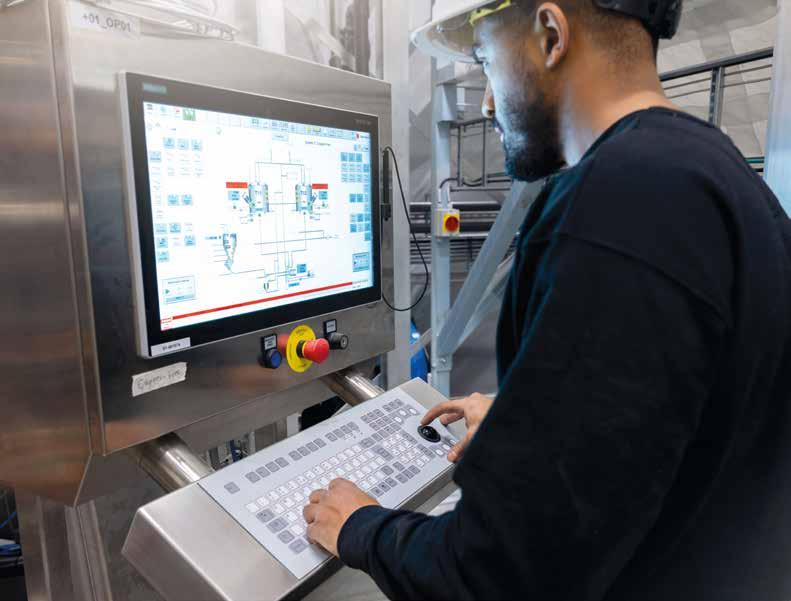
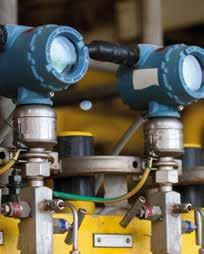
SAFETY
18 PUMPS
Interface Portfolio for Ex and SIL Applications
19
Hermetically Sealed Pump with Magnetic Coupling
SAFETY
18 PUMPS
Interface Portfolio for Ex and SIL Applications
19
Hermetically Sealed Pump with Magnetic Coupling
Steen-Hansen – a Norwegian manufacturer of fouling prevention and net protecting solutions for aquaculture use as well as of specialized industrial paint systems – has not only successfully overcome quality problems with its newly developed antifouling coatings, but also significantly shortened process times, simply by switching its production facilities to state-of-the-art mixing and dispersion technology.
Steen-Hansen has been a leading provider of antifouling coatings for nets in industrial fish farming for more than 30 years. Antifouling coatings reduce the growth of algae and other organisms on the nets, meaning they can be used for longer periods of time. In addition to conventional copper-based antifouling coatings, copper-reduced – not to mention completely copper-free and biocide-free coatings – are becoming increasingly important in the fish farming industry. SteenHansen is a pioneer in the development and manufacture of coating solutions like these with a reduced environmental footprint.
Innovative coatings call for new process technology
Manufacturer Steen-Hansen initially used dissolvers, which it also used for its copper-
based coatings, to make these innovative antifouling coatings. However, the company found that using conventional production techniques for copper-reduced or copperfree coatings resulted in quality deficiencies, since the long process times in the dissolver caused strong, undesirable foaming in the product.
Several factors were responsible for this foaming. On the one hand, powders contain a great deal of air. Even heavy powders such as titanium dioxide contain more than 75% air by volume. If this air is not fully substituted by liquid and separated, but rather dispersed together with the powder particles, this creates micro foam, which is exactly what happens in a dissolver process. Additionally, the fact that – in a dissolver – the powder is added to the open vessel from above leads
to the creation of vortexes, which introduce large amounts of additional air. Since SteenHansen‘s products are water-based, another factor is the process water foaming, regardless of the technology used.
Steen-Hansen managed to counteract this undesirable foaming by using defoamers, but only to a certain extent. This is why the company was looking for a way to disperse the powdered raw materials in a gentler, more product-friendly way, ultimately opting for the technology offered by mixing and dispersion technology specialist ystral. ‘ystral’s process engineering solution allowed us to overcome the quality problems and, at the same time, significantly shorten our production times,’ reported Stig Bjarte Fagerlid (plant manager at Steen-Hansen AS).
