NEWS
Case IH Quadtrac 715 takes Tractor of the Year 2025 prize

PROFILE
& LARGE SCALE FARMER
Dan and Jill Bingham; family friendly work culture a winner
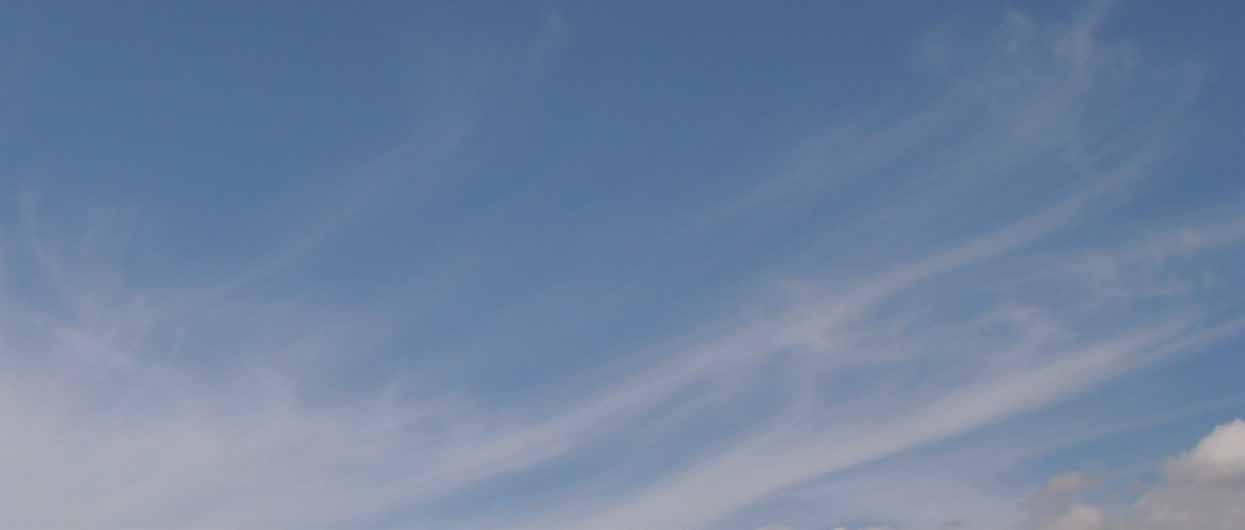
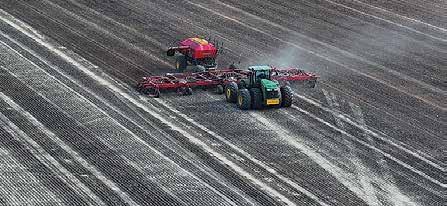
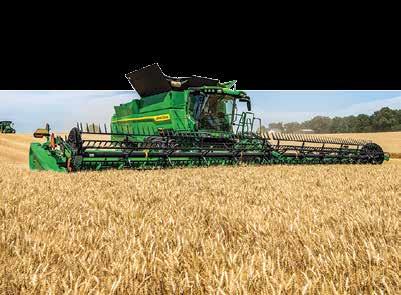
NEWS
Meet the new John Deere S7 combine harvester
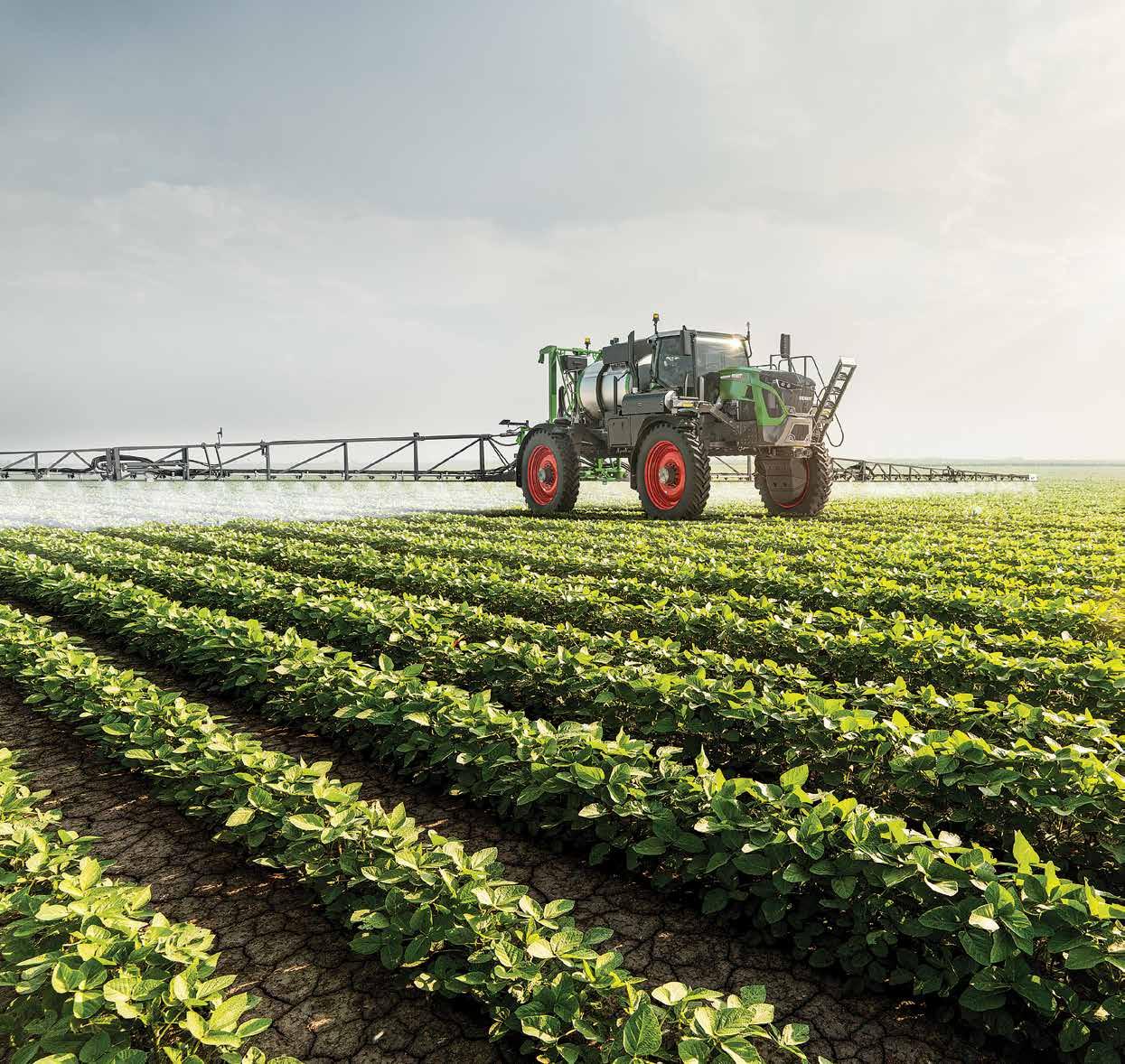
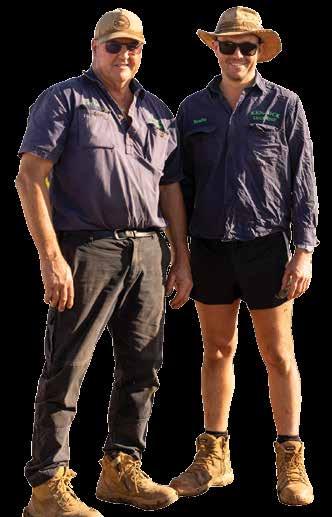
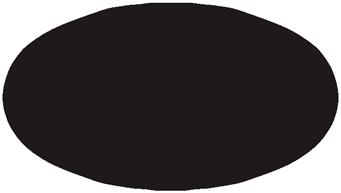

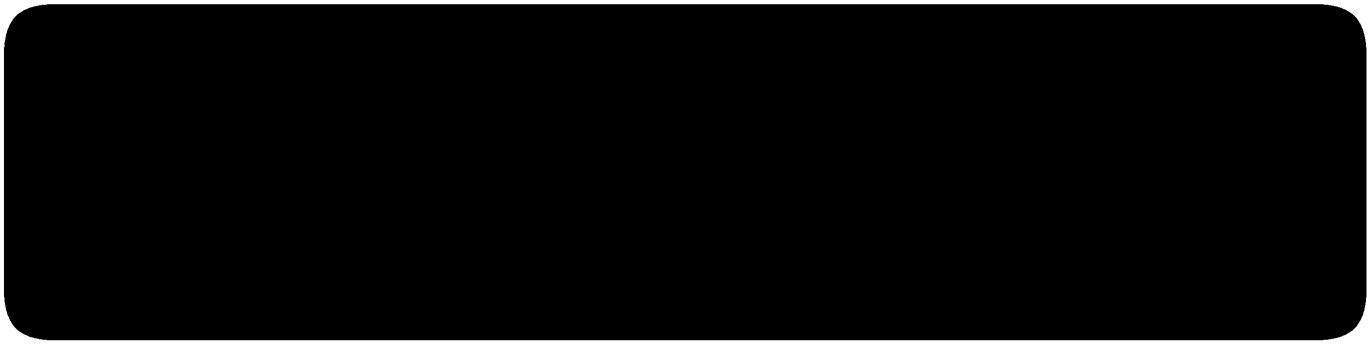
PUBLISHERS
NEWS
Case IH Quadtrac 715 takes Tractor of the Year 2025 prize
Dan and Jill Bingham; family friendly work culture a winner
NEWS
Meet the new John Deere S7 combine harvester
PUBLISHERS
PO Box 36753
Merivale, Christchurch 8146
ph: +64 3 329 6555 www.agrimedia.co.nz
Publishers of Rural Contractor & Large Scale Farmer, AgriBusiness, AgriVet, NZ Cropping, Australian AG Contractor & Large Scale Farmer, NZ Novachem Manual.
EDITOR
Scott Wilson
Mob: +64 21 725 061
Email: scott@agrimedia.co.nz
ADVERTISING SALES
Pulse – Media Sales
Justin Bowler
Ph: 0429 699 553
Email: justin.bowler@mmg.com.au
CIRCULATION
DDI: +64 3 329 6555
Email: admin@agrimedia.co.nz
PRODUCTION, LAYOUT & DESIGN
Mark Winstanley
Email: art@agrimedia.co.nz
Contributors: Delwyn Dickey, Gerhard Uys
Printed by PrintGraphics Pty Ltd
AC © AUSTRALIAN AG CONTRACTOR AND LARGE SCALE FARMER - No part of this publication may be reproduced in any form without the prior written permission of the publisher. Opinions expressed in this publication are not necessarily that of the publisher and suggest independent advice be sought before acting on information or suggestions contained herein.
CONTRIBUTIONS - Editorial and photographic contributions are welcomed and should be sent directly to AML. Editing of submissions is at the sole discretion of the editor and will accept no responsibility for unsolicited material.
03 New Axial-Flow series feature as combine ordering period opens for 2025
04 Meet the new John Deere S7 combine harvester
05 Case IH support for organisation with laser focus on increasing technology take- up among nation’s farmers
06 Amazone favours green and orange for a strong brand identity
07 Case IH Quadtrac 715 takes Tractor of the Year 2025 prize
08 Benefits of landforming in drought-prone Australia
10 Land Watch launches new thermal camera
11 Aussie farmers key to success
12 Dan and Jill Bingham; family friendly work culture a winner
16 Holm family continues family legacy
22 Across the ditch: Young contractor adapts after cyclones with hard work, new technology
28 What’s new in sprayers and spraying technology
38 What’s new in precision agriculture EQUIPMENT
44 Optimising cropping with the Bourgault 4420DKD
45 ‘All-rounder’ Maxxum tractor fleet keeps business ticking over for ag contractor
46 Seed Terminator for the New Holland CR11
47 Kubota’s new RTV-X is built to be tough and dependable
48 Claas revolutionises forage harvesting with the new V-Flex chopping cylinder for Jaguar 900 Series
50 More precision with Precea seeders
51 Loader integration sets Landini Powerfarm II tractor apart
52 Big savings, limited time to secure hi-tech sprayer
53 Soil health focus boosts contract tillage work
54 The baron of balers
55 New kid on the block
56 HIVE removes bottlenecks, boosts harvest efficiency 02 FROM
AS WE STEP INTO THE NEW YEAR, IT’S NATURAL TO REFLECT ON THE CHALLENGES AND TRIUMPHS OF THE PAST AND LOOK AHEAD TO THE OPPORTUNITIES THAT LIE BEFORE US.
As we step into 2025, it's a time to reflect on the challenges and triumphs of the past while looking ahead to the opportunities the new year brings. In agriculture, the turning of the calendar is symbolic—some are already in the thick of harvest, while others are preparing for a new growing season. Regardless, one constant remains: the landscape of Australian agriculture is evolving, and with it, our practices and commitment to sustainable success must adapt.
However, our industry is not without its risks. Recent health and safety incidents throughout 2024 have underscored the inherent dangers faced by those working in agriculture. From machinery accidents to on-site injuries, these events have highlighted the critical need to prioritize the health, safety, and well-being of workers across the sector.
Australian agriculture is a cornerstone of
the economy, driven by farmers and contractors pushing innovation, food production, and sustainability. But with this responsibility comes the need for ongoing vigilance. Each year introduces new machinery and technologies, but these also require continuous training, risk assessment, and safety protocols. The lessons from recent incidents must not be forgotten; instead, they should be integrated into our practices moving forward. Now, more than ever, we must make the agricultural workplace safer for everyone—from the tractor seat to the office desk.
Health and safety need to be a constant conversation, requiring everyone in the supply chain—farmers, contractors, machinery operators, and workers—to be vigilant and proactive. Regular equipment maintenance, up-to-date safety training, and proactive risk management are all vital steps in improving safety standards across the country. But safety isn’t just about accident prevention— it’s about creating a culture where well-being is a top priority. In rural and remote communities, mental health is an increasing concern, and addressing this aspect of safety is crucial.
Looking ahead, the agricultural sector
faces multiple pressures—climate change, labour shortages, shifting markets, and evolving regulations. Yet, within these challenges lie opportunities for growth. Contractors and farmers must embrace new technologies that improve efficiency, enhance safety, and support sustainability. Whether through smarter machinery, better management software, or more efficient resource use, technology offers many solutions. However, no technology can replace the importance of a well-trained, safety-conscious workforce.
As we move through 2025, our success will not only be measured by the crops we grow or contracts we secure, but by the safety and well-being of those who make it all possible. Let’s make this the year we prioritize health and safety—on every site, in every operation. Here’s to a safe, prosperous, and successful 2025.
SCOTT WILSON
WITH HARVEST HAVING JUST WRAPPED UP IN SOME REGIONS, AND BEING FULL-STEAM AHEAD IN OTHERS, CASE IH IS ALREADY LOOKING TO 2025 WITH ITS COMBINE ORDERING PERIOD FOR NEXT YEAR NOW OPEN.
Farmers in the market for a new Case IH Axial-Flow have until February to place an order for a current Axial-Flow 250 Series, a new 260 Series, and the new AF9 and AF10 Series. However, AF9 and AF10 Series are in limited supply for next year.
“This is a busy time for our customers and dealers, with customers looking to their harvest needs for 2025, while many are still in the paddock harvesting this year, and our dealers readying combine orders for next season and helping ensure their customers get the right equipment for their particular needs,” said Product Manager Marc Smith.
Marc said the new Axial-Flow 260 Series represented the value of feedback from Case IH customers on their requirements for a combine, incorporating the latest in harvest technology and seamlessly integrating that into the machine’s operation.
The Axial-Flow 260 Series includes dual Pro 1200 displays, providing a comprehensive view of every aspect of the 260 Series’ operation.
The large displays feature an anti-glare screen for optimum visibility and allow for instant grain quality imaging for a real-
time, high-definition look at harvested grain.
The entire display system is also designed for easy navigation among key functions, allowing the operator to customise the display, input Harvest Command settings, set up guidance and share real-time data and critical machine information where appropriate.
“Our Axial-Flow combines have set the standard for grain quality and the highest levels of efficiency and productivity for many years now, and that remains unsurpassed in this latest series. But what customers will really appreciate in the 260 Series are in the cab with the likes of dual Pro 1200 displays, and the easyto-use and customisable features that give operators access to every aspect of the combine’s functions and performance,”
Marc said.
“The comfort of the cab, which we know is absolutely critical given the number of hours an operator spends in the seat during harvest, has also been elevated, with an emphasis on helping alleviate the fatigue and stress associated with such long days.”
Case IH’s Harvest CommandTM combine automation technology
really comes to the fore in the Axial-Flow 260 Series, and AF9 and 10 Series, designed to help refine the harvesting process by reducing the number of functions operators need to monitor in the cab.
Also available on the Case IH Axial-Flow 250 Series, Harvest Command monitors everything from ground speed and engine load all the way up to feed-rate control and sieve settings, which are based on the feedback received from the loss sensors, a grain camera and sieve pressure sensors.
The AF9 and AF10 Series have been designed with enhanced power, efficiency and throughput in mind. The AF9’s 634 horsepower and the AF10’s 775
THE NEW CASE IH 260 SERIES COMBINES CAN BE ORDERED FROM YOUR LOCAL DEALER NOW.
horsepower provide the power to maximise crop flow while increasing speeds, but without putting any additional pressure on the machine.
Built upon the legacy of Axial-Flow single-rotor technology, the AFXL rotor of the AF9 and AF10 is 40% longer than the 250 Series, offering increased throughput, and grain-handling capacity is enhanced with a 16,000L grain tank on the AF9, 20,000L on the AF10. They also include a full suite of precision technology, including dual Pro 1200 displays, Harvest Command and connectivity.
“We continue to remain focused on enhancing the operations of our customers, and giving them the very best in terms of productivity and the value on investment they make. Harvest is one of the most critical periods in any cropping business, with technology features that save time and boost productivity, so that ultimately the machine is helping to maximise the business’ bottomline,” Marc said.
For more information on the Axial-Flow 250 Series, 260 Series, AF9 and AF10 Series, or to place an order for 2025, speak to your local Case IH dealer.
AFTER THE LAUNCH OF THE ALL-NEW JOHN DEERE S7 COMBINE HARVESTER IN FEBRUARY, JOHN DEERE NOW HAS MACHINES ON THE GROUND ACROSS THE COUNTRY FOR CUSTOMER DEMONSTRATIONS.
In a video filmed near Toowoomba, Queensland, John Deere Manager, Production System Specialists, Max Cusack, walks through the new features and automation designed to deliver more productivity and fuel efficiency, when it matters most.
The acclaimed John Deere S Series combine, now known as the S7 combine, one of the world’s most loved pieces of farm equipment since its inception in 2012, has been redesigned and optimised with new technologies to build on its proven performance in Australian and New Zealand conditions.
The all-new updates to the S Series will deliver productivity gains of up to 20%1 , with 10% less fuel2 used, taking the performance of this proven workhorse to the next level.
In addition to visible styling changes to the cab, a re-designed grain loss sensing system will provide more accurate grain
THE NEW S7 FAMILY INCLUDES:
loss measurements, and new automation features will take operator performance to the next level.
The new S7 combine harvesters will be equipped with either the JD14 13.6L engine, or the JD9 9L engine, Tier 3 configuration. Designed to produce higher power at lower rpms, these powerhouses offer improved all-condition performance and advanced diagnostic capabilities to help keep the S7 combine running strong, all day.
The S7 combine also offers a new high-efficiency residue management system. Featuring straight knives, a mechanical tailboard drive, and the available Premium PowerCast tailboard, the new machines can more consistently size and spread fineor extra-fine cut residue up to
S7 600: 333hp/249kw rated power; 367hp/274kw max power
S7 700: 402hp/300kw rated power; 460hp/343kw max power
S7 800: 473hp/353kw rated power; 540hp/402kw max power
S7 900: 543hp/405kw rated power; 617hp/460kw max power
https://www.youtube.com/watch?v=_xybtAeITGM
13.7m (45 ft.), while drawing up to 15 fewer hp (11 kw) for residue management functions.
A new, adjustable unloading spout ensures grain is going into the bin and not on the ground. After the grain tank is emptied, the new cross-auger shutoff feature completely empties the unloading system, reducing weight in the unloading auger and wear on the associated belts.
The new machines also feature an improved grain loss monitoring system in base equipment three times more accurate than the previous system. The loss rate is shown clearly on the in-cab display, so operators can quickly make required adjustments.
The new S7 combine has been designed to be among the most comfortable combine harvesters ever produced, with a new operator station offering more storage space for food and drink, a more comfortable seat and more glass for better visibility – all designed to help the operator remain alert and focused through even the longest days of harvest.
Along with the operator comfort upgrades, the base S7 combine will be equipped with the G5PLUS CommandCenterTM , the Integrated StarFireTM 7500 receiver, JDLink™ modem and new corner post display, paving
the way for new automation features and functionality into the future.
The Model-Year 2025 S7 and X9 combines have three technology packages operators can choose from – select, premium and ultimate. Available options in the ultimate package include:
- Ground speed automation to manage the combine’s speed based on operator inputs for grain loss, engine load and rotor pressure to maintain consistent throughput.
