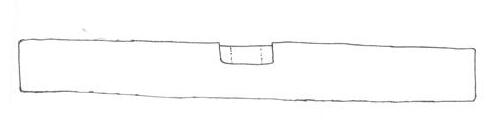
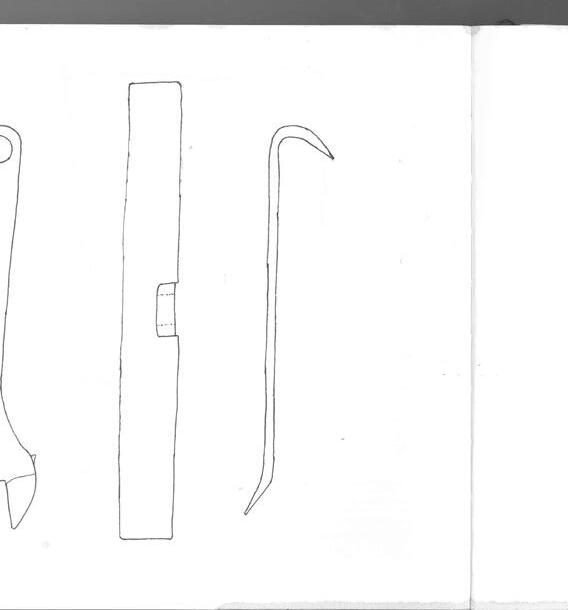
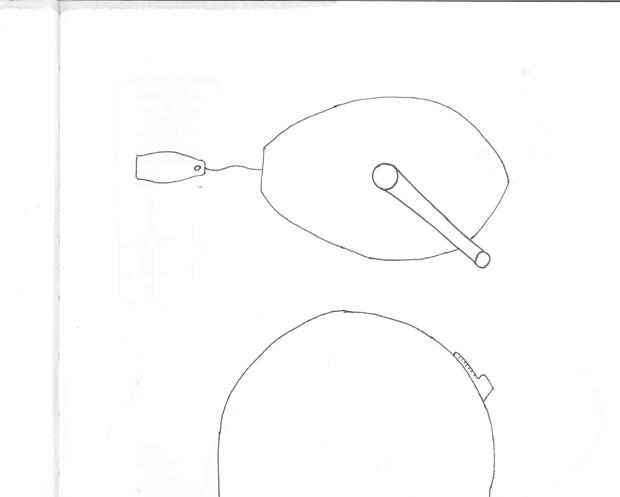

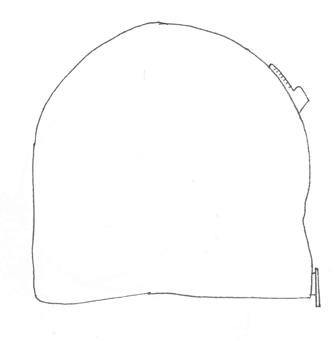

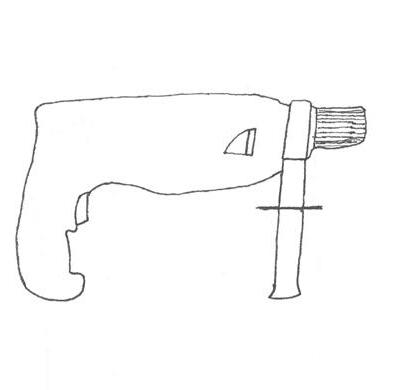
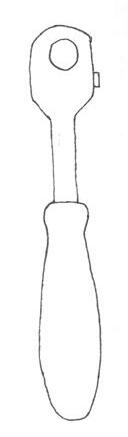
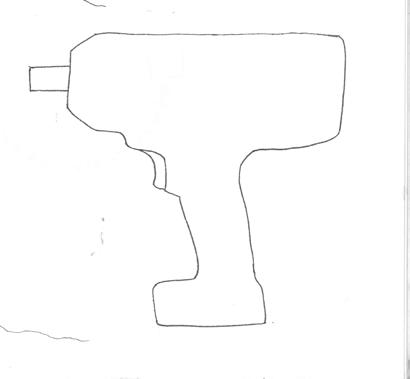
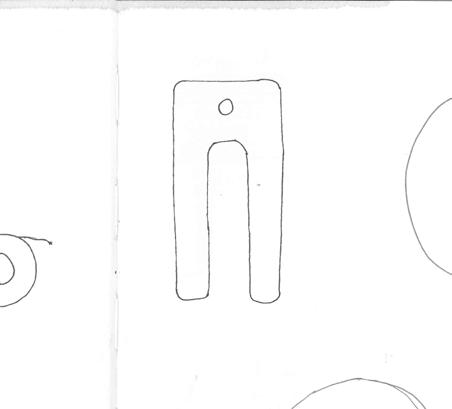
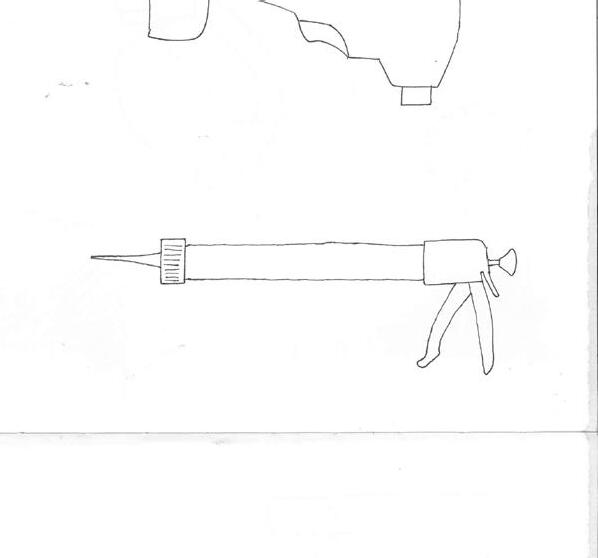
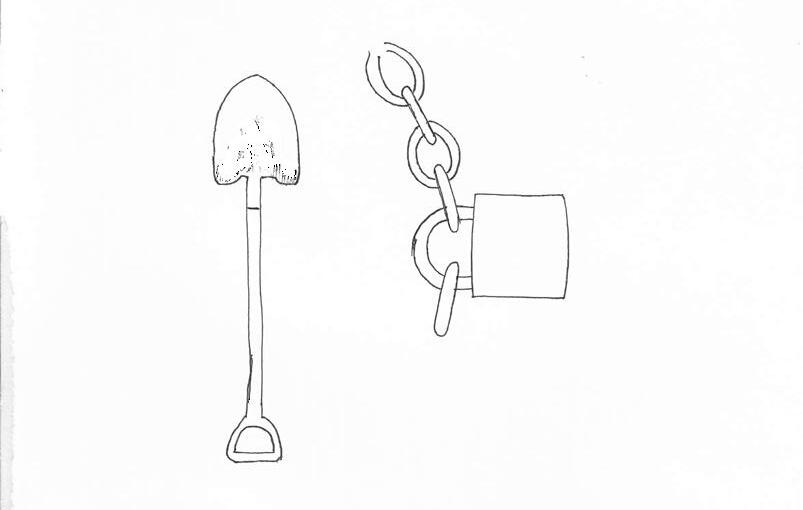
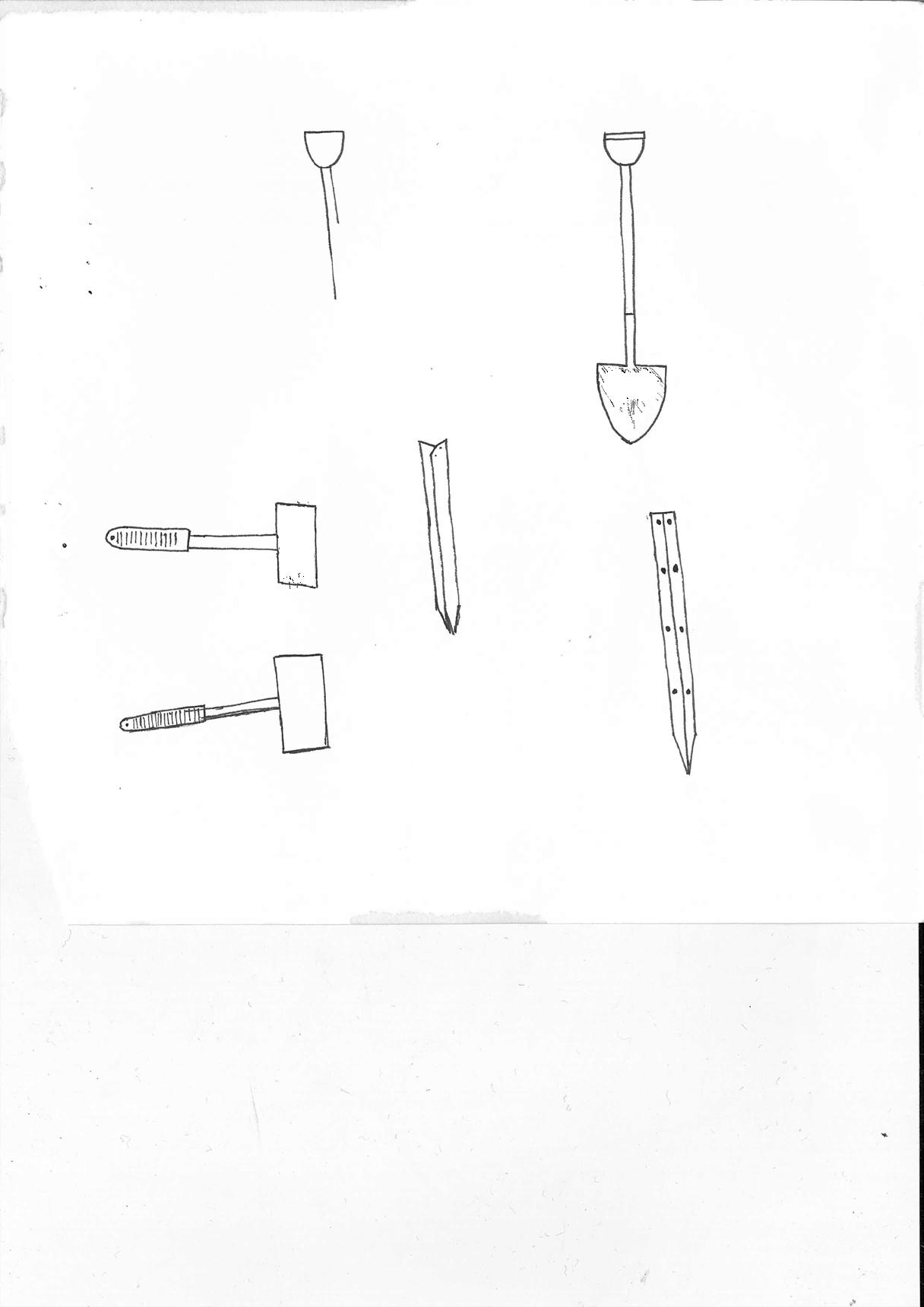
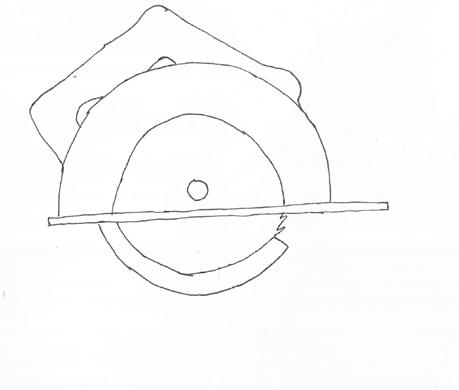

By Thomas Glassock-Warren
Is building your own home a feasible response to Australian housing unaffordability?