In the ystral process system installed in
2019, the intense process steps of powder wetting and dispersion take place outside the vessel with the YSTRAL Conti-TDS inline powder wetting and dispersing machine, while the contents of the vessel are simultaneously mixed in a continuously homogeneous manner with a YSTRAL Jetstream Mixer.
Using the vacuum expansion method, the inline disperser achieves complete deagglomeration and wetting of the powder particles in a matter of microseconds. Due to an induction vacuum built up directly in the wetting and dispersing zone, the air contained in the powder is expanded many times over, enormously increasing the distances between the particles and allowing the particles to be completely wetted immediately, one by one, on contact with the liquid. The air contained in the powder is separated from the significantly heavier dispersion through the centrifugal effect of the fast-running rotor and coalesces to large air bubbles. These are then pumped to the process vessel with the liquid flow, where they can easily escape. There are no vortexes and there is no additional air intake during the entire process. This can help to significantly reduce the use of defoamers.
Based on this experience, the company decided to install two more ystral process systems while modernising and expanding its production capacities. ‘We completely reorganised our production facilities as part of a relocation, and aligned our entire production infrastructure with ystral technologies,’ commented Mr Fagerlid. ‘ystral technologies allow us to fully automate our production processes. But, at our old site, we were unable to exploit this potential. So we used the move as an opportunity to comprehensively automate the peripheral devices of the ystral systems with powder and liquid handling.’ Whereas, at the old production site, the operators still opened bags manually and poured their contents into the ystral system’s powder hopper, now all the powder materials are fed from the silo to the ystral systems by means of a fully automatic chain conveyor.
At its new site, Steen-Hansen uses one system each for producing antifouling coatings containing copper, for making copper-free coatings, and for manufacturing industrial paints. A system consists of two process vessels with YSTRAL Jetstream Mixers, a powder vessel and the YSTRAL Conti-TDS inline dis-
perser, which is operated alternately on one of the two process vessels. While powder and liquid handling at Steen-Hansen is performed using a central control system, each system is fed from separate silos and tanks. This eliminates the possibility of the copperfree coating products being contaminated with copper particles, for example.
The YSTRAL Control System (YCS) Professional + – the ystral control system with the highest degree of automation – is used as the control software for the three systems. The operator starts and monitors the process using a graphical user interface, and dosing and feeding of the liquid components and solids is fully automatic. Every single process step is exactly reproducible, and creating new recipes is child’s play with the recipe handler.
By using modern mixing and dispersing technology and centrally controlled peripheral devices with automated feeding and dosing of powder and liquid components, Steen-Hansen successfully tripled its production capacity at its new site, all the while keeping its staff levels the same. The three ystral systems can be operated by just one employee. With the dissolvers previously used, the process often lasted one to two hours, but this was shortened to between 10 and 15 minutes with the ystral technology. While Steen-Hansen was barely able to meet the rapidly growing demand for its products with the production infrastructure it used previously, even in two-shift operation, it has now switched to one-shift operation in the new factory.
The significantly shorter process time also goes hand in hand with a considerable reduction in energy consumption - which is particularly important to Norwegian producer Steen-Hansen, since electricity prices are high in Norway. Measured in terms of electricity demand per litre of finished product, Steen-Hansen cut its electricity demand at the new site by about 75% –simply by using more efficient mixing and dispersing technology and energy-saving building technology.
64511 at www.pcne.eu
Forflexibleanddecentralisedmonitoringsolutions
Turck expandsitsFluid+series withanIO-Linkprocessingunit forremoteflowsensorswitha plaintextdisplayandIP67protection.Theflexibleuseofdifferentmeasuringprobesenablesthe FS121tocoverabroadrangeof applicationsandthusallowsconsiderablecostsavings.Forexample,theflowsensorsolutionis idealforuseinmodularprocessskids,lubricationsystems,compressorcoolingsystemsinconfinedspaces,cleaningandwashing systems,aswellasforapplicationsinthefoodandbeverageindustry. TherobustFS121withIP67protectionallowsdecentralized cabinet-freeinstallationclosetotheprocess,makingitidealfor applicationswithfewmeasuringpointsorspecificpositioningrequirements.Itoffersuser-friendlyoperationthankstoits12-segmentalphanumericplaintextdisplayandtheIO-LinkSmartSensor Profile(SSP),aswellasothersmartfunctionssuchasQuickTeach forfastsetupandDeltaFlowMonitoringformonitoringflow changes.ThecompactFS121iscompatiblewiththeflowsensors oftheFCS,FP100(immersionsensors)andFCI(inlinesensors) series.ItintegratesseamlesslywithTurck'sIO-LinkTBENI/O modulesandthelatestversionoftheTurckAutomationSuite(TAS) includingTASCloudindecentralizedautomationsolutions.
