
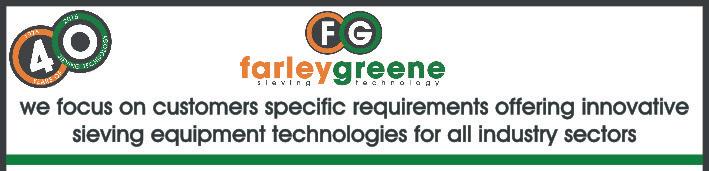
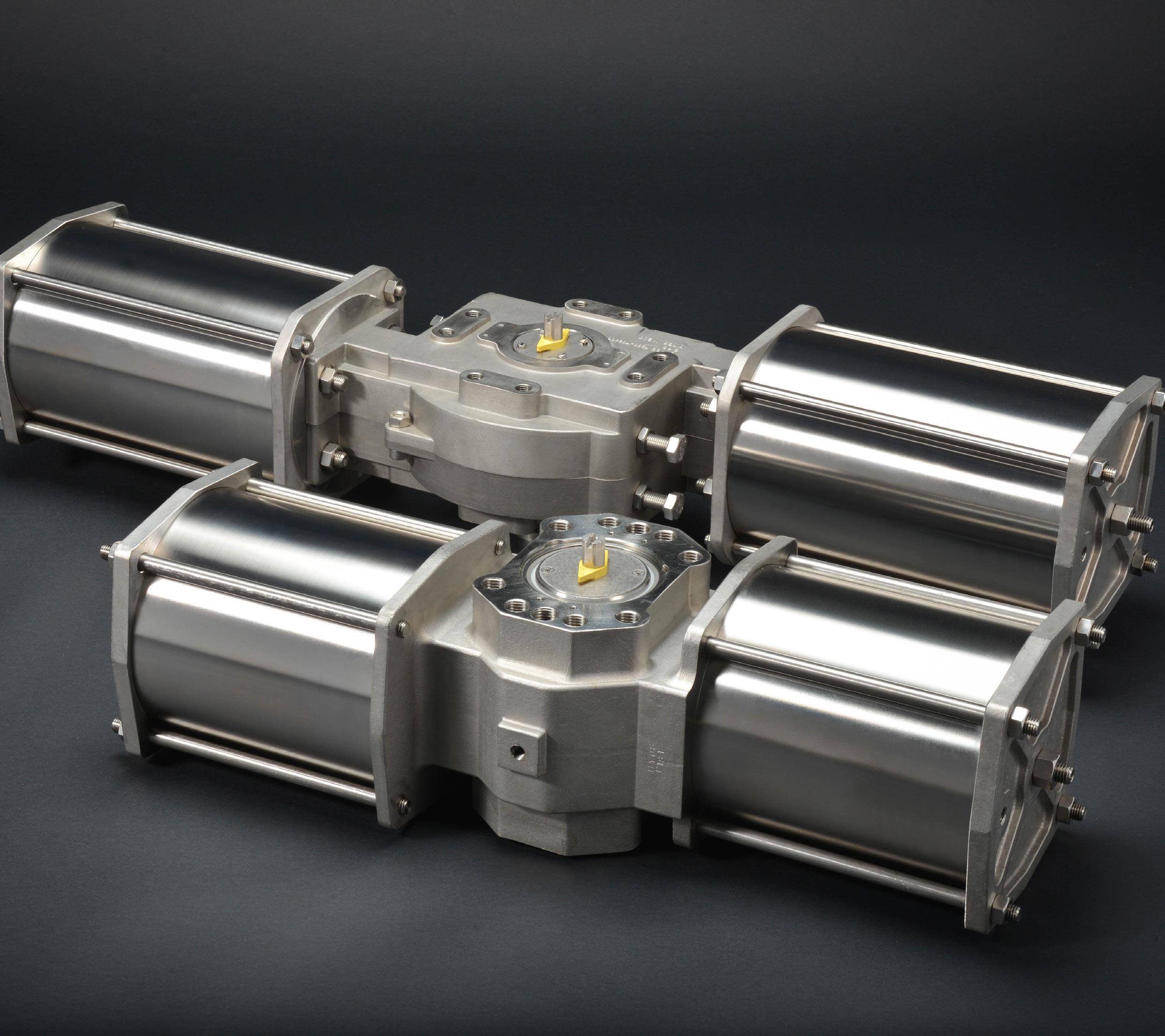
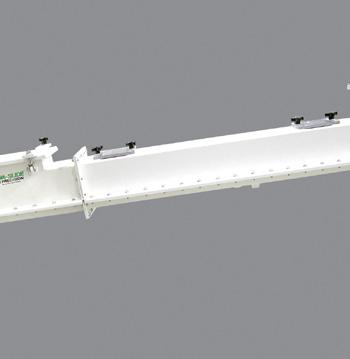
4
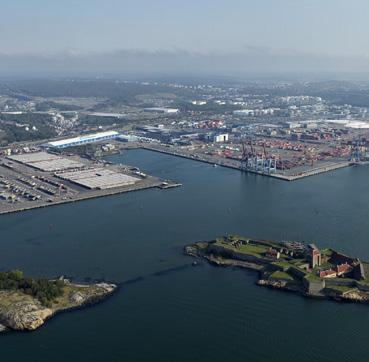
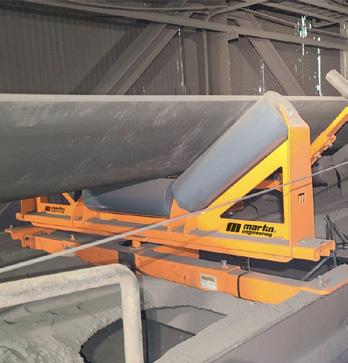
4
From micron sized powders to large pellets and everying in between, Dynamic Air can move your dry granular materials gently, reliably and with significant reductions in product degradation and/or system wear.
