THE SAFETY NET
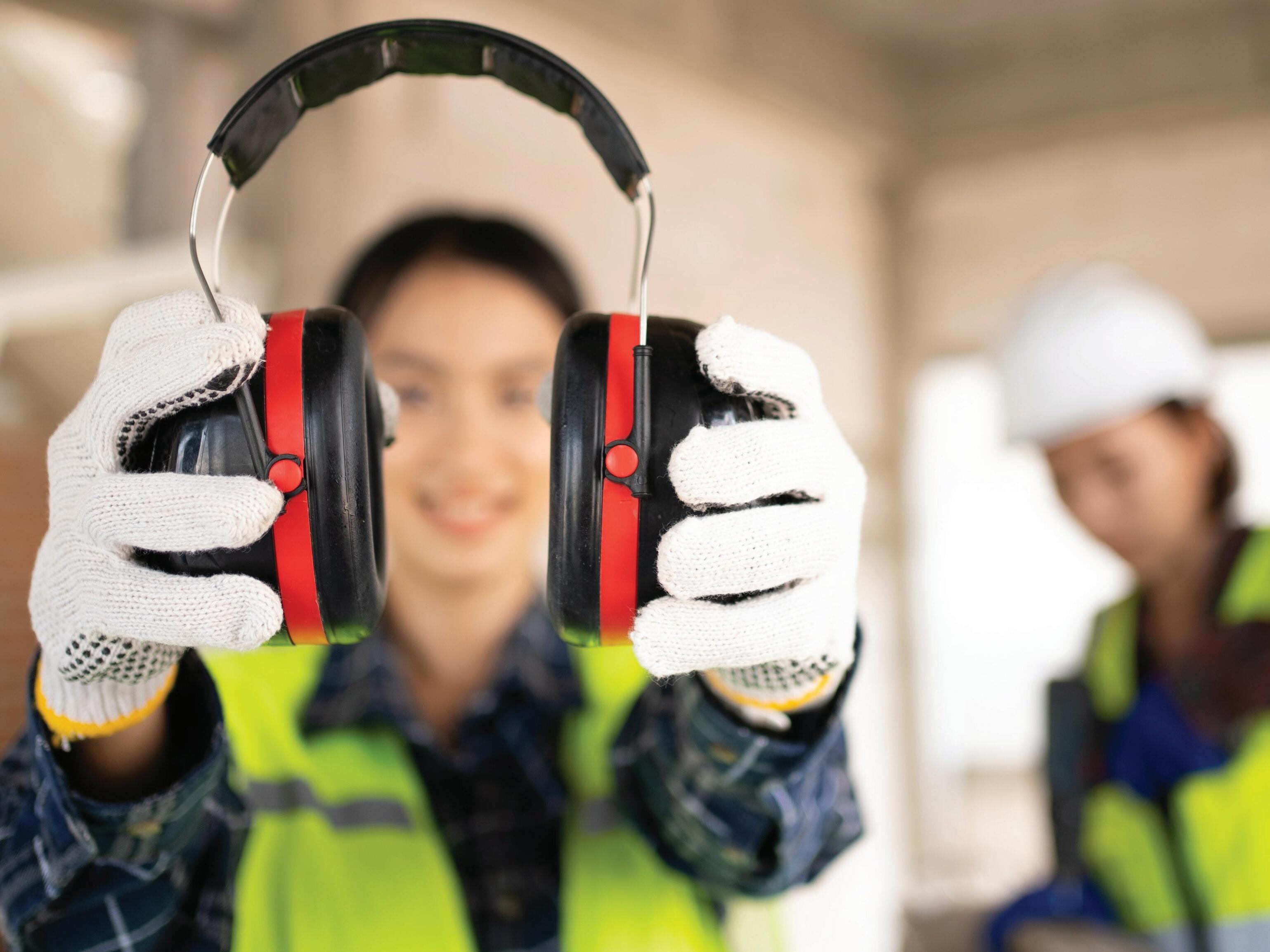
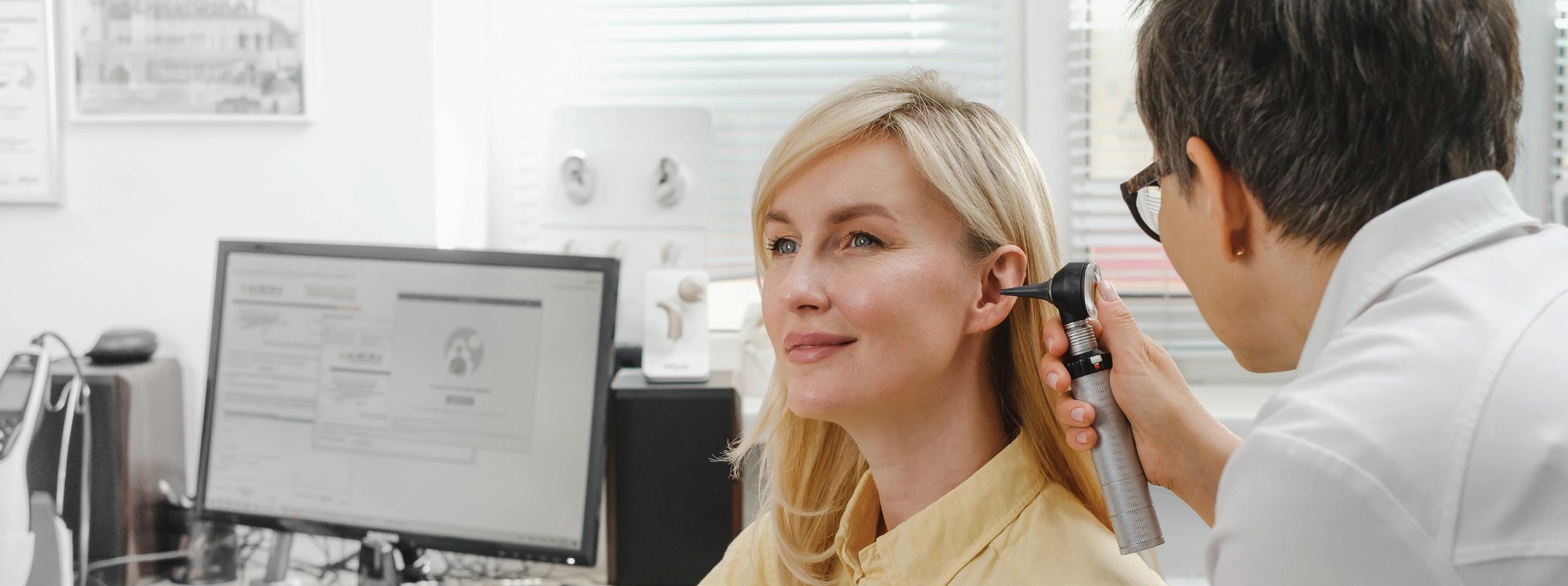
• Personnel with elevated noise exposures in the workplace (as described in the table below) are required to follow the requirements in the UW Hearing Loss Prevention Program. This includes the use of required hearing protection, completing Hearing Conservation training, and receiving annual audiometric tests.
• Units and departments are required to implement noise controls, post signs, provide hearing protection and audiometric testing when required. Units are also responsible for identifying tasks, equipment, or environments with the potential for elevated noise exposure, requesting evaluation of noise hazards, conducting an annual self-audit , among other requirements for preventing work related hearing loss.
DESCRIPTION
Personnel may be exposed to noise by working in areas with loud noise, operating machinery or equipment, using tools, and performing noise-producing activities.
Washington State Department of Labor and Industries (L&I) requires that hearing loss prevention measures are implemented when the noise levels reach specified action levels summarized in the following table.
EH&S is available to conduct noise assessments, assist with noise controls and hearing protection selection. Units, departments and supervisors can request noise monitoring anytime there is a change in activities or tools that may change the noise level.
Visit the Hearing Loss Prevention Program webpage and contact EH&S with questions.
REQUIREMENTS
• Training (initial and annual)
• Audiometric testing (initial and annual)
• Hearing protection (provided and used)
exposure equals or exceeds this level for one or more individuals (averaged over 8 hours)
noise level in an area where personnel are working (greater than one second)
Extreme impulse or impact noise in an area where personnel are working (less than one second)
• Training (initial and annual)
• Audiometric testing (initial and annual)
• Hearing protection (provided and used)
• Noise controls
• Hearing protection (provided and used)
• Post signage
• Hearing protection (provided and used)
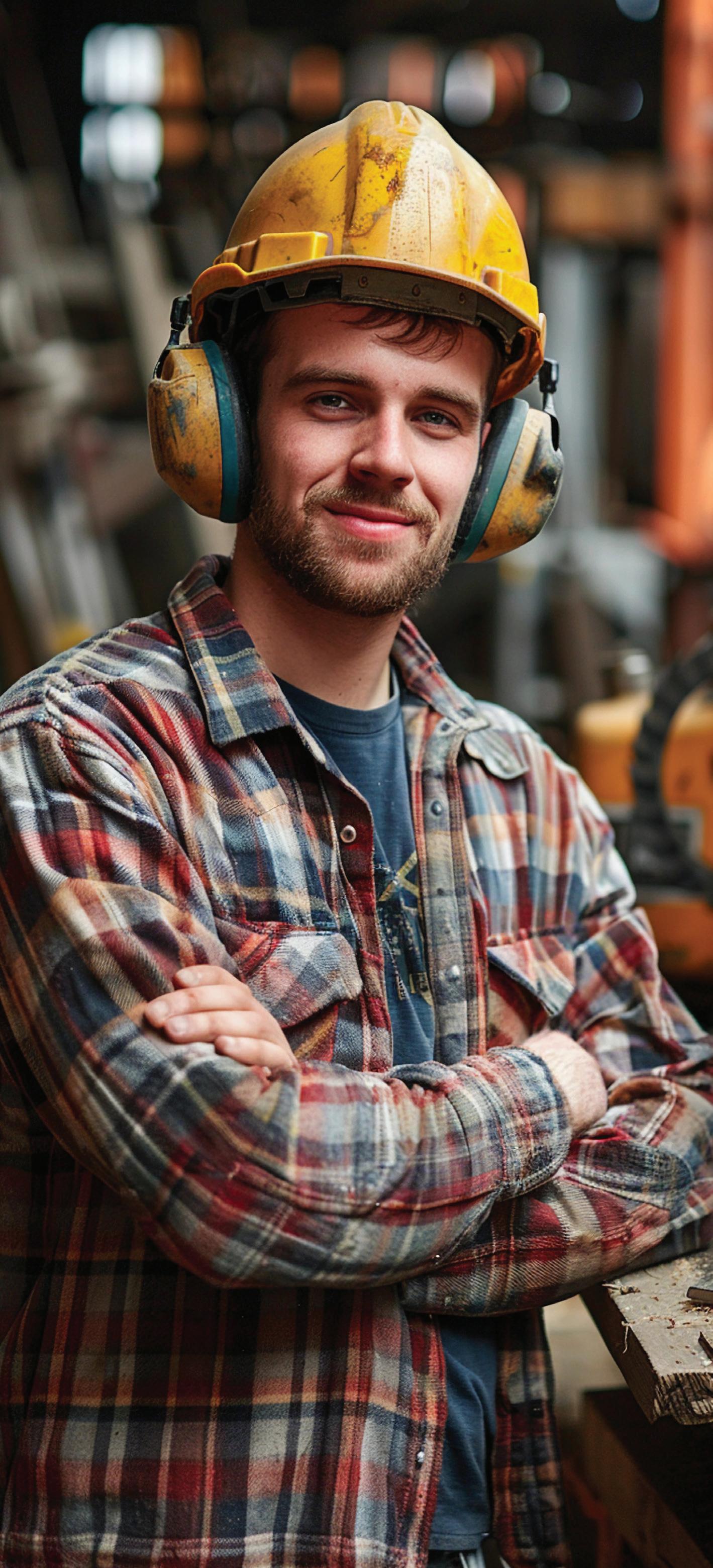
Every October, businesses across the nation come together to raise awareness about noiseinduced hearing loss during National Protect Your Hearing Month.
