Sustainability Report 2022
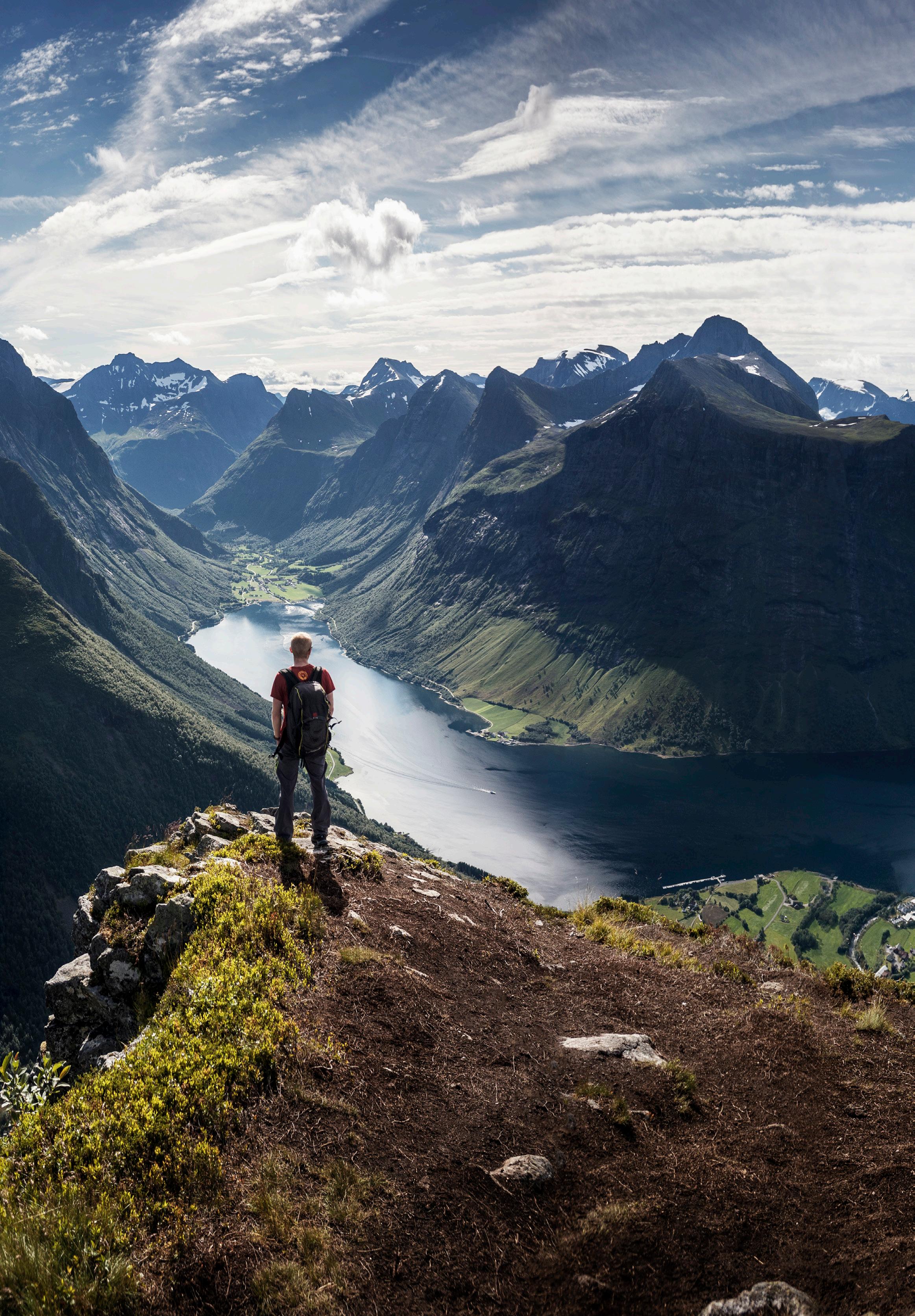
Optimar is a global leader in automated fish processing systems for use on board fishing vessels, on land and in the aquaculture sector. Aside from its headquarters and manufacturing facility in Ålesund, on Norway’s west coast, Optimar operates other facilities in Norway, the United States, Spain and Romania. The company delivers to international customers in more than 40 countries.
The challenges of our time are becoming even greater, and we are convinced that there is no alternative to focusing on sustainability. For Optimar, this means taking a holistic view of our actions and thinking through their consequences from beginning to end. There is no option but to step up and focus on our mission to create value for present and future generations.