Dynamic Air dense phase pneumatic conveying systems have been proven in over 15,000 installations worldwide. They handle a wide range of materials and bulk densities at rates from less than a hundred kilograms per hour to 400 tonnes per hour, over distances exceeding 1500 metres.
Each Dynamic Air system is custom designed from one of our sixteen different conveying concepts. So you get a conveying solution that fits your process perfectly, without compromises.
Our high material-to-air ratios reduce energy and compressed air requirements. Our low conveying velocities provide significant process savings in both operation and maintenance.
Dynamic Air Ltd.
Milton Keynes, United Kingdom
+44 (0) 1908 622344 • sales@dynamicair.co.uk
www.dynamicair.com
Issue 166
Sales Director: James Scrivens
Production: Sarah Daviner
Accounts Manager: Avery Hudson
Office Manager: Katie Brehm
BULK SOLIDS TODAY is published 6 times a year by Abbey Publishing Ltd
ADVERTISING & EDITORIAL
Please contact us at:
Tel: 01933 316931
Email: editorial@bulksolidstoday.co.uk advertising@bulksolidstoday. co.uk
Web: www.bulksolidstoday.co.uk
Twitter: www.twitter.com/ BulkSolidsToday
CIRCULATION
To receive a copy free of charge, please send your details to subs@bulksolidstoday.co.uk
No part of this publication may be reproduced by any means without prior permission from the publishers. The publishers do not accept any responsibility for, or necessarily agree with, any views expressed in articles, letters or supplied advertisements.
ISSN: 1365/7119
All contents © Abbey Publishing Ltd 2017
When it comes to weighing and batching, choosing the proper dosing feeder is crucial to achieving a reliable and accurate system. Although scale accuracy is important, the accuracy of the feeder is even more important since the feeding needs to stop when the desired weight is
achieved. Because each material and application are unique, Dynamic Air offers a variety of feeders for weighing and batching, including screw feeders, air-activated feeders, vibratory feeders and more. Dynamic Air also offers complete custom designed weighing and batching systems.
https://www.dynamicair. com/products/dynaslidehp. html
info@dynamicair.com
www.dynamicair.com
Bulk Solids Today is the bi-monthly digital journal covering the storage, processing and handling of materials ranging from fine powders to the heaviest raw materials. To subscribe to Bulk Solids Today magazine or for more information, please feel free to visit www.bulksolidstoday.co.uk
Contract with Linde Material Handling UK (Ltd) is delivering health and safety innovation along with savings in operating costs and carbon emissions.
A novel way of integrating weighing scales into Linde Material Handling forklift trucks has brought health and safety benefits and greater efficiencies to Palletline’s Birmingham and London sites.
The contract for 78 upgraded forklifts, ten of which are electric, is saving Palletline more than £100,000 over five years, including a 25% cut in gas (LPG) consumption. Meanwhile they are reducing the palletised freight distribution network’s carbon emissions by 27kg a day.
Weighing capability was a key requirement for Palletline’s new fleet. The company had previously relied upon a bolt-on arrangement for weighing scales, and had needed larger capacity trucks to handle the extra weight.
Linde MH partnered with specialists from B&B Attachments to devise an integrated weighing solution which allows Palletline to operate a smaller, more fuelefficient truck.
Linde MH’s fleet management system which ensures that only fully trained staff are authorised to operate them.
Importantly, an automated alarm prevents drivers from lifting a pallet weighing more than 400kg above a height of 1.2m. This aligns the company’s operations with the latest double-deck trailer loading guidelines from the DVSA, HSE and other regulatory bodies.
The upgraded fleet of forklifts are also fitted with
Rob Carney, Facilities Manager of Palletline, said: “The trucks are brilliantly robust yet incredibly agile when compared to the previous trucks we had on site, perfect for our network freight environment. Our drivers love the electric trucks too, which provide additional flexibility across our fleet and impressive range.”
The company plans further collaboration with the Linde team on the future of Palletline’s
forklift truck fleet.
Graham Leitch, Group Managing Director, added: “We are currently working with Linde to investigate the use of hydrogen fuel cells in forklifts to further reduce the environmental impact of our operation while at the same time reducing fuel costs.
“Hydrogen is expected to be a significant opportunity for this partnership and we are hoping to be one of the first to introduce a hydrogen-fuelled fleet of forklifts in the industry, further reinforcing our marketleading position.”
Gericke is celebrating an impressive anniversary: 130 years of bulk handling solutions. For over a century, the Swiss family-owned company has been a leader in the manufacture of systems and machines for processing bulk solids. What once began in a modest location in Zurich has developed into a global group of companies with 350 employees. Starting out in the milling industry, Gericke has firmly established its place as a leader in industries such as food, chemicals, environmental technology, battery manufacturing and pharmaceuticals.
In 1894, Walter H. Gericke founded “W. Gericke, Maschinenfabrik, Schleiferei und verwandte Industrien” in Zurich. At that time, grain mills were among the pioneers using automated conveying systems for bulk materials. But other core technologies such as dosing, grinding, mixing, separating and filling were also available in the early days.
From 1924, the two sons of the company founder, Otto H. Gericke and Walter H. Gericke,
continued the tradition. The company began to expand and the brothers acquired a new site near Zurich’s main railway station. Together with engineer O. Soder, Gericke developed a pioneering roller mill with a horizontal millstone. This patented innovation led to considerable improvements in flour production in the 1930s and 1940s.
In 1954, the third generation joined the company: Otto H. Gericke’s sons, Willi and Hermann Gericke. In 1957, Gericke expanded its production capacity with a new factory in Regensdorf near Zurich. The site was significantly expanded in autumn 2023 with the construction of an additional production hall.
