
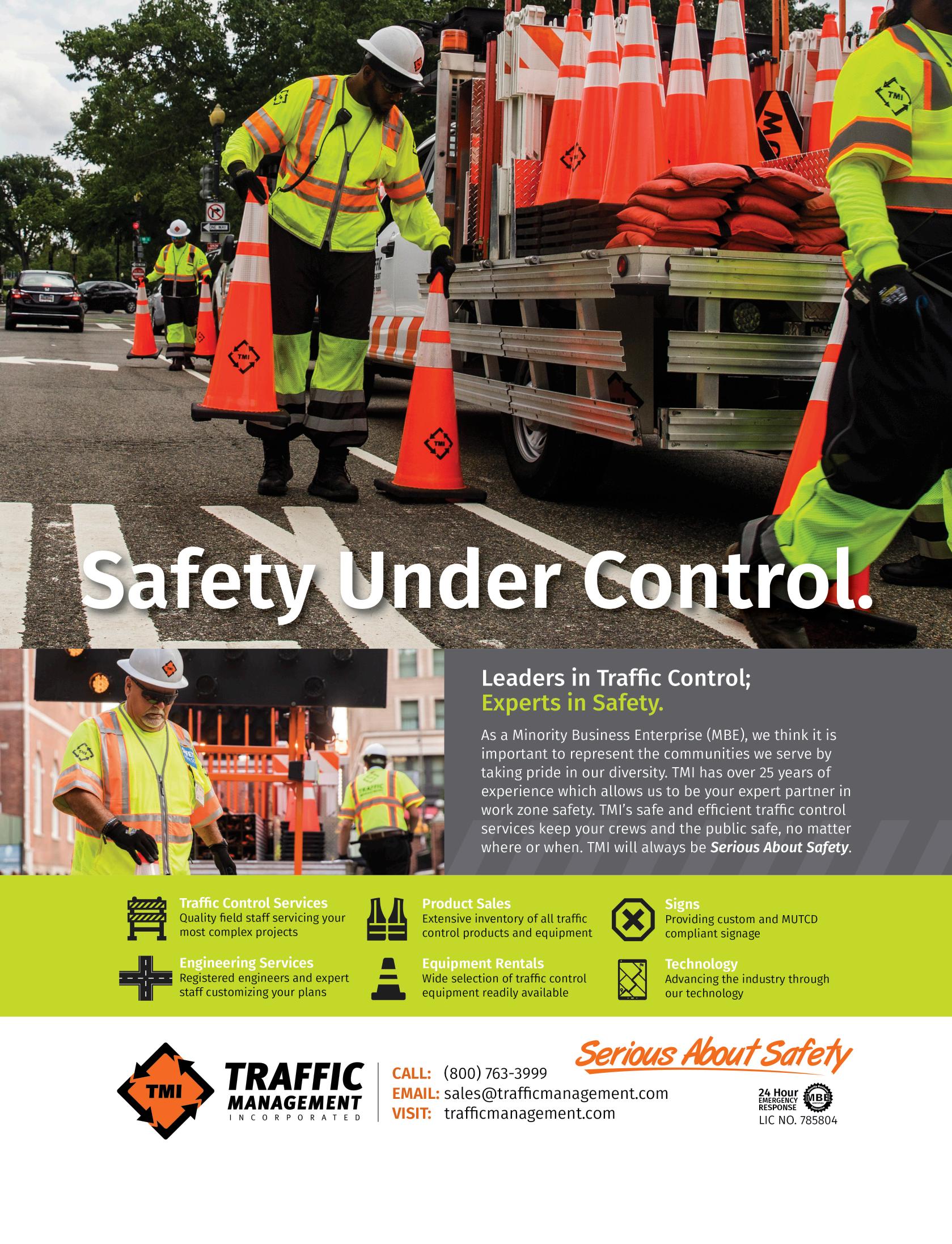

From
One of the things that has impressed me since becoming involved with the UTCA has been the approach, quality, and then impact of how this association addresses issues and challenges. A good example of that was the 2020/2021 development and then issuance of the UTCA Five Year Strategic Plan. The plan is wonderfully crafted and descriptive of the things that move this association forward and make it so vital in our industry. For example, our vision is succinctly and clearly stated as:
“The UTCA creates a positive impact on New Jersey citizens, the health of the environment and our shared economic prosperity by leveraging its respected expertise and relationships to promote a sustainable infrastructure sector.”
Our mission further indicates:
“The UTCA assists its members in achieving success through a collective focus on infrastructure funding, legislative and regulatory advocacy, labor relations, improved working conditions and project-based problem solving. The UTCA strives to achieve an even playing field for fair competition and to drive investment in New Jersey infrastructure for future generations.”
Of the five stated guiding principles, one jumps out and motivates me, namely that the UTCA will be a “problem solver”, aiming as an association to be the “do-er” in our industry. As I think about all of the important and coordinated steps that staff and members take on behalf of our industry, the UTCA is notably the “do-er” in our industry!
Just as that principle motivates me to action to advance our industry, I want also to encourage you to be similarly motivated to action. The success of the UTCA really relies upon individuals who become the hands and feet of the association.
So what can your organization do to be that “do-er” that moves our industry forward? In a word – engage! The ways
to do that are many but start by becoming a member if you are not already. Enroll the right employees within your organization in the events that they can themselves both contribute to and learn from – training, membership meetings, the Annual Convention, and in events that will broaden and reward them – the golf outing, the clay shoots.
Just as we need our companies to be engaged, so too do we need individuals from those companies to be “do-ers”. What can that look like within the UTCA? Start by encouraging other associates or contractors to become members. Join one of the vital committees and contribute to how they shape our collective thought and subsequently our industry. Contribute to our well run and important PAC.
Next, read and respond to the many notices, queries, and questionnaires that are sent out to you where staff seeks input and data. Call or write to congressional members and offices to express your thoughts about steps they need to take to advance our industry and state. In short, find ways to contribute. Clearly, our voices are only effective when we speak out about issues that impact us all, and when we do so in unison with others within our industry. And remember, even the littlest deed, is greater than the grandest intention!
Lastly, I want to congratulate Barnard Construction for achieving 75 years in business and PS&S for likewise completing 60 years. Well done!
Enjoy the magazine, and may this holiday season be joyous, memorable, and reflect you as a “do-er” in all the realms that you endeavor!
Are we headed toward a recession? The answer is, we’ll get there… eventually. Read on for the “road signs” that can help us estimate when we might arrive and what we can do before we get there.
Over the past few months, it’s felt like I’ve been on an extended road trip with a recession destination. Everyone from my friends, family, colleagues, and social media followers have been asking, “are we there yet?” much like my kids do when we’re on a family road trip. The truth is, we’ll get there … eventually. So, if we’re headed down the road towards the next recession, let’s use the “road signs” along the way to help us estimate when we might arrive and what we can do before we get there.
Throughout my career, I’ve leaned on two key indicators that have proven to be reliable signals of a future recession—the Treasury yield curve and the ISM Manufacturing Index. Let’s see what these indicators are telling us.
We can understand a lot about the economy by looking at the Treasury yield curve and evaluating short-term yields relative to their longer-dated siblings. In essence, yield curves measure interest rates of bonds with equal credit quality but different maturity dates. In normal times, when the economy is growing, the yield curve will tend to be upward-sloping, with yields on longer maturity bonds higher than shorter-term bonds. Understandably, investors typically expect to be paid more for, say, a 10-year bond versus a 2-year bond.
But in times of trouble, this relationship changes. The Federal Reserve may start hiking short-term interest rates, as they are now, sending them above longer-term rates. Hence an inverted, downward-sloping yield curve in which shorter-term bonds carry higher yields than longer-term bonds.
To measure this relationship, we can examine 10-year Treasury yields relative to 2-year Treasury yields. When those two points are inverted for an extended period, this is a clear sign that a recession is on the horizon, but the timing can vary significantly. Since 1950, any time we have had 10-year Treasury yields above their 2-year counterparts, a recession has occurred anytime from six months to two years after the yield curve inverts.
In addition to simply reaching an inversion, we can examine how deeply the yield curve is inverted (i.e. how much lower is the 10-year yield relative to the 2-year) and for how long. Here’s where we’re at currently:
1. The 10-year to 2-year Treasury yields have been inverted since May 7, 2022 and were recently inverted by more than 40 basis points. Relative to previous inversions, this would rank among the more severe.
2. The curve has been inverted a total of 146 days. Going back to 1986, the yield curve has stayed inverted for an average duration of 256 days.
