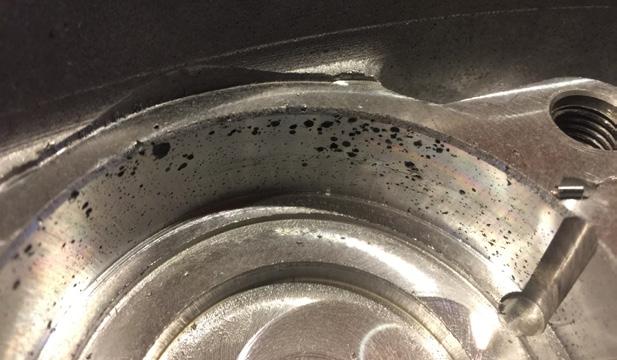
10 minute read
Vätgas i aluminium
Text av Tomas Liljenfors, vd på Bryne
Vätgas i aluminium
Vätgas som energikälla är en möjlig ersättare till fossila gaser vid smältning av aluminium. Som jag tidigare skrivit om i denna tidskrift används vätgas både som bränsle och som råvara i många kemiska produkter. Denna gång ska vi behandla den sida av vätet som inte är positiv, dvs vätgas som förorening. Väte är det lättaste grundämnet, men trots att en vätgasmolekyl är liten till storleken så får den inte riktigt plats mellan aluminiumatomer. Anledningen till att väte bildar porer i aluminium är för att den löser sig i smält aluminium men vätet får inte plats mellan atomer när aluminium stelnar. Vätgas i aluminium är en förorening som kan skapa stor skada i aluminiumprodukter. En felaktig design eller tillverkningsprocess kan skapa håligheter i form av vätgasporer hos aluminiumprodukten.
I smält aluminium kan det vara en viss mängd vätgas inlöst. En högre temperatur skapar större mellanrum mellan aluminiumatomerna i den smälta metallen så att fler vätgasatomer kan rymmas i metallen. Den inlösta vätgasen kommer främst från fukten som finns i omgivande luft men kan också komma från ugnsinfodring, metallråvaran eller andra tillsatsmaterial. En hög temperatur på metallen liksom en hög temperatur på omgivande luft ger en högre vätgashalt. Det är därför som vätgasporer vanligen uppkommer under fuktiga sommardagar när luftens temperatur är hög och mängden vatten som ryms i luften därmed också är hög. Ofta mäts luftfuktighet som relativ luftfuktighet. Mängden vatten i luften vid en relativ luftfuktighet på 50 % och en lufttemperatur på 10°C är mycket lägre än för samma relativa luftfuktighet vid 25°C.
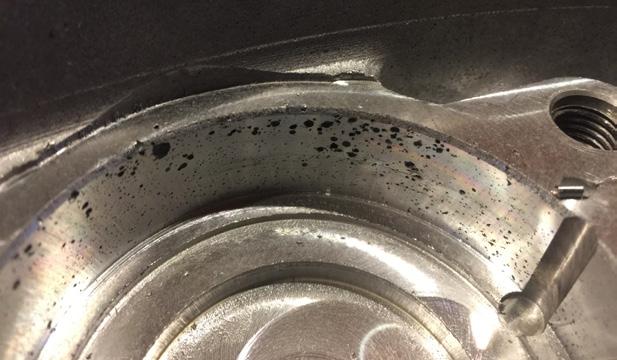
Bild 1 Vätgasporer i aluminium är typiskt runda. Storleken varierar från mikrometer upp till flera centimeter.
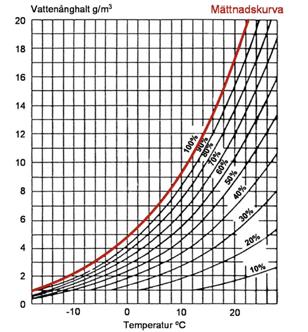
Bild 2 Relativ luftfuktighet mäts i procent. Diagrammet visar att den maximala lösligheten av vatten i luft är temperaturberoende och ökar medtemperatur. En relativ fuktighet på 100% vid 10°C motsvarar sammavattenmängd i luft som vid 20% relativ luftfuktighet vid 23°C.