Animal health and welfare, human working conditions, raw material utilization, energy consumption and carbon emissions are important considerations in sustainable food production. Consumer awareness of and emphasis on these considerations is changing how our industry operates. We have used 2022 to take a step back and see where and in what areas we can do the most, and make real changes in the industry.
The situation in 2022 made it extremely difficult for us to achieve the ambitious targets we set ourselves in the year before. The fallout from the ongoing war in Ukraine,
combined with supply chain issues and rising prices, also had a major impact on our market. In response to the uncertain economic outlook, many of our customers were reluctant to embark on major new investment projects. For this reason, we were forced to make far-reaching organizational changes and concentrate our limited resources entirely on stopgap adjustments. But by taking action at an early stage, we were able to secure a sustainable financial footing for our business and secure the jobs of over 300 employees in Norway, Spain, Romania and the USA.
Optimar’s dedicated and highly skilled workforce is our
Sustainability is no longer a project or initiative; it is the core of our business and will continue to set the future course of both the industry and the people involved in it.
Georg Saint-Denis | CEO, Optimar
most valuable resource. For us, it is important to value each and every team member. We know that it takes people, engagement and considerable effort to make the changes necessary to develop in the right direction. Our people and their engagement in Optimar gave us the strength to ride out the rough water we faced in 2022.
By taking advantage of our position, we can influence a great part of the industry. Our value chain – from initial idea to complete delivery – affects many different sub-suppliers and partners. By setting high standards concerning working conditions, safety, emissions and environmental impact, Optimar, along with its suppliers and business associates, has the opportunity to positively impact not only the industry but also those who more broadly depend on it.
We offer complete solutions that minimize energy consumption and carbon emissions along the value chain by enabling our customers to process fish more effectively, safely and with higher quality. In doing so, our goal is an ethically sound end-product, with the highest level of animal welfare and 100% yield. We will achieve this through the innovation that Optimar has been renowned for for many years. In order to initiate and control improvement processes, data is needed. Our digital solutions therefore provide our customers with a wealth of valuable data and control options.
Optimar reaffirms its support of the Ten Principles of the United Nations Global Compact in the areas of human and labour rights, the environment and anti-corruption. We disclose our continuous efforts to integrate the Ten Principles into our business strategy, culture and day-to-day operations, and contribute to the achievement of United
Nations goals, particularly the UN’ Sustainable Development Goals (SDGs).
ࣽ Increased focus on animal welfare, with support from animal welfare organizations. Through the year, we established close connections with several animal welfare organizations with the aim of improving animal welfare in the harvesting process.
ࣽ CatchID, we are a chosen partner. We have started a close collaboration with the Norwegian Directorate of Fisheries to develop a common platform for sustainable fishing and reporting by the fishing fleet.
ࣽ Solar panels were installed at our facility in Spain, which reduced CO2 emissions from electricity consumption at that site by 65%.
Sustainability is no longer a project or initiative; it is the core of our business and will continue to set the future course of both the industry and the people involved in it.
We look forward to continuing our work in creating value for generations.
Georg Saint-Denis CEO OptimarWe have been a member of UN Global Compact since 2020 and published our first sustainability report for that same year. We reported our first GHG emission calculation for the year 2021. In 2022 we followed up on initiatives and adjusted our Sustainable Development Goals
We have been a member of UN Global Compact since 2020 and published our first sustainability report for that same year. We reported our first GHG emission calculation for the year 2021. In 2022, we followed up on initiatives and adjusted our SDG-related endeavours.
ESG is incorporated as a natural part of our overall business strategy. We have matured in our sustainability work since 2020. For example, when we restructured the business in 2022, we did not retain a defined sustainability team, but integrated sustainability goals, tasks and reporting into the business lines and departments. In doing so, we have enhanced sustainability ownership and quality in our day-to-day business.
Optimar’s board of directors is responsible for determining company guidelines and strategy , while the CEO is responsible for implementing the strategy.
Our top management are responsible for company compliance, and ensures that our reporting is compliant with applicable legislation and directives.
Our Sustainability Lead (SL) has overall responsibility for the preparation and follow-up of the strategy and goals. The SL coordinates the various sustainability initiatives driven by our departments and reports to top management and the board.
Through a variety of contact points, such as union dialogue meetings, exhibitions, supplier questionnaires, employee surveys and partnerships with non-government organizations (NGOs) and academia, our stakeholders have shown us which topics are important for them and what they need and expect from us as a company going forward.