National Protect Your Hearing Month takes place throughout the entire month of October and gives employers plenty of time to plan activities that bring further awareness to the workforce on the importance of hearing loss prevention.
SOME GREAT IDEAS INCLUDE:
• Lead a safety meeting or toolbox talk on any topic related to workplace noise reduction or hearing protection.
• Host a workshop to demonstrate the correct way for workers to wear (or insert) their hearing protection devices.
• Plan an activity to demonstrate how workers can use NIOSH’s free Sound Level Meter app that they can download to their cell phones
• Conduct a safety audit or workplace inspection to re-evaluate the noise hazards in the workplace. Decide if the hearing program in place is sufficient or if additional changes should be made to protect workers.
• Provide information to employees, that they can also share with their families, on ways that everyone can prevent hearing loss outside of work.
• Ensure that all workers who require hearing protection devices, like earplugs or earmuffs, have access to the equipment they need, when they need it.
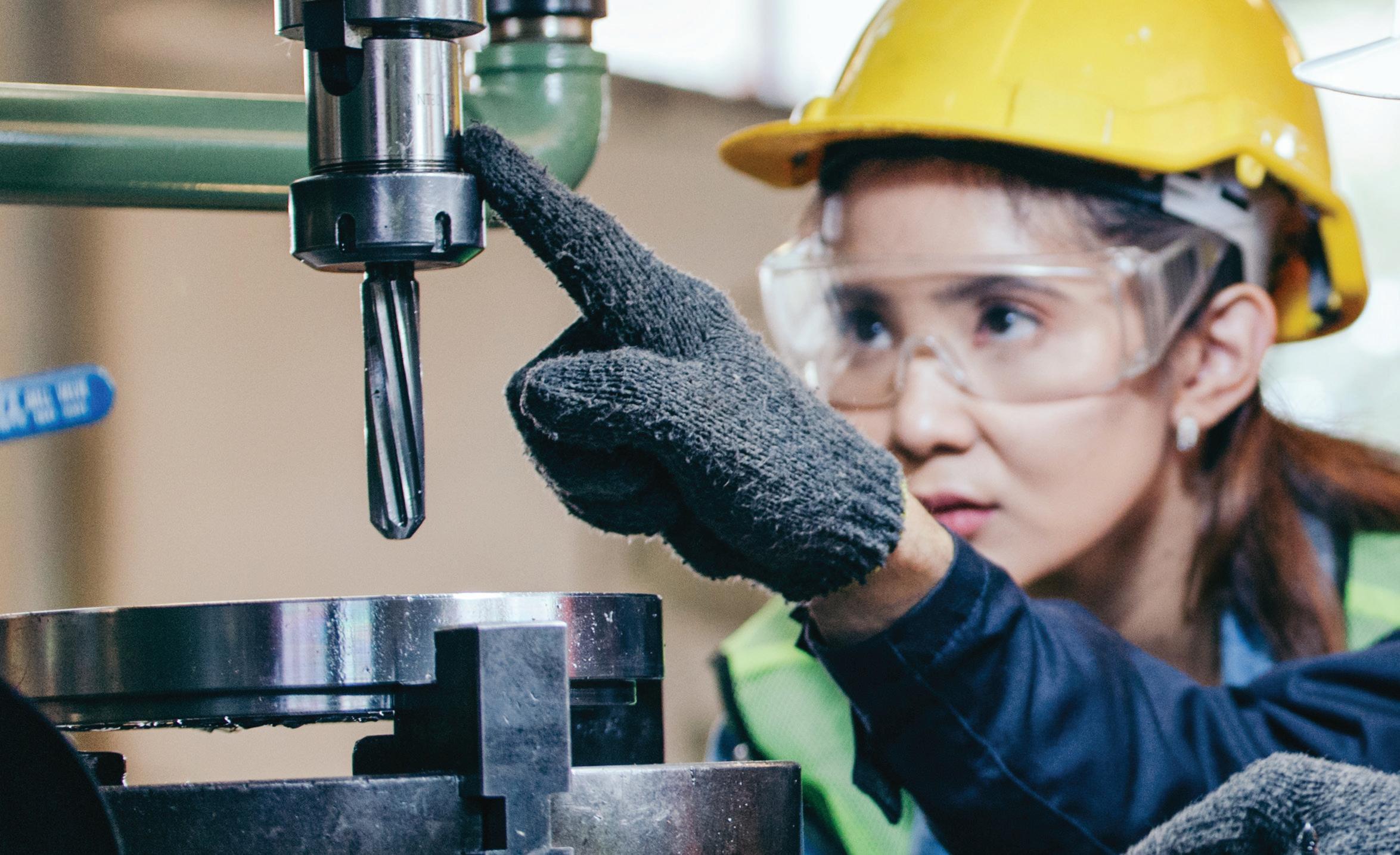
Best Practices for 2024: Driving Safety in a Changing Manufacturing Environment
In a constantly evolving manufacturing environment, fostering a culture of safety through employee engagement, data-driven analysis, interactive training and strategic automation is essential for mitigating risks and ensuring workplace safety.
Manufacturing is a constantly evolving industry. Shifts in factory technology, growing customer demand for manufactured products across a wide variety of industries and labor shortages are creating additional stress on manufacturers. Additionally, the increased adoption of automation is changing the makeup of manufacturing, bringing with it both risks and opportunities. However, manufacturing leaders have a responsibility to ensure that high-pressure environments do not disrupt the most important consideration on the manufacturing floor: safety.
The key to driving safety in an environment with anticipated hazards is building best practices into everyday work so that good habits become ingrained in the workplace. This culture of safety takes time to build and requires commitment from everyone who comes into contact with or makes decisions about a manufacturing
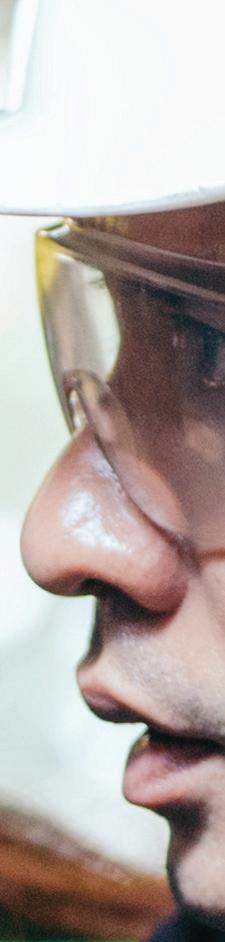
floor. Management must be committed to safety and encourage time to be spent on safety initiatives. Floor leaders must be committed to reinforcing good safety behaviors and pointing out bad ones, and every worker in a manufacturing environment must take responsibility for their and others’ safety. While safety programs must be customized to fit each unique environment, there are a few best practices everyone can follow.
FOCUSED EMPLOYEE ENGAGEMENT
Employee engagement needs to be a key part in any successful safety program both to make sure employees are understanding safety concepts and to solicit safety improvement ideas from those who work on the manufacturing floor every day. Driving strong participation in safety committees and safety activities must be accompanied by empowering employees to identify safety concerns and potential solutions. Management must recognize that production employees are experts in their work environment and build strong relationships to support communication, training, appropriate corrective action and other safety aspects.