65107atwww.pcne.eu
Supportforover100hardwareandsoftwareprotocols
HSYCO hasannouncedaplatform tosimplifycommunicationbetweenthearrayofdisparate proprietaryconnectivityprotocols usedinindustrialandbuilding automationsystems.Called HSYCOGateway,theplatform supportsover100differenthardwareandsoftwareprotocols,includingallthemostwidespread andusedincontrolapplications.Functionssupportedthroughthe HSYCOGatewayrangefromindustrialtobuildingautomation, includingsecurityandfireprotectionsystems,lighting,environmentalandenergymanagementtechnologies,Modbus,BACnet, MQTT,andradioprotocolssuchasLoRaWANandSigfox.These includewell-knownindustryleadersandnichevendors. Amongthe highlightsoftheHSYCOGatewayisitspowerfulscriptinglanguage,whichallowsquickandflexiblecustomizationofthecontrolapplication.Anotheruniquefeatureisthatthesoftwarelicense doesnothavedatapointslimitation;furthermore,manyextra servicesareincluded,suchasbackup/restoreandtunneling,for secureremoteaccess.TheHSYCOGatewayisdesignedtobe compatiblewithawiderangeofhardwareservers.Itisflexible enoughtoadapttoeachproject'sspecificneedsandoffersa varietyofstorageoptions,includinghigh-availabilityconfigurations,toensurethatdataisalwaysaccessibleandsecure.
Moduleswithbroadrangeoffunctionsandcertifications Safetyisputfirstwiththeuse oftheK-Systemfrom P Pepperl+ Fuchs:Itsbarrierfunctionlimits theenergyfedintotheintrinsicallysafecircuit.Thegalvanic isolationofthemeasuringand controlcircuitsprotectscontrol systemsandfielddevicesfrom interferencecausedbygroundloops,ensuringsignalreliability.The K-SystemisG3compliantandenablesuptoSIL3tobeachieved forallsignaltypes. With200isolatedbarriersand150signal conditioners,thepossibleapplicationsarepractical-lyunlimited, bothinhazardousareasandinmixedExandnon-Exareas.Simple installationandmaintenanceareensuredbyremovableterminal blockswithtestsocketsandtheinternaldiagnosticfunctionofthe modules.HARTsignaltransparencyallowseasyaccesstothefield devices.Themodulescanbemountedhorizontallyandvertically withoutde-ratingtheoperatingvalues.Downtimeisminimizedas themodulescanbehotswappedduringoperation.Theoperating temperaturerangeextendsfrom-40°Cto+70°C. Asthefirst 2-channelAI/AOintrinsicsafetybarrierwithdualfunction,the newKCD2-SCS*canbeconfiguredindividuallyforanaloginputor analogoutputcontrolsignals.Withacompact12.5mmhousing andapackingdensityof6mm/channel,thenewmodulesaves spacein thecontrolcabinet.
65013atwww.pcne.eu
Terminalcombinesweighingandsensorpowersupply WithitsfourEL336xEtherCAT analoginputterminals, B Beckhoff isofferingaparticularlycompact andcost-effectivesolutionfor integratingweighingfunctions intocontrolsystems.Theintegrationofthesupplyvoltageforthe loadcellsisparticularlyadvantageous. TheEL3361-0100andEL3362-0100EtherCATanaloginput terminalsfeatureanaloginputsforthedirectconnectionofoneor tworesistancebridges(straingauges)orloadcellsina4-wireor 6-wireconnectionsystem.The10Vsensorsupplyisalreadyintegrated.Theanalogvalueresolutionis24bitsand10ksps.Formore demandingapplications,theEL3361andEL3362alsooffera switchablesensorsupply(5/10V)anddigitalinputs(e.g.,fortare) andoutputs(e.g.,forreadymessages)thatcanbecontrolledeither locallyorviathecontroller. TheEL336xanalogterminalsarea welcomeadditiontoBeckhoff'sexistingrangeofweighingtechnology,slottingintotheportfolioabovetheEL3351andalongside theEL3356withadditionalfunctionalities.TheELM350xEtherCAT measurementterminals,whichsupportfreelyadjustablefilters, quarter/halfbridgecapability,andevenhighersamplingrates(also inconnectionwiththeTwinCAT3WeighingLibrary),aretheideal solutionforthemostdemandingdynamicapplicationsthatrequire anevengreaterlevelofmeasurementtechnology.
