
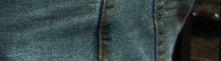
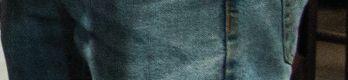

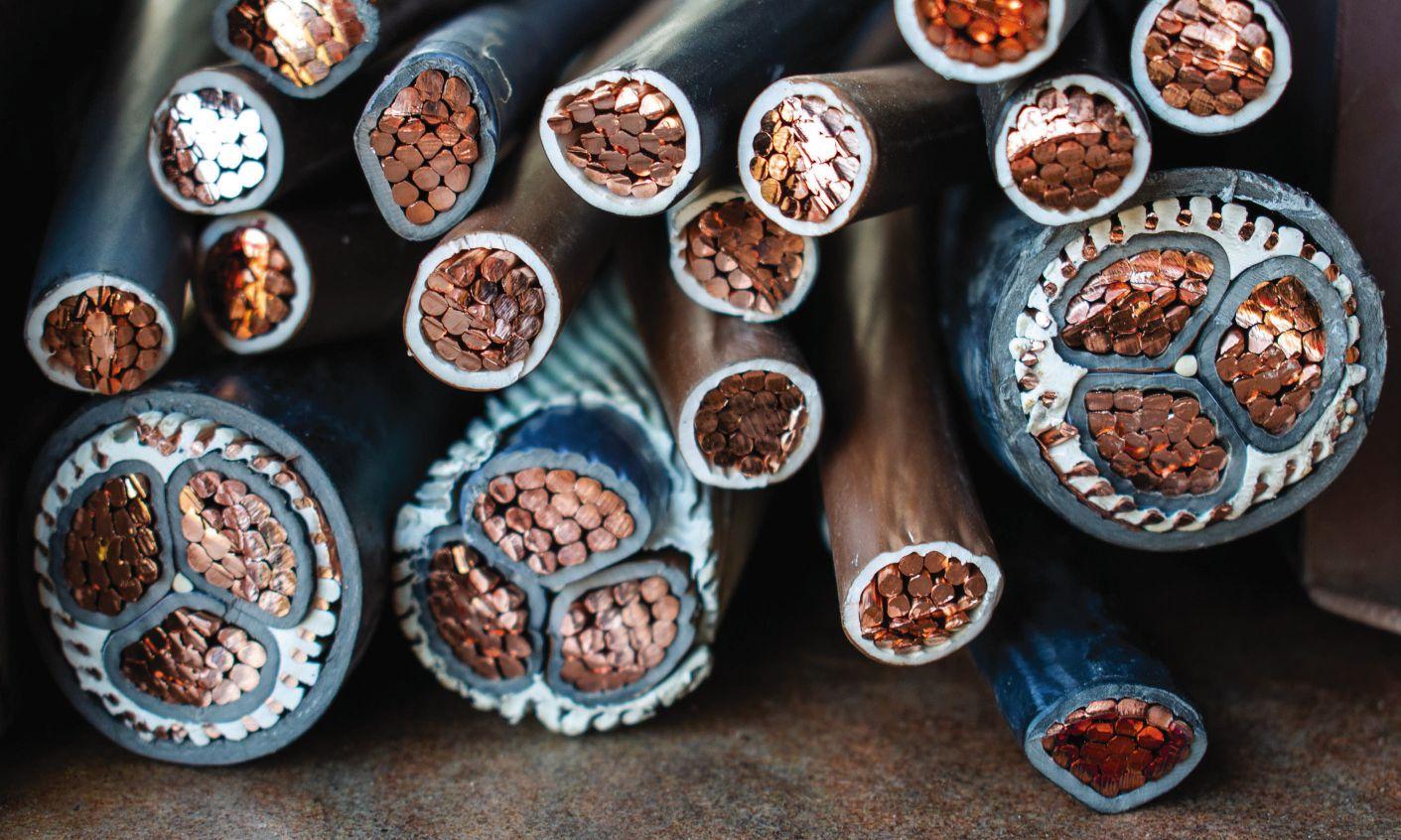

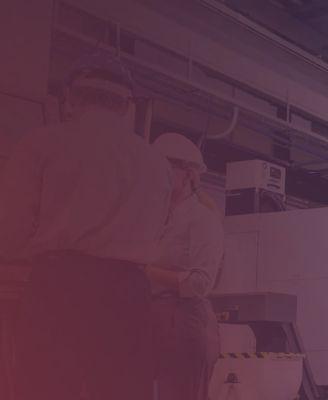
Unlimited Licensing Model
Add unlimited clients, screens, tags, connections & devices.
Cross-Platform Compatibility
Ignition works with any major operating system, even iOS and Android.
Install on a server in just 3 minutes, push updates to clients everywhere, instantly.
Build Mobile-Responsive HTML5 Applications That Run Natively on Any Screen
System Integration Views
6 Editor’s note: Best of a Breed
7 SIs bring automation advances to an installed base of legacy systems
2024 System Integrator of the year
8 Systems integrators apply technology to very human endeavors
2024 System Integrator Giants
13 The Time is Now: Labor and skills shortages justify increased automation; SIs occupy key positions in today's supply chains; SI Giants embrace the opportunities
Integrators in action
24 Integrators address competing production priorities
27 Batch solutions specialist ECS and Inductive Automation deliver for AmeriQual
30 Process clarity achieved using Industry 4.0 solutions
32 Enhanced technology addresses manufacturing challenges
34 The worth systems integrators bring to industrial automation
36 The role of data in navigating change
39 Robotic cell alleviates labor shortages for Tier 1 automotive supplier
42 The dark side of the IT/OT integration equation
44 American SpiralWeld Pipe drives efficiency through automation
46 Innovative integration extended by main automation contractors
See our digital edition for full coverage
System integration vendor partners p. 48
System Integration corporate close-ups p. 49
With the AutomationDirect
network, good help is never hard to find.
AutomationDirect’s SI Direct program provides expert system integration service to AutomationDirect customers, with particular emphasis on programmable controller, HMI, and motion products. These numerous ready-to-hire integrators, across the USA & Canada, have demonstrated specific product and application expertise and also receive ongoing training and equipping assistance from AutomationDirect.
Hire a skilled SI Direct integrator for help with:
• Electrical design
• Software programming
• Panel building and assembly
To learn more about the SI Direct program or to find the SI Direct integrator near you, go to: www.automationdirect.com/si-direct
• Turn-key systems
• Field service needs
• Consulting services
FREE CONFIGURATION SOFTWARE with thousands of ready-to-use objects
The NEW C-more CM5 HMI series offers low-cost, high-performance HMIs in sizes from 4 inches (only $340.00) to an impressive 22 inches (only $2,299.00). With an amazing 1.6 GHz processor in the larger units (10” and above) and 43 Mbytes of memory, these HMIs provide better trending, extra data storage, faster communication, improved file types, and 16.7 million screen/object color options.
All CM5 panels have serial and Ethernet ports (dual Ethernet ports on 10” or larger models) that support many of the most popular industry protocols, including EtherNet/IP, MQTT, and Modbus. The included USB ports provide in-an-instant connections for keyboards, barcode scanners, memory storage, etc. and the embedded SD-card slot provides easy project transfers or up to an additional 2TB of data storage (depending on model) for important log files. Plus, all C-more HMIs come with FREE, powerful, easy-to-use programming software and FREE technical support!
• Autonomous vehicles tackle labor and supply chain complexities
—Mike Belzen, RAMP, Inc.
• Coty Cosmetics saves half a million dollars with flexible cobot application
—Bryan Bird, Universal Robots
• Knowledge and experience actualized by powder processing technology
—Doan Pendleton, Vac-U-Max
• Pharma manufacturer embraces supply chain risk mitigation practices
—Bryon Hayes, Grantek
• Tea manufacturer enhances flow synchronization and efficiency
—Nathan Ferrin, Cornerstone Automation
• Calibration and asset management integration deliver productivity gain
—Heikki Laurila, Beamex
• Chevron Phillips addresses enterprise demand for real-time process data
—Matrikon
THE HISTORIAN Edmund Gibbon in his Decline and Fall, speaks of a field general who “transported his person to the scenes of danger,” or, as in a chess game, to the points of greatest tension. And that’s what systems integrators do. Systems integration brings together for a one-time event a menu of role-defined individuals to execute a project in a constrained environment that requires highly trained individuals to execute detailed, complex protocols. At the same time, flexibility may be the group’s mostly highly prized individual behavior. Talk about wearing two hats.
It’s possible to wax rhapsodic on the topic of systems integration because history’s most renowned military and scientific engineering breakthroughs were all case studies in systems integration. The Global System Integrator Report’s narrative may take place on a smaller scale. But if you think about it, even the grandest decisions are influenced by the dynamics of small work groups.
The System Integrator of the Year program selects winners in three categories defined by annual SI-related revenues: small, medium and large. Coverage begins on page 8, and includes some relevant comments by engineering managers at the winning companies on current issues that SIs and those who partner with them are sure to find of interest.
Extensive case study coverage based on a wide solicitation from integrator companies includes more than a dozen examples, including digital-only coverage. Other editorial features mirror the issues addressed by the System Integrator of the Year winners, including the critical relationship between the information and operations technology functions, growing supply chain complexity and 21st century project management ways and means. Finally, a good number of the case studies address robotics applications.
Of course, many of the case studies talk about the familiar combination of PLCs and supervisory control, but today’s SCADA environments keep pace with
“
Systems integration brings together for a one-time event a menu of role-defined individuals to execute a project in a constrained environment that requires highly trained individuals to execute detailed, complex protocols.“
technology’s most current advances, including edge and cloud, enterprise integration and growing use of analytics and artificial intelligence. GSIR
Kevin Parker is a content manager at CFE Media & Technology.
Jose Rivera,
CEO, Control System Integrator Association (CSIA)
Plenty of opportunity, but you need to know your stuff
Business boomed for systems integrators the last several years, while slackening a bit recently. Some welcomed this assuredly temporary return to a more sustainable pace.
Let’s look at the drivers of this dynamic technology services market, including those specific to systems integration. Let’s ponder what opportunities the current market state suggests, as well as what SIs might do to seize these opportunities.
While COVID-19 seems to be in the rear-view mirror, it was a cataclysmic global event. Several SI market drivers derive from this post-pandemic dynamic. For one, a commitment to supply-chain resiliency contributes to increased re- and nearshoring.
However, the pandemic dramatically reduced the available labor pool. Labor constraints impacting manufacturers ended up setting the pace for automation projects and SI work engagements. At the same time, engineering managers are demanding broader solutions from management, often expanding a project’s scope. Unfortunately, SIs themselves encounter a competitive labor market when recruiting.
The relationship between goods makers and system integrators has expanded in recent years. Manufacturers most often opt to focus on key strategic areas. Some still assign automation of manufacturing processes — their secret sauce - to internal teams. The rest engage the experts: design firms, EPCs (engineering, procurement and construction) contractors, automation equipment providers and SIs.
Manufacturers do today what they only dreamt about in the past. Deploying computational power on the plant floor is what smart manufacturing is about. But again, it expands the scope of work SIs are asked to perform.
While interfaces are ever more friendly, integration remains a challenge due to an installed base of legacy equipment. One way SIs play an expanded role is as consultants to goods makers overwhelmed by a myriad of possibilities.
Besides specializing in operations, enterprise or supply chain automation, many SIs focus on the
industry verticals in which they’re experienced. While all industries evolve, some see more dramatic transformations.
System integration market fundamentals look solid for years to come and represent an opportunity. SIs should consider the following. Realistically assess company strengths and weaknesses to set a viable growth strategy with realistic targets. Not every SI company has the same capabilities.
Develop a broader perspective by joining CSIA and attending the annual conference to benchmark with peers and collaborate with vendor partners.
The talent shortage will persist. As a business driven by talent resources, SIs need to to scale their workforce to leverage boom periods. SIs should reexamine their approaches to recruiting and onboarding. If STEM graduates are highly sought for, how can they be won over? Are there unidentified non-STEM resources available?
SIs having the competence and desire to grow quickly should explore the following options:
• Hire resources that help deliver on newer opportunities: digital transformation consulting, on-going services, software license management, cybersecurity and others.
• Experiment, understand and embrace new business models. Automation suppliers feature application subscription models. Can an SI leverage subscription models?
• In general, end users find it easier to contract for OPEX versus CAPEX funded projects.
Opportunity often entails risk. The automation market has benefited from exciting growth backed by solid fundamentals. Opportunities are abundant, but not all SIs will benefit. Some will fail to adapt to an evolving market and lose out. Others will move forward even if they, just like the rest of us, are a bit unsure of the final destination. GSIR
Jose Rivera has been CEO of the Control System Integrators Association (CSIA) since March 2015.
“SIs need to to scale their workforce to leverage boom periods. SIs should reexamine their approaches to recruiting and onboarding.“
—Jose Rivera, CEO
Interstates, Sioux Center, IA. - Above $30 million
Polytron, Duluth, GA. - $5 million to 30 million
APCO, Inc., North Salt Lake, UT. - Under $5 million
MANY great control system integrators exist, and many are expanding system integration capabilities and talent to help clients remain competitive, relevant and useful in an accelerating world of technology developments and market demands. Congratulations to the applicants who took the time to answer questions and assembled supporting documents to meet requirements to become finalists. Thank you.
Meet the 2023 System Integrator of the Year judges, who volunteer time for the challenging and rewarding selection process. They are asked to rank the finalists in each of three categories, divided by system integration revenue. Judges consider the assembled descriptions, metrics and examples of business skills (a thriving business enables engineering creativity), technical competence and customer satisfaction.
Dennis Brandl, chief consultant, BR&L Consulting, www.brlconsulting.com
Larry O’Brien, vice president of research, ARC Advisory Group, www.arcweb.com
Don Roberts, principal, Exotek LLC, www.exotek.com
Shari Worthington, PhD, president, Telesian Technology Inc., www.telesian.com
Mark T. Hoske, content manager, Control Engineering, www.controleng.com
Kevin Parker, content manager, Plant Engineering, www.plantengineering.com
Steve Rourke, co-founder, CFE Media and Technology, www.cfemedia.com
Chris Vavra, content manager, CFE Media & Technology, www.cfemedia.com
While winners are announced in the Global System Integrator Report, a supplement to the November/December 2023 issues of Control Engineering and Plant Engineering, the award is dated for the following year, in recognition of anticipated excellent system integration work to come. Note that prior winners are also found in the Control Engineering and Plant Engineering System Integrator of the Year Hall of Fame found at www.controleng.com/SIY. Now, please, learn more about the 2024 System Integrator of the Year companies in three categories.
Edited by Kevin Parker, content manager, CFE Media, kparker@cfemedia.com. Chris Vavra, web content manager, CFE Media and Technology, collaborated on questions. Amanda McLeman, director of research and awards programs, administers the System Integrator of the Year program.
As the workplace changes, the integration imperative persists
Systems integrators are a diverse lot. The same is true of the three winners of the Control Engineering and Plant Engineering System Integrator of the Year awards. To start, the winners occupy different size categories based on revenue. Further, integrators may be regional, national or international. They may focus on specific vertical industries, such as discrete automotive parts manufacturing or batch-process production in food & beverage. Finally, their focus may be on the control system, operations management or business enterprise, or some combination of the three.
At the same time, integrators hold much in common. Below please find some trenchant comments on topics of current interest from this year’s system integrators of the year. We salute and thank them.
“Automation, at its heart, is about using technology to deliver resources and goods to the world, and some of what we are most proud of stems from the impact we’ve been able to make,” said Eric Smith, president of APCO Inc., North Salt Lake, Utah, winner of the System Integrator of the Year Award in the small system integrator category, i.e., under $5 million in SI-related revenue.
“Something that comes to mind is the impact we have had within the state of Utah on both fresh water and water reclamation,” Smith said. “A large percentage of the state’s population gets water from systems that we have had an important hand in setting up. That isn’t to say that there aren’t many other people and organizations that are primarily responsible, but to the extent we’ve played a part it's something we’re proud of and we are thankful for our association with those organizations.”
APCO also participates in include petroleum refining, mining, and manufacturing in the medical and food industries.