Housing affordability is at an all-time low in Australia with homeownership and the ‘great Australian dream’ an ever-distant fantasy for most Australians. The effects of housing unaffordability impacts more than an Australians' access to secure refuge with many financial systems built around the expectation of ownership including financing retirement.1 This is not the first time that housing issues have been prevalent in Australia with early settlement, post-World War 2 and the late 1960’s all containing periods of housing scarcity. Australians during these eras responded by taking construction of their home into their own hands to save on costs and overcome labour shortages, in a process known as owner-building.2 Australia is once again trending towards a climate for increased owner-building with the economy narrowly missing a recession combined with cost-of-living increases and the construction industry facing significant labour shortages due to declining new apprentices and increasing worker demand. Many of us may need to pick-up the tools to accomplish our dream home.
Housing and the construction industry in Australia has changed dramatically since the last major housing crisis of the 1960s with owner-builders now having to navigate highly challenging legal, financial, social and political systems in addition to more complex construction practices. The amalgamation of these systems is designed to discourage people from owner-building with insurances, construction licences, permits and financial loans heavily weighted against prospective owner-builders, placing them at severe financial and personal risk. This systematic dissuasion against owner-building has led to only a small percentage of Australia’s population fulfilling the necessary requirements to owner-build and the savings potential of owner-building to be difficult to achieve.3 Semi-prefabricated modular systems have been developed to aid owner-builders, responding to the demands of the regulatory authorities through clear, quick, quantifiable construction. However, these systems are currently limited to rural areas requiring significant space and are unresponsive to unique site conditions and client lifestyle, dictating a design response onto the owner-builder and their property.
BuildIY, a semi-prefabricated modular system developed within this project creates a greater accessibility to owner-building by both responding to the key challenges of the regulatory systems and providing a design adaptable enough to suit the site and lifestyle of any ownerbuilder. Designed to function within a suburban context the from the outset, the proposed system acts as a weatherproof and structurally sound canvas for owner-builders to then adapt to their specific aesthetic tastes and design ambitions, leaning into the greatest benefits of doingit-yourself, freedom, control and self-actualisation. The system developed considers the needs, challenges and motivations of an owner-builder at every stage of the project from site selection to final completion, designing a process of delivery tailored to improving the owner-builder experience and likelihood of the project being successfully completed. The success of this project in responding the legal, financial, social, political and construction constraints of ownerbuilding, as well as the design adaptability to various sites and lifestyles, will test the overall feasibility of owner-building as a response to housing unaffordability.
WHY OWNER-BUILD?
Housing Unaffordability
The Need for Ownership
Saving by Owner-Building
Additional Motivations
Regulatory Systems
Financial Systems
Keys To Success
Playing the System
THE DESIGN
BuildIY
How BuildIY Works
Adapting to Clients abd Site
Responding to Authorities
WHO CAN OWNER-BUILD?
Support System Is
Housing unaffordability in Australia is returning to its pre-COVID peak with house prices 16.4 times the average household income and continuing to rise. Whilst there are various contributors to the rise of house prices including the profitability of housing speculation through government policy such as negative gearing and capital gains discount creating additional demand.4 The rise of material and labour costs postCOVID are also exacerbating the issue with construction costs on average 30% higher than pre-COVID values.5 Labour shortages are the largest contributor to the increasing construction costs, currently sitting around 40% of total build costs with the construction industry suffering a chronic shortage of workers. There has been a year-on-year decline of new apprentices with the previous year reporting a significant drop of 25% causing the construction workforce to be deemed as aging. Continued government pushes for new infrastructure and housing development have further exacerbated the issue with the national goal of building 1.2 million new homes over the next 5 years, works for the 2032 Olympics and the 2050 Net Zero Plan amplifying.6 Projections from the Master Builders Association suggest Australia needs at least 500 000 more tradespeople by 2029 to keep up with construction demand with only 21 000 new qualified tradespeople last year, this figure is highly unlikely.7
The result of all this will be extreme demand for construction workers, increasing hourly rates and continuous project delays. Wages
across the industry expected to incrementally increase to a total of 26% by 2027, which will see qualified tradespeople weekly wages go from $1948 to $2454 per week raising labour costs to over 50% of total build costs.8 Current recommendations from the Master Builders Association and the Housing Industry Association are to alleviate labour shortages through the immigration of construction workers. “Skilled migration is a vital piece of the workforce puzzle in the building and construction industry.” 9 This may have adverse effects on the quality and sustainability of Australia’s housing stock as these workers are not familiar with Australian Construction regulations and how to build for the Australian climate.
Home ownership has become a societal expectation in Australia and the cornerstone of the ‘Australian dream’ with this ‘normality’ becoming a necessity for one’s well-being, welfare, financial and living stability. Australia has a multitude of financial systems built around the expectation of home ownership with the ‘home’ leveraged to generate equity which Australians use regularly to pay large, unexpected expenses such as surgeries, finance new business ventures and fund eventual retirement.10 Home ownership has become closely tied to the mental wellbeing of most Australians with the secure, self-determined living afforded by ownership aspirational over the volatility of renting and unbalanced landlord-tenant relationship.11 Therefore, the project has sought to create more options of accessing the traditional style of home
ownership that has seemingly become a necessity for full participation in Australia’s social and financial systems rather than proposing an alternate financial model of ownership such as build-to-rent.
“The Commission believes build-to-rent has a valuable role to play in the Australian housing market, but in considering the international and domestic experience with build-to-rent, has not found strong evidence to suggest that governments should favour build-to-rent over other kinds of housing. In general, there is a risk that measures to encourage build-to-rent developments will simply substitute one form of ownership for another, without materially improving housing supply or affordability.”12
Owner-building has the capacity to reduce the cost of housing and alleviate demand for construction workers, mitigating housing delays due to labour shortages. The greatest saving factor of owner-building is not having to pay the builders margin typically valued 20%-30% of the total build cost by taking on this role of managing the project.13 Further savings can be achieved by the owner-builder completing aspects of the construction work themselves with some owner-builders by completing much work of themselves able to save over 50% of the total build cost with the average home build costing $473 000 this would be hundreds of thousands of dollars saved.14 However, the typical savings target for owner-builders is 25% of the total build cost through project management and DIYing aspects of the home.15 Broad figures
on the true savings of owner-building are difficult to ascertain due to the numerous factors associated. A survey by the OwnerBuilder Magazine suggested that 62.5% of owner-built projects ran over budget and result in the construction cost running closely to that of what a builder would have charged.16 This budget over-run is generally caused by project creep, project home builders use the most cheap and basic methods and materials available whilst owner-builders are willing to spend to get the exact home they want. Therefore, their potential savings are put back into the project to create a better-quality home than what a traditional builder could have provided.17
Australia has a long history of ownerbuilding with the scarcity builders throughout Australia’s history and the freestanding, single cottage nature of Australian housing creating an environment for owner-building to thrive. The timeline tracks the history of housing in Australia and the proportion of which
home construction was completed by ownerbuilders. Tracking the trends of ownerbuilding in Australia revealed increases in owner-building had direct correlation to periods of financial hardship and trade shortages.
Primary Method
OWNER-BUILDER CONSTRUCTION
Standard Practice
Common Choice
Unusual Method
Rare Practice
Settlement
Formal estabilshment of builders & tradespeople.
Hiring a builder became common with construction supply industries established & housing construction becoming more complex.
Commonwealth Government introduced war service housing schemes.
Post World War 2 tradespeople shortage lead to increased amount of owner-building.
1972 Builders Licensing Act came into affect.
In 2002 the NSW Government increased the regulations within the OwnerBuilders Permit.
The first ‘owner-builders’ were Australia’s Indigenous people, nomadic they would use materials locally available to construct semi-permanent structures. Construction methods and materials were repeated between locations with Stringy-Bark for weatherproofing, brushwood for wind protection and saplings lashed together to create a framework which the most typical construction method.18
Early European settlers to Australia disregarded Indigenous construction methods and attempted to recreate European huts and cabins using local materials. The houses constructed during this time were largely owner-built with only the most affluent people able to use convict labour. Known as ‘Bark Huts’ these early homes were entirely made of timber with bark used to weatherproof the structure, with high quality lumber available these structures could last up to thirty years.19 Upon the realisation that native black and green wattles could be used to reproduce European wattle and daub wall construction in which flexible wattle branches are weaved between vertical ‘studs’ like basket work to allow a clay, water, straw mix to be rendered across the wall. Wattle and daub homes became the most popular construction method of this period because they were better insulated and longer
lasting than Bark Huts.20
With European settlement now established in Australia a middle class started to emerge through the increased commerce in the region. Whilst the working class continued to owner-build the increased wealth led to the formal establishment of building companies and tradespeople. Architecturally, with sawmills and other industries now working natural materials into standardised elements, settlers could more closely mimic European style, resulting in the rise of the Georgian and Regency inspired Colonial Cottage.21
5: History of Australian housing and owner-building 1850-1930.
1930-1946
1955-1965
1965-1975
8: History of Australian housing and owner-building 1965-present.
Financial necessity and construction labour shortages are shown to have been historically the primary motivator behind ownerbuilding; however, Australia also has a strong societal affection towards do-it-yourself home improvement. The freedom, control and eventual satisfaction of completing a self-directed project has become so popular in Australia that it is part of our cultural identity with significant business and media programs established to support and inspire DIY practices such as Bunnings and Better Homes and Gardens. The approach of DIY has been present throughout Australia’s history being first terminologically linked to ownerbuilding by Garrrett Winslow in the 1912 publication of Suburban Life magazine where he was encouraging homeowners to paint their homes themselves.34 DIY popularity and formalisation as a societal phenomenon truly began during the 1950s in North America. Albert Roland of the United States Information Agency tracked the growth of DIY during this period producing an essay in 1958 where he identified the primary motivators behind cultural adoption of DIY to be self-actualisation and transformation.35 The self-actualisation in completing a DIY project offered an avenue of escape through renewed self-worth and a “positive psychological release for individuals bewildered or worn by the vicissitudes of ordinary existence.”
36 Transformation refers to the motivation of the outcome of the DIY project as it functions to fulfil one’s lifestyle ambitions. This motivation has a strange internal tension between social conformity and individualism creating a spectrum of outcomes as ‘DIYers’
and owner-builders choose between creating their personal ideal home and societal dream home. This tension is present within many manuals and guides produced for ‘DIYers’ that both encourage individualism whilst also presenting ‘right’ and ‘wrong’ forms of home improvement.37
“Redecorating makes your dreams come true. It’s easy to decorate when you follow the simple ‘howto’ steps in this book. The following pages show you just how other families like yours achieved the homes of their dreams.”38
The degree to which Australian DIYers have sought social conformity over individualism in their home improvements has shifted overtime. During the 1970s the Counterculture movement inspired unique individualistic housing that conflicted with mainstream ways of living and housing regimes.39 In the early 2000s DIY projects became about ‘value adding’ with changes to the home closely following housing trends with ‘lifestyle’ shows such as the ‘The Block’ which premiered in 2003 pushing the desirability of social conformity in home improvement as means to convey status and improve financial returns in a now highly commodified housing market.40 Today the self-actualisation motivation to DIY remains constant, offering an avenue to Australia’s longstanding cultural emphasis on resourcefulness, self-reliance and a ‘can-do’ attitude and a means to display these values. The underlying objectives motivating transformation have become more case-by-case today with
some seeking home improvement that continue to be closely tied to social trends whilst the desire for more individualistic projects servicing unique lifestyles has been increasing since COVID-19 pandemic.41 Design that promotes the motivations of self-actualisation and transformation will encourage more Australians to owner-build and assist in their perseverance with the project because construction a new home at any scale is a major undertaking. To support self-actualisation within the project the design maximises the time on the tools by streamlining the bookkeeping and project management. Transformation to fulfil lifestyle ambitions will be unique from project to project as each owner-builder determines their balance between social conformity and individualism. The design therefore cannot prescribe a type of lifestyle onto the ownerbuilder rather act as a canvas that facilitates the fulfilment of an owner-builder’s lifestyle ambitions for their home.
