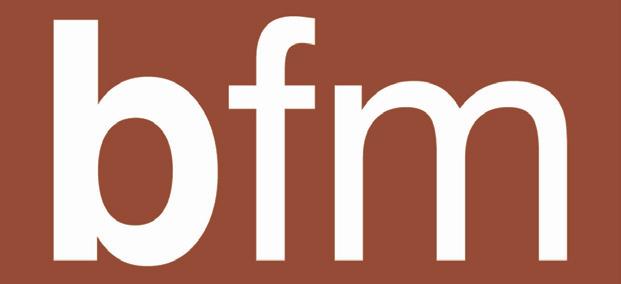
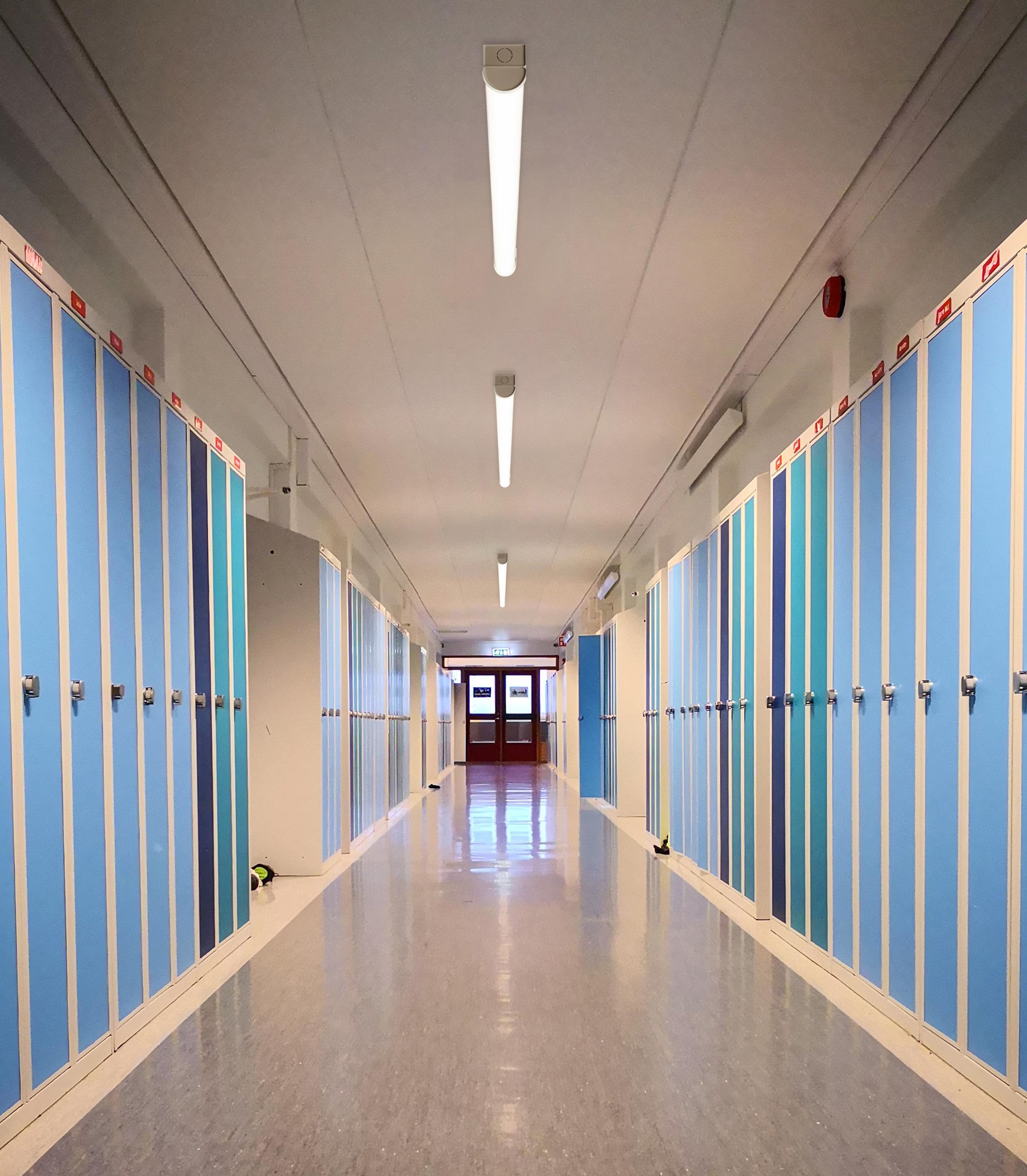
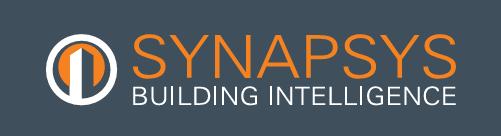
Optimise energy use and create adaptable spaces with intelligent lighting controls
Cut costs not performance
Eliminate unnecessary energy waste, helping budgets go further without compromising lighting quality
made simple
Optimise energy use in real-time, helping you meet carbon reduction targets and regulatory requirements
Scalable systems integrate with existing infrastructure, ensuring compliance and longterm savings with minimal disruption
Synapsys Lighting Control Systems help buildings to unlock smarter, more efficient lighting solutions - reducing waste, cutting costs, and enhancing comfort.
Email | enquiries@synapsys-solutions.com
Web | synapsys-solutions.com
Business Development Director James Scrivens james@abbeypublishing.co.uk
Production Sarah Daviner sarah@abbeypublishing.co.uk
Accounts Manager Katie Brehm accounts@abbeypublishing.co.uk
BFM is published digitally 10 times a year by Abbey Publishing Ltd. To receive a copy free of charge, contact our offices.
Tel: 01933 316931
Email: bfm@abbeypublishing.co.uk www.bfmmagazine.co.uk www.abbeypublishing.co.uk
www.twitter.com/ BFM_Magazine
Subscriptions are available via www.bfmmagazine.co.uk/subscribe
“At a time when travel is increasing, facilities must offer environments that are both hygienic and reassuring.”
Joanne Gilliard, CEO of Jangro, comments:
“Airports are some of the busiest public spaces, especially during the summer holidays, with thousands of people moving through shared, enclosed areas each day. In such high-traffic environments, hygiene is not just a nice-tohave, it’s a frontline defence for public health.
“Washrooms, in particular, play a central role. Shared facilities, high-touch surfaces, and heavy footfall create ideal conditions for viruses like cold and flu to spread. Research has shown that exposure to these conditions during travel significantly increases the risk of illness, making ‘post-travel flu’ an all-too-familiar experience for many.
“That’s why airport washrooms must be not only regularly cleaned but also well-stocked and frequently monitored to maintain higher hygiene standards. In an environment where thousands pass through daily, even minor oversights can have major consequences for travellers.
“With travel volumes rising over the summer, now is the time for facilities teams to reassess their strategies and invest in staff training, adopt effective and sustainable cleaning products and implement real-time monitoring systems to track refill levels throughout the day. These efforts not only save time and resources but also ensure consistency and reliability.
“At a time when travel is increasing, facilities must offer environments that are both hygienic and reassuring. Clean, well-managed washrooms are not only essential for public health, but they also enhance trust, comfort and the overall passenger experience.”
Building & Facilities Management editorial content covers all the major FM areas of interest within the workplace and the built environment.
This includes industry developments, company news, case studies and application stories, product news as well as articles from leading authorities within the marketplace.
To find out more information about BFM Magazine or to subscribe, please visit
www.bfmmagazine.co.uk
Summer is your prime opportunity to prepare your estate for the seasons ahead.
At OUTCO, we help clients take full advantage of the longer daylight hours and drier conditions to address surfacing issues, manage vegetation growth, and schedule critical inspections.
With expert planning, professional insight and technology-led solutions, OUTCO keeps your outdoor spaces compliant, safe, and always one step ahead.
0800 0432 911 enquiries@outco.co.uk
Mechline Developments are excited to announce the launch of their latest AquaTechnix tap – the TX-i
Designed with the most advanced electronics on the market, Mechline’s intelligent TX-i boasts a whole host of benefits including a super-smart instant shut-off valve, extended battery life, and enhanced antibacterial properties as John Newell, Director at Mechline Developments, details:
“The huge water savings, hygiene and durability benefits of our brand-new TX-i tap are largely made possible thanks to our smart-valve, coupled with latest time of flight IP67 rated infrared sensor technology. This clever technology instantly detects hand motion without false triggers and provides instant shut-off. As such, water need not be wasted, and therefore money saved. To put this into perspective, operators of the TX-i can expect to reduce water consumption by up to 72% in comparison to a standard, traditional basin tap.”
This clever, contactless method of hand-washing also helps to reduce touch-points across an entire handwashing area. Increasingly, this is becoming a necessity in kitchen, bar, washroom and healthcare settings where minimising the spread of bacteria is paramount.
The AquaTechnix TX-i sensor tap is available in two sizes, 200mm and 300mm, offering flexibility to suit different installation needs. Designed for seamless integration, it can be easily fitted directly onto countertops. Its sleek design perfectly complements Mechline’s full range of basins, pairing the advanced
functionality of the TX-i with the durability and practicality of our BaSix Basin range.
Taking hygiene precautions yet another step-further, the TX-i is also configured to run an independent anti-stagnation flush every 24 hours. This service flush serves to prevent legionella colonies from forming.
Built to cope in the most demanding environments, the battery operated TX-i is designed to run for up to 5 years, or 365,000 hand-washing cycles. What’s more, the tap spout is engineered from highstrength tubular 316L stainless steel to provide superior sturdiness and strength and
hygiene, coupled with latest water aeration technologies and a PEX lined braided hose. Making it the perfect solution for retrofitting and upgrading existing facilities.
Universally suitable and easy to maintain and install, the TX-i comes complete with a universal horseshoe clamp that can be secured to any work surface up to 65mm thick. DZR and leadfree with 4MS valve fittings, the TX-i has been designed to satisfy the worldwide market.
For more information on Mechline’s AquaTechnix TX-i range, please visit https://www.mechline.com/tx-i/
Thomann-Hanry® have revolutionised the way building façade cleaning and restoration is achieved, through our patented conservation grade cleaning system ‘Façade Gommage®’.
The system reduces time, money, and the inconvenience of needing unsightly scaffolding. Works are normally completed in half the time of conventional methods and without the use of high pressures, harsh solvents, or damaging aggregates.
Thomann-Hanry® will serve as your principal façade contractor; we seamlessly manage all areas of façade restoration with minimal disruption — from surveys, permit application, restoration of stone masonry and render, intricate internal and external painting, window and roofing works, and our highly specialised techniques to delicately strip away layers of grime to unveil the original splendour.
With construction costs under constant scrutiny and site safety more critical than ever, Liftroller UK is helping real estate developers and project owners improve site efficiency through advanced material handling technology— now available exclusively in the UK for over a year.
The Liftroller system is a proven solution for moving large, heavy materials safely and efficiently into buildings—particularly useful during complex urban developments, mixed-use builds, and retrofit schemes.
“We’ve helped developers accelerate build programmes while reducing site disruption
and logistics costs,” says Jon Kates, Business Development Manager at Liftroller UK. “The savings go beyond labour—they include improved safety, fewer delays, and reduced reliance on scaffolding and reduce the repeated use of cranes.”
The Liftroller range includes:
• Liftroller Wall –Deliver plant and materials through existing facade openings, maintaining architectural integrity.
• Liftroller Floor –Improve ground-level logistics with minimal setup.
• E Wagon & E Mover – Electric, remote-controlled transport for internal or restricted-access zones.
✅ Fewer delays in handover schedules
✅ Minimised structural modifications during build
✅ Reduced HSE risk exposure
✅ Lowered equipment and labour costs
Liftroller equipment has been used successfully across flagship developments in urban environments, including multistorey apartment buildings, hospitals, data centres, and commercial office projects— making it a reliable choice for developers focused on efficiency and ROI.
To explore purchase or hire options, or request a project consultation: jon@liftrolleruk.com www.liftrolleruk.com
Follow: Liftroller UK on LinkedIn
Vanguard Healthcare Solutions is proud to highlight the success of its day case unit at Milton Keynes University Hospital, which has delivered significant benefits to the hospital, its staff, patients, and the wider community. Claire McGillycuddy, Associate Director of Operations for Surgery & Elective Care at the Trust, shared her insights on the transformative impact of the Vanguard solution.
The day case facility, comprising a mobile operating theatre and a recovery ward staffed by Vanguard’s clinical team, has dramatically reduced waiting lists and improved
operational efficiency. Within just three months, over 330 procedures were performed, reducing the overall waiting list by approximately 600 patients, including 554 long waiters. Claire emphasised the flexibility of the unit, which allows the hospital to adapt to waiting list pressures and address the most urgent needs across various specialties, including general surgery, urology, gynaecology, orthopaedics, and oral surgery. Claire also highlighted the positive working environment provided by the Vanguard unit, which has been praised by surgeons and staff for its calm atmosphere and efficient
workflows. Patients have expressed their appreciation for the seamless care and clear communication, noting the significant reduction in waiting times and the highquality experience provided by the Vanguard team.
The wider social value of the day case unit is evident in its ability to alleviate pressure on the hospital’s main theatres, enabling the Trust to focus on delivering exceptional care to its community. By addressing elective surgery backlogs and improving patient outcomes, the Vanguard solution has made a meaningful impact on healthcare delivery in the region.
Steve Juson, Managing Director,
Smarter Building Management Through Continuous Monitoring and Actionable Insight
As the UK edges closer to its legally binding net zero targets, building owners and facilities managers face mounting pressure to reduce energy consumption, cut carbon emissions and deliver more efficient spaces—without compromising comfort or productivity. But with modern buildings becoming increasingly complex, one question remains critical: how well are you using your energy data?
The Cost of Not Knowing
Energy is often one of the highest controllable costs in commercial buildings, yet it remains one of the least understood. In most organisations, procurement teams meticulously track everything from office supplies to service contracts—but energy often escapes the same scrutiny. The result? Missed savings, underperforming systems, and energy strategies that fail to deliver long-term value.
You can’t manage what you can’t measure—and measuring alone isn’t enough. Raw data must be transformed into insight. That’s the role of an Energy Management System (EMS).
Why a BMS Isn’t Enough
A Building Management System (BMS) is essential for real-time control of plant equipment like HVAC, lighting, and power systems. However, it’s not designed for long-term data analysis. It operates on fixed rules, and without ongoing adjustment, even a wellcommissioned BMS will drift from its original efficiency goals.
An EMS bridges this gap. Think of it like a car dashboard:
while the BMS steers and drives the building’s systems, the EMS provides the live feedback—energy consumption, performance metrics, trends— that helps you decide when and how to adjust course.
Too often, energy-saving measures are treated as oneoff initiatives: replacing light fittings, upgrading HVAC, or improving insulation. While valuable, these improvements rarely deliver sustained benefits without monitoring. A lighting control system, for instance, may be bypassed if it fails to meet user expectations— undoing any energy gains.
An EMS enables continuous monitoring of all building systems, highlighting inefficiencies before they become costly. Platforms like iNSIGHT EBIS (Energy & Building Information Software) from Synapsys Solutions
gather and analyse data across entire estates, turning isolated data points into actionable insights. Managers can easily spot anomalies, benchmark performance across sites, and develop long-term strategies that adapt with the building.
Data is often trapped in silos—different systems, formats, and platforms— making it difficult to get a clear picture. A successful EMS strategy requires integration.
That’s why Synapsys developed the SIP+ Data Interface, a device that collects data from systems including ModBus, M-Bus, BACnet, LoRaWAN, MQTT-enabled devices, and many more protocols. This means building managers can consolidate energy usage data from across their estate into a single, consistent platform, where it can be visualised, analysed, and shared.
The result? Faster decisionmaking, more targeted energysaving actions, and a stronger return on investment.
Energy efficiency is not just about systems—it’s also about people. Occupants play a key role in shaping how a building performs. But getting them to adopt energy-saving behaviours isn’t easy unless they can see the results.
That’s where an intuitive, realtime dashboard makes all the difference. From simple floor-byfloor comparisons to full estatelevel metrics, visualising energy use empowers everyone— facilities teams, management, and everyday occupants—to make smarter choices. Public displays in communal areas, for example, can highlight real-time usage versus historical data,
turning everyday decisions into visible, measurable actions.
As energy prices fluctuate and ESG reporting becomes more rigorous, the ability to demonstrate how and where savings are being made is vital. A robust EMS provides:
• Verified ROI for energy upgrades
• Accurate reporting for compliance and ESG frameworks
• Early warnings of underperformance
• Support for smart control strategies
• Engagement tools to change occupant behaviour
Whether managing a single building or a nationwide estate, integrating an EMS into your strategy turns raw data into one of your most powerful assets.
The journey to net zero is complex—but it doesn’t have to be confusing. At Synapsys Solutions, we help building owners and operators harness their data, simplify integration, and develop energy management strategies that truly work. By combining advanced data interfaces, cloud-based analytics, and expert support, we give you the tools to unlock long-term efficiency and real energy savings.
Let’s talk.
To find out how Synapsys Solutions can support your energy strategy:
• Call us on 01444 246 128
• Visit www.synapsyssolutions.com
• Email us at enquiries@ synapsys-solutions.com
ABM, the leading provider of facility, engineering, and infrastructure solutions, has been awarded a contract by Iron Mountain Data Center’s (IMDC) UK team to provide technical cleaning services at the global information management and data storage company’s first data centre.
The highly secure site occupies 4.5 acres in Slough and was originally built for one of the world’s largest banking institutions. The data centre offers multiple infrastructure designs with six data halls and marking-leading Power Usage Effectiveness as well as a loading dock, offices, conference rooms and break out spaces.
To deliver a market-leading service, ABM will deploy four permanent onsite team members, who will undergo training bespoke to IMDC. They are supported by mobile technicians and an in-house out of hours helpdesk to respond and adapt at speed to evolving business needs.
The yearly rolling contract will
see ABM’s Critical Solutions division provide elevated technical cleaning services using sustainable cleaning products within data room and server spaces as well as window and carpet cleaning, waste removal and feminine hygiene management.
As part of its strong sense of social purpose, ABM is employing local people for this contract and will be working closely with IMDC to strengthen its CSR objectives.
In addition to the use of specialist equipment and PPE, IMDC will benefit from the use of ABM’s proprietary technology, with the ability to log in and review data and trends to inform business decisions and aid cost savings, operational improvements and maximise productivity.
Lewis Cannell, Head of Critical Solutions at ABM, comments, “What began as a one-off technical cleaning project in a data hall has evolved into a long-term partnership with IMDC, aimed at elevating
operational standards at their flagship data centre.
“This achievement is testament to the expertise and dedication of our highly trained specialists, who consistently deliver world-class service in complex environments. Moving forward, the entire ABM team will collaborate closely with IMDC to implement a shared strategy centred on innovation, safety, technology, sustainability and people.”
Adam Gilio Miet, Senior Data Centre Operations Manager, said, “There has been a notable uptick in quality since ABM have taken over the contract with regular site visits by the area manager ensuring that we are all aligned on expectations and delivery, thanks ABM!”
ABM has extensive experience in providing high-quality, consistent FM services to data centre and critical environments, working with some of the biggest names in the sector, including Vodafone, Google, Santander and JP Morgan Chase.
Building & Facilities Management editorial content covers all the major FM areas of interest within the workplace and the built environment.
This includes industry developments, company news, case studies and application stories, product news as well as articles from leading authorities within the marketplace.
To find out more information about BFM Magazine or to subscribe, please visit www.bfmmagazine.co.uk
UK provider of temporary heating and cooling solutions, is pleased to announce the appointment of Matt Stapley as its new Technical Director. This strategic addition to the leadership team underscores the company’s commitment to technical excellence and innovation in the HVAC hire industry.
With over 25 years of experience in the HVAC sector, Matt brings a wealth of knowledge and expertise to Rapid Energy. His career has been marked by significant contributions to the development and deployment of energy-efficient heating and cooling solutions across various sectors. Matt’s leadership is expected to drive Rapid
Energy’s technical operations to new heights, ensuring the delivery of high-quality, reliable, and sustainable services to clients nationwide.
In his new role, Matt will oversee the technical strategy and operations of Rapid Energy, focusing on enhancing service delivery, expanding the company’s product offerings, and fostering innovation. His appointment is part of Rapid Energy’s broader strategy to strengthen its position in the market and continue providing exceptional service to its clients.
“I am thrilled to join Rapid Energy at such a pivotal time,” said Matt Stapley. “The company’s dedication to excellence and innovation aligns perfectly with my
professional values. I look forward to contributing to Rapid Energy’s growth and success in the HVAC hire industry.”
Rapid Energy offers a comprehensive range of temporary heating and cooling solutions, including packaged boilers, chillers, heaters, and air conditioning units. The company’s services cater to various industries, such as healthcare, education, construction, and facilities management, ensuring clients receive tailored solutions to meet their specific needs.
For more information about Rapid Energy and its services, please visit https://rapidenergy.co.uk.
Providing a platform to collectively improve the delivery of estates, facilities and patient services through peer knowledge sharing, expert insights and the presentation of the latest technologies and service solutions.
• Entry to the Exhibition is FREE OF CHARGE and includes access to a full programme of Keynotes and seminars.
• Upgrade to a Conference Delegate Pass to unlock exclusive access to an additional multi-stream programme, plus on-site extras.
Discover the 2025 programme online now
21-22 October 2025
Sandman Hotel Group UK & Ireland is boosting its sustainability commitment, with the introduction of the first smart water management technology featuring behavioural science - significantly cutting water, energy and CO2 emissions.
Showerkap’s system and sensors have been installed in 20 bedrooms as part of a ground-breaking trial at the four-star Sandman Signature London Gatwick Hotel in Crawley, which attracts guests from Gatwick, the UK’s second busiest airport, as well as visitors to London and Sussex.
The pioneering UK startup, based in Warnham, near Horsham, has designed a new platform that enables organisations to monitor and manage water remotely, while nudging users to make more eco-friendly decisions. The solution will also support the operational team with realtime reports - analysing and improving water use and efficiency and highlighting any potential safety risks and waste.
The innovation features small smartboxes in every room, which upload data from the sensors to a centralised cloud system, to remotely monitor and manage water temperature and safety. Working closely with hotel staff, the Showerkap team will help raise guest awareness about water scarcity and the importance of shorter showers to help conserve water. In future projects, guests will have the option to connect directly to the smart devices, with the ability to use the patented, fade technology, which gradually reduces the water temperature at the end of a shower - creating a ‘nudge’ and behavioural cue to promote shorter showers
and conserve water.
The hotel has a long-standing commitment to sustainability and resource conservationfrom its community work to recycling - resulting in it being the first hotel in Crawley to achieve Green Key status (the eco-label and standard of excellence for tourism facilities since 1994). This echoes an increasing trend for customers, with over 80% of travellers citing sustainable travel and hospitality as important[1].
Showerkap founder and CEO Steve Harding said: “We are delighted to be partnering with such a forward-thinking hotel group, which has sustainability at its core and which is committed to operating in the most environmentallyfriendly way. Every day in the UK, we send two billion litres of shower water down the drain, but we can change that using engineering innovation and the power of behavioural science to make taking shorter showers rewarding for guests.”
Sandman Signature London Gatwick Hotel general manager Gints Skieris added: “We are excited to be the first hotel nationally to adopt this new technology, which will benefit our local community, guests, staff and the environment. This will enable users to monitor and reduce water usage and, at the same time, empower people to make more ecofriendly decisions that will hopefully become part of their daily lives. We look forward to providing guests with the same high standards, while offering them the chance to be part of a unique initiative, which is kinder to the planet and which we hope the hospitality industry will collectively embrace to
bring about significant change.”
The issue of water scarcity is ranked by the UN among the top five global risks, with the hospitality industry among some of the planet’s biggest water consumers. A hotel can use an average of 1,500 litres per room per day and tourism can use up to eight times more water per person than the local population.[2]
Showerkap estimates that based on a hotel with 100 rooms, over a year, its innovation could save 2,190,000 litres of water and 13,500 kg of carbon, helping businesses to reach their Environmental, Social, and Governance (ESG) targets. Costs are also significantly reduced, saving around £6,500 for water and £15,000 for electricity.
Founded by engineer Steve Harding, Showerkap applies behavioural science to help motivate people to make better choices and take shorter showers, to conserve water, save money and use less energy. The innovation gives organisations – such as hotels and universities – the ability to track and analyse their water usage, measure CO2, detect abnormal events like leaks and maintain water safety.
With the average shower in the UK using around 150 litres of water, this not only exacerbates water shortages, but also has a significant impact on CO2 production, due to the energy needed to heat the water.
First opened in 1875, Sandown Park is a historic venue in British horse racing, playing host to a number of competitions. However, due to the rising maintenance costs of the existing flooring in the venue’s main hall –Surrey Hall – it was decided that new flooring would be installed. For this, RB Flooring Solutions suggested Forbo Flooring Systems’ innovative Allura Puzzle.
A renowned horse racing venue located in Surrey, Sandown Park is known for its rich history and picturesque surroundings, making it a
popular choice with racing enthusiasts. A versatile venue, it offers both flat and jumps racing, as well as restaurants, bars and hospitality suites catering to a number of events. However, maintenance of the venue’s Surrey Hall was considerable, with owners The Jockey Club needing to have the original flooring resanded and re-sealed every year. As well as the high costs associated with the works, it also led to the space being out of action once a year. For this reason, the organisation opted to have new flooring installed, with RB Flooring
Solutions suggesting Forbo’s Allura Puzzle luxury vinyl tiles. Robin Butcher, Director at RB Flooring Solutions, spoke more on this: “Originally installed in the 1980s, Surrey Hall’s flooring was becoming dated and a real financial burden on the owners, due to the regular maintenance needed for its upkeep. As a result, they wanted to change the flooring to something more modern, with the original idea being polished concrete. However, due to the near constant usage of the space, they couldn’t afford the downtime required to implement this. So, we suggested a floor
covering that would be quicker to install but also durable enough to last: Allura Puzzle.”
Part of Forbo’s Fast Flooring collection, Allura Puzzle is a unique adhesive-free luxury vinyl tile floor covering. With a large scale 96x96cm puzzle piece shape, each durable tile can be easily connected together and also easily removed, without compromising on the integrity of the flooring.
Robin explained why RB Flooring Solutions suggested Allura Puzzle: “The specification of Allura Puzzle meant that there were no preparation works required, in turn speeding up the installation time. What’s more, if any damage is caused to the flooring, it can be easily swapped out. It took our team of five floor layers just two and a half weeks to complete the entire installation, something that would have taken almost twice as long with traditionally adhered flooring solutions. Thanks to Forbo’s unique puzzle connector system, we were able to easily place the tiles down one by one, until the whole space was covered.
“Another reason we recommended Allura Puzzle is its durability. Like all LVTs, there is a tough wear layer that allows it to withstand sustained traffic, whether that be feet or wheels. In addition to this, the flooring system comes with a warranty, covering us for 10 years in the event of damage. This was extended by a further five years, as we also specified Forbo’s Coral Duo barrier matting in all entrances. This specification will help to further prolong the lifespan of the Allura Puzzle flooring, reducing walked-in dirt and moisture.
“We installed Allura Puzzle in the contemporary grey colourway, which was reminiscent of the original polished concrete look that the owners had wanted. The Coral Duo matting was installed in the Black Diamond design, chosen due to its modern look,
further enhancing the space’s new contemporary feel.”
Robin spoke about the finished project, saying: “The overall project went very well, and we have since returned to complete an additional staircase, with plans to work on a further two staircases and the food hall in the near future. There were some initial concerns about how robust a flooring we would need, due to the sheer number of forklifts, pump trucks and general movement of materials there would be each week. However, upon visiting the project a year on from the original installation, we were incredibly happy with how well it’s held up.”
A spokesperson from The Jockey Club spoke on the finished space, saying: “Forbo’s flooring has completely revolutionised how our Grandstand space looks and has had a hugely positive impact on customer experience. The team were really efficient to work with, delivering to our
tight deadlines and we are delighted with the outcome. The flooring has also held up really well to the wear and tear of race days and events since it has been installed, which we are also very happy with.”
Find out more about Allura Puzzle, here: https://www.forbo. com/flooring/en-uk/commercialproducts/fast-flooring/fastflooring-tiles-planks/allurapuzzle/byqcra#63604pz7
A New Web Shop selling Jung Pumpen replacement pumps and pump spares has just been launched by Pump Technology Ltd the UK’s largest authorised Jung Pumpen distributor and stockist.at www. jung-pumps.co.uk/shop/
Replacement waste water pumps, including the Jung Pumpen U3K, U3KS special, U6K, US62, US73, US102, US103 plus Compli pump heads and spares, are all available.
Pump Technology Ltd have specialised in the specification and supply of waste water and sewage pumps and pumping systems for over 30 years
The company’s head office and warehouse are based in Aldermaston, Berkshire, where they hold the most comprehensive stock of Jung Pumpen equipment in the UK. This means that for orders placed before 2pm goods will be dispatched same day for next day delivery to mainland UK.
Traditionally, customers would speak to one of the company’s pumping experts to order a pump and of course this is still a great option. However, if they are confident about the specification of the replacement pump required, the advantage of the Web Shop is that orders can be
paced immediately at any time of day or night, including outside of working hours.
Because Pump Technology Ltd are the largest supplier of Jung Pumpen equipment in the UK today they are able to offer competitive prices for all Jung Pumpen products. They
promise that if customers can buy at a lower cost they will do their best to price match. Just one more way that the dedicated team at Pump Technology Ltd are working to provide the Facilities Management sector with the best possible service!
The BATM range of single colour and tri-CCT, quadwattage modular LED battens from Knightsbridge – one of the UK’s leading manufacturers of wiring accessories and lighting – is versatile, efficient and easy to install, Knightsbridge’s uses advanced modular design to meet a wide range of lighting needs with fewer parts, reducing stock requirements for suppliers and installers.
The BATM’s flexible design allows for easy conversion to emergency, microwave, or a combination of both using plug-and-play accessories. This adaptability ensures the product can be customised quickly and simply, without the need for extra components or complex processes.
It is also an innovative replacement for the BATS LED battens, delivering the
same reliable performance with enhanced versatility.
Installation is quick and straightforward thanks to pushfit terminals, loop-in/loop-out wiring, rear and end 20mm conduit entries, and standard 600mm fixing centres. BESA box compatibility and a hinged gear tray further enhance convenience, ensuring a retrofit-friendly installation that saves both time and effort.
With an efficiency of up to 140 lumens per watt, the BATM reduces energy consumption significantly compared to traditional lighting fixtures. This improved efficiency lowers operating costs, reduces the carbon footprint, and delivers substantial energy savings over time.
The range can be further enhanced with a selection of accessories, including an emergency kit and a microwave sensor.
The emergency kit features a threehour lithium iron phosphate (LiFePO4) battery, ensuring reliable emergency lighting operation for maintained and non-maintained use. The microwave sensor is fully adjustable so that the detection area, hold time, and lux level can all be optimised for energy efficiency and user convenience.
5 and 6 are tri-CCT – 3000K, 4000K and 57000K – and each quad-wattage adjustable between 17W and 49W depending on the model.
Operating at 230V with an IP20 rating, the BATM entry batten offers a 4000K colour temperature and is available in wattage options of 10W, 20W, 32W, 36W, 43W, and 48W. Beyond that, the BATMCW4,
Warranties of five-years for BATM and seven years for BATMCW4, 5 and 6 ensure long-term performance and reliability, reflecting Knightsbridge’s commitment to delivering lighting products
that meet the highest standards of innovation and quality. By combining advanced modularity, installation simplicity, and long-term reliability, Knightsbridge’s BATM range sets the benchmark for LED battens. It is a versatile and efficient product that offers exceptional value for installers and end-users alike.
Clivet launches EDGE PRO the innovative air-to-water packaged heat pump from 4 to 16 kW, ideal solution for new buildings and renovations, thanks to the ALTODesign aesthetics, versatile and sustainable for heating, cooling and domestic hot water.
EDGE PRO heat pumps are an efficient and environmentally friendly solution for home comfort. Designed to provide heating, cooling and domestic hot water in homes as a valid alternative to traditional boilers, they use the natural refrigerant R-290, which has a very low
environmental impact. They are also quiet and easy to use. In terms of energy efficiency, they achieve class A+++ for heating with both low-temperature (35 °C) and medium-temperature (55 °C) water, while also offering outstanding performance in hightemperature water production.
Winner of the iF DESIGN AWARD 2025 and of RED DOT DESIGN AWARD 2025, thanks to its ALTODesign aesthetics, it is the ideal solution for new buildings and renovations, versatile and sustainable for heating, cooling and domestic hot water.
These heat pumps are also a valid answer for those installations where high quietness is required, guaranteed by the special design of the fans and the two silent operation modes. In addition, in EDGE PRO, the compressor is positioned inside a ‘silent box’ composed of several layers of soundabsorbing material specially designed to reduce compressor noise by up to -25 dB(A).
EDGE PRO stands out for its wide operating ranges, guaranteeing reliable performance down to -25
°C outside temperature: it can produce water at 80 °C even at -10 °C outside.
The extended operating ranges, combined with new control logics and different system types, allow a wide range of applications for these units. In larger systems, up to six units can also be cascaded.
The control system is intuitive, with a full-colour graphic interface that facilitates daily use. The Wi-Fi connection also allows the heat pump functions to be managed via a dedicated app, enabling remote control.
The EDGE PRO heat pumps are an integral part of the Clivet Smart Living system, compatible with CONTROL4 NRG, for efficient management of the entire apparatus. Equipped with the Smart-grid function, it operates within advanced electricity grids or in combination with photovoltaic systems.
EDGE PRO (4 to 16 kW) is the new air-to-water packaged heat pump with natural refrigerant R-290 for heating, cooling and domestic hot water in residential applications, also as an alternative to traditional boilers. It has some of the widest operating limits on the market, guaranteeing reliable performance down to -25 °C outside temperature. EDGE PRO can produce water at 80 °C even with -10 °C outside air. Energy class A+++ in heating with both low temperature water (35 °C supply water) and medium temperature water (55 °C supply water). Market-leading quietness. New ALTODesign aesthetics, combining elegance and functionality. This series was awarded the prestigious iF DESIGN AWARD 2025 in the ‘Product’ discipline, category ‘1.20 Building Technology’ and of RED DOT DESIGN AWARD 2025.
Every CHSA member has signed our Code of Practice, which includes the
As the number of electric vehicles (EVs) on our roads continues to grow, the way people think about charging is changing. Elizabeth Warren, Director of Public Charging at Mer, talks about how new charging attitudes and habits have opened up a unique opportunity for retailers.
When people transition to an EV, they are often surprised by how different the process of charging is. With petrol or diesel cars (also known as internal combustion engine or ICE vehicles), most people drive until they’re low on fuel, spend 5 minutes filling up in a petrol station, and carry on.
But for electric cars, charging from empty can take a long time – even a fast charge can take 15 to 30 minutes to charge a car from 0-80%, depending on battery capacity and temperature. It’s why in practice; EV owners top up more regularly.
If you have space for a home charger, regular charging is easy – plug in when you arrive home, and you’re always ready with a full tank. But if you’re heading further afield or are staying away from home for a longer period of time, then you’ll need to use public charging alternatives.
We’ve become used to seeing EV charge points in public places: in car parks, at motorway services and, increasingly, at retail parks. Public charging has become an essential part of EV infrastructure, with most people using a charging station more than 10 times in a year. And in fact, we’re seeing a continual increase in the number of EV owners who only ever charge on the public network.
We’re arguably still in the early stages of EV adoption – but the number of fully electric cars continues to grow. Nearly 1.5 million of the 34 million cars on the road today are EVs, and the Society of Motor Manufacturers and Traders (SMMT) projects that by 2030 it will be 9 million.
Nearly half (49%) of all EV charging is currently destination charging: where we choose to charge at a public location while we take part in other activities. The demand for destination charging options will grow alongside EV usage, and this creates a real opportunity for retail land owners and operators.
EV charging hubs are not only revenue-generating by themselves, but also deliver an increase in customer footfall and spending within the retail park. When drivers are choosing a public charging location, our research shows that they are heavily influenced by the amenities available on site. Over 50% of EV drivers say they use charging time
to visit a restaurant or café, and 46% say they use the time to shop or run errands.
It’s not just local people doing their weekly shop who use charging hubs at retail parks – they also provide a valuable service to longer distance travellers. Many people are increasingly choosing retail parks to break their journeys, swapping traditional motorway service stations (with a small number of food outlets) for a retail park with restaurants, shops and other activities.
In fact, retail parks that don’t have a charging hub are arguably at a disadvantage. Online shopping remains popular, and when customers do visit a physical store, they can be highly influenced by additional factors such as the ability to charge while they’re there. It’s similar to buyone-get-one-free thinking.
And the availability of charging facilities can also influence retailers looking to open new locations. It can bring new partners into the park more quickly and reduce vacant times for units.
Most retail parks are already designed around the car, sited in locations that are easy to access and with plenty of space for cars to park. It means you can usually install a charging hub without significant disruption.
But what are the other factors you need to consider if you want to install a charging hub at your retail site?
Chargers and speed of charge. The top factor in attracting people to a particular charging environment is the speed of charging that is available. A short dwell time will favour rapid chargers whilst an all-day or overnight car park may require fast chargers or a combination of both fast and rapid.
The number of charging bays. It’s important to install enough bays to meet demand, so people can reliably get a charging space, without there being so many that your
resources are underutilised.
Highly reliable kit. We’ve all heard stories from EV drivers who’ve stopped at a location only to find the chargers out of order. This can quickly have a long-term impact on people’s habits – you need to deliver a consistently good experience to keep people coming back to your charging hub – and therefore your retail location.
User friendly equipment. Particularly if someone is travelling outside of their usual area, finding and accessing a new charging location can be stressful. Equipment should be easy to use and with clear instructions on the charger.
Good customer service. We all accept that, no matter how good your setup, sometimes people struggle – or things don’t work as planned. Your charging supplier needs to have a great customer service team so that customers can be happy with the support they receive.
Early buy-in drives consumer habit
In an increasingly complex
and competitive retail environment, providing charging facilities at your retail site can bring you more customers, and as people wait for their cars to charge, you’ll see an increase in the time and money they spend with you.
If you don’t already offer EV charging, now is the time to invest. Consumers are quick to adopt habits, and slow to change them, so the earlier you become embedded in people’s routines, the greater the business value you can achieve. It’s important to make sure you are offering an excellent customer experience, not only in terms of the charging environment you provide, but also in customer support.
At Mer, our EV charging hubs provide a convenient way for electric vehicle drivers to charge. With retail parks already occupying strategic locations, we help land owners and managers to leverage a golden opportunity to generate incremental revenue. Download our Charging Hubs guide for more details.
Daikin UK welcomes the UK Government’s recent changes to planning regulations, which are set to significantly ease the installation of heat pumps across England. These reforms mark a pivotal step towards broader adoption of low-carbon heating solutions, aligning with the nation’s Net Zero ambitions.
The government’s Warm Homes Plan introduces several amendments to permitted development rights, including:
Removal of the OneMetre Rule: Homeowners are no longer required to maintain a one-metre distance between heat pumps
and property boundaries, eliminating a common barrier for installations in terraced and semi-detached homes.