“Being recognized and receiving this award is significant. It is tangible representation that our core values of character, service, excellence, passion, creativity, trust and teamwork are being lived out in dayto-day work recognized by our clients, suppliers and the industry. It reflects our mission statement: Putting
innovation to work and making a positive impact on the quality of life.” said Ron Rich, CEO, Polytron, winner in the medium system integrator category of $5 to $30 million in SI related revenue annually.
With the proliferation of the industrial Internet of Things (IIoT), cloud computing and analytics, not to mention the dawn of AI-based applications, some experts say there’s more technology innovation coming to light at the moment than any time since the introduction of programmable logic controllers (PLC), enterprise resources planning (ERP) and computer-aided design (CAD) in the 1980s.
As the technology has evolved, the tools that a systems integrator uses to accomplish client projects, as well as run its business, changes as well.
LARGE SYSTEM INTEGRATOR CATEGORY
$30 million and above system integrator revenue
“We see awareness building about important concepts related to IT and OT, and I think it is great that more people are getting cross-training on understanding the differences between the two,” said Smith.
Manufacturing environments have always focused on maximizing both uptime and efficiency, said Daren Dieleman, VP of operations, Interstates, winner in the large system integrator category for companies with annual SI-related revenues of $30 million or more.
“With the OT environment connected, the overall drivers of uptime and efficiency remain but also include the need to protect and understand data flowing from devices. Clients ask integrators to shield their data and facilities from cybersecurity threats, while simultaneously asking them to organize and interpret data from an increasing density of devices and sensors into actionable intelligence,” said Dieleman.
The expectations surrounding this activity are central to success, Dieleman added. They include clear communication between IT, OT, and definition of roles and responsibilities for all parties; onboarding of human and device resources; and assistance in selecting the right infrastructure to accommodate the goals of all parties.
MEDIUM SYSTEM INTEGRATOR CATEGORY
$5 million to $30 million in system integrator revenue
In recent years, “We’ve grown the number of manufacturing clients that we’re helping develop and implement their long term, sustainable Smart Manufacturing strategy and journey,” said Richard Phillips, director of smart manufacturing, Polytron.
Too many manufacturers struggle with how they should start this journey, not to mention lack of awareness of best practices, technologies to use and architecture, Phillips said. “Many have experienced the ‘pilot purgatory’ phenomenon and hesitate to continue funding these initiatives though they realize success is needed to stay competitive.”
The global supply chain, in the wake of the pandemic, has had a significant impact on SI clients and projects. Interstates’ Dieleman pointed to his company’s use of a dedicated supply chain team that supports the system integrator’s projects and clients and that has proved an asset in recent years. “We have seen projects get delayed, but in general, we continue to work closely with our vendors, partners, and clients to ensure projects can be completed as planned.”
Dieleman shared some specific ways and methods to address supply chain challenges:
• Standardization: allows for equipment to be purchased early before a detailed design is accomplished. It can shorten the design time needed to specify a custom equipment order.
• Flexible product selection: Work with vendors to select equipment options that minimize lead time impacts or actually in stock. Small changes to features can make a large impact on availability.
• System design approach: For electrical and control systems, consider what can be done to allow work to proceed despite long lead times for equipment.
Rande Allen, VP of sales at Polytron, said project managers now aggressively assess and manage supply chain risks as part of project planning. This involves identifying potential vulnerabilities, establishing contingency plans, and diversifying supply chain sources to mitigate future disruptions.
Allen also noted that to mitigate supply chain challenges, clients are more receptive to digital solutions such as supply chain planning and execution software, predictive analytics and real-time visibility tools.
“It is important for project managers to closely monitor supply chain issues, adapt their project plans accordingly and establish strong communication channels with suppliers and stakeholders to address any potential impacts on project delivery and success,” Allen said.
Automation systems sit at the heart of customer processes, Smith said. “The control system is the glue that holds the process together as the eyes and ears of the operations staff. Solid relationships are important to reduce friction and ensure problems are solved effectively and quickly, but particularly with the critical nature of the control system in enabling system function."
Working with an integrator looking after a customer's best interest can make all the difference in making good decisions that will have a long-term impact for the client. “We are the clients' advocate, supporting their decision making with a frank and honest relationship,” Smith said.
Interstates’ Dieleman, like all engineering project managers, has thought about the management of complex projects. “Interstates is a process-driven organization and has benefitted from its involvement in the Control Systems Integrator Association (CSIA),” he said. “We have been certified seven times by CSIA.”
In addition, he said, Interstates developed a 22step project methodology that covers every aspect of a project, from project initialization through project planning, execution, monitoring, controlling and closing. Each step in the methodology includes template meeting agendas and forms and instructions on locations where deliverables should be stored.
Polytron's Allen noted that the waterfall methodology is the most common in industry when it comes to traditional projects, involving sequential phases where each is completed before moving to the next. It emphasizes thorough planning and documentation.
However, depending on the project type and timeline, other methodologies include the following:
Agile methodology: Agile methodologies, such as Scrum and Kanban, prioritize flexibility, collaboration and iterative development. They focus on delivering value to customers in shorter cycles, allowing for frequent feedback and adaptation.
Lean philosophy: The Lean approach aims to eliminate waste, optimize processes, and deliver value efficiently. It emphasizes continuous improvement and customer-centricity.
Six Sigma: Six Sigma focuses on reducing defects and improving quality by utilizing statistical analysis and process improvement techniques. It aims to minimize variations and enhance process efficiency.
With “pervasive digitization” in recent years, these methodologies and philosophies have evolved, Allen said.
SMALL SYSTEM INTEGRATOR CATEGORY
Under $5 million in system integrator revenue
“For example, agile methodologies have gained significant popularity due to their ability to adapt to changing digital landscapes,” he said. “Agile principles have been embraced beyond software development, extending to diverse industries and projects, including ours.”
In a world where many people spend the best part of their day in front of a computer screen, system integration is highly defined discipline but benefits from flexibility as much as anything.
“The best thing our young engineers have going for them is great mentors,” said Smith. “We believe in building up those around us and really emphasize this as a core within our company. I think the new engineers feel this and benefit from the wealth of experience that their peers have to offer. Additionally, we provide both internal and external training aligned with their role. Specific training may be related to PLCs, HMI packages and best practices, networking, cybersecurity, electronics, regulatory control and data science, to name a few.” GSIR
Kevin Parker, is a content manager at CFE Media & Technology.
Jason Deets, Group manager, Chemicals, RoviSys
Aglobal supplier of agricultural commodities overhauled its outdated control infrastructure at one U.S. facility. With the initiative, the company also developed a template to replicate at its other sites throughout North America.
A vital link in the producer-to-consumer food chain since the early 1900s, this goods producer grew and evolved, focusing on innovation and quick response to consumer food trends, while adding capabilities such as value-added processing, refining and milling.
At the Illinois facility, the company shifted from producing chicken feed to refining soybean oils for in-demand food products and healthier frying oils. The refinery made food products on the leading edge of consumer preferences, but the decades-old control system was a drag on operational efficiency. The company opted to bolster competitiveness by modernizing its control backbone.
The Illinois facility ran multiple product recipes simultaneously and performed quick changeovers of production lines for flexible response to variable demand.
Unfortunately, the control hardware was approaching obsolescence. Operational data was unreliable. System reporting and analytics failed to support meaningful, actionable insights. Engineers and operators struggled with system alarms and interfaces. Maintaining the system was onerous because replacement parts were hard to find — and expensive when available. With the replacement decision made the focus shifted to implementation, and establishing a model planned for use at other company locations as part of a ten-year digital transformation initiative.
This project was in the proverbial “sweet spot” for RoviSys, which brought to bear more
than three decades’ experience with control of batch production environments in food & beverage and other industries. The goods producer selected Rockwell Automation hardware and software for its control platform. RoviSys is a Rockwell Automation Platinum System Integrator Partner – the highest level of partnership within the Rockwell program.
A nine-month timeline was agreed upon. Commissioning coincided with the facility’s annual two-week maintenance shutdown. RoviSys dedicated six full-time engineers to bring the project to a successful conclusion.
Engineers defined project scope, goals and benchmarks as well as requirements and risks. The team drafted functional specifications and offered system recommendations, including use of Rockwell FactoryTalk Historian to capture real-time process and production data and Rockwell FactoryTalk Batch to reduce recipe management complexity.
Finalizing project parameters and details was a collaborative effort between RoviSys and the goods producer’s leadership and operations teams. With plans approved, coding and implementation began. RoviSys conducted factory acceptance testing (FAT) at its engineering office in Aurora, Ohio.
Engineers worked around the clock during the two-week installation. Thorough recipe and phase testing followed.
The complex implementation and start up was delivered on time and budget. While the goods producer hoped to recoup its investment in six months, the company realized a return on investment (ROI) within three months. The result has served as a catalyst – and a model –for similar initiatives at other sites throughout North America. GSIR
A WORLDWIDE LEADER in automation and information solutions, RoviSys has made businesses more secure and more profitable since 1989. We deliver solutions that drive productivity, improve product quality, increase asset utilization and integrate technology. Our reputation is built on technical expertise, dedicated customer service, quality, and continuity.
www.rovisys.com
• Process Automation
• Building Automation
• Discrete Manufacturing Automation
• Warehouse Automation
• Control Systems Integration
• Manufacturing Execution Systems (MES)
• Industrial Network Solutions
• Building Management Systems
• Electrical Power Management Systems
• Electrical & Instrumentation Design
• Industrial AI
• Consulting
NORTH AMERICA: Ohio, North Carolina, Texas, Michigan, Illinois, Massachusetts, California, Georgia
ASIA-PACIFIC: Singapore, Taiwan, Indonesia, Malaysia
EUROPE: The Netherlands, Ireland
ccording to a 2021 assessment from Deloitte, the manufacturing industries are hobbled by a skills gap that could leave as many as 2.1 million manufacturing jobs unfilled by 2030. In response to that challenge, systems integrators (SIs) offer goods producers’ access to highly trained resources and advanced technologies, which otherwise might not be available.
Labor and skills shortages justify increased automation; SIs occupy key position in today’s supply chains; SI Giants embrace the opportunities
The SI Giants chart supplies important information regarding the wide variety of systems integrators available.
Integrators combine sophistication regarding technology innovation with practical, hands-on experience. Collaborating with systems integrators is the means to significant productivity improvement powered by information and operations technology (IT/OT) convergence.
What’s more, with the proliferation of the industrial Internet of Things (IIoT), cloud computing and analytics, and the dawn of AI-based applications, some experts say there’s more technology innovation coming to light at the moment than any time since the introduction of programmable logic controllers (PLC), enterprise resources planning (ERP) and computer-aided design (CAD) in the 1980s.
SIs come in all different shapes and sizes. Some are part of much larger engineering, procurement and construction (EPC) companies. One common way of classifying SIs is by industries and geographies covered. An SI may be operations, enterprise or supply-chain centric.
Jose Rivera is CEO of the CSIA.“Systems integrators have a role in helping U.S. manufacturers address labor and skills shortages,” Rivera said.
“Besides reshoring, the infrastructure bill and renewables demand are impacting U.S. manufacturing. Greater use of automation can help manage costs, improve quality and ensure safety.”
Karen Griffin is vice president of Hargrove Controls & Automation, the SI branch of the larger EPC firm. She is also chair of the Control Systems Integrators Association (CSIA).
When it comes to Industry 4.0, Griffin says Hargrove clients sometimes want to implement a specific technology but more often they want support generating a roadmap that determines future directions and then help implementing the necessary steps.
“The technology supplier sales force inundates manufacturers with different options. The technologies are on display at trade shows, each promising significant return on investment. But when it comes down to the implementation, some crucial factors to consider are if the facility is ready, if the workers are properly trained, and if the workflow is appropriate to accommodate the new technology.”
System integrators are more diverse today than in the past. For example, SCADA used to be almost solely a plant-floor concern. Today, it’s less about individual workers than it is about a range of functions interested in plant-floor data.
“SIs have changed. In the past they were mainly small companies doing similar things. Today, what SIs contribute is more diverse in terms of talent, training, project management and more,” Rivera said.
Skilled labor shortages will be addressed by market mechanisms that attract talented individuals to higher paying jobs. It’s also the case that what’s needed isn’t so much specific skill sets as individuals equipped with a propensity to learn.
There can be many avenues for identifying people equipped with this propensity, in school or otherwise. In fact, many would say work experience is more important than formal education.
“We learn on the job throughout our careers,” Griffin said. “It's not a field to choose because you want to get good at something and do that for the rest of your career. In this technology-driven environment, about the time you master your job, it changes.” GSIR
Kevin Parker, content manager, CFE Media and Technology.
Alpharetta, GA, United States Energy (coal, hydro, nuclear, wind); mining, aggregates, cement; pulp, paper,
Aurora, OH, United States
Township, MI,
Bottling, canning, brewing, distilling; building envelope, controlled atmosphere; chemicals, petrochemicals; electronics, semiconductor; food, beverage; glass, stone, clay; household, personal care products; information and communication systems; life sciences, biotechnology; material handling, logistics, warehousing; mining, aggregates, cement; oil & gas refining; paints, coatings; pharmaceuticals; pipelines; plastics; pulp, paper, converting; quality control, test and measurement; transportation equipment; water, wastewater; wood, lumber products
San Pedro Garza García, Mexico
Baton Rouge, LA, United States
Fishers, IN, United States
Phoenix, AZ, United States Energy (coal, hydro, nuclear, wind);
TN,
Long Beach, CA, United States
Andover, MA, United States
Indaiatuba, São Paulo, Brazil
North Salt Lake, UT, United States
Fort Lauderdale, FL,
Aerospace, aircraft; automotive (OEMs, suppliers); bottling, canning, brewing, distilling; chemicals, petrochemicals; computer systems; electrical equipment; electronics, semiconductor; entertainment; food, beverage; government, defense; household, personal care products; information and communication systems; life sciences, biotechnology; machine building; material handling, logistics, warehousing; metals (fabricated, steel, primary, forming); packaging; pharmaceuticals; research, R&D, laboratories; transportation equipment
By Stephen Greene, Vice president of global marketing, Stratus Technologies
Systems integrators meet information technology (IT) and operational technology (OT) demands
All organizations have their nuances — and the same goes for every digital transformation journey. The road to successful transformation is paved with plenty of challenges, not just pertaining to information technology (IT), but to operational technology (OT), as well. Many IT organizations have already largely turned their focus toward the cloud. In OT, the focus has been primarily on solutions that improve and foster success at the edge.
What do these competing priorities mean for systems integrators (SIs)? And how can SIs deliver solutions that effectively walk the tightrope between the needs of IT and OT? While the differences present an obstacle, there’s an opportunity to build solutions that address both worlds with edge computing technology. According to IDC, in 2023 alone, investments in edge computing are projected to reach over $200 billion — and for good reason. Edge computing has emerged as a powerful way for organizations to gather and analyze data at the source, quickly and effectively. For IT and OT, the ability to manage data is critical, and it’s a task edge computing solutions are well-positioned to solve.
uEdge computing addresses critical information technology (IT) and operational technology (OT) needs by providing control over hardware, enabling efficient data processing and reducing operational costs, benefiting both domains.
uEdge computing platforms offer autonomous operation, alleviating workforce constraints and ensuring reliability, ultimately maximizing the value of data in digital transformation efforts.
IT leaders have many variables to consider when building a digital transformation initiative. Interoperability, easy manageability, cost efficiency and cybersecurity support all rank among the most important features — particularly as IT teams weigh their options with edge computing platforms. When building IT solutions, SIs need to ensure they deliver greater uptime and fault tolerance to give users transparency and eliminate modifications or extra scripting.
On the OT side, transformation hinges on how well a new technology or tool supports missioncritical applications and infrastructure at edge locations. Teams rely on OT devices to collect data from remote locations, on factory floors or in production facilities. OT devices bring in huge volumes of data generated from remote areas.
To manage high volumes of data and many edge devices, OT leaders are investing in automation tools that rely heavily on edge computing platforms to run complex industry 4.0 software. OT teams want an edge computing platform that delivers continuous availability for critical applications.
Given the differences between IT and OT, what makes edge computing the right approach to effectively meet both sets of needs?
Edge computing platforms can satisfy application needs across IT and OT. For SIs and their clients, these platforms should be simple, protected and autonomous. Edge computing gives organizations control over their hardware. IT benefits from a hybrid edge-to-cloud approach, where edge and cloud computing work together to create efficiencies, optimize data flow and reduce operating costs. OT benefits from IT tools accessible at the edge.
