
FEATURE
What’s new in hay and silage making equipment

Contractor’s lifelong journey with Case IH and New Holland EQUIPMENT
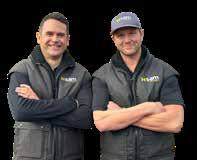
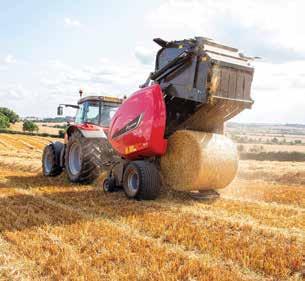
What’s new in hay and silage making equipment
Contractor’s lifelong journey with Case IH and New Holland EQUIPMENT
Take your planter to the next level of accuracy and performance with SeedCommand® precision technology from Ag Leader. SureSpeed® metering ensures perfect singulation and placement at operating speeds from 2 km/h to 19 km/h! SureForce® hydraulic downforce maintains consistent planting depth in all operating conditions. SureDrive® electric drives reduce overlap and wastage. SureStop® electric clutches provide instantaneous row and section control. Contact your local Ag Leader dealer and find out how SeedCommand can turn your existing planter into a high-speed precision planter for a fraction of the cost of a new implement.
04 36 29
02 From The Editor: What’s in those genes?
INDUSTRY NEWS
03 Award recognises young spray contractors
04 Don’t let your guard down against velvetleaf
06 Gifted tractors rays of sunshine after cyclone
08 Quality built into Kverneland balers’ DNA
10 TAMA forum chance to eye the big picture
12 Fuso Canters keep improving to stay ahead of the pack
13 Contractor takes iron fist to slugs
14 Badly designed roads a talking point at RCNZ conference
15 Industry ties, good communication vital for Hanz On Jobs’ success
17 Norwood offers broad range of Landini tractors
18 Proud of its past, Landini eyes the future
22 Bomb-proof Australian spreaders reach New Zealand shores
23 Fatigue still killing rural people
24 Government gives big tick to Agrecovery recycling scheme
TECHNOLOGY
26 Many benefits of humates
27 Electric Mercedes-Benz truck now on NZ roads
28 ‘Hybrid’ PneuTrac enhances traction, safety and comfort
29 Tractor Implement Management – Rise of the (Friendly) Machines
30 Technology key to finding efficiencies for May Brothers Contracting
92 Kverneland baler meets contractor’s high standards 70
PROFILES
32 Expanding contractor keeps hands-on approach
38 Two generations of earthmoving expertise
42 Smart decisions, good friends help young contractor grow
46 Across The Ditch: Getting the balance right
FEATURES
52 What’s new in hay and silage making equipment
EQUIPMENT
80 Contractor’s lifelong journey with Case IH and New Holland
82 Beefy JCB 457S keeps pace with high-output forage harvester
83 Unique strip tiller at work near you
84 Agri-Spread gives contractor more capacity, more options
86 Allen unveils new triple disc drill
88 New Holland FR 780’s reliable performance earns contractor’s respect
90 Contractor reaches new heights with Bale Baron
PAUL TITUS, EDITOR
APPARENTLY NEW ZEALANDERS’ ATTITUDES TOWARDS GENETIC TECHNOLOGY IN AGRICULTURE ARE CHANGING AND MORE PEOPLE ARE OPEN TO THE IDEA.
According to the consultancy group Primary Purpose, depending on how the question is put to people, the public is not opposed to the idea.
Respondents to Primary Purpose’s survey of 1029 Kiwis were evenly divided. That is, 34 percent support genetic technology, 31 percent oppose it, and 34 percent are unsure.
More people are willing to consider using gene editing on a case-by-case basis. More are also willing to consider it when given more details about how the technology could be used.
For example, in scenarios such as using the technology to develop plants that are more resistant to pest or drought, or have more nutritional value – up to 69 percent of respondents are in favour and 9-13 percent are opposed.
All of this was in my mind when I read a recent article in the Guardian about an amazing collection of wheat varieties that was put together about a century ago. After WWI English plant scientist Arthur Watkins collected 827 different types of wheat from all around the world.
Recently scientists from China and the UK completed DNA profiles of all of them. This was no easy task since the wheat genome is made up of 17 billion units of DNA (versus 3 billion in the human genome).
Wheat grown around the world today only has about 40 percent of the gene combinations found in the Watkins collection. With the genetic maps of all the other varieties, it will be possible to add new traits to the commercial gene pool. Studies are already under way to breed varieties that will grow in salty soils or with less
nitrogen fertiliser.
On that hopeful note, welcome to our latest edition. We have had some changes around Agrimedia, the company that publishes this magazine. For one thing, the magazine is now online. On the Agrimedia website select this publication and you will find a Read Online tab.
Also, our long-serving advertising manager Paula Forde has left and she has been replaced by Michael Lightborne. Paula is still available on her old phone number if anyone wishes to contact her.
We still have the usual lame jokes though. Here’s the latest:
Two Aussie mates, Trev and Bazza, were huge cricket fans. They attended every game they could and spent hours discussing the sport. During the winter months, they analysed results from games around the world.
They lived and breathed cricket. They even agreed that whoever died first would come back and tell the other if they play in heaven.
One night, Trev passed away in his sleep. A few mornings later, Bazza awoke to the sound of Trev’s voice from beyond.
“Trev is that you?” Bazza asked.
"Of course, it's me,” Trev replied.
"This is unbelievable!” Bazza exclaimed. "So tell me, is there cricket in heaven?”
"Well, I have some good news and some bad news.”
"Tell me the good news first,” Bazza said.
"Well, the good news is that there is cricket in heaven.”
"That’s great! So what could possibly be the bad news?”
"You're bowling tomorrow night.”
PO Box 36753
Merivale, Christchurch 8146 ph 03 329 6555 www.agrimedia.co.nz
Publishers of Rural Contractor & Large Scale Farmer, AgriBusiness, AgriVet, NZ Cropping, Australian AG Contractor & Large Scale Farmer, NZ Novachem Agrichemical Manual.
© RURAL CONTRACTOR AND LARGE SCALE FARMER - No part of this publication may be reproduced in any form without the prior written permission of the publisher. Opinions expressed in this publication are not necessarily that of the publisher and suggest independent advice be sought before acting on information or suggestions contained herein.
CONTRIBUTIONS - Editorial and photographic contributions are welcomed and should be sent directly to AgriMedia Ltd. Editing of submissions is at the sole discretion of the editor and will accept no responsibility for unsolicited material.
EDITOR
Paul Titus
87 Stanbury Avenue, Christchurch mob 021 655 092
email titus@agrimedia.co.nz
ADVERTISING MANAGER
Michael Lightbourne mob 021 403 853
email michael@agrimedia.co.nz
CIRCULATION
email admin@agrimedia.co.nz
PRODUCTION, LAYOUT & DESIGN
Hannah Kincaid email art@agrimedia.co.nz
CONTRIBUTORS
Joanna Ibell, Brendon Burns, Mark Hamilton-Manns
Printed by Blueprint Ltd
A YOUNG WAIKATO BOOM SPRAY OPERATOR AND MANAGER HAS TAKEN OUT THE INAUGURAL NUFARM RCNZ AGRICHEMICAL APPLICATOR OF THE YEAR AWARD.
Harri Moss, who is operations manager for Cambridge-based spray contractor Spraylink, was announced as the winner at the awards dinner at the Rural Contractors NZ conference in June.
The runner-up was Todd Ealam who works for Methven-based spraying business Molloy Agriculture.
Nufarm national product manager Matt Strahan announced the winners. Matt says there were a number of good entries and it was great to have both a North Island and South Island finalist.
“The award recognises individuals who demonstrate excellence in agrichemical application and innovation. It highlights those leaders in the sector who are investing in the next generation coming through as demand for the services of agrichemical contractors grows,” Matt says.
“They and their staff are performing at high levels on delivering crop protection solutions and ensuring these are applied sustainability.”
Harri won a trophy and a $5000 fund to support his education and training related to the crop protection industry.
To be eligible for the award, entrants need up to five years’ experience in the industry and to either hold or be working toward a recognised agrichemical qualification. Their employer is required to be a member of Rural Contractors NZ and to hold a current Registered Chemical
Applicator qualification.
Harri grew up on a family dairy farm near Matamata and did a Diploma in Agriculture at Lincoln University before driving harvest machinery in Western Australia and South Canterbury. When Covid hit, Spraylink owner and family friend Michael Butler offered him a job.
After Harri drove spray trucks for Spraylink he was offered the role of operations manager, supervising five drivers.
“I am pretty keen to stick in the
NUFARM’S MATT STRAHAN PRESENTS HARRI MOSS WITH THE AGRICHEMICAL APPLICATOR OF THE YEAR AWARD.
spraying industry. There is a lot of variety and opportunity,” he says.
RCNZ CEO Andrew Olsen says the awards reflected the highest level of expertise, compliance and innovation and Harri and Todd were worthy inaugural winners.
The all-new Continental Farm Tyre range has extra grip to help lower fuel costs and get the job done faster. Then there’s N-Flex resilience for extra damage resistance and a longer lasting, more comfortable ride. All backed by a 10-year manufacturer's warranty.
Technology that’s ahead of its field. So you can stay ahead in yours.
275 897
FARMERS NEED TO TREAT THEIR FARM GATE AS A BORDER OR RISK THE ARRIVAL OF DIFFICULT-TO-ELIMINATE WEEDS SUCH AS VELVETLEAF, SAYS NORTH ISLAND VELVETLEAF COORDINATOR SALLY LINTON.
Sally is concerned that velvetleaf ( Abutilon theophrasti ) has fallen off many growers’ radars. That is because there has been a lot of hard work to get it under control and there have been very few new incursions in recent years.
She says the weed is still a risk because its seeds remain viable for 50 years.
“It only takes one inadvertent error for a velvetleaf seed to turn up on a property. One plant can drop 30,000 seeds, so you do the math on what can happen by year two if that first plant is not found.”
Velvetleaf was found on two new properties in Waikato in April. They are concerning because field staff have not been able to find the source property.
“The worst-case scenario is there is velvetleaf on other properties that we do not know about,” Sally says. “It is an annual weed so we will have to wait until spring and the new season before continuing our tracing efforts.”
Velvetleaf is a tall, large-leafed, highly competitive weed that is difficult to control because of its progressive emergence over summer.
Tracing has found machinery and infested maize silage to be the most common cause of its spread. This shows the need for farmers to be vigilant and for contractors to keep up rigorous machinery hygiene protocols.
As a declared pest, velvetleaf plants and seed must be removed and disposed of. It is illegal to move them off a property.
“This is not a big deal if farmers are growing maize silage to feed to stock on their farm because there are pre- and post- emergent sprays that do a good job of keeping it under control, if you get the rates and timing right.
“If you are selling maize under contract for silage or grain then you have a big problem, however. It is your responsibility to confirm that there is not one velvetleaf seed in that crop before it is moved off.”
Sally believes one of the recently-infested farms is returning the property from maize to pasture because they do not want to take a risk of spreading it.
The first initial velvetleaf outbreak associated with maize in Auckland and Waikato, occurred more than 15 years ago. It involved about 80 properties.
The problem escalated in 2015-2016 with an incursion of contaminated fodder beet seed lines imported from overseas. They were sown on hundreds of properties around
NORTH ISLAND VELVETLEAF CO-ORDINATOR SALLY LINTON SAYS FARMERS SHOULD INSPECT THEIR CROPS AND MAKE SURE CONTRACTORS AND ANYONE ELSE VISITING THEIR PROPERTY IS CLEAN.
New Zealand, but predominantly in Canterbury, Otago and Southland.
South Island velvetleaf co-ordinator and FAR biosecurity officer Ash Mills says farmers should carry out routine surveillance. This is especially important when paddocks are cultivated, as seeds can lie dormant in the soil and then germinate years later.
In 2023, nine velvetleaf plants were found in a Mid Canterbury paddock which was associated with the earlier fodder beet incursion.
The 2015-16 incursion led to a three-year project by FAR and AgResearch to find management options to control velvetleaf. They include alternative crops, better efforts to deplete the soil seed bank and herbicide and non-herbicide controls.
FEILDING TRC Tractors 06 323 4117
Sally says that to reduce the risk of spread, farmers should make sure contractors or anyone coming on their property is clean.
MASTERTON Brandt NZ 06 377 3009
NELSON Drummond & Etheridge 03 543 8041
BLENHEIM Drummond & Etheridge 03 579 1111
“If they charge extra to do so, put it down as an insurance cost. Inspect your crops, call in any unknown weeds.
KAIKOURA Drummond & Etheridge 03 319 7119
GREYMOUTH Drummond & Etheridge 03 768 5116
CHRISTCHURCH Drummond & Etheridge 03 349 4883
“One tip is that the most likely incursion point is where the harvester turns on or cultivating equipment starts working. Inspect those areas regularly because if you find a plant before it seeds, you could well dodge a bullet,” Sally says.
ASHBURTON Drummond & Etheridge 03 307 9911
TIMARU Drummond & Etheridge 03 687 4005
OAMARU Drummond & Etheridge 03 437 1111
MOSGIEL JJ Limited 03 489 8199
GORE JJ Limited 03 208 9370
INVERCARGILL JJ Limited 03 211 0013
KAITAIA Kaitaia Tractors 09 408 0670
WHANGAREI Piako Tractors Northland 09 438 1319
SILVERDALE Brandt NZ 09 427 9137
PUKEKOHE Brandt NZ 09 237 0043
MORRINSVILLE Piako Tractors 07 889 7055
MATAMATA Matamata Tractors & Machinery (07) 888 6292
HAMILTON Brandt NZ 07 847 0425
CAMBRIDGE Brandt NZ 07 827 5184
ROTORUA Piako Tractors Ltd 07 345 8560
TAUPO Taupo Tractors & Machinery 07 378 4533
STRATFORD FeildTorque Taranaki 06 765 8643
HASTINGS Stevenson and Taylor 0800 4273 2273
WAIPUKURAU Stevenson and Taylor 06 858 6041
DANNEVIRKE Lancaster Tractor Services 2022 Ltd 06 374 7731
FEILDING TRC Tractors 06 323 4117
MASTERTON Brandt NZ 06 377 3009
NELSON Drummond & Etheridge 03 543 8041
BLENHEIM Drummond & Etheridge 03 579 1111
KAIKOURA Drummond & Etheridge 03 319 7119
GREYMOUTH Drummond & Etheridge 03 768 5116
CHRISTCHURCH Drummond & Etheridge 03 349 4883
ASHBURTON Drummond & Etheridge 03 307 9911
TIMARU Drummond & Etheridge 03 687 4005
OAMARU Drummond & Etheridge 03 437 1111
MOSGIEL JJ Limited 03 489 8199
GORE JJ Limited 03 208 9370
INVERCARGILL JJ Limited 03 211 0013
AFTER CYCLONE GABRIELLE
DEVASTATED HAWKE'S BAY AND TAIR ĀWHITI LAST YEAR CNH WORKED WITH STEVENSON & TAYLOR AND FEDERATED FARMERS TO HELP FARMERS REINSTATE KILOMETRES OF LOST FENCING.
The project was called Commence the Re-Fence, and CNH donated two tractors to it – a Case IH JX100 and a New Holland TD5.90.
When Commence the Re-Fence came to an end, CNH decided to donate the two tractors to farmers who were in need of some additional support. It did so in June.
The Case IH went to Lil Poulton who farms in the Patoka district near Hastings, while Colin Skudder from Tokomaru Bay, took home the New Holland. Both expressed their thanks for the generous gifts.
To determine who would receive the tractors, the public was asked to nominate farmers severely impacted by the cyclone. Dozens of nominations were made, and CNH develop -
ment manager Murray Grant says it was a tough task for those making the final decision.
“Deciding who would receive them was a very moving and difficult experience. Many nominations came from neighbours or community leaders who knew first-hand what people had been through.
“It was inspiring to see the resilience, courage and bravery of these farmers in the wake of the disaster, and the amazing support everybody provided to help people get back on their feet,” Murray says.
Lil Poulton and her family have a 440-ha property where they run sheep and beef. They lost a lot of fences and two bridges in the cyclone, and many of their tracks and culverts were damaged by erosion.
Commence the Re-Fence helped reinstate some of the fences and rebuild a bridge. Lil says a year later they were almost back to the pre-cyclone production levels. But it has been a tough road, given Lil lost her husband Rob only a few months after Gabrielle hit.
She says the new tractor will be a big help since she has been relying on a 20+ year-old tractor up to now.
“It is just so incredible to have been given this tractor. We are so grateful and very humbled. The level of support we received has been amazing. It shows our rural communities are just the best of people,” Lil says.
Colin Skudder is the manager of Marotiri Farm Partnership in Tokomaru Bay on the East Coast. The cyclone badly affected the property, which lost stock, fencing and land.
It was Colin’s efforts as the Civil Defence lead for Tokomaru Bay that secured him the New Holland TD5.90.
“To be honest there were so many who were worthy of the nomination. We all worked so hard over the five weeks we were locked in Tokomaru Bay,” Colin says.
His community was isolated for weeks after the cyclone, and Colin was instrumental in clearing a track that gave access to medical supplies, nurses and doctors, food and water as well as tradesman.
For two weeks no vehicles could get in and out of Te Puja Springs, north of Tokomaru Bay. Colin's track and his ability to drive on it in hazardous conditions was vital for the welfare of staff, patients and residents of the settlement, Colin’s nominee said.
If it wasn’t for Colin, staff of Te Puja hospital who had been working around the clock for five days would not have been relieved of their duties, the shop would not have had its power connected up to the generator, and residents would not have received medication or gas to cook with.
Colin says he will likely use the tractor on the farm he manages. It is a handy upgrade from the “bit old and tired” one he was using.
ACROSS ITS NINE EUROPEAN FACTORIES, KVERNELAND GROUP BUILDS IMPLEMENTS TO HANDLE ALL STAGES OF CROP AND PASTURE ESTABLISHMENT, CARE AND HARVESTING.
The factory that produces Kverneland round balers and bale wrappers is near the Italian city of Ravenna, an ancient centre that once served as the capital of the Western Roman Empire.
In 2012 the Kubota Corporation bought Kverneland Group, and in the same year it purchased the Ravenna factory from the Italian baler manufacturer Gallignani.
Kubota invested heavily in the factory and transferred a team of baler specialists and mechatronics engineers there to develop a new generation of Kverneland balers from scratch. It is now the Group’s Centre of Excellence for balers.
All research and development for balers is done there, as is all the work needed to produce them – parts production, painting and assembly.
Technological advancements that the Kverneland baler team have achieved include producing the first commercially available non-stop baler-wrapper combination, the Fast Bale.
It is also making big advances alongside Kubota tractor engineers to develop balers with Tractor Implement Management (TIM). TIM allows the baler to control the tractor’s forward hydraulic valves and PTO rotation speed.
In 2023 the Ravenna factory produced more than 2000 balers. They sell under the Kverneland, Vicon and Kubota brands.
It is also the Group’s mulcher factory and it produces roadside, municipal and agricultural mulchers sold into a number of markets, including Australia, in the Kubota brand.
Managing director of the Ravenna factory, Filippo Gallieri says since 2013 the Ravenna factory has tripled its turnover.
The US and Canada snap up the majority of the balers the factory produces. France is another large market followed by Germany, Italy, Australia and the UK.
Filippo says, while 2024 sales will be down on 2023, the Group aims to nearly triple turnover by 2030 after the market recovers.
“This year we are adding a new 2500 m2 building to the factory and in 2026 we will add another 3000 m2 building. We will expand the factory by another 20 percent by 2030,” he says.
To increase its capacity, over the past seven years Kverneland has upgraded the factory’s manufacturing, painting and testing equipment. It has installed robotic welding, laser cutting and folding machines and it will continue to upgrade this technology going forward.
“Output is 15 percent higher with robotic folding machines. Robotic welders improve welding quality and speed and they reduce scrap. Laser cutting is six times faster than traditional cutting. When we increase efficiency we minimise costs and place our products at better price positions.”
As important as robotic machinery is Kubota-Kverneland’s focus is on people and how
THE KVERNELAND FACTORY IN RAVENNA, ITALY CARRIES OUT ALL RESEARCH, DEVELOPMENT AND PRODUCTION OF THE COMPANY’S BALERS.
their work is organised in the factory.
“We believe that if people are treated well, they will work with passion and deliver a great performance. We invest in people to retain our experienced assembly operators. We have a stable organisation with very low resignation rates.
“We develop the skills of our employees and 78 percent of our mid-level managers have been promoted from within our factory staff. The leaders of our assembly and service teams all started on the shop floor.”
Filippo says Kverneland also promotes values that support its people. This includes making the factory as healthy and ‘green’ as possible, with solar power, for example.
It also supports and engages staff. Weekly management meetings provide input from staff on the assembly lines, and this feeds into the way production is carried out. Social activity outside of work includes a factory motorcycle club, football team (the Coyotes), and a tennis group.
Along with new technology, the factory has implemented Kubota systems to increase the efficiency of the assembly lines. Balers are built using an automotive platform concept, in which a base machine is built and then specified with any additional accessories to meet a particular order.
Logistics are organised on a ‘pull system’ which provides assembly workers with a trolley that contains exactly those components needed to carry out their stage of the build. Another policy that ensures quality is the
KVERNELAND’S RAVENNA FACTORY CAN PRODUCE 2000 VARIABLE AND FIXED CHAMBER BALERS AS WELL AS 600 BALE WRAPPERS EACH YEAR.
‘First Time Right’ approach to customer service. If a mistake happens during production or there is a flaw in a machine, the first step is to fix the problem and make it right for the customer. The second step is to determine why the mistake happened and ensure it is not repeated.
Kverneland Ravenna produces several models of fixed chamber round balers and two ranges of variable chamber round balers, the 6600 and 6700.
New Zealand’s Kverneland distributor, Power Farming, has focused primarily on the variable chamber models. It is promoting the KV 6716, which produces bales up to 1.65m in diameter and the KV 6720, which produces bales up to 2m in diameter.
KV 6716 and 6720 balers are ideal for large Kiwi farmers and mid-sized contractors. They come with Kverneland’s full two-year warranty programme.
Bale equipment product manager for Kverneland Ravenna, Adrian Ploscar, says KV variable chamber balers produce consistently-sized, high-density bales. They are easy to stack and transport and preserve the crop to create the best possible forage.
“6700 balers have a heavy duty chamber with three profiled rollers and five heavy duty endless belts. It starts rotating and rolling the crop right from the core so the bale is formed in a series of thin layers. This creates a higher bale density and bales with a more
KVERNELAND 6700 VARIABLE CHAMBER BALERS PRODUCE HIGH-DENSITY BALES THANKS TO THEIR HEAVY DUTY CHAMBER AND FIVE HEAVY DUTY ENDLESS BELTS.
stable structure,” Adrian says.
The chamber features hydraulic proportional density control which has help from twin density springs. As the bale diameter grows the pressure increases so there is higher density throughout the bale.
Adrian says 6700 balers also feature Intelligent Density 3D, which gives the operator electronic control of bale density.
“There are pre-programmed settings so the driver can easily select the best bale formation for silage, hay and straw. They can also easily customise each setting to match
their specific crop conditions.
Another important feature of the KV 6716 and 6720 balers is the PowerBind netwrap system. It is a high-speed, reliable device that secures the net right to the edge of the bale. It has no feed rollers, which eliminates the possibility of net getting wrapped around them.
PowerBind is the most convenient and secure net roll exchange on the market, Adrian says. Operators can install a new roll in one minute without putting a foot on the baler because it is done from the ground.
THE TRACTOR & MACHINERY ASSOCIATION’S BIENNIAL CONFERENCE AND AGM WILL BE A CHANCE FOR FARM MACHINERY AND TRACTOR WHOLESALE DISTRIBUTORS AND SUPPORT SERVICES TO TAKE A LOOK AT INDUSTRY TRENDS AT A TIME WHEN THE LATEST FIGURES CONFIRM THE SECTOR IS IN THE MIDST OF A SERIOUS DOWNTURN.
The conference will be held on the 27th and 28th of August at the Intercontinental Hotel in Wellington. The theme is ‘Geared for Success’.
TAMA general manager Phil Holden says the gathering will give members a chance to hear from Agriculture Minister Todd McClay, Federated Farmers chief executive Terry Copeland and other leading lights from the industry who can help shape thinking about where things are heading.
“The conference provides a platform for members to step out of their day-to-day challenges and take some time to think about the next step in their businesses’ evolution.
Melinda Haley will present Kynetec’s annual ‘state of the industry’ report and FMG’s Lucie Douma will present insights into the global trends impacting farmers,” Phil says.
“Our after-dinner speaker is fishing legend Matt Watson, who has some amazing stories to tell, which will be well received after
a full day of speakers. The second day will start with our AGM, followed by more speakers before concluding the conference with an informal lunch.
Planning for the conference comes as TAMA released its June half year sales figures. They show a similar negative trend as previous months this year and annual results to date are well below 2023.
TAMA members’ deliveries for June were down 45 percent from June a year ago, and there was a 28 percent decline on year-todate performance compared to June 2023.
“Quite simply it is a very tough trading environment at the moment. Growers, farmers, and rural contractors across the country are focusing mainly on replacing only essential equipment.
“They are taking a more deliberate approach to larger tractor and machinery purchases. They are either pushing those decisions out or postponing them completely,”
Phil says.
The sales slump is affecting both Islands. Monthly deliveries in the North Island were down 51 percent from a year ago and deliveries in the South Island were 34.3 percent behind June 2023.
While there has been more settled weather than previous years across the country, the potential for a more favourable harvest is not translating into tractor sales.
“Dryer conditions are beginning to drive some positive signs in the horticulture segment, particularly kiwifruit, but beef and
TAMA SALES FIGURES SHOW THAT THE AG MACHINERY SECTOR IS DOING IT TOUGH WITH A 28 PERCENT DROP IN SALES OVER THE YEAR FROM JUNE 2023 TO JUNE 2024.
sheep prices across the country continue to be very flat.
“Positive signs in the diary sector have resulted in modest price movement and, with the better weather, there is plenty of grass in the paddocks. How that translates in the mid-to-long term on tractor and machinery movement will be something TAMA members will be reviewing closely.”
All tractor segments have been hit by the current market. Total deliveries of 1167 for the June half year are well down on the 1620 deliveries at June last year.
On a rolling 12-month basis, deliveries for the June 2024 period are 2980, down from 3883 annual deliveries in June 2023.
A brighter note for TAMA members is that shipping and logistics are catching up with demand. Both whole goods and parts timeframes are significantly better than the last couple of years.
Phil says TAMA members are aware that in the current climate farmers and contractors will be more thorough and take more time to make decisions about major purchases. To address the current market headwinds, it is important for TAMA members to maintain close contact with their customer base to ensure they are well aware of their needs.
TAMA’s biennial conference presents as the ideal place for members to reflect and take stock of the current market environment and, hopefully, get some insights on where the agriculture industry is heading.
These insights should better inform them of what their customers might be focused on. For regular updates and to register your attendance visit the webpage tama.org.nz/ agm.
Enjoy the productivity gains that come with John Deere’s Mower Conditioners and Balers. With a broad range of equipment to suit your specific needs underpinned by John Deere’s trusted reliability and quality, you can confidently expect to maximise uptime, enhance performance, and drive efficiencies across your operation. So, if you want to get more done in a day and do it better, talk to your local John Deere dealer today.
F FUSO CANTER HAS BEEN A TRUSTED KIWI WORKMATE IN INDUSTRIES AS DIVERSE AS AGRICULTURE, CONSTRUCTION, LANDSCAPING, GENERAL FREIGHT, FOOD DELIVERY AND MORE. NOW, THE NEW 2024 CANTERS BUILD ON THEIR MARKETLEADING POSITION WITH NEW FEATURES THAT IMPROVE THE COMFORT AND SAFETY OF DRIVERS.
Kevin Smith says, for the first time Fuso’s Advanced Safety Features come standard across the full Fuso 4x2 range. These include active emergency brak ing, lane departure warning, electronic braking system, and
THE LATEST FUSO 6T CITY TIPPER HAS A NEW LED LIGHTING PACKAGE AND 8-INCH TOUCHSCREEN, AND IS THE ONLY LIGHT-DUTY TIPPER TO COMBINE A 3-TONNE
from the crowd with its stylish new front grille, which is flanked by the LED lighting that both looks good and improves performance.
Highlights of the Fuso Canter range include the Canter Tipper with limited slip differential and the class-leading Duonic 2.0 automatic transmission. Duonic 2.0 gives smoother, more economical driving and is available in various Canter models.
There are 29 models in the 2024 Canter range with wheelbases from 2.5m to 4.75m and up to 9 tonne gross vehicle mass (GVM).
