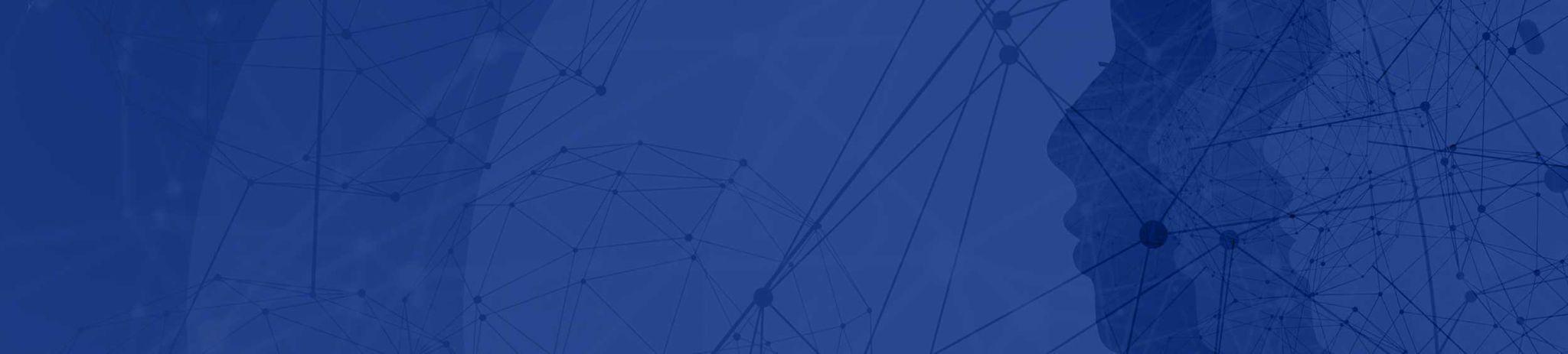

WHAT ARE THE MOST EFFECTIVE SILICA CONTROLS?

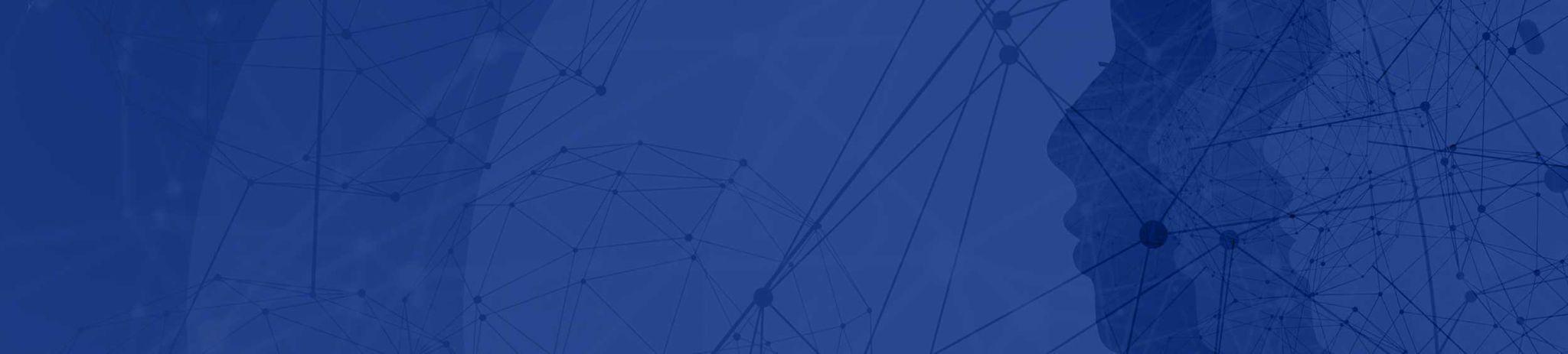
Work Health and Safety Regulations (Crystalline Silica Substances) Amendment 2024 requires that control measures to eliminate or minimise risks are implemented so far as is reasonably practical, and at least 1 of these measures are used:
• isolation of a person from dust exposure,
• a fully enclosed operator cabin fitted with a high efficiency air filtration system,
• an effective wet dust suppression method,
• an effective on-tool extraction system, and
• an effective local exhaust ventilation system.
While the prescribed controls may seem to provide a measure of reassurance there is evidence that not all controls may adequately protect workers against exposure to CS dust. Each measure has its own requirements to be effective and all controls have limitations. Even when controls substantially reduce airborne dust concentrations workers may still be at risk of exposure and require respiratory protection for residual risk. This guidance was developed by AIOH occupational hygienists and ventilation specialists to help in the recognition of what makes CS controls effective – or not.
