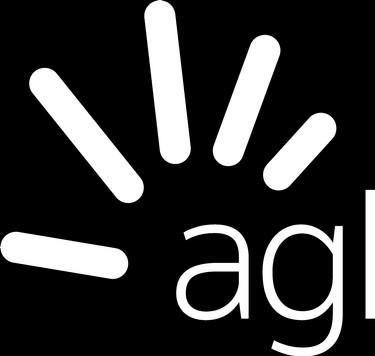
Working at Heights and Fall Prevention Technical Guide
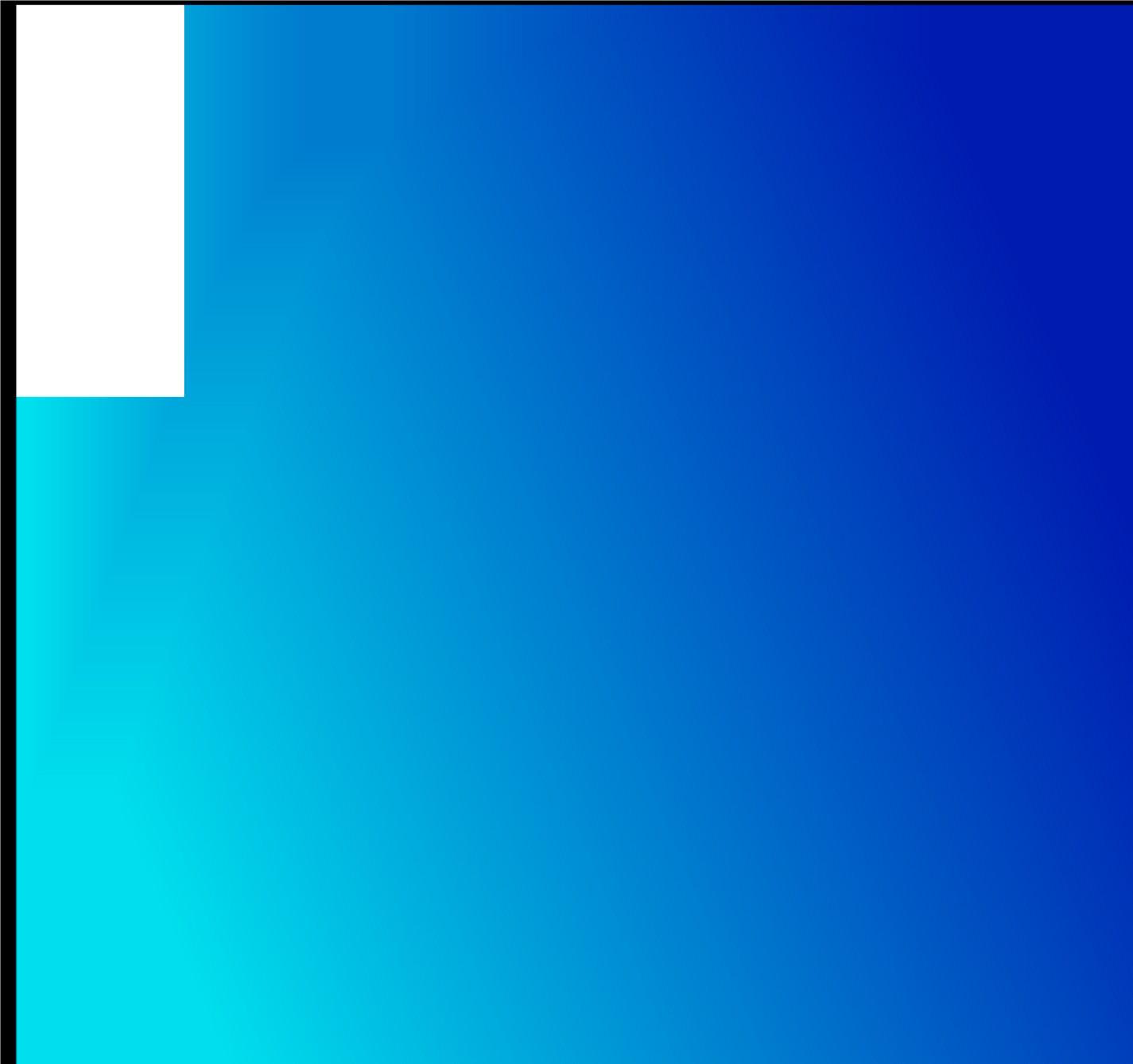
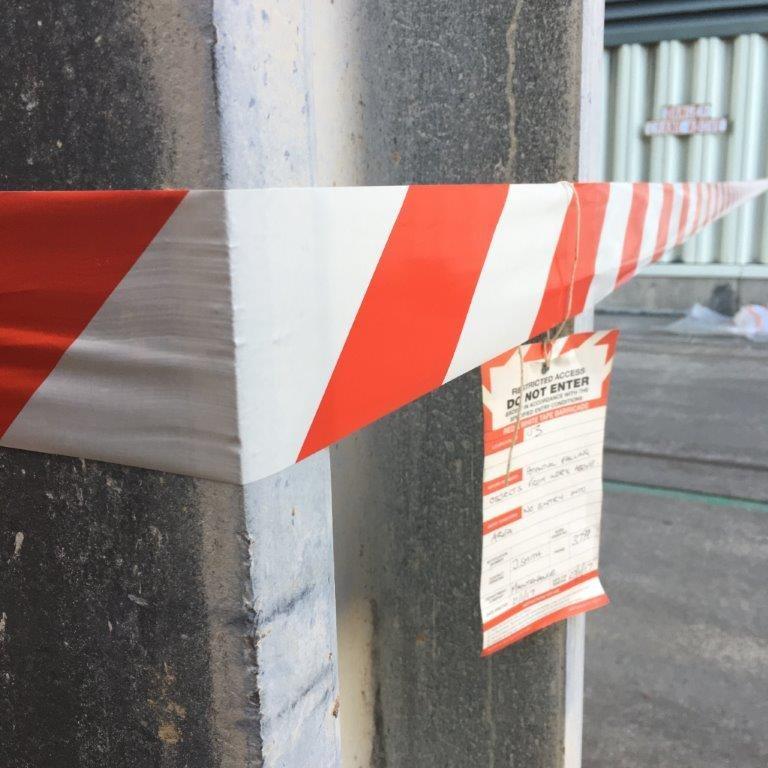
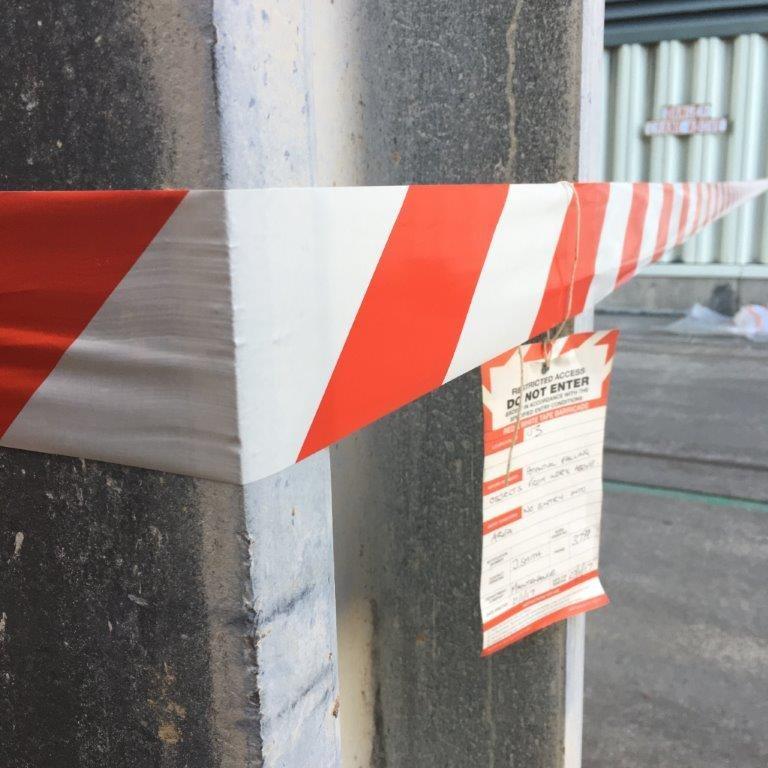
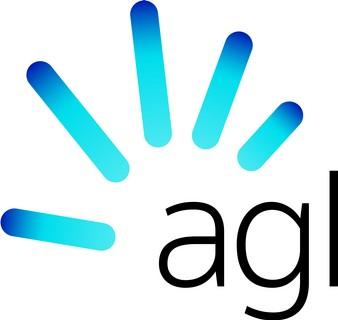
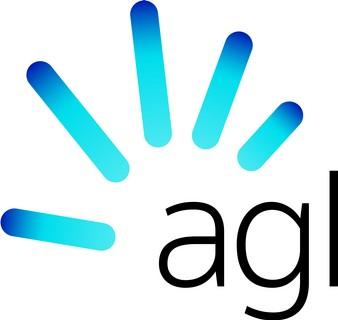
1 Introduction
The purpose of this document is to inform users of the technical aspects of working at heights. The information provided in this document is for information only. Only persons who have appropriate training and experience are to undertake working at heights work where there is a risk of a fall that may result in a significant injury.