Owner-builder rights have been progressively restricted by regulations and laws, with the days where anyone could act as an ownerbuilder if they obeyed the basic habitation and construction codes, are long gone. The primary legislation restricting owner-builders is the Owner-Building Permit, varying from state to state the New South Wales version containing five key requirements.
1. Complete Owner-Builders Course containing information on finance administration, works scheduling, contract requirements, project management and insurances. Courses are available online and are in the form of a study guide, typically costing $120.
2. Have proven ownership of the land to be built upon and intend to live in the home after completion.
3. Complete the White Card Safety Course where basic risk management is taught as a 6-hour face to face seminar.
4. Various insurances including Homeowner Warranty and Public Liability are needed with Workers Compensation, Personal Accident/Injury and Voluntary Works insurances highly recommended to cover any potential accidents
5. Show the property is not within a multidwelling strata complex. The Owner-Builders
Permit has unique restrictions that a licenced builder does not have to contend with, these make it harder for people to successfully owner-build.
1. Specialist work must be completed by licensed tradespeople including plumbing, electrical, gas fitting and air-conditioning.
2. An Owner-Builder permit can only be issued to an individual once every 5 years.
3. Only work covered within the development application can be completed under an Owner-Builder Permit.
4. Owner-Builders are responsible for their own defect resolution, and should they choose to sell the house within 7 years after completion the new owners can hold them liable for any defects they identify until the 7 years has elapsed.
5. Home building compensation cover which protects homeowners if a builder is unable to complete building work or defects is not required by an owner-builder however is it required by every licensed subcontractor that works on the project.42
The unique restrictions placed upon ownerbuilders through the owner-builder permit do not directly increase the challenge of owner-building however they do generate indirect impacts that affect the both the ability to owner-build and the financial risk. The responsibility of the owner-builders to resolve defects creates a huge degree of financial exposure, many defects require resolution before occupant certification can be achieved. Defect resolution is costly and timely to during a period when most owner-builders will have little left in their budget. Waterproofing issues and structural concerns are some of the most common and expensive building defects to resolve in NSW, with the capacity force owner-builders into a financially venerable position as they seek to push their project over the line.43 An owner-builders financial exposure to defects remains for up to 7 years after the completion of the home and impacts saleability within this time. Potential buyers within this 7-year period need to be forewarned that the home
was owner-built, and should they discover any defects they can hold the owner-builder responsible for their resolution. This can lock owner-builders into a house until the 7 years have elapsed out of fear that they may be held accountable for any issues a new buyer may have.44
The requirement for subcontractors to have home building compensation cover makes it harder for owner-builders to source tradespeople because this is an additional cost to the contractor and increases their personal risk because they are working under their own insurance. Home building compensation is generally only carried by the head builder of a home with all sub-contractors operating underneath this one insurance policy. By requiring all sub-contractors to have this insurance on owner-builder projects there is a variable risk verse reward for any potential sub-contractor often result in higher quoted prices for owner-builders.45
Local councils generally do not place any formal requirements on owner-builders however they often have criteria that assists in obtaining development application approval. The nature of these informal criteria relates to local concerns about the capacity for owner-builders to complete their construction project within a reasonable timeframe and maintain building standards. Local Council expect construction to commence within 12 months of acquiring the Owner-Builders Permit with a construction timeline not exceeding 18 months.46 Whilst local councils do not want explicit financial documentation they appreciate owner-builders providing a payment strategy for the project as a means of assurance that the project will not be left in a semi-finished state.
Construction regulations such as those created by the Australian Building Codes Board, Standards Australia and SafeWork are covered within the construction guide aspect of the ‘Design Delivery’ book.
Financing for owner-builders is very challenging to acquire with few lenders today willing to offer loans to owner-builders. This is due to the high-risk nature of the loan as historically many owner-builder projects have failed with the broker unable to recoup their loan due to the property being significantly devalued by having a half-built home. Westpac and St. George are the main two lenders available to owner-builders with St. George historically seen as the go-to lender likely due to their loan to value ratio being higher than Westpac’s at 75% compared to 60%. The loan to value ratio is calculated using the lesser value of either property value plus construction cost estimate or a valuer’s estimation of property value upon completion with an owner-builder able to borrow a maximum of 75% of the lesser value. Payments are made as progress payments with owner-builders providing a schedule of works for the project detailing when payments are required and for what, with the lender having final approval over the amounts and frequency.47 A valuer is required to inspect the construction before each progress payment is approved which means that the owner-builder needs to be able to fund each stage up-front and finance continued construction until approval A key stipulation of the loan is the requirement for the ownerbuilder to maintain the serviceability of the loan meaning at least one member of the owner-builder team needs to have a highincome during construction and evidence provided that the household income will return to the current level once the project has been completed. 48
Typical percentage of total loan amount released at the completion of each stage:
1. Deposit and site preparation: 10%
2. Foundations, footings and slab: 10%
3. Framing and structure: 20%
4. Lockup: 20%
5. Finishes and Fix-out: 30%
6. Completion and handover: 10%
Documentation lenders generally require from owner-builders applying for a loan:
- Proof of Identification
- Income details
- List of your existing assets and liabilities
- Council building permits and plans
- Professional building plans
- Proof of land purchase
- Your contract with the builder
- Progressive payment schedule
- Proof of insurance
- A contingency plan in case things go wrong (for example, proof that additional insurance has been taken out to fully protect the ownerbuilder)49
“An owner-builder needs to have significant funds up-front even if you are going to borrow for an OwnerBuilder Loan.”
-Mortgage
Broker Consultation 26/8/24
The set of requirements one needs to successfully owner-build a traditional home has been collated and outlined in the following section. This information has then been cross referenced with census data to demonstrate just how few of Australians can owner-build using traditional construction processes, breaking down the financial, regulatory and physical requirements necessary. The financial data uses the real family of six, client referenced within the upcoming design chapter to generate the financial data as they recently completed a traditionally constructed family home in 2023.
Due to the nature and amount available from lenders an owner-builder will need at least 40% of the total construction cost saved to account for the staged back-pay of the lender's loan as this ensures stages can be completed, progress is maintained whilst payments are being processed and cover any unexpected expenses such as mistakes.50 Whilst the project is under construction owner-building a traditionally constructed home would be full-time work. However, someone within the owner-builder team will need to maintain their employment both to provide the lender with assurances over the serviceability of the loan and prevent an over usage of savings on general household expenses. The ability for someone within the owner-builder team to take extended paid leave and be guaranteed a return to a position after the project's completion will significantly reduce the financial strain of daily expenses and assist the loan serviceability evaluation.51 Being physically
able to complete a full day of labour is not an absolute requirement however it is very helpful as it reduces your reliance on hired or volunteer help, improving savings and reducing risk of delays.
The skills an owner-builder needs:
Clear understanding of standard construction methods.
Skilled in project planning and management
Know how to control budgeting and maintain organised bookkeeping.
Understand the processes of the building industry including material and equipment ordering and trade hire.
Able to use tools and equipment to a moderate proficiency.
Have a strong knowledge of Work Health and Safety Requirements
Following data breakdowns down the financial requirements of owner-building that are constant across owner-builder projects with amounts present sourced using the situation of the family of 6, client.
Costs
Total Construction Cost
Owner-Builder Permit
White Card
First Aid
Construction Insurance* (public liability insurance included)
Personal Injury Insurance
Workers Compensation Insurance**
Owner-Builder Training
Land Cost
Documentation Architect
Land Surveyor
Land Valuer
Structural Engineer***
Quantity Surveyor
TOTAL
Deductions
HomeBuilder Grant
$843 000 $219 $120 $228 $3 826.31
474.72 $2 800 $120 $860 000
$67 440 (8% of total build)
$5000 (boundary & set-out)
$990 $3000 $2000 $1 791 218.03
First Home Owner Grant**** TOTAL $25 000 $10 000 $1 756 218.03
Owner-Builder Savings***** Expenses during construction******
Bank Loan Loan Approval Fee
$478 968.03 $2307 (per week)
Maximum Amount Loan Servicing $700 $1 277 250 $240 000 (yearly income)
Figure 12: Information within this table has been ascertained by recieving direct quotes from the applicaible providers.
From the financial information collected and the requirements necessary to successfully owner-build, various aspects of Australia’s population data can be referenced to reveal the number of Australians that could ownerbuild this project. Australia’s population is 26 785 028 as of October 10th, 2024, to obtain an Owner-Builder Permit you must be over the age of 18 whilst Australian’s over the age of 65 will likely be unable to endure the physical demands and stress of the project leaving 61.6% of Australia’s population within the 18-65 age range, 16 499 577 Australians can owner-build.52 18% of Australia’s population are identified as having a disability whilst severity varies due to this it is likely these people would not choose to ownerbuild, 13 529 653 Australians could ownerbuild.53 Australia’s employment to population ratio 64.2% to gain approval for an ownerbuilder construction loan the applicants will need to be employed, 8 686 037 Australians could owner-build.54 50.6% of Australia’s employees can accrue paid leave, 4 395 135 could owner-build.55 Household income necessary to service this loan and in turn gain loan approval will need to be at least $240 000 per year to not experience mortgage stress, only 15% of Australian households earn at this threshold or higher, 659 270 Australians could owner-build.56
The proposed house to be constructed is large with 5-bedroom and a 396sqm floor area whilst the average new Australian home is 245sqm. However, the total cost of $843 000 is on the lower end for a 5-bedroom house and a land cost of $860 000 is also considered an affordable price.57 Yet, considering the key requirements to owner-build, only 2.5% of Australia’s population could undertake this project as an owner-builder with a high likelihood of success. This demonstrates the
degree to which regulatory and financial systems have sought to restrict ownerbuilding as a method of home building and with total build cost being the only figure with any flexibility this will need to be reduced further to make owner-building a more broadly accessible option.
*Owner-builders are entitled to a 50% levy discount on this figure through NSW Fair Trading with automatic approval for work costing less than $500 000.
**Contractors may be classified as ‘workers’ when hired; this would require the ownerbuilder to have workers compensation figures calculated based on $100 000 wages paid directly from owner-builder to worker.
***Structural Engineer costs will vary greatly depending on the amount of issues identified.
****Applicable for owner-builder contracts under $750 000.
*****Up front savings includes various initial costs such as permits, approvals, training, insurances and 40% of the total construction cost.
******Expenses during construction factors average weekly household spending in addition to the fees outside of the new construction’s total build cost. Income does not have to exactly match this figure as the savings are expected to also be used to off-set these expenses.
