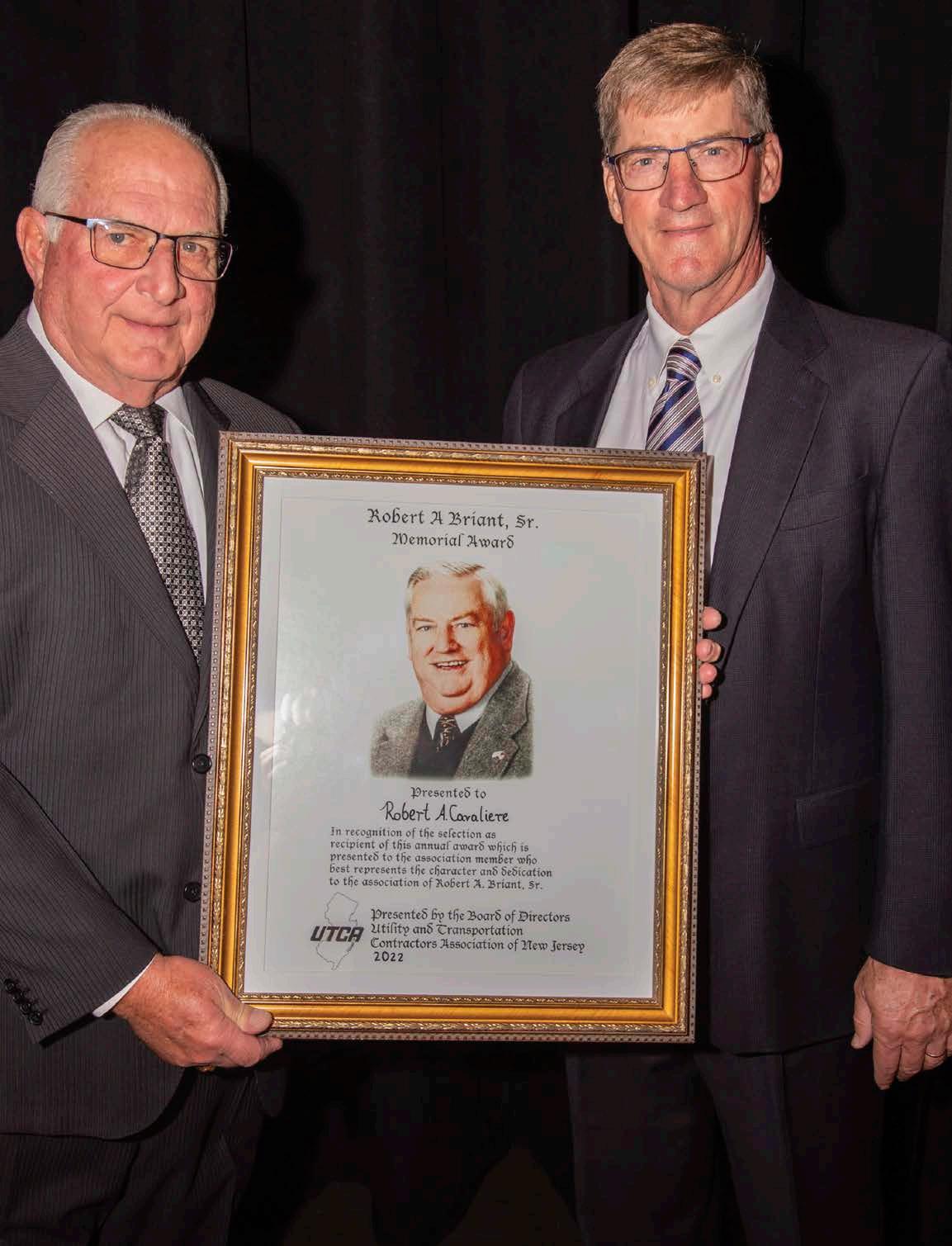

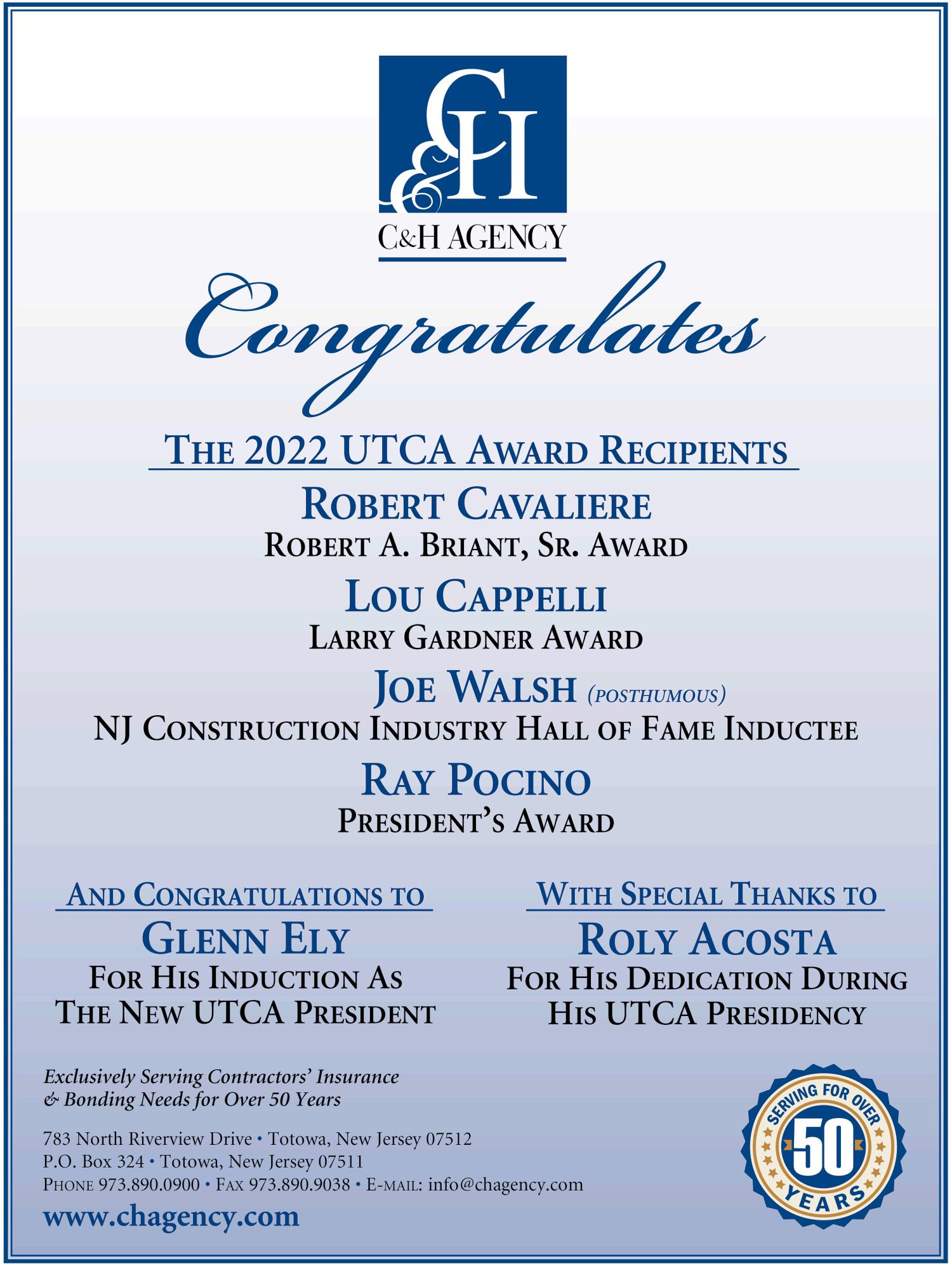
Having watched leaders in our industry who I have great respect for, previously serve and lead as UTCA’s presi dents, I am awe inspired and excited to serve our indus try in that role for the coming year. As I think back on those past icons, I recall vivid examples of individuals who understood the nuts and bolts of our work, knew the impact that would result from changes in funding or legislation, who were quick to listen but also to boldly provide input (sometimes in flowery ways), and most of all, who passionately led our industry in moving it all the while forward. I will endeavor to do the same in this com ing year.
Likewise inspiring to me has been the UTCA staff. As I have watched staff individually and collectively over the many years that I have been involved with them, I know that our staff brings the greatest knowledge, terrific experience and perspectives, and a tremendous drive to serve our members in all that they do. They also inspire me and have me very much looking forward to this year ahead.
The dynamic combination of member leadership and staff, posi tion the UTCA as an association to uniquely serve our industry in ways that exceed all others. I have clearly seen this association as the mover and shaker in our industry, and whose services and pursuits so vitally align with the topics that most impact all of us as members.
In addition to expressing those perspectives, I want to let each of you know what goals that I have set as highest priorities for this coming year. First among them is funding in general and how we can push facility owners in NJ to not only avail themselves of all of the funding opportunities within the recently enacted Infrastructure Bill, but to actually spend those funds by getting jobs designed, out to bid, and awarded. Opportunities for all our members rise and fall with funding, so this must be priority one. Secondly, critical in this coming year is the ongoing evaluation and support for members regarding the current PLA and ap prenticeship laws/regulations. The UTCA will remain vigilant in ensuring that these requirements are administered in ways that ensure a level playing field for our members as we all deal with understanding and compliance. Thirdly, as an association, we need to fully evaluate the Carpenters recent change in their pen sion structure to include a defined contribution as opposed to a defined benefit moving forward, and if deemed appropriate and beneficial for our members, seek to move that model forward within other of our union agreements. Fourthly, we will evalu ate a perceived opportunity to partner with owner agencies in
promoting our combined in dustry and then ultimately in jointly recruiting individuals to enter into it. This partnering effort could include visits to high schools/vocational tech nical schools as well as colleges, with an expressed intent to tout industry opportunities while at the same time building rapport and good will with owner agencies. Lastly and what will notably be included in a subsequent article, is the completion and prom ulgation of the UTCA Strategic Planning effort that has been started and continues through this year and beyond.
In laying out these goals, it is my hope that any of you who have input or important perspectives on any of these issues, will for ward that input to myself or any member of our Executive Com mittee, as a means of pursuing our goals that are most beneficial to the whole of our members. Likewise, if during the year, when new issues arise, please feel free to bring those ideas to us.