64793atwww.pcne.eu
CompatiblewithEtherNet/IP,ModbusTCPandPROFINET
Rotork introdudesanintegratedEthernetsolutionfortheintelligentIQ3 Proactuator.Adatagatewayisno longerrequired,thisreducescomplexityandincreasesthevolumeand speedofdataextraction,withtransfer ratesupto100Mbps.Thesolutionis alsohousedwithinarobustweatherprooforexplosionproofenclosureand supportsRJ45andM12connectionstandards.Compatibilityextendstoindustry-standardprotocols,withPIcertification,GSDML filesforPROFINET,andODVAcertificationwithsupportingEDS filesforEtherNet/IP. Dataiskeytooperationalexcellenceinthe eraofIndustry4.0.ThenewEthernetsolutionacceleratesdata transferandenhancesthecapabilityforin-depthdataanalysis.
65059atwww.pcne.eu
Magneticcouplingforconveyingofhigh-viscosityfluids
NETZSCH is presenting a new version of the NEMO® MY magnetically coupled pump. In addition to the previously available version with a flexible coupling rod made of PA12, a versionwitharobustBorKjointisnowalsoavailable,which enablesawiderrangeofapplications. Themagneticallycoupled pumpishermeticallysealedandthereforeleak-free,which guaranteesthesafetyofallemployeesandthesystem.Thepump hasbeenspeciallydesignedforsaferandmoresustainable conveyingoffluidswithhighviscosity,suchasslurriesinbattery production.ThemagneticcouplingoftheNEMO®MYwasspecially developed. Comparedtoconventionalpumpswithmechanical sealsorothersealingsystemsitofferssignificantcostadvantages.
65111atwww.pcne.eu
Eliminationofreflectionsinunfavourablelightconditions
Thestainless-steelpressuregauges andmechanicalthermometersfrom W WIKA havebeengivenafacelift.All visibleelastomerpartsarecoloured inthebrand'scharacteristicblue.In addition,thegaugesnowhaveaQR codeonthedialthatconnectsusers directlytoastandardisedWIKA productpassportwithallthedataontherespectiveinstrument. Lastbutnotleast,thisprotectsusersfromunauthorisedimitations ofWIKAproducts. Notonlythecolourofthewindowsealhasbeen changed,butalsoitscontour,sothattherearenolongerany metallicsurfacesinsidethecase.Thiseliminatestheriskofreflectioninunfavourablelightconditions.Themeasuredvaluecanbe clearlyregisteredinanysituation,especiallyoutdoors.
65136atwww.pcne.eu
Advanced pressure measurement technologies not only provide outstanding accuracy and reliability in chemical industry applications, but also help to minimise operational costs without compromising plant safety.
Chemical manufacturers depend on accurate and reliable pressure measurements in applications such as reactors, distillation columns, heat exchangers and storage tanks, to help optimise processes and ensure plant and worker safety. Some pressure measurement applications are relatively straightforward, which enables continued deployment of older and relatively basic instrumentation. However, in more critical and complex applications, the functionality provided by modern, advanced technologies create some significant benefits, including reduced costs and increased safety.
Distillation columns
For example, pressure measurements are vital for the operation of distillation columns, but the size of these columns can make it complex and costly to install and maintain measurement devices. For many years this application has relied on differential pressure (DP) transmitters in wet leg and dry leg systems. These devices, which use impulse piping as well as capillary-based solutions, are wellunderstood, but have certain disadvantages. For example, impulse lines are prone to plugging and can freeze in extreme cold, while DP transmitters with remote seals and capillaries have a limited measurement range and are difficult to install. Capillary systems are complicated to calibrate and maintain, have a relatively slow response time, and are sensitive to temperature changes, vibrations and physical stress. Capillaries are also fragile and prone to damage from physical impacts. If a seal is damaged, the complete capillary sys-
tem must be replaced, which makes inventory costs high. With all these challenges, the cost of installing a DP transmitter with capillaries can be five times higher than the cost of the device itself.