In ‘A systematic review of the effectiveness of dust control measures adopted to reduce workplace exposure’ it was found that ‘while the identified interventions drastically reduce dust levels, workers may still be overexposed to respirable crystalline silica (RCS) even under high-efficiency levels’ [1]. This study recommended using multiple layers of controls. The QLD Code of Practice Managing respirable crystalline silica dust exposure in construction and manufacturing of construction elements 2022 [2] details engineering and work practice control methods for a range of construction equipment and task durations. Based on the U.S. Safety and Health Regulations for Construction 1926.1153Respirable crystalline silica [3] it considers the duration of the construction task (<= 4 hours or >4 hours) and whether it occurs outdoors, indoors or in an enclosed area.
‘The Evaluation of Worker Exposure to Airborne Silica Dust During Five OSHA Table I
Construction Tasks’ [5] study conducted personal respirable crystalline silica air monitoring during five different construction tasks. The results also suggest that exposure to hazardous levels of respirable CS may still occur even when OSHA-specified engineering controls are implemented and warn that background construction site silica concentrations may potentially cause overexposures, even when the Table 1 control methods have been put in place.
In consideration of the research cited, the AIOH advises that determining whether a crystalline silica process (CSP) is effectively controlled (or not) should involve a technical evaluation by an engineer or Certified Occupational Hygienist (COH)®. Air monitoring conducted under the direction of a COH® may be needed to quantify the respirable crystalline silica air concentrations by suitable methods outlined here.
AIOH offers the following general guidance on the ‘real world’ factors that can limit (or enhance) the effectiveness of various control methods commonly applied to CS work.
Booths, cabins or offices may be suitable in environments with significant ambient dust concentrations such as tunnel construction areas, surface construction areas or in indoor work areas where dust generating processes are occurring. To be effective, booths, cabins or offices need to be well sealed with a filtered air supply. High efficiency particulate air (HEPA) filters remove airborne dust and can substantially reduce dust concentrations.
Booths, cabins or offices are unlikely to protect if:
• The air conditioning system or fan draws unfiltered air from outside into the space,
• The space is negatively pressurized which allows dusty outside air to be drawn into the workplace,
• Windows or doors are not well sealed and/or not kept closed.
Enclosed cabins can serve as a critical line of defense against the health risks posed by respirable crystalline silica (RCS) because they physically isolate operators from the external environment, significantly reducing exposure.
For a cabin to be an effective control they should be designed to provide operators with a comfortable, safe, and healthy work environment [6]. To further enhance protection, most enclosed cabs incorporate air filtration and pressurization systems within their heating, ventilation, and air conditioning units.
Determining whether your specific equipment cabs meet international and local standards can be challenging for the workplace. While some cabs may be enclosed, they might lack adequate pressurization and filtration systems, potentially compromising the air quality inside the cab. Additionally, even cabs initially designed to meet cabin design or health standards can become compromised due to insufficient maintenance of their components.
The current industry benchmark for cabin filtration is ISO 23875, adopted locally as AS/NZS 23875. This standard comprehensively outlines design, testing, operational, and maintenance criteria for enclosed cabins to ensure optimal cabin air quality. Preceding ISO 23875 was ISO 10263 targeting earthmoving equipment, which addressed air quality, temperature control, noise reduction, pressurization, and ergonomics.
Enclosed cabins can be a critical component of a comprehensive CS control strategy. However, the suitability of enclosed cabins depends on the specific risks associated with different machinery and crystalline silica processes (CSP). A risk-based approach is essential to determine the most appropriate control measures and what standard to aim for. Standards like AS/NZS 23875 provide valuable guidelines for cabin design and performance, though they may not be universally applicable. Continuous monitoring of the way the control measure is working is crucial to maintain a safe working environment when processing crystalline silica substances.
For enclosed cabins to be and remain effective over time they require specific design and consistent maintenance. This typically includes: -
The cabin must be positively pressurized to prevent dusty air from entering through seals. This creates an outward airflow, pushing contaminants away from the operator. Pressure should be in the range of 20 to 200 pascals(Pa) according to AS/NZS 23875.
All gaps, doors, and windows should be sealed to maintain positive pressure and prevent dust ingress. Regular inspections and maintenance are crucial to ensure these remain effective. Policies may need to state the need to keep doors and windows closed as protection against dust inhalation.
The job of a High-efficiency Particulate Air (HEPA) filter is to clean incoming air. They must be regularly inspected and replaced before becoming clogged to ensure optimal performance. Various filters will have relevant standards with specific instructions for use and limitations. AS/NZS 23875 specifies operator cabins have an external and a recirculating filter.
4). Recirculation and make up air.
