March/April 2025
www.housingspecification.co.uk

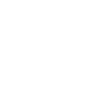
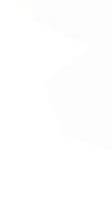
HYDRATED LIME CYCLE FOR DRY WALLS

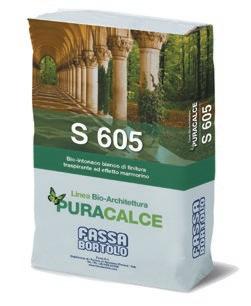




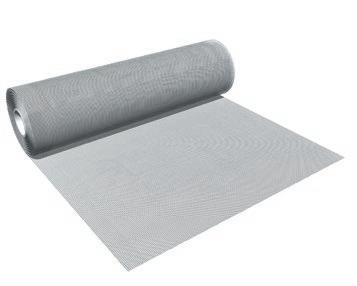
March/April 2025
www.housingspecification.co.uk
High breathability
TO FIND OUT MORE about Fassa Bortolo and its range of render systems and building products. Visit www.fassabortolo.co.uk or call 01684 218 305
Suitable water repellency
UNDERCOAT
1 S 650 Bio white undercoat
BASE COAT
Ready-to-use top coat in different gradings
2 KB 13 Bio lime base coat plaster OR K 1710 Bio traditional fibre reinforced base coat
FINISH COAT
3 S 605 Bio white finish coat plaster
4 FASSANET 160 Reinforcing mesh
PRIMER AND DECORATIVE COAT
5 FS 412 Primer
6 RSR 421 Siloxane-enhanced coating
7 SKIN 432 Siloxane-enhanced finish
Up to 170,000 homes in England will benefit from energy efficiency upgrades as the rollout of the Warm Homes Plan gathers pace, helping more families lower their energy bills and improve their homes.
Government support of £1.8 billion in will be allocated to local authorities and social housing providers, in a new boost which will support them to deliver warmer, more energy efficient homes in local communities across England.
This funding will be targeted towards low-income households and tenants living in social housing, with thousands of families set to receive energy performance and clean heating upgrades in the form of insulation, solar panels and heat pumps.
Gavin Smart, chief executive of the Chartered Institute of Housing (CIH), welcomed this investment as another important step towards making homes warmer, healthier, and more affordable to run.
“Social landlords have worked hard to improve the energy efficiency of their homes, and this funding will help them to continue that work — supporting retrofit programmes that will reduce fuel poverty, lower carbon emissions, and bring down energy bills for tenants,” he said.
“CIH will continue to work with government and our members to support the effective rollout of this funding and advocate for the long-term investment needed to make all homes warmer and safer.”
He added: “The strong demand for this funding highlights how vital energy efficiency investment is for the social housing sector. While this latest allocation will support important retrofit work, we know that many landlords will have bid for more than they have received.
“To maximise the impact of this programme, we encourage the government to build on this commitment and ensure the full £13.2 billion Warm Homes Plan funding is delivered at the forthcoming Spending Review, with a minimum allocation of £5 billion for the social housing sector."
Paul Groves Group Editor paul.groves@tspmedia.co.uk
Pendock’s ‘Profiles’ brand is now one of the most comprehensive available and is widely used to support ongoing heating system improvements and fire safety upgrades, as well as the growth in low carbon heating solutions.
Our cover image shows bespoke metal boxing used to conceal heating pipework, building services and electrical conduits in a 7-storey tower block refurbishment in Walsall.
Discover more by reading ‘Pendock –Thinking inside the box’ on pages 16-17
Industry has welcomed the sweeping changes to the planning system which the Government has outlined in its Planning and Infrastructure Bill, in order to deliver 1.5million homes by 2030.
The Bill, which was announced by the Deputy Prime Minister and Secretary of State for Housing, Rt Hon. Angela Rayner MP, proposes measures aiming to speed up planning decisions and deliver necessary development.
RIBA’s President, Muyiwa Oki said: “This is a welcome shot in the arm for the construction industry. To ensure the much needed high quality housing and infrastructure, urgent action is required.
“However, to deliver the seismic changes proposed, local planning departments will need to be adequately resourced and supported with the right people, skills and design expertise they need.
Sama Investment Group, a Birminghambased developer and investor, has announced that it is partnering with Lambert Smith Hampton, a leading UK commercial and residential real estate consultancy and agency, for the sale of its Lawson Street purpose-built student accommodation (PBSA) properties.
The scheme – which offers 184 studios in an eight-storey building – is located at the corner of Lawson Street and Staniforth Street in Birmingham’s city centre, is 150 yards away from Aston University and Birmingham City University’s campus is also located nearby, providing an ideal location.
“We look forward to examining the Bill and working with the Government to ensure we create well-designed homes and places that meet the needs for communities to thrive. The Bill signifies a step in the right direction to speeding up the planning system. What’s not in question is the desperate need to build quality homes and vibrant places up and down the country.”
The Bill sets out a range of measures designed to deliver the government’s programme of housebuilding and infrastructure reforms through reforming the operation of the planning system.
Sir John Armitt, Chair of the National Infrastructure Commission said: “This bold and broad-ranging package of measures should deliver a planning system optimised to enable the significant amounts of new energy, transport and water infrastructure the country will need to thrive over the long term.
“By adopting a spatial approach to planning decisions, enabling more streamlined decisions on major infrastructure projects and funding better environmental mitigation, the Bill covers all the bases for an infrastructure planning system built for speed, fairness and sustainable growth.”