International Growth International growth began in the 1960s with subsidiaries in Europe, including Germany,
France, the Netherlands and Great Britain. From the 1990s, Gericke also expanded overseas, with subsidiaries in Singapore, Thailand, Indonesia, Malaysia, China, Brazil and the USA.
Markus H. Gericke joined the company in 1993 as Managing Director of Gericke France and is now the fourth generation to manage the company. Gericke manufactures all key components in its own production facilities, including equipment for mixing, pneumatic conveying, dosing, big bag handling, screening and crushing. The company also develops its own control systems, which enable easy integration into higher-level automation systems.
Since 2010, Gericke has been involved in the development and establishment of continuous processes in the production of solids in the pharmaceutical industry. The GFS Formulation Skid is now used worldwide in this pioneering technology.
LOGiQ combines yard management and weighing technology fully automatically
Schenck Process, a leading specialist for process-critical bulk materials applications, offers the LOGiQ yard management system, a cloud-based software solution that combines smooth and efficient truck loading operations with fully automated weighing of bulk materials - supported by log-on terminals, which are also part of the LOGiQ product family.
LOGiQ is a proven system in the cement and steel industry. However, the solution is also suitable for yard management in other segments of industrial production.
LOGiQ handles all logistical steps from the entry of an authorized truck onto the company premises to the exit in a seamless process. The software system monitors and controls access, supports weighing processes, ensures correct loading and records all relevant data without delays. All information is integrated into the ERP system, for example SAP, to provide up-to-date sales and administrative data.
weighing, feeding, conveying, milling and grinding, and related digital applications of the CONiQ product family.
For more information, please visit www. schenckprocess.com
Multilingual terminals included in the LOGiQ complete package
Access is controlled via LOGiQ registration terminals, which are intuitive to use and available in several languages on request. The truck drivers operate these terminals themselves and record their weighing processes and all steps during loading and unloading. The processes run automatically without the need for manual intervention by staff: “zero-touch fulfillment”. This reduces the susceptibility to errors in the process and increases safety. The basic need for personnel on the factory premises is also noticeably reduced thanks to automation. In addition, the responsible employees and support staff at Schenck Process can access and support all data in real time, regardless of location, if required.
Further information can be found at https://www. schenckprocess.com/yard-management. Click here for the information page with explanatory videos of the LOGiQ process: https://www.schenckprocess.com/ technologies/software-automation/logiq.
Schenck Process is a global provider of sustainable products, integrated solutions, and services in missioncritical applications for bulk materials. Headquartered in Darmstadt, Germany, the group has more than 1,100 employees with a presence in over 12 countries focused on markets alongside chemicals and performance materials, and infrastructure and energy as well as alternative fuels.
The product range includes solutions for industrial
Dynamic Air BulkBuster bulk bag unloaders provide the solution for safely and effectively emptying large bulk bags. The Series 422 Model H1900 BulkBuster bulk bag unloader provides a clean method of discharging bulk bags since it includes internal dust collection for containing fugitive dust. The removable bayonet mounted cartridge filters provide continuous cleaning, and they recycle fugitive dust by discharging it back into the process hopper
below. The Series 422 Model H1900 unloader also features a viewport, work gloves to allow the bulk bags to be untied and emptied without contacting the bag contents, and a bag closing mechanism, which allows partial bag unloading. Also included are air operated bulk bag jostlers for faster discharging of difficult to handle materials.
https://www.dynamicair. com/products/bagunloaders. html
Dynamic Air Inc. St. Paul, MN 651 484-2900 info@dynamicair.com www.dynamicair.com
If you would like to subscribe to receive a regular copy of the digital edition of Bulk Solids Today magazine, you can subscribe on our website - www.bulksolidstoday.co.uk
If you are interested in advertising within Bulk Solids Today magazine or supplying editorial content, please feel free to get in touch using the details on our website or below.
Bulk Solids Today is sent to our digital readership of over 9,000 Chief Engineers, Operations Managers and Technical Managers from within sectors including Chemicals, Food & Drink, Mining, Quarrying, Transport/Distribution, Recycling & Waste Management and more.
www.bulksolidstoday.co.uk
Develon, formerly Doosan Construction Equipment, has opened the company’s new European Training Centre at Allonnes close to Nantes in the west of France.
Among the aims of the new Training Centre is to provide dedicated conditions to update and develop the knowledge and skills of dealer personnel and the company’s service technicians and demonstrators, to enhance Develon customer experience and satisfaction throughout the European market.
Located in an easily accessed location close to the beautiful chateaux region of the Loire Valley, the new Training Centre is designed to provide a relaxing and attractive environment for all attending the new facility.
Patrice Pesnot, Head of Training at Develon in Europe, said: “The new Training Centre is intended to provide an environment to allow participants to concentrate on Develon products, allowing them to remove themselves from their daily work and focus entirely on the training activities.”
The new Training Centre consists of a main building with several areas that can be set up for training. In addition to the classroom space, the facility also includes offices, workshops for service training and an impressive 3000 m² outdoor area which is devoted to hands-on try outs of machines from Develon and competitor machines.
Providing a Safe and Secure Area for Training
Patrice Pesnot added: “Another aspect of the Training Centre is to provide a secure and safe environment with excellent conditions for training, in a fully equipped area that demonstrates the professionalism of Develon, allowing testing of machines both in the workshop but also in the working conditions in the outside demonstration area.
“The new Develon Training Centre is dedicated to helping Develon dealers and company personnel to enhance their knowledge and skills in all possible ways, as we believe personal development is the foundation of further dealer performance growth.
The new Training Centre also aims to greatly enhance Develon customer experience right across the European region.”
