CATALOGUE 2022
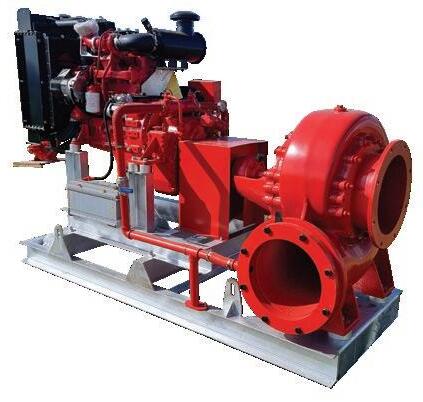
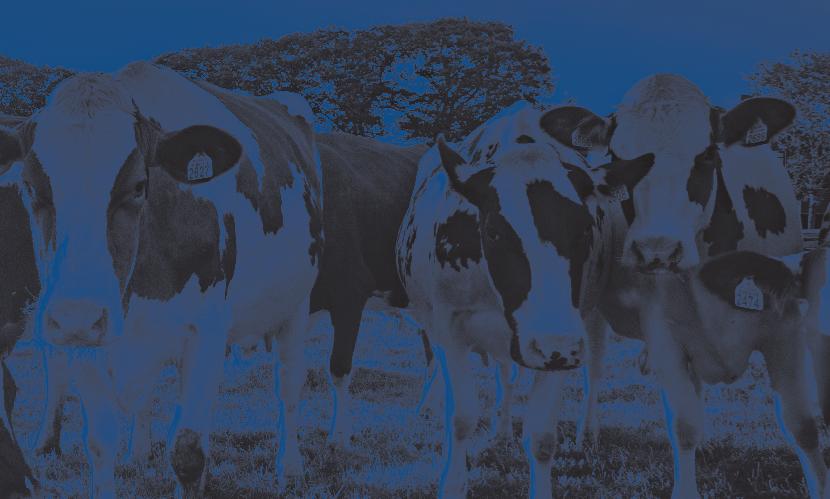
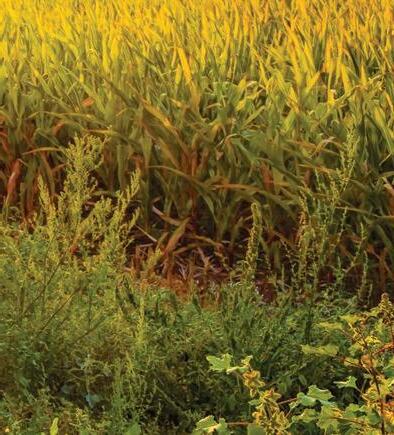
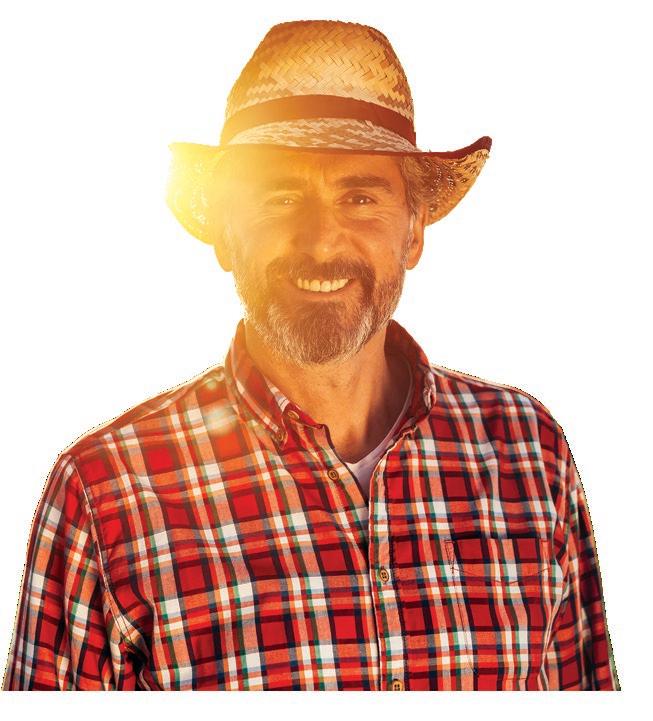
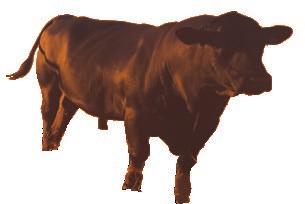