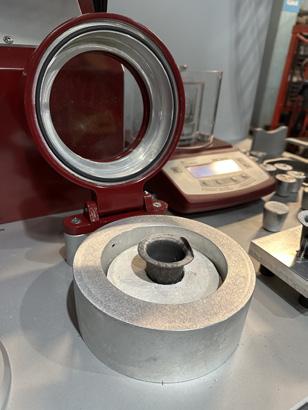
Bild 3 Reduced Pressure Test (RPT) används för densitetsindexmätningar, slaggprovning och andra vakuumtekniker. Denna utrustning tillverkas iTyskland för MK.
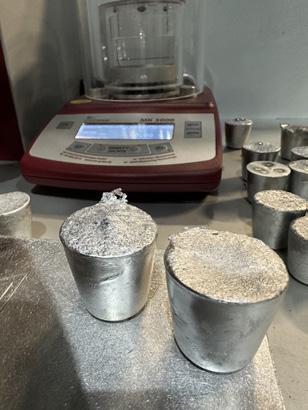
Bild 4. Två prover, ett som stelnat i vakuum och ett i luft, vägs för att fastställa densiteten på proverna.
Jag skulle rekommendera att mäta luftfuktigheten i lokaler där den smälta metallen processeras. Ett enkelt loggande instrument som mäter absolut luftfuktighet ger en enkel anvisning om och hur mycket vattenhalten i luften har förändrats sedan sist. Speciellt vid den plats där metallen hälls från ett kärl till ett annat spelar luftfuktigheten roll eftersom det smälta aluminiumet då exponeras av luften.
En annan viktig orsak till höga vätgasnivåer i aluminiumet är själva råvaran. Skrot som faller i den egna processen eller inköpt skrot har ofta ett tunt lager av fukt eller olja (skärvätska) när de smälts ned. Det går att tvätta och torka skrotet eller att använda en schaktugn där fukten förångas och försvinner med avgaserna. Även råvaruleverantörer bidrar med ett tillskott av vätgas. Det finns till och med tackproducenter som kyler sina tackor med vatten innan ytan har stelnat. Utöver en hög vätgashalt skapar detta också aluminiumoxider så att en del av det du köper som aluminiumråvara i själva verket är skräp. För varje millimeters tjocklek av en yta av en tacka som är oxid blir det ca 15 kg skräp per levererat ton aluminiumråvara.
För tackor som stelnat i luft kan man få en indikation på vätgasinnehållet genom att titta noga på dess yta. Vid högt vätgasinnehåll kan man se små ”maskhål”, som i själva verket är vätgasporer som vid stelnandet trängt genom ytoxiden. Ett tränat öga kan bedöma om en leverantör har avgasat metallen inför utgjutning eller inte, helt utan avancerad (och dyr) analysutrustning. Säkrare är dock att begära en mätning av halten vätgas i varje leverans.
Hur mäter man då vätgas? Den erfarne smälteriarbetaren kan se mycket med blotta ögat, men just vätgashalten är svår att se. Ett klassiskt vätgastest är att använda en gas-sten. Egentligen kan det vara vilken sten som helst så länge den är slät och torr. Efter att hällt metall på stenen låter man metallen svalna på stenen. När metallen börjar stelna drar man med till exempel en kniv genom metallen så att ett tunt halvstelnat lager av metall bildas på stenen. Mängden bubblor som syns kan användas som ett mått på huruvida det är mycket eller lite gas i metallen. Det kräver förstås lång erfarenhet och två olika bedömningar ger antagligen inte samma svar. Om man vill ge ett mer precist svar på om det finns lite eller mycket vätgas i metallen finns det andra metoder att tillgå, vilket dock kräver en investering i en apparat. Den enklaste apparaten, och antagligen den med lägst pris, förekommer under flera olika beteckningar. Reduced Pressure Test (RPT), DensitetsIndex (DI), Straube Pfeiffer, Ideco test, Dross test är alla namn på utrustning som baseras på samma teknik. Den smälta metallen som ska analyseras placeras i en kopp i en vakuumkammare. Innan provet börjat stelna pumpas luften ut så att ett undertryck uppnås. När en metall stelnar i undertryck så kommer den inlösta gasen expandera så att vätgasen bildar gasbubblor i provet.