Anna Hollyman, UKGBC’s Co-Head of Policy & Places said every planning decision is an opportunity to create greener, safer and healthier communities: “This bill indicates a welcome move towards longer-term strategic planning, investment in planning capacity and an acceleration towards clean energy.
“However, communities must have a meaningful voice in ensuring developments meet their local needs, and ‘streamlining’ environment assessments must not be code for weakening standards.”
Cambridge Investment Partnership (CIP), the equal partnership between Cambridge City Council and award-winning housebuilder, The Hill Group, celebrated the official start on site at Fanshawe Road in Cambridge’s Coleridge ward, with a ground-breaking ceremony.
Ward Councillors joined CIP board members and the project team to mark this significant milestone in the development, which will deliver 84
much-needed sustainable homes, comprising both council and market sale properties. The development will include 45 council homes, designed to meet Passivhaus-equivalent performance standards, and 39 market sale homes.
Of the 45 council homes, 34 will be offered at affordable rent - set at 60% of the market rate in line with the Council’s standard for new builds – while the remaining 11 will be available at 80% of the market rate.
Reinvestment in new and existing homes reached record levels as housing associations continued to focus on development, building safety, energy efficiency and stock decency, according to the new Value for Money report published by the Regulator of Social Housing.
RSH publishes Value for Money metrics annually so boards and other stakeholders can assess how each housing association is performing against its peers.
Reinvestment into existing stock and acquisition or development of new homes increased to £14.6bn from £12.5bn in the previous year – the highest level recorded since the Value for Money metrics were introduced in 2018.
The median headline cost per property rose by 12% to £5,136 – the highest level
recorded. However, the sector projects cost increases to fall below the rate of inflation over the next five years.
Following several years of high inflation, and rising borrowing costs, the financial performance of the sector has weakened. Many organisations are managing competing demands on their resources, particularly between investment in the existing stock and new supply.
However, the sector continued to sustain the high levels of new development seen in recent years, even as financial pressures intensify. Despite a number of providers scaling back development ambitions, 49,287 new social homes were delivered over the year to 31 March 2024- the highest level since 2021.
Around 10% of providers (excluding forprofit organisations) develop nearly half (45%) of new social homes.
MCI Developments, a subsidiary of the national top 10 housebuilder, Keepmoat, is celebrating construction starting on site that will see the transformation of a disused piece of land in Wigan into 38 modern, affordable homes.
When complete, the homes will be made available in partnership with leading social housing provider Your Housing
Group (YHG), representing a multi-million pound investment into the regeneration of the Aspull area.
The two-acre site will feature a mix of two and three bed homes consisting of 19 properties available for shared ownership and 19 for affordable rent, with all homes fitted with solar PV panels and electric vehicle charging points.
Will Perry, Directory of Strategy at RSH, said: “The sector as a whole is proving resilient at grappling with competing demands on their resources, investing record amounts on new and existing homes, though inflation and high levels of repairs works are driving up unit costs.
“This year, we have also carried out new and expanded analysis which allows us to understand in greater detail some of the structural factors that can impact on value for money. This supports our ongoing scrutiny and regulation of the sector, especially as pressures intensify, and provides important insight for landlords as they consider what drives their businesses.
“It is crucial that landlords challenge themselves on their efficiency so they can continue to build more homes and deliver better services for people who need them.”
A brand new development is launching this March in the family-friendly neighbourhood of Waddon, South East London.
Parkside Triangle, from Hyde New Homes will deliver a first phase of 70 homes, set around a lush communal green space and children’s playground.
The area offers fantastic travel links into Central London, making it perfect for commuters looking for quick and easy access to the heart of the city.
All homes will be available to buy through shared ownership, providing local property buyers with an affordable route to owning their own home.
BESPOKE DESIGN IS AVAILABLE
E.G. with added overflow channel to conform with local requirements
Fundo shower elements with or without integrated drainage (shown: bespoke wedi Fundo Integro with a total installation height of just 93mm including integrated drainage)
Seamless, preformed design surfaces for the shower floor (shown: Flake white)
Large fomat, panel type design surfaces for walls (shown: Flake white)
Metallic drain covers to match bathroom fittings (shown: Metallic Gold)
√ Fully tanked, directly tileable floor-to-ceiling system
√ Interlocking modular XPS elements with 40 years’ pedigree
√ Unrivalled ease and safety of installation
√ On-site training for contractors
Futurebuild 2025 has once again proven itself as the premier event uniting the built environment, bringing together thousands of industry professionals to drive lasting change.
From the very start, Futurebuild 2025 was not just about discussing change— it was about making it happen. The National Retrofit Conference opened with a compelling keynote from Minister Miatta Fahnbulleh, Minister for Energy Consumers and Parliamentary UnderSecretary of State at DESNZ, who laid out the government’s strategy for tackling one of the biggest challenges of our time: retrofitting the UK’s ageing housing stock and accelerating the path to net zero.
Policy discussions remained at the heart of the event, with thought leaders, policymakers, and industry pioneers driving conversations on overcoming barriers and shaping a greener built environment.
But Futurebuild is about more than dialogue—it’s about action. Nowhere was this clearer than in the Big Retrofit Challenge, which saw an incredible 75 groundbreaking entries from across the sector. Seven finalists pitched live in front of an expert panel, with each securing direct meetings with contractors ready to integrate their solutions into real-world projects.
This wasn’t just innovation on display; it was innovation moving into implementation.
