
www.durlon.com
info@durlon.com
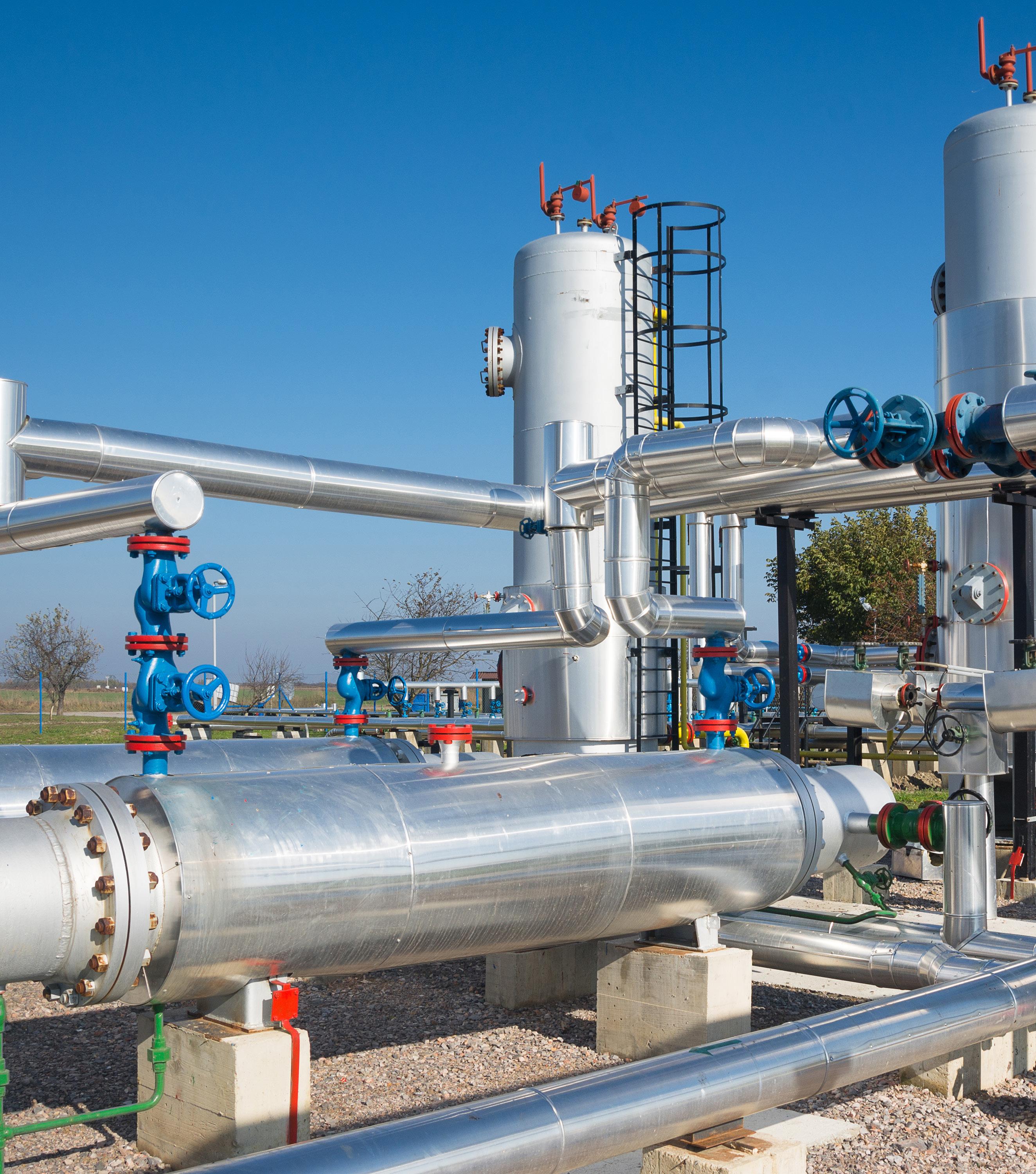

www.durlon.com
info@durlon.com
Evolution isn’t a choice in today’s business landscape, it’s the only way to succeed.
Progress relies on everything moving forward; from people to machinery to production. Everything must flow.
As we engineer our way to a better world, we are breaking down barriers, making sure each process is in place, always reflecting and improving. We are experts at delivering the best sealing solutions to help our customers unlock their highest potential.
Our global community of industry leading specialists drive our innovative production and materials to consistently raise the bar.
Whether through the stress of everyday use, or specialized applications and hightemperature environments, liquid or gas, our products deliver sustainable integrity.
At Durlon, we succeed when you succeed.
The oil and gas industry is a major global sector that involves the exploration, production, refining, and distribution of petroleum products. The industry plays a critical role in meeting the world’s energy needs, providing fuel for transportation, heating, and electricity generation, as well as a wide range of other industrial and consumer applications. Here is an overview of the oil and gas industry, including its flow process and major challenges.