What can be ascertained from analysing the regulatory and financial systems is that very few Australians have the skills and requirements to successfully build their own home using traditional construction processes. Therefore, new methods of construction have been developed that play into the system, providing greater accessibility to owner-builders and improving the likelihood of success. The key factors this construction method needs to address is quick progression through construction stages to maintain income streams from loan payments, simplified construction methods to allow tasks to be completed by workers with limited skill, clear project sequencing to prevent unexpected expenses and high-cost estimation accuracy to improve the chances of loan approval. Semi-prefabricated modular systems address these key areas with rapid construction due to reduced work being completed on site, easy construction, a clear, predefined construction sequence and highly accurate cost estimations as most material and labour costs are included within the cost of the modular components.
Prefabricated housing has been present in Australia since the post-war period where they were used to address housing and labour shortages with mass produced packaged kits containing construction instructions suitable for unskilled labour. Ownerbuilders could choose between forty-four housing types of various sizes all of which used the same basic system.58 This early explosion of prefabricated housing in many ways influenced Australia’s current housing conditions as they suburbanised Australia’s population with 40 of these flat-pack homes being constructed per week by the 1950s. Homeownership increased in Australia from 46% to 72% during the post-war period with the affordability and constructability of flat-pack homes a key contributor as it allowed more Australians the opportunity to buy land and construct a home.59 The popularity of post-war prefabricated homes set consumer expectations over housing quality and standardised Australian suburban living and homeownership. Which is not a good thing because these homes were of poor design and material quality with minimal insulation, asbestos cladding and openings in pre-set locations making them extremely unresponsive to specific site conditions.60
PAAL Kit Home is Australia’s oldest and most established kit home company in Australia being highly recommended within owner-builder online forums and is representative of how semi-prefabricated modular housing has developed since the post-war flat-pack. PAAL’s various kit home products are organised as preset plans of various sizes that have the capacity for internal layouts to be customised within the 1.8mx1.8m grid system of the light gauge, structural steel frames because no internal walls are load bearing. PAAL products use a number system for components that directly relates to the instruction manual for ownerbuilders to easily identify parts and follow construction processes with most framing components bolt-in. PAAL kit homes have variability in project timelines between products, but the general targets are lock-up stage achieved 8 weeks after floor is complete, internal fix-out 6 weeks and fit-out 5 weeks. The compressed timeline of achieving lock-up is incredibly advantageous for owner-builders as it alleviates time pressures being typically the longest stage, mitigates the effects of poor weather and allows more flexibility in when and how owner-builders work.61
PAAL’s products have exclusively been built in rural areas to date, due to their product requiring completely flat sites and a large amount of space to store all the components as the materials for the homes are delivered in only three stages. PAALs products are limited in sustainable performance and slow to adopt new systems as changes would require a complete review of the entire manufacturing process. The degree of responsibility placed onto the owner-builder by PAAL is concerning with the owner-builder expected to organise the services and connections, manage the pouring of a completely flat slab and resolve how any material choices not offered by PAAL would connect to their system e.i. different cladding.62 PAAL kit-homes also suffer from the same issues as the post-war flat-pack homes in relation to design quality with little adaptability to site characteristics to improve building performance and occupant experience. In fact, the system requires a complete destruction of a site’s unique qualities for the flat foundation.
Dimensions X is a series of kit homes designed by Peter Stutchbury Architecture for unskilled owner-builders with the goal of creating site-conscious, planet friendly, architecturally designed homes with simple assembly in a suburban context. The current product line consists of two similar products that are designed for clients at different budgets; OM1 a highly customisable structure that utilises family portal frames that can be configured in any ordering on footings to allow thousands of configurations of internal layout. PS1 a prescribed, prefabricated shell to minimise manufacturing cost with openings that function as either windows or doors and preset GPOs that allow the client to determine and do their own fit-out including lighting.63
Peter Stutchbury Architecture provides owner-builders with a construction manual and guide for each of these products and an onsite consultation with the client as to how best configure the OM1 or PS1 to suit site conditions. The process of development focused upon taking out as much as possible and simplification in all aspects to recurring techniques to minimise the learning curve. Dimensions X products have a series of design innovations that address key issues of current kit home products; driven footings allow the buildings to be built even on sloped sites and have minimal soil disruption. Prefabricated wall segments including insulation and building wrap allow the outer shell of the building to be quickly constructed and weatherproofed. The usage of crosslaminated timber is more workable than steel, more sustainable whilst maintaining
high accuracy in CNC cutting. Services are easily run in concealed channels below and above walls and behind cabinetry which in conjunction the additional GPOs for lighting allows for clients to set out internal layouts in any manner without the need for changes to accommodate services. The design of internal walls and spaces allow for the most standard fix-out products including bunnings cabinetry to be installed and simple external horizontal battens capable of fixing a wide range of external claddings to.64
An issue with the Dimension X homes is that they too forcefully prescribe Peter Stutchbury Architecture's set of design principles onto the owner-builder and how they perceive one's lifestyle should be. This leaves little capacity for a prospective owner-builder to determine how they would like this building to feel, function and be inhabited because whilst there is design flexibility of spatial arrangement the building cannot escape the determined lifestyle. Ultimately the capacity for the Dimensions X to be an appropriate option for owner-building becomes limited to those seeking the lifestyle envisioned by Peter Stutchbury Architecture due to there being little scope for individualism or wider social conformity.
The design developed is inspired by the ethos and methods of Australia's 1970s countercultural owner-builders. In which basic construction methods and materials acting as the start point to adapt building conventions and practices to create highly individualistic buildings safe in the knowledge, they would remain structurally sound.65 BuildIY, the semi-prefabricated modular system proposed is not concerned with property value adding or dictating a lifestyle onto you, it is to facilitate the construction of shelter, your shelter. Acting as a blank canvas for owner-builders to “realise their philosophies and beliefs in the very walls they inhabit.” in such a manner to be responsive to site allowing for a renewed relationship between Australian housing, local contexts and nature.
Sheathing replaced with fire rated Fibre Cement for areas with increased requirements.
Not to Scale
10mm Sheathing
80mm Rigid Insulation
90x45mm Lightweight RHS
90x45mm Lightweight RHS
90x90mm Structural SHS
90x45mm Timber
Building Wrap
80mm Rigid Insulation
30x30mm Timber Battens
18mm Wall Brace Sheeting
12mm Plywood Sheeting
90x45mm Nogging
125x75mm Floor Joist
75x50mm Angled Steel
Structural PFC
200x100mm
Level Master Adjustable Stump Footing
Concrete Pile Footing
Details of how BuildIY is incorporated into the and facilitates the construction of an owner-builders dream home.
The system is designed to amplify the building experience by focusing the owner-builders role around their personal motivations for undertaking the project; self-actualisation and transformation to one's lifestyle ambitions. Typically, ownerbuilders act as project managers on the phone and computer constantly managing the administration including invoicing, procurement and planning of the project. This is rarely what owner-builders imagine themselves doing whilst building their home rather they expect to be ‘doing-it-themselves’ on the tools with the autonomy to construct to their desires.67 BuildIY’s prefabricated
‘shell’ system facilitates this motivation by simplifying much of the administration work required. Additionally, the owner-builder is allowed complete construction freedom after the lock-up stage, being hands on safe in the knowledge the home is structural sound and waterproof with the 600x600 standardised grid making their work during the internal fix-out easy. By having non-structural internal walls, standardised dimensioning, high flexibility in the design stage and finishes including external cladding the owner-builder has the capacity to shape the home to match their lifestyle ambitions.
24: Demonstrating how BuildIY’s 600x600 grid can incorporate easily accessible and cheap components for fix-out.
BuildIY is simple to use, layout a 600x600 grid over the site and place your desired components in any configuration within the building envelope. Only one consideration needs to be followed, to place walls on opposite sides of a room on the same side of the grid lines. This is to make sure the distances will fit at least one of the kit-ofparts. Outside of this the design is completely open with the capacity to determine your own materials, room sizes and floorplan to create your dream home. What this means is each home built using this system can be completely unique and tailored to both you and your site for a fraction of what a completely architecturally designed home would cost.
Experimentation of floorplan design using the consultation model.
Remove internal Sheeting, trims and cut cladding.
2 3 4
Unscrew panel from surrounding componets and push out.
Prop steel top plate. Until new panel is ready. Insert new panel replace trims and internal sheeting.
Sequence of diagrams documenting how you can remove a panel from your home to create a home extension.
Models documenting the construction sequencing of the project.
Models documenting the construction sequencing of the project.
Selection of an initial site was predicated on the most atypical set of site conditions present in the New South Wales housing market and used to develop the system’s design and process of construction. This is because a successful design intervention onto such a site will act as a baseline to test the feasibility of owner-building. The desired site will facilitate the construction of the most common housing type, in an area where this housing type is being continually built, on the type of site most commonly available. Developing the design to satisfy these criteria at the outset will result in the corresponding proposal having the broadest applicability to owner-builders and the most repeatable processes.
The most common housing type in Australia is separate freestanding houses with 70% of private dwellings counted in the 2021 Census falling into this categorisation.68 Western Sydney has the largest number of freestanding houses being built based upon the NSW Government’s current data on
building approvals and 5-year housing supply forecast with the Local Government Areas (LGAs) of Penrith, Blacktown, The Hills Shire, Liverpool and Camden expected to have the largest growth in development.69 Vacant land parcels are the most consistently available property type suitable for the construction of a freestanding house in Western Sydney with developers actively seeking to create flat, vacant blocks because they are easiest to construct on. Land parcels between 400-800m2 are the most common lot size according to Australian Bureau of Statistics 2022 Land Supply Indicators with 55% of all land parcels counted within this range.70 The number of vacant blocks available will only increase over the next 5 years as the NSW Government is set to release large areas of land for residential development supported by incentives such as the Greenfield Housing Code to fast-track home construction approval in an attempt to reach the National Housing Accord 2029 target of delivering 377 000 new homes.71
400m2 to 800m2
Selection of a site was narrowed to a vacant block between 400m2 and 800m2 in one of Western Sydney’s highest development LGA’s that a freestanding house can be built upon. For the final selection of a site real estate websites such a Domain were used to mimic the process a true owner-builder would follow in finding a property based upon listings available with the previous criteria identified included as search filters. To narrow the search results further additional site conditions, of the land being in an established suburb, with neighbouring buildings, minimal building restrictions and no additional considerations such as being in a bushfire or flood prone area were considered. This set of criteria was not based on data of the most typical conditions rather to streamline the project's initial focus of testing the feasibility of owner-building without having to negotiate case-by-case strict regulations such as BAL requirements. Locating the site in an established suburb will add some additional constraints because the impact on neighbours will need to be considered during the design and construction; however, this will be a common challenge many owner-builders will have to navigate and would therefore need to be represented within this design project. Existing Suburb
The chosen site located at 12 Nancy Street, St. Marys accomplishes this full set of criteria, with St. Marys to undergo significant growth as it forms part of the direct link to the Western Sydney Airport with all traditional challenges of building within an established suburban area including confined streets, limited access and neighbours.72 The site is 600m2, flat rectangular block with no existing trees and therefore has the conditions of land parcels frequently available for purchase. (see appendix for breakdown of LEP & DCP requirements)
The client is based upon a real family of three children aged 7,11 and 14, their mother, father and grandmother with the mother and father acting as the primary stakeholders. An initial design consultation with the primary stakeholders has been completed to develop a brief of basic requirements to govern the design response to be owner-built. This allows for the early desires and ambitions of a would-be owner-builder to directly respond to the unique challenges of owner-building and assess the extent to which these initial ambitions can be retained.
