
Address:
Email:
Rapid No.
Phone: Post Code:
Please sign here if you wish to receive a regular copy of this publication and send the form to AgriMedia Ltd, P.O. Box 37151, Halswell, Christchurch 8245. Freepost No. 114059.
Sign: Date:
Credit Card: Mastercard Visa
Card Number:
Name on Card:
Expiry Date: / CSC:
Signature:
If you have moved, please write clearly your name and new address above and your old address (including post code) below.
Name:
Company:
Address:
Email: Rapid No.
Phone: Post Code:
WHEN CANTERBURY FARMER CRAIG CLUCAS WAS LOOKING FOR A NEW REAR MOWER, A MATE SUGGESTED HE CONSIDER GETTING A POTTINGER.
Craig purchased a Pottinger NovaCat 442 rear mounted disc mower, with a 4.3m cutting width, six years ago and has not looked back since. He went for a large 10-disc mower for cutting grass seed and grass silage.
“We used to do it with a sixdisc mower, but we wanted to go wider without going to a front and rear mower,” Craig says.
“I am very happy with it. I like the width it cuts and it has proven to be value for money. I would certainly buy another one and would definitely recommend it to other growers.”
Craig has added top hats in the middle of his NovaCat plus a full set of swath wheels. When harvesting grass seed, this creates two even rows that the tractor can straddle. They dry more quickly and are easy to pick up with the header front.
A unique feature of NovaCat mowers is the cutting direction of the two inner and outer discs, which gives a significant advantage over other mowers. They both turn inward, so they don’t fight with the disc beside them.
This means they leave a nice tidy swath with limited clumping.
The Clucas family has been farming Foxdale Farm at Lismore in Mid Canterbury since the 1930s. Craig says the family is passionate about the farm.
He is the fourth generation to manage the 430-ha operation which is mainly arable, with a bit of stock, including store lambs, ewes and cows for grazing.
Around 400 ha are set aside for crops on a rotation. They grow ryegrass seed, cereals, other small seeds, maize, kale and peas.
“We turn ground over all the time, so we need reliable machinery. The Pottinger NovaCat 442 gives us control over when we cut paddocks. Timing
WITH HIS NOVACAT 442’S 4.3M CUTTING WIDTH AND UNIQUE MOWING ACTION, CRAIG CLUCAS CAN HARVEST RYEGRASS WITHOUT USING A CONTRACTOR OR SELFPROPELLED MOWER.
CRAIG CLUCAS HAS ADDED TOP HATS AND A FULL SET OF SWATH WHEELS TO HIS POTTINGER NOVACAT 442 SO HE CAN EFFICIENTLY MOW AND WINDROW WHEN HARVESTING RYEGRASS SEED.
is crucial and can have a huge bearing on yield. By having our own mower, we don’t have to rely on a contractor,” Craig says.
They can run the mower with their 120-hp John Deere 6120M tractor, or alternatively they hook it onto their 175-hp John Deere 6175 with skinny tyres to mow grass seed.
In large paddocks, the mower can cruise along at 15 kph and cut about 5 ha an hour doing silage.
“In grass seed we drive at 10 kph and cut 3.5 ha per hour. We go through up to 25 litres of fuel per hour when cutting grass seed because it is quite thick, but when we do silage we use less fuel.”
With its hydraulic centre pivot mounting, the cutter bar is evenly supported over the entire
cutting width which gives close ground tracking.
Its large cutting width means Craig is able to get through mowing jobs in half the time.
“I get up at 3:00 a.m. when it is cool and dewy and do about 20 ha. It is done before 9:00 a.m., when it is getting too warm. When we had a smaller mower, we did two shifts through the
night. Now we only need one operator.
“It takes less time at a difficult part of the season. We need to make the most of our time at that time of year, and having the bigger mower makes a difference.”
The NovaCat 442 is such a reliable mower, Craig has had no breakdowns.
“We just change the oil every
second year and we replace the blades. It is just basic wear and tear.”
Craig bought the mower from Drummond & Etheridge in Ashburton. He says they have been fantastic to deal with. He has had good service from Pottinger sales specialist Graham Booth, although the NovaCat has never given him any trouble.