- Harvest settings automation to automatically adjust rotor speed, fan speed, and concave, chaffer, and sieve clearances based upon acceptable limits for grain loss, foreign material, and broken grain. This delivers a more consistent and higher quality harvest, irrespective of operator skill level.
- Predictive ground speed automatio n using Ground Speed Automation as the foundation, plus two forward-looking cameras, to visually assess changing crop conditions and a pre-harvest satellite image to generate a predictive field map. The combine merges the two inputs to proactively manage ground speed and maximise combine throughput. For the latest news and product information see your local John Deere dealer.
1 Based on anonymised Ops Center data comparing John Deere combine models with and without Predictive Ground Speed Automation. Productivity represented by tonnes of crop per hour. Results will vary depending on model, crop and field and operating conditions.
2 S7 800 & S7 900 models only.
LEADING AGRICULTURAL MACHINERY BRAND, CASE IH, HAS RECOMMITTED TO ITS LONG-STANDING SPONSORSHIP OF THE SOCIETY OF PRECISION AGRICULTURE AUSTRALIA (SPAA), A NON-PROFIT ASSOCIATION THAT ADVOCATES FOR THE ADOPTION OF PRECISION AGRICULTURE AMONG AUSTRALIAN PRODUCERS.
SPAA had its beginnings in 2002 and provides independent, objective, timely and relevant precision agriculture information to the grains, sugarcane, horticulture, and livestock industries. It acts as an umbrella group, supporting precision agriculture initiatives within industries that have the funding and capabilities to explore and adopt new technologies.
Case IH has been a silver sponsor of SPAA for more than a decade, and CNH Commercial Director – Agriculture ANZ, Aaron Bett, said it was a great fit for the brand, given the shared goals of the two organisations.
“Case IH is a leader in the development of agricultural machinery technology, so SPAA’s commitment to the advocacy of precision agriculture aligns perfectly with our shared goals of enhancing on-farm efficiencies and profitability. What SPAA is doing across the industry in this space is so important for the continued growth and evolution of Australian
The Highline NT Rock Picker is built for Aussie conditions and offers capacities up to 2.56m3.
High 2.13m lift design suits trailers and compact piling
Two hitch positions for improved visibility
Large tyres for excellent flotation
Minimal moving parts and easy to service
agriculture,” Aaron said.
SPAA’s membership includes Australian farmers, agronomists, consultants, researchers and academics working across broadacre, sugar, cotton, dairy, livestock and horticulture.
Phil Honey, President of SPAA, said the organisation had a national focus, achieved
THE COLOUR SCHEME FOR GROUNDCARE AND HOES TO MATCH THAT OF AGRICULTURAL MACHINERY.
As part of its brand strategy, and from the new price list in December 2024, the Amazone Group is changing the design of its groundcare and hoeing divisions over to the colour combination of green and orange. Amazone is thus continuing the standardisation of its differing colour schemes within the different divisions of the company. All product lines will, therefore, match the long-established Amazone agricultural machinery colour scheme, which in many countries is protected under trademark law. The aim is to strengthen the corporate identity throughout the entire group of companies.
The Amazone Group has been successfully represented in the groundcare market for over 40 years. The mounted and self-propelled mowers/collectors, previously available in green and beige, are renowned, both by local authorities and service providers, for their high level of functionality and quality.
by collaborating with organisations like Case IH and being an active partner in national and industry alliances.
“Case IH has been a longstanding partner of SPAA, and their continued support is important to our mission of driving the adoption of precision agriculture across Australian farming. Their advanced machinery, from tractors to precision planting systems, enables growers to work smarter, not harder,” he said.
“The partnership we have with Case IH helps to bridge the gap between technology and practical, on-farm implementation, ensuring Australian producers have the tools, expertise, and ongoing support needed to embrace the future of farming and increase their productivity and sustainability.”
The range covers a wide variety of applications. From scarifying and mowing to collecting leaves, these all-rounders are in use all year round. The fresh green-orange colour scheme not only gives the kit a striking visual change, but also new dynamic lines.
Schmotzer Hacktechnik has been part of the Amazone Group since 2019 with its implements offered in the colour combination of blue and orange. In recent years, the collaboration between Schmotzer and Amazone has resulted in new technical impetus and equipment options for even more efficient plant care solutions.
In future, this product line will also be presented in the Amazone colours of green and orange. In the course of this process, the Schmotzer brand will also be transferred to the Amazone brand. This will emphasise visually the affiliation to the Amazone Group as well as accentuating the synergy of the agricultural product lines. This relaunch of the hoeing systems is intended to help market the equipment even more successfully, particularly internationally. The company is
relying on the significantly higher global recognition value of the green and orange livery under the Amazone brand.
There will be a transitional phase in both divisions, during which both groundcare and hoes will still be shown at exhibitions and sold in their existing colours. However, this is not a disadvantage because the level of technology and functionality of the kit will remain unchanged.
The standardisation of the colour scheme across all product lines shows that the Amazone Group is sending out a clear signal for its innovative green and orange colours and is thus aiming to further strengthen the market presence of the Amazone brand worldwide in the long term.
The fresh green-orange colour scheme not only gives the Amazone groundcare a striking visual change, but also new dynamic lines.
In future, the hoes will also be presented in the Amazone colours of green and orange. In the course of this process, the Schmotzer brand will also be transferred to the Amazone brand.
THE STEIGER QUADTRAC 715, THE NEW TOP MODEL IN THE CASE IH TRACTOR RANGE, HAS WON THE TRACTOR OF THE YEAR 2025 HIGHPOWER CATEGORY FOR MODELS OF 300HP, AT EIMA 2024 IN BOLOGNA, ITALY.
This recognition follows the Quadtrac’s earlier win of an EIMA Technical Innovation Award.
Designed to help the largest farm businesses cover ground as efficiently as possible, the latest Quadtrac minimises fuel use, labour hours and soil compaction.
It features an all-new heavy duty undercarriage with larger drive wheel to maximise positive drive through greater lug engagement, and a larger overall footprint boosts traction and reduces soil compaction.
This is aided by rubber damped mid rollers providing cushioning to absorb shocks and compen-
sate for rolling terrain, eliminating point loading. Greater comfort allows operation at higher field speeds, enhancing workrates.
Service time is minimised through automatic track tensioning, elimination of undercarriage greasing points, clear-view oil caps and maintenance-free bushings and pins.
The pan-European judging panel of farm machinery journalists based their assessments on areas including engine performance, fuel efficiency and emission standards, transmission smoothness and reliability. Featuring an FPT
Cursor 16 TST twin-stage-turbo engine, the Quadtrac 715 produces 778hp at 1,900 rpm and maximum torque of 3,356Nm at 1,400 rpm.
A PowerDrive powershift transmission minimises torque loss, while a multicontroller-mounted right-hand powershuttle switch controls driving direction in combination with a left-hand steering column-mounted shuttle.
Other innovations on the latest Quadtrac include configurable buttons allowing operators to set up controls to suit preferences, AccuTurn – a fully automatic
headland turn system – and up to 428 l/min of oil flow with smart torque hydraulic pump to match demanding implements.
Comfort and convenience features include automatic pivoting steps and 76,620 lumens total output from a new lighting package.
The new Quadtrac 715 also features AccuGuide auto steering and works with the new Case IH FieldOps™ monitoring and management app. For more information on the Case IH range of machinery, contact your local Case IH dealer.
By Justin Van Viersen
EFFICIENCY HAS BEEN A TOP PRIORITY FOR AUSTRALIAN FARMERS FOR SEVERAL YEARS, AND IT WILL CONTINUE TO BE A CRITICAL DRIVER OF SUCCESS IN 2025 AND BEYOND AS WE ARE CHALLENGED TO MEET INCREASING DEMAND WITH FEWER RESOURCES.
Adding to this challenge is Australia’s climate, which presents one of the harshest growing environments on the planet. Farmers are looking to precision ag technologies that can help them be more efficient in how they manage and deploy natural resources, including water use.
Landforming is one underutilised strategy that can deliver significant value by enabling farmers to use water more efficiently, and it also opens up more possibilities to positively impact ROI through increased crop yield and reduced irrigation costs.
PTx Trimble recently launched its next-generation water solution, WM-FieldForm, to enable farmers to control the movement of water onto, off and within fields. The solution moves landforming capability into Precision-IQ, and offers much of the same functionality of FieldLevel II with a new feel, improved vis-
ualisation and enhanced tools and features. From simple topsoil levelling right through to complex multiplane landforming, grading, levelling and terracing projects, farmers who use the system have the advantage in terms of:
- Optimised water distribution, which translates to reduced moisture runoff and better management of expensive irrigation water on fields.
- Improved crop yields of up to 30% in the first year after landforming.
- Greater positioning accuracy through top-of-the-line GNSS corrections.
- More uptime to get the work done quicker.
By simplifying every stage of the landforming process, including design, execution and verification, WM-FieldForm enables farmers to form and/or maintain fields on their own. Without hav-
ing to hire contractors to manage landforming projects, farmers have another opportunity to increase their cost savings on labour resources.
As part of PTx Trimble’s commitment to a retrofit-first, mixedfleet strategy, WM-FieldForm integrates with the GFX-1260 display and the NAV-900 guidance controller, offering additional cost-savings benefits by utilising visiting tractor equipment. Farmers simply need to add a NAV900 and hydraulic machine controls to a bucket scraper. With NAV-900 compatibility, farmers have greater positioning accuracy and more uptime to get the work done faster.
We know that implementing new technologies and adapting farm practices increases the risk farmers carry, and especially in today’s economic environment, farmers don’t have a lot of wiggle room to explore the benefits these tools can offer. It’s important to work with your dealer to understand the range of benefits that a landforming project could offer your specific operation. Learn more at ptxtrimble.com, or by contacting your PTx Trimble water management dealer.
About Justin Van Viersen
Justin is a commercial director with PTx Trimble, a new venture established in 2024 to better serve farmers worldwide with industry-leading smart farming solutions. Based in Perth, Justin oversees operations throughout the Asia-Pacific (APAC) region.
Marcrest bale packaging equipment offers hay producers innovative solutions to reduce expenses by virtually eliminating manual labour. Their line of bale packaging and bale handling products maximise efficiencies of forage management operations.
CLEAR NIGHT TIME VISION PROVIDES ADDITIONAL LEVEL OF PROTECTION AND PEACE OF MIND FOR LANDOWNERS.
Leading on-farm security provider Land Watch Australia have launched their new offer, a category first thermal camera.
Two cameras are better than one, with the new Entry Guard Thermal simply designed with both a standard camera and thermal camera - so that nothing can sneak past.
The launch of the new entry guard thermal enables 24/7 security, providing day and night alerts, ensuring safety and peace of mind. Typically, security camera systems have limited night time vision, often lacking surveillance at the time that matters most. Using advanced thermal technology, temperatures are detected by recognising levels of infrared radiation emitted by objects.
The thermal technology effectively cuts through the blindness of headlights, successfully identifying the structure of the vehi-
John Hill, co-founder of Land Watch Australia, stated: “The product is engineered to thrive in the toughest environments of the Australian outback. We understand the unique challenges our customers face, and we’ve built a product tough enough to meet those demands, ensuring peace of mind and
uncompromised security, even in the harshest of climates.”
The entry guard thermal camera expands the product range, offering new security solutions that can be easily integrated with existing systems.
The addition provides a flexible way to enhance security without replacing current setups. “By offering products that seamlessly integrate with our existing systems, secu
SOUTH WALES FARMERS WAYNE AND BRODIE WILLIAMS’ LOCAL EXPERTISE IN INTENSIVE CANOLA HYBRID SEED PRODUCTION HAS BEEN CRITICAL TO MAXIMISING THE AVAILABILITY OF DG BULLER G FOR THE 2025 SEASON.
Australian knowledge and farming knowhow have been key features of the development of the new glyphosate-tolerant canola hybrid by Dyna-Gro Seed, from genetic selection at the beginning of the breeding process, through to final seed production via crossing of the hybrid’s two parent lines.
The Williams family business, Kenlock Cropping, regularly undertakes this intensive form of crop production from within their broader commercial irrigated farming operation 50km south of Griffith.
“We’ve been doing seed crops for 15 years, although it’s not every year as there’s a lot of parameters you have to work within,” Wayne Williams said.
“For example, we can’t do a hybrid canola line if there’s a neighbour growing a conventional canola crop within five kilometres because of the risk of cross-pollination contaminating the seed line.
“The crop rotation on our farm is also a factor – we grow corn, maize, cotton, lucerne and canola – and we can’t use a paddock for hybrid breeding if there’s been another canola crop on that paddock within the last three years.
“We also can’t grow a breedleaf crop in that paddock the season following the glyphosate-tolerant canola.”
The introduction of the Optimum® GLY herbicide-tolerant hybrid trait into Dyna-Gro canola hybrids offers commercial growers improved crop safety and enhanced weed
control through a wider window of application, helping to maximise yield potential.
The process of canola hybrid seed production also involves a lot more work than a typical broadacre crop.
“Compared to a conventional canola crop, there’s a lot more passes,” Wayne said. “From ground preparation to finish, we’ll go over that field 15 times.”
That includes having to set up a special shielded sprayer for herbicide application over the female lines, which carry the Optimum GLY herbicide-tolerant trait technology. This prevents any chemical impacting the male lines, which do not carry the gene, where inter-row cultivation was used instead for weed control.
“The glyphosate didn’t affect the female plants at all. It was really easy to control all the weeds – it’s definitely glyphosate-tolerant,” Wayne said.
Late in the season the male lines are removed and mulched to prevent contamination of the progeny seed collected from the female line.
“The parent lines are quite different, and it’s
effective. This way our customers can continually receive on-farm security without the hassle and expense of replacing systems,” said John.
As a homegrown Aussie agtech success story, John and James attest their family as key in setting them up for success. With
the hybrid progeny that is collected from the female plants that commercial growers buy and that seed has to meet purity standards.”
The parent lines of DG Buller G were sown onto two, 20-hectare plots of red loam soils on raised beds for furrow irrigation.
The use of a precision vacuum planter in a two-row pattern resulted in nearly 100 per cent germination rate, maximising the response of just 32 kilograms of available seed.
Good winter rainfall ensured the crop was sown into a full moisture profile, with irrigation not needed until later in the growing season.
Despite the in-season rainfall and wet winter conditions, the crop showed no signs of disease.
The crop was sown in late May to ensure the availability of bees for the critical pollination process.
The Williams’s place their hives about 50 metres apart to fully surround the crop.
“It is extra work, but it is really important. The further away the bees are, the pollination rate gets lower and that is critical in hybrid production.
“The team at Nutrien and Dyna-Gro have been great to work with and we’re really looking forward to doing a lot more of this work in the future.”
3000+ cameras installed across Australia, the team continue to deliver on tough, made -for-purpose remote on-farm surveillance systems.
FOURTH GENERATION FARMERS IN THE MINGAY AREA OF SOUTHERN VICTORIA, DAN AND JILL BINGHAM ARE ENJOYING THE REWARDS FROM THE YEARS OF HARD WORK BUILDING THEIR FARMING AND CONTRACTING BUSINESS.
Along the way, they have built a professional work culture that supports women in the industry and is helping their daughters achieve their own farming aspirations.
Together since their teens, having met at a Christmas party in a local hall when Dan was 18 and Jill was 17, their business partnership has also been a remarkably successful one over more than 35 years.
The farming side of their operation covers 9000 acres made up of adjoining farms that have been added to over the years.
Cropping is the main income earner with around 60 per cent wheat, 20 per cent canola, and 10 per cent beans grown each year. On less suitable land, they run about 5000 head of Merino sheep and first cross ewes for fat lambs.
Along with their farming oper-
ation they also run a successful contracting business – Bingham Agriculture.
They have been regularly contracting for many of the same group of farmers over the years and built up a good relationship with them, growing with them as their farms expand in size.
This sees their 30 headers on the annual harvesting migration from the Queensland border
down to western Victoria.
With one of their clients having also bought in Tasmania in recent years, this now sees some of the crew loading their gear and heading across the Bass Strait to Julia Creek.
Having been involved with all aspects of the contracting and farming operation over the years, Dan reckons he’s still just one of the crew and won’t ask anyone to do what he wouldn’t do himself.
From sleeping in the shearer’s quarters, to carrying a swag in the car when he goes to jobs, Dan says he just enjoys the camaraderie of being one of the team.
Along with harvesting, they often do a lot of different work for these customers including bed forming, ripping, and sowing.
Seeding is done exclusively with Seed Hawk air seeders with three staff managing each seeder - two drivers and a leader that fills the truck and oversees the operation.
Dan is impressed with the Seed Hawks’ ability to handle all the different soil types they work with, including heavy clay.
In paddocks with swampy areas and clay loam on the banks, they don’t have to keep changing the air seeders as it can handle both.
“Each tine has a separate wheel and that sets the height, and then they have two tines and one puts the fertilizer down lower than the seed. So, the fertilizer is lower and the seed is on a little shelf.”
Originally sheep country, the land tends to be undulating which the air seeders handle very well, Dan reckons.
When it comes to farm vehicles, Dan is a big fan of Toyotas, especially the Land Cruisers.
“You’ve got to have a reliable vehicle and they never let me down. We run them up to 800,000 kms and they’ve never broken down once.”
His also has high praise for their Kenworth trucks.
While all of their 12 tractors are John Deere, there is an old tractor, now tucked safely away in the shed, that has a special place in Dan’s heart.
Some tractors become legends, and are spoken of in almost hushed tones by older farmers.
So it was when Dan, at the tender age of 20, decided he wanted to become a cropping man.
His father Rob immediately knew what tractor he needed and where to find one.
The pair set off from the family farm at Mingay in the south to Mallee in northern Victoria.
There, in a clearance sale, they found the perfect tractor. While the old Chamberlain Super 90 with its garish orange livery may have been in its prime several decades earlier, and being pretty worn out with the cabin falling off, Rob knew it was a winner for his boy.
The $3,000 price tag clinched the deal.
Production of these big, grunty, two-stroke, three-cylinder supercharged diesel tractors began in Perth in 1962. Designed specifically for Australian conditions and broadacre work, they were beasts of machines and were often seen pulling two 22-disc ploughs coupled together in tandem. While able to compete in power with the machines coming out of the US later that decade, the Chamberlain Super 90s were expensive to produce. This ultimately led to their demise and saw the last one roll out of the Welshpool factory in 1967.
Rob’s admiration for this tough old Australian-made workhorse was well placed.
With Jill, still Dan’s girlfriend at the time, helping to fix the cabin Dan was soon out on the machine, working all hours to get
CONTRACT WORK IS DONE MOSTLY ON LARGE FAMILY FARMS AND HELPS KEEP THE BUSINESS VERY FAMILY ORIENTATED. BEING FARMERS THEMSELVES HELPS THEM TO UNDERSTAND AND EMPATHISE WITH THEIR CUSTOMERS NEEDS, DAN RECKONS.
the contract cropping operation underway.
The Chamberlain continued to be used for a good many years although Dan admits the open half cab made working out in the cold and wet unpleasant at times, with plenty of rugging up necessary during the colder months.
When Jill turned the house upside down one night, looking for her tracky gear to wear to netball, Dan had to sheepishly admit he was wearing them under his work clothes to get the three layers he had needed to stay warm on the tractor.
Both Jill and Dan came off sheep and cropping farms, with small-scale share contracting on the side. This saw them naturally pick up a lot of the ins and outs of each of these operations.
Farming had always been on the cards for Dan who hadn’t really considered another career. Staying on the farm just seemed like a natural progression.
Jill, meanwhile, had headed off to Melbourne for a couple of years to go nursing, but eventually returning to farming remained her goal.
THEIR ABILITY TO HANDLE DIFFERENT SOIL TYPES AND UNDULATING COUNTRY SEES SEED HAWK AIR SEEDERS EXCLUSIVELY USED.
BINGHAM: FROM
Rob, who left school at 12 to work on the farm was always a very hard worker and he installed this work ethic in Dan.
As the family wasn’t well off when Dan left school at 16, he worked for his father for 10 years for not much money. Once Dan was established however, Rob returned the favour by working for him for 10 years.
“He’d work harder than a lot of the young ones. Showed them how to work – had a hard work culture,” says Dan.
But success for the business didn’t just come from hard work.
“Dad’s philosophy was always do what you say you’re going to do and harvest the crop like your own,” Dan reckons.
He has continued with that philosophy and incorporated it throughout the contracting, including with the 20-odd people father and son have trained to also be contractors over the years.
“The business keeps growing. Our customers trust us and our staff trust us,” says Dan. “That comes down to reliability.”
As with most farming/contracting combos, the contracting provides the cash flow.
It wasn’t long before the contracting saw Jill and Dan get some appreciating assets under their belt in the early days, buying their first property for $128,000.
By the time Dan’s parents decided to retire and move into Ballart - selling them the family farm at market value - Dan was around 30 and the pair already owned three other farms.
Their partnership saw Dan involved in the day-to-day running of both the farms and contracting arms of their business, while Jill had focused more on raising their five daughters.