Based on both the depth and length of the current yield curve inversion, it appears clear that the economy will face a recession sometime in the future.
The other indicator that can help us understand the timing of entering or exiting a recession is the ISM Manufacturing Index or Purchasing Managers’ Index (PMI). This index surveys supply manufacturers on a monthly basis to give us a quick glimpse into the demand for products based on the ordering activity of manufacturers. The manufacturing industry has a solid track record of providing a leading view of overall economic conditions. The PMI is comprised of a diffusion index that summarizes whether market conditions are expanding, contracting, or staying the same:
1. Anything above 50 indicates growth, and anything below means shrinking
2. Historically, when the index falls below 47, there is a confirmed recession
We can peer into the future by analyzing one specific component of the PMI—New Orders. The New Orders component measures the number of new orders a company receives relative to the previous month. That number usually precedes the overall PMI by several months. New Orders briefly dipped below 50 in July for the first time since April 2020 but have since slid and are currently sitting at 47.1.
In recessionary periods, one helpful tool can be dollar cost averaging: invest a fixed dollar amount on a regular basis (weekly or monthly), regardless of the share price. If prices decline, an investor will buy more shares, potentially providing greater chances for growth in the future.
On all road trips, you’re bound to run into some bumpy roads that make the drive more stressful, uncomfortable, and uneasy. But it won’t last the whole trip. And when you think about the entire journey, those bumpy roads account for just a small fraction of your trip.
To put that into a financial perspective, as the investor and author Brian Feroldi recently said, “when in doubt, zoom out.” The S&P 500 has declined 23% so far in 2022. But over the past five years, it has returned 58% and a whopping 207% over the last ten. Recessions won’t last forever, zoom out and keep that big picture in mind when the markets make you feel uneasy.
Dollar cost averaging does not assure a profit and does not protect against a loss in declining markets. This strategy involves continuous investing; you should consider your financial ability to continue purchases no matter how prices fluctuate.
If the yield curve tells us that a recession is coming, the ISM is telling us not quite yet. But if the downward momentum that we have seen over the last few months continues, it would suggest we could see an official recession by the first half of 2023.
Answering the question of whether a recession is on the horizon, as difficult as it may be, is easier than predicting what the market will do. Stocks have a tendency to turn down before a recession even starts and then to rebound well before it’s over. Investors who wait until the coast is clear inevitably miss accretive opportunities. It’s helpful to remember that markets go up much more often than they go down.:
1. Going back to the 1960s, on average, bear markets have declined by -38% over 446 days
2. By contrast, bull markets have typically risen by 209% over 2,069 days
The opinions expressed in this commentary are those of the author and may not necessarily reflect those held by Kestra Advisor Services Holdings C, Inc., d/b/a Kestra Holdings, and its subsidiaries, including, but not limited to, Kestra Advisory Services, LLC, Kestra Investment Services, LLC, Bluespring Wealth Partners, LLC, and Grove Point Financial, LLC. The material is for informational purposes only. It represents an assessment of the market environment at a specific point in time and is not intended to be a forecast of future events, or a guarantee of future results. It is not guaranteed by any entity for accuracy, does not purport to be complete and is not intended to be used as a primary basis for investment decisions. It should also not be construed as advice meeting the particular investment needs of any investor. Neither the information presented nor any opinion expressed constitutes a solicitation for the purchase or sale of any security. This material was created to provide accurate and reliable information on the subjects covered but should not be regarded as a complete analysis of these subjects. It is not intended to provide specific legal, tax or other professional advice. The services of an appropriate professional should be sought regarding your individual situation. Kestra Advisor Services Holdings C, Inc., d/b/a Kestra Holdings, and its subsidiaries, including, but not limited to, Kestra Advisory Services, LLC, Kestra Investment Services, LLC, Bluespring Wealth Partners, LLC, and Grove Point Financial, LLC. Does not offer tax or legal advice
On August 2, 2022, the New Jersey Supreme Court in East Bay Drywall, LLC v. Department of Labor & Workforce Development, considered whether certain workers employed by a contractor were to be classified as employees or independent contractors under the Unemployment Compensation Law. The test under the Unemployment Compensation Law, referred to as the “ABC Test” is used to determine whether a worker serves as an employee or independent contractor of the employer.
Under the ABC Test, N.J.S.A. 43:21-19(i)(6)(A)-(C), to determine the classification of a worker as an employee or an independent contractor, a court will undertake a fact sensitive inquiry into the employer-worker relationship. The default is that a worker is considered an employee unless an employer can satisfy all three of the following factors to prove the worker is an independent contractor. The three statutory factors reviewed by a court of competent jurisdiction are:
1. Such individual has been and will continue to be free from control or direction over the performance of such service, both under his contract of service and in fact; and
2. Such service is either outside the usual course of the business for which such service is performed, or that such service is performed outside of all the place of business of the enterprise for which such service is performed; and
3. Such individual is customarily engaged in an independently established trade, occupation, profession, or business.
Failure of the employer to prove all three factors will result in a worker being classified as an employee.
In East Bay Drywall, East Bay, a drywall installation business, hired workers on a per-job basis. Specifically, when East Bay’s bid for a particular project was accepted by a builder, East Bay would contact workers, classified by East Bay as subcontractors, to check the availability of such workers for the project. The workers were permitted to accept or decline East Bay’s offer to work on the project. When a worker accepted the offer, East Bay would provide all materials, but the worker was required to provide all labor, tools, and transportation to the worksite.
In 2013, East Bay stopped reporting wages to the New Jersey Department of Labor and Workforce Development, which triggered an audit by the Department for the years between 2013 and 2016. The purpose of the audit was to determine whether the workers used by East Bay were independent contractors, as claimed by East Bay, or employees under the ABC Test. Following the audit, the auditor found that approximately half of the alleged subcontractors working for East Bay between 2013 and 2016 were misclassified as independent contractors. East Bay was informed it owed unpaid employment and temporary disability contributions in the amount of $42,120.79 for that period. The Commissioner of the Department, on appeal by East Bay, found that all 16 workers at issue were employees of East Bay. The Appellate Division reversed finding only 5 of the 16 workers were employees of East Bay.
However, the New Jersey Supreme Court reversed the Appellate Division and agreed with the Commissioner of the Department that all 16 workers were employees and remanded the matter to the Department for the assessment of appropriate back-owed contributions from East Bay.
In rendering its decision, the Supreme Court found East Bay did not supply the proper evidence to satisfy the third prong of the ABC Test. The Supreme Court noted that the third factor of the ABC Test is construed broadly and questions whether a worker can maintain a business independent and apart from the employer. Further, the Supreme Court noted, under factor three, that the factor is satisfied “when a person has a business, trade, occupation, or profession that will clearly continue despite termination” of the relationship. However, if a worker would be
unemployed when the relationship ends with the employer, the worker cannot be considered independent under the third factor of the ABC Test.
The Supreme Court noted that wholly dependent employees may choose to work for more than one employer or abruptly resign from their position but the probative value of a refusal to accept or complete work is limited because, like an employee, even a bona fide independent contractor is not free from the pressure to accept a job. Further, a certificate of insurance could be an indication of independence because an employer is generally “not vicariously liable for the negligent acts of the contractor in the performance of the contract” but insurance documents and certificates do not, by themselves, determine whether the workers were engaged in independent business separate and apart from East Bay. As such, based on a totality of the circumstances and evidence presented, the Supreme Court determined the eleven workers at issue were employees of East Bay.
A crucial takeaway for contractors from East Bay is an understanding of the requirements necessary to classify a worker as an employee and an independent contractor. For each worker that an employer intends to classify as an independent contractor, the employer must examine the ability of the worker to maintain a business separate and apart from the employer, the ability of the
worker’s business, trade, occupation, or profession to continue despite the termination of the employer-worker relationship, and a determination whether the worker’s business is able to survive the termination of the employer-worker relationship.
Moving forward, it is critical for contractors to review the classification of workers as employees and independent contractors. As demonstrated by the ABC Test, the default is a worker is an employee unless all three factors of the ABC Test are met. A contractor should keep in mind that a business practice which requires workers to assume the appearance of an independent contractor, when the worker is an employee, could give rise to an inference that such a practice was intended to obscure the employer’s responsibility to comply with all State laws and regulations regarding payment and contributions for employees. Such a finding by a court could require an employer to be responsible for back-owed contributions and penalties.
About The Author. . .Nicholas A. Sullivan, Esq., is an Associate in the Cherry Hill office of Florio, Perrucci, Steinhardt, Cappelli, Tipton and Taylor, LLC. He may be contacted at nsullivan@floriolaw. com
Inflation, supply chain disruptions, geopolitical unrest, and other influences are significantly cutting into profits. Contractors must watch changes and trends that could negatively affect the company. Here are key metrics that should be monitored, as well as profit improvement strategies to safeguard your bottom line:
Global and regional metrics give a macroeconomic view of consumer and industry buying behavior.
• Unemployment: The U.S. Bureau of Labor Statistics releases monthly and yearly employment data. Look at employment figures to determine if the labor markets are going up or down. A steep or rapid decline could indicate that a recession is imminent. Employers should keep a close eye on employment levels within their organization. A drop in output often accompanies a decline in employment.
• Consumer confidence: The Consumer Confidence Report gauges how people feel about the economy. When consumer confidence is high, customers spend more and feel financially stable. When it is low, consumers spend less. A decline in consumer confidence is a warning sign that customer behavior may change. This metric can indicate the estimated demand for products now and in the immediate future.
• Consumer spending: The U.S. Department of Commerce releases a monthly report on economic activity. This report assesses individual wealth and how much disposable personal income people have. When people have higher disposable income, they are more likely to spend.
A business’s financial metrics can signal that the company is in trouble or provide reassurance that everything is fine.
• Sales revenue is a metric that companies need to watch consistently. If sales are declining month-over-month, an issue needs to be addressed. If sales increase, the company could be in good shape to face a recession.
• Cost of goods sold (COGS) measures the total cost of goods sold (overhead, labor, shipping, and storage costs). COGS is a crucial business metric directly affecting a company’s bottom line.
• Cash flow refers to the amount of money that comes in and goes out of a business. A positive cash flow means the amount received exceeds spending. A negative cash flow means that the company cannot pay its bills.
• Net profit margin is a financial ratio used to calculate the percentage of profit a company produces from its total revenue. It measures the amount of net profit a company obtains per dollar of revenue gained.
• Unpaid invoices indicate that payment terms must be adjusted to speed up customer payments and slow down payments to vendors. Staying on top of receivables and payables is essential to ensure accounts are not delinquent.
The implementation of the following profit improvement strategies will help to mitigate some of the negative economic effects on your business:
• Plan for success. Look at every aspect of the company, from its fleet to insurance. Identify where too much money is being spent and which debt to attack first. Analyze the entire cost ecosystem, from labor to office supplies. Understand what's making money and where the money is being lost.
• Improve productivity. Contractors can dramatically increase profits with improved productivity. Jobsite efficiency and productivity are critical to minimizing costs, keeping projects on track, and avoiding expensive delays. Productivity can be compromised by scheduling mishaps, supply-chain issues, and rework. Construction project management software can improve profitability by managing these problems.
• Benchmark KPI’s. Another key to boosting profitability is benchmarking the company’s key performance indicators (KPIs). Track results from every area of the business. Compare them to industry standards and local, regional, and national companies similar to yours. Common metrics to benchmark include job costs, wage rates, change orders, technology expenses, capital ratios, and profit margins.
• Schedule jobs. Carefully schedule projects and ensure that workers are trained and adequately equipped for the job. Be aware of the key factors contributing to high output, including employee morale. Even minor inefficiencies can drive up the cost of a project.
• Track time. One of the most critical components of construction profitability is a streamlined system for tracking time. Paper data entry is time-consuming and prone to errors. An efficient process will help capture more accurate data. Furthermore, better time tracking improves job costs and minimizes overhead.
• Motivate employees. Incentives such as performance rewards can help motivate employees and increase overall profitability. Some companies use the money to come in under budget to give bonuses to employees. This incentivizes them to finish work and projects on time.
• Use cloud technology. Cloud-based construction management software can help streamline project collaboration. For example, it can track access to building information and reduce misunderstandings about design updates. Cloud technology can also make communication easier. Answers to change orders and requests for information can be shared instantly. Construction project management software can improve profitability by reducing problems caused by scheduling mishaps, supply-chain issues, poor communications, and rework.
• Reduce waste. There are many ways to reduce construction waste. Contractors can examine job records, trends, and forecasts to identify why one job is not as profitable as another. The use of specific products should be analyzed to determine if other products would be better.
• Cut costs. Construction companies can increase their profit margin by finding ways to cut costs. Evaluate construction processes and identify areas where changes can be made without compromising quality.
• Lower taxes. Contractors must invest in tax planning throughout the year to gain the maximum impact. Many tax planning strategies specific to construction contractors should be considered. While most tax strategies strive to accelerate income in the current tax year and defer expenses to the following year, strategic tax planning considers many factors, such as how reducing income for tax purposes will affect your financial statements, cash position, working capital, and financial ratios.
Contractors can improve profitability by setting realistic goals, developing a long-term business strategy, analyzing costs, and expanding into new markets. Contractors looking only to reduce costs can miss growth opportunities. Take the time to look for the silver lining in this situation, and you may become a much stronger, more robust company.
About the Author. . . Salvatore Schibell, CPA, CFP®, CGMA, MS Taxation, MBA, is the tax partner at Lawson, Rescinio, Schibell & Associates, P.C. He is a profit improvement expert who focuses on helping construction contractors make more money. Sal can be contacted at 732-539-7328 or salschibell@lrscpa.com.
325 Columbia Turnpike, Suite 308
Florham Park, New Jersey 07932
TEL: (973) 325-3030 FAX: (973) 325-7360 7:30 A.M. - 5:00 P.M. Monday - Friday
308 North 14th Street
Kenilworth, New Jersey 07033
TEL: (908) 686-3832
7:30 A.M. - 4:30 P.M. Monday - Friday EMERGENCY
It may be hard to believe but 10 years have now passed since Superstorm Sandy made a decidedly unwelcome appearance on our shores. This historic storm resulted in upwards of 40 deaths in New Jersey and damaged or destroyed hundreds of thousands of homes and businesses and wreaked havoc on our state’s utility and transportation infrastructure. The damage caused by Sandy has been estimated at nearly $37 billion.
As we look back on the decade after Sandy, it is evident that much has changed. Tiny bungalows have been replaced by larger homes, often lifted high in the air. Businesses have rebuilt and many are thriving. And the critical infrastructure damaged in Sandy has been rebuilt, replaced, and made more resilient with much of the restoration being performed by UTCA members who rebuilt roads and bridges and helped restore vital services like heat, gas, and electricity.
The Legislature recently looked back at Sandy with an eye toward assessing our state’s preparedness for future storms. In October, the Assembly Environment Committee and Infrastructure and Natural Resources Committee held a joint hearing on Sandy recovery efforts, including the post storm-response and the continuing efforts to mitigate damage from weather events.
A number of speakers offered testimony that questioned the state’s ability to handle similar weather events. Many mentioned Hurricane Ida which marched through New Jersey last September, leaving 30 dead and causing over $2 billion in damage. The consensus from speakers and many lawmakers was that, while we have made progress, we are still vulnerable and unprepared to handle severe weather which may become more frequent and intense as a result of climate change.
Also taking center stage in Trenton was work zone safety which was the subject of an Assembly Transportation Committee hearing in October. During this hearing various speakers testified on the dangers workers face on our roadways, with many citing driver inattentiveness and excessive speed as the cause of many accidents and near misses.
UTCA and our members were invited to address the Committee and the views of the industry were well-represented by Anthony Izzo from J. Fletcher Creamer & Son and Gregg Johanesson from Spiniello Companies who spoke about their experience on roadway job sites. It is expected that legislation affecting the industry will result from this hearing.
Another issue drawing the attention of lawmakers is the material cost escalation experienced by contractors throughout the industry over the past two years. Legislation extending the dates covered by the cost escalation law is moving through the process and may be enacted soon. This measure, S-3124 would extend the eligibility date from projects that were bid before June 1, 2020 to those bid before December 1, 2021.
In addition, another bill that would offer a more expansive cost escalation program was recently introduced. This measure, A-4718 would expand cost adjustments to additional contractors and project owners and is not limited to Small Business Enterprises (SBE’s).
Issues related to water infrastructure also continue to be a focus in Trenton. Likely the biggest news was the decision by the state to take over the operations of Trenton Water Works which has been unable to move forward with critical upgrades to it facilities and recently found the bacteria that causes Legionnaire’s Disease in its water supply.
In addition, the Legislature has acted on several water-related bills, including measures requiring increased testing and a bill that would allow water utilities to recoup monies invested in safety and infrastructure upgrades. A bill package that approves the operations and budget of New Jersey’s Infrastructure Bank received the approval of a key legislative committee and is likely on the path to approval.