Responsible business, plans, operations and investments are essential to achieving transformational change through sustainable development goals (SDGs). The UN’s 17 Sustainable Development Goals (SDGs) provide a framework for achieving the agenda and targets set by UN Member States. Together, the SDGs signpost what needs to be done to end extreme poverty, fight inequality and injustice, and protect our planet. We have determined four SDGs where we assess that we have the greatest impact. Focusing primarily on these four goals will, however, also contribute positively to others of the UN’s 17 SDGs.
Goal 12
We wish to help reduce the environmental footprint of the value chain in which we participate, not only by reducing the emissions associated with our own production process but also those relating to customers’ use of our products, by making them more energy efficient and operationally robust.
Our equipment has a long service life and to extend it even further, we offer customers a rebuilding, reconfiguration and upgrade service for their pre-used machinery.
The design of our equipment and systems plays an important role in maintaining the high quality of the raw materials that are processed in the customers’ factories. High quality results in less food waste in the production chain, and more food with a high nutritional content. We are therefore constantly striving to further improve the design of our products and services.
Goal 8
When developing our factory solutions, we work for increased catch utilization and a higher quality end-product. This contributes to increased economic productivity among our customers and maximum utilization of our marine resources.
Fishing is generally associated with heavy manual labour. Our automated solutions assist the industry to provide better factory working conditions, and we focus strongly on health, safety and ergonomics both at our own production facilities and wherever our products are used.
Goal 14
Through design, engineering, automation and control we provide our customers with the opportunity to gather data that helps document their operations from a production, environmental and efficiency perspective. We are helping to develop an advanced fish sorting and grading system that will enable improved traceability and sustainability in the fishing industry. It will also facilitate better verification and reporting of harvested fish stocks as a means of reducing overfishing.
Goal 17
We are contributing our expertise and technology to partnerships with academia, public authorities, animal welfare organizations and marine clusters. We value our relationship with business partners and customers globally, and mutual cooperation ultimately leads to product designs based on worldwide experience.
Based on our four main SDGs we have identified the following GRI topics as material for Optimar. It is in relation to these topics that we can reinforce ours, and the fish handling industry’s positive impact and reduce our and the fish handling industry’s adverse impacts. SDGs 2, 3, 13 and 15 are not our main goals but will be affected by our focus on SDGs 8, 12, 14 and 17.
Based on our aim to deliver fish handling with care by improving the sustainability of food production, and the material sustainability topics we have uncovered, we have set ourselves strategic goals to ensure that we achieve our objectives.
Growth SDG 14 Sustainable product development Align our internal product development guidelines with our sustainability goals.
SDG 17 Partnerships for sustainable development
Be an innovative contributor to the industry by challenging established solutions.
Be the chosen partner for the project CatchID in Norway.
SDG 8 Sustainable economic growth Anchor plan for ISO 9001-certification with the board, top management and organization.
Operations SDG 12 Responsible supply chain
Map and risk assess all suppliers.
Establish a Suppliers Code of Conduct.
Establish a policy for supplier risk management.
Renewable energy share Increase renewable energy share from 50% to 70%.
Emissions Establish full Scope 3 screening.
People SDG 8 Occupational health and safety
All employees to have downloaded and activated app for incident reporting in the new system Optimize.
Be the chosen partner for sustainable development of the fish handling industry in cooperation with public authorities, non-profit organizations and academia.
Achieve ISO 9001-certification.
Audit process established and implemented, and auditors trained.
100% of the energy used in our factories is from renewable sources.
Net zero by 2050.
Achieved ISO 45001-certification.
Sick leave total under 3%. Zero work-related sick leave. Attractive employer Re-establish regular employee surveys. Resignations < 3 per month.
Steady high score on employee surveys and 3 or more qualified applicants for each vacant position in the company.
Optimar believes there is a strong correlation between long-term profitability and responsible business practices. This attitude is reflected in the company’s environmental, social and governance (ESG) standards and our ethical guidelines. We support the UN Global Compact’s ten principles on human and labour rights, the environment and anti-corruption, and require the same from our business partners and suppliers
Our ethical guidelines are known by and available to all our employees. They describe key ethical principles to which Optimar is committed and provide basic principles for expected behaviour and business practice. Our whistleblower e-mail is open for both internal and external disclosures, and both are handled with the same discretion.