Pushing the boundaries of possibility even further, the Big Innovation Pitch chaired by Dr Oliver Jones, Cundall put the industry’s most exciting breakthroughs in the spotlight. In a high-stakes, ‘Dragon’s Den’-style showdown, four pioneering companies went head-to-head, presenting game-changing solutions that could redefine the future of construction. Agreka Build emerged victorious, impressing the judges with their revolutionary product WHEATEX, the world’s first circular bio-based insulation board made from 100% waste wheat straw, a testament to Futurebuild’s role as a launchpad for industry-defining advancements.
The Futurebuild Arena took centre stage in driving critical conversations, with each of its three daily themes tackling the industry’s most pressing challenges. From unlocking the circular economy to accelerating net zero strategies, the Arena provided a platform for trailblazing experts like Duncan Baker Brown and the Dr David Greenfield (Circular Economy Taskforce), who delivered powerful insights on how designers, manufacturers, and policymakers can transform theory into practice. With tangible, scalable solutions now within reach, the Arena proved that sustainability is no longer an aspiration—it’s an expectation.
A call to action: the future starts now
Reflecting on the success of this year’s event, Martin Hurn, Event Director at Futurebuild, reinforced the show’s growing impact: “Futurebuild is not just a conversation—it’s action. For 20 years now, Futurebuild has been instrumental in making real progress, from groundbreaking innovations securing industry backing, to pioneering circularity solutions on the exhibition floor, and companies demonstrating tangible decarbonisation strategies. The challenge now is bringing more people on this journey. That’s why we call on the entire sector to connect, collaborate, and push forward together.”
As Futurebuild 2025 closes its doors, its legacy continues. For those who couldn’t attend every session, all event content will soon be available on-demand, ensuring that the insights, innovations, and solutions shared here continue to inspire and drive change long after the event has ended.
The momentum is building. The transformation is happening. Futurebuild 2025 has set the stage—now it’s up to us to build the future we need.
▸ Timber frame construction
▸ Spandrel panels
▸ Modular build
▸ Rainscreen cladding
▸ Render carrier board
▸ High performance dry lining
▸ Tilebacker
▸ Fire resistant floors and ceilings
▸ Passive fire protection
▸ Steel frame construction
Chris Hall, Technical Innovation Manager at NHBC, explains why the UK house building sector stands at a pivotal crossroads.
With challenging sustainability targets ahead, evolving building standards, and a rapid acceleration in Modern Methods of Construction (MMC), the industry is undergoing its most significant transformation in decades. As we navigate this changing landscape, understanding the key drivers of innovation becomes essential for everyone involved in delivering tomorrow's homes.
One of the most significant challenges facing innovative construction is the absence of established standards. In the UK, national and international standards bodies often struggle to keep pace with rapidly developing products, materials and systems.
Innovators in timber, concrete, steel, and integrated home systems frequently outpace the standardsetting process.
Our approach extends beyond just developing the NHBC Standards. For innovative solutions lacking established criteria, such as ultrahigh performance concrete or integrated solar facades, we develop positions based on thorough technical evaluation. This allows us to provide clear guidance on what we will and won't underwrite, enabling innovation while managing risk.
Looking ahead, the construction landscape will undergo dramatic changes over the next five years. Major builders are significantly shifting their production models, with more components manufactured in off-site environments.
The most transformative change may be in how we power our homes. We anticipate a definitive shift towards gas-free developments, necessitating significant investment in the UK power grid to support an all-electric model. Meanwhile, homes themselves are evolving to become more sophisticated living environments.
While the industry has the workforce to deliver current build levels, meeting the Government's ambitious target of 1.5 million homes by 2029 will require a 25 per cent increase in recruitment –equal to 224,900 additional workers. This workforce expansion presents perhaps one of our most pressing challenges.
If the Government can address broader barriers to housing delivery, these workforce requirements will become increasingly pressing.
Ensuring quality in MMC systems requires unprecedented collaboration between manufacturers, developers, and regulatory bodies like NHBC.
Our approach is multifaceted, focusing on writing standards that align with industry demand while working alongside organisations such as the New Home Quality Board and considering regulations like the Consumer Duty Act.
At the upcoming BEYOND '25 LIVE event, I'm particularly looking forward to engaging with SME builders which believe they're too small to implement innovative construction methods. This is a common misconception that needs addressing – innovation isn't exclusive to large developers.
The event provides an opportunity to dispel myths and demonstrate that innovative construction has moved beyond the pilot stage to become an established reality. The industry is experiencing a definitive shift in production models, and builders of all sizes need to prepare for this transformation.
To book your place and join the conversation about the future of house building, visit https://www.nhbc. co.uk/awards-and-events/beyond
A new roadmap to get britain building with the use of sustainable and low carbon building materials, will help solve the housing crisis and achieve 2050 net zero targets.
New, ambitious plans to increase the use of timber in construction to boost the domestic timber industry, economic growth, rural jobs and housebuilding targets, have been announced by Environment Minister Mary Creagh at the Timber in Construction (TiC) Summit in London with Timber Development UK.
The government has outlined new methods to deliver on its Plan for Change that will help to build 1.5million sustainable and affordable homes, create a low-waste circular construction sector and drive further investment into domestic timber and wood-processing supply chains.
Speaking at the TiC Summit, Minister Creagh confirmed the government will recommit to the Timber in Construction Roadmap, which outlines measures to increase the use of timber in the construction sector.
Using timber in construction is one of the best ways to reduce emissions from buildings. Around 25% of the UK’s greenhouse gas emissions are from the built environment, and larger buildings can store up to 400% more carbon when built out of engineered timber products
compared to when built with concrete. Currently only 80% of the timber the UK uses is imported.