Despite IT and OT’s different needs, there are similarities — particularly when it comes to data. Both groups collect and are being flooded with data for analysis that must be protected, stored and secured. A platform equipped with tools helps SIs and their clients address pressing challenges pertaining to bandwidth, latency and security at the edge, enabling data acquisition.
Edge computing platforms provide benefits including predictive fault tolerance, protection of mission-critical applications and data, manageability and serviceability and consolidation of workloads — all while still running complex software stacks behind advanced operations.
An edge computing solution can form a natural bridge between IT teams’ cloud-based services and OT teams’ need for on-premise highly available infrastructure to run critical operations — bringing the best of both worlds together. When SIs deliver edge computing solutions, everyone wins, and the full value of digital transformation can be realized from the cloud to the edge. GSIR
Stephen Greene is vice president of global marketing at Stratus Technologies. Its solutions collect and analyze data at the source.
The Bridging the Gap Podcast discusses major industry topics and features experts covering everything from Arti cial Intelligence to technology integration.
OCTOBER 24, 2023
NOVEMBER 7, 2023
EPISODE 1: Challenges of AI Integration with Jeff Winter EPISODE 2: AI Implementation with Jeff
By Kevin Parker, Senior contributing editor
ECS Solutions partnered with AmeriQual Group to implement a batch solution running on Inductive Automation’s Ignition platform. The project was delivered on an aggressive timeline.
What does it take to successfully implement a systems integration project that includes aspects of both operations technology and information technology?
Success in many industries – in many walks of life, in fact – is the product of preparation meeting opportunity. This may be especially true in private label food manufacturing. “The people, processes and equipment must be able to adapt to ever changing market demands,” said Wes Blankenberger, VP of operations & maintenance for AmeriQual Group, Evansville, IN.
Much as brand owners make timely use of private-label manufacturers, the goods makers themselves leverage systems integrators and others to assemble existing and new equipment into functional processing systems.
Moreover, similar qualities define success for the control system integration space. Integrators are often recognized for their ability to deliver in specialized market segments. Having as a team a rational mix of technology professionals allows the integrator to apply staff, often on short notice, to priority projects. Integrators tackle projects or parts of projects, often in concert with yet other partners.
At Evansville, IN-based ECS, daily conversations revolve around equipment modules, recipe procedure models and equipment availability, including from entry-level technicians to the highest-order software specialists and project managers. One tool the entire team knows well is Inductive Automation’s SCADA solution.
“Every ECS teammate learns Ignition from day one with us,” said Mark Randall, ECS project manager. “The training is online, free of charge, and modular. That makes it relevant upon hire at ECS and then regularly as a teammate matures.
AmeriQual Group is frequently called upon by major food companies and the U.S. Department of Defense to provide packaged solutions. AmeriQual’s reputation for quality gives the company opportunities to work on these challenging projects.
When presented with a chance to land a series of large contracts with a well-known label, AmeriQual quickly pressed all their assets into action to create an entirely new kitchen.
AmeriQual ordered long lead-time items with less-than-optimal information available. Equipment from its local storage cache was inspected, tuned up and prepared for deployment. Existing relationships with local contractors allowed it to prepare the plant infrastructure and quickly move into detailed piping and wiring. Perhaps most important, its relationship with ECS allowed for a quick project assessment and documentation of a framework to establish budgets and obtain bids.
AmeriQual also gave ECS personnel a tour of the facility and explained what it had in mind. “From that point ECS came back to us with ideas and showed us what its systems looked like and could do. We came up with a strategic path and a phased approach to implementation. The phased approach allowed us to implement operations improvements on shorter timelines and simplify the training requirements for our team members,” Blankenberger said.
A fully integrated solution from ECS was integral to AmeriQual’s long-term success. The solution would allow for as much automation as reasonable, minimizing the number of new operators needed to run the system.
“We didn’t consider using manpower as a stop gap because it is tough to find manpower and the processing requirements for the product would be challenging to accomplish manually,” said Blankenberger.
Following these conversations, ECS received an order in early January of 2022. Working from preliminary piping and instrumentation diagrams
“Success in many industries –in many walks of life, in fact – is the product of preparation meeting opportunity.“
According to MES provider Tulip, the benefits of batch processing in the food industry include the following:
uMore control over quality and better traceability
u Shorter production time
u Lower cost equipment
u Lower chance of contamination.
“We have more than twenty custom faceplates in our Ignition library that we’ve deployed to tie into Rockwell PlantPAx process objects,” Randall said. The team used elements of ECS’ S88 builder, developed in Ignition, to make connections via Rockwell’s existing API for PlantPAx. Image courtesy ECS Solutions.
(P&IDs), the ECS team crafted a flexible batch solution on the Ignition platform.
Folsom, CA-based Inductive Automation’s Ignition is an integrated development platform that can be applied to supervisory control, manufacturing execution and achieving digital connectivity by means of the industrial internet of things.
“This project encompassed a few elements that we’re uniquely positioned to address,” said Randall. “The fact that it was batch processing put it squarely in our wheelhouse and the fact that it was based on Ignition opened up many options for the team delivering the solution.”
ECS extends Ignition’s capabilities by developing custom faceplates that tie into the Rockwell FT Batch engine running behind the scenes. “We have more than twenty custom faceplates in our Ignition library deployed to tie into Rockwell’s PlantPAx process objects,” Randall said.
The team used elements of ECS’ S88 builder, developed in Ignition, to make the connections via Rockwell’s existing API for PlantPAx. “This level of integration allowed us to speed development in a way that keeps things from getting unruly. Our R&D and prior use of these elements made a real difference on this project,” Randall said.
In addition to the process control and SCADA tie-in, ECS also addressed the client’s multilingual requirements. “Approximately 20% of our staff is Spanish speaking,” Blankenberger said. “Operator interfaces are easily toggled from English to Spanish depending on the team member. This has improved willingness to work in this area of our facility as well as reduced training time.”
PlantPAx prompts are mirrored as well. “We used the localization capabilities within Ignition to accomplish the switching,” Randall said. “Before we could do that, however, we used our native Spanish speaking teammates to examine and tweak the generic translations that were delivered via software. The adjustments add contextual value to the translations that software alone cannot deliver. Batch operations require specific terminology.
AmeriQual’s Blankenberger agreed. “Transparency, accountability, and communication are the attributes critical on projects with short timelines. AmeriQual and ECS were true partners in the project. There were many challenges and tough discussions throughout, but we were able to prioritize tasks based on what was best for the project.” GSIR
By Heath Stephens, Digitalization leader, Hargrove Controls & Automation
Virtualization efforts pave the way for predictive analytics
An ongoing multi-site program at a global manufacturer collects and analyzes production data using relatively common Industry 3.0 technologies and newer Industry 4.0 concepts, including cloud connectivity, AI-based analytics and predictive reliability.
As a result, a system integrator and engineering firm, together with the asset owner/operator, can make informed, data-driven control system and process improvements based on system feedback.
uVirtualization is a computing technology that creates virtual representations of physical machines. Virtualization uses software to simulate hardware functionality. This allows multiple virtual machines (VMs) to run simultaneously on a single physical machine.
To begin, the global manufacturer recognized the need to improve visibility of the processes running in its plants. In addition, its data collection methods were labor-intensive and posed potential cybersecurity risks. Moreover, process quality and reliability needed improvement.
Process data was manually recorded from human-machine interfaces (HMIs) by operators using paper and pencil. Often, the documentation was routinely filed away until a problem arose. If an event did occur, employees delayed acting as
WATERFALL CHART: Quantifying sources of plant. Images courtesy Hargrove Controls & Automation.
they sought to decipher the information by sifting through the paper documents.
In addition, methods for other local data collection needed improvement. Engineers walked around the plant floor with a USB stick to move data from shop floor computers to their office laptop. They only retrieved data when a problem needing to be addressed was identified. This was also a significant cybersecurity issue.
In addition to data-visibility challenges, the manufacturer recognized it faced certain labor constraints. It understood that by reducing the time employees spent putting out fires, or troubleshooting to get production running, their focus on value-added tasks would increase.
Keeping equipment running has an immediate impact on the bottom line that management can see. However, a well-run plant also allows personnel to spend more time working on continuous improvement to top-quality products.
The manufacturer wanted to identify the reasons for its quality issues and for the reliability problems it faced. It was aware of the increasing efficacy of Industry 4.0 initiatives and witnessed other companies in different sectors advancing with data-analysis efforts. The manufacturer asked Hargrove Controls & Automation to develop a roadmap and execution plan to improve its data retrieval and analytics strategy.
Hargrove Controls & Automation planned and executed the job employing experienced personnel spanning a range of engineering and technical disciplines.
To relieve the manufacturer’s IT management burden, Hargrove used both VMware and Microsoft HyperV virtualization technologies to reduce the company’s hardware footprint.
In addition, the company selected a cloudbased industrial artificial intelligence (AI) platform to generate insights into running processes. As a result, process data is analyzed to provide real-time insights into how the process and associated equipment are running. Beyond the cloud data visualization tools, Hargrove Controls & Automation’s
upgrades allowed company engineers to locally review data and trends to discern correlations. At the same time, the AI engine sifted through variables to find nuanced interactions among parameters that might be difficult for onsite engineers to recognize.
The company had better tools for predicting downtime and understanding what machines needed, including addressing such things as the need for a bigger heat exchanger, an instrument calibrated incorrectly or a motor not running fast enough. Once known issues are mitigated, the data validates that the changes made addressed the problem.
When gaps and challenges are addressed, efficiency improvements are realized. With more reliable equipment, a facility sees improved production throughput since machine uptime increases and variability decreases.
The manufacturer achieved production efficiency gains through improved quality control. Reducing manual tasks improved worker efficiency. The company is still in the process of digitalizing its facilities. To date, about a half-dozen facilities have received some type of improvement with the help of
Hargrove’s team, with plans to continue the partnership.
The manufacturer started as a company driven by the skill and experience of its employees. It is transforming into a data-driven company. It knows that the labor force is changing. Newer employees may not share the same ideas about tenure as previous generations. The manufacturer will always count on the people it employs, but now supported by optimized processes and equipped with data for informed decision making.
The end goal of digitalization and Industry 4.0 is to have a single process portal for process, business, maintenance and laboratory data, collated and analyzed by both people and machines in a single platform.
The factory of the future won’t appear overnight, but with the right partners and resources, having a roadmap to get there is increasingly imperative. GSIR
Heath Stephens is digitalization leader, Hargrove Controls & Automation, specializing in control strategy development and implementation, as well as legacy system migration.
PLANT FLOOR: Regardless of where the work cells are located, data analytics employing statistical methods can find interdependencies. and recommend improvements.
By Keith Mandachit, Huffman Engineering, and Barbara Padgett, SmartSights
Deloitte and the Manufacturing Institute, in a recent report, said as many as 2.1 million manufacturing jobs will be unfilled through 2030, and warns that the worker shortage will hurt revenue and production and could ultimately cost the US economy up to $1 trillion by 2030.
Folks over 55 years of age make up increasingly larger portions of the technical workforce in the US. Meanwhile, technical demands for manufacturing have grown, making it more difficult to hire the right workers. Manufacturing is being squeezed by both labor and skills shortages.
Given these facts, manufacturers face enormous pressures to stay competitive. It’s not all doom-and-gloom though. To combat these labor challenges, manufacturers are looking to new technologies that expand productivity, decrease labor costs, increase uptime and slash error rates.
By leveraging technology, manufacturers lessen reliance on manual labor. Increased automation reduces errors and costs while increasing productivity, quality and safety. For example, adding sensors detects performance aberrations that simply wouldn’t be found through manual spot checks and personnel monitoring. By locating the underpinnings of potential issues in real-time, sensors alert maintenance teams to investigate to prevent a machine aberration before failure happens.
While manufacturing plants have long used supervisory control and data acquisition (SCADA) the technology has evolved with increasing digitalization (See sidebar, “Terms and definitions”).
The manufacturing industry is going through some big changes. As analytics, sensors, robotics, cloud computing and IIoT technology become less expensive and easier to implement, more manufacturers
go digital with their business and production process to stay competitive in the market.
The ability to monitor critical process variables and be notified when something is not right is vitally important in every stage of industrial manufacturing and utility processes. Seamlessly transferring these notifications to operations and automation teams, and even beyond to business offices or whoever needs to know, is something system integrators (SI) have been talking about for a long time.
Digital transformation is not so much a technology initiative as it is a business initiative. Business owners and C-level executives typically don't fully understand engineering concepts and practices that bring digital transformation, IIoT, and Industry 4.0 to life. Their focus usually is on the big picture. It's important for SIs to help them understand how and why this technology affects day-to-day business operations. By thoroughly explaining this technology and bringing data to life for end-users, management will see the return on investment of digital transformation.
Smart manufacturing software provider L2L recently surveyed 125 manufacturing leaders. The findings were enlightening. For example, only 24% have a digital transformation strategy. According to survey results, this is because a clear path to implemention is the most common challenge, followed by a lack of funds and problems with moving away from legacy systems. The survey illustrates that manufacturers need guidance and counsel on implementing digital transformation from subject matter experts. SIs who typically work across industries with exposure to multiple control systems daily can provide that expertise.
In addition to providing counsel to clients about embracing digital transformation, SIs can partner with technology companies to further offer solutions for manufacturers to increase productivity and efficiency. Seamlessly integrating software that notifies manufacturers in every way possible about equipment problems – via mobile app, text, voice, email, or in-plant announcements – helps fix
problems faster, reduce waste, and lessen maintenance and staff costs.
The importance of reducing unplanned downtime by seamlessly integrating remote alarm notification software into the existing SCADA system should not go unnoticed. This allows fewer people to monitor many more assets using devices they already have, such as smartphones and tablets, addressing the worker shortage through increased automation. Uninterrupted remote availability is essential to ensuring systems can be continuously monitored, even without staff onsite or with fewer people working at the facility.
Remote monitoring of critical plant systems has been extended beyond email, texts and phone calls to include apps that feature time-saving tools like real-time alarm acknowledgements, team chats to troubleshoot and resolve plant problems, and detailed reporting for preventing future incidents. Not only does this mean fewer emergency shutdowns, but also less resources spent on overtime and maintenance.
Rapid globalization, technological advancements, changing consumer preferences and evolving government policies are reshaping the manufacturing industry. To meet these challenges with manually intensive processes and outdated technology is difficult. However, by incorporating advanced technology, manufacturers can increase productivity and efficiency, and reduce maintenance costs.
SIs play an important role as honest brokers in this process by listening to clients’ challenges and recommending solutions. The unique skillset brought by a skilled controls system integrator provides an invaluable link between IT vendors who
offer solutions – like remote alarm notification software – and clients with complex projects. GSIR
Keith Mandachit, PE, is the engineering manager at Huffman Engineering, Inc., and may be reached at kmandachit@huffmaneng.com. Barbara Padgett is the marketing manager atSmartSights, and may be reached at Barbara.padgett@smartsights.com
Life science manufacturer wants to be in the know
A prominent Midwest-based animal health life science manufacturer knows the value of integrating remote alarm notification software with their robust SCADA system. Because of their seamless relationship with its SI, this manufacturer has continuously added alarms over the years to monitor four bioreactors, six fermenters, and two specialized systems that include a water building system and bio kill system. There are 250 alarm tags within these 12 systems and the SI and remote alarm notification team have standardized each tag to have three escalation levels on each alarm tag: five minutes; two hours; and four hours.
Additionally, this company is expanding production into a new facility on another project and integrating alarm systems with the entire building management system. Once this expansion is complete, it will rise to human health life sciences compliance standards.
FIGURE 3: Remote alarm monitoring software utilizes a variety of communication platforms to send the right notification to the right person at the right time. Image courtesy SmartSights
FIGURE 2: Chat helps the entire team converse, brainstorm, and share solutions on-the-fly, from any location — whether in the plant, at home, or on the road. Image courtesy SmartSights
Supervisory control and data acquisition (SCADA) is a system of software and hardware elements that can control processes either locally or remotely. SCADA components include the supervisory computer, remote terminal units (RTUs) or programmable logic controllers (PLCs) and human machine interfaces (HMIs) that display a schematic representation of the system, amongst other information. Besides process control, at SCADA, production throughput can be matched to supply based on shortterm factors.