We strive to ensure that all our activities worldwide are conducted in accordance with basic human rights. Optimar supports internationally recognized human rights, such as the UN Declaration of Human Rights and the standards promoted by the International Labor Organization (ILO).
Material human rights related to the business are:
ࣽ Freedom of association and collective bargaining.
ࣽ Safe and healthy working environment.
ࣽ Labour standards, including prevention of forced labour, child labour and non-discrimination in employment and occupation.
ࣽ Working conditions (wages, working hours).
ࣽ Freedom of expression.
Optimar is vehemently opposed to all forms of corruption and works actively to ensure that this does not occur within the company. Corruption is not tolerated at Optimar, and violations will lead to disciplinary action.
Our people will make a difference
Fish handling with care is our purpose and we enable our customers to process the fish as sustainably as possible by means of the equipment we supply. Our key objective and passion is to continuously improve the standard of fish handling and enable our customers to process fish more efficiently, safely and with higher quality. Fish welfare, food safety and safe working conditions for operators are always of primary importance
In the table to the right, we describe a selection of our accomplishments in 2022 and what we are aiming for in the short and long term regarding our contribution to sustainable fisheries.
Animal welfare
ࣽ Collaboration with Food Safety Authorities to ensure products in our portfolio that handle live animals adequately safeguard animal welfare.
ࣽ Investigated, documented and determined equipment parameters to ensure gentle handling.
ࣽ Tested and documented how connecting our Optiflush solution to the Optilice Flush System can remove sea lice more efficiently, while better safeguarding fish welfare, because the water temperature needed is reduced by 2–4 degrees Celsius. This also offers the benefits of reduced energy consumption. The system has been designed specifically to ensure the gentle handling of fish and lice removal without the use of chemicals.
ࣽ Increase availability of stunners to smaller customers (small-scale aquaculture production) in emerging markets
ࣽ Make the Optiflush available to all actors in the market.
Supply fish farms worldwide with delousing solutions that safeguard fish welfare and avoid the use of harmful chemicals or other threats to marine life.
Food quality and food safety
ࣽ Optimized performance to achieve higher quality fish bleeding. Introduced a new system for flow control and a solution that is more cleanable and gentler compared to the previous solution.
ࣽ Testing and approving optimized bleeding systems that improve the quality of the seafood products, since bleeding will be performed in a more controlled timespan based on the FIFO principle, using equipment that is more cleanable and gentler than previous versions.
ࣽ Level 1 EHEDG training for our engineers to increase knowledge of hygienic design.
Improve cleanability of our standard tanks and bulk seafood handling systems. Combined with more gentle treatment, this will lead to fewer losses and higher quality food products, increased food safety and reduced use of water, chemicals and time needed for cleaning.
Energy consumption in the value chain
ࣽ Released new CO2-freezing plates onto the market, showing satisfactory results with short freezing times.
ࣽ Developed a new onboard freezer design.
ࣽ Perform testing and tracking of energy consumption and freezing time, with the aim of further optimizing the design to achieve a shorter freezing time and reduced energy consumption in the freezing process.
Optimize energy consumption and freezing time for various species in our plate freezer solutions.
Working conditions (safety, heavy lifting, etc)
Process control and data harvesting
ࣽ Commander Web platform rolled out to multiple new customers, enabling data capture from operations.
ࣽ Customers in general are more interested in data capture from operations. Commander OnSite delivered to multiple customers, enabling better overall control and diagnostics.
ࣽ Applied for participation in the Norwegian Directorate of Fisheries’ CatchID project.
ࣽ Launch new designs for our main conveyor products where we improve personnel safety without compromising on food safety.
ࣽ Release an automated packing solution for the onboard market.
ࣽ Standardize Commander Web as the platform for production data capture in all of our segments.
ࣽ Help customer to integrate factory-related fuel and emission data.
ࣽ Participation in the Norwegian Directorate of Fisheries’ CatchID project.
Become a solution provider for weighing, grading and packing whole fish and fillets without the need of heavy manual labour.
Gather operational data that helps document customers’ operations, from a production, environmental and efficiency perspective.
Greater focus on increasing factories’ energy efficiency, based on harvested data.
The entire fishing industry has a responsibility to manage our global fish resources in the best possible way. At Optimar, we always focus on making products and systems that ensure a high-quality end product, with as little waste as possible. Our target is to reduce our adverse impact and promote our positive impact, as well as exploit possibilities related to the climate and environment
Our commitment:
ࣽ Map and reduce our carbon footprint.