“Over several decades, Canter has been one of the most popular light trucks in New Zealand. A Canter is a tried and trusted investment for businesses from single-unit owner-operators to
giant multinationals,” Kevin says.
“We understand what operators expect from a truck and we are committed to delivering that across all categories. We also place a priority on the wellbeing of drivers, which is critical to the health of our industry.
“In terms of efficiency and performance, Fuso’s Duonic automated manual transmission is still best-in-class and Canter Tipper remains the only light-duty truck in New Zealand to feature a limited slip differential.
“We were also the first truck brand in New Zealand to introduce advanced safety features across our light, medium and heavy-duty ranges. Now these are standard across the 4x2 Canter range.”
Canter owners have the option of Fuso NZ’s industry-best fiveyear or 200,000-km bumperto-bumper extended warranty, which is a step up from the standard three-year or 100,000-km warranty.
“The optional extension delivers a huge amount of value at no additional cost. The only stipulation is that the truck is serviced at an authorised Fuso dealer,” Kevin says.
For more information on the new Canter range, go to the website fuso.co.nz.
MAIZE GROWING IS NOT FOR THE FAINT HEARTED. TIME FRAMES ARE TIGHT AND THE VALUE OF THE CROP IS HIGH.
As UPL NZ Upper North Island regional manager Pieter Van Der Westhuizen says, if something in your maize crop gets mucked-up, you do not have the luxury to go back and fix it. This is especially true when it comes to slug control.
Reliance on cultivation for slug control, which is sketchy at best, is becoming a less viable option these days as more and more land is being planted with strip till or direct drilled (the latter across multiple crops).
Therefore, you would definitely be “chancing your arm” if you did not have a slug control programme, Pieter says.
Waikato contractor Darcy Finch was one of the first to catch on to the benefits of BioGro certified Ironmax Pro for slug control.
Darcy and his wife Rachel operate Finch Contracting based in Te Awamutu. It is a busy, successful business and Darcy is an early adopter.
Finch Contracting employs up to 40 staff at peak season and provides a ‘nose-to-tail’ service for farmers. They offer everything from cultivating, drilling and fertilising to harvesting, baling and carting.
if you get the same performance, it is a win/ win for everyone,” he says.
“They
“We have had no issues with the product. It flows well, which is important with
WAIRARAPA SPRAY CONTRACTOR
CLINTON CARROLL WAS SELECTED TO BE THE NEW PRESIDENT OF RURAL CONTRACTORS NZ AT ITS ANNUAL CONFERENCE IN MASTERTON IN JUNE.
Clinton runs Wairarapa Weedsprayers and was elected by the RCNZ board to replace Helen Slattery, who stood down after three years in the role of president. Clinton has served on the board since 2018 and was Helen’s vice-president.
At its AGM, which was held on the first day of the conference, RCNZ also welcomed three new board members. They are Taupo’s Gordon Brown, Taranaki’s Alistair Kalin and Canterbury’s David Molloy.
Transport issues were a hot topic at the RCNZ conference. Of particular concern are new roading developments that don’t allow motorists to pass slow-moving vehicles.
This is particularly true when median barriers, which prevent cars from passing, are combined with side barriers, which prevent vehicles from pulling over to let others pass.
Associate Agriculture Minister Andrew Hoggard opened the RCNZ conference and he touched on the issue. He says he sees the issues when he drives to Parliament from his Manawatu home.
Median barriers prevent over-taking between Levin and Otaki and there is no shoulder space to allow vehicles such as tractors to pull over.
“There are a lot of tractors trying to get in and out of paddocks. Motorists get angry as a result. There is lots of screaming, fingers
our metering systems.”
Finch Contracting uses Ironmax Pro for a range of crops – chicory and turnips through to grass and maize.
“Slug pressure can vary a lot even from one paddock to another on a single property. With direct drilling and strip till particularly, slugs are something you really need to think about.”
Pieter says contractors like Darcy have a strong focus on best practice and doing the best by their clients, their staff, and the environment.
“They appreciate the Ironmax Pro BioGro certification, but they want to see it delivering for them as well, and it does. Yes, it is gentle on beneficial insects and your dogs and other animals but it’s got an iron fist in that velvet glove.”
You should assume slugs are present when planting because of the real risk they pose to
WAIRARAPA SPRAY CONTRACTOR CLINTON CARROLL IS THE NEW PRESIDENT OF RURAL CONTRACTORS NZ.
out the windows and potentially stupid decisions being made,” Andrew says.
Roading developments needed to allow traffic to get past slow-moving machinery.
Canterbury rural contractor Steve Murray asked the minister if he would support signage to alert motorists when they entered areas where there is agricultural activity and the need to drive safely.
Andrew says he is wary of the cost of NZTA signage but people needed to recognise that primary production made up 80 percent of NZ’s income. He says he will take up the issue with the Transport Minister.
Rural Contractors NZ CEO Andrew Olsen
vulnerable seedlings, Pieter says.
“Yields can take a real hit if you are not on top of the slug population. When you think about the fact that slugs can consume more than 50 percent of their own body weight in a night’s feeding and produce 300 eggs in their 13-month lifespan, that’s pretty sobering.”
Manufactured by De Sangosse, a world leader in molluscicides, Ironmax Pro has all the benefits of market leader and sister product Metarex Inov, with the sustainability factor Pieter says contractors are looking for.
“There is that reassurance and, also, some of our feedback says Ironmax Pro is more pleasant to deal with because it doesn’t have a strong smell when you are working with it in more confined spaces.
“In some areas, there was some fairly challenging slug pressure in the past season, but contractors tell us Ironmax Pro has more than proven itself. It has been really well received.”
says the organisation has written to the Transport Minister but any help was very welcome.
“This issue is not limited to Horowhenua. Rural contractors have to do a 7-km run on SH2 in the Bay of Plenty where there are no areas to pull over or slow down. Rural contractors in Waikato and other parts of the country face anger from motorists because of median barriers and no pull over space.
“We support reducing the road toll but giving rural contractors no capacity to pull over for kilometres at a time is actually adding to the risk of fatalities. We want the Transport Minister to act.’’
Ironmax Pro contains the optimized active ingredient 24.2 gm/kg ferric phosphate anhydrous, referred to as IPMax. Iron (ferric) phosphate is a natural component of soil.
In Ironmax Pro, it works as a stomach poison on slugs and is fatal once ingested. Moreover, Ironmax Pro uses Colzactive technology developed from oil seed rape molecules selected for palatability, feeding preference, and rapid detection by slugs.
Pieter says it’s a myth that juveniles won’t ingest on the bait. All slugs and snails will feed on it.
Ironmax Pro has high field integrity (it is rainfast) thanks to unique wet process manufacturing. “It won’t disintegrate in the first shower, and that’s important since slugs thrive in those damp conditions.”
For more information, talk to your local technical merchant or contact Pieter Van Der Westhuizen at UPL NZ on 021 392 740.
RICHARD HOUSTON STARTED HIS JOB RECRUITMENT SERVICE HANZ ON JOBS IN 2007 WHEN HE WAS DRIVING SILAGE HARVESTERS IN THE UK.
“I recognised the talents of English drivers and their eagerness to work in New Zealand, so I began connecting them with opportunities here,” Richard says.
“Our business has flourished because it is driven by a passion to optimise the agricultural season for both employers and employees.
“We have a lot of repeat customers and others who have got in touch because someone recommended us, which is a testament to the positive experiences we have facilitated.”
Hanz On Jobs specialises in filling critical roles – such as buck
require specific expertise. Their approach is deeply personal and, as it says on the tin, hands-on.
With years of experience in the industry, the Hanz On team understands what drives both employers and employees. They have also embraced generational change so they can adapt new ideas and ensure smooth transitions.
Richard says recruiting drivers from the Northern Hemisphere in September and October aligns perfectly with their quiet season. They travel to NZ when their work is slowing down and they return home in late March or early April for another spring.
TO MAKE HANZ ON JOBS SUCCESSFUL, RICHARD HOUSTON ATTENDS THE CEREALS SHOW IN ENGLAND TO KEEP UP WITH NEW TRENDS IN THE INDUSTRY AND HE GETS BEHIND THE WHEEL OF THE LATEST EQUIPMENT.
timing needs of both parties. For example, Irish drivers often prefer to return home when the slurry ban is lifted, so we place them with Kiwi contractors whose work finishes earlier.
“On the other hand, buck rake drivers need to stay until the
we select individuals who can commit to a longer stay. This planning ensures everyone’s needs are met.
“Our goal is also to match candidates based on their experience, so they bring the required skills but also gain new experi-
The Sulky brand you know and trust, now with a new look.
A hopper capacity f rom 900 to 1500 litres, and working widths of between 9 and 18 metres, the double cone hopper with steeply slanted walls guarantees a very regular fertiliser flow
Plus, with a seven-year paint warranty you know the ECONOV will go the distance.
Each year, Hanz On Jobs finds employment for 50 to 60 machine operators. They are placed with 20 to 30 Kiwi contractors and large-scale farmers.
While challenges are rare, Richard provides support if issues arise, which could mean finding replacements or new job opportunities.
In June Richard was in the UK and Ireland to interview keen drivers. He says the trip was a big success.
“I started in Ireland and Northern Ireland, and then flew to England for the Cereals event, which highlights arable farming. Then I travelled to Devon to conduct interviews and help a friend with his maize drilling.
“After that I went to Wales and Cumbria, which is known for its skilled drivers, before heading to Edinburgh and the Highland Show. Finally, I went to Suffolk to meet the last group of candidates and assist with the rye harvest. It is always nice to get back in a machine and get amongst the harvest," he says. Candidates complete a handwritten form to assess their basic literacy and life skills. Group discussions cover all aspects of travel to New Zealand – from booking flights to navigating gravel roads.
Afterwards, smaller group or individual meetings are held to answer any remaining questions and plan travel dates.
Experience in the industry and effective communication are both crucial, Richard says. Establishing an open and fair relationship from the start ensures mutual understanding and alignment of expectations.
He ensures both parties are aware of their responsibilities and offers support when needed. With his extensive network in the close-knit NZ-UK agricultural community, someone is always available to assist.
Last season, Hanz On Jobs placed Edward Hatton with Pankhurst Contracting in North Canterbury. It was their first time employing a UK driver, and Hanz On Jobs supported them
HANZ ON JOBS DIRECTOR
RICHARD HOUSTON HAS HAD A SUCCESSFUL SOJOURN IN THE UK AND IRELAND RECRUITING SKILLED AG MACHINERY OPERATORS FOR THE UPCOMING SEASON IN NZ.
throughout the process.
Ben has told Richard, “I don't think you will find another fella as good as Edward, but if you can please do the same again this season.”
Hanz On Jobs will continue to provide pathways for those seeking work with ag machinery worldwide.
"We take great satisfaction in helping people create wonderful memories while working in excellent jobs," Richard says.
“For employers, our focus is on delivering top-notch staff each season. There is also a driver shortage in the UK. I am now looking to place 20 Kiwi drivers in the UK, which will create a reciprocal exchange of talent.”
To register your interest in Hanz On Jobs’ services go to the webpage hanzonjobs.co.nz/getstaff or call Richard on 027 615 6693.
WEIGHT DISTRIBUTION
Unique design allows the spreader to sit closer to the tractor.
• Improves weight distribution for larger payloads with less front weight stress.
DURABILITY
• One-piece stainless steel body integrated with the frame. Eliminates corrosion risk and extends the spreader’s lifespan.
VERSATILE SPREADING
• Conveyor system delivers product to spinners.
Bin shape prevents bridging, allowing smooth spreading of various materials, from urea to lime.
ISOBUS COMPATIBILITY
• Plug-and-play control system compatible with all ISOBUS-compliant terminals.
Variable rate ready, facilitating easy transfer between machines.
L5 CAPACITY
Loading Height: 2,150 mm
• Urea Capacity: 3,750 kg
• Lime Capacity: 6,000 kg
LANDINI NEW ZEALAND’S DISTRIBUTION AGREEMENT WITH NORWOOD WILL SEE A WIDER RANGE OF LANDINI TRACTORS AVAILABLE AROUND THE COUNTRY
THROUGH A RETAIL NETWORK THAT INCLUDES BOTH NORWOOD AND INDEPENDENT DEALERSHIPS.
A benefit of the new distribution arrangement is that a wider range of Landini models from Argo Tractors will be available here.
Norwood product specialist Andrew Dunlop says the company can now offer tractors that have not been available in the New Zealand market.
The extended range includes five high-horsepower tractor series, 20 models of specialty tractors and 22 models of hard-working utility tractors.
Andrew says Landini high horsepower tractors are high spec machines for farmers and contractors who demand a high level of efficiency and performance. All Landini high horsepower tractors can be specified with full loader kit except for the Series 8.
High horsepower Landini tractors now available in NZ are:
Series 6 RS Stage 5. A cab-only three model range that range from 113 hp to 136 hp. All feature a four-cylinder, 4.5-litre, FPT engine, and Robo Shift and Smart Auto Power Shift (APS) transmission.
Series 7 SWB Dynamic Stage 5. There are four models in this Series 7 range, two four-cylinder and two six-cylinder models, which deliver from 165 to 175 hp. The two transmission offerings are the Robo Six with Smart APS and the V-Shift CVT.
Series 7 RS Tier 3: The three models in this range have a larger frame, a six-cylinder, 6.7-litre, Tier 3 FPT engine (151 to 215 hp) and EPM for a power boost when using the PTO for transport and hydraulic operations. With active
THE REX4 IS LANDINI’S TOP SPECIALITY TRACTOR AND WON THE 2024 SPECIALTY TRACTOR OF THE YEAR AWARD AT AGRITECHNICA.
transmission top speed is 40 kph only, with the dynamic transmission top speed is 50 kph. Both have Robo Six with Smart APS.
Series 7 VS Dynamic Tier 3/
Stage 5. This is the larger framed V-Shift or CVT transmission
Series 7, available with Tier 3 or Stage 5 engines. Both engines are six –cylinder and range from 215 to 230 hp.
Series 8 VS Dynamic Tier 2/
Stage 5. The most powerful Landini tractor is available in two models, Stage 5 at 250 hp and Tier 2 at 292 hp. Both versions are six-cylinder, 6.7 litre FPT with VS and a choice of 40-kph or 50-kph CVT transmission. Front hitch and dynamic PTO is standard.
The Landini specialty tractor range has something for orchardists, horticulturalists, viticulturalists, market gardeners, or greenhouse operations.
REX3: Compact low and narrow tractor. The REX3 is available in two models, 68 or 75 hp, F ROPS, standard and Low Profile cab or GE Low Profile ROPS for kiwifruit.
REX T3: There are five models of the REX T3 from 75 to 110 hp. Also with F ROPS and cab, or low profile ROPS for under trellis kiwifruit operations.
REX4: This is the flagship in Landini’s speciality tractor range. The REX4 is a high-end, highspec, customisable specialty tractor with five models from 75 to 112 hp. The 120 T3 112-hp REX4 model received the 2024 Specialty Tractor of the Year Award at Agritechnica last year.
REX4 is available in six different versions including a V Cab for narrow vineyard rows, an S Cab with a wider tractor base with a narrow cab up top, and a standard F
IN MAY, A TEAM OF NORWOOD STAFF VISITED THE ARGO TRACTORS FACTORY IN ITALY, WHICH BUILDS SERIES 7 AND SERIES 8 LANDINI TRACTORS.
Series in ROPS and cab.
Super HC: A high clearance tractor available in four models from 80 to 111 hp in both cab and ROPS.
Series 5 HC Stage 5: A Cab only high-spec high clearance tractor available in two models from 93hp to 103hp with customisable tyre options. Landini utility tractors are
THERE IS SOMETHING SPECIAL ABOUT THE PROVINCE OF EMILIA-ROMAGNA IN NORTH-CENTRAL ITALY. NOT ONLY DOES IT HAVE A REPUTATION FOR PRODUCING THE COUNTRY’S BEST FOOD, IT IS ALSO KNOWN AS MOTOR VALLEY, HOME TO FERRARI, LAMBORGHINI, MASERATI AND DUCATI.
This year another iconic motor technology brand from Emilia-Romagna marks a major milestone as Landini Tractors celebrates its 140th birthday.
In 1884 Giovanni Landini established Officine Landini to manufacture wine-making machinery in the town of Fabbrico. In 1910 Landini introduced a stationary hot-bulb engine and in 1925 it introduced its first tractor, making it a pioneer in agricultural mechanisation.
Today the main factory that produces Landini tractors is still in Fabbrico, but it is now complemented by several other factories in nearby towns.
And while the Landini family no longer owns the company, it is part of another proud fam-
ily-owned industrial group, Argo Tractors. The Morra family bought Landini in 1994 and McCormick tractors in 2000.
After they shifted production of McCormick tractors from England and France to Fabbrico, they consolidated both brands under the umbrella of a new company, Argo Tractors.
Argo Tractors designs, builds and distributes Landini and McCormick tractors throughout the world. The Landini range extends from specialist vineyard, orchard and vegetable tractors to the high-horsepower 7 and 8 Series.
The numbers tell an impressive story. Argo Tractors have the capacity to produce 22,000 tractors a year. It has 2000
ARGO TRACTORS IS PROUD OF THE FACT THAT IT PRODUCES 65 PERCENT OF THE COMPONENTS USED TO BUILD ITS LANDINI AND MCCORMICK TRACTORS.
employees and six manufacturing plants.
It is an export driven company with 130 importers around the world. Its sales in Italy account for 15 percent of its earnings while sales in the rest of Europe contribute 35 percent of the total. Another 16 percent of its turnover comes from the USA and 22 percent from Africa, thanks to its strong presence in the South African market.
Argo Tractors is proud of the fact that, in terms of value, 65 percent of their tractors’ components are manufactured in-house because it gives them control over quality, costs and time to market.
Components that Landini
ARGO TRACTORS HAS THE CAPACITY TO PRODUCE 22,000 TRACTORS A YEAR AT ITS SIX MANUFACTURING PLANTS IN ITALY.
designed for general farm work and they are perfect for New Zealand livestock farms.
Series 4 Stage 5: This new offering is available in three models, 61 to 75hp, in both ROPS and cab configurations. They are available loader-ready or with full kit option.
Super: A robust farm tractor with models from 82 to 111 hp. They are available in ROPS, cab and high clearance versions with a full loader option.
Powerfarm II: A higher spec cab-only tractor in three models (93 to 110 hp). All have a three step transmission with Power
Shuttle. They can be specified loader ready or with a full kit.
Series 5 Stage 5: Another highspec tractor in four models up 112 hp. They are available in both ROPS and cab versions. Options include a full kit loader and an Active or Dynamic transmission.
Landforce: Ideal for Kiwi live-
builds itself include transmissions for all models up to 160 hp, gearbox housings, wheel hubs, axles, gears and shafts. It also builds its own platforms and cabs in a dedicated facility at Fabbrico that can churn out 105 units per day.
To stay at the forefront both tractor and manufacturing technology requires constant investment. Argo Tractors returns 5.5 percent of its annual turnover or about €30 million (NZ$53 million) to research and development. This is vital as electronics and software are now critical factors in today’s agricultural machinery. Landini’s approach is to equip its tractors with advanced technology that is easy to use.
This approach bore fruit when the Landini Rex 4-120GT Dynamic was awarded the 2024 Tractor of the Year award for the Best of Specialised category. Tractor of the Year judges highlighted the Rex 4-120GT’s innovative RoboShift transmission, new cab with a swivel driver's seat, SmartPilot Plus joystick and Advanced Driving System.
Another project that builds on new technology is the Landini Rex4 Full Hybrid tractor. It combines a 55 kW diesel engine with 25 kW electric engine. It can work in full diesel, in hybrid mode with
stock farmers. The two models are 112 hp or 120 hp. Both are available with ROPS and cab and full loader options.
Landpower II: Available in four models (117 to 157 hp) with ROPS or cab and a full loader kit.
To see the full Landini range, visit landininewzealand.co.nz.
Power through every job with over 300HP of grunt, four-stage V-Shift transmission technology, and a tailor-made hydraulic system. The Landini Series 8 can handle all your farming applications and offers real productivity and efficiency benefits.
Ask us about the Landini Series 8 and let’s grow together.
ARGO TRACTORS USES ROBOTICS, ARTIFICIAL INTELLIGENCE AND SENSORS TO IMPROVE PRODUCTIVITY AT ITS FACTORIES.
an output of 80 kW, or in full electric mode (for three hours with a peak output of 65 kW).
Like a hybrid electric car, the diesel engine in the Rex4 Full Hybrid recharges the battery and its Power Management System monitors power flows and sets the best operating point for the two propulsion systems.
But advanced technology is not only available on certain specialised models. All Landini tractors can be fitted with ISOBUS and they can be used with the My Landini suite of precision farming applications.
My Landini digital tools include the telematics package Landini Fleet and Remote Diagnostics Management, which allows you or other trusted parties to monitor your machines and carry out diagnostics remotely.
PSM is Landini’s Precise Steering Management system, which links with ISOBUS and can provide RTK accuracy. Landini Farm is a digital platform for managing farm data, sensors, prescription maps and traceability.
The drive to incorporate new technology also applies to Landini’s manufacturing facilities. To maintain its cutting edge, Argo Tractors invests in what is called ‘Industry 4.0’ manufacturing technology. This encompasses robotics, artificial intelligence and sensors that collect and share data to improve productivity.
The R&D unit at the Fabbrico and San Martino in Rio factories develop prototypes. These units have testing rooms for engines and transmissions to test all tractors from 50 hp to 313 hp with advanced software.
Along with its cab and platform facility, the Fabbrico plant has a cast iron processing area and three production lines, which together can build up 55 tractors per day. Solar panels provide one third of the electricity used to run the plant.
One of Argo Tractors satellite factories is in the town of Luzzara and it is dedicated to the production of front axles. It produces rigid axles as well as suspended axles for tractors up to 120 hp.
Its factory at San Martino in Rio machines transmission components and builds specialist tractors, and the company’s newest factory, in Campagnola, builds transmissions.
THE
In New Zealand Landini is best known for its orchard, vineyard and other specialist tractors. The new nationwide distributor, Norwood, will expand this offering but it is also promoting the larger Series 7 and Series 8 machines.
Landini Series 7 tractors are available with either a Tier III or Stage V engine. The Tier III version delivers 225 hp and has a ZF CVT transmission, while a number of Series 7 models are available with Stage V engines.
Stage V models have an FPT engine that delivers excellent traction and fuel efficiency. They include three models with a Robo-Six powershift transmission (180 hp, 200 hp and 215 hp) and a 225 model with a ZF V-Shift CVT transmission.
The V-Shift CVT has four mechanical ranges and Landini says it delivers gear changes from 0 to 50 kph that are as smooth as the leading CVT transmissions in the market.
A power reverse shuttle on the V-Shift lets the driver shift from forward to reverse using a control lever near the steering wheel, so there is no need to use the clutch pedal.
The Robo-Six transmission offers 30 forward and 15 reverse speeds. With the creeper option
ARGO TRACTORS’ NEWEST FACTORY IN THE TOWN OF CAMPAGNOLA BUILDS TRANSMISSIONS.
it offers 54 forward speeds and 27 in reverse.
All Series 7 Landini models have a front axle with independent wheel suspension that delivers very efficient road travel. They have contemporary dynamic look and a quiet, spacious four-post cab with intuitive controls for maximum comfort and efficiency.
The hydraulic system supplies up to 160 litres/min to the hitch and remote valves, and it always delivers exactly the quantity of oil that the system requires.
The Landini Series 8 V-Shift model now available in New Zealand is the 8-310. Its maximum power output is 305 hp and it delivers maximum torque at 1400 rpm.
It has a Tier II FPT engine that is mounted on a cast iron chassis, which forms the main structure of the tractor. Because the engine does not have an exhaust gas recirculation unit, it can deliver very high torque at low engine speeds.
The Landini 8-310 has an external 90-litre tank for hydraulic oil, which keeps it separate from the transmission oil, so there is no danger of cross contamination.
Its hydraulic system delivers 212 litres/min to the hitch and remote valves and 115 litre/minute to the electronic steering system. A powerful rear three-point linkage provides the capacity to lift 12,000 kg and it can be specified with a front hitch (5000 kg) and PTO.
Another option is an automatic centralised greasing system and Landini is set to release a centralised tyre inflation system that works off a water-cooled air compressor.
All Series 7 and 8 models can be specified GPS ready with ISOBUS and they have the capacity to work with My Landini precision farming tools.
THERE IS A NEW SPREADER IN TOWN – THE HANSA RANGE OF TRACTORDRAWN SPREADERS MADE BY AUSTRALIAN COMPANY SOUTHERN SPREADERS. SOLD HERE BY EUROAGRI IMPORTS, THE HANSA RANGE INCLUDES LINKAGE-MOUNTED AND TRAILED MODELS.
EuroAgri Imports general manager James McCloy says since he took over the business in 2009, he has always looked to add more specialised brands of machinery to its lineup.
“We have the best brands of machinery that are most suited to the New Zealand market.”
Hansa spreaders easily meet this brief. The bins are stainless steel to resist corrosion. Delivery to the twin spinners is via a hydraulically-driven conveyor chain. This keeps products moving even on slopes and minimises blockages.
James says they deliver an even spread on hills and use up all the product in the bin.
Another feature ticked off the wish list James had when considering the Hansa range is their ability to spread general fertiliser to 36m.
Hansa spreaders are ISOBUS-compatible and easily swapped between tractors. When combined with GPS, they can apply at variable rates over 14 sections and carry out headland management and independent side-to-side application.
The rate controllers allow operators to vary their speed according to the conditions, knowing the rate will stay consistent. Proof of placement is available.
James sees Hansa as a brand that is well-suited to New Zealand conditions. “Plus Southern Spreaders gives good delivery
times and amazing quality and back-up.”
Southern Spreaders sales and business development manager Ashley Dinning says the company developed the Hansa spreaders after supplying the Australian contractor market for more than 30 years.
“It’s proven at the top end of the market by contractors who do a lot more work than farmers in all conditions.”
Ashley says an important feature is their ability to handle not only a variety of products but also variability within a type of product.
“Products can vary year to year. Our spreaders are easy to calibrate and adjust for changes. They can spread fertiliser, gypsum, compost and manure, and they love chicken manure.”
Hansa spreaders come in three ranges – the L-Series, S-series and T-Series.
L-Series models are linkage spreaders. The model number gives the capacity in 1000-litres. The L2 can carry 2000 litres, for example, and the other models are the L2.5 and L3.
“The three-point linkage spreaders are capable of doing anything a trailer spreader will do including lime, manure, compost, urea, bait and seed. There is no other threepoint linkage that will spread all types of lime,” James says.
Maximum payload is 8 tonnes. Lime is spread out to 26m and urea out to 36m.
Bins sit close to the tractor, minimising the amount of front counterweight required.
Hansa S-Series spreaders are on single axle trailers. The models range from T3 to T12.
It is not just a simple increase in capacity. The various models also consider loading height required and stability on hills.
T-Series spreaders are on a tandem axle. There are two models, the T15 and T23. The T15 can carry 10 tonnes of urea while the T23 can handle 15 tonnes of urea.
EUROAGRI IMPORTS SAYS THE HANSA L-SERIES IS THE ONLY RANGE OF LINKAGE SPREADERS ON THE MARKET THAT CAN SPREAD UREA, MANURE, COMPOST, BAIT, SEED AND ALL TYPES OF LIME.
Both models have a steerable rear axle and hydraulic drawbar suspension. The option of an automatic door removes the need to get out of the cab to adjust settings.
All Hansa models are available in New Zealand. EuroAgri Imports has had them in the country since the beginning of the year.
James sees Hansa as a suitable spreader for any part of the rural industry – contractors, farmers and growers.
He says Hansa linkage spreaders have started well here, and he thinks the market will soon include the Southern Spreaders truck-mounted spreaders.
“The quality of the build and the spinner design are great. The shape of the chutes has been refined through years of testing. They deliver a better spread and more accuracy.”
Ashley says Southern Spreaders has a focus on research and development.
“We rely heavily on feed-back from customers. We are keen listeners and maintain close relationships with our contractor base. We are always open to suggestions. So if anyone has an unusual product they want spread, get in touch.”
That listening has led Southern Spreaders to offer such options as variable tyre sizes, wheel track options, tarps and load cells.
Maintenance is simple – just grease and clean. Chains require very little maintenance and last up to 17,000 hours.
“Hansa spreaders are designed around the needs of contractors. They are busy people who want to spend time spreading, not crawling around fixing stuff,” Ashley says.
EuroAgri holds parts and has certified testers and a full-service team, though James is not expecting the team to be over-worked.
“This is bomb-proof machinery,” he says. “Hansa spreaders are very well-built machines with fantastic back-up from the manufacturers.”
ALL HANSA SPREADERS HAVE STAINLESS STEEL BINS THAT RESIST CORROSION AND, WHEN USED WITH GPS, THEY CAN SPREAD AT VARIABLE RATES OVER 14 SECTIONS.
KEEPING CONTRACTORS AND THEIR EMPLOYEES
AND HEALTHY IS
MAJOR PRIORITY FOR RURAL CONTRACTORS
AND ONCE AGAIN THIS WAS A
AT THE
CONFERENCE IN JUNE.
The keynote speaker at the conference dinner was chair of the agricultural industry’s Safer Farms initiative, Lindy Nelson, and the conference also held a full session devoted to the topic.
Lindy says the agriculture sector is one of New Zealand’s most important primary industries but it is one of the most dangerous sectors to work in.
Last year, Safer Farms launched its ‘Half Arsed Stops Here’ campaign to create safer farm culture in New Zealand.
Yet, Lindy says, there have already been a dozen farm bike fatalities alone this year.
“Unfortunately, I think this is going to be our worst year yet for farm bike fatalities.”
She says farmers could not function without rural contractors but sometimes they put contractors under a lot of pressure and this increases the risk of accidents caused by fatigue.
In her talk, she told the imaginary story of
contractor Jim and his wife Sarah. At 52, Jim’s ‘no matter what’ approach to juggling farmers’ demands, weather windows and other challenges is taking its toll. Sarah notices a change in Jim. He has lost weight, seems constantly tired, grumpy and has little time for her or the family.
Then one Friday night at 11:30 pm two police arrive to tell her Jim has driven off the road after completing a job and is in critical condition. Lindy says Jim and Sarah’s story is not an
RURAL SUPPORT TRUST REGIONAL COORDINATOR SARAH DONALDSON.
isolated case.
The message of her talk was echoed the following day by Wairarapa psychologist and Rural Support Trust regional coordinator Sarah Donaldson.
Sarah had a call the previous morning from the wife of a contractor whose husband was under similar stress to the fictional Jim. The call was one of many she receives from farmers and rural contractors.
“The vast majority of people I see are
IN A SIGNIFICANT MILESTONE FOR NEW ZEALAND AGRICULTURE, AGRECOVERY HAS ANNOUNCED THAT ITS GREENFARMS PRODUCT STEWARDSHIP SCHEME (GPSS) HAS BEEN ACCREDITED UNDER THE WASTE MINIMISATION ACT.
Agrecovery chairman Anders Crofoot says accreditation is a pivotal moment in the country’s move towards sustainable agricultural practices because it will help achieve responsible management of plastic in the primary sector.
Agrecovery’s Green-Farms scheme aims to tackle the challenge of farm plastic waste head-on. In the next three years it will focus on four farm plastics waste streams. These are agrichemical containers, bale wrap and silage sheets, small seed and feed bags, and large 1-tonne and 500-kg fertiliser sacks.
The GPSS has also been accredited to recycle animal health and some household plastic packaging.
Anders say accreditation of the GPSS is a testament to the hard work and commitment of the Agrecovery team, stakeholders, and
AGRECOVERY PLANS TO WORK WITH GOVERNMENT TO EXPAND THE RANGE OF PLASTICS THE SCHEME CAN RECYCLE.
the agricultural community.
“Together, we are setting a new standard for environmental responsibility. This will ensure that our actions today pave the way for a more sustainable tomorrow.”
Agrecovery’s product stewardship scheme takes a phased approach to include a broader range of materials over time. It plans to increase the range of recyclable plastics GPSS collects over the next seven years.
Its expansion is a response to the feedback from the farming community and it acknowledges the evolving needs of the agricultural sector.
By incorporating more types of farm plastics into the recycling scheme, Agrecovery will address the waste management challenges that farmers and growers face, and instil a culture of kaitiakitanga and environmental stewardship in the primary sector.
Agrecovery CEO Tony Wilson says accreditation is a landmark for both Agrecovery and New Zealand’s entire primary industry. He looks forward to working with government to expand the scheme.
“Our accredited scheme underscores our dedication to sustainable practices, and it is driven by the demands of New Zealand’s farmers and growers. We look forward to expanding our schemes and fostering innovation and collaboration to ensure a sustainable future for all,” Tony says.
GPSS will operate as a voluntary scheme
staunch blokes. Fatigue is the biggest issue. Crash and burn – that’s 75 percent of what I see in the rural sector,” she says.
Sarah says, like everyone else, rural contractors need recovery time from work and other stresses. They should see their work as being on phones and laptops as well as operating machinery.
It is not soft to have downtime, leisure and good sleep. They are critical to recovery from stress but people under stress often have dif-
ficulty finding their off button.
“Elite athletes have recovery built into their schedules. Sleep is our number one recovery mode. Exercise and other ways to reduce stressful thoughts are also important,” Sarah says.
Sarah gives several bullet points on how to stay well. They include:
• Have good connections. Talk, listen and be there for people who matter in your life.
• Be active.
AGRECOVERY CEO TONY WILSON SAYS THE SCHEME’S SUCCESS IS DUE TO THE COLLABORATIVE APPROACH IT HAS TAKEN TO MEET THE DEMANDS OF NEW ZEALAND’S FARMERS AND GROWERS.
until regulations are in place to ensure all producers of targeted products participate. Under the industry-led scheme, businesses selling targeted products will pay levies to fund a free nationwide collection network for farmers and growers.
Horticulture NZ CEO Nadine Tunley says accreditation of the Agrecovery scheme aligns with the organisation’s strategic goals. Coordinating operations and sharing costs will help the horticultural sector manage farm plastics and improve sustainability.
“The GPSS is a game-changer for our industry. It will enable growers to recycle a more diverse range of plastic packaging. It is a simple and efficient way for growers to optimise environmentally positive growing practices,” Nadine says.
DairyNZ general manager for policy Dr David Burger confirms the scheme's importance to the dairy sector.
"New Zealand dairy farmers are committed to reducing their environmental footprint, including plastic waste. The GPSS will enable our farmers to progress further along this journey,” David says.
• Recover from stress.
• Learn new things and have new experiences.
• Have purpose and give others your time, words and presence.
• Eat well. Good nutrition keeps us healthy. An important thing rural contractors can do to achieve a healthier work life is to have conversations with farmers and set things up ahead of the season to reduce pressure points.
2.8-5.6m working widths
Suits 80-170HP
Fixed or folding hydraulic models
4.05 – 5.85m working widths
Suits 150-350hp
Hydraulic folding models
For over 150 years GASCON have built gear that lasts.
3.05 – 3.55m working widths
Suits 100-180hp
Fixed width models
KAITAIA Kaitaia Tractors 09 408 0670
WHANGAREI Piako Tractors Northland 09 438 1319
SILVERDALE Brandt NZ 09 427 9137
PUKEKOHE Brandt NZ 09 237 0043
MORRINSVILLE Piako Tractors 07 889 7055
MATAMATA Matamata Tractors & Machinery (07) 888 6292
HAMILTON Brandt NZ 07 847 0425
CAMBRIDGE Brandt NZ 07 827 5184
ROTORUA Piako Tractors Ltd 07 345 8560
TAUPO Taupo Tractors & Machinery 07 378 4533
STRATFORD FieldTorque Taranaki 06 765 8643
HASTINGS Stevenson and Taylor 0800 4273 2273
WAIPUKURAU Stevenson and Taylor 06 858 6041
DANNEVIRKE Lancaster Tractor Services 2022 Ltd 06 374 7731
PALMERSTON NORTH Transag Centre 06 354 7164
MASTERTON Brandt NZ 06 377 3009
NELSON Drummond & Etheridge 03 543 8041
BLENHEIM Drummond & Etheridge 03 579 1111
KAIKOURA Drummond & Etheridge 03 319 7119
GREYMOUTH Drummond & Etheridge 03 768 5116
CHRISTCHURCH Drummond & Etheridge 03 349 4883
ASHBURTON Drummond & Etheridge 03 307 9911
TIMARU Drummond & Etheridge 03 687 4005
OAMARU Drummond & Etheridge 03 437 1111
MOSGIEL JJ Limited 03 489 8199
GORE JJ Limited 03 208 9370
INVERCARGILL JJ Limited 03 211 0013
BUYING EXPENSIVE FERTILISER TO WASH INTO WATER WAYS OR EVAPORATE WITH THE WIND HELPS NO ONE. THERE IS A SIMPLE SOLUTION: HUMATES.
Fred Harvey began using humates on his Te Puke kiwifruit orchard about 23 years ago. He imported a tonne from Australia and applied it to his orchard.
At the time, Fred was in a compost tea business with two associates. They also tried the humates, and they all noticed healthier vines with greener, larger leaves. So they decided to market them.
“When humate sales began surpassing compost tea sales, we formed a separate company called New Zealand Humates Ltd,” he says.
Four years ago, Fred’s daughter, Julia Uffindell, joined the company and she now runs the business side.
Humates are from plant and animal residues which have undergone long-term decomposition.
Fred says humates have three parts – carbon and humic acid, which are better applied to the soil, and fulvic acid, which is best used as a foliar.
“Fulvic acid is the cream of the milk. It does most of the work carrying nutrients directly into plants. It works extremely well with foliar feeds. Adding humates to a fertiliser mix is crucial to increasing soil organic matter.”
New Zealand Humates imports their raw
HUMIC SUPREME LIQUID IS A HUMIC ACID CONCENTRATE THAT CAN BE APPLIED VIA GROUND SPRAY, FERTIGATION OR CENTRE PIVOTS IN ALL AGRICULTURAL AND HORTICULTURAL APPLICATIONS.
humate from Australia. It is extracted from leonardite, a mineraloid layer found above coal seams.
Fred says the Australian humate they use is considered the ‘champagne’ of humates due to its superior quality.
“We are taking a very important product, importing it and putting it on orchards and farms.”
Humates have a very high cation exchange capacity (CEC), so they bind to nitrogen and keep it in the soil longer. Fulvic acid can have a CEC of 1400, whereas healthy soil typically has a CEC of around 25.
“Humates can reduce nutrient leaching. For example, urea usually lasts 12 to 15 days in the soil, but with humates it lasts longer. By holding onto ammonia it helps reduce nitrogen leaching, and can extend the nitrogen sometimes up to 60 days.”
This means growers can apply less urea, less often, which saves money and improves the soil.
Humates also stimulate the soil biology, including the mycorrhizal fungi. They act in symbiosis with bacteria in the soil to help turn nutrients into bioavailable forms.
“It holds it there for the plant to take when required.”
Julia says holding more carbon in the soil, rather than in the air is also an advantage. It is another tool that can negate the effects of climate change.
“In the soil humates increase the value of the farm. Work done by the CSIRO (the Australian government’s Commonwealth Scientific and Industrial Research Organisation)
SOME FARMERS USES FULVIC EXPRESS LIQUID WHEN APPLYING GLYPHOSATE BECAUSE FULVIC ACID AIDS THE TRANSPORTATION OF THE CHEMICAL INTO PLANTS’ ROOT SYSTEMS AND PROTECTS SOIL MICROBES FROM IT.
confirms that organic carbon or humus is the single most important determinant of profitability in farm enterprises.
“For every 0.1 percent that you build up your organic carbon levels and cation exchange capacity, there could be an associated increase in your net profits and land value,” she says.
Some farmers use New Zealand Humates’ Fulvic Express liquid when spraying glyphosate.
“Fulvic acid aids the transportation of glyphosate into the root system and the presence of fulvic acid in the soil profile with glyphosate suppresses weed re-growth up to twice as long as glyphosate alone. Fulvic acid also protects soil microbes from the harmful effects of glyphosate.
“Our clients use Fulvic Express liquid at a rate of 1 litre/ha mixed in with the glyphosate,” Fred says.
Humates also increase the soil’s capacity to store water because they hold up to seven times their weight in water.
Most of New Zealand Humates’ clients are in the North Island, and the majority are on dairy farms or in horticulture. But there are clients in every field including cropping and sheep
THE FIRST MERCEDES-BENZ MEDIUM-DUTY 100 PERCENT ELECTRIC TRUCK – THE EACTROS 300 – HAS ARRIVED IN NEW ZEALAND SAYS NORTH ISLAND MERCEDESBENZ DISTRIBUTOR KEITH ANDREWS.
After 4000 km of testing on New Zealand roads, the eActros 300 is now fine-tuned and available for Kiwi businesses that want to transition away from internal combustion engines (ICE).
With a range of more than 300 km on a single charge, the eActros 300 is perfectly suited to metro and inter-regional work, says Keith Andrews product planning manager Matt Gillatt.
“When fully loaded with a 4.5-tonne payload, the eActros achieved a 300 km range with 20 percent battery charge remaining. This places it squarely in the market for metro operators and those driving between large population centres.”
The eActros 300 is available in 4x2 or 6x2 rigid configurations. It is powered by three lithium-ion battery packs with a combined 336 kW capacity, which produces a peak performance output of 400 kW and 330 kW continuous output.
CCS Type 2 DC charging takes a battery from 20 percent to 80 percent in 75 minutes with
a 150 kW charger.
Operators can also plan where they charge by using the Mercedes-Benz range prediction tool. The tool has also been tested and validated in New Zealand conditions.
Mercedes-Benz engineers have produced an eAxle for its electric units. It incorporates two electric motors that are driven through a two-speed transmission.
“The eAxle has fewer moving parts, which makes it highly efficient,” Matt says. “It offers the same axle limits as a similar-sized diesel truck, and with its design the batteries can be placed for optimal weight distri-
and beef. Farm sizes range from lifestyle blocks to large-scale farms.
Some of their products are BioGro certified. Products are available in liquid or solids, and can be mixed with other products such as sprays and fertilisers. Many clients mix it with fish or seaweed products.
“A number of our clients contacted us because they wanted to switch from hard to soft fertilisers but didn’t know how. Humic material is one tool and a very easy way to improve soil and plant health,” Julia says.
It seems one of those too-good-to-be-true stories, but Fred says there is research from universities around the world that supports the use of humates.
IN LOCAL TESTS A FULLY-LOADED EACTROS ACHIEVES A 300 KM RANGE WITH 20 PERCENT BATTERY CHARGE REMAINING
bution and performance.”
The eActros cab gives drivers plenty of space to do their work, and the driving position, instrument display and switchgear layout will be familiar to those who have driven a diesel Mercedes-Benz.
Noise levels in the cab are about 50 percent (10dB) less than in an ICE truck, and the cab has a multimedia cockpit with two 10-inch high-resolution screens.
Like its diesel Mercedes-Benz counterparts, the eActros has advanced safety features as standard. These include Active Brake Assist 5 with pedestrian
“There is lots of information around now. It is a fairly new product here, but is used a lot in Europe and the US.”
Julia says it is also a low-risk product to try out.
“We had a couple come up to our stand at the National Fieldays to say they recently tried using humic products on one paddock and could see the results so they wanted to do more.”
Fred compares using humates with humans taking probiotics.
“The soil is the plants’ stomach. If you don’t have the correct bacteria in your stomach, what happens? It is harder for ionisation to take place.”
detection, Advanced Emergency Braking, Stability Control Assist, and Tyre Pressure Monitoring.
The second-generation MirrorCam system is also standard. It has two in-cab A-pillar mounted 15-inch monitors.
“If you are thinking about moving away from diesel engines, the time is now,” Matt says.
“eActros has proven its ability to tackle predictable, inter-regional routes. It provides operators with a safe, comfortable, and quiet working environment.
“Keith Andrews staff are ready and waiting to assist with the transition to electric trucks, so give us a call on 0800 487 825.”
New Zealand Humates’ products include Liquid Humate Trimate, which is a BioGro-certified mix of humic acid, fulvic acid and carbon. It can be mixed with fertiliser or used on its own as a foliar for plant health.
Fulvic Express is a liquid formula rich in fulvic acid, which can be sprayed on the ground or as a foliar. It is BioGro-certified and delivers results.
Nitrogen Express is used to decrease leaching and retain N in the soil longer. Humic granules can be spread on the ground or mixed with fertiliser and seed.
For more information call 0800 HUMATES or visit the website humates.co.nz.
VINEYARDS AND ORCHARDS
Vineyards are often on steep terrain and, like orchards, they typically have narrow rows and small spaces between vines or trees. Tracked vehicles are often too wide to pass between rows with a comfortable margin of error.
Trelleborg’s PneuTrac is a hybrid system that combines the efficiency, comfort and handling of a radial agricultural tyre with the wide footprint and traction of a track.
PneuTrac delivers outstanding performance on both steep slopes and muddy terrain. This can reduces stress on roots which contributes to healthy crops and better yields.
On-road, the hybrid nature of the PneuTrac gives better safety, handling and comfort along with
lower fuel consumption in line with a modern radial pneumatic tyre.
Ross Tanner of Tanner Spraying is a very happy user of PneuTrac tyres. Ross is a contractor based in Katikati. He has been running the Trelleborg PneuTrac on his New Holland tractor since 2022.
Ross says the PneuTrac tyres allow him to go places he couldn’t go before and with less mess.
TRS Tyre & Wheel national sales manager Mark Prentice says the PneuTrac is a game changer for the NZ viticulture market, and it demonstrates Trelleborg’s commitment to sustainable farming
“When they designed the PneuTrac, Trelleborg focused on the requirements of key producers. For example, the roots of vines are incredibly precious and sus-
ceptible to damage,” Mark says.
“Just as with conventional agriculture, the topsoil needs to be protected and tractor slippage can easily be a disaster for both the soil and roots. PneuTrac can help protect some of our most valuable agricultural assets.”
Pneutrac has the Omega Design sidewall. Its extended footprint ensures outstanding flotation, traction and lateral stability. It can deliver solid traction even on slippery slopes, typical of wine country.
It can also help reduce machine downtime, a critical concern for farmers looking to increase productivity and gain substan-
THE PNEUTRAC TYRE FROM TRELLEBORG COMBINES THE EFFICIENCY AND HANDLING OF A RADIAL TYRE WITH THE WIDE FOOTPRINT AND TRACTION OF A TRACK.
tial cost savings in fuel, maintenance and labour.
PneuTrac is available in VF sizes 280/70R18, 280/70R20, 420/70R28 and 480/65R28.
TRS Tyre & Wheel offers a wide range of Trelleborg and Mitas tyres across New Zealand. Contact TRS via the website trstyreandwheel.co.nz or on 0800 336 334.
By Mark Hamilton-Manns, AGCO product marketing manager
MOST MANUFACTURERS
OFFER TRACTOR IMPLEMENT MANAGEMENT (OR TIM). IT IS NOT UNIQUE TO ANY SINGLE MANUFACTURER BUT RATHER A STANDARD THAT MANUFACTURERS MUST CONFORM TO IF THEY WANT TIM FUNCTIONALITY.
In most ISOBUS systems, the tractor controls the towed implement. TIM is ISOBUS technology in which the implement controls certain tractor functions and optimises the work process.
Covid lockdowns showed New Zealand contractors the varying skill levels of operators who are not from the UK or Ireland. TIM is a tool to mitigate this risk.
The journey to TIM began in 1991 when the International Organization for Standardization (ISO) set up a working group. Its mandate was to develop a standardised communication protocol for agricultural equipment.
A decade later, in 2001, ISOBUS started to make its way into practical applications. Tractors and implements began to incorporate this technology. It was patchy, with different versions and unreliable communications, so it heralded a blame game
between tractor and machine manufacturers.
Then, between 2003 and 2005, significant strides were made, and ISOBUS became increasingly efficient. This period saw the introduction of ‘plug fests', where manufacturers tested the compatibility of their equipment with ISOBUS, to ensure seamless communication across various brands and models.
The Agricultural Industry Electronics Foundation (AEF) was established in 2008. The AEF plays a crucial role in setting standards and facilitating collaboration among different stakeholders in the agricultural electronics industry. They have introduced recent improvements to ISOBUS, including TIM.
A critical point is that TIM is not embedded on every tractor or implement. It must be fitted at the factory.
When connecting a TIM baler to a tractor for the first time, information is exchanged between the tractor and the implement. Sending the information can take about five minutes as a considerable data package is transferred. Both machines check the validity and currency of their on-board digital certificates.
If both are in agreement, the tractor and implement exchange a shared key, which is effectively a virtual handshake. This key will be checked when starting the same combination of tractor and
TIM REMOVES THE NEED FOR BALER OPERATORS TO CARRY OUT REPETITIVE ACTIONS, SUCH AS STOPPING AND STARTING, AND INCREASES THE PRODUCTIVITY OF BALING.
implement every time. If either is not current or broken, the partnership will not work.
Tractor Implement Management has two main functions:
1. To remove repetitive actions from the operator. These might include stopping and starting and selective control valve (SCV) operation when baling.
2. To assist the operator in achieving increased productivity. As the machine takes control, it removes a high degree of operator input.
Autopilot is a good analogy for TIM. It takes away the complexity of multiple tasks and assumes control over the aircraft. The pilot is generally resting at the wheel, alert for problems.
As the story goes, a plane can be flown by a pilot and a dog: The pilot is there to feed the dog and the dog is there to bite the pilot if he touches anything. Maybe that’s the future for tractors too?
Fendt Rotana balers feature TIM, which gives improved operator control and productivity. Advantages are:
• TIM stops the tractor. There is no need to declutch, hold brakes or shuttle the forward reverser. The tractor does the work. Simply touch the drive lever and go.
• The tailgate functions automatically so there is no need for operators to cycle SCVs repetitively.
• The pick-up is automatically
raised when weighing the bale so it doesn’t interfere with the tare weight.
• Knife slots are cycled to prevent blocking. This has the added benefit of removing the need to change to blind knives.
• Moisture sensors trigger when the material is too wet to avoid bale spoilage and deterioration of quality due to mould.
• Every bale is weighed to record yield and assist contractors in adding value to their customers.
• The last bale layer is uncut to ensure edges and corners don’t crumble and retain their integrity when storing or shipping.
• Finally, side panels light up automatically when opened.
Austrian test magazine, LandWirt published some recent data on TIM. They measured performance increases of around 15 percent in binding and ejecting with TIM. In the overall baling process, efficiency increases were around 7 percent. This equates to around three more bales per hour, with less operator input.
Extend this performance increase over a full day and it could result in an additional 36 bales. It is important to underline that no more fuel and time were expended; the gains were made by simply increasing efficiency.
Talk to your local Fendt dealer about Tractor Implement Management on Rotana balers.
CANTERBURY CONTRACTORS PHIL AND TIM MAY HAVE PUT TOGETHER A FLEET OF MACHINES WITH THE TECHNOLOGY THAT HELPS THEM ACHIEVE HIGH PRODUCTIVITY AND MAINTAIN THEIR REPUTATION FOR EFFICIENT, RELIABLE SERVICE.
Since the two brothers started May Brothers Contracting as teenagers 17 years ago, they have grown the business to a fleet of more than 30 John Deere tractors, as well as combine harvesters, forage harvesters and windrowers.
Based near Methven, Phil and Tim have a reputation for innovation. In addition to providing contracting services to Canterbury farmers, they grow potatoes for a global company.
Phil says their ability to streamline their operation, closely monitor expenses and offer a cost-effective service has been made easier by having John Deere machines equipped with JDLink and John Deere Operations Center.
“A lot has changed over 17-odd years. As far as technology goes, everything is so much more efficient and it is right there on your phone,” Phil says.
“We always manage our costs when we run machinery, and Ops Center shows us how efficient the machines are, our working times, idle times and how much fuel is getting burnt.
WITH OPS CENTER, MAY BROTHERS CAN SEND DATA FROM THEIR JOHN DEERE X9 1100 COMBINE HARVESTER TO THE OFFICE COMPUTER TO PRODUCE YIELDS MAPS.
“It has transport as well, so we can see how much time we spend on the roads. We can factor all of that into what we charge and offer a cost-effective service.”
Phil says the technology available now is a far cry from the days when a USB stick was needed to transfer information from a machine to a computer to create yield maps. With Ops Center, they can send yield data from the combine harvester to the office computer and produce maps immediately.
“You have got all the benefits of sending information from the forage harvester straight back to the office. It is a lot more user-friendly and all remote. It is brilliant.”
When they were growing up, Phil and Tim got to know another local, Pete Etheridge, whose John Deere dealership, Drummond & Etheridge, has been operating in Ashburton for 50 years.
“You do business with the dealership, but it is people who make the business. Knowing Pete has been a big part of our
John Deere background,” Phil says.
“Our machines can now send error codes to the dealership. Often when we phone to tell them we have had a breakdown, they are almost one step ahead of us.”
Phil says while it was hard to put a dollar value on connectivity for the business, it saves time by collating data and providing detailed information on their fleet and crop yields.
Recently May Brothers invested in a John Deere X9 1100 combine harvester which they have to harvest a variety of crops, including ryegrass, rapeseed,
METHVEN CONTRACTORS PHIL AND TIM MAY USE THE CONNECTIVITY OF THEIR JOHN DEERE FLEET TO SUPERCHARGE EFFICIENCY.
kale seed, wheat and barley.
“We have only done the one harvest with the X9 so far, but the performance in cereal crops is probably twice the capacity of anything we have ever owned,” Phil says.
“John Deere spends a lot of money on R&D and they are working years ahead of where we are today. They are already onto the next thing.”
TARANAKI
GEOFF HART SAYS FARMERS
"They want someone who knows their farms and how they like the job done. They get frustrated when someone different turns up all the time,” he says.
HAVING THE SAME GUY TURN UP YEAR IN AND YEAR OUT.
You can see their point. Farms are not only homes and workplaces - they are part of a farmer’s identity.
Hart Contracting specialises in spraying and Geoff and his two drivers (Tony Brophy and Damian Hill) know their clients and their farms. They also appreciate the variety of work they do.
“We see all types of farms and everyone does things a bit differently and has different opinions,” Geoff says.
Hart Contracting is based in Inglewood. It is a diverse business. Aside from the spraying, Geoff does earthmoving and snow ploughing with Fulton Hogan Stratford. Also he and business partner Gareth Littley recently bought a quarry.
It was a meandering path to get to this position and it required manoeuvring around some obstacles.
Geoff grew up in Stratford where his parents had close ties to the ag industry. In 2003 he went to Taratahi Agriculture Training Centre in Masterton. He returned to Taranaki and managed various dairy farms. Then some obstacles loomed in his path.
In 2013 the farm he was on was about to be sold and the jump to 50:50 share-milking was just too
FROM ITS TWO BASES AT INGLEWOOD AND STRATFORD, HART CONTRACTING DOES CONTRACT SPRAYING AND EARTHMOVING THROUGHOUT WESTERN AND CENTRAL TARANAKI.
high. He got around that problem by landing a job as a field rep for Farm Source.
Geoff has always been interested in pasture management, so at the same time he started
doing pasture readings for farmers. He provided an estimate of what they were actually growing and helped with feed budgets, so farmers could make informed decisions about crops and supplements.
On weekends and after work, Geoff visited farms and did his calculations. Demand for the service grew until it became a full-time job.
In about 2017 the dairy payout dropped significantly and farm-
ers started cutting services. This created another obstacle in his path, and Geoff side-stepped it by working with a mate in Wairarapa who needed help building forestry roads.
For two and a half years Geoff did earthmoving in Masterton and came home on the weekends to work with his remaining farm clients.
When the forestry contract came to an end, Geoff adapted again.
“It was just before Covid and I discovered there was a gap in my home area for someone with an agronomy background to do spray work.”
This was the start of Hart Contracting. Geoff already had chemical applicator and approved handler certificates, so he bought a John Deere 6125M tractor and a Bertolini LS1300 sprayer and got to work.
“It was right on the start of Covid and it was nerve-wracking. But I had a lot of work from previous contacts and I worked through that.”
Using a tractor with a threepoint linkage sprayer keeps him flexible. “It is so versatile. I can unhook and do something else with the tractor, but a spray truck is just a spray truck.”
HART CONTRACTING’S NEWEST TRACTOR IS A NEW HOLLAND T7190 WITH 19-SPEED POWERSHIFT.
In fact, after a year Geoff had enough work that he bought a Land Cruiser spray truck so he could get to clients faster and look after farms that are further away.
A year later, he had even more work, so Geoff got another John Deere tractor and another sprayer, and employed Tony Brophy. At the same time he began doing some roading work with
FOR HIS EARTHMOVING WORK GEOFF HART HAS A SIX-TONNE DIGGER AND TWO 12-TONNE MCINTOSH FARM TRAILERS.
Fulton Hogan in east Taranaki. He bought a six-tonne digger, and trailers for the tractors.
“Tractors work in all weather, and we can use them on forestry roads. We have two 12-tonne McIntosh farm trailers. They are a suitable size for what we do. They are nice and safe when hauling a 10-tonne load and they are a good match with a six-wheel truck.”