Scott Kiser, Sr., global partner development manager, ICONICS
global partner development manager, ICONICS
The discrete manufacturing and process production industries embrace technology to improve productivity and stay competitive. However, many companies don’t have the skills or are spread too thin to immediately benefit. This is where system integrators (SIs) play a pivotal role, one like Shane Stevens, the owner of Impact Automation and Controls in Lewisville, Texas. Stevens is an ICONICS gold-certified system integrator with more than 20 years’ experience, primarily in water & wastewater and secondarily in buildings, and was the SI for the integration project at the Lake Cities Municipal Utility Authority (LCMUA).
LCMUA is located in Lake Dallas, Texas, and provides drinking water, fire protection and pressure to the Shady Shores, Lake Dallas and Hickory Creek areas (together known as the Tri-Cities). LCMUA operates 21 lift stations, 3 elevated storage tanks, 3 ground storage tanks, 10 pumps on the water side (with 3 altitude valves), and 46 sewer pumps on the wastewater side.
LCMUA had an aging infrastructure system that needed help from top to bottom. For example, a
large portion of LCMUA’s budget at the time was spent on callouts, false alarms and failing equipment. The existing supervisory control (SCADA) system was a combination of three competitor products, which ended up giving LCMUA personnel three different sets of operating data. The company prioritized an upgrade to better manage and maintain the facility.
LCMUA needed a unified solution with a new human-machine interface (HMI) and SCADA system that could handle distributed network protocol (DNP3) communications and interface with the existing Ovarro Connecting Technologies TBox combined programmable logic controller/remote terminal unit (PLC/RTU) hardware installed at every lift station, pump station and elevated storage tank in its system. To accommodate a lean, often remote workforce, it needed a solution with 24/7 operational visibility and notification alerts whenever the situation warranted attention to potential issues.
LCMUA wanted to replace the older SCADA system, reduce related costs and efficiently manage the facility with a lean workforce. LCMUA chose to work with Impact Automation and Controls and together selected to deploy product solutions as follows:
• GENESIS64 web-based HMI/SCADA suite with WebHMI
• MobileHMI data mobility software suite
• AlarmWorX64 Multimedia OPC alarm management software
• ReportWorX64 enterprise reporting, charting and analysis software
• CFSWorX intelligent notification software
• Hyper Historian high-speed plant data historian.
The HMI/SCADA met quality and maintenance needs within the water and wastewater system without any of the previous issues or data discrepancies. The upgraded SCADA improved data quality, visualization and management of water
“Know the capabilities and limitations of the software package before committing. A system integrator will advise and help plan, which will avoid headaches later.“
and sewer levels, monitoring and control of potable water and wastewater, elevation, PSI, intrusion pumps, pump monitors/controls, pump failure status and temperature.
Intelligent notification software streamlined work and empowered personnel to move past the break/fix model toward more proactive facilities and equipment management. The human/machine interfaces provided crucial monitoring and control of connected systems from the field using iPads through “Any Glass” (a user interface that delivers 2D and 3D real-time operational visualization and intelligent dashboards).
LCMUA now considers its visualization to be “top notch,” its alarming to be “solid” and its data mobility to have an “impressively fast response time.”
With graphic displays in place, the system integrator completed the system upgrade. Alarms and notifications capabilities, including voice and text messages, added to team efficiency and collaboration. Rather than everyone getting the same alarms all the time, managers decide who gets what alarm and when. That’s important because operators are not always on shift.
Messages can go to personal smartphones, which allows personnel to switch to the mobile app for contextualized details before acknowledging alarms or making relevant decisions.
Team resources are allocated based on real-time data for improved response times and reduced downtime. The software addresses challenges around efficient onboarding of new hires into the present workforce. The team is better equipped to run the facility efficiently, even with a lean workforce.
Mark DiCiaccio, Lake Cities Municipal Utility Authority operations manager had this to say, “CFSWorX has been great. With the previous application, we would constantly worry if the system was working. Before we would leave on Friday, we would always send a test alarm to make sure we would get alarms over the weekend. That is no longer the case. We have yet to miss a single alarm since moving to CFSWorX.”
It takes years to develop the expertise and experience system integrators possess. An organization that hires a system integrator is banking on this investment. Five key areas where system integrators play a pivotal role are the following:
1. Specialized expertise and experience: Digital transformation encompasses a range of technologies, including the internet of things (IoT), data analytics, cloud computing and machine learning. SIs not only possess in-depth knowledge of the technologies but also help to drive trends, best practices and industry standards. Their expertise enables them to design, implement, and thus optimize complex digital solutions tailored to the client’s unique needs.
2. Seamless integration of systems and technologies: Integration of disparate systems and technologies to create a unified central system of control can be challenging. SIs can bridge gaps among different data sources, software applications and hardware components. They also have the know-how to connect to legacy systems with modern solutions, achieving seamless data flow and interoperability.
3. Customization and scalability: Every organization has distinct requirements and digital transformation goals. SIs know the importance of project customization and scalability. They assess each organization’s infrastructure and processes and take into consideration the organization’s expectations and needs, including future needs. System integrators then implement solutions that align with the organization’s objectives and design systems that can scale with the capacity to grow and evolve over time.
4. Change management and risk mitigation: Since digital transformation involves significant changes in technology, processes and culture, substantial operations disruption can manifest itself as resistance from employees. SIs have experience with change management strategies. They can support the human element of digital transformation to enhance user understanding of the technology’s value.
5. Continuous innovation and futureproofing: Technology continuously evolves. Staying up to date is hard work, but crucial for success. Since SIs constantly monitor the technology landscape, they can help organizations identify innovative and best-fit solutions. They can also ensure systems are future-proofed, so organizations more easily adopt evolving technologies.
Beyond the value already recognized, Lake Cities Municipal Utility Authority anticipates expanding remote worker support with worker location capabilities, push notifications and priority calling.
When implementing or upgrading, be sure to plan thoroughly. Stevens recommends, “Know the capabilities and limitations of the software package before committing. A system integrator will advise and help plan, which will avoid headaches later. The keys to success are communication and project understanding. A system integrator can develop the best system in the world, but if it doesn't do what the customer expects, it’s junk.”
Given today’s labor shortages and supply chain complexities, there is demand for automation solutions and experts on design and implementation of these systems. Leverage the expertise and specialized knowledge of system integrators. Companies can maximize investments in new technologies and ensure smooth, successful digital transformations. GSIR
Scott Kiser, Sr., global partner development manager, ICONICS
Some recent innovations in water and wastewater technology include the following:
uAutomatic variable filtration is a water purification technology that cleans an upward flow of influent through a downward flow of filter media.
uMembrane bioreactors are a combination of a suspended growh bio reactor that breaks down waste with microbes followed by membrane filtration.
uPhoto catalytic water purification can treat industrial wastewater polluted with high loads of organic substances or metal.
Michael De Boer, Director of automation, Interstates
The systems integrator’s mission today involves using data for smart, lean production, innovative supply management, pre-engineering involvement, simplified interfaces, in-depth system understanding and provision of readily available hands-on support. Harnessing the power of data streamlines processes, reduces waste and optimizes productivity.
“Systems that support quality-assurance testing without taking samples to a lab save time. Automating data collection means less paper, less human error,” said Heather Johnson, automation manager, Interstates. Automation has streamlined
production by collecting data more efficiently, reducing paperwork, and enabling real-time data acquisition. Operators are relieved from manual testing tasks, as automated systems ensure the collection of data at the required frequency.
Demand for and reliance on automation follows from widespread labor shortages. This data-driven approach aids clients in enhancing accounting processes, safety procedures and regulatory compliance.
“Tailored dashboards allow clients to have access to accounting files or safety procedures at their fingertips. On the process side, having this data available is critical in the event of state or government audit,” Robert Phillips, also an Interstates automation manager, said.
Because of bottlenecks associated with supply chain management, supply orders appear earlier in project timelines than ever before. “Many clients proactively order materials before projects are fully funded. This approach ensures long lead time materials are secured in a timely manner,” Johnson said.
In some cases, custom or reengineered equipment is needed to overcome supply chain constraints. Timely resource decisions allow projects to progress smoothly.
SI guidance on alternative possibilities and potential redesigns address supply chain challenges and avoid dependence on any particular supplier or material. Considering lead times on critical parts or types of equipment during the pre-engineering phase promotes efficient project execution.
Collaboration during the pre-engineering phase ensures designs align with client needs and budgetary constraints. “This approach allows clients to have a clear understanding of the project scope and associated costs well in advance,” Phillips said. “During this stage, the point is to provide design options and suggest volume engineering to optimize resources.”
Johnson emphasized that deep understanding of industrial processes is the basis for insights.
“Experience in a range of industrial sectors is a major enabler of efficient project execution and quick ramp-ups,” she said. Additional requirements identified can include network integration or interfacing with enterprise business systems. Considering these factors early on leads to accurate cost estimates and optimizes the project timeline.
Simplifying operator interfaces ensures operators have the tools and information to run processes smoothly, even with relatively new hires. Leveraging automation and advanced control systems reduces complexity at a time when the workforce is experiencing significant changes.
“To make the interface simpler to use, we create control narratives, which are basically step-by-step documents that guide operators through the operation. Narratives help operators understand how various instruments and devices should behave under different conditions, minimizing the need for manual intervention,” Phillips said.
Interstates Automation Manager, Raymond Berning emphasized that the younger generation of operators expects intuitive and user-friendly interfaces. “Everybody uses iPads, cell phones and smart devices where information is at your fingertips. We take this into account, ensuring that interfaces align with modern user experiences. Our aim is to build on what was provided by previous
A data-driven approach aids clients in enhancing accounting processes, safety procedures and regulatory compliance.
“Many clients proactively order materials before projects are fully funded. This approach ensures long lead time materials are secured in a timely manner.“
—Heather
Johnson, automation manager, Interstates
generations and give the next generation of workers a platform to go further,” he said.
Understanding clients’ systems is a key factor for success as a system integrator. “Interstates’ expertise spans diverse sectors, including pet care, food & beverage, and value-added agriculture, allowing us to transfer knowledge and best practices across many kinds of projects,” Johnson said.
Interstates is continually expanding its support capabilities. In closing, Johnson mentions its ongoing efforts to develop regional EIC (Electrical, Instrumentation, and Controls) tech teams. “These teams, consisting of skilled technicians located strategically, will aim to provide on-site support for electrical, instrumentation, and control issues,” she said. GSIR
Michael De Boer is director of automation at Interstates, Sioux Center, IA.
According to Mingo Smart Factory:
u Big Data involves the extremely large data sets tat can be analyzed to reveal patterns, trends and associations.
u Big Data in manufacturing is generated by "software machines" such as sensors, pumps, motors, compressors or conveyors.
u Big Data is often managed using a hub and spoke methodology: create one hub or centralized view fed by spokes to form a single view of the truth.
By L. John Shipley, P.E., CAP, Engineering director, Indiana operations; senior electrical engineer, Patti Engineering
Challenges addressed ranged from design through development, implementation and start up
Struggling to hire and retain new employees to fill gaps left by retiring operators, a Tier 1 automotive supplier set ambitious goals for reducing headcount through automation. In response, the supplier automated an area of the facility where operators performed dull, repetitive tasks at three machine stations. Besides reducing headcount, the goal was to increase throughput and reduce errors.
The automotive supplier envisioned a robotic solution; however, it was unsure of how best to eliminate manual operators given the narrow, confined space around the machine stations.
Auburn Hills, MI-based integrator Patti Engineering designed and developed a solution that met the project’s ambitious requirements to eliminate the need for one operator from each of two to three shifts per day.
The return on investment (ROI) payback period required to justify this automation project had been 20 months. Interestingly enough, after moving forward with it, continuing pressure to reduce headcount led the supplier to lengthen the time period allowed for justification of automation projects to 36 months.
A press station, a weld station and a laser station, which included some testing functions, were combined into a single automated cell. The two robots were programmed to handle eight models of parts, with each model including additional variations.
• Station #1 - Press station
• Station #2 - Weld station
• Station #3 - Laser marker with an additional test station
The new robotic cell included two automated conveyors, one infeed and one outfeed, with a third gravity-fed conveyor for empty bin collection. The first robot uses 3D vision to pick parts from a bin.
Intermediary transfer stands are for hand-off between the robots. The second robot tends the first two stations and uses 2D vision to pick the part. The first robot tends the third station. The first robot also removes and adds bins vis-a-vis the conveyors.
Safety fencing and a new control panel located outside the cell area were added to house the controls hardware, including the cell control PLC, safety controls, and new interface for operators to interact with the cell.
The retrofit of existing automation hardware and software presents inherent risk due to unknowns and potential incompatibility of system components. Adapting a new robotic automation solution into a space-constrained footprint of three existing machine stations required building a hybrid solution. During development of the robotic cell project, Patti Engineering encountered several obstacles.
The first challenge involved the manufacturer’s specification to use a globally specified robotics maker. The lead time for delivery of these robots would have caused major setbacks, delaying the project beyond the manufacturer’s targeted installation period.
Patti Engineering proposed use of FANUC robots as the best choice for the project, which could also meet the desired delivery timeline. As an added benefit, FANUC’s integrated 2D and 3D system iRVision also significantly reduced the overall project cost since there was no need to incorporate the third-party vision system otherwise required.
Approval for using FANUC robots as an alternative to the originally specified robots was achieved by presenting a factual comparison of the FANUC selected robot to that previously specified in 18
uAccording to Prophecy Market Insights, motion control software in robotics markets was a nearly $11 billion market in 2022 and is expected to rise to $68 billion in 2032, for a CAGR of fully 21%.
categories including motion range, speed, payload, arm-reach and repeatability data. For the requirements of this application, FANUC had an advantage in 14 of 18 categories.
The next major issue revolved around end-of-arm tooling (EOAT). Patti Engineering had to design custom pole shoe magnetic end-of-arm tools capable of handling numerous part variations consistently and equally.
“There were significant challenges in creating the interface hardware on the end of the tooling because there are a number of part types for these machines. Overall, they have the same general dimensional feel, but there are some significant differences in the stamping,” said Dan Ragozzino, senior controls engineer at Patti Engineering. “Some of the parts have contours, different tabs and things in different places, so we had to come up with tooling that would allow the cell to run a number of different part variants with equal capability.”
Each robot required two custom designed EOAT. From picking the parts to placement in the machine stations, the two EOAT accommodated different clearance requirements and application needs.
Enabling the first robot to handle empty bins using a third hook EOAT required a creative strategy to minimize the complication of the end of arm tooling itself and also to reduce weight due to the limited payload for the robots. To address this
challenge, a custom EOAT attachment housed in a tool holder within the cell was developed. When the robot needs to move an empty bin from one place to another, it uses the bin picking magnetic EOAT to attach to the hook tool, remove it from the tool holder, manipulate the bin and then return it to the tool holder when it's finished.
Integrating the vision systems into the robotic cell required planning and precision. The team ensured seamless coordination between the 3D vision camera used by the first robot for picking parts from bins and the 2D vision capability of the second robot at the other machine stations. Implementing intermediary transfer stands facilitated smooth hand-offs between the robots but added to the complexity of the vision system integration.
To enhance visualization and streamline development, FANUC ROBOGUIDE, a simulation tool, allowed for testing and optimization of system performance before physical implementation. Smooth, efficient commissioning of the automated cell was ensured.
Lastly, the manufacturer had one unique requirement: it wanted the flexibility to switch back to manual labor with an operator running the cell, if needed at any point. For example, if a new part had to be run that the robotic automation was not programmed for, the flexibility would be there to accomplish that.
“This project was a hybrid between a turnkey solution and a retrofit: using preexisting equipment and modifying it to suit our application, but also providing whole new sets of equipment to perform this operation automatically,” explained Ragozzino. “Another project challenge was meeting requirements the customer had to return to manual operation for whatever reason they wanted at any point and they wanted it to be seamless.”
To meet this challenge, the robots and additional hardware components are mounted on mobile platforms to return the station to manual operation when needed.
Working within the narrow existing footprint, FANUC’s LR-10iA 6-axis robot designed for machine tending and picking applications was chosen for a variety of reasons. At just over 100 pounds, the
robot’s compact, lightweight design met the space limitations, arm reach, payload and speed needed, as well as being roughly the same cost as the robots the plant had originally specified. Attaching the robots to mobile platforms met the requirement of being able to return the cell to manual operation if needed.