ࣽ Improve waste management, reduce residual waste and increase utilization of purchased materials.
ࣽ Increase product lifespans through rebuilding and retrofitting.
ࣽ Reduce non-renewable energy consumption.
ࣽ Contribute to animal welfare, enable full utilization of raw materials and traceability for sustainable fisheries.
By reducing our operational footprint, we will reduce the footprint of the products we deliver to our customers.
CEMAsys is Optimar’s system partner for carbon accounting. This report provides an overview of Optimar’s greenhouse gas (GHG) emissions, which form an integrated part of our climate strategy. The presentation is based on consumption data from internal and external sources, converted into tonnes of CO2-equivalents (tCO2e).
Scope 1 includes all direct emission sources. This includes all use of fossil fuels for stationary combustion, transportation by company vehicles (both leased and owned) and process emissions.
Emission factors per fuel type are based on assumptions in the IEA methodological framework. Our Scope 1 emissions are lower than in 2021 mainly because we closed one facility in Braila, Romania. Closing the site reduced the annual use of natural gas for heating and internal transport between sites in Romania. The use of diesel decreased in 2022 because we eliminated four diesel cars from our vehicle fleet, three in Norway and one in Spain. The four cars were replaced by one electric car in Norway. The use of company cars was needed in connection with fewer projects in 2022.
In June 2022, we finalized installation of solar panels at our production facility in Spain. This led to a reduction in electricity consumption from 135 MWh in 2021 to 61 MWh in 2022, and a reduction in tCO2e of 65%. We also reduced our services in Seattle, USA, and the remaining employees in the US have been working from home since April 2022. The closure of the production facility in Braila, Romania, also contributed to reduced electricity consumption in 2022 compared to 2021.
Scope 3 is so far only partially accounted for, and for 2022 scope 3 includes the categories waste and business travel.
2022 was the first year where we report business travels by air for all units globally. We see that the number of travels is increasing again after reliefs of corona restrictions, but compared to the last pre-pandemic year 2019, we are significantly below. In 2019 business travels by air for the Norwegian unit alone contributed with 788,3 tCO2e to our GHG emissions
In 2021, we experienced an acid leakage incident which, in addition to its local environmental impact, meant a large increase in hazardous waste during the cleanup process. 380 out of 412 tCO2e from our waste handling was due to the acid leakage. If we exclude the hazardous waste from the incident, we note a 30 per cent reduction in GHG emissions from waste handling in 2022 compared with 2021. One initiative for reducing residual waste was the implementation of waste sorting stations at all Norwegian sites.
In 2022, we ended our use of water jets, and the disposal of the sand gave a non-recurring increase in residual waste in 2022. The handling of the sand alone contributed 9.8 tCO2e.
We apply our expertise in pursuit of more sustainable fisheries
We have a steady focus on measures for improvement in our own operations. This may include changes for reduced emissions, a safer working environment or to make the company robust against future changes
Having three facilities located nearby in Norway and two in Romania generates a lot of transport between the sites. Now that we have optimized production at one facility in Norway and one in Romania we have significantly reduced internal transport and thereby decreased our fuel consumption. We have not included this in our Scope 3 emission calculations yet, so the reduction is not visible in the data set.
Since the acid leak in 2021, we have worked hard to find a replacement for our acid treatment of steel. The solution had to be not only effective and offer a high capacity, but also environmentally friendly, with a low risk of leakage, and ensure the safest possi-
ble working environment for our operators. We have successfully identified a container solution that fulfils all our requirements. In addition, the ability to perform acid treatment in-house again will reduce our need for transportation. Over a period of six months in 2022, 46 tonnes of steel were transported back and forth to a third-party facility for acid treatment, a process requiring 100 separate journeys. Roughly calculated, this initiative will reduce CO2 emissions from transport relating to acid treatment by 20–25 tCO2e per year compared to 2022.
We are convinced that diversity and inclusion are important factors for growing our business and our results. Diversity in gender, background, culture and experience contributes to a strong work environment
A blend of different voices and thoughts makes Optimar an exciting and inclusive place to work that fosters personal development and professional growth. Equal rights is a fundamental principle at Optimar, and this is safeguarded through our open and fair employment policy, salary policy and ethical guidelines for all employees and business partners.
Our goal is to have a workplace that is free from all discrimination and harassment.
This section on equality, diversity and inclusion constitutes Optimar’s response to the activity and reporting obligation pursuant to the Norwegian Equality and Anti-Discrimination Act for the period 1 January to 31 December 2022.