He bought his Komatsu digger second-hand. “It was on low hours. I have had a lot to do with Komatsu diggers and this one ticked all the boxes. I have had a good run with it.”
Most of Hart Contracting’s earthmoving is with Fulton Hogan, but they also do some races and drainage jobs for farmers.
A year and a half later, they were struggling to keep up with the workload.
“Another spray contractor was shutting down and field reps were hounding me to do the work. I said I couldn’t do it unless I could get another guy who could hit the ground running.”
He did find that operator, Damian Hill. “Damian does that area now. He organises his day and off he goes though I am there if he needs me. It is bloody great.”
The next big investment was a tow and fert sprayer made in Dannevirke.
Geoff says it is an unbelievable machine. “We haven’t put it anywhere near its limits.”
Farmers had been asking Geoff about liquid fertiliser. Initially he used his existing sprayers, but, he says, it is hard on them.
“Fertiliser is really corrosive and you have got to cover a large area fast.”
He asked his clients and enough said they were interested to justify the Tow and Fert. It also provided the tractors more work.
“Farmers have got to get more profitable production from the same land, so it would be silly not to look at more options.”
Some go for fish brews. Some want liquid urea and/or ProGibb. Some do molasses and humates.
“There are all sorts of things that farm advisors are dreaming up.” He says lots of farmers are interested and they just need to start small, try something and then tailor it to suit themselves.
Geoff has Tow and Fert’s Multi 2800, which is the second biggest in their range. He decided not to go for the largest because
he was worried about the extra weight in wet areas and because Taranaki paddocks are mostly small.
“A lot of the time we’re struggling to find 20 ha to do at once. We did not want bulky machines making a big mess.”
He says Tow and Fert has developed a very good app. He enters the brew and the app gives a good idea of what nozzles to use, the travel speed and rate to aim for.
“I think this side will grow more and more. The Tow and Fert has stainless steel or plastic components, which fertiliser can’t corrode. I saw the damage it did to the boom sprayer in only a couple of days.”
Geoff also adds small seeds to the fertiliser mixes. He says it does chicory, clover and plantain, no worries. He has also had success with turnips.
He says one client added chicory and clover to the urea at 2 kg to the ha. “The farm is now riddled with chicory and clover.”
About 95 percent of Hart Contracting’s ag clients are dairy farmers. He is now also doing roadside spraying and snow ploughing on Mt Taranaki for Fulton Hogan. “They have the maintenance contract and were doing it, but struggling to keep up.”
Geoff did some number crunch-
TO TAKE ON ROAD SPRAYING GEOFF HART BOUGHT A CASE IH PUMA WITH A CVT TRANSMISSION AND BUILT HIS OWN REACH ARM SPRAYER.
RECENTLY GEOFF HART ADDED A LAND CRUISER SPRAY TRUCK TO THE BUSINESS SO HE COULD LOOK AFTER FARMERS FURTHER AWAY FROM HIS BASE.
ing, then bought another tractor and built his own reach arm sprayer. “It reaches further and carries more spray in a day than their little trucks were doing.”
Part of that job requires getting more standards on the chemical applicator certificate to cover total vegetation control.
One problem Geoff had to sort out was no-spray zones. These are important for some landowners, but at times it is challenging to recognise them. Signs may be knocked over or obscured.
His spray operators had to operate from a list of no-spray zones, but it was often out of date. Besides it is not ideal for a spray operator to scan through lists when they should be paying attention to driving and spraying.
Geoff approached Tabula (formerly Tracmap) to map these areas. Now when the operators cruise along working, the no-spray zones are coloured in, it is obvious without being distracting.
“As far as we know, we are the only contractors in New Zealand doing it.”
He says Tabula were very helpful setting it up. “There is no real cost to this extra feature, but we do spend plenty each year with Tabula.”
It fits in nicely with the overall need for proof of placement, and nips in the bud any potential arguments over harm in no-spray areas.
When Hart Contracting sprays farm land, Tabula produces a PDF file that has a Google Earth image with the sprayed paddocks coloured in.
“Tabula is an extra cost, but
MOST OF HART CONTRACTING’S EARTHMOVING IS WITH FULTON HOGAN, BUT THEY ALSO DO RACES AND OTHER JOBS FOR FARMERS.
HIS FATHER, GEORGE, WAS A JOHN DEERE MECHANIC, SO GEOFF HART KNOWS THEM WELL AND SAYS THEY ARE ALWAYS RELIABLE.
hart contracting works all over taranaki
They travel north to Awakino, down to Eltham on SH3, and south along the coast road.
It is a big area which means they can spray early crops in the north and by the time they have worked their way south, those northern crops are ready for a second spray.
Winter is quieter, but then the Fulton Hogan work keeps them busy, and now they have 50 ha of land and a quarry to play with.
The aim is to fully utilise the gear they have and even out the income stream over the year without getting too big.
“Cara and I talked about it and we want to stay small and keep control and farmers like the same guy turning up year in and year out.”
well worth it. We might get extra work because we supply that proof of spraying.”
Traffic management is another cost. Hart Contracting uses a pilot vehicle on busy roads or where there are lots of dips and hollows.
“It is so costly to comply these days. It is starting to hinder contractors because we have to pass it on.”
Geoff began contracting with John Deere tractors. “Dad was a John Deere mechanic and I grew up with them. Lots of farms I worked on had John Deeres. I find them reliable and in a business you need reliability. I have had a very good run out of them.”
Hart Contracting still has two John Deeres – a 6125M and 6140M – both with PowrQuad transmissions. Then came the pragmatic leap to other brands.
Now a Case IH Puma 165 with CVT does the roadside spraying.
“We started looking around for a new tractor and the TransAg salesman came up with a good deal. I am quite impressed with it.”
The CVT makes life easy when there is enough to think about spraying roadsides. It is also comfortable with leather seats and other such luxuries.
When they got the Tow and Fert, Geoff went hunting for another tractor. He was thoroughly
impressed with the Case IH but then he got a good offer on a New Holland T7190 with 19-speed PowerShift and he went with that.
The quarry that Geoff runs with Gareth Littley used to be run by another contractor, but it had shut down. When the 50-ha farm the quarry is on came on the market, Geoff and Gareth bought it.
“I will run the cropping farm and he will run the quarry. It creates diversity for my guys and security on the days when they can’t be spraying. They can crush in the quarry if it is blowing or wet for days,” Geoff says.
His dad, George Hart, has been
GEOFF HART SAYS HIS DAD GEORGE HELPED HIM GET HIS YOUNG CONTRACTING BUSINESS OFF THE GROUND.
a huge help in getting this venture off the ground. George has extensive knowledge of heavy machinery and has lent a helping hand almost daily.
Central Quarries and Crushing is in Stratford, while Geoff’s yard is in Inglewood, so they now have two bases in Taranaki.
They took over the quarry on May 1st and the first trucks carted metal out the gate on the 16th. They have excavators, loaders and crushers on site and supply a range of aggregates.
They have also applied for consent for clean fill to be stockpiled for sale or reinstatement.
“Our quarry is another arrow for our bow. It will generate more work for tractors and trailers.”
In addition to cropping, the farm will take dairy cows over winter.
A vital part of the whole operation is Geoff’s partner Cara Muir. They have two children Milly (3) and Frankie (1). Geoff also has an older daughter Mia, who is 16.
Cara used to do the office work, but is now busy with the two youngsters plus working on her own home business.
“She is a busy lady. She runs around sorting everything out. I wouldn’t have achieved what I have achieved without her.”
Geoff’s mum, Annette Hart, has now taken over the book work for the contacting and quarry. “It takes so much pressure off, having someone do that.”
IN MAY, GEOFF HART AND BUSINESS PARTNER GARETH LITTLEY STARTED CARTING AGGREGATES FROM A DEFUNCT QUARRY THEY BOUGHT AND REACTIVATED.
CONTRACTING IS NOT ALL BALERS, DRILLS AND TRACTORS. FARMERS ALSO NEED DIGGERS.
Waikato-based Glenn McGuire and his company McGuire Drainage & Contracting Ltd provide a range of earthmoving services.
Like most things rural, at first thought it sounds straightforward enough, until you start pondering the details. Such as: How do you stabilise a mains pipe undercut by a flooded creek? How do you clean up a slip with tonnes of soil still above you? What is the best way to drain a particular paddock?
This is why the world needs experts. McGuire Drainage & Contracting specialises in erosion control and it does other waterway works, such as creating gradient structures and fish passes.
Glenn is based in Pirongia, where he grew up. His father, David, was also a contractor. He started contracting in 1996 with a Bobcat.
Glenn undertook a diesel mechanic apprenticeship at Land Power. Then, at age 21,
went to Darwin, to work on a farm closely associated with a mine. At first he was a mechanic and then drove diggers and bulldozers. It was all big gear, such as a Caterpillar D11.
Back at home his father had purchased a truck and was getting busier. Glenn came home to give him a hand.
David passed away 10 years ago, but Glenn has kept the business going and has expanded it.
Now, 21 years since he joined
GLENN MCGUIRE HAS A SOFT SPOT FOR HITACHI DIGGERS. HE HAS THREE OF THEM AND TENDS TO WORK THEM FOR 6000-8000 HOURS BEFORE TRADING THEM IN.
the business, Glenn has two Hitachi diggers as his frontline machines. One is 13.5 tonne and the other is 13 tonne. He can also call on a 12-tonne Sumitomo and
GLENN MCGUIRE’S FATHER DAVID STARTED THE CONTRACTING BUSINESS IN 1996. GLENN LATER JOINED HIM AND HAS KEPT THE BUSINESS GOING AFTER DAVID PASSED AWAY 10 YEARS AGO.
a 20 tonne Hitachi with an 18m boom.
Glenn says Hitachi is a good strong machine. He has found it optimum to purchase diggers new and update them after about three years or at 6000 to 8000 hours.
These days he uses Leica laser level-guidance and GPS to add precision and save time.
One of McGuire Drainage & Contracting’s diggers is usually on farm work. It cleans overflows and maintains or establishes raceways and drainage channels. Their farm clients cover the range and include a bit of everything – dairy, dry stock and deer farms.
Glenn says these days lots of farmers have their own digger, so he needed to diversify. He still does farm work for those who do not have a digger and those
who maybe under-estimate the complexities and all the regulations and consents required to do some jobs.
Wetlands are a good example. If you are working on a wet area and over half of it is in native species or rushes, then draining is not permissible.
“Some places really have no value in being drained and should be planted and retired. After all, wetlands have value in both drought and flood. Forming and maintaining an ecological
balance is primary.”
McGuire Drainage & Contracting is also proficient when it comes to clearing house sites, constructing horse arenas, and cleaning calf sheds.
Glenn says emergency works can be challenging and it is vital to be aware of all legislation and the consent processes involved.
One example of this occurred in late 2023, where a water main was left suspended when 30m of river bank became eroded by the Waikato River. McGuire
ONE OF MCGUIRE DRAINAGE & CONTRACTING’S SERVICES IS MULCHING, WHICH GLENN MCGUIRE SAYS IS A GOOD WAY TO MANAGE OVERGROWN WATERWAYS.
Drainage & Contracting was the lead contractor, positioning tonnes of rock and metal to stabilise the bank.
Hamilton’s western water supply is no longer at risk, after work to protect a critical piece of
THE COMPANY WAS THE LEAD CONTRACTOR IN AN EMERGENCY PROJECT TO SECURE AN ERODED BANK ALONG THE WAIKATO RIVER THAT WAS THREATENING A WATER MAIN.
glenn mcguire is happy to use subcontractors if he needs help
He says this ensures he gets good operators. It also limits the amount of money and time he has to invest in buying machinery or training labour for a type of job that may only last a short term.
“We mainly work with three companies that are all experts in their fields. Pooling of resources is a viable and cost effective use of time and gear.”
Glenn’s brother, Brent, runs McGuire Bulk Haulage, and also gives a hand when required.
water infrastructure wrapped up late last month.
McGuire Drainage & Contracting and the Hamilton Council’s Three Waters unit spent seven weeks reinforcing the bank of the Waikato River at the mouth of the Mangakotukutuku Stream, where river flow had worn away a 30m-long section of bank.
The erosion was underneath pipes that supply drinking water to about 30,000 properties on the western side of the Hamilton, including Dinsdale, Frankton, Rotokauri, and the CBD.
Up to 25 truckloads of material were delivered to the site each day. This included about 1100 tonnes of metal and 2300 tonnes of large rock. This rock was then carefully placed along the riverbank and underneath the river level by a long-reach digger, strengthening the bank and reducing any chance of future erosion at the site.
Glenn and his team mostly work in the greater Waikato area but they are not limited to it. They source all the materials they work with from quarries that work on an environmentally sustainable basis, in accordance with the appropriate rock specs.
McGuire Drainage & Contracting Ltd is also skilled in mulching, which they do with the 13-tonne Hitachi. Glenn says mulching is a very efficient and practical way to manage herbage and it is also an environmentally sound practice.
MCGUIRE DRAINAGE & CONTRACTING HAS A SMALL, WELL-TRAINED TEAM OF DRIVERS, WHO ARE TAUGHT TO GET THE JOB DONE RIGHT AND SAFELY.
THE MCGUIRE DRAINAGE & CONTRACTING TEAM USES TRACTORS TO SPREAD EFFLUENT AND CRUSHER DUST. ITS CURRENT DEUTZ FAHR ALSO HAS WINCHES ON THE BACK TO CLEAR LOGS AND OTHER BLOCKAGES FROM GULLIES.
The mulching digger has 1500mm mulcher heads, meaning that it can easily deal with pest species such as willows which cause blockages to waterways, or barberry and hawthorn. The mulcher also can tackle small trees up to 300 mm in diameter. McGuire Drainage & Contracting has its own trucks and trailers to move its diggers and cart rock and metal. The preferred truck option is Isuzu six-wheel tippers.
Glenn says Isuzu are a good brand, but in general he considers trucks to be rather expensive items to run and they cannot compete for his affection with the beloved diggers.
Also part of the team is a 620 Deutz Fahr tractor with a manual transmission. “We find a manual is better for this work. We’ve had IVT on another brand and didn’t like it. The four-wheel drives didn’t cope either. So we’re back to manuals and using a Deutz Fahr.”
The tractor has two winches on the back so that it can be used to clear gullies of logs and blockages. This work is not for the faint hearted.
“We have the second cable to drag out the main cable. Training is a big part of our company’s health and safety programme. We need a small, well-trained group that can operate a variety
MCGUIRE DRAINAGE & CONTRACTING SPECIALISES IN EROSION CONTROL, AND DOES EARTHMOVING FOR DAIRY, DRY STOCK AND DEER FARMS.
of machinery and equipment.”
There are four operators who run the diggers (including
Glenn). The company’s policy is to leave people in the same digger and not swap around. In this way, everyone is comfortable in their own machine and they can have it set up as they like it.
Glenn employs an engineer who also does the tractor work and winching.
All earthmoving work is permitted to be carried between 1st
October and 1st May. So from May onwards, the focus is on maintenance and carrying out any modifications necessary on the machinery and equipment.
Glenn has two horse-mad daughters, so when he’s not at work, his weekends can involve equine events or farm trekking with them.
MCGUIRE HITACHI DIGGERS FITTED WITH ROTATING GRAPPLE AND MODIFIED GRAB BUCKETS.
He says McGuire Drainage & Contracting is a small nimble organisation, with a depth of experience. “My operators’ attention to details makes us what we are.”
IT ONLY TOOK A WEEK OF MILKINGS FOR KYLE SELMAN TO REALISE HE WOULD NOT BE FOLLOWING IN HIS PARENTS’ FOOTSTEPS INTO DAIRY FARMING. HIS DIFFERENT PATH EVENTUALLY LED TO KYLE SELMAN CONTRACTING LTD.
Kyle’s parents had a dairy farm near Hobbiton (Matamata), in the Waikato. When he had his ‘stuff this’ moment with the cows, Kyle worked for a wellknown local contractor for a couple of seasons.
Then he headed off overseas and drove for an arable and silage contractor in Buckingham, England. He had five summers in a row alternating between contractors in the UK and New Zealand. Then Kyle’s daughter was born, so he stayed put in the Southern Hemisphere.
It was during this time he bought his first under-sower as a do-up project.
“I walked into a dealership and it was sitting there. Half an hour later I owned it. It was a Duncan Enviro 3000E.
“I learned a lot of engineering by rebuilding it. It took a bit of maintenance to keep it going, but it got me to where I am now.”
KYLE AND KIDS: KYLE SELMAN WITH HIS CHILDREN (FROM LEFT) CELIA, ALEX AND LILA.
The year was 2018. Kyle needed a tractor to tow the Duncan Enviro, so he went on the hunt. He came across a 2014 Massey Ferguson 7624 Dyna VT on 2300 hours.
That was the start of everything and it snowballed from there, he says. He moved from being a sole trader to a company, Kyle Selman Contracting Ltd.
In the background all this time
KYLE SELMAN SAYS HIS VÄDERSTAD RAPID SINGLEDISC DIRECT-DRILL IS “DEADLY ACCURATE” AND VERY RELIABLE.
was his mate Jacob Klaus. Kyle and Jacob had been friends since primary school, and both of them are hard-working and ambitions.
Jacob started Klaus Ag when he was also working for the local AGCO dealer, Matamata Tractors and Machinery.
Kyle was working for two other well-known contractors in the district but he also drove on weekends for Jacob and his father Robert, who helped get Klaus Ag off the ground.
Eventually both Kyle and Jacob left their other gigs to do their own contracting work full-time. It was Jacob who helped Kyle buy his first tractor.
gle-disc direct-drill with a 4m working width and five-inch row spacing.
“It was half the price of other machines of the same width, and ended up being the most reliable machine out there,” he says.
In one pass the Rapid A400S drills the seed, adds fertiliser and spins on slug bait. Kyle says it is “deadly accurate” and easy to use with the iPad control system.
harrow. He got an excellent deal on a 6m Pottinger Lion, which he mainly uses in spring to prepare maize ground.
“The Lion leaves a smooth finish in the paddock and has not missed a beat. There are probably better machines on the market, but for what I paid for it and for what we do it fits the bill perfectly. I would be interested in getting another when I need to upgrade.”
Two years ago he bought a Maschio Attila subsoiler. “The Attila is easier to use than discs. It doesn't ridge up the paddock. The finish is a lot smoother with rippers than discs and you don’t get a pan like you do with ploughs and discs.”
At the time Kyle was looking to buy a second-hand Fendt 824 that had done a lot of work. Jacob sent him a TradeMe link to a Massey Ferguson that was for sale in Taranaki. They went to look at it on ANZAC day and Kyle bought it on the spot.
“Jacob knew all about Massey Ferguson. It was better value for money than anything else I was looking at.”
Even though it was a good deal, buying the second-hand Massey Ferguson was still a lot of money to pay out at once. Most contractors likely remember those early days and sleepless nights, hoping to God you’ve done the right thing and the calculated risk pays off.
It did work out for Kyle. He kept working for another contractor, but he also sent out a flier announcing that he was offering under-sowing services. From there his business grew through word of mouth.
The Duncan drill started him off for two seasons and by then there was enough work that he needed something newer and faster.
He bought an ex-demo Väderstad Rapid A400S. It is a sin-
He got it in February 2020, just in time for the Covid-19 lockdowns. That created more sleepless nights. “I was worried I wouldn’t be able to use it because of Covid.”
After he bought the Rapid, he ran it for 12 months. He did not really like the way the second hopper was set up, so he merged the two hoppers together, which shortened the whole setup.
“Before I modified it, we would fill it with five bags of seed. Now it can take 12 to 15 bags and it still holds 1.5 tonne of DAP. We added a StocksAg Rotor Meter to spin on slug bait and clover seed.
After that, Kyle’s work load really took off. The first season with the Väderstad Rapid he did 500 ha. He did twice that in his second season.
It drills chicory, turnips, kale and swedes in spring and in autumn mainly grass and oats. This past season, he also drilled barley with it for the first time.
“I could not be happier with that drill. It is extremely reliable. The only problem is that I have done 7000 ha with it and it is worn out.”
Kyle’s strategy is to lease gear when he needs it. Then, as his clients and finances build up, he buys an implement if the workload justifies it.
A recent example is a power
He did have a set of discs, but he traded them in. “Personally I just don’t like discs, I prefer rippers.”
Although the Attila can theoretically rip down to a depth of 900 mm, Kyle reckons you would need a bulldozer on the front to do so.
He generally works down to 30cm. He mostly uses it to plant maize in sprayed-out pasture. The routine is first a pass with the DIRECT DRILLING AFTER A MAIZE CROP WITH THE VÄDERSTAD RAPID A400S, WHICH HAS A 4M WORKING WIDTH AND 5-INCH ROW SPACINGS. TO ESTABLISH MAIZE KYLE SELMAN GENERALLY DOES A PASS WITH HIS RIPPERS, THEN HIS POWER HARROW, AND THEN THE MAIZE PLANTER.
ALONG WITH ITS BLACK PAINT JOB, THE 305-HP MASSEY FERGUSON 8S 205 HAS A BIG CAB, TIGHT TURNING CIRCLE AND DYNA VT TRANSMISSION.
rippers, then the power harrow, and finally the maize planter.
“After harvest we go back in with the under-sower and job’s done.”
The maize planter is an eightrow Kverneland Optima, which does both seed and fertiliser. Kyle bought it second-hand as a good deal.
“When we got it we put in seed and DAP and grew one of the best crops of maize I have seen for a long time. It hasn’t missed a beat.”
Planting maize is Kyle’s favourite job. “It is nice and smooth, with no bumps. You cruise all day.”
His Optima is getting old and ideally Kyle would like to trade it in for a Väderstad Tempo F8. “I think the Tempo has a higher working speed and everyone else in the district has one.”
When Kyle got the maize planter, he also updated his tractor. Over the four years he had the MF 7624, he put 5000 hours on it.
“It was easy to work on if anything went wrong. It performed well and it sounded cool. It only had a couple of hiccups and it never let me down.”
Initially he ordered a MF 7720S with Dyna VT from Matamata Tractors, but then they told him the new Massey Ferguson 8S was available.
“I have been interested since the MF 8S was released a couple of years ago in Europe.” He was allowed to change his order and a year later in January 2023 he became the owner of a new black MF 8S 205.
“I always wanted a black tractor. I thought it would look cool, and it does.”
He says the 8S has a lot bigger cab than the 7624. “The amount of space is massive. It is a slightly bigger tractor than the 7624 but is much more manoeuvrable.
“The turning circle is freaking amazing. That’s one of the main things people say when they come for a ride – it turns sharp.”
In his young contracting career Kyle has made some sensible financial decisions. Starting out he has mainly bought second-hand gear. Only his latest tractor is brand new while his Vaderstäd Rapid under-sower is an ex-demo machine.
It means he can get through more gateways, even though it is slightly wider.
While it is possible to drive the MF 8S in manual mode, Kyle cannot see the point. He leaves the tractor to work out the best gear, utilising the full Dyna VT continuously variable transmission.
“It is a high-spec tractor. I ticked every box I could when I ordered it. I wanted it to do everything with the gear I have now and I wanted to future-proof it for machinery I get in future. For example, I ordered it with air brakes because I am considering heavy trailer work.”
He says the MF 8S has been a good investment. It is very quiet inside and has front suspension, front linkage and front PTO.
It also has auto-steer, full sun blinds on each window, side window wipers, fridge and air-conditioning in the seat. (“The air conditioned seat is a game-changing invention. It’s awesome.”)
For now Kyle is happy to remain an owner/operator. He mostly works for dairy farmers, ranging around eastern Waikato.
These days Jacob Klaus works
While it is not an easy time to be contracting, Kyle’s business model is working.
“It has gone further than I ever thought it would. It has been exciting to see how far everything has come. It will be very interesting to see how the next six years go.”
WHILE HE WAS STILL WORKING FOR OTHER CONTRACTORS, KYLE SELMAN LAUNCHED HIS OWN BUSINESS BY OFFERING AN UNDERSOWING SERVICE.
TO FUTURE PROOF THE BUSINESS, KYLE SELMAN ORDERED HIS MF 8S WITH SOME ADVANCED FEATURES, INCLUDING AIR BRAKES, FRONT SUSPENSION, FRONT LINKAGE AND FRONT PTO.
full-time with his father Robert at Klaus Ag, and Kyle works in with them a lot. He does his work and then joins them.
For example in summer, he drives one of their balers. Or he may mow or work the stack for bulk silage, using his own 2.7m, Albutt push-off buck rake.
“Stacking is enjoyable. It’s repetitive – the load is dumped out and I push it. I don’t have to think about seeding rates or anything else.”
On the other hand, if Kyle gets behind, then Jacob turns up with a tractor and tows one of the implements, mainly the power harrow.
Working with other contractors is great. It is more efficient to have fewer implements that work more often, spread between two businesses. It also means skilled operators are available.
“Farmers really like it too. Jacob does have a couple of staff now, but Robert, Jacob or myself are always on the job.”
Kyle’s Dad, Raymond, also drives if things get really busy, but most of the time he does his own thing contracting with a digger.
Clients get to say who they want working, and most want Kyle on the under-sowing.
Under-sowing usually begins in August along with ground work and maize planting. Silage and hay take over summer, then maize harvest and under-sowing in autumn.
Over winter, life goes from insanely busy to merely busy. Kyle does maintenance, some engineering work and a bit of truck driving. It is also the time to go hunting.
Drive your business forward with the Fendt IDEAL combine, a combine that is truly forward thinking and brings the future of reliable and efficient farming to your paddock today.
With a range of combines spanning up to class 10 models, Fendt IDEAL gives you more power and more productivity with less effort. Experience clever features such as IDEALDrive that provides joystick-steering for simple and intuitive operation.
No matter your crop, harvest better returns by running an advanced combine from Fendt. It's different. It's better. It's IDEAL.
Speak to your nearest Fendt dealer to find out more.
SAM FRYER IS A BUSY MAN, BUT DETERMINED TO MAINTAIN A HEALTHY WORK-LIFE BALANCE WITH HIS FAMILY.
Having lived most of his life in the farming area of Hughenden in northern Queensland, and long been involved with his parent’s beef breeding operation, Sam knows first-hand the challenges that go with farming in remote rural areas.
This has stood him in good stead in his role as Regional Area Manager for the North West and Gulf for Queensland Rural and Industry Development Authority, helping farmers with advice and financial support, especially when areas are hit by big events like droughts or flooding.
affecting their mental health.
This, in turn, has indirectly led to Sam to starting his own podcast - A Place to call Home with Sam Fryer
While still a bit of a hobby, the podcast’s popularity is growing and this recently saw him taking on sponsors for each episode. It’s here, Sam reckons, that peo-
ple’s integrity can start to be compromised and he is careful he doesn’t get pulled into that.
But the remoteness of farming communities brings pressures that don’t just involve running a business a long way from suppliers or a handy mechanic.
Sam has also experienced firsthand the impacts on families caring for children and young adults who have special needs, or are going through tough times
GETTING THE MOST OUT OF FARMING IN REMOTE AREAS CAN MEAN LOOKING OUT FOR EACH OTHER’S WELL BEING. WHILE
“Just about everyone has a podcast nowadays and it’s not hard to set up. That’s why it comes down to integrity,” he says.
There are podcasts out there that are a marketing ploy to bring in people, he says, while others, once they have a partnership or advertising person on board, get caught in the trap of playing toward where their advertising dollar is coming from, and lose their integrity.
The strength of his new project, Sam feels, is the topics he covers are of genuine interest to him as he looks to focus on his dream of farm ownership further down the track.
While he gets downloads, it is the 5-stars on Spotify and personal messages of thanks that are his biggest drivers for continuing – that people are gaining something from it.
But the podcast now sees him too busy and is making him re-evaluate some other commitments he’d taken on as he got up to speed with industry developments.
He started the project after pulling out of the succession process with his parents and their farming business.
“I had been in partnership with them, but it was falling apart so I got out and then felt really lost.”
His dream is still to one day be chasing cows as a full-time beef producer, so he began asking people how to do that. He looked at what he personally wanted to learn to achieve that dream for his wife Emily, himself and their three children.
A fifth-generation grazier with strong family ties to the Townsville area, Sam was a baby when his parents moved to Hughenden to manage a farm his grandparents had bought. They were young - in their mid-twenties. Like many farming families,
three generations often worked together on the land so Sam saw a lot of his grandfather while he was growing up on the farm. By the time his parents began their succession process of buying out the grandparents in the farm, they had three young children. This saw Sam’s father often away contracting in the mines to supply much needed cash flow. While this would have been hard on any family, with Sam’s younger sister Alex having been born with cerebral palsy, it put significant pressure on his mother carrying the load of not only looking after the property with young children, but also deal-
SAM AND EMILY REVEL IN FAMILY LIFE WITH THEIR THREE CHILDREN, IN REMOTE NORTHERN QUEENSLAND.
ing with the high demands of a special needs child, including regularly taking all three children to Townsville – a four-hour drive away, for specialist appointments.