Ett prov som stelnar i vakuum får ett utseende likt en svamp om den innehåller mycket gas och är helt platt om det inte innehåller gas. Vid densitetsindex så jämförs två prover, ett som stelnat i luft och ett som stelnat i vakuum (80mbar). Arkimedes princip används sedan för att bestämma densiteten för de båda proverna med hjälp av en noggrann våg och genom att väga ett prov i luft och sedan i vatten. Genom att dividera densiteten för det vakuumstelnade provet med det luftstelnade erhålls ett index, där ett lågt index anger att provet har mindre porer och ett högt index att det har mer porer. Det vore enkelt att här dra slutsatsen att mer porer innebär mer inlöst vätgas, men så lätt är det inte. Ett ”Dross test” använder endast vakuumprovet för att helt enkelt efter stelning kapa provet mitt itu och visuellt jämföra mängden bildad slagg. I Dross test undersöker man hur många oxider metallen innehåller. Samma utrustning kan användas för att både ge ett svar på vätgashalten och halten slagg (oxid). Vad händer då med provresultatet om mängden slagg ökar samtidigt som vätgashalten minskar? Eller tvärtom? Det är faktiskt så lurigt att en högre vätgashalt kan döljas av oxidhalt och tvärtom. Ett högre värde i densitetsindex säger att vätgashalten eller oxidhalten är högre.
Att utföra ett densitetsindexprov tar cirka 10 minuter, där provtagning och stelning tar 4 till 6 minuter plus en vägning som tar några minuter till.
Ett känt problem med vätgasprovning är att det är oerhört beroende av provtagningstekniken. Om provtagningsbägaren doppas ned i metallen ges ett mycket lägre värde än om man slevar ned metall i bägaren. Lika så är kondenserad fukt i provtagningskoppar och mätutrustning ett problem eftersom detta också påverkar resultatet kraftigt. Med en uppstyrd provtagningsmetod kan dessa metoder dock vara en god indikator med en robust teknik som faktiskt fungerar industriellt i en tuff miljö.
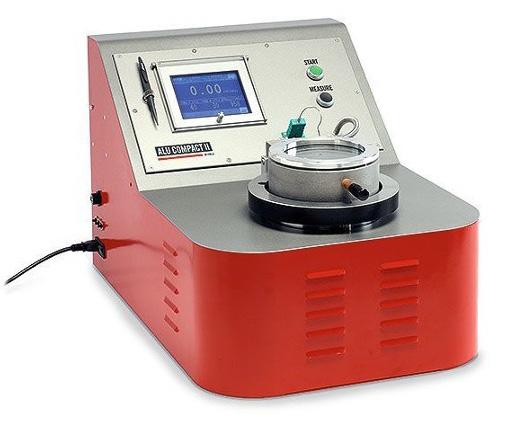
Bild 5 First bubble utrustning för effektiv mätning av vätgas i gjuterier, här från FMA (Liechtenstein).

Bild 6 Gasbubblor vid vätgasprovning med first bubble.
En variant på RPT tekniken är ”First bubble test” där provet igen placeras i en vakuumkammare, men denna gång en uppvärmd kammare. Sieverts lag säger att koncentrationen av inlöst gas i en vätska är proportionell mot kvadratroten av det partiella trycker vid konstant temperatur. Utrustningen sänker trycket i kammaren och mäter temperaturen tills den första bubblan uppstår på ytan av provet. Operatören använder sitt öga för att se när den första bubblan når provets yta och trycker då på en knapp. Utrustningen mäter metalltemperaturen samt undertrycket och beräknar vätgashalten i provet. Ett digitalt värde visas på instrumentet och mätningen tar mindre än en minut att genomföra. Den lämpar sig för mätningar i ugnar eller som stickprov i kontinuerliga processer. Även denna metod är robust och industriellt lämpad.