A Mitsubishi Q-Series PLC was chosen as the central control system for the entire cell. Each station was controlled by its own Mitsubishi Q-Series PLC, requiring programing modifications and integration into the central control PLC to ensure smooth coordination and synchronization between the robots and the different machine stations.
Additionally, a Keyence GC-1000 safety controller was included to maintain supervisory control over safety aspects, ensuring a secure working environment for the operators and technicians. The safety controller allowed integration of safety features without upgrading the PLC to a specialized controller the plant did not have on site and with which it was inexperienced. Integrating the safety control reduced training time.
Plant maintenance and engineering staff have an awareness of possible future challenges. This comprehensive PLC setup allowed for seamless communication and coordination between all components of the automated cell.
The new control panel located outside the cell area houses the controls hardware, including the cell control PLC, safety controls and operator interface. The control panel also contains the distribution and connection components for added devices and sensors.
The solution used FANUC vision systems for accurate part detection and orientation. The first robot in the cell was equipped with a 3D vision camera, to precisely pick parts from bins. Intermediary transfer stands facilitated smooth exchanges between the robots during the production process. The second robot used 2D vision to tend to the first two machine
stations, picking parts with accuracy and efficiency. The first robot then tended to the third station, demonstrating its flexibility and multitasking capabilities. The system ensured correct handling and verification of various part models, reducing errors and enhancing production efficiency.
A Keyence color touch screen HMI panel with operator fingerprint reader was selected to display cell status. The HMI software has a similar look and feel to other HMIs in the facility, minimizing training. The fingerprint reader allows operators to access restricted operations and features depending on authorization.
The existing gravity-fed part-in and part-out conveyors were replaced with three new conveyors integrated into the cell. Two automated Hytrol EZ-Logic Powered Roller Zone conveyors process incoming unfinished parts bins and outgoing finished parts bins.
A third unpowered gravity roller conveyor stows empty parts bins until needed for placement onto the exit conveyor to be filled with finished parts.
The fully automated cell delivers a range of benefits to the Tier 1 automotive supplier. Integration of the two robots eliminated the need for manual operators. Operators are no longer exposed to repetitive and potentially hazardous tasks. HMI incorporation allowed easy monitoring and real-time visibility. The intuitive interface required minimal training of staff, for a smooth transition to automated operations and an employee-friendly work environment.
The solution led to a 33% increase in throughput, running a part every 12 seconds. Moreover, use of robotics allowed for consistent and uninterrupted production, ensuring efficient cell operations. Overall cell availability rose to more than 95%, based on reduced downtime and maximized output.
The project may also serve as a pilot for adoption of similar automated solutions in other areas in the plant. Plant management is considering expanding automation use to other laborintensive processes. The potential is to drive significant improvements and efficiencies across the manufacturing facility. GSIR
L. John Shipley is engineering director, Indiana operations, senior electrical engineer, Patti Engineering, which uses its experience and digital strategies to improve facilities' productivity and quality.
McKinsey says the pandemic’s aftermath accelerates trends already apparent in the automation supply chain. OEMs experienced record margins in 2021.
Suppliers' margins, while higher than the previous two years, were substantially lower than prior to the pandemic.
According to an online article from Boston Consulting Group, “As automakers transform, so must suppliers,” growth in suppliers' OEM related revenues and profits will come from emerging technologies driven by two areas: software and electric power trains. In liight of semiconductor supply chain disruptions and other factors, OEMs will push to diversify and localize their supplier base.
By Dino Busalachi, CTO and cofounder, Velta Technology
Are operations cyber-vulnerable due to lack of resources, lack of understanding or both?
The risk of adverse cyber events impacting industrial networks is rising faster than organizations can train talent to address the challenge. How does a company acquire qualified operations technology (OT) cybersecurity protection? The answer isn’t as straightforward as one might wish.
Let’s start with the basics. OT cybersecurity and industrial control systems (ICS) themselves may
at first seem unfamiliar. Once the concept of OT cybersecurity is established – before tackling talent or resource determination – agreement is needed around its ownership.
IT traditionally handled enterprise network security. A closed-loop network of industrial equipment, including programmable logic controllers (PLCs) and supervisory control (SCADA) wasn’t an IT consideration. OT teams focused on ensuring that production was up and running efficiently, continuously and at full capacity.
Remote monitoring and support of plant-floor operations altered the level of risk to industrial environments. Original equipment manufacturers (OEMs) and system integrators (SIs) rely on the internet for access to OT environments, exposing critical machine controls to threats first faced by IT.
Awareness, acknowledgment of risk, and subsequent action haven’t kept pace with the sophisticated hacking evidenced across enterprise and OT environments using Windows, Linux / Unix and other legacy technology. IT’s blind spot regarding OT environments leaves ICS assets exposed, due to unpatched or end-of-life technologies like Windows XP, still used by OT assets. The rapid shift to the use of Remote Access and IIoT technologies has exacerbated the airgap ‘myth’ between IT and OT. On average, 94% of IT security incidents affect OT environments, according to data published by TXOne Networks.
IT and OT security priorities are out of whack, partly because each have polarized objectives. OT assumes isolated, air-gapped ICS assets are in place, when in most cases they are not.
IT protects what it is comfortable with and what it knows: networks, infrastructure, enterprise business applications and databases. They oversee security of enterprise environments with cybersecurity software, as well as firewalls, EDR and anti-virus technologies.
Expecting IT to understand OT cybersecurity needs can be likened to expecting a round peg to fit in a square hole.
“IT and OT security priorities are out of whack, partly because each have polarized objectives. OT assumes isolated, air-gapped ICS assets are in place, when in most cases they are not.“
To bolster the OT environment, organizations must educate themselves and identify gaps in understanding, expertise, ownership and accountability.
To improve security of manufacturing and infrastructure, companies should adopt a multi-pronged approach, including:
• A workforce with skillsets to leverage the tools for OT / ICS cybersecurity
• A cybersecurity framework i.e., NIST, IEC62443, or other guidelines or regulations
• IT cybersecurity best practices, including policies, procedures, audits and security segmentation
• Traditional technologies such as firewalls / IPS, EDR, SIEM, SDN.
The challenge in buttressing the cybersecurity posture of an organization is found in the ecosystem itself. Clearly, the automation vendors, such as Siemens, Rockwell Automation, Honeywell, ABB, Emerson and GE, have achieved maturity regarding OT cybersecurity. Systems integrators bring automation’s benefits to bear, acting as a bridge between suppliers and users of automated control systems. A clear roadmap exists to get where you need to be with cybersecurity. The good news is that experienced and talented resources exist.
The question remains, is the source of the problem a talent shortage or a lack of OT cybersecurity knowledge and expert resources? We think both contribute to the challenge organizations face. The important thing is to take action, because it’s not ‘if’ you’ll experience a cyber event but when. GSIR
Dino Busalachi is CTO and cofounder of Velta Technology, a provider of digital safety and security for industrial environments.
Dragos and Rockwell Automation strengthen controls cybersecurity for manufacturers
THE NEWEST industrial cyber security solutions aim to improve automation system protection through access control, encrypted communication, vulnerability management and end-point protection. It also involves improved network security through anomaly detection, secure remote access and OT/IT data exchange.
Dragos Inc., a supplier of cybersecurity resources for industrial controls systems and operational technology (OT) environments, announced expansion of its combined capabilities in partnership with Rockwell Automation. Rockwell will be making the Dragos Platform available to organizations for enhanced control system/OT cybersecurity threat detection, while also providing global deployment services and support capabilities.
The threat detection capabilities build on the previous global agreement between Dragos and Rockwell for the OT Incident Response Retainer (IRR) program that helps industrial organizations prepare for, respond to, and recover from cyber incidents in OT environments. The Dragos Platform is codified with OT-specific threat intelligence and insights. It provides visibility into assets and vulnerabilities, detects cyber threats to industrial systems, and enables efficient response through forensic investigation and OT-specific playbooks.
Expanded capabilities allow improved threat detection and response across the entire industrial OT network. Visibility into the OT environment allows industrial organizations to inventory and monitor assets, track vulnerabilities, and leverage network monitoring to investigate issues and incidents. Threat detection helps maintain safety and uptime as a result of knowledge packs focused on ICS networks for Rockwell-specific and third-party vendor hardware.
The collective experience and intelligence of Dragos and Rockwell to enhance knowledge for industrial defenders, includes whitepapers, webinars, and other resources.
Dragos believes five critical controls for OT cybersecurity include the following:
1. A defensible architecture, whether through firewalls or software defined networks, with the ability to get access into and insights from the environment.
2. Comprehensive visibility and monitoring to cover inventory, topology, vulnerability management, threat detection, and system to system interactions.
3. Multi-factor authentication, “anywhere and everywhere you can put it.” Multi-factor authentication (MFA) is one of the few IT controls that can be appropriately and relatively easily applied to OT.
4. An ICS-specific incident response plan. Unlike MFA, your incident response plan can NOT be copied and pasted from IT, but must be dedicated to the OT environment. You need to know which people with which skill sets need to be inside the plant when something happens.
5. Collaboration between IT and OT. Last but not least, IT and OT must work together at the people and technology levels. While this collaboration isn’t easy, it is critical to lasting security success.
By communicating and aligning with company leadership, cybersecurity professionals can ensure that both IT and OT get the resources they need to keep the business secure.
By Thea Sander, Technical marketing, Vertech
In the wake of global labor shortages and supply chain issues, many manufacturers turn to system integrators and automation to improve efficiency and productivity. But what does innovation look like for slower, low-volume manufacturing processes that have traditionally been manual?
One such company, American SpiralWeld Pipe (ASWP), engaged systems integrator, Vertech, to implement a comprehensive automation plan for a new state-of-the-art facility in Paris, TX.
But it takes more of a supporting role when it comes to labor needs. “I want to be clear that the use of automation at ASWP is not a labor reduction focus. We use automation to make the job task easier for the employee… allowing them to make decisions faster and more accurately based on data and facts instead of intuition,” Davis said.
Given the large scale of its manufacturing operations, automation also protects ASWP employee safety. Davis said that advances in mechanical automation have allowed them to take a “hands-off” approach to pipe production and transport throughout the facility. Operators interact with machinery HMIs (human-machine Interfaces) rather than the pipes.
SCREEN 1. MES Overview
The MES Overview displays critical information for all core production lines during the shift. It reports equipment utilization as well as OEE, production status, work order information, and time spent for each core line. Note: Screenshot is simulated and does not represent actual process data. All images courtesy Vertech.
ASWP, a division of the American Cast Iron Pipe Co. is a spiral-welded steel pipe manufacturer that supports the municipal water and wastewater transmission industry as well as hydroelectric, industrial, and power markets. It’s not a small operation. ASWP makes pipes up to 50 feet long with diameters up to 12 feet wide. They have three plant locations that produce a combined average of 6,000 pipes, equating to more than 20,000 tons of steel, annually.
ASWP faces the same labor shortages as other manufacturing companies and is always looking for ways to improve production efficiency. Kent Davis, director of business process automation and operational excellence, said that for ASWP, automation primarily increases quality and throughput.
ASWP approached Vertech in 2020 to implement supervisory control and data acquisition (SCADA), manufacturing execution (MES) and statistical process control (SPC) systems at their greenfield facility in Paris, TX, and roll out the technology at their Columbia, SC and Flint, MI locations.
Phase 1 of the project, completed in 2021, tackled the SCADA system. The system tracks current and historical production data and funnels it to a centralized control room at the Paris company headquarters. The control room has 18 48-inch industrial monitors that display real-time Industry 4.0 data and analytics. Eventually, all divisional operations will be managed across multiple locations via SCADA, MES, and SPC from the centralized control room.
Phase 2, discussed below, focused on implementing the MES. ASWP wanted a system that tracked labor and production data, transforming it into useful OEE (overall equipment effectiveness), downtime efficiency and resource efficiency metrics.
For OEE accuracy, ASWP wanted to track downtime and production, maintenance, and changeover times.
Labor tracking typically involved operators working on a pipe and then self-reporting the time it took to complete the process. However, this resulted in inaccurate data, unreliable for business decisions or improvement efforts. ASWP needed a more automatic way to track process start and end times without depending on the operators.
Kevin Finnan, Strategy advisor,Yokogawa
The main automation contractor (MAC) concept enables drastic cost savings to the overall project compared to traditional project management.
For many years, leading control systems integrators and control systems suppliers have been providing main automation contractor (MAC) services. The MAC services include the full scope of project execution capabilities. By assuming responsibility over the entire automation related aspects of the project, the MAC provider better enables the end-user customer to satisfy requirements in terms of budgeting, timing, people resources, delivery and risk management.
The ability to deliver the full scope of project execution in industrial automation projects is more important than ever. Plant managers are under constant pressure to achieve high quality project execution, plant operations and maintenance.
However, companies are constrained by personnel issues, budgets and shrinking timetables. In addition to grassroots construction activity in emerging markets, companies face the task of executing multiple projects simultaneously in disparate geographic regions.
Also, many engineering, procurement and construction contractors (EPC's) have pared down their automation departments and no longer possess the resources to deal with multiple automation suppliers on a project. An automation supplier with the appropriate capabilities and experience can provide a single point of responsibility for project management and coordinate the work among multiple suppliers and subcontractors.
Compared to a traditional project management approach, the MAC concept enables drastic cost savings to the overall project. Many end users, particularly in the process industries, have applied the MAC approach to entire capital projects. That can result in project cost savings of up to 30% compared to a traditional approach.
Since automation suppliers are encouraged to consolidate industry and application expertise to execute projects in a consistent manner, costs are reduced in almost all phases of the project. This has led to the development of standardized practices and procedures, which can be applied across multiple projects to reduce costs. In addition, MAC suppliers often have introduced innovative project management practices such as decoupling hardware and applications software, removing dependencies to allow multiple aspects of projects to be executed in parallel, reducing the number of project gates and simplifying the commissioning process.
While typical MAC services could comprise all aspects of the automation scope, MAC suppliers have expanded their services in many directions. For example, in recent projects, the extended services, often referred to collectively as “MAC+,” have included the supply of instrumentation, process equipment such as pumps and valves, communications services and IT services. By consolidating additional services, MAC+ providers offer end-users even further savings.
In response to increased cost pressures, major end-users in the process industries have devised new cost control measures, which require MAC+ providers to expand the scope of their services even further.
At a large energy company, internal competition placed considerable pressure on new project costs. Although the company had been able to reduce project costs, management called for repeatable solutions that would further reduce costs.
Project management addressed the challenge with a new concept, in which designs would begin with the absolute minimum scope and justify additions upward. Among the results were simplified designs whose construction, integration and installation were within the capabilities of multiple suppliers rather than “one in the world.” Future projects will re-use replicated designs from prior projects.
The energy company selected Yokogawa as the MAC for the first project to use the new design concept. In line with an innovative approach to cost control, the MAC contract encompassed an unconventional scope. A streamlined program created a single-source solution for all measurement and automation products plus related services. The MAC scope included procurement, engineering, fabrication, delivery management, inspection, logistics and warehousing — hence “Beyond MAC+.”
Included in the product scope were the following:
• The distributed control system (DCS) and safety instrumented system (SIS)
• Control valves
• On-off valves
• Transmitters and gauges
• Flowmeters
• Skids.
The service scope included the following:
• Delivery management and coordination
• Inspections
• Logistics
• Warehousing.
In the procurement scope, 34 suppliers and 60 packages were managed. The value of third-party products was four times the value of the manufactured products. The MAC responsibilities included all contract management, flow-downs, terms and conditions and liquidated damages. With suppliers spread throughout the world, the MAC team literally worked in all time zones.
Inspection management required in-depth knowledge of all products as well as inspection criteria. There were cargo transit inspections at seven points. The MAC team required a thorough understanding of logistics, import/export, ocean and air freighting and overseas coordination. Warehousing required an understanding of inventory management, preservations, delivery of goods and care.
The automation system project management used an agile execution methodology, which enables global team collaboration. The methodology also decouples the application software environment from such hardware as standard smart junction boxes for input/ output (I/O), flowmeters, transmitters and valves. A significant portion of the factory acceptance test (FAT) was automated and conducted collaboratively from multiple, remote locations.
Also expediting the MAC process was a subcontract to address non-conforming (or non-confirmative) reports (NCRs) on-site.