I also want to express my personal congratulations to our recent ly announced 2022 award winners, including: Bob Cavaliere of B. Anthony Construction, who received the Robert A. Briant, Sr. Memorial Award, Lou Cappelli of Florio Perrucci Steinhardt Cappelli Tipton & Taylor LLC, who received the Larry Gardner Memorial Award, and the family and colleagues of Joe Walsh of J. Fletcher Creamer & Son, who posthumously was inducted into the NJ Construction Hall of Fame. I have worked with each of these men firsthand and seen the energy, passion, and leadership of each as they have fiercely and so ably represented you in our industry. Thanks to each of them. I also want to extend a hearty thank you and congratulations to Ray Pocino of LIUNA for re ceiving the UTCA’s 2022 President’s Award. Ray has provided tireless decades of service to his members and to our industry.
Finally, I want to specifically thank Roly Acosta for all of his hard work and leadership over this past year. His business savvy and ability to first formulate and then decisively lead in implement ing ideas that become strategies for this association, are exem plary and have fully served us well. Likewise, with the Executive Committee members serving this year, I thank each of them for their continued willingness to serve and for their help in this coming year. Together with them, we look forward to what the UTCA will accomplish this year!
Economic indicators have provided conflicting views as to whether or not we have entered a recessionary period. By definition, a recession is generally identified as a fall in Gross Domestic Product (GDP) for two successive quarters. A broader analysis suggests a recession being a period of tempo rary economic decline in trade and industrial activity. A simpler analysis can be done by looking at your recent 401k statement or buying a gallon of milk. Seems like a recession to me.
Economists and political pundits have difficulty agreeing on whether current market conditions indicate a recession. This of course leaves many of us not only pondering the present but also the future. What is certain, however, is that inflationary pressure on energy, food and durable goods prices reduces consumers’ discretionary income. This, coupled with an increasing rate en vironment, will curtail retail and housing sales as well as the pur chases of other non-essential needs. These factors also suggest a recession.
Empirical economic data is often used to fill in the gaps provided by economic statistics, but it can be subjective and influenced by political leanings. Intuitive data can be much more useful when provided by individuals in the workforce who have ‘boots on the ground’ every day. A few examples include ship activity out on the fishing grounds, spewing smokestacks along the interstate, empty shelves in stores and the number of active construction sites. While it is difficult to quantify how or where these observa tions are accounted for in the economic calculator, they are most assuredly impactful.
Based on recent economic activity it would seem we have en tered a recession, but it is not like any others; it is another ‘new’ normal. Prior recessions left many workers in search of employ ment, yet today many companies continue in vain searching for new hires in a low unemployment marketplace. The most recent recession of ‘08/’09 was largely driven by weak financial markets. Subsequently, regulatory remedies put in place have mitigated many of those risks. Recessions prior to that period shared sim ilar symptoms, including high inflation, increasing unemploy ment, escalating interest rates, falling retail sales, lower home prices, a declining stock market, a tighter money supply, etc.
There are many other factors that make this recession differ ent, not the least of which are significant government subsidies that seem to have no end. These sources of cash have bolstered balance sheets both personal and corporate, providing added liquidity and reduced levels of debt. Having cash on-hand and modest levels of debt can do wonders to help sustain oneself during a weak economic period.
One of the more important items making this recession different in the residential mortgage market; the homeowner. While hous ing prices have gone through the roof (pardon the pun), over the past few years, homeowners availed themselves of historically low interest rates for 30-year terms. This lessens the likelihood of a glut of inventory coming as a result of forced sales/foreclosure, thereby driving down home prices. It also means homeowners can continue to be consumers as their housing costs are fixed and relatively manageable. The detrimental effect adjustable rate and interest only mortgages had on the economy during prior recessions cannot be overstated.
The commercial real estate market has also demonstrated resil iency despite the impact Covid, and other factors have had on the industry. Doom-sayers suggested that the office building market would collapse due to vacancies, yet workers have re turned, albeit slowly. Companies have adjusted their space needs downwards, thereby providing efficiencies in their occupancy costs resulting in improved earnings. Retail space has been vio lently impacted by the pandemic and the “Amazon effect” of online shopping. Many malls have been successfully repositioned into multi-purpose use and become income generating assets. New retailers have taken over empty storefronts utilizing a mod ified business model with less space. The industrial real estate
market may have reached its capacity as job sites seemed to have slowed, but demand remains strong in this asset class as well.
Lastly, despite weak economic indicators and mixed views of a recession, most banks have continued to lend money. Funding for working capital, equipment, M&A, R&D and real estate is readily available, providing needed capital to combat a recession. While some tightening in loan struc turing has occurred, banks have reported strong earnings while building loan-loss reserves in anticipation of weak er economic times. Putting money aside for a rainy day is prudent and the foresight will benefit lending activity in the future.
What to do? Hoard your cash, retire debt and closely scru tinize future borrowings. Monitor material costs so that you can quickly respond to a decline in profit margins. Closely watch operating expenses so lower revenue can be offset by quickly reducing overhead. Review your customers’ pay ment habits so that you are prepared for a deterioration in
accounts receivable. Ensure cash flow is sustainable and reliable. Lastly, maintain open and proactive dialogue with critical busi ness partners including your CPA, banker, and insurance agent.
Now that I have your head spinning, let’s look at the bright side. While there are many uncertainties regarding the economy, there are also many positive items to help ward off a recession. Weak economic times have happened in the past and well managed organizations have been successfully guided through the diffi culties. It reminds me of a John Prine song… “That’s the way the world goes ‘round, one day you’re up and the next your down.”
May all your days be up!
Congratulations to Robert Cavaliere, recipient of the 2022 Robert A. Briant, Sr. Award; Lou Cappelli, recipient of the Larry Gardner Award; the Family of Joseph Walsh, posthumous 2022 NJ Construction Industry Hall of Fame Inductee; Glenn Ely, UTCA President 2022-2023; and Sussman Enterprises’ new leadership.
Although bidders will typically reach out to legal counsel before filing a formal bid notice, it is useful for contrac tors to have a general understanding of what the proce dures are depending on which public entity has solicited bids. This article provides an outline of timing and steps to take to preserve your rights.
The bid and award process for municipalities, counties, and oth er divisions of local government is governed by the Local Public Contracts Law, N.J.S.A. 40A:11-1 et seq. (LPCL). The process by school boards is governed by the Public School Contracts Law, N.J.S.A. 18A:18A-1 et seq. The procedures are almost (but not completely) identical in both statutory schemes.
Construction contracts above the bid threshold must be solicit ed by public advertisement and awarded to the lowest responsible bidder. There are certain exceptions to this requirement that may be important for contractors, such as that a contract for the pur chase of water supply services or wastewater treatment services may be solicited through a request for proposals and awarded in what the owner determines to be its best interests, price and other factors considered. N.J.S.A. 40A:11-5(gg).
Public owners may only reject all bids and readvertise a project for limited reasons: the lowest bid substantially exceeds the cost estimates or the contracting unit’s appropriation for the goods or services; the governing body decides to abandon the project; the contracting unit wants to substantially revise the specifications for the goods or services; or the governing body determines that the purposes or provisions of the applicable statute have been violat ed. While the justification of “substantial revision” of the specifi cations is somewhat amorphous, our courts have recognized that revelation of bid prices prior to a re-bid has a negative effect on competition.
There are statutory terms prohibiting the inclusion of certain re quirements in specifications such as requiring any “restriction or condition not directly related to the purpose, function or activity for which the contract is awarded;” requiring that a bidder or its business be a resident of or located in the municipality in which the contract will be awarded or performed; or requiring the fur nishing of any “brand name” unless certain conditions are met. Other statutory terms require that certain bid elements must be included, such as identifying subcontractors who will perform a prime trade if the contractor will not be performing that work it self.
There are also certain bid elements that are material, while others may be waived at the discretion of the owner. Mandatory bid ele ments that are specified in the LPCL include the submission of a bid bond; a surety guarantee that it will provide a performance and payment bond if the bidder is awarded the contract; a statement of corporate ownership; a listing of subcontractors; and an acknowl edgement of addenda. N.J.S.A. 40A:11-23.3.
Advertisements for bids must be published in an official newspa per no less than 10 days prior to the date specified for the receipt of bids. That date may not fall on a Monday or any day directly following a State or federal holiday. Most local units and school boards still require bids to be submitted by hard copy (in person or by delivery), but the Electronic Procurement Act, PL 2018, c.156, now permits local agencies to use electronic bidding if certain pro cedures have been adopted. Notice of addenda must be provided seven days, Saturdays, Sundays, or holidays excepted, prior to the acceptance of bids.
The contracting unit must award the bid or reject all bids no later than 60 days from receipt of bids, unless the bidders consent to an extension of that time.
If a bidder objects to the specifications, they must file a challenge directly with the contracting unit no less than three business days prior to the opening of the bids. Challenges filed after that time shall be considered void and have no impact on the contracting unit or the award of a contract. N.J.S.A. 11-13.1.
If a bidder objects to the award of a contract to another bidder, the best practice is to notify the contracting unit immediately explain ing the general basis of the challenge, while advising that counsel will be retained. In that initial protest letter, demand that copies of the other bidder’s bid be provided promptly. This will likely require filing an OPRA request. Also demand that you be provided with any responses submitted on behalf of the bidder whose bid you are challenging, any recommendations by the architect or engineer that may have been made to the governing body, and any Resolu tions that have or will be adopted. Emphasize that you want timely notice of when the award of the contract will be put on the agenda so that you can attend in person or at least have your attorney file a more in-depth protest prior to the award. You also want to doc ument that you are taking meaningful steps to expedite the protest prior to award of the contract, which would then allow your com petitor to commence performance. Importantly, if you do not hear back from the contracting unit following your initial protest letter, follow up by telephone regularly, until you are provided with the information that you seek.
Similarly, if more than a week has passed since the receipt of bids and you have not heard anything about the anticipated award of the contract, make yourself heard! Too often, contracting units do not follow the procedures you would expect to promptly notify you about award of a contract, rejection of all bids, or other actions that you may want to protest until too much time has passed that the court may be reluctant to undo what has transpired.
Once award of the contract has been made, you technically have 45 days to file suit in court challenging that decision, but the earli er the formal complaint is filed the better the chance that the court will order injunctive relief to prohibit the project from commenc ing until the matter is decided. Your attorney will likely seek a tem porary restraining order, and then ask for a fairly brief schedule for both parties to submit briefs and certifications, followed by oral argument. Depositions may be allowed, but are infrequent in bid protest challenges, since the decision typically rests on the bid specifications and the bids that were submitted.
For local agencies, the complaint is filed in the Superior Court of New Jersey, usually in the Law Division – the trial level. Either side may then take an appeal to the Appellate Division. Again, the par ties may seek an emergent stay and an acceleration of the briefing schedule. If those are not granted, it is likely that by the time the court’s decision is reached, the project will have progressed to the point where even if you win you lose – because the court will not order the contract to be rescinded and awarded to you, and bid ders are not entitled to money damages. Although the court may choose to issue an opinion, on a practical level, the case is moot.