Continuous air circulation with filtered air is essential to maintain a clean cabin environment while introducing sufficient fresh air flow to maintain carbon dioxide (CO2) within safe levels for operator alertness. AS/NZS23875 stipulates CO2 level of no more than 400 ppm above ambient levels.
5). Visibility.
The filtration and recirculation system should not inadvertently add any obstruction in the operator's visibility to safely operate the machine.
6). Maintenance and testing.
Regular cleaning, inspection, and filter replacement are essential for the overall filtration and pressurization requirements. This may require pressure tests or smoke test to identify leaks.
Below is a representation of a typical cabin filtration unit.
Figure 1 Reproduced with permission of MineGear, 2024
This refers to the use of water or water mixtures to suppress dust generation during tasks that would otherwise liberate dust to air. This includes the use of free flowing water over cutting blades, sprays on tools and the use of fine water mists to reduce airborne dust concentrations.
Use of wet methods can be effective in suppressing dust. However, for some highenergy tasks such as high-speed cutting a fine mist can be generated even during wet cutting and airborne dust aerosol levels may exceed the Workplace Exposure Standards (WES) for respirable crystalline silica Using water mist to reduce airborne dust requires that the water droplets be of similar size to the airborne dust particles. Airborne dust particles are typically <100 microns (1 millionth of a meter) in diameter and respirable crystalline silica (RCS) particles usually <4 microns. So to be an effective control for silica the water misting system must produce very fine water droplets in that size range. In practice this means that the water must be filtered so that the nozzles producing the fine mist do not clog. Another consideration with wet methods is the runoff. Crystalline silica containing slurry, if dried must also be controlled such that dust is not released and made airborne again.
On-tool extraction is a type of LEV system which is fitted directly onto the tool. It consists of a capture hood which attaches to the tool, tubing and extraction unit.
To be effective on-tool extraction requires:
• An attachment that allows air to be extracted at the point of and in the direction of dust creation
• A strong vacuum – a High (H) Class vacuum is required for carcinogenic dusts v
• Pre-filters and built-in ‘back-flushing’ filter cleaning mechanisms can reduce the need for filter changes.
Extraction systems that expel or release dust containing crystalline silica into the work environment are likely to increase the risk to users and others in the workplace, including cleaners and maintainers. If dust collection systems, such as bag houses are used there may be risks associated with handling the collected dust and during maintenance tasks such as filter change-outs. Using air pressure to clean these filters introduces a high exposure risk and is not recommended.
The U.K. Health and Safety Executive, Construction Information Sheet No 69Controlling construction dust with on-tool extraction [9] is a good source of information as are the increasing number of tool manufacturers who can provide on-tool capture hoods and extraction systems specific to their tools.
Local exhaust ventilation (LEV)
LEV is an engineering control to reduce exposures to dust. It comprises:
• A hood where the dust is drawn into, sometimes called a capture hood or canopy
• Ducting to move the dusty air
• Air filters which are effective barriers for various sizes of dust particles
• Air mover or air handler which powers the extraction system
The primary task of LEV is to remove dust at the point of generation. Important considerations for assessing LEV effectiveness are:
• Type of capture hood. The design, location, and efficiency of hoods and enclosures are critical when dealing with fine silica particles.
• ‘Capture velocity’. This is the velocity required to overcome the movement of the dust cloud and draw it into the hood.
• Duct velocity. This is the air velocity required to move the dust through the duct work. For dusts such as cement dust the minimum duct velocity is 20 m/s [8].
• Filtration and Emission Control. The toxicity and size of silica particles necessitates the use of high-efficiency filtration systems to capture particles of 4 micron or less. Baghouses and cartridge collectors are commonly used, and in situations where venting to the atmosphere is not feasible, additional controls such as HEPA filters and exhaust dust monitors should be implemented.
• Airflow Measurement and Monitoring: To ensure that extraction rates remain effective, continuous or frequent airflow measurement and monitoring are essential. This involves regular checks of dust collector, fan performance, ductwork integrity and hood efficiency against applicable dust control standards.
• Maintenance and Cleanliness: Regular maintenance of the LEV system is critical when handling silica. This includes routine inspections, replacements of filters as well as the cleaning of ductwork, hoods, and filters to prevent dust buildup,
which can compromise system efficiency and increase exposure risks. Safeguarding personnel during maintenance tasks and when changing filters requires training on the specific tasks and how to exchange filters.
Examples of where LEV may be used to meet requirements to control CS processes: -
• Laboratory Workstations: While a capture velocity of 0.5 m/s might be adequate for non-toxic dusts, a capture velocity of 0.75 - 1.0 m/s is recommended for tasks involving high silica concentrations to ensure effective containment.