Although the overall project was delayed by the COVID-19 pandemic, significant content such as factory acceptance testing used augmented reality (AR) technology to minimize the team members required to be present at any facility.
In light of the progress on the first project, which is now operational, the end-user awarded the company the MAC contract for a follow-on project, which is in process today. With 34 suppliers and 58 packages, the scope is similar to the first project.
The Beyond MAC+ experience can be transferred from fossil fuel projects to sustainable energy development. For example, Yokogawa recently announced the company has been selected to be the MAC for the construction of a hydrogen production plant in Europe. The plant will produce renewable hydrogen by using electricity from an offshore wind farm. The MAC optimizes operations at the plant by integrating its systems and equipment.
The plant will use a high capacity electrolyzer that will produce green hydrogen. The green hydrogen produced at this plant will be transported via a pipeline to a refinery, where it will replace grey hydrogen, partially decarbonizing the facility's production of energy products such as gasoline, diesel and jet fuel. GSIR
Kevin Finnan is a market intelligence and strategy advisor at Yokogawa.
uMain automation contractor (MAC) services streamline project management, reducing costs up to 30%, enabling efficient execution in diverse global locations.
uYokogawa's approach integrates diverse services, demonstrating adaptability in sustainable energy projects, envisioning a future of interconnected systems
Software Toolbox has reduced risk for System Integrators since 1996. We reduce risks associated with the use of third party or add-on software to major HMI/SCADA/MES packages, and the risks of writing custom software to meet a specific need. The software products we provide involve applications in reporting, data collection, device integration, remote data connectivity, logging, visualization, OEE, SCADA, cloud services, and more are used in all industrial verticals and are trusted by users in over 110 countries.
Collaboration is what the Software Toolbox experience is about.
Our clients benefit from this culture that loves working together; committed to reliability and responsiveness. Thousands of integrators and users around the world experience our knowledge of how industrial software can work together through our ability to work patiently with multiple vendors and customers.
Visit us at info.softwaretoolbox.com/integrators to learn more.
Our risk reduction formula is equal parts of providing a variety of off-the-shelf software products, combined with the knowledge of how they work with major supplier’s software products or together on their own, to solve real manufacturing operations challenges, and back it with support that, well, you just have to experience the difference.
John Weber Partner Program Manager
Software Toolbox Inc.
Email: jweber@softwaretoolbox.com
Telephone: 704-849-2773
Charlotte, NC
Actemium’s North American network of system integrators is structured to provide local support, regional expertise, and, as needed, global scale. With over a dozen offices on the continent, and 400+ business units around the globe, Actemium can meet the operational technology development and support needs of every manufacturer regardless of their size or location.
With experience spanning over forty years of solutions for industry, we can help on any project in the OT spectrum. Our services and solutions span system upgrades due to obsolescence, new system implementations to expand production, MES and Data Analytics to optimize operations and integrate to the enterprise, or 24x7 support to close gaps and keep the plant running. No matter what your OT or MES challenge is, Actemium is prepared to provide a solution.
We provide these services across a wide variety of industries:
Why Actemium? Our clients work with Actemium because we have a unique balance to deliver technically while at the same time address the human element and the change impact of the new systems. We know that, in OT, a system is often judged by how well the people understand, embrace, and further its use.
• Automotive
• Brewing
• Chemicals
• Consumer Products
• Energy
• Entertainment
Solutions:
• Electrical Engineering
• Panel Design
• Automation / Control Systems
• Manufacturing Execution Systems (MES, MOM)
Locations:
USA
• Atlanta, GA
• Cincinnati, OH
• Detroit, MI
• Indianapolis, IN
• Philadelphia, PA
• Assorted Satellite Locations
• Feed, Food, & Beverage
• Government
• HVAC
• Life Sciences
• Material Handling
• Metals and Mining
• Data & Analytics
• Robotics and Vision
• Consulting and Requirement Definition
• 24x7 Support / System Adoption
• Training and Education
Canada
• Mississauga, ON
• Bedford, NS
• Langley, BC
• Quispamsis, NB
• Moncton, NB
• Assorted Satellite locations
• Oil and Gas
• Pulp and Paper
• Transportation
• Water & Wastewater
• Process Engineering
• Project Management
Mexico
• Querétaro, Qro.
Wilfred Misener, Director of Business Development, North America wilfred.misener@actemium.com (902) 464-4862 ext. 202 (902) 293-4393 mobile
As a leading system integrator, Hargrove Controls & Automation is one of few multidiscipline automation groups in the country capable of providing turnkey solutions for plant automation, safety systems, cybersecurity/OT, and industrial digitalization. Our system integration team provides simplified solutions for our clients by working handin-hand with the engineering and execution team throughout the project life cycle.
Our Team specializes in DCS/PLC/SIS system integration & migration, digitalization, and process safety. We can implement the vision of Industry 4.0 through digitalization such as AI-enabled advanced process control, equipment failure predictions, reliability and availability analyses, and multi-variate analysis. Our process safety Team is TÜV Rheinland certified in Functional Safety and has many years of experience in all phases of the Safety Life-cycle including Process Hazard Analysis, SIL Calculations, Safety Requirement Specifications, and SIS logic solver programming. We provide process safety training courses, and we host TÜV Rheinland certification courses facilitated by authorized providers.
and SIS solver
Hargrove Controls & Automation implements control systems for pulp & paper, petroleum & chemical, heavy manufacturing, and other industrial facilities. Our Team consists of process control engineers and specialists, certified process safety engineers, cybersecurity professionals, networking specialists, instrumentation designers, and panel builders. We foster a culture of safety that cultivates quality throughout the project lifecycle while leveraging industry best practices. Based on your needs, our team will operate as an independent system integrator or with the full complement of our global EPC firm, Hargrove Engineers & Constructors and our asset life cycle management company, Tormod.
Together, Hargrove and Tormod offer clients a differentiator in the marketplace by providing a complete solution for total asset life cycle management including engineering, automation, full-service EPC, maintenance, reliability, commissioning & startup, and technical services. Tormod specializes in transitioning engineered facilities into operating assets with both short-term commissioning assistance and longterm operations contracts. The success of our Team of companies stems from cultivating the most talented engineering and construction professionals while valuing long-term client relationships.
For more information about Hargrove Control & Automation, please visit https://hargrove-ca.com . For more information about Tormod, please visit https://tormod.com/.
Capabilities
• System Integration
• System Migration
Corporate Headquarters
Mobile, Alabama / 251.476.0605
KEY EXECUTIVE
Karen Griffin, Vice President
Hargrove Controls & Automation
• Process Safety
• Machine Safety
Other Office Locations:
• Angleton, TX
• Atlanta, GA
• Baton Rouge, LA
• Beaumont, TX
• Birmingham, AL
• Columbus, OH
• Concord, CA
• Decatur, AL
• Greenville, SC
• OT/Cybersecurity
• Digital Transformation
• Houston, TX
• Lake Charles, LA
• Memphis, TN
• Monterrey, MX
• Pasadena, TX
• Pascagoula, MS
• Philadelphia, PA
• Savannah, GA
• Mexico City, MX
• Panel Fabrication
• Lifecycle Services Solution
CONTACT INFORMATION:
Nick Hausman, Marketing Leader
Hargrove Engineers & Constructors | Controls & Automation Life Sciences | Tormod | p: 251.375.5924 | c: 618.954.9071
www.hargrove-epc.com
A worldwide leader in automation and information solutions, RoviSys has made businesses more secure and more profitable since 1989. Customers rely on RoviSys for information management solutions, manufacturing automation, control systems integration, building automation, warehouse automation enterprise and industrial networks, MES, and Industrial AI.
We deliver solutions that drive productivity, improve product quality, increase asset utilization and integrate technology. Our reputation is built on technical expertise, dedicated customer service, quality, and continuity.
Companies with large, enterprise-wide initiatives and small-scale operations, across nearly every industry, and across the globe partner with RoviSys for services and solutions ranging from problem identification to project completion.
Engineering Offices
• North America: Ohio, North Carolina, Texas, Michigan, Illinois, Massachusetts, California, Georgia
• Asia-Pacific: Singapore, Taiwan, Indonesia, Malaysia
• Europe: The Netherlands, Ireland
Capabilities:
• Process Automation
• Building Automation
• Discrete Manufacturing Automation
• Warehouse Automation
• Control Systems Integration
• Electrical Power Management Systems
• Manufacturing Execution Systems (MES)
• Industrial Network Solutions
• Building Management Systems
• Electrical & Instrumentation Design
• Industrial AI
• Consulting
Companies with large and small-scale operations, across nearly every industry partner with RoviSys for services and solutions ranging from problem identification to project completion. When asked why RoviSys is preferred over the competition, the prevailing answer is experience and vendor independence, paired with a unique ability to manage, deliver and support projects. Our flexibility to do what’s right for customers is the key to satisfaction and success.
• Chemicals
• Life Sciences
• Consumer Goods
• Data Centers
• Glass
• Mining & Metals
• Oil & Gas
• Paper & Wood
• District Energy & Microgrids
• Water/Wastewater
• Semiconductor
• Automotive
• Federal Solutions
Falon Simmons, Vice President McKinney, TX
Telephone: (469) 270-5503
fsimmons@adaptiveresources.com www.adaptiveresources.com
Primary Industries
• Food & Beverage
• Power
• Consumer Products
• Automotive
• Medical Devices
Other Office Locations
• Calgary, AB
• McKinney, TX
• Guadalajara, Mexico
Adaptive provides a range of solutions and a unique combination of technology and expertise for managing processes. More than systems integrators or software engineers, we provide the consulting and design services to minimize process variability and yield better quality and less power usage or waste.
Since 1992, Adaptive Resources has applied scientific principle to advance process control. From their Quick Study suite of advanced control technology solutions to process consulting, systems integration, Adaptive has always focused on delivering the information and tools needed to manage the most complex manufacturing processes.
Core competencies
• Quick Study APC Advanced Process Controls software suite (MPC)
• Systems Integration
• Machine Vision and Robotics
• UL 508 Industrial Control Panel Fabrication
Strategic Partnerships
• ABB Robotics
• B&R
• Cognex Partner SI
• Datalogic
• Denso Robotics
• Festo
• Keyence
• Microscan SI
• Rockwell Automation Recognized SI
• Siemens Solution Provider
• Universal Robots
Full Profile at www.cfemedia.com/systemintegrator/adaptiveresources
+43 316 6902 0 automation@andritz.com andritz.com
Primary Industries
• Pulp and Paper
• Mining & Mineral Processing
• Hydro
• Seperation
• Process Equipment Automation & Optimization
• ANDRITZ operates over 280 sites worldwide. Please obtain contact details of our global locations online.
• Headquartered in Graz, Austria, founded in 1852.
ANDRITZ is a globally leading supplier of plants, equipment, and services for hydropower stations, pulp and paper, metalworking and steel industries, mining, and solid/liquid separation in the municipal and industrial sectors, as well as for animal feed and biomass pelleting.
ANDRITZ Pulp & Paper: Continuous research and development activities focus on supporting customers to achieve sustainable production with higher capacities and higher energy efficiency while minimizing the consumption of energy, chemicals, and water.
ANDRITZ Hydro: A global supplier of electromechanical systems and services (“from water-to-wire“) for hydropower plants and one of the leaders in the world market for hydraulic power generation. More than 180 years of accumulated experience in turbine design. Over 31,900 turbines (more than 471,000 MW) installed globally. Over 125 years of experience in electrical equipment.
ANDRITZ Automation & Digitalization is a leading supplier of machine and plant control systems with 110 company locations worldwide. ANDRITZ provides automation services and tools for a wide range of process industries, including pulp and paper, mining, lime and cement, power, and oil and gas. ANDRITZ automation defines electrical system capacity and utility requirements, establishes an equipment numbering system, works with process engineers to accurately assign control devices to process equipment, and produces effective E&I construction and maintenance packages. As a technology leader with extensive and long-term experience in supplying industrial measurement, control, and optimization solutions for various industries, ANDRITZ is combining its process and equipment expertise with the latest advancements in the digital era. The result of this powerful combination is Metris: a portfolio of ANDRITZ Digital Solutions.
Gerry Gallo
Hialeah, FL 33016
Telephone: 305) 805-3700
Fax: 305-818-5976
https://cct-inc.com
Primary Industries
• Pumping Systems
• Baggage & Handling
• Industrial Automation
• Oil & Gas
• Power Generation
Other Office Locations
• Central and South America
CCT is a premier custom control panel builder in the South Florida with capacity to serve National and International markets. We provide full services for design, fabrication, and integration of industrial control systems. Our main focus is Industrial Automation, System Integration, Custom Control Panels, Custom Programming, Operator Visualization and more.
We are presenting our New Product a Submersible Panel for Pump Stations tested 8.4 feet of water(measured from panel legs on a 24 inches concrete slab) fully energized and functioning. This Submersible Panel is patented and UL Verified V420512 for No water ingress after 72 hours, 10 inches above Panel (24" slab + 67" enclosure + 10" UL requirement equal 101" or 8.4ft). UL verification was recently upgraded to V986660 for No Water Ingress after 30 days, giving you more confidence when install this control panel. This is the perfect solution for flood prone areas. Although this panel is not intended to work indefinitely under water, it is designed to have a resilience to flood conditions. CCT has tested it more than ten times submerged more than two or three weeks at the time and with no water ingress. Seventeen of our customized enclosure have been installed at City of Coral Gables, FL where flooding can occur during major storms. Having the water pump control system working during the heavy rain fall is critical to minimize the flooding. Our application can keep the system dry and intact during the catastrophic situations.
CCT is a UL 508A, UL 698A and pending UL 1741 certified panel shop and proud supporter of the Buy American Act. Please call or email us if you have any questions. We are here to Serve You!
Full Profile at www.cfemedia.com/systemintegrator/customcontrolstech
(812) 479-5170
Evansville, IN www.ecssolutions.com info@ecssolutions.com
Primary Industries
• Chemical
• Beverage & Distilleries
• Food & Bakery
• Life Science
• Metals
Other Office Locations
• Atlanta, GA
• Bowling Green, KY
• Hattiesburg, MS
• Henderson, KY
• Joplin, MO
• Knoxville, TN
• Lexington, KY
• Phoenix, AZ
• Raleigh, NC
• Venice, FL International:
• Colombia
ECS is dedicated to performance improvement and innovation in batch manufacturing. Our vision of steady, sustainable growth with a diverse customer base is the foundation for making ECS a good place to work. ECS is a recognized leader in the delivery of process control systems, having achieved that status by aggressively pursuing solutions that provide the information and controls our customers need to manufacture more products faster and at a lower cost. We understand that rapid developments in technology necessitate new approaches to control systems – approaches that allow people to filter and consume information more quickly so they can make the best decisions and take immediate action to follow those decisions through. Our leadership team is focused on adding value to our customers’ process and ultimately improving their bottom line.
ECS operates under the guiding principles of excellence in all we undertake, measured internally by profitability and externally by satisfying requirements, and trust that we earn by demonstrating integrity and technical prowess, that we extend to those who prove trustworthy, and that we maintain through communication. ECS’ core values are instilled in every employee to consist communicate candidly, build trusting relationships, serve others well by being responsive, lead with the courage to take risks, continuously improve in response to changing markets and technologies, disarm conflict by handling it one on one, seek excellence rather than perfection to meet the objective, and make ECS a better place to work by being trusting and trustworthy.
EOSYS Group
615-355-7200
www.eosysgroup.com/contact
Primary Industries
• Food and Beverage
• Chemical
• Consumer Products
• Automotive
• Pulp and Paper
Other Office Locations
• Nashville, TN (HQ)
• Atlanta, GA
• Cincinnati, OH
• Huntsville, AL
• Minneapolis, MN
www.etechgroup.com
Telephone: 1-513-935-0100
Headquarters: 8614 Jacquemin Dr, West Chester Township, OH 45069
Primary Industries
• Life Sciences
• Mission Critical
• Food and Bev/CPG
• Manufacturing
• Material Handling
Other office locations
• Alabama
• California
• Indiana
• Michigan
• New Hampshire
• New York
• North Carolina
• Ohio
• South Carolina
• Texas
• Mexico and Canada
2023 has been an exciting year for EOSYS with several big announcements. Control Engineering named EOSYS the 2023 System Integrator of the Year in the Large Systems Integrator category. EOSYS was cited for excelling in digital transformation, batch control, and other control and automation system project integration, with an emphasis on mentoring and continuing education.