2 Scope
This guide is to be used by all AGL employees, contractors, and visitors on AGL Macquarie controlled sites. This document is to be read in conjunction with the working at height and fall prevention procedure .
3 Planning
Key to a successful task is to undertake planning for that task. This should involve persons who will undertake the task as they will have unique experience on the practical nature of the task. Planning involves:
Understanding the scope of work in detail
Undertaking risk assessments to identify the issues that need to be managed.
Determining how to control the risks that have been identified.
Developing contingency plans if an incident occurs
Identifying and completing necessary permits
Organising the necessary equipment and personnel to implement the controls developed.
3.1 Hazard Identification and Risk Assessment
A risk assessment must be completed for all work where there is a risk of fall from one level to another that is reasonably likely to result in injury. The aim of the Risk Assessment to identify hazards associated with the work and determine the appropriate controls which are to be implemented to mitigate these risks . Typical hazards associated with working at heights include, but are not limited to:
• Persons falling from or through a structure, roof, or item of plant;
• Falling objects;
• An exposed and unprotected opening through which a person could fall;
• The adequacy of inspection and maintenance of the plant and equipment used to control the risk (for example, scaffolding);
• Electrical hazards when working beside or under electricity power lines and conductors;
• Weather conditions;
• Unstable platforms;
• Inadequate edge protection;
• Unstable footings;
• The suitability of footwear and clothing for the conditions;
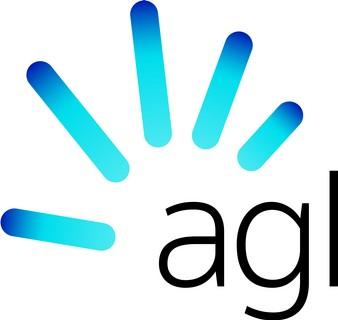
Working at Heights and Fall Prevention Technical Guide
• Suitability of attachment points including anchor points;
• Safety of other persons working under or near an area where work at heights is performed;
• Poor housekeeping;
• The adequacy of current knowledge and training to perform the task safely (for example, new or inexperienced workers may be unfamiliar with a task or contractors unfamiliar with the AGL Macquarie site); and
• The adequacy of procedures for all potential emergency situations.
• Operational interactions including fixed structures, mobile plant, overhead cranes and operational access through or in the vicinity of the worksite.
• Worker Suspended in harness.
• Ground condition, sloped, unstable,
It is important that personnel work together (consult) to identify any hazards from working at heights and select the most effective method of fall prevention that is compatible with the type of work being done.
3.2 Determining how to control risk
All identified hazards and risks identified in the risk assessment process, must be eliminated where possible, or at least minimised to a level as low as reasonably practicable. This shall be achieved through the implementation of appropriate risk control measures using the hierarchy of controls. These risk control measures must be documented. Examples of the hierarchy of control are shown in Figure 1 below.
In managing the risks of falls, the controls outlined in the Controlling the risk of Falls section are to be implemented, where it is reasonably practicable to do so with the Most Effective option being the most preferred and the Least Effective option the least preferred:
All work where there is a risk of fall that is reasonably likely to result in injury must utilise the fall prevention hierarchy of controls. These are outlined in the following section Controlling the risk of Falls.

• Elimination – removing the hazardous plant, tool, substance, etc., so that the hazard or risk no longer exists;
• Substitution – replacement with a less hazardous tool, chemical, operation;
• Isolation – of an activity, plant, etc., to prevent exposure or contact;
• Engineering – erecting screens or guards or platforms, installing ventilation, etc.;
• Administrative – procedures, warning signs, training, job rotations; and
• Personal Protective Equipment – the least effective means of risk control.
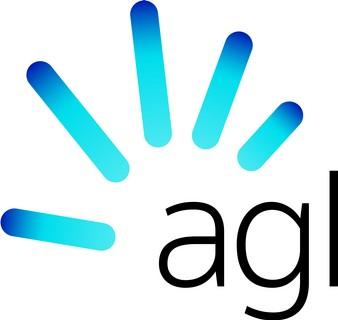
Working at Heights and Fall Prevention Technical Guide
In some cases a combination of control measures may be necessary, for example using a safety harness (fall-arrest) whilst working from an elevating work platform (fall prevention).
3.3 Contingency Plans (Rescue Plan)
When planning for working at height work consideration must be given to how emergencies situations are to be managed. The existing emergency plan is to be used if it covers the work being undertaken. Where work involves the use of EWP’s or Fall arrest equipment a specific emergency plan is to be developed and consulted on with the work party. The AGL Macquarie Rescue Checklist provides the requirements that need to be considered. A key issue is suspension trauma which is possible when fall arrest equipment is activated. As such persons shall not work alone when fall arrest equipment is required.
The purpose of a Working at Heights Rescue Plan is to outline the rescue operations for the risks associated with working at heights, as identified in the task risk assessment/JSEA. The Rescue Plan should enable a fallen person to be removed from a suspended position as quickly as possible to prevent them suffering suspension intolerance.
A Rescue Plan should be considered for all work at heights but is *mandatory for tasks where a person will be using a fall arrest/restraint system to ensure that provisions for rescue have been considered during the planning of the work. The rescue plan must be completed before any work commences. Where there is a rescue plan developed, notification to relevant site personnel and emergency site authority will be the responsibility of the Person in Charge of the work.
*The only exception to this requirement is where a fall arrest harness is being worn for the purposes of moving a boom lift that is not in an elevated state. The moving of a boom lift, where the operator is wearing fall arrest PPE, does not require a rescue plan; however, a rescue plan must be in place for any other operation of the boom lift, i.e. when it will be used in an elevated position.
Whilst scissor lifts and vertical lifts do not require the operator to wear fall arrest PPE, there may be times when the work being carried out could potentially place the operator in a situation where a rescue is required. In these circumstances, while not mandatory, the need to develop a rescue plan should be considered during the risk assessment process. Key to this plan is determining who and how to bring the piece of plant to ground level or access the basket.
All Working at Heights Rescue Plans must be developed using the AGL Macquarie Rescue checklist template and should include the following information;
• Work Description/Scope
• Characteristics of Work Area
• Communication
• Rescue Resourcing
• Rescue Arrangements
• Rescue Methodology
• Rescue Equipment
• Photos and Drawings if applicable
• Review and Approval
• Work Party Sign on
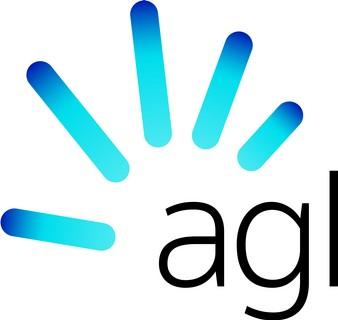
Working at Heights and Fall Prevention Technical Guide
All members of the work party that are performing or involved in the working at heights, or may play a role in rescue are required to read and sign onto the rescue plan prior to starting work.