“This Government is getting Britain building,” said the Minister. “Our Plan for Change will build 1.5 million homes this
Parliament. Timber will play a vital role benefitting development and nature.”
Forestry Commission Chief Executive, Richard Stanford said: “To reach net zero, we must increase timber production from homegrown trees and use that timber in our buildings to sequester carbon. The Timber in Construction Roadmap will propel forestry production in England to ensure timber security, reduce our dependence on imports, and address the nature crisis by boosting biodiversity, improving water quality, and providing more green spaces for people.
“The Forestry Commission will continue to collaborate closely with partners from the timber, forestry, and construction sectors in this critical area of work for many years ahead.”
Alex Goodfellow, Chair of the Confederation of Timber Industries, and CEO of Donaldson Offsite said: “Timber frame construction is a well-proven technology and business model for delivering houses rapidly and sustainably while improving quality. By accelerating this growth we can build more lowcarbon housing today while providing a market pull for expanding forests.
As a supply chain we will support the Government to deliver on all of the goals in the Roadmap and help build a more sustainable future.”
The amended Roadmap goes further than previous Government commitments, setting out more ambitious targets and actions to increase the use of homegrown timber in construction in a move to reduce carbon emissions, provide green jobs of the future, create affordable and sustainable housing, and drive-up economic growth.
Increasing the domestic production of timber will create new green jobs in the forestry and wood processing sectors, which contribute over £3bn to the UK economy.
Modular green build on Isle of Skye
An architect, whose work involves residential new-builds and extensions across the Highlands and Islands of Scotland, has chosen to use an innovative mew modular construction system for a small scale development of his own on the Isle of Skye, with West Fraser's SterlingOSB Zero featuring as a key component for the assembly of individual wall and floor units.
Aiden Junor and Rhiann Junor have acquired a small piece of land on the beautiful isle, North-west of Glasgow and are in the process of building a "Tiny House," a trailer mounted cabin which makes use of the WikiHouse system which was launched just four years ago to offer an eco-friendly and economic means of erecting domestic and other properties, potentially in situations not
accessible to many timber frame and other off-site solutions.
The couple ‘learnt on the job' carrying out the assembly work themselves; and realising how rapidly their productivity was rising.
Aiden explained: " The primary attraction of the Wiki solution was the ease of assembly, the buildability, and then the energy efficiency, with the 200mm wide insulation filled units offering a much better U-value than is required by Scotland's Caravan Act -plus very good airtightness. And externally, the structure is going to be clad in a Proctor PassivHaus standard membrane, and a bitumen sheeting in a green colour.
“The actual Wiki modules have been supplied in a kit form by Geo:Ply which is a fabricator from near Edinburgh that is actually treating our project as a trial for the system. This has included some 135 sections of the OSB, which is a material
I am quite familiar with, as it has also featured in many of the domestic builds I have helped design with contactors such as AJ Contractors. And with the WikiHouse wall and floor units you quickly pick up speed once you've completed the first block."
Taylor Lane Timber Frame has boosted its commercial credentials after securing STA Gold Assure membership for another year. This demonstrates the manufacturer’s continued commitment to superior quality and performance through conformity and compliance.
Taylor Lane is a long-standing member of the Structural Timber Association. In recent years, the timber frame manufacturer has held the highest level of membership, STA Gold Assure.
This membership level confirms that Taylor Lane Timber Frame holds the relevant accreditations or standards and is Site Safe fire compliant, Uses STA Installer Training Scheme (ITS) certified and competent erector/installer companies, holds Conformity compliance (for components), is subject to STA Assure third-party assessment 85% + assessment score, and Utilises STA Gold/Silver Assure designers (or equivalent standard).
To retain its STA membership, Taylor Lane is subject to an annual assessment by the Structural Timber Association, this includes providing evidence of the STA and third party accreditations and affiliations required to meet the membership criteria.
In holding this certification, Taylor Lane also has the necessary accreditation to comply with Construction Products Regulation (CPR), plus relevant and applicable construction product conformity compliance. CE/UKCA marking of products (where applicable) is a condition of STA membership.
The use of pre-formed boxings and casing for concealing pipework on social housing refurbishment projects is now common practice, replacing the previously time-consuming process of fabricating and finishing individual boxings on site. We explore Pendock Profiles boxing solutions.
With the increased use of low carbon heating systems, including heat networks, air source and ground source heat pumps, as well as shared ground loop arrays, Pendock boxing offers an effective solution for concealing pipework for external distribution, as well as those located within individual flats.
The wide range of pipe boxing and casing products available makes the Pendock Profiles range one of the most comprehensive for use on local authority and housing association refurbishment projects.
Pre-formed boxing saves time Pendock’s principle of using pre-formed plywood casings to conceal interior pipework was developed to reduce onsite time and associated costs, which is increasingly important as labour costs
continue to escalate. Unlike traditional site-fabricated alternatives, pre-formed boxing is curved to form a smooth ‘L’ shaped profile, eliminating sharp corners or joints along the edges of the profiles, providing a more aesthetic finish to the installation.
Also, due to the wide range of sizes available, the correct profiles can be selected to fit closely over the pipework, minimising intrusion and visual impact in flats where skirting-level heating pipework or high-level fire sprinkler systems are being concealed.
Using an 'off the shelf' purposedesigned boxing range enables consistent finishes to be achieved in individual flats, even with different profile styles or sizes installed. This consistency becomes more beneficial when complete blocks are refurbished, ensuring continuity of finish, which is more difficult with site-made boxing.