EOSYS was also recognized by Rockwell Automation as one of only four U.S.-based system integrators to achieve the level of Rockwell Automation Platinum System Integrator Partner. This is a significant accomplishment as becoming a Platinum System Integrator Partner means EOSYS has achieved exclusive recognition within the Rockwell Automation Partner Network reserved for less than 1% of their partners.
Minnesota has its first Rockwell Automation System Integrator Platinum Partner. In September of 2023, EOSYS announced the opening of its new office location in Minneapolis, Minnesota. "The Minneapolis expansion is an exciting step forward for EOSYS and its customers in the Upper Mid-west. We are looking forward to meeting new engineers in the area and growing our team," said Vice President of Operations, Andy Ask.
Headquartered in Nashville, Tennessee, the Minnesota office is one of four satellite office locations, with other locations in Ohio, Alabama, and Georgia. The expansion to the Upper Mid-west will help EOSYS better serve its many customers as well as attract new engineering talent from the area.
Profile at www.cfemedia.com/systemintegrator/eosysgroup
E Tech Group is one of the largest engineering and system integration firms in the United States. With locations throughout the United States, Canada and Mexico and with over 380 engineers, we provide automation, control, and information solutions to the Life Sciences, Mission Critical, Metals, Parcel, Consumer Products and Food & Beverage industries. Four respected system integration brands – E Technologies, Glenmount Global Solutions, Superior Controls and Banks Integration - came together to deliver consistent solutions across the United States, pairing deep industry knowledge and experience with innovative and comprehensive engineering solutions.
Our scale allows us to help our clients develop and implement standardized solutions at any of their facilities regardless of physical location. We have the capability to bring together large teams of diverse professionals to provide turnkey projects, as well as offer professional project and program management, procurement, panel builds, site and subcontractor supervision, installation and commissioning services, and more.
From full turnkey design/build projects, to staff augmentation, small upgrade projects, E Tech Group has the right people, expertise, and industry experience to deliver for you.
Full Profile at www.cfemedia.com/systemintegrator/etechgroup
Daniel Lyrek
VP, Sales & Marketing
Primary Industries:
• Food & Beverage
• Consumer Packaged Goods
• Life Sciences
• Chemical
• Lexington, KY (headquarters)
• St. Louis, MO
• Fullerton, CA
• Charlotte, NC
• Denver, CO
Huffman Engineering, Inc. 5301 North 57th Street Lincoln, NE 68507 www.huffmaneng.com info@huffmaneng.com (402) 464-6823
Colorado
112 Inverness Cir E, Ste E Englewood, CO 80112
Primary Industries
• Pharmaceuticals & Life Sciences
• Food & Beverage
• Water & Wastewater
• Electrical & Gas Utilities
• Manufacturing & Material Handling
At Gray Solutions, we're a bunch of intellectual rebels on a mission to revolutionize smart manufacturing through innovation. As a leading system integrator, we let curiosity lead us to creative ways of solving unique problems to ensure our customers succeed. We never settle for average or cut-and-paste solutions; we thrive on doing things that have never been done before. Our toolbox includes cutting-edge expertise in Automation + Controls, Digital Transformation, EPC Turnkey, OT + Cybersecurity, Process + Packaging, Robotics + Vision, and Technical Support. Our team of Solutioneers is in the trenches every day with our customers, fighting the challenges of modern manufacturing with collaboration and ingenuity. Founded in 2018 in Lexington, Kentucky, we employ more than 275+Solutioneers across the country in a work-fromanywhere model. As a global CSIA Certified System Integrator, we collaborate with customers in the Food & Beverage, CPG, Life Sciences, and Chemical industries. We love what we do, and have been recognized for it; named Rockwell Automation’s 2023 Partner of the Year, recipient of Rockwell Automation’s 2023 Ecosystem Award, and a multi-year SI Giant by CFE Media. In 2023, Gray Solutions achieved Ignition Premier Integrator status with Inductive Automation and Platinum Partner with Rockwell Automation.
www.graysolutions.com
Daniel.Lyrek@graysolutions.com 612-716-3187 www.graysolutions.com Full
Recognized in the Control System Integrators Hall of Fame, Huffman’s Engineering Inc. (HEI) is a full-service engineering firm specializing in process automation and control systems with expertise in highly regulated industries.
Our experienced engineering team is bolstered by the integrator certifications we hold. We have been a Control Systems Integrators (CSIA) Certified member since 2005, a Rockwell Recognized Systems Integrator in Process, Control and Safety, Ignition Gold Certified System Integrator, AVEVA/ Wonderware Certified Systems Integrator, and Schneider Certified Alliance System Integrator and are Siemens, Fortinet, GE Digital and Smart Sights certified among others.
HEI designs and builds robust and reliable automation systems to meet the expectations of the CDPHE, FDA, USDA and EPA. Our documentation is detailed and consistent, allowing our customers to meet stringent regulatory requirements.
We house the oldest UL508 and UL698 shop in Eastern Nebraska and a fully certified UL508 shop in Colorado. Control panels are custom built in-house by experienced technicians to exacting industry standards that are clearly labeled, documented and tested before leaving the shop to ensure quality to customers.
With a focus on pharmaceutical & life sciences in both human & animal health, food & beverage, water/wastewater, electric & gas utilities, material manufacturing and networking, data analytics & cybersecurity, our resident expertise in the Midwest is second to none.
www.cfemedia.com/systemintegrator/huffmanengineeringinc
Kimberly Pelkey
Wilson, NC
Telephone: (252) 237-3399
kpelkey@ias-nc.com www.ias-nc.com
Primary Industries
• Life Science
• Tire & Rubber
• Wire and Cable
• Chemical Film & Plastics
• Food & Beverage
Other Office Locations
• Cedar Point, NC
• Garner, NC
• Lucama, NC
• Rocky Mount, NC
Your plant comes with its own set of unique challenges and goals. Our automation specialists collaborate with your team to produce solutions tailored specifically to your needs. Whether we’re designing a new system or updating your existing systems, IAS will devise a plan to both enhance productivity and reduce costs.
Manufacturing Automation
• PLC Programming
• Motion Control Engineering & Servo Systems
• Process Batch Solutions
HMI & SCADA Programming
IIoT
Project Management
• Owner’s Representative
• Qualification Testing
Continuous Improvement
• Performance Tracking and Reporting • Reporting and Analytics
Partners / Affiliates • Rockwell Automation Silver System Integrator
Malisko Engineering, Inc. malisko.com info@malisko.com (314) 621-2921
St. Louis, MO
Primary Industries
• Food & Beverage
• Dairy
• Consumer Packaged Goods
• Life Sciences
• Metal, Mining, & Cement
Other Office Locations
• Denver, CO
• Eau Claire, WI
Profile at www.cfemedia.com/systemintegrator/industrialautomatedsystems
For nearly 30 years, we have connected people, process, and technology to improve manufacturing productivity and efficiency. Our team of engineers, designers, programmers, automation, and network & security specialists listen to understand your needs and develop personalized solutions. When you work with us, you’re not just investing in process automation. You’re investing in a business partnership with a group of dedicated, multi-disciplined efficiency professionals.
Malisko offers a full suite of services that work well independently or together. Our foundation in Industrial Control Systems brings practical OT experience and perspectives to Digital Transformation and Industry 4.0 initiatives.
We have the unique ability to bridge the gap between IT and OT with our Industrial Network, Security, and Information Specialists. Our specialists have instant credibility with both sides based on practical experience.
Plant Floor Control & Process Automation Solutions
We have nearly three decades helping manufacturers streamline their process by integrating various technologies and components to enhance efficiency, productivity, and data accuracy on the plant floor.
Manufacturing Intelligence
We help manufacturers harness the power of manufacturing intelligence by collecting, analyzing, and utilizing data to optimize processes, reduce costs, and improve overall performance in a customized and sustainable manner.
Full Profile at www.cfemedia.com/systemintegrator/malisko
Kevin Overmyer, Director of Client Solutions & Success
Maumee, OH matrix@matrixti.com
419-897-5630 www.matrixti.com
Primary Industries
• Food & Beverage
• Wine & Spirits
• Consumer Products
• Life Sciences
• Chemical
• Metals
• Oil & Gas
• Feed/Grains/Oilseed
• Aggregates & Mining
Other Office Locations
• Atlanta, GA
• Cincinnati, OH
• Denver, CO
• Indianapolis, IN
• Kansas City, KS
• Maumee, OH
• Minneapolis, MN
Pacific Blue Engineering info@pacificblueengineering.com www.pacificblueengineering.com (657) 201-8603
Primary Industries
• Food and Beverage
• Entertainment
• Transportation
• Life Sciences
• Manufacturing
Office Locations
• Long Beach, CA
• Irvine, CA
• Orlando, FL
• Phoenix, AZ
Matrix Technologies is the only company you need to call for your next capital investment.
We are a truly single-source solution for all of your engineering, automation and information needs.
87% of our projects are repeat engagements with satisfied clients.
• Consulting
– Pre-Engineering for capital project scope and cost development
– 3D Facility and Process Laser scanning for baseline/ ground penetrating radar
–Automation Master Planning
–Digital transformation
–Network Investigation and Design
–Cyber Security
–MFG. Transformation Assessement
– Arc Flash
–Machine Safety
• Detailed Engineering
–Facility Design
–Process Conceptual and Detailed Design
–Network Design
–Mechanical and Piping Design
–Virtualized Server Systems
–Electrical Distribution and Control
–Process Automation
–Manufacturing Intelligence/MES Systems
–Energy Tracking and Reduction
–Performance Monitoring and Improvement
–Standards Development & Governance
• Application Expertise
–Industrial OT/I4.0
– Virtual Server Environments/Distributed Technology
–Raw Material Handling
–Batch System Design
–Batch System Automation
– Filling and Packaging Systems
–Track and Trace Systems
–Manufacturing Intelligence/Continuous Improvement
–Manufacturing Operations Management, MES & Systems
• Engineer, Procure and Construct Services (EPC)
–Upfront Engineering Scope and Construction Planning
–Full Engineering Design through Stage Gate Project Delivery
–Industrial Controls/Automation, Startup/Commissioning
–Coordination with Preferred local Contractors and Vendors
–Project and Construction Management
– PMI Practices
–Greenfield and Brownfield Capital Investments
– Industrial Buildings, Process and Packaging Line Expansions
Full Profile at www.cfemedia.com/systemintegrator/matrixtechnologies
Pacific Blue Engineering is a premier automation integrator that leverages the latest industrial automation technology to deliver unique solutions for our customers’ challenges in a broad range of industries. Our true end-to-end services provide a single vision for our customers’ projects, from planning and design, to programming, building, installation, commissioning, testing, and validation. We have served 200+ customers, in 4 countries, for 8 industries, and executed more than 1,196 jobs.
Our culture is the attitude we bring to work every morning. We work hard, do what’s right, pay attention to detail, and focus on achieving measurable results. We take pride in crossing our t’s and dotting our i’s so our customers don’t have to.
Services and Solutions
• Machine Safety Controls
• Turn-Key Control System Integration
• SCADA
• Networks & Infrastructure
• Legacy Controls Migration
• UL508A Panel Build & Design
• AutoCAD Electrical Drafting
Certifications & Associations
• TUV SUD and TUV Rheinland Functional Safety Engineers
• UL 508A Panel Shop
• CSIA member
• ISNetworld / Avetta
Patti Engineering
Telephone: (800) 852-0994 sales@pattieng.com www.pattiengineering.com
Primary Industries
• Aerospace
• Automotive
• Consumer packaged goods
• Distribution & sortation
• Food & Beverage
• Glass
• Heavy Industry
• Pharmaceutical
• Semiconductor
Premier Automation Sales
Sales@premierautomation.com Monroeville, PA Telephone: 412-373-3700 www.premierautomation.com
Primary Industries
• Metals
• Aerospace
• Entertainment
• Glass & Plastics
• Oil & Gas
Other Office Locations
• Alpharetta, GA
Founded in 1991, Patti Engineering, Inc. offers high-caliber engineering and software development services to integrate automation technology in world-class industrial facilities so that your business runs faster, smarter, and more reliably. Patti Engineering is a seventime CSIA Certified Integrator and partners with the world’s leading industrial automation suppliers, including: Siemens, FANUC, Beckhoff, Mitsubishi, and Ignition.
Modern solutions for today’s automation challenges. Digital manufacturing strategies and project management are our strong suits. Functional specs are standard and all projects have a dedicated project manager that provides regular communication throughout the process. Patti Engineering is known for becoming trusted advisors to our clients, helping them improve OEE, safety and quality in their facilities.
We have a wide range of Manufacturing Automation and Intelligence expertise:
• IIoT/Industry 4.0
• PLCs & CNCs
• Robotics
• Digital Twins
• Virtual Commissioning
• MES/SCADA
• Motion Control
• RFID/RTLS
• Vision Systems
Experienced, degreed engineers complete all of our engineering, and Licensed Professional Engineers are on staff. Patti Engineering has experience not only in floor level automations, but also with applying Industry 4.0 technologies for Digital Transformation.
Outstanding customer satisfaction and project success earned Patti Engineering placement in Control Engineering magazine’s System Integrator Hall of Fame.
Premier Automation is an engineered solutions company that specializes in providing automation, drive and electrical control solutions and services to industrial markets. Premier Automation offers cost effective, industry specific technology solutions to help our customers increase their industrial productivity, efficiency and overall systems performance. We take the time to understand your unique process and requirements, and then work closely with you to develop the best control solution for your need. What sets Premier Automation apart is the wide range of in-house services that we offer which provides reliable, complete, fully integrated customer solutions. From concept to completion, our engineering, production & field service staff are unmatched in industrial automation experience and ability. Premier Automation serves as a true electrical control partner to companies that are in need of innovative solutions, strategies & support to help them compete successfully in today’s highly competitive global environment.
Full Profile at www.cfemedia.com/systemintegrator/premeirautomation
Quantum Design Inc.
Caledonia, IL 61011
815-885-1300
qdisales@quantumdi.com www.quantumdi.com
Primary Industries
• Agriculture
• Aerospace, aircraft
• Food & Beverage
• Pharmaceutical
• Material handling, logistics, warehousing
Since 1986, Quantum Design Control Systems has been a leading systems integrator serving the automation controls market by designing, building and deploying control systems throughout the world. We are committed to providing our customers with cost effective solutions using the most appropriate technology and products with proven reliability in a wide range of demanding environments and applications. Our controls engineering knowledge and panel production excellence is unique and provides customers a complete, turnkey solution.
Quantum Design’s team of engineers come from many different industry backgrounds and deliver broad ranging expertise in the following key areas:
• electrical engineering/design
• control system and panel design
• motion control a/programming
• CNC design/implementation
• Legacy system upgrades
• Logic programming and HMI development
• plant data integration, reporting and visualization
• and more….
Quantum Design provides full support throughout the project including installation support, start up, field service and training.
In addition, Quantum Design is a self-certifying, UL508A panel assembly shop and proficient at developing CE compliant controls systems. We employ the best technicians and assemblers and each system is inspected by our dedicated Quality Assurance team. Our ISO 9001:2015 Quality Management System ensures adherence to requirements and empowers us to continually improve. Quantum Design has been featured on Control Engineering’s System Integrator Giants list since 2019.
Full Profile at www.cfemedia.com/systemintegrator/quantumdesigncontrolsystems
Quantum Solutions, Inc.
504 DD Rd. Columbia, IL 62236
Email: sales@qsicontrols.com
Primary Industries
• Food and Beverage
• Distillation and Brewing
• Metal
• Chemical
• Water and Wastewater Treatment
Offices
• St. Louis, MO
• Dallas, TX
Yes, we can help with that! With over 26 years of experience, we’ve seen it all. We've been a dedicated and trusted partner to our clients, some since the very beginning. Our clientele range from small startups to numerous Fortune 100 Food & Beverage companies. No matter the size, Quantum Solutions can build a custom control system that integrates into your entire manufacturing facility driving efficiencies and productivity. We are centrally located but can be found throughout the US. We are actively building 3 greenfield facilities (1 West Coast, 2 Midwest). Let us help you design and build with the latest technologies and environmental considerations in mind.
