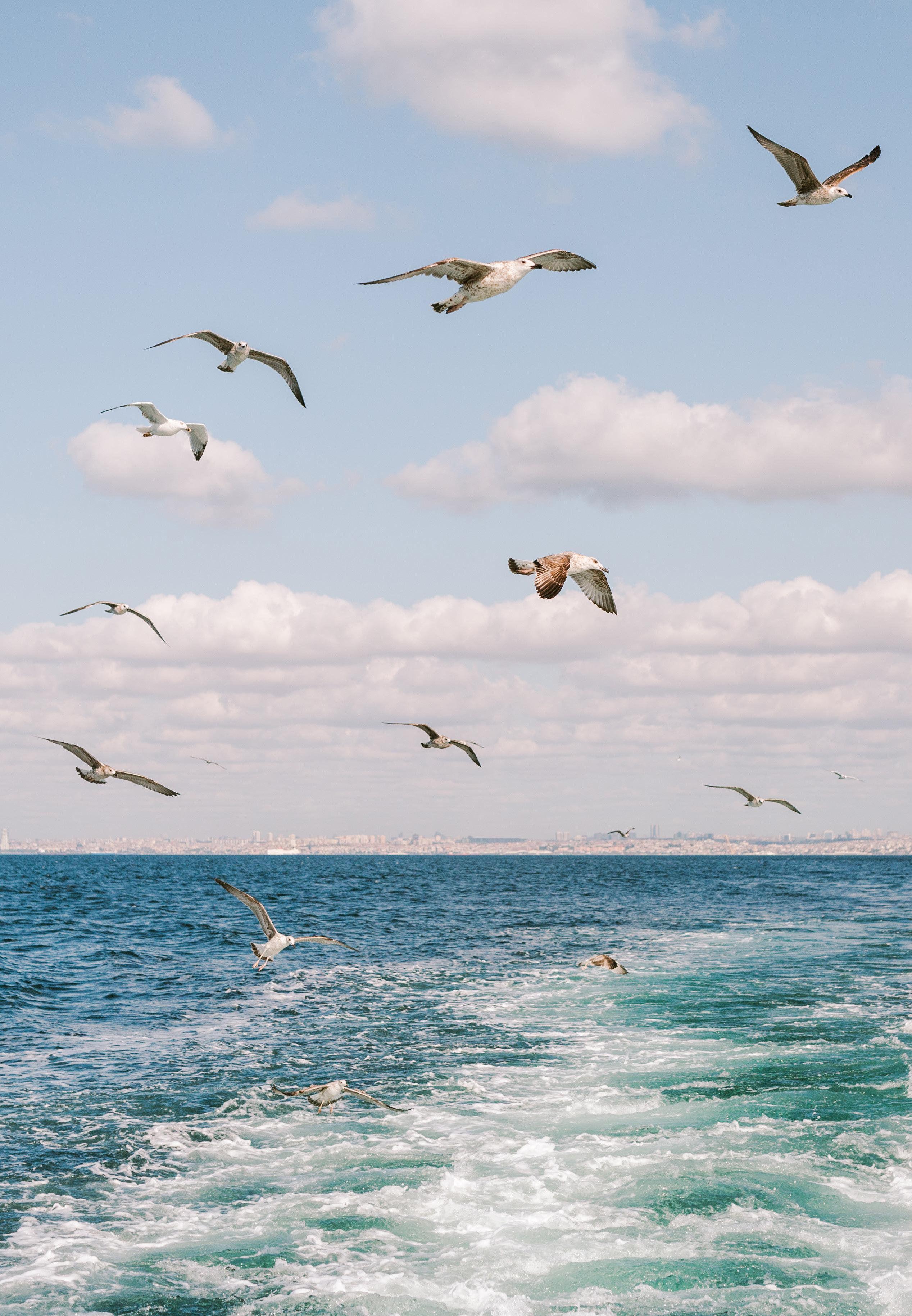
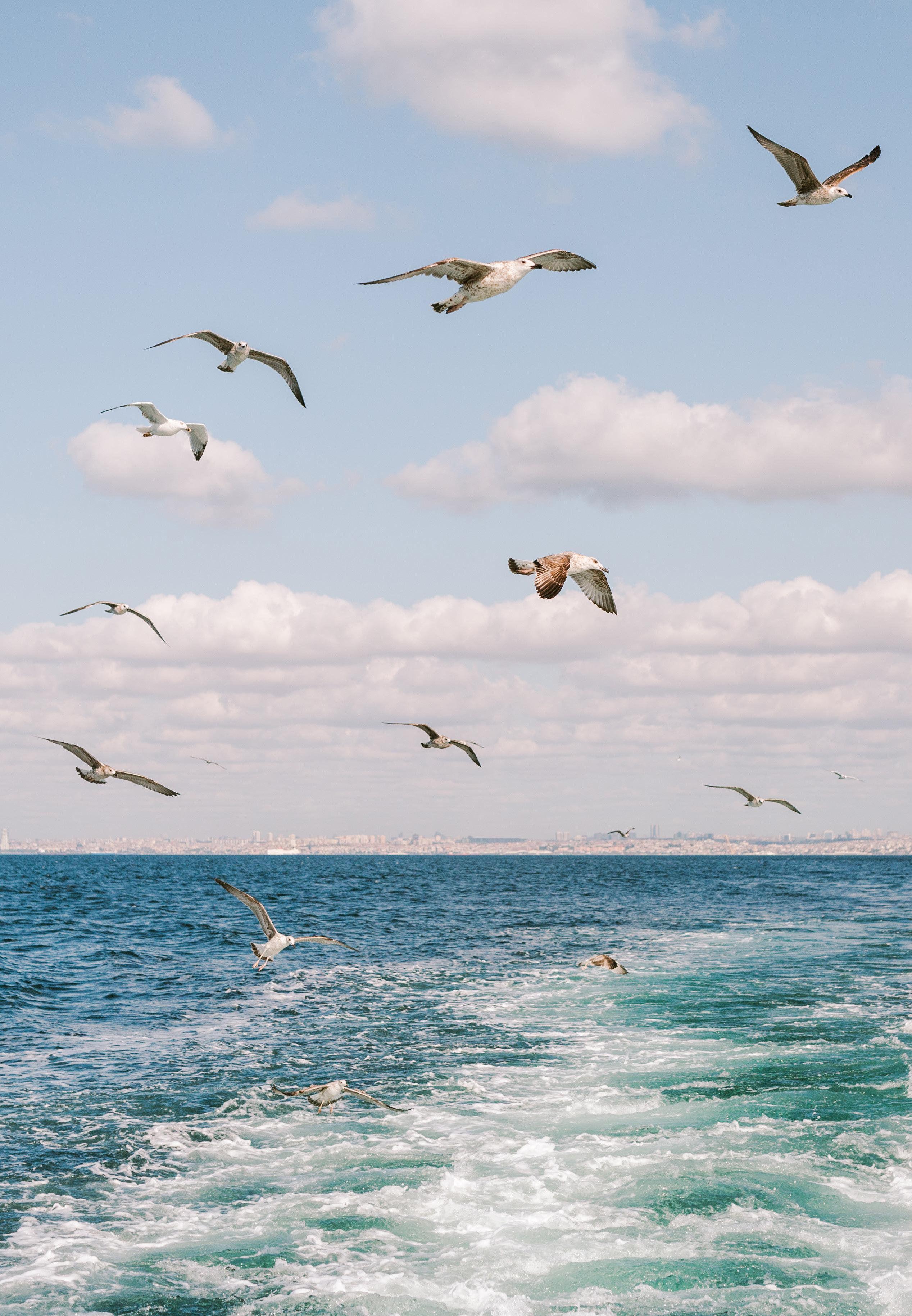
Sustainability Report 2023

Together we create value for generations
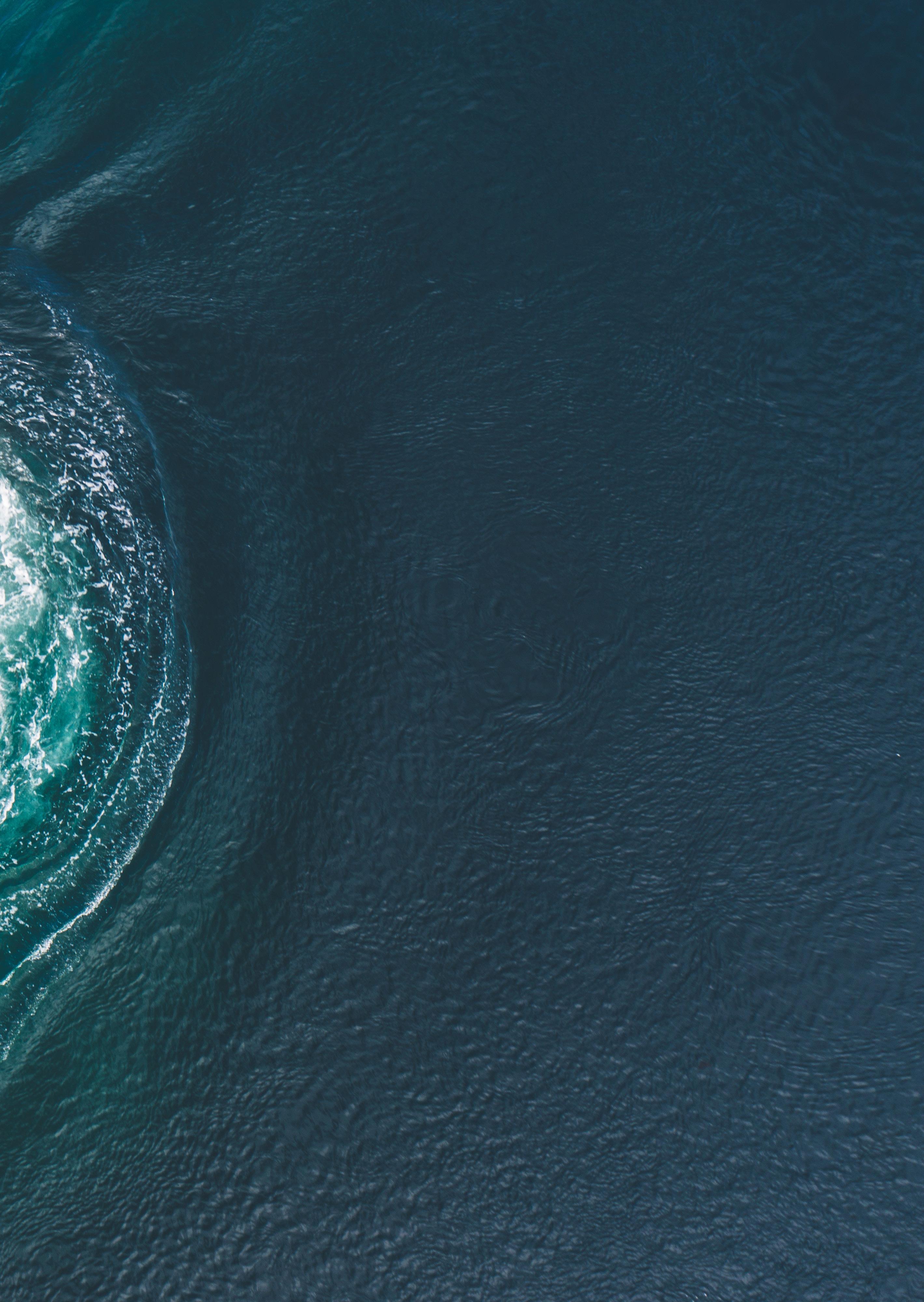
Our goal is an ethically sound end product with the highest level of animal welfare and 100% yield.
Siggi Olason | CEO, Optimar
Optimar is a global leader in automated fish processing systems for use on fishing vessels, on land and in the aquaculture sector. The company’s headquarter and manufacturing plant are at Valderøya ouside of Ålesund, on Norway’s west coast. Optimar also operates other facilities in Norway, the United States, Spain and Romania, and delivers to customers in more than 50 countries.