They coped with the help of neighbours who would often come in to deal with problems around the property while Sam’s father was away, showing Sam the value of community.
Boarding school is common for rural youngsters and, when Sam was 10, he left behind his four fellow students at the tiny local school and joined 1500 other kids at boarding school.
While it might have been exciting in other circumstances - getting off the farm and out into a bigger world - his younger sister Alex at eight, had just tragically died from complications from an epileptic seizure. Away from home and family, and surrounded by strangers, her death really hit him hard, playing on his mind.
They teach you about physical fitness and eating healthy at school, he says, but they don’t teach you how to deal with grief and looking after your own mental health.
Years later, in his early 20’s, this
trauma came back when a close friend was killed on the job while they were both working on a station in the Northern Territory, and saw him develop post-traumatic stress disorder (PTSD).
Emily, his girlfriend at the time, came to work on the farm as a book-keeper giving him support.
But his mood started spiralling. He was working hard as a contractor but began drinking hard and partying hard. It was a year that tested friendships, he says.
He broke down and cried for a couple of hours in the kitchen one day when his family asked what was happening and if he was ok.
Counselling followed and, since then, Sam - now in his mid 30shas been mindful of looking after his own mental health and look-
ing out for others too. And why he got involved with Movember, raising awareness of men’s mental health issues, particularly for rural men.
This mindfulness has also seen him building a close relationship with his own three children, sixyear-old Bella, Charlie (five) and Lucy, who’s three. He wants to be the best Dad he can be for them, he says, and for them to be able to talk to him about anything that’s happening in their lives.
It’s these strong bonds with his children that were part of the fracture with his own parents when they started going through the succession process.
With his father doing the hard yards at the mines in the early days, sometimes away from his family for long periods, and the
FARMERS NEED TO ACCEPT THE CLIMATE IS CHANGING AND ADAPT THEIR FARMING SYSTEMS, SAYS SAM.
resulting hard times experienced by his mother, Sam wanted a different kind of homelife for Emily, himself and their children and says he couldn’t commit to the long hours his father wanted him to put in.
“It was a classic case of poor communication and a lot of family conflict starting to happen.”
Things were deteriorating and it was really affecting his mental health, Sam reckons.
By the time they got out of the family business he admits he was “pretty broken”.
Going it alone, along with breeding cattle, they also do some trading, with Emily working on the property as well as looking after the behind-the-scenes work with the podcast.
The break has also given Sam the space to continue to get up to speed with Australian agriculture more broadly and what’s going on globally.
“It’s important to keep looking abroad so you don’t fall behind as a business and as an industry. You’ve got to keep up with the latest trends, developments with tech and genetics.”
Queensland’s beef industry –like the rest of Australia – faces issues with climate change, carbon, and renewables, along with needing to be more consumer focused, he says. Through his work with QRIDA he gets to see the impacts of the warming climate.
“Looking at northern Queensland, in the last five years we’ve had a dozen once-in-100-year floods, and that’s a pretty scary trend.”
Many, mostly younger, farmers are very aware of these issues with some making quite dramatic changes to make a difference, Sam reckons.
But with a predominantly older demographic in the industry - the average age of a primary producer is 63 – many farmers haven’t kept up and see no need
THE NORTHERN REGION.
DON’T GET CAUGHT OUT - Make sure you are up-to-date!
• Over 140 new listings
• 160 deleted products
• 100 existing labels updated (new weed, pest & disease claims)
Plus the latest regulatory amendments
The definitive guide to agrichemicals registered for use in New Zealand.
A comprehensive alphabetical listing of products, active ingredients, crop & weed tables, weed & pest identification and much, much more all in one single publication. It really is the definitive agrichemical guide and the only one you’ll ever need.
Purchase a manual to receive a FREE 12-month subscription to our subscriber only website.
The website is continually updated and contains product listings, a fully searchable online product manual, a powerful search engine of weeds, diseases & pests, including photo galleries with all the agrichemical options to use on individual crops as well as up-to-date SDS’s, Haznotes and product labels, plus posts about industry news and information.
ORDER NOW to receive your FREE pair of SureShield Coveralls
SureShield Coveralls supplied by pH7, provides both protection and comfort with exceptional liquid and particulate protection. Ideal for a wide range of industrial applications. One size fits all.
Shigematsu Respirators supplied by pH7.
* Available to those who order directly from www.novachem.co.nz - while stocks last.
Print up-to-date SDS’s & Haznotes from novachem.co.nz to ensure you are compliant.
to change production, or plan for a different kind of farming future. This affects the industry going forward, he says.
While many farmers don’t like discussing climate change, including within his own family, he believes it is important for the next generation to keep asking questions, keep bringing things up, to keep looking around the corner, and the next one after that.
“Otherwise, you end up with that old saying – if you always do what you’ve always done, you’ll always get what you’ve always got. We can’t keep doing that any more - we’ve got to keep moving forward and being progressive.”
It is with this background, where he sees the need for more renewable energy as it all ties in with meeting the challenges of climate change, that Sam now finds himself somewhat conflicted when it comes to the significant push for wind farms in the northern Queensland region.
While leasing land for wind turbines and solar farms is a massive opportunity for some people, he’s worried what impacts this will have on the area as a community.
“Will people just cash in and move away, because you make more from a wind farm than from breeding cows?
“Or is there an opportunity where people could now retire early and you could still lease that farmland off them?”
While he would always have reservations of good agricultural land potentially falling out of production, he says, it is more the concern over the disposal of the wind towers once they reach their end of life in 30 years’ time that worries him. While there are payments into trusts designed to meet the costs of removal and regeneration of the land, will they be enough, he wonders.
Impacts on farming communities also sees Sam disappointed so many family farms are being bought up by corporate entities, as he doesn’t believe corporates look after the land as well as generational farmers do.
While he recognises corporates do well at bringing improved genetics, improved data, and focus more on the consumer - which moves the industry forward, Sam also thinks that long term views around land care and
YOUNG LUCY AND HER SIBLINGS WILL BE THE SIXTH GENERATION GROWING UP ON THE LAND.
animal welfare need to be recognised.
“With generational farming you look at the land differently when you’re caretaker for that time. You’re looking forward to what it’s going to look like when your grandkids take it over. You have to think like that.
“There are companies out there that do a great job and families that do a terrible job but it’s the overview that family farms are generally better at looking after the land and animals.”
There are also shared challenges on the smaller family farms that corporates wouldn’t have to deal with, that bind farming communities together and makes them more resilient to the challenges of remote living, he says.
Co-operation in sending stock to market is one of these areas that Sam knows the benefits of first hand with his smaller operation.
“Because of the isolation of where we live it takes a long time for trucks to get here. To make it viable for a B-double to travel those distances, you really need to sell three or four decks of stock. Selling one deck up here is nearly impossible.”
This sees Sam and Emily coordinating sales with neighbours so the B-doubles decks are full, making the trip viable.
After a cooling down period that initially saw Sam and Emily leasing land elsewhere, they have recently started to lease part of a farm off his parents and now live on one of their other properties.
Sam is hopeful they will be able to build bridges with his parents and eventually be involved with the family business again. But, in the meantime, they are forging ahead with their own business and plans for the future – making time for both farm and family.
A Place to call Home with Sam Fryer https://aplacetocallhome. buzzsprout.com
A LIFE LONG PASSION FOR HORSES SEES HORSEBACK AS SAM’S PREFERRED MODE OF TRANSPORT AROUND THE FARM.
WE ALL KNOW FODDER IS THE LIFEBLOOD OF NEW ZEALAND AGRICULTURE. TO MAKE TOP QUALITY SILAGE AND HAY, YOU NEED TOP QUALITY EQUIPMENT. HERE IS OUR SURVEY OF THE LATEST MOWERS, RAKES, TEDDERS, BALERS, SILAGE WAGONS, FORAGE HARVESTERS AND TRAILERS AVAILABLE TO KIWI FARMERS AND CONTRACTORS.
The Schuitemaker Rapide is a genuine dual-purpose loader wagon and transport wagon that can be used for harvesting and cutting all types of grass, as well as for carting heavy loads of maize silage.
In addition, Rapide loader wagons can be specified with a feeding unit. These models have a left-hand and/or right-hand side discharge conveyor in the tailgate so that feeding grass to livestock is quick and easy.
The unique trailing pick-up on Schuitemaker loader wagons does an excellent job of following ground contours to guarantee efficient harvesting in all conditions. The pick-up runs on a tandem runner wheel, which ensures a smooth run.
While a forward-facing pick-up on the front of a wagon can be liable when working on uneven surfaces, the trailing pick-up runs over bumps and folds away if met by obstructions.
Rapide 100 and 1000 Series
loader wagons have a 2m and 2.2m wide star-shaped rotor and pick up respectively with 20 mm wide curved rotor tines. This design ensures that all crops are perfectly cut and loaded, while the wide rotor channel and the sunken bottom help move the crop efficiently into the wagon.
New features Schuitemaker has added to the pick-up are the RapidFlow hydraulically-driven intake roller and new Power Rotor. The RapidFlow feed roller
‘sucks’ the grass into the wagon and provides a smooth flow of crops.
New swivel pick up wheels on the pickup make it even more adaptable to challenging contours.
HiSpec’s Kompactor is a multipurpose trailer with a unique compaction and off-loading mechanism. With compaction the Kompactor’s payload can be increased by as much as 30 percent, which makes it ideal
for transporting and off-loading silage and other material.
Kompactor is available in two sizes, K36 (36m3) and K40 (40m3). Standard features include commercial running gear, super single wheels, air over hydraulic brakes and a hydraulically sprung drawbar.
Industry research has shown that an average tractor spends up to 70 percent of its time doing haulage. Increasing the density of the load can reduce the overall number of trips to increasing efficiency and profitability.
HiSpec has adopted this idea to develop Kompactor trailers.
The tandem-axle K36 trailer features a 22-foot long body on a heavy-duty chassis that uses high-speed commercial running gear and super single tyres.
With its steel body and extensive vertical bracing Kompactor trailers retain rigidity to overcome any compaction loadings and deliver a long working life.
Compaction is achieved by a multi-stage hydraulic ram that moves the floor and headboard rearwards to compact and eventually discharge the load. The moving floor carries the load and reduces the pressure on the moving headboard.
When filling the Kompactor, the harvester or loaders start at the rear and move forwards. During loading the tractor driver can see the load through a large vision panel in the front bulkhead. Compaction can be started during loading, or during headland turns when harvesting.
The tailgate on the Kompactor is secured with a drop and lock system that can resist compaction forces. After compaction, the floor and headboard return to the start position at the front of the trailer.
A moveable headboard ejects
the load, which means it can discharge when there is little headroom. The unloading system is safer because there is no need to tip the trailer at steep angles and it eliminates a vertical jack-knife caused by ‘sticking’ loads.
During unloading, the rear door raises to 90 degrees from the closed position to clear the trailer body. This enables an unimpeded discharge in about one minute.
The headboard stops flush with the rear edge of the trailer body, to completely empty the trailer body. A discharge chute incorporated into the floor gives controlled discharge of free run-
ning material.
HiSpec offers a number of options with the Kompactor, including a passive rear steering system that gives tighter turning and a lock-out system for reversing.
Other options are 200 mm deep ‘greedy boards’ to increase capacity and a hydraulically actuated load cover for safe road travel. A ball and spoon drawbar coupling can increase comfort and reduce wear, while a fully independent weighing system can accurately measure loads.
For more details visit the website gaz.co.nz.
Elho’s Cobra 7710 trailed forage harvester offers an option to achieve cost-effective but very efficient harvesting that will appeal to both farmers and contractors.
Driven by the tractor’s PTO, the Cobra has a 3m wide pickup and chopper rotor that is 1m wide and 770 mm in diameter. It can work with tractors from 250 hp to 400 hp to produce volumes of fine chop silage that match.
Diesel Tech is the Elho distributor in New Zealand, and Diesel Tech managing director Chris Barnes says the cost of a Cobra is about a quarter of most medium and large-sized self-propelled foragers, but it can match their output.
“A Cobra would suit a larger farmer, a group of farmers working together, or even a contractor who is looking for a second or third machine.
“It has the largest cutting cylinder of any forage harvester in the market, which runs off a direct drive from the PTO. The pick-up and everything else is hydraulically-driven, so it is both very efficient and low maintenance.
“With its direct drive there are minimal power losses, and the more power the tractor has, the more power there is to chop. There is really no upper limit to the size of tractor it will handle. In all the tests that Elho has run, the limiting factor is always
the tractor, never the chopping unit,” Chris says.
Power is maximised because the crop travels in a straight line through the Cobra. The 3m pickup feeds the crop to a 1m conveyor. The revised pickup feeds the crop to the pre-compression rollers.
Both the pick-up and conveyor are powered by the Cobra’s own hydraulic system. Since the conveyor belt, feeder and knife drum are all the same width, the crop flow and load remain even.
The Cobra can harvest without the need for an accelerator. The absence of an accelerator significantly reduces the chopper’s power requirement and fuel consumption.
Chris says other convenient features include a telescopic axle, which extends out wide in the field and narrows down for road transport. It also has pallet forks so that it can transport a 1000-lt pod of silage inoculant.
Sitrex’s MKS Europe range of V rakes are designed to be used at high working speeds on any terrain with any type of fodder, including silage.
According to Chris, Italian company Sitrex is the world’s largest rake manufacturer.
“Sitrex makes a lot of V rakes for big brand OEMs in the North American market. V rakes are very popular in the US and Canada but less so in Europe. They wanted to get into their domestic market, so they developed the MKS Europe range, which is a V rake on steroids.
“It is built to handle silage as well as straw and hay. It is very, very good at following ground contours and its finger tines flick the material, rather than roping it. This allows it to handle heavy, wet crops.”
Chris says Sitrex V rakes offer three definite advantages over a traditional rotor rake:
1) Their working speed is significantly faster than a rotor rake.
2) They are low cost and easy to maintain, because the only moving parts are the finger tine reels.
3) The purchase price of a V rake is less than a rotor rake.
“Not only are Sitrex V rakes faster than rotor rakes, operators can adjust the working width and the width of the swath from the cab. They also have a rear wheel steering system, which gives them a very good turning circle. Hydraulic brakes make road transport safer.”
The frame is made from heavygauge tubular steel. The opening system with a telescopic drawbar reduces the length of the rake during transport and stabilises the wings during work.
Chris says Sitrex MKS Europe V rakes will suit contractors and farmers anywhere in New Zealand that produces lots of silage.
John Deere has launched its new powerhouse baler that produces longer, heavier bales to save the contractor time, fuel and labour, and it comes with all the precision agriculture integration that the company is renowned for.
100 per cent designed and built by John Deere in the US, the L341R High-Density Large Square Baler features a bigger build chamber, reinforced hoops and is 45.7cm longer than a standard unit, which enables the machine to compress hay into a 3x4 bale with 30% more density.
Since fewer bales need to be removed from the field, farmers spend less time travelling across the crop and trucks are loaded with the maximum amount of hay for enhanced efficiency, creating savings on each trailer load.
Despite its increased power and compression ability, the L341R operates under the same PTO power requirements as its predecessor, negating the necessity to invest in new machinery to pull it.
The machine’s MegaWide™ pickup comes in two sizes on the L341R, a 2.2 metre wide pickup and a 2.5m wide pickup, which
makes it easier to produce neatly shaped bales and improves crop pickup in wide, windblown or scattered windrows.
Other highlights include the low-profile pickup drum with a large-diameter roller baffle to efficiently pick crop up and compress it against the pickup tines, meaning more crop in the bale and less debris in the field.
While the L341R High-Density Baler leverages product components, functions, and technology that John Deere customers are familiar with, it introduces the local hay industry to new levels of sophistication through the data acquisition system, Bale Doc.
John Deere Australia and New Zealand Product Specialist, Hay and Forage, Roberto Scheidt, said Bale Doc was standard in the L341R, providing customers with information they didn’t previously have to boost productivity and profitability.
“Bale Doc provides customers with yield data to inform decisions on whether to apply fertiliser to parts of the field, whether to let the hay re-grow for more cuts or plant a new crop,” Roberto said.
“It allows operators to monitor bale characteristics such as weight and moisture as bales are made, so they can make more consistent, high-quality bales,
Claas Disco 9700 triple-combination mowers set new benchmarks in throughput, efficiency, and forage quality.
They have a variable working width of 8.8m to 9.5m, the proven eight-disc Max Cut mower beds, Active Float suspension, and a range of conditioning and auto swathing options.
The new Disco 9700 Series expands the Claas range of largescale mowers and closes the gap between the Disco 9200/9300 and the Disco 1100.
All Claas Disco front, rear and trailed mowers are built to withstand maximum loads and deliver top-quality cutting. They maintain outstanding efficiency with minimal power requirements.
The five models in the new 9700 range are Disco 9700 Comfort, 9700 C Business (tine conditioner), 9700 RC Business (roller conditioner), 9700 C Auto Swather (tine conditioner and swath grouping) and 9700 RC Auto Swather (roller conditioner and swath grouping).
Disco 9700 C Business and Disco 9700 C Auto Swather will be available in New Zealand for sale this spring.
With Max Cut mower beds
and Active Float suspension they deliver clean forage, maximum sward protection and high capacity. In light crops, the mower beds can be operated with a PTO speed down to 850 rpm, reducing fuel consumption by up to 20 percent.
RC models have two counter-rotating polyurethane rollers that are actively driven and synchronised with a scissor gearbox for maximum throughput and processing quality.
The rollers extend across the width of the mower bed and gently crush the crop and optimise crop flow. This conditioning system is ideal for gently processing large volumes of lucerne, forage crops and whole-crop silage.
RC Auto Swather models have two 1100-mm wide Kevlar-reinforced conveyor belts that consolidate harvested crop from the left and right-hand mowers into a single, perfectly shaped swath, for a forage harvester.
Auto Swather models can also be ordered with a central lubrication system, on-board hydraulics, or an oil cooler.
On all Disco 9700 models, the new swinging arms can be hydraulically pivoted outwards to adjust the overlap when turning corners and working across
and the moisture maps allow the operator to understand where there are issues in the field with dry down.
“This precision technology seamlessly integrates data in near real-time for record keeping in the John Deere Operations Center™. It’s the same system
slopes to avoid unmown strips. The swing arm travel can be infinitely adjusted from the cab.
The Disco 1010 Trend is the widest mounted mower without a telescopic boom on the market. It has two booms suspended at the centre of gravity. They have a vector folding system which gives unrivalled compact and safe road transport.
Thanks to vector folding, even the impressive working width of the Disco 1010 can be driven safely and, above all, legally on the road and on narrow tracks.
In 2023 Claas celebrated 50 years of leadership in the self-propelled forage harvester market. With more than 45,000 units manufactured since the Jaguar was introduced in 1973, they have earned a hard-won reputation for productivity, efficiency and reliability.
The top of the range Jaguar 970 boasts a number of technological advancements, including a new 790-hp MAN S6 engine.
Optional features on the Jaguar include power and fuel saving operator assistance systems such as CEMOS Auto Performance and CEMOS Auto Crop Protection. They maintain the engine speed set by the operator and adjust the engine output and ground speed to match the volume of crop harvested.
CEMOS Auto Crop Protection
allows the operator to set a minimum engine rpm. If the minimum setpoint is reached the machine cuts the feed drive to avoid any blockages.
When its assistance systems are switched on, the Jaguar can achieve up to 10 percent higher throughput and up to 13 percent lower fuel consumption.
Assistance systems also make life more comfortable and less stressful for the operator. Studies have shown that operator assistance systems can reduce control lever clicks to operate the discharge chute by 50.6 percent, reduce control lever movement by 15.2 percent, and reduce steering wheel turns by 35.4 percent.
All operator settings can be programmed as favourites and accessed by switches on the multifunction C-Motion control lever for maximum operator comfort.
The CEBIS touch control hub implements the operator’s adjustments at any point while chopping is underway. The clear, user-friendly control system can be operated without previous knowledge.
Other advanced features are the continuously variable front attachment drive, hydraulic pre-compression, enhanced crop flow systems, Auto Fill automatic loading and dynamic steering.
Steering options include CEMIS 1200 GPS steering, Cam PILOT swath detection and Auto Pilot row sense, all with Dynamic Steering for the headlands.
being used in broadacre cropping machinery, but the hay industry can now benefit from these new efficiencies.”
The L341R has been trialled under Western Australian conditions and hit the ground running, Roberto said, with excellent reliability.
“The farmer remarked on the ride and driveability of the new baler too, as the usual rocking motion of the tractor when baling was much smoother thanks to the Ride Control™ feature on the JD tractor,” he said.
“The new baler also features an integrated preservative appli-
cator, to provide more precise application of innoculant to preserve the crop.”
The John Deere L341R High-Density Baler was on show at the Australian Fodder Industry Association conference in Coffs Harbour, NSW, on 23-24 July, 2024.
Car rier disc cultivators
speed soil tillage prepares a seedbed that’s perfect for planting. Get your hands on a true workhorse and one that makes cultivation easy.
3-12.2m working width
5-13cm working depth
125mm disc spacing
The new Krone VariPack 190 round balers are designed to bale wet and dry crops. They offer an uncomplicated design, high throughputs and high baling densities.
The VariPack 190 produces round bales from 0.8m to 1.9m in diameter. When specified with the XCut cutting system, it can be used with 17 or 26 cutting blades, which delivers cut lengths of 128 mm or 64 mm.
Operators select the number of blades in operation from the cab, so it is easy to adjust the chop length in changing conditions.
The cutting system’s double tines pull the material in a consistent flow through the blades. This prevents any material from slipping through, so bale weights are higher. The cutting unit’s helix design ensures there are no peak loads in the cutting system, so its operation is smooth and quiet.
Whenever a blade hits an object, it retracts from the crop flow and automatically returns to its working position after the object has passed.
The VariPack 190 has Krone’s EasyFlow pick-up. Unlike a system whose tines are controlled by a cam track with many moving parts that are prone to wear, the EasyFlow pick-up has special strippers that ensure the tine angle is always at the right length.
The pick-up tines’ arrangement and the integral rotor distribute the material perfectly across the width of the chamber to create uniform bales. The tines are spaced at just 55 mm, so the EasyFlow can pick up short and heavy crops without losses.
With a working width of 2.15m,
the EasyFlow pick-up delivers high outputs. Its double tines are 6 mm in diameter and mounted with large coils. They are hard-wearing and arranged in a chevron-line to reliably pick up even the widest swaths and feed it consistently to the rotor cutter.
Pivoting and spring-loaded, EasyFlow provides perfect ground contouring even in the roughest terrain. The EasyFlow pick-up rides on two castering gauge wheels that pivot flexibly for smooth tracking in all curves without scuffing.
VariPack’s feed auger is integrated at both ends with the rotor cutter and the feed rotor. This means that only one drive is required to power the pick-up and the rotor.
The integral rotor has a drop floor that can easily be opened and closed from the cab. This allows you to open the floor under the cut-and-feed rotor to remove any blockages.
Finally, the hydraulic cylinders that operate the rear door of the VariPack 190 have stroke end cushioning. This gives fast unloading cycles and maximum throughput. Bales are unloaded in a few seconds.
The trailed Vendro T900 is a
new addition to the Krone tedder family. It can handle all types of forage crops and has such proven Krone technology as OptiTurn tines with generously overlapping rotors to optimally lift and spread the crop. This ensures fast wilts and better quality forage.
Two shafts in each pair of tines have different lengths. This ensures their tips are always parallel as they hover above the ground, so they lift the crop cleanly and prevent contamination.
Vendro T900 tedders have a pin-and-hole system, which alters the spreading angle between 13° to 19° for optimal conditioning. A steep angle results in intensive tedding, a shallow angle results in gentle turning.
This is ideal for crops such as lucerne that require a gentle touch. The spring-loaded pin adjusts the angle quickly and easily in only four steps without needing to change cotter pins.
OctoLink finger clutches make a reliable connection inside the driveline and provide consistent power flow to the next rotor. The finger clutches are extremely robust and require no lubrication.
Along the edge of a paddock, the Vendro T900’s border spreading control throws the material
away from the border, so no crop is lost.
All the running wheels are connected to each other via the border spreading control linkage to ensure stable castering during uphill work and uniform spreads on steep slopes.
The new Krone M steel roller is the ideal conditioner for gentle treatment and fast wilting.
Two drives deliver double power. The top roller of the M-Rolls is driven by a separate gearbox on the right end of the cutterbar which synchronizes the speed of the top and bottom rollers. This enables it to handle wet and heavy crops.
The profiled, counter-rotating M-Rolls mesh together to crush the material at two pressure points. Yet they leave a sufficiently wide gap for the material to pass through.
This helps the crop dry faster and delivers uniform conditioning and wilting without fragmentation. It is the perfect system for lucerne or clover.
M-Rolls are available as an option on most Krone mowers. For more information or to find your nearest dealer, visit kronenewzealand.co.nz.
Bogballe offers you a world of possibilities with GPS automatic section control and automatic start/stop on headlands with your existing tablet or GPS unit** Stops overspreading & wastage and increases your fertiliser placement accuracy.
KAITAIA Kaitaia Tractors 09 408 0670
WHANGAREI Piako Tractors Northland 09 438 1319
SILVERDALE Brandt NZ 09 427 9137
PUKEKOHE Brandt NZ 09 237 0043
MORRINSVILLE Piako Tractors 07 889 7055
MATAMATA Matamata Tractors & Machinery (07) 888 6292
HAMILTON Brandt NZ 07 847 0425
CAMBRIDGE Brandt NZ 07 827 5184
ROTORUA Piako Tractors Ltd 07 345 8560
TAUPO Taupo Tractors & Machinery 07 378 4533
STRATFORD FieldTorque Taranaki 06 765 8643
HASTINGS Stevenson and Taylor 0800 4273 2273
WAIPUKURAU Stevenson and Taylor 06 858 6041
DANNEVIRKE Lancaster Tractor Services 2022 Ltd 06 374 7731
PALMERSTON NORTH Transag Centre 06 354 7164
MASTERTON Brandt NZ 06 377 3009
NELSON Drummond & Etheridge 03 543 8041
BLENHEIM Drummond & Etheridge 03 579 1111
KAIKOURA Drummond & Etheridge 03 319 7119
GREYMOUTH Drummond & Etheridge 03 768 5116
CHRISTCHURCH Drummond & Etheridge 03 349 4883
ASHBURTON Drummond & Etheridge 03 307 9911
TIMARU Drummond & Etheridge 03 687 4005
OAMARU Drummond & Etheridge 03 437 1111
MOSGIEL JJ Limited 03 489 8199
GORE JJ Limited 03 208 9370
INVERCARGILL JJ Limited 03 211 0013
Also referred to as ejector trailers, Fliegl ASW trailers have double acting hydraulic rams that enable the contents to be pushed out from the trailer's body through a hydraulic opening rear door.
ASW push-off silage trailers unload faster than walking and chain floor systems. They have fewer moving parts and require very little maintenance.
In the 25 years Fliegl have been producing the ASW range, improved safety and stability have become the two most notable advantages that customers
have reported.
The push-off system allows for a near-constant and low centre of gravity during unloading versus the instability that can result when a tipping trailer's box is hoisted.
Fliegl’s ASW Push-Off models range in capacities from 20m3 to 55m3 and they can be specified with tandem and tridem axles.
As well as being an excellent option for harvesting silage, Fliegl ASW push-off trailers can be fitted with rear PTO driven attachments, including a muck spreader, dosing rollers and overloading grain auger.
For large scale harvesting
operations, local distributor Power Farming offers the ASW271 and ASW391 models.
The ASW271 model is the universal workhorse in Fliegl's push-off range. It is a safe, stable and a flexible transport option for silage, root crops, grain, gravel, manure, soil and woodchips, and for the New Zealand market it is specified with a number of heavy-duty upgrades.
The double acting two-stage hydraulic system has a very low oil requirement and does not use telescopic cylinders. With minimal moving parts, the Push-Off system is extremely robust in comparison to chain and walking-floor systems.
The tridem axle ASW391 mod-
el has an uncompressed capacity of 50m3 and a permitted total weight 30,000 kg (27,000 kg axle load and 3000 kg drawbar load). Other features are a hydraulic drawbar suspension and axle suspension, 650/55 R26.5 tyres, hydraulic brakes and trailed steering.
ASW push-off trailers can also be fitted with Fliegl’s ULS400 overloading grain auger. The ULS400 can unload up to 7.5 tonnes/min to a height of 4.3m. This makes it a very useful option for cereal and maize grain harvesting.