Activities at the new Training Centre include:
• Dealer Service Training
• Dealer Product Training
• Internal ‘Train The Trainer’ sessions to widen the training capabilities for the region
• Training development: including video tutorials and other tools
• Virtual Classrooms
• Future events to include promotion of Develon in schools (in France and Europe)
More than Simply Training
Patrice Pesnot concluded: “The Develon Training Centre aims to enhance dealer and staff performance with the right training, support and tools for enhanced customer experience. To achieve this, the Training Centre builds on our strong training foundations to also focus on the
competition’s equipment with proactive sales materials, complemented by supporting dealers further with equipment demonstrations and other positive action.”
For more on Develon, please visit the website: https://eu.develon-ce.com/en/ Gothenburg named Sweden’s top logistics location
The Gothenburg region tops the list in Swedish industry magazine Intelligent Logistics’ annual ranking of Sweden’s best logistics locations. As Sweden’s largest freight hub, the Port of Gothenburg plays a crucial role in the award, which has been presented since 2001. It is the 23rd time that the Gothenburg region has topped the list.
“We are pleased and proud to once again be named Sweden’s best logistics location. Together with the region’s other logistics actors, we have worked hard throughout the year to create additional conditions for an innovative and constantly growing freight hub that strengthens the competitiveness of Swedish foreign trade both regionally and nationally,” says Jacob Minnhagen, Senior Market Development Manager at the Gothenburg Port Authority.
More than 55% of Sweden’s total container traffic is handled at the Port of Gothenburg, and volume growth is stable. After thirteen consecutive quarters of increased container volumes, the port achieved an all-time high result for the full year 2023 with 914,000 handled containers. Intelligent Logistics also highlights the fact that the EU has given clearance for a deepened fairway to the Port of Gothenburg, which means future-proofing with increased flexibility and the ability to accommodate ships that are both larger and more loaded than possible today. The groundbreaking ceremony for the project will take place on April 8th.
Access to logistics areas is crucial for the functionality of a logistics region, and therefore an important assessment criterion in the designation of Sweden’s best logistics location. The magazine notes that there is now plenty of buildable land for logistics in the region, including in the immediate vicinity of the port, as well as in Mölndal and around Landvetter. New areas of 780,000 square meters in the past five years and an additional 182,000 square meters in 2024 are contributing factors to the Gothenburg region retaining its top ranking according to Intelligent Logistics’ assessment.
“We are several parties collaborating in our region. For example, we have close cooperation with Swedavia Landvetter Airport, Business Region Borås, and Business Region Gothenburg to jointly strengthen ourselves as an attractive region for business establishments. Here, there is competent labor, good infrastructure, buildable land ready for establishment both today and in the future,” Jacob Minnhagen commented further.
The renowned list of Sweden’s best logistics locations has been published since 2001, with the Port of Gothenburg ranked first 23 out of 24 times. The ranking is based on access to logistics areas, flows/ geography, infrastructure, market access, competence, and collaboration climate in the region.
The Gothenburg region is awarded first place on the list along with the Helsingborg region.
If you would like to subscribe to receive a regular copy of the digital edition of Bulk Solids Today magazine, you can subscribe on our websitewww.bulksolidstoday.co.uk
If you are interested in advertising within Bulk Solids Today magazine or supplying editorial content, please feel free to get in touch using the details on our website or below.
Bulk Solids Today is sent to our digital readership of over 9,000 Chief Engineers, Operations Managers and Technical Managers from within sectors including Chemicals, Food & Drink, Mining, Quarrying, Transport/ Distribution, Recycling & Waste Management and more.
www.bulksolidstoday.co.uk
bst@abbeypublishing.co.uk
Tuf-Lok ring grip pipe and tube couplings are rugged, heavy duty, self-aligning and self-grounded couplings with a high end pull. They can be used for almost any application where pipe or tube ends need to be connected. The Tuf-Lok self-aligning couplings install quickly and easily with little effort.
Features
• Self-aligning
• Self-grounding
• High pressure rated
• Full vacuum rated
• Stainless or mild steel
• Usable on thin or thick wall pipe or tube
• Low cost
• Reusable
• Absorbs vibration
• Externally leakproof
Tuf-Lok (UK)
Tel: +44 (0) 1706 822512
Email: sales@tuflok.co.uk
• www.tuflok.com
New from Flexicon is a Twin Tilt-Down Flexible Screw Conveyor system with dual hoppers on a common mobile base, constructed and finished to 3-A sanitary standards.
Ready to plug-in and run, the self-contained system can fill two vessels with the same material simultaneously, or convey two different materials. Mounted on a frame with locking castors for in-plant mobility, it can be utilised in multiple locations, and rolled to a wash-down booth.
Each 113-liter hopper is equipped with grates capable of supporting a 115 kg bag of material, level sensors, and mechanical agitator assemblies to promote flow into the conveyor inlets.
The two BEV-CON™ conveyors are engineered to move dry bulk solids efficiently without product degradation, especially non-free-flowing materials that pack, cake, smear, fluidise, compress, or are otherwise problematic to convey. The screws are the only moving parts contacting material, and are driven beyond the point at which material is discharged, eliminating wear and contamination related to product contacting seals and bearings.
Discharge housings of the conveyors are supported by dual motorised booms that cantilever
from the mobile base, allowing discharge of material into processing equipment or storage vessels. The support boom and conveyor assembly can be tilted down to manoeuver through standard doorways and aisles, and around corners for use anywhere in the plant.
The system is constructed to 3-A standards, and features sanitary quick-release clean out caps, quick-disconnect discharge box access covers, and wash-down motors.
The stainless IP65 (NEMA 4X) control panel allows operation of either or both conveyors. HMI controls allow manual and automatic start/stop, reverse and variable speed adjustment.
Flexicon also manufacture other types and sizes of flexible screw conveyors as well as tubular cable conveyors, pneumatic conveying systems, bulk bag dischargers, bulk bag conditioners, bulk bag fillers, bag dump stations, drum/box/container tippers, drum fillers, weigh batching and blending systems, and engineered plant-wide bulk handling systems with automated controls.
For information contact Flexicon Europe Ltd, +44 (0)1227 374710, sales@flexicon.co.uk, www.flexicon.co.uk
Solids handling specialist, Ajax Equipment, has supplied atomising technology and atomised metal powder provider, Atomising Systems Limited, with an ATEX rated feed hopper and mass flow screw feeder for metal powder handling. The stainless steel equipment will expand Atomising Systems’ production capacity at its Sheffield, UK production facility.
The powder handling system is based on a proven design previously supplied to Atomising Systems with increased robustness to allow for the modest pressure rating required. In this case Ajax ensured mass flow by using a specially designed screw feeder below the suitably stiffened two stage plane flow hopper to provide a consistent feed.
Commenting, Craig Winfield, Project Manager at Atomising Systems Limited, said, “We’ve used Ajax on several occasions for screw feeders
and mass flow hoppers and so when this new requirement came up, we were happy to work with Ajax again and have not been disappointed.”
“Ajax has worked with Atomising Systems successfully on many projects, so we were happy to provide a new system hopper and feeder design, updated to meet their new capacity requirements and modest pressure needs,” said Eddie McGee, managing director, Ajax Equipment. “Ajax’s screw feeders are used across a wide range of industries around the world to ensure reliable powder handling from a few grams per minute to hundreds of tonnes per hour.”
For more information on Ajax Equipment’s powder handling equipment call +44(0)1204 386723, email: sales@ajax.co.uk and visit www.ajax.co.uk.
The pioneer in belt conveyor accessories has launched the next generation of tracking technology for a global marketplace. Martin Engineering designed the highly responsive Martin® Tracker™ HD (heavy-duty) belt conveyor alignment system with widely available plate steel to increase availability and affordability across all 6 continents it serves. A mistracking belt produces excessive spillage which increases labor costs for cleanup and may cause contact with the mainframe. This seriously damages both the belt and the structure and increases the potential for a friction fire. The Martin Tracker HD upper and lower units provide immediate, continuous, and precise adjustment of the mistracking belt. The result is greater productivity with less unscheduled downtime from both equipment replacement and spillage cleanup for a lower cost of operation.
“Since most OEM mistracking devices are only designed to prevent contact with the stringer and don’t actually realign the belt, operators can spend a lot of time monitoring the system and adjusting idlers to achieve consistent alignment,” explained Dave
Mueller, Product Manager for Martin Engineering. “With enough manual adjusting, operators find that idlers must be recentered if there’s a change in cargo characteristics or to install a new belt. The Tracker HD automates the alignment process, eliminating the need for constant monitoring and manual adjustments, reducing the labor and downtime for maintenance.”
The Martin Tracker HD’s unrivaled precision comes from sensing rollers that ride either side of the belt edge and are attached to the end of an arm assembly. As the rollers detect slight variations in the belt path, the force of the wandering belt causes the arms to automatically position a pivoting idler in the opposite direction of the misalignment. The lever action requires less force to initiate the correction and only slight adjustments mean the consistent contact between the belt and idlers reduces the energy needed to bring the belt back into alignment.
“Certain countries can’t buy the square tubing, so we’re now manufacturing the equipment from readily available plate steel without any changes to
the performance or life of the unit,” Mueller pointed out. “This allows the Tracker HD to be produced and supplied across all global business units.”
Easy to install and designed to withstand the stress associated with wider, thicker belts moving at higher speeds and carrying heavier loads, the Martin Tracker HD is suitable for a belt thickness up to 1.125 in. (28.5 mm) and speeds up to 800 fpm (4 m/s). Both the upper and lower units accommodate belt widths of 36-72 in. (915-1828 mm) with an effective tracking distance of 150 ft. (45.72 m).
Available in 20-, 35-, and 45-degree trough angles, there are options for the addition of a Martin® Trac-Mount™ Idler, which allows the entire troughed idler unit to be slid away from the mainframe and safely serviced from outside of the system by a single worker. This important safety element can considerably reduce the amount of labor and maintenance time for the replacement of broken or frozen idlers. Also available are rubber-lagged rollers on the lower tracker and a grease kit for both the upper and lower assemblies. The unit is not suitable for reversing conveyors, belts with substantial rollback, or paddle or chevron belts.
It is recommended operators install Martin Tracker HDs after the load zone on belts wider than 24 in. (610 mm) with additional units placed down the system to keep the belt centered and tracking. By placing an upper unit before the discharge, operators ensure the belt is centered on the head pulley allowing for optimal
belt cleaning with maximum cargo discharge.
The lower tracker has been redesigned to include an extra safety feature not found in competitor units. Regardless of the conveyor, return rollers have been known to detach and drop, creating a serious safety issue, so the Martin Tracker HD has been equipped with safety guarding on the steering roll to prevent the roller from coming off or putting workers in harm’s way. On the return, it is recommended to place a tracker after the discharge zone or take-up pulley, as well as periodically down the system depending on length. To ensure centered loading, the belt must enter the loading zone aligned, so installing a lower unit approximately five times the belt’s width in distance from the tail pulley will support an efficient loading process.
Since the basic design of the Martin Tracker HD is similar to that of its predecessors with square tube construction, the testing focused on performance, durability and installation time. Tested in bulk handling operations including mining and cement where mistracking leading to spillage had historically been a concern, the unit performed up to Martin Engineering’s high standards.
“Martin Engineering believes safety should be a core function in any conveyor accessory we design, and the Tracker HD is no different,” Mueller said. “By automating consistent belt tracking, this solution reduces equipment wear, maintenance time, and downtime. These factors lower the cost of operation offering the best return on investment of any tracker on the market.”