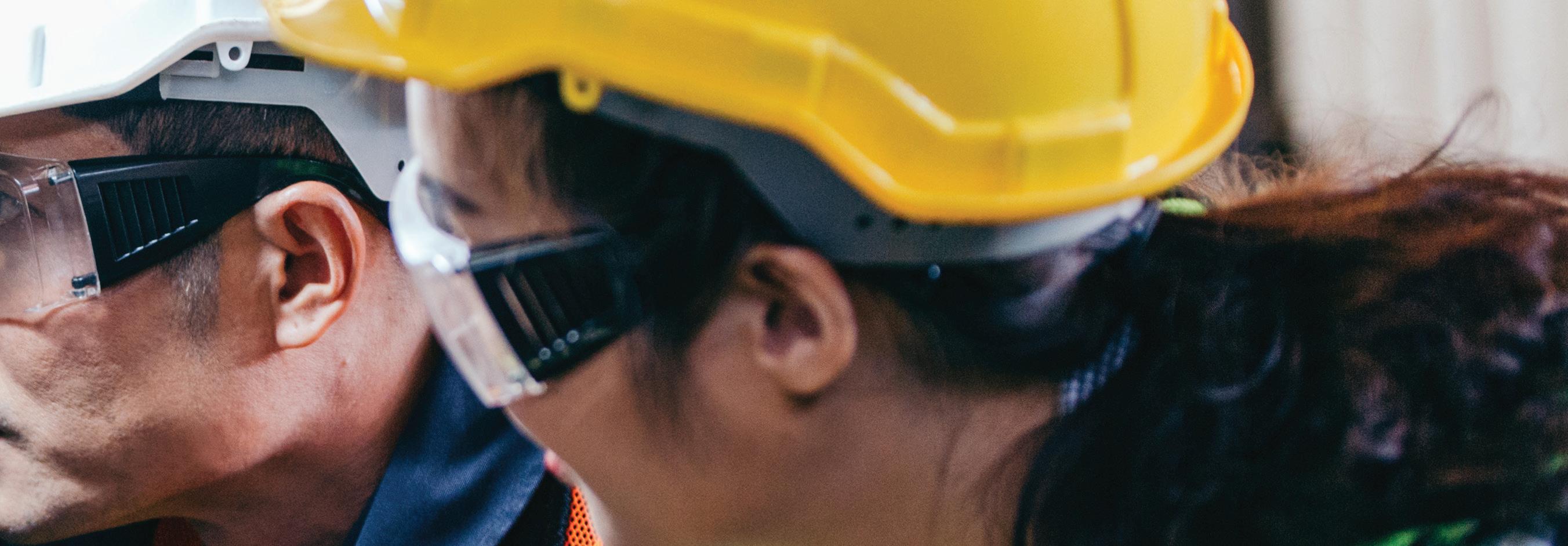
One way to successfully engage employees is through a “Safety Net” program. This approach breaks down the larger work environment into different areas, with rotating assessors from local teams focusing on a specific area and topic each week. These assessors record actions that need to be taken, track the closure of those actions and communicate progress with employees. These rotations help ensure that safety inspections do not become mindless and regularly bring fresh eyes to each part of the facility.
DATA-DRIVEN ANALYSIS
It is important to encourage reporting even of minor incidents and track those incidents in a way that helps illuminate trends before they become serious concerns. This helps leaders take steps to mitigate future issues by prioritizing specific areas for improvement. Identifying the root causes of minor incidents and near-miss events can help inform injury prevention efforts, including best practice sharing between employees about certain kinds of incidents.
It is important to not only collect and analyze safety information but be transparent in sharing it with employees. Utilizing department-specific Gemba boards or installing digital dashboards around workstations to display both leading and lagging safety indicators is a good step that leaders can take to keep employees informed about safety priorities and progress.
INTERACTIVE TRAINING
It is important to make sure that safety training is not simply a “check the box” item for both employees and visitors to the manufacturing floor. Interactive training—instead of just passive video or presented training—is a great way to encourage better understanding and adoption of safety best practices. Dedicating space to training and filling that space with interactive displays and visual aids helps
immerse people in the safety concepts being discussed. It is also important to make sure to not only build safety expectations but also check for the understanding of those expectations before allowing anyone—employees or visitors—into the production environment.
STRATEGIC AUTOMATION DEPLOYMENT
In addition to behavior-based activities and robust safety program deployment, manufacturing leaders must invest in technology that helps to improve safety. This includes installing ergonomic equipment and making the right investments in automation to reduce high-repetition and high-force tasks. This type of automation helps reduce safety risks in manufacturing and warehousing environments, especially related to musculoskeletal disorders and the prevention of strains and sprains. Before implementing any robotic or automated equipment, it is important to deploy a strong management of change program, set safety standards and communicate those standards across project teams. This includes implementing robust machine guarding, electrical safety and energy control programs to reduce risks for employees who may program, operate, diagnose, repair or routinely adjust equipment.
SAFETY IS NOT ONE-SIZE-FITS-ALL
When implementing any of these ideas, it is critical to work with employees to determine how they fit into a specific manufacturing environment. While adopting some best practices is fairly straightforward, manufacturing leaders must always maintain open and honest communication about what is and isn’t working in their workplaces. Maintaining a safe working environment for all employees and visitors must be the first priority for all manufacturers, and adopting these key behaviors is a great place to start.
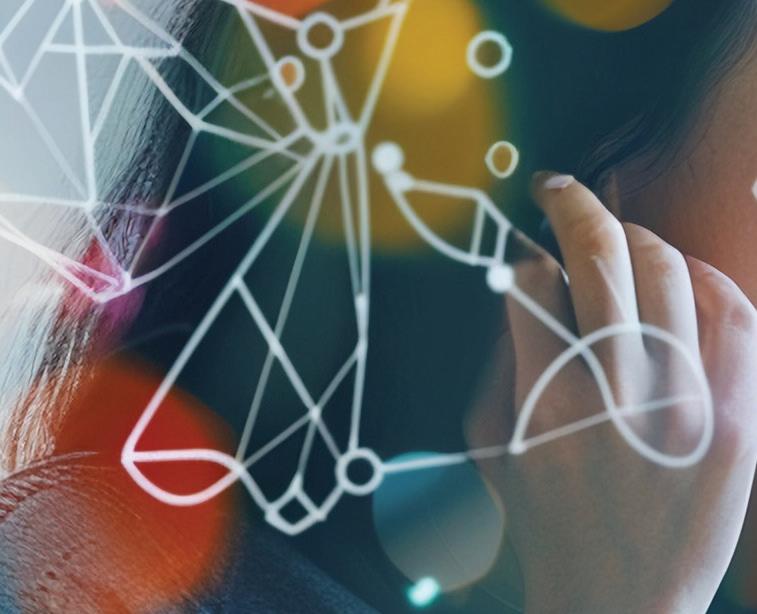
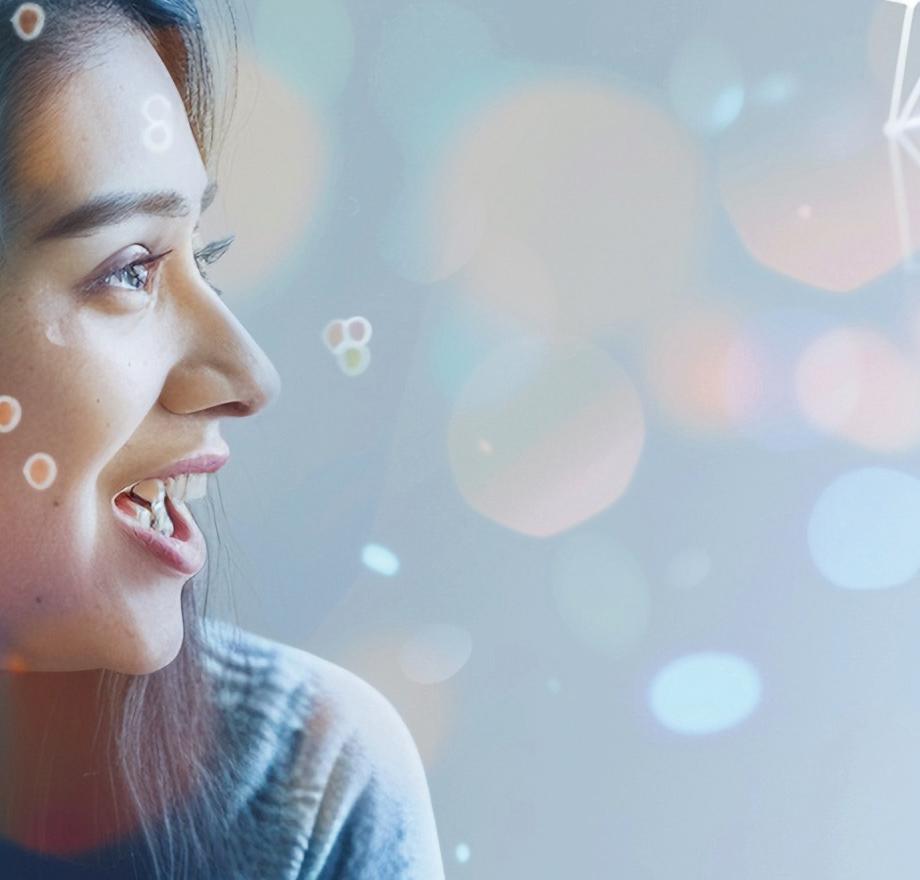
Empowering Employees to Speak Up is the Foundation to Creating a Safer Workplace
08.02.2024 | NSC
NSC MSD Pledge member Schneider Electric shares key insights on building a successful safety culture.
In 2022, there were more than 4.5 million work-related, medically consulted injuries, according to NSC Injury Facts. These injuries are estimated to cost U.S. businesses more than $1 billion per week. But what’s not reflected in these figures is the toll they take on employees, whether it prevents them from coming to work or missing out on family activities because they are in too much pain.
That’s why at Schneider Electric, a global leader in energy management and automation and an NSC and Campbell Institute member, we take workplace safety extremely seriously. More than a principle, our safety culture is a core business directive and everyday practice. This is also true for our suppliers, contractors and partners. It’s because of our forward-thinking approach that we have been successful at reducing all safety incidents over the last decade and we’re outpacing our competitors. In fact, we’re proud to lead the electrical manufacturing industry with less than one medical incident per 1 million hours worked.
While we’re pleased with this progress, we recognize there’s always more we can do to improve safety at our company. Over the next three years, our goal is to cut our medical incident rate in half. Further, as the number of lacerations,
fractures and electrical events have gone down, musculoskeletal disorders, or MSDs, have unfortunately risen. As part of our efforts to combat these ailments, we were one of the first organizations to sign the NSC MSD Pledge in June 2022 to reduce MSD risks and enhance the physical and psychological wellbeing of all workers.
One of the core tenets of the pledge is to share learnings that improve safety practices, so all workplaces can benefit. To help broadcast some of what makes our safety culture successful, we recently took members of the NSC MSD Solutions Lab on a tour of our Lincoln, Nebraska, facility to showcase how we’re putting safety into action. Here are some of the key takeaways:
Involving the workforce is the foundation of building a safer workplace. Whether it’s employees working on the facility floor or directors in the office, it’s critical to speak with people at all levels of an organization about their safety experiences. Encourage them to speak up and listen closely to any concerns or potential changes they believe can have a positive impact. At Schneider Electric, this starts on a worker’s first day at new employee orientations, where we promote early reporting and saying something if they see something. We also have safety and ergonomics committees at our facilities, which include a range of employees at different levels. We rely on them to
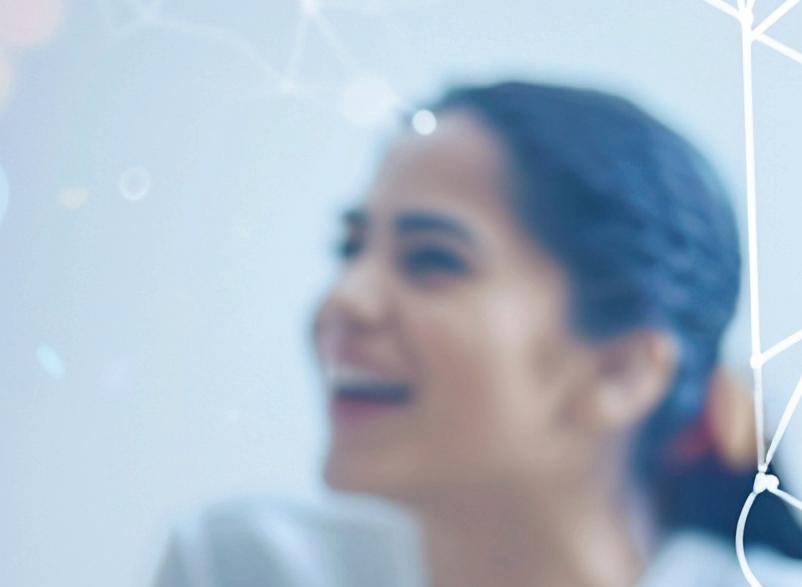
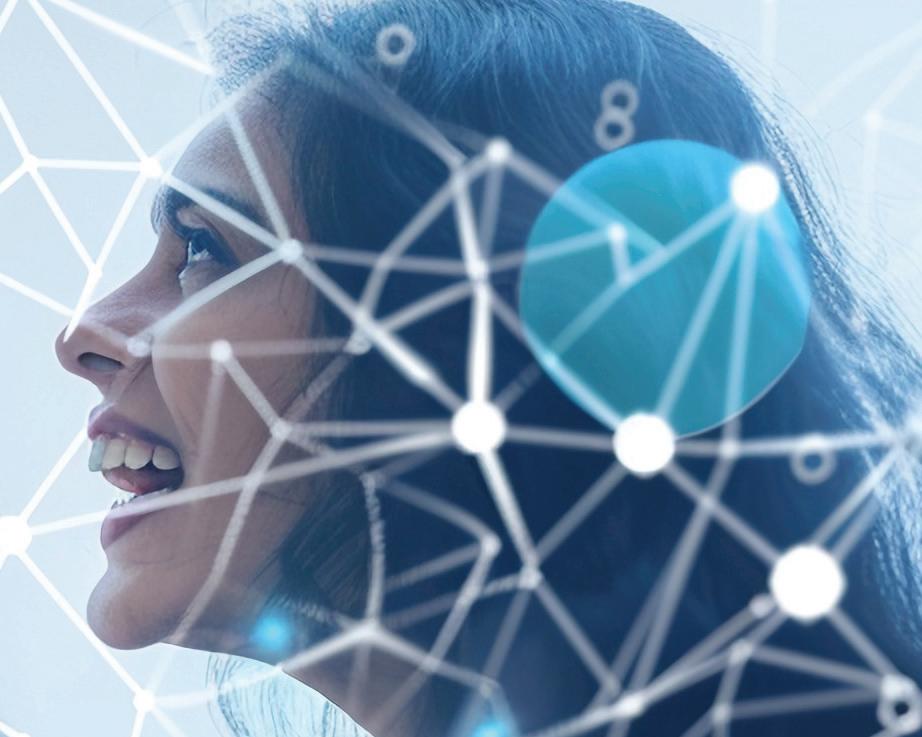
bring ideas and solutions based on their work firsthand or observing colleagues. For example, when a new line was introduced in the Lincoln facility, the committee shared some ideas about how to eliminate bending and twisting by simply adding a lift cart, which helped resolve many of these issues. The bottom line is, empowering employees to share their opinions freely without fear of retribution leads to greater collaboration and accountability by everyone, and ultimately contributes to a safer work environment.
Focus on being proactive and not reactive. Three decades ago, when our safety program was still in its infancy, our approach to safety was more reactive and centered on making improvements after someone got hurt. Since that time, we’ve evolved vastly and are looking to stay ahead of any issues. We do this in several ways, including training on proper body mechanics, developing a safety database that helps us gather all safety-related information and monitor if there are any trends to reduce accident rates, and constantly exploring different technology to prevent injuries, whether it’s tools like wearables or exoskeletons.
Not all safety initiatives require a major investment. While we’re fortunate at Schneider Electric to have the resources to implement leading-edge technology, like AVGs and robotics, in addition to offering physical, trigger point and massage therapists on site for employees, not all safety initiatives require a large investment. In fact, some of our most impactful safety efforts don’t require any additional budget, including soliciting input from employees on job design, stretching at the beginning of a shift and throughout the day, establishing job rotations so no one
is in the same position all day, and instituting a 26-pound weight-lift limit to minimize strain.
Safety is all about continuous improvement. We’re always looking for ways to enhance our safety efforts, and a major part of that is looking inward. Each year, we strive to raise the bar. It starts by doing a self-evaluation, where we come up with goals for each site, and then have directors from outside the facilities come in and validate them. We also do a corporate audit on our safety, environmental and ergonomics programs every three years. Regularly evaluating ourselves and giving an honest assessment allows us to improve upon areas of opportunity and build on where we excel.
A culture of safety starts at the top. When safety is the first thing the CEO mentions during organizational meetings and by making bold statements like, “safety will define us as a company,” that speaks volumes to employees. As an EHS professional, a lot of our work starts on the ground level and, when the top of an organization stands behind safety, then we can meet in the middle and truly implement the improvements we need to move the needle.
At the heart of our safety philosophy is the desire for our employees to leave work in the same or better condition than when they arrived. We will not be fully satisfied until this is achieved and there are zero work-related medical incidents. We know we have more work to do to accomplish this, and joining the MSD Pledge community is yet another way we can advance along our safety journey.
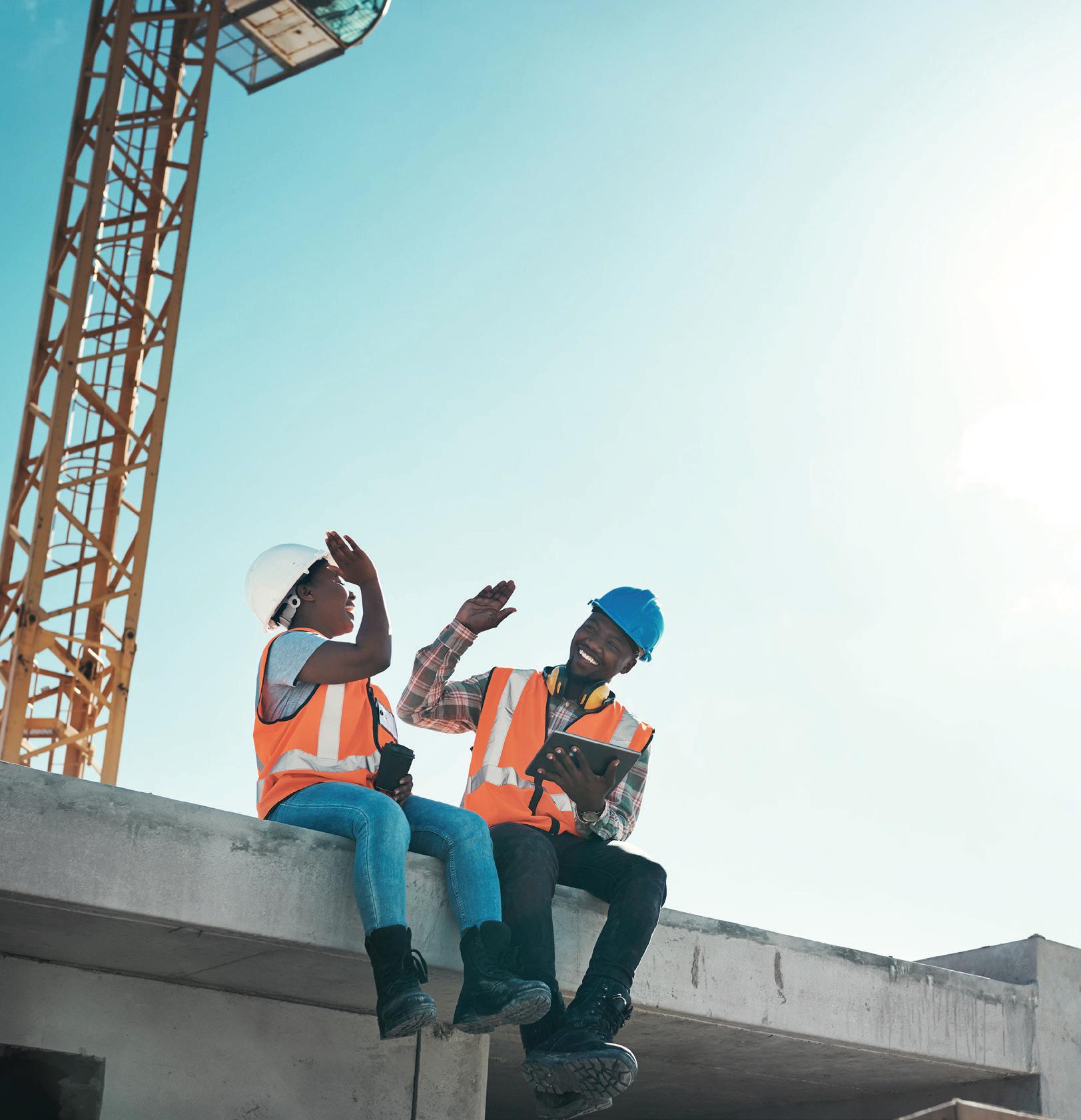
How To Identify Workplace Safety Champions
Workplace safety champions are the beating heart of a strong health and safety culture. They are people who are passionate about safety, take an active role on safety committees or lead by example among their peers.
Anyone can be a workplace safety champion—at one organization it might be a shift supervisor who is skilled at supporting safe behavior, and at another it could be an accountant who sits on an H&S committee and pushes for cutting-edge human error training.
It’s incredibly difficult to replicate their keen awareness, insight and enthusiasm for safety. But it’s possible to spot people who could be the next safety champion if they only had a little additional encouragement.
No two workplace safety champions are identical. But almost every single one of them has at least one standout
quality that helps them excel. Here are some of those qualities to look for when trying to identify potential workplace safety champions.
THEY LEAD BY EXAMPLE
Looking out for the safety of others and adjusting their own behavior to inspire a change is one of the hallmarks of a health and safety champion. Champions don’t tout the importance of safety to others only to apply a different set of rules to themselves. The pride they take in being safe can influence others to feel the same.
Even entry-level employees can lead the way with their enthusiasm, inspiring confidence and helping develop a healthy safety culture. And safety champions in a leadership position will know that workers are more likely to take safety seriously if their top managers regularly
show up to training and follow the rules just like everyone else. It helps build an understanding that safety applies to everyone and those in charge are not above anyone else. After all, they’re all in it together.
THEY’RE SAFE 24/7
A world-class safety system requires a 24/7 approach and safety champions are pioneers in this regard. They are natural motivators, treating their personal safety with deep respect whether they’re in the middle of a task at work or enjoying time off with their family. They recognize that injuries can happen at any time.
They wear the appropriate PPE consistently, report damaged machinery or equipment, and take care whenever they’re on the shop floor. They take the same careful approach to safety when they’re off the job too, whether they’re on the road with their family or working on a DIY project over the weekend. By sharing this attitude with their team, they increase their peers’ view of health and safety.
These individuals participate in workplace training regularly and do their best to extend their knowledge to others, improving overall performance on the job and awareness outside of the workplace. They are superstars who demonstrate concern for their own well-being and the wellbeing of their peers, regardless of whether they’re at work, at home or on the road.
THEY START SAFETY CONVERSATIONS
For conversations to affect change, first they must occur, and workplace safety champions are often the ones leading the discussion. They bring up problems and work hard on trying to resolve them, showing their dedication to safety improvements. They are always open to discussing safety issues and growing awareness. They lead or actively participate in toolbox talks , helping foster an open safety culture that welcomes input and rewards questions. Even if they’re not overly talkative, they truly commit to communications regarding safety.
THEY TAKE INITIATIVE
Safety champions in higher positions will create safety policies that guarantee every employee receives proper orientation and training. They will also ensure that regular safety visits are scheduled, and training is updated as needed. Moreover, whether they’re management or staff, they will have the courage to endorse practices that reinforce a culture of safety in the workplace and make sure the rules
are followed. When they witness bad habits, they will bring it up and try to influence positive change.
THEY ARE WILLING TO LEARN AND ENGAGE WITH NEW IDEAS
New discoveries, new research and new equipment continuously build and shape an organization’s safety culture. For example, more effort is now being put by many companies into human factors training, safety harnesses are widely used at heights, and new regulations are added to modernize safety laws. But sometimes people can get stuck in the past, and companies might ignore or miss out on newer approaches as they concentrate on compliance.
But safety champions are open to new ideas and new discoveries. If there is a chance to improve the safety of their team, they will be excited to try it. Sure, sometimes implementing something new might take a lot of effort, but in the end, the possible improvement to everyone’s safety is worth the work.
THEY RECOGNIZE THE HUMAN FACTORS THAT PREVENT COMPLIANCE
A person’s state of mind greatly influences their compliance with health and safety; champions seek to better understand these factors and address them in order to reduce errors and improve decision making. Rushing, fatigue, frustration and complacency are often just as responsible for injuries as the hazards themselves, and champions will encourage their team to take breaks, slow down, and take the safest route at all times. They will also provide training and support so that employees have the skills required to identify and deal with human factors in real time. For a safety champion, safety is the most important aspect of the workplace. Yes, there are deadlines, but there is no reason to jeopardize lives in the process.
THEY ARE ENCOURAGING
Finally, as much as a champion will bring issues to attention, they will also celebrate their coworkers’ successes , thank them for being mindful, and when in a supervisory position, reward their employees for being perceptive and taking care of the communal well-being of the workplace.
The first step to creating a strong culture of safety is to notice those who are doing a good job; through them, you can create improvements and build upon existing structures. It’s also prudent to reward these champions accordingly, which will encourage them to continue promoting workplace safety.
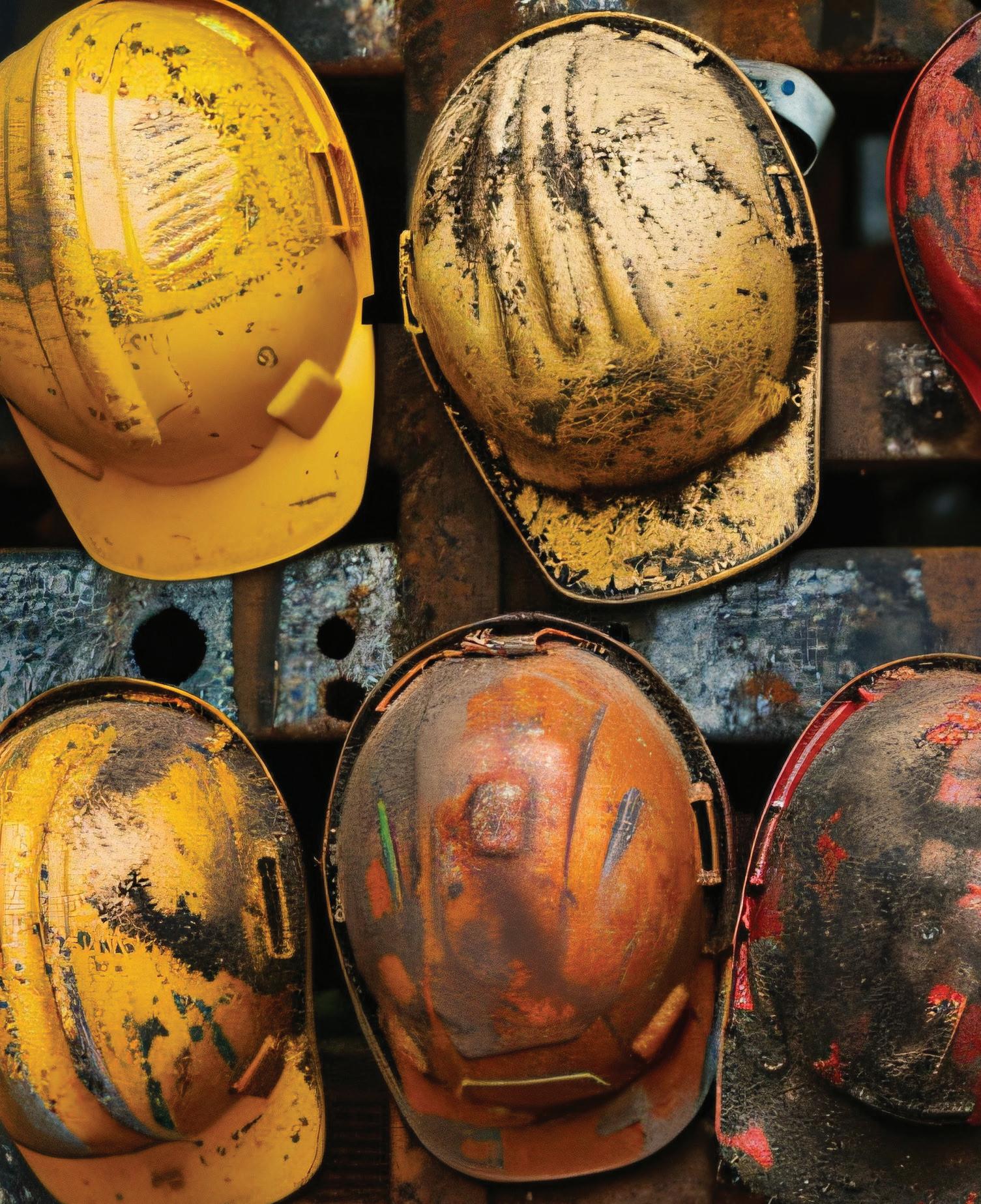
OSHA Provides Enforcement Update, Details New Safety Helmet Pilot Program at NAHB Meeting
12.11.2023 | OSHA.gov
At the NAHB Spring Leadership Meeting in Washington last week, Scott Ketcham, director of OSHA’s Office of the Directorate of Construction, provided a robust update on the safety agency’s activities and enforcement agenda in the NAHB Construction Safety and Health Committee meeting.
Ketcham explained key changes in OSHA’s Severe Violators Enforcement Program (SVEP) that went into effect last fall. The SVEP carries elevated penalties and stricter inspection requirements for employers “committing willful, repeated, or failure-to-abate violations.” Significantly, under OSHA’s multi-employer citation policy, “[a]n employer can qualify for SVEP even if none of its own employees were exposed to [SVEP-related] hazards.”
Late last year, the SVEP was expanded to include all OSHA standards and hazards. In addition, the requirements to be placed in the SVEP were dropped to just two willful or repeated violations or failure-to-abate notices based on serious violations.
Ketcham shared the most-cited OSHA violations for the first seven months of the federal fiscal year 2023:
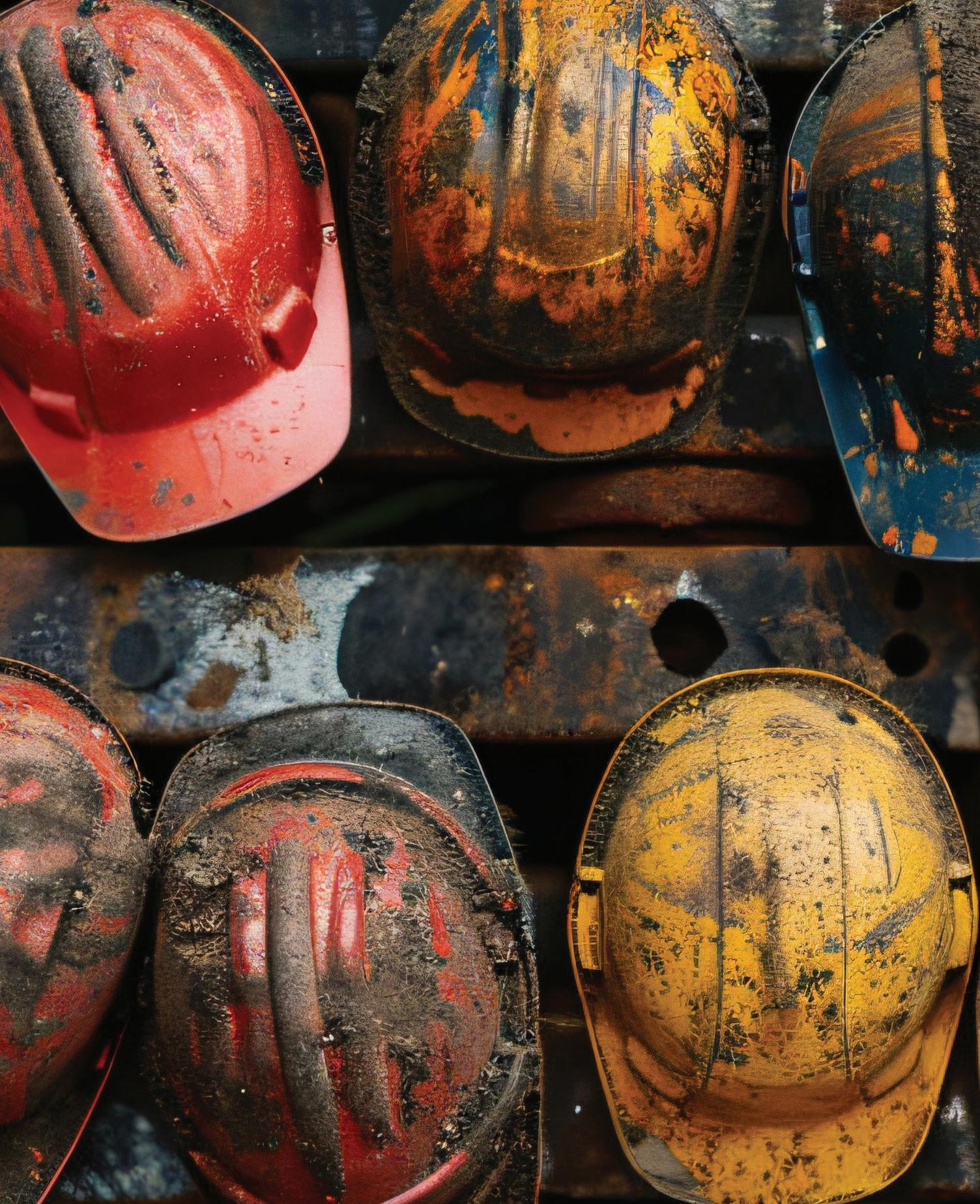
Ketcham also detailed enforcement emphasis programs within the Directorate of Construction, including the fall protection program announced just last month and one on outdoor and indoor heat-related hazards, which was issued in April 2022.
Beyond enforcement, OSHA’s construction office is working on guidance to improve jobsite safety. One initiative shared at the meeting is a pilot program for safety helmets meant to eventually replace hardhats as the preferred head protection in construction. Ketcham noted that 20% of head injuries in construction are the result of slips, trips, and falls and that hardhats do not protect against such injuries while helmets with chinstraps may stay on the head during a fall and offer protection.
OSHA is also working on revising construction standards to include explicit requirements that PPE must fit workers properly. This would align construction standards with those in general industry and maritime and address concerns heard from women in construction. A notice of proposed rulemaking is expected shortly.
Ketcham noted that OSHA, and especially the Directorate of Construction, is devoting a lot of resources and energy to going beyond enforcement with strategies to make health and safety a core value on jobsites.
Using an Activity Hazard Analysis effectively is critical to identify, assess, and control jobsite hazards in a way that ensures a safe work environment.
An Activity Hazard Analysis (AHA) is very similar to a Job Hazard Analysis (JHA). The primary goal of an Activity Hazard Analysis is to enhance workplace safety by systematically identifying and controlling hazards associated with specific tasks.
3. Implement Controls: Develop and implement measures that will eliminate or minimize the identified hazards.
4. Use as a Reference: Regularly review and use the AHA as a reference to ensure ongoing safety throughout the job.
An Activity Hazard Analysis typically contains some or all of the following information:
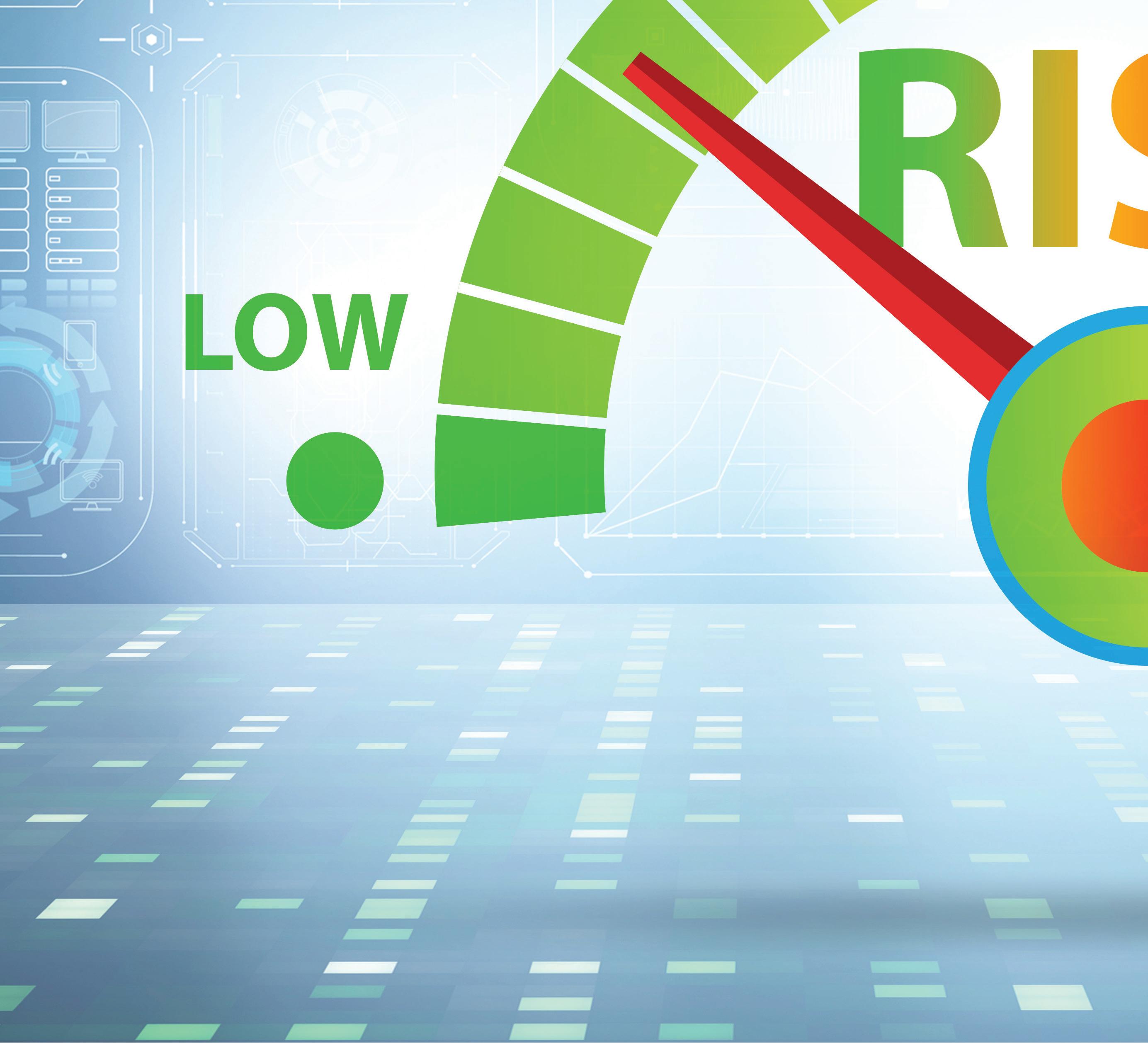
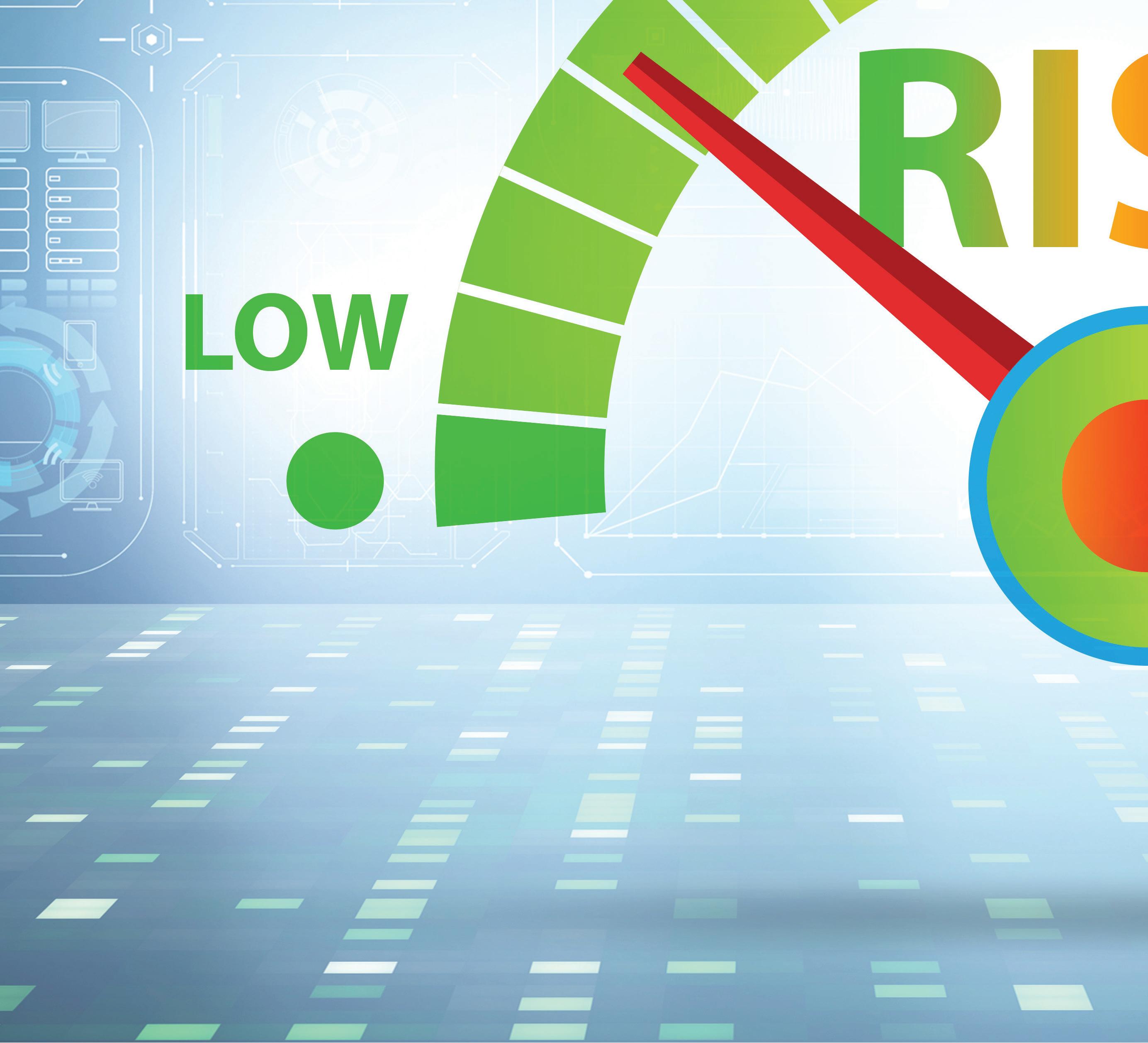
An Activity Hazard Analysis (AHA) is commonly associated with military projects and contracts, but its application extends even further. AHAs are now widely used across various industries as part of an organization’s overall risk management plan.
THE PURPOSE OF AN ACTIVITY HAZARD ANALYSIS IS TO:
1. Identify Job Tasks: Break down the job into individual tasks to understand each component.
2. Determine Hazards: Identify potential hazards associated with each task.
Basic Information about the project including the date(s), project name, contractor, activity type and location, and names of who prepared the AHA and who reviewed the document.
Job Steps involved and the sequence of work activities.
Potential Hazards associated with each job step.
Recommended Controls and precautionary actions to eliminate or minimize each hazard.
Equipment to be used during the work activities.
Training Requirements for personnel (example: equipment operator training).
Inspection Requirements for the equipment and work activities (example: inspect scaffold daily.)
PPE Requirements including the minimum PPE required for all job steps, and special PPE requirements for some job steps.
Competent and Qualified Person(s) and their areas of expertise.
An Activity Hazard Analysis may also have a Risk Assessment Code (RAC) Matrix that is used to assign a RAC to each job step.
A Risk Assessment Code (RAC) Matrix is a tool used to evaluate and categorize the level of risk associated with specific hazards identified during an Activity Hazard Analysis (AHA).
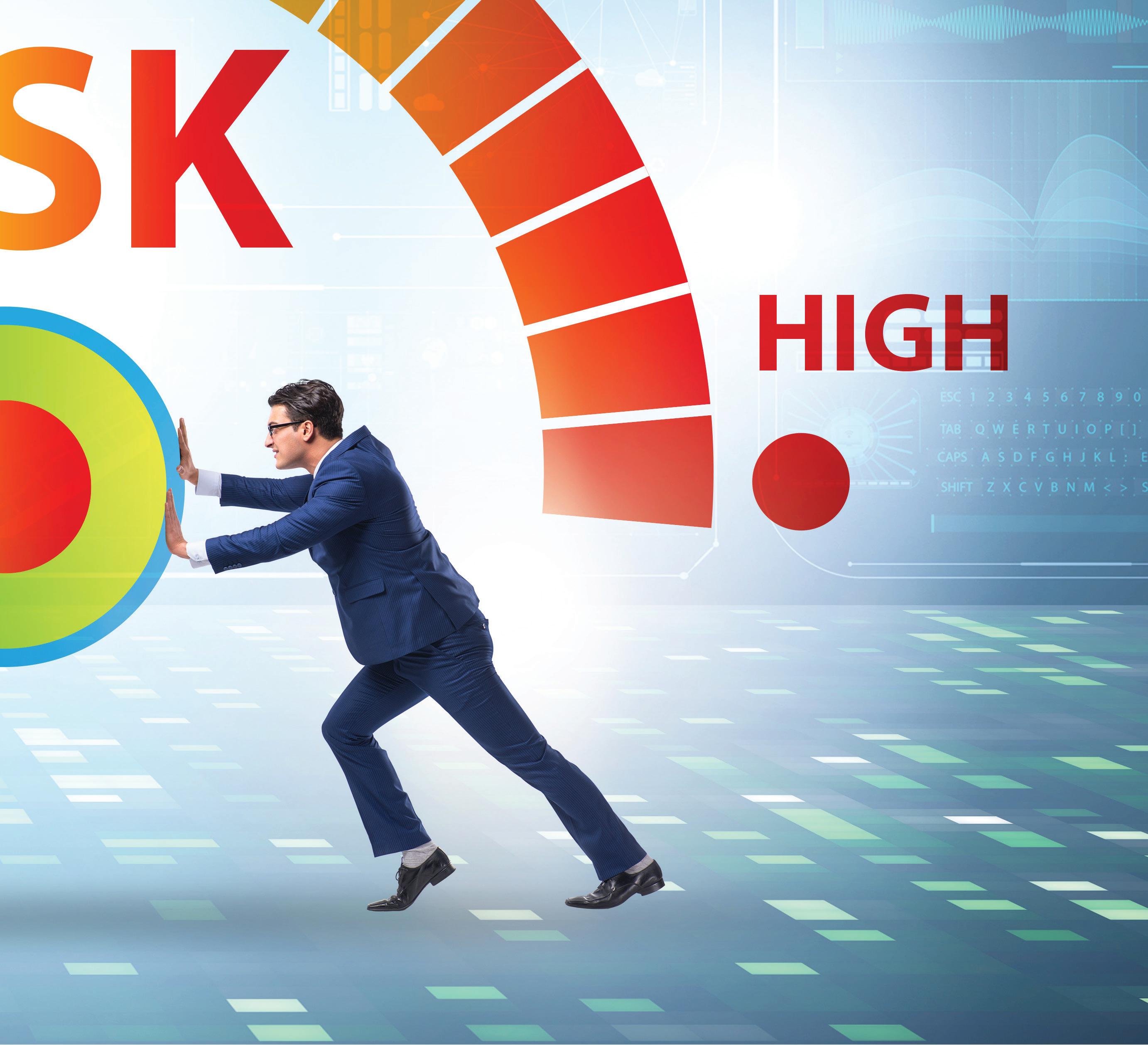
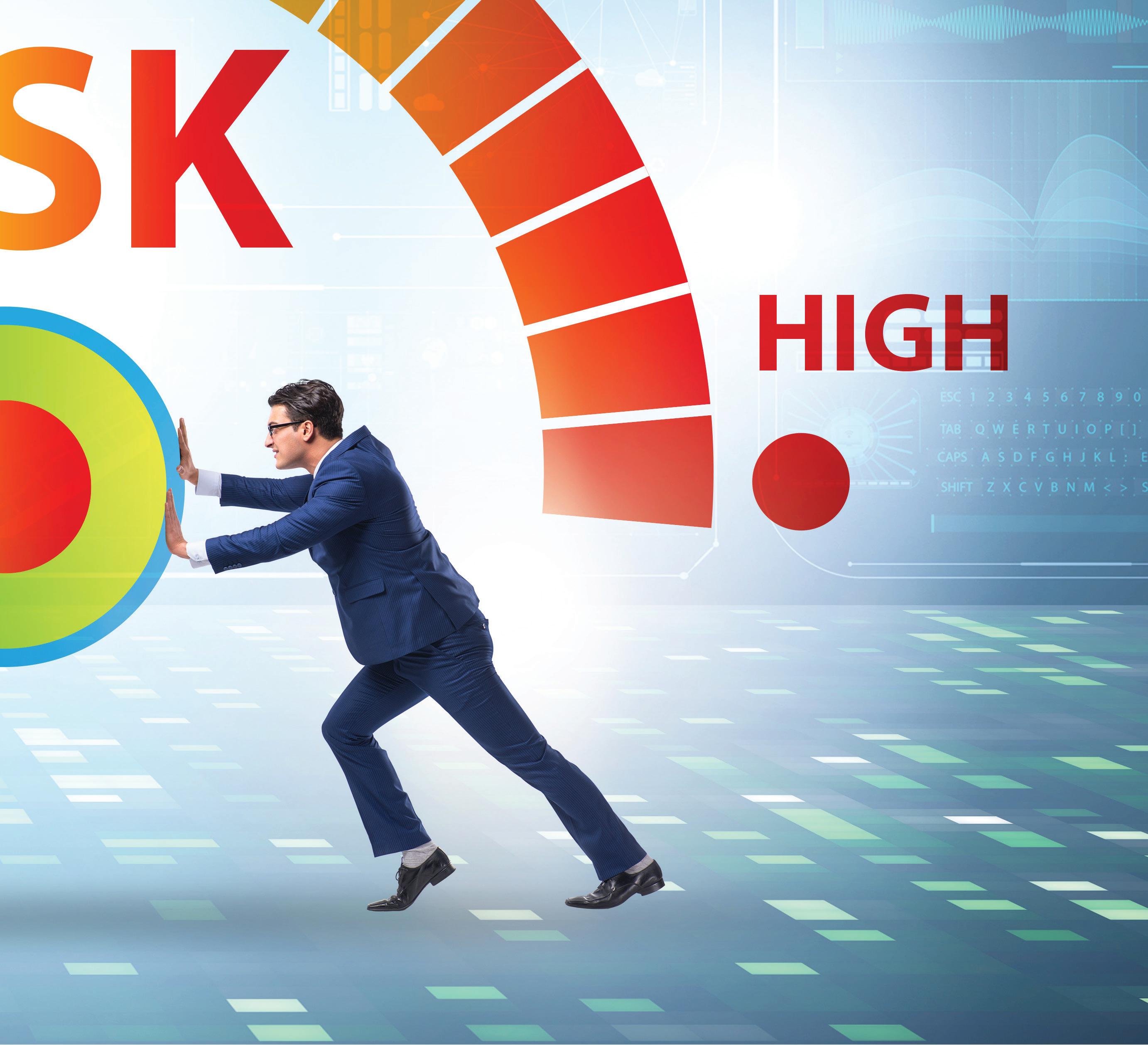
The RAC Matrix combines severity and probability to determine the overall risk level. The intersection of severity and probability in the matrix provides a risk code or rating, such as:
• Extremely High Risk: Do not proceed until risk is reduced to acceptable level.