While there is not enough space to list all of the industry issues being considered in Trenton, it’s worth mentioning that UTCA is keeping a close eye on many legislative and regulatory initiatives and is in constant communication with policymakers. Some of the issues we are monitoring include, green energy mandates, New York’s congestion pricing proposal, asphalt pavement standards and the transition to electric vehicles.
In Washington, economic issues have garnered the attention of officials who continue to look for ways to tame record inflation which remains close to 8% and caused the Federal Reserve to raise interest rates to their highest level since 2008. In addition, many experts believe we are heading toward a recession while some say we are already in a recession.
It is also important to take note of the recent midterm elections which saw the Democrats maintain their majority in the Senate while the Republicans took control of the House of Representatives. This divided government will likely have a significant impact on any number of policy issues that will impact our industry and could also affect the race for the White House in 2024.
Finally, here in New Jersey, with Governor Murphy barred from seeking another term, the jockeying for Governor has already begun. Rumored potential candidates for the 2025 election include
Jack Ciattarelli, who was the Republican nominee in 2021, and former Senate President Steve Sweeney, Jersey City Mayor Steve Fulop and Congresswoman Mikie Sherrill on the Democrat side. However, there is always the possibility that a dark horse candidate emerges and wins the nomination. And don’t forget that next year our entire Legislature is up for election under a redrawn map that could potentially shift the balance of power in Trenton.
Worker classification – meaning whether a worker is considered an employee or an independent contractor – is a critical concern for contractors, with implications ranging from taxes to employee benefits to application of employment laws, and more. With so much at stake, a proposed United States Department of Labor (“DOL”) rule change underscores the need for contractors to pay close attention to developments in worker classification law. While other industries, most notably the ride-sharing companies and other “gig economy” businesses, have been the focus of headlines on worker classification issues, the construction industry typically finds itself among the nation’s largest users of independent contractors.
The Fair Labor Standards Act (“FLSA”) requires contractors to pay employees certain minimum wages and overtime. Those requirements, however, are inapplicable to workers who are properly categorized as independent contractors. On October 13, 2022, the DOL formally published proposed modifications to the test used to determine whether a worker is an employee or an independent contractor.
The current FLSA worker classification rule, which was issued in the final days of the Trump Administration, utilizes an “economic realities” test to determine if a worker is an employee or independent contractor. Under the “economic realities” test, there is a non-exhaustive list of factors that are considered when determining a worker’s classification. The current rule, however, permits a streamlined analysis based upon two “core factors”: (1) the nature and degree of control over the work; and (2) the worker’s opportunity for profit or loss based on initiative or investment. The Trump Administration’s emphasis on the two “core factors” has been generally regarded as employer-friendly, making it easier to categorize workers as independent contractors.
The Biden Administration, taking a more employee-friendly approach, seeks to institute a “totality of the circumstances” analysis in place of the current “economic realities” test. The current administration has asserted that the proposed “totality of the circumstances” test more closely aligns with prior rulings of federal courts. Unlike the current rule, the “totality of the circumstances” analysis does not weigh certain factors more heavily than others.
Instead the rule prescribes six evenly-weighed factors to determine whether the worker is economically dependent upon the employer or is in business for him or herself: (1) the opportunity for profit or loss depending on managerial skill; (2) investments by the worker and the employer; (3) degree of permanence of
the work relationship; (4) nature and degree of control, including whether the employer uses technology to electronically supervise the worker, reserves the right to supervise or discipline workers, or places demands on workers’ time that do not allow them to work for others or work when they choose; (5) the extent to which the work performed is an integral part of the employer’s business; and (6) skill and initiative of the workers (i.e., whether the worker possesses specialized skills for the job or the worker is dependent upon employer-provided training). The proposed rule also allows for additional factors to be considered.
Contractors – particularly those who changed their classification practices following the enactment of the current rule in January 2021 – should continue to monitor developments concerning the proposed rule to ensure compliance with the FLSA. The proposed rule, if adopted, will likely result in a nationwide increase in the number of workers subject to the FLSA, with fewer workers qualifying for status as independent contractors
Contractors should bear note, however, that the proposed federal rule changes (which relate to compliance with, among other things, the FLSA) are separate and apart from New Jersey’s own requirements concerning worker classification. Unlike the test applied at the federal level – whether it be the current streamlined “economic realities” test or the proposed “totality of the circumstances” test – New Jersey uses a typically more worker-friendly ABC Test to assess worker classification as it relates to compliance with State employment laws. Given New Jersey’s strict application of this State’s ABC Test for worker classification, New Jersey contractors who properly classify workers under New Jersey’s standards will likely find themselves on the right side of the proposed changes to the federal rules concerning worker classification for purposes of FLSA compliance.
Worker classification will continue to remain a topic of interest and evolution at both the state and federal levels. Following the close of the public comment period on November 28, 2022, the DOL will consider the implementation of the proposed rule and take further action in connection therewith. Contractors should pay attention to the proposed changes as they progress through the regulatory process in order to avoid costly misclassifications.
About the Authors . . . Kevin S. Brotspies, a member of Trif & Modugno LLC, represents businesses, including contractors and subcontractors, in all areas affecting the construction industry, including in employment and labor matters. Alyssa Puccio, an associate with Trif & Modugno, represents businesses, including sureties, contractors, and subcontractors in all areas of law affecting the construction industry.
It’s not often that you come across a business that has been continuously operating for 75 years. And it’s even more unusual to find one that has been run by the same family for that entire time. But that’s exactly the case at Barnard Construction Company which recently marked 75 years in business and is now operated by the third generation of Barnards.
In talking to Dean Barnard and his sons, Ryan and Jeff at their Pompton Plains office, it’s clear that Barnard Construction is still a family affair with Ryan serving as CEO and Jeff in the role of President. Dean is still very much involved in the business that he ran for 40 years after taking charge of the company following the passing of his father, Clarence who founded Barnard in 1946. In addition, Dean’s wife, Karen is the secretary and Jeff’s wife is the company accountant.
The Barnards take great pride in their family’s history with the business which started when World War II veteran Clarence left the service and purchased an old dump truck and began paving driveways and roads. He soon expanded to become a site
development contractor, offering additional services, including excavation and even, golf course construction. Upon the death of Clarence, Dean, himself a veteran of the Vietnam War, took the helm of Barnard and oversaw the company for nearly four decades as Barnard continued to grow and flourish.
Dean’s younger brother Tim began working as a laborer in the summers at age 14. Tim was successful at bidding and completing projects for Barnard before leaving for Montana in 1975 to start his own construction company.
As teenagers, Dean’s sons spent their summers working in the family business which helped prepare them for their current roles managing the day-to-day operations of Barnard. While they started as self-described “gophers”, Ryan and Jeff learned all aspects of the construction business and each spent time as laborers, machine operators and foremen on job sites. The “handson” experience they acquired growing up in the business allowed them to build on the legacy of success created by their father and grandfather and take Barnard Construction to unprecedented levels of success. In fact, they note the company will do upwards of $12 million in work this year.
Jeff remembers life at the family dinner table even as young kids, started and ended with talk about the construction jobs. His mom would always say no more talk about work at the dinner table, but the conversations would always come back to work. “Construction has always been our life,” he said.
Dean’s daughter Amy also worked in the family business before her untimely passing in 2012. She, like her brothers, began in the field as a laborer and then worked her way up the ranks to ultimately become Dean’s assistant in the office. She was an integral
ing, retaining walls, and pad preparation. These and the other services they provide have them in high demand among a number of general contractors, many of whom utilize Barnard on a regular basis, including Dobco, Inc., Joseph Natoli Construction, Phelps Construction Group, Premier Design and Build Group and R.C. Andersen.
Among the public projects they have worked on are the New Jersey State Police Troop D Station in Bloomfield, Lyndhurst Junior
part of the company for many years utilizing her background in insurance. She saved the company a considerable amount of money and headaches over the years.
Ryan and Jeff attribute much of their success to their employees, noting that many have been with the company for decades, including their construction operation manager who has been with Barnard for 20 years, their office manager who has been with the company for over 24 years, one operator who has been with the company for 34 years and an estimator who is in his 40th year at Barnard. The presence of these longtime employees allows Barnard to strategically locate their foremen at job sites to maximize their specific skill sets. The brothers are also quick to praise their labor partners, including the Operating Engineers Local 825 and the Laborers Local 472. They also point out that both they and their father are members of Local 825.