But problem solving and business direction were worked out together, with Dan crediting Jill with being the smarter of the two and being very canny around business.
Having come a cropper when he hasn’t listened to her, Dan says he has a real appreciation of Jill’s good judgement and problem solving skills.
As their family grew and, with Dan out working so much, the girls were regularly out with him, either in the headers or on the farm as they grew up. Like their parents, this also gave them a good grounding in both arms of the business and has meant they have been able to choose which operation they enjoyed the most, also taking on more responsibility within the business.
This has seen 27-year-old Sophie now overall manager of the farm with her husband, Sam Sedgwick the cropping manager. They have a young son, Archie.
A strong affinity to the livestock has seen 23-year-old Ruby working under Sophie and managing the sheep.
Lily, at 25, is involved with the contracting side of things with Dan, and is starting to take over from him looking after customers, staff, planning, and machinery purchasing.
Nineteen-year-old Tess is currently header driving and will be studying agriculture in some form at university next year.
At 14, Bella is at school in Ballarat, and looks to be the only one not really interested in farming.
Dan admits having the girls about the work place, especially
when they were younger, saw him taking particular care with the character of the people he hired and to the work environment.
“We had to make sure the business was really culturally clean, proper and professional.
“So we employ on culture, not skill - we employ good people. We can teach them the skills they need.”
THE BIGGEST MACHINES AVAILABLE ARE PURCHASED SO THEY WILL STILL HAVE COMMERCIAL VALUE WHEN ONSOLD SOME YEARS LATER.
THE BUSINESS HAS REMAINED VERY FAMILY ORIENTATED, WITH PROFESSIONAL STANDARDS EXPECTED.
As the business has grown over the years, Dan feels that care with their work culture has also had a positive impact on their reputation as an employer, espe-
cially for young people just entering farming.
With labour shortages industry-wide, encouraging more young people, especially women into agriculture is important, Dan reckons. To do that, operations need to be run in a way that women feel comfortable, he says. They need to be more family friendly.
Around 20 per cent of his staff are women, with Dan appreciating the different qualities women tend to bring to the operation, including being easier on equipment and machinery, and being very good with animals.
While Jill and the girls take out the top spots, followed by his constant companion border collie Nelly, the other loves of Dan’s life are old farm machinery and helping to give it an extended life.
The place the Chamberlain Super 90 has in Australian agricultural history and its significance in the early days of his own business hasn’t been lost on Dan.
While the trusty orange monster may have long been replaced by younger machines, the old tractor with the big heart was never sent to the scrap heap or left to rust away. Instead it became the first member of
Dan’s now extensive 80-piece tractor collection.
“I don’t want to see them under a tree, I want to see them in a shed.”
The oldest tractor in his collection is a 1920 International Harvester 1020.
There is also a collection of headers including 10 John Deeres. The oldest header is a 1913 Sunshine headerdesigned by Headlie Shipard Taylor of Henty, New South Wales.
A collection of trucks used over the years in the business will also have a long life on the farm.
While he may be spending less time in the business as his daughters get more involved, it doesn’t mean Dan is going to have more time on his hands.
He is still hosting visits of agricultural students to show them the ropes around his operation and he and Jill have recently bought what is the crowning
beautiful old historic sheep farm ‘Banongill’.
Situated near Skipton, the lovely ‘Banongill’ homestead on the farm was built in 1905 and has a 13-acre garden. Dan reckons he is making good use of the swimming pool.
There are also a couple of Airbnb houses on the property to run.
Although it has been well maintained, the homestead hadn’t
their love of heritage and preserving the past, have thrown themselves into renovations and are starting to also have weddings there.
“It’s about keeping it good for the next generations,” says Dan. “We don’t want it to fall down
MALCOLM HOLM HAS SEEN A LOT OF CHANGES OVER THE 42 YEARS HIS FAMILY HAS OPERATED THEIR DAIRY FARM NEAR FINLEY, NEW SOUTH WALES.
From shifting operations from near Byron Bay in the 1980s, to weathering the variable climate of the past two decades, and having to change operations drastically after a farm accident, the Holm family has had to adapt to maintain their multi-generational farming legacy.
The Holms milk 600 cows across three farms, which span 580 hectares. The farm produces about 480,000kg of milk solids per year.
The area receives around 350mm of rain annually, predominantly in winter when temperatures dip to -1°C at times, with summer highs topping out at 40°C.
The Holms are multi-generational farmers. Malcolm’s grandfather and father farmed, with the family’s farming roots traceable back to the 1700s. In the early 1980s when urban pressure meant their operations could not
MALCOLM (LEFT), HERD
expand, the family shifted from Byron Bay to Finley.
Malcolm says the shift was a good one because, in Finley, farming is seen as the backbone of the economy. Now Malcolm, wife Jenny and daughters Ellena (29) and Talei (27) have their roots firmly established in the region.
“There aren’t many dairy farmers left, but the ones left employ a lot of people and are investing heavily in dairy,” Malcolm says.
“Cow housing sheds are popping up everywhere with a “lot of concrete being poured,” he says, adding that existing dairy farmers are investing heavily into infrastructure.
Malcolm wears a few hats and,
MANAGER JOESPH OWINO AND WIFE JENNY PLANNING THE
WEEK AHEAD.
besides farming, also chairs both the New South Wales Farmers Dairy Committee and the National Farmers Federation Water Committee.
Farming operations have been heavily influenced by challenges, but the Holm family seem to have a knack for turning challenges into opportunities.
Malcolm’s role on the farm changed 18 years ago when he had a serious accident that cost him his hand. His hand was reattached and, while he has reasonably good use of it, he isn’t able to milk anymore and lacks the fine motor skills needed for tasks such as putting cups on.
The incident means the family focuses on farm safety, and understands better than most that in times of stress, wet weather, or when conditions change, accidents can happen.
Malcolm says the first few years after the accident were “tough going”, but the entire mindset on the farm changed and, for the last 18 years, he has had to rely heavily on farm labour.
“The last full milking I did was the morning of my accident. I can help, but I can’t milk anymore; I am in a facilitation role,” he says.
MALCOLM ALSO RECENTLY RAISED 60 CALVES THAT HE WILL SELL TO THE WORKS. HE SAYS THE APPETITE FOR BOBBY CALVES IN THE INDUSTRY IS DIMINISHING AND THE INTEREST IN BEEF DAIRY IS INCREASING.
Malcolm says, to keep production up, his main role is ensuring there’s enough feed in front of cows and the farm has ample feed conserved.
“I have to make sure everything’s running smoothly and think about where we will be in six months.
“To some degree the farm is a semi-corporate farm, because we rely on our labour to manage animals.”
The farm is run by 10 staff. Four are on working visas with the option of permanent residency. On top of that, Malcolm also relies on backpackers and some locals who milk part-time.
Four Kenyans and a Ugandan manage the herd and Malcolm describes their animal husbandry skills as fantastic.
Dr Joe, Joseph, Stephen and Calleb are really valued on the Holm’s dairy farm.
Finding labour and jumping through regulatory hoops has been an ongoing battle for regional rural Australia and the entire agriculture industry, and Malcolm deems himself lucky to have a good crew.
Even though he wants to stop using backpackers, he says the last few backpackers who have helped him were great workers.
Malcolm says when it makes the news that large companies such as Coles and Woolworths,
or universities and organisations with large human resources departments, “get it wrong”, then it is tough to be a small business and be expected to get requirements right.
An unpredictable climate is another massive challenge the area faces.
“The first 20 years here were pretty smooth, the last 20 years have just been really erratic,” he says.
“You’re in drought for a couple
ing aids irrigation’s effectiveness.
has not been land formed or isn’t under irrigation.
to stand in muddy paddocks in winter.
of years, the next minute it’s really wet.”
Malcolm says the farm operated on a traditional rotational grazing system, but it is becoming increasingly difficult in today’s environment to run a pasture-only system.
To this end, irrigation is critical and helps maintain control of the seasons.
Malcolm says maize is critical in his feed base and the family have become croppers that grow forage to feed cows. The climate cycle impacts how much he grazes.
“There are dairy farms who graze a lot and others who don’t graze any animals. We are still grazing. However, I can see a time where we won’t be grazing. It will be sooner rather than later.
“It comes back to economics; 100ML of water can grow about 100t - 150t dry matter of ryegrass, or 320t - 350t of maize/winter crop. When temporary irrigation water is at $200/ML, that’s $133/t for the pasture for water alone, compared to $57 for the cropping.
“We can kick off a season in the autumn and then help finish it off through the spring and grow maize through the summer.”
The farm uses some pivots, but relies mostly on flood irrigation while well-structured land form-
Malcolm says, 40 years ago managing irrigation was almost a full-time job on each farm, but now he irrigates all three farms and calls it a “parttime job”.
“Forty years ago you used a motorbike and a shovel; today, paddocks that had a hundred irrigation bays may only have six. With land forming, the technology around irrigation has really changed.”
Only about 80ha of the farm
Due to the inconsistent climate, Malcolm is also considering housing cows and he says farmers in the region who house cows are managing climate impacts better.
Keeping cows under shelter has definite production benefits.
“They’re getting better feed efficiency. Feed costs don’t drastically increase. It keeps the cows out of the heat in summer and they’re not walking down muddy laneways or have
“It takes a bit more to manage but it’s better from a cow health point of view.”
Many farmers in the area are, therefore, switching from pasture-only grazing to systems they can manage better.
“We’re running a hybrid system
MALCOLM SAYS HE CAN FORESEE A TIME IN THE REGION WHEN MOST COWS WILL BE HOUSED.
MALCOLM IS
at the moment. We don’t have the efficiencies and benefits of a pasture system, and we don’t have the efficiencies and benefits of a total mixed ration system.”
In this hybrid system he has been operating over the last number of years, cows are currently grazing twice a day, with a top-up from the mixer wagon.
But it is likely that soon all the cow feed will be coming from the mixer wagon.
The timing of the switch is influenced by temporary water pricing and seasonal heat. Once there are consistently hot days of 35°C-plus, rye grass stops growing.
Mating heifers are fed a fixed ration.
The right equipment makes managing the hybrid system easier and will also help if cow sheds become the norm.
To this end Malcolm recently bought a new Ausmix XL30 mixer wagon from Farmtech. In the early 2000s he didn’t need a silage wagon, but when the millennium drought hit he realised he would have to deal with climate ups-and-downs, and feed issues, for extended periods.
Now cows depend on the Ausmix, built by Brad Modra and the team at Farmtech, twice a day for feed.
“There isn’t a day of the year that it isn’t used. There is always a mating mix, weaners or a top up for the milkers. During summer and autumn it might be doing five -seven loads a day.”
He turned to Ausmix because the quality of imported brands seemed to drop.
Malcolm says the new XL 30 has a number of small upgrades from the previous XL 30 Ausmix model he relied on.
Farmtech’s approach to manufacturing, especially with the new machine, means maintenance and servicing is easier.
“When things are easier, you tend to maintain machines more because it’s not a pain”.
Small adjustments also make for a stronger machine. Galvanised adjusting rods have been replaced with stainless steel. A stainless steel skin means when a machine is traded, the skin can be cut out and the machine is like new, and the barrel remains protected.
“In the end it comes back to local service and availability of parts. Because Farmtech makes them, I know they will have spare parts and they are not relying on an importer. That’s a massive plus when something goes wrong. Farmtech now are building their machines in-house, so there is a consistently high quality product.
“What the critical test is, when something goes wrong, you want them standing behind you. You don’t want to look around and can’t find anyone. You get that with Farmtech.
“I reckon the majority of dairy farms in the region now have one of their machines.
“For us being only two hours from Wodonga, if there is a major breakdown we can have another machine here in a few hours.
“Farmtech also ensures there are regular inspections of the machine for blade wear and oil changes.”
The machines come with Top con software, and staff use a tab let that connects to the machine
via bluetooth, so they can precisely mix rations.
One of the challenges in TMR systems is making sure that each mix is consistently the same and the software’s ease of use helps
keep mixes consistent across different staff members and differing mixing experience and abilities, Malcolm says.
Of course the quality of cows is crucial to success. Malcolm says
he hasn’t had a bull on the farm in 15 years.
Traditionally, he used sexed Holstein genetics but, when bobby calves became unpopular, he switched to conventional Angus semen from the USA on cows and heifers.
Replacements receive Holstein semen.
“We are now using the genomic results to better select what sexed semen goes into animals.
“We lean towards health traits and look at the bottom third of animals. These will get mated to Angus, the others will get sexed for a couple of inseminations, and, if unsuccessful, get Angus semen.
“We were using a lot more sexed semen, however, since the Chinese heifer market dried up we have changed our focus.”
Almost 70% of the milkers have now had their DNA tested.
Malcolm recently raised 60 calves that he will sell to the works, as he wasn’t able to move them at five days old.
COWS GET A DAILY TOP UP FROM THE MIXER WAGON, BUT IT IS LIKELY ALL THE COW FEED WILL SOON COME FROM THE WAGON.
He says the appetite for bobby calves in the industry is diminishing.
Beef dairy still has a long way to go, however he believes given time it will “get there”.
“Beef-dairy crosses are great low carbon footprint animals.
“There is a willingness on farms to breed these calves and, at the market end, there is a willingness to sell them; we just need the piece in the middle. As an industry we need to progress.”
Angus genetics, for example, means calves are feed efficiently, grow fast and are “turned over weeks earlier and grow into animals the abattoir wants”.
In the end, the market also wants that product, he says.
Water is fast becoming a massive challenge for the region. Not only because of droughts, but because some government initiatives are not managed satisfactorily, such as the Murray-Darling Basin Plan, he says.
Through the plan the government is investing in water saving infrastructure in the Basin through the Sustainable Rural Water Use and Infrastructure Program and the Commonwealth On-Farm Further Irrigation Efficiency Program.
However, the government struck a deal with the Greens last year where as much as 700 gigalitres of water used for farming could be bought for the environment.
Water, Malcolm says, could have been better applied.
“The government is too focused on buying entitlements and not focused on environmental outcomes.”
He says environmental concerns could also have been addressed better by initiatives, like, for example, building fish ladders.
Malcolm says the farm is
THE HOLM’S MILK 600 COWS ACROSS THREE FARMS, WHICH SPAN 580 HECTARES. THE FARM PRODUCES ABOUT 480,000 KG OF MILK SOLIDS PER YEAR.
IRRIGATION FROM MURRAY IRRIGATION LIMITED COMING ONTO THE FARM. A SHALLOW GROUND WATER PUMP AND ON-FARM CONTROL STRUCTURES IN THE FOREGROUND. ONLY ABOUT 80HA OF THE FARM HAS NOT BEEN LAND FORMED OR ISN’T UNDER IRRIGATION.
going through an interesting time because they are considering selling the farm.
Depending on expression of interest, he will either sell or refinance and then put in hous
“We are at a critical juncture, given our ages, of late 50s and early 60s. If we put the housing up, we will have to commit for another five to 10 years at least.”
aren’t being stopped by these decisions and he and the Holm family and team are charging full steam ahead.
“This is a really great region to live and farm in, it is hard work though.
“There are some really inspiring dairy farms around and with the right skills, capability and good financing there is no limit.
STEPHEN KIMANI ON THE CUPS. WITH MALCOLM RELYING ON 10 STAFF MEMBERS, HE SEES THE FARM AS SEMI CORPORATE.
their capacity to change and adapt. We still need help in research and facilitation in these changes, however it can be successfully done,” Malcolm
LIVING IN THE WAKE OF CYCLONE GABRIELLE AND MULTIPLE WEATHER EVENTS SINCE HAS BEEN A CHALLENGE BUT TOBY PARKER IS DETERMINED TO KEEP GOING.
Toby runs Broadlands Contracting Ltd from his parents’ farm in Tolaga Bay, north of Gisborne. He does drainage, levels paddocks, plants and harvests maize for himself and other farmers, and does long-haul trucking to deliver feed wherever it is needed.
“The last two seasons have been extremely challenging which has taken a real toll on all of us. We pretty much had a rain event every month leading up to Cyclones Hale and Gabrielle and afterwards, it still didn’t stop.”
shed, yard and gate buried, with no idea where to start.
“Almost two years on, we are still very much in recovery mode. Only now are we at a stage where we can start putting fences back up.”
TOLAGA BAY CONTRACTOR TOBY PARKER FOCUSES ON DRAINAGE, EARTHMOVING AND MAIZE PLANTING AND HARVESTING.
In the wake of the disaster, Toby had more work to do than hours in the day. That included piling up slash and moving mountains of silt.
Everything was covered in silt and slash, fences were gone, and heavy rain left paddocks flooded, and unable to drain. The Parker family farm was particularly hard hit.
across ditch the
PROFILED IN NZ’S RURAL CONTRACTOR & LARGE SCALE FARMER DECEMBER-JANUARY 2025, WE VISIT BROADLANDS CONTRACTING IN TOLAGA BAY, NORTH OF GISBORNE, NEW ZEALAND.
“Imagine waking up to every single inch of the property covered in silt. Every house, every
AFTER CYCLONE GABRIELLE, TOBY PARKER BEEFED UP HIS FLEET OF EARTHMOVERS WITH A 13-TONNE DIGGER, A 21-TONNE DIGGER AND A KOMATSU BULLDOZER.
Today, he is future proofing paddocks by levelling them with new technology, so water can run off as quickly as possible.
Having 50 ha of maize on his lease land completely wiped out by Cyclone Gabrielle and unable to be harvested, was a huge hit financially.
“It was soul destroying to watch entire paddocks of maize fall over, and not be able to do a thing about it. Maize and drainage is my passion, but it’s been a real struggle to keep our heads above water. Now, with the sun shining and our 2024 crops in the ground early things are finally starting to look up.”
Last year he planted 630 ha of crops on his parents’ farm, leased properties and neigh-
bouring farms. Most of that was maize and some sweet corn, but he also sowed grass and chicory.
“Pretty much 90 percent of the farms we work with are local. I have enough area around me to keep me busy, so I don’t have to go far. It is all about keeping a good relationship with farmers close by.”
Toby wasn’t always dead set on being an agricultural contractor. He spent his school years following in his fathers’ footsteps as a boarder at King’s College in Auckland. After that he took a year off to work as a teacher’s aid in England and travel around Europe.
Upon returning home, Toby found a passion for engineering, took a course at the Eastern Institute of Technology and worked for Gisborne Engineering where he learned the trade. He then headed out on his own to set up Parker Engineering.
“I loved the challenge. My business was running for about five years, but I worked too hard and just got burned out. A lot of what we did was heavy duty welding for forestry companies. There were plenty of nights staying late on site to get the job done.”
He realised those hours weren’t sustainable in the longterm, and it was difficult finding staff willing to travel.
When his parents decided to grow organic kiwifruit for Zespri,
TOBY PARKER’S JOHN DEERE 8RX ON QUAD TRACKS WAS A GODSEND AFTER THE CYCLONES BECAUSE IT COULD WORK IN PLACES WHERE A WHEELED TRACTOR WOULD GET STUCK.
Toby took the opportunity to join them on the farm.
“I moved back to Tolaga and we got to work researching and building the kiwifruit orchard. Having no previous experience constructing something like this, it was a great learning curve.”
After about a year, the project finished and Toby was ready for a new challenge. With house prices skyrocketing he sold his
TO IMPROVE MAIZE YIELDS, TOBY PARKER LEVELS PADDOCKS USING TRIMBLE GPS AND OPTISURFACE EARTHWORKS DESIGN SOFTWARE.
renovated property in Gisborne, and bought some machinery off his parents.
As work began to pick up, more clients came on board, so starting Broadlands Contracting Ltd seemed like the natural next step.
“It’s been a hell of a journey –
a lot of highs, some real testing lows, but we are pushing through and making good progress.
Everything we do is to get a step ahead of the game and grow the best crops we possibly can.
“It is one thing to deliver in the good times, but as we have learned the past couple of years, we need to be prepared for the bad.”
Having owned the agricultural contracting business for about four years now, he has expanded to take on several staff, all with a different set of skills.
“They are all pretty flexible, some of them like having a
break in the winter, but I try to keep work going with the digger and some engineering. There is always plenty to do, year-round, so it is important to have the right people for the job.”
Putting his engineering background to good use, Toby maintains and services his machinery. He also makes hoses and fixes gear for others.
The Parker family has eight John Deere tractors in all, including Toby’s 370-hp 8RX 370 on tracks. All up the fleet also includes three big tractors in the
300-hp range and two smaller 125-hp tractors, which are perfect for planting and spraying.
There’s an ‘old classic’ John Deere 4450, which is 160hp and dates from the 1980s and two 85-hp orchard tractors.
“The 8RX arrived just as Gabrielle hit, so it is not even twoyears-old, but it has been an incredible investment already. There is just no way we could have even attempted planting some of our paddocks without it.
“It’s basically my home now, it has a massager, heated seat and a fridge, so it keeps your back warm and beers cold,” Toby jokes.
“Having a quad track tractor means there is not much we can’t do, the problem is there is only one of them. In areas where a wheeled tractor would get stuck the 8RX makes it look easy. It has changed the game for us because we are able to push through even in some really tough conditions.”
Toby admits John Deere machinery is expensive, but it is all about parts and support.
Brandt Gisborne is the John Deere dealer in town and offers a wide variety of machinery with
LEVELLING AND DRAINING PADDOCKS REMOVES WET, BOGGY AREAS THAT REDUCE MAIZE YIELDS AND MAKE HARVESTING DIFFICULT.
TOBY PARKER SAYS THE 9770 STS IS THE BEST COMBINE JOHN DEERE HAS EVER MADE AND WITH TRACKS IT CAN HARVEST IN PRETTY MUCH ANY CONDITIONS.
a big presence and “there is not really anyone else who comes close”.
Brandt has a number of mechanics on deck, meaning someone is able to get out in the field to offer support at short notice.
The Parkers brought an eightrow planter and John Deere 6125R tractor brand new in 2015. Back then they were top of the line, but in recent years Toby has upgraded with Precision Planting technology.
“It allows me to see soil temperature and how clean and uniform the soil is. It helps to get the best planting conditions possible and in turn, increases yields. The planter keeps track, so I can vary planting depths based on optimal conditions for growth.
“Maize isn’t the highest value crop out there, but if you can produce a high yield it’s rewarding. That is why I am so passionate about levelling and drainage, because every hollow is costing money in a dry or a wet year. Having an even paddock gives you the best chance to be as productive as possible.”
He has made a significant investment to his planter in the last three years, adding speed
Looking ahead, Toby says he would like to buy his own land and to build a house. He would also like to get married.
“I made a vision board in 2017 and I have just about ticked it all off. My goal for 10 years was to get a grain dryer in place, an 8RX John Deere tractor and a combine harvester on tracks, and I have managed to do that.”
For now his focus is on getting the family farm back looking like it did before Cyclone Gabrielle and level every contour and drain in Tolaga Bay.
There are always new dreams, big plans, and Toby has no intention of slowing down any time soon.
“For now it is about looking to the future. It finally feels like there’s light at the end of the tunnel, and as always I have plenty more projects on the horizon.”
tubes, which means he can now plant twice as fast.
Toby has a Freightliner truck and trailer unit, and he runs a couple of diggers, a bulldozer and a John Deere 9770 combine harvester on tracks.
“It’s the best combine John Deere has ever made. She’s a bit of a beast. It goes over the ground without too much com-
paction and you can pretty much harvest in any conditions. The tracks have been worth their weight in gold.”
The truck is his newest addition. He uses it to cart maize from sources to suppliers. It can carry a 38.5-tonne payload and gives him the ability to bring fertiliser in and take grain away.
After Cyclone Gabrielle, he
bought his 13-tonne digger to help remove slash and silt from paddocks. He also added a 30-tonne dump trailer on Stryder tracks, which has been invaluable for clean-up work and harvesting in wet conditions. This year he added a 21-tonne digger and a Komatsu bulldozer.
The Parkers built a grain drying complex in April, which has
proven to be a good move already, Toby says. It means maize can come off the paddock and into a silo, without having to wait for trucks or drier space.
“Living in a relatively remote
location, logistics can be a nightmare, especially with road closures and delays. Having these systems in place takes the pressure off and gives us a lot more control.
“I love having a great team of staff around, living in Tolaga. We are always on the lookout for people with varied skills so we can tackle most jobs in house.
“We are about to start build-
A 30-TONNE DUMP TRAILER ON AUSTRALIAN-MADE STRYDER TRACKS HAS BEEN INVALUABLE FOR CLEAN-UP WORK AND HARVESTING MAIZE IN WET CONDITIONS.
AFTER THEIR MAIZE PADDOCKS ARE HARVESTED, THE PARKER FAMILY OVERSOWS ANNUAL RYEGRASS, WHICH THEY GRAZE SHEEP ON OR CUT FOR SILAGE.
ing a large storage dam to store water, so we can protect ourselves and the wider community in case of a drought.”
As technology evolves, Toby’ can use data to make small adjustments that have a big impact over time.
Levelling paddocks using Trimble GPS and OptiSurface prevents water from pooling in low lying areas, meaning less re-planting and higher yields. Trimble GPS knows where all the highs and hollows are, which has allowed him to level 180 ha on his parents’ farm to increase efficiencies.
“It’s eliminated wet areas making the paddocks far easier to work. After the Cyclone we had a lot of very wet, boggy spots that were putting pressure on our machinery. We were getting stuck multiple times a day just trying to get the crops harvested before they fell over.”
A Polaris buggy makes it simple for Toby to take data off paddocks and send it to OptiSurface in Australia, who map out the area and help get the best results for his clients.
“They basically design each paddock from across the Ditch. A couple of phone calls later we hop in the tractor and go round and round to get it looking like Eden Park. You don’t see any puddles on Eden Park.
“There are massive areas in many paddocks which aren’t performing. It is my passion to help people sort that out, so they can start making money off their land. They need to, because costs only keep rising. Once it is level, you see instant benefits so you don’t have to worry.
THE PARKER FAMILY RECENTLY INSTALLED THEIR OWN GRAIN DRYING COMPLEX, SO THEY CAN DRY MAIZE IMMEDIATELY AND GET IT INTO A SILO WITHOUT TRUCKING IT TO A DIRER.
ALTHOUGH IT IS PRIMARILY DESIGNED TO LAY DRAINAGE TILES, TOBY PARKER ALSO USES HIS SOILMAX GOLD DIGGER (RIGHT) TO MIX SILT FROM THE CYCLONES INTO THE TOPSOIL.
“Whether it is lush green grass or lush green maize crops, as far as I’m concerned if you are not producing more off the same land, you are going backwards. As soon as a crop turns yellow, you are losing money – it is as simple as that.”
The Parker family has been farming in Tolaga Bay since 1956, when Toby’s grandfather first moved into the area.
BROADLANDS CONTRACTING’S FREIGHTLINER TRUCK HAS A 38.5 TONNE PAYLOAD AND IS USED TO BRING IN FERTILISER AND TAKE AWAY GRAIN.
His parents, Mike and Bridget Parker, have around 250 ha, while sisters Penny and Clare and their husband’s Matt and Ben have 40 ha. Toby leases an additional 100 ha of land.
Having sold his house in Gisborne two-years-ago, Toby is now living on the family farm with his partner Amy and his three-year-old step-daughter Freya.
With his parents looking to retire, he is gradually taking over the farming operation alongside Clare and Ben. The farm is a mix of horticulture and agriculture, with the kiwifruit orchard taking up 7.3 ha.
“It is really starting to come on now. We should get a big harvest in March, which will all be destined for export.”
They grow maize over the spring and summer period on 80-100 ha.
Once they have harvested it, they oversow a crop such as grass. They can either harvest it or put sheep on it, depending on
the season and the price.
“The biggest challenges are the rising cost of inputs, including diesel, parts and freight. Farming right now is the toughest it has been for quite a while.”
AS SPRAYING TECHNOLOGY GETS MORE SOPHISTICATED, IT GIVES FARMERS AND CONTRACTORS THE ABILITY TO APPLY CHEMICALS MORE ACCURATELY AND AT FASTER SPEEDS. HERE ARE THE LEADING PRODUCTS AVAILABLE IN AUSTRALIA FOR APPLYING CROP PROTECTION AND FOLIAR FERTILISERS.
AUSTRALIAN FARMING PRACTICESBROADACRE CROPPING AND CROP CARE
Australia is a dry continent. Rainfall is low and unreliable in most of Australia’s grain growing regions, making management of crop water supply vital to profitability. Crop yields in Australia are most limited by water supply, and efficient use of this resource is a key element of farm management.
For decades, Australian farmers have been developing sustainable and drought resilient farming systems using larger equipment and advanced technology to save on labour costs, expanding the size of their farming footprints, and implementing advanced and innovative farming practices and technologies into their businesses.
The 2024 growing season, for large portions of the Australian broadacre cropping regions, was a prime example of the effectiveness of summer spraying for
water retention and highlights the necessity of an efficient and reliable sprayer within the farming systems across Australia.
“Ensuring that your spray operation is as efficient and effective as possible is a key to profitable farming in drier than average seasons,” explains Tom Draffen, AGCO’s Product Marketing Manager, Fendt Rogator for ANZ.
“Research has shown that good fallow management throughout the dry season can preserve up to 70% of water which has carried over or fallen throughout the fallow management period. This year, in some parts of the broadacre regions, we’ve seen farmers harvesting a crop grown on decile 1 rainfall during the growing season, well below the average rainfall, and which in times gone past would have meant a failed crop, unable to be utilized for any return on investment.
“In studies undertaken to determine the mean additional grain yield across numerous agricultural sites in the Southern
Australian grain growing region, it was found that between 0.8 and 2.3 t/hectare additional grain could be produced with good summer fallow management,” continued Tom.
“There are numerous examples of side-by-side paddocks where one has been well-managed for summer fallow and one has not and the results in yield performance are starkly different,” he explained.
“I have seen a few examples where there is a patch of underperforming crop in a paddock where something like a field bin left insitu after harvest impacting the ability to manage that small part of the field is visually obvious during the growing season and harvest – conserving that summer rainfall was that important this year.”
In 2023, AGCO, a global leader in the design, manufacture and distribution of agricultural machinery and precision ag technology, launched the new Fendt Rogator 900 Series applicator with adjustable clearance and
a combo-chassis designed for multiple application systems, as well as industry-leading technology and first-class performance and operator comfort.
The Rogator sprayer has a long and proven heritage which is now coupled with the new technology in the machine, reflecting passion and innovation which is synonymous with the Fendt brand.
This Rogator is a step forward from the previous models with a new chassis, a larger engine and horsepower offering, a Fendt cab with excellent visibility for the operator, and customer selectable options on the tech-stacks available. The Rogator can come configured with OptiStop electric control valves wired in at 35 or 36 sections, depending on nozzle spacings as a baseline, liquid application control system, or, for operators looking for greater control, the OptiPulse PWM systems allows for induvial nozzle control and turn compensation. Fendt offer another innovative solution called OptiTwin which combines both nozzle control valves through a specially designed T-body that works as a tiered PWM system.
“OptiTwin is a great option for growers who are looking to maximise their speed window while maintaining an efficacy in the application,” explained Tom. “OptiTwin is only available with the ProTech+ tech stack which includes the AGCO/ RAVEN RCM-S. The PWM system controls application up to a set duty-cycle, say 80%, before
THE UPDATED CAB ON THE NEW FENDT ROGATOR PROVIDES GREATER VISIBILITY AND OPERATOR COMFORT WHEN CHASING DOWN HOURS AND HAS COMMONALITY WITH THE FENDT WHEELED TRACTOR RANGE.
the OptiStop nozzle is engaged, at which point the duty-cycle for the PWM drops back and has the ability to ramp-up again to hold rate at higher speeds.
The benefit here is that the OptStop On/Off electric valves don’t pulse, so the spray pattern is perfectly uniform at the set rate for that side of the T-body, with the PWM nozzle side allowing for turn compensation at the same time.”
The Rogator also boasts one of the most stable boom rides on the market. Using a boom-tree mounting system developed by AGCO, the boom raises and lowers directly behind the rear wheels rather than moving outwards from the chassis in an arc, as it does on a parallelogram mounting design. The boom
THE OPTIONAL OPTITWIN NOZZLE CONTROL COMBINES BOTH NOZZLE CONTROL VALVES THROUGH A SPECIALLY DESIGNED T-BODY THAT WORKS AS A TIERED PWM SYSTEM FOR OPERATORS LOOKING TO MAXIMISE THEIR SPEED WINDOW WHILE MAINTAINING AN EFFICACY IN THE APPLICATION.
itself is mounted to the boom tree using a single pivot point, allowing the boom to hold gravitational balance unaffected by chassis roll in rougher paddocks or chewed-out wheel tracks.
“It’s a simple design, but it’s very effective in keeping the boom stable and level,” says Tom. “It also helps keep the operator comfortable during long hours as the weight of the boom isn’t shifting outwards behind the boom when the autoheight control is working; this keeps the front end and the cab stable.”
The boom mounting design is coupled with an advanced automatic height control system Fendt call OptiHeight.
“OptiHeight is our white label name for the RAVEN XRT system which is installed at the factory in Jackson during production,” says Tom. “The system takes a proactive approach to ensuring the boom is where it needs to be. We use a gyroscope in the ABM module mounted on the chassis of the sprayer to detect chassis roll.
This information sends a signal to the electromagnetic dampers on the centre rack of the boom which can stiffen up to hold the wings in place. The centre rack potentiometer, wing-tilt sensors and boom height sensors mounted under the boom send a signal back to the brains to confirm boom position and make slight
THE FENDT ROGATOR CAN BE CONFIGURED WITH A COMBO-READY CHASSIS GIVING OWNERS THE OPTION TO QUICKLY CHANGE BETWEEN LIQUID AND DRY SYSTEMS FOR MORE VERSATILITY IN THEIR MACHINE USAGE THROUGHOUT THE YEAR.
The Massey Ferguson ® 500R Series sprayers offer fast, efficient, and easy-to-use spraying solutions for farmers worldwide.
Built on over 60 years of AGCO experience in application technology, the MF 500R Series sprayers are based on the 9100 MF and Rogator 1100 and combine durability and flexibility, giving operators more control and confidence in their daily operations.
Designed with user-friendliness in mind, the MF 500R Series features an intuitive layout that balances cutting-edge technology with simple operation, ensuring smooth and efficient spraying. The tractor-style cab is spacious and ergonomic, inspired by the award-winning MF S Series tractors, providing exceptional comfort for long working hours.
With nearly 360-degree visibility, operators can easily monitor
booms and tyres without straining. The cab is also designed to reduce vibration and noise, enhancing operator comfort throughout the day. Built into the chassis, the sprayer’s flexible self-levelling, C-Channel design ensures all four wheels maintain optimal ground contact, even during the full 762mm of suspension travel.
The Smart AWD all-wheeldrive system provides AGCO’s industry leading power-toground traction, ensuring consistent coverage while reducing pump pressure at lower engine speeds. This results in lower fuel consumption, extended engine life, extended transmission life, a wider peak power rpm range and more reliable spraying performance in a wider range of conditions than some of its competitors.
The MF 500R Series comes equipped with MF telemetry and guidance sub-meter accuracy packages as standard. Should you need even greater precision, it’s easily upgradeable to
adjustments as needed to keep the boom in place. Using this system combined with the boom mounting design we’ve had independently conducted testing tell us that we can keep our boom in optimal spray position 95% of the time.”
Operators of the new Rogator 900 machines will also benefit from some well proven technology on previous models with the automatic traction control of the AWD SmartDrive™ system whereby, turn-compensat-
RTK OTA. Maintenance is made simple with easily accessible service points, boom systems that require no lubrication, and a ‘recirculate to tank’ feature that eliminates end-cap cleanouts, ensuring a hassle-free ownership experience.
Owning an MF 500R Series sprayer means you can apply product at the optimal time, maximizing yield potential and minimizing chemical waste. With its user-friendly design and low total cost of ownership, the MF 500R gives operators the confidence to spray when and where it’s needed, without relying on custom applicators.
The LiquidLogic® system, standard on every model, primes the sprayer in under 50 seconds without wasting chemicals.
Choose between 3000L – or 3500L – tanks, each equipped with a rotating rinse nozzle, a 350-litre freshwater tank, a 40litre hand-wash tank, adjustable agitation, and high- and low-level tank sensors.
The easy-to-use reload station includes a 2” and 3” camlock fill point, an optional 568 l/minute reload pump, a 26.5l HyPro chemical eductor, and an air connection for nozzle cleaning. To track performance, all spray data can be recorded on the terminal and easily saved to a USB drive for accurate record keeping and analysis.
The MF 500R Series provides the control, flexibility and efficiency you need to get the job done with confidence, every time.
ed wheel speed provides independent control of each wheel to assist in tight turns and reduce soil disruption and crop damage.
The Fendt Tractor Management System (TMS) automatically adjusts engine rpm’s to optimize power output and minimise fuel usage, and the optional GatorTrak™ 4-Wheel Steer offers a tight turning radius that dramatically improves field manoeuverability, crosses fewer rows, and reduces compaction.
“It all comes down to a value
proposition to owners looking to maximise the efficacy and efficiency of their application. Ensuring the boom is in optimal spray position is the most important thing for me,” explains Tom. “As with so many things in agriculture today – the cost of product being used to manage crops is going up and staying up, so making sure that we can use those products effectively is so important. We also know that farm businesses are time-poor and application timing windows
are shrinking. Getting across the paddocks in good time while holding rate and spray position makes a huge difference to the bottom line of the business, particularly in seasons like we’ve just seen, where efficiency of application and good product usage have paid dividends in the pointy end of the year.”
The Rogator 900 Series is being exclusively distributed through select Fendt dealers across Australia. Contact your local AGCO dealer to know more.
The FM9380-F75 is a brandnew design of flow meter from TeeJet® Technologies. This innovative design contains no moving parts which means no service or maintenance requirements and has no risk of clogging. With an extremely wide flow range of 166:1 plus fast response times, it has been optimised for modern agricultural application control equipment.
This clean-sheet design offers the best operating range in the industry. It balances excellent low-flow performance with the ability to handle high flow rates without pressure loss. It is unaffected by changes in fluid temperature, density, viscosity, concentration, and electrical conductivity. The FM9380 comes
with lifetime factory calibration and will never require any field calibration.
“The engineering team at TeeJet really delivered with this electromagnetic flow meter,” says Jake Lanyon, Technical Specialist with TeeJet Australasia. “The innovative product was designed with today’s spraying applications in mind. It requires no maintenance, and is easy to connect to your TeeJet control system or other control systems as well. The FM9380 is designed for years of trouble-free operation. Plus, the unprecedented wide flow range means it can handle the widest booms, but also provide flawless performance with just one or two nozzles spraying.”
The FM9380 has a flow range from 2.3 LPM to 380 LPM with a low pressure drop of 0.276 bar at 380 LPM. It is rated to a
When it comes to crop protection, an in-furrow application of fungicide with a liquid system delivers a ‘Prevention is better than cure’ approach. By factoring in crop protection in your seeding program, you can reduce the need to post spray, saving thousands of dollars. However, still worth noting is that the best management strategy against plant diseases is by promoting plant health in the first place. In-furrow application at seeding with its targeted placement gives the plant the best possible start.
Sprayers are a major piece of equipment that often facilitates necessary crop requirements, and sometimes after the issue arises. With unpredictable weather conditions, nutrient
deficiencies and increasing fuel and labour costs, nutrient and operational efficiencies are top of the priority list when it comes to looking at new equipment and ROI.
Trevor Walters from Manangatang, Vic, protected his crop and recouped his investment in Liquid Systems (SA) technology in its first season, injecting zinc and fungicide with water while seeding. By injecting these products in-furrow, he avoided the need entirely to spray for stripe rust that was prevalent in the region. He did not require any additional crop care products post seeding.
Trevor said, “I needed to have a constant rate of crop protectant of fungicide and zinc products, along with handling and safety issues. The Liquid Systems unit proved to be very reliable, very easy to use and calibrate and
maximum pressure rating of 14 bar and is fully compatible with TeeJet 75 Series and Banjo® 200 Series flanged connections.
TeeJet Technologies manufactures a comprehensive line of products including agricultural spray nozzles for various herbicide/fungicide applications, boom components, valves/manifolds, strainers, and spray guns, as well as GPS guidance sys-
tems, sprayer control systems, ISOBUS job computers, assisted steering systems and other precision farming products. In addition, TeeJet Technologies continues to invest in research and development to advance precision application and control technology.
For more information, please contact your local TeeJet distributor or go to www.teejet.com.
paid for itself in the first season.”
Since 2002 Liquid Systems (SA) have been manufacturing liquid delivery systems for in-furrow application of liquids.
The LQS range of pump sizes suit any size implement, wide or narrow implements, big or small tanks, intense or light agitation, high or low application rates. The liquid kits come with a controlled positive pressure ‘Stacker’ distribution kit that can configure to suit any size air tool or planter, different openers, application rates, products and row spacing for even and precisely targeted liquid application.
All Plug’n’play with most leading Precision Ag Displays and Controllers, made easy with offthe-shelf LQS adaptor looms. A range of ISOBus control options are available. The inte-
gration with a variety of precision systems enables advanced application features like liqud section control and map/GPSbased variable rate application.
In January 2022, a Liquid Systems (SA) customer survey found users are achieving greater nutrient efficiency: - 93% reported improved farm profitability, - 88% reported quicker crop emergence, - 55% reported reduced post-spraying, - 74% reported improved operational efficiency, reducing fuel and labour costs, and - 73% reported increased crop yields. (18%) reported yield responses of 15% and higher. There were 77 % of customers who use their Liquid Systems (SA) equipment to apply multi-
Managing spraying technology
Across South Australia, farmers are leading a movement toward sustainable agriculture, embracing Hardi’s GeoSelect spraying technology to manage their spraying programs more efficiently and sustainably.
As the focus on environmental, social, and governance (ESG) criteria grows, farmers are showing their commitment to environmental stewardship and responsible practices that resonate with consumers who value sustainability.
The GeoSelect advantage
Based on a sample area of 7660ha, GeoSelect has demonstrated impressive results, with 2024 studies showing a 58.3 per cent reduction in chemical usage – equating to savings of 214 litres per farm.
Water savings have also been significant, with a 58.2pc reduction in water consumption, conserving more than 356,000L, equivalent to 36 full tank refills for sprayers with capacities between 7000 and 9000L.
This efficiency reduces costs, supports healthier ecosystems, and promotes soil quality, giving farmers a competitive edge.
GeoSelect empowers farmers through precision agriculture, allowing them to identify and target specific areas that require treatment.
This targeted approach minimises unnecessary chemical
application while maintaining crop health.
Unlike traditional camera-based systems, which often involve cumbersome on-boom hardware, GeoSelect’s decoupled system employs high-resolution aerial imagery captured by drones. This streamlined method reduces equipment burden and eliminates the hassle of cleaning, servicing, or calibrating complex systems.
Farmers using GeoSelect enjoy regained time and efficiency in their operations.
The technology allows for pre-spraying analysis, enabling informed decision-making about when and where to spray.
This proactive strategy means less time spent in the field and more focus on enhancing yields and overall farm management.
By calculating spray volumes before entering the field, GeoSelect optimises chemical use, achieving savings of up to 90pc.
The system provides real-time feedback and precise GPS tracking, ensuring that only targeted weeds are treated.
This precision not only helps maintain healthy crops but also significantly reduces the environmental impact of farming practices.
Heath Thompson, innovation manager at Hardi Australia, emphasises the benefits of this technology.
“GeoSelect increases the
spraying efficiency by calculating the spray volume required prior to entering the field,” Heath said. “This reduces chemical costs, water volume, and sprayer running costs.”
Farmer Sam Correll, who participated in the study, said, “GeoSelect provides us the ability to know the amount of chemical required to be loaded into the sprayer before we go spraying –there is no wastage.”
This insight underscores the system’s effectiveness in promoting sustainability and cost efficiency.
The adoption of GeoSelect represents a significant step toward achieving robust ESG goals.
Farmers are increasingly aware that their practices impact not just their immediate environment, but also broader social and governance issues.
By reducing chemical dependency and conserving water resources, they are contributing to a healthier ecosystem and promoting biodiversity.
This commitment aligns with growing consumer expectations for sustainably produced food and agricultural practices.
In the corporate world, similar principles are reflected in corporate social responsibility (CSR) initiatives.
However, ESG encompasses a broader framework, evaluating a company’s sustainability practices across environmental impact, social responsibility, and governance transparency.
For farmers, demonstrating adherence to ESG criteria
enhances their marketability, proving that sustainable practices are not just beneficial for the planet but also for their bottom lines.
Farmers in South Australia are set- ting a commendable example for agricultural practices nationwide.
By investing in GeoSelect, they are embracing a sustainable future – one that prioritises profitability while remaining deeply committed to environmental stewardship.
Looking ahead, the potential of GeoSelect continues to grow.
Upcoming features, such as Green on Green (GoG) capabilities powered by AI, will further enhance functionality without the need for additional hardware.
Farmer’s use of satellite imagery and advanced data analytics in conjunction with GeoSelect, promises to keep them at the forefront of precision agriculture.
In a rapidly advancing agricultural industry, Hardi Australia’s GeoSelect technology leads in innovation and sustainability.
By choosing GeoSelect, farmers are optimising their operations, reducing chemical usage, conserving resources, and contributing to a healthier ecosystem.
Embrace GeoSelect today and join the movement toward a greener, more sustainable future in Australian agriculture.
For more information go to hardi.com/en-au.
The top three Liquid Systems benefits reported were: 1. Ability to apply multiple inputs in one pass 77%, 2. Targeted and even distribution
ple liquids in one pass at seeding. Fungicides (59%), micronutrients (59%) and UAN (55%) were the most common liquids applied in-furrow, although some farmers are also using inoculants (33%), soil wetters (22%), carbon products (10%) and biologicals (9%).
of nutrients 73%, 3. Reliable operation 70%. Switching to Liquid Systems will improve input use efficiency. It will also mean you can gain accurate, targeted and even distribution of nutrients, improve
disease resistance and have the flexibility to work at a wide range of application rates and operating speeds.
For more information call (08) 8357 4437 or visit www.liquidsystems.com.au.
In the vast, sun-scorched landscapes of rural Australia, few names resonate as deeply with agricultural innovation as Goldacres. Founded in 1978, this company represents more than just a manufacturer of farming equipment—it embodies the spirit of Australian rural ingenuity.
Goldacres began as a small workshop in St Arnaud Victoria, addressing the critical needs of local farmers, at a time when
agricultural technology was rapidly evolving, In the 1970s, an investor conference entitled ‘Grain, the other gold’ included field demonstrations held at the Condobolin NSW property of Dr Allan Bond. It was opened by the Federal Minister for Primary Industry, Mr Ian Sinclair. The conference was innovative in Australian agriculture for its time and illustrated the long-term, low-risk investment and returns from large scale cereal production.
The interest in Dr Bond’s conference spread far and wide,
Plough, mulch and achieve your ideal soil bed with independent discs, tines and packers
identifying the trend toward large scale grain farming. Fuelled by this popular conference, John Richards of St Arnaud Victoria, recognized the importance of developing robust, efficient spraying equipment that could withstand Australia’s challenging farming conditions. He wanted a name for his new venture, identifying his machines as part of the progressive expansion of cereal farming in Australia. So ‘Grain, the other gold’ inspired the name ‘Goldacres’ identifying the opportunities in grain farms. What started as a modest family enterprise quickly grew into a national powerhouse of
agricultural machinery design. The company’s signature boom sprayers became synonymous with precision and reliability, helping farmers maximize crop treatment while minimizing environmental impact. Their commitment to research and development set them apart in an increasingly competitive market.
Throughout the decades, Goldacres has navigated significant technological shifts, in mechanical designs to sophisticated computerized systems. They’ve consistently anticipated farmers’ needs, creating equipment that improves efficiency, reduces
Plough, mulch and achieve an ideal soil bed with independent discs, tines and packers
• Exclusive, on-the-go tine adjustment to 440mm depth, disc gang angle for more aggressive cut, and packing pressures
• Winged point option available
• Strong, durable with 2.9 - 7.2m working widths
• Folds to less than 3m
Plus speed and subsoil tillers, disc harrows and semi-mounted ploughs
In 2023 Amazone released AmaSelect, an electric control system that automatically selects the best nozzle according to operating conditions. The AmaSelect system featured four individually-controlled nozzles in carriers that are positioned at 50 cm intervals, which, depending on the field size, working width and the number of partwidth sections used, allowed the operator to enter optimum pressure ranges for each nozzle type, fitted on the carriers, into the ISOBUS operator terminal.
“With a low maintenance cost, and large rate application from the tractor seat, AmaSelect makes it easy for the operator,” says Murray Tuck, Amazone Product Manager.
AmaSelect automatically
selects and activates the best nozzle according to the desired application rate and forward speed. Once the nozzle is operating outside of the optimum pressure range, AmaSelect automatically switches over to a smaller or bigger nozzle or adds a second nozzle to the spray circuit, reducing crop protection costs.
In order to keep the application rate as constant as possible across the whole of the boom width when driving round bends, Amazone has introduced a new CurveControl feature available for the AmaSelect nozzle control on UX trailed sprayers and the Pantera self-propelled sprayer.
The new curve control feature
chemical usage, and supports sustainable farming practices.
Current technologies include the integration of autonomously controlled swarmbot sprayers featuring Weedetect camera technology for green-on-green spot spraying capability.
Designed to address the challenges of modern farming, these autonomous robotic systems offer farmers unprecedented precision and efficiency.
Unlike traditional farming
will facilitate the best possible automatic optimisation while driving around curves,” says Murray.
“In the past, application of plant protection products when driving round bends has led to an over-application on the inside of the bend and an under-application on the outside of the bend. The problem increases with increasing boom widths,” he says.
When applying herbicides to the inside of a bend, over-dosing may lead to significant weakening of the crop or even total crop failure. Under-dosing in the outside area results in incomplete suppression of the weeds and fungal diseases and might lead to resistance developing as a consequence of under-dosing.
“AmaSelect CurveControl will ensure that crop yield losses are prevented,” says Murray. Loss of yield is a possible as a result of under-dosing or over-dosing.
AmaSelect CurveControl determines the curve radius using sensors, and thanks to the ability to automatically change the nozzles across the boom, ensures fully uniform application rates during cornering.
The application rate can be adapted independently of the part-width section control, since the AmaSelect individually controls each nozzle body at a part-width section distance of 50 cm.
The AmaSelect CurveControl
provides the option of adapting the amount applied by selecting one of four different nozzles or three nozzle combinations. Different nozzle options provide AmaSelect CurveControl with an enormous range of application rates and thus also facilitates their best-possible automatic optimisation while driving around curves.
An additional special advantage of the AmaSelect CurveControl is the high-speed switching of the AmaSelect nozzle bodies, the automatic calculation of the variable distribution of the nozzle control versions within the boom, and the automatic adjustment of the pressure to the changed flow rate resulting from the change of the nozzles on the boom.
AmaSelect CurveControl takes into account the application rate of each individual nozzle, within the specified pressure range, to ensure functionality and reduction in spray drift, particularly in the marginal areas.
Provided with an appropriate set of nozzles, the variable functions of the AmaSelect CurveControl make it possible to vary the application rate across the boom to an enormous extent, and independently of the partwidth section control, in order to compensate for over-dosing and under-dosing as much as possible while driving round a bend. AMAZONE is adding to their range by introducing a 48m boom width soon.
methods, these autonomous machines can navigate paddocks with remarkable accuracy, performing tasks like crop monitoring, targeted spraying, and data collection with minimal human intervention.
Prairie Auto products designed and manufactured by Goldacres complement this technological advancement, providing farmers with sophisticated automated solutions that optimize field management.
These systems integrate advanced GPS tracking, precise navigation, and real-time data analysis to help farmers make more informed decisions about crop treatment, resource allocation, and overall farm management.
In 2025 Goldacres will release its latest model, the G8 Crop Cruiser Series 3, a self-propelled 8000 litre high clearance sprayer – set for release in October.
The G8 Crop Cruiser Series 3
will deliver more capacity and refined efficiency, which Goldacres self-propelled sprayers have been renowned for.
Today, Goldacres represents more than a business—it’s a testament to Australian engineering prowess and agricultural innovation. From family farms in the Mallee to large-scale agricultural operations across the country, their equipment continues to play a crucial role in feeding the nation.
Attending to liquid kit issues on seeding bars has become an accepted part of applying liquid cropping inputs today. However, McIntosh Distribution has moved to ensure the liquid kits on its Morris seeding bars are simple to manage and, more importantly, the most reliable to use.
The latest development follows extensive work by the McIntosh Distribution team on liquid kit designs across the Morris range to conveniently specialise the kits to each individual system.
Duncan Murdoch, the company’s National Morris Product Manager, said widespread reviews of working machines in recent seasons had identified air and liquid kits as largely the two main areas that could be further improved.
Duncan said air kit problems, in many cases, highlighted the need for correct fitment, while reliability issues with liquid kits resulted in leaks and corrosion concerns, which were compounded where growers were using dual liquid kits or had added to existing systems.
He said the company decided to mirror the new liquid kits to its air kit designs and it had collaborated with Furrow Management Systems Australia (FMSA) to tailor-make the liquid kits to each individual bar and tine assembly.
“Growers appear to put up with issues with their liquid kits. They accept that there is going to be some mucking around, but we wanted to come up with a completely designed liquid kit for each given bar – and to remove any items that could cause issues,” Duncan said.
“For users of dual liquid kits, which can present challenges, we wanted to provide a solution where growers can immediately see that it works.
“Most bars have tines fixed to a frame that moves up and down, whereas the Morris tines move up and down relative to the frame. They also fold very tight, with tines passing through the frame.
“Rather than use a generic kit to suit every bar, we have worked with Furrow Management (Systems Australia), who also are located just down the road and have an engineering focus, to individually design liquid kits for improved performance and reliability. We are aiming to make the systems as reliable as possible.
“They also use better quality fittings and more durable tube – and on the bulkheads we have switched from plastic to stainless-steel fittings.”
The new liquid kits have been designed to suit all models of the Morris Quantum air drills and C3 and C2 Contour drills, with precut and pre-formed friction tube and standardised layouts.
Single and dual liquid kits are
available to suit bars set on 250mm (10-inch), 300mm (12in) or 381mm (15in) tine spacings, and they can be used with existing pumps and controllers, as well as with systems featuring variable rate control and section control technologies. They also can be retrofitted to earlier-manufactured Quantum air drills and Contour drills.
Liquid fertiliser (red) and soil wetter (green) friction tube has been configured to suit growers’ typical application rate ranges and operating speeds at the different tine spacing settings (see table).
“The typical rate ranges will suit more than 90 per cent of growers, and custom-designed kits can be arranged to suit rates outside of these ranges,” Duncan said.
“The total solution with UAN applied is generally 45-70 litres per hectare, and with wetter it’s 35-55L/ha, and we are comfortable with growers going up to 3-bar of pressure. The sweet spot tends to be 1-2.5 bar.”
He said standardising the kits was a great step for growers and dealers.
“Up until now, they have had to calculate the length of tube based on a number of measurements including speed, viscosity, spacings and bar pressure, and the correct length has required getting all of that right.
“We wanted to achieve fixed lengths of tube, where it can arrive to the dealers and they can just fit it to the boots with no calculation required.
“Growers won’t have to worry about working out anything with dealers. There’s every chance it will suit what they need and if they damage a tube, they can have the spare tube part sitting on the shelf and just fit it.”
Duncan said the new liquid kit system was trialled on a bar in the northern wheatbelt this season without fault, and the dealer involved quickly indicated their preference exclusively for the new kits.
He said further work on the air kits involved precise configuration of every seed and fertiliser hose, including to within 10mm of required lengths and suitably arranged to each port linked to heads.
“Sometimes hoses are not routed correctly. They can be too short or too long and pull out of boots. We have started with an air kit system on a 24-metre, tow-between Quantum and we have looked at every hose and configured things individually.
“We would now like to roll this level of detail out with our air kits, starting with the most popular Morris bars, to help further improve the reliability of the kits,” Duncan said.
In the rapidly evolving world of agriculture, the push for greater precision and efficiency is reshaping the way crops are managed. One technology that is gaining significant traction is camera systems. These systems are becoming more important within modern farming, as they allow for targeted, efficient application of chemicals, which not only reduces waste but also minimises environmental impact, preserves moisture, and improves overall crop health.
Among the most advanced of these technologies is the Carbon Bee Smart Striker X, a product from the French-based company Carbon Bee.
Precision Spraying:
A game-changer for farmers
Traditional sprayers apply chemicals uniformly across an entire field, which lead to wasted resources and unnecessary environmental impact. In contrast, the Carbon Bee Smart Striker X leverages advanced sensor technology to target specific areas with remarkable precision, applying chemicals only where they are needed while also collecting ever important data for you to utilise at a later date.
The system offers several working modes, allowing farmers to tailor their spraying approach for maximum efficiency:
- Spot spray mode: This mode applies chemicals only to the
areas where weeds are detected, reducing chemical usage and minimising environmental impact.
- Dual spray mode: Ideal for early summer spray applications, this mode allows for a blanket spray across the machine’s width, with a boost to a maximum set rate when the Sensor X detects a weed.
- Modulation mode: This sophisticated mode adjusts spray rates based on the biomass detected by the Sensor X. It customizes the application rate for each nozzle, allowing for targeted treatment of both crops and weeds based on their size.
The Smart Striker X is also capable of spraying in green on green and green on brown situations:
- Green on green: This mode targets weeds emerging within crop rows, treating only the areas that have the problem weeds.
- Green on brown: Designed for summer spraying in fallow paddocks, this mode ensures that the sprayer focuses on weed control without wasting chemicals on the soil, and controlling summer moisture loss.
At the core of the Smart Striker X is the powerful Sensor X, which plays a critical role in the system’s precision. Equipped with both RGB and hyperspectral sensors, the Sensor X provides realtime data on the field. The RGB sensors capture the visible light spectrum, while the hyperspec-
tral sensors extend detection beyond the visible range, allowing the system to differentiate between crop types, weeds, and biomass with exceptional accuracy.
The Sensor X is also IP69K-rated, ensuring it withstands harsh conditions. Whether working in heavy rain, dust, or extreme temperatures, the sensors remain highly effective, providing reliable performance in even the toughest farming environments.
Key components like the Controller X (available in both ISOBUS and non-ISOBUS versions), Display X, and Sensor X are designed for ease of use, durability and longevity giving you the ability to switch the system between sprayers.
Connections are made using Deutsch plugs, known for their ruggedness and resistance to wear and tear. These points ensure that the system will continue to function optimally over its life span.
Additionally, the system when fitted by Fieldworks includes a lighting package that provides consistent illumination for the camera system, ensuring that the sensors can operate effectively, even in varying light conditions.
bility. Unlike many other camera systems, the Smart Striker X is designed to be easily retrofitted to most existing sprayers. This means farmers don’t need to replace their entire sprayer to take advantage of cutting-edge technology.
Whether upgrading a modern sprayer or updating an older model, the system integrates seamlessly with most setups, making it an attractive option for farmers seeking a cost-effective solution to precision spraying.
The Carbon Bee Smart Striker X is not just a piece of technology—it’s an investment in the future of farming.
Backed by a two-year warranty, this system offers peace of mind and long-term reliability. With its ability to reduce chemical use, save moisture and enhance operational efficiency, the Smart Striker X is a compelling option for farmers looking to stay ahead in the increasingly competitive and environmentally-conscious agricultural industry.
Speak to the friendly team at Fieldworks if you have any more questions in regards to one of these systems.
What sets the Carbon Bee Smart Striker X apart is its flexiFieldworks
www.fieldworkssa.com.au (08) 8832 2610
admin@fieldworkssa.com.au
NEW TECHNOLOGY GIVES CONTRACTORS AND FARMERS THE POWER TO ACHIEVE HIGHER YIELDS WITH FEWER INPUTS WHILE PROTECTING THE ENVIRONMENT. IN THIS FEATURE THE INDUSTRY’S LEADING MANUFACTURERS AND DISTRIBUTORS PROVIDE DETAILS ABOUT THEIR GUIDANCE SYSTEMS, SECTION CONTROL, MAPPING, TELEMATICS, ISOBUS AND OTHER PRECISION FARMING PRODUCTS.
Few will debate the merits of precision ag and its influence in shaping the future of the ag industry in Australia. Thanks to early adoption of these technologies, Australian farmers have positioned themselves as global leaders in the precision ag space. To maintain that foothold, we have to keep our focus on the future, taking a strategic approach to technology upgrades and adjusting proven practices to maximise the accu-
racy, efficiency and productivity of our farm tech.
No matter where you invest in precision ag technology in 2025, it’s important to consider how technology advances can benefit your operation. Here are a few areas to pay attention to so you don’t overlook opportunities for value creation.
Let’s say you invested in a green-on-brown or green-on-
green spot spraying technology, like PTx Trimble’s retrofit solution WeedSeeker ® 2 and the Bilberry system, to deliver herbicide only where needed. You may see immediate cost savings with reduced chemical use without making adjustments to your chemical program, but are you maximising its full potential? When implementing new technology, you need to bring an experimental mindset to your field practices too. In this case, ask yourself, how can I adjust spray practices and the chemical mix to get even more value out of a smart sprayer? You don’t have
PTx Trimble, formerly Trimble Agriculture, continues to support Australian farmers with the same industry-leading products and commitment to help make farming easier.
This includes retrofit solutions for sprayers, and spot spraying technology that enables farmers to get the most out of existing equipment. These solutions are designed to maximize accuracy, efficiency and most importantly, enhance ROI.
PTx Trimble’s next-generation WeedSeeker ® 2 spot spray system enables farmers to transform their existing spray equipment with green-on-brown technology. WeedSeeker 2 has advanced optical sensors and powerful processing that detects chlorophyll and automatically turns spray nozzles on and off as they pass over weeds. The spray nozzle applies herbicide in the exact amount
needed to kill the weed so farmers can be more efficient and effective with every application. Using WeedSeeker 2 limits the number of tank refills needed and reduces the amount of chemical applied by up to 90%. This translates into more sustainable practices that generate useful cost savings, which farmers can reinvest in other areas of their operation.
Farmers can utilise PTx Trimble’s FieldIQ™ ISOBUS Advanced Sprayer solution for maximum customization and control of any machine, regardless of the brand, make or model. With this technology, farmers control rate, section and frame managed through any of the GFX displays. The benefits of implementing this technology include significant cost savings from reduced downtime and lower input costs, but farmers who use FieldIQ™ are also seeing the impact when
to overhaul your entire program. Start small to manage your risk and understand that even making incremental changes to your chemical program to align with the technology will yield results.
The current economic climate is forcing farmers to take a close look at their budgets and consider cutting costs to take some pressure off the bottom line. Every dollar you spend should expand your existing capabilities so you can do more than you’re able to now, and/or deliver a measurable return through cost savings and/or yield enhancements.
Avoid big-ticket expenses
that don’t create new value or enhance your capabilities, like a new tractor.
Retrofit solutions that add capabilities to your existing equipment, like adding PTx Trimble guidance and steering will give you all of the benefits of cutting-edge technology and still enable you to preserve capital so you have financial flexibility.
Another example where a retrofit approach can benefit farmers is in PTx Trimble’s next-generation water solution, WM-FieldForm, which optimises water usage by controlling the movement of water onto, off of and within fields utilising uniform surfaces.
From simple topsoil levelling right through to complex multiplane landforming, grading,
it comes to generating greater net farm income and improving their overall financial position.
PTx Trimble brings together a variety of precision ag technologies to support the success of farmers throughout Australia, creating a single ecosystem that provides integrated data management solutions to connect the entire operation. Farmers have real-time access to data with the ability to share and automate workflows, cut down on training time and reduce errors. As farmers know, there are many products on the market with similar claims to improve yield, save time and money, but you cannot understate the value that comes from a connected ecosystem. Integrating data from any product and having it seamlessly synchoronise across devices gives you timely information for better decision making and value generation.
levelling and terracing projects, WM-FieldForm integrates with the GFX-1260 display and the NAV-900 guidance controller. Farmers simply need to add a NAV-900 and hydraulic machine controls to a bucket scraper and they can take on these projects by themselves, without the added cost of involving a contractor. These are just a few examples of where farmers can get additional value and ROI benefits by taking a retrofit approach.
It’s one thing to have the tools and technology at your fingertips, but many farmers simply aren’t aware of the breadth and depth of capabilities already available through their existing equipment and precision
ag systems tools. You can build that understanding and capture more value by inviting participation from people you trust and connecting with a robust dealer network that has access to field experts, resources and training. When evaluating which technologies offer the greatest benefit to your operation, you’ll be better off if you involve people you trust, who can help assess how these tools can impact your success. Leveraging the expertise of your dealer will also help you connect the dots and get even more value out of your investments. Farmers who involve their dealer in decisions around implementation and field practices put themselves in the best position possible to be successful.
A recent independent trial undertaken by three respected European trade publications echoed what our customers have been saying for years: “Valtra’s autoguidance capabilities and user interface were found to be the best of all systems tested.”
Mark Hamilton-Manns, Valtra’s Product Marketing Manager explained that the field study was undertaken in Denmark and aimed to evaluate different brands’ autoguidance and automatic headland turning capabilities.
“Seven tractors were assessed, including a Valtra Q285 and six competitors. The Valtra came out on top, scoring a total of 43.5 points compared to 40.1 for the next closest tractor and 33.6 points for the poorest result.”
The judges acknowledged that all brands tested offered good guidance features that make practical work easier, however, Valtra came out on top thanks to its ease of use and functionali-
ty. The judging panel concluded that “Valtra is the best when it comes to the user interface in general”.
In terms of speed, Valtra’s system also scored highly. The SmartTouch terminal took only 20 seconds to start up, compared to about 55 seconds for the slowest tractor tested.
Simplicity is another area where the Valtra impressed. Judges noted that the Valtra Go Mode made everything much simpler and liked the fact that the information icon (SmartTouch Help) remained in the top right corner of the display in most menus.
When it comes to headland management and automatic headland turns, the trial concluded that, once again, Valtra offered the best solution as all four, or even more, headlands can be individually adjusted.
“Complimenting the simplicity of the Smart Touch terminal and guidance package are Valtra’s SmartFarming solutions,” says Mark.
Valtra operators benefit from
completely automatic headland turns. Together with Auto U-Pilot headland automation and Valtra Guide automated steering, the SmartTurn feature completes field task automation by automatically turning the tractor on the headland.
The operator does not have to touch the steering wheel. This feature improves precision, saves time and fuel, prevents soil compaction and enables the driver to focus entirely on the job.
Working with SmartTurn begins by defining the field boundary and headland. The turning radius is calibrated according to implement type. The final step is to select between four turning options:
U-turn mode: The tractor turns automatically in the headland into the adjacent undriven wayline. The tractor makes a small U-shaped turn in the headland according to the maximum turning radius. This requires a relatively large headland.
Part-field mode: The tractor turns automatically in the headland into the third, fourth or further wayline. This requires a smaller headland than for U-turns.
K-turn mode: The tractor turns away from the worked area, reverse must be triggered manually, following a straight reverse line, shuttling forward must be again triggered manually, tractor turns toward new line.
Y-Turn mode: The tractor turns towards worked area, reverse must be triggered manually, following a curved line, shuttling forward must be again triggered manually, tractor turns toward new line.
U-turns and part-field mode are suitable for both mounted and trailed implements.
“Guidance and headland management are pivotal to precision agriculture,” commented Mark. “And now Valtra customers can benefit from Section Control 96 with Multiboom feature.
“Section Control automation has previously been able to divide the boom of an ISOBUS-compatible sprayer, for example, into 24 or 36 sections. The new Section Control 96, by comparison, can divide the boom into up to 96 different sections, while the Multiboom feature makes it possible to simultaneously control up to three different booms.
“On a seed drill, for example, fertiliser can be spread in the first feed system, seed in the next and starter fertiliser or small seed in the third. Depending on the implement, the seed and fertiliser hoppers are often divided between two or more sections. The new Section Control 96 with Multiboom can control each of these sections and feeders with centimetre accuracy,” says Mark.
Alternatively, one implement can be in front of the tractor and the other at the rear. As the width of implements is growing year by year, ISOBUS implement management is increasingly required to control them precisely. The more irregular the fields, the greater the benefit.
“Valtra’s Section Control is very easy to operate from the touchscreen on the SmartTouch armrest. The tractor must have Valtra Guide auto guidance and ISOBUS implement control,” Mark adds.
The addition of precision guidance technology has propelled two 25-year-old tractors into the 21st century.
Fraser McIntyre, together with parents, Ben and Kerry, and sister, Kate, own and share-farm about 680 hectares across four properties based around ‘Tanami’ at Mt Tyson, 40 km west of Toowoomba.
Approximately 580 ha is double-cropped to barley, chickpeas, sorghum and mung beans each year.
Transitioning from dairy farming to cropping about 20 years ago, the McIntyres operate an older machinery fleet.
“Our long-term goal is always to upgrade our machinery but at the moment we are more focussed on what the tractors are pulling rather than the tractors themselves,” Fraser says.
“To us, it doesn’t make a lot of sense to have a brand new tractor pulling a 30-year-old planter.
“We’d rather have it the other way around.”
Fraser says the addition of Ag Leader SteerCommand guidance and DirectCommand precision application systems is allowing him to implement precision planting and spraying operations with minimal outlay.
“We’re running a zero-till, 30’ controlled traffic, strip-cropping program and we simply couldn’t do this without GPS guidance,” Fraser says.
“We have lots of small or irregular-shaped strips and point rows where we are not coming onto headlands perpendicular.
“Automated steering makes us more efficient.
“You might only save a minute here or there, but it adds up.”
The McIntyres have been using Ag Leader precision agriculture technology for more than a decade, commencing with the purchase of a tractor that had an AutoFarm A5 steering system.
The purchase of a new 12-row Norseman precision planter in 2016 triggered the need to upgrade to a new SteerCommand system and InCommand 1200 universal display, which
were installed in 2018.
“Our summer planter has electric drives and section control, so we needed to update,” Fraser says.
“We paid about $70,000 for the tractor and then $30,000 for the steering, but that’s nothing compared to the cost of a new tractor.
“To be honest, we like the older tractors because they’re relatively simple and they aren’t loaded up with lots of electronics, so they’re easy to keep going.
“This tractor had about 7,000 hours on it when we bought it and we don’t see any reason why we won’t get another 10,000 hours out of it.”
The autosteer system is controlled using the InCommand 1200 display, a 30 cm high visibility touchscreen that also controls Ag Leader’s precision spraying, spreading and harvesting applications.
The display has built-in lightbar guidance, four camera inputs and split-screen capability.
“We’ve had machines with other guidance systems and Ag Leader is streets ahead,” Fraser says.
“The InCommand display is chalk-and-cheese in terms of visibility and functionality compared to our old A5 display.
“It’s simple to use and it’s easy to teach others how to use it.”
Dalby-based Ag Leader dealer, Darling Downs Precision, installed a new InCommand 1200, SteerCommand Z2 and DirectCommand L2 systems on the McIntyres’ Case Patriot 3320 self-propelled sprayer last year, while a second John Deere 8300 tractor is about to be fitted with a new Ag Leader autosteer system.
DirectCommand L2 controls all spraying operations, including AutoSwath, which controls each individual section of the sprayer.
“This reduces input costs but more importantly, it avoids problems with residual herbicides,” Fraser says.
“It’s all about better application and record keeping – we know exactly what was applied and where.”
The system can be upgraded to RightSpot, which provides individual control of up to 144 nozzles.
RightSpot utilises ‘pulse width modulation’ (PWM) technology to ensure boom pressure remains constant regardless of operating speed.
This ensures consistent droplet size, minimising the risk for spray drift and ensuring correct application of crop protection products.
“Our next step will be to add DirectCommand to our airseeder, which will give us section and variable rate application, and we’ll definitely look at RightSpot when the time comes,” Fraser says.
“Ultimately, we want to get into AgFiniti, which allows maps, guidance lines and field data to be wirelessly synchronised and
shared across all of our displays and remote devices.
“The big thing we like about Ag Leader is the service and support we get from Ben and his team at Darling Downs Precision.
“They are genuinely interested in helping us to succeed and to grow our business.”
Ag Leader is recognised as a global leader in precision agriculture technology.
It produces a range of integrated and easy-to-use guidance, steering, application control, monitoring and decision support systems that help to make farming easier.
Based in Iowa, USA, the family-owned business employs about 400 people worldwide.
Precision Agronomics Australia set to launch the V3 Fertiliser spreader controller
Precision Agronomics Australia (PAA) will release the updated version 3 i4M fertiliser spreader controller to the Australian market in February 2025.
Originally released in 2017, the i4M fertiliser spreader controller, has proved popular with Australian farmers, enabling a cost-effective solution for variable rate spreading, machine auto-shut off and coverage mapping and the new Version 3 improvements, further extending the capabilities of the system.
A major improvement is the integration of on-the-go calibration of fertiliser calibration factors by using dynamic feedback from the spreader loadcells. Electronic modules located at each loadcell take accurate highspeed readings of the weight in the spreader and send this data via a high speed link to the main control unit.
If the calibration factor changes due to fertiliser properties, such as moisture content or bulk density, the controller will detect the change from the load-
Spray nozzle selection is often based upon droplet size and for an increasing number of products, particularly herbicides such as 2,4-D, the droplet size is specified on the label and must be followed.
Droplet size classification follows strict and concise measurement parameters or standards, the first of which was created in 1985 in England by the British Crop Protection Council (BCPC). Since then, the classification standards have evolved and changed as drop size measurement technology improves, nozzle design has progressed, and the industry focus shifts to coarser sprays to reduce spray drift.
In 1999, the American Society of Agricultural and Biological Engineers (ASABE) developed
cell readings and compensate accordingly. Instead of waiting until the end of the load to detect the calibration factor error, the controller will immediately make adjustments to ensure the correct application rate is applied.
The core of any i4M system is the mobile app that runs on Android-based tablets. The Version 3 fertiliser spreader controller is the first i4M Android app to feature the rebuilt work screen which includes more precise auto shut-off, coverage mapping and icon-based step-through menus.
Adjustments of the spreader control as it moves in and out of work areas is more complex than other implements such as seeders and sprayers. As such the PAA engineers have built more flexibility into the Version 3 system to allow for changes when spreading both granulated and non-granulated fertilisers. As a result of the increased complexity, the map screen was built from scratch to enable high speed rendering of coverage and prescription maps on the Android tablet. Coverage maps that are recorded in the Version 3 app can be exported from the i4M app for
use in 3rd party Precision Ag software for as-applied analysis. For spreaders with conveyor belt systems, a belt slip sensor can be integrated with the i4M version 3 controller, to alert the operator if the conveyor belt is slipping under load, eliminating potential under-application of fertiliser.
The i4M version 3 fertiliser
spreader controller is the result of two years of development and field testing and is available on both new spreaders as well as a retro fit kit for farmers running either the version 1 or version 2 systems.
For more information, contact Precision Agronomics Australia on +61 8 9072 0542 or visit i4M. net.au.
a new standard for droplet size classification, ASABE S572, in which the droplet size boundaries were set by a series of defined TeeJet reference spray tips and operating pressures (ASABE, 2009). The ASABE S572 original standard established six droplet size classes (VF, F, M, C, VC, and XC), with five reference nozzles establishing the boundaries between them. Two additional droplet size classes were added in the same year on the review of the standard, ASABE S572.1, totalling eight classes (XF, VF, F, M, C, VC, XC, and UC).
The International Organization for Standardization (ISO) worked on the development of an international droplet size classification standard.
In 2018, the ISO 25358 standard was published (ISO, 2018), which carried out the update of some droplets size classifica-
tion ranges to better distribute the classification boundaries, particularly in the coarser ranges that are important for drift reduction. Only the C/VC, VC/ XC and XC/UC boundaries have changed.
The ASABE has updated the standard to match with the ISO 25358 as ASABE S572.3.
All TeeJet nozzles are classified according to the new ISO 25358 classification standard, however TeeJet Australasia’s Technical Specialist, Jake Lanyon, says care must be taken when comparing data found in older
TeeJet literature and/or different nozzle manufacturers that have not specified the classification standard used.
“Most reputable nozzle manufacturers have adopted ISO 25358, but not all, so when comparing drop size between nozzles and manufacturers, make sure you check the data has been measured to the same standard,” Jake said.
For the latest accurate information about spray nozzles and their droplet size, please contact your nearest TeeJet representative or visit www.teejet.com.
› It’s available free of charge to readers who qualify under the publisher’s criteria and who supply proof of occupation.
› All the latest news, views and information from the industry.
If you are not a registered reader but would like to receive a regular bi-monthly copy, please fill in the details below of your contracting or farming business and post this form to us.
Alternatively, you can fill in the subscription form on our website: www.agcontractormag.com
Australian AgContractor is available free of charge to readers who qualify under the publisher’s criteria and who supply proof of occupation (ie. printed letterhead, business card, invoice etc.) and to others upon payment of the $50.00 annual Australian Subscription (Rest of the World: $65.40 AUD).
› In-depth profiles on contractors and farmers from all across Australia.
› Six issues per year, delivered direct to your door.
› Subscriptions from as low as $50.00 annually to non-industry subscribers.
Please email admin@agrimedia.co.nz or phone +64 3 329 6555 to arrange payment if you are a non-industry subscriber.
Name:
Business/Farm Name:
Postal Address:
Postcode:
Country:
Phone:
Email:
coNTracTor
Main contracting services offered:
Criteria: Broadacre - over 1000ha and/or Sheep or Beef - over 12,000 stock units and/or Dairy - milk over 400 cows (owner or sharemilker)
Total farm ha: No. of dairy cows: No. of beef cattle: No. of sheep: Area in arable crop:
Please sign here if you wish to receive a regular copy of this publication and send the form, together with proof of occupation or cheque to: aML, Po Box 37151, christchurch 8245, New Zealand.
Signature:
Date:
ALWAYS WORKING TOWARDS THE LATEST INNOVATION IN QUALITY FARM MACHINERY HAS LED BOURGAULT AUSTRALIA TO LAUNCH ITS LATEST SEEDING IMPLEMENT – THE 4420DKD, WHICH, OVER THE LAST YEAR, HAS SHOWN GREAT RESULTS.
Launched in 2024, the 4420DKD™ (Deep Knife Drill™ ) is a testament to Bourgault’s commitment to helping Australian growers achieve optimal seeding application with purpose-built solutions.
The 4420DKD combines a robust, easyto-adjust deep knife opener with a durable and versatile frame that can be paired with any Bourgault air cart and accommodate on-board liquid tanks.
This groundbreaking implement sets a new standard for precision seeding with an innovative design that allows farmers to penetrate the soil to greater depths, facilitating improved fertiliser separation and precise seed placement.
Third-generation WA farmer and Roma Farming Company Director Frank Varone assisted with in-field testing in 2023. Frank was so impressed with the 4420DKD’s performance that he purchased the machine for the 2024 season.
“With the 4420, it almost doesn’t matter what the tines are doing,” he says. “The seed placement is always precise, and the germination is very even.
“Because it has good flotation, it’s very even and accurate across the whole bar.”
Bourgault Australia General Manager Craig Christensen says there has been a lot of work engineering and tailoring the new 4420DKD
to meet the requirements of Australian farms.
“The development of this implement was a fantastic process of collaboration with local growers to ensure we delivered exactly what they need,” he says.
Built with novel dual-tine DK (Deep Knife) openers, the 4420DKD can penetrate the soil to depths of 120mm to 165mm, enabling growers to facilitate improved fertiliser separation and precise seed placement.
Enhanced control with the on-the-go adjustable hydraulic breakout on the openers offers a force range of 68kg to 450kg for increased adaptability to soil conditions with consistent depths.
The adaptability of the 4420DKD allows it to be optionally paired with the Bourgault TruTrac Coulter™ system to optimise soil throw and residue management in high-stubble fields.
Wrapping up the opener assembly, the packing wheels are available in V, U, and VU
profiles, all using Bourgault’s semi-pneumatic design to eliminate punctures.
Boasting an all-new frame design, growers can be assured they have the quality-of-life inclusions expected of Bourgault equipment, such as a floating hitch as standard and a steerable front axle.
“With 12m and 18m models, the new 4420DKD gives growers unparalleled crop management, while both models can conveniently fold to a narrow 5.5m, enabling easier transportation,” Craig says.
The 4420DKD Seeder caters to a wide range of field requirements with row spacings of 250mm to 300mm.
The heavy-duty frame option makes the 4420DKD Streamliner™ compatible, allowing a pair of liquid tanks with a total capacity of 5400 litres to be fitted.
When fitted with liquid tanks, a hydraulic lift assist kit is available, ensuring you have the lift capacity to raise the bar on headlands.
Any worries about soil compaction from the weight can be put to rest with Hi-Flotation™ tyres provided as standard, minimising compaction and further promoting healthy crop growth.
The Bourgault 4420DKD’s feature-rich design makes precision seed and fertiliser placement more efficient while causing minimal soil disturbance.
There’s still some time to order your 4420DKD and have it ready for seeding. “We have high stock levels, and with two assembly plants, we can spare growers lengthy wait times by delivering the best local service,” says Craig.
“Using the new Bourgault 4420DK Seeder, we’re expecting growers to achieve great results.”
For more information about the Bourgault 4420DK Seeder and its features, chat with your local Bourgault Australia representative at +618 9399 9700.
NICO ROMANO GREW UP ON A VICTORIAN DAIRY FARM AND HAS AGRICULTURE RUNNING THROUGH HIS VEINS, BUT WHEN IT CAME TIME TO LEAVING SCHOOL AND DECIDING ON A FUTURE CAREER PATH, TRADITIONAL FARMING LIFE WASN’T FOR HIM.
Instead he became a heavy vehicle mechanic, working at a number of tractor dealerships before a new path beckoned.
“Growing up on the farm, I loved the machinery, and used it on my parents’ farm for the hay and silage, and jobs like that. After I started working in the tractor dealerships, I bought a couple of trade-in tractors that were the right price and some people started asking me to do a bit of work for them on their places,” Nico said.
“It got to the stage where I was doing more and more, and still working full-time, so I realised
I had a decision to make. The thought of leaving my job and a regular wage to start my own business was a bit daunting, but I really enjoyed the contracting so I made the jump.”
Romano Ag Services, based at Tatura in Victoria, had its beginnings in 2018 and Nico hasn’t looked back. The small number of clients with smaller holdings that he started with has grown to a broader client base with larger properties. Now, his year is dictated by the hay, silage and sowing seasons.
The heavy-lifters of his machinery and equipment team are three Case IH Maxxum tractors,
which Nico says tick every box for his business.
“I like the size of them, and the simplicity – they’re very user-friendly making it easy to show someone else how to use
when needed. Another big plus for me is the comfort which is really important. I love them, I could sit in them all day,” Nico said.
“They’ve also got plenty of
SEED TERMINATOR, RENOWNED FOR ITS RELENTLESS INNOVATION IN HARVEST WEED SEED CONTROL, IS SET TO UNVEIL A FORMIDABLE NEW PLATFORM TAILORED FOR NEW HOLLAND’S CR11 COMBINE HARVESTER. TESTED DURING THE 2024 WESTERN AUSTRALIAN HARVEST, THIS SYSTEM IS DESIGNED TO HANDLE THE COMBINE’S IMPRESSIVE TONNAGE PER HOUR WITH EASE AND RELIABILITY.
This milestone aligns with Seed Terminator’s mission which is to empower farmers with technology to efficiently feed the world and improve their farms for future generations.
“We are investing in more development than ever,” says Dr. Nick Berry, Seed Terminator’s Founder and Director of R&D.
“From fast tracking platforms for the New Holland CR11 and Case IH AF, to launching the FLEX and our Pro series Seed Terminators, we’re ensuring farmers have cutting-edge options to control weeds.”