The bid and award process of each State agency is governed by separate statutes: the New Jersey Department of Transportation is governed by N.J.S.A. 27:7-30. The New Jersey Turnpike, School Development Authority, Department of Environmental Protec tion and Department of the Treasury each have their own statu tory frameworks with specific quirks, such as whether award must be made to the low bidder or may be awarded based on price and other factors. Most State agencies are using electronic bidding.
The basic principles of public bidding outlined above, with respect to the bid forms to be submitted, whether they are considered ma terial or may be waived, the need for advertisements, and pre-bid challenge procedures are all fairly consistent with local practice.
One key difference is that appeal from a State agency decision is made directly to the Appellate Division – not to the trial level court. Because of this, it is important to establish a “record on ap peal” – the pleadings and documents that the Appellate court will review in considering the appeal. To do this, the aggrieved bidder must first file a bid protest with the State agency, for example, with the Commissioner of Transportation. Once the agency issues a “fi nal agency decision,” that decision and the documents that were considered by the agency become the record which the Appellate court will consider.
While bidders cannot be expected to be familiar with all the nu ances of the bid and award process and the differences among local and State agencies, it is important to keep in mind that the clock is ticking. Find out when you must file a challenge to the bid spec ifications themselves if you believe they are improperly prepared. When is the award being made? Has the other bidder commenced work? Is the project being funded through a grant that may have deadlines? Has a resolution been adopted by a local agency? What is the process for filing a bid protest either to a State agency? Be proactive in getting as many answers as possible to these questions on your own, and demand answers and information from the con tracting unit. Your attorney will then be best prepared to move forward with your case.
About the Author. . .Adrienne L. Isacoff, Esq. Adrienne is Co-Chair of the Construction Law Practice Group at Florio Perrucci Stein hardt Cappelli Tipton & Taylor, in the firm’s New Providence office. Adrienne also serves as an arbitrator and mediator for the American Arbitration Association. You can contact her at aisacoff@florioper rucci.com
Many provisions have been implemented under legisla tion in the past several years to help businesses and individuals reduce their tax obligation. Here are 10 tax planning strategies for contractors to consider:
Use the Right Accounting Method. Contractors should ensure that the tax reporting method for each contract is appropriate by determining which projects are not considered long-term (more than one year). Most contractors must use the percent age-of-completion method for long-term contracts, but excep tions exist. For example, residential builders generally qualify to use a different tax reporting method. In addition, contrac tors may be eligible for other elections for pay if paid contract language, unit price contracts, Guaranteed Maximum Price contracts, and retainage receivable. Under the Tax Cuts & Jobs Act (TCJA), tax accounting methods previously available only to smaller contractors can generally be used by contractors with average annual gross receipts of up to $26 million (adjusted for inflation). Choosing the appropriate method for each contract to reduce taxes is an overlooked tax planning tool.
Qualify as a Real Estate Professional. Rental activities and in come are generally considered passive income unless the inves tor qualifies as a real estate professional for tax purposes. Then it is treated as non-passive income. Losses can be deducted if the real estate professional materially participates in the rental activity. More than 50% of the person’s time and 750 hours must be spent on real estate activities. Holding a real estate license is not required. Other rules apply. Generally, contractors qualify for this provision under the Internal Revenue Code.
Depreciate Properties. According to the IRS, the lifespan of a residential building is 27.5 years. Therefore, owners can de duct 1/27.5 of the property’s building cost each year for the first 27.5 years they own the property. Capital improvements to the property can also be depreciated. However, when the property is sold, the owner may owe taxes for “depreciation recapture” on profits they previously avoided paying taxes on through de preciation. Land cannot be depreciated or the costs of clearing, planting, and landscaping. Those activities are considered part of the cost of the land and not the buildings. Real estate investors that acquired, renovated, or built a building should consider a cost segregation study to determine if the property qualifies for accelerated depreciation. Personal property acquired as part of a building may be eligible for immediate expensing under TCJA
by claiming 100% bonus depreciation.
Take Advantage of the 20% Pass-Through Deduction. A TCJA provision allows small business owners to deduct 20% of domes tic qualified business income (QBI) from a pass-through entity. The deduction is taken on the net number of eligible items of income, gain, deduction, and loss concerning any qualified trade or business of the taxpayer. The deduction cannot exceed taxable income. Rules apply.
Take the Employee Retention Credit (ERC). The Employee Re tention Credit (ERC) can still be claimed in 2022, even though the program ended last October. Employers can go back to March 13, 2020 and claim wages until September 30, 2021. This refundable tax credit can be taken against certain employment taxes. Employer-paid health insurance costs may also be eligible, even if the employer has furloughed workers and is not otherwise paying wages. A maximum of $7,000 per employee per quarter for a total of $21,000 can be claimed by qualified employers in 2021 and $5,000 for 2020 for a total of $26,000 per employee. Businesses may qualify for the ERC even if they receive funding through the Paycheck Protection Program (PPP).
Take Advantage of Bonus Depreciation Changes. The CARES Act includes a technical correction to TCJA that permits 100% bonus depreciation for eligible Qualified Improvement Proper ty (QIP) placed in service after December 31, 2017, and before January 1, 2023. As a result, taxpayers who placed eligible QIP in service during 2022 may be eligible to claim 100% bonus depre ciation. In addition, REITs, manufacturers, and other businesses that own certain types of non-residential real estate improve ments on leased land may also be eligible. After 2022 the Bonus Depreciation is reduced to 80% of the cost of the QIP.
Take the Energy Efficient Building Deduction. The Consoli dated Appropriations Act (CAA) of 2021 made the Energy Effi cient Building Deduction (Section 179D) permanent. Business owners and government contractors can deduct energy-efficient improvements to commercial and government buildings. A tax deduction is available to new or existing building owners who install interior lighting, building envelope, heating, cooling, ventilation, or hot water systems that reduce energy and power costs by 50% or more. Any accrued tax deductions from these buildings can be carried back two tax years or forward for up to 20 years. The Inflation Reduction Act of 2022 (the IRA) in
creases the value of the section 179D tax deduction to $5.00 (up from $1.88) per square foot. Contractors can qualify for the full deduction by designing and installing qualified energy-efficient systems in certain buildings, provided they meet prevailing wage and apprenticeship requirements. Certain nonprofit organiza tions, schools and universities, churches, and other public en tities are eligible for this deduction under the IRA. Eligible de signers and builders (such as architects, engineers, contractors, environmental consultants, and energy service providers) can qualify for 179D under a special rule for public property.
Take the 45L Energy Efficient Home Tax Credit. The IRA also expands upon section 45L of the Internal Revenue Code, where eligible builders of energy-efficient apartment buildings could receive a tax credit of up to $5,000 per dwelling unit.
The R&D tax credit is a federal tax credit for increasing research and development activities during the year. This credit is of ten overlooked because many construction companies feel that they do not qualify. However, an improved business component alone counts as R&D, so construction companies may be eligible for the credit. The credit ranges based on various factors but can be up to 20% of the company’s R&D cost.
Buy an Electric Vehicle. The IRA includes a $4,000 tax credit to purchase used electric vehicles and up to $7,500 in tax credits for
new cars. These tax credits apply to any “clean vehicle,” including hydrogen fuel cell cars. In addition, the Act extends existing elec tric vehicle tax credits for 10 years until December 2032.
The IRA introduces new renewable energy tax credits and ex tends others. These include incentives to companies and con sumers who make cleaner energy choices, a tax credit for energy efficiency in commercial buildings, and grants and loans to help companies reduce gas methane emissions from oil and gas. The IRA also creates a $1B incentive program for energy-efficient af fordable housing and $3B to improve roads.
Taking tax credits in one area of the business may offset the ben efits of another. So, it is vital to take a holistic approach to tax planning. Contractors must weigh the costs versus the benefits of each credit or incentive before implementing a strategy.
About the Author. . . Andrew Russo, CPA, MST, is the Direc tor of Tax Strategies for McCarthy & Company, PC. Andy helps clients by providing them with a strategic approach to tax plan ning to reduce their income tax liability. He can be contacted at 610.828.1900 or andrew.russo@mccarthy.cpa.
Disclaimer: This article is for informational purposes only and does not constitute professional advice. We strongly advise you to seek professional assistance with respect to your specific issue(s).
Asphalt Paving Systems
J. Fletcher Creamer & Son Crisdel Group
D’Annunzio & Sons
George Harms Construction Montana Construction Mount Construction Northeast Remsco
PKF Mark III
Union Paving & Construction
Governor’s Level
Black Rock Enterprises Colliers Engineering Schifano Construction South State Inc.
Ambassador Level
Anselmi & DeCicco Bayshore Family of Companies Gray Supply Corp. Haines & Kibblehouse
P&A Construction
R.E. Pierson Construction Traffic Lines
Leadership Level
B. Anthony Construction Dewcon Inc.
M.S.P Construction
Orchard Holdings Smith-Sondy Asphalt Construction
Platinum Level
James J. Anderson Construction C&H Agency Carbro
Grade Construction Green Construction HBC Company Hoffman Equipment Mathis Construction Matina & Sons Metra Industries
New Prince Concrete Construction P.M. Construction Penn Bower Inc. Pennoni Associates Persistent Construction Pillari Brothers Construction Corp. Pioneer Pipe Skoda Contracting United Construction Services Yonkers Contracting Gold Level
Advanced Coring & Cutting Corp. American Shoring Apartment Rehabilitation Corp. Brent Material CATS Sweeping Caterina Supply Concrete Construction Corp. Eastern Landscape Contractors
First Montgomery Management Arthur R. Henry Inc. J.A. Alexander Inc.
Kinsley’s Landfill Menard USA
Ritacco Construction Rockborn Trucking & Excavation
SJA Construction V.A. Spatz & Sons
Silver Level
B&W Construction S. Batata Construction Bil-Jim Construction CIS
Coppola Services
Curchin Group DiMilia Inc.
Industrial Welding Supply Perna Finnigan SAX LLP
Scafar Contracting Shark Transportation Inc. Smolin Lupin & Co. Taylor Oil Company Trap Rock Industries Trench Technologies
Trevcon Construction Walters Marine Construction Zack Painting
Bronze Level
AJM Contractors
JM Ahle Co.