With their vast experience and dedicated staff, Barnard offers a variety of services in site development, including excavation, water service, sanitary sewer, stormwater management, road build-
High School, and the Mountain Ave Water Tank in Pequannock. A small sampling of their commercial projects includes the Home Depot in Mahwah, Dick’s Sporting Goods and Costco in Wayne, and Lowe’s in Paterson. They also note that one of the busiest growth areas in their portfolio is in the warehouse sector.
One of their more interesting projects involved one of the most iconic sites in the world—the Statue of Liberty. The unique location and history of this site provided tremendous opportunity as well as significant challenges.
Beginning in 2011, Barnard worked to install new water lines and perform excavation work, among other projects, on Liberty Island which houses the statue and its base. While this may seem like a relatively straightforward project, a number of factors made this work quite challenging, not the least of which was the fact that the landmark had to remain open to the approximately 10,000 people who visit the island every day.
In addition, since there are no bridges to the island, all the equipment had to be transported by barge and the only way for staff to get to the job site was to take the ferries that transport visitors to the island. This meant that one forgotten tool could result in a two-hour round trip ferry ride to retrieve the missing item. Moreover, everyone working on the job site had to pass through airport-like security screenings.
The historic nature of the island presented other unusual complications. For instance, they were required to have an archeologist on site who would date any fragment or discoloration in excavated
soil that could potentially be of historic significance. Ryan says he found an arrowhead and foundations for cold cellars, which were utilized to store root crops in the days before refrigeration. While he was excited to find these pieces of our nation’s history, he notes that these and other requirements made the project take three times longer than a typical project of this scope.
However, Barnard’s unique experience at this location turned out to be of tremendous value to the company, their general contractors and the project owner, the National Park Service. In fact, the day after completing the first part of their site work, Superstorm Sandy struck the island with a 12-foot storm surge that washed away much of their surface work and inflicted tremendous damage.
Barnard’s intimate knowledge of the island proved to be invaluable for both Sandy recovery efforts and for additional projects. As a result, they have been working on Liberty Island since 2011 and will soon begin work on several projects on nearby Ellis Island, including the American Immigrant Wall of Honor.
This type of unique experience, as well as the knowledge and experience of their longtime staff, has helped propel Barnard to incredible success. In addition, their longstanding relationships and reputation for quality work have made Barnard the first choice of many general contractors and projects owners. In fact, they currently have eight active projects, dozens more potential projects and they are submitting an average of one to two bids a week.
When asked what makes their company unique, the Barnard brothers point to being a family company as one of the things that make them stand out. As they note, if someone calls about a problem with a job, they are able to talk to the company owner. Moreover, being a family company ensures they care deeply about the quality of their work.
The tremendous success they have achieved does not come without challenges. Like others in the industry, they are contending with increased costs and supply chain issues which have forced them to be creative in scheduling material purchases. In addition, they sometimes struggle with securing necessary equipment as dealers remain critically low on inventory.
Ryan and Jeff are by no means complaining about the challenges or the busy pace of projects, noting this is the nature of the industry they grew up in where hard work comes with the territory and being on call “24-7” is the norm. They point to the example set by their father who worked long days and weekends and only started slowing his work schedule when he reached his 70’s. “You have to love the work if you want to be successful,” said Ryan.
That love of their work and commitment to the construction industry has propelled Barnard to an incredible, sustained run of success that is poised to continue for years to come. The fourth generation of Barnards could be on their way as the oldest is entering college this upcoming year. Congratulations to Barnard Construction Company on its 75th Anniversary and we look forward to seeing what the future brings for this remarkable construction company.
The U(T)CA was founded in 1965 without the “T” for transportation. The founders of the UTCA had an early focus on wastewater treatment because in New Jersey, opportunities in our state and the region were advancing faster than at the federal level, creating clear opportunities for the construction industry. UTCA’s founding leaders had the foresight to begin organizing the interests of contractors to fight for a level playing field and their share of work that was to come from one of the most aggressive federal environmental laws to date, the Clean Water Act of 1972.
What was happening at the time in New Jersey and the nation is important to consider. In the late 1960s, many water bodies were a cocktail of toxicity, with some capable of catching on fire. Some did!
In New Jersey, centralized sewer systems had been in place since the late 1900’s. However, these rudimentary systems discharged untreated human, animal and industrial waste from urban centers into the nearest stream and, as a result, into our rivers, bays and eventually, the ocean. While an improvement from earlier practices, this resulted in deplorable conditions in our waterways which often served as a source of drinking water.
The historical focus of sewage treatment was on moving raw sewage to a natural body of water, like a river or ocean, where it would be diluted and dissipated. In the early 19th century, sanitation was largely left up to individuals, and outhouses, often known as privies, prevailed.
Typically, residents and shopkeepers disposed of garbage on their own properties, sometimes in pits dug behind their buildings, and in some cases in town dumps where residents could haul their own waste. Later, as municipalities grew in population, either government-run or private haulers commenced operations on a larger scale, with dumps eventually established to service disposal by towns in a county or region.
Then, as piped water connections increased and more people adopted water closets, wastewater began to overwhelm cesspools and storm drains. Facing serious public health issues from the lack of proper sanitation in booming industrial centers, cities in New Jersey started some of the first sewer systems in the United States.
New Jersey’s First Sewer System – Newark
As New Jersey’s economy grew in the nineteenth century, industrial plants and factories disposed of their waste on their own sites or hired haulers, who often disposed of the waste on whatever land appeared available or abandoned. As our cities grew in population, however, the past methods of disposing of garbage and sewage could not keep pace with the growing numbers of people living closely together in tenements and other housing.
Streets were sites for disposal of household garbage and animal carcasses, along with holding feces and urine from the many horses used for everyday transport and hauling. The contents of chamber pots often were dumped from windows, sometimes landing on pedestrians passing below.
The population of Newark more than tripled between 1840 and 1856 and the frequency of outbreaks of diseases like cholera, yellow fever, diphtheria, and typhoid was linked by some physicians and scientists to humans living and working in close proximity to rotting animal carcasses, garbage and untreated human waste
In the last half of the nineteenth century, the state and local governments began to take limited actions to address concerns over the impact of waste on public health. In the 1850s, Newark started building its first underground sewers serving the city center, with their outfall dumping untreated human waste into the Passaic River, which was already heavily polluted by the disposal of waste from upstream factories. In addition to the newly built sewers, attempts were made to control odors by paving over streams that residents used to dump waste.
Laws passed in the early and mid-20th century were intended to expand the state's authority to regulate the discharge of pollution into waterways. However, the laws delegated enforcement authority to the state Department of Health (parts of which became the NJDEP) which tended to intervene only in the cases of epidemics of diseases caused by waterborne pathogens.
The histories of these systems are fascinating and track with major shifts in our society and perhaps the establishment and growth of some of your companies.
50 years ago, sweeping amendments to the Federal Water Pollution Control Act of 1948 brought both awareness and action to control water pollution. It also brought with it big opportunities for construction. For states like New Jersey that were attempting unsuccessfully to control pollution, it brought teeth and the power of the federal government and its checkbook.
These amendments, commonly known as the Clean Water Act (CWA) gave the EPA and states (when the delegated authority was accepted) the right to regulate pollutant discharges into the waters of the United States and implement pollution control programs, such as setting wastewater standards for industry. Additional components of the CWA:
• Maintained existing requirements to set water quality standards for all contaminants in surface waters.
• Made it unlawful for any person to discharge any pollutant from a point source into navigable waters, unless a permit was obtained under its provisions.
• Funded the construction of sewage treatment plants under the construction grants program.
• Recognized the need for planning to address the critical problems posed by nonpoint source pollution.
The biggest controversy of the CWA was how to pay for the infrastructure upgrades necessary to meet the lofty goals set forth by this transformational law. At first, there was the “construction grant” program, which was eventually phased out and replaced with the State Water Pollution Control Revolving Fund, more commonly known as the Clean Water State Revolving Fund (CWSRF). This program is still very much active in New Jersey
and is recognized by state leaders as one of the top programs in all of state government.
Run jointly by the NJDEP and the NJ Infrastructure Bank (IBank), the CWSRF program provides financial assistance for the construction of projects that protect, maintain, and improve water quality. This program is now commonly known as the “Water Bank” and funds not just clean water projects but projects that provide safe drinking water.
From its first loan in 1987 through this summer, the Water Bank has delivered more than $9.1 billion in clean water investment, mostly in construction projects. This is through more than $7.7 billion in long-term loans and had an additional $1.4 billion in short-term construction loans outstanding. This program has saved taxpayers and ratepayers more than $2.8 billion on longterm financing costs through lower interest charges, refunding of outstanding bond deals, and principal forgiveness loans.