In addition, all plywood profiles are prefinished with a white resin impregnated décor paper, as standard, which removes the need for painting on site, saving even more time and costs, while further improving the final project finish. The combined benefits of reduced installation time and improved finish quality can also support tenant
satisfaction levels by minimising disruption during refurbishment programmes.
Tough and durable metal boxing
Engineered to provide weather-resistant and durable solutions for concealing external pipework, building services, and other utilities, it also protects against accidental damage or vandalism where pipes may be accessible.
Bespoke manufactured to individual project specifications from 2mm aluminium, as standard, metal boxing is available as a three-sided channel profile - CHM - for securing to a single flat surface or as a two-sided 90-degree design - MXM - for fixing to adjacent surfaces, such as corners or like walls and ceilings.
Supplied with a PPC finish in lengths up to 4000mm, both CHM and MXM can be used to conceal vertical and horizontal pipework installations.
The two products are also supported by dedicated ranges of accessories, including corners, stop-ends and joint covers.
Metal boxing is also used to cover fire sprinkler supply pipework mounted in open balconies or externally to flats, to provide added security and weather resistance. As it is non-combustible, it is regularly used in high rise residential blocks to conceal interior runs of pipework where no sprinkler heads are present, such as in communal areas.
Box clever
While Pendock metal boxing is popular for its specific applications, pre-formed plywood boxing and casings are still the most widely used for concealing interior pipework. At the core of the 'Profiles' range are the TK and MX products, which are already utilised in countless social housing projects across the UK.
TK incorporates a 115-degree angle on the shorter leg, creating a sloping top surface. Designed primarily for hiding small bore heating system pipework at skirting level, TK blends into living areas, bedrooms and kitchens while the angled top surface prevents its use as a step.
A three-sided version, the TKD, is also available for mid-wall or vertical use, incorporating the 115-degree angle on both sides. Both are manufactured from 5mm plywood and prefinished with a white resin impregnated décor paper.
Unlike the TK, the MX has a 90-degree ‘L’ shaped profile, and the wide range of available sizes make it suitable for boxing in horizontal or vertical pipework in a variety of residential applications, such as heating and mains water, plus larger diameter drainage and waste pipework.
This versatility is increased further as two ‘L’ shaped MX profiles can be joined together in different size configurations to create ‘U’ shaped channel sections. These can be used to conceal interior pipework or building utilities, such as vertical pipe runs or ceiling mounted fire sprinkler pipework.
The MX range is manufactured in 5mm or 8mm thicknesses and finished with a white resin impregnated décor paper. A range of dedicated accessories is
available for both MX and TK, including internal and external corners, stop ends, butt joint covers, and access panels.
Sprinklers, boilers and ventilation
MXF fire sprinkler boxing is also a preformed, pre-finished ‘L’ shaped profile, and is the preferred choice of many LA and HA contractors when concealing surface mounted sprinkler pipework in high-rise blocks.
Available in 5mm or 8mm thicknesses, it can be readily cut to length and drilled to accommodate sprinkler heads, on site, while the range of dedicated accessories help give a high quality finish to the project.
MXV boxing is a recent addition to the Profiles range and is designed specifically for covering flexible ducting used in Positive Input Ventilation (PIV) schemes. MXV includes options to conceal installations both with and without coving.
Completing the interior casings range are the ‘BC’ pre-formed boiler pipe casings, which are designed to conceal boiler pipework, valves, filters, and flues while avoiding the time and cost issues associated with site-fabricated boiler boxing. They also allow easy access for gas safety checks, routine inspection, or boiler maintenance, as they can be removed, reused, and refitted without damage.
With such a diverse and comprehensive product range, Pendock’s website hosts a range of information. Alongside downloadable drawings in PDF and DWG format, there are also NBS specification clauses for every product, located in the ‘Tech Info’ section. In addition, Pendock also offers technical support and advice to specifiers by phone or e-mail.
Pendock - Enquiry 9
In the pursuit of sustainable building materials, lime render has emerged as a key player in reducing environmental impact while enhancing the performance and longevity of buildings. Fassa Bortolo, a leader within the construction materials industry, with over 300 years of experience, has developed a range of high-performance lime renders that combine traditional materials with modern innovation.
Fassa’s lime render offers not only superior structural and aesthetic benefits but also significant environmental advantages, making it a vital solution for sustainable construction practices.
A key advantage of Fassa’s lime is its exceptional breathability. Unlike cementbased renders, which can trap moisture and lead to structural damage, lime render allows moisture to pass through walls. This natural permeability prevents dampness and mould, ensuring a healthier environment. Additionally, the flexibility of lime render allows it to accommodate minor structural movements without cracking, which enhances the longevity of the building’s exterior finish.
Lime render stands out for its low environmental impact throughout its lifecycle. The production of lime requires lower firing temperatures than Portland cement, resulting in significantly lower CO2 emissions. More importantly, the carbonation process involved in curing lime render allows the material to reabsorb a substantial portion of the CO2 released during production, effectively contributing to carbon neutrality.
Unlike cement-based products, which are often difficult to recycle and contribute to construction waste, lime render from Fassa is fully recyclable. When a building is demolished, lime render can be crushed and reused as aggregate or allowed to return to the earth without causing environmental harm. This cradle-tocradle lifecycle reduces landfill waste and supports circular economy principles in the construction industry.
Another sustainability benefit of Fassa lime is its contribution to thermal regulation within buildings. By allowing walls to breathe and managing moisture levels, lime render helps maintain stable temperatures. This improved energy efficiency lowers the overall carbon footprint of the building and contributes to long-term operational savings.
