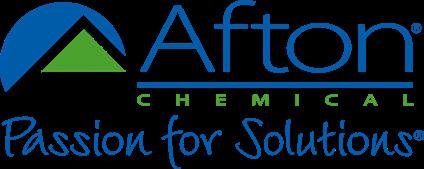

February 2024
Charlotte Edwards, Industrial Marketing Specialist, Afton Chemical
Hayley Hammond, Industrial Customer Technical Services Specialist, Afton Chemical
With heightened lithium demand and price volatility, many grease producers are diversifying their technology portfolio to include calcium sulfonate greases. Afton’s latest solution provides manufacturers with greater flexibility, while addressing traditional safety handling risks and retaining performance.
Afton’s improved patented process speeds up calcium sulfonate grease production. In addition to requiring less thickener, it now also utilizes a promoter with improved health and safety handling. This ultimately gives grease manufacturers control over their own production and reassurance on safety.
Thanks to a buoyant battery electric vehicle market, the heightened demand for lithium shows little sign of slowing down. In response to this, lithium prices have become more volatile, prompting grease manufacturers to consider calcium as an alternative option. The longer-term stability in supply of calcium has made a calcium sulfonate grease approach more attractive and it offers improved performance. Therefore, manufacturers are looking to pivot in response.
Calcium sulfonate has long-been considered the performance champion with its high shock load protection, good structural strength, seal protection and water washout resistance. In response, Afton Chemical created a patented-process that enables manufacturers to make a high-performing complex
Lithium
Lithium-calcium mix
Calcium
Lithium / polymer mix
Calcium sulfonate complex
grease from its 300TBN calcium sulfonate grease. This innovative method delivers both time and cost savings, which manufacturers could take advantage of without having to invest in production upgrades. As well as being faster, this process also uses less thickener, which results in both financial and performance benefits. Previous field trials have shown this new calcium sulfonate grease is effective in demanding automotive and commercial vehicle applications, such as wheel bearings.
However, the promoter used in this patented grease process, isopropyl alcohol, has multiple safety classifications - such as flammable liquid - due to its very low flashpoint of 13 degrees Celsius.
Isopropyl alcohol may be a relatively common component for sites that already produce calcium sulfonate complex greases. However, for lithium grease plants expanding their product range to include calcium alternatives, they may not be as comfortable working with this promoter. Investment in new equipment may even be required to help with handling it.
Considering the difficulties in handling, Afton worked to identify a replacement promoter with a higher flashpoint and lower safety restrictions, recognizing that any substitute would not increase the formulation costs, nor detract from the finished grease’s performance.
• Proven technology for decades
• Cost / value balance
• Lower cost (less lithium)
• Lower cost
• Good water tolerance
• Good structural strength
• Lower cost
• Very high dropping point
• Excellent shock load protection
• Good thermal stability, good for many applications
• Seal protection
• Pricing volatility
• Safety concerns
• Inconsistent quality (dropping point), limits application suitability
• Low dropping point, limits application suitability
• Lower pumpability
• Low pumpability (central lubrication)
• Higher soap content: more suited to high load, low speed applications
path forward to improve handling?
Afton identified potential alternative promoters, based on those already commonly used in grease manufacturing. Screenings were conducted based on their flashpoint and safety classifications. A team of Afton chemists examined the impact of each promoter’s molecular shape, polarity and other key characteristics to evaluate the potential impact on the manufacturing process to create a shortlist of final candidates.
In partnership with a grease manufacturer, Afton used small batch production to tweak the process with a new promoter, ensuring formulation costs did not escalate, and the production yield was maintained. Once both the promoter and process were optimized, production was scaled up and the resulting grease checked for quality, aesthetics and performance.
The new promoter exhibits a transparency and brightness similar to that of isopropyl alcohol, using Afton’s calcium sulfonate grease.
After this process was completed, other benefits were realized; the speed, yield and cost savings of production with the new promoter were retained - with only 0.5% of the new promoter being required - but the same superior performance was achieved.
What began as a business continuity exercise to help manufacturers add calcium sulfonate complex grease to their portfolio instead of lithium or lithium complex greases, has ultimately resulted in a solution with health and safety benefits and added value whilst delivering both price and performance benefits.
For more information, contact your Afton Chemical Representative.