For more information on Fliegl trailers and implements contact your local Power Farming dealership.
Case IH’s RB6 HD Pro Series is the latest addition to the brand’s variable chamber round baler range. It offers a range of new features aimed at boosting productivity and performance.
The two models in the RB6 Series are the RB 456 and the RB 466. The RB 456 produces bales 90 cm to 165 cm in diameter, while the RB 466 produces bales 90 cm to 190 cm in diameter.
Both models produce larger diameter bales than the RB5 Series balers and both are available with a rotor feed or a 25-knife rotor cutting system.
CNH hay and forage equipment product specialist Ross Aylwin says RB6 HD Pro Series balers not only produce larger bales, they are also designed to deliver high volume output of silage, hay or straw bales.
“The two RB6 Series balers were designed from the ground up to meet the needs of contractors and larger hay producers who produce high numbers of bales each year. They are built for longevity and will produce more bales between servicing.
“They are basically completely new balers from the RB5 Series. They have larger rollers and beefed up chains, sprockets, bearings and drivelines. They actually weigh about a tonne more than RB5 Series balers,” Ross says.
“We believe the RB6 Series will be a popular baler in New Zealand. It is ideal for contractors who want to produce a lot of bales of any crop type.
“With the over-sized bale chamber, operators can be confident they will produce typical bale sizes without meeting or exceeding the capacity of the bale chamber.”
The driveline on RB6 HD Pro Series balers is a heavy-duty T-type gearbox that delivers power to both sides of the baler. It has a straightforward design and transmits power evenly for better balance and smoother operation.
The five-bar pick-up has been modified from the RB5 Series. It has a different mount, which increases the forward angle to allow for an even smoother crop flow as it transitions between the pick-up and the rotor.
A new feature is the active drop floor which moves automatically to allow heavy crop flow to pass and avoid plugging. A sensor constantly monitors the movement of the drop floor and it alerts the operator if it detects excessive floor movement.
A large 520-mm rotor increases the baler's capacity.
In the chamber a new belt path and roller configuration creates a compact core right from the beginning and quickly produces a tight bale.
The four belts are deflected only 10 times as they rotate, and the floor roller carries most of the bale’s weight. This reduces stress on the belts and increases their service life.
Only two sets of hydraulic remotes are needed on the tractor because RB6 Series balers have a new hydraulic valve bank that allows the operator to select the hydraulic function through the display. One of the hydraulic units controls the tailgate and the other is for controlling the pickup.
Ross says while the RB6 balers feature a number of new features they also retain Case IH’s renowned netwrap system, which has been used for many years on RB5 Series balers.
Other notable features the new RB6 Series offer include a new user interface that gives operators a clear layout, sharp graphics, and easy-to-use setup menus. They can control the knives, rotor cut, and hydraulic drop floor through the display.
ISOBUS connectivity and an ISOBUS display are standard
with RB6 balers. There is also an option to configure the baler to operate with ISOBUS Class 3-compatible Case IH tractors to control several tractor and baler functions without any operator input.
With an ISOBUS 3 tractor, the baler can tell the tractor’s hydraulics what to do at the end of the baling cycle. The baler monitors its own actions and knows when to slow down and stop. It con-
firms when the bale is wrapped, and knows when to eject it.
The baler controls the tractor’s forward speed and tells it when to slow down and stop. It then lets the operator know when it is time to resume moving forward again.
Other options with RB6 balers are moisture sensors and an automatic greasing system.
For more information, contact your local Case IH dealer.
TAMA is the national body for New Zealand’s Tractor and Machinery industry and has been doing so since 1949. Our members, keep the wheels of New Zealand’s agricultural economy turning.
We proudly represent almost the entire industry including importers, manufacturers and retailers.
• We unify and consolidate the opinions and views of our sector.
• We advocate and take a stand for our members on industry issues and opportunities.
• We provide access to detailed and relevant market data and sales trends to inform your business decisions.
To find out more about memberships & benefits, contact Phil Holden:
When making silage, high quality pasture is where it all begins. Pasture must be in the best condition possible to ensure high quality forage. Nutritional values of forage crops are well-documented, and most farmers know that ensiling the crop is not a silver bullet and does not improve pasture quality.
What they can do to improve forage quality is to minimise soil contamination when they process the crop, and the Fendt range of green harvest equipment is designed with a goal of reducing soil impact as much as possible
Good examples of this are the streamlined cutterbar on Fendt Slicer mowers, the high performance tines on Fendt Lotus tedders and the cardanic suspension on Fendt Former rakes.
To make high quality silage, grass needs to rapidly wilt from about 15 percent dry matter content to about 25 percent DM content. Solid compaction and sealing are the final steps in best practice silage making.
Transpiration is the process whereby moisture plants lose moisture through the stomata on the underside of the leaf. Healthy plants have open stomata and they ingest CO2 and expel O2 and water.
Plants close their stomata around 30-40 minutes after mowing to prevent permanent moisture loss and death (because the plant doesn’t know it’s already game over!).
To get from 15 percent to 25 percent DM with spring pasture, the aim is to increase wilting
moisture loss and a mower conditioner does exactly that.
Scraping the waxy cuticle on the outer layer of the leaf increases the surface area where moisture can be lost, which achieves faster dry-down. This occurs as the steel tine and counter comb action hit the leaf. It also occurs with leaf on leaf scraping action that damages the cuticle.
Fendt Green Harvest product marketing manager Mark Hamilton-Mann says for Model Year 2025 Fendt has expanded the Slicer Butterfly product range to a total of 16 models.
“We continue to offer the smaller 8.6m and 9.6m mowers, and we are now offering 9.6m and 10.1m models to harvest large areas quickly,” Mark says.
“These mowers can be specified with either tine or roller conditioners and they can be used in combination with our current 3.1m or 3.6m front mowers. We now have belt models for merging windrows and mowing sensitive crops like lucerne or clover.”
Fendt Slicer Pro models have ISOBUS control and smart features. The new 960 and 1010 Pro models have tine conditioners and the unique Automatic Conditioning Intensity.
No paddock is the same throughout. There can be areas with more grass because they are wetter or have higher fertility, or there can be drier areas with less grass. Variable adjustment ensures all forage is conditioned evenly to ensure uniform dry down and more consistent forage quality across the paddock.
Variable adjustment is done via a linear motor connected to the counter combs of the mower conditioner. Operators don’t need to get in and out of the tractor to adjust the conditioning rate. They can make adjustments three ways:
1. Satellite. A low earth orbit satellite measures paddock biomass and generates a prescription map that is exported to the tractor. The task controller communicates the target conditioning values as the tractor passes across the various parts of the variable rate map. When the tractor hits high or low growth spots, the conditioning intensity adjust automatically.
2. Sensors. Three sensors fitted to the tractor scan the biomass of the crop in real-time and adjust conditioner intensity immediately.
3. ISO control. Operators can adjust all three mowers through the ISOBUS terminal.
Mark says this technology reduces set-up times and eliminates the need to get out of the cab to adjust settings.
“Therefore, the crop lies in the paddock for less time, which reduces losses and risk of losing the crop to rain or wind. Uniform drying ensures consistent forage quality and reduces the chance of mould and mildew in bales.
“Other benefits are lower fuel use with targeted adjustments in heavy spots because the mowers are not working intensely through the entire paddock.”
Fendt’s Automatic Conditioning Intensity won a Silver award at 2023 Agritechnica.
Fendt range front mowers feature the unique Automatic Side Shifting. Front mowers can drift from their correct path on hills or corners. Until now, operators had to manually adjust the front mower by eye using a selective control valve.
Now, when matched to an ISOBUS rear mower, the front mower automatically adjusts up to 200 mm to the left or right. The steering sensor on the tractor directs the front mower to match the vector of the tractor’s front wheels.
With a category-leading power-to-weight ratio of 14 hp to every tonne, JCB’s new 457S agricultural wheeled loader is the king of the clamp for material loading, handling or spreading.
JCB product manager Steve Gorman says the high-capacity loader sets the benchmark for productivity, efficiency and comfort in demanding agricultural applications.
The 457S features the spacious JCB CommandPlus cab, which provides excellent allround visibility. The controls are well laid out, easy to use and include a full colour LCD display and single-lever joystick.
Its 6.7-litre six-cylinder Cummins B6.7 engine gives the 457S the ability to deliver a maximum output of 282 hp and peak torque of 1,200 Nm.
This is combined with a new six-speed automatic/manual powershift with a top speed of 40 kph.
“The torque converter lock-up provides direct mechanical drive
in all six forward gears as standard,” Steve says.
“Alternatively, the operator can select the lock-up for the three lowest forward gears or any of the three reverse gears to suit different applications.
“For less demanding applications, the operator can revert to the standard power output of 224 hp to reduce fuel consumption.”
In addition, the engine automatically shuts down after an idle period (which the operator
can specify), further reducing fuel consumption.”
457S wheeled loaders are available with either standard or high lift arms, which provide a maximum lift of 4.3m or 4.8m at the attachment pivot pin, respectively.
Steve says the non-parallel lift links allow the attachment to roll back when the loader arms are raised for improved load retention.
The loader arms have unloaded spool valves, which allows
them to lower by gravity for increased productivity and reduced fuel consumption. The arms can also be equipped with two auxiliary services to allow a wide range of attachments to be used with the loader.
Implements are quickly attached via the hydraulic quick hitch.
An optional 20-tonne rear hitch, twin-line hydraulic or airready trailer brakes and integrated camera further increases the loader’s versatility.
Rigid or 3-section frame and flexible cutterbar (Razor)
Widest centre section allows greatest wing flexibility
Exclusive, fully integrated air system behind knife for lowest losses
Floating, mechanical drive intake auger
Slim side panels for minimal disturbance of high value crops
Tough, bolt together, non-cracking bins with in-built scales, auto outload
Full auger pivot, suits grain baggers
4 wheel steer, auto steer lock
Direct drive gearbox – no belts, chains
Built to tackle the big jobs, and designed for contractors and larger farms, the heavy duty DM 8612 and DM 9614 butterfly mowers offer exclusive features that provide high performance and low operating costs.
Ranging in size from 8.3m to 9.3m, the Massey Ferguson DM butterfly mowers have an extremely robust and efficient spur gear drive. The spur gear drive gives minimal backlash and has gear shaft overload protection, which ensures a longer lifespan.
The spur gear drive runs with less noise and friction, and features easy access from the top to make maintenance easier.
Massey Ferguson engineers have also developed a robust flat cutter bar that ensures a long working life. The flat, welded cutter makes deep cutting possible even under difficult forage conditions and its flat cutting pattern achieves optimum outputs and high forage quality. It is also easy to service, which adds to the low cost of ownership.
DM butterfly mowers also have a compensation cylinder to lock the mower unit in headland position. This protects the PTO shaft from damage by preventing the mower from pivoting.
Other features of the DM butterfly mowers include:
• A low mounting point, so the mower unit has a transport height under 4m.
• Lateral swing angle of +30°/-19° to provide ground following in hilly areas.
• Profiled cutter bar, which allows smooth soil flow and prevents forage contamination.
• A working position indicator that is visible from the cabin to save setup time.
• Compatible with 850 rpm from the PTO, saving fuel.
With a simple and effective driveline and a compact overall cutter bar height, you can expect optimal regrowth in most crops.
Massey Ferguson’s DM butterfly mowers have been engineered from the ground up to be as durable and efficient as possible, contributing to a lower cost of ownership in the long run.
MF RK Series rotary rakes gently sweep your crop in even fluffy windrows for faster drying and better baling. Driven by the PTO, RK rakes hug paddock contours and control the raking tines to create a clean raking action.
Their rugged box-beam frame ensures both stability on rough terrain and a long service life.
Tine arms rotate on a cam track within the gear head that enables the tine to lift the hay then rotate by at the precise time, discharging the hay against a robust vinyl curtain in order to produce the perfect windrow.
Cardanic suspension lets the rotors closely follow field topography so tines operate close to the ground without making contact for cleaner hay in your windrow.
An adjustable drawbar allows you to level the rake wheel beams to match the tractor drawbar height.
RK Series rakes are all equipped with a headland position feature. With it, the rotors do not need to be switched off at the end of the field.
The ‘jet effect’ of the rotor undercarriage when lifting and lowering on headlands ensures the tines do not gouge the ground. This provides longer service life of the equipment and quality hay by eliminating ash injection.
There are 11 models in the Massey Ferguson range of TD tedders covering working widths from 5.2m to 12.7m. There are eight straight tine models for light to medium crop, and three
hook tine models for heavier lodged crops.
MF tedders are easy to set up and adjust to achieve efficient coverage.
With MF tedders, the tines pick up the forage and gently turn it without damage. This creates a light, loose and well-mixed mat of forage to ensure a top-quality end-product.
All tedders in the MF TD range offer multiple easily-adjusted spreading angles, so the operator can always adapt the machine to the harvesting situation.
A centralised hydraulic lift system synchronises the lift of the exterior rotors, while pressure cylinders ensure optimum performance and eliminate heavier loads on one side, even on slopes.
A central edge spreading device is standard on TD tedders. This means that the edges of paddocks no longer present any problems. You can achieve high quality forage down to the last blade of grass.
Tine arms on MF tedders are made of galvanised flat steel bar, which allows a wide contact surface between tine and rotor disc and therefore excellent power transmission.
Rotor heads are enclosed to protect all important components from dirt and dust and give years of trouble-free work.
Individual rotors are driven via a large shaft and robust universal joints. Power transmission is smooth and reliable and free from backlash.
All MF hay tedders are built with thick-walled frame tubes to ensure rigidity and a very long service life.
15-27 ton capacity - Built with HARDOX High-tensile wear resistant steel
OTHER TRAILERS
JOSKIN TRAILERS
KAITAIA Kaitaia Tractors 09 408 0670
WHANGAREI Piako Tractors Northland 09 438 1319
SILVERDALE Brandt NZ 09 427 9137
PUKEKOHE Brandt NZ 09 237 0043
MORRINSVILLE Piako Tractors 07 889 7055
MATAMATA Matamata Tractors & Machinery (07) 888 6292
HAMILTON Brandt NZ 07 847 0425
CAMBRIDGE Brandt NZ 07 827 5184
ROTORUA Piako Tractors Ltd 07 345 8560
TAUPO Taupo Tractors & Machinery 07 378 4533
STRATFORD FieldTorque Taranaki 06 765 8643
HASTINGS Stevenson and Taylor 0800 4273 2273
WAIPUKURAU Stevenson and Taylor 06 858 6041
DANNEVIRKE Lancaster Tractor Services 2022 Ltd 06 374 7731
PALMERSTON NORTH Transag Centre 06 354 7164
MASTERTON Brandt NZ 06 377 3009
NELSON Drummond & Etheridge 03 543 8041
BLENHEIM Drummond & Etheridge 03 579 1111
KAIKOURA Drummond & Etheridge 03 319 7119
GREYMOUTH Drummond & Etheridge 03 768 5116
CHRISTCHURCH Drummond & Etheridge 03 349 4883
ASHBURTON Drummond & Etheridge 03 307 9911
TIMARU Drummond & Etheridge 03 687 4005
OAMARU Drummond & Etheridge 03 437 1111
MOSGIEL JJ Limited 03 489 8199
GORE JJ Limited 03 208 9370
INVERCARGILL JJ Limited 03 211 0013
Giltrap Ag has five decades of experience manufacturing forage wagons for Kiwi farmers and it has built on that heritage to develop its exciting new G-Max range.
G-Max forage wagons have a fresh, contemporary look and they are packed with new features and technology. They are built tough and are designed to make both feeding out and maintenance easier.
The six models in the G-Max range are built to handle all types of feed, including grass, maize and wholecrop silage as well as long or precision chopped round or square bales. When specified with the optional chain and slat conveyor system they can readily handle heavy, bulky feeds, such as fodder beet or big square bales.
Models in the range extend from the G-Max 9 (9m3) to the G-Max 25 (25m3). All have corrosion-proof stainless steel sides and tandem axles. (A single axle option is available on the three smallest models.)
Giltrap Ag NZ sales manager Matt Moodie says notable new features on the G-Max range are a high density polyethylene floor, 13 mm chains for the floor and elevator on the four larger models, and gearbox transmissions for the floor and elevator.
“Our new HDPE floor is one of
the most durable plastic products available. It offers great properties such as abrasion and corrosion resistance, and high impact strength,” Matt says.
“The 13 mm chains are twice as strong as the chains on our previous silage wagons. They have a tested breaking load of 22 tonnes each and they are paired with bigger sprockets. The whole system is heavier and stronger, so there is less chance of breaking, and the bigger chains stretch less, so you spend less time tightening them. Link chains have proven to be far more durable and stronger than low strength roller chains, which can be found on other wagon brands.”
Matt says the hydraulic gear-
box on the new wagons is less complex than the chain and gears system it replaces, so there are fewer things that can go wrong. It also delivers smoother torque than the chain system on earlier models.
Another new feature is a 1200 mm wide conveyor which is standard, as opposed to the to the old 900 mm conveyor. The wider conveyor makes it easier to feed bales.
“We have put a big emphasis on making the G-Max easier to operate and service. We have engineered countless features to make maintenance easier.
“For example, the chain tensioners are easy to get at from behind the wagon. The conveyor
tracks nicely, and if it does need to be straightened, the adjustors are also outside the wagon and easy to get at,” he says.
The mesh front screen on the G-Max is larger than previous Giltrap forage wagons. The increased visibility makes it easier for the operator to view the load and see what’s happening.
With the G-Max back gate closed there is a cover over the feed-out chains. This provides added safety and prevents hungry or curious animals from sticking their head where it shouldn’t be.
A broad range of options and accessories are available for the G-Max. All wagons are built ‘scale-ready’ and can have electronic load cells fitted for weighing on-the-go. This means it is straight forward to fit the optional wireless weigh scales later.
“With the weigh scales you can program the G-Max to feed out a set weight over a predetermined distance. You could, for example, tell it to feed out 3 tonnes over 100m and then you just drive. This is a good option for feeding out in barns or on feed pads,” Matt says.
This is all done through a 7inch touchscreen in the tractor cab using the Smart Ag controller. This is the same controller proven for years on Giltrap Ag’s fertiliser spreaders and Duncan drills.
Other options include hydraulic brakes, extended cross conveyor and sprung axles with steering.
The GA 8731+ Gyrorake rounds out the Kuhn range of large width semi-mounted rakes with central delivery.
Kuhn Gyrorakes deliver reliable, safe, and efficient operation. They are simple and practical to use.
The GA 8731+ addresses the needs of large farmers, baling and bulk silage contractors with its ability to cleanly rake forage at working widths from 7.7m to 8.6m.
Its sturdy, double curved rotor arms make clean, even windrows for optimum harvesting.
Swath widths are adjustable from 1.4m to 2.3m so at maximum working width, the GA 8731+ can be used in front of both balers and forage harvesters.
The GA 8731+ has 13 arms on each of its rotors. They are driven by a rotor drive through a double reduction with the Master Drive GIII gearbox. The strength and effectiveness of this system has proven itself in all conditions on many Kuhn rakes,
Perfect ground adaptation is achieved with the 3D articulation system, which provides a large travel range.
Operators can easily adjust the working or windrow width and the raking height. GA 8731+ rakes also feature rotor suspension kits as standard in NZ.
Kuhn’s exclusive StabiLift device locks the rotors in the windrow clearance phase. This maximises ground clearance in the ‘headland turn’ position, while maintaining a low centre of gravity and good stability, including on slopes. In addition, it locks the rotors during trans-
port for increased safety and driving comfort.
GA 8731+ rakes deliver maximum manoeuvrability for easier operations and higher productivity. A control box is used to carry out critical operations (such as remote height adjustments and separate lifting of the rotors).
Since their introduction to the NZ market more than 15 years ago, Alpha Motion front disc mowers have been well recognised for their innovative front-mounted systems.
It has gained Pöttinger a worldwide reputation for ground hugging abilities. The secret lies in Pöttinger’s patented headstock with its advanced carrier headstock.
On conventional headstocks, only the leading linkage responded to bumps in the ground. With the Alpha Motion Pro headstock, the entire carrier frame adapts to the ground contours.
Each movement controls the carrier to ensure a ‘floating cut’, even over high speeds or wet ground. The result is a unique conservation of the surface layer of grass.
The new Alpha Motion Pro models are available in three sizes – the NovaCat 261 (2.62m cut), 301 (3m cut) and 351 (3.46m cut).
All models can be purchased
with or without a conditioner. A big advantage with Pöttinger’s design is that you can add or remove the conditioner in minutes, to switch from a mower conditioner to a mower in different crop conditions.
New to the NZ market is the Top FlowTask 882C with an adjustable working width of 7.7m to 8.8m with flexible swath widths between 1.3m and 2.6m. This offers the advantage of wider swaths for forage harvesters and narrower swaths for loader wagons and balers.
The 882C is available with a normal bogie axle and six contour wheels, or with the new FlowTask glide bar with hydraulic suspension, which replaces the wheels.
FlowTask guide bars glide effortlessly over uneven deep ruts and are suitable for soft and damp soil conditions providing perfect ground tracking. They deliver a quiet, smooth opera-
tion without vibration even in rough surfaces, such as pugged ground.
Pöttinger’s new 7000 Series model range is the third generation of their Jumbo Series. They feature a number of patented innovations that boost harvesting efficiency.
Six models are available in the 7000 Series with volumes from 38m3 to 54m3 , all offering different axle suspension systems from sprung to hydro-pneumatic.
All types of suspension ensure the load is evenly distributed and provide smooth running in-field and on-road. The hydro-pneumatic chassis gives outstanding stability on steep ground, better shock absorption, and more safety when travelling at high speeds.
A large 2.3m wide, seven-row floating pickup is fitted with a new hydraulically adjustable
drive system, which automatically adjusts the pickup tine speed to match the driving conditions. This eliminates any dragging effect and improves chop quality. The cutter bar bank features 48 knives, each designed with a long cutting arc surface. They slice the full length of the knife so the forage is cut extra short with uniformity.
Pöttinger’s Impress 3000 Series baler range is doing what it says on the box, impressing contractors and farmers nationwide.
OriginAg North Island sales manager Liam Hines says a baler demonstration tour last season was very popular. “The Impress baler was well received because of its usability and its huge crop flow, which allows it to handle higher crop volumes,” Liam says.
Impress balers are fitted with a patented 2.3m controlled floating pickup system with a centralised suspension. It allows for side-toside movement of 120 mm providing exceptional ground contouring.
A key feature of the Impress baler is the rotor’s Lift-Up flowover technology, which directs the forage up and over the rotor into the baling chamber. The forage is not deflected at any point, and this smooth straight feed flow results in fewer blockages, lower power requirements, and higher bale density.
Pöttinger is proudly imported and distributed by the OriginAg group of 27 nationwide dealers. For further information, or to find your local dealer, go to the website originag.co.nz or phone to talk to a Pöttinger product specialist on 07 823 7582.
At the top end McHale’s F5000 fixed chamber baler range is the McHale F5600. The F5600 is a 25-knife chopper baler with a load sensing control valve and an Expert Plus ISOBUS control console, which together make round baling fully automatic.
With this system, once the high density bale is fully formed in the F5600’s chamber, net is automatically applied. The tailgate automatically opens to release the bale, and then it automatically closes and pressurises.
Operators use the Expert Plus control screen to make all necessary adjustments to the F5600. This includes bale density, net layers, and net delay.
A new feature to the F5600 software and ISOBUS controller is the ability to customise the fully automatic rear door function and other features depending on their tractor’s capabilities.
The rear view camera can now also be integrated into the ISOBUS display and the software features a function to automatically switch to the camera view when releasing the bale.
Another new feature on the latest F5600s is McHale’s Profi-Flo pick-up with adaptive intake, which was available last season on their Fusion and V6 balers. The 2.1m wide Profi-Flo pickup is more efficient so it boosts crop intake volumes and it can work in all crop conditions.
5600 balers have the same high capacity chopper unit and rotor as the McHale Fusion 3. It gives a theoretical chop length of 46 mm and it has hydraulic knife protection as well as a drop floor unblocking system. The operator can engage and disengage the knives from the cab.
McHale has also improved F5600’s density system and door sensors to achieve even higher bale densities.
The ISOBUS user interface shares a similar look to McHale’s V6 and V8 range of balers. It provides a very simple means to navigate through the menus when making adjustments.
As with the rest of its baler range, McHale’s ISOBUS terminal options are the ISO-Play 7 or ISO-Play 12. Or you can simply use the tractor’s ISOBUS screen.
The Fusion Vario Plus is McHale’s first variable chamber baler-wrapper with the ability to secure the bale with either netwrap or film.
Whether you choose to apply net or film to the barrel of the bale, the Fusion Vario Plus produces high-density bales with the ideal shape.
Many farmers now prefer to have their silage bales made with film-on-film, however. Studies have shown that filmon-film bales produce better quality silage that is easier to feed out because film can be
stretched to a higher degree than net, so it expels more air.
Fusion Vario Plus also has a number of improvements that give it more capacity and faster working speeds than previous Fusion Vario combi balers.
One is the new Profi-Flo pickup. It improves crop flow, is more forgiving in poor swaths, and ultimately increases output.
In the bale chamber Vario Plus has a single belt, which reduces leaf loss and makes for seamless application of film around the circumference of the bale. The heavy-duty endless belt applies high pressure to the material in the chamber.
A heavy-duty double drive system powers the belt and bale rotation.
Both the Fusion Vario Plus and Fusion 4 Plus are available with weighing and a moisture sensor. These features are now a popular option in NZ.
The new Profi-Flo pick-up is also a feature on the latest Fusion 4 fixed chamber baler wrappers. Profi-Flo has a heavier driveline and ‘adaptive intake’, which reduces the chance of blockages and allows the intake to automatically adjust to the volume of the crop in the windrow.
All versions of the Fusion 4 sold here come with a 1000-rpm gearbox as standard, along with a swivel hitch and wind-up stand. The faster speed with reduced torque reduces sharp loads on the driveline.
All Fusion 4s have increased density pressure, which produces tighter, well-shaped bales.
The three versions of the Fusion 4 are the standard specification, Fusion 4 Pro, and Fusion 4 Plus. Fusion 4 Plus features film-on-film binding, while both the Pro and Plus versions have ISOBUS compatible controls as standard.
Kverneland’s 6700 Plus variable chamber balers can handle moist and dry crops, and they deliver both high output and market-leading bale density.
Plus series models are new and have upgrades that increase output and reduce maintenance. The pick-up has been updated with longer tines and wider stripper plates, for better cleaning. Both pick-up and main bale chamber drives are fitted with new high specification HBC chain.
The two models in the Kverneland 6700 Plus range are the KV 6716, which produces bales with diameters up to 1.65m, and the KV 6720, which produces bales up to 2m in diameter.
Both models suit mid-sized contractors or large farmers and they come with Kverneland’s full two-year warranty programme.
KV 6720 Plus balers can be specified with a PowerFeed or SuperCut intake system. Both intakes efficiently feed the crop to the bale chamber to maximise capacity.
The PowerFeed rotor has 14 rotor tines to force crop into the bale chamber. It can handle wet or dry crops in all conditions.
KV 6700 Plus balers produce dense bales, thanks to the Intelligent Density 3D. It gives operators the ability to choose the bale density that suits current crop conditions.
Intelligent Density 3D offers three pre-programmed bale density settings to suit straw, hay or silage. The operator can also customise the density settings for three different zones of the bale – core, middle, and outer layer.
KV 6700 Series balers use the PowerBind net wrap system to secure the bale. They are ISOBUS compatible and can run through
the tractor’s monitor or a Kverneland IsoMatch Tellus terminal.
Another option is Tractor Implement Management (TIM), which enables the baler to control certain tractor functions.
Kverneland 2800 M rear mounted mowers are popular with Kiwi contractors and farmers. The range offers working widths of 2.8m-4m with corresponding weights of 805-1045 kg. This means they are ideal for farmers with smaller tractors who harvest lots of grass.
Major features include the ability to operate at 540 or 1000 rpm and even weight distribution thanks to the centre pivot suspension. Paired with a KV 2828 F or 2832 F front mower, they have working widths up to 6.8m. Hydraulic adjustment of ground pressure is an option.
The 3.6m KV 2836 M is the biggest selling Kverneland mower in New Zealand. It has nine discs and 18 knives, and like other models in the 2800 M range, a transport width of 2.3m.
Kverneland also offers heaps of options for larger front, rear and butterfly mowers.
Wider rear mower conditioners include the 3.2m KV 3332 MT
with semi-swing conditioners and KV 3332 MC with roller conditioners. Both have Kverneland’s unique QuattroLink suspension system.
QuattroLink uses four suspension arms fitted onto a fixed carrying arm. The mower floats over the ground and the operator can adjust its height accurately and instantly to adapt to contours.