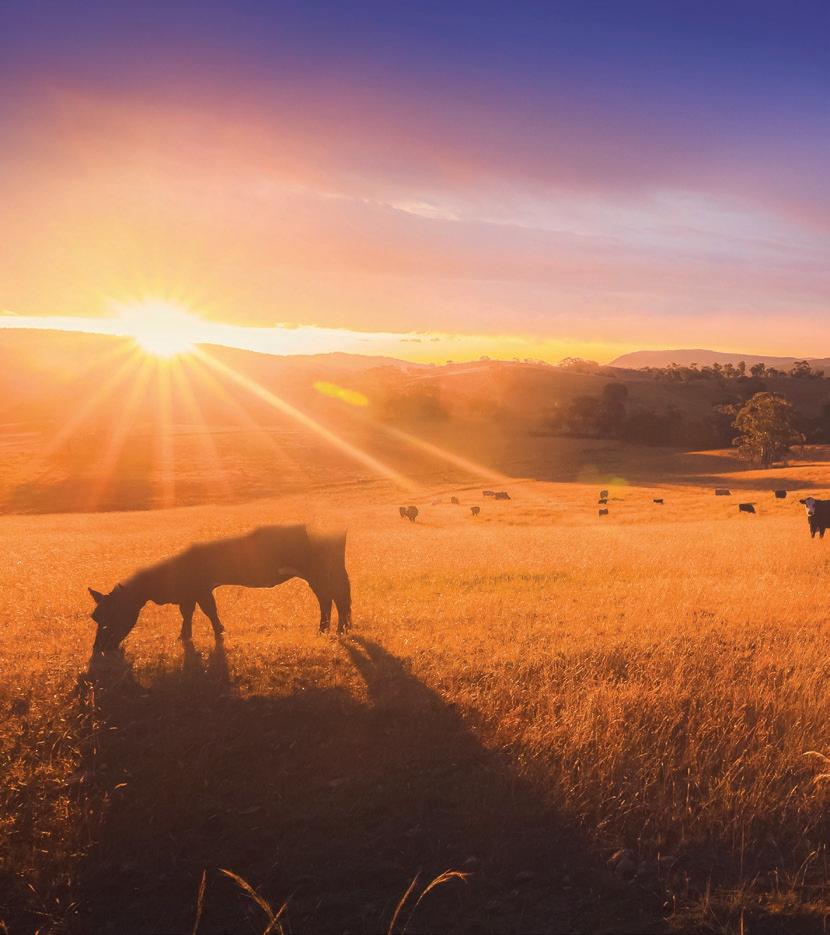
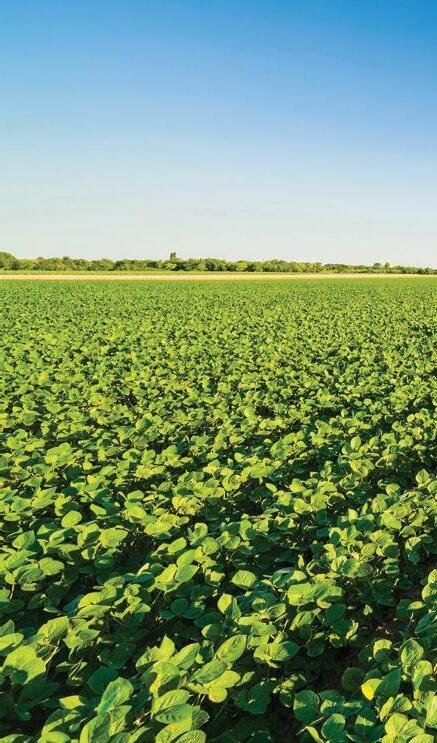
RELIABLE OPERATION
HWG Type Mixed Flow Pumps are horizontal, single stage, single suction volute mixed-flow pumps.