Arawak Paving
Capital Steel Service Clearsite Industrial Cooper Plumbing & Mechanical Creative Employee Benefit Services
Patrick DiCerbo Diacon USA
ICON Equipment Rencor T&T Commonwealth TKT Construction
Top Line Construction Wyndham Construction
Della Pello PavingAfter taking its summer recess, the Legislature is now back in action after a relatively quiet summer that involved only a handful of official legislative meetings. In the meantime, Congress too, has returned from their own recess af ter tackling some significant issues during the summer.
One of the most noteworthy developments in Washington was the enactment of the Inflation Reduction Act which implements sig nificant components of President Biden’s agenda. Since the Build Back Better plan stalled, ongoing negotiations resulted in this re named and pared down $430 billion legislative package that is sig nificantly smaller than the $2 trillion Build Back Better Act that passed the House in November.
Notably, the measure invests $370 billion to address climate change through tax credits for consumers who purchase energy efficient appliances and technologies and extends incentives for drivers who purchase electric vehicles. It also directs $90 billion to clean energy manufacturing and provides tax credits for wind and solar energy production.
While the likelihood the bill will actually reduce inflation has been sharply debated, the issue that drew the ire of many observers is the allocation of additional funding for the Internal Revenue Ser vice (IRS). This funding will be used in part to bolster enforce ment of tax laws by hiring additional staff and conducting more audits which experts say will likely be focused on high income earners and large corporations.
In other news from Washington, New Jersey is once again being shortchanged by the federal government. A recent report from the Natural Resources Defense Council found that we are receiv ing the second least amount of water infrastructure funding from the Infrastructure Investment and Jobs Act, per lead line, than any other state.
This is particularly irresponsible when considering that New Jer sey has some of the oldest water infrastructure in the country, in cluding upwards of 350,000 lead service lines. Members of our Congressional delegation wrote a letter demanding the Environ mental Protection Agency reconsider New Jersey’s lead service line allocation to correct what they called an “absurd disparity” in funding.
And California was once again in the news, voting to ban the sale of gasoline-powered cars and trucks by 2035 and then, days later, asking motorists to refrain from charging their electric vehicles due to the strain on their electric grid. UTCA’s Executive Director,
Dave Rible urged New Jersey to look closely at California’s struggles before following their lead in rushing to tran sition to electric vehicles.
Here in New Jersey, the Legislature is back in full swing after meeting only a handful of times since passing the Budget in June. While the Senate met once, the only other legislative meeting was a Joint Senate and Assembly Environment Committee meeting which took place in Toms River in August and focused on climate change and resiliency.
A variety of speakers testified on these issues and on legislation to increase the percentage of the state’s energy that comes from renewable sources and a bill to divest state pension funds from fossil fuel companies. New Jersey Department of Environmental Protection Commissioner Shawn LaTourette spoke about the need to prepare for climate change and rising sea levels that will have a serious impact on coastal communities.
He mentioned Hurricane Ida and Superstorm Sandy and increas ing rainfall totals as evidence of the urgent need to take action to protect the state’s residents. While the Committee did not vote on any legislation, UTCA will continue to monitor these bills which may be considered in the next few months.
Also worth noting is the announcement from the State Treasurer that New Jersey would reduce the gas tax by a penny, beginning October 1. This reduction is based on the Transportation Trust Fund (TTF) law that UTCA and its members advocated for in 2016. In order to ensure the funding for critical infrastructure projects remains stable, the law included a provision to adjust the tax annually based on gasoline consumption.
While the tax was raised last year, officials said increased fuel con sumption prompted this year’s reduction. This development il lustrates the law is functioning as intended by ensuring the TTF is properly funded while passing on savings to motorists when possible.
As we move deeper into fall, the mid-term elections are just a few weeks away and control of both the Senate and House could change hands. Earlier in the year, many pundits predicted a Republican wave that would give them a majority in one or both houses of Congress. However, recent events, including the Supreme Court’s Roe v. Wade decision, President Biden’s legislative victories and the influence of former President Trump could have a major im pact on this election.
Finally, while the State Legislature is not up for election this year, it will have a significant change due to the retirement of New Jersey’s longest serving black lawmaker, Senator Ron Rice of Newark. The long-time leader of the Legislative Black Caucus was a fierce advo cate for social justice and civil rights who was known to buck New Jersey’s power brokers, including those in his own party. Senator Rice is a legendary figure in Trenton and he will be sorely missed.
In the meantime, both the Legislature and Congress have a busy fall schedule and we will be watching closely as there will surely be even more developments in the infrastructure industry before the end of the year.
recognizing hazards, making straight-forward changes can significantly reduce workzone accidents, injuries
By: lucy perry, ceg correspondent - reprinted with permission from construction equipment guideThe top four causes of accidents on the construction site remain falls, strikes from objects, crushes between ob jects and electrical shock. Too often, though, workplace accidents and injuries can be attributed to the materials being used on the job site. There are easy methods to avoid incidents and keep workers safe on the construction job.
OSHA safety standards spell out the exact process for preventing injuries to crew members. There are many causes for these inci dents, but Grant Law Office points to negligence as chief among them.
Lack of proper worker training contributes to that negligence. The law team said improper use of or malfunctioning tools and equipment; failure to properly secure tools or components and improper stacking of tools, equipment, supplies or materials contribute, as well.
Inadequately securing loads on a boom, hoist or crane; loads that are too heavy; failure to use safety devices designed to stop fall ing debris and objects; faulty parts or materials that break down or lead to structural collapse; and lack of posted warning signs can all be tied to accidents.
Legal experts say recognizing hazards and making simple chang es in work processes as a result can improve conditions expo nentially.
“For instance, the seemingly common-sense requirement to bolt new steel instead of welding it in pre-existing wood structures
can significantly reduce the risk of costly and dangerous fires,” attorney Neill Flynn, The Plata Law Firm, told Structure maga zine. “Whether made of steel, lead, cast iron or copper, pipes are invariably denser, heavier and capable of making short work of the human body.
“Required safety precautions, most notably hard hats, have sig nificantly reduced the number of injuries caused by construction workers coming into unintended contact with metal pipes.”
Unfortunately, these materials are still the source of a “signifi cant” percentage of workplace accidents, he noted.
So do incidents related to working around pipes. Due to their weight and “unyielding nature,” Flynn said pipes are inherently dangerous whether they fall on an unsuspecting worker or cause an impact injury from improper storage.
“Something as simple as an unevenly stacked rebar can easily cut a worker or cause one to trip and fall,” he said. “Given the na ture of construction sites, where almost everything is sharp, hard and/or heavy, what might otherwise be a benign occurrence can quickly become a career or an even life-ending event.”
Electrical wiring and other dangerous materials such as conduit and fixtures, invariably found on construction sites, can be haz ards.
The most obvious source of injury from such materials is the risk of electrical shock, said Flynn.
He added while it’s most closely associated with injuries to elec tricians, a significant number of electrical injuries are sustained by construction workers in every trade.
Wiring by its very nature creates a high risk of trip and fall inju ries stemming from entanglements in loosely or otherwise im properly stored materials, he said.
Flammable materials pose an inherent danger on the construc tion site. Solvents, liquid petroleum gas and adhesives pose mul tiple risks ranging from flammability and combustion to inhala tion dangers, said Flynn.
Taking required safety precautions, most notably wearing hard hats, has significantly reduced the number of injuries caused by construction workers coming into unintended contact with pipes and structures.
“As the general public has become inured over the last two years to wear masks due to the COVID pandemic, construction work ers and especially safety officers have long been aware of proper breathing protection procedures.”
Such materials must be stored and used in adequately ventilated spaces, he continued.
“Fire or even explosions are the most obvious risk associated with combustible and/or flammable substances. However, they pose additional risks that are often overlooked.”
Simple skin contact with these materials can cause injury, said Flynn. They’re often more dangerous when inhaled due to the lack of or failure to use proper respiratory protection.
“Damage to the lungs and respiratory system overall can range from immediate to long-term and can, in many cases, be fatal.”
Foot injuries are a very common occurrence on construction sites, especially from falling objects. But there are many other causes and types of injuries.
Rhoades Legal notes that in addition to electrical shock, workers can suffer broken bones, punctures, cuts and lacerations, burns and sprains all involving the feet and negligence.
The law firm noted that workers can be crushed or suffer bro ken foot bones due to falling objects, moving vehicles and being trapped or caught between objects.
Punctures of the sole of the foot are caused by loose nails, sharp metal or glass objects.
“Puncture wounds can easily get infected if not treated promptly. You can even get tetanus from a puncture injury,” according to the legal team.
Cuts and lacerations of the feet can be caused by chainsaws, ro tary mowers and unguarded or improperly guarded heavy ma chinery.
Foot-related burn injuries can result from splashing molten met al, chemical spills, contact with fire and flammable or explosive materials.
Electrical shock is caused by static electricity, contact with sourc es of electricity, including exposed hot wiring or wiring that is not properly grounded.
Finally, sprains can happen in slip and fall accidents. A work er could slip and fall on scaffolding or from wearing improper footwear.
Many local jurisdictions provide legal means to compensate in jured workers, but both site owner and contractor can be proac tive by integrating a mix of strictly enforced site safety practices, OSHA regulations and simple common sense, said Flynn.
“By collecting and monitoring information about the project, in creasingly in real-time, structural engineers can anticipate prob lems before they reach the critical stage and can be managed be fore someone gets hurt.”
He urged frequent site inspections, regular safety meetings and rigorously enforced site safety standards supplemented with re al-time data collection systems.
“Comprised of wireless onsite sensors coupled with data col lection nodes, such systems streamline the structural engineer’s ability to monitor the entire building site and anticipate problems before they arise,” said Flynn. “These systems can be customized to monitor material storage and the location and movement of workers throughout the site, thereby giving the engineer the abil ity to anticipate and prevent dangerous or even deadly accidents before they happen.”
What simple common-sense measures can be implemented on the job site? The list is long, but Rhoades refers to OSHA’s rules for preventing workplace injuries:
• Workers must wear safety shoes when working in locations where there is a risk of slipping and falling or objects piercing the sole.
• Protective footwear must meet ANSI Z4 or have equivalent de sign requirements. Impact and compression protection are pro vided by all ANSI-approved shoes.
“However, the level and sort of protection may not always be the same. Different footwear protects users in various ways. Make sure to review the label of the footwear.”
Shoes or boots may need to have special electrical conductivity insulation or other non-conductive protective material in order to prevent electrical shock.
Chemical-resistant boots may be required to protect against caustic, reactive, toxic or corrosive substances during cleaning or surface preparation.
Slip-resistant shoes should always be worn in any type of con struction or production facility environment, but especially if the worker will have to be in icy or rainy weather conditions.
Many construction work settings require boots with toe caps and puncture-proof soles. Non-slip soles, chemical-resistant materi als, insulation or other protective features may be required in your profession.