Rescue Plans for height work in a confined space shall be developed using AGLM-HSE-PRO-007.02.02
Rescue Plan Work at Heights.
Suspension Trauma
Suspension trauma or intolerance can occur with a fall-arrest system when a person has an arrested fall and is suspended in an upright, vertical position with the straps of the full body harness causing pressure on and restricting blood flow to the legs.
The lower legs’ capacity to store large amounts of blood reduces the return of blood to the heart, slowing the heart rate, which can cause the person to faint. If left to develop, the condition can become fatal. This condition may be affected by several factors including heat and dehydration.
To prevent suspension intolerance occurring because of an arrested fall:
• Workers shall not work alone when using a harness as fall protection;
• The time a worker spends in suspension after a fall should be minimised;
• Suspension trauma straps shall be fitted to all harnesses to allow workers to move their legs whilst suspended and maintain blood flow; and
• Rescue plans should be developed to allow for quick response and rescue of personnel.
The quick rescue of a person suspended in a full body harness, as soon as is possible, is vital. For this reason, workers should be familiar with the relevant works rescue plan, be familiar with and have all the necessary equipment on hand and be capable of conducting a rescue of a fallen worker if required. Workers and emergency response personnel must be trained in the rescue procedures and be able to recognise the risks of suspension intolerance and act quickly in the rescue of a person.
The provision of first aid treatment for persons suffering from suspension intolerance should be in accordance with the Australian Resuscitation Council Guideline 8.25, Harness Suspension Trauma—First Aid Management, which recommends normal first aid treatment plus the administration of oxygen, if available.
3.4 Permits
A Permit is not generally required for Working at Heights, however a permit may be required if the work includes other Specific Hazard Work Categories. A permit is mandated for the following:
Scaffolding where the scaffolding is likely to impact/be impacted by operating plant including:
Scaffolding is to be erected in the path of moving plant equipment (e.g. conveyors/shuttles/cranes)
Scaffolding is to be erected within 1m of operating plant that is subject to expansion/contraction
Scaffolding is likely to restrict operator access to operating plant such as walkways, switch boards, safety valves, emergency valves/systems or main steam valves
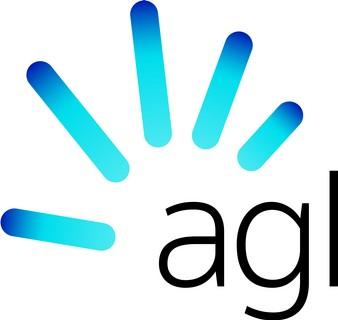
Working at Heights and Fall Prevention Technical Guide
Scaffolding is within the boundaries of a HV switchyard
Any other circumstance where the risk assessment requires plant out of service to provide a safe environment
Elevating Work Platforms where the following applies:
Isolation of plant/equipment is required for the safety of the EWP work activity
If any part of the EWP or load will come within 10m of:
Overhead power lines;
An open switchboard with exposed components (e.g. connections or bare busbars);
An exposed overhead conductor (e.g. substation busbar, travelling or gantry crane busbars);
Any exposed electrical part which may present risk to personnel; or
Any area defined as HV Vicinity in AGLM-HSE-PRO-007.01.01 HV Electrical Procedure
For more information, refer to the AGLM-HSE-004.02 Permit to Work Procedure
4 Controlling the Risk of Falls
The following provides information on the types of controls that are to be implemented in the hierarchy of control format. Fall prevention methods include any equipment that is designed to prevent a person from falling whilst working at heights, which, once in place does not require any further adjustment by workers using the device. All work where there is a risk of a fall of greater than 2 metres must apply physical controls that prevent a person from falling or are designed to arrest a fall
4.1 Elimination
Eliminating the need to work at heights is the most effective way of protecting workers from the risk of falls. Examples of eliminating the risk. Whilst eliminating the work a heights risk may be achieved an assessment needs to be undertaken to manage other risks which maybe introduced by the alternate method.
4.1.1
Work on the Ground or Solid Construction
Moving work to the ground or area where there are no fall risk eliminate the risk. Some examples include:
• Reducing shelving heights so that workers can access items from ground level;
• Moving elevated equipment that requires maintenance to the ground to be worked on;
• Fitting valves or controls with extendable handles that can be operated from the ground or accessible platform/walkway;
• Fitting outlets, inlets and controls of large tanks and silos near the ground; and
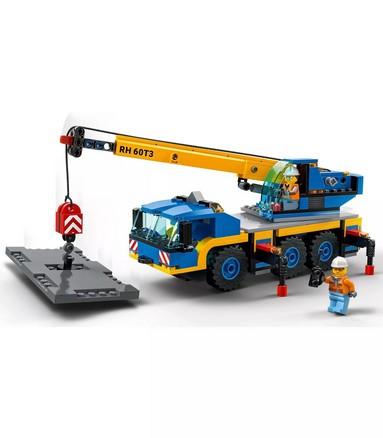
• Using tools with extendable handles, such as paint rollers (the risk of musculoskeletal disorders will need to be considered when deciding whether to use such tools).
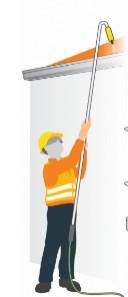
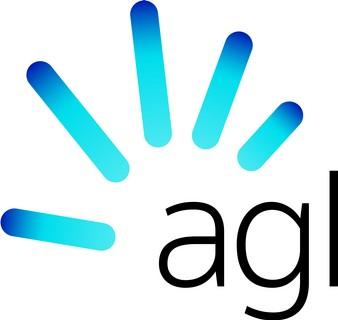
Working at Heights and Fall Prevention Technical Guide
4.1.2
Remote methods
As technology progresses work is increasing being undertaken by remote methods. One example is the use of drones to undertake inspections.

4.2 Isolation
Isolation of workers from the fall from heights is achieved by providing edge protection or covering penetrations which workers may fall through.
Edge protection, in the form of guard rails, can provide effective fall prevention:
• At the edges of roofs;
• At the edges of mezzanine floors, walkways, stairways, ramps and landings;
• On top of plant and structures where access is required;
• Around openings in floor and roof structures; and
• At the edges of shafts, pits and other excavations;
Guard rails should incorporate a top rail 1100mm above the working surface, a mid rail and a toe board.
All edge protection systems installed shall be checked by a competent person to ensure that they are adequate to support the potential load of all workers undertaking the work at one time.
All temporary edge protection must be installed to meet the requirements of Australian Standards.
For penetrations in the floor or on a wall that are large enough for a person to fall through a cover may be used instead of edge protection. The cover must have sufficient strength to support the weight of workers as well as any other load that may be subjected to it. It must also be secured to the ground /wall so that it cannot inadvertently move.
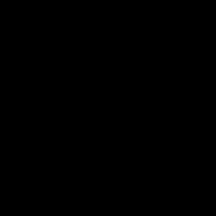
4.3 Engineering
4.3.1 Mobile Scaffolds
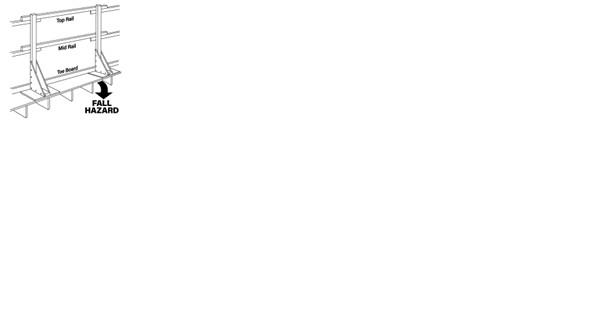

Portable scaffolds can be used where the high required is less than 4m. Portable scaffolds can be erected and used by workers following the manufactures instructions. Portable Scaffolds are only to be used on level stable ground and where only the workers and light loads are being used. Workers are to check that the portable scaffold is setup correctly and all connection points are tight before use. Where a scaffold has wheels, these are to be lock before using the scaffold.