Lime render is highly valued in both historic preservation and contemporary construction. In the restoration of heritage buildings, lime render’s compatibility with traditional masonry materials ensures that the original architectural integrity is maintained. Its ability to allow for moisture transfer helps prevent structural degradation, which can occur when
modern, impermeable cement renders are used on older buildings.
In modern construction, Fassa’s lime render is increasingly being specified for its aesthetic versatility and environmental benefits. Fassa’s commitment to research and development has resulted in innovative lime render solutions that meet the performance demands of contemporary construction while preserving the environmental benefits associated with traditional lime products.
Fassa’s commitment to sustainability extends beyond product development. The company continues to invest in environmentally responsible manufacturing processes, renewable energy sources, and research into new materials and techniques. This proactive approach ensures that Fassa Bortolo remains at the forefront of sustainable building innovation.
If you’d like to find out more about Fassa’s lime render products and systems, please call 01684 218305, or email our team at info.fassauk@fassabortolo.com
Fassa Bortolo - Enquiry 10
For developers, Section 106 is a necessary, yet often challenging, aspect of project delivery requiring careful planning to ensure compliance. While developers may manage some elements like affordable housing, inhouse, they often seek specialist partners like TG Escapes for facilities like schools, sports pavilions, community hubs and healthcare.
TG Escapes has a proven track record delivering permanent buildings for education, sports and leisure, and community hubs. Their modular timber frame system offers several critical benefits for developers navigating Section 106:
TG Escapes' modular approach delivers significant cost savings through reduced labour, minimised waste, and efficient material utilisation. Their in-house design and build service eliminates the need for multiple contractors, streamlining the process and further reducing expenses.
Modular construction dramatically reduces on-site build time, minimising disruption to the surrounding community and ensuring rapid project completion.
TG Escapes provides a complete solution, ensuring full compliance. Their team
handles all aspects of the project, from initial design and planning to final handover, providing developers with a "safe pair of hands" and peace of mind. Their in-house design team can even liaise directly with local authorities, navigating potentially complex specifications.
TG Escapes' biophilic design principles with options for green roofs, bat and bird boxes and planters, naturally contribute
to achieving BNG targets. Their design team also provide expertise in helping to achieve any BREEAM requirements imposed.
TG Escapes' modular panelised system allows for complete customisation, ensuring that the final building precisely meets the required specifications. This could be a school providing appropriate spaces for their specific age range in line with BB103, DfE-compliant SEND provision (with the required acoustic, access and space standards for pupils with additional needs), or a community centre requiring flexible internal space designed for multiple user groups.
“The quality is outstanding, as is the speed of construction. The TG Escapes buildings have been right first time and snag free give or take. We get a good quality product that is delivered on time and absolutely meets the needs of our delivery programme.” David Webb, Surrey County Council.
For more information call 0800 917 7726, email info@tgescapes.co.uk or scan this QR code.
TG Escapes - Enquiry 11
Vericon Systems, a leading manufacturer of remote technologies to manage and control essential building services, has launched HomeHub, a sophisticated in-property device that has been specifically developed to help Housing Associations and property managers monitor and manage their resident’s living environment.
HomeHub, with its intuitive user-friendly touchscreen, provides real-time visibility into environmental conditions within a property, such as humidity levels and alerting residents to potential issues such as damp and mould, by assessing the risk in each room every five minutes rather than providing a general view over a 24hour period.
Kidde launches wireless fire alarm controller
Kidde Safety Europe has launched its innovative CV9101 Fire Alarm Controller, designed to simplify the regular testing and maintenance of its Cavius family of wireless alarms. This user-friendly controller eliminates the need for physical access to alarms, making fire safety more accessible than ever before. The CV9101 Fire Alarm Controller allows homeowners to remotely test and silence their Cavius wireless alarms using a convenient Test/Hush button. This advancement is particularly beneficial for elderly or disabled individuals who may struggle to access alarms, as well as for properties where physical access is challenging, such as alarms installed in high ceilings or non-occupied loft spaces.
Kidde - Enquiry 13
Thanks to its intelligent machine learning, the HomeHub system ‘learns’ the property’s unique heating characteristics, enabling it to accurately calculate the time needed to achieve the desired temperature. This data can also help landlords and property managers better identify properties with inefficient heating systems or inadequate insulation, providing valuable insights for optimisation and improvement.
HomeHub enables direct communication between landlords and residents, including proactive communication with residents, available in multiple languages, to address concerns or when an issue occurs, with regular updates to provide tenants with reassurance that the relevant parties are working to resolve the issue.
The system can also be used by property managers to notify residents of any disruption to boiler performance, as well as provide reminders for annual gas safety checks.
Vericon Systems - Enquiry 12
With the findings of the Grenfell Inquiry continuing to reshape building practices across the UK, the annual construction show at the capital’s famous Olympia venue is this year doubling in size and being refocused as the London Build Fire & Security Expo (November 2021st) with insulation specialist Marmox UK Ltd on hand to demonstrate its recently launched Fireboard product on Stand L42.
The Marmox Stone Wool based product shares the unique Marmox honeycomb surface structure with its XPS forerunner and is suitable for both internal and external wall insulation (IWI/EWI) applications.
Externally the A1 non-combustible certified Fireboard can serve as a weatherproof render-backer, or be used internally across walls and ceilings to take a plaster finish, while providing sound absorption properties, along with thermal insulation.