Utrustningar för att mäta vätgas har under åren utvecklats av de stora aluminiumproducenterna, där Telegas utvecklats av Alcoa och ALscan av Alcan, som båda lämpar sig för kontinuerliga processer. Det är metoder som baseras på att mäta termisk konduktivitet på en drivgas (vanligen kvävgas) som flödar genom en sensor som är nedstucken i metallen. Den porösa sensorn tillåter vätgasen från den smälta metallen att tränga in i det porösa materialet. Vätgasen följer med den flödande drivgasen så att en jämvikt mellan väte och kvävgas uppnås. Mängden vätgas kan avläsas genom att mäta ändringen i den termiska ledningsförmågan i gasen som sedan kan översätts till vätgashalt. De utbytbara sonderna finns för olika typer av legeringar, men dessa är känsliga och har begränsad livslängd, och kräver att hanteras med varsamhet. Det tar typiskt 5 till 10 minuter för utrustningen att ställa in sig vid start för att därefter mäta kontinuerligt i en flödande metall. Metoden lämpar sig inte för stickkontroller eller stillastående metall i till exempel hållugnar.
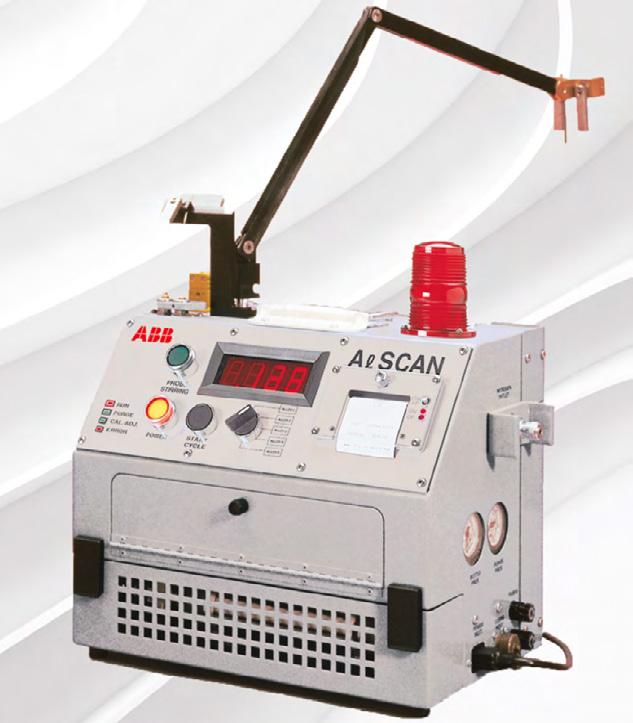
Bild 7 ALscan vätgasmätningsutrustning från Kanadensiska ABB finns på många råvarutillverkande företag.