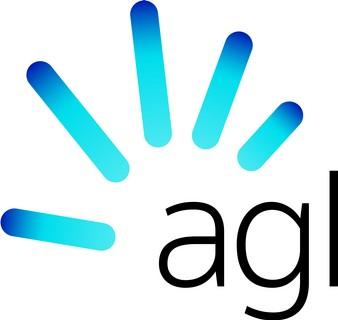
4.3.2
Scaffolds
Working at Heights and Fall Prevention Technical Guide
All work involving the erection, use, inspection and dismantling of scaffolding on the AGL Macquarie site shall be done in accordance with the AGL Macquarie Scaffolding Procedure, which incorporates the relevant legislative requirements.
All built scaffolding must comply with the relevant Australian Standard and must be erected by a licenced installer (scaffolder) holding a high risk work license. Personnel erecting scaffold shall provide evidence of currency of qualification. Where a scaffold is not of a standard design or the use of a scaffold is outside of standard parameters a suitably qualified engineer is to design the scaffold to meet the abnormal requirements.
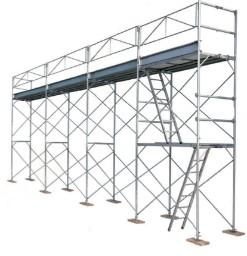
All scaffolds will have a scaftag attached to indicate the status of the scaffold and be inspected at least monthly to ensure the scaffold is fit for purpose.
4.3.3
Elevated Work Platforms
Elevating Work Platforms (EWP) provide a temporary safe working platform for personnel required to access and work at heights. EWPs come in a variety of types and sizes, suitable for a range of work scenarios and requiring different levels of competency to operate. EWPs include boom lifts, scissor lifts, cherry pickers, workboxes hung from crane structures and platforms lifted by a forklift.
The safe operational use of EWPs requires specific considerations including:
• Pre-start checks to be carried out prior to use or before the beginning of each shift. The log book shall be filled out and signed by the operator.
• A inspection of ground conditions to ensure stability and no obstructions or hazards, for example electrical leads, hoses etc.;
• EWPs shall only be set and operated by competent persons;
• All persons shall stand on the floor of the platform at all times;
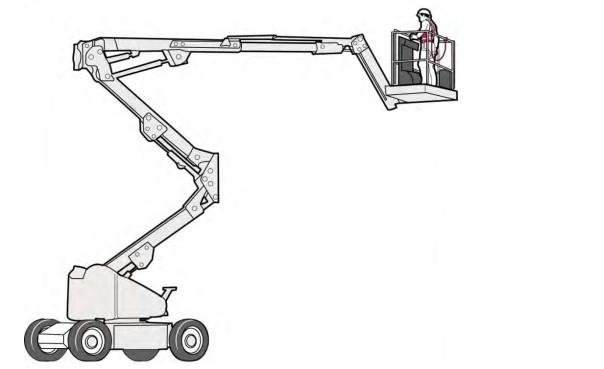
• A fall-arrest harness and shock absorbing lanyard, complying with the Australian Standards, shall be worn by all personnel on the platform of a boom type elevating work platform and be secured to a suitable anchor point provided for purpose.
• Fall arrest harnesses are not required for use in scissor lifts.
• When work above personnel access/pedestrian areas cannot be avoided, appropriate actions shall be taken to prevent access to the area and objects falling from the basket or platform. Where practicable, all tools and other loose objects shall be secured with lanyards.
• Maintain approach limits to live electrical conductors in accordance with the Australian Standards for Electrical safety.
• If slewing is to occur, consider the possibility of a collision with the structures and ensure barricades and safety observer are correctly positioned for encroaching hazards.
• Mobile and Elevated Work Platforms (MEWP/ EWP) operated over 11 meters must only be operated by a person with a high risk licence.

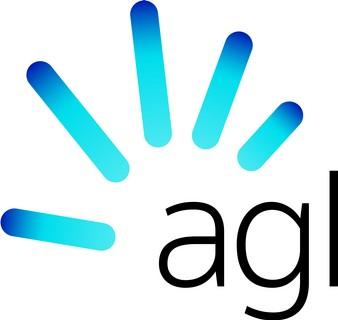
Working at Heights and Fall Prevention Technical Guide
• Access and egress from the work platform shall only be from fit for purpose access/egress positions unless the MEWP/EWP is an emergency or breakdown situation.
4.3.4
Work Positioning and Restraint Systems
Restraint systems consist of the worker wearing a full body harness connected by a lanyard to a suitable anchorage point or horizontal lifeline. They must be set up so that they prevent the worker from reaching an edge from where a fall may occur.
Restraint systems must only be used where it is not reasonably practicable to use fall prevention devices.
All equipment used in restraint scenarios must be rated for fall-arrest to account for unforeseen circumstances or situations that could lead to a worker being involved in a fall, such as the following:
• The worker can reach a position where a fall is possible;
• The worker has set the adjustable lanyard to an incorrect length;
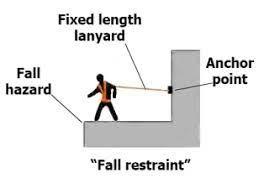
• There is a danger of the worker falling through the surface (e.g. fragile roofing material);
• The slope of the surface the worker is on is greater than 15 degrees; or
• There is any other reasonably likely misuse of the system which could lead to a fall.
For these reasons, a shock-absorbing lanyard must be used in restraint systems rather than a conventional lanyard.
All equipment used for restraint shall meet the requirements of the AS 1891 series of Standards, however rope access equipment may also be used for restraint, provided the equipment complies with the relevant AS, ISO or EN Standard and is configured by a competent person.
4.3.5 Fall-Arrest system
Fall-arrest systems are intended to safely stop a person falling an uncontrolled distance and reduce the impact of the fall.
Fall-arrest must only be used if it is not reasonably practicable to use higher level controls (i.e. controls that prevent a person from falling) or if higher level controls, used on their own, may not be fully effective in preventing a fall.
All equipment used for fall-arrest at AGL Macquarie must be designed, manufactured, selected and used in accordance with the Australian Standards.
Key safety considerations in using fall arrest systems are:
• The correct selection, installation and use of the equipment;
• That the equipment and anchorages are designed, manufactured and installed to withstand the force applied to them as a result of a person’s fall;
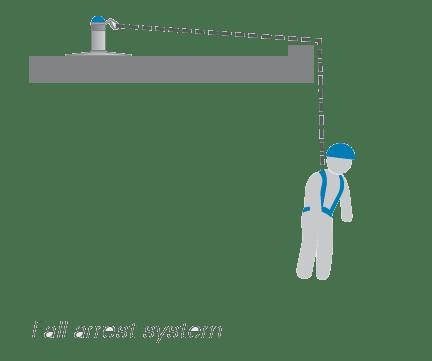
• That the system is designed and installed so that the person travels the shortest possible distance before having the fall arrested;
• That workers using a fall-arrest system wear adequate head protection to protect them in the event of a fall; and
• That if the equipment has been used to arrest a fall it is not used again until it has been inspected and certified by a competent person as safe to use.
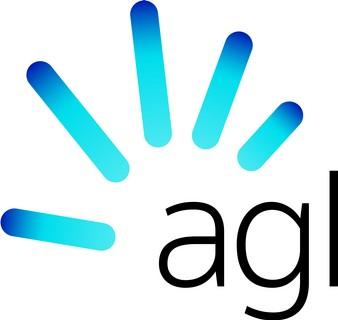
Working at Heights and Fall Prevention Technical Guide
Individual fall-arrest systems consist of some or all of the following components:
• Anchorages
• Lifelines
• Inertia reel
• Lanyard of fixed length
• Retractable lifelines
• Rope grabs
• Wire grabs
• Rail system
• Shock absorbers, both personal and industrial
• Harness
• Snap hooks (must be double or triple action to prevent rollout)
• Karabiners (double or triple action to prevent rollout)
• Rescue equipment
Temporary Lifelines
Temporary lifeline systems are available in kit form and are pre-engineered systems that meet the requirements of AS1891.2:2001 – Industrial Fall Arrest Systems – Horizontal Lifeline and Rail Systems that have not been tested and certified to AS1891.2:2001 are not to be used (i.e. onsite developed temporary systems).