Selection of this specific set of real clients was primarily based upon the breadth of design response this multi-generational household will require and the opportunity to explore how owner-building can be engaged with by people of various ages. The ages of the children are also representative of a key moment many Australians look to up-size their home with the children hitting their teenage years where shared bedrooms become less suitable. The design desires and ambitions of the client are also very popular within Australia’s current housing trends with open
plan living, white walls, timber floors, strong outdoor connections and a sense of spatial generosity features of many homes being built. Additionally, this client has recently completed the construction of a new custom designed home by a builder, whilst the sites and design responses will differ between this built home and this project’s design proposal. The opportunities to compare construction processes, timelines and costs will provide a degree of insight into the potential savings of owner-building.73 (See ‘Design Delivery’ Book for site photos)
Not to Scale
Axonometric of home materiality.
Conceptual perspective of creating one’s dream home using BuildIY.
Selection of 47 Edith Street as a second site to test the adaptability of the system on a tighter, inner-city block with increased fire regulations and an existing structure to preserve and integrate into the system. The design is used to demonstrate how one could use the system in an extension and construct compact yet comfortable home.
The client for this project was a young couple moving out of home for the first time and closer into the Sydney CBD. They have a very limited budget and are hoping to construct a two-bedroom home, with the second bedroom starting as a study and being converted into a baby’s room. The couple is very social and keen cooks spending most of their time in the kitchen. (See ‘Design Delivery’ Book for site photos)
Connection from existing structure to system.
Not to Scale
Study/ Bedroom
Entry
Axonometric of home materiality.
Conceptual perspective of creating one’s dream home using BuildIY.
Experimenting with how BuildIY could be used to create duplex style homes. The design for two, two-bedroom homes that are mirrored with the capacity to house two
The design was created using the consultation model and sketching to experiment with potential layouts using the modular system.
Detail of weatherboard and tile wall and roof claddings fixed onto the system with the weatherboard fixed directly to the panel sheathing and tile battens fixed off sheathing.
Not to Scale
Designing a small holiday surf shack. This design experimented with incorporating a verandah into the system and a small compact floorplan with minimal internal walls.
The design was created using the consultation model and sketching to experiment with potential layouts using the modular system.
Detail section of surf shack verandah incorported into the BuildIY system.
Not to Scale
A homage to the 1970s owner-builders that inspired the design development of BuildIY.
built in high Bushfire Attack Level (BAL)
The design was created using the consultation model and sketching to experiment with potential layouts using the modular system.
Fibre-Cement Cheathing
Cladding Metal Battens
Using Colourbond cladding, metal battens and fire rated fibre-cement sheathing the BuildIY system can be adapted to suit BAL-40 requirements defined in AS 3959:2018.74
Not to Scale
The Owner-Builder Permit places all the responsibility for defect resolution onto the owner-builder with these issues often costly and timely to resolve during a period when most owner-builders will have little left in their budget. Waterproofing issues and structural concerns are some of the most common and expensive building defects to resolve in NSW. By using this prefabricated system, the potential for these forms of defects is highly unlikely due to the ease of installation and incorporation of waterproofing into the system.
Local council requirements for the project construction timeline to be less than 18 months is far more achievable because the prefabricated components can be prebuilt ahead of time and delivered to site when necessary. The flexibility of the design and materiality also allows for easy adaptation to unique regulations imposed by Local Councils such as ‘Neighbourhood Character’ aesthetic compliances and any irregular building envelope forms.
Lower labour costs associated with prefabricated systems should reduce the overall construction costs and in turn the size of loan necessary to fund the project. The system is designed to quickly move through the construction stages up until lock-up which will reduce the time between lender progress payments reducing the risk of any
cash flow issues. By having a clear sequencing of construction and the labour and material usage easily quantifiable lenders will be more likely to look favourably on owner-builders using this system as they can clearly see what money is going where and when.
Designing to an owner-builder experience is not a direct regulatory requirement however as the key authority dictating the success or failure of the project, creating a system that both protects owner-builders from themselves and enhances their enjoyment improves the likelihood of success. The standardisation and prefabricated nature of the system helps to protect the owner-builder from budget blow-outs due to scope creep because despite any last-minute design changes the construction process will remain simple and pre-determined by the construction guide which prevents overspending. Burnout is a real risk for owner-builders with any home construction causing all sorts of stress and pressure which can lead to owner-builders resenting their own home. To help prevent this from happening the design delivery document has been produced with processes and recommendations tailored to ownerbuilders which facilitate both the do-ityourself motivations and produce your dream home.
“We
finished our home 6 months ago and I cannot walk around the home without noticing mistakes that need to be fixed and having reminders of stress and bad memories.
My wife is expecting soon which is why we built the house but I don’t think I can live in it anymore.”75
-Anonymous Owner-Builder in Owner-Builder Forum
Owner-building your own home within Australia remains a daunting challenge inspite of how the design proposal for this project seeks to reduce the challenge. Systematically there remains an aversion against owner-building. Local councils often push for strict, constrained timelines to prevent prolonged construction and are wary of potential non-compliance with regulations with random inspections of owner-builder sites often occuring.76 The finances required and the stipulations within loans incur a significant amount of risk for owner-builders and large sums of money to front the construction costs until the progress payments begin to come in. Additionally, they require tight construction schedules and material quantities which puts more pressure on the owner-builder as it leaves little capacity for learning on the job.77 Trades often charge extra on owner-builder projects or avoid them due to uncertainty of work and material quality provided by the ownerbuilder and the additional risk they incur by requiring homeowner’s warranty insurance.78
What this all amounts to is there being fewer financial benefits to owner-building than first thought, especially when the loss of income for the owner-builders due the time-off is also considered. Most of the aversion to owner-builders and the extra cost they incur is well founded because there is historic data that almost all owner-builder projects run overtime and over budget with a high potential of failing completely. This is due to various reasons, most of all that the construction industry is volatile. In the past
financial year 2832 construction companies entered insolvency as the continued “increases in interest rates and cost of materials, labour shortages and supply-chain issues”79 put many builders into financial distress.80 If this is the current situation for professional builders then it is clear why lenders and councils would be incredibly wary of unskilled, inexperienced owner-builders working with constrained finances entering this industry.
The design project does alleviate some of these issues with the prefabricated systems, shrinking the construction time and making costs far more predictable. However, there is no substitute for experience and a support network for owner-builders that allows consultation with trusted professionals would provide the assurances lenders, councils and trades need when considering involvement with owner-builder projects. The support network would consist of architects to assist in the design development and documentation necessary for financial and council applications and retired builders acting as construction consultants providing support through their expertise and industry connections to owner-builders in their local area. (see ‘Design Delivery’ book)
Owner-building has the capacity to be an affordable alternative to the traditional construction of a home and would alleviate demand for tradespeople. The savings potential on offer through the usage of this construction system and the process of delivery tailored to improving the successful completion of owner-built homes increases the viability of this practice. By having a highly adaptable system to both site and client requirements the system can facilitate unique, personalised design responses to suit any potential lifestyle, making it universally applicable to Australians and capable of being developed in various contexts. The prefabricated panels determining the process up until fix-out, aids the owner-builder in maintaining budget and construction quality by mitigating the risk of defects and project creep. The semi-prefabricated system proposed also acts to maintain the 25% of the total build cost savings expected by owner-building, through clear design and construction processes that reduce unexpected challenges with a support system to resolve any issues that may emerge. Furthermore, the flexibility of the prefabricated components means it can be modified to fulfill the lifestyle ambitions of any Australian.
BuildIY and relating process proposed, respond well to the unique regulatory requirements placed onto owner-builders satisfying all key criteria. Simple, expediated sequencing through construction stages assist with loan and development applications with most of the construction contained
within the prefabricated components making feasibility and cost reviews precise. By having most of the costs within the prefabricated system, material and stage costing can be closely estimated allowing for owner-builders and lenders to split the progress payment amounts to align with the true costs. The overall responsiveness of the project to regulatory requirements will only improve with continuous usage because ownerbuilders successfully completing homes using this system can be referenced as a precedent during application processes. As a process and system, BuildIY would give an ownerbuilder the best opportunity to navigate and adhere to the unique regulatory requirements without major adverse effects on project pricing or budget typically associated.
Owner-building using this system and process represents the greatest capacity for it to be a widespread affordable option. However, there remain core issues that limit the capacity for owner-building to meaningfully address housing unaffordability. The physical and time requirements laidout in the ‘keys to success’ chapter limit the number of Australian’s who can reasonably complete an owner-builder project before a desire to do-it-yourself is even considered. The level of financial exposure remains high for owner-builders due to the staged backpay loan structure provided by lenders, requiring significant savings or upfront equity to offset the delayed loan payments. This would also place risk onto the supplier of the proposed system with the supplier
needing to align their payment scheme with a smaller deposit up-front despite most of the supplier expenses being at the early stages of the construction process.81 Realistically there needs to be more flexibility in lender payment scheduling for owner-building to fully be considered an affordable option because the current up-front saving requirements and risk associated with the loan discourage and price out a significant number of Australians. Lenders follow government incentives, becoming more flexible with loan structures; with the NSW government recently putting 10 million dollars towards prefab modular housing development to deliver affordable housing the potential for policy intervention necessary for owner-building to be a widespread affordable option may happen soon.82
1 Australian Institute of Health and Welfare. “Housing Affordability.” Australian Government. July 12, 2024. https://www.aihw.gov.au/reports/australias-welfare/ housing-affordability
2 Wilkie, George. “Building your own home.” Lansdowne-Rigby Publishers, 2012. Accessed August 7, 2024.
3 “Owner-Builder frequently asked questions.” APEX Training Courses. nd. Accessed August 6, 2024. https://www.ownerbuildercourses.com/owner-builderfrequently-asked-questions.html#:~:text=Construction%20time%20should%20not%20 exceed,to%20your%20site%20or%20project.
4 Jericho, Greg. “Housing affordability is so bad that 2020 now looks good.” The Guardian. March, 2024. ttps://australiainstitute.org.au/post/housing-affordabilityis-so-bad-that-2020-now-looks-good/
5 Martin, Mina. “Construction cost growth slows.” Australian Broker. July 11, 2024. https://www.brokernews.com.au/news/breaking-news/construction-cost-growthslows-285119.aspx#:~:text=After%20years%20of%20accelerated%20growth,the%20 0.8%25%20increase%20in%20Q1.
6 “Building industry faces labour shortage and drop in apprentices.” Build Australia. March 28, 2024. https://www.buildaustralia.com.au/news_article/buildingindustry-faces-labour-shortage-amid-housing-crisis/#:~:text=The%20number%20 of%20apprentices%20in,industry%2C%20as%20highlighted%20by%20Wawn.
7 Rachwani, Mostafa. “Australian construction industry calls for skilled migration overhaul to ease ‘desperate’ shortage of tradies.” The Guardian, November 2nd, 2024. https://www.theguardian.com/australia-news/2024/nov/02/australianconstruction-industry-calls-for-skilled-migration-overhaul-to-ease-desperate-shortageof-tradies
8 Eyers, Paul. “Increased labour rates to keep construction costs on the rise.” Build-it. May 29, 2024. Accessed August 20, 2024. https://build-it.au/general/ increased-labour-rates-set-to-keep-construction-costs-on-the-rise
9 Rachwani, Mostafa. “Australian construction industry calls for skilled migration overhaul to ease ‘desperate’ shortage of tradies.” The Guardian, November 2nd, 2024. https://www.theguardian.com/australia-news/2024/nov/02/australianconstruction-industry-calls-for-skilled-migration-overhaul-to-ease-desperate-shortageof-tradies
10 Australian Institute of Health and Welfare. “Housing Affordability.” Australian Government. July 12, 2024. https://www.aihw.gov.au/reports/australias-welfare/ housing-affordability
11 “The advantages of owning your first home.” Mortgage Advice Bureau. July 26, 2023. . https://www.mortgageadvicebureau.com.au/services/the-advantages-ofowning-your-first-home/
12
“Review of housing supply challenges and policy options for New South Wales.” NSW Productivity and Equality Commission. August 2024. Page 33. https:// www.productivity.nsw.gov.au/sites/default/files/2024-09/20240911_NSW-PEC-reportReview-of-housing-supply-challenges-and-policy-options-for-New-South-Wales.pdf
13 Nicholson, Scott. “The basics of being an owner-builder in NSW.” Design Plus Drafting. February 27, 2020. https://designplusdrafting.com.au/the-basics-ofbeing-an-owner-builder-in-nsw/#:~:text=What%20are%20the%20benefits%20of%20 being%20an%20owner%2Dbuilder%3F&text=It%20is%20estimated%20that%20 owner,and%2040%25%20on%20construction%20costs.