In 2022, Optimar carried out a significant restructuring and downsizing of its organization in Norway. Considerable efforts were made to implement the process while maintaining a constant focus on the people in the organization an
The day-to-day activities are carried out by our HR organization. Responsibility lies with the Top Management. HR and management cooperate with unions in quarterly dialogue meetings
Issues and decisions relating to the working environment are discussed in our Working Environment Committee (WEC). Four such meetings were held in 2022, and a new WEC was established following the restructuring process. The new WEC consists of four employee representatives and four management representatives, and quarterly meetings are planned for 2023.
At the close of 2022, we had 334 employees, 15 per cent of whom were women, 85 per cent men and 0 per cent identifying as non-binary.
The table below shows the gender distribution per position level, stated as a percentage (GRI 405-1).
Even though the total percentage of women compared to men in the global organization remains the same as in 2021, there are differences at each level.
The table shows women’s pay as a percentage of men’s pay in full-time positions at the different levels (GRI 405-2) The figures are based on the Norwegian workforce.
Listed salary statistics do not consider factors such as different levels of education, seniority, job complexity and responsibility, nor labour market conditions for specific professions. We nevertheless acknowledge that the pay gap between women and men at the most senior levels is substantial and further investigations will be conducted in 2023. If the underlying reason is attributable to gender or other types of discrimination, we will strive continuously to reduce the gap, because equal pay is important to be an attractive employer and foster a culture of diversity.
Optimar complies with the regulations related to parental leave in each of the countries we operate in. In the figures, we also see the impact of the regulations in the different countries.
The table below shows the total period of parental leave taken in weeks and as a percentage of the leave taker’s own gender in the workforce. No employees in the USA took parental leave in 2022.
The table shows the number of employees globally in part-time and temporary positions, by gender.
Our eight apprentices are not included in the data for temporary positions.
Every published job advertisement is for full-time employment with Optimar. In every case where an employee works part-time, it is by the employee’s own choice. The company offers reduced hours to be inclusive and adapt to the employee’s situation. Temporary employment is used only when the work itself is of a temporary nature, for instance in connection with a project or as a substitute for an employee taking leave of absence.
A blend of backgrounds, genders, ages, competence and mindsets contributes to the successful development of our company, when acknowledged and taken advantage of in the right way. Our workforce consists of many different disciplines and nationalities, and cooperation is a vital part of our success, although it can be challenging.
The table shows a breakdown of our workforce by age, stated in % (GRI 405 -1).
Our personnel policy is gender neutral in all areas and states that we work to promote equality and hinder discrimination. Work tasks and workplaces are organized and adjusted where there are special needs
For example, all our general staff meetings are conducted with an interpreter for the hearing impaired. Our recruitment policy is open and fair, but there was little new recruitment in 2022 due to the implementation of the restructuring process.
Area Risk Actions Status and goal Recruitment Fear of the “other”. Prejudice.
Unconscious discrimination.
ࣽ HR attends all interviews. In 2023, we aim to train our leaders to use our uniform interview questionnaire to ensure and document
Wages and working conditions
Individual salary negotiations, men are often more likely to negotiate salary compared to women.
Some professions have a higher salary expectation than others due to the scarcity of skills in the market.
ࣽ Annual local salary negotiations with trade unions.
ࣽ Unions are provided with salary data for men and women to reveal gender-based differences.
Assess further improvements in the salary policy to secure equal pay for equal work.
Promotion and talent development
Discrimination in employees chosen for training and promotions.
ࣽ All employees are included in our performance management programme: “Talent”.
ࣽ Our annual employee dialogue meetings contain standardized questions for promotion, development wishes and opportunities.
ࣽ All employees are reviewed based on standardized Core Behaviours and Results.
ࣽ After the performance review, all leaders are calibrated to ensure that everyone is assessed on the most equal basis possible.
No further actions planned at the moment.
Work/life balance
Always available – the boundary between work and leisure is unclear.
Career possibilities may be affected when starting a family.
ࣽ Flexible working hours.
ࣽ Working from home may be agreed on a temporary or permanent basis.
ࣽ Paid free time for breastfeeding.
Consider coverage of full salary during parental leave, including the intermediate payment above 6G for employees in the Norwegian workforce. Other solutions apply to employees abroad.
Harassment, sexual harassment and gender-based violence
Male dominated industry. Work abroad in various cultures.
Work performed outside our company.