IMPROVING EFFICIENCY TO MAKE FARM WORK AND LIFE
A LITTLE EASIER IS AN AIM OF MANY DAIRY FARMERS. FOR MICHAEL AND SANDY CLARK, THIS HAS MEANT REDUCING TO ONCE-A-DAY MILKING AND INVESTING IN A HIGH-TECH FERTILISER SPREADER.
Michael and Sandy run a small, 42-ha dairy farm near Kaponga, Taranaki, where they milk 92 Friesian and Friesian cross cows. They also run a contracting business – MEC Contracting, which bales hay and silage, sows grass and turnips, mulches hedges, and spreads fertiliser.
Sandy says they run the herd at less than a cow per acre and average 450 kilograms of milk solids per head each season, before the cows dry-off from mid-May.
Rather than use maize silage and palm kernel, the Clarks have simplified and mainly grow their own feed. “We only buyin molasses in the spring when
we are calving down for four months,” Sandy says.
They switched from two to one daily milking in recent years to free-up time for their contracting business. Sandy says it is the best thing they have ever done.
Another major step they have made is upgrading to an AgriSpread AS65 trailed spreader. It has been a boon for the business.
Agri-Spread spreaders give hydraulic control of the spinners and drop point adjustment. They
also have load cells to ensure accurate spreading right across the working width.
Convenience is another plus with Agri-Spread spreaders. They are compatible with most ISOBUS and GPS systems so it is easy to monitor and control spread rates from the cab of the tractor. They come ready for variable rate applications, but there is not much demand for this around Kaponga at this stage.
Sandy says the Agri-Spread’s accuracy has helped them meet more stringent proof of placement requirements.
“Our nitrogen applications come under the Taranaki Regional Council N Cap, which indicates the highest rates that can be used. Growers send spread requests to their fertiliser company and that then comes through to us with a GPSmapped application area and the rate to be applied.
“The spreader can spread out to 30m, including through fence lines from paddock to paddock, which is all mapped. It saves us a lot of time.
“You set up the application per hectare on the monitor and the machine just does it. With the load cells, you can continuously check what you have done and
TARANAKI FARMERCONTRACTORS MICHAEL AND SANDY CLARK SAY THEIR AGRI-SPREAD AS65 IS VERY ACCURATE AND HAS DELIVERED A GREAT RETURN-ON-INVESTMENT.
what’s left in the spinners and you know that it is doing it. It is straight-forward once you get your head around the computer.
“We also have section control, which turns off spinners especially in headlands and when we have thin pieces to complete in the middle. It is very accurate. If you end up with a cup full in the spinner, then it didn’t run out of the machine.”
She and Michael are impressed with the huge flotation tyres on the AS65 Agri-Spread. They can spread in wet conditions and not leave a mark in a paddock.
Thanks to the engineering skills of Sandy’s son, Brad, the Clarks added an extension to the top of their spreader bin.
The addition of the specially-designed ‘hungry sides’ increased its capacity from 5 tonnes to 7 tonnes. It can carry 8 tonnes of lime, which only requires a change of the spinners to apply.
Lime is applied at 1-2 tonnes/ha at a narrower spreading width, while nitrogen is applied at 50-100 kg/ha. Muriate of potash goes on at 120-150 kg/ha and super potash blends at 250-500 kg/ha.
So far, they have completed 36,500 ha of spreading with their AS65 Agri-Spread and they have applied 8100 tonnes of products. They have not encountered any major problems.
Sandy says it has given them one of the best returns-on-investment of any machine they have operated.
EUROPEAN MOWER MANUFACTURER SAMASZ AND THEIR NEW ZEALAND DISTRIBUTOR FARMSHOP HAVE SET AN AMBITIOUS GOAL TO BE THE NEW ZEALAND MARKET LEADER IN HAY MOWERS BY 2027.
It takes many factors to excel in the farm machinery sector, and today having ISOBUS connectivity to improve mower performance is vital.
Samasz has introduced ISOBUS in their flagship mowers, making them more convenient for large contractors working in challenging conditions. Samasz likens it to looking after your health. You wouldn’t side-step a specialist if you needed one, and when it comes to mowing, a specialist working with advanced technology can protect farmers’ bottom lines.