Butterfly options include the KV 5095 and KV 53100 MT-BX. The 9.5m-wide KV 5095 is a straight disc mower while the KV 53100 has tine or roller conditioners.
KV 5095 rear twin mowers deliver excellent contouring with their adjustable pressure springs. They give break-back protection from obstacles, clean headland turns, and centre suspension for even weight distribution across the full width of the mowers.
KV 53100 mowers have a working width of 10.2m and hydraulic adjustment of both the working width and overlap.
When fitted with BX swath belts, the KV 53100 MT can group all the grass cut by its front mower and two rear mowers into a single swath or lay it down in other configurations.
With the optional GeoMow feature, it automatically adjusts the overlap between rear and front
mowers to avoid mowing ground that has already been mowed.
High capacity raking options from Kverneland include the KV 9584 and KV 9590. These heavy-duty two-rotor rakes give working widths of 8.4m and 9m respectively.
They are built to handle tough conditions with a high-performance gearbox and strong frame. It has hydraulically-adjusted working and swath widths, and the ability to make sharp turns of up to 80°.
For a four-rotor option there is the KV 95130C Pro. Designed to handle all types of crops, it gives hydraulically adjustable working widths 10m-12.5m.
The 95130 has load-sensing hydraulics, ISOBUS, and a sophisticated headland management system, which raises the rotors clear during headland turns and has adjustable timings for lifting and lowering of the front and rear rotors.
Kverneland tedders include the KV 85134 C and 85156 C. They have 13.4m and 15.6m working widths and 12 and 14 rotors respectively, and are designed for high output and excellent crop quality.
SAM feed wagons are strong, simple and smart. They are built to deliver a reliable, efficient performance year in, year out, and, like all SAMs, they are designed to be easy to use and maintain.
The range encompasses models with capacities of 10m3 , 12m3 and 15m3. They can be specified with either a low maintenance stainless steel chain side-feed or a simple centre-feed delivery system.
All versions provide an even flow of feed with excellent throw. They can handle a large range of feed types – green feed, grass silage, maize and PK.
You can also add smart weigh scales to have simple, accurate electronic weighing of feed quantities.
The standard stainless sidefeed conveyor has 25-mm conveyor bars that provide a strong flow of feed. Heavy roller chains for the feed conveyor are standard and a belt option is also available. The conveyor eliminates tracking, so operators face less maintenance issues.
Stainless sides and a strong
stainless front provide durability and eliminate any worry about rust. If you are feeding fine product, front mesh can be customised to suit your needs.
All SAM feed wagons have extra corrosion protection. First comes a grit blast, then a thermal-arc spray and finally a special SAM coating. It is a mega tough finish.
Standard on all SAM feed wagons is a Trans-Tex 21-mm highstrength timber ply floor. TransTex is widely used in the trucking industry because of its high bending stiffness and high-impact resistance.
Heavy duty 13-mm high-tensile floor chains ensure a long working life and low maintenance.
The teaser bars that lift the feed to the side feed delivery floor have individually welded teeth, which are designed for optimal grab and lift. Although they are more labour intensive to build, they last longer and they are great for handling grass silage.
Weigh scales can be factory fitted or retrofitted. The loadcell system can be used with a display to provide simple, accu-
A new option for New Holland’s BigBaler range offers the potential for greater productivity, bale quality, fuel efficiency and operator comfort by automating key baler and tractor functions.
Operating a BigBaler manually demands that operators focus for long hours and make regular steering adjustments to follow the swath. They must observe the swath density and crop flow to prevent overloads and blockages and adjust the speed of the tractor to match.
To ensure production of consistent bales, drivers must observe the bale fill indicator and correct the tractor steering accordingly, while also monitoring bale slice numbers and weights.
By proactively automating tractor steering according to the swath path, and speed adjustment with regard to swath volume, IntelliSense bale automa-
tion relieves the driver of these demands.
At its heart is a LiDAR (light detection and ranging) sensor located at the front of the tractor cab’s roof. The sensor emits a laser pulse several meters ahead of the tractor which is reflected off the swath.
The system then automatically adjusts the steering to follow the swath and ensure even filling of the chamber according to the baler’s plunger load sensors.
IntelliSense can work in daylight or at night and can deal with dusty conditions. It delivers great bale quality, saves fuel and makes the operator’s life easier over long working days and nights.
The swath cross-section measured by the LiDAR is also used to govern the tractor’s speed control. It reduces the speed when necessary to avoid overloads and increases it in thin swath areas.
This can significantly increase
productivity, because the system adjusts the forward speed to its optimum.
CNH NZ-Australia product manager Sune Nielsen says he is delighted with IntelliSense technology.
“I had the opportunity to validate this system locally. I have spent many hours behind the wheel of a baler in the past, and it was pleasing to see how simple and effective IntelliSense really is,” Sune says.
“It is not always straight forward to make a uniform bale, especially if the windrows are narrow or not-uniform. If you don’t feed the baler right the bales can come out bananashaped with more material on one side that can also lead to broken twine.
“IntelliSense takes care of this, steering the tractor so material is evenly distributed into the baler feed system.”
With IntelliSense, the operator has two assisted baling modes to choose from. They can be used together or independent from each other.
In Feedrate mode the operator can set the maximum speed limit and number of slices per bale set. A low number gives thicker slices and a higher throughput. The tractor will then continuously adjust its forward speed to match the target slice number.
The second mode is Swath Guidance. It uses the tractor’s SmartSteer technology to give hands-free driving whenever a swath is detected ahead of the tractor. It ensures the swath enters the centre of the pick-up, and makes adjustments as necessary according to the plunger load cells to ensure a perfect bale shape.
Both functions can be disengaged at the press of a button or by moving the steering wheel.
IntelliSense is available on all BigBaler Plus models. It is available as a kit which can be retrofitted to all existing BigBalers HD models starting from model year 2020.
It can work with all New Holland T7 LWB, T7 HD and T8 AutoCommand tractors equipped with Class 3 ISOBUS unlocked for steering and speed control.
A specific intuitive run screen has been developed to provide a simple overview of the IntelliSense functions and key main information. Differential GPS provides a sufficient signal, so RTK is not necessary.
The system was also recognised with a Silver Medal Award at Agritechnica 2022 and is now available in Australia and New Zealand for the New Holland BigBaler Plus range and BigBaler High Density models for 2024.
a chassis designed with ample ground clearance, to save bellying out in rough terrain.
To improve machine maintenance, they have a remote axle-greasing system. It saves
time and effort and gives access to all axle greasing points from an easy to reach location. It is standard on 12m3 and 15m3 models (and available as an upgrade on 10m3 models).
Heavy duty swivel coupling is also standard on 12m3 and 15m3 models. You can use a donut eye for coupling with a quick hitch or the insert option for tractor coupling.
SAM have been making feed wagons in New Zealand since the 1960s - that's six decades of testing and R&D. All are backed up by their fast parts support service from the heart of the Waikato.
KAITAIA Kaitaia Tractors 09 408 0670
WHANGAREI Piako Tractors Northland 09 438 1319
SILVERDALE Brandt NZ 09 427 9137
PUKEKOHE Brandt NZ 09 237 0043
MORRINSVILLE Piako Tractors 07 889 7055
MATAMATA Matamata Tractors & Machinery (07) 888 6292
HAMILTON Brandt NZ 07 847 0425
CAMBRIDGE Brandt NZ 07 827 5184
ROTORUA Piako Tractors Ltd 07 345 8560
TAUPO Taupo Tractors & Machinery 07 378 4533
STRATFORD FieldTorque Taranaki 06 765 8643
HASTINGS Stevenson and Taylor 0800 4273 2273
WAIPUKURAU Stevenson and Taylor 06 858 6041
DANNEVIRKE Lancaster Tractor Services 2022 Ltd 06 374 7731
PALMERSTON NORTH Transag Centre 06 354 7164
MASTERTON Brandt NZ 06 377 3009
NELSON Drummond & Etheridge 03 543 8041
BLENHEIM Drummond & Etheridge 03 579 1111
KAIKOURA Drummond & Etheridge 03 319 7119
GREYMOUTH Drummond & Etheridge 03 768 5116
CHRISTCHURCH Drummond & Etheridge 03 349 4883
ASHBURTON Drummond & Etheridge 03 307 9911
TIMARU Drummond & Etheridge 03 687 4005
OAMARU Drummond & Etheridge 03 437 1111
MOSGIEL JJ Limited 03 489 8199
GORE JJ Limited 03 208 9370
INVERCARGILL JJ Limited 03 211 0013
It’s in your power to protect it from introduced predators and preserve it for future generations
Without predator control, these habitats and the native wildlife that depends on them will continue to decline — even with stock exclusion. Our toolbox will guide you through how to manage pests in these unique spaces.
predatorfreenz.org/farms
A Strautmann Magnon loader wagon is the go-to option for contractors and large farmers who need to harvest and cart large volumes of silage to meet tight schedules or weather windows.
Thanks to the unique design of the Continuous Flow System (CFS), Magnon loader wagons can achieve a high throughput.
With CFS, the swath is evenly spread across the full width of the rotor. The roller then accelerates the swath from the pick-up and maintains a constant feed to the rotor to ensure smooth crop flow without feed jams.
Other features that give the Strautmann Magnon the ability to produce higher quality silage are the Flex-Load pick-up and the Exact Cut knife bank. The pick-up lifts the crop cleanly while the 48 double-sided knives deliver a theoretical chop length of 35mm.
The three models in the Magnon 10 Series are the Magnon 10-430, with a capacity of 42 m3 , Magnon 10-470 (46 m3) and the flagship Magnon 10-530 (52 m3).
All three models have a solid all-steel superstructure with easy access side door. A new addition is the hydraulically swivelled front panel, which gives better compression and higher capacity.
When the Magnon loader wagon is completely full, the headboard automatically moves forward either all the way or in three stages guided by a timer.
Its new moving headboard allows for an extra capacity of 5m3 in the front of the wagon. By compressing the crop and swivelling forward, the headboard allows Magnon loader wagons to be shorter and have a more compact design than their predecessors.
A standard feature is the steel floor with twin powerful hydraulic motors and low-wear steel chains. It unloads even heavy crops very quickly. Dosing units can also be fitted for even silage discharge, which improves the compression in the stack and, therefore, silage quality.
Beginning at the front, the 2.25m-wide Flex-Load pick-up has a plastic tine system, which suffers 50 percent less wear than
a steel-on-plastic system. The tines are hard enough to pick up large swaths but flexible enough to adapt to ground conditions, which minimises wear and contamination.
Flex-Load pick-ups are camless and hydraulically driven, and they adapt automatically to changing travel speed. Operators can also adjust them manually. For better travel over uneven terrain there is the option of a sensing wheel that sits behind the pick-up.
A double-drummed crop roller evenly feeds the crop to the rotor. Because the crop rotor sits higher up, it reduces the distance the crop needs to travel. The benefit of this design is faster loading with lower diesel consumption, a win-win.
The rotor on Strautmann Magnon 10 Series loaders has an overall width of 2.1m and a conveying width of 1.75m. It has eight helical rows of tines and augers on either side that bring the material in from the pick-up to ensure uniform cutting.
The Exact Cut knife bank has an automatic ‘reset’ system that ensures consistent quality and efficiency, because the operator can load without the need to stop.
With its 48 double-sided knives, the Exact Cut has a long service life. It is easy to replace knives during a job thanks to its quick-change system. Buttons on the side of the wagon are used to retract the knife bank for
servicing and for positioning the drawbar to easily hook up the Magnon.
Standard features include LED light strips inside the bin for night time loading and unloading, as well as rear twin LED lights for reversing and unloading.
Strautmann offers a number of options to customise your Magnon loader wagon. These include extra LED lights beside the knife bank for servicing or navigating the machine around tight laneways at night.
Folding mesh covers can be fitted to minimise losses during transport. A range of cameras can be fitted inside the bin for better loading or on the rear for reversing.
The Magnon range comes standard with tandem hydraulic suspension on the 10-430 and 10-470, whereas the Magnon 10-530 is standard with tridem hydraulic suspension. This is optional on the 10-470.
A range of steering options are available: passive steering on
tandems and the optional extra of SES (Strautmann Electronic Steering) or hydraulically forced steering.
Strautmann Hopkins has been the New Zealand importer of Strautmann products for more than 40 years. Its dealer network provides support for the sale and service of Strautmann machinery throughout the country.
Strautmann Hopkins holds a large inventory of spare parts at its headquarters in Palmerston North. The headquarters serve as a hub for importing, assembling, spare parts distribution and technical support.
The company thanks contractors Daryl Thompson (DTC Contracting) and Graham Laidlaw (B&R Contracting) for their help demonstrating and photographing the Magnon 10-530.
For more information call Conor Hopkins on 021 246 0689 or conor@strautmann.co.nz or to find a dealer near you visit the website strautmann.co.nz.
European mower manufacturer Samasz and agricultural machinery specialist FarmShop have set an ambitious goal to be the New Zealand market leader in hay mowers by 2027.
Samasz has produced more than 160,000 mowers since its inception in 1984 and is a leader on the international stage with a presence in more than 70 countries. They are celebrating 40 years in business with sharp deals on hay mowers in New Zealand all backed up by FarmShop’s customer service.
To demonstrate their commitment to the NZ market, Samasz sent sales representative Greg Biedrzycki to join the FarmShop team at National Fieldays. Greg also took the opportunity to visit customers in the North and South Island.
Because Samasz devotes time and energy to understand New Zealand conditions and then sends that information straight back to their R&D team in Poland, it is respected by Kiwi farmers. It also puts Samasz on track for its
goal of ‘NZ number 1’ by 2027.
Fieldays 2024 saw more than 106,000 visitors over four days. It highlighted the resilient farming community and raised hopes for an improved payout in October.
FarmShop staff enjoyed chatting with new customers and hearing firsthand from those who have already chosen a Samasz mower. They included Otago contractor, Joe Herbert, who is very happy with his decision.
“I have been running Samasz mowers for nine seasons, and I have had a real good run with them. We do 1500 to 2000 hectares a year with them, which
includes stony conditions, rolling hills, and a lot of steeper stuff.
“I hit a big lump of concrete with our original set, and it just lifted, came back down, and didn’t even break a blade, module or anything. Another time the front mower hit a four-inch steel hydrant in a paddock. It sliced it off and kept going. It didn’t even break a blade.”
Joe says the floatation on his Samasz mowers is second to none.
“They sit well on the ground, follow contours, don’t leave too much behind, and leave a nice clean finish – probably the clean-
est finish I have seen. We are real happy with them.
“The side-shift on the front mower is awesome – you can slide it across along the sides of hills or around corners, I couldn’t do without it really. It should have it on more gear, especially going through gateways; it makes it a lot easier.”
Another thing Joe likes is that when he is under pressure, parts are easily sourced, and downtime is eliminated. He finds the mowers extremely durable and easy to work on if something does go wrong.
Samasz grouper mowers have
Webbline Agriculture has a wide range of agricultural equipment from leading European manufacturers suitable for New Zealand.
With branches in Waikato, Manawatu, Canterbury and Southland, there is a fully equipped Webbline branch within a three hours’ drive for over 80 percent of New Zealand’s farming regions.
Italian-made ROC continuous mergers provide a significant number of advantages over traditional raking systems.
ROC mergers lift the crop vertically on to a conveyor belt before discharging it out either side of the machine, versus rotary rakes, which ‘drag’ the crop horizontally along the ground to the swath.
One major advantage is that ROC mergers’ pick up tynes improve feed quality. They handle the crop gently, which reduces stripping or shattering of the forage and reduces the amount of foreign material. This improves quality and reduces wear on foragers and balers.
Available in New Zealand is the 10m RT1000 with a pick-up that can build a wide swath on each pass. By reversing the direction of the conveyor, the RT1000 can deposit the crop from the second pass in the pre-existing swath, to form a large swath that reduces the number of passes required by the baler or silage chopper.
If necessary, ROC mergers can then pick up the entire swath and deposit it one row further out to create an even larger swath.
With durable wheels on adjustable bogies under each section, ROC mergers can han-
dle undulating terrain. A set of four modulating tandem wheels can be adjusted to suit the height of the cut.
SIP has recently unveiled its new range of swather rakes –the Star R930, R870, R770, and R670.
The Star R930 is the flagship of the series. It features a working width of 9.3m, making it ideal for large-scale operations. Its robust construction ensures long-lasting performance, while the advanced tine arm technology provides a clean and efficient raking process.
Hydraulic adjustment allows for easy customisation of the working width and height, and ensures optimal performance in a range of field conditions.
While the Star R870 offers a slightly narrower working width (8.7m), it retains all the innovative features of its larger counterpart. The R870 is perfect for operators who want high performance and reliability.
Its precision-engineered tine arms and adjustable rotor speed guarantee consistent raking quality and boost the efficiency of the harvesting process.
Designed for farms that require a reliable rake capable of handling diverse field conditions, the Star R770 strikes a balance between performance and versatility.
With a working width of 7.7m, the R770’s compact design ensures easy manoeuvrability, while the high-quality materials used in its construction provide durability and low maintenance.
The most compact model in the range is the Star R670, with a working width of 6.7m. This rake is ideal for small farms or fields with tight spaces.
Despite its smaller size, the
Star R670 does not compromise on performance. It features the same advanced tine arm technology and hydraulic adjustment system found in the larger models, ensuring efficient and precise raking.
Wilson SuperMove bale transporters are perfect for New Zealand contractors and large farmers who need robust, reliable gear.
The range includes models with the capacity to carry eight, 10, 12 or 16 bales.
A big advantage of the Wilson SuperMove is the ability for a single operator to pick up wrapped or unwrapped bales from the paddock without leaving the cab.
Because the bales don’t need
to be secured for transportation, there is no need for loading machinery or truck-and-trailer units when transporting bales. Bales are transported gently in the innovative loading cradle, which reduces potential damage to wrapped bales. The Wilson transporter is also up to 60 percent faster than traditional methods.
The SuperMove has a robust chassis and high-capacity hydraulic rams to ensure durability. They have strong axles and suspension systems to manage uneven surfaces and provide smooth, stable transportation.
For more information, contact Webbline Agriculture on 0800 932 254, email sales@webbline. co.nz, or visit the website webbline.co.nz.
a robust frame, conditioners, stone-proof knife holders and replaceable stone protectors. The thicker 25-mm spur gears with a bevelled edge reduce maintenance costs and there are no sharp edges to catch or break They are available with either
tine or roller conditioners and they offer easy adjustment of the grouper's belt speed. They are the perfect option to increase productivity and eliminate the need of a tedder and rake.
Another reason the mowers are respected is because Samasz
can boast one of the fastest blade tip speeds of 3200 rpm. This is an important factor in mower performance because it provides a cleaner and faster cut.
FarmShop is currently providing 20 percent off retail prices and 0 percent finance over three
years. Plus anyone who places an indent order for a Samasz grouper mower this season will be in the draw to win a Can-Am Defender valued at $31,500.
For more information visit the Farmshop website: farmshop. co.nz.
Goweil machinery is designed to significantly enhance efficiency and productivity in baling and wrapping operations. Among Goweil’s top-tier products are LT Master stationary baler-wrappers and the G1-F125 fixed chamber baler.
The high-performance Goweil LT Master is both versatile and efficient. It is engineered to process a wide variety of materials, including maize, hemp, corn cob mix (CCM), and sugar beet pulp.
A standout feature of the LT Master is its integrated feed hopper, which ensures a steady and continuous flow of material into the machine. Coupled with a scraper floor and a re-feeder belt, the hopper guarantees efficient material handling and consistent operation.
Its hydraulic drive system is another of the LT Master’s critical components. It allows the operator to precisely match the baling speed to the material being processed. This adaptability maintains optimal performance and ensures high-quality bales.
The LT Master can produce bales with a diameter of 0.60m to 1.15m, to meet different storage and transport requirements. Its robust construction and advanced features enable it to process up to 60 bales per hour, depending on the material and conditions, showcasing its impressive efficiency.
In 2024, Goweil expanded the LT Master range with the introduction of the F60 model. This new addition offers the same exceptional quality and performance as the LT Master but in a more compact and affordable package.
The LT Master F60 is specifically designed for smaller operations or farms with limited space. Despite its smaller size, the LT Master F60 retains all the advanced features of its larger counterpart.
It processes a wide range of materials, including maize, hemp, CCM, and sugar beet pulp. The integrated feed hopper, scraper floor, and re-feeder belt ensure smooth and efficient material handling, while the hydraulic drive system allows for precise adjustment of the baling speed.
LT Master F60 produces bales with a diameter of 0.60m, maintaining the same standard as the larger model. Its compact dimensions and ease of transport make it an ideal choice for operations that require mobility or have space constraints.
Both the LT Master and LT Master F60 set the standard in stationary baler-wrapper technology.
The innovative Goweil G1-F125 fixed chamber baler has established itself as one of the best on the market since its arrival a couple of seasons ago. It produces bales that are tightly formed right from the centre and have great density throughout.
Contractors who run Goweil G1-F125 balers say that their clients love the bales they make because they are easier to cart and stack, heavier, and contain high quality forage.
The G1-F125 is user-friendly for operators and it offers great performance and durability. Maintenance is reduced thanks to a heavy-duty split gearbox drive system and heavy-duty drive chains.
Bale formation starts with the innovative 570-mm diameter Shot Over rotor, which feeds the grass over the top of the rotor (not under it like other balers on the market). When it goes over the rotor, the grass takes the most direct route to the bale chamber.
This greatly improves the crop flow, minimises the possibility of blockages and produces bales that are formed consistently from the start.
Standard on the G1-F125 is an easy-to-use ISOBUS terminal. It provides a wide range of infor-
mation to the operator, and it can be operated through the tractor’s own ISOBUS compatible screen.
The Goweil G1-F125 is available in two versions – the G1-F125 baler or a G1-F125 Kombi baler-wrapper combination. Both are available with the five year-30,000 bale Goweil Gold warranty and servicing programme.
For more information, contact Webbline Agriculture on 0800 932 254, email sales@webbline. co.nz, or visit the website webbline.co.nz.
Step into a New Holland and get 1.95% p.a.* finance across the range.
New Holland understands the cost pressures facing farmers today across New Zealand and we want to step up and get you into a new tractor.
Whether you are buying for the first time or upgrading, New Holland are giving you, the farmer, the option of purchasing your new tractor at 1.95%* with deferred repayment until March 2025. This gives you peace of mind to hop into a new tractor this winter without having to worry about repayments until next year. So, what are you waiting for? Head to your local New Holland dealer to secure a deal. Hurry, offer ends 31 August 2024.
newholland.co.nz
ANDREW DALZELL KNOWS WHAT HE LIKES IN TRACTORS.
“I HAVE BEEN A CASE MAN ALL MY LIFE, AND MY FATHER WAS A CASE MAN.”
Over the years Andrew has had flings with New Holland and another brand but he keeps coming back to Case IH. His newest two tractors are both red. One is a Puma 240 and the latest is an Advanced Farming Systems (AFS) Connect Optum 300.
Andrew also has a Case IH CVX 1190, which he says is his favourite, as well as two New Hollands – a T7270 and a T7245.
Dalzell Contracting is based in Culverden, North Canterbury. Clients are dairy farmers in the Amuri basin and sheep farmers in the surrounding hill country.
Over summer Andrew and three operators are flat-out baling rounds and large squares. During their downtime over winter they clear shelter belts and
ALL OF DALZELL CONTRACTING’S CASE IH AND NEW HOLLAND TRACTORS HAVE CONTINUOUSLY VARIABLE TRANSMISSIONS, WHICH COME INTO THEIR OWN DURING BALING AND MOWING.
run a firewood business.
In the background, Andrew’s partner Vicki Collett does the paperwork, relocates staff and drives if necessary.
A lot of Vicki’s time is spent on the Hurunui Garden Festival Committee. They organise the annual festival, which is held at the end of October and includes hers and Andrew’s garden ‘Coldstream’.
All of Dalzell Contracting’s tractors have continuously variable
THE NH BIGBALER 1290 MOSTLY MAKES BIG SQUARE SILAGE BALES BUT IT ALSO BALES UP HAY AND CEREAL STRAW.
transmissions. Andrew says it lets the driver select their speed, from zero to 50 kph.
“You can’t do that in powershift. With baling and mowing you get the full benefit of the CVT, and it is easy to drive. The
operator doesn’t have to select a gear. It is all done for you.”
The Optum arrived in autumn this year. Its first job in spring will be baling, which it will do for six months and then over winter it will pull two diggers around the district.
“The Optum has everything. I ticked all the boxes because if you order it out of the factory it doesn't cost a lot more compared to adding it on afterwards.”
AFS Connect is all about advanced farming technology and making connections –between the tractor and home computer as well as with the dealer. It makes it easy to send and receive job orders and other data.
The main reason Andrew opted for the Optum was its size, however. “I needed the extra weight to tow around our two diggers.”
He has specified the Optum with front linkage and PTO so it can eventually serve as a backup triple-mower tractor.
The Optum is set up with GPS and auto-steer, and in time Andrew will incorporate other AFS components. “Farmers will want to know where their bales are coming from in the blocks and it will all be GPS logged.”
Powering the Optum is a 7.6-litre FPT engine, famed for its fuel efficiency.
It has a luxurious cab with heaps of room and a gentle ride, courtesy of front suspension, cab suspension and an air-ride seat. Added comfort comes from the heating and cooling seat.
Five hydraulic remotes are on the back. It also has mid-mounts for the front linkage and a set of remotes on the front for the mower. Oil flow is 220-litres per minute.
Andrew has just bought a new New Holland large square baler, and his older one, also New Holland, will become the back-up.
In fact, he has had a series of New Holland square balers. The latest is a BigBaler 1290 with Loop Master knotter system.
“Every baler I have bought has had improvements in plunger design. This one is no exception with more reinforcing to last longer, especially in wetter crops.
“It copes well with wet or dry crops. That is one of the reasons I got a New Holland baler.”
The pick-up on the BigBaler 1290 is 2.35m wide and it has five rows of tines.
“It picks up cleanly, so long as you use the conditioners on the mowers. It is only when farmers mow their own crop that it is hard to rake and bale.”
A set of 21 knives is another feature of the BigBaler 1290, although Andrew mostly uses six when farmers want a chopped crop.
He says the knives retract if they hit an obstacle, and when they wear out, they are easy to replace. No tools are required. He just pulls out the knife drawer and locks them in with a halfcam system.
The BigBaler 1290’s pre-compression chamber is adjustable for the different crop types. With this feature and the ability to choose the number of slices, Andrew and his team always make perfect bales.
Most baling is grass silage on dairy platforms, but Andrew also uses the NH BigBaler 1290 for hay and cereal straw.
In good going, it makes about 50 bales per hour. They can make around 700 bales in a day with two balers, before the
moisture levels rise too high. Andrew has opted for moisture meters and scales on his balers. He also knows the lengths of all the bales.
The Loop Master knotting system is the star of the show. This is the second Loop Master Andrew has owned. The knotting system ensures there is no twine wastage and no off-cuts are left in the paddock.
“I don’t know what knots would do in the gut of a cow, but it can’t be good. And there is no contamination of sheep’s wool.”
There is storage for 36 XL twine spools, which are all connected, saving time in the field. This is enough twine to last two days, but they tend to load up every morning.
Andrew also has two tube wrappers and one individual wrapper. His team carts silage bales to the wrapping site where they are wrapped and stored, either individually or in tubes.
His team make 1.6m big square silage bales, which weigh 800900 kg.
Andrew’s Dad worked with Cochranes and Andrew has
maintained the relationship.
“They provide good back-up service, and I get on well with the mechanics and with Dan the branch manager.”
Cochranes do all the warranty servicing and provide a full callout service, although Andrew can sort most issues himself. If he does need help, he chooses to leave it to a more civilised hour.
“If it is serious I may talk to the on-call person and get it teed up for the next morning.”
Andrew has been using Case IH tractors and New Holland gear over 35 years of contracting. “I know a lot about them. They are very similar tractors, and I have never had a reason to change.”
Both his new Puma and Optum are painted viper-red which is the colour celebrating 175 years of Case. The two New Holland tractors also have non-standard ‘Blue-Power’ paintwork.
“They stand out. Everyone knows who owns those tractors. We keep them clean, which prevents contamination, especially for organic farmers, but it also looks professional.
“It is very reliable equipment and it is all that I have used through my whole life.”
NORTH CANTERBURY
CONTRACTOR SIMON BROOM RECKONS IT WAS A GOOD THING HE REPLACED HIS JCB 435S AGRI WHEELED LOADER WITH A BIG 280-HP JCB 457S VERSION TO BUILD HIS SILAGE STACKS BACK IN 2022.