14 “Tips for owner-builders.” Builders Academy, July 23, 2023. https:// buildersacademy.edu.au/building-and-construction/tips-for-owner-builders/
15 Kennedy, Jessica. “How much will I save if I owner-build my house?” How to build a better house, August 12, 2023. https://howtobuildabetterhouse.com/how-muchwill-i-save-if-i-owner-build-my-house/
16 Amelia. “Budget-blowing mistakes when building or renovating.” Undercover Architect, March 30, 2015. https://undercoverarchitect.com/how-to-keep-on-budget/
17 Kennedy, Jessica. “How much will I save if I owner-build my house?” How to build a better house, August 12, 2023. https://howtobuildabetterhouse.com/how-muchwill-i-save-if-i-owner-build-my-house/
18 “Early settlers’ homes and bush huts in Australia.” Romsey Australia. January 1, 2018. Accessed August 28, 2024. http://romseyaustralia.com/houses.html
19 Wilkie, George. “Building your own home.” Lansdowne-Rigby Publishers, 2012.
20 “Early settlers’ homes and bush huts in Australia.” Romsey Australia. January 1, 2018. Accessed August 28, 2024. http://romseyaustralia.com/houses.html
21 Wilkie, George. “Building your own home.” Lansdowne-Rigby Publishers, 2012.
22 “The definitive guide to Australia House Styles.” Fat Shack Vintage. n.d. https://www.fatshackvintage.com.au/pages/the-definitive-guide-to-australian-homestyles?srsltid=AfmBOor0tuU-xhd32yAO-lm53aINrBKYLuOdYUssNAzvl3LR9UdTJ r5F
23 Wilkie, George. “Building your own home.” Lansdowne-Rigby Publishers, 2012.
24 Wilkie, George. “Building your own home.” Lansdowne-Rigby Publishers, 2012.
25 “Skint! Making do in the Great Depression.” Museums of History New South Wales. n.d. Accessed August 28, 2024. https://mhnsw.au/stories/general/skint-makingdo-great-depression/
26 ANZAC Square Memorial Galleries. “Industry in World War II.” State Library of Queensland . July 15, 2024. Accessed August 28, 2024. https://www.slq.qld.gov.au/
blog/industry-world-war-ii
27 Wilkie, George. “Building your own home.” Lansdowne-Rigby Publishers, 2012.
28 Wilkie, George. “Building your own home.” Lansdowne-Rigby Publishers, 2012.
29 Smith, Cathy. “Handy, hippies and healing: Social transformation through the DIY movement (1940-1970) in North America.” Architectural Histories, University of Newcastle, Australia. 2014. https://journal.eahn.org/article/id/7461/
30 Stickells, Lee. “Negotiating off-grid: Counterculture, conflict and autonomous architecture in Australia’s Rainbow Region.” Fabrication, 2015, Vol 25, Iss 1: 104-129. https://www.tandfonline.com/doi/ full/10.1080/10331867.2015.1006755?scroll=top&needAccess=true
31 Taylor, Retreat or Advance; Holland, “Planning and Building Regulations and Alternative Lifestyles”; Munro-Clark, Communes in Rural Australia. Appendix 1, 88.
32 “Home Building Licensing in NSW.’ NSW Government. n.d. https://www. fairtrading.nsw.gov.au/about-fair-trading/how-we-work/protection-schemes-andsystems/home-building-licensing-in-nsw
33 Wilkie, George. “Building your own home.” Lansdowne-Rigby Publishers, 2012. Accessed August 7, 2024. https://www.aihw.gov.au/reports/australias-welfare/ housing-affordability
34 Smith, Cathy. “Handy, hippies and healing: Social transformation through the DIY movement (1940-1970) in North America.” Architectural Histories, University of Newcastle, Australia. 2014. https://journal.eahn.org/article/id/7461/
35 Roland, Albert (1958). “Do-It-Yourself: A Walden for the Millions?” American Quarterly, 1958, Vol 10, Iss 154. Part 1.
36 Starr, J. Fifty Things to Make for the Home. New York: Whittlesey House, McGraw-Hill Book Company, Inc. 1941.
37 Smith, Cathy. “Handy, hippies and healing: Social transformation through the DIY movement (1940-1970) in North America.” Architectural Histories, University of Newcastle, Australia. 2014. https://journal.eahn.org/article/id/7461/
38 Better Homes and Gardens. Better Homes and Gardens Decorating Book. Des Moines, Iowa: Meredith Publishing Company, 1961.
39 Stickells, Lee. “Negotiating off-grid: Counterculture, conflict and autonomous architecture in Australia’s Rainbow Region.” Fabrication, 2015, Vol 25, Iss 1: 104-129. https://www.tandfonline.com/doi/ full/10.1080/10331867.2015.1006755?scroll=top&needAccess=true
40 Buchanan, Ian. “Renovating reality TV.” Australian Humanities Review, n.d. https://australianhumanitiesreview.org/2004/04/01/renovating-reality-tv/#footnotes1
41 Sarah. “The love affair with DIY: Why Australians can’t get enough of home improvement projects.” Flexspec Australia, March 14, 2024. https://flexspec.com.
au/the-love-affair-with-diy-why-australians-cant-get-enough-of-home-improvementprojects/#:~:text=The%20love%20of%20DIY%20projects,an%20expression%20of%20this%20mentality
42 “Owners-builder permit.” NSW Government. n.d. https://www.fairtrading. nsw.gov.au/housing-and-property/building-and-renovating/becoming-an-ownerbuilder/owner-builder-permits
43 “The most common building defects in new homes.” Select Building Inspections, n.d. https://selectbuildinginspections.com.au/common-building-defectsin-new-homes/#:~:text=Rickety%20and%20jamming%20doors%20don,of%20 moisture%20into%20the%20house.
44 “Owner-Builder frequently asked questions.” APEX Training Courses. nd. Accessed August 6, 2024. https://www.ownerbuildercourses.com/owner-builderfrequently-asked-questions.html#:~:text=Construction%20time%20should%20not%20 exceed,to%20your%20site%20or%20project.
45 Jennion, Craig. “Performing work for owner-builders.” NHS, September 20, 2021. https://www.nhs.trade/news/post/performing-work-for-owner-builders.html
46 “Owner-Builder frequently asked questions.” APEX Training Courses. nd. Accessed August 6, 2024. https://www.ownerbuildercourses.com/owner-builderfrequently-asked-questions.html#:~:text=Construction%20time%20should%20not%20 exceed,to%20your%20site%20or%20project.
47 “Guide to residential building loans.” St.George. May 17, 2020.
48 Swatridge, Paul. “Personal Correspondance.” August 21, 2024.
49 Savvy Editorial Team. “Owner-builder loans.” Savvy, August 7, 2023. https:// www.savvy.com.au/home-loans/owner-builder-loans/
50 Swatridge, Paul. “Personal Correspondance.” August 21, 2024.
51 “Securing loans with favourable terms for owner-builder in NSW.” Contract Specialist, April 22, 2024. https://www.contractsspecialist.com.au/articles/ownerbuilder-loans-nsw/
52 Statista Research Department. “Population distribution in Australia in 2024, by age. https://www.statista.com/statistics/608088/australia-age-distribution/ “Australia population.” WorldoMeter, n.d. https://www.worldometers.info/worldpopulation/australia-population/
53 Australian Institute of Health and Welfare. “People with disability in Australia.” Australian Government, April 23, 2024. https://www.aihw.gov.au/ reports/disability/people-with-disability-in-australia/contents/people-with-disability/ prevalence-of-disability
54 “Labour force, Australia.” Australian Bureau of Statistics, September 17, 2024.
55 “Australians have 200 million days of annual leave due.” Roy Morgan, December 19, 2023. https://www.roymorgan.com/findings/australians-have-200million-days-of-annual-leave-due
56 Read, Micheal. “How wealthy you are compared to everyonee else.” Financial Review, January 20, 2023. https://www.afr.com/politics/how-wealthy-are-youcompared-to-everyone-else-in-eight-charts-20221214-p5c6a8
57 “New houses being built on smaller blocks.” Australian Bureau of Statistics, July 7, 2022. https://www.abs.gov.au/articles/new-houses-being-built-smaller-blocks Sorensen, Emma. “How much does it cost to build a house in Sydney?” Realestate. com, October 3, 2024. https://www.realestate.com.au/advice/how-much-does-it-costto-build-a-house-in-sydney/
58 Edgar, Ray. “Postwar Melbourne needed homes and workers: Snail kits gave us both.” The Sydney Morning Herald, August 21, 2020. https://www.smh.com.au/ culture/art-and-design/postwar-melbourne-needed-homes-and-workers-snail-kitsgave-us-both-20200819-p55n4o.html
59 Murray, Cameron. “Did public housing create the Australian dream?” Fresh Economic Thinking, April 2, 2023. https://www.fresheconomicthinking.com/p/didpublic-housing-create-the-australian
60 Thomas, Maddie. “All of a sudden there’s a house’: could prefab be the future of Australian homes?” The Guardian, May 21, 2023. https://www.theguardian.com/ australia-news/2023/may/21/could-prefab-homes-be-future-australian-house-houses
61 “Anyone can build.” PAAL Kit Homes. n.d. https://www.paalkithomes.com. au/about/anyone-can-build.php
62 “PAAL... Kit homes for the hands-on owner-builder.” PAAL Kit Homes. n.d. https://www.paalkithomes.com.au/about/kit-homes-owner-builder.php
63 Peter Stutchbury Architecture, “Dimensions X.” n.d. https://www.dimensions. com.au/
64 De Achaval, Alejo. “Personal Correspondence.” August 27, 2024.
65 Smith, Cathy. “Handy, hippies and healing: Social transformation through the DIY movement (1940-1970) in North America.” Architectural Histories, University of Newcastle, Australia. 2014. https://journal.eahn.org/article/ id/7461/
66 Stickells, Lee, et al. “Not quite square: the story of Northern Rivers architecture.” Lismore Regional Gallery: Lismore, New South Wales, 2013. Page 2
67 Nicholson, Scott. “The basics of being an owner-builder in NSW.” Design Plus Drafting. February 27, 2020. https://designplusdrafting.com.au/the-basics-of-being-anowner-builder-in-nsw/#:~:text=What%20are%20the%20benefits%20of%20being%20an%20 owner%2Dbuilder%3F&text=It%20is%20estimated%20that%20owner,and%2040%25%20 on%20construction%20costs.