Facilitation Lack of accommodation for employees with regard to functional ability, gender identity, religion and age.
ࣽ We have ethical guidelines that state our zero tolerance for harassment and abuse of any kind.
ࣽ All new employees and leaders are informed of our ethical guidelines.
ࣽ Field service engineers are given training in the topic.
ࣽ Every second year we conduct a survey specifically designed to reveal harassment and other forms of abuse.
ࣽ We are an Inclusive Working Life partner (IA company) and strive to make arrangements for employees with reduced functional abilities through individual adaptation of both the workplace and work tasks.
ࣽ Our buildings have elevators and HC-restrooms available.
ࣽ General staff meetings are conducted with an interpreter for the hearing impaired.
ࣽ Production workers who work in a noisy and/or dusty environment are, in addition to protective equipment, offered a health check every second year, while the rest of our employees are offered a free health check every third year.
ࣽ We have developed a senior employee policy.
threats and how to handle and report them.
No further actions planned at the moment.
In 2022, we performed an employee survey that focused on psychosocial issues in the workplace. The survey was global and anonymous. We had a 71% response rate, and the results showed us that, in general, we have a good psychosocial working environment. However, the results also showed that it is important to keep a continuous focus on the topic and that we need to improve the way our Whistleblower Policy is implemented in the organization.
In 2023, we will provide training for all employees in our ethical guidelines and provide some dilemmas that groups of employees can use as training materials. The same training will also provide detailed information on our Whistleblower Policy and how reported cases are handled. The survey will be repeated in 2024 to follow up on the impact of the additional training.
For people to be receptive to development and perform at their best, they require a good work/life balance and good health. Optimar is an industrial company, and employees perform tasks associated with risk, such as welding, use of heavy machinery, automation and assembly. We believe in building a strong safety culture through involvement and training
Our goal is zero workplace injuries that result in employees being absent for a workday or more, otherwise known as Lost Time Injuries (LTIs). In 2022, we focused heavily on the reporting of near misses and actual injuries. We also launched a new reporting system where HSE and quality-related non-conformances can be reported via an app, to make it more convenient for our field service engineers and production workers. Easier access to reporting created an increase in reported events and reported LTIs, which we consider a step in the right direction towards a transparent and strong safety culture.
In 2022, we experienced 11 recorded injuries at Optimar, seven of which were LTIs.
The table below shows the number and rate of work-related injuries per million hours worked (GRI 403-9) for Optimar globally.
*(FTE*1940h per year) x 1 million hours
Average sick leave increased from 3.6 per cent in 2021 to 4.3 per cent in 2022. Our target is a monthly global sickness absence rate of less than 3 per cent, and we follow up both managers and employees to track performance in this area. In comparison, the average sick leave rate for industrial companies in Norway was 5.9 per cent in 2022 according to the Confederation of Norwegian Enterprise (NHO).
A total of eight sick leave events were registered as work-related sick leave or LTIs in 2022. No special measures to lower the rate of sick leave were implemented in 2022 and our target of 3.0 per cent remains the same for 2023.
We used to measure employee engagement twice a year with the eNPS model. We experienced that the method chosen was not well implemented and very time consuming, while managers did not find it provided particularly high-value insights. In September 2022, we decided to abandon the survey. Our goal for 2023 is to implement a new employee engagement survey during the year.
It is our responsibility as an organization to ensure that our employees have the skills, training and certification they need to perform their work. In 2022, we expanded our established Certified to Operate programme to include production workers as well as field service engineers. Among other things, our employees are trained in:
ࣽ Electrical safety
ࣽ Work at height and personal lift
ࣽ Scaffolding and ladder safety
ࣽ Hot work
ࣽ Extensive first-aid
ࣽ Forklift and crane handling
ࣽ Personal protective equipment.
We are an approved apprenticeship company and have eight apprentices in our production department, seven men and one woman in the reporting year.
In 2022 we focused on skills training for 20 of our managers or management candidates through the leadership training programme “Nature of leadership”. Dedicated leadership is the key to driving engagement and development, and recognizing leadership as a skill that needs to be trained and developed results in conscious and competent managers.
Our sales team and procurement department conducted training in negotiation and contract standards. It is important that we are professional and reliable in processes with our customers and suppliers, and raising competence in this area contributes to our reputation as a solid and trustworthy supplier.
Employees are actively participating in networks and clusters to keep updated and continuously learn from other businesses and academic institutions in our local area.