A better alternative is a measurement system based on electronic remote sensors (ERS), such as the Rosemount™ 3051S ERS System from Emerson. Rather than using a single DP transmitter with mechanical impulse piping or capillary, ERS systems use two pressure sensors connected with nonproprietary electrical wire that is immune to
the effects of temperature variations. The DP is calculated in one of the two sensors and transmitted to the distributed control system or a PLC using a standard two-wire 4-20 mA HART® signal. By removing mechanical connections, ERS systems not only provide a faster response time than traditional DP technologies but are also easier to install and maintain, thus reducing costs. Replacing difficult-to-install impulse piping with electrical wire makes installation quicker and 60% less costly compared to DP transmitters with capillaries. Additionally, while cold weather
Thousands of pressure transmitters can be deployed in a large chemical plant, so configuring them all can be time-consuming and costly.
installations of impulse piping and capillaries often require heat tracing or insulation to prevent freezing, electrical wire does not require heat tracing or insulation, which significantly reduces installation costs.
In applications with high levels of pressure and vibration, mechanical instruments such as Bourdon tube gauges are typically used to provide pressure monitoring and control. These simple devices can be cost-effective in some applications but have limitations that make them less suitable for critical applications where high accuracy, real-time monitoring and data integration capabilities are vital. Extreme temperatures, humidity, vibration and shock can make Bourdon tube gauges difficult to read, possibly leading to inaccurate readings which could affect product quality and profitability. Bourdon tube gauges are also sensitive to overpressure and lack diagnostics, creating a safety risk for personnel. In challenging applications, they may require additional options such as syphons, seals and glycol fill, which raises costs. In addition, their components wear out over time, creating a high failure rate and necessitating regular maintenance and calibration. Furthermore, mechanical gauges provide only a visual display and lack digital output options, which means that time-consuming and error-prone manual readings are required.
To support increased reliability, electronic wireless devices, such as the Rosemount Wireless Pressure Gauge from Emerson, replace Bourdon tube gauges with a solid state pressure sensor based on piezoresistive technology. Wireless gauges provide correct pressure information even in highpressure and high-vibration environments, and reduce costs by delivering up to 10 years of maintenance-free operation. These devices feature a large dial, making it easy for personnel to accurately read pressure
levels, while a blinking diagnostics LED indicates that a device is operating correctly. In addition, WirelessHART® communication technology enables them to deliver reliable pressure readings and device health status back to the control room as often as once per minute, supporting the central logging of historical data, improved maintenance planning and reduced costs.
Safety instrumented systems (SIS) are another challenging and critical application, requiring high levels of accuracy, repeatability and reliability. Pressure transmitters deployed in SIS must be regularly proof-tested to verify that they are working correctly and comply with safety standards. Performing a proof-test has traditionally been a timeconsuming, labour-intensive and costly procedure. However, the latest devices provide guides to easily lead operators through a step-by-step process outlined by the transmitter’s software or a handheld communicator, which saves time and reduces both complexity and costs.
Poorly performing pressure transmitters can impact safety and operational efficiency, so issues need to be identified quickly. To enable this, advanced instruments feature built-in diagnostics to continuously moni-
tor electrical loops and impulse lines. Issues can then be identified and alerts transmitted quickly, enabling corrective measures to be taken before process quality is impacted. The early detection of issues also enables maintenance to be scheduled during planned downtime, to minimise disruption and avoid additional costs.
Thousands of pressure transmitters can be deployed in a large chemical plant, so configuring them all can be time-consuming and costly. However, the Rosemount 3051 Pressure Transmitter from Emerson includes features that makes it easy to install, commission, configure, maintain and use. A user interface provides a straightforward, taskbased menu structure, enabling quick configuration in just a couple of clicks, saving a great deal of time and significantly reducing costs. The device offers Bluetooth® connectivity to reduce complexity further. This eliminates the need for a physical connection via a cable, which enables configuration and maintenance to be performed from a distance. This is especially beneficial if devices are installed on large storage tanks or distillations columns.
at www.pcne.eu