68 “Housing Census.” Australian Bureau of Statics. July 18, 2022. https://www.abs.gov.au/statistics/people/housing/housing-census/latest-
release#:~:text=Housing%20tenure%2C%202021%20Census,-This%20 image%20shows&text=Of%20all%20the%20occupied%20private,and%20 other%20non%2Dclassifiable%20households.?trk=article-ssr-frontend-pulse_ little-text-block
69 Greater Sydney urban development program dashboard.” NSW Government. November 15, 2023. Accessed August 22, 2024. https://app. powerbi.com/
70 “Land and housing supply indicators.” Australian Bureau of Statistics July 15, 2022. https://www.abs.gov.au/statistics/industry/building-andconstruction/land-and-housing-supply-indicators/latest-release
71 “Housing targets.” NSW Government. n.d. https://www.planning.nsw. gov.au/policy-and-legislation/housing/housing-targets
72 “Planning for the future of St Marys Town Centre.” Your Say Penrith. n.d. Accessed August 22, 2024. https://yoursaypenrith.com.au/stmarys2041
73 Warren, Carl. “Personal Correspondence.” August 24, 2024.
74 “Fire performance.” Colourbond. n.d. https://colorbond.com/whycolorbond-steel/fire-performance
75 “Owner-Builder Forum.” HomeOne. January 26, 2021. https://forum. homeone.com.au/viewforum.php?f=38
76 Build 10. “Owner Builder SA.” September, 2023. https://i-build.com.au/ownerbuilder-south-australia/.
77 “Guide to residential building loans.” St.George. May 17, 2020.
78 NHS Trade. “Performing work for owner-builders.” N.d. https://www.nhs.trade/news/ post/performing-work-for-owner-builders.html
79 Dervisevic, Hanan. “Hundreds of Australian construction firms have collapsed. Here’s what to do if your builder goes bust.” September 28, 2023. https://www.abc.net.au/news/202309-28/builders-collapsing-state-breakdown-of-legal-rights/102878514
80 Schlesigner, Larry. “Nearly 3000 building companies go broke in a year.” July 2, 2024. https://www.afr.com/property/commercial/nearly-3000-building-companies-go-brokein-a-year-20240701-p5jq86
81 Swatridge, Paul. “Personal Correspondance.” October 28, 2024.
82 The Premier, Minister for Homelessness, Minister for Housing, Minister for Planning and Public Spaces. “Modular homes to deliver more social housing, sooner.” NSW Government, July 22, 2024. https://www.nsw.gov.au/ media-releases/modular-homes-to-deliver-more-social-housing-sooner
Figure 1: Whittaker, Noel. “Housing Affordability.” December 21, 2016. https://www. noelwhittaker.com.au/essential_grid/housing-affordability/
Figure 2: Bassi, Isha. “An ode to The Castle, one of the most wholesome and charming Aussie flicks.” BuzzFeed, Febuaray 8, 2022. https://www.buzzfeed.com/ishabassi/the-castle-movieappreciation-post
Figure 3: Australian Glass Group. “NCC 2022 Confirmed.” n.d. https://agg.com.au/ncc-2022-confirmed//
Figure 4: Created by student.
Figeure 5: Created by student.
Figure 6: Created by student.
Figure 7: Created by student.
Figure 8: Created by student.
Figure 9: Taken by student
Figure 10: Pandey, Swati.” Australian Home Prices Rise for Second Straight Month in Sign of Market Stabilization.” bloomberg, April 30, 2023. https://www.bloomberg.com/news/articles/2023-04-30/australian-home-prices-rise-for-secondstraight-month-in-sign-of-stabilization?in_source=embedded-checkout-banner
Figure 11: Taken by student.
Figure 12: Table Sources for quoted figures “Workers compensation insurance.” Fully Insured, n.d. https://fullyinsured.com.au/insurance/ workers-compensation-insurance/ Business Insurance. “What insurance do owner-builders need?” CGU, June 4, 2018. https:// www.cgu.com.au/blog/what-insurance-do-owner-builders-need “Building insurances.” Buildsafe. n.d. https://buildsafe.com.au/term-policy/ Fair Trading. “Professional Indemnity insurance information sheet.” NSW Government, 2003. chrome-extension://efaidnbmnnnibpcajpcglclefindmkaj/https://www.fairtrading.nsw.gov.au/__ data/assets/pdf_file/0010/371872/Professional_indemnity_insurance_information_sheet.pdf ABLIS. “Owner-builder permit: New South Wales.” Australian Government. n.d. https://ablis. business.gov.au/service/nsw/owner-builder-permit/16675 Revenue NSW. “First home owner (new homes) grant.” n.d. https://www.revenue.nsw.gov.au/ grants-schemes/first-home-buyer/first-home-owner-new-homes-grant “First-home buyer’s guide: What grants, incentives and discounts do first-home buyers get?” Domain. n.d. https://www.domain.com.au/guides/first-home-buyers-guide-what-grants-
incentives-and-discounts-do-first-home-buyers-get-872680/ Sudarshan, Saranga & Wallis, Sophie. “Australian household spending statistics.” Finder, August 28, 2024. https://www.finder.com.au/insights/australian-household-spending-statistics Kagan, Julia. “Loan servicing: Definition, how it works, example.” Investopedia, November 30, 2020. https://www.investopedia.com/terms/l/loan_servicing.asp#:~:text=This%20fee%20 usually%20amounts%20to,amount%20to%20the%20note%20holder “Land surveying costing guide Australia 2023.” Avian, n.d. https://www.avian.net.au/landsurveying-costing-guide/ Ashington Homes. “DA Application Cost Estimate.” HomeOne. April 5, 2022. https://forum. homeone.com.au/viewtopic.php?f=31&t=104797
Fignure 13: Bladwinson, Arthur. “Beaufort Home Construction.” State Library New South Wales. https://www.sl.nsw.gov.au/volume-5-beaufort-home-construction-photographs-arthurbaldwinson-collection
Fignure 14: Gropius, W. & Wachsmann, K. The General Panel Corporation. In The Dream of the Factory-Made House. MIT Press, Cambridge, 2021. https://parametricmonkey. com/2023/10/05/modular-construction-amp-its-henry-ford-syndrome/
Fignure 15: Lange, Kate. “Modular homes: Home Smitten.” Pinterest, n.d. https://au.pinterest. com/pin/346988346269852139/
Fignure 16: Image scan from catalogue. PAAL. “Kit homes for country Australia.” July 2023, p.51
Figure 17: Image scan from catalogue. PAAL. “Kit homes for country Australia.” July 2023, p.30.
Figure 18: PAAL. “Wall frame assembly.” n.d. ccessed August 23, 2024. https://www. paalkithomes.com.au/blog/post-details-36.php
Figure 19: PAAL. “Catalogue Image.” n.d. https://www.paalkithomes.com.au/blog/postdetails-36.php
Figure 20: Peter Stutchbury Architecture, “PS1 construction.” n.d. Accessed August 23, 2024. https://www.dimensions.com.au/
Figure 21: Peter Stutchbury Architecture, “OM1 construction.” n.d. Accessed August 23, 2024. https://www.dimensions.com.au/
Figure 22: Peter Stutchbury Architecture, “OM1 finished photos” n.d. Accessed August 23, 2024. https://www.dimensions.com.au/
Figure 23: Bolinas, Callif. “Shelter.” Random House, New
York. 1973. https://sydney.primo.exlibrisgroup.com/discovery/ fulldisplay?docid=alma991002687359705106&context=L&vid=61USYD_ INST:sydney&lang=en&search_scope=MyInst_and_CI&adaptor=Local%20Search%20 Engine&tab=Everything&query=any,contains,shelter&mode=basic
Figure 24: Screenshot Sources: “Billy.” IKEA. n.d. https://www.ikea.com/au/en/p/billy-bookcase-white-00522047/ “Niva.” Fantastic Furniture. n.d. https://www.fantasticfurniture.com.au/Categories/ Living-&-Dining/Living-Room/Entertainment-Units/Niva-160cm-Entertainment-Unit/p/ NIVLOWMEDOOOFOIOAK
“Hume 2040x820x35mm Internal door primed MDF finish.” Bunnings. n.d. https://www. bunnings.com.au/hume-2040-x-820-x-35mm-internal-door-primed-mdf-flush-prehung-fhlh_p1972955
“1800mm Kitchen Island Sintered stone white modern with storage kitchen cabinet.” Homely. n.d. https://au.homary.com/item/72-sintered-stone-white-kitchen-island-with-storage-modernkitchen-cabinet-47645.html
“Premier housewares bar stool/wooden = stool/breakfastbar stool - natural, 64,32,32. Amazon. n.d. https://www.amazon.com.au/Premier-Housewares-Revolving-Rubberwood-Stool/dp/ B0018819EE
“Gabby walnut dining chair.” Home Gallery Stores. n.d. https://homegallerystores.com/gabbywalnut-dining-chair
Figure 25: Screenshot. “Property map.” Domain. n.d. https://www.domain.com.au/ sale/?excludeunderoffer=1&displaymap=1
Figure 26: Construction Industry Federation. “Mental Health in the Construction Sector.” n.d. Accessed 29 October, 2024. https://cif.ie/wp-content/uploads/2020/09/1237-CIF-MentalHealth-Report-LR.pdf
Consultation with a Mortgage Broker. 21/8/24
Have you ever dealt with an owner-builder loan?
Yes. St George NAB do them. Not done one in the last 10 years
What is the process of applying for the loan? What documents are required?
Unsure about the exact documents required having not reviewed an application in a while. Is going to put in a ‘placeholder’ claim to find out and email the answer.
There seems to be a reluctance towards approving owner-builder loans. Why is this? The loan is very high risk with historical data of many owner-builder projects failing to reach completion resulting in the mortgage broker incurring significant losses as they are rarely able to recoup their money on an abandoned half-built project.
What can owner-builders do to improve their chances of getting a loan?
Need all the necessary qualifications a builder would have, prove that they will maintain a reasonable income for the duration of the construction and have a large amount of money already saved to cover the cost of each stage of construction and possible contingencies.
Are their major red flags lenders look for when reviewing documents that should be avoided?
It’s seen as high risk by lenders every aspect of the project needs to be fully documented and approved for any loan to be offered. In essence any aspect not fully complete in the application is a red flag. Need to be able service the loan e.i. Maintain a source of income during the build so lenders.
What is the process of payment to ownerbuilders? Research I have conducted so far has mentioned that payments are made based on the project reaching certain stages of completion within a timeframe.
Generally do lines of credit. Draw down. The owner-builder needs to be able to fund each stage up front. There’s ruffly 6 stages of payments. The bank then pays the money to the OB for that stage. Need to have inbuilt contingencies for unexpected costs. Can’t borrow any money to push through a stage.. Non-completion is borrowed against the land and in-progress build.
Conversation with Builder of Peter Stutchbury PS1 Mark: Building Process
“What was your experience of constructing the Dimensions buildings?”
“Did the process seem simplified with the prefabricated parts?”
Yes, when everything was to the correct compliances and lined up the total construction only took two days with the project relatively straightforward for a builder.
“Were there unforeseen challenges of working
with prefabricated parts?”
Project sequencing so that the correct parts were on site and ready to go when needed and decisions about when a crane needs to be brought in e.i. Do you use it to unload the truck and install building walls in the same day or just unload and bring it back tomorrow. Site access will also play into this with the current examples
“How much work was done on site?” Was it as simple as fixing components together or was there additional steps before things could go in?”
“What was the delivery method of materials? Was everything you needed to build all brought at once or was it in stages? Did you need to go out and buy additional things to complete the project?”
What did you think about the project overall? Do you feel this style of design and construction process should become more common in the construction industry?’