Our vision
Fish handling with care – we improve the sustainability of food production by enabling our customers to process fish and other aquatic species more effectively, safely and with higher quality.

Optimar in 2023
Carbon footprint (Scopes 1 and 2)
230
UN Global Compact Signatory since 4
SDGs where our business has the greatest impact
Workforce from 20+ nationalities
LTIs in 2023 4
Countries served 50+
Workforce
258 Production sites
people
Norway
Administrative sites
Norway
Innovation and Cooperation for a Sustainable Future
The seafood industry relies on our oceans and marine ecosystems. The climate crisis has already led to changes that will require collective action to secure the planet for future generations. Transitioning both energy and food systems to more sustainable alternatives is crucial, since both are major contributors to greenhouse gas emissions.
As the world’s population grows, feeding everyone sustainably is becoming increasingly challenging. A dietary shift is necessary, with a greater emphasis on ocean-derived proteins. Technology plays a key role in this transition, and Optimar is at the forefront, delivering state-of-the-art equipment and solutions for sustainable, efficient and secure seafood production. Innovation is central to our business model, and we aim to lead the way with the world’s best processing solutions.
Sustainability Underpins Our License to Operate
We collaborate closely with customers, public authorities and research institutes to find the best designs and solu-
tions, sharing knowledge and experience for the benefit of the seafood industry.
Animal welfare is a key concern for retail chains, NGOs and consumers alike. We help enhance animal welfare through the development of new equipment and solutions. For example, our electric stunner reduces stress and pain for fish before slaughter, and our OptiFlush system provides efficient and gentle delousing.
At Optimar, we deliver robust, long-lasting products and solutions. Embracing sustainability, we leverage AI and advanced technology to support our customers with superior processing solutions and decision-making tools.
Sustainability is no longer a project – it is integral to our business. Our goal is to reduce our adverse impact, enhance our positive impact, and explore opportunities to preserve the climate and environment.
Siggi Olason | CEO, Optimar
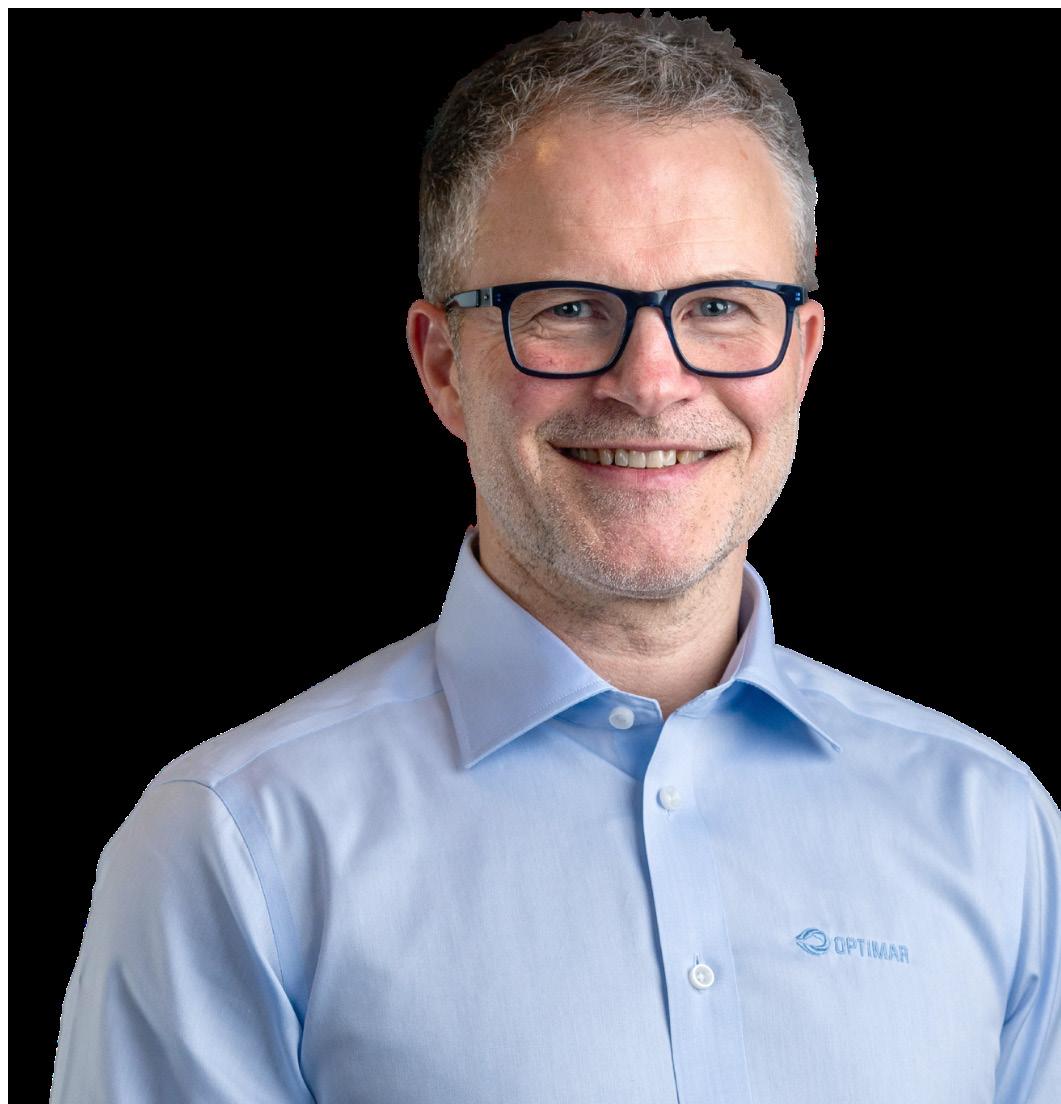
A Challenging Year
In 2023, our efforts to meet strategic sustainability ambitions was made more difficult by the Russia/Ukraine war, resource tax imposed on the aqua industry in Norway, higher prices and interest rates, and lower quotas for wild-caught fish in Norway. The salmon tax made the aquaculture industry reluctant to embark on new projects, significantly reducing investment levels. However, we anticipate increased investments going forward.
In 2022/23, organizational changes were made to ensure Optimar’s future as a leading provider of state-of-the-art solutions for the aquaculture and seafood industry.
Our Most Valuable Resource
Optimar’s dedicated and skilled workforce is our most valuable asset. We know that achieving progress requires people, engagement and effort. We are grateful for our employees’ perseverance and dedication.
Many employees participated in the “Ocean Clean Up Project”, clearing plastic and waste from the local area through “Hold Norge Rent”. Protecting marine life and the environment is critical for the seafood industry, and our employees’ dedication reflects our core values and mission to create lasting value for future generations.
Our Contribution to the Industry
“Fish handling with care” is our mantra. Our key objectives are to continuously improve fish handling standards and enable our customers to engage in efficient, safe and high-quality fish processing. Fish welfare, food safety and safe working conditions for operators are always primary concerns.

As a system integrator, we offer complete factory solutions. Our highly qualified team of experienced engineers and managers allows us to handle projects of any size and complexity. We turn ideas into reality – from initial planning to completed projects. Our goal is an ethically sound end product with the highest level of animal welfare and 100% yield.
Our Commitment
Optimar supports the ten principles of the United Nations Global Compact regarding human and labour rights, the
environment and the fight against corruption. We integrate these principles into our business strategy, culture and operations, contributing to the UN Sustainable Development Goals (SDGs). We are currently preparing for the EU Corporate Sustainability Reporting Directive (CSRD), which will be mandatory for Optimar from the 2025 fiscal year. Our first CSRD-compliant report will be published in 2026.
Key Highlights from 2023
Focus on animal welfare continued, supported by animal welfare organizations. Our electrical stunner was introduced to new customers in emerging markets.
OptiFlush was released as a product for integration with various delousing technologies.
We released an automated fillet packing solution for the onboard market, with delivery expected in the second half of 2024.
In partnership with the Norwegian Directorate of Fisheries, Optimar is participating in the CatchID project, which is developing a platform for sustainable fishing and reporting.
Sustainability is no longer a project; it is integral to our business. Our goal is to reduce our adverse impact, enhance our positive impact, and explore opportunities to preserve the climate and environment. New ownership in early 2024 with extensive experience, and a positive market outlook, makes us ready to continue our sustainability journey.
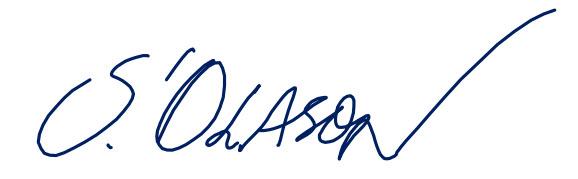
Siggi Olason CEO Optimar
E GS
Sustainable and Profitable Growth

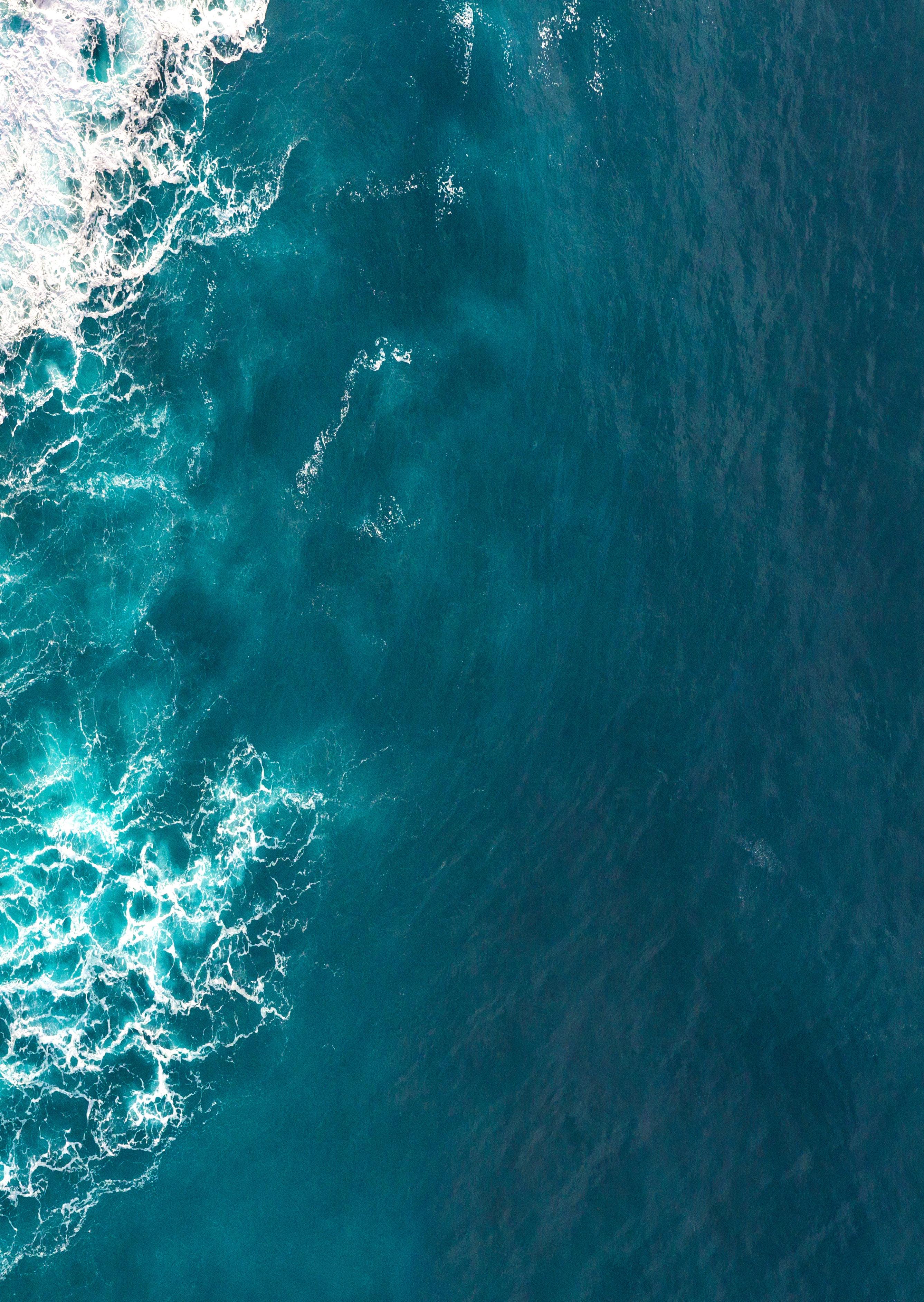
Our ESG strategy
At Optimar, we strive to incorporate sustainability as an integral part of our overall business strategy and our day-to-day activities. We believe this creates commitment throughout our organization.
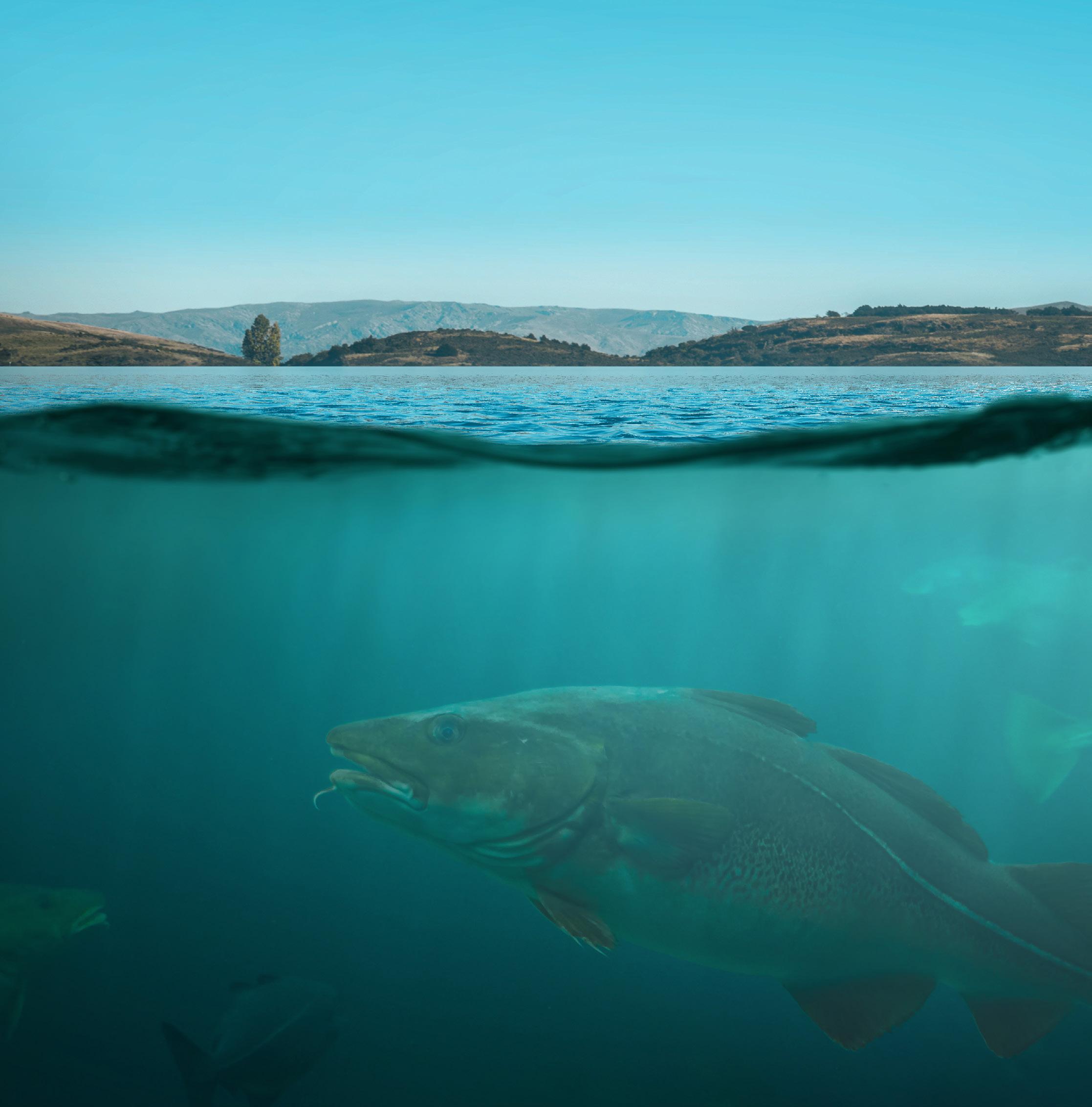
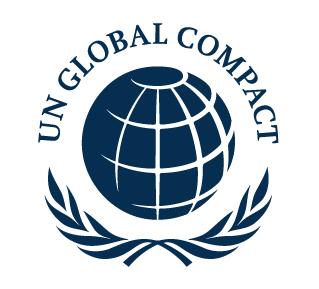
United Nations Global Compact
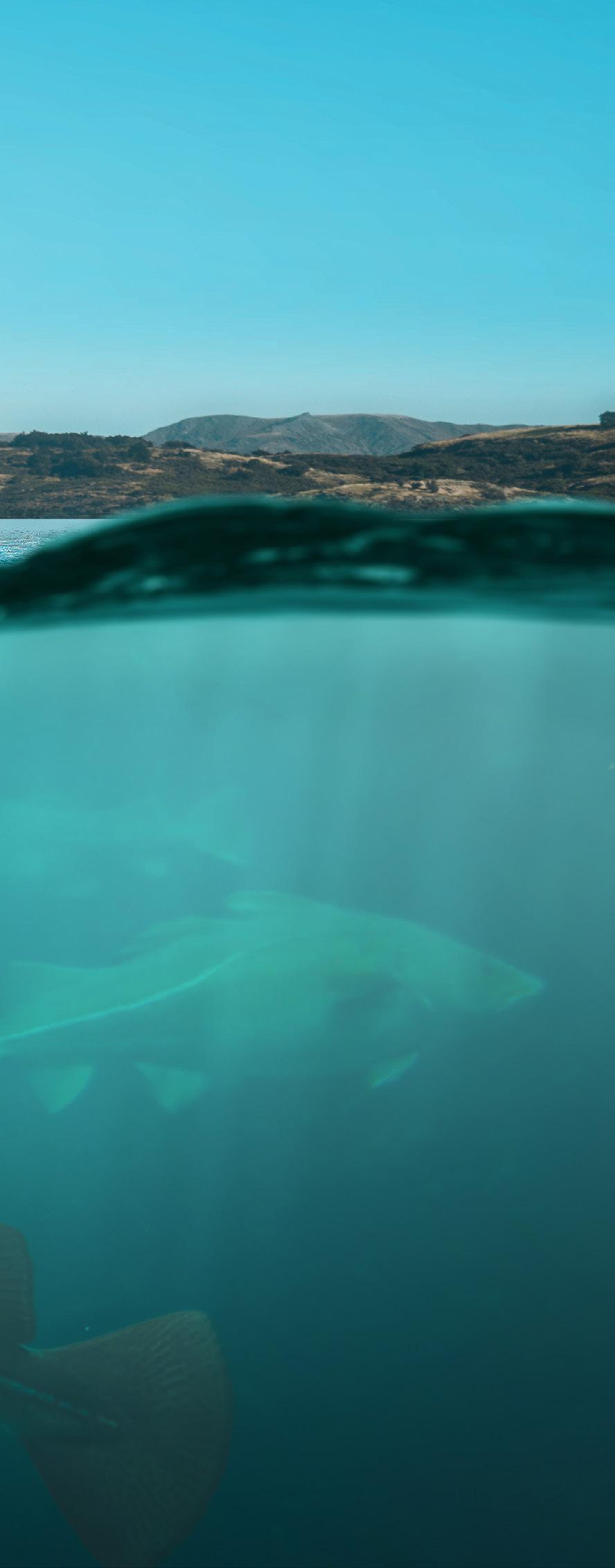
How we work with
sustainability in
our company
Optimar has been a member of the UN Global Compact since 2020 and published its first sustainability report for that same year. The company published its first Greenhouse gas (GHG) emission calculations for the year 2021. In 2022, we followed up on initiatives and adjusted the goals we have set in relation to the UN’s Sustainable Development Goals (SDGs).
2023 was a challenging year for the whole fishing and aquaculture supply industry. The Norwegian government’s sudden decision to impose a resource tax on salmon farming caused huge uncertainty and resulted in many investment plans being halted or put on hold. In addition, higher inflation, increased costs and geopolitical issues made market conditions even more difficult.
Sustainability as part of our business model
We aim to incorporate sustainability as an integral part of our overall business strategy. Sustainability goals, tasks and reporting are therefore integrated into the day-to-day operations of business lines and departments. This not only improves the quality of our sustainability-related activities but also creates a strong sense of ownership and commitment throughout the organization.
Ownership
Optimar’s Board of Directors is responsible for determining company guidelines and strategy, while the Chief Executive Officer (CEO) is responsible for implementing the strategy.
Our Chief Financial Officer (CFO) is our compliance officer and ensures that our reporting is compliant with applicable legislation and directives.
Our Sustainability Lead (SL) has overall responsibility for the preparation and follow-up of the strategy and goals. The SL coordinates the various sustainability initiatives driven by our departments and reports to top management and the board. To step up the focus on integrating sustainability in our business model, Optimar decided to onboard a new resource with responsibility for sustainability and business development with effect from 2024. In partnership with our customers and other stakeholders, Optimar aims to lead the way in the processing of sustainable seafood.
One of our goals is to further increase our own organization’s awareness of sustainability as a vital factor in Optimar’s continued success. We therefore emphasize the importance of incorporating environmental, social and governance (ESG) considerations in our strategies and day-to-day activities.
Sustainable and Profitable Growth (Governance)
Our defined stakeholders
Through a variety of contact points, such as dialogue meetings with trade union representatives, participation at trade fairs and exhibitions, supplier questionnaires, employee surveys and partnerships with non-government organizations (NGOs) and academia, our stakeholders have shown us which topics are important.
Optimar aims to communicate transparently with our stakeholders to ensure that we are aligned and are addressing the most significant matters.
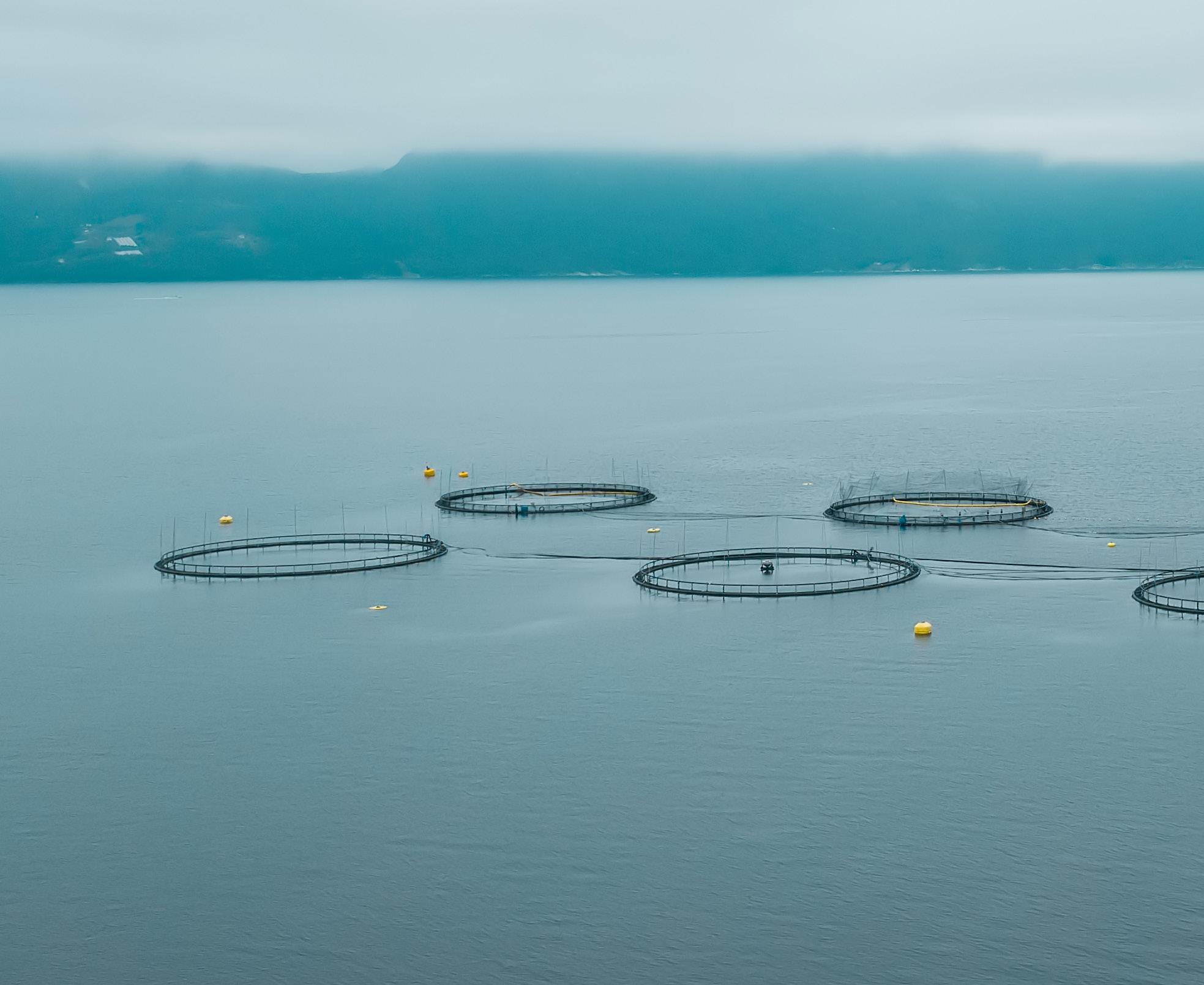

Sustainable and Profitable Growth (Governance)
Our commitment
Responsible business plans, operations and investments are essential to achieving transformational change. The UN’s 17 Sustainable Development Goals (SDGs) provide a framework for achieving the agenda and targets set by UN Member States. Together, the SDGs signpost what needs to be done to end extreme poverty, fight inequality and injustice, and protect our planet. We have identified four SDGs where, in our assessment, we have the greatest impact. Focusing primarily on these four goals will, however, also contribute positively to additional SDGs.

Goal 8
The working conditions in fish processing factories have always been physically demanding and involved a great deal of manual work
Optimar builds solutions onshore and onboard fish processing factories that contribute to increased productivity and automatization. This results in less strain on employees, changed physical requirements and an increased opportunity to stay longer in the job. This also
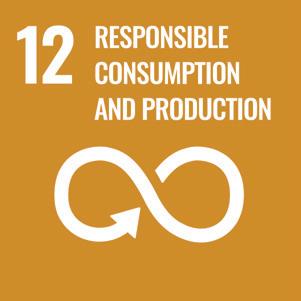
Goal 12
Optimar strives to reduce its own carbon footprint by focusing on its direct and indirect emissions and energy consumption.
A low footprint in the company’s own production process will contribute to a lower total footprint in the whole value chain. We aim to continue focusing on reducing the amount of waste generated through both minimizing and recycling.
Optimar produces long-lasting equipment that can be upgrad-
contributes to SDGs 3 (Good Health and Well-Being) and 5 (Gender Equality).
Optimar supplies products that maximize the usable percentage of aquatic raw materials and eliminate waste. Automated solutions provide an opportunity to increase efficiency on board and thereby increase our customers’ financial gain.
Optimar is an industrial company, and our safety culture
is present at every level of our organization. We promote a safe and secure working environment, with proper employment terms and conditions, and a commitment to labour rights both in-house and throughout our supply chain. Machine safety is highly prioritized when we design our systems and products, with all precautions being taken. The customer is given training in the safe use of Optimar’s equipment.
ed during its lifespan, rebuilt to fit new requirements at the same facility or adjusted to fit into a new factory. We strive to extend the life of the products with as little downtime as possible. Reduced downtime will cut the number of times a boat must return to shore for maintenance and contributes to reduced energy consumption and fuel used during transportation.
Animal welfare is a crucial concern for retail chains, NGOs, and consumers. We contribute
to this cause by developing innovative equipment and solutions that minimize stress and pain for fish prior to slaughter.
A major challenge for the marine fleet is fuel consumption and concomitant emissions. Our contribution to greater fuel efficiency is to develop equipment where moving parts stop automatically when not in use. The stand-still function reduces energy consumption and wear and tear.
Continued on the next page
Heating and cooling equipment consume a lot of energy. When designing such equipment, it is therefore important to analyse how
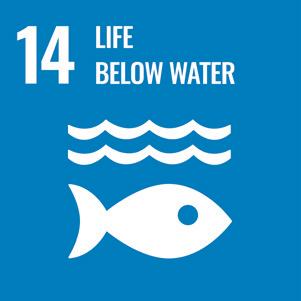
Goal 14
Life below water is considered in the design and engineering of our automation and control systems.
Our digital platform has been developed to gather operational data that documents the individual customer’s operations, from a production, environmental and efficiency perspective.
Together with our customers, we are focusing on more
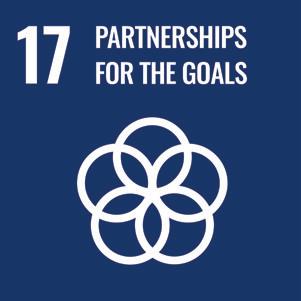
Goal 17
Optimar contributes its expertise and technology to partnerships with academia, public authorities, animal welfare organizations and marine clusters.
When it comes to design and solutions, we always work in close collaboration with our customers. Where relevant, we also use the opportunity to
energy consumption may be reduced, thereby lowering our customers’ operating costs and shortening the investment payback time. This will also
make it possible to lower food costs, indirectly affecting SDGs 2 (Zero Hunger) and 13 (Climate Action).
energy-efficient factories and how we can help to monitor and avoid pollution to the sea. We supply advanced fish sorting and grading systems, enabling improved traceability and sustainability in the fishing industry.
By always prioritizing cleanable designs, we decrease the amount of scrubbing and chemicals needed to clean our equipment. This reduces the amount of waste discharged
into the sea. Our delousing system has been developed to remove lice without the use of chemicals. The chemicals used in traditional delousing methods are a threat to marine life surrounding open-pen fish farms.
We design factories to achieve 100% fish utilization, ensuring high-quality final products for the market.
collaborate with public authorities and research institutes. It is our policy to learn from each other and share competence and experience for the benefit of the industry.
Optimar has a global presence and aims to learn from its global network of stakeholders, particularly regarding issues that impact the drive
towards sustainability. We are always keen to receive actionable feedback from any corner of the world. Needs and requirements are first entered in the quality system and then incorporated into our products when the improvements are considered to be beneficial. This ultimately leads to product designs based on worldwide experience.
Sustainable and Profitable Growth (Governance)
Material topics for Optimar
Based on our four main SDGs, the following GRI topics has been included as material topics for Optimar. It is in relation to these topics that we can reinforce our own and the fish handling industry’s positive impact, and reduce our adverse impacts. SDGs 2 and 3 are not our main goals but will be affected by our focus on SDGs 8, 12, 14 and 17. SDG
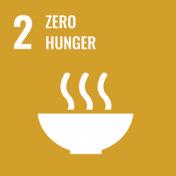
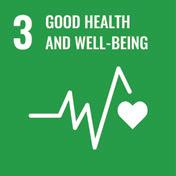
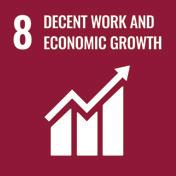

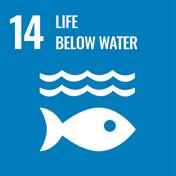
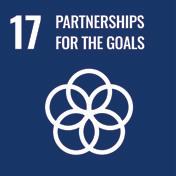
Optimar’s potential impacts in the value chain
Targeted goals
Based on our aim to deliver fish handling with care by improving the sustainability of food production, and the material sustainability topics we have uncovered, we have set ourselves strategic goals to ensure that we achieve our objectives.
Strategic Area SDG Topic
Growth
Operations
SDG 14 Sustainable product development
SDG 17 Partnerships for sustainable development
SDG 8 Sustainable economic growth
SDG 12 Responsible supply chains
Short term goal
Align our internal product development guidelines with our sustainability goals.
Be the chosen partner for the project CatchID in Norway.
Anchor plan for ISO 9001-certification with the board, top management and organization.
Map and risk assess all suppliers.
Further develop Suppliers Code of Conduct.
Establish a policy for supplier risk management.
Long term goal
Be an innovative contributor to the industry by challenging established solutions.
Chosen partner for sustainable development of fish handling industry in cooperation with customers, authorities, non-profit organizations and academia.
ISO 9001-certification.
Audit process established and implemented, and a trained auditors.
People
SDG 8
Renewable energy share
Map the opportunities and increase use of renewable energy.
Emissions Full Scope 3 screening.
100% of the energy used in our factories is from renewable sources.
Net zero by 2050.
Occupational health and safety
Attractive employer
ISO 45001-certification.
Sick leave total under 3.7%. Zero work-related sick leave.
Re-establish regular employee survey.
Staff turnover < 3 per month.
Steady high score on employee surveys and three or more qualified applicants to available positions in the company.
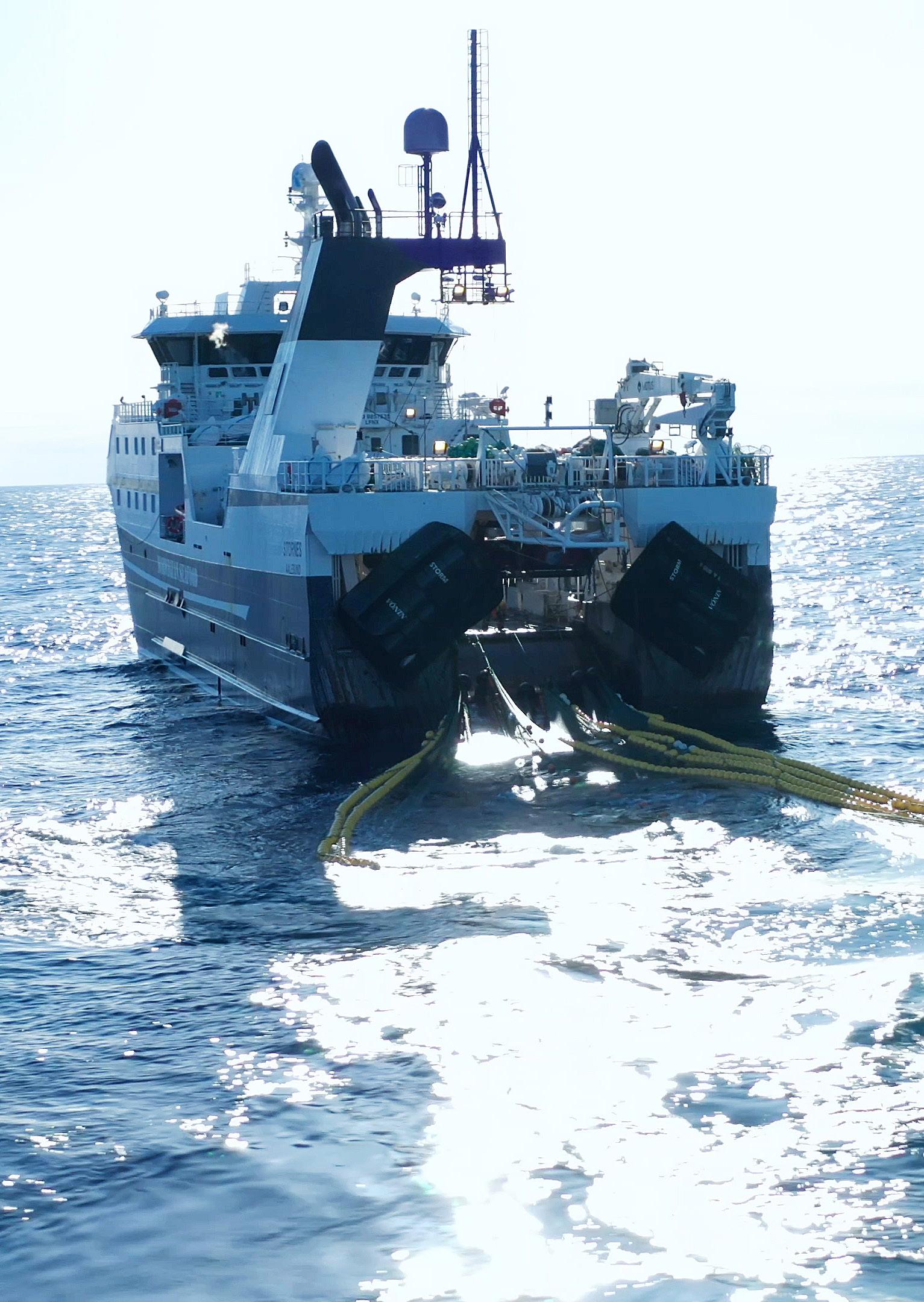
Our ethical responsibility
Optimar believes there is a strong correlation between long-term profitability and responsible business practices.
This view is reflected in the company’s environmental, social and governance (ESG) standards and our ethical guidelines. We support the UN Global Compact’s ten principles on human and labour rights, the environment and anti-corruption, and urge the same from our business partners and suppliers.
Ethical guidelines and whistleblower policy
Our ethical guidelines are known by and available to all our employees. As a part of their onboarding process, new employees must complete an e-learning programme covering our ethical guidelines (Code of Conduct) and whistleblower policy. These describe key ethical principles to which Optimar is committed and establish a shared platform for expected behaviour and business practices. Both employees and external stakeholders may use our dedicated “whistleblowing” e-mail address to report concerns or suspected wrongdoing. All such disclosures are handled with appropriate discretion.
Human rights and labour standards
We strive to ensure that all our activities worldwide are conducted in accordance with basic human rights. Optimar supports internationally recognized human rights, such as the UN Declaration of Human Rights and the standards promoted by the International Labor Organization (ILO).
Material human rights related to the business are:
Freedom of association and collective bargaining.
Safe and healthy working environments.
Labour standards, including a ban on the use of forced labour, child labour and all forms of discrimination in the workplace.
Employment terms and conditions (wages, working hours etc).
Freedom of expression.
Anti-corruption
Optimar is vehemently opposed to all forms of corruption and works actively to ensure that this does not occur within the company. Corruption is not tolerated at Optimar, and violations will lead to disciplinary action.
Our contribution to the industry
Fish handling with care is our core business purpose. Our primary objective is to continuously improve the standard of fish handling and enable our customers to process fish more sustainably, efficiently and safely, and achieve a higher quality output. Fish welfare, food safety and safe working conditions for operators are always of primary importance.
In the table below, we describe a selection of our accomplishments in 2023 and the short and long-term goals we have set for our contribution to sustainable fisheries going forward.
Focus area Accomplishments in 2023
Animal welfare Collaborated with food safety authorities on how to ensure animal welfare in our product portfolio.
Broadened the availability of our electrical stunner to smaller customers (small-scale aquaculture production) in emerging markets.
Released the Optiflush for integration with all types of surface delousing technologies.
Aiming for in 2024 Long term goals
Continue our collaboration with customers and relevant authorities/institutions to ensure animal welfare.
Introduce the electric stunner to emerging markets in Asia.
Develop the electric stunner for Nephrops to ensure humane tailing operation.
Start the process to validate the electrical stunner’s effect on several new species.
Prepare to host an animal welfare conference in 2025.
Optiflush to be delivered together with Optimar OptiLice. This reduces the temperature required on thermal delicing, and causes less stress for the animals.
Participate in the “Catch Welfare Platform”, a three-year project initiated by the Marine Research Institute of Norway (Havforskningsinstituttet) to develop innovative ideas and solutions to improve the welfare of wildcaught fish and crustaceans.
Collaborate with customers, NGOs, scientists, fish health companies, institutions etc. to continue research into and the development of methods and technology to ensure animal welfare.
Deliver delousing solutions that are proven to safeguard the welfare of farmed fish, while posing no threat to nearby life under water.
Increase collaboration with animal welfare specialists to expand the use of our electrical stunner. Validate its stunning effect on additional species.
Cooperate with others to improve transport systems that safeguard the welfare and quality of the fish.
Further develop the Optiflush to achieve increased independence from dual lice-treatment requirements.
Focus area Accomplishments in 2023
Food quality and food safety Analysed and designed an optimized bleeding solution to improve the quality of the seafood. Further system testing and verification will be carried out in 2024.
More than half our engineers and other personnel underwent training to increase their knowledge of hygienic design principles.
Aiming for in 2024 Long term goals
Test and approve optimized bleeding systems that improve the quality of the seafood.
Continue to explore new solutions for each corner, each radius and each drop in an Optimar fish factory, to minimize impacts that can affect the quality of the final product.
Increase our focus on how factories, systems and pipelines are integrated.
Continue Optimar’s policy of delivering only first-in-first-out solutions that minimize treatment times and maximize fish welfare.
Continue to develop novel fish processing and logistics solutions.
Improve the cleanability of our standard tanks and bulk seafood handling systems. This will lead to less waste and higher quality of food products, increased food safety, and reduced use of water, chemicals and time needed for cleaning.
Develop systems that handle the fish even more gently.
Develop and deliver traceable product flows.
Energy consumption in the value chain
Working conditions
Tested and tracked energy consumption and freezing time in order to further optimize the design of the freezing process and improve its performance.
Entered into a partnership agreement with the Norwegian University of Science and Technology (NTNU), where a laboratory freezer has been installed.
Released an automated fillet packing solution for the onboard market.
Performed numerous commercial and physical demonstrations to potential customers. The work is ongoing.
Continue to test and monitor the energy consumption and freezing times for various fish products and types of packaging in our Lab Plate Freezer.
Launch new designs for Optimar’s main conveyor products, offering enhanced operator safety without compromising on food safety.
Plan the delivery of the first automated onboard fillet packing solution.
Optimize energy consumption and freezing times for various species in Optimar’s plate freezer solutions.
Perform Air Blast tests on shrimps and IQF systems to optimize the energy consumption and design and size of these products.
Continue to develop products and solutions that will ease and improve factory working conditions and efficiency.
Process control and data harvesting
Standardized the Commander Web as a data harvesting platform for all our segments.
Help customers to integrate fuel and emission data in the factory.
Participation in the CatchID project organized by the Norwegian Directorate of Fisheries. The project aims to track the amount of catch divided by species as early as possible in the value chain.
Release a new freezer to the market, featuring lower power consumption, a smaller footprint and better freezing quality.
Be one of three remaining competitors for CatchID after the concept phase is finished.
Gather data that documents customers’ operations from a production, environmental and efficiency perspective.
Higher focus on energy-efficient factories.
Release an onboard solution to package shrimps directly for the consumer market. This will provide a better quality endproduct by reducing the need for repackaging on land.
Design and deliver onboard facilities to package multiple species directly for the consumer market. This will reduce the need for repackaging and save on energy and packaging materials.
Sustainable and Profitable Growth (Governance)
for better fish welfare, reduced energy consumption and improved working conditions
Optimar strives to develop new and improved solutions to ensure sustainable food production. For example, Optimar’s electric stunner has been documented to enhance fish welfare and will be available for more markets and species in the years to come. The focus on fish welfare is increasing globally. Several retail chains and end-customers demand that fish welfare, food safety and food quality can be fully documented.
In 2022, Optimar hosted the “Fish welfare week” with great success. People from the whole industry gathered
to discuss fish welfare issues and how to resolve them. Optimar plans to host a new gathering in 2025. We believe that more knowledge and a greater awareness of fish health and welfare can lead to the development of new technologies that safeguard animal welfare.
Food quality is another important area where Optimar strives to supply the best solutions. One example is an improved bleeding process that both fully drains and cools the fish at the same time. Thorough bleeding and
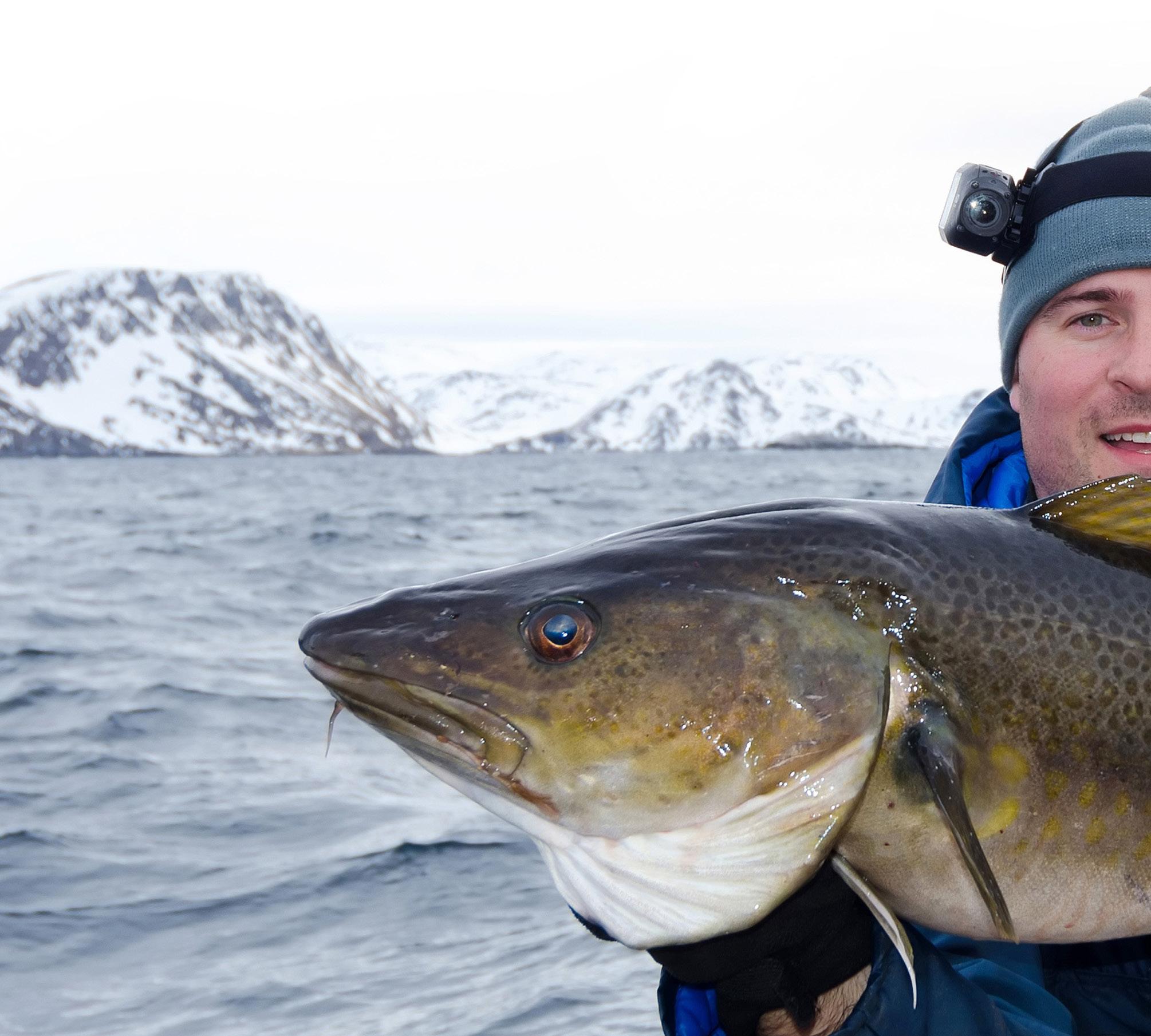
control of the fish’s temperature is crucial to ensure a high product quality. The bleeding pipes are equipped with fully automated cleaning systems that eliminates risk of bacterial contamination. Optimar also supplies tracking systems which can document that the freezing chain is not broken, and thereby ensure the quality of the fish through the value chain.
Optimar continues to invest heavily in the integration of factories, systems and pipelines. This is a key factor for our designers and engineers because
we believe in the vital importance of eliminating pinch points in the production process that can impair food quality.
Optimar is a partner in the project “Fish 4.0”, which is being led by Møreforskning and the Norwegian University of Science and Technology (NTNU). The project is investigating how the fourth industrial revolution (“Industry 4.0”), with its emphasis on smart manufacturing and the creation of intelligent factories, could influence what a trawler could look like in 2030.
Optimar aims to continue collaborating with others to investigate and develop methods and technologies to ensure animal welfare, food safety and quality, efficient and safe work conditions, and reduced energy consumption.

E SG
Sustainable and Scalable Operating Platform
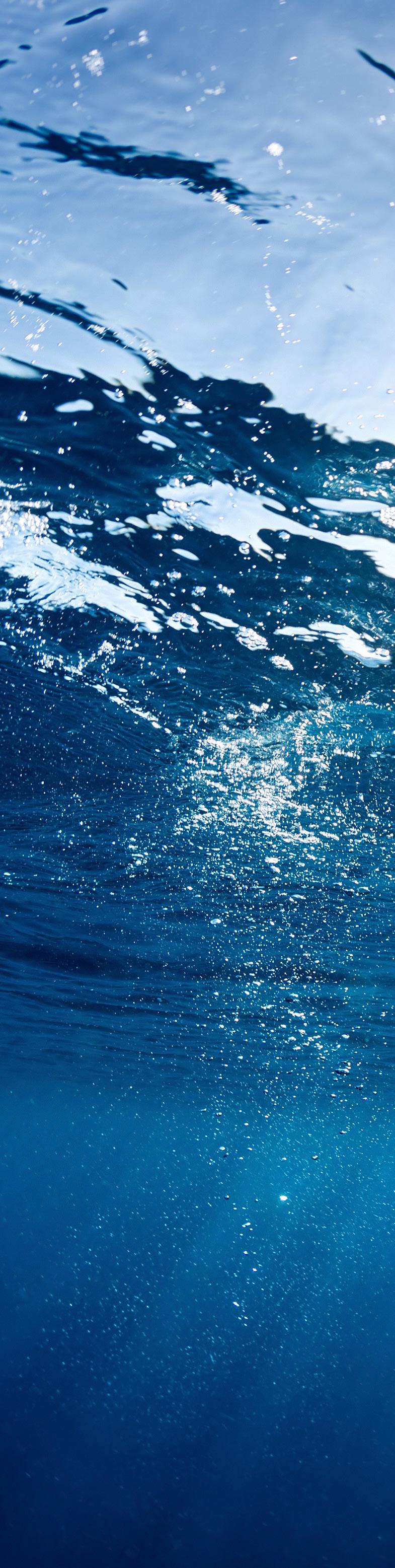
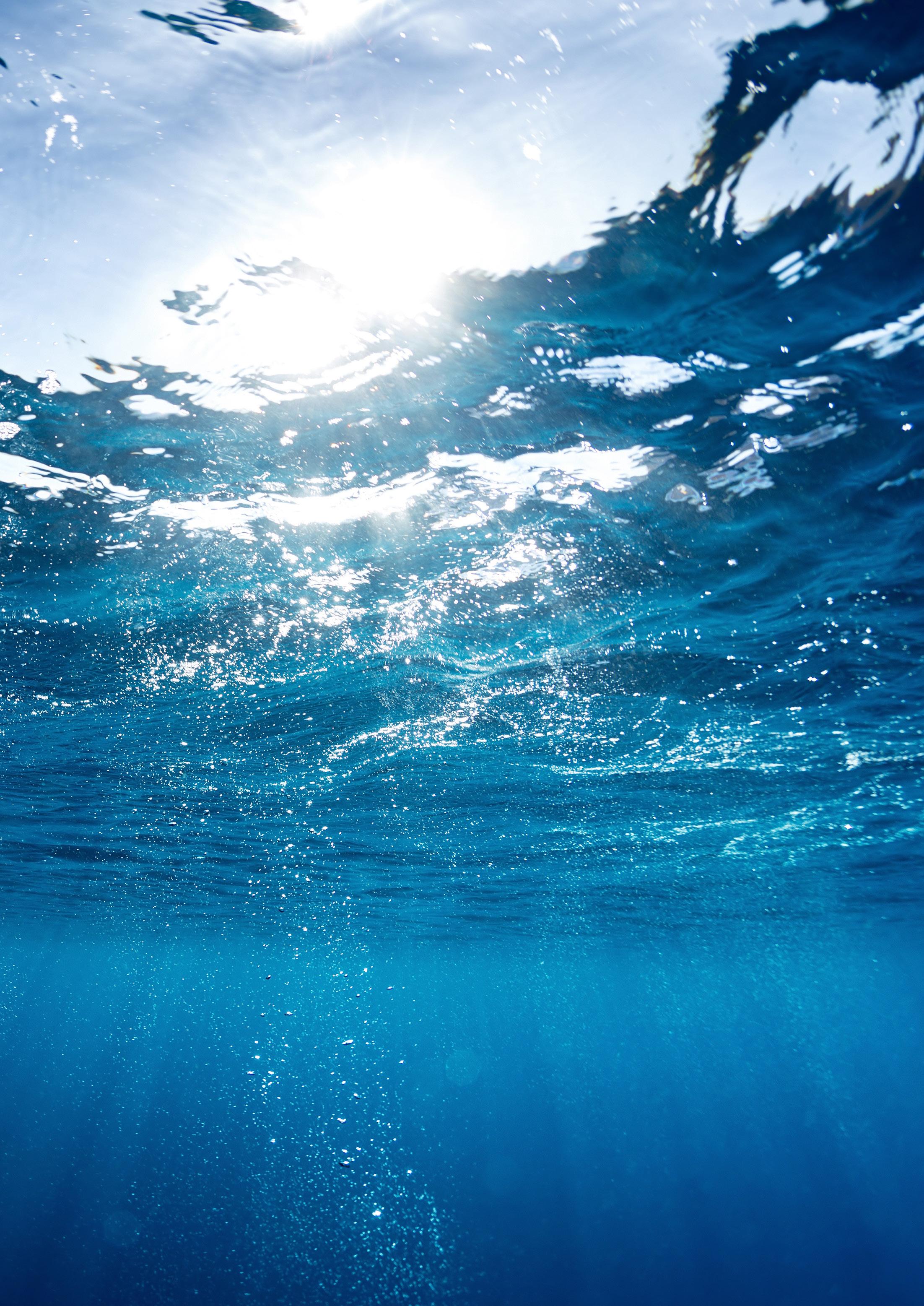
Our environmental policy
The whole fishing industry has a responsibility to manage our global fish resources in the best possible way. At Optimar, we focus on making products and systems that ensure a high-quality end product, with as little waste as possible.
Our target is to reduce our adverse impact and increase our positive impact, as well as exploit any opportunities related to the climate and environment.
Our commitment:
Map and reduce our carbon footprint.
Improve waste management, reduce residual waste and increase utilization of purchased materials.
Increase systems lifespan through upgrades and retrofits.
Reduce non-renewable energy consumption.
Contribute to animal welfare.
Enable full utilization of raw materials and traceability for sustainable fisheries.
Ensure our products and solutions contribute to a safe and attractive workplace.

Greenhouse gas (GHG) emissions
Optimar started calculating its carbon footprint in 2021. Data for 2023 is compared with 2022 and commented on accordingly.
CEMAsys is Optimar’s system partner for carbon accounting. This report provides an overview of Optimar’s greenhouse gas (GHG) emissions, which forms an integrated part of our climate strategy. The presentation is based on consumption data from internal and external sources, converted into tonnes of CO2-equivalents (tCO2e).
Emissions (tCO2e) from our global business
Global Scope 1 & 2 emissions (tCO2e) per employee and per NOK million in revenue

Sustainable and Scalable Operating Platform (Environmental)
Scope 1
Scope 1 covers all direct emission sources. This includes all use of fossil fuels for stationary combustion, transportation by company vehicles (both leased and owned) and process emissions.
Emission factors per fuel type are based on assumptions in the IEA methodological framework. The reduction in Scope 1 emissions in 2023 compared with 2022 is mainly attributable to a lower level of commercial activity due to difficult market conditions. The use of diesel decreased in 2023. This is due to fewer projects and a reduction in internal transportation between sites resulting from the relocation of production at Stette and Stranda to Valderøya in 2022 and 2023. Furthermore, a better solution for our acid process has reduced the need for acid and associated transport. In 2023, Optimar had only one electric vehicle, which handled most of our internal transport. As battery capacity increases, we will buy/lease more electrical vehicles.
Scope 1
Scope 2
In 2022, we finalized installation of solar panels at our production facility in Spain. This led to a reduction in electricity consumption. In 2022 and 2023, Optimar has made some changes and reduced activities in Seattle, USA, repatriated production to Norway by closing the production facilities in Braila, Romania, and relocated production from Stette and Stranda to Valderøya. This move led to a reduction in electricity consumption and transport between the sites. We will investigate how we can improve our buildings to use less energy for heating and how we can increase the use of renewable energy.
Scope 2 Unit
Scope 3
Scope 3 is so far only partially accounted for. The Scope 3 figures for 2023 include the categories waste and business travel.
In 2023, business-related air travel accounted for a substantial part of Optimar’s carbon footprint. However, the total of 533.2 tCO2e is a slight reduction from 2022.
Scope 3 Category
In 2023, the total figure for waste is substantially lower than the year before. This is mainly due to the previously mentioned reduction in projects and commercial activity. All our waste is sorted at source and recycled. We are working with our suppliers to ensure that the supply of raw materials is sustainable, and we also work to reduce the amount of non-recyclable packing materials in/out of the company.
*In 2021, we experienced an acid leakage incident which, in addition to its local environmental impact, meant a large increase in hazardous waste during the cleanup process. 380 out of 412 tCO2e from waste handling was due to the acid leakage. We have now installed a new high-capacity solution that is both efficient and more environmentally friendly. It has a low risk of leakage and ensures the safest possible working environment for our operators. With the implementation of this acid treatment facility in-house, we have also reduced our need to transport acid and other products.

People E SG
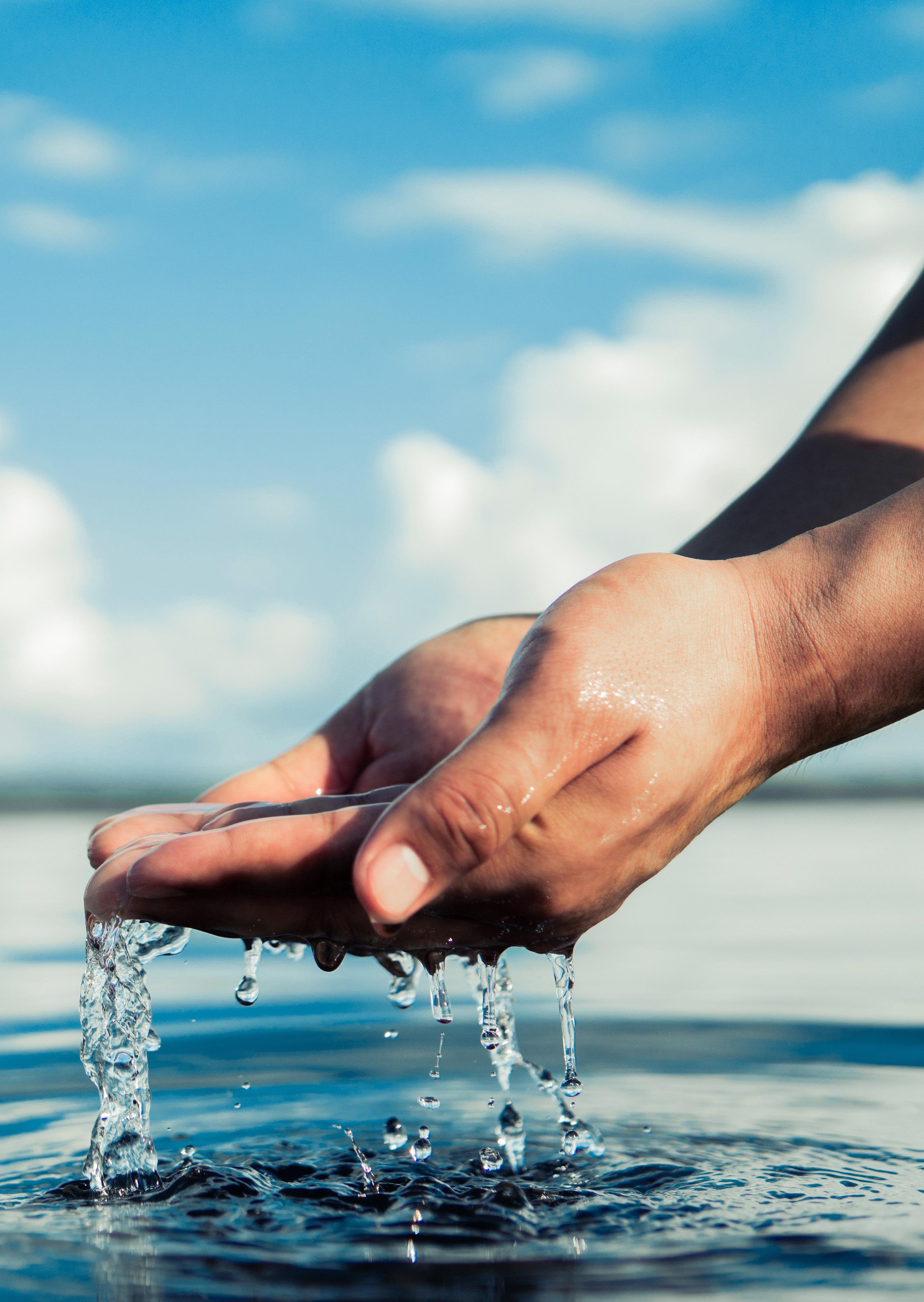
Our social responsibility
We are convinced that diversity and inclusion are important factors for growing our business and our results. Diversity in gender, background, culture and experience contributes to a strong work environment.
A blend of different voices and thoughts makes Optimar an exciting and inclusive workplace that seeks to foster personal development and professional growth. Equal rights are a fundamental principle at Optimar, and this is safeguarded through our open and fair employment policy, salary policy and ethical guidelines.
Our goal is to have a workplace that is free from all discrimination and harassment.
The section below on diversity, equality, and inclusion (DEI) constitutes Optimar ’s response to the activity and reporting obligation pursuant to the Norwegian Equality and Anti-Discrimination Act for the period 1 January to 31 December 2023.
In 2023 we were just emerging from a significant restructuring and downsizing process that was implemented at the end of 2022. Our focus was on stabilizing the organization and creating a good workplace. Although recruitment was minimal in 2023, we continued to focus on diversity and equality in those recruitment processes that were undertaken.
Organization of our diversity, equality and inclusion (DEI) activities
Diversity, equality and inclusion are basic principles in the company’s strategy and documented in the ethical guidelines and code of conduct. The Management is responsible for organizing the business operations to ensure adherence and compliance to these policies.
The HR organization carries out the day-to-day DEI related activities. HR and management engage with trade union representatives in quarterly dialogue meetings. Issues and decisions relating to the working environment are discussed by our Working Environment Committee (WEC). In 2023 the WEC held four meetings.
Gender equality
At the close of 2023, we had 258 employees, 15 percent of whom were women, 85 per cent men and 0 per cent identifying as non-binary.
The table below shows the percentage of each gender category at the various levels in the organization (GRI 405-1).
Even though the total ratio of women to men in the global organization remains the same as in 2022, there are differences at each level.
The table below shows women’s pay as a percentage of men’s pay in full-time positions at the different levels (GRI 4052). The figures are based on the Norwegian workforce.
Listed salary statistics do not consider factors such as different levels of education, seniority, job complexity and responsibility, nor labour market conditions for specific professions. We nevertheless acknowledge that the pay gap between women and men at the most senior levels is substantial and further investigations will be conducted. If the underlying reason is attributable to gender or other types of discrimination, we will strive to reduce the gap. Equal pay is important if we are to be an attractive employer and foster a culture of diversity.
Parental leave
Optimar complies with the regulations relating to parental leave in each of the countries in which we operate. The figures below reflect the regulations in effect in the different countries.
SPAIN
No employees of Optimar US took parental leave in 2023.
In Norway, eligible women took an average of 29.5 weeks of parental leave in 2023, while eligible men took an average of 14.1 weeks.
Part time and temporary positions
The table below shows the number of employees globally in part-time and temporary positions, by gender. This overview does not include our eight apprentices.
Every published job advertisement is for full-time employment with Optimar.
In every case where an employee works part-time at Optimar, it is the employee’s own choice. The company offers reduced hours to be inclusive and adapt to the employee’s situation.
Temporary employment is used only when the work itself is of a temporary nature, for instance in connection with a specific project or as a substitute for an employee taking leave of absence. Apprenticeships are also defined as temporary positions.
Age diversity
A blend of backgrounds, genders, ages, competence and mindsets contributes to the successful development of our company. Leveraging the benefits of such diversity for the good of the entire company requires sensitivity and an emphasis on cooperation and team spirit.
The table shows a percentage breakdown of our workforce by age (GRI 405 -1).
Diversity, equality and inclusionrelated activities
Our personnel policy is gender neutral in all areas and states that we work to promote equality and prevent discrimination.
Work tasks and workplaces are organized and adjusted where there are special needs. For example, all our general staff meetings are conducted with an interpreter for the hearing impaired. Our recruitment policy is open and fair. However, there was little new recruitment in 2023 due to the difficult market-conditions and implementation of changes in the organization.
Area Risk
Recruitment
Pay and working conditions
Promotion and talent development
Fear of change in daily routines. Prejudice. Unconscious bias.
Some individuals are more inclined to negotiate their salaries. Certain professions command higher salary expectations due to the scarcity of skills in the market
Some employees may not be chosen for training and promotions due to discrimination/unconscious bias.
Actions
HR attends all interviews.
Standard set-up and contracts are used in all recruitments.
Annual local salary negotiations with trade unions (collective bargaining).
Unions are provided with salary data for men and women to reveal gender-based differences.
We strongly encourage employees to apply for all published vacancies.
Status and goal
In 2024, we aim to use more pictures showing both women and men in our job advertisements.
Assess further improvements in the pay policy to secure equal pay for work of equal value.
No further actions planned at the moment.
Work-life balance
Always available – the boundary between work and leisure is unclear. The need to care for children/ elderly relatives may impact career progression.
Flexible working hours.
Working from home may be agreed on a temporary or permanent basis.
Paid time off for breastfeeding.
Consider coverage of full salary during parental leave. Other solutions apply to employees abroad.
Area Risk Actions
Bullying, sexual harassment and gender-based violence
Male dominated industry. Work abroad in various cultures.
Facilitation
Lack of accommodation for employees with regard to functional ability, gender identity, religion and age.
We have ethical guidelines that state our zero tolerance for harassment and abuse of any kind.
All new employees and leaders are informed of our ethical guidelines.
Field service engineers are given training in the topic.
Every second year we conduct a survey specifically designed to reveal harassment and other forms of abuse.
We are an Inclusive Working Life partner (IA company) and strive to make arrangements for employees with reduced functional abilities through individual adaptation of both the workplace and work tasks.
Our buildings have elevators and HC-restrooms available.
General staff meetings are conducted with an interpreter for the hearing impaired.
Production workers who work in a noisy and/or dusty environment are provided with personal protective equipment and offered a health check every second year. Other employees are offered a free health check every third year.
We have developed a policy specifically for older employees.
Status and goal
Conduct training in our ethical guidelines and dilemma-related discussions to increase awareness of possible threats and how to handle and report them.
No further actions planned at the moment.
In 2022, we conducted an employee survey that focused on psychosocial issues in the workplace. The survey was global and anonymous and achieved a 71 per cent response rate. The results showed that, in general, we have a good psychosocial working environment. However, the results also showed that it is important to keep a continuous focus on this topic and that we need to further improve the way our Whistleblower Policy is implemented in the organization. The survey will be repeated in 2024.
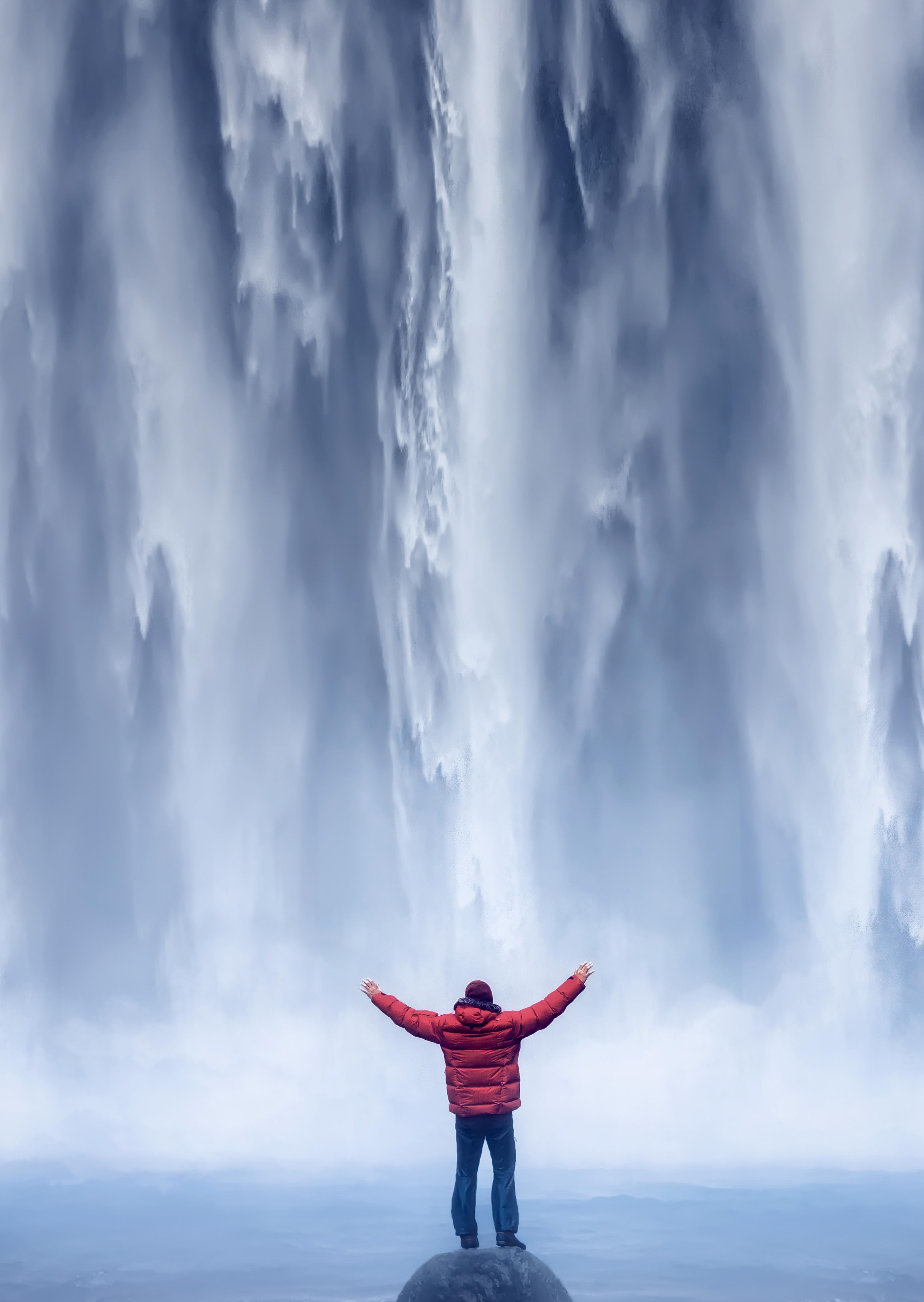
Health, Safety and Work Environment
For people to be receptive to development and perform at their best, they require a good work-life balance and good health. Optimar is an industrial company and employees perform tasks associated with risk, such as welding, use of heavy machinery, automation and assembly. We believe in building a strong safety culture through personnel involvement and training.