Temporary lifelines shall be assembled, installed used and maintained in accordance with the manufacturer’s instructions.
Fall Clearance Distances
Whenever a work at heights activity is conducted that requires the use of fall-arrest, fall clearance distances must be considered. If a fall-arrest system is to be used, it is essential that there is adequate clearance under the system so that in the event of a fall the worker will not strike the ground or any other obstacle beneath the system.
Fall-arrest systems should be installed so that the maximum distance a person would free fall before the fall-arrest system takes effect (i.e. shock absorbing lanyard or an inertia reel) is two metres. There should be enough distance between the work surface and any surface below to enable the system, including the action of any shock absorber to fully deploy and effectively arrest a fall. If this cannot be achieved, the task should be re-assessed, considering the benefit of the fall-arrest system keeping a person upright in the event of a fall.
To work out whether there is enough distance available, you should take into account the factors in figure 3.
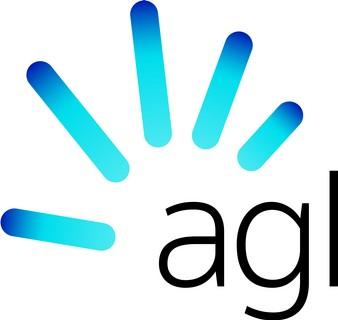
Working at Heights and Fall Prevention Technical Guide

Figure 3: Example of fall clearance calculation using a shock absorbing lanyard. Total distance from the anchorage in this example is 6.5 meters.
The fall clearance is always expressed as a vertical distance from the anchorage point.
Adjustments to clearance distances can be made by:
• Repositioning the anchorage point (to reduce free fall distance);
• Using a shorter length lanyard (to reduce free fall distance); or
• Using an inertia reel type fall arrestor (type 2 device) instead of a lanyard (reduce extension).
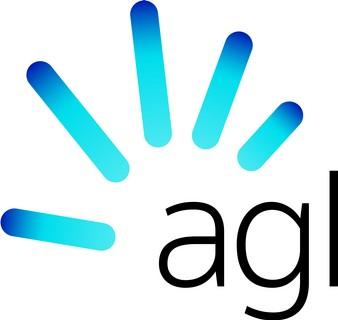
Free fall distances (i.e. the distance a person falls before the fall-arrest device takes effect) should never exceed two metres as this can cause excessive force to be placed on the body in the event of a fall. In the example shown in Figure 4, below, the anchorage is at the worker’s feet. If the worker is also using a two metre lanyard, the free-fall distance could potentially be 3.5 metres.
This is because the anchorage is at the worker’s feet, so an allowance must be made for the distance from the point of the anchorage (the ground) and the point that the lanyard is attached to the worker’s harness, which is generally high on their back, for example 1.5 metres. The length of the two metre lanyard is then added to this, leading to a free fall distance of 3.5 metres. Therefore, anchorage points should be positioned above the worker, wherever practicable.

Figure 4: Example of a lanyard and anchorage set up that can result in a free fall distance greater than 2 metres.
Fall-arrest devices
Inertia reels and self-retracting lines are typically known as Type 2 fall-arrest devices. Inertia reels are devices designed to limit free fall distance. One end is attached to the worker’s harness and the other end is attached to an anchorage point. When attached to the worker’s harness, a spring-loaded reel allows a length of wire rope or webbing to deploy and retract from the housing of the device in response to the movements of the worker. In the event of a fall, the device locks (similar to the locking mechanism of a car seat-belt). A type 3 device is similar to a type 2 device with the addition of a winching mechanism.
Type 2 devices are useful in providing a significant range of movement for the worker and decreasing freefall distances to no more than 600mm. However, there are limitations to their use. They generally should not be used in the horizontal position or in situations where a worker could fall down a slope and the slope is such that the worker slides down the slope at a speed that is insufficient to activate the arresting mechanism.
They are typically erected above the worker, but the worker should not move outside an angle of 30 degrees from the vertical (or the distance specified by the manufacturer), to ensure that a pendulum effect is not created in the event of a fall.
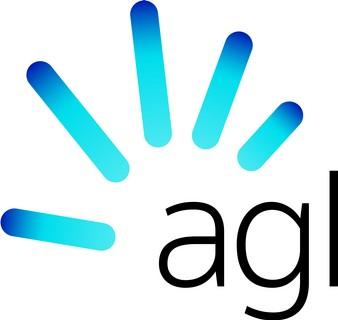
Type 2 devices are useful in that they can remain attached to an anchorage point high above the ground or work surface, ready for use with a tag line attached, using rope or similar material. A user can then use the tag line to deploy the device and pull the attachment point to the worker to connect their harness to. The line of a type 2 device should not be left extended when not in use as this can allow dirt and debris to contaminate the device and cause the spring mechanism to fatigue.
A lanyard and an inertia reel must never be connected. Similarly, two or more lanyards should never be connected, as this increases the forces on the body to unacceptable levels during a fall.
Snap-hooks
Snap-hooks must comply with AS1891.4:2009 – Industrial Fall Arrest Systems and Devices – Fall Arrest Devices. Only double-action snap-hooks that require two separate forces to open the gate for disengagement shall be used to minimise the risk of “roll out”. Locking snap-hooks must always be connected to compatible hardware. The use of non-compatible components may also lead to ‘roll-out’ with some hook / karabiner configurations allowing the snap-hook gate to be depressed by a turning motion of the snap-hook. Persons who are unsure whether components of a fall-arrest system are compatible should stop work and contact their Team Leader.
Two snap-hooks must never be attached together.
Unless designed by the manufacturer, a snap-hook must never be attached to a webbing loop or back onto its own lanyard.
Cross-gate loading
Snap hooks and carabiners are designed to be used and loaded along their long axis, or parallel to the spine. Through various means such as movement of lanyards and attachments, loading of the gate can occur. Many devices (which are still compliant to Australian Standards) do not have gates rated to handle the forces of a fall and if the gates of these devices are loaded in this way, their strength is reduced from about 22 kN when loaded parallel to the spine, to 12 kN or less when loaded across the gate. If a fall was to occur, the loading could cause the gate to fail and the hook to be detached from the anchorage.
To reduce this risk, snap hooks should be purchased and selected with gates rated, and marked, to at least 16kN. Where snap hooks are used with gates that are not rated, correct set up and monitoring of equipment must occur to ensure correct loading. Existing snap hooks owned by AGL Macquarie that do not have gates rated to 16kN may continue to be used for the remainder of their normal service life, but shall be replaced with snap hooks with gates rated to 16kN.
4.3.6 Anchorage Point
Anchorage point refers to a secure point of attachment for a lanyard, lifeline or other components of a fall protection system, such as fall restraint or fall arrest.
Anchorage points may be permanently installed, engineer designed points, or temporary points set up on building structures at the time of use.
All anchorages used for fall-arrest must be able to withstand the following forces, in accordance with AS1891.4:
• For a single person – 15kN
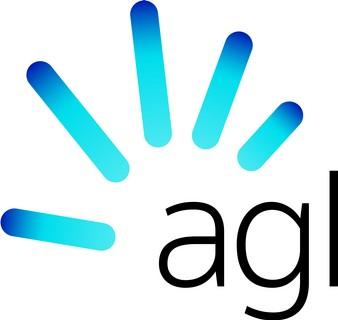
Working at Heights and Fall Prevention Technical Guide
• For two people using the same anchorage – 21kN
Each anchorage point should be located so that a lanyard can be attached to it before the person using equipment moves into a position where they could fall.
All temporary anchorages should be assessed and approved by a competent person before use and included in the risk assessment documentation for the task.
It must be clear to a competent person that the anchorage system is structurally adequate. If any doubt exists as to the structural adequacy of the anchorage, an engineer shall make the assessment.
The engineer shall certify in writing that the proposed structure and anchorage points can safely support all combinations of loads in the worst-case situation. The D2 notification process to be used for installation of permanent anchorage points. Once the process is completed, a nameplate complete with unique identifier and load rating shall be installed as close as reasonably practicable. The D2 notification process will also identify the inspection frequency and method to be incorporated into new SAP routine for the new point.