Do you think a group of unskilled people could construct a Dimensions X building?
What are your thoughts on unskilled ownerbuilders attempting to build their own home? Do you think this is something that is achievable?
Would you have any advice for someone attempting to build their own home? Pitfalls? Or things someone might overlook when starting this type of project?
Conversation with the Architect of Peter Stutchbury Architecture’s Prefab systems Alejo: 22/8/2024
Introduction
What was your role on the project? Project Architect.
Is the project designed in such a way that a group of unskilled people could build this project? If so, were there any specific design decisions or detailing that was done to accommodate unskilled people building the structure? If not, why not?
Responsiveness to site is one of Pete’s key ideologies something that prefabricated homes often struggle to achieve. How did Dimensions seek to address these challenges? Whilst reducing the amount of different prefabricated elements? How flexible and scalable is the modularity of the structure and the internal spaces? Can the size of Dimension X structures and the internal finishes be changed to a client's desires? How does it achieve this modular setup via a grid system or a series of building blocks that can be configured in various ways.
The first Dimensions X structure was built in a rural context, how do you feel this style of building would perform in a suburban area? Would any adjustments to the design be required?
Continually refining process refine by taking out as much as you can minimising details continually refining through practical development. To take away from all aspects. First design is OM 1 second PS 1 as affordable as possible. Portal frame structure with wall of different size. Building can increase in length and 4 types of wall panels
and four types floor panels. Same a best built house but has the flexibility. PS 1 takes out the flexibility is fixed openings to make things faster the shell is always the same with the openings able to be used as either able to move around internal fixtures around e.i lights.
Loss of accessibility with bigger panels requiring cheapest crane (scissor crane) to to place panels.
CLT is far more workable than steel with the flexibility to be used as a structure, finish and acoustic barrier.
Process was to continually construct aspects of the project to test each aspect of the construction process, refining aspects such as double handling, amount of material required, tips and tricks, tools needed and how to adjust things to personal preference.
Bal meets 2029 rating and can be improved to higher rating by changing out windows and doors and adding an additional cladding.
Phone Consultation with primary stakeholder (Mother & Father) 24/8/24
Objectives: To understand more about design preferences and layout of their desired home.
Let’s start with room relationships. Which rooms do we want nearby? For example, do we want all the bedrooms close together? The kitchen, dining & living room open plan and connected? Continue working through the key spaces of the home.
How do you want these spaces to look? Do you have any ideas on materiality?
Timber floors for all dry areas, white walls, white cabinetry. Furniture to be the statement pieces.
Wet areas tiled need natural light, white bench tops.
How do you want these spaces to feel? Do you want living spaces to be open and filled with natural light? Continue through key spaces.
Standard room sizes, that aren’t small but to standard dimensions such as 2.4m ceil heights etc.
Wide and high hallway.
Wanting everything to feel light and generous but not delicate.
Are there any areas you want a close relationship to landscape or key outside views?
Living area and the kitchen need a view. Bedrooms are less important, requiring mainly natural light as they function mainly as change rooms. The master bed having direct access to the outside is also important.
If you had to list your most important things the house needs to achieve, what would they be?
Has to function for the three generations at the same with the ability to have their own space within the house but also be able to inhabit the same areas at the same time. 5 bedrooms and a study at least.
Spatial Connections Diagram Produced Post Client Consultation Phone Call.
Ensuite -Shower -Storage -Toilet
Landscape -Native Plants -Outdoor Seating -BBQ Area
Master Bed -King Bed -Walk-in Robe -Natural Light
Parlour -Lounge -Table -TV
Kitchen -Double Sink -Bench Seating -Dishwasher -Large Fridge -Large Pantry
Dining -8 Person
Dining Table -Close to Outdoors
Kids Bed 1 -Double Bed -Wardrode -Natural Light
Kids Bed 2 -Double Bed -Wardrode -Natural Light
Playroom
Main Bath -Bath -Toilet -Shower Laundry
Kids Bed 3 -Double Bed -Wardrode -Natural Light
Ensuite -Shower -Storage -Toilet
Grandmother’s Bed -Queen Bed -Storage -Display space
Open Plan Living
Living -Seating for 8 -Coffee table -Large TV -Display Cabinetry
Entry
Study -Storage -Desk
Carport -Space for 2 Cars -Storage -Workspace
Spatial diagram developed after client consultation.
Key: Has a degree of separation Direct connection
How do you want these spaces to look? Do you have any ideas on materiality?
‘Timber floors for all dry areas, white walls, white cabinetry. Furniture to be the statement pieces. Wet areas tiled need natural light, white bench tops.’
-Client Consulation 24/8/24
Collages of Finished Produced Post Client Consultation Phone Call.
How do you want these spaces to feel? Do you want living spaces to be open and filled with natural light?
‘Wanting everything to feel light and generous but not delicate.’
-Client Consulation 24/8/24
Collages of Finished Produced Post Client Consultation Phone Call.
Housing Construction Forcast over the next 5 years.
Image created by student using data from “Greateer Sydney urban development program dashboard.” NSW Government. November 15, 2023. Accessed August 22, 2024. https://app.powerbi. com/
10 SARDAM AVENUE
Council: Penrith City
LEP: Penrith Local
Environment Plan 2010
Land Zoning: R2 Low
Density Residential
FSR: NA
Build Height: 8.5m
Lot Size: 550m2
Special Considerations: At risk of flooding.
Existing trees create poor site access.
19 BRIDGE VIEW STREET
Council: Blacktown City
LEP: Blacktown Local
Environment Plan 2015
Land Zoning: R2 Low
Density Residential
FSR: NA
Build Height: 9m
Lot Size: 550m2
Special Considerations: NA
Site’s researched but not chosen. Images edited by student. Original source: “Six maps.” NSW Goverment. n.d.
19 PANDOREA STREET CLAREMONT
Council: Penrith City
LEP: Penrith Local
Environment Plan 2010
Land Zoning: R2 Low
Density Residential FSR: NA
Build Height: NA
Lot Size: 550m2
Special Considerations:
Local provisions LEP clauses apply.
30 NAGLE STREET JORDAN SPRINGS
Council: Penrith City
LEP: Penrith Local
Environment Plan 2010
Land Zoning: UR Urban
FSR: NA
Build Height: NA
Lot Size: 375m2
Special Considerations: NA
Site’s researcedh but not chosen. Images edited by student. Original source: “Six maps.” NSW Goverment. n.d.
Information within this table has been created in close reference to Penrith LEP and DCP docuemtns and may contain some areas of copy-paste text.
Document Part Section Subsection
Penrith LEP 2010
Principle development Standards Height of Buildings N/A
Principle development Standards Floor Space Ratio
Penrith DCP 2014 D2 - Residential Development 2.1. Single Dwellings
2.1.2 Setback and building envelope
2.1.4 Landscaped Area
Page Control Control Text
N/A
5 1a
Maximum height of building 8.5m.
No defined floor space ratio for site.
Front set back 5.5m or average of adjoining properties, whichever is bigger.
1c Verandahs and pergolas can encroach 1.5m into front setback.
1d Side setbacks minimum 900mm
1e i) Minimum rear setback for single story component is 4m.
ii) Minimum rear setback for a two-storey building 6000m.
iii) Minor encroachments into rear setbacks will be considered on irregular blocks.
iv) Rear setbacks are to be used predominantly for landscaped area.
1f Exceptions to rear setbacks are considered for non-habitable buildings/structures if it can be demonstrated it will have minimal adverse impact on subject property or adjoining properties.
5 2a
2b
8 1
Building envelope is 1.8m off the ground on the side boundaries and the projected at a 45-degree angle into the centre of the site.
Considerations may be given for minor encroachments into the building envelope e.i. eaves, gutters, chimneys, antennas, pergolas where it is demonstrated encroachment improves the design, appearance or utility of the building.
Minimum landscaped area for R2 is 50%
2 Calculation for landscaped area does not include areas less than 2m in width and hard surface areas such as driveways.
3 Calculation of landscape area includes up to 15m2 of any deck/patio attached to the dwelling at ground floor level and associated with the landscaped area.
4 A portion of the landscaped area should be connected to or directly adjacent to a living area.
2.1.5 Building Design/ Site Works
2.1.6 Solar Planning
2.1.7 Garden Design and Fences
9 1 Articulation of all building forms and façades including stepping floor plans capped by various roof forms and pitches, every window should have windows and wall should be overhung.
2a Two storey buildings should mix one and two storey elements.
2b External walls cannot be an uninterrupted length longer than 8m e.i. no windows, verandahs.
2c Balconies and decks above 800mm should include screening and landscape planting.
3 Design should front street with a traditional configuration front door, window to habitable room, garage integrated into façade, driveway size minimised.
4a Garage setback 1m from building line of dwelling.
4b Width of garage doors cannot exceed 6m.
1 Existing neighbouring private open spaces and proposed open spaces receive adequate solar access. Maximise solar gain by exposing windows to Northern sun, living zones have a minimum of 3 hours of sunlight between 9am and 3pm on June 21.
3 hours of sunlight between 9am and 3pm on June 21 to 40% of main living zones. Sunlight is not to be reduced further than 20% of existing overshadowing.
10 1 Retaining walls, no taller than 600mm and should be separated from fence by 500mm wide planter and driveway by 500mm wide landscape verge.
2a Dividing Fences Act 1991 requirements.
2b Fences should be no taller than 1.8m including any retaining wall.
2c Fences on boundaries in front of the building should not be taller than 1.2m and be see-through.
2e Fences seen from the street cannot be constructed out of solid metal panels.
2f Fencing with a timber frame or between brick piers as long as it is no taller than 600mm and palings are spaced.
3a Rear boundary setback should be private open space.
3b Habitat corridor and green backdrop visible from the street.
2.1.8 Significant Landscapes
2.1.9 Significant Townscapes
Land Environment Plan and Development Control Plans have been summarized with all relevant controls extracted and applied to a site context model containing topography.
4
5
6
3
Planting along boundaries small-medium to provide shading and privacy.
Planting in service areas to create ground cover.
Street frontage to be sympathetic to the setting in the materials, colour, planting choices and maintain natural surveillance from the street.
Ensure the long-term survival of existing trees.
8 New planting should be indigenous species to the local soil type.
No controls applicable.
FUNCTIONAL & DURABLE
QUICK PROGRESS TO LOCK-UP 1 2 3
SIMPLIFCATION & STANDARDISATION
NON-PRESCRIPTIVE DESIGN
LIGHT & GENEROUS
FLEXIBILITY IN MATERIALS & LAYOUT
Early Ideas Matrix of key concepts of the design.
Mortgage Broker Conversation 28/10/24
The goal is to pitch the project to the broker and see if he feels this would improve the of overall financial viability and improve the chances of getting a loan.
The lender was flexible with the staging, staging the costing how much the it aligns with the supplier payment requirements. Smaller deposit up front. Then repaying the modular parts purchased in full upon completion of a stage.
Would work well satisfying the key requirements accurate costing, staging and timelines. Costings looked at closely. Don’t think it’ll a problem.
A history behind the system will help and the success of owner-builders. Whole idea sounds good. Lender requirements will be show and addressed justification. Lenders will follow initiates via government incentives and do become more flexible, offering more favourable loans. Upfront equity is whether or not they are going to lose. Land ownership for that early upfront payments. High upfront first down payment
Completion scenario as they take ages to do and run over costs. Lendering on partially completed properties . High land value with equity really helps this system front end costs.
Up front and in one heavy payment makes it hard for small start-ups to produce a system like this.