These pumps are designed to convey clear water or any other kind of liquid with similar physical and chemical properties of water, consequently they are largely used in the Agricultural, Aquacultural, Industrial and Municipal industries for drainage or lifting applications in low head situations as they can move a relatively large amount of water efficiently in these applications.
HIGH EFFICIENCY
HIGH FLOW RATES
BENEFITS OF MIXED FLOW PUMPS:
Simple construction
High flow rates in low head applications
Large variation of flowrate for supplying multiple duties in one application
Small size and light weight
Ease of maintenance and repair
Pump Casing Cast Iron
304 & 316 Stainless Steel, Duplex Stainless Steel & Super Duplex Stainless Steel
Pump Shroud Cast Iron 304 & 316 Stainless Steel, Duplex Stainless Steel & Super Duplex Stainless Steel
Bearing Housing Cast Iron 304 & 316 Stainless Steel, Duplex Stainless Steel & Super Duplex Stainless Steel
Shaft 304 Stainless Steel 316 Stainless Steel, Duplex Stainless Steel & Super Duplex Stainless Steel, 4110 High Tensile Steel
Impeller Brass Cast Iron, 304 & 316 Stainless Steel, Duplex Stainless Steel & Super Duplex Stainless Steel
Impeller Nut Brass Cast Iron, 304 & 316 Stainless Steel, Duplex Stainless Steel & Super Duplex Stainless Steel
Seal Cover Cast Iron 304 & 316 Stainless Steel, Duplex Stainless Steel & Super Duplex Stainless Steel
Bearing End Caps Cast Iron 304 & 316 Stainless Steel, Duplex Stainless Steel & Super Duplex Stainless Steel
Our casting quality is completed to a high standard and quality checked, any components with risk of corrosion are painted in Marine Grade Paint for maximum corrosion protection.
Impeller and Nut is constructed in Brass for proven longevity and has superior wear and corrosion resistance.
Bearings are NSK Brand Single Row Radial Ball Bearings.
Shaft Seal is a Silicon Carbide / Viton / Carbon / 316 Stainless Steel Seal.
Pump Flanges cast with Extra Thickness added for better strength and come standard universally drilled in both Chinese Bolt Pattern (Table H) and AUS Standard Bolt Pattern (Table D) providing better flexibility whether you are installing a new system or replacing an old system, removing the need to modify existing pipework to suit either bolt pattern.
Our Sealing Method is a Silicon Carbide / Viton / Carbon / Stainless Steel mechanical seal which runs in its own enclosed sealed chamber which is lubricated by food grade white oil, this sealing method protects the pump in instances where it may run for extended durations of time without water “ran dry” without risking damage to the pump or seal. This innovative new sealing method is a superior sealing method due to the reliability and the little maintenance required, mechanical seals provide a 100% seal rather than the outdated gland packing method which constantly leaks or sucks air, mechanical seals are proven to increase longevity of the pump mainly by protecting the bearings from residual moisture which is a proven factor in premature bearing failure.
EXAMPLE MODEL NO: 300HWG-8A
Ambient Temperature: 50˚ C
Liquid Maximum Temerature : 50˚ C
Maximum Suction Lift: 6 Meters (Vertical)
Can be direct coupled
Direction of Rotation: Anti-Clockwise
Designed Tolerance Between Suction Shroud and Impeller Face: 3mm ± 2mm
Flange Bolt Pattern: Universal China (Table H) + Table D Drilled Flanges
Mechanical Seal Oil Bath: STELLA White Oil (ISO 15, 22, 32, 46 & 68)
PART NUMBER FORMAT:
(Pump Model)-(Series Number)P(Part Identification Number)(Material Code S = Standard Material)(Trim Impellers Only)
Example 1: 200HWG-8-P3-S Standard 304 Stainless Steel Shaft for a 200HWG-8 Mixed Flow Pump
Example 2: 300HWG-5-P13-304SS-A 304 Stainless Steel Impeller for a 300HWG-5 Mixed Flow Pump with A Level Trim (if ordering without Trim it would just be 300HWG-5-P13-304SS)
MATERIAL CODES: CI Cast Iron B Brass 304SS 304 Grade Stainless Steel 316SS 316 grade Stainless Steel
2205DSS 2205 Duplex Stainless Steel
All prices exclude GST and are list prices without any dealer discounts applied.