⁃ Increased Size
Allowance: The permissible size for heat pump units has been expanded from 0.6m³ to 1.5m³, accommodating more efficient systems.
Multiple Units for Detached Homes: Detached properties can now install up to two heat pumps without additional planning permissions, facilitating advanced heating and cooling configurations.
Hamid Salimi, National Product Manager at Daikin
UK, said: “Daikin fully supports these regulatory changes, recognising their potential to broaden the access to heat pumps in the UK, with many households now considering them as viable alternatives to traditional heating systems. Through the simplification of installation processes, we hope to see an even greater uptake of heat pumps across the UK, which would be a significant step towards achieving the UK’s target of Net Zero by 2050.”
For more information about Daikin, and their heat pumps, visit: https://www.daikin. co.uk/en_gb/residential.html
Specifying CFA members for your flooring projects means you’ll be gaining a wealth of experience from vetted contractors with the knowledge and products to fulfil your specification with a sustainability criteria.
CFA members are part of a supply chain that includes specialist contract flooring contractors, manufacturers and distributors, all of whom promote the highest standards and expertise.
Summer is the prime season for outdoor FM teams to ramp up grounds care, tackle maintenance, and plan to keep estates thriving year-round.
Understanding the specific demands of the season is key to optimising the many and varied demands on grounds maintenance and outdoor FM teams. Invariably a key focus is on grounds care and addressing increased lawn and turf management needs, keeping shrubs and hedges in check, and keeping flourishing blooms and weeds under control. However, drier months are also ideal for proactively spotting issues and preparing for future seasons. Less rainfall and longer daylight make it the best time for site inspections and essential maintenance.
Before this busy period, it’s vital to work with staff and contractors to draft a work programme, create a seasonal schedule, agree on objectives, and set KPIs. Every estate has its own priorities, but this article covers some key areas to consider.
Inspections and troubleshooting - from drainage to surfacing, line marking and pothole repairs
Although the British summer doesn’t guarantee dry conditions, this relatively dry period is ideal to maintain drainage systems, address flooding issues and to inspect and maintain car parks to catch issues before the
onset of heavier rains and colder weather. Drainage issues can arise from the temperatures affecting piping, while summer growth can see increased root damage and debris in pipes that causes blockages or cracking. Hot, arid weather can also dry up drains to produce nuisance odours. All of these factors can increase the need for reactive investigations and repairs. To get ahead of these issues, proactively schedule drain surveys to identify any hidden problems and give you the insight needed to better manage maintenance costs. Early action can also help to prevent issues later in the year such as water damage or flooding in car parks.
Summer is also a good time to take action on surfacing repairs, e.g identifying and fixing cracks before they develop into potholes during the colder months. During the summer holidays when traffic levels are reduced, consider other repair tasks, such as refreshing line marking in car parks that can help to improve safety and visibility during the darker nights of autumn and winter.
Growing grounds maintenance demands
During summer much of the grounds care budget may be focused on maintaining the status quo (with more grass cutting and pruning demanding more contractor visits to keep lawns and shrubs in check). In addition, early summer is also ideal for improvements such as new bedding plants and hanging baskets to increase the aesthetic appeal of sites. Alternatively, this can be a good time to make changes that encourage biodiversity or improve environmental impacts – for example, wildflower meadows that add visual interest while also supporting pollinators. In this way, effective grounds care planning can proactively support organisations’ environmental (ESG) commitments. It’s also worth looking at how different
approaches can help to control budgets – for example, setting aside areas as wildflower meadows can also help to reduce the increased overhead of keeping lawns tidy.
Catching risks early
Proactive works aim to “fix the roof while the sun is shining” – well-timed interventions help avoid greater maintenance costs down the line. They also help prevent serious risks and liabilities.
Summer is an important time to keep an eye out for reportable invasive species such as Japanese Knotweed and Giant Hogweed. Japanese Knotweed starts its rapid growth in spring and flourishes vigorously during the summer. Making sure grounds staff are trained to identify species can be vital to ensure early intervention and control measures are applied by specialist contractors.
Tree surgery and arboriculture activity in autumn is key to keep sites safe ahead of strong winds and winter storms. Prepare during summer by scheduling a professional tree to identify risks and prioritise tree works.
Counter-intuitively, late summer is the best time in the calendar to start planning for frosts and snowfall. Prudent organisations work to lock in contracts for winter gritting and snow clearance at this stage to ensure budget certainty and guarantee of service provision. This is also a good time to engage new contractors as it will provide plenty of time for them to survey your sites to identify high-risk areas. Helping you take on every seasonal challenge
At OUTCO we provide year-round support to help our clients maintain the safety, functionality, and longevity of their external estate. During the summer this involves striking the right balance between managing the increased grounds care pressures of the peak growing season but also maintaining a forward view of challenges and risks ahead. Despite the budget pressures of this busy time, proactive planning and professional surveying is critical to identifying risks before they escalate and helping to plan essential maintenance with confidence.
For more information on how OUTCO can support your organisation make the most of its outside spaces this summer, contact us on 0800 0432 911 email enquiries@ outco.co.uk or visit www.outco.co.uk
The Public Sector Sustainability Association (PSSA) provides a professional association and network for all those working in the Public Sector who have a common interest in sustainability. The aim of the association is to bring together a wide group of people working across all areas of the Public Sector – to help educate, train, support and connect as we work towards a more sustainable future.
• Access to up to date info on all issues of sustainability affecting the public sector including the latest news, case studies, legislation, policy and reports
• Reminders and invitation to trade events, exhibitions, conferences and seminars involving sustainability
• Networking opportunities
• Discounted training and education courses
• Access to a PSSA Members-Only online forum to discuss issues, problem solve and connect (Launch date TBC)
For more information on becoming a member of the PSSA, please visit www.pssa.info.