• Hood Design in Drum Filling: For non-toxic dusts, a simple tapered hood might suffice. However, with silica, a slotted drum hood is preferred as it provides better control and capture of dust generated during filling operations and thus a higher capture efficiency.
• Work Benches: A hood positioned at the back of a workbench might be acceptable for non-toxic dusts. When working with fine silica dust, however, a more enclosed design, such as a partial or full enclosure, is typically required to prevent dust from escaping into the worker's breathing zone. This also should consider air movements into the enclosure and the position of the operator.
• Grinding Operations: In stone-cutting applications where crystalline silica dust is generated, traditional open hoods may not provide sufficient protection. Enclosed grinding booths with front-facing slots or downdraft tables that draw dust away from the worker are often necessary.
• Abrasive Blasting: In blasting operations where large amounts of crystalline silica dust are generated, the enclosure must fully encapsulate the work area, and inlet velocities are typically set above 1 m/s.
• Conveyor Transfer Points: For crystalline silica-rich materials, inlet velocities through openings are typically set above 1 m/s.
In ‘real world’ workplace conditions LEV may not work as effectively as designed. In a 2004 study of ‘The Efficacy of Local Exhaust Ventilation for Controlling Dust Exposures
During Concrete Surface Grinding’ [2] it was reported that despite the effective control of dust during surface grinding 26% of samples collected while LEV was being used were greater that exposure standard value for RCS.
Dilution ventilation
Dilution ventilation uses clean mechanically supplied air or ambient air flow to reduce the airborne dust concentration in a space. Dilution ventilation can be effective in an enclosed area such as tunnel construction and underground mining. How effective it is
will depend on the amount of airborne dust being generated and how much air is being moved out of the space.
The Australian Tunnelling Society and Engineers Australia produced an information package known as Ventilation during Tunnel Construction Industry - Considerations Air Quality [9]. They advise that if dilution ventilation is to be considered the primary control, a ventilation engineering assessment is required which considers dust concentrations being generated and the volume and flow of dilution air required. Dilution ventilation is not suitable when workers are located at the source of dust generation and directly exposed. A consistent finding in the literature [12] and in the real-world experience of occupational hygienists is that interventions which utilize water, surfactant, foam and air currents offer varying degrees of dust control effectiveness against respirable dust and respirable crystalline silica (RCS).
The AIOH recommends a multiple barrier approach to controlling CS risk and undertake air monitoring to determine if the risk from CS processing is effectively controlled in accordance with the requirements of the Work Health and Safety Regulations (Crystalline Silica Substances) Amendment 2024
[1] Anlimah, F. etal ‘A systematic review of the effectiveness of dust control measures adopted to reduce workplace exposure’, Environmental Science and Pollution Research (2023) 30:54407–54428.
[2] Workplace Health and Safety Queensland Code of Practice Managing respirable crystalline silica dust exposure in construction and manufacturing of construction elements 2022.
[3] U.S. Safety and Health Regulations for Construction [3] 1926.1153(c)(1) Respirable crystalline silica .
[4] Cothern, E. J. etal in ‘The Evaluation of Worker Exposure to Airborne Silica Dust During Five OSHA Table I Construction Tasks’ , Annals of Work Exposures and Health, 2023, 67, 572–583 .
[5] John A. Organiscak and Andrew B. Cecala. (2008) Key Design Factors of Enclosed Cab Dust Filtration Systems. National Institute for Occupational Safety and Health. https://www.cdc.gov/niosh/mining/UserFiles/works/pdfs/2009-103.pdf .
‘The Evaluation of Worker Exposure to Airborne Silica Dust During Five OSHA Table I Construction Tasks’
[6] U.K. HSE Controlling Airborne Contaminants at Work, A guide to local exhaust ventilation (LEV) HSG258 (Third edition) 2017
[7] US NIOSH publication RI 9689 Report of Investigations/2012 Dust Control Handbook for Industrial Minerals, Mining and Processing
[8] U.K. Health and Safety Executive, HSE has produced Construction Information Sheet No 69 - Controlling construction dust with on-tool extraction
[9] Australian Tunnelling Society and Engineers Australia Air Quality Working Group Ventilation during Tunnel Construction Industry Considerations - Information Package - Part 7 of 12, 2018
[10] International organization for standardization. (2021). Mining Air quality control systems for operator enclosures Performance requirements and test methods (ISO 23875:2021) https://www.iso.org/standard/77249.html
[11] International organization for standardization. (2009). Earth-moving machinery Operator enclosure environment (SO 10263-1:2009) https://www.iso.org/standard/42453.htmll.