Handrails, cable ladders, etc. are unsuitable for fall-arrest and shall not be used as an anchorage point unless certified by an engineer as being suitable.
Equipment used to create a temporary anchorage point shall be purpose designed for that application (e.g. anchor straps or beam clamps). Lifting slings should not be used unless designated for fall-arrest use only.
Cranes shall not be used as an anchorage point, except in emergency rescue situations. For emergency rescue use, approval must be obtained from the General Manager AGL Macquarie or their delegate. Approval will only be given if the following requirements are met:
• There is no other, more appropriate means of anchoring;
• The use of the crane is risk assessed;
• The crane must be a fixed (non-mobile) overhead crane rated to at least 3 tonnes;
• The crane hook must be positioned above the worker;
• The crane controls/power supply must be isolated, locked and tagged; and
• The hook of the crane must be a closed hook, i.e. fitted with a one-way gate, to prevent any lanyard attached from slipping off the hook.
For additional information and guidance on setting temporary anchorage points, personnel should consult with an AGL Macquarie Team Leader.
Permanent Horizontal Lifelines
A competent person must approve permanent lifelines and associated systems used for securing permanent lifelines. Lifelines must comply with AS1891.2:2001 and must be used in accordance with manufacturer’s instructions. Inspections of lifelines must be in accordance with the inspection schedule shown in Section 10 and included as a SAP routine
4.3.7 Lanyards
The purpose of a lanyard is to connect a harness worn by a worker to an anchorage point, horizontal lifeline or rail, or other acceptable anchorage point. All lanyards shall incorporate an energy shock absorber and comply with AS1891.1:2007 – Industrial Fall Arrest Systems – Harnesses and Ancillary Equipment
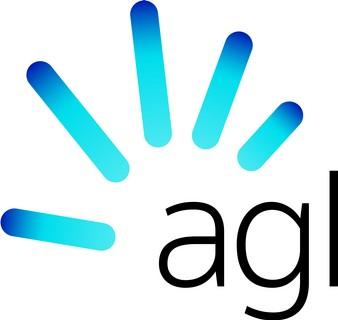
Working at Heights and Fall Prevention Technical Guide
Lanyards can be purchased in fixed lengths or be adjustable, but in any case, shall be no more than two metres in length and shall be selected and used to ensure that free fall distance does not exceed two metres.
Twin-tail lanyards
A twin-tail (or double tail) lanyard generally comprises a single shock absorbing device fitted at one end with a snap hook, screw connector or carabiner. The second end of the shock absorber is connected to two, equal length, lanyard tails - each terminating in identical snap hooks or carabiners.
They are intended for use when transferring between attachment points so that the user is always connected to an anchorage via one or other of the tails.
Use of a twin-tail lanyard requires that the tail that is not in use be stored either on a manufacturer provided point on the other tail or another point on the lanyard, depending on where the manufacturer has provided the attachment points. The second tail should never be attached to the worker’s harness, unless the manufacturer has provided a specific point for this purpose, as this can result in excessive forces being applied to the body in the event of a fall.
Lanyard stowage points can be fitted to harnesses, which are designed as a point to attach spare lanyard tails. They are attached with velcro and are designed to tear away from the harness in the event of a fall or the tail being caught. All harnesses used by AGL Macquarie personnel should be fitted with lanyard stowage points.
When twin-tail lanyards are provided, an information sheet is to be provided to and read by the operator, to ensure correct techniques for using twin-tail lanyards is understood.
4.3.8 Safety Harness
Safety harnesses are a critical piece of equipment for fall restraint and fall arrest systems. All safety harnesses used must:
comply with Australian Standards,
be inspected by a competent person every 6 months
be inspected by the user prior to use for obvious damage and that all carabiners and attachment rings are functioning.
Have suspension
4.4 Administration
4.4.1 Unprotected edge
Where any handrail, walkway, stairs, etc. are removed, subsequently creating an unprotected edge, an assessment of the risk of falls shall be conducted and controls shall be implemented to manage the risk.
The requirements shall be followed when creating an unprotected edge:
• All other reasonable means of undertaking the job without the need for removing flooring and handrails shall be considered before commencing the job;
• No work is to take place within 2m of the unprotected edge unless appropriate fall protection is in place.
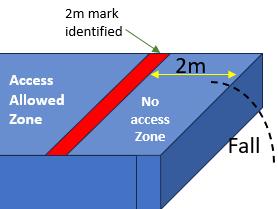
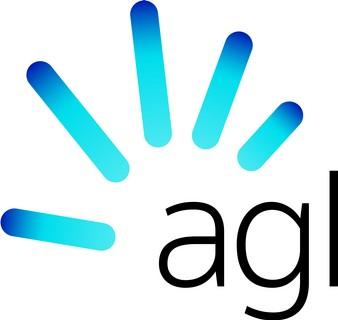
Working at Heights and Fall Prevention Technical Guide
• The 2m mark is to be clearly identified with barrier tape and signage so workers know where the no access zone is.
• A toolbox talk is to be held at the start of each shift explaining the unprotected edge and no access zone.
• The provision of Emergency Response access to the area must be considered and provided;
• Fall protection (Harness/restraint lanyards, etc.) shall be worn and suitably attached by all personnel working within the immediate area (no access zone) surrounding the walkway penetration or unprotected edge where there is a potential to fall;
• The possibility of dropped objects shall be evaluated and controls implemented;
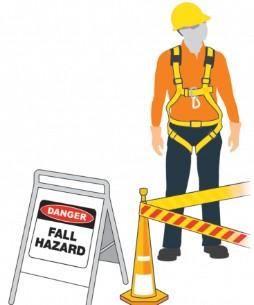
• The integrity of the floor is to be checked to ensure that the surrounding area would not be affected structurally by the floor being removed;
• Work should be planned to include a designated lay down area for the sections to be removed; and
• Identify the correct lifting requirements for the sections to be removed.
5 Requirements for specific hazards
5.1 Dropped/Falling Objects
All work at heights activities shall consider the risk of dropped/falling objects and potential for injury or damage to personnel or equipment below. This shall be included as part of the risk assessment for the task. These risks shall be controlled in accordance with AGL Macquarie Dropped/Falling Objects Procedure.
Where a risk exists, control measures must be implemented, which may include:
• Materials and equipment properly secured, especially during dismantling, lifting or moving;
• Placing tar paper, scaffold mesh, plastic sheeting or other material on grid mesh or working surfaces where items could fall through;

• Installation of scaffold mesh infill, brickie guards or screens between handrails and toe boards;
• Scaffolding erected to correct standards (e.g. kick/toe boards);
• Using buckets/ tool pouch/tool belt or suitable containers for tools, off-cuts, welding rods stubs, nuts and bolts, etc.;
• Use of heavy duty lifting bags for larger items
• Using lanyards/wrist straps on hand tools (including mobile phones) and chin strap on safety helmets;
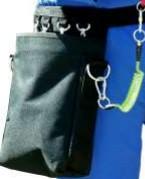
• Removing items from clothing pockets or preventing items from falling by securing zips and/or buttons;
• Providing catch scaffold or safety net under the job; and
• Providing adequate exclusion zone with barricades and warning systems to prevent people entering an area where falling objects may injure them.
Barricading and warning signage shall be placed on all lower levels where personnel or objects may fall. The area to be barricaded should consider the height at which the work is being carried out, as well as pipe work and
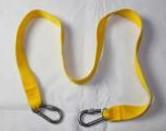
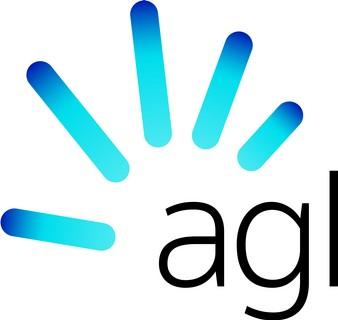
Working at Heights and Fall Prevention Technical Guide
structures that could deflect a falling object. All barricading shall be in accordance with the AGL Macquarie Barricading Procedure SAFP 003.