ORDERING DETAILS ARE AS BELOW:
(Model)-(Impeller Material B is Standard, 304SS is 304 Stainless Steel) (-WC if with Weed Chopper)-(Trim)
Example 1: 250HWG-5-B-WC
250HWG-5 with Brass Impeller and Weed Chopper no Trim
Example 2: 300HWG-5-304SS-WC
300HWG-5 with 304SS Impeller and Weed Chopper
Example 3: 350HWG-8-B-A
350HWG-8 with Brass Impeller, No Weed Chopper and an A level trim
These pumps can be installed underground, semi-underground or above-ground.
1 High water level should not be higher than the lowest part of the bearings.
2 Low water level should be considered so that the low water level will not exceed the pump maximum suction lift for the duty required.
3 The pump must be located as close to the water source as possible to ensure efficient performance.
4 The pump inlet and outlet manifold should be designed in such a way it is as short and straight as possible with minimal reduction in size.
5 When designing or assessing existing pump suction size, the water velocity should be calculated and checked to minimise the risk of cavitation, maximum allowable velocity of the pumped fluid entering the pump is 1.8m a second, however the recommended velocity is 1.2-1.3 Meters a second.
6 Mixed flow pumps are not self-priming, when a suction is being designed either a foot valve, full-flow swing type check valve or priming system (eg. vacuum pump or firefighter pump) should be utilised.
7 Pump suction should always have some type of strainer installed, in any case to ensure foreign objects larger than 50mm in size cannot enter the pump.
8 Pumps can be mounted in any orientation, however if deviating from standard orientation make sure to consider mechanical seal bath filling point will need to be moved into correct orientation for both operation and ease of maintenance, and bearings in pump will likely have to be changed to sealed unserviceable bearings or new grease filling point on bearing housing will have to be drilled and plugged, old filling point will have to be permanently closed off to prevent leakage of grease.
9 Any reducers, bends or check valves should be installed at minimum 1m away from the suction inlet of the pump and the pipe leading into the pump should be the same size or larger leading straight into the pump to reduce turbulence of water entering the pump ensuring even velocity of fluid into the pump.
10 Pump flanges are not load bearing devices, any pipework should be adequately supported as to not be putting stress on the pump or flanges.
11 Pump should be fully mounted utilising all mounting points to frame using the correct size bolts which will be the largest size that will fit, bolts should be correctly fastened tight, and pump should be solid mounted to frame, not rubber mounted.
12 Eccentric reducers entering pump should be installed the correct orientation with the reduction on top of the pipework. See Australian Standards for more details.
13 It is recommended that the suction have a vacuum gauge installed on the suction to read suction head to help diagnose potential issues or monitor performance of pump.
14 It is recommended that the pump discharge manifold include a pressure gauge to suit the application, a priming point with ball valve and an extra 25mm thread for installation of pressure switch / flow switch either immediately or in future for added protection.
15 It is recommended that pump is direct coupled to the engine / motor not belt driven for best efficiency and performance.
16 Is it recommended that the coupling utilised be a PTO shaft or jaw coupling and to be aligned with use of a laser alignment tool by a qualified person to ensure maximum efficiency / life of the coupling and pump.
It is recommended that the pump be regularly serviced and operated throughout its lifetime.
PRE-OPERATIONAL CHECKS:
Check Bearing Grease Level
Check Mechanical Seal Oil Level
Check for any Leaks or Damage
Check Coupling
EVERY 500 HOURS OR EVERY 6 MONTHS, WHICHEVER OCCURS EARLIER:
Change Bearing Grease
Change Mechanical Seal Oil
NOTE: The pump should be serviced and operated when not being utilized for extended periods of time, in such periods where the pump is not being operated it is recommended that the pump be operated regularly to identify any potential issues early so it can be repaired or replaced ready to operate when it is needed, taking these extra steps will mitigate the risk of any losses or delays caused by the pump being inoperable/under performing.