“Ensure that the shoes are safe according to necessary safety standards.”
Grant Law Office noted the adoption of additional safety precau tions to reduce the risk of injury specifically from falling objects on the construction site:
• Always wear protective gear, such as helmets, goggles and hardtoe boots. Avoid hazardous areas for falling materials.
• Never walk or stand under heavy equipment, such as a front loader, hoist or crane, particularly when it is carrying a load.
• Use the proper equipment for the job at hand. Never stack ma terials or objects too high. And inspect equipment and tools be fore using them.
• Never use improperly maintained or faulty equipment or tools; never exceed the lifting capacity of a hoist, crane or lift; and se cure tools and equipment properly when working overhead.
Despite two tumultuous years of lockdowns, restrictions and canceled events, there was no pandemic-related hangover for this year’s UTCA Convention. In fact, this year’s convention was one of the best yet and this annual gather ing continues to be a “can’t miss” event for contractors, vendors and anyone involved in the infrastructure industry.
The convention once again shattered prior attendance records with over 1,000 people, representing nearly 350 companies, mak ing the early fall trip to the Borgata in Atlantic City. Longtime members and new faces alike took part in the festivities which unfolded over the 3-day convention. As always, the exhibit floor served as the center of activity with approximately 100 exhibitors from all facets of the construction industry displaying all types of goods and service.
As in past years, the convention kicked off with the Fall Golf Out ing at Atlantic City Country Club in Northfield. With all slots sold out months in advance, the addition of another mini-outing at Seaview Golf Club in Galloway gave an additional 28 golfers
the opportunity to hit the links before the convention. Thank you to our golf sponsor, Spiniello Companies and to everyone who played and helped make both outings a tremendous success.
After golf, the festivities began at the Borgata with the Opening Reception, which was followed by the Awards Dinner. Both the reception and dinner again proved wildly popular with nearly 600 people attending one or both events.
The highlight of the dinner was the presentation of the industry awards. This year’s Robert A. Briant, Sr. Memorial Award was presented to Bob Cavaliere of B. Anthony Construction while Lou Cappelli of Florio Perrucci Steinhardt Cappelli Tipton & Taylor, LLC. was the recipient of the Larry Gardner Memorial Award.
After the awards presentation, UTCA’s outgoing president Roly Acosta was honored for his service to the Association over the past year. In his remarks, Roly thanked his colleagues and men tioned a number of accomplishments during his tenure, includ ing the adoption of the New Jersey DOT’s steel escalation specifi cations and the passage of the Infrastructure Investment and Jobs Act which included UTCA’s toll credit study.
In addition, he highlighted the creation of a reimbursement pro gram for material cost escalation, lauded the continuation of UT CA’s strategic plan and expressed pride in his role in UTCA CEO Bob Briant, Jr.’s election to the American Road and Transporta tion Builders Association (ARTBA) Hall of Fame. Thank you to our reception and dinner sponsors, Jesco Inc./Wirtgen, Foley Inc. and South Jersey Industries, and to everyone who participat ed in these wonderful events.
The luncheon then continued with a tribute to our dear friend, the late Joe Walsh of J. Fletcher Creamer, who was posthumous ly inducted into the New Jersey Construction Industry Hall of Fame. Dave Rible offered heartfelt remarks about Joe’s life and tremendous legacy while Joe’s sons, JT and Andrew, accepted the award on behalf of the Walsh family. As you can imagine, there was hardly a dry eye in the room during this salute to a truly leg endary figure in the industry who is terribly missed by so many.
The Exhibit Floor re-opened on Friday morning with exhibitors that ran the gamut of goods and services, including construc tion equipment, safety devices and a wide variety of innovative construction materials as well as engineering, insurance, and ac counting services.
The luncheon program was opened by UTCA Executive Director Dave Rible who offered a warm welcome to everyone in atten dance and acknowledging the many years of service of longtime Laborers’ official, Ray Pocino who is retiring in November.
Following that was the installation of the next UTCA president, Glenn Ely of PKF-Mark III. Lou Cappelli administered the oath of office and Glenn expressed his gratitude in being chosen to lead the UTCA and laid out his vison for the association for the upcoming year. Glenn has an ambitious agenda and in his speech he focused on the need to move more projects into the construction phase, recruit more young people into the industry and to continue strengthening and improving the UTCA He also urged his colleagues to take an active role in the Association.
After Glenn concluded his remarks, the crowd was engrossed by this year’s guest speaker, country music star Jimmy Wayne. An award-winning song writer and recording artist, Wayne is the au thor of the novel and made-for-TV movie Paper Angels and the New York Times bestseller, Walk To Beautiful. Once a foster child himself, he walked halfway across America to raise awareness for children in the foster care system.
Wayne credited his success to both his hard work and the support of a local couple who took him in when he became homeless as a teenager. In a speech that was both humorous and heartbreaking, he stressed that his story illustrates how the actions of one person can change someone’s life.
Thanks to our labor partners, the Engineers Labor-Employer Cooperative who sponsored this year’s riveting guest speaker and to our premier lunch sponsor, Komatsu.
After lunch, the Exhibit Floor reopened and was again abuzz with activity, highlighted by the sight of attendees grabbing as many bills as possible as cash swirled around them in the Money Booth. Other lucky winners from the day took home an iPad, Apple Watches, a Yeti Cooler, and a trip to St. Maarten.
Friday evening’s President’s Reception once again drew a large crowd that enjoyed delicious food, including an amazing raw bar, and a few cocktails thanks to the generosity of our sponsors, C & H Agency, and the Eastern Atlantic States Regional Council of Carpenters.
The PAC Auction was also a resounding success with attend ees bidding on over 40 items, many of which were donated by our members. Winning bidders took home a Gucci handbag, Yankees-Red Sox tickets, exclusive golf packages and many oth er luxury goods and experiences that were auctioned off. These fantastic auction items-and the generosity of the bidders-helped raise more than $20,000 for the UTCA’s Constructors for Good Government Political Action Committee which helps ensure the voice of our industry is represented in Trenton.
Thank you to our PAC Auction Party sponsors, Capitol Supply Construction Products, JESCO-Wirtgen, Northeast Remsco Construction, EIC Associates, M.L. Ruberton Construction, Atlantic Concrete Products, Earle Asphalt, Cohen Seglias Pallas Greenhall & Furman, and South State.
Despite the whirlwind of activity, the night was just getting start ed for many attendees, including our Emerging Leaders who hosted a late-night happy hour at the Borgata Pool. Thanks to our premier sponsors, McCarthy & Co. and Trif & Modugno, more than 100 young professionals enjoyed cocktails and net working that lasted well into the morning with their colleagues from in and around the construction industry.
The convention concluded on Saturday morning with a farewell breakfast, courtesy of Construction Risk Partners, where attend ees enjoyed a hearty meal before hitting the road ahead of the wet and windy remnants of Hurricane Ian.
Everyone at the UTCA is incredibly grateful to all who helped make this year’s convention an overwhelming success. We thank everyone who participated, including all of the sponsors, exhib itors and attendees. It is because of your generosity that we are able to stage this event year after year to support our members and strengthen the construction industry. We can’t wait to see everyone again at next year’s convention which promises to be even better!
Ihave been practicing labor and employment law for almost 25 years. Like most lawyers, I spend a lot of time on the phone counseling my clients and trying to keep them out of trouble. In this article, I share a few real-life scenarios to help clear up some common misconceptions about employment law and for you to learn from the mistakes of others.
As I was driving into the office the other morning, my day be gan with a call from a small paving contractor. After exchanging pleasantries, my client told me he was getting ready to termi nate one of his longtime project managers. He explained that this project manager used to be a good employee but had slowed down in recent years. When I started asking questions, my client disclosed that the project manager was the oldest employee in the entire company and that he had taken a lot of time off be cause he has diabetes. I was in the middle of advising my client that we needed to slow down when he interrupted with a line that I’ve heard from countless contractors: “Can’t we just say that we are firing him because he’s an at-will employee?”
That brings us to our first employment law misconception; that relying upon employment at will is okay. If you do a Google
While that definition is technically correct, any employer who relies upon employment at will as a justification for making a ter mination decision is making a terrible and potentially very costly mistake. In the event of a discrimination lawsuit, an employer needs to be able to articulate and explain a legitimate, non-dis criminatory business reason for all of its termination decisions. Saying that we terminated someone because they are an at-will employee just doesn’t fly.
Whenever I’m counseling an employer about the risks associated with a termination, I consider a number of factors, including:
a) Whether the employee’s personnel file, including perfor mance reviews and progressive disciplinary documentation, tells a story that is up to date and consistent with reality
b) Whether the employer has consistently applied written workplace policies to other similarly situated employees;
c) Whether the employee belongs to a protected class (based on age, race, religion, disability, national origin, etc.) that cre ates a greater risk exposure; and
d) Whether it makes sense to use a severance agreement to buy a general release and avoid potential claims.
search on employment at will, you will quickly see hundreds of articles stating that at-will employees can be terminated for any reason or no reason, and at any time, with or without notice.
My next client call came in just as I arrived at my desk. A gen eral contractor had an employee in the office complaining about not getting overtime pay. My client explained that all of the of fice employees are salaried and that they have never paid any of them overtime. With this, we can now debunk our second misconception: that paying someone a salary means that they are not entitled to overtime. There are federal and state wageand-hour laws that specifically define who may be considered an exempt employee. Paying someone a salary is only part of the equation. In addition, you must satisfy the Department of La bor’s no-docking rules, called the salary basis test, and an exempt employee needs to perform “white collar” job duties. There are three types of white collar employees: executive, administrative, and professional. Each of these categories has detailed and often counterintuitive definitions and terms. Making assumptions
about an employee’s exempt status can be a very expensive mis take, especially because this area of the law is ripe for collective and class action litigation.
After reviewing the ins and outs of exempt status with another client and giving them practical tips for converting some of their office staff to hourly status, I began preparing for a deposition scheduled for the following day in a noncompete case. My client, a specialty electrical contractor, had hired an estimator from a direct competitor even though the estimator had signed a non compete agreement. The company found itself in this situation because it believed that noncompete agreements are generally unenforceable and that the three-year restriction in the estima tor’s agreement was especially unfair. That brings us to our third common misconception; that noncompetes won’t hold up in court. As an attorney who has litigated dozens of these cases in court, I can assure you that noncompete agreements are enforce able under New Jersey law. While many judges disfavor them and view them as anticompetitive and un-American, the law says that noncompete agreements and non-solicitation agreements should be upheld and deemed enforceable to the extent that they
are necessary to protect an employer’s legitimate business inter ests, which can include its customer relationships and confidential trade secrets. But what about agreements that include three-year restrictions or other overly burdensome terms? New Jersey is a “blue pencil” jurisdiction. This means that if a judge determines that a noncompete goes too far, the court can essentially re-write the agreement to shorten the restriction or otherwise narrow the noncompete so that it is reasonable.