På marknaden har utrustning för elektrokemisk vätgasmätning med mer avancerad elektronik utvecklats. De första utrustningarna såg dagens ljus för mer än 20 år sedan men återkallades för att de inte var tillräckligt robusta. Dagens generation baseras på teknik som ursprungligen utvecklades för bränsleceller men som nu finns på marknaden och kan köpas både som mobila enheter som stationära. Även för dessa instrument används en flödande gas och en mätsensor som sänks ned i metallen. Sensorerna baseras på keramiska halvledare som ger olika elektrisk potential för olika vätgashalter. Dessa keramer har en struktur som tillåter vätgasjoner (det vill säga protoner) att fylla vakanser i den keramiska kristallen. När de positiva protonerna tar en plats i kristallen kan en potentialskillnad (likspänning) avläsas över kristallen. Den avlästa spänningen kan relateras till vätgashalt så att instrumentet mäter vätgasen i metallen. För att klara den tuffa miljön i smält aluminium används en termisk stabil keram som baseras på calcium-zirkonat (CaZrO3) men som dopas med indium för att få rätt känslighet mot vätgasjoner. En mätning utförs genom att sätta på ett gasflöde innan mätstickan nedsättes i metallbadet. Efter cirka 5 minuter har instrumentet stabiliserats och mätning kan påbörjas. Mätningen kan ske kontinuerligt eller under begränsad tid. Sensorerna för denna typ av utrustning är mer robusta än tidigare sensorbaserade utrustningar, men bör fortfarande hanteras med silkesvantar. Att hantera känsliga sensorer, gasflaskor, och elkopplingar i en tung industri är en utmaning. Som laborativt instrument är dessa instrument noggranna, men får än idag anses vara för ömtåliga för de flesta industriella applikationer. En fördel är att tekniken mäter vätgashalten och inte en kombination av vätgas- och oxidhalt som vakuumteknikerna gör.
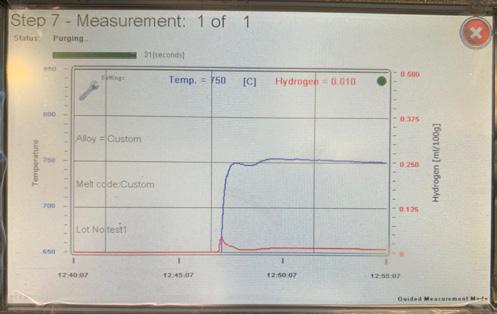
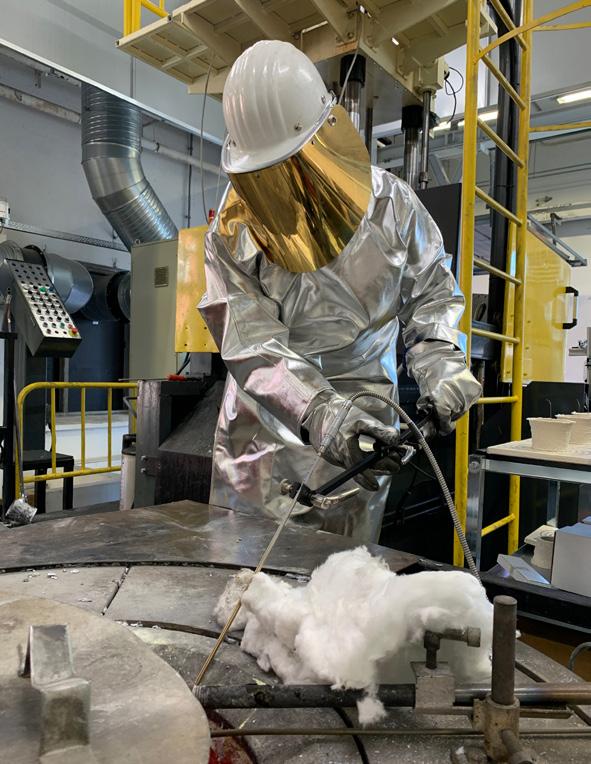
BILD 8-9 Hycal är ett exempel på elektrokemisk vätgasmätning med fasta keramiska elektrolyter. Hycal tillverkas av EMC (England)
Sammanfattningsvis behöver man mäta för att säkert veta. Att mäta är inte alltid så enkelt. Man kan tycka att med avancerad teknik skulle det vara svårare att mäta fel. Tyvärr är många av mätmetoderna för varma processer helt avhängda av operatörsutförandet. Akademiska mätutrustningar fungerar dåligt i industriell miljö och skapar ibland mer oreda än sanning. Jag tror vi kommer se fler mätmetoder användas industriellt för att möta de nya utmaningarna med till exempel att ha mer återvunnen metall i högprestandaprodukter. Viktigt är att metoderna är robusta och lätta att använda. Att tro att man mäter rätt men i stället mäta fel är värre än att inte mäta alls.