Sick leave and work-related injuries
Our goal is zero workplace injuries that result in employees being absent for a workday or more, other wise known as Lost Time Injuries (LTIs). In 2023, we continued to focus on the reporting of near misses and actual injuries. In 2022, we launched a new reporting system that enables HSE and quality-related non-conformances to be reported via an app. This is much more convenient for our field service engineers and production workers and has proved a great success.
In 2023, we recorded six injuries at Optimar, four of which were LTIs.
The table below shows the number of LTIs and the Lost Time Injury Frequency Rate (LTIFR) for Optimar globally (GRI 403-9).
*The LTIFR is calculated as follows: ([Number of lost time injuries in the reporting period] x 1,000,000) / (Total hours worked in the reporting period).
The average sick leave in the Optimar group in 2023 was 2.8% which is significantly down from 4.3% in 2022. Our target KPI is below 3.7%. As reference, the average sick leave rate for industrial companies in Norway was 5.2% in 2023 according to the Confederation of Norway Enterprise (NHO).
Employee engagement
We used to measure employee engagement twice a year with the eNPS (Employee Net Promoter Score) model. However, we experienced that this method was very time-consuming, and failing to provide managers with high-value insights. In September 2022, we decided to discontinue the survey. In the fourth quarter of 2024, a new survey tool will be implemented, and we will relaunch the eNPS survey.
Competence, skills development and training
We
have a responsibility to ensure that our employees have the skills, training and certifications they need to perform their work.
In 2023, our Certified to Operate scheme continued to ensure that our production workers and field service engineers are properly trained and have the required certificates. Among other things, our employees are trained in:
Electrical safety.
Work at height and elevating work platforms.
Scaffolding and ladder safety.
Hot work.
Extensive first-aid.
Forklift and crane handling.
Personal protective equipment.
We are an approved apprenticeship company and have eight apprentices
in our production department, seven men and one woman in the reporting year.
Employees participate actively in networks and clusters to keep updated and continuously learn from other businesses and academic institutions in our local area.
At the end of 2023 we acquired a new Learning Management System (LMS). This solution will help us to maintain a complete overview of the documented competence needed in each position at Optimar, and will be implemented in 2024/2025.
Supply chain responsibility
Optimar is committed to upholding responsible business standards and actively seeks to avoid purchases that could compromise human rights and decent working conditions.
More information on the company’s supply chain initiatives can be found elsewhere in this report. This section constitutes our response to the Norwegian Transparency Act for the reporting period 1 July to 31 December 2023.
Under the Transparency Act, our Global Procurement & Logistics Department oversees supplier-related activities, while our top management has overall responsibility for compliance with relevant laws and ethical standards. In our purchasing orders (POs) and framework agreements, we state clearly that our suppliers must abide by our ethical principles and general Code of Conduct. However, Optimar wanted to be clearer about what we expect from our suppliers and business partners. Our new Supplier Code of Conduct was therefore finalized in 2023. We will continue to follow up our suppliers through contract obligations.
Readers interested in more detailed information regarding human rights and working conditions in our supply chain are welcome to reach out to us using the contact information provided on our website www.optimar. no. We will respond to such enquiries within three weeks. Additionally, we encourage suppliers to report any potential or actual breaches of our Code of Conduct through our whistleblower e-mail. This channel is open for both internal and external disclosures, and both are handled in accordance with the same procedure and with the same discretion.
In 2022, we engaged with 379 of our suppliers. In 2023, we narrowed our focus to 151 suppliers, that were selected on the basis of volume and risk to ensure a more comprehensive overview. Our supply chain varies from project to project, but steel-related products account for the bulk of our purchases. We also purchase
Optimar Supplier Code of Conduct
products from original equipment manufacturers (OEMs), which may, in turn, use components made by a variety of subcontractors. This makes it difficult to perform a risk assessment on the entire supply chain.
With effect from 2022, we conduct an annual evaluation of our suppliers, where the prioritized risk areas investigated are:
Fundamental human and labour rights.
Health and safety.
Anti-corruption and bribery.
Supplier risk management
Optimar recognizes that it cannot address every potential adverse impact in its supply chain. However, being aware of risks helps us prioritize our endeavours to achieve a sustainable supply chain.
We use a third-party system for supplier mapping and initial risk assessment. A complete overview of our first-tier suppliers and business partners, broken down by category, is included in the platform and is continuously updated. An initial risk assessment is performed based on the supplier’s location and their industry, product or service category, and the volume of goods purchased from that specific supplier as a percentage of Optimar’s total purchases.
Upon registration, suppliers receive a survey with questions based on GRI standards. Using the initial risk assessment and survey responses, we assign each supplier a total score and
risk rating for their potential adverse impact on human rights and decent working conditions.
While it is challenging to survey beyond the first tier of the supply chain, we encourage our direct suppliers to assess their subcontractors using the corresponding survey.
We will continue to work with our suppliers to document their work with climate performance, corruption and workers’ rights. Optimar’s efforts to map and do a risk assessment on our suppliers are an ongoing process, as we also experience that it is challenging and takes time to get feedback from all.
Action priorities have been set for the most significant risks of human and labour rights abuses. The following table shows the main risks that have been identified.
Component/Activity Risks
Steel
Plastic
Environmental impact. The steel industry is responsible for 7–9 percent of the world’s CO2 emissions.
Mining and metal sector. Small-scale operations tend to use low-skilled manual labour and have poor health and safety standards. Small-scale mines may be linked to organized crime and corruption.
Plastic has a high environmental impact. The plastics industry is responsible for 3.8 percent of the world’s CO2 emissions.
Forced labor, unsafe working conditions etc.
Measures
Supplier Code of Conduct.
Inclusion of specific contractual requirements.
Monitoring (Assess/Audit/Visit).
Supplier Code of Conduct.
Inclusion of specific contractual requirements.
Monitoring (Assess/Audit/Visit).
Original Equipment Manufacturer (OEM)
Outsourcing
Optimar’s suppliers buy engineered components from a variety of subcontractors for assembly in their own workshops. Optimar has limited insight into the lower tiers of the supply chain. We consider that the most likely adverse impacts relate to poor working conditions and inequality at sub-contractor workshops.
Human rights and working conditions controlled by other companies and other statutory requirements than those applicable in Norway.
Supplier Code of Conduct.
Inclusion of specific contractual requirements.
Supplier survey with questions covering subcontractors.
Monitoring (Assess/Audit/Visit).
Supplier Code of Conduct.
Inclusion of specific contractual requirements.
Supplier survey with questions covering sub-contractors.
Monitoring (Assess/Audit/Visit).
Should our supplier risk assessment reveal an unacceptable level of risk or result in unanswered questions, we initiate a pre-defined internal process. To ensure that all suppliers and business partners are treated equally, our risk response plan contains a description of the prescribed actions to be taken in relation to each identified risk.
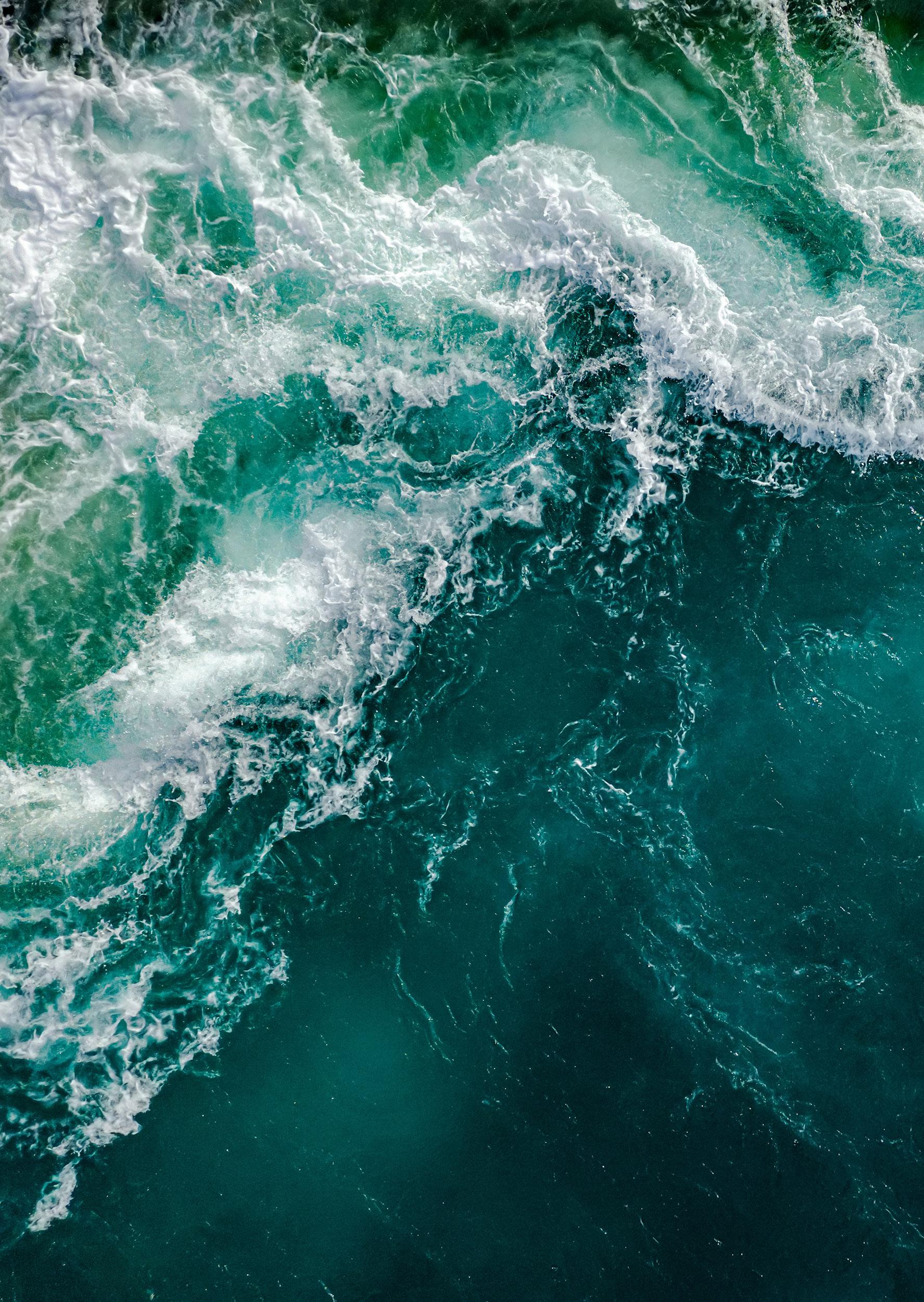
Together we create value for generations