So welcome to my world. These real-life examples present a snap shot of the misconceptions I regularly encounter as a labor and employment lawyer. The big takeaway here is that employment law is often counterintuitive and that investigating and learning about an issue is the best way to avoid getting caught in the jaws of an employment lawsuit.
Co-chair of Cohen Seglias’ Labor & Employment Group, Jonathan Landesman counsels his clients on proactive and preventative strat egies to ensure the long-term health of their business. When litiga tion is necessary, Jon aggressively defends his clients to protect their interests. He can be reached at jlandesman@cohenseglias.com or 267.238.4726.
In late 2018, I used this column to update UTCA members about growing concerns with previously unregulated chem icals in our drinking water. In the column I speculated that we were about to hit a tipping point of public awareness/gov ernment action that will lead to a renewed push for expanded treatment in drinking water systems not seen in decades. I am checking back in with UTCA members to explain what’s hap pened since I made that prediction.
New Jersey is known for many positive things. On the negative side, it has equal to or more historic environmental contamina tion issues than any other state. As a result, we often find our selves at the forefront of addressing environmental challenges resulting from our largely unregulated industrial past. The scope of the issues we face are enormous and diverse. Nothing, I mean nothing, gets the attention of the public and politicians like chal lenges with drinking water.
What has grabbed the attention of New Jersey residents relates to PFAS, an acronym representing a group of manmade chemicals that have been used in industrial and commercial applications for many decades. While smart people can argue the exact im pact, ongoing research confirms that these chemicals, which are long-lasting in the environment and accumulate in the human body over many years, can present health concerns for the public over time. Since human health effects are associated with even low-level exposures to PFAS, it is important to minimize expo sure from drinking water. That we can all agree on.
Since 2018, the NJ Department of Environmental Protection (DEP) has adopted rule amendments to:
• Establish drinking water maximum contaminant levels (MCLs) for three PFAS chemicals (PFOA, PFOS, and PFNA… saving you the long full names of each compound);
• Expand testing of private wells subject to sale or lease for PFOA, PFOS, and PFNA under the Private Well Testing Act (PWTA);
• Establish specific ground water quality standards for PFOA, and PFOS, and PFNA;
• Add PFOA, and PFOS, and PFNA to New Jersey’s List of Hazardous Substances; and
• Expand the New Jersey Pol lutant Discharge Elimination System (NJPDES) permit application testing require ments/pollutant listings and requirements for discharges to ground water to include PFOA, PFOS, and PFNA.
So formal government standards (technically referred to as “MCLs”) for these “Big 3” PFAS chemicals made their way through the rule-making process and now must be complied with. What this means is that monitoring for these chemicals becomes a requirement for public water systems and those with levels above the individual standards will have to take steps to address their exceedances. While there are impacts to industry and redevelopment from these standards, my focus here for UTCA is with the drinking water aspects.
The new standards require all public water systems to mon itor for the contaminants. All have complied. According to DEP data, we know that as of January 21, 2022, 34 communi ty water systems and 40 non-transient non-community water systems have had MCL violations for PFNA, PFOA, and/or PFOS. Compliance is based on a running average of quarterly samples taken over the course of one year for each contami nant. Samples are taken at the point of entry within a regulated system, namely treatment plants and/or wells. Systems appear ing on the list have had at least one treatment plant or well experience an MCL violation for a regulated PFAS.
To its credit, DEP has provided resources to assist drinking water systems understand and comply with these new stan dards. For example, the DEP now has a group within the Di vision of Water Supply & Geoscience that is providing com pliance assistance to public water systems that have incurred MCL violations. This group helps guide water systems through the regulatory steps needed to return to compliance.
The DEP and the Water Bank are providing financial resources that are available to community water systems and nonprof it noncommunity water systems with violations through the Drinking Water State Revolving Fund (DWSRF) loan pro-
gram. DEP is also attempting to document instances where these drinking water systems have been damaged by discharg es of PFAS and connect them to funding through the Spill Compensation Fund and other actions. Water industry part ners like AEA and AWWA NJ have provided a tremendous amount of support to their members in this difficult transition from rule making to compliance.
In 2018, I speculated that most water companies that have exceedances of these new standards will install a treatment technology to bring the water produced by the system into compliance. The DEP’s advisory council evaluated all possi ble approaches to treatment and concluded that at the present time the use of granulated activated carbon (GAC) treatment would be the most effective to install. This treatment technol ogy has been installed proactively in several water systems, in cluding NJ American Water’s Penns Grove Water System. This treatment, when properly designed, constructed and main tained, will achieve the goal of removing a wide spectrum of contaminants, including this suite of three PFOAs.
While there are other options for compliance, as I speculat ed, new treatment is the path being chosen to address these exceedances by most water systems. The costs to construct these new treatment technologies are all recoverable in the rate structure and the projects themselves are eligible for loans/ grants from the I-Bank. Additional state and federal funding has been set aside to assist systems with this necessary con struction. Many projects are already in design or otherwise underway. Some have already been constructed. New Jersey’s water companies are well aware of this issue and the challeng es ahead. UTCA has been at the forefront of the advocacy to make these additional funding resources available to offset (to
the extent possible) any unreasonable shocks to monthly bills of customers.
Middlesex Water Company recently announced that it has completed Phase 1 construction of a water treatment facility in Edison. The wells used to produce water were turned off when the high levels of PFOA were found in newly required groundwater samples. This new advanced treatment facility (constructed by Northeast Remsco Construction) is designed to treat groundwater to ensure compliance with all state and federal drinking water standards. Middlesex Water is already working with the DEP and has begun a phased, start-up of its Park Avenue wellfield.
Ringwood Village has been approved for a $2.8 million federal Environmental Protection Agency grant to pay costs associat ed with PFAS chemicals from the water supply. The grant will offset a $3.5 million renovation of the village's Ravine Treat ment Plant to remove the PFAS found in the local drinking water.
To their credit, a handful of water systems have proactively ad dressed the issue and have been monitoring and taking actions to eliminate PFOS from their systems before the DEP put reg ulations in place. The reality is that it is hard to rationalize in vestment until it is required by some higher authority like the federal or state government. These new DEP standards make that imperative. Many treatment projects throughout the state are making their way through the DEP / Water Bank approval process and will be heading to construction in the foreseeable future. Please contact me via email (kennedy@utcanj.org) if you would like to discuss this matter further and better under stand where these construction opportunities may be.
Fourth Quarter is officially upon us and that means employ ers will soon be busy navigating the changing landscape of another employee benefits open enrollment. Rising healthcare costs, a tight labor market, uncertain economy, a mul tigenerational workforce, hybrid work arrangements, a heavy fo cus on employees’ emotional well-being and work/life balance are some challenges that employers are tasked with. It is clear the pandemic has changed the way employees view health and wellness and what is really important to them.
How an employer responds to some of these challenges can be a factor in keeping a good employee or losing them to a compet itor.
Below are items to consider for a successful open enrollment:
Now more than ever, employees are looking for protections for themselves and their families and health benefits are one of the top drivers of employee attraction and retention.
Is your current benefit package effectively meeting the needs of your employees? If not, now is the time to make changes.
insurance, identity theft protection, etc. This can be done in a way that it does not cost the employer anything.
A lack of understanding about health benefits can lead to em ployee uncertainty and stress during open enrollment. With in flation and rising costs everywhere we turn, employee education is now more important than ever to help ensure employees are getting the most out of their benefits so as not to miss potential cost savings.
Use open enrollment as an opportunity to educate employees on items such as the importance of using in-network provid ers, understanding how deductible, copay/coinsurance and out of pocket maximums work, using generic medications when it makes sense, taking advantage of wellness incentives, etc.
Consider some “out of the box” benefits to help retain and at tract top talent. A few examples are—flexible work hours, float ing holidays, anniversary rewards, employee referral incentives, and spot bonuses—just to name a few.
How do you plan to push open enrollment information out to your employees? There is no one-size fits-all solution for every organization. Solutions can vary based on company size, and complexity of the benefit packages being offered. Employee de mographics and culture can also play a role. Tailoring strategies to meet your specific needs encourages employee engagement and ultimately helps pave the way for a more efficient enrollment for both the employer and the employee. Many platforms may also be available on a continued year-round basis, making infor mation easily accessible throughout the entire year.
Here's to a successful Open Enrollment!
Offering a wider mix of benefits in 2023 can give employees ver satility to choose the benefits that meet their individual or family needs. Think about adding supplemental benefits such as hos pital, accident, critical illness, employee assistance programs, pet
An immigrant to the United States when she was five years old, Teresa Brill is the embodiment of the Ameri can Dream. A passion for engineering, combined with a desire to serve her adopted country, led her to a military career that provided her with unique experience that she believes will help her thrive as the new owner of Sussman Enterprises, Inc. a longtime New Jersey construction contractor.
A native of Peru, Brill’s family settled in New York and she grew up in Brooklyn. She attended New York University School of Engineering and joined the United States Air Force where she served in the Civil Engineering Squadron out of Joint Base Mc Guire-Dix-Lakehurst. She also has her Master of Business Ad ministration (MBA) and is a certified Professional Project Man ager (PMP).
Her first deployment in the Air Force was part of Operation En during Freedom where she was stationed at Al Dhafra Airbase in the United Arab Emirates (UAE). For her second tour, she served in Operation Inherent Resolve and was a part of the First Expeditionary Civil Engineering Group, which took her to Qa tar, UAE and Saudi Arabia.
In both deployments, Brill served as a Project Manager for infra structure projects on the base designed to support the military personnel who were utilizing the base as they engaged in their missions in Iraq, Afghanistan and the entire Middle East.
She credits her time in the military with providing her with unique experience in construction that cannot be replicated, not ing that she literally got her hands dirty on these projects. This experience of overseeing projects in difficult and often hostile en vironments gave her insights that few in the industry possess. In fact, Brill notes that she has worked “in places that people can’t even get into.”
“My time in the Air Force has given me life experiences like no other,” she said. “The military has prepared me to face challeng es head on and succeed at my missions. I was able to travel the world, learn from amazing leaders, and most importantly, had the opportunity to serve my country.”
After ten years in the Air Force, she made the difficult decision to leave the military and enter the private sector. She initially worked for a construction company in New York City before tak ing a position with an aerospace defense contractor. She was a Program Manager in the Electronic Warfare Division and team lead for its F-22 program—a fighter jet that remained close to her heart from her time in the Air Force.
Between tours she put her expertise to work on a project to help her sister redevelop a building. During this process, Brill discov ered her love of entrepreneurship, noting her ability to navigate the many challenges she faced on this project, including permit ting, insurance and bonding requirements. This experience and her desire to be her own boss inspired her to make the decision to leave her corporate job and run her own company.
Based on her experience in the construction industry, Brill knew that she wanted to purchase an established company instead of starting from scratch. After some initial research, she found that Sussman Enterprises, Inc. (SEI), a company with more than 38
years of experience in the infrastructure industry, was available.
In March of this year, she finalized the purchase of SEI and Brill and her team are hard at work on projects that were initiated prior to her purchase and are seeking to secure additional work. She credits much of their success to the vast experience of her staff—all of whom remained with the company after the sale. In addition, she has relied on the assistance of Jeff Sussman who remains with the operation as a consultant. Moreover, Brill em phasizes that she is continuing SEI’s commitment to delivering projects on time and under budget.
While she touts the legacy created by the previous owner, Brill wants to take the company to even bigger heights. After acquir ing SEI, she immediately began to expand the services offered to include projects that align with her vison and experience.
While they continue to perform mostly specialized contractor work, such as playground construction, athletic fields, and land scaping, she wants to expand their scope of work to more varied and larger projects and ultimately, transition to a general con tractor or construction manager role.
proposals for many types of site work, including utility excava tion and grading.
While they currently work in New Jersey, Pennsylvania and Del aware, Brill expects SEI to expand into New York very soon and is actively seeking both public and private work. She also plans to move their operations from South Jersey to a more convenient location in Central Jersey before end of the year.
When asked about challenges she is facing, Brill cites many of the issues affecting contractors throughout the industry, including fuel costs, labor shortages and material delays. Additionally, she is looking to connect with the companies that need her services and her certifications as a minority-owned, woman-owned, and veteran-owned small and disadvantaged business enterprise.
As SEI emerges from this transition stage, Brill plans to increase her marketing efforts and will continue to forge relationships in the industry. To that end, she is continuing SEI’s membership in the UTCA and is looking forward to participating in the UTCA Convention.
In addition to her aspirations for SEI, Brill says her real mission is to strengthen the woman, minority, and veteran representa tion in the construction industry. She also plans to capitalize on her unique credentials as one of the few, if any, minority-owned, woman-owned, veteran-owned small businesses in this space.
Working in a male-dominated field in both the military and ci vilian world has prepared her well for working in this industry in which, despite recent progress, women are still a decided minori ty. Citing her extensive experience on the ground, Brill says she “can handle her own”, but is quick to point out that her reception in the industry has been overwhelmingly positive.
While she maintained the SEI staff, in order to achieve her goals of growing the company and expanding services, Brill is current ly in a hiring phase. In fact, she hopes to double the number of employees by next year and recently became a signatory with the Operating Engineers Local 825.
Sussman Enterprises, Inc. is currently working to complete ex isting projects, is ready to mobilize on new projects this fall, and is bidding new site work for the upcoming year. Current projects include numerous playgrounds at various locations and real es tate development sites.
Upcoming work includes plantings at St. Luke’s Hospital in Pennsylvania, work on a playground and fitness installation project at Garret Mountain Reservation in Passaic County, and hydroseeding for PSEG in Salem, NJ. Most recently, SEI won the contract for Doc Cramer Sports Complex in Stafford Town ship, which is comprised of three different fields – little league, softball, and football. Brill says they are excited to be preparing
“Being a woman, minority, and veteran business owner in a field dominated by men gives me an advantage because I have a dif ferent point of view than my counterparts,” she said. “It is this difference in life experience and perspective that allows me to derive solutions to tough challenges that construction brings. There is a need in the industry for more representation, and I am doing my part to help fill that gap with my resources, team, and credentials.”
While she enjoys tackling the challenges of being a construction contractor, she is also looking forward to indulging her passion for travel. Although she has already been to more than 20 coun tries and four continents, she has plans to keep adding to that list with trips to Africa & Australia on the horizon.
While still adjusting to being a company owner, Brill feels her certifications, along with her formal education and unique hands-on construction background, are tremendous assets for SEI and the construction industry as a whole. Combining these attributes with the vast experience of her team have SEI well-po sitioned to succeed in the construction industry and, with this Air Force veteran at the controls, the sky is the limit for Sussman Enterprises, Inc.
The road to profit can be rough, especially if you are with out a map to guide you through the obstacles and barriers you will encounter along the way. These challenges throw you off course – turning your focus away from the final destina tion and toward alternative paths.
While dealing with issues as you approach them, keeping your long-term goals in mind is crucial to avoid going so far off course that it is difficult or impossible to turn things around.
There are many management theories to guide you along the way. For example, five avenues to success can be adopted from the 5Ps of Marketing (Marketing Management. Philip Kotler and Kevin Lane Keller. 15th Edition. 2016):
1. People – focuses on the needs of the company’s customers, employees, and stakeholders.
2. Processes – these are the internal activities needed to produce a product or service.
3. Programs – are the company’s customer-directed engage ment, marketing, promotion, and sales activities.
4. Performance – reporting on various outcomes from a finan cial and non-financial perspective. This includes metrics such as profitability, brand and client equity, and implications beyond the company like social, legal, ethical, and environmental re sponsibilities.
5. Productivity – includes production, deliverables, quality con trol, and other programs that deliver value to customers.
Another theory – Open Book Management (OBM), is at the junction of the five paths described above. OBM is a way of running a company that engages employees in making money. People learn to understand the economics of the business. They track and forecast key numbers. They figure out how to move those numbers in the right direction and share in the rewards of better performance.
Definitions of OBM vary, but they generally include the follow ing components:
• Sharing the income statement and balance sheet with most em ployees
• Sharing other data with employees (such as productivity and plant utilization/quality data)
• Encouraging employees to use the information in their daily work
• Training employees to understand financial numbers
• Sharing financial results through a gain-sharing program
OBM has been called the most important management trend in the country for a good reason. OBM nearly always improves near-term financial results. Some companies reported as much as a 30% increase in productivity and profitability in the first year alone. Besides the economic benefits, OBM strengthens a company over the long haul. It improves the lives of employees, building loyalty and commitment. It helps create a business that can thrive year after year in today’s mercurial economy.
A Powerful Competitive Advantage Companies that use the OBM approach have a competitive ad vantage – their people. A major shift happens when leaders trust their employees to the extent required by OBM. Employees be come invested in the company. They think of the company as their own and work hard to ensure it is successful. Instead of showing up to do a job, they show up to perform at a higher level. As a result, companies will have:
• More engaged employees
• Lower supervisory costs
• Better front-line relations with customers
• Faster, more agile response to changing customer needs
•
•
fun
company valuation
•
With conventional initiatives, a company’s decision to hire con sultants is usually the critical step. The consultants work direct ly with managers and employees to implement the prescribed changes. With OBM, consultants typically coach from the side
lines. Because it affects many different parts of a business, OBM requires senior managers' ongoing support and involvement. Because OBM is, in many ways, a cultural change, everybody in the organization learns new ways of thinking and acting. It also requires the ongoing involvement of middle managers and frontline employees. While the groundwork for change is being laid, an OBM company must develop “scoreboards” or vehicles for regular communication of key metrics to the workforce. Busi ness-unit scoreboards include an income statement, a balance sheet, and other numbers critical to the unit’s long-term health.
The hallmark of OBM isn’t just seeing and understanding finan cial metrics. It’s taking joint responsibility for focusing on and meeting company goals and objectives. Like any system of re sponsibility and accountability, OBM needs a structure. The hall mark of OBM is employees’ joint responsibility for moving the numbers in the right direction. OBM usually begins with depart ment-level meetings, which must develop and monitor numbers from the ground up. Then employees start experimenting with ways of affecting the numbers, which may also encourage them to create better metrics to handle the most critical drivers.
Traditional bonus plans are typically designed to reward im provements in the company’s bottom line and procedural ef ficiencies. The bonus plan is thus an indispensable part of the management system because it answers the inevitable question: What’s in this for me?
OBM can be made competitive and rewarding with gameplay. A game is an initiative focusing on immediate improvement in a given area. Companies call it a game because it has a starting point, set of rules, goal, and reward for winning. Every game focuses on financial results. Employees learn that what they do on the job daily affects some number that ultimately impacts the business's financial performance. The satisfaction comes from figuring out how to win and benefiting from the rewards of win ning. Gameplaying teaches employees to understand and care about the business. In open-book companies, people understand that games are a fun and exciting way to learn about the business and that the real payoff will come as the whole business unit im proves its performance.
Because OBM is a system rather than a how-to program, it is not a quick fix. Implementation is a long and cumbersome pro cess, particularly in a large company. The effect of the new way of thinking on the bottom line may not be apparent for some time.
The power of OBM lies not in the short term but in the long term. In its ability to change how people think and act, day in and day out. Business success always depends on a wide variety of factors. But this is a constant: whether a company’s employees care if it does well, know how to help it do better, and have a rea son for learning new skills and attempting new tasks.
About the Author Salvatore Schibell, CPA, CFP®, MS Taxation, MBA, CGMA, is the tax partner at Lawson, Rescinio, Schibell & Associates, P.C. One of his specialties is working with contractors to maximize profitabil ity utilizing his certified global management, financial planning, and tax planning specialties. Sal has many years of experience and can be contact ed at 732-539-7328.
George Harms Construction Company continued work on the replacement of the Raritan River Bridge on a frigid January day as a major winter storm barreled to ward New Jersey. This determination, along with a unique deci sion-making strategy centered on a specific piece of equipment, are keeping this critical infrastructure project on track.
The material under the riverbed largely dictated the need for a rig the size of the BG 55. The upper layers were soft, silty clay underlain by varying depth sand layers. Beneath that was dense clay and Siltstone.
A group of key project executives from Harms and Equipment Corporation of America (ECA) gathered on the shoreline as work progressed and crews secured the barges holding the equipment.
“We can handle cold temperatures and snow, but our biggest nemesis out here is the wind,” says Jason Hardell, P.E., Senior Vice President of Operations. “That's why we all have beards.” The group erupted in laughter.
This 112-year-old bridge carries an active New Jersey Transit line across the river from Perth Amboy to South Amboy. Damaged by Superstorm Sandy in 2012, the new span will incorporate structural designs and materials to bolster its defenses against severe weather.
shafts per pier. It was the first of three construction phases that will replace the bridge with a lift span. This bridge represents the largest project Harms has ever done in terms of dollar value, but not in terms of scope.