New funding in the amount of approximately $1.2 billion is available for clean water construction projects for at least the next two years. None of this would be possible without the Clean Water Act of 1972. We are far from “mission accomplished” as we have many old pipes to fix and treatment components to maintain and upgrade. That said, we have the tools in place for the next 50 years to incrementally achieve the lofty goals set forth in this transformational federal legislation.
I have been reminding those celebrating this important anniversary not to forget the role of contractors, our partners in labor and the entire ecosystem of construction for the progress made to date. UTCA is at the table to advance progress over the next 50 years and ensure that the interests of our members are at the table at every critical juncture.
From its early days as a single-discipline, single-office practice to a fully-integrated architecture, engineering, environmental, and surveying firm with 11 offices throughout the U.S., PS&S has evolved into one of the most prominent AE firms in the greater New York City/New Jersey metro area.
From humble beginnings, PS&S has grown into a company offering planning, design, and regulatory compliance services on diverse projects across a number of market segments.
William "Bill" Paulus Jr., P.E. and Wallace Sokolowski, P.E. founded P&S LLC in 1962, as a structural engineering company. The small firm’s first client was the Hillier Group, and the company was selective in choosing projects to work on, growing slowly to six employees three years later and 15 by 1970.
Dr. Anthony "Tony" Sartor, PhD, PE, PP, joined the company in 1973 and the following year, spearheaded the addition of environmental services to the offerings. In 1977, civil and industrial engineering disciplines were added, and the firm’s name was changed to PS&S the next year.
“I know my dad was proud to add the ‘S’ of our last name to what became PS&S,” said John Sartor, PE, President, who was promoted from COO to CEO in June 2014. “His joining the firm turned out to be a pivotal moment in the firm’s history as the addition of new capabilities led to rapid growth in terms of projects and headcount.”
Indeed, growth skyrocketed in the 1980s: surveying services were added in 1986 and by 1987 the firm had completed its 5,000th project and boasted 160 employees. PS&S was afforded the opportunity to work on several large-scale, high-profile real estate projects, notably the Harrah’s, Taj Mahal, and Bally’s Park Place casinos in Atlantic City; PNC Bank’s “Tower Center” office complex in New Brunswick; the New Jersey Performing Arts Center in Newark, and campus buildings at Montclair State University and Ramapo College.
The firm was under different ownership for several years. In 2000, PS&S was acquired by KeySpan Corporation, now part of
National Grid USA, which at the time was the fifth-largest distributor of natural gas in the U.S. Nine years later, PS&S’ company management purchased the company back to seek additional growth opportunities.
With renewed strength, PS&S began implementing its own acquisition strategy to catalyze growth, incorporating CSCA in 2015 to expand the firm’s healthcare practice; DW Smith Associates in 2019 to expand into South Jersey, to begin community association services and increase the firm’s surveying presence across the U.S.; and B. Thayer Associates in April of 2022 to broaden the transportation practice and the firm’s presence in New York City.
The company has four divisions: Architecture and Vertical Engineering; Energy and Environment; Surveying; and Site and Civil Engineering. PS&S works in six market sectors: Education; Energy and Utilities; Healthcare; Public Works; Real Estate Development; and Science and Technology.
PS&S delivers innovative solutions for utilities’ energy infrastructure needs. The firm provides desktop and feasibility analysis to field services, detailed engineering and permitting, through bidding and construction support.
PS&S led several natural gas main replacement projects over the last several years. For Elizabethtown Gas, PS&S mandated work for AIRP, SMART, DIMP, & IIP Replacement Programs. A total of 260 miles of pipeline replacement were designed and installed and 37,550 customers were upgraded. This work is still ongoing today.
Similarly, for South Jersey Gas, a total of 70 miles of natural gas pipeline replacement were designed and installed and 2,581 customers were upgraded.
As environmental and engineering consultant to the South Jersey Transportation Authority (SJTA), PS&S provided environmental, cultural resource, civil, and survey services for the proposed third lane widening of the Atlantic City Expressway.
During the Concept Development phase of the project, PS&S delineated environmental features within the right of way and obtained a Freshwater Wetlands Letter of Interpretation (LOI)Line Verification and Flood Hazard Area Control Act Riparian Zone Verification from the Pinelands Commission and the New Jersey Department of Environmental Protection (NJDEP) approved those delineations. In addition, PS&S also conducted cultural resource investigations and reconnaissance for the project, hazardous waste screening, air quality, noise, and socioeconomic studies.
Together with team partners and the SJTA, the Concept Development phase was successfully completed on time and on budget. PS&S has also been retained to advance the project during the Preliminary Engineering phase. As part of that, PS&S is conducting a Hydrologic and Hydraulic Study and will be preparing the Environmental Impact Statement for the project.
Daylighting of the Saw Mill River, a true conservation project.
Over 10 years ago, Superstorm Sandy severely damaged Route 35 in New Jersey, requiring a full roadway reconstruction. As a coastal emergency evacuation route serving the barrier peninsula between Barnegat Bay and the Atlantic Ocean, Route 35 needed to be reconstructed to better withstand future storms.
PS&S worked with a partner firm and the New Jersey Department of Transportation (NJDOT) to rebuild and deliver a more innovative, resilient drainage infrastructure system. The firm implemented several improvements to Route 35, including the design and installation of pump stations that would quickly evacuate storm water should there be another severe storm in the future.
“We’re long-time corporate citizens of New Jersey, of course, but many of us also live in the state and it is safe to say that everyone at PS&S knew someone who was negatively impacted by Superstorm Sandy,” said Sartor. “We’re proud to have worked side by side with NJDOT to make Route 35 safer for driving in the worst of weather.”
PS&S stepped into the role of Engineer of Record for the CCMUA (Camden County Municipal Utilities Authority) when its longtime professional engineer retired. The strength of the firm’s wastewater, engineering, environmental, permitting, and architectural divisions and staffing placed PS&S solidly in the position to perform these services and other “owner’s representative” tasks as needed by the Authority. PS&S has been functioning in this role since 2019.
The CCMUA is Camden County’s Regional Wastewater Treatment System, treating over 55 million gallons per day from properties in Camden County. As Engineer of Record, PS&S works closely and collaboratively with the Administration as well as other contracted and on-call professionals to assist with moving projects forward in design and implementation. Under this model, the Authority has been able to address a variety of desired projects and improvements.
The team became a trusted partner and advisor to the Authority. Projects that PS&S professionals continue to work on include staffing support, combined sewer overflow (CSO) permitting, long-term control plan implementation, sewer main replacements, dredge management, plant upgrades and replacements, renovation of the existing physical plant and office buildings, flood control projects and green infrastructure.
The Saw Mill River was buried beneath the City of Yonkers, New York at the beginning of the 20th century. “Daylighting” the river, or returning the river to a more natural, open-air condition,
provided community and ecological benefits and was part of the City of Yonkers's plan for social and economic progress. PS&S led a team in creating a new urban river and park through the center of downtown Yonkers, featuring two dynamic pools and three strategic low waterfalls.
The PS&S design included a fish ladder that supports the American eel migration, an outdoor learning enclave and a hydroelectric water wheel that powers streetlights near City Hall.
In recognition of PS&S’s work, the Yonkers Saw Mill River Daylighting Park was one of four parks featured in the September 2022 issue of National Geographic, ‘America the Beautiful; New Ideas for Protecting Land, Water and Wildlife.’
“This was a true conservation project that resulted in a win-win for the environment as well as for the community economically,” said Sartor. “PS&S is proud to have helped create such a visionary project that included so many local, state and federal entities to make this a reality.”
At 60 years old, PS&S felt it was time to re-brand the company.
Leadership wanted the re-brand to exemplify a path forward and embody the mission, vision, and values of the company. PS&S considers its employees its most important asset, and it was important that employees be recognized for the work they do as the foundation for the company’s new look.
PS&S constantly evaluates itself on its managerial expertise, technical excellence, and business development acumen. Those three pillars of excellence are the building blocks the firm used for the design of its new headquarters and logo.
Naturally, PS&S looked to its own talent pool of engineers and architects to help come up with a solution for the new brand. The firm tackled the issue in the same way it works with clients--by solving a problem in a systematic way to reach a goal. This intense focus on clients continues to be an underlying principle PS&S brought into its new workspace and logo, helping guide employees every day.