The 600 x 1200mm Fireboards are available in thicknesses of 20mm, 50mm and 100 mm and with the polymer modified mortar honeycomb coating applied to both faces.
With a nominal density of 150 kg/m3 the boards’ core material offers a compressive strength of 90kPa (9 tonnes/m2), while its high insulation performance will help combat thermal-bridging and the formation of surface condensation, as well as having the potential to cut energy bills.
Marmox – Enquiry 14
You may just see a roof. But by specifying a complete Marley Solar Roof System, you can be sure of a secure and robust solution, that also delivers more desirable, energy efficient homes. It’s more than a roof, it’s building to make a difference.
Passive fire protection manufacturer Promat has launched a new digital portal to allow for faster, accurate design of passive fire protection systems at the earliest stage in a project.
The basic version of the portal – MyPromat – has been designed to give architects and specifiers the information and design capabilities needed to identify and design correct systems for built-in fire protection.
Architects and specifiers signing up for the advanced MyPromat+ platform, however, are also able to access design tools – including BIM and CAD files – to add an additional level of specification support, again at no cost. Built-in performance calculators can also be used within the portal in to help to identify the level of protection needed.
Nigel Morrey, Technical Director at Promat UK, says, “Passive fire protection is a critical part of the safety of any building and is a driving force for the Building Safety Act. Choosing the right passive fire protection systems and products at the earliest stage is vital, and rightly so, but this can be confusing and time consuming without specialist support. Importantly, we wanted to create a trail so all parties involved can show the building meets safety standards and supports the transparency needed for the golden thread, and throughout the lifetime of the building. This is where MyPromat+ comes in.”
Gold certification for low VOCs Promat has secured Indoor Air Comfort Gold certification in Eurofins VOC testing to demonstrate its fire protection boards support a healthy indoor environment and sustainability-led building design.
All of Promat’s standard calcium silicate and mineral bound fire protection boards have now been certified under the leading global scheme that measures emissions of volatile organic compounds (VOCs) to prove the product fulfils low emissions requirements.
Tested to EN 16516, the third-party certification also demonstrates that the products, which are used to create structural protection and fire resistant compartments in buildings, comply with leading sustainability certifications such as BREEAM and LEED.
The testing has been carried out as part of Promat’s commitment to evidencebased sustainability within both the company’s own operations, and in the buildings protected by its passive fire protection systems. Eurofins is the largest global laboratory for testing VOCs, with certification through the
scheme being updated in line with any industry changes introduced, ensuring it supports sustainable building performance documentation with no further need for testing.
As part of its ‘6 steps to CLEARCHANGE’ programme, Promat has set out all of its sustainability targets to provide transparent aims and achievements. This includes supporting sustainable design by actively contributing to BREEAM, LEED and WELL Building Standard projects.
Promat already has 26 Environmental Product Declarations (EPDs) in place across the global brand that further support sustainable building design by detailing the environmental impacts of fire protection boards.
Promat - Enquiry 16
A proven and scalable solution for the challenges faced by social housing providers, while generating a return on investment. The HomeLINK Connected Home Solution assists with:
Mayplas, a specialist in passive fire protection, acoustic and thermal insulation for the housebuilding industry, has introduced two new products. The new Party Wall Head Cap System and Therma Soffit add to Mayplas’ comprehensive portfolio of products for timber and masonry frame applications.
The new Party Wall Head System provides fire protection compartmentation at the party wall junction. Installed together as per Mayplas’ Installation Guide, the two-component system - a party wall head cap and a tile batten barrier, achieves 60 minutes fire integrity and insulation tested to the principles of EN 1363-1:2012 and EOTA TR31:2008 and independently assessed in accordance with BS 47620:1987 and BS 476-22:1987. The system addresses Building Regulations requirements to maintain the continuity of fire resistance between a compartment party wall and the underside of the roof covering, so preventing the spread of fire and smoke.
Mayplas’ new Therma Soffit product also works at the party wall junction providing thermal insulation within the soffit. It is available in two thicknesses, 100mm and 150mm, facilitating required thermal resistance values (Approved Document L) and providing resistance to the passage of sound synonymous with stone mineral wool insulation (Approved Document E).
These new products join Mayplas’ MP552 Cavity Stop Socks, MP556 Fire Stop Slab, MP551 Timber Frame Cavity Barriers and MP557 Acoustic Party Wall DPC Cavity Carrier, all recently tested to BS EN 1366-4:2021, to meet a wide range of housebuilders’ specialist insulation needs.
“Builders are putting fire safety first and foremost. Our new Party Wall Head System together with our existing passive fire protection range addresses that need,” explains Michael Hunter, Mayplas’ Technical Director.
“We now provide a comprehensive solution for realising passive fire protection, for reducing heat loss and for minimising sound transmission in both timber frame and masonry construction to help housebuilders create protected, energy-efficient and comfortable homes.”
New technical data sheets are available at: www.mayplas.co.uk/housebuildingsolutions
Mayplas is a member of the Association for Specialist Fire Protection and the Structural Timber Association. An insulation specialist for over 40 years, Mayplas manufactures a range of fire, acoustic and thermal insulation products at its facility in Bury, Greater Manchester, ideally located for distribution throughout the UK. Mayplas can accommodate virtually any insulation specification, working with architects, contractors, developers, distributors and merchants. Mayplas is part of the Performance Technology Group.
www.mayplas.co.uk
Mayplas - Enquiry 18
The UK’s First Fully Fire-Tested EWI System for below DPC & Base Areas
Visit: www.wall-systems.co.uk
A2 Fire Rated EWI System
Ideal for Remediation Projects.