High cycle actuators are often seen as having a short lifespan, with costly installation and maintenance requirements. However, many leading processors are realizing that well-designed actuators can offer reliable performance for years with minimal maintenance or repair.
In food, pulp and paper, pharmaceutical, and chemical plants, processors often operate around the clock to produce chemicals, paints, resins, lubricants, ingredients, and other raw materials. To manufacture these products, high-speed, high cycle actuators open, close, or throttle valves to regulate, direct, or control the flow of gases, liquids, fluidized solids, or slurries.
Regrettably, many processors today have become accustomed to the idea that high cycle actuators have a short lifespan and necessitate regular maintenance to replace parts prone to wear, such as O-Rings, springs, cylinders, and others. In some facilities, this task can consume a technician’s entire work schedule.
However, many leading processors are beginning to reassess this expectation, given the high costs for installation and maintenance.
The truth is that a well-designed actuator should be able to provide reliable performance for many years beyond the warranty period. If maintenance or repair is needed, it should be infrequent and simple enough for a single technician to handle, using common tools. For maintenance or repair purposes, the actuator should be easily accessible without the need to remove it from the valve. This is a crucial factor, as valve manufacturers will invalidate warranties if the actuator is detached from its mount.
Actuator usage and stress are often linked to the frequency of valve opening and closing cycles. The cycle count often varies based on the environment or application. Some actuators are seldom used, while others operate regularly. High cycle, high-speed valve actuators – often found in processor operations – can fire rapidly and repeatedly many times per hour, nonstop throughout the year.
The core issue lies in the high utilization and demand placed on the actuator.
Actuators come in different styles based on the mechanical action required, such as linear or rotary, but all involve moving parts that experience considerable force, wear, and stress. In processing plants, actuators are also installed in highly corrosive industrial settings. Many designs fail to account for these factors and are poorly engineered, leading to excessive side loading, wear on non-wearing parts, and various other issues.
High reliability is another crucial factor that holds significance for Scott Howard of NewGen Products, a specialist in valve automation. Many of his customers are in the aerospace industry, where valves with actuators regulate the flow of cryogenic gases for fueling and storage operations.
For critical applications like these, Howard often recommends a top-of-the-line actuator, purpose built for the application. Although there may be a higher initial cost, these actuators are designed to perform reliably in challenging
and harsh environments. Even within this category, however, many actuators are not expected to last. “Many of the higher end actuators are rebuilt every three to four years,” says Howard.
There are exceptions, including what Howard refers to as the “Ferrari” of actuators from Tomball, Texas based QTRCO actuators. Founded in 1998, QTRCO has innovated designs specifically for high cycle, high speed, high reliability applications.
The actuators are built with a robust mechanical design that eliminates common failure points like sliding parts, side load forces, and multiple seals. This makes them perfect for demanding applications in extreme temperature, corrosive, or submerged environments.
Among the more innovative designs from QTRCO is its answer to the common aluminum “lunchbox” actuator and its inherent design limitations.
The actuator, which gets its name from its onepiece aluminum extruded body and cylinder that resembles a lunchbox, is popular because it is compact, inexpensive, and works well. Aluminum lunchbox actuators are not very reliable and often break, however, in more demanding environments or applications.
To resolve many of these issues, QTRCO designed an actuator with an internal “rack and gear” mechanism as an alternative to its traditional
rack and pinion design.
The actuators are designed with offset cylinders that align the piston axis with the pinion gear pitch circle diameter, eliminating cantilever forces and friction. The company also replaced the sliding blocks, wear pads, and bushings with specialized rollers. As a result, the rack and gear actuators have extremely low internal friction.
The new design also eliminates one of the primary causes of failure of a lunchbox actuator: the O-rings on the shaft. In a lunchbox actuator, air is forced through ports in the body. The air pushes the piston outwards, and springs push the piston back in. Each cycle pressurizes the shaft, which typically has two O-rings, one at the top and one at the bottom. As the shaft cycles back and forth 90 degrees, the reciprocating motion places significant stress on the O-rings.
In QTRCO’s design, this action is reversed, and the air is forced inward through the end cap. The spring return applies no pressure to the shaft seals, which prevents premature O-ring wear.
This configuration also has benefits when valve throttling is required. Due to the design of the company’s Q Series and because the piston is located close to the end cap, much less air fill volume is required, and the actuator responds much quicker and is easier when throttling.
QTRCO took a similar approach as an
alternative to Scotch yoke actuators. Also known as a slotted link mechanism, the Scotch Yoke is a simple and effective mechanism that has been used for a long time. However, with typical Scotch Yoke actuators, the force applied to the piston rod is also applied to the shaft and shaft bushings, resulting in friction and bushing wear.
To resolve these issues, QTRCO designed a patented Flat Yoke mechanism that can accurately and reliably position any rotary control valve requiring up to 500,000-inch lbs. of torque.
The Flat Yoke is designed with quad body slots that absorb the mechanism’s side loading forces, leaving the piston rod completely free of bending stresses while allowing termination of the rod at the yoke. Like the Q Series, these F Series actuators also have extremely low internal friction, consume minimal air volume, and can handle the most severe throttling applications.
With an actuator specifically designed for reliable and long-lasting performance, processors can save on costs associated with more frequent replacements.
In one processing plant he visited, Howard says the actuator fired twice a minute throughout the entire year, adding up to over a million cycles per year. Given the usage, the plant would replace the actuator annually during planned outages.
According to Howard, the replacement of an actuator typically requires an entire day for a single technician, often with the help of at least two
additional individuals. If the actuator is large enough, a crane is required. Considering the potential costs for hourly labor rates and rentals, a plant could save thousands of dollars every time it eliminates the need to replace an actuator.
“If a plant doesn’t have to change the actuator every year, they just saved a fortune,” says Howard.