Phone: (618) 281-9574 Full Profile at www.cfemedia.com/systemintegrator/quantumsolutions
Proficient with Allen Bradley PLC’s, FT/Ignition/Wonderware, Electrical and Control System Design, 480VAC Motor Controls and Control Panel Design, SCADA/OEE/MES/Historian, Site Commissioning and Training.
Danny Smith
Head of Business Development
danny.smith@gotoSAGE.com www.gotoSAGE.com
Primary Industries
• Manufacturing
• Mining/Resources
• Utilities/Water/Energy
• Transport / Smart Cities
• Defence Office Locations:
• Australia - South Australia, Victoria, New South Wales, Western Australia, Queensland, Northern Territory and Tasmania
• India – Pune, Mumbai
SAGE Group is a global company with a team of more than 720 people over two continents, committed to creating a Smarter Future, Better World.
As an integrated industrial digitalization services provider, SAGE has specialist brands and software solutions that combine to support clients to lead into the future on their digital transformation journey, with the perfect balance of technology, process, and capability. SAGE clients are world leaders and innovators looking for a smarter way of doing things and together, we are on a mission to make the lives of everybody smarter, safer, and more sustainable.
SAGE Automation Industrial automation design, delivery, and support Nukon Digital operations consultancy and delivery for smart decision making using whole-of-business insights
Embedded Expertise Matching high-calibre technical expertise with agile clients Skills Lab Creating a workforce that thinks smarter with industry 4.0 capability
TilliT Manufacturing’s low-code digital platform
Addinsight Unlocking powerful transport insights using real-time movement data
Hamid Sarshar, President Sacramento, CA
Telephone: (916) 395-8800 sales@tescocontrols.com https://tescocontrols.com
Primary Industries
• Water, Wastewater
• Renewable Energy
• Transportation Office Locations:
• Baton Rouge, LA
• Irving, TX
• Orlando, FL
• Salinas, CA
• Temecula, CA
TESCO is a national system integrator focused on delivering well-designed control system solutions that automate processes for water/wastewater treatment, distribution, and storage. We partner with clients to deliver end-to-end systems, from initial concepts, assessment and design, to programming, manufacturing, installation, and commissioning.
TESCO’s ability to offer a complete suite of professional services, manufacturing, and installation capabilities helps clients to manage schedule, quality, performance risk, and final outcomes.
Client services: system assessments, system design, engineering, programming, SCADA-HMI development, project management, commissioning, 24/7/365 technical support, training, and long-term service options. We are CSIA-certified and certified in all major control system software platforms.
TESCO designs, fabricates, and customizes control panels, MCCs, PLCs, VFDs, switchgear and instrumentation at our 130,000 sq. ft. Sacramento facility, offering options for custom dimensions, cabinet colors, configurations, and materials. We are a UL-certified OEM for all major industry equipment vendors.
TESCO’s project execution methodologies range from design-bid-build to design-build and collaborative delivery. With over 50,000 projects completed since 1972, client satisfaction is our primary objective. At TESCO you are not “just a project;” instead, each project is part of our long-term client commitment to consistently meet and exceed your expectations
Mike King, Principal Director of Operations
Toledo, OH (Maumee)
Telephone: (419) 725-7161 mking@thejdigroup.com www.thejdigroup.com
Primary Industries
• Food & Beverage
• Chemicals
• Manufacturing
• Fats & Oils
• Agricultural / Fertilizer
Global Headquarters
119 South Main Street St. Charles, MO 63301 www.veltatech.com asktheexperts@veltatech.com 314-463-3600
Primary Industries
• Manufacturing
• Chemicals, Petrochemicals
• Utilities
• Food, Beverage
• Process Industries
• Pharmaceuticals
Functional Safety Eng (TÜV Rheinland) | ISA/IEC 61511 SFS (SIS)
• Automation & Instrumentation
• PLC / DCS / HMI Programming
• Panel Design & Fabrication
• Safety Systems Design
• Commissioning & S/U Support
• Operator & Maintenance Training
• PFD and P&ID Development
• Instrument Specification
• Arc Flash & Power Distribution
• SCADA / MES
• Network Design
• IT / Cybersecurity
Velta Technology specializes in Digital Safety and Cybersecurity for the industrial space. We understand industrial assets and infrastructure to bridge the gap between Industrial IoT and OT/IT convergence. We are knowledgeable of the differences between industrial and IT infrastructures and the toolsets required to secure them.
Who are we?
The Velta Technology team is comprised of multi-disciplinary industrial manufacturing and critical infrastructure experts. Recognized as a Cisco IoT Advantage Partner, TXOne Networks Certified Partner, and Claroty Partner of the Year in North America, we have relationships and partner with the world’s leading solution providers in the industrial space.
We offer clients:
• Over 100 years of combined OT/ IT Industrial, Enterprise & C-suite experience
• Laser-focused on the industrial and manufacturing space
• Platform agnostic solutions with world-class partners across technologies & environments
• Proprietary Velta Technology Standards, Platforms & Methodologies
• Specialized Digital Safety / Cybersecurity Training program
• Expert resources and support as an extension to your internal terms
We help companies and organizations integrate digital safety solutions, expertise and tools, with existing technologies. We bridge the gap in expertise and understanding from industrial assets on the plant floor across to the enterprise. With over 1,000 points of entry, they only need one.
Velta Technology - Get Safer Sooner
Full Profile at www.cfemedia.com/systemintegrator/veltatechnology
Michelle Hammer
Business Development Manager
4409 E Baseline Rd #127 Phoenix, AZ 85042
615-208-4979
vertech.com
Primary Industries:
• Food & Beverage
• Solar Energy
• Water & Wastewater
• Manufacturing
• Irvine, CA
• Phoenix, AZ
• Nashville, TN
• Austin, TX
Paul Sondreaal, Director of Business Development
Eden Prairie, MN Telephone: (952) 933-3222 paul.sondreaal@wmeng.com www.wmeng.com
Primary Industries
• Water / Wastewater
• High tech
• Oil & Gas
• Pharmacuetical or Life Sciences
• Food and Beverage
Other Office Locations
• Over 30 offices Nationally
At Vertech, we believe there's a human way to do industrial automation.
Yes, we design bulletproof MES, SCADA, OT, and Controls solutions that are a joy to use. But we're also your long-term ally. No more endless change orders. No more paying good money for a half-solution. We're here to reduce your tech-related stress, not add to it. And who knows? You might even enjoy the process.
If you need a long-term guide to help you traverse the ever-changing rapids of industrial technology, we’ve got a paddle. Jump on in.
WUNDERLICH-MALEC: THE GO-TO TEAM FOR YOUR ENGINEERING, SYSTEM INTEGRATION, AND FABRICATION NEEDS.
Clients in a wide variety of industries rely on Wunderlich-Malec for advanced engineering solutions. The demands on today’s leaders require complex solutions to help manage their business. Cost reduction, regulatory requirements, security, and rapidly changing market dynamics require fully integrated operations. Since 1981 Wunderlich-Malec has excelled at creating and deploying the total solutions they need to meet these business objectives. We believe the key to our success is our depth of talent, proven methodologies and exceptional flexibility. Our people are passionate about solving your unique engineering challenges, and with the support of industry experts behind them, they can successfully execute projects of any size while meeting the demands of your industry.
Wunderlich-Malec is a 100% employee-owned company (ESOP). With offices throughout the US and over 500 professionals on our staff, we are one of the largest and most well established engineering companies in the United States. Our success is fueled by our strong and long-lasting customer relationships guided by our 3 part culture – Our Pledge, Process and People. We’re confident that our qualified staff has the knowledge, experience and talent to create and deliver the solutions you need for your integration needs.
Profile at www.cfemedia.com/systemintegrator/wunderlichmalec
In 2023 Avanceon joined forces with the North American network of Actemium System Integrators. We are bringing our expertise and innovation in Digital Transformation to this large global integration organization. In the next year you’ll see us transform our brand, expand our scale, and offer new services but one thing will remain the same - our commitment to providing innovation and value to our customers.
Expertise
Susan Schlegel
Vice President of Sales
610.458.8700
610.858.4936 mobile susan.schlegel@actemium.com www.avanceon.com www.actemium.us
Primary Industries
• Food & Beverage / CPG
• Water / Wastewater
• Life Sciences
Digital Transformation Services encompassing all technology from the electrical control panel through PLC, SCADA, MES, Analytics to the ERP
Reach out to find out how we can bring value to your company through our new network.
As “System Integrator of the Year,” APCO is outstanding in industrial control and automation. APCO excels in:
• Serving Diverse Industries: We cater to various sectors, including freshwater and water reclamation; oil, gas, and refining; and manufacturing
• Control System Mastery: Our specialization encompasses SCADA Master Planning, SCADA Programming (all platforms), System Integration, and Industrial Process Controls Consulting
• UL-Listed Panel Fabrication: high-capacity in-house panel fabrication guarantees smooth project integration. UL-listed control panels for both hazardous and classified area locations, incl. NEMA 7 and Purge Systems
• Award-winning Excellence: APCO is recognized for exceptional contributions to industrial automation
Primary Industries
• Water/Water Reclamation
• Oil, Gas and Refining
• Manufacturing
Contact: (801) 519-9500 apco-inc.com North Salt Lake, UT St George, UT
aeSolutions, from the earliest inception phases to final turn over, provides project development and technical expertise to guide you to success on your project and business objectives. Through a proven project delivery model, aeSolutions integrates diverse hardware, software, and services from multiple vendors and client stakeholders into a unified, integrated system
• Process Control
• Batch Control
• Complex Migrations & Upgrades
• Burner Management
• Combustion Control
• Industrial Fire & Gas
• Industrial Networks
• Material Handling
Stephen Powell
Client Success Manager aeSolutions Greenville, SC (864) 404-3026 www.aeSolutions.com
Primary Industries
• Petrochemical & Oil & Gas
• Pharmaceutical
• Specialty & Agricultural Chemical
Our full range of services will lead you through the controls integration process to deliver a fully integrated, cohesive control system in a wellexecuted project.
Our talented and dedicated engineers at Automation Plus utilize a wealth of industrial control system expertise to deliver plant centric, business driven, automation solutions for our clients.
We work directly with your management, operations, and maintenance staff to ensure that your goals are realized while designing and implementing control systems that are operator-friendly, maintainable, and cost-effective.
Dennis Romak dromak@plusgroups.com 513-742-7590
Primary Industries
• Chemical • Pharmaceutical
• Food & Beverage
Our engineers and specialist possess substantial operating floor and system startup experience in manufacturing, process, and packaging systems. In addition, we have a team of industry-seasoned professionals to address Cybersecurity concerns and ensure your business is protected. Our team utilizes proven best practices for project execution and design, leading to a nimble, best in class solution, customized for each client.
George T. Hall (GTH) is a full-service solutions provider. With a legacy of 90 years in business, we are experts in the areas of:
• PLC Modernization
• SCADA/ OEE Solutions
• Combustion Technology
• Process Control Upgrades
Corporate Headquarters Anaheim, CA 714-939-7100
https://www.georgethall.com/si/ integrationsupport@georgethall.com
Primary Industries
• Water/Wastewater
• Mining, Minerals, & Metals
• Pharmaceutical
GTH brings experience and intuition to automation challenges and creates sustainable, reliable control solutions. Certified to ISO 9001:2015 by DQS, we craft custom panels in UL-certified shops in California and Nevada. Our UL 508A and 698A panels meet regulatory needs, tailored precisely for OEMs' specifications.
MartinCSI is a highly-qualified systems integrator that has been providing complete automation solutions to the manufacturing community for over 30 years. We offer a broad scope of automation services including control panel design, upgrades, motion controls, PLC programming, SCADA/HMI development, and robotics. We specialize in Smart Manufacturing solutions, machine vision, and machine safety. Being hardware agnostic and trained on multiple platforms allows us to work across a variety of different industries in discreet and process manufacturing. You can expect to receive detailed scopes, expert engineering, honest and regular status assessments, attention to quality, and a focus on exceeding your expectations.
Lindsey
Kielmeyer,
Business Development Director
Telephone: (614) 761-5600
Fax: (614) 761-5601 saleseng@martincsi.com www.martincsi.com
Primary Industries:
• Automotive
• Chemical
• Factory Automation
• Food and Beverage
• Life Sciences
Interstates, Inc. is a total systems integrator with the ability to automate all of a plant's equipment, collect and provide data reporting from operations, and design the interface with business systems to give an owner real-time tracking and control. With decades of experience and proven expertise, we partner with our clients to find industrial solutions from operational technology to analytics to automation.
Interstates, Inc.
1400 7th Avenue NE
Sioux Center, IA 51250
712-722-1662
bdev@interstates.com www.interstates.com
Primary Industries:
• Consumer Packaged Goods
• Food & Beverage
• Value-Added Agriculture
• Warehouse & Distribution
Since 1953, Interstates has thrived on solving the most complex challenges to ensure your facilities stay up and running with no unplanned downtime. As a system integrator, we have the capacity and the know-how to deliver solutions on schedule, on budget, and on target with your needs.
LEADING SYSTEMS INTEGRATORS TRUSTED TO OPERATE IN HIGH-RISK, LOW-TOLERANCE ENVIRONMENTS.
From power distribution and chemical manufacturers to transportation and data center operators, success is often measured in milliliters or microseconds. The requirement for repeatability, precision, and efficiency is absolute. M.C. Dean initiates and implements complex, large-scale automation projects from design and programming to production and site commissioning, offering our customers a one stop shop for project execution. With a combination of experience, diversity, and depth of knowledge, we are a certified systems integrator for many leading controls equipment vendors.
M.C. Dean
(703) 802-6231
Automation_Solutions@mcdean.com
Primary Industries
• Energy Management Control Systems
• Power Control Systems
• Industrial Control Systems
Contact us today to learn more about our full-lifecycle solutions that drive consistency, quality, and resiliency for our customers.
McEnery Automation combines extensive process control knowledge with OT and IT expertise to deliver scalable, cost-effective solutions that optimize assets and productivity. We help clients with their digital transformation journey by integrating the plant floor with information systems.
McEnery Automation’s engineers are experts in Process, Control and Information systems. Now in our 30th year, our success is built upon hiring and developing engineers that are skilled in each of these areas.
Steve Holland
Info@McEneryAutomation.com
St. Louis, MO 636-717-1400
www.McEneryAutomation.com
Primary Industries:
• Food & Beverage
• Consumer Products
• Lubricants & Chemicals
This unique approach allows our team to not only understand the process data, but also how to put it to use by business systems and analytical tools to optimize assets and productivity.
Who we are: Triad has revolutionized the industrial sector serving our clients for the past 50 years delivering tested and proven solutions. Whether it is E/I Design, DCS/PLC programming or MCC modular building fabrication, to E/I construction, Triad is the absolute leader when it comes to your E/I/A project.
What we offer:
• Automation Services
• Design Services
• Fabrication/Integration
• Analytical
• Burner Management
Who we serve:
• Petro/Chemical
• Refining
• Power Generation
• Pulp/Paper
• Midstream
• Green Energy/Renewables
With full-system engineering expertise, our advanced knowledge and project management best practices, ensure the highest degree of project success at a lower risk. Polytron supports your business goals from start-to-finish including controls, process, mechanical, packaging, and digital transformation solutions. Our strong leadership and project managers are your trusted partners to help you design, implement, and validate your vision for a sustainable future.
We deliver:
• Advanced Smart Manufacturing solutions
• Long-time expertise in process and packaging
• Proven results-driven project management
Rande Allen, Vice President 855-794-7659
marketing@polytron.com www.polytron.com
Primary Industries:
• Food & Beverage
• Consumer Packaged Goods
• Life Sciences
• Industry-recognized Industrial Networks and Security expertise
• Professional PEs, PMPs, and TÜV safety engineers
• Certified expertise in major industry technologies for unique solutions
Automation/Analytical/Design
• Baton Rouge, LA
• Deer Park, TX
Metal/Fabrication/Integration
• Baton Rouge, LA (833) 501-4858
TCSInfo@TheNewtonGroup.com
Contact us at QR code below:
Data security has never been more critical
DataHub technology is redefining industrial IoT. New security enhancements, unmatched mirror capabilities to bridge on-premise and cloud, unparalleled flexibility with MQTT.
One solution that does it all. Secure, fast, easy.