Superior Impact Resistance. Moisture & Weather Protection. Blends Seamless with Rendered Façades.
Below DPC, Base Areas, Balconies, Walkways, and Pla
Wetherby Wall Systems, part of the ROCKWOOL Group, is delighted to announce the launch of SOQEL A2, a fully compliant, impact-resistant, and moisture-protected External Wall Insulation (EWI) system designed for below damp-proof course (DPC) applications.
Launching on March 17th, SOQEL A2 sets a new benchmark for fire safety and durability in external wall insulation. It’s the first fully fire-tested system for below DPC applications, meeting the latest A2-s1,d0 fire classification required for materials in buildings over 11 meters. This ensures compliance with the UK Building Regulations and provides a solid solution for the construction industry.
With UK building regulations now requiring that materials used in buildings over 11 meters must meet a minimum A2-s1,d0 fire rating, SOQEL A2 offers architects, contractors and specifiers a reliable solution in line with these regulations.
Designed for use in below DPC areas, as well as balconies, walkways and plant rooms, the system improves fire resistance, impact protection and long-term moisture durability. Unlike traditional solutions, such as bitumen paint, SOQEL A2 delivers a more effective and resilient alternative.
This game-changing system integrates Coverrock x-2 pre-coated insulation,
which ensures a strong and durable bond for coatings while protecting the A1-rated Stone Wool core during installation. Paired with Heck K+A SL coating and Heck CER Mesh, it also provides superior impact and moisture resistance, withstanding harsh weather and high foot traffic in exposed areas like balconies and plant rooms.
SOQEL A2 incorporates Heck 4S Silicone Render, ensuring a seamless finish that matches the overall façade system.
Unlike traditional below DPC treatments, which may distrupt the building's aesthetics, it offers a modern, integrated look while maintaining full regulatory compliance.
Joe Ragdale, Technical Director at Wetherby Wall Systems: “We have worked alongside our ROCKWOOL Group sister company, HECK in Germany to launch this innovative system into the UK market. We are delighted to introduce SOQEL A2, the first system of its kind for below DPC and base areas."
"This solution provides architects and contractors working on remediation projects with a compliant, durable, and efficient way to enhance building safety while ensuring a seamless finish alongside insulated façade systems.”
For more information about SOQEL A2 or to discuss your project requirements, visit www.wall-systems.co.uk
Wetherby Wall Systems - Enquiry 20
An architect’s home near Dundee is seeing the benefits of its new roof underlay – even though the reroofing hasn’t finished yet.
Neil Simpson, a Partner at Wellwood Leslie Architects, is fitting the Proctor Air himself while renovating the roof of his stone-walled property built in 1902.
“Proctor Air has been excellent,” explained Neil. “It is relatively easy to install, and has protected us from the weather. The wind used to whistle through the roof before, but we’ve seen a difference straight away in reducing that infiltration.”
Using Proctor Air to protect against the elements – during and after reroofing Situated in an exposed location overlooking the River Tay, the house is subject to the elements. As Neil has continued to live in the property during the work, the underlay had to be capable of protecting the property and its occupants. Proctor Air has a water resistance classification of W1, and
its BBA certificate states the hydrostatic head is greater than 1m. This water hold out performance means Proctor Air can be left exposed for up to three months (although should not be relied upon as being waterproof). As the frequency and intensity of extreme weather increases, roofs and their underlays need to be capable of withstanding more severe levels of rainfall. A hydrostatic head of at least 1m is the minimum that an underlay should be capable of.
While the reroofing work has not experienced too much rain, there have been strong winds. Proctor Air can be used in wind zones 1-4 without additional measures such as taping joints or additional battens.
A. Proctor Group - Enquiry 21
Swish Building Products has extended its NatureClad cladding range with the addition of a new colour.
Moonlight Anthracite has been introduced to meet the continued demand from customers and the industry for a contemporary anthracite grey tone of premium wood effect cladding.
Available in both the 300mm Double Shiplap and 270mm Double Feather Edge cladding profiles, Moonlight Anthracite features the same high-definition woodgrain texture and super matt finish as the rest of the collection. Its lightweight cellular PVC composition makes it easy to install, extremely durable and simple to maintain.
This latest addition to the range now means NatureClad is available in six stunning shades; Morning Dew Silver, a light grey; Cumulus Grey, a mid-grey tone; Chiminea Charcoal, a dark grey; Coastal Sand, a nature inspired light brown; and Rich Espresso, a dark brown. Complementary trims and joints are also available which help to achieve a seamless, cohesive finish every time.
“The addition of Moonlight Anthracite to our NatureClad range means we can now offer one of the most comprehensive colour collections of contemporary, wood effect PVC cladding on the market, from neutral browns to modern greys. This allows homeowners to protect their properties in the most stylish way possible,” explains Lewis Litchfield, Product Marketing Manager.
Swish Building Products - Enquiry 22
Keylite helps housebuilders meet ambitious targets
With the UK government targeting 1.5 million new homes over the next five years, Keylite Roof Windows is poised to support this growth with innovative solutions designed to address industry challenges. Keylite has become the preferred supplier for numerous national and regional housebuilders, offering market-leading products that simplify compliance with updated Building Regulations in England and Wales. Keylite tackles thermal bridging with its patented Integrated Expanding Thermal Collar, which ensures the thermal integrity of the window. This innovation eliminates the need for an extra thermal collar, helping meet Part L requirements, enhancing airtightness, and improving Psi values for SAP calculations.
Keylite Roof Windows - Enquiry 23