The first stage in the oil and gas industry is exploration, which involves the search for underground reservoirs of hydrocarbons, such as oil and natural gas. This is typically done using a combination of geologic, geophysical, and seismic data analysis, as well as drilling test wells to assess the presence and quality of the hydrocarbon deposits.
Once a viable reservoir is identified, the production phase begins. This involves drilling one or more production wells to extract the hydrocarbons, using a variety of technologies and techniques to optimize the efficiency and yield of the extraction process. The extracted oil and gas are typically transported to a processing facility, such as a refinery or a gas plant, for further processing and distribution.
The refining and processing of oil and gas involves a complex series of steps that are designed to separate the hydrocarbons into their various components, such as gasoline, diesel fuel, and jet fuel. The process typically begins with the separation of crude oil into its different fractions, using techniques such as distillation, cracking, and blending.
Once the different fractions are separated, they are subjected to further processing and treatment to remove impurities and improve their quality and properties. This may involve additional refining steps, such as hydro-treating, reforming, and alkylation, as well as the addition of additives and other chemicals to enhance the performance and environmental characteristics of the final products.
Once the refined products are produced, they are transported to various distribution points, such as terminals, pipelines, and storage facilities. From there, they are delivered to retailers, wholesalers, and other end users, such as gas stations, airports, and industrial consumers.
The oil and gas industry faces a number of challenges and opportunities in the current
global economy. One of the major challenges is the transition to a low-carbon future, which is driving increased investment in alternative energy sources, such as wind, solar, and biofuels. This has led to growing pressure on the industry to reduce its carbon footprint and adopt more sustainable practices.
Another major challenge is the volatility of oil and gas prices, which are subject to a range of economic, political, and environmental factors. Companies must be able to navigate these
fluctuations in order to remain competitive and profitable, while also investing in new technologies and innovations to improve efficiency and reduce costs.
Despite these challenges, the oil and gas industry remains a vital and dynamic sector that plays a critical role in meeting the world’s energy needs. As the global economy continues to evolve and transform, the industry must adapt and innovate in order to stay ahead of the curve and continue to provide value to its customers and stakeholders.
Durlon® Durtec® gaskets are made with a specially engineered machined metal core that is bonded on both sides with soft covering layers, typically flexible graphite. The core is produced by proprietary technology that allows the finished gasket to have the best possible mechanical support function. The Durtec® core is virtually uncrushable, unlike conventional corrugated metal core gaskets. The precision construction guarantees that Durlon® Durtec® gaskets will have excellent sealing characteristics even under low bolt loads.
The Durtec® gasket is designed to withstand high temperatures and pressures, to be blowout resistant, to be fire safe, and to resist toxic and or corrosive chemicals for such applications as: pipeline flanges, valves, small & large pressure vessels, heat exchangers, towers, and tanks.
Gasket Factors
**Passed modified API 607 fire test and meets the requirements of Shell Specification MESC SPE 85/203 & PVRC SCR Flexible Graphite Spec for FG 600 material.
Durtec® is a registered trademark of Triangle Fluid Controls Ltd.
pH range, Room Temperature 0-14
*Depends on facing material and metallurgy of core. Note: Data shown above is for Inconel® 625 core and HT1000® covering layers.
SIZE, TYPES & MATERIALS:
• Standard ASME, DIN, JIS and BS EN sizes
• Non-standard flanges ½” through 157” diameter
• Standard core material is 316L stainless steel. Other core materials: SS304, SS321, SS316Ti, Monel®, Titanium, Hastelloy® & Alloy 20 can be manufactured to your specifications on request
• Alternate facing material is available upon request. Popular materials include Durlon® 9600 expanded PTFE (ePTFE), mica & ceramic
API 607 fire test:
• Average bolt torque loss (with no adjustments): Upstream 45%; Downstream 33%
• Fire, Cool-Down & Post-Burn: Combined Leak Rate (2 gaskets) 0 mL/min at 30 psig avg.
• Exxon requirements post burn: Combined Leak Rate (2 gaskets) with no flange bolt re-torques at any test pressure 0 mL/min at 30 psig, 0mL/ min at 50 psig, 0 mL/min at 100psig and, 0mL/ min at 200 psig.
Composition
Aramid -Inorganic NBR
Inorganic Filler / Pure PTFE Resins
Temperature:
-40°C (-40°F)
496°C (925°F)
400°C (752°F)
(-350°F)
(520°F)
(500°F)
Spiral Wound Gasket Extreme Temperature Gasket
650°C (1,200°F)
to 1,000°C (1,832°F)
Specially Engineered Metal
(-328°F)
(1,832°F)
(1,200°F)
Durlon® SWG - All Durlon® SWG’s are manufactured according to ASME B16.20 standards. Quality Assurance complies with API Specifications Q1 and ISO 9001 standards. Super Inhibited Graphite meets the requirements of Shell Specification MESC SPE 85/203 and meets PVRC SCR Flexible Graphite Spec for FG 600 material.