This ‘blueprint’ guides PS&S along its journey, reminding the firm of its past and giving the company a glimpse of a bright future ahead. With 60 years behind us, PS&S looks ahead to another 60 years—or more.
“Is the new infrastructure law having an impact?” That is the question I am most often asked in my travels to industry events and on Zoom calls.
One year after enactment of the historic Infrastructure Investment and Jobs Act (IIJA) the answer is definitively, “Yes.”
Although IIJA was signed into law November 15, 2021, things did not move as quickly as predicted. States did not have access to the full amount of the historic increase until Congress approved the annual appropriations bill in mid-March 2022. The Federal Highway Administration released the official funding notice April 1, and in May, state departments of transportation began to ramp-up their commitment funds in earnest.
The IIJA provides New Jersey with $8.1 billion to improve roadway and bridge infrastructure networks over five years. The first installment was $1.4 billion for FY 2022, which began October 1 of last year. As of August 30, New Jersey was leading the way by obligating $1 billion (82 percent) of its FY 2022 IIJA highway formula.
Out of all 50 states and D.C., the Garden State ranks 29 in the number of new transportation construction projects started since IIJA became the law of the land. The funds currently support 396 new projects with more to follow during the year – a sign of the confidence the new law brings to the transportation construction market. By comparison, Ohio came in at the top with 1,363 new projects in the pipeline. Reimbursements for work related to New Jersey’s new projects stand at $60.9 million as of August 30.
Some of the most notable projects supported by IIJA funds in the state include the Route 18 East Brunswick drainage and pavement rehabilitation project ($91.8 million), the Ocean County highway reconstruction project ($57.6 million), and interchange and bridge replacement along Route 3 and Route 46 in Passaic County ($32.3 million).
While the commitment of IIJA funds is a positive development for our industry, ARTBA is carefully tracking increases in project costs and material availability. Since late 2020, transportation construction professionals have confronted unprecedented pandemic-related cost increases and often-limited availability for key commodities and materials. The severity of the situation varies from state-to-state. In July, ARTBA leaders met with U.S. Department of Transportation (DOT) officials regarding increases
for a variety of inputs and urged the department to allow price adjustment clauses for existing federal-aid contracts, which would provide contractors temporary relief from unforeseen inflationary pressures.
U.S. DOT officials also engaged ARTBA members in a detailed dialogue on the pending expansion of Buy America requirements to certain construction materials and discussed availability of domestically produced materials and challenges in increasing that supply during the short term.
Despite these challenges, IIJA remains a net positive for the industry and the country. As we enter the second year of the most significant investment in U.S. infrastructure since the Interstate era, we will continue to see its positive impacts flow through to state and local economies in the form of increased gross domestic product, disposable income, and local tax revenue. The longterm economic benefits of these investments – improved mobility and flow of commerce – will last decades.
Editor’s note: ARTBA tracks the economic impacts of the IIJA in all 50 states and D.C., along with national commodity and material prices for transportation construction. This information can be accessed in the “Economics” section of www.artba.org
About the Author... Dr. Alison Premo Black joined the American Road & Transportation Builders Association (ARTBA) in August 2000. In addition to serving as senior vice president and chief economist for ARTBA, she is managing director of the the Transportation Investment Advocacy Center program. Dr. Black manages ARTBA’s economics staff and is responsible for over 100 studies examining national and state transportation funding and investment patterns, including the association’s landmark economic profile of the transportation construction industry, state bridge condition profiles and annual modal forecast.
Bringing a new product to market is never an easy task, especially when it is being supplied to a large joint venture working on a high-profile project like the $8-billion Central Terminal Replacement Project at New York’s LaGuardia Airport. Walsh Construction and Skanska USA, operating as the Design-Build Joint Venture of Skanska-Walsh on this project for the Port Authority of New York and New Jersey (PANYNJ), decided to put Stay-In-Place-Fascia-Forms (SIPFF) to work on two bridges that carry vehicular traffic between terminals.
This precast fascia form was patented by Precasteel LLC of Skillman, New Jersey. It is essentially an L-shaped piece of precast concrete designed to stay in place and serve as a form for the bridge deck pour and subsequent barrier pour. Precasteel is the brainchild of Gary M. Dinmore, P.E. It was conceived based on a trend he noticed over the course of 20 years working on numerous New York City bridge projects with bridge bracket and conventional overhang construction issues.
Dinmore recalled learning about the graying of America – caused by the aging of the Baby Boomers – during a Penn State Economics class. He didn’t recognize the significance of this trend at the time and the window of opportunity eventually closed. Despite
the missed opportunity it left him looking for another trend, which he discovered while inspecting bridges early in his career.
“Rather than the graying of America,” Dinmore recalls, “I started thinking of the rusting of America and the fact that our bridges are getting old and need to be replaced.”
Recognizing that the seemingly endless inventory of bridges would eventually have to be fixed, especially those built in the post-World War II era, he set out to identify market inefficiencies. Dinmore found what he was looking for in bridge overhang brackets. During his deployment to Lebanon as a member of a Special Forces ‘A’ Detachment, he saw stone aqueducts dating back to the B.C. era with overhangs reportedly constructed in a similar manner with timber falsework for support. He believed there had to be a better way because of advancements in modern materials where concrete can nearly mimic the strength of mild steel; hence the name PRECASTEEL®.
Design work at LaGuardia was done in 2018, but construction unfolded in 2019. Precasteel had done research and development and built prototypes and full-scale mock-ups in the past, but this was the first actual job.
“This is the first production job on a permanent structure,” says Dinmore. “It was probably the hardest project we could have asked to start with.”
There could be no production mistakes on a project of this magnitude. Precasteel had to slip form a full-scale mock-up at the Lehighton, Pa. facility of its precast supplier, J&R Slaw. It also had to clear the design review process under the scrutiny of WSP USA and HOK.
LaGuardia was challenging on several levels. It was a large project requiring approximately 1,800 linear feet of SIPFF panels for two structures, each with nine 100-foot spans of varying soffit widths and two spans with curvature. It also required a deviation from the standard shape. The architect wanted a “Lazy L” shape for aesthetic reasons. The placement of light blisters also required the soffits to be bumped out from 30 to 44 inches. The fact that one bridge used prestress concrete Bulb T Beams and the other steel girders wide flange beams also required Precasteel to modify hardware during the project to accommodate the geometry of the two different bridge beam types.
The Precasteel design allowed for a ¼-inch gap between panels to provide some construction tolerances since no closure pours were allowed on the structures to avoid contrasts in color. It also helped with the camber, which is essentially the upward deflection built into the bridge beam during fabrication. The camber was necessary for the structure to lay level after the entire deadload was applied. Dinmore confirmed that the gap closed and the panels settled into position along the beams’ edge without consequence when Skanska-Walsh poured the deck.
“Everything behaved the way we anticipated,” he says. “The ¼-inch gap gave them a lot of leeway in the field.” One unexpected benefit was that the gap was hidden in the shadows of the chamfered edges upon completion, which made the façade even more aesthetically pleasing.
The gap also eliminated rework and scheduling issues for Skanska-Walsh. In one instance, a panel was damaged prior to installation and needed to be replaced. The crew was able to continue setting panels, butting them tightly together, and skipping over the damaged panel location until a new one could be installed. They used a flat bar to make some minor adjustments to adjacent panels and the final panel fit perfectly.
“You don’t have to stop just because you don’t have one piece of the puzzle,” says Dinmore. “That ¼-inch gap helped. It gave the contractor plenty of room to drop it in without banging against the other panels.”
Precasteel was originally designed with a 90-degree angle. The architect at LaGuardia; however, was going for a different aesthetic. The vertical axis tilts back as a result, which Dinmore dubbed the “lazy L.”
Aesthetics are, in fact, what drove the specification of Precasteel over conventional methods at LaGuardia. The tilted back panel would have required extra bracing, whereas precast concrete was able to be formed without additional costs.
The architect discussed the use of white concrete for the facade, but Precasteel suggested that standard concrete would be a close match. They worked with its precast supplier J&R Slaw to provide samples and it was approved.
“There are inherent problems with bridge brackets,” said Dinmore. These triangular brackets, consisting of steel and heavy-duty plywood, jut out from the edges of the bridge to provide support during deck construction. “The conventional alternative to using bridge brackets,” he continues, “is fraught with wasted money and materials.”
Dinmore spent 20 years working on high-profile infrastructure projects in Metropolitan New York, the last 6 years as Chief Engineer for a Fortune 500 heavy civil contractor. He saw money wasted on transportation, unnecessary tasks, and the disposal of
Skanska-Walsh workers had to have all the hardware on before they flew the panels up to the bridge deck to achieve the production rate of one minute per linear foot. The hardware on each panel includes swivel hoist rings (aka swivel lifts), and two eye bolts, primary ties, and secondary ties.
plywood after bridge brackets were disassembled. Most contractors don’t own bridge brackets that conform to the requirements of today’s construction and those that do often spend time digging them up in the yard for the next project only to find that they have fallen into disrepair.
“Every time I would find an area where we were losing money, it traced back to these bridge brackets,” Dinmore says passionately. “The money was going everywhere except into the structural deck where it belonged.”
The closer spacing of these costly brackets has exacerbated the problem, according to Dinmore. Contractors used to set them around 36 to 48 inches apart. “They are now putting them much closer and that gets very, very expensive,” he says. “Precasteel eliminates the need for brackets altogether.”
Bridge brackets can also impact paving quality. The proximity of the bridge paver screed rail to the brackets causes them to deflect during paving and creates a wave, or a washboard affect, in the concrete deck along the barrier that often collects water and eventually scales. The damage is often discovered after the project is completed but the warranty has not expired, leaving the contractor with the unexpected cost of diamond grinding or deck replacement depending upon available concrete cover over the deck reinforcing steel. Precasteel is not subject to this issue since the paver screed rail is located along the centerline of the fascia beam as opposed to the panel itself.
J&R Slaw produced the panels at its Lehighton plant with Precasteel performing periodic quality inspections for quality assurance, especially on the first bridge known as the Frontage Road Structure (FRS). No plant inspectors were present from
PANYNJ; although the authority did station an inspector at the plant for ramp L29, the second of the structures. All Precasteel sections were five feet long and 1,000 pounds on average.
“It was shown in the design that soffit widths varied requiring each panel to be custom,” Dinmore recalls. “At the end of the day Slaw did a really good job, especially on the geometry, because everything fit like a glove.”
There was no specification for Precasteel so guidelines from the Architectural Precast Association (APA) were adopted early on. The recommended slender ratio dictated an increase in thickness from 2 ½ to 3 inches and a minimum concrete compression strength of 6,500 psi to avoid shrinkage and stress cracks.
All Precasteel sections were palletized, stacked on a flatbed trailer, and shipped off to LaGuardia. Upon arrival, Skanska-Walsh crews offloaded and moved the sections to a staging area where workers installed the hardware before hoisting them to the bridge deck one by one with a small crane.
“They had to have all the hardware on before they flew the panels up,” says Dinmore. “That was the only way to achieve the production rate of one minute per linear foot.”
The hardware on each panel includes swivel hoist rings (aka swivel lifts), and two eye bolts, primary ties, and secondary ties.
flown back down with the rigging on the crane hook and the process was repeated on the next section. Another set of swivel lifts were used on the next section to save time.
The plus 90-degree angle of the notch, better known as the bird’s beak, allows a panel to be set at almost any angle without any chipping or breakage. And it fits nearly any member that might be used for a bridge fascia beam. The only requirement is a 90-degree edge along the beam, whether curved, straight, concrete, or steel. No positive connection is made between the notch and the beam’s flange. “The notch is the secret sauce,” says Dinmore. “It’s what makes Precasteel work.”
Precasteel was initially designed to improve productivity, but it turned out that the conventional method of installing parapets was causing safety headaches.
Dinmore was approached by several insurance agents at the 2018 Utility & Transportation Contractors Convention of New Jersey (UTCA NJ) in Atlantic City. All were seeing frequent safety claims associated with the improper installation of bridge brackets or the vulnerability to wind uplift causing damage prior to concrete placement. The bracket and plywood are often unsecured before concrete is poured, acting like a kite that can get blown upward by moderate to heavy winds.
“This is a typical scenario for a lot of contractors,” Dinmore says. “It has probably happened to most of them at least once.” Many owners now specify that a cable needs to be threaded through the brackets to prevent the brackets from falling into the roadway below after uplifting winds rip the entire forming system off the bridge.
Precasteel allows the paver screed rail to be located along the centerline of the fascia beam as opposed to the panel itself, which eliminates the paving quality issues that can occur when using bridge brackets.
Skanska-Walsh workers waited on the bridge deck as sections were floated into place like puzzle pieces. The panels featured a notch slightly greater than 90-degrees along the bottom longitudinal edge that rested directly upon the top outboard flange of the fascia beam. Once the connection was engaged, a worker bolted the ties onto a threaded stud shot on the beam and tightened it. The swivel lifts were disconnected from the panel and
Skanska-Walsh crews were able to work safely from the bridge deck at LaGuardia, focusing on connecting the hardware properly. Each Precasteel section is equipped with two ties, one of which is redundant. Even in a worst-case scenario where a heavy load bangs into a panel, it would break rather than fall. This was proven on the last barrier pour on a section installed more than 6 months before barrier concrete placement. Precasteel panels at LaGuardia were designed to withstand all anticipated construction and OSHA loads with up to six times the factor of safety on deck pours and two times on barrier pours; the current standards have increased safety factors even more to facilitate the usage of pick brackets attached to the panels on the inside to allow workers to move freely up and down the line of panels and to account for reverse stresses that could be implied on the panels during slip forming operations.
At 42 inches tall from the soffit top, the installed Precasteel panels eliminated the need for fall protection, which is required when using bridge brackets. This not only prevented tripping and other nuisances that arise when connecting self-retracting lifelines, but also improved productivity for the trades waiting behind Skans-
ka-Walsh’s panel installation crew. The time savings gained by not having to tie off were incremental at the end of the project but the real schedule booster was not having to come back after the panels were installed; hence the Precasteel motto, “Set ‘em & Forget ‘em!.”
Skanska-Walsh finished successfully installing all Precasteel panels on the Central Terminal project in September 2019, and Delta Airlines had designed approximately 1,700 linear feet of Precasteel panels into the project at its neighboring terminal. DeFoe Construction Inc. had been slated to perform the work in early 2020; however, the pandemic caused precast plant closures that resulted in the need for conventional construction. The fact that Delta Airlines incorporated the panels into their design after witnessing the ease of construction and aesthetically pleasing finish is a testament to Precasteel.
Dinmore was proud to see Precasteel reaching the tipping point after more than 20 years of seeking a solution and six years researching and developing the concept. “My goal is to see Precasteel on bridges in every state across this great nation and eventually the world,” he says. “I’m thankful to Skanska-Walsh for recognizing the simplicity and potential of my idea and putting it to the ultimate test at LaGuardia.”
Gary M. Dinmore, P.E. conceived Precasteel based on a trend he noticed over the course of 20 years working on numerous New York City bridge projects with bridge bracket and conventional overhang construction issues.
But Dinmore does not consider himself a sale person or a politician, nor does he have the distribution or manufacturing facilities in place that are needed to launch his product on the grand scale it deserves. Now that proof of concept is behind him and the Infrastructure Bill is imminent, he’s looking for a helping hand to reach his goal of getting SIPFF’s on bridges across the U.S. Go to www.precasteel.com if you want to lend a hand.
No matter how hard we try to control it, life happens. That is why voluntary benefits are so critical. Your employees need protection for their families, finances and futures beyond core benefits — and you need a partner you can trust to help you do that.
IOA believes in delivering exceptional value to our clients, which is why we've selected Colonial Life as a preferred partner for voluntary benefits. Our relationship is rooted in our shared ideals:
• Benefit flexibility and personalization are essential to employees
• Businesses and employees have different needs that deserve equal attention
• Communicating the value of benefits to employees
• Results are what matter most
Also called “supplemental insurance,” these benefits offer protections beyond major medical and other insurance coverages. They are often paid for by the employees themselves, allowing them to choose plans that meet their needs and goals.
They help employees personalize benefits packages to their individual needs, including using them for co-pays or co-insurance, travel expenses, household bills and replacing wages or savings. A list of available benefits is showcased below:
* Accident Insurance
* Cancer Insurance
* Critical Illness * Hospital Confinement
* Disability Insurance
* Term and Whole Life Insurance
Colonial Life has a simple enrollment promise: educate and enroll employees in their benefits, all year round, at their convenience. Whether it be voluntary and core benefits or just voluntary, IOA and Colonial Life can make your open enrollment a breeze.
To learn more about the benefits that you can offer to your employees, please contact:
Insurance Office of America
Margaret Fitzgerald, SHRM-CP, REBC, ChHC, RHU
Senior Account Executive -Team Leader
margaret.fitzgerald@ioausa.com
Direct: 732 378 7388