When preventative maintenance or repair is required, it should be easily conducted using common tools and without removing the actuator from the valve. With large, metal-seated ball valves, it is critical to mount the actuator with extreme precision. A slight misalignment during mounting can result in severe damage to a valve that carries a hefty price tag of hundreds of thousands of dollars. The connection is so crucial that most major valve manufacturers will void warranties if the actuator is removed.
In rare cases, like with QTRCO designs, the actuators can be easily maintained without removal from the valve. This enables hassle-free removal and replacement of end caps, cylinders, and O-rings, often without special tools.
According to Ross Evans, also with NewGen Products, safety is another concern during preventative maintenance and repair. Actuators of considerable size may require two people for lifting and moving.
“Imagine being in a plant environment and climbing six flights of stairs to a catwalk to service an actuator. With that kind of weight, what does it take to get your cranes and rigging in place to
safely take off the actuator? You have to remove all the pneumatic airlines, disconnect the electrical, and you need a couple hands. There’s a lot of cost and time and risk involved,” explains Evans.
“The alternative is, I can do maintenance on the valve while it is in place,” adds Evans. “I shut down the unit, tag it out, take off the end cap, inspect the cylinder, remove an O-ring, grease it, and put it back in place. In about 10 minutes per cylinder, we are back and running.”
The actuator’s design can also contribute to safety concerns. Many Scotch Yoke designs feature a lone piston assembly on one side of the unit. Lifting or rigging an unbalanced, single piston assembly is challenging due to its significant lean on one side.
retainers and there is a safety collar that locks it into place. Replacing the springs simply requires removing the end cap and replacing the cartridge.
For high speed, high cycle processing applications, QTRCO recommends sizing up to a two-piston version of its Flat Yoke design. The two pistons balance the forces on both sides of the shaft, preventing bushing wear. The design also includes the addition of a weight and force balancing second force module diagonally offset from the first.
By balancing the forces, there is less friction and wear and no net force applied to shaft bushings. The balanced weight also makes lifting and handling of the actuators safer and easier, while reducing valve neck stress that can occur in unbalanced scotch yoke actuators.
Another issue is the spring set used in many lunchbox actuators, which are under load and must safely be controlled once the end cap is removed. If the spring becomes jammed and the mechanism that contains the spring fails, the force exerted can be equivalent to a shotgun.
“In one actuator, the end cap corroded and failed. It discharged the spring out of the actuator across the shop,” says Evans.
He says he has personally observed experienced field technicians that regularly work on actuators, who move out of the line of the cylinder to remove the end cap on the actuator.
“Anybody that’s done any type of maintenance on an actuator, they know the potential energy contained in the spring,” says Evans.
With QTRCO, the spring is fully captured using a solid stainless-steel rod that goes through the spring
“Once they capture those springs, it is designed not to ever come apart again – it remains captured. It is a big safety feature,” says Evans.
Installing actuators that are built to last and require minimal maintenance or repair not only brings significant benefits, but also proves to be more cost-effective in the long run, even if the initial cost of ownership is higher. When multiple actuators are installed in a processing plant, the savings can add up.
“If you put a well designed actuator in one of these demanding applications and rarely have to do any maintenance or replace it very quickly, the total cost of ownership is far less,” says Evans.
“If you can get an extra three or four years of run time on an actuator, you just made up whatever cost difference you had on the initial price,” notes Evans, adding that does not even take into consideration the number one thing that costs the plant money: downtime.
Today, design advancements in high speed, high cycle actuators make it easier for food, pulp and paper, pharmaceutical, and chemical processors to create high-quality products.
With an actuator specifically designed for reliable and long-lasting performance, processors can reduce costs associated with a labor-intensive manufacturing component that today too often requires frequent maintenance, repairs, and replacement.
Danfoss Power Solutions, a leading global supplier of mobile and industrial hydraulics as well as electric powertrain systems, has partnered with Australian crane manufacturer Franna to improve the performance of its MAC 25 crane. With the PVG 48 proportional valve at the heart of the work and steering subsystems, Danfoss is delivering a reliable, precise, future-proof solution.
Franna, a Terex brand, is a leading manufacturer of pick and carry cranes with a rich heritage of design and engineering excellence. For more than 40 years, Franna has been a leader in the Australian market, and today its products are at work in more than 30 countries across the globe.
Franna’s MAC 25 mobile articulated crane features a maximum lifting capacity of 25 tonnes (27 tons) and a maximum boom length of 18.4 meters (60 feet). The crane offers maximum safety, excellent roadability, intuitive operation, and unmatched versatility. True to the company’s heritage, the crane’s design has been tested, proven, and continuously improved over the years.
In 2021, Franna began looking at other options
for the MAC 25 crane’s main control valve. The company required a solution that was precise, reliable, and future proof to accommodate increasingly sophisticated electronic control systems. The Danfoss PVG 48 proportional valve, then in development, emerged as the superior solution.
PVG 48 is a pre-compensated proportional control valve for applications requiring flow rates of up to 180 liters per minute (47.6 gallons per minute). The latest member of the PVG load-sensing valve family, PVG 48 is ideal for machines such as wheel loaders, aerial lifts, and cranes in which precise flow and controllability are essential.
Danfoss launched the PVG 48 valve to the general market in June 2023 with Franna as a key pilot customer. On the MAC 25, the valve turns operator joystick inputs into quick, accurate boom movement.
“The PVG is extremely precise and reliable. It does what you want it to do repeatedly,” said Adam Murchie, project engineer, Franna. “It’s the ideal choice for MAC 25 and likely to end up in other of our cranes, too – not least in future launches where more advanced electronic controls are key. We wanted a
future-proof valve. PVG 48 is it.”
The PVG 48 valve integrates easily with electric actuators, sensors, and digital controls, opening a range of possibilities. One of them is to automate certain machine functions so the crane assists – or even takes over from – the operator. Such a function can be advantageous in many situations, particularly when instant reaction is required to ensure safety.
With the change to PVG 48, Franna also switched to Danfoss counterbalance valves. Together with PVG 48, they ensure smooth and safe activation of the crane’s boom.
“Controllability is smooth and even – very refined,” said Quentin Bourke, product support technician, Franna. “The initial tiny bounce on the front tires, which you sometimes see when operators raise or lower the boom, is completely gone. Extension or subtraction of the boom is impressively smooth, too.”
Bourke adds that initial feedback from crane operators using MAC 25 with a PVG 48 and Danfoss counterbalance valves is positive, too.
“Together with Danfoss, we’ve managed to create the exact kind of MAC 25 crane feel that we hoped for,” Bourke said.
The Danfoss PVG 48 proportional valve is already at work in more than 100 of Franna’s MAC 25 cranes throughout Australia.
To learn more, read the full Franna MAC 25 success story.
RAVAS, a leading player in mobile weighing technology, is proud to announce its nomination for the esteemed International Forklift Truck of the Year (IFOY) Award. The nomination recognizes the innovative Weigh in Motion technology on an intelligent carriage plate (iCP), developed for forklifts.
“This nomination for the IFOY Award is confirmation of our commitment to innovation and quality,” says Michael van Dijk, International Key Account Manager at RAVAS. “With the Weigh in Motion technology, we are taking a major step forward in optimizing logistic processes and increasing safety in the workplace. We are honored by this recognition and look forward to the official launch of the Weigh in Motion technology at LogiMAT in March.”
process of weight registration, improves inventory accuracy, and facilitates data-driven decision-making.
The IFOY Award, recognized as one of the most prestigious honors in the international forklift industry, shines a spotlight on the most innovative and impactful developments in the sector. RAVAS is excited to be nominated in the ‘Special of the Year’ category, focusing on improving profitability, sustainability, and physical and psychological working conditions.
RAVAS is making a revolutionary leap forward in the world of mobile weighing technology with its advanced Weigh in Motion technology, developed for integration in forklifts. This technology, which was also recently recognized with the ‘Most Innovative Product for Logistics, Transport, and Production 2023’ award at the Logistyki, Transportu i Produkcji gala in Warsaw, Poland, enables loads to be weighed directly while the forklift is in motion.
The Weigh in Motion technology on an intelligent carriage plate (iCP) ensures accurate and reliable weight determination while a forklift is moving. This results in significant time savings, and thus cost savings, as the driver can weigh without stopping. It also prevents unnecessary additional transport movements and manual activities, contributing to higher efficiency, lower chances of accidents, better sustainability, and increased employee satisfaction compared to traditional weighing methods.
Moreover, the calibrated value provided by the Weigh in Motion technology can be used for direct billing.
The seamless integration of Weigh in Motion technology with TMS, WMS, or ERP systems enables real-time weight control, optimization of loads, and prevention of over- or under-loading of trucks, ensuring streamlined operations and maximum productivity. Additionally, data can be automatically collected, stored, and analyzed. This integration enhances the
Forklift scales with Weigh in Motion technology are particularly suitable for situations where large amounts of palletized goods need to be moved within a limited time. Ideal for logistics, storage, reweighing, and LTL shipments.
RAVAS, founded in the 1970s in Zaltbommel, the Netherlands, has evolved over the years into a global player with 200 employees. RAVAS is present in 8 European countries and the United States and serves other customers with their equipment, software and consultancy through a worldwide network of professional partners.
As a leading manufacturer and supplier of mobile weighing solutions, RAVAS integrates weighing and measuring technology into various logistic equipment, such as hand pallet trucks, electric warehouse trucks, stackers and forklifts. Focusing on optimizing material handling in logistic and industrialapplications. By generating real-time data on material flows, RAVAS contributes to improving productionand logistic supply chains, with data being exchanged with TMS, WMS, or ERP business systems.
With an innovative team of specialists, RAVAS aims to provide intelligent solutions and services for global supply chains. The mobile weighing solutions collect accurate data, including legal for trade, on material flows in weight and volume, in real-time and during movement. Additionally, the solutions seamlessly integrate with existing material handling equipment, allowing current systems to be transformed into efficient weighing machines. This enables working safer, more efficiently and faster;saving costs and creating extra revenue, supported by RAVAS’ excellent after-sales service.
For more information about RAVAS and their products, visit www.RAVAS.com.
Schenck Process, a leading specialist for processcritical bulk materials applications, offers the LOGiQ yard management system, a cloud-based software solution that combines smooth and efficient truck loading operations with fully automated weighing of bulk materials - supported by log-on terminals, which are also part of the LOGiQ product family.
LOGiQ is a proven system in the cement and steel industry. However, the solution is also suitable for yard management in other segments of industrial production. LOGiQ handles all logistical steps from the entry of an authorized truck onto the company premises to the exit in a seamless process. The software system monitors and controls access, supports weighing processes, ensures correct loading and records all relevant data without delays. All information is integrated into the ERP system, for example SAP, to provide up-to-date sales and administrative data.
Access is controlled via LOGiQ registration
terminals, which are intuitive to use and available in several languages on request. The truck drivers operate these terminals themselves and record their weighing processes and all steps during loading and unloading. The processes run automatically without the need for manual intervention by staff: “zero-touch fulfillment”. This reduces the susceptibility to errors in the process and increases safety. The basic need for personnel on the factory premises is also noticeably reduced thanks to automation. In addition, the responsible employees and support staff at Schenck Process can access and support all data in real time, regardless of location, if required.
Further information can be found at https:// www.schenckprocess.com/yard-management.
Click here for the information page with explanatory videos of the LOGiQ process: https:// www.schenckprocess.com/technologies/softwareautomation/logiq.