• Pump is not primed correctly
• Leak in suction pipework or leaking pump seal
• Suction lift is too high
Pump is not discharging water
• Direction of pump rotation is incorrect
• The total dynamic head exceeds range of application
• Blockage / restriction in suction line
• Foreign object / blockage in impeller
• Insufficient water cover or vortexing over the suction pipe inlet / strainer causing air to enter suction line
• The suction line is not fully primed and contains trapped air
Pump operates normally for a short period then ceases discharging water.
• Leak in suction pipework
• Foreign object / blockage in impeller
• Ensure pump is primed correctly
• Inspect suction for leaks, inspect seal for leak, if nothing found pressure test pump and suction line
• Move pump closer to water source to decrease suction lift
• Change the direction of rotation
• Decrease the total head of the system
• Check pipework and impeller for foreign objects and remove
• Check motor / engine for issues
• Check rpm of pump and motor / engine is as designed
• Lower total dynamic head of the system
• Check gap between impeller face and pump shroud is correct
• Check pump isolation valve and checkvalves
• Move pump closer to water source
Pump stops suddenly when turning off engine/motor
• Impeller face is rubbing against the pump shroud face
• The pump shaft is bent
• Bearings have failed
• If belt driven the belts are too tight
• Check belts are not too tight
• Check bearings have not failed
• Check pump shaft not bent
• Check impeller is not rubbing against pump shroud and check impeller nut is tight
• Misalignment of coupling or belts
• The pump shaft is bent or the bearings have failed
• The mounting bolts are loose
• The impeller is blocked with a foreign object
• Cavitation due to the pump duty being outside of the designed performance parameters or suction lift being too high
• Impeller nut has come loose or off the shaft casing the impeller to be loose
• Foreign object in the pump
• Oil level in bearing housing is low or empty
• Misalignment of coupling or pulleys
• Overtightened belts
• Moisture / water in bearing housing
Pump seal is leaking
• Mechanical seal has failed
• Check alignment of belts and coupling
• Check mounting bolts are tight
• Check impeller is not blocked with foreign objects
• Check pump casing for foreign objects
• Check designed duty vs actual duty
• Check suction lift is too high
• If suction lift is too high move pump closer too water source
• Check oil level in bearing housing, if empty or low refill
• Check alignment of coupling or pulleys
• Check belt tension correct
• Check bearing housing for moisture or water
• Replace mechanical seal
Legend Diesel Stationary Engines have been in Australia for over 30 years, they are tried and tested engines that have been developed and designed in Australia to handle the harsh Australian conditions.
FEATURES OF LEGEND STATIONARY DIESEL ENGINES:
Mechanical Governor ensures reliable operation of engine with easy vernier type adjustment, E-Governor is also available by request.
SAE Standard Flywheel and Bellhousing ensures easy adaptation of engine to existing installations.
Comes standard with SmartGen electronic watchdog protection with unpluggable loom, extension looms are also available for remote mounting of electronic watchdog away from the engine
Simple design ensures reliability and ease of use
Spin on filters ensures ease of service and maintenance
Radiators come standard with Top & Bottom Stainless-Steel Tanks for corrosion protection
Engine is supplied on a heavy-duty hot dip galvanised base as standard
Engine comes standard with Stub Shaft bolted onto flywheel with flyheel guard for safety
Comes standard with Marine Grade Paint
All prices exclude GST and are list prices without any dealer discounts applied.
PRE-OPERATIONAL CHECKS:
Check engine oil level
Check coolant level
Check for any leaks or damage
Check belts for tightness and damage / excessive wear
EVERY 500 HOURS OR EVERY 6 MONTHS, WHICHEVER OCCURS EARLIER:
Change engine oil
Flush radiator and cooling system and refill coolant
Change oil, air and fuel filter
Check valve clearances
Change fan belts
Engine Oil: 15W40
Coolant: Green LLO
NOTE: The Engine should be serviced and operated when not being utilized for extended periods of time, in such periods where the engine is not being operated it is recommended that the pump be operated regularly to identify any potential issues early so it can be repaired or replaced ready to operate when it is needed, taking these extra steps will mitigate the risk of any losses or delays caused by the pump being inoperable / underperforming.