That’s because the following season he upgraded his forage harvester to a new Claas Jaguar 970, and, he says, the smaller wheel loader would not have been able to keep up with it.
SW Broom Contracting is based at Culverden and looks after dairy farmers in the Amuri Basin. Virtually of them are on irrigated land and Simon and his team establish their crops and do their baling and bulk silage.
He says the JCB 457S has boosted the capacity of their bulk silage work and does a lot of other jobs as well.
On the stack, the JCB 457S has plenty of power thanks to its 6.7-litre, six-cylinder Cummins engine, which puts out a maximum 188 kW and 1200 Nm peak torque. It is also heavy enough to really compact the stack.
“It weighs 20 tonnes with the 16-ft buck rake we have on it,”
Simon says. “Our other JCB wheel loaders did a good job and lasted well, but this one is beefier and
SIX-CYLINDER
gives a lot more push than those smaller ones.
“With the extra weight and power it can stack half as much again as the prior one. Plus it is nimble enough to lift fodder beet, load trucks with hay and straw bales, and push up fire heaps. We wouldn’t go back to a smaller one.
“We got it just after Christmas 2022, so it has now done oneand-a-half seasons. We have put 1500 hours on it, or 1000 hours a year, so we use it all the time. It tends to put in more hours than our tractors.”
Scott Bunt is Simon’s stack driver. He has been doing the job for a decade and during that time he has used three different
JCB wheel loaders. He is quite impressed with the 457S.
“One of the things that you notice on the stack is that they have lengthened the tool bar by 250 mm. It does not sound like much, but it gives much better visibility of the tines on the buck rake. It is also easier to see the front on other jobs like lifting fodder beet,” Scott says.
“When we demoed the JCB 457S, some people were saying it is too big and unstable to work on the stack, but it has been fine. We make stacks with square edges rather than traditional buns, and it has never been a problem.”
With its 20-tonne weight the 457S can really compact the stack. Scott recently had to feed
CONTRACTOR SIMON BROOM SAYS HIS JCB 457S WEIGHS 20 TONNES WITH ITS BUCK RAKE, SO IT HAS THE WEIGHT AND POWER TO BUILD DENSE STACKS QUICKLY BUT IT IS NIMBLE ENOUGH TO DO OTHER JOBS LIKE STACKING BALES.
out from a stack that he made with it more than a year ago using a tractor and front-end loader. He says he was surprised how hard it was to do because it was packed so densely.
“It is also fast. We can comfortably drive it 40 or 50 kph across a paddock to pick up bales, and it is quick on the road, so we can travel between jobs faster,” he says.
At the start of the 2023-2024 season, SW Broom Contracting added a new Jaguar 970 forage harvester to its fleet. It has a 24-litre MAN V12 engine that can crank up to 990 hp.
It has a much higher output than their previous Jaguar, and Simon says that can take five trucks or more working flat-out to keep up with it.
“We use a self-propelled mower in front of the Jaguar. We can use a big rake to pull in two rows from the mower and the Jaguar 970 eats it up.
“There is no point in having a big forage harvester like that if you can’t keep up with it on the stack. If we didn’t have the JCB 457S we would need two stack tractors to match its output.”
It is fully specified with a near-infrared (NIR) dry matter sensor as well as weigh scales. He can provide his customers an accurate account of the tonnages he chops for them along with a full run down of the quality of the silage including DM, wet tonnage, and protein and sugar levels.
WITH THE STRIPCAT’S PNEUMATIC PRESSURE SYSTEM OPERATORS CAN CONTROL DOWN PRESSURE ON THE TILLAGE UNITS, TRASH CLEARANCE, AND THE REAR PACKER WHEELS FROM THE CAB.
FRENCH COMPANY AGRISEM HAS TAKEN AN INNOVATIVE APPROACH TO STRIP TILLAGE AND NEW ZEALAND IMPORTER NC EQUIPMENT SAYS THE COMPANY’S STRIPCAT MACHINES HAVE LOTS TO OFFER KIWI CONTRACTORS AND FARMERS.
NC Equipment received a shipment of Stripcat strip tillers in June and several are now at work around the country. The Stripcat line-up offers liquid and solid fertiliser options on 8 to 12 row machines.
With its large range of adjustments, the Stripcat can be set up to suit many scenarios, even in challenging field conditions.
Operators can control the key elements of
each row pneumatically from the cab. With the pneumatic system they can make adjustments precisely and on the fly.
A demonstration Stripcat is now in Waikato and it will soon be working on farms from Taranaki to Tauranga. Any interested growers or contractors can enquire about a demo.
NC Equipment strip till consultant Cameron Bassett says people are always surprised at the conditions they can work in and the seedbeds they can create.
“The Stripcat can handle everything from 60 cm of bean stubble, to dry North Canterbury soils or wet clay in Southland. One grower uses it to strip till and apply dry fertiliser at 500 kg/ha,” Cameron says.
Agrisem Stripcats come in sizes up to 12m wide. Both mounted and trailed versions are available. Spacings between the rows are
easily adjusted from 40 cm to 80 cm with only two U-bolts to loosen per row.
The Stripcat can be used in tandem with most major European brands of precision planters. This gives a one-pass system to cultivate, fertilise and plant, which has proved successful in crops such as maize, beet, carrot, hemp, rape seed and other row crops.
Its ability to create tilth for a seedbed at relatively low speeds suits planters in one-pass tilling and planting scenarios. The carbide tungsten winged point fitted to Agrisem’s C shaped leg does an exceptional job of cultivating, mixing the soil and bringing the tilth to the top of the row.
For more information on the Agrisem Strip tillage range call NC Equipment on 0800 908 908, contact Cameron Bassett on 021 193 3964 or visit the website ncequipment.co.nz.
Ironmax Pro is next gen science that’s building on the toughness of Metarex® Inov. And it’s a great fit for all farming and growing practices – conventional, sustainable, regenerative, and organic.
MAYFIELD ARABLE FARMERS RICKY AND REBECCA TAYLOR STARTED THEIR CONTRACTING BUSINESS FIVE YEARS AGO BECAUSE THEY COULD SEE THERE WAS A NEED FOR A SPREADING OPERATION IN MID-CANTERBURY THAT FOCUSED ON SERVICE AND JOB QUALITY.
Their business, Fert Solutions, applies the full range of liquid, solid and granulated products that farmers use these days.
Ricky and Rebecca started Fert Solutions in 2019 with a Tow and Fert. They later brought in a
spreading truck to apply granular fertiliser and then another spreading truck. Last year they added an Agri-Spread AS2100SC trailed spreader to the business.
With its large bin and its ability to do both variable width and variable rate spreading, the AgriSpread has boosted the capability of Fert Solutions.
“We take a lot of pride in the quality of the job we do and the great service we provide our clients. Our aim is to provide a precision spreading service. All our spreaders are fully calibrated and Spreadmark certified,” Rebecca says.
Fert Solutions spreads all types of granulated nitrogen products, high analysis fertiliser, capital fertiliser, lime, phosphate, com-
post and a variety of liquid products – from liquid nitrogen to fish fertiliser and biologicals.
“We don’t really advise people on what to spread, but it has been interesting to see the changes in the industry in the last five years. When we started, farmers mainly used mainstream products,” Ricky says.
“Now there are lots of different liquids, granulated biologicals and other products. One of our trucks has a chain drive so it can handle the lumpier biological products.
“We got the Agri-Spread for extra capacity. We could see it fitting into our business because many of our clients are close by. Its also great at the end of the season when we need to get onto certain farms. A tractor and trailed spreader are better able to handle wet, heavy soils.”
In addition to its ability to work in wetter conditions, the single axle Agri-Spread AS2100SC has a larger capacity than Fert Solutions’ two truck-mounted spreaders. It can carry 6 tonnes of urea or 10 tonnes of lime.
Ricky says it is well built and has some handy features,
FERT SOLUTION’S AGRISPREAD AS2100SC HAS A BIGGER CAPACITY THAN THEIR TRUCK MOUNTED SPREADERS PLUS THE ABILITY TO DO VARIABLE WIDTH AND VARIABLE RATE SPREADING.
sprung drawbar, stainless steel bin and fittings. It can comfortably spread granulated fertiliser up to 36m or even 38m (depending on the product and the weather) and lime up to 12m.
“Another reason we got the Agri-Spread is its twin belts, which give it the ability to do accurate section control. We can spread in the inconsistently shaped paddocks on farms with pivot irrigators without overlaps,” Ricky says.
“In fact it is very rare to get a paddock that is a perfect square or rectangle or has perfect bout widths. With variable width and rate spreading we have an even spread in variable shaped paddocks. Getting a consistent rate without overlaps is important when farmers have to work within nitrogen caps.”
Ricky runs the Agri-Spread with a John Deere 175R tractor. It connects to the tractor through its ISOBUS monitor and uses the tractor’s Greenstar GPS to work out its position to do section control.
The Agri-Spread has also accurate weigh scales, which contribute to its accuracy.
“When we calibrate the spreader we enter the weight of a litre of the product. It then knows the target bulk density and with the weigh scales it takes constant measurements and adjusts the application rate if the density varies from the target to get the desired spread rate. It is very good if you are using fert mixes that are not blended quite right and are not consistent,” Ricky says.
Another plus with the AgriSpread is its hydraulic drive rather than ground drive, so there is no ground wheel that can get soil
RICKY AND REBECCA TAYLOR ADDED AN AGRISPREAD AS2100SC TO THEIR CONTRACTING BUSINESS BECAUSE TRAILED SPREADERS ARE BETTER ABLE TO HANDLE THE WET, HEAVY SOILS THAT THEY HAVE TO DEAL WITH AT THE END OF THE SEASON.
ASHBURTON-BASED ALLEN CUSTOM DRILLS DESIGN AND MANUFACTURE
INNOVATIVE AIR SEEDER
DRILLS THAT ARE AT WORK IN A RANGE OF CONDITIONS ACROSS NEW ZEALAND AND AUSTRALIA.
The company collaborates closely with their customers to develop and build air seeder drills that suit the needs of individual farmers and contractors based on their five base models. This is a unique and appealing factor of Allen Custom Drills.
Optional extras can be added to the tried and tested base models to improve efficiency even further.
Triple disc drills are a popular option in the Allen air seeder range. They offer many advantages to achieve high strike rates, including minimum soil disturbance, accurate seed depth placement, and efficiencies in terms of time, cost and performance.
Reducing soil disturbance helps preserve soil structure, moisture and beneficial microorganisms. Combined with the other advantages that triple disc drills offer, this can provide the long-term benefits of increased yields, drilling efficiency and less environmental damage.
Triple disc drills have an opening disc that penetrates and creates tilth in the soil. The opening disc is followed by a seeding disc arrangement and then a press wheel to consolidate the seed into the ground.
Allen Custom Drills offer two triple disc series, the E-D (Ergonomic Drill) series and C-D (Con-
tour Drill) series.
The E-D series has an entry level triple disc system. They are available in 3m to 4m working widths with either 5-inch or 6-inch row spacings.
The C-D series has a triple disc system with a heavier and more robust design than the E-D series. Contour drills are available in 3m to 6m working widths with either 5-inch or 6-inch row spacings.
Allen Custom Drills recently designed and built a new model, the E-D 4500C, which was on display at this year’s National Fieldays. It is a combination of their E-D Series and C-D Series.
The E-D 4500C is 4.5m wide and available with 36 runs at 5-inch (125-mm) row spacings or 30 runs at 6-inch (150-mm) row spacings.
build up and alter the spreading rate.
Some of Fert Solutions’ customers want to be able to spread fertiliser at different rates across different parts of their paddocks, and the Agri-Spread can do that too.
They upload a map using Tabula which tells the rate controller to adjust the application rate on the go.
“We use Tabula for proof of placement and invoicing, but if farmers want to apply a product at variable rates, they can upload a map
The new drill has Allen’s proven triple disc system, with no greasing on the row units. The row units have active hydraulic down force with pressure adjustment. It features hydraulic accumulator down force on the folding wings and folds to a transport width of 3m.
As with all Allen Custom Drills, the E-D 4500C uses an Accord metering system. This is combined with the company’s own 7115 drill controller which has a 7-inch touchscreen or the option of ISOBUS-ready.
This gives the operator full control of sowing rates and area covered as well as audible and visual alarms. The system can be configured to apply seed and fertiliser, and it has the ability to run optional small seed and slug bait applicators.
using one of the various systems out there which then links through to Tabula. There is not a big demand for it at the moment but we are seeing more and more of it,” Ricky says.
Fert Solutions works from the mountains to the sea in a region bounded by the Rakaia and Rangitata Rivers. Clients include the whole gamut of Canterbury farmers – dairy, dairy support, arable, sheep and beef, and deer.
Ricky and Rebecca did their research before
THE NEW ALLEN E-D 4500C IS 4.5M WIDE AND FEATURES THE COMPANY’S PROVEN TRIPLE DISC SYSTEM AS WELL AS ACTIVE HYDRAULIC DOWN FORCE ON THE ROW UNITS.
Allen Custom Drills understands that no season is the same when it comes to farming and contracting, and they incorporate this knowledge into their drills. Their drills can operate in many different terrains from harsh, dry ground, through to wet, sticky, flat and undulating ground. They are built tough and built to last.
For more information on Allen Custom Drills, phone the team at 03 308 4094 or visit their website allencustomdrills.co.nz.
opting for the Agri-Spread AS2100SC. They bought it from Power Farming Ashburton. Ricky says the team there under Simon Jackson has been great to deal with. They are knowledgeable, helped with the set-up and have provided good back-up support.
“There are at least a dozen Agri-Spread spreaders around Canterbury now,” Ricky says. “Up our way a couple of dairy farmers have them and one arable farmer runs one. We are the first contractor.”
either
Ivan Burrows - ivan.burrows@trelleborg.com or register online at www.trstyreandwheel.co.nz/optimisation
NZ Rural Contractor is available free of charge to readers who qualify under the publisher’s criteria and who supply proof of occupation (printed letterhead, business card, invoice etc) and to others via subscription and payment of the $68.00 inc GST annual NZ Subscription. Australian Subscription $130, Rest of World $270.
If you are not a registered reader, but would like to receive a regular bi-monthly copy, fill in the details of your contracting or farming business below.
Subscription criteria for owners/sharefarmers:
Dairy milk over 600 cows
Sheep & Beef 12,000+ stock units
Cropping over 250 ha in arable
Main contracting services offered:
Equipment operated
Total farm Ha.: No. of sheep: No. of dairy cows: No. of beef cattle: Area in arable crop:
Make, Year, Model
To subscribe to NZ Rural Contractor & Large Scale farmer, please complete the credit card form below: $68.00 (NZ), $130 (Australia), $270 (Rest of World).
Name:
Company:
Address:
Email:
Rapid No.
Phone: Post Code:
Please sign here if you wish to receive a regular copy of this publication and send the form to AgriMedia Ltd, P.O. Box 37151, Halswell, Christchurch 8245. Freepost No. 114059.
Sign: Date:
PAYMENT:
Credit Card: Mastercard Visa
Card Number:
Name on Card:
Expiry Date: / CSC:
Signature:
If you have moved, please write clearly your name and new address above and your old address (including post code) below.
Name:
Company:
Address:
Email: Rapid No.
Phone:
Post Code:
KING COUNTRY CONTRACTOR JOHN CLARK IS HAPPY WITH THE PERFORMANCE OF HIS NEW HOLLAND FR 780 FORAGE HARVESTER. HE SAYS HE WOULD DEFINITELY CONSIDER GETTING ANOTHER ONE.
“We started out with a smaller FR 650 seven years ago,” John says. “After we put an axe head through it, we had to send it back to the dealer for repairs and they lent us a FR 780.
“Its extra power made a big difference so I told them they were not getting it back. We have now had two FR 780s.”
John and his wife Julie (who is on the board of Rural Contractors NZ) have been full-time contracting for 26 years. They are based at Otorohanga and work in a huge area – from Te Awamutu in the north, along the coast from Marokopa southward, and east to Taumarunui and Turangi.
John Clark Contracting runs 15 tractors and has 10 full-time staff. Employee numbers jump to 17 during the harvest season.
“Every year we produce over 30,000 square and round bales of silage and hay. We also make 600 to 700 ha of bulk grass silage and 600 ha of maize
silage,” John says.
“We work for dairy and sheep and beef farmers and we also buy standing grass to bale. We have three truck and trailers that we use to cart bales all around the North Island.”
The trucks also cart the fine chop grass and maize silage they produce with the NH FR 780.
New Holland’s FR 780 has a large comfortable cab and an FPT engine that delivers 775 hp (570 kW) maximum power at 17001900 rpm. It features a wide, heavy drum that delivers high quality cutting even in heavy crops.
John and Julie run the HD version of the FR 780, which has
JOHN CLARK APPRECIATES THE POWER HIS NH FR 780 GIVES, THANKS TO ITS FPT ENGINE, WHICH DELIVERS 775 HP MAXIMUM POWER AT 1700-1900 RPM.
heavy duty rollers and headstock.
“We like the FR 780 because it is reliable. It comes home every night after a big day without any problems. We have never had a major breakdown and if anything has gone wrong, we have been able to fix it and get going again.”
Although they do equal hectares of grass and maize, John says maize is the more important crop for the business financially.
“We would like to do more grass silage but there is not a big demand for it in the areas we work. Maize takes longer to harvest and we earn more from it,”
John says.
“To chop maize we run a 10-row New Holland maize front and a New Holland corn processor. The FR 780 has all the winches needed to install and remove the kernel processor.
“A good thing about the kernel processor is that you can swing it out of the way if you need to do a paddock of lucerne or grass during the maize harvest. It only takes five minutes to whip it out of the way so the crop does not go through it.
“When we start the maize season, we don’t have to replace
JOHN
wear parts. We just change the knives and put in the kernel processor and keep going.”
John says the NH FR 780 he currently runs has moisture and yield sensors, which means he can provide customers some information about their silage. When he upgrades it will be to one that has an NIR sensor so that he can provide farmers more details on the quality of their forage.
The 1200 ha of forage harvesting that John Clark Contracting does each year amounts to about
800 hours. At that rate, John says, they can trade in their forage harvester every three years at about 2500 hours and get a very good resell price for it.
“In that time the harvester is always under warranty. We have never had any major repair or maintenance costs over that period, so there are no costs associated with it.”
Their local New Holland dealer is Giltrap Agrizone, which conveniently enough has its main branch in Otorohanga. John says they give his forage harvesters
a big service when they hit 600 hours.
“We worked with Andrew Giltrap and his team before they became New Holland dealers. They have always looked after us and we have a good relationship with them.
“We don’t really shop around just to get the best price. We work with people who support us and hope they provide us the best price and best service that they can. Andrew relies on his team to do the best for his clients, just like we do.”
UPGRADING TO A BALE BARON 4245P BALE ACCUMULATOR HAS BOOSTED THE OUTPUT OF RANGIORA-BASED CONTRACTOR TOP GUNN AGRICULTURE.
Angus (Gus) Gunn says the trailed Bale Baron 4245P from Canadian company Marcrest easily keeps up with his two New Holland BC5070 conventional balers. It gathers them and binds them into large, tight packs that are easy to stack.
“With the Bale Baron we can effectively bale and pack 4000 to 5000 bales a day. The packs are very easy to stack using our specialist claw grabs from Marcrest or with traditional bale forks.
“We have had customers show up at our yard with a team of four or five guys to hand load their bales onto a truck. We load up the packs onto their truck in five minutes and send them on their way,” Gus says.
Top Gunn Agriculture works throughout Canterbury’s Waimakariri district. They make round and conventional bales in the spring and summer and do fencing in the autumn and winter.
The business serves dairy and sheep and beef farmers as well as a few lifestyle properties. It can provide a full baling service –mowing, raking and baling – and Gus also has some lease paddocks and buys standing grass to produce hay and silage bales to sell around the country.
At the beginning of last season he added the Bale Baron 4245P to his fleet. The ‘P’ means it is
a pick-up version, which gathers the bales off the ground (although Gus says he may get a kit to connect it directly to a baler in future).
“The Bale Baron is an absolute breeze to operate. It is very manoeuvrable and the pick-up is brilliant. It operates out to the right side of the tractor but in tight areas we can run it directly behind the tractor. We then drive the tractor over the bales and the Baron picks them up.
“We have not had a single issue with the knotter. It is a low maintenance machine and I can tell we are not going to have any mechanical issues with it. It is a slow moving machine without a lot of moving parts because it is all hydraulic.”
Bale Barons have a Rasspe double knot system that uses four strings of standard baling twine to makes packs of 9, 18 or 21 conventional bales. During the binding cycle, a plunger compresses the bundle and then the knotters engage and tie off the bundle.
Gus says the bales are compressed in all directions, so the packs are tight and compact.
He generally makes packs of 18 bales with his Bale Baron 4245P. They are 1m wide, 2.1m long and 1.35m high.
“The 18-bale packs are about
ANGUS GUNN USES HIS BALE BARON TO MAKE PACKS OF 18 BALES, WHICH ARE 1M WIDE, 2.1M LONG AND 1.35M HIGH.
the size of a medium square bale. They can be stacked two at a time side-by-side in a standard hay shed. We can stack them as high as a telehandler will reach.”
Marcrest also produces a range of grabs designed specifically to handle the packs that the Bale Baron produces. Gus has one of their claws, which grasps the bale pack along the side with a set of hooks.
“We can use the grab to stack the bales two high on the back of a truck and trailer. Or we can lay them on their side and load them three high with standard forks. If we load them with forks, then our customers can also use forks to unload them.”
When Gus was looking at buying his Bale Baron, a Marcrest representative from Canada and staff from the New Zealand importer, NC Equipment, visited
him and discussed it in detail.
“The Marcrest guy was unbelievably knowledgeable. We have also had good support from our local dealer, NC Equipment in Amberley. They came out and worked with us when we set it up. Fortunately we have not had to go back to them because we have not had any issues with it.”
Last season Top Gunn Agriculture made and transported about 25,000 conventional bales. Gus says there is absolutely no way he could have done that without his Bale Baron.
CANTERBURY CONTRACTOR ANGUS GUNN SAYS HIS BALE BARON 4245P IS “AN ABSOLUTE BREEZE” TO OPERATE AND ITS PICK-UP IS BRILLIANT.
KAITAIA Kaitaia Tractors 09 408 0670
WHANGAREI Piako Tractors Northland 09 438 1319
SILVERDALE Brandt NZ 09 427 9137
PUKEKOHE Brandt NZ 09 237 0043
MORRINSVILLE Piako Tractors 07 889 7055
MATAMATA Matamata Tractors & Machinery (07) 888 6292
HAMILTON Brandt NZ 07 847 0425
CAMBRIDGE Brandt NZ 07 827 5184
ROTORUA Piako Tractors Ltd 07 345 8560
TAUPO Taupo Tractors & Machinery 07 378 4533
STRATFORD FieldTorque Taranaki 06 765 8643
HASTINGS Stevenson and Taylor 0800 4273 2273
WAIPUKURAU Stevenson and Taylor 06 858 6041
DANNEVIRKE Lancaster Tractor Services 2022 Ltd 06 374 7731
PALMERSTON NORTH Transag Centre 06 354 7164
MASTERTON Brandt NZ 06 377 3009
NELSON Drummond & Etheridge 03 543 8041
BLENHEIM Drummond & Etheridge 03 579 1111
KAIKOURA Drummond & Etheridge 03 319 7119
GREYMOUTH Drummond & Etheridge 03 768 5116
CHRISTCHURCH Drummond & Etheridge 03 349 4883
ASHBURTON Drummond & Etheridge 03 307 9911
TIMARU Drummond & Etheridge 03 687 4005
OAMARU Drummond & Etheridge 03 437 1111
MOSGIEL JJ Limited 03 489 8199
GORE JJ Limited 03 208 9370
INVERCARGILL JJ Limited 03 211 0013
a purchase of any Modulo2 12000/14000/16000Lt
tanker. Includes 8inch pit hose and funnel Limitedoffer,while stocks
WHEN POWER FARMING
INTRODUCED THE NEW KVERNELAND 6700 PLUS SERIES BALER TO NEW ZEALAND, THEY ASKED BAY OF PLENTY CONTRACTOR NEVILLE MARSH TO TAKE IT FOR A SPIN. NEVILLE HAS MORE THAN 40 YEARS’ EXPERIENCE OPERATING BALERS AND HE KNOWS WHAT WORKS.
After trying it out, he decided the KV 6700 Plus is a good, efficient machine, so he kept it. It is now Marsh Contracting’s dedicated hay baler and back-up silage baler.
“We have run it for two seasons. We did 5000 bales with it last season and 3000 bales with it the first season. We haven’t even had to replace a pick-up tine on it and the belts have never given us trouble,” Neville says.
Kverneland’s 6700 Plus variable chamber baler range consists of two models, the KV 6716 Plus and the KV 6720 Plus.
The 6716 version, which Neville has, produces bales up to 1.65m (5 ft) in width, whilst the 6720 version produces bales up to 2m (6 ft) wide.
“Our main silage baler is a baler-wrapper, which is more convenient and cheaper to run because we only need one driver. But when
things get busy, we can use the Kverneland to make silage bales with a standalone wrapper. It makes good silage bales,” Neville says.
But its main job is baling hay. Because they are near the coast, Marsh Contracting can start making hay with it in December or even late November and go through the summer.
“It is a very good little hay baler. The belts in the chamber have never given us any trouble and the pick-up goes well.
“We can vary the density of the core. We make a semi hard core, because it makes the bales easier to feed out. Then the last twothirds of the bale are very tight. It makes a well-formed bale with nice straight edges, and it applies the net very fast.”
Kverneland says the KV 6716 and 6720 have a robust, powerful intake system that can handle wet or dry crops. The intake has a 450 mm diameter rotor and a drop floor to clear blockages.
They have a heavy duty split driveline with an automatic lubrication system, which Neville says is very convenient. “You just fill it up with liquid grease and forget about it. It saves a lot of time greasing and oiling the chains.”
Kverneland has designed the 6700 Plus balers to handle silage, hay and straw. The Intelligent Density 3D system allows the operator to quickly adapt to the changing crop conditions.
Marsh Contracting generally makes 1.2m silage bales and 1.5m hay bales, but if a farmer wants something different they can accommodate.
“The PTO has a minimum speed of 540 rpm, but I like to drive slow, and run the PTO at 580 or 600 rpm. If you drive at about 7 kph, you can run the PTO at that speed and the baler rolls the bale and wraps better.
“Because the hydraulics only run the pickup and the tailgate, you could run the baler with a 40 hp tractor. We use it on a 180 hp or 220 hp tractor at 1600 revs with the economy PTO and save diesel.”
Another of the KV 6716’s positive features in Neville’s book is the Kverneland monitor. He says he is old fashioned and prefers to use a dedicated monitor for the machine, rather than the tractor’s ISOBUS monitor.
“Sometimes the ISOBUS monitor won’t hook up and I find the machine’s own monitor works better anyway. This baler has an easy-to-use monitor that tells you to steer right or left when you are not filling exactly right.”
NEVILLE MARSH USES HIS KVERNELAND 6716 PLUS AS HIS HAY BALER. HE SAYS IT CHURNS OUT WELL-FORMED BALES AND IT APPLIES THE NET VERY FAST.
• Compact and sturdy
• Good penetration
• Simple adjustment
• Long lasting discs
• Perfect cutting angle
• Maintenance-free bearings
* INTEREST 36 MONTHS | 30% DEPOSIT ON SELECTED CULTIVATION AND SEEDING EQUIPMENT
DRILL COMBINATION
KVERNELAND PLOUGHS
Front & rear tyre packers present a uniform seed bed
CD coulter ensures consistent seed depth for greater germination
• 2-12 furrows
• Robust and reliable construction
• Variomat Vari-width® system for furrow width adjustments that save fuel and time as standard
• Unique heat treated steel
Seed & Seed & fertiliser options
3m, 4m & 6m models
The JCB Series lll has taken telehandling to a new level. Redesigned and re-engineered from the ground up, the JCB Series lll has raised the bar - literally.
f All new CommandPlus cab provides the ultimate operator experience
f JCB EcoMAX engine provides fuel-efficient matching of transmission and hydraulics
f Smart Hydraulics package improves cycle times and reduces fuel consumption
f Designed to be productive, without compromising safety or comfort
f New Zealand’s #1 telehandler
*Standard CLAAS Financial Services lending criteria, terms, and conditions apply. 0.99% p.a requires a minimum 30% deposit followed by monthly repayments over 36 months, GST back in month 3. Offer applies to in-stock new JCB SERIES III LOADALL telehandlers only. If finance base rates move by more than 0.25%, CLAAS Financial Services reserve the right to re-quote. Offer valid until 31/07/2024 or while stocks last. Images illustrative only.