ISOBUS is the communication protocol that allows tractors and agricultural implements to ‘speak’ a common language. With ISOBUS compatibility, Samasz mowers have smoother integration and communication with the tractor, enhancing operational efficiency and control.
Samasz 911 and 941 double rear mowers are the two models
with ISOBUS. Thanks to their large working width, they are ideal for large farmers and contractors who need to cut large areas quickly and efficiently.
The Samasz KDD 911 STH ISOBUS rear mower combination is AEF-certified, which ensures it complies with ISOBUS standards. This makes it easy for farmers to connect them to different tractors and use them seamlessly.
An additional benefit Samasz offers (at no additional cost) with its ISOBUS rear mowers is that it controls the front mower as well as the rear mowers. Some other mower manufacturers charge extra for this.
The Samasz KDD 911 STH rear-mounted mowers deliver comfort, efficiency and reliability. With ISOBUS integration, operators can control all functions directly from the tractor's control panel. This means they can set mowing height, speed, and swath width on a single screen.
This connectivity provides a streamlined and user-friendly experience, so contractors can focus on their work without juggling multiple controls or leaving their seat. It is the ultimate in ease and control.
KDD 911 STH mowers also have innovative flail conditioners that speed up drying and can elimi-
nate additional tedding.
They can be equipped with one, two or three swath rollers and conveyor belts, so it can be adapted to different work conditions. Their adaptable configurations help increase efficiency by streamlining material handling and reducing mowing times.
By simplifying control through ISOBUS, operators can focus more on navigation and less on handling multiple interfaces. It also supports precision adjustments to limit operator error, which is especially important in challenging paddock conditions.
Samasz has designed the KDD 911 STH to deliver cleaner fodder and a long working life. The geometry of the blades, the knife holder and the pressure relief system all work together to provide faster, cleaner cuts while protecting the turf and minimising wear.
Pressure monitoring and automatic adjustments ensure smooth operation even at higher speeds, ultimately extending the life of mower parts.
FarmShop mechanic, Scott Teal, says the Samasz KDD 911
SAMASZ NOW OFFERS ISOBUS ON ITS 911 AND 941 DOUBLE MOWERS SO THEY CAN BE RUN THROUGH ANY TRACTOR’S ISOBUS MONITOR.
STH stands out for its build quality.
“With their quick-change blade modules, downtime is reduced. This is ideal for contractors on tight schedules. Now ISOBUS control from the cab will make it a reliable choice for demanding conditions. I am looking forward to seeing it in action.”
Backed by a two-year warranty and Samasz’s 40 years of engineering expertise, the KDD 911 STH is a durable, high-performance addition to any farm operation.
FarmShop currently provides 0% finance over three years. Plus, anyone who buys a set of Samasz groupers will go in the draw to win a Can-Am Defender valued at $31,500.
• Innovative QuattroLink racecar suspension concept
• Dual adjustment of conditioner hood - both front and rear end can be adjusted
• ISOBUS control with intuitive joystick or terminal control
• Flexible suspension – 700mm movements, 400mm upwards and 300mm downwards
• Fast ground adaption with center suspension
• NonStop BreakBack to protect the mower
• Vertical transport position for good
weight distribution
• Easy and convenient vertical parking stand
• 1000RPM PTO gearbox
• High-performance maintenancefree gearbox
• Excellent manoeuvrability with steered wheels for tight turns of up to 80°
• TerraLink Quattro – excellent ground adaptation
• Comes standard with individual rotor lift
• Pro-line duo rake tines
CLAAS DISCO mowers are highly sought after for their efficiency and durability. Get your hands on a CLAAS DISCO 24, 28, 32, 320, 360, 2800, 3200, 3600, 4000 or 4400 model mower courtesy of the sharpest deal we’ve ever had. Purchase your DISCO mower at your local CLAAS Harvest Centre today and you won’t have to pay till August 2025*. Plus you’ll receive a FREE* accessory pack containing additional wear skids and 50 spare knives valued up to $1184 plus GST, and a two year warranty (double the normal warranty). This is an unbeatable deal so hurry now, offer ends 28 February 2025.