Optimar seeks to ensure responsible business practices by avoiding purchases that contribute to or entail adverse impacts on human rights and decent working conditions. Information regarding our company and our work can be found in the opening pages of the sustainability report. The part of this report under the headline Responsible Supply Chain is also our response to the Norwegian Transparency Act for the reporting period 1 July to 31 December 2022.
Our Global Procurement & Logistics Department is responsible for supplier-related activities under the Transparency Act, while top management has overall responsibility for compliance with applicable law and ethical standards.
So far, we have had contract requirements stating that our suppliers must abide by our code of conduct. We want to be clearer about what we expect from our suppliers and business partners, and our new Supplier Code of Conduct will be finalized in 2023. We will continue to follow up our suppliers through contract obligations. Those interested in information regarding human rights and working conditions in our supply chain are referred to the contact information on our website www.optimar.no. We will respond no more than three weeks after the request has been received.
If suppliers wish to report possible or actual breaches of our code of conduct, they are invited to use our whistleblower e-mail. This is open for both internal and external disclosures, and both are handled in accordance with the same procedure and with the same discretion.
Members of our procurement team are each responsible for following up a specific portfolio of suppliers, on which they also perform periodic risk assessments. In 2022, we had 379 unique suppliers and business partners. Our supply chain varies from project to project, but our main purchase category is steel-related products. We also purchase products from Original Equipment Manufacturers (OEMs), which makes it challenging for us to risk assess the entire supply chain.
With effect from 2022, we now conduct an annual evaluation of our suppliers. Prioritized risk areas investigated in the supplier evaluation are:
ࣽ Fundamental human and labour rights
ࣽ Health and safety
ࣽ Anti-corruption and bribery
Optimar acknowledges that we cannot handle all potential adverse impacts in our supply chain, but being aware of risks helps us prioritize our actions in pursuit of a sustainable supply chain.
We use a third-party system for supplier mapping and initial risk assessment. A complete overview of our first-hand suppliers and business partners broken down by category is included in the platform and is continuously updated. An initial risk assessment is performed based on the supplier’s geographic profile and their industry, product or service category, and the percentage of goods purchased from that specific supplier compared to total purchases.
A survey with fully defined questions based on the GRI standard is sent out to suppliers upon registration and annually thereafter. Based on the initial risk assessment and responses to our surveys, we give our suppliers a total score and risk rating with regard to their potential adverse impact on human rights and decent working conditions.
It is challenging to survey beyond the first link in the supply chain, but our first-hand suppliers are encouraged to give an assessment of their subcontractors in the same survey.
Optimar’s ESG risk rating for suppliers in 2022, shown as a map indicating the risk rating for workers’ rights.
Risk of workers’ rights violations: International Trade Union’s Global Rights Index
Risk of corruption: Corruption Perception Index
Action priorities have been set for the most significant risks of human and labour rights abuses. The main risks identified are described below.
Steel
ࣽ Environmental impact. Steel industry is responsible for 7–9% of the world’s CO2 emissions.
ࣽ We buy steel from China, which scores low on international human rights evaluations.
ࣽ Mining and metal sector. Small-scale operations tend to use low-skilled manual labour and have poor health and safety standards. Small-scale mines may be connected to organized crime and corruption
ࣽ Frequent supplier visits.
ࣽ Supplier Code of Conduct.
OEM
ࣽ Optimar’s contracting parties buy engineered components from a variety of sub-suppliers and usually undertake assembly in their own workshops. Optimar has limited transparency with respect to the lower tiers of the supply chain. We consider that the most likely adverse impacts are: poor working conditions and inequality at sub-supplier workshops (in rough machining and welding workshops), and unreasonable working hours, inadequate leave periods and low wages for workers during equipment installation on site.
Outsourcing ࣽ Human rights and working conditions controlled by another company and other statutory requirements than those applicable in Norway.
ࣽ Supplier survey with sub-supplier coverage.
ࣽ Onsite visits or audits.
ࣽ Visits to subcontracting factories.
ࣽ Contract requirements.
We have established an internal escalation process to deal with suppliers about which we still have unanswered questions or where our risk assessment has revealed an unacceptable level of risk. To ensure that all suppliers and business partners are treated equally, our risk response plan contains a description of the prescribed actions to be taken in relation to each identified risk.
Everything looks great from a distance. We get up close to find solutions
Content: Optimar AS Design: Optimar AS
various artists, Adobe Stock June 2023
Optimar AS www.optimar.no Optimar