The New Holland CR11, after its unveiling at Agritechnica 2023 in
power for what they are, and I find them efficient in getting the job done.
”When I was in the market for new tractors, I got plenty of quotes, and when it came down to it, the Maxxums represented the best value for money,” he said.
Case IH’s Maxxum tractor is described as ‘the ultimate all-rounder’, offering state-ofthe-art features to help deliver better productivity and greater profitability.
It’s designed to handle a multitude of tasks with enhanced cab visibility plus power, fuel economy, ease-of-use and solid performance.
Nico has two Maxxum 140s, and a Maxxum 125, which he uses year-round for cutting, raking and baling hay, sowing a variety of crops from pasture varieties through to wheat, barley and sorghum, and spraying. Having the three tractors gives
Germany, has certainly created a buzz.
Interest in the platform is high, and farmers around the world are eager to see its performance in action.
Its advanced features, including a 775-horsepower engine, dual 24-inch rotors, and a 20,000-liter grain tank, make it a standout in the combine market.
Paired with Seed Terminator’s Pro platform, this combination promises to set new standards in sustainable and efficient farming practices.
Building upon the success of Seed Terminator's Pro series, first introduced in 2022, the
him greater flexibility and saves valuable time.
“When we’re coming into hay season, one of the Maxxum 140s is attached to the mower and the other to a round baler, and the 125 has the likes of the hay rake on it.
“Coming into sowing season, one of the 140s has the seeder, the other does the discing and ploughing and the 125 is on the boom sprayer. This just means you’re not having to swap out implements all the time,” Nico said.
Currently, Nico’s preparing for the end of hay season, describing this year’s season as “average”.
“We were probably three good rains away from having a fantastic season. Not the worst season, but not a great season,” he said.
Nico says they did between 11,500 and 12,000 bales this year, over 610ha, compared with his best season to date last
Pro CR platform for the New Holland CR11 combine harvester is engineered for highcapacity performance.
It features the latest AeroIMPACT 4 multi-stage hammer mills to maximise seed kill, delivering proven results in harvest weed seed control.
This advancement aids farmers in combating herbicide-resistant weeds while maintaining optimal harvest operations.
Seed Terminator’s commitment to providing tailored solutions is showcased in recent innovations, including the Pro 1000 for CLAAS Lexion, Pro X for John Deere X-Series and the FLEX platform—a low-maintenance solution for farmers prioritising flexibility.
These advances ensure that
year, when they topped 15,000 bales.
He’ll get a bit of a break over Christmas, although there’s still some preparation for the sowing season ahead, including his equipment maintenance.
Nico’s local Case IH dealership, O’Connors Shepparton, keeps his Maxxums running smoothly and in the paddock – their
the next generation of weed control is not just here—it’s also continuing to evolve.
With platforms under development for the John Deere S7 and Case IH AF 9 and 10 combines, and the ongoing development of their FLEX technology, Seed Terminator remains on track with their vision to make weed seed control a standard feature on all combines by 2030.
Farmers worldwide can trust Seed Terminator to continue leading the charge in integrated harvest weed seed control technology. As excitement builds for the CR11, Seed Terminator has announced that there will be a limited release for the 2025 harvest.
This is the future of farming— and it’s happening now.
responsiveness and customer service a big plus for his business.
“When you’ve got a limited amount of time to get around multiple properties and do the best job you can for them, you can’t afford to have machinery out of the paddock for too long. Yes, time is money – 110 per cent it is.”
KUBOTA AUSTRALIA IS TAKING COMFORT AND DEPENDABILITY TO THE NEXT LEVEL WITH ITS BRAND NEW RTV-X RANGE LAUNCHING THIS MONTH.
Complete with all the familiar features that made Kubota’s previous diesel RTV models so popular, the RTV-X comes with a dependable three-cylinder Kubota diesel engine, power steering, VHT-X transmission and hydraulic dump bed.
In addition to these foundational features, the new model comes with a stylish, revamped exterior, LED headlights, all-new multipurpose tyres, black alloy wheels and a new Pro-Konvert fully convertible cargo box with spray on bed liner.
To Kubota Australia’s Marketing Manager, Mark Basile, the RTV-X is a step into the future for what is already a well-regarded product.
“The RTV is one of Kubota’s most popular vehicles internationally, and the RTV-X is the culmination of years of development, and perhaps even more importantly, customer feedback,” Mark says.
“Every feature of this all-new model has been informed by the feedback and work of our customers. Across Australia, Kubota rough terrain vehicles are trusted for their versatility, durability and reliability. We’re proud to continue to build upon that reputation with this release.”
The RTV-X 2-seater model offers higher capacities for towing up to 1000 kilograms, thanks to its increased engine power and updated HST system, as well as increased uphill driving performance. Even with heavy loads, the RTV-X provides superior traction, making it an ideal machine for all terrains. The mechanical 4WD system can easily be turned off, when driving on more even ground.
The new RTV-X Crew allows users to easily transform the machine from a 1-row model with extra cargo bed space, to a 2-row machine to accommodate additional pas-
sengers. Farmers and contractors alike will enjoy the addition of the all-new 3-Way Pro-Konvert tray. The tray, which opens on all sides, enables a greater degree of flexibility and enables operators to transport oversized items.
“Along with some of these more dramatic new additions, we’ve also been hard at work bringing about quality improvements that matter most,” Mark says.
“The RTV-X is in every way a continuation of Kubota’s commitment to fulfilling the needs of Australians.
“With this new model, there has been a focus on maintaining a balance between new features, and global improvements. It’s our constant aim to remain dynamic, while still delivering on the promise of safe, capable machinery.
“We’re proud to offer equipment that demonstrates an understanding of our customers, their projects and their needs.”
Deliveries of these RTV-X are available from March 2025 through your local Kubota dealer.
Better weed detection, control for increased herbicide savings up to 90%
Work night or day, in dust, dense stubbles, over fencelines
Section control, helping to reduce residual concerns
Weed mapping, assisting with resistance plans
Quick-attach brackets for easy install
CLAAS HAS RAISED THE BAR FOR FORAGE HARVESTING WITH THE V-FLEX CHOPPING CYLINDER, NOW OPTIONALLY AVAILABLE FOR PRE-ORDERED JAGUAR 900 SERIES FORAGE HARVESTERS.
This innovation sets new productivity, flexibility, and efficiency standards, enabling farmers and contractors to achieve exceptional results.
This new development continues Claas‘s legacy of customer-focused innovation, backed by over 50 years of forage harvesting expertise. Farmers and contractors using the V-Flex-equipped Jaguar can expect a season of reliable, efficient harvesting, with advanced precision and ease of use.
Additionally, Claas has streamlined sharpening and shear bar adjustment processes, completing them in just one minute, minimizing downtime, and boosting operational efficiency.
THE 2025 JAGUAR 900 SERIES ENHANCEMENTS INCLUDE:
- New V-Flex chopping cylinder for Jaguar 900 / Jaguar 900 Terra Trac as optional alternative to the V-Max for even greater versatility.
- V-Flex knives: 23 mm anti-wear coating for exceptional service life and new geometry with 10 degree cutting angle for precise cut in all crops. Significant reduction in noise levels and improved chopping quality.
- Optimised process management for knife sharpening and shear bar adjustment – now available as a combined option for even fewer downtimes.
- Factory-fitted speed differential of up to 40 per cent for MCC Classic and MCC Max corncrackers and new MCC Classic with fine sawtooth profile for use in small-seeded crops such as sorghum.
- Larger maintenance compartment for faster, more convenient changeover of corncracker module.
- Pick Up: new intake auger with four paddles ensures uniform crop flow with reduced torque peaks and higher throughput
- New Carraro rear axle with fourwheel drive engagement under load and option of extending track by 460 or 620 mm.
Product Business Manager – Green Harvest, Luke Wheeler says, “Reduced setup time, lower fuel consumption per tonne, and a significant boost in throughput, alongside faster sharpening and shearbar settings ensures the avoidance of any harvesting delays.”
The new V-Flex chopping cylinder offers unparalleled versatility for all applications and chop lengths with full and half sets of knives, as well as half-knives.
The V-Flex cylinder brings remarkable versatility with a unique design supporting multiple knife configurations, allowing operators to effortlessly adjust chop lengths and adapt to varied crop conditions, enhancing performance and precision. The triple-bolted knives, equipped with a durable 23mm antiwear coating and angled at 10 degrees to the shear bar, offer superior stability, reduced wear, and greater operational intervals.
With its optimised V-angle and new V-Flex knives, the cylinder delivers higher throughput, lower noise levels, and smoother operation, ensuring a more consistent crop flow, especially at chop lengths over 12mm.
The V-Flex cylinder is available in four configurations—20, 24, 28, and 36 knives— offering adaptable settings such as full-knife, half-knife, and one-third knife modes to extend chop lengths.
The V-Flex 36 can operate in multiple modes: 36 knives for full capacity, 18 knives in half mode, or a third mode with 12 knives. A new variant, with 36 half-knives, doubles the length of cut for optimal crop flow and chopping quality.
These configurations provide a versatile cutting range from 3.5 mm up to 53 mm, supporting maize harvesting at lengths up to 30mm in combination with MCC Classic, MCC Max, and MCC Shredlage corn crackers.
This versatility ensures a smooth material flow, precise cuts, and reduced processing costs, contributing to superior feed quality.
THE NEWLY DEVELOPED V-FLEX KNIVES FEATURE SEVERAL OUTSTANDING IMPROVEMENTS IN TERMS OF WEAR PROTECTION, THROUGHPUT AND SMOOTH RUNNING.
The new Pick Up 300 for Jaguar 800, 900 and 900 Terra Trac is characterized by less soiling in the intake and more even, slightly increased throughput.
When it comes to the Pick Up 300, the shape of the auger has been redesigned with four offset central feed paddles. This ensures even more uniform crop flow, which in turn has a positive effect on throughput. The flat or toothed paddle extensions are easy to replace or changeout in challenging conditions.
The extended dust screen now covers the entire working width of the Pick Up. This reduces material buildup on the top of the feeder housing, cutting cylinder and front windscreen. It effectively captures all crop types, avoiding harvest losses. The widemesh screen still provides a clear view of crop flow from the cab.
“The new one-piece dust screen can easily be swung open for maintenance work,” Luke says.
The MCC Classic and MCC Max now work with a speed difference of up to 40 percent, and the MCC Classic is also available with fine gearing. Thanks to the larger maintenance space, installation and removal of the corn cracker module is quicker and less stressful.
For years the Claas Multi Crop Cracker concept (MCC) comprising the MCC Classic, MCC Max and MCC Shredlage has offered the widest choice of corn cracker options for highly efficient processing of kernels, leaves and stalks - from short-cut to longcut and shredlage.
For more intensive kernel processing, the differential speed has been increased from 30 to 40 percent in the MCC Classic with a sawtooth profile, and the MCC Max, with unique ring segments and cutting and shearing effects. Furthermore, the MCC Classic is optionally available with a new 190 sawtooth profile-roller designed for particularly small kernels like sorghum.
The maintenance compartment on all Jaguar 900 Series machines has been enlarged to provide additional space for the fitting and removal of the corn cracker.
Luke said, “Having the extra room in the side opening makes it easier to fit the corn cracker when changing from grass to maize.”
The 2025 Jaguar will be fitted with the new Carraro rear axle. Sporting a load capacity of
9 tonnes and 10-hole rims in the Power Trac variant, the Carraro axle enables four-wheel drive to be engaged under load.
Furthermore, wheel spacers of 460mm for the standard axle and 620mm for the Power Trac four-wheel drive axle are available to widen the track.
AMAZONE IS EXPANDING ITS RANGE OF PRECISION SEEDERS WITH THE NEW TRAILED PRECEA 6000-TCC, 9000-TCC AND 12000-TCC MODELS, IN WORKING WIDTHS OF 6, 9 AND 12 M RESPECTIVELY.
This variant, which has been developed specially for large-scale farms and contractors, stands out with its high-performance overpressure singling, large tank capacities and innovative Central Seed Supply seed delivery system. The high-precision seed placement ensures optimum field emergence, even at increased forward speeds of up to 15 km/h.
The new Central Seed Supply seed delivery system carries the seed from the central hopper to the singling units via an air stream. There, the seed for each row is temporarily stored in a small reception unit. Once this reception unit reaches the maximum fill level, the air stream is automatically cut off, thereby shutting off any further seed supply. When the fill level decreases, the air stream automatically restarts and conveys seed from the main hopper to the individual rows.
Thanks to the intelligent air stream system of the Central Seed Supply, every singling unit is independently supplied with seed, without the need for complex sensor systems or electronic controls. Whilst the Precea 9000 and 12000 models feature a central seed hopper with a capacity of 2,000 L for up to two big bags, the Precea 6000-TCC model has an 850 L central seed supply, or 70 L seed hoppers.
Product Manager - Amazone (AU) Murray Tuck says, “The 6000-TCC encompasses all of the features of the Precea in a more compact version.”
For seed singling, Amazone uses its precision PreTeC singling units, whose functionality is based on the overpressure principle. This means the seed is pressed against the singling disc by air pressure.
The seal rotates along with the singling disc, which considerably reduces the power consumption of the electric drives across the individual rows.
The remotely controlled, automatic SmartControl stripper finger adjustment is coupled with the optical sensors and effectively prevents any misses or doubles.
Meanwhile, the electrically-driven singling disc turns in relation to the forward speed and desired seed rate, conveying the seed towards the propulsion channel. At this point, the contact pressure is broken, the seed is shot precisely into the seed furrow, caught by the catcher roller and then securely embedded in the furrow bottom.
The furrow formers ensure the precise seed placement. Two carrying rollers and the highdown force, hydraulically adjustable coulter pressure ensure uniform depth control.
For even greater convenience, Amazone offers the SmartForce automatic coulter pressure regulation.
This ensures that the set contact force remains constant for a consistently uniform seed placement, especially in variable soil conditions. The ElectricDrive electric metering drive allows the desired seed rate to be conveniently set via the ISOBUS terminal and serves as the basis for precise, part-area, site-specific rate control using GPS and field zone maps. In addition to this, Section Control actively saves seed row-by-row in wedgeshaped fields and on headlands, particularly useful at these large working widths. Ideal conditions are also provided for mechanical weed control with a hoe.
The electric metering drive to the individual rows makes it possible to maintain an evenly-spaced placement across the entire working width, even when driving round bends. A yaw sensor is used to calculate the difference between the forward speed on the inside and outside of the bend.
The innovative CurveControl then adjusts the speed of each singling disc accordingly, ensuring that the seed spacing remains uniform, even when seeding around bends. The even spacing allows the plants to be adequately supplied with nutrients. This results in uniform crops and ensures even ripening.
For the simultaneous application of fertiliser, the Precea-TCC 9000/12000 is equipped
THE FRONT-END LOADER IS THE MOST POPULAR TRACTOR ATTACHMENT FOR TRACTORS UP TO 150 HP. AND FOR GOOD REASON. IT OFFERS GREAT VERSATILITY AND UTILITY FOR GENERAL PURPOSE TRACTORS AROUND A FARM, CONTRACTING OR PUBLIC WORKS, ASSISTING WITH A WIDE RANGE OF MATERIALS HANDLING AND MAINTENANCE TASKS.
As we rely more on the loader to undertake these tasks, ergonomics of the loader operation are a major factor in the efficiency of that work and the level of fatigue and errors experienced. A high level of loader integration with the tractor is the key to improving ergonomics.
The new Landini Powerfarm II 120 tractor makes this leap with superb loader integration directly from the factory.
First, it starts with the loader. Gary Surman, Sales and Marketing Manager at distributor Inlon, explains, “Three years ago, the Morra family behind Landini tractors acquired the largest Italian loader manufacturer, Sigma4. They made Sigma4 the OEM supplier of loaders to Landini. With this direct connection to the factory, the Powerfarm II 120 loader is now fitted during the tractor assembly process ensuring it is fitted as the original engineers intended.
“The integration in the cabin is obvious in the easy-to-reach location and layout on the right-hand side of the driver. But it is the extra controls on the loader joystick that lift that integration to the next level.”
The Landini Powerfarm II 120 Cabin model is powered by a 4.4 litre Perkins Tier 3 diesel engine. Its transmission has a hydraulic power shuttle main clutch, 36 forward and 12 reverse gears incorporating a HML 3-speed power shift, and a top speed of 40 km/h.
When manoeuvring the loader, the forward-reverse shuttle control on the steering column is essential, but the Powerfarm II also incorporates HML transmission speed shift-
with an easily accessible, twin-chamber hopper with a total filling volume of 6,000 L, whilst the Precea-TCC 6000 delivers a 3,000 L volume. Each hopper chamber has its own electric metering unit that is connected to a distributor head, meaning that half-side shutoff is available as standard.
Fertiliser is placed via the FerTeC twin HD fertiliser coulter. The relationship between the placement depth of the fertiliser and the
ing with a press of the thumb on the loader joystick. Hydraulic third function is operated with the trigger button on the front of the joystick, with optional hydraulic fourth function and hydraulic implement latch and un-latch also available.
For efficient and tireless operation, all the key loader and tractor driving controls are within finger reach of the steering wheel and loader joystick.
Visibility is another essential when stacking bales. The Landini Powerfarm II Series has the latest slimline rounded cabin bulkhead providing the operator with superb visibility when placing bales high in the shed.
Both Italian manufacturer Landini and distributor Inlon celebrated milestones in 2024. Landini celebrated its 140th anniversary as a machinery manufacturer. It was 1884 when Giovanni Landini founded Officine Landini, a wine-making machinery factory in Fabbrico, Italy. The first tractor went into production in 1925.
Australian family business Inlon Pty Ltd recently celebrated its 40th anniversary. Established in 1984 by Joe and Lolita Jardim, Inlon first imported, assembled and distributed Universal Farmliner tractors from Romania. Forty years later, Inlon is a major importer and distributor of 15 brands of farm
seed sowing depth is set only once. If the sowing depth is subsequently changed, the fertiliser placement depth is automatically adjusted in relation to the seeding depth.
The Precea 9000 and 12000-TCC models offer 12 or 16 rows for row widths of 70, 75 and 80 cm. The Precea 6000-TCC is 8 rows, with 70, 75 and 80cm spacing.
machinery from across Europe, Korea, India and Japan.
The Landini Powerfarm II 120RPS 4WD Cab with integrated level lift loader with quick detach, Euro hitch, soft ride, 3rd function, independent loader valve and joystick plus a 2,000mm 4-in-1 bucket is $138,446 including GST from Inlon dealers, with finance from 1.99% (offer ends 31st December 2024) .
See website for details.
A telescopic axle is available for the running gear of the Precea. During field operation, this allows the position of over-sized tyres to be adjusted so that the wheels run between the seed rows, preventing compaction directly beneath the seed rows. With the wheels fully retracted, the Precea-TCC can be conveniently transported by road with an overall width of 3m.
GROWERS KEEN TO UPGRADE TO THE LATEST IN SPRAYING SYSTEM TECHNOLOGIES AND MACHINE DATA CONTROL COULD SAVE THEMSELVES TENS OF THOUSANDS OF DOLLARS BY TAKING A LOOK AT THIS OPTION OVER THE NEXT TWO MONTHS.
McIntosh Distribution, national distributor of the Miller sprayer line-up, recently announced a 3.5 per cent finance offer with the popular front-mounted machines, including the manufacturer’s latest Intelligence models. However, grower orders must be received by December 31, 2024.
The new Miller Intelligence sprayers feature Sidewinder Ultra consoles, larger screens and updated cabs that come with greater comfort, numerous luxury appointments and improved, 270-degree panoramic visibility.
The consoles also have introduced advanced telematics, raising spraying application and machine data control and transfer to industry-leading levels, and which, critically, seamlessly integrate with all major data management systems available, including New Holland, Case IH, John Deere and other data platforms.
Peter Vella, National Miller Sales Manager with McIntosh Distribution, said the special finance offer required a 30pc deposit on new machines and provided for the interest rate of approximately 3.5pc over four years. However, he said depending upon the trade-in of existing grower sprayers, the low interest rate could become significantly more attractive.
Peter said the finance offer already had generated strong interest in recent weeks, with machine sales recorded in Western Australia, South Australia and New South Wales.
“Growers have moved quickly and, as a result, are saving thousands of dollars,” Peter said.
“We still have good stocks of sprayers currently available, but growers looking to upgrade should lock-in their orders by the end of this year to grab the attractive finance offer and ensure timely delivery of their new machine, ready for summer spraying.”
Ongoing demonstrations of the Miller Intelligence sprayers with growers right across the country is contributing to the healthy interest in the machines.
In WA, two 7380 Miller Intelligence models have been applying growers’ crop protection products in the northern and southern agricultural zones. They feature 6000 L and 8000L tank capacities and both have been equipped with 36-metre truss booms, Bil-
berry weed identification systems and Miller Intellispray II pulse width modulation (PWM) nozzle control systems.
The Bilberry systems have been demonstrating green-on-green (GoG) and greenon-brown (GoB) spot spraying at Mullewa, as well as GoG spraying in the Merredin, Katanning, Lake King and Esperance areas.
“Growers have been putting their chemical through the machines in personal, on-farm demonstrations and have seen the hit rate and effectiveness. They have seen what the Bilberry has treated and the results seven days later,” Peter said.
The latest Bilberry Intelligent Spot Spraying System, which is available on the Miller truss booms up to 41.5m and the 48m Pommier boom, incorporates generation III architecture, featuring less componentry, and it fully integrates with Miller’s electronics.
“Previously, there was one computation module per camera, whereas now there is only one for every four cameras, so across a 36m boom there are only three modules for 12 cameras,” Peter said.
The Miller Intellispray II nozzle system is the next generation of PWM control that can run at user-defined hertz rates of 10, 15 and up to 20 hertz, whereas Intellispray I ran at 10 hertz.
“The latest system helps to maintain consistent spray application at wider speed variations. By not requiring as much power, it allows the PWM to be set at 25-centimetre spacings on booms of up to 48m. On the larger boom, that’s individual nozzle control via 193 nozzles, compared with 92 nozzles set at 50cm spacings with Intellispray I,” Peter said.
“It provides greater consistency at higher speeds and it allows higher resolution with spot spraying. At 25cm resolution, but with
side safety engaged, you are at 75cm resolution, versus 1.5 metres, so it further reduces chemical usage whilst maintaining ultimate coverage.”
The 7380 Miller Intelligence model with 6000L tank, 36m truss boom and Intellispray II nozzle control system is being demonstrated in SA and Victoria, while a 7420 Miller Intelligence model with 8000L tank and 48m Pommier boom in NSW is demonstrating the easy integration of third party data management systems, particularly the John Deere and Topcon platforms.
“It is working with a John Deere G5 screen, MTG modem device and Starfire receiver, allowing seamless transfer of spray and machine data to the John Deere Operations Centre,” Peter said.
He said a number of similar John Deere systems already were operating with Miller Intelligence machines in the field for growers, including three in the Geraldton area.
A smaller 7310 Miller Intelligence sprayer with 4500L tank is being demonstrated to growers in the Griffith area of NSW.
Peter said growers continue to be impressed with the ease of use of the Miller Intelligence sprayers despite their sophisticated technologies, as well as the access to data and machine analytics, such as fuel consumption, and receival of alerts, which can help them better support operators.
“Better data can help growers to do budgets with greater accuracy, like with fuel costs.”
Fuel economy in the latest Miller Intelligence sprayers has improved by several litres per hour compared with the previous 6000 Series machines, and by more than 50pc compared with earlier ranges.
Peter said the latest data control and transfer capability was assisting dealers to check
IN EARLIER TIMES IT USED TO BE LOOKING TO THE SKIES, BUT GROWERS HAVE SINCE LOOKED INTO THE GROUND, PARTICULARLY AT THEIR SOIL HEALTH, TO HELP MAXIMISE THE POTENTIAL OF GOOD SEASONS AND MINIMISE LOSSES IN POOR PERFORMING YEARS, AND FOR WESTERN AUSTRALIAN TILLAGE CONTRACTOR JOHN DAVIS THIS HAS MEANT PLENTY OF TIME ON THE ROAD.
Based from York, John operates Total Tillage Contracting and Hire and has been assisting growers across the WA wheatbelt with soil amelioration work.
The business’ tillage equipment fleet includes a spader, speed tiller and delver, while he has recently upgraded from a chisel plough style machine to a Gregoire Besson ‘Discordon One-Pass Finisher’, which comprises two rows each of independent tines and notched or smooth discs, plus a following packer.
Compared with the chisel plough, he said the disc machine was more versatile and provided a better soil bed finish leading into seeding programs.
“As a result, we can rip more soils with the machine and it doesn’t leave a mess – ever, John said.
“A spader is probably the best machine on the market for soil amelioration, but they are way too fussy. They can’t handle rocks and stumps.
“On most farms, about 70-80 per cent of the land would be suitable for amelioration, but only 10pc could be handled with the spader –unless you are on sandplain country.
“The Discordon can go just about anywhere and on all soil types.”
He said Gregoire Besson was renowned for manufacturing some of the industry’s best ploughs, and particularly for its mouldboard plough.
The Discordon One-Pass Finisher features a parallelogram setup, and, compared with other similar machines, the tine and disc frames are completely independent, allowing the disc and tine depths to be adjusted separately – and also on-the-go with the packing pressure.
machine fault codes prior to service visits, which was helping reduce downtime and, hence, further pleasing growers.
Growers interested in arranging a Miller
THE GREGOIRE BESSON DISCORDON ONE-PASS FINISHER, WHICH COMPRISES TWO ROWS EACH OF INDEPENDENT TINES AND NOTCHED OR SMOOTH DISCS, PLUS A FOLLOWING PACKER, CAN GO JUST ABOUT ANYWHERE, ON ALL SOIL TYPES, ACCORDING TO WESTERN AUSTRALIAN WHEATBELT CONTRACTOR JOHN DAVIS. JOHN SAYS COMPARED TO HIS PREVIOUS CHISEL PLOUGH STYLE MACHINE, IT ALSO LEAVES A BETTER SOIL BED LEADING INTO SEEDING PROGRAMS.
The tines dig to a depth of about 450 mm and the discs to about 230mm, while the disc gang angle can be adjusted for a more aggressive cut. This allows the Discordon to carry out shallow stubble ploughing through to deeper subsoiling, as well as mulching, decompacting and reconsolidating all in the one pass.
John said one of the best attributes of the Gregoire Besson Discordon was the fact the ripper tines could be lifted independently of the rest of the machine.
“We run the discs at full depth all the time, and with full pressure on the packer all the time, and we rip as deep as the conditions, or tractor, allows.
“We have a crumble packer with the machine, which has also performed way better than we thought it would.
“The job the Discordon has done has been most impressive and we have had great support from (Australian distributor) Waringa Distribution.
“Due to it performing so well, we’ve probably deep ripped at times when you shouldn’t. We started mid-January this year and didn’t stop – and for about three weeks we did night shift only because it was so hot.”
John’s 6.2-metre Discordon One-Pass Finisher, which folds to less than 3m in width, has worked in medium to heavy country in the eastern wheatbelt through to sandy soils
Intelligence demonstration, including GoB spot spraying over summer, as well as in the latest finance offer on the machines, can contact their local dealer. For further infor-
near Dandaragan, covering about 5000 hectares in just over a 12-month period at a travelling speed of around 8 kilometres per hour.
He said most of the soil types were non-wetting, including forest gravels and sands, and almost all involved lime incorporation as well.
“You need to fix these soils from the top down. Mixing fixes the top, you can bury the non-wetting sand and incorporate the lime.
“The more you mix, the better it is and the longer it lasts before looking to do it again. I would rather rip and mix to a depth of 300mm than straight rip to 600mm, and the mixing with the discs is ideal with this machine.”
John said grower feedback from works completed by the Gregoire Besson Discordon had been outstanding, largely because it produced a “tidy finish”.
“Out of the 5000ha, we have only had one complaint that it was a little rough, but most of our customers are return customers.
“With land so expensive now, soil improvement is becoming important to do and can significantly increase your land value. Rather than considering buying more land, it can be a better move to fix what you have got.
“Bringing poor areas back to good production provides a huge benefit and improves your property value per arable acre,” he said.
mation on the new Miller range and various application systems available with the sprayers, growers also can visit millersprayers.com.au.
MARCREST’S BALE BARON HAS HELPED A SOUTH AUSTRALIAN HAY GROWER TO INCREASE TO BE EFFICIENT AND STAY PROFITABLE.
Hay grower James Stacey from Langhorne Creek in South Australia relies on Marcrest’s Bale Baron to remain profitable and optimise operations.
James grows lucerne, rye grass and hay grain across two farms that span 800 hectares.
He supplies mostly to the racing industry and horse lovers in the region.
James says Marcrest’s Bale Baron helped him, wife Rachael and sons Zac and Ashton increase their production from 5000 small square bales to about 50,000 bales this year.
James has been a hay contractor for 25 years, doing mostly large round bales. But after doing a Nuffield Scholarship on the impact of urban growth on agriculture he realised he had to capitalise on his location, living just 65km from Adelaide.
In 2016, James bought a small square baler and a 10 bale accumulator, and started off producing some lucerne and rye grass hay, producing 4,000 bales in his first year.
It was in 2018 that he completed the Nuffield scholarship and then bought his first Bale Baron in 2019, and ramped up production.
He ran his first 4250T Bale Baron in line between a 1840 Massey Ferguson Baler, and hasn’t looked back since, upgrading to a 5250P Bale Baron this season.
“We've got two small square balers operating so we can cover a lot of country quicker. The Bale Baron allowed us to grow. Bale
Baron makes it easy to handle, especially truck loading.”
“That gives you peace of mind that you're not sending people out who don't have a load that's terribly secure.”
According to Marcrest, there are two unique Bale Baron models. The pickup model Bale Baron 5250P is tractor-assisted and well-suited for larger acreage and will keep up to two to three balers, with full control of the baling operation accessed from the comfort of the cab.
The trail-behind model, Bale Baron 5250T, is also tractor-assisted and is towed directly behind the baler, making it an ideal option for smaller acreages.
It uses an articulated chute to guide bales directly off the existing baler and is powered by either the remote hydraulics on the tractor or the optional power unit.
James says Bale Barons are built tough.
They don't have many wearing parts, and except for one incident over years of using Bale Baron where a seal broke, they have been reliable every day. James also runs a Marcrest single bale grapple to load bales.
James sources his baling equipment from G & J East in Strathalbyn, which is home to the latest farm machinery from the best brands in the industry.
His location close to G & J East means he is near if a service is needed or he needs parts.
G & J East Strathalbyn is the Australian distributor for Mar-
crest Manufacturing products, which hail from Ontario, Canada.
Marcrest Manufacturing President, Mark Horst says he always tells people that, “necessity is the mother of invention”.
“That’s why I invented a system that changes small bale handling to eliminate backbreaking work and allow you to work your fields more quickly and efficiently. Marcrest offers the ultimate alternative to existing bale wagons, thrower wagons and accumulators.”
At the heart of Marcrest is a dedicated family and team of employees that has found the most effective way for farmers to transport hay bales off their fields and into the marketplace.
“More and more hay producers each year are realising that the full line of Marcrest equipment gives them the edge they need in today’s tough economy. Like so many of our satisfied customers, I truly believe our bale handling equipment will meet your demanding expectations.”
Marcrest Product Manager in Australia Philip Wigzell says G & J East has a fully serviced workshop and parts department with factory-trained technicians able to handle all manner of repairs and maintenance.
James has worked with other manufacturers’ hay equipment but says in terms of logistics and handling, the Bale Baron is far superior.
Especially when he was operating on his own, before his sons joined the operation, the Bale Baron was a logical solution, with the ability to make a 21 bale pack, cutting out other pieces of equipment and requiring less manpower
With an accumulator, for example, it might take a fair portion of the day to move the hay off a center pivot.
However, with a Bale Baron it takes two or three hours to move 2000 or 3000 bales of hay.
The fact that it tightly bundles
packs means you are more confident when you're loading for customers, and packs are easy to tie down on trailers.
Word from Marcrest in Canada is that small-square bales are among the most in-demand form of bale used across North America and beyond by equine, specialty, and general livestock producers for everyday feeding and bedding.
“Those same bales are also the most expensive and labour-intensive to produce. At least that was the case before the arrival of the Bale Baron, which removes all manual handling and additional labour costs, and saves time.”
Anyone who has ever handled a small-square bale understands the benefit of this more manageable size as it is far easier to handle.
Additionally, the Bale Baron functions to create remarkable efficiencies in packaging, transporting, and storing by bundling up to 21 small bales. A full row consists of three bales that will build a pack of 21, 18, or nine bales in total.
Then, once the injector positions the final bale in place, the Bale Baron compresses and ties the pack together with twine, using a Rasspe Knotter.
As the next bundle is formed, the pack is pushed out of the chamber, rolls down the ramp and is gently placed on the ground.
This process means bales can be easily stacked for transportation from the field and efficiently stored and organized in the barn.
This design also allows for the bales to be loaded directly into a semi-truck or van trailer for immediate delivery.
This inventive system effectively eliminates the backbreaking work and gets the commodity into the marketplace quicker and easier, which has never been more important than in today’s tough economy.
A BOBCAT TELEHANDLER HAS JUST PROVEN IT CAN GET THE JOB DONE AT A WESTERN AUSTRALIAN TRANSPORT COMPANY WHERE NO PIECE OF EQUIPMENT LIES IDLE.
The Bobcat TL43.80HF Telehandler, has fast become a trusted piece of kit in SimRon Transport’s bulk grain and hay cartage operations, says co-owner Andrew Sims.
Based in the Wheatbelt town of Narrogin, SimRon Transport specialises in hay and straw cartage and storage as the main leg of their business, but also cart bulk grain, lime and fertiliser, sheep and cattle as well as general haulage, wool and oversize machinery.
In 2007, Rhonda and her late husband Brad began the business with one truck and added a truck per year until they had 10 trucks.
Rhonda and Brad’s eldest son Andrew, who was five days old when he took his first ride in a truck, and Brad’s stepson Braiden, are now running the business with Rhonda.
Youngest son and brother Blade runs sheep on the side and grows hay and cereal crops.
Besides Andrew, the drivers at SimRon also give the Bobcat TL43.80HF the thumbs up.
For example, the day Agrimedia spoke to Andrew, it was 38°C outside, but no-one operating the Bobcat TL43.80HF had complained of the heat, because its aircon system is so efficient. Plus, it’s got a fridge inside to keep water bottles cold.
“That was a good idea,” Andrew says.
In temperature extremes it's not only the driver that needs to be cool, but a cool engine is a must. Andrew says the way the radiator is designed, sitting on top of the engine, helps it stay cool.
“The fact that it doesn't overheat, that's significant, it’s anywhere from 30°C to 40°C degrees on a Narrogin summer's day.”
The Bobcat performs in heat, even on days when it has a massive workload.
“We don’t muck around when we load and unload because we have to get product into sheds as fast as we can”.
Andrew says operating in a warm and dusty environment means he often has to blow out radiators that block up but, unlike other makes he has used, the Bobcat’s system only needs a clean every few days. The manufacturer says this is because the Bobcat TL43.80HF self-cleans the cooling system thanks to an automatic reverse fan that kicks in with the flick of a switch.
Rhonda says Brad had a vision of creating a stable income for the trucks and as a result they built two hay sheds, and lease three, where they store and cart hay from. They also stack hay for clients who have their own sheds.
Rhonda says they are all full by December. Then they have about 18 sheds to empty by the following September, before it starts all over again.
That means the Bobcat TL43.80HF is part of an operation that handles almost 100,000 bales of hay in any given year, and as such does not have easy days at SimRon.
According to the manufacturer, precise work at heights can be done with surgical precision, thanks to the incredibly smooth transmission, a Boom Position-
THE BOBCAT TL43.80HF TELEHANDLER IS PUT THROUGH ITS PACES AT SIMRON TRANSPORT.
ing System, an updated joystick, an inching function, and great visibility from the cab.
The Bobcat TL43.80HF handle heavy loads at any height easily and safely, thanks to the low center of gravity, heavy counterweight, and a long wheelbase.
Andrew says a wide field of vision is where the Bobcat TL43.80HF’s design excels.
“I like the vision you get from the full windscreen as you're sitting back in the seat looking up. Because we stack 10 high and the Bobcat TL43.80HF is fully extended getting to the top. The windows go all around there is nothing obstructing your view in the back”.
The 7,505mm lift height and the 4,300kg lift capacity also comes into play here. The cab is also roomy.
“I'm not a short bloke, and I've got plenty of room in there. It's comfortable to sit in for long periods of time.”
Rhonda says a Clarke Equipment salesman helped them buy a TL43.80 last year.
“The salesman was very knowledgeable and helpful and knew if we purchased a machine, there was only a short delivery window with the hay season on the verge of starting.
“Clarke Equipment promised and delivered the machine within two weeks and also offered the option of finance if required. Rates starting at 0% to 3.49% on offer at that time.”
Clarke Equipment has been very easy and uncomplicated to deal with, she says.
Andrew says the Bobcat TL43.80HF has a future with them.
“At the end of the day, we will buy another one, and that's a fact.”
IT’S APTLY CALLED THE HIVE, WITH GRAIN HARVEST CHASER BIN DRIVERS FEEDING INTO IT AND TRUCKING OPERATORS FEEDING OUT OF IT, AND FOR WESTERN AUSTRALIAN GROWER BRAD JONES, IT HAS REMOVED ALL BOTTLENECKS AND MADE HARVESTING, STORAGE AND TRANSPORTING OF GRAIN TO END-USERS SO MUCH MORE EFFICIENT, FAST AND ACCURATE.
“This harvest, we have one truck servicing our on-farm silos and two trucks servicing markets in Perth twice a day. Last year the trucks were doing one trip a day to Perth and we were mucking around with bulkheads and chucking grain on the ground and tarping it, which is a big job,” said Brad, who farms with his wife, Kate, and their family at Tammin.
“If we had three trucks going into CBH we would probably be held up.”
The portable, 225-tonne Elmer’s HIVE Motherbin, which also is available in 150t capacity, has more than doubled the Jones’ in-field grain storage to in excess of 300t.
“It is much quicker and easier because there are no bottlenecks anywhere in the chain. With a bin of this size, 50t only looks like a drop in the bottom of it too,” Brad said.
“Recently we loaded two road trains with 136t and it took 15
minutes from the truck tarps coming off, going back on and then getting out the gate.
“We also had a storm recently and the trucks were not back from Perth and there were fires on a neighbour’s place, but we had the capacity during the day to push for an extra 20 minutes so the trucks could come in and then load and go.”
Together with national equipment distributor, Waringa Distribution, the Jones’ assisted the development of the Elmer’s HIVE Motherbin, which has been introduced into Australia for this harvest.
The family’s 225t bin features two tank compartments; easyto-access cleanout gates at the end of each tank; weigh scales; Elmer’s HM Connect and Pro data management system for tracking weights and loads; electronic tarps; and 55-centimetre discharge augers with semi-automated fold and movement controls, as well as four-
KELLY GOOSSEN, ELMER’S BUSINESS DEVELOPMENT MANAGER, SAM ABBOTT, WARINGA DISTRIBUTION GENERAL MANAGER, WA GROWER BRAD JONES, TAMMIN, AND BEN JOHNSON, ELMER’S SALES MANAGER, WITH THE 225-TONNE HIVE MOTHERBIN DURING HARVEST AT THE JONES FAMILY’S PROPERTY.
THE 225-TONNE ELMER’S HIVE MOTHERBIN HAS MORE THAN DOUBLED THE JONES FAMILY’S IN-FIELD GRAIN STORAGE AT TAMMIN IN WA, ALLOWING MULTIPLE LOADING AND OUTLOADING AND REMOVING ALL BOTTLENECKS IN THE HARVEST, STORAGE AND TRANSPORTING PROCESS.
way spout control.
“At the click of a button, the spout can move laterally and vertically, so you can tilt it to fill trucks exactly where you want it to go. Then a double click puts it back into fold configuration,” Brad said.
“The beauty with the HIVE is we recently had a fair wedge of barley to come off and we were switching to wheat, but we were able to work into the evening and fill a load to go to Perth, with everything weighed and measured, and then it was cleaned and ready to go onto the wheat. Previously we would have just been guessing.”
He said the Elmer’s HIVE Motherbin allowed significantly more control of grain logistics, with the ability to use the in-field storage and have less concerns over on-farm storage.
“From the headers to the chaser bins, to the HIVE with the HM Connect and Pro, and into the trucks that also have scales, everything is measured and cross-checked quickly and easily. Communication with the truck drivers is also easy because we know what’s in the Motherbin.
“We know what and where everything is, including what has been taken from the Moth-
erbin into on-farm storage. We recently finished loading into a silo and the operator was able to quickly say there was 1350t in the on-farm silo.
“We also recently changed paddocks and a truck driver was wanting another 16t and we were able to arrange it quickly.”
Brad said side and end windows on the Elmer’s HIVE Motherbin were a handy feature, providing another good reference of the grain levels “as you drive past”.
Brad and Kate run the Bungulla Farming enterprise at Tammin. They also have four children, Zoe, Alex, Sam and Nina.
They grow wheat, barley, canola and lupins for domestic and export container markets, while significant grain is marketed from their 10,000t on-farm storage holding.
The crops are harvested with three John Deere headers and, in addition to the HIVE Motherbin, they also use two (36t and 41t) Elmer’s Haulmaster chaser bins as well as an Agri-Spread spreader sourced from the Waringa Distribution product line-up.
Brad said the ongoing support and backup for their equipment fleet from the Waringa Distribution team had been exceptional.
You deserve technology that’s both compatible with your existing fleet and easy to use. That’s why PTx Trimble leads the way in engineering solutions – including displays, steering systems and guidance control – that allow you to connect your farm, your way for seamless work all season long.
This farmer uses: GFX-1060™ display with Precision-IQ™, Autopilot ® steering system, NAV-900 guidance controller, and Trimble ® CenterPoint ® RTX correction service. Scan to learn more and contact a local dealer.