Durlon® ETG adds an inner and outer protection boundary in the form of a mica-phyllosilicate based sealing material - Durlon® HT1000® : consists of phlogopite mica paper impregnated with an inorganic binder at less than half the binder amount found in a typical vermiculite-phyllosilicate filled product. This lower binder content allows for superior weight retention and results in ultimate extreme temperature sealing performance. Durlon® Durtec® - Physical Properties: dependent on facing material and metallurgy of core, data shown above is for Inconel® 625 core and HT1000® covering layers. Durlon® Kammprofile* - Max temperature is dependent on material used.
Style
Certifications
8900 ANSI/API 607 Fire Test with 6th Ed., Zero leakage, RoHS Reach Declaration compliant.
9000 Passed API 6FA, 3rd Edition Fire Test, Met requirements of 121ºC (250ºF) for USP for Plastic Class VI, Conforms to required 21 CFR 177.1550 for FDA, TA-luft (VDI Guideline 2440) approved material, ABS-PDA & Pamphlet 95 approved material - chlorine institute, (EC) 1935/2004 & EU (10/2011) approved material.
SWG TA-luft (VDI Guideline 2440), API Standard 6FB Fire Test- 6 inch Class 300 SWG FG
ETG API 6FB, Fourth Edition 2019,Type 1 (Onshore Test), API 6FB, Fourth Edition 2019,Type 2 (Offshore Test), API 607, 4th edition Fire Test with Exxon modifications.
Durtec® Passed modified API 607 fire test and meets the requirements of Shell Specification MESC SPE 85/203 & PVRC SCR
Kammprofile RoHS Reach Declaration compliant. Physical Properties
Flexible Graphite Specification for FG 600 material, RoHS Reach Declaration compliant.
Note: ASTM properties are based on 1/16” sheet thickness, except ASTM F38 which is based on 1/32” sheet thickness. This is a general guide only and should not be the sole means of accepting or rejecting this material. The data listed here falls within the normal range of product properties, but should not be used to establish specifications limits nor used alone as the basis of design. For applications above Class 300, contact our technical department.
Warning: Durlon® gasket materials should never be recommended when both temperature and pressure are at the maximum listed. Properties and applications stated are typical. No applications should be undertaken by anyone without independent study and evaluation for suitability. Never use more than one gasket in one flange joint and never reuse a gasket. Improper use or gasket selection could cause property damage and/or serious injury. Data reported is a compilation of field testing, field service reports and/or in-house testing. While the utmost care has gone into publishing the information contained herein, we assume no responsibility for errors. Specifications and information contained within are subject to change without notice. This edition cancels and obsoletes all previous editions.
TRANSPORTATION
The oil and gas industry is divided into three main segments: Upstream, Midstream, and Downstream.
Here is an overview of each segment:
UPSTREAM
Product List
SWGs, Durtec®, ETG, Kammprofile
SWGs, Durtec®, ETG, Kammprofile
8300, 8500, 9000, Durtec®
8300, 8500, 8900, 9000, 9002, 9200, ETG, Durtec®, SWG, Kammprofile, FGL316
8500, 9000, 9002
8300, 8500, 8900, 9000, 9002, 9200, Durtec®, SWG, Kammprofile, FGL316
8500, 9000, SWG
8500, 9000, 9002, FGS95
The upstream phase of oil and gas production involves the exploration and drilling of oil and gas wells.
1. Well heads: Used to control the flow of oil and gas from the well (Well head equipment, artificial lift systems, and flow control equipment).
2. Drilling rig: Used to drill oil and gas wells (Drilling rigs, drilling bits, drill pipes, casing, and cementing equipment).
MIDSTREAM
The mid-stream phase of oil and gas production involves the transportation of crude oil and natural gas from the well site to processing facilities.
3. Gathering lines: These are used to transport crude oil and natural gas from the well site to processing facilities (Pipeline systems, pumping stations, and storage tanks).
4. Processing facilities: Used to separate crude oil and natural gas from other impurities such as water and sediment (Distillation columns, heat exchangers, separators, and de-salters).
5. Transportation: To transport crude oil and natural gas from processing facilities to refineries and other distribution centers (Pipelines, tankers, and trucks).
DOWNSTREAM
The downstream phase of oil and gas production involves the refining and distribution of petroleum products.
6. Refineries: Used to convert crude oil into various petroleum products such as gasoline, diesel, and jet fuel (Distillation columns, catalytic crackers, hydro-crackers, reformers, and hydro-treaters).
7. Storage: Used to store refined petroleum products before they are transported to distribution centers (Storage tanks, pumps, and valves).
8. Tanker trucks and ships: Used to transport refined petroleum products from storage facilities to retail outlets (Tank trucks, railcars, pipelines, and tanker ships).
The core of the Durlon® brand is to provide fluid sealing solutions that make sense, both financially and strategically. We accomplish this through process-oriented design, sector-specific knowledge, and extensive testing. Our goal is to ensure
performance and safety while adhering to the quality management system registered to ISO 9001:2015.
At Durlon, we offer specially developed sealing solutions tailored directly to your specific needs.
Distributed by: