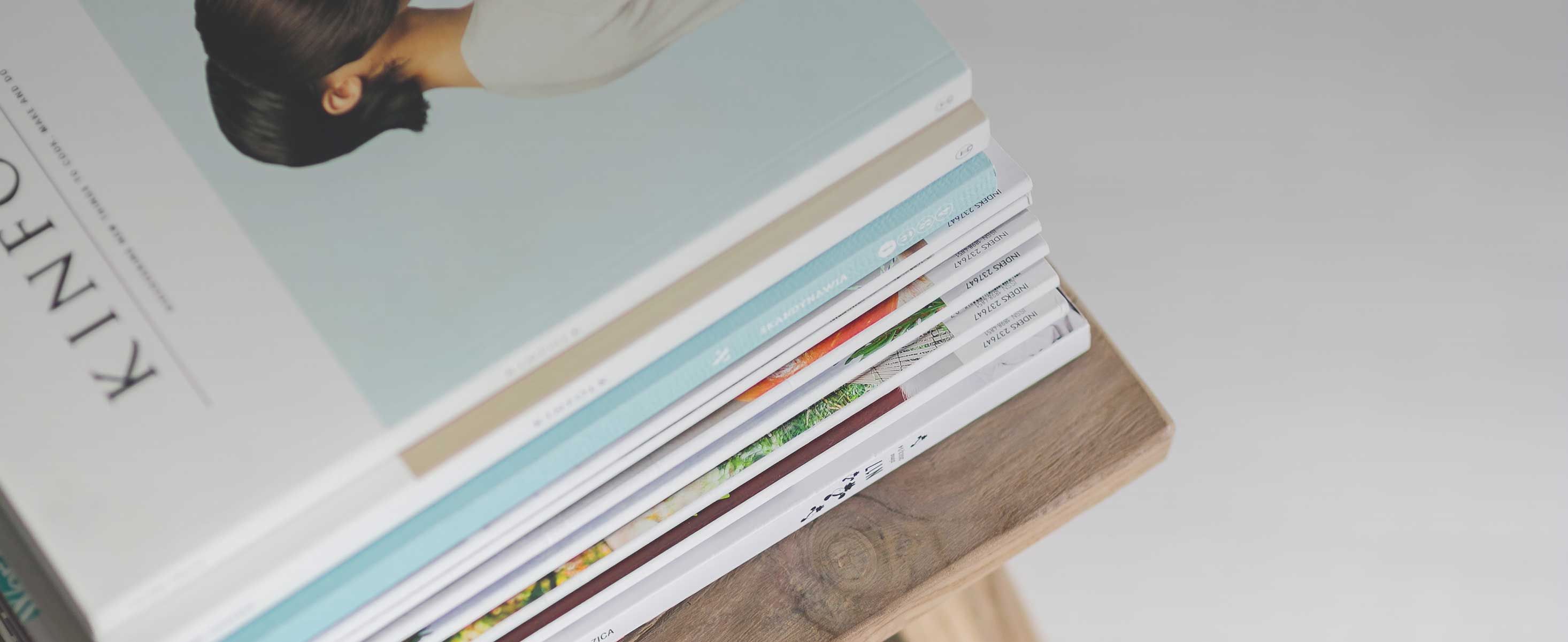
2 minute read
y comercialización
con Eli Whitney para suministrar 10.000 mosquetes en dos años. Se diseñaron máquinas específicas para construir algunos elementos del mosquete y se formó a artesanos para el diseño de otras partes del mosquete. La suma de todas las partes, formaría el mosquete final, tal y como se había planteado en su diseño. Sin embargo, Eli Whitney no tuvo en cuenta el efecto de variaciones en la fabricación de los elementos, lo que supuso un retraso de diez años la entrega final de los mosquetes contratados (Hounshell 1984). De acuerdo con Evans y Lindsay (2015), gracias a Whitney, se reconoció el valor de las piezas intercambiables, lo que supuso un avance en el aseguramiento de la calidad como componente necesario en el proceso de producción.
1 .1 .2 . La revolución en los métodos de producción y comercialización
La Revolución Industrial, que empieza en Europa durante la segunda mitad del siglo XVIII, implicó el nacimiento de las grandes fábricas que pronto superaron a los artesanos y pequeñas tiendas, e hicieron que su sistema de producción quedase obsoleto (Juran y De Feo 2010). La meta de las fábricas era incrementar la productividad y reducir costes, por lo que se introducen sistemas más sofisticados en los procesos productivos. Las tareas que hasta la fecha realizaba un artesano, en la fábrica se dividían entre varios operarios. Por ejemplo, las tareas más propias de diseño y planificación del producto las asumían gerentes e ingenieros, y las tareas de ejecución eran asumidas por supervisores y operarios. Esta división del trabajo, apoyada en los principios de Organización Científica del trabajo de Taylor, conocido como «el padre de la administración científica», tuvo un gran impacto en la producción en masa y en la calidad (Provost y Clifford 1990).
La división del trabajo tuvo efectos significativos en el incremento de productividad, pero también efectos adversos, al menos en estas primeras etapas, en las relaciones humanas y en la calidad de los productos. De acuerdo con Juran y Gryna (1995), los enormes errores de producción se trataron de solucionar a través de inspectores (con frecuencia y de forma masiva) y departamentos de calidad específicos, que trataban de eliminar y separar aquellos productos defectuosos de los productos de buena calidad en las etapas finales de los procesos. Por tanto, los fabricantes eran capaces de lograr productos de buena calidad, pero el uso de masivos inspectores y el enorme coste asociado a los desechos incrementaba los costes productivos (Hounshell 1984). Dado que la demanda era superior a la oferta, los productores, en aquella época, daban mayor prioridad a la productividad que a la reducción crónica del desperdicio (Juran y Gryna 1995).