The selection of the BG 55 was founded on a 30-plus year busi ness relationship and friendship between ECA New York, New Jersey Regional Sales Manager Bruce Langan and Harms Presi dent Emeritus Tom Hardell.
Harms was awarded this project when the original low bidder re tracted its bid. No stranger to $200-million-plus bridges, Harms wasted no time mobilizing and starting work in July 2020.
Harms worked with ECA’s Director of BAUER Product Sales and Service Gordian Ulrich to spec the BG 55 into the project during the pre-bid phase. His career started in 2007 at BAUER Maschin en’s method development department in Germany and he has been involved with various drilling applications on a global scale.
Other brands of equipment were considered, but Harms con cluded that only the BG 55 could cost-effectively drill 8-foot-di ameter shafts up to 240 feet. “We went out on the limb and pur chased it before we were even low,” says President and CEO Rob Harms.
The smaller BAUER BG 40 was also considered but lacked the winch capacity Harms needed. With the massive Kelly bar, tool ing, and heavy clay, the BG 55 was the only choice.
ECA had the rig shipped from BAUER Maschinen in Germany to the Port of Newark and hauled to the Harms waterfront fa cility in Newark, N.J. Once assembled, the BG 55 crawled onto a 200-foot-long Flexifloat Barge and was floated to the Raritan River Bridge site. This barge would serve as its mobile working platform.
ECA and Harms gathered for a key ceremony in October 2020 to commemorate the purchase of the BG 55
In May 2020, Harms was awarded a contract to install 87 drilled shafts across the Raritan River in configurations from two to 10
Barge stability was critical with the 118-foot-tall BG 55 mast sub jected to heavy winds during drilling. The barge is constructed of Flexifloats and the configuration is unique and specifically designed for this project and this application. Its 10-foot-wide sections in 10- and 20-foot lengths snap together like Legos, so Harms had the flexibility to add and remove.
Six hydraulic spuds with 24-inch diameter pipes anchored the
barge to the soft riverbed. Despite the added stability, Harms and ECA had to overcome up and down movement every time the Kelly bar moved.
Harms worked with Flexifloat at the pre-bid stage to design the barge around the BG 55. The polymer slurry tanks on the op posite side served as a counterweight. The hurdle Harms had to overcome was that the weight fluctuated during drilling as the Kelly bar turned and slurry was pumped to the BG 55 to support drilling.
“We had to analyze different drilling scenarios, including worst case scenarios,” says Jason Hardell. “Then we calculated the for ward- and rear-leaning barge trim, conveyed that to BAUER, and received confirmation that there would be no issue with the ma chine (BG 55).”
Harms installed rock sockets into the Siltstone out in the channel in the deepest part of the river. Some of the shallower shafts were socketed into dense clay. The Siltstone had tested unconfined compressive strength as high as 7,000 psi.
According to Vice President of Construction Kevin Harms, the BG 55 excelled when drilling in hard materials. He says, “The BG 55 has been good in terms of its performance in harsh geotechni cal conditions and overall capabilities.”
Harms did two test shafts in November 2020 using the BG 40. A third test shaft was completed with the BG 55 in January 2021. The installation of the production shafts started in February 2021.
Pre-planning seems to be a recurring theme for Harms. Rob Harms says, “We looked at different options and different ways to do it, and it has paid off. We had some large, difficult challeng es to overcome that weren’t in the planning process. That’s when you really see the value of the team.”
From the workers in the field that barely pause to make eye con tact with visitors, to the project management team, a get it done attitude seems to be the norm at Harms. “Our people have the same mindset: we’ve got to get this done no matter what it takes,” says Rob Harms. “When major issues arise, we focus on address ing the problem before considering the cost.”
Harms only buys equipment. Once the contractor is convinced that a certain machine is the right fit for a certain project, it with make the purchase with the conviction that it can keep it busy on future projects. Harms also has a reputation for maintaining equipment, which translates into an above-average resale value. “If you own it, you're only making money when it's running,” says Kevin Harms. “If it goes down on a job, we lose money, so making sure it's serviced, and running is crucial.”
“It's a 24-hour operation,” ECA’s Gordian Ulrich says. “If the phone rings in the middle of the night, we need to have boots on the ground immediately to support the customer.”
It was critical to have the right people to assemble the BG 55, start up the project with Harms, conduct operator training, and service the equipment. ECA’s team included technicians, opera tor trainers, and even welders for the tooling.
“Projects of this size and scope are what the ECA BAUER Service Team lives for,” says Ulrich. “In 2019 we started building a team of BAUER product specialists to be able to support our custom ers in the field when it is showtime. Our crew set up and com missioned the rig before our in-house operator trainers started working with three Harms operators to ensure safe operation with this massive 84-meter-long Kelly bar together with the big gest rig on the East Coast.”
ECA knows how to control the risk above ground, but once the drill breaks ground, all bets are off. With offshore drilling, no backup rig could be brought in if the BG 55 went down. The movement of the barge was also a factor, especially drilling at depths of up to 240 feet. The time frame Harms had to drill a shaft was fixed, which added yet another layer of complexity.
“Everything we need is on that drill barge,” says Jason Hardell. “The whole operation is self-sufficient.”
Harms first pinned a square-shaped casing guide to the BG 55 barge to ensure that the casing was straight and properly located. Sections up to 145 feet were set with a 330-ton crane on a neigh boring barge. The drilled shafts were 102-inch diameter from top of casing to the bottom with 96-inch rock sockets, the longest of which was 30 feet.
The BG 55 was not the only massive piece of equipment on site. Harms used a crane-supported 100,000-pound ICE 200C Vibra tory Driver/Extractor to drive the casing that will remain in place
as part of the structure. The BG 55 was then used to drill out the material within the cas ing to the depth Harms required.
The depth of the shafts and the uncased sec tion below the casing presented the greatest complexity for Harms. Polymer slurry was required to keep the hole open in sandy soils between the casing and the rock socket.
The BG 55 was used strictly to excavate ma terial and drill the rock sockets. Its cleanout bucket removed the spoils with the help of polymer slurry pumped from nearby tanks. A floating tank was moved back and forth to supply clean water for the reuse of the polymer slurry. The spoils were loaded into a hopper barge by excavator and transported to the shoreline for disposal.
Workers spliced the galvanized rebar cages on an adjacent barge. Once completed, the crane hoisted them into the casing. The shafts were completed with the pumping of 4,000-psi Self-Con solidating Concrete (SCC).
Harms also used its BAUER BG 40 for backup. The rig was po sitioned on a pile-supported trestle to Kelly drill the shallower shafts near the shoreline.
Vibration was also a concern. Reducing it is why drilled shafts were chosen over driven piles. Harms installed and monitored vibra tion sensors on the existing bridge for safe measure.
Harms equipment operators, namely for the BG 55 and crane, had to work carefully to avoid contact with overhead lines on the ex isting bridge. The wires carried up to 38,000 volts. Working from barges in a windy area further complicated matters.
Casing was sourced from Illinois. Fabricators that can produce sections up to 143 feet in length with the ability to roll one-inch walls are uncommon.
The fabricator and supplier Nucor Skyline shipped the casing by rail and truck in 75-foot sections. Harms needed a way to as semble them on site. “We set up a semi-automated shop to weld the sections quickly,” recalls Jason Hardell. “We talked to a few different welding equipment manufacturers early on and came up with this system.”
Two sections are placed on an automated roller assembly, joined, full penetration welded in several passes, and ultrasonic tested to verify strength. The completed full-length casing was trucked to the shoreline and shipped to the BG 55 barge for installation.
The welding system proved to be an effective alternative to workers doing the job by hand. “You're doing a full penetration V-shaped weld on one-inch casing,” says Rob Harms. “It's a seri ous welding job.”
Passenger trains chugging past the Harms barges were a con stant reminder of the challenges of working next to an existing bridge. Drilling 240-foot shafts in proximity to an active railroad requires caution and finesse.
Project specifications required Harms to complete the shaft con crete within 36 hours from when drilling advanced below the permanent casing. “We had to drill it, clean it out, get the rebar in, and fill it as quick as possible,” says Rob Harms. “The potential for collapse increases the longer you leave the hole open so we had to move quick.”
ECA and Harms chose conventional tooling for the BG 55 during the pre-bid phase. “We chose to drill with a lockable Kel ly bar combined with BAUER tools including double-cut rock buckets and a cleanout bucket,” says ECA’s Gordian Ulrich. “For better guidance, verticality, and production reasons we designed and built these tools extra-long and equipped them with BETEK bullet teeth.”
Drilling up to 240 feet with a telescoping four-section Kelly bar was no easy task. This 84-meter (275.5-foot) bar is custom-made for the BG 55. It is among the largest of the few that exist in the U.S. and the longest ECA has sold. “The telescopic Kelly bar is like a long asparagus-type bar; the longer you extend it, the more it tends to wobble,” says Ulrich. “When you crowd down on the bar the tip tends to take the path of least resistance below the casing, so putting the right tool on it and having well trained operators are key factors in the drilling success.”
"Everything we need is on that drill barge. The whole operation is self-sufficient"
- Jason Hardell
The project had a tough vertical tolerance spec of 1.5 percent. Harms purchased Kelly bar stabilizers BAUER had used on sev eral other deep holes around the world, but the skill of its opera tors in combination with the specially tailored tools made them unnecessary. The tolerance was achieved starting with the first drilled shaft. Harms had no regrets because being prepared up front was better than shutting down the project for months while tooling was manufactured.
Harms is on track to complete this roughly 4 ½ year project on schedule. It will then pass the torch to the phase two contractor to construct the lift bridge and flanking spans superstructure, communications, and signal and overhead catenary work. The old bridge will be demolished, and rail traffic will be transferred to the new structure in phase three.
“The drilling rig (BG 55) is really what’s driving the job,” says Rob Harms. “The shift from two 12-hour shifts to three 8-hour shifts really made a difference. It’s going really good.”
Building a foundation for a structure of this size and complexity is a challenge regardless of the construction method chosen. In
the case of the Raritan River Bridge, Harms combined innova tion, teamwork, pre-planning, vendor partnerships, and the right equipment to make the project a success.
Rob Harms – President, Chief Executive Officer
Kevin Harms – Vice President of Construction
Jason Hardell P.E. – Senior Vice President of Operations
Chris Standke – Equipment Superintendent Tim Fogarty – Project Superintendent
Tom Hardell – President Emeritus
Brian M. Fraley
Owner, Fraley Construction Marketing fraleyconstructionmarketing.com 610.906.7275