• High Risk: Work may not begin until management agrees on safe course of action.
• Moderate Risk: Corrective action needed as soon as possible.
• Low Risk: Monitor and manage with routine procedures.
The RAC Matrix helps determine likelihood of potential accidents or incidents, allowing organizations to prioritize and implement appropriate control measures.
Conducting an Activity Hazard Analysis starts with systematically identifying job tasks, followed by a thorough review of potential hazards , and then the assignment of control measures.
First, break down the scope of work activity into job steps. List each job step in the order it is performed. Do not make the steps too generic or too detailed. Identify the hazards for each step of the process and ask these questions:
• What can go wrong and what are the ways it could go wrong?
• What are the consequences if something does go wrong?
• How likely is it that something will go wrong?
• What contributing factors will increase the likelihood of something going wrong?
• What are the contractual and regulatory requirements associated with the hazard?
Be specific when identifying the controls that will be used to eliminate or reduce the hazards. For each hazard, there should be at least one control, but there may be more than one.
Consider the hierarchy of controls and always try to eliminate hazards. If elimination isn’t possible, substitution and engineering efforts should reduce the hazard, and administrative controls along with personal protective equipment can add further protection for workers.
Ensure that administrative controls include required work permits, inspections, and training. Be specific when identifying the type of required personal protective equipment.
Utilizing an Activity Hazard Analysis (AHA) helps create a safer work environment by fostering a proactive approach to hazard identification and risk management.
An Activity Hazard Analysis is not just a corporate document but is intended to be created and used in the field.
Review the job steps, hazards, and controls listed on the AHA with workers who have performed the same tasks or have worked on a similar project to ensure that no items have been left out.
Before work begins, review the contract to ensure all conditions of the Activity Hazard Analysis have been met, including approvals of the completed AHA.
Keep a copy of the AHA at the job site during work activities. All workers must review the Activity Hazard Analysis before work begins.
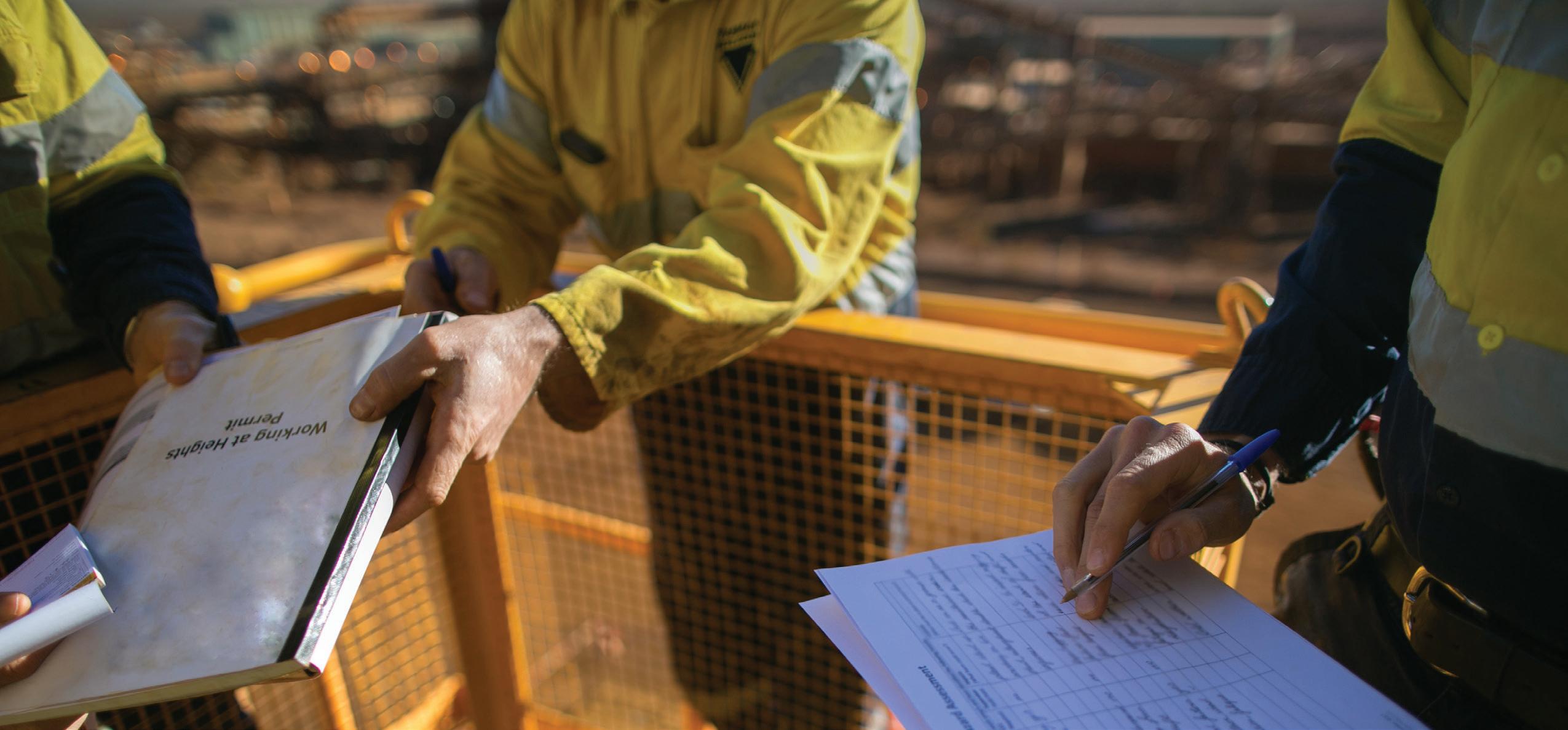
The AHA should be reviewed and modified as necessary to address changing site conditions, operations, or any change to the competent persons .
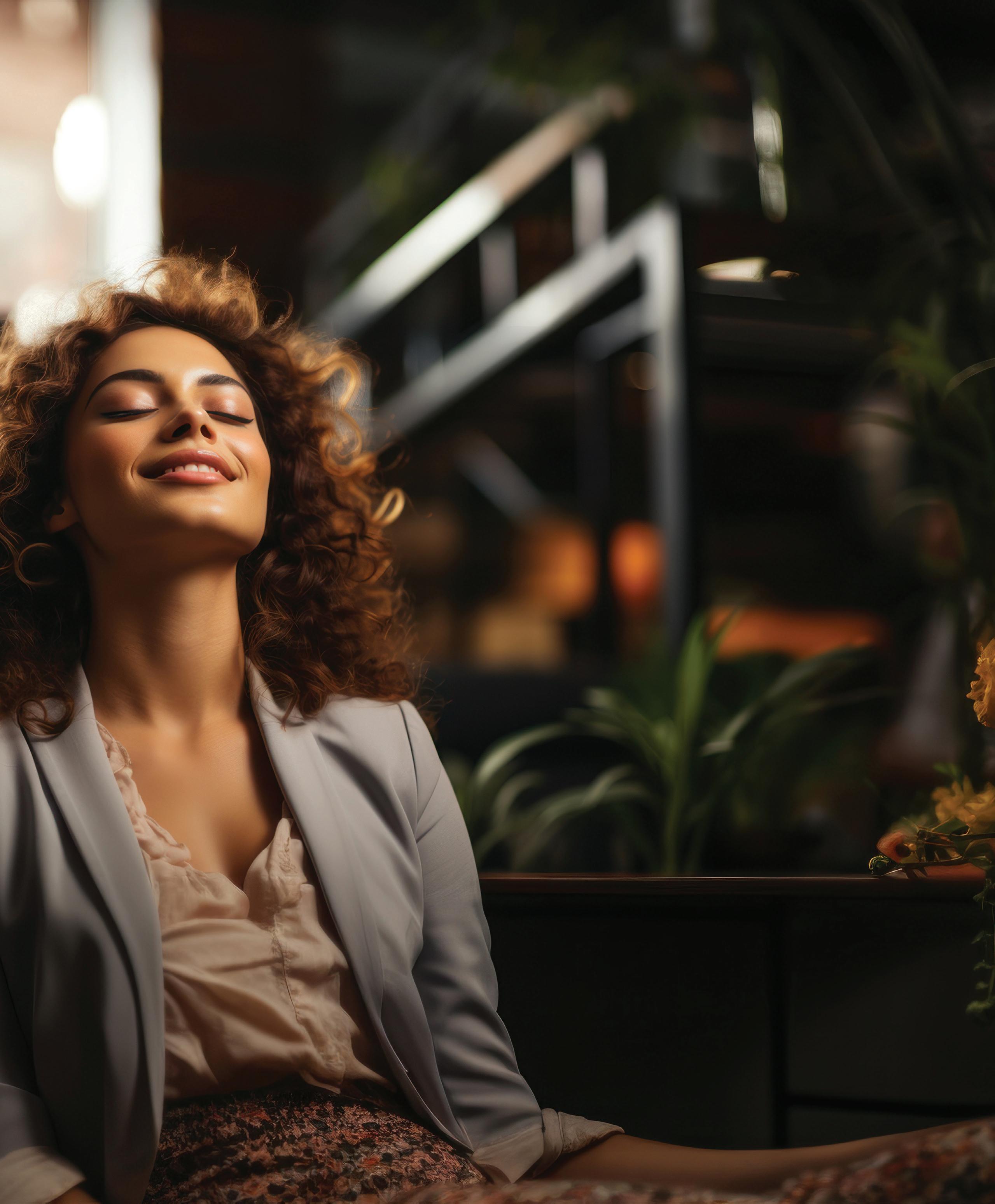