Our pumpsets are constructed on a heavy duty skid base, supplied with either a diesel engine, electric motor or pto drive, pto driven in cases of diesel engines with driveshaft guard, jaw coupling in cases of electric motors with coupling guard, watchdog protection is also available with automation or remote monitoring solutions.
PRODUCTS:
Mixed Flow Pumps
Self-Priming Pumps
Trailer Mounted Pumps
PTO Driven Pumps with 3 Point Linkage
ISO Spec Pressure Pump sets
Level Switch Start / Stop
Flow Switch Start / Stop
Clutch Kits
Marine Gearbox Reduction Drives
Belt Driven Pump sets
Belt Driven Generator Off Engine for Power Generation
Electronic Engine Protection or Mechanical Engine Protection
Auto – Prime Vacuum Priming Systems
Remote Monitoring and Control
Pumpset Supplied with a 150mm Mixed Flow Volute Pump direct coupled to a Legend 380 3 Cylinder Diesel Engine via PTO Shaft, with heavy duty forkable base, Coupling guard and Smartgen Electronic Engine Protection.
Pumpset Supplied with a 200mm Mixed Flow Volute Pump direct coupled to a Legend 480 4 Cylinder Diesel Engine via PTO Shaft, with heavy duty forkable base, Coupling guard and Smartgen Electronic Engine Protection.
All prices exclude GST and are list prices without any dealer discounts applied.
Pumpset Supplied with a 200mm Mixed Flow Volute Pump direct coupled to a Legend 490 4 Cylinder Diesel Engine via PTO Shaft, with heavy duty forkable base, Coupling guard and Smartgen Electronic Engine Protection.
Pumpset Supplied with a 250mm Mixed Flow Volute Pump direct coupled to a Legend 4102 4 Cylinder Diesel Engine via PTO Shaft, with heavy duty forkable base, Coupling guard and Smartgen Electronic Engine Protection.
All prices exclude GST and are list prices without any dealer discounts applied.
Pumpset Supplied with a 300mm Mixed Flow Volute Pump direct coupled to a Legend 4102 4 Cylinder Diesel Engine via PTO Shaft, with heavy duty forkable base, Coupling guard and Smartgen Electronic Engine Protection.
WP Pumps offer extended 24 Months Warranty on their Products as Standard. Once a product sold to the purchaser has been identified as faulty, WP Pumps should be notified as soon as possible in writing via email sent from the client to: warranty@wppumps.com.au
MINIMUM INFORMATION REQUIRED IN INITIAL EMAIL:
Model of pump
Proof of purchase
Serial number (if available)
Photos of installation before any dismantling of pipework or couplings
Pump and motor / engine
Pump in position
Mounting method and fastening bolts
Coupling (remove guard)
Water source
Suction pipework
Foot valve / check valve / strainer
Delivery pipework
Photos of removal
Any blockages / objects or particulates in impeller or suction line
Photos of suspected faulty part / damaged parts and disassembly of pump
Designed duty of pump
Suction lift of pump
RPM of pump
Coupling details
Suction size and length
If pump can be repaired or need complete replacement
If the new pump / repairs are required urgently
The above information will help WP Pumps process and assess your claim quickly and organise corrective actions promptly and ensure any costs / losses incurred by the affected parties can be compensated by WP Pumps, providing detailed information can also help WP Pumps to identify any potential issues with the installation and ensure that replacement / repairs are not going to result in the system failing in future due to incorrect selection or application of products.
Any labour compensation will not exceed the rate of $80+GST per hour.
WP Pumps strive to assess and rectify warranty claims in a timely manner.
WP Pumps reserve the right to send a representative to the installation site to assess the claim in person to ensure accurate information is provided.
WP Pumps are not liable for any damage or losses to crops or livestock.