The leaning of tools and equipment, etc. against handrails must not occur. Tools and equipment that are required to be left unattended at a work at heights job site for any length of time are to be secured in such a way as to prevent them falling. Consideration should be given to securing tools and equipment in the case of a change in weather i.e. winds, rain, etc.
Upon completion of the work, staff shall ensure that all tools and equipment have been removed prior to removing any barricading.
5.2 Work on roofs
All work on roofs, including roofs of buildings, structures, and tanks, shall be subjected to a risk assessment, and must consider both the potential to fall over an unprotected edge as well as through the roof itself.
All roof surfaces shall be considered fragile or brittle unless written evidence is obtained that the roof complies with the load requirements of Australian Standard or is approved by a suitably qualified engineer. Warning notices should be mounted on fragile or brittle roofs (where access is possible) advising of the hazard and must detail access requirements.
Where roof access is required, access should be via the following methods, as deemed appropriate to the task and level of risk:
• Stairways;
• Permanent ladders;
• Scaffolding;
• Properly secured temporary ladders where the height to the roof does not exceed 6 metres; or
• EWP (subject to a risk assessment and requirements of the EWP Procedure).
Where access ways and designated walkways are provided, they are to be used at all times. All work on fragile roofs that do not have designated walkways is to have secured roof ladders, walkways or planking installed for use. Scaffold planks are to be secured to prevent them moving or falling. Where planks do not provide sufficient safety, scaffolding platforms shall be used. Where planks or walkways do not provide sufficient levels of safety (i.e. slipping/stepping off planks onto fragile roofing), additional precautions such as fall prevention or fall-arrest shall be used.
Where there is a risk of falling over an unprotected edge of a roof, temporary edge protection shall be installed, or fall restraint/fall-arrest used, where edge protection is not assessed as possible.
Any scaffolding components erected for walkways or temporary edge protection are to be inspected at least quarterly, in accordance with the AGL Macquarie Scaffolding Procedure.
Other considerations when working on roofs include:
• The slope of the roof;
• How tools, materials and equipment will be raised, lowered, and stored on the roof;
• How a person will be anchored to a suitable anchor point;
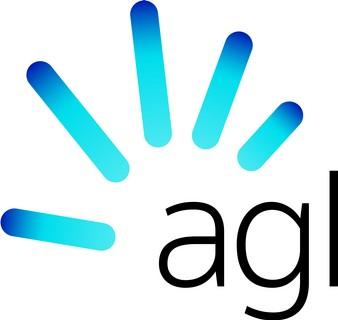
• Weather conditions;
• The contents of any tanks;
Working at Heights and Fall Prevention Technical Guide
• The proximity to live power lines or other overhead hazards; and
• Rescue arrangements.
5.3 Ladders
General requirements for safe use of ladders are:
• The ladder shall be compliant to the relevant AS Standards;
• Ladders shall only be used primarily as a means of access and egress and shall only be used as a working platform if there is no higher level of risk control that is reasonable and practicable;
• Only light duty work shall be undertaken on a ladder;
• Welding, oxy-cutting and using grinders is prohibited from being conducted on all ladders;
• Extension or single ladders should only be used as a means of access and egress from a work area, not as a working platform. Scaffolding, EWPs or Platform Ladders should be used as alternatives;
• Working from ladders, where the height of the user’s feet is at or above 2.0 meters, or where there is a risk of falling 2.0 metres or more, is deemed to be high risk and additional fall prevention measures are required, such as wearing a harness and lanyard attached to an anchorage;
• All extension, step and platform ladders shall be fitted with a Multitag “ladder Inspection Record” Tag, which when completed, indicates that the ladder has been visually inspected and deemed fit for use;
• Ladders should extend at least one meter above the access level;
• Ladders should be firmly secured. This includes being either tied off at the top and/or bottom or firmly held by another employee at the base;
• Barricade or tape the work area while ladder in use; and
• Only platform ladders with edge protection and guards should be used for working off, and their use is to be minimised to that which cannot be done by other means. EWP’s or scaffolding are always preferable to ladders for accessing heights
Fixed ladders

The use of fixed ladders on AGL Macquarie sites should be avoided wherever practicable. Install stairs and platforms, where practical to provide access. Some fixed ladders have fixed barricades over them, restricting their use to authorised personnel with the appropriate safety controls in place.
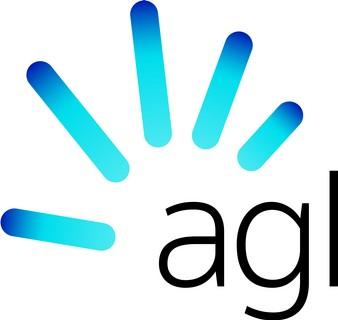
Working at Heights and Fall Prevention Technical Guide
Fixed ladders should be designed, installed and maintained in accordance with the relevant Australian Standard (e.g. ladders in chutes or cages).
General ladder considerations
When using ladders the following should be adhered to:
• Use the correct ladder for the task;
• The tag of the ladders should be checked and the ladder should be inspected prior to use;
• The ladder used should be manufactured for industrial use and have a load rating of at least 120kg;
• Examine ladders for any defects and damage before use;
• The use of extension ladders should be managed in the same way as any other ladder;
• The ladder shall be set up on an angle of 4 in 1 (ladders should be angled out one and four up);
• Ladders should extend at least one metre above the level being accessed.;
• Ladders shall be firmly secured. This includes being either tied off at the top and/or bottom or held firmly by another employee at the base;
• When securing the ladder the ties shall be attached to the stiles of the ladder and not the rungs;
• Persons should remain within the stiles of the ladder while carrying out short duration tasks;
• The ladder shall not be “walked” by the employee standing on the ladder;
• Only one employee may be on a ladder at one time;
• Employees on a ladder should maintain 3 points of contact;
• Do not climb higher than the third rung from the top on the ladder;
• Metal or wire reinforced ladders should not be used during electrical tasks;
• Ladders shall not be used as support planks or work platforms;
• Ladders should be cleaned and well maintained; and
• Barricade or tape the work area while the ladder is in use.
Ladder Maintenance
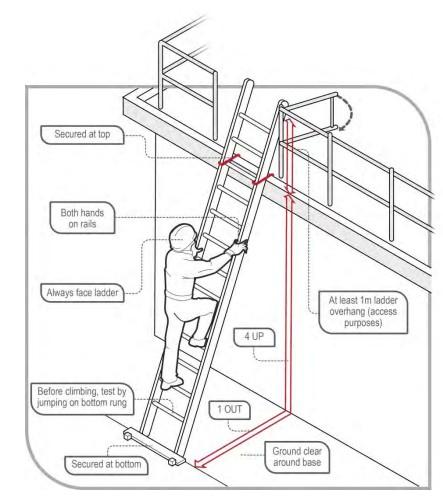
Ladders are to be inspected and tagged annually and documented in a register. Pre-use inspections are to occur and ladders found with any of the following faults must be replaced or repaired:
• fibreglass stiles cracked, chipped or severely faded with fibres exposed
• timber stiles warped, splintered, cracked or bruised
• metal stiles twisted, bent, kinked, crushed or with cracked welds or damaged feet
• rungs, steps, treads or top plates that are missing, worn, damaged or loose
• tie rods missing, broken or loose
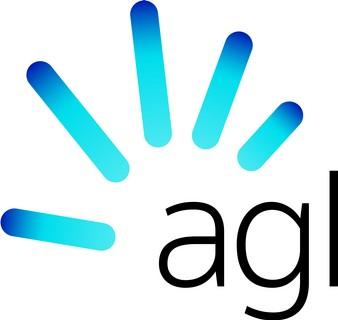
Working at Heights and Fall Prevention Technical Guide
• ropes, braces, or brackets that are missing, broken or worn
• timber members that are covered with opaque paint or other treatment that could disguise faults in the timber
• missing, loose, bent or worn fasteners, i.e. rivets, bolts and pins
• worn or damaged feet, including non-slip material
6 Inspection and Testing
Inspection and testing of fall-arrest equipment shall be carried out in accordance with AS1891.4. The requirements for the inspection of fall-arrest equipment are summarised in the table below.
Operator inspection
The following items must be subjected to inspection by the operator of each before and after each use to ensure that it is in a serviceable condition:
a) Personal equipment-harnesses, lanyard assemblies, connectors, fall-arrest devices.
b) Common use equipment-ropes, slings, fall-arrest devices, mobile attachment devices together with any other items in Item (a) above that are provided for common use.
c) All fall arrest and restraint devices including harnesses and anchor points must be inspected and certified.
d) All fall arrest equipment must be maintained and inspected in accordance with the relevant Australian Standards.
Inspection must be by sight and touch. Operation of the locking mechanism on fall-arrest devices must also be checked.
The continued efficiency and durability of equipment used by personnel is essential to protecting them from serious injury or death in the event of a fall. Proper and thorough inspection at the time of each use is the first line of defence against the hazards of faulty equipment. Any damaged equipment shall be reported upon return and taken out of service so appropriate means of repair can be arranged.
Activity Application
Inspection by operator before and after each use
6-monthly inspection by a competent person*
• Personal equipment, including harnesses, lanyards, connectors and fall-arrest devices (including common-use devices).
• Harnesses, lanyards, associated personal equipment.
• Fall-arrest devices (external inspection only)
• Ropes and slings.
• Horizontal or vertical lifelines – fibre rope or
Summary of Inspection Requirements in Accordance with AS1891.4:2009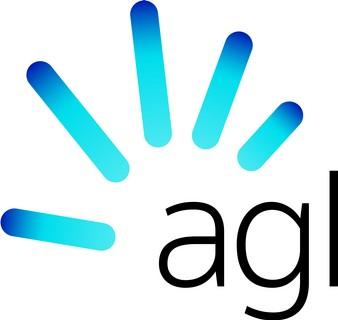
Working at Heights and Fall Prevention Technical Guide webbing.
• Permanently installed anchorages.
12-monthly inspection by competent person*
Inspection on entry or re-entry into service by competent person
Inspection after a fall-arrest (and before further use) by a competent person
• Fall-arrest devices – full service.
• Horizontal and vertical lifelines – steel rope or rail.
• All items of personal and common use.
• All items that have been involved in a fall.
Equipment used in harsh environments (chemical areas, in hot work or exposed to weather for extended periods) should be inspected more frequently – typically twice as often as is listed in the table above.
Equipment which has Arrested a Fall or Shows a Defect
Any piece of equipment, including both personal and permanently installed items, which has been used to arrest a fall or which shows any defect during operator or periodic inspection must be withdrawn from service immediately and a replacement obtained. An information tag indicating the condition or defect should be attached to the equipment, and it should be examined by a competent person who will decide whether the equipment is to be destroyed or repaired if possible and returned to service.
Life Expired Equipment
Life expired equipment must be taken out of service as follows:
• Personal equipment – items which have been marked with a date by which they are to be taken out of service, in accordance with AS1891.4:2009 – Industrial Fall Arrest Systems and Devices – Selection, Use and Maintenance and that date has been reached, must be taken out of service and destroyed.
• Horizontal life lines and rails – items which according to their associated system information plate are either to be taken out of service or re-certified by a certain date must either be dismantled or have recertification that the system is safe for continued use completed before the nominated date.
Destroyed means to render the equipment un-useable, such as cutting up components prior to disposal.
Record of Inspections
Inspection records shall be maintained for all inspections of equipment, except those carried out as part of pre and post use inspections.
Fall Protection Equipment
Inspection requirements for equipment including scaffolds and EWPs are to be carried out in accordance with the relevant site procedures referred to in this document. All inspections are to be carried out by competent persons in line with Australian or industry standards.
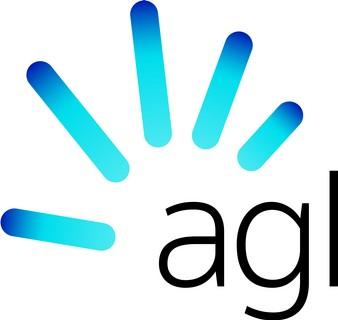
7 Definitions
Term Definition
Competent Person
Fall-Arrest Device
Fall-Arrest System
Free Fall
Fall Prevention
Fall Restraint
Height Safety Equipment Inspector
Inertia Reel
Lifeline or Static line
Observer
Working at Heights and Fall Prevention Technical Guide
A person who has, through a combination of training, qualification and experience, acquired knowledge and skills enabling that person to correctly perform a specified task.
A self-locking device meeting the requirements of AS 1891.3 with the function is to arrest a fall.
A system of interconnected components comprising a harness connected to an anchorage point or anchorage system either directly or by means of a lanyard or fall-arrest device and whose purpose is to arrest a fall in accordance with AS 1891.4 and this procedure. This includes rescue equipment (e.g. peer rescue systems and tripods).
Any fall or part of a fall where the person falling is under the unrestrained influence of gravity over any fall distance, either vertically or on a slope on which it is not possible to walk without the assistance of a handrail or hand line.
Refers to methods, devices and controls that prevent a person from falling whilst working at height.
A method of fall prevention that does not allow a person to reach a position where they could fall, by limiting the distance or amount of movement a person has.
A person who is competent in the skills needed to detect faults in height safety equipment and to determine remedial action.
(Also known as a self-retracting lanyard or fall-arrest block) is a type 2 or 3 fall-arrest device that arrests a fall by locking onto a line and at the same time allows freedom of movement.
A horizontal or substantially horizontal line to which a lanyard may be attached and which is designed to arrest a free fall.
A person who is trained in working at heights and peer rescue and who is in the immediate vicinity of the work. The Observer must constantly observe the work at heights and be ready to initiate emergency response including peer rescue if needed. The observer must not conduct any other work which may interfere with their primary role of monitoring the work being conducted at height.
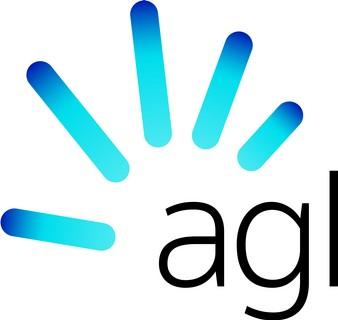
Term
Personal Energy Absorber (or deceleration device):
Rollout
Shall ensure that
Total Fall Distance
Working at height
Working at Heights and Fall Prevention Technical Guide
Definition
A device which reduces the deceleration force imposed when a fall is suddenly arrested, and correspondingly reduces the loadings on the anchorage and the person’s body. The energy absorber may either be a separate item or manufactured as part of the lanyard.
An involuntary disconnection of components when the snap-hook disengages from the anchor point. It is commonly caused by incompatible hardware such as small D-rings or anchor eyebolts causing the snap-hook gate to push open in a twisting action.
Must ensure, so far as is reasonably practicable.
The total distance a person is likely to fall during both the free and restrained parts of a fall and includes the maximum dynamic extension of all supporting components.
Working at Heights refers to any work activities where there is a risk of a fall by a person, object, or material from one level to another that is reasonably likely to cause injury.
8 Referenced Documents
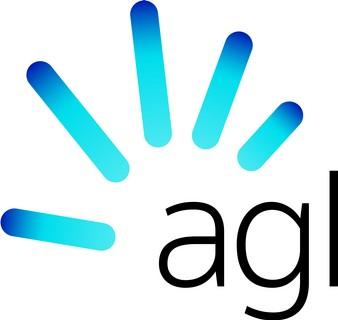
Document Number
AS1891.4:2009
Working at Heights and Fall Prevention Technical Guide
Document Title
Industrial fall-arrest systems and devices—Selection, use and maintenance
AS1892 Portable Ladders series
AS 4488
Industrial Rope Access Systems series
AS 4576:1995 Guidelines for Scaffolding
AS/NSZ 4994
ISO 22846.2
To be developed
Temporary Edge Protection series
Personal Equipment for Protection Against Falls – Rope Access Systems Code of Practice
Working at Heights Activity Register
AGLM-HSE-PRO-004.02 Permit to Work Procedure
AGL-HSE-STD-007.2 Working at Heights and Fall Prevention Standard
AGL-HSE-SDM-007.2 